Bryant 502A User manual
Add to my manualsadvertisement
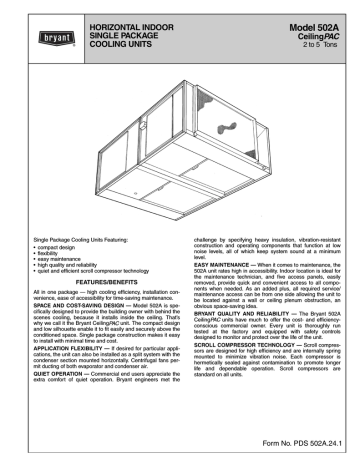
HORIZONTAL INDOOR
SINGLE PACKAGE
COOLING UNITS
Model 502A
CeilingPAC
2 to 5 Tons
Single Package Cooling Units Featuring:
• compact design
• flexibility
• easy maintenance
• high quality and reliability
• quiet and efficient scroll compressor technology
FEATURES/BENEFITS
All in one package — high cooling efficiency, installation convenience, ease of accessibility for time-saving maintenance.
SPACE AND COST-SAVING DESIGN — Model 502A is specifically designed to provide the building owner with behind the scenes cooling, because it installs inside the ceiling. That’s why we call it the Bryant CeilingPAC unit. The compact design and low silhouette enable it to fit easily and securely above the conditioned space. Single package construction makes it easy to install with minimal time and cost.
APPLICATION FLEXIBILITY — If desired for particular applications, the unit can also be installed as a split system with the condenser section mounted horizontally. Centrifugal fans permit ducting of both evaporator and condenser air.
QUIET OPERATION — Commercial end users appreciate the extra comfort of quiet operation. Bryant engineers met the challenge by specifying heavy insulation, vibration-resistant construction and operating components that function at low noise levels, all of which keep system sound at a minimum level.
EASY MAINTENANCE — When it comes to maintenance, the
502A unit rates high in accessibility. Indoor location is ideal for the maintenance technician, and five access panels, easily removed, provide quick and convenient access to all components when needed. As an added plus, all required service/ maintenance access can be from one side allowing the unit to be located against a wall or ceiling plenum obstruction, an obvious space-saving idea.
BRYANT QUALITY AND RELIABILITY — The Bryant 502A
CeilingPAC units have much to offer the cost- and efficiencyconscious commercial owner. Every unit is thoroughly run tested at the factory and equipped with safety controls designed to monitor and protect over the life of the unit.
SCROLL COMPRESSOR TECHNOLOGY — Scroll compressors are designed for high efficiency and are internally spring mounted to minimize vibration noise. Each compressor is hermetically sealed against contamination to promote longer life and dependable operation. Scroll compressors are standard on all units.
Form No. PDS 502A.24.1
TABLE OF CONTENTS
Page
Features/Benefits . . . . . . . . . . . . . . . . . . . . . . . . . . . . . . . . . . 1
Model Number Nomenclature . . . . . . . . . . . . . . . . . . . . . . . . . 2
ARI Capacity Ratings. . . . . . . . . . . . . . . . . . . . . . . . . . . . . . . . 2
Physical Data . . . . . . . . . . . . . . . . . . . . . . . . . . . . . . . . . . . . . 3
Field-Installed Accessories . . . . . . . . . . . . . . . . . . . . . . . . . . . 4
Base Unit Dimensions . . . . . . . . . . . . . . . . . . . . . . . . . . . . . . . 5
Selection Procedure . . . . . . . . . . . . . . . . . . . . . . . . . . . . . . . . 6
Performance Data . . . . . . . . . . . . . . . . . . . . . . . . . . . . . . . . .6-8
Controls . . . . . . . . . . . . . . . . . . . . . . . . . . . . . . . . . . . . . . . . . 9
Electrical Data . . . . . . . . . . . . . . . . . . . . . . . . . . . . . . . . . . . 9,10
Typical Wiring Schematics . . . . . . . . . . . . . . . . . . . . . . . . 10-13
Typical Piping and Wiring . . . . . . . . . . . . . . . . . . . . . . . . . . . 14
Application Data . . . . . . . . . . . . . . . . . . . . . . . . . . . . . . . . . . 14
Guide Specifications . . . . . . . . . . . . . . . . . . . . . . . . . . . . 15,16
Model Designation
502A Horizontal, Indoor
Single-Package Cooling Unit
MODEL NUMBER NOMENCLATURE
502A P X 048 000 AB
Indoor Fan Motor
AA — Standard Motor
AB — 1.5 hp Optional Motor*
Electric Heaters
000 — No factory-installed electric heaters
Nominal Tons
024 — 2
036 — 3
048 — 4
060 — 5
Voltage
J — 208/230-1-60
P — 208/230-3-60
E — 460-3-60
T — 575-3-60
X — Heat Not Installed
(field-installed electric heaters available)
*Factory-Installed option, contact your local representative for specific information.
ARI* CAPACITY RATINGS
UNIT
502A
024
V-PH-Hz
TOTAL kW
2.6
NET TOTAL
COOLING CAP. (Btuh)
25,000
036
048
060
208/230-1-60
208/230-1-60
208/230-3-60
460-3-60
208/230-1-60
208/230-3-60
460-3-60
575-3-60
208/230-1-60
208/230-3-60
460-3-60
575-3-60
4.3
5.5
6.9
36,000
49,500
58,500
LEGEND dB — Decibels
EER — Energy Efficiency Ratio
SEER — Seasonal Energy Efficiency Ratio
TDR — Time-Delay Relay
*Air-conditioning and Refrigeration Institute.
NOTES:
1. Ratings are at zero condenser air static and rated in accordance with ARI
Standard 210.
