- No category
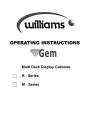
advertisement
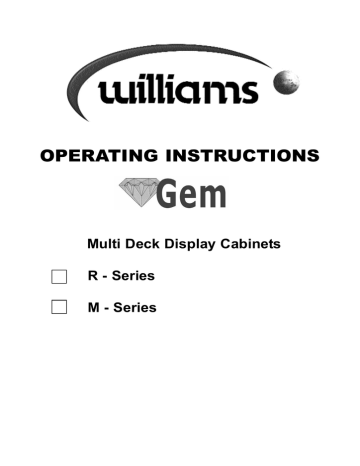
OPERATING INSTRUCTIONS
Multi Deck Display Cabinets
R - Series
M - Series
Please read the Operating Instructions before using the cabinet.
The Williams GEM range temperature parameters are set as follows:
+3°C (37°F) / +5°C (41°F)
OLD CABINETS
Please ensure the old / redundant cabinet and refrigeration equipment are disposed of safely and legally.
We would recommend that any internal fittings/doors are removed prior to disposal to ensure safety.
UNPACKING
Ensure that the cabinet has arrived in good order and that no damage during transport has ocurred.
Remove all external and interior packing and accessories, please ensure all packaging is disposed of safely.
MAINS CONNECTION
The cabinet comes fitted with moulded plug for safety and must be earthed. We recommend that should the plug or cable fail contact Williams Refrigeration for a replacement part, (contact details can be found at the back of this booklet).
INSTALLATION
The Multi Deck Display cabinet should be installed in a dry place, avoiding direct exposure to sunlight and sources of heat or draughts including air currents such as radiators, fans, air conditioning units and doors etc. Ensure there is a gap at the back of the cabinet if positioned against a wall of at least 60mm to ensure the condensing unit operates effectively and efficiently. The cabinet is fitted with castors as standard, please ensure the cabinet is level and in a stable position for safe and efficient usage.
If the cabinet has been laid on its back or tipped, DO NOT switch on immediately. Leave the cabinet in the upright position for at least1 hour before switching on.
The minimum ambient required is 16°C with a maximum of 25°C and a relative humidity of 60°C.
To ensure optimum operation of the refrigeration system, DO NOT block the front of the cabinet and air flow vents.
Locking Castors
When the cabinet has been positioned please ensure brakes have been activated by pressing the metal bar down. Remember to release the brakes before trying to move the cabinet.
Shelf/Slide Fitting
To adjust the position of the trayslides insert the ends into the vertical support with the ‘hooks’ pointing downwards and slot downwards into position. Ensure trayslides are parallel and level after fitting.
Shelf Weight Distribution
When loading the cabinet please ensure the load is equally distributed throughout the cabinet and ensure air can circulate around and through stored products.
VENTILATION
It is essential to ensure that the room in which the equipment is installed is adequately ventilated. Multi Decks can generate considerable amounts of heat and if operated in small unventilated rooms, especially in warm weather, will quickly cause the room temperature to rise to excessive temperatures which can cause motor overheating and possible damage to the windings.
Ensure there is a gap at the back of the cabinet if positioned against a wall of at least 60mm for the condensing unit to operate effectively and efficiently.
LOCKING FACILITY
On models fitted with a security shutter which has a locking facility it is recommended that the key be removed from the lock during normal working use. If the key is left in the lock it can be knocked causing it to bend or break in the barrel, making the lock inoperative.
THERMOMETER
The controller is marked in Centigrade for the thermometer display. The thermometer should be checked daily to ensure that the equipment is maintaining the correct temperature.
CONTROL PANEL
Set-up Procedure
The controller is factory set therefore you should not have to enter the set-up procedure. A qualified refrigeration engineer should be called if any parameters need changing.
SET: To display target set point; in programming mode it selects a parameter or confirm an operation.
(DEF): To start a manual defrost.
(UP): To see the maximum stored temperature; in programming mode it browses the parameter codes or increases the displayed value.
(DOWN): To see the minimum stored temperature; in programming mode it browses the parameter codes or decreases the diaplsyed value.
Meaning of LED’s
Each LED function is described in the following table.
LED MODE FUNCTION
ON
Flashing
Compressor enabled
- Programming Phase
- Anti-short cycle delay enabled
ON
Flashing
Defrost enabled
- Programming Phase
- Drip time in progress
INITIAL OPERATION
Your cabinet is delivered ready to operate. Check that the cabinet is connected to the correct electricity source (230V - 50Hz). Plug into the mains and the cabinet is ready for use. Wait until the cabinet has reached its normal operating temperature (shown on the control panel) before loading it.
