Graymills Fluid Conditioning Oil Coalescer OSEP-2 Owner's Manual
Add to my manuals
4 Pages
Graymills Fluid Conditioning Oil Coalescer OSEP-2 is a reliable and efficient solution for removing tramp oil and suspended solids from water-based coolants. It's designed for continuous operation and features an automatic air bleeder, a fluid conditioning filter vessel, and a coalescing chamber for effective oil removal. The OSEP-2 is easy to install and maintain, requiring only a level surface, plant air, and a coolant sump/tank connection. It operates on standard cartridges and comes with a one-year warranty.
advertisement
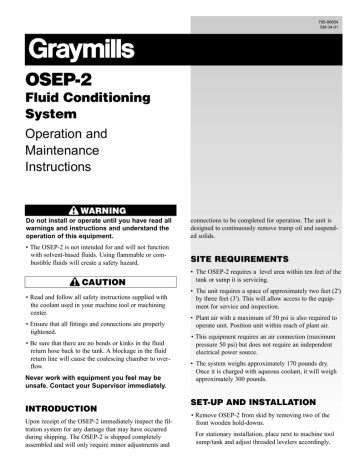
795-90654
GM 04-01
OSEP-2
Fluid Conditioning
System
Operation and
Maintenance
Instructions
Do not install or operate until you have read all warnings and instructions and understand the operation of this equipment.
• The OSEP-2 is not intended for and will not function with solvent-based fluids. Using flammable or combustible fluids will create a safety hazard.
• Read and follow all safety instructions supplied with the coolant used in your machine tool or machining center.
• Ensure that all fittings and connections are properly tightened.
• Be sure that there are no bends or kinks in the fluid return hose back to the tank. A blockage in the fluid return line will cause the coalescing chamber to overflow.
Never work with equipment you feel may be unsafe. Contact your Supervisor immediately.
INTRODUCTION
Upon receipt of the OSEP-2 immediately inspect the filtration system for any damage that may have occurred during shipping. The OSEP-2 is shipped completely assembled and will only require minor adjustments and connections to be completed for operation. The unit is designed to continuously remove tramp oil and suspended solids.
SITE REQUIREMENTS
• The OSEP-2 requires a level area within ten feet of the tank or sump it is servicing.
• The unit requires a space of approximately two feet (2') by three feet (3'). This will allow access to the equipment for service and inspection.
• Plant air with a maximum of 50 psi is also required to operate unit. Position unit within reach of plant air.
• This equipment requires an air connection (maximum pressure 50 psi) but does not require an independent electrical power source.
• The system weighs approximately 170 pounds dry.
Once it is charged with aqueous coolant, it will weigh approximately 300 pounds.
SET-UP AND INSTALLATION
• Remove OSEP-2 from skid by removing two of the front wooden hold-downs.
For stationary installation, place next to machine tool sump/tank and adjust threaded levelers accordingly.
For portable installation, remove threaded levelers and replace with heavy-duty dual wheel swivel casters
(provided).
• Connect the 3/8" clear suction skimmer hose to the inlet strainer basket and clamp.
• Connect 1" oil discharge hose to clean coolant outlet on side of OSEP-2 tank. Hoses have been provided in 10 foot lengths. Do not exceed 10 feet. However, if all your sumps can be serviced with shorter suction and discharge hoses, cut hoses as short as possible for optimum performance.
• Close all system drain valves.
• Make sure clear inlet strainer gasket is in place and bowl is secure.
• Open fluid conditioning filter vessel. Make sure filter cartridge is securely in place.
• Lift the oil intake nozzle (orange and blue) straight up even with top.
• Fill the coalescing chamber and fluid conditioning filter vessel (approximately 17 US gallons) with fresh charge of coolant used for normal machining operation.
• Close fluid conditioning filter vessel and tighten wing nuts.
• Open black cap on auto air bleeder on fluid conditioning filter vessel lid.
• Be sure that machine tool sump/tank is full (especially on low profile coolant tanks).
• Locate floating skimmer in coolant sump/tank as close to machine tool discharge as possible. Use the handy hose spring clamp to stabilize and/or secure the floating skimmer in place. Be sure the skimmer is floating with the proper side up and is level to assure optimum flow through the OSEP-2 system.
• Clamp the return hose to the sump/tank, as far away from the skimmer as possible. Be sure to leave an air gap for positive flow and to provide the best possible circulation and accelerate turnover.
• Place an oil recovery pail, supplied by customer, under oil outlet (1/2" hose).
• Close 1/4" ball valve on air regulator.
• Install 1/4" male air fitting on 1/4" ball valve and connect air line. (Air fitting is supplied by customer.)
START UP
• Open 1/4" ball valve on air regulator.
• Be sure regulator is set at 50 psi. Higher or lower pressure will adversely effect system performance. Do not use an air lubricator.
