advertisement
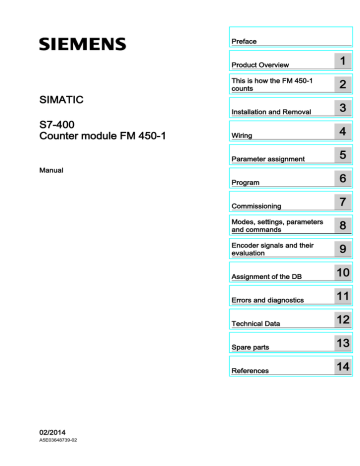
Counter module FM 450-1
SIMATIC
S7-400
Counter module FM 450-1
Manual
02/2014
A5E03648739-02
Legal information
Warning notice system
This manual contains notices you have to observe in order to ensure your personal safety, as well as to prevent damage to property. The notices referring to your personal safety are highlighted in the manual by a safety alert symbol, notices referring only to property damage have no safety alert symbol. These notices shown below are graded according to the degree of danger.
DANGER indicates that death or severe personal injury will result if proper precautions are not taken.
WARNING indicates that death or severe personal injury may result if proper precautions are not taken.
CAUTION indicates that minor personal injury can result if proper precautions are not taken.
NOTICE indicates that property damage can result if proper precautions are not taken.
If more than one degree of danger is present, the warning notice representing the highest degree of danger will be used. A notice warning of injury to persons with a safety alert symbol may also include a warning relating to property damage.
Qualified Personnel
The product/system described in this documentation may be operated only by personnel qualified for the specific task in accordance with the relevant documentation, in particular its warning notices and safety instructions.
Qualified personnel are those who, based on their training and experience, are capable of identifying risks and avoiding potential hazards when working with these products/systems.
Proper use of Siemens products
Note the following:
WARNING
Siemens products may only be used for the applications described in the catalog and in the relevant technical documentation. If products and components from other manufacturers are used, these must be recommended or approved by Siemens. Proper transport, storage, installation, assembly, commissioning, operation and maintenance are required to ensure that the products operate safely and without any problems. The permissible ambient conditions must be complied with. The information in the relevant documentation must be observed.
Trademarks
All names identified by ® are registered trademarks of Siemens AG. The remaining trademarks in this publication may be trademarks whose use by third parties for their own purposes could violate the rights of the owner.
Disclaimer of Liability
We have reviewed the contents of this publication to ensure consistency with the hardware and software described. Since variance cannot be precluded entirely, we cannot guarantee full consistency. However, the information in this publication is reviewed regularly and any necessary corrections are included in subsequent editions.
Siemens AG
Industry Sector
Postfach 48 48
90026 NÜRNBERG
GERMANY
A5E03648739-02
Ⓟ 03/2014 Subject to change
Copyright © Siemens AG 2014.
All rights reserved
Preface
Purpose of this manual
This manual describes all steps required to use the FM 450-1 function module efficiently. It supports you in installing and commissioning the module. The procedures for installing and removing, wiring, assigning parameters, and programming are explained.
This manual is intended for the programmers of STEP 7 programs and for those responsible for configuring, commissioning, and servicing automation systems.
Basic knowledge required
This manual requires general knowledge of automation engineering.
You also require knowledge of the use of computers or PC-type equipment (such as programming devices) based on a Windows 95/98/2000 or NT operating system as well as
STEP 7 programming skills.
Scope of this manual
The present manual contains the description of the FM 450-1 valid at the time the manual is published. We reserve the right to describe changes to the functions of the FM 450-1 in the form of product information.
Standards
The S7-400 automation system meets the requirements and criteria of IEC 61131-2.
Recycling and disposal
Owing to the fact that its equipment is low in contaminants, the FM 450-1 can be recycled.
For environmentally compliant recycling and disposal of your discarded device, please contact a company certified for the disposal of electronic waste.
Additional support
If you have any further questions about the use of products described in this manual and do not find the right answers here, contact your local Siemens representative
( http://www.siemens.com/automation/partner ):
A guide to the technical documentation for the various products and systems is available on the Internet:
● SIMATIC Guide manuals ( http://www.siemens.com/simatic-tech-doku-portal )
The online catalog and online ordering systems are also available on the Internet:
● A&D Mall ( http://www.siemens.com/automation/mall )
Counter module FM 450-1
Manual, 02/2014, A5E03648739-02
3
4
Preface
Training center
To help you get started with automation technology and systems, we offer a variety of courses. Contact your regional Training Center or the central Training Center in
D-90327 Nuremberg, Germany.
● Internet: SITRAIN homepage ( http://www.sitrain.com
)
Technical Support
You can access technical support for all A&D projects via the following:
● Online support request form: ( http://www.siemens.com/automation/support-request )
Service & Support on the Internet
In addition to our documentation, we offer a comprehensive online knowledge base on the
Internet at:
Industry Automation and Drive Technologies - Homepage
( http://www.siemens.com/automation/service&support )
There you will find the following information, for example:
● The newsletter that provides up-to-date information on your products.
● The documents you need via our Search function in Service & Support.
● A forum for global information exchange by users and specialists.
● Your local partner for Automation and Drives.
● Information about on-site service, repairs, and spare parts. Much more can be found under "Services".
Counter module FM 450-1
Manual, 02/2014, A5E03648739-02
Table of contents
1
2
3
4
5
6
1.1
1.2
1.3
1.4
1.5
2.1
2.2
3.1
3.2
3.3
3.4
6.1
6.2
6.3
6.4
6.5
4.1
4.2
4.3
4.4
5.1
5.2
Counter module FM 450-1
Manual, 02/2014, A5E03648739-02
5
6
Table of contents
7
8
8.4
8.5
8.6
8.7
8.8
8.9
8.10
8.11
7.1
7.2
7.3
8.1
8.2
8.3
9
8.12
9.1
9.2
9.3
9.4
9.5
10
10.1
11
11.1
11.2
11.3
11.4
11.5
12
12.1
12.2
Counter module FM 450-1
Manual, 02/2014, A5E03648739-02
Table of contents
13
14
Counter module FM 450-1
Manual, 02/2014, A5E03648739-02
7
Table of contents
8
Counter module FM 450-1
Manual, 02/2014, A5E03648739-02
Product Overview
1.1 Chapter overview
Section overview
This section provides you with an overview of the FM 450-1 function module.
● It informs you of what the FM 450-1 can do.
● Examples demonstrate some of the possible applications of the FM 450-1.
● You will learn how the FM 450-1 is integrated into the S7-400 automation system, and familiarize yourself with the vital components of FM 450-1.
1
Counter module FM 450-1
Manual, 02/2014, A5E03648739-02
9
Product Overview
1.5 The FM 450-1 software
1.2
Properties
Properties
The FM 450-1 is a fast counter module to be used in the S7-400 automation system. There are two counters on the module which can work in the following counting ranges as required:
● 0 to 4 294 967 295 (0 to 2
32
- 1)
● - 2 147 483 648 to + 2 147 483 647 (-2
31
to 2
31
- 1).
The maximum input frequency of the counter signals is up to 500 kHz depending on the encoder signal.
The FM 450-1 can be used for the following counting tasks:
● Continuous counting
● Single counting
● Periodic counting
You can start and stop the count either via the user program (software gate) or via external signals (hardware gate).
Comparison values
You can store two comparison values per counter on the module; they are assigned to the two corresponding outputs on the module. If the counter status reaches one of the comparison values, then the output assigned to it can be set so that it triggers control operations directly in the process.
Load value
You can determine an initial value (load value) for each counter on the FM 450-1 The counter is set at the initial value if a software or hardware-related signal to the module comes up.
Hardware interrupts
When comparison values are reached, for overflow, underflow and/or for zero crossing of a counter, the FM 450-1 can trigger a Hardware interrupt.
10
Counter module FM 450-1
Manual, 02/2014, A5E03648739-02
Product Overview
1.5 The FM 450-1 software
Diagnostic interrupt
When the following events occur, the FM 450-1 can trigger a diagnostic interrupt:
● External auxiliary voltage faulty
● Encoder 5.2 VDC supply faulty
● Module not assigned parameters or errors in parameter assignment
● Watchdog timeout
● RAM defective
● Hardware interrupt lost
● Fault in signal A, B, or N of the 5 V encoder
Pulse duration
You can determine a pulse duration for the digital outputs of the FM 450-1. The pulse duration is used to specify how long the corresponding digital output is to be set. You can specify a value between 0 and 500 ms for the pulse duration. This value applies to both outputs. By prescribing a pulse duration you can adapt the FM 450-1 to existing actors.
Which signals can the FM 450-1 count?
The FM 450-1 can count signals that are generated by the following encoders:
● Incremental 5-V encoders
● Incremental 24-V encoders
● 24-V pulse encoders with direction level
● 24-V initiators without direction level e.g., light barrier or BERO
Input filter
For the purpose of suppressing interference, you can assign input filters (RC elements) with a uniform filter time for the 24 V inputs A*, B*, and N* and for the digital inputs. The following two input filters are available:
Table 1- 1 Input filter
Characteristics Input filter 2
Typical input delay
Maximum count frequency
Minimum pulse width of the count signals
Input filter 1
(default)
1 μs
200 kHz
2.5 μs
15 μs
20 kHz
25 μs
Counter module FM 450-1
Manual, 02/2014, A5E03648739-02
11
Product Overview
1.5 The FM 450-1 software
1.3 Fields of applications of the FM 450-1
You can use the FM 450-1 as follows:
The main field of application of the FM 450-1 is where it is necessary to count signals with high frequencies and fast reactions must be triggered when a prescribed counter reading is reached.
Examples are:
● Packaging plants,
● sorting plants,
● dosing plants
Example application for an FM450-1
Here a specific number of parts is to be filled into a box. An FM 450-1 counter assumes the job of counting the parts and controlling the two motors for transporting the parts and the box.
If the box is in the right position, belt A is stopped via the light barrier, the counting process is started and the motor for belt B switched on. If the programmed number of parts are in the box, the FM 450-1 stops the motor for belt B and switches on the motor for belt A so that the box can be transported away. The counting process can start again when the next box reaches the light barrier
12
Figure 1-1 Example application for an FM450-400 in the S7-400
Counter module FM 450-1
Manual, 02/2014, A5E03648739-02
Product Overview
1.5 The FM 450-1 software
1.4 The FM 450-1 hardware
View of module
The illustration shows the FM 450-1 module with front connector plugged in.
Figure 1-2 Illustration of the FM 450-1
Order number and version
The full order number of the FM 450-1 is shown on the rating plate.
The abbreviated order number and the version of the FM 450-1 are marked on the top end of the front of the module.
Counter module FM 450-1
Manual, 02/2014, A5E03648739-02
13
Product Overview
1.5 The FM 450-1 software
Diagnostic and status LEDs
The FM 450-1 has 16 LEDs. The LEDs are for diagnostic purposes and indicate the state of the FM 450-1 and its digital inputs and outputs. The following table lists labeling, color and function of the LED displays.
Table 1- 2 Labeling, color and function of the LEDs
Labeling
INTF
EXTF
CH1 CR
CH2 CR
CH1 DIR
CH2 DIR
CH1 IN 0
CH2 IN 0
CH1 IN 1
CH2 IN 1
CH1 IN 2
CH2 IN 2
CH1 OUT 0
CH2 OUT 0
CH1 OUT 1
CH2 OUT 1
Color Function
Red Internal error
Red External error
Green Counter in operation; status of the lowest value bit of counter 1 (CH 1) or counter 2 (CH2)
Green Count direction; LED illuminated if counter 1 (CH1) or counter 2 (CH2) is counting backwards.
Green Status of input 1I0 of counter 1 and/or 2I0 of counter 2
Green Status of input 1I1 of counter 1 and/or 2I1 of counter 2
Green Status of input 1I2 of counter 1 and/or 2I2 of counter 2
Green Status of output 1Q0 of counter 1 and/or 2Q0 of counter 2
Green Status of output 1Q1 of counter 1 and/or 2Q1 of counter 2
Front connectors
The front connector has the following terminals:
● 5-V or 24-V encoder signals for counters 1 and 2
● Encoder supply
● Digital input signals to start, stop and set counters 1 and 2
● Digital output signals Q0 and Q1 for counters 1 and 2
● Auxiliary voltage 1L+ to generate the encoder supply voltages
● Load voltage 2L+ to supply the digital outputs
The front connector can be ordered separately (see chapter "Spare parts (Page 119)").
14
Counter module FM 450-1
Manual, 02/2014, A5E03648739-02
Product Overview
1.5 The FM 450-1 software
Front connector coding
If you hook in the front connector, the front connector coding engages. Thereafter this front connector can only be attached to an FM 450-1 module.
Labeling strips
A plate block with four labeling strips is included with the module. These strips can be labeled individually with the corresponding signal names.
Counter module FM 450-1
Manual, 02/2014, A5E03648739-02
15
Product Overview
1.5 The FM 450-1 software
1.5 The FM 450-1 software
Software packages of the FM 450-1
You will require the software package on the supplied CD to integrate the FM 450-1 into the
S7-400. It includes:
● Parameterization software with parameterization interfaces
● Software for the CPU (blocks)
● Documentation
parameter assignment screen forms
The FM 450-1 is adapted to the respective task via parameters. These parameters are stored in an SDB and transferred to the module by the CPU.
The parameters can be determined via the parameter assignment screen forms. These parameter assignment screen forms are installed on your programming device and opened in STEP 7.
16
Counter module FM 450-1
Manual, 02/2014, A5E03648739-02
Product Overview
1.5 The FM 450-1 software
Software for the S7-400-CPU
The software for the CPU consists of the FC CNT_CTRL function, which is invoked in the
CPU user program. This FC enables communication between the CPU and the FM 450-1. In addition, there is also the FC DIAG_INF for the FM 450-1 with which you can transmit diagnostic data into the DB of FC CNT_CTRL.
This figure shows an S7-400 layout with an FM 450-1 and several signal modules.
Figure 1-3 Layout of a SIMATIC S7-400 with an FM 450-1
Counter module FM 450-1
Manual, 02/2014, A5E03648739-02
17
Product Overview
1.5 The FM 450-1 software
18
Counter module FM 450-1
Manual, 02/2014, A5E03648739-02
This is how the FM 450-1 counts
2
2.1 Basics
What is counting?
Counting refers to the recording and totaling of events. In the case of the FM 450-1 function module encoder signals are captured and evaluated accordingly.
Count range, count limits
The FM 450-1 can count both forwards and backwards. When you select the count range, you determine the limits between which the FM 450-1 can count.
Count range
Count range 1:
0 to +32 bit
Count range 2:
-31 to +31 bit
Low count limit
0
-2 147 483 648
High count limit
+4 294 967 295
+2 147 483 647
Load value
You can lay down an initial value for each of the two FM 450-1 counters from which the counting is to begin. This initial value is the load value. You can specify any value within the count limits for the load value.
Comparison values
You can use two digital outputs on the module for each counter in order to trigger reactions in a process at a certain counter reading, independently of the CPU. You store two comparison values for each counter on the FM 450-1. If the counter reading reaches one of the two comparison values, the digital output assigned belonging to the comparison value is set and/or a Hardware interrupt is generated.
Operating modes
You can count rectangular pulses in three different ways with the FM 450-1:
● Continuous counting, with or without gate function
● Single counting with hardware or software gate
● Periodic counting with hardware or software gate
The differences manifest themselves in the way the FM 450-1 behaves when a counter reaches a count limit.
Counter module FM 450-1
Manual, 02/2014, A5E03648739-02
19
This is how the FM 450-1 counts
2.2 Gate functions
Continuous counting
If when counting in the up direction a counter has reached the high count limit and a further count pulse comes, then the counter jumps to the low count limit and begins to total the count pulses; thus, it counts continuously.
Figure 2-1 Continuous counting in the up direction
If when counting in the down direction a counter has reached the low count limit and a further count pulse comes, then it jumps to the high count limit and then goes on counting down from there.
Single counting
For single counting the counter starts from the load value. If when counting up a counter has reached the high count limit and a further count pulse comes, then the counter jumps to the low count limit and comes to a halt even if further count pulses come.
Figure 2-2 Single counting in the up direction
If when counting down a counter has reached the low count limit and a further count pulse comes, then the counter jumps to the high count limit and comes to a halt even if further count pulses come.
20
Counter module FM 450-1
Manual, 02/2014, A5E03648739-02
This is how the FM 450-1 counts
2.1 Basics
Periodic counting
For periodic counting the respective counter starts from the load value. If when counting up the counter reaches the high count limit and further count pulses come, then the counter jumps to the load value and starts totalizing the count pulses.
