advertisement
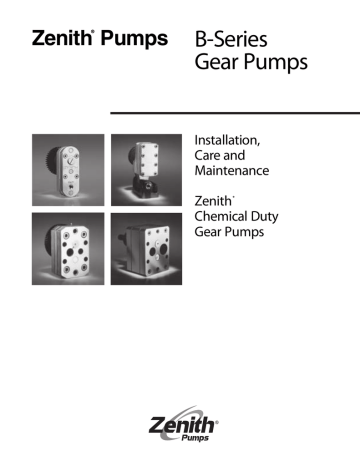
Zenith
®
Pumps B-Series
Gear Pumps
Installation,
Care and
Maintenance
Zenith
®
Chemical Duty
Gear Pumps
2
Zenith
®
Thoroughly read and understand this entire manual before installation and operation of pump.
In 1926, Zenith
® was approached by the synthetic fiber industry to design a pump to provide a precise, pulseless, repeatable flow and assure better quality control. The options then were the same as those in the chemical process industry today — diaphragm, lobe, coarse gear, piston, plunger and screw pumps. Each had problems with pulsation, flow inaccuracies, multiple seal areas and slippage, which required constant calibration, high maintenance and extended downtimes.
Zenith
® met the challenge and designed a rotary external gear pump of unique precision and simplicity. Manufacturing techniques were developed to hold tolerances to ±.00005", minimizing internal clearance to assure accurate and precise metering. The pump’s simplistic design of only three moving parts–two metering gears and a drive shaft–provided long life and easy maintenance.
For years since, chemical engineers have relied on Zenith
® to provide precision fluid handling solutions for their most difficult pumping applications. Zenith
® gear pumps can be found wherever precise, pulseless, repeatable metering of fluids is required.
Benefits
High Accuracy
Stable, repeatable flows are assured even under varying conditions of temperature, viscosity and pressure.
Minimum Pulsation
Unique design offers virtually pulseless flow without valves or flexible elements to hinder performance.
Precision Construction
Ground and lapped components and built-in dowels allow for close control of operating clearances.
High Volumetric Efficiency
Maximum efficiency is achieved with optimum operating clearances.
Corrosion Resistance
400 series stainless steel provides good bearing qualities and the necessary corrosion resistance for most standard chemical processes.
Maximum Life
Only three moving parts; components are through hardened to HRc 54 or better.
Specifications
Pump Type: Rotary external spur gear, single stream.
Rotation: See pump drawing.
Operating Speed: 3-180 rpm depending upon application conditions and fluid viscosity.
Temperature: To 300° F (150° C). Heat jacket required for above ambient temperatures.
Design
The B-Series pumps are constructed from cutlery grade 420 and 440C stainless steel. The pumps consist of two or three gears rotating in mesh within a closely fitted housing that is comprised of three plates. The center or gear plate fits closely around the outside diameter of the metering gears. The front and rear plates sandwich the gear plate and restrict axial movement of the gears. In the BPB, BMB, BLB, and BXB series, the gear set is comprised of a driving and a driven gear. The BMC series is comprised of a driving gear and two driven gears. In all series, the driving gear is keyed to the drive shaft while the driven gears ride on stationary arbors.
The B-Series pumps have two seal designs: a mechanical face seal and a lip seal (the BMB/BMC has only a lip seal). The standard seal is a single or double lip seal while the mechanical face seal is available as an option. The mechanical face seal design consists of a rotating universal seal coupling that acts as a coupling between the inner and outer drive shafts and, at the same time, seals against a fixed seal plate or anchor washer. The mechanical face seal is dependent upon sufficient inlet pressure
(usually 25-50 psi) to force the inner rotating coupling against the outer stationary anchor. This design is common in abrasive fluid applications.
Since the metal seal requires sufficient inlet or working pressure to be effective, a spring-loaded lip seal design is usually recommended. Pumps with lip seals normally will only require a flooded inlet.
The BPB pumps use a lip seal with an
“O” ring; the BMB/BMC pumps use a lip seal alone; and the BLB and BXB pumps use two lip seals. The Teflon lip seal with stainless steel spring is chemically inert and is most commonly used for general-purpose metering in a variety of applications.
All B-Series pumps (with the exception of the BXB) come equipped with an outer drive gear and drive strap. The
BXB Series is direct drive. The outer drive gear is meshed with a pinion gear mounted on the output shaft of a motor or gear box. The drive strap is incorporated into the design to act as the weak element in the pump. Should something go wrong in the process, such as line blockage, the increased back pressure will increase the amount of torque required to turn the pump. The drive strap is designed with a critical breaking torque that will allow it to fail before any excess stress is exerted on the internal pump parts. This protects the precision manufactured inner workings of the metering pump.
3
4
Operation
In the trunnion-ported BPB, BMB and
BMC pumps, fluid enters the pump at the outer drive gear side of the pump. A passage has been drilled from the inlet port up through the front plate into the center plate gear pocket. Fluid flows into the gear pocket and fills the gear tooth volumes. As the gears rotate, the fluid is transported around the outer diameter of the gear pocket to the discharge side.
