advertisement
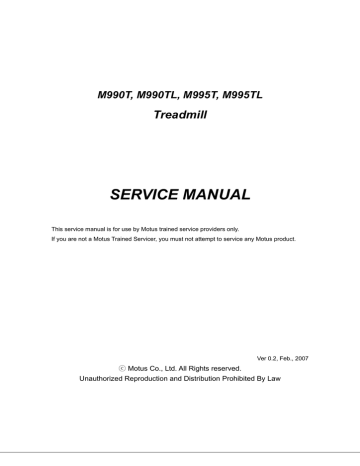
M990T, M990TL, M995T, M995TL
Treadmill
SERVICE MANUAL
This service manual is for use by Motus trained service providers only.
If you are not a Motus Trained Servicer, you must not attempt to service any Motus product.
Ver 0.2, Feb., 2007 ⓒ Motus Co., Ltd. All Rights reserved.
Unauthorized Reproduction and Distribution Prohibited By Law
Motus Treadmills M990T, M990TL, M995T and M995TL
Table of Contents
SECTION I TROUBLESHOOTING GUIDE
SECTION II HOW TO REPLACE & REPAIR GUIDE
General
SECTION III HOW TO REPLACE & REPAIR GUIDE,
Electronic PCB
SECTION IV ELECTRONIC PCB, CONNECTOR AND
CABLE OVERVIEW
APPENDIX EXPLODED VIEW
1
Motus Treadmills M990T, M990TL, M995T and M995TL
SECTION I
TROUBLESHOOTING GUIDE
1.1 System Block Diagram
1.2 Troubleshooting Guide
1.3 Troubleshooting Guide for LCD
1.4 Protective Function & Display Code
1.5 Lubrication Guide
2
1.1 System Block Diagram
1) AC 220V/230V INPUT
AC
220V/230V
Circuit
Breaker
Line
Filter
Power ON/OFF
Switch
Video & Audio Input
(Coaxial, RCA)
Lift/
Power Supply
PCB
Motor
Controller
(Inverter)
U
V
W
LCD Power
Supply PCB
Lift Motor
Touch -Sensitive
Key PCB (L/R)
Speed/Incline/
Start/Enter
Drive
Motor
A/D
PCB
Oil Pump Motor
Transformer
Emergency
Switch
MPU PCB
(Main
Processing
Unit)
CHR PCB
Wireless HR
PCB
Membrane Overlay Key
Audio Interface
Headphone Jack
LCD Screen Back-Light
LCD Lamp Inverter PCB
OSD Button PCB for Channel/Volume/Power-on
3
2) AC 100V/120V INPUT (USA, Japan)
AC 230V/240V
Boost
Transformer
AC
100V/120V
Circuit
Breaker
AC 100V/120V
Power ON/OFF
Switch
Line
Filter
Video & Audio Input
(Coaxial, RCA)
Lift
/Power Supply
PCB
Motor
Controller
(Inverter)
LCD Power
Supply PCB
U
V
W
Lift Motor
Touch -Sensitive
Key PCB (L/R)
Speed/Incline/
Start/Enter
Drive
Motor
Oil Pump Motor
Transformer
MPU PCB
(Main
Processing
Unit)
Emergency
Switch
CHR PCB
Wireless HR
PCB
Membrane Overlay Key
Headphone Jack
Audio Interface
LCD screen Back-Light
A/D
PCB
LCD Lamp Inverter PCB
OSD Button PCB for Channel/Volume/Power-on
4
1.2 Troubleshooting Guide
SYMPTOM
No power to treadmill console
PROBABLE CAUSE
Line voltage is not present at treadmill.
Circuit breaker on the rear of the Treadmill Is tripped.
(Countries using 220V or 230V Supply Voltage)
CORRECTIVE ACTION
Check the main circuit breaker and wall outlet voltage at the Facility.
If wall outlet voltage is present, then replace line cord.
If tripped, a white button has popped out. Press the white button to reset the circuit breaker after eliminating the cause of the trip. The circuit breaker is located next to power ON/OFF switch on the outside of the treadmill.
Power-on switch with built-in circuit breaker is tripped.
(US/Canada market or Japan market using 100V or 120V
Supply Voltage)
In the United States, Canada and Japan, circuit breaker is combined with power ON/OFF switch. If tripped, the switch is turned to OFF position. Turn the switch on after eliminating the cause of the trip. Replace it if necessary
Power-on Switch is damaged.
Defective Line Filter.
Electronic components of Lift/Power Supply PCB are damaged.
Fuses 1, 2 on Lift/Power Supply PCB are blown.
Replace Power-on Switch if the output voltage of Power
Switch is not present.
Replace Line Filter if the output of Line Filter is not present.
Disconnect CN3 cable at Lift/Power Supply PCB and then measure the voltage between pin 2 and pin 1.
Measure the voltage between pin 2 and pin 3. The voltage should be 5VDC. If there is no voltage, replace the PCB.
Replace Fuses or the PCB.
5
SYMPTOM
No power to treadmill console
Striding belt does not move or treadmill pauses randomly
SYMPTOM
PROBABLE CAUSE
Defective wire harness
Defective MPU PCB
Due to normal protective function.
(E□□ is displayed on Console Display.)
Magnetic switch for emergency stop is not firmly attached.
CORRECTIVE ACTION
Disconnect CN6 (3-pin connector) on MPU PCB
(M990T/M995T) and then measure the voltage between pin 2 and pin 1 at the cable. Measure the voltage between pin 2 and pin 3 at the cable. If there is no voltage, replace the cable.
Disconnect CN1 (3-pin connector) on MPU
(M990TL/M995TL) and then measure the voltage between pin 2 and pin 1 at the cable. Measure the voltage between pin 2 and pin 3 at the cable. If there is no voltage, replace the cable. If the cable is normal, secure the connector firmly.
Replace MPU PCB.
Refer to
“Protective Function & Display Code”
Mount magnetic switch in position.
If it is in position, adjust the position of magnetic sensor under properly or replace it if necessary.
Emergency Push Button Switch is locked. Unlock it by rotating clockwise.
Insufficient power source
Unstable power connection.
RS485 connection for communication is loose.
Plug treadmill into a dedicated 20-amp circuit.
Find unstable connection at electrical outlet and at treadmill
If the Console display is normal, check the electrical connection between MPU of Console and Motor
Controller under motor hood is firm.
3-pin connectors at MPU of Display Console or Lift/Power
Supply PCB are not secure.
Check the connection is secure.
PROBABLE CAUSE CORRECTIVE ACTION
6
Treadmill pauses
Randomly and then
Program Profile
Window of Console start displaying from the beginning as if
Power-on Switch is turned on.
Maximum speed is reduced
Power-on switch is unstable or defective.
Supply voltage to MPU PCB is too low.
Unstable cable connection.
The deck laminate worn through or the underside of striding belt became hard or glossy.
Manual lubrication is not sufficient.
Automatic lubrication system does not work.
Replace power-on switch.
If the voltage between pin 2 and pin 1 at CN1 on MPU
PCB (M990T/M995T) is under 4.8V, replace Lift/Power
Supply PCB.
If the voltage between pin 2 and pin 1 at CN6 on MPU
PCB (M990T/M995T) is under 4.8V, replace Lift/Power
Supply PCB .
Check the connection between CN3 on Lift/Power
Supply PCB and CN1 (M990TL/M995TL) on MPU PCB is connected firmly.
Check the connection between CN3 on Lift/Power
Supply PCB and CN6 (M990T/M995T) on MPU PCB is connected firmly.
Replace belt and deck.
(Refer to section “How to replace Striding Belt”, “How to replace Deck”)
Check if the lubrication is proper by pushing striding belt backward using your feet while holding front handlebar after turn OFF the treadmill. If insufficient, apply lubrication.
Check if the lubrication is proper by pushing striding belt backward using your feet while holding front handlebar after turn OFF the treadmill. If insufficient, apply lubrication.
Verify lubricant tank is not empty, or lubrication system works well.
7
SYMPTOM
Incline is not adjusted by Incline-
Up or Incline-Down
Button.
Speed is not adjusted by Speed-
Up or Speed-Down
Button.
PROBABLE CAUSE
Touch-Sensitive Buttons does not work.
Unplugged or defective cables.
Unplugged or defective cable
Lift/Power Supply PCB is damaged.
Touch-Sensitive Buttons does not work.
Unplugged or defective cable
RS485 connection for communication is loose.
CORRECTIVE ACTION
If all 3 lamps on Start/Stop, Speed Down and Speed UP do not light up, replace the Touch-Sensitive Key PCB.
If a lamp on Start/Stop, Speed Down or Speed UP does not light up any more than before pressing each button, replace the Touch-Sensitive Key PCB.
Check the connection between CN4 on Lift/Power
Supply PCB and CN2 (M990TL/M995TL) on MPU PCB is exact or connected firmly.
Check the connection between CN4 on Lift/Power
Supply PCB and CN3 (M990TL/M995TL) on MPU PCB is exact or connected firmly.
Check the cable from the incline motor is connected firmly to CN20 on Lift/Power Supply PCB.
Replace Lift/Power Supply PCB.
If all 3 lamps on Start/Stop, Speed Down and Speed UP do not light up, replace the Touch-Sensitive Key PCB.
If a lamp on Start/Stop, Speed Down or Speed UP does not light up any more than before pressing each button, replace the Touch-Sensitive Key PCB.
Check the cable from the Drive motor is connected firmly to the terminal of Motor Controller..
If the Console display is normal, check the electrical connection between MPU of Console and Motor
Controller under motor hood is firm.
3-pin connectors at MPU of Display Console or Lift/Power
Supply PCB are not secure.
Motor Controller or MPU PCB is defective.
Check the connection is secure.
Replace Motor Controller or MPU PCB if necessary.
8
SYMPTOM
Treadmill changes
Speed or Incline on its own.
PROBABLE CAUSE
Touch-Sensitive Key PCB is affected by some noise.
Sweat or water over the buttons.
Treadmill shuts Touch-Sensitive Key PCB is affected by some noise. down on its own. Sweat or water over the buttons.
Membrane Overlay
Key is not responding when depressed.
Oil leakage
Loose ribbon connection.
Defective Membrane Overlay Key.
Defective MPU PCB.
Too much amount of lubrication.
Uneven floor surface
Striding belt drifts off center Striding belt tension or tracking adjustment is needed.
Striding belt slips during footfall.
Loud groaning on footfall
Squeaking noise under motor hood
Knocking sound from deck.
Electrostatic discharge
Worn striding belt.
Belt tension is loose.
High friction between deck and striding belt.
Foreign objects.
Drive Motor Belt may be worn or damaged.
Drive Motor Belt tension is loose.
Foreign objects on the groove of the belt.
Deck is not fixed.
The underside of Striding belt is worn away.
9
CORRECTIVE ACTION
Replace the Touch-Sensitive Key PCB.
Remove sweat or water.
Replace the Touch-Sensitive Key PCB.
Remove sweat or water.
Verify the ribbon connection is firmly inserted into the corresponding socket of MPU PCB.
Replace Membrane Overlay Key.
Replace MPU PCB.
Reduce the amount to be lubricated.
Level or balance treadmill. (Refer to section “Level
Adjustment”)
Align striding belt by using belt adjustment bolt after
Level Adjustment is done.
