advertisement
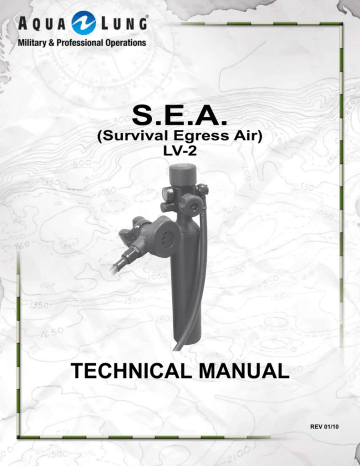
S.E.a.
(Survival Egress air) lV-2
TEchnical Manual
REV 01/10
2
SEa lV2 Technical Maintenance Manual copyRighT noTicE
©2010 aqua lung aMERica.
S.E.a. lV2 TEchnical Manual, p/n 108448
You can contact a Technical Adviser via e-mail at: [email protected] [email protected]
[email protected] [email protected]
Aqua Lung ®
Trademark notice
is a registered trademark of Aqua Lung America, Inc.
Warnings, cautions, & notes
Pay special attention to information provided in warnings, cautions and notes that are accompanied by one of these symbols:
A WaRning indicates a procedure or situation that, if not avoided, could result in serious injury or death to the user.
A cauTion indicates any situation or technique that could cause damage to the product, and could subsequently result in injury to the user.
A
note
is used to emphasize important points, tips, and reminders.
3
conTEnTS
Copyright Notice ...................................................................................................................................2
Change Record ....................................................................................................................................................4
General Guidelines ...............................................................................................................................5
General Conventions ............................................................................................................................5
Initial Inspection Procedure ..................................................................................................................6
External Inspection ..........................................................................................................................6
Immersion/Leak Test ......................................................................................................................6
Medium Pressure (Over-Bottom) Test .............................................................................................6
DISASSEMBLY PROCEDURE .............................................................................................................7
First Stage Disassembly ..................................................................................................................7
Second Stage Disassembly ...........................................................................................................10
REASSEMBLY PROCEDURE ............................................................................................................12
First Stage Reassembly .................................................................................................................12
First Stage Testing .........................................................................................................................15
Filling Procedures ..........................................................................................................................15
Second Stage Reassembly ...........................................................................................................18
FINAL TESTING .................................................................................................................................21
Subjective Test ..............................................................................................................................21
Immersion Test .............................................................................................................................21
Final Assembly ............................................................................................................................................21
Initial Pre-Issue Procedures for the SEA MK/LV2/HESP ....................................................................22
Table 1: Troubleshooting Guide for First Stage/Valve Assembly .........................................................23
Table 2: Troubleshooting Guide for Second Stage..............................................................................24
Table 3: List of Tools and Service Kits ................................................................................................25
Table 4: Torque Specifications ............................................................................................................29
Table 5: Checking Specifications .......................................................................................................29
Table 6: Recommended Cleaners and Lubricants ..............................................................................29
Procedure A: Cleaning and Lubricating ..............................................................................................30
S.E.A. First Stage with Cylinder Assembly, Exploded View ...............................................................31
LV-2 Second Stage, Exploded View ...................................................................................................32
Maintenance Notes ............................................................................................................................33
4
SEa lV2 Technical Maintenance Manual
changE REcoRD
change no.
001-11
Date
10/6/11
Title or Description p. 25-28 Table 3: list of Tools and Service
Kits updated change made by aqa
introduction
This manual provides factory prescribed procedures for the correct service and repair of the Aqua Lung SEA LV-2. It is not intended to be used as an instructional manual for untrained personnel.
The procedures outlined within this manual are to be performed only by personnel who have received Factory Authorized training through an
Aqua Lung Service & Repair Seminar. If you do not completely understand all of the procedures outlined in this manual, contact Aqua Lung to speak directly with a Technical Advisor before proceeding any further.
LV-2 has black external parts, however, chrome parts are used in this manual for clarification.
Scheduled Service
The SEA LV-2 should be given the same care and maintenance as life support equipment. It is therefore important to perform scheduled overhaul service for the complete unit, according to the procedures outlined in this manual on a regularly scheduled basis; once every two years with normal use.
5
.
general conventions
Unless otherwise instructed, the following terminology and techniques are assumed:
1. When instructed to remove, unscrew, or loosen a threaded part, turn the part counterclockwise.
2. When instructed to install, screw in, or tighten a threaded part, turn the part clockwise.
3. When instructed to remove an o-ring, use the pinch method
(see illustration below) if possible, or use a brass or plastic o-ring removal tool. Avoid using hardened steel picks (unless directed), as they may damage the o-ring sealing surface. All o-rings that are removed are discarded and replaced with brand new o-rings.
4. The following acronyms are used throughout the manual: lp is Low Pressure; M p is Medium Pressure; and hp is High
Pressure.
5. Numbers in parentheses reference the key numbers on the exploded parts schematics on pages 31 and 32. For example, in the statement, “...remove the o-ring (31) from the...”, number 31 is the key number to the piston head o-ring.
Pinch Method
Press upwards on sides of o-ring to create a protrusion. Grab o-ring or insert o-ring tool at protrusion.
general guidelines
1. In order to correctly perform the procedures outlined in this manual, it is important to follow each step exactly in the order given. Read over the entire manual to become familiar with all procedures before attempting to disassemble the product in this manual, and to learn which specialty tools and replacement parts will be required. Keep the manual open beside you for reference while performing each procedure. Do not rely on memory.
2. All service and repair should be carried out in a work area specifically set up and equipped for the task. Adequate lighting, cleanliness, and easy access to all required tools are essential for an efficient repair facility.
3. Before beginning any disassembly, it is important to first perform the
Initial Inspection procedure, and refer to Tables 1 & 2: Troubleshoot-
ing p. 23 & 24, to determine the possible cause of any symptoms which may be present.
4. As each unit is disassembled, reusable components should be segregated and not allowed to intermix with nonreusable parts or parts from other units. Delicate parts, including inlet fittings and crowns which contain critical sealing surfaces, must be protected and isolated from other parts to prevent damage during the cleaning procedure.
5. Use only genuine Aqua Lung ® parts provided in the overhaul parts kit for this product. DO NOT attempt to substitute an Aqua Lung ® part with another manufacturer’s, regardless of any similarity in shape or size.
6. Do not attempt to reuse mandatory replacement parts under any circumstances, regardless of the amount of use the product has received since it was manufactured or last serviced.
7. When reassembling, it is important to follow every torque specification prescribed in this manual, using a calibrated torque wrench. Most parts are made of either marine brass or plastic, and can be permanently damaged by excessive stress.
6
initial inspection procedure
External Inspection
1. When possible, inspect the filter of the fill adapter for
any signs that contaminants, such as moisture or
particulate matter, may have entered the system.
2. Visually inspect the MP hose along its length for any
signs of deterioration or damage, such as blistering,
abrasion, or corrosion of the fittings.
3. Slowly pressurize the system by turning the on-off
handwheel counterclockwise
4. Examine the pressure indicator (pin or dial) to deter-
mine whether the pin is within the full range or dial is
in the green, indicating that the SEA LV-2 cylinder is
full.
noTE : If the pin indicator or dial indicator does not indi- cate that the cylinder is completely full, it will be necessary to perform the filling procedure outlined in the SEA LV-2 owner’s Manual before proceeding further.
WaRning: only use the SEa lV-2 with normal, atmospheric, compressed air (21% oxygen and 79% nitrogen by volume).
DO NOT attempt to fill with pure oxygen, or enriched air which contains more than 23.5% oxygen. Failure to observe this warning may result in serious injury or death due to fire and explosion, or the serious deterioration and failure of the equipment.
immersion / leak Test
1. After ensuring that the system is pressurized and the cyl-
inder is full, listen for any obvious signs of leakage from
the system, including free flow from the second stage.
cauTion: if a second stage leak is detected, carefully perform the medium pressure test. use caution and avoid over pressurizing the Mp test gauge. performing this test may cause damage to the test gauge, and possibly result in serious personal injury.
