- Computers & electronics
- Networking
- Gateways/controllers
- ProSoft Technology
- 5201-DFNT-DNPSNET
- Specification
ProSoft Technology 5201-DFNT-DNPSNET ProductsEtherNet/IP to DNP 3.0 over Ethernet Gateway Specifications
Add to My manuals124 Pages
advertisement
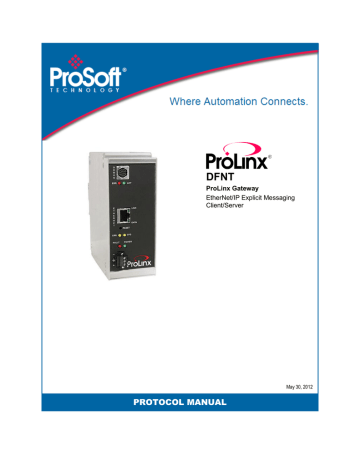
DFNT
ProLinx Gateway
EtherNet/IP Explicit Messaging
Client/Server
PROTOCOL MANUAL
May 30, 2012
Your Feedback Please
We always want you to feel that you made the right decision to use our products. If you have suggestions, comments, compliments or complaints about our products, documentation, or support, please write or call us.
How to Contact Us
ProSoft Technology
5201 Truxtun Ave., 3rd Floor
Bakersfield, CA 93309
+1 (661) 716-5100
+1 (661) 716-5101 (Fax) www.prosoft-technology.com [email protected]
Copyright © 2012 ProSoft Technology, Inc., all rights reserved.
DFNT Protocol Manual
May 30, 2012
ProSoft Technology
®
, ProLinx
®
, inRAx
®
, ProTalk
®
, and RadioLinx
®
are Registered Trademarks of ProSoft
Technology, Inc. All other brand or product names are or may be trademarks of, and are used to identify products and services of, their respective owners.
ProSoft Technology
®
Product Documentation
In an effort to conserve paper, ProSoft Technology no longer includes printed manuals with our product shipments.
User Manuals, Datasheets, Sample Ladder Files, and Configuration Files are provided on the enclosed CD-ROM, and are available at no charge from our web site: www.prosoft-technology.com
Important Installation Instructions
Power, Input, and Output (I/O) wiring must be in accordance with Class I, Division 2 wiring methods, Article 501-4 (b) of the National Electrical Code, NFPA 70 for installation in the U.S., or as specified in Section 18-1J2 of the Canadian
Electrical Code for installations in Canada, and in accordance with the authority having jurisdiction. The following warnings must be heeded:
A WARNING - EXPLOSION HAZARD - SUBSTITUTION OF COMPONENTS MAY IMPAIR SUITABILITY FOR
CLASS I, DIV. 2;
B WARNING - EXPLOSION HAZARD - WHEN IN HAZARDOUS LOCATIONS, TURN OFF POWER BEFORE
REPLACING OR WIRING MODULES
C WARNING - EXPLOSION HAZARD - DO NOT DISCONNECT EQUIPMENT UNLESS POWER HAS BEEN
SWITCHED OFF OR THE AREA IS KNOWN TO BE NON-HAZARDOUS.
D THIS DEVICE SHALL BE POWERED BY CLASS 2 OUTPUTS ONLY.
ProLinx
®
Products Warnings
WARNING – EXPLOSION HAZARD – DO NOT DISCONNECT EQUIPMENT UNLESS POWER HAS BEEN
SWITCHED OFF OR THE AREA IS KNOWN TO BE NON-HAZARDOUS.
AVERTISSEMENT
– RISQUE D'EXPLOSION – AVANT DE DÉCONNECTER L'EQUIPMENT, COUPER LE
COURANT OU S'ASSURER QUE L'EMPLACEMENT EST DÉSIGNÉ NON DANGEREUX.
ProLinx Gateways with Ethernet Ports
Series C ProLinx™ Gateways with Ethernet ports do NOT include the HTML Web Server. The HTML Web Server must be ordered as an option. This option requires a factory-installed hardware addition. The HTML Web Server now supports:
8 MB file storage for HTML files and associated graphics files (previously limited to 384K)
32K maximum HTML page size (previously limited to 16K)
To upgrade a previously purchased Series C model:
Contact your ProSoft Technology distributor to order the upgrade and obtain a Returned Merchandise Authorization
(RMA) to return the unit to ProSoft Technology.
DFNT ♦ ProLinx Gateway
EtherNet/IP Explicit Messaging Client/Server
Contents
Contents
Protocol Manual
Your Feedback Please ........................................................................................................................ 2
How to Contact Us .............................................................................................................................. 2
ProSoft Technology
®
Product Documentation .................................................................................... 2
Important Installation Instructions ....................................................................................................... 3
ProLinx
®
Products Warnings ............................................................................................................... 3
ProLinx Gateways with Ethernet Ports ............................................................................................... 3
To upgrade a previously purchased Series C model: .................................................................... 3
1 Start Here
1.1
1.2
1.3
1.4
1.5
1.5.1
9
System Requirements ............................................................................................. 10
Package Contents ................................................................................................... 11
Mounting the Module on the DIN-rail ...................................................................... 12
Connecting Power to the Unit ................................................................................. 13
Installing ProSoft Configuration Builder Software ................................................... 14
Using the Online Help ............................................................................................. 14
2 Functional Overview
2.1
2.2
2.2.1
2.2.2
2.2.3
2.3
2.3.1
2.3.2
2.4
2.5
2.3.3
2.3.4
2.6
15
EtherNet/IP (Explicit Messaging) Compatible Devices ........................................... 16
EtherNet/IP (DFNT) Port ......................................................................................... 17
ProLinx DFNT Client Counts ................................................................................... 18
Module Internal Database ....................................................................................... 19
DFNT EtherNet/IP Client Access to Database ........................................................ 19
DFNT Server Access to Database .......................................................................... 20
EtherNet/IP Explicit Messaging Server Command Support .................................... 22
Basic Command Set Functions ............................................................................... 22
PLC-5 Command Set Functions ............................................................................. 22
SLC-500 Command Set Functions ......................................................................... 22
Other Ethernet Services (HTTP/FTP) ..................................................................... 23
Installing the .EDS file with RSLinx ......................................................................... 24
Browsing the module using RSLinx ........................................................................ 28
3 Configuring the Gateway 31
3.1
3.1.1
3.1.2
3.2
3.2.1
3.2.2
3.2.3
3.3
3.3.1
3.4
3.3.2
3.4.1
3.5
3.4.2
3.4.3
ProSoft Technology, Inc.
July 24, 2013
Using ProSoft Configuration Builder ....................................................................... 31
Setting Up the Project ............................................................................................. 31
Renaming PCB Objects .......................................................................................... 33
[DFNT Client x] ........................................................................................................ 34
Minimum Command Delay ...................................................................................... 34
Response Timeout .................................................................................................. 34
Retry Count ............................................................................................................. 34
[DFNT Client x Commands] .................................................................................... 35
Command List ......................................................................................................... 35
Command Entry Formats ........................................................................................ 38
[DFNT UClient 0] ..................................................................................................... 42
Minimum Command Delay ...................................................................................... 42
Response Timeout .................................................................................................. 42
Retry Count ............................................................................................................. 42
[DFNT UClient 0 Commands] ................................................................................. 43
Page 5 of 124
Contents
Protocol Manual
3.6
3.6.1
3.6.2
3.6.3
3.6.4
3.6.5
3.7
3.6.6
3.8
DFNT ♦ ProLinx Gateway
EtherNet/IP Explicit Messaging Client/Server
Using the CommonNet Data Map ........................................................................... 44
Moving Data ............................................................................................................ 45
From Address ......................................................................................................... 45
To Address .............................................................................................................. 45
Register Count ........................................................................................................ 45
Swap Code ............................................................................................................. 45
Delay Preset ........................................................................................................... 47
Ethernet Port Configuration - wattcp.cfg ................................................................. 48
Downloading the Project to the Module Using a Serial COM port .......................... 49
4 Diagnostics and Troubleshooting
4.1
4.1.1
4.1.2
4.2
4.1.3
4.3
4.2.1
4.3.1
4.3.2
4.3.3
4.3.4
4.3.5
4.3.6
4.4
4.4.1
4.5
4.4.2
4.5.1
4.5.2
4.5.3
4.5.4
4.6
4.6.1
4.6.2
4.6.3
4.6.4
51
Using ProSoft Configuration Builder (PCB) for Diagnostics ................................... 52
Required Hardware ................................................................................................. 52
Using the Diagnostic Window in ProSoft Configuration Builder ............................. 52
Navigation ............................................................................................................... 54
Base Module LEDs ................................................................................................. 56
Ethernet LED Indicators .......................................................................................... 56
Client Error/Status Data .......................................................................................... 57
DFNT Client 0 Status .............................................................................................. 57
Unconnected Msg DFNT Client 0 Status ................................................................ 58
DFNT Client 1 through 4 Status.............................................................................. 58
DFNT Server 0 ........................................................................................................ 59
DFNT Servers 1 Through 4 .................................................................................... 59
DF1 Pass-Through Server ...................................................................................... 60
EtherNet/IP Client Command List Error Data ......................................................... 61
DFNT Client 0 (Command List Error Data) ............................................................. 61
DFNT Client 1 Through 4 Command List Error Addresses .................................... 61
Error Codes ............................................................................................................. 62
Local STS Error Codes ........................................................................................... 62
Remote STS Error Codes ....................................................................................... 63
Errors When EXT STS Is Present .......................................................................... 64
Module Specific Error (not DFNT Compliant) ......................................................... 65
TCP/IP Interface Errors .......................................................................................... 66
Timeout Errors ........................................................................................................ 66
Register Session Response Errors......................................................................... 66
Forward Open Response Errors ............................................................................. 66
PCCC Response Errors .......................................................................................... 67
5 Reference
5.1
5.2
5.2.1
5.2.2
5.2.3
5.2.4
Page 6 of 124
5.2.5
5.2.6
5.2.7
5.2.8
5.2.9
5.2.10
69
Command Function Codes ..................................................................................... 70
General Command Structure .................................................................................. 71
Function Code #1 - Protected Write (Basic Command Set) ................................... 72
Function Code #2 - Unprotected Read (Basic Command Set) .............................. 72
Function Code #3 - Protected Bit Write (Basic Command Set) .............................. 73
Function Code #4 - Unprotected Bit Write (Basic Command Set) ......................... 73
Function Code #5 - Unprotected Write (Basic Command Set) ............................... 74
Function Code #100 - Word Range Write (PLC-5 Command) (Binary Address) ... 75
Function Code #101 - Word Range Read (PLC-5 Command) (Binary Address) ... 76
Function Code #102 - Read-Modify-Write (PLC-5 Command) (Binary Address) ... 77
Function Code #150 - Word Range Write (PLC-5 Command) (ASCII Address) .... 78
Function Code #151 - Word Range Read (PLC-5 Command) (ASCII Address) .... 78
ProSoft Technology, Inc.
July 24, 2013
DFNT ♦ ProLinx Gateway
EtherNet/IP Explicit Messaging Client/Server
5.2.11
5.2.12
5.2.13
5.2.14
5.2.15
5.2.16
Fields)
5.3
5.3.1
5.4
5.5
5.4.1
5.6
5.5.1
5.7
5.8
5.7.1
5.7.2
5.9
5.9.1
5.9.2
5.10
5.10.1
5.10.2
5.11
5.11.1
5.11.2
5.12
Contents
Protocol Manual
Function Code #152 - Read-Modify-Write (PLC-5 Command) (ASCII Address) .... 79
Function Code #501 - Protected Typed Logical Read (Two Address Fields) ......... 80
Function Code #502 - Protected Typed Logical Read (Three Address Fields) ...... 81
Function Code #509 - Protected Typed Logical Write (Two Address Fields) ......... 82
Function Code #510 - Protected Typed Logical Write (Three Address Fields) ...... 83
Function Code #511 - Protected Typed Logical Write with Mask (Three Address
84
PLC-5 Processor Specifics...................................................................................... 85
PLC-5 Sub-Element Codes ..................................................................................... 85
SLC Processor Specifics ......................................................................................... 87
SLC File Types ........................................................................................................ 87
MicroLogix Processor Specifics .............................................................................. 88
SLC File Types ........................................................................................................ 88
ControlLogix Processor Specifics ........................................................................... 89
RSLinx Software ...................................................................................................... 90
DDE Connection ...................................................................................................... 93
OPC Connection ..................................................................................................... 97
RSView Software .................................................................................................. 100
ControlLogix (CLX) Processor .............................................................................. 103
Encapsulated PCCC Messages ............................................................................ 103
CIP Data Table Operations ................................................................................... 107
PLC5 Processor .................................................................................................... 111
PLC5 Write Commands ......................................................................................... 111
PLC5 Read Commands ........................................................................................ 112
SLC 5/05 Processor .............................................................................................. 114
SLC5/05 Write Commands.................................................................................... 114
SLC5/05 Read Commands ................................................................................... 115
DFNT Command Entry Form ................................................................................ 117
6 Support, Service & Warranty 119
Contacting Technical Support ......................................................................................................... 119
6.1
Warranty Information ............................................................................................. 120
123 Index
ProSoft Technology, Inc.
July 24, 2013
Page 7 of 124
Contents
Protocol Manual
DFNT ♦ ProLinx Gateway
EtherNet/IP Explicit Messaging Client/Server
Page 8 of 124 ProSoft Technology, Inc.
July 24, 2013
DFNT ♦ ProLinx Gateway
EtherNet/IP Explicit Messaging Client/Server
1 Start Here
In This Chapter
System Requirements ........................................................................... 10
Mounting the Module on the DIN-rail ..................................................... 12
Connecting Power to the Unit ................................................................ 13
Installing ProSoft Configuration Builder Software .................................. 14
Start Here
Protocol Manual
ProSoft Technology, Inc.
July 24, 2013
Page 9 of 124
Start Here
Protocol Manual
1.1 System Requirements
DFNT ♦ ProLinx Gateway
EtherNet/IP Explicit Messaging Client/Server
The ProSoft Configuration Builder configuration software for the DFNT module requires the following minimum hardware and software components:
Pentium ®
II 450 MHz minimum. Pentium III 733 MHz (or better) recommended
Supported operating systems: o o
Microsoft Windows Vista
Microsoft Windows XP Professional with Service Pack 1 or 2 o o
Microsoft Windows 2000 Professional with Service Pack 1, 2, or 3
Microsoft Windows Server 2003
128 Mbytes of RAM minimum, 256 Mbytes of RAM recommended
100 Mbytes of free hard disk space (or more based on application requirements)
256-color VGA graphics adapter, 800 x 600 minimum resolution (True Color
1024
768 recommended)
CD-ROM drive
Page 10 of 124 ProSoft Technology, Inc.
July 24, 2013
DFNT ♦ ProLinx Gateway
EtherNet/IP Explicit Messaging Client/Server
1.2 Package Contents
The following components are included with your DFNT module, and are all required for installation and configuration.
Start Here
Protocol Manual
Important: Before beginning the installation, please verify that all of the following items are present.
Qty. Part Name
1
1
DFNT module
Cable
Varies Cable
Varies Adapter
1 ProSoft Solutions CD
Part Number
PLX-####
Cable #15, RS232
Null Modem
Cable #9, Mini-
DIN8 to DB9 Male
Adapter
1454-9F
Part Description
ProLinx communication gateway
For RS232 Connection from a PC to the
CFG Port of the module
For DB9 Connection to module’s Port. One
DIN to DB-9M cable included per configurable serial port, plus one for module configuration
Adapters, DB9 Female to Screw Terminal.
For RS422 or RS485 Connections to each serial application port of the module
Contains sample programs, utilities and documentation for the DFNT module.
If any of these components are missing, please contact ProSoft Technology
Support for replacements.
ProSoft Technology, Inc.
July 24, 2013
Page 11 of 124
Start Here
Protocol Manual
1.3 Mounting the Module on the DIN-rail
DFNT ♦ ProLinx Gateway
EtherNet/IP Explicit Messaging Client/Server
ProLinx 5000/6000 Series module
Page 12 of 124 ProSoft Technology, Inc.
July 24, 2013
DFNT ♦ ProLinx Gateway
EtherNet/IP Explicit Messaging Client/Server
1.4 Connecting Power to the Unit
Start Here
Protocol Manual
WARNING: Ensure that you do not reverse polarity when applying power to the module. This will cause damage to the module’s power supply.
ProSoft Technology, Inc.
July 24, 2013
Page 13 of 124
Start Here
Protocol Manual
DFNT ♦ ProLinx Gateway
EtherNet/IP Explicit Messaging Client/Server
1.5 Installing ProSoft Configuration Builder Software
You must install the ProSoft Configuration Builder (PCB) software to configure the module. You can always get the newest version of ProSoft Configuration
Builder from the ProSoft Technology website.
Installing ProSoft Configuration Builder from the ProSoft website
1 Open your web browser and navigate to http://www.prosoft-
technology.com/pcb
2 Click the D OWNLOAD H ERE link to download the latest version of ProSoft
Configuration Builder.
3 Choose S AVE or S AVE F ILE when prompted.
4 Save the file to your Windows Desktop, so that you can find it easily when you have finished downloading.
5 When the download is complete, locate and open the file, and then follow the instructions on your screen to install the program.
If you do not have access to the Internet, you can install ProSoft Configuration
Builder from the ProSoft Solutions Product CD-ROM, included in the package with your module.
Installing ProSoft Configuration Builder from the Product CD-ROM
1 Insert the ProSoft Solutions Product CD-ROM into the CD-ROM drive of your
PC. Wait for the startup screen to appear.
2 On the startup screen, click P RODUCT D OCUMENTATION . This action opens a
Windows Explorer file tree window.
3 Click to open the U TILITIES folder. This folder contains all of the applications and files you will need to set up and configure your module.
4 Double-click the S ETUP C ONFIGURATION T OOL folder, double-click the
PCB_*.
