SICK ICR890 Operating instructions
Add to My manuals128 Pages
ICR890 is a high-end CCD camera system designed to read 1-D and 2-D codes with superb image quality suitable for OCR and video coding applications. It is a versatile device that can be used in various industrial applications, such as reading codes on conveyor belts, reading labels on products, and inspecting parts. The ICR890 system is equipped with a range of features that allow you to optimize its performance for specific applications, including adjustable illumination, focus control, code configuration, and data processing.
advertisement
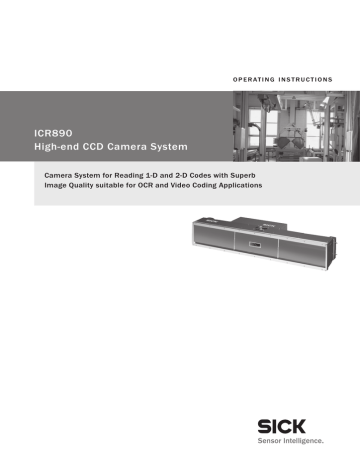
O P E R AT I N G I N S T R U C T I O N S
ICR890
High-end CCD Camera System
Camera System for Reading 1-D and 2-D Codes with Superb
Image Quality suitable for OCR and Video Coding Applications
Operating Instructions
ICR890 High-end CCD Camera System
Software Versions
Software/Tool
ICR890 System
Function
SICK Firmware
ICR890 Device
Description
SOPAS-ET
Device-specific software module for SOPAS-ET
Configuration Software
Configuration software
Version
From version
1.0 0000
From version
1.00
From version
2.10
RF interference in case of use in residential areas.
¾ ICR890 High-end CCD Camera System is exclusively intended for use in an industrial environment.
2
Copyright
Copyright © 2006
SICK AG Waldkirch
Auto Ident, Reute Plant
Nimburger Strasse 11
79276 Reute
Germany
Trademark
Windows98 TM , NT TM , ME TM , 2000 TM , XP TM and Internet Explorer TM are registered trademarks or trademarks of the Microsoft Corporation in the USA and other countries.
Latest manual version
For the latest version of this manual (PDF), see www.sick.com.
© SICK AG · Division Auto Ident · Germany · All rights reserved 8011325/0000/2006-10-24
Operating Instructions
ICR890
Quick Finder
ICR890 High-end CCD Camera System
Quick Finder …
• Included in the delivery ...
–
Chapter 3.1.2 Included in delivery, page 25
• System projection
–
Chapter 3.2 System requirements, page 26
• PLEASE NOTE
–
Chapter 2 Safety information, page 17
• Installing the device in the reading station
–
Chapter 4 Installation, page 45
• Connecting the device to the electricity supply
–
Chapter 5 Electrical installation, page 53
• Familiarizing yourself with the device and its functions
–
Chapter 3 Product description, page 23
–
Chapter 6.3.6 Changing the device password for the user level "Authorized Client", page 88
–
Chapter 9 Technical data, page 103
• Starting up the device with the default setting
–
Chapter 6.3 First startup, page 80
• Installing the SOPAS-ET Configuration Software on the PC
–
Chapter 6.2.3 Installation of the Configuration Software SOPAS-ET, page 79
• Optimizing the device to the reading conditions
–
Chapter 6.3.3 Configuring the ICR890 System/MSC800, page 83
• Assistance in case of problems
–
Chapter 8 Troubleshooting, page 97
• Where is everything?
–
8011325/0000/2006-10-24 © SICK AG · Division Auto Ident · Germany · All rights reserved 3
4
Quick Finder
Operating Instructions
ICR890 High-end CCD Camera System
Overview of installation sequence
The following list summarizes the most important installation sequences for the ICR890
System as a stand-alone device in combination with the MSC800 for reading from above:
1.
Check delivery for completeness.
2.
Insert the ICI890 Illumination into two 180° brackets on the frame and screw tight. The front window of the ICI890 Illumination should face downwards.
3.
Remove the yellow and black protective caps from the lens protection tube and from ICD890
Camera lens.
Do not touch the lens!
4.
Align the ICD890 Camera from the correct side to the illumination and carefully insert the lens protection tube into the ICI890 Illumination opening.
5.
Attach the ICD890 Camera to the ICI890 Illumination. Align the entire unit parallel to the conveyor level and screw on the 180° brackets.
6.
Connect the control line and the ICI890 Illumination power supply to the ICD890 Camera.
7.
Insert and tighten the deflection mirror incl. the protective film on the opposite side to the ICI890
Illumination in two additional 180° brackets, parallel to the conveyor level.
The deflection mirror must be positioned at the same height as and exactly parallel to the illumination.
8.
Install the MSC800 close to the reading location.
9.
Install the photoelectric reflex switch on the conveyor system in front of the reading location in opposite direction of transport.
10. Install the MLG Light Grid on the conveyor system in front of the photoelectric reflex switch in opposite direction of transport.
11. Install the incremental encoder on the conveyor system at the reading location.
12. Electrically connect the ICR890 System to the MSC800.
13. Connect the photoelectric reflex switch, MLG Light Grid, incremental encoder as well as data processing host and PC to the MSC800 configuration.
14. Connect the MSC800 to the supply voltage (100 to 264 V AC/50 to 60 Hz).
15. Switch on the MSC800 using the main switch.
The ICR890 System and the MSC800 start up automatically.
16. Switch on the PC and install the SOPAS-ET Configuration Software (minimum requirements:
Windows 98 TM ).
17. Start the SOPAS-ET Configuration Software and set up the new SOPAS-ET Project by choosing the appropriate ICR890 and MSC800 Device Descriptions.
18. Establish communication with the MSC800.
19. Configure the ICR890 System via the register tabs in the SOPAS-ET Configuration Software
(position of the ICR890 in relation to conveyor system, focus control, code configuration, reading pulse, etc.).
20. Trigger the ICR890 System (start reading pulse). To achieve this, move the object into the range of the photoelectric reflex switch and keep it in this position.
The illumination switches on.
21. Remove the protective film from the deflection mirror and set up the deflection mirror ensuring that the ICI890 Illumination light hits the stationary object (code) at a 15° angle (skew angle on the conveyor level).
22. Carry out a test reading with the 1-D/2-D code. Move the object carrying the code several times across the conveyor level beneath the ICR890 System and display the reading results in the
SOPAS-ET Configuration Software.
23. Repeat the test reading under real conditions and check that the data has been transferred to the host.
24. Correct or optimize the parameter values where necessary via the SOPAS-ET Configuration
Software.
25. Save the parameter set as an “*.spr” configuration file to the SOPAS-ET Configuration Software.
The ICR890 System is ready for operation once the application-specific setting has been set.
Note Detailed instructions can be found in Chapters
,
and
© SICK AG · Division Auto Ident · Germany · All rights reserved 8011325/0000/2006-10-24
Operating Instructions
ICR890
Contents
Contents
Installation and maintenance....................................................................17
Electrical installation and the replacement of system components.......17
Startup, operation and configuration........................................................17
General safety precautions and protection measures .................................19
LED radiation from the ICI890 Illumination..............................................19
Switch off the ICR890 System...................................................................20
Switch on the ICR890 System ...................................................................20
Dispose of the device after decommissioning .........................................21
General system requirements ...................................................................26
Electrical installation requirements ..........................................................28
Product features and functions (overview) ...................................................29
Data processing.............................................................................................37
LEDs of the ICD890 Camera......................................................................42
8011325/0000/2006-10-24 © SICK AG · Division Auto Ident · Germany · All rights reserved 5
6
Contents
Operating Instructions
ICR890 High-end CCD Camera System
Layout the components which are to be installed................................... 45
Selecting the installation location............................................................. 46
Arrangement at the conveyor system....................................................... 47
Installing the ICI890 Illumination and the ICD890 Camera.................... 50
Installing the incremental encoder ........................................................... 52
Installing the MSC800 Controller.............................................................. 52
Electrical installation of the ICR890 System (without MSC800) ............ 54
Electrical installation of the ICR890 System with MSC800
Electrical installation of the ICR890 System with MSC800
Electrical connections of the ICD890 Camera......................................... 60
Electrical connections of the ICI890 Illumination.................................... 61
Electrical connections of the MSC800 (overview) ................................... 62
Assembled cables (overview) .................................................................... 63
Power supply of the ICR890 System ........................................................ 64
Data interfaces HOST/AUX........................................................................ 65
Data interface CAN 1-IN/OUT.................................................................... 66
Wiring the Ethernet interface HOST ETHERNET....................................... 68
Wiring the Ethernet interfaces GBIT 1 and GBIT 2 .................................. 69
Wiring the switching inputs IN 1 and IN 2 ............................................... 69
Wiring the switching outputs Result 1 and Result 2 (OUT connection). 70
Pin assignments and conductor colouring assignment............................... 71
ICD890 Camera connections .................................................................... 71
ICI890 Illumination connections............................................................... 75
Wire colours assignment of assembled cables with open end............... 75
Configuration Software SOPAS-ET................................................................. 79
Functions of the SOPAS-ET Configuration Software for the
ICR890 System/MSC800 (overview)........................................................ 79
System requirements for the SOPAS-ET Configuration Software ........... 79
Installation of the Configuration Software SOPAS-ET.............................. 79
Default setting for the SOPAS-ET Configuration Software....................... 80
Overview of the configuration procedure ................................................. 81
Establishing communication with the ICR890 System/MSC800........... 81
Configuring the ICR890 System/MSC800 ............................................... 83
Load changed parameter sets into the device ........................................ 87
Save, display and print the current parameter set.................................. 87
Changing the device password for the user level "Authorized Client".... 88
Resetting the default setting in the ICR890 System ............................... 88
© SICK AG · Division Auto Ident · Germany · All rights reserved 8011325/0000/2006-10-24
Operating Instructions
ICR890
Contents
Cleaning the deflection mirror ...................................................................91
Cleaning further optical effective surfaces...............................................92
Replacing a system or a component .............................................................93
Replacing the ICD890 Camera or ICI890 Illumination ............................93
Replacing the deflection mirror .................................................................94
Overview of errors and malfunctions which could occur..............................97
Malfunctions during operation ..................................................................97
ST error status in the reading result of a 1-D code (bar code) ................. 101
Data sheet for ICR890 Camera................................................................... 103
Data sheet for ICI890 Illumination ............................................................. 105
Reading conditions for the diagram....................................................... 106
Reading areas of the ICR890 System.................................................... 106
Max. resolution across the direction of transport ................................. 107
Max. resolution in the direction of transport ......................................... 107
System dimensional drawing ICR890......................................................... 108
Deflection mirror dimensional drawing ...................................................... 110
Configuring the ICR890 System with command strings............................ 111
Calculating code length of a bar code ........................................................ 112
10.4.1 ICR890 High-end CCD Camera System ................................................. 113
10.4.2 Accessories: Controller and object distance detector .......................... 114
10.4.3 Accessories: Cables and connectors ..................................................... 115
10.4.5 Accessories: Cleaning agents for front window of the illumination ..... 116
Supplementary documentation................................................................... 117
8011325/0000/2006-10-24 © SICK AG · Division Auto Ident · Germany · All rights reserved 7
Contents
Operating Instructions
ICR890 High-end CCD Camera System
8
© SICK AG · Division Auto Ident · Germany · All rights reserved 8011325/0000/2006-10-24
Operating Instructions
ICR890
Figures and tables
Abbreviations
BMP Bitmap (pixel-oriented Windows format for saving photos)
CAN C ontroller A rea N etwork (field bus protocol based on the CAN bus)
CCD C harge C oupled D evice
DOF D epth O f F ield dpi d ots p er i nch ( 1 inch = 25.4 mm)
EEPROM E lectrically E rasable P rogrammable R ead Only M emory
FTP F ile T ransfer P rotocol
HTML H yper T ext M arkup L anguage
ICD
I I nput
I mage C apture D evice
ICI I mage C apture I llumination
ICR I mage C ode R eader (High-end CCD Camera System)
JPEG J oint P hotographic E xpert G roup (pixel-oriented file format for saving high compression photos, compression process for tiff formats)
LED lpi
L ight E mitting D iode
L ines p er i nch ( 1 inch = 25.4 mm)
MAC M edium A ccess C ontrol
MLG M odular L ight G rid
MSC M odular S ystem C ontroller (MSC800)
MTBF M ean T ime B etween F ailure
MTTR M ean T ime T o R epair
O O utput
RAM R andom A ccess M emory
ROM R ead O nly M emory
SD
SMART
S
S ecure
ICK M
D igital Card odular A dvanced R ecognition T echnology
SOPAS-ET S ICK O pen P ortal for A pplication and S ystems Engineering Tool (PC software for Windows for configuration of the ICR890 System and the MSC800)
PLC P rogrammable L ogic C ontrollers
TCP/IP T ransmission C ontrol P rotocol/ I nternet P rotocol
UDP U ser D atagram P rotocol
VMS V olume M easuring System
8011325/0000/2006-10-24 © SICK AG · Division Auto Ident · Germany · All rights reserved 9
Figures and tables
Operating Instructions
ICR890 High-end CCD Camera System
Note The ICR890 System components and other components in this document are referred to in the following simplified terms:
• ICR890 High-end CCD Camera System , simplified: ICR890 System
• ICD890 Image Capture Device, simplified: ICD890 Camera
• ICI890 Image Capture Illumination, simplified: ICI890 Illumination
• MSC800 Modular System Controller, simplified: MSC800
• MLG Light Grid (Modular Light Grid), simplified: MLG Light Grid
• VMS4xx/5xx Volume Measuring System, simplified: VMS4xx/5xx
• SICK Open Portal for Application and Systems Engineering Tool, simplified:
SOPAS-ET Configuration Software
The register tabs for configuration of the ICR890 System are referred to in the SOPAS-ET
Configuration Software online help as "device pages".
10
© SICK AG · Division Auto Ident · Germany · All rights reserved 8011325/0000/2006-10-24
Operating Instructions
ICR890
Figures and tables
Tables
Tab. 3-1: Included in the delivery of the ICR890 High-end CCD Camera System ........ 25
Tab. 5-7: ICD890 Camera: Function of the electrical connections ............................... 61
Tab. 5-8: ICI890 Illumination: Function of the electrical connections .......................... 61
Tab. 5-11: Maximum cable lengths between ICR890 and the host................................ 65
Tab. 5-12: CAN bus: Maximum cable lengths, depending on the data transfer rate..... 66
Tab. 5-16: Ratings of the switching outputs Result 1 and Result 2................................ 70
Tab. 5-17: ICD890 Camera: Pin assignment of the 8-pole RJ-45 sockets
Tab. 5-18: ICD890 Camera: Pin assignment of the 5-pole M12 sockets
Tab. 5-19: ICD890 Camera: Pin assignment of the 5-pole M12 plugs
Tab. 5-21: ICD890 Camera: Pin assignment of the 8-pole M12 plug “AUX“ .................. 72
Tab. 5-22: ICD890 Camera: Pin assignment of the 8-pole M12 plug “HOST“ ............... 72
Tab. 5-23: ICD890 Camera: Pin assignment of the 4-pole M12 plug “OUT“.................. 73
Tab. 5-24: ICD890 Camera: Pin assignment of the 5-pole M12 socket “IN 1“.............. 73
Tab. 5-25: ICD890 Camera: Pin assignment of the 5-pole M12 socket “IN 2“.............. 73
Tab. 5-26: ICD890 Camera: Pin assignment of the 4-pole M12 socket
Tab. 5-27: ICD890 Camera: Pin assignment of the 8-pole Harting HanQ8 plug
Tab. 5-28: ICD890 Camera: Pin assignment of the 8-pole Harting HanQ8 socket
Tab. 5-29: ICI890 Illumination: Pin assignment of the 8-pole Harting HanQ8 plug
Tab. 5-30: ICI890 Illumination: Pin assignment of the 8-pole M12 plug
Tab. 5-31: Wire colours assignment: Cable no. 6028420 (HOST/AUX), standard ........ 75
Tab. 5-32: Wire colours assignment: Cables no. 6021166/no. 6021175
8011325/0000/2006-10-24 © SICK AG · Division Auto Ident · Germany · All rights reserved 11
Figures and tables
Operating Instructions
ICR890 High-end CCD Camera System
Tab. 5-33: Wire colours assignment: Cable no.6024861 (IN 1/IN 2), standard ............76
Tab. 5-34: Wire colours assignment: Cable no. 6027559 (OUT), standard....................76
Tab. 6-1: Default setting for the SOPAS-ET Configuration Software (excerpt) ..............80
Tab. 6-2: Connection between the PC with the SOPAS-ET Configuration
Software and the ICR890 System/MSC800 ...................................................81
Tab. 10-2: Ordering information: ICR890 High-end CCD Camera System ................... 113
Tab. 10-3: In stock accessories: Controller and object distance detector ................... 114
Tab. 10-7: Supplementary documentation for the ICR890 System.............................. 117
12
© SICK AG · Division Auto Ident · Germany · All rights reserved 8011325/0000/2006-10-24
Operating Instructions
ICR890
Figures and tables
Figures
ICR890 System in combination with the MSC800 (single-side reading) ...... 23
View of the ICD890 camera and the ICI890 Illumination .............................. 24
Work area of the ICR890 System (standard device)...................................... 26
Example of simple system installation on the installation frame.................. 27
The ICR890 System at a conveyor system, single-side reading from above 31
System diagram for single-side reading from above ...................................... 32
Diagram of the illumination with illuminated area ......................................... 33
ICR890 System with deflection mirror for reading from above ..................... 34
Position of the ICR890 System and the tilt angle........................................... 35
Fig. 3-11: Image analysis (blue rectangle: Regions of interest; green rectangle:
Fig. 3-12: Reading operation modi of the ICR890 System in stand-alone operation ... 38
Fig. 3-15: Pixel resolution across the direction of transport (standard device,
Fig. 3-16: Line resolution in the direction of transport (standard device,
Abb. 4-1: Example of a project-specific dimensional sheet for installation.................. 46
Abb. 4-2: Free space required for connecting the camera and the illumination.......... 47
Abb. 4-4: Arrangement at the conveyor system for multi-side reading with
Abb. 4-7: 180° bracket for the deflection mirror and the illumination......................... 49
Abb. 5-1: Block diagram: connection principle of the ICR890 (standard system) ....... 54
Abb. 5-3: Block diagram: Connection principle of several ICR890
Abb. 5-4: ICD890 Camera: Position of the electrical connections
Abb. 5-5: MSC800-0000 logic controller: Position of the electrical connections ........ 62
Abb. 5-6: ICD890 Camera: Wiring of the HOST/AUX data interfaces............................ 66
Abb. 5-10: ICD890 Camera: Electrical connections (standard system) .......................... 71
Abb. 7-5: ICD890 Camera: Position of the battery on the internal PC card.................. 95
Abb. 9-1: Reading areas of the ICR890 System (standard).........................................106
Abb. 9-2: Pixel resolution across the direction of transport (standard device,
8011325/0000/2006-10-24 © SICK AG · Division Auto Ident · Germany · All rights reserved 13
Figures and tables
Operating Instructions
ICR890 High-end CCD Camera System
Abb. 9-3: Line resolution in the direction of transport (standard device,
Abb. 10-1: EC Declaration of Conformity for the ICD890 Camera
Abb. 10-2: EC Declaration of Conformity for the ICI890 Illumination
Abb. 10-3: Code samples of 1-D codes of various module widths
(print ratio 2:1) and 2-D code of various cell sizes ...................................... 127
14
© SICK AG · Division Auto Ident · Germany · All rights reserved 8011325/0000/2006-10-24
Operating Instructions
ICR890
Notes on this document
Chapter 1
1
Notes on this document
1.1
Purpose
This document provides instructions for technical staff on the installation and operation of the following ICR890 System models:
• The ICR890 System equipped with focus control, CCD sensor 8,192 pixels, standard lens (focal distance 135 mm (5.32 in))
This document contains the following information:
• Installation and electrical installation
• Startup
• Operation and configuration
• Maintenance
• Troubleshooting
• Replacing system components
A step-by-step approach is taken for all tasks.
1.2
Target audience
The target audience of this document is persons assigned the following tasks:
Tasks
Installation, electrical installation, maintenance, replacing system components
Startup, operation and configuration
Operation of the conveyor system
Target audience
Qualified staff, e. g. service technicians and factory electricians
Qualified staff, e. g. technicians and engineers
Qualified staff for startup and operation of the conveyor system
Tab. 1-1: Target audience
1.3
Information content
This document contains all the required information for installation, electrical installation and operation of the ICR890 System at the installation location. The factory configuration
(default setting) of the ICR890 System as a stand-alone device is optimized to a single-side reading (from above or from the side).
Configuration of the ICR890 System for the application-specific reading conditions and operation is carried out via the SOPAS-ET Configuration Software at a Windows TMPC. The
SOPAS-ET Configuration Software contains an online help system to facilitate configuration.
Electrical installation of the MSC800 controller for a ICR890 System as stand-alone device and its configuration is detailed in the MSC800 Operating Instructions (no. 8011540).
These instructions also described use of the MSC800 as a controller for a multi-side reading.
Note Further information on High End CCD Camera Systems, Volume Measurement Systems and
Bar Code Scanners is available from SICK AG, Auto Ident division.
On the Internet at www.sick.com.
8011325/0000/2006-10-24 © SICK AG · Division Auto Ident · Germany · All rights reserved 15
Chapter 1
Notes on this document
Operating Instructions
ICR890 High-end CCD Camera System
1.4
Symbols used
Some of the information in this document is marked specially so that you can access it quickly:
Warning!
Warnings are provided to prevent injury to operating personnel or serious damage to the
ICR890 System.
¾ Always read warnings carefully and observe them at all times.
Reference Italics are used to refer to more detailed information elsewhere.
Note Notes indicate special features or characteristics.
Explanation Explanations provide background information on technical correlations.
Recommendation Recommendations help you carry out certain procedures more effectively.
TIP Tips explain settings in the SOPAS-ET Configuration Software.
P ROJECT This font indicates a term in the user interface of the SOPAS-ET Configuration Software.
Icons refer to buttons in the user interface of the SOPAS-ET Configuration Software.
“0x0“ This font indicates messages output by the ICR890 System.
This symbol identifies sections that describe steps carried out with the SOPAS-ET
Configuration Software.
This symbol refers to additional technical documentation.
¾ There is a procedure which needs to be carried out. This symbol indicates operational instructions which only contain one operational step or operational steps in warning notices which do not have to be followed in any particular order.
Operational instructions comprising several steps are denoted using consecutive numbers.
Ö This symbol indicates a glossary entry.
16
© SICK AG · Division Auto Ident · Germany · All rights reserved 8011325/0000/2006-10-24
Operating Instructions
ICR890
Safety information
Chapter 2
2
Safety information
This chapter deals with your safety and operator safety.
¾ Read this chapter carefully before using the ICR890 System.
2.1
Authorized users
For correct and safe functioning, the ICR890 System must be installed, operated and maintained by sufficiently qualified staff.
Repairs to the ICR890 System should only be carried out by qualified and authorized SICK
AG service staff.
¾ The operating instructions should be made available to the end user.
¾ The end user should be briefed and urged to read the operating instructions by the technicians.
The following chapters summarize the required qualifications for the various tasks.
2.1.1
Installation and maintenance
• Practical technical training
• Knowledge of current health and safety regulations at the workplace
2.1.2
Electrical installation and the replacement of system components
• Practical electrical training
• Knowledge of current electrical safety regulations
• Knowledge of startup and operation of the device in each operational area
(e. g. conveyor system)
2.1.3
Startup, operation and configuration
• Knowledge of the mechanical and electrical parameters of the conveyor system and the characteristics of the conveyor system regarding startup and operation
• Basic knowledge of the Windows TM operating system
• Basic knowledge of data transfer
• Basic knowledge of designing and setting up (addressing) Ethernet connections for connecting the ICR890 System to the Ethernet
• Basic knowledge of working with an HTML browser (e.g. Internet Explorer) for using the online help
• Basic knowledge of 1-D/2-D code technology
8011325/0000/2006-10-24 © SICK AG · Division Auto Ident · Germany · All rights reserved 17
Chapter 2
Safety information
Operating Instructions
ICR890 High-end CCD Camera System
2.2
Intended use
The ICR890 High-end CCD Camera System is an intelligent sensor for the automatic recognition and decoding of 1-D/2-D codes on moving objects in a reading station.
In combination with the MSC800 modular system controller, the ICR890 System is used as a stand-alone device for single-side reading, e.g. from above or from the side. For a similarly possible multi-side reading on the conveyor system, the corresponding number of systems is combined with other SICK bar code scanners and with the co-coordinating MSC800.
The intended use of the system results from the following description of the system components and their functions:
• The system consists of the ICD890 Camera, the ICI890 Illumination and a deflection mirror. The ICD890 Camera is installed in a frame together with the ICI890 Illumination as a unit parallel to the deflection mirror, either above the conveyor system (reading from above) or at the side (side reading).
• The necessary object distance information is contained in the ICR890 System either by an MLG Light Grid (in the case of readings from above) or by a VMS4xx/5xx Volume
Measurement System for focus control during S ingle or multi-side reading.
• The ICR890 System transfers the reading data via its HOST main data interface (serial
RS 232, RS 422/485, Ethernet or CAN), with optionally selectable diagnosis data, to a superordinate host processor for further processing.
The ICR890 System transfers its data via the CAN interface to the MSC800, in combination with the MSC800. The data can then be accessed from the HOST data interface.
• The processed image information of the ICD890 Camera is located on two fast GBit
Ethernet channels. The image information can be transferred to the client display at extremely high data transfer rates on a special PC with compatible GBit Ethernet interface cards and GigE Vision Standard licence (real time image data transfer). The high image quality also allows use in OCR and video coding applications.
• Configuration/Operation of the ICR890 System is carried out as standard via the AUX auxiliary data interface (serial RS 232 or Ethernet) using the SOPAS-ET Configuration
Software, which runs on a standard client PC. Alternatively, the configuration can also be carried out via the PC connection to the MSC800 (serial RS 232 or Ethernet).
Any warranty claims against SICK AG shall be deemed invalid in the case of other system use or system modifications, this includes modifications during installation and electrical installation or changes to the SICK software.
Note The ICD890 Camera and ICI890 Illumination must not be opened. If the devices are opened, the manufacturer's warranty shall not apply.
