advertisement
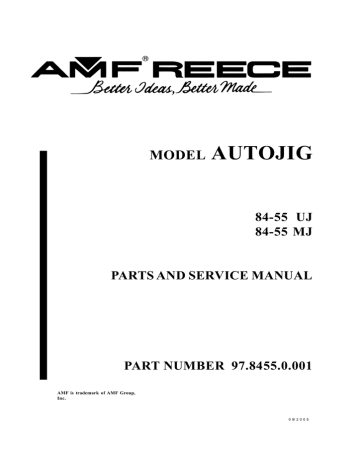
MODEL
AUTOJIG
84-55 UJ
84-55 MJ
PARTS AND SERVICE MANUAL
PART NUMBER 97.8455.0.001
AMF is trademark of AMF Group,
Inc.
0 9/ 2 0 0 5
LIMITED WARRANTY ON NEW AMF REECE EQUIPMENT
Warranty provisions:
A ninety (90) day limited service labor warranty to correct defects in installation, workmanship, or material without charge for labor. This portion of the warranty applies to machines sold as ”installed” only.
A one (1) year limited material warranty on major component parts to replace materials with defects. Any new part believed defective must be returned freight prepaid to AMF Reece, Inc. for inspection. If, upon inspection, the part or material is determined to be defective, AMF Reece, Inc. will replace it without charge to the customer for parts or material.
Service labor warranty period shall begin on the completed installation date. Material warranty shall begin on the date the equipment is shipped from AMF Reece, Inc.
Exclusions:
Excluded from both service labor warranty and material warranty are: (1) Consumable parts which would be normally considered replaceable in day-to-day operations. These include parts such as needles, knives, loopers and spreaders. (2)
Normal adjustment and routine maintenance. This is the sole responsibility of the customer. (3) Cleaning and lubrication of equipment. (4) Parts found to be altered, broken or damaged due to neglect or improper installation or application. (5)
Damage caused by the use of non-Genuine AMF Reece parts. (6) Shipping or delivery charges.
There is no service labor warranty for machines sold as ”uninstalled”.
Equipment installed without the assistance of a certified technician (either an AMF Reece Employee, a Certified Contractor, or that of an Authorized Distributor) will have the limited material warranty only. Only the defective material will be covered.
Any charges associated with the use of an AMF Reece Technician or that of a Distributor to replace the defective part will be the customer’s responsibility.
NO OTHER WARRANTY, EXPRESS OR IMPLIED, AS TO DESCRIPTION, QUALITY, MERCHANTABILITY, and FITNESS
FOR A PARTICULAR PURPOSE, OR ANY OTHER MATTER IS GIVEN BY SELLER OR SELLER’S AGENT IN CONNECTION
HEREWITH. UNDER NO CIRCUMSTANCES SHALL SELLER OR SELLER’S AGENT BE LIABLE FOR LOSS OF PROFITS
OR ANY OTHER DIRECT OR INDIRECT COSTS, EXPENSES, LOSSES OR DAMAGES ARISING OUT OF DEFECTS IN OR
FAILURE OF THE EQUIPMENT OR ANY PART THEREOF.
WHAT TO DO IF THERE IS A QUESTION REGARDING WARRANTY
If a machine is purchased through an authorized AMF Reece, Inc. distributor, warranty questions should be first directed to that distributor. However, the satisfaction and goodwill of our customers are of primary concern to AMF Reece, Inc. In the event that a warranty matter is not handled to your satisfaction, please contact the appropriate AMF Reece office:
Europe/Africa/Americas
Prostejov, Czech Republic
Phone: (+420) 582-309-286
Fax: (+420) 582-360-608 e-mail: [email protected]
Warranty Registration Card
(Please Fax or Mail immediately after installation)
Note: All Warranty Claims Void, unless Registration Card on file at AMF Reece HQ
Machine model number:
(S101, S100, S104, S105, S211, Decostitch, S4000 BH, EBS Mark II, etc)
Manufacturer‘s serial or production number:
Installation Site Information:
Customer‘s Name:
Customer‘s Mailing Address:
Customer‘s Telephone Number:
Supervising Mechanic‘s or Technician‘s Name:
Signature of Supervising Technician:
AMF Reece Technician‘s Name:
AMF Reece Technician‘s Signature:
Type of garment produced at this location?
Average Daily Production Expected from this machine?
(number of buttonholes, jackets sewn, pants produced, buttons sewn, etc)
Any special requirements required at this location?
What other AMF Reece Machines are at this location?
How can we serve you better?
Tovární 837, 796 25 Prostìjov, Czech Republic
Fax: +420 582 360 606, e-mail: [email protected], website: www.amfreece.com
84-55 UJ / MJ
TABLE OF CONTENTS
Introduction .......................................................................................................................................... 1-2
Safety instructions ............................................................................................................................ 1-3
Introduction .......................................................................................................................................... 1-4
Introduction .......................................................................................................................................... 1-5
Important notes ................................................................................................................................ 1-5
Using Jigs ............................................................................................................................................. 1-6
2.0 Loading of material into the jig (e.g. Collar) ............................................................................. 1-6
2.1 Program selection ..................................................................................................................... 1-6
2.2 Loading jig to the machine ........................................................................................................ 1-6
2.2.1 Manual start ............................................................................................................................. 1-6
2.2.2 Auto start ................................................................................................................................. 1-7
2.3 Jig set up ................................................................................................................................. 1-8
2.3.0 Auto start metal tab .................................................................................................................. 1-8
2.3.2 Photocell tapes ......................................................................................................................... 1-8
2.3.2 Fly fronts ................................................................................................................................. 1-8
Operating Instructions ........................................................................................................................... 1-9
3.1 To start up the machine ............................................................................................................... 1-9
3.2 Instalation of needle .................................................................................................................... 1-9
3.3 Threading of upper thread ........................................................................................................... 1-9
3.4 Bobbin winding ........................................................................................................................ 1-10
3.5 Bobbin setting into bobbin case ................................................................................................ 1-10
3.6 Adjusting the needle thread tension........................................................................................... 1-11
3.7 Adjust the bobbin thread tension ............................................................................................... 1-11
3.8 Adjusting the thread take-up stroke ........................................................................................... 1-11
3.9 Thread take-up spring ............................................................................................................... 1-12
Clearing .................................................................................................................................... 1-12
3.10 Regulating foot pressure on jig ............................................................................................... 1-13
3.11 Emergency stop ...................................................................................................................... 1-13
3.12 Needle and thread ................................................................................................................... 1-14
Mechanical Setting Procedures ........................................................................................................... 1-15
4.0 Introduction ......................................................................................................................... 1-15
4.1 Jig drive settings ................................................................................................................... 1-15
4.1.1 Common settings .................................................................................................................. 1-15
4.1.1a Drive wheel cylinder ............................................................................................................ 1-15
4.1.1b Drive wheel surface ............................................................................................................. 1-15
4.1.1c Drive arm eccentric .............................................................................................................. 1-15
4.1.1d Drive wheel assembly .......................................................................................................... 1-15
4.1.1e Drive arm spring compression .............................................................................................. 1-17
Revised 09 /2005
E-mail: [email protected]; [email protected] ; website: www.amfreece.com
Phones: +420 582 309 146 (Service), +420 582 309 286 (Spare Parts) ; Fax: +420 582 360 606
84-55 UJ / MJ
TABLE OF CONTENTS
4.1.2. Index feed settings ............................................................................................................... 1-17
4.1.2a Feed timing .......................................................................................................................... 1-17
4.1.2b Drive linkage ....................................................................................................................... 1-17
4.1.3 Continuous feed settings ....................................................................................................... 1-17
4.1.3a D.C. Motor ......................................................................................................................... 1-17
Mechanical Setting Procedures ........................................................................................................... 1-18
4.1.3.b Clutch ................................................................................................................................. 1-18
4.2 Stitch size adjustment ........................................................................................................... 1-18
4.2.0 Index feed ............................................................................................................................ 1-18
4.2.1 Continuous feed .................................................................................................................... 1-18
4.3.0 Photocell setting ................................................................................................................... 1-19
4.4 Snubber and jig align ............................................................................................................. 1-19
4.4.0 Snubber setting ..................................................................................................................... 1-19
4.4.1 Jig alignment cylinder setting ................................................................................................ 1-19
4.5 Jig eject / reverse correction .................................................................................................. 1-20
4.6 Jig flap adjustment ................................................................................................................. 1-20
4.7 Auto start proximity sensor .................................................................................................... 1-21
4.7.0 Jig proximity sensor adjustment ............................................................................................. 1-21
4.7.1 Jig metal insert ...................................................................................................................... 1-21
4.8 Side knife .............................................................................................................................. 1-21
4.8.0 Indication .............................................................................................................................. 1-22
4.8.1 Sensitivity adjustment ............................................................................................................ 1-22
4.8.2 Photocell head alignment ....................................................................................................... 1-23
4.9 Photo electric switch ................................................................................................................. 1-23
Controls & Program Description ........................................................................................................ 1-24
5.0 Control display ......................................................................................................................... 1-24
5.1 Machine functions .................................................................................................................... 1-26
5.1.0 Error messages ...................................................................................................................... 1-27
5.2 Modes of operation ................................................................................................................... 1-28
5.2.1 Input testing mode: ................................................................................................................ 1-31
5.2.2 Output testing mode ............................................................................................................... 1-34
5.2.3 Needle test ............................................................................................................................. 1-41
5.3 Programming mode: ................................................................................................................. 1-42
5.3.1 Back tack parameters at cycle start: ........................................................................................ 1-44
5.3.2 Dense stitch parameters at cycle start: .................................................................................... 1-47
5.3.3 Program functions .................................................................................................................. 1-49
5.3.3a Function types: ..................................................................................................................... 1-53
5.2 Batch programming .................................................................................................................. 1-57
Diagram display ............................................................................................................................. 1-58
Parameters value chart & default programs ..................................................................................... 1-62
Revised 09/2005
E-mail: [email protected]; [email protected] ; website: www.amfreece.com
Phones: +420 582 309 146 (Service), +420 582 309 286 (Spare Parts) ; Fax: +420 582 360 606
84-55 UJ / MJ
TABLE OF CONTENTS
Pneumatics ......................................................................................................................................... 1-66
6.0 Pneumatics ............................................................................................................................... 1-66
6.1 S1 Jig flap ................................................................................................................................ 1-66
6.2 S3 Stitch size adjusters 1 & 2 .................................................................................................... 1-66
6.3 S4 Jig drive/presser foot ........................................................................................................... 1-66
6.4 S5 Knife ................................................................................................................................... 1-66
6.5 S6 Jig eject ............................................................................................................................... 1-66
6.6 Waste disposal .......................................................................................................................... 1-66
6.7 S7 Jig alignment ...................................................................................................................... 1-67
6.8 S9 Jig drive clamp ................................................................................................................... 1-67
6.9 S10 Air blowers ....................................................................................................................... 1-67
7.0 Air flow controls ...................................................................................................................... 1-67
7.1 Air pressure regulators and water filters ................................................................................... 1-67
Pneumatic Diagram............................................................................................................................. 1-68
Head Setting Procedures ..................................................................................................................... 1-69
7.1 Adjusting the feed timing .......................................................................................................... 1-69
7.2 Needle-to-hook relationship ...................................................................................................... 1-69
7.3 Lubrication ............................................................................................................................... 1-70
7.4 Adjusting the amount of oil (Oil splashes) in the hook .............................................................. 1-70
7.5Cloth cutting knife ..................................................................................................................... 1-72
Trimming and Synchronizer ................................................................................................................ 1-73
8.1 Replacing the moving knife (DLM-5400N-7) ........................................................................... 1-73
8.2 Adjusting the initial position of the moving knife (DLM-5400n-7) ........................................... 1-73
8.3 Replacing the counter knife (DLM-5400N-7) ........................................................................... 1-74
8.4 Adjusting the pressure of the counter knife ............................................................................... 1-74
8.5 Synchronizer setting ................................................................................................................. 1-75
Electrical Diagram .............................................................................................................................. 1-76
Revised 09 /2005
E-mail: [email protected]; [email protected] ; website: www.amfreece.com
Phones: +420 582 309 146 (Service), +420 582 309 286 (Spare Parts) ; Fax: +420 582 360 606
84-55
INTRODUCTION
Quick Reference Specification Sheet
Electrical requirement : 220V, 60Hz, Single phase, 850W
Air Supply : Pressure – 80 Psi ( 5.5 Bar )
Noise Level : 75.5 DB (A)
Sewing Head : Juki DLM 5400-7-00 Lockstitch with under
bed trimmer
Sewing Head Motor : 0.55KW
Sewing Head speed : 3600 RPM maximum
Stitch size : Up to 4mm
Lubrication system : Sensate Head – Sump Reservoir, Wick &
Pump distribution, System Jig track – Silicon
spray
Needle Type : 134R
Recommended Thread : Core spun polyester/cotton
Table Height : 930mm ( 36.5”)
Operator Position : Standing
1-2
Revised 09/2005
E-mail: [email protected]; [email protected] ; website: www.amfreece.com
Phones: +420 582 309 146 (Service), +420 582 309 286 (Spare Parts) ; Fax: +420 582 360 606
84-55
INTRODUCTION
SAFETY INSTRUCTIONS
- The machine must only be used for the purpose it was designed for. In case of conversion into another version all valid safety instructions have to be considered.
- Do not operate this machine without the safety devices it is equipped with.
- The machine must only be switched on and operated by persons who have been instructed accordingly.
- When exchanging parts and when doing maintenance work, the machine must be disconn ected either by actuating the master switch or by removing the mains plug.
- When threading the machine, Emergency stop must be engaged or the machine switched off.
- When carrying out maintenance or repair work on pneumatic devices, the machine must be disconnected from the pneumatic supply source.
- Work on electrical equipment on this machine must only be carried out by electricians or other persons who have been instructed accordingly.
- The actual ‘A’ weighted sound pressure level taken on an identical machine is 82.5DB (A).
- Take appropriate measures for protection of hearing if sound pressure of 85DB (A) is ex ceeded.
- Ensure lifting rail is used when lifting with fork lift truck.
Revised 09 /2005
E-mail: [email protected]; [email protected] ; website: www.amfreece.com
Phones: +420 582 309 146 (Service), +420 582 309 286 (Spare Parts) ; Fax: +420 582 360 606
1-3
84-55
INTRODUCTION
1-4
Revised 09/2005
E-mail: [email protected]; [email protected] ; website: www.amfreece.com
Phones: +420 582 309 146 (Service), +420 582 309 286 (Spare Parts) ; Fax: +420 582 360 606
84-55
INTRODUCTION
IMPORTANT NOTES
To avoid trouble or damage, it is absolutely necessary to observe the following instructions.