EXE file and follow the instructions on your screen to install the software on your PC. The information represented by the "*" character in the file name is the PCB version number and, therefore, subject to change as new versions of PCB are released.
Note: Many of the configuration and maintenance procedures use files and other utilities on the
CD-ROM. You may wish to copy the files from the Utilities folder on the CD-ROM to a convenient location on your hard drive.
1.5.1 Using the Online Help
Most of the information needed to help you use ProSoft Configuration Builder is provided in a Help System that is always available whenever you are running
ProSoft Configuration Builder. The Help System does not require an Internet connection.
To view the help pages, start ProSoft Configuration Builder, open the H ELP menu, and then choose C ONTENTS .
Page 14 of 124 ProSoft Technology, Inc.
July 24, 2013
DFNT ♦ ProLinx Gateway
EtherNet/IP Explicit Messaging Client/Server
Functional Overview
Protocol Manual
2 Functional Overview
In This Chapter
EtherNet/IP (Explicit Messaging) Compatible Devices .......................... 16
EtherNet/IP (DFNT) Port ....................................................................... 17
DFNT Server Access to Database ........................................................ 20
Other Ethernet Services (HTTP/FTP) .................................................... 23
Installing the .EDS file with RSLinx ....................................................... 24
Browsing the module using RSLinx ....................................................... 28
The ProLinx EtherNet/IP (DFNT) driver can be used to interface many different protocols into the Rockwell Automation family of processors as well as other software-based solutions. The DFNT driver supports Client connections as well as Server connections. With the addition of the WEB hardware option, the module also provides HTTP, FTP and Email capability.
The Ethernet driver interfaces with a common internal database in the module.
This permits the sharing of data across many different networks. Rockwell
Automation processors supported on the TCP/IP network include ControlLogix,
PLC5 Ethernet and SLC 5/05.
The module also supports unconnected client through the UClient section.
Unconnected messaging is a type of Ethernet/IP explicit message that uses
TCP/IP implementation. Certain devices, such as the AB Power Monitor 3000 series B, support unconnected messaging. Check your device documentation for further information about its Ethernet/IP implementation.
The following illustration shows the functionality of the DFNT driver.
ProSoft Technology, Inc.
July 24, 2013
Page 15 of 124
Functional Overview
Protocol Manual
DFNT ♦ ProLinx Gateway
EtherNet/IP Explicit Messaging Client/Server
2.1 EtherNet/IP (Explicit Messaging) Compatible Devices
List of Rockwell Automation material that support EPIC:
PLC5/E rev C/N, D/E, E/D
SLC5/05 series A, OS503 frn4
1785-ENET Series A, rev D
Interchange V6.2
MicroLogix 1100/1400/ANY via 1761-NET-ENI
CompactLogix 1768-L43/L45 via 1768-ENBT
CompactLogix 1769-L32E/L35E/ANY via 1761-NET-ENI
CompactLogix L23E
RSLinx Gateway V1.7+
ControlLogix 1756-ENET/ENBT/EN2T
Page 16 of 124 ProSoft Technology, Inc.
July 24, 2013
DFNT ♦ ProLinx Gateway
EtherNet/IP Explicit Messaging Client/Server
2.2 EtherNet/IP (DFNT) Port
Functional Overview
Protocol Manual
The module supports two independent clients on the TCP/IP network to interface with processors using a user constructed command list of up to 100 entries for each client. The use of two clients permits the module to have a high priority
(small number of commands) and low priority (larger number of commands) simultaneously. The module’s internal database is used as the source for write commands to the remote processors. Data collected from the processors using read commands is placed in the module’s database.
ProSoft Technology, Inc.
July 24, 2013
Page 17 of 124
Functional Overview
Protocol Manual
2.2.1 ProLinx DFNT Client Counts
DFNT ♦ ProLinx Gateway
EtherNet/IP Explicit Messaging Client/Server
The following table lists the number and type of DFNT Clients and Servers available on ProLinx gateways based on the companion protocol installed on the gateway.
ProLinx
Model Number /
Part Number
5201-DFNT-101M
5201-DFNT-101S
5201-DFNT-103M
5201-DFNT-104S
5201-DFNT-ASCII
5201-DFNT-BACNET
5201-DFNT-BSCH
5201-DFNT-CLVM
5201-DFNT-DFCM
5201-DFNT-DH485
5201-DFNT-DNPM
5201-DFNT-DNPS
5201-DFNT-DNPSNET 2
5201-DFNT-EGD 1
5201-DFNT-GRCM
5201-DFNT-ISDA
2
2
5201-DFNT-MCM
5201-DFNT-PNPM
5201-MNETC-DFNT
5201-MNET-DFNT
2
2
1
1
5202-DFNT-ASCII4
5202-DFNT-BSCH4
5202-DFNT-CLVM4
5202-DFNT-DFCM4
5202-DFNT-GRCM4
5202-DFNT-ISDA4
5202-DFNT-MCM4
2
2
2
2
2
2
1
2
1
2
2
2
2
2
1
2
2
Number of
Connected
DFNT Clients
(TCP/IP)
2
2
5202-DFNT-PNPM4
5204-DFNT-PDPM
5204-DFNT-PDPMV1
5205-DFNT-PDPS
5206-DFNT-DEM
5207-DFNT-HART
5208-DFNT-HART
5209-DFNT-CCLINK
5210-DFNT-RIO
5228-DFNT-HART(2)
5303-MBP-DFNT
2
5
4
2
5
4
4
2
5
2
5
1
1
1
1
1
1
1
0
1
1
1
0
0
1
1
0
0
1
1
0
1
1
1
1
0
0
1
1
1
1
0
0
1
1
1
1
Number of
Unconnected DFNT
Clients
(UDP)
1
1
5
5
5
5
5
5
5
5
5
5
5
5
5
5
10
5
5
5
5
5
5
5
5
5
5
5
5
5
5
5
5
5
10
Number of
Connected DFNT
Servers
( TCP/IP)
5
5
5
5
10
Page 18 of 124 ProSoft Technology, Inc.
July 24, 2013
DFNT ♦ ProLinx Gateway
EtherNet/IP Explicit Messaging Client/Server
2.2.2 Module Internal Database
Functional Overview
Protocol Manual
The internal database is central to the functionality of the module. This database is shared between all the ports on the module and is used as a conduit to pass information from one device on one network to one or more devices on either connected network. This permits data from devices on one communication port or network to be viewed and controlled by devices on another port or network.
In addition to data from the Master and <SlaveServer> ports, status and error information generated by the module can also be mapped into the internal database.
2.2.3 DFNT EtherNet/IP Client Access to Database
The client functionality places data from the DFNT module automatically in data tables established in ControlLogix, PLC5 and SLC 5/05 processors. The command list defined in the user configuration defines what data is to be transferred between the module and one of the processors. No ladder logic is required in the processor for client functionality.
The following diagram describes the flow of data between the Ethernet clients and the internal database.
ProSoft Technology, Inc.
July 24, 2013
Page 19 of 124
Functional Overview
Protocol Manual
2.3 DFNT Server Access to Database
DFNT ♦ ProLinx Gateway
EtherNet/IP Explicit Messaging Client/Server
The DFNT module supports server functionality using the reserved ControlNet service port 0xAF12. Services supported in the module permit client applications
(that is, RSView, ControlLogix processors and RSLinx) to read from and write to the module’s database. This document discusses the requirements for attaching to the module using several client applications.
The following illustration shows the relationship of the DFNT module’s functionality to devices on an Ethernet network:
Server functionality places all data transfer operations outside the module. There is no configuration required in the module other than setting up the network and database parameters in the configuration file. Ladder logic in attached processors use MSG instructions to perform read and write operations on the module’s internal database.
When RSLinx links a user application to the module, the module ’s server functionality must be used. RSLinx exists on an Ethernet network only as a client application. It cannot act as a server. User applications can use the DDE/OPC capabilities built into RSLinx to interface with the data in the DFNT module.
RSView can link directly to the module using drivers supplied by RSLinx.
The internal database of the DFNT module is used as the source (read requests) and destination (write requests) for requests from remote clients. Access to the database depends on the MSG command type executed to interface with the database. The following table defines the relationship of the module’s internal database to the addresses required in the MSG instructions:
Page 20 of 124 ProSoft Technology, Inc.
July 24, 2013
DFNT ♦ ProLinx Gateway
EtherNet/IP Explicit Messaging Client/Server
MSG Instruction Type
Database Address PLC2 PLC5 or SLC
Functional Overview
Protocol Manual
0
999
1000
1999
2000
2999
3000
3999
0
999
1000
1999
2000
2999
3000
4000
N10:0
N19:99
N20:0
N29:99
N30:0
N39:99
N40:0
N49:99
ControlLogix
PCCC
N10:0
N19:99
N20:0
N29:99
N30:0
N39:99
N40:0
N49:99
CIP Integer
Int_data[0]
Int_data[999]
Int_data[1000]
Int_data[1999]
Int_data[2000]
Int_data[2999]
Int_data[3000]
Int_data[3999]
MSG Instruction Type
0
999
1000
1999
2000
2999
3000
3999
Database
Address
CIP Boolean
BoolData[0]
BoolData[15984]
ControlLogix
CIP Bit Array
BitAData[0]
CIP Byte CIP Double
Int
SIntData[0]
SIntData[1998]
DIntData[0]
CIP Real
RealData[0]
BoolData[16000] BitAData[500] SIntData[2000] DIntData[500] RealData[500]
BoolData[31984] SIntData[3998]
BoolData[32000] BitAData[1000] SIntData[4000] DIntData[1000] RealData[1000]
BoolData[47984] SIntData[5998]
BoolData[48000] BitAData[1500] SIntData[6000] DIntData[1500] RealData[1500]
BoolData[63999] SIntData[9998]
When using PLC5 or SLC commands, access to the database is through simulated "N" files. For example, to access database element 3012, use the file address of N40:12. When using CIP Data Table Read or Write commands, use the various data[ ] tag arrays described in the following table. For example, use int_data[3012] to access database register 3012 as an integer value.
Data Type Tag Name
BOOL
Bit Array
SINT
INT
DINT
REAL
BOOLData[ ]
BITAData[ ]
SINTData[ ]
INT_Data[ ]
DINTData[ ]
REALData[ ]
2
4
4
Length of Each Element in
CIP message
1
4
1
Array Range for 4000
Element Database
0 to 63999
0 to 1999
0 to 7999
0 to 3999
0 to 1999
0 to 1999
ProSoft Technology, Inc.
July 24, 2013
Page 21 of 124
Functional Overview
Protocol Manual
DFNT ♦ ProLinx Gateway
EtherNet/IP Explicit Messaging Client/Server
Before attempting to use the module on a network, verify that the DFNT module is correctly configured and connected to the network. A network program such as
PING can be utilized to make certain the module can be seen on the network.
Use ProSoft Configuration Builder to verify correct operation, and to transfer configuration files to and from the module.
2.3.1 EtherNet/IP Explicit Messaging Server Command Support
The current version of the module will respond to the following list of commands.
Future releases may support more functions as required by user applications.
2.3.2 Basic Command Set Functions
Command Function Definition
0x00
0x01
0x02
0x05
0x08
N/A
N/A
N/A
N/A
N/A
Protected Write
Unprotected Read
Protected Bit Write
Unprotected Bit Write
Unprotected Write
2.3.3 PLC-5 Command Set Functions
Command Function Definition
0x0F
0x0F
0x00
0x01
Word Range Write (Binary Address)
Word Range Read (Binary Address)
0x0F
0x0F
0x0F
0x0F
0x0F
0x0F
0x26
0x00
0x01
0x26
Typed Range Read (Binary Address)
Typed Range Write (Binary Address)
Read-Modify-Write (Binary Address)
Word Range Write (ASCII Address)
Word Range Read (ASCII Address)
Read-Modify-Write (ASCII Address)
Supported in Server
X
X
X
X
X
X
X
X
X
Supported in Server
X
X
2.3.4 SLC-500 Command Set Functions
Command Function Definition
0x0F 0xA1 Protected Typed Logical Read With Two
Address Fields
0x0F 0xA2 Protected Typed Logical Read With Three
Address Fields
0x0F
0x0F
0x0F
0xA9
0xAA
0xAB
Supported in Server
X
X
Protected Typed Logical Write With Two
Address Fields
Protected Typed Logical Write With Three
Address Fields
X
X
Protected Typed Logical Write With Mask (Three Address Fields)
Page 22 of 124 ProSoft Technology, Inc.
July 24, 2013
DFNT ♦ ProLinx Gateway
EtherNet/IP Explicit Messaging Client/Server
2.4 Other Ethernet Services (HTTP/FTP)
Other network services are provided on the module, if the WEB option is installed.
Functional Overview
Protocol Manual
Important: The WEB option is an additional hardware component that is installed on the module during manufacturing. If the WEB option is not installed, the following features are not enabled.
The module contains an HTTP server to serve Web pages containing database data and error/stat us values present in the module’s internal database to a Web browser. The pages presented can be those built into the module or custom designed by the user. Additionally, Web pages can be constructed to alter (write) the values contained in the module’s database.
An FTP server is present to handle file operations controlled from a remote computer on the network.
The following table describes the capabilities of the WEB option.
Type Specifications
HTML Server (See note below)
Key features of the HTML server include:
Max HTML page size: 1MB
Max File Storage: 32MB
Supported context types: jpeg, bmp, css
Supported data types: bit, ASCII, integer, float
Sockets: Up to ten connections. Note that this limits the number of simultaneous graphic file and frame references per HTML page
FTP Server Permits remote HTML file transfer between the module and remote host.
Capabilities of the FTP Server include:
Single socket connection
Non-passive transfers only
WS_FTP or Command Line FTP recommended
CuteFTP, Internet Explorer, Netscape, or NCFTP all support multiple socket connections and therefore will not support the ProLinx module
For detailed information on these services, refer to the WEB Driver Manual.
ProSoft Technology, Inc.
July 24, 2013
Page 23 of 124
Functional Overview
Protocol Manual
2.5 Installing the .EDS file with RSLinx
DFNT ♦ ProLinx Gateway
EtherNet/IP Explicit Messaging Client/Server
1 Click on RSLinx Tools / EDS Hardware Installation Tool
2 Click on the Add button.
Page 24 of 124 ProSoft Technology, Inc.
July 24, 2013
DFNT ♦ ProLinx Gateway
EtherNet/IP Explicit Messaging Client/Server
Functional Overview
Protocol Manual
3 Select Single File and Browse the .EDS file in your computer. Make sure that the same folder contains the .ICO file (ProLinx ICON). Click on the Next button.
4 Select the file once it was evaluated for errors and click the Next button.
ProSoft Technology, Inc.
July 24, 2013
Page 25 of 124
Functional Overview
Protocol Manual
DFNT ♦ ProLinx Gateway
EtherNet/IP Explicit Messaging Client/Server
5 This window displays how the module will be displayed. Click on the Next button
6 The following window allows the user to review the configuration.
Page 26 of 124 ProSoft Technology, Inc.
July 24, 2013
DFNT ♦ ProLinx Gateway
EtherNet/IP Explicit Messaging Client/Server
7 The procedure is concluded. Click the Finish button.
Functional Overview
Protocol Manual
8 Click the Exit button to quit the Hardware Installation Tool.
ProSoft Technology, Inc.
July 24, 2013
Page 27 of 124
Functional Overview
Protocol Manual
2.6 Browsing the module using RSLinx
DFNT ♦ ProLinx Gateway
EtherNet/IP Explicit Messaging Client/Server
1 With RSLinx running, click on C OMMUNICATIONS /C ONFIGURE D RIVERS .
2 Select E THERNET D EVICES .
3 Enter a name for the RSLinx Driver, "AB_ETH-PROLINX", for example.
Page 28 of 124 ProSoft Technology, Inc.
July 24, 2013
DFNT ♦ ProLinx Gateway
EtherNet/IP Explicit Messaging Client/Server
4 Configure the IP address for the module.
Functional Overview
Protocol Manual
5 Configure the IP addresses for any other EtherNet/IP devices on the network.
ProSoft Technology, Inc.
July 24, 2013
Page 29 of 124
Functional Overview
Protocol Manual
DFNT ♦ ProLinx Gateway
EtherNet/IP Explicit Messaging Client/Server
6 Click on C OMMUNICATIONS /RSW HO to browse the network and display the module's icon.
Page 30 of 124 ProSoft Technology, Inc.
July 24, 2013
DFNT ♦ ProLinx Gateway
EtherNet/IP Explicit Messaging Client/Server
Configuring the Gateway
Protocol Manual
3 Configuring the Gateway
3.1 Using ProSoft Configuration Builder
ProSoft Configuration Builder (PCB) provides a quick and easy way to manage module configuration files customized to meet your application needs. PCB is not only a powerful solution for new configuration files, but also allows you to import information from previously installed (known working) configurations to new projects.
3.1.1 Setting Up the Project
To begin, start ProSoft Configuration Builder (PCB). If you have used other
Windows configuration tools before, you will find the screen layout familiar.
ProSoft Configuration Builder’s (PCB's) window consists of a tree view on the left, an information pane, and a configuration pane on the right side of the window. When you first start PCB, the tree view consists of folders for Default
Project and Default Location, with a Default Module in the Default Location folder. The following illustration shows the PCB window with a new project.
To add the module to the project
1 Use the mouse to select D EFAULT M ODULE in the tree view, and then click the right mouse button to open a shortcut menu.
ProSoft Technology, Inc.
July 24, 2013
Page 31 of 124
Configuring the Gateway
Protocol Manual
DFNT ♦ ProLinx Gateway
EtherNet/IP Explicit Messaging Client/Server
2 On the shortcut menu, choose C HOOSE M ODULE T YPE . This action opens the
Choose Module Type dialog box.
3 In the Product Line Filter area of the dialog box, select the appropriate product type radio button.
4 In the STEP 1: Select Module Type dropdown list, select the model number that matches your module, and then click OK to save your settings and return to the PCB Main window.