18
© SICK AG · Division Auto Ident · Germany · All rights reserved 8011325/0000/2006-10-24
Operating Instructions
ICR890
Safety information
Chapter 2
2.3
General safety precautions and protection measures
¾ Read the general safety precautions thoroughly and observe them during all ICR890
System activities. Also observe the warning notices above the operational instructions of each chapter.
2.3.1
Radio interferences
RF interference in case of use in residential areas.
¾ ICR890 High-end CCD Camera System is exclusively intended for use in an industrial environment.
2.3.2
Installation work
Risk of injuries due to falling components!
The combined weight of the ICD890 Camera and the ICI890 Illumination is approx. 37 kg
(81.6 lb) without installation accessories.
¾ Do not carry out installation work alone.
¾ A second person should always secure components during installation.
2.3.3
Electrical installation work
Risk of injuries due to electrical current!
Connect the MSC800 Controller to the mains power supply (100 to 264 V AC/50 to 60 Hz).
¾ Observe current safety regulations when working with electrical equipment.
2.3.4
LED radiation from the ICI890 Illumination
Output opening
Fig. 2-1: LED radiation outlet opening
LED radiation escapes from the entire front window of the ICI890 Illumination.
8011325/0000/2006-10-24 © SICK AG · Division Auto Ident · Germany · All rights reserved 19
Chapter 2
Safety information
Operating Instructions
ICR890 High-end CCD Camera System
Class 1M LED radiation (in accordance with EN/IEC 60825-1)!
Incorrect use can result in hazardous radiation exposure and the LED class being exceeded!
The accessible radiation of the ICI890 Illumination is not hazardous under reasonably foreseeable conditions, provided that the beam width is not reduced by optical instruments, e.g. magnifying glass, lenses or telescopes. Visual glare, loss of colour vision and eye injuries cannot be ruled out.
The entire window surface is the LED radiation outlet opening.
¾ Do not look directly into the radiation source with optical instruments.
¾ Do not open the housing. (The illumination is not switched off if the housing is opened).
¾ Always observe the latest valid version of laser protection regulations.
Note The ICI890 Illumination works with LEDs on the λ = 620 nm (red light) wavelength.
The radiation emitted is not harmful to human skin.
Regular maintenance is not required to ensure compliance with laser class 1M.
The ICI890 Illumination operates as follows:
• The reading pulse (pulse source) controls the on and off mechanism of the LED illumination during the reading process. The LEDs are switched on in pulsed mode during the reading operation depending on the reading gate duration.
• A time stage (illumination timeout) automatically switches off the illumination during the reading operation after 3 seconds (default setting) following the start of a continuous reading pulse. This, however, does not switch off the reading pulse. The reading pulse should be stopped via a relevant pulse signal. The next reading pulse switches the illumination back on.
• The illumination timeout can be set or switched off within a range of 3 s to 25 h. For safety reasons, the minimum illumination power on time is 3 seconds.
2.4
Quick stop and quick start
The ICR890 System is operated via the MSC800 Controller as standard and can be switched on and off using the controller main switch.
2.4.1
Switch off the ICR890 System
¾ Switch off the power supply of the MSC800.
When the system is switched off the following data is lost:
• Application-specific parameter sets in the ICR890 System and in the MSC800
Controller which were only temporarily saved in the devices
• The last reading result of the ICR890 System
• Daily operating hours counter of the ICR890 System
2.4.2
Switch on the ICR890 System
¾ Switch on the power supply of the MSC800 again.
The ICR890 System starts up using the most recent permanently saved configuration.
The daily operating hours counter is reset.
20
© SICK AG · Division Auto Ident · Germany · All rights reserved 8011325/0000/2006-10-24
Operating Instructions
ICR890
Safety information
Chapter 2
2.5
Environmental information
The ICR890 System has been constructed with minimum environmental pollution in mind.
Excluding the housing, the system does not contain any materials using silicone.
2.5.1
Energy requirements
The ICR890 System is electrically powered via the MSC800 Controller as standard
(functional extra-low voltage in accordance with IEC 364-4-41).
The following power consumption details apply to the system components and the controller:
• ICD890 Camera: typically 75 W with 24 V DC ± 10 % (via MSC800 power supply)
• ICI890 Illumination: typically 350 W with 24 V DC ± 10 % (via MSC800 power supply)
• MSC800-0000 logic controller: typically 10 W with 24 V DC ± 10 %
2.5.2
Dispose of the device after decommissioning
At present SICK AG will not accept the return of any devices which can no longer be operated or repaired.
¾ Inoperable or irreparable devices must be disposed of in an environmentally friendly manner and in accordance with valid country-specific waste disposal guidelines.
The design of the ICR890 System allows for its separation as recyclable secondary raw materials and hazardous waste (electronic scrap).
Please see
Chapter 7.4 Disposal, page 95 .
Note The battery on the internal PC card of the ICD890 Camera must be removed before the device is scrapped.
¾ Dispose of the battery separately in accordance with ROHS regulations (Europe).
8011325/0000/2006-10-24 © SICK AG · Division Auto Ident · Germany · All rights reserved 21
Chapter 2
Notes:
Safety information
Operating Instructions
ICR890 High-end CCD Camera System
22
© SICK AG · Division Auto Ident · Germany · All rights reserved 8011325/0000/2006-10-24
Operating Instructions
ICR890
Product description
Chapter 3
3
Product description
This chapter describes the design, the features and the functions of the ICR890 System.
¾ For installation, electrical installation and startup assistance as well as system configuration using the SOPAS-ET Configuration Software, please read this chapter prior to carrying out any of the tasks.
3.1
Design
The ICR890 System consists of the ICD890 Camera (Image Capture Device), the ICI890
Illumination (Image Capture Illumination) and a deflection mirror. The ICR890 System is operated in combination with the MSC800 (Modular System Controller) via a CAN bus. The
MSC800 supplies the ICR890 System with power.
For further information on the MSC800, see the MSC800 Operating Instructions
(no. 8011540).
External sensors are required for the reading pulse, detection of the object distance and for creation of the increment signal. These sensors and the superordinate host processor are connected to the MSC800.
ICR890 System
MSC800
Mains connection
Power supply
CAN bus
HOST
MLG Light Grid/
VMS4xx/5xx
Object distance/
Object geometry
Reading pulse
Conveyor speed
Fig. 3-1: ICR890 System in combination with the MSC800 (single-side reading)
Alternatively, connection of the external sensors and the superordinate host processor can be carried out directly at the ICR890 System.
8011325/0000/2006-10-24 © SICK AG · Division Auto Ident · Germany · All rights reserved 23
Chapter 3
Product description
3.1.1
Device view
2
3
Operating Instructions
ICR890 High-end CCD Camera System
4
Complete ICR890 System, from above
1
6
5
7
8
Complete ICR890 System, from below
7
ICD890 Camera, from below
9 bl bo bn bm
Legend:
1
ICI890 Illumination
2 ICD890 Camera
3
Air inlet opening for cooling the ICI890 Illumination
4
Guide pins (4 x) for use in
180° bracket
5
ICD890 Camera reading window
6
Electrical connections for the
ICI890 Illumination
7 Electrical connections for the
ICD890 Camera
8 Fixing for bracket (2 x)
9
Handhold for camera (2 x) bl Threaded centering pin for fixing to the ICI890 Illumination bm LEDs for status indicator (5 x) bn
SD memory card for parameter cloning bo Lens protection tube
Fig. 3-2: View of the ICD890 camera and the ICI890 Illumination
24
© SICK AG · Division Auto Ident · Germany · All rights reserved 8011325/0000/2006-10-24
Operating Instructions
ICR890
Product description
Chapter 3
3.1.2
Included in delivery
Delivery of the ICR890 System includes the following components:
4
1
1
1
1
1
Piece(s) Components
1 ICD890 Camera
ICI890 Illumination
Deflection mirror
MSC800
MLG Light Grid (preconfigured) height distance detector with connection cable and installation kit
1
1
1
1
1
1
1
1
1
Comment
ICR890 System
Without connection cables
Application-specific
- or -
Object distance detector VMS4xx/5xx with connection cables and installation kit
180° brackets with installation accessories For ICR890 System and deflection mirror
Triggering the reading procedure WL18-3 Reading Pulse Sensor (pulse photoelectric reflex switch) with connection cable and installation kit
Connection cable
Connection cable
Connection cable
CAN bus data link
Terminal resistance
For the power supply of the ICR890
System
For the power supply of the ICI890
Illumination via the camera
For control of the ICI890 Illumination via the camera
For networking the ICR890 System with
MSC800 via the CAN bus
For CAN bus termination at the ICR890
System
Optional (application-specific) GigE Vision Standard licence for real time image data transfer
Incremental encoder, resolution
10 mm (394 mil)/pulse
- or -
Optional (application-specific)
Incremental encoder, resolution
0.2 mm (7.9 mil)/pulse (using VMS4xx/5xx)
Installation frames Optional (application-specific)
1 Notes on Device with electrical connection diagram as primary information min. 1 CD-ROM
Operating Instructions ICR890 System in printed form, in German and/or English
Included in the device packaging of the
ICR890 System
Depending on number of ordered devices
Optional, depending on the number of issues explicitly ordered upon purchase
Tab. 3-1: Included in the delivery of the ICR890 High-end CCD Camera System
An overview of system components, in stock installation accessories, incremental encoders, cables and plug connections is available in
Chapter 10.4 Ordering information, page 113
.
8011325/0000/2006-10-24 © SICK AG · Division Auto Ident · Germany · All rights reserved 25
Chapter 3
Product description
Operating Instructions
ICR890 High-end CCD Camera System
3.1.3
Contents of the CD-ROM
• “SOPAS-ET Engineering Tool“: Configuration software for Windows TM PCs with integrated online help system (HTML files)
• ICR890 Operating Instructions: PDF version in German and English as well as further publications for MSC800, VMS4xx/5xx
• “Acrobat Reader“: Freely available PC software for reading PDF files
Note The current versions of publications and programs on the CD-ROM can be downloaded at www.sick.com.
3.1.4
Device versions
The system components are available in the following versions:
ICD890-0000000 1027582 Camera with lens (focal distance 135 mm (5.32 in)), standard device
ICD890-0000001 1040277 the same as 1027582, but includes GigE Vision licence
ICI890-00000 1028219 ICI890 Illumination
Tab. 3-2: System component versions
3.2
System requirements
3.2.1
General system requirements
26
25°
600 mm
1.000 mm
Fig. 3-3: Work area of the ICR890 System (standard device) mm
600
1,000
1,400
2,400
3,000 inch
23.6
39.4
55.2
94.6
118.2
© SICK AG · Division Auto Ident · Germany · All rights reserved 8011325/0000/2006-10-24
Operating Instructions
ICR890
Product description
Chapter 3
Requirement
Max. reading distance
Shortest permissible distance to the object
Aperture angle
Value Comment
3,000 mm (118.2 in)
from reading window ( Fig. 3-3, page 26
)
1,400 mm (55.2 in)
Max. track width
Achievable ICD890
Camera resolution
25 ° Work area up to 2,400 mm (94.6 in)
1,000 mm (39.4 in)
also see reading area diagram in Fig. 9-1, page 106
depends on the distance to the object and on the
conveyor speed (see Chapter 3.4.12 Data interfaces, page 39 )
4.8 m/s (945 ft/min) with pixel size 0.25 mm (9.8 mil) Max. conveyor speed
Tab. 3-3: General system requirements (standard device)
3.2.2
Installation requirements
• Typical space requirements above the highest object (for reading from above): application-specific
• Unobstructed view of the objects for the ICR890 System
• Stable installation frames with sufficient load capacity and measurements suited to the
ICR890 System (see
Chapter 9.5 System dimensional drawing ICR890, page 108
)
• Four 180° brackets for the ICR890 System and the deflection mirror (included in delivery)
• Shock absorbent and vibration free attachment
Note An installation frame made of 80 mm (3.15 in) item aluminium profiles can be used for simple system installation (
). The 180° brackets are aligned to these profiles.
Fig. 3-4: Example of simple system installation on the installation frame
8011325/0000/2006-10-24 © SICK AG · Division Auto Ident · Germany · All rights reserved 27
Chapter 3
Product description
Operating Instructions
ICR890 High-end CCD Camera System
3.2.3
Electrical installation requirements
• Power supply (via MSC800): 100 to 264 V AC/50 to 60 Hz
• Reading pulse sensor (start/stop), e.g. photoelectric reflex switch (included in delivery):
For detecting an object with external reading pulse
• Additional appropriate reading pulse sensor (stop), e.g. photoelectric reflex switch: For detecting the end of pulse with extended external reading pulse
• Preconfigured MLG Light Grid(included in delivery): when reading from above to detect the object distance
• VMS4xx/5xx Volume Measurement System: when reading from the side or for multiside reading to detect the object distance
• Suitable incremental encoder, e.g. no. 2039455 (resolution 10 mm (394 mil)/pulse) or no. 2039457 (resolution 0.2 mm (7.9 mil)/pulse) when using the VMS4xx/5xx.
Device is included in delivery depending on the system configuration
• Host processor with RS 232, RS 422/485 data interface or Ethernet: For further processing of the reading data via MSC800 also PROFIBUS-DP
• Suitable visualization PC or PLC: To display the system status
•
Connection cables: See Chapter 5.3.4 Assembled cables (overview), page 63
3.2.4
Operation requirements
• PC in the following version:
– Minimum Pentium III, 500 MHz, 128 MB RAM, CD drive, RS 232 serial data interface or Ethernet interface card, mouse (recommended) and colour monitor
(recommended resolution 1,024 x 768 pixels)
– Operating system Windows 98 TM , Windows NT4.0
TM , Windows ME TM , Windows
2000 TM or Windows XP TM
– Free storage space on the hard drive: Approx. 100 MB for the SOPAS-ET
Configuration Software (V. 2.08) with help files and approx. 70 MB for “Acrobat
Reader“
•
Connection cables see Chapter 5.3.4 Assembled cables (overview), page 63
• PC HTML browser, e.g. Internet Explorer TM : For online help system to the SOPAS-ET
Configuration Software
• Special PC for client display of the processed camera image information in real time equipped with the following:
– Two 1 GBit Ethernet “IntelPro/1000 network card“ interface cards with 8254x
(x = 0, 1, 2, 4, 5, 6, 7) chip set
– GigE vision standard licence for real time image data transfer
28
© SICK AG · Division Auto Ident · Germany · All rights reserved 8011325/0000/2006-10-24
Operating Instructions
ICR890
Product description
Chapter 3
3.3
Product features and functions (overview)
High-end CCD Camera ICD890
• CCD line with 8,192 pixels (standard device)
• Dynamic focus setting
• Lens with 135 mm (5.32) focal distance (standard device)
• Reading area 1,400 to 3,000 mm (55.2 to 118.2 in) (standard device)
• Image resolution 170 to 350 dpi (standard device)
• Conveyor speed max. 4.8 m/s (945 ft/min) with 0.25 mm (9.8 mil) pixel size
• Scanning frequency max. 19.1 kHz (standard device)
• Can be adapted to the print quality of the code
• Analysis area of the CCD line can be restricted
• Real time image output (grey values: “*.bmp“ or “*.jpg“)
User safety and convenience
• Robust, compact metal housing, enclosure rating max. IP 64, CE mark
• Laser class 1M, switching off the LED ICI890 Illumination in case of prolonged active reading gate or if the output capacity is exceeded, minimum power on-time 3 s
• Automatic self-test on system startup
• Diagnosis tools for system setup and system (distance) monitoring
• Configurable reading diagnosis data display in two reading result formats
• Operational data retrieval, error code display on request in case of errors
• Activatable test string function for signalling readiness for operation
• Password protected configuration mode
• Back up of configuration parameter values (cloning) also on SD memory card
(can be removed when replacing the camera)
• Future proof due to firmware update (flash PROM) via data interface
• Future proof SOPAS-ET Configuration Software
• Extended power supply scope
• Necessary maintenance or service task displayed via LED and system report
• The camera or illumination can be replaced within 20 mins
Convenient operation/configuration
• Configuration (online/offline) and display of image memory contents via the SOPAS-ET
Configuration Software (incl. help system)
• Status indicators via five LEDs
Operating modes
• Configuration mode
• Reading operation
Reading operation modi
• Start/Stop operation
• Object tracking (max. 10 objects per second, minimum gap 50 mm (1.97 in))
8011325/0000/2006-10-24 © SICK AG · Division Auto Ident · Germany · All rights reserved 29
Chapter 3
Product description
Operating Instructions
ICR890 High-end CCD Camera System
1-D/2-D code detection
• Data Matrix ECC200 (PDF417 in preparation)/all conventional bar codes
• Max. number of 1-D codes: 50 per reading pulse
• Max. number of 2-D codes: 10 per reading pulse
• Separation of identical codes of the same code type using the code position
• Output sorting: Code position, FIFO, LIFO, code lengths list
• Manipulation of output strings via filter or format masks
Data communication
• Main data interface HOST: Configurable output format of the reading result, communication redirectable to Ethernet interface
• AUX auxiliary data interface: Permanent output format with special diagnosis functions, communication redirectable to Ethernet interface
• Two 1 GBit Ethernet interfaces for fast image output
Reading pulse
• External reading pulse via switching input(s) or data interface
Electrical interfaces
• HOST data interface: RS 232, RS 422/485 serial, Ethernet or CAN (various transfer rate and protocol configurations possible)
• AUX data interface: RS 232, RS 422/485 serial, Ethernet or CAN (permanent transfer rate, data format and protocol)
• CAN interface for integration into SICK CAN-SENSOR Network with the MSC800 or into a CAN Open Network
• Ethernet interface (10/100 MBps), TCP/IP and FTP
• Two 1 GBit Ethernet interfaces, FTP and GigE Vision Standard
• Two digital switching inputs for external reading pulse sensor and incremental encoder via optocoupler
• Two digital switching outputs for signalling definable results in the reading process
(system status)
• Connection to PROFIBUS-DP via MSC800
Connection technology (design)
• Data and function interfaces: M12 connector for industrial use
• GBit Ethernet: Phoenix VARIOSUB RJ-45 sockets, enclosure rating IP 67
• Power supply: Harting connectors
30
© SICK AG · Division Auto Ident · Germany · All rights reserved 8011325/0000/2006-10-24
Operating Instructions
ICR890
Product description
Chapter 3
3.4
Method of operation
This ICR890 System is an intelligent sensor system for automatic and non-contact detection and decoding of 1-D/2-D codes. In principle, the codes can be detected on any side of moving objects in a conveyor system.
For single-side readings, the codes are detected from above, below or from the side using a camera. In order to allow easier installation and setup of the system, the camera image is recorded using a deflection mirror.
Fig. 3-5: The ICR890 System at a conveyor system, single-side reading from above
Note Several cameras can be combined to allow detection of several sides in one passage (multiside reading). The method of operation is described here using the example of single-side reading from above.
8011325/0000/2006-10-24 © SICK AG · Division Auto Ident · Germany · All rights reserved 31
Chapter 3
Product description
Operating Instructions
ICR890 High-end CCD Camera System
The system is operated in combination with an MSC800 Controller. The reading results are output at the data interfaces via the controller. External sensors deliver information via the reading pulse, the object distance and the conveyor speed.
Deflection mirror ICD890 Camera and ICI890
Illumination
Object distance
(Top view)
Reading pulse
(start/stop)
Reading area
Object release point
Direction of transport
Object
MSC800
Controller
Direction of transport
Conveyor system
ICR890 System
(camera, illumination and deflection mirror)
Incremental encoder
VMS4xx/5xx or MLG
Light Grid
Photoelectric reflex switch
Fig. 3-6: System diagram for single-side reading from above
3.4.1
Reading configuration
The ICD890 Camera detects 1-D/2-D codes line by line with the help of a CCD line. The lines are written successively and with a high frequency into an image storage. Continuous feeding of the object on the conveyor system produces a two-dimensional image of the object.
Note The ICR890 System cannot recognize codes on stationary objects.
A moving 1-D/2-D code on an object is displayed as a grey level matrix in the image storage.
Contrast jumps are analyzed in order to scan the codes. The threshold value can be adapted to the ambient conditions.
For more rapid analysis, the analysis area can be restricted to across the direction of transport (code position).
The SOPAS-ET Configuration Software can, among other things, be used to configure features, such as the code position and the symbol contrast:
P ROJECT T REE , ICR890, P ARAMETER , R EADING CONFIGURATION , register tab C ODELABEL PROPERTIES
Moreover, the image resolution across the direction of transport (digital zoom in dpi) and in the direction of transport (dynamic scanning frequency in lpi) can be configured:
P ROJECT T REE , ICR890, P ARAMETER , R EADING CONFIGURATION , register tab I MAGE CAPTURING
PROPERTIES
32
© SICK AG · Division Auto Ident · Germany · All rights reserved 8011325/0000/2006-10-24
Operating Instructions
ICR890
Product description
Chapter 3
3.4.2
Object trigger control
In order to initiate a reading process, the ICR890 System requires an appropriate signal
(trigger). The start signal is emitted via an external reading pulse sensor (photoelectric reflex switch) as standard. As soon as an object has passed the reading pulse sensor, an
“internal reading gate“ opens for the reading process.
Alternatively, a command activates the reading process via a data interface or the CAN-
SENSOR network.
The trigger source can be configured using the SOPAS-ET Configuration Software:
P ROJECT T REE , ICR890, P ARAMETER , R EADING CONFIGURATION , O BJECT T RIGGER C ONTROL , register tab S TART /S TOP OF O BJECT TRIGGER
3.4.3
Focus control
For dynamic focus control, the ICD890 Camera requires continuous information on the distance to the object surface. This data is provided by a lateral MLG Light Grid for readings from above. The object dimensions are taken from the VMS4xx/5xx Volume Measurement
System and processed via the MSC800 for readings from the side.
The SOPAS-ET Configuration Software can, among other things, be used to configure features, such as the default position and the source of the distance measurement:
P ROJECT T REE , ICR890, P ARAMETER , R EADING CONFIGURATION , F OCUS C ONTROL , register tabs
O PTIONS and D ISTANCE M EASUREMENT S OURCE
3.4.4
Illumination control
The area which is to be read must be illuminated with a high-performance LED illumination when recording with the camera. The ICI890 Illumination produces a thin red illuminated area (wavelength λ = 620 nm).
Illuminated area
Fig. 3-7: Diagram of the illumination with illuminated area
During reading from above, the light is deflected onto the conveyor system using the deflection mirror.
8011325/0000/2006-10-24 © SICK AG · Division Auto Ident · Germany · All rights reserved 33
Chapter 3
Product description
Operating Instructions
ICR890 High-end CCD Camera System
Fig. 3-8: ICR890 System with deflection mirror for reading from above
The illumination is controlled by the camera and can be switched on permanently or for the duration of the internal reading gate.
If the reading gate does not run to the end due to an error (e. g. when the conveyor system comes to a halt), the illumination automatically switches off once the settable timeout has expired. In order to prevent epilepsy, the minimum power-on time of the illumination is 3 s.
The illumination mode and the timeout for the ICI890 Illumination can be configured using the SOPAS-ET Configuration Software:
P ROJECT T REE , ICR890, P ARAMETER , R EADING CONFIGURATION , L AMP C ONTROL , register tab
I LLUMINATION MODE
34
© SICK AG · Division Auto Ident · Germany · All rights reserved 8011325/0000/2006-10-24
Operating Instructions
ICR890
Product description
Chapter 3
3.4.5
Position
To ensure correct functioning of the ICR890 System, the position and angle of the camera and the deflection mirror have to be adjusted to the conveyor level.
Fig. 3-9: Position of the ICR890 System and the tilt angle
The position of the object trigger control (photoelectric reflex switch) on the outer right-hand edge of the conveyor system is considered the point of reference, as viewed in the direction of transport.
The α and γ angles must be set depending on the position of the System (e. g. on top or at the side). In order to prevent direct reflectance, the light must be incident at an angle of approx. 15 ° (β = skew) on the object surface against the direction of transport.
The position and the angle of the camera and the deflection mirror can be configured using the SOPAS-ET Configuration Software:
P ROJECT T REE , ICR890, P ARAMETER , P OSITION , register tabs O FFSET , C OORDINATES and A NGLES
3.4.6
Increment configuration
In order to control the camera line frequency, the ICR890 System requires information on the conveyor speed. An external incremental encoder delivers pulses which are used to determine the current conveyor speed.
The conveyor speed results from the number of pulses and the resolution of the external incremental encoder.
The increment source and resolution/speed can be configured using the SOPAS-ET
Configuration Software:
P ROJECT T REE , ICR890, P ARAMETER , I NCREMENT CONFIGURATION , register tab I NCREMENT
8011325/0000/2006-10-24 © SICK AG · Division Auto Ident · Germany · All rights reserved 35
Chapter 3
Product description
Operating Instructions
ICR890 High-end CCD Camera System
3.4.7
Image requirement
The recorded image can be generated irrespective of the decoding result for further processing via the GBit Ethernet interface. This enables, e. g., an analysis if decoding has been unsuccessful.
36
Fig. 3-10: Example of an image recording for analysis
If data processing has been successful (decoding), the marking of the corresponding image areas can also be displayed.
The image format and the scaling/quality can be configured using the SOPAS-ET
Configuration Software:
P ROJECT T REE , ICR890, P ARAMETER , I MAGE A CQUISITION , register tab R EQUEST
Decoding
The recorded image is analyzed by the ICR890 System. This identifies regions of interest in which codes are suspected.
blue rectangle green rectangle green line
Fig. 3-11: Image analysis (blue rectangle: Regions of interest; green rectangle: Successful decoding; green line: Decoder runtime at end of the reading pulse)
© SICK AG · Division Auto Ident · Germany · All rights reserved 8011325/0000/2006-10-24
Operating Instructions
ICR890
Product description
Chapter 3
3.4.8
Code configuration
The ICR890 System can decode the following code types:
1-D codes (bar codes)
• Codabar
• Code 39
• UPC/EAN family
• 2/5 Interleaved
• Code 93
• Code 128 family
2-D codes
• Data Matrix EEC200
• PDF417 (in preparation)
The code types for 1-D and 2-D codes can be selected using the SOPAS-ET Configuration
Software:
P ROJECT T REE , ICR890, P ARAMETER , 1D C ODE CONFIG ., register tab S YMBOLOGIES
P ROJECT T REE , ICR890, P ARAMETER , 2D C ODE CONFIG ., register tab S YMBOLOGIES
The selected code types can be configured individually. The SOPAS-ET Configuration
Software has individual register tabs for each type.