2. If there are no detectable leaks, immerse the entire sys-
tem in fresh water. Check for any bubble streams to
locate the source of any leakage.
3. Note the source of any leakage found and refer to Table
2: Troubleshooting, p. 23-24 to determine its possible
cause.
4. Close the valve and depress the second stage purge
to completely depressurize the system. Wait at least five
minutes, and depress the second stage purge to deter-
mine whether any air pressure has built up inside the
MP hose and second stage valve.
noTE : A buildup of pressure is caused by either a bad valve seat (20) or damaged sealing surface inside the body (36). If a buildup of air pressure occurs, check both items. Replace the valve seat first. If the problem still occurs, replace the body.
SEa lV2 Technical Maintenance Manual
Medium (over-Bottom) pressure Test
1. With the valve closed, purge the second stage to depres-
surize the system. While securely holding the second
stage inlet fitting (51) with a thin 3/4" open-end wrench,
apply an 11/16" open-end wrench to the female fitting
of the MP hose. Turn the hose fitting counterclockwise to
loosen and remove the hose from the second stage.
2. Connect the medium pressure test gauge (PN
111610) to the female fitting of the MP hose, and tighten
the hose fitting by hand until finger tight.
3. While holding the MP test gauge positioned so that it is
facing away from you, pressurize the system by slowly
turning the SEA LV-2 valve handle counterclockwise.
Check the SEA LV-2 pin indicator or dial gauge to ensure
that it indicates the cylinder is filled with at least 2,700
psi.
4. Note the medium (over-bottom) pressure indicated by the
test gauge, and briefly open and shut the bleed valve
of the test gauge to ensure that lockup is achieved without
“creeping” or fluctuating back and forth.
5. If the medium pressure “creeps” up or otherwise
fluctuates after cycling the regulator, wait for it to stabilize
(if possible) before noting the final medium pressure.
noTE : Correct medium pressure for the SeA LV-2 is 135
(±20) psi, with an inlet pressure between 2,500 - 3,000 psi.
6. Partially open the bleed valve of the IP test gauge to
empty the SEA LV-2 cylinder very slowly. DO NOT fully
open the test gauge bleed valve to empty the cylinder, as
this may cause condensation of moisture to form inside
the first stage and hose, as well as the cylinder itself. If
the cylinder or valve becomes cold to the touch while
performing this step, the air has been relieved too rapidly.
WaRning: Failure to completely empty the SEa lV-2 of air prior to performing any disassembly may cause the sudden separation of components or ejection of parts, and may result in serious personal injury.
DiSaSSEMBly pRocEDuRE
noTE:
Before performing any disassembly, refer to the exploded parts drawing, which references all mandatory replacement parts. these parts should be replaced with new and must not be reused under any circumstances – regardless of the age of the regulator or how much use it has received since it was last serviced.
cauTion: use only a plastic or brass o-ring removal tool (p/n 944022) when removing o-rings to prevent damage to the sealing surface. Even a small scratch across an o-ring sealing surface could result in leakage. once an o-ring sealing surface has been damaged, the part must be replaced with new. Do noT use a dental pick or any other steel instrument, except where instructed.
First Stage Disassembly
1. Completely open the on-off handwheel (10). Make sure all the air is completely drained from the cylinder (see step
6, p. 6) or use the purge button intermittently.
7
4. Using a 3/16" hex key, unscrew the swivel port plug (1) from the first stage body. Separate the hose (4) and spacer
(5) from the fitting. Remove the o-rings (2 & 3) from the swivel port plug.
5. Unscrew the burst plug (6) from the first stage using a
3/8” socket and discard.
6. Unscrew the handwheel retaining nut (7) using a notched medium flat blade screwdriver. Remove the washer (8), spring (9), handwheel (10), indicator ring (12) and washer
(11) from the stem (19).
2. While holding the second stage inlet fitting (52) with a thin 3/4" wrench (not wider than the nut), use an 11/16" wrench to unscrew the hose from the second stage.
3. Remove the o-ring (16) located inside the hose-end swivel fitting using the o-ring tool (p/n 10-102-400) and discard. DO
NOT use this tool on any other parts or damage may result.
7. Using a 3/4" wrench or socket, unscrew the bonnet (13) from the first stage body (36). Pull the valve stem (19) out of the bonnet.
8
8. Remove the backup ring (15), o-ring (16), spacer (17) and washer (18) from the stem. (note: It is possible that some
or all of these parts are in the bonnet.) Discard the backup ring, o-ring and washer.
SEa lV2 Technical Maintenance Manual
12. If the SEA LV-2 is equipped with a dial-type pressure indicator (27), remove the gauge using a 7/8" wrench. cauTion: use caution to not damage the fill adapter port.
check bonnet
9. Remove the o-ring (14) from the bonnet and discard.
13. If equipped with a pin-type pressure indicator (27a), remove the gauge with valve handling retainer tool (PN
053035). For either gauge, remove the o-ring (22) and discard.
10. Insert the squared end of the stem into the valve seat
(20), then unscrew the valve seat from the first stage body and discard.
11. Using a magnifier, inspect the condition of the crown.
There should be no scratches, nicks or dents on the crown sealing surface.
14. Disassembly of pin-type pressure indicator cauTion: The pin indicator parts are under spring pressure. Be sure to apply pressure against the retaining screw (27g) while unscrewing it from the indicator body (27b).
a. If the o-ring (22) has not been removed yet, do so
now and discard.
b. Using a 1/8" hex key unscrew the retaining screw
(27g) from the pin indicator body (27b). Remove the
spring (27e) and pin (27f).
27b
27g
27b
27e
27f
27g
c. Turn the indicator body upside down to remove the
washer (27d) and o-ring (27c). Discard the o-ring.
If they do not exit the body freely, use the o-ring
removal tool (p/n 944022) to extract these parts.
17. Remove and discard the fill adapter port o-ring (22).
9
27c
27d
15. Using your fingers, unscrew the fill port plug (21) from the end of the fill adapter port (23). Remove the o-ring (22) from the fill port plug and discard.
18. Using your fingers, peel the cap protector (29) off the first stage.
19. Insert the pins of an adjustable spanner wrench into the two corresponding holes in the top of the piston cap (30). noTE: there is a small pin inside the adapter port. take care not to lose the pin when the adapter port is removed.
16. Using a 9/16" wrench or socket, unscrew the fill adapter port (23) from the first stage body (36). Remove and discard the o-ring (22). Remove the fill pin (26) and the o-ring (25) from the check valve. Discard the o-ring (25).
20. Unscrew the piston cap from the first stage body. Sep- arate the piston (32) from the cap. Remove the spring (35) from the first stage.
noTE: The check valve may be in either the first stage or the fill adapter port.
10
21. Remove the o-rings (31 & 33) from the piston and discard. Insert the pin of the seat extraction tool (p/n 109437)
SEa lV2 Technical Maintenance Manual
Second Stage Disassembly
1. Using small wire cutters, carefully snip the plastic mouthpiece clamp (55) and remove the mouthpiece (66) from the box bottom (63). Inspect the mouthpiece to ensure it is free of any tears or cuts that may cause leakage of water into the second stage or other discomfort. Discard the mouthpiece or set it aside to be reused, depending on its condition.
22. Use a cylinder vise or place a rubber strap wrench onto the cylinder (38) to hold it secure while it is turned in a clockwise direction. While holding the cylinder secure with the strap wrench, unscrew the first stage body (36) from the cylinder using a 1 3/16" crowfoot & flex handle drive.
2. Using your fingers, unscrew the front cover (59) from the box bottom (63). Using the Micra Retaining Ring Tool
(p/n 100188), unscrew the retaining ring (60).
CAUTION: Ensure that the crowfoot is not over the hole for the bonnet (13) as damage to the bonnet opening could result.
23. Remove and discard the o-ring (37) from the cylinder threads.
3. Lift out the purge cover (61) and diaphragm (43). Inspect the diaphragm for any tears or pin holes by holding it up to a light and gently stretching around the perimeter.