Figure 2-3 Periodic counting in the up direction
If when counting down a counter has reached the low count limit and a further count pulse comes, then the counter jumps to the load value and then continues counting down from there.
Counter module FM 450-1
Manual, 02/2014, A5E03648739-02
21
This is how the FM 450-1 counts
2.2 Gate functions
2.2 Gate functions
Counting with gate functions
Many applications require that the counting process should be started or stopped at a specifically defined point in time, depending on other events. In the case of the FM 450-1 starting and stopping the counting process like this take place via a gate function. If the gate is opened, count pulses can reach a counter and the counting process is started. If the gate is closed, count pulses can no longer reach the counter and the counting process is stopped.
Software gate and hardware gate
The module possesses two gate functions for each counter:
● A software gate (SW gate) which is controlled via the user program in the CPU.
● A hardware gate (HW gate) that is controlled via the 1I0 and 1I1 (counter 1) and/or 2I0 and 2I1 (counter 2) digital inputs on the module. When assigning parameters for the FM
450-1 you determine if the operation of the hardware gate is to be level controlled or edge controlled.
Example
When the gate signal is set, the gate is opened and the count pulses are counted. If the gate signal is taken away, the gate is closed and the count pulses are no longer picked up by the counter. The counter status remains constant.
The figure shows a gate opening and closing and the pulses being counted:
Figure 2-4 Opening and closing a gate
Ending counting process with the gate stop function
You can end the counting process when counting with the SW gate and when counting with the HW gate with the respective gate stop function. For this purpose you set the GATE_STP input parameter of the FC CNT_CTRL.
22
Counter module FM 450-1
Manual, 02/2014, A5E03648739-02
Installation and Removal
3.1
Overview
Chapter overview
In this chapter you will find information on the installation and removal of the FM 450-1
● You will find out what you have to pay attention to during installation. You will obtain information on project planning and on the design of an FM 450-1
● Step by step you will be shown how to install and remove the FM 450-1.
3
Counter module FM 450-1
Manual, 02/2014, A5E03648739-02
23
Installation and Removal
3.4 Removal of the FM 450-1
3.2 Preparing for Mounting
Important safety rules
There are important rules to be observed when integrating an S7-400 with an FM 450-1 into a plant or a system.
These rules and regulations are explained in manual /1/.
Defining the slots
The FM 450-1 function module can be installed like a signal module in any central device or extension device.
Designing the mechanical structure
Manual /1/ provides you with information on how the mechanical structure can be designed and how to proceed.
Define start address
The start address of the FM 450-1 is required for the purpose of communication between the
CPU and the FM 450-1. The start address is entered into the DB of the FC CNT_CTRL (refer
to chapter "Program (Page 45)" and chapter "Assignment of the DB (Page 103)"). The entry
is either made with the program editor or out of the user program.
You specify the start address for the module under STEP 7.
24
Counter module FM 450-1
Manual, 02/2014, A5E03648739-02
Installation and Removal
3.3 Installing the FM 450-1
3.3
Rules
Installing the FM 450-1
No special protective measures (EGB guidelines) are required for installing the FM 450-1.
Tools required
You require a 4.5 mm screwdriver to install the FM 450-1.
Installation procedure
Proceed as follows to install an FM 450-1
1. Hook the FM 450-1 in at the top and rotate it down.
2. Screw the FM 450-1 tight (torque approx. 0.8 to 1.1 Nm).
3. Label the FM 450-1 with its slot number. For this purpose use the number wheel enclosed with the rack.
The system according to which you must perform then numbering and the procedure for defining the slot number are described in manual /1/.
Further information
Further information on the installation and removal of modules is to be found in manual /1/.
Counter module FM 450-1
Manual, 02/2014, A5E03648739-02
25
Installation and Removal
3.4 Removal of the FM 450-1
3.4
Rules
Removal of the FM 450-1
No special protective measures (EGB guidelines) are required for removing the FM 450-1.
Tools required
You require a 4.5 mm screwdriver to remove the FM 450-1.
Procedure for removal
Proceed as follows to remove an FM 450-1
1. Release the front connector and pull it out.
2. Undo the module fixing screw.
3. Rotate the module out of the rack and unhook it.
4. If necessary, install a new module.
Further information
Further information on the installation and removal of modules is to be found in manual /1/.
26
Counter module FM 450-1
Manual, 02/2014, A5E03648739-02
Wiring
4.1 Chapter overview
Chapter overview
In this chapter you will find information on wiring the FM 450-1
● Terminal assignment of the front connector.
● Terminal functions.
● Notes on the selection of cables.
● Procedure when wiring the front connector.
● State of module after it has been wired and the power supply is switched on.
4
Counter module FM 450-1
Manual, 02/2014, A5E03648739-02
27
Wiring
4.4 Module status after power is switched on
4.2 Terminal assignment of the front connector
Front connectors
You connect the following to the 48-pin front connector:
● count signals,
● digital inputs
● digital outputs
● encoder power supply
● auxiliary voltage and load voltage.
The following illustration shows the front side of the front connector, the strip with the terminal assignment printed on and the labeling strips.
28
Counter module FM 450-1
Manual, 02/2014, A5E03648739-02
Wiring
4.4 Module status after power is switched on
Figure 4-1 Front connector of the FM 450-1
Counter module FM 450-1
Manual, 02/2014, A5E03648739-02
29
Wiring
4.4 Module status after power is switched on
Assignment of front connector
3
4
1
2
Table 4- 1 Assignment of front connector
Terminal Name Inputs/ outputs
10
11
12
13
14
15
7
8
9
5
6
16
21
22
23
24
17
18
19
20
25
26
27
28
1L+
1M
1 A
1 /A
1 B
1 /B
1 N
1 /N
1 A*
1 B*
1 N*
1M
ON
ON
ON
ON
ON
ON
ON
ON
ON
OFF
5.2 VDC OFF
24 VDC
2 A
2 /A
2 B
2 /B
2 N
2 /N
2 A*
2 B*
ON
ON
ON
ON
ON
ON
ON
ON
2 N*
1M
ON
OFF
5,2 VDC OFF
24 VDC
ON
ON
OFF
OFF
Function
5 V encoder RS
422, symmetrical
24 V encoder, asymmetric
-
-
24-V pulse encoder with direction level
24 V auxiliary voltage supply for encoders
Auxiliary voltage ground to supply encoders
Counter 1
Encoder signal A
Encoder signal /A
-
-
24 V initiator
Encoder signal B
Encoder signal /B
Encoder signal N
-
-
-
Encoder signal /N
-
-
-
Encoder signal /A
Encoder signal B
Encoder signal /B
-
Encoder signal A*
Encoder signal B* Directional signal -
Encoder signal N* -
Ground for encoder power supply
5.2 V encoder power supply
-
Counter 2
Encoder signal A
-
24 V encoder power supply
-
-
-
-
Encoder signal N
Encoder signal /N
-
-
-
5,2 V encoder power supply
-
-
-
Encoder signal A*
Encoder signal B*, directional signal
Encoder signal N*
Ground for encoder power supply
-
24 V encoder power supply
30
Counter module FM 450-1
Manual, 02/2014, A5E03648739-02
Wiring
4.4 Module status after power is switched on
Terminal Name Inputs/ outputs
2I0
2I1
2I2
2Q0
2Q1
2L+
2M
1I0
1I1
1I2
1Q0
1Q1
41
42
43
44
45
46
47
48
33
34
35
36
37
29
30
31
32
38
39
40
ON
ON
ON
OFF
OFF
ON
ON
ON
ON
ON
OFF
OFF
Function
5 V encoder RS
422, symmetrical
24 V encoder, asymmetric
24-V pulse encoder with direction level
Counter 1
Digital input 1I0
Digital input 1I1
Digital input 1I2 (set counter)
-
24 V initiator
Digital output 1Q0
Digital output 1Q1
-
-
-
-
-
-
Counter 2
Digital input 2I0
Digital input 2I1
Digital input 2I2 (set counter)
-
Digital output 2Q0
Digital output 2Q1
24 V load voltage for the digital inputs and outputs
Load voltage ground for digital inputs and outputs
Note
The circuits for the counter inputs (encoder power supply, encoder signals) are isolated electrically toward the ground of the CPU. Hence you must connect terminal 4 (1M) to the ground of the CPU with a low impedance!
If you supply the encoders with external voltage, you must also connect the mass of this external voltage supply to the ground of the CPU.
Auxiliary voltage 1L+, 1M
To supply the 5 V and 24 V encoders with voltage, connect a 24 DC V to the 1L + and 1M terminals.
An integrated diode protects the module from reversing the polarity of the auxiliary voltage.
The module monitors whether the auxiliary voltage is connected.
Counter module FM 450-1
Manual, 02/2014, A5E03648739-02
31
Wiring
4.4 Module status after power is switched on
5.2 VDC encoder power supply
The module generates a 5.2 VDC voltage from the 1L+/1M auxiliary voltage at a maximum current of 300mA per count channel; this voltage is available on the respective "DC5.2V" terminal to supply a 5 V encoder with short circuit-proof voltage.
24 VDC encoder power supply
1l+/1M voltage is provided on output "24 VDC" to supply an encoder with short circuit-proof
24-V voltage. The encoder power supply is short-circuit checked.
5 V encoder signals A and /A, B and /B, N and /N
You can connect incremental encoders with 5 V differential signals in compliance with
RS422, i.e. incremental encoders with the differential signals A and /A, B and /B, N and /N.
The A and /A, B and /B, N and /N signals are connected via the correspondingly labeled terminals
The signals N and /N are only to be connected if you wish to set the counter to the zero mark of the encoder.
The inputs are not electrically isolated from the S7-400 bus.
24-V encoder signals A*, B* and N*
24 V signals are identified with the letters A*, B* and N*.
You can connect three different types of encoders to each counter:
● Incremental encoders with 24- V signals:
The signals A*, B* and N* are connected via the correspondingly labeled pins.
● Pulse encoders without directional level:
The signal is connected to terminal A*
● Pulse encoders with directional level:
The count signal is connected to the terminal A*. The directional level is connected to terminal B*.
The inputs are not electrically isolated toward the S7-400 bus.
32
Counter module FM 450-1
Manual, 02/2014, A5E03648739-02
Wiring
4.4 Module status after power is switched on
Input filter for 24 V encoder signals
To suppress faults you can assign parameters to the input filters (RC elements) with a uniform filtering time for the 24 V inputs A*, B* and N*. The following two input filters are available for each counter:
Table 4- 2 Input filter for 24 V encoder signals
Features Input filter 2
Typical input delay
Maximum count frequency
Minimum pulse width of the count signals
Input filter 1
(default setting)
1 μs
200 kHz
2.5 μs
15 μs
20 kHz
25 μs
Digital inputs
You can use the digital inputs 1I0 and 1I1 for the gate control of counter°1.
You can use the digital inputs 2I0 and 2I1 for the gate control of counter°2.
The gates can be operated both in the level-controlled and edge-controlled modes (see
chapter "Modes, settings, parameters and commands (Page 65)").
The 1I2 digital input is for setting counter 1 to the load value.
The 2I2 digital input is for setting counter 2 to the load value.
The digital inputs are operated with a 24 V nominal voltage.
The digital inputs are electrically isolated from bus and count inputs.
Input filters for digital inputs
To suppress faults you can assign parameters to the input filters (RC elements) with a uniform filtering time for the digital inputs 1I0, 1I1 and 1I2 or 2I0, 2I1 and 2I2. The following two input filters are available:
Table 4- 3 Input filters for digital inputs
Characteristics Input filter 2
Typical input delay
Maximum frequency of the input signals
Minimum pulse width of input signals
Input filter 1
(default setting)
1 μs
200 kHz
2.5 μs
15 μs
20 kHz
25 μs
Counter module FM 450-1
Manual, 02/2014, A5E03648739-02
33
Wiring
4.4 Module status after power is switched on
Digital outputs
For the purpose of directly initiating control processes, the FM 450-1 has the digital outputs
1Q0 and 1Q1 (for counter 1) or 2Q0 and 2Q1 (for counter 2) that are supplied via the load voltage 2L+.
The digital inputs are potentially isolated from the S7-400 bus and count inputs.
The digital outputs are P switches and can carry a load current of 0.5 A. They are protected against overload and short circuit.
Note
The direct connection of relays and cutouts can be executed without external wiring
The time-related behavior of the digital outputs depends on the parameter assignment and is
described in greater detail in the chapter "Setting: Behavior of the digital outputs (Page 76)".
2L+ /2M load voltage
To ensure the power supply of the digital outputs 1Q0 and 1Q1 or 2Q1 and 2Q2 you have to connect a load voltage of 24 V to the module terminals 2L+ and 2M.
An integrated diode protects the module from reversing the polarity of the load voltage.
The 2L+ / 2M load voltage is not monitored by the FM 450-1.
34
Counter module FM 450-1
Manual, 02/2014, A5E03648739-02
4.3
Cables
Wiring Front Connectors
Wiring
4.4 Module status after power is switched on
There are a few rules you must observe when selecting the cables:
● The cables for the digital inputs must be shielded.
● The cables for the count signals must be shielded.
● You must apply the shields to the count signal cables both on the pulse encoder and in close proximity to the module, e.g. via the shield application element.
● Cables A and /A, B and /B, N and /N of the incremental 5-V encoder must be twisted in pairs.
The following figure shows details relating to the connection of incremental 5-V encoders.
Counter module FM 450-1
Manual, 02/2014, A5E03648739-02
35
Wiring
4.4 Module status after power is switched on
36
Figure 4-2 Connecting incremental 5 V encoders
Terminal 4 (1M) of the front connector must be connected with the ground of the CPU with a low impedance. If you supply the encoder with external voltage, you must also connect the ground of this external voltage supply to the ground of the CPU.
The following figure shows details relating to the connection of incremental 24 V encoders.
Counter module FM 450-1
Manual, 02/2014, A5E03648739-02
Wiring
4.4 Module status after power is switched on
Figure 4-3 Incremental 24 V encoder connection
● Use flexible cables with cross sections of 0.25 to 1.5 mm
2
.
Note
If the encoder is supplied via the module, the cable cross section must be selected large enough for sufficient voltage to be applied to the encoder via the cable in spite of a drop in voltage. This applies in particular in the case of incremental 5 V encoders.
● A wire end ferrule is not required. If you use wire end ferrules, they must be of the type without insulating collars in compliance with DIN 46228 Form A, short type!
Counter module FM 450-1
Manual, 02/2014, A5E03648739-02
37
Wiring
4.4 Module status after power is switched on
Wiring steps
Proceed as follows when wiring the front connector:
WARNING
Injury to persons can occur.
If you wire the FM 450-1 front connector when the power is switched on, you may injure yourself owing to an electric shock.
Always switch off power before you wire the FM 450-1!
1. Pull the cover off the front connector.
2. Insulate the cables (length 6 mm).
3. Do you use wire end ferrules?
If so: Press-fit the wire end ferrules with the the conductors.
4. Load the enclosed strain relief clamp into the front connector
5. Start wiring from the bottom. If you have a front connector with screw-type contacts also screw unassigned terminals (torque 0.6 to 0.8 Nm).
6. Tighten the strain relief for the cable chain.
7. Close the front connector.
8. Label the terminals on the enclosed labeling strip.
A detailed description of the wiring of a front connector is to be found in manual /1/.
38
Counter module FM 450-1
Manual, 02/2014, A5E03648739-02
Wiring
4.4 Module status after power is switched on
4.4 Module status after power is switched on
Characteristics
After the power supply has been switched on and before any data have been transmitted, the module status is as follows:
● Counter inputs with default setting for 5 V differential signals, track B not inverted; single
evaluation (refer to the section "Signal evaluation (Page 100)")
● 0 to +32 bit counting range
● Counter status zero
● Counter setting with digital input 1I2 or 2I2 (and zero mark) disabled
● Input delay for the digital inputs: typically 1 μs
(max. frequency: 200 kHz, minimum pulse width: 2.5 μs)
● Input delay for 24-V count inputs: typically 1 μs
(max. frequency: 200 kHz, minimum pulse width: 2.5 μs)
● Outputs 1Q0 and 1Q1 or 2Q0 and 2Q1 switched off
● Pulse duration = 0
● No Hardware interrupts set
● "Continuous counting" mode set
● Gate function switched off (i.e. gate open)
● Status messages are updated
This setting corresponds to the default setting of the module.
RESET status
This module status (default setting) is also called RESET status.
Counter module FM 450-1
Manual, 02/2014, A5E03648739-02
39
Wiring
4.4 Module status after power is switched on
40
Counter module FM 450-1
Manual, 02/2014, A5E03648739-02
Parameter assignment
5.1 Chapter overview
Chapter overview
In this chapter you will learn how to install and start parameter assignment screen forms.
