- No category
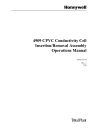
advertisement
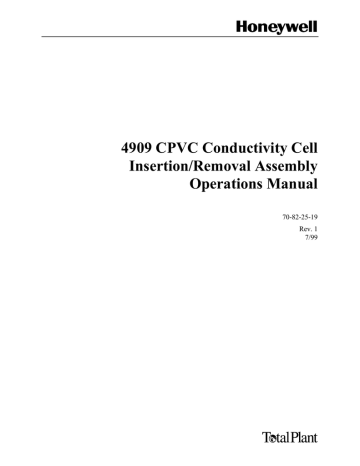
4909 CPVC Conductivity Cell
Insertion/Removal Assembly
Operations Manual
70-82-25-19
Rev. 1
7/99
Copyright, Notices, and Trademarks
Printed in U.S.A. – © Copyright 1999 by Honeywell Inc.
Revision 1– 7/99
While this information is presented in good faith and believed to be accurate, Honeywell disclaims the implied warranties of merchantability and fitness for a particular purpose and makes no express warranties except as may be stated in its written agreement with and for its customer.
In no event is Honeywell liable to anyone for any indirect, special or consequential damages. The information and specifications in this document are subject to change without notice.
ii
Honeywell
Industrial Automation and Control
Automation College
2820 West Kelton Lane
Phoenix, AZ 85023
(602) 313-5669
4909 CPVC Conductivity Cell Insertion/Removal Assembly– Operations Manual 7/99
About This Document
Abstract
The purpose of this document is to support the installation operation and maintenance of the 4909 CPVC
Conductivity Cell Removal/Insertion Assembly.
Revision Notes
The following list provides notes concerning all revisions of this document.
Rev. ID
0
1
Date
11/96
6/99
Notes
This revision is the initial release of the Honeywell version of the L&N manual p/n 277731 Rev. E1. There were no major changes to the L&N version when it was Honeywellized.
Edits were made to standardize terminology and to add the new Model
Selection Guide.
References
Honeywell Documents
The following list identifies all Honeywell documents that may be sources of reference for the material discussed in this publication.
Document Title
9782 Series Conductivity/Resistivity Analyzer/Controller Operator’s Manual
7079-17 Two-Wire Transmitter for Conductivity/Resistivity Operation and
Maintenance Manual
ID #
70-82-25-74
70-82-25-51
Non-Honeywell Documents
The following list identifies select non-Honeywell documents that may be sources of reference for the material discussed in this publication.
Title Author Publisher ID/ISDN #
Contacts
The following list identifies important contacts within Honeywell.
7/99 4909 CPVC Conductivity Cell Insertion/Removal Assembly– Operations Manual iii
Organization
Honeywell TAC
Telephone
1-800-243-9883 Voice
Address
1100 Virginia Drive
Fort Washington, PA 19034
iv 4909 CPVC Conductivity Cell Insertion/Removal Assembly– Operations Manual 7/99
Contents
1.
INTRODUCTION....................................................................................................1
1.1
Overview.........................................................................................................................................1
1.2
4908 Conductivity Cell ...................................................................................................................1
1.3
31074357 Removal Device............................................................................................................2
2.
SPECIFICATIONS AND MODEL SELECTION GUIDE .........................................7
2.1
Specifications..................................................................................................................................7
Cell Constants....................................................................................................................................7
Electrode Material .............................................................................................................................7
Wetted Parts.......................................................................................................................................7
Pressure and Temperature (See Fig. 1-1) ..........................................................................................7
Maximum Pressure ............................................................................................................................7
Mounting ...........................................................................................................................................7
Purge Port ..........................................................................................................................................7
Insertion Depth ..................................................................................................................................7
Electrical Connections.......................................................................................................................7
Integral Automatic Temperature Compensation ...............................................................................8
Leadwire ............................................................................................................................................8
Weight ...............................................................................................................................................8
2.2
Model Selection Guide ...................................................................................................................8
...........................................................................................................................................................8
3.
INSTALLATION ...................................................................................................11
3.1
Requirements ................................................................................................................................11
3.2
Location and Position ...................................................................................................................11
Considerations .................................................................................................................................11
3.3
Prepare Assembly .........................................................................................................................12
Initial Prep .......................................................................................................................................12
Mounting into the Process ...............................................................................................................12
3.4
Insertion ........................................................................................................................................13
3.5
Removal ........................................................................................................................................14
3.6
Electrical Connections ..................................................................................................................14
7/99 4909 CPVC Conductivity Cell Insertion/Removal Assembly– Operations Manual v
4.
MAINTENANCE AND REPLACEMENT PARTS .................................................17
4.1
To Clean The Cell.........................................................................................................................17
4.2
Replacing Removal Device Parts..................................................................................................17
Ball Valve ........................................................................................................................................17
Nipples.............................................................................................................................................17
Bushing And Washer.......................................................................................................................17
4.3
Replacement Parts.........................................................................................................................18
5.
PLATINIZATION AND PLATINUM BLACK .........................................................19
vi 4909 CPVC Conductivity Cell Insertion/Removal Assembly– Operations Manual 7/99
Tables
Table 4-1 Replacement Parts __________________________________________________________ 18
Table 4-2 Voltage and Time Limits for Platinizing Cells ____________________________________ 18
Figures
Figure 1-1 Temperature/Pressure* Range__________________________________________________ 2
Figure 1-2 4909 CPVC Conductivity Cell Insertion/Removal Assembly with Conductivity Cell Installed3
Figure 1-3 4909 CPVC Conductivity Cell Insertion/Removal Assembly with Universal Head_________ 3
Figure 1-4 4908 Conductivity Cell _______________________________________________________ 4
Figure 1-5 31074357 Removal Device ____________________________________________________ 4
Figure 1-6 Universal Head _____________________________________________________________ 5
Figure 3-1 Outline and dimension drawing for 4909-X-X-X-X-03-X-X Conductivity Cell, Insertion Type with CPVC Removal Device _______________________________________________________ 15
Figure 3-2 Outline and Dimension drawing for 4909-X-X-X-X1-03-X-X Conductivity Cell, Insertion
Type with CPVC Removal Device and Universal Head __________________________________ 16
Figure 5-1 Installation Diagram-Cat. 4909 Cells with Junction Box Head Connected to 7082
Conductivity/Resistivity Analyzer ___________________________________________________ 20
Figure 5-2 Installation Diagram-Cat. 4909 Cells with Junction Box Head Connected to 9782
Conductivity/Resistivity Analyzer ___________________________________________________ 21
Figure 5-3 Installation Diagram-Cat. 4909 Cells with 7 or 20 Foot Leads Connected to 7082
Conductivity/Resistivity Analyzer ___________________________________________________ 22
Figure 5-4 Installation Diagram-Cat. 4909 Cells with 7 or 20 Foot Leads Connected to 9782
Conductivity/Resistivity Analyzer ___________________________________________________ 23
7/99 4909 CPVC Conductivity Cell Insertion/Removal Assembly– Operations Manual vii
Introduction
1. Introduction
1.1 Overview
The 4909 Conductivity Cell Insertion/Removal Assembly is designed for use in a pipeline or closed vessel where it is desirable to remove the cell for inspection and maintenance without shutting down the system and releasing the pressure. The assembly comprises a 4908 Conductivity Cell and a 31074357 Removal
Device which are shown assembled in Figs. 1-2 and 1-3. It is to be used in applications for which maximum pressure does not exceed 125 psig, and can be reduced to 50 psig during insertion and removal of the cell. Maximum operating temperature is determined by the temperature compensator range. Do not use in solutions above 80
°
C.