3.4.9
Data processing
Start/Stop operation
There is only one object in the reading area during start/stop operation, i. e. all the read codes should be unambiguously assigned to the object. The start and stop of the reading process control two reading pulse sensors at the beginning and at the end of the reading area as standard (
Fig. 3-12, page 38 ). The distance between each sensor is determined by
the size of the reading area. The reading process can be alternatively controlled with command strings via the data interface. The output of the reading results is carried out either at the end of the reading pulse (the rear edge of the object has left the end of the reading area) or during the reading pulse if certain parameterizable conditions have been fulfilled.
8011325/0000/2006-10-24 © SICK AG · Division Auto Ident · Germany · All rights reserved 37
Chapter 3
Product description
Operating Instructions
ICR890 High-end CCD Camera System
Tracking operation
During the reading process, a maximum of 10 objects can be simultaneously situated, one behind the other, in the tracking operation, i. e. the ICR890 System must be able to unambiguously assign the read codes to the objects (
Fig. 3-12 ). A reading pulse sensor
controls initiation of the reading process at the start of the reading area as standard (see
Chapter 3.4.2 Object trigger control, page 33
), the end is determined by the object release point. This also defines the size of the resulting reading area.
A regular pulse is required in order to track objects in the reading area. This is generated by the external incremental encoder, which delivers a constant pulse at least every 10 mm
(394 mil) of movement in the direction of transport (see
Chapter 3.4.6 Increment configuration, page 35
). This allows the ICR890 System to generate a clear display of the distance between the reading pulse sensor and the object release point. Any fluctuations during startup of the conveyor technology or reductions in speed caused by heavy objects are also detected. For clear separation of consecutive objects, a gap of at least 50 mm
(1.97 in) is required. Reading results for an object are displayed after the rear edge of the object has passed the object release point. Alternatively, the reading process can be initiated by a command string via the data interface.
Tracking operation
Data output
Start/Stop operation
Trigger 2:
Stop
Data output
Trigger 1:
Start
Fig. 3-12: Reading operation modi of the ICR890 System in stand-alone operation
Trigger 1:
Start
The reading operation mode and object release point can be configured using the SOPAS-
ET Configuration Software:
P ROJECT T REE , ICR890, P ARAMETER , D ATA PROCESSING , register tab T RACKING
38
© SICK AG · Division Auto Ident · Germany · All rights reserved 8011325/0000/2006-10-24
Operating Instructions
ICR890
Product description
Chapter 3
3.4.10
Output format
The reading result (decoded codes) is displayed via definable data interfaces. Two different output formats (telegrams) can be defined for this task.
Two output formats can be configured using the SOPAS-ET Configuration Software:
P ROJECT T REE , ICR890, P ARAMETER , D ATA PROCESSING , O UTPUT F ORMAT
3.4.11
Network
Although all important interfaces for displaying the reading results are available at the
ICR890 System, the system is operated via the MSC800 Controller as standard. The
MSC800 assumes system coordination for multi-side readings. The ICR890 System and the
MSC800 can be networked via the CAN bus.
The network parameters can be configured using the SOPAS-ET Configuration Software:
P ROJECT T REE , ICR890, P ARAMETER , N ETWORK A RCHITECTURE , register tabs N ETWORK O PTIONS and
M ASTER /S LAVE
3.4.12
Data interfaces
Numerous data interfaces are available at the ICR890 System.
Data interface
Serial host interface
Serial host interface
Ethernet
Connection
HOST
AUX
Function
Preparation of the reading result for further processing by the host processor
Reading diagnosis
GBit Ethernet:
CAN bus
HOST ETHERNET Preparation of the reading result for further processing by the host processor
GBIT ETHERNET Preparation of the image data of the current reading for further processing
CAN 1 (Out/In),
CAN 2 (Out/In)
Networking one or several systems with the MSC800
Tab. 3-4: Data interface function
The data interfaces can be configured using the SOPAS-ET Configuration Software:
P ROJECT T REE , ICR890, P ARAMETER , I NTERFACES , S ERIAL
P ROJECT T REE , ICR890, P ARAMETER , I NTERFACES , E THERNET
P ROJECT T REE , ICR890, P ARAMETER , I NTERFACES , GB IT E THERNET
P ROJECT T REE , ICR890, P ARAMETER , I NTERFACES , CAN
8011325/0000/2006-10-24 © SICK AG · Division Auto Ident · Germany · All rights reserved 39
Chapter 3
Product description
Operating Instructions
ICR890 High-end CCD Camera System
3.4.13
Digital outputs
Under certain system conditions (e. g. for unsuccessful decoding “No Read“), two independent switch signals can be generated at both digital outputs and can be used to display the system status.
The digital outputs can be configured using the SOPAS-ET Configuration Software:
P ROJECT T REE , ICR890, P ARAMETER , D IGITAL O UTPUTS , register tabs O UTPUT 1 and O UTPUT 2
3.4.14
Digital inputs
The external sensor for the object trigger control (photoelectric reflex switch) and the incremental encoder can, e. g., be connected to the two digital inputs.
The digital inputs can be configured using the SOPAS-ET Configuration Software:
P ROJECT T REE , ICR890, P ARAMETER , D IGITAL I NPUTS , register tabs S ENSOR 1 and S ENSOR 2
40
© SICK AG · Division Auto Ident · Germany · All rights reserved 8011325/0000/2006-10-24
Operating Instructions
ICR890
Product description
Chapter 3
3.5
Indicators and control elements
3.5.1
User interface
The ICR890 System is configured application specifically using the SOPAS-ET Configuration
Software (see Chapter 6.3.1 Overview of the configuration procedure, page 81 ). The
software for this runs on a PC which must be connected to one of the data interfaces
(“HOST/AUX“ RS 232 or “HOST Ethernet“) of the MSC800 or the ICD890 Camera.
As an alternative to the SOPAS-ET Configuration Software, command strings are available upon which the user interface of the SOPAS-ET Configuration Software is based (see
Chapter 10.2 Configuring the ICR890 System with command strings, page 111 ).
In case of an error, startup and diagnosis can only be carried out via the SOPAS-ET
Configuration Software. The system works fully automatically in normal operation. Further operating elements are not available at the ICR890 System.
Parameter set on the SD memory card
The configured parameter values are saved as a parameter set in the internal EEPROM of the ICR890 System and on the SD memory card of the ICD890 Camera (cloning). If the camera needs replacing, the memory card allows convenient and rapid transfer of the
parameter set to a new device (also see Chapter 7.3 Replacing a system or a component, page 93
).
Note To prevent data loss, the SD memory card should only be removed or inserted in a new device when the system is switched off.
The card can be accessed from the rear of the camera and is located behind a cover on the panel with the electrical connections.
removed cover
SD memory card
Opening for insertion of the SD memory card
Fig. 3-13: SD memory card for parameter set
8011325/0000/2006-10-24 © SICK AG · Division Auto Ident · Germany · All rights reserved 41
Chapter 3
Product description
Operating Instructions
ICR890 High-end CCD Camera System
3.5.2
LEDs of the ICD890 Camera
There are five LEDs for the electrical connections of the ICD890 Camera. These LEDs display the operating status, the status of the reading result, the illumination switch status, necessary maintenance or service tasks and data transfer to the serial main data interface.
LED
DEVICE READY
Colour green
RESULT
IllUMINATION
SERVICE
DATA
Tab. 3-5: LED indications green green red yellow
Fig. 3-14: LEDs at the ICD890 Camera
The LEDs indicate the following:
Indication
• Lights up after switching on and a successful self-test
• Lights up permanently during reading operation
• Goes off when the configuration mode changes
• Lights up during reading operation after a successful reading (default setting: Good Read, 100 ms)
• Lights up during reading operation if the ICI890 Illumination of the camera is switched on (depends on the reading pulse)
• Flashes if system maintenance is required
• Lights up permanently if the system requires servicing
• Flashes during reading operation if data is being transferred between the ICR890 System and the main data interface at the host
42
© SICK AG · Division Auto Ident · Germany · All rights reserved 8011325/0000/2006-10-24
Operating Instructions
ICR890
Product description
Chapter 3
3.6
Impacts on the reading quality
The image/reading quality of the ICD890 Camera is affected by the resolution across the direction of transport (pixel resolution, dpi) and the resolution in the direction of transport
(line resolution, lpi). A quadratic resolution is selected in the default setting (dpi = lpi).
Max. pixel resolution across the direction of transport
The pixel resolution across the direction of transport depends on the reading distance to the object.
Fig. 3-15 shows the curve gradient for the standard 135 mm (5.32 in) lens and the
CCD with 8,192 pixels.
CCD line
Reading distance (mm) dpi = dots per inch
Fig. 3-15: Pixel resolution across the direction of transport (standard device, 135 mm (5.32 in) lens)
Max. line resolution in the direction of transport
The line resolution in the direction of transport depends on the conveyor speed. Fig. 3-16
shows the curve gradient for the standard 135 mm (5.32 in) lens and the CCD with 8,192 pixels with a max. line rate of 19.1 kHz.
CCD line lpi = line per inch
Conveyor speed (m/s)
Fig. 3-16: Line resolution in the direction of transport (standard device, 8,192 pixels CCD sensor)
8011325/0000/2006-10-24 © SICK AG · Division Auto Ident · Germany · All rights reserved 43
Chapter 3
Notes:
Product description
Operating Instructions
ICR890 High-end CCD Camera System
44
© SICK AG · Division Auto Ident · Germany · All rights reserved 8011325/0000/2006-10-24
Operating Instructions
ICR890
Installation
Chapter 4
4
Installation
4.1
Overview of installation sequence
This chapter describes the installation sequence for components of the ICR890 System and external components.
Note Prerequisite for the installation of components is a suitable installation frame at the installation location. The installation frame has to be assembled according to the specifications of a project-specific dimensional sheet.
The typical installation sequence is displayed below:
• Installation of the photoelectric reflex switch
• Installation and alignment of the deflection mirror
• Installation and alignment of the ICI890 Illumination and the ICD890 Camera
• Installation of the MSC800 Controller
• Installation of the MLG Light Grid or the VMS4xx/5xx
• Installation of the incremental encoder
Note Do not open the ICD890 Camera or the ICI890 Illumination. If the devices are opened, the manufacturer's warranty shall not apply.
4.2
Installation preparations
4.2.1
Layout the components which are to be installed
The following components of the ICR890 System have to be placed ready for installation:
• Deflection mirror with protective film
• ICI890 Illumination with protective caps
• ICD890 Camera with yellow and black protective caps
For further components see Chapter 4.4 Installing external components, page 51 .
4.2.2
Layout accessories
The following accessories are included and have to be placed ready for installation:
• 2 x 180° bracket for the deflection mirror incl.
– 2 clamping screws for each bracket
– 2 bolts for each bracket with 2 slot nuts for attachment to the installation frame
• 4 fastening screws for the deflection mirror
• 2 x 180° bracket for the ICI890 Illumination incl.
– 2 clamping screws for each bracket
– 2 bolts for each bracket with 2 slot nuts for attachment to the installation frame
• 4 fastening screws for the ICI890 Illumination
The following tools and resources are required for installation:
• Project-specific dimensional sheet
• Allen key (6 mm (0.24 in)) suitable for all screws
• Tape measure
• Goniometer
8011325/0000/2006-10-24 © SICK AG · Division Auto Ident · Germany · All rights reserved 45
Chapter 4
Installation
Operating Instructions
ICR890 High-end CCD Camera System
4.2.3
Selecting the installation location
Dimensional sheet
The general installation location requirements are described in Chapter 3.2.2, page 27
. The project-specific specifications (position of the components, distances, angles, etc.) are contained in a dimensional sheet and have to be adhered to when installing components.
46
Abb. 4-1: Example of a project-specific dimensional sheet for installation
© SICK AG · Division Auto Ident · Germany · All rights reserved 8011325/0000/2006-10-24
Operating Instructions
ICR890
Installation
Chapter 4
Free space required for connecting
Select an installation position for the illumination and for the camera which allows easy access to the connections.
Free space required for connecting
(L x W x H: 496 mm (19.5 in) x 250 mm (9.85 in) x 210 mm (8.3 in))
Abb. 4-2: Free space required for connecting the camera and the illumination
4.2.4
Arrangement at the conveyor system
The arrangement of the components above the conveyor system depends on the projectspecific requirements and the number of systems.
Abb. 4-3: Arrangement above the conveyor system for single-side reading from above
8011325/0000/2006-10-24 © SICK AG · Division Auto Ident · Germany · All rights reserved 47
Chapter 4
Installation
Operating Instructions
ICR890 High-end CCD Camera System
48
Abb. 4-4: Arrangement at the conveyor system for multi-side reading with VMS4xx/5xx
Generally, each unit consisting of an ICI890 Illumination and a ICD890 Camera is always installed together with a deflection mirror. The front of the illumination and the reflector surface have to be exactly parallel to each other and aligned at a right angle to the conveyor system.
90°
90° 90°
90°
Arrangement for reading from above/below
(top view)
Abb. 4-5: Arrangement at the conveyor system
Arrangement for side reading
(side view)
© SICK AG · Division Auto Ident · Germany · All rights reserved 8011325/0000/2006-10-24
Operating Instructions
ICR890
Installation
Chapter 4
4.3
Installing and adjusting the device
The position of the components on the installation frame is specified project specifically in a dimensional sheet (
). The specifications have to be adhered to as far as possible during installation, since the values influence the configuration of the system to some extent.
Note A final (fine) adjustment of the components can only occur during startup (see
). Prerequisite for this is the complete electrical installation of the system (
ICI890 Illumination with ICD890
Camera
Distance of the illumination and the camera to the deflection mirror
Deflection mirror
Reference point
Direction of transport
Reading location 15°
Distance of the deflection mirror to the reference point
Abb. 4-6: Position of the components
In order to facilitate component alignment, the deflection mirror and the unit consisting of the illumination and the camera are attached to the installation frame via 180° brackets.
Bore holes for fastening screws
Grooves for guide pins
Clamping screws
Pivotal point
Bolts with slot nuts for attachment to the installation frame
Abb. 4-7: 180° bracket for the deflection mirror and the illumination
After loosening the clamping screws, the angle of the brackets can be adjusted from 0° to
180° as required. To achieve this, the clamping screws can be screwed into the various threaded holes.
8011325/0000/2006-10-24 © SICK AG · Division Auto Ident · Germany · All rights reserved 49
Chapter 4
Installation
Operating Instructions
ICR890 High-end CCD Camera System
4.3.1
Installing the deflection mirror
The deflection mirror is attached to the installation frame via two 180° brackets. The position of the deflection mirror results from the distance to the reference point in the direction of transport (plumb line above the pivotal point of the bracket) and the angle to the conveyor level (see
). The deflection mirror has to be installed parallel to the conveyor level.
1. Attach a 180° bracket to each side of the installation frame using two bolts and two slot nuts on each side.
2. Place the mounting plate of the 180°bracket vertically and tighten the clamping screws.
3. Insert the guide pins of the deflection mirror into the grooves of the 180° brackets.
The grips point upward.
4. Use two fastening screws to attach the deflection mirror to the 180° brackets.
5. Loosen the clamping screws, use the goniometer to adjust the deflection mirror to the desired angle and retighten the clamping screws.
6. Remove the protective film from the deflection mirror.
4.3.2
Installing the ICI890 Illumination and the ICD890 Camera
The illumination is attached to the installation frame via two 180° brackets. The position of the illumination is the result of the distance to the deflection mirror (see pivotal point of the
brackets, Fig. 4-6, page 49 ). The illumination has to be parallel to the deflection mirror.
Risk of injuries due to falling components!
The combined weight of the ICD890 Camera and the ICI890 Illumination is approx. 37 kg
(81.6 lb) without installation accessories.
¾ Do not carry out installation work alone.
¾ A second person should always secure components during installation.
1. Attach a 180° bracket to each side of the installation frame using two bolts and two slot nuts on each side.
2. Place the mounting plate of the 180°bracket vertically and tighten the clamping screws.
3. Insert the guide pins of the illumination into the grooves of the 180° brackets. Always ensure free space for connecting (
).
4. Use four fastening screws to attach the illumination to the 180° brackets.
5. Remove the protective cap from the illumination and ensure that the sealing ring on the illumination is positioned correctly.
50
© SICK AG · Division Auto Ident · Germany · All rights reserved 8011325/0000/2006-10-24
Operating Instructions
ICR890
Installation
6. Remove both protective caps from the camera.
Chapter 4
Protective caps
Abb. 4-8: Removeable protective camera caps
7. Place the camera on the illumination and screw it to the illumination using the four hexagon socket screws (centering pin with thread).
8. Loosen the clamping screws at the 180° brackets, horizontally rotate the illumination and retighten the clamping screws.
4.4
Installing external components
MLG Light Grid
Reference point
MSC800
Controller
Direction of transport
Photoelectric reflex switch
Incremental encoder
Abb. 4-9: Position of the external components
4.4.1
External sensors for triggering
The reading pulse sensor (photoelectric reflex switch) is attached to the right-hand edge of the conveyor system according to the specifications in the project-specific dimensional sheet. The position of the photoelectric reflex switch is the reference point for the position of the other components (see
). The photoelectric reflex switch has to be aligned as vertically as possible in the direction of transport.
¾ Install the photoelectric reflex switch onto the conveyor system.
8011325/0000/2006-10-24 © SICK AG · Division Auto Ident · Germany · All rights reserved 51
Chapter 4
Installation
Operating Instructions
ICR890 High-end CCD Camera System
4.4.2
Installing the incremental encoder
The incremental encoder is attached directly to the conveyor system according to the specifications in the project-specific dimensional sheet. The position of the incremental encoder should be as close as possible to the reading location.
¾ Install the incremental encoder to the reading location. Ensure that the friction wheel has direct and permanent contact with the conveyor surface and does not slip.
4.4.3
Installing the MLG Light Grid
The MLG Light Grid is attached directly to the installation frame according to the specifications in the project-specific dimensional sheet. Select a position for the light grid which ensures that a large area above the conveyor level is detected by the sensors of the
MLG. The lower sensors should not be permanently covered by the conveyor system.
¾ Install the MLG Light Grid to the installation frame.
For further information see the MLG Modular Light Grid Operating Instructions
(no. 8009403).
4.4.4
Installing the MSC800 Controller
The MSC Controller is attached directly to the installation frame according to the specifications in the project-specific dimensional sheet. Select a position for the MSC800 which ensures that the cables to the controller are easy to lay.
¾ Install the MSC800 close to the reading location.
For further information see the MSC800 Operating Instructions (no. 8011540).
4.5
Removing the device
Risk of injuries due to falling components!
The combined weight of the ICD890 Camera and the ICI890 Illumination is approx. 37 kg
(81.6 lb) without installation accessories.
¾ Do not carry out removal work alone.
¾ A second person should always secure components during removal.
Removal of the components is described in
Chapter 7.3 Replacing a system or a component, page 93 .
Note Prior to removing the camera, always clean the cooling ribs on the illumination and on the
camera (see Chapter 7.2.3 Cleaning the deflection mirror, page 91
). This prevents dirt from entering into the illumination housing.
Carry out environmentally friendly disposal after decommissioning according to
.
52
© SICK AG · Division Auto Ident · Germany · All rights reserved 8011325/0000/2006-10-24
Operating Instructions
ICR890
Electrical installation
Chapter 5
5
Electrical installation
5.1
Overview of installation sequence
Note Complete installation of all the components is a prerequisite for electrical installation
(see Chapter 4 Installation, page 45 ).
The following list provides an overview of a typical installation sequence:
• Connecting the power supply of the ICI890 Illumination and the illumination control line to the camera (system-internal connections)
• Connecting the ICD890 Camera to the external power supply (24 V DC)
• Connecting the host processor (RS 232, RS 422/485, Ethernet or CAN)
• Connecting the reading pulse sensor(s)
• Connecting the MLG Light Grid (RS 485) or the VMS4xx/5xx (CAN)
• Connecting the incremental encoder
• Connecting a PC/laptop temporarily for startup/configuration (RS 232 or Ethernet)
• Optional: Wiring the switching outputs for system status indication
• Optional: Connecting the special PC with 2 GBit Ethernet interfaces and software
(driver) for real-time image transfer/presentation
The actual installation work which has to be carried out depends on the respective system
). Once electrical installation has been completed, the
8011325/0000/2006-10-24 © SICK AG · Division Auto Ident · Germany · All rights reserved 53
Chapter 5
Electrical installation
Operating Instructions
ICR890 High-end CCD Camera System
5.2
Electrical installation preparation
The ICR890 System can be used for single-side reading with or without the MSC800 or for multi-side reading with the MSC800.
These three possibilities of use are described in the following chapters, each one by means of a block diagram and a table of connections. Instructions on how to carry out the individual
installation sequences are contained in Chapter 5.4, page 64 .
5.2.1
Electrical installation of the ICR890 System (without MSC800)
Block diagram of the ICR890 System without MSC800 for single-side reading from above
ICR890 System
ILLUMINATION
POWER OUT
POWER IN
IN 2
Incremental encoder
Increment
24 V DC
IN 1
HOST ETHERNET
Photoelectric reflex switch
Reading pulse
OUT (1/2)
AUX/
HOST ETHERNET
GBIT 1/2 ETHERNET
HOST
PC/laptop
Configuration/ diagnosis
(temporary)
MLG
Light Grid
Detection object height
Abb. 5-1: Block diagram: connection principle of the ICR890 (standard system)
Special PC
Real-time
HOST
Host processor
Reading result presentation of images
54
© SICK AG · Division Auto Ident · Germany · All rights reserved 8011325/0000/2006-10-24
Operating Instructions
ICR890
Electrical installation
Chapter 5
Wiring of the ICR890 System without MSC800 for single-side reading
The following connections have to be established if one ICR890 is used as a stand-alone device without the MSC800 (e.g. reading from above):
No. ICD890 Camera connection
1
2
3
4
5
6
7
8
POWER OUT
ILLUMINATION
POWER IN
IN 1
HOST or AUX
IN 2
OUT (1/2)
HOST or
HOST ETHERNET
Function
Illumination power supply
Illumination control
Power supply 24 V DC
Connection to ...
Reading pulse trigger signals External reading pulse sensor
Detection of object height MLG Light Grid (RS 485)
Increment signals
Indication of system status
Data output of the reading result
POWER IN connection of the ICI890 Illumination No. 2039397
ILLUMINATION connection of the ICI890
Illumination
No. 6030216
Power supply provided by the client
Incremental encoder
(resolution 10 mm (394 mil)/incr.)
PLC (optional)
Host processor (RS 232, RS 422/485 or
Ethernet)
Cable to be used
No. 2039398
(10 m (32.8 ft))
Included in delivery
Included in delivery
Included in delivery
No. 6027559
(10 m (32.8 ft))
– RS 232, RS 422/485: no. 6028420
(10 m (32.8 ft))
– Ethernet: patch cable: no. 6030928
(3 m (9.84 ft)) no. 6029630
(5 m (16.4 ft))
9 GBIT 1/2
ETHERNET
10 AUX or
HOST or
HOST ETHERNET
Real-time image transfer
Configuration/Diagnosis
Special PC for image presentation (optional)
Standard PC, temporarily,
(RS 232 or Ethernet)
Crossover cable no. 6029775
(10 m (32.8 ft)) or patch cable no. 6029776
(10 m (32.8 ft))
– RS 232: no. 6028420
(10 m (32.8 ft)) no. 6028420
(10 m (32.8 ft))
– Ethernet: patch cable: no. 6030928
(3 m (9.84 ft)) no. 6029630
(5 m (16.4 ft))
Tab. 5-1: ICR890 System (stand-alone device) without MSC800: Overview of the ICD890 Camera connections which have to be established
8011325/0000/2006-10-24 © SICK AG · Division Auto Ident · Germany · All rights reserved 55
Chapter 5
ICR890 System
Electrical installation
Operating Instructions
ICR890 High-end CCD Camera System
5.2.2
Electrical installation of the ICR890 System with MSC800 (single-side reading)
Block diagram of the ICR890 System with MSC800 for single-side reading from above
ILLUMINATION
POWER OUT
MSC800
OUT (1/2)
GBIT 1/2
ETHERNET
POWER IN
CAN 1-IN
Incremental encoder
Increment
CAN 1
INC (1)
OUT (1/2)
100 to 264 V AC/
50 to 60 Hz
AUX/ USB/
ETHERNET
HOST/
AUX
Special PC
Real-time presentation of images
TRIGGER PC/laptop
Configuration/
Diagnosis
(temporary) Photoelectric reflex switch
Reading pulse
HOST
HOST/
ETHERNET/
PROFIBUS
MLG
Light Grid
Detection object height
Host processor
Reading result
Abb. 5-2: Block diagram: Connection principle of a ICR890 (standard system) with MSC800
Wiring of the ICR890 System with MSC800 for single-side reading
The following connections have to be established if one ICR890 is used as a stand-alone device with the MSC800 (e.g. reading from above):
No.
ICD890 Camera connection
1 POWER OUT
Function Connection to ...
Cable to be used
2
3
4
5
6
ILLUMINATION
POWER IN
CAN 1-IN
CAN 1-OUT
GBIT 1/2
ETHERNET
Illumination power supply
Illumination control
Power supply 24 V DC
Communication with MSC800
(CAN-SENSOR network)
Terminal resistance
Real-time image transfer
POWER IN connection of the ICI890
Illumination
ILLUMINATION connection of the ICI890
Illumination
Internal power supply of the MSC800
"CAN 1" connection of the MSC800
–
Special PC for image presentation
(optional)
No. 2039397
No. 6030216
No. 2039398 (10 m (32.8 ft))
No. 6021166 (5 m (16.4 ft)) or
No. 6021175 (10 m (32.8 ft))
No. 6021167
Crossover cable no. 6029775
(10 m (32.8 ft)) or patch cable no. 6029776
(10 m (32.8 ft))
Tab. 5-2: ICR890 System (stand-alone device) with MSC800: Overview of the ICD890 Camera connections which have to be established
56
© SICK AG · Division Auto Ident · Germany · All rights reserved 8011325/0000/2006-10-24
Operating Instructions
ICR890
Electrical installation
Chapter 5
2
3
No. MSC800 connection
1
4
Power supply input terminals
TRIGGER
HOST or
AUX
INC
Function
Power supply of the MSC800
Reading pulse trigger signals
Detection of object height
Connection to ...