2. EER =
NET CAPACITY (Btuh)
TOTAL WATTS
NOMINAL
CFM
800
1200
1600
2000
EER
—
—
9.0
9.0
—
9.1
9.1
9.1
—
8.55
8.55
8.55
SEER
10.80
10.00
—
—
10.20
—
—
—
9.75
—
—
—
SEER
(with TDR)
11.00
10.05
—
—
10.40
—
—
—
10.05
—
—
—
SOUND RATING
(dB)
78
82
82
82
2
PHYSICAL DATA
UNIT 502A
SHIPPING WEIGHT (lb)*
OPERATING WEIGHT (lb)
Base Unit
REFRIGERANT TYPE
Operating Charge (lb)†
COMPRESSOR — TYPE
Quantity...Model
Oil (oz)
HPS Setting (psig)
Cutout
Reset
LPS Setting (psig)
Cutout
Reset
CONDENSATE DRAIN CONNECTION
Size (in.)...Type
CONDENSER FAN
Nominal Cfm
Maximum Rpm
Blower Size (in.)
Pulley Pitch Diameter (in.)
Blower
Motor (Variable)
Motor Hp
Motor Rpm
EVAPORATOR AIR FAN (Standard)
Nominal Cfm
Max Rpm
Blower Size (in.)
Motor Hp (Rpm)
EVAPORATOR AIR FAN (Optional)
Nominal Cfm
Max Rpm
Blower Size (in.)
Motor Hp
Motor Rpm
Pulley Pitch Diameter (in.)
Blower
Motor (Variable)
CONDENSER COIL
Size (L x H) (in.)
Number of Rows...Fins/in.
EVAPORATOR COIL
Size (L x H) (in.)
Number of Rows...Fins/in.
INDOOR-AIR FILTERS
Number...Size (in.)
INTERCONNECTING TUBING SIZE (in.)**
Hot Gas
Liquid
024
560
450
5.4
(1)...ZR23
24
Centrifugal — Direct Drive
LEGEND
HPS — High-Pressure Switch
LPS — Low-Pressure Switch
*Shipping weights include base unit plus packaging.
†If components are to be split, additional refrigerant will be needed.
**Use Type L copper only.
1
1350
None
None
1 /
2
825
800
1100
10 x 5
/
6
(850)
40 x 15
4...13.6
34 x 15
4...14.4
1 /
3 /
2
8
1100
12 x 6
Not
Available
1...14 x 34 x 1
036
590
480
5.5
(1)...ZR34
42
1350
R-22
Scroll
426 ± 7
320 ± 20
27 ± 4
67 ± 7
048
690
580
8.0
(1)...ZR49
48
3 /
4
...FPT
Centrifugal — Belt Drive
2250
1500
12 x 9
2450
5.0
2.4-3.4
3 /
4
1725
6.0
1.9-2.9
1
1725
Centrifugal — Direct Drive
1200
1150
1 /
10 x 6
2
(1075)
1600
1050
3 /
10 x 6
4
(1050)
Centrifugal Belt Drive
1600
1300
10 x 8
1 1 /
2
1725
6.0
2.4-3.4
1 1 /
2
1725
2000
2000
Copper Tubes — Aluminum Fins
40 x 16
4...17
Copper Tubes — Aluminum Fins
34 x 16
4...15
Factory-Supplied Cleanable Type
4.2
2.4-3.4
40 x 22
4...13.6
34 x 22
4...14.4
1...21 x 34 x 1
060
700
590
7.6
(1)...ZR57
54
1 /
2
3 /
8
1 /
2
3 /
8
1 /
2
3 /
8
NOTE: If components are to be split, the maximum length of refrigerant tubing to be used is 50 equivalent ft, assuming components will be installed in same horizontal plane.
If components are not to be installed in same horizontal plane, contact your Bryant representative for more information.
NOTE: Fasten threaded rods through holes in end frames. Use 2 rods on each side of unit for a total of 4.
All panels must be in place when rigging.
UNIT
502A
024
036
048
060
OPERATING WEIGHT DISTRIBUTION AND
CENTER OF GRAVITY
1
WEIGHT (lb/kg)
OF CORNER
2 3 4
93/42 108/49 139/63 120/54
95/43 113/51 148/67 124/56
112/51 143/65 183/83 142/64
114/52 143/65 186/84 147/67
2-5 /737
2-4
2-5 /737
2-4
3
3
A
DIMENSIONS
(ft-in./mm)
B
/
/
4
4
/730
/730
2-1
2-2 /660
2-3
5 /
8
/651
/686
2-2 3 /
4
/679
3
FIELD-INSTALLED ACCESSORIES
Thermostat and Subbase — Attractive wall-mounted 24-v accessory provides precise temperature control. Automatic and
Manual changeover models available. A thermostat subbase is available that works with Cycle-LOC™ circuitry. If a safety device trips, compressor locks out and subbase warning light
(LK OUT) alerts occupant.
Two models available: Two stage cool/two stage heat and one stage cool/one stage heat.
Time Guard® II Circuit (standard on single-phase units) —
Time Guard II device prevents short cycling of compressor if thermostat is rapidly changed; automatically prevents compressor from restarting for 5 minutes after shutdown.
Electric Heaters — A wide range of models available from 5 to
30 kW, 208-, 240- and 480-v, single- and 3-ph units. Mount easily on 502A discharge opening. Heater control box accessible from the bottom of heater.
Condensate Pump — The condensate pump is used when the distance and slope to the nearest drain is far enough to prevent the natural drainage of unit. The pump is mounted remotely from the unit and includes a signal light (field-installed) which illuminates when the reservoir rises beyond a certain level. The unit automatically shuts down when this reservoir level is achieved.
Head Pressure Control Damper — This accessory is duct mounted and allows unit to mechanically cool down to 0° F.
Damper dimensions fit 024, 036 sizes.
NOTE: For use with 048 and 060 size units, ductwork from unit to damper must be reduced in size to fit damper dimensions.
Vibration Isolators — Package of four isolators used for dampening any unit vibration so that vibrating sounds are not transmitted to building structure. Isolators are spring, ceiling type.
88EN ELECTRIC HEAT MODULE
ACCESSORY
HEAD PRESSURE CONTROL DAMPER (in.)
DIMENSIONS (in.)
UNIT
502A
A B C
024,036 13 1 /
2
16 2 1 /
2
048,060 24 21 3 /
4
3
D
8 1 /
2
DUCT
OPENING
7 1 /
8
x 14
19 7 1 /
8
x 20 7 /
8
4
BASE UNIT DIMENSIONS
UNIT
502A
024
036
048
060
DIMENSIONS (ft-in.)