The depth of insertion is given in Figs. 3-1 and 3-2.
The conductivity cell is made of polyethersuflone (PES), which is resistant to most corrosive inorganic chemicals over a wide range of temperatures (common exceptions are chlorinated hydrocarbons and ketones). Sample solutions come into contact with the PES and the platinum or nickel electrode surface of the cell. (Any cell constant can be supplied with either electrode material). The only materials of the 4909
Assembly with which the sample solution may come into contact are in the removal device which is comprised of CPVC plastic, Teflon, EPDM and Viton materials. The automatic temperature compensator may be built into the cell as shown in Section 2.2, Model Selection Guide.
CAUTION
Specific parameters of your process may prohibit the use of nickel electrodes. For example, always use a platinum cell (Table II = 44) if the cell will measure or be exposed to regeneration acids or bases.
1.2 4908 Conductivity Cell
The molded conductivity cell and its one-inch diameter by 3-inch long adapter comprise a one piece cell unit and are made of polyethersulfone (PES). This adapter serves as a stop during the removal operation.
The cell can be supplied with a two, three or four conductor, Tefzel-sheathed cable, Fig. 1-2. Either of two different lengths of cable can be furnished as specified in the Model Selection Guide (MSG) number, see
Section 2.2, Model Selection Guide. Or the insertion/removal assembly can be supplied with a Universal
Head, Fig. 1-3.
The cells having constants of 5, 10, 20, 25 or 50 cm
-1
are intended for making measurements in highly conductive solutions. They differ in construction from those having constants of 0.01, 0.1, or 1. On the 5 to 50 constant cells, the electrodes are short tubes located midway inside the two parallel tubular channels that run lengthwise through the cell, and are open to the sample at both ends of the cell. The channels are larger on the 25 constant cell and they are elliptical on the 5 and 10 constant cell. The 0.01, 0.1, and 1.0
constant cells have a removable cell guard which is screwed onto the cell body to protect the electrode surfaces. Cells with a guard tube must be used with the guard in place or the cell constant may differ from that specified. Electrodes are three discs on the 1 constant cell, parallel plates on the 0.1 constant cell, and a pair of concentric wires wound on the cell body on the 0.01 constant cell.
7/99 4909 CPVC Conductivity Cell Insertion/Removal Assembly– Operations Manual 1
4909 CPVC Conductivity Cell Insertion/Removal Assembly Operations Manual
1.3 31074357 Removal Device
This device consists of a ball valve which is connected to the closed system by a 1-1/2 inch CPVC schedule
80 mounting nipple and to a housing by a 6 inch long schedule 80 CPVC nipple into which the support tube for the cell mounting is inserted. The compression handle provides a seal around the cell support tube.
Depending on the Key Number selected in Section 2.2, MSG, the 31074357 Removal Device may or may not include the 4908 Cell preinstalled in the device.
If Key Number 04908 is selected, the 4908 Cell (Fig. 1-4) is shipped apart from the removal device.
If Key Number 04909 is selected, the 4908 Cell is preinstalled into the removal device, Fig. 1-3. Details of each type of installation are given in Section 3.3.
130
80
70
60
50
40
30
120
110
100
90
20
10
0
-10 -5 0 10 60 70 80 20 30 40
DEGREES CELSIUS
50
a/n 23349
Figure 1-1 Temperature/Pressure* Range
* 50 psig max. during insertion or removal of 4908 cell.
2 4909 CPVC Conductivity Cell Insertion/Removal Assembly– Operations Manual 7/99
Introduction
Conductivity Cell
Valve
Purge Port
1/4" NPT Plug
Compression Handle
Support Grip
6" Nipple
1-1/2" NPT Nipple
Housing
Adapter (Contains Automatic Temperature Compensator when Specified)
Cable
Cable Grip a/n 23350
Figure 1-2 4909 CPVC Conductivity Cell Insertion/Removal Assembly with Conductivity Cell Installed
Universal Head Assembly a/n 23351
7/99
Figure 1-3 4909 CPVC Conductivity Cell Insertion/Removal Assembly with Universal Head
4909 CPVC Conductivity Cell Insertion/Removal Assembly– Operations Manual 3
4909 CPVC Conductivity Cell Insertion/Removal Assembly Operations Manual
Conductivity
Cell
Adapter *
* Automatic Temperature Compensator,
when specified by catalog number, is
mounted inside adapter.
Cable
a/n 23352
Figure 1-4 4908 Conductivity Cell
Do not nick outside of support tube
Note: Apply a thin film of Silicone grease to all surfaces of bushing and to diameter of support tube as shown.
Apply grease
(See Note above)
Modify per sketch*
Tighten securely to pipe
Apply teflon tape to both ends of support tube. Tighten all pipe thread fittings two turns beyond hand tight.
