- Home
- Domestic appliances
- Large home appliances
- Water heaters & boilers
- Viadrus
- Hercules P 1
- Datasheet
advertisement
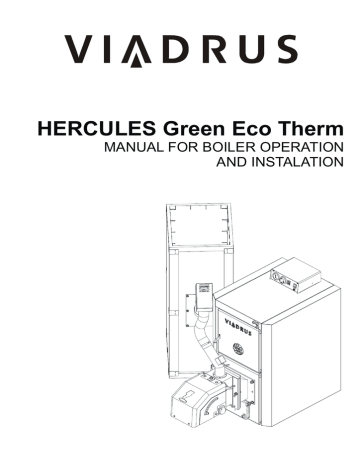
AND INSTALATION
Contents:
page
1.
Produced variants of boiler .......................................................................................................................... 3
2.
Technical data of the boiler ......................................................................................................................... 4
3.
Boiler description ......................................................................................................................................... 6
3.1
Boiler drum construction ..................................................................................................................... 6
3.2
Control, regulation and safety elements ............................................................................................. 6
3.2
The construction of burner and transport routes of the fuel ................................................................ 9
4.
Location and installation ............................................................................................................................ 11
4.1
Regulations and directives ................................................................................................................ 11
4.2
Positioning possibilities ..................................................................................................................... 12
5.
Order, delivery and assembly .................................................................................................................... 14
5.1
Order ................................................................................................................................................. 14
5.2
Delivery and accessories .................................................................................................................. 14
5.3
Assembly procedure ......................................................................................................................... 16
5.3.1
Boiler drum installation .................................................................................................................. 16
5.3.2
Mounting of partitions of the combustion chamber and turbulators .............................................. 17
5.3.3
Mounting of burner ........................................................................................................................ 17
5.3.4
Mounting of the fuel reservoir ....................................................................................................... 19
5.3.5
Mounting of the shells ................................................................................................................... 20
5.3.6
Installation of electrical wiring ....................................................................................................... 21
5.3.6.1
Version HERCULES Green Eco Therm XJ .......................................................................... 21
5.3.6.1
Version HERCULES Green Eco Therm XS .......................................................................... 22
5.3.7
Assembly tools for brush............................................................................................................... 22
5.3.8
Filling of the heat system with water ............................................................................................. 22
5.3.9
Electrical scheme .......................................................................................................................... 23
5.3.10
Boiler hydraulic diagram ............................................................................................................... 27
6.
Putting into operation - instructions for contractual service organization .................................................. 28
6.1
Inspections before start-up ............................................................................................................... 28
6.2
Boiler putting into operation .............................................................................................................. 28
7.
Boiler operation by user ............................................................................................................................. 29
7.1
Version HERCULES Green Eco Therm XJ ...................................................................................... 29
7.1.1
Setting of the heat output of burner .............................................................................................. 32
7.2
Version HERCULES Green Eco Therm XS...................................................................................... 37
7.2.1
Setting of the heat output of burner .............................................................................................. 39
8.
IMPORTANT WARNINGS ........................................................................................................................ 42
9.
Maintenance .............................................................................................................................................. 43
10.
Faults and their removal ........................................................................................................................ 45
11.
Instructions for product liquidation after its operating life ....................................................................... 47
12.
Warranty and defect liability ................................................................................................................... 47
2
Dear customer, thank you for the purchase of HERCULES Green Eco Therm boiler; this purchase demonstrates your confidence in VIADRUS a.s.
In order to get used to a proper treatment of your new product from the start please read these instructions for its use (first of all the chapter no. 7 – Boiler attendance by user, chapter no. 11 – Important warnings and chapter no. 12 – Maintenance by user). Please observe the information given below in order to ensure a longstanding trouble-free operation of boiler so that both you and we are satisfied.
1. Produced variants of boiler
• Order specification code
HERCULES Green Eco Therm X X
Burner output:
25: 25 kW
32: 32 kW
Type of burner:
J: Junior
S: Senior
The fuel tank is included in the standard boiler accessories
• Optional accessories (see chapter no. 5.2)
The boiler design you received is only destined for wooden pellets combustion (specification see page 6) and its trade name is HERCULES Green Eco Therm. It is the boiler with automatic fuel supply. The burner is cleaned manually.
The boiler is manufactured as warm-water boiler with forced heating water circulation and working overpressure up to 400 kPa (4 bar). The boiler is tested for tightness by applying 800 kPa (8 bar) overpressure before despatch.
The use:
The version of boiler HERCULES Green Eco Therm 25X is particularly destined for heating of individual housing units, weekend houses, cottages etc.
The version of boiler HERCULES Green Eco Therm 32X is particularly destined for heating of cottages, weekend houses, small business premises, smaller leisure amenities etc.
Advantages of boiler:
automatic boiler operation guarantees the heating comfort,
mechanical fuel feed from any reservoir
automatic ignition
simple, not time-consuming attendance and maintenance
high efficiency reaching 87,9 %,
boiler drum construction proven on a long-term basis
high service life of the cast iron boiler drum
five-year guarantee for the boiler drum
3
2. Technical data of the boiler
Tab. no. 1 Dimensions, thermal parameters of boiler
Version of boiler
HERCULES Green Eco Therm
25X
5 Section number
Class of boiler according to
EN 303-5
Weight including the supplied fuel tank
Fuel tank weight on demand
Water space volume
Diameter of smoke socket
Boiler dimensions (incl. burner): - height x width
- depth
Capacity of the supplied fuel tank
Fuel tank capacity on demand
Water operating overpressure
Testing water overpressure
Hydraulic loss
Recommended heat water operating temperature
Recommended return water operating temperature
Noise level
Chimney draught
Boiler connections - heat water
- return water
Connected voltage
Operating electric power/max.
Electric protection pcs
- kg kg l mm mm mm dm
3 kg dm
3 kg kPa (bar) kPa (bar)
-
°C
°C dB mbar
W
3
332
65
40,9
156
1218 x 1309
1335
130
85
725
470
400 (4)
800 (8)
See picture Nr.1
60 - 90
Doesn´t exceed level 65 dB (A)
0,15 - 0,25
G 1 1/2"
G 1 1/2"
1/N/PE 230 V AC 50 Hz TN-S
100/1200
IP 20
Tab. no. 2 Heat - technical parameters of the boiler
60
HERCULES Green Eco Therm
32X
7
3
401
65
50,3
156
1218 x 1309
1527
130
85
725
470
400 (4)
800 (8)
See picture Nr.1
60 - 90
60
Doesn´t exceed level 65 dB (A)
0,2 - 0,3
G 1 1/2"
G 1 1/2"
1/N/PE 230 V AC 50 Hz TN-S
100/1200
IP 20
Version of boiler
Section number
Nominal output
Minimum output
Efficiency
The approximate fuel consumption at rated output
The approximate fuel consumption at minimum output
Burning time at nominal output - supplied tank / the tank by request.
Burning time at minimum output - supplied tank / the tank by request
Heating value
Maximum flue gas temperature pcs kW kW
% kg.h
-1 kg.h
-1 h h
MJ. kg
-1
°C
HERCULES Green Eco Therm
25X
5
25
7,5 až 86,8
14,17
60,7
5,8
1,74
17,189
205
78,33
335,71
HERCULES Green Eco Therm
32X
7
32
9,6 až 87,9
10,625
35,42
8,2
2,45
17,189
210
58,75
195,83
Specified fuel:
The pellets must comply at least with one of the standards or regulations as follows:
Direction no. 14-2000 MŽP Č R
DIN 517 31
ÖNORM M 7135
Specified pellets granularity: between 6 and 8 mm
Maximum fuel water content. 12%.
Ash content max. 1,5 %
WARNING! A poor quality of fuel can markedly negatively affect the boiler output and emission parameters.
4
Pa
300
250
200
150
100
50
0
15 20 25 30 35 40 45 50 55
Power in kW
60
Fig. no. 1 Hydraulic loss of the boiler drum
Version of boiler
L
L1
HERCULES Green Eco Therm 25X
1335
809
HERCULES Green Eco Therm 32X
1527
1001
Fig. no. 2 Boiler dimensions
5
3. Boiler description
3.1 Boiler drum construction
The cast iron section boiler drum is the main part of boiler and it is manufactured of grey cast iron according to EN 1561
•
• central sections – quality 150 (previously Č SN 42 2415) front and rear sections – quality 200 (previously Č SN 42 2420)
The pressure parts of boiler conform to the strength requirements according to:
EN 303-5 Boilers for central heating– part 5: Solid fuel boilers for central heating, with a manual or automatic feed, with nominal thermal output max. 300 kW: terminology, requirements, testing and marking.
The boiler drum is assembled of sections by means of pressed on boiler insertions and secured by means of anchor bolts. The sections create the combustion and ash-pan space, the water space and convection part.
The inlet and outlet of heating water are situated in the rear part of boiler.
The rear section of boiler in its upper part has a smoke extension piece and heating water flange, in the lower part there is the return water flange with a sleeve piece for inlet and outlet cocks. The cleaning door and ash door with mounted burner are affixed to the front boiler section.
The whole boiler drum is insulated by means of a health harmless mineral insulation which reduces the losses caused by the heat transfer into ambient. The steel shell colour is treated by means of high-quality komaxit spray.
3.2 Control, regulation and safety elements
Elements for control, regulation and safety placed in the control cabinet
Thermomanometer serves for measuring the temperature and pressure of water in the heating system and is located in the upper part of the boiler shell. The check valve for pressure gauge connection is located in the upper part of the rear boiler section.
Operating thermostat switches off / switches on the operation of the burner according to the set temperature of heating water.
Signalling of safety thermostat signals the activation of the safety thermostat (overheating of the heating system above 97 °C)
The safety thermostat is placed in the control box and serves for ensuring the heating system against overheating. This thermostat is set by the manufacturer to a temperature of 95°C, i.e. to a higher temperature than can be set as the desired temperature on the boiler. When you turn off the safety thermostat unblocking must be done manually. The safety thermostat can be turned on only after the temperature has dropped below the set value. We have to unscrew the black cap of the safety thermostat and by using a suitable object we press the button.
In case of repeated switching of the thermostat the boiler must be shut down and the reason of repeated overheating of the boiler must be found out.
The thermostat of the pump switches on and switches off the pump of heating water according to the set temperature.
1. Termomanometer
2. Operating thermostat
3. The switch "start of burner"
4. Signalling of safety thermostat
5. Fuse 10A
6. Main switch
7. Safety thermostat
8. Thermostat of pump
Fig. no. 3 Control box
6
Elements for control, regulation and safety placed on the boiler body
The air rosette of cleaning door and the lower stifling element is not used at the boiler with an automatic combustion of wooden pellets and must be permanently closed.
Elements for control, regulation and safety placed on the burner
• Control Module of boiler (version HERCULES Green Eco Therm XJ) or automatic (version
HERCULES Green Eco Therm XS).