The parameter assignment screen forms have an integrated help function to support you with parameter assignment and commissioning of the FM 450-1.
5
Counter module FM 450-1
Manual, 02/2014, A5E03648739-02
41
Parameter assignment
5.2 Installing and calling parameter assignment screen forms
5.2 Installing and calling parameter assignment screen forms
Marginal conditions
The following conditions apply to the transfer of parameter assignment data to the CPU:
● STEP 7 must be correctly installed on your programming device.
● The programming device must be correctly connected to the CPU.
● The CPU must be in STOP
Note
During data communication via the MPI you must not pull out or plug in any S7-400 modules!
Installing the Parameterization Interfaces
To install the configuration package:
1. Place the supplied CD in the CD drive of your programming device or PC.
2. Start the program "Setup.exe".
3. Follow the operating instructions provided by the installation program.
Important information can be found in the readme file.
Result
The components of the configuration package are installed in the following directories:
● SIEMENS\STEP7\S7LIBS\FMx501LIB:FCs, UDTs
● SIEMENS\STEP7\S7FCOUNT: Configuration software, Readme, Online Help
● SIEMENS\STEP7\EXAMPLES: Examples
● SIEMENS\STEP7\S7MANUAL\S7FCOUNT: Getting Started, Manuals
Installing parameter assignment screen forms
Call the SETUP.EXE program on the backup copy of your installation diskette. This installs both the parameter assignment screen forms and the FC CNT_CTRL and the FC DIAG_INF on your programming device. The FCs are added to the standard library in the "FM_CNT_L" catalog. Follow the instructions displayed in the SETUP menu on the display.
Example Program
A comprehensive example program is inserted into the "Examples" sub catalog in the STEP
7 catalog in the FM_ZAEHL project during installation.
42
Counter module FM 450-1
Manual, 02/2014, A5E03648739-02
Parameter assignment
5.2 Installing and calling parameter assignment screen forms
Reading the readme file
Important up-to-date information about the provided software can be found in a readme file.
You can read this file with the WORDPAD editor in Windows.
Calling parameter assignment screen forms
The parameter assignment screen forms are displayed automatically after successful installation, if you assign the FM 450-1 parameters within the hardware configuration
Calling the integrated help
There is an integrated online help for the parameter assignment screen forms that you can call in any phase of parameter assignment either with the F1 key or with the Help button.
Counter module FM 450-1
Manual, 02/2014, A5E03648739-02
43
Parameter assignment
5.2 Installing and calling parameter assignment screen forms
44
Counter module FM 450-1
Manual, 02/2014, A5E03648739-02
Program
6
6.1 Chapter overview
Chapter overview
In this chapter you can find all the information you require to program the FM 450-1 in the
S7-400. Two STEP 7 blocks are provided for integrating the FM 450-1 into a user program and make handling the desired functions as easy as possible for you.
This chapter describes these blocks.
Block number
FC 0
FC 1
Block name
CNT_CTRL
DIAG_INF
Meaning
Controlling the FM 450-1 counters
Read diagnostic data set of the FM 450-1
In addition, an example program demonstrates how to use the blocks. The example program shows how to call the blocks and contains the necessary data block.
Counter module FM 450-1
Manual, 02/2014, A5E03648739-02
45
Program
6.5 Technical specifications of the blocks
6.2
Functionality
The FC CNT_CTRL function
The data required for the FC CNT_CTRL are stored in a DB on the CPU. The
FC CNT_CTRL transfers data cyclically from this DB to the FM and fetches data from the
FM.
Requirement
● You have created a DB under STEP 7 as a data block with assigned user-specific data type.
For this purpose select the UDT 1 as the source. The UDT 1 was copied into the block library for the counter (FM_CNT) when the FCs were installed. You must not modify the
UDT 1. Copy the UDT 1 into your project together with the FCs.
● The following valid data must be assigned to the DB required for the FC CNT_CTRL:
– Module address
Set the module address (basic address of the FM 450-1) when you configure your hardware.
The module address must be entered in the MOD_ADR parameter in the DB.
To enter the module address, the following methods can be used:
Recommended procedure
Make the assignment of the module address to the DB in the user program so that the assignment of the module address occurs when user program is called in OB 100 (see example below).
Alternative procedure
You can have the module address entered automatically when you select the module in HW Config, open the "Properties" dialog box with the menu command Edit > Object
Properties, and select the DB using the "Mod Addr" button there. However, in this case, the values entered in the DB (including the module addresses) will be reset to their initial values when a consistency check (menu command Edit > Check Block
Consistency opens the "Check Block Consistency" dialog box) is performed followed by compilation (menu command Program > Compile All in the "Check Block
Consistency" dialog box).
If a consistency check is performed without compilation, the values are not changed.
The menu command Edit > Compile All is only required within a consistency check when the project has been edited with STEP 7 V5.0 Service Pack 2 or earlier.
– Channel address
The channel address of count channel 1 is the same as the module address in pointer format. The channel address of count channel 2 is the same as the module address +
32 in pointer format.
– User data length
The user data length is 32.
46
Counter module FM 450-1
Manual, 02/2014, A5E03648739-02
Program
6.5 Technical specifications of the blocks
Example
The following contains an example of how you can implement the transfer of the module address, the channel address, and the length of the user data to the DB in OB 100. The symbol table contains the following assignments for this example:
FM450_DB_K1
FM450_DB_K2
DB 10
DB 11
DB with the counter data for channel 1
DB with the counter data for channel 2
You program the transfer in STL as follows:
STL
Channel 1
L 512
T FM450_DB_K1.MOD_ADR
L P# 512.0
T FM450_DB_K1.CH_ADR
L 32
T FM450_DB_K1.U_D_LGTH
Channel 2
L 512
T FM450_DB_K2.MOD_ADR
L P# 544.0
T FM450_DB_K2.CH_ADR
L 32
T FM450_DB_K2.U_D_LGTH
// Module address = 512
// Transfer of module address
// Module address in pointer format
// Transfer of the channel address for channel 1
// User data interface length = 32
// Transfer of the user data interface length
// Module address = 512
// Transfer of module address
// Module address + 32 in pointer format
// Transfer of the channel address for channel 2
// User data interface length = 32
// Transfer of the user data interface length
Counter module FM 450-1
Manual, 02/2014, A5E03648739-02
47
Program
6.5 Technical specifications of the blocks
Call
The FC CNT_CTRL can be called once per counter either cyclically or in a time-controlled program. Calling in the interrupt program is not permissible.
Calling the FC CNT_CTRL in the STL and LAD representations is rendered below.
Figure 6-1 Calling the FC CNt_CTRL
Parameters of the FC CNT_CTRL
Name
DB_NO
SW_GATE
GATE_STP
OT_ERR_A
OT_ERR
Declaration type Data type
INPUT BLOCK_DB
Meaning
Number of the data block with the counter data
INPUT
INPUT
INPUT
OUTPUT
BOOL
BOOL
BOOL
BOOL
"SW gate (start/stop)" counter control bit
"Stop gate" counter control bit
The user... enters this sets and resets this sets and resets this
Acknowledge operator error sets and resets this
Operator error occurred queries this
L_DIRECT
L_PREPAR
T_CMP_V1
T_CMP_V2
IN-OUT
IN-OUT
IN-OUT
IN-OUT
BOOL
BOOL
BOOL
BOOL
Trigger bit for "direct loading" of a counter
Trigger bit for "preparatory loading" of a counter
Transfer trigger bit for
"comparison value 1"
Transfer trigger bit for
"comparison value 2" sets sets sets sets
The block... queries this queries this queries this queries this sets and resets this queries and resets this queries and resets this queries and resets this queries and resets this
48
Counter module FM 450-1
Manual, 02/2014, A5E03648739-02
Program
6.5 Technical specifications of the blocks
Name Declaration type Data type
RES_SYNC IN-OUT BOOL
RES_ZERO IN-OUT BOOL
Meaning
Delete "synchronization" status bit
Reset status bits for zero crossing, overflow, underflow and comparator or measurement end
The user... sets sets
The block... queries and resets this queries and resets this
Processing jobs
You initiate a job for the FM 450-1 by means of the L_DIRECT, L_PREPAR, T_CMP_V1,
T_CMP_V2, RES_SYNC, RES_ZERO, OT_ERR_A and GATE_STP FC parameters.
Depending on the job you must enter the load value or a comparison value into the instance
DB prior to the calling the FC.
A set in/out parameter (L_DIRECT, L_PREPAR, T_CMP_V1, T_CMP_V2, RES_SYNC and
RES_ZERO) is deleted again by the FC CNT_CTRL after the job has been completed. This enables you to recognize that the job has been completely executed by the FM 450-1 and, if necessary, to evaluate this information in the user program.
Startup characteristics
As soon as the FC CNT_CTRL identifies a startup (CPU or FM startup), a pending job is deferred and the startup is acknowledged. Any job you have already initiated is carried out once the startup is finished and is therefore not lost.
Error Messages
If an operator error occurred when the FC is called, it is reported in the OT_ERR parameter.
You can read the error information in the DB 1 (variable OT_ERR_B). Thereafter you can acknowledge the operator error with the OT_ERR_A parameter. No new operator error will be reported until you have acknowledged the previous one.
Counter module FM 450-1
Manual, 02/2014, A5E03648739-02
49
Program
6.5 Technical specifications of the blocks
6.3
Functionality
The FC DIAG_INF function
The FC DIAG_INF reads data record DS1 from the FM 450-1 and makes it available to you in the DB of the FC CNT_CTRL. Transfer proceeds as follows:
● If initiation parameter (IN_DIAG=TRUE) the DS1 is read out from the FM°450-1.
● The DS1 is entered into the DB of the FB CNT_CTRL from DW 54 with the aid of the
SFC RD_REC.
● The return code of the SFC (RET_VAL) is copied onto the RET_VAL parameter of the
FC DIAG_INF.
● As soon as the function has been performed, the initiation parameter IN_DIAG is reset and hence the transfer is reported as completed.
A full description of the SFC RD_REC is to be found in manual°/2/.
Call
The FC DIAG_INF can be called in the cycle and in the interrupt program. However, it is not expedient to call it in the time-controlled program.
Calling the FC DIAG_INF in the STL and LAD representations is rendered below.
Figure 6-2 Calling the FC DIAG_INF
Parameters of the FC°DIAG_INF
Name
DB_NO
Declaration type Data type
INPUT INT
RET_VAL
IN_DIAG
OUTPUT
IN-OUT
INT
BOOL
Meaning The user...
Number of the data block of the FC CNT_CTRL enters this
Return code of the SFC 59 queries this
Initiation bit reads diagnostics record DS 1 sets and scans this
The block... queries this enters this resets this
50
Counter module FM 450-1
Manual, 02/2014, A5E03648739-02
Program
6.5 Technical specifications of the blocks
6.4 Example application
Example for the use of the FC CNT_CTRL
The following example is representative for all functions and demonstrates the "Transfer load value to FM 450-1" and "Start counter" functions to show how the FC°CNT_CTRL can be applied.
STL
CONT:
END:
SET
S
...
SPA
...
AN
S
JC
L
T
AN
L
T
U
+1000;
KANAL1.LOAD_VAL;
INITIATION;
S
R
LOAD_DIRECT;
TRIGGER;
CALL CNT_CTRL, (
SW_GATE
GATE_STP
OT_ERR_A
OT_ERR
L_DIRECT
L_PREPAR
T_CMP_V1
T_CMP_V2
RES_SYNC
RES_ZERO
OPERATOR_ERROR;
CONT;
:=START,
:=GATE_STOP,
:=ERROR_ACKN,
:=OPERATOR_ERR,
:=LOAD_DIRECT,
:=LOAD_INDIRECT,
:= COMP1_LOAD
:=COMP2_LOAD,
:=RES_SYNCHRO,
:= RES_ZERO);
CHANNEL1.OT_ERR_B;
OUTPUT;
ERR_ACKN
END;
LOAD_DIRECT;
START;
// Enter load value into
// the DB.
// DIRECT input parameters
// Call the FC with the DB
// Channel 1.
// Control software gate
// Stop GATE
// Acknowledge operator error
// Operator error occurred
// Load new counter value
// Prepare new counter value
// Load new comparison value 1
// Load new comparison value 2
// Delete synchronization status bit
// Delete "zero crossing" status bit
// If no error has occurred,
// CONTinue
// *** Error evaluation START ***
// Read additional information
// and output.
// Generate RLO 1
// Acknowledge error
// Further error responses
// *** Error evaluation END ***
// Continue with normal processing
// Load direct function is ready
// Open software gate
Counter module FM 450-1
Manual, 02/2014, A5E03648739-02
51
Program
6.5 Technical specifications of the blocks
Description of the symbols
The tables lists the symbols used in the example. You specify your own symbol assignments in the S7 symbol table.
Table 6- 1 Symbols in the user program
Symbols used
CHANNEL1
CHANNEL1.LOAD_VAL
INITIATE
LOAD_DIRECT
START
GATE_STOP
ERR_ACKN
LOAD_INDIRECT
COMP1_LOAD
COMP2_LOAD
RES_SYNCHRON
RES_ZERO
OPERATOR_ERROR
CHANNEL 1.OT_ERR_B
Absolute (example)
DB 1
DB1.DBB14
M 10.0
M 20.0
M 20.1
M 20.2
M 20.3
M 20.4
M 20.5
M 20.6
M 20.7
M 21.0
M 21.1
DB1.DBX40.0
Comment
Data block for FC°CNT_CTRL
Counter value specified in DB 1
Initiation bit generated to meet technological requirements
Accept counter value directly
Start counter
Close counter gate
Acknowledge operator error
Load counter value in preparation
Load comparison value 1
Load comparison value 2
Reset synchronization status bit
Reset zero crossing, overflow and underflow status bit
Operator error occurred
Operator error information in DB 1
Description of the sequence
Prerequisite:
The value to be transferred must have been entered in the DB°1.
The load value is transferred and started:
When the FC is called, the load value of a channel is transferred to the FM 450-1. Calling the
FC°CNT_CTRL selects either the L_DIRECT parameter or the L_PREPAR parameter. The
L_DIRECT selection bit specifies that the load value will be loaded directly onto the counter
(L_DIRECT=1). The L_PREPAR selection bit specifies that the load value is to be stored in the load register (L_PREPAR=1). The load value in the load register is then loaded onto the counter when the counter is next set. L_PREPAR=1 prepares a new counter value. Load value transfer lasts a minimum of 3 FC calls.
The FC must be called until it has reset the selected initiation bit (L_DIRECT or L_PREPAR).
While the job is in progress the I/O parameter remains set. The FC°CNT_CTRL does not output an error message regarding data exchange with the FM.
If the FC CNT_CTRL resets the parameter you had set, the FM 450-1 has accepted the load value. The read-back load value stored in the DB°1 is updated by the FC°CNT_CTRL.
You must generate the "initiation" bit to comply with your technological requirement. This bit may be set at "1" for one cycle only. Please note, that the FC must be called until the I/O parameter of the FC CNT_CTRL is reset.
52
Counter module FM 450-1
Manual, 02/2014, A5E03648739-02
6.5 Technical specifications of the blocks
Table 6- 2
Technical Specifications
Block number
Version
Assignment in work memory
Assignment in load memory
Assignment in local data area
System function called
FC CNT_CTRL
FC 0
3.0
540 bytes
634 bytes
4 bytes
-
● Internal update time of the FM°450-1: 0.5°ms.
● SDB 100: approx. 240°bytes
Program
6.5 Technical specifications of the blocks
FC DIAG_INF
FC 1
3.0
246 bytes
326 bytes
38 bytes
SFC 51 RDSYSST
Counter module FM 450-1
Manual, 02/2014, A5E03648739-02
53
Program
6.5 Technical specifications of the blocks
54
Counter module FM 450-1
Manual, 02/2014, A5E03648739-02
Commissioning
7.1 Chapter overview
Chapter overview
In this chapter you will find checklists for commissioning the FM 450-1. These checklists enable you to
● check all working steps up to full operation of the module,
● avoid operating faults by the module.
7
Counter module FM 450-1
Manual, 02/2014, A5E03648739-02
55
Commissioning
7.3 Working steps for parameter assignment
7.2 Working steps during mechanical installation
Check list
Working step
Define the slot
Install the FM 450-1
Use the following checklist to check and document the working steps during mechanical installation of the FM 450-1.
Select cables
Connect 5 V encoders
Options/procedure
All slots that are not already occupied or due to be occupied by a power supply module, a CPU or an IM.
1. Hook FM into position and screw tight
2. Attach slot number
Observe rules and specifications in chapter "Wiring (Page 27)".