4
These parts should be hand-tightened only
*
Slice through one side as shown
Compression
Bushing
Figure 1-5 31074357 Removal Device
4909 CPVC Conductivity Cell Insertion/Removal Assembly– Operations Manual
a/n 23353
7/99
Introduction
Nipple (3/4" NPT)
Set Screw
Base
#6-32 Screw
Wire
Gasket
Cap
#6-32
Binding Head
Screw &
Washer
#6-32 Screw
Chain
A
B
D
C
Terminal
Board
Assembly
View of Base with Cap Removed
O
C
D
N
C
U
IV
T
Y
IT
E
C
L
L a/n 23354
Figure 1-6 Universal Head
7/99 4909 CPVC Conductivity Cell Insertion/Removal Assembly– Operations Manual 5
4909 CPVC Conductivity Cell Insertion/Removal Assembly Operations Manual
6 4909 CPVC Conductivity Cell Insertion/Removal Assembly– Operations Manual 7/99
Specifications and Model Selection Guide
2. Specifications and Model Selection Guide
2.1 Specifications
Cell Constants
0.01, 0.1,1.0, 5, 10, 20, 25 and 50 cm
-1
.
Electrode Material
Nickel or Platinum, as specified.
Wetted Parts
Cell Body: Polyethersulfone (PES).
Mounting Materials: Chlorinated Polyvinyl Chloride (CPVC).
Internal Sealing Materials: Viton, Teflon & EPDM
Pressure and Temperature (See Fig. 1-1)
125 psig (862 kPa) max. @ 23
°
F (-5
°
C)
90 psig (621 kPa) max. @ 122
°
F (50
°
C)
50 psig (345 kPa) max. @ 176
°
F (80
°
C)
Maximum Pressure
During Insertion or Removal: 50 psig.
Mounting
1-1/2” NPT male pipe. Overall length of removal device: approximately 20 or 22 inches (allow additional clearance for cell withdrawal). See Figs. 3-1 and 3-2.
Purge Port
1/4” NPT female opening.
Insertion Depth
Varies between 4.5” and 6.8” nominal, depending upon cell constant. Greater insertion depths are optional.
See Figs. 3-1 and 3-2.
Electrical Connections
Three leads with integral automatic temp. compensator. Two leads without integral automatic temp.
compensator. Four leads with integral automatic temp. compensator)Table III = 333).
7/99 4909 CPVC Conductivity Cell Insertion/Removal Assembly– Operations Manual 7
4909 CPVC Conductivity Cell Insertion/Removal Assembly Operations Manual
Integral Automatic Temperature Compensation
Refer to Section 2.2 – Model Selection Guide
Leadwire
Tefzel covered, 18-gage cable (7 feet, 20 feet, or Universal Head, as specified).
Weight
Approximately 3.5 lb (1.6 Kg) (including cell).
2.2 Model Selection Guide
KEY NUMBER
Description
04909 Complete Conductivity Cell Assembly
04908 Replacement Cell Only
TABLE I
Cell Constant
TABLE II
Electrode Material
TABLE III
Automatic Temperature Compensator (ATC)
No Temperature Compensator
Available for 9782 and 7082 Only
Nickel
Platinum
(Note 2) (Note 3)
(Note 1) (Note 3)
0.01
0.1
1
5
10
20
25
50
Selection Availability
04909
04908
001
X01
XX1
XX5
X10
X20
X25
X50
g g g g
Available for 7079C Transmitter or already withdrawn analytical instrumentation. (Refer to Tables 1 and 6 under Steps to Selecting
Appropriate Conductivity Instrumentation & Cells for available
Temp. Compensator/Conductivity range.)
33
44
074
088
090
091
093
113
114
160
164
168
000
333
009
013
014
071
072
073
f f
8 4909 CPVC Conductivity Cell Insertion/Removal Assembly– Operations Manual 7/99
Specifications and Model Selection Guide
TABLE IV
Leadwire Length ’7 ft. Leadwire
20 ft. Leadwire
Junction Head (Aluminum)
TABLE V
Valve/Cell Material
4909 Stainless Steel (SS) Valve
Assembly
4908 PES Replacement Cell for
4909 SS Valve Assembly
4909 CPVC Valve Assembly
Material
Includes SS Valve assembly and
Standard insertion cell
Standard insertion cell only
Includes CPVC assembly and standard CPVC Support tube
(15 3/8") and cell
Cell only 4908 PES Replacement Cell for
CPVC Valve Assembly
TABLE VI
Special Mounting Options - select one option per unit
None
SS support tube for 4909 SS Valve assemblies only. Use Table V
Option = 02
4908 replacement cells for 4909 SS
Valve Assembly containing SS Support tube. Use Table V Option = 02
Special insertion lengths for new/ replacement cells for 4909 SS
Valve Assemblies. Only available for Table V Option = 02
Uses special insertion cell to increase standard insertion cell depth by 4.4"
Uses special insertion cell to
Extended Length CPVC Support tube.
Only available for Table V Option = 03 increase standard insertion cell depth by 8.8"
(Note 4)
Uses special insertion cell to increase standard insertion cell depth by 13.2"
(Note 4)
Uses special insertion cell to decrease standard insertion cell depth by 4.4"
Supplies special CPVC support tube (21 3/8") to increase cell insertion depth by 6.0" in a new CPVC Valve
Assembly. Note: Allow additional 6.0" for cell removal
049
Selection
09 08
X7
20
X1
02
02
03
03
000
930
930
910
920
925
940
950
c d e j c d e h h h h
7/99 4909 CPVC Conductivity Cell Insertion/Removal Assembly– Operations Manual 9
4909 CPVC Conductivity Cell Insertion/Removal Assembly Operations Manual
049
TABLE VII - OPTIONS
Tagging
Certificate of Calibration
None
Linen
Stainless Steel
No
Yes
0_
L_
S_
_ 0
_ 1
Notes:
1. Replacement cells only, caution look at Restrictions for insertion depth dimensions based on valve assembly type.
2. When converting from 4806 to 4909, order 4908 directly.
3. Replacement 4908 cells for existing 4908’s and 4909’s manufactured before 8/85 must specify Table V = 02.
4. This option is application sensitive. You must contact Analytical Instruments Marketing for approval.
RESTRICTIONS
Restriction Letter c
Table
Available Only With
Selection Table
Not Available With
Selection
V Standard insertion cell for SS valve assemblies consists of a conductivity cell of variable length based on the cell constant and a 13.2" PES tube molded to the cell. The conductivity cell insertion depth is listed below:
d e f g h j
V
III
V
V
001, X01, XX1 = 7.5"
XX5 = 6.5"
X10 = 7.7"
X20 = 8.0"
X25, X50 = 8.8"
V Standard conductivity cell insertion depth dimensions according to cell constants for CPVC assemblies is listed below:
001, X01, XX1 = 5.5"
XX5 = 4.5"
X10 = 5.7"
X20 = 6.0"
X25, X50 = 6.8"
02
For 9782 and 7082 Analyzers only
02
03
I
I X25, X50
Not for 9782 and 7082 Analyzers
10 4909 CPVC Conductivity Cell Insertion/Removal Assembly– Operations Manual 7/99
Installation
3. Installation
3.1 Requirements
To insure that a representative sample is being measured at all times, the solution must move through and completely purge out the cell channels or guard tube. If the measurement is made in a rapidly moving liquid, the existing circulation of the solution can be utilized by mounting the assembly as described in the next section so that the flow of the solution forces liquid through the cell. However, when measurements are to be made in quiescent solutions, means must be provided for forcing the solution through the conductivity cell so no air bubbles accumulate or care taken to place the cell in a position to measure the true value of the solution.
Do not use the cells in solutions which will attack the fittings used or the wetted cell materials. The PES and platinum or nickel of the electrode are the cell materials with which the solution will come into contact.
The wetted materials of the removal device with which the process may come into contact with are CPVC,
Teflon, EPDM and Viton.
Do not use the cell in a solution having temperatures greater than 80
°
C. The maximum limit set by the temperature compensator range must be observed.
For cells having a constant of 0.01, 0.1 or 1, make certain that the guard is in place and is not loose on the cell body. The guard tube must be hand-tightened only. There is a 1/16 inch space between the guard tube and the cell body.
Do not install the 4909 Assembly where pressures and/or temperatures may occur outside the operating range given in Fig. 1-1. Both pressure and temperature must be within the shaded area of the curve.
Avoid installations where the 4909 Assembly will be exposed to pressure shock caused by water hammer.
3.2 Location and Position
Refer to Fig. 3-1 or Fig. 3-2 for mounting dimensions.
Considerations
The cross-channel in the high constant cells or the guard tube holes in the low constant cells must be covered by the solution during measurements.
Vertical insertion (from above) or horizontal insertion can be used. Make certain the tank or pipeline is full under all process conditions. If a pipeline is not always full, use a vertical mounting and insert the cell far enough into the vertical pipe that the cross-channel is below the horizontal exit pipe which may empty out.
Make certain an air bubble in the pipe does not prevent the cell from filling properly. (If the cell becomes dry after use, it may require cleaning in accordance with Section 4.1 before again being placed in service.)
For best results, whether vertical or horizontal mounting is used, position the cell so that the sample will flow through the channels or guard tube towards the mounting end of the cell, exiting through the crosschannel or guard-tube holes. In applications where vertical mounting is required, avoid a position with the cell channels pointed up, as this will permit solution to flow down into the open end of the cell and may result in clogging by solids settling in the cell channels.
Allow for insertion depth from the outside wall of the mounting surface as indicated by the dimensions in
Fig. 3-1 or 3-2.
7/99 4909 CPVC Conductivity Cell Insertion/Removal Assembly– Operations Manual 11
4909 CPVC Conductivity Cell Insertion/Removal Assembly Operations Manual
Allow at least 1/2 inch clearance beyond the end of the cell and 1/8 to 3/16 inch radius clearance surrounding the cell to permit circulation of the solution.
Avoid locations where excessive temperature changes may occur.
Allow clearance behind the support grip to permit removal of the cell per dimensions in Fig. 3-1 or 3-2.
Locate the insertion/removal assembly on the pressure side of pumps; not the vacuum side.
Avoid locations where the operator must take an awkward position to perform the cell insertion or removal operation.
The 4909 Insertion/Removal Assembly is designed to support only its own weight. Do not install in locations where it would be used as a foot rest or where it would be used as a hand grip. Do not hang or support any other piping or objects from the assembly.
The removal device should not be mounted onto pipelines or vessels displaying excessive vibration unless a support is provided on the 6” long valve nipple.
3.3 Prepare Assembly
If X7 or 20 are selected in Table IV of the Model Selection Guide, then the 4908 Conductivity Cell (Fig. 1-
4) must be joined with the support tube of the 31074357 Removal Device as discussed in Section 1.3.
Refer to Fig. 1-5.
Initial Prep
1.
Loosen compression handle by turning it counterclockwise until it is free from housing.
2.
Withdraw the support tube, bushing, washer and handle assembly keeping the bushing and washer in place on the support tube. When greater insertion depth of the conductivity cell into the process solution is desired, p/n 074344 Support Tube will give an additional 6 inches immersion beyond the standard depth. See Figs. 3-1 and 3-2. If 074344 Support Tube is to be used, it must be secured to the support grip.
3.
Slide the bushing and washer off of the standard support tube.
4.
Turn the compression handle counterclockwise to remove it from the support grip.
5.
Using a strap wrench, loosen and remove the standard support tube.
6.
Install 074344 Support Tube by wrapping one end with Teflon tape overlapping by 50% on each wrap.
Wrap the tape in a clockwise direction as viewed from the threaded end of the support tube.
7.
Thread this end into the support grip by hand and tighten an additional two turns by using a strap wrench. Do not use stillson or chain type wrenches as they may damage or score the support tube and prevent a good seal with the bushing.
8.
Replace the compression handle, washer and bushing removed earlier. Note the proper orientation of the bushing with the tapered surface facing away from the compression handle.
Mounting into the Process
The valve nipples and housing can now be mounted into the process pipeline or tank wall.
1.
Remove the protective cap and apply Teflon tape to mounting nipple. Wrap the tape on the threads in a clockwise direction as viewed from the threaded end. Overlap the tape by 50% on each wrap. Cover the threaded area twice in this manner.
2.
Install the mounting nipple and valve assembly hand tight.
12 4909 CPVC Conductivity Cell Insertion/Removal Assembly– Operations Manual 7/99
Installation
3.
Using a strap wrench on the mounting nipple, tighten the assembly an additional 1-1/2 to 2 turns. Do not use stillson or chain type wrenches as they may damage and weaken the CPVC plastic. Do not use the valve handle for leverage.
4.