• LCD display with control buttons, that is designed for change of the values of operating parameters
(version HERCULES Green Eco Therm XJ).
•
•
•
Potentiometer – for setting the boiler output (version HERCULES Green Eco Therm XS).
Photo sensor, which monitors the intensity of the combustion process.
Transport hose with reinforcing spiral, which melts in the case of penetration of fuel back through the knee of burner, thus preventing further supply of pellets into the burner.
• Sensor of penetration of fuel (TD) is placed on the knee of burner and is activated in case of the surface temperature above 90 °C. Burner and fuel feeder are stopped in case of activation of this sensor and the system is switched over into reporting of a failure. The failure mode is deactivated by switching off and on of the main switch. It is necessary to determine the cause of the failure and take appropriate measures, namely before restarting of the burner;
• Reversible thermal label displays the operating temperature of the burner body. This temperature is an indicator for operating mode of the burner and temperature of flue gases which pass the combustion chamber back into the fuel tank. The initial state is shown in black colour for all thermally active parts. If the temperature is increased, the segments gradually are getting a light colour, according to the temperature range of individual heat-active segments. The reversible thermal label should be checked as needed. Increased temperature in this section signals the necessity to clean the boiler, grate of burner or routes of flue gasses and smoke flue. During cooling of the main burner body the colour of the label returns to its original state (all segments are black).
• Irreversible thermal label displays overheating of the knee of burner. This label in case exceeding of temperature of the burner knee irreversibly changes its colour.
The initial status, the active segment is white, the temperature hasn’t reached the degree of activation 104 °C;
THERMAX
°C
104
°F
219
The status at activation, the active segment is dark, the temperature has exceeded the degree for activation 104 °C; activation of 104 °C;
THERMAX
°C
104
°F
219
CAUTION:
•
Activation of irreversible thermal label is signalling overheating of the knee of burner. Status of this label is irreversible and in case of damage it has to be replaced. Control and service of burner may be performed only by an authorized technician.
•
This thermal label is activated for example when hot combustion products pass back via the fuel feeder due to an increased resistance of the smoke flue or a lower draft in the chimney. In such cases the transport hose that connects the fuel feeder and burner body can be damaged and will be necessary its replacement.
•
In case of these emergency statuses the warranty for the burner is void.
7
1. Boiler drum
2. Boiler shell with ashtray
3. Cleaning door
4. Burner
5. Transitionary flange
6. Insulation of transitionary flange
7. The ash door
8. Fuel tank
9. Fuel feeder
10. Transport hose with reinforcing spiral
11. Control box
12. Flange of heating water
13. Flange of return water
14. Fill and drain cock
15. Sealing 90 x 60 x 3
16. Assembly of smoke adapter
17. Turbulators
18. Partition of flue way
19. Partition of the combustion chamber- the front section
20. Partition of the combustion chamber
21. Hose clamp
22. Screw M10 x 50
23. Screw M10 x 30
Fig. no. 4 Boiler assembly
8
3.2 The construction of burner and transport routes of the fuel
The version HERCULES Green Eco Therm XJ
•
Control module with microprocessor;
•
LCD display with control buttons, that is designed for change of the values of operating parameters;
Version HERCULES Green Eco Therm XS
•
Control panel on which there is placed a potentiometer for setting the boiler output;
•
Colour scale on which we can set the position of throttle flap of the fan (the output power of fan) to the same colour as the setting of the thermal output potentiometer.
•
Manual setting of throttle flap of the fan.
Version of boiler
Nominal heat output power range
25J
25
7,5 - 25
HERCULES Green Eco Therm
25S
25
7,5 - 25
32J
32
9,6 - 32
32S
32
9,6 - 32
The burner consists of following components:
• Combustion chamber, which serves for burning pellets and made from high quality stainless steel;
• Removable grate of combustion chamber;
• Electric spiral, by means of which the fuel is ignited. It is located behind the inclined plate of grate in the combustion chamber;
• Fan for intake of air, equipped with Hall effect sensor for sensing the rotational speed;
• Photo sensor, which monitors the intensity of the combustion process;
• Sensor for penetration of burning fuel (TD) which stops the operation of the burner in case of break forth of flame into the fuel feeder;
• Socket for connecting the fuel feeder, which ensures power supply into the motor of the fuel feeder;
• Reversible thermal label from a liquid crystal with the indicator of current temperature of the body of burner.
• Irreversible thermal label from a liquid crystal which signals the high temperature of the knee of burner, preliminarily sets the conditions for the non-warranty service of the main module of burner and of any kind of damage to the hose for fuel supply;
• Fuel feeder with an inlet cable and 1 ~ plug.
• Transport hose with reinforcing spiral, which is made partly of a transparent heat-resistant material
(in case of burning does not emit toxic substances and does not maintain the process of burning), that interconnects the fuel feeder and the knee of burner;
Fuel feeder Transport hose with reinforcing spiral
Knee of the burner
Burner
Fig. no. 5 Burner and fuel feeder
9
Sensor for penetration of burning fuel
(TD)
LCD display with control buttons
Photo sensor
Combustion chamber
Control module of boiler
Transitionary flange for mounting the burner to the door of boiler
Inlet of electricity
Socket for connection of the fuel feeder
Fig. no. 6 Basic components of the burner of boiler HERCULES Green Eco Therm XJ
Control panel
Sensor for penetration of burning fuel (TD)
Photo sensor
Combustion chamber
Control module of boiler
Throttling flap of the fan
Transitionary flange for mounting the burner to the door of boiler
Inlet of electricity
Fig. no. 7 Basic components of the burner of boiler HERCULES Green Eco Therm XS
10
Irreversible thermal label
Reversible thermal label with indicator of current temperature of the body of burner
Fig. no. 8 Positioning of thermal labels on the burner
4. Location and installation
4.1 Regulations and directives
The solid fuel boiler can only by mounted by a company holding a valid authorization to install these equipments.
A project according to the valid regulations must be prepared for the installation.
The heating system must be filled with water that matches the requirements of Č SN 07 7401 and especially its hardness must not exceed the required parameters.
Recommended values
Hardness
Ca
2+
Concentration of total Fe + Mn
*) Recommended value mmol/l mmol/l mg/l
1
0,3
(0,3)*
WARNING!!! The use of anti-freeze mixture is not recommended by the manufacturer. a) regarding the heating system
Č SN 06 0310 Thermal systems in buildings – Design and installation
Č SN 06 0830
Č SN 07 7401
Thermal systems in buildings – Protecting devices
Water and steam for thermal energetic devices with steam working pressure up
EN 303-5 to 8 MPa.
Boilers for central heating – Part 5: Solid fuel boilers for central heating with manual or automatic feed and max. 300 kW nominal thermal output: terminology, requirements, testing and marking. b) regarding the chimney
Č SN 73 4201 Chimneys and flue gas ducting– designing, implementation and connection of fuel consumers.
We recommend that HERCULES Green Eco Therm boiler is connected to the smoke flue with min.
160 mm diameter and the chimney draught must be 0,15 - 0,3 mbar – see Tab. no. 1. c) regarding the fire regulations
Č SN 06 1008 Fire safety of thermal equipments
EN 13 501-1 + A1 Fire classification of construction products and building elements – Part 1:
Classification using test data from reaction to fire tests. d) regarding the electric network
Č SN 33 0165
Č
Č
SN 33 1500
SN 33 2000-3
Electrical regulations; marking the leading wires by colours or digits; implementing regulations
Electrical regulations; revision of electrical equipments
Electrical regulations; electrical equipments Part 3: Setting the basic characteristics.
11
Č SN 33 2000-4-41 Electrical equipments: part 4: Safety chap. 41: Protection against electric shock
Č SN 33 2000-5-51 ed. 2 Electrical regulations: Electrical equipments construction
Č SN 33 2130
Č SN 33 2180
Electrical regulations: Internal electricity distribution
Electrical regulations: Connection of electric instruments and appliances
Č SN 34 0350
EN 60 079-10
EN 60 252-1
Electrical regulations: Regulations for flexible cords and cord lines
Electrical regulations: Regulations for electrical equipments at the places with explosion hazard with flammable gases and vapours.
Capacitors for AC motors – Part 1: In general – Design, testing, dimensioning –
Safety requirements – Instructions for installation and operation.
EN 60 335-1 ed.2
EN 60 335-2-102
EN 60 445 ed. 3
EN 60 446
Electric appliances for household and similar purposes – Safety – Part 1:
General requirements
Electric appliances for household and similar purposes – Safety – Part 2-102:
Special demands on appliances containing the electric connections and burning the gas, oil and solid fuels
Basic and safety principles for man – machine interface, marking and identification
Basic and safety principles of machinery operation - Marking the leading wires with colours or digits e) regarding the system for HWS heating
Č SN 06 0320 Thermal systems in buildings– Hot water preparation– Design and project
Č
Č
SN 06 0830
SN 73 6660 engineering
Thermal systems in buildings – Protecting devices
Internal water piping
4.2 Positioning possibilities
The boiler is approved for installation in non – residential spaces (for example – cellar, corridor, etc.)
The installation of the boiler must comply with all requirements of Č SN 06 1008.
ATTENTION!
In the event that it is installed the delivered wooden fuel reservoir, then it is necessary to install a fireproof bulkhead between the reservoir and boiler.
Boiler placing with regard to fire regulations:
1. Placing on floor of flame resistant material (Fig. no. 9)
boiler to be put on a flame resistant backing exceeding the boiler platform over 20 mm at sides and only on the boiler drum depth.
if the boiler is situated in a cellar we recommend to place it on a bedding of minimum 50 mm height.
Section number
L [mm]
5
680
7
872
Fig. no. 9 Bedding dimensions
12
2. A safe distance from the combustible materials:
when installing and operating the boiler it is necessary to keep a safety distance of 200 mm from the materials of combustibility grade A1, A2, B and C (D);
for easily combustible materials of combustibility grade E (F), which quickly burn and burn themselves even after removal of ignition source (such as paper, cardboard, asphalt and tar paper, wood and wood-fiber boards, plastics, floor coverings) the safe distance has to be doubled, i.e. to
400 mm;
safe distance should be doubled as bulb where the grade of reaction to fire has not been proved.
Tab. no. 3 Grade of reaction to fire
Grade of reaction to fire
Examples of building materials and products included in the reaction to fire
(Extract from EN 13 501-1 + A1)
A1 – incombustible Granite, sandstone, concrete, bricpcs, ceramic tiles, mortars, fireproof plasters, …
A2 – combustible with difficulty acumin, izumin, heraklit, lignos, boards and basalt felt, fibreglass boards,...
B – hardly combustible Beech and oak wood, hobrex boards, plywood, werzalit, umakart, sirkolit,...
C (D) – medium combustible Pinewood, larch, whitewood, chipboard and cork boards, rubber flooring,...
