- Home
- Domestic appliances
- Large home appliances
- Water heaters & boilers
- Vaillant
- ecoTEC pro
- User manual
advertisement
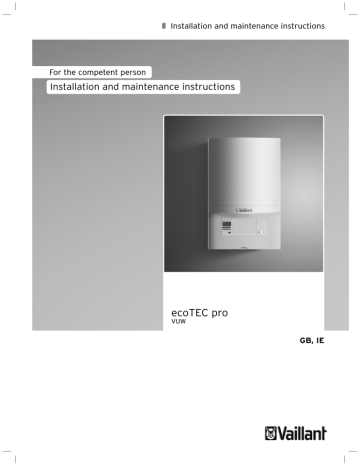
Installation and maintenance instructions
For the competent person
Installation and maintenance instructions ecoTEC pro
VUW
GB, IE
Table of contents
2 i BEFORE PROCEEDING - ENSURE BOILER IS
CORRECT FOR GAS GROUP SUPPLIED!
Table of contents
1 Notes on the documentation .....................................4
1.2 Symbols ....................................................................4
1.3 Applicability of the instructions ...................................4
1.4 Identification ...........................................................4
1.5 CE ...............................................................................4
5.1
5.2
2 Safety .................................................................................6
2.1 Safety and warning information ..................................6
2.1.1 Classification of warnings ..............................................6
2.1.2 Structure of warnings .....................................................6
2.3
2.4
Basic safety instructions ................................................6
Important information regarding propane-fired boilers ....................................................... 7
7
7.1
6.1
6.2
6.3
6.4
6.5
6.6
Preparing for installation ..............................................19
Connecting the gas pipe ...............................................19
Preparing for installation ............................................ 20
Connecting the hot and cold water ............................21
Connecting the heating flow and heating return....21
Low loss header ..............................................................21
Connecting the condensate discharge pipework ....21
Connecting the discharge pipe to the expansion relief valve on the boiler ..............................................22
Flue gas installation ...................................................23
Air/flue gas duct .............................................................23
2.5.7 Water supply Combination boilers ...............................9
2.5.8 Water circulation system................................................9
2.5.9 Pressure relief valve ...................................................... 10
8.1
8.2
8.3
8.4
Preparing for installation .............................................26
Opening/closing the electronics box .........................26
Establishing the mains connection ............................26
Connecting the controller ............................................27
8.4.1 Fitting the controller .....................................................27
8.4.2 Connecting controllers to the electronic system ...28
8.5 Connecting additional components via VR 40 – connecting a "2 in 7" multi-functional module ......28
8.6 Connection wiring diagram .........................................29
3 Description of the appliance ......................................11
9 Operation ....................................................................... 30
9.1 Overview of the read-off and setting options ........ 30
9.2 Calling up the installer level ....................................... 30
4 Installation ......................................................................12
4.1.2 Installation and operation .............................................12
4.2 Scope of delivery ............................................................12
4.2.1 Unpacking the boiler ......................................................12
4.2.2 Checking the scope of delivery ...................................12
4.2.3 Disposing of the packaging ..........................................13
4.3
4.4
Transporting the appliance ..........................................13
Requirements for the installation site .......................15
4.4.1 Required minimum clearances/ installation clearances ...................................................15
4.4.2 Using installation templates .........................................15
4.5
4.6
4.7
4.8
Dimension drawing and connection measurements .................................................................16
Wall-mounting the boiler ...............................................17
Removing/fitting the front casing ..............................17
Removing/fitting the side panel ................................. 18
10 Commissioning ...............................................................31
10.1 Switching on the boiler ..................................................31
10.2 Using test programs .......................................................31
10.3 Preparing the heating water .......................................32
10.4 Read off the filling pressure ........................................32
10.5 Filling and purging the heating installation ............32
10.5.1 Filling the heating installation ....................................32
10.5.2 Purging the heating system ........................................33
10.5.3 Flushing the system for the first time ("cold") ......33
10.6 Avoiding low water pressure .......................................33
10.7 Fill and purge the hot water system .........................33
10.8 Filling the condensate trap ..........................................33
10.9 Checking the gas setting............................................. 34
10.9.2 Checking for tightness of the flue gas installation and flue gas recirculation ..................... 34
10.9.3 Checking the gas flow rate ......................................35
10.9.4 Checking the gas inlet working pressure .................35
Installation and maintenance instructions ecoTEC pro 0020129672_03
Table of contents
10.10
10.10.1
Carrying out a full function test.................................36
Checking the heating mode ........................................37
10.10.2 Checking the hot water generation ...........................37
10.11 Final flush of the heating system ("hot") ................37
13.2.6 Reading off the fault codes ........................................ 56
13.2.7 Querying the fault memory ........................................ 56
13.2.8 Resetting the fault memory ....................................... 56
13.2.9 Overview of fault codes ................................................57
13.3 Running test programs ................................................ 58
13.4 Resetting parameters to factory settings ............... 58 11
11.1
Adapting the boiler to the heating installation 38
Diagnosis codes – Overview ....................................... 38
11.1.1 Setting the heating partial load ................................ 42
11.1.2 Setting pump overrun time and pump
11.1.6
11.1.7
11.2 operating mode ............................................................. 42
11.1.3 Setting the maximum flow temperature ................. 42
11.1.4 Setting the return flow temperature control ......... 42
11.1.5 Burner anti-cycling time .............................................. 42
Setting the maintenance interval ............................. 43
Setting the by-pass valve ............................................ 43
Handing over the boiler to the operator ................. 44
12
12.1
Inspection and maintenance ................................... 45
Inspection and maintenance intervals ..................... 45
12.1.1 General inspection and maintenance instructions ..................................................................... 46 15 Decommissioning .........................................................63
15.1 Temporarily shutting down the boiler ......................63
15.2 Taking the boiler permanently out of service ........63
15.3 Disposing of the boiler .................................................63
12.1.3 Checking the CO/CO
2
ratio and the CO
2 concentration ................................................................. 46
12.1.4 Adjusting the CO
2 concentration
(or the air ratio) ..............................................................47
12.2 Inspection and maintenance work steps ................. 49
12.2.1 Filling the boiler and the heating installation ........ 50
12.2.2 Draining the boiler ........................................................ 50
12.2.3 Draining the entire heating installation .................. 50
12.3 Carrying out maintenance work ................................ 50
12.3.1 Removing the compact thermal module ................. 50
12.3.2 Cleaning the heat exchanger .......................................51
12.3.3 Checking the burner ......................................................51
12.3.4 Cleaning the condensate trap .....................................52
12.3.5 Cleaning the filter in the cold water inlet ................52
12.3.6 Installing the compact thermal module ...................53
12.3.7 Checking the charge pressure of the expansion vessel ............................................................53
12.4 Checking the gas flow pressure ................................ 54
CO
2
content .................................................. 54
14.1 Preparing for and completing replacement work . 59
14.1.1 Preparing for replacement work ............................... 59
14.1.2 Completing replacement work ................................... 59
14.2 Replacing the burner ................................................... 59
14.3 Replacing the fan or the gas valve ........................... 60
14.4 Replacing the expansion vessel................................. 60
14.5 Replacing the heat exchanger .....................................61
14.6 Replacing the PCB and/or the display ......................62
14.6.1 Replacing either the display or the PCB ..................62
14.6.2 Replacing the PCB and the display at the same time ........................................................................62
16
20
21
Guarantee and customer service ............................63
18 Glossary ......................................................................... 65
19 Appendix ........................................................................ 66
Benchmark Log Book ..................................................67
EC declaration of conformity .................................. 69
Index ............................................................................................70
13 Troubleshooting ........................................................... 55
13.1 Contact Vaillant Service Solutions
(0870 6060 777) .......................................................... 55
13.2.1 Calling up Live Monitor (status codes) .................... 55
13.2.2 Status codes – Overview ............................................. 55
13.2.3 Status codes – Overview ............................................. 55
13.2.5 Calling up diagnosis levels .......................................... 56
Installation and maintenance instructions ecoTEC pro 0020129672_03 3
1 Notes on the documentation
4
1 Notes on the documentation
The following instructions are intended to guide you throughout the entire documentation. Further documents apply in combination with these installation and maintenance instructions.
We accept no liability for any damage caused by nonobservance of these instructions.
Other applicable documents
> When installing the ecoTEC pro, follow all installation instructions for the various parts and components of the system without exception.
These installation instructions are enclosed with the various system components as well as additional components.
> Also observe all the operating instructions included with the system components.
The identification plate of the Vaillant ecoTEC pro is attached to the underside of the boiler in the factory.
The article number of the gas fired wall hung boiler can be found in the serial number. The seventh to sixteenth numbers constitute the article number.
The serial number can also be found on the lift out badge located at the bottom of the front casing of the boiler.
The serial number can also be shown on the display of the boiler (¬ Operating instructions).
The CE label shows that the boilers comply with the basic requirements of the applicable directives as stated on the identification plate.
> Pass these installation instructions and all other applicable documents and, if necessary, any required aids to the system operator.
The system operator should retain these instructions and tools so that they are available when required.
The symbols used in the text are explained below:
1.3 i
>
Symbol that denotes useful tips and
information
Symbol for a required action
Applicability of the instructions
These installation instructions are only valid for boilers with the following article numbers:
– Directive 2009/142/EEC of the Commission with amendments "Directive for Harmonisation of Legal Regulations of the Member States for Gas Cosumption Appliances"
(Gas equipment directive)
– Directive 92/42/EEC of the Commission with amendments "Directive Concerning the Efficiency of New Hot
Water Heating Boilers Fired by Liquid or Gaseous Fuels"
(Efficiency directive)
– Directive 2006/95/EC of the Council with amendments
"Directive Concerning Electrical Equipment for Use
Within Specific Voltage Limits" (Low voltage directive)
– Directive 2004/108/EC of the Council with amendments
"Directive Concerning Electromagnetic Compatibility"
The boilers comply with the type sample described in the
EC Type testing certificate.
PIN No. CE-0085CM0320
The boilers comply with the following standards:
– EN 483
– EN 625
– EN 677
– EN 55014
– EN 60335-1
– EN 60335-2-102
– EN 61000-3-2
– EN 61000-3-3
Boiler Type designation
Article number
Gas
Council
Number ecoTEC pro 24 (VUW GB 246/5-3) 0010011689 47-044-44 ecoTEC pro 28 (VUW GB 286/5-3) 0010011690 47-044-45 ecoTEC pro
28 (VUW GB 286/5-3)
(LPG)
0010011718 47-044-47
1.1 Appliance types, article numbers and Gas Council Number
The article number of the boiler can be found on the identification plate.
Installation and maintenance instructions ecoTEC pro 0020129672_03
1.6 Benchmark
Vaillant Ltd. supports the Benchmark Initiative.
You will find the Benchmark Logbook on the last pages of this instruction manual. It is very important that this document be filled out properly when installing, commissioning, and fully explained at hand over to the operator of the installation. Installers should point out also the service record section for completion following service calls to this appliance.
Vaillant Ltd. is a licensed member of the Benchmark
Scheme which aims to improve the standards of installation and commissioning of domestic heating and hot water systems in the UK and to encourage regular servicing to optimize safety, efficiency and performance. Benchmark is managed and promoted by the Heating and Hot water
Industry Council.
> For more information visit www. centralheating .co .uk
Notes on the documentation 1 i Vaillant supply a special self adhesive sticker on top of the boiler for use in entering the serial number details straight onto the commissioning checklist found in the last pages of this document.
Unit type ecoTEC pro
24 (VUW GB 246/5-3)
28 (VUW GB 286/5-3)
1.2 Type overview
Designated country (designation in accordance with
ISO 3166)
Approval category
GB (Great Britain)
IE (Ireland)
II
2H3P
GB (Great Britain)
IE (Ireland)
II
2H3P
5 Installation and maintenance instructions ecoTEC pro 0020129672_03
a 2 Safety
6
2 Safety
2.1 symbol
Safety and warning information
> When installing the ecoTEC pro, take account of the
general safety instructions and the warning notes that appear before all of the actions.
2.1.1 Classification of warnings
The warning notes are classified in accordance with the severity of the possible danger using the following warning symbols and signal words:
Warning a
Signal word
Danger!
Explanation
Immediate danger to life or risk of severe personal injury e
Danger!
Risk of death from electric shock a
Warning.
Risk of minor personal injury b
Caution.
Risk of material or environmental damage
2.1 Classification of warnings
The Vaillant ecoTEC pro boilers are constructed using stateof-the-art technology in accordance with recognised safety rules and regulations. Nevertheless, there is still a risk of injury or death to the operator or others or of damage to the boiler and other property in the event of improper use or use for which it is not intended.
This boiler is not designed to be used by persons (including children) with limited mental and sensory capabilities or by persons who do not have enough experience and/or knowledge, unless they are supervised by a person who is responsible for their safety or they have been instructed by him/ her about how to use the boiler.
Children must be supervised to ensure that they do not play with the boiler.
The boiler is intended as a heater for closed hot water/central heating installations and for hot water generation.
The use of the ecoTEC pro in vehicles, such as mobile homes and caravans, is not classed as intended use. Units that are not classed as vehicles are those that are installed in a fixed and permanent location and that do not have any wheels (fixed installation).
Any other use, or use beyond that specified, shall be considered as improper use. Any direct commercial or industrial use is also deemed to be improper.
The manufacturer or supplier is not liable for any damage resulting from such use. The user alone bears the risk.
Intended use includes the following:
– observance of accompanying operating, installation and maintenance instructions for Vaillant products as well as for other parts and components of the system
– installing and fitting the appliance in accordance with the boiler and system approval
– complying with all of the inspection and maintenance conditions listed in the instructions.
Caution.
Any improper use is forbidden.
2.1.2 Structure of warnings
2.3 Basic safety instructions
Warning signs are identified by an upper and lower separating line and are laid out according to the following basic principle:
> Observe the following safety instructions at all times.
a Signal word!
Type and source of danger!
Explanation of the type and source of
danger
> Measures for averting the danger
European installation directive
Installation and maintenance of the appliance should only be undertaken by a competent person (referred to in these instructions as "competent person" or "skilled trade company", thus making these terms gender-neutral) approved at the time by the Health and Safety executive and in accordance with the gas safety (installation and use) regulations 1998. The existing regulations, rules and guidelines must be observed when doing so. The competent person is also responsible for inspection, maintenance and repairs to the unit, as well as alterations to the gas volume setting.
Only IE: The installation must comply with the current Version of I.S.813 "Domestic Gas Installations" and the current
Building Regulations.
Installation and maintenance instructions ecoTEC pro 0020129672_03 a
a Safety 2 a
The current ETCI Regulations for installing electrical equipment must also be observed.
Installation and settings
In the following cases, the boiler must be operated only with the front casing fitted and closed and with a completely mounted air/flue gas duct:
– starting up
– test purposes
– continuous operation,
Otherwise, under unfavourable operating conditions, injury, death or material damage may occur.
Exclusively for test purposes such as gas working pressure testing the boiler may be operated with the front casing removed for short durations ONLY but must have a completely mounted air/flue gas duct.
> Do not use sprays, solvents, chlorinated cleaning agents, paint, adhesives or similar substances in the vicinity of the boiler.
Under unfavourable circumstances, these substances may cause corrosion.
Material damage due to improper use and/or unsuitable tools
The use of unsuitable tools or improper use thereof may cause damage, such as gas or water leaks.
> When tightening or loosening threaded connections, always use suitable open-end spanners, but do not use pipe wrenches, extensions, etc.
2.4 Important information regarding propane-fired boilers
What to do if you smell gas
Installation errors, damage, manipulation, an unauthorised installation site or similar can cause gas to escape and result in a risk of poisoning and explosion. If there is a smell of gas in the building, proceed as follows:
> Avoid rooms that smell of gas.
> If possible, open doors and windows fully and ensure air is circulating.
> Avoid the use of naked flames (e.g. lighters, matches).
> Do not smoke.
> Do not use any electrical switches, plugs, doorbells, telephones or other communication systems in the building.
> Close the gas meter isolator device or the main isolator device.
> If possible, close the gas stop cock on the unit.
> Warn the occupants in the building by knocking or calling.
> Leave the building.
> If you can actually hear gas leaking, leave the building immediately and ensure that no third parties enter the building.
> Alert the police and fire brigade when you are outside the building.
> Use a telephone outside the building to inform the gas supply company or National Grid Transco 0800 111999.
Purging the liquid gas tank when installing the system:
> Before installing the boiler, make sure that the gas tank has been purged.
The liquid gas supplier is responsible for proper ventilation of the tank. Ignition problems can result if the tank is not purged properly.
> In such cases, first contact the person in charge of filling the tank.
> Also observe the information on conversion to liquid gas in (¬ section 10.9) of this manual.
Using the correct gas type
Using the wrong gas type may cause a fault shutdown on the boiler. Furthermore, ignition and combustion noise may occur in the boiler.
> Only use propane gas G31.
Affix tank sticker
Affix the enclosed tank sticker (propane quality) to the tank where it will be clearly visible, or on then cylinder cabinet near the filler nozzle if possible.
What to do if you smell exhaust fumes
Installation errors, damage, manipulation, unauthorised installation sites or the like can cause flue gas to escape and result in a risk of poisoning. If there is a smell of exhaust fumes in the building, proceed as follows:
> If possible, open doors and windows fully and ensure adequate ventilation.
> Switch the boiler off.
> Check the flue gas route in the boiler and the flue gas pipes.
Material damage caused by corrosion
To prevent corrosion on the boiler and also on the air/flue gas duct, note the following:
To ensure the safe installation and continued satisfactory operation of your appliance, all works shall be carried out by a competent installer fully conversant with the required current and up to date, acts standards, laws and regulations relevant for this range of equipment at the time of installation. In addition any special requirements of Local Authorities, gas undertakings or insurers must be complied with.
Installers shall carryout a full site risk assessment and put into place all necessary steps and procedures to comply with Health and safety at work act and ensure safety of themselves and others with regard to manual handling and working at height requirements.
Installation and maintenance instructions ecoTEC pro 0020129672_03 7
a 2 Safety
8
Attention shall be paid to (but not restricted to) the
following:
– Gas Safety (Installation and Use) regulations.
– All Building Regulations 2000 for England and Wales,
(as amended).
– (Includes Approved Codes of Practice and Approved Documents for building regulations e.g. L1, L1A, L1B, L8.)
– The Building Standards, Scotland, and any requirements determined by the local authorities within.
– The current Version of I.S.813 „Domestic Gas Installations“ and the current Building Regulations for IE.
– The current ETCI Regulations for installing electrical equipment for IE.
– BS 7671 Requirements for electrical installations.
IEE Wiring Regulations
– The Electricity at Work Regulations.
– The Water supply (water fittings) regulations 1999.
– BS 5854 Code of practice for flues and flue structures in buildings.
– BS EN 12828 Design of water-based heating systems.
– BS EN 806 parts 1 - 5
– BS 8558
– BS 6880 Code of practice for low temperature heating systems with outputs greater than 45 kW.
Part 1 Fundamental and design considerations.
Part 2 Selection of equipment.
Part 3 Installation, commissioning and maintenance.
– BS 6981 Installation of low pressure gas pipework of up to 35 mm in domestic premises.
– BS 4814 Specification for: Expansion vessels using an internal diaphragm, for sealed hot water and heating systems.
– BS 7074 Application, selection and installation of expansion vessels and ancillary equipment for sealed water systems.
Part 1 Code of practice for domestic heating and hot water.
Part 2 Code of practice for low and medium temperature hot water systems.
