Trio MC405 Quick Connection Manual
Add to My manuals8 Pages
Trio MC405 is a versatile motion coordinator with a range of capabilities that cater to diverse industrial automation needs. It offers 5 encoder connections, which can be utilized for either 6MHz encoder inputs or 2MHz stepper outputs. The device features 8 registration inputs, 8 bi-directional I/O, 2 analog inputs, 4 analog outputs, and a watchdog relay. It supports various communication protocols, including CANopen, Modbus-RTU, Ethernet IP, and Modbus-TCP, enabling seamless integration into different control systems.
advertisement
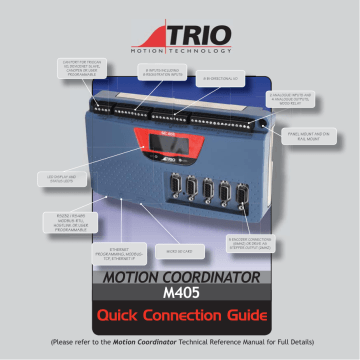
CAN PORT FOR TRIOCAN
I/O, DEVICENET SLAVE,
CANOPEN OR USER
PROGRAMMABLE
8 INPUTS INCLUDING
8 REGISTRATION INPUTS
8 BI-DIRECTIONAL I/O
2 ANALOGUE INPUTS AND
4 ANALOGUE OUTPUTS,
WDOG RELAY
PANEL MOUNT AND DIN
RAIL MOUNT
RS232 / RS485
MODBUS-RTU,
HOSTLINK OR USER
PROGRAMMABLE
MICRO SD CARD
5 ENCODER CONNECTIONS
(6MHZ) OR DRIVE AS
STEPPER OUTPUT (2MHZ)
ETHERNET
PROGRAMMING, MODBUS-
TCP, ETHERNET IP
MOTION
M405
Quick Connection Guide
(Please refer to the Motion Coordinator Technical Reference Manual for Full Details)
5-WAY
CONNECTOR
RJ45
CONNECTOR
This is a 5 way 3.5mm pitch connector. The connector is used both to provide the 24 Volt power to the MC405 and provide connections for I/O expansion via Trio’s CAN I/O expanders.
A 24V dc, Class 2 transformer or power source must be provided as this powers the unit.
This 24 Volt input is internally isolated from the
I/O 24 Volts and the +/-10V voltage outputs.
!
The 24V (V+) and 0V (V-) MUST be connected as they power the MC405. The MC405 is grounded via the metal chassis. A screw is provided on the chassis at the rear to allow an earth strap connection if needed. It MUST be installed on an unpainted metal plate or
DIN rail which is connected to earth. The CAN connections are optional.
V+ CAN
-H
SHIELDCAN
-L
V-
A standard ethernet connector is provided for use as the primary programming interface.
The Trio programming software, Motion Perfect 2, must be installed on a Windows based PC that is fi tted with an Ethernet connection. The IP address is displayed on the MC405 display for a few seconds after power-up or when an Ethernet cable is plugged in.
SERIAL
CONNECTIONS
I/O CONNECTOR 1
Serial Connector
6
7
8
5
3
4
1
2
Pin Function
1 RS485 Data In A Rx+
2 RS485 Data In B Rx-
3 RS232 Transmit
4 0V Serial
5 RS232 Receive
6 5V
7 RS485 Data Out Z Tx-
8 RS485 Data Out Y Tx+
Note
Serial Port #2
Serial Port #1
Serial Port #1
Serial Port #2
I/O 0V
I/O 0V
Input 0
Input 1
Input 2
Input 3
Input 4
Input 5
Input 6
Input 7
Input Pin
Optical
Input
Signal
6k8
0V Pin
Any input, 0 - 7, may be mapped to any axis as a registration input.
I/O CONNECTOR 2
Optical
Output
Control
Signal
Optical
Input
Signal
6k8
I/O 0V
I/O 24V
Input / Output Channel 8
Input / Output Channel 9
Input / Output Channel 10
Input / Output Channel 11
Input / Output Channel 12
Input / Output Channel 13
Input / Output Channel 14
Input / Output Channel 15
24V Power / I/O 8-15
24V Pin
Protected
Switch
Input / Output Pin
0V Pin
I/O CONNECTOR 3
Analogue 0V
Analogue Out Axis 1
Analogue Out Axis 0
Analogue Input 1
Analogue Input 0
Analogue 0V
WDOG
WDOG / Analogue Inputs / Analogue Outputs
I/O 24V must be applied to power the voltage outputs.
