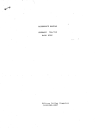
advertisement
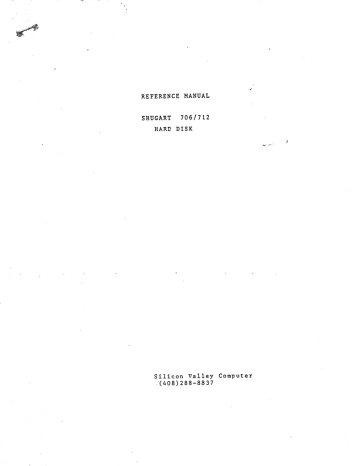
...•..
~ ~
...
REFERENCE MANUAL
SHUGART 706/712
HARD DISK
.I
Silicon Valley Computer
.'. ( 4 0 8 ) 2 8 8 - 8 8 3 7
-
~
-
-
~
"
-
~
-
.~
TABLE OF CONTENTS
Page
~
,~
-
~
-
:
.~
-, i
..
:
~ .
..
..
~.
..
-
I ! I
..
-.
.
.
'.
• 'f8
'.
••
•
••
•
·
~
•
. .j
t
,
TABLE OF CO~S . . . . . . . . . . . . . . . . . . . . . . . . . . . . . . . . . . . . . . . . . .
UST OF AGURES
UST OF TABLES
ABBREVlAllONS/MNEMONlCS
NOTICE TO USERS
.
ill vi vii viii viii
PRODUCTION DESCRIPTION
SECTION I
~ODUCT10N
1.1
1:1
I-I
1.2
General Description . . . . . . . . . . . . . . . . . . . . . . . . . . . . . . . . . . .
1.3
Specifications
. . . . . . . . . . . . . ..
1·1
Summmy . . . . . . . . . . . . . . . . . . . . . . . . . . . . . . . . . . . . . . . . . .
. . . ..
1-2
1.4
Purpose..........................................................
1.3.1
1.3.2
Perfonnanc~ Specifications. . . . . . . . . . . . . . . . . . . . . . . . . . . . . . . . . . . . . ..
. . . . . . . ..
1-2
1-2
1-2
1.3.3
Functional Specifications. . . . . . . . . . . . . . . . . . . . . . . . . . . . . . . .
Physical Specifications . . . . . . . . . . . . . . . . . . . . . . . . . . . . . . . . . . . ..
. . . . . . . . . ..
1-3
1.3.4
Reliabtlrty Specifications
Functional Characteristics . . . . . . . . . . . . . . . . . . . . . . . . . . . . . . . . . . . . .
1.4.1
General Operation . . . . . . . . . . . . . . . . . . . . . . . . . . . . . . . .
. . . . . . . ..
1·3
. . . . . . . . . . . ..
1·3
1.4.2
Read/Write and Control Electronics
1.4.3
Drive Mechanism. . . . . . . . . . . . . . . . . . . . . . . . . . . . . . . . . . . . .
. . . . . . . ..
1-4
1-4
. . . . . . . . . . . . . . ..
1-4
'. . . . . ..
1-4
1.4.4
Positioning Mechanism. . . . . . . . . . . . . . . . . . . . . . . . . .
1.4.5
R~d/Write'Heads and Disk(s)
'
1.4.6
A1r Altration System. . . . . . . . . . . . . . . . . . . . . . . . . . . . . . . . . . .
. . . . . . . ..
1-4
. . . . . . . . . . . ..
1-6
1.5
1.4.7
Spindle Lock and Brake. . . . . . . . . . . . . . . . . . . . . . . . . . . .
1.4.8
R~d/Write Head Shipping
Zone. . . . . . . . . . . . . . . . . . . . . . . . . . . . . . . . ..
Functional Operations
. . . . . . . . . . . . . . . . . . . . . . . . ..
1-6
1-6
1.5.1
Power
1.5.3 Track
Sequendng
1.5.2
Drive Selection
Accessing. . . . . . . . . . . . . . . . . . . . . . . . . . . . . . . . . . . . . . . . .
. . . . ..
1-6
1-6
1-7
. . . . . . . . . . . ..
1-8
1.5.4
Read Operation. . . . . . . . . . . . . . . . . . . . . . . . . . . . . . . . . .
1.5.5 Write Operation. . . . . . . . . . . . . . . . . . . . . . . . . . . . . . . .
. . . . . . . . . . . . . ..
1-8
1·8
1.5.6
Head Selection
SECTION n
ElECI'R.lCAL OOERFACE . . . . . . . . . . . . . . . . . . . . . . . . . . . . .
2.1
Introduction
2.2
Control Input Unes
2.2.3
2.2.4
Head Select ~ and 2' . . . . . . . . . . . . . . . . . . . . . . . . . . . . . . . . . . . . . . . . . ..
2.2.5
Write Gate. . . . . . . . . . . . . . . . . . . . . . . . . . . . . . . . . . . . . . . . . .
2.2.6
Reduced Write Current and Precompensation
. . . . . . . . . . . . . . . .
. .. 2-1
2-1
2.2.1
Drive Select 1-4. . . . . . . . . . . . . . . . . . . . . . . . . . . . . . . . . . . . . . . . . . . . ..
2.2.2
Direction In . . . . . . . . . . . . . . . . . . . . . . . . . . . . . . . . . . . . . . . . . . . . . . . .
2-4
2-4
Step.......................................................
. . . . . . . .. 2-6
2-6
2.3
Control O\Jtput Unes . . . . . . . . . . . . . . . . . . . . . . . . . . .
. . . . . . . . . . . . . . . . . . . . ..
2.3.1
Tr&ek 00 . . . . . . . . . . . . . . . . . . . . . . . . . . . . . . . . . . . . . . .
. . . . . . . . . . . ..
2.3.2
Index......................................................
2.3.3
Ready......................................................
2-2
2-4
2-5
2-6
2-6
2-6
2-6
Ul
TABLE OF CONTENTS (CONT.)
.
2.3.4
Wrtte Fault
2.3.5
Seek Complete
2.4
Data Transfer Unes
2.4.1
~ Write Data
2.4.2
~ Read Data
· · · · · · · · · · · · ·
· .. · . ·
· .. · . · · · . · · · · · ·
.
· · · . · .. · · · . · .. · ·
.
.
2.5
Select Status
2.6
General Timing
2.7
Power Interface
2.8
Frame Grounding
· · · · · · · · . · · · ·
ReqUirements .................•.....••••..•............
· · . · . · · · · · . ·
·
· · · · · · · · · · · · . · . ·
SECTION III PHYSICAL INTERFACE
3.1
Introduction
3.2
Jl!Pl
Connection
3.3
J5/P5 Connection
3.4
J6/P6 Connection
·
·
· . · · · .. · · · · · . · ·
· · . · · . · .. · ·
· .. · · · · · · .. · · · · · · · · · ·
.
.
2-7
2-7
2-7
2-8
2-8
2-8
2-8
2-9
2·9
3-1
3-1
3-1
3-2
3-2
SECTION IV PHYSICAL SPECIACAll0NS
4.1
Mechanical
Dimensions
4.2
Mounting
· ' · . · · · · ·
.
.
4-1
4-1
4-2
SECTION V MEDlA DEFECTS AND ERRORS
5.1
Error Mapping and Qualification
.
.
5.1.1
Cause.s of Errors
5.1.2
Error Definition . . . . . . . . . . . . . . . . . . . . . . . . . . . . . . . . .
• . . . . . . . . . . . . .
.
5.1.3
Media Defed Definition
.
5.1.4
Error Map
.
5.1.5
User Error Mapping
.
5.2
Error Acceptance
Criteria
5.3
System Generated Errors
.
.
5-1
5-1
5-1
5-1
5-1
5-2
5-2
5-2
5-2
.
SECTION VI RECORDING FORMAT
6.1
Track Fonnat
6.2.3
Gap 3
6.2.4
Gap 4
£ • • • • • • • • •
• • • • •
"• • • •
.
6.2
Gap Length Calculations
I • • " • • • • • • • • • • • •
6.2.1
Gap 1 .
~
• • • • • • • • •
6.2.2
Gap 2
~
• • • • • • • • • • • •
~
~
• • • • • • • • • • • • • • • • • •
• • • • • • • • •
.
.
.
.
. 6.3
Write ?recompensation
6-1
6-1
6-1
6-1
6-2
6-2
6-2
6-2
SECTION VII CUSTOMER INSTAllABLE OPTIONS
7.1
FuU-Height Faceplate
Kit
7.2
Low-Power
Slow Start Jumper
.
.
.
7-1
7-1
7-2
OPERATIONS DESCRIPTIONS
8-1
SECTION VIII niEORY OF OPERAnONS
8-1
8.1
Introduction .•••••.•...•........•.•.•••••••••.•.....•.••...........
8.2
High Priority Critical Tasks (Foreground)
8.2.1
8.2.2
8.2.3
Foreground Loop Control
Spindle Motor Foreground . . . . . . . . . . . . . . . . . . . . . . . .
. . . . . . . . . . . . . ..
Motor Fault Foreground . . . . . . . . . . . . . . . . . . . . . . . . . . . . . . .
. . . . . . . . ..
8.2.4
Step Input Buffering Function . . . . . • . . . . . . . . . . . . . . . . . . . . . . . . .
. . . . ..
8.2.5
Stepper Damping Time Out Routine . . . . . . . . .. . . . . . . . . . . . . . . . . . . . . ..
8.2.6
Seek Function Foreground. . . . . . . . . . . . . . . . . . . . . . . .
8.2.7
Foreground End and Interrupt Return
. . . . . . . . . . . . . ..
. . . . . . . . . . . . . . . . . . . . ..
. . . . . . . . ..
8-2
8-2
8-2
8-2
8-2
8-2
8-3
8-4
8.3
Lesser
8.3.1
Priority Critical Tasks (Background) . . . . . . . . . . . . . . . . . . . . . . . .
System Startup Code . . . . . . . . . . . . . . . . . . . . . . . . . . . . . .
8.3.2
Spindle Motor InltializZltion ..... . . . . . . . . . . . . . . . . . . .
. . . . . . . . . . . ..
8-5
. . . . . . . . . . . . . ..
8-4
8-5 tv
)
)
TABLE OF CONTENTS (CONT.)
,
8.3.3
Microprocessor
8.3.5
Inttialize
Control
Code End
Fault indicator
8.3.4 . Seek Function lnitiallzZltion
Function
· . · · · . ·
· . . . . . . . . . . . . . . . ..
8-7
~ . . . . . . . . . . .. 8-7
· . . . . . . . . . . . . . . . . . . .. 8-7
8.3.6
Spindle Motor Background. . . . . . . . . . . . . . . . . . . . . . . . . . . . . . . . . . . . . .. 8-7
8.3.7
Motor Status Monitor. . . . . . . . . . . . . . . . . . . . . . . . . . . . . . . . . . . . . . . . . .. 8-7
8.3.8
Warm-up Settling Extension Countdown · . . . . . . . . . . . . . . . . . . ..
8-7
8.3.9
System Background Loop Control
8.3.10
8-8
Loss of Index Monitor. . . . . . . . . . . . . . . . . . . . . . . . . . . . . . . . . . . . . . . . ..
~8
8.3.11
CyUnder Address Rezero Monitor 8-8
8.3.12
Seek Ramping Calculate Function . . . . . . . . . . . . . . . . . . . . . . . . . . . . . . . ..
8-8
8.3.13
Drive Actuator Self-exerdse Function. . . . . . . . . . . . . . . . . . . . . . . . . . . . . .. 8-8
8.3.14
Actuator Lube Unstick Routine . . . . . . . . . . . . . . . . . . . . . . . . . . . . . . . . . ..
8-8
8.3.15
Automatic Actuator Reset to Track
Zero
(Recal Function) 8-8
8.3.16
Write Current Control Function. . . . . . . . . . . . . . . . . . . . . . . . . . . . . . . . . ..
8-9
8.3.17
8.3.18
Drive Select LED Monitor . . . . . . . . . . . . . . . . . . . . . . . . . . . . . . . . . . . . . ..
8-9
Background Code End ' . . . . . . . . . . . . . . . . . . . . . ..
8-9
8.4
System Initialization Tasks. . . . . . . . . . . . . . . . . . . . . . . . . . . . . . . . . . . . . . . . . . . . .. 8-9
SEcnON IX PACKAGING INSTRUcnONS 9-1
9. 1 Uncrating.........................................................
9-1
9.2
Recommended Receiving Inspection . . . . . . . . . . . . . . . . . . . . . . . . . . . . . . . . . . . . .. 9-1
9.2.1
Packaging and Identification . . . . . . . . . . . . . . . . . . . . . . . . . . . . . . . . . . . . .. 9-1
9.2.2
Mechanicallnspeetion 9-1
9.2.3
Functional Testing ,. . . . . . . . . . . . . . . . . . . ..
94
9.3
Packing for Reshipping. . . . . . . . . . . . . . . . . . . . . . . . . . . . . . . . . . . . . . . . . . . . . . ..
9-4
SEcnON X DRIVE INTERCONNECT . . . . . . . . . . . . . . . . . . . . . . . . . . . . . . . . . . . . . . . . . . . . . . . . . . . 10-1
SERVICING INFORMATION
SEcnONXI SPAREPARTS
11.1
11-1
Routine Order Entry. . . . . . . . . . . . . . . . . . . . . . . . . . . . . . . . . . . . . . . . . . . . . . . . . 11-1
11.2
Emergency Order Entry ' ' ,.11-1
SEcnON VII MAINl"'ENANCE
12.1
Introduction
12-1
12-1
12.2
Maintenance Equipment. . . . . . . . . . . . . . . . . . . . . . . . . . . . . . . . . . . . . . . . . . . . . . 12-1
12.3
Diagnostic Techniques 12-1
12.4
Test Point Locations
12.5
Troubleshooting
12.6
Checks and Adjustments
12.7
Removal and Replacement Procedures
12.7.1
Removal of Control PCB
12.7.2
Replacement of Control PCB
12.8
Alignment Procedures
12.9
Preventive Maintenance
12-1
12-1
12-2
12-4
. . . . . . . . . . . . . . . . . . . . . . . . . . . . . . 12-4
12-4
12-5
12-5
SEcnON XIII ILLUSTRATED PARTS CATAlOG . . . . . . . . . . . . . . . . . . . . . . . . . . . . . . . . . . . . . . . . . .
