Duerkopp Adler 1281/5-1 Operating instructions
Add to my manuals
62 Pages
Beisler 1281/5-1 is a sewing unit designed for closing seams for trousers and skirts, featuring a user-friendly interface with a touch-screen monitor for easy operation, customization, and monitoring of sewing processes. It offers various seam programs with adjustable seam parameters, machine parameters, and global parameters for diverse sewing requirements. Additionally, it includes a roll-out device, puller, input-output test, stepper motor test, and data protection via USB stick.
advertisement
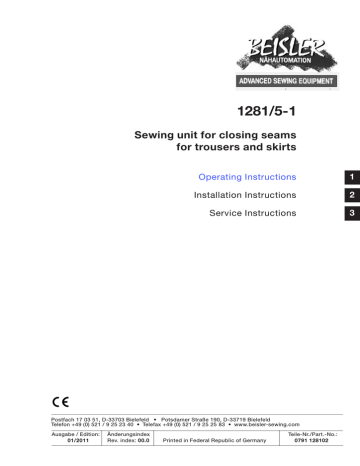
1281/5-1
Sewing unit for closing seams for trousers and skirts
Operating Instructions
Installation Instructions
Service Instructions
1
2
3
Postfach 17 03 51, D-33703 Bielefeld • Potsdamer Straße 190, D-33719 Bielefeld
Telefon +49 (0) 521 / 9 25 23 40 • Telefax +49 (0) 521 / 9 25 25 83 • www.beisler-sewing.com
Ausgabe / Edition: Änderungsindex
01/2011 Rev. index: 00.0 Printed in Federal Republic of Germany
Teile-Nr./Part.-No.:
0791 128102
All rights reserved.
Property of Beisler GmbH and copyrighted. Reproduction or publication of the content in any manner, even in extracts, without prior written permission of Beisler GmbH, is prohibited.
Copyright © Beisler GmbH - 2011
Foreword
This instruction manual is intended to help the user to become familiar with the machine and take advantage of its application possibilities in accordance with the recommendations.
The instruction manual contains important information on how to operate the machine securely, properly and economically. Observation of the instructions eliminates danger, reduces costs for repair and down-times, and increases the reliability and life of the machine.
The instruction manual is intended to complement existing national accident prevention and environment protection regulations.
The instruction manual must always be available at the machine/sewing unit.
The instruction manual must be read and applied by any person that is authorized to work on the machine/sewing unit. This means:
– Operation, including equipping, troubleshooting during the work cycle, removing of fabric waste,
– Service (maintenance, inspection, repair) and/or
– Transport.
The user also has to assure that only authorized personnel work on the machine.
The user is obliged to check the machine at least once per shift for apparent damages and to immediatly report any changes (including the performance in service), which impair the safety.
The user company must ensure that the machine is only operated in perfect working order.
Never remove or disable any safety devices.
If safety devices need to be removed for equipping, repairing or maintaining, the safety devices must be remounted directly after completion of the maintenance and repair work.
Unauthorized modification of the machine rules out liability of the manufacturer for damage resulting from this.
Observe all safety and danger recommendations on the machine/unit!
The yellow-and-black striped surfaces designate permanend danger areas, eg danger of squashing, cutting, shearing or collision.
Besides the recommendations in this instruction manual also observe the general safety and accident prevention regulations!
General safety instructions
The non-observance of the following safety instructions can cause bodily injuries or damages to the machine.
1. The machine must only be commissioned in full knowledge of the instruction book and operated by persons with appropriate training.
2. Before putting into service also read the safety rules and instructions of the motor supplier.
3. The machine must be used only for the purpose intended. Use of the machine without the safety devices is not permitted. Observe all the relevant safety regulations.
4. When gauge parts are exchanged (e.g. needle, presser foot, needle plate, feed dog and bobbin) when threading, when the workplace is left, and during service work, the machine must be disconnected from the mains by switching off the master switch or disconnecting the mains plug.
5. Daily servicing work must be carried out only by appropriately trained persons.
6. Repairs, conversion and special maintenance work must only be carried out by technicians or persons with appropriate training.
7. For service or repair work on pneumatic systems, disconnect the machine from the compressed air supply system (max. 7-10 bar).
Before disconnecting, reduce the pressure of the maintenance unit.
Exceptions to this are only adjustments and functions checks made by appropriately trained technicians.
8. Work on the electrical equipment must be carried out only by electricians or appropriately trained persons.
9. Work on parts and systems under electric current is not permitted, except as specified in regulations DIN VDE 0105.
10. Conversion or changes to the machine must be authorized by us and made only in adherence to all safety regulations.
11. For repairs, only replacement parts approved by us must be used.
12. Commissioning of the sewing head is prohibited until such time as the entire sewing unit is found to comply with EC directives.
13. The line cord should be equipped with a country-specific mains plug. This work must be carried out by appropriately trained technicians (see paragraph 8).
It is absolutely necessary to respect the safety instructions marked by these signs.
Danger of bodily injuries !
Please note also the general safety instructions.
Content
Preface and General Safety Notes
Page:
Part 1: Operating Instructions Cl. 1281/5-1 – Original Instructions
(Edition: 01/2011)
1.
1.1
1.2
1.3
2
3
3.1
3.2
3.3
3.4
4
4.1
4.2
4.3
Product Description
Description of use for the intended purpose . . . . . . . . . . . . . . . . . . . . . . . . . . . . .
Brief Description . . . . . . . . . . . . . . . . . . . . . . . . . . . . . . . . . . . . . . . . . . . . . .
Technical Data . . . . . . . . . . . . . . . . . . . . . . . . . . . . . . . . . . . . . . . . . . . . . . .
Optional Equipment . . . . . . . . . . . . . . . . . . . . . . . . . . . . . . . . . . . . . . . . . . .
Switching On - Switching Off - Program Stop
Switching On . . . . . . . . . . . . . . . . . . . . . . . . . . . . . . . . . . . . . . . . . . . . . . . .