- Before you put the machine into operation for the first time, clean it thoroughly, remove all the dust which has accumulated on it.
- Oil all necessary parts ensuring drive wheel section is free from any type of lubricant.
- Check to make sure line voltage agrees with the voltage indicated on the motor rating plate.
If it does not, be sure not to plug the machine.
- Check you have the correct pneumatic line pressure.
- Always make sure the correct program is selected on the AMF Reece controller related to the type of jig being used.
Revised 09 /2005
E-mail: [email protected]; [email protected] ; website: www.amfreece.com
Phones: +420 582 309 146 (Service), +420 582 309 286 (Spare Parts) ; Fax: +420 582 360 606
1-5
84-55
USING JIGS
2.0
LOADING OF MATERIAL INTO THE JIG (E.G. COLLAR)
1. Open jig and position lower ply of cloth to the jig location marks.
2. If the jig has a filling bar (i.e. middle section) close this on the lower ply of cloth.
3. Position the upper ply of cloth to jig location marks.
4. Close the top plate of the jig.
5. Jig is now ready to insert into machine
2.1
PROGRAM SELECTION
This machine has a LCD display control with function keys. Any program editing is possible with the help of keys. Programming instructions have neen explained in detail in section 5.
2.2
LOADING JIG TO THE MACHINE
The 84-55 has two start options, Manual start or Auto start. In Manual start mode the green start button must be pressed to start the machine. In Auto start mode, the machine will begin automatically once the jig has been loaded safely.
2.2.1 MANUAL START
a) Slide the loaded jig towards the needle, lining up the start position approximately ½”
(13mm) behind the needle.
b) Push the jig over the raised flap in front of the needle plate.
c) As the jig is pushed to the right, the jig flap will drop to its normal position.
d) If the jig is located correctly, the raised “D” shape of the needle plate will locate in the track of the jig.
e) Pull jig back to closed end of track. (Double jig should be pulled back so jig contacts presser foot).
f) When the jig is loaded, press the green start button on the table top; the sew cycle will begin.
g) At the end of the cycle the jig will be ejected (or in case of a double jig, wait for the operator to reposition the jig for second half).
1-6
Revised 09/2005
E-mail: [email protected]; [email protected] ; website: www.amfreece.com
Phones: +420 582 309 146 (Service), +420 582 309 286 (Spare Parts) ; Fax: +420 582 360 606
USING JIGS
2.2.2 AUTO START
The auto start function may not be used on double jigs.
e) Pull jig back to close end of track. At this point the proximity sensor in the needle plate will detect the metal tab in the jig. See fig.2.0.
f) If the jig is loaded correctly and both the snubber switch and photocell have been activated, the machine will start automatically. See fig.2.0.
g) At the end of the cycle, the jig will be ejected.
84-55
Revised 09 /2005
E-mail: [email protected]; [email protected] ; website: www.amfreece.com
Phones: +420 582 309 146 (Service), +420 582 309 286 (Spare Parts) ; Fax: +420 582 360 606
1-7
84-55
USING JIGS
2.3
JIG SET UP
Before the jig can be used the auto start metal tab and all the photocell activating tapes must be positioned correctly.
2.3.0 AUTO START METAL TAB
The metal tab is located at the start of track. A Tufnol locating patch holds it in place. Set the metal tab to activate the proximity sensor 2mm before the raised
“D” makes contact with the end of the inner track.
This setting may have to be altered if the start of the sew seam is incorrectly posit ioned.
2.3.2 PHOTOCELL TAPES
The tapes on the surface of the jigs are used to trigger the programs in the controller. See section 5 for full instructions on program editing.
Figure 2.2 shows a simple slow sew corner jig, with dense in and out of the corners.
Each tape sends a signal to the control box to activate a particular function.
2.3.2 FLY FRONTS
The AMF Reece controller will allow the use of fly front jigs. To set up the jig for this operation, position tapes are shown in figure 2.3 and refer to section 5 for programming instructions.
1-8
Revised 09/2005
E-mail: [email protected]; [email protected] ; website: www.amfreece.com
Phones: +420 582 309 146 (Service), +420 582 309 286 (Spare Parts) ; Fax: +420 582 360 606
OPERATING INSTRUCTIONS
3.1
TO START UP THE MACHINE
a) Turn the power on switch.
b) If airfloation is required in case of bigger sewing parts like.“Large Jacket Front”, turn the blower switch on to make are air pass throught small holes on the table.
Note: The presser foot of the machine is always in the raised position when the machine is the “Stop” mode with the air and power switched on.
Carry out the following steps of procedure after the power switch has been turned OFF.
3.2
INSTALATION OF NEEDLE
Insert the so it is fully up the needle bar with its longer groove to the left and firmly fasten by using the needle clamps screw. (Figure 3.1)
Applicable needle 134R
Note: Needle size and point are depent on the type of material being used. (Refer to needle and thread section 3.12)
3.3
THREADING OF UPPER THREAD
Turn the handwheel toward you to make the thread take-up reach the highest position and run a thread from the spool pin to the needle through each part in the numbered order in figure 3.2. At the needle run the thread from left to right and leave the thread end approx. 5 cm.
84-55
Revised 09 /2005
E-mail: [email protected]; [email protected] ; website: www.amfreece.com
Phones: +420 582 309 146 (Service), +420 582 309 286 (Spare Parts) ; Fax: +420 582 360 606
1-9
84-55
OPERATING INSTRUCTIONS
3.4
BOBBIN WINDING
a) Set the bobbin with the bobbin winder spindle and wind the thread on the bobbin for a few turns by hand.
b) Push fully the bobbin winder setting lever to make the winder pulley contact with the V-belt.
c) Set winding capacity at 80% using the bobbin winding capacity regulating screw.
d) If bobbin winding is uneven, adjust the position of bobbin winder complete so that winding becomes even.
e) When winding finishes, the bobin winder setting lever flips up and the bobbin winding pulley stops.
3.5
BOBBIN SETTING INTO BOBBIN CASE
a) Install the bobbin in the bobbin case so that the thread wound direction is counterclockwise.
b) Pass the thread through thread slid and pull the thread in direction . By so doing , the thread will pass under rhe tension spring the come out from notch .
c) Check that the bobbin rotates in the direction of the arrow when thread is pulled.
1- 1 0
Revised 09/2005
E-mail: [email protected]; [email protected] ; website: www.amfreece.com
Phones: +420 582 309 146 (Service), +420 582 309 286 (Spare Parts) ; Fax: +420 582 360 606
OPERATING INSTRUCTIONS
3.6
ADJUSTING THE NEEDLE THREAD TENSION
a) As you turn thread tension No. 1 nut Ê clockwise (in direction ) the thread remaining on the needle after thread trimming will be shorter.
As you turn nut Ê counterclockwise (in will direction ), the thread length will be longer.
c) As you turn thread tension nut Ë clockwise( in direction ), the needle thread tension will be increased.
As you turn nut Ë counterclockwise (in direction ), the needle thread tension be decreased.
3.7
ADJUST THE BOBBIN THREAD TENSION
As you turn tension adjust screw Ì clockwise
(in direction ), the bobbin thread tension will be increased.
As you turn screw Ì counterclockwise (in direction ), the bobbin thread tension will be decreased.
84-55
3.8
ADJUSTING THE THREAD TAKE-UP STROKE
Carry out the following steps of procedure after the power switch has been turned OFF.
a) When sewing heavy-weight materials, move thread guide Ê to the left (in direction ) to increase the length of thread pulled out by the thread take-up.
b) When sewing length-weight materials, move thread guide Ê to the right (in direction ) to decrease the length of thread pulled out by the thread take-up.
c) Normally, thread guide Ê is positioned in a way that marker line is aligned with the center of the screw.
Revised 09 /2005
E-mail: [email protected]; [email protected] ; website: www.amfreece.com
Phones: +420 582 309 146 (Service), +420 582 309 286 (Spare Parts) ; Fax: +420 582 360 606
1- 1 1
84-55
OPERATING INSTRUCTIONS
3.9
THREAD TAKE-UP SPRING
1. Changing the stroke of thread take-up spring Ê.
a) Loosen setscrew Ë .
b) As you turn tension post Ì clockwise (in director ), the stroke of the thread take-up spring will be increased.
c) As you turn the knob counterclockwise (in direction ), the stroke will be decreased.
2. Changing the pressure of thread take-up spring Ë a) Loosen setscrew Ë , and remove thread tension (assembly) Î.
b) Loosen setscrew Í.
c) Loosen setscrew Ë , and remove thread (in direction ), the pressure will be increased.
d) As you turn the post counterclockwise (in direction ), the pressure will be decreased.
CLEARING
Clean the hook and base area once every day, removing any lint or thread which may have accumulated. For this purpose the jig flap may be removed. Switch off the machine, remove the jig and remove the lint with the air gun provided.
Remove the jig drive cover and clean away any dust or lint which may have accumulated.
Note: Never oil the jig wheel.
1- 1 2
Revised 09/2005
E-mail: [email protected]; [email protected] ; website: www.amfreece.com
Phones: +420 582 309 146 (Service), +420 582 309 286 (Spare Parts) ; Fax: +420 582 360 606
OPERATING INSTRUCTIONS
3.10 REGULATING FOOT PRESSURE ON JIG
Adjustment of Presser Pressure
Turn the presser regulating screw clockwise to increase, and counterclockwise to decrease.
Be sure to tighten the nut after adjustment.
A foot pressure of approximately 1,5 to 2 kg will give best results on all materials.
84-55
3.11 EMERGENCY STOP
This is activated by pressing the Stop Button. This will activate the Emergency Stop Sequence.
The machine will not restart until the mushroom type red color emergency stop button has been released. Failure of air pressure or safety cover kept-opened will stop the machine operation. Before these signals are restored, these signals before ensure the needle is in up position, if not turn the handwhell to bring it to this position. Releasing of Emergency Stop will execute machine to home position and jig eject operation will be executed..
EMERGENCY STOP
Revised 09 /2005
E-mail: [email protected]; [email protected] ; website: www.amfreece.com
Phones: +420 582 309 146 (Service), +420 582 309 286 (Spare Parts) ; Fax: +420 582 360 606
1- 1 3
84-55
OPERATING INSTRUCTIONS
3.12 NEEDLE AND THREAD
Selection of the proper needle depends on the material and used.
NEEDLE
SIZE
(NM)**
THREAD SIZE
COTTON SILK SINTETIC LINEN NEEDLE
SYSTEM
For selection of the proper needle and thread sizes refer to the table below:
A
B
C
A
B
C
NM**
110
120
130
140
60
70
80
90
100
100 — 80 140
70 — 60 120
60 — 50 100
50 — 40 80
40 — 30 70
30— 24
20
12
10
60
50
40
30
200 — 150
180 — 120
120 — 100
100 — 80
80 — 60
60 — 50
50 — 40
40 — 30
30 — 20
70
60
50
40
35
30
134k
134k
134k
= LINGHT WEIGHT MATERIALS
= MEDIUM WEIGHT MATERIALS
= HEAVY WEIGHT MATERIALS
= NEEDLE SIZE IN HUNDRETHS OF MM
1- 1 4
Revised 09/2005
E-mail: [email protected]; [email protected] ; website: www.amfreece.com
Phones: +420 582 309 146 (Service), +420 582 309 286 (Spare Parts) ; Fax: +420 582 360 606
84-55
MECHANICAL SETTING PROCEDURES
4.0 INTRODUCTION
This section deals with the mechanical settings for parts not found on standard Juki head.
4.1 JIG DRIVE SETTINGS
Figure 4.0 shows the jig drive assembly. On the 84-55 a jig may be driven continuously or with an indexed motion. The settings for these two styles of motion are given in separate sections below. Any settings common to both types of motion are also given in separate sections.
4.1.1 COMMON SETTINGS
4.1.1A DRIVE WHEEL CYLINDER
The rod end bearing ( item 8, figure 4.0) should be set so that when the cylinder is fully extended the drive wheel is taken 3mm past its point of contact with the jig.
CAUTION :
IF THE DRIVE WHEEL TRAVELS TOO FAR, IT WILL DAMAGE THE PHOTOCELL IF THE MA-
CHINE IS RUN WITHOUT A JIG.
4.1.1B DRIVE WHEEL SURFACE
The surface of the drive wheel must not be contaminated with any lubricant or silicon Aerosols etc. Such contamination will affect jig feeding. If contamination occurs, clean the tapered groove of the drive wheel with solvent. See section 11.0 on cleaning.
4.1.1C DRIVE ARM ECCENTRIC
The drive arm eccentric ( item 34, fig 4.0 ) is used to adjust the point of contact between the drive wheel and the jig face in relation to the throat plate ‘D’. Location holes drilled into the base plate, item 62, ensure the eccentric does not move from the position it has been set to.
The factory setting for the eccentric is shown by a center pop mark next to the relative hole. If any adjustment is required slacken off nut 64 and lift drive arm item 43, up allowing the eccentric to rotate. Ensure the pin is located in one of the holes and tighten the nut. Set the spring 47 to the correct compression, see section 4.1.2.d.
4.1.1D DRIVE WHEEL ASSEMBLY
To replace a worn drive wheel detach the drive arm 43, from the machine bed, unfasten the rod end bearing 21 from the drive post and remove screw 3 from the drive cylinder. Disconnect the
DC motor and clutch bullet connectors, taking care not to pull on the wires and carefully lift the assembly out.
Undo screw 6 and remove the drive wheel and its housing 30 from the drive arm. Using the two
M5 holes in the base of the drive wheel as an anchor, loosen gear 17 taking great care not damage any teeth on the gear. Remove the wheel from the assembly. When reassembling, care should be taken that all surfaces are free from lint etc. the pivot spindle 28 should be lubricated with graphite grease before replacement into the drive wheel.
ONLY GREASE CONTAINING GRAPHITE OR MOIBDENUM DISULPHATE MUST BE USED.