Cable to be used
Mains voltage 100 to 264 V AC/50 to 60 Hz Cable provided by the
External reading pulse sensor
MLG Light Grid (RS 485) client
Included in delivery
Included in delivery
5 HOST or
ETHERNET or
PROFIBUS
OUT (1/2)
Increment signals
Data output of the reading result at the ICR890 System
Incremental encoder
(resolution 0.2 mm (7.9 mil)/incr.)
Host processor (RS 232, RS 422/485 or
Ethernet)
Included in delivery
Cable provided by the client
6
7 AUX or
USB or
ETHERNET
Indication of system status
Configuration/Diagnosis
PLC (optional)
Standard PC, temporarily
Cable provided by the client
Cable provided by the client
Tab. 5-3: ICR890 System (stand-alone device) with MSC800: Overview of the MSC800 connections which have to be established
Note Please refer to the MSC800 Operating Instructions (no. 8011540) for connection to the
MSC800.
8011325/0000/2006-10-24 © SICK AG · Division Auto Ident · Germany · All rights reserved 57
Chapter 5
Electrical installation
Operating Instructions
ICR890 High-end CCD Camera System
5.2.3
Electrical installation of the ICR890 System with MSC800 (multi-side reading)
Block diagram of the ICR890 System with MSC800 for multi-side reading
Power Supply
ILLUMINATION
POWER OUT
MSC800
HOST
Host processor
Reading result
POWER IN
CAN 1-IN/OUT
GBIT 1/2
ETHERNET
CAN 1
Special PC
Real-time presentation of images
TRIGGER
TACHO
Photoelectric reflex switch
Reading pulse
VMS4xx/5xx
Detection object distance
Incremental encoder
Increment
HOST/ETHERNET/PROFIBUS
OUT (1/2)
Abb. 5-3: Block diagram: Connection principle of several ICR890 (standard systems) with MSC800
24 V DC
100 to 264 V AC/
50 to 60 Hz
AUX/ USB/
ETHERNET
PC/laptop
Configuration/
Diagnosis
(temporary)
Wiring of several ICR890 with MSC800 for multi-side reading.
The following connections have to be established if several ICR890 with MSC800 are used:
No.
ICD890 Camera connection
1 POWER OUT
2
3
4
5
6
Function Connection to ...
ILLUMINATION
POWER IN
CAN 1-IN
CAN 1-OUT
Illumination power supply
Illumination control
Power supply 24 V DC
Communication with MSC800
(CAN-SENSOR network)
Communication with CAN bus
(CAN-SENSOR network)
POWER IN connection of the ICI890
Illumination
ILLUMINATION connection of the ICI890
Illumination
Internal power supply of the MSC800
“CAN 1“ connection of the MSC800
“CAN 1-IN“ connection of the next ICR890
System
GBIT 1/2
ETHERNET
Real-time image transfer Special PC for image presentation
(optional), temporary connection to every
ICR890 System, if required
Cable to be used
No. 2039397
No. 6030216
No. 2039398 (10 m (32.8 ft))
No. 6021166 (5 m (16.4 ft)) or
No. 6021175 (10 m (32.8 ft))
No. 6021164 (1 m (3.28 ft))
No. 6021165 (3 m (9.84 ft))
No. 6021168 (5 m (16.4 ft))
Crossover cable no. 6029775
(10 m (32.8 ft)) or patch cable no. 6029776
(10 m (32.8 ft))
Tab. 5-4: ICR890 System with MSC800 (multi-side reading): Overview of the ICD890 Camera connections which have to be established
58
© SICK AG · Division Auto Ident · Germany · All rights reserved 8011325/0000/2006-10-24
Operating Instructions
ICR890
Electrical installation
Chapter 5
No. MSC800 connection
1 Power supply input terminals
2 TRIGGER
3
4
HOST or
ETHERNET or
PROFIBUS
OUT 1/2
Function Connection to ...
Power supply of the MSC800 Mains voltage 100 to 264 V AC/50 to 60 Hz
Reading pulse trigger signals External reading pulse sensor
Data output of the reading result of all ICR890 Systems via the MSC800
Indication of system status
Host processor (RS 232, RS 422/485 or
Ethernet)
PLC (optional)
Cable to be used
Cable provided by the client
Included in delivery
Cable provided by the client
5 AUX or
USB or
ETHERNET
Configuration/Diagnosis Standard PC, temporarily
Cable provided by the client
Cable provided by the client
Tab. 5-5: ICR890 System with MSC800 (multi-side reading): Overview of the MSC800 connections which have to be established
Note Please refer to the MSC800 Operating Instructions (no. 8011540) for connection to the
MSC800.
No.
1
VMS4xx/5xx connector cap connection
Power/CAN IN
Function
Communication with CAN bus
(CAN-SENSOR network)
Connection to ...
“CAN 1-IN“ connection of the next ICR890
System
Cable to be used
No. 6021164
(1 m (3.28 in))
No. 6021165
(3 m (9.84 ft))
No. 6021168
(5 m (16.4 ft))
Included in delivery 4 Tacho Increment signals Incremental encoder (resolution 0.2 mm
(7.9 mil)/incr.)
Tab. 5-6: ICR890 System with MSC800 (multi-side reading): Overview of the VMS4xx/5xx connections which have to be established
Note Please refer to the VMS410 Volume Measurement System Operating Instructions
(no. 8010592) for connection to the VMS410 or to the VMS 420/520 Volume
Measurement System Operating Instructions (no. 8010448) for connection to the
VMS420/520 as well as to the connector cap installation instructions for the VMS400/500
Volume Measurement Systems (no. 8010817).
8011325/0000/2006-10-24 © SICK AG · Division Auto Ident · Germany · All rights reserved 59
Chapter 5
Ethernet
(GBit channels)
Electrical installation
Operating Instructions
ICR890 High-end CCD Camera System
5.3
Electrical connections and cables
Prerequisites for enclosure rating IP 64
All the electrical connections of the camera and illumination have been provided with appropriate protective caps for delivery.
To maintain the enclosure rating IP 64, unused connections have to be provided with protective caps during operation. The connectors attached to used connections have to be firmly screwed or engaged.
The same applies to the EMC requirements (ESD) according to CE.
The protective caps have the following colours:
– M12 connectors: yellow (plugs) and black (sockets)
– RJ-45 connections: Grey, fixed to the device via a strap (cannot be lost)
– Power supply: black
RF interference in case of use in residential areas.
¾ ICR890 High-end CCD Camera System is exclusively intended for use in an industrial environment.
5.3.1
Electrical connections of the ICD890 Camera
The electrical connections of the ICR890 System comprise eleven M12 connectors attached to the housing of the ICD890 Camera (on and next to the panel), two Harting connectors for the power supply as well as two RJ-45 connections (enclosure rating IP 67) for the GBit Ethernet.
Ethernet
(host)
Panel
Abb. 5-4: ICD890 Camera: Position of the electrical connections (standard system)
60
Power supply
(IN and OUT)
© SICK AG · Division Auto Ident · Germany · All rights reserved 8011325/0000/2006-10-24
Operating Instructions
ICR890
Electrical installation
Chapter 5
The following interfaces are realized via the ICD890 Camera connections:
-
Connection Design
GBIT 1 ETHERNET RJ-45
GBIT 2 ETHERNET RJ-45
CAN 1-OUT M-12
CAN 1-IN
CAN 2-OUT
CAN 2-IN
ILLUMINATION
AUX
M-12
M-12
M-12
M-12
M-12
HOST
OUT
IN 1
IN 2
M-12
M-12
M-12
M-12
HOST ETHERNET M-12
POWER IN Harting
HanQ8
POWER OUT Harting
HanQ8
Number of poles
Function
8, socket Image data output, channel 1
8, socket Image data output, channel 2
5, socket Output CAN-SENSOR network 1
5, plug Input CAN-SENSOR network 1
5, socket Output CAN-SENSOR network 2 (reserved)
5, plug Input CAN-SENSOR network 2 (reserved)
8, socket Control data interface ICI890 Illumination
8, plug Auxiliary data interface (RS 232, RS 422/485)
8, plug
4, plug
Main data interface (RS 232, RS 422/485)
Two digital switching outputs (system status)
5, socket Digital switching input (reading pulse)
5, socket Digital switching input (reading pulse, increment)
5, socket Main data interface (10/100 MBps)
8, plug Power supply input 24 V DC
8, socket Output 24 V DC, to ICI890 Illumination
Tab. 5-7: ICD890 Camera: Function of the electrical connections
5.3.2
Electrical connections of the ICI890 Illumination
The ICI890 Illumination is equipped with a Harting connector for the power supply and an
M12 connector for the control line.
The following interfaces are realized via the ICI890 Illumination connections:
-
Design
M-12
Harting
HanQ8
Number of poles
8, plug
8, plug
Function
Control data interface ICD890 Camera
Power supply input 24 V DC
Tab. 5-8: ICI890 Illumination: Function of the electrical connections
8011325/0000/2006-10-24 © SICK AG · Division Auto Ident · Germany · All rights reserved 61
Chapter 5
Electrical installation
Operating Instructions
ICR890 High-end CCD Camera System
5.3.3
Electrical connections of the MSC800 (overview)
Please refer to the MSC800 Operating Instructions (no. 8011540) for connections of the
MSC800-0000 logic controller.
Abb. 5-5: MSC800-0000 logic controller: Position of the electrical connections
-
The following interfaces are realized via the MSC800-0000 connections:
Connection
PROFIBUS
USB 2
ETHERNET 3
ETHERNET 2
USB 1
ETHERNET 1
AUX 2
AUX 1
OUT
IN
TRIGGER
INC
HOST (1/2)
CAN 2
CAN 1
POWER
Design
D-Sub
USB
RJ-45
RJ-45
USB
RJ-45
Block
D-Sub
Block
Block
Block
Block
Block
Block
Block
Block
Number of poles
9, socket
4
8, socket
8, socket
4
Function
Main data interface
Auxiliary data interface
Auxiliary data interface
Auxiliary data interface
Auxiliary data interface
8, plug Main data interface
14, terminals Auxiliary data interface (RS 232, RS 422/485)
9, plug Auxiliary data interface (RS 232, RS 422/485)
14, terminals Digital switching outputs (system status)
12, terminals Digital switching inputs
12, terminals Digital switching inputs (reading pulse)
12, terminals Digital incremental encoder inputs
14, terminals Main data interface (RS 232, RS 422/485)
12, terminals Input/Output CAN-SENSOR network 2
12, terminals Input/Output CAN-SENSOR network 1
8, terminals Power supply input 24 V DC
Tab. 5-9: MSC800-0000 logic controller: Function of the electrical connections (overview)
62
© SICK AG · Division Auto Ident · Germany · All rights reserved 8011325/0000/2006-10-24
Operating Instructions
ICR890
Electrical installation
Chapter 5
5.3.4
Assembled cables (overview)
Interface from ICD890
Camera to
HOST/AUX
(RS 232, RS 422/485)
Cable no.
Type
6028420 Connection cable for host processor or
PC, TPU/PUR bundle jacket
CAN-SENSOR network 6021164 CAN data cable,
PVC-free
CAN-SENSOR network 6021165 CAN data cable,
PVC-free
CAN-SENSOR network 6021168 CAN data cable,
PVC-free
CAN-SENSOR network 6021166 CAN data cable to MSC800,
PVC-free
CAN-SENSOR network 6021175 CAN data cable to MSC800,
PVC-free
CAN-SENSOR network 6021167 CAN terminal resistance
Length
10 m
(32.8 ft)
1 m
(3.28 ft)
3 m
(9.84 ft)
5 m
(16.4 ft)
5 m
(16.4 ft)
10 m
(32.8 ft)
–
Cable ends
ICD890
8-pole M12 socket
5-pole M12 socket
5-pole M12 socket
5-pole M12 socket
5-pole M12 socket
5-pole M12 socket
5-pole M12 plug
RJ-45 plug external open
5-pole M12 plug
5-pole M12 plug
5-pole M12 plug open open
–
Enclosure rating
IP 65
IP 65
IP 65
IP 65
IP 65
IP 65
IP 65
Ethernet
Ethernet
HOST Ethernet
HOST Ethernet
Reading pulse sensor
Incremental encoder
PLC
ICI890 Illumination
ICI890 Illumination
6029776 Patch cable for GBit Ethernet,
CAT6, PVC-free
6029775 Crossover cable for GBit Ethernet,
CAT6, PVC-free
6030928 Patch cable for HOST Ethernet,
(10/100 MBps), CAT5
6029630 Patch cable for HOST Ethernet,
(10/100 MBps), CAT5
6024861 Connection cable for switching inputs,
PUR bundle jacket
6027559 Connection cable for switching outputs
6030216 Illumination control line
(included in delivery), PUR, halogenfree
2039397 Illumination power supply
(included in delivery)
0.75 m
(29.6 in)
10 m
(32.8 ft)
10 m
(32.8 ft)
3 m
(9.84 ft)
10 m
(32.8 ft)
5 m
(16.4 ft)
10 m
(32.8 ft)
0.6 m
(23.6 in)
Power supply
ICI890 Illumination
Power supply
2039398
2032922
Connection cable for power supply
Illumination power supply,
PVC-free
2032926 Connection cable for power supply,
PVC-free
Tab. 5-10: Cables for connecting the ICR890 System
RJ-45 plug
4-pole M12 plug
4-pole M12 plug
5-pole M12 plug
4-pole M12 socket
8-pole M12 plug
RJ-45 plug
RJ-45 plug
RJ-45 plug
RJ-45 plug open open
8-pole M12 socket
IP 65/20
IP 65/20
IP 65/20
IP 65/20
IP 65
IP 65
IP 65
10 m
(32.8 ft)
0.75 m
(29.6 in)
10 m
(32.8 ft)
8-pole Harting
HanQ plug
8-pole
Harting
HanQ socket open
IP 65
IP 65 8-pole Harting
HanQ socket
8-pole Harting
HanQ plug
8-pole Harting
HanQ socket
8-pole
Harting
HanQ socket open
IP 65
IP 65
All the cables included on the list are suitable for the temperature range 0 to +40 °C
(32 to 104 °F).
See
Chapter 10.4.3 Accessories: Cables and connectors, page 115
for technical cable data. See
Chapter 5.5.3 Wire colours assignment of assembled cables with open end, page 75
for the wire colour assignment of cables with open cable end.
8011325/0000/2006-10-24 © SICK AG · Division Auto Ident · Germany · All rights reserved 63
Chapter 5
Electrical installation
Operating Instructions
ICR890 High-end CCD Camera System
5.4
Performing electrical installation
Risk of injuries due to electrical current!
The MSC800 Controller is connected to the power supply (mains voltage 100 to 264 V AC/
50 to 60 Hz).
¾ Observe current safety regulations when working with electrical equipment.
¾ Make sure the equipment has been deenergized before performing any installation work.
Note To ensure secure fastening of the plugged connectors and adherence to the enclosure rating IP 64 for the ICR890 System, the knurled nuts/coupling rings of the M12 connectors have to be tightened and the Harting connectors for the power supply secured by means of the fastening bows.
¾ Wire all connections provided by the client using shielded copper wires!
¾ Pay attention to the required wire cross sections:
– Switching inputs/outputs: At least 0.25 mm 2 (24 AWG)
– Data interfaces: At least 0.22 mm 2 (24 AWG)
¾ Lay all the cables in such a manner that persons cannot trip over them and that the cables are protected against damage.
Recommendation Attach suitable wire end ferrules to the open wire ends of flexible cables which are fixed to terminal screws. However, do not use wire end ferrules when fixing open wire ends to spring terminals, since secure contact is otherwise not ensured.
5.4.1
Connecting the power supply cable and the ICI890 Illumination control line
The system-internal connection between the ICD890 Camera and the ICI890 Illumination is realized via two short cables (no. 2039397 and no. 6030216) included in the delivery.
¾ Plug the power supply cable no. 2039397 into the 8-pole Harting HanQ8 socket
POWER OUT of the ICD890 Camera and fix it.
Plug the other cable end onto the corresponding 8-pole Harting HanQ8 plug of the
ICI890 Illumination and fix it.
¾ Plug the control line no. 6030216 into the 8-pole M12 socket ILLUMINATION of the
ICD890 Camera and fix it.
Plug the other cable end onto the corresponding 8-pole M12 plug of the ICI890
Illumination and fix it.
5.4.2
Power supply of the ICR890 System
Power supply requirements
A supply voltage of 24 V DC ± 10 % is required for the operation of the ICR890 System
(functional extra-low voltage according to standard IEC 364-4-41 (VDE 0100 (Part 410)).
This voltage is generated by the power supply in the MSC800 as standard. The typical power consumption per ICD890 Camera and ICI890 Illumination amounts to a total of 425 W.
Note The wire cross section for the power supply of the ICR890 System has to be at least 3 mm 2
(12 AWG). To ensure protection against short circuit/overload of the supply line, the cable has to be protected according to the wire cross sections used. The valid standards must be observed.
64
© SICK AG · Division Auto Ident · Germany · All rights reserved 8011325/0000/2006-10-24
Operating Instructions
ICR890
Electrical installation
Chapter 5
Connecting the power supply of the ICR890 System via the MSC800
1. Ensure that the external power supply for the MSC800 has been switched off.
2. Plug the 8-pole Harting HanQ8 socket of the power supply cable no. 2032926 into the
8-pole Harting HanQ8 plug POWER IN of the ICD890 Camera and fix it.
3. Attach the open cable end to the terminal strip for power supply in the MSC800. (See
Tab. 5-35, page 77 for pin/wire colour assignment of cable no. 2032926.)
Note The supply voltage remains switched off during the subsequent installation work!
5.4.3
Data interfaces HOST/AUX
General conditions of the data interfaces HOST and AUX
Both the HOST data interface (main data interface) as well as the AUX data interface
(auxiliary data interface) of the ICR890 System can be operated as RS 232 version or as
RS 422/485 version or be rerouted to the Ethernet interface. Tab. 5-11
shows the recommended maximum cablelengths, depending on the interface version and the data transfer rate.
Interface type
RS 232
Data transfer rate up to 19.2 kbd
38.4 to 115.2 kbd
RS 422 1) max. 38.4 kbd max. 57.6 kbd max. 115.2 kbd
10/100 MBps Ethernet
GBit Ethernet 10 Mps to 1GBps
1) with corresponding line termination according to specification
Tab. 5-11: Maximum cable lengths between ICR890 and the host
Distance to target processor (host) max. 10 m (32.8 ft) max. 3 m (9.84 ft) max. 1,200 m (3,936 ft) max. 500 m (1,640 ft) max. 10 m (32.8 ft) max. 100 m (328 ft) max. 100 m (328 ft)
Recommendation ¾ Use shielded data cables (twisted pair).
¾ To prevent interference, do not lay data cables parallel to power supply cables and motor lines over a longer distance, e. g. in cable channels.
Wiring the HOST/AUX data interface
Damage to the interface modules!
Incorrect wiring of the HOST/AUX data interfaces can damage electronic components in the
ICR890 System.
¾
Wire the data interfaces correctly according to Fig. 5-6, page 66 .
¾ Check the wiring carefully before switching on the ICR890 System.
¾ Connect the data interfaces to the host/PC paying attention to the EMC and using a
shielded cable. Adhere to the maximum cable lengths ( Tab. 5-11, page 65 ).
¾
Wire the versions RS 232 or RS 422 according to Fig. 5-6, page 66
.
Use cable no. 6028420 for each of the connections.
(See
Tab. 5-31, page 75 for pin/wire colour assignment.)
8011325/0000/2006-10-24 © SICK AG · Division Auto Ident · Germany · All rights reserved 65
Chapter 5
66
Electrical installation
RS 232
ICR890
4
6
7
Operating Instructions
ICR890 High-end CCD Camera System
(3)
(2)
(5)
( ) = 9-pole D-Sub plug at PC
RS 422
5
6
3
4
7
ICR890
Abb. 5-6: ICD890 Camera: Wiring of the HOST/AUX data interfaces
5.4.4
Data interface CAN 1-IN/OUT
General conditions of the CAN interface
The SICK-specific CAN-SENSOR network is based on the CAN bus, which is structured in line topology.
Tab. 5-12 shows the maximum permissible CAN bus length, depending on the selected data
transfer rate.
Data transfer rate
10 kBps
20 kBps
50 kBps
100 kBps
125 kBps
Maximum data cable length
4,976 m (16,325 ft)
2,476 m (8,123.3 ft)
976 m (3,202 ft)
576 m (1,889.7 ft)
476 m (1,561.7 ft)
226 m (741.5 ft) 250 kBps 1)
500 kBps
1) Default setting in the ICR890 System
76 m (249.3 ft)
Tab. 5-12: CAN bus: Maximum cable lengths, depending on the data transfer rate
Tab. 5-13 shows the maximum permissible overall length of all stub cables, depending on
the data transfer rate. This overall length must not be exceeded. The maximum length of each individual stub cable must not exceed 6 m (19.7 ft).
Data transfer rate
125 kBps
250 kBps
500 kBps
Total of all stub cable lengths
156 m (512 ft)
78 m (256 ft)
39 m (128 ft)
Tab. 5-13: CAN bus: Maximum stub cable lengths, depending on the data transfer rate
© SICK AG · Division Auto Ident · Germany · All rights reserved 8011325/0000/2006-10-24
Operating Instructions
ICR890
Electrical installation
Chapter 5
The required wire cross section of the data cable depends on the overall length of the network.
Tab. 5-14 shows an overview according to ISO 11898.
Cable length Required wire cross section (data cable)
0 to 40 m (0 to 131 ft) ≥ 0.25 mm 2
(24 AWG)
40 to 300 m (131 to 984 ft) ≥ 0.34 mm 2 (22 AWG)
300 to 600 m (984 to 1968 ft) ≥ 0.5 mm 2 (21 AWG)
600 to 1,000 m (1968 to 3280 ft) ≥ 0.75 mm 2 (20 AWG)
Tab. 5-14: CAN bus: Required wire cross section, depending on the data cable length
Wiring the data interface CAN 1-IN/OUT
The CAN interface of the ICR890 System is used in the following configurations:
• In the case of single-side reading, the peripheral equipment should be wired centrally at the MSC800.
• In the case of multi-side reading, the ICR890 System works with the MSC800 together with further camera systems, bar code scanners and volume measurement systems
(camera control).
¾ Connect the ICD890 Camera to the 5-pole M12 socket and the open end via the CAN
1-IN connection using the cable no. 6021166. (See
Tab. 5-32, page 76 for pin/wire
colour assignment.)
¾ Attach the open cable end to the CAN 1 connection in the MSC800.
¾ Attach the terminal resistance no. 6021167 to the CAN1-OUT connection of the
ICD890 Camera.
The signals for the reading pulse and increment are transmitted to the ICR890 System via the CAN bus. Direct connection to the ICR890 System is, thus, not required. The HOST and
AUX data interfaces as well as the signals of both switching outputs (for single-side reading) are accessible via the CAN bus at the MSC800. The ICR890 System and the MSC800 have to be configured accordingly as Slave or Master for this purpose (see
Chapter 6.3 First startup, page 80
).
8011325/0000/2006-10-24 © SICK AG · Division Auto Ident · Germany · All rights reserved 67
Chapter 5
Electrical installation
Operating Instructions
ICR890 High-end CCD Camera System
5.4.5
Wiring the Ethernet interface HOST ETHERNET
The Ethernetinterface HOST ETHERNET of the ICR890 System has several functions:
• Output of the reading result of the HOST data interface via TCP/IP as an alternative to the serial interface version RS 232, RS 422/485
• Output of data of the AUX data interface (reading result + reading diagnosis data) via
TCP/IP as an alternative to the serial interface version RS 232, RS 422/485
• Access to the ICR890 System via the SOPAS-ET Configuration Software
• Connection as RDT400 Client (system distance monitoring)
PC ICR890
RS 232, RS 422/485
Aux
Host
RS 232, RS 422/485
CAN
Ethernet
Port 2111: AUX
Port 2112: Host
Port 21: FTP
SOPAS-ET
FTP server
VMS4xx/5xx MSC800
Abb. 5-7: Block diagram: Function of the Ethernet interface
Connecting the ETHERNET HOST interface
¾ Connect the ICD890 Camera directly to the Ethernet card of the PC (point-to-point
connection) using the crossover cable (see Tab. 10-4, page 115 ).
- or -
Connect the ICD890 Camera to the Ethernet network using the standardized data cable
(patch cable ) no. 6029630.
See
Chapter 6.3.2, page 81 for required settings at the PC and the ICR890 System.
68
© SICK AG · Division Auto Ident · Germany · All rights reserved 8011325/0000/2006-10-24
Operating Instructions
ICR890
Electrical installation
Chapter 5
5.4.6
Wiring the Ethernet interfaces GBIT 1 and GBIT 2
The two GBit Ethernet interfaces facilitate fast output of images to a special PC which is also equipped with two GBit Ethernet interfaces.
Connecting the GBIT 1-ETHERNET and GBIT 2-ETHERNET interfaces
¾ Connect the ICD890 Camera directly to the Ethernet card of the PC (point-to-point
connection) using the crossover cables no. 6029775 (see Tab. 5-10, page 63 ) .
- or -
Connect the ICD890 Camera to the GBit Ethernet network using the standardized data cables (patch cables) no. 6029776.
5.4.7
Wiring the switching inputs IN 1 and IN 2
The reading pulse sensor is connected via the digital switching input IN 1.
The incremental encoder is connected via the switching input IN 2. Fig. 5-8
shows the wiring of switching input IN 1 as an example.
Tab. 5-15 contains ratings for both inputs.
ICR890 System PNP sensor Switch
Vo
V
S
= +24 V DC
*) V imax
= 28 V!
Abb. 5-8: Wiring of the switching inputs IN 1 and IN 2
Switching behaviour
Features
Electrical values
IN 1: Power fed to the input opens the reading gate of the ICD890 Camera.