As the gears mesh together, the fluid is displaced back down a passage drilled into the rear plate and out the discharge port at the rear side of the pump.
In rear-ported BPB, BLB and BXB pumps, fluid enters the pump through a port drilled into the rear side plate (the side opposite the outer drive gear/shaft).
The fluid again fills the exposed gear tooth volumes and is transported around the outer diameter of the gear pocket.
As the gears mesh, the fluid is displaced out through the discharge port that is drilled alongside the inlet port in the rear plate.
Since Zenith ® pumps are not selfpriming, a flooded suction is usually the minimum inlet pressure required. However, when high-viscosity fluids are used, more time is required to fill the tooth volumes. As a result, the inlet pressure must be increased or the gears must rotate at a slower speed to ensure complete volume filling and to prevent cavitation.
Zenith ® pumps rely on the metered fluid for lubrication of internal bearing areas. The pump should never be allowed to run dry or be allowed to run with non-lubricating fluids such as water.
Because of close clearances in the bearing areas, lack of sufficient lubrication can cause pump seizure and possibly catastrophic failure.
Under extreme conditions, slip may occur across the face of the gears from in between the high-pressure side to the low-pressure side. Pump efficiency depends on four factors: fluid viscosity, pump speed, differential pressure and gear clearances. Under reasonably stable operating conditions, slip is repeatable and predictable, and pump operation can be adjusted to compensate.
The Zenith ® B-Series pumps are designed for low-temperature operation.
As such, the maximum operating temperature should not exceed 300° F.
When operating at temperatures above ambient, heat jackets should be used, and pumps should be heated slowly and uniformly.
The 400-Series stainless steels used in the construction of the B-Series pumps provide sufficient corrosion resistance for most standard chemical processes. The material hardness will provide a high degree of wear resistance as well. However, processes involving corrosive or abrasive fluids should always be approved by Zenith ® .
Installation
Pumps should be carefully unpacked and checked to make sure that the shipment is complete. If any items are missing or damaged, the freight carrier and
Zenith ® should be notified immediately.
The following is a general installation procedure. For special applications, considerations, or simply to ask for advice, please contact our Applications
Engineering Group.
It is not recommended to flush downstream process equipment utilizing
Zenith ® precision metering pumps. Most fluids used as flushing agents, such as solvents and water, have a low viscosity and have poor lubricating qualities.
Catastrophic failure may occur under certain operating conditions. If it is necessary to flush the system, the following suggestions are recommended to prevent premature pump failure:
1) If possible, flush the system using a lubricating fluid.
2) Minimize the differential pressure across the pump ports to 25 psi.
3) Reduce the pump speed to an acceptable level (approximately 10 rpm).
4) Flush the pump for the shortest allowable time, yielding effective cleansing of the system, and no longer than necessary.
5) It is recommended to use a bypass around the pump as illustrated in
Figure A. This will allow for high velocity flushing of the system while minimizing risk to the metering pump. During the flush cycle, fluid will pass through and around the pump. This will allow the system to be flushed quickly and effectively.
Figure A
Pump
To prepare the pump for use:
1) Always flush out the plumbing system before connecting the pump.
2) Filters should be installed prior to the pump inlet and should filter ideally to half the pump gear clearances.
3) Turn pumps by hand before running.
Pumps should turn freely.
4) Pivot mount pumps should be mounted in the L-5677 mounting saddle, and the trunnions should be loosely tightened to support but not restrict movement of the pump. Fixed-mount pumps should be installed on an
L-shaped saddle, and mounting screws securely tightened.
5) Make certain that bearing grease has been applied between the hub and
Outer Drive Gear. If necessary, apply a suitable lubricant to the grease fitting located on the pump. Rotate the Outer
Drive Gear, by hand, to ensure that a layer of grease is evenly spread between the hub and outer drive gear bearing area. Pumps without a grease fitting do not require lubrication.
Note: Lubrication applied to a grease fitting will not lubricate internal bearings or come in contact with the pumped fluid.
6) Carefully mesh the outer drive gear with the drive pinion gear. A backlash of .005" is recommended. Trunnions can then be securely tightened.
7) Make sure the pump is primed before starting. Be sure to apply positive inlet pressure when metering high-viscosity fluids. Pumps with universal face seals require approximately 25-50 psi inlet pressure to seat the seal.
8) Start the pump slowly and, if possible, operate with a lubricating fluid.
9) When satisfactory operation is achieved, the pump and system may be gradually brought up to normal operating conditions.
10) If, at any time during operation, the pump does not appear to be running smoothly, stop the pump immediately to avoid serious internal damage.
Bypass
Valve
5
6
Cleaning,
Inspection and Repair
Zenith ® metering pumps are made for exacting duty. All parts are machined to extreme accuracy; critical dimensions are held between one and two tenthousandths of an inch (.0001"/.0002").
Accurate performance is dependent upon proper handling. Please treat them with care, and if it’s at all possible, set aside a separate clean area for pump maintenance.