13-1
13.1
De-scription.......................................................
13-1
13.2
Indented Level 13-1
13.3
Quantity per Assembly . . . . . . . . . . . . . . . . . . . . . . . . . . . . . . . . . . . . . . . . . . . . . . . 13-1
13.4
Recommended Spare Parts Stocking Guide . . . . . . . . . . . . . . . . . . . . . . . . . . . . . . . . 13-4 t
SEcnON XN SCHEMATIC DIAGRAMS 14-1
APPENDICES
APPENDIX A ORDERING INFORMATION A·l v
LIST OF FIGURES
2-3
2-4
2-5
2-6
27
2-8
2-9
2-10
2-11
3-1
3-2
3-3
I-I
1-2
1-3
1-4
1-5
2-1
2-2
8-2
8-3
9-1
9-2
10-1
12-1
12-2
13-1
13-2
14-1
3-4
4-1
6-1
7-1
7-2
7-3
8-1
Figure Title Page
Shugart 706/712 Rigid Disk Storage Drive
Read/Write Head Positioning Mechanism
0 • • 0 • • • • 0 • • 0 • • • • • • • • • • • • • • •
0 • • • 0 • • •
0 . . . . . . . . . . . .
• • • • • • • • • • • • •
I-a
1-5
AIr Filtration System ·
0 • 0 • • • • • • • • • • • 0 • • • • 0 • 0 • • • • • 0 0 • • • • • • 0 • • • 0 • • • • • • • • • • • • • • • •
1-5
Spindle Lock
0 • • • • • • • • • • • • • 0 • • • • • • • • • • • • • • • • • • • • • • • • • • • • • • • • • • • • • • • •
1-6
Shipping Zone 1-7
0 • • • • • • 0 • • • • • • • • • • • • • • • • • • •
J51nterface and Jl Power Connections. . . . . . . . . . . . . . . . . . . . . . . . . . . . . . . . . . . . . . . . . ..
J61nterface Connection
2-1
0 • • • • • • • • • • • • • • • • • • • • • • • • • • • • • • • • • • • • • • • •
2-2
Control Input Driver/Receiver Combination 2-3
Jumper Locations ....
Normal Step Mode ..
0
0
0
• •
0
0 • • • • • • • • • • • • • •
• • • • • • • • • • • • • • • • • • • • • • • •
MFM Read/Write Data Timing ....
General Control Timing Requirement
0
Interface Connector Locations
Jl Connector
0 • 0
0
0
0
• • • • • • • • • • • •
• •
• •
0
• • • • • •
• • • • •
0
0 0
0 • • • • •
0 • 0
0
0
• •
0
• •
• • •
• • • • • • • • • • • • • •
• • • • • • • • • • •
0
0
0
0
0 •
0 • • • • • • • • • •
• • • • • •
• • • • • • • •
•
0
•
• • • • • • •
• • • • • •
•
0
•
•
• • •
0
0
•
•
•
•
•
•
•
0
•
0
•
0
•
• •
•
•
•
• • • •
•
•
•
•
•
0
•
•
•
•
•
•
•
•
•
•
•
•
•
0
•
•
•
•
•
•
•
•
•
•
•
•
•
•
•
•
•
•
•
•
•
•
•
•
•
•
•
•
•
•
•
•
•
•
•
•
•
•
•
•
•
•
•
•
•
•
•
•
•
•
•
• •
• •
• •
• •
• •
• •
2-3
2-4
Buffered Step Mode .
Head Selection Timing
0 • • • • • • • • • • • • 0 • • • • • • • 0 • • • • • • • • • • • • • • • • • • • • • • • • • • • • • • • • • •
2-5 o.
0 • • • • 0 • 0 0 • • 0 • • 0 • 0 • • • • • • • • 0 0 • • • 0 • • • • • • • 0 • • • • • • • 0 • • • • • •
2-5
Index Timing.
0 • • • 0 • • • • • • • 0 • • • • • • • • • 0 • • • 0 • • • •
Data Transfer Line Driver/Receiver Combination ...
0
0
•
• • • • • • • •
0 • • • • 0
0 •
• • • •
•
0
• • • • •
• • • • •
•
0
•
0
•
•
•
•
•
•
•
•
•
•
•
•
•
•
•
•
•
• •
• • •
• •
2-6
27
2-8
2-9
3-1
3-1
J5
J6
Connector Dimensions
Connector Dimensions
Mounting Dimensions
0 • • • 0 • • • • • • 0
0 . 0
• • • • • • • •
• • • • • • • • • • • • • • • • • •
0 0 • • • • • • • • • • • • • • • • • ' .
~
0 • • • • • • • • • • • •
• • • • • • • • • • •
"
• •
. . . . . . . . . . . . . . . . . . . . . . . . . . ..
Track Format
Full-Height Faceplate Kit. . . . . . . . . . . . . . . . . . . . . . . . . . . . . . . . . . . . . . . . . . . . . . . . . . . . ..
Low Power Option (Early Models) . . . . . . . . . . . . . . . . . . . . . . . . . . . . . . . . . . . . . . . . . . . . . ..
Jumper Installation and Fabrication. . . . . . . . . . . . . . . . . . . . . . . . . . . . . . . . . . . . . . . . . . . . ..
Logic Diagram
0 • • ' .
• • • • • • • • • • • • • •
3-2
3-2
4-1
6·1
7·1
7-2
7-2
8-1
Foreground Routines Sequencing . . . . . . . . . . . . . . . . . . . . . . . . . . . . . . . . . . . . . . . . . . . . . ..
8-3
Background Routines sequencing
Single Unit Packaging Configuration . '
Ten Units Packaging Configuration
Multiple Drive Configuration
Locations Diagram
Removal/Replacement of Control PCB
Shugart 706/712 Assembly
Front Panel and Rail Assembly
Control PCB Schematic (2 Sheets)
0 • • • • • • • • • • • • • • • • • • • • • • • • • • • • • • • • • • • • • • • • • •
8-6
~ ..
0 • • • • • • • 0 • • • • • • • • • • 0 • • • • • • • • • • • • •
9-2
. . . . . . . . . . . . . . . . . . . . . . . . . . . . . . . . . . . . . . . . ..
9-3
10-1
12-3 o • • • • • • • • • • • • • • • • • • • • • • • • • • • • • • • • • • • • • • • •
12·4
13·2
13-3
14-3
)
-
-
-
-
•
-
~
•
-
-
••
.
-
-
..
..
•
-.
•
-
.. I
-
•
" -,
....
-
I
-
•
-
.
•
-
.
-
•
-
-
-
~
"
a
..
-
, t
•
-
-
-
-
-
-
-
-
-
-
...
;'.
~
.:.
.•
-
.~
••
...
-
-
-
-
-
-
-
-
-
.~
.~
~~
,~
I~
,
~
-
-
~
-
-
.~
Table
2-1
2-2
6-1
8-1
8-2
9-1
9-2
12-1
12-2
12-3
13-1
A-I
LIST OF TABLES
Page
Tltl.
Head Select (1
DC
Print Parameters
=
Requirements · · · .. · · · . · . · · · · . · · · . · · - ·
Write Precompensation · · · · · · · . · · . · . · · . · · ·
I/O Port Configuration .. · · . · · · · · · · · · · · · · · · · . . . . . . . . . .
LED Fault Codes. · · · · · .. · · · · · · · · · · ·
· · . · · . · · · · . . . . . . . . . . . . . . . . . . . . . . . . . . . . . . . . . . ..
Test Program - . . . . . . . . . . . . . . . . . . . . . . . . . . . . . . . . . .
PCB Versus Drive Failures
-
Inspection of the Drive
Signals Inspection
False. 0 = True) · · · · · · · · . · . . . . . . . . . . . . . . . . . . . . . . . . . . . . . . . .
Shugart 706/712 Spare Parts Stocking Guide
Shugart 706/712
PSI .. ·
. . ..
2-5
· · . . . . . . . . . . . . . . . . . ..
· . . . . . . . . . . . . . . . . . ..
. . . . . . . . . . . . . . . . . . . . . . ..
· · . . . . . . . . . . . . . . . . ..
. . . . . . . . . . . . . . . . . . . . . . . . . . .
,
2-9
6-2
8-4
8-7
9-4
9-4
12-1
12-2
12-2
13-4
A·I vii
BKPC Background Port C
0 bpi Bits per Inch eRe
Cyclic Redundancy Check
Prompt Character fel Flux Change per Inch
10 Identification
I/O Input/Output
IP Inspect Phase
LED
Light Emitting Diode
LSI Large ~ale Integration
ABBREVIATIONS /MNEMONICS
MFM Modified FM
MLC Machine Language Code
PCB Printed Circuit Bo.ard
pp
Print Parameters
PWM Pulse Width Modulation
RCFLG Recalibrate Rag
R/W
Read/Write
SEL Select tpl
TRK
Tracks per Inch
Track
NOTICE TO USERS
This manual, P/N 39402-0, supersedes, replaces, and incorporates the OEM manual. P /N 39252-1, published
April.
1983.
and further includes the Publication Change Notice No. 1 dated August 18. 1983. and Publication
Change Notice No.2 dated February 20, 1984. All technical changes have been indicated with a change bar in the text margin or a star symbol in the illustration. While every effort has been made to ensure that the information provided herein is correct, please notify us in the event of an error or inconsistency. Direct any comments on the form at the back of this manual to:
Shugart Corporation
Technical Publications. MS 3-14
475 Oakmead Parkway
Sunnyvale, CA 94086 (U.S.A.)
Phone (408) 737-7900
Shugart makes no representations or warranties with respect to the contents hereof and specifically disclaims any implied warranties of merchantability or fitness for any purpose.
Further, Shugart reserves the right to revise this publication and to make changes from time to time in the contents hereof without obligation to notify any person of such revisions or changes.
The information contained herein has been copyrighted by the Shugart Corporation. No portion of this document can be duplicated in any form, or sold, without the express written consent of Shugart Corporation. Failure to comply could entail legal action to remedy such violation.
viII
-
-
-
~,
-
,~
--:,
.- :3
:3
..3
j
~
..
..
~
., :!
--
.~
~:
.
:
.~~
.'.
: J
: .~
= I~
: ·3
:
I~
:: ;~
}
-~ 3
..
~
-
- 3
'"
, t
SECTION I
INTRODUCTION
1.1
PURPOSE
This publication is designed as a reference source for technicians. and knowledgeable end users.
OEM engineers. system Integrators. service and maintenance
It is assumed that the reading audience is sufficiently versed in the stateof-the-art with respect to rigid disk drives .
1.2
GENERAL DESCRIPTION
The Shugart 706/712 Disk Drives are random access 5.25
inch (130 mm) Winchester storage devices with one
(706) or two (712) non-removable disks as storage media. Ellch disk surface employs one movable head to service
320 data tracks. These drive are available in half-height or fun height configurations.
I
Low cost and high reliability are acheived through the use of a unique rotary band actuator design, a self-contained microcomputer. and custom LSI circuitry .
The 706/712 interface is either ST506 or ST412 compatible, allowing easy integration into existing systems.
Some of the key features of this series are as follows: a.
Microprocessor-based electronics.
b.
Three custom LSI devices for reliability .
c.
BuUt-in diagnostics.
I d.
Jumper selected exercise routines.
e.
Dedicated landing zone.
f.
Single track seek time is less than latency.
g.
Read/write pre-amp on head arm.
h.
3370 head flexure design .
l.
Brushless dc spindle motor.
j.
k.
Winchester design reliability In a half-height or fun-height package.
Improved shock and vibration characteristics.
1-1
...
-.
"----'
1.3
SPECIFICATIONS SUMMARY
1.3.1
Performance Speclflcatlona
Capacity
Unformatted
Per Drive
Per Surface
Per Track
Formatted (33 sectors/track)
Per Drive
Per Surface
Per Track
Per Sector
Formatted (32 sectors/track)
Per Drive
Per Surface
Per Track
Per Sector
Transfer Rate
I Access Time (includes settling time)
Track to Track
Average
Maximum
Average Latency
Start Up Time (typical)
1.3.2
Functional Specification.
Read/Write Heads
Disks
I Cylinders
Data Tracks
Index/Revolution
-I Rotational Speed
Recording Density
Aux Density
Track Density
Data Encode Method
Write Precompensation
Reduced Write Current
I Shipping Zone (track number)
1.3.3
Phy.lcal Speclftcatlon.
Mechanical Dimensions without Faceplate (nominal):
Height
Width
Depth
Weight
= 1.63
in ( 4.14
cm)
=
5.75
In (14.61
cm)
= 8.00
In (20.32 cm)
=
3.0
Ibs { 1.36 kg)/706
3.6 Ibs ( 1.63 kg)/712
706
6.4 Mbytes
3.2
Mbytes
10,416 bytes
5.2
Mbytes
2.6
Mbytes
8.4
kbytes
256 bytes
5.0
Mbytes
2.5
Mbytes
8.2
kbytes
256 bytes
5.0
Mbits/sec
16.2
msec
85
msec
175 msec
8.37
msec
12 sec
2
1
320
640
1
3.600 (±0,-72) rpm
9.036
bpi
9.036
fci
360 tpi
MFM
12 (± 2) nsec
Automatic
353
4
2
320
1,280
712
12.7
Mbytes
3.2
Mbytes
10,416 bytes
10.3
Mbytes
2.6
Mbytes
8.4
kbytes
256 bytes
10.0
Mbytes
2.5
Mbytes
8.2
kbytes
256 bytes
5.0
Mbits/sec
16.2
msec
85
msec
175 msec
8.37
msec
12 sec
1-2
1.3 SPEClFlCAnONS SUMMARY
1.3.1 Paformaace
SpecUicadoD8
Capacity
Unformatted
Per Drive
Per Surface
Per Track
Formatted (33 sedon/track)
Per Drive
: Per Surface
Per Track
Per Sector
Formatted (32
Per Drive
Per Surface
Per Track
Per Sector
Transfer Rate seeton/track)
I
Access Time (includes settling time)
Track to Track
Average
Maximum
Average Latency
Start Up Tune (typical)
1.3.2 .