E (F) – easily combustible
Asphaltboard, fibreboards, cellulose materials, polyurethane, polystyrene, polyethylene, PVC,…
The boiler placing with respect to the necessary handling space:
•
•
•
•
• basic surroundings of AA5/AB5 according to Č SN 33 2000-3 handling space of minimum 1000 mm in front of the boiler must be maintained a minimum distance of 400 mm between the back part of the boiler and the wall from the side of the boiler there must be maintained a space at least 500 mm for the door opening and for the access to the rear part of the boiler; a minimum distance of 100 mm from the side wall.
Fig. no. 10 Boiler placing in a boiler room
Fuel placing:
•
•
dry fuel (up to the 12% moisture) must be used in order to guarantee the correct combustion in the
boiler. The pellets should be stored in their original packing from the manufacturer
(e.g. PET sacpcs) at a dry place; it is impossible to store fuel behind the boiler or unload it next to the boiler in a distance smaller than
400 mm;
13
• the manufacturer recommends that min. 1000 distance is kept between the boiler and fuel or the fuel is placed in a room different from that where the boiler is installed
Boiler positioning with regard to electricity network:
•
•
• the boiler must be placed so that the plug in socket (230V/50Hz) is always accessible; the boiler is connected to the mains by a fixed movable inlet with a normalized plug; the electric shock prevention must be guaranteed according to valid EN (see chap. 5.1.)
A permanent air supply for combustion and ventilation must be guaranteed in the room where the boiler is installed (the air consumption of HERCULES Green Eco Therm 5X boiler amounts to approx. 80 m
3
.h
-1
, the air consumption of HERCULES Green Eco Therm 7X boiler amounts to approx.
160 m
3
.h
-1
.
The connection of heating system piping must be carried out by a person authorised according to
. the valid regulations.
CAUTION: When connecting the boiler to the heating system there must be installed a inlet and outlet cocpcs in the lowest point and as near as possible to the boiler (at the return water flange).
5. Order, delivery and assembly
5.1 Order
In the order the following is needed to be specified:
1. Output and type of burner (see chap. 1)
2. Requirements for accessories offered on request
5.2 Delivery and accessories
Boiler HERCULES Green Eco Therm is supplied so that on a pallet there is placed the complete boiler drum and on the side there is attached the wrapped boiler shell. The accessories are stored inside the boiler drum and are accessible after opening the cleaning door. On the other pallet there is stored wooden fuel container, in which there is stored the burner, the fuel feeder and their accessories. The boiler is packed into a shipping container and must not be flipped during shipping; it is only permitted to tilt to the sides in order to remove the wrapping from the boiler drum.
•
•
•
Standard accessories to boiler:
•
•
•
•
Boiler with the appropriate number of boiler sections on the palette
Flange of heating water G 1 1/2"
•
•
•
•
•
•
•
Return water flange G 1 1/2 "with socket Js 1/2" for the fill and drain cock
• Sealing
φ
90 x 60 x 3
Washer 10,5
Nut M10
The fill and drain cock Js 1/2“
Three-position sump of thermostat G 1/2" spring of the capillary
Blind plug Js 6/4“
Sealing 60 x 48 x 2
Fasteners for mounting of a transitionary flange
- screw M10 x 50
-
- screw M10 x 30 spring washer 10
-
- washer 10,5 nut M10
Insulation of the transitionary flange
The boiler shell including the ashtray and insulation in the adequate size
Fasteners for jacketing
- console 1 assembly
-
- console 2 assembly washer 10,5
-
-
- nut M10 connecting pin screw M5 x 12
2 pcs
2 pcs
4 pcs
4 pcs
4 pcs
4 pcs
1 pc
1 pc
2 pcs
8 pcs
8 pcs
1 pc
1 pc
1 pc
1 pc
1 pc
1 pc
3 pcs
4 pcs
4 pcs
4 pcs
14
•
•
-
-
-
- washer 5,3 screw into the plate ST 4,2 x 9,5 spring clamp bushing PG 9 control box
- screw M5 x 12
- serrated washer 5,3 cleaning equipment
- hook
•
•
•
•
•
•
-
-
-
- brush with handle pike cleaning equipment holder handling key turbulator partition of combustion chamber – the front segment the partition of combustion chamber the partition of smoke channel burner fasteners for mounting of burner
•
•
•
-
-
-
-
-
- screw M10 x 50 screw M10 x 30 spring washer 10 washer 10,5
- nut M10 insulation of burner transitionary flange of the burner fuel feeder transport hose with reinforcing spiral hose clamp
•
• fuel reservoir
- sloping bottom
- flange of the fuel feeder fasteners for the fuel reservoir
-
- screw M8 nut M8
- washer 8,4 flexo cord 5 m •
•
• boiler label business – technical documentation
Accessories delivered by request:
• fuel reservoir 725 l
- the side of fuel reservoir
- the side of fuel reservoir with the hole for spiral worm
- the foot of fuel reservoir
- the bottom of fuel reservoir
•
- the bottom of fuel reservoir A
- the cover of fuel reservoir
- handle connection accessories for fuel reservoir assembly
- pendant chainlet
- screw M6 x 12
- washer 6,4
- nut M6
- screw M6 x 16
- washer 8,4
The boiler equipment delivered “by request“ is not included in the basic price of boiler
4 pcs
6 pcs
4 pcs
7 pcs
1 pc
4 pcs
4 pcs
1 pc
1 pc
1 pc
1 pcs
1 pc
4 pcs
1 pc
4 pcs - 7 sect.
2 pcs
1 pc
3 pcs
3 pcs
6 pcs
6 pcs
6 pcs
1 pc
1 pc
1 pc
1 pc
2 pcs
1 pc
2 pcs
1 pc
10 pcs
10 pcs
10 pcs
1 pc
1 pc
3 pcs
1 pc
4 pcs
2 pcs
2 pcs
1 pc
1 pc
1 pcs
72 pcs
72 pcs
72 pcs
2 pcs
2 pcs
15
5.3 Assembly procedure
5.3.1 Boiler drum installation
1. Position the boiler body on a retaining wall.
2. Put sealing 90 x 60 x 3 (1) onto the upper flange of the rear boiler section and screw the flange of heating water (2) and then interconnect the other end with the heating system.
3. Put sealing 90 x 60 x 3 (5) onto the lower flange of the rear boiler section and screw the flange of heating water with a sleeve (6) for the fill and drain cock and then interconnect the other end with the heating system.
4. After connecting the boiler to the heating system screw a knee with the fill and drain valve (9) into the sleeve of the flange of return water.
5. Then screw the sump of thermostat G 1/2 "into the hole in the upper part of the rear boiler section
(Fig. no. 11).
1 Check valve for the manometer
2 Boiler basin
Fig. no. 11
6. Then carry out blinding of the threaded hole Js 6/4 "in the front boiler section by using a blinding plug Js
6/4". Place the seal 60 x 48 x 2 under the blinding plug.
7. Fit the smoke pipe onto the smoke adapter and insert it into the chimney opening.
1. Sealing
φ
90 x 60 x 3
2. Heating water flange
3. Washer10,5
4. Nut M10
5. Sealing
φ
90 x 60 x 3
6. Return water flange
7. Washer 10,5
8. Nut M10
9. Filling and draining cock
Fig. no. 12 Boiler drum installation
16
5.3.2 Mounting of partitions of the combustion chamber and turbulators
1. 1.According to Fig no. 13 insert the partitions of the combustion chamber (1, 2) into the combustion chamber in number of 4 pcs (for HERCULES Green Eco Therm 5X) or 5 pcs (for HERCULES Green
Eco Therm 7X).
2. Insert 2 pcs partitions of the smoke channel (3) between the front and middle boiler section.
3. 3.Put 4 pcs turbulators (4) into the route of flue gases
1. Partition of the combustion chamber– the front section
2. Partition of the combustion chamber
3. Partition of the smoke channel
4. Turbulator
Fig. no. 13 Positioning of the partitions of combustion chamber in boiler
5.3.3 Mounting of burner
567 mm for HERCULES Green Eco Therm 5X
630 mm for HERCULES Green Eco Therm 7X
Fig. no. 14 Dimensions of burner
17
1. Please screw the flange of burner (see Fig. no. 15) onto the ash door by means of 3 pcs screws
M10 x 30 (2), 1 pc screw M10 x 50 (2), 4 pcs nuts M10, 4 pcs washers 10,5 and 4 pcs spring washers
10,5.
2. Screw the knee of the burner on the body of burner with the throat directed onto the positioning of the fuel reservoir.
3. Mount the burner insulation onto the flange of the burner.
4. Screw the burner with insulation to the transitionary flange by means of 2 pcs screws M10 x 50, 2 pcs nuts M10, 2 pcs washers 10,5 and 2 pcs spring washers 10,5.
1. Screw M10 x 50
2. Screw M10 x 30
Ash door
Transitionary flange for installation of burner
Fig. no. 15 The lower door with the flange of burner
18
5.3.4 Mounting of the fuel reservoir
ATTENTION!
In the event that it is installed the supplied wooden fuel reservoir, it is necessary to place a fireproof bulkhead between it and the boiler.
• According to Fig no. 16 you must screw the flange of fuel feeder (3) to the lateral part of the fuel reservoir (6) by using 6 pcs screw M8 x 20 (5), M8 nuts (2) and washers 8.4 (4);
• Then you must screw together inclined bottom (7) by means of 4 pcs screw M8 x 30 (8), M8 nuts (2) and washers 8.4 (4);
• Put the assembled inclined bottom (7) into the fuel tank;
• Insert the fuel feeder (1) into the flange of fuel feeder (3).
• The fuel feeder should form an angle of 45 degrees with the horizontal floor in order to ensure optimal operating conditions. The lower part of the feeder should be placed at the lowest point of fuel reservoir.
The fuel feeder and reservoir must be placed so that there is ensured a safe operation of equipment and an easy access and maintenance.
ATTENTION: Any change in the angle of the fuel feeder affects the amount of the dosed fuel:
• reduction of the angle will lead to an increased dosing of fuel;
• Increase of the angle will lead to a reduced dosing of fuel;
• Then position the fuel tank with the fuel feeder in the proximity of the burner so as to prevent clogging of the transport hose with the pellets during supply of fuel and also to make it possible to open the cleaning door and ash door.
• After mounting of the shells (see chap. 5.3.5) interconnect the transport hose with the knee of burner and secure by means of hose clamps. ps.