Counter 1: Terminal Name Function
5 V incremental encoders with differential signals A and /A, B and /B, N and /N
14
15
5
6
7
8
9
10
1M
5.2 VDC
A
/A
B
/B
N
/N
Counter 2:
5 V incremental encoders with differential signals A and /A, B and /B, N and /N
Terminal
26
27
17
18
19
20
21
22
Name
1M
5.2 VDC
A
/A
B
/B
N
/N
Ground for encoder power supply
5.2 V encoder power supply
Encoder signal A
Encoder signal /A
Encoder signal B
Encoder signal /B
Encoder signal N
Encoder signal /N
Function
Ground for encoder power supply
5.2 V encoder power supply
Encoder signal A
Encoder signal /A
Encoder signal B
Encoder signal /B
Encoder signal N
Encoder signal /N
(X)
56
Counter module FM 450-1
Manual, 02/2014, A5E03648739-02
Commissioning
7.3 Working steps for parameter assignment
Working step Options/procedure
Connect 24 V encoders Counter 1: Terminal
24V incremental encoders 14
16
11
12
13
Counter 2: Terminal
24V incremental encoders 26
28
23
24
25
Counter 1:
24V pulse encoder without direction level initiator/BERO)
Terminal
14
16
11
Counter 2:
24V pulse encoder without direction level initiator/BERO)
Terminal
26
28
23
Counter 1:
24-V pulse encoder with direction level
Counter 2:
24-V pulse encoder with direction level
Terminal
14
16
11
12
Terminal
26
28
23
24
Name
1M
24 VDC
A*
B*
N*
Name
1M
24 VDC
A*
Name
1M
24 VDC
A*
B*
Name
1M
24 VDC
A*
B*
Name
1M
24 VDC
A*
B*
N*
Name
1M
24 VDC
A*
Function
Ground for encoder power supply
24 V encoder power supply
Encoder signal A*
Encoder signal B*
Encoder signal N*
Function
Ground for encoder power supply
24 V encoder power supply
Encoder signal A*
Encoder signal B*
Encoder signal N*
Function
Ground for encoder power supply
24 V encoder power supply
Encoder signal A*
Function
Ground for encoder power supply
24 V encoder power supply
Encoder signal A*
Function
Ground for encoder power supply
24 V encoder power supply
Encoder signal A*
Direction level B*
Function
Ground for encoder power supply
24 V encoder power supply
Encoder signal A*
Direction level B*
(X)
Counter module FM 450-1
Manual, 02/2014, A5E03648739-02
57
Commissioning
7.3 Working steps for parameter assignment
Working step
Wiring digital inputs and outputs
Connecting auxiliary voltage and load voltage
Options/procedure
Counter 1: Terminal
Digital inputs and outputs 29
30
Counter 2:
Digital inputs and outputs 41
42
43
45
46
Terminal
Encoder supply
Supply for digital inputs and outputs
3
4
47
48
31
33
34
Terminal
Name
1I0
1I1
1I2
1Q0
1Q1
Name
2I0
2I1
2I2
2Q0
2Q1
Name
1L+
1M
2L+
2M
Function
Digital input START
Digital input STOP
Digital input SET
Digital output Q0
Digital output Q1
Function
Digital input START
Digital input STOP
Digital input SET
Digital output Q0
Digital output Q1
Function
24V auxiliary voltage
Auxiliary voltage ground
24V load voltage
Load voltage ground
(X)
58
Counter module FM 450-1
Manual, 02/2014, A5E03648739-02
Commissioning
7.3 Working steps for parameter assignment
7.3 Working steps for parameter assignment
Check list
Working step
Assign the FM 450-1 parameters
Use the following checklist to check and document the working steps during parameter assignment of the FM°450-1. Assign the parameters of the FM°450-1 counters in the same order as the check list.
Options/procedure
Select encoders for counter 1
5-V encoder with symmetrical signals
24-V encoder with asymmetrical signals
24V encoders with a pulse train and direction signal
24-V initiator
Signal evaluation
Monitoring
Interface
A + B + N
A + B
A
None
Sinking output
Sourcing output/push-pull
≤200 kHz/≥2.5 μs Frequency range/ minimum pulse width
Interface
Frequency range/ minimum pulse width
≤20 kHz/≥25 μs
Current-sinking output
Current-sourcing output/push-pull
≤200 kHz/≥2.5 μs
≤20 kHz/≥25 μs
Single
Double
Quadruple
Frequency and direction (with 24V encoders)
(X)
Counter module FM 450-1
Manual, 02/2014, A5E03648739-02
59
Commissioning
7.3 Working steps for parameter assignment
Step
Assign the FM 450-1 parameters
Options/procedure
Select encoders for counter 2
5-V encoder with symmetrical signals
24-V encoder with asymmetrical signals
24-V encoder with a pulse train and direction signal
24-V initiator
Signal evaluation
Monitoring
Interface
Frequency range/ minimum pulse width
A + B + N
A + B
A
None
Current-sinking output
Current-sourcing output/push-pull
≤200 kHz/≥2.5 μs
≤20 kHz/≥25 μs
Interface
Frequency range/ minimum pulse width
Current-sinking output
Current-sourcing output/push-pull
≤200 kHz/≥2.5 μs
≤20 kHz/≥25 μs
Single
Double
Quadruple
Frequency and direction (with 24-V encoders)
Step
Assign the FM 450-1 parameters
Options/procedure
Specify mode for counter 1
Continuous counting
Single counting
Periodic counting
Set count range
Without gate
With SW gate
With HW gate
With SW gate
With HW gate
With SW gate
With HW gate
0 to +32 bit
-31 bit to +31 bit
(X)
(X)
60
Counter module FM 450-1
Manual, 02/2014, A5E03648739-02
Step
Assign the FM 450-1 parameters
Options/procedure
Specify mode for counter 2
Continuous counting
Single counting
Periodic counting
Set count range
Without gate
With SW gate
With HW gate
With SW gate
With HW gate
With SW gate
With HW gate
0 to +32 bit
-31 bit to +31 bit
Specify the behavior of the digital inputs for counter 1
HW gate Level-controlled
Edge-controlled
Minimum pulse width
Set counter
≥2.5 μs
≥25 μs
Single setting
Evaluate zero mark for setting
Multiple setting
Specify the behavior of the digital inputs for counter 2
HW gate Level-controlled
Minimum pulse width
Set counter
Edge-controlled
≥2.5 μs
≥25 μs
Single setting
Evaluate zero mark for setting
Multiple setting
Commissioning
7.3 Working steps for parameter assignment
(X)
Counter module FM 450-1
Manual, 02/2014, A5E03648739-02
61
Commissioning
7.3 Working steps for parameter assignment
Step
Assign the FM 450-1 parameters
Options/procedure
Specify the behavior of the digital outputs for counter 1
Output 1Q0 Disable
Active from comparison value 1 to overflow
Active from comparison value 1 to underflow
Active for "pulse duration" when comparison value 1 is reached in up direction
Output 1Q1
Active for "pulse duration" when comparison value 1 is reached in down direction
Active for "pulse duration" when comparison value 1 is reached in up or down direction
Disable
Active from comparison value 2 to overflow
Active from comparison value 2 to underflow
Active for "pulse duration" when comparison value 2 is reached in up direction
Active for "pulse duration" when comparison value 2 is reached in down direction
Active for "pulse duration" when comparison value 2 is reached in up or down direction
0 to 500 ms Pulse duration
Specify the behavior of the digital outputs for counter 2
Output 2Q0 Disable
Active from comparison value 1 to overflow
Output 2Q1
Pulse duration
Active from comparison value 1 to underflow
Active for "pulse duration" when comparison value 1 is reached in up direction
Active for "pulse duration" when comparison value 1 is reached in down direction
Active for "pulse duration" when comparison value 1 is reached in up or down direction
Disable
Active from comparison value 2 to overflow
Active from comparison value 2 to underflow
Active for "pulse duration" when comparison value 2 is reached in up direction
Active for "pulse duration" when comparison value 2 is reached in down direction
Active for "pulse duration" when comparison value 2 is reached in up or down direction
0 to 500 ms
(X)
62
Counter module FM 450-1
Manual, 02/2014, A5E03648739-02
Step
Assign the FM 450-1 parameters
Integrate FCs in user program
Commissioning
7.3 Working steps for parameter assignment
Options/procedure
Enable digital outputs
CTRL_DQ0 in DB 1
CTRL_DQ1 in DB 1
Specify load value and comparison values for counter 1 and enter in DB
Load value
Comparison value 1
Comparison value 2
Specify load value and comparison values for counter 2 and enter in DB
Load value
Comparison value 1
Comparison value 2
Enter basic data in DB 1
Module address
Channel address
User data length
Select interrupts for counter 1
Interrupt when door is opened
32
Interrupt when door is closed
Interrupt in case of overflow
Interrupt in case of underflow
Interrupt in case of zero crossing
Interrupt when comparison value 1 is reached in the up direction
Interrupt when comparison value 1 is reached in the down direction
Interrupt when comparison value 2 is reached in the up direction
Interrupt when comparison value 2 is reached in the down direction
Interrupt when setting counter
Select interrupts for counter 2
Interrupt when door is opened
Interrupt when door is closed
Interrupt in case of overflow
Interrupt in case of underflow
Interrupt in case of zero crossing
Interrupt when comparison value 1 is reached in the up direction
Interrupt when comparison value 1 is reached in the down direction
Interrupt when comparison value 2 is reached in the up direction
Interrupt when comparison value 2 is reached in the down direction
Interrupt counter is set
Integrate FC CNT_CTRL
Integrate FC DIAG_INF
(X)
Counter module FM 450-1
Manual, 02/2014, A5E03648739-02
63
Commissioning
7.3 Working steps for parameter assignment
64
Counter module FM 450-1
Manual, 02/2014, A5E03648739-02
Modes, settings, parameters and commands
8.1 Chapter overview
Chapter overview
This chapter gives you
● an overview of the three modes, the various settings and the commands available and how to call them.
● A description of the three modes
● A description of the settings
● A description of the two commands
● Marginal conditions and notes which you must heed when using these functions.
8
Counter module FM 450-1
Manual, 02/2014, A5E03648739-02
65
Modes, settings, parameters and commands
8.12 Initiating a process interrupt
8.2 Overview of modes, settings and commands
Which modes are available?
For the FM°450-1 there are the three following modes:
Table 8- 1 Operating modes of FM°450-1
Name
Continuous counting
(with or without gate)
Single counting with SW gate or with HW gate
Periodic counting with SW gate or with HW gate
Description
Starting from the current counter status the FM°450-1 counts continuously.
When the gate opens, the FM 450-1 counts from the load value to the count limit.
When the gate opens, the FM 450-1 counts between the load value and the count limit.
You can configure the two FM 450-1 counters in different modes.
The default setting is the "Continuous counting" mode.
Choice of count range, behavior of the two digital outputs, pulse duration, evaluation of the count signals, and the selection of the signal to set the counter all depend on the mode.
Which settings are available?
You can adapt the FM 450-1 to your count job by means of the following five settings:
Table 8- 2 The FM 450-1 settings
Name
Count range
Behavior of digital outputs Q0 and Q1
Pulse duration
Triggering hardware interrupts
Encoders
Description
You select the count limit with the count range.
You can choose between six possibilities for the behavior of the outputs on reaching the comparison value.
Pulse duration indicates the time for which the output is to be set.
When the various selectable events occur, the FM 450-1 can trigger a hardware interrupt.
You must specify different settings for the encoder used. These are
described in section "Encoder signals and their evaluation
66
Counter module FM 450-1
Manual, 02/2014, A5E03648739-02
Modes, settings, parameters and commands
8.12 Initiating a process interrupt
Which commands are available?
You can influence the counting process of the FM 450-1 by means of the following commands:
Table 8- 3 The FM 450-1 commands
Name
Open and close gate
Set counter
Description
The counting process starts when a gate opens and ends when it closes.
The counter can be set to the load value using various signals.
Basic parameter assignment
When configuring the hardware you define the basic parameter assignment of each FM 450-
1. The following table shows the significance of the relevant parameters.
Table 8- 4 Parameters for the basic parameter assignments
Name
Interrupt selection
Reaction to a CPU
STOP
Option
None
Diagnostics
Process
Process and diagnostics
STOP
Description
You enable the corresponding interrupts via this selection.
Continue operating
Terminate active job
Outputs immediately disabled counting process aborted
The module continues operating.
The single count process continues until it terminates itself or, in modes with a HW gate, until it is terminated by closing the HW gate.
The periodic counting process is reparameterized into a single counting process and is terminated as such.
Counter module FM 450-1
Manual, 02/2014, A5E03648739-02
67
Modes, settings, parameters and commands
8.12 Initiating a process interrupt
8.3 Basics on calling modes, settings and commands
Calling modes, settings and commands
● You select modes and settings in the FM°450-1 parameter assignment screen forms.
The parameter assignment data are automatically stored on the programming device and in the rack SDB.
Notes on installing parameter assignment screen forms and on assigning the FM°450-1
parameters can be found in the chapter "Parameter assignment (Page 41)" and, after the
software has been installed, also in the integrated Help function.
● Modes and settings are modified in the parameter assignment screen forms. The new mode or setting is valid from the next time the FM 450-1 starts.
● Commands are either generated via hardware signals, which are connected to the front connector, or by setting the relevant input parameters of the FC CNT_CTRL in the user program to influence the count process. The input parameters are stored as control bits in the DB of the FC CNT_CTRL.
Control and status bits in the DB
In addition to the control bits, there are status bits in the DB which signalize the status of the count process. The control and status bits are each allocated two bytes in the DB (see the
chapter "Assignment of the DB (Page 103)".)
Transferring control and status bits
You transfer control and status bits between the CPU and module with the FC°CNT_CTRL, which you must integrate into your user program:
Use symbolic names for the control and status bits in the user program. The symbolic names are used in this chapter in the description of the FC.
The exact description of the FC CNT_CTRL is to be found in the chapter "Program
(Page 45)"; the DB assignments are to be found in the chapter "Assignment of the DB
68
Counter module FM 450-1
Manual, 02/2014, A5E03648739-02
Modes, settings, parameters and commands
8.12 Initiating a process interrupt
8.4
Overview
Infinite counting
In this mode an FM 450-1 counter counts infinitely from the current counter status:
● When counting up, if the counter reaches the upper count limit and a further count pulse comes, it jumps to the lower limit and continues counting from there without any pulse loss.
● When counting down, if the counter reaches the lower count limit and a further count pulse comes, it jumps to the upper limit and continues counting from there without any pulse loss.
Select gate function
In this mode you can select the gate function Options:
● Without gate (default)
● SW gate
● HW gate, level-controlled or edge-controlled
Figure 8-1 Infinite counting with load value and gate function
Open and close SW gate
You open and close the SW gate of the relevant counter with the input parameter SW_GATE
of the FC CNT_CTRL (see chapter "The FC CNT_CTRL function (Page 46)").
Action
Open SW gate
Close SW gate
Initiating event
Set SW_GATE
Reset SW_GATE
Counter module FM 450-1
Manual, 02/2014, A5E03648739-02
69
Modes, settings, parameters and commands
8.12 Initiating a process interrupt
Opening and closing HW gate
You open and close the HW gate of the relevant counter by applying or removing the corresponding signals to or from the inputs 1I0 and 1I1 (counter 1) and/or 2I0 and 2I1
(counter 2).
Action
Opening HW gate (level controlled)
Closing HW gate (level controlled)
Opening HW gate (edge controlled)
Closing HW gate (edge controlled)
Initiating event
Applying signal to input 1I0 (2I0)
Removing signal from input 1I0 (2I0)
Applying positive edge to input 1I0 (2I0)
Applying positive edge to input 1I1 (2I1)
When the HW gate opens the counter resumes counting from the current counter status.
Terminating counting process with the gate stop function
In addition you can end the count process when counting with the SW gate or HW gate by means of the gate stop function of the relevant counter. For this purpose you set the
GATE_STP input parameter of the FC CNT_CTRL.
70
Counter module FM 450-1
Manual, 02/2014, A5E03648739-02
Modes, settings, parameters and commands
8.12 Initiating a process interrupt
8.5
Overview
Single counting
In this mode an FM°450-1 counter counts once from the load value up to the count limit.
Select gate function
In this mode you can select the gate function Options:
● SW gate
● HW gate, level-controlled or edge-controlled
Figure 8-2 Single counting with load value and gate function
Open and close SW gate
You open and close the SW gate and set the counter to the load value with the input parameter SW_GATE of the FC CNT_CTRL.