(Refer to section ”Striding belt alignment”)
Replace striding belt.
Adjust the belt tension.
(Refer to section ”Belt Tension adjustment”)
Lubrication is needed between deck and striding belt.
Remove any debris or objects under striding belt.
Replace Drive Motor Belt.
Adjust the tension.
Remove any debris or objects on the groove of the belt.
Tighten Deck by using the bolt to fix DECK.
Replace the striding belt.
SYMPTOM
Heart rate reading is abnormally high or is displayed even when
Chest Strap or
Contact Heart Rate sensors are not in use.
PROBABLE CAUSE
Electromagnetic interference from television sets, cell phones, refrigerator, or motor driven exercise equipment.
RF energy source from another chest straps.
CORRECTIVE ACTION
Keep the treadmill away from the probable cause until the heart rate readings are accurate.
Keep another chest strap away more than 1 meter until the heart rate readings are accurate.
Heart rate reading using wireless chest strap is erratic or not displayed
Contact Heart Rate reading is erratic or not displayed .
Contact Heart Rate cables are pinched at handle bars. Replace damaged cables.
Chest strap electrodes are not wet enough to sense accurate heart rate.
The distance between cardio equipments are too close.
Dampen the Chest strap electrodes with tap waters.
Chest strap electrodes are out of monitoring range.
Chest strap battery is discharged.
Chest strap electrodes are not laid flat or horizontally across your skin.
Faulty chest strap.
Faulty Wireless HR PCB.
Defective cable or bad connection between Wireless HR PCB and MPU PCB.
Faulty CHR PCB.
Dirty handlebar sensors.
Defective cable or bad connection between CHR PCB and MPU
PCB.
User may have an unusual heart rate condition.
Maintain the distance more than 30 cm.
Make sure the chest strap is within 60cm from Wireless
HR PCB.
Replace chest strap or the battery.
Make sure the chest strap electrodes lies flat and horizontally across your skin.
Replace chest strap.
Replace Wireless HR PCB.
Check the cable and connection is no problem.
Replace CHR PCB
Wipe stainless steel sensors with a clean soft cloth.
Check the cable and connection is no problem
Let different user grasp sensors to detect any variances.
10
1.3 Troubleshooting Guide for LCD
CAUSE
Air/cable setting is not correct
Follow the set up procedures in LCD manual.
Snow and noise are scattering on LCD screen. Any picture is not found even though channel-up button or channel-down button is pressed.
LCD screen is uniformly white
LCD screen is dark or black.
- Check if the TV signal source is correctly supplied to A/D PCB from external source.
TV signal source is not supplied.
- Make sure the cable is properly secure.
- If external TV signal is correct, try to connect the coaxial cable directly to the internal connector in AD
PCB of Console to check whether the internal cables are wrong or not.
75 ohm coaxial cable is bad.
Replace 75 ohm coaxial cable.
A/D Board is damaged. Replace A/D Board with new one.
Internal cable connection is loose or disconnected.
Check if the connection between LCD screen and
A/D Board is tight.. In other word, LVDS cable shown in picture.
1) Whenever you press Volume down button, words are displayed in following order on the left upper
When LCD power is turned on by pressing TV on/off, “VIDEO”, “S-VIDEO” or “ANALOG” appears temporarily and then disappears on the left upper corner of LCD screen.
TV mode is not set-up. corner of LCD screen.
“ANALOG”=>”VIDEO”=>”S-VIDEO”=>”TV”
2) Press the button until “TV” is displayed.
3) As soon as “TV” is displayed, snow and noise will be scattering on LCD screen or any picture will be captured.
When LCD power is turned on by pressing TV on/off, “VIDEO”, “S-VIDEO” or “ANALOG” is NOT displayed on the left upper corner of LCD screen.
LCD Power Supply has a problem. Power Supply is
Check if LCD Power supply is normally operated or its LED lamp is turned on. used for supplying 12 VDC to LCD Overlay Bezel
If LED is off, z replace Power Adapter.
Assembly.
11
If LED is on,
Channels or sound does not change
No sound z tighten midpoint (LCD Power Supply side)
& endpoint(A/D Board side) connection. z or make sure the voltage of end point is
DC 12 volt.
The cable related to LCD
Lamp Inverter is loose in either side.
TV on/off button is wrong or stuck.
Check if the connection is secure.
Replace OSD Button Board.
A/D Board is damaged. Replace A/D Board.
LCD Lamp inverter is damaged.
Replace LCD Lamp inverter.
LCD Back Light is damaged. Replace LCD screen.
The connector or cable is bad.
Button to change channels or sound does not work.
Replace the connector or cable
Replace the button, OSD Button Board or harness related to it.
Air/cable setting is not correct
Follow the set up procedures in LCD manual.
Faulty headphones Replace headphones assembly.
12
1.4 Protective Function & Display Code
If a treadmill stops suddenly, it means a protective function works properly. This is normal function to protect the treadmill. As the result of protective function, a code indicating the cause of error is displayed on the display console or the display panel of Motor Controller (or Motor
Inverter) which is located under motor hood. Motor is driven directly by Motor Controller according to the command from the console.
If this protective function occurs, turn off the treadmill and then turn on the treadmill after 20 seconds even though the cause is eliminated. Even though the cause is eliminated, the treadmill stop due to protective function will remain unsolved if you turn on the treadmill within 20 seconds after turning off the treadmill.
Display
Code
Protective
Function Name
PROBABLE CAUSE or DESCRIPTION CORRECTIVE ACTION
E05 Overload
Excessive current flows in Motor Controller. In other word, the
Motor Controller output current exceeds the rated current by more
- Reduce impact load or lubricate between belt and deck than approximately 180%.
- The load is in abnormal condition like impact load.
- The output is short
- Replace Motor Controller with new one. - - Check the cables and wires between motor and Motor Controller are loose or if there is any short between wires.
Overheated Motor Controller caused by worn or damaged belt and
Replace the deck or belt. deck.
An excessive load is applied to motor, which is judged by detecting Motor Controller output current.
Unexpected high voltage is detected at DC voltage of Motor
- Lubricate between belt and deck
- Input voltage of Motor Controller is too high.
- Check the input voltage fluctuates abnormally.
- Don’t push the striding belt backward
13
E60
E34
Communication
Error
Short-circuited output
- Regenerative energy from motor is too much.
- External noise
- Trouble in internal memory due to or high temperature.
- Cable connection between MPU and Motor Controller
Unexpected low voltage is detected at DC voltage of Motor
- Instantaneous power failure compulsorily by foot.
- Replace Motor Controller cable with new one
- Replace Motor Controller with new one
- Check the input voltage to treadmill.
- Connect the treadmill to dedicated circuit.
- Supply stable power to treadmill
Excessive current flows in Motor Controller when the output of
Motor Controller is short
- Check the cables and wires between motor and Motor Controller are loose or if there is any short circuit between wires.
E08 EEPROM
E12
Trouble in internal EEPROM due to high temperature. A lot of parameters are saved in the EEPROM.
- Make a service call.
Tripped out due to external input signal
Failure caused intentionally by input terminal. It is not implemented in the treadmill.
Replace the Motor Controller
E14 Ground fault trip
Grounding protection when an Motor Controller output line - Check the cables and wires from dropped to earth. Current leaks from an output cable or the motor to ground.
Motor Controller are dropped to the earth
The temperature of power module in Motor Controller is too high.
- Ambient temperature is too high.
- Do not place heat generating device near the treadmill.
Overheated Motor Controller caused by worn or damaged belt and deck.
Replace the deck or belt.
14
1.5 Lubrication Guide
Basically, initial lubrication is performed at factory, but the oil could be dried during transportation or stock in your warehouse.
As soon as you complete installing, please lubricate and then make sure that oil is enough or not as below.
1) Turn off treadmill .
2) Push the striding belt backward using your feet while holding the front handle bar or side handle bar.
3) You can judge whether the friction is enough or not by feeling the smooth move of the belt. Lubrication is needed if the belt is not pushed well.
z Lubricant prevents the belt and deck from being damaged by frictional heat, which extends life span of the deck and belt. z Use the lubricant provided by Motus only. KF54 silicone fluid made from Shin-Etsu Chemical Co. Ltd.
How to manage automatic lubrication system (M990T, M990TL)
A certain amount of oil is lubricated automatically every lubrication interval which is preset at Manager Mode. Default lubrication amount and lubrication interval are set up to, for instance, 30cc and 500km, respectively, which can be set at Manager Mode. Therefore, it is recommended that fitness club manger set up the lubrication amount and interval according to club condition.
A volume of lubricant tank is about 270cc, and if residual amount of oil is less than 20%, the warning SYMBOL is displayed on the screen with a beep. At that time, fill the tank as instructions below.
1) Turn OFF the treadmill and open motor hood.
2) Open the cap of oil tank by turning it with hand.
3) Fill the empty tank fully with the oil provided by Motus. Keep in mind that automatic lubrication system doesn’t work properly if oil is not filled full.
4) Close the cap of oil tank and put the motor hood in place.
5) Turn ON the treadmill. Message indicating oil lack will be still displayed on the screen with the beep.
6) To input “finishing oil-filling”, press buttons in the order as below.
15
‘INCLINE ▽’ -> ‘INCLINE △’ -> ‘SPEED ▽’ -> ‘SPEED △’ -> ‘ENTER’
Keep in mind that this step must be done after filling the tank fully.
7) The warning SYMBOL and beep disappears.
How to inject lubricant manually (M995T, M995TL)
To judge proper lubrication timing, you can feel the friction intensity by pushing the striding belt backward using your feet while holding the front handle after turn OFF the treadmill.
1. Fill the lubricator with the oil Motus provided.
2. The conduction hole for the lubrication is at the right corner on the front of the treadmill as shown in the picture.
3. Insert the pipe tip of the lubricant to the end through the conduction hole to spread out the lubricant on the center of the belt.
4. Inject the lubricant into the conduction hole by squeezing the lubricator about 20 times under the belt speed of 4km.
The amount of 30 cc is recommended.
5. To spread out the lubricant all round on the belt, operate the treadmill for a few minutes.
6. Lubricate more than twice a month.
How to eliminate warning beep & symbol requiring lubrication (M995T, M995TL)
Although lubricant is not injected automatically, lubrication interval can be set up at Manager Mode, for instance, 500km. If the interval is too short or long, you can adjust the interval at Manager Mode. Warning beep & symbol every lubrication interval makes you easy to lubricate without any need to consider lubrication timing.
To reset the warning beep and symbol after completing manual lubrication, press buttons in the order as below.
‘INCLINE ▽’ -> ‘INCLINE △’ -> ‘SPEED ▽’ -> ‘SPEED △’ -> ‘ENTER’
The warning beep and SYMBOL disappear.
16
Numeric value 5 in management mode means interval of 500 km. If you exercise on treadmill at 8km/h for 10 hours a day, total distance a day is
80km and the warning beep and symbol appears every 6.25 days corresponding to 500 divided by 80.
The speed (8km/h) and workout duration for a day (10 hours) depend on the numbers of the users or utilization rate ay Gym.