4. While depressing the lever (45), unscrew the inlet fitting
(52) using a 3/4" wrench or socket. Remove and discard the inlet fitting o-ring (14).
inlet fitting
5. Gently grasp the lever and remove the entire valve assembly (44-51) from the box bottom (63). It may be necessary to push in on the valve assembly through the inlet hole into the box bottom (63).
11
8. Remove the exhaust valve (64) by grasping the flap of the valve and pulling straight outward. Discard exhaust valve.
CAUTION: Valve assembly parts are under spring pressure.
When removing the locknut (44), be sure to keep the poppet side of the valve assembly against the work surface or place a finger over the poppet to prevent the parts from ejecting from the valve body (46).
6. Hold the valve assembly, poppet side facing down, firmly against the work surface. Using a 1/4" nut driver, remove the locknut (44) and discard. Separate the locknut, washer (46), lever (45), poppet (50), and spring (49) from the valve body
(47). Using the threaded end of the poppet, press the poppet bearing (48) out of the valve body and discard.
9. Using the tip of the o-ring tool (p/n 944022), or any type of pointed tip type tool, pierce the center of the LP seat (51) and remove it from the poppet. DO NOT discard the seat, as it will be used later to aid in reassembly.
50
49
47
45
46
44
ThiS EnDS DiSaSSEMBly
Before starting reassembly, perform partscleaning and lubrication in accordance with
Procedure A: Cleaning and Lubricating, p. 30.
7. Using your fingers, unscrew the exhaust cover (65).
12
REaSSEMBly pRocEDuRE
First Stage Reassembly
CAUTION: Before proceeding, visually inspect the cylinder according to compressed gas association
(cga) standards pamphlet (cga c-6.1--2002, "STan-
DaRDS FoR ViSual inSpEcTion oF high pRESSuRE aluMinuM coMpRESSED gaS cylinDERS"). This inspection requires a visual inspection light. if the cylinder does not pass the visual inspection, it must be serviced or replaced with a new cylinder before it can be assembled and filled.
1. Install a new, lightly lubricated o-ring (37) over the cylinder threads so that it is seated against the first stage body.
Lubricate the first 4 to 5 threads on the first stage body with
Christo-lube ® .
SEa lV2 Technical Maintenance Manual
4. Place the spring (35) into the body. Press the piston into the cap (30) so that the piston head is seated flat against the cap. Lightly lubricate the male threads on the body.
5. Pass the piston shaft through the spring. While pressing down on the cap, hand tighten the cap onto the first stage by turning clockwise. Tighten the cap with an adjustable spanner wrench (p/n 107394) until the cap stops against the first stage body.
2. Thread the first stage into the cylinder until hand tight.
Attach a 1 3/16" crowfoot adapter to a torque wrench. Place in cylinder vise or apply a strap wrench to the cylinder. While holding the cylinder firmly, torque the first stage body to a torque value of 25±2 ft/lbs.
6. Install a new, lubricated o-ring (25) onto the shaft of the check valve (26). Install a new, lubricated o-ring (22) onto the fill port plug (21).
3. Install a new, lubricated piston shaft o-ring (33) and piston head o-ring (31) onto the piston (32). Closely inspect the edges of new HP seat (34). One edge is sharp and one edge has a chamfer. With the chamfered edge facing outward, press the HP seat into the small, recessed hole in the end of the piston. Put the piston down on a clean, hard, flat surface to seat completely.
7. Install a new, lubricated o-ring (22) onto the fill adapter port. Insert the check valve (26), o-ring side first, into the male-threaded end of the fill adapter port (23).
22
34 23
23
26
32
33
8. Thread the fill adapter port into the lower of the two HP ports. Attach a 9/16" socket to a torque wrench and tighten the fill adapter port (23) to 90±3 in/lbs.
13
c. Using a 1/8" hex key socket, tighten the retaining
screw by turning it clockwise until it stops. Install a
new, lubricated o-ring (22) onto the threaded end of
the indicator body.
22
CAUTION: Do not over torque. Damage will result to the fill adapter port.
9. SeA LV-2 with a pin-type pressure indicator (27a): a. Drop a new, lubricated o-ring (27c) into the pin indicator body (27b); make sure it is properly seated in the small recess inside the body. Drop the washer (27d) over the o-ring, making sure it is laying flat atop the o-ring.
d. Thread the pressure indicator into the upper HP port
until firmly finger tight, then tighten with a valve hand
wheel tool (p/n 053035).
10. SeA LV-2 with a dial-type pressure indicator (27):
a. Install a new, lubricated o-ring (22) onto the dial
pressure indicator (27). Thread the pressure indicator
into the upper HP port and tighten using a 7/8" crow
foot wrench and torque to 45±3 in/lbs.
CAUTION: Do not damage fill adapter port (23).
b. Insert the spring (27e) into the indicator body and insert
the pin (27f) into the spring. Place the retaining screw
(27g) on top of the pin and press the retaining screw
against the indicator body. While keeping the retaining
screw pressed against the indicator body, turn the
indicator body counterclockwise to engage the screw
threads.
27b
27e
27f
27g
Turn body to engage threads
CAUTION: Do not lubricate the burst plug (6).
11. Thread a new, unlubricated burst plug (6) into the lower port on the first stage body (the side opposite of the fill adapter). Attach a 3/8" socket to a torque wrench and torque the burst plug to 90±3 in/lbs.
14
12. Install new, lubricated o-rings (2) into the grooves located on either side of the center hole of the swivel port plug (1). Install a new, lubricated o-ring (3) on the threaded end of the swivel port plug.
SEa lV2 Technical Maintenance Manual
15. Install lubricated back-up ring (15).
13. Pass the threaded end of the swivel port plug through the hose swivel, then through the spacer (5). Make sure that both o-rings (2) are covered by the hose swivel. Thread the swivel adapter into the first stage body. Attach a 3/16" hex key socket to a torque wrench and torque the swivel port plug to 60±3 in/lbs.
Backup ring
O-ring
16. Lubricate the threads of a new HP seat (20) with Christo-
Lube ® . Using the squared end of the stem (19), screw a new valve seat (20) into the first stage body until finger tight. Leave the stem in the HP seat. Place the handwheel over the stem and tighten the valve seat. Remove the handwheel (10).
5 2
14. Place a new washer (18) onto the valve stem (19), followed by the metal spacer (17) and o-ring (16).
17. Install a new, lubricated o-ring (14) onto the bonnet (13) so that the o-ring fits into the groove located above the larger threads. Lubricate the bonnet threads, then pass the bonnet over the stem and thread it into the body.
18. Attach a 3/4" medium deep-well socket to a torque wrench and torque the bonnet to 90±3 in/lbs.
NOTE : Before continuing, closely examine the back up ring (15). You will note that it has a flat side and a concave side. For correct assembly the concave side should be against the o-ring
(16), as shown in the picture below.
19. Place the washer (11) over the stem, against the bonnet.
With the rounded edge of the indicator ring (12) facing outward, lightly thread the indicator ring onto the bonnet.
15
20. When the indicator ring bottoms out, turn it slightly counterclockwise so the corners of the square shaft of the stem point towards the centers of the square cut outs of the indicator ring. Turn an additional 90° counterclockwise.
First Stage Testing
21. Place the handwheel (10) over the indicator ring. Place the spring (9) into the handwheel, followed by the washer (8).
Using a medium flat bladed screwdriver, screw the retaining nut (7) onto the end of the stem until the retaining nut will not turn any further. Avoid cross threading the nut.
8
7
9
22. Install a new, lubricated o-ring (16) into the swivel end
(second stage end) of the hose.
NOTE: Initial first stage testing is done WITHOUT anything attached to the end of the hose. For proper filling instructions, refer to the following section:
Filling Procedures for either cylinder fill adapter to fill from a larger cylinder, or yoke fill adapter to fill from a compressor.