Switching Off . . . . . . . . . . . . . . . . . . . . . . . . . . . . . . . . . . . . . . . . . . . . . . . .
Program Stop . . . . . . . . . . . . . . . . . . . . . . . . . . . . . . . . . . . . . . . . . . . . . . .
Renewed setting in motion after program stop . . . . . . . . . . . . . . . . . . . . . . . . . . .
Operation of the sewing machine head
General Information . . . . . . . . . . . . . . . . . . . . . . . . . . . . . . . . . . . . . . . . . . . .
Recommended yarn . . . . . . . . . . . . . . . . . . . . . . . . . . . . . . . . . . . . . . . . . . .
Detaching/ Attaching the fabric sliding plate. . . . . . . . . . . . . . . . . . . . . . . . . . . . .
5
5.1
5.2
5.3
5.4
5.5
5.6
5.7
Operating the sewing unit
Positioning table and work table . . . . . . . . . . . . . . . . . . . . . . . . . . . . . . . . . . . .
Mouse with guide rail and retraction mechanism . . . . . . . . . . . . . . . . . . . . . . . . . .
Inserting the sewing parts and starting the sewing operation. . . . . . . . . . . . . . . . . . .
Adjusting the blow air for the nozzles in the table top . . . . . . . . . . . . . . . . . . . . . . .
Adjusting the retraction speed of the mouse. . . . . . . . . . . . . . . . . . . . . . . . . . . . .
Adjusting the pressure of the puller . . . . . . . . . . . . . . . . . . . . . . . . . . . . . . . . . .
Stacker . . . . . . . . . . . . . . . . . . . . . . . . . . . . . . . . . . . . . . . . . . . . . . . . . . .
6
6.1
6.3
Operation of the control unit
Operation of the touch-screen monitor . . . . . . . . . . . . . . . . . . . . . . . . . . . . . . . .
Main screen . . . . . . . . . . . . . . . . . . . . . . . . . . . . . . . . . . . . . . . . . . . . . . . .
6.4
6.4.1
Sewing programs
Selecting the program and seam number . . . . . . . . . . . . . . . . . . . . . . . . . . . . . . .
6.4.2
Creating a new seam program with seam number . . . . . . . . . . . . . . . . . . . . . . . . .
6.4.2.1
Number of seam programs and seams . . . . . . . . . . . . . . . . . . . . . . . . . . . . . . . .
6.4.3
6.4.4
Editing, deleting the seam program or seams . . . . . . . . . . . . . . . . . . . . . . . . . . . .
Manual sewing, driven by the pedal . . . . . . . . . . . . . . . . . . . . . . . . . . . . . . . . . .
6.4.5
Changing the seam programs . . . . . . . . . . . . . . . . . . . . . . . . . . . . . . . . . . . . . .
6.4.5.1
Seam Parameters . . . . . . . . . . . . . . . . . . . . . . . . . . . . . . . . . . . . . . . . . . . . .
6.4.5.2
Machine Parameters . . . . . . . . . . . . . . . . . . . . . . . . . . . . . . . . . . . . . . . . . . .
17
18
19
10
11
13
16
20
21
27
32
33
35
24
25
26
39
7
8
9
2
2
3
4
6
6
5
5
1
Content Page:
7
7.1
7.2
7.3
7.4
7.5
7.6
7.8
8
8.1
8.2
8.3
6.4.5.3
Roll-out Device . . . . . . . . . . . . . . . . . . . . . . . . . . . . . . . . . . . . . . . . . . . . . .
6.4.5.4
Puller. . . . . . . . . . . . . . . . . . . . . . . . . . . . . . . . . . . . . . . . . . . . . . . . . . . . .
6.4.5.5
Global Parameters . . . . . . . . . . . . . . . . . . . . . . . . . . . . . . . . . . . . . . . . . . . .
6.4.5.6
Input - Output Test . . . . . . . . . . . . . . . . . . . . . . . . . . . . . . . . . . . . . . . . . . . .
6.4.5.7
Stepper Motor Test . . . . . . . . . . . . . . . . . . . . . . . . . . . . . . . . . . . . . . . . . . . .
6.4.8
Version Data . . . . . . . . . . . . . . . . . . . . . . . . . . . . . . . . . . . . . . . . . . . . . . . .
Data protection by means of USB stick
General Information . . . . . . . . . . . . . . . . . . . . . . . . . . . . . . . . . . . . . . . . . . . .
Formatting the USB stick . . . . . . . . . . . . . . . . . . . . . . . . . . . . . . . . . . . . . . . .
Saving the seam programs and seam parameters on the USB stick . . . . . . . . . . . . . . .
Loading the seam programs and seam parameters from the USB stick. . . . . . . . . . . . .
Saving global parameters on USB stick . . . . . . . . . . . . . . . . . . . . . . . . . . . . . . . .
Loading global parameters from the USB stick . . . . . . . . . . . . . . . . . . . . . . . . . . .
Removing the USB stick . . . . . . . . . . . . . . . . . . . . . . . . . . . . . . . . . . . . . . . . .
Maintenance
Cleaning and Testing . . . . . . . . . . . . . . . . . . . . . . . . . . . . . . . . . . . . . . . . . . .
Lubrication . . . . . . . . . . . . . . . . . . . . . . . . . . . . . . . . . . . . . . . . . . . . . . . . .
Repair . . . . . . . . . . . . . . . . . . . . . . . . . . . . . . . . . . . . . . . . . . . . . . . . . . . .
54
56
57
40
41
42
44
46
48
52
53
53
53
49
49
50
1 Product Description
1.1
Description of use for the intended purpose
The 1281/5-1 is a sewing unit which can be used according to the intended purpose of sewing of light to medium-heavy workpieces.
Such workpieces are as a rule materials made of textile fibers. These sewing materials are used in the apparel industry.
In general, only dry sewing fabrics may be processed with this sewing unit. The material must not contain any hard objects.
In general, the seam is prepared from core thread, polyester fibre or cotton yarn.