The assembled
bottom
1 Fuel feeder
2 Nut M8
3 Flange of fuel feeder
4 Washer 8,4
5 Screw M8x20
6 Fuel reservoir
7 Inclined bottom
8 Screw M8x30
Fig. no. 16 The fuel feeder with the supplied fuel reservoir
1 pc
10 pcs
1 pc
14 pcs
6 pcs
1 pc
2 pcs
4 pcs
19
5.3.5 Mounting of the shells
1
2
3
4
5
6
7
8
9
Anchor screw
Console 1
Washer 10,5
Nut M10
Console 2
Right side part of shell
Insulation of the side part of shell
Connecting pin
Washer 6,4
10 Screw M5 x 12
11 Right side part of shell
12 Screw ST 4,2 x 9,5
13 Insulation of the rear part of shell
14 Rear part of shell
15 Upper part of shell
16 Insulation of the upper part of shell
17 Spring clamp
18 Control box
19 Washer 5,3
20 Cable gland PG 9
Fig. no. 17 Mounting of jacketing
1. Remove shells out of the carton wrapping.
2. Fitting is carried out according to Fig no. 17th
3. Put the consoles (1) (2) and 2 (5) on the threads of the upper anchor screw (1) (2) and 2 (5) and screw them by using 2 pcs M10 nuts (4) and 2 pcs 10.5 washers (3)
20
4. You will mount the connecting pins 2 pcs (8) on the right side part of the shell (6) and then insert the insulation (7). Then you will install the jacket (shell) (6) on lower anchor screws and connect the upper part with consoles 1 and 2 by using 2 pcs M5 x12 screw (10) and 2 pcs 5.3 washers (9).
5. Put the consoles 1 (2) and 2 (5) on the threads of the left upper anchor screw and screw them by using the 2 pcs M10 nuts (4) and 2 pcs 10.5 washers (3).
6. You will mount the connecting pins 2 pcs (8) on the left side part of the shell (11) and then insert the insulation (7). Then you will install the jacket (shell) (6) on lower anchor screws and connect the upper part with consoles 1 and 2 by using 2 pcs M5 x12 screw (10) and 2 pcs 5.3 washers (9).
7. Then you will mount the insulation of the rear part of the shell (13) on the rear part of the shell (14) and screw it to the side parts of the shell by using 6 pcs screw ST 4,2 x 9,5 (12).
8. Put the insulation of the upper part of the shell (16) on the boiler drum.
9. Mount spring clamps 4 pcs (17) on the upper part of the shell (15).
10. The next assembly process of the control box and wiring see chap. Section 5.3.6.
5.3.6 Installation of electrical wiring
5.3.6.1 Version HERCULES Green Eco Therm XJ
1. According to Fig no. 17 equip the upper part of the shell (15) with the glands PG 9 (20)
2. Attach the control box (18) to the upper part of the shell (15) by using of screws M5 x 12 (10) and serrated lock washers 5.3 (19) and pull the capillary tube of safety thermostat, capillary tubes of thermomanometer and the capillary tube of the thermostat of pump through the hole.
3. Pull the supply cable of burner WL4 through the gland PG 9 (located in front part of the upper section of the shell) and connect the cable wires to the control box to the terminals: black terminal X1: 5 brown terminal X1: 10 grey (blue) terminal X1: 11 yellow-green terminal X1: 12
4. Unscrew the cover of burner and pull the cable of burner control WL2 through a rubber grommet and connect the cable to the terminals black grey blue brown
A1: K22
A1: K23
A1: K10
A1: K11
5. Secure the cable of burner control WL2 against pulling out by using a tightening tape.
6. Pull the other end of the cable of burner control WL2 through the gland PG 9 (located in front part of the upper section of the shell) and connect the cable wires to the control box to the terminals: black terminal X1: 6 grey brown terminal X1: 9 terminal X1: 16 blue terminal X1: 17
7. Pull the sensor of heating water B1 through the gland PG 9 ( located in front part of the upper section of the shell).
8. Connect the supply flexo-cord to the control box to the terminals: brown blue
X1: L
X1: N yellow-green X1: PE
9. Connect the pump and room thermostat according to the electrical scheme, see chap. No. 5.3.9.
10. Insert B1 sensor of heating water, capillary tube of safety thermostat, capillary tubes of thermomanometer and the capillary tube of thermostat of pump into the sump of boiler (see Fig no. 12) and secure with a spring.
11. Screw the capillary tube for pressure of manometer into the reverse valve for pressure gauge in the rear section of boiler drum (see Fig no. 12)
12. Fit the upper part of the shell on the boiler and screw the upper part of the control box.
13. Insert 1 ~ plug of the fuel feeder into the socket of burner.
WARNING: Version HERCULES Green Eco Therm XJ is equipped with sensor B1 of hot water.
For this reason the operating thermostat in the control box is shunted to terminals
X1: 7 and X1: 8 and does not serve for control of the operation of burner.
21
5.3.6.1 Version HERCULES Green Eco Therm XS
1. According to Fig no. 17 equip the upper part of the shell (15) with the glands PG 9 (20)
2. Attach the control box (18) to the upper part of the shell (15) by using of screws M5 x 12 (10) and serrated lock washers 5.3 (19) and pull the capillary tube of safety thermostat, capillary tubes of thermomanometer and the capillary tube of the thermostat of pump through the hole..
3. Pull the supply cable of burner WL4 through the gland PG 9 (located in front part of the upper section of the shell) and connect the cable wires to the control box to the terminals: black brown terminal X1: 5 terminal X1: 10 grey (blue) terminal X1: 11 yellow-green terminal X1: 12
4. Connect the supply flexo-cord to the control box to the terminals:: brown X1:L blue yellow-green
X1:N
X1:PE
5. Connect the pump and room thermostat according to the electrical scheme see chap. No. 5.3.9.
6. Insert the capillary tube of safety thermostat, capillary tubes of thermomanometer and the capillary tube of thermostat of pump into the sump of boiler (see Fig no. 12) and secure with a spring.
7. Screw the capillary tube for pressure of manometer into the reverse valve for pressure gauge in the rear section of boiler drum (see Fig no. 12)
8. Fit the upper part of the shell on the boiler and screw the upper part of the control box.
9. Insert 1 ~ plug of the fuel feeder into the socket of burner.
5.3.7 Assembly tools for brush
Use the leather gloves and common assembly tools for mounting or dismounting of the brush and the spike point (if they are included in the delivery) .
5.3.8 Filling of the heat system with water
Water for filling of the boiler and the heat system must be pure and colourless, without suspended substances, oil and chemically aggressive substances. Its hardness must correspond to Č SN 07 7401 and in case it does not correspond it is necessary the water to be adjusted. Even multiplying heating of the water with higher hardness does not prevent from excluding of soils on the boiler drum walls. The precipitation of
1 mm of limestone reduces in the given place the heat transfer from metal to water by 10 %.
Heat systems with an open expansive tank allow direct contact of the heat water with atmosphere. In the heat period the expansive water in the tank absorbs oxygen that increases the rust effects and at the same time a considerable vaporization of water occurs. Only water adjusted to values according to Č SN 07 7401 can be used for fill – up. The heat system is needed to be rinsed so as all impurities have been washed out.
During heat period it is necessary to keep consistent water volume in the heat system. While filling – up of the heat system with water it is necessary to prevent the air from leeching onto the system. The water from boiler and heat system must never be impregnated or taken out for use except for cases necessarily needed such as repairs, etc. By draining the water and filling with new one the risk of rust and scale creation is increased.
If it is needed to fill water into the heat system we fill it only to a cooled down boiler to prevent
section cracking. After filling of the boiler and heat system checking of tightness of all joints is needed.
The finishing of assembly and the heat test performance must be recorded in the warranty card.
22
5.3.9 Electrical scheme
Fig. no. 18a) Circuit diagram of HERCULES Green Eco Therm XJ
23
Central heating pump
(HO5VV - F 3Cx0,5)
Supply cable of burner
(HOSRR - F 4G1)
Room thermostat
(HO5VV - F 2Dx0,5)
Control of burner
(HO5VV - F 5Cx0,5)
BU (A1:K10)
BN (A1:K11)
GNYE
BU
BN
GNYE (A1:PE)
GR * (A1:K1)
BN (A1:K3)
GR (A1:K23)
GNYE
BU
BN
BK (A1:K22)
BK (A1:K2)
Supply flexo-cord
HO5VV - F 3Cx0,75
GNYE
BU
BN
Fig. no. 18b) Circuit diagram of HERCULES Green Eco Therm XJ
24
Fig. no. 19a) Circuit diagram of HERCULES Green Eco Therm XS
25
Central heating pump
(HO5VV - F 3Cx0,5)
Supply cable of burner
(HOSRR - F 4G1)
Room thermostat
(HO5VV - F 2Dx0,5)
GNYE
BU
BN
GNYE (A1:PE)
GR * (A1:K1)
BN (A1:K3)
BK (A1:K2)
Supply flexo-cord
HO5VV - F 3Cx0,75
GNYE
BU
BN
Fig. no. 19b) Circuit diagram of HERCULES Green Eco Therm XS
26
5.3.10 Boiler hydraulic diagram
Fig. no. 20 HERCULES Green Eco Therm boiler hydraulic diagram
Fig. no. 21 HERCULES Green Eco Therm boiler hydraulic diagram with HWS reservoir and Danfoss valve
Legend:
1. Boiler
2. Heating system
3. Thermostatic valve
4. Pump
5. Safety valve
6. Expansion tank
7. HWS reservoir
8. Danfoss FJVR valve
27
6. Putting into operation - instructions for contractual service organization
The boiler can only be put into operation by a contractual service organization authorized to carry out this activity.
6.1 Inspections before start-up
Before putting the boiler into operation it I necessary to check:
1. Filling the heat system with water (thermomanometer check).
2. Tightness of heating system.
3. Connection to the chimney – it must be approved by a chimney-sweepers’ company.
4. Connection to the electricity network - it must be approved by an authorized company.
When connecting the sockets the grounding pin must be upward and the phase conductor is connected to the left female connector in front view. The same applies to the double receptacles.
6.2 Boiler putting into operation
1. Fire the boiler (see chap. 7.). When firing up the protective spraying of boiler section is baked and this process is accompanied by a slight smell. Mind the boiler room ventilation.
2. Bring boiler to the necessary service temperature. The recommended heating water temperature is between 60 and 90 °C.
3. Check whether the set parameters of burner correspond to the required power of a given heating system. Setting the operating parameters (see chap. 7.1.1 and 7.2.1)
4. Carry out the heating test according to relevant standards (see the Guarantee certificate).
5. Recheck visually the boiler tightness.
6. Make the user acquainted with boiler attendance (see chap. 7).
7. Make a registration in the Guarantee certificate.
28
7. Boiler operation by user
Before putting the boiler into operation or in case that the fuel feeder is empty during operation and it is necessary to fill the fuel feeder with pellets:
• pull out the plug 230 V from the socket of burner;
• insert the plug of power supply (230 V/50 Hz);
• wait until the wooden pellets start to discharge from the throat of the fuel feeder;
• pull out the plug from the power supply and insert it back into the socket of burner.