Page 32 of 124 ProSoft Technology, Inc.
July 24, 2013
DFNT ♦ ProLinx Gateway
EtherNet/IP Explicit Messaging Client/Server
3.1.2 Renaming PCB Objects
Configuring the Gateway
Protocol Manual
Notice that the contents of the information pane and the configuration pane changed when you added the module to the project.
At this time, you may wish to rename the Default Project and Default Location folders in the tree view.
1 Select the object, and then click the right mouse button to open a shortcut menu. From the shortcut menu, choose R ENAME .
2 Type the name to assign to the object.
3 Click away from the object to save the new name.
Configuring Module Parameters
1 Click on the [+] sign next to the module icon to expand module information.
2 Click on the [+] sign next to any icon to view module information and configuration options.
3 Double-click any icon to open an Edit dialog box.
4 To edit a parameter, select the parameter in the left pane and make your changes in the right pane.
5 Click OK to save your changes.
Printing a Configuration File
1 Select the module icon, and then click the right mouse button to open a shortcut menu.
2 On the shortcut menu, choose V IEW C ONFIGURATION . This action opens the
View Configuration window.
3 In the View Configuration window, open the F
ILE menu, and choose P
RINT
.
This action opens the Print dialog box.
4 In the Print dialog box, choose the printer to use from the drop-down list, select printing options, and then click OK.
ProSoft Technology, Inc.
July 24, 2013
Page 33 of 124
Configuring the Gateway
Protocol Manual
3.2 [DFNT Client x]
DFNT ♦ ProLinx Gateway
EtherNet/IP Explicit Messaging Client/Server
This section defines the configuration for the DFNT Client (master) device simulated on network port
3.2.1 Minimum Command Delay
0 to 65535 milliseconds
This parameter specifies the number of milliseconds to wait between the initial issuances of a command. This parameter can be used to delay all commands sent to servers to avoid "flooding" commands on the network. This parameter does not affect retries of a command as they will be issued when failure is recognized.
3.2.2 Response Timeout
0 to 65535 milliseconds
This is the time in milliseconds that a Client will wait before re-transmitting a command if no response is received from the addressed server. The value to use depends on the type of communication network used, and the expected response time of the slowest device on the network.
3.2.3 Retry Count
0 to 10
This parameter specifies the number of times a command will be retried if it fails.
Page 34 of 124 ProSoft Technology, Inc.
July 24, 2013
DFNT ♦ ProLinx Gateway
EtherNet/IP Explicit Messaging Client/Server
3.3 [DFNT Client x Commands]
Configuring the Gateway
Protocol Manual
This section defines the EtherNet/IP commands to be issued from the module to server devices on the network. These commands can be used for data collection and/or control of devices on the TCP/IP network.
3.3.1 Command List
In order to interface the virtual database with DF1 slave devices, you must construct a command list. The commands in the list specify the DF1 slave device to be utilized, the function to be performed (read or write), the data area in the device to interface with and the position in the virtual database to be associated with the device data. There is a separate command list for each DF1 master device emulated. The list is processed from top (command #0) to bottom. A poll interval parameter is associated with each command to specify a minimum delay time between the issuance of a command. If the user specifies a value of 10 for the parameter, the command will be executed no more frequently than every 10 seconds for the serial implementation and 1 second for the network implementation.
Write commands have a special feature, as they can be set to execute only if the data in the write command changes. If the data in the command has not changed since the command was last issued, the command will not be executed. If the data in the command has changed since the command was last issued, the command will be executed. Use of this feature can lighten the load on the DF1 network. In order to implement this feature; set the enable code for the command to a value of 2.
ProSoft Technology, Inc.
July 24, 2013
Page 35 of 124
Configuring the Gateway
Protocol Manual
DFNT ♦ ProLinx Gateway
EtherNet/IP Explicit Messaging Client/Server
If the module is configured for the serial DF1 half-duplex protocol, the module can act as a master device routing messages between attached slave devices.
This peer-to-peer communication is defined in the DF1 protocol specification.
The master polls each DF1 slave device until no more data is available from the device. Response messages from the slaves that have a destination address that do not match the module are routed with a request message header back out onto the network. This facility offers communication between the slave devices for control and data monitoring. This feature is not available if the module is configured for DF1 full-duplex mode (point-to-point).
The module supports numerous commands. This permits the module to interface with a wide variety of DF1 protocol devices. This includes PLC2, PLC5, SLC-500 series, MicroLogix and ControlLogix processors. Additionally, other devices supplied by Rockwell Automation that use the DF1 protocol are supported.
The format of each command in the list depends on the function being executed.
To simplify command construction, the module uses its own set of function codes to associate a command with a DF1 command/function type. The tables below list the functions supported by the module:
Basic Command Set Functions
3
4
1
2
Function
Code
5
Comman d
0x00
0x01
0x02
0x05
0x08
Function Definition
N/A
N/A
N/A
N/A
N/A
PLC5
Protected Write
Unprotected Read
Protected Bit Write X
Unprotected Bit Write X
X
X
Unprotected Write X
X
SLC500 &
MicroLogix
X
Powermonitor II
ControlLogix
X
X
X
X
X
PLC-5 Command Set Functions
Function
Code
100
Command Function Definition
0x0F 0x00
101
102
150
151
152
0x0F
0x0F
0x0F
0x0F
0x0F
0x01
0x26
0x00
0x01
0x26
Word Range Write
(Binary Address)
Word Range Read
(Binary Address)
Read-Modify-Write
(Binary Address)
Word Range Write
(ASCII Address)
Word Range Read
(ASCII Address)
Read-Modify-Write
(ASCII Address)
X
X
X
X
X
PLC5
X
SLC500 &
MicroLogix
Powermonitor II
ControlLogix
X
X
X
X
X
X
Page 36 of 124 ProSoft Technology, Inc.
July 24, 2013
DFNT ♦ ProLinx Gateway
EtherNet/IP Explicit Messaging Client/Server
SLC-500 Command Set Functions
Function
Code
501
Command Function Definition
0x0F 0xA1
502
509
510
511
0x0F
0x0F
0x0F
0x0F
0XA2
0XA9
0XAA
0XAB
Protected Typed
Logical Read With
Two Address Fields
Protected Typed
Logical Read With
Three Address Fields
Protected Typed
Logical Write With
Two Address Fields
Protected Typed
Logical Write With
Three Address Fields
Protected Typed
Logical Write With
Mask (Three Address
Fields)
PLC5 SLC500 &
MicroLogix
X
Powermonitor II
X
X
X
X
X
X
Configuring the Gateway
Protocol Manual
ControlLogix
X
X
X
X
X
Each command list record has the same general format. The first part of the record contains the information relating to the communication module and the second part contains information required to interface to the DF1 or EtherNet/IP slave device.
ProSoft Technology, Inc.
July 24, 2013
Page 37 of 124
Configuring the Gateway
Protocol Manual
3.3.2 Command Entry Formats
DFNT ♦ ProLinx Gateway
EtherNet/IP Explicit Messaging Client/Server
The format of each command in the list depends on the function being executed.
Refer to Command Function Codes (page 38) for a complete discussion of the
commands supported by the module and of the structure and content of each command.
The following table shows the structure of the configuration data necessary for each of the supported commands.
Module Information Data
Column
#
1 2
Functio n Code
FC 1
FC 2
Enabl e
Code
Internal
Addres s
3
Poll
Interval
Time
Code Register Second s
Code Register Second s
FC 3
FC 4
Code Register Second s
Code Register Second s
FC 5 Code Register Second s
FC 100 Code Register Second s
4
FC 101 Code Register Second s
FC 102 Code Register Second s
FC 150 Code Register Second s
FC 151 Code Register Second s
FC 152 Code Register Second s
FC 501 Code Register Second s
FC 502 Code Register Second s
FC 509 Code Register Second s
FC 510 Code Register Second s
5 6
Device Information Data
7 8 9 10 11
Coun t
Swap
Code
IP
Address
Slot
Numbe r
Count Code Node Slot
Count Code Node
Count Code Node
Count Code Node
Count Code Node
Count Code Node
Count Code Node
Count Code Node
Count Code Node
Count Code Node
Count Code Node
Count Code Node
Count Code Node
Count Code Node
Count Code Node
Funct ion
Code
1
Function Parameters
2
3
4
Word
Address
Word
Address
Word
Address
Word
Address
5 Word
Address
100 File
Number
Elemen t
101
102
File
Number
File
Number
Elemen t
Elemen t
Sub-
Elemen t
Sub-
Elemen t
Sub-
Elemen t
150 File
String
151 File
String
152 File
String
501 File
Type
502
509
510
File
Type
File
Type
File
Type
File
Numbe r
File
Numbe r
File
Numbe r
File
Numbe r
Elemen t
Elemen t
Elemen t
Elemen t
12
Sub-
Elemen t
Sub-
Elemen t
Page 38 of 124 ProSoft Technology, Inc.
July 24, 2013
DFNT ♦ ProLinx Gateway
EtherNet/IP Explicit Messaging Client/Server
Configuring the Gateway
Protocol Manual
Module Information Data
Column
#
1 2
Functio n Code
Enabl e
Code
Internal
Addres s
3
Poll
Interval
Time
FC 511 Code Register Second s
4 5 6
Device Information Data
7 8 9 10 11
Coun t
Swap
Code
IP
Address
Count Code Node
Slot
Numbe r
Funct ion
Code
Function Parameters
511 File
Type
File
Numbe r
Elemen t
IP Address = IP address of processor to reach
Slot Number = -1 for PLC5 & SLC, processor slot number of ControlLogix
12
Sub-
Elemen t
The first part of the record is the Module Information, which relates to the module. The second part contains information required to interface to the Server device. An example of a command list section of the configuration file is shown in the following illustration.
[DFNT Client 0 Commands]
#
# The file contains examples for a ControlLogix processor with the N7 file
# configured. This example uses SLC and PLC5 commands.
#
# LOCATION :
# DATE : 04/05/2000
# CONFIGURED BY: RAR
# MODIFIED :
#
# 1 2 3 4 5 6 7 8 9 10 11 12
# DB Poll Swap Func File File Elm Sub
#Enab Addr Delay Count Code Node IP Address Slot Code Type # # Elm
START
# 1 2000 0 10 0 192.168.0.100 0 501 N 11 0
# 1 2000 0 10 0 192.168.0.100 0 509 N 12 0
#
# DB Poll Swap Func File Elm Sub
#Enab Addr Delay Count Code Node IP Address Slot Code # # Elm
END
ProSoft Technology, Inc.
July 24, 2013
Page 39 of 124
Configuring the Gateway
Protocol Manual
The following table describes each parameter
Parameter
Enable
Internal
Address
Poll Delay
Count
Swap Code
DFNT ♦ ProLinx Gateway
EtherNet/IP Explicit Messaging Client/Server
Range
0, 1, 2
Description
This field defines whether the command is to be executed and under what conditions.
Value Description
0 The command is disabled and will not be executed in the normal polling sequence.
1
2
The command is executed each scan of the command list if the
Poll Interval Time is set to zero. If the Poll Interval time is set, the command is executed when the interval timer expires.
The command executes only if the internal data associated with the command changes. This value is valid for write commands only.
0 to 3999
0 to 1000
This field specifies the database address in the module's internal database to be associated with the command. If the command is a read function, the data received in the response message is placed at the specified location. If the command is write function, data used in the command is sourced from the specified data area.
This parameter specifies the minimum interval to execute continuous commands (Enable code of 1). The parameter is entered in 1/10th of a second. Therefore, if a value of 100 is entered for a command, the command executes no more frequently than every 10 seconds.
Command dependent. This parameter specifies the number of registers or digital points to be
associated with the command. See Command Function Codes (page 38) for
information
0, 1, 2, 3 This parameter defines if the data received from the Server is to be ordered differently than that received from the Server device. This parameter is helpful when dealing with floating-point or other multi-register values, as there is no standard method of storage of these data types in Server devices. This parameter can be set to order the register data received in an order useful by other applications. The following table defines the values and their associated operations: xxx.xxx.xxx.xxx
1
2
Swap Code Description
0 None - No Change is made in the byte ordering (1234 =
1234)
Words - The words are swapped (1234=3412)
Words & Bytes - The words are swapped then the bytes in each word are swapped (1234=4321)
3 Bytes - The bytes in each word are swapped (1234=2143)
The words should be swapped only when using an even number of words.
The IP address of the device being addressed by the command. Node IP
Address
Slot When addressing a ControlLogix processor, the slot number corresponds to the slot in the rack containing the controller being addressed. In the
ControlLogix platform, the controller can be placed in any slot and the rack may contain multiple processors. This parameter uniquely selects a controller in the rack.
Use a value of -1 when interfacing to an SLC 5/05 or a
PLC5. These devices do not have a slot number.
Page 40 of 124 ProSoft Technology, Inc.
July 24, 2013
DFNT ♦ ProLinx Gateway
EtherNet/IP Explicit Messaging Client/Server
Parameter Range
Function Code See Command
Function Codes (page
Function
Parameters
See Command
Function Codes (page
Configuring the Gateway
Protocol Manual
Description
These parameters specify the function to be executed by the command. The
Reference chapter in this manual describes the meaning of these values for each of the available supported commands. Following is a complete list of the command supported by the Client driver.
Function Code Listing
Basic Command Set
1
2
Protected Write
Unprotected Read
3
4
Protected Bit Write
Unprotected Bit Write
5 Unprotected Write
PLC-5 Command Set (0x0F)
100
101
102
150
Word Range Write (Binary Address)
Word Range Read (Binary Address)
Read-Modify-Write (Binary Address)
Word Range Write (ASCII Address)
151
152
Word Range Read (ASCII Address)
Read-Modify-Write (ASCII Address)
SLC Command Set (0x0F)
501 Prot Typed Read with 2 addr fields
502 Prot Typed Read with 3 addr fields
509
510
511
Prot Typed Write with 2 addr fields
Prot Typed Write with 3 addr fields
Prot Type Write with Mask 3 addr field
The number of auxiliary parameters required depends on the function code selected for the command.
ProSoft Technology, Inc.
July 24, 2013
Page 41 of 124
Configuring the Gateway
Protocol Manual
3.4 [DFNT UClient 0]
DFNT ♦ ProLinx Gateway
EtherNet/IP Explicit Messaging Client/Server
This section defines the configuration for the unconnected master device simulated on network port
3.4.1 Minimum Command Delay
0 to 65535 milliseconds
This parameter specifies the number of milliseconds to wait between the initial issuances of a command. This parameter can be used to delay all commands sent to servers to avoid "flooding" commands on the network. This parameter does not affect retries of a command as they will be issued when failure is recognized.
3.4.2 Response Timeout
0 to 65535 milliseconds
This is the time in milliseconds that a Client will wait before re-transmitting a command if no response is received from the addressed server. The value to use depends on the type of communication network used, and the expected response time of the slowest device on the network.
3.4.3 Retry Count
0 to 10
This parameter specifies the number of times a command will be retried if it fails.
Page 42 of 124 ProSoft Technology, Inc.
July 24, 2013
DFNT ♦ ProLinx Gateway
EtherNet/IP Explicit Messaging Client/Server
3.5 [DFNT UClient 0 Commands]
Example PLC5 Binary Command List
Configuring the Gateway
Protocol Manual
Example PLC5 ASCII Command List
Refer to Command List for a description of command list syntax.
ProSoft Technology, Inc.
July 24, 2013
Page 43 of 124
Configuring the Gateway
Protocol Manual
3.6 Using the CommonNet Data Map
DFNT ♦ ProLinx Gateway
EtherNet/IP Explicit Messaging Client/Server
The Data Map section allows you to copy data between areas in the module's internal database.
You can copy a maximum of 100 registers per Data Map command, and you can configure a maximum of 200 separate copy commands.
You can copy data from the error or status tables in upper memory to internal database registers in the User Data memory area.
You can rearrange the byte and/or word order during the copy process. For example, by rearranging byte or word order, you can convert floating-point values to the correct format for a different protocol.
You can also use the Data Map to condense widely dispersed data into one contiguous data block, making it easier to access.
Page 44 of 124 ProSoft Technology, Inc.
July 24, 2013
DFNT ♦ ProLinx Gateway
EtherNet/IP Explicit Messaging Client/Server
3.6.1 Moving Data
Configuring the Gateway
Protocol Manual
The following illustration shows an example Data Map. The Data Map allows you to move data to different addresses within the module database in order to create simpler data requests and control.
3.6.2 From Address
0 to highest Status Data address
This field specifies the beginning internal database register address for the copy operation. This address can be any valid address in the User Data Area or the
Status Data Area of the gateway.
3.6.3 To Address
0 to 3999
This parameter specifies the beginning destination register address for the copy operation. This address must always be within the User Data registers area.
Take care to specify a destination address that will not overwrite data that has been stored in memory by one of the communication protocols running on the gateway.
3.6.4 Register Count
1 to 100
This parameter specifies the number of registers to copy.
3.6.5 Swap Code
N O C HANGE , W ORD S WAP , W ORD AND B YTE S WAP , B YTE S WAP
ProSoft Technology, Inc.
July 24, 2013
Page 45 of 124
Configuring the Gateway
Protocol Manual
DFNT ♦ ProLinx Gateway
EtherNet/IP Explicit Messaging Client/Server
You may need to swap the order of the bytes in the registers during the copy process in order to change the alignment of bytes between dissimilar protocols.
This parameter is helpful when dealing with floating-point or other multi-register values, as there is no standard method of storage of these data types in slave devices.
The following table defines the values and their associated operations:
Swap Code Description
No Swap No change is made in the byte ordering (1234 = 1234)
Word Swap The words are swapped (1234=3412)
Word and
Byte Swap
The words are swapped, then the bytes in each word are swapped (1234=4321)
Bytes The bytes in each word are swapped (1234=2143)
Page 46 of 124 ProSoft Technology, Inc.