• Check system for leaks.
• Once system has run for approximately 10 minutes, adjust oil intake nozzle in coolant sump/tank to approximately 3/16" above coolant level.
BE PATIENT! The OSEP-2 may take several hours or even days to begin discharging tramp oil. This is due to the fact that the system must reach its saturation point based on the amount of tramp oil in each machine.
OPERATION & MAINTENANCE
Turn unit off prior to servicing.
The OSEP-2 is designed to run continuously and unattended. A periodic check of the oil recovery pail is needed to prevent an overflow situation. Use proper judgement when leaving the unit unattended for long periods.
Be sure to follow all federal and local EPA requirements when disposing of waste oil.
Cycle Times
Cycle times will vary due to tramp oil levels in coolant tank. Run OSEP-2 until sump is noticeably free of floating tramp oil.
Servicing inlet strainer basket
Periodically remove clear canister on front of unit and check stainless mesh screen. Wash out and replace, return to normal operation.
Servicing fluid conditioning filter
Periodically monitor the pressure gauge on the inlet of the fluid conditioning filter. When the gauge reads 15 psi change the filter cartridge.
Service instructions:
• Close 1/4" ball valve on air supply.
• Remove wing nuts on the vessel. Remove lid.
• Lift out cartridge and replace.
• Inspect and clean vessel rim gasket.
• Return system to normal operation.
Diaphragm Pump
Refer to manual 795-08691 enclosed with this unit for pump operation/maintenance. For replacement pump use DPHG-50 Diaphragm Pump 1/2", 1/1 Hytrel.
SUCTION
STRAINER
BOWL
INSTALLATION DIAGRAM
DIRTY COOLANT INLET
CLEAN COOLANT RETURN
FILTER
VESSEL
AIR OPERATED
DIAPHRAGM PUMP
(DPHG-50)
OIL
COALESCER
COOLANT SUMP/TANK
OIL
RECOVERY
PAIL
1/4" FNPT PLANT AIR INLET
MAX 50 PSI REQUIRED
FLOATING
SKIMMER
INLET
HEADER
REPLACEMENT CARTRIDGES
767-90700 Standard cartridge
767-90706 Optional cartridge for fine particulate removal
767-90707 Optional cartridge for extra-fine particulate removal
Graymills Corporation warrants that the equipment manufactured and delivered, when properly installed and maintained, shall be free from defects in workmanship and will function as quoted in the published specification. Graymills does not warrant process performance, nor assume any liability for equipment selection, adaptation, or installation.
Warranty does not apply to damages or defects caused by shipping, operator carelessness, misuse, improper application or installation, abnormal use, use of add-on parts or equipment which damages or impairs the proper function of the unit, and modifications made to the unit.Warranty does not apply to expendable parts needing replacement periodically due to normal wear and tear.
A new Warranty period shall not be established for repaired or replaced materials or products. Such items shall remain under
Warranty for only the remainder of the Warranty period of the original material or product.
THE FOREGOING WARRANTIES ARE IN LIEU OF ALL
OTHER WARRANTIES, WHETHER ORAL, WRITTEN,
EXPRESSED, IMPLIED OR STATUTORY. GRAYMILLS COR-
PORATION MAKES NO OTHER WARRANTY OF ANY KIND,
EXPRESS OR IMPLIED. ALL IMPLIED WARRANTIES OF
WARRANTY
MERCHANTABILITY AND FITNESS FOR A PARTICULAR
PURPOSE WHICH EXCEED THE AFORESTATED OBLIGA-
TION ARE HEREBY DISCLAIMED BY GRAYMILLS COR-
PORATION AND EXCLUDED FROM THIS SALE. Graymills warranty obligations and Buyer remedies (except to title), are solely and exclusively stated herein. In no case will Graymills be liable for consequential damages, loss of production, or any other loss incurred due to interruption of service.
Graymills’ obligation under this Warranty shall be limited to:
(a) Repairing or replacing (at Graymills sole discretion) any nonconforming or defective component within one year from the date of shipment from Graymills.
(b) Repairing or replacing (at Graymills sole discretion), components supplied by, but not manufactured by Graymills, to the extent of the warranty given by the original manufacturer.
Buyer must give Graymills prompt notice of any defect or failure.
If you believe you have a Warranty claim, contact Graymills at
(773)248-6825. Any returned material must have an RMA number on the outside of the package and shipped prepaid or shipment will be refused. Graymills will promptly examine the material and determine if it is defective and within the Warranty period.
Graymills Corporation 3705 N. Lincoln Avenue Chicago, IL 60613-3594 (773) 248-6825 FAX (773) 477-8673 www.graymills.com
advertisement
* Your assessment is very important for improving the workof artificial intelligence, which forms the content of this project
Related manuals
advertisement