7.1 Version HERCULES Green Eco Therm XJ
Home screen
S button to enter a submenu or to confirm the setting
+ And - buttons for movement in menu and modifying of values
ESC key for return to the higher level of menu or return to the main menu
GREEN ecoTHERM v2s 1
Software version number of control module of burner
S
-
ESC +
Activate?
ENTER
S
-
•
For putting the burner into operation press the button "S"
Activate? (activate) putting the burner into operation
+ ESC
29
After putting the burner into operation the following message appears on the display:
TEST – BLOWING
ON 32
o
FC: 0%
S
+ ESC
The display shows information about the current operating mode of the burner:
• TEST - BLOWING (blowing through the burner) the burner performs the initial blowing through with the purpose to remove all debris from the grate of burner;
• 32° actual water temperature in the boiler. The water temperature in the boiler is displayed in case the burner is started in the mode of sensing the water temperature by means of a sensor;
• FC: 0% intensity of flame, measured by means of a photosensor (%)
The display shows information about the operating mode of the burner - the burner is in the mode of ignition of fuel:
IGNITION 1 150
ON 32
o
FC: 0%
S
+ ESC
After removal of debris by means of a fan the fuel feeder starts to supply the initial quantity of fuel and the burner performs the ignition of fuel. The display shows the operating mode "IGNITION 1" (ignition) - this is the first attempt (denoted as 1) of ignition of fuel which lasts for a period that can be set in the service software;
30
After a successful ignition of fuel the operation of burner will continue to operate according to the factory setting in order to stabilize the combustion process according to the data on the display - see the Figure below:
TRANS.: 10kW
ON 32
o
FC: 65%
S
+ ESC
TRANS.:10kW the burner is in the mean operating mode and it works with a heat output of 10 kW;
The burner from the mode of stabilization passes into automatic mode. The performance will change depending on the desired temperature of outlet water from the boiler.
COMBUST 5 32kW
ON 72
o
FC: 98%
•
COMBUST 5 – 32kW
•
72
°
•
FC: 98%
S
+ ESC the degree of operating heat output of the burner (in the event that the burner works in the degree 5 of heat output and its power is 32 kW); temperature of outlet water from the boiler, [°C]; intensity of flame measured by means of a photosensor [%];
31
Items of user menu of control module of burner
The user menu starts up on the display by a long pressing the button "S".
By pressing the button "S" you go to the selection of menu of control module of burner.
To exit the current item of menu press "ESC".
COMBUST 5 32kW
ON 75
o
FC: 98%
S
+ ESC
7.1.1 Setting of the heat output of burner
You can set the heat output of burner through the selection of the degree of heat output (EFFECT LEVEL).
EFFECT LEVEL
ENTER EXIT
S
+ ESC
Degree of heat output (EFFECT LEVEL)
Heat output of burner [kW]
25J 32J
1
2
3
4
7.0
15.0
20.0
25.0
10.0
20.0
25.0
32.0
5 28.0 32.0
We recommend that you use the burner up to the degree 4 of its heat output. The degree 5 is intended for operation only at high heat consumption during a short period of time.
To select "Effect level" press "S". Use the + and - buttons to select the degree of heat output according to the required output of burner. To confirm your choice, press "S".
To return to a higher level menu or return to the main menu, press "ESC".
32
N:5
[n] Effect level
O:5
S
+ ESC
ATTENTION: In case that the fuel has changed (for instance the class of pellets has changed), then an additional adjustment of operating parameters of the burner should be done.
NOTE: The burner in case of a change of the degree of heat output automatically re-adjusts the fan power and the quantity of fuel;
Stopping of the operating mode of the burner by switching off the button „START OF
BURNER“
Use "START OF BURNER" button for switching on and the operation of the burner and the subsequent switching off and stopping of burner. The display of control module after switching off the burner shows the message: „FINAL COMBUSTION“ (the final combustion).
ATTENTION: To turn off the burner, use the "START OF BURNER". Do not turn off power supply of burner.
The reason for this measure is that the button "START BURNER" activates the controlled process of switching off of the control module of burner, which also cools the unit and ensures that all carbonaceous residues are burnt, and thus retains the reliability and performance of the burner.
Stopping of the operating mode of burner by setting the item in menu of its control module.
To stop the burner operation is necessary to proceed as follows:
• Press and hold the "ESC" (longer than 5 seconds);
• Give an answer to the question "Make final comb.?" (should be carried out the final combustion?) that appears on the display of control module by selecting "YES" (yes);
If you select "YES" (yes), the display shows "MAN FINAL COMB" (final combustion) and the control module will shut down the burner.
Other way to stop the operation of the burner, see below:
To stop the burner operation it is necessary to enter into the item "MAKE FINAL COMB." (Carry out the final combustion) in the menu of control module of burner.
MAKE FINAL COMB.
ENTER EXIT
S
+ ESC
To confirm your choice press "S"; in case of refusal press "ESC" and in for moving to other items, use the "+" and "-".
33
Make final comb.?
[YES] [NO]
S
+ ESC
After the extinction of the burner, the display shows "Activate" (initial screen display).
If the burner is not in use for a long time, unplug it from the power supply and then clean the combustion chamber, combustion grate and photosensor from deposition of ashes.
Switching off the burner by means of external control module
Turn off the burner by pressing START OF BURNER. Then the control module of burner performs a
"controlled shutdown process" during which the fan is kept in operation (burner is cooled down) while simultaneously are monitored the operating parameters. After cooling the burner (to the room temperature) switch off the burner by means of its disconnecting from the main power supply.
Faulty statuses of the burner
When a faulty status occurs on the burner, then the display of control module shows the message of alarm. A detailed description of error messages and their solutions can be found in Tab. no. 4 and 5
ATTENTION:
• In case of boiler overheating the safety thermostat is activated. Safety thermostat must be manually reset: Safety thermostat can be turned on only after the temperature has dropped below the set value.
We shall unscrew the black cap of safety thermostat and with a suitable tool we press the button. In case of a repeated shutdown of the safety thermostat the boiler has to be shut down and then the cause of repeated overheating of the boiler must be found out. After checking of boiler and burner and determining and correction of the cause of overheating restart the burner by switching off the power supply and its subsequent switching on.
• In case of activation of thermal sensor against the penetration of burning fuel the fuel feeder switches off and the burner becomes extinct. After finding the cause of high temperature on the knee of burner we reset the fault by switching off and on of the burner. In the event of damage to the sensor this must be replaced by a service worker.
34
The list of latest 10 faults that occurred during the burner operation
To check the latest faults that occurred during the burner operation, enter into the menu „LOG“.
LOG error 1:22
EXIT
S
+ ESC
The display of control module of burner shows the selected item „LOG“ in menu, i.e. the number of faults in the list of faults and their codes.
To exit the menu press the button „ESC“.
Fault conditions and the procedure for their solution are described in Tab. no. 4 and 5
Reset of faulty statuses of burner
We carry out the reset by switching off and then switching on of the main switch in the control box of boiler.
Tab. no. 4 The error codes, stored in the list "LOG" in the items of menu of burner (25J and 32J).
Error codes
Description of fault The way of repair
10
11
12
13
14
15
16
18
19
20
21
22
23
24
Failed ignition
Fault of control module faulty fan functionless fan
Low speed fan failed ignition
Clean the burner grate;
Check whether in the fuel feeder and fuel reservoir there is a sufficiency of fuel;
In case of a sufficiency of fuel - ask an authorized technician for assistance
For assistance, contact an authorized technician The flame goes out during operation of the burner
Photoreceptor function error
Temperature around the control module is above set limit
Too low temperature of boiler outlet water (5 °C)
Too high temperature of boiler outlet water 120oC
Failure of the fuel feeder failure of photoreceptor
Photoreceptor fails to sense/scan a successful ignition
For assistance, contact an authorized technician
Turn off the burner and allow the equipment to cool;
For assistance, contact an authorized technician
The risk of frost and mechanical damage, increase the degree of heat output of the burner
For assistance, contact an authorized technician to check the whole heating system;
The risk of overheating the boiler and the heating system, reduce the degree of heat output of the burner
For assistance, contact an authorized technician to check the whole heating system;
For assistance, contact an authorized technician;
For assistance, contact an authorized technician;
For assistance, contact an authorized technician;
For assistance, contact an authorized technician;
Check whether in the fuel feeder and fuel reservoir there is a sufficiency of fuel;
In case of a sufficiency of fuel - ask an authorized technician for assistance
For assistance, contact an authorized technician
For assistance, contact an authorized technician
For assistance, contact an authorized technician
35
Tab. no. 5 The faults which are displayed on the display of the burner (25J and 32J).
The text which is
Description The way of repair shown on display
IGNITION FAILED Failed ignition Check whether in the fuel feeder and fuel reservoir there is a sufficiency of fuel;
In case of a sufficiency of fuel - ask an authorized
LOST FIRE IN
COMBUSTION
STOKER FAULT
The flame goes out during normal operation of burner
Disconnection of fuel technician for assistance
Check the electricity connection, fuel feeder, restart the burner
Check connection of the fuel feeder,
LOW TEMPERATURE
SENSOR
PHOTOSENS
TEMP SENSOR
OVERHEAT feeder
Activation of the sensor against penetration of burning fuel placed on the knee of burner
Clean the deposits of dirt in the knee and the combustion chamber of burner or clean the boiler drum. Restart the burner. Check the condition of irreversible label - in case of damage to ask for assistance from an authorized technician;
Check the connection of water temperature sensor NTC Disconnection of water temperature sensor NTC
The problem with the operation of a photoreceptor
Check the condition and function of the photoreceptor.
Carefully clean the transparent portion of the photoreceptor - Do not use solvents. If necessary, replace it - this operation should be performed by an authorized technician;
High water temperature The risk of overheating the boiler and the whole heating system;reduce the degree of heat output of the burner
Ask an authorized technician to check the whole heating system
36
7.2 Version HERCULES Green Eco Therm XS
Putting the burner into operation:
• The main switch must be in the position on(I) - (green light of main switch on the control box is alight- see Fig. no. 3 and signalling "POWER" on the burner drum - see Figure 22);
• By pressing the switch "START OF BURNER" on the control box (see Fig no. 3) the burner is put into operation. Also operational thermostat and the room instrument have to be switched. The signalling of
"START" (see Fig no. 22) lights up on the burner drum.
Potentiometer for setting of output
Colour scale
Signalling "START"
(orange) - burner in operation
Signalling "POWER"
(green) -
Burner under voltage
Fig. No.22
Adjustment of the burner output
Adjustment of the burner output is done by means of setting the position of the potentiometer of heat output
(i.e. the amount of supplied fuel ) and the amount of air flow that is controlled by means of a throttle flap of the fan into the burner. Set the position of the lever of throttle flap of the fan on the colour scale
(see Fig. no. 23) to the same colour as the setting of potentiometer of heat output (see Fig no. 22).