A
2-5
2-4 3 /
4
2-5
2-4 3 /
4
B
2-1 5 /
8
2-2
2-3
2-2 3 /
4
C
1- 5 3 /
4
1- 5 3 /
4
1-11 5 /
8
1-11 5 /
8
D
1-2
1-2
1-8 7 /
8
1-8 7 /
8
E
1-1
1-1
1-7 7 /
8
1-7 7 /
8
Unit Component Locations
5
SELECTION PROCEDURE (with example)
I DETERMINE COOLING REQUIREMENTS AT DESIGN
CONDITIONS.
Given:
Gross Cooling Capacity
Required (TC) . . . . . . . . . . . . . . . . . . . . . . . . . 39,000 Btuh
Sensible Heat Capacity (SHC) . . . . . . . . . . . . 30,500 Btuh
Temperature of Air Entering Condenser . . . . . . . . . . . 95 F
Temperature of Air Entering
Evaporator. . . . . . . . . . . . . . . . . . . . . 80 F edb/67 F ewb
Evaporator Air Quantity . . . . . . . . . . . . . . . . . . . 1,200 cfm
External Static Pressure:
Condenser . . . . . . . . . . . . . . . . . . . . . . . . . . 0.50 in. wg
Evaporator (includes static pressure drop of factory-supplied filter of 0.06 in. wg) . . . . . . . . . . . . . . . . . . . . . . 0.20 in. wg
II SELECT UNIT BASED UPON REQUIRED COOLING
CAPACITY.
Enter cooling capacity table at temperature of air entering condenser of 95 F. The 502A036 unit at 1200 cfm and
67 F ewb will provide a Total Capacity (TC) of 44,200 Btuh and a Sensible Heat Capacity (SHC) of 31,300 Btuh.
Since the entering air is 80 F edb, an SHC correction is not required.
III DETERMINE EVAPORATOR FAN PERFORMANCE.
Enter Evaporator Fan Performance table at 1200 cfm and 502A036 data. The external static pressure shown
(0.23 in. wg) will exceed the 0.20 in. wg required. The fan motor will require 0.52 kW.
IV DETERMINE CONDENSER FAN PERFORMANCE AND
MOTOR PULLEY SETTING REQUIREMENTS.
Enter Condenser Fan Performance table at the selected cfm and required static pressure of 0.50 in. wg. The fan motor will require 0.73 kW and the motor pulley should be set at 2 turns open at 1350 cfm of condenser air required.
NOTE: Unit 502A024 contains a direct-drive condenser fan assembly.
PERFORMANCE DATA
GROSS COOLING CAPACITIES
502A024
Temp
Air Ent
Condenser
(F)
85
Evaporator Air Quantity — Cfm/BF
600/0.02
800/0.03
1000/0.04
Evaporator Air Ewb Temp (F)
72 67 62 72 67 62 72 67 62
TC 27.1 25.3 23.0 27.7 26.4 24.6 27.8 26.9 25.8
SHC 13.5 17.0 20.2 14.7 19.4 23.7 15.6 21.5 25.8
kW 1.64 1.62 1.61 1.65 1.63 1.62 1.65 1.64 1.63
95
105
115
TC 26.6 24.5 20.8 27.4 25.8 22.9 28.0 26.5 25.2
SHC 13.4 16.7 19.1 14.7 19.4 22.8 16.0 21.7 25.2
kW 1.85 1.84 1.80 1.86 1.85 1.82 1.87 1.85 1.84
TC 25.8 22.3 18.4 27.1 24.5 21.2 27.7 25.6 23.6
SHC 13.1 15.8 17.9 14.7 18.9 21.2 16.2 21.5 23.6
kW 2.09 2.05 1.99 2.11 2.08 2.04 2.12 2.10 2.07
TC 24.6 19.9 16.5 26.1 22.0 19.8 26.8 23.6 22.3
SHC 12.7 14.8 16.5 14.4 17.9 19.8 16.0 20.7 22.3
kW 2.36 2.29 2.22 2.39 2.33 2.29 2.39 2.35 2.33
See Legend on page 7.
502A036
Temp
Air Ent
Condenser
(F)
85
Evaporator Air Quantity — Cfm/BF
900/0.01
1050/0.01
1200/0.02
Evaporator Air Ewb Temp (F)
72 67 62 72 67 62 72 67 62
TC 45.0 41.1 37.3 45.8 42.3 38.6 46.5 43.4 39.8
SHC 22.5 27.7 32.6 23.6 29.9 35.6 24.6 32.0 38.3
kW 3.19 3.07 2.96 3.22 3.11 3.00 3.25 3.14 3.04
95
105
115
TC 43.0 38.8 34.3 44.1 40.1 35.8 45.0 44.2 37.4
SHC 21.8 26.8 31.1 23.1 29.1 34.1 24.4 31.3 36.8
kW 3.42 3.28 3.15 3.46 3.33 3.20 3.49 3.37 3.25
TC 40.4 35.8 29.6 41.6 37.1 31.3 42.6 38.2 33.2
SHC 20.9 25.6 28.5 22.3 27.9 30.8 23.7 30.2 33.2
kW 3.63 3.48 3.38 3.68 3.53 3.44 3.73 3.58 3.49
TC 37.7 30.6 25.8 38.7 31.6 37.8 39.7 32.8 29.7
SHC 19.9 23.3 25.8 21.3 25.5 27.8 22.7 27.8 29.7
kW 3.85 3.71 3.59 3.90 3.76 3.67 3.94 3.80 3.73
6
PERFORMANCE DATA (cont)
GROSS COOLING CAPACITIES (cont)
502A048
Temp
Air Ent
Condenser
85
95
105
115
(F)
Evaporator Air Quantity Cfm/BF
1200/0.06
1600/0.08
Evaporator Air Ewb Temp (F)
2000/0.10
72 67 62 57 72 67 62 57 72 67 62 57