– BS 7593 Code of practice for treatment of water in domestic hot water central heating systems
– BS EN 13831 Closed expansion vessels with built in diaphragm
– BS EN 14336 Heating systems in buildings. Installation and commissioning of water based heating systems.
– BS 5440 – 1 Installation of flues and ventilation for gas appliances of rated input not exceeding 70 kW*
– BS 5440 – 2 Flueing and ventilation for gas appliances of rated input not exceeding 70 kW*
* 1st 2nd and 3rd family gases.
– BS EN 6798 Installation & maintenance of gas fired hot water boilers of rated input not exceeding 70 kW net
Institute of Gas Engineers Publications:
– IGE/UP/1B (Edition 2) Tightness testing and direct purging of small natural gas installations.
– IGE/UP/ 7 (Edition 2) Gas in timber and light steel framed buildings.
– I.S. 813 – Domestic Gas Installations - 2nd edition
( Ireland)
– BS 5482 – Part 1 Domestic butane and propane gas burning installations
The location chosen for the boiler must permit the provision of a satisfactory flue termination. The location must also provide adequate space for servicing and air circulation around the boiler.
Before commencement of any works the installer should carry out a full risk assessment in accordance with Health and Safety executive regulations.
The boiler may be installed in any room, although particular attention is drawn to the requirements of BS 7671 (IEE Regulations), the electrical provisions of the Building Regulations (Scotland) and in IE the current edition of IS 813 and the current ETCI rules, in respect of the installation of a boiler in a room containing a bath or shower.
In case of installation of the boiler in an unusual location, special procedures may be necessary and BS 5546 and
BS 6798 give detailed guidance on this aspect. The boiler must be mounted on a flat, vertical wall, which must be sufficiently robust to take the weight of the boiler.
The boiler may be installed on a combustible wall, subject to the requirements of the Local Authorities and Building
Regulations. A compartment used to enclose the boiler must be designed and constructed specifically for this purpose. (An existing cupboard or compartment may be used provided that it is modified for the purpose). Details of essential features of cupboard/compartment design including airing cupboard installations are given in BS 6891. In IE the current edition of IS 813.
i b
If the boiler is to be installed in an airing cupboard it is not required to separate the boiler with a non-combustible partition. However installation and servicing clearances must be maintained, and the boiler kept clear of any clothing.
Caution.
site
Risk of damage caused by aggressive vapours and dust.
Aggressive vapours and dust in the installation room may cause corrosion damage to the boiler and to the flue gas installation.
> Ensure that the boiler is room sealed if the air in the installation room contains aggressive vapours or dust.
> Observe the following when choosing the installation site and operating the boiler,
– Do not install the boiler in rooms prone to frost.
– Do not install the boiler in rooms in which the combustion air contains chemical substances, such as fluoride, chlorine, sulphur, dust, etc. (e.g. sprays, solvents, cleaning agents, paint, adhesives).
Installation and maintenance instructions ecoTEC pro 0020129672_03 a
a Safety 2 a
> Please ensure that the boiler is room sealed or in a separate installation room if
– the combustion air supply contains the aforementioned substances,
– you install the boiler in hairdresser salons, painter's or joiner's workshops, cleaning businesses or similar.
> Do not route the combustion air through an old oil furnace chimney, as this can also cause corrosion.
means of completely isolating the boiler and its ancillary controllers. Isolation is preferably by the use of a fused three pin plug and unswitched shuttered socket outlet, both complying with the requirements of BS 1363. Alternatively, a 3 Amp. fused doublepole switch with a 3 mm contact opening on both poles may be used.
An existing gas meter should be checked to ensure that it is capable of passing the rate of gas supply required.
Installation pipes should be fitted in accordance with
BS 6891, in IE in accordance with the current issue of
IS 813. Pipework from the meter to the boiler must be of an adequate size.
Do not use pipes of a smaller size than the boiler gas connection. The complete installation must be tested and purged in accordance with:
– IGE/UP /1B for systems up to 0.035 m 3 capacity
– for larger systems IGE/UP/1A and
– for LPG installations refer to BS 5482 - 1 or
– IGE/UP1 Edition 2 for larger volume installations.
Detailed recommendations for air supply are given in
BS 5440: Part 2. It is not necessary to have an air vent in the room or internal space in which the boiler is installed.
Designers and installers must ensure that all pipe work and fittings connected to the ecoTEC complies with the necessary water fittings regulations. See related documents above (ref BS 6700 and new BSEN 806 parts 1 - 5 plus BS
8558) For combination boilers the incoming water supply should be checked to ensure that sufficient pressure and flow rate are available to suite the intended use, see the technical data at the back of this manual.
All mains water heated by the ecoTEC combination boiler will be classed as Category 2 fluid and small expansion volumes created during warm up must be allowed to flow back into the supply pipe. No back flow prevention is necessary with this appliance as the very small expansion volume is unlikely to heat the incoming service pipe above 25 Deg C.
Note that where back flow prevention devices are fitted
(this may include water meters) these can prevent the permitted expansion into the cold supply. This along with the effects of pumping and / or water hammer can result in a pressure build-up that may cause damage to the boiler (and other household devices such as showers). Vaillant cannot accept responsibility for damage caused to the boiler or its surroundings where an appliance has been fitted to supplies with mechanical back flow prevention. In these cases the requirement would be that a competent installer correctly installs a suitable shock arrestor / mini-expansion vessel adjacent to the boiler in the cold water supply pipe.
The boilers are very high efficiency appliances. As a consequence the heat loss from the appliance casing during operation is very low. Compartment ventilation is required if the flue used is not concentric and air is supplied from the room or compartment the boiler is installed in.
a Danger!
Risk of death from electric shock.
If the appliance is not earthed, it may hold voltage if a defect occurs.
> Earth the appliance.
A 230 V, ~ 50 Hz single phase electricity supply fused to 3
Amp. must be provided in accordance with the latest edition of BS 7671 (IEE Wiring Regulations) and any other local regulations that may apply. In IE reference should be made to the current edition of the ETCI rules. The method of connection to the mains electricity supply must provide a
Detailed recommendations concerning the water circuit system can be taken from BS 6798 and BS 5449, Part 1 (for
"Small Bore" and "Micro Bore" central heating installations). Lines which do not form part of the usable heating surface should be insulated to prevent heat losses and possible freezing up, especially where the lines run under rooves and ventilated cellar rooms. The drain connections must be easily-accessible, so that the entire system including the boiler and hot water system can be drained. The drain connections should be at least 1/2 " (BSP nominal size) and must be in accordance with BS 2879.
The boiler is suitable for Minibore and Microbore systems.
Water lines are to be copper pipes in accordance with
BS 2871, Part 1. These must be thoroughly cleaned, especially when connecting a new boiler to an existing system.
9 Installation and maintenance instructions ecoTEC pro 0020129672_03
a 2 Safety
Risk of damage if the heating water is treated with unsuitable frost or corrosion protection agents.
Frost and corrosion protection agents can cause changes to seals, noise during heating mode and may lead to other consequential damage.
> Do not use any unsuitable frost or corrosion protection agents.
Mixing additives with the heating water can result in material damage. However no incompatibility with Vaillant boilers has been detected with proper use of the following products over a long period.
> When using additives, follow the manufacturer's instructions without exception.
Vaillant accepts no liability for the compatibility of any additive or its effectiveness in the rest of the heating installation.
Additives for cleaning measures
(subsequent flushing required)
– Fernox F3
– Sentinel X 300
– Sentinel X 400
Total heating output kW
< 50
> 50 to £ 200
>200 to £ 600
> 600
Overall hardness at smallest boiler heating surface 2)
20 l/kW
> 20 l/kW <
50 l/kW mol/m 3
(mg/l CaCO
3
)
> 50 l/kW mol/m 3
(mg/l CaCO
3
) mol/m 3
(mg/l CaCO
3
)
No requirement or
< 3 1)
< (300)
1)
2
(200)
2
(200)
1.5
(150)
0.02
(2.0)
0.02
(2.0)
1.5
(150)
0.02
(2.0)
0.02
(2.0)
0.02
(2.0)
0.02
(2.0)
0.02
(2.0)
1) on systems with circulation water heaters and for systems with electric heating elements
2) from the specific system volume (nominal capacity in litres/ heating output; for multiple boiler systems, the lowest individual heating output should be used).
This data only applies up to 3 times the system volume for filling and top-up water. If 3 times the system volume figure is exceeded, the water must be treated in exactly the same way as if the limits quoted in table 2.2 were exceeded (softening, desalination, hardness stabilisation or desludging).
Additives intended to remain permanently in the system
– Fernox F1
– Fernox F2
– Sentinel X 100
– Sentinel X 200
2.5.9 Pressure relief valve
Additives for frost protection intended to remain permanently in the system
– Fernox Antifreeze Alphi 11
– Sentinel X 500
> Inform the operator of the necessary measures if you have used these additives.
> Inform the operator about the required measures for frost protection.
The boiler is equipped with a pressure relief valve. This safety device is required for all sealed central heating systems, is preset to 3 bar and is fitted with a 15 mm compression connection for the discharge pipe, whose diameter must not be less than 15 mm. The pressure relief valve must not be used for draining purposes.
For situations where the discharge cannot be easily routed
Vaillant have a remote pressure relief valve mounting kit available which can be used to provide a suitable way to achieve this.
Permissible water hardness
> Observe all valid national and technical regulations when conditioning filling and supplementary water.
Provided the national regulations and technical standards do not stipulate more stringent requirements, the following applies:
> You must condition the heating water in the following cases:
– If the entire filling and supplementary water quantity during the operating life of the system exceeds three times the nominal volume of the heating installation or
– If the limit values shown in the tables are not observed.
2.5.10 Venting
The boiler is fitted with an automatic air vent. Other measures need to be taken to allow the heating system to be either automatically or manually vented during filling and during commissioning.
a
10 Installation and maintenance instructions ecoTEC pro 0020129672_03
Description of the appliance 3
3 Description of the appliance
Design
4
3
2
1
18
17
16
Key
2 Water pressure sensor
4 Connection for the air/flue gas duct
6 Air intake pipe
7 Compact thermal module
9 Fan
10 Automatic air vent
12 Internal pump
13 Diverter valve with bypass
14 Expansion relief valve
Installation and maintenance instructions ecoTEC pro 0020129672_03
15 Electronics box
16 Impeller sensor (hot water)
17 By-pass valve
18 Secondary heat exchanger
15
5
6
7
8
11
12
9
10
13
14
11
4 Installation
4 Installation
The current price list shows the complete range of hydraulic accessories for the ecoTEC pro series.
i BEFORE PROCEEDING - ENSURE BOILER IS
CORRECT FOR GAS GROUP SUPPLIED!
The work described in this section must only be carried out by a competent person.
i The pipes can be routed upwards behind the boiler in front of the wall (surface installation) using the spacer frame. Which means the distance between the wall and the boiler increases by 65 mm.
4.2 Scope of delivery
The Vaillant ecoTEC pro is delivered pre-mounted in a packaging unit.
4.1.1 Controller
To control the ecoTEC, Vaillant offers various controller versions for connecting to the switching rail or for plugging into the operator control screen.
> Remove the boiler from its box.
> Remove the protective film from all parts of the boiler.
Room Thermostats
VRT 30 – Room Thermostat (230 V)
VRT 50 – Room Thermostat eBUS
Timers / Programmers timeSWITCH 150 – mechanical clock timeSWITCH 160 – 7 day programmer
Digital Room Temperature Controls
VRT 350 – Programmable Room Control
VRT 392f – RF Programmable Room Control *
VRT 350f – RF Programmable Room Control
Weather Compensating Controls
VRC 470 – Weather Compensator
VRC 470f – RF Weather Compensator
Communication vrnetDIALOG comDIALOG
Accessories
VR 65 – Control Centre
VR 66 – Control Centre
VR 61/2 – Two Zone Wiring Centre
VR 81/2 – Remote Control Unit
VR 68/2 – Solar Module
4.1 Controller accessories
* Note 392f RF transmitter wired external to boiler
> Check that all parts have been delivered and are intact
(¬ fig. 4.1 and ¬ table 4.2)
7
1
6
5
4
2
3
Optional accessories are available for use in conjunction with the installation and operation of the ecoTEC.
12 Installation and maintenance instructions ecoTEC pro 0020129672_03
Installation 4
Item Qty Description
5
6
7
3
4
1
2 1
1
2
4
1
1
3
Wall bracket
Boiler
Connectors (hot water, expansion relief valve)
Service valves
Installation template
Enclosure documentation
Bags with parts incl. electrical plug and cable clamps
1 Addition for propane boilers: tank sticker
> Dispose of the cardboard packaging used on the eco-
TEC pro at a cardboard recycling site.
> Dispose of the plastic film and plastic filling at an appropriate plastic recycling site.
> Observe national regulations.
Carriage of carton from point of delivery to point of installation – ground floor.
Recommend 2 person lift or 1 person with use of sack truck.
> If 1 person is performing lift, straddle the load, tilt and place carton into position on truck.
> Recommend secure appliance onto truck with suitable straps.
> Ensure safe lifting techniques are used – keep back straight – bend using legs.
> Keep load as close to body as possible.
> If 2 persons performing lift, ensure co-ordinated movements during lift.
> Clear the route before attempting the lift.
> If removing boiler from truck straddle the load and tilt forwards to facilitate secure grip.
> Ensure safe lifting techniques are used – keep back straight – bend using legs.
> Do not twist – reposition feet instead.
> Take care to avoid trip hazards, slippery or wet surfaces and climbing steps and stairs.
> Always use assistance if required.
4.3 Transporting the appliance
Important:
With regards to the Manual Handling Operations, 1992 Regulations, the following lift operation exceeds the recommended weight for a one man lift.
General recommendations when handling
> Clear the route before attempting the lift.
> Ensure safe lifting techniques are used – keep back straight – bend using legs.
> Keep load as close to body as possible. Do not twist – reposition feet instead.
> If 2 persons performing lift, ensure co-ordinated movements during lift.
> Avoid upper body/top heavy bending - do not lean forward/sideways.
> Recommend wear suitable cut resistant gloves with good grip to protect against sharp edges and ensure good grip.
> Always use assistance if required.
Carriage of carton from point of delivery to point of installation – first or higher floor, cellar.
Recommend 2-person lift or 1 person with use of sack truck.
> If 1 person is performing lift, straddle the load, tilt and place carton into position on truck.
> Recommend secure appliance onto truck with suitable straps.
> Ensure safe lifting techniques are used – keep back straight – bend using legs.
> Keep load as close to body as possible.
> If 2 persons performing lift, ensure co-ordinated movements during lift.
> Avoid upper body/top heavy bending - do not lean forward/sideways.
> Clear the route before attempting the lift.
> If removing boiler from truck straddle the load and tilt forwards to facilitate secure grip.
> Ensure safe lifting techniques are used – keep back straight – bend using legs.
> Do not twist – reposition feet instead.
> Take care to avoid trip hazards, slippery or wet surfaces and climbing steps and stairs.
> Always use assistance if required.
Removal of carton from delivery van
Recommend 2 person lift or 1 person with use of sack truck.
> If 1 person is performing lift, straddle the load, tilt and place carton into position on truck.
> Recommend secure appliance onto truck with suitable straps.
> Ensure safe lifting techniques are used – keep back straight – bend using legs.
> Keep load as close to body as possible.
> If 2 persons performing lift, ensure co-ordinated movements during lift.
> Always use assistance if required.
Carriage of carton from point of delivery to point of installation – roofspace.
> Recommend 2-person lift.
> Ensure co-ordinated movements during lift.
> Avoid upper body/top heavy bending - do not lean forward/sideways.
> Clear the route before attempting the lift.
> Take care to avoid trip hazards, slippery or wet surfaces and climbing steps and stairs.
> When transferring appliance into roofspace, recommend 1 person to be in roofspace to receive the appliance and other person to be below to pass up and support appliance.
Installation and maintenance instructions ecoTEC pro 0020129672_03 13
4 Installation
> Ensure safe lifting techniques are used – keep back straight – bend using legs.
> Keep load as close to body as possible.
> Always use assistance if required.
> It is assumed safe access, flooring and adequate lighting are provided in the roof space.
> It is recommended a risk assessment of the roof space area be carried out before moving the appliance into the area to take into account access, stability of flooring, lighting and other factors, and appropriate measures taken.
Unpacking of appliance from carton.
> Recommend 2 persons unpack appliance from carton.
> Always keep working area clear.
> Recommend straps and open carton flaps, then remove items from the top including the polystyrene packing and remove carton by sliding up over the boiler.
> Ensure safe lifting techniques are used – keep back straight – bend using legs.
> Keep load as close to body as possible.
> Always use assistance if required.
> Dispose of packaging in a responsible manner.
> Recommend wear suitable cut resistant gloves with good grip to protect against sharp edges and ensure good grip when handling appliance outside packaging.
Positioning of Appliance for Final Installation – no obstructions.
> If appliance weight is over 25 kg always use 2 persons to move where practical.
> Fit bracket securely onto wall before lifting appliance into position.
> Obtain firm grip on front and sides of appliance, lift upwards, ensure stable balance achieved and lift upwards to position in place on bracket.
> Ensure safe lifting techniques are used – keep back straight – bend using legs - when lifting load from floor level.
> Do not twist – reposition feet instead.
> Keep boiler as close as possible to body throughout lift to minimise strain on back.
> Ensure co-ordinated movements to ensure equal spread of weight of load.
> Always use assistance if required.
> Recommend wear suitable cut resistant gloves with good grip to protect against sharp edges and ensure good grip when handling appliance.
> If 2 persons positioning onto bracket obtain firm grip at front and sides/base of boiler.
> Ensure coordinated movements during 2 person lifts to ensure equal spread of weight of load.
> Ensure safe lifting techniques are used – keep back straight – bend using legs - when lifting load from floor level.
> Do not twist – reposition feet instead.
> Keep boiler as close as possible to body throughout lift to minimise strain on back.
> Avoid upper body/top heavy bending - do not lean forward/sideways.
> Always use assistance if required.
> Recommend wear suitable cut resistant gloves with good grip to protect against sharp edges and ensure good grip when handling appliance.
Positioning of Appliance for Final Installation – within compartment etc. restricting installation.
> If appliance weight is over 25 kg always use 2 persons to move where practical.
> Fit bracket securely onto wall before lifting appliance into position.
> Obtain firm grip on front and sides of appliance, lift upwards, onto worktop if practicable.
> Ensure stable balance achieved and lift upwards to drop into place onto bracket.
> If 2 persons positioning onto bracket obtain firm grip at front and sides/base of boiler.
> Ensure coordinated movements during 2 person lifts to ensure equal spread of weight of load.
> If 1 person positioning onto bracket recommend obtain firm grip supporting base of boiler.
> Ensure safe lifting techniques are used – keep back straight – bend using legs - when lifting load from floor level.
> Do not twist – reposition feet instead.
> Keep boiler as close as possible to body throughout lift to minimise strain on back.
> Always use assistance if required.
> Recommend wear suitable cut resistant gloves with good grip to protect against sharp edges and ensure good grip when handling appliance.
Positioning of Appliance for Final Installation – above worktop, foreseeable obstructions etc.
> If appliance weight is over 25 kg always use 2 persons to move where practical.
> Fit bracket securely onto wall before lifting appliance into position.
> Obtain firm grip on front and sides of appliance, lift upwards, onto worktop if practicable.
> Ensure stable balance achieved and lift upwards to position in place on bracket.