CAUTION: In case of change of the type of fuel it is necessary to re-adjust the output of burner.
Setting the operating parameters of the burner may be performed only by an authorized trained technician.
Reducing the heat output of the burner
Burner output is reduced by turning the potentiometer counterclockwise which results in lowering the fuel consumption. It is also necessary to reduce the amount of air flow by means of closing the throttle flap of fan.
Increasing the heat output of the burner
Burner output is increased by turning the potentiometer clockwise, which results in increasing the fuel consumption. It is also necessary to increase the amount of air flow by opening the throttle flap of the fan.
WARNING:
The potentiometer of setting the heat output must not be set to the full value (i.e. into the red zone of the scale) in any case, because thus the heat output of burner would be exceeded.
37
Colour scale
Lever for setting the position of the throttling flap of the fan
Fig. No.23
The burner is automatically shut down after reaching the desired temperature that is set by the operating thermostat (the fan carries out cleaning of the combustion grate).
In case of a request for heating the fan carries out the operations of blowing through, filling fuel and ignition.
In the event that the first portion of fuel is not ignited then a second ignition is performed.
In case the flame is not identified by photosensor after this cycle, the burner is put into failure (see chap.9).
Closing of the throttling flap
Opening of the throttling flap
Fig. no. 24
ATTENTION:
The amount of air flow significantly affects the operating mode of the burner, including performance and efficiency of the whole system - if the amount of air flow is less than required, then the fuel partially is unburned due to the low intensity of combustion. The situation when the amount of air flow exceeds the optimum value of the air flow will result in a reduction in combustion efficiency due to the intensive cooling of the combustion process and increased amount of unburned fuel. The above mentioned characteristics should be considered carefully and appropriate adjustment of the properties of the combustion process should be performed so as to achieve high efficiency and economic performance of the system. Adjusting the amount of air flow should be done by changing the lever position synchronized with the position of potentiometer for
setting the heat output, which achieving of the optimal operating conditions and a high efficiency of boiler.
38
Putting the burner out of operation
• The burner is put out of operation by pressing "START OF BURNER" button (signalling of "START" on the body of the burner is off). The burner during becoming extinct performs so called "process of controlled switching off" during which the fan keeps working (and the burner gradually is cooled down) and the operating parameters are monitored.
• After the burner is cooled down to ambient temperature we can switch it off by pressing the main switch on the control box of boiler (see Figure 3).
• In the event that the burner is out of service for a long time, it is recommended to disconnect the boiler from the mains and clean the combustion chamber, sweep off the ash from the grate and to clean the photosensor.
7.2.1 Setting of the heat output of burner
The operating parameters of burner may only be set by an authorized and trained technician.
WARNING:
Every adjustment, which requires removing of the cover of the burner and any other potential interventions into the equipment that is under voltage may only be carried out by an authorized and trained technician.
The control module is equipped with light emitting diodes LEDs (green, yellow and red) that by flashing indicate the operating mode of the burner and the set values according to the index of potentiometer. LEDs are located under the cover of burner and are observable through the transparent window.
Green LED - number of flickers (1-5 times) indicates the index of the potentiometer:
P1 – initial dose of fuel for ignition;
P2 – dosing of fuel;
P3 – operation of fan at burning out;
P4 - stabilization (transfer from the minimum output of a given outlet output of burner.);
P5 – Operating value of sensibility of the photosensor
Yellow LED - number of flickers (0-9 times) indicates the values of the operating time (s) for the relevant index of potentiometer P1 to P5.
Green LED flashes once (P1), then follows a series of flickers of yellow LED (0-9 times), according to their number you can search the adequate value of operating time (s) in the Tab. no. 6 and 7 in column P1.
Then the green LED flashes 2 x (P2), then follows a series of flickers of yellow LED (0-9 times), according to their number you can search the adequate value of operating time (s) in the Tab. no. 6 and 7 in column P2.
Flashing of LEDs goes on in the same way for index of the potentiometer P3 - P5.
Then the whole cycle repeats.
Red LED - lights up when the photosensor is in the stage of sensing the flame. If it flashes, it is a fault condition (see Tab. No. 9).
Tab. no. 6 Description of the operating parameters of the control module of burner 25S number of flickers of yellow LED
[-]
P1 P2
Index of potentiometer
P3
Operating time (s)
P4
4
5
6
7
8
9
0
1
2
3
30
45
60*
75
90
105
120
135
150
165
1,50
1,65
1,82
2,18
2,83
3,68
4,79
6,22
---
---
30
60
90
120
150*
180
210
240
270
300
45
90
135
180
225
270
315
360
405
450*
* factory setting
Note: The maximum value of lighting up of yellow LED for parameter P2 is 7.
P5
Index
4
5
6
7*
8
9
0
1
2
3
39
Tab. no. 7 Description of operating parameters of control module of burner 32S number of flickers of yellow LED
0
1
2
3
4
5
6
7
8
9
P1
30
45
60*
75
90
105
120
135
150
165
P2
Index of potentiometer
P3 P4
Operating time (s)
1,50
1,65
1,82
2,18
2,83
3,68
4,79
6,22
7,46
8,21
30
60
90
120
150*
180
210
240
270
300
45
90
135
180
225
270
315
360
405
450*
P5
Index
5
6
7*
8
9
0
1
2
3
4
* factory setting
Tab. no. 8 Setting of burner output by means of potentiometer
P2
Heat output of boiler [kW]
HERCULES Green Eco Therm
( number of flickers of yellow LED ) 25S 32S
0
1
2
3
4
5
6
7
8
9
5,0
6,0
8,0
11,0
14,0
18,0
21,0
25,0
-
-
5,0
6,0
8,0
11,0
14,0
18,0
21,0
25,0
28,0
32,0
WARNING:
In case a dark yellow flame and black smoke escape from the chimney, we should reduce burner output by means of potentiometer or the valve of fan should be opened.
When using the recommended fuel, the parameters that are listed in Tab. no. 8 correspond to a good quality of combustion and operation of burner.
• Setting of burner output could be achieved by determining the amount of supplied fuel at nominal operating mode - the amount of fuel transported by auger during a certain time interval in nominal operating mode. Here it is necessary to take into account the fuel heat efficiency and boiler efficiency.
• To determine the amount of dosed fuel proceed as follows:
• Disconnect the transport hose from the knee of the burner.
• Insert the end of the hose into a prepared vessel.
• Turn on the main switch of boiler to ON position and select the operating temperature of the operating thermostat.
• Disconnect the photosensor by pulling it out of the fixture (this is evaluated on the control panel as the ignition and operation at rated power)
• Dosing of fuel for rated output will run in this mode
For example:
The measured time interval is 15 minutes (which is 1/4 hours) and the amount of fuel accumulated in the vessel is 1,325 kg. Calculation shows that the amount of supplied fuel is 5.3 kg / h;
40
Example of calculating the heat output of the burner:
• Determine the amount of fuel supplied per hour - m fuel
= 5.3 kg / hr.
Calculate the instantaneous amount of supplied fuel m' fuel
: m' fuel
=
M fuel
(kg/h)
3600 (s)
= 0,001472 kg/s
• Take into account fuel efficiency –e.g. wood pellets have a calorific value
H fuel
= 17,2 MJ/kg = 17200 kJ/kg.
In case of another unit of fuel efficiency it is more convenient to apply - kWh / kg, and the calculation is as follows: normal wood pellets have calorific value of 4.77 kWh / kg (equivalent to 17.2 MJ / kg);
• Take into account the efficiency η system
= 89 %=0,89.
• Calculate the input of boiler:
P heat consumption
= η system
* H fuel
* m' fuel
= 0,89 * 17200 * 0,001472 = 22,5 kW, if the unit MJ / kg is used for the calorific value of the fuel.
If the fuel efficiency is indicated in kWh / kg, then the calculation is as follows:
P heat consumption
= η system
* H fuel
* m fuel
= 0,89 * 4,77 * 5,3 = 22,5 kW.
•
The same formula should be used for the calculation of the burner output in the case where the calorific value of the fuel differs from the value as described above or the required output of burner is lower than nominal;
Fault statuses of burner
The fault status is signalled by LEDs on the control module. A detailed description of the faults and their removal can be found in Tab. no. 9.
After the fault removal, restart the burner by means of switching off and on the switch "START OF BURNER" on the control box of boiler (see Fig no. 3).
Tab. no. 9 Indication of fault statuses by means of LEDs
No. Indication
1. Yellow LED is always alight
2. fast blinking yellow
LED
3. Green LED is always alight
Importance
4. fast blinking red
LED
Sensor of fan speed sensor
(Hall sensor) is not connected correctly or the fan is functionless
5. Yellow and green
LED is always alight
Motor of fuel feeder is disconnected or functionless
Operating relay of the control panel is defective
Removal of fault
Has been reached maximum number of attempts to ignite and ignition of the fuel failed
Check the reasons why the fuel could not be ignited.
Check the cause of problems with the ignition
High intensity of light sensing that exceeds the settings or a short circuit of the photosensor
Operating signal of photosensor disappeared during the regime of combustion
Failed ignition of the fuel
Check the potentiometer that controls the sensitivity adjustment of the photosensor - repair should be performed only by an authorized technician
Check and clean the photosensor; if necessary, call the service for assistance.
Check the reasons
The assistance of the service is required, but this only can be performed by an authorized technician
Check if there is not disconnect the supply cable of fuel feeder from the main unit of burner. Check the status and functionality of the feeder
The assistance of the service is required, but this only can be performed by an authorized technician
ATTENTION:
In case of boiler overheating the safety thermostat is activated. This thermostat must be manually reset and can be switched on again after the temperature drops below the set value. We have to unscrew the black cap of the safety thermostat and then press the button by using a suitable tool. In case of repeated shutdown of the safety thermostat the boiler must be shut down and the cause of repeated overheating of the boiler must be found out. Once you have checked the boiler and burner and you have determined and repaired the cause of overheating, restart the burner by switching off the power supply and its subsequent switching on.
In case of activation of thermal sensor against penetration of combusted fuel the fuel feeder is turned off and the burner becomes extinct. Once the cause of high temperature on the knee of burner has been determined we reset the fault by switching off and switching on the burner. In the event of damage to the sensor this must
be replaced by a service worker.
41
8. IMPORTANT WARNINGS
1. The boiler must not be used for other purposes than those it is designed for.
2. The boiler can only be operated by adults who are acquainted with this operation manual. It is forbidden to leave children unattended near the boiler that is working.
3. The boiler is not destined for use by persons (including children) whose physical, sensual or mental inability or lack of experience and knowledge prevents from a safe use of the appliance in case they are not under supervision or are not instructed regarding the use of the appliance by a person responsible for their safety.