Functional Specification.
Read/Write Heads
Disks
I Cylinders
Data Tracks
Index/Revolution
I
Rotational Speed
Recording Density .
Aux Density
Track Density
Data Encode Method
Write Precompensation
Reduced Write Current
I Shipping Zone (track number)
1.3.3 Pbplcal SpeclftcatloDa
Mechanical Dimensions without Faceplate (nominal):
Height • 1.63
in ( 4.14 cm)
Width = 5.75
In (14.61 em)
Depth
Weight
=
8.00 In (20.32
em)
= 3.0 Ibs ( 1.36 kg)/706
3.6
Ibs·( 1.63 kg)/712
706
6.4
Mbytes
3.2
Mbyte.
10,416 byte_
5.2 Mbytes
2.6
Mbytu
8.4 kbytes
256 bytes
5.0
Mbyte.
2.5 Mbyta
8.2 kbyta
256 bytes ·
5.0 Mbltl/sec
16.2
msec
85maec
175
mMe
8.37
maec
12 He
2
1 .
320
640
1
3,600 (:0,-72) rpm
9,036 bpi t
9,036 fd
360 tpi
MFM
, 12 (± 2) nsec
Automatic
353
4
2
320
1.280
712
12.7 Mbytes
3.2
Mbytes
10,416 bytes
10.3 Mbytes
2.6 Mbytes
8.4
kbytes
256 bytes
10.0 Mbytes
2.5 Mbytes
8.2
kbytes
256 bytes
5.0 Mbits/sec
16.2
msec
85 msec
175 msec
8.37
msec
12 sec
1·2
)
·
·
:.L·
·
·
.,
--
~l
-
-
I
.
·
.: 4
"
.
• ~: i
"
..
'~
-
..
,-
· Oil
-
~CI
· : ~ II
-
d'
·
°
\1
~
,...-
..
..
.j
.~
....'.9
-
-
-
-
.
-
..
.oj
...
I j
~
-
..
.~!t
-
-
~,
-
-
-
-
~!
-
-
•
.,
.o~
••
.:~
•
.:~
•
!I
~
,
Environmental Umtts:
Host Ambient Temperature:
Operating - 41 ° to 113°F (5° to 45°C)
Non-operating _40° to 140°F (_40° to 60°C)
.
,
Temperature Gradient:·
Operating - 10°F (5.~OC) per
1/2
.
hour
Non-operating - 212°F (100°C) per hour non-condenllng
Relative Humidity:
Operating 8% to 80%
Non-operating - 1% to 959.»
Maximum Wet Bulb:
Operating - 78°F (25.6°C) non-eondenslng
Non~operatlng - Non-eondenslng
Elevation:
Operating - 0 to 10,000 ft (0 to 3048 m)
.
Non-operating -1.000
to 30,000 ft (-305 to 9144 m)
Acoustic Noise: Less than 50 dbA at 3.3
It (1.0
m)
Shock:
Operating 10 G max (11 msec half sine wave)
Non-operating - 40 G max (11 msec half sine wave)
Vibration:
Operating:
5 17 Hz = 0.036
In
17 - 150 Hz = 0.55 G
200 - 500 Hz :: 0.25 G
Non-operating:
5 22 Hz
44- 500 Hz
= 0.50 G
=
2.00 G
DC Voltage Requirements: .
± 12 Vdc ± 5% .75 A typical (3.9 A max starting for 10 sec) (2.7 A max starting with low power option)
± ·5 Vdc ± 5% 1.6 A typical (2.4 A max)
I .
Heat Dissipation
=
86 BTU/hr typical (18.4 watts)
1.3.4 Reliability Speclflcatlona
Mean Time Between Failure:
Preventive Maintenance:
Mean Time to Repair:
Component ute:
20,000
Power-on
Houn typical usage
None Required
12
minutes
(PCB only)
5 yean
1.4 FUNCTIONAL CHARACTERISTICS
1.4.1
General Oper.dOD
The 706/712 fixed disk drives consist of read/writ., heada, read/write and con;ol electronics, track positioning mechanisms, media, and air filtration systems.
TheM components perform the foUowing functions: a.
Interpret and generate control signals.
I b.
Position the heads over the seleded track.
c.
Read and write data.
d.
Provide a contaminant-free environment.
1·3
--
.~
1.-4.2 Read/Write anel Control
Electroalea
The standard
~iaoproceS50r and electronics are packaged o~ one printed circuit board containing the foUowing circuits: a.
Index Generator Circuit b.
Head Position Actuation Drivers
c.
Read/Write Amplifiers d.
Drive (READY) up to Speed Circuit
e.
Drive Select Circuit f.
Write Fault Detection Circuit g.
Read/Write Head Select Circuit
h.
Ramped (Buffered ) Stepper Circuit
I.
Track 00 Indicator
Brushless Spindle Motor Control Circuits j.
1.4.3
Drive Mechanlam
I The brushless dc drive motor rotates the spindle at .3.600
(:t 0, - 72) revolutions per minute.
1.4.4
Poaltlonlng Mechanl••
The read/write heads are mounted on an arm which is positioned
by
I
Fasflex™ IV rotary actuator.
A stepper motor is used to precisely position the rotary actuator utilizing a unique metal band/capstan concept.
Figure 1-2 ulustrates thiS positioning mechanism.
.
1.4.5 Read/Write Head. and DI.k(l)
The recording media consists of a thin, lubricated, magnetic oxide coating on a 130 mdUmeter diameter aluminum substrate.
This coating formulation, together
with
the low load force/low mass Winchester-type flying heads, permits reliable contact stan/stop operation.
I Data on each disk surface are read by one read/write head, each of which accesses 320 data tracks.
The drive is available in two basic configurations: one disk with two read/write heads (706) or two disks with four read/write heads (712). The heads should be positioned at cybnder 353 via IOftware prior to power down in order to minimize the potential for damage to the recorded data on portable systems.
Refer to paragraph 1.4.8.
1.4.6
AIr flltratioD Syatem
The disk(s) and read/write heads are fuUy encased In a protective cover using an integral recirculating air system, with a recirculating filter. to maintain a contaminant-free environment. A separate absolute breather filter allows
.
to the ambient air without contamination.
See figure 1-3.
)
'-4
ACTUATOR
SPINDLE ASSEMBLY
PJW HEAD
ASSEMBLY
STEPPER CAPSTAN BAND
.MOTOR
*
FIGURE 1·2.
READ/WRITE HEAD POSITIONING MECHANISM
0.3 MICRON
BAROMETRIC
FILTER
. COVER
0.3 MICRON
FILTER
*
FIGURE 1·3. AIR FILTRATION SYSTEM
1·5
These drives are provided with an integral fall·sal.
spindle lock and brake.
ThIs lOIenold operated. mechanical brake is actuated when de power is applied to the drive, allowing the spindle to rotate. When the drive is powered off, the solenoid is deae:ttvated allowing the brake to engage the spindle.
This prevents the possibility of disk move· ment during shipping or movement of the drive.
During spin down, the brake decelerates the spinning disks quickly to reduce the amount of time that the heads are In unltable flight.
Se.
figure 1-4.
STEPPER MOTOR
BRUSHLESS DC
SPINDLE MOTOR
)
FIGURE 1-4. SPINDLE LOCK
1.4.8
Read/Write Head Shipping Zoae
The unused area of the disk surface. Inside the data bands, is designated as a "shipping zone." The heads should be positioned to this area via software before the drive 15 powered off.
prior to moving or shipping the drive. This ensures that damaged if the drive is exposed to severe handling (shock). the data storage area of the disk surface will not be by heads movement on the disk(s). See figure }-5.
1.5 FUNCTIONAL OpERATIONS
1.5.1 Power SequencIDl
The required power-on sequence for early production units (1.8., 706/712 that are MLC 4 or less) is that both the 5 and 12 volts supplies be
M on" within 20 seconds of each other. The order is not important.
No power-on sequence is required for
MLC 5 and
above.
All
drtves have a speed
sense
ctrcult to prevent stepping until the disk is rotating at the proper speed (3,600 rpm). A READY signal will be presented to the controller interface once the disk is up to' Its normal rotational speed (:t 2%) for two seconds.
At .READV
time, after an initial power-up, the drive will recalibrate Itself to track 00. When the recallbration procedure Is complete. SEEK COM-
PLETE will go true. Normal seek and read functions can now begin. Refer to paragraph 2.6.
!
·1.5.2
Drive SelectlOD
Drive selection occurs when one of the DRIVE SELECT Ilnes II activated. Only the drive appropriately jumpered will respond to the input signals. and the output signals of that drive are then gated to the controller.
1·8
) i l
130 mm
DISK 00 TRt< 00
- DATA
TRACKS
.'@ ....
:~
-
..
...
:
..
~
.:1
.,
• lJ
" t
I
..
,
..
.'
•
..
, t• . '
,
.• l
._'
..
,
· l
..
I,
.
" u t'
.
...
...
·
..
.
( t
HEAD SHIPPING ZONE
CYLINDER 353
FIGURE 1·5. SHIPPING ZONE
40mm
DISK 10
1.5.3 Track Acceaalng
Read/write head positioning is accomplished by: a.
Deactivating the WRITE GATE.
b.
Activating the appropriate DRIVE SELECT line .
c.
Being in the
READY
condition with SEEK COMPlETE true.\ d.
Selecttng the appropriate direction .
e.
Pulsing the STEP Un•.
f.
Checking for the edge of the -SEEK COMPLETE line (changing from false to true).
Stepping can occur at either the normal or buffered rate. DUring normal stepping,-the heads are repositioned at the rate of incoming step pulses.
In the case of buffered stepping, Incoming step pulses are received at a high rate and are buffered Into counters.
When all of the steps have been received, they are Issued to the stepper drivers at a ramped stepping rate.
Each pulse will cause the heads to move either one track In or one track out, depending on the level of the DIREC-
TION IN line.
A true on the DIRECTION IN line wUI toward track 00.
cause an Inward seek: a false will result in an outward seek
'·7
1.~4 Reacl OperaUoUl
Reading data &om the d1sk Is accompUshecl by: a.
Deactivating"the WRITE GATE line.
r b.
Activating the appropriate D~ SELECT line.
c.
Assuring that the drive ts READY.
d.
Selecting the appropriate head.
1.5.5 Write Operation
Writing data onto the disk is accomplished by: a.
Activating the appropriate DRIVE SELECT Une.
b.
Assuring that the drive is READY.
c.
Clearing any write fault conditions (if that exist).
by reselceting the drive.
d.
Selecting the proper head.
e.
Activating the WRITE GATE and plactng data on the WRITE DATA
Un••
1.5.6 Head Selection
Any of the two to four possible heads can be seleded by placing the binary address of that head on the two HEAD
SELECT Unes.
1·8
)
~
\ t
• l.
..
.1
1
(.
tC
'.
-
• ,r
.1
.r
•
·
"
•
•
-
..
•
-
•
•
•
·
·
.
."
·
· '-'
.
·
,.
. -'
.,.
·
.
• ',a
I
• .1
:
-'
:
:~
• .J
J
· • .J
,
SECTION
II
ELECTRICAL INTERFACE
2.1
INTRODUCTION
The interface for a 706/712 has pin assignments.
drive control signal pin ualgnmentl per Industry standards.
See figure 2·1 for the
HOST
~
RESERVED
RESERVED
-WRITE GATE
-SEEK COMPLETl
-TRACK 00
-WR'TE FAULT
-HEAD SELECT 2'
RESERVED
-HEAD SELECT 2' •
7OeI712 ,
~~
-
2
-
•
•
7
• t
5
10
I'
13
"
3
t.
-
-
11.
17
'1
11
15
FLAT
AlIBON
20 FT. MAX.
ce"mm)
-INDEx
-
~ -~EADY a
~
-STEP
-DAIVE SELECT t
-DRIVE SILECT 2
-DAIVE IllECT 3
22
-
N
25
23
a
zr
•
21
3D
31
- DRIVI SILECT •
-DIRECTION IN
-
-
-
3Z
33 ,.
•
.
3
-
1
2
rh--=-
IfRAUEGND
..,,1P1
•
~ v
DC --..
..£:
-
~
DCGNO
A
-
X
• ~
• '2
RETURN
Y DC
• 12 RETURN rJ
GND
TWISTED PAIR
*
FIGURE 2·1. J5 INTERFACE AND J1 POWER CONNECTIONS
2·1
The sJgna11nterface consists of three categories: a.
Control Input Una b.
Control Output Una c.
Data Transfer Una
I
AD control lines are digitalin nature and either provide signals to the drive (input) or provide signals to the host (output) via the interface connector JS/P5.
The data transfer slgnall are differentialln nature. They provide data either to or from the drive. via
J6/P6.
See figure
2-2
for the
J6/P6
pin assignments.
706n12
HOST
FLAT CABLE
20 FT MAX
(8.6
mm)
--:
-
-
-
- DRIVE SELECTED
GND
SPARE
GND
SPARE
GNO
RESERVED
GND
SPARE
GND
GND
+
GND
MFM WRITE DATA
-MFM WRITE DATA
+
GND
GND
MFM READ DATA
-MFM READ DATA
GNO
GND
3
5
,
7
1
-
, ..
13
17
18
2
~
8
8
10
'1
12
15
16
19
20
..
~
J6/Pe
*
FIGURE 2·2. J6 INTERFACE CONNECTION
2.2
CONTROL INPUT
UNES
The control1nput signals are of two types; those Intended for multiplexing In a multiple drive system, and those intended to control the multiplexing. The controllnput Ilgnals to be multiplexed are: a.
The STEP signal b.
The DIRECTION SELECT signal c.
The HEAD SELECT 20 and 2 1 signals d.
The WRITE GATE signal
The signals which are intended to control the multiplexing are DRIVE SELECT 1 through DRIVE SELECT 4.
The controllnput lines have the following
.lectrical
specifications.
541.
figure 2-3 for the recommended cIrCuit.
Only one drive In the system should be terminated. h should a
220/330
ohm resistor pack. This resistor pack can be
be
disabled located at the end of the cable and terminated with by removing the jumper block located near the P5 connector. See figure 2-4 for the location.