July 24, 2013
DFNT ♦ ProLinx Gateway
EtherNet/IP Explicit Messaging Client/Server
3.6.6 Delay Preset
Configuring the Gateway
Protocol Manual
This parameter sets an interval for each Data Map copy operation. The value you put for the Delay Preset is not a fixed amount of time. It is the number of firmware scans that must transpire between copy operations.
The firmware scan cycle can take a variable amount of time, depending on the level of activity of the protocol drivers running on the ProLinx gateway and the level of activity on the gateway's communication ports. Each firmware scan can take from 1 to several milliseconds to complete. Therefore, Data Map copy operations cannot be expected to happen at regular intervals.
If multiple copy operations (several rows in the Data map section) happen too frequently or all happen in the same update interval, they could delay the process scan of the gateway protocols, which could result in slow data updates or missed data on communication ports. To avoid these potential problems, you should set the Delay Preset to different values for each row in the Data Map section and set them to higher, rather than lower, numbers.
For example, Delay Preset values below 1000 could begin to cause a noticeable delay in data updates through the communication ports. And you should not set all Delay Presets to the same value. Instead, use different values for each row in the Data Map such as 1000, 1001, and 1002 or any other different Delay Preset values you like. This will prevent the copies from happening concurrently and prevent possible process scan delays.
ProSoft Technology, Inc.
July 24, 2013
Page 47 of 124
Configuring the Gateway
Protocol Manual
3.7 Ethernet Port Configuration - wattcp.cfg
DFNT ♦ ProLinx Gateway
EtherNet/IP Explicit Messaging Client/Server
The wattcp.cfg file must be set up properly in order to use a TCP/IP network connection. The ProLinx Reference Guide provides detailed information on setting up this file, as well as how to load it to ProLinx modules.
Page 48 of 124 ProSoft Technology, Inc.
July 24, 2013
DFNT ♦ ProLinx Gateway
EtherNet/IP Explicit Messaging Client/Server
Configuring the Gateway
Protocol Manual
3.8 Downloading the Project to the Module Using a Serial COM port
For the module to use the settings you configured, you must download (copy) the updated Project file from your PC to the module.
1 In the tree view in ProSoft Configuration Builder, click once to select the module.
2 Open the Project menu, and then choose M
ODULE
/D
OWNLOAD
. The program will scan your PC for a valid com port (this may take a few seconds). When
PCB has found a valid COM port, the Download dialog box will open.
3 Choose the COM port to use from the dropdown list, and then click the
D OWNLOAD button.
The module will perform a platform check to read and load its new settings.
When the platform check is complete, the status bar in the Download dialog box will display the message Module Running.
Page 49 of 124 ProSoft Technology, Inc.
July 24, 2013
Configuring the Gateway
Protocol Manual
DFNT ♦ ProLinx Gateway
EtherNet/IP Explicit Messaging Client/Server
Page 50 of 124 ProSoft Technology, Inc.
July 24, 2013
DFNT ♦ ProLinx Gateway
EtherNet/IP Explicit Messaging Client/Server
Diagnostics and Troubleshooting
Protocol Manual
4 Diagnostics and Troubleshooting
In This Chapter
Using ProSoft Configuration Builder (PCB) for Diagnostics................... 52
EtherNet/IP Client Command List Error Data ........................................ 61
There are two ways to troubleshoot ProLinx Gateways:
Using the LEDs located on the front of the gateway
Using the Debug port that provides a view into the gateway's internal database.
ProSoft Technology, Inc.
July 24, 2013
Page 51 of 124
Diagnostics and Troubleshooting
Protocol Manual
DFNT ♦ ProLinx Gateway
EtherNet/IP Explicit Messaging Client/Server
4.1 Using ProSoft Configuration Builder (PCB) for Diagnostics
The Configuration and Debug menu for this module is arranged as a tree structure, with the Main menu at the top of the tree, and one or more submenus for each menu command. The first menu you see when you connect to the module is the Main menu.
Because this is a text-based menu system, you enter commands by typing the
[command letter] from your computer keyboard in the Diagnostic window in
ProSoft Configuration Builder (PCB). The module does not respond to mouse movements or clicks. The command executes as soon as you press the
[ COMMAND LETTER ] — you do not need to press [E
NTER ].
When you type a
[ COMMAND LETTER ], a new screen will be displayed in your terminal application.
4.1.1 Required Hardware
You can connect directly from your computer’s serial port to the serial port on the module to view configuration information, perform maintenance, and send or receive configuration files.
ProSoft Technology recommends the following minimum hardware to connect your computer to the module:
80486 based processor (Pentium preferred)
1 megabyte of memory
At least one UART hardware-based serial communications port available.
USB-based virtual UART systems (USB to serial port adapters) often do not function reliably, especially during binary file transfers, such as when uploading/downloading configuration files or module firmware upgrades.
4.1.2 Using the Diagnostic Window in ProSoft Configuration Builder
To connect to the module’s Configuration/Debug serial port
1 Start PCB, and then select the module to test. Click the right mouse button to open a shortcut menu.
Page 52 of 124 ProSoft Technology, Inc.
July 24, 2013
DFNT ♦ ProLinx Gateway
EtherNet/IP Explicit Messaging Client/Server
2 On the shortcut menu, choose D IAGNOSTICS .
Diagnostics and Troubleshooting
Protocol Manual
This action opens the Diagnostics dialog box.
3 Press [?] to open the Main menu.
If there is no response from the module, follow these steps:
ProSoft Technology, Inc.
July 24, 2013
Page 53 of 124
Diagnostics and Troubleshooting
Protocol Manual
DFNT ♦ ProLinx Gateway
EtherNet/IP Explicit Messaging Client/Server
1 Click to configure the connection. On the Connection Setup dialog box, select a valid com port or other connection type supported by the module.
2 Verify that the null modem cable is connected properly between your computer’s serial port and the module. A regular serial cable will not work.
3 On computers with more than one serial port, verify that your communication program is connected to the same port that is connected to the module.
If you are still not able to establish a connection, contact ProSoft Technology for assistance.
4.1.3 Navigation
All of the submenus for this module contain commands to redisplay the menu or return to the previous menu. You can always return from a submenu to the next higher menu by pressing [M] on your keyboard.
The organization of the menu structure is represented in simplified form in the following illustration:
The remainder of this section shows the menus available for this module, and briefly discusses the commands available to you.
Page 54 of 124 ProSoft Technology, Inc.
July 24, 2013
DFNT ♦ ProLinx Gateway
EtherNet/IP Explicit Messaging Client/Server
Keystrokes
Diagnostics and Troubleshooting
Protocol Manual
The keyboard commands on these menus are usually not case sensitive. You can enter most commands in lowercase or uppercase letters.
The menus use a few special characters (?, -, +, @) that must be entered exactly as shown. Some of these characters will require you to use the SHIFT, CTRL, or
ALT keys to enter them correctly. For example, on US English keyboards, enter the ? command as SHIFT and /.
Also, take care to distinguish the different uses for uppercase letter "eye" (I), lowercase letter "el" ( L ), and the number one (1). Likewise, uppercase letter "oh"
(O) and the number zero (0) are not interchangeable. Although these characters look alike on the screen, they perform different actions on the module and may not be used interchangeably.
ProSoft Technology, Inc.
July 24, 2013
Page 55 of 124
Diagnostics and Troubleshooting
Protocol Manual
4.2 Base Module LEDs
LED
Power
Fault
Cfg
Err
DFNT ♦ ProLinx Gateway
EtherNet/IP Explicit Messaging Client/Server
State
Off
Description
Power is not connected to the power terminals or source is insufficient to properly power the module (minimum required is 800mA at 24 Vdc)
Green Solid Power is connected to the power terminals.
Off Normal operation.
Red Solid
Off
A critical error has occurred. Program executable has failed or has been user-terminated and is no longer running. Press Reset p/b or cycle power to clear error. If not, use the Debug procedures described later in this manual.
Normal operation.
Amber Solid The unit is in configuration mode. The configuration file is currently being downloaded or, after power-up, is being read, the unit is implementing the configuration values, and initializing the hardware.
This will occur during power cycle, or after pressing the reset button. It also occurs after a cold/warm boot command is received.
Off
Flashing
Normal operation.
An error condition has been detected and is occurring on one of the application ports. Check configuration and troubleshoot for communication errors.
Solid Red This error flag is cleared at the start of each command attempt
(Master/Client) or on each receipt of data (slave/adapter/server); so, if this condition exists, it indicates a large number of errors are occurring in the application (due to bad configuration) or on one or more ports
(network communication failures).
4.2.1 Ethernet LED Indicators
LED
Data
Link
State
OFF
GREEN Flash
OFF
GREEN Solid
Description
No activity on the Ethernet port.
The Ethernet port is actively transmitting or receiving data.
No physical network connection is detected. No Ethernet communication is possible. Check wiring and cables.
Physical network connection detected. This LED must be ON solid for Ethernet communication to be possible.
Page 56 of 124 ProSoft Technology, Inc.
July 24, 2013
DFNT ♦ ProLinx Gateway
EtherNet/IP Explicit Messaging Client/Server
4.3 Client Error/Status Data
Diagnostics and Troubleshooting
Protocol Manual
The second and most thorough troubleshooting method for debugging the operation of the DFNT driver (and the module in general) is the powerful Debug port on the module which provides much more complete access to the internal operation and status of the module. Accessing the Debug capabilities of the module is accomplished easily by connecting a PC to the Debug port and loading a terminal program such as ProSoft Configuration Builder or HyperTerminal.
The Client connection Error and Status Data areas are discussed in this section
The error/status data table is located in virtual address assigned by ProLinx. If the address is set to -1, the data will not be placed in the database. It will only be available through the Configuration/Debug Port. If a valid address value is assigned, the module will update the data area.
The data area is initialized with zeros whenever the module is initialized. This occurs during a cold-start (power-on), reset (reset push-button pressed) or a warm-boot operation (commanded or loading of new configuration).
Note: The ProLinx Reference Guide contains detailed information on accessing the contents of the following registers.
4.3.1 DFNT Client 0 Status
Description
7904
7905
7906
7907
7908
7909
Internal Database
Address
7900
7901
7902
7903
Offset
4
5
6
7
8
9
0
1
2
3
Number of Command Requests
Number of Command Responses
Number of Command Errors
Number of Requests
Number of Responses
Number of Errors Received
Number of Errors Sent
Configuration Error Code
Current Error Code
Last Error Code
ProSoft Technology, Inc.
July 24, 2013
Page 57 of 124
Diagnostics and Troubleshooting
Protocol Manual
DFNT ♦ ProLinx Gateway
EtherNet/IP Explicit Messaging Client/Server
4.3.2 Unconnected Msg DFNT Client 0 Status
Status Register
12800
12801
12802
12803
12804
12805
12806
12807
12808
12809
12810 to 12909
12910 to 12999
Description
Command Request Count
Command Response Count
Command Error Count
Number of Request Packets
Number of Response Packets
Errors Sent
Errors Received
Configuration Error Word
Current Error
Last Error
Command List Errors
No Valid Data
4.3.3 DFNT Client 1 through 4 Status
DFNT Clients 1 through 4 have the same description and order as shown in the
DFNT Client 0 Status Table. The following table shows the internal database addresses for clients 1 through 4:
DFNT Client
1
2
3
4
Address Range
8100 through 8109
8300 through 8309
8500 through 8509
8700 through 8709
Page 58 of 124 ProSoft Technology, Inc.
July 24, 2013
DFNT ♦ ProLinx Gateway
EtherNet/IP Explicit Messaging Client/Server
4.3.4 DFNT Server 0
8910
8911
8912
8913
8914
8915
Internal Database
Address
Description
8900
8901
8902
Socket Size
Connection State
Socket Open Count
8903
8904
8905
8906
8907
8908
8909
Socket Established Count
Socket Close Count
Socket Read Count
Processed Message Count
Socket Write Count
Socket Timeout Count
Host s_type
Host Port
Host IP
Host IP
Reserved
Reserved
Reserved
Diagnostics and Troubleshooting
Protocol Manual
4.3.5 DFNT Servers 1 Through 4
DFNT Servers 1 through 4 have the same description and order as shown in the
DFNT Server 0 Status Table. The following table shows the internal database addresses for servers 1 through 4:
DFNT Server
1
2
3
4
Address Range
8916 through 8931
8932 through 8947
8948 through 8963
8964 through 8981
The following table defines the values represented in the Connection State parameter:
State
0
1
2
Definition
No session exists on socket
Session established but no connections
Session established and connected
ProSoft Technology, Inc.
July 24, 2013
Page 59 of 124
Diagnostics and Troubleshooting
Protocol Manual
4.3.6 DF1 Pass-Through Server
DFNT ♦ ProLinx Gateway
EtherNet/IP Explicit Messaging Client/Server
8989
8990
8991
8992
8993
8994
8995
8996
8997
8998
8999
Internal Database
Address
Description
8982
8983
8984
8985
8986
8987
8988
Socket Size
Connection State
Socket Open Count
Socket Established Count
Socket Close Count
Socket Read Count
Processed Message Count
Socket Write Count
Socket Timeout Count
Host s_type
Host Port
Host IP
Host IP
Reserved
Reserved
Reserved
No Valid Data
No Valid Data
Refer to Error Codes to interpret the status/error codes present in the data area.
Page 60 of 124 ProSoft Technology, Inc.
July 24, 2013
DFNT ♦ ProLinx Gateway
EtherNet/IP Explicit Messaging Client/Server
4.4 EtherNet/IP Client Command List Error Data
Diagnostics and Troubleshooting
Protocol Manual
Each command in the command list for each EtherNet/IP client has a reserved word value for a status/error code. This error data list can be read using the
Debug/Config Port and can be placed in the module’s internal database. Each network client has its own register location parameter.
The first word in the register location defined contains the status/error code for the first command in the client’s command list. Each successive word in the command error list is associated with the next command in the list. Therefore, the size of the data area is dependent upon the number of commands defined. The structure of the data area is displayed in the following tables:
4.4.1 DFNT Client 0 (Command List Error Data)
Description
8007
8008
8009
Internal Database
Address
7910
7911
7912
7913
7914
Offset
.
.
.
97
98
99
0
1
2
3
4
Command #0 Error Status
Command #1 Error Status
Command #2 Error Status
Command #3 Error Status
Command #4 Error Status
.
.
.
Command #97 Error Status
Command #98 Error Status
Command #99 Error Status
4.4.2 DFNT Client 1 Through 4 Command List Error Addresses
DFNT clients 1 through 4 have the same description and order as shown in the
DFNT Client 0 Status Table. The following table shows the internal database addresses for clients 1 through 4:
DFNT Client
1
2
3
4
Address Range
8100 through 8209
8310 through 8409
8510 through 8609
8710 through 8809
Note that the values in the Command List Error Status tables are initialized to zero(0) at power-up, cold boot and during warm boot. Refer to the following topic containing Error Codes to interpret the status/error codes present in the data area.
ProSoft Technology, Inc.
July 24, 2013
Page 61 of 124
Diagnostics and Troubleshooting
Protocol Manual
4.5 Error Codes
DFNT ♦ ProLinx Gateway
EtherNet/IP Explicit Messaging Client/Server
The module error codes are listed in this section. Error codes returned from the command list process are stored in the command list error memory region. A word is allocated for each command in the memory area. The error codes are formatted in the word as follows: The least-significant byte of the word contains the extended status code and the most-significant byte contains the status code.
Use the error codes returned for each command in the list to determine the success or failure of the command. If the command fails, use the error code to determine the cause of failure.
Note: The Module Specific error codes (not DF1 compliant) are returned from within the module and never returned from an attached DF1 slave device. These are error codes that are part of the
DF1 protocol or are extended codes unique to this module. The standard DF1 error codes can be found in the DF1 Protocol and Command Set Reference Manual (Publication 1770-6.5.16) from
Rockwell Automation. The most common errors for the DF1 protocol are shown in the following tables:
4.5.1 Local STS Error Codes
Code (Int) Code (Hex) Description
0
256
512
0x0000
0x0100
0x0200
Success, no error
DST node is out of buffer space
Cannot guarantee delivery (Link Layer)
768
1024
1280
1536
1792
2048
0x0300
0x0400
0x0500
0x0600
0x0700
0x0800
Duplicate token holder detected
Local port is disconnected
Application layer timed out waiting for response
Duplicate node detected
Station is offline
Hardware fault
Page 62 of 124 ProSoft Technology, Inc.
July 24, 2013
DFNT ♦ ProLinx Gateway
EtherNet/IP Explicit Messaging Client/Server
4.5.2 Remote STS Error Codes
Diagnostics and Troubleshooting
Protocol Manual
Code (Int) Code (Hex) Description
0 0x0000 Success, no error
4096 0x1000 Illegal command or format
8192
12288
16384
0x2000
0x3000
0x4000
Host has a problem and will not communicate
Remote node host is missing, disconnected or shut down
Host could not complete function due to hardware fault
20480
24576
26872
-32768
-28672
-24576
-20480
-16384
-12288
-8192
0x5000
0x6000
0x7000
0x8000
0x9000
0xA000
0xB000
0xC000
0xD000
0xE000
0xF0nn
Addressing problem or memory protect rungs
Function not allowed due to command protection selection
Processor is in Program mode
Compatibility mode file missing or communication zone problem
Remote node cannot buffer command
Wait ACK (1775-KA buffer full)
Remote node problem due to download
Wait ACK (1775-KA buffer full)
Not used
Not used
Error code in the EXT STS byte (nn contains EXT error code)
ProSoft Technology, Inc.