(Default setting: Not inverted (active high); debouncing: 10 ms; pulse start delay: 0 ms, pulse end: 0 ms)
– Optodecoupled, reverse polarity protected
– Can be wired with the PNP output of a sensor
Low:
–1 V ≤ V
–0.3 mA i
≤ +1 V
≤ I i
≤ +0.3 mA
High:
+8 V ≤ |V
+1.4 mA i
| ≤ +28 V
≤ |I i
| ≤ +18 mA
Tab. 5-15: Ratings of the switching inputs IN1 and IN 2
Connecting the switching inputs IN 1 and IN 2
1. Connect the reading pulse sensor (photoelectric reflex switch) to switching input IN 1, as shown in
.
2. Connect the incremental encoder to switching input IN 2, as shown in Fig. 5-8 .
3. For power supply via the ICD890 Camera, additionally establish connections between
SGND and GND in the connector of the connection cable.
8011325/0000/2006-10-24 © SICK AG · Division Auto Ident · Germany · All rights reserved 69
Chapter 5
Electrical installation
Operating Instructions
ICR890 High-end CCD Camera System
5.4.8
Wiring the switching outputs Result 1 and Result 2 (OUT connection)
An appropriate visualization PC or PLC for system status indication is connected via these two digital switching outputs.
Fig. 5-9 shows the wiring of switching output Result 1 as an
example.
Tab. 5-16 contains ratings for both outputs.
ICR890 System
Result 1: Pin 1 and 2
Result 2: Pin 3 and 4
Abb. 5-9: Wiring of the switching outputs Result 1 and Result 2
Switching behaviour
Features
Electrical values
PNP-switching against the supply voltage V
S
– Optodecoupled, reverse polarity protected
– In the event of a short circuit, the current is limited to 0.7 A
– The polarity is irrelevant due to a bridge connection
I
0 V ≤ V o o
≤ 30 V guaranteed: V o
≤ V
S
− 1.3 V at I o
≤ 100 mA
≤ 100 mA
Tab. 5-16: Ratings of the switching outputs Result 1 and Result 2
Connecting the switching outputs Result 1 and Result 2
¾ Connect the visualization PC/PLC to switching output Result 1 and/or Result 2, as
shown as an example in Fig. 5-9 .
Note In the "Device Ready" function, the output supplies a static pulse if the ICR890 System is in reading operation.
Recommendation ¾ Wire the outputs with a load resistance to test the switching functions using a highresistance digital voltmeter. Indication of incorrect voltages/switching statuses is avoided this way.
70
© SICK AG · Division Auto Ident · Germany · All rights reserved 8011325/0000/2006-10-24
Operating Instructions
ICR890
Electrical installation
5.5
Pin assignments and conductor colouring assignment
5.5.1
ICD890 Camera connections
Chapter 5
Ethernet
(host)
Ethernet
(GBit channels)
Abb. 5-10: ICD890 Camera: Electrical connections (standard system)
Power supply
Note All connections have been provided with protective caps for delivery.
-
“GBIT 1“/“GBIT 2“ connections (Ethernet, max. 1GBps)
5
6
3
4
7
8
Pin
1
2
Ethernet signal
TD+
TD–
RD+ n. c.
n. c.
RD– n. c.
n. c.
–
–
Function
Transmitter+
Transmitter–
Receiver+
–
–
Receiver–
Tab. 5-17: ICD890 Camera: Pin assignment of the 8-pole RJ-45 sockets “GBIT1“ and “GBIT2“
-
“CAN 1-OUT“/“CAN 2-OUT“ connections (CAN-SENSOR networks)
4
5
2
3
Pin
1
CAN signal
Shield
CAN_V+
CAN_GND
CAN_H
CAN_L
Function
Shielding
Supply voltage 24 V
Ground
CAN bus (IN/OUT)
CAN bus (IN/OUT)
Tab. 5-18: ICD890 Camera: Pin assignment of the 5-pole M12 sockets “CAN 1-OUT“/“CAN 2-OUT“
8011325/0000/2006-10-24 © SICK AG · Division Auto Ident · Germany · All rights reserved 71
Chapter 5
72
Electrical installation
Operating Instructions
ICR890 High-end CCD Camera System
-
“CAN 1-IN“/“CAN 2-IN“ connections (CAN-SENSOR networks)
4
5
2
3
Pin
1
CAN signal
Shield
CAN_V+
CAN_GND
CAN_H
CAN_L
Function
Shielding
Supply voltage 24 V
Ground
CAN bus (IN/OUT)
CAN bus (IN/OUT)
Tab. 5-19: ICD890 Camera: Pin assignment of the 5-pole M12 plugs “CAN 1-IN“/“CAN 2-IN“
“ILLUMINATION“ connection (control data interface for illumination)
Pin
1
2
3
4
5
7
8
Signal n. c.
LAMP_ON+ n. c.
n. c.
RD+/TD+ (RS 485)
GND n. c.
Function
–
Illumination ON/OFF
–
–
Transmitter+/Receiver+
Transmitter–/Receiver–
Ground
–
Tab. 5-20: ICD890 Camera: Pin assignment of the 8-pole M12 socket “ILLUMINATION“
“AUX“ connection (auxiliary data interface)
6
7
4
5
8
2
3
Pin
1
Signal n. c.
n. c.
RD+ (RS 485)
RD–/RxD (RS 485/RS 232)
TD+ (RS 485)
TD–/TxD (RS 485/RS 232)
GND
Shield
Function
–
–
Receiver+
Receiver–/Receiver
Transmitter+
Transmitter–/Transmitter
Ground
Shielding
Tab. 5-21: ICD890 Camera: Pin assignment of the 8-pole M12 plug “AUX“
“HOST“ connection (main data interface)
5
6
3
4
7
8
Pin
1
2
Signal n. c.
n. c.
RD+ (RS 485)
RD–/RxD (RS 485/RS 232)
TD+ (RS 485)
TD–/TxD (RS 485/RS 232)
GND
Shield
Function
–
–
Receiver+
Receiver–/Receiver
Transmitter+
Transmitter–/Transmitter
Ground
Shielding
Tab. 5-22: ICD890 Camera: Pin assignment of the 8-pole M12 plug “HOST“
© SICK AG · Division Auto Ident · Germany · All rights reserved 8011325/0000/2006-10-24
Operating Instructions
ICR890
Electrical installation
“OUT“ connection (digital switching outputs)
2
3
Pin
1
4
Signal
Result 1+
Result 1–
Result 2–
Result 2+
Function
Switching output 1
Switching output 1
Switching output 2
Switching output 2
Tab. 5-23: ICD890 Camera: Pin assignment of the 4-pole M12 plug “OUT“
“IN 1“ connection (digital switching input 1)
4
5
2
3
Pin
1
Signal
+24 V DC
IN 1–
GND
IN 1+
–
Function
Power supply for sensor
Switching input 1 (optocoupler)
Ground
Switching input 1 (optocoupler)
–
Tab. 5-24: ICD890 Camera: Pin assignment of the 5-pole M12 socket “IN 1“
“IN 2“ connection (digital switching input 2)
3
4
5
Pin
1
2
Signal
+24 V DC
IN 2–
GND
IN 2+
–
Function
Power supply for sensor
Switching input 2 (optocoupler)
Ground
Switching input 2 (optocoupler)
–
Tab. 5-25: ICD890 Camera: Pin assignment of the 5-pole M12 socket “IN 2“
“HOST ETHERNET“ connection (Ethernet 10/100 MBps)
3
4
Pin
1
2
Signal
TD+
RD+
TD–
RD–
Function
Transmitter+
Receiver+
Transmitter–
Receiver–
Tab. 5-26: ICD890 Camera: Pin assignment of the 4-pole M12 socket “HOST ETHERNET“
Chapter 5
8011325/0000/2006-10-24 © SICK AG · Division Auto Ident · Germany · All rights reserved 73
Chapter 5
Electrical installation
Operating Instructions
ICR890 High-end CCD Camera System
“POWER IN“ connection (power supply IN)
8
3
6
1
Pin
1
2
3
4
5
6
7
8
Signal Function
+24 V DC (ICD890) Power supply IN
GND (ICI890_1) Ground
+24 V DC (ICI890_1) Power supply IN
–
– n. c.
n. c.
GND (ICD890) Ground
+24 V DC (ICI890_2) Power supply IN
GND (ICI890_2)
PE
Ground
Protective ground
Tab. 5-27: ICD890 Camera: Pin assignment of the 8-pole Harting HanQ8 plug “POWER IN“
“POWER OUT“ connection (power supply OUT for illumination)
6
1
8
3
Pin
1
2
3
4
5
6
7
8
Signal
–
Function n.c.
GND (ICI890_1) Ground
+24 V DC (ICI890_1) Power supply OUT
–
– n.c.
n.c.
– n.c.
+24 V DC (ICI890_2) Power supply OUT
GND (ICI890_2)
PE
Ground
Protective ground
Tab. 5-28: ICD890 Camera: Pin assignment of the 8-pole Harting HanQ8 socket “POWER OUT“
74
© SICK AG · Division Auto Ident · Germany · All rights reserved 8011325/0000/2006-10-24
Operating Instructions
ICR890
Electrical installation
Chapter 5
5.5.2
ICI890 Illumination connections
“POWER IN“ connection (power supply IN)
8
3
6
1
Pin
1
2
3
4
5
6
7
8
Signal
–
Function n.c.
GND (ICI890_1) Ground
+24 V DC (ICI890_1) Power supply IN
–
– n. c.
n. c.
– n. c.
+24 V DC (ICI890_2) Power supply IN
GND (ICI890_2)
PE
Ground
Protective ground
Tab. 5-29: ICI890 Illumination: Pin assignment of the 8-pole Harting HanQ8 plug “POWER IN“
“ILLUMINATION“ connection (control data interface)
Pin
1
2
3
4
5
7
8
Signal n. c.
LAMP_ON+ n. c.
n. c.
RD+/TD+ (RS 485)
GND n. c.
Function
–
Illumination ON/OFF
–
–
Transmitter+/Receiver+
Transmitter–/Receiver–
Ground
–
Tab. 5-30: ICI890 Illumination: Pin assignment of the 8-pole M12 plug “ILLUMINATION“
5.5.3
Wire colours assignment of assembled cables with open end
Cable no. 6028420 for the camera (HOST/AUX connections), standard
6
7
4
5
8
2
3
Pin
1 socket
Signal n. c.
n. c.
RD+ (RS 485)
RD–/RxD (RS 485/RS 232)
TD+ (RS 485)
TD–/TxD (RS 485/RS 232)
GND
Shield
Wire colour white brown green yellow grey pink blue red
Tab. 5-31: Wire colours assignment: Cable no. 6028420 (HOST/AUX), standard
8011325/0000/2006-10-24 © SICK AG · Division Auto Ident · Germany · All rights reserved 75
Chapter 5
Electrical installation
Operating Instructions
ICR890 High-end CCD Camera System
Cables no. 6021166/no. 6021175 for the camera (CAN 1-IN connection), PVC-free socket
4
5
2
3
Pin
1
Signal
Shield
CAN_V+
CAN_GND
CAN_H
CAN_L
Wire colour
– red black white blue
Tab. 5-32: Wire colours assignment: Cables no. 6021166/no. 6021175 (CAN 1-IN), PVC-free
Cable no. 6024861 for the camera (IN 1/IN 2 connections), standard plug
4
5
2
3
Pin
1
Signal
+24 V DC
IN 1–/IN 2–
GND
IN 1+/IN 2+
–
Wire colour brown white blue black grey
Tab. 5-33: Wire colours assignment: Cable no.6024861 (IN 1/IN 2), standard
Cable no. 6027559 for the camera (OUT connection), standard socket
3
4
Pin
1
2
Signal
Result 1+
Result 1–
Result 2–
Result 2+
Wire colour brown white blue black
Tab. 5-34: Wire colours assignment: Cable no. 6027559 (OUT), standard
76
© SICK AG · Division Auto Ident · Germany · All rights reserved 8011325/0000/2006-10-24
Operating Instructions
ICR890
Electrical installation
Cable no. 2039398 for the camera (POWER IN connection), standard
Chapter 5
6 8
1 3 socket
6
7
4
5
8
2
3
Pin
1
Signal
+24 V DC (ICD890)
GND (ICI890_1)
+24 V DC (ICI890_1)
–
–
GND (ICD890)
+24 V DC (ICI890_2)
GND (ICI890_2)
PE
Wire colour (numbers printed on wires)
Wire 1: black
Wire 4: black
Wire 3: black n. c.
n. c.
Wire 2: black
Wire 5: black
Wire 6: black green-yellow
Tab. 5-35: Wire colours assignment: Cable no. 2039398 (ICD890 Camera power supply), standard
Cable no. 2032926 for the camera (POWER IN connection), PVC-free
6 8
1 3
5
6
3
4
7
8
Pin
1
2 socket
Signal
+24 V DC (ICD890)
GND (ICI890_1)
+24 V DC (ICI890_1)
–
–
GND (ICD890)
+24 V DC (ICI890_2)
GND (ICI890_2)
PE
Wire colour (numbers printed on wires)
Wire 1: black
Wire 4: black
Wire 3: black n. c.
n. c.
Wire 2: black
Wire 5: black
Wire 6: black green-yellow
Tab. 5-36: Wire colours assignment: Cable no. 2032926 (ICD890 Camera power supply), PVC-free
8011325/0000/2006-10-24 © SICK AG · Division Auto Ident · Germany · All rights reserved 77
Chapter 5
Notes:
Electrical installation
Operating Instructions
ICR890 High-end CCD Camera System
78
© SICK AG · Division Auto Ident · Germany · All rights reserved 8011325/0000/2006-10-24
Operating Instructions
ICR890
6
Operation
Operation
Chapter 6
The ICR890 System does not require manual operation. Startup, adjustments and diagnosis are carried out via the SOPAS-ET Configuration Software.
6.1
Overview of the startup procedure
• Start up the ICR890 System with the factory default settings.
• Connect the PC with the SOPAS-ET Configuration Software to the ICR890 System or the
MSC800.
• In order to optimize the functionality of the system, adjust, if necessary, the ICR890
System and optimize the configuration of the system or the MSC800.
• Check correct functioning of the system in reading operation.
6.2
Configuration Software SOPAS-ET
The SOPAS-ET Configuration Software optimizes the ICR890 System to the reading conditions on site. The configuration data can be saved and archived as a parameter set
(project file) on the PC.
6.2.1
Functions of the SOPAS-ET Configuration Software for the ICR890 System/
MSC800 (overview)
The online help in the SOPAS-ET Configuration Software describes the general functions of the software and their operation:
M ENU , H ELP , H ELP F1
• Selecting the menu language (German, English)
• Setup communication with the ICR890 System/MSC800
• Password protected configuration for various operating levels
• Presentation of the image storage contents of the ICR890 System
• Recording of data during the current mode (recording and analyzing the data of certain system memory areas via the data recorder)
• System monitoring
6.2.2
System requirements for the SOPAS-ET Configuration Software
PC system requirements: see
Chapter 3.2.4 Operation requirements, page 28
or the booklet in the cover of the CD-ROM “Manuals & Software ICR890“ (no. 2039442).
6.2.3
Installation of the Configuration Software SOPAS-ET
Note For installation instructions, also see the booklet in the cover of the CD-ROM “Manuals &
Software ICR890“ (no. 2039442).
1. Start the PC and insert the installation CD.
2. If installation does not start automatically, call setup.exe on the CD.
3. Follow the operating instructions to conclude installation.
8011325/0000/2006-10-24 © SICK AG · Division Auto Ident · Germany · All rights reserved 79
Chapter 6
Operation
Operating Instructions
ICR890 High-end CCD Camera System
6.2.4
Default setting for the SOPAS-ET Configuration Software
Parameter
User interface language
Units of length
User group (operating level)
Download parameter for changes
Upload parameter after online switching
Window layout
Serial communication
Value
English 1)
Metric
Machine operator
Immediate, temporary (RAM of the ICR890
System)
Automatic
3 (project tree, help, work area)
COM 1: 9,600 Bd/19,200 Bd, 8 data bits, 1 stop bit, no parity
1) the software has to be restarted after changes
Tab. 6-1: Default setting for the SOPAS-ET Configuration Software (excerpt)
6.3
First startup
The ICR890 System is optimized to the reading conditions on site via the SOPAS-ET
Configuration Software. Starting point for this is the factory default setting which can be adjusted to optimize the system. The SOPAS-ET Configuration Software is used to create an application-specific parameter set which can be loaded into the system and saved/archived as a project file (spr file with configuration data) on the PC.
System ICR890
Parameter set in the main memory of the system
RAM
Permanently saved parameter set
EEPROM
Factory default setting of the system
ROM
Abb. 6-1: Configuration with SOPAS-ET
PC with Configuration
Software SOPAS-ET
Opened project file with current parameter set
RAM
Saved project file (*.spr) with archived parameter set
Database
(hard drive)
Note The ICR890 System does not provide a reading result in configuration mode.
80
© SICK AG · Division Auto Ident · Germany · All rights reserved 8011325/0000/2006-10-24
Operating Instructions
ICR890
Operation
Chapter 6
6.3.1
Overview of the configuration procedure
• Connect data interfaces of the PC and the ICR890 System/MSC800
• Start the SOPAS-ET Configuration Software and create a new project file
• Configure the scan assistant (activate PC communication)
• Establish communication with the ICR890 System/MSC800
• Accept current configuration of the ICR890 System/MSC800 in the project tree
• Use the password “client“ to register at the system as an “authorized client“
• Configure the ICR890 System/MSC800 for use
• Activate the image output of the SOPAS-ET Configuration Software (“Image Viewer“) to check the reading
• If necessary, apply the diagnosis tools “Reading Diagnosis“ and “Event Monitor“
(online presentation/recording of the switching statuses of switching inputs and outputs as well as data transfers to the host)
• Load the optimized configuration into the ICR890 System and save permanently
• Save the project file with the configuration data of the ICR890 System/MSC800 at the
PC
6.3.2
Establishing communication with the ICR890 System/MSC800
Prerequisite The TCP-IP protocol at the PC has to be active to enable communication via TCP-IP.
Connection via:
MSC800
MSC800 (optional)
ICR890 System
ICR890 System (optional) s
Connecting data interfaces
¾ Interconnect the PC and the ICR890 System/MSC800 according to
.
At data interface:
ETHERNET 1
(10/100 MBps)
AUX 1 or HOST 1
(RS 232)
HOST ETHERNET
(10/100 MBps)
AUX or HOST
(RS 232)
Comment
Connect the PC (Ethernet interface), MSC800 (ETHERNET 1 connection) and the ICR890 System (HOST ETHERNET connection) to a joint switch using a patch cable no. 6030928 (10 m (32.8 ft)) or no. 6029630 (3 m (9.84 ft)) for each connection.
Connect the PC via a 3-wire null modem cable no. 2014054 to the
9-pole D-Sub connector AUX 1 of the MSC800.
Directly connect the PC (Ethernet interface) to the HOST ETHERNET connection of the ICR890 System via a crossover cable.
- or -
Use the patch cable (1:1) no. 6030928 (3 m (9.84 ft)) or no.
6029630 (10 m (32.8 ft)) when connecting via a hub.
Provide the cable no. 6028420 (open end) for connection to the PC with a 9-pole D-Sub socket and, depending on the interface type, configure it as a null modem cable.
(For wire colour assignment: see
Tab. 5-31, page 75 , transmitter and
receiver signals are crossed, see Fig. 5-6, page 66 ).
Connect the PC via the cable no. 6028420 to the AUX connection or the ICR890 System HOST.
Tab. 6-2: Connection between the PC with the SOPAS-ET Configuration Software and the ICR890 System/MSC800
8011325/0000/2006-10-24 © SICK AG · Division Auto Ident · Germany · All rights reserved 81
Chapter 6
Operation
Operating Instructions
ICR890 High-end CCD Camera System
Sta rting the SOPAS-ET Configuration Software and calling the scan assistant
1. Switch on the power supply to the ICR890 System/MSC800.
The ICR890 System and the MSC800 carry out a self-test and are initialized.
2. Switch on the PC and start the SOPAS-ET Configuration Software.
The SOPAS-ET Configuration Software opens the program window with an English program interface as standard.
3. In order to change the language setting, click on C ANCEL and change the language of the program interface to G ERMAN /D EUTSCH via the menu T OOLS /O PTIONS .
4. Once the language setting has been changed, shut down the SOPAS-ET Configuration
Software, restart.
5. In the dialog window select the option C REATE A NEW P ROJECT and click on OK to confirm it.
6. In the main window under S CAN -A SSISTENT click on the C ONFIGURATION button.
The dialog window S CAN W IZARD appears.
Configuring the serial connection
1. In the dialog window S CAN W IZARD under S ERIAL P ORT /S TANDARD P ROTOCOL check the check box for E NABLE S ERIAL C OMMUNICATION .
2. Click on the A DVANCED ... button.
3. Under B ITS PRO S EKUNDE deactivate all the baud rates except 57.6 kbd.
4. Select the following P ORT SETTINGS : 8 data bits, no parity, 1 stop bit.
5. Click on OK to confirm settings.
The dialog window A DVANCED SCAN SETTINGS closes.
Configuring the Ethernet connection
1. In the dialog window S CAN W IZARD under I NTERNET P ROTOCOL /I NTERNET P ROTOCOL IP check the check box for E NABLE IP C OMMUNICATION .
2. Click on the A DD button.
3. Enter the IP address of the ICR890 System and confirm it via OK in the dialog window.
The dialog window closes. A new entry appears in the IP A DDRESS CONFIGURATION list.
4. Click on OK to confirm settings.
The dialog window A DVANCED SCAN SETTINGS closes.
Carrying out a scan
1. In the dialog window S CAN W IZARD click on the S CAN button.
2. Select the listed devices (ICR890 and MSC800) and confirm via A DD DEVICE .
Connected devices are searched for via the connection. The SOPAS-ET Configuration
Software inserts the found devices in the project tree and uploads the current parameter set (S YNC C HECK ).
3. For configuration of the devices see
82
© SICK AG · Division Auto Ident · Germany · All rights reserved 8011325/0000/2006-10-24
Operating Instructions
ICR890
Operation
Chapter 6
6.3.3
Configuring the ICR890 System/MSC800
The following tables
and
Tab. 6-4 (ICR890 System with MSC800) or
(ICR890 System without MSC800) act as guidelines for the configuration.
The function of each respective parameter is explained in a context-sensitive manner in an online help (F1 key). The valid value range and the default setting list the display window
“Parameter Info“ (right mouse button, when the cursor is positioned over the parameter).
In order to configure a device via the SOPAS-ET Configuration Software, the respective operating level has to be selected in advance. After the start, the SOPAS-ET Configuration
Software functions at the operating level “Maintenance“.
1. In the menu bar under E XTRAS select the command L OGIN TO DEVICE .
2. In the dialog window under U SERLEVEL in the list box select the entry A UTHORIZED C LIENT and enter the word “client“ under P ASSWORD .
Click on OK to confirm the dialog window.
The previously greyed out parameters on the register tabs are now accessible.
Settings at the ICR890 System for application as a stand-alone device with MSC800
(single-side reading)
Step
1.
2.
3.
4.
5.
6.
7.
8.
9.
10.
11.
Entry in the project tree
Reading config.
Reading config.
Object Trigger Control
Focus Control
Focus Control
Lamp Control
Position
Position
Position
Increment config.
Image Acquisition
Register tab
Codelabel properties
Image capturing properties
Start/Stop of Object trigger
Optionen Fokussteuerung
Distance Measurement Source
Illumination mode
Offsets
Coordinates
Angles
Increment
Request
Parameter
Minimum code position
Maximum code position
Symbol Contrast
Digital zoom
Image Resolution
Control
Start
Default Position
Focus Control Mode
MLG
VMS
Lamp on
Lamp timeout active
Timeout
X-Offset
Y-Offset
Z-Offset
X-Coordinate
Y-Coordinate
Z-Coordinate
Distance to deflecting mirror
Alpha
Beta
Gamma
Increment source
Resolution/Speed
Request
Image format
Bitmap scaling/JPEG Quality
Activate Diagnosis Output
Output limited by code position
Tab. 6-3: ICR890 System (stand-alone device) with MSC800: Overview of parameters which have to be set
8011325/0000/2006-10-24 © SICK AG · Division Auto Ident · Germany · All rights reserved 83
Chapter 6
Operation
Operating Instructions
ICR890 High-end CCD Camera System
Step
12.
13.
14.
Entry in the project tree
1D Code config.
2D Code config.
Data processing
Register tab
Symbologies
Symbologies
Tracking
Parameter
Codabar
Code 39
UPC/EAN Familie
2/5 Interleaved
Code 93
Code 128 Familie
Data Matrix
PDF 417
Tracking Mode
Object release point
15.
16.
17.
18.
19.
20.
21.
22.
23.
Output Format
Network Architecture
Serial
Serial
Ethernet
GBit Ethernet
CAN
Digital Outputs
Digital Inputs
Output Formating #1/#2
Master/Slave
Serial Host Interface
Serial Auxilliary Interface
General
GBit Ethernet 1/2
CAN 1/2
Output 1/2
Sensor 1/2
Network function
Output format
Baudrate
Stopbits
Databits/Parity
Hardware
Protocol
Blockcheck
Mode
IP-Address
IP-Mask
IP-Gate-Address
Speed
IP-Address
IP-Mask
IP-Gate-Address
Speed
Mode
Node-ID
Baudrate
Output format
Output 1/2
Inverted
Control
Duration
Control
Inverted
Debouncing
Tab. 6-3: ICR890 System (stand-alone device) with MSC800: Overview of parameters which have to be set (cont.)
84
© SICK AG · Division Auto Ident · Germany · All rights reserved 8011325/0000/2006-10-24
Operating Instructions
ICR890
Operation
Chapter 6
Settings at the MSC800 for application of the ICR890 System as stand-alone device
(single-side reading)
Step
1.
Entry in the project tree
Object Trigger Control
Register tab
Start/Stop of Object trigger
Parameter
Control
Start
2.
3.
4.
5.
6.
MLG settings
Increment config.
1D Code config.
2D Code config.
Data processing
Increment
Symbologies
Symbologies
Tracking
Increment source
Resolution/Speed
Codabar
Code 39
UPC/EAN Familie
2/5 Interleaved
Code 93
Code 128 Familie
Data Matrix
PDF 417
Tracking mode
Object release point
7.
8.
9.
10.
11.
12.
13.
14.
15.