17
Motus Treadmills M990T, M990TL, M995T and M995TL
SECTION II
HOW TO REPLACE & REPAIR GUIDE
2.1 How to Stabilize the Treadmill
General
2.2 How to Align Striding Belt
2.3 How to Adjust Striding Belt Tension
2.4 How to Adjust Motor Drive Belt Tension
2.5 How to Replace the Rear Roller
2.6 How to Replace the Front Roller
2.7 How to Replace the Striding Belt
2.8 How to Replace the Motor Drive Belt
2.9 How to Replace the DECK
2.10 How to Replace Drive Motor
2.11 How to Replace the Incline Motor
2.12 How to Replace the Oil Pump
2.13 How to Replace the Contact Heart Rate Sensor
18
2.1 How to Stabilize the Treadmill
Two front casters and two adjustable rear feet (or stabilizing leg) support the weight of both the treadmill and a user exercising on it. The rocking motion or striding belt misalignment may be caused when one of them is not resting on the floor.
1) Check if the treadmill is even on a solid and flat surface. A BUBBLE LEVEL can be used to ensure proper leveling. Determine which foot is not resting on the floor.
2) Loosen the nut on the top of adjustable foot by turning it clockwise.
3) Once the nut is loosened, turn adjustable foot with hand until the rocking motion ceases.
4) After leveling, turn the nut counterclockwise and tighten it.
Note: Adjusting height must be done while rear side of treadmill is lifted up. Do not adjust more than 1/4 of entire adjustable rear foot’s height.
19
2.2 How to Align Striding Belt
The belt is properly aligned at the factory before shipment. However, while delivering or exercising, the belt can be misaligned from the original center position. The correct alignment or striding belt is critical to the smooth operation of the treadmill.
2.2.1 When the belt is off center to either right direction or left direction
1) Level and stabilize the treadmill prior to any alignments or tracking adjustments.
* The belt may move off center by using the treadmill on uneven surface.
2) Turn on the treadmill and then check if the belt drifts off center or not while treadmill is operated with the speed of 5km/h for a few minutes.
3) Turn off the treadmill after keeping in mind whether the belt is off center to which direction, left or right.
4) Make sure the striding belt has completely stopped.
5) Find the right belt tensioning bolt in the rear end cap of the treadmill.
Make tracking adjustments using the 10 mm hex key wrench provided as shown. z If the belt is off center to the right, turn the right adjusting bolt 1/4 turn clockwise, which brings the striding belt back to the left. z If the belt is off center to the left, turn the right adjusting bolt 1/4 turn counterclockwise, which brings the striding belt back to the right.
Note: Do not turn the adjusting bolt more than 1/4 at a time. Over-tightening the bolt can damage the treadmill. Do not exceed one full turn of the adjusting bolts in either direction.
6) Turn ON the treadmill, press START/STOP, and then operate the treadmill with the speed of
5km/h.
7) Observe the striding belt for a few minutes. The belt should be centered on the deck.
8) If you need additional alignment, repeat step 2) through 7) of this procedure until the belt is properly aligned.
CAUTION: If you hear any chafing, the belt is not center-aligned or the belt appears to be
20
getting damaged, stop the treadmill and contact authorized local dealer.
2.2.2 When the belt is diagonally tilted
When the Striding Belt is diagonally tilted as shown, the Front Roller (F4) needs to be aligned by following steps.
1) Turn off the unit power at the switch and then unplug the line cord at wall outlet.
2) Remove three Motor Cover screws (B20) and then lift the cover
(T1) out from between the upright Supports.
3) Turn the Hex Bolt (B2) in either direction to compensate for the tilted
Striding Belt.
When the Striding Belt is tilted as shown in A), turn the Hex Bolt (B2) by 1/4 turn in the direction of (1).
When the Striding Belt is tilted as shown in B), turn the Hex Bolt (B2) by 1/4 turn in the direction of (2).
Note: Make adjustments in 1/4 turn.
The position of the Front Roller to be changed by the direction of the Hex Bolt (B2) is indicated in the figure.
4) Re-assemble the Motor Cover in the reverse order of removal and make sure that the Striding Belt is properly aligned after turning on the unit power and operating it with the speed of 5km/h for a few minutes..
5) Repeat this adjustment until the
Striding Belt is properly aligned.
21
2.3 How to Adjust Striding Belt Tension
Belt tension is properly adjusted before delivery. However, while exercising for a long time, the tension can be loose. Belt tension is adjusted by moving the position of rear roller using the belt tensioning bolt of END CAP.
Note: it is very important to keep belt’s tension constant to avoid belt slips during footfall for user’s safety.
1) Turn on the treadmill, press START/STOP, and then operate the treadmill with the speed of
4km/h. Walk on the treadmill. Tightly grip the front handlebar and apply force with feet on the striding near the motor cover against the moving direction. If the belt slips, do steps from 2). If it does not slip, the tension is proper.
2) Stop the treadmill for a safety during adjustment and prepare 10mm wrench
Do not adjust tension while treadmill is in operation.
Warning: If you adjust the belt tension when the treadmill is in operation, it is very dangerous because sleeve or a part of body may be caught in roller or belt.
3) Locate the two belt tensioning bolts in the end caps on each rear side of the treadmill as shown, which enables to adjust belt tension. When turning this bolt, a position of roller moves back and forth. To move backward the roller, turn the bolts clockwise. To move forward the roller, turn the bolts counterclockwise.
4) Put 10mm wrench into the hole of the Right End
Cap as shown and then turn the wrench 1/4 turn clockwise.
5) Put 10mm wrench into the hole of the Left End Cap as shown and then turn the wrench 1/4 turn clockwise. Equal amount of rotations should be performed on right tensioning bolt and left tensioning bolt. If not so, the belt is off center to either right direction or left direction.
6) Repeat steps 1) through 5) until the belt no longer slips.
Do not exceed one full turn of the adjusting bolts in either direction. Over-tightening of the bolts may over stretch and damage the striding belt or roller bearings.
If the belt continues to slip in spite of the belt tension adjustment, verify that Drive Motor Belt can be the cause of the slip.
22
2.4 How to Adjust Motor Drive Belt Tension
The tension of Motor Drive Belt (M3, Poly-V Belt) can be loosened by a long time use and it can cause a slip between The Drive Motor Pulley and Motor Drive Belt. The tension is corrected by adjusting the mounting position of the Drive Motor (M1).
Do the steps below while referring to the following Exploded Views in Appendix.
A.1 M990T
B.1 MAIN BODY_FRONT A
C.1 MAIN BODY_REAR
1) Stop the treadmill after lifting up the unit at maximum by operating Incline Motor.
2) Turn off the unit power at the switch at the state of the treadmill lifted-up and then unplug the line cord at wall outlet.
3) Remove three bolts (B20) and then lift Motor Cover (T1) out from between the upright
Supports.
4) Loosen four nuts (N2) securing the Drive
Motor (M1) by one or two turns to allow the
Drive Motor to be moved by the Tension
Bolt (B7).
5) Turn the nut (N3) in the direction of arrow
‘1” to allow adjusting the tension on the
Drive Motor Belt by using the Tension Bolt
(B7).
6) Turn the Tension Bolt (B7) in 1/4 turn in the direction of arrow ”2” to move the Drive
Motor (M1) toward the outside of the unit, and then measure the tension of the Belt..
1
2
Note: One turn of the Tension Bolt makes the Drive Motor move by 1.5 mm. Keep in mind that tightening the Tension Bolt too much can damage the internal bearings of the Drive Motor or Front Roller .
7) When the tension reaches 160 Hz, secure two nuts (N2) diagonally.
Note: It is desirable to set the tension to
150Hz before tightening two nuts (N2)
23
because tightening two nuts (N2) increases the tension of the Motor Drive Belt.
8) Measure the Tension again. If the tension is lower than 155Hz or higher than 165Hz, readjust the tension 4 through 8) until it reaches 155Hz to 165Hz.
9) When the tension reaches 160 Hz, tighten the nut (N3) securing the Tension Bolt (B7).
10) Tighten remaining two nuts (N2) diagonally.
11) Make sure that the nut (N3) securing the Tension Bolt (B7) is tightened.
12) Re-assemble remaining parts in the reverse order of removal.
24
2.5 How to Replace the Rear Roller
Do the steps below while referring to the following Exploded Views in Appendix.
A.1 M990T
B.1 MAIN BODY_FRONT A
C.1 MAIN BODY_REAR
1) Turn off the unit power at the switch and then unplug the line cord at wall outlet.
2) Remove three Motor Cover screws (B20) and then lift the cover(T1) out from between the upright Supports.
3) Remove one bolt (B18) inside the left End Cap on the rear side of the unit and then remove
END CAP_L (F10) from the unit.
Remove one bolt (B18) inside the right End Cap on the rear side of the unit and then remove
END CAP_R(F11) from the unit.
4) Pull out two NONSLIP_PVC (F9) toward the rear side of the unit, which are inserted into the left NONSLIP_TOP (F8) /NONSLIP SIDE_L(F6) and the right NONSLIP_TOP(F8)/NONSLIP
SIDE_R (F7).
5) Remove eight bolts (B13) and then remove the left NONSLIP_TOP (F8) /NONSLIP
SIDE_L(F6) and the right NONSLIP_TOP(F8)/NONSLIP SIDE_R(F7).
6) Remove two bolts (B1) and then remove REAR ROLLER (F5) out under the Striding Belt.
7) Install a new Rear Roller in the reverse order of disassembly.
8) Refer to “How to Align Striding Belt” and “How to Adjust Striding Belt Tension”.
25
2.6 How to Replace the Front Roller
Do the steps below while referring to the following Exploded Views in Appendix.
A.1 M990T
B.1 MAIN BODY_FRONT A
C.1 MAIN BODY_REAR
1) Stop the treadmill after lifting up the unit at maximum by operating Incline Motor.
2) Turn off the unit power at the switch at the state of the treadmill lifted-up and then unplug the line cord at wall outlet.
3) Remove three bolts (B20) and then lift Motor Cover(T1) out from between the upright
Supports.
4) Remove one bolt (B18) inside the left End Cap on the rear side of the unit and then remove
END CAP_L (F10) from the unit.
5) Remove one bolt (B18) inside the right End Cap on the rear side of the unit and then remove
END CAP_R (F11) from the unit.
6) Loosen two bolts (B1) by turning it counterclockwise to slacken the Striding
Belt enough to allow side-to-side movement of the FRONT ROLLER (F4).
Count the number of rotations when loosening the bolts (B1) for re-tensioning the Striding Belt.
7) Loosen the nut (N3) securing Tension
Bolt (B7) for the Drive Motor Belt (M3) using spanner as shown in arrow mark 1.
9) Loosen the Tension Bolt (B7) for the
Drive Motor Belt (M3) as indicated in arrow mark 2 to allow the movement of the Drive
Motor (M1).
10) Loosen four nuts (N2) securing the
Drive Motor (M1) by one or two turns to allow the Drive Motor to be moved by the
Tension Bolt (B7).
11) Move the Drive Motor (M1) toward the
FRONT ROLLER to slacken the Drive Motor
1
2
26
Belt (POLY-V BELT).
12) Remove two bolts (B16, B2) securing the FRONT ROLLER (F4) and then remove the
FRONT ROLLER out from the left side of the frame, through the underside the Striding Belt.