It is recommended that pump users institute a program of dimensional inspection of critical parts in order to keep maintenance and operating costs at a minimum. By noting the performance of a pump immediately before removing it from service and correlating the performance to measured component wear, the user can establish the maximum wear limits for the pump’s critical components. Further, the service life of the pump can be predicted and downtime scheduled accordingly.
As with any other Zenith ® pump,
B-Series pumps may be returned to
Zenith ® for complete rehabilitation. This procedure may be desirable if only a few pumps are involved. If a large number of pumps are to be maintained at the user’s plant, it may be worthwhile to have key personnel attend a maintenance seminar at Zenith ® to learn the manufacturing, gauging, and assembly techniques involved in producing the
B-Series pump. In addition, Zenith ® also offers a contract service program. Please contact Zenith ® for further information on these items.
Remember: Zenith ® pumps are precision instruments. You can’t keep them too clean. The slightest bit of debris may cause damage.
Lapping
Or Blocking
Place two layers of 400-Grit Emery Cloth on a lapping block or plate–a granite flat is suitable. Apply light pressure to the component and turn it in a “Figure 8” pattern (as shown in Figure 1) approximately 10 times until a smooth finish appears. Components that are commonly lapped are the sides of metering gears and the inside faces of front, rear and center plates. The components are now ready to be cleaned. An ultrasonic cleaner with a safe industrial solvent (Nu solution) is preferred, but you may also use a large container filled with about four inches of solution.
Caution: Never drop the components into a tank or container; place them gently onto the bottom to avoid damage.
Always use clean, lint-free rags and compressed air to clean components.
Paper towels are not acceptable; they may leave small pieces of paper and dust on the components. Use chemical brushes to clean between gear teeth, bores and reliefs. Tooth brushes are not acceptable. After all components are
“hospital clean,” the pump is ready for assembly.
New parts should be deburred and cleaned using the above procedures.
*
*
*
*
*
Figure 1 Note: Part should be rotated by quarter turns as it moves through a "Figure 8" pattern.
*
BPB Series
Disassembly
Refer to Diagram 1 on Page 10 (general reference only).
Note: As parts are disassembled, place them carefully on a clean surface such as a soft cloth. Do not allow them to knock together.
1) Remove Outer Drive Gear (18) by first removing Drive Strap Screws (28) and
Drive Strap (20). Slide Yoke Retainer
(19) out of slot in Hub (12).
2) Pull Outer Drive Shaft (11) out of
Hub (12).
3a) LIP SEAL DESIGN. Place pump in a soft-jawed vise with the Hub (12) facing upward. Never clamp on lapped surfaces. Remove three #10-
24 Hub Screws (27) and Hub (12).
Note: We strongly advise removing the Lip Seal (14) from the Hub (12) and discarding it.
3b) METAL SEAL DESIGN. Place pump in a soft-jawed vise with the Hub (12) facing upward. Never clamp on lapped surfaces. Upon removal of the three #10-24 Hub Screws (27), the Hub (12), Coupling Housing (13),
Anchor Washer (15) and Universal
Seal Coupling (14) are all easily removed. Remove and carefully store the Compression Spring (16).
4) Turn the pump over and clamp the vise onto the Front Side Plate (1).
Remove two of the diagonally opposed
#12-24 Binder Screws (21). Loosen the other two screws but leave them engaged by two or three threads.
5) Separate the Front Side Plate (1) and
Rear Side Plate (3) by gently tapping the slightly engaged Binder Screws
(21) with a plastic hammer.
6) Lift off the Rear Side Plate (3), Center
Plate (2) and Spacer (9).
Caution: Do not allow the metering gears to be lifted out with the Center Plate (2).
They may drop, causing damage to the gear teeth. On Metal Seal Design pumps, be careful to retain Ball (29).
7) Remove Driving Metering Gear Assembly (6) by gently turning and lifting.
Repeat for Driven Metering Gear (7).
Never use pliers to lift gears. Never use a screwdriver to pry gear upward.
If there is a film of oil or other tenacious fluid between the gear and the side plate, it helps to immerse the parts in solvent. On Metal Seal Design pumps, Driving Metering Gear (6) and
Drive Shaft (4) are not a press fit assembly.
8) Remove Port Seal Screws (23 & 25) and Gaskets (22 & 24). Repeat for
Shaft Seal Screw (31) and Gasket (30).
9) If the Arbor (5) is to be replaced or thoroughly checked, press out by using an arbor tool, pressing towards the inside of the pump (the shortest press direction). Repeat for Dowels (10).
7
8
BPB Series
Assembly
Considerable care should be taken to prevent wedging or jamming. Never force the parts together. They will drop into place if properly aligned.
1) Provide a can of clean oil, preferably
SAE-50 motor oil or mineral oil.
2) Press Arbor (5) and Dowels (10) into
Rear Side Plate (3) using the Driven
Metering Gear (7) as a guide for press-ing the arbor upright and perpendicular to the plate. See Figure 2.