1. Cycle the handwheel on and off several times to ensure the proper function of the indicator ring and valve seat. Close the on-off valve by turning the handwheel (10) clockwise until it stops.
2. Install unit in MRS III or attach the fill adapter. Attach a
3000 psi supply to the fill adapter. Secure the end of the hose prior to pressurizing.
3. Slowly begin to fill the cylinder with 3000 psi of air (Do not exceed 500 psi/minute). During the fill process, check any air leaking from the open end of the hose. If an air leak is detected, immediately stop the filling process consult the Table
1: Troubleshooting guide p. 23. If a leak is not detected, finish filling the cylinder to 3000 psig. Turn off the supply line valve and bleed the line pressure. Remove the supply line from the fill adapter port and unscrew the fill adapter from the fill port.
4. Thread a medium pressure (MP) gauge to the hose until finger tight. Slowly turn the handwheel (10) and open the valve. Check the MP to make sure it "locks up" at 135±20 psig. Closely monitor the MP gauge for a few minutes to make sure the MP does not begin to creep upward. Any
MP creep indicates a small high pressure leak somewhere in the system. If an MP creep is detected, consult Table 2:
Troubleshooting guide on page 24.
5. Assuming the MP is properly set, close the SEA LV-2 valve and open the bleeder valve on the MP gauge to relieve the air from the system. Remove the MP gauge from the end of the hose.
6. Since there is nothing attached to the end of the hose and the cylinder is fully charged, set the system in a secure place so that the valve cannot be accidently opened.
Filling procedures
WARNING: use safety glasses when charging with hp air.
Filling the SEa from a scuba cylinder
NOTE: this o-ring is in the second stage overhaul kit, p/n 108344 or 108444.
NOTE: the SeA system does not include a
SCUBA fill adapter. This adapter (P/N 108325) may be purchased separately. (Refer to Figure A shown on page 5 of the SEA User’s Manual for component identification.)
1. Using a calibrated pressure gauge, check the supply cylinder to ensure that it contains at least 2,700 PSI/ 186
BAR and less than 3,100 PSI/ 214 BAR. It is very important to ensure that the SEA is filled to its total capacity, but not overfilled.
2. Remove the protector cap from the threaded nozzle of the fill adapter. Inspect the nozzle to ensure the o-ring is present and seated evenly at the base of the threads.
16
3. Mate the threaded nozzle of the fill adapter into the open fill port, and turn clockwise by hand until snug. DO NOT apply a wrench or otherwise overtighten the fill adapter into the first stage.
4. Loosen the fill adapter yoke screw as needed so that the dust cap can be removed from the inlet fitting and the yoke can be placed over the valve of the supply cylinder.
5. While supporting the SEA with one hand, place the yoke of the fill adapter over the cylinder valve to align the inlet fitting flush against the valve o-ring. Tighten the fill adapter yoke screw clockwise into the small dimple on the backside of the cylinder valve only until finger snug.
WARNING: DO NOT attempt to fill the SEA from a supply cylinder which contains more than 3,100 pSi/ 213.5 BaR.
Doing so may weaken and damage the safety burst plug assembly and/or SEa cylinder.
NOTE: Part number 108382 does not have an on/ off valve; therefore, the pressure indicator gauge and second stage are always active when the cylinder is pressurized.
6. While holding the first stage and fill adapter secure, turn the valve handwheel counterclockwise until it is completely open. When the handwheel is in the open position, the red indicator ring is not visible.
SEa lV2 Technical Maintenance Manual
7. Support the cylinder with one hand, and slowly turn the supply cylinder valve handwheel counterclockwise to open and begin filling. As the SEA cylinder begins to fill, make sure the pressure indicator (pin or dial) shows that the cylinder is filling properly.
NOTE: Always fill the cylinder as slowly as possible by turning the handwheel of the supply valve slowly to control the rate of fill. Rapid filling will generate heat and will result in an incomplete fill after the cylinder cools. If the cylinder is warm to the touch afterward, the fill rate was too rapid.
8. When at least two minutes have elapsed and air can no longer be heard flowing from the supply cylinder into the
SEA, turn the supply cylinder valve completely open.
9. To conserve the limited air supply of the SEA, it is strongly recommended that you perform a preflight inspection of the second stage purge while it is connected to the supply cylinder as follows:
a. Depress the purge button to ensure that sufficient
airflow is provided to clear the second-stage of water.
b. Immediately after releasing the purge button, listen
closely to ensure that the second-stage does not
continue to flow any air.
10. While holding the first-stage and fill adapter secure, turn the SEA valve handwheel clockwise until it stops and the red indicator is visible. Turn the handwheel of the supply cylinder valve clockwise until shut.
11. Hold the second stage purge button depressed until airflow can no longer be heard from the second stage and the
LP hose between the first and second stages is completely depressurized.
12. Slightly open the pressure relief screw on the fill adapter to relieve the line pressure.
13. While supporting the SEA cylinder with one hand, turn the yoke screw of the fill adapter counterclockwise to loosen until the complete system can be lifted off and removed from the supply cylinder valve.
14. While holding the SEA securely, turn the fill adapter counterclockwise at the fitting to loosen and remove from the first stage. Replace the dust cap over the inlet fitting, then tighten the yoke screw until finger snug.
15. Thread the port plug back into the fill port until fingertight.
Filling the SEA with compressor fill adapter
NOTE: the Compressor Fill Adapter (P/n 1006-56) is not included with SeA, and must be purchased separately.
WARNING: Do not attempt to fill the SEA directly from a compressed air filling station unless you have received the necessary training and authorization to do so. if done incorrectly, this procedure poses certain hazards which may cause severe injury or death.
NOTE: Part number 108382 does not have an on/ off valve; therefore, the pressure indicator gauge and second stage are always active when the cylinder is pressurized.
1. Inspect the fill adapter to ensure that the o-ring is present and seated evenly inside its groove, and the male fitting is clean and free of any damage to its threads.
2. Mate the male fitting of the fill adapter into the high pressure fill port of the first stage, and turn clockwise only by hand until lightly snug. DO NOT apply a wrench or otherwise overtighten the fill adapter.
3. Loosen the yoke screw of the compressor fill yoke as needed so that the yoke can be placed over the block of the fill adapter.
4. While supporting the SEA with one hand, place the yoke of the compressor fill yoke over the block of the fill adapter to align the inlet fitting flush against the valve o-ring. Tighten the fill yoke screw clockwise into the small dimple on the backside of the fill adapter block only until finger snug.
CAUTION: DO NOT attempt to fill the SEA from a compressor or air supply where the regulated pressure exceeds 3,000 pSi/ 206 BaR. Doing so may weaken and damage the safety burst plug assembly and/ or
SEa cylinder.
17
5. While holding the first stage and fill adapter secure, turn the SEA valve handwheel counterclockwise until it is completely open. When the handwheel is in the open position, the red indicator ring is not visible.
6. Ensure that the SEA is supported, then turn the compressor valve very slowly until it is slightly open to fill the cylinder with approximately 500 PSI/ 34.5 BAR. Turn the fill valve shut and wait 45-60 seconds before proceeding to fill the cylinder any further. Repeat this procedure to fill the cylinder very slowly in small increments of 500 PSI/ 34.5 BAR or less, until it is filled to exactly 3,000 PSI/ 206 BAR.
WARNING: use safety glasses when charging with hp air.
NOTE: Always fill the SEA as slowly as possible by turning the hand-wheel of the supply valve slowly to control the rate of fill. Rapid filling will generate heat and will result in an incomplete fill after the cylinder cools. If the cylinder is warm to the touch afterward, the fill rate was too rapid.
7. To conserve the limited air supply of the SEA, it is strongly recommended that you perform the following preflight inspection of the second stage purge while the SEA is connected to the compressor fill yoke and pressurized via the compressor fill adapter:
a. Briefly depress the purge button to ensure that suf-
ficient airflow is provided to clear the second stage.
b. Immediately after releasing the purge button, listen
closely to ensure that the second stage does not
continue to flow any air.