Revised 09 /2005
E-mail: [email protected]; [email protected] ; website: www.amfreece.com
Phones: +420 582 309 146 (Service), +420 582 309 286 (Spare Parts) ; Fax: +420 582 360 606
1- 1 5
84-55
MECHANICAL SETTING PROCEDURES
1- 1 6
Revised 09/2005
E-mail: [email protected]; [email protected] ; website: www.amfreece.com
Phones: +420 582 309 146 (Service), +420 582 309 286 (Spare Parts) ; Fax: +420 582 360 606
84-55
MECHANICAL SETTING PROCEDURES
4.1.1E DRIVE ARM SPRING COMPRESSION
To allow the jig drive wheel to find its optimum location point a floating drive arm, 43, fig 4.0, has been used.
The spring 47, is used to prevent the drive arm from moving up and down the stud,67.
The correct compression setting for the drive arm spring is shown in fig. 4.1. when the nut 64, is tightened onto the spring, the distance between washers, 46, should be
11mm.
4.1.2. INDEX FEED SETTINGS
The index feed only drives the jig when the needle is clear of the material. The linkages in the sewing machine head control the timing for the drive.
Alterations to the stitch size are made in the usual manner using the stitch regulator.
4.1.2A FEED TIMING
The feed should be timed so that when the descending needle is approximately 6mm above the material the feed motion is complete. See section 7.1 for adjustment procedures.
4.1.2B DRIVE LINKAGE
As well as providing the drive to the drive wheel , the drive linkage , item 22, figure 4.0, also determines the angle of the drive clamp cylinder, item 27, figure 4.0. if the angle of this cylinder is incorrect it can foul on the sewing jig or collide with the drive linkage itself.
Set the linkage so that when the stitch size regulator is set to 4. The drive clamp cylinder does not interfere with either the sewing jig or the drive linkage.
4.1.3 CONTINUOUS FEED SETTINGS
The continuous feed differs from the index feed because instead of only driving the jig when the needle is clear of the material it drives all the time.
4.1.3A D.C. MOTOR
The DC motor, item 1, figure 4.0, is used to obtain the continuous drive feed . The motor has two speed settings.
Figure 4.2 shows the drive enclosure, which is located on the side of electrical cabinet. To increase the drive speed , rotate the potentiometer anticlockwise, to decrease turn it clockwise.
Figure 4.2
Revised 09 /2005
E-mail: [email protected]; [email protected] ; website: www.amfreece.com
Phones: +420 582 309 146 (Service), +420 582 309 286 (Spare Parts) ; Fax: +420 582 360 606
1- 1 7
84-55
MECHANICAL SETTING PROCEDURES
4.1.3.B CLUTCH
The clutch, item 11, figure 4.0, engages and disengages the DC drive motor. The gap between the two clutch faces must be set correctly to avoid slippage and binding. Figure 4.2 shows how to increase and decrease the clutch power. Figure 4.3 shows the gap setting between the faces. Release the cap head screw 1 and move clutch body up or down until the correct setting is achieved.
4.2 STITCH SIZE ADJUSTMENT
When using the index drive system alterations to stitch size are made in the usual manner using the stitch regulator and dense. When the machine is using the continuous feed system the stitch size is altered, using the sewing machine head speeds and DC motor drive speeds.
4.2.0 INDEX FEED
Three settings are available on the index feed stitch size adjuster item 1 fig 4.4, small, medium or full. The full stitch size is adjusted using the stitch regulator on the sewing head, but the small and medium stitch sizes are adjusted on the stitch size adjuster. To set the small stitch size set both cylinders 11 and 12 figure 4.4 and use the lock nuts 8 to the set the size. For the medium stitch size activate cylinder 12 and adjust rod end bearing 4 using adjuster screw 13. lock off screw with nut 3.
To ensure that the stitch size adjuster will give the full size stitch indicated on the stitch size regulator, activate both cylinders 11 and 12. if the required stitch size is not achieved, adjust adjuster screw 7 and lock off with nut 2. Set both cylinders in again and check the small stitch size has not been effected.
4.2.1 CONTINUOUS FEED
To set the stitch size using the continuous feed both the sewing head speed and the DC motor drive speed must be balanced. If the sewing head speed is set too slow and the DC drive speed set too high then an unusable large stitch will be formed and possible needle damage result. For information on setting the DC drive and sewing head speeds in the program see the Section 5.
1- 1 8
Revised 09/2005
E-mail: [email protected]; [email protected] ; website: www.amfreece.com
Phones: +420 582 309 146 (Service), +420 582 309 286 (Spare Parts) ; Fax: +420 582 360 606
84-55
MECHANICAL SETTING PROCEDURES
Section 4.1.3a gives details on how to adjust the DC drive speed.The spool sensor uses a photocell to detect the speed of rotation of the spool. As the amount of thread on the spool decreases so the speed of the spool increases and once the number of rotations reaches the value in the controller, set by the operator ( see section 5), the machine will give an audible warning.
4.3.0 PHOTOCELL SETTING
Figure 4.5 shows the face of a spool used with the spool sensor. The grey segment of the spool is the ‘OFF’ state and the light segment is ‘ON’.
Set the photocell to read the spool so that when the signal is ‘ON’ or ‘OFF’ the green light on the photo cell amplifier is ‘ON’.
4.4 SNUBBER AND JIG ALIGN
The snubber and jig align assembly is used to keep the jig running straight and also to signal the presence of a loaded jig and corners
.
4.4.0 SNUBBER SETTING
The snubber head, (item 2, Figure
4.6), should be set to allow 5mm of travel before the snubber block comes into contact with the damper when a jig is being loaded. This gap is to allow the jig to be loaded with minimal resistance from the damper.
The micro switch, ( item 1, Figure
4.6), should be set so that when the jig is loaded the switch is activated by the collar, (item 3, Figure 4.6).
4.4.1 JIG ALIGNMENT CYLINDER SETTING
The jig alignment cylinder must not bind on any part of the snubber block, ( item 4, Figure
4.6), through its full travel. The two M5 lock nuts must be tight at all times. The pressure regulator located in the frame cabinet should be set to allow the cylinder to guide the jig in a straight line.
TOO MUCH PRESSURE CAN CAUSE OVER CORRECTION AND POSSIBLE BINDING.
Revised 09 /2005
E-mail: [email protected]; [email protected] ; website: www.amfreece.com
Phones: +420 582 309 146 (Service), +420 582 309 286 (Spare Parts) ; Fax: +420 582 360 606
1- 1 9
84-55
MECHANICAL SETTING PROCEDURES
4.5
JIG EJECT/ REVERSE CORRECTION
The jig eject assembly acts as both an ejection system and a jig correction system. The jig eject bearing, ( item 1, Figure 4.7), must be set up to clear a jig from under the head at the end of the sew cycle. To adjust the position of the jig eject assembly undo screws 3,
Figure 4.7 and move the assembly in or out. Once the optimum position has been achieved, tighten the screws, load the jig into the machine and check to make sure it ove freely without binding between the jig eject bearing and the snubber head, (item 2, Figure 4.6).
4.6
JIG FLAP ADJUSTMENT
To allow the jig to be loaded into the machine the jig flap must be set above the throat plate
‘D’. If the flap is set too high the jig may catch on the presser foot.
To adjust the jig flap cylinder, (item 1, Figure 4.7), release screw 2, Figure 4.8 and adjust the cylinder up or down until the jig can be loaded into the machine without obstruction.
1- 2 0
Revised 09/2005
E-mail: [email protected]; [email protected] ; website: www.amfreece.com
Phones: +420 582 309 146 (Service), +420 582 309 286 (Spare Parts) ; Fax: +420 582 360 606
84-55
MECHANICAL SETTING PROCEDURES
4.7
AUTO START PROXIMITY SENSOR
The jig proximity sensor detects a block of metal located in the base of the jig, which determines the reverse back tack position. The jig proximity sensor also detects the jig for the auto start function.
4.7.0 JIG PROXIMITY SENSOR ADJUSTMENT
The jig proximity sensor must be set below the top of the jig flap to avoid damage from the jig.
Figure 4.9 shows the adjustment.
4.7.1 JIG METAL INSERT
The metal insert placed in the jig behind the track can be adjusted by releasing the tufnol tab from the jig and moving it until the jig proximity sensor detects the metal. To test the sensor is detecting the metal, place the jig on the machine, with the foot up and use the system check in section 5.
4.8
SIDE KNIFE
The knife adjustment mechanism allows adjustment of the side knife in three planes, vertical, horizontal and in a rotation plane to allow a certain amount of rake to be introduced.
Revised 09 /2005
E-mail: [email protected]; [email protected] ; website: www.amfreece.com
Phones: +420 582 309 146 (Service), +420 582 309 286 (Spare Parts) ; Fax: +420 582 360 606
1- 2 1
84-55
MECHANICAL SETTING PROCEDURES
4.8.0 INDICATION
The green and red indicators turn on and off as shown in Figure 5.0. Set the sensitivity adjuster at an appropriate position so that the photo electric switch operates within the stable operating range.
4.8.1 SENSITIVITY ADJUSTMENT
C A U T I O N : WHEN ADJUSTING SENSITIVITY DO NOT TURN THE SENSITIVITY
ADJUSTER BEYOND ITS MAXIMUM SCALE POSITION, OTHERWISE THE ADJUSTER
WILL BE DAMAGED.
1- 2 2
Revised 09/2005
E-mail: [email protected]; [email protected] ; website: www.amfreece.com
Phones: +420 582 309 146 (Service), +420 582 309 286 (Spare Parts) ; Fax: +420 582 360 606
MECHANICAL SETTING PROCEDURES
4.8.2 PHOTOCELL HEAD ALIGNMENT
To ensure the drive wheel or trimmed fabric does not give a false signal; the photocell must be aligned as shown in Figure 5.2.
84-55
4.9 PHOTO ELECTRIC SWITCH
The lens of the photocell head should be kept clean at all times to prevent any malfunction of this unit.
C A T U T I O N : DO NOT CLEAN WITH ALKALI, AROMATIC HYDROCARBON OR
CHLORIDE HYDROCARBON AS THE LENS MAY BE DISSOLVED.
Revised 09 /2005
E-mail: [email protected]; [email protected] ; website: www.amfreece.com
Phones: +420 582 309 146 (Service), +420 582 309 286 (Spare Parts) ; Fax: +420 582 360 606
1- 2 3
84-55
CONTROLS & PROGRAM DESCRIPTION
Auto Jig 84-55 is equipped with a sophisticated LCD display control. Detailed information has been provided in earlier steps by explaining function of each and every key on the display board while describing different parameters of the machine. But it is assumed that the reader becomes familiar with basic operation of Function Keys and can understand easily in the later part of the manual and would be able to make any sort of parameter editing even if the basic function of each key is not explained.
5.0 CONTROL DISPLAY
AMF REECE Display board has total number of six membrane push buttons designated as F1,
F2……F6, also called function keys. Different functions of the machine can be accessed with the help of these function keys. The sequence of operation is divided into different menus/screens. If we have a look at the display, keys F1 and F2 are also designated as keys NEXT and PREV respectively.
In most of the times F1 is used to switch over to next screen and F2 is used to go back to the previous screen, in case these keys are used for some other operation then same has been explained in the manual. Key F5 is also designated as CLR, this key functions to clear the value of any function selected to zero. Key F6 is designated as ENT. Main function of this key is to write the value of any function into the memory of control system. The values of any functions may be altered with the help of arrow keys. Let us study the following example.
We assume that we have to run a motor from display. We have two options, we can run the motor continuously or we can run the motor defined by a function.
Refer to Screen A. “Cont” stands for continuous run and “Fun” stands for function based running of motor. To choose the parameter “Cont” or “Fun” in Screen A, one must press the key
F6
and parameter “Cont/Fun” would start flashing. Pressing key
F4
while display is flashing would change the state Cont to Fun or vice versa and pressing key
F4
more than once will toggle the state between “Cont” and “Fun”. Then to enter the selected parameter one must press the key
F6
again. If a state “Cont” is selected that means we want to run the motor continuously and press key
F1
to enter into Screen C.
F1 F2
NEXT PREV
Motor Run
Cont/Fun
F3 F4 F5
CLR
F6
ENT
Screen A
In case parameter “Fun” is selected then pressing key
F1
means next Screen B would appear..
1- 2 4
Revised 09/2005
E-mail: [email protected]; [email protected] ; website: www.amfreece.com
Phones: +420 582 309 146 (Service), +420 582 309 286 (Spare Parts) ; Fax: +420 582 360 606
84-55
CONTROLS & PROGRAM DESCRIPTION
Motor Speed- 000
Time - 0.0 Rev - 0000
Sreen B
Screen B defines three parameters, motor speed, run the motor for a pre defined time or run the motor for a particular number of revolutions.
1. Motor Speed – Number of RPMs from 0 to 999
2. Time – Time in 0.0 to 9.9 seconds.
3. Rev – Number of revolutions
To edit Parameter 1, press key
F6
once, data value for “Motor Speed” would flash, pressing key
F6
twice would flash the data value for Parameter 2 and pressing key
F6
thrice would result in flashing of data for Parameter 3. Data of any of the three parameters can be edited when a particular data value is flashing. For example if the data for Parameter 1 i.e. Motor Speed is flashing, then press key
F5
to clear the value to “000”. Then increment the value by pressing key
F4
. The value cannot be decremented. Key
F3
may be used to shift the value of one digit to the other from right to left. For example if a value “001” is displayed, pressing
F3
once will change the value to “010”, pressing key
F3
twice will change the value to “100” and pressing key
F3
again will change the value to “000”. After a desired data value has been selected, press key
F6
again to store the value into the system. Similarly data can be edited for parameter “Time” and “Rev”. we have assumed that motor can be run either for a fixed interval of time or for a fixed number of revolutions. So a value selected more than zero would hide the parameter “Rev” and “*****” would appear. Press key
F1
to switch to next Screen C or press key
F2
to switch back to Screen A.
Motor Run – Yes/No
Screen C
In Screen C there is one parameter, which has two values Yes or No. Pressing key
F6
would make the Yes or No value to flash. Press key
F4
to toggle between Yes and No. Selecting Yes would make the motor run. The motor would stop after certain time or after the number of revolutions are completed depending upon the parameter selected in Screen B. In case parameter ‘Cont’ is selected in
Screen A, motor can be stopped by selecting ‘No’ in Screen C.
Above example is just demonstrated to explain the function of different keys on the Display
Board and no such parameter would display on the machine.
Revised 09 /2005
E-mail: [email protected]; [email protected] ; website: www.amfreece.com
Phones: +420 582 309 146 (Service), +420 582 309 286 (Spare Parts) ; Fax: +420 582 360 606
1- 2 5
84-55
CONTROLS & PROGRAM DESCRIPTION
5.1 MACHINE FUNCTIONS
To start with let us switch on the power of the machine and we see the screen1 flashing on the display.