TC 56.0 52.1 47.9 44.4 57.7 54.5 50.6 49.6 59.4 56.0 52.7 52.3
SHC 27.8 34.8 41.6 44.4 30.2 39.6 48.0 49.6 32.8 43.9 52.5 52.3
kW 3.77 3.68 3.59 3.53 3.81 3.74 3.66 3.64 3.85 3.77 3.70 3.69
TC 54.0 50.1 45.7 42.4 55.7 52.3 48.6 47.3 57.4 53.8 51.0 50.9
SHC 27.1 34.0 40.4 42.4 29.6 38.8 47.0 47.3 32.4 43.2 50.9 50.9
kW 4.21 4.11 4.01 3.95 4.25 4.18 4.09 4.07 4.31 4.21 4.15 4.15
TC 51.8 47.9 42.3 40.2 53.6 50.0 45.1 45.0 54.6 51.4 48.9 48.6
SHC 26.3 33.1 38.8 40.2 29.0 38.0 44.8 45.0 31.3 42.4 48.9 48.6
kW 4.69 4.58 4.45 4.40 4.75 4.65 4.54 4.53 4.77 4.69 4.63 4.63
TC 49.5 45.5 38.6 37.7 51.2 47.6 41.9 42.1 52.2 49.1 45.8 45.8
SHC 25.5 32.2 37.0 37.7 28.3 27.3 41.8 42.1 30.7 42.0 45.8 45.8
kW 5.21 5.09 4.92 4.89 5.27 5.17 5.03 5.03 5.30 5.23 5.14 5.14
LEGEND
BF — Bypass Factor
Ewb — Entering Wet-Bulb kW — Compressor Motor Power Input (kilowatts)
SHC — Gross Sensible Heat Capacity (1000 Btuh)
TC — Gross Total Cooling Capacity (1000 Btuh)
NOTES:
1. Performance based on nominal condenser airflow listed in physical data table on page 3.
2. SHC is based on 80 F db temperature of air entering the coil.
Below 80 F db, subtract (corr factor x cfm) from SHC.
Above 80 F db, add (corr factor x cfm) to SHC.
502A060
Temp
Air Ent
Condenser
85
95
105
115
(F)
Evaporator Air Quantity — Cfm/BF
72
1500/0.06
67
2000/0.09
Evaporator Air Ewb Temp (F)
62 72 67 62 72
2250/0.10
67 62
TC 64.8
58.5
52.9
68.0
61.5
56.3
68.9
62.5
58.0
SHC 33.2
41.1
48.5
37.2
47.3
55.7
38.9
50.0
57.7
kW 4.49
4.29
4.13
4.59
4.83
4.22
4.62
4.41
4.27
TC 61.9
55.7
50.2
65.1
58.7
54.0
66.1
59.7
55.8
SHC 32.3
40.1
47.3
36.4
46.5
54.0
38.2
49.3
55.8
kW 4.94
4.72
4.57
5.04
4.81
4.67
5.07
4.84
4.72
TC 58.5
52.4
47.2
61.5
55.2
51.4
62.6
56.3
53.3
SHC 31.1
38.8
45.8
35.2
45.2
51.4
37.1
48.1
58.2
kW 5.41
5.20
5.04
5.51
5.28
5.16
5.55
5.32
5.22
TC 54.9
49.0
44.1
57.8
51.7
48.7
58.7
52.6
50.4
SHC 29.8
37.5
44.0
34.0
43.9
48.7
35.9
46.7
50.4
kW 5.93
5.72
5.56
6.04
5.80
5.70
6.07
5.83
5.75
The following formulas may be used: t ldb
= t edb
– sensible capacity (Btuh)
1.10 x cfm tlwb = Wet-bulb temperature corresponding to enthalpy of air leaving evaporator col (hlwb).
h lwb
= h ewb
– total capacity (Btuh)
4.5 x cfm
Where: hewb = Enthalpy of air entering evaporator coil
BYPASS
FACTOR
(BF)
.025
.05
.10
.20
.30
.35
79
ENTERING AIR DRY-BULB TEMPERATURE (F)
78 77 76 75 Under 75
81 82 Over 85
1.07
1.04
.98
.87
.76
.71
2.12
2.07
1.96
1.74
1.53
1.42
83 84 85
Correction Factor
3.19
3.11
2.94
2.62
2.29
2.13
4.25
4.14
3.92
3.49
3.05
2.83
5.32
5.18
4.90
4.36
3.82
3.54
Use formula shown below
Correction Factor = 1.10 x (1 – BF) x db – 80)
EVAPORATOR FAN PERFORMANCE
CFM
600
700
800
900
1000
1100
1200
1300
1400
1500
1600
1700
1800
1900
2000
ESP
.60
.54
.43
.29
.11
—
—
—
—
—
—
—
—
—
—
024
Fan kW
.20
.22
.24
.26
.29
—
—
—
—
—
—
—
—
—
—
ESP
—
—
—
.69
.57
.42
.23
—
—
—
—
—
—
—
—
036
LEGEND
ESP — External Static Pressure (in. wg) kW — Total Fan Motor Power Input (kilowatts)
*Standard direct drive indoor (evaporator) fan motor (IFM). For optional belt drive IFM performance, see table on page 8.
NOTES:
1. Above fan performance is based on wet coil and deducted casing losses, and clean factory-installed permanent cleanable filter.
UNIT SIZE — 502A
Fan kW
—
—
—
.44
.46
.49
.52
—
—
—
—
—
—
—
—
048* 060*
ESP
—
—
—
—
—
1.10
1.01
.90
.79
.67
.54
.39
.22
.03
—
Fan kW
—
—
—
—
—
.45
.49
.51
.55
.58
.61
.64
.67
.70
—
ESP
—
—
—
—
—
1.11
1.045
.97
.88
.78
.67
.53
.52
.40
.28
Fan kW
—
—
—
—
—
.52
.55
.57
.59
.62
.64
.67
.70
.74
.78
2. Evaporator fans are direct drive (except 048, 060 special order evaporator-fan motor option). Refer to Belt Drive Evaporator Fan
Performance table on page 8.