July 24, 2013
Page 63 of 124
Diagnostics and Troubleshooting
Protocol Manual
4.5.3 Errors When EXT STS Is Present
DFNT ♦ ProLinx Gateway
EtherNet/IP Explicit Messaging Client/Server
-4076
-4075
-4074
-4073
-4072
-4071
-4070
-4083
-4082
-4081
-4080
-4079
-4078
-4077
Code (Int) Code (Hex) Description
-4096 0xF000 Not used
-4095 0xF001 A field has an illegal value
-4094
-4093
-4092
0xF002
0xF003
0xF004
Less levels specified in address than minimum for any address
More levels specified in address than system supports
Symbol not found
-4091
-4090
-4089
-4088
-4087
-4086
-4085
-4084
0xF005
0xF006
0xF007
0xF008
0xF009
0xF00A
0xF00B
0xF00C
Symbol is of improper format
Address does not point to something usable
File is wrong size
Cannot complete request
Data or file is too large
Transaction size plus word address is too large
Access denied, improper privilege
Condition cannot be generated - resource is not available
-4069
-4068
-4067
-4066
-4065
0xF00D
0xF00E
0xF00F
0xF010
0xF011
0xF012
0xF013
0xF014
0xF015
0xF016
0xF017
0xF018
0xF019
0xF01A
0xF01B
0xF01C
0xF01D
0xF01E
0xF01F
Condition already exists - resource is already available
Command cannot be executed
Histogram overflow
No access
Illegal data type
Invalid parameter or invalid data
Address reference exists to deleted area
Command execution failure for unknown reason
Data conversion error
Scanner not able to communicate with 1771 rack adapter
Type mismatch
1171 module response was not valid
Duplicate label
File is open; another node owns it
Another node is the program owner
Reserved
Reserved
Data table element protection violation
Temporary internal problem
Page 64 of 124 ProSoft Technology, Inc.
July 24, 2013
DFNT ♦ ProLinx Gateway
EtherNet/IP Explicit Messaging Client/Server
4.5.4 Module Specific Error (not DFNT Compliant)
Diagnostics and Troubleshooting
Protocol Manual
Code (Int) Code (Hex) Description
-1 0xFFFF CTS modem control line not set before transmit
-2 0xFFFE Timeout while transmitting message
-10
-11
-12
0xFFF6
0xFFF5
0xFFF4
Timeout waiting for DLE-ACK after request
Timeout waiting for response after request
Reply data does not match requested byte count
-20
-21
-200
0xFFEC
0xFFEB
0xFF38
DLE-NAK received after request
DLE-NAK sent after response
DLE-NAK received after request
ProSoft Technology, Inc.
July 24, 2013
Page 65 of 124
Diagnostics and Troubleshooting
Protocol Manual
4.6 TCP/IP Interface Errors
DFNT ♦ ProLinx Gateway
EtherNet/IP Explicit Messaging Client/Server
4.6.1 Timeout Errors
Error (Int) Error (Hex) Description
-33
-34
-35
0xFFDF
0xFFDE
0xFFDD
Failed to connect to target
Failed to register session with target (timeout)
Failed forward open response timeout
-36
-37
-47
-48
0xFFDC
0xFFDB
0xFFD9
0xFFD7
PCCC command response timeout
No TCP/IP connection error
ARP could not resolve MAC from IP (bad IP address, not part of a network, invalid parameter to ARP routine).
Error during ARP operation: the response to the ARP request did not arrive to the module after a 5 second timeout.
Note: When the client gets error -47 or -48, it uses the adjustable ARP Timeout parameter in the configuration file to set an amount of time to wait before trying again to connect to this non-existent server. This feature allows the client to continue sending commands and polling other existing servers, while waiting for the non-existent server to appear on the network.
4.6.2 Register Session Response Errors
Error (Int)
-49
-50
-51
-52
-53
-54
Error (Hex) Description
0xFFCF Invalid response length
0xFFCE
0xFFCD
0xFFCC
0xFFCB
0xFFCA
Command field invalid
Invalid length field parameter
Status error reported
Context field not matched
Invalid version
4.6.3 Forward Open Response Errors
-68
-69
-70
-71
-72
-73
-74
-75
Error (Int)
-65
-66
-67
Error (Hex) Description
0xFFBF
0xFFBE
0xFFBD
Message Length received not valid
Command code returned not valid
Session handle field invalid
0xFFBC
0xFFBB
0xFFBA
0xFFB9
0xFFB8
0xFFB7
0xFFB6
0xFFB5
Status error reported
Context field not matched
CPF item count not correct
CPF address field error
CPF packet tag invalid
CPF bad command code
CPF invalid IOI
CPF status error reported
Page 66 of 124 ProSoft Technology, Inc.
July 24, 2013
DFNT ♦ ProLinx Gateway
EtherNet/IP Explicit Messaging Client/Server
4.6.4 PCCC Response Errors
-87
-88
-89
-90
-91
-92
-93
Error (Int)
-81
-82
-83
-84
-85
-86
-94
-95
-96
Error (Hex) Description
0xFFAF Message Length received not valid
0xFFAE Command code returned not valid
0xFFAD
0xFFAC
0xFFAB
0xFFAA
Session handle field invalid
Status error reported
Context field not matched
CPF item count not correct
0xFFA9
0xFFA8
0xFFA7
0xFFA6
0xFFA5
0xFFA4
0xFFA3
0xFFA2
0xFFA1
0xFFA0
CPF address field error
CPF packet tag invalid
CPF bad command code
CPF invalid IOI
CPF status error reported
TSN in PCCC message not matched
CPF not correct message number
CPF incorrect connection ID value returned
Incorrect session handle returned
Diagnostics and Troubleshooting
Protocol Manual
ProSoft Technology, Inc.
July 24, 2013
Page 67 of 124
Diagnostics and Troubleshooting
Protocol Manual
DFNT ♦ ProLinx Gateway
EtherNet/IP Explicit Messaging Client/Server
Page 68 of 124 ProSoft Technology, Inc.
July 24, 2013
DFNT ♦ ProLinx Gateway
EtherNet/IP Explicit Messaging Client/Server
5 Reference
In This Chapter
Command Function Codes .................................................................... 70
General Command Structure ................................................................. 71
PLC-5 Processor Specifics .................................................................... 85
SLC Processor Specifics ....................................................................... 87
MicroLogix Processor Specifics ............................................................. 88
ControlLogix Processor Specifics .......................................................... 89
ControlLogix (CLX) Processor ............................................................. 103
DFNT Command Entry Form ............................................................... 117
Reference
Protocol Manual
ProSoft Technology, Inc.
July 24, 2013
Page 69 of 124
Reference
Protocol Manual
5.1 Command Function Codes
DFNT ♦ ProLinx Gateway
EtherNet/IP Explicit Messaging Client/Server
In the following discussion, the Column values are described for the serial DFCM
Command list (See Node Address parameter #6). In the DFNT module, the Node address has been replaced with two parameters; the IP Address and the Slot
Number, causing the Function Code and Function Parameters to occupy positions 8 to 12 instead of 7 to 11. Aside from this difference, all other information is correct.
DFNT Configuration Form
Module Information Data
1 2 3
Enable
Code
Internal
Address
Poll
Interval
Time
4 5
Count Swap
Code
6
Device Information Data
7 8 9 10
IP
Address
Slot
Number
Function
Code
Function Parameters
11 12
DFNT Command Structure
Module Information Data
Column # 1 2
Function
Code
Enable
Code
Internal
Address
3
Poll
Interval
Time
4 5
Count Swap
Code
6
IP
Address
Device Information Data
7
Slot
Number
8
Function
Code
9 10 11 12
Function Parameters
Page 70 of 124 ProSoft Technology, Inc.
July 24, 2013
DFNT ♦ ProLinx Gateway
EtherNet/IP Explicit Messaging Client/Server
5.2 General Command Structure
Reference
Protocol Manual
Communicati on Module
Information
Device
Information
DF1 Master Port Command
Structure (File for each Master
Port)
Enable/Type Word
Description
Virtual Database Address
Poll Interval
Count
Swap Type Code
Node Address
Function Code
Parameters
0=Disabled, 1=Continuous, 2=Conditional and 999=Poll. The conditional type only applies to the write functions.
This parameter defines the virtual database register to be associated with the command.
Minimum time in tenths of a second to wait before polling with this command.
Number of data values or registers to be considered by the function.
Swap type code for command: 0=None, 1=Swap words, 2=Swap words & bytes and 3=swap bytes in each word.
Node address of unit to be reached on the data highway.
This parameter defines the module function code to be associated with the command. Each function code requires a set of parameters to construct the DF1 message.
Up to four parameter fields can follow the function code field to define the element or data register to be considered by the function.
Note that the Node Address field in the serial implementation has been expanded to two fields: IP Address and Slot Number in the DFNT Ethernet implementation.
This is required for network support. The IP Address specifies the IP address of the device to reach on the network. The Slot Number has specific meaning determined by the processor. For ControlLogix processors, the Slot Number is the location in the ControlLogix rack of the processor. For a four-slot rack, this parameter would have a valid range of 0 to 3. For the PLC5 and SLC family of processors, the Slot Number parameter is always set to -1. These processors do not have a slot number in the path field as the Ethernet interface is resident on the processor.
The following tables define the parameters required for each function.
ProSoft Technology, Inc.
July 24, 2013
Page 71 of 124
Reference
Protocol Manual
DFNT ♦ ProLinx Gateway
EtherNet/IP Explicit Messaging Client/Server
5.2.1 Function Code #1 - Protected Write (Basic Command Set)
Column
1
2
3
4
5
6
7
8
9
10 to 12
Parameter
Enable/Type Word
Virtual Database Address
Poll Interval
Count
Swap Type Code
Node Address
Slot Number
Function Code = 1
Word Address
Not Used
Description
0=Disabled, 1=Continuous and 2=Conditional.
This parameter defines the database address of the first data point to be associated with the command.
Minimum time in tenths of a second to wait before polling with this command.
Number of data word values to be considered by the function.
Parameter
Swap type code for command: 0=None, 1=Swap words,
2=Swap words & bytes and 3=swap bytes in each word.
Address of unit to reach on the data highway.
Processor slot number in Control/CompactLogix rack.
Use -1 for PLC5 & SLC processors.
Protected Write Function
Word address where to start the write operation.
These fields are not used by the command. Values entered in these columns will be ignored.
P1
P2 to P4
This function writes one or more words of data into a limited area of the slave device. This function should work on the following devices: 1774-PLC, PLC-2,
PLC-3, PLC-5 and PLC-5/250.
5.2.2 Function Code #2 - Unprotected Read (Basic Command Set)
Column
1
2
3
4
5
6
7
8
9
10 to 12
Parameter
Enable/Type Word
Virtual Database Address
Poll Interval
Count
Swap Type Code
Node Address
Slot Number
Function Code = 2
Word Address
Not Used
Description
0=Disabled and 1=Continuous.
This parameter defines the database address of the first data point to be associated with the command.
Minimum time in tenths of a second to wait before polling with this command.
Parameter
Number of data word values to be considered by the function.
Swap type code for command: 0=None, 1=Swap words,
2=Swap words & bytes and 3=swap bytes in each word.
Address of unit to reach on the data highway.
Processor slot number in Control/CompactLogix rack.
Use -1 for PLC5 & SLC processors.
Unprotected Read Function
Word address where to start the read operation.
These fields are not used by the command. Values entered in these columns will be ignored.
P1
P2 to P4
This function reads one or more words of data from the PLC memory. This function should work on the following devices: 1774-PLC, PLC-2, PLC-3, PLC-5,
SLC 500, SLC 5/03, SLC 5/04 and MicroLogix 1000.
Page 72 of 124 ProSoft Technology, Inc.
July 24, 2013
DFNT ♦ ProLinx Gateway
EtherNet/IP Explicit Messaging Client/Server
Reference
Protocol Manual
5.2.3 Function Code #3 - Protected Bit Write (Basic Command Set)
5
6
7
Column
1
3
4
8
9
10 to 12
Parameter
Enable/Type Word
Virtual Database Address
Poll Interval
Count
Swap Type Code
Node Address
Slot Number
Function Code = 3
Word Address
Not Used
Description
0=Disabled, 1=Continuous and 2=Conditional.
This parameter defines the database address for the data to be associated with the command. The address defined represents a register address and not a bit address. This function will update one or more words of data as defined by the count parameter.
Minimum time in tenths of a second to wait before polling with this command.
Number of data word values to be considered by the function.
Swap type code for command: Always zero (0).
Address of unit to reach on the data highway.
Processor slot number in Control/CompactLogix rack.
Use -1 for PLC5 & SLC processors.
Protected Bit Write Function
Word address where to start the write operation.
These fields are not used by the command. Values entered in these columns will be ignored.
Parameter
P1
P2 to P4
This function sets or resets individual bits within a limited area of the PLC data table. This function should work on the following devices: 1774-PLC, PLC-2,
PLC-3, PLC-5 and PLC-5/250.
3
4
5
6
7
5.2.4 Function Code #4 - Unprotected Bit Write (Basic Command
Set)
Column
1
2
8
9
10 to 12
Parameter
Enable/Type Word
Virtual Database Address
Poll Interval
Count
Swap Type Code
Node Address
Slot Number
Function Code = 4
Word Address
Not Used
Description
0=Disabled, 1=Continuous and 2=Conditional.
This parameter defines the database address for the data to be associated with the command. The address defined represents a register address and not a bit address. This function will update one or more words of data as defined by the count parameter.
Minimum time in tenths of a second to wait before polling with this command.
Number of data word values to be considered by the function.
Swap type code for command: Always zero (0).
Address of unit to reach on the data highway.
Processor slot number in Control/CompactLogix rack.
Use -1 for PLC5 & SLC processors.
Unprotected Bit Write Function
Word address where to start the write operation.
These fields are not used by the command. Values entered in these columns will be ignored.
Parameter
P1
P2 to P4
ProSoft Technology, Inc.
July 24, 2013
Page 73 of 124
Reference
Protocol Manual
DFNT ♦ ProLinx Gateway
EtherNet/IP Explicit Messaging Client/Server
This function sets or resets individual bits within a limited area of the PLC data table. This function should work on the following devices: 1774-PLC, PLC-2,
PLC-3 and PLC-5.
5.2.5 Function Code #5 - Unprotected Write (Basic Command Set)
6
7
Column
1
2
3
4
5
8
9
10 to 12
Parameter
Enable/Type Word
Virtual Database Address
Poll Interval
Count
Swap Type Code
Node Address
Slot Number
Function Code = 5
Word Address
Not Used
Description
0=Disabled, 1=Continuous and 2=Conditional.
This parameter defines the database address of the first data point to be associated with the command.
Minimum time in tenths of a second to wait before polling with this command.
Number of data word values to be considered by the function.
Swap type code for command: 0=None, 1=Swap words,
2=Swap words & bytes and 3=swap bytes in each word.
Address of unit to reach on the data highway.
Processor slot number in Control/CompactLogix rack.
Use -1 for PLC5 & SLC processors.
Unprotected Write Function
Word address where to start the write operation.
These fields are not used by the command. Values entered in these columns will be ignored.
Parameter
P1
P2 to P4
This function writes one or more words of data to the PLC memory. This function should work on the following devices: 1774-PLC, PLC-2, PLC-3, PLC-5, SLC
500, SLC 5/03, SLC 5/04 and MicroLogix 1000.
Page 74 of 124 ProSoft Technology, Inc.
July 24, 2013
DFNT ♦ ProLinx Gateway
EtherNet/IP Explicit Messaging Client/Server
Reference
Protocol Manual
5.2.6 Function Code #100 - Word Range Write (PLC-5 Command)
(Binary Address)
Column Parameter
1 Enable/Type Word
2 Virtual Database Address
3
4
5
8
9
6
7
10
11
12
Poll Interval
Count
Swap Type Code
Node Address
Slot Number
Function Code = 100
File Number
Element Number
Sub-Element Number
Not Used
Description
0=Disabled, 1=Continuous and 2=Conditional.
This parameter defines the database address of the first data point to be associated with the command.
Minimum time in tenths of a second to wait before polling with this command.
Number of data word values to be considered by the function.
Swap type code for command: 0=None, 1=Swap words,
2=Swap words & bytes and 3=swap bytes in each word.
Address of unit to reach on the data highway.
Processor slot number in Control/CompactLogix rack.
Use -1 for PLC5 & SLC processors.
Word Range Write Command.
PLC-5 file number to be associated with the command.
If a value of -1 is entered for the parameter, the field will not be used in the command, and the default file will be used.
The parameter defines the element in the file where write operation will start. If a value of -1 is entered for the parameter, the field will not be used in the command, and the default element will be used.
This parameter defines the sub-element for the command. Refer to the AB documentation for a list of valid sub- element codes. If the value is set to -1, the default sub-element number will be used.
This field is not used by the command. Values entered in this column will be ignored.
P1
P2
P3
P4
Parameter
This function writes one or more words of data to a PLC data table. This function should work on the following devices: PLC-5.
ProSoft Technology, Inc.
July 24, 2013
Page 75 of 124
Reference
Protocol Manual
DFNT ♦ ProLinx Gateway
EtherNet/IP Explicit Messaging Client/Server
5.2.7 Function Code #101 - Word Range Read (PLC-5 Command)
(Binary Address)
Column Parameter
1 Enable/Type Word
2 Virtual Database Address
3
4
5
8
9
6
7
10
11
12
Poll Interval
Count
Swap Type Code
Node Address
Slot Number
Function Code = 101
File Number
Element Number
Sub-Element Number
Not Used
Description
0=Disabled and 1=Continuous.
This parameter defines the database address of the first data point to be associated with the command.
Minimum time in tenths of a second to wait before polling with this command.
Number of data word values to be considered by the function.
Swap type code for command: 0=None, 1=Swap words,
2=Swap words & bytes and 3=swap bytes in each word.
Address of unit to reach on the data highway.
Processor slot number in Control/CompactLogix rack.
Use -1 for PLC5 & SLC processors.
Word Range Write Command.
PLC-5 file number to be associated with the command.
If a value of -1 is entered for the parameter, the field will not be used in the command, and the default file will be used.