Positioning of Appliance for Final Installation – in roof space restricting installation.
> If appliance weight is over 25 kg always use 2 persons to move where practical.
> Obtain firm grip on front and sides of appliance, lift upwards, ensure stable balance achieved and lift upwards to drop into place onto bracket.
> If 2 persons positioning onto bracket obtain firm grip at front and sides/base of boiler.
> Ensure co-ordinated movements during 2 person lifts to ensure equal spread of weight of load.
> If 1 person positioning onto bracket recommend obtain firm grip supporting base of boiler.
14 Installation and maintenance instructions ecoTEC pro 0020129672_03
Installation 4
> Ensure safe lifting techniques are used - keep back straight – bend using legs - when lifting load from floor level.
> Do not twist – reposition feet instead.
> Keep boiler as close as possible to body throughout lift to minimise strain on back.
> Always use assistance if required.
> Recommend wear suitable cut resistant gloves with good grip to protect against sharp edges and ensure good grip when handling appliance.
> It is recommended a risk assessment of the roof space area be carried out before moving the appliance into the area to take into account access, stability of flooring, lighting and other factors, and appropriate measures taken.
4.4 Requirements for the installation site least approx. 50 mm) in order to facilitate maintenance or repair work (¬ section 4.8).
It is not necessary to ensure sufficient clearance between the boiler and combustible materials or components as the temperature of the boiler will always be less than the maximum permissible temperature of 85 °C due to its nominal heat output.
4.4.2 Using installation templates
An installation template is supplied with the boiler to aid wall mounting.
The template shows the following:
– The position of the fixing holes for the hanging bracket.
– The position of the connections.
– The position of the wall breakthrough of the air/flue gas duct.
4.4.1 Required minimum clearances/ installation clearances
> When using accessories, observe the minimum clearances/installation clearances (¬ fig. 4.2).
Position the installation template vertically over the installation site.
> Attach the template to the wall, using tacks for example.
> Mark the drill holes for the hanging bracket on the wall.
> If necessary, mark the position for the wall breakthrough for the air/flue gas duct.
> Remove the installation template from the wall.
> Drill 2 holes Æ 10 mm for the hanging bracket in the wall.
> If necessary, cut the wall breakthrough for the air/flue gas duct.
C C
Key
A 165 mm (air/flue gas duct
Æ 60/100 mm)
246 mm (air/flue gas duct
Æ 80/125 mm)
C 5 mm; optimum approx. 50 mm
500 mm in front of the boiler to enable easy access for servicing (may be provided by an opening door).
Clearance at the side is not required, but the side panels can also be removed if there is adequate side clearance (at
Installation and maintenance instructions ecoTEC pro 0020129672_03 15
4 Installation
4.5 Dimension drawing and connection measurements
440
1
2
8
3
4
5
6
7
35
100
35
100
4.3 Connection measurements in mm
Key
1 Wall breakthrough for air/flue gas duct
3 Heating flow (
Æ 22 x 1.5)
4 Hot water connection (
Æ 15 x 1.5)
5 Gas connection (
Æ 15 x 1.5)
6 Cold water connection (
Æ 15 x 1.5)
7 Heating return (
Æ 22 x 1.5)
8 Air/flue gas duct connection
10 Condensate discharge connection,
Æ 19 mm
11 Heating expansion relief valve drain line connection,
Æ 15 mm
Minimum dimension from wall bracket to center line of air/flue gas duct wall breakthrough
Dimension A
[mm]
60/100 with elbow 87°, PP
80/125 with elbow 87°, PP
175
223
3 4 5 6 7 11
9 10
16 Installation and maintenance instructions ecoTEC pro 0020129672_03
Installation 4
1
2
1 a Danger!
Risk of death if the load-bearing capacity of the fixing elements used is insufficient!
If the fixing elements or wall do not have sufficient load-bearing capacity, the boiler can come loose and fall down. This may also cause leaks in the gas line, which is potentially fatal.
> When fitting the boiler, ensure that the fixing elements and the wall have a sufficient load-bearing capacity.
> Check the quality of the wall.
4.5 Removing the front casing
2
3
4.4 Wall-mounting the boiler
> Mount the hanging bracket (1) on the wall using the wall plugs and screws (2) provided with the unit.
> Hang the boiler (3) on the hanging bracket from above using the hanging bracket.
Removing the front casing
> Loosen the screw (1) on the bottom of the boiler using a screwdriver or small spanner.
> Push in both retaining clips (2) on the bottom of the boiler so that the front casing is released.
> Pull the front casing forwards using the bottom edge.
> Lift the front casing upwards from the bracket.
Fitting the front casing
> Place the front casing on the upper brackets.
> Push the front casing onto the boiler so that until both retaining clips (2) snap into place at the front casing.
> Fasten the front casing by screwing in the bolt (1) on the underside of the boiler.
17 Installation and maintenance instructions ecoTEC pro 0020129672_03
4 Installation
You can also remove a side panel for installation or maintenance purposes.
> Unscrew the two screws (2.) from the top and bottom of the side panel.
> Hold onto the side panel (3.) when doing this.
> Swivel the side panel outwards and remove it from below by pulling it downwards (4.).
> Install the side panel in reverse order.
b Caution.
Risk of damage caused by mechanical tension.
Removing both side panels may cause mechanical distortion in the boiler, which can cause damage to the piping and potentially result in leaks.
> Always only remove one side panel, never both side panels at the same time.
2.
3.
18
1.
4.
4.6 Removing/fitting the side panel b Caution
Risk of damage to the side panel.
Unscrewed side panels that are merely suspended from the back wall can fall down.
> Hold onto the side panel when you are unscrewing it, and always remove it from the boiler.
> Fold the electronics box (1.) forwards.
Installation and maintenance instructions ecoTEC pro 0020129672_03
Gas installation 5
The work described in this section must only be carried out by a competent person.
a Danger!
Risk of death from incorrectly installed gas system!
An incorrect gas installation can result in leaks and an explosion.
> During installation, the legal directives and the local regulations for gas supply companies must be observed.
1 a Danger!
Risk of death from incorrectly installed gas system!
Tension in the gas line can result in leaks or an explosion.
> Make sure there are no stresses in the gas lines when it is installed.
5.1 Fitting the gas connection b Caution.
Risk of damage caused by incorrect gas installation.
Excess test pressure or operating pressure can cause damage to the gas valve.
> When the entire gas installation is tested for leaks, the maximum pressure at the gas valve must not exceed 0.75 kPa
(75 mbar).
> Make the gas connection as shown.
7
6
5 b Caution.
Risk of damage caused by contaminated lines.
Foreign bodies such as welding remnants, sealing residue or dirt in the supply lines for gas can cause damage to the boiler.
> Blow the gas line clean prior to installation.
b Caution.
Risk of damage caused by using the wrong gas type.
Using the wrong gas type can cause a fault shutdown on the boiler. Furthermore, ignition and combustion noise may occur in the boiler.
> Only use propane gas for propane-fired boilers in accordance with BS 4250: Part
1 (1987).
4
3
2
19 Installation and maintenance instructions ecoTEC pro 0020129672_03
20
6 Hydraulic installation
The work described in this section must only be carried out by a competent person.
6.1 Preparing for installation b Caution.
Risk of damage caused by heat transfer when soldering.
Heat that is transferred during soldering can cause damage to the seals in the service valves.
> Do not solder the connection pieces if the connection pieces are screwed to the service valves.
a Danger!
Risk of death caused by an incorrectly installed system!
Heating water that leaks from the discharge pipe of the expansion relief valve can cause severe burns.
> Install the expansion relief valve and the opening for the drain line in such a way that there is no danger to any persons in or around the building. This may be outside or to a suitable open drain in the installation room.
> Make sure that the drain is visible.
i Seals made of rubber-like materials may be subject to plastic deformation, which can lead to pressure losses. We recommend using seals made of a paste-like fibre material.
The Vaillant ecoTEC boiler is equipped with an 8 l expansion vessel with a gas-side filling pressure of 0.075 MPa
(0.75 bar), which is suitable for a closed heating system with a maximum water volume of 80 litres.
b Caution.
Risk of damage caused by contaminated lines.
Foreign bodies such as welding remnants, sealing residue or dirt in the water pipes can cause damage to the boiler.
> Flush the heating installation thoroughly prior to installation.
b Caution.
Risk of damage from corrosion.
If non-diffusion-tight plastic pipes are used in the heating installation, this may cause air to enter the heating water and corrosion of the heat generation circuit and the boiler.
> If using non-diffusion-tight plastic pipes in the heating installation, separate the system by installing an external heat exchanger between the boiler and the heating installation.
> Before installing the boiler, check whether the volume of the installed expansion vessel is sufficient.
> If the volume of the expansion vessel is insufficient, then install an additional expansion vessel connected as close to the boiler as possible into the boiler return pipe. i When using an external expansion vessel together with a VUW boiler, it is advisable to install a non-return valve in the outlet (boiler flow) or take the internal expansion vessel out of service.
Otherwise, the warm start function may be more frequently activated because of backflow, which causes unnecessary energy loss.
Initial system pressure (in bar)
Expansion relief valve setting
(in MPa (bar))
With system volumes greater than 80 l, multiply the volume by the adjacent factor.
Vessel volume
(in l)
1.0
1.5
0.3 (3.0)
0.109
0.156
a Danger!
Risk of scalding and/or damage due to incorrect installation leading to leaking water.
Stresses in the supply line can cause leaks.
> Make sure there are no stresses in the supply lines when they are installed.
Installation and maintenance instructions ecoTEC pro 0020129672_03
Hydraulic installation 6
6.4 Low loss header
A low loss header disconnects the boiler from the heating system. The system is no longer dependent on the remaining feed head of the boiler. In conjunction with the heating pump, the low loss header ensures that a sufficiently high minimum quantity of water is always circulating through the boiler. No electrical accessories are required in order to use a low loss header.
7
6 pipework
5
4
3
2
1
6.1 Fitting the hot and cold water connection
> Make the domestic hot and cold water connections as shown.
> Ensure correct water pressure and flow requirements and that any expansion can be accommodated with the cold supply pipe work (¬ section 2.5.7).
return a Danger!
Risk of death from flue gases!
An empty or insufficiently filled condensate trap may allow flue gas to escape into the room air.
> Make sure that the condensate trap is filled with water when switching on the boiler.
a Danger!
Risk of death from flue gases!
If the condensate discharge pipework is connected tightly to a fixed connection to the waste water piping, the internal condensate trap can be drained fully.
> Do not connect the condensate discharge pipework tightly to the waste water
piping.
ecoTEC pro boilers are equipped with a condensate trap that continually deposits the contents to the discharge pipe.
1
> Make the water connections as shown.
5
4
3
2
Installation and maintenance instructions ecoTEC pro 0020129672_03
4 a
3
Internal stackpipe b c
6
3
Internal discharge system
5
Gulley
1
2
3 d
7
Soakaway
6.3 Condensate discharge pipework
21
22
6 Hydraulic installation
> Connect the condensate discharge (1) of the boiler to a condensate discharge pipework (3) which has a minimum internal diameter of 19 mm (22 mm outside diameter for all external pipes) and is made from an acid-resistant material (e.g. plastic overflow pipe).
i The condensate drain pipework must have a continuous fall (45 mm per metre) and should whenever possible terminate at a suitable drain point within the heated envelope of the build- ing that will remain frost free under long periods of low external temperatures.
min.
180
1
2
3
> During installation remove all burs from inside of cut pipe work and avoid excessive adhesive which may trap small pockets of water close to the pipe wall which can freeze and build into a larger ice plug.
> As with other pipe work insulate the condensate discharge pipe to minimise any risk of freezing and beware when crossing cavities that the fall is maintained and the pipe sleeved.
> The condensate discharge pipework must terminate in a suitable location.
Further information can be obtained from "BS 6798 Specification for installation of gas–fired boilers of rated input not exceeding 70 kW net". Before starting up the boiler, the condensate trap (2) must be filled with water, as described in the relevant section.
6.6 Connecting the discharge pipe to the expansion relief valve on the boiler
> Insert a seal (1) in the cap nut (2).
> Screw the discharge pipe (3) onto the expansion relief valve.
> Make the drain line routing as short as possible and sloping away from the boiler.
> Allow the line to terminate in such a way that nobody can be injured and no cable or other electrical components can be damaged if water or steam is ejected.
> Note that the end of the line must be visible.
> If the pipe cannot fall to a safe discharge point then the
Vaillant remote pressure relief valve mounting kit can be used to provide a suitable way to achieve this.
> Ensure the discharge pipe work is installed, routed and terminated correctly to minimise the risk of freezing up.
The expansion relief valve for the heating installation is integrated in the boiler.
> Install the discharge pipe for the expansion relief valve so that it does not interfere with the removal and fitting of the condensate trap. i We recommend not to shorten the discharge pipe supplied.
> Leave an installation space of at least 180 mm beneath the condensate trap.
Installation and maintenance instructions ecoTEC pro 0020129672_03
Flue gas installation 7
7.1 Air/flue gas duct a Danger!
Risk of death and risk of damage from use of non-approved air/flue gas ducts!
Vaillant boilers are certified only with genuine Vaillant air/flue gas ducts. The use of other accessories can cause personal injury and material damage as well as operating faults.
> Only use genuine Vaillant air/flue gas ducts.
Article number 0020060570 and 0020065937
The CE mark is valid only if the appliance is operated with
Vaillant air/flue gas ducts.
All ecoTEC pro boilers feature a
Æ 60/100 mm diameter air/ flue gas connection as standard. Selecting the most suitable system depends on the individual installation and application conditions.
Optional 125 mm air/flue gas duct
A concentric air/flue gas ducting with an outer diameter of
125 mm is available that can be extended depending on the boiler output range. The flues gas spigot Ø 80/125 (with 2 measuring apertures) Art. No.: 0020147469 will be required.
You can also get a vertical system. For more information refer to the ¬ installation manual for the air/flue gas
duct.
Standard 100 mm air/flue gas duct 1020
667 87 65 48
70
Article number 303933
A concentric air/flue gas ducting with an outer diameter of
100 mm that can be extended depending on the boiler output range is available.
You can also get a vertical system. For more information refer to the ¬ installation manual for the air/flue gas
duct. 87° elbows and 45° elbows are also available for greater flexibility during the installation.
Article number 303209
Installation and maintenance instructions ecoTEC pro 0020129672_03
Article number 303200
23
7 Flue gas installation
The following details refer to all flue systems.
a. The terminal must be positioned such that the products of combustion can disperse freely at all times.
b. A plume of water vapour will sometimes be visible from the flue terminal. Positions where this could be a nuisance should be avoided.
c. If the terminal is fitted less than 2 m above a balcony, above ground or above a flat roof to which people have access then a suitable terminal guard must be provided and fitted (contact Tower Flue Components,
Tonbridge, TN9 1TB).
i Vertical flues must not terminate within
600 mm of an openable window, air vent or any other ventilation terminal.
The flue system shall be so placed or shielded as to prevent ignition or damage to any part of the building.
P
R
S
T
D, E
J
L
G
B
A
II
C
H
O
H
N
N
K
24 Installation and maintenance instructions ecoTEC pro 0020129672_03
Location
Minimum dimensions
A
Directly below an opening, air brick, opening windows, etc.
300 mm
B Above an opening, air brick, opening window, etc.
300 mm
C
Horizontally to an opening, air brick, opening window, etc.
300 mm
D
Below temperature-sensitive building components e.g. plastic gutters, soil pipes or drain pipes
75 mm
E Below eaves
F Below balconies or car port roof
G From a vertical drain pipe or soil pipe
H From an internal or external corner
I Above ground, roof or balcony level
J From a surface facing the terminal
K From a terminal facing the terminal
200 mm
200 mm
150 mm
200 mm
300 mm
600 mm
1200 mm
L
R
From an opening in the car port (e.g. door, window) into the dwelling
1200 mm
M Vertically from a terminal on the same wall
N Horizontally from a terminal on the same wall
1500 mm
300 mm
O From the wall on which the terminal is mounted 0 mm
P From a vertical structure on the roof N/A
Q Above intersection with roof 300 mm
Horizontally to a window or opening on pitched or flat roofs
600 mm
S
T
Above a window or opening on pitched or flat roofs
Below a window or opening on pitched or flat roofs
600 mm
2000 mm duct
BS 5440–1 It is recommended that the fanned flue terminal should be positioned as follows: a) at least 2 m from an opening in the building directly opposite, and b) so that the products of combustion are not straightly directed to discharge across a boundary.
1) Dimensions D, E, F and G:
These clearances may be reduced to 25 mm without affecting the performance of the boiler. In order to ensure that the condensate plume does not affect adjacent surfaces the terminal should be extended as shown in ¬ fig. 7.6.
This clearance may be reduced to 25 mm without affecting the performance of the boiler. However, in order to ensure that the condensate plume does not affect adjacent surfaces a clearance of 300 mm is preferred. For IE, recommendations are given in the current edition of IS 813.
For 1 and 2 above you can use the Variable Termination Kit to move the termination point away from the building
fabric.
Article numbers:
0020060584 - White
0020060585 - Black
Installation and maintenance instructions ecoTEC pro 0020129672_03
Flue gas installation 7
25
26
8 Electrical installation
3 e Danger!
Risk of death from electric shock!
Touching live connections can cause serious personal injury.
> Switch off the power supply.
> Secure the power supply against being switched on again.
e Danger!
Risk of electrocution as a result of an improper electrical connection!
An improper electrical connection may negatively affect the operational safety of the boiler and result in material damage or personal injury.
> The electrical connection must be carried out by a suitably qualified competent person who is responsible for complying with the existing standards and guidelines.
> Connect the boiler in accordance with
BS 7671 (IEE Regulations).
> For IE: Please observe the latest edition of the ETCI regulations (Electro-Technical
Council for Ireland).
> Earth the boiler.
4
> Fold the electronics box (1) forwards.
> Undo the 4 clips of the rear cover (2) of the electronics box from the brackets (3) at the rear and sides of the electronics box.
> Fold up the cover.
Closing the electronics box
> Close the rear panel on the electronics box.
> Push in the panel until it clicks into place in the clips.
> Fold up the electronics box.
> Push the right and left clips of the box against the side panels on the boiler until they click into place.
> Replace the front casing on the boiler (¬ section 4.7).
2
1
Opening the electronics box
> Remove the front casing from the boiler (¬ section 4.7).
e Danger!
Risk of death from electric shock!
Mains connection terminals L and N remain live even if the continuous voltage on/off switch is turned off.
> Before establishing a mains connection, switch off the power supply.
b Caution.
Risk of damage from erroneous connected voltage.
At mains voltages greater than 253 V and less than 190 V, the functions may be impaired.
> Make sure that the rated voltage of the mains is 230 V.
Installation and maintenance instructions ecoTEC pro 0020129672_03
Electrical installation 8
1 b Caution.
Risk of damage caused by incorrect installation.
A mains voltage at the incorrect plug terminals on the ProE system can destroy the electronics.
> Only connect the mains connection cable to the terminals marked for the purpose.
b Caution.
Risk of damage caused by incorrect installation.
Connecting wires that have been stripped too far can cause short circuits and damage the electronics if a strand accidentally comes loose.
> Only strip the outer sheathing of flexible cables for a maximum of 3 cm to prevent short circuits.
> Lay the lines correctly.
> Use strain reliefs.
2 i If you install the boiler in safety area 2, it can only be operated if it is room sealed. Installation method B53P is not permitted in this case.