Ensure all shelves are fitted so they are in contact with back panel. To ensure effective air circulation leave a gap of 60mm between products and the shelf above. The products should be evenly distributed on the shelf. (See Fig.1)
We recommend the night blind or security shutter be used overnight or when the Multi Deck is not in use to save on electricity.
Fig.1
ADJUSTING THE OPERATING TEMPERATURE
To access the parameters, enter the programming mode by pressing the SET and UP key for 3 seconds
(? and ? start blinking), then select the required parameter in the following sequence:
-
-
Press the “SET” key to display its value (? LED starts blinking).
Use “UP” or “DOWN” to change its value.
Press “SET” to store the new value and move to the next parameter.
To exit: Press SET and UP or wait 15 seconds without pressing a key.
NB: The set value is stored even when the procedure is exited by waiting for the time-out to expire.To adjust the operating temperatures, press and hold the SET key for more than 3 seconds, while the maximum or minimum temperature is displayed. (rSt message will be displayed). To confirm the operation the
“rSt” message starts blinking and the normal temperature will be displayed.
NB: All machines are preset at the factory, however conditions on site will vary compared with test conditions and it may be necessary to perform the above adjustments several times in order to obtain a perfect temperature cycle. We would recommend this is done by a qualified refrigeration engineer.
DEFROST OPERATION
Push the DEF key for more than 2 seconds and a manual defrost will start.
IdF Interval between defrost cycles: (1/120h)
Determines the time interval between the beginning of two defrost cycles.
MdF Length for defrost: (0/255mins)
It sets the defrost duration.
Fault Diagnosis/Display Conditions
Fault/Display Possible Cause Action
Cabinet not Operating No Power Supply Check fuse or power source
Ensure that the general switch is on
Cabinet not maintaining 1. Dirty Condenser temperature
2. Air circulation restricted
Clean
Remove Restriction
3. Check that shelves and goods are properly installed and loaded
4. Check that the cabinet is not near draughts or heat sources
5. Check that the air return of the air curtain is not blocked
BREAKDOWN
In the event of a breakdown, please check the thermostat setting and fuse before calling the service engineer. When calling the engineer, please advise him of the model and serial number of the machine.
These details are on the identification plate on the back of the cabinet and should also be noted on the back cover of this booklet. Please ensure any redundant parts are disposed of safely and legally.
CLEANING
Normal day to day cleaning of the exterior and interior of the cabinet should be carried out with lukewarm soapy water and a soft cloth. Never use abrasive materials or cleaners, or chemical cleaners. Do not wash the cabinet with a hose or spray. (Fig.2)
Fig.2
ROUTINE MAINTENANCE
All maintenance should be carried out by a competent, qualified person. We recommend that you undertake regular preventative maintenance using a qualified service provider in order to get the best from your equipment.
CONDENSER CLEANING
The condenser, which is part of the refrigeration unit, is sited in the unit compartment and requires cleaning, approximately 4 times per year.
Fig.3
Disconnect the cabinet from the electrical supply by unplugging it then, to achieve access to the condenser you must remove the screws followed by the front panel.
(Fig. 3)
To clean the condenser, disconnect mains supply before
starting, then brush the fins vertically with a stiff brush, taking care not to damage the fins or push dirt or dust further in and vacuum away. Remember to reconnect mains supply once finished.
PARTS ONLY WARRANTY
Warranty applies to equipment manufactured by Williams Refrigeration and equipment bearing the Williams
Refrigeration name plate and serial number identification tag.
We undertake, in conjunction with the supplying agent, distributor or representative, to replace free of charge any such piece of equipment or part thereof used under normal conditions for which the equipment was designed which is found to be faulty in either materials or workmanship. This warranty applies to the Gem range of Display Cabinets within
12 months of date of purchase on condition that annual servicing has been carried out:
Replacement of defective equipment will only be made where Williams Refrigeration or its authorised agent, representative or distributor has determined that effective repair is not practical
. Responsibility is limited to the replacement of the equipment of components (excluding labour) and in no case is Williams Refrigeration liable for consequential loss or damage. If you purchased direct from the main distributor, your warranty may also include labour costs. Please check with your supplier in conjunction with his terms of sale.
In instances where a piece of equipment fails to perform to the reasonable satisfaction of the customer, the customer may apply for a refund of the purchase price in full, provided that notification of dissatisfaction is received within 10 days of installation and subject to the following;
1)
2)
3)
The equipment is functioning incorrectly, and has been installed correctly and has not been subject to misuse.