4. Children should be watched to make sure that that they do not play with the appliance.
5. If there occurs the danger of flammable vapours or gases development and their penetration into boiler room or during the works that are accompanied by transient danger of fire or explosion
(gluing the flooring materials, painting with combustible paints etc.) the boiler must be put out of operation prior to the start of works
6. The fuel transport into combustion chamber is watched visually. There is a danger of injury caused by rotating worm shaft.
7. In the event that it is installed the supplied wooden fuel reservoir, it is necessary to place a fireproof bulkhead between it and the boiler.
8. It is forbidden to use flammable liquids (petrol, oil, furnace oil and others) for making fire in boiler.
9. During the boiler operation it is forbidden to overheat it in any way.
10. It is forbidden to put any things made of flammable materials on the boiler or within the distance smaller than the safe distance.
11. When removing the ash from boiler there must not be found any flammable substances within
1500 mm from the boiler. The ash must be collected in a non-flammable ashbin with a cover.
12. During the operation at the temperature below 60 °C the cast iron heat exchanger becomes dewy which initiates so called low-temperature corrosion that reduces the boiler service life. Therefore we recommend the boiler operation at the temperature 60 °C and higher.
13. After the end of heating season the user is obliged to clean thoroughly the boiler including the smoke flue and smoke extension piece. Lubricate the pivot bolts and other mobile parts on the boiler with graphite grease. Boiler room must be kept clean and dry.
14. It is forbidden to interfere with construction and electric installation of boiler.
15. WARNING! A poor quality of fuel can markedly negatively affect the boiler output and emission parameters
16. During assembly, installation and operation of the appliance it is necessary to comply with standards that apply in the relevant country of destination.
17. The ashes must be thrown out into a non-combustible container with a lid. When working is necessary to use protective equipment and respect the personal safety.
18. In case the heating system is not daily used in winter season, then the water from boiler must be drained.
If you fail to meet these conditions you cannot requisite the guarantee repairs.
42
9. Maintenance
1) Regularly remove ashes from the combustion chamber and the ash drawer. The ashes must be thrown out into non-combustible containers with lids. When working is necessary to use protective equipment and respect the personal safety.
2) The boiler has to be put out of operation at least 1 hour before cleaning (incl. the electric
disconnection). Boiler cleaning frequency is dependent on the quality of fuel. In case of pellets that do not contain more than 0.5% ashes, the cleaning is performed in 3 to 4 week intervals. In case of pellets containing 1.5% and more ashes the boiler must be inspected and cleaned once a week, or more often as needed. Boiler cleaning means the removal of ashes or deposited foulness from the boiler drum
(combustion chamber, flue ways, etc.).
3) Grate of burner should be cleaned regularly (depending on the operation of boiler). After cooling down of the combustion chamber remove the grate, by tapping on the grate the hardened ashes can be emptied and then check the patency of the holes for intake of air! This is influenced by the quality of pellets. The protective gloves must be used.
4) It is necessary to ensure a timely refilling of fuel. If in the reservoir only a small amount of fuel is left it must be added immediately in order to prevent aspiration of "false" air
5) It is recommended to clean the transport hose regularly, because during the transport of fuel there settle fine particles inside the hose and they could ultimately hinder the passage of fuel through a hose.
Moreover the sedimentary layer of fine fuel particles could ignite in case of a reverse burst of flame;
6) After cleaning or any handling with the fuel feeder check the correct attachment of hose on both its ends by means of hose clamps.
7) For a slight positive pressure in the combustion chamber during fan operation we ensure a perfect tightness of the boiler (cleaning door, ash door, cleaning lid of smoke adapter, etc.).
8) The operator of boiler must not remove the cover of the burner or in any other way interfere in
these units. This may be done only by qualified service personnel.
Removing of the grate of burner during maintenance and cleaning of the burner
• Remove the grate of burner from the body of burner once the burner has cooled down to a safe temperature and clean it thoroughly. For a safe handling the grate is necessary to use protective equipment and tools.
• During cleaning of the grate is necessary to clean the air passage apertures.
• After cleaning return the grate into the body of burner.
• Position the rack grate so that small feet touch the bottom of the combustion chamber of the burner.
• Insert the grate until it snaps under the inclined grate of burner.
43
Fig. no. 25
The body of burner
Inclined grate of combustion chamber
1. Initial position of the grate
2. End position of the grate
Small feet of the grate
Fig. no. 26 End position of the grate
44
10. Faults and their removal
Tab. no. 10 Faults and their removal
Operating fault The cause Solution
Failure to reach the desired room temperature
Exceeding the specified room temperature
Difficult ignition
Boiler overheating
(safety thermostat is activated)
Lack of fuel on the grate of combustion chamber
Failed ignition
Fuel is located in the burner grate, completely burned, but the ignition process is terminated.
Functionless burner
Insufficient heat output of the burner
Low temperature setting value in the operating thermostat of burner
A low setting of the value of temperature on the room thermostat (if connected)
A high heat output of burner
A high setting of the value of temperature on the operational thermostat of burner
High set temperature values on the room thermostat (if connected)
Low quality of fuel
System without heat removal, incorrect setting of burner parameters or an unbalanced operation of the system
Increase the degree of heat output of the burner
Increase the set values of operating thermostat of burner (up to 90 °C)
Increase the set values of room thermostat
Reduce the degree of heat output of the burner
Reduce the set values of operating thermostat of burner (It is recommended to keep it above 60 °C)
Reduce the set values of room thermostat
Failure of pumps
Lack of fuel in the fuel reservoir
Change the fuel
Modification of the operation parameters of burner
(degree of heat output).
The safety thermostat must be manually reset. The safety thermostat can be switched on only after the drop of temperature below the set value. You have to unscrew the black cover of the safety thermostat and press the button by using a suitable tool. In case of repeated switching off of the safety thermostat, the boiler must be put out of operation and the cause of repeated overheating of boiler must be found out. Then restart the burner (switch off and again switch on the power supply).
Repair or exchange the pumps.
Refill the fuel in the fuel reservoir. Disconnect the flexible hose and the body of burner. Insert the end of the hose into a prepared vessel. Disconnect the supply cord of fuel feeder from the burner, and then plug it into an electricity socket. Wait until the pellets begin to fall out from the feeder into the vessel. Disconnect the feeder from mains and reconnect with the burner. Push the hose on the knee of burner.
Check or exchange the ignition spirals. Fuel is located in the burner grate, but does not burn.
Functionless sensing of the flame by means of photosensor
Clean or exchange the photosensor. The exchange can be carried out only by an authorized technician.
;
No power supply Check the function of display of the control module located on the panel of interface of burner.
Check the connection and the electrical parameters of the main unit of burner and the power supply of the heat appliance - parameters should be as follows: 220 V, 50 Hz - may be performed only by an authorized technician;
Make sure that the power supply is properly connected - may be performed only by an authorized technician;
Check the wiring of electrical connections of control module - may be performed only by an authorized technician;
No signal from the control box of boiler Check the availability of signal to start the burner.
Check the interconnection between the burner and control box.
The burner does not start and the signal is alight
Check whether burner is not in a fault status - see
Tab. no. 4 and 5 (HERCULES Green Eco Therm
XJ) and 13 (HERCULES Green Eco Therm XS)
Burned safety fuses This inspection may be performed only by an authorized technician: check the status of each fuse and, if necessary, replace it with a new one
(Caution: Safety fuses F1, F2, F3 and F4 have a fast activation);
45
Operating fault The cause Solution
Flame has a purple colour and at the outlet to the chimney can be observed smoke
Fuel ignition was successful, but the unit did not reach a stable operating mode
Burner operation is not stable
Warming of knee of burner and activation of temperature sensor against penetration of burning fuel
Increased temperature displayed on the return temperature label of the liquid crystal
Activation of reversible heat label, located on the knee of burner
Unburned fuel in an ashtray
In the combustion chamber of the burner is deposited ash
(especially on the grate)
Fuel of poor quality
Setting of incorrect operating parameters
Incorrect placement of photoreceptor
It is recommended to replace the fuel, the moisture is higher than recommended - see chap. 2 -
Prescribed fuel.
Modify the the operating parameters - this operation may be performed only by an authorized and trained technician;
Change ( slightly rotate or rotate along the axis) the position of the photosensor
Photosensor is dirty on the surface Carefully clean the transparent part of the photosensor - Do not use solvents
Photosensor is functionless- its working surface is damaged and burned areas can be observed
Malfunction of photosensor
The operating parameters of the control module were changed
Replace the photosensor - this operation may be performed only by an authorized technician
Check the status and function of the photoresensor
Check the position of the potentiometer of heat output (HERCULES Green Eco Therm XS)
Check the degree of operational heat output of the control module of burner (HERCULES Green Eco
Therm XJ);
Check the values of operational parameters of the control module of burner- this operation may be performed only by an authorized technician
Insufficient chimney draft or deposition of dirt in the knee of burner
Insufficient chimney draft, clogged flue path.
Clean up the deposits of dirt in the knee and in the combustion chamber of burner or clean the boiler drum. A possible solution is to also the installation of an additional exhaust fan * - is performed by an authorized technician;
It is necessary to restart the burner.
Clean up the deposits of dirt in the knee and in the combustion chamber of burner or clean the boiler drum. A possible solution is to also the installation of an additional exhaust fan * - is performed by an authorized technician;
Clean up the deposits of dirt in the knee and in the High temperature of the knee of burner because of an insufficient chimney draft combustion chamber of burner or clean the boiler drum. A possible solution is to also the installation of an additional exhaust fan * - is performed by an
Ash content in fuel is higher than the recommended values authorized technician;
Inefficient process of combustion of fuel Modify the operational parameters of the burner – has to be performed by an authorized technician;
Exchange the fuel – see chap. 2 – Prescribed fuel
The burner operates at heat output which is higher than the nominal values
Reduce the degrees of the heat output of burner
High temperature of flue gas
Clogged boiler drum, flue gas ways and smoke flue
Clean the boiler drum, flue gas ways and smoke flue
46
11. Instructions for product liquidation after its operating life
VIADRUS a.s. is contractual partner of firm EKO–KOM a.s. with client number F00120649.
The packages comply with EN 13427.
With respect to the fact that the product is designed out of common materials the individual parts are recommended to be liquidated in the following manner:
exchanger (grey cast iron), by a company engaged in salvage and liquidation of waste
tube distributions, jacketing, by a company engaged in salvage and liquidation of waste
other metal parts, by a company engaged in salvage and liquidation of waste
ROTAFLEX and IZOBREX sealing materials in common waste
We recommend to dispose the packages in the following way:
- plastic foil, cardboard cover, use a salvage point
- metal strapping tape, use a salvage point
- wooden base, is designated for a single usage and no longer can be used as a product. Its disposal is subject to Act. 477/ 2001 Sb. a 185/2001 Coll. as amended.
In case that the product has lost its manufacture qualities there can be taken the advantage of product taking back (if this is established), in case that the originator has declared that this is a waste and it must be handled according to the valid legislation of the relevant country.