Observe the latest edition of the "IEE Wiring
Regulations – BS7671, Requirements for Electrical Installation".
In IE, reference should be made to the current edition of the ETCI (Electro-Technical Council for Ireland) rules.
The boiler is supplied for connection to 230 V, ~ 50Hz supply fused at 3 A rating. Connection to the mains supply shall be made via a fused 3 pin plug to an unswitched shuttered socket, both complying with the requirements of
BS 1363. (Alternatively, connection may be made via a 3 A fused double pole isolator having a contact opening of at least 3 mm in all poles and supplying the boiler and controllers only). The point of connection to the mains supply must allow complete electrical isolation of the boiler and its ancillary controllers. It should be readily accessible and adjacent to the boiler. A flexible cord fulfilling BS6500 or comparable standard, conductor diameter between 0,75 and 1,5 mm 2 and an allowed temperature range including 90 °C should be used.
The nominal voltage of the mains must be 230 V; at mains voltages greater than 253 V and less than 190 V the functions may be impaired.
> Use the strain reliefs (1) provided.
> Shorten the mains connection cable as necessary.
> Only strip the outer sheathing of flexible cables to a maximum of 3 cm.
> Ensure inner conductor insulation is not damaged during stripping of outer sheathing.
> Only strip inner conductors sufficient to make good sound connections.
> Fit the stripped ends of the conductors with crimp pin terminals to ensure a secure connection free from loose strands to prevent short circuits.
> Connect the provided green ProE plug for the mains
connection to the mains connection cable using a screwdriver.
> Insert the ProE plug into the corresponding PCB slot
(L, N and earth) (¬ fig. 8.2).
> Lay the lines correctly.
> Secure the cable in the electronics box using the strain reliefs.
> Close the electronics box (¬ section 8.2).
i Make sure that the connection cables are securely fastened to the plug terminals.
> Open the electronics box (¬ section 8.2).
> Use a normal commercial mains connection cable that is compliant with standards.
> Route the mains connection cable through the left cable duct (¬ fig. 8.1, pos. 4) on the base of the boiler.
> Fit the controllers in accordance with the relevant operating and installation instructions.
27 Installation and maintenance instructions ecoTEC pro 0020129672_03
8 Electrical installation
28
8.4.2 Connecting controllers to the electronic system b Caution.
Risk of damage caused by incorrect installation.
Connecting wires that have been stripped too far can cause short circuits and damage the electronics if a strand accidentally comes loose.
> Only strip the outer sheathing of flexible cables for a maximum of 3 cm to prevent short circuits.
> Lay the lines correctly.
> Use strain reliefs.
> If you connect a weather compensator or room temperature control via eBUS, then bridge input 24 V = RT (X100 or X106) if no bridge exists.
> I If using low voltage (24 V) controls connect these in place of the bridge marked RT 24 V (X100 or X106).
> Close the electronics box (¬ section 8.1).
> In order to achieve pump operating mode "Comfort"
(continuously running pump) for multi-circuit controllers, change diagnosis code D.018 Pump operating mode from 3 = "Eco" (intermittent pump) to 1 = "Comfort"
(¬ section 11.1.2).
i Please note that the bridge at the ProE plug
(Burner off) must be removed when connecting a maximum thermostat (contact thermostat) for underfloor heating.
b Caution.
Risk of damage caused by incorrect installation.
A mains voltage at the incorrect plug terminals on the ProE system can destroy the electronics.
> Do not connect a mains voltage to the eBUS terminals (+/-).
8.5 Connecting additional components via
VR 40 – connecting a "2 in 7" multifunctional module i Make sure that the conductors are securely fastened to the plug terminals of the ProE plug.
> Open the electronics box (¬ section 8.2).
> Route the supply lines of the components to be connected (e.g. external controllers, external sensors) through the left cable duct (¬ fig. 8.1, pos. 4) on the underside of the boiler.
> Use the strain reliefs provided.
> Shorten the supply lines as necessary.
> Only strip the outer sheathing of flexible cables to a maximum of 3 cm.
> Ensure inner conductor insulation is not damaged during stripping of outer sheathing.
> Only strip inner conductors sufficient to make good sound connections.
> Fit the stripped ends of the conductors with crimp pin terminals to ensure a secure connection free from loose strands to prevent short circuits.
> Connect the ProE plug to the supply lines of the controller using a screwdriver.
> Insert the ProE plug into the associated PCB slot
(¬ fig. 8.3).
> Lay the lines correctly.
> Secure the cable in the electronics box using the strain reliefs.
> If you connect a 230 V AC time and temperature control to the boiler, then remove the bridge at input 24 V = RT
(X100 or X106) if a bridge exists.
b Caution.
Risk of damage caused by incorrect installation.
Connecting wires that have been stripped too far can cause short circuits and damage the electronics if a strand accidentally comes loose.
> Only strip the outer sheathing of flexible cables for a maximum of 3 cm to prevent short circuits.
> Lay the lines correctly.
> Use strain reliefs.
You can connect additional components to the ecoTEC pro using the Vaillant multi-functional module 2 in 7 (accessories).
> Fit the components in accordance with the corresponding operating and installation instructions.
> Select diagnostic code "D.027" to actuate relay 1 on the multi-functional module at installer level (¬ section 11.1).
> Select diagnostic code "D.028" to actuate relay 2 on the multi-functional module at installer level (¬ section 11.1).
The following components can be actuated:
1 = Circulation pump
2 = External pump
3 = Cylinder charging pump
4 = Extractor hood
5 = External solenoid valve
6 = External fault message
7 = Solar pump (not active)
8 = Remote control eBUS (not active)
9 = Legionella protection pump (not active)
10 = Collective solar valve (not active)
Installation and maintenance instructions ecoTEC pro 0020129672_03
Electrical installation 8
24 V
230 V~
X51
X2 blue
6
4
12
5
1
8
17
7
18
14
13
11
3
2
X20 pink
12
13
2
15
16
4
3
17
8
7
5
7 orange
1
3
2
5
4
6
M
Diverter valve
3
4
2
3
J
Impeller sensor
Warm start sensor red blue
+
J Flow sensor
J Return sensor
Safety fuse
Gas valve
X41
Edge connector
1
6
FB
AF
RF
DCF
0
0
X106
-
+
External sensor
DCF connection
Earth
Contact thermostat/burner off
24 V DC room thermostat
Bus connection
(Controller/room th. digital)
1 2 4 5
PWM Earth
Fan
Ignition transformer
L
N
Internal pump *
RT
L
N
Mains connection
Appliance earth
Installation and maintenance instructions ecoTEC pro 0020129672_03
Ignition electrode
* ... variant-dependent
29
30
9 Operation
9 Operation
The Vaillant ecoTEC pro boiler is fitted with a digital information and analysis system (DIA). You can use the DIA to display the current status of your boiler (Live monitor) and fault codes, to view and change parameters and to start test programs.
b Caution.
Risk of damage caused by incorrect
handling.
Incorrect settings at installer level can cause damage to the heating installation.
> You should only access installer level if you are an approved competent person.
The operating concept and operation of the boiler is described in the ¬ operating instructions for the boiler.
The read-off and setting options for the installer level are also described in the ¬ operating instructions.
You can find further read-off and setting options in ¬ sec-
tion 13.2.1.
The following overview shows the read-off and setting facilities of the installer level.
Installer level is secured against unauthorised access with a password, as incorrect parameter settings at this level can cause functional faults and damage to the heating installation.
> Press the left and right selection buttons
("i") at the same time 9.1 Overview of the read-off and setting options
S.31
Code
D.---
The Live monitor is shown in the display (current status of the boiler).
> Press the right selection button menu point.
to select the
"Code" and the value "00" appear in the display.
> Select the value 17 (code) using the minus button
or the plus button
> Press the right selection button
.
to confirm the entered code.
You are at the installer level. The diagnostic codes are shown in the display.
Use the left-hand selection button
– to cancel the change to a set value.
:
– to return to the basic display.
PF
Use the right-hand selection button :
– to access the test programs (P), to access the fault codes
(F) and to return to the diagnostic codes (D).
– to confirm a set value or the start of a test program.
P.--
D F i If you exit the installer level and then access it again within 15 minutes, you do not have to enter the code again.
--/--
DP installer level
Installation and maintenance instructions ecoTEC pro 0020129672_03
Commissioning 10
10 Commissioning
At the time of commissioning, complete all relevant sections of the benchmark checklist found within the back pages of this document.
Ensure that the filling and purging programs P.06 and P.00 have been allowed to run fully before the boiler is ignited for the first time.
By activating various test programs, you can trigger special functions on the boilers.
The following four test programs are available:
Display Meaning
P.00
1)
Purging test program
The heating circuit and the hot water circuit are purged using the automatic air vent (the cap of the automatic air vent must be released).
a Danger!
Risk of poisoning and burns caused by escaping hot flue gas!
Hot flue gas can escape and cause poisoning and burns if the boiler is operated with an incompletely mounted or open air/flue gas duct or if the boiler is operated with internal leaks with the front casing open.
> Operate the boiler
- for commissioning
- for testing purposes
- in continuous operation only when the front casing is fitted and closed and the air/flue gas duct is completely fitted.
> Exclusively for test purposes such as gas working pressure testing the boiler may be operated with the front casing removed for short durations ONLY but must have a completely mounted air/flue gas duct.
i The automatic air vent cap must be released before filling the heating circuit or recharging circuit and during operation.
Purge the heating circuit or the recharging circuit using the purge program P.00 (¬ sec-
tion 10.2).
P.01
P.02
P.06
1 x right selection button: Start heating circuit purging
2 x right selection button (" -> "): Start purging hot water circuit
3 x right selection button (" -> "): Restart heating circuit purging
1 x left selection button ("Cancel"): Exit purging program
The internal pump is cyclically actuated.
Note: The purge program runs 7.5 min per circuit.
Maximum load test program:
The boiler is operated at maximum heat input after successful ignition.
Minimum load test program:
The boiler is operated at minimum heat input after successful ignition.
Filling mode test program:
The diverter valve (VUV) is moved to the mid-position.
The burner and pump are switched off (to fill or drain the boiler).
1) Purging the heating circuit:
Diverter valve in heating position, actuation of internal pump for 9 cycles: 30 sec. on, 20 sec. off. Display: "Active heating circuit".
Purging the hot water circuit:
After the above-mentioned cycles have run or the right-hand selection button has been pressed again: Diverter valve in the hot water position, actuation of the internal pump as above.
Display: "Active hot water circuit".
Auxiliary service equipment:
The following test and measuring equipment is required for commissioning:
– CO
2
measuring instrument
– Digital or U-tube manometer i If you do not press a button for more than
15 minutes. the test programs are stopped automatically. The boiler switches to normal operating mode.
To terminate the test programs, you can press the left-hand selection button " " ("Back", "Cancel") at any time.
10.1 Switching on the boiler
> Press the on/off button (¬ Operating instructions).
The basic display appears on the display.
P.00
1,0 bar
You can call up the test programs for the commissioning
(¬ section 9.2).
Installation and maintenance instructions ecoTEC pro 0020129672_03 31
32
10 Commissioning i If the boiler is in error condition, you cannot start any test programs. You can detect an error condition by the fault symbol shown in the left bottom corner of the display (¬ fig. 10.1). You must first reset.
If the heating installation extends over several storeys, higher filling pressures may be required to avoid air entering the heating installation.
> Remove the front casing from the boiler (¬ section 4.7).
1
10.3 Preparing the heating water
Pay attention to the specifications concerning heating water preparation in (¬ section 2.5.7).
The boiler is equipped with an analogue pressure gauge
(¬ fig. 3.1) and also has a symbolic bar display for the filling pressure of the heating system and a digital pressure and temperature display.
You can see the pressure gauge once you have removed the front casing of the boiler.
Press the right selection button twice to read off the digital filling pressure value.
10.2 Automatic air vent
> Release the cap of the automatic air vent (1) by up to two rotations.
> Open all thermostatic radiator valves.
b Caution.
Risk of damage caused by contaminated lines.
Foreign bodies such as welding remnants, sealing residue or dirt in the water pipes can cause damage to the boiler.
> Flush the heating installation thoroughly prior to commissioning.
i The ecoTEC pro purges the heating circuit independently during continuous operation via the automatic air vent.
> Select test program P.06 (¬ section 10.2).
The diverter valve moves to the mid-position, the pumps do not run and the boiler does not switch to heating mode.
The system is filled via a customer-installed filling connection, which must be attached in a suitable position in the heating circuit. This connection must be removed again after the filling process is complete. If the local Water
Authority regulations do not allow temporary connection a sealed system filler pump with break tank must be used.
The heating system will not be filled automatically from the domestic hot water side. (Alternative methods of filling sealed systems are given in BS 5449)
To ensure the correct operation of the heating installation, the indicator on the pressure gauge must point to the upper half of the grey area or in the middle of the bar graph display (marked by the dashed limit value) when the heating installation is cold. This corresponds to a filling pressure of between 0.1 MPa and 0.2 MPa (1.0 bar and
2.0 bar).
You can display the exact filling pressure (¬ section 10.4).
i Ensure that the filling and drainage cock on the heating installation is connected to a cold water valve as per standard.
> In order to fill the heating installation, first open the cold water valve.
> Open all thermostatic radiator valves.
> Check that both service valves on the boiler are open.
> Slowly open the stop valve on the filling line so that the water flows into the heating system.
Installation and maintenance instructions ecoTEC pro 0020129672_03
Commissioning 10 i If the water pressure in the heating system is too low, the display switches between fault message F.22 and the display of the current pressure when the boiler is switched on.
> Purge the lowest radiator until water flows out of the purging valve without bubbles.
> Purge all other radiators until the entire heating system has been filled with water. Close all purging valves.
> Use the display to monitor the rising filling pressure in the heating installation.
> Top up with water until the pressure gauge display is in the middle of the grey area and the required filling pressure appears on the display.
> After filling, close the stop valve at the filling line and the cold water valve.
> Check all connections and the entire system for leaks.
> To purge the heating installation, select test program
P.00 (¬ section 10.2).
remove the contamination caused during installation out of the heating system before the boiler is started up.
> Close the drain cocks.
> Refill the heating system with water, as described in
(¬ section 10.5).
> Check that the expansion relief valve of the heating system is functioning correctly by turning the handle on the valve.
> Check the pressure in the heating system and top up with water if necessary.
> Close the filling valve and the cold water valve.
To prevent damage to the heating installation caused by low water pressure, the ecoTEC pro is fitted with a water pressure sensor.
If the water pressure falls below 0.08 MPa (0.8 bar), the boiler indicates low pressure by displaying a flashing pressure value.
If the water pressure falls below 0.05 MPa (0.5 bar), the boiler switches off.
The fault message F.22 appears in the display.
The boiler does not start up, the internal pump operates intermittently and, as an option, purges the heating circuit or the hot water circuit. The display shows the filling pressure of the heating installation.
> Top up the water and switch the boiler on again.
A flashing pressure value appears on the display until a pressure of 1.1 bar or higher has been reached.
> The filling pressure of the heating system must not fall below 0.08 MPa (0.8 bar) when purging is in progress as, otherwise, this will not be carried out properly.
The test program P.00 runs for 7.5 minutes per circuit.
At the end of the filling procedure, the filling pressure of the heating installation should be at least 0.02 MPa
(0.2 bar) above the counterpressure of the expansion vessel
(P
Installation
³ P
Exp
+ 0.02 MPa (0.2 bar)).
i If you notice frequent drops in pressure, then determine and eliminate the cause, i.e water leaks in the system. Failure to do so along with frequent topping up will result in system corrosion and subsequent failures.
> If there is still too much air in the heating installation at the end of test program P.00, repeat the test program.
> Check all connections for leaks.
> Open the cold water stop valve on the boiler.
> Fill the hot water system by opening all the hot water draw-off points until water comes out.
As soon as water comes out of all the hot water draw-off points, the hot water circuit is filled completely and also purged.
("cold") i The entire heating system must be flushed through completely at least twice: once cold and once hot, in accordance with the following instructions.
> Check whether all thermostatic radiator valves and both service valves on the boiler are open.
> Connect a hose to the drain valve that is located at the lowest position in the heating system.
> Open the drain cocks and all the purging valves on the radiators so that the water flows quickly and completely out of the heating system and the boiler, in order to a Danger!
Risk of poisoning from escaping flue gas!
An empty or insufficiently filled condensate trap may allow flue gas to escape into the room air.
> Fill the condensate trap with water before starting up the boiler.
33 Installation and maintenance instructions ecoTEC pro 0020129672_03
34
10 Commissioning
If the boiler version does not correspond to the local gas family:
> Call Vaillant Service Solutions (0870 6060 777); Gas conversions must only be carried out by Vaillant Service
Solutions.
> You must not start up the boiler yourself.
i If a gas conversion to liquid gas has been carried out by Vaillant Service Solutions, the smallest possible partial load is higher than is shown in the display. The current values can be found in the technical data (¬ section 17).
1
The combustion of this boiler has been checked, adjusted and preset at the factory for operation on the gas group defined on the identification plate. No measurement of the combustion is necessary to set up the boiler.
10.3 Filling the condensate trap
> Remove the lower part (1) of the condensate trap by turning the bayonet fitting anti-clockwise.
> Fill the lower section with water until about 10 mm below the upper edge.
> Re-attach the lower section to the condensate trap.
Do not adjust the gas valve.
> Ensure
– that the boiler has been installed in accordance with these instructions,
– the integrity of the flue system and the flue seals, as described in the ¬ flue installation instructions enclosed with this boiler, and as described below,
– a visual check is carried out on the boiler combustion circuit and the relevant seals,
– that any defects have been corrected at this stage.
To further validate the integrity of the flue system and confirm correct operation of the boiler it is possible to conduct flue gas and air measurements on this boiler - for details see ¬ section 10.9.2.
b Caution!
An incorrect gas group setting can cause operating faults or a reduction in the working life of the boiler.
If the boiler version does not correspond to the local gas group, there will be malfunctions or you have to change components of the boiler ahead of schedule, e. g. do not use a LPG boiler on natural gas.
> Before starting up the boiler compare the details of the gas group specified on the identification plate with the gas group supplied at the installation site.
installation and flue gas recirculation
> Check the integrity off the flue gas installation according to TB 008.
> Should the flue gas installation be longer than 2 m we strongly recommend to check the system for flue gas recirculation as described below.
If the boiler version corresponds to the local gas family:
> Proceed as described below.
Proceed to put the boiler into operation as follows:
> Check the maximum gas flow rate as detailed in ¬ sec-
tion 10.9.3.
> Check the gas inlet working pressure as detailed in
¬ section 10.9.4.
> Note that you must re-measure the gas flow rate or the gas inlet working pressure, if changes were required to correct any issues found.
Installation and maintenance instructions ecoTEC pro 0020129672_03
Commissioning 10
1
2
– terminating test program P.01 as described in ¬ sec-
tion 10.2.
– Allow the boiler to cool down by turning off water taps and allow pump overrun to operate for a minimum of two minutes.
> Record the boiler maximum gas flow rate onto the
Benchmark gas boiler commissioning checklist.
Nominal net heat output in kW
18.5
23
24
28
Gas flow rate (as per BS EN 483)
Natural gas in m 3 /h Propane in kg/h nominal
+ 5 % - 10 % nominal
+ 5 % - 10 %
2.02
2.12
1.82
1.48
1.56
1.34
2.50
2.63
2.25
2.61
3.10
2.74
2.35
1.84
1.92
1.93
2.02
1.66
1.73
3.26
2.79
2.25
2.36
2.03
10.4 Flue gas and air measure points
Legend:
1 Flue gas measure point
2 Air measure point
For checking the system for recirculation use the air measure point (2).