3) Install Port Seal Screws (23 & 25) in both plates with new Gaskets (22 &
24). Repeat for Shaft Seal Screw (31) and Gasket (30).
4) Fix the Rear Side Plate (3) in a bench vise inside face up.
5) Lubricate the drive shaft bearing hole and arbor with a few drops of oil. See
Figure 3.
6a) LIP SEAL DESIGN. Place Driving
Metering Gear Assembly onto plate.
Place the shaft into bearing hole, rotating several times to insure free rotation.
6b) METAL SEAL DESIGN. Place Ball
(29) into depression on shaft seal screw. Assemble loose-fit Driving
Metering Gear (6), Drive Shaft (4) and Key (8). Place stub end of drive shaft into bearing hole and rotate several times to insure free rotation.
7) Position Driven Metering Gear (7) over the Arbor (5), rotating several times to insure free rotation.
8) With a thin film of oil on your fingertips, lubricate the gear pockets of the
Center Plate (2).
9) Carefully lower Center Plate (2) over gears.
10) Lower Spacer (9) over Dowel (10).
11) Place a drop of oil into each port in
Center Plate (2) (i.e. either side of meshing gear teeth) and turn Drive
Shaft (4) several times to insure free rotation. See Figure 3.
12) Carefully lower the Front Side Plate
(1) over the Dowel (10) and Drive
Shaft (4).
13) Flip pump over in the vise, clamp to
Front Side Plate (1), and insert
Binder Screws (21) until finger tight.
Check for free rotation.
14) Tighten binder screws to 60 lbs.-in.,
50% of the recommended tightening torque. Follow the order shown in
Figure 4 depending on whether the pump has 4 or 6 binder screws. Be sure the pump turns freely.
15) Tighten binder screws to the recommended tightening torque of 120 lbs.-in.; follow the order shown in
Figure 4.
Note: If the pump will not turn freely after each component is installed, then the last piece installed needs additional attention or replacement.
16) Flip pump over and fix it in a vise. Set leading chamfer of Lip Seal (14) into
Hub (12) opening. For Metal Seal
Design pumps, place Compression
Spring (16) into hole on top of Drive
Shaft (4).
17) LIP SEAL DESIGN only. Use of the
Zenith ® Lip Seal Installation Guide is recommended to prevent lip seal damage. [P/N 14-00131-0001-1
(Items A,B & C)].Set guide (B) down over Lip Seal (14) and against the
Hub (12) in order to compress the seal O.D. and ease its entry into the hub. See Figure 5.
18a) LIP SEAL DESIGN. Holding the Lip
Seal Guide (B) against the Hub
(12), press the Lip Seal Inserter (C) down firmly, but gently, until Lip
Seal (14) is seated against the bottom of the hole. Be careful not to crush the seal. See Figure 5.
18b) METAL SEAL DESIGN. Place the Universal Seal Coupling (14) over the drive shaft and slide the Coupling
Housing (13) over the coupling. The
Anchor Washer (15) is then inserted into the coupling housing right on top of the coupling itself. The two ears on the anchor washer fit into grooves in the housing. See
Diagram 1 Inset.
19) LIP SEAL DESIGN only. Place “O” Ring
(32) over the Drive Shaft (4) and using the Bullnose (A) on end of
Drive Shaft (4), carefully lower hub and seal assembly down over Drive
Shaft (4). See Figure 6.
20a) LIP SEAL DESIGN. Remove Bull-nose
Installation Tool and rotate Hub (12) until grease fitting is facing in the desired orientation.
20b) METAL SEAL DESIGN. Place the Hub
(12) on top of the Coupling Housing
(13) and orient the Grease Fitting
(26) as desired.
21) Insert Hub Screws (27) and tighten to first 32 lbs.-in. in a circular rotation, then complete tightening to recommended torque of 64 lbs.-in.
BPB Series
Assembly
(continued)
22) Place Outer Drive Shaft (11) into Hub
(12) (when applicable), and rotate until Drive Shaft (4) and Outer Drive
Shaft (11) mate.
23) Place Outer Drive Gear (18) over
Hub (12), insert Yoke Retainers (19) into appropriate grooves followed by
Drive Strap (20) and tighten down with Drive Strap Screws (28).
24) Pour oil into inlet port to lubricate internal components, then rotate pump to check for free rotation.
25) Apply standard gun grease to
Grease Fitting (26). Conoco Super
Lube M EP Grease or equivalent is recommended.
Figure 2
Figure 3 Figure 4
Figure 5 Figure 6
9
BPB Series
Diagram 1
BMB/BMC Series
Diagram 2
10
BLB Series
Diagram 3
BXB Series
Diagram 4
11
BMB/BMC
Series
Disassembly
Refer to Diagram 2 on Page 10.
Note: As parts are disassembled, place them carefully on a clean surface such as a soft cloth. Do not allow them to knock together.
1) Remove Outer Drive Gear (2) by first unscrewing the two #10-24 Drive Strap
Screws (32). Remove Drive Strap (31) and Retaining Rings (30) from Drive
Shaft (8).