Action
Open SW gate
Close SW gate
Initiating event
Set SW_GATE
Reset SW_GATE
Counter module FM 450-1
Manual, 02/2014, A5E03648739-02
71
Modes, settings, parameters and commands
8.12 Initiating a process interrupt
Opening and closing HW gate
You open and close the hardware gate and set the counter to the load value by applying or removing the relevant signals at the inputs 1I0 and 1I1 (Counter 1) and/or 2I0 and 2I1
(Counter 2).
Action
Opening HW gate (level controlled)
Opening HW gate (edge controlled)
Closing HW gate (level controlled)
Closing HW gate (edge controlled)
Initiating event
Applying signal to input 1I0 (2I0)
Applying positive edge to input 1I0 (2I0)
Removing signal from input 1I0 (2I0)
Applying positive edge to input 1I1 (2I1)
In the case of a level-controlled HW gate, a signal at output 1I0 (2I0) is used to reopen the gate and set the relevant counter to the load value.
If in the case of an edge controlled HW gate a positive edge is again applied to input 1I1
(2I1), the counter resumes counting from the load value irrespective of whether the gate is closed or still open (retriggering) provided input 1I1 (2I1) is not set.
Behavior at count limits
If the counter reaches the upper or lower count limit and another count pulse arrives, the counter is set to the other count limit.
Thereafter the gate is closed and the counting process terminated, even if the SW_GATE parameter is still set or the HW gate is still open. The corresponding status bit is set in the
DB of the FC CNT_CTRL.
Count limit reached
Upper count limit
Lower count limit
Bit in the DB
STS_OFLW is set
STS_UFLW is set
If you want to restart the counter, you must reset the SW_GATE parameter and/or reopen the HW gate. The counting process is then continued from the load value.
Terminating counting process with the gate stop function
In addition you can terminate the counting process at any time using the gate stop function.
For this purpose you set the GATE_STP input parameter of the FC°CNT_CTRL.
72
Counter module FM 450-1
Manual, 02/2014, A5E03648739-02
Modes, settings, parameters and commands
8.12 Initiating a process interrupt
8.6
Overview
Periodic counting
In this mode an FM 450-1 counter counts once from the load value up to the count limit, jumps back to the load value and continues to count.
Select gate function
In this mode you can select the gate function Options:
● SW gate
● HW gate, level-controlled or edge-controlled
Figure 8-3 Periodic counting with load value and gate function
Open and close SW gate
You open and close the SW gate and set the counter to the load value by setting or resetting the relevant bit in the DB of the FC°CNT_CTRL in the user program (see chapter
"Assignment of the DB (Page 103)"). When you open the SW gate, the FM 450-1 starts
counting from the load value.
Action
Open SW gate
Close SW gate
Initiating event
Set SW_GATE
Reset SW_GATE
If you want to restart the counter, you must reset the bit. The counter then starts counting from the load value.
Counter module FM 450-1
Manual, 02/2014, A5E03648739-02
73
Modes, settings, parameters and commands
8.12 Initiating a process interrupt
Opening and closing HW gate
You open and close the HW gate and set the counter to the load value by applying or removing the relevant signals at the inputs 1I0 and 1I1 (counter 1) and/or 2I0 and 2I1
(counter°2).
Action
Opening HW gate (level controlled)
Closing HW gate (level controlled)
Opening HW gate (edge controlled)
Closing HW gate (edge controlled)
Initiating event
Applying signal to input 1I0 (2I0)
Removing signal from input 1I0 (2I0)
Applying positive edge to input 1I0 (2I0)
Applying positive edge to input 1I1 (2I1)
If in the case of an edge controlled HW gate a positive edge is again applied to input 1I0
(2I0), the relevant counter again starts counting from the load value irrespective of whether the gate is closed or still open (retriggering) provided input 1I1 (2I1) is not set.
Behavior at the Count Limits
If a counter reaches the upper or lower count limit and a further count pulse comes, it begins counting from the load value again. The count process is thereby continued without pulse loss. A corresponding status bit is set in the DB:
Count limit reached
Upper count limit
Lower count limit
Bit in the DB
STS_OFLW is set
STS_UFLW is set
Terminating counting process with the gate stop function
In addition you can terminate the counting process at any time using the gate stop function.
For this purpose you set the GATE_STP input parameter of the FC CNT_CTRL.
74
Counter module FM 450-1
Manual, 02/2014, A5E03648739-02
Modes, settings, parameters and commands
8.12 Initiating a process interrupt
8.7
Introduction
Count range
There is a 32°bit-wide count register on the module. With the count range you specify if the module counts only in the positive range or if the 32nd°bit is interpreted as a sign bit and hence negative numbers can be represented. This section describes these two count ranges, "0 to +32 bits" and "-31 to +31 bits".
Count ranges
The FM 450-1 counts within different limits in the count ranges 0 to +32 bits and -31 to
+31 bits. In each case an overflow or an underflow is identified at the range limits.
In the "-31 to +31 bits" count mode, the counter status is represented in the two's complement.
Count range Overflow
0 to +32 bits
1)
0 to 4 294 967 295 0 to
FFFF FFFFH
-31 to +31 bit -2 147 483 648 to
2 147 483 647
8000 0000H to
7FFF FFFFH
When the counter status changes from 4 294 967 295 to 0
When the counter status changes from +2 147 483 647 to -
2 147 483 648
1)
In this count range, you can only specify and evaluate values in hexadecimal.
Underflow
When the counter status changes from
0°to 4 294 967 295
When the counter status changes from
-2 147 483 648 to +2 147 483 647
Overflow, underflow and zero crossing
A bit is set in the DB of FC°CNT_CTRL for both count limits in the case of overflow and
underflow (see section "Assignment of the DB (Page 103)").
In the "-31 to +31 bit" count range, a bit is similarly set in the DB on a zero crossing.
In the "0 to +32 bit" count range, an overflow or underflow, depending on the direction of counting, is additionally indicated on a zero crossing.
Event
Overflow
Underflow
Zero crossing
Bit in the DB
STS_OFLW is set
STS_UFLW is set
STS_ZERO is set
Triggering hardware interrupts
You can also signalize the events overflow, underflow and zero crossing by means of hardware interrupts.
Counter module FM 450-1
Manual, 02/2014, A5E03648739-02
75
Modes, settings, parameters and commands
8.12 Initiating a process interrupt
8.8
Introduction
Setting: Behavior of the digital outputs
You can store two comparison values (comparison value 1 and 2) for the counters on the module; these are assigned to the respective digital outputs (comparison value°1: 1Q0 and
2Q0, comparison value 2: 1Q1 and 2Q1). The comparison values are compared to the current counter status. When the counter status reaches a comparison value, the relevant output can be set.
Comparison values 1 and 2
You enter the two comparison values in the DB of the FC CNT_CTRL (CMP_V1, CMP_V2) and transfer them to the FM 450-1 by setting the bits T_CMP_V1 or T_CMP_V2 (see the
section "Assignment of the DB (Page 103)"). The count is not affected by this.
The comparison values must be within the limits of the respective count range. The comparison value is interpreted according to the selected count range. If you give
FFFF FFFF H, for example, as the comparison value, the value is interpreted as
4 294 967 295 within the 0 to +32 bit count range, and as -1 within the -31 to +31 bit count range.
Enabling the outputs
Before you can activate the outputs, you must first enable them by setting the appropriate
bits in the DB (see the section Assignment of the DB (Page 103)). If you reset one of these
bits, the associated output is disabled immediately even if you have assigned a pulse duration for them.
Output
Q0
Q1
...is enabled by
CTRL_DQ0
CTRL_DQ1
Status of the outputs
You can identify the state of the two outputs from the green status LEDs and the relevant bits in the DB.
Output status
1Q0 (2Q0) is set
1Q0 (2Q0) is reset
1Q1 (2Q1) is set
1Q1 (2Q1) is reset
LED status
CH 1 OUT 0 (CH2 OUT 0) is alight
CH 1 OUT 0 (CH2 OUT 0) is dark
CH 1 OUT 1 (CH2 OUT 1) is alight
CH 1 OUT 1 (CH2 OUT 1) is dark
Bit status
STS_COMP1 is set
STS_COMP1 is reset
STS_COMP2 is set
STS_COMP2 is reset
76
Counter module FM 450-1
Manual, 02/2014, A5E03648739-02
Modes, settings, parameters and commands
8.12 Initiating a process interrupt
Behavior of the outputs
For the two outputs you can set one of six possible responses to reaching the comparison value. The various options are shown in the following table.
Digital output parameter assignment
Disable
Behavior of the outputs
The output remains deactivated and is not affected by the comparison value, zero crossing, overflow, and underflow events.
Active between comparison value and overflow
The output is enabled when the counter is within the range between comparison value n and overflow. The output is activated by setting the counter to a value between the comparison value and overflow.
Active between comparison value and overflow
The output is activated when the counter is within the range between comparison value and underflow. The output is activated by setting the counter to a value between the comparison value and underflow.
Active for "pulse duration" when the comparison value is reached in up direction
The output is activated when the comparison value is reached in the up counting direction for the time the pulse lasts.
Active for "pulse duration" when the comparison value is reached in down direction
The output is activated when the comparison value is reached in the down count direction for the time the pulse lasts.
Active for "pulse duration" when comparison value is reached in up or down direction
The output is activated when the comparison value is reached for the time the pulse lasts, irrespective of the counting direction.
A shaded in area in the table signifies: The output is active. t = pulse duration
Counter module FM 450-1
Manual, 02/2014, A5E03648739-02
77
Modes, settings, parameters and commands
8.12 Initiating a process interrupt
Boundary conditions
If you assign the behavior of the digital outputs, you must observe the following boundary conditions.
If ...
... you want to assign parameters for the output to be "active between the comparison value and the overflow or underflow" ...
...you want to assign the parameters for the output to be "active for the pulse duration in the up counting direction"...
...you want to assign the parameters for the output to be "active for the pulse duration in the down counting direction"... then...
...you must ensure that the time between the events is longer than the minimum operating time of the outputs (operating time: 300°µs); otherwise the control pulses at the outputs are lost.
If the counter status again reaches the comparison value while the output is still active, no new pulse will be initiated. A further pulse can only be initiated when the output is no longer active.
... you must not enable a hardware interrupt when
"the comparison value 1 or 2 in the down direction is reached".
...you must not enable a hardware interrupt when
"the comparison value 1 or 2 in the up direction is reached".
Disabling the outputs
The outputs are disabled by the following events, irrespective of the parameter assignment:
● Module watchdog timeout (internal error)
● Removal of the enable bit (CTRL_DQ0 for Q0 and CTRL_DQ1 for Q1 in the DB, see
section "Assignment of the DB (Page 103)")
Default setting
The outputs are disabled in the default setting.
78
Counter module FM 450-1
Manual, 02/2014, A5E03648739-02
Modes, settings, parameters and commands
8.12 Initiating a process interrupt
8.9
Introduction
Setting: Pulse duration
As a means of adaptation to the actors used in your process (contactors, control elements etc.) you have the possibility of specifying a pulse duration during which the outputs are set when a comparison value is reached. This section describes what you must take into account if you want to define a pulse duration for the outputs.
The effect of the pulse duration setting
Via the pulse duration you also specify for how long the output should be set at minimum.
This setting is only effective if you preselect the behavior of the output accordingly. The pulse duration is without effect if the output is to be set between the comparison value and overflow or underflow.
Pulse duration begins when the output is set. Inaccuracy of the pulse duration is less than
1°ms.
Value range
You can prescribe a value between 0 and 500°ms for the pulse duration. This value applies to both outputs together.
Note
If you specify the pulse duration to be zero you must ensure that the count pulse times are greater than the minimum operation time of the digital outputs (operating time:°300°µs, i°e. the count frequency is less than 3333°Hz); otherwise the control pulses are lost at the outputs.
In this case check if your actor can respond with the operating time 300°µs.
Default value
The default value for the pulse duration is 0.
Counter module FM 450-1
Manual, 02/2014, A5E03648739-02
79
Modes, settings, parameters and commands
8.12 Initiating a process interrupt
8.10
Overview
Command: Open and close gate
The FM 450-1 counters have the following gates:
● A hardware gate (HW gate) which you can open and close level controlled or edge controlled.
● A software gate (SW gate) which you can open and close via control bits in the user program.
Selecting a gate
In the "Operating Mode" dialog (see section "Overview of modes, settings and commands
(Page 66)"), you specify which gate you want to use for the count process.
The following figures demonstrate the various possibilities for opening and closing the
FM°450-1 gates.
Level controlled opening and closing of the HW gate
The following figure shows the level controlled opening and closing of the HW gate of counter°1.
Figure 8-4 Level controlled opening and closing of the HW gate of counter 1
If you set input 1I0 to 1 the count signals can reach counter 1 and are counted. If you reset input 1I0 to 0, the door is closed. The count pulses are no longer counted, counter 1 stops.
If the gate of counter 1 is closed owing to overflow or underflow, you must first reset input 1I0 and apply a positive edge to input 1I0 to reopen the door.
80
Counter module FM 450-1
Manual, 02/2014, A5E03648739-02
Modes, settings, parameters and commands
8.12 Initiating a process interrupt
Edge controlled opening and closing of the HW gate
The following figure shows the edge controlled opening and closing of the HW gate of counter 1.
Figure 8-5 Edge controlled opening and closing of the HW gate of counter 1
With the edge controlled door function the HW gate of counter 1 is opened by a positive edge on input 1I0. The door is closed by a positive edge on input 1I1.
If positive edges occur simultaneously on inputs 1I0 and 1I1 an open gate is closed or a closed gate remains closed. If input 1I1 is set a positive edge on input 1I0 cannot open the gate.
The same applies analogously to counter 2 (inputs 2I0 and 2I1).
Status of inputs 1I0 (2I0) and 1I1 (2I1)
The status of the inputs 1I0 (2I0) and 1I1 (2I1) are indicated by the green LEDs CH1 IN 0
(CH 2 IN 0) and CH 1 IN 1 (CH 2 IN 1) and, within the user program, in the STS_STA and
STS_STP bit of the DB of the FC°CNT_CTRL.
Gate status
The gate status is indicated in the STS_GATE bit within the user program.
Counter module FM 450-1
Manual, 02/2014, A5E03648739-02
81
Modes, settings, parameters and commands
8.12 Initiating a process interrupt
Opening and closing the SW gate
The following figure shows the opening and closing of the SW gate of counter 1.
Figure 8-6 Opening and closing the SW gate
The SW gate is opened and closed by setting and resetting the input parameter SW_GATE of the FC CNT_CTRL.
The closed gate can be reopened by setting the input parameter SW_GATE again.
Status of the SW gate
The status of the SW gate is signalized on the STS_SW_G bit of the DB of the
FC°CNT_CTRL.
Terminating the count with the gate stop function
In addition, you can terminate the counting process at any time using the gate stop function of the relevant counter, irrespective of the signals applied or the status of the SW gate. For this purpose you set the GATE_STP input parameter of the FC CNT_CTRL.
When you reset the GATE_STP parameter, you can only open the gate for the counter concerned by means of a positive edge, either at input 1I0 or 2I0 (HW gate) or resetting the
SW_GATE input parameter (SW gate).
Hardware interrupt
Opening and closing of a HW or SW gate can be used to trigger a hardware interrupt (see
section "Initiating a process interrupt (Page 90)".)
Default setting
In the default setting all gates are open; the count pulses are counted.
82
Counter module FM 450-1
Manual, 02/2014, A5E03648739-02
Modes, settings, parameters and commands
8.12 Initiating a process interrupt
8.11
Overview
Command: Set counter
If you want to start or continue the counting process of a counter from a specific value (the load value), you must assign parameters for the signal with which the counter is to be set to the load value. You can set the counter as follows:
● With the L_DIRECT input parameter of the FC_CNT_CTRL
● With an external signal either via input 1I2 (2I2) or via the input in conjunction with the zero mark of the encoder.
This section describes the different methods and the time sequence for setting a counter.
Load value
Any number within the count range can be set for the load value.
The load value is interpreted according to the selected count range. If, for example, you specify FFFF FFFF H as the load value, this is interpreted as 4 294 967 295 within the count range 0 to +32 bit and as -1 within the count range -31 to +31 bit.
The load value is entered in the DB of the FC°CNT_CTRL.
Setting the counter via the user program
Regardless of the external events, you can set a counter with the FC°CNT_CTRL by means of the L_DIRECT input parameter. This is also possible while a count is in progress.
The input parameter L_DIRECT is reset by FC CNT_CTRL once the job is successful completed.
If you set the counter via the FC_CNT_CTRL call, setting cannot trigger a hardware interrupt.