Remove the DRIVE BELT (M3) out and save for a new Front Roller.
13) Install the new Front Roller and the Drive Motor Belt into position and secure in place with the mounting bolt (B16, B2). Adjust the Front Roller to be in parallel with the Rear Roller and the
Drive Motor by using the right side bolt (B2).
14) Make sure that the Motor Drive Belt (M3) is positioned on the grooves of the Front Roller
Pulley and the grooves of the Drive Motor Pulley.
15) Adjust the Motor Drive Belt Tension while referring to “How to Adjust Motor Drive Belt
Tension”.
16) Install the REAR ROLLER and other parts in the reverse order of disassembly.
17) Refer to “How to Align Striding Belt” and “How to Adjust Striding Belt tension”.
27
2.7 How to Replace the Striding Belt
Do the steps below while referring to the following Exploded Views in Appendix.
A.1 M990T
B.1 MAIN BODY_FRONT A
C.1 MAIN BODY_REAR
1) Stop the treadmill after lifting up the unit at maximum by operating Incline Motor.
2) Turn off the unit power at the switch at the state of the treadmill lifted-up and then unplug the line cord at wall outlet.
3) Remove three bolts (B20) and then lift Motor Cover (T1) out from between the upright
Supports.
4) Remove one bolt (B18) inside the left End Cap on the rear side of the unit and then remove
END CAP_L (F10) from the unit.
Remove one bolt (B18) inside the right End Cap on the rear side of the unit and then remove
END CAP_R (F11) from the unit.
5) Pull out two NONSLIP_PVC (F9) toward the rear side of the unit, which are inserted into the left NONSLIP_TOP (F8)/NONSLIP SIDE_L (F6) and the right NONSLIP_TOP (F8)/NONSLIP
SIDE_R (F7).
6) Remove eight bolts (B13) and then remove the left NONSLIP_TOP (F8)/NONSLIP SIDE_L
(F6) and the right NONSLIP_TOP (F8)/NONSLIP SIDE_R (F7).
7) Remove two bolts (B1) and then remove REAR ROLLER (F5) out under the Striding Belt.
8) Loosen the nut (N3) securing Tension Bolt (B7) for the Drive Motor Belt (M3) using spanner as shown in arrow mark “1”.
9) Loosen the Tension Bolt (B7) for the
Drive Motor Belt (M3) as indicated in arrow mark “2” to allow the movement of the Drive Motor (M1).
10) Loosen four nuts (N2) securing the
Drive Motor (M1) by one or two turns to allow the Drive Motor to be moved by the
Tension Bolt (B7).
11) Move the Drive Motor (M1) toward the
FRONT ROLLER to slacken the Drive
1
2
Motor Belt (POLY-V BELT).
12) Remove two bolts (B16, B2) securing the FRONT ROLLER (F4) and then remove the
28
FRONT ROLLER out from the left side of the frame, through the underside the Striding Belt.
Remove the DRIVE BELT (M3) out and save for a new Front Roller.
13) Remove the eight mounting bolts (B13) and then remove the DECK (F2).
14) Position a new Striding Belt (F3) onto the center of the frame inside unit and then install the saved DECK (F2) by tightening the eight mounting bolts (B13).
15) Install the new Front Roller and the Drive Motor Belt into position and secure in place with the mounting bolt (B16, B2). Adjust the Front Roller to be in parallel with the Rear Roller and the
Drive Motor by using the right side bolt (B2).
16) Make sure that the Motor Drive Belt (M3) is positioned on the grooves of the Front Roller
Pulley and the grooves of the Drive Motor Pulley.
17) Adjust the Motor Drive Belt Tension while referring to “How to Adjust Motor Drive Belt
Tension”.
18) Install the REAR ROLLER and other parts in the reverse order of disassembly.
19) Refer to “How to Align Striding Belt” and “How to Adjust Striding Belt tension”.
29
2.8 How to Replace the Motor Drive Belt
Do the steps below while referring to the following Exploded Views in Appendix.
A.1 M990T
B.1 MAIN BODY_FRONT A
C.1 MAIN BODY_REAR
1) Stop the treadmill after lifting up the unit at maximum by operating Incline Motor.
2) Turn off the unit power at the switch at the state of the treadmill lifted-up and then unplug the line cord at wall outlet.
3) Remove the three bolts (B20) and then lift Motor Cover (T1) out from between the upright
Supports.
4) Remove one bolt (B18) inside the left End Cap on the rear side of the unit and then remove
END CAP_L (F10) from the unit. Remove one bolt (B18) inside the right End Cap on the rear side of the unit and then remove END CAP_R (F11) from the unit.
5) Loosen two bolts (B1) by turning it counterclockwise to slacken the Striding Belt enough to allow side-to-side movement of the FRONT ROLLER (F4).
Count the number of rotations when loosening the bolts (B1) for re-tensioning the Striding Belt.
6) Loosen the nut (N3) securing Tension Bolt (B7) for the Drive Motor Belt (M3) using spanner.
7) Loosen the Tension Bolt (B7) for the Drive Motor Belt (M3, POLY-V BELT) to allow the movement of the Drive Motor (M1).
8) Loosen four nuts (N2) securing the Drive Motor (M1) by one or two turns to allow the Drive
Motor to be moved by the Tension Bolt (B7).
9) Move the Drive Motor (M1) toward the FRONT ROLLER to slacken the Drive Motor Belt.
10) Remove two bolts (B16, B2) securing the FRONT ROLLER (F4) and then remove the
FRONT ROLLER out from the left side of the frame, through the underside the Striding Belt.
Remove the DRIVE BELT (M3) out and save for a new Front Roller.
11) Install the new Front Roller and the Drive Motor Belt into position and secure in place with the mounting bolt (B16, B2). Adjust the Front Roller to be in parallel with the Rear Roller and the
Drive Motor by using the right side bolt (B2).
12) Make sure that the Motor Drive Belt (M3) is positioned on the grooves of the Front Roller
Pulley and the grooves of the Drive Motor Pulley.
13) Adjust the Motor Drive Belt Tension while referring to “How to Adjust Motor Drive Belt
Tension”
14) Install the REAR ROLLER and other parts in the reverse order of disassembly.
15) Refer to “How to Align Striding Belt” and “How to Adjust Striding Belt tension”.
30
2.9 How to Replace the DECK
Do the steps below while referring to the following Exploded Views in Appendix.
A.1 M990T
B.1 MAIN BODY_FRONT A
C.1 MAIN BODY_REAR
1) Turn off the unit power at the switch and then unplug the line cord at wall outlet.
2) Remove three bolts (B20) and then lift Motor Cover (T1) out from between the upright
Supports.
3) Remove one bolt (B18) inside the left End Cap on the rear side of the unit and then remove
END CAP_L (F10) from the unit.
Remove one bolt (B18) inside the right End Cap on the rear side of the unit and then remove
END CAP_R (F11) from the unit.
4) Pull out two NONSLIP_PVC (F9) toward the rear side of the unit, which are inserted into the left NONSLIP_TOP (F8)/NONSLIP SIDE_L (F6) and the right NONSLIP_TOP (F8)/NONSLIP
SIDE_R (F7).
5) Remove eight bolts (B13) and then remove the left NONSLIP_TOP (F8)/NONSLIP SIDE_L
(F6) and the right NONSLIP_TOP (F8)/NONSLIP SIDE_R (F7).
6) Remove two bolts (B1) and then remove the REAR ROLLER (F5) out under the Striding Belt.
7) Remove the eight mounting bolts (B13) and then remove the DECK (F2) out from under the
Striding Belt.
8) Mount a new DECK (F2) through the Striding Belt and secure it in position by tightening the eight mounting bolts (B13).
10) Install the REAR ROLLER and other parts in the reverse order of disassembly.
11) Refer to “How to Align Striding Belt” and “How to Adjust Striding Belt tension”.
31
2.10 How to Replace Drive Motor
Do the steps below while referring to the following Exploded Views in Appendix.
A.1 M990T
B.1 MAIN BODY_FRONT A
C.1 MAIN BODY_REAR
1) Stop the treadmill after lifting up the unit at maximum by operating Incline Motor.
2) Turn off the unit power at the switch at the state of the treadmill lifted-up and then unplug the line cord at wall outlet.
3) Remove three bolts (B20) and then lift Motor
Cover (T1) out from between the upright Supports.
4) Remove the nut (N3) securing the Tension Bolt
(B7) by using a spanner.
5) Remove the Tension Bolt (B7) to reserve a space to move the Drive Motor.
6) Remove the upper small Cover by pushing it in the direction of arrow while pushing it downward.
7) Remove the screw on the lower left side of the
Motor Controller and then open the Cover.
8) Disconnect three Cables from the Motor Controller by removing three bolts securing three
32
cables to the Motor Controller as shown. U, V or W is marked on three Cables.
9) Remove four bolts (B9), washers (W2) and four nuts (N2) and then lift the Drive Motor (M1) out.
10) Install a new Drive Motor in the reverse order of removal and then connect the three Cables from the Drive Motor to the Motor
Controller. Keep in mind that each three cables should be connected exactly as shown. In other word, connect the
U V W
Cable “W” to rightmost terminal, Cable
“V” to second rightmost terminal and
Cable “U” to third rightmost terminal.
11) Re-install two Covers of the Motor
Controller in the reverse order.
12) Install the Motor Drive Belt onto the
Drive Motor Pulley and then refer to
“How to Adjust Motor Drive Belt Tension” to adjust the tension of the Motor Drive Belt.
13) Refer to “How to Align Striding Belt” and “How to Adjust Striding Belt tension”.
33
2.11 How to Replace the Incline Motor
Do the steps below while referring to the following Exploded Views in Appendix.
A.1 M990T
B.1 MAIN BODY_FRONT A
1) Turn off the unit power at the switch and then unplug the line cord at wall outlet.
2) Remove three Motor Cover screws (B20) and then lift the cover (T1) out from between the upright Supports.
3) Disconnect the 3-pin Connector from the Lift/Power Board
(M10) as indicated in arrow “1”.
4) Disconnect the Incline Motor ground wire by removing one bolt (B30) securing small Transformer (M6).
5) Tilt the treadmill over on its right or left side after putting down soft materials to avoid a scratch on the side of the treadmill.
6) Remove the bolt (B6) and nut (N2) securing the LEG FRAME (M13) and the
1
Shaft Tube of the Incline Motor (M7).
7) Remove the bolt (B8) and nuts (N2 and
N3) and then lift the Incline Motor (M7) out from the Main Frame (F1).
8) Install a new Incline Motor in the reverse order of the removal and then make sure that the clearance between the
CASTER (M14) and the underside of the
Main Frame is between 12 mm and 15 mm as shown. When the clearance is too narrow, remove the bolt (B6) and nut (N2), and then turn the Shaft Tube of the Incline
Motor in the direction of the arrow “1” to increase the stroke of the Tube as shown.
When the clearance is too wide, turn the
Shaft Tube of the Incline Motor in reverse direction of the arrow “1” to adjust the stroke of the Shaft Tube.
34
10) Reassemble remaining components in the reverse order of removal.
11) Turn on the treadmill and then make sure that the Incline function is working properly.