2) Remove Seal Plate (16) by unscrewing three #10-24 x 1/2" Seal Plate Screws
(20).
3) Clamp Body (1) in a bench vise with
Rear Side Plate (3) facing upward and remove Binder Screws (28).
Never clamp on lapped surfaces.
4) Lift off Rear Side Plate (3) and Center
Plate (4).
Caution: Do not allow metering gears to be lifted out with the Center
Plate. They may drop, causing damage to the gear teeth.
5) Remove Driven Metering Gears (6) from Arbors (10) by turning and lifting simultaneously. Never use pliers to lift gears. Never use a screwdriver to pry gears upward.
6) Remove Driving Metering Gear (7) and
Round Key (12) in the same way, while also pulling Drive Shaft (8) outward.
7) Remove Port Plate (5).
8) Remove Lip Seal (15) and discard.
9) Remove Port Seal Screws (24 & 26) and
Gaskets (25 & 27). Discard gaskets.
10) If the Arbors (10) and/or Sleeve
Bearing are to be replaced or thoroughly checked, press out by using an arbor press, pressing toward the inside of the pump (the shortest press distance.) Removing these items during general maintenance is not recommended.
Caution: Extreme care must be taken with arbors when pressing out of or installing into cast body.
P/N 15-00131-0009-1
Figure 7 Figure 8
12
Figure 9 Figure 10
BMB/BMC
Series
Assembly
Considerable care should be taken to prevent wedging or jamming. Never force the parts together. They will drop into place if properly aligned.
1) Provide a can of clean oil, preferably
SAE-50 motor oil or mineral oil.
2) Fix Body (1) in a bench vise, inside face up. Install Port Seal Screws (24 &
26) with new Gaskets (25 & 27).
3) Lubricate Arbors (10). If the Arbors and Sleeve Bearing were removed, press Arbors into the Pump Body (1) using a Driven Metering Gear (6) as a guide for pressing arbors perpendicular
(upright) to the plate. Reinstall Sleeve
Bearing lead end first into Body (1) and press in place allowing Sleeve
Bearing to project from inside face slightly less than the thickness of the
Port Plate (5).
Caution: Extreme care must be taken with arbors when pressing out of or installing into cast body.
4) Carefully place Port Plate (5) over
Arbors (10) making sure ports line up with ports in Body (1). Make sure plate is not 180° out of position; relief grooves face up toward Center Plate (4).
5) Assemble Driving Metering Gear (7),
Round Key (12) and Drive Shaft (8).
6) Lubricate Sleeve Bearing and place
Driving Metering Gear assembly into
Body (1) and through Sleeve Bearing.
Rotate several times to insure free rotation.
7) Place one Driven Metering Gear (6) on its arbor and rotate several times to be sure it is free. Repeat process for the other Driven Metering Gear (6).
8) Rub a slight amount of oil over gear recesses of the Center Plate (4), then carefully lower over the Metering
Gears.
9) Put a drop of oil in the port recesses on either side of the meshing point of the gears. Turn the shaft to make sure the gears turn freely.
10) Place Rear Side Plate (3) over
Center Plate (4) and screw in Binder
Screws (28) finger tight. Again, make sure pump turns freely.
11) Tighten the Binder Screws (28) to
150 lbs.-in., 50% of the recommended tightening torque. Follow the order shown in Figure 7. Make sure the pump turns freely.
12) Tighten Binder Screws (28) (following the order shown in Figure 7) to recommended tightening torque of 305 lbs.-in. and make sure pump turns freely.
Note: If the pump will not turn freely after each component is installed, then the last piece installed needs additional attention or replacement.
13) Turn the pump over (so the Drive
Shaft is facing upward) and clamp on edges of Rear Side Plate (3) in vise.
14) Use of a Zenith ® Lip Seal Installation
Guide (Bullnose) is recommended to prevent seal damage. Place a new
Lip Seal (15) over the Bullnose with spring-loaded open end facing down and push down firmly to slightly expand Lip Seal inside diameter.
See Figure 8.
Caution: Do not push the Lip Seal completely down the bullnose or permanent damage to the seal may result.
15) Remove Lip Seal from Bullnose and attempt to slide Lip Seal onto Drive
Shaft.
16) If the seal does not slip on easily, repeat Step 14, being careful not to over-expand the Lip Seal. (The seal will soon recover from the slight expansion necessary.)
17) Once the Seal is installed onto the
Drive Shaft, place the Seal Plate (16) into position as shown in Figure 9.
18) Install the three Seal Plate Screws
(20) and tighten evenly to draw the
Lip Seal into the pump body, being careful not to cock the seal or damage it in any way. See Figure 9.
19) Torque the three Seal Plate Screws
(20) to 50 lbs.-in.
20) Reinstall Outer Drive Gear (2) with relieved side upward. Replace
External Locking Retaining Ring (30) onto Drive Shaft (8).
21) Install Drive Strap (31) and Drive
Strap Screws (32).
22) After pouring oil into the inlet port, rotate pump to lubricate internal components and check for free rotation.