Counter module FM 450-1
Manual, 02/2014, A5E03648739-02
83
Modes, settings, parameters and commands
8.12 Initiating a process interrupt
Setting the counter with an external signal
The L_PREPAR input parameter prepares a new load value. You can choose between two different external signals with which you set a counter to the load value
● Only input 1I2 (2I2)
● Input 1I2 (2I2) and the zero mark of the encoder
You use the zero mark of the encoder if you want to synchronize the counter to a specific counter status at a specific point in your process. Hence you achieve greater precision in the count process.
The counter is set independent of the mode.
After setting the counter with an external signal, the STS_SYNC bit is set in the DB. The
STS_SYNC bit is cleared by the RES_SYNC bit.
Note
The synchronization of a counter with the zero mark only makes sense if the gate is open.
When setting a counter with an external signal, if you have only enabled one count direction, please note the following: When the door closes, only the current count direction is stored
(frozen). Hence it is possible for the counter to be synchronized in the opposite direction to the enabled count direction.
Hardware interrupt
Setting a counter with an external signal can be used to trigger a hardware interrupt.
84
Counter module FM 450-1
Manual, 02/2014, A5E03648739-02
Modes, settings, parameters and commands
8.12 Initiating a process interrupt
Setting counter with input 1I2 (2I2)
A counter can be loaded with the load value via a rising edge at input 1I2 (2I2).
You can specify the behavior of an FM°450-1 counter with a positive edge at input 1I2 (2I2) with the ENSET_UP and ENSET_DN variables in the DB of the FC_CNT_CTRL and by means of parameter assignment.
Bit
ENSET_UP set
ENSET_DN set
ENSET_UP and
ENSET_DN set
Behavior of the FM 450-1
The counter is only set in the case of up counting
The counter is only set in the case of down counting
Counter is set for up and down counting.
Parameter assignment
Parameter assignment
"single setting of counter"
Parameter assignment
"multiple setting of counter"
Behavior of the FM 450-1
The counter is set only at the first rising edge at input 1I2 (2I2).
If the counter is to be set again, you must first set ENSET_UP or
ENSET_DN again. The counter is then set again with the next positive edge at input 1I2 (2I2).
As long as ENSET_UP or/and ENSET_DN are set, the counter will be set with each rising edge at input 1I2 (2I2).
Note
It is imperative that you set one of the two variables, ENSET_UP or/and ENSET_DN, so that the relevant counter can be set via input 1I2 (2I2).
Counter module FM 450-1
Manual, 02/2014, A5E03648739-02
85
Modes, settings, parameters and commands
8.12 Initiating a process interrupt
Setting counter once with input 1I2 (2I2)
The following figure shows counter 1 being set once with input 1I2. The situation is analogous for counter 2 with input 2I2. In the case represented here, only ENSET_UP is set, i.e., the counter is set during up counting.
The relevant counter is set with the first rising edge at input 1I2, as long as ENSET_UP is set. If you want to set this counter again, first you must reset the relevant ENSET_UP and then set it again. Then the next positive edge at input 1I2 results in the counter being set.
Figure 8-7 Single setting of counter 1 with input 1I2
86
Counter module FM 450-1
Manual, 02/2014, A5E03648739-02
Modes, settings, parameters and commands
8.12 Initiating a process interrupt
Multiple setting of the counter with input 1I2 (2I2)
The following figure shows the multiple setting of counter 1with input 1I2. The situation is analogous for counter 2 with input 2I2. In the case represented here, only ENSET_UP is set, i.e., the counter is set during up counting.
The relevant counter is set with the first rising edge at input 1I2, as long as ENSET_UP is set. When you reset ENSET_UP you cannot set the counter with input 1I2. Only after you have set ENSET_UP again will the next positive edge at input 1I2 result in the setting of the counter.
Figure 8-8 Multiple setting of counter 1 with input 1I2
Setting the counter with the zero mark
If you assign the parameters for setting a counter with the zero mark of the encoder, the relevant counter is set with the rising edge of the zero mark.
Setting is only performed if input 1I2 (2I2) of the relevant counter is set at the time of the rising edge of the zero mark.
With the ENSET_UP and ENSET_DN variable is the DB of the FC CNT_CTRL and by assigning parameters, you specify the behavior of the respective FM 450-1 counter in the case of a rising edge of the zero mark.
Bit
ENSET_UP set
ENSET_DN set
ENSET_UP and
ENSET_DN set
Behavior of the FM 450-1 counter
The counter is only set in the case of up counting.
The counter is only set in the case of down counting.
Counter is set for up and down counting.
Counter module FM 450-1
Manual, 02/2014, A5E03648739-02
87
Modes, settings, parameters and commands
8.12 Initiating a process interrupt
Parameter assignment
Parameter assignment
"single setting of counter"
Parameter assignment
"multiple setting of counter"
Behavior of the FM 450-1 counter
The counter is set only at the first rising edge of the zero mark.
If the counter is to be set again, you must first set ENSET_UP or
ENSET_DN again (edge evaluation). The counter is then set again with the next rising edge of the zero mark.
As long as ENSET_UP and/or ENSET_DN are set, the counter will be set with each rising edge of the zero mark.
Note
It is imperative that you set one of the two variables, ENSET_UP or/and ENSET_DN and input 1I2 (2I2) so that the relevant counter can be set with the zero mark.
Single setting with the zero mark
The following figure shows counter 1 being set once with the zero mark. In the case represented here, only ENSET_UP is set, i.e., the counter is set during up counting.
The relevant counter is set with the first rising edge of the zero mark as long as ENSET_UP and input 1I2 are set.
If you want to set counter°1 again, you must reset ENSET_UP and then set it again. If input
1I2 is not set, setting is performed with the first zero mark after setting 1/2. If input 1I2 is set, setting takes place with the next zero mark.
The situation is analogous for counter 2 with input 2I2.
88
Figure 8-9 Single setting of counter 1 with the zero mark
Counter module FM 450-1
Manual, 02/2014, A5E03648739-02
Modes, settings, parameters and commands
8.12 Initiating a process interrupt
Multiple setting with the zero mark
The following figure shows multiple setting of counter 1 with the zero mark. In the case represented here, only ENSET_UP is set, i.e., the counter is set during up counting.
The relevant counter is set with each first rising edge of the zero mark as long as
ENSET_UP and input 1I2 are set.
The situation is analogous for counter 2 with input 2I2.
Figure 8-10 Multiple setting of counter 1 with the zero mark
Counter module FM 450-1
Manual, 02/2014, A5E03648739-02
89
Modes, settings, parameters and commands
8.12 Initiating a process interrupt
8.12
Introduction
Initiating a process interrupt
For the individual counters of the FM 450-1 you can set which events are to trigger a hardware interrupt during operation. For this purpose you parameterize the counter interrupts in the parameter assignment screen marks.
What is a hardware interrupt?
If a response is to be made to an event regardless of the cycle of the CPU, each counter of the FM 450-1 can trigger a hardware interrupt. The CPU then interrupts the cyclical program and handles the hardware interrupt OB.
Which events can trigger a hardware interrupt?
In the FM 450-1 count mode, the following events can trigger a hardware interrupt
(independently of each other for each of the two counters):
● Opening of the gate (in modes with HW or SW gate)
● Closing of the gate (in modes with HW or SW gate)
● Overflow
● Underflow
● Zero crossing
● Reaching comparison value 1 in the up direction
● Reaching comparison value 1 in the down direction
● Reaching comparison value 2 in the up direction
● Reaching comparison value 2 in the down direction
● Setting the counter with an external signal
You can select a random number of events for triggering hardware interrupts, as long as the boundary conditions are observed.
Enabling the hardware interrupt
When configuring the hardware, in the parameter assignment screen masks you enable the interrupts for the module and choose whether the module is to initiate a diagnostic and/ or a hardware interrupt.
90
Counter module FM 450-1
Manual, 02/2014, A5E03648739-02
Modes, settings, parameters and commands
8.12 Initiating a process interrupt
Hardware interrupt OB, OB 4x
If a hardware interrupt occurs, the user program is interrupted, the data are transferred from the module to the start information of the OB 4x and the OB 4x is called. The hardware interrupt is acknowledged by quitting the OB 4x.
If no OB 4x is programmed the CPU goes into STOP. If you then switch back to RUN, the hardware interrupt requirements are deleted.
Start information
The temporary variable OB4x_POINT_ADDR is described in the start information of the
OB4x.
The OB4x_POINT_ADDR variable (bytes 8 - 11) consists of four bytes. The information on the event that initiated the hardware interrupt is entered into these four bytes. The following table shows which bits are set for which interrupt. All bits not listed have no meaning and are zero.
Byte
0
1
2
3
Bit
4
5
6
7
0
5
0
1
2
3
5
6
3
4
0
1
2
7
0
5
Significance: Interrupt in the case of...
Counter 1
Opening the gate
Closing the gate
Overflow
Underflow
Reaching comparison value 1 in the up direction
Reaching comparison value 1 in the down direction
Reaching comparison value 2 in the up direction
Reaching comparison value 2 in the down direction
Zero crossing
Setting of the counter
Counter 2
Opening the gate
Closing the gate
Overflow
Underflow
Reaching comparison value 1 in the up direction
Reaching comparison value 1 in the down direction
Reaching comparison value 2 in the up direction
Reaching comparison value 2 in the down direction
Zero crossing
Setting of the counter
Counter module FM 450-1
Manual, 02/2014, A5E03648739-02
91
Modes, settings, parameters and commands
8.12 Initiating a process interrupt
Lost hardware interrupt
If an event occurs that is to trigger a hardware interrupt and the same previous event has not yet been acknowledged, no further hardware interrupt is triggered; the hardware interrupt is lost.
This can result in the diagnostic interrupt "hardware interrupt lost" depending on the parameters assigned.
Default setting
No hardware interrupt is assigned in the default setting.
92
Counter module FM 450-1
Manual, 02/2014, A5E03648739-02
Encoder signals and their evaluation
9.1 Chapter overview
Chapter overview
This chapter describes:
● which encoders you can connect to the counter module
● the time profile of the encoder signals
● the multiple evaluation of encoder signals by the counter module
● how the module monitors the various encoder signals
● which signals can be assigned input filter parameters.
9
Counter module FM 450-1
Manual, 02/2014, A5E03648739-02
93
Encoder signals and their evaluation
9.5 Signal evaluation
9.2
Introduction
Encoders which can be connected
The counter module can process rectangular count signals which were generated by incremental encoders or pulse generators.
Incremental encoders scan a barcode to generate rectangular electrical pulses. They differ in terms of pulse amplitude and number of signals.
Pulse generators such as light barriers or proximity switches (BEROs) return only a rectangular signal at a specific amplitude.
Connecting different encoders
The counter module supports different encoders which return pulses for the count signals.
The table shows these encoders and the corresponding signals.
Table 9- 1 Encoders which can be connected
Encoders
5-V incremental encoder
24-V incremental encoder
24-V pulse encoder
24-V proximity switch
Signal
Differential signals A and /A, B and /B, N and /N
A*, B* and N*
24-V with directional signal
24 V without directional signal
94
Counter module FM 450-1
Manual, 02/2014, A5E03648739-02
Encoder signals and their evaluation
9.5 Signal evaluation
9.3 5-V differential signals
Count signals of 5-V incremental encoders
RS422 signals returned by the 5-V incremental encoder to the module:
● A and /A
● B and /B
● N and /N
The signals /A, /B and /N are the inverted signals of A, B and N. Signals A and B are phaseshifted by 90°.
The tracks A and B of 5-V incremental encoders are used for counting. Track N is used to initialize the counter with the load value, if programmed accordingly.
Encoders featuring these six signals are symmetrical encoders.
The diagram shows the time profile of the encoder signals:
Figure 9-1 Signals of the 5-V incremental encoder
The module detects the count direction by evaluating the ratio of signals A and B. The
diagrams in the chapter "Signal evaluation (Page 100)" show which edges of signals A and B
are counted in down or up direction.
Changing the count direction
You can change the count direction using the "Count direction normal" and "Count direction inverted" parameters without having to modify the wiring.
Counter module FM 450-1
Manual, 02/2014, A5E03648739-02
95
Encoder signals and their evaluation
9.5 Signal evaluation
Monitoring encoder signals
The module monitors the cable connection, and detects wire-break or short-circuit.
You can define which of the three signal pairs to include in monitoring in your program.
There is no need to wire any unused signal pairs, if you have disabled the corresponding diagnostics functions in the program (monitoring.)
An error state at all three signals indicates a defective encoder, or a short-circuit at the
"5.2 V DC" encoder supply, or a missing encoder.
When programming is completed, and the module detects an error, the error information will be written to the diagnostics data records DS0 and DS1. This situation my lead to a diagnostics interrupt if programmed accordingly.
Coding plug (only for FM 350-1)
To operate this encoder, insert the coding plug in position A.
96
Counter module FM 450-1
Manual, 02/2014, A5E03648739-02
Encoder signals and their evaluation
9.5 Signal evaluation
9.4 24-V signals
Count signals returned by 24-V encoders
24-V incremental encoders
The 24-V incremental encoder returns the 24-V signals A*, B* and N* to the module. The A* and B* signals are phase-shifted by 90°.
24-V signals are marked with an asterisk "*" character.
The tracks A* and B* of a 24-V incremental encoder are used for counting. Track N* is used to initialize the counter with the load value, if programmed accordingly.
Encoders which do not return inverted signals asymmetrical encoders.
The diagram shows the time profile of the encoder signals:
Figure 9-2 Signals of the 24-V incremental encoder
The module detects the count direction by evaluating the ratio of signals A* and B*. The
diagrams in the chapter "Signal evaluation (Page 100)" show which edges of the A* and B*
signals are incremented or decremented.
You can program the inputs of 24-V encoder signals for the connection of source outputs, or push-pull outputs, or sink outputs. For further information, refer to the encoder manual.
You can change the count direction using the "Count direction normal" and "Count direction inverted" parameters without having to modify the wiring.
Counter module FM 450-1
Manual, 02/2014, A5E03648739-02
97
Encoder signals and their evaluation
9.5 Signal evaluation
24-V pulse encoders without/with direction signal
Encoders such as proximity switches (BERO) or light barriers return only a count signal which you wire to terminal A* of the front connector. in additional, you can wire a signal for direction detection to terminal B* of the relevant counter. If your encoder does not return a corresponding signal, you can wire a corresponding ID signal you generate within the user program, or use a corresponding process signal.
The diagram shows the time profile of the encoder signals, and the resultant count pulses
Figure 9-3 Signals of a 24-V pulse generator with direction signal
Programming the encoder inputs
The count direction is defined by programming the encoder inputs. The diagram shows a change of the count direction based on parameter settings.
Table 9- 2 Count direction determined by input parameters
Programming current sourcing, push-pull current sinking
Terminal B* not wired
24 V connected not wired
Short-circuited to ground
Count direction
Up
Down
Down
Up
Set the "24 V pulse and direction" parameter for the selected encoder.
You can not reverse the direction of these count signal by inverting the B* signal.
Note
This type of evaluation may cause the count value to "drift off" at the edges if count signal oscillates, as all signals are added.
98
Counter module FM 450-1
Manual, 02/2014, A5E03648739-02
Encoder signals and their evaluation
9.5 Signal evaluation
Input filters for the 24-V count inputs
For the purpose of suppressing interference, you can parameterize input filters with a uniform filter time for the 24 V inputs A*, B* and N* and for the digital inputs. Input filters available:
Table 9- 3 Input filters
Features Input filter 2
Typical input delay
Maximum count frequency
Minimum pulse width of count signals
Input filter 1
(default)
1 µs
200 kHz
2.5 µs
15 µs
20 kHz
25 µs
Monitoring encoder signals
The 24-V count signals are not monitored to detect wire-breaks or short-circuits.
Coding plug (only for FM 350-1)
To operate this encoder, insert the coding plug in position D.
Counter module FM 450-1
Manual, 02/2014, A5E03648739-02
99
Encoder signals and their evaluation
9.5 Signal evaluation
9.5
Overview
Signal evaluation
The counter module supports the count of signal edges. It usually evaluates the edge at A
(A*) (single evaluation). Options in the program of increasing the resolution:
● Single evaluation
● Double evaluation
● Quadruple evaluation
Multiple evaluation is only supported for 5-V incremental encoders which return the A and B signal with a phase shift of 90°, for 24-V incremental 24 V encoders with a phase shift of 90° of the A* and B* signals.
Single evaluation
In this mode, the module evaluates only one edge of signal A. Up count pulses are recorded at the positive edge at track A, and if track B is low. Down count pulses are recorded at the positive edge at track A, and if track B is low.
The diagram shows a single evaluation of signals:
Figure 9-4 Single evaluation
100
Counter module FM 450-1
Manual, 02/2014, A5E03648739-02
Encoder signals and their evaluation
9.5 Signal evaluation
Double evaluation
Double evaluation refers to the evaluation of the positive and negative edges of signal A.