Close the ball valve; handle perpendicular to valve.
A purge port is provided on the removal device housing. Water or some other fluid source can be piped to this port for the purpose of cleaning out the valve assembly from accumulated debris. For most conductivity applications, the process stream will not have high particle content and the purge port is not used.
If purging is required remove plug and install a purge line to the ¼” NPT opening. Note that the purge fluid temperature and pressure must not exceed the 4909 Assembly temperature and pressure specifications as shown in Fig. 1-1. Also, the purge line must have a shutoff valve located near the removal device.
Another use for the purge port can be realized if a pressure gage is installed in the ¼” NPT opening. It will serve as a local indication of process pressure to confirm that the pressure is below 50 psig during insertion or removal of the cell.
Make sure the bushing and washer are in place on the support tube, then feed the cable of the 4908
Conductivity Cell through the support tube and turn the tube hand tight onto the conductivity cell. Using a strap wrench, tighten the 4908 Cell an additional 1-1/2 to 2 turns. Do not score or gouge the support tube surface because the bushing makes a seal on the tube surface.
Tighten the cable grip to provide strain relief from the cell cable.
If X1 is selected in Table IV of the Model Selection Guide, then the 4908 Conductivity Cell has been premounted by Honeywell onto the support tube. Also cable wiring to the universal head terminal board has been completed. The valve assembly can then be mounted to the process by following steps under
“Mounting into the Process” mentioned earlier.
3.4 Insertion
1.
Make sure the bushing and washer (Fig. 1-5) are in place on the support tube. A thin film of silicone grease is applied at the factory to the bushing and to the support tube area covered by the compression handle. If this film has been wiped off or if dirt or grit is present, clean these areas and reapply a new film of silicone grease (p/n 090011, 0.3 oz. tube).
2.
Obtain the cell and support tube assembly prepared earlier. Separate the compression handle from the support grip by turning the support grip counterclockwise approximately two turns. Slide the compression handle along the support tube until the bushing and washer are sandwiched between the handle and 4908 Cell Adapter.
3.
Slide the cell and tube assembly into the removal device housing and tighten the compression handle clockwise until drag is felt on the tube. This can be determined by rotating the tube by hand.
4.
REDUCE PROCESS PRESSURE TO 50 PSIG OR LESS. Open the ball valve; handle parallel to valve.
5.
Push the cell and support tube assembly all the way in using the support grip.
6.
Tighten the support grip by turning clockwise two turns.
7/99
ATTENTION
This step is important to prevent blow-back of cell and support tube assembly. The bushing acts as a safety stop against the cell adapter if the support tube does blow back.
7.
Return the process to normal operating pressure.
8.
Further tighten the compression handle if leakage occurs from the bushing seal area.
4909 CPVC Conductivity Cell Insertion/Removal Assembly– Operations Manual 13
4909 CPVC Conductivity Cell Insertion/Removal Assembly Operations Manual
3.5 Removal
1.
REDUCE PROCESS PRESSURE TO 50 PSIG OR LESS. Shut off purge line, if used. Disconnect wiring connections if X1 is selected for Table IV in the MSG.
2.
DO NOT STAND BEHIND THE TUBE WHEN PERFORMING THIS STEP. While holding the compression handle from turning, turn the support grip two turns counterclockwise. Loosen the compression handle until the process pressure pushes the cell and support tube assembly out to its internal stop. If necessary, pull out by hand until stop is reached.
3.
Close the ball valve. If the valve does not close easily, make sure the support tube is pulled all the way back.
4.
Completely loosen the compression handle to withdraw the cell.
3.6 Electrical Connections
The terminal board connections for recorder or analyzer are given in the appropriate directions furnished with the measuring instrument.
When the cell assembly includes a built-in temperature compensator, all leads are used. The cell is connected between black and white and the compensator is between red and white, except when MSG Table
III=333. In this case, the built-in temperature compensator is between red and green. See Figs. 5-1 and 5-2 when wiring cells with MSG option=333.
To avoid the possibility of ac pick-up in the cell leads, separate them from all AC line voltage wiring or run them in a separate grounded conduit.
Cells are available with leadwire up to 20 feet as specified in the MSG assembly. For distances greater than
20 feet, use the required length of cable and a junction box, both listed in Section 4.3. For assemblies supplied with a Universal Head, Fig. 3-2, a junction box is not required.
14 4909 CPVC Conductivity Cell Insertion/Removal Assembly– Operations Manual 7/99
Installation
X "
See Below
* Standard Insertion Depth
Table I
X" Approx.
mm
001
0 1
5.5
5.5
140
140
1
5
5.5
140
114
1 0
20
4.5
5.7
6.0
145
152
25
50
6.8
6.8
173
173
Approx 4.1"
(105mm)
Approx 12.5"
(317mm)
Approx 19.7" max.
(502mm)
1/4" NPT
Purge connection. Do not exceed Temp./Press.
specifications of removal device
Allow a minimum clearance of 36"
(914 mm) beyond this point for removal of electrode.
Allow 42" (1067mm) if alternate support tube is used.
2.5"
(64mm)
* Add 6" (152 mm) to
Dimensions if 074344
Support Tube is Used.
0.940"
(24mm)
Dia
Temp.
Comp.
1 1/2 NPT
Schedule 80 Nipple
RED
WHITE
Cell
BLACK
Linear Micromho,
Resistivity, or
Concentration Ranges
RED
Shunt
Comp.
WHITE
Series
Comp.
Cell
BLACK
Non-Linear
Micromho Ranges
Cell
WHITE
BLACK
Without Temp.
Compensation
RED
Temp.
Comp.
GREEN
WHITE
Cell
BLACK
Linear Ranges
Electrode Cable, approx 0.25" (6.4mm)
O.D. max with 2, 3, or
4 conductors of
#18 AWG wire a/n 23355
Figure 3-1 Outline and dimension drawing for 4909-X-X-X-X-03-X-X Conductivity Cell,
Insertion Type with CPVC Removal Device
7/99 4909 CPVC Conductivity Cell Insertion/Removal Assembly– Operations Manual 15
4909 CPVC Conductivity Cell Insertion/Removal Assembly Operations Manual
X "
See Below
* Standard Insertion Depth
Suffix A
001
0 1
1
5
X" Approx.