12. Warranty and defect liability
VIADRUS a.s. grants a warranty:
– For boilers 24 months after the boiler putting into operation, but maximum 30 months after the date it was dispatched from the manufacturing factory.
– For boiler drum 5 years after the date its dispatch from the manufacturing factory.
The user is obliged to leave the boiler installation to an assembly company, putting into operation and defect removing only to a professional contractual service accredited by the boiler producer VIADRUS a.s. otherwise the warranty for proper boiler operation is not valid.
If the boiler is operated according to the instructions mentioned in the “Instructions for the boiler operation and installation”, the boiler does not require any special professional service interventions.
“Certification of the quality and completeness of the HERCULES Green Eco Therm“ serves for filling in by a contractual service organization as the ”Warranty card”.
For an eventual jacket reclamation is the customer obliged to submit a packing label of the boiler jacket. It is placed on the cardboard in which the jacket is expedited.
The user is obliged to perform a regular control of the boiler – see chap. 9.
Failing to keep the mentioned instructions the warrants provided by the producer are not granted.
Each notice of defect must be made immediately after its finding always in written form and by a phone agreement.
The grant does not apply for:
- Faults caused by improper assembly and improper attendance of the product and faults caused by improper maintenance see chap. 9
- Faults and damage caused by failure to observe water quality in heating system see chap. no. 4.1 and 5.3.2 or by using the anti-freeze mixture
- Faults caused by failure to observe instructions stated in this manual
Defects caused by a wrong assembly or incorrect operation of the product
Damage of the product during transfer or other mechanical damage
Defects caused by improper storage
The producer grants the right for changes performed within the frame of product innovation that may
not be included in this instruction.
47
Information for customer
Packaging edentification
PE Plastic sacks, folie, corrugaled board, iron and plastic fix
Assessment reference line
Identification od principál materials used. Paper, Polyethylene, iron, wood
Part 1: Summary of assessment
Standard/Report
1.1 Prevention by source reduction
1.2 Heavy metals and
Assessment requirement Claim
YES
Note
1.3 Other noxious/hazardous substances
2 Reuse ensure below maximum permitted levels for components
(CR 13695-1:2000) ensure in compliance with
(CR 13695-2:2002, EN 13428:2000)
YES
YES
3.1 Recovery by material recycling
3.2 Recovery in the form of energy
3.3 Recovery by composting ensure reusability in all terms of the standard for the functional packaging unit (EN 13429:2000) ensure recyclability in all term sof the standard for the functional packaging unit (EN 13430:2000) ensure that calorific gain is achievable for the functional packaging unit
(EN 13431:2000) ensure compost ability in all terms of the standard for the functional packaging unit (EN 13432:2000)
NO
YES
YES
NO
Iron - NO
NOTE Conformity with EN 13427 requires affirmative responses to sections 1.1; 1.2; 1.3 and to at least one of 3.1; 3.2; 3.3. In addition, where a claim of reuse is made section 2 should also record affirmative responses.
Part 2: Statement of conformity
In the light of the assessment results recorded in part I above, this packaging is claimed to comply with the requirements of EN 13427:2000.
48
Destined for user VIADRUS a.s
Bezru č ova 300
735 81 Bohumín
Guarantee certificate and Quality & completeness certificate for
HERCULES Green Eco Therm boiler
Boiler serial number
User (surname, name)
..............................………… Boiler output ............................................
………………………………………………………………………………………...
Address (street, city, postcode) ………………………………………………………………………………………...
Telephone/Fax ………………………………………………………………………………………...
Boiler matches the requirements
EN 303-5 Boiler for central heating – Part 5: Solid fuel boiler for central heating, with manual or automatic feed and nominal thermal output max. 300 kW: terminology, requirements, testing and marking.
VIADRUS a.s. provides the guarantee:
– for boiler for 24 months after the date of putting it into operation, but maximally 30 months after the date of despatch from the production plant
– for cast iron boiler drum for 5 years after the date of despatch from the production plant let
The conditions for the guarantee validity:
• the boiler installation must be carried out according to „Boiler operation and installation manual “ by a qualified installation company
• the boiler must be put into operation according to „Boiler operation and installation manual “ by a contractual service organization accredited by the manufacturer
• the defects elimination must be carried out by the contractual service organization accredited by the manufacturer
The boiler delivery completeness is guaranteed by the seller.
Unfilled guarantee certificate is invalid.
Measured values
Chimney draught (mbar)
Numerical value
Temperature of combustion products (°C)
The user confirms that:
• the boiler adjusted by the contractual service organization did not show any fault during the heating test
• he received the “Boiler operating and installation instruction” incl. the duly filled-out Guarantee certificate and Quality certificate
• he was made acquainted with boiler attendance and maintenance
……………………………………..
Boiler manufacture date
……………………………………..
Date of installation
……………………………………..
Manufacturer’s stamp
……………………………………..
Installation company
(stamp, signature)
……………………………………..
Checked by (signature)
……………………………………..
User’s signature
……………………………………..
Date of putting the boiler into operation
……………………………………..
Contractual service organization
(stamp, signature)
……………………………………..
User’s signature
49
Annex to the guarantee certificate for the customer-user
Record of the carried out guarantee and after-guarantee repairs and regular product inspections
Date of record
Carried out activity
Contractual service organization
(signature, stamp)
Customer’s signature
50
Destined for service organization VIADRUS a.s
Bezru č ova 300
735 81 Bohumín
Guarantee certificate and Quality & completeness certificate for
HERCULES Green Eco Therm boiler
Boiler serial number
User (surname, name)
..............................………… Boiler output ............................................
………………………………………………………………………………………...
Address (street, city, postcode) ………………………………………………………………………………………...
Telephone/Fax ………………………………………………………………………………………...
Boiler matches the requirements
EN 303-5 Boiler for central heating – Part 5: Solid fuel boiler for central heating, with manual or automatic feed and nominal thermal output max. 300 kW: terminology, requirements, testing and marking.
VIADRUS a.s. provides the guarantee:
– for boiler for 24 months after the date of putting it into operation, but maximally 30 months after the date of despatch from the production plant
– for cast iron boiler drum for 5 years after the date of despatch from the production plant let
The conditions for the guarantee validity:
• the boiler installation must be carried out according to „Boiler operation and installation manual “ by a qualified installation company
• the boiler must be put into operation according to „Boiler operation and installation manual “ by a contractual service organization accredited by the manufacturer
• the defects elimination must be carried out by the contractual service organization accredited by the manufacturer
The boiler delivery completeness is guaranteed by the seller.
Unfilled guarantee certificate is invalid.
Measured values
Chimney draught (mbar)
Numerical value
Temperature of combustion products (°C)
The user confirms that:
• the boiler adjusted by the contractual service organization did not show any fault during the heating test
• he received the “Boiler operating and installation instruction” incl. the duly filled-out Guarantee certificate and Quality certificate
• he was made acquainted with boiler attendance and maintenance
……………………………………..
Boiler manufacture date
……………………………………..
Date of installation
……………………………………..
Manufacturer’s stamp
……………………………………..
Installation company
(stamp, signature)
……………………………………..
Checked by (signature)
……………………………………..
User’s signature
……………………………………..
Date of putting the boiler into operation
……………………………………..
Contractual service organization
(stamp, signature)
……………………………………..
User’s signature
51
52
Destined for manufacturer VIADRUS a.s
Bezru č ova 300
735 81 Bohumín
Guarantee certificate and Quality & completeness certificate for
HERCULES Green Eco Therm boiler
Boiler serial number
User (surname, name)
..............................………… Boiler output ............................................
………………………………………………………………………………………...
Address (street, city, postcode) ………………………………………………………………………………………...
Telephone/Fax ………………………………………………………………………………………...
Boiler matches the requirements
EN 303-5 Boiler for central heating – Part 5: Solid fuel boiler for central heating, with manual or automatic feed and nominal thermal output max. 300 kW: terminology, requirements, testing and marking.
VIADRUS a.s. provides the guarantee:
– for boiler for 24 months after the date of putting it into operation, but maximally 30 months after the date of despatch from the production plant
– for cast iron boiler drum for 5 years after the date of despatch from the production plant let
The conditions for the guarantee validity:
• the boiler installation must be carried out according to „Boiler operation and installation manual “ by a qualified installation company
• the boiler must be put into operation according to „Boiler operation and installation manual “ by a contractual service organization accredited by the manufacturer
• the defects elimination must be carried out by the contractual service organization accredited by the manufacturer
The boiler delivery completeness is guaranteed by the seller.
Unfilled guarantee certificate is invalid.
Measured values
Chimney draught (mbar)
Numerical value
Temperature of combustion products (°C)
The user confirms that:
• the boiler adjusted by the contractual service organization did not show any fault during the heating test
• he received the “Boiler operating and installation instruction” incl. the duly filled-out Guarantee certificate and Quality certificate
• he was made acquainted with boiler attendance and maintenance
……………………………………..
Boiler manufacture date
……………………………………..
Date of installation
……………………………………..
Manufacturer’s stamp
……………………………………..
Installation company
(stamp, signature)
……………………………………..
Checked by (signature)
……………………………………..
User’s signature
……………………………………..
Date of putting the boiler into operation
……………………………………..
Contractual service organization
(stamp, signature)
……………………………………..
User’s signature
53
54
55
56
Update 2/2013 – GB
advertisement
Related manuals
advertisement
Table of contents
- 3 Produced variants of boiler
- 4 Technical data of the boiler
- 6 Boiler description
- 6 Boiler drum construction
- 6 Control, regulation and safety elements
- 9 The construction of burner and transport routes of the fuel
- 11 Location and installation
- 11 Regulations and directives
- 12 Positioning possibilities
- 14 Order, delivery and assembly
- 14 Order
- 14 Delivery and accessories
- 16 Assembly procedure
- 16 Boiler drum installation
- 17 Mounting of partitions of the combustion chamber and turbulators
- 17 Mounting of burner
- 19 Mounting of the fuel reservoir
- 20 Mounting of the shells
- 21 Installation of electrical wiring
- 21 Version HERCULES Green Eco Therm XJ
- 22 Version HERCULES Green Eco Therm XS
- 22 Assembly tools for brush
- 22 Filling of the heat system with water
- 23 Electrical scheme
- 27 Boiler hydraulic diagram
- 28 Putting into operation - instructions for contractual service organization
- 28 Inspections before start-up
- 28 Boiler putting into operation
- 29 Boiler operation by user
- 29 Version HERCULES Green Eco Therm XJ
- 32 Setting of the heat output of burner
- 37 Version HERCULES Green Eco Therm XS
- 39 Setting of the heat output of burner
- 42 IMPORTANT WARNINGS
- 43 Maintenance
- 45 Faults and their removal
- 47 Instructions for product liquidation after its operating life
- 47 Warranty and defect liability