F1 F2
NEXT PREV
Better Ideas
Better Made
F3 F4 F5
CLR
F6
ENT
Screen 1
Screen 1 will flash for 3 seconds, after that Screen 2 will appear on the display.
F1 F2
NEXT PREV
AMF Reece v00-00
F3 F4 F5
CLR
F6
ENT
Screen 2
Screen 2 describes the software version of the machine. The same could be referred for any future correspondence for any technical queries.
After a delay of 3 seconds Screen 3 will appear on the display.
1- 2 6
Revised 09/2005
E-mail: [email protected]; [email protected] ; website: www.amfreece.com
Phones: +420 582 309 146 (Service), +420 582 309 286 (Spare Parts) ; Fax: +420 582 360 606
CONTROLS & PROGRAM DESCRIPTION
5.1.0 ERROR MESSAGES
84-55
F1 F2
NEXT PREV
M: Insert Jig
Prg-1 Knife-Yes
F3 F4 F5
CLR
F6
ENT
Screen 3
The screen3 shows a message (M) that machine is ready for operation. It directs the operator to insert the jig. Prg-1 indicates that Program no. 1 is selected. Knife is ON during the operation. The program no. and Knife option may be altered from this screen. Press key
F6
, Knife selection Yes or No starts blinking and this status can be toggled by pressing key
F4
, pressing key
F6
again will enter the
Yes/No value for the knife and display stops blinking. To alter the program number press key
F6
twice and program no. Prg -… starts blinking. The value can be incremented with the help of key
F4
and can be reset with key
F5
and selected value can be stored by pressing the key
F6
again. It is possible to have total number of ten programs and the parameter Prg -… can have values 0 to 9.
In certain situations machine may not be ready for operation, in that case the corresponding Error
Message would be displayed on the screen. These error messages could be as follows:
E: Emergency Stop
Prg-1 Knife-Yes
a) This message refers to the Emergency switch and it must be released to put the machine ready for operation.
E: Inverter Err
Prg-1 Knife-Yes
b) This message refers to some error with the frequency inverter drive. The frequency inverter drive is used to control the speed of sewing motor. Any malfunction in this drive will generate a signal and above error message will be displayed. The type of the fault will be displayed on the LED display of the inverter drive inside the control cabinet. The fault state of the inverter must be cleared to put the machine ready for operation. Operator must call upon a qualified technician when this message is displayed.
Revised 09 /2005
E-mail: [email protected]; [email protected] ; website: www.amfreece.com
Phones: +420 582 309 146 (Service), +420 582 309 286 (Spare Parts) ; Fax: +420 582 360 606
1- 2 7
84-55
CONTROLS & PROGRAM DESCRIPTION
E: Spool Alarm
Prg-1 Knife-Yes
c) This message appears on the screen when the bobbin of thread roll is running out of thread. But this is an optional feature and all machines may not have this feature.
E: Tape Sensor
Prg-1 Knife-Yes
d) sensor is not sensing the tape on jig.
This message will appear on the display, if tape
E: Air Pressure
Prg-1 Knife-Yes
e) This message will appear on the display, when the pneumatic air pressure to the machine is disconnected or it goes low and machine is not ready for operation.
E: Safety Cover
Prg-1 Knife-Yes
f) This message will appear on the display, when the acrylic sheet safety cover around the needle area is open and must be closed to make the machine ready for operation.
5.2 MODES OF OPERATION
From screen3 pressing the key
F1
will take us to the Screen 4.
1- 2 8
System Check-F3
Edit-F4 Seq.-F5
F3 F4 F1 F2
NEXT PREV
F5
CLR
F6
ENT
Screen 4
Revised 09/2005
E-mail: [email protected]; [email protected] ; website: www.amfreece.com
Phones: +420 582 309 146 (Service), +420 582 309 286 (Spare Parts) ; Fax: +420 582 360 606
84-55
CONTROLS & PROGRAM DESCRIPTION
Looking at screen4 tells us about the different modes of the machine. Pressing key
F2
will display the previous screen and pressing the key
F1
will display the next screen i.e. Screen5.
Production Count
000000 Rst-F3
F3 F4 F1 F2
NEXT PREV
F5
CLR
F6
ENT
Screen 5
Screen 5 is the production counter. The production counter will increment after the completion of every sewing cycle. The value of this Production Counter may be reset to zero by pressing the key
F3
. Pressing key
F2
will display the previous screen and pressing the key
F1
will display the next screen i.e. Screen6.
Spool Count
000000 Rst-F3
F3 F4 F1 F2
NEXT PREV
F5
CLR
F6
ENT
Screen 6
Screen 6 is the spool counter. The spool counter will increment after the completion of every sewing cycle. The value of this Production Counter may be reset to zero by pressing the key
F3
. Pressing key
F2
will display the previous screen and pressing the key
F1
will display the next screen i.e.
Screen7. This is an optional feature. The display may show the spool counter even though the machine is not equipped with this feature.
Revised 09 /2005
E-mail: [email protected]; [email protected] ; website: www.amfreece.com
Phones: +420 582 309 146 (Service), +420 582 309 286 (Spare Parts) ; Fax: +420 582 360 606
1- 2 9
84-55
CONTROLS & PROGRAM DESCRIPTION
Batch Count
000000 Rst-F3
F3 F4 F1 F2
NEXT PREV
F5
CLR
F6
ENT
Sceen 7
Batch counter is a function that is used to count the number of pieces sewn for a particular program.
It counts on irrespective of the production counter value as the production counter is value that counts on every piece sewn irrespective the program type selected and hence gives a total number of pieces sewn on the machine for different programs selected. The value of a batch counter may be reset to zero by pressing key
F3
and pressing key
F1
will switch the display back to the Screen3.
A glance at Screen4 tells us about the different modes of operation. One of these modes is System
Check, press key
F3
i.e. System Check and Screen 4.1 will appear on the display..
F1 F2
NEXT PREV
Input test – F3
Output test – F4
F3 F4 F5
CLR
F6
ENT
Screen 4.1
After switching to Screen 4
This mode is used to diagnose the proper working of different input and output signals.
1- 3 0
Revised 09/2005
E-mail: [email protected]; [email protected] ; website: www.amfreece.com
Phones: +420 582 309 146 (Service), +420 582 309 286 (Spare Parts) ; Fax: +420 582 360 606
84-55
CONTROLS & PROGRAM DESCRIPTION
5.2.1 INPUT TESTING MODE:
Pressing the key
F3
will enter into the input testing mode and first screen of input testing mode i.e.
Screen 4.1.a.1 will appear. Pressing key
F2
will take back to the previous Screen 4.
Needle Up Proxy
X00 – On
F3 F4 F1 F2
NEXT PREV
F5
CLR
F6
ENT
Screen 4.1a.1
In this mode if the proximity switch for needle up sensing is energized, the display will show
X00 – On, otherwise it will display X00 – Off.
Pressing
F1
will enter into the next Screen 4.1.a.2 and pressing key
F2
Motor Run – Yes/No
Screen 4.1.a.2
In this mode if the proximity switch for needle down sensing is energized, the display will show
X01 – On, otherwise it will display X01 – Off. Pressing
F1
will enter into the next Screen 4.1.a.3
& pressing
F2
will enter into the previous screen 4.1.a.1.
Start PB
X02 - Off
Screen 4.1.a.3
In this mode if the start push button for cycle start, mounted on the machine table is pressed, the
display w ill show
X02 – On, otherwise it will display X02 – Off.
Revised 09 /2005
E-mail: [email protected]; [email protected] ; website: www.amfreece.com
Phones: +420 582 309 146 (Service), +420 582 309 286 (Spare Parts) ; Fax: +420 582 360 606
1- 3 1
84-55
CONTROLS & PROGRAM DESCRIPTION
Pressing key
F1
will enter into the next Screen 4.1.a.4 and pressing key
F2
will enter into the previous screen 4.1.a.2.
Emergency Stop
X03 - Off
Screen 4.1.a.4
In this mode if the mushroom type emergency switch mounted on the machine table is pressed, the display will show X03 – On, when released it will display X03 – Off. Pressing key
F1
will enter into the next Screen 4.1.a.5 and pressing key
F2
will enter into the previous screen 4.1.a.3.
Tape Photo Cell
X04 - On
Screen 4.1.a.5
In this mode if the tape sensing photocell is energized by putting below a dark object like tape, the display will show X04 – On, otherwise it will display X04 – Off. Pressing key
F1
will enter into the next Screen 4.1.a.6 & pressing key
F2
will enter into the previous screen 4.1.a.4
Spool Photo Cell
Bypass-N X05 - On
Screen 4.1.a.6
In this mode if the photocell for sensing the spool is energized manually, the display will show
X05 – On, otherwise it will display X05 – Off. This feature is optional and all machines may not be equipped with this photocell. Pressing key
F1
will enter into the next Screen 4.1.a.7 and pressing key
F2
will enter into the previous screen 4.1.a.5.
Snubber Limit sw
X06 - Off
Screen 4.1.a.7
In this mode if the snubber switch meant for jig alignment is pressed manually, the display will show
X06 – On, otherwise it will display X06 – Off. Pressing key
F1
will enter into the next
1- 3 2
Revised 09/2005
E-mail: [email protected]; [email protected] ; website: www.amfreece.com
Phones: +420 582 309 146 (Service), +420 582 309 286 (Spare Parts) ; Fax: +420 582 360 606
84-55
CONTROLS & PROGRAM DESCRIPTION
Screen 4.1.a.8 and pressing key
F2
will enter into the previous screen 4.1.a.6.
Auto Start Proxy
X07 - On
Screen 4.1.a.8
This is the proximity switch mounted on the machine table to sense the start point in a jig. When this proximity switch is energized by bring a metal object close to its sensing range, the display will show
X07 – On, otherwise it will display X07 – Off. Pressing key
F1
will enter into the next Screen
4.1.a.9 and pressing key
F2
will enter into the previous screen 4.1.a.7.
Inverter Ok
X10 - On
Screen 4.1.a.9
The motor speed is controlled by the frequency inverter drive; any fault detected in the inverter drive would result in an output and would display X10 – Off and energize an error message Inverter Err, with, otherwise display shows Inverter Ok. With X10 – On. Pressing key
F1
will enter into the next Screen 4.1.a.10 and pressing key
F2
will enter into the previous screen 4.1.a.8.
Air Pressure sw
Bypass-N X11 - Off
Screen 4.1.a.10
This input may be diagnosed by blocking the pneumatic pressure line. There is a switch that is on when there is enough air pressure developed to run the machine. Any drop in air pressure would result in the change of status of this input and display would change from X11 – On to X11 – Off.
Pressing key
F1
will enter into the next Screen 4.1.a.11 and pressing key
F2
will enter into the previous screen 4.1.a.9.
Revised 09 /2005
E-mail: [email protected]; [email protected] ; website: www.amfreece.com
Phones: +420 582 309 146 (Service), +420 582 309 286 (Spare Parts) ; Fax: +420 582 360 606
1- 3 3
84-55
CONTROLS & PROGRAM DESCRIPTION
Safety Cover
Bypass-N X12 - Off
Screen 4.1.a.11
There is an Acrylic sheet cover for the safety of operator around the needle area. A micro switch is attached with this cover. When this cover is opened or closed the display changes from X12 - On to
X12 - Off accordingly. Pressing key
F1
will enter back to Screen 4.1 and pressing key
F2
will enter into the previous screen 4.1.a.10.
5.2.2 OUTPUT TESTING MODE
Screen 4.1 also shows output testing mode. Pressing key
F4
enters into the first screen of this mode i.e. Screen 4.1.b.1. This screen shows Knife solenoid valve output. Press key
F6
, Y00 – Offf will
Knife S/V
Y00 – On
F3 F4 F1 F2
NEXT PREV
F5
CLR
F6
ENT
Screen 4.1.b.1
start flashing, then pressing key
F4
once, will change the output status from Y00 – Offf to Y00 –
On and then pressing key
F6
will energize pneumatic solenoid for knife up/down operation (Pressing the key
F4
again while the display is flashing will toggle the On/Off status) and the display will stop flashing. Pressing key
F1
will enter into the next Screen 4.b.1.2 and pressing key
F2
will enter into the previous screen 4.1.
1- 3 4
Revised 09/2005
E-mail: [email protected]; [email protected] ; website: www.amfreece.com
Phones: +420 582 309 146 (Service), +420 582 309 286 (Spare Parts) ; Fax: +420 582 360 606
84-55
CONTROLS & PROGRAM DESCRIPTION
Jig Flap S/V
Y01 - Off
Screen 4.1.b.2
Screen 4.1.b.2 shows Jig flap solenoid valve output. This output may be tested by changing the Y01 On/
off status on the display with a procedure as mentioned above and pneumatic solenoid for jig flap up/ down operation will be energized. Pressing key
F1
will enter into the next Screen 4.b.1.3 and pressing key
F2
will enter into the previous screen 4.1.b.1.
Stitch size1 S/V
Y02 - Off
Screen 4.1.b.3
Screen 4.1.b.3 shows Stitch size1 solenoid valve. There are two positions of twin type pneumatic cylinder and are controlled by two solenoid valves Stitch size1 S/V and Stitch size2 S/V to opt for two different stitch densities. Stitch size2 S/V is displayed on Screen 4.1.b.4. and this screen can be viewed by pressing key
F1
. In both the screens selected cylinders can be operated by energizing respective solenoids. Press the key
F6
, Y02 – Offf will start flashing, then pressing key
F4
once will change the output status from Y02 – Off to Y02 – On and then pressing key
F6
will energize pneumatic solenoid for stitch size1 cylinder (Pressing the key
F4
again while the display is flashing will toggle the On/Off status) and the display will stop flashing. Repeat the above procedure in
Screen 4.1.b.4 to diagnose the stitch size2 output.
Stitch size2 S/V
Y03 - Off
Screen 4.1.b.4
Pressing key
F1
will enter into the next Screen 4.1.b.5 and pressing key
F2
will enter into the previous screen 4.1.b.3.