35
2.12 How to Replace the Oil Pump
Do the steps below while referring to the following Exploded Views in Appendix.
A.1 M990T
B.1 MAIN BODY_FRONT A
1) Stop the treadmill after lifting up the unit at maximum by operating Incline Motor.
2) Turn off the unit power at the switch at the state of the treadmill lifted-up and then unplug the line cord at wall outlet.
3) Remove three bolts (B20) and then lift
Motor Cover (T1) out from between the upright Supports.
4) Locate the Hosepipe (M18) and Socket
(M17) under the bottom of the front Frame.
5) Turn the Socket (M17) in the direction of arrow until the Oil Pump (M15) is removed.
6) Re-assemble a new Oil Pump (M15) in the reverse order of removal.
7) Re-assemble the Motor Cover in the reverse of removal.
36
2.13 How to Replace the Contact Heart Rate Sensor
Do the steps below while referring to the following Exploded Views in Appendix.
E.1 CONSOLE ASSEMBLY
1) Turn off the unit power at the switch and then unplug the line cord at wall outlet.
2) Remove four screws (B25) and two screws (B21) securing SIDE HANDLE TOP/BOTTOM
(C6, C7, C8 & C9) and then remove SIDE HANDLE TOP/BOTTOM from the Console Assembly..
3) Remove six screws (B27) securing the FRONT HANDLE TOP and FRONT HANDLE
BOTTOM to the HANDLE CROSS PIPE (C10) and then remove the FRONT HANDLE
TOP/BOTTOM from the Console
Assembly.
4) Disconnect the sensing wire from the inside TERMINAL of the SENSOR PLATE which is located on the FRONT HANDLE
TOP.
Note: The FRONT HANDLE
TOP has four SENSOR PLATEs and each SENSOR PLATE has one TERMINAL.
5) Remove the SENSOR PLATE from the FRONT
HANDLE TOP by straightening the bent fixing tips indicated as A.
6) Install new sensor in reverse order while bending four fixing tips.
7) Repeat the above steps for the remaining SENSOR
PLATE 4) through 6).
37
Motus Treadmills M990T, M990TL, M995T and M995TL
SECTION III
HOW TO REPLACE & REPAIR GUIDE
Electronic PCB
3.1 How to Replace the LCD Screen
3.2 How to Replace the MPU Board in Model M990TL and M995TL
3.3 How to Replace the MPU Board in Model M990T and M995T
3.4 How to Replace the Touch Sensitive Key Board
3.5 How to Replace the Lift/Power Board
3.6 How to Replace the A/D Board
3.7 How to Replace the Lamp Inverter Board
3.8 How to Replace the Program Button, OSD Button & Audio Interface
Board in Model M990TL and M995TL
3.9 How to Replace the Logo-Lighting & Key Conversion Board in Model
M990T and M995T
3.10 How to Replace the CHR (Contact Heart Rate) Board
38
3.1 How to Replace the LCD Screen
Do the steps below while referring to the following Exploded Views in Appendix and Section 4
ELECTRONIC PCB, CONNECTOR AND CABLE OVERVIEW.
D.1 OVERLAY BEZEL ASSEMBLY
E.1 CONSOLE ASSEMBLY
1) Turn off the unit power at the switch and then unplug the line cord at wall outlet.
2) Remove eleven screws (B23) from the Console Bottom (C2).
3) Lift off the Console Bottom from the Console Case (C1) while disconnecting the Download
Cable (C41) from the MPU PCB (L9).
4) From the underside of the Console Case (C1), remove three screws (B26) securing the
Overlay Bezel Assembly to the Console Case.
5) Remove green Earth Cables connected between MPU PCB (L9) and Handle Frame (C3) by removing two screws (B21) from Handle Frame.
6) Disconnect all of electrical connectors from MPU PCB (L9) and the Co-axial Cable(TU1),
Stereo Cable (CN12), RCA Cable(CN5, 8, 9), S-VIDEO Cable(CN2) and DC12V Cable(CN3) from the A/D Board (L13).
<The Connectors of A/D Board>
7) Lift out the Overlay Bezel Assembly from the front of Console Case and then put it down on the flat and clean surface so that LCD Screen faces downward.
8) Remove six screws (B33) securing the LCD Metal Bracket (L12) to the LCD Overlay Bezel and then remove the LCD Metal Bracket (L12) from the Overlay Bezel.
9) Disconnect LVDS Cable (CB16) from the LCD screen (L11).
10) Disconnect the Lamp Cable from the Lamp Inverter (L14).
39
11) Disconnect the OSD Button Cable from either OSD Button PCB (L7) or A/D Board (L13).
12) Reverse LCD Metal Bracket (L12) so that the LCD Screen (L11) faces upward.
13) Remove four bolts (B34) securing the LCD Screen to LCD Metal Bracket and then lift the
LCD Screen off.
14) Install new LCD Screen in reverse order.
40
3.2 How to Replace the MPU Board in Model M990TL and M995TL
Do the steps below while referring to the following Exploded Views in Appendix and Section 4
ELECTRONIC PCB, CONNECTOR AND CABLE OVERVIEW.
D.1 OVERLAY BEZEL ASSEMBLY
E.1 CONSOLE ASSEMBLY
1) Turn off the unit power at the switch and then unplug the line cord at wall outlet.
2) Remove eleven screws (B23) from the Console Bottom (C2).
3) Lift off the Console Bottom from the Console Case (C1) while disconnecting the Download
Cable (C41) from the MPU PCB (L9).
4) From the underside of the Console Case (C1), remove three screws (B26) securing the
Overlay Bezel Assembly to the Console Case.
5) Remove green Earth Cables (J3) connected between MPU PCB (L9) and Handle Frame (C3) by removing two screws (B21) from Handle Frame.
6) Disconnect all of electrical connectors from MPU PCB (L9) and the Co-axial Cable(TU1),
Stereo Cable (CN12), RCA Cable(CN5, 8, 9), S-VIDEO Cable(CN2) and DC12V Cable(CN3) from the A/D Board (L13).
7) Lift out the Overlay Bezel Assembly from the front of Console Case (C1) and then put it down on the flat and clean surface so that the LCD Screen faces downward.
8) Disconnect the Program Button Cable (CB12) from the MPU Board (L9).
9) Disconnect the Ribbon Cable (L4) from the connector CN13 of MPU Board (L9).
10) Remove eight screws (B35) securing MPU Board to the LCD Overlay Bezel and then remove MPU Board from the Overlay Bezel.
11) Install new MPU Board in reverse order. Make sure that all connectors and the Ribbon
Cable are securely fastened.
41
3.3 How to Replace the MPU Board in Model M990T and M995T
Do the steps below while referring to the following Exploded Views in Appendix and Section 4
ELECTRONIC PCB, CONNECTOR AND CABLE OVERVIEW.
D.1 OVERLAY BEZEL ASSEMBLY
E.1 CONSOLE ASSEMBLY
1) Turn off the unit power at the switch and then unplug the line cord at wall outlet.
2) Remove eleven screws (B23) from the Console Bottom (C2).
3) Lift off the Console Bottom from the Console Case (C1) while disconnecting the Download
Cable (C41) from the MPU PCB (D4).
4) From the underside of the Console Case (C1), remove three screws (B26) securing the
Overlay Bezel Assembly (DOT TYPE) to the Console Case.
5) Remove green Earth Cables (J3) connected between MPU PCB (D4) and Handle Frame
(C3) by removing two screws (B21) from Handle Frame.
6) Disconnect all of electrical connectors from the MPU PCB (D4).
7) Lift out the Overlay Bezel Assembly (DOT TYPE) from the front of Console Case (C1) and then put it down on the flat and clean surface so that the Display faces downward.
8) Disconnect the Logo Backlight Cable (CB9) from the MPU Board (D4).
9) Disconnect the Key Conversion Cable (CB6) from the MPU Board (D4).
10) Disconnect the Ribbon Cable (D2) from the connector CN13 of MPU Board (D4).
11) Remove nine screws (B33) securing MPU Board to the Overlay Bezel (DOT TYPE) and then remove MPU Board from the Overlay Bezel.
12) Install new MPU Board (D4) in reverse order. Make sure that all connectors and the Ribbon
Cable are securely fastened.
42
3.4 How to Replace the Touch Sensitive Key Board
Do the steps below while referring to the following Exploded Views in Appendix and Section 4
ELECTRONIC PCB, CONNECTOR AND CABLE OVERVIEW.
E.1 CONSOLE ASSEMBLY
1) Turn off the unit power at the switch and then unplug the line cord at wall outlet.
2) Remove eleven screws (B23) from the Console Bottom (C2).
3) Lift off the Console Bottom from the Console Case (C1) while disconnecting the Download
Cable (C41) from the MPU PCB.
4) Disconnect the Touch Sensitive Key Cable (CB3L) from the left Touch Sensitive Key Board
(C14).
For the right Touch Sensitive Key Board (C15), disconnect the Cable (CB3R).
5) Remove eight screws (B35) and then remove the Touch Sensitive Key Board (C14 or C15) from the Console Case (C1).
6) Install new the Touch Sensitive Key Board (C14 or C15) in reverse order.
43
3.5 How to Replace the Lift/Power Board
Do the steps below while referring to the following Exploded Views in Appendix and Section 4
ELECTRONIC PCB, CONNECTOR AND CABLE OVERVIEW.
A.1 M990T
B.1 MAIN BODY_FRONT A
1) Turn off the unit power at the switch and then unplug the line cord at wall outlet.
2) Remove three bolts (B20) and then lift Motor Cover(T1) out from between the upright
Supports.
3) Disconnect all of cables from the Lift/Power Board (M10).
4) Remove four screws (B30) securing the Lift/Power Board (M10) and lift out the Lift/Power
Board (M10) from the base frame.
5) Install new Lift/Power Board (M10) in reverse order.
44
3.6 How to Replace the A/D Board
Do the steps below while referring to the following Exploded Views in Appendix and Section 4
ELECTRONIC PCB, CONNECTOR AND CABLE OVERVIEW.
D.1 OVERLAY BEZEL ASSEMBLY
E.1 CONSOLE ASSEMBLY
1) Turn off the unit power at the switch and then unplug the line cord at wall outlet.
2) Remove eleven screws (B23) from the Console Bottom (C2).
3) Lift off the Console Bottom from the Console Case (C1) while disconnecting the Download
Cable (C41) from the MPU PCB (L9).
4) Disconnect all of cables from the A/D Board (L13).
5) Remove four screws (B34) securing the A/D Board (L13) and then remove the A/D Board
(L13) from the LCD Metal Bracket (L12).
6) Install new A/D Board (L13) in reverse order.
45
3.7 How to Replace the Lamp Inverter Board
Do the steps below while referring to the following Exploded Views in Appendix and Section 4
ELECTRONIC PCB, CONNECTOR AND CABLE OVERVIEW.
D.1 OVERLAY BEZEL ASSEMBLY
E.1 CONSOLE ASSEMBLY
1) Turn off the unit power at the switch and then unplug the line cord at wall outlet.
2) Remove eleven screws (B23) from the Console Bottom (C2).
3) Lift off the Console Bottom (C2) from the Console Case (C1) while disconnecting the
Download Cable (C41) from the MPU PCB (L9).