The dimensions for needle thread and looper thread may be derived from the tables in Chapter 4.2.
If you wish to use other threads, you must first estimate the inherent risks and take safety measures, where required.
This sewing unit may be set up and operated only in dry and well-kept rooms. If the sewing unit is used in other rooms that are not dry and well-kept, further measures may become necessary that must be agreed to by the manufacturer (see EN 60204-31: 1999).
As manufacturers of industrial sewing machines, we assume that our products are operated by at least trained personnel, so that all the usual operations, and possibly dangers, can be presumed to be known.
1
1.2
Brief Description
The Beisler 1281/5-1 is a sewing unit for closing of long seams such as e.g.
® trouser side seams and inside seams,
® Side seams without vent in outer fabric and lining in skirt parts
Depending upon the machine head used,
® Double chain stitch seams (401),
® Safety seams 4-thread (515) or 5-thread (516) can be generated.
All the workplace components are arranged on a rack welded from square-cut steel tubes and are controlled by a micro-processor system.
The sewing workplace is operated by means of the operating panel.
Various control programs can be called up, new programs can be defined and all the inputs and outputs can be checked here for maintenance and repair jobs.
Machine head
– Pegasus Serging Machine EXT 3216-03
– Direct-Drive Efka Type DC 1500 /AB 425S
– Microprocessor control, freely programmable
– Light barrier for detecting seam start and seam end for automatic seam start and stop.
– Programmable edge guide for different material strengths, moving crosswise from feeding direction.
– External Operating Panel Efka V900 with:
Menu Guide
3
Freely programmable parameters for
“Differential lower feed (optional)”, “Upper feed
(optional)”, “Roll-out Device”, “Puller”, “Machine
Parameters”,
“Global Parameters”, “Program Sequences”
Input and Output Tests
Test routine for stepper motors
20 Program Memory Capacity
up to 7 seam programs per program storage space
– Vertical cutter with suction device for overseaming and serging in a work step.
– Programmable chain cutting device with suctioning.
– Adjustable blow nozzles in the table top for supporting the sewing material feed, mechanical regulation of the blow strength by means of adjusting knob, duration of table blowing is programmable.
– Positioning table with mouse and retraction device for the workpiece; for uniform workpiece guidance and higher productivity.
– Special sewing equipment for trouser side seams with side seam pockets and slant pockets.
– Narrow gauge parts including narrow sewing foot for problem-free feed/ sewing of the pocket openings.
– Automatic contour control through programmable puller.
– Height-adjustable rack, infinitely variable from 850 mm up to 1200 mm.
– Automatic fullness distribution through stepper motor controlled upper and lower feed (optional).
Within a seam program, the fullness of the upper and lower feed can be programmed at the operating panel by means of 3 freely selectable segments.
User-friendly adjustment option for fullness in a segment by means of one control each.
– Integrated destacking device.
– Manual destacking by means of the shortcut key.
1.3
Technical Data
Machine Head:
Type of stitch:
Number of needles:
Needle system:
Needle thickness:
Type of hook:
Yarn:
Speed:
Speed at delivery:
Stitch length: min.
max.
Seam width:
Optional
Workpiece:
Operating pressure:
Air consumption:
Pegasus EXT 3216-03/233-K 5x5-KH-021A
401, 515, 516
1 or 2
B27
Nm 80 to Nm 110
Looper crosswise to feeding direction
Serging looper see table in Chapter 4.2
6,500 min
6,500 min
-1
-1
0.5 mm
3.5 mm
10 mm
8 - 12 mm
Light weight to medium weight
6 bar
20 NL per working cycle
4
2 Optional Equipment
Rated voltage:
Rated power:
Dimensions:
Work height:
Weight:
1 x 230 V 50/60 Hz
1.00 KVA
2300 x 1300 x 1500 mm (L x B x H)
850 … 1200 mm
(upper edge of table top)
125 kg
Rated noise level: LC = 81 dB (A)
Workplace-related emission value according to DIN 45635-48-B-1
Stitch length: 2.6 mm
Seam length:
Number of stitches:
1,000 mm
6,500 min -1
Workpiece G1 DIN 23328: 2-ply
Measuring point according to DIN 4895
Part 1 X = 550 mm Y = 350 mm Z = 600 mm
X - axis = crosswise to direction of feed
Y - axis = main feed direction
Z - axis = height
1
See Appendix.
5
3 Switching On - Switching Off - Program Stop
3.1
Switching On
1
– Switch on the main switch 1 (turn in clockwise direction).
The control unit loads the machine program.
The starting screen is displayed on the display screen of the operating panel.
3.2
Switching Off
– Switch off the main switch 1 (turn in anti-clockwise direction).
6
3.3
Program Stop
2
The safety system of 1281/5-1 foresees the following options for immediate stoppage in case of faulty operation, needle breakage etc.:
– Press the program stop switch 2 at the operating panel.
Ongoing work steps at the sewing unit are immediately aborted.
– Turn main switch 1 in anti-clockwise direction.
The sewing unit is powered off immediately; all the movements at the sewing unit stop immediately.
1
3.4
Renewed setting in motion after program stop
Caution: Risk of Injury!
Switch off the main switch.
Repair the fault only when the sewing unit is switched off.
Renewed setting in motion of the machine is allowed only after the fault has been repaired.
– Switch on the main switch 1 (turn in clockwise direction).
– Unlock the program stop switch.
The control unit loads the machine program.
The start screen appears on the display screen of the operating panel.
The sewing unit is once again ready for operation.
7
4 Operation of the sewing machine head
4.1
General Information
The operation of the sewing machine head (inserting the needle, threading the needle thread and looper thread etc.) is described in the separately enclosed Pegasus operating instructions.
The operating instructions are in the accessories pack of the sewing unit.
Caution: Risk of Injury!
Kindly read the operating instructions of the sewing machine head carefully and follow all the safety instructions.