5.5
5.5
5.5
4.5
mm
140
140
140
114
1 0
20
5.7
6.0
145
152
25
50
6.8
6.8
173
173
Approx 4.1"
(105mm)
Approx 12.5"
(317mm)
Approx 19.7" max.
(502mm)
2.5"
(64mm)
1/4" NPT
Purge connection. Do not exceed Temp./Press.
specifications of removal device
* Add 6" (152 mm) to
Dimensions if 074344
Support Tube is Used.
0.940"
(24mm)
Dia
RED
Temp.
Comp.
WHITE
Cell
BLACK
Linear Micromho,
Resistivity, or
Concentration Ranges
1-1/2" NPT
Schedule 80 Nipple
RED
Shunt
Comp.
WHITE
Series
Comp.
Cell
BLACK
Non-Linear
Micromho Ranges
WHITE
Cell
BLACK
Without Temp.
Compensation
Cell Wiring
1/2" female NPT for user’s flexible electrical conduit connection. For insertion or removal of cell, disconnect conduit connections.
RED
Temp.
Comp.
Cell
GREEN
WHITE
BLACK
Linear Ranges
(Table III = 333)
Allow a minimum clearance of 36"
(914 mm) beyond this point for removal of electrode.
Allow 42" (1067mm) if alternate support tube is used.
3"
(76mm) a/n 23346
Figure 3-2 Outline and Dimension drawing for 4909-X-X-X-X1-03-X-X Conductivity Cell,
Insertion Type with CPVC Removal Device and Universal Head
16 4909 CPVC Conductivity Cell Insertion/Removal Assembly– Operations Manual 7/99
Maintenance and Replacement Parts
4. Maintenance and Replacement Parts
If a series of below normal conductivity readings or above normal resistivity readings occur, this may indicate that the cell is not filled with process solution. Check the cell installation. Refer to Sections 3.1
and 3.2.
The only maintenance which may be required is occasional cleaning in certain applications. The 0.01, 0.1, and 1.0 cm
-1
low constant electrodes are not platinized.
4.1 To Clean The Cell
CAUTION
The cell assembly is PES (polyethersulfone). Do not clean with acetone, chloroform, toluene, benzene, or any chlorinated hydrocarbon.
The cell will require cleaning if sludge, slime, etc., accumulates in the flow channels. Since the materials of construction are chemically inert, chemical agents may be used and are recommended for cleaning the cells.
The particular cleaning agent used must be selected according to the type of contamination to which the cell is exposed. In general, soap and hot water cleaning solution is effective. Immerse the plastic body of the cell in this solution. A 10 or 15 minute soaking period should be adequate. If necessary, a soft bristle brush of appropriate diameter may be used to clean out the tubular channels of the 5, 10, 20, 25 and 50 constant cells. Care must be taken not to scratch the electrode surfaces. Do not use a brush on the low (0.01, 0.1
and 1) constant cells and be especially careful not to bend the electrode plates of the 0.1 constant cell.
Rinse the cell thoroughly in tap water and then in distilled water if available. To remove the platinum black from electrodes (5 to 50 constants only), refer to Section 5. Replatinizing after each cleaning (5 to 50 constant cells only) may not be necessary unless brushing was used.
4.2 Replacing Removal Device Parts
Ball Valve
If a new ball valve is installed, orient the valve body so that the heavy walled end is toward the process connection for added support strength. See Teflon tape note below.
Nipples
If nipples are replaced, use exact replacement to ensure pressure and temperature ratings, proper immersion length and proper operation of removal device.
Use only Teflon tape on all valve, nipple and support tube pipe threads. Other liquid or paste sealants may contain solvents that weaken the CPVC material.
Bushing And Washer
Replace these parts if swollen, cracked or damaged in a way that prevents a good seal on the support tube.
Lightly grease the new bushing with silicone grease before installing.
Note that the support grip must be removed from the support tube before replacing the bushing and/or washer. Orient the bushing so that the tapered surface faces away from the compression handle, Fig. 1-5.
7/99 4909 CPVC Conductivity Cell Insertion/Removal Assembly– Operations Manual 17
4909 CPVC Conductivity Cell Insertion/Removal Assembly Operations Manual
4.3 Replacement Parts
Table 4-1 Replacement Parts
Description
Complete Assembly
Cell Assembly
Complete CPVC Removal Device
Universal Head Parts
Part Number
See Figs. 1-5 and 1-6
Cat. 4908
31074357
See Fig. 1-6
Platinizing Solution (3 oz. bottle)
Cell Guard Tube (0.01, 0.1, and 1.0 Constants Only)
Support Tube, 1/2” NPT Sch. 80, CPVC (12” Immersion)
Support Tube, 1/2” NPT Sch. 80, CPVC (6” Immersion)
Junction Box
Cell Extension Leadwire (Table III other than 333)
Three conductor 18 gage cable PVC (105
°
C max.)
Three conductor 18 gage cable Tefzel (150
°
C max.)
9782/7082 Standard Ranges
Up to 500 ft.
Three conductor, 18 gage cable (Belden 9493)
and Coax Cable (Belden 9259)
Up to 1000 ft
Four conductor (3 used), 16 gage cable,
Belden 9494 or equivalent and Coax Cable (Belden 9259)
9782/7082 Wide Ranges
Up to 500 ft - Four Conductor, 18 gage
Up to 1000 ft - Four Conductor, 16 gage
31103011
065602
074344
074343
31316260
834059
834086
834059
835024
834055
835024
31834052
834055
Table 4-2 Voltage and Time Limits for Platinizing Cells
Cell Constant
DC Voltage 5 10 20 25 50
1.5
3.0
6.0
12.0
----
200 sec
80 sec
----
----
240 sec
100 sec
----
----
----
180 sec
120 sec
----
----
200 sec
150 sec
----
----
300 sec
240 sec
18 4909 CPVC Conductivity Cell Insertion/Removal Assembly– Operations Manual 7/99
Platinization and Platinum Black
5. Platinization and Platinum Black
Only the electrodes having constants from 5 to 50 must be replatinized if the velvety-black deposit has been rubbed off the electrodes in service or in cleaning, or if platinized electrodes are recommended and this black deposit is not present when the cell is received. Always replatinize if a brush was used in cleaning the electrodes. The indication of a need for replatinization of the electrodes is a long term drift of the measuring instrument caused by an apparent increase in cell constant as the platinum black coating is depleted from the electrode surfaces. The electrodes of the high constant cells are not visible since they are located near the middle of the flow channels. Therefore the need for platinization is only indicated by the effect on the measuring instrument. Do not platinize cells intended for measuring high purity water.