)
) l t t
-
-
..
tI
• II
II
· .
II
· .
• a
•
•
• 'II
....
·
.
• ' .. =!I
-
·
·
.
-
~
.,
.1
.
.
,
-
i
....
")
~l
..
!
-
...
-
..
~
~
..
: ..
..
-
-
-
-
.. ill
.~
-
-
-
-
- •
.
•
.
• ~
-
-
-
.~
..
...
• C!I
t
20 FT (MAX)
(6.0
mm)
True
False
-
-
=
0.0
to 0.• V de fl lin
=
.0 mA (max)
=
2.5
to 5.25
V de " lin
=
0 mA (open)
-
-
3i026-06·A
FIGURE 2·3. CONTROL INPUT DRIVER/RECEIVER COMBINATION
REAR VIEW
DRIVE SELECT.
DRIVE SELECT
I /
3./.
j
DRIVE SELECT 2
NOTE: These eight Jumper. are for drive control line termination and .r.
to be removed from ai, but the Int drive in a multiple drive configuraUon
(r.fer to Section IX).
STEP
UNDEFINED
UNDEFINED
WRITE GATE
DRIVE SELECT 1
HEAD SELECT 21
DRIVE ALWAYS
UNDEFINED
5 LECTED
DIRECTION HEAD SELECT 2'
*
FIGURE 2·4. JUMPER LOCATIONS
2·3
..
DrIve
Select 1-4
DRIVE SELECT, when logically true, connects the drive to the control Una.
be active at a time.
Only
one DRIVE SELECT line may
Jumper options 051-4 are used to choose which DRIVE SELECT lin.
drive.
See figure 2-4 for the jumper locations.
wID
activate the Interface for that unique
.
2.2.2 Direction
10
This
signal
defines the direction
of
motion
of the read/write
heads when
the STEP bne
Is pulsed.
An
open ctrcult, .
or logical false.
defines
the direction as
"out" and
a
pulse applied
to the STEP lin.
wID move the R/W
head away from the center of the disk. U the Input is shorted to ground (logical true) and a
pulse
is applied, the heads
wID
move toward the center of the disk.
I.e.
''In.,.
2.2.3 Step
This
line causes the read/write heads
to
move In the direction
defined
by
the DIRECTION IN
line.
The motion
Is initiated at each logical
true-ta-false
transition.
Any
change In
the DIRECTION IN line must
be made before
the
leading e ige of the STEP pulse. Stepping can
be performed in
lither
the
normal or
buffered
mode:
Normal Step Mode
In
this mode.
the
read/write heads will move
at the rate
of the Incoming
STEP
pulses. The minimum
time
between successive steps is 3.0
msec, with a minimum pulse width of 500 nsec. See figure 2-5.
-DIRECTION
-STEP
-SEEK COMPLETE
~
I
~I
J
1'00
,nslC MIN'
I
--., p550nsecTYP
1
~1oon"CMIN
I
I
I3.0maec MIN
*
FIGURE 2·5. NORMAL STEP MODE
(5141215T5OI TYPE UO)
~·'3-A
Buffered Step Mode
In this mode, the
STEP
pulses are received at a high rate and buffered Into a counter. After the last STEP
pulse.
the read/write heads will begin stepping the desired number of cylinders and SEEK COMPlETE (refer to paragraph
2.4.5) will go true after the heads settle on the cylinden. This mode of operation is
automatically
selected when the time between STEP pulses is less than 200
pee.
.
.
The DRIVE SElECT line may be dropped and a different drive selected 500 nsec after the last STEP pulse has been sent to the drive.
The maximum time between steps is
200 1d8C.
with a minimum pulse width of 3.0
~.
See figure 2-6.
)
)
"'
•
)
2·4
· u
• u
• II
• u
• \t
·
\
•• l
• I
·
· '-'
· -
•• 1
· -
•• I
• !
..
,
•••
:
:
-
-
: _I
.
.
--
...
:
'.'
: ..
'
• u
.1
-STEP
-SEEK COMPLETE
-DRIVE SELECT X
NOTE: VARIES WITH SeEK L~NGTH.
11•• mMC MIN, .a.o
maec MAX.
FIGURE 2·8. BUFFERED STEP MODF
Shipping Zone
The read/write heads can be accessed to the shipping zone by doing.
seek to cylinder 353.
NOTE
STEP pulses with periods between 200 "sec curacy is not guaranteed and 3.0
msec are not permitted. Seek ac-
If.
this timing requirement is violated.
2.2.4
Head
Select
2- and
2
1
These two lines provide for the selection of each individual read/write head In a"binary coded sequence. HEAD
SELECT 2° is the least significant line. When all HEAD SELECT 11nes are false, head 0 will be seleded. Table 2·1 shows the HEAD SELECT sequence and model variations for the ing sequences.
HEAD
SELECT lines.
,"
See figure 2-7 for the tim-
TABLE 2·1. HEAD SELECT (1
=
FALSE, 0
=
TRUE)
!
HEAD SELECT LINE HEAD SELECTED HEAD SELECTED
20 2 1 701 712
1
0
1
0
0
0
1
1
0
1
IMPROPER SELECT
IMPROPER SELECT
2
3
0
1
I
HEADS SWITCHED
READ DATA
VAUD
+ WRITE GATE
WRITE DATA
(FROM CONTROLLER)
VALID
-...-..--...1
-.f
~
8 "lee MAX
-.-.-_1
- .....-
l
....1
I
8 "aec '1
~(
FORMAT SENSITIVE)
_ _ _ _I 400 MAX 1-._ _
FIGURE 2·7. HEAD SELECTION TIMING
2·5
')
2.2.5 Write Gate
The active state of this signal (logical 0 level)
enables
WRITE DATA to be Written onto the disk. The inactive state of the signal (logical 1 level) enables data to be transferred from the drive and STEP pulses to reposition the head arm.
See figure 2-7 for the tlm1ng sequences.
2.2.6 Reducecl Write ClII1'eDt and Precom,...AtloD
The 706/712 provides for automatiC reduced write current switching. Optimum precompensation 15 12 nsec and should be used on cyUnders 128 through 320.
2.3
CONTROL OUTPUT UNES
The control output signals are driven with an open collector output stage capable of sinking a maximum of 40 rnA at logical 0 (true), with a maximum voltage of 0.4 V measur.d at the driver. When the line driver is at logical 1
(false).
the driver transitor is off and the collector cut-off current is a maximum of 250 ~.
I All
J5 output lines are enabled by their respective DRIVE SELECT .lines.
Agure 2-3 shows the recommended control signal driver/recetver comblnation~
2.3.1 Track 00
This interface signal Indicates a true state (Ioglcal 0) only when the read/write heads of the seleded drive are at track 00 (the outermost track) and the access circuitry is driving current through phase one of the stepper motor.
This signal is false (logical 1) when the read/write heads of the selected drive are not at track 00. The state of this line is undefined when SEEK COMPLETE is
false.
2.3.2 ladex
The drive provides this interface signal once I!very revolution (16. 74 msec typical) to Indicate the beginning of the track.
Normally this signal is a logical 1 (false) and makes the transition to logical 0 (true) for a period of approximately 200 I1sec once each revolution (see figure 2-8).
INDEX mMC TYP
----~.~
I
.
FIGURE 2·8. INDEX TI.MING
2.3.3 Ready
This interface level, when true Oogical 0).
together with SEEK COMPLETE, Indicates the drive is ready to read.
write, or seek, and that the signals are valid. When the drive.
this
Une is false (Iogicall).
aU
seeking and writing is inhibited at
.
READY will be true after the drive is up to· speed (± 2%) for two seconds. The typical time for READY to become true after power-on is 12 seconds(21 seconds when the low power option has been utilized). After the automatic aduator recalibration process. typically six seconds. SEEK COMPLETE wiD the drive. but an additional two minutes also become true.
It is now safe to seek should be allowed for thermal expansion to stabUlze before any write operations are perfonned.
t t t
C
C
t
I t t t t
C t
I
I
I
~I
I f
I f
I t t
I
I
I
I
C
2·6
-
..
.l
~
-
-
:~
-
-
-
-
.~
.,
-
,!
-
..
-
-
'-
:i
..
] .,
:, t
.
-
.
-
-
•
•
•
•
•
,.
I
.,.
-
• t
·
·
·
J
.
.
.
I
,
·
.
2.3.4 Write Fault
This signal. when active (logical 0), Is luued to indicAte.
condltlon exists at the drive that could cause improper writing on the disk. A WRITE FAULT occun whenever one of three conditions occurs: a.
The read/write heads are Improperly ..Ieded., b.
The dc volta~e Is more than 2S percent out of tolerance.
c.
The actuator or spindle controllystem II faulted.
To reset the WRITE FAULT line, deseled the drive for at
least
500 nsec.
NOTE'
The WRITE FAULT Une will not reset of the drive.
if
the fault condition still exists after deseleetion
2.3.5 Seek Complete
The SEEK COMPLETE signal will go true Oogical 0) when the read/write heads have settled on the final track at the completion of a seek. Reading or writing should not be attempted until SEEK COMPLETE Is true.
The SEEK COMPLETE will go false In two cases: a.
A recalibration sequence Is initiated (by the drive logic) at power-on if the read/write heads are not over track 00.
Refer to paragraph 2.7.
b.
After the leading edge
2.4
DATA TRANSFER UNES of a.
STEP pulH (550 nMC typical) or the first of a series of Step pulses.
All lines associated with the transfer of data·between the drive and the host are differential in nature and may not be multiplexed.
These two pairs of balanced signals are:· a.
MFM WRITE DATA b.
MFM READ DATA
These signals are provided at the J6/P6 connector on aU drives. Figure 2-9 Ulusttates the driver/receiver combina-I tion.
See figure 2-2 for the J6/P6 interface connection.
HIGH
TRUE
26LS31
OR EQUIVALENT
FLAT CABLE
20 FT MAX
(8.8
mm)
.....- - - - - -....... 100 0
+ SIGNAL
-SIGNAL
HIGH
~--TRUE
26LS32
OR eQUIVALENT
FIGURE 2·8. DATA TRANSFER LINE DRIVER/RECEIVER COPv1BINATION
2·7
-_._-~
2.4.1
MfM Write Data
This pair of signals defines the transitions (bits) to than be written on the dlIk.
+ MFM WRITE DATA going more positive
-MFM WRITE
DATA will cause • flux reversal on the track under the selected head providing WRITE GATE
15 active.
This
signal must be driven to an Inactive state (+
MFM
WRITE DATA more negative than
-MFM WRITE
DATA) by the host system when in the rod mode.
Figure 2·10 aho.WI
the timing for MFM WRITE DATA.
- DRIVE SELECT
HEAD SELECT
+MFM VALID
READ DATA
-WRITE GATE
12
+MFM
WRITE DATA
(PRE·COMP
= nSle SINGLE LEVEL)
--,
---,
.J
81lsec
MAX f.
~ J.
50 nl.e
TVP
1+
~1~ciE;:.c
TYP °1
~--35I'I.c
MIN
-i
-i
~
35l'sec MAX i
400 nlee MAX
solnaec
____________ruui MIN to 150 nlee MAX _
200naec :t 0.1%
~ ~
FIGURE 2·10. MFM READ/WAITE DATA TIMING
2.4.2
MFM Read Data
The data recovered by reading a pre-recorded track are transmitted to the host system via the differential pair of
MFM READ DATA lines. This transition of the + MFM READ DATA line going more positive than -MFM READ
DATA lines represents a flux reversal on the track of the selected
head whUe
WRITE GATE is inactive. See figure
2·10.
2.5
SELECT STATUS
I A status line is provided at the J6/P6 connector to Inform the, host system of the selection status of th~ drive.
The DRIVE SELECT line is driven by a Tn.
open collector driver' as shown only when the drive is programmed as drive X (X iii
1, 2, in
figure
2-8.
This signal will go
active
3. or
4) by
proper placement
of the shorting plug in the
• vicinity of J5.
and DRIVE SELECT X line at J5/P5 is activated by the host system. See figure 2-4 for the jumper location.
2.6
GENERAL TIMING REQUIREMENTS
The timing diagram shown in figure 2-11 Ulustrates the nec811ary sequence of eventl (with associated timing restrictions) for the proper operation of the drive.
I
Note that a recalibrate to track 00 sequence Is Initiated at every dc power-on.
For this auto-recall sequence to function, the following conditions must be met:
Zl.
b.
The STEP input at JS/PS is h.ld
active.
The spindle Is spinning at Its regular speed.
2·8
: o~
- 0.
: :j
• -.if
- OJ
: o-.!
-
-
-
~
~
: ..
~
:
-~
~
:
.~ j
~
: 'o!
- j
-
~
-
~
-
~.
- 0'
.~
~
-
=.~
., j
~
- r;
.
~
- '..!
DC POWEAON
DISK AT SPEED
-READY
-TKOO
---I
I...-
12 SEC TVP
I I.
I
I
J
I
+f
J
r---
9.0 SEC MAX
_
_
-SEEK COMPLETE
I ~
-----~i
1__ 18
~ ~
46 male TYP male MAX -_
*
FIGURE 2·11. GENERAL CONTROL TIMING REQUIREMENT
39026·t6-C
2.7
POWER INTERFACE
These drives require only dc power for operation .
The de power to a 706/712 drive Is via connector Jl/Pl located on the solder side of the PCB. The two de vohages and their specifications, along with the Jl/Pl pin designations are shown in table 2·2.
I
Power from the + 5 and within 20 seconds of the
+ 12V supplies may be applied In any order. However. the + 5V power must be assened
+ 12V power-on application.
'*
TABLE 2·2. DC REQUIREMENTS oc
VOLTAGE PI PIN.
TOLERANCE CURRENT MAX RIPPLE (P TO P)
. 1 +12 V
~0.6
:t
V DC
1.2 V STARTING'
.75 A TYPICAL
3.9 A STARTING-
500 mV MAX
ALLOWABLE
2 + 12 V RETURN
3 +5 V RETURN
4 +5V :0.25 V DC
1.6 A TYPICAL
. 2.4 A MAX
50 mV MAX ALLOWABLE
·10SECMAX.