8
4.2
Recommended yarn
Needle system:
Recommended needle thickness:
B27
Nm 80 for very thin sewing material
Nm 90 for thin sewing material
Nm 100 for medium weight sewing material
High sewing safety and good sewability are achieved with the following covering threads:
– Double polyester continuous polyester core spun
(e.g. Epic Poly-Poly, Rasant x, Saba C, ...)
– Double polyester continuous cotton core spun
(e.g. Frikka, Koban, Rasant, ...)
In case these yarns cannot be procured, even polyester fibers or cotton yarn specified in the table can be sewed up.
Double core threads are often offered by yarn producers under the same designation as triple polyester fibre yarn (3-cyl. spun). This results in doubts in respect of twist and yarn thickness.
In case of doubt, untwist the yarn and check as to whether it is double or triple twisted.
The Label No. 120 on the yarn roll of a core thread e.g. corresponds to the yarn thickness Nm 80/2 (see table values in brackets).
In case of monofil threads, needle threads and looper threads of the same thickness can be used. In doing so, the best results are achieved with soft and elastic threads (software) with thread thickness of 130 Denier.
1
Recommended yarn thicknesses:
Needle Thickn.
Nm
Needle thread
Polyestercontinuous
Label No.
Core thread
Looper thread
Polyestercore spun
Label No.
80
90
100
120 (Nm 80/2)
100 (Nm 65/2)
120 (Nm 80/2)
100 (Nm 65/2)
Core thread
Needle thread
Polyestercontinuous
Label No.
Looper thread
Cotton core spun
Label No.
120 (Nm 80/2)
100 (Nm 65/2)
120 (Nm 80/2)
100 (Nm 65/2)
Needle Thickn.
Nm
80
90
100
Polyester fibre yarn
(3cyl.-spun)
Needle thread
Nm 120/3
Nm 80/3-120/3
Nm 70/3-100/3
Looper thread
Nm 120/3
Nm 80/3-120/3
Nm 70/3-100/3
Cotton yarn
Needle thread
Ne
B
60/3-80/3
Ne
B
50/3-70/3
Ne
B
40/3-60/3
Looper thread
Ne
B
60/3-80/3
Ne
B
50/3-70/3
Ne
B
40/3-60/3
9
4.3
Detaching/ Attaching the fabric sliding plate
2 3 2 1
The fabric sliding plate 2 is held in the recess of the table top with the help of the magnet 1.
The edge guide 3 is fastened to the fabric sliding plate.
Detaching the fabric sliding plate
– Detach the edge guide 3 carefully upwards from the magnet.
– Swivel the fabric sliding plate to the side.
The lower area of the sewing machine head is now accessible.
Attaching the fabric sliding plate
– Push the fabric sliding plate into the recess of the table top and insert downwards.
10
5 Operating the sewing unit
5.1
Positioning table and work table
2 1 4 3
The sewing unit is equipped with two positioning tables 1 and 2. The skirt parts or trouser parts are prepared on them respectively.
On work table 4, the trouser parts or skirt parts are positioned and clamped with the mouse 3.
1
11
5.2
Mouse with guide rail and retraction mechanism
3 2 1 7 6 5 4
The mouse is used for clamping of the trouser parts or skirt parts, in order to prevent them from sliding.
The guide rail 3 is flexible and must be adjusted to the contour of the sewing part.
Caution: Risk of Injury !
Do not reach into the mouse when it is open.
Insert sewing part
– Place the sewing part between the mouse plate 2 and the clamping arm 1.
– Press shut the mouse.
During the sewing operation, the mouse is drawn along the guide rail 3 until the opening of the clamping arm 1 is actuated by a limit switch.
Then, the mouse is drawn back by the retraction mechanism 4 until the adjustable limit stop 5 is contacted.
12
9 3 9 8
Adjusting the guide rail 3
– Place the sewing part 8 on the work table in opposite direction to the feed direction.
– Loosen the toggle screw 9.
– Advance the guide rail 3 towards the contour of the sewing part.
– Retighten the toggle screw 9.
1
Opening the mouse manually
– Actuate lever 10.
The mouse opens.
10
13
5.3
Inserting the sewing parts and starting the sewing operation
The closing seam sewing unit 1281/5-1 works semi-automatically at high production speed.
In the process, the operator of the sewing unit must perform the following tasks:
® Call up the desired seam program;
® Insert the workpiece neatly;
® Actuate the sewing operation with the foot switch;
® Monitor the sewing operation of the sewing unit;
® Remove the finished parts from the stacker.
Side Seam M02 5_7
1
1) Select the seam program at the operating panel.
2) Lay out and adjust the trouser parts on the positioning table.
3) Insert the sewing parts in the mouse 1.
4) Close the mouse.
5) Insert the trouser parts under the sewing foot up to the point that the feed dogs securely grasp the trouser parts.
6) Hold the trouser parts to be sewed up with the left hand.
7) Sew the hip curve manually with the “forward” pedal.
14
8) With the right hand, grasp the trouser parts to be sewed such that the middle finger is below the lower trouser part, the index finger is between the two and the thumb is on the upper trouser part.
9) With pedal “-1” “backwards”, the contour guide moves forward.
10) Should a correction be needed, the contour guide can be moved back with the reset button.
Once the trouser parts have been corrected, the contour guide can once again be moved forward with the “backwards” pedal.
11) Step on forward pedal.
The automatic sewing operation starts.
12) The transport puller is lowered and transports the workpiece.
- At the seam end, the roll-out device is lowered in order to secure chain separation and prevent the trouser parts from sliding.
- The completely sewed trouser parts are destacked.
1
15
16
Inside seam M 01 4_6
1) Select the seam program at the operating panel (see Chapter 6.3).
2) Lay out and adjust the trouser parts on the positioning table.
3) Insert the trouser parts in the mouse.
4) Close the mouse.
5) Insert the trouser parts under the sewing foot up to the point that the feed dogs securely grasp the trouser parts.
6) With the left hand, hold the trouser parts to be sewed.