P/F Jig Drive S/V
Y04 - On
Screen 4.1.b.5
Revised 09 /2005
E-mail: [email protected]; [email protected] ; website: www.amfreece.com
Phones: +420 582 309 146 (Service), +420 582 309 286 (Spare Parts) ; Fax: +420 582 360 606
1- 3 5
84-55
CONTROLS & PROGRAM DESCRIPTION
Screen 4.1.b.5 shows Presser Foot/Jig Drive solenoid valve. Press the key
F6
, Y04 – Offf will start flashing, then pressing key
F4
once, will change the output status from Y04 – Offf to Y04 – On and then pressing key
F6
will energize pneumatic solenoid for Presser Foot/Jig driver pneumatic cylinder (Pressing the key
F4
again while the display is flashing will toggle the On/Off status) and the display will stop flashing. Pressing
F1
will enter into the next Screen 4.1.b.6 & pressing
F2
will enter into the previous Screen 4.1.b.4.
Spare/Jig Turn
Y05 - On
Screen 4.1.b.6
Screen 4.1.b.6 shows Jig Turn solenoid valve. Press the key
F6
, Y05 – Offf will start flashing, then pressing key
F4
once, will change the output status from Y05 – Offf to Y05 – On and then pressing key
F6
will energize pneumatic solenoid for jig turn operation (Pressing the key
F4
again while the display is flashing will toggle the On/Off status) and the display will stop flashing. Pressing key
F1
will enter into the next Screen 4.1.b.7 and pressing key
F2
will enter into the previous screen
4.1.b.5. This feature is not used in all the machines and some machines may not be equipped with this feature and this parameter may not be displayed.
Jig Eject S/V
Y06 - Off
Screen 4.1.b.7
Screen 4.1.b.7 shows Jig Eject solenoid valve. Press the key
F6
, Y06 – Offf will start flashing, then pressing key
F4
once, will change the output status from Y06 – Offf to Y06 – On and then pressing key
F6
will energize pneumatic solenoid for jig eject operation (Pressing the key
F4
again while the display is flashing will toggle the On/Off status) and the display will stop flashing. Pressing key
F1
will enter into the next Screen 4.1.b.8 and pressing key
F2
will enter into the previous screen
4.1.b.6.
1- 3 6
Revised 09/2005
E-mail: [email protected]; [email protected] ; website: www.amfreece.com
Phones: +420 582 309 146 (Service), +420 582 309 286 (Spare Parts) ; Fax: +420 582 360 606
84-55
CONTROLS & PROGRAM DESCRIPTION
Jig Aligner S/V
Y07 - On
Screen 4.1.b.8
Screen 4.1.b.8 shows Jig Aligner solenoid valve. Press the key
F6
, Y07 – Offf will start flashing, then pressing key
F4
once, will change the output status from Y07 – Offf to Y07 – On and then pressing key
F6
will energize pneumatic solenoid for jig align operation (Pressing the key
F4
again while the display is flashing will toggle the On/Off status) and the display will stop flashing.
Pressing key
F1
will enter into the next Screen 4.1.b.9 and pressing key
F2
will enter into the previous screen 4.1.b.7.
Drive Wheel Clamp
S/V Y10 - off
Screen 4.1.b.9
Screen 4.1.b.9 shows Stitch size1 solenoid valve. Press the key
F6
, Y10 – Offf will start flashing, then pressing key
F4
once, will change the output status from Y10 – Offf to Y10 – On and then pressing key
F6
will energize pneumatic solenoid for drive wheel clamping operation (Pressing the key
F4
again while the display is flashing will toggle the On/Off status) and the display will stop flashing. Pressing key
F1
will enter into the next Screen 4.1.b.10 and pressing key
F2
will enter into the previous screen 4.1.b.8.
Start PB Lamp
Y11 - off
Screen 4.1.b.10
Screen 4.1.b.10 shows cycle start push button lamp. Press the key
F6
, Y11 – Offf will start flashing, then pressing key
F4
once, will change the output status from Y11 – Offf to Y11 – On and then pressing key
F6
will make the lamp in the start push button glow (Pressing the key
F4
again while the display is flashing will toggle the On/Off status) and the display will stop flashing. Pressing key
F1
will enter into the next Screen 4.1.b.12 and pressing key
F2
will enter into the previous screen
4.1.b.9.
Revised 09 /2005
E-mail: [email protected]; [email protected] ; website: www.amfreece.com
Phones: +420 582 309 146 (Service), +420 582 309 286 (Spare Parts) ; Fax: +420 582 360 606
1- 3 7
84-55
CONTROLS & PROGRAM DESCRIPTION
Inverter Speed - 1
Y23,Y22,Y21 - 001
Screen 4.1.b.12
Screen 4.1.b.12 shows inverter speed selection mode. There are total number of seven speeds that can be selected and it may have values Inverter Speed – 0 to 6. To select a particular speed press key
F6
, the value for the Inverter speed starts flashing. Press key
F5
(CLR) to clear the value.
Then with the help of key
F4
value of Inverter Speed can be incremented. After selection of certain value press key
F6
to enter the desired value. Pressing key
F1
will enter into the next Screen
4.1.b.13 and pressing key
F2
will enter into the previous screen 4.1.b.10.
N o t e 1 : Screen 4.1.b.12 also shows status of PLC outputs for a particular speed selected. For example, if for a particular Inverter Speed the display shows Y23, Y22, Y21 – 101, it means for that speed PLC outputs Y36 and Y34 will be On and Y35 will be Off.
Note 2: For editing of Inverter Speed value use key
F5
to clear the value as the value can only be incremented with the help of key
F4
.
Inverter Fwd – F3
Y24,Y04 - 01
Screen 4.1.b.13
Screen 4.1.b.13 shows inverter forward run display. In this screen Y37 (Input command for Inverter forward run), Y04 (Presser Foot/Jig Drive) and – .. (Inverter Speed 0 to 6 selected in Screen
4.1.b.12) are also displayed. Switching to this screen automatically leads to the energizing of presser foot/Jig drive solenoid thro PLC output Y37 and presser foot comes down. Press key
F3
and PLC output Y37 will send a signal to Inverter drive to forward run at a speed selected in Screen 4.1b.12
and sewing head motor starts rotating till key
F3
is kept pressed. Pressing key
F1
will enter into the next Screen 4.1.b.14 and pressing key
F2
will enter into the previous screen 4.1.b.12.
1- 3 8
Revised 09/2005
E-mail: [email protected]; [email protected] ; website: www.amfreece.com
Phones: +420 582 309 146 (Service), +420 582 309 286 (Spare Parts) ; Fax: +420 582 360 606
84-55
CONTROLS & PROGRAM DESCRIPTION
Th. Trim Relay
Y26 - Off
Screen 4.1.b.14
Screen 4.1.b.14 shows Thread trim relay. Press the key
F6
, Y26 – Offf will start flashing, then pressing key
F4
once, will change the output status from Y26 – Offf to Y26 – On and then pressing key
F6
will energize magnetic thread trim solenoid (Pressing the key
F4
again while the display is flashing will toggle the On/Off status) and the display will stop flashing. Pressing key
F1
will enter into the next Screen 4.1.b.15 and pressing key
F2
will enter into the previous screen
4.1.b.13.
DC Motor Clutch
Y30 - Off
Screen 4.1.b.15
Screen 4.1.b.15 shows clutch for DC motor. Press the key
F6
, Y30 – Offf will start flashing, then pressing key
F4
once, will change the output status from Y30 – Offf to Y30 – On and then pressing key
F6
will energize magnetic coil of clutch for holding the DC motor (Pressing the key
F4
again while the display is flashing will toggle the On/Off status) and the display will stop flashing. Pressing key
F1
will enter into the next Screen 4.1.b.16 and pressing key
F2
will enter into the previous screen 4.1.b.14.
DC Motor Enable
Y31 - Off
Screen 4.1.b.16
Screen 4.1.b.16 shows DC Motor Enable. Press the key
F6
, Y31 – Offf will start flashing, then pressing key
F4
once, will change the output status from Y31 – Offf to Y31 – On and then pressing key
F6
will energize PLC output Y31 and that will further send a signal at enable pin of DC drive inside the electrical cabinet (Pressing the key
F4
again while the display is flashing will toggle the
On/Off status) and the display will stop flashing. Pressing key
F1
will enter into the next Screen
4.1.b.17 and pressing key
F2
will enter into the previous screen 4.1.b.15.
Revised 09 /2005
E-mail: [email protected]; [email protected] ; website: www.amfreece.com
Phones: +420 582 309 146 (Service), +420 582 309 286 (Spare Parts) ; Fax: +420 582 360 606
1- 3 9
84-55
CONTROLS & PROGRAM DESCRIPTION
DC Motor Direct.
Y32 - Off
Screen 4.1.b.17
Screen 4.1.b.17 shows DC motor direction. Press the key
F6
, Y32 – Offf will start flashing, then pressing key
F4
once, will change the output status from Y32 – Offf to Y32 – On and then pressing key
F6
will change the direction of DC motor. (Pressing the key
F4
again while the display is flashing will toggle the On/Off status) and the display will stop flashing. Pressing key
F1
will enter into the next Screen 4.1.b.18 and pressing key
F2
will enter into the previous screen 4.1.b.16.
DC Speed1 – F3
Y33,Y32,Y31 - 001
Screen 4.1.b.18
Screen 4.1.b.18 shows DC motor speed selection. DC motor has two speeds. This screen shows speed1. Press key
F3
and PLC output Y33 will send a signal to DC drive to run at speed1 and DC motor starts rotating till key
F3
is kept pressed. Pressing key
F1
will enter into the next Screen
4.1.b.19 and pressing key
F2
will enter into the previous screen 4.1.b.17.
DC Speed2 – F3
Y34,Y32,Y31 - 001
Screen 4.1.b.19
Screen 4.1.b.19 shows DC motor speed2 selection. Press key
F3
and PLC output Y27 will send a signal to DC drive to run at speed1 and DC motor starts rotating till key
F3
is kept pressed. Pressing key
F1
will enter back into the first Screen 4.1.b.1 and pressing key
F2
will enter into the previous screen 4.1.b.18.
Note: Screen 4.1.b.18 and Screen 4.1.b.19 display Y33,Y32,Y31 – 001 and Y34,Y32,Y31 – 001 respectively. Status 001 describes the status of outputs Y32 (DC motor direction) and Y31 (DC motor Enable) and motor speed (Y27 or Y33).
1- 4 0
Revised 09/2005
E-mail: [email protected]; [email protected] ; website: www.amfreece.com
Phones: +420 582 309 146 (Service), +420 582 309 286 (Spare Parts) ; Fax: +420 582 360 606
84-55
CONTROLS & PROGRAM DESCRIPTION
5.2.3 NEEDLE TEST
Pressing key
F1
in Screen 4.1 will enter into Screen 4.1.1.
Position test – F3
Restore Pgm – F4
Screen 4.1.1
Screen 4.1.1 displays two modes i.e. Position test and Restore Program. Pressing key
F3
will enter into Screen 4.1.2.
Needle Position –
Up X01,X00 - 01
Screen 4.1.2
In Screen 4.1.2, pressing key
F6
will result in flashing of Up or Dn characters on the display. Press key
F4
once to change from Up to Dn or vice versa while the display is flashing. Then press key
F6
again. This will make the sewing motor run till needle up or needle down position is acquired by the machine. On the display, X01,X00 – 01 will appear when machine is at needle up position and
X01,X00 – 10 will appear when machine is at needle down position. Pressing key
F1
will enter into
Screen 4.2.
In Screen 4.1.1, when key
F4
is pressed, it will enter into Screen 4.1.1.c1. This screen is used to
Restore Pgm – 4
F3 - Yes
Screen 4.1.1.c1
select a default program. This default program is nothing but a reset program, where all the Yes conditions in the program are set to No and all the integer value parameters are set to zero. To select a program that is intended to be reset, press key
F6
the program number Pgm - … starts blinking.
Then press key
F4
to increment the number or press key
F5
to clear the Pgm number and press key
F6
to store the value. Press key
F3
for Yes
F1
to enter into Screen 4.1.1.c2 or press key
F2
to return to Screen 4.2.
Revised 09 /2005
E-mail: [email protected]; [email protected] ; website: www.amfreece.com
Phones: +420 582 309 146 (Service), +420 582 309 286 (Spare Parts) ; Fax: +420 582 360 606
1- 4 1
84-55
CONTROLS & PROGRAM DESCRIPTION
Sure to Restore
No Exit – F3
Screen 4.1.1.c2
Screen 4.1.1.c2 confirms the restoring of default values, press key
F6
, No or Yes status starts blinking, press key
F4
to toggle between Yes or No status and press key
F6
to store the selected status to the control system memory. If a status Yes is selected, then after pressing key
F6
, the screen starts blinking for 2-3 seconds with a message “Saving”. Press key
F3
to exit and enter to
Screen 4.1.1 or key
F2
to previous return to Screen 4.1.1.c1.
5.3 PROGRAMMING MODE:
Screen 4 also displays program editing mode. Pressing key
F4
will enter into Screen 4.2.
Select Prg No - 2
Edit – F3
Screen 4.2
This screen will display a program no. that has been selected in Screen 3, but can be altered by pressing key
F6
and enter the desired program no. with the help of key
F4
and press
F1
again to store the value. To edit a particular program press key
F3
This will enter into Screen 4.2.d.
Enter Password
0000
Screen 4.2.d
Enter the right password or press key
F2
to return to Screen 4.2. After entering the right password will show a message “Wait” on Screen 4.2.1 and will enter into Screen 4.2.d1.
1- 4 2
Prg – 2 Type - 2
Point Collar
Screen 4.2.d1
Revised 09/2005
E-mail: [email protected]; [email protected] ; website: www.amfreece.com
Phones: +420 582 309 146 (Service), +420 582 309 286 (Spare Parts) ; Fax: +420 582 360 606
84-55
CONTROLS & PROGRAM DESCRIPTION
Screen 4.2.d1 displays the program no. Prg -… selected in Screen 4.2 and type of the program. The type of program must be selected in this mode. There are total numbers of 6 types of programs. The type of program may be changed with the help of keys
F1
and
F4
as mentioned in previous screens. The program type value may vary from 0 to 5. Different types are mentioned below:
0 – 1 (Single) Pocket Flap
1 – 2 (Double) Pocket Flap
2 – Point Collar
3 – Round Collar
4 – Single Breast (Point Corner)
5 – Double Breast (Round Corner)
Pressing key
F1
will enter into Screen 4.2.d2 and pressing
F2
will enter previous Screen 4.2.d.
Fast Sew Prg - Off
Auto Start - Off
Screen 4.2.d2
Screen 4.2.d2 begins with Start parameters of a program. There are two parameters Fast Sew Program and Auto Start. A Fast Sew program means the cycle will cancel all the back tack or index functions even if such parameters are selected. This function is mainly used when sewing simple parts, such as pocket flaps or cuffs.