3. Interpolation is permissible, do not extrapolate.
4. For units installed with accessory electric heaters, see Electric
Heater Static Pressure Drop table for additional performance losses.
7
PERFORMANCE DATA (cont)
BELT DRIVE EVAPORATOR FAN PERFORMANCE
(Special Order Only, Pricing and ordering on related price pages.)
CFM
1800
1850
1900
1950
2000
2050
2100
2150
2200
2250
ESP
—
—
—
.81
.72
.63
.55
.47
.42
.34
UNIT SIZE — 502A
048
Fan kW
—
—
—
1.03
1.05
1.07
1.08
1.11
1.14
1.17
ESP
—
—
—
—
—
—
1.02
.93
.84
.75
060
Fan kW
—
—
—
—
—
—
1.17
1.21
1.24
1.27
LEGEND
ESP — External Static Pressure (in. wg) kW — Total Fan Power Motor Input (kilowatts)
NOTE: Pulley setting must be adjusted to limit cfm to 450 cfm/ton
maximum. Unit operation beyond that limit may result in blow-off and condensate problems.
CONDENSER FAN PERFORMANCE
EXTERNAL STATIC PRESSURE (in. wg)
0.2
0.3
0.4
—
—
.80
—
—
.68
—
.57
—
—
—
.83
—
.74
—
—
—
—
1.24
—
—
—
1.01
—
—
—
.90
kW
—
—
.63
—
—
Turns
—
—
Note 4
—
—
—
3
—
4
—
—
2
—
—
—
—
2
—
3
—
—
—
—
4
—
—
—
5
—
—
—
3
Turns
—
—
—
Note 4
—
—
—
3
—
—
—
—
2
—
—
—
1
2
—
—
—
—
2
—
—
3
—
—
—
—
4
—
—
—
—
.78
—
—
.67
—
—
—
—
.89
.80
—
—
—
—
1.39
—
—
1.17
—
—
—
—
.97
— kW
—
—
—
.62
—
Turns
—
—
—
—
Note 4
2
—
—
3
—
—
—
1
—
—
—
—
1
—
2
2
—
—
—
3
—
—
—
—
—
—
—
—
—
—
.84
.76
—
—
.65
—
—
—
—
.86
—
.77
—
—
—
—
1.32
—
—
—
1.12
—
—
— kW
—
—
—
—
.62
Turns
1
—
2
—
—
—
—
—
—
—
—
—
—
0
1
—
—
—
2
—
—
—
3
—
—
—
—
—
—
—
—
—
0.5
kW
—
—
—
—
—
—
—
—
—
—
—
—
—
.83
—
.73
—
—
—
—
—
—
.90
.82
—
—
—
1.26
—
—
—
1.08
5. Minimum one turn open of motor pulley is required on unit sizes 036 and 060.
6. Number of turns open applies to field setting of motor pulley.
7. Factory setting as follows: 036, 4 turns open; 048, 2 turns open; 060,
5 turns open.
—
1
—
2
—
—
—
—
—
—
—
—
—
—
0
—
—
1
—
—
—
2
—
—
—
—
—
Turns
—
—
—
—
—
0.6
—
—
—
—
—
.81
—
.71
—
—
—
—
—
—
.86
—
—
—
—
—
—
1.37
—
—
—
1.21
— kW
—
—
—
—
—
8
OPERATING SEQUENCE
Cooling
1. Thermostat calls for cooling.
a. Indoor (evaporator) fan relay is energized and starts evaporator fan.
b. Compressor contactor is energized to start compressor and condenser fan (up to a 5-minute delay on singlephase units).
CONTROLS
2. When room thermostat is satisfied, the evaporator fan, compressor, and condenser fan shut off.
Continuous Fan Operation — The thermostat can be set for continuous operation by setting the fan switch to ON.
UNIT
502A
024
036
048
048*
060
060*
V-PH
(60 Hz)
230-1
230-1
208/230-3
460-3
230-1
208/230-3
460-3
575-3
208/230-3
460-3
230-1
208/230-3
460-3
575-3
208/230-3
460-3
VOLTAGE RANGE
Min
207
207
187
414
207
187
414
518
187
414
207
187
414
518
187
414
Max
254
254
254
508
254
254
508
632
254
508
254
254
508
632
254
508
COMPRESSOR
RLA
11.5
17.2
10.2
4.3
23.7
13.5
7.4
5.8
13.5
7.4
28.8
17.3
9.0
7.1
17.3
9.0
LEGEND
HACR — Heating, Air Conditioning, and Refrigeration
Hp — Horsepower
FLA — Full Load Amps
LRA — Locked Rotor Amps
MOCP — Maximum Overcurrent Protection (HACR breaker)
RLA — Rated Load Amps
LRA
62.5
96.0
77.0
37.0
129.0
99.0
49.5
40.0
99.0
49.5
169.0
123.0
62.0
50.0
123.0
62.0
ELECTRICAL DATA
.50
.50
.50
.75
.75
.75
.75
1.5
1.5
.75
.75
.75
.75
1.5
1.5
FAN MOTORS
Evaporator
Hp FLA
.17
1.10
Condenser
Hp
.50
FLA
3.40
3.20
3.20
1.50
4.00
4.00
2.15
1.40
5.60
2.80
4.00
4.00
2.15
1.40
5.60
2.80
.75
.75
.75
1.0
1.0
1.0
1.0
1.0
1.0
1.5
1.5
1.5
1.5
1.5
1.5
6.06
3.93
1.97
8.35
3.93
1.97
1.45
3.93
1.97
9.50
4.82
2.41
1.90
4.82
2.41
*Optional evaporator-fan motor nameplate data.