> Use the flue gas analyser.
> If you detect any CO or CO
2
in the fresh air, search for the flue gas leakage or recirculation.
> Correct the defects.
> Check again as described before, if there is any CO or
CO
2
in the fresh air.
> If you cannot correct the defects you must not start up the boiler.
> Ensure that the gas inlet working pressure can be obtained with all other gas appliances in the property working.
> Remove the front casing from the boiler (¬ section 4.7).
> Close the gas isolation valve of the boiler.
10.9.3
The boiler is fitted with a multifunctional automatic gas valve which ensures that the precise air/gas ratio is provided under all operating conditions. The gas flow rate has been set during production and does not require adjustment. With the front casing fitted check the gas flow rate of the boiler as follows:
> Start the boiler by activating the test program P.01 as described in ¬ section 10.2.
> In addition, ensure that maximum heat can be dissipated into the heating system by turning up the room thermostat.
> Alternatively, fully open the hot water taps to ensure full flow rate through the boiler.
> Wait at least 5 minutes until the boiler has reached its operating temperature.
> Ensure that all other gas appliances in the property are turned off.
> Measure the gas flow rate at the gas meter.
> Check that the gas flow rate is as stated in ¬ table 10.2.
If the measured gas flow rate lies outside the tolerance limits specified in ¬ table 10.2, do not operate the boiler and inform the Vaillant Service Solutions (0870 6060 777).
If the measured gas flow rate is within the tolerance limits shown in ¬ table 10.2, then proceed as follows:
> Take the boiler out of operation by 10.5 Measuring the gas inlet working pressure
1
2
Installation and maintenance instructions ecoTEC pro 0020129672_03 35
10 Commissioning
> Undo the sealing screw of the measuring nipple (1) (lefthand screw) at the gas valve using a screwdriver.
> Connect a digital pressure gauge or U-tube manometer
(2) to the measuring nipple (1).
> Open the gas isolation valve of the boiler.
> Start the boiler by activating the test program P.01 as described in ¬ section 13.3.
> In addition, ensure that maximum heat can be dissipated into the heating system by turning up the room thermostat.
> Alternatively, fully open the hot water taps to ensure full flow rate through the boiler.
> With the boiler operating at full load check that the gas inlet working pressure at the reference test point (1) complies with the requirements of ¬ table 10.3.
> Should the pressure recorded at the reference test point in the boiler be lower than indicated (¬ table 10.3) check if there is any blockage in the pipework or if the pipework is undersized.
> Record the appliance gas inlet working pressure (kPa resp. mbar) in the Benchmark gas boiler commissioning checklist.
Boiler
24
28
Natural gas (G20) LPG (G31)
Minimum pressure at reference test point in kPa (mbar)
Maximum pressure at reference test point in kPa (mbar)
Minimum pressure at reference test point in kPa (mbar)
Maximum pressure at reference test point in kPa (mbar)
1.6 (16)
1.5 (15)
2.3 (23)
2.3 (23)
2.3 (23)
2.3 (23)
4.3 (43)
4.3 (43)
If the supply pressure is out of tolerance contact your
Emergency Service Provider.
If the gas inlet working pressure at the reference test point
(1) is not within the permissible range and you cannot correct the failure, notify the gas supply company or the
Vaillant Service Solutions (0870 6060 777) and proceed as
follows:
> Take the boiler out of operation by
– terminating test program P.01 as described in ¬ sec-
tion 10.2.
– Allow the boiler to cool down by turning off water taps and allow pump overrun to operate for a minimum of two minutes.
> Close the gas isolation valve of the boiler.
> Remove the pressure gauge and retighten the sealing screw (1) for the measuring nipple.
> Turn on gas at the gas isolation valve.
> Make sure that there is no leakage at the sealing screw.
> Turn off gas at the gas isolation valve.
> Put the front casing back on.
> Turn off electrical supply to the boiler.
> You must not start up the boiler.
> After completing the installation and the gas setting, perform a complete function check of the boiler before starting up the boiler and handing it over to the operator.
> Start up the boiler in accordance with the relevant operating instructions.
If the gas inlet working pressure is within the permissible range, proceed as follows:
> Take the boiler out of operation by
– terminating test program P.01 as described in ¬ sec-
tion 10.2.
– Allow the boiler to cool down by turning off water taps and allow pump overrun to operate for a minimum of two minutes.
> Close the gas isolation valve of the boiler.
> Remove the pressure gauge and retighten the sealing screw (1) for the measuring nipple.
> Open the gas isolation valve of the boiler.
> Make sure that there is no leakage at the sealing screw.
> Put the front casing back on.
> Reset boiler controls for normal operation.
> Check the gas supply line, the flue gas installation, the heating installation and the hot water pipes for leaks.
> Check the air/flue gas duct for correct installation.
> Make absolutely sure that the front casing is properly
fitted.
> Check the heating mode (¬ section 10.10.1)
> Check the operation of the hot water generation (¬ sec-
tion 10.10.2)
36 Installation and maintenance instructions ecoTEC pro 0020129672_03
Commissioning 10
You can display the current operating condition of the boiler in the "Live monitor" on the boiler display (¬ sec-
tion 13.2.1).
> Switch on the boiler.
> Make sure that there is a heat requirement.
> Activate the Live monitor (¬ section 13.2.1).
S.04
If the boiler is operating correctly, the display will show status code "S.04".
> Close the drain valve.
> Fill the heating system again with water as described in
¬ section 10.5.3.
> Re-fill the system until the system design pressure of
0,1 MPa (1,0 bar) is attained. (The actual reading on the digital pressure gauge should ideally be 0,05 MPa
(0,5 bar) plus an additional pressure corresponding to the highest point of the system above the base of the boiler – 10 m head equals an additional 1 bar reading on the pressure gauge. The minimum pressure should not be less than 0,1 MPa (1 bar) in any installation.) If the system is to be treated with an inhibitor it should be applied at this stage in accordance with the manufacturer’s instructions. Further information can be obtained from
Sentinel, Betz Dearborn Ltd., Tel: 0151 420 9595, or Fernox, Alpha–Fry technologies. Tel: 0870 8700362.
> Refit the boiler casing (¬ section 4.7).
> Attach the bottom cover to the boiler by sliding the front edge of the cover into the lip at the bottom front edge of the appliance chassis.
> Carefully push the rear of the bottom cover upwards until the spring retaining clips engage at the side of the appliance. It may be necessary to adapt the bottom cover by removing the easy break sections.
10.10.2 Checking the hot water generation
> Switch on the boiler.
> Open a hot water valve all the way.
> Activate the Live monitor (¬ section 13.2.1).
If hot water generation is working correctly, the display shows "S.14".
S.14
10.11 Final flush of the heating system ("hot")
> Operate the appliance until the boiler and the heating system are up to temperature.
> Check the heating system for leaks.
> Connect a hose to the drain valve located at the lowest position of the heating system.
> Shut off the boiler, open the drain valve and all purge valves on the radiators and allow the water to flow out of the heating system and the boiler quickly and fully.
Installation and maintenance instructions ecoTEC pro 0020129672_03 37
11 Adapting the boiler to the heating installation
installation
You can find all setting options in the diagnostic codes in the installer level (¬ section 9.2).
You can use the parameters that are marked as adjustable in ¬ table 11.1 to adapt the boiler to the heating installation and the needs of the customer: i You can enter your settings in the last column after setting the system-specific parameters.
> Switch to the installer level (¬ section 9.2) and select the diagnostic codes.
> Press the minus button or the plus button
to switch between the displayed diagnosis codes.
With modifiable parameters:
> Press the right-hand selection button to select the parameter to make a change.
> Press the minus button or the plus button
to change the current setting.
> Press the right-hand selection button firm the change.
to con-
The change is saved.
38 Installation and maintenance instructions ecoTEC pro 0020129672_03
Adapting the boiler to the heating installation 11
Code
D.000
Parameters
Heating partial load
Adjustable values
Adjustable heating partial load in kW
Auto: Boiler automatically adjusts max. partial load to current system demand
Factory
setting
Auto
D.001
Overrun time of internal pump for heating mode
D.002
Max. burner anti-cycling time heating at 20 °C flow temperature
D.003
Outlet temp. actual value
1 - 60 min
2 - 60 min in °C
5 min
20 min
D.004
Measured value of hot water sensor Not relevant
D.005
Flow temperature target value (or return target value)
D.006
Hot water temperature target value
(VUW boilers only)
D.007
Warm start temperature target value
(only with VUW boilers)
Cylinder temperature target value
(only with VU boilers)
In °C, max. of the value set in d.71, limited by an eBUS controller if connected)
35 to 65 °C
40 to 65 °C
15 °C frost protection, then 40 to 70 °C;
(max. temperature can be adjusted under D.020)
D.008
Room thermostat at terminal RT
D.009
Target value from external eBus controller
D.010
Status of internal pump
Room thermostat open (no heat requirement)
Room thermostat closed (heat requirement) in °C
1 = on, 0 = off
D.011
Status of external heating pump 1 to 100 = on, 0 = off
Not relevant D.012
Status of cylinder charge pump
D.013
Status of hot water circulation pump Not relevant
D.014
Target pump speed (high-efficiency pump)
D.015
Actual pump speed (high-efficiency pump)
D.016
Room thermostat 24 V DC open/ closed
D.017
Heating flow/return regulation changeover
D.018
Pump operating mode setting
D.019
Operating mode of 2-stage pump
Not relevant
Not relevant
0 = Room thermostat open (no heating mode)
1 = Room thermostat closed (heating mode)
0 = Flow, 1 = Return
1 = Comfort (continuously operating pump)
3 = Eco (intermittently operating pump)
Not relevant
0
3
D.020
Max. setting for cylinder target value Not relevant
D.022
Hot water demand via C1/C2, internal hot water control system
Not relevant
D.023
Summer/winter operating mode (heating on/off)
1 = Heating on, 0 = Heating off (summer mode)
D.025
Hot water generation enabled by eBUS 1 = Yes, 0 = No controller
D.026
Auxiliary relay control Not relevant
Your own setting
Not adjustable
Not adjustable
Not adjustable
Not adjustable
Not adjustable
Not adjustable
Not adjustable
Not adjustable
Not adjustable
Not adjustable
Not adjustable
Not adjustable
Not adjustable
Not adjustable
Not adjustable
Not adjustable
Not adjustable
Not adjustable
Not adjustable
Not adjustable
Installation and maintenance instructions ecoTEC pro 0020129672_03 39
11 Adapting the boiler to the heating installation
Code Parameters
D.027
Switching of relay 1 on the
"2 in 7" multi-functional module VR 40
Adjustable values
1 = Circulation pump
2 = External pump
3 = Cylinder charging pump
4 = Extractor hood
5 = External solenoid valve
6 = External fault message
7 = Solar pump (not active)
8 = Remote control eBUS (not active)
9 = Legionella protection pump (not active)
10 = Collective solar valve (not active)
D.028
Switching of relay 2 on the
"2 in 7" multi-functional module VR 40
1 = Circulation pump
2 = External pump
3 = Cylinder charging pump
4 = Extractor hood
5 = External solenoid valve
6 = External fault message
7 = Solar pump (not active)
8 = Remote control eBUS (not active)
9 = Legionella protection pump (not active)
10 = Collective solar valve (not active)
D.033
Fan speed target value In rpm
D.034
Fan speed actual value
D.035
Position of the diverter valve
In rpm
0 = Heating; 100 = Hot water; 40 = Mid-position
D.036
Hot water flow quantity
(impeller sensor)
D.039
Solar feed temperature
D.040
Flow temperature
In l/min
Actual value in °C
Actual value in °C
Factory
setting
2
2
Your own setting
Not adjustable
Not adjustable
Not adjustable
Not adjustable
Not adjustable
Not adjustable
D.041
D.044
Return temperature
Digitised ionisation value
Actual value in °C
Display range 0 to 1020,
> 800 no flame
< 400 good flame
Not relevant
Not adjustable
Not adjustable
D.046
Pump type Not adjustable
D.047
Outside temperature (with weather- controlled Vaillant controller)
D.050
Offset for minimum speed
Actual value in °C
D.051
Offset for maximum speed
In rpm, setting range: 0 to 3000
In rpm, setting range: -990 to 0
D.058
Activation of solar post-heating for VUW boilers;
Switch hot water mode
0: Solar post heat mode deactivated
3: DHW activation target value minimum 60 °C
Number of shutdowns D.060
Number of temperature limiter shutdowns
D.061
Number of ignition device cutoffs Number of unsuccessful ignitions in the last attempt
Nominal value set in factory
Nominal value set in factory
0
Not adjustable
Not adjustable
Not adjustable
D.064
Average ignition time
D.065
Maximum ignition time
In seconds
In seconds
Not adjustable
Not adjustable
11.1 Diagnosis codes (continued)
40 Installation and maintenance instructions ecoTEC pro 0020129672_03
Adapting the boiler to the heating installation 11
Code Parameters
D.067
Remaining burner anti-cycling time
D.068
Unsuccessful ignitions at 1st attempt
D.069
Unsuccessful ignitions at 2nd attempt
Adjustable values
In minutes
Number of unsuccessful ignitions
Number of unsuccessful ignitions
D.070
Setting diverter valve position 0 = Normal mode
1 = Mid-position (parallel mode)
2 = Permanent heating setting
D.071
Target value maximum heating flow temperature
40 to 80 °C
Not relevant D.072
Internal pump overrun after cylinder charging
D.073
Warm start target offset Adjustable from -15 K to 5 K
D.075
Max. charging time for domestic hot water cylinder without independent control system
Not relevant
D.076
Device specific number
D.077
Limit on cylinder charging output in kW
D.078
Limit on cylinder charging temperature in °C
D.080
Operating hours, heating
7 = VUW 24
8 = VUW 28
Not relevant
Not relevant
In hours (h)
D.081
Operating hours, hot water generation In hours (h)
Factory
setting
0
75 °C
0
D.082
Number of burner start-ups in heating mode
Number of burner start-ups
D.083
Number of burner start-ups in hot water mode
Number of burner start-ups
D.084
Maintenance indicator: Number of hours until the next maintenance
Setting range: 0 to 3000 hrs and "---" for deactivated "---"
D.088
Start delay for hot water draw-off detection via impeller (VUW boilers only)
0 = 1.5 l/min and no delay,
1 = 3.7 l/min and 2 sec. delay
D.090
Status of digital controller 1 = Recognised, 0 = Not recognised
0
D.091
Status DCF with external sensor connected
D.092
actoSTOR module recognition
D.093
Invalid device specific number (DSN)
D.094
Delete fault history
0 = No reception, 1 = Reception, 2 = Synchronised, 3 =
Valid
Not relevant
Setting range: 0 to 99
Delete fault list
D.095
Software version of PeBUS components PCB (BMU)
Display (AI)
D.096
Factory setting Reset all adjustable parameters to default setting
11.1 Diagnosis codes (continued)
Your own setting
Not adjustable
Not adjustable
Not adjustable
Not adjustable
Not adjustable
Not adjustable
Not adjustable
Not adjustable
Not adjustable
Not adjustable
Not adjustable
Not adjustable
Not adjustable
Not adjustable
Not adjustable
Not adjustable
Installation and maintenance instructions ecoTEC pro 0020129672_03 41
42
11 Adapting the boiler to the heating installation
The heating partial load of the Vaillant ecoTEC pro boiler is factory-set to "auto". This means that the boiler independently determines the optimum heating output depending on the current heat demand of the system. A setting is normally no longer required. If you still want to set a fixed maximum heating partial load, you can set a value under diagnostic code "D.000", which equates to the boiler output in kW.
operating mode
The pump overrun time for the heating mode is set at the factory to a value of 5 minutes. You can set the pump overrun time under diagnosis code "D.001" within the range of
1 minute to 60 minutes. You can set a different pump operating mode under diagnosis code "D.018". Here you have the choice between 3 = Eco and 1 = Comfort.
Setting the burner anti-cycling time
To prevent frequent switching on and off of the burner and therefore energy loss, an electronic restart lockout is activated for a specific period each time the burner is switched off. You can adjust the burner anti-cycling time to the conditions of the heating installation.
The burner anti-cycling time is only activated for the heating mode.
Hot water handling during a burner anti-cycling time does not affect the timer.
You can set the maximum burner anti-cycling time at installer level under diagnosis code "D.002" within the range 2 minutes to 60 minutes (factory setting: 20 min).
The effective burner anti-cycling time depends on the current target flow temperature and the maximum burner anticycling time set.
The effective burner anti-cycling times with respect to the target flow temperature and the maximum set burner anticycling time can be found in the following table.
Comfort (continuously operating pump)
The internal pump is switched on when the heating flow temperature is not at "Heating off"(¬ Operating instruc-
tions) and the heating requirement is enabled via an external controller.
i The remaining burner anti-cycling time following a regular shutdown in heating mode can be called up under diagnosis code "d.067".
Eco (intermittently operating pump)
Pump operating mode Eco is the factory setting. This pump operating mode is useful for removing residual heat after hot water generation when the heat demand is extremely low and large temperature spreads exist between the hot water generation and heating mode target values. This prevents living rooms from being under-supplied. If there is a heat demand, the pump is switched on every 25 minutes for
5 minutes once the overrun time has elapsed.
Reset remaining burner anti-cycling time
> Press the fault clearance key (¬ Operating instruc-
tions).
The maximum flow temperature for the heating is set at the factory to 75 °C. This can be set to a value in the range of
40 °C to 80 °C under diagnosis code "D.071".
If the boiler is connected to an underfloor heating system, the temperature control can be changed from flow temperature regulation (default setting) to return flow temperature control under diagnosis code "D.017".
Installation and maintenance instructions ecoTEC pro 0020129672_03
Adapting the boiler to the heating installation 11
T
Feed
(target)
[°C]
Set maximum burner anti-cycling time [min]
1 5 10 15 20 25
60
65
70
75
40
45
50
55
20
25
30
35
2.0
2.0
2.0
2.0
2.0
2.0
2.0
2.0
2.0
2.0
2.0
2.0
5.0
4.5
4.0
4.0
3.5
3.0
3.0
2.5
2.0
1.5
1.5
1.0
10.0
9.2
8.5
7.5
6.5
6.0
5.0
4.5
3.5
2.5
2.0
1.0
15.0
14.0
12.5
11.0
10.0
8.5
7.5
6.0
5.0
3.5
2.5
1.0
20.0
18.5
16.5
15.0
13.0
11.5
9.5
8.0
6.0
4.5
2.5
1.0
25.0
23.0
20.5
18.5
7.5
5.5
3.0
1.0
16.5
14.0
12.0
10.0
11.2 Effective burner anti-cycling times
30
30.0
27.5
25.0
22.0
9.0
6.5
3.5
1.0
19.5
17.0
14.0
11.5
35
35.0
32.0
29.0
25.5
22.5
19.5
16.5
13.5
10.5
7.0
4.0
1.0
40
40.0
36.5
33.0
29.5
11.5
8.0
4.5
1.0
26.0
22.5
18.5
15.0
45
45.0
41.0
37.0
33.0
29.0
25.0
21.0
17.0
13.0
9.0
5.0
1.0
50
50.0
45.0
41.0
36.5
32.0
27.5
23.5
19.0
14.5
10.0
5.5
1.0
55
55.0
50.0
45.0
40.5
35.5
30.5
25.5
20.5
15.5
11.0
6.0
1.0
60
60.0
54.5
49.5
44.0
17.0
11.5
6.5
1.0
38.5
33.0
28.0
22.5
i On completion of the set operating hours, you must set the maintenance interval again in diagnosis mode.