8. While holding the first stage and fill adapter securely, turn the SEA valve handwheel clockwise until it stops and the red indicator is visible. Turn the compressor fill valve until it is completely closed.
9. Hold the second stage purge button depressed until airflow can no longer be heard from the second stage and the
LP hose is depressurized.
10. Open the pressure relief screw on the compressor fill yoke to relieve the line pressure.
11. While holding the SEA cylinder supported, turn the yoke screw of the compressor fill yoke counterclockwise to loosen until the compressor fill valve can be removed from the block of the fill valve adapter. Return the compressor fill yoke to its storage location.
12. While holding the SEA secure, turn the fill adapter block counterclockwise at the fitting to loosen and remove from the first stage.
13. Thread the port plug back into the fill port until finger tight.
18
SEa lV2 Technical Maintenance Manual
Filling the SEa with the MRS iii Mobile
Refill Station
The MRS III is a self-contained Mobile Refill Station with an onboard supply of approved breathing air pressurized up to 4500 psi. The MRS III is designed to fill up to two (2) Aqua Lung SEA
(Survival Egress Air) units simultaneously to the operating pressure of 3000 psi. The following instructions are the same for filling one unit or two.
1. Verify that both panel mounted fill valves on the MRS III are closed (clockwise).
2. Open the valves on the MRS III supply cylinders and verify that the SUPPLY Pressure Gauge on the panel reads between 3000 and 4500 psi.
3. Verify that the REGULATED Pressure Gauge on the
MRS III panel reads 3000 psi.
4. Remove the fill port plug from the SEA unit and store the plug in the mounted retainer located on each MRS III. Verify that the SEA fill port is clean and dry, and place the SEA in the blast tube.
5. Install the MRS III fill hose connector into the SEA fill port by rotating the knob clockwise until the o-ring is fully seated.
DO NOT USE A WRENCH OR PLIERS TO TIGHTEN. If the fitting leaks during filling, the connector threads and o-ring must be inspected for damage. Replace the damaged parts as needed.
6. Slowly open the MRS III panel mounted fill valve (counterclockwise) that corresponds to the fill hose being used.
There is no need to open any valve on the SEA unit.
7. Slowly fill the SEA at a rate not to exceed 500 psi per minute, to the maximum of 3000 psi.
Second Stage Reassembly
1. Install a new, unlubricated exhaust valve (64) by inserting the stem of the exhaust valve through the center hole of the exhaust port. Pull the stem all the way through until the mushroom plug pops through the hole and keeps the valve securely in place. Examine the flap of the exhaust valve to make sure it is laying flat and is not distorted or folded under. Using a pair of small wire cutters, snip the stem of the exhaust valve so it is only about 1/4" long.
2. Using your fingers, screw the exhaust cover (65) onto the box bottom (63) until hand tight.
NOTE: If the SeA cylinder becomes excessively warm to the touch while filling, allow additional filling time for the unit to cool before removing the SeA unit.
3. Press a new LP seat (51) into the end of the poppet (50) until it is flush and seated evenly. Ensure the dimpled side is toward the poppet.
51
50 8. When the SEA has cooled and is full, close the MRS III panel mounted fill valve.
9. Open the bleeder valve knob on the MRS III fill hose connector and vent the pressure from the fill hose.
10. Verify that the small pressure indicator on the SEA indicates zero pressure.
11. Disconnect the MRS III fill hose connector from the SEA by rotating the connector knob counterclockwise.
12. Replace the port plug into the fill port of the SEA unit and hand tighten.
13. When all filling operations are complete, close the valves on the MRS III supply cylinders. Firmly grasp one of the MRS
III fill hose connectors, point in a safe direction, and bleed any remaining pressure from the system by slowly opening the corresponding panel mounted fill valve for that hose.
14. Close both panel mounted fill valves and both bleeder valve knobs on the MRS III.
15. Attach the fill connectors to the provided mounting brackets, close and securely latch the MRS III cover.
4. Place the poppet bearing (48), rounded side first, onto the stem of the poppet (50). Using the poppet as an installation tool, insert the bearing into the barrel of the valve body (47).
Align the squared side of the poppet bearing with the square hole in the valve body and press it into place. Remove the poppet.
48 47
NOTE: If the poppet bearing does not stay in place, put a small amount of Christo-Lube ® on the square flats and reinsert.
5. Install a new, lubricated inlet fitting o-ring (14) in the groove located between the wrench flats and shorter threads on the inlet fitting (62).
19
8. Place the "feet" of the lever (45) into the groove on the face of the valve body (47) such that the lever is pointing away and up from the air outlet hole.
45
6. Take the used LP seat that was removed during disassembly and place it on top of the crown sealing surface inside the inlet fitting (62). Place the spring (49) over the stem of the poppet (50) and set this assembly into the inlet fitting, on top of the used LP seat.
52 51
50
49 air outlet hole feet
9. Place the washer (46) over the threads of the stem.
Thread a new locknut (44) onto the stem. Using a 1/4" nut driver, tighten the locknut until two threads show past the locknut. two threads
46
44
10. Unscrew the inlet fitting (62) from the valve body. Discard the used LP seat. While depressing the lever with your finger, thread the inlet fitting back into the valve body.
NOTE: the used LP seat is only used to aid in reassembly. It will be removed and discarded later in the reassembly procedure.
7. Place the barrel of the valve body (47) over the top of the poppet. While pressing down on the valve body to compress the spring, screw the valve body onto the inlet fitting. This will fully expose the threads of the poppet.
11. Attach the valve assembly to the end of the hose until finger tight. Slowly turn the SEA LV-2 handwheel (10) counterclockwise to open the valve. If a leak is detected while opening the valve, immediately close the valve. Loosen the locknut a 1/2 turn and slowly open the valve again. Repeat this step until the unit does not leak.
If air leaks when pressurized, loosen locknut until leak stops
20
12. Using a 1/4" nut driver, tighten the locknut until air starts to leak. As soon as a leak is detected, loosen the locknut until the leak stops, then continue to loosen for another 1/4 to 1/2 turn.
SEa lV2 Technical Maintenance Manual
16. Place the diaphragm (43) over the lever, making sure the perimeter of the diaphragm is seated below the threads and against the box bottom (63). Place the purge cover (61) on top of the diaphragm.
Tighten until air leaks.
Loosen until air leak stops, then loosen
1/4-1/2 turn more.
13. Close the SEA LV-2 valve by turning the handwheel clockwise. Purge the air from the system by pressing down on the lever. Remove the valve/inlet assembly from the hose.
While depressing the lever with your finger, unscrew the inlet fitting from the valve body.
Press lever to relieve pressure.
17. Using the Micra Retaining Ring Tool (p/n 100188), screw the retaining ring (60) into the box bottom (63) until finger tight. Screw the front cover (59) onto the box bottom until hand tight.
Red indicates "off".
14. With the lever facing upward, reinsert the valve body (47) back into the box bottom (63). Make sure the flat sides of the valve body (47) are within the plastic slot. This will prevent the valve body from rotating when installing the inlet fitting.
18. Install the mouthpiece (66) onto the box bottom and position as required. Loosely fasten a tie-strap clamp (55) over the slots at the base of the mouthpiece. Orient the clamp buckle to the side of the mouthpiece with the hose.
Pull the clamp tight and snip the excess strap flush with the buckle using a small pair of diagonal cutters (p/n 9-45771).
15. While depressing the lever (45), lubricate and thread the inlet fitting (52) into the valve body (47). It may be necessary to press inward on the valve body to prevent it from rotating.
Attach a 3/4" socket to a torque wrench and torque the inlet fitting (52) to 50±3 in/lbs.
19. Thread the hose onto the inlet fitting. Attach an 11/16" crowfoot to a torque wrench. While holding the inlet fitting
(52) with the thin 3/4" wrench, torque the hose to 45±3 in/lbs.