7) With the right hand, grasp the trouser parts to be sewed such that the middle finger is below the lower trouser part, the index finger is between the two and the thumb is on the upper trouser part.
8) Step on the forward pedal.
The sewing operation is performed automatically.
9) The transport puller is lowered and transports the workpiece.
At the seam end, the roll-out device is lowered in order to secure chain separation and prevent the trouser parts from sliding.
The completely sewed trouser parts are destacked.
5.4
Adjusting the blow air for the nozzles in the table top
1 2
The blow nozzles 1 in the table top support the neat destacking of the workpiece.
– Adjust the blow air strength with the hand wheel 2 under the table top.
Turning the hand wheel to the right
= blow air is stronger
Turning the hand wheel to the left
= blow air is weaker
1
17
5.5
Adjusting the reverse motion speed of the mouse.
3 2 1
The cylinder 2 presses the mouse mechanism 3 downwards and thus draws the mouse back into insertion position.
The return speed can be adjusted.
– Adjust the speed with the hand wheel 1.
Turning the hand wheel to the right
= speed is higher
Turning the hand wheel to the left
= speed is lower
18
5.6
Adjusting the pressure of the puller
2
1
The pressure of the puller rollers 1 can be influenced using the turning knob 2.
– Turning the knob 2 to the right.
Pressure is increased.
– Turning the knob 2 to the left.
Pressure is reduced.
1
19
5.7
Stacker
2 1 3
The finished sewing parts are destacked on the flip stacker 2.
The destacked and clamped sewing parts can be removed by actuating the foot switch 1.
The triggering of the stacker is done by means of a control impulse.
The pneumatic functions are shown in the pneumatic circuit diagram.
Caution: Risk of Injury !
Do not reach into the operating range of the flip stacker while the stacking operation is on.
Manual destacking
– Press button 3 on the operating panel.
A destacking operation is performed.
Removal of destacked parts
– Actuate foot switch 1 and hold it in that position.
– Remove the destacked parts.
20
6 Operating the control unit
6.1
Operating the touch-screen monitor
To start a function, the display screen is touched with the finger-tip at the point where the respective icon is shown.
Tap directly on the desired function symbol with the finger-tip.
The symbol will appear against a yellow background.
1
21
6.3
Main screen
– Switch on the main switch 1 (turn in clockwise direction).
The control unit loads the machine program.
The start screen is displayed on the display screen of the operating panel.
= Seam pattern is active seam in program
= Pedal Start
= Designation of the program (M01)
A program can comprise several seams ( 4, 6)
= Seam number of the active program
= Adjusting the upper feed (only stepper motor version)
Increasing or decreasing the value using the plus/minus symbols
= Adjusting the lower feed (only stepper motor version)
Increasing or decreasing the value using the plus/minus symbols
= Calling up the machine parameters
= Automatic seam change
= Adjusting the puller
= Adjusting the puller transport
= Daily pieces counter
= Display of the current seam
22
= Calling up the main menu
= Increasing (+) or decreasing (-) values for the upper and differential feed
(only stepper motor version)
= Activating manual sewing
= Manual stacking
= Contour guide back to home position
Note:
When the symbols are tapped, the highlighting of the symbols in white background signifies that the function is activated.
1
23
6.4
Sewing programs
4
The sewing unit is pre-programmed with four programs ex-works.
5
6
Program
No.
1
2
3
4
Seam-
No.
6
7
5
4
5
4
6
7
Operation
Closing the inside seam
Closing the inside seam
Closing the inside seam
Closing the inside seam
Closing the inside seam
Closing the inside seam
Closing the inside seam with fullness
Closing the inside seam with fullness
Trouser position Remarks
Hind trouser top
Hind trouser bottom
Hind trouser top
Hind trouser bottom
Hind trouser top
Hind trouser bottom
Hind trouser top
Hind trouser bottom
Automatic sewing with contour guide
Manually guiding and sewing over the hip curve, then automatic sewing
Automatic sewing with contour guide
Manually guiding and sewing over the hip curve, then automatic sewing
24
6.4.1
Selecting the program and seam number
– Press the symbol when the main screen is displayed.
The display changes to the screen programs.
1
– Tap the symbol for the desired program, e.g. “M04”.
The symbol appears in inverted image.
– Tap the symbol “P” in order to adopt the selection and in order to return to the main screen.
25
6.4.2
Creating a new seam program with seam number
– Press the symbol on the displayed main screen.
The display changes to the screen programs.
– Tap the symbol for the new seam program (e.g. “M05”).
The program number appears in inverted image.
– Tap the symbol in order to adopt the selection.
The display changes to the seam program “M05”.
– Tap the symbol.
The display is inverted.
– Select a seam (e.g. “4”).
The display changes to confirmation prompt.
Selection: Yes/ No
– Confirm with “Yes” in order to adopt the selection and in order to return to the seam program “M05".
26
– Tap the symbol.
The display is inverted.
– Select a seam (e.g. “6”).
The display changes to confirmation prompt.
Selection: Yes/ No
1
– Confirm with “Yes” in order to adopt the selection and in order to return to the seam program “M05".
– Tap the symbol “P” in order to adopt the selection and in order to return to the display screen program.
– Tap the symbol “P” in order to return to the main screen.
6.4.2.1
Number of seam programs and seams
Seam programs max: M01 – M20
Seams per seam program: 1 - 7
27
6.4.3
Editing, deleting the seam program or seams
Symbol Meaning
Save
Delete
Enter
Insert
Scroll pages
Exchanging
Delete seam
Example: Seam “6”
– Press the symbol when the main screen is displayed.
The display changes to the screen programs.
– Tap the symbol for the new seam program (e.g. “M05”).
The program number appears in inverted image.
– Tap the symbol “E” in order to adopt the selection.
The display changes to the seam program “M05”.
28
– Tap the seam “6”.
The display is inverted.
– Tap the symbol “Delete”.
The display changes to the confirmation prompt Yes / No.
– Confirm with “Yes” in order to delete the seam 6.