Output Format
Network Architecture
Serial
Serial
Ethernet
CAN
Protokoll
Digital Outputs
Digital Inputs
Output Formating #1/#2
Master/Slave
Serial Host Interface
Serial Auxilliary Interface
General
CAN 1/2
RDT400
Output 1/2
Sensor 1/2
Network function
Output format
Baudrate
Stopbits
Databits/Parity
Hardware
Protocol
Blockcheck
Mode
IP-Address
IP-Mask
IP-Gate-Address
Speed
Mode
Node-ID
Baudrate
Output format
RDT ID
Enable internal index telegram
Output 1/2
Inverted
Control
Duration
Control
Inverted
Debouncing
16.
Realtime clock
Tab. 6-4: ICR890 System (stand-alone device) with MSC800: Overview of parameters which have to be set
8011325/0000/2006-10-24 © SICK AG · Division Auto Ident · Germany · All rights reserved 85
Chapter 6
Operation
Operating Instructions
ICR890 High-end CCD Camera System
Settings at the ICR890 System for application as stand-alone device without MSC800
Step
1.
2.
3.
4.
5.
6.
7.
8.
9.
10.
11.
12.
13.
14.
Entry in the project tree
Reading config.
Reading config.
Object Trigger Control
Focus Control
Focus Control
Lamp Control
Position
Position
Position
Increment config.
Image Acquisition
1D Code config.
2D Code config.
Data processing
Register tab
Codelabel properties
Image capturing properties
Start/Stop of Object trigger
Optionen Fokussteuerung
Distance Measurement Source
Illumination mode
Offsets
Coordinates
Angles
Increment
Request
Symbologies
Symbologies
Tracking
Parameter
Minimum code position
Maximum code position
Symbol Contrast
Digital zoom
Image Resolution
Control
Start
Default Position
Focus Control Mode
MLG
VMS
Lamp on
Lamp timeout active
Timeout
X-Offset
Y-Offset
Z-Offset
X-Coordinate
Y-Coordinate
Z-Coordinate
Distance to deflecting mirror
Alpha
Beta
Gamma
Increment source
Resolution/Speed
Request
Image format
Bitmap scaling/JPEG Quality
Activate Diagnosis Output
Output limited by code position
Codabar
Code 39
UPC/EAN Familie
2/5 Interleaved
Code 93
Code 128 Familie
Data Matrix
PDF 417
Tracking Mode
Object release point
15.
16.
17.
18.
Output Format
Network Architecture
Serial
Serial
Output Formating #1/#2
Master/Slave
Serial Host Interface
Serial Auxilliary Interface
Network function
Output format
Baudrate
Stopbits
Databits/Parity
Hardware
Protocol
Blockcheck
Mode
Tab. 6-5: ICR890 System (stand-alone device) without MSC800: Overview of parameters which have to be set
86
© SICK AG · Division Auto Ident · Germany · All rights reserved 8011325/0000/2006-10-24
Operating Instructions
ICR890
Operation
Chapter 6
Step
19.
20.
21.
22.
23.
Entry in the project tree
Ethernet
GBit Ethernet
CAN
Digital Outputs
Digital Inputs
Register tab
General
GBit Ethernet 1/2
CAN 1/2
Output 1/2
Sensor 1/2
Parameter
IP-Address
IP-Mask
IP-Gate-Address
Speed
IP-Address
IP-Mask
IP-Gate-Address
Speed
Mode
Node-ID
Baudrate
Output format
Output 1/2
Inverted
Control
Duration
Control
Inverted
Debouncing
Tab. 6-5: ICR890 System (stand-alone device) without MSC800: Overview of parameters which have to be set (cont.)
6.3.4
Load changed parameter sets into the device
Changed parameter values are immediately transferred to the ICR890 System depending on the option (“Download Immediately“). To ensure that the changes remain even after a system restart, the configuration has to be permanently saved in the system.
1. In order to load current settings into the ICR890 System, in the menu bar under ICR890 select the command P ARAMETER /S AVE PERMANENT .
- or -
In order to load the current settings in the MSC800, select the command P ARAMETER /
S AVE PERMANENT in the menu bar under MSC800.
2. Restart the ICR890 System/MSC800.
6.3.5
Save, display and print the current parameter set
When archiving a parameter set it is recommended to not only save the project file but also print out the contents of the file.
1. In order to save the current parameter set, select the menu item S AVE P ROJECT AS in the menu bar under P ROJECT .
2. Enter a file name in the dialog window and confirm it via S AVE .
The SOPAS-ET Configuration Software saves the current settings in a configuration file
“*.SPR“.
3. In order to print out the current parameter set, select the command P RINT /P RINT P REVIEW in the menu bar under P ROJEKT .
The SOPAS-ET Configuration Software displays a preview of a table with a list of all the parameter values.
4. Click on in the tool bar at the top of the dialog window.
The dialog window P RINT for printer configuration appears.
5. Edit setting accordingly and confirm via OK.
The current project settings are printed as a table on several pages.
8011325/0000/2006-10-24 © SICK AG · Division Auto Ident · Germany · All rights reserved 87
Chapter 6
Operation
Operating Instructions
ICR890 High-end CCD Camera System
6.3.6
Changing the device password for the user level "Authorized Client"
The device password for the user level "A UTHORIZED C LIENT " can be altered device specifically by the customer. This prevents unwanted or unauthorized changes to the configuration.
1. Establish communication with the device (see Chapter 6.3.2, page 81
).
2. In the menu bar under ICR890 select the command P ASSWORD /C HANGE P ASSWORD .
3. Ensure that the user level "A UTHORIZED C LIENT " has been selected in the dialog window
R EGISTER .
4. Enter the new password in the field N EW P ASSWORD .
The entry occurs as hidden text.
5. Re-enter the new password in the field C ONFIRM N EW P ASSWORD .
The entry occurs as hidden text.
6. Confirm entries via the L OGIN button.
A message confirms successful device password changes.
6.4
Default setting
The values of the default setting are permanently saved in the ICR890 System (ROM) and in the database of the SOPAS-ET Configuration Software in the device-specific jar file (see
Fig. 6-1, page 80 ). A PC is not required for system startup with the default setting.
6.4.1
Resetting the default setting in the ICR890 System
Prerequisite The SOPAS-ET Configuration Software is connected online to the ICR890 System.
1. In order to completely discard changes to the parameter set, in the menu bar under
ICR890 select the command P ARAMETER /L OAD FACTORY DEFAULT .
The SOPAS-ET Configuration Software loads the default setting from the database and displays the parameter values in the register tabs.
2. In the menu bar under E XTRAS select the command L OGIN TO DEVICE .
3. In the dialog window under U SERLEVEL in the list box select the entry A UTHORIZED C LIENT and enter the word “client“ under P ASSWORD .
Click on OK to confirm the dialog window.
4. In the menu bar under ICR890 select the command P ARAMETER /S AVE P ERMANENT .
The SOPAS-ET Configuration Software transfers the default setting to the permanent parameter memory (EEPROM) of the ICR890 System.
6.4.2
Default setting MSC800
See MSC800 Operating Instructions (no. 8011540).
88
© SICK AG · Division Auto Ident · Germany · All rights reserved 8011325/0000/2006-10-24
Operating Instructions
ICR890
7
Maintenance
Maintenance
Chapter 7
7.1
Maintenance during operation
The ICR890 System functions maintenance free. Regular maintenance is not required to guarantee LED class 1M of the ICR890 System.
Note Do not open the ICD890 Camera or the ICI890 Illumination.
If the devices are opened, the manufacturer's warranty shall not apply.
Checking the incremental encoder
If an incremental encoder is used, the position of the friction wheel at the drive system should be checked at regular intervals.
¾ Ensure that the incremental encoder has contact with the drive system and that the friction wheel rotates without slipping.
7.2
Cleaning the ICR890 System
Recommendation In order to make use of the full optical reading capacity of the ICR890 System, the front window should be checked regularly (e. g. weekly) for soiling. This is especially recommended when operating the device in harsh conditions (dust, abrasion, humidity, finger prints, etc.).
If possible, do not clean the deflection mirror due to its structure.
7.2.1
Cleaning the front window
LED radiation of class 1M (according to EN/IEC 60825-1)!
Incorrect use can result in hazardous radiation exposure and the LED class being exceeded!
The accessible radiation of the ICI890 Illumination is not hazardous under reasonably foreseeable conditions, provided that the beam width is not reduced by optical instruments, e.g. magnifying glass, lenses, telescopes. Visual glare, loss of colour vision and eye injuries cannot be ruled out.
The entire window surface is the LED radiation outlet opening.
¾ Do not look directly into the radiation source with optical instruments.
¾ Do not open the housing. (The illumination is not switched off if the housing is opened!)
¾ Always observe the latest valid version of laser protection regulations.
Damage to the front window!
Reduced reading capacity due to scratches or smears on the front window!
The front window of the illumination is made of glass. The opening for the camera within the front window is made of special glass.
¾ Do not use aggressive cleaning agents.
¾ Do not use cleaning agents which cause increased abrasion (e. g. powder).
¾ Avoid cleaning motions at the front window which could cause scratches or abrasion.
8011325/0000/2006-10-24 © SICK AG · Division Auto Ident · Germany · All rights reserved 89
Chapter 7
Maintenance
Operating Instructions
ICR890 High-end CCD Camera System
Cleaning the front window
Note Electrostatic charges cause dust particles to stick to the front window.
This effect can be combated by using anti-static SICK synthetic cleaner (no. 5600006) in combination with a SICK lens cloth (no. 4003353).
¾ Use a clean, soft brush to free the front window from dust.
¾ If necessary, additionally clean the front window with a clean, damp, lint-free cloth and a mild, anti-static window cleaning fluid.
clean here
Abb. 7-1: Cleaning the front window
If the front window is scratched or damaged (cracked, broken), it must be replaced. Please contact the SICK Service.
7.2.2
Cleaning the housing
In order to ensure sufficient cooling for the illumination, make sure that the air inlet and outlet opening are always clean.
¾ Use a soft brush to free the openings at the ventilator on top of the housing and at the cooling ribs of the air outlet openings on both narrow sides from dust.
90 clean here
Abb. 7-2: Cleaning the air inlet and outlet openings at the system's illumination ICR890
© SICK AG · Division Auto Ident · Germany · All rights reserved 8011325/0000/2006-10-24
Operating Instructions
ICR890
Maintenance
Chapter 7
7.2.3
Cleaning the deflection mirror
Damage to the optical effective surface of the deflection mirror!
Incorrect cleaning or aggressive cleaning agents can damage the deflection mirror, thus impairing the reading quality of the ICR890 System.
¾ If possible, do not clean the deflection mirror.
¾ Only clean the reflector surface if absolutely necessary (e. g. heavy soiling). Never touch the entire reflector surface.
¾ Do not use canned compressed air.
¾ To avoid irreversible scratches, never clean the mirror with a cloth.
Removing dust and loose dirt particles
¾ Carefully blow off dust and loose dirt particles using cleaned, oil-free air.
Do not use canned compressed air, since it can contain alkaline substances which corrode the surface of the mirror.
Removing solid particles
¾ Carefully remove more solid particles with a degreased camel hair brush (previously treated with acetone). Ensure that acetone does not come into direct contact with the reflector surface.
Cleaning the deflection mirror intensively
1. Fill a clean plastic spray bottle with distilled water.
2. Evenly spray distilled water onto the reflector surface.
Keep the mirror tilted, allowing the distilled water to drip dry.
3. Allow the mirror to dry. Do not wipe the mirror dry!
Removing grease deposits
1. Spray affected areas with household glass cleaner.
2. Use a paper towel (recommended: “Kleenex“) to wipe the affected area. Only apply slight pressure to the mirror. Do not scour.
3. Allow the mirror to dry. Do not wipe the mirror dry!
8011325/0000/2006-10-24 © SICK AG · Division Auto Ident · Germany · All rights reserved 91
Chapter 7
Maintenance
Operating Instructions
ICR890 High-end CCD Camera System
7.2.4
Cleaning further optical effective surfaces
Depending on the system equipment, further sensors with optical effective surfaces can be installed (e. g. photoelectric reflex switch for external reading pulsing or MLG Light Grid for detecting the object distance). Soiling of these sensors can cause incorrect switching behaviour.
¾ In order to prevent incorrect switching behaviour, remove soiling from the optical effective surfaces of the external sensors.
: clean here
Trigger stop
(optional)
Trigger start
Abb. 7-3: Cleaning of the external optical sensors (reading pulse generator, detector for object distance)
92
© SICK AG · Division Auto Ident · Germany · All rights reserved 8011325/0000/2006-10-24
Operating Instructions
ICR890
Maintenance
Chapter 7
7.3
Replacing a system or a component
Incorrect or damaged system components have to be removed and replaced with either new or repaired components.
Repairs to the ICR890 System should only be carried out by qualified and authorized SICK
AG service staff.
Risk of injuries due to falling components!
The combined weight of the ICD890 Camera and the ICI890 Illumination is approx. 37 kg
(81.6 lb) without installation accessories.
¾ Do not carry out removal / installation work alone.
¾ A second person should always secure components during removal / installation.
7.3.1
Replacing the ICD890 Camera or ICI890 Illumination
Removing connection cables
1. Switch off the power supply to the ICR890 System.
2. Loosen and disconnect all external cable connectors and sockets at the camera.
3. Remove both connecting cables between the camera and the illumination.
Disconnecting system components
1. Loosen, but do not remove, the two clamping screws in the curved grooves of both
180° brackets!
Bore hole for the illumination fastening screws
Clamping screws
Abb. 7-4: 180° bracket: Loosening clamping screws
2. Carefully swing the ICR890 System until the front window of the illumination is facing downwards.
3. Remove the camera from the illumination.
To achieve this, loosen the four hexagon socket screws of the camera (
Fig. 3-2, page 24, centering pin with thread
) and carefully extract the camera upwardly out of the illumination.
8011325/0000/2006-10-24 © SICK AG · Division Auto Ident · Germany · All rights reserved 93
Chapter 7
Maintenance
Operating Instructions
ICR890 High-end CCD Camera System
Replacing the illumination
1. Note the installation position of the illumination when suspended (e. g. position of the round ventilator opening in relation to the direction of transport).
2. Remove both clamping screws for the illumination from the two 180° brackets.
3. Lift the illumination out of the bracket grooves and remove it from the frame.
4. Insert a new illumination the right way round into the two 180° brackets and subsequently tighten the two clamping screws in each bracket.
The front window of the illumination faces downwards.
Replacing the camera
1. Remove the memory card with the saved parameter set from the defective camera
(
).
2. Insert the memory card into the empty slot of the new camera accordingly.
Close the slot cover.
3. Remove the yellow and black protective caps from the lens protection tube and from the lens of the new camera. Do not touch the lens!
4. Align the camera the right way round on the illumination and carefully insert the lens protection tube into the illumination opening.
5. Place the camera on the illumination and attach it using four hexagon socket screws.
6. Align the complete unit parallel to the conveyor level.
7. Use the clamping screws to fix the 180° brackets.
Reconnecting cables
1. Reconnect both connecting cables between the system components.
2. Reconnect all external cables to the camera.
3. Switch on the power supply to the ICR890 System.
The ICR890 System starts up and loads the parameter set from the memory card into its permanent parameter memory (EEPROM) after initialisation.
7.3.2
Replacing the deflection mirror
1. Mark the installation position of the deflection mirror when suspended (e. g. mark the position of the illumination surface).
2. Loosen the clamping screws on both sides, place the mounting plate of the
180° bracket in a vertical position and retighten the clamping screws.
3. Unscrew the fastening screws and remove the deflection mirror from the
180° brackets.
4. Insert the guide pins of the new deflection mirror into the grooves of the 180° brackets.
5. Use two fastening screws to attach the deflection mirror to the 180° brackets.
6. Loosen the clamping screws, adjust the deflection mirror to the desired angle with the illumination switched on and retighten the clamping screws.
7. Remove the protective film from the new deflection mirror.
Note The deflection mirror can also be removed without changing the angle of the 180° brackets.
The deflection mirror must, however, be held securely when removing the fastening screws.
94
© SICK AG · Division Auto Ident · Germany · All rights reserved 8011325/0000/2006-10-24
Operating Instructions
ICR890
Maintenance
Chapter 7
7.4
Disposal
Inoperable or irreparable devices must be removed and disposed of in an environmentally friendly manner in accordance with valid country-specific waste disposal guidelines.
At present SICK AG will not accept the return of any devices which can no longer be operated or repaired.
Removing ICR890 Systems for decommissioning
1. Switch off the power supply to the ICR890 System.
2. Disconnect all the connection cables at the ICR890 System.
3. Release the ICR890 System from the two brackets and remove it from the frame.
4. Remove both connecting cables between the camera and the illumination.
5. Loosen the four hexagon socket screws (
) and carefully extract the camera from the illumination.
Disposing of the ICI890 Illumination
1. Remove the illumination housing.
2. Remove the electronic assemblies of the illumination and dispose of them as hazardous waste.
3. Remove the front window of the illumination and set it aside for glass recycling.
4. Set aside the fresnel lens for plastics recycling.
5. Set aside the illumination housing for the recycling of aluminium pressure die castings.
Disposing of the ICD890 Camera
1. Remove the camera housing.
2. Remove the electronic assemblies of the camera.
3. Remove the battery on the internal PC card from its holder and dispose of it as hazardous waste according to ROHS Directives (Europe).
Battery
Abb. 7-5: ICD890 Camera: Position of the battery on the internal PC card
4. Set aside the camera lens for glass recycling.
5. Dispose of electronic assemblies as hazardous waste.
6. Set aside the housing and the cover of the camera as well as the lens assembly for the recycling of aluminium pressure die castings.
7. Set aside the connection cables for metal recycling.
8011325/0000/2006-10-24 © SICK AG · Division Auto Ident · Germany · All rights reserved 95
Chapter 7
Notes:
Maintenance
Operating Instructions
ICR890 High-end CCD Camera System
96
© SICK AG · Division Auto Ident · Germany · All rights reserved 8011325/0000/2006-10-24
Operating Instructions
ICR890
Troubleshooting
Chapter 8
8
Troubleshooting
This chapter describes how errors at the ICR890 High-end CCD Camera System can be recognised and eliminated.
8.1
Overview of errors and malfunctions which could occur
8.1.1
Installation error
• The ICR890 System has been unsuitably aligned to objects with 1-D/2-D codes (e.g. visual glare)
• Reading pulse sensor has been incorrectly positioned (e.g. internal reading gate opens too late or shuts too early)
• Focus switching: Sensors for detecting object heights positioned incorrectly
• Incremental encoder (optional) positioned incorrectly
8.1.2
Electrical installation error
• Interfaces of the ICR890 System wired incorrectly
8.1.3
Configuration error
• Functions have not been adjusted to the local conditions, e. g. parameters for the main data interface set incorrectly
• Device-related limits have not been considered, e. g. reading distance, aperture angle
• Selected trigger source for reading pulse incorrect
8.1.4
Malfunctions during operation
• Start/Stop operation: External reading pulse is missing, more than one object is in the reading area
• Tracking operation: Minimum gap of the objects in the direction of transport not achieved
• Timeout of the ICI890 Illumination exceeded
• Device error (hardware/software)
8011325/0000/2006-10-24 © SICK AG · Division Auto Ident · Germany · All rights reserved 97
Chapter 8
Troubleshooting
Operating Instructions
ICR890 High-end CCD Camera System
8.2
Detailed malfunction analysis
8.2.1
LEDs at the camera
The following statuses can, among other things, be read at the LEDs for the electrical
connections of the ICD890 Camera (see Chapter 3.5.2, page 42
):
• Result of the self-test
• Operating status
• Status of the reading result
• Required maintenance or service work
The LEDs can display possible malfunctions or errors. Please refer to the system information for further details.
8.2.2
System information
The ICR890 System displays errors in various ways. The error output is hierarchised and always allows a detailed analysis:
• Communication errors can occur while transmitting telegrams to the ICR890 System.
In this case, the ICR890 System returns an error code.
• Error codes are written into a status protocol for errors which occur during a reading.
8.2.3
Status protocol
Note • The status protocol remains even after switching the device off and on again.
• The system differentiates between four error types:
– Information
– Warning
– Error
– Fatal error
The system only saves the last five entries for each of the error types.
Displaying the status protocol with the aid of the SOPAS-ET Configuration Software
In order to display the status protocol, the SOPAS-ET Configuration Software has to be online and connected to the ICR890 System.
¾ Connect the SOPAS-ET Configuration Software to the device.
¾ Open the project tree IRC890, S ERVICE , S YSTEM S TATUS , register tab S YSTEM I NFORMATION .
Reading the status protocol with the aid of command strings
The status protocol can also be read with the aid of command strings. There is a telegram available for each error type.
¾ Send the telegram from the command sRN (SOPAS read by name) and the telegram name to the ICR890 System, e. g. via the terminal in the SOPAS-ET Configuration
Software.
The ICR890 System sends an answer consisting of sRA (SOPAS write answer) the telegram name, an error code (00000000h = no error) and information, warnings, errors or fatal errors.
98
© SICK AG · Division Auto Ident · Germany · All rights reserved 8011325/0000/2006-10-24
Operating Instructions
ICR890
Troubleshooting
Chapter 8
Query warnings
Request: sRN MSwarn
Telegram part
Type of command
Command
Description
Request (SOPAS write by name)
Query warnings
Variable type string string
Length (byte) Value range
3
6 sRN
MSwarn
Tab. 8-1: Request “Query warnings“
Answer: sRA MSwarn ParameterWARNING1 (Error code FirstTimePwrOnCnt FirstTimeOpHours
FirstTimeDailyOpHours LastTimePwrOnCnt LastTimeOpHours LastTimeDailyOpHours Number
ReservedBytes) ParameterWARNING2 ParameterWARNING3 ParameterWARNING4
ParameterWARNING5
Telegram part
Type of command
Command
Error code
FirstTimePwrOnCnt
FirstTimeOpHours
FirstTimeDailyOpHours
LastTimeOpHours
LastTimeDailyOpHours
Number
Description
Answer (SOPAS answer)
Variable type string
Query warnings string
Hex value of the saved error code uint_32
Status of the power on counter at the time of the first occurrence uint_16
Status of the total operating hours counter at the time of the first occurrence
Status of the operating hours counter at the time of the first occurrence uint_16 uint_16 uint_16 the time of the last occurrence
Status of the total operating hours counter at the time of the last occurrence
Status of the operating hours counter at the time of the last occurrence
Displays a number of the occurrence uint_16 uint_16 uint_16
Reserved bytes Reserved
Tab. 8-2: Answer to the request “Query warnings“ uint_16
6
4
Length (byte) Value range
3 sRA
MSwarn
00000001h
…
FFFFFFFFh
2
2
2
2
0000h
…
FFFFh
0000h
…
FFFFh
0000h
…
FFFFh
0000h
…
FFFFh
2
2
2
2
0000h
…
FFFFh
0000h
…
FFFFh
0000h
…
FFFFh
0000h
Example for querying warnings
Request: sWN MSwarn
Answer: sWA MSwarn 4C0ACC0Ah 00A4h 0255h 0005h 00A4h 0256h 0006h 0256h 0000h 4C0ACC0Bh
00A4h 0255h 0005h 00A4h 0256h 0006h 0256h 0000h 4C0ACC0Ch 00A4h 0255h 0005h 00A4h
0256h 0006h 0256h 0000h 4C0ACC0Bh 00A4h 0255h 0005h 00A4h 0256h 0006h 0256h 0000h
4C0ACC0Ch 00A4h 0255h 0005h 00A4h 0256h 0006h 0256h 0000h
8011325/0000/2006-10-24 © SICK AG · Division Auto Ident · Germany · All rights reserved 99
Chapter 8
Troubleshooting
Operating Instructions
ICR890 High-end CCD Camera System
Query errors
Request: sRN MSerr
Telegram part
Type of command
Command
Description
Request (SOPAS write by name)
Query errors
Variable type string string
Length (byte) Value range
3
5 sRN
MSerr
Tab. 8-3: Request “Query errors“
Answer: sRA MSwarn ParameterWARNING1 (Error code FirstTimePwrOnCnt FirstTimeOpHours
FirstTimeDailyOpHours LastTimePwrOnCnt LastTimeOpHours LastTimeDailyOpHours Number
ReservedBytes) ParameterWARNING2 ParameterWARNING3 ParameterWARNING4
ParameterWARNING5
Telegram part
Type of command
Description
Answer (SOPAS answer)
Command
Parameters see
Reserved bytes
Query errors
Reserved
Tab. 8-4: Answer to the request “Query errors“
Variable type string string uint_16
Length (byte) Value range
3 sRA
5 MSerr
2 0000h
Example
Request: sRN MSerr
Answer: sRA MSerr 4303C303h 00A4h 0255h 0005h 00A4h 0256h 0006h 0256h 0000h 00000000h
0000h 0000h 0000h 0000h 0000h 0000h 0000h 0000h 00000000h 0000h 0000h 0000h 0000h
0000h 0000h 0000h 0000h 00000000h 0000h 0000h 0000h 0000h 0000h 0000h 0000h 0000h
00000000h 0000h 0000h 0000h 0000h 0000h 0000h 0000h 0000h
Query fatal errors
Request: sRN MSfat
Telegram part
Type of command
Command
Description
Request (SOPAS write by name)
Query fatal errors
Variable type string string
Length (byte) Value range
3 sRN
5 MSfat
Tab. 8-5: Request “Query fatal errors“
Answer sRA MSfat ParameterFATALERROR1 (Error code FirstTimePwrOnCnt FirstTimeOpHours
FirstTimeDailyOpHours LastTimePwrOnCnt LastTimeOpHours LastTimeDailyOpHours Number
ReservedBytes) ParameterFATALERROR2 ParameterFATALERROR3 ParameterFATALERROR4
ParameterFATALERROR5
Telegram part
Type of command
Command
Description
Answer (SOPAS answer)
Query fatal errors
Parameters see
Reserved bytes Reserved
Tab. 8-6: Answer to the request “Query fatal errors“
Variable type string string uint_16
Length (byte) Value range
3
5 sRA
MSfat
2 0000h
Example
Request: sRN MSfat
Answer: sRA MSfat 4912C912h 00A4h 0255h 0005h 00A4h 0256h 0006h 0256h 0000h 00000000h
0000h 0000h 0000h 0000h 0000h 0000h 0000h 0000h 00000000h 0000h 0000h 0000h 0000h
0000h 0000h 0000h 0000h 00000000h 0000h 0000h 0000h 0000h 0000h 0000h 0000h 0000h
00000000h 0000h 0000h 0000h 0000h 0000h 0000h 0000h 0000h
100
© SICK AG · Division Auto Ident · Germany · All rights reserved 8011325/0000/2006-10-24
Operating Instructions
ICR890
Troubleshooting
Chapter 8
8.3
ST error status in the reading result of a 1-D code (bar code)
With the respective configuration, the ICR890 System transfers the ST error status to the output string of the HOST data interface.