The equipment was purchased by the supplying distributor direct from Williams Refrigeration and not through a wholesaler or other supplier whose warranty may be different.
Made to measure modular cold storage is excepted.
Our responsibility under this warranty shall cease if: a) Authorised representatives of Williams Refrigeration are denied full and free rights of access to the equipment b) for inspection at a convenient time.
The customer permits persons other than those authorised by Williams Refrigeration to perform or effect c) d) e) repairs or adjustments to the equipment.
The customer has not properly maintained the equipment or carried out annual servicing, in accordance with instructions, literature or directions issued by Williams Refrigeration.
The customer fails to observe commonly accepted operating practices.
f)
Repairs are made using spare parts or replacements not of the same make as those supplied originally as components of the equipment unless authorised by Williams Refrigeration.
Equipment fails through misuse, accidental damage or power surges.
Specials
Where equipment is manufactured to the customers’ own design, Williams Refrigeration will not be liable for any non performance or operation of the equipment as a result of a design fault or defect.
Claim Procedure
If a customer wishes to make a claim under the terms of this warranty, the following procedure should be observed:
1)
2)
Contact the supplying agent, representative or distributor
Quote the model, date of installation and serial number of the cabinet. The serial number is located on the
3)
4) cabinet identification plate inside the cabinet. It should also be recorded on the operating instruction booklet supplied with the cabinet. Details of annual servicing should be available for presenting to Williams
Refrigeration.
Note: contents risk and insurance responsibility remains at all times with the customer.
This warranty does not cover consumable items such as batteries, fuses, light bulbs, printer cartridges, keys, glass, paper roll and condenser filters.
Williams Standard Terms and Conditions of Sale apply to this warranty.
This warranty does not affect your statutory rights.
Customer Satisfaction Questionnaire
Thank you for selecting a Williams product for your business. We would be very grateful if you could please complete the Customer Satisfaction Questionnaire below along with any comments you may have regarding our products or the service you have received. We have a commitment to continuing improvement and your feedback will help us to ensure we develop our products and services to meet your requirements now and in the future. Please tick the relevant box:
What was your main reason for purchasing new refrigeration?
New premises Needed additional refrigeration
Replacement of broken equipment Replacement of old equipment
Kitchen refurbishment
What influenced your decision to purchase a Williams product?
Price Model Specifications meet requirement
Brand Recommendation
Sales Person
Specified Product
Previous experience
How did you become aware of Williams?
Advertising Article in Trade Magazine
Reputation Recommendation
Sales Person
Direct Mail Leaflet Website
Please circle your response:
How was our response to your enquiry?
Poor Average Good
How was the advice you received?
Poor Average Good
How was the service you received?
Poor Average Good
Other Comments:-
Very Good
Very Good
Excellent
Excellent
Excellent
Name: .................................................................................. Position: ........................................................................
Company: .........................................................................................................................................................................
Address: ...........................................................................................................................................................................
..................................................................................................................................... Tel: ............................................
Serial No: ....................................................................................................................
Thank you for taking the time to complete the questionnaire. Please fax your completed form to the
Marketing Department on 01553 817111 or return it to the Norfolk address printed on the back cover of this booklet.
Data Protection:
The details you supply will be stored on computer for use by Williams Refrigeration or any companies within Aga Foodservice
Equipment Ltd for producing performance data on customer satisfaction and to send you information on new product developments.
If you would prefer not to receive this information please tick this box:
Model No: ....................................................................................................................................
Serial No: ....................................................................................................................................
Supplied & Serviced by: ...............................................................................................................
Telephone No: .........................................................................................................................
WILLIAMS REFRIGERATION
Bryggen Road
North Lynn Industrial Estate
King’s Lynn, Norfolk PE30 2HZ
Sales Tel: +44 1553 817000 Fax: +44 1553 817111
Spares Tel: +44 1553 817017 Fax: +44 1553 817020
Email: [email protected]
Website: www.williams-refrigeration.com
WILLIAMS SILVER FROST
30 Route d’Ahun
23150 Lavaveix Les Mines
France
Tel: +33 5 55 52 27 88 Fax: +33 5 55 62 10 61
Email: [email protected]
Website: www.williamssf.fr
WILLIAMS REFRIGERATION AUSTRALIA
38-42 Gaine Road
Dandenong South
Victoria 3175, Australia
Tel: +61 3 8787 4747 Fax: +61 3 8787 4787
Email: [email protected]
Website: www.williamsref.com.au
GEM O&M
Rev 2
March 2008
advertisement
* Your assessment is very important for improving the workof artificial intelligence, which forms the content of this project
Related manuals
advertisement