POWER SUPPLY
Min Ckt
Amps
19.1
29.5
19.9
8.8
42.0
24.8
13.4
10.1
26.4
14.0
49.5
30.4
15.8
12.2
32.0
16.5
MOCP
Amps
70
45
25
20
40
25
60
35
15
15
35
20
25
40
25
15
ELECTRIC HEATER
UNIT 88EN
0050CA01
0075CA01
0115CA01
0075EA01
1150EA01
0100EA01
0150EA01
0200EA01
0300EA01
USED WITH
UNIT 502A
024, 036
1-Stage Heat
048, 060
2-Stage Heat
0300CA01
0100FA01
0150FA01
0200FA01
0300FA01
LEGEND
MCA — Minimum Circuit Ampacity
MOCP — Maximum Overcurrent Circuit Protection
(Fuses or Circuit Breaker)
V-PH
(60 Hz)
240-1
240-1
240-1
208-3
240-3
208-3
240-3
208-3
240-1*
240-3
208-3
240-1*
240-3
208-3
240-1*
240-3
208-3
240-3
240-1
480-3
480-3
480-3
480-3
ELECTRIC HEATER DATA
CAP. (kW)
5.0
7.5
11.5
5.6
7.6
11.3
15.0
7.5
10.0
10.0
11.3
15.0
15.0
15.0
20.0
20.0
22.5
30.0
30.0
10.0
15.0
20.0
30.0
Heater Amps
20.8
31.3
47.9
15.6
18.0
31.2
36.1
20.8
41.7
24.1
31.2
62.5
36.1
41.7
83.3
46.9
62.5
72.2
124.0
12.0
18.1
24.1
36.1
BRANCH CIRCUIT
MCA
26.0
39.1
59.9
19.5
22.6
39.0
45.1
26.0
52.1
30.1
39.0
78.1
45.1
52.1
104.2
58.6
78.2
90.2
155.0
15.0
22.6
30.1
45.1
MOCP (Amps)
30
40
60
20
25
40
50
30
60
35
40
80
50
60
110
60
80
100
175
15
25
35
50
*May be field converted to single-phase units, see electric heat installation instructions.
NOTE: Separate power source is required for all heaters. Control from base unit 502A (24 v).
9
ELECTRICAL DATA (cont)
ELECTRIC HEATER STATIC PRESSURE DROP (in. wg)
ELECTRIC HEATER
UNIT 88EN
0050CA01
0075CA01
0115CA01
0075EA01
1150EA01
0100EA01
0150EA01
0200EA01
0300EA01
0300CA01
0100FA01
0150FA01
0200FA01
0300FA01
UNIT
502A
024, 036
1-stage heat
048, 060
2-stage heat
MIN
CFM
400
510
620
320
720
970
1240
1350
1220
1220
1130
1360
1350
1270
600
.02
.03
.04
—
—
—
—
800
.04
.06
.08
—
—
—
—
1000
.06
.10
.13
—
—
—
—
1200
.10
.16
.19
.04
.08
.04
.08
UNIT CFM
1400
—
—
—
.06
.11
.06
.11
1600
—
—
—
.08
.14
.08
.14
1800
—
—
.12
.18
.12
.18
NOTE: Above electric heaters are not UL or CSA listed for use with optional high-static evaporator-fan motor (048, 060 units only).
—
TYPICAL WIRING SCHEMATICS
2000
—
—
—
.15
.22
.15
.22
2200
—
—
—
.17
.26
.17
.26
NOTES:
1. Compressor and fan motors are thermally protected 3-phase motors protected against primary single-phase condition.
2. If any original wires furnished must be replaced, it should be replaced with 90 C or its equivalent.
3. Numbers indicate the line location of used contacts. A bracket over 2 numbers signifies a single-pole double-throw contact. An underlined number signifies a normally closed contact.
4. Must use thermostat HH07AT170, 172 or 174 with subbase HN63AZ176, 177 or 178.
5. Separate field power supply required for electric heater accessory.
6. CLO locks out the compressor to prevent short cycling on compressor overloads and safety devices. Before replacing CLO check devices.
AHA
C
CB
CC
CLO
CT
— Adjustable Heat Anticipator
BKR W/AT — Brakes with Amp Turns
— Contactor Compressor
— Circuit Breaker
— Cooling Compensator
— Compressor Lockout
— Current Transformer
EQUIP GND — Equipment Ground
HPS — High-Pressure Switch
HR
IFC
IFR
JB
L
LOR
— Heater Relay
— Indoor (Evaporator) Fan Contactor
— Indoor (Evaporator) Fan Relay
— Junction Box
— Light
— Lockout Relay
LEGEND
LPS
NEC
PL
TB
TC
TH
— Low-Pressure Switch
— National Electrical Code
— Plug Assembly
— Terminal Block
— Thermostat-Cooling
— Thermostat-Heating
TRAN — Transformer
Marked Wire
Denotes connection point between subbase and thermostat
Terminal (Marked)
Terminal (Unmarked)
502A036,048,060, 208/230-3-60, 460-3-60; and 502A036, 208/230-1-60
Terminal Block
Field Splice
Splice (Marked)
Factory Splice
Factory Wiring
Accessory or Optional Wiring
Field Control Wiring
Field Power Wiring
To indicate common potential only, not to represent wiring
10
TYPICAL WIRING SCHEMATICS (cont)
LEGEND
L
LPS
NS
OAT
OFC
OFM
PL
QT
RC
SW
TB
TC
FU
GND
HPS
HR
IFC
IFM
IFR
JB
AHA
C
CAP
CB
— Adjustable Heat Anticipator
— Contactor Compressor
— Capacitor
— Circuit Breaker
CC
CDT
— Cooling Compensator
— Compressor Discharge Thermostat
COMP — Compressor Motor
EQUIP — Equipment
—
—
—
—
—
—
—
—
Fuse
Ground
High-Pressure Switch
Heater Relay
Indoor-Fan Contactor
Indoor-Fan Motor
Indoor-Fan Relay
Junction Box
—
—
—
—
—
—
—
—
—
—
—
—
Light
Low-Pressure Switch
Night Setback Switch
Outdoor-Air Thermostat
Outdoor-Fan Contactor
Outdoor-Fan Motor
Plug Assembly
Quadruple Terminal
Run Capacitor
Switch
Terminal Block
Thermostat-Cooling
TH
TRAN
— Thermostat-Heating
— Transformer
Marked Wire
Denotes connection point between subbase and thermostat
Terminal (Marked)
Terminal (Unmarked)
Terminal Block
Field Splice
Splice (Marked)
Factory Splice
Factory Wiring
Accessory or Optional Wiring
Field Control Wiring
Field Power Wiring
To indicate common potential only, not to represent wiring
502A024, 230-1-60 Units
11
NOTES:
1. Neutral for 240/416 v supply (Canada only).
2. If any original wires furnished must be replaced, it should be replaced with 90 C or its equivalent.
3. Numbers indicate the line location of used contacts. A bracket over 2 numbers signifies a single-pole double-throw contact. An underlined number signifies a normally closed contact. Plain (no line) number signifies a normally open contact.