Before platinizing, clean the cell with detergent and brush as described in Section 4.1.
Support the cell in a cylindrical vessel with the end of the cell raised from the bottom. It is not necessary to remove the cell from the fittings for platinizing. However, the guard tube must be removed from the low constant cells. Pour in platinizing solution (p/n 31103011) to a level above the cross-channel.
To platinize the 5, 10, 20, 25 and 50 constant cells, immerse an auxiliary platinum electrode* in the solution to a point about midway between the cross-channel or tube hole and the open end of the cell. Both electrodes of the cell are platinized simultaneously by connecting the negative terminal of the battery (see
Table 4.2 for voltage) to both leadwires of the cell.
ATTENTION
* This third electrode should be chemically pure platinum. Its shape is unimportant. It may be one of the electrodes in another conductivity cell or a platinum strip, sheet, rod, wire, etc.
Connect the positive terminal of the battery to the auxiliary platinum electrode. Note the time in seconds listed in Table 4.2. During the platinizing operation, move the cell up and down gently to keep the solution stirred. Then disconnect the battery and remove the cell. Rinse the cell thoroughly in tap water and then rinse in distilled water.
Pour the platinizing solution back into its container as it may be used a number of times.
7/99 4909 CPVC Conductivity Cell Insertion/Removal Assembly– Operations Manual 19
4909 CPVC Conductivity Cell Insertion/Removal Assembly Operations Manual
Four Point Terminal Plate with #6-32 Screw Terminals
Five Point Terminal Board.
Each Terminal Will Accept
#16 Gage Max. Wire
1000 ft. max.
RED
B
Temp.
Comp.
GREEN
D
Cell
WHITE
C
BLACK
A
Internal Cell Assembly
Configuration
A
B
D
C
Note 3
B
D
A
C
Coax Cable Shield
4905
View of Junction Box Head with Cap Removed
l l A s l y n n
I II III IV
V VI
- - 333 - X1
4973
4974
I II III
- 333 - X1 -
IV V
4908
4909
I II III IV V VI
- - 333 - X1
VII
Note 2
Note 1
An
W K SH G
Conductivity/Resistivity
l y r I np
Analyzer
t C e n
R
NOTES:
1. For pure water samples in non-conductive (plastic, glass, etc.) piping, ground the black cell electrode lead near the cell. Alternatively,
connect to the 7082 ground screw as shown dotted. Do not ground 10, 25, or 50 constant cells.
2. 70 1 17 , (only)
Use 22 gage minimum coaxial cable type RG59/U connecting shield to terminal "SH" only.
3. 70 2 , 1 , 1 9
For cable runs of up to 500 ft., use: 18 gage minimum, three conductor cable.
For cbale runs of 500 - 1000 ft., use: 16 gage minimum, three conductor cable.
7 2 , , 1 [coax and shield (SH) not used]
For cable runs of up to 500 ft., use: 18 gage minimum, four conductor cable.
For cable runs of 500 - 1000 ft., use: 16 gage minimum, four conductor cable.
4. Cell to analyzer cables are considered low level. Run seperate from high level wiring.
GND
Figure 5-1 Installation Diagram-Cat. 4909 Cells with Junction Box Head
Connected to 7082 Conductivity/Resistivity Analyzer
a/n 23345
20 4909 CPVC Conductivity Cell Insertion/Removal Assembly– Operations Manual 7/99
Platinization and Platinum Black
Five Point Terminal Board.
Each Terminal Will Accept
#16 Gage Max. Wire
RED
B
Temp.
Comp.
GREEN
D
WHITE C
Cell
BLACK
A
Internal Cell Assembly
Configuration
Four Point Terminal Plate with #6-32 Screw Terminals
A
B
D
C
1000 ft. max.
Note 3
D
B
Note 2
R
W
K
W
K
SH
G
R
G
(Note 5)
#2 Temp
Compensator
#1 Temp
Compensator
Cell 2
(Note 5)
Electrodes
Cell 1
Electrodes
View of Junction Box Head with Cap Removed
C
A
Coax Cable
Shield
Note 1
4905
4973
4974
l l A s l y n n
I II III IV V VI
- - 333 - X1
I II III
- 333 - X1 -
IV V
Conductivity/Resistivity
Analyzer
An l y r I np t C e n
4908
4909
I II III IV
- - 333 - X1
V VI VII
NOTES:
1. For pure water samples in non-conductive (plastic, glass, etc.) piping, ground the black cell electrode lead near the cell. Alternatively,
connect to the 9782 ground screw as shown dotted. Do not ground 10, 25, or 50 constant cells.
2. 97 2C (only)
Use 22 gage minimum coaxial cable type RG59/U connecting shield to terminal "SH" only.
3. 9 8 0
For cable runs of up to 500 ft., use: 18 gage minimum, three conductor cable.
For cbale runs of 500 - 1000 ft., use: 16 gage minimum, three conductor cable.
9 2C
For cable runs of up to 500 ft., use: 18 gage minimum, four conductor cable.
For cable runs of 500 - 1000 ft., use: 16 gage minimum, four conductor cable.
4. Cell to analyzer cables are considered low level. Run seperate from high level wiring.
5. If 2 Cells are to be appplied, the same wiring guidelines are applied to Cell 2 as are followed for Cell 1.
Figure 5-2 Installation Diagram-Cat. 4909 Cells with Junction Box Head
Connected to 9782 Conductivity/Resistivity Analyzer
GND
7/99 4909 CPVC Conductivity Cell Insertion/Removal Assembly– Operations Manual 21
4909 CPVC Conductivity Cell Insertion/Removal Assembly Operations Manual
Temp.
Comp.
Cell
RED
GREEN
WHITE
BLACK
4905
4973
4974
4908
4909
s s e l y e i o
I II III IV V VI
- - 333 - X1
I II III
- 333 - X1 -
IV V
I II III IV V VI
- - 333 - X1
VII
20 ft. max.
Five Point Terminal Board.