The parameter defines the element in the file where write operation will start. If a value of -1 is entered for the parameter, the field will not be used in the command, and the default element will be used.
This parameter defines the sub-element for the command. Refer to the AB documentation for a list of valid sub- element codes. If the value is set to -1, the default sub-element number will be used.
This field is not used by the command. Values entered in this column will be ignored.
P1
P2
P3
P4
Parameter
This function reads one or more words of data from a PLC data table. This function should work on the following devices: PLC-5.
Page 76 of 124 ProSoft Technology, Inc.
July 24, 2013
DFNT ♦ ProLinx Gateway
EtherNet/IP Explicit Messaging Client/Server
Reference
Protocol Manual
5.2.8 Function Code #102 - Read-Modify-Write (PLC-5 Command)
(Binary Address)
3
4
5
6
7
8
9
Column Parameter
1 Enable/Type Word
2 Virtual Database Address
10
11
12
Poll Interval
Count
Swap Type Code
Node Address
Slot Number
Function Code = 102
File Number
Element Number
Sub-Element Number
Not Used
Description
0=Disabled, 1=Continuous and 2=Conditional.
This parameter defines the database address for the data to be associated with the command.
Minimum number of seconds to wait before polling with this command.
Number of data word values to be considered by the function.
Swap type code for command: Always zero (0).
Address of unit to reach on the data highway.
Processor slot number in Control/CompactLogix rack.
Use -1 for PLC5 & SLC processors.
Read-Modify-Write Command.
PLC-5 file number to be associated with the command.
If a value of -1 is entered for the parameter, the field will not be used in the command, and the default file will be used.
The parameter defines the element in the file where write operation will start. If a value of -1 is entered for the parameter, the field will not be used in the command, and the default element will be used.
This parameter defines the sub-element for the command. Refer to the AB documentation for a list of valid sub-element codes. If the value is set to -1, the default sub-element number will be used.
This field is not used by the command. Values entered in this column will be ignored.
Parameter
P1
P2
P3
P4
This function writes one or more words of data to a PLC data table. This function should work on the following devices: PLC-5. The command constructed contains an AND mask and an OR mask. Values in the AND mask have the following definitions: 0=Reset and 1=Leave the Same. Values in the OR mask have the following definitions: 0=Leave the Same and 1=Set. The module is responsible for setting the mask values to correctly construct the message from the virtual database values.
ProSoft Technology, Inc.
July 24, 2013
Page 77 of 124
Reference
Protocol Manual
DFNT ♦ ProLinx Gateway
EtherNet/IP Explicit Messaging Client/Server
5.2.9 Function Code #150 - Word Range Write (PLC-5 Command)
(ASCII Address)
Column Parameter
1 Enable/Type Word
2 Virtual Database Address
3
4
5
8
9
6
7
10 to 12
Poll Interval
Count
Swap Type Code
Node Address
Slot Number
Function Code = 150
File String
Not Used
Description
0=Disabled, 1=Continuous and 2=Conditional.
This parameter defines the database address of the first data point to be associated with the command.
Minimum time in tenths of a second to wait before polling with this command.
Number of data word values to be considered by the function.
Swap type code for command: 0=None, 1=Swap words,
2=Swap words & bytes and 3=swap bytes in each word.
Address of unit to reach on the data highway.
Processor slot number in Control/CompactLogix rack.
Use -1 for PLC5 & SLC processors.
Word Range Write Command.
PLC-5 address as specified as an ASCII string. For example, N10:300.
These fields are not used by the command. Values entered in these columns will be ignored.
Parameter
P1
P2 to P4
This function writes one or more words of data to a PLC data table. This function should work on the following devices: PLC-5.
5.2.10 Function Code #151 - Word Range Read (PLC-5 Command)
(ASCII Address)
Column Parameter
1 Enable/Type Word
2 Virtual Database Address
3
4
5
8
9
6
7
10 to 12
Poll Interval
Count
Swap Type Code
Node Address
Slot Number
Function Code = 151
File String
Not Used
Description
0=Disabled and 1=Continuous.
This parameter defines the database address of the first data point to be associated with the command.
Minimum time in tenths of a second to wait before polling with this command.
Number of data word values to be considered by the function.
Swap type code for command: 0=None, 1=Swap words,
2=Swap words & bytes and 3=swap bytes in each word.
Address of unit to reach on the data highway.
Processor slot number in Control/CompactLogix rack.
Use -1 for PLC5 & SLC processors.
Word Range Read Command.
PLC-5 address as specified as an ASCII string. For example, N10:300.
These fields are not used by the command. Values entered in these columns will be ignored.
Parameter
P1
P2 to P4
This function reads one or more words of data from a PLC data table. This function should work on the following devices: PLC-5.
Page 78 of 124 ProSoft Technology, Inc.
July 24, 2013
DFNT ♦ ProLinx Gateway
EtherNet/IP Explicit Messaging Client/Server
Reference
Protocol Manual
5.2.11 Function Code #152 - Read-Modify-Write (PLC-5 Command)
(ASCII Address)
Column Parameter
1 Enable/Type Word
2 Virtual Database Address
3 Poll Interval
Description
0=Disabled, 1=Continuous and 2=Conditional.
This parameter defines the database address for the data to be associated with the command. The first database register is used as the AND mask for the command, and the second is used for the OR mask.
Values in the AND mask have the following definitions:
0=Reset and 1=Leave the Same. Values in the OR mask have the following definitions: 0=Leave the Same and 1=Set.
Minimum time in tenths of a second to wait before polling with this command.
Parameter
4 Count Number of data word values to be considered by the function.
5
6
Swap Type Code
Node Address
Swap type code for command: Always zero (0).
Address of unit to reach on the data highway.
7
8
9
10 to 12
Slot Number
Function Code = 152
File String
Not Used
Processor slot number in Control/CompactLogix rack.
Use -1 for PLC5 & SLC processors.
Read-Modify-Write Command.
PLC-5 address as specified as an ASCII string. For example, N10:300.
These fields are not used by the command. Values entered in these columns will be ignored.
P1
P2 to P4
This function writes one or more words of data to a PLC data table. This function should work on the following devices: PLC-5. The command constructed contains an AND mask and an OR mask. Values in the AND mask have the following definitions: 0=Reset and 1=Leave the Same. Values in the OR mask have the following definitions: 0=Leave the Same and 1=Set. The module is responsible for setting the mask values to correctly construct the message from the virtual database values.
ProSoft Technology, Inc.
July 24, 2013
Page 79 of 124
Reference
Protocol Manual
DFNT ♦ ProLinx Gateway
EtherNet/IP Explicit Messaging Client/Server
5.2.12 Function Code #501 - Protected Typed Logical Read (Two
Address Fields)
Column Parameter
1 Enable/Type Word
2 Virtual Database Address
3
4
5
8
9
6
7
10
11
12
Poll Interval
Count
Swap Type Code
Node Address
Slot Number
Function Code = 501
File Type
File Number
Element Number
Not Used
Description
0=Disabled and 1=Continuous.
This parameter defines the database address of the first data point to be associated with the command.
Minimum number of seconds to wait before polling with this command.
Number of data word values to be considered by the function.
Swap type code for command: 0=None, 1=Swap words,
2=Swap words & bytes and 3=swap bytes in each word.
Address of unit to reach on the data highway.
Processor slot number in Control/CompactLogix rack.
Use -1 for PLC5 & SLC processors.
Logical Read Command
SLC file type letter as used in file name string. Valid values for the system are N, S, F, A, ….
P1
SLC file number to be associated with the command. P2
The parameter defines the element in the file where write operation will start.
P3
This field is not used by the command. Values entered in this column will be ignored.
P4
Parameter
This function reads one or more words of data from a PLC data table.
Page 80 of 124 ProSoft Technology, Inc.
July 24, 2013
DFNT ♦ ProLinx Gateway
EtherNet/IP Explicit Messaging Client/Server
Reference
Protocol Manual
5.2.13 Function Code #502 - Protected Typed Logical Read (Three
Address Fields)
Column Parameter
1 Enable/Type Word
2 Virtual Database Address
3
4
5
8
9
6
7
10
11
12
Poll Interval
Count
Swap Type Code
Node Address
Slot Number
Function Code = 502
File Type
File Number
Element Number
Sub-Element Number
Description
0=Disabled and 1=Continuous.
This parameter defines the database address of the first data point to be associated with the command.
Minimum number of seconds to wait before polling with this command.
Number of data word values to be considered by the function.
Swap type code for command: 0=None, 1=Swap words,
2=Swap words & bytes and 3=swap bytes in each word.
Address of unit to reach on the data highway.
Processor slot number in Control/CompactLogix rack.
Use -1 for PLC5 & SLC processors.
Logical Read Command
SLC file type letter as used in file name string. Valid values for the system are N, S, F, A, ….
P1
SLC file number to be associated with the command. P2
The parameter defines the element in the file where write operation will start.
P3
This parameter defines the sub-element for the command. Refer to the AB documentation for a list of valid sub-element codes.
P4
Parameter
This function reads one or more words of data from a PLC data table. This function should work on the following devices: SLC 500, SLC 5/03 and SLC 5/04.
ProSoft Technology, Inc.
July 24, 2013
Page 81 of 124
Reference
Protocol Manual
DFNT ♦ ProLinx Gateway
EtherNet/IP Explicit Messaging Client/Server
5.2.14 Function Code #509 - Protected Typed Logical Write (Two
Address Fields)
Column Parameter
1 Enable/Type Word
2 Virtual Database Address
3
4
5
8
9
6
7
10
11
12
Poll Interval
Count
Swap Type Code
Node Address
Slot Number
Function Code = 509
File Type
File Number
Element Number
Not Used
Description
0=Disabled, 1=Continuous and 2=Conditional.
This parameter defines the database address of the first data point to be associated with the command.
Minimum time in tenths of a second to wait before polling with this command.
Number of data word values to be considered by the function.
Swap type code for command: 0=None, 1=Swap words, 2=Swap words & bytes and 3=swap bytes in each word.
Address of unit to reach on the data highway.
Processor slot number in Control/CompactLogix rack.
Use -1 for PLC5 & SLC processors.
Logical Write Command
SLC file type letter as used in file name string. Valid values for the system are N, S, F, A, ….
P1
SLC file number to be associated with the command. P2
The parameter defines the element in the file where write operation will start.
P3
This field is not used by the command. Values entered in this column will be ignored.
P4
Parameter
This function writes one or more words of data to a PLC data table.
Page 82 of 124 ProSoft Technology, Inc.
July 24, 2013
DFNT ♦ ProLinx Gateway
EtherNet/IP Explicit Messaging Client/Server
Reference
Protocol Manual
5.2.15 Function Code #510 - Protected Typed Logical Write (Three
Address Fields)
Column Parameter
1 Enable/Type Word
2 Virtual Database Address
3
4
5
8
9
6
7
10
11
12
Poll Interval
Count
Swap Type Code
Node Address
Slot Number
Function Code = 510
File Type
File Number
Element Number
Sub-Element Number
Description
0=Disabled, 1=Continuous and 2=Conditional.
This parameter defines the database address of the first data point to be associated with the command.
Minimum time in tenths of a second to wait before polling with this command.
Number of data word values to be considered by the function.
Swap type code for command: 0=None, 1=Swap words,
2=Swap words & bytes and 3=swap bytes in each word.
Address of unit to reach on the data highway.
Processor slot number in Control/CompactLogix rack.
Use -1 for PLC5 & SLC processors.
Logical Write Command
SLC file type letter as used in file name string. Valid values for the system are N, S, F, A, ….
P1
SLC file number to be associated with the command. P2
The parameter defines the element in the file where write operation will start.
P3
This parameter defines the sub-element for the command. Refer to the AB documentation for a list of valid sub-element codes.
P4
Parameter
This function writes one or more words of data to a PLC data table. This function should work on the following devices: SLC 500, SLC 5/03 and SLC 5/04.
ProSoft Technology, Inc.
July 24, 2013
Page 83 of 124
Reference
Protocol Manual
DFNT ♦ ProLinx Gateway
EtherNet/IP Explicit Messaging Client/Server
5.2.16 Function Code #511 - Protected Typed Logical Write with Mask
(Three Address Fields)
3
4
5
6
7
8
9
Column Parameter
1 Enable/Type Word
2 Virtual Database Address
10
11
12
Poll Interval
Count
Swap Type Code
Node Address
Slot Number
Function Code = 511
File Type
File Number
Element Number
Sub-Element Number
Description
0=Disabled, 1=Continuous and 2=Conditional.
This parameter defines the database address of the data to be associated with the command. The first word of data contains the bit mask and the second word contains the data.
Minimum time in tenths of a second to wait before polling with this command.
Number of data word values to be considered by the function.
Swap type code for command: Always zero (0).
Address of unit to reach on the data highway.
Processor slot number in Control/CompactLogix rack.
Use -1 for PLC5 & SLC processors.
Logical Write with mask
SLC file type letter as used in file name string. Valid values for the system are N, S, F, A, ….
P1
SLC file number to be associated with the command. P2
The parameter defines the element in the file where write operation will start.
P3
This parameter defines the sub-element for the command. Refer to the AB documentation for a list of valid sub-element codes.
P4
Parameter
This function writes one or more words of data from a PLC data table controlling individual bits in the table. The bit mask used for the command is 0xFFFF. This provides direct manipulation of the data in the device with the internal data of the module. The function requires that all data associated with the command use the same mask.
Page 84 of 124 ProSoft Technology, Inc.
July 24, 2013
DFNT ♦ ProLinx Gateway
EtherNet/IP Explicit Messaging Client/Server
5.3 PLC-5 Processor Specifics
Reference
Protocol Manual
This section contains information specific to the PLC-5 processor with relation to the DF1 command set. The commands specific to the PLC-5 processor contain a sub-element code field. This field selects a sub-element field in a complex data table. For example, to obtain the current accumulated value for a counter or timer, the sub-element field should be set to 2. The tables below show the subelement codes for PLC-5 complex data tables.
5.3.1 PLC-5 Sub-Element Codes
Timer / Counter
Code
0
1
2
Description
Control
Preset
Accumulated
Control
Code
0
1
2
Description
Control
Length
Position
BT
Code
0
1
2
3
4
5
PD*
Code
0
2
4
Description
Control
SP
Kp
6
8
Ki
Kd
26 PV
*All PD values are floating point values, so they are two words long.
Description
Control
RLEN
DLEN
Data file #
Element #
Rack/Grp/Slot
ProSoft Technology, Inc.
July 24, 2013
Page 85 of 124
Reference
Protocol Manual
MG
Code
0
1
2
3
Description
Control
Error
RLEN
DLEN
DFNT ♦ ProLinx Gateway
EtherNet/IP Explicit Messaging Client/Server
Page 86 of 124 ProSoft Technology, Inc.
July 24, 2013
DFNT ♦ ProLinx Gateway
EtherNet/IP Explicit Messaging Client/Server
5.4 SLC Processor Specifics
Reference
Protocol Manual
This section contains information specific to the SLC processor based family when used with the DF1 command set. The SLC processor commands support a file type field entered as a single character to denote the data table to interface with in the command. The following table defines the relationship of the file types accepted by the module and the SLC file types:
5.4.1 SLC File Types
N
F
Z
A
File Type
S
B
T
C
R
Description
Status
Bit
Timer
Counter
Control
Integer
Floating-point
String
ASCII
The File Type Command Code is the ASCII character code value of the File Type letter. This is the value to enter into the "File Type" parameter of the DF1
Command configurations in the data tables in the ladder logic.
Additionally, the SLC specific functions (502, 510 and 511) support a subelement field. This field selects a sub-element field in a complex data table. For example, to obtain the current accumulated value for a counter or timer, the subelement field should be set to 2.
ProSoft Technology, Inc.
July 24, 2013
Page 87 of 124
Reference
Protocol Manual
5.5 MicroLogix Processor Specifics
DFNT ♦ ProLinx Gateway
EtherNet/IP Explicit Messaging Client/Server
This section contains information specific to the MicroLogix processor based family when used with the DF1 command set. The MicroLogix processor commands support a file type field entered as a single character to denote the data table to interface with in the command. This field is the same as that used for a SLC processor. The following table defines the relationship of the file types accepted by the module and the SLC file types:
5.5.1 SLC File Types
R
N
F
Z
A
File Type
S
B
T
C
Description
Status
Bit
Timer
Counter
Control
Integer
Floating-point
String
ASCII
The File Type Command Code is the ASCII character code value of the File Type letter. This is the value to enter into the "File Type" parameter of the DF1
Command configurations in the data tables in the ladder logic.
Additionally, the SLC specific functions (502, 510 and 511) support a subelement field. This field selects a sub-element field in a complex data table. For example, to obtain the current accumulated value for a counter or timer, the subelement field should be set to 2.
Page 88 of 124 ProSoft Technology, Inc.
July 24, 2013
DFNT ♦ ProLinx Gateway
EtherNet/IP Explicit Messaging Client/Server
5.6 ControlLogix Processor Specifics
Reference
Protocol Manual
This section contains information specific to the ControlLogix processor when used with the DF1 command set. The current implementation of the DF1 command set does not use functions that can directly interface with the
ControlLogix Tag Database. In order to interface with this database, the tablemapping feature provided by RSLogix 5000 must be used. The software permits the assignment of ControlLogix Tag Arrays to virtual PLC 5 data tables. The
ProSoft module using the PLC 5 command set defined in this document can then reach this controller data.
ProSoft Technology, Inc.
July 24, 2013
Page 89 of 124
Reference
Protocol Manual
5.7 RSLinx Software
DFNT ♦ ProLinx Gateway
EtherNet/IP Explicit Messaging Client/Server
RSLinx is used by many personal computer-based applications to interface with
Rockwell Automation products. For example, RSView requires the use of RSLinx for communication to remote nodes on a network. The following procedure is recommended for accessing the DFNT database using RSLinx version 2.54, or higher.