13
BLB Series
Disassembly
Refer to Diagram 3 on Page 11.
Note: As parts are disassembled, place them carefully on a clean surface such as a soft cloth. Do not allow them to knock together.
1) Remove Drive Strap Screws (28) and
Drive Strap (20). Remove Seal Plate
Screws (41) and Seal Plate (19) and remove the Outer Drive Gear (1).
2) Remove Seal Housing (13) and Lip
Seals (14) in the housing. In all cases we strongly advise removing and discarding used Lip Seals (14).
3) For pumps with a mechanical face seal, remove Outer Drive Gear (1) by first removing Drive Strap Screws
(28), Drive Strap (20) and Outer Drive
Shaft (11). Remove Coupling Housing
Screws (41) and Seal Plate (2) to allow outer drive gear to be removed.
4) With the pump ports facing upward, clamp the sides of the Front Side
Plate (2) in a vise. Note: Never clamp the pump on a lapped surface.
Loosen the four 1/2-13 Binder Screws
(21) and remove two diagonal screws completely. Back the other two screws out until only one or two threads are engaged.
5) Remove the pump from the vise and lay it on its long side on the bench.
Separate the Front Side Plate (2),
Center Plate (4) and Rear Side Plate
(3) by gently tapping the engaged
Binder Screws (21) with a plastic hammer. Some process fluids make disassembly difficult, and a soft-face, dead blow hammer may have to be used in these cases.
6) After the plates are apart, completely remove the partially engaged Binder
Screws (21). Pull the Front Plate (2) off the Dowels (10) and carefully remove the Drive Shaft (5), Key (8) and Metering Gears (6 & 7). Never pry the pump parts with a screwdriver or similar tool or use pliers to lift the gears.
7) The Center Plate (4) may, at times, be difficult to separate from the Rear Side
Plate (3). If this is the case, it can sometimes be loosened by jarring the dowel ends against a table top. To do this, grasp the Center Plate (4) and, with the Rear Plate (3) upward, give a downward thrust with the plates parallel to the table top. If this doesn’t work, the Dowels (10) must be pressed out in the direction from the
Rear Plate (3) through the Center
Plate (4).
8) If the Arbor (9) or Hollow Dowels (10) are to be replaced or checked, use an arbor tool and press toward the inside of the pump (the shortest press distance). If there is residue present on the surfaces of the front and rear side plates, it is better to remove the
Arbor (9) and Dowels (10) in order to hand lap, or “block” the plates as described earlier.
14
BLB Series
Assembly
Considerable care should be taken to prevent wedging or jamming. Never force parts together. They will drop into place if properly aligned.
1) Provide a can of clean oil, preferably
SAE-50 motor oil or mineral oil.
2) Using the Driven Metering Gear (7) as an upright guide, press the Arbor (9), using an arbor press, into the Front
Side Plate (2) until flush with the outside of the plate. Apply a light film of oil to the Arbor (9) before pressing it into the plate.
3) Making sure that the surfaces are clean, place the Center Plate (4) on top of the inside surface of the Rear
Side Plate (3). Be sure that the port hole sizes on the Center Plate coincide with the port holes on the Rear
Side Plate. The thicker center plates have only a short portion of the dowel hole precision ground. This ground portion should be placed adjacent to the rear plate.
4) Insert the lightly oiled Dowels (10) into the Center Plate (4) and carefully press them into the Rear Side Plate
(3) and flush with its outer surface.
5) Place the sub-assembly on a clean bench top. Making sure that the
Center Plate (4) and Rear Side Plate
(3) are in close contact, insert the
Driving Gear (6) and Driven Gear (7) into their respective gear pockets.
Do not force the gears into the gear pockets. If force is necessary, there is something wrong, and the plates and gears should be checked for burrs, dents, or the like.
6) Install the Drive Shaft (5) and the
Drive Shaft Key (8) into the Driving
Gear (6) and the lightly oiled bearing of the Rear Side Plate (3). Turn the drive shaft to assure free rotation of the gears. If there is any binding, remove the gear shaft and key and examine for damage.
7) Apply a thin coat of oil to the drive shaft bearing and arbor of the Front
Side Plate (2) and place into position over Center Plate (4).
8) Insert Binder Screws (21) finger tight and rotate drive shaft to insure free rotation.
9) Clamp pump into vise by front side plate edges, Rear Side Plate (3) facing upward. Tighten Binder Screws (21) in the order shown in Figure 11 to 390 lbs.-in., 50% of the full recom-mended tightening torque. Rotate to make sure the pump turns freely.
10) Tighten Binder Screws (21) in the order shown in Figure 11 to the full recommended tightening torque of
780 lbs.-in. Rotate to insure free rotation.
11) Install Seal Assembly per instructions on page 18.
Note : If the pump does not turn freely after each component is installed, then the last piece installed needs additional attention or replacement.
New pumps may occasionally develop intermittent bind points or tight spots.
Since precision metering requires minute tolerances, this is perfectly normal and will pass quickly as the pump “wears in.”