Auto Start is a function when the operator does not have to press the start button. The templates are loaded under the sewing head and machine automatically starts. This parameter should be turned
OFF if using manually loaded jigs (Section 2.0). Auto Start function is possible only on jigs with metal insert.
Press key
F6
, Fast Sew Prg - On or Off starts blinking and this status can be toggled by pressing key
F4
, pressing key
F6
again will enter the On/Off value for this parameter and display stops blinking. To alter the Auto Start status press key
F6
twice and Auto Start -… starts blinking. The value can be toggled with the help of key
F4
and selected value can be stored by pressing the key
F6
again. Pressing key
F1
will enter into Screen 4.2.d3 and pressing
F2
will enter previous
Screen 4.2.d1.
Revised 09 /2005
E-mail: [email protected]; [email protected] ; website: www.amfreece.com
Phones: +420 582 309 146 (Service), +420 582 309 286 (Spare Parts) ; Fax: +420 582 360 606
1- 4 3
84-55
CONTROLS & PROGRAM DESCRIPTION
Knife Delay - off
Kn Delay Typ - Tim
Screen 4.2.d3
Screen 4.2.d3 displays two parameters. Knife Delay parameter at start and then type of knife delay. If knife delay is set at Off that means knife starts operating as the sewing cycle begins. If it is set at On, then type of knife delay is to be defined.
Kn Delay Typ (Knife Delay Type) is either time based or tape type. If this parameter is set to Tape, then knife will start operating at the trailing edge of start tape. If this type is selected Tim (Time), then time value will be defined in Screen 4.2.d4 by pressing key
F1
In case Tape type delay is selected, pressing key
F1
will enter into Screen 4.2.d5.
Knife Delay
Time – 0.04s
Screen 4.2.d4
Knife delay time may be set in seconds in this screen. Press key
F1
to enter the next Screen 4.2.d5.
5.3.1 BACK TACK PARAMETERS AT CYCLE START:
Select Back Tack
Yes
Screen 4.2.d5
Screen 4.2.d5 is a selection of Back tack at the start of sewing cycle. Selecting a value “Yes” for this parameter will disable the knife delay even if it was selected “On” in Screen 4.2.d3. If this parameter is selected “Yes” then pressing
F1
will enter into Screen 4.2.d6, if “No” it will switch to Screen
4.2.d9.
1- 4 4
Revised 09/2005
E-mail: [email protected]; [email protected] ; website: www.amfreece.com
Phones: +420 582 309 146 (Service), +420 582 309 286 (Spare Parts) ; Fax: +420 582 360 606
84-55
CONTROLS & PROGRAM DESCRIPTION
BT Length – 0.0s
BT head speed - 4
Screen 4.2.d6
Screen 4.2.d6 displays two parameters.
a)
BT Length: This is the length of back tack. This length is defined in terms of time in seconds till the DC motor for back tack moves the jig backward from point B to point C, so BT Length is the distance covered in time (parameter set in Screen 4.2.d6). The other parameter is
b)
BT head speed: This is the speed parameter for sewing head motor when the jig moves from point B to C. There are 7 sewing head speeds and this parameter may be set from
0 to 6. Press key
F1
to enter next Screen 4.2.d7.
Pwd speed
A
C
C
Back Tack
B
B
Side 1
‘C’ Type Back Tack
No Stitch
Stitch
BT Drive Speed – 1
Fwd Head Speed - 3
Screen 4.2.d7
Screen 4.2.d7 displays two parameters.
a)
BT Drive Speed: This is the speed of DC motor set during back tack operation from point B to C. There are 2 speeds available for DC motor and this parameter may be set
1 or 2.
b)
Fwd Head Speed: This is the speed parameter set for the sewing head motor when the jig is moving from point A to B. This parameter is active in case of “Z type” (Screen 4.2.d26) back tack only. In case of “C type” back sewing head motor does not operate for jig movement from point A to B i.e. no stitch.
Revised 09 /2005
E-mail: [email protected]; [email protected] ; website: www.amfreece.com
Phones: +420 582 309 146 (Service), +420 582 309 286 (Spare Parts) ; Fax: +420 582 360 606
1- 4 5
84-55
CONTROLS & PROGRAM DESCRIPTION
Press key
F1
and enter into next parameters of back tack for cycle start in Screen 4.2.d8.
Fwd Drive Speed – 1
Time – 0.0s Index - 1
Screen 4.2.d8
There are 3 parameters on this screen.
a) Fwd Drive Speed: This is the DC motor speed during the jig movement from point
A to B.
b) Time: This is a time parameter in seconds. During this time DC motor will rotate to move the jig from point A to B.
c) Index: This parameter is an integer value to select different stitch densities. But in Screen
4.2.d8 this parameter will be active only in case of “Z Type” back tack (Screen 4.2.d26) and if parameter Fwd Drive Speed is set ‘0’. It means jig movement from A to B in “Z
Type” back tack is not controlled by DC motor and is intended to be controlled with main sewing motor. In case Fwd Drv Speed selected other than ‘0’ the parameter “Index” will hide and display will show ‘****’. When performing whole stitching operation with main
1- 4 6
Pwd speed
A
C
C
Back Tack
B
B
Side 1
‘Z’ Type Back Tack
No Stitch
Stitch sewing motor only, then stitch density may be controlled by three index values 0,1 and 3.
Press key
F1
to enter Screen 4.2.d13 for Side1 parameters.
Index 1
Index 2
Index 3
Stitch Density with Sewing Head Motor
Revised 09/2005
E-mail: [email protected]; [email protected] ; website: www.amfreece.com
Phones: +420 582 309 146 (Service), +420 582 309 286 (Spare Parts) ; Fax: +420 582 360 606
84-55
CONTROLS & PROGRAM DESCRIPTION
5.3.2 DENSE STITCH PARAMETERS AT CYCLE START:
In Screen 4.2.d5, If Back tack parameter is selected “No” it will switch to Screen 4.2.d9.
Soft Head Speed - 3
Screen 4.2.d9
Whenever using dense stitching mode, the machine makes a few stitches before moving into actual dense stitching mode and this mode is called “Soft Start”. Soft Head Speed is the sewing head motor speed selected for a soft stitching mode. Press key
F1
to enter next parameter of soft start mode in
Screen 4.2.d10.
Soft Drv Speed – 0
Time – 0.0s Index - 1
Screen 4.2.d10
Screen 4.2.d10 displays three parameters.
a) Soft Drv Speed: This is the DC motor speed during soft start.
b) Time: This is a time parameter in seconds. During this time DC motor will rotate in soft start mode.
c) Index: This parameter is an integer value to select different stitch densities during soft start. But in Screen 4.2.d10 this parameter will be active only if parameter Soft Drv Speed is set ‘0’ and any other value than ‘0’ will hide the Index parameter and screen will display ‘*****’, soft start operation will be controlled both by Soft head speed parameter and DC motor speed parameter. Otherwise only Index parameter and Soft head speed parameter will control the soft start operation.
Press key
F1
to enter next Screen 4.2.d11.
Dense head Speed – 3
Screen 4.2.d11
Dense head Speed parameter is the speed value for sewing head motor during the dense stitch operation after soft start. Similar to back tack and soft start, stitch density may be controlled with Dense head Speed and Index or Dense head speed and Dense drive speed parameters as mentioned below in
Screen 4.2.d12. Press key
F1
to enter next Screen 4.2.d12.
Revised 09 /2005
E-mail: [email protected]; [email protected] ; website: www.amfreece.com
Phones: +420 582 309 146 (Service), +420 582 309 286 (Spare Parts) ; Fax: +420 582 360 606
1- 4 7
84-55
CONTROLS & PROGRAM DESCRIPTION
Dense Drv Speed – 0
Time – 0.0s Index - 1
Screen 4.2.d12
Screen 4.2.d12 displays three parameters.
a) Dense Drv Speed: This is the DC motor speed during dense stitching mode.
b) Time: This is a time parameter in seconds. During this time DC motor will rotate in dense
stitch mode.
c) Index: This parameter is an integer value to select different stitch densities during dense stitch mode. But in Screen 4.2.d12 this parameter will be active only if parameter Dense
Drv Speed is set ‘0’ and any other value than ‘0’ will hide the Index parameter and screen will display ‘*****’, dense start operation will be controlled both by dense head speed parameter and DC motor speed parameter. Otherwise only Index parameter and dense head speed parameter will control the dense start operation.
Press key
F1
to enter Screen 4.2.d13 for Side1 parameters.
Side1 head speed – 0
Screen 4.2.d13
Side 1 head speed is the sewing head speed selected for side1. Press key
F1
to enter next Screen
4.2.d14. This screen has two parameters. These parameters are used to control stitch density for
Side1. Parameter Side 1Drv spd is kept zero, if stitch density is intended to be controlled by index
Side 1 Drv spd – 0
Index - 1
Screen 4.2.d14
size, otherwise it will be controlled by a combination of DC motor speed to move the jig and a corresponding Side 1 head speed selected in Screen 4.2.d13.
Press key
F1
to enter Screen 4.2.d15
1- 4 8
Revised 09/2005
E-mail: [email protected]; [email protected] ; website: www.amfreece.com
Phones: +420 582 309 146 (Service), +420 582 309 286 (Spare Parts) ; Fax: +420 582 360 606
84-55
CONTROLS & PROGRAM DESCRIPTION
5.3.3 PROGRAM FUNCTIONS
Function used – 2
Edit – f1 Press F3
Screen 4.2.d15
Screen 4.2.d15 displays function selection. Total number of 6 functions may be used in a single program. There are three types of functions that may used in a program.
1.
Corner
2.
Fly back
3.
Cycle End
There are two parameters on this screen.
Function used – This is the number of functions used in a program. If this parameter is set to ‘0’ that means no function has been used and it will not be possible to edit a function. For example if this parameter is set ‘2’ that means two functions are used and to edit these function parameters, first select f.. with the help of key
F6
and then press key
F3
to make any changes to the function related parameters by entering Screen 4.2.e1. pressing key
F1
will enter into Screen 4.2.d16. This screen also displays two parameters.End Knife Dl is delay for knife operation. Unlike Start Knife
FEnd Knife Dl – No
End Back tack - Yes
Screen 4.2.d16
delay (Screen 4.2.d3) this is only a tape function, it cannot be adjusted with time. If this parameter is selected ‘Yes’ then knife operation will stop at the start edge of cycle end tape, if selected ‘No’ then it will stop at trailing edge of the tape. Other parameter is a selection of Back Tack at the end of cycle. If this parameter is selected ‘No’ then dense stitch parameters in Screen 4.2.d9 to Screen
4.2.d12 will be automatically applied at the cycle end.
If this parameter is selected ‘Yes’ then pressing key
F1
will continue from Screen 4.2.d17 for back tack parameters at cycle end.
End Fw Hd Spd – 3
Screen 4.2.d17
This parameter defines the sewing head speed during forward movement of jig in back tack. Press key
F1
to enter into other parameters related to back tack at end of cycle in Screen 4.2.d18. this
Revised 09 /2005
E-mail: [email protected]; [email protected] ; website: www.amfreece.com
Phones: +420 582 309 146 (Service), +420 582 309 286 (Spare Parts) ; Fax: +420 582 360 606
1- 4 9
84-55
CONTROLS & PROGRAM DESCRIPTION
to enter Screen 4.2.d23.
screen displays three parameters used to control stitch density for the back tack at the cycle end.
End Fwd Drv Spd – 0
Time – 0.0s Index - 1
Screen 4.2.d18
a) End Fwd Drv Spd: This is the DC motor speed during forward movement of back tack at cycle end. (This parameter is set for jig movement from point ‘C’ to ‘End’ in ‘Z Type’ back Tack.
And is not active in case of ‘C Type’ back tack.) b) Time: This is a time parameter in seconds. During this time DC motor will rotate for forward movement.
c) Index: This parameter is an integer value to select different stitch densities during this mode.
But in Screen 4.2.d18 this parameter will be active only if parameter End Fwd Drv Spd is set
‘0’ and any other value than ‘0’ will hide the Index parameter and screen will display ‘*****’, this operation will be controlled both by End Fwd Hd Spd parameter and DC motor speed parameter. Otherwise only Index parameter and End Fwd Hd Spd parameter will control this operation.
Side 1
A
Back Tack
C
C
Side 1
Side 1
No Stitch
Stitch
End
Back Tack
B
B
Press key
F1
to enter into next Screen 4.2.d19.
End BT Hd spd – 4
End BT Drv spd – 4
Screen 4.2.d19
1- 5 0
Revised 09/2005
E-mail: [email protected]; [email protected] ; website: www.amfreece.com
Phones: +420 582 309 146 (Service), +420 582 309 286 (Spare Parts) ; Fax: +420 582 360 606
84-55
CONTROLS & PROGRAM DESCRIPTION
Screen 4.2.d19 displays two parameters.
a)
End BT Drv Spd: This is the speed of DC motor set during back tack operation at the cycle end.
b)
End BT Hd Spd: This is the speed parameter set for the sewing head motor when the jig is moving for back tack operation at the end of cycle end. Press key
F1
to enter into next
Screen 4.2.d20.
End Feed out – No
End Rev Feed - No
Screen 4.2.d20
There are certain jigs for which it is required to move the jig forward or backward after the completion of cycle. To have this feature included in our program it is necessary to select End Feed out –
Yes. If this parameter is selected ‘No’ then other parameter End Rev Feed has no significance. When the other parameter End Rev Feed is selected ‘Yes’ then after the completion of cycle DC motor will rotate the jig in reverse otherwise in forward direction and the sewing head motor stands still.
Press key
F1
to enter into Screen 4.2.d21.
End Feed out
Time – 0.0s
Screen 4.2.d21
This parameter defines the time for how long DC motor should run for the feed out parameter defined in Screen 4.2.d20. Press key
F1
to enter into Screen 4.2.d22.
Jig Flap Use - Yes
Screen 4.2.d22
To keep the jig flap up at time of cycle start and cycle end this parameter must be set to ‘Yes’. If this parameter is set ‘No’, then jig will not be ejected automatically after the cycle end. Press key
F1
to enter Screen 4.2.d23.