20. Slowly open the SEA LV-2 valve to pressurize the system. Ensure there is no leakage from the second stage.
21
Final TESTing
Subjective Test
1. Slowly open the SEA LV-2 First Stage valve to pressurize the system.
2. Press the purge cover a few times to ensure there is a strong purge.
3. Perform a subjective breathing test to ensure that the second stage is operating properly.
NOTE: the regulator must be cleaned and sanitized per local instructions before issue
Final aSSEMBly
1. Once completely dry, install cap protector (29).
2. Thread the fill port plug (21) into the fill adapter port (23) until finger tight.
immersion Test
1. Refill the SEA LV-2 to 3000 psi. Turn the SEA LV-2 valve to the "ON" position to repressurize, and check the pressure gauge to ensure that the SEA LV-2 cylinder is completely filled to 3,000 psi. If the SEA LV-2 has a pin gauge, ensure that the gauge indicates pressure.
2. Submerge the entire system in a test tank of clean water with the valve turned all the way open. Shake the unit to remove trapped bubbles. Observe any bubbles arising from the submerged system over a one minute period. The recommended time is necessary due to slower bubble formation that occurs in smaller leaks. Bubbles indicate a leak, which requires that the system must be disassembled at the source to check sealing surfaces, assembly sequence and component positioning in order to correct the problem(s).
21
23
This Ends Reassembly
This concludes the service procedures for the SEa lV-2 First and Second Stages
NOTE: Do not confuse bubbles from trapped air with a true leak. If there is an air leak, bubbles will come out in a constant stream.
WARNING: The SEa lV-2 is designed to assist helicopter crew members and passengers in emergency egress situations from submerged aircraft. it is very critical to ensure that no leakage is present, and that the unit has met all requirements in the Final Testing procedures outlined above. Do noT issue to a crew member or passenger any SEa lV-2 which exhibits any signs of leakage or unsatisfactory performance until the problem has been thoroughly diagnosed and repairs have been made as needed, including the possible replacement of a damaged component or subassembly.
3. As a final test, leave the unit pressurized with the valve completely open at a stable temperature for a period of at least twelve hours, and check the pressure gauge to determine whether any air loss has occured.
WARNING: if the pressure gauge is not in the green or the pin indicator has dropped flush with the body, refer to trouble shooting section (table 1 &2).
4. Upon completion of air test, ensure all water is removed from unit. Blow clean LP air through the cap holes to remove excess water from cap.
22
iniTial pRE-iSSuE pRocEDuRE FoR ThE
SEa MK/lV2/hESp
Upon initial receipt of the SEA MK/LV2/HESP (here after referred to as SEA) from the OEM or storage and prior to the initial issue of the SEA, the following procedure must be performed.
1. Remove the SEA from the OEM packaging
2. Inspect the SEA IAW local instructions and verify it is in good condition.
3. Remove the Fill Port Plug and set it aside. Ensure there is no debris in the Fill Port Adapter. Remove the Protective
Rubber Cover from the top of the SEA and set it aside.
4. Turn on the SEA On/Off Valve.
5. Connect the Air Charging Source Connector to the SEA and slowly charge the unit to 3000 psi IAW local procedures.
6. Depress the 2nd Stage purge cover two times for about
5 seconds each with a 5 second pause between each purge.
7. Turn off the Air Supply. Vent/purge the charging lines and remove from the charging source.
8. With the SEA On/Off valve still in the OPEN position, submerge the entire SEA in water for no less than 2 minutes and observe for leaks. Verify that no residual air is in the void spaces of the unit.
a. If no leaks – remove from the water, shake out any excess water and conduct the pressure drop test, set the
SEA aside for a minimum of 8 hours in a stable temperature environment, note the pressure on the gauge. Recheck the unit after the time has elapsed and verify the pressure is the same +/- 300 psi or still in the green. If the pressure is stable continue to step 9.
b. If a leak is detected go to step 15 and continue procedure c. If the unit fails the leak test a second time go to step 16
SEa lV2 Technical Maintenance Manual
9. Connect the Charging system to the SEA unit and recharge to 3000 psi.
10. Secure the Air supply and remove the SEA from the charging connector.
11. Upon completion of the pressure drop test, verify no water is remaining in the unit and reinstall the Protective Rubber
Cover on the Regulator.
12. Reinstall the Fill Port Cap.
13. The SEA unit is now ready for service.
14. Prior to issue perform the Pre-Flight checks IAW Local
Procedures
TRouBlEShooTing
15. If a 2nd stage leak is detected, remove the unit from the water and shake out any excess water. Purge the 2nd Stage regulator as follows: a. Depress the Purge Cover for 15 seconds, then release.
b. Wait 5 seconds.
c. Depress the Purge Cover for 15 seconds, then release.
d. Wait 5 seconds e. Continue to repeat this procedure until the gauge reads
1500 psi.
f. After the cylinder is at 1500 psi, refill the cylinder to 3000 psi IAW local procedures. Repeat step 8.
16. If a leak is still present – 2 options a. Return to OEM thru local command instructions b. Shut the On/Off valve and purge the 2nd stage. When the pressure has been relieved, remove the medium hose from the 2nd stage. Remove the Inlet fitting. Inspect the gray seat for debris or damage. Remove the seat using the pointed Brass O-ring Tool (DO NOT puncture), clean it and put it back in with the DIMPLE UP. Depress the purge cover and re-install the Inlet Fitting and Torque to 50+/-3 in.lbs.
Connect the Medium hose to the 2nd Stage and torque to
45 +/-3 in.lbs. Open the On/Off valve and repeat the entire procedure from step 5.
Table 1: Troubleshooting guide
First Stage/Valve assembly
SyMpToM
System will not remain depressurized after valve is shut and second stage is purged.
poSSiBlE cauSE TREaTMEnT
1. The valve seat (20) is worn or damaged.
1. Replace valve seat
2. The valve seating surface is damaged.
2. Replace body (36)
1. The valve seat (20) is worn or damaged.
1. Replace valve seat high or unstable ip “creep” low ip
External air leak
2. The valve seating surface is damaged.
3. The main spring (35) is defective
2. Replace body (36)
3. Replace main spring
4. The HP seat (34) is worn or damaged.
4. Replace HP seat
5. The HP crown sealing surface is
damaged.
1. Main spring (35) is weakened or
damaged.
1.The piston head o-ring (31) or shaft o-ring
(33) is worn or damaged.
2. The o-ring grooves on the piston (32)
are damaged.
5. Replace body (36)
1. Replace spring
1. Replace o-ring (s)
2. Replace piston and o-rings
3. The piston head o-ring sealing surface in
the piston cap (30) is damaged.
4. The piston shaft o-ring sealing surface in
the body is damaged.
3. Replace piston cap
4.Replace body
23
24
SEa lV2 Technical Maintenance Manual
SyMpToM
Table 2: Troubleshooting guide Second Stage
poSSiBlE cauSE
1. High first stage IP (should be 135±20
psi).
TREaTMEnT
1. Refer to First Stage Table 1: Troubleshooting Guide on p. 23
2. The LP seat (51) is worn or damaged.
2. Replace LP seat
Leakage or free flow from the second stage
low purge or labored breathing
(full cylinder)
External air leak
(immersion Test)
3. The lever (45) is set too high.
4. The lever (45) is damaged.
5. The crown sealing surface on the inlet
fitting (52) is worn or damaged.
6. The poppet (50) is worn or damaged.
3. Readjust locknut
4. Disassemble second stage
and replace lever
5. Replace inlet fitting
6. Replace poppet and LP seat
7. The poppet spring (49) is damaged.
1. Low IP (should be 135±20 psi).
2. The lever (45) is set too low.
3. The lever (45) is bent.
4. The poppet spring (49) is incorrectly
installed.
5. The IP hose is clogged or obstructed.
1.The IP hose is loose.