If a tight spot is interfering with operation, it can be reduced or minimized by lifting one of the metering gears out of the center plate and rotating it a few teeth.
#1
#4
#5 #3
#6 #2
Figure 11
#1
#4
#3
#2
15
BXB Series
Disassembly
Refer to Diagram 4 on page 11.
Note: As parts are disassembled, place them carefully on a clean surface such as a soft cloth. Do not allow them to knock together.
1) Remove the Key (17) from the end of the Drive Shaft.
2) Remove the Seal Plate Screws (20).
3) Slide the Seal Plates (13) and Flush
Plate (14) over the end of the shaft.
4) Pry the Lip Seals (31) from the Seal
Plates and discard. It is recommended that the Lip Seals be replaced anytime the pump is taken apart.
5) Remove the Dowels (9) and Arbor (5) and press in the direction which disengages the press fit in the shortest distance.
Note: Dowels are press fit in the Rear Side Plate and slip fit in the Front and Gear Plates. The arbor is press fit in the Front Plate and slip fit in the Gear and Rear Plates.
6) Place the pump in a vise with the ports facing upward.
Note: Never clamp the pump on lapped surfaces.
Loosen the four Binder Screws (21) and remove two Diagonal Screws.
Back out the remaining two screws until only two or three threads are engaged.
7) Remove the pump from the vise and lay it on its side.
8) Separate the Front Side Plate (1),
Gear Plate (2), and Rear Side Plate
(3) by gently tapping the engaged
Binder Screws with a plastic hammer.
Some process fluids make disassembly difficult and therefore a soft-face hammer may be used.
9) After the plates are apart, completely remove the two remaining Binder
Screws. Separate the plates by gently tapping them with a soft-head dead blow hammer.
Note: Do not attempt to pry the plates apart or damage to lapped surfaces may occur.
10) Carefully remove the Drive Shaft (4),
Key (8), and Driving Gear Assembly
(6) from the Gear Plate (2). Next, remove the Driven Gear (7).
11) After all components are thoroughly cleaned, inspected, or replaced, the pump may be reassembled. Note: If the Drive Shaft Bearings (49, 50) are replaced, they must be honed to the proper inner diameters after being pressed into the Front (1) and Rear
(3) Plates. Contact Zenith ® for details.
16
BXB Series
Assembly
Note: Considerable care should be taken to prevent wedging or jamming of parts. Never force parts into place. All parts should drop into place if properly aligned. During assembly, manually turn the metering gears to ensure free rotation.
If binding occurs at any time, determine the cause and correct it immediately. A small nick, burr, or foreign particle may cause extensive damage to pump components.
1) Provide a can of clean oil, preferably
SAE-50 motor oil or mineral oil.
2) Lubricate the dowel and arbor holes in the Front and Rear Plates. Using the Driven Gear as a guide, press the arbor (5) into the Front Side Plate (1).
The thermocouple hole in the arbor should be facing upwards. Press the dowels (9) into the rear side plate (3).
3) Place the rear side plate onto a bench with the dowels and arbor facing up.
4) Lower the gear plate (2) over the dowels and onto the rear side plate.
Ensure that the correct port location of the gear and rear plates are maintained.
5) Gently insert the drive shaft (4), key
(8), and driving gear assembly (6) into the gear pocket and rear side plate bearing. Ensure free rotation of the drive shaft.
6) Carefully insert the driven gear (7) onto the arbor (5) and lower into the gear plate. Again, ensure free rotation of the driving and driven gears.
7) Place the front side plate (1) and arbor
(5) over the end of the drive shaft and into position over the dowels.
8) Turn the pump onto its side and insert the binder screws (21).
9) Place the pump into a vice with the drive shaft facing down. Tighten the binder screws to 50% of their rated torque using a crossing pattern. Turn the drive shaft to ensure free rotation.
If no binding occurs, completely tighten the binder screws to 100% of their rated torque. Again, check for free rotation.
10) Turn the pump over so that the drive shaft is facing up.
11) Insert new lip seals (31) into the seal plates (13).
12) Use of a Zenith ® Lip Seal Installation
Guide is recommended to expand the ID of the seals prior to sliding the seals down the drive shaft preventing seal damage (P/N 15-00131-0026-2).
A piece of tape can also be used over the keyway located at the end of the drive shaft. This is to prevent damage to the seals during assembly.
13) Slide the seal plates (13) and flush plate (14) over the end of the shaft and onto the front side plate.
14) Insert the seal plate screws (20) into the seal plates. Allow the plates to center themselves around the shaft before tightening the screws. Torque the screws to 50% and then 100% of their rated torque using a crossing pattern.
15) Remove the tape from the end of the shaft and insert the key (17).
16) Lubricate the pump by squirting mineral oil into the inlet port and rotating the pump shaft until oil appears at the outlet port.
17
“Seal Area”
For BLB Lip
Seal Type
Pump
1) Use of a Zenith ® Lip Seal Installation
Guide is recommended to expand the
ID of the seals prior to sliding the seals down the drive shaft preventing
Lip Seal damage (P/N 15-00131-
0071-2). Install Lip Seals (14) into Seal
Housing (13) as shown in Figure 12.