Photocell Retry
Quantity - 00
Screen 4.2.d23
Revised 09 /2005
E-mail: [email protected]; [email protected] ; website: www.amfreece.com
Phones: +420 582 309 146 (Service), +420 582 309 286 (Spare Parts) ; Fax: +420 582 360 606
1- 5 1
84-55
CONTROLS & PROGRAM DESCRIPTION
Photocell retry is a time parameter in milliseconds. This time is a delay in execution of signal to the control system after the tape is sensed by the photocell. This parameter helps to eliminate inaccuracies in sensing of tape due to uneven response at the edges of tapes and sensing begins after the tape edge has been crossed. Press key
F1
to enter Screen 4.2.d24.
Spool Check – No
Spool Warn No - 00
Screen 4.2.d24
This is an optional feature and may not be displayed for certain machines and may not be active even if it is displayed. Spool Check set to ‘Yes’ and fed a value for Spool warn will indicate after specified number of spool cycles have been crossed to warn that thread will be finished soon in the bobbin.
Press key
F1
to enter Screen 4.2.d25.
Jig Align On – No
Jig Align Qty - 00
Screen 4.2.d25
This parameter is used to align the jig at any stage of running cycle. When the jig is moving and Jig
Align On parameter is set ‘Yes’ if snubber switch operates jig align cylinder will operate for a time mentioned in parameter Jig Align Quantity. If Jig Align On is set ‘No’ then the parameter Jig Align
Quantity will not activate. Press key
F1
to enter Screen 4.2.d26.
Pgm BT Type – C
Fun BT Type - C
Screen 4.2.d26
Screen 4.2.d26 defines the type of back parameter. It could be a ‘C’ type back tack or ‘Z’ type back tack. Parameter Pgm BT Type defines the type of back tack for the cycle start and cycle end. Parameter Fun BT Type define the type of back tack within a function. If more than one function are used in a program then type selected in this parameter would be applicable for all the functions. Press key
F1
to enter Screen 4.2.d27.
Save Program – 2
F3 – Yes F4 - No
1- 5 2
Screen 4.2.d27
Revised 09/2005
E-mail: [email protected]; [email protected] ; website: www.amfreece.com
Phones: +420 582 309 146 (Service), +420 582 309 286 (Spare Parts) ; Fax: +420 582 360 606
84-55
CONTROLS & PROGRAM DESCRIPTION
In Screen 4.2.d27 press key
F3
to save the program or press key
F4
to retrieve the previously entered parameters and enter to program edit mode in Screen 4.2.
5.3.3A FUNCTION TYPES:
There are total three types of functions that can be programmed in any Program.
a) Cor(0) – Corner b) Fly(1) – Fly Back c) Cy End(2) – Cycle End
a ) C o r n e r T y p e F u n c t i o n ( C o r ) :
In Screen 4.2.d15, if a value other than zero is set for parameter Function used, then it is possible to edit parameters of selected function f.. by pressing key
F3
and it will enter Screen
4.2.de1
Fun Type: 0 – Cor
In f1 head spd - 4
Screen 4.2.e1
In this screen if parameter “Fun Type” is set ‘0’ that means a corner. Select value for function number ‘f..’ for which parameters need to be edited. Parameter “head spd” is sewing head speed for the selected function number. Press key
F1
to enter Screen 4.2.e2.
In f1 Drv Spd – 0
Index - 1
Screen 4.2.e2
This screen has the parameters to control stitch density for entry zone of a function. If stitch density is intended to be controlled with index cylinders then parameter “In f1 Drv Spd” which is the DC motor speed is set ‘0’. Any value other than ‘0’ will hide the Index parameter and
“*****” will be displayed. Press key
F1
to enter Screen 4.2.e3.
f1 Head Speed – 4 f1 Drive Speed - 1
Screen 4.2.e3
This screen displays two parameters. Parameter “f1 Head Speed” defines sewing head motor speed and parameter “f1 Drive Speed” defines DC motor speed during the corner. But these
Revised 09 /2005
E-mail: [email protected]; [email protected] ; website: www.amfreece.com
Phones: +420 582 309 146 (Service), +420 582 309 286 (Spare Parts) ; Fax: +420 582 360 606
1- 5 3
84-55
CONTROLS & PROGRAM DESCRIPTION
parameters are not active if parameter “Type” in Screen 4.2.d1 is set ‘2’ which means Point
Collar. These parameters are active only in case of round corner. Press key
F1
to enter Screen
4.2.e4.
Needle Stop position
Up
Screen 4.2.e4
In point corner program this parameter is used to define the position of needle. It may be set to
‘Up’ or ‘Down’. Press key
F1
to enter Screen 4.2.e5.
b ) F l y B a c k F u n c t i o n ( F l y ) :
There are certain flaps where stitching needs to be avoided in between a continuous sewing cycle. This function helps to leave that zone unstitched.
In Screen 4.2.e1, if parameter “Fun Type” is set ‘1’ that means a fly back function and pressing key
F1
will enter into Screen 4.2.e.fb1 for fly back parameters.
f1 Back tack – Fly
In – No Out - No
Screen 4.2.e.fb 1
This screen displays Back tack selection for fly back function. In and Out selected Yes/No define back tack required or not in entry and exit zones of a fly back function respectively. The head motor will stop for fly back, needle will stay in up position and forward drive parameters will remain the same as defined in Screen 4.2.e3 (f1 Drive Speed).
The back tack parameters at the time of entry will remain the same as for starting parameters of back tack defined in Screen 4.2.d6,7 & 8 and back tack parameters at the time of exit will remain the same as for parameters of end back tack defined in Screen 4.2.d17,18 & 19. Press key
F1
to enter Screen 4.2.e.fb2.
In f1 Thread Trim
Time – 0.0s
Screen 4.2.e.fb 2
1- 5 4
Revised 09/2005
E-mail: [email protected]; [email protected] ; website: www.amfreece.com
Phones: +420 582 309 146 (Service), +420 582 309 286 (Spare Parts) ; Fax: +420 582 360 606
84-55
CONTROLS & PROGRAM DESCRIPTION
This screen defines the time delay parameter set in seconds and thread trim cylinder will activate after this time parameter once jig enters the fly back zone. Press key
F1
to enter Screen
4.2.e.fb3.
f1 Soft Start
Yes
Screen 4.2.e.fb 3
This parameter activates soft start feature for a selected function number f.. If this parameter is set ‘No’ then parameter related to soft start have no significance. Press key
F1
to enter Screen
4.2.e.fb4.
f1 Soft Head Spd – 2
Screen 4.2.e.fb 4
Parameter ‘f1 Soft Head Spd’ defines sewing motor head speed for soft start operation in a function. Press key
F1
to enter Screen 4.2.e.fb5.
f1 Soft Drv Spd – 0
Time – 0.0s Index - 1
Screen 4.2.e.fb 5
Stitch density control is maintained by either parameter ‘f1 Soft Drv Spd’ the DC motor speed, if this parameter set ‘0’ then Index becomes active as explained in previous cases. Pressing key
F1
will enter into Screen 4.2.e.5.
f1 Out Head Spd – 2
Screen 4.2.e.fb 6
The parameter “f1 Out Head Spd” is defines sewing head motor speed when the jig is moving out of function zone. Press key
F1
to enter Screen 4.2.e6.
Revised 09 /2005
E-mail: [email protected]; [email protected] ; website: www.amfreece.com
Phones: +420 582 309 146 (Service), +420 582 309 286 (Spare Parts) ; Fax: +420 582 360 606
1- 5 5
84-55
CONTROLS & PROGRAM DESCRIPTION
The parameter “f1 Out Drv Spd” is defines DC motor speed when the jig is moving out of function zone. Press key
F1
to enter Screen 4.2.e7.
f1 Side2 Head Spd –2
Screen 4.2.e.fb 7
The parameter “f1 Side2 Head Spd” is defines sewing head motor speed when the jig next side after moving out of a function zone. Press key
F1
to enter Screen 4.2.e8.
f1 Side2 Drv Spd – 0
Index - 1
Screen 4.2.e.fb 8
The parameter “f1 Side2 Drv Spd” defines DC motor speed when the jig enter into the next side after moving out of a function zone. In Screen 4.2.e7 and Screen 4.2.e8 display will automatically change the Side number depending on the function number f.. If f1 is selected Side 2 will be displayed and f2 means Side3 will be displayed.
Figure below explains a typical example of stitching using four functions. The four functions are Fly Back, Corner 1, Corner 2 and Cycle End.
1
Side 1
Side 1
Side 2
Side 3
Side 4
2
Fly Back
3
Side 2
4
Tape 2-Function 1-In
(Fly Back)
Tape 3-Function 1-Out
(Fly Back)
Tape 6-Function 3-Int
(Corner 2)
Tape 7-Function 3-Out
(Corner 2)
5
Side 3
6
7
Side 4
8
1- 5 6
Revised 09/2005
E-mail: [email protected]; [email protected] ; website: www.amfreece.com
Phones: +420 582 309 146 (Service), +420 582 309 286 (Spare Parts) ; Fax: +420 582 360 606
84-55
CONTROLS & PROGRAM DESCRIPTION
Press key
F1
to enter Screen 4.2.end and the parameters will be updated and will enter back to
Save f1 Param
Screen 4.2.end
Screen 4.2.d15 to edit parameters for some other function number.
5.2 BATCH PROGRAMMING
Looking at Screen 4, if we press key
F5
, this will enter into Screen 4.3.1 for Batch Sequence
Mode. This mode may be used to run different program types for different parts.
Batch Seq. - Yes/No
No. of Batch - 10
Screen 4.3.1
This screen has two parameters, Batch Seq. and No. of Batch. Parameter “Batch Seq” if selected
“yes” then other parameter which defines the number of batches to used will be entered. There could be maximum number of 10 batch numbers. Press key
F1
to enter into next Screen 4.3.2.
Set Pgm in Batch
Seq. 1 3 4 ……
Screen 4.3.2
Depending on the value of “No. of Batch” in Screen 4.3.1 the same number of digits would be displayed in Screen 4.3.2. If this parameter selected “5” that means we want to run five different programs. The programs will run turn by turn depending on the sequence selected. A sequence 4 3 6 8 7 means Pgm 4, will be followed by 3, 6, 8 and 7 respectively.
Pressing key
F1
will enter back to Screen 4.
Revised 09 /2005
E-mail: [email protected]; [email protected] ; website: www.amfreece.com
Phones: +420 582 309 146 (Service), +420 582 309 286 (Spare Parts) ; Fax: +420 582 360 606
1- 5 7
84-55
CONTROLS & PROGRAM DESCRIPTION
DIAGRAM DISPLAY
1- 5 8
Revised 09/2005
E-mail: [email protected]; [email protected] ; website: www.amfreece.com
Phones: +420 582 309 146 (Service), +420 582 309 286 (Spare Parts) ; Fax: +420 582 360 606
CONTROLS & PROGRAM DESCRIPTION
DIAGRAM DISPLAY
84-55
Revised 09 /2005
E-mail: [email protected]; [email protected] ; website: www.amfreece.com
Phones: +420 582 309 146 (Service), +420 582 309 286 (Spare Parts) ; Fax: +420 582 360 606
1- 5 9
84-55
CONTROLS & PROGRAM DESCRIPTION
DIAGRAM DISPLAY
1- 6 0
Revised 09/2005
E-mail: [email protected]; [email protected] ; website: www.amfreece.com
Phones: +420 582 309 146 (Service), +420 582 309 286 (Spare Parts) ; Fax: +420 582 360 606
CONTROLS & PROGRAM DESCRIPTION
DIAGRAM DISPLAY
84-55
Revised 09 /2005
E-mail: [email protected]; [email protected] ; website: www.amfreece.com
Phones: +420 582 309 146 (Service), +420 582 309 286 (Spare Parts) ; Fax: +420 582 360 606
1- 6 1
84-55
CONTROLS & PROGRAM DESCRIPTION
PARAMETERS VALUE CHART & DEFAULT PROGRAMS
1- 6 2
Revised 09/2005
E-mail: [email protected]; [email protected] ; website: www.amfreece.com
Phones: +420 582 309 146 (Service), +420 582 309 286 (Spare Parts) ; Fax: +420 582 360 606
CONTROLS & PROGRAM DESCRIPTION
PARAMETERS VALUE CHART & DEFAULT PROGRAMS
84-55
Revised 09 /2005
E-mail: [email protected]; [email protected] ; website: www.amfreece.com
Phones: +420 582 309 146 (Service), +420 582 309 286 (Spare Parts) ; Fax: +420 582 360 606
1- 6 3
84-55
CONTROLS & PROGRAM DESCRIPTION
PARAMETERS VALUE CHART & DEFAULT PROGRAMS
1- 6 4
Revised 09/2005
E-mail: [email protected]; [email protected] ; website: www.amfreece.com
Phones: +420 582 309 146 (Service), +420 582 309 286 (Spare Parts) ; Fax: +420 582 360 606
CONTROLS & PROGRAM DESCRIPTION
PARAMETERS VALUE CHART & DEFAULT PROGRAMS
84-55
Revised 09 /2005
E-mail: [email protected]; [email protected] ; website: www.amfreece.com
Phones: +420 582 309 146 (Service), +420 582 309 286 (Spare Parts) ; Fax: +420 582 360 606
1- 6 5
84-55
PNEUMATICS
-
-
-
-
-
-
-
-
6.0 PNEUMATICS
The pneumatics are switched by a bank of solenoids mounted on the rear out side of the electrical control box. This bank of solenoids control the following:
Jig Flap
Stitch Size Adjuster 1
Stitch Size Adjuster 2
Jig Drive/Presser Foot
Knife
Jig Eject
Jig Alignment
Jig Drive Clamp
Air is normally on the B lines and is switched to A line when the solenoid is energized. Refer to the pneumatics diagram on page 1-68
6.1 S1 JIG FLAP
When the solenoid is energized this allows air through line A1 causing jig flap to lift.
6.2
S3 STITCH SIZE ADJUSTERS 1 & 2
When both stitch size adjuster 1 and 2 are energized the full stitch is achieved. When stitch size adjuster 1 is energized and stitch size adjuster 2 is de-energized then a medium dense is achieved.
When both stitch size adjuster 1 and 2 are de-energized then a small dense is achieved. See section
4.2 Stitch Size Adjustment.
6.3
S4 JIG DRIVE/PRESSER FOOT
When this solenoid is energized air flows through line A4 causing the jig drive cylinder to operate and grip the jig. When the solenoid is de-energized air flows through both lines of B4 causing drive to return and presser foot to lift. There is no air to presser foot through line A4, as this is a spring return cylinder.
6.4
S5 KNIFE
When this solenoid is energized air flows thro’ line A5 causing the knife to engage. When the solenoid is de-energized air through line B5 causes the knife to return to up position.