1
29
30
Inserting a seam
Example: No. “1”
The seam to be inserted is always inserted in front of an existent seam.
– Tap the seam “6”.
The display appears inverted.
– Tap the symbol ”Insert”.
The seam or several seams are shifted one place to the right and the free storage space flashes in negative image.
– Select one seam, e.g. Number “1”.
The display changes to confirmation prompt Yes/ No.
– Confirm with “Yes” in order to insert the seam “1”.
– Tap the symbol “P” in order to adopt the selection and in order to return to the display screen program.
Exchanging the seam
Example: No. “6” with No. “4”
– Tap the seam “6”.
The seam “6” flashes.
– Tap the symbol ”Exchange”.
The other seams are marked for selection.
1
– Tap one seam “4”.
The seams “4” and “6” flash in inverted image.
– Confirm with “Yes” in order to exchange the seams “4” and “6”.
– Tap the symbol “P” in order to adopt the selection and in order to return to the display screen program.
31
32
Deleting the seam program
Example: M05
– Tap the symbol “Delete”.
The display changes to the confirmation prompt Yes/ No.
– Confirm with Yes in order to delete the seam program M05.
The display changes to the program screen.
– Select the desired seam program, e.g. 04.
The seam program is displayed in inverted image.
– Tap the symbol “P” in order to adopt the selection and in order to return to the display screen program.
6.4.2
Manual sewing, driven by the pedal
Switching on the function
– Tap the symbol “MAN”.
The display changes to the “manual mode”.
Switching off the function
– Tap the symbol “P” in order to return to the main screen.
Note
The maximal speed in “Manual Mode” can be changed in the global parameters with the help of Parameter No. “103”.
1
33
6.4.5
Changing the seam programs
·
Seam parameters are parameters that can be changed for individual seams (e.g. “4” or “6”).
·
Global parameters are parameters that are identical for all the seam programs and seams.
Seam parameters
Global parameters
Automatic seam change
Note
The quick access keys function only for the option “Fullness regulation by means of stepper motors”.
34
35
1
6.4.5.1
Seam Parameters
6.4.5.1.1
1
Editing the fullness regulation
– Tap the symbol for upper or lower feed.
The following display screen appears.
3
1 2 3
7
4
8
With cylinder
Segment 1 Segment 2 Segment 3
Stitches Stitches Stitches
5
6
7
With cylinder With stepper motor
8
1 = Display of the current seam
2 = Display of the fullness in the home position (stepper motor)
3 = Fullness regulation is enabled
4 = Switching on the segments
5 = Switching on the segments for quick adjustment on the main display screen (stepper motor)
6 = Fullness in the 5 segments towards which the sewing motor moves
7 = Number of stitches in the segments 1 - 5
8 = Saving
Segment 1
Basic seam
With stepper motor
Segment 2 Segment 3 Segment 4 Segment 5
Stitches Stitches Stitches Stitches Stitches Basic seam
Note
The parameters of the home positions 2 are located in the “Global
Parameters” with the numbers “40” and “42”.
36
Switching on the fullness regulation
– Tap the symbol 3.
The display is inverted.
– The fullness regulation is therewith enabled and is also displayed in inverted image on the main screen on exiting the fullness regulation.
Programming the stitches and quantities
– Tap on the symbols for the stitches “6” or Item “5”.
The display changes to input mode.
– Enter the desired values.
– Save the values with the key “P”.
The display changes back to fullness regulation.
Machine with fullness regulation by means of cylinder
– Tap on the symbol for the segment 2.
The display appears inverted.
.
In segment 2, fullness is switched on by means of the number of programmed stitches
Machine with fullness regulation by means of stepper motor
– Tap on the symbols 1, 3, 5
.
The display appears inverted.
– The segments 1, 3, 5 are switched on for the quick adjustment in the main view
.
ATTENTION !
The following must be borne in mind while working with fullness by means of stepper motor:
The enabling of the fullness always applies to all 5 segments.
1
37
38
Quick adjustment of fullness regulation
– Tap on the symbol for the desired quick adjustment.
The display appears inverted.
– Enable the fullness with the keys “+” and “-”.
Change segments 1, 3 and 5.
– Tap on the symbol “+17”.
The value is saved.
Parameters of fullness regulation by means of cylinder
Upper feed
Parameter 01: switched on
Parameter 02:
Parameter 03: which the upper feed
Parameter 04:
Parameter 05: which the upper feed
Parameter 06:
Segment 1
Number of stitches before the upper feed is
Quantity of fullness 1 OFF/ ON
Segment 2
Number of stitches, the length of time during is switched on
Quantity of fullness 2 OFF/ ON
Segment 3
Number of stitches, the length of time during is switched on
Quantity of fullness in segment 3 OFF/ ON
Differential lower feed
Parameter 07:
Parameter 08:
Parameter 09: which
Parameter 10:
Parameter 11: which
Parameter 12:
Segment 1
Number of stitches before differential feed is switched on
Quantity of fullness 1 OFF/ ON
Segment 2
Number of stitches, the length of time during differential transport is switched on
Quantity of fullness 2 OFF/ ON
Segment 3
Number of stitches, the length of time during differential transport is switched on
Quantity of fullness in segment 3 OFF/ ON
Parameters of fullness regulation by means of stepper motor
Upper feed
Parameter 01:
Parameter 02:
Parameter 03:
Parameter 04:
Parameter 05:
Parameter 06:
Parameter 107:
Parameter 108:
Parameter 109:
Parameter 110:
Segment 1
Number of stitches
Quantity of fullness in segment 1
Segment 2
Number of stitches
Quantity of fullness in segment 2
Segment 3
Number of stitches
Quantity of fullness in segment 3
Segment 4
Number of stitches
Quantity of fullness in segment 4
Segment 5
Number of stitches
Quantity of fullness in segment 5
1
Differential upper feed
Parameter 07:
Parameter 08:
Parameter 09:
Segment 1
Number of stitches
Quantity of fullness in segment 1
Segment 2
Number of stitches
Parameter 10:
Parameter 11:
Parameter 12:
Parameter 113:
Quantity of fullness in segment 2
Segment 3
Number of stitches
Quantity of fullness in segment 3
Segment 4
Number of stitches
Quantity of fullness in segment 4 Parameter 114:
Parameter 115: Segment 5
Number of stitches
Parameter 116: Quantity of fullness in segment 5
39
6.4.5.2
Machine parameters
– Tap the symbol.