392521().A
2.8 FRAME GROUNDING
These drives require ac grounding of the buepl~te.
Thls grounding is accomplished in either of two ways: a.
The de voltage returns (+ 12 V and
+
5 V) are tied to the ac ground at the power supply .
b.
A separate ground wire (#18 AWG or larger) is attached to a grounding lug on the baseplate in the vicinity of the interface connectors.
2·91 2·10 (blank)
•
,
:
.
..
•
.
••
..
SECTION III
PHYSICAL INTERFACE
·-a
- . a
.
-
..
II
• II
..
"
•
•
I u
3.1
INTRODUCTION
The elecmcallnterface between a 706/712 drive and the host system Is via three connectors. The first connector,
Jl. provides the de power: the second connector, J5. provides the control signals for the drive; and the third connector. J6. provides for the radial connection of the read/Write Ilgnals.
P6
- - - - -
P5
J6 --~~
-
---------
JIl ____..........""'-
._~
~-
I
•
•
•
•
•
· ,
•
•
•
· .
•
• _I
•
•
•
•
·
•
•
· .
••
•
"
-
•
• I
"
I
•
·
·
','
•
J1
*
FIGURE 3-1. INTERFACE CONNECTOR LOCATIONS
38~·"·8
3.2 Jl/Pl CONNECTION
The dc power connector, Jl.
is mounted on the component Iide of the PCB.
Jlls a 4-pin AMP Mate·N·Lok nector.
PIN 350211·1. The recommended mating connector II AMP PIN 1-480424-0 utilizing AMP pins con-I
PIN
61473-1.
Jl. pin I, is labeled on the component side of the PCB. Wire used should be -18 AWG. Figure 3-2 U· lustrates the connector as seen on the component sid. of the drive PCB.
PIN •
3
4
1
2
DESIONAnON
+12 V
+ 12 V RETURN
+5 V RETURN
+5V
*
FIGURE 3-2. Jl CONNECTOR
3·1
I
3.3 J5/P5 CONNECTION
Connection to J5 is through a 34-pln PCB edge connector. Th. dimensions for this connector are shown In figure
3-3. The pins are numbered 1 through 34 with the odd numbered pin, located on the component and even pins located on the solder side of the PCB. Pin 2 Is located at the end of the PCB connector closest to t h e :
~
I
Jl side of the PCB, connector and is labeled.
A key slot is provided between pin.
3 and 5. The recommended mating connector for aJ.
€a
I
PS Is a Scotchflex ribbon connector.
PIN 3463-0001.
~~
--- II ~
0.036 : O.OCM
(o.a
:t 0.1)
.E-'
~I
0.400
:t 0.010
(10.2 : 0.3)
--L
BOARD THICKNESS
0.062
~ 0.007
(1.6
~ 0.2)
T
0.450
:t 0.010
0.3) (11.4 :
I
-.....J
~
0.050 NOM (1.3)
~
- 11-
0.050 NOM 0.100 NOM
~
~
I
(1.3) (2.6)
1.775
% 0.010
(~5.1
; 0.3)
I i
I I
I i
. - .
.
-.11--~;~3
NOM (2 x) I
NOTE: X.xx
(x.JUt
~
~ x.xx
x.xx)
= in.
= mm •
E-'
,
Ea~
~~
I
~6
~i
~I
,
3.4
J6/P6 CONNECTION
Connection to J6 is through a 20·pin PCB edge connector.
The pins are numbered 1 through 20 with the odd
I numbered pins located on the component side of the PCB.
The recommended mating connector for P6 is a Scotchflex ribbon connector, PIN 3461-0001. A key slot is provided between pins 3 and 5. Figure 3-4 shows the dimensions of the connector.
0.400
~ 0.010
(10.2
:t 0.3)
--L
BOARD THICKNESS
0.062
~ 0.007
(1.6
:t 0.2)
FIGURE 3·3. J5 CONNECTOR DIMENSIONS
-...II....
0.036 : 0.004
- I (O.Q
% 0.1)
T
O.ASO : 0.010
(11.~ % 0.3)
I,
...J
f.-
0.050 NOM (1.3)
... J,...
0.050 NOM (1.3)
,........
1.075
:t 0.010
(27.3
:t 0.3)
I •
I
•
I ,
I
I
Ji..
J"
0.063 NOM (1.6)
0.100 NOM (2.5)
- - -..........1
NOTE: x.xx
% x.xx
(x.xx
:t x.xx)
= in.
= mm
FIGURE 3-4. J6 CONNECTOR DIMENSIONS
3
(.1
f:.
f
~
J
~
~
~
I
~
I
~
I
~
I fa ,
(.'
I r
(.1
~.
, fa~
.!
(.1
E-
(.
3.. 2
e-
I
..
.-
.
,
.
.-
.
,
)
SECTION IV
PHYSICAL SPECIFICATIONS .
·
"
..
·
.\
-
\\
· .,
.
...
~.'
·
~.
• 1':-1
·
• l.
t
-
I(
.
.1
t
4.1
MECHANICAL DIMENSIONS
See figure 4-1 for the dimensions of the Shugart 700 Mries
drives.
163 • 0011·0.02
141 • • 0.31-0.5)
-~
\------
SIDE Z
+ t
1.00
1203.2) MAX - - - -
038 : 002
It I : 0.5)
. . .
3.12 : 0
171.3 :
0.,
-"1.
----------T
SWAY SPACE
007511 9) MIN·
1-32 MOUNTING HOLIS ca • • o
5 II • 0031· 001
114t • • 01
02)
- e -
BonOM I
·CLEARANCE OF .O~ (3.•,0) MINIMUM IN THE Z
DIRECTION AND 01 MINIMUM FOR THE Y DIRECTION
MOTI: ••
1 I • I ' • 1ft
, • • • I • . • • • • fftm
MUST BE Pf'OV10ED FOR MACHINE SWAY.
*
FIGURE 4·1.
MOUNTING DIMENSIONS
5~ • 002
1131 7 : 0 ~J
~ 7~
C1~0
• 0
01~
• 04.
013
"I!
0015
(3.3
I 0 •• t
" a
"
• - I
"
• ,:'.1
• s.02
(21.1)
~·12.c
o
4.2 MOUNTING
The 706/712 drives are capable of being mounted In any position.
CAunON'
,These drives must 1),e mounted wtth four machine screws. The screws may be installed
In either the vertical or horizontal plains into the Iide rads. The saews must to ten inch/pounds. The required sway space is 0.075
inch.
be torqued
( c
C
(
C t
C
C f f f f
C
,
$
.
6:
~
~
~
~
~ .
I
6:
I
~
C
~
~
~
~
J t t t t
4·2
-.
.
..
e·
...
..
-
• c
~ ,
-
,
.
(
• I
I
• &
• I
SECTION V
MEDIA DEFECTS AND ERRORS
.
...
.
.
-
..
'
.
,
5.1
ERROR MAPPING AND
QUALIFICATION
In high density digital recording storage systems, it is necessary to Increase rellabdlty and Improve operational performance.
This is done by providing an error detection and correction scheme.
For disk storage systems, the predominant error pattern is a burst of etlon occuring in one or more
tracks·.
These errors are drop-outs (absent bits). drop-ins (bits added)
1 or bits shifted from their nominal position beyond the tolerance of the data separator.
5.1.1
CauH8 of Errora
The following conditions may result in errors: a.
Marginal signal to noise ratio of the read/write circuits.
b.
Marginal characteristics of the me~ia and the read/write heads.
c.
Mispositioning of the read/write heads on the disk.
d.
Defects or imperfections in the disk media .
5.1.2
Error Definition
An can error is a discrepancy between recorded data and original data. There be transformed into a "1" or vice versa.
can be an extra or missing bit. i.e ..
a ·'0·'
Errors fall into two categories: "hard" or repeatable. Soft errors are often caused
"soft.·, Hard errors are usually the result of media defects and will be by items "a" through. "c" of paragraph 5.1.1.
and will normally not be repeatable.
.
5.1.3
Media Defect Definition
Most errors resulting from media defects are classified as hard erron.
They are attributable to small imperfections in the oxide coating of the disk, such as an impUrity within the oxide Itself.
or a saatch on the surface of the Oxide coating.
As the storage size and density of information lnaeases.
th.M
defects become more apparent to the system. Winchester technology utilizes a higher bit packing ratio than older types of drives and is therefore more susceptible to this type of error.
t
..
5·1
(J
5.1.4 Error Map
All drives are scanned for hard etTon during the manufACturing process.
AU hard errors (media defects) are logged and an error map is attached to each drive. Each defed listed contains the foUowing information a.
Track number
I b.
Head number c.
Byte
I .
count accurate to ± 4-bytes (Indicates the defective bytes as a location from physical index) d.
Length of defect in bits
The error map accompanying each drive will typically provide the locations of more hard errors than will be detected by the user system. There are situations, however, where a magnetic anomaly or extra defects caused by improper handling may cause an error that is unique to a particular format or bit pattern. Such a itself as a hard error, in addition to those reported on the error map. In the mended that the defect be added to the error map and mapped out.
.
flaw may present event this situation occurs, it is recom-
5.1.5
Uaer Error Mapping
Occasionally, errors shown on system.
the error map~ supplied with the drive will not show up as errors in the user's
Similarly, the user may find hard errors In addition to those on the error map dUring the user's functional tests
The recommended method of mapping is to aeate a defect directory at cylinder 00. This directory should include the locations of all defective areas, as well as alternate track assignments for those areas.
5.2
ERROR ACCEPTANCE CRITERIA
The drive, as received from the factory. wUl'meet the following error criteria: a.
No disk will have more than ten defective tracks.
Of these ten tracks. no more than three will contain multiple defects. Additionally, track 00 of ,all heads Is g~anteed to be error free.
b.
Errors separated one error.
by less than 20 bytes from beginning to end.
or less, 20 bytes long, are considered
5.3
SYSTEM GENERATED ERRORS·
It should be noted that errors may also be present as a result of system electrical noise, marginal timing conditions, ground loops in the dc power distribution cable. electro-magnetic interference, radio frequency interference, etc.
)
5·2
•
-. J
-
I
~
•• J
...
'.
(" -'
-:
..
.'
...
SECTION
VI
RECORDING FORMAT
..
..
.
-
•.
-
.~
-
..
..
..
..
-
.
..
6.1
TRACK fORMAT
The pupose of a format is to organize a data track Into smaller, Mquentlally numbered blocks of data called sectors.
The 706/712'5 format is a soft sectored ten identification type.
which means that the beginning of each sector is defined by a prewrit-
(10) field which contains the physical Hctor 'address, plus cylinder and head information. The 10 field is then followed by a user data field. '
"(
The soft sectored format is a slightly modified version of the IBM system 34 double density format commonly used on 8-inch floppy disk drives. The encoding method used here Is modified &equency modulation (MFM).
Figure 6-1 shows each track divided Into 32 sectors. Each sector has a data field 256 bytes in length. However, if sector interleaving is used, Gap 4 can be reduced to 32 bytes minimum to accommodate 33 sectors per track.
If sector interleaving is not used, and 33 sectors are desired, Gap 3 is 25 bytes and Gap 4 becomes 26 bytes
, minimum.
1~~fXJ1-----------------fl\..-------------------_rL
G»' SYM:
I
22 a
'.e
2M • USER DATA
~
10 ....
w~ITE
UPDATE - - - - - - - - - - - - - -
NOTES:
1.
MINIMUM TRACK CAPACITY 1CM11IYTES.
2.
WRITE TO READ RECOVERY TIME • • MICROSECONDS.
3.
HEAD SWITCHING TIME • • "MICROSECONDS•
FIGURE 8·1.
TRACK FORMAT
The beginnings of.
both the 10 field and the data field are flagged by unique characters called address marks .
An address mark is two bytes in length. The first byte is always ali "At" data pattern. This is followed by either an
"FE" pattern which is the pattern used to define an 10 address mark. or an MFS·· which is a data address panern.
The MAl" pattern violates the encode rules for MFM by omitting on 'clock transition between bits 4 and 5.
This makes the address mark panen unique to any other serial bit combination.
AllID and data field are followed by a 16·bit cyclic redundancy check (CRC) character used for data verification.
Each eRe polynomial is unique for a particular data panern.
Surrounding the 10 and data fields are gaps called Intenecord gaps.
6.2
GAP LENGTH CALCULATIONS
C,
6.2.1
Gap 1
The purpose of Gap 1 is to provide a head switching recovery period 10 that. when switching from one track to another, sequential sectors may be read Without waiting the rotational latency time. In ~ddition.
Gap 1 allows
8·1
physical position "drift" of the index pulse as a functton of drive ~emperature.
Gap 1 should be at least 22 ~1es (30 bytes recommended) 10llg to correspond with the head switching time and index drift.
Gap 1 is immediately followed by a sync field for the 10 field of the first sector.
6.2.2
Gap 2
Following the 10 field. and separating it from the data field, is Gap 2. Gap 2 provides a known area for the data field write update to occur. The remainder of this gap Also serves as the sync-~p area for the data field address mark. The length of Gap 2 is determined by the data separator lock-up performance.
6.2.3
Gap 3
Gap 3, following the data field. is a speed variation tolerance area.
This
aUows for
a
situation where a track has
I been formatted while the disk is running two percent slo'.uer (3531 rpm).
then write updated with the disk running at highest speed (3603 rpm).
Gap 3 should be at least 15 bytes In length (this includes two bytes for write tum off).
6.2.4
Gap 4
Gap 4 is a speed tolerance buffer for the entir4 track.
This allows the disk to rotate at the highest rated speed without overflowing the track dUring a format operation. The format operation which writes the 10 fields, begins with the first encountered index and continues to the next index.
6.3
WRITE PRECOMPENSATION
Whenever two bits are written in close proximity to each other, a phenomenon called pulse superposition occurs, which tends to cause the two bits to move
away
from
each
other.
This
is a large factor contributing to bit shift. Other phenomena such as random noise, speed variation.
etc .. will also cause bit
shift,
but to a lesser degree.
The
effect of bit shift can be reduced by a technique call precompensation,
which.
by detecting which
bits
wUI occur early and which bits will occur late, can effectively minimize the shift by writing these bits in the opposite direction of the expected shift. Bit shift is more apparent on the innermost dat tracks due to pulse crowding. Therefore.
precompensation should only be at track numbers greater than or equal to 128.