You can define maintenance intervals for the ecoTEC pro.
After the set burner operating hours have elapsed, in addition to the current flow temperature, the maintenance symbol (open-end spanner) appears in the display and this shows that the boiler must be serviced. The display on the eBUS controller (accessory) shows the information "Maintenance" "MAIN".
Heat demand
5.0 kW
10.0 kW
15.0 kW
20.0 kW
25.0 kW
> 27.0 kW
Number of persons
Burner operating hours until the next inspection/service
(depending on the system type)
1 - 2
2 - 3
1 - 2
2 - 3
2 - 3
3 - 4
3 - 4
4 - 5
3 - 4
4 - 6
3 - 4
4 - 6
1,050 h
1,150 h
1,500 h
1,600 h
1,800 h
1,900 h
2,600 h
2,700 h
2,800 h
2,900 h
3,000 h
3,000 h
The boilers have a by-pass valve.
The pressure is adjustable in the range between 17.0 MPa
(170 mbar) and 35.0 MPa (350 mbar). Approx. 25.0 MPa
(250 mbar) is pre-set (mid-position). The pressure changes by approx. 1.0 MPa (10 mbar) each time the adjusting screw is rotated. By turning right, the pressure increases and turning left decreases it.
1
> Set the operating hours until the next service using diagnosis code "d.084".
Guideline values for the setting can be found in
¬ table 11.3. The values stated correspond to an average boiler operating time of one year.
You can set the operating hours in increments of ten from
0 to 3,000 h.
If you do not enter a figure under diagnosis code "D.084" but instead enter the symbol "–", then the "Maintenance display" function is not active.
11.1 Setting the by-pass valve
Installation and maintenance instructions ecoTEC pro 0020129672_03 43
11 Adapting the boiler to the heating installation
> Regulate the pressure using the setting screw (1).
Position of the
setting screw
Right-hand stop
(turned all the way down)
Pressure in MPa
(mbar)
Notes/application
35.0 (350)
If the radiators do not get properly hot in the default
setting.
Note: In this case, you must set the pump to the maximum stage.
Mid-position (5 turns to the left)
5 further turns to the left from the mid-position
25.0 (250) Factory setting
17.0 (170)
If noises in the radiators or radiator valves are produced
11.4 Setting value for the by-pass valve (feed head) a Danger!
Risk of poisoning and burns caused by escaping hot flue gas!
Hot flue gas can escape and cause poisoning and burns if the boiler is operated with an incompletely mounted or open air/flue gas duct or if the boiler is operated with internal leaks with the front casing open.
> Operate the boiler
- for commissioning
- for testing purposes
- in continuous operation only when the front casing is fitted and closed and the air/flue gas duct is completely fitted.
> Exclusively for test purposes such as gas working pressure testing the boiler may be operated with the front casing removed for short durations ONLY but must have a completely mounted air/flue gas duct.
If this boiler is not installed and commissioned in accordance with the manufacturer's instructions, this may void the guarantee (Note: Your legal rights remain unaffected by this.)
> Handover the boiler to the operator.
> Explain the basic operation of the heating installation to the operator.
> Provide the operator with all relevant instructions and boiler documentation.
> Go through the operating instructions with the operator
> Reply to his questions if necessary.
> Make the operator aware of the need to keep the instructions in a handy location near the boiler, but not in or on the boiler.
> Draw special attention to the safety instructions, which the operator must follow.
> Instruct the operator that no changes or adaptations must be made to the flue system or combustion air supply. These must both terminate outside of the building and be constructed only from approved components.
> Explain to the operator how he should monitor the water level/filling pressure of the system.
> Explain to the operator which measures are required to top up and purge the heating installation if required.
> Explain to the operator how to correctly set the temperatures, the controllers and the thermostatic radiator valves (economically).
> Complete and sign off the Benchmark commissioning check list.
> Complete and sign off the guarantee documentation.
> After completing the installation, stick the 835593 sticker in the user's language to the front of the boiler.
The sticker is delivered with the boiler.
You must brief the operator of the boiler on the handling and function of the ecoTEC pro.
> Explain the importance of regular maintenance by a competent skilled trade company to the operator.
It is strongly recommended that a maintenance contract be taken out to ensure regular maintenance. Important information is available from Vaillant Service Solutions
(0870 6060 777).
> Complete the benchmark Benchmark gas boiler commissioning checklist which is found at the end of these instructions.
44 Installation and maintenance instructions ecoTEC pro 0020129672_03
Inspection and maintenance 12
12 Inspection and maintenance
After servicing, complete the relevant Service Record section of the Benchmark Checklist located on the inside back pages of this document.
We recommend the conclusion of an inspection and maintenance contract with an approved company or installer.
The inspection serves to determine the actual condition of the respective boiler and compare it with the specified condition. This is done by measuring, checking and observing.
Maintenance is required in order to eliminate any deviations of the actual condition from the specified condition.
a Danger !
Risk of injury and risk of damage to property due to neglected inspection and maintenance!
Neglected inspection and maintenance works or not observing the stated inspection and maintenance intervals can interfere with the operational safety of the boiler and can result in damage to property and to persons.
> Point out to the operator that he must observe the demanded inspection and maintenance intervals as a minimum.
> Carry out proper regular inspections once a year.
> Carry out regular maintenance as dictated by findings during the inspection process.
This normally is done by cleaning, adjustment and, if necessary, replacing individual components that are subject to wear.
In any case, regular servicing in line with column 2 in
¬ table 12.2 must be carried out to ensure continued efficient and reliable operation of the boiler.
You must carry out an annual inspection of the Vaillant
ecoTEC.
The annual inspection can be effectively performed without removing components by requesting data from the DIA system, carrying out the simple visual checks indicated in
¬ table 12.2 and performing a flue gas measurement.
The maintenance intervals and their scope are determined by the heating engineer based on the condition of the boiler found during the inspection.
All inspection and maintenance work should be performed in the order specified in ¬ table 12.2.
a Danger!
Danger of life and limb due to improper inspection/maintenance!
Inspections/Maintenance work carried out improperly can result in leakages and explosion.
> The boiler may only be inspected/maintained by a competent person.
All service work must be carried out by a competent person in accordance with the Gas safety, installation and use regulations. In the UK this is considered to be a person approved at the time by the Health and Safety Executive.
In addition BS 6798: 2009 "Specification for installation and maintenance of gas-fired boilers of rated input not exceeding 70 kW net" advises that:
– The person carrying out a combustion measurement must be assessed as competent in the use of a flue gas analyser and the interpretation of the results.
– The flue gas analyser used must be one meeting the requirements of BS 7927 or BS-EN50379-3 and be calibrated in accordance with the analyser manufacturers’ requirements.
– Competence can be demonstrated by satisfactory completion of the relevant ACS standard assessment, which covers the use of electronic portable flue gas analysers’ in accordance with BS 7967, parts 1 to 4.
– The flue gas analyser is set to the correct fuel setting.
a Danger!
Risk of poisoning and burning caused by escaping hot flue gas!
Hot flue gas can escape and cause poisoning and burning if the boiler is operated with an incompletely mounted or open air/ flue gas duct or if the boiler is operated with internal leaks with the front casing open.
> Operate the boiler
- for commissioning
- for testing purposes
- in continuous operation only when the front casing is fitted and closed and the air/flue gas duct is completely mounted.
> Exclusively for test purposes such as gas working pressure testing you can operate the boiler may be operated with the front casing removed for short durations ONLY but must have a completely mounted air/ flue gas duct.
45 Installation and maintenance instructions ecoTEC pro 0020129672_03
12 Inspection and maintenance
46
12.1.1 General inspection and maintenance instructions
To ensure the faultless operation, long term availability of all functions and long working life of your Vaillant boiler and to prevent modifications to the approved series status only genuine Vaillant spare parts must be used when carrying out inspection, maintenance and repair work.
For an overview of the available original Vaillant spare parts, contact the Vaillant sales office on 0870 6060 777.
During any inspection and maintenance or after change of parts of the combustion circuit, the following must be checked:
– The boiler has been installed in accordance with the relevant installation instructions.
– The integrity of the flue gas installation and flue seals is in accordance with the relevant flue installation instructions enclosed.
– Visual, the integrity of the boiler combustion circuit and relevant seals (paying particular attention to the burner door seal).
– The gas inlet working pressure at maximum rate as described in ¬ section 10.9.4.
– The gas flow rates as described in ¬ section 10.9.3.
– Correctness of electrical, water and gas connections.
– Correctness of the water pressure.
– The condition of the whole system, in particular the condition of radiator valves, evidence of leakage from the heating system and dripping taps.
> Correct any faults before proceeding.
Always perform the following steps prior to inspection or maintenance work:
> Switch off the main switch.
> Disconnect the boiler from the power mains by
– disconnecting the mains plug or
– de-energising the boiler via an isolating device with a contact opening of at least 3 mm (e. g. fuses or power switches).
> Further check for electrical isolation of the appliance by use of a test meter.
> Close the gas isolation valve.
> Close the service valves in the heating flow and return.
> Remove the front casing from the boiler.
> When removing any water carrying components ensure that water is kept away from all electrical components.
Always perform the following steps after performing any inspection or maintenance work:
> Always use new seals and O-rings when parts are replaced.
> Open the service valves in the heating flow and return.
> Open the cold water stop valve if necessary.
> Reconnect the boiler to the power mains.
> Switch on the boiler using the on/off switch.
> Fill the heating circuit of the boiler to a pressure of between 0,1 and 0,2 MPa (1,0 and 2,0 bar) if required.
> If you have topped up with water, purge the heating installation using test program P.00 (¬ section 10.5.2).
> Open the gas isolation valve.
> Check the boiler for gas and water leaks.
> Replace the front casing to the boiler (¬ section 4.7).
> Carry out a functional check of the boiler (¬ sec-
tion 10.10).
> Always check earth continuity, polarity and resistance to earth with a multimeter after any service work and after replacing any electrical component.
> If necessary, refill and re-purge the heating installation.
> Complete the benchmark gas boiler commissioning service record on the back pages of these instructions.
a Danger!
Danger of life and limb by electric shock!
The supply terminals of the boiler are under mains voltage even if the boiler main switch is off.
> Don’t touch the supply terminals.
> Protect the electronic box from any water or spray.
> Before working on the boiler, turn off the power and secure against restart.
Checking the CO/CO
2
ratio and the CO
2 concentration a Danger!
Danger of explosion, fire or poisoning caused by incorrect flue gas value adjustment.
Safe combustion can only be verified by measuring CO/CO
2
ratio.
> Make sure that the CO/CO
2
ratio does not exceed the value shown in ¬ table 12.1
.
i If it is necessary to keep the electricity to the boiler switched on for certain inspection and maintenance, this is indicated in the description of the maintenance task.
i Checking/adjustment of the CO2 concentration is required in the following instances:
- replacement of gas valve,
- conversion to or from Natural Gas/LPG
- or if an incorrect combustion is suspected.
Installation and maintenance instructions ecoTEC pro 0020129672_03
Inspection and maintenance 12
1
1
Measuring the CO
2
concentration i The boiler is fitted with a flue gas analysis point
(1). A suitable flue gas analyser can be connected to this point to establish the combustion performance of the boiler.
> Remove the front casing (¬ section 4.7).
> Start the testing program P.01 (¬ section 10.2).
> Wait at least 5 minutes until the boiler reaches its operating temperature.
> Measure the CO
2
concentration at the flue gas analysis point (1). Compare the measured value with the corresponding value in ¬ table 12.1.
> If all these points are as required, proceed as described in ¬ section 12.2.
> If one of the flue gas values is greater than the acceptable values in ¬ table 12.1, then proceed as described in the following ¬ section 12.1.4.
ing screw (gas setting) and making the air ratio setting
2
Adjusting the CO
2 concentration (or the air ratio) a Danger!
Increased risk of poisoning due to incorrect settings!
If one of the flue gas values is greater than the acceptable values in ¬ table 12.1 then:
> Check the integrity of the complete flue gas installation.
> Check the integrity of the combustion circuit seals.
> Check the gas inlet working pressure.
> Check the gas flow rate.
If the flue gas value needs to be adjusted, proceed as
follows.
The adjusting screw for making the air ratio setting is located beneath a blue covering cap (1), which is easy to remove.
> Remove the yellow sticker.
> Remove the covering cap.
> Set the relevant CO
2
value (value with removed front casing ¬ table 12.1) by turning the screw (2). Use a
2.5 mm Allen key for this.
– Turn to the left: higher CO
2
concentration,
– Turn to the right: lower CO
2
concentration.
i i
Natural gas: Only perform the adjustment in small increments of 1/8 turn and wait approximately 1 minute after each adjustment until the value stabilises.
Liquid gas: Only perform the adjustment in very small increments (approximately 1/16 turns), and wait approximately 1 minute after each adjustment until the value stabilises.
> Press the "Cancel" selection button once the settings have been adjusted.
> When the adjusting work is complete, put the covering cap back on again.
> Put the front casing back on (¬ section 4.7).
47 Installation and maintenance instructions ecoTEC pro 0020129672_03
12 Inspection and maintenance
Settings Unit
CO
2
after 5 minutes full load mode with boiler front casing fitted
CO
2
after 5 minutes full load mode with boiler front casing removed
Vol.–%
Vol.–%
Set for Wobbe index Ws kWh/m 3
CO value with full load
CO/CO
2 ppm
Natural gas
(H)
9.2 +/
9.0 +/
15
- 1.0
- 1.0
< 250
< 0.0031
Propane
10.2 +/
10.0 +/
- 0.5
- 0.5
22.5
< 250
< 0.0026
a Danger!
Risk to life due to poisoning!
CO is an extremely toxic gas. Risk to life due to excessive CO concentrations.
> If you are not able to adjust the boiler correctly and the flue gas values remain higher than allowed in ¬ table 12.1, call the Vaillant Service Solutions
(0870 6060 777).
> Do not start up the boiler!
48 Installation and maintenance instructions ecoTEC pro 0020129672_03
Inspection and maintenance 12
No. Activity
1
Check the air flue gas installation for leaks and for proper fixation and ensure it is not blocked or damaged and is fitted correctly, complying with the relevant installation instructions.
2 Carry out a general inspection of the boiler for dirt and dust and clean as necessary.
3
4
Visually inspect the complete heat engine for its general condition and for signs of corrosion, sooting or other forms of damage (paying particular attention to the burner door seal). If damage is evident proceed to column 2.
Measure the gas flow rate during operation with maximum load (¬ section 10.9.3). If the gas flow rate complies to the ¬ table 10.2 continue with column 1, if not proceed to column 2.
5
6
Check the gas inlet working pressure (¬ section 10.9.4) operation with maximum load. If the gas inlet working pressure complies to the ¬ table 10.3 continue with column 1, if not proceed to column 2.
Check combustion by measuring CO, CO
2
and CO/CO
2
. If the values are outside the tolerances of ¬ table 12 proceed to maintenance column 2. You must not proceed with the maintenance if a new burner door seal kit is not available.
7
Isolate the boiler from the power mains. Check whether the electrical plug connections and the other electrical connections are fitted tightly and correct them if necessary.
8 Close the gas isolation valve and the service valves.
9
Drain the pressure in the boiler on the water side (observe pressure gauge) and check the charge pressure of the expansion vessel. Top up if necessary.
10 Remove the compact thermal module.
11
Check the integrity of all combustion circuit seals, especially the burner door seal. Ensure any damage found is repaired before proceeding.
12 Clean the heat exchanger (¬ section 12.3.2).
13 Check whether the burner is dirty and clean it if necessary.
14
Check the condensate trap in the boiler, clean and fill. Flush through all discharge pipe work
(ensure route and termination are correct and it is unlikely to freeze up in severe weather).
15 Install the compact thermal module. Caution: Use new seals and nuts!
16
Replace the hot water heat exchanger if the volume of water is insufficient or the output temperature is not reached
17
18
Remove the impeller sensor, clean the filter in the cold water inlet of the sensor and refit the sensor.
Open the gas isolation valve, reconnect the boiler with the power mains and switch on the boiler.
19
20
Open the service valves and fill up the boiler/appliance to approximately 0,1 - 0,2 MPa (1,0 -
2,0 bar) (depending on the static height of the system). Start the purging program P.00.
Perform a test operation of the boiler and heating installation, including hot water generation and purge again if necessary.
21 Check visually the ignition and burner performance.
22
23
24
Check the boiler for leaks of any kind (gas, flue gas, water, condensate) and rectify as necessary.
If you had problems with the CO, CO
2
, CO/CO
2
-values in Step 6 before the maintenance, check them again now ( ¬ table 12.1). If they are outside of the tolerances of ¬ table 12.1 make an adjustment, see ¬ section 12.1.4.
Complete the Benchmark gas boiler commission service record on the back pages of this manual.
Column 1
Inspection must be carried out each year
Column 2
Maintenance must be carried out at regular intervals x x x x x x x x x x x x x x x x x x x x x x x x x x x x x x x x x x x x
Installation and maintenance instructions ecoTEC pro 0020129672_03 49
50
12 Inspection and maintenance
12.2.1 Filling the boiler and the heating installation
The compact thermal module consists of five main components:
A description of how to fill the boiler and the heating installation is provided in ¬ section 10.5.
2. Gas/air mixture fitting
3. Gas supply (mixture pipe) to the premix burner
12.2.2 Draining the boiler
> Close the service valves of the boiler.
> Start test program P.06 (diverter valve mid-position)
(¬ section 10.5).
> Open the drain valves on the service valves.
> Make sure that the cap of the automatic air vent on the internal pump is open so that the boiler can be drained fully.
12.2.3 Draining the entire heating installation
> Attach a hose to the draining device on the system.
> Bring the open end of the hose to an appropriate drain point.
> Start test program P.06 (diverter valve mid-position)
(¬ section 10.5).
> Make sure that the service valves on the boiler and the cap of the automatic air vent on the internal pump is open.
> Open the drain cock.
> Open the purging valves on the radiators.
Start from the highest radiator and then work from the top to the bottom.
> Once the water has drained off, close the purging valves of the radiators and the drain cock.
> Switch off the boiler using the on/off switch.
> Close the gas isolator cock on the boiler.
> Close the service valves on the boiler.
> Remove the front casing from the boiler (¬ section 4.7).
> Fold the electronics box forwards (¬ section 8.2).
1
2
3
4
12.3 Carrying out maintenance work
> Unscrew the retaining screw (2, ¬ fig. 12.3) and detach the air intake pipe (1, ¬ fig. 12.3) from the intake stub.
> Unscrew either the cap nut (3, ¬ fig. 12.3) from the gas valve or the cap nut (4, ¬ fig. 12.3) between the gas pipes.
> Secure the gas pipe against twisting by holding the pipe against the spanner flat when undoing the cap nut.
a Danger!
Risk of being burned or scalded by hot components!
There is danger of being burned or scalded at the compact thermal module and at all water-carrying components.
> Only carry out work on these components if they have cooled down.
Installation and maintenance instructions ecoTEC pro 0020129672_03
Inspection and maintenance 12
7
1
2
> Remove the compact thermal module (¬ section 12.3.1).
2
3
3
6
5
4
1
12.5 Cleaning the heat exchanger b Caution.
Risk of damage to the heat exchanger.