1 Start RSLinx software.
2 Open the C OMMUNICATIONS menu, and then select C ONFIGURE D RIVERS . This action opens the C ONFIGURE D RIVERS dialog box.
3 Click the arrow to the right of the Available Driver Types field, and then select
E THER N ET /IP D RIVER from the dropdown list.
Page 90 of 124 ProSoft Technology, Inc.
July 24, 2013
DFNT ♦ ProLinx Gateway
EtherNet/IP Explicit Messaging Client/Server
Reference
Protocol Manual
4 Click the A DD /N EW button, and then click OK in the A DD N EW RSL INX D RIVER dialog box.
5 In the C ONFIGURE D RIVER dialog box, make sure the Browse Local Subnet item is selected.
6 Make sure the B ROWSE L OCAL S UBNET item is selected. RSLinx software will browse your local subnet and retrieve the IP address.
ProSoft Technology, Inc.
July 24, 2013
Page 91 of 124
Reference
Protocol Manual
DFNT ♦ ProLinx Gateway
EtherNet/IP Explicit Messaging Client/Server
7 Click OK to save your settings and dismiss the C ONFIGURE D RIVER dialog box. The new driver will appear in the list of configured drivers.
8 Close RSLinx software.
Page 92 of 124 ProSoft Technology, Inc.
July 24, 2013
DFNT ♦ ProLinx Gateway
EtherNet/IP Explicit Messaging Client/Server
5.7.1 DDE Connection
Reference
Protocol Manual
This section discusses setting up a DDE connection to the module in order to transfer data between the module and a DDE compliant application.
Each DDE connection requires three basic elements: Application, Topic and
Item. These three properties of a DDE link define the program providing the connection, the topic to connect to and the item in the topic that you wish to interface. All three are required for a connection. For this discussion, the
Application will always be RSLinx. The Topic is defined in the RSLinx OEM release software and the Item is defined in the DDE client application where the data is required. The link between the DDE server and the DDE client can be established after these parameters are defined. The following illustration shows the relationship of these elements and the facilities used in the DDE link.
1 The DDE Client application specifies the DDE link by specifying the
APPLICATION, TOPIC, and ITEM elements. For example, in Excel, enter
=RSLINX|CIP_Sample! 'ReadData[0]' into a cell.
2 RSLinx is the DDE Server: APPLICATION = RSLINX.
And
RSLinx defines the TOPIC.
This is the communication link to the DFNT module. In this example, a DDE
TOPIC is called "CIP_Sample" for the communication link to the DFNT module.
3 The DFNT module is used to serve data to RSLinx using the EtherNet/IP driver with explicit messaging. Database is accessed using tag names (e.g.
ReadData[0]).
ProSoft Technology, Inc.
July 24, 2013
Page 93 of 124
Reference
Protocol Manual
DFNT ♦ ProLinx Gateway
EtherNet/IP Explicit Messaging Client/Server
As discussed in the previous section, RSLinx must be used to define the Topic element for the DDE link definition. This is accomplished using the following procedure. It is assumed that the module can be seen in the RSLinx software.
Refer to the RSLinx section of this manual to set up this connection. To define a new Topic, select the T OPIC C ONFIGURATION option on the DDE/OPC menu from the RSLinx Main Menu. This causes the following dialog box to appear:
Page 94 of 124 ProSoft Technology, Inc.
July 24, 2013
DFNT ♦ ProLinx Gateway
EtherNet/IP Explicit Messaging Client/Server
Click the N EW button to add a new Topic to the T OPIC L IST . This displays a default name. Edit the Topic name for the link to be formed. This name should reflect the unit or location to which the connection is being made. Do not press the Enter key. Instead, double-click the mouse on the DFNT device you want to connect to the entered Topic name. The dialog should now appear as follows:
Reference
Protocol Manual
Now select the D ATA C OLLECTION tab on the dialog box. Fill in the form to define the characteristics of the DDE link. The following screen shows an example:
ProSoft Technology, Inc.
July 24, 2013
Page 95 of 124
Reference
Protocol Manual
DFNT ♦ ProLinx Gateway
EtherNet/IP Explicit Messaging Client/Server
You must set the P ROCESSOR T YPE to Logix5000. Refer to the RSLinx on-line help for a discussion of each of the parameters on the form. Next select the
A DVANCED C OMMUNICATION tab on the dialog box. The following is displayed after selecting the tab.
The C OMMUNICATION D RIVER should be set to the ETHIP driver. Make sure the
L OCAL option is selected in the L OCAL OR R EMOTE A DDRESSING section of the dialog box. You should not have to alter any data on this tab, as RSLinx knows the communication path. Now click the A PPLY button to implement the options and to establish the topic.
You are now ready to use the DDE link in a DDE client application. The following example shows how to define a DDE link in an Excel Spreadsheet. It is also possible to define a DDE link in a Visual Basic program. Any other Windows DDE client application could be used including SoftLogix and RSSql.
Defining a DDE link in Excel
This is the simplest DDE link to define and should be used to make sure the
Topic is defined correctly before using more advanced applications. Before attempting to make the link, verify that RSLinx is running and that the DFNT module is seen. To make a DDE link in Excel, enter the application, topic and item elements as a formula into a cell. The format for the formula is as follows:
=APPLICATION|TOPIC!ITEM
The "|" character (piping symbol) separates the application and topic fields and the "!" (exclamation symbol) separates the topic and item fields. For our example topic of ProLinx1, the entry into the cell is:
=RSLinx|CIP_Sample!'RealData[500]'
Page 96 of 124 ProSoft Technology, Inc.
July 24, 2013
DFNT ♦ ProLinx Gateway
EtherNet/IP Explicit Messaging Client/Server
Reference
Protocol Manual
This causes the current value at the database double-word offset 500 (starting at word address 1000) in the DFNT module to be displayed in the cell as a floatingpoint value. This value updates at the frequency defined in the Topic configuration in RSLinx. You can now place any database point in the DFNT module using the same procedure in your work sheet. Note that the tag array name is used for the item property and must be enclosed within the quote marks.
This is because the tag array name item reference looks like an Excel work sheet reference. If you do not include the quotes, a formula error occurs. You can select any of the defined tag array names defined in the module on your spreadsheet.
When the items are used for the topic, RSLinx displays the following after selecting the Active Topic/Items command on the DDE/OPC menu option:
Any DDE compliant program can be used in the same manner. For maximum utility Visual Basic applications can be used to interface with module’s database using DDE connectivity.
5.7.2 OPC Connection
This section discusses setting up an OPC connection to the module in order to transfer data between the module and an OPC compliant client. Follow the instructions for setting up the DDE connection outlined in the previous section.
This will define the connection required by the OPC server. RSLinx will now be configured to interface with an OPC client application.
The example used in this section uses the OPC test client (opctest.exe) available from Rockwell Automation. Fir st start the application and select the Connect… option from the Server Menu. In the dialog box shown, select the RSLinx OPC server. Next add a group using the Group menu option and fill in the Group
Name using any name that is meaningful for the points to be monitored and controlled. The following dialog displays an example:
ProSoft Technology, Inc.
July 24, 2013
Page 97 of 124
Reference
Protocol Manual
DFNT ♦ ProLinx Gateway
EtherNet/IP Explicit Messaging Client/Server
Next, add items to the client. The following shows an example dialog used to add a floating-point data item:
It is important to set the Access Path value to the Topic name assigned in
RSLinx and to set the Item Name to a valid controller tag in the DFNT module.
The Datatype parameter must be set to match that of the controller tag. In the example shown, the VT_R4 data type is selected for the floating-point tag. The
Validate button can be used to verify that the point is valid in the OPC server.
After configuring the new data item, click OK to add the point. The following illustration shows the new item and event windows.
Page 98 of 124 ProSoft Technology, Inc.
July 24, 2013
DFNT ♦ ProLinx Gateway
EtherNet/IP Explicit Messaging Client/Server
You have now connected an OPC client to data in the DFNT module. In order to change the value for the item, select the Sync Write option from the Item menu and enter a new value as shown in the following dialog box:
Reference
Protocol Manual
Click OK to transfer the new value to the module. The following illustration shows the updated item data window.
ProSoft Technology, Inc.
July 24, 2013
Page 99 of 124
Reference
Protocol Manual
5.8 RSView Software
DFNT ♦ ProLinx Gateway
EtherNet/IP Explicit Messaging Client/Server
RSView is a client application for building user interfaces to control systems. This tool requires RSLinx to be loaded and operational (refer to the RSLinx section of this document). In order to interface RSView to a DFNT module, the following steps are required:
First select the C HANNEL option from the E DIT M ODE tab as shown in the following window.
After selecting the option, the following dialog box is displayed:
Select the N ETWORK T YPE and P RIMARY C OMMUNICATION D RIVER for the channel to be associated with the DFNT module. The N ETWORK T YPE should be TCP/IP and the P RIMARY C OMMUNICATION D RIVER name should match that set up in
RSLinx. Click OK to save the information.
Page 100 of 124 ProSoft Technology, Inc.
July 24, 2013
DFNT ♦ ProLinx Gateway
EtherNet/IP Explicit Messaging Client/Server
Next select the N ODE option from the E DIT M ODE tab. After selecting the option, the following dialog box is displayed:
Reference
Protocol Manual
Enter a record in the dialog box for the DFNT module to be addressed. The
N AME field identifies the module to the RSView system. The C HANNEL parameter should be that defined in the channel set up defined above. The S TATION parameter should be set to the IP address of the DFNT module. Select the
C LOSE button after completing the node entry. If your version of the RSView supports ControlLogix controller tag read and write operations, select the device type consistent with the ControlLogix processor. This will permit direct access to the controller tags simulated in the module. Use of controller tags simplifies handling of the data in RSView as the data will be passing in the correct data format (that is, bit, word, float).
ProSoft Technology, Inc.
July 24, 2013
Page 101 of 124
Reference
Protocol Manual
DFNT ♦ ProLinx Gateway
EtherNet/IP Explicit Messaging Client/Server
Next select the T AG D ATABASE option from the E DIT M ODE tab. After selecting the option, the following dialog box is displayed:
Set up tags for each element to be transferred between RSView and the DFNT module. In the example above, D ATA 1 is associated with the first element in the
DFNT module’s database (N10:0). A tag should be setup for each register in the module’s database to be interfaced. If RSView is set in run mode, values for the tags should match those in the module’s database. Use the module controller tag names if using CIP data table read and write operations.
Refer to the RSView documentation for a full discussion of database tags and reading and writing data between RSView and a processor.
Page 102 of 124 ProSoft Technology, Inc.
July 24, 2013
DFNT ♦ ProLinx Gateway
EtherNet/IP Explicit Messaging Client/Server
5.9 ControlLogix (CLX) Processor
Reference
Protocol Manual
In order to exchange data between a ControlLogix processor and the module, the
MSG instruction is used. There are two basic methods of data transfer supported by the module when using the MSG instruction: Encapsulated PCCC messages and CIP Data Table messages. Either method can be used, and the selection is left to the application developer.
5.9.1 Encapsulated PCCC Messages
PLC5 and SLC5/05 processors containing an Ethernet interface use the encapsulated PCCC message method. The module simulates these devices and accepts both read and write commands. The following topics describe the support for the read and write operations.
Encapsulated PCCC Write Message
Write commands transfer data from the ControlLogix processor to the module.
The following encapsulated PCCC commands are supported from a ControlLogix
Processor:
PLC2 Unprotected Write
PLC5 Typed Write
PLC5 Word Range Write
PLC Typed Write
An example rung used to execute a write command is shown in the following diagram:
The M ESSAGE C ONFIGURATION dialog box must be completed to define the data set to be transferred from the processor to the module. An example of the dialog box follows:
ProSoft Technology, Inc.
July 24, 2013
Page 103 of 124
Reference
Protocol Manual
DFNT ♦ ProLinx Gateway
EtherNet/IP Explicit Messaging Client/Server
Complete the dialog box for the data area to be transferred. For PLC5 and SLC messages, the D ESTINATION E LEMENT should be an element in a data file (such as, N10:0). For the PLC2 Unprotected Write message, the D ESTINATION E LEMENT is the ad dress in the module’s internal database and cannot be set to a value less than ten. This is not a limitation of the module but of the RSLogix software.
For a PLC2 unprotected write or read function, the database address should be entered in octal format. Additionally, the C OMMUNICATION information must also be configured. The following is an example of the dialog box.
Verify that the CIP radio-button is selected as the C OMMUNICATION M ETHOD . The
P ATH specifies the message route from the ControlLogix processor to the DFNT module. Path elements are separated by commas. In the example path shown, the first element is "Enet", which is the user-defined name given to the 1756-
ENET module in the chassis (you could substitute the slot number of the ENET module for the name), the second element, "2", represents the Ethernet port on the 1756-ENET module, and the last element of the path, "192.168.0.75", is the
IP address of the DFNT module, the target for the message.
More complex paths are possible if routing to other networks using multiple 1756-
ENET modules and racks. Refer to the Rockwell Automation Support
Knowledgebase for more information on Ethernet routing and path definitions.
Page 104 of 124 ProSoft Technology, Inc.
July 24, 2013
DFNT ♦ ProLinx Gateway
EtherNet/IP Explicit Messaging Client/Server
Encapsulated PCCC Read Message
Reference
Protocol Manual
Read commands transfer data from the module to a ControlLogix processor. The following encapsulated PCCC commands are supported from a ControlLogix
Processor:
PLC2 Unprotected Read
PLC5 Typed Read
PLC5 Word Range Read
PLC Typed Read
An example rung used to execute a read command is shown in the following diagram:
The M ESSAGE C ONFIGURATION dialog box must be completed to define the data set to transfer to the processor from the module. An example of the dialog box follows:
ProSoft Technology, Inc.
July 24, 2013
Page 105 of 124
Reference
Protocol Manual
DFNT ♦ ProLinx Gateway
EtherNet/IP Explicit Messaging Client/Server
Complete the dialog box for the data area to be transferred. For PLC5 and SLC messages, the S OURCE E LEMENT should be an element in a data file (such as,
N10:0). For the PLC2 Unprotected Read message, the S OURCE E LEMENT is the address in the module’s internal database and cannot be set to value less than ten. This is not a limitation of the module but of the RSLogix software.
Additionally, the C OMMUNICATION information must also be configured. An example of the dialog box follows:
Verify that the CIP radio-button is selected as the C
OMMUNICATION
M
ETHOD
. The
P ATH specifies the message route from the ControlLogix processor to the DFNT module. Path elements are separated by commas. In the example path shown, the first element is "Enet", which is the user-defined name given to the 1756-
ENET module in the chassis (you could substitute the slot number of the ENET module for the name), the second element, "2", represents the Ethernet port on the 1756-ENET module, and the last element of the path, "192.168.0.75", is the
IP address of the DFNT module, the target for the message.
More complex paths are possible if routing to other networks using multiple 1756-
ENET modules and racks. Refer to the Rockwell Automation Support
Knowledgebase for more information on Ethernet routing and path definitions.
Page 106 of 124 ProSoft Technology, Inc.
July 24, 2013
DFNT ♦ ProLinx Gateway
EtherNet/IP Explicit Messaging Client/Server
5.9.2 CIP Data Table Operations
Reference
Protocol Manual
This method of data transfer uses CIP messages to transfer data between the
ControlLogix processor and the module. Tag names define the elements to be transferred. The following topics describe the support for the read and write operations.
CIP Data Table Write
CIP data table write messages transfer data from the ControlLogix processor to the DFNT module. An example rung used to execute a write command is shown in the following diagram:
The M ESSAGE C ONFIGURATION dialog box must be completed to define the data set to be transferred from the processor to the module. An example of the dialog box follows:
Complete the dialog box for the data area to be transferred. CIP Data Table messages require a tag database element for both the source and destination.
The S
OURCE
T
AG is a tag defined in the ControlLogix Tag database. The
D ESTINATION E LEMENT is the tag element in the DFNT module.
The module simulates a tag database as an array of elements defined by the maximum register size for the module (user configuration parameter "Maximum
Register" in the [Module] section) with the tag name INT _ DATA .
ProSoft Technology, Inc.
July 24, 2013
Page 107 of 124
Reference
Protocol Manual
DFNT ♦ ProLinx Gateway
EtherNet/IP Explicit Messaging Client/Server
In the previous example, the first element in the database is the starting location for the write operation of ten elements. Additionally, the C OMMUNICATION information must also be configured. An example of the dialog box follows:
Verify that the CIP radio-button is selected as the C OMMUNICATION M ETHOD . The
P ATH specifies the message route from the ControlLogix processor to the DFNT module. Path elements are separated by commas. In the example path shown, the first element is "Enet", which is the user-defined name given to the 1756-
ENET module in the chassis (you could substitute the slot number of the ENET module for the name), the second element, "2", represents the Ethernet port on the 1756-ENET module, and the last element of the path, "192.168.0.75", is the
IP address of the DFNT module, the target for the message.
More complex paths are possible if routing to other networks using multiple 1756-
ENET modules and racks. Refer to the Rockwell Automation Support
Knowledgebase for more information on Ethernet routing and path definitions.
CIP Data Table Read
CIP data table read messages transfer data to the ControlLogix processor from the DFNT module. An example rung used to execute a read command is shown:
Page 108 of 124 ProSoft Technology, Inc.
July 24, 2013
DFNT ♦ ProLinx Gateway
EtherNet/IP Explicit Messaging Client/Server
The M ESSAGE C ONFIGURATION dialog box must be completed to define the data set to transfer to the processor from the module. An example of the dialog box follows:
Reference
Protocol Manual
Complete the dialog box for the data area to be transferred. CIP Data Table messages require a tag database element for both the source and destination.
The D ESTINATION T AG is a tag defined in the ControlLogix Tag database. The
S OURCE E LEMENT is the tag element in the DFNT module. The module simulates a tag database as an array of elements defined by the maximum register size for the module (user configuration parameter "Maximum Register" in the [Module] section) with the tag name INT _ DATA .