The logic level at signal B determines the count direction, i.e. the up or down count pulse.
The diagram shows the double evaluation of signals:
Figure 9-5 Double evaluation
Quadruple evaluation
Quadruple evaluation refers to the evaluation of the positive and negative edges of signals A and B. The logic level at the signals A and B determines the count direction, i.e. the up or down count pulse.
The diagram shows quadruple evaluation of signals:
Default
Figure 9-6 Quadruple evaluation
Single evaluation is set by default.
Counter module FM 450-1
Manual, 02/2014, A5E03648739-02
101
Encoder signals and their evaluation
9.5 Signal evaluation
102
Counter module FM 450-1
Manual, 02/2014, A5E03648739-02
Assignment of the DB
10
10.1 Assignment of the DB
DB for the FC°CNT_CTRL
All data associated with a channel of the module are located in the DB of FC CNT_CTRL.
The data structure and the length of the DB is determined by the variable declaration in
FC CNT_CTRL. Prior to configuring the module, the DB must have the following valid data
assigned to it (see section "Program (Page 45)"):
● Module address (address 6.0)
● Channel starting address (address 8.0)
● User data length (address 12.0)
The DB was generated from the UDT 1 as a data block with associated, user-specific data
type (see section "Program (Page 45)"). The DB assignments resulting from this are shown
below.
Table 10- 1 Assignment of the DB
12.0
13.0
14.0
18.0
22.0
Address
0.0
4.0
5.0
6.0
8.0
26.0
26.1
26.2
26.3
26.4
26.5
26.6
26.7
27.0
27.1
Variable
AR1_BUFFER
FP
RESERVED
MOD_ADR
CH_ADR
U_D_LGTH
A_BYTE_0
LOAD_VAL
1
CMP_V1
1
CMP_V2
1
A_BIT0_0
TFB
A_BIT0_2
A_BIT0_3
A_BIT0_4
A_BIT0_5
A_BIT0_6
A_BIT0_7
ENSET_UP
1
ENSET_DN
1
Data type
DWORD
BYTE
BYTE
WORD
DWORD
BYTE
BYTE
DINT
DINT
DINT
BOOL
BOOL
BOOL
BOOL
BOOL
BOOL
BOOL
BOOL
BOOL
BOOL
FALSE
FALSE
FALSE
FALSE
FALSE
FALSE
FALSE
FALSE
FALSE
FALSE
Initial value Comment
DW#16#0 AR1 buffer
B#16#0
B#16#0
W#16#0
DW#16#0
Flag byte
Reserved
Module address
Channel address
B#16#0
B#16#0
L#0
L#0
L#0
User data length
Reserved
New load value (write user)
New comparison value 1 (write user)
New comparison value 2 (write user)
Reserved
Test enabled
Reserved
Reserved
Reserved
Reserved
Reserved
Reserved
Enable setting in up direction (write user)
Enable setting in down direction (write user)
Counter module FM 450-1
Manual, 02/2014, A5E03648739-02
103
Assignment of the DB
10.1 Assignment of the DB
Address
40.0
41.0
41.1
41.2
41.3
41.4
41.5
41.6
41.7
29.6
29.7
30.0
34.0
38.0
42.0
43.0
43.1
43.2
43.3
43.4
43.5
43.6
28.2
28.3
28.4
28.5
28.6
28.7
29.0
29.1
29.2
29.3
29.4
29.5
27.2
27.3
27.4
27.5
27.6
27.7
28.0
28.1
Data type
BOOL
BOOL
DINT
DINT
WORD
BYTE
BOOL
BOOL
BOOL
BOOL
BOOL
BOOL
BOOL
BOOL
BYTE
BOOL
BOOL
BOOL
BOOL
BOOL
BOOL
BOOL
BOOL
BOOL
BOOL
BOOL
BOOL
BOOL
BOOL
BOOL
BOOL
BOOL
BOOL
BOOL
BOOL
BOOL
BOOL
BOOL
BOOL
BOOL
BOOL
BOOL
Variable
A_BIT1_2
A_BIT1_3
A_BIT1_4
A_BIT1_5
A_BIT1_6
A_BIT1_7
CTRL_DO0
1
CTRL_DO1
1
A_BIT2_2
A_BIT2_3
A_BIT2_4
A_BIT2_5
A_BIT2_6
A_BIT2_7
DIAG
E_BIT0_3
DATA_ERR
1
E_BIT0_5
E_BIT0_6
PARA
1
E_BYTE_0
STS_RUN
STS_DIR 1
STS_ZERO
1
STS_OFLW
1
STS_UFLW
1
STS_SYNC
1
STS_GATE
1
A_BIT3_0
A_BIT3_1
A_BIT3_2
A_BIT3_3
A_BIT3_4
A_BIT3_5
A_BIT3_6
A_BIT3_7
LATCH_LOAD 1
ACT_CNTV
1
DA_ERR_W
1
OT_ERR_B
1
E_BIT0_0
STS_TFB
Initial value Comment
B#16#0
FALSE
FALSE
FALSE
FALSE
FALSE
FALSE
FALSE
FALSE
FALSE
L#0
L#0
W#16#0
B#16#0
FALSE
FALSE
FALSE
FALSE
FALSE
FALSE
FALSE
FALSE
FALSE
FALSE
FALSE
FALSE
FALSE
FALSE
FALSE
FALSE
FALSE
FALSE
FALSE
FALSE
FALSE
FALSE
FALSE
FALSE
FALSE
FALSE
FALSE
FALSE
Reserved
Reserved
Reserved
Reserved
Reserved
Reserved
Enable digital output DO0 (write user)
Enable digital output DO1 (write user)
Reserved
Reserved
Reserved
Reserved
Reserved
Reserved
Reserved
Reserved
Reserved
Reserved
Reserved
Reserved
Reserved
Reserved
Current load or latch value (read user)
Current count value (read user)
Data error word (read user)
Operator error byte (read user)
Reserved
Status test free
Reserved
Reserved
Data error bit (read user)
Reserved
Reserved
Module parameters assigned (read user)
Reserved
Status, counter working
Status count direction (read user)
Status zero crossing (read user)
Status overflow (read user)
Status underflow (read user)
Status counter synchronized (read user)
Status internal gate (read user)
104
Counter module FM 450-1
Manual, 02/2014, A5E03648739-02
Assignment of the DB
10.1 Assignment of the DB
Address Variable Data type Initial value Comment
54.5
54.6
54.7
55.0
56.0
56.1
56.2
56.3
54.0
54.1
54.2
54.3
54.4
43.7
44.0
44.1
44.2
44.3
44.4
44.5
44.6
44.7
45.0
45.1
45.2
45.3
45.4
STS_SW_G
1
STS_SET
1
STS_LATCH
1
STS_STA
1
STS_STP
1
STS_CMP1
1
STS_CMP2
1
STS_COMP1
1
STS_COMP2 1
E_BIT3_0
E_BIT3_1
E_BIT3_2
E_BIT3_3
E_BIT3_4
BOOL
BOOL
BOOL
BOOL
BOOL
BOOL
BOOL
BOOL
BOOL
BOOL
BOOL
BOOL
BOOL
BOOL
FALSE
FALSE
FALSE
FALSE
FALSE
FALSE
FALSE
FALSE
FALSE
FALSE
FALSE
FALSE
FALSE
FALSE
Status SW gate (read user)
Status digital input SET (read user)
Reserved
Status digital input START (read user)
Status digital input STOP(read user)
Status output comparison value 1 (read user)
Status output comparison value 2 (read user)
Reserved
Reserved
Reserved
Reserved
Reserved
Reserved
Reserved
45.5
45.6
45.7
46.0
E_BIT3_5
E_BIT3_6
E_BIT3_7
ACT_CMP1
1
BOOL
BOOL
BOOL
DINT
FALSE
FALSE
FALSE
L#0
Reserved
Reserved
Reserved
Current comparison value 1 (read user)
50.0 ACT_CMP2
1
DINT L#0
The following diagnostics data are entered by the FC_DIAG_INF
Current comparison value 2 (read user)
56.4
56.5
56.6
56.7
57.0
57.1
57.2
MDL_DEFECT
INT_FAULT
EXT_FAULT
PNT_INFO
FLD_CNNCTR
NO_CONFIG
CONFIG_ERR
RACK_FLT
PROC_FLT
EPROM_FLT
BOOL
BOOL
BOOL
BOOL
EXT_VOLTAGE BOOL
BOOL
BOOL
BOOL
MDL_TYPE BYTE
SUB_MDL_ERR BOOL
COMM_FAULT BOOL
MDL_STOP BOOL
WTCH_DOG_FAU
LT
INT_PS_FLT
BOOL
BOOL
PRIM_BATT_FLT BOOL
BCKUP_BATT_FL
T
BOOL
RESERVED_2 BOOL
BOOL
BOOL
BOOL
FALSE
FALSE
FALSE
FALSE
FALSE
FALSE
FALSE
FALSE
B#16#0
FALSE
FALSE
FALSE
FALSE
FALSE
FALSE
FALSE
FALSE
FALSE
FALSE
FALSE
Module faults
Internal error
External error
Channel error
Auxiliary voltage fault
Front connectors
Missing parameters
Faulty parameters
Module type
Incorrect/missing interface module
Communication error
RUN/STOP operating status indicator
Watchdog (FM)
Internal power supply fault
Battery monitoring
Backup fault
Reserved
Module rack fault
CPU fault
EPROM fault
Counter module FM 450-1
Manual, 02/2014, A5E03648739-02
105
Assignment of the DB
10.1 Assignment of the DB
Address Variable Data type Initial value Comment
61.0
61.1
61.2
61.3
61.4
61.5
61.6
61.7
62.0
62.1
62.2
62.3
57.3
57.4
57.5
57.6
57.7
58.0
59.0
60.0
RAM_FLT
ADU_FLT
FUSE_FLT
HW_INTR_FLT
RESERVED_3
CH_TYPE
LGTH_DIA
CH_NO
GRP_ERR1
GRP_ERR2
D_BIT7_2
D_BIT7_3
D_BIT7_4
D_BIT7_5
D_BIT7_6
D_BIT7_7
CH1_SIGA
CH1_SIGB
CH1_SIGZ
CH1_BETW
BOOL
BOOL
BOOL
BOOL
BOOL
BYTE
BYTE
BYTE
BOOL
BOOL
BOOL
BOOL
BOOL
BOOL
BOOL
BOOL
BOOL
BOOL
BOOL
BOOL
FALSE
FALSE
FALSE
FALSE
FALSE
B#16#0
B#16#0
B#16#0
FALSE
FALSE
FALSE
FALSE
FALSE
FALSE
FALSE
FALSE
FALSE
FALSE
FALSE
FALSE
RAM fault
ADC/DAC fault
Fuse
Hardware interrupt lost
Reserved
Channel type
Diagnostics data length per channel
Channel number
Group error channel 1
Group error channel 2
DS1 byte 7 bit 2
DS1 byte 7 bit 3
DS1 byte 7 bit 4
DS1 byte 7 bit 5
DS1 byte 7 bit 6
DS1 byte 7 bit 7
Channel 1, error signal A
Channel 1, error signal B
Channel 1, error zero signal
Channel 1, error between channels
64.0
64.1
64.2
64.3
64.4
64.5
64.6
64.7
65.0
62.4
62.5
62.6
62.7
63.0
CH1_5V2
D_BIT8_5
D_BIT8_6
D_BIT8_7
D_BYTE9
CH2_SIGA
CH2_SIGB
CH2_SIGZ
CH2_BETW
CH2_5V2
D_BIT10_5
D_BIT10_6
D_BIT10_7
D_BYTE11
BOOL
BOOL
BOOL
BOOL
BYTE
BOOL
BOOL
BOOL
BOOL
BOOL
BOOL
BOOL
BOOL
BYTE
FALSE
FALSE
FALSE
FALSE
B#16#0
FALSE
FALSE
FALSE
FALSE
FALSE
FALSE
FALSE
FALSE
B#16#0
Channel 1, 5.2 V encoder supply fault
DS1 byte 8 bit 5
DS1 byte 8 bit 6
DS1 byte 8 bit 7
DS1 byte 9
Channel 2, error signal A
Channel 2, error signal B
Channel 2, error zero signal
Channel 2, error between channels
Channel 2, 5.2V encoder supply fault
DS1 byte 10 bit 5
DS1 byte 10 bit 6
DS1 byte 10 bit 7
DS1 byte 11
66.0
67.0
D_BYTE12
D_BYTE13
BYTE
BYTE
B#16#0
B#16#0
DS1 byte 12
DS1 byte 13
68.0
69.0
D_BYTE14
D_BYTE15
BYTE
BYTE
B#16#0
B#16#0
DS1 byte 14
DS1 byte 15
1
Variables in the DB that you have to/can enter or read out during work with the FM
106
Counter module FM 450-1
Manual, 02/2014, A5E03648739-02
Errors and diagnostics
11
11.1 Chapter overview
Chapter overview
Errors can occur owing to operator errrs or incorrect wiring which the module must communicate to the user.
The errors and faults are divided into the following classes on the module:
● Faults displayed by the diagnostics LEDs that indicate internal and external module faults.
● Faults that can trigger a diagnostics interrupt.
● Operator errors caused by incorrect operation.
The different classes of errors are indicated and displayed in different positions and must be acknowledged in different ways.
This chapter describes
● which errors and faults can occur,
● where these errors and faults are displayed and
● how you acknowledge them.
Counter module FM 450-1
Manual, 02/2014, A5E03648739-02
107
Errors and diagnostics
11.5 Operator error
11.2 Faults indicated via the diagnostics LEDs
Where are the faults displayed?
Faults are indicated by the two red diagnostics LEDs:
● The INTF diagnostics LED displays internal faults of the module.
● The EXTF diagnostics LEDdisplays external faults to the cable connections.
Which fauts are displayed?
The following faults are indicated by the two red diagnostics LEDs lighting up:
Fault type/LED
Internal fault
INTF diagnostics LED
External fault
EXTF Diagnostics LED
Cause of fault
Fault in EPROM TEST
Fault in RAM TEST
Watchdog has responded
Process interrupt lost
Auxilliary voltage 1L+/1M is not connected or
24 VDC encoder supply is short circuited
5.2 VDC encoder supply short circuited or overloaded
5 V encoder signals faulty (wire breakage, short circuit, cable missing)
Correction
Module replacement
Module replacement
Module replacement
Is acknowledged by processing the process interrupt.
Correct connection
Correct connection
Correct connection
Initiation of a diagnostics interrupt
All faults, except for the fault in the EPROM test can initiate a diagnostics interrupt if you have enabled the diagnostics interrupt in the relevant parameter assignment screen form.
You will find out which fault has caused the LED to light up from the diagnostic data records
DS0 and DS1. The assignment of the diagnostics data records DS0 and DS1 is described in the next section.
108
Counter module FM 450-1
Manual, 02/2014, A5E03648739-02
Errors and diagnostics
11.5 Operator error
11.3 Initiation of diagnostics interrupts
What is a diagnostics interrupt?
If the user program is to respond to an internal or external fault, you can set the parameters for a diagnostic interrupt that will break off the cyclical program of the CPU device and calls the diagnostics interrupt OB (OB 82).
Which events can initiate a diagnostic interrupt?
The following events can initiate a diagnostic interrupt:
● The external auxiliary 1L+/1M voltage is faulty.
● 5.2 VDC encoder supply short circuited or overloaded.
● The module parameters are incorrectly assigned.
● Watchdog timeout
● RAM defective
● Hardware interrupt lost
● Signal A faulty (wire breakage, short circuit, cable missing)
● Signal B faulty (wire breakage, short circuit, cable missing)
● Signal N faulty (wire breakage, short circuit, cable missing)
Enabling the diagnostic interrupt
You disable or enable the interrupts for the module and you choose whether the module is to initiate a diagnostic interrupt and/or a hardware interrupt.
Responses to a diagnostic interrupt
If an event occurs that can trigger a diagnostic interrupt, the following happens:
● The diagnostic information is stored in the diagnostic data records DS0 and DS1 on the module.
● An error LED lights up.
● The diagnostic interrupt OB is called (OB82).
● Diagnostic data record DS0 is entered in the start information of the diagnostic interrupt
OB.
● The count process continues unchanged.
If no OB82 has been programmed, the CPU goes into STOP.
Counter module FM 450-1
Manual, 02/2014, A5E03648739-02
109
Errors and diagnostics
11.5 Operator error
Diagnostic Data Records DS0 and DS1
The information as to which event triggered a diagnostic interrupt is stored in diagnostic data records DS0 and DS1. Diagnostics data record DS0 consists of 4 bytes; DS1 consists of
12 bytes, the first 4 bytes of which are identical to DS0.