4) Disconnect the Lamp Inverter Cable (CB17) from the Lamp Inverter Board (L14).
5) Disconnect the Lamp Cable between the Lamp Inverter Board (14) and LCD Screen (L11).
5) Remove two screws (B34) securing the Lamp Inverter Board (L14) and then remove the
Lamp Inverter Board (L14) from the LCD Metal Bracket (L12).
6) Install new Lamp Inverter Board (L13) in reverse order.
46
3.8 How to Replace the Program Button, OSD Button & Audio Interface
Board in Model M990TL and M995TL
Do the steps below while referring to the following Exploded Views in Appendix and Section 4
ELECTRONIC PCB, CONNECTOR AND CABLE OVERVIEW.
D.1 OVERLAY BEZEL ASSEMBLY (LCD TYPE)
E.1 CONSOLE ASSEMBLY
1) Turn off the unit power at the switch and then unplug the line cord at wall outlet.
2) Remove eleven screws (B23) from the Console Bottom (C2).
3) Lift off the Console Bottom from the Console Case (C1) while disconnecting the Download
Cable (C41) from the MPU PCB (L9).
4) From the underside of the Console Case (C1), remove three screws (B26) securing the
Overlay Bezel Assembly to the Console Case.
5) Remove green Earth Cables (J3) connected between MPU PCB (L9) and Handle Frame (C3) by removing two screws (B21) from Handle Frame.
6) Disconnect all of electrical connectors from MPU PCB (L9) and the Co-axial Cable(TU1),
Stereo Cable (CN12), RCA Cable(CN5, 8, 9), S-VIDEO Cable(CN2) and DC12V Cable(CN3) from the A/D Board (L13).
<The Connectors of A/D Board>
7) Lift out the Overlay Bezel Assembly from the front of Console Case (C1) and then put it down on the flat and clean surface so that the LCD Screen faces downward.
Program Button Board
8) Disconnect the Program Button Cable (CB12) from the Program Button Board (L6).
47
9) Remove three screws (B33) securing Program Button Board (L6) and lift off the Program
Button Board (L6) from the LCD Overlay Bezel (L5).
10) Install new Program Button Board in reverse order.
OSD Button Board
8) Disconnect the OSD Button Cable (CB15) from the OSD Button Board (L7).
9) Remove three screws (B33) securing the OSD Button Board (L7) and lift off the OSD Button
Board (L6) from the LCD Overlay Bezel (L5).
10) Install new OSD Button Board in reverse order.
Audio Interface Board
8) Disconnect the Audio Interface Cable (CB5) from the Audio Interface Board (L8).
9) Remove four screws (B35) securing the Audio Interface Board (L8) and lift off the Audio
Interface Board (L8) from the LCD Overlay Bezel (L5).
10) Install new Audio Interface Board (L8) in reverse order.
48
3.9 How to Replace the Logo-Lighting & Key Conversion Board in Model
M990T and M995T
Do the steps below while referring to the following Exploded Views in Appendix and Section 4
ELECTRONIC PCB, CONNECTOR AND CABLE OVERVIEW.
D.1 OVERLAY BEZEL ASSEMBLY (DOT TYPE)
E.1 CONSOLE ASSEMBLY
1) Turn off the unit power at the switch and then unplug the line cord at wall outlet.
2) Remove eleven screws (B23) from the Console Bottom (C2).
3) Lift off the Console Bottom from the Console Case (C1) while disconnecting the Download
Cable (C41) from the MPU PCB (D4).
4) From the underside of the Console Case (C1), remove three screws (B26) securing the
Overlay Bezel Assembly (DOT TYPE) to the Console Case.
5) Remove green Earth Cables (J3) connected between the MPU PCB (D4) and Handle Frame
(C3) by removing two screws (B21) from Handle Frame.
6) Disconnect all of electrical connectors from the MPU PCB (D4).
7) Lift out the Overlay Bezel Assembly (DOT TYPE) from the front of Console Case (C1) and then put it down on the flat and clean surface so that the Display faces downward.
Logo-Lighting Board
8) Disconnect the Logo Backlight Cable (CB9) from the MPU Board (D4).
9) Remove two screws (B33) securing the Logo Backlight Board (D5) and lift off the Logo
Backlight Board (D5) from the Overlay Bezel (D3).
10) Install new Logo Backlight Board (D5) in reverse order.
Key Conversion Board
8) Disconnect the Key Conversion Cable (CB6) from the MPU Board (D4).
9) Remove two screws (B35) securing the Key Conversion Board (D6) and lift off the Key
Conversion Board (D6) from the Overlay Bezel (D3).
10) Install new Key Conversion Board (D6) in reverse order.
49
3.10 How to Replace the CHR (Contact Heart Rate) Board or Combo Board
3.10.1 Old Version CHR Board
Note: Old version CHR Board is mounted on MPU Board as Piggy Back Board.
Do the steps below while referring to the following Exploded Views in Appendix and Section 4
ELECTRONIC PCB, CONNECTOR AND CABLE OVERVIEW.
D.1 OVERLAY BEZEL ASSEMBLY
E.1 CONSOLE ASSEMBLY
1) Turn off the unit power at the switch and then unplug the line cord at wall outlet.
2) Remove eleven screws (B23) from the Console Bottom (C2).
3) Lift off the Console Bottom from the Console Case (C1) while disconnecting the Download
Cable (C41) from the MPU PCB (L9 or D4).
4) From the underside of the Console Case (C1), remove three screws (B26) securing the
Overlay Bezel Assembly (LCD TYPE/DOT TYPE) to the Console Case.
5) Remove green Earth Cables (J3) connected between MPU PCB (L9 or D4) and Handle
Frame (C3) by removing two screws (B21) from Handle Frame.
6) Disconnect all of electrical connectors from MPU PCB (L9 or D4).
If the Model is M990TL or M995TL with LCD Screen, disconnect the Co-axial Cable(TU1),
Stereo Cable (CN12), RCA Cable(CN5, 8, 9), S-VIDEO Cable(CN2) and DC12V Cable(CN3) from the A/D Board (L13).
7) Lift out the Overlay Bezel Assembly (LCDTYPE/DOT TYPE) from the front of Console Case
(C1) and then put it down on the flat and clean surface so that the Display faces downward.
8) Cut Cable Tie Strap securing CHR Board to MPU Board and remove the Cable Tie Strap.
9) Lift off the CHR Board from the MPU Board (L9 or D4).
10) Install new CHR Board(old-version) in reverse order.
50
3.10.2 Replacing Old Version CHR Board with New Version CHR Board
Note: Replacing Old version CHR Board with New Version CHR Board. Old version CHR
Board is located on MPU Board as Piggy Back Board.
Do the steps below while referring to the following Exploded Views in Appendix and Section 4
ELECTRONIC PCB, CONNECTOR AND CABLE OVERVIEW.
D.1 OVERLAY BEZEL ASSEMBLY
E.1 CONSOLE ASSEMBLY
1) Turn off the unit power at the switch and then unplug the line cord at wall outlet.
2) Remove eleven screws (B23) from the Console Bottom (C2).
3) Lift off the Console Bottom from the Console Case (C1) while disconnecting the Download
Cable (C41) from the MPU PCB (L9 or D4).
4) From the underside of the Console Case (C1), remove three screws (B26) securing the
Overlay Bezel Assembly (LCD TYPE/DOT TYPE) to the Console Case.
5) Remove green Earth Cables (J3) connected between MPU PCB (L9 or D4) and Handle
Frame (C3) by removing two screws (B21) from Handle Frame.
6) Disconnect all of electrical connectors from MPU PCB (L9 or D4).
If the Model is M990TL or M995TL with LCD Screen, disconnect the Co-axial Cable(TU1),
Stereo Cable (CN12), RCA Cable(CN5, 8, 9), S-VIDEO Cable(CN2) and DC12V Cable(CN3) from the A/D Board (L13).
7) Lift out the Overlay Bezel Assembly (LCD TYPE/DOT TYPE) from the front of Console Case
(C1) and then put it down on the flat and clean surface so that the Display faces downward.
8) Cut Cable Tie Strap securing CHR Board to MPU Board and remove the Cable Tie Strap.
9) Lift off the CHR Board from the MPU Board (L9 or D4).
10) Prepare new CHR Board (4000EX) or Combo Board(8500) which functions as both
Wireless Receiver & Contact Heart Rate Monitor) and cut off Ground Line of the CHR Board in green if any. M990 series treadmill requires the Ground Line of the Board eliminated.
11) Attach new CHR Board on the position as shown in figure. Make use of foam which is attached on the backside of CHR Board for fixing the board.
51
12) Connect 3-pin cable between the CHR Board and MPU PCB (CN7 on L9 Board or CN10 on
D4 Board).
13) Connect two 2-pin cables coming from Contact Sensor to the CHR Board.
14) Re-install all of disassembled parts in reverse order.
52
3.10.3 New Version CHR Board
Do the steps below while referring to the following Exploded Views in Appendix and Section 4
ELECTRONIC PCB, CONNECTOR AND CABLE OVERVIEW.
D.1 OVERLAY BEZEL ASSEMBLY
E.1 CONSOLE ASSEMBLY
1) Turn off the unit power at the switch and then unplug the line cord at wall outlet.
2) Remove eleven screws (B23) from the Console Bottom (C2).
3) Lift off the Console Bottom from the Console Case (C1) while disconnecting the Download
Cable (C41) from the MPU PCB (L9 or D4).
4) Disconnect three cables from CHR Board (or Combo Board) and remove the Board from the
Console Case.
5) Prepare new CHR Board (or Combo Board which functions as both Wireless Receiver &
Contact Heart Rate Monitor) and cut off Ground Line of the CHR Board in green if any. M990 series treadmill requires the Ground Line of the Board eliminated.
6) Install new CHR Board (New Version) in reverse order.