The optimum amount of precompensation for a 706/712 drive is 12 nsec for both early and late written bits. Table 6-1 shows various bit patterns for precompensation. Precompensation pattern detection bits are shifted through a 4-bit shift register.
The bit is written out of the third position.
1( TABLE
~1.
WRITE' PRECOMPENSATION
WRITE POS,nON o 0 0 0
000 1
001 0
001 1 o
1 0 0 o
1 0 1 o
1 1 0 o
1 1 1
100 0
100 1
101 0
10' 1
1 1 0 0
1 101
1 110
111 1
DtREcnON OF SHIFT
::
=
ON TIME CLOCK
=
LATE CLOCK
=
ON TIME DATA
=
EARLY DATA
::
= LATE DATA
:: ON TIME DATA
=
EARLY CLOCK
:: ON TIME CLOCK
:: ON TIt.4E DATA
::
::
=
LATE DATA
;:; ON TIME DATA
BIT IS WRITTEN CUT OF THIRD POSITION 310»24
)
8·2
• e
.J
• · .l
-
·
..
• e •
.
.
.
-
•
• • ,J
' . '-J
0"
• oJ
\
(
• t
· • • J
-
.
J
SECTION VII
CUSTOMER INSTALLABLE OPTIONS
7.1
FUll-HEIGHT FACEPLATE KIT
One of the customer instaUllble options currently available for the Shugart 706/712 disk drives is the Full-height
Faceplate Kit, PIN 061597-0. See figure 7-1.
.
.J
0.~
.J
-
J
• .J
-
-
-
-
I
,
( e_
I
@
•• J
-
-
-
.
•
·
, •
·
,
,.
.
•
·
, .,
·
·
.-
-
\
•
·
··
·
-
• e_
.
)
-
·
.
•_1
.
·
· .
· -
-
• ',-1
0'
-
.
~
-
"
',~
·
,
-
....:.
.
t
•
~t
A - -
TORQUE SCREWS. B • TO 10 IN.-LIS.
TORQUE FRONT PANEL MOUNTING SCREWS A TO 2.5 IN.-LIS.
FIGURE 7·1. FULL HEIGHT FACEPLATE KIT
7-1
7.2 LOW-POWER SLOW START JUMPER
In
certain system configurations It may be desirable to use a Low-Power Slow Start mode of initialization of the drive.
In cases when this Is
necessary.
the mode can be selected by grounding pin 13 of the microprocessor.
( )
On early versions (i.e.
t
MLC 4 only) of the between pins 12 and 13. See figure 7-2.
706/712 PCB (PIN 26141 and 26159)
.
this is accomplished by shorting
PIN 12 PIN 13
•
(SHORT THESE PINS)
FIGURE 7·2. LOW POWER OPTION (EARLY MODELS)
On later versions (MLC 5 and above) It Is
PCB.
See figure
'-3.
necesSary to fabricate a
amaD
Jumper and install it in location E3 of the
.
(
3
NOTE: The ends of the jumper should be cut to a chi,el point to pierce the socket insulation.
FIGURE 7·3.
JUMPER INSTALLATION AND FAB.RICATION
In each of the above applications. grounding board is not necessary.
is to be applied to the solder sid. of the PCB.
and removal of the
7·2
.J
t
E f
t
E
E t t
, t t t
C
t
C
C
C
4
-
..
,,- I •
..
- a.'.
- I I
-
..
.
)
SECTION VIII
THEORY OF OPERATIONS
·
..
· I
•••
· ...
•• I
..
,
· .'
..
,
.
· .'
,
·
·
'.'
·
. ' J
·
·
-
'-'
..
•• a
....
·
...
·
·
· · .-.
I-.
I
-
..
.
-'
•
_I
•
•
· . I
· I )
8.1
INTRODUCTION
All of the tasks of the PCB miaoprocessor are separated into the following groups: a.
High priority time aitical tasks b.
Lesser priority time critical tasks.
c.
System initialization tasks
POWER
ON
RESET
.
-
SPINDL£
BRAKE t
STEPPER -
MOTOR ~
CONTROL
~
~
CONTROLLER
......
~
110
LOGIC
AIW
LOGIC
-
~
~
~ liP fVW
PRE-AMP
•
-
:
FIGURE '~1.
LOGIC DIAGRAM
8·1
SPINDLE
MOTOR
CONTROL
~
~
STEPPER
MOTOA
SPINDLE
MOTOR
~O'
8.2
HIGH PRIORITY CRITICAL TASKS (fOREGROUND)
The high priority time critical tasks consist of the following: a.
Generate the
spindle
motor
waveform
and measure
the
revolution time.
b.
Deted and accumulate the step pulses from the Interface.
c.
Generate the stepping waveforms applied to the stepper motor, ramping (up and down) including pulse width modulation.
and perform the
actuator
velocity d.
Time out the actuator damping interval.
These tasks are updated once each 90 lisec by using the mlcroprocessor'slntemal timer to generate each update.
These tasks cannot be Interrupted by another task while they are being executed.
an
interrupt for
The set of program routines associated with these task.
II collectively caned the
IIforeground."
Foreground routines are arranged so that forming any necessary they will sequlntlally,.xlcute'one after the other, with each routine peraction, then handing control to th. next routine. The last routine turns processing over to other tasks until the next timer interrupt anives, at which the foreground process starts over. See figure 8-2.
The folloWing subparagraphs detail the actual foreground routines.
8.2.1
Foreground
Loop Control
This is the entry point for the 90 routines. Refer to paragraph 8.3.
lisec Interrupt requelt which II set up at the beginning of the "background"
This routine saves the accumulator, clears the timer interrupt flag, and updates the background gate counter. Control then passes to the Spindle Motor Foreground.
8.2.2
Spindle
Motor Foreground
This measures the revolution period in lnaements of foreground time by being triggered by INDEX.
It then generates a Pulse Width Modulated (PWM) waveform to control spindle motor power. Control now passes to
Motor Fault Foreground.
,8.2.3
Motor
Fault
Foreground
This routine determines if the spindle, motor speed is correC1.
and Interrupt Return routine and
Buffering Fundion.
If It is not, controlls passed to the Foreground End all seek fundions are skipped..
If speed is correct, control passes to the Step Input
.
8.2.4 Step Input Buffering
Function
If Step Input is not enabled, this means that actuator seek.
are stilltn process, In which case this routine exits immediately to the Stepper Damping Time Out routine.
If
Slip
Input
is enabled,
this
routine adds any additional steps to the total step count; the directioJ:\ls saved: the Step Input flag
'I disabled: and the Ramp Calculate flag is set true.
Control will then pass to the Stepper Damping Time Out Routtne.
8.2.5
Stepper
Damping
Time Out
Routine
Damping can
(Background).
be enabled through the Seek Function Foreground or Actuator Lubricant Unstick Routine
If it is not enabled, the routine exits to the Seek Function Foreground. U it is enabled, the actuator is decelerated somewhat with a track arrival delay. This is followed by an additional settling delay which also allows checking for any additional step pulses. If any more step pulses are received, the routine exits early without Setting
Seek Complete true. Exit is made to Seek Fundion Foreground.
!
)
8·2
: 1{1
..
-
• '0
·
·
'.
~
·
'.
·
• !.O
• c.
a
...
~
-
-
•
.
•
·
· I
~
•
4)
-
"" • _I
-
..
.
..
-
-
I
,
•
•
•
)
-
·
-
•
•
·
-
"
'
•
•
_I
-
-
-
-
L
•
I
-~
•
«
-
· I j
-
-
-
I.' a.'
• a'
-
..
•
·
· .
."
U'
·
• ,lJ
~
..
OFFE '
INTERRUPT
REQUEST
VECTOR
OCD1 IENTRY
FOREGROUND
LOOP CONTROL
EVERY 10 liMe occe
SPINDLE MOTOR
FOREGROUND
0003
MOTOR FAULT
FOREGROUND
ERAA
STEP INPUT
BUFFERING
FUNCTION
Oc.A
DAMA
STEPPER DAMPING
TIME OUT
ROUTINE
0078 seEK FUNCTION
FOREGROUND
SEEK
IEXIT
FOREGROUND END
AND INTERRUPT
RETURN
~IGURE
1-2.
FOREGROUND ROUTINES SEQUENCING
8-3
8.2.6
Seek FunctioD Foregrouacl
The seek flag is set from the Seek Ramping Calculate Function (background). U the seek flag is set, then a step delay is provided to allow time for step settling. Uthe delay is not done. then the routine exits to Foregr~und End ) and Interrupt Return. Otherwise the routine gets a ramp table value and determines if ramping is up or down.
It ramping is down and seek is complete. then the actuator slew vohage Is tuned off; the seek fuetion is disabled; and the damping fuetion is enabled.
If seek is not complete, and rarpping is up or down, then step timing is saved: direction is determined; the cylinder address is updated: the new stepper phase is output on port B (see table 8-1); and the routine exits to Foreground
End and Interrupt Return.
.
TABLE 8-1.
I/O PORT CONFIGURATION
PORTA
PORT B
PORTe
PORT D
PIN NO.
PA7
PA8
PA5
PA4
PA3
PA2
PA1
PAO
PB7
PB6
PB5
PB4
PB3
PB2
PBl
,PBO
PC7
PeS
PC5
PC4
PC3
PC2
PCl
PCO
PD7
P06
POS
P04
PD3
PD2
PD1
PDQ
AssiGNMENT
+OIA
+ TRK 000
+ FAULT
-FAULT CLEAR
-READV
+ SeEK COMPLETE
UNUSED
... INDEX (
+
EDGE)
+COILA
+ COIL B
+ COIL C
+ COIL 0
-STEPPER ENABLE
UNUSED
UNUSED
UNUSED
-SLOW SPIN-UP
+ REDUCE IW
-RUN SPINDLE
+ BRAKE PICK
+ LED
UNUSED·
UNUSED
UNUSED
+SEL
-DELAY
-EXERCISE
+ ACTUATOR SLEW
· ... STEP INPUT COUNT 0
+.
STEP INPUT COUNT C
+ STEP INPUT COUNT B
+ STEP INPUT COUNT A
39~2·oe
8.2.7
Foreground End and Interrrupt Return
This routine simply restores the accumulator from the stack and returns to the background.
8.3 LESSER PRIORITY CRITICAL TASKS (BACKGROUND)
The less time critical tasks are referred to as the "background" and are performed in between foreground interrupts, after the last foreground routine has ended, but before the foreground restarts. Average foreground execution time is approximately 55 Ilsec; therefore, out of every 90 psec time period. the background has about 40 I£sec to perform its tasks.
The background tasks are arranged sequentially like the foreground. however the last background routine hands control back to the first, thereby establishing a continuous loop. For co.nvenlence in timing certain non-critical events, the background loop rate in made self-synchronous with the foreground.
~
)
8·4
-
·
C
·
I
-
-
&.
·
(
-
~ c:
...
I
r
•
..
Col
-
[.
-
-
I
· t
I
· • It
·
• U
·
, U
·
· ,
\ U
··
U
.
·
,
.
• ·.U
· .
• ' U
.
· -
',~
~
" ~,
·
',1:-
· ..
~
·
· ..
·
•
.
,
·
· ..
• J
•
J
· •
D j
)
This is accomplished by allowing
the
beginning of background loop execution t~ proceed only on every fifth foreground interrupt. Therefore, background loop execution time is 450 p.SeC
(5 x 90 I£Sec). The only exception to this Is that the spindle motor background control routines ar. exempted from this "gating" process In order to minimize control system phase error.
The less time atticaJ tasks consist of the foUowing: a.
Calculating the duty cycle of the spindle motor power waveform·, based upon the measured revolution time.
b.
Monitoring the disk revolution time to generate the Drive Ready signal to the interface, and to determine if spindle motor fauks
have
occurred.
c.
Determining the necessary ramp-up and ramp-down parameters to perform a seek, given the step pulse count as received from the interface.
d.
Performing the automatic actuator reset to cylinder 0 dUring the drive power-up.
e.
Moving the actuator a fun stroke in and out twice In order to distribute the actuator bearing lubricant dUring drive power-up.
f.
Self-exercising the actuator with continuous drive exercise jumper has been Installed.
random seeks and checking for seek errors when the
The following subparagraphs detail the actual background routines. See figure 8-3.
8.3.1
Sy.tem Startup Code
This code initializes the stack pointer and binary arithmetic mode with the foUowing results (see table 8·1):
Cl.
On Port A the READY and FAULT flags are set to false. and the FAULT CLEAR line is momentarily pulsed true.
b.
On Port B the stepper coil bits are put Into Phase A and the Stepper Enable is made· false.
c.
On Port C, Reduce Write Current and Brake Pick are tru~; Run Spindle and LED are false.
d.
On Port 0 the Aduator Slew is false.
On
aU
four ports, all bits not assigned as outputs are coofigured as Inputs.
The routine then jumps to Spindle Motor InltlallzaUon .
8.3.2
Splndl~ Motor Initialization
This routine initializes the spindle motor control conltAnts and variables. The spindle brake is held at high current for about one second. Brake power is then reduced and the .pindle motor is ramped up to 100 percent for about 8 seconds, using pulse width modulation.
FuU spindle power is held for an additional X seconds while the spindle index Is counted.
If X or more Index pulses have occurred, then control goes to Seek Function Initialization. otherwise there is a spindle failure and control goes to the Miaoprocessor Control Fauh Indicator function.
8·5
SYlE... STAAT
PORT PAE.
0878
SPINDLE MOTOR
IN'T
IMTA
YES
0822 FAULT
,.P
CONTROL
FAULT
INDICATE
FUNCTION
0917
SEEK FUNCTION
INIT.