4. Must use thermostat HH07AT170, 172 or 174 with subbase
HN63AZ176, 177 or 179.
5. Separate field power supply required for electric heater accessory.
TYPICAL WIRING SCHEMATICS (cont)
LEGEND
AHA
C
CAP
CB
— Adjustable Heat Anticipator
— Contactor Compressor
— Capacitor
— Circuit Breaker
CC
CDT
— Cooling Compensator
— Compressor Discharge Thermostat
CH — Crankcase Heater
COMP — Compressor Motor
EQUIP — Equipment
GND — Ground
HPS
HR
—
—
High-Pressure Switch
Heater Relay
IFC
IFM
IFR
JB
—
—
—
—
Indoor-Fan Contactor
Indoor-Fan Motor
Indoor-Fan Relay
Junction Box
L
LPS
NEC
OFM
PL
QT
RC
TB
—
—
—
—
—
—
—
—
Light
Low-Pressure Switch
National Electrical Code
Outdoor-Fan Motor
Plug Assembly
Quadruple Terminal
Run Capacitor
Terminal Block
TC
TH
—
—
Thermostat-Cooling
Thermostat-Heating
TRAN — Transformer
Marked Wire
Denotes connection point between subbase and thermostat
Terminal (Marked)
Terminal (Unmarked)
Terminal Block
Field Splice
Splice (Marked)
Factory Splice
Factory Wiring
Accessory or Optional Wiring
Field Control Wiring
Field Power Wiring
To indicate common potential only, not to represent wiring
502A048,060, 230-1-60 Units
12
NOTES:
2. If any original wires furnished must be replaced, it should be replaced with 90 C or its equivalent.
3. Numbers indicate the line location of used contacts. A bracket over 2 numbers signifies a single-pole double-throw contact. An underlined number signifies a normally closed contact. Plain (no line) number signifies a normally open contact.
4. Must use thermostat HH07AT170, 172 or 174 with subbase
HN63AZ176, 177 or 179.
5. Neutral for 240/416 v supply (Canada only).
6. Separate field power supply required for electric heater accessory.
7. The 10-kW, 15-kW and 20-kW heater assemblies for
502A048,060 are wired for 3 phase. See heater label diagram for
1-phase rewiring procedure.
TYPICAL WIRING SCHEMATICS (cont)
GND
HPS
IFC
IFM
IFR
JB
L
LOR
AHA — Adjustable Heat Anticipator
BKR W/AT — Breaks with Amp Turns
C
CC
—
—
Contactor Compressor
Cooling Compensator
CLO
COMP
CT
EQUIP
—
—
—
—
Compressor Lockout
Compressor Motor
Current Transformer
Equipment
—
—
—
—
—
—
—
—
Ground
High-Pressure Switch
Indoor-Fan Contactor
Indoor-Fan Motor
Indoor-Fan Relay
Junction Box
Light
Lockout Relay
LPS
NEC
OFM
PL
PRI
TB
TC
TH
TRAN
— Low-Pressure Switch
— National Electrical Code
— Outdoor-Fan Motor
— Plug Assembly
— Primary
— Terminal Block
— Thermostat-Cooling
— Thermostat-Heating
— Transformer
Marked Wire
LEGEND
Denotes connection point between subbase and thermostat
Terminal (Marked)
Terminal (Unmarked)
Terminal Block
Field Splice
Splice (Marked)
Factory Splice
Factory Wiring
Accessory or Optional Wiring
Field Control Wiring
Field Power Wiring
To indicate common potential only, not to represent wiring
502A048,060, 575-3-60 Units
13
NOTES:
1. Compressor and fan motors are thermally protected, three-phase motors protected against primary single-phase conditions.
2. If any original wires furnished must be replaced, it should be replaced with 90 C or its equivalent.
3. Numbers indicate the line location of used contacts. A bracket over 2 numbers signifies a single-pole double-throw contact. An underlined number signifies a normally closed contact. Plain (no line) number signifies a normally open contact.
4. Must use thermostat HH07AT170, 172 or 174 with subbase
HN63AZ176, 177 or 179.
5. Neutral for 240/416 v supply (Canada only).
6. The CLO locks out the compressor to prevent short cycling on compressor overloads and safety devices, before replacing CLO check these devices.
TYPICAL PIPING AND WIRING
LEGEND
NEC — National Electrical Code
NOTES:
1. Wiring and piping shown are not intended for or to include all details for specific installation.
2. All wiring must comply with applicable local and national codes.
3. All piping must follow standard refrigerant piping techniques.
4. For other installation details refer to Installation Instructions.
5. If unit sections are field split, 8 threaded support rods are required.
6. Ensure condenser air recirculation is minimized.
APPLICATION DATA
OUTDOOR-AIR TEMPERATURE OPERATING LIMITS (F)
UNIT 502A
Without Head Pressure Control Minimum
Maximum
With Head Pressure Control Minimum
Maximum
Field Splitting Instructions — If components are split, maximum length of refrigerant tubing to be used is 50 ft, assuming components are installed in same horizontal plane. Condenser may be mounted up to 12-ft above evaporator. Liquid line tubing is 3 /
8
-in. OD copper tubing, and discharge line is 1 /
2
-in. OD copper tubing. Units should always be within line of sight from each other, or separate NEC (National Electrical Code)
024
35
126
0
126
036
35
126
0
126
048
40
126
0
126
060
40
126
0
126 disconnects will be required. Junction boxes should be installed in both the evaporator and condenser sections adjacent to
D-shaped grommets, to provide a location to splice the outdoorfan motor factory wiring (no. 16 AWG [American Wire Gage],
4 /
64
-in. thick insulation). Field wiring should be a minimum of no. 16 AWG, 4 /
64
-in. thick insulation. Check all applicable electrical codes to ensure proper compliance.