Value
0
1
2
5
7
9
A
D
Meaning
Error-free reading “Good Read“
Wrong check digit
Possible cause
–
The check digit which the ICR890 System calculated during the reading does not correspond to the printed check digit in the bar code area.
• No bar code during the reading pulse in the reading area of the ICR890 System
Remedy n/a
Check the correctness of the check digit created during the printing process in the bar code area.
No code of the released bar code type found according to the analysis conditions
• Synchronize the reading pulse of the ICR890 with the occurrence of a bar code in the reading area.
• Configure the bar code correctly.
Required number of identical multiple readings for the bar code not achieved
• Bar code type/length in the ICR890
System not released for decoding
•
•
•
Reading window covered/soiled
Conveyor speed of the object too high
Scanning frequency too low
• With scalariform arrangement of the bar code in the direction of transport:
Bar code height (strip length) to small
• Poor print quality
• Check the reading window.
• Check conveyor speed.
• Adjust the parameter “Object speed“ in the ICR890 System.
• Check the bar code height
The source of the reading result is the auxiliary input via the Aux interface
The function O comparison.
UTPUT FILTER
is additionally active for the bar code
The ICR890 System has detected valid bar codes, but these do not correspond to the active set code(s)
Function C
HECK MAX
.
NUMBER OF CODES is active.
The ICR890 System has detected more valid bar codes in the reading pulse than specified under N
UMBER OF
CODES : MAXIMUM .
Instead of the bar code contents, it displays the number of the defined error string, as defined under N
UMBER
OF CODES : M INIMUM .
For code 39 the analysis option
“Code 32“ is activated. The ICR890
System attempts to interpret 6-digit
C39 bar codes as C32 bar codes
(output of 9-digit decimal numbers).
The bar code was not been detected by the reading of the ICR890 System, but subsequently entered via the auxiliary function of the Aux interface and transferred to the host in a separate data string.
The detected object does not have a bar code which corresponds to the specified set code.
In a batch of objects with a constant number of bar codes, an object has, e.g., more bar codes than defined.
The read 6-digit bar code is not a C32 bar code.
ICR890 System displays the defined error string instead.
• Check the print quality n/a n/a
The message serves as the display of an error for the objects (e.g. test for sort pure: mixing with the incorrect object).
n/a
Tab. 8-7: Meaning of the ST error status in the reading result
8011325/0000/2006-10-24 © SICK AG · Division Auto Ident · Germany · All rights reserved 101
Chapter 8
Troubleshooting
Operating Instructions
ICR890 High-end CCD Camera System
Value
F
Meaning
Function C HECK MIN . NUMBER OF CODES
PRÜFEN
is active.
The ICR890 System has detected less valid bar codes in the reading pulse than specified under N UMBER OF
CODES
:
MINIMUM
.
Instead of the bar code contents, it displays the number of the defined error string, as defined under N UMBER
OF CODES
: M
INIMUM
.
Possible cause
In a batch of objects with a constant number of bar codes an object has less bar codes than defined.
Tab. 8-7: Meaning of the ST error status in the reading result (cont.)
Remedy
The message serves as the display of an error for the objects (e.g. test for sort pure: mixing with the incorrect object).
8.4
SICK support
If a system error occurs repeatedly or if you cannot correct an error using the above measures, the ICR890 System may be defective. The system components cannot be repaired by the user, meaning that it is not possible to re-establish functions after a failure.
However, the camera or the illumination can be rapidly replaced by the user. See
Chapter 7.3 Replacing a system or a component, page 93 .
¾ Please contact our local SICK office or subsidary if an error occurs which cannot be eliminated:
• The telephone numbers and email addresses are listed on the back page of this manual.
For postal addresses see also www.sick.com.
¾ Do not send the device to the SICK service without first contacting us.
102
© SICK AG · Division Auto Ident · Germany · All rights reserved 8011325/0000/2006-10-24
Operating Instructions
ICR890
Technical data
Chapter 9
9
Technical data
9.1
Data sheet for ICR890 Camera
Type
Function
MTBF of the device
MTTR of the device 1)
ICD890 Camera (standard)
Camera
> 50,000 h
< 20 min
CCD sensor (lines)
Line frequency (line rate)
Image resolution 250 dpi for a reading distance of 2 m (6.56 ft)
170 dpi for a reading distance of 3 m (9.84 ft)
Max. 25 ° up to a reading distance of 2.4 m (7.87 ft) Useable aperture angle
Cover track width of the conveyor system 1,000 mm (39.4 in) for a resolution of 170 dpi
600 mm (23.6 in) for a resolution of 250 dpi
DOF (depth of field) 1,600 mm (63.0 in) for a resolution of 170 dpi
600 mm (23.6 in) for a resolution of 250 dpi
Reading areas 1,4 to 3 m (4.59 to 9.84 ft)
Max. conveyor speed (objects)
Line camera with 8,192 pixels
Max. 19.1 kHz
Supported objects
Focus
Image data output format
Ambient light compatability
PCS (print contrast)
1-D code types (bar codes)
2-D code types
Number of objects per second
Minimum object gap
Number of codes per object
Number of characters per 1-D code
Number of characters per 2-D code
Pressure ratio 1-D code
Number of multi-readings (1-D code)
Memory card for parameter (cloning)
Optical indicators
Reading pulse
Pulse start/Pulse end delay
“Host“ data interface
Data transfer rate
Protocols
1.9 m/s (374 ft/min) for a resolution of 250 lpi
2.8 m/s (551 ft/min) for a resolution of 170 lpi
4.8 m/s (945 ft/min) for a resolution of 100 lpi
Standard (focal distance 135 mm (5.32 in))
Dynamic
GigE Vision Standard
Max. 10
RS 232, RS 422/485, adjustable data output format
9.6 to 115.2 kbd
SICK standard
2) or FTP
2,000 lx (on 1-D/2-D code)
≥ 40 %
2/5 interleaved, code 39, code 128, EAN/UPC with add-on, Codabar, EAN 128
Data Matrix ECC200, PDF417 (in preparation)
50 mm (1.97 in)
1-D: max. 50, 2-D: max. 10
Max. 50 characters (max. 1,000 characters across all 1-D codes per reading gate)
Max. 1,556 bytes
2:1 to 3:1
1 to 99
SD card, 64 MB
5 x LED (status indicators)
Switching input “sensor 1“/“sensor 2“ command (data interface)/CAN
0 to 10,000 ms (for reading pulse switching input/serial interface)
“CAN“ data interface
“Ethernet“ data interface
“GBit Ethernet“ data interface
2 x, 10 KBps to 1 MBps, CAN open protocol, CAN-SENSOR network
10/100 MBps, TCP/IP, FTP, half/full duplex
2 x, 10 MBps to 1 GBps, real-time image output, FTP and Gig-E Vision standard,
Half/Full duplex
Tab. 9-1: Technical specifications for the ICR890 Camera
8011325/0000/2006-10-24 © SICK AG · Division Auto Ident · Germany · All rights reserved 103
Chapter 9
Technical data
Operating Instructions
ICR890 High-end CCD Camera System
Type
“AUX“ data interface
Data transfer rate
IN switching inputs
OUT switching outputs
Electrical connections
Operating voltage
Current consumption
Housing
Enclosure rating
Protection class
EMC/vibration/shock test
ICD890 Camera (standard)
RS 232, RS 422/485, adjustable data output format
57.6 KBps
2 x digital (“sensor 1/2“), configurable, optically decoupled, V imax
= 28 V, reverse polarity protected
Function: “Start/Stop reading pulse“, increment signal or ICI890 Illumination triggering
Control: Time or path-based
Debouncing: Min. 3 ms
Selectable logic analyzer (low -> high, high -> low)
2 x digital (“Out 1/2“), configurable, PNP, I omax
= 100 mA, short-circuit proof
Function: Good read, no read or device ready
Adjustable impulse duration (stat., 10 to 990 ms)
Selectable logic analyzer (low -> high, high -> low)
4 x 5-pole M12 (CAN 1-IN, -OUT; CAN 2-IN, -OUT)
3 x 8-pole M12 (AUX, HOST, ILLUMINATION)
4 x 4-pole M12 (IN 1, IN 2, OUT, HOST ETHERNET)
2 x RJ-45 socket (GBIT ETHERNET)
2 x 8-pole Harting connector POWER IN/POWER OUT
24 V DC ± 10 % in accordance with IEC 364-4-41 (VDE 0100 Part 410)
Typically 75 W
Aluminium die-casting.
Excluding the housing, the system does not contain any materials using silicone.
IP 64 (in accordance with DIN 40 050)
Class 3 (in accordance with IEC 1010-1)
In accordance with EN 61000-6-2:2001, EN 61000-6-4:2001/ IEC 68-2-6/ IEC 68-2-27,
IEC 68-2-29
Dimensions 3)
Weight
Approx. 13.5 kg (29.7 lb)
Fixing
Ambient operating temperature/Storage temperature
Max. rel. humidity
To the ICI890 Illumination, 4 x M8 bolt with centering pin
0 to +40 °C (+32 to +104 °F)/–20 to +70 °C (–4 to +158 °F)
Colour
95 %, no condensation
SICK Blue (RAL 5012)
1) Camera and illumination can be replaced independently of each other.
2) In preparation
3) Including decoder
Tab. 9-1: Technical specifications for the ICR890 Camera (contd.)
104
© SICK AG · Division Auto Ident · Germany · All rights reserved 8011325/0000/2006-10-24
Operating Instructions
ICR890
Technical data
Chapter 9
9.2
Data sheet for ICI890 Illumination
Type
Function
Wavelength
LED class
ICI890 Illumination
LED illumination
Red light ( λ = 620 nm)
1M (in accordance with EN/IEC 60825-1), illumination switches off after 3 s 1)
Power-on time
MTBF of the device
Operating voltage
Current consumption
Housing
Reading pulse-dependent, minimum power-on time 3 s
> 50,000 h
< 20 min MTTR of the device 2)
Electrical connections 1 x 8-pole M12 (camera control)
1 x 8-pole Harting connector Power IN
24 V DC ± 10 % in accordance with IEC 364-4-41 (VDE 0100 Part 410)
Typically 350 W
Aluminium die-casting.
Excluding the housing, the system does not contain any materials using silicone.
IP 64 (in accordance with DIN 40 050), IP 54 ventilator Enclosure rating
Protection class
EMC/vibration/shock test
Dimensions
Class 3 (in accordance with IEC 1010-1)
In accordance with EN 61000-6-2:2001, EN 61000-6-4:2001/ IEC 68-2-6/ FC Test /
IEC 68-2-27 EA Test
See
Weight
Fixing
Approx. 23.5 kg (51.7 lb)
2 x angle support (U-shaped), including 2 x guide pin each ∅ 6 mm (0.24 in) and 2 x M8 threaded hole for use in 180° brackets
0 to +40 °C (+32 to +104 °F)/–20 to +70 °C (–4 to +158 °F) Ambient operating temperature/Storage temperature
Max. rel. humidity
Colour
95 %, no condensation
SICK Blue (RAL 5012)
1) (Default setting)
2) Camera and illumination can be replaced independently of each other.
Tab. 9-2: Technical specifications for the ICI890 Illumination
9.3
Data sheet for deflection mirror
Order no.
Function
Material
MTTR of the device
Housing
Dimensions
Weight
Fixing
2039600
Deflection mirror
Glass
< 20 min
Aluminium
See
7 kg (15.4 lb)
2 sided, 2 x guide pin each ∅ 6 mm (0.24 in) and 2 x M8 threaded hole, for use in 180 ° brackets
0 to +40 °C (+32 to +104 °F)/–20 to +70 °C (–4 to +158 °F) Ambient operating temperature/Storage temperature
Max. rel. humidity
Colour
95 %, no condensation
SICK Blue (RAL 5012)
Tab. 9-3: Technical specifications for deflection mirror
8011325/0000/2006-10-24 © SICK AG · Division Auto Ident · Germany · All rights reserved 105
Chapter 9
Reading area height
(mm)
Technical data
9.4
Specification diagram
9.4.1
Reading conditions for the diagram
Test code
Code quality
Print contrast
Ambient light
Code 128
A or B, in accordance with ANSI
> 90 %
< 2,000 lx
Minimum resolution
Tilt
Pitch
Skew
2 pixels/module
360 °
–15 ° to +15°
–15 ° to +15°
Tab. 9-4: Reading conditions for the specification diagram
Operating Instructions
ICR890 High-end CCD Camera System
9.4.2
Reading areas of the ICR890 System
Min. module width
7.9 mil
9.8 mil
11.8 mil
Reading distance (mm)
55.2
63.0
70.9
78.8
86.7
94.6
102.4
110.3
118.2
inch
3.9
7.8
11.8
15.8
19.7
23.6
47.3
1,400
1,600
1,800
2,000
2,200
2,400
2,600
2,800
3,000 mm
100
200
300
400
500
600
1,200
Abb. 9-1: Reading areas of the ICR890 System (standard)
106
© SICK AG · Division Auto Ident · Germany · All rights reserved 8011325/0000/2006-10-24
Operating Instructions
ICR890
Technical data
9.4.3
Max. resolution across the direction of transport
CCD line
Chapter 9 dpi = dots per inch
Reading distance (mm)
Abb. 9-2: Pixel resolution across the direction of transport (standard device, 135 mm (5.32 in) lens)
9.4.4
Max. resolution in the direction of transport
CCD line lpi = line per inch
Conveyor speed (m/s)
Abb. 9-3: Line resolution in the direction of transport (standard device, 8,192 pixels CCD sensor)
8011325/0000/2006-10-24 © SICK AG · Division Auto Ident · Germany · All rights reserved 107
Chapter 9
Technical data
Operating Instructions
9.5
System dimensional drawing ICR890
ICR890 High-end CCD Camera System mm
9
40
50
95
110
148
154
348
6.1
13.7
1,190 46.9
1,224 48.2
1,400 55.2
3,000 118.2
inch
0.35
1.58
1.97
3.7
4.3
5.8
All dimensions in mm
Abb. 9-4: Dimensions of the ICR890 System
108
© SICK AG · Division Auto Ident · Germany · All rights reserved 8011325/0000/2006-10-24
Operating Instructions
ICR890
Technical data
(L x W x H: 1,224 x 255 x 212)
(L x W x H: 496 x 208 x 214)
(L x W x H: 1,224 x 348 x 231)
214
231
255
348 mm
180
208
212
496
1,224 inch
7.1
8.2
8.35
8.4
9.1
10.1
13.7
19.5
48.2
Chapter 9
Free space required for connecting
(L x W x H: 496 x 250 x 210)
All dimensions in mm
Abb. 9-5: Total dimensions of the ICR890 System and the free space required for connecting
8011325/0000/2006-10-24 © SICK AG · Division Auto Ident · Germany · All rights reserved
7.5
8.3
8.7
9.9
11.2
19.5
39.4
55.2
82.7
118.2
inch
1.4
2.4
3.55
4.0
4.2
5.7
190
210
222
250
283
496
1,000
1,400
2,100
3,000 mm
35
60
90
102
107
144
109
Chapter 9
Technical data
Operating Instructions
9.6
Deflection mirror dimensional drawing
ICR890 High-end CCD Camera System mm
4
19
69.8
inch
0.16
0.75
2.8
101.6
170
4.0
6.7
178 7.0
1125.6
44.3
All dimensions in mm
Abb. 9-6: Dimensions of the deflection mirror
110
© SICK AG · Division Auto Ident · Germany · All rights reserved 8011325/0000/2006-10-24
Operating Instructions
ICR890
10
Appendix
Appendix
Chapter 10
10.1
Appendix overview
The appendix contains the following additional information:
• Configuring the ICR890 System with command strings
• Help table for calculating code length of a bar code
• Ordering information
• Supplementary documentation (overview)
• Glossary
• Image of EC Declaration of Conformity
• Decodeable 1-D codes/2-D codes
10.2
Configuring the ICR890 System with command strings
As an alternative to the SOPAS-ET Configuration Software, the ICR890 System can also be configured and operated with command strings via all the data interfaces. Each command string can be displayed via the SOPAS-ET Configuration Software.
¾ To request a command string in the SOPAS-ET Configuration Software, use the right mouse button to click on a parameter.
Note Both the command strings and the SOPAS-ET Configuration Software are based on command language which directly accesses the command interpreter of the ICR890
System. This command language must be used with care as the ICR890 System executes sent commands immediately. Parameter values altered via commands are at first only active in the current parameter set in the working memory (RAM) of the ICR890 System. To save in the permanent memory, the altered parameter set must be copied into the EEPROM using a special command, this ensures that the alterations are not lost when the power supply is switched off.
8011325/0000/2006-10-24 © SICK AG · Division Auto Ident · Germany · All rights reserved 111
Chapter 10
Appendix
Operating Instructions
ICR890 High-end CCD Camera System
10.3
Calculating code length of a bar code
The code length of a bar code corresponds to the number of characters used in the print image, including the check digit (if available).
To scan (decode) a code, the code length must be input using the SOPAS-ET Configuration
Software. Depending on the bar code type, the code length can, according to the relevant formula in
Tab. 10-1 , be calculated by counting the bars and spaces.
Calculating the length of a bar code:
1. Determine the bar code type and count the bars or wide elements (bars and spaces), incl. start and stop characters according to the information in
2. Calculate the bar code length according to the relevant formula.
3. Enter the results via the SOPAS-ET Configuration Software, as shown in column 4 of the table.
Bar code type
Code 39
2/5 Interleaved
EAN
UPC
Count
Number of bars
Number of wide elements
(bars and spaces) n/a n/a
Calculating the bar code length 1)2) Input in the SOPAS-ET
Configuration Software
Number – 10
I
Code
= —————————
5
Calculated code length
Calculated code length
I
Number – 1
Code
= —————————
2
13 characters (normal version)
8 characters (short version)
12 characters (UPC A, normal version)
6 characters (UPC E, short version)
Activate 13-digit
Activate 8-digit
Activate version A
Activate version E
Codabar
Code 128
(Character set A)
EAN 128
Number of bars
Number of bars
Number of bars
I
Number – 8
Code
= —————————
4
Number – 10
I
Code
= —————————
3
I
Number – 10
Code
= —————————
3
Number
Calculated code length
Calculated code length
Calculated code length
Pharmacode Number of bars Number = code length
1) Check digit optional for code 39, 2/5 Interleaved, Codabar.
Check digit is always integrated into the bar code print for EAN, UPC, code 128, code 93, EAN 128 according to the specification
(automatically eliminated when the ICR890 System reading results are generated)
2) Apart from a few exceptions, every printed character represents an ASCII character which has to be decoded.
Extended for code 39. The number of characters in the ICR890 System data string may be greater than the number of characters in the print image for code 93, code
128 and EAN 128, since they are made up of several character sets.
Tab. 10-1: Help table for calculating code length of a bar code
112
© SICK AG · Division Auto Ident · Germany · All rights reserved 8011325/0000/2006-10-24
Operating Instructions
ICR890
Appendix
10.4
Ordering information
10.4.1
ICR890 High-end CCD Camera System
Order no.
Complete ICR890 System, consisting of:
On request 1 x ICI890 Illumination and ICD890 Camera
1 x power supply cable for the illumination (no. 2039397)
1 x control line for the illumination (no. 6030216)
1 x deflection mirror (no. 2039600)
Display
4 x 180° bracket (no. 2034457 for one bracket)
Chapter 10
1 x WL18-3 Reading Pulse Sensor (photoelectric reflex switch) with connection cable and installation kit (no. 2034693)
1 x ICD890 Camera power supply cable (no. 2039398)
1 x “ICR890 Manuals & Software“ CD-ROM (no. 2039442)
Tab. 10-2: Ordering information: ICR890 High-end CCD Camera System
Note For an exact type designation of the ICR890 System, see the type plate on the device.
8011325/0000/2006-10-24 © SICK AG · Division Auto Ident · Germany · All rights reserved 113
Chapter 10
Order no.
1040386
Description
MSC800-2300
Appendix
Operating Instructions
ICR890 High-end CCD Camera System
10.4.2
Accessories: Controller and object distance detector
Display
On request MLG Modular Light Grid
On request VMS410/VMS510 Volume Measurement System
On request VMS410/VMS510 Volume Measurement System
1 x
2 x
Tab. 10-3: In stock accessories: Controller and object distance detector
114
© SICK AG · Division Auto Ident · Germany · All rights reserved 8011325/0000/2006-10-24
Operating Instructions
ICR890
Appendix
Chapter 10
10.4.3
Accessories: Cables and connectors
Order no.
Description
6028420 Connection cable for Host/AUX (RS 232, RS 422/485),
∅ 6.3 mm (0.25 in), screened, with 8-pole M12 socket and open end (wire end ferrules), IP 65, TPU/PUR bundle jacket
6021164 CAN data cable, screened, twisted pair, with 5-pole M12 socket and 5-pole M12 connector, IP 65, PVC-free
6021165 CAN data cable, screened, twisted pair, with 5-pole M12 socket and 5-pole M12 connector, IP 65, PVC-free
6021168 CAN data cable, screened, twisted pair, with 5-pole M12 socket and 5-pole M12 connector, IP 65, PVC-free
6021166 CAN data cable, ∅ 6.8 mm (0.27 in), screened, twisted pair, with
5-pole M12 socket and open end (wire end ferrules), IP 65, PVCfree
6021175 CAN data cable, ∅ 6.8 mm (0.27 in), screened, twisted pair, with
5-pole M12 socket and open end (wire end ferrules), IP 65, PVCfree
6021167 CAN terminal resistance, screened, with 5-pole M12 connector,
IP 65
6029776 Patch cable for GBit Ethernet connection, screened, twisted pair, with RJ-45 connector (IP 65) and RJ-45 connector (IP 20), CAT6,
PVC-free
6029775 Crossover cable for GBit Ethernet connection, screened, twisted pair, with RJ-45 connector (IP 65) and RJ-45 connector (IP 20),
CAT6, PVC-free
6030928 Patch cable for host connection, screened, twisted pair, with RJ-
45 connector (IP 65) and RJ-45 connector (IP 20), CAT5
6029630 Patch cable for host connection, screened, twisted pair, with RJ-
45 connector (IP 65) and RJ-45 connector (IP 20), CAT5
Crossover cable for host connection, screened, twisted pair, with
RJ-45 connector (IP 65) and M12 connector (IP 20), CAT5
6024861 Connection cable for switching inputs IN 1/IN 2, ∅ 5.7 mm
(0.22 in), screened, with 5-pole M12 socket and open end, IP
65, PUR bundle jacket
Wires
8 x 0.34 mm 2
(22 AWG)
–
5 x 0.25 mm
(24 AWG)
2
Length
10 m
(32.8 ft)
1 m
(3.28 ft)
3 m
(9.84 ft)
5 m
(16.4 ft)
5 m
(16.4 ft)
10 m
(32.8 ft)
–
10 m
(32.8 ft)
10 m
(32.8 ft)
Connection
ICD890 Camera to Host or PC (open end)
ICD890 Camera to CAN bus
ICD890 Camera to CAN bus
ICD890 Camera to CAN bus
ICD890 Camera to
MSC800 (open end)
ICD890 Camera to
MSC800 (open end)
ICD890 Camera to CAN bus
ICD890 Camera to GBit
Ethernet
ICD890 Camera to GBit
Ethernet
10 m
(32.8 ft)
3 m
(9.84 ft)
10 m
(32.8 ft)
5 m
(16.4 ft)
10 m
(32.8 ft)
ICD890 Camera to
Ethernet
ICD890 Camera to
Ethernet
ICD890 Camera to
Ethernet
ICD890 Camera to reading pulse sensor/ incremental encoder
(open end)
ICD890 Camera to PLC
(open end)
6027559 Connection cable for switching outputs OUT, ∅ 5.2 mm
(0.20 in), screened, with 4-pole M12 socket and open end, IP
65, PUR bundle jacket
6030216 ICI890 Illumination control line, screened, twisted pair, with 8pole M12 socket and 8-pole M12 connector, IP 65, PUR bundle jacket (halogen free)
2039397 Power supply cable for ICI890 Illumination, with 8-pole Harting
HanQ8 connector and 8-pole Harting HanQ8 socket, IP 65
2039398 Power supply cable for ICD890 Camera, with 8-pole Harting
HanQ8 socket and open end (wire end ferrules), IP 65
2032922 Power supply cable for ICI890 Illumination, with 8-pole Harting
HanQ8 connector and 8-pole Harting HanQ8 socket, IP 65, PVC-free
2032926 Power supply cable for ICD890 Camera, with 8-pole Harting
HanQ8 socket and open end (wire end ferrules), IP 65, PVC-free
Tab. 10-4: In stock accessories: Cables and connectors
4 x 0.34 mm 2
(22 AWG)
7 x 4 mm 2
(11 AWG)
7 x 4 mm 2
(11 AWG)
7 x 4 mm 2
(11 AWG)
7 x 4 mm 2
(11 AWG)
0.6 m
(23.6 in)
ICD890 Camera to
ICI800
0.75 m
(29.6 in)
10 m
(32.8 ft)
0.75 m
(29.6 in)
10 m
(32.8 ft)
ICD890 Camera to
ICI800
ICD890 Camera to power supply (open end)
ICD890 Camera to
ICI800
ICD890 Camera to power supply (open end)
8011325/0000/2006-10-24 © SICK AG · Division Auto Ident · Germany · All rights reserved 115
Chapter 10
Appendix
Operating Instructions
ICR890 High-end CCD Camera System
10.4.4
Accessories: Incremental encoder
Order no.
2039455
2039457
2039456
Description
Incremental encoder with friction wheel, resolution 10 mm (394 mil)/pulse, max. 100 kHz, operating voltage
10 to 30 V DC, operating temperature 0 to +60 °C (+32 to +140 °F). With fixing bracket and fixing material, 10 m
(32.8 ft) connection cable with 5-pole M12 socket and open end. For operation with the ICR890 System and an MLG
Light Grid.