INIT COOE END
INTERRUPT TIMER
ENABLE
095B
SPINOLE MOTOR
BACKGROUND
MTRB
NO
MOTOR STATUS
MONITOR yel
WARM UP
SETTLING
EXTN COUNT DN
OA3O IKGA
SYSTEM
LOOP
IACKGND
CONTROL
NO
'YES
DRIVE ACTUATOR
SELF·EXERCISE
FUNCTION
YES
ACTUATOR LUBE
UNSTICK ROUTINE
LUBA
AUTO ACTUATOR
RESET TO TRK 0
AREA
Losa 0" INDEX
MONITOR
VES
CYLINDER
ADDAI
R£ZERO MONITOR
OA5E "AMe
SEEK AAMPtNQ
CALCULATE fUNCTION
WAITE CURRENT
CONTROL FUNCTION
OCl8
DRIVE SELECT
L£D MONITOR
LED
OCCE
BACKGROUND
COOEEND
SKEND
FIGURE 8-3. BACKGROUND ROUTINES SeQUENCING
8·6
I·
-.e,
- • 1:.'
: '_Ci
- IU
: 1..
':1
• L
:.~
--
._L.~
. ..l:J
-.
Il.j
-.
.. J
_u,
-
_
--
8.3.3
M~croproc ...or Coatrol Fault ladlcator FUDCtI~
f
This
routine removes power to the spindle motor and Rapper motor;
th8
foreground interrupts are
halted,
and the .
READY line
is set false.
The FAULT latch
Is
pulled and:
a.
If no jumpers are InstaUed, or
If
the delay Jumper and the LED is flashed u shown In tabl. 8-2.
(EI) 1I1nstaDed.
then aU motor power II removed b.
If only the exeidse Jumper (E2) IIlnstaU8d.
then the microprocessor returns to System Startup and restarts.
TABLE 1-2.
LED FAULT CODeS
IOURCI Of FAULT ..
HUMBleR OF FLASHES
RESERVED.
1
RESERVED.
2
6
7
3
~
5
SPINDLE FAILED AFTER ACHIEVING FULL SPEED SUCCESSFULLY.
ACTUATOR FAILED TO RESTORE TO CYUNDEA ZERO.
ACTUAl:oR seEK ERROR DETECTED DURING DRIVE SELF-EXERCISE.
LOSS OF SPINDLE INDEX SIGNAL
•
-
-
I.~ I
--
.
_
: -
...
'.'
-
'.'
:.~
..
..
'
..
~
-
8.3.4
Seek Function Inltlallzatloa
This
initializes the aduator seek
function control constants
and
variables. The
routine then goes directly to Initialize
Code End.
8.3.5
Initialize ~de £ad
This starts the 90 ".sec
foreground intenupts. and directly to Spindle Motor Background.
th.
system enters the continuous background
loop
by
going
8.3.6
Spindle .Motor Background
This takes the index time flag, passed from the foreground, and determines If the speed is correct.
If it is, no changes are made and the routine goes
to
the Motor StatUi
Monitor.
If the speed is not correct. the Index time error 11 lntegr.ted
and added to the current index time error to ~etermine and set the motor power factor.
The
routine then goes to the Motor Status Monitor.
8.3.7
Motor Statua Monitor t
This monitors the index time to determine if the motor speed II out of tolerance. It sets the FAULT line to true if the speed varies more the :t 1.61 percent for six revolution•.
Uthe speed drops below 92 percent for more than ten revolutions. the routine jumps to Control Fauk Indicate Fune:tton (paragraph 8.3.3). otherwise it ~s to the Warmup Settling Extension Countdown.
.
8.3.8 Warm-up Settling ED....loa Couatdo...
A countdown of two minutes allows drive warm-up time and provides longer seek settling time during warm-up.
The
routine then goes to System Background
Loop
Control.
8·7
8.3.9
Syatem Background Loop Control
If five 90 Jolsec foreground loops have occurred since thal.5t
time thiS funetton was entered, then control proceeds to Loss of Index Monitor; otherwise control goes back to Spindle Motor Background (paragraph 8.3.6).
8.3.10
Lo.. of Index Monitor
If INDEX has not occurred during the last 115 msec. then control goes to the Control Fault Indicate Function
(paragraph 8.3.3); otherwise control proceeds to Cylinder Address Rezero Monitor.
.
8.3.11
Cylinder
Address Rezero Monitor
If the actuator is on cylinder 0 and the exercise jumper (E2) is not installed. then the cylinder address variables are set to zero; otherwise control proceeds to the next step.
8.3.12
Seek Ramping Calculate Function
If Ramp Calculate is not enabled by either the Step Input Buffering Fundion (paragraph 8.2.4) or the Drive Actuator Self-exercise Function (paragraph 8.3.13). the control proceeds to the Drive Actuator Self-exercise Function.
.
If Ramp Calculate is enabled.
it accepts the step sum and direction of inputs and produces the necessary seek control values to effect a buffered seek. The actuator track zero flag i.
monitored and outward seeks from cylinder 0 are inhibited. unless the delay jumper (E1) is installed in which
CASa such seeks are allowed (this facilitates the adjustment of the crash stop and track zero flag).
.
If the exercise jumper (E2) is installed. the aduator cylinder address variable will flag to detect possible seek errors during self-exercise.
be compared with the track zero
If seek errors are detected. control goes to the Control Fault Indicate Function (paragraph 8.3.3). otherwise control passes to Drive Actuator Self-exercise Function.
8.3.13
Drive Actuator Self-exercl8e Function
If the exercise jumper (E2) is installed then this routine uses its internal random number generator to create a continuing series of pseudo-random seek values which insure full disk coverage dUring exercise.
If the delay jumper (El) is not installed. this function will delay itself for 10.msec; if it is installed. the delay will be
500 msec. If the exercise jumper (E2) is not installed the control proceeds to Actuator Lube Unstick Routine.
8.3.14
Actuator Lube Un.tlck Routine
This routine is enabled by a flag passed hom the Automatic Actuator Reset to Track Zero function. otherwise
.known·as Recal (recalibrate).
It seeks from cylinder 0 to the end cylinder and back twice.
It enables the damping function when done, and control passes to the next step .
. 8.3.15
Automadc Actuator Ra.t to Track Zero (Ree.1 Function)
Upon system start. the Seek Function Initialization (paragraph 8.3.4) sets the Recal Aag (RCFLG) to indicate that the actuator arm has not been calibrated to track zero and to provide for a ten revolution delay before Recal. The
Motor Status Monitor (paragraph 8.3.7) checks to see of the unit has been recalibrated.
If not. it checks the disk revolution period to see if the disk is running fast enough.
If it is.
RCFlG is incremented once each time the Motor StatuI Monitor is entered. After ten entries. i.e., ten disk revolutions. RCFLG is incremented to zero.
If
it is not, the routine Is exited. If it is, the actuator is stepped outward
512 steps or until track zero is found.
The Actuator Lube Unstick Routine is enabled by setting the LUBE flag (paragraph 8.3.14) and control pasSes to the Write Current Control Function.
.
~ )
)
8·8
• • l'
• r
·
.~
• C'
• I
·
...
(
·
..
• .l
·
..
,
.
,'''';'-:''.'
·
·
, ]
.
• .u
U,J
:
(~
I.J
:
.~,
- . I
• ~
I
...J
-
•
..
{J .
.
• u o
8.3.16 Write Current Control
Function
+ REDUCE IW lignal on port C. bit 6 high. when the t This routine sets greater than the write cUlTent switchovcr point
(WRITS~).
See table 8-1.
cybnder address (TRKL and TRKH) is
The routine' then passes control to Drive Seled LED Monitor.
8.3.17
DrIve Select LED Monitor
This function checks port 0.
bit 7 (+ SEl).
to see
BKPC (port C Backgroung Bit Control) Is set high.
If It is high: Indicating that the drtve Is selected. U it Is.
If bit 3 in
+ SEL is low, then bit 3ln BKPC is set low. See table 8-1.
Control now proceeds to the next routine.
8.3.18
Background Code End
This routine merely jumps to the beginning of Spindle Motor Background, continuing the background loop.
8.4 SYSTEM IN_TIALIZATION
TASKS
System initialization tasks are performed only once for each are completed.
the microprocessor foreground interrupts are started and control restart. Once most initialization tasks
I.
given to the continuous background loop. Reand make use of its time (as gated in the maining initialization tasks are completed in the background loop foreground) to time necessary events.
These initialization tasks consist of: a.
Setting up the miaoprocessor into the proper initial state.
internal registers and placing the various input and output pins of such b.
Clearing the drive fault latch.
c.
Applying power to the spindle motor and verifying that It begins to rotate properly.
"
• ~I
• , u
• II
..
8·91 8·10 (blank)
SECTION IX
PACKAGING INSTRUCTIONS
• . r
·
• • l
.
,
• 0
·
..
L
·
.
• ' (1
.
•• 0
• • C
· c
·
(
•• Co
· • l
·
·
., .
·
..
-
"
"
· 0 . . .
·
'.-~
..
•·...9
~
9.1
UNCRATING
Due to the integral spindle actuator lock, no spec14llnstrudlonl for unaating or packaging are required.
The Shugart 706/712 drives are shipped in two manners .. follows: a.
A single unit In a single carton (figure 9·1).
b.
Ten units in a single carton (figure 9·2).
It is suggested that packing materials be kept in case the unit must be returned to Shugart for repair.
Regardless.
the unit must be indiVidually packaged in comparable packing al shipped to preclude damage in shipping and handling. Damage to the unit as a result of inadequate packaging will void the warranty on the unit.
Inspection of the unit(s)" should be made in accordanc.
,
9.2
RECOMMENDED RECEMNG INSPECnON
with
the spectfications of paragraph 9.2.
9.2.1
Packaging and Identlftcatlon
The individual and paUeted containers should be inspected for exterior damage.
Each shipment contains a packing slip, listing as a minimum the Customer Purchase Order Number, quantity. stock number, dash level, and MlC level.
Each
unit
is individually protected
as shown
In
figures 9-1 and 9-2.
The container should be free of foreign matter and clean.'
9.2.2
Mechanical IDapec:tloa
The following visual checks should be made for eAch unit: a.
Verify
the model number,
serial number.
and b.
Check for loose saews and sub-assemblies.
MlC
level.
c.
Inspect for loose connectors or missing
Jumpcn.
d.
Check for exposed wires on cables and conn.eton.
9·1
FIGURE 9·1. SINGLE UNIT PACKAGING CONFIGURATION
9-2
:~ f t t f t t t t t t t
,
,
, f
, f
~
~t
E t f
~ t
C
3: t f
, t t
~.
FIGURE 1-2 TEN UNITS PACKAGING CONFIGURATION
9·3
( t
"9.2.3
FUDetiODU
latinS
Shugart recommends using the
ACe
T
-650
Tester wtth Lev.1 E-6 Software.
This tester Is speCiaDy programmed for
aU
5.25 and 8-inch fixed disk products.'
()
The functional tests performed by the
ACe
Tester arc as follows: .
o
: I
Prompt character and Indicates the program is rcady to accept
Commands
from the user.
IP = Inspect Phase command code is availAble for displaying the contents of a phase.
PP = Print Parameters. See table 9-1
TABLE
8-1.
PRINT PARAMETERS
STEP RATE ( )( 0.1 MS)
MARGIN CODe
MAX. HEAD
STEP MODE
MAX. CYLINDER
MAX. ERROR eNT
BUFFER ERROR RETRY LIMIT
PRECOMP START CYLINDER
LOW WRITE I START CYLINDER
DENSITY MODE
The following example (table 9-2) is a print out ~f th~ test program with the Printer Option for the ADC.
TABLE e.2.
TeST PROGRAM
WHICH PHASE?
0 a30
11
3
:a 3
:=
:s
0
319
:a0
=
5
.128
=200
:a 1 MKM 32+256 aG·"
() ( f t t t t t f t f f
MSJ
TMI
P21
F1/
WT/
ATI
RRI
RV/
WAJ
RAJ
WCJ
TMI
HOI
PKl
4
1
,.
1
1
1
500
1
1
1
1
1
1
353
I
SET MARGIN CODE
TEST MARGINS
=
3
SET WORST CASE PATTERN
FORMAT DISK DENSITY 1
WRITE DATA INTEGRITY TeST.
READ DATA INTEGRITY TEST
RANDOM READ DATA TeST
READ REveRSE TeST
OVERWRITE TEST
OVERREAD TEST
WORST CASE seEK TEST
TEST MARGINS
HOME THE DRIVE
MAX CYLINDER
( t
( f
9.3 PACKING FOR RESHIPPING
To prepare a drive for shipment: a.
Locate the heads to the Shipping Zone (refer to para.
1.4.8).
b.
Place the drive in the proteetlve plastic sleeve.
c.
Place this configuration Into the inner container.
d.
The inner container is to be sandwiched between the foam inserts.
e.
The entire array is then placed Into the outer container and Haled.
Failure to follow these procedures may result in damage to the drtve(s).
9-~
0 t
E
E
~ t
~ t
~
, f
,
,
,
, f
•
• "
•
· • , J -
- I .J
(
)
-1.1
• ! ,
• : .J
SECTION X
DRIVE INTERCONNECT
• • J
·
- • oJ
· • .1
• J
-
.J
- • J
·
• J (
...
)
• J
·
·
]
·
·
-
.
J
·
·
-
.
~
.
.
•
· · ..
'
· ·
.
.
.
·
..
-
.
..
~
..
·
· ..
--
.
-
·
,
.
(
.)
· ·
·
.
-
·
.
-
..:
The electrical connection between the Shugart 706/712 and the controi system Is shown
chain configurations, the
terminating paragraph 2.3.
in
figure
10-1.
For daisynetworks
must be
r.moved
from
aD but the last
drive
in
the
chain.
Refer
to
HOST
7061712
J6
JI
DRIVE 1 -
J1
CONTROlLER
------
DATA SEPARATOR
DC
POWER
(
"-
(
J5
JI
DRIVE 2·
J1
J5 ,
Je
DRIVE 3·
J1
J5
Je
DRIVE ~
J1
-TERMINATOR NETWORK REMOVED
*
FIGURE 10-1.
MULTIPLE DRIVE CONFIGURATION
10-1/10·2 (blank)
.
-
•
.
-.
&
·
,
• J
·
'-~
·
-
• !, •
·
,
--.
.
• r 1
SECTION
XI
'SPARE PARTS
t
L
.