The display changes to the machine parameters.
– Select the desired parameter with the arrow keys.
– Tap the symbol “E” in order to adopt the selection.
– Changing the value.
– Tap the symbol “P” in order to save the selection.
Parameter 30:
Parameter 31:
Parameter 32:
Adjusting the main speed
Manual sewing on/ off
Length of time during which table blowing remains switched on
Number of stitches before start of sewing is followed Parameter 33: by automatic start
Parameter 34: lowered
Parameter 35:
Number of stitches until the contour guide is
Parameter 36:
Parameter 37:
Number of stitches until the contour guide moves in sideways
Number of stitches until the transport unit is lowered
Start mode for contour control
0 = front right
1 = front left
2 = rear right
3 = rear left
Parameter 60:
Parameter 61:
Parameter 77:
Parameter 78:
Soft-start speed
Switching on or switching off the soft-start
Switching on or switching off the auto-start
Number of stitches before the auto-start begins
Parameter 120: Sewing foot lift in the seam
Parameter 121: Sewing foot lift at seam start
40
6.4.5.3
Roll-out Device
– Tap the symbol.
The display changes to the parameters.
– Select the desired parameter with the arrow keys.
– Tap the symbol “E” in order to adopt the selection.
– Changing the value.
– Tap the symbol “P” in order to save the selection.
Parameter 16: chain
Number of stitches for the length of which the thread
1 is suctioned (seam start)
Parameter 17:
Parameter 21: roll-out device
Switching on or switching off the stacker
Parameter 20: Number of stitches before the roll-out device is lowered
Number of stitches, for the length of which the
Parameter 22: before the is switched on.
Number of stitches after unblocked light barrier roll-out device stops.
Parameter 23: Period of time during which the smoothening takes place.
Parameter 47: Point of time of stacker movement
Parameter 53: Point of time when the roll-out device is lifted.
41
6.4.5.4
Puller
– Tap the symbol.
The display changes to the parameters.
For programming, see
Chapter 6.5.6.2 Roll-out Device
Parameter 26:
Parameter 27: puller
Parameter 51:
Parameter 100: puller is opened.
Number of stitches before the puller is lowered
Number of stitches, for the length of which the is lowered.
Puller speed
Value lower = Puller is quicker
Value higher = Puller is slower
Number of stitches, for the length of which the
42
6.4.5.5
Global Parameters
– Tap the symbol for “Main Menu”.
The display changes to main menu.
– Tap the symbol for global parameters.
The display changes to the global parameters.
– Select the desired parameter with the arrow keys.
– Tap the symbol “E” in order to adopt the selection
.
– Changing the value.
– Tap the symbol “P” in order to save the selection.
Parameter 29: Upper feed maximum track (option of stepper motor)
Parameter 38:
Parameter 39:
Delayed start of light barrier
Differential feed (option of stepper motor)
Maximum track
Parameter 40:
Parameter 42:
Base value for upper feed (option of stepper motor)
Base value for differential lower feed
(option of stepper motor)
Parameter 45: Number of stitches before table blowing is switched on.
Parameter 46: Duration of the stacker impulse
Parameter 48: Max. speed
Parameter 49:
Parameter 50:
Speed during warp thread separation
Number of stitches before thread tensioning is opened (seam end).
Parameter 52: Speed of roll-out device
Parameter 54: Impulse duration of retracted mouse
Parameter 55: Time until after the roll-out device is lifted on the transport unit.
Parameter 58:
Parameter 59: roll-out device
Display of the software version
Number of stitches, for the length of which the suctions the thread chain (seam start)
Parameter 65: Thread tension lift
1
43
44
Parameter 79:
Parameter 80:
Soft-start after “Stop in the seam”
Resetting the daily pieces counter.
Parameter 102: Language
Parameter 103: Manual speed
Parameter 126: Chaining-off speed
6.4.5.6
Input - Output Test
– Tap the symbol for “Main Menu”.
The display changes to main menu.
– Tap the symbol for Input-Output.
The display changes to Input.
Checking the inputs e.g. Start light barrier In1
– Switching the light barrier to dark.
The display In1 appears inverted.
In 1 = Start light barrier
In 5 = Program Stop
In 8 = Upper Feed Switch (Option)
In 9 = Differential Lower Feed Switch (Option)
Checking the pedal
– Actuate the pedal.
The display 2 to 12 appears in stepped mode.
0 to 2 = backwards
0 to 12 = forwards
1
45
46
Checking the outputs
– Tap the symbol for the outputs.
The display changes to Outputs.
– Tap the symbol “Y 1”.
The display appears inverted and the output is switched on at the same time.
– Tap the symbol “Y 1” once again.
The output is returned to its original position.
– Tap the symbol.
The subsequently selected output is automatically switched on/off.
Output element
Switch Designation
Y06
Y07
Y08
Y09
Y10
Y11
Y12
Y13
Y01
Y02
Y03
Y04
Y05
Y14
Y15
Y16
Sewing foot up/ down
Thread tension lift
Contour guide up/ down
Stacker off / on
Roll-out device up/ down
Transport unit up/ down
Contour guide forward / backward
Contour guide blowing on
Move contour guide sideways
Differential lower feed on / off
Upper feed on / off
Warp thread separator off / on
Table blowing off / on
Dirt suctioning off / on
Puller up/ down
Mouse retracted
6.4.5.7
Stepper Motor Test
– Tap the symbol “Stepper Motor Test”.
The display changes to the inputs.
– Tap the symbol.