Reading the data record from the module
Diagnostic data record DS0 is automatically transferred to the start information when the diagnostic OB is called. These four bytes are stored there in the local data element
(bytes 8-11) of OB 82.
You can read out the diagnostic data record DS 1 and hence also the contents of DS0 from the module using FC DIAG_INF. This is only useful if DS0 signals an error in one channel.
1
2
3
Assignment of the Diagnostic Data Record DS0 and the Start Information
The table below shows the assignment of the diagnostic data record DS0 in the start information. All bits not listed have no meaning and are zero.
Table 11- 1 Assignment of diagnostic data record DS0
Byte
0
Bit
0
1
Meaning
Module error
Internal error
2
3
3
3
6
4
7
0 ... 3
4
External error
Error in one channel
External auxiliary voltage faulty
Faulty parameter assignment
Type class
Channel information
Watchdog timeout
RAM defective
Hardware interrupt lost
Remark
Is set at each diagnostic event.
Is set for all internal faults:
•
Fault in RAM TEST
•
Watchdog timeout
•
Lost hardware interrupt
Is set for all external faults:
• Auxiliary voltage 1L+/1M is not connected or 5.2 VDC encoder supply is short circuited
•
5.2 VDC encoder supply short circuited or overloaded.
• 5V signals faulty
•
Faulty parameter assignment
1 is always assigned for internal and external faults.
Always assigned with 8.
Always assigned with 1.
Event no.
8:x:00
8:x:01
8:x:02
8:x:03
8:x:04
8:x:07
8:x:33
8:x:43
8:x:46
110
Counter module FM 450-1
Manual, 02/2014, A5E03648739-02
Errors and diagnostics
11.5 Operator error
Diagnostic data record DS1
Diagnostic data record DS 1 consists of 12 bytes. The first 4 bytes are identical to diagnostic data record DS0. The following table shows the assignment of the remaining bytes. All bits not listed have no meaning and are zero. This data record is entered into DB 1 from DW54 with the FC DIAG_INF.
Table 11- 2 Assignment of the bits of bytes 4 to 12 of the diagnostic data record DS1
5
6
7
Byte
4
8
9
10
11
Bit
0 ... 6
7
0 ... 7
0 ... 7
0
0
1
2
4
0
1
2
4
Meaning
Channel type
Other channel types
Diagnostic information length
Number of channels
Channel fault vector
Signal A - faulty channel 1
Signal B - faulty channel 1
Signal N faulty channel 1
5.2V encoder supply faulty channel 1
Reserved
Signal A - faulty channel 2
Signal B - faulty channel 2
Signal N faulty channel 2
5.2V encoder supply faulty channel 2
Reserved
Remark
76H is always assigned.
0 is always assigned.
Always allocated to CH.
2 is always assigned.
Bit 0 = 1: Fault on channel 1
Bit 1 = 1: Fault on channel 2
Event no.
8:x:B0
8:x:B1
8:x:B2
8:x:B4
8:x:B0
8:x:B1
8:x:B2
8:x:B4
How does the diagnostic text appear in the diagnostic buffer?
If you want to enter the diagnostic message in the diagnostic buffer, you must call the
SFC 52 (Enter user-specific message in the diagnostic buffer" in the user program. The event number of the diagnostic message in each case is specified in the input parameter
EVENTN. The interrupt is entered in the diagnostic buffer with x=1 as incoming and x=0 as outgoing. The diagnostic buffer contains the relevant diagnostic text in the "Meaning" column as well as the time of the entry.
Default setting
The diagnostic interrupt is disabled in the default setting.
Counter module FM 450-1
Manual, 02/2014, A5E03648739-02
111
Errors and diagnostics
11.5 Operator error
11.4 Data error
When do data errors occur?
If new parameters are transferred to the module, the FM 450-1 checks these parameters. If errors occur during this check, the module reports these data errors.
Wrong parameters are not accepted by the module.
Where are data errors indicated?
The FC CNT_CTRL enters the data errors in DB1 with the error numbers. You can access this data word via the variable name "DA_ERR_W" in the user program The following table shows the numbers of the data errors and the significance of these errors.
Table 11- 3 Data error numbers and their significance
No. Meaning
0 No fault
201 Value too great for receiver selection
202 Value too great for the diagnostics of the pair of signals
203 Value too great for the evaluation of the signals
204 Value too great for the input filter of the 24V count signals
205 Value too great for the input filters of the digital inputs
206 Reversing the direction not permitted
207 Value too great for the behavior of digital output 1Q0 (2Q0)
208 Value too great for the behavior of digital output 1Q1 (2Q1)
209 Pulse duration wrong or too long
211 Wrong mode selected
212 No gate or both gates specified
215 When assigning the process interrupt "Reaching the comparison value in the up and/or down count direction" parameters a different count direction was specified than the parameter assignment for the behavior of the outputs "Output active for on pulse duration in up and/or down direction". The directions must match.
216 Gate control interrupts are only possible for modes with gate control
217 No interrupt on reaching the comparison values is permitted for behavior of the digital outputs
"active between comparison value and overflow" or "active between comparison value and underflow".
How are data errors acknowledged?
Correct the values for the parameters to comply with the specifications. Transfer the corrected set of parameters to the FM 450-1 again. This again checks the parameters and deletes the data error in DB 1.
112
Counter module FM 450-1
Manual, 02/2014, A5E03648739-02
Errors and diagnostics
11.5 Operator error
11.5 Operator error
When do operator errors occur?
Operator errors occur if you operate the module incorrectly by specifying the wrong control signals.
Where are operator errors indicated?
FC CNT_CTRL enters the operator error numbers in DB1. You can access this data word via the variable name "OT_ERR_B" in your program.
Which operator errors exist?
The table below shows the possible numbers of operator errors and their meaning.
Table 11- 4 Operator error numbers and their meaning
Error code
0
1
2
4
Meaning
No fault
Mode cannot be started using the SW gate.
Mode cannot be aborted.
Permitted only if OD is active
How are operator errors acknowledged?
Acknowledge the error with parameter OT_ERR_A in DB 1.
Counter module FM 450-1
Manual, 02/2014, A5E03648739-02
113
Errors and diagnostics
11.5 Operator error
114
Counter module FM 450-1
Manual, 02/2014, A5E03648739-02
Technical Data
12
12.1 General technical specifications
These general technical specifications are described in the manual /3/:
● Standards and certifications
● Electromagnetic compatibility
● Shipping and storage conditions
● Mechanical and climatic environment conditions
● Specifications for insulation tests, safety class, and degree of protection
Design Guidelines
SIMATIC products meet the requirements if you observe the design guidelines described in the manuals when installing and operating the equipment.
Counter module FM 450-1
Manual, 02/2014, A5E03648739-02
115
Technical Data
12.2 Technical Data
12.2 Technical Data
Technical data
Dimensions and Weight
Dimensions WxHxD (mm)
Weight
Voltages, currents, potentials
Auxiliary voltage 1L+/1M
•
Range, static
•
Range, dynamic
• Reverse polarity protection
2L+/2M load voltage
•
Range, static
•
Range, dynamic
• Reverse polarity protection
•
Electrical isolation
5 V encoder power supply
•
Output voltage
• Output current
24 V encoder power supply
•
Output voltage
• Output current
• Non-periodic overvoltage
Current consumption
•
From the backplane bus 5 V DC, max.
• From load voltage 1L+ (no load), max.
• From load voltage 2L+ (no load), max.
Power loss of the module
25x290x210
Approx. 650 g
24 VDC
20.4 ... 28.8 V
18.5 ... 30.2 V
Yes
24 VDC
20.4 ... 28.8 V
18.5 ... 30.2 V
Yes
Yes, toward all other voltages
5.2 V ± 2%
Maximum 300 mA per count channel, short-circuit proof
1L+ - 3 V
Maximum 300 mA per count channel, short-circuit proof
Value: 35 V
Duration: 500 ms
Recovery time: 50 s
Approx. 300 mA
Approx. 50 mA
Approx. 60 μA
Approx. 6 W
116
Counter module FM 450-1
Manual, 02/2014, A5E03648739-02
Technical Data
12.2 Technical Data
Status, interrupts, diagnostics
Status display
Interrupts
• Hardware interrupt
•
Diagnostic interrupt
Diagnostics functions
•
Fault indication for internal and external faults
• Reading diagnostics information
Yes, 14 green LEDs for status of CR, DIR, inputs and outputs
Yes, configurable
Yes, configurable
Yes
Yes, 2 red LEDs
Yes
Data to the count signals and the digital inputs and outputs (applies to both counters)
Counter inputs 5 V (A , /A; B, /B; N, /N)
• Level
In compliance with RS 422
•
Terminating resistor approx. 220 Ohms
•
Differential input voltage
Min. 0.5 V
• Maximum count frequency
500 kHz
No
• Electrical isolation toward S7-400 bus
Counter inputs 24 V (A*, B*, N*)
•
Low Level
- 30 ... + 5 V
• High level
+ 11 ... + 30 V
• Input current
Typically 9 mA
•
Minimum pulse width (maximum count frequency) ≥ 2.5 µs (200 kHz)
≥ 25 µs (20 kHz)
(configurable)
Digital inputs
• Low Level
- 28.8 ... + 5 V
•
High level
+ 11 ... + 28.8 V
•
Input current
Typically 9 mA
•
Minimum pulse width (maximum input frequency) ≥ 2.5 µs (200 kHz)
≥ 25 µs (20 kHz)
(configurable)
Counter module FM 450-1
Manual, 02/2014, A5E03648739-02
117
Technical Data
12.2 Technical Data
Data to the count signals and the digital inputs and outputs (applies to both counters)
Digital outputs
•
Supply voltage
2L+ / 2M
• Electrical isolation
Yes, toward all others except the digital inputs
• Output voltage
– High signal "1"
– Low signal "0"
Min. 2L+ - 1.5 V
Max. 3 V
•
Switching current
– Nominal value
– Range
0.5 A (Res./P.D. 5W Tungsten 24VDC)
5 mA to 0.6 A
•
Switching time
Max. 300 µs
• Cutoff voltage (inductive)
Limited to 2L+ -39V
•
Short-circuit proof
Yes
Note
Other relevant data, e.g. environmental conditions, are listed in Manual /1/.
118
Counter module FM 450-1
Manual, 02/2014, A5E03648739-02
Spare parts
Spare parts
13
The table lists all the spare parts for the FM 450-1 you can order for this module either additionally or at a later date.
Table 13- 1 Accessories and spare parts
Parts for the FM 450-1
Labeling sheet for the front connector, petrol blue
Labeling sheet for the front connector, light beige
Labeling sheet for the front connector, yellow
Labeling sheet for the front connector, red
Front connector (48-pin) with screw terminals
Front connector (48-pin) with spring-loaded terminals
Front connector (48-pin) with crimp snap-on terminals
Order number
6ES7492-2AX00-0AA0
6ES7492-2BX00-0AA0
6ES7492-2CX00-0AA0
6ES7492-2DX00-0AA0
6ES7492-1AL00-0AA0
6ES7492-1BL00-0AA0
6ES7492-1CL00-0AA0
Counter module FM 450-1
Manual, 02/2014, A5E03648739-02
119
Spare parts
120
Counter module FM 450-1
Manual, 02/2014, A5E03648739-02
References
14
Supplementary references
The table below lists all manuals to which reference is made in the present manual.
No. Title
/1/ SIMATIC; S7-400 Automation System; Installation
( http://support.automation.siemens.com/WW/view/en/1117849 )
/2/
/3/
SIMATIC; System software for the S7-300/400 system and standard functions
( http://support.automation.siemens.com/WW/view/en/44240604 )
SIMATIC; S7-400 Automation System S7-400 Module Data
( http://support.automation.siemens.com/WW/view/en/1117740 )
Order number
Part of package
6ES7498-8AA04-8AA0
Part of package
6ES7810-4CA07-8AW1
Counter module FM 450-1
Manual, 02/2014, A5E03648739-02
121
References
122
Counter module FM 450-1
Manual, 02/2014, A5E03648739-02
Glossary
Asymmetrical signals
Refers to two pulse sequences, phase-shifted by 90°, and with zero mark signal where applicable.
Configuration
Assignment of modules to racks, slots and addresses. Users configuring the hardware fill out a configuration table in STEP 7.
Double evaluation
In this mode, the module evaluates all positive edges of the pulses at track A and B of an incremental encoder.
Encoders
Encoders are used to for the precise recording of rectangular signals reflecting distances, positions, velocity, speed, dimensions, etc.
Encoders with asymmetrical output signals
These encoders return two differential pulse sequences with 90° phase-shift, including a zero mark signal where applicable.
Encoders with symmetrical output signals
These encoders return two differential pulse sequences with 90° phase-shift, including inverted signals to form a zero mark as required.
Function (FC)
According to IEC 1131-3 notations, this is a code block which does not contain static data. A function supports the transfer of parameters in a user program. Functions are thus particularly suitable for programming complex, recurrent functions
Function module (FM)
A module which relieves the CPU of the S7 automation system of process signal processing tasks which are critical in time or memory-intensive. As a rule, FMs use the internal communication bus for high-speed data exchange with the CPU. Examples of FM applications: Counting, positioning, controlling
Counter module FM 450-1
Manual, 02/2014, A5E03648739-02
123
Glossary
Incremental encoder
Incremental encoders are used to record distance, position, velocity, speed or weight units by counting small increments.
Increments per encoder revolution
Defines the number of increments the encoder outputs per revolution.
OD
The "output disable" (OD) signal is used in STOP and HOLD state to force all modules of an
S7 automation system to safe state. A safe state could be: all outputs are shut off, or supplied with a substitution value.
Power control
The power control unit controls the motor; its simplest form is a contactor relay circuit.
Proximity switch
A simple BERO switch, without directional information. The device returns only a single count signal. The counter records only the positive edges at signal A. The count direction is user-specific.
Pulse duration
The pulse duration setting defines the minimum on time of an output.
Push-pull
Quadruple evaluation
In this mode, the module evaluates all pulse edges at the tracks A and B of an incremental encoder.
SFC
Push-pull output of an encoder; supplies an active low signal to 0 V (ground) and an active high signal to +24 V.
An SFC (system function) is an integrated function of the CPU operating system. The SFC can be called in the STEP 7 user program as required.
Single evaluation
Refers to a the evaluation of positive edges of the pulses at track A of an incremental encoder.
124
Counter module FM 450-1
Manual, 02/2014, A5E03648739-02
Sinking output
Encoder output which returns an active low signal to 0 V (ground)
Sourcing output
Sourcing output of the encoder which returns an active high signal +24 V.
STOP
STOP as an international term, for example, as an operating command.
Glossary
STOPP
STOPP (German spelling) as a term used in the manual to define an action which is not a command.
Zero mark
The zero mark is positioned on the third track of an incremental encoder. It returns a zero mark signal after each rotation.
Zero mark signal
The incremental encoder returns one zero mark signal per revolution.
Counter module FM 450-1
Manual, 02/2014, A5E03648739-02
125
Glossary
126
Counter module FM 450-1
Manual, 02/2014, A5E03648739-02
Index
0
0 to +32 bit counting range, 75
2
24 VDC encoder power supply, 32
5
A
B
Basic parameter assignment, 67
Behavior of the digital outputs
C
Check list
Command
Open and close gate,
Set counter, commands
Count range -31 to +31 bit, 75
Counter module FM 450-1
Manual, 02/2014, A5E03648739-02
D
Diagnostic data record DS0
Diagnostic data record DS1
Digital input I0
Digital input I1
digital outputs
E
F
FCs
FM 450-1
Overview of operating modes, 66
127
Index
G
Gate stop function, 72, 74, 82
H
HW gate
Edge controlled opening and closing of, 81
Level controlled opening and closing of, 80
I
L
LEDs
M
modes
O
OB 4x
Open and close SW gate, 69, 71, 73
Opening and closing hardware gate, 74
128
P
parameter assignment screen forms
Parameter assignment screen forms
Pulse duration
Q
R
S
Select gate function, 69, 71, 73
Setting
Behavior of the digital outputs, 76
Count range,
Pulse duration,
Setting the counter
settings
Counter module FM 450-1
Manual, 02/2014, A5E03648739-02
Supply
SW gate
V
VDC 5.2 encoder power supply, 32
Z
Index
Counter module FM 450-1
Manual, 02/2014, A5E03648739-02
129
Index
130
Counter module FM 450-1
Manual, 02/2014, A5E03648739-02
advertisement
* Your assessment is very important for improving the workof artificial intelligence, which forms the content of this project
Related manuals
advertisement