Incremental encoder with friction wheel, resolution 0.2 mm (7.9 mil)/pulse, max. 100 kHz, operating voltage
10 to 30 V DC, operating temperature 0 to +60 °C (+32 to +140 °F). With fixing bracket and fixing material, 10 m
(32.8 ft) connection cable with 5-pole M12 socket and open end. For operation with the ICR890 System and a
VMS4xx/5xx.
Incremental encoder with friction wheel, resolution 1 mm (39.4 mil)/pulse, max. 100 kHz, operating voltage
10 to 30 V DC, operating temperature 0 to +60 °C (+32 to +140 °F). With fixing bracket and fixing material, 10 m
(32.8 ft) connection cable with 5-pole M12 socket and open end. Application-dependent usage
(not for operation with VMS4xx/5xx).
Tab. 10-5: In stock accessories: Incremental encoder
10.4.5
Accessories: Cleaning agents for front window of the illumination
Order no.
4003353
5600006
Description
SICK lens cloth (do not use for deflection mirror)
SICK synthetic cleaner (do not use for deflection mirror)
Tab. 10-6: In stock accessories: Cleaning agents for front window of the illumination
116
© SICK AG · Division Auto Ident · Germany · All rights reserved 8011325/0000/2006-10-24
Operating Instructions
ICR890
Appendix
Chapter 10
10.5
Supplementary documentation
Order no.
Title
8011539 Operating Instructions
“Modular System Controller MSC800“
8011540 Operating Instructions
“Modular System Controller MSC800“
8009403 Operating Instructions
“Modular MLG Light Grid“
Language
German
English
German/
English
German
Contents
Description of installation, startup and configuration of the MSC800
Description of installation, startup and configuration of the MSC800
Description of installation, startup and configuration of the MLG Light Grid
Description of installation, startup and configuration of the VMS410/VMS510
8010591 1) Operating Instructions
“VMS410/VMS510 Volume Measurement
System“
8010592 1) Operating Instructions
“VMS410/VMS510 Volume Measurement
System“
8010447 2) Operating Instructions
“VMS420/VMS520 Volume Measurement
System“
8010448 2) Operating Instructions
“VMS420/VMS520 Volume Measurement
System“
English
German
English
Description of installation, startup and configuration of the VMS410/VMS510
Description of installation, startup and configuration of the VMS420/VMS520
Description of installation, startup and configuration of the VMS420/VMS520
8010817 3) Installation Instructions
“Connector caps for VMS4xx/VMS5xx
Volume Measurement System“
8009992
8009993
4)
4)
Operating Instructions
“CLV490 Bar Code Scanner“
Operating Instructions
“CLV490 Bar Code Scanner“
German/
English
German
English
Description of installation and connection of the connector caps
Description of installation, startup and configuration of the CLV490
Description of installation, startup and configuration of the CLV490
1) “VMS410/VMS510 Manuals & Software“ on CD-ROM (no. 2034044), enclosed with VMS410/VMS510
2) “VMS420/VMS520 Manuals & Software“ on CD-ROM (no. 2038921), enclosed with VMS420/VMS520
3) see 1) and 2)
4) “Bar Code Scanners Manuals & Software“ on CD-ROM (no. 2029112), enclosed with CLV490
Tab. 10-7: Supplementary documentation for the ICR890 System
8011325/0000/2006-10-24 © SICK AG · Division Auto Ident · Germany · All rights reserved 117
Chapter 10
118
Appendix
Operating Instructions
ICR890 High-end CCD Camera System
10.6
Glossary
Also see the SOPAS-ET Configuration Software online help for further terms.
1-D code (bar code, strip code)
Field of dark strips (bars) and light spaces (elements) arranged in parallel, which, by working to a certain rule (specification), can be represented on the medium (subsurface) by various print processes. A user-readable (alpha)numeric character is produced from each machinereadable, corresponding number and combination of strips and spaces. Since the entire coded information, framed by start and stop characters, is available as a whole in one dimension and is also mostly analyzed by line, these bar codes are referred to as linear codes. The various code types differ in their codeable character inventory, design (number of elements per character, number of characters, start/stop characters, check characters), their information density and in their print tolerances. The length of the code strips and spaces has no bearing on the information content. However, longer code strips and spaces can be more easily analyzed by the reading device.
2-D codes
In two dimensional codes the information is arranged more densely in a matrix with the help of dark and light cells (quadrates). The vertical and horizontal arrangement of the cells in relation to the reference points in the centre and on the edges, determines the data content which is defined by the specification. In the case of error correction during reading, the code is tagged with a redundancy by way of a mathematical process (e. g. for Data Matrix ECC200 via error correction code words). The unidirectional reading of 2-D codes is carried out by way of image processing.
Aperture angle α
Aperture within the boundaries of which the ICR890 System is able to analyze codes
(through the lenses). A V-shaped area appears radially in front of the reading window, across the direction of transport (reading from above), in which the codes to be read must be positioned.
Aspect ratio
For bar codes with the code height (strip length) to code length (number of characters) ratio.
Bar codes with very low ratios can be read using the SMART decoder.
Aux interface
Auxiliary data interface (RS 232) of the ICR890 System with fixed data output format.
Access to the ICR890 System for operation and configuration is always possible via this interface, using the SOPAS-ET Configuration Software. Among other things, the interface controls the output of Ö system and error messages and can be allocated various functions. Aux interface communication can also be executed via the Ethernet interface
(port 2111).
CAN interface
Controls construction of a rapid SICK-specific CAN SENSOR network with various functions
(e. g. multiplexer, master/slave) or integration into existing CAN networks after the CAN open protocol. Access to the ICR890 System for operation and configuration is possible via the CAN interface (network) using the SOPAS-ET Configuration Software in remote mode.
© SICK AG · Division Auto Ident · Germany · All rights reserved 8011325/0000/2006-10-24
Operating Instructions
ICR890
Appendix
Chapter 10
Capture area
Zone which the ICR890 System sets up around a moving code using the increment manager and the code position comparison. Allows, among other functions, the separation of codes with identical content, where the code type is the same.
Code geometry
Code length and height dimensions.
Code position (CP value)
Position of the first dark strip of a recognized bar code along the Ö red illumination line.
Recorded by the ICR890 System in the mapped memory and used, e.g., for the separation of bar codes with identical data contents. For the Ö decoding process, the active analysis area within the illumination line can be restricted application-specifically by presetting the minimum and maximum CP values.
Command strings, commands
An alternative to the SOPAS-ET Configuration Software. User interface to the ICR890
System. A simple yet clearly structured command language for online modification of the parameter set in the ICR890 System. Directly accesses the command interpreter of the
ICR890 System. Use of the host requires a corresponding programming task.
The SOPAS-ET Configuration Software is based on the command strings.
Configuration file
SOPAS-ET Configuration Software file in which a complete Ö parameter set of the ICR890
System is stored for archiving. Can be printed out as a table.
Data forwarding
Possibility to transparently forward data sent from the host via the ICR890 System to a terminal using identifying information. The direction can also be reversed. The function also permits data received at one of the serial interfaces to be immediately sent, unaltered, via the same interface (echo).
Application: Forwarding reading results or reading pulse commands in pass through mode, e.g. for master/slave combination.
Data output string
Structured data telegram of the Ö reading result, generated on the Ö Host/CAN or Ethernet interface. The design is flexible and can be widely adapted to the subsequent data processing requirements. However, the data output format of the Ö Aux interface cannot be altered.
Decoder, decoding
From the code type-dependent analysis routine to reconstruction of the codes read in electronic form, in order to decipher the data content.
8011325/0000/2006-10-24 © SICK AG · Division Auto Ident · Germany · All rights reserved 119
Chapter 10
Appendix
Operating Instructions
ICR890 High-end CCD Camera System
Download
Transfer process of the Ö parameter set, modified in Ö SOPAS-ET, from the PC to the
ICR890 System. The SOPAS-ET Configuration Software always transfers the just modified parameter values in the background (“online“ communication mode) to the working memory (RAM) of the ICR890 System. Either the just processed parameters (D OWNLOAD
CHANGED PARAMETER TO DEVICE ) or all parameters on the indicated register tab (D OWNLOAD ALL
PARAMETERS TO DEVICE ) can be transferred using the right mouse button context menu. The previous parameter set in the ICR890 System is permanently written onto the EEPROM via the “permanent“ memory option.
Ethernet interface (Host)
Data interface with transfer rate (10/100 MBps).
The Ethernet interface can be used as an alternative to the Aux interface (port 2111) for configuration via TCP/IP using the SOPAS-ET Configuration Software or as an alternative to the host interface for generation of the reading result.
Error messages
Optical Ö messages in coded form (4-digit alphanumerical characters) with which the
ICR890 System detects a diagnostic error during the reading operation. The output is executed via the Aux interface only. The error messages can be displayed by the user in the
SOPAS-ET Configuration Software.
Focus position
Distance of the lens focal point in front of the reading window. The distance determines the
DOF (depth of field) via the ICR890 System lenses, in which the code can be analyzed. The depth of field depends on the resolution.
Function interfaces
For the switching inputs and outputs of the ICR890 System.
GBit Ethernet interface
Allows rapid image transfer.
Good Read
The ICR890 System successfully recognized the code or the requested number of codes specified by the configured analysis conditions during the last Ö reading pulse.
Header
Data block in reading result of the Ö Host/CAN or Ethernet interface. Is the header in the
Ö data output string for the subsequent code data content. Consists of reading diagnosis data and/or constants (control characters, letters, digits). In the default setting of the
ICR890 System the “header“ block is empty.
Help input
Special function of the Ö Aux interface. Allows the additional manual input of code data for completion of the reading results sent to the host.
120
© SICK AG · Division Auto Ident · Germany · All rights reserved 8011325/0000/2006-10-24
Operating Instructions
ICR890
Appendix
Chapter 10
Host interface
Main data interface of the ICR890 System with configurable data output format. Allows, among other functions, the output of the Ö reading result in telegram form to the host/PLC.
Works as a gateway in conjunction with the SICK-specific CAN-SENSOR network. Available with either RS 232 or RS 422/485 version. Provides various transfer protocols. Access to the ICR890 System for operation and configuration is also possible via the host interface using the SOPAS-ET Configuration Software. Host interface communication can also be executed via the Ethernet interface or the CAN interface.
Master/Slave configuration
Special arrangement and technical circuit connection of maximum 8 ICR890 Systems to one reading station (e. g. multi-side reading) using the CAN interface. Via the master the combination acts on the host as just one device.
Multi-reading
Selectable number of readings which must each deliver internal results from one and the same bar code before the ICR890 System generates the reading result.
No read
The ICR890 System did not recognize any or the requested number of codes specified by the configured analysis conditions during the last Ö reading pulse.
No read format
Special configurable data block as a replacement for each expected and unrecognised code in the data output string of the Host/CAN or Ethernet interface in case of a Ö no read.
Consists of the reading data with/without defined error string or is completely eliminated.
In its default setting, the ICR890 System generates the reading data as no read format with the "NOREAD" error string.
Object distance
Gauge for focusing the camera. Determined, e. g., by means of an MLG Light Grid or
VMS4xx/5xx Volume Measurement System on the conveyor system during reading from above.
Object height
See object distance.
Parameter set
Data set which is used to initialize and activate the implemented functions of the ICR890
System. Transferred using the Ö upload or Ö download from the ICR890 System to the
SOPAS-ET Configuration Software or vice versa.
Reading area (DOF)
Depth of field on both sides of the lens focal point at the reading level. Size of the area depends on the resolution and the reading distance.
Reading diagnosis data
Data which the ICR890 System derives directly from the reading process. The data allows, among other things, an assessment of the reading quality.
8011325/0000/2006-10-24 © SICK AG · Division Auto Ident · Germany · All rights reserved 121
Chapter 10
122
Appendix
Operating Instructions
ICR890 High-end CCD Camera System
Reading gate, reading interval
Time window in which the ICR890 System switches on the illumination and attempts to recognize valid codes from the read information. The reading gate can be shorter than the external reading pulse, depending on the output mode of the selected reading result.
Reading pulse
Triggering of the internal Ö reading gate via an ICR890 System external pulse is carried out by means of a photoelectric reflex switch or a command from the host via the serial interface.
Reading result
Electronic representation of the data contents of the code which has been read together with Ö reading diagnosis data in a Ö data output string after completion of the reading pulse.
Result status output
Functions of both switching outputs “OUT 1“ and “OUT 2“ during reading operation.
Indicates each status of the reading result without displaying its contents (e.g. “good read“).
One status per output can be provided with the SOPAS-ET Configuration Software. The
“result“ LED is coupled with the “Result 2“ output.
Saving to the ICR890 System
The application-specific Ö parameter set can be stored on the ICR890 System either temporarily of permanently. In the case of temporary storage, the parameter set is only contained in the working memory (RAM) and is lost as soon as the power supply is switched off. In the case of permanent storage, the parameter set is also transferred to the EEPROM of the ICR890 System and saved as a current data set after switching off. The default setting is deposited in a Read Only Memory (ROM) irrespective of this.
Sending point
Output time of the reading result in relation to the start of the Ö reading pulse and the internal Ö reading gate.
SMART decoder
Specially developed Ö decoder for reading bar codes with extremely small code heights and or bad or soiled print images.
SOPAS-ET
PC configuration software, to run on Windows 98 TM , ME TM , NT 4.0
TM , 2000 TM and Windows
XP TM . Allows offline configuration (adaptation to local reading conditions) and online operation of the ICR890 System in dialogue. The Ö parameter set to be processed using the ICR890 System can be exchanged by means of Ö upload and Ö download.
SOPAS-ET Help
Online help which supports use of the SOPAS-ET Configuration Software. The parameter functions of the ICR890 System and the respective value range are explained in the online help. Runs using an HTML browser, such as “Internet Explorer TM “, and can be called up in the SOPAS-ET Configuration Software.
© SICK AG · Division Auto Ident · Germany · All rights reserved 8011325/0000/2006-10-24
Operating Instructions
ICR890
Appendix
Chapter 10
Start/Stop operation
In this type of reading pulse, only one object per reading pulse is located in the reading area.
External sensors, command strings or the free running of the ICR890 System control the beginning and end of the reading pulse for the ICR890 System (stand-alone device). In the case of combined use with other ICR890 Systems in a master/slave combination with the
MSC800 (e. g. unidirectional double-side reading), the ICR890 System receives its pulse signals via the MSC800. The length of the reading area is determined in this case by the distance of both external sensors for the start (beginning of the reading area) and stop (end of the reading area) of the reading pulse. The minimum reading distance between two objects must always be greater than the length of the reading area. Networking the ICR890
System to the MCS800 is carried out via the CAN interface.
Terminator
Data block in the reading result of the Ö Host/CAN or Ethernet interface. Serves as completion of the preceding code data contents. Consists of reading diagnosis data and/or constants (control characters, letters, digits). The “terminator“ block is empty in the default setting of the ICR890 System.
Tracking operation
In this type of continuous reading pulse, several objects are simultaneously located in a row in the reading area. For unambiguous allocation of the read codes to the objects, a minimum gap must be maintained between two objects and band increment signals have to be available. The ICR890 System can be used with other ICR890 Systems using the
MSC800 (e.g. unidirectional triple-side reading). The ICR890 System contains pulse signals and increment values via the MSC800. The length of the reading area is determined in this case by the distance of the external sensor for the beginning/end of the object at the beginning of the reading area and the object entry point (data output) in the direction of transport of the MSC800 at the end of the reading area. Networking the ICR890 System to the MCS800 is carried out via the CAN interface. The ICR890 System manages recorded objects by means of an internal object tracking list.
Upload
Transfer process of the Ö parameter set of the ICR890 System to the PC according to
Ö SOPAS-ET. The SOPAS-ET Configuration Software loads a complete copy of the current parameter set from the working memory (RAM) of the ICR890 System ( UPLOAD ALL
PARAMETERS TO DEVICE ). Parameter values must be represented in the register tabs before the current parameter set can be modified.
User interface
Windows-oriented input interfaces in the SOPAS-ET Configuration Software for operation and configuration of the ICR890 System.
8011325/0000/2006-10-24 © SICK AG · Division Auto Ident · Germany · All rights reserved 123
Chapter 10
Appendix
Operating Instructions
ICR890 High-end CCD Camera System
10.7
EC Declaration of Conformity
and
Fig. 10-2 show a scaled down version of the EC Declaration of Conformity
(page 1) for the ICD890 Camera and the ICI890 Illumination.
¾ The complete EC Declaration of Conformity can be requested from SICK AG.
Abb. 10-1: EC Declaration of Conformity for the ICD890 Camera (page 1, scaled down version)
124
© SICK AG · Division Auto Ident · Germany · All rights reserved 8011325/0000/2006-10-24
Operating Instructions
ICR890
Appendix
Chapter 10
Abb. 10-2: EC Declaration of Conformity for the ICI890 Illumination (page 1, scaled down version)
8011325/0000/2006-10-24 © SICK AG · Division Auto Ident · Germany · All rights reserved 125
Chapter 10
Notes:
Appendix
Operating Instructions
ICR890 High-end CCD Camera System
126
© SICK AG · Division Auto Ident · Germany · All rights reserved 8011325/0000/2006-10-24
Operating Instructions
ICR890
!
Appendix
10.8
Code samples (decodeable)
" § $
Code 39
EAN 13-digit
2/5 Interleaved
%
Data Matrix
ECC200
PDF417
Chapter 10
Module width
0.30 mm
(11.8 mil)
Module width
0.35 mm
(13.8 mil)
Module width
0.5 mm
(19.7 mil)
Cell size
0.5 mm
(19.7 mil)
Cell size
0.3 mm
(11.8 mil)
Abb. 10-3: Code samples of 1-D codes of various module widths (print ratio 2:1) and 2-D code of various cell sizes
8011325/0000/2006-10-24 © SICK AG · Division Auto Ident · Germany · All rights reserved 127
Australia
Phone +61 3 9497 4100
1800 33 48 02 – tollfree
E-Mail [email protected]
Belgium/Luxembourg
Phone +32 (0)2 466 55 66
E-Mail [email protected]
Brasil
Phone +55 11 5091-4900
E-Mail [email protected]
Ceská Republika
Phone +420 2 57 91 18 50
E-Mail [email protected]
China
Phone +852-2763 6966
E-Mail [email protected]
Danmark
Phone +45 45 82 64 00
E-Mail [email protected]
Deutschland
Phone +49 (0)2 11 53 01-270
E-Mail [email protected]
España
Phone +34 93 480 31 00
E-Mail [email protected]
France
Phone +33 1 64 62 35 00
E-Mail [email protected]
Great Britain
Phone +44 (0)1727 831121
E-Mail [email protected]
India
Phone +91–22–2822 7084
E-Mail [email protected]
Italia
Phone +39 02 27 43 41
E-Mail [email protected]
Japan
Phone +81 (0)3 3358 1341
E-Mail [email protected]
Nederlands
Phone +31 (0)30 229 25 44
E-Mail [email protected]
Norge
Phone +47 67 81 50 00
E-Mail [email protected]
More representatives and agencies in all major industrial nations at www.sick.com
Österreich
Phone +43 (0)22 36 62 28 8-0
E-Mail [email protected]
Polska
Phone +48 22 837 40 50
E-Mail [email protected]
Republic of Korea
Phone +82-2 786 6321/4
E-Mail [email protected]
Republika Slowenija
Phone +386 (0)1-47 69 990
E-Mail [email protected]
Russia
Phone +7 495 775 05 34
E-Mail [email protected]
Schweiz
Phone +41 41 619 29 39
E-Mail [email protected]
Singapore
Phone +65 6744 3732
E-Mail [email protected]
Suomi
Phone +358-9-25 15 800
E-Mail [email protected]
Sverige
Phone +46 8 680 64 50
E-Mail [email protected]
Taiwan
Phone +886 2 2365-6292
E-Mail [email protected]
Türkiye
Phone +90 216 587 74 00
E-Mail [email protected]
USA/Canada/México
Phone +1(952) 941-6780
1 800-325-7425 – tollfree
E-Mail [email protected]
SICK AG | Waldkirch | Germany | www.sick.com
advertisement
Key Features
- High-end CCD camera system
- Reads 1-D and 2-D codes
- Superb image quality
- Suitable for OCR and video coding applications
- Adjustable illumination
- Focus control
- Code configuration
- Data processing
Related manuals
Frequently Answers and Questions
How do I install the ICR890 system?
What types of codes can the ICR890 system read?
What are the system requirements for the ICR890 system?
How do I configure the ICR890 system?
What are the technical specifications for the ICR890 system?
advertisement
Table of contents
- 15 Notes on this document
- 15 Purpose
- 15 Target audience
- 15 Information content
- 16 Symbols used
- 17 Safety information
- 17 Authorized users
- 17 Installation and maintenance
- 17 Electrical installation and the replacement of system components
- 17 Startup, operation and configuration
- 18 Intended use
- 19 General safety precautions and protection measures
- 19 Radio interferences
- 19 Installation work
- 19 Electrical installation work
- 19 LED radiation from the ICI890 Illumination
- 20 Quick stop and quick start
- 20 Switch off the ICR890 System
- 20 Switch on the ICR890 System
- 21 Environmental information
- 21 Energy requirements
- 21 Dispose of the device after decommissioning
- 23 Product description
- 23 Design
- 24 Device view
- 25 Included in delivery
- 26 Contents of the CD-ROM
- 26 Device versions
- 26 System requirements
- 26 General system requirements
- 27 Installation requirements
- 28 Electrical installation requirements
- 28 Operation requirements
- 29 Product features and functions (overview)
- 31 Method of operation
- 32 Reading configuration
- 33 Object trigger control
- 33 Focus control
- 33 Illumination control
- 35 Position
- 35 Increment configuration
- 36 Image requirement
- 37 Code configuration
- 37 Data processing
- 39 3.4.10 Output format
- 39 3.4.11 Network
- 39 3.4.12 Data interfaces
- 40 3.4.13 Digital outputs
- 40 3.4.14 Digital inputs
- 41 Indicators and control elements
- 41 User interface
- 42 LEDs of the ICD890 Camera
- 43 Impacts on the reading quality
- 45 Installation
- 45 Overview of installation sequence
- 45 Installation preparations
- 45 Layout the components which are to be installed
- 45 Layout accessories
- 46 Selecting the installation location
- 47 Arrangement at the conveyor system
- 49 Installing and adjusting the device
- 50 Installing the deflection mirror
- 50 Installing the ICI890 Illumination and the ICD890 Camera
- 51 Installing external components
- 51 External sensors for triggering
- 52 Installing the incremental encoder
- 52 Installing the MLG Light Grid
- 52 Installing the MSC800 Controller
- 52 Removing the device
- 53 Electrical installation
- 53 Overview of installation sequence
- 54 Electrical installation preparation
- 54 Electrical installation of the ICR890 System (without MSC800)
- 56 (single-side reading)
- 58 (multi-side reading)
- 60 Electrical connections and cables
- 60 Electrical connections of the ICD890 Camera
- 61 Electrical connections of the ICI890 Illumination
- 62 Electrical connections of the MSC800 (overview)
- 63 Assembled cables (overview)
- 64 Performing electrical installation
- 64 control line
- 64 Power supply of the ICR890 System
- 65 Data interfaces HOST/AUX
- 66 Data interface CAN 1-IN/OUT
- 68 Wiring the Ethernet interface HOST ETHERNET
- 69 Wiring the Ethernet interfaces GBIT 1 and GBIT
- 69 Wiring the switching inputs IN 1 and IN
- 71 Pin assignments and conductor colouring assignment
- 71 ICD890 Camera connections
- 75 ICI890 Illumination connections
- 75 Wire colours assignment of assembled cables with open end
- 79 Operation
- 79 Overview of the startup procedure
- 79 Configuration Software SOPAS-ET
- 79 ICR890 System/MSC800 (overview)
- 79 System requirements for the SOPAS-ET Configuration Software
- 79 Installation of the Configuration Software SOPAS-ET
- 80 Default setting for the SOPAS-ET Configuration Software
- 80 First startup
- 81 Overview of the configuration procedure
- 81 Establishing communication with the ICR890 System/MSC
- 83 Configuring the ICR890 System/MSC
- 87 Load changed parameter sets into the device
- 87 Save, display and print the current parameter set
- 88 Changing the device password for the user level "Authorized Client
- 88 Default setting
- 88 Resetting the default setting in the ICR890 System
- 88 Default setting MSC
- 89 Maintenance
- 89 Maintenance during operation
- 89 Cleaning the ICR890 System
- 89 Cleaning the front window
- 90 Cleaning the housing
- 91 Cleaning the deflection mirror
- 92 Cleaning further optical effective surfaces
- 93 Replacing a system or a component
- 93 Replacing the ICD890 Camera or ICI890 Illumination
- 94 Replacing the deflection mirror
- 95 Disposal
- 97 Troubleshooting
- 97 Overview of errors and malfunctions which could occur
- 97 Installation error
- 97 Electrical installation error
- 97 Configuration error
- 97 Malfunctions during operation
- 98 Detailed malfunction analysis
- 98 LEDs at the camera
- 98 System information
- 98 Status protocol
- 101 ST error status in the reading result of a 1-D code (bar code)
- 102 SICK support
- 103 Technical data
- 103 Data sheet for ICR890 Camera
- 105 Data sheet for ICI890 Illumination
- 105 Data sheet for deflection mirror
- 106 Specification diagram
- 106 Reading conditions for the diagram
- 106 Reading areas of the ICR890 System
- 107 Max. resolution across the direction of transport
- 107 Max. resolution in the direction of transport
- 108 System dimensional drawing ICR
- 110 Deflection mirror dimensional drawing
- 111 10 Appendix
- 111 Appendix overview
- 111 Configuring the ICR890 System with command strings
- 112 Calculating code length of a bar code
- 113 Ordering information
- 113 10.4.1 ICR890 High-end CCD Camera System
- 114 10.4.2 Accessories: Controller and object distance detector
- 115 10.4.3 Accessories: Cables and connectors
- 116 10.4.4 Accessories: Incremental encoder
- 116 10.4.5 Accessories: Cleaning agents for front window of the illumination
- 117 Supplementary documentation
- 118 Glossary
- 124 EC Declaration of Conformity
- 127 Code samples (decodeable)