2) Carefully lower Seal Housing (13) over Drive Shaft (5) making sure that the grease hole in the Front Side Plate
(2) coincides with the grease hole in the Seal Housing (13).
3) Apply a thin coat of oil inside the bore of the Outer Drive Gear (1) and carefully place over Seal Housing (13).
4) Place Seal Plate (19) into Outer Drive
Gear (1) and install Seal Housing
Screws (41) finger tight.
5) Tighten Seal Housing Screws (41) (in order shown in Figure 13) to 60 lbs.in., 50% of the full recommended tightening torque. Check for free rotation.
6) Tighten Seal Housing Screws (41) (in order shown in Figure 13) to the full recommended tightening torque of
120 lbs.-in. Check for free rotation.
7) Place Drive Strap (20) over Drive
Shaft (5) and install Drive Strap screws (28). Tighten to full recommended tightening torque of 305 lbs.in. Check for free rotation.
8) Apply standard gun grease to Grease
Fitting (26). Conoco Super Lube M EP
Grease or equlvalent is recommended.
“Seal Area”
For BLB
Mechanical
Face Seal
Type Pump
1) Place Coupling Housing (13) on Front
Side Plate (2) making sure that the grease hole in the coupling housing coincides with the grease hole in the front side plate.
2) If the pump is equipped with an
Anchor Washer (15), drop it into the
Coupling Housing (13). Make sure it lies flush on the Front Side Plate (2).
3) Place Universal Coupling (14) with proper (shallow) female tang over
Drive Shaft (5).
4) Apply a thin coat of oil to the inside bore of the Outer Drive Gear (1) and carefully place over Coupling
Housing (13).
5) Place Seal Plate (19) onto Outer Drive
Gear (1) and install Seal Plate Screws
(41) finger tight.
6) Tighten Seal Plate Screws (41) (in order shown in Figure 13) to 60 lbs.in., 50% of the full recommended tightening torque. Check for free rotation.
7) Tighten Seal Plate Screws (41) (in order shown in Figure 13) to full recommended tightening torque of
120 lbs.-in. Check for free rotation.
8) Install the Drive Strap (20) over the tang on the Outer Drive Shaft (11) and fasten to the Outer Drive Gear (1) with Drive Strap Screws (28). Torque to 305 lbs.-in.
9) Apply standard gun grease to Grease
Fitting (26). Conoco Super Lube M EP
Grease or equivalent is recommended.
14 13
#1
#4 #3
#2
Figure 12 Figure 13
18
Bolt Torque
Troubleshooting
(UNC Alloy Steel)
#10-24
#12-24
5/16-18
1/2-13
5/8-11
(in -lbs)
64
120
305
780
900
Trouble
Pump will not turn
No flow from pump
Excessive seal assembly leakage
Reduced pump efficiency
Probable Cause
1) Drive malfunction
2) Process conditions Check process conditions changed for proper temperature, pressures, viscosities and materials.
3) Entrained particle Disassemble and clean pump; replace any damaged parts.
4) Possible internal damages
Remedy
Verify drive powered.
Check to assure all alarm circuits are clear. Check drive motor current and speed settings.
1) Same as above
2) Pump rotation
1) Worn lip seal
Disassemble and clean pump; replace damaged parts. Consult factory.
Same as above
Correct drive arrangement or power leads
Replace lip seals.
2) Worn seal plate
3) Insufficient inlet pressure
1) Worn gear(s)
Replace seal plate and coupling if necessary.
(Mechanical Face Seal version)—increase inlet pressure.
Replace worn gears.
2) Worn bearings Replace worn bearings.
3) Process conditions Consult factory for clearance changed recommendations on new process conditions.
19
FAILURE, IMPROPER SELECTION OR IMPROPER USE
OF THE PRODUCTS AND/OR SYSTEMS DESCRIBED
WARNING
HEREIN OR RELATED ITEMS CAN CAUSE DEATH,
PERSONAL INJURY AND PROPERTY DAMAGE.
This document and other information from Zenith
Pumps, its subsidiaries and authorized distributors provide product and/or system options for further investigation by users having technical expertise. It is important that you analyze all aspects of your application and review the information concerning the product or system in the current product catalog. Due to the variety of operating conditions and applications for these products or systems, the user, through its own analysis and testing, is solely responsible for making the final selection of the products and systems and assuring that all performance, safety and warning requirements of the application are met.
The products described herein, including without limitation, product features, specifications, designs, availability and pricing, are subject to change by Zenith Pumps and its subsidiaries at any time without notice.
A Colfax Buisiness Unit
ISO 9001: 2000 Registered
Zenith ® Pumps
1710 Airport Road
Monroe, NC 28110
Phone: 704-289-6511 • Fax: 704-289-9273 [email protected] • www.zenithpumps.com
© Copyright 2000 Zenith Pumps B C&M 10/04
advertisement
Related manuals
advertisement