6.5
S6 JIG EJECT
When this solenoid is energized air flows thro’ line A6 causing the jig cylinder to operate. When the solenoid is de-energized air through line B6 causes the jig cylinder to return to ‘A’ position.
6.6
WASTE DISPOSAL
Ensure jets are directed in area of cut-out, otherwise trimmed material will not be directed down chute.
1- 6 6
Revised 09/2005
E-mail: [email protected]; [email protected] ; website: www.amfreece.com
Phones: +420 582 309 146 (Service), +420 582 309 286 (Spare Parts) ; Fax: +420 582 360 606
84-55
PNEUMATICS
6.7
S7 JIG ALIGNMENT
When solenoid is energized, air flows thro’ line A7. This causes the jig align cylinder to activate and pull on the snubber arm block and straightens out the jig. An air pressure regulator is fitted in line to control the force applied to the snubber block. When the solenoid is de-energized air flows through
B7 releasing the pressure on the snubber block.
6.8
S9 JIG DRIVE CLAMP
When the solenoid is energized air flows through line A8 causing the jig drive clamp cylinder to operate. This clamps the drive bearing outer race. When this solenoid is de-energized air flows through B8 causing the cylinder to release the clamp ring.
CAUTION: THE JIG DRIVE CLAMP CYLINDER MUST NOT BE ACTIVATED IF THE DC MO-
TOR AND CLUTCH ARE ACTIVATED.
6.9
S10 AIR BLOWERS
There are 3 blowers on the machine:
One to the throat plate, one to cloth disposal and one to the presser foot side blower. The three air regulators located onside the cabinet door individually control these. These are labeled as TP, CD and PF respectively. The blowers only work when a signal is sent from the knife solenoid valve to the pilot valve.
7.0 AIR FLOW CONTROLS
Some cylinders are fitted with flow control valves to adjust the speed of operation of a cylinder. For example the drive wheel cylinder (Figure 4.0) must be adjusted so that the drive wheel is brought smoothly into contact with the edge of the jig. Otherwise damage may be caused to the jig.
7.1 AIR PRESSURE REGULATORS AND WATER FILTERS
When the air is released to the machine from the main pneumatic line, full line pressure is fed into the regulator. Regulator should be set to 80PSI. The gauge on the machine shows the pressure out of the regulator, this supplies air to the
Revised 09 /2005
E-mail: [email protected]; [email protected] ; website: www.amfreece.com
Phones: +420 582 309 146 (Service), +420 582 309 286 (Spare Parts) ; Fax: +420 582 360 606
1- 6 7
84-55
PNEUMATIC DIAGRAM
1- 6 8
Revised 09/2005
E-mail: [email protected]; [email protected] ; website: www.amfreece.com
Phones: +420 582 309 146 (Service), +420 582 309 286 (Spare Parts) ; Fax: +420 582 360 606
HEAD SETTING PROCEDURES
7.1
ADJUSTING THE FEED TIMING
84-55
7.2
NEEDLE-TO-HOOK RELATIONSHIP
Revised 09 /2005
E-mail: [email protected]; [email protected] ; website: www.amfreece.com
Phones: +420 582 309 146 (Service), +420 582 309 286 (Spare Parts) ; Fax: +420 582 360 606
1- 6 9
84-55
7.3
LUBRICATION
HEAD SETTING PROCEDURES
7.4
ADJUSTING THE AMOUNT OF OIL (OIL SPLASHES) IN THE HOOK
1- 7 0
Revised 09/2005
E-mail: [email protected]; [email protected] ; website: www.amfreece.com
Phones: +420 582 309 146 (Service), +420 582 309 286 (Spare Parts) ; Fax: +420 582 360 606
HEAD SETTING PROCEDURES
84-55
Revised 09 /2005
E-mail: [email protected]; [email protected] ; website: www.amfreece.com
Phones: +420 582 309 146 (Service), +420 582 309 286 (Spare Parts) ; Fax: +420 582 360 606
1- 7 1
84-55
HEAD SETTING PROCEDURES
7.5
CLOTH CUTTING KNIFE
1- 7 2
Revised 09/2005
E-mail: [email protected]; [email protected] ; website: www.amfreece.com
Phones: +420 582 309 146 (Service), +420 582 309 286 (Spare Parts) ; Fax: +420 582 360 606
TRIMMING AND SYNCHRONIZER
8.1
REPLACING THE MOVING KNIFE
(DLM-5400N-7)
84-55
8.2
ADJUSTING THE INITIAL POSITION
OF THE MOVING KNIFE (DLM-5400N-7)
Revised 09 /2005
E-mail: [email protected]; [email protected] ; website: www.amfreece.com
Phones: +420 582 309 146 (Service), +420 582 309 286 (Spare Parts) ; Fax: +420 582 360 606
1- 7 3
84-55
TRIMMING AND SYNCHRONIZER
8.3
REPLACING THE COUNTER KNIFE
(DLM-5400N-7)
8.4
ADJUSTING THE PRESSURE OF THE
COUNTER KNIFE
1- 7 4
Revised 09/2005
E-mail: [email protected]; [email protected] ; website: www.amfreece.com
Phones: +420 582 309 146 (Service), +420 582 309 286 (Spare Parts) ; Fax: +420 582 360 606
TRIMMING AND SYNCHRONIZER
8.5
SYNCHRONIZER SETTING
84-55
Revised 09 /2005
E-mail: [email protected]; [email protected] ; website: www.amfreece.com
Phones: +420 582 309 146 (Service), +420 582 309 286 (Spare Parts) ; Fax: +420 582 360 606
1- 7 5
84-55
ELECTRICAL DIAGRAM
1- 7 6
Revised 09/2005
E-mail: [email protected]; [email protected] ; website: www.amfreece.com
Phones: +420 582 309 146 (Service), +420 582 309 286 (Spare Parts) ; Fax: +420 582 360 606
ELECTRICAL DIAGRAM
84-55
Revised 09 /2005
E-mail: [email protected]; [email protected] ; website: www.amfreece.com
Phones: +420 582 309 146 (Service), +420 582 309 286 (Spare Parts) ; Fax: +420 582 360 606
1- 7 7
84-55
ELECTRICAL DIAGRAM
1- 7 8
Revised 09/2005
E-mail: [email protected]; [email protected] ; website: www.amfreece.com
Phones: +420 582 309 146 (Service), +420 582 309 286 (Spare Parts) ; Fax: +420 582 360 606
ELECTRICAL DIAGRAM
84-55
Revised 09 /2005
E-mail: [email protected]; [email protected] ; website: www.amfreece.com
Phones: +420 582 309 146 (Service), +420 582 309 286 (Spare Parts) ; Fax: +420 582 360 606
1- 7 9
84-55
ELECTRICAL DIAGRAM
1- 8 0
Revised 09/2005
E-mail: [email protected]; [email protected] ; website: www.amfreece.com
Phones: +420 582 309 146 (Service), +420 582 309 286 (Spare Parts) ; Fax: +420 582 360 606
84-55
TABLE OF CONTENTS
9.1 Stitching ...........................................................................................................................................2-2
9.2 Machine Control ...............................................................................................................................2-3
Revised 09 /2005
E-mail: [email protected]; [email protected] ; website: www.amfreece.com
Phones: +420 582 309 146 (Service), +420 582 309 286 (Spare Parts) ; Fax: +420 582 360 606
2-1
84-55
TROUBLESHOOTING
2-2
FAULT
9.1 Stitching:
9.1.1 General
9.1.2 Slip Stitching
CAUSE CORRECTION
Thread is caught in the thread path.
Tension is wrong
Thread take up spring misadjusted.
Problem with needle.
Spool spin.
Material wrongly positioned in jig.
Jig damage.
Material flagging.
Problem with needle.
Problem with the sewing hook.
Needle thread tension is too high.
Sewing head speed too high/low.
Drive speed too high/low.
Check lubrication.
Correct threading (Sec.3)
Adjust tension (Sec. 3).
Adjust the take up (Sec.
3).
Check or Replace
(Sec.3)
Fit friction washer.
Ensure all stitching is in material (Sec. 2).
Repair jig or replace jig.
Check jig is clamping material
Check for needle damage and for correct needle orientation. Check the needle size is correct for thread being used.
(Sec. 3)
Check to see if the hook point is blunt or worn.
Check the hook timing.
(Sec 7)
Decrease thread tension.(Sec. 3)
Decrease or increase the head speed (Sec 5).
Decrease or increase the drive speed. ( Sec. 5)
Revised 09/2005
E-mail: [email protected]; [email protected] ; website: www.amfreece.com
Phones: +420 582 309 146 (Service), +420 582 309 286 (Spare Parts) ; Fax: +420 582 360 606
TROUBLESHOOTING
9.1.3 Short end on top or needle unthreads
9.1.4 Thread not
trimmed.
Tension release mechanism.
Thread catcher moved.
Loose plug on solenoid lead.
Loose plug on synchronizer.
Synchronizer loose on hand wheel.
Sewing hook slipping last stitch.
Blunt trimming knife.
9.1.5 Thread not picked up.
Short end on spool due to spool spin.
Check the tension plate is functioning properly.
Reset synchronizer and timing. (Sec.8)
Reset synchronizer.
(Sec.8)
Check to see if hook is blunt or worn. Check hook timing. (Sec. 7)
Check knife. (Sec.8)
Increase bobbin thread tension.
Check friction disc.
(Sec. 3.5)
Correct as 9.1.3. 9.1.6 Spool thread picked up late after first few stitches.
9.1.7 First few stitches looped underneath.
Short end on needle thread.
Foot lift cylinder sluggish on return.
9.2 Machine Control
9.2.1 Machine Fails To
Power on
Power on plug not connected properly
Power on switch not on
Clean and lubricate assembly.
Connect properly
Turn the Switch on(SSW1) & still not power on then open the cabinet & check if voltage relay VR Green LED is off then check the wiring by wiring diagram if wiring ok Voltage relay is faulty so contact AMF
Reece for new & replace
84-55
Revised 09 /2005
E-mail: [email protected]; [email protected] ; website: www.amfreece.com
Phones: +420 582 309 146 (Service), +420 582 309 286 (Spare Parts) ; Fax: +420 582 360 606
2-3
84-55
TROUBLESHOOTING
2-4
9.2.2 Air Blower fails to start
9.2.3 All Sensors & MMI fails Power on
9.2.4 Table Lamp fails to on
9.2.5 Control Cabinet
Cooling Fan Not
Functional
Blower power on switch is off
No power to Blower motor
24 V Power supply unit not powered
Power on switch off
Lamp Bulb Blown
Lamp unit is faulty
Fan not powered
Fan is faulty
Turn the switch on
(SSW2)
Check Fuse F1 if blown then change, still not power on Check Blower
Motor supply terminals for power 220 V AC & rectify by the help of wiring diagram if wiring ok then Blower motor is faulty contact AMF
Reece for new & replace
Check Fuse F2 if Blown then Change if still no
Green LED at Power
Supply Unit then Power
Supply faulty contact
AMF Reece for new & replace
Turn on power switch at two locations one at lamp head & another at Lamp
Base
Change the bulb
Rectify by the help of wiring diagram if wiring ok then Lamp Unit faulty contact AMF Reece for new & replace
Check Fuse F3 if blown then change
Check power supply 24 V
DC at Fan Input terminals, rectify by the help of wiring diagram If still not working then fan is faulty contact AMF
Reece for new & replace
Revised 09/2005
E-mail: [email protected]; [email protected] ; website: www.amfreece.com
Phones: +420 582 309 146 (Service), +420 582 309 286 (Spare Parts) ; Fax: +420 582 360 606
84-55
TROUBLESHOOTING
9.2.6 MMI fails to power on
PLC not powered
PLC ok but MMI to PLC connections
MMI cable connection ok but still not powered on
9.2.7 DC motor for jig movement fails to functional
DC motor card in cabinet is not powered
Necessary command signals for function is missing
DC card faulty
Revised 09 /2005
E-mail: [email protected]; [email protected] ; website: www.amfreece.com
Phones: +420 582 309 146 (Service), +420 582 309 286 (Spare Parts) ; Fax: +420 582 360 606
Check fuse F4 if blown then change & check power on indication on
PLC if not rectify by the help of help of wiring diagram, if wiring ok then
PLC faulty contact AMF
Reece for new & replace
Check MMI cable connection
Chance of MMI faulty or
PLC to MMI connection
Port is faulty contact AMF
Reece for new & replace
Check Fuse F5 if Blown then Change if still not functional then check 24
V DC power at input terminals, rectify by the help of wiring diagram
Go to MMI System Check
Menu – Output test- DC drive speed 1 screen & give command for test.
While test command is on check 24 V DC between P24 sleeve wire terminal & Y31,Y33 sleeve wire terminals. If no voltage rectify by wiring diagram, if signal is ok then check DC voltage at M+ & M- sleeve terminals turn the speed potentiometer on card to anticlockwise DC voltage at M+ & M- should increase. if it increases check the DC motor power cable & rectify by wiring diagram.
2-5
84-55
TROUBLESHOOTING
2-6
DC motor is faulty
9.2.8 Thread trim engagement mechanism fails to work
Trim Solenoid not powered
Thread trim Relay faulty
Trim solenoid faulty
9.2.8 Error message on
MMI like “E: Emergency
Stop”
Required safety signals missing
9.2.9 Sew cycle fails to Start push button
Voltage between M+ &
M- sleeve wire terminal doesn’t increase DC drive card is faulty contact AMF Reece for new & replace
DC motor power cable is ok but motor doesn’t run then DC motor is faulty contact AMF Reece for new & replace
Check fuse F6 if blown then replace,
Go to MMI System Check
Menu – Output test-
Thread trim relay test screen turn the S/V on,
Check 24 VDC at N24 &
Y26 sleeve wire terminals at relay. If no voltage then rectify wiring by wiring diagram. If voltage is there then check relay(RLY) if relay faulty or in same cases but very rarely relay base can also be faulty if so contact
AMF Reece for new & replace
Check cable for 24 VDC for trim solenoid mounted at sewing head if cable is ok then solenoid is faulty so contact AMF
Reece for new & replace
Follow the error message
& rectify the cause
Go to MMI System Check
Revised 09/2005
E-mail: [email protected]; [email protected] ; website: www.amfreece.com
Phones: +420 582 309 146 (Service), +420 582 309 286 (Spare Parts) ; Fax: +420 582 360 606
advertisement
* Your assessment is very important for improving the workof artificial intelligence, which forms the content of this project