Each Terminal Will Accept
#16 Gage Max. Wire
Red
Green
Black
White
Cell cable is approx. .250"
(6.4mm) O.D. max. with 4 conductors of #18 AWG wire, 7 or 20 foot length.
i r e t C A a r I n t a t i o
W K SH G R
Note 1
Conductivity / Resistivity Analyzer
An l y ze t C e ti o s
GND
20 ft. max.
1000 ft. max.
Note 3
4905
4973
4974
4908
4909
l l A s l y Co e i o s
I II III IV V VI
- - 333 - X1
I II III
- 333 - X1 -
IV V
I II III IV V VI
- - 333 - X1
VII
Red
Green
Black
White
Junction Box
R
G
K
W
C l l t o a r T r o h n t i o o
Note 2
Coax Cable Shield
Note 1
W K
SH G R
NOTES:
1. For pure water samples in non-conductive (plastic, glass, etc.) piping, ground the black cell electrode lead near the cell.
Alternatively, connect to the 7082 ground screw as shown dotted. Do not ground 10, 25, or 50 constant cells.
2. 70 1 , 1 , (only)
Use 22 gage minimum coaxial cable type RG59/U connecting shield to terminal "SH" only.
3. 70 -1 , 1 , 1 , 1
For cable runs of up to 500 ft., use: 18 gage minimum, three conductor cable.
For cbale runs of 500 - 1000 ft., use: 16 gage minimum, three conductor cable.
7 2 , , 1 [coax and shield (SH) not used]
For cable runs of up to 500 ft., use: 18 gage minimum, four conductor cable.
For cable runs of 500 - 1000 ft., use: 16 gage minimum, four conductor cable.
4. Cell to analyzer cables are considered low level. Run seperate from high level wiring.
Conductivity/Resistivity
Analyzer
An l y r I
Co n
n u
t i on
t
s
GND a/n 23346
Figure 5-3 Installation Diagram-Cat. 4909 Cells with 7 or 20 Foot Leads
Connected to 7082 Conductivity/Resistivity Analyzer
22 4909 CPVC Conductivity Cell Insertion/Removal Assembly– Operations Manual 7/99
Temp.
Comp.
Cell
RED
GREEN
WHITE
BLACK
Platinization and Platinum Black
Five Point Terminal Board.
Each Terminal Will Accept
#16 Gage Max. Wire
20 ft. max.
Red
Green
Black
White
K
W
K
R
W
SH
G
R
G
#2 Temp
#1 Temp
Compensator
Cell 2
(Note 5)
Electrodes
Cell 1
Electrodes
Cell cable is approx. 0.250"
(6.4mm) O.D. max. with 4 conductors of #18 AWG wire, 7 or 20 foot length.
Note 1
i r e t C A a r I n t a t i o
Conductivity/Resistivity
Analyzer
An l y r I np t C e s
(Note 5)
Compensator
GND 4905
4973
4974
4908
4909
l l A s l y n n
I II III IV
V VI
- - 333 - X1
I II III
- 333 - X1 -
IV V
I II III IV V VI
- - 333 - X1
VII
4905
4973
4974
4908
4909
s s e l y e i o
I II III IV
V VI
- - 333 - X1
I II III
- 333 - X1 -
IV V
I II III IV V VI
- - 333 - X1
VII
20 ft. max.
Red
Green
Black
White
Junction Box
R
G
K
W
1000 ft. max.
Note 3
C l l t o a e r o h n t i o B
Note 2
Coax Cable
Shield
Note 3
Note 1
K
W
K
SH
G
R
G
R
W
#2 Temp
Compensator
#1 Temp
Compensator
Cell 2
(Note 5)
Electrodes
Cell 1
Electrodes
Conductivity/Resistivity
Analyzer
An l y r I np t C e ti o s
NOTES:
1. For pure water samples in non-conductive (plastic, glass, etc.) piping, ground the black cell electrode lead near the cell.
Alternatively, connect to the 9782 ground screw as shown dotted. Do not ground 10, 25, or 50 constant cells.
2. 97 - S (only)
Use 22 gage minimum coaxial cable type RG59/U connecting shield to terminal "SH" only.
3. 9 8 - S
For cable runs of up to 500 ft., use: 18 gage minimum, three conductor cable.
For cbale runs of 500 - 1000 ft., use: 16 gage minimum, three conductor cable.
9 78 - W0
For cable runs of up to 500 ft., use: 18 gage minimum, four conductor cable.
For cable runs of 500 - 1000 ft., use: 16 gage minimum, four conductor cable.
4. Cell to analyzer cables are considered low level. Run seperate from high level wiring.
5. If 2 Cells are to be applied, the same guidelines are applied to Cell 2 as wereused for Cell 1.
(Note 5)
GND a/n 23346
Figure 5-4 Installation Diagram-Cat. 4909 Cells with 7 or 20 Foot Leads
Connected to 9782 Conductivity/Resistivity Analyzer
7/99 4909 CPVC Conductivity Cell Insertion/Removal Assembly– Operations Manual 23
Industrial Automation and Control
Honeywell, Inc.
1100 Virginia Drive
Fort Washington, Pennsylvania 19034
advertisement
* Your assessment is very important for improving the workof artificial intelligence, which forms the content of this project
Related manuals
advertisement
Table of contents
- 9 INTRODUCTION
- 9 Overview
- 9 4908 Conductivity Cell
- 10 31074357 Removal Device
- 15 SPECIFICATIONS AND MODEL SELECTION GUIDE
- 15 Specifications
- 15 Cell Constants
- 15 Electrode Material
- 15 Wetted Parts
- 15 Pressure and Temperature (See Fig. 1-1)
- 15 Maximum Pressure
- 15 Mounting
- 15 Purge Port
- 15 Insertion Depth
- 15 Electrical Connections
- 16 Integral Automatic Temperature Compensation
- 16 Leadwire
- 16 Weight
- 16 Model Selection Guide
- 19 INSTALLATION
- 19 Requirements
- 19 Location and Position
- 19 Considerations
- 20 Prepare Assembly
- 20 Initial Prep
- 20 Mounting into the Process
- 21 Insertion
- 22 Removal
- 22 Electrical Connections
- 25 MAINTENANCE AND REPLACEMENT PARTS
- 25 To Clean The Cell
- 25 Replacing Removal Device Parts
- 25 Ball Valve
- 25 Nipples
- 25 Bushing And Washer
- 26 Replacement Parts
- 27 PLATINIZATION AND PLATINUM BLACK