2. The IP hose o-ring is damaged.
1. The mouthpiece (58) has a hole.
7. Replace poppet spring
1.Refer to Table 1: Troubleshooting
Guide First Stage, p. 23
2. Readjust locknut
3. Disassemble the second stage and
replace lever
4. Disassemble the second stage and
reinstall poppet spring
5. Clean or replace hose
1. Tighten hose to 45 in/lbs at second
stage fitting
2. Disassemble and replace o-ring
1. Replace mouthpiece
2. The demand diaphragm (43) is damaged. 2. Replace demand diaphragm
Water entering second stage
3. The exhaust valve (56) is damaged.
4. The diaphragm is improperly seated
between the box bottom (54) and purge
cover ring (41).
5. The box bottom (54) is damaged.
6. The inlet fitting o-ring (53) is damaged.
3. Replace exhaust valve
4. Disassemble and properly
reassemble (check for distortion)
5. Check exhaust valve sealing
surface, replace box bottom
6. Disassemble and replace o-ring
NOTE: this is a partial list of possible problems and recommended treatments.
For more information contact Aqua Lung technical Service Department for assistance with problems not described here.
CAUTION: Recommended treatments which require disassembly of the regu-
Table 3: list of Tools and Service Kits
paRT # DEScRipTion applicaTion
108361
Tool Pouch
SEA MK / LV2
Tool holder
111610
Test Gauge
0-400 psi
108362
Soft Case,
IP Test Gauge
108325
SCUBA Fill
Adapter
944022
O-ring Tool
Kit
Checking medium pressure
IP test gauge
IP testing and filling
Removing and installation of o-rings
Internal hose o-ring (16) 10-102-400 O-ring Tool
100188
Micra Retaining
Ring Wrench
107394
Adjustable
Spanner
Wrench
109437
Seat
Extraction
Tool
108357
Repair Mat with Windows
Retaining ring removal and installation
Piston cap (30) removal and installation
HP seat (34) removal
Service and maintenance
25
26 paRT #
820466
SEa lV2 Technical Maintenance Manual
Table 3: list of Tools and Service Kits (continued)
DEScRipTion applicaTion
Christo-Lube MCG III
2 oz. tube
Lubrication
9-aM11708
9-46661
Hex Bit Tool (1/8”)
Hex Bit Tool (3/16”)
Pin-type pressure indicator (27a) and LP swivel port plug (1)
9-45171
Diagonal Pliers
(small)
9-47709
Cylinder
Light
Mouthpiece clamp (55)
Cylinder (38) visual inspection
9-Ba819008
Magnifier w/Illumination
9-43001
9-43004
9-43226
3/8” Socket
9/16” Socket
3/4” Socket
9-43625
9-43628
9-43626
11/16” Crowfoot
7/8” Crowfoot
3/4” Crowfoot
Sealing surface spring inspection
Burst plug (6) (3/8”), Fill adapter port (23) (9/16”) , Bonnet (13) and 2nd stage inlet fitting (52) (3/4”)
Hose fitting (11/16”) , Dial pressure indicator (27) (7/8”),
Bonnet (13) (3/4”)
Fc38a 1 3/16” Crowfoot 1st stage body (36)
9-44388 lTa2428
Tappet
Wrench
(7/8” & 3/4”)
9-44584
Wrench
(11/16”)
Wrench
(7/8” & 3/4”)
Hose fitting (11/16”)
Inlet fitting (52)
Pressure indicator, bonnet (13)
Table 3: list of Tools and Service Kits (continued)
paRT # DEScRipTion applicaTion
9-44572
9-44385
9-44592
3/8” & 7/16” Wrench
1/2” Wrench
5/8” & 9/16” Wrench
MRS III
9-44605
12’ Adjustable
Wrench
MRS III
947448
Medium Blade
Modified
Screwdriver
Handwheel retainer nut (7)
9-41971
1/4” Nut
Driver
5682a28
#2 Phillips
Screwdriver
Lock nut (44)
MRS III
111100 Circlip Pliers MRS III
9-44363
3/8” Drive,
Flex Handle
053035
Valve Handle
Retainer Tool
54325a22
Strap
Wrench
Removal of parts
Pin Type Pressure Indicator (27a) / MRS III
Cylinder removal (52)
108342
Tool Kit (includes all items listed above for SEa lV-2, SEa-MK and MRS iii)
SEa lV-2 / SEa-MK / MRS iii Maintenance
27
28 paRT #
SEa lV2 Technical Maintenance Manual
Table 3: list of Tools and Service Kits (continued)
DEScRipTion applicaTion
820467 Christo-Lube MCG III
16 oz. tube
Lubrication
100398
HABD/SEA
Vise Jaw Inserts
100397 n/a
HABD/SEA
Table Mount
Cylinder Vise
Torque
Wrench ft/lbs / in/lbs
SEA cylinder removal and installation for use w/ existing vice
SEA cylinder removal & installation
Apply torque to parts listed in
Table 4: Torque Specifications, p. 24
NOTE: Photos of tools contained in the SeA tool kit are representative. tool manufacturers and part numbers are subject to change without notice.
TEST
Leak Test
IP
IP Creep
Flow Effort
Purge Flow paRT #
108312
108305
054201
108318
108308
742537
108346
Various
108338
108369
Table 4: Torque Specifications
DEScRipTion / KEy iTEM #
1st Stage Body (item 36/1st stage)
Swivel adapter (item 1/1st stage)
Burst Plug (item 6/1st stage)
Bonnet (item 13/1st stage)
Fill adapter port (item 23/1st Stage)
Pressure Gauge (item 27/1st stage)
Pin type Pressure Indicator (item 27a/
1st stage)
IP Hose (item 4/1st stage)
Inlet Fitting (item 52/2nd stage)
Plug, Blank, 5/8, Black
ToRquE
25±2 ft/lbs
60± in/lbs
90±3 in/lbs
90±3 in/lbs
90±3 in/lbs
45±3 in/lbs
T” wrench
45±3 in/lbs
50±3 in/lbs
90±2 in/lbs
Opening Effort
Table 5: Checking Specifications
conDiTion SpEciFicaTion
Inlet 2,500-3,000 (±100) psi
Inlet 2,500-3,000 (±100) psi
Inlet 2,500-3,000 (±100) psi
No leaks allowed
135±20 psi
5 psi max between 5 to 15 seconds after cycling regulator (purge)
Inlet 2,500-3,000 (±100) psi
IP 135±20 psi
IP 135±20 psi at 5 SCFM
IP 135±20 psi
+1.4 to +3.0 inch H
2
0
+5 inches H
2
0 (maximum)
5.0 SCFM flow rate (minimum)
Table 6: Recommended cleaners and lubricants
luBRicanT/clEanER applicaTion SouRcE christo-lube Mcg 111
All o-rings
Aqua Lung, PN 820466, or
Lubrication Technologies
310 Morton Street
Jackson, OH 45640
(800) 477-8704 oakite #31
CAUTION: Silicone rubber requires no lubrication or preservative treatment.
Do noT apply grease or spray to silicone rubber parts. Doing so may cause a chemical breakdown and premature deterioration of the material.
Acid bath for reusable stainless steel and brass parts.
Oakite Products, Inc.
50 Valley Road
Berkeley Heights, NJ 07922
White distilled vinegar liquid dish washing detergent
(diluted with warm water)
CAUTION: Do not use muriatic acid for the cleaning of any parts. Even if strongly diluted, muriatic acid can harm chrome plating and may leave a residue that is harmful to o-ring seals and other parts.
Acid bath for reusable stainless steel and brass parts.
“Household” grade
Degreaser for brass and stainless steel parts; general cleaning solution for plastic and rubber
“Household” grade
29
30
SEa lV2 Technical Maintenance Manual
procedure a: cleaning and lubricating
cleaning Brass parts
1. Preclean in warm, soapy water* using a nylon bristle tooth brush.
2. Thoroughly clean parts in an ultrasonic cleaner filled with soapy water. If there are stubborn deposits, household white distilled
vinegar (acetic acid) in an ultrasonic cleaner will work well. DO NOT place plastic, rubber or silicone or parts in vinegar.