In the example above, the first element in the database is the starting location for the read operation of ten elements.
Additionally, the C OMMUNICATION information must also be configured. An example of the dialog box follows:
Page 109 of 124 ProSoft Technology, Inc.
July 24, 2013
Reference
Protocol Manual
DFNT ♦ ProLinx Gateway
EtherNet/IP Explicit Messaging Client/Server
Verify that the CIP radio-button is selected as the C OMMUNICATION M ETHOD . The
P ATH specifies the message route from the ControlLogix processor to the DFNT module. Path elements are separated by commas. In the example path shown, the first element is "Enet", which is the user-defined name given to the 1756-
ENET module in the chassis (you could substitute the slot number of the ENET module for the name), the second element, "2", represents the Ethernet port on the 1756-ENET module, and the last element of the path, "192.168.0.75", is the
IP address of the DFNT module, the target for the message.
More complex paths are possible if routing to other networks using multiple 1756-
ENET modules and racks. Refer to the Rockwell Automation Support
Knowledgebase for more information on Ethernet routing and path definitions.
Page 110 of 124 ProSoft Technology, Inc.
July 24, 2013
DFNT ♦ ProLinx Gateway
EtherNet/IP Explicit Messaging Client/Server
5.10 PLC5 Processor
The module can be used to receive messages from a PLC5 containing an
Ethernet interface. The module supports both read and write commands. A discussion of each operation is provided in the following topics:
Reference
Protocol Manual
5.10.1 PLC5 Write Commands
Write commands transfer data from the PLC5 processor to the DFNT module. An example rung used to execute a write command is shown in the following diagram:
In order to complete the configuration of the MSG instruction, select the S ETUP
S CREEN area of the MSG object. This displays the following dialog box.
Select the C
OMMUNICATION
C
OMMAND
to execute from the following list of supported commands.
PLC5 Type Write
PLC2 Unprotected Write
PLC5 Typed Write to PLC
PLC Typed Logical Write
The T ARGET D EVICE D ATA T ABLE A DDRESS must be set to a valid file element
(such as, N11:0) for SLC and PLC5 messages. For the PLC2 Unprotected Write message, set the address to the database index (such as, 1000) to consider with the command.
ProSoft Technology, Inc.
July 24, 2013
Page 111 of 124
Reference
Protocol Manual
DFNT ♦ ProLinx Gateway
EtherNet/IP Explicit Messaging Client/Server
The M ULTI H OP option must be set to Y ES .
The M ULTI H OP tab portion of the dialog box must be completed as shown in the following window:
Set the IP address value to the module’s Ethernet IP address. You must press the "Insert" key to add the second line for ControlLogix Backplane and set the slot number to zero.
5.10.2 PLC5 Read Commands
Read commands transfer data to the PLC5 processor from the DFNT module. An example rung used to execute a read command is shown in the following diagram:
In order to complete the configuration of the MSG instruction, select the S ETUP
S CREEN area of the MSG object. This displays the following dialog box.
Select the C OMMUNICATION C OMMAND to execute from the following list of supported commands.
PLC5 Type Read
PLC2 Unprotected Read
PLC5 Typed Read to PLC
PLC Typed Logical Read
Page 112 of 124 ProSoft Technology, Inc.
July 24, 2013
DFNT ♦ ProLinx Gateway
EtherNet/IP Explicit Messaging Client/Server
Reference
Protocol Manual
The T ARGET D EVICE D ATA T ABLE A DDRESS must be set to a valid file element
(such as, N11:0) for SLC and PLC5 messages. For the PLC2 Unprotected Read message, set the address to the database index (such as, 1000) to consider with the command.
The M ULTI H OP option must be set to Y ES .
The M ULTI H OP tab portion of the dialog box must be completed as shown in the following window:
Set the IP address value to the module’s Ethernet IP address. You must press the "Insert" key to add the second line for ControlLogix Backplane and set the slot number to zero.
ProSoft Technology, Inc.
July 24, 2013
Page 113 of 124
Reference
Protocol Manual
5.11 SLC 5/05 Processor
DFNT ♦ ProLinx Gateway
EtherNet/IP Explicit Messaging Client/Server
The module can be used to receive messages from a SLC 5/05 containing an
Ethernet interface. The module supports both read and write commands. A discussion of each operation is provided in the following topics.
5.11.1 SLC5/05 Write Commands
Write commands transfer data from the SLC processor to the DFNT module. An example rung used to execute a write command is shown in the following diagram:
Set the R EAD /W RITE parameter to W RITE .
The module supports a T ARGET D EVICE parameter value of 500CPU or PLC5. In order to complete the configuration of the MSG instruction, select the S ETUP S CREEN area of the MSG object. This displays the following dialog box.
Page 114 of 124 ProSoft Technology, Inc.
July 24, 2013
DFNT ♦ ProLinx Gateway
EtherNet/IP Explicit Messaging Client/Server
The T ARGET D EVICE D ATA T ABLE A DDRESS must be set to a valid file element
(such as, N11:0) for SLC and PLC5 messages. The M ULTI H OP option must be set to Y ES .
The M ULTI H OP tab portion of the dialog box must be completed as displayed in the following window:
Reference
Protocol Manual
Set the IP address value to the module’s Ethernet IP address. You must press the "Insert" key to add the second line for ControlLogix Backplane and set the slot number to zero.
5.11.2 SLC5/05 Read Commands
Read commands transfer data to the SLC processor from the DFNT module. An example rung used to execute a read command is shown in the following diagram:
ProSoft Technology, Inc.
July 24, 2013
Page 115 of 124
Reference
Protocol Manual
DFNT ♦ ProLinx Gateway
EtherNet/IP Explicit Messaging Client/Server
Set the R EAD /W RITE parameter to R EAD .
The module supports a T ARGET D EVICE parameter value of 500CPU or PLC5. In order to complete the configuration of the MSG instruction, select the S ETUP S CREEN area of the MSG object. This displays the following dialog box.
The T ARGET D EVICE D ATA T ABLE A DDRESS must be set to a valid file element
(such as, N11:0) for SLC and PLC5 messages. The M ULTI H OP option must be set to Y ES .
Fill in the M
ULTI
H
OP tab portion of the dialog box as shown in the following illustration.
Set the IP address value to the module’s Ethernet IP address. You must press the "Insert" key to add the second line for ControlLogix Backplane and set the slot number to zero.
Page 116 of 124 ProSoft Technology, Inc.
July 24, 2013
DFNT ♦ ProLinx Gateway
EtherNet/IP Explicit Messaging Client/Server
5.12 DFNT Command Entry Form
Reference
Protocol Manual
The following form can be used to design the application’s command list:
Module Information Data
Column
#
1 2
Functio n Code
Enabl e
Code
Internal
Addres s
3
Poll
Interva l Time
4
Coun t
5
Swa p
Code
Device Information Data
6
IP
Addres s
7
Slot
Numbe r
IP Address = IP address of processor to reach
Slot Number = -1 for PLC5 & SLC, processor slot number of ControlLogix
8
Functio n Code
9 10 11 12
Function Parameters
ProSoft Technology, Inc.
July 24, 2013
Page 117 of 124
Reference
Protocol Manual
DFNT ♦ ProLinx Gateway
EtherNet/IP Explicit Messaging Client/Server
Page 118 of 124 ProSoft Technology, Inc.
July 24, 2013
DFNT ♦ ProLinx Gateway
EtherNet/IP Explicit Messaging Client/Server
Support, Service & Warranty
Protocol Manual
6 Support, Service & Warranty
In This Chapter
Contacting Technical Support ............................................................. 119
Return Material Authorization (RMA) Policies and Conditions ............. 120
Contacting Technical Support
ProSoft Technology, Inc. (ProSoft) is committed to providing the most efficient and effective support possible. Before calling, please gather the following information to assist in expediting this process:
1 Product Version Number
2 System architecture
3 Network details
If the issue is hardware related, we will also need information regarding:
1 Module configuration and associated ladder files, if any
2 Module operation and any unusual behavior
3 Configuration/Debug status information
4 LED patterns
5 Details about the serial, Ethernet or fieldbus devices interfaced to the module, if any.
Note: For technical support calls within the United States, an after-hours answering system allows
24-hour/7-days-a-week pager access to one of our qualified Technical and/or Application Support
Engineers.
ProSoft Technology, Inc.
July 24, 2013
Page 119 of 124
Support, Service & Warranty
Protocol Manual
Internet
DFNT ♦ ProLinx Gateway
EtherNet/IP Explicit Messaging Client/Server
Asia Pacific
(location in Malaysia)
Asia Pacific
(location in China)
Europe
(location in Toulouse,
France)
Europe
(location in Dubai, UAE)
North America
(location in California)
Web Site: www.prosoft-technology.com/support
E-mail address: [email protected]
Tel: +603.7724.2080, E-mail: [email protected]
Languages spoken include: Chinese, English
Tel: +86.21.5187.7337 x888, E-mail: [email protected]
Languages spoken include: Chinese, English
Tel: +33 (0) 5.34.36.87.20,
E-mail: [email protected]
Languages spoken include: French, English
Tel: +971-4-214-6911,
E-mail: [email protected]
Languages spoken include: English, Hindi
Tel: +1.661.716.5100,
E-mail: [email protected]
Languages spoken include: English, Spanish
Latin America
(Oficina Regional)
Latin America
(location in Puebla, Mexico)
Tel: +52-222-3-99-6565,
E-mail: [email protected]
Languages spoken include: Spanish
Brasil
(location in Sao Paulo)
Tel: +1-281-2989109,
E-Mail: [email protected]
Languages spoken include: Spanish, English
Tel: +55-11-5083-3776,
E-mail: [email protected]
Languages spoken include: Portuguese, English
6.1 Warranty Information
For complete details regarding ProSoft Technology’s TERMS & CONDITIONS
OF SALE, WARRANTY, SUPPORT, SERVICE AND RETURN MATERIAL
AUTHORIZATION INSTRUCTIONS please see the documents on the Product
CD/DVD or go to www.prosoft-technology/warranty
Documentation is subject to change without notice
Page 120 of 124 ProSoft Technology, Inc.
July 24, 2013
DFNT ♦ ProLinx Gateway
EtherNet/IP Explicit Messaging Client/Server
Support, Service & Warranty
Protocol Manual
ProSoft Technology, Inc.
July 24, 2013
Page 121 of 124
Support, Service & Warranty
Protocol Manual
DFNT ♦ ProLinx Gateway
EtherNet/IP Explicit Messaging Client/Server
Page 122 of 124 ProSoft Technology, Inc.
July 24, 2013
DFNT ♦ ProLinx Gateway
EtherNet/IP Explicit Messaging Client/Server
Index
[
[DFNT Client x Commands] • 35
[DFNT Client x] • 34
[DFNT UClient 0 Commands] • 43
[DFNT UClient 0] • 42
B
Base Module LEDs • 56
Basic Command Set Functions • 22, 36
Browsing the module using RSLinx • 28
BT • 85
C
CIP Data Table Operations • 107
CIP Data Table Read • 108
CIP Data Table Write • 107
Client Error/Status Data • 57
Command Entry Formats • 38, 40, 41
Command Function Codes • 70
Command List • 35
Configuring Module Parameters • 33
Configuring the Gateway • 31
Connecting Power to the Unit • 13
Contacting Technical Support • 119
Control • 85
ControlLogix (CLX) Processor • 103
ControlLogix Processor Specifics • 89
D
DDE Connection • 93
Defining a DDE link in Excel • 96
Delay Preset • 47
DF1 Pass-Through Server • 60
DFNT Client 0 (Command List Error Data) • 61
DFNT Client 0 Status • 57
DFNT Client 1 Through 4 Command List Error
Addresses • 61
DFNT Client 1 through 4 Status • 58
DFNT Command Entry Form • 117
DFNT EtherNet/IP Client Access to Database • 19
DFNT Server 0 • 59
DFNT Server Access to Database • 20
DFNT Servers 1 Through 4 • 59
Diagnostics and Troubleshooting • 51
Downloading the Project to the Module Using a Serial
COM port • 49
E
Encapsulated PCCC Messages • 103
Encapsulated PCCC Read Message • 105
Encapsulated PCCC Write Message • 103
Error Codes • 62
Errors When EXT STS Is Present • 64
Ethernet LED Indicators • 56
ProSoft Technology, Inc.
July 24, 2013
Index
Protocol Manual
Ethernet Port Configuration - wattcp.cfg • 48
EtherNet/IP (DFNT) Port • 17
EtherNet/IP (Explicit Messaging) Compatible Devices •
16
EtherNet/IP Client Command List Error Data • 61
EtherNet/IP Explicit Messaging Server Command
Support • 22
F
Forward Open Response Errors • 66
From Address • 45
Function Code #1 - Protected Write (Basic Command
Set) • 72
Function Code #100 - Word Range Write (PLC-5
Command) (Binary Address) • 75
Function Code #101 - Word Range Read (PLC-5
Command) (Binary Address) • 76
Function Code #102 - Read-Modify-Write (PLC-5
Command) (Binary Address) • 77
Function Code #150 - Word Range Write (PLC-5
Command) (ASCII Address) • 78
Function Code #151 - Word Range Read (PLC-5
Command) (ASCII Address) • 78
Function Code #152 - Read-Modify-Write (PLC-5
Command) (ASCII Address) • 79
Function Code #2 - Unprotected Read (Basic
Command Set) • 72
Function Code #3 - Protected Bit Write (Basic
Command Set) • 73
Function Code #4 - Unprotected Bit Write (Basic
Command Set) • 73
Function Code #5 - Unprotected Write (Basic
Command Set) • 74
Function Code #501 - Protected Typed Logical Read
(Two Address Fields) • 80
Function Code #502 - Protected Typed Logical Read
(Three Address Fields) • 81
Function Code #509 - Protected Typed Logical Write
(Two Address Fields) • 82
Function Code #510 - Protected Typed Logical Write
(Three Address Fields) • 83
Function Code #511 - Protected Typed Logical Write with Mask (Three Address Fields) • 84
Functional Overview • 15
G
General Command Structure • 71
H
How to Contact Us • 2
I
Important Installation Instructions • 3
Installing ProSoft Configuration Builder Software • 14
Installing the .EDS file with RSLinx • 24
K
Keystrokes • 55
Page 123 of 124
Index
Protocol Manual
L
Local STS Error Codes • 62
M
MG • 86
MicroLogix Processor Specifics • 88
Minimum Command Delay • 34, 42
Module Internal Database • 19
Module Specific Error (not DFNT Compliant) • 65
Mounting the Module on the DIN-rail • 12
Moving Data • 45
N
Navigation • 54
O
OPC Connection • 97
Other Ethernet Services (HTTP/FTP) • 23
P
Package Contents • 11
PCCC Response Errors • 67
PD* • 85
Pinouts • 3
PLC-5 Command Set Functions • 22, 36
PLC5 Processor • 111
PLC-5 Processor Specifics • 85
PLC5 Read Commands • 112
PLC-5 Sub-Element Codes • 85
PLC5 Write Commands • 111
Printing a Configuration File • 33
ProLinx Gateways with Ethernet Ports • 3
ProLinx® Products Warnings • 3
ProSoft Technology® Product Documentation • 2
R
Reference • 69
Register Count • 45
Register Session Response Errors • 66
Remote STS Error Codes • 63
Renaming PCB Objects • 33
Required Hardware • 52
Response Timeout • 34, 42
Retry Count • 34, 42
RSLinx Software • 90
RSView Software • 100
S
Setting Up the Project • 31
SLC 5/05 Processor • 114
SLC File Types • 87, 88
SLC Processor Specifics • 87
SLC5/05 Read Commands • 115
SLC5/05 Write Commands • 114
SLC-500 Command Set Functions • 22, 37
Start Here • 9
Support, Service & Warranty • 119
Page 124 of 124
DFNT ♦ ProLinx Gateway
EtherNet/IP Explicit Messaging Client/Server
Swap Code • 45
System Requirements • 10
T
TCP/IP Interface Errors • 66
Timeout Errors • 66
Timer / Counter • 85
To Address • 45
To upgrade a previously purchased Series C model: •
3
U
Unconnected Msg DFNT Client 0 Status • 58
Using ProSoft Configuration Builder • 31
Using ProSoft Configuration Builder (PCB) for
Diagnostics • 52
Using the CommonNet Data Map • 44
Using the Diagnostic Window in ProSoft Configuration
Builder • 52
Using the Online Help • 14
W
Warranty Information • 120
Your Feedback Please • 2
Y
ProSoft Technology, Inc.
July 24, 2013
advertisement
Related manuals
advertisement
Table of contents
- 123 Your Feedback Please
- 123 How to Contact Us
- 123 Product Documentation
- 124 Important Installation Instructions
- 124 Products Warnings
- 124 ProLinx Gateways with Ethernet Ports
- 124 To upgrade a previously purchased Series C model
- 124 System Requirements
- 124 Package Contents
- 124 Mounting the Module on the DIN-rail
- 124 Using the Online Help
- 124 Module Internal Database
- 124 PLC-5 Command Set Functions
- 124 SLC-500 Command Set Functions
- 124 Other Ethernet Services (HTTP/FTP)
- 124 Using ProSoft Configuration Builder
- 124 Setting Up the Project
- 124 Renaming PCB Objects
- 124 Minimum Command Delay
- 124 Response Timeout
- 124 Retry Count
- 124 Minimum Command Delay
- 124 Response Timeout
- 124 Retry Count
- 123 Using the CommonNet Data Map
- 124 Moving Data
- 124 From Address
- 124 To Address
- 124 Register Count
- 124 Swap Code
- 124 Using ProSoft Configuration Builder (PCB) for Diagnostics
- 124 Required Hardware
- 124 Using the Diagnostic Window in ProSoft Configuration Builder
- 124 Navigation
- 124 Unconnected Msg DFNT Client 0 Status