53
Motus Treadmills M990T, M990TL, M995T and M995TL
SECTION IV
ELECTRONIC PCB, CONNECTOR AND
CABLE OVERVIEW
4.1 Cable Connection Block Diagram
4.2 Electronic PCB, Connector and Pin Description
4.3 Cables & Connectors
4.4 Cable Diagram
54
4.1 Cable Connection Block Diagram
1) MPU PCB (LCD Type)
55
2) MPU PCB (DOT Type)
56
3) A/D BOARD
57
4) Lift/Power BOARD
4-1) Supply Voltage: 220/230VAC
58
4-2) Supply Voltage: 100/120VAC (USA, Japan)
59
4.2 Electronic PCB, Connector and Pin Description
1) MPU (LCD Type), M990TL/M995TL
Connector
CN 1: Main Power
It Is connected to
Lift/Power PCB
CN 2 :
Lift/Power Control
It Is connected to
Lift/Power PCB
Location Pin
1
3
Pin Name
VCC3A
Functional Description
5V for DOT Display
VCC_MPU 5V for System Power
2 V_HR Vcc for HR
8
9
10
11
12
13
14
15
GND_TCH
V_TCH
VCC_12V
Oil_PMP
Touch Board Ground
Touch Board Vcc
12V for Buzzer
Oil Pump On/Off
N.C N/C
N.C N/C
60
Connector
CN 3 :
TV Power Control
CN 5 :
Serial Port (RS-232)
(Reserved)
Location Pin
2
3
CN 6 :
Program Download
It is connected to
Download PCB
1
CN 7 :
Wireless Receiver which is connected to
Wireless HR PCB
CN 8 :
Emergency Magnet
CN 9 : Contact
Heart Rate Sensor
Connector
CN 10 : Contact
Heart Rate Sensor
CN 18 : Emergency
Push Button Switch
Location Pin
1
2
1
2
2
3
Pin Name Functional Description
TXD_PC
RXD_PC
Transmit data ( M990T Æ PC)
Receive data( PC Æ M990T )
T232/PDO Program Data Output
VCC
GND
Heart Rate +5V
Heart Rate Ground
Signal 1
Signal 2
Pin Name
Signal 1
Signal 2
Touch Plate signal 1-1
Touch Plate signal 1-2
Functional Description
Touch Plate signal 2-1
Touch Plate signal 2-2
61
Connector
CN 13 :
Ribbon Connector for Membrane Overlay
Location Pin
7
8
9
10
5
6
CN 14 :
Speed & Start Key
Pin Name
Q6
Q5
Q4
Q3
Q2
Q1
Functional Description
Data Output 6
Data Output 5
Data Output 4
Data Output 3
Data Output 2
Data Output 1
4
5
SPEED-
SPEED+
Speed Down Key
Speed Up Key
6 LIGHT_CON 않음.
7 VCC3A System +5V Vcc
CN 15 :
Incline & Enter Key
3
4
INCLINE-
INCLINE+
Incline Down Key
Incline Up Key
CN 16 :
Program Button
1
2
3
4
Q1
Q2
Q3
Q4
Data Output 1
Data Output 2
Data Output 3
Data Output 4
62
Connector
CN 17 : Push Button
Switch
RJ 1 : Communication for Motor Controller
Location Pin Pin Name Functional Description
63
2) MPU (DOT TYPE) M990T/M995T
CN 2 :
Key Conversion for
Speed/Incline
Connector
CN 1 :
Program Download
Location Pin
1
Pin Name
T232/PDO
Functional Description
Program Data Output
2
3
Key 1
Key 2
Key Invert signal
Key 1 Invert signal
64
Connector
CN 3 :
Lift/Power Board
Control
It is connected to
Lift/Power PCB.
Location Pin
2
Pin Name
V_HR Vcc for HR
Functional Description
13
14
15
10
11
12
VCC_12V
Oil_PMP
12V for Buzzer
Oil Pump On/Off
SEN_PMP Oil Pump sencing
N.C N/C
N.C N/C.
CN 5 :
Serial Port (RS-232)
CN 6 : Main Power which is connected to
Lift/Power PCB
CN 8 :
Magnetic Emergency
CN 9 : Contact
Heart Rate Sensor
CN 10 : Wireless
Receiver which is con- nected to WHR PCB.
1
2
1
2
3
1
3
2
3
TXD_PC
RXD_PC
Transmit data ( M990T Æ PC)
Receive data( PC Æ M990T )
VCC3A
VCC_MPU
5V for DOT Display
5V for System Power
Signal 1
Signal 2
Signal
VCC
GND
Touch Plate signal 1-1
Touch Plate signal 1-2
Wireless Receive Signal
Heart Rate +5V
Heart Rate Ground
65
Connector
CN 12 : Touch
Heart Rate Sensor
CN 13 :
Ribbon Cable for
Membrane Overlay
Location Pin
1
2
8
9
10
5
6
7
CN 15 :
Speed & Enter Key
4
5
Pin Name
Signal 1
Signal 2
Functional Description
Touch Plate signal 2-1
Touch Plate signal 2-2
Q6
Q5
Q4
Q3
Q2
Q1
SPEED-
SPEED+
Data Output 6
Data Output 5
Data Output 4
Data Output 3
Data Output 2
Data Output 1
Speed Down Key
Speed Up Key
CN 16 :
Incline & Enter Key
3
4
INCLINE-
INCLINE+
Incline Down Key
Incline Up Key
CN 18 : Push Button
Switch
66
Connector
CN 17 :
Logo Backlight
Location Pin Pin Name
RJ 1 :
Communication for
Motor Controller
Functional Description
67
3) Touch Sensitive Key Board
Connector
CN 1 :
Right Touch Sensitive
Key.
(Start/Stop, Speed Up &
Speed Down)
Location Pin
4
5
CN 2 :
Left Touch Sensitive
Key.
(Enter, Incline Up &
Incline Down)
3
4
Pin Name Functional Description
SPEED-
SPEED+
Speed Down Key
Speed Up Key
INCLINE-
INCLINE+
Incline Down Key
Incline Up Key
68
4) Lift/Power Board
Connector
CN 1 :
Transformer Output
Location Pin
CN 2 :
Transformer Output
Pin Name Functional Description
CN 3 :
Main Power
1
3
VCC3A
VCC_MPU
5V for DOT Display
5V for System
69
Connector
CN 4 :
Lift/Power Board
Control
Location Pin
2
Pin Name
V_HR Vcc for HR
Functional Description
13
14
15
10
11
12
VCC_12V
Oil_PMP
12V for Buzzer
Oil Pump On/Off
N.C N/C
N.C N/C
CN 5 :
Transformer Input
CN 6 :
Oil Pump Control
CN 7 :
I/O Interface for Motor
Controller
CN 8 :
Encoder Pulse
1
2
3
4
Motor+
Motor-
Limit Switch-
Limit Switch+
Oil pump motor
Oil pump motor
Oil pump motor
Oil pump motor
70
Connector
CN 9 :
Reserved
CN 10 :
Reserved
CN 11 :
Oile Pump Control
CN 20 :
Lift Motor Control
AC 1 : AC Power
AC 2 : AC Power
Location Pin Pin Name
1
1
AC
AC
Functional Description
220VAC Power Input
220VAC Power Input
71
5) A/D Board
Connector
CN 1 : Audio Out
CN 2 : S-VIDEO
CN 3 : DC In
CN 5 : Video In (RCA)
CN 8 : Audio In (RCA)
CN 9 : Audio In (RCA)
CN 10 :
LAMP Inverter
Control
Location Pin
1
3
Pin Name
Audio Left Audio Left
Functional Description
Audio Right Audio Right
SVIDEO Input
DC 12V/3.5A Input
Video Input (Yellow)
Audio Input (Red)
Audio Input (White)
7
8
DIM CTRL
On/Off
Back Light Intensity Control (DC 0 - 5V)
Back Light On/Off Control
72
Connector
CN 11 :
OSD Button
Location Pin Pin Name
4
Functional Description
5V Vcc DC 5V
CN 12 : S-AUDIO In
CN 14 : RGB In
TU 1 : RF ANT In
CN 13 :
LVDS Control
S-AUDIO In S-AUDIO Input
N/C
RF ANT In
N/C
Coaxial TV
CN 13 :
11
12
13
14
8
9
10
15
16
17
18
19
20
E 3+
E 3-
E CLK +
LVDS EVEN
LVDS EVEN
LVDS EVEN
E CLK -
E 2+
LVDS EVEN
LVDS EVEN
E 2- LVDS EVEN
GND Ground
E 1+
E 1-
LVDS EVEN
LVDS EVEN
GND Ground
E 0+
E 0-
O 3+
LVDS EVEN
LVDS EVEN
LVDS ODD
73
LVDS Control 21
22
23
24
25
26
27
28
29
30
O 3-
O CLK +
LVDS ODD
LVDS ODD
O CLK - LVDS ODD
GND Ground
O 2+ LVDS ODD
O 2-
O 1+
LVDS ODD
LVDS ODD
O 1-
O 0+
O 0-
LVDS ODD
LVDS ODD
LVDS ODD
74
6) LAMP Inverter Board
CN 2 :
CN 3 :
CN 4 :
CN 5 :
Connector
CN 1 :
Location
7
8
9
10
11
12
Pin
1
2
3
4
5
6
Pin Name Functional Description
Lamp Inverter Control
Lamp Inverter Control
Lamp Inverter Control
Lamp Inverter Control
Lamp Inverter Control
Lamp Inverter Control
Lamp Inverter Control
Lamp Inverter Control
Lamp Inverter Control
Lamp Inverter Control
Lamp Inverter Control
Lamp Inverter Control
Lamp Power
Lamp Power
Lamp Power
Lamp Power
75
7) OSD Button Board
Connector
CN 3 :
Location Pin Pin Name Functional Description
Key
(Volume up, Channel down & Channel up)
(Volume down, Power)
8) Program Button Board
Connector
CN 4 :
Location Pin
1
2
3
4
5
Pin Name
Q1
Q2
Q3
Q4
B4
Functional Description
Key Output (Program)
Key Output (CARDIO)
Key Output (MANUAL)
Key Output (USER)
Key Scan Signal
76
9) Key Conversion Board
Connector
CN 2 :
Location Pin Pin Name Functional Description
2 10KEY_LED Key LED RED
10) Logo Backlight Board
Connector
CN 1 :
Location Pin Pin Name
77
Functional Description
11) Audio Interface Board
Connector
CN 6 :
Location
12) Wireless Heart Rate Board
13) Contact Heart Rate Board
Pin Pin Name Functional Description
78
4.3 Cables & Connectors
Cable
No.
Start Board
Connector
No.
CB11
Main PCB
(Dot Type)
End Board
Connector
No.
Wire
Length
[mm]
Housing Remark
CN4 SMH250-15
CN3 LH1143-03
CN1 8P 270 SMH250-08
CN2 8P 270 SMH250-08
- SMH250-02
- SMH250-02
CN2 SMH250-03
- 2P SMH250-02
CN1 SMH250-04
HR SMH250-03
- 8P 2,000 RJ-45(8P)
SMH250-02
CB12
A/D Board
CB5
CB22
CB7
LCD Power
Supply
Motor
Controller
CB21
CN16 Program 120
-
-
CN3
CN11
Audio Interface
Board
-
A/D Board
LCD
Supply
CN3
TU1
CN2
CN12
SMH250-05
79
Cable
No.
Start Point or Board
Connector
No.
End Point or Board
Connector
No.