The display screen for the stepper motor test appears.
– Tap the symbol “Differential Feed” .
The display screen for the differential transport test appears.
– Tap on the symbol once again.
The stepper motor for differential transport moves to reference position.
1
– Tap the symbol once again.
The stepper motor moves through its steps.
47
48
– Tap the symbol “Upper Feed” .
The display screen for the upper feed test appears.
– Tap on the symbol once again.
The stepper motor for differential feed moves to reference position.
– Tap the symbol once again.
The stepper motor moves through its steps.
6.4.8
Version Data
– Tap the symbol Global Parameters in the main menu.
The following display screen appears.
– Tap the symbol Version .
The version data appears.
1
49
7.
Data protection using the USB stick
7.1
General Information
1
The USB stick 1 serves the purpose of preserving and transferring the sewing unit software.
With its help, program and parameter data can be transferred even to other sewing units and workplaces.
Even customary USB sticks can be used.
7.2
Formatting the USB stick
Before a new USB stick is used, it must be formatted accordingly.
The file format is the “FAT 16” system.
Format the USB stick using a PC with the FAT 16 system.
50
7.3
Saving the seam programs and seam parameters on the USB stick
– Switch off the main switch.
– Insert the USB stick in the slot of the operating panel.
– Switch off the control element.
– Tap the symbol.
The display changes to the main menu.
– Tap the symbol.
The display changes to the display screen “Saving the seam
parameters”.
1
– Tap the symbol “Control on USB stick”.
The display screen changes to selection.
– Tap one file out of the five file options.
– Tap the symbol “Control on USB stick”.
The display changes to the screen “Save”.
– Tap the symbol.
The display changes to the main menu without saving.
Or
– Tap the symbol.
The seam program and all the parameters are saved.
51
52
This is followed by the message:
– Confirm with “OK”.
The display changes to the main menu.
– Tap the button “P” in order to return to the main screen.
Note
Five variously programmed files can be saved.
The files can be renamed using the PC.
ATTENTION: In the process, make sure that the file name does not exceed 8 characters.
7.4
Loading the seam programs and seam parameters from the USB stick
– Switch off the main switch.
– Insert the USB stick in the slot of the control element.
– Switch on the main switch.
– Tap the symbol.
The display changes to the main menu.
– Tap the symbol.
The display changes to the display screen “Saving the seam
parameters”.
1
– Tap the symbol “USB stick in the control unit”.
The display screen changes to selection.
– Select the desired file with the arrow keys.
– Tap the symbol.
The display changes to the main menu without saving.
Or
– Tap the symbol.
The seam program and all the parameters are loaded.
53
This is followed by the message:
– Confirm with “OK”.
The display changes to the main menu.
– Tap the button “P” in order to return to the main screen.
7.5
Saving global parameters on USB stick
Procedure:
See Chapter 7.3
7.6
Loading global parameters from the USB stick
Procedure:
See Chapter 7.4
7.8
Removing the USB stick
– Switch off the main switch.
Pull out the USB stick from the slot of the Efka control unit
54
8.
Maintenance
8.1
Cleaning and Testing
Caution: Risk of Injury !
Switch off the main switch.
The sewing unit may be serviced only when it is switched off.
The maintenance jobs must be performed latest after the maintenance intervals specified in the tables (see column “Operating Hours”).
Shorter maintenance intervals can ensue for the processing of lint collecting materials.
A clean sewing unit protects against faults.
1
1
2
6 5 4 3
55
Operating hours
Maintenance Job
Remove machine head
.
- Lint and thread waste
(e.g. with air blow gun)
Explanation
Clean the entire area 1 of the thread guides under the thread sliding plate
Suctioning Device Empty the container 2 of the suctioning device
- Turn the lower part of the container to the left and remove the lower part
- Empty the container
- Screw back the lower part by turning it to the right.
Pneumatic System
- Check the water level in the pressure regulator
3
- Clean the filter insert 4
- Check the leak tightness of the system
Make sure that the water level does not rise up to the filter insert 4.
- After pressing the drain screw 5, blow out the water under pressure from the water separator.
Dirt and condensate are discharged by means of filter insert 4.
- Separate the sewing unit from the compressed air supply.
- Press in the drain screw 5.
The pneumatic system of the sewing unit must be pressureless.
- Unscrew the water separator 6
- Extract the filter insert 4.
Wash and blow out the contaminated filter cup and filter insert with petroleum ether
(no solvent!).
- Reassemble the water separator and connect the maintenance unit.
Operating Job to be performed
8
8
40
500
500
56
8.2
Lubrication
Maintenance work to be carried out
Lubrication
1
Caution: Risk of Injury !
Oil can induce skin rashes.
Avoid long-term skin contact.
Wash yourself thoroughly after contact.
ATTENTION !
The handling and disposal of mineral oils is subject to legal regulation.
Deliver used oil to an authorised collection point.
Protect your environment.
Take care not to spill oil.
1
For lubrication the sewing unit head, use exclusively the lubricant
DA 10 or an equivalent oil with the following specification:
– Viscosity at 40° C:
– Flash point
10 mm²/s
150° C
DA 10 can be ordered from the sales outlets of DÜRKOPP ADLER AG while referring to the following part numbers:
250-ml container:
1-litre container:
2-litre container:
5-litre container:
9047 000011
9047 000012
9047 000013
9047 000014
Explanation Operating hours
8 Check the oil level in the sewing unit head regularly (inspection glass 1 and 2).
For more detailed information, kindly refer to the enclosed operating instructions for the sewing machine head.
57
8.3
Repair
When the machine is damaged or parts are worn please contact:
Dürkopp Adler AG
Potsdamer Str. 190
33719 Bielefeld
Tel.:
Fax:
+49 (0) 180 5 383 756
+49 (0) 521 925 2594
E-mail: [email protected]
Internet: www.duerkopp-adler.com
58
advertisement
* Your assessment is very important for improving the workof artificial intelligence, which forms the content of this project