,
:
:
:
=
Shugart Corporation, in its commitment to sional Spare Part/Logistic support provide service to Its customers, has available group to support the OEM cUllomer a dedicated and profesbase as well as the end user.
t
11.1
ROUTINE ORDER ENTRY
TWX, or by mail. AU verbal orders before the order is processed
In the U.S. may be placed with for confirmation or shipment.
Shugart Corporation
Routine orders (domestic open accounts) boo~ed as received but will require confirming by phone. facsimile.
purchase documents
Spares)
PHONE:
(408) 737-7900 (Ask operator for
(910) 339-9355
TWX:
.-
FACSIMILE:
(408) 735-7486
MAll:
Shugart Corporation
475 Oakmead
Parkway
Sunnyvale. CA 94086
ATIN: Spare
Parts Dept.
11.2
EMERGENCY ORDER ENTRY
Requests for parts required on an
. TWX or phone.
emergency basls
Be particularly, careful to ensure should be communicated that all applicable information to is
Shugart Corporation by either communicated.
11·11 11·2 (blank)
SECTION XII
MAINTENANCE
12.1
INTRODUCTION
The Shugart 706/712 has tion been designed to require no maintenance under normal operating conditions. This sec· will discuss those steps to be taken in the event of a .drive malfunction.
12.2
MAINTENANCE EQUIPMENT
The only equipment required ls procedure.
an ADC T-650 Tester and an oscilloscope.
Refer to paragraph 9.2.3.
for ADC test
12.3
DIAGNOSTIC TECHNIQUES
The 706/712'5 are eqUipped with a self-exerciser that supplements any diagnostic requirements.
12.4 TEST POINT LOCATIONS
Although test points are evident on the testing is reqUired of the end user.
PCB.
these are used for testing during the manufacturing operations. No
12.5 TROUBLESHOOTING
Tables 12.1 through 12.3 show the procedures for determining possible problems.
TABLE 12·1. PCB VERSUS DRIVE FAILURES
DESCRIPTION
MOST ERRORS OCCUR ON TRK 00
PROBLEM IS IN
THE DRIVE THE PCI'S
X
EXTERNAL
ERROR OCCURS ON TRK 317 X
WRITE FAULT IN WRITE MODE
ONLY SELECT HEAD 0 AND HEAD 1 NOT HEAD 2 AND 3
SYSTEM TIME OUT ERROR·
DRIVE UNABLE TO COME UP TO SPEED·
:
X
X
X
X
X
X
DRIVE NOT RUNNING TESTS WITH OTHER FIXED DRIVES·· X
BRAKE NOT FUNCTIONING RIGHT··· X
GND BUTTON NOISY X ~
-TRY WITH KNOWN GOOD PCS'S. IT COULD BE THE DRIVE OR PCS'S.
·-MAKE SURE TO CHECK THAT THE PCS'S HAVE DRIVE SELECT JUMPER AND TERMINATING JUMPERS.
---ADJUSTMENT OF BRAKE IS VERY IMPORTANT. USE 20 MIL SHIM FOR PROPER ADJUSTMENT BETWEEN BRAKE
AND SPINDLE.
12·1
fABLE 12·2. INSPECTION OF THE DRIVE"
DESCRIPTION
COVER DAMAGE/BEND IN COVER ETC.
,
LEAK IN THE COVER GASKET
CUT IN THE FLEX CABLE OR 1fRACES BROKEN IN FLEX CABLE
"
. t
.
,
,
'.
# 0•
..
'
~.
.
' °.'0 0 • • ,-
,
.
,
PR08LEII IS IN .
l\~<'-:.
THE DRIVE THEPCa..
EXTERNAL
X
X
X
PeS·S SMOKED/BURN OUT X
MISCELLANEOUS BROKEN PARTS X
X
X
X
X
X
NOISE FROM HDA MAY BE OUETO: HEAD DAMAGE
BAND BROKEN
DISC NOT CLAMPED
NOISY
DAMPER LOOSE
SPINDLE MOTOR
DRIVE NOT COMING UP TO
ON LEO
SPEED~
COUNT THE NUMBER OF FLASHES
1 TIME
2 TIME (NOT ASSIGNED)
3 TIME
4 TIME
5 TIME·
6 TIME
7TIME
-TRY WITH KNOWN GOOD PCS'S.
--MOST LIKELY THE POWER SUPPLY.
X
X
X
X
X
X
X··
3t'02·14
TABLE 12·3. SIGNALS INSPECTION
CHECK THE DIFFERENTIAL SIGNAL ON TP11 AND TP12 IN BOTH WRITE AND READ MODE ON ALL THE HEADS AND
RECORD AMPLITUDE AND RESOLUTION.
..
'
PROBLEMaSIN
DESCRIPTION
SIGNAL LOOKS OK ON SOME HEADS AND NOT ON OTHERS
SIGNAL LOOKS GOOD ON TP11 AND TP12 AND NOT ON TP1.
AND TP16
THE DRIVE THE PCB'S EXTERNAL
X·
X
DRIVE NOT HANDLING DATA
WRITE FAULT WHEN TRYING TO WRITE
X
X
X DRIVE NOT SEEKING
SIGNAL LOOKS GOOD ON TPll AND TP12 DURING WRITE MODE BUT
NO SIGNAL DURING READ MODE
X X
12.6 CHECKS AND ADJUSTMENTS
The only adjustment necessary to the 706/71215 brake adjustment after instaUlJ1g
The foUowing steps define the procedures to be followed (see figure 12·1):
a
new PCB, or when
necessary.
a.
With the control PCB Is Its normal position, note that the brake pad and spindle motor can be seen through the slot opening.
b.
Loosen the five saews securing the PCB to the drive: do not remove.
)
12·2
-
.
•
••
:
.~
:,
: ..
~
INSERT SHIM HERE
~
:\ t;:;;i.
o
...
~:
~ - - _
.... '6'
~
@
@)
@)
I
•
•
•
•
· I
•
· ,
·
:
,"
,
,
.
.
.
..
• , I
,
•
·
• ,
-
I
· -
• , J
I o
•
·~.1
• , J o
~8 o
FIGURE 12·1. LOCATIONS DIAGRAM c.
Insert a flexible 0.020 Inch (0.5 mm)
.him
between the brake pad and the spindle motor. Pull the
PCB.
from the connector end, allowing the brake pad to press firmly against the shim and spindle rotor.
d.
Tighten the two screws labeled "A" to 5 'n/lb (0.56
J) without releasing the PCB.
brake pad is pressed firmly against the rotor.
Be sure that the e f.
Insert another 0.020 Inch (0.5 mm) shim under the screws labeled "8" and tighten them individually.
Remove that shim and check for a 0.01·0.02 Inch (0.3-0.5 mm) gap between the screw head and the board when light pressure is applied against the PCB. When properly fastened. the board should be allowed to ·'float tt at the connedor edge.
Remove all shims.
12·3
g.
Push the brake pad awa~J spincUe. The stroke
: ·mn the spindle ,·otor to see that the brake has sufficient stroke to about 0.020 lnch (O.~ mm).
dear the h.
After the five mounting saews have been properly tightened.
fiD the saew heads with glyptol.
12.7
REMOVAL AND REPLACEMENT PROCEDURES
I
12.7.1 Removal of Control PCB
()
The foUowing steps define the process to be followed for the removal of the Control PCB (see figure 12·2): a.
Remove and retain the five mounting screws.
b.
Lift the Control PCB and stepper t and flex circuits.
Front Panel Rall Assembly about
2 inches (51 mm)
.
.
and unplug the spindle.
c.
Remove the PCB.
d.
Replace the Front Panel Rail Assembly and mountir:'9 screws.
~
~
i
E
I
E
E
E
E
E
~
~
I
~
E
FIGURE 12·2. REMOVAUREPLACEMENT OF CONTROL PCB
12.7.2 Replacement of Control PCB
The foUowing steps give the sequence with which to install a control PCB (see figure 12-2): a.
Remove and retain the five mounting screws.
b.
c.
Place the Control PCB on the drive at an angle••••hown. to allow the cables to be plugged in.!Place ".....
lid..
rail.
but over the stand-offs.
' J
Plug In the three circuit cables.
Be sure the cllble.
are fuUy Inserted Into position.
12·4
• f •
·
,
,
· ,
,
.,
,
., t
.
, ,
•• I
.
-
• I ,
-:
-"
: =-
· I
•
•
·
·
-
.
..
.
•
.
•
•
•
(t
-
-
-
-
-
.
•
.
.
.
.
•
•
I d.
e.
Lower the Control PCB carefuUy on to the ..and-offs with the cables not interferring with the spindle motor.
Be
baseplate.
sure the spindle motor
cable
Is nlot sandwiched between the miaoprocessor and the
Insert the five mounting screws through the board and Into the stand-offs but DO NOT TIGHTEN
UNTIL BRAKE ADJUSTMENT IS MADE (refer to paragraph 12.6).
12.8 ALIGNMENT PROCEDURES
The 706/712 drives require no special allgnment.
12.9 PREVENTIVE MAINTENANCE
The 706/712 drives require no preventive maintenance.
(t
• r ,
• I J
4
I •
12·51 12·8 (blank)
• II
·
-~
-
·
·
·
"
-
"II
.
- J
.-)
J
: .8
-
)
:
--'
- J
.J
SECTION XIII
ILLUSTRATED PARTS CATALOG
-
:..~
.~
-
-
•
.
.1
.
.
~
13.1 . DESCRIPTION
The Illustrated Parts Catalog (lPC)ls arranged possible. will appear directly above the parts list
10 thlt the figure will always precede the parts listing and, when or on the left hand p~ge immediately preceding it.
The first number in the list will aly/ays refer
~o the ref.renci number of the part within the figure .
Part numbers enclosed in parenthesis refer to parts belonging to a Next Higher Assembly tance only to those customers with alternate assembU...
NHA PIN c·ustomer's quantity
(NHA) and are of impor-
Following the desaiption of these parts, the designation gives the part number of the assembly to which they pertain. When assembly. these alternate parts will be used tn lieu of the part listed directly above per assembly for these alternate parts is th! I4me unless otherwise directed.
them.
applicable to the
Assume that the
When an assembly is referred to within a figure and a further breakdown referenced number will be caUed out.
is shown on another figure. then the
(t
13.2 INDENTED LEVEL
The parts list is indented to show the levels of assembly within a figure. The major assembly will always be will be indented one space. Pans within these unindented. All parts or assemblies that attach to the assembly assemblies will be indented two spaces and so on.
13.3
QUANTITY PER ASSEMBLY.
The quantity listed is the quantity used on the major assembly. Major assemblies quantity listed.
· themselves wiD never have a
• .1
_ II
: '.i
13·1
I
Tf..---2
I
I
I
I
I .......
~
__ '
.....-~,..",a
~::tIfIiI'/I~
I
I
I I
FIGURE 13-1. SHUGART 7061712 ASSEMBLY
13·2
»tQ2-,.
._
..
~
(.
,
~
r"
(
REFERENCE
NUMBER
1·1
2
3
PAJIT
NUll." .
·28173-0
28177-0
12233-0
~ e121~2
.' DllCIUPTION
· CONTROL PCB (708)
CONTROL PCB (712)
SCREW, PHILUPS. PAN HEAD ('~ x 5118)
. WITH NYLON PAD fRONT PANEL AND RAIL ASSEMBLY
I
QUANTITY
1
5
1
(
(.
(oE
(~
(~
(~
(~
€C
[b.
.~ ~
(r
€r
.
~.
~~
€~
€~
€~
(
€ [
f (
r ( •
~(
€[ t.
~
REFERENCE
NUMBER
2-1
2
3
4
5 e
3~02·19
FIGURE 13·2. FRONT PANEL AND RAil ASSEMBLY
PART
NUMIER
11306-0
81282·1
8128&0
113384
12207-0
812i1·1
DESCRIPnON
SHOCK MOUNT
RAIL. RIGHT sloe
FRONT PANEL
LENS
SCREW. THREAD FORMING ('4-20 x 1/4)
RAIL. LEFT SIDE
QUANTITY
1
..
1
1
2
1
13·3
· lS.4
RECOMMENDED SPARE PARTS STOCKING GUIDE
The spare parts stocking guide is broken down Into three level'. The..
(level 1). Branch Office (level 2). and Depot or Headquarter. (liv.1
3).
levels
are: Site or
F~eld
Suppon
Engineer
The
quantities listed assume that the Site is replenished by the Branch Immediately and the Branch replenllhad by the Depot within 30 Days.
The inventories that the levels can m~nta1n are:
Site
Branch
Depot
1 to 20 machines
1
to 100 machine.
Depot only parts Unlimited
Branch replenishment Same as Branch ratio
Table 13-1 shows the spare parts required to support the 706/712 in the field.
PART HUM.EII
1133&0
26173-0
26177-0 .
81218-2
8128&0
81291·1
81292·1
61306-0
TABLE 13-1. SHUGART 7061712 SPARE PARTS STOCKING GUIDE
DESCRIPTION
LENS
CONTROL PCB (708)
CONTROL PCB (712)
FRONT PANEL AND RAIL ASSEMBLY
\ FRONT PANEL
RAIL. LEFT SIDE
RAI~ RIGHT SIDE
SHOCK MOUNT
QUANTITY PEA LEVEL
SITE BRANCH DEPOT
2
2
1
.-
.-
.-
.-
8
8
8
8
·2
2
.-
~
2 4
18 100
JSMQ2·20
( t
() t t t t
, i i
E
~
~
€a itl-
If.
(.
()
~
~
~
~
~
~
~
~ ee-
t:
ef:.
13·4
..
,
~
.!
.~
...
•
-
•
I~
II:
: i~
:1 's
I
~I
.. I I~
!
:~
E J~
• ifi
!
~
!
~ i
--i
_.
S
~
!
~
!
Ij e
~
S!t
s L.
E!~ e l ..
e·~
~!~
~ :~
!
~ ~ e
,
;~ e ;
~ r
~.:
•
, I t)
!
~ t) p
I
I
!
t) i~t) t e:~
•
•
SECTION XIV
SCHEMATIC DIAGRAMS.
The following schematic diagrams are furnished to
.'d
In malfundlon analysis.
14·1/14·2 (blank)
~
.
-_.~._._-
advertisement
* Your assessment is very important for improving the workof artificial intelligence, which forms the content of this project
Related manuals
advertisement