Wire
Length
[mm]
Housing Remark
CN5 Yellow
CN8 Red
CN9 White CB19 -
J4 Switch-21
- Switch-11
- Switch-12
- Earth
-
Circuit
Protector-1
-
-
-
-
J5
Circuit
Protector-2
J6 Switch-22
J7
Noise Filter-
21
J8
AC1
AC2
CB7
Noise Filter-
22
Motor
Controller
Motor
Controller
Motor
Controller
- Noise
-
R/T/Earth
Noise
- Motor
- Motor
R Lift/Power
T Lift/Power
LCD Power
Supply
-
-
AC1
AC2
-
80
4.4 Cable Diagram
Cable No. Cable Name
CB2 Main Power Cable
CB1
Lift/Power Control
Cable
CB3R,CB3L
Touch Sensitive
Key Cable
CB12
CB9
CB6
CB11
J7, J8
Program Button
Cable
Logo-Backlight
Cable
Key Conversion
Cable
Communication
Cable (RJ-45)
-
AC1, AC2 -
CB4L, CB4R Contact HR Cable
CB7
LCD Power Supply
Cable
CB8
Emergency Push
Button Cable
81
Cable Spec Remark
Cable No. Cable Name
J1, J2, J4,
J5, J6
-
CB5
Audio Interface
Cable
CB17 Lamp Inverter Cable
CB18
CB18
CB18
Coaxial Cable
(NTSC)
Coaxial Cable
(PAL/SECAM)
Coaxial Cable
(NTSC/PAL/SECAM)
Cable Spec
Old type
Old type
New type
Remark
82
Cable No. Cable Name
CB22
LCD Power Supply
Cable
`
Cable Spec
`
Remark
83
Motus Treadmills M990T, M990TL, M995T and M995TL
APPENDIX
EXPLODED VIEW
A. M990T – PART LIST
A.1. M990T – EXPLODED VIEW
B. MAIN BODY_FRONT – PART LIST
B.1 MAIN BODY_FRONT A – EXPLODED VIEW
B.2 MAIN BODY_FRONT B – EXPLODED VIEW
C. MAIN BODY_REAR – PART LIST
C.1. MAIN BODY_REAR – EXPLODED VIEW
D. OVERLAY BEZEL ASSEMBLY – PART LIST
D.1. OVERLAY BEZEL ASSEMBLY – EXPLODED VIEW
E. CONSOLE ASSEMBLY – PART LIST
E.1 CONSOLE ASSEMBLY - EXPLODED VIEW
F. BOLT, WASHER, NUT & ETC – PART LIST
F.1 BOLT A
F.2 BOLT B
F.3 BOLT C
F.4 WASHER & NUT
84
A. M990T
NO. CODE P/NAME SPEC Q’TY
C1 MAP151010 1
(CONSOLE ASSEMBLY)
C4 MAP184100 1
C5 MAP184110
C6 MAP184010 SIDE
1
1
1
C8 MAP184020 SIDE
T1 MAP191010
T2 MAC191020
T3 MAP181000
T4 MAP182000
T5 MAP197010
BADGE-COVER
SUPPORT_L
SUPPORT_R
STICKER_SIDE
T6 MAO197020
T7 MAQ197020
T8 MAP197020
T9 MAR197020
T10 MAP151320
STICKER_MODEL
STICKER_MODEL
STICKER_MODEL
STICKER_MODEL
CONSOLE BACK LABEL
1
1
1
1
1
1
2
2
2
2
2
1
85
A.1 M990T
86
B. MAIN BODY_FRONT
NO. CODE P/NAME SPEC Q’TY
M1 MAK131010 MOTOR 1
M2 MAOD31090 MOTOR BASE PLATE BAKELITE 1
M3 MAP141041
1
M5 MAK171010
M6 MAP171030
M7 MAP122010
M8 MAO499200
BRACKET
INVERTER
M8 MAC199200 LINE FILTER for WIRELESS H/R
M8 MAOD99201
N100 1
RF215-TS
RF415
RF435
1
1
1
1
1
1
12V/3.5A 1
1
M11
M12
MAO167210
MAO131100
LCD POWER SUPPLY
LCD PPWER SUPPLY
BRACKET
M13 MAP121020
M14 MAC114000
M15 MAP195020
M16 MAP195020
M17 MAP195020
M18 MAP195040
M19 MAP171060
CASTER
SOCKET
HOSEPIPE
AC POWER SOCKET
M20 MAC193000
M21 MAC192000
M22 MAO174010
M22 MAO174020
M23 MAO111010 TERMINAL
M24 MAP161010 AUDIO INTERFACE BOARD
M25 MAC121010
15AMP
NT
PAL
1
1
1
1
1
1
2
1
2
1
1
1
1
1
87
NO. CODE
M26 MAP131060
P/NAME
DRIVE MOTOR PULLEY
M28 MAPD93000
WITH CIRCUIT BREAKER
M29 MAOD94001
M30 MAOD90500 POWER CODE HOLDER
M31 MAP111010 TERMINAL
M32 MAOD11010 TERMINAL
M33 MAPD11010 TERMINAL
BRACKET
SPEC Q’TY
1
1
1
1
1
1
1
1
1
1
1
1 M37
88
B.1 MAIN BODY_FRONT A
89
B.2 MAIN BODY_FRONT B
90
C. MAIN BODY_REAR
NO. CODE
F1 MAP111000
P/NAME SPEC Q’TY
1
F2 MAP142010 DECK 1
F3 MAP142000
F4 MAP141011
F5 MAP141021
F6 MAP144030
F7 MAP144040
F8 MAP144010
F9 MAP144050
F10 MAP145010
F11 MAP145020
F12 MAP112000 STABILIZER
F13 MAP113000 STABILIZER
F14 MAP195050
F15
F16
MAOD11090
MAOD11100
F17 MAP144060
FRONT ROLLER FENCE_L
FRONT ROLLER FENCE_R
F18 MAP111080
F19 MAP191040 MOTOR COVER BRACKET
F20 MAC145030 R-ROLLER RUBBER
F21 MAC116000 R-CUSHION
M3 MAP141041 MOTOR DRIVE BELT
(POLY-V BELT)
2
2
3
4
1
1
2
2
1
1
1
4
1
1
1
1
1
2
2
1
91
C.1 MAIN BODY_REAR
92
D. OVERLAY BEZEL ASSEMBLY
NO. CODE
L1 MAO151060
P/NAME
ACRYLIC PANEL LCD
SPEC Q’TY
1
L2 MAO151140 1
L3 MAO151140
L4 MAO451020 LCD MEMBRANE OVERLAY
L5
L6
MAO151050
MAO167221
LCD OVERLAY BEZEL
PROGRAM BUTTON BOARD
L7 MAO167121 OSD BOARD
L8 MAP161010
L9 MAO162011
AUDIO INTERFACE BOARD
L10 MAP151290
L11 MAO167050
L12 MAO157060
L13 MAO167070
L14 MAO167080
D1
D2
D3
MAP151060
MAP451020
MAP151050
LCD METAL BRACKET
ACRYLIC PANEL DOT
DOT MEMBRANE OVERLAY
DOT MEMBRANE OVERLAY
D4 MAP162010
D5 MAP168010 LOGO BACKLIGHT BOARD
ENGLISH
ABS
LCD
15”
ENGLISH
DOT
1
1
1
1
1
1
1
1
2
1
1
1
1
1
1
1
3
1
1
1
93
D.1 OVERLAY BEZEL ASSEMBLY
94
E. CONSOLE ASSEMBLY
NO. CODE P/NAME SPEC Q’TY
C1 MAP151010 1
C2 MAP152010 1
C3 MAP184090
C4 MAP184100
C5 MAP184110
C6 MAP184010 SIDE
C8 MAP184020 SIDE
C10 MAP185000 HANDLE CROSS PIPE
C11 MAP185010 FRONT
1
1
1
1
1
1
1
1
1
1
4
1
C13 MAJ182030
C14 MAP164021
C15
C16
C17
MAP164011
MAP151080
MAP151090
TOUCH SENSITIVE KEY
BOARD_LEFT
TOUCH SENSITIVE KEY
BOARD _RIGHT
LIGHTING SPEED UP
LIGHTING SPEED DOWN
C18 MAP151100
C19 MAP151110
C20 MAP151120
LIGHTING INCLINE UP
LIGHTING INCLINE DOWN
C21 MAP151200 BUTTON SPEED UP
BUTTON SPEED DOWN C22 MAP151210
C23 MAP151220
C24 MAP151230
C26 MAC162020
1
PC
PC
PC
PC
PC
ABS
1
1
1
1
2
1
ABS
ABS
ABS
1
2
1
ABS 1
1
1
SWITCH
95
1
NO. CODE
C29 MAP154030
C30 MAP151180
C31 MAP151190
SWITCH KNOB
P/NAME
C32 MAP451160 CONSOLE
C32 MAP151160 CONSOLE
C33 MAP451170 CONSOLE
C33 MAP151170 CONSOLE
C34 MAP151040
C35 MAP151320 STICKER CONSOLE BACK
C36 MAPD11040
C37 MAP111010 EMERGENCY
SWITCH
C38 MAOD11010 EMERGENCY
C39 MAPD11010
C40 MAP151250
C41 MAP152020
C42 MAP151030 EARPHONE
C44 MAC153040 EMERGENCY
SPEC Q’TY
1
1
1
ENGLISH
KOREAN
ENGLISH
KOREAN
MOTUS
1
1
1
1
1
1
1
1
1
1
4
1
2
2
1
1
96
E.1 CONSOLE ASSEMBLY
97
F. BOLT, WASHER & NUT
P/NAME NO. CODE
B1 MA0A12100
B2 MA0K12065
B3 MA0C12060
B4 MA0K12030
B5 MA0K12025
B6 MA0I10120
B7 MA0K10045
B8 MA0I10050
B9 MA0J10045
B10 MA0J10040
ALLEN BUTTON BOLT
H/S HEX BOLT
SPEC
M12*L100
M12*L65
M12*L60
M12*L30
M12*L25
M10*L45
M10*L45, TAP30
Q’TY
B11 MA0K10071
ALLEN PILLOW BOLT
ALLEN PILLOW BOLT
M10/M9,L70
TAP10
M8*L35
M8*L30
M8*L25
M8*L20
B12
B13
MA0D08035
MA0D08025
B14 MA0F08025
B15 MA0F08020
B16 MA0I06035
B17 MA0M06016
B18 MA0A06015
B19 MA0V06010
B20 MA0W05016
B21 MA0F05015
B22 MA0Y04020
B23 MA1G04020
B24 MA1G04018
B25 MA1G04016
B26 MA0F04015
B27 MA1G04012
B28 MA0F04012
B29 MA0Y70103
B30 MA0F04008
TRUSS CROSS BOLT
BUTTON CROSS BOLT
BUTTON CROSS BOLT
BUTTON CROSS BOLT
BUTTON CROSS BOLT
M6*L16
M6*L15
M6*L10
M5*L16
M5*L15
M4*L20
M4*L20
M4*L18
M4*L16
M4*L15
M4*L12
M4*L12
M4*L10
M4*L8
NO CODE P/NAME SPEC Q’TY
98
B31 MA0M04008
B32 MA1G03016
B33 MA1G03012
B34 MA0F03008
B35 MA1G03008
B36 MA0L73008
B37 MA0Y03008
B38 MA0K10020
B39 MA1G04008
W1 MA0S12000
W2 MA0S10003
W3 MA0Y40302
W4 MA0S06001
W5 MA0U05000
TRUSS CROSS BOLT
BUTTON CROSS BOLT
PILLOW CROSS BOLT
W7 MA0S03000
N1 MA0O12000
N2 MA0O10000
N3 MA0P10000
N4 MAU113020
N5 MA0Y90103
99
M4*L8
M3*L16
M3*L12
M3*L8
M3*L8
M3*L8
M3*L8
M10*L20
M4*L8
M12x3t
M10x3t
M8,D20,6t
M6x1.5t
M5
M4
M3
M12
M10
M10
3/8”
M5
F.1 BOLT A
100
F.2 BOLT B
101
F.3 BOLT C
102
F.4 WASHER & NUT
103
Ver 0.1, Feb., 2007 ⓒ Motus Co., Ltd. All Rights reserved.
Unauthorized Reproduction and Distribution Prohibited By Law
104
advertisement
Related manuals
advertisement