> You should neither loosen nor tighten the four screws (1).
i The plug on the fan motor has a latching lug with which it engages in the slot. You have to release the latching lug by pushing it in to pull off the plug.
> Remove the plug of the ignition line (5, ¬ fig. 12.4) and the ground connection (6, ¬ fig. 12.4) from the ignition electrode.
> Remove the plug (3, ¬ fig. 12.4) from the fan motor.
> Remove the plug from the gas valve (4, ¬ fig. 12.4).
> Unscrew the four nuts (7, ¬ fig. 12.4).
> Remove the entire compact thermal module (2,
¬ fig. 12.4) from the heat exchanger (1, ¬ fig. 12.4).
> Once removed, check the burner and the heat exchanger for damage and dirt.
> If necessary, clean the components according to the following sections.
> Check the burner flange insulation on the module. If signs of damage, other than small cracks, are apparent you must replaced it (article number 193 595).
> Clean the heating coil (3) of the heat exchanger (4) using water or if required commercially-available white vinegar.
> Allow the vinegar to act on the heat exchanger for
20 minutes.
> Rinse away any loose dirt with a sharp jet of water or use a plastic brush.
> Do not point the water jet directly at the insulating surface (2) on the back of the heat exchanger.
The water flows out of the heat exchanger through the condensate trap.
1
4 b Caution.
Risk of damage from water spray.
If you fail to protect the electronics box adequately, water can penetrate the box during cleaning and may damage the electronics.
> Protect the folded down electronics box against sprayed water.
Installation and maintenance instructions ecoTEC pro 0020129672_03
12.6 Checking the burner
51
12 Inspection and maintenance
As the burner (1) is maintenance-free, it does not require cleaning.
> Check the surface of the burner for damage.
> If necessary, replace the burner.
1 a Danger!
Risk of death caused by improper maintenance.
If you operate the boiler with an empty condensate trap, flue gas can escape into the room air.
> Top up the condensate trap after each cleaning session.
> Close the cold water stop valve.
> Drain the hot water from the boiler.
> Undo the nut (1, ¬ fig. 12.8) of the cold water supply line from the casing of the boiler.
1
1
12.7 Cleaning the condensate trap
> Remove the lower part (1) of the condensate trap by turning the bayonet fitting anti-clockwise.
> Clean the bottom of the condensate trap by flushing it out with water.
> Fill the lower part of the condensate trap with water up to about 10 mm below the upper edge.
> Re-fit the lower part of the condensate trap.
> Flush through all discharge pipe work (ensure route and termination are correct and it is unlikely to freeze up in severe weather).
2
> Fold the electronics box forwards (¬ section 8.2).
> Remove the clamp (1, ¬ fig. 12.9) from the flow sensor.
> Pull off the cold water pipe from the flow sensor.
> Remove the pipe (2, ¬ fig. 12.9) from the boiler.
> Rinse the filter under a jet of water holding against the direction of flow.
> Refit the pipe with the cleaned filter in the reverse order.
> Always use new seals.
12.3.5 Cleaning the filter in the cold water inlet
There is a filter in the cold water inlet of the boiler which must be cleaned during maintenance work.
52 Installation and maintenance instructions ecoTEC pro 0020129672_03
Inspection and maintenance 12
7
8
10
9 a Danger!
Risk of death and risk of damage caused by hot flue gas!
If you do not renew the seal and the selflocking nuts on the burner door, hot flue gases may escape and cause personal injury and material damage.
> Replace the seal each time you open the burner door.
> Replace the self-securing nuts each time you open the burner door.
> If the burner flange insulation on the module shows signs of damage other than small cracks it must be replaced
(article number 193 595).
1
2
3
4
> Tighten either the cap nut (6, ¬ fig. 12.10) on the gas valve or the cap nut (7, ¬ fig. 12.10) between the gas pipes. Use a new seal for this.
> Secure the gas pipe against twisting (¬ fig. 12.11) by holding the pipe against the spanner flat when tightening the cap nut.
> Open the gas isolator cock on the boiler and ensure there are no leaks.
> Check that the sealing ring in the air intake pipe is positioned correctly in the seal seat.
> Insert the air intake pipe (1, ¬ fig. 12.3) back into the intake stub.
> Attach the air intake pipe using the retaining screw (2,
¬ fig. 12.3).
5 expansion vessel
6
> Attach the compact thermal module (4, ¬ fig. 12.10) to the heat exchanger (1, ¬ fig. 12.10).
> Tighten the four nuts (3, ¬ fig. 12.10) crosswise until the burner door fits closely and uniformly onto the mating surfaces (If a torque spanner is available, set at 6 Nm).
> Attach the plug of the ignition line (10, ¬ fig. 12.10) and the ground connection (9, ¬ fig. 12.10) to the ignition electrode.
> Attach the plug (5, ¬ fig. 12.10) to the fan motor.
> Attach the plug (8, ¬ fig. 12.10) to the gas valve.
12.12 Checking the charge pressure of the expansion vessel
1
The service valves of the boiler must be closed.
> Measure the charge pressure of the expansion vessel at the testing nozzle (1) of the vessel with the boiler depressurised.
> Top up the expansion vessel at a pressure of less than
0.75 bar in accordance with the static height of the heat-
Installation and maintenance instructions ecoTEC pro 0020129672_03 53
12 Inspection and maintenance ing installation, ideally with nitrogen, otherwise with air.
Ensure drain valve on boiler is open during topping up.
> If water escapes from the measuring stub pipes (1) of the expansion vessel, you must replace the expansion vessel.
> Check the gas flow pressure (¬ section 10.9.4).
2
content
> Check the CO
2
content (¬ section 12.1.3).
54 Installation and maintenance instructions ecoTEC pro 0020129672_03
Troubleshooting 13
13 Troubleshooting
13.1 Contact Vaillant Service Solutions
(0870 6060 777)
> If you contact Vaillant Service Solutions (0870 6060
777) or your Vaillant service partner, if possible, please mention
– the fault code displayed (F.xx),
– the boiler status that is displayed (S.xx) in the "Live monitor" (¬ section 13.2.1).
You can call up the boiler status codes in the display which provide information on the current operating status of the boiler.
> Press the left-hand buttons
and right-hand selection
("i") at the same time
S.04
13.1 Status code display view
Display Meaning
DHW mode (VUW boiler)
S.10
Hot water demand via impeller sensor
S.11
S.13
DHW mode, fan start-up
DHW mode, ignition
S.14
S.15
S.16
S.17
DHW mode, burner on
DHW mode, pump/fan overrun
DHW mode, fan overrun
DHW mode, pump overrun
VUW Comfort mode, warm start
S.20
DHW demand
S.21
S.22
DHW mode, fan start-up
DHW mode, pump running
S.23
S.24
S.25
S.26
S.27
S.28
DHW mode, ignition
DHW mode, burner on
DHW mode, pump/fan overrun
DHW mode, fan overrun
DHW mode, pump overrun
Hot water burner anti-cycling time
Special cases
S.30
Room thermostat (RT) is blocking heating mode
S.31
Summer mode active or no heat requirement from eBUS controller
S.32
S.34
S.39
Waiting period because of fan speed deviation
Frost protection mode active
"Burner off contact" has triggered (e.g. contact thermostat or condensate pump)
S.40
S.41
S.42
Comfort safety mode is active: Boiler is running with limited heating comfort (¬ section 13.2.4)
Water pressure > 2.8 bar
Flue non-return flap return signal blocks burner operation (only in connection with VR40 accessory) or condensate pump faulty, heat requirement is blocked
S.46
S.53
S.54
Comfort safety mode, flame loss at minimum load
Boiler is in waiting period of modulation block/operation block function due to water shortage (supply-return spread too large)
Boiler is in waiting period of operation blocking function as a result of water shortage (temperature gradient)
Display Meaning
Heating mode
S.00
Heating, no heat demand
S.01
S.02
S.03
S.04
Heating mode fan start-up
Heating mode pump flow
Heating mode, ignition
Heating mode, burner on
S.05
S.06
S.07
S.08
Heating mode, pump/fan overrun
Heating mode, fan overrun
Heating mode, pump overrun
Heating mode, burner anti-cycling time
13.1 Status codes
S.76
S.96
S.97
S.98
System pressure too low; top up water
Return temperature sensor test running, heating demands are blocked
Water pressure sensor test running, heating demands are blocked
Flow/return temperature sensor test running, heating demands are blocked
13.1 Status codes (continuation)
55 Installation and maintenance instructions ecoTEC pro 0020129672_03
13 Troubleshooting
13.2.8 Resetting the fault memory
If the "open-end spanner" maintenance symbol appears on the display, a service message is present. The maintenance symbol appears if you have set a maintenance interval, for example, (¬ section 11.1.6) and it has elapsed. The boiler is not in fault mode but continues to operate.
To obtain more information about the service message:
> Call up the "Live monitor" (¬ section 13.2.1).
You can delete the entire fault list.
> Call up the installer level (¬ section 9.2).
> Set the diagnostic code "D.094" to 1 (¬ section 11.1).
13.2.5 Calling up diagnosis levels
You can use the diagnostic codes to view parameters and modify certain parameters (¬ section 9.2) An overview of the diagnostic codes can be found in ¬ table 11.1.
If a fault develops in the boiler, the display shows a fault code F.xx.
Fault codes have priority over all other displays. If a fault occurs, the display no longer shows the current heating flow temperature of the heating installation.
If multiple faults occur at the same time, the display shows the corresponding fault codes for two seconds each in sequence.
> Remedy the fault.
> To restart the boiler, press the fault clearance key
(¬ Operating instructions).
> If you are unable to remedy the fault and the fault reoccurs despite having carried out several resets, contact
Vaillant Service Solutions (0870 6060 777).
The boiler has a fault memory. ¬ section 9.2 describes how you can call up the fault memory.
Here you can query the last ten faults that occurred in chronological order.
The display shows:
– the number of faults that have occurred
– the fault currently selected with fault number F.xx.
> You can display the last 10 faults that occurred using the minus button or the plus button .
56 Installation and maintenance instructions ecoTEC pro 0020129672_03
Troubleshooting 13
Code
F.00
F.01
F.10
Meaning
Flow temperature sensor interruption
Return temperature sensor interruption
Flow NTC short circuit
Cause
NTC plug not plugged in or has come loose, multiple plug on the PCB not plugged in correctly, interruption in cable harness, NTC defective
NTC plug not plugged in or has come loose, multiple plug on the PCB not plugged in correctly, interruption in cable harness, NTC defective
NTC defective, short circuit in cable harness, cable/casing
NTC defective, short circuit in cable harness, cable/casing F.11
Return NTC short circuit
F.20
F.22
F.23
F.24
F.25
F.26
F.27
F.28
F.29
F.32
F.49
F.61
F.62
Safety switch-off: temperature limiter
Safety switch-off: low water pressure
Incorrect earth connection between cable harness and boiler, flow or return NTC defective (loose connection), black discharge via ignition cable, ignition plug or ignition electrode
No water pressure, or water pressure is too low in the boiler, water pressure sensor defective, cable to pump or water pressure sensor loose/not connected/defective
Safety switch-off: Temperature difference too great Pump blocked, insufficient pump output, air in boiler, flow and return
NTC interchanged
Safety switch-off: Temperature rise too fast
Safety switch-off: Flue gas temperature too high
Fault: Gas valve without function
Pump blocked, poor pump performance, air in boiler, system pressure too low, non-return valve blocks/incorrectly installed
Break in plug connection for optional flue gas safety thermostat (STB), break in cable harness
Gas valve stepper motor not connected, multiple plug on the PCB not plugged in correctly, interruption in cable harness, gas valve stepper motor defective, electronics defective
Safety switch-off: Flame simulation
Failure during start-up: ignition unsuccessful
Moisture on the electronics, electronics (flame monitor) defective, gas solenoid valve leaking
Gas meter defective or gas pressure regulator has triggered, air in gas, gas flow pressure too low, thermal isolator device (TAE) has triggered, condensate duct blocked, incorrect gas restrictor, incorrect ET gas valve, fault on the gas valve, multiple plug on PCB incorrectly plugged in, break in cable harness, ignition system (ignition transformer, ignition cable, ignition plug, ignition electrode) defective, ionisation current interrupted
(cable, electrode), incorrect earthing of boiler, electronics defective
Failure during operation: Re-ignition unsuccessful Gas supply temporarily stopped, flue gas recirculation, condensate duct blocked, faulty earthing of boiler, ignition transformer has spark failure
Fan fault Plug at fan not correctly plugged in, multiple plug on PCB not correctly plugged in, break in cable harness, fan blocked, Hall sensor defective, electronics defective eBUS fault
Fault: Gas valve regulation
Fault: Gas valve switch-off delay
Short circuit on eBUS, eBUS overload or two power supplies with different polarities on the eBUS
- Short circuit/short to earth in cable harness for the gas valve
- Gas valve defective (coils shorted to earth)
- Electronics defective
- Delayed shutdown of gas valve
- Delayed extinguishing of flame signal
- Gas valve leaking
- Electronics defective
F.63
F.64
F.65
F.67
EEPROM error
Electronics/NTC fault
Electronic temperature fault
Electronics/flame fault
13.2 Fault codes
Electronics defective
Supply or return NTC short circuited, electronics defective
Electronics overheating due to external influences, electronics defective
Implausible flame signal, electronics defective
Installation and maintenance instructions ecoTEC pro 0020129672_03 57
13 Troubleshooting
Code
F.68
F.70
F.71
F.72
F.73
F.74
F.75
F.76
F.77
F.78
F.83
Meaning Cause
Unstable flame signal fault
Invalid device specific number (DSN)
Flow NTC fault
Air in gas, gas flow pressure too low, wrong air ratio, condensate route blocked, wrong gas restrictor, ionisation flow interruption (cables, electrodes), flue gas recirculation, condensate route
Spare part case: Display and PCB changed at the same time and appliance code not reset
Flow temperature sensor signalling constant value:
- Flow temperature sensor incorrectly positioned at supply pipe.
- Flow temperature sensor defective.
Flow/return NTC fault
Water pressure sensor signal in the wrong range
(too low)
Flow/return NTC temperature difference too great -> flow and/or return temperature sensor defective
Interruption/short circuit of water pressure sensor, interruption/short circuit to GND in supply line to water pressure sensor or water pressure sensor defective
Water pressure sensor signal outside correct range
(too high)
Fault, no pressure change detection when starting pump
Overheating protection on primary heat exchanger has responded
Flue non-return flap/condensate pump fault
Interruption to DHW outlet sensor at external controller
Flow and/or return temperature sensor temperature change fault
Cable to water pressure sensor has short-circuited at 5 V/24 V or internal fault in water pressure sensor
Water pressure sensor and/or pump defective, air in heating installation, too low water pressure in boiler; check adjustable bypass, connect external expansion vessel to return
Cable or cable connections for safety fuse in primary heat exchanger or primary heat exchanger defective
No response from flue non-return flap or condensate pump defective
UK link box is connected, but hot water NTC not bridged
When the burner starts, the temperature change registered at flow and/or return temperature sensor is non-existent or too small.
- Not enough water in the boiler
- Flow and/return temperature sensor not in correct position at pipe.
F.84
F.85
Fault: Flow/return temperature sensor temperature difference implausible
Flow and return temperature sensors returning implausible values.
- Flow and return temperature sensors have been inverted.
- Flow and return temperature sensors have not been correctly fitted.
Fault: Flow and return temperature sensors incorrectly fitted
Flow and/or return temperature sensors
have been fitted to the same pipe/wrong pipe.
No communication with the PCB Communication fault between display and PCB in the electronics box connection
13.2 Fault codes (continued)
By activating various test programs, you can trigger special functions on the boiler (¬ table. 10.1). The display shows which test program you have chosen.
> Read how to start the test programs in ¬ section 10.2.
13.4 Resetting parameters to factory settings
As well as the option to manually reset individual parameters to the default settings specified in ¬ table 11.1, you can also reset all parameters at once.
> Set the value of the diagnosis code parameter D.096 to
"1" (¬ section 11.1).
You have now reset all parameters to factory settings.
58 Installation and maintenance instructions ecoTEC pro 0020129672_03
Replacing components 14
14.1.2 Completing replacement work
The work described in this section must only be carried out by a competent person.
> Only use genuine Vaillant spare parts for repairs .
An overview of the available genuine Vaillant spare parts can be obtained:
– From your parts wholesaler
– Alternatively contact Spares Technical Enquiries on
01773 596615 or via email: [email protected]
> Check the boiler for gas leaks.
> Reattach the front casing (¬ section 4.7).
> Perform a function check (¬ section 10.10).
> Remove the compact thermal module (¬ section 12.3.1).
14.1 Preparing for and completing replacement work
14.1.1 Preparing for replacement work e Danger!
Risk of death from electric shock!
Mains connection terminals L and N remain live even if the continuous voltage on/off switch is turned off.
> Before carrying out maintenance work on the boiler, switch the boiler off using the on/off button.
> Disconnect the boiler from the power mains by disconnecting the mains plug or by de-energising the boiler via a partition with a contact opening of at least
3 mm (e. g. fuses or power switches).
14.1 Replacing the burner
> Undo the four screws (1) on the burner.
> Remove the burner.
> Fit the new burner with a new seal. Make sure that the nose on the burner window grips the seal inside the recess in the burner.
> Reinstall the compact thermal module.
(¬ Section 12.3.6).
i When carrying out any repair to the boiler, make sure that you observe the following instructions for your own safety and to avoid material damage to the boiler.
> Switch off the boiler.
> Disconnect the boiler from the power mains (¬ sec-
tion 11.3).
> Remove the front casing (¬ section 4.7).
> Close the gas isolator cock.
> Close the service valves in the heating flow and in the heating return.
> Close the service valve in the cold water pipe.
> Drain the boiler if you want to replace components that carry water (¬ section 11.3.2).
> Make sure that water does not drip on live components
(e.g. the electronics box).
> Use only new seals and O-rings.
1
59 Installation and maintenance instructions ecoTEC pro 0020129672_03
14 Replacing components
4
5
6
7
8
1
2
3
> If you want to replace the gas valve, unscrew the cap nut
(2, ¬ fig. 14.3) if the gas pipe is still secured to the gas valve.
> Unscrew the two fixing screws (1, ¬ fig. 14.3) from the gas valve and remove the fan from the gas valve.
> Replace the defective fan or the defective gas valve.
> Fit the gas valve and the fan in the same position as before. Use new seals.
> Screw the fan to the gas valve.
> If you had replaced the gas valve, screw the cap nut of the gas pipe (2, ¬ fig. 14.3) only loosely to the gas valve.
Only tighten the cap nut on the gas valve after completing the installation work.
> Refit the entire fan/gas valve unit in reverse order. You
must use a new seal for this (5, ¬ fig. 14.2).
> Pay attention to the order in which the three screws between the fan and the mixture pipe are screwed in, as per the numbering 3, 2 and 4 (¬ fig. 14.2).
> Remove the air intake pipe (¬ section 12.3.1).
> Remove the plug from the gas valve (7, ¬ fig. 14.2).
i The plug on the fan motor has a latching lug with which it engages in the slot. You have to release the latching lug by pushing it in to pull off the plug.
> Remove the plug (6, ¬ fig. 14.2) from the fan motor.
> Unscrew either the cap nut (2, ¬ fig. 14.3) from the gas valve or the cap nut (8, ¬ fig. 14.2) between the gas pipes.
> Secure the gas pipe against twisting by holding the pipe against the spanner flat when undoing the cap nut.