3. Remove parts from the ultrasonic cleaner and rinse with fresh water. If tap water is extremely “hard,” place the parts in a bath
of distilled water to prevent any mineral residue. Agitate lightly, and allow to soak for 5-10 minutes. Remove and blow dry
with low pressure (25 psi) filtered air, and inspect closely to ensure proper cleaning and like-new condition.
cleaning plastic & Rubber parts
Parts made of plastic or rubber, such as box bottoms, box tops, dust caps, etc., may be soaked and cleaned in a solution of warm water mixed with mild dish soap. Use only a soft nylon toothbrush to scrub away any deposits. Rinse in fresh water and thoroughly blow dry, using low pressure filtered air.
CAUTION: Do not place plastic and rubber parts in acid solutions.
Doing so may alter the physical properties of the component, causing it to prematurely degrade and/or break.
cleaning hoses
1. Hose fittings: Ultrasonically clean with soapy water*; vinegar OK on tough corrosion – ( only hose ends)
2. Run soapy water through hose if needed
3. Thoroughly rinse with fresh water– ( hang with hose ends down)
4. Blow out hose before installing
lubrication and Dressing
All o-rings should be lubricated with Christo-Lube ® MCG 111. Dress the o-rings with a very light film of grease, and remove any visible excess by running the o-ring between thumb and forefinger. Avoid applying excessive amounts of Christo-Lube grease, as this will attract particulate matter that may cause damage to the o-ring.
*Soapy water is defined as “household” grade liquid dishwashing detergent diluted in warm water.
CAUTION: Silicone grease and sprays must be strictly avoided for the
SEA LV-2, since silicone does not provide adequate lubricity in extreme weather conditions.
S.E.a. First Stage with cylinder assembly
29
38a, 38b, 38c
30
31
32
27g
27b
25
27d
27e
27f
22
Wrench
Tight
27a
45 ± 2 in. lbs.
(5.0 ± .5 nm)
27
25
26
22
21
22
23
90 ± 3 in. lbs.
(10.2 ± .3 nm)
NLA - No Longer Available
Key # part # Description
.......108343 overhaul Service Kit
.......108311 First Stage, Spare
.......108469 First Stage Spare, USCG/CBP
1 .......108305 Port Plug, Swivel, Black
.......108333 Port Plug, Swivel, Chrome
2 .......820312p o-ring (10 pk)
3 .......820311 o-ring (10 pk)
4 .......100625 Hose Assy. MK, 27" Black
.......102835 Hose Assy. MK, 20" Black
.......108392 Hose Assy. LV2, 27” Black
.......108391 Hose Assy. LV2, 20” Black
5 .......108306 Spacer, Black
.......108334 Spacer, Chrome
6 .......054201 Burst plug
7 .......108304 Retaining Nut, Handwheel, Black
.......108314 Retaining Nut, Handwheel, Silver (NLA)
8 .......108329 Washer, Handwheel
9 .......108316 Spring, Handwheel
10 .......108313 Handwheel
11 .......108326 Washer
12 .......108317 On-off indicator ring
13 .......108318 Bonnet
14 .......820015 o-ring (10 pk)
15 .......828009 Backup ring
16 .......820010 o-ring (25 pk)
17 .......108328 Spacer, metal
18 .......108327 Washer, white Teflon ®
19 .......108319 Stem
20 .......108322 Valve seat
21 .......108307 Fill port plug
22 .......820319 o-ring (10 pk)
4
33
34
35
5
3
2
1
60 ± 5 in. lbs.
(6.8 ± .5 nm)
20
6 90 ± 3 in. lbs.
(10.2 ± .3 nm)
37
36
19
18
17
25 ± 2 ft. lbs.
(33.9 ±2.7 nm)
16
15
14
13
90 ± 3 in. lbs.
(10.2 ± .3 nm)
12
On/Off Valve
Conversion Kit
PN 108441
10
On-off valve assembly may be replaced with optional "no onoff" plug, part number 108367
(see key # 39 below) & part number 820015 ( see key # 14 below).
14 11
39
90 ± 3 in. lbs.
(10.2 ± .3 nm)
Key # part # Description
23 .......108308 Fill adapter port
25 .......820304 o-ring (10 pk)
26 .......108309 Check valve
27 .......742537 Pressure indicator, Dial, Black
27a .......108346 Pressure indicator, Pin
27b .......108347 Body, Pin indicator
25 .......820304 o-ring (10 pk)
27d .......845034 Washer
27e .......100688 Spring
27f .......100613 Pin
27g .......100607 Retaining screw
29 .......108302 Cap protector
30 .......108303 Piston cap
31 .......820062 o-ring (10 pk)
32 .......106769 Piston
33 .......820007 o-ring (20 pk)
34 .......106726 hp Seat
35 .......106771 Spring
36 .......108312 First stage body
37 .......820316 o-ring (10 pk)
38a .......079105 Cylinder, 1.5 cu.ft.
38b .......079120 Cylinder, 2.0 cu.ft.
38c .......079125 Cylinder, 2.5 cu.ft.
39 .......108367 Plug, Blank, 5/8, Black
9
7
8
31
32
59
SEa lV2 Technical Maintenance Manual
lV-2 Second Stage
45 ± 3 in. lbs.
(5.0 ± .3 nm)
16
50 ± 3 in. lbs.
(5.6 ± .3 nm)
60
51
50
61
52
49
43
4847
14
63
45
46
44
55
66
64
65
Key # part # Description
.......108402 LV2 Second Stage Assy., Complete
.......
108344 overhaul parts Kit
14 .......820015 o-ring (10 pk)
16 .......820010 o-ring (25 pk)
59 .......100652 Front Cover
60 .......100119 Retaining Ring
61 .......100104 Purge Cover
43 .......100181 Diaphragm
44 .......102510 locknut
45 .......100923 Lever
46 .......104129 Washer
47 .......100945 Valve Body
48 .......104134 poppet Bearing
Part numbers in BOLD ITALICS indicate standard overhaul replacement part.
Key # part # Description
49 .......104127 Spring
50 .......104122 Poppet
51 .......106738 lp Seat
52 .......108438 Inlet Fitting, Black
63 .......108374 Box Bottom
55 .......104913 clamp
64 .......100122 Exhaust Valve
65 .......108371 Exhaust Cover
66 .......108373 Mouthpiece, LV2
Parts not shown
n/s .......108453 Mouthpiece Cover, LV2, PU
n/s .......108391 Hose Assy, LV2, 20” Black
n/s .......108392 Hose Assy, LV2, 27” Black
Maintenance notes
33
S.E.a. lV2
©2010Aqua Lung International
2340 Cousteau Court • Vista, CA 92081
Phone: (760) 597-5000 • Fax: (760) 597-4900 www.aqualung.com/militaryandprofessional
P/N 108448 REV 01/10
advertisement
* Your assessment is very important for improving the workof artificial intelligence, which forms the content of this project
Related manuals
advertisement
Table of contents
- 2 Copyright Notice
- 4 Change Record
- 5 General Guidelines
- 5 General Conventions
- 6 Initial Inspection Procedure
- 6 External Inspection
- 6 Immersion/Leak Test
- 6 Medium Pressure (Over-Bottom) Test
- 7 DISASSEMBLY PROCEDURE
- 10 Second Stage Disassembly
- 12 REASSEMBLY PROCEDURE
- 12 First Stage Reassembly
- 18 Second Stage Reassembly
- 21 FINAL TESTING
- 21 Immersion Test
- 21 Final Assembly
- 22 Initial Pre-Issue Procedures for the SEA MK/LV2/HESP
- 23 Table 1: Troubleshooting Guide for First Stage/Valve Assembly
- 24 Table 2: Troubleshooting Guide for Second Stage
- 25 Table 3: List of Tools and Service Kits
- 29 Table 4: Torque Specifications
- 29 Table 5: Checking Specifications
- 29 Table 6: Recommended Cleaners and Lubricants
- 30 Procedure A: Cleaning and Lubricating
- 31 S.E.A. First Stage with Cylinder Assembly, Exploded View
- 33 Maintenance Notes