14
GUIDE SPECIFICATIONS
INDOOR PACKAGED UNIT
HVAC GUIDE SPECIFICATIONS — SECTION 15787
SIZE RANGE: 2 TO 5 TONS, NOMINAL
BRYANT MODEL NUMBER: 502A
PART 1 — GENERAL
1.01 SYSTEM DESCRIPTION
Indoor mounted, electrically controlled packaged horizontal cooling unit utilizing a hermetic type scroll compressor.
1.02 QUALITY ASSURANCE
A. Unit shall be certified in accordance with ARI Standard 210.
B. Unit shall be UL listed and carry a UL label.
C. Unit shall be CSA approved (except 3 ton, 3-phase units).
D. Unit shall be factory run-tested to ensure proper performance prior to delivery.
1.03 DELIVERY, STORAGE, AND HANDLING
A. Unit shall be shipped completely assembled and ready to operate.
B. Unit shall be shipped factory charged with refrigerant
R-22.
C. Unit shall be stored and handled in accordance with the unit manufacturer’s instructions.
PART 2 — PRODUCTS
2.01 EQUIPMENT
A. General:
Factory assembled horizontal, single piece, air cooled, indoor, ceiling plenum mounted electric cooling unit. Contained within the unit enclosure shall be all factory wiring, piping, controls, refrigerant charge (R-22), and special features required prior to start-up.
B. Unit Cabinet:
1. Constructed of galvanized steel.
2. Interior shall be insulated with 1 /
2
-in. thick neoprene coated fiberglass. Insulation shall be bonded to interior surfaces by sprayed water reduceable adhesive.
3. Equipped with 3 same side access panels and 2 bottom hanging removable doors to facilitate ease of maintenance. Side panels allow access to the control box, refrigeration components, and condenser coil.
Control box shall be hinged allowing access to the compressor and pressure switches. Bottom doors shall allow access to and easy removal of the condenser and evaporator motors and blower assemblies.
4. Equipped with two 3 /
4
-in. threaded condensate drain connections below the evaporator coil and one 3 /
4
-in.
threaded connection for condenser coil wash down.
Connections shall be factory plugged for field removal.
5. Field splittable through the removal of 4 bolts and extending refrigerant piping and wiring to allow remote horizontal or vertical condenser mounting.
6. Unit shall have an integral hanging bracket requiring only 4 threaded rods (8 if unit is split) run to the top flange of the unit for hanging, eliminating need for external hanger brackets.
7. Contains junction box for power connection and opening for routing of control wiring.
C. Fans:
1. Evaporator: a. Blower shall be of the forward-curved, centrifugal, direct-drive type or belt drive (4 and 5 tons only).
bearings.
c. Unit sizes 048, 060 shall be available with an optional 1.5 hp fan motor.
2. Condenser: a. Blower shall be of the forward-curved, centrifugal, direct-driven type (024 only), or belt drive
(036,048,060).
* bearings.
D. Compressor:
1. Fully hermetic scroll type.
2. Mounted on suitable spring vibration isolators.
3. Equipped with internal line break protection.
E. Coils:
Evaporator and condenser coils shall be of non-ferrous construction with aluminum fins mechanically bonded to seamless copper tubes with all joints brazed.
F. Refrigerant Components:
Refrigerant components shall include:
1. Capillary tube feed system.
2. Refrigerant filter-drier.
G. Filter Section:
Filter section shall consist of factory-installed, permanent, cleanable air filter, removable from the same side as the access panels without the use of tools.
H. Controls and Safeties:
Control system shall include a high-pressure switch, a low-pressure switch, and a compressor lockout feature which upon tripping of any safety device shall prevent compressor from restarting until reset at the thermostat
(on all 3-phase units and 036 single-phase units only).
I. Operating characteristics:
1. Unit shall operate using refrigerant R-22.
2. Unit shall be designed for indoor suspended horizontal mounting and operation.
J. Electrical Requirements
Unit shall have single point power connection to leads in terminal box.
K. Special Features:
Certain standard features are not applicable when the features designated by * are specified. For assistance in amending the specifications, your local Bryant Sales
Office should be contacted.
1. Electric Heat Module: a. Provides encased heater elements that shall attach directly to the base unit discharge.
b. Shall have bottom access.
c. UL listed.
2. Thermostat Assembly:
Provides cooling and fan control. Standard subbase shall include ‘‘Compressor malfunction light’’ designed to illuminate if compressor lockout is activated.
15
*
*
GUIDE SPECIFICATIONS (cont)
3. Compressor Cycle Delay:
Prevents compressor from restarting for a minimum of 5 minutes after shutdown.
4. Condensate Pump:
Unit shall be equipped with remotely located condensate pump. A field-installed light shall illuminate when reservoir rises above a preset level. Unit shall shut down upon reservoir light illumination.
5. Head Pressure Control Package:
Allows unit to mechanically cool down to 0° F ambient temperature. Package shall include damper operating device and all necessary hardware.
6. Vibration Isolation Package:
Shall provide 4 spring hangers for ceiling mounted unit to damper vibration that may be transmitted to building structure.
7. Time Guard® II Device:
Time Guard II device (024,048,060 single-phase only) shall prevent the compressor from restarting for a minimum of 5 minutes after shutdown.
Copyright 2001 Bryant Heating & Cooling Systems
SPECIFICATIONS SUBJECT TO CHANGE WITHOUT NOTICE
UNIT MUST BE INSTALLED IN ACCORDANCE
WITH INSTALLATION INSTRUCTIONS
Printed in U.S.A.
1-01 Catalog No. 5250-200
advertisement
* Your assessment is very important for improving the workof artificial intelligence, which forms the content of this project