> Unscrew the three screws (2-4, ¬ fig. 14.2) between the mixture pipe (1, ¬ fig. 14.2) and the fan flange.
> Tighten the cap nut (2, ¬ fig. 14.3) on the gas valve and the cap nut (8, ¬ fig. 14.2) between the gas pipes. Use new seals.
> Secure the gas pipe against twisting (¬ fig. 14.4) by holding the pipe against the spanner flat when tightening the cap nut.
> After completing the work, perform a gas-tightness check and function check (¬ section 10.10).
> If you have fitted a new gas valve, adjust the gas setting
(¬ section 10.9).
> Drain the boiler (¬ section 12.2.2).
1
2
> Remove the entire fan/gas valve unit from the boiler.
60 Installation and maintenance instructions ecoTEC pro 0020129672_03
Replacing components 14
1
1
2
3
4
2
3
14.5 Replacing the expansion vessel
> Loosen the screw connection (4) at the water connection on the underside of the expansion vessel.
> Remove both screws (1) on the support plate (2).
> Remove the support plate (2).
> Pull out the expansion vessel (3) from the front.
> Insert the new expansion vessel into the boiler.
> Screw the new expansion vessel to the water connection.
Use a new seal for this.
> Attach the support plate using both screws (1).
> If necessary, adjust the pressure to the static height of the heating installation (¬ section 12.3.7).
> Fill and purge the boiler and, if necessary, the system after installing the new expansion vessel (¬ sec-
tion 10.5).
> On completion of the work, check for water leaks.
> Detach the clamps (2, ¬ fig. 14.6) and (3, ¬ fig. 14.6) from the flow connection and the return connection.
> Detach the flow connection from the heat exchanger.
> Detach the return connection from the heat exchanger.
> Remove two screws (1, ¬ fig. 14.6) from each of the two brackets of the heat exchanger.
1
2
3
1 b Caution.
Risk of damage to the heat exchanger.
> You can neither loosen nor tighten the four screws (¬ fig. 14.7, pos. 1).
> Drain the boiler (¬ section 12.2.2).
> Remove the compact thermal module (¬ section 12.3.1).
> Detach the condensate discharge hose from the heat exchanger.
> Disconnect the plug connection (2, ¬ fig. 14.7) of the thermal fuse in the heat exchanger.
> Remove the bottom three screws (3, ¬ fig. 14.7) from the rear part of the heat exchanger bracket.
> Swivel the bracket around the top screw (1, ¬ fig. 14.7) to one side.
> Pull the heat exchanger downwards and to the right, and remove it from the boiler.
61 Installation and maintenance instructions ecoTEC pro 0020129672_03
62
14 Replacing components b Caution.
Risk of damage to the boiler.
Mineral oil-based lubricants may damage the seals. The seals should therefore not be lubricated.
> Only use water or commercially available soft soap, if necessary, to assist with installation.
14.6.1 Replacing either the display or the PCB
> Replace the PCB or display according to the assembly and installation instructions supplied.
If you are replacing only one of the two components (PCB or display), the parametrisation functions automatically. By switching on the boiler, the new component takes over the previously set parameters from the unreplaced component.
> Install the new heat exchanger in the reverse order.
> Replace the seals.
> Insert the flow and return connections into the heat exchanger as far as they will go.
14.6.2 Replacing the PCB and the display at the same time i Make sure that the brackets are seated correctly on the flow and return connections.
> Reinstall the compact thermal module.
(¬ section 12.3.6).
> Fill and purge the boiler and, if necessary, the heating installation (¬ section 10.5).
Setting the appliance type
> Set the correct value for the appliance type in accordance with ¬ table 14.1 for diagnostic code D.093.
After confirmation, the display restarts itself automatically.
ecoTEC pro
24 (VUW GB 246/5-3)
28 (VUW GB 286/5-3)
Device specific number (DSN)
7
8 e Danger!
Risk of death from electric shock!
Mains connection terminals L and N remain live even if the continuous voltage on/off switch is turned off.
> Before carrying out repair work on the boiler, switch the boiler off using the on/ off button.
> Disconnect the boiler from the power mains by disconnecting the mains plug or by de-energising the boiler via a partition with a contact opening of at least
3 mm (e. g. fuses or power switches).
The electronics are now set to the appliance type and the parameters of all adjustable diagnosis codes are set to default settings.
> Make the system-specific settings (¬ section 11).
b Caution.
Risk of material damage caused by incorrect repairs.
Using an incorrect spare part display can cause damage to the electronics.
> Before replacing, check that the correct spare part display is available.
> ONLY fit the correct spare part display.
i Comply with the assembly and installation instructions provided with the spare parts.
Installation and maintenance instructions ecoTEC pro 0020129672_03
Decommissioning 15
15 Decommissioning
15.1 Temporarily shutting down the boiler
The Vaillant ecoTEC pro boiler consists primarily of materials that can be recycled.
The boiler and its accessories must not be disposed of with household waste.
> Make sure that the boiler and any existing accessories are disposed of properly.
b Caution.
Risk of frost damage due to incorrect shutdown.
If you switch off the boiler using the on/off switch or disconnect it from the power mains, this can cause frost damage to the heating installation.
> Only shutdown the boiler fully if the heating installation is otherwise protected from frost.
> Drain the heating installation fully.
One year guarantee for ecoTEC pro appliances
Vaillant undertakes to rectify any manufacturing defect that occurs within twelve months of the installation date.
2
50
Registering with us
Registration is simple. Just complete the Guarantee Registration Card and return to Vaillant within 30 days of installation. Your details will then be automatically registered within the Vaillant scheme.
Note: No receipt will be issued.
1
Immediate help
If your Vaillant boiler develops a fault your first action should be to contact your installer, as his professional assessment is needed under the terms of our Guarantee. If you are unable to contact your installer, phone Vaillant
Service Solutions: 0870 6060 777 15.1 Switching off the boiler
> Close the gas isolator cock.
> Close the cold water stop valve.
> Drain the heating installation fully
(¬ section 12.2.2).
> Press the on/off switch (1).
The display (2) goes off.
To ensure regular servicing, it is strongly recommended that arrangements are made for a Maintenance Agreement.
Please contact Vaillant Service Solutions
(0870 6060 777) for further details.
15.2 Taking the boiler permanently out of service
> Close the gas isolator cock.
> Close the cold water stop valve.
> Drain the heating installation fully
(¬ section 12.2.2).
> Press the on/off switch (1).
The display (2) goes off.
> Isolate the boiler from the power mains.
> Dispose of the boiler correctly (¬ section 15.3).
63 Installation and maintenance instructions ecoTEC pro 0020129672_03
17 Technical data ecoTEC pro Unit
Nominal heat output range P at 50/30 °C
Nominal heat output range P at 80/60 °C
Maximum heat output for hot water generation
Maximum heat input for hot water generation
Maximum heat input at the heating side
Minimum heat input G20
Minimum heat input G31
Minimum heat output G31
Heating setting range
Heating
Max. flow temperature
Max. flow temperature setting range(factory setting: 75 °C)
Min. pressure for full operation
Permissible total over-pressure
Expansion vessel capacity
Circulation water quantity (with reference to
DT = 20 K)
Condensate rate approx. (pH value 3.5 – 4.0) in heating mode 50 °C supply/30 °C return
Remaining feed head of pump (at nominal circulation water volume)
DHW mode
Lowest water volume
Water volume (at
DT = 42 K)
Water volume (at
DT = 35 K)
Water volume (at
DT = 30 K)
Permitted overpressure
Required connection pressure
Hot water output temperature range
General
Boiler-side gas connection
Flow/return heating connections, boiler side
Connecting the hot and cold water, boiler side
Connector expansion relief valve (minimum)
Condensate discharge pipework (minimum)
Flue gas spigot
Gas connection pressure (gas inlet working pressure)
natural gas, G20
Gas connection pressure (gas inlet working pressure)
propane, G31
Gas flow rate at 15 °C and 1013 mbar
(based on hot water generation if applicable) G20
G31
Flue gas mass flow min./max.
°C
°C
MPa/bar
MPa/bar l l/h l/h
MPa/bar l/min l/min l/min l/min
MPa/bar
MPa/bar
°C mm mm
Inches mm mm mm kPa/mbar kPa/mbar m 3 /h kg/h g/s
°C Flue gas temperature min./max.
Certificated flue gas connections
NOx class
NOx
SEDBUK (2005)
SEDBUK (2009) (G20/G31)
Boiler dimensions (H x W x D)
Mounting weight approx.
Electrical connection
Built-in fuse
Electrical power consumption min./max.
Standby electrical consumption
Level of protection
Certification number mg/kWh mm kg
V/Hz
W
W kW kW kW kW kW kW kW kW kW
17.1 Technical data pro 24 (VUW GB 246/5-3)
5.7 - 19.9
5.2 - 18.9
23.4
23.7
19.1
5.5
—
—
5 - 19
796
1.9
7.8
9.4
11.0
1.5
9.6
11.5
13.4
1.0/10.0
0.035/0.35
35-65
15
22
G 3/4
15
19
60/100 (concentric), optional 80/125 (concentric)
0.20/20
0.37/37
2.5
1.84
2.5/10.6
85
30-80
8 pro 28 (VUW GB 286/5-3)
0.08/0.8
0.3/3.0
0.025/0.25
6.9 - 25.7
6.2 - 24.4
28.6
28.9
24.7
6.6
8.7
8.2
6 - 24
1032
2.5
3.1
2.25
3.0 (H gas); 3.9 (P gas)/13.0
40/70 40/75
C13, C33, C43 , C53, C83, C83, B53P
5
27.3
33.4
A
89.1/89.3/90.3
720 x 440 x 335
35 36
230/50
2 A, slow-blow
90/105
< 2 < 2
IP X4 D
CE-0085CM0320
64 Installation and maintenance instructions ecoTEC pro 0020129672_03
Glossary 18
18 Glossary
Air/flue gas duct
An air/flue gas duct is a line system with two separate flow channels. The flue gas is routed into separate chambers at the same time as the required combustion air is pumped to the boiler. The air/flue gas duct can be designed as a concentric or adjacent double flue gas pipe (the flue gas channel is sealed from the air channel). Floor-standing boilers and gas-fired wall-hung boilers can be operated as roomsealed through the air/flue gas duct. As a result, boilers can be installed in new buildings that do not offer sufficient combustion air for open-flued heaters due to their airtight construction.
Burner anti-cycling time
The burner is electronically locked for a specific time after each time it is switched off ("restart interlock") to avoid frequent switching on and off of the burner (energy losses) and to extend the working life of the boiler.
The burner anti-cycling time is only activated for the heating mode.
Hot water handling is not affected if burner anti-cycling time is running.
Digital information and Analysis system (DIA)
The Vaillant ecoTEC pro boiler is fitted with a digital information and analysis system (DIA). If additional settings are required, which have not been configured using the installation assistant, you can view and modify further parameters using the DIA.
eBUS eBUS is an abbreviation for energyBUS. The eBUS is a special bus used in heating technology, which assists the communication between intelligent components in the heating technology. In a Vaillant system, up to eight different heaters can be connected via the eBUS.
The eBUS communications protocol simplifies the controlrelated linking of different system components within a heating installation. It provides particular flexibility for retrofitting and expanding the system. This simplifies the installation of boiler cascades or the subsequent addition of components such as solar hot water generation.
The eBUS provides extended facilities for connecting controllers.
Calorific value
Unlike the heating value, the calorific value of a fuel describes the total useable heat during combustion, based on the quantity of fuel used, including the condensation heat in the steam.
The energy contained in steam can also be used if the steam liquefies on cooling.
Multi-functional module
The multi-functional module is an accessory that controls additional functions or components in combination with
Vaillant boilers with eBUS electronics. It also allows you to select and control 2 in 7, e. g. circulation pump, external heating pump, external solenoid valve or response from the flue non-return flap.
Compact thermal module
The compact thermal module is an assembly of Vaillant condensing units that consists of the following four main components in the ecoTEC pro: speed-regulated fan, gas-air mixture fitting, gas supply (mixture pipe) for the premix burner and premix burner
Condensing technology
Technology which maximises the use of the calorific value of the fuel. The flue gas is cooled until the water vapour that it contains condenses. The condensation heat that this releases can also be used.
In particular, the flue gas losses are greatly reduced. The losses from conduction of heat and radiation are also reduced by the lower system temperatures. The entire heating installation should therefore be designed for low system temperatures (flow/return temperature) for the effective use of the calorific value. The level of efficiency attainable for boilers is always given based on the heating value of the gas. Due to the additional condensation heat used, the calculated values can exceed 100 %.
Installation and maintenance instructions ecoTEC pro 0020129672_03 65
19 Appendix
19 Appendix
Installation,
Commissioning and
Service Record
66 Installation and maintenance instructions ecoTEC pro 0020129672_03
Please affix the label from the rear cover of the control box over this area.
20 Benchmark Log Book
Benchmark Log Book 20
Installation and maintenance instructions ecoTEC pro 0020129672_03 67
0020008345-06
20
It is recommended that your heating system is serviced regularly and that you complete the appropriate Service Interval Record Below .
Service Provider. Before completing the appropriate Service Interval Record below, please ensure you have carried out the service as described in the boiler manufacturer’s instructions. Always use the manufacturer ‘s specified spare part when replacing all controls.
SERVICE 1
Date
Energy Efficiency Checklist completed?
Engineer Name
Company Name
Telephone Number
Engineer ID Number
Comments
Yes No
SERVICE 2
Date
Energy Efficiency Checklist completed?
Engineer Name
Company Name
Telephone Number
Engineer ID Number
Comments
Yes No
Signature
Signature
SERVICE 3
Date
Energy Efficiency Checklist completed?
Engineer Name
Company Name
Telephone Number
Engineer ID Number
Comments
Yes No
SERVICE 4
Date
Energy Efficiency Checklist completed?
Engineer Name
Company Name
Telephone Number
Engineer ID Number
Comments
Yes No
Signature
SERVICE 5
Date
Energy Efficiency Checklist completed?
Engineer Name
Company Name
Telephone Number
Engineer ID Number
Comments
Signature
SERVICE 7
Date
Energy Efficiency Checklist completed?
Engineer Name
Company Name
Telephone Number
Engineer ID Number
Comments
Signature
SERVICE 9
Date
Energy Efficiency Checklist completed?
Engineer Name
Company Name
Telephone Number
Engineer ID Number
Comments
68
Signature
Yes
Yes
Yes
No
No
No
Signature
SERVICE 6
Date
Energy Efficiency Checklist completed?
Engineer Name
Company Name
Telephone Number
Engineer ID Number
Comments
Signature
SERVICE 8
Date
Energy Efficiency Checklist completed?
Engineer Name
Company Name
Telephone Number
Engineer ID Number
Comments
Yes
Yes
No
No
Signature
SERVICE 10
Date
Energy Efficiency Checklist completed?
Engineer Name
Company Name
Telephone Number
Engineer ID Number
Comments
Yes No
Installation and maintenance instructions ecoTEC pro 0020129672_03
Signature
21 EC declaration of conformity
EC declaration of conformity 21
Installation and maintenance instructions ecoTEC pro 0020129672_03 69
Index
Index
A E
Accessories.................................................................................... 12
Air/flue gas duct .................................................................. 23, 65
Air/flue system ............................................................................ 23
Article numbers ............................................................................ 4 eBUS .............................................................................................. 65
F
B
Burner ............................................................................................. 51
Burner anti-cycling time ............................................. 42, 55, 65
C
Calorific value .............................................................................. 65
Checking
Burner ....................................................................................... 51
Connection pressure ............................................................. 35
Expansion vessel charge pressure .................................... 53
Function of boiler .................................................................. 36
Gas flow rate ........................................................................... 35
Heating mode .......................................................................... 37
Leaks ........................................................................................ 36
Scope of delivery .................................................................... 12
Circulation pump.................................................................. 28, 39
Commissioning ............................................................................. 31
Compact thermal module .................................................. 50, 65
Condensate discharge pipework .............................................. 21
Condensate trap ................................................................... 33, 52
Condensing technology ............................................................. 65
Connecting
Cold and hot water ................................................................. 21
Condensate discharge pipework ......................................... 21
Controller................................................................................. 27
Flow and return ....................................................................... 21
Gas line ..................................................................................... 19
Multi-functional module ....................................................... 28
Connection diagram ................................................................... 29
Connection measurements ....................................................... 16
Customer service ........................................................................ 63
I
Fault codes ............................................................................ 56, 57
Fault memory ............................................................................... 56
Filling
Condensate trap .................................................................... 33
Heating installation ............................................................... 32
Hot water system .................................................................. 33
Filling pressure ............................................................................ 32
Fitting
Boiler ......................................................................................... 17
Controllers ............................................................................... 27
Front casing ............................................................................. 17
Side panel ................................................................................. 18
Flue gas system ........................................................................... 23
Frost protection ............................................................................ 10
G
Gas Council Number .................................................................... 4
Gas flow pressure ....................................................................... 35
Gas flow rate ................................................................................ 35
Gas setting.................................................................................... 34
H
Heating mode ............................................................................... 37
Heating water
Preparation ............................................................................... 9
Installation clearance .................................................................. 15
Installation site ........................................................................ 8, 15
Installation template ................................................................... 15
Installer level ................................................................................ 30
D
Diagnosis codes....................................................... 38, 39, 40, 41
DIA system.................................................................................... 65
Disposal
Boiler ........................................................................................ 63
Packaging ................................................................................. 13
Domestic hot water cylinder ..................................................... 41
Draining
Boiler ........................................................................................ 50
Heating installation ............................................................... 50
L
Low loss header ........................................................................... 21
70 Installation and maintenance instructions ecoTEC pro 0020129672_03
Index
M S
Mains connection ........................................................................ 26
Manufacturer’s guarantee ........................................................ 63
Minimum clearance ..................................................................... 15
Multi-functional module ............................................................ 65
O
Overview
Inspection and maintenance work .................................... 49
Parameters ................................................................. 39, 40, 41
Read-off and setting options .............................................. 30
Status codes ........................................................................... 55
Setting
Burner anti-cycling time ...................................................... 42
By-pass valve .......................................................................... 43
Heating partial load .............................................................. 42
Maintenance interval ............................................................ 43
Maximum flow temperature ................................................ 42
Pump operating mode .......................................................... 42
Pump overrun ......................................................................... 42
Return flow temperature control....................................... 42
Unit type .................................................................................. 62
Status codes................................................................................. 55
T
P
Test programs ............................................................................... 31
Type overview ................................................................................. 5
Preparing
Electrical installation ............................................................ 26
Gas installation ....................................................................... 19
Hydraulic installation ............................................................ 20
Pump operating mode ........................................................ 39, 42
Pump overrun .............................................................................. 42
Purge
Heating installation ............................................................... 33
W
Water pressure ..................................................................... 33, 55
Water pressure sensor ................................................ 33, 55, 57
Wiring diagram ............................................................................ 29
R
Removing
Burner ...................................................................................... 59
Compact thermal module .................................................... 50
Display ...................................................................................... 62
Fan ............................................................................................. 60
Front casing ............................................................................. 17
Heat exchanger ....................................................................... 61
PCB ........................................................................................... 62
Side panel ................................................................................. 18
Repair ............................................................................................ 59
Replacement parts ..................................................................... 59
Reset .............................................................................................. 56
Installation and maintenance instructions ecoTEC pro 0020129672_03 71
Supplier
Manufacturer
advertisement
* Your assessment is very important for improving the workof artificial intelligence, which forms the content of this project
Related manuals
advertisement