Analogue Out Axis 2
Analogue Out Axis 3
Analogue 0V
N/C
N/C
Analogue 0V
N/C
N/C
AMPLIFIER
ENABLE
(WATCHDOG)
RELAY OUTPUT
ANALOGUE INPUT S
AIN0: 0 TO 10V
AIN1: 0 TO 10V
Ain
22k
22k
0V
30pF
A to D
CONVERTER
0V
An internal relay is used to enable external amplifi ers when the controller has powered up correctly and the system and application software are ready. The amplifi er enable is a single pole solid state relay with a normally open “contact”. The enable relay contact will be open circuit if there is no power on the controller OR a following error exists on a servo axis OR the user program sets it open with the WDOG=OFF command.
ALL STEPPER AND SERVO AMPLIFIERS MUST BE INHIBITED WHEN
THE AMPLIFIER ENABLE OUTPUT IS OPEN CIRCUIT
To other axis enables
Amplifi er
Enable 1
24V 0V 0V
Amplifi er
Enable 2
V+
V-
Trio Controller
Enable
VIN +
VIN-
Servo Amplifi er
ANALOGUE OUTPUTS
AOUT 0 TO AOUT 3
Output: +/-10V at 5mA
Output impedance: 100 Ohms.
Common 0V return. Isolated from I/O & Encoders.
Aout
100R
D to A
CONVERTER
100nF
0V
0V
STEPPER
OUTPUTS /
ENCODER INPUTS
5 4 3 2 1
9 8 7 6
5 4 3 2 1
9 8 7 6
5 4 3 2 1
9 8 7 6
5 4 3 2 1
9 8 7 6
5 4 3 2 1
9 8 7 6
STEP
A
DIRECTION
B
0V
BOOST / ENABLE
Z
5V
Current Limit
NC
8
9
6
7
1
2
3
4
5
5
6
3
4
7
8
9
Pin
1
2
Servo Axis
Enc. A
Enc. /A
Enc. B
Enc. /B
0V
Enc. Z
Stepper Axis
Step +
Step -
Direction +
Direction -
0V
Enable +
Enc. /Z
5V*
Enable -
5V*
Not Connected Not Connected
* Current limit is 150mA total, shared between all axes.
Absolute Encoder
Clock
/Clock
--------
--------
0V Enc.
Data
/Data
5V*
Not Connected
GROUNDING AND
SHIELDING
Ensure that:
1. The shield pin is grounded as close to the MC405 as possible.
2. 0V, V- and E- connections are
NOT used for terminating screens.
3. Pin 5 of Encoder/Stepper plug is connected to 0V on drive.
4. Encoder cable screen is clamped to 9 way D shell.
5. The MC405 24V supply has common 0V with the drive(s).
Power 24V+
CANbus (H)
SHEILD
CANbus (L)
24V Return (-)
POWER CONNECTOR
3
4
5
1
2
Watchdog Relay
Watchdog Relay
I/O CONNECTOR 3
1
2
Analogue Out 0V Common
8
6
Analogue Out Axis 0
Analogue Out Axis 1
7
!
When wiring MC405 Stepper outputs to a differential input stepper drive, use the 0V and shield connections shown for the encoder. The stepper drive must have its common
0V connected to the MC405
24V return. (24V -)
Enc 0V
ENCODER INPUT (9 WAY D-TYPE)
5
1
Quadrature A
2
Quadrature B
Z Marker Pulse
3
4
6
7
CONNECTOR SHELL
24V POWER SUPPLY
24
0
*
0V
A+
A-
B+
B-
Z+
Z-
SERVO DRIVE
Input Common 0V
Hardware Enable
Speed ref.
Ain -
Ain +
Sheild / Ground
* Encoder input 0V MUST be connected to pin 5
LCD DISPLAY
6
7
4
5
0
1
2
3
12
13
14
15
8
9
10
11
Display at start-up
2
3
0
1
4
5
6
7
ENABLE
10
11
8
9
12
13
14
15
Display with WDOG on
The IP address and subnet mask of the MC405 is shown on the LCD display for a few seconds after power-up. The factory default IP address is 192.168.0.250. This can be changed using the ETHERNET or IP_ADDRESS commands via Motion Perfect 2.
Good quality screened cables should be used for the serial ports. The serial ports and CANbus port are not galvanically isolated, therefore the 0V return MUST be connected to all peripheral devices. In addition, bond together the 0V (24V return) terminals of all system components so as to minimise current fl owing in the serial cables.
Trio Motion Technology Ltd.
Trio Motion Technology LLC [email protected]
Trio Shanghai [email protected]
Trio India [email protected]
Website: www.triomotion.com
quick start v1-October 2011
advertisement
Related manuals
advertisement