advertisement
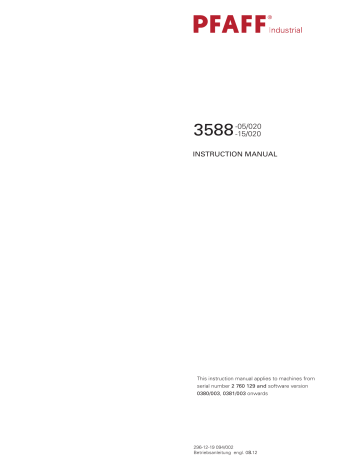
3588
-05/020
-15/020
INSTRUCTION MANUAL
This instruction manual applies to machines from serial number 2 760 129 and software version
0380/003, 0381/003 onwards
296-12-19 094/002
Betriebsanleitung engl. 0
8.12
This instruction manual applies to all versions and subclasses listed under
"Specifi cations".
Reprinting, copying or translation of PFAFF instruction manuals, whether in whole or in part, is not permitted without our prior permission and not without written indication of the source.
PFAFF Industriesysteme und Maschinen AG
Hans-Geiger-Str. 12 - IG Nord
D-67661 Kaiserslautern
Index
Contents ..................................................................................Page
Register 01
.................................................................................................5
1
Safety
1
.01 Directives
1
.02 General notes on safety ......................................................................................................... 7
1
.03 Safety
1
.04
1
.05
Important notes for the user .................................................................................................. 8
Notes for operating and technical staff .................................................................................. 9
1
.05.01 Operating
1
.05.02 Technical
1
.06 Danger
Register 02
.................................................................................................9
2
Proper
3
Specifi cations ..................................................................................................................... 12
4
Disposal of Machine .......................................................................................................... 13
5
5
.01
Transportation, packing and storage ................................................................................ 14
Transportation to customer‘s premises ............................................................................... 14
5
.02
5
.03
Transportation inside the customer‘s premises ................................................................... 14
Disposal of packing materials .............................................................................................. 14
5
.04 Storage
6
Explanation of symbols ..................................................................................................... 15
Register 03
...............................................................................................15
7
Controls
7
.01 On/off
7
.02 Stopptaster
7
.03 Switch for the loading function ............................................................................................ 18
7
.04 Double-start
7
.05 Handwheel
7
.06 Control
Register 04
............................................................................................... 19
8
Mounting and commissioning the machine .................................................................... 21
8
.01 Mounting
8
.02 Removing the transit support bracket .................................................................................. 22
8
.03 Mounting the spool holder ................................................................................................... 22
8
.04 Commisioning
8
.05 Switching the machine on/off .............................................................................................. 24
8
.06 PC
8
.07
8
.08
8
.09
Selecting the language ........................................................................................................ 25
Adjusting the control panel .................................................................................................. 26
Checking / adjusting the zero points .................................................................................... 27
Index
Contents ..................................................................................Page
Register 05
...............................................................................................31
9
Preparation
9
.01
9
.02
Inserting the needle ............................................................................................................. 33
Winding the bobbin thread, adjusting the thread tension .................................................... 34
9
.03
9
.04
9
.05
9
.06
Changing the bobbin / adjusting the bobbin thread tension ................................................ 35
Threading the needle / adjusting the needle thread tension ................................................ 36
Selecting the program number ............................................................................................ 37
Selecting / confi guring a sequence ...................................................................................... 38
9
.06.01 Selecting a sequence ........................................................................................................... 38
9
.06.02 Confi guring a sequence ....................................................................................................... 39
9
.07 Slide
9
.08
9
.08.01
9
.08.02
9
.09
9
.10
9
.11
Jig monitor (optional) ........................................................................................................... 41
Activating jig monitor ........................................................................................................... 41
Determining the jig code ..................................................................................................... 42
Setting the bobbin thread stitch counter .............................................................................. 43
Changing the part set .......................................................................................................... 44
Loading the pre-cut parts ..................................................................................................... 46
12
12
.01
12
.02
12
.03
12
.04
12
.05
12
.06
12
.07
12
.08
12
.09
Register 06
...............................................................................................45
10
Sewing
10
.01
10
.02
Automatic sewing mode ...................................................................................................... 48
Manual sewing mode .......................................................................................................... 49
10
.03 Sewing with sequences ....................................................................................................... 51
10
.04 Program
10
.05 Error
11
Input
11
.01
11
.02
Overview of the functions in the input mode ...................................................................... 54
Creating / editing seam programs ........................................................................................ 56
11
.02.01 Block
11
.02.02 Image
11
.02.03 Inserting
11
.02.04 Other
11
.03 Seam programming example ............................................................................................... 66
11
.04 Program
11
.05 Rights of access .................................................................................................................. 79
Register 07
...............................................................................................81
Care and maintenance ....................................................................................................... 83
Care and maintenance intervals ........................................................................................... 83
Cleaning the machine .......................................................................................................... 84
Cleaning the hook ................................................................................................................ 85
Cleaning the blower air fi lter ................................................................................................ 85
Cleaning the air fi lter of the air-fi lter/lubricator .................................................................... 86
Checking/adjusting the air pressure ..................................................................................... 86
Checking the oil level of the sewing head lubrication .......................................................... 87
Lubricating the needle bar frame eccentric ......................................................................... 87
Lubricating sewing jig feed .................................................................................................. 88
Index
Contents ..................................................................................Page
12
.10 Lubricating the pocket plate guide ....................................................................................... 89
13
Adjustment
13
.01
13
.02
Notes on adjustment ........................................................................................................... 90
Tools, gauges and other accessories for adjusting ............................................................. 90
13
.03 Abbreviations
13
.04
13
.05
Removing/inserting sewing head ......................................................................................... 91
Adjusting the sewing head .................................................................................................. 92
13
.05.01 Spacing between sewing head and bedplate ...................................................................... 92
13
.05.02 Sewing head position in relation to the bedplate ................................................................. 93
13
.05.03 Upper and lower toothed belt guards ................................................................................ 94
13
.05.04 Counterweight
13
.05.05 Preadjusting the needle height ............................................................................................ 96
13
.05.06 Zero
13
.05.07 Centering the needle in the needle hole .............................................................................. 98
13
.05.08 Zigzag stitch movement ....................................................................................................... 99
13
.05.09 Needle bar rise, hook-to-needle clearance, needle height and needle guard .................... 100
13
.05.10 Bobbin case opener stroke ................................................................................................ 102
13
.05.11 Counter presser lifting stroke............................................................................................. 103
13
.05.12 Counter presser height ...................................................................................................... 104
13
.05.13 Counter presser position ................................................................................................... 105
13
.05.14 Zigzag stitch width ............................................................................................................. 106
13
.05.15 Resting position of the roller lever / radial position of the control cam .............................. 107
13
.05.16 Thread catcher height ........................................................................................................ 108
13
.05.17 Thread catcher position and knife height ........................................................................... 109
13
.05.18 Knife
13
.05.19 Bobbin thread clamp spring ................................................................................................111
13
.05.20 Manual cutting test .............................................................................................................112
13
.05.21 Presser
13
.05.22 Bobbin
13
.05.23 Needle thread tension release ............................................................................................115
13
.05.24 Thread check spring and slack thread regulator ..................................................................116
13
.05.25 Sewing head lifting cylinder ................................................................................................117
13
.05.26 Hook
13
.06 Adjusting the folding, feed and stacker devices ................................................................. 120
13
.06.01 Aligning the sewing jig ....................................................................................................... 120
13
.06.02 Height of the pocket plate guide ........................................................................................ 121
13
.06.03 Aligning the pocket plate arm ............................................................................................ 122
13
.06.04 Aligning the pocket plate guide .......................................................................................... 123
13
.06.05 Front pocket plate position ................................................................................................. 125
13
.06.06 Monitoring the sewing jig feed .......................................................................................... 126
13
.06.07 Positioning the edge folding unit ........................................................................................ 127
13
.06.08 Aligning the die .................................................................................................................. 129
13
.06.09 Control sequence of the folder plates ................................................................................ 130
13
.06.10 Position of folder plates ..................................................................................................... 131
13
.06.11 Position of corner folders ................................................................................................... 132
13
.06.12 Aligning the seam in relation to the pocket........................................................................ 133
13
.06.13 Seam backtack distance .................................................................................................... 134
13
.06.14 Stacking
Index
Contents ..................................................................................Page
13
.06.15 Aligning the feed rollers ..................................................................................................... 136
13
.07 Shaping folder plates ......................................................................................................... 137
13
.07.01 New installation / self-manufacture of folder plates........................................................... 137
13
.07.02 Slanting the lateral folder plates ......................................................................................... 138
13
.08 Service
13
.08.01 Coldstart
13
.08.02 Loading / updating the operating program ......................................................................... 141
13
.09 Sewing motor adjustments ................................................................................................ 142
13
.10 Parameter
13
.10.01 Selecting and altering parameters. .................................................................................... 143
13
.10.02 List of parameters .............................................................................................................. 144
13
.10.03 Carriage start (NIS) ............................................................................................................. 149
13
.10.04 Zig-zag delay on/off ............................................................................................................ 150
13
.10.05 Stacker rolling time ............................................................................................................ 150
Register 08
............................................................................................. 149
14 Control
............................................................................................................................. 151
14
.01 Basic setting / Diagnosis / Pin assignment ........................................................................ 151
14
.01.01 Basic control unit A20 ........................................................................................................ 151
14
.01.02 Sewing
14
.01.03 Stepping motor drive A21 .................................................................................................. 155
14
.01.04 Stacker motor drive ............................................................................................................ 156
14
.01.05 AC-Line-Controller
14
.02 Description of the error messages .................................................................................... 157
14
.02.01 General
14
.02.02 CAN-errors
14
.02.03 Stitch generation error ....................................................................................................... 160
14
.02.04 Sewing motor errors .......................................................................................................... 161
14
.02.05 Errors – Stepping motor drive ............................................................................................ 162
14
.02.06 Errors - Stacker drive .......................................................................................................... 163
14
.03 List of outputs and inputs .................................................................................................. 164
14
.03.01 CAN-Nodes
14
.03.02 CAN-Nodes
14
.03.03 CAN-Nodes
14
.03.04 Special
14
.04 Boot
15
Pneumatics-switch
16
Circuit
Register 09
.............................................................................................131
Register 10
.............................................................................................131
Miscellaneous
Safety
1 Safety
1
.01
Directives
The machine has been constructed in accordance with the requirements listed in the
EC Declaration of Conformity and the Declaration of Incorporation.
In addition to this Instruction Manual, also observe all generally accepted, statutory and other regulations and legal requirements and all valid environmental protection regulations!
The regionally valid regulations of the social insurance society for occupational accidents or other supervisory organizations are to be strictly adhered to!
1
.02
General notes on safety
● This machine may only be operated by adequately trained operators and only after having completely read and understood the Instruction Manual!
● All Notes on Safety and Instruction Manuals of the motor manufacturer are to be read before operating the machine!
● The danger and safety instructions on the machine itself are to be followed!
● This machine may only be used for the purpose for which it is intended and may not be operated without its safety devices. All safety regulations relevant to its operation are to be adhered to.
● When exchanging sewing tools (e.g. needle, roller presser, needle plate and bobbin), when threading the machine, when leaving the machine unattended and during maintenance work, the machine is to be separated from the power supply by switching off the
On/Off switch or by removing the plug from the mains!
● Everyday maintenance work is only to be carried out by appropriately trained personnel!
● Repairs and special maintenance work may only be carried out by qualifi ed service staff or appropriately trained personnel!
● Work on electrical equipment may only be carried out by appropriately trained personnel!
● Work is not permitted on parts and equipment which are connected to the power supply!
The only exceptions to this rule are found in the regulations EN 50110.
● Modifi cations and alterations to the machine may only be carried out under observance of all the relevant safety regulations!
● Only spare parts which have been approved by us are to be used for repairs! We expressly point out that any replacement parts or accessories which are not supplied by us have not been tested and approved by us. The installation and/or use of any such products can lead to negative changes in the structural characteristics of the machine. We are not liable for any damage which may be caused by non-original parts.
7
Safety
1
.03
Safety symbols
Danger!
Special points to observe.
Danger of injury to operating or technical staff!
Caution
Do not operate without fi nger guard and safety devices.
Before threading, changing bobbin and needle, cleaning etc. switch off main switch.
I
8
1
.04
Important notes for the user
● This instruction manual belongs to the equipment of the machine and must be available to the operating staff at all times.
● This instruction manual must be read before the machine is operated for the fi rst time.
● Both operating and technical staff must be instructed on the safety devices of the machine and on safe working methods.
● It is the duty of the user to operate the machine in perfect running order only.
● The user must ensure that none of the safety devices are removed nor put out of working order.
● The user must ensure that only authorized persons operate and work on the machine.
For further information please refer to your PFAFF agency..
1
.05
1
.05.01
Safety
Notes for operating and technical staff
Operating staff
Operating staff are the persons responsible for setting up, operating and cleaning the machine and for eliminating any malfunctioning in the sewing area.
The operating staff is obliged to observe the following points:
● The notes on safety in this instruction manual must always be observed!
● Any working methods, which adversely affect the safety of the machine, must be avoided.!
● Loose-fi tting clothing should be avoided. No jewellery, such as chains and rings, should be worn!
● Ensure that only authorised persons enter the danger area of the machine!
● Any changes occurring on the machine, which may affect its safety, must be reported to the user immediately.
1
.05.02
Technical staff
Technical staff are persons who have been trained in electrical engineering/electronics and mechanical engineering. They are responsible for lubricating, servicing, repairing and adjusting the machine.
The technical staff is obliged to observe the following points:
● The notes on safety in this instruction manual must always be observed!
● Before carrying out any adjustment or repair work the main switch must be switched off and measures taken to prevent it from being switched on again!
● Never work on parts or equipment still connected to the power supply! Exceptions are only permissible in accordance with the regulations EN 50110.
● All safety covers must be replaced after the completion of maintenance or repair work!
9
Safety
1
.06
Danger warnings
A working area of 1 m must be kept free both in front of and behind the machine, so that easy access is possible at all times.
Never put your hands in the sewing area during sewing!
Danger of injury by the needle!
1
Never leave objects on the table while adjusting the machine settings! Objects can become trapped or be slung away! Danger of injury by hurled objects!
4
6
2
5
8
3
Fig. 1 - 01
7
Do not operate the machine without protective covers 1, 2, 3, 4 and 5!
Danger of crushing between moving parts of the pneumatic or feed systems!
Do not operate the machine without take-up lever guard 6!
Danger of injury by the movement of the take-up lever!
Do not operate the machine without the fi nger guard 7!
Danger of injury by the needle!
Do not put your hands or fi ngers in needles 8 of the fabric retainer!
With the needle strip engaged (needles up) there is danger of injury near the needle strip due to the projecting needles!
10
Proper use
The PFAFF 3588-05/020 and PFAFF 3588-15/020 is used for folding and sewing on pockets on jeans, workwear and similar garments.
Any and all uses of this machine which have not been approved of by the manufacturer are considered to be inappropriate! The manufacturer cannot be held liable for any damage caused by the inappropriate use of the machine!
The appropriate use of the machine includes the observance of all operational, adjustment, maintenance and repair measures required by the manufacturer!
11
Specifi cations
3 Specifi cations
▲
Sewing head: ..................PFAFF sewing head for mechanized sewing units with vertical hook
Max. speed:
PFAFF 3588-05/020 ........................................................................................... max. 4000 spm
PFAFF 3588-15/020 ........................................................................................... max. 3600 spm
Stitch length: ............................................................................................................ max. 6 mm
Stitch type: ..........................................................................................................301 (lockstitch)
Needle system: .......................................................................................................... 134, 1955
Needle size: .................................................................................... 100 - 140 Nm / MR3 - MR5
Motor speed: .....................................................................................................max. 4000 rpm
Connection voltage: .......................................................................230 V ± 10%, 50 - 60 Hz AC
Power requirement: ........................................................................................................2.2 kW
Leakage current ........................................................................................................... < 5 mA
◆
Max. control range:
PFAFF 3588-05/020 ............................................................................................. 250 x 250 mm
PFAFF 3588-15/020 ............................................................................................. 280 x 280 mm
Storage capacity: ......................................................................................... 5 000.000 stitches
Working air pressure: ................................................................................................. min. 6 bar
Air consumption: .......................................................................................... approx. 25 l / cycle
Ambient temperature
85% rel. humidity (condensation not permitted): ...................................................... 5 – 40° C
Noise data
Emission sound pressure level at the workplace at a sewing speed of 4000 spm ........................................................................ L pA
< 78 dB(A) ■
(Noise measurement in acc. with DIN 45 635-48-A-1, ISO 11204, ISO 3744, ISO 4871)
Dimensions of machine:
Length: .......................................................................................................... approx. 2250 mm
Width: .............................................................................................................approx. 1150 mm
Height: ........................................................................................................... approx. 1450 mm
Table height: ....................................................................................................... 870 - 1170 mm
Net weight: ..................................................................................................................... 600 kg
▲
Subject to alteration
◆
Due to the use of network fi lters there is a nominal leakage current of < 5 mA.
■
K pA
= 2,5 dB
12
4
Disposal of Machine
Disposal of Machine
● Proper disposal of the machine is the responsibility of the customer.
● The materials used for the machine are steel, aluminium, brass and various plastic materials. The electrical equipment comprises plastic materials and copper.
● The machine is to be disposed of according to the locally valid pollution control regula-tions; if necessary, a specialist ist to be commissioned.
Care must be taken that parts soiled with lubricants are disposed of separately according to the locally valid pollution control regulations!
13
Transportation, packing and storage
5
5
.01
Transportation, packing and storage
Transportation to customer‘s premises
The machines are delivered completely packed.
5
.02
5
.03
5
.04
Transportation inside the customer‘s premises
The manufacturer cannot be made liable for transportation inside the customer‘s premises nor to other operating locations. It must be ensured that the machines are only transported in an upright position.
Disposal of packing materials
The packing materials of this machine comprise paper, cardboard and VCE fi bre. Proper disposal of the packing material is the responsibility of the customer.
Storage
If the machine is not in use, it can be stored as it is for a period of up to six months, but It should be protected against dust and moisture.
If the machine is stored for longer periods, the individual parts, especially the surfaces of moving parts, must be protected against corrosion, e.g. by a fi lm of oil.
14
6
Explanation of symbols
Explanation of symbols
In this instruction manual, work to be carried out or important information is accentuated by symbols. These symbols have the following meanings:
Note, information
Cleaning, care
Lubrication
Maintenance, repairs, adjustment, service work
(only to be carried out by technical staff)
15
7 Controls
7
.01
On/off switch
Controls
1
Fig. 7 - 01
● By turning on/off switch 1, the power supply to the machine is switched on or off.
7
.02
Stopptaster
1
● By pressing the stop switch 1, the complete work cycle is stopped, see chapter
10.04 Program interruption.
Fig. 7 - 02
17
Controls
7
.03
Switch for the loading function
1
● The function of the switch 1 can be adapted to the various requirements for loading the workpiece.
The adjustment is made with parameter "113" and "114", see
Chapter 13.10.02 Parameter
List.
With the needle strip engaged
(needles up) there is danger of injury near the needle strip due to the projecting needles!
Fig. 7 - 03
18
7
.04
Double-start keys
1
1
Controls
7
.05
Fig. 7 - 04
● In MANUAL operation mode, when both double-start keys 1 are activated simultaneously the folder is moved lowered.
● In AUTOMATIC operation mode, when both double-start keys 1 are activated simultaneously the entire program sequence is started.
● The double-start keys 1 also are used to continue the program after the bobbin has been replaced or the program has been interrupted.
Handwheel
● By turning and simultaneously pushing the handwheel 1 in, the needle bar can be positioned manually as required.
1
Fig. 7 - 05
19
Controls
7
.06
Control panel
1
Fig. 7 - 06
The current operating conditions are displayed on control panel 1. Operation takes place in a constant dialogue between the control unit and the operator. For this purpose, depending on the operating condition of the machine, different symbols and/or texts are displayed. If the symbols or texts are framed, these show functions which can be selected by pressing the appropriate position on the monitor. By pressing the corresponding function this is carried out or switched on or off immediately, or a further menu appears, e.g. for entering a value.
Activated functions are shown with inverted symbols. Unframed symbols or texts are only used for display purposes and cannot be selected by pressing.
Description of the functions
Normal symbol = function switched off (inactive)
Inverted symbol = function switched on (active)
20
8
8
.01
Mounting and commissioning the machine
Mounting and commissioning the machine
After unpacking the machine, check it for any transport damage. In case of damage, inform the shipping company and the responsible PFAFF dealer.
The machine must only be mounted and commissioned by qualifi ed personnel!
All relevant safety regulations are to be observed!
Mounting
At the machine’s location, there must be a stable and horizontal surface as well as suitable electricity and compressed air supplies (see chapter 3 Specifi cations).
Fig. 8 - 01
● Lift the machine with a forklift from the shipping pallet.
For machines without vertical adjustment:
● Align the machine horizontally just above the fl oor and move the four legs accordingly before setting the machine down on the ground.
For machines with vertical adjustment:
● Set down the machine on the ground and align it by turning the four spindles.
The vertical adjustment is available as an optional feature.
Fig. 8-01 shows a machine with vertical adjustment.
21
Mounting and commissioning the machine
8
.02
Removing the transit support bracket
1
Before the machine is commissioned, transit support bracket
1 must be removed!
Transit support bracket 1 serves to secure the sewing machine during transit and must not be used during sewing.
Fig. 8 - 02
8
.03
Mounting the spool holder
● Mount the spool holder according to
Fig. 8.03.
22
Fig. 8 - 03
8
.04
Commisioning
Mounting and commissioning the machine
Fig. 8 - 04
● Before commissioning the machine, clean it thoroughly and lubricate it, or pour in oil, see Chapter 12 Care and Maintenance!
● The machine, in particular the electric wires and pneumatic connection tubes, must be examined for any damage.
● Have skilled personnel check if the machine can be operated with the available mains voltage.
Do not operate the machine if there is any discrepancy.
The machine may only be connected to an earthed socket!
● Connect machine to the compressed air system.
The manometer on the air fi lter/lubricator unit must display a pressure of 6 bar.
If necessary, set to the correct value (see chapter 12.06 Checking / regulating air compression).
23
Mounting and commissioning the machine
8
.05
Switching the machine on/off
2
1
4
2
6
8
100
150
10
12
200
230
16
14
0
50
0
3
Fig. 8 - 05 Fig. 8 - 06
● Check air pressure on pressure gauge 1 and, if necessary, adjust air pressure with adjusting knob 2.
● Turn main switch 3 to position "I".
24
● After booting the machine control unit, to start the machine, move it back to its basic position.
● Carry out a test run, see Chapter 10 Sewing.
When commissioning the machine, the zero points must be checked or adjusted (see Chapter 8.09 Checking / adjusting the zero points).
● To switch off the machine, turn main switch 3 to position "0".
Description of other functions on the display
Input menu
This function is used to call up the input mode, see Chapter 11 Input.
8
.06
PC interface
Mounting and commissioning the machine
● To read sewing programs or install machine software, use the sd-card-slot in the control panel.
● Socket 2 is for connecting the programming system OSCA.
With OSCA existing CAD data records can be used to generate seam programs.
2
1
2 GB max.
8
.07
Fig. 8 - 07
Selecting the language
● Switch on the machine.
● Call up the input menu.
● Call up the settings menu
● Select the appropriate language.
25
Mounting and commissioning the machine
8
.08
Adjusting the control panel
● Switch on the machine.
● Call up the input mode.
● Select the service menu.
● Select control panel functions.
26
● Change the display contrast.
● Switch the key tone off or on.
Never reduce the display contrast to the extent, that the display can no longer be read!
● Conclude the input.
8
.09
Mounting and commissioning the machine
Checking / adjusting the zero points
When commissioning the machine and after changing the control unit or one of the initiators of the sewing jig feed unit, it is necessary to adjust the zero points!
● Call up the input mode.
● Select the service menu.
● Call up the "adjusting the zero points" function and enter the code number with the number keys.
27
Mounting and commissioning the machine
● Call up the "teach-in position" function.
1
Fig. 8 - 08
● Check if adjustment pin 1 can be inserted in the holes of the sewing jig and table when the sewing jig is in this position.
28
● If necessary, correct the position of the sewing jig accordingly using the direction symbols.
● Save the setting.
If this position is altered, the needle position must also be adjusted, as described in the following section!
● To quit the menu without taking over the change in position, use the "Esc" function.
Mounting and commissioning the machine
● Call up the "needle position" function
1
2
3
Fig. 8 - 09
● Fix adjustment pin 1 in the needle bar with screw 2.
● By turning balance wheel 3, check whether adjustment pin 1 can be guided into the hole in the sewing jig.
● If necessary, correct the position of the sewing jig accordingly using the direction symbols.
● Save the setting, loosen screw 2 and remove adjustment pin 1.
29
Mounting and commissioning the machine
● Call up the "folder position".
1
Fig. 8 - 10
● Check whether adjustment pin 1 can be guided into the adjustment hole of the sewing jig and the pocket plate.
● If necessary, correct the position of the sewing jig accordingly using the direction symbols.
● Save the setting.
● Conclude the zero points input.
30
Mounting and commissioning the machine
● Move the machine to its basic position, the machine is ready for operation.
31
Preparation
9 Preparation
All regulations and instructions in this Instruction Manual are to be observed!
Special attention is to be paid to the safety regulations!
All preparation work is only to be carried out by appropriately trained personnel!
9
.01
Inserting the needle
2
1
Switch the machine off!
Danger due to unintentional starting of the machine!
Only use needles from the system intended for the machine, see Chapter 3 Specifi cations.
● Raise the needle bar to its highest postion by turning the handwheel.
● Loosen screw 1 and insert needle 2 in the needle bar as far as it will go.
● Align needle 2 in such a way that the long needle groove is pointing to the folder station and tighten screw 1.
Fig. 9 - 01
33
Preparation
9
.02
Winding the bobbin thread, adjusting the thread tension
4
+
-
34
7
5
1
3
2
6
Fig. 9 - 02
● Switch on the machine.
● Place an empty bobbin 1 onto bobbin shaft 2.
● Thread the bobbin in accordance with Fig. 9-02 and wind it anti-clockwise around bobbin
1 a few times.
● Switch on the bobbin winder while at the same time pressing bobbin winder spindle 2 and lever 3.
The bobbin fi lls up during sewing.
● The tension of the thread on bobbin 1 can be adjusted with knurled screw 4.
● The bobbin winder stops automatically when bobbin 1 is full.
● Remove the fi lled bobbin 1 and cut the thread on knife 5.
If the thread is wound unevenly, loosen nut 6 and turn thread guide 7 accordingly. Retighten nut 6 after the adjustment
To adjust the fi lling capacity, see Chapter 13.05.22 Bobbin winder.
9
.03
Preparation
Changing the bobbin / adjusting the bobbin thread tension
1
2
+
-
4
3
Fig. 9 - 03
● When the number of stitches entered previously under the "bobbin thread stitch counter" function (see Chapter 9.09) have been sewn, the sewing jig moves automatically to the folding station and stops there. Hook compartment cover 1 opens.
● Changing the bobbin /adjusting the bobbin thread tension, see following section.
● Confi rm the bobbin change.
● Press the double start keys, see Chapter 7.04 Double start keys.
(Program cycle continues) or
● Call up the "change bobbin" function.
● Changing the bobbin /adjusting the bobbin thread tension (see following section).
● Press the double start keys (hook compartment cover 1 closes).
Changing the bobbin / adjusting the bobbin thread tension
● Lift latch 2 and remove empty bobbin.
● Insert a full bobbin into the hook so that it rotates in the direction of the arrow when pulling the thread.
● Close latch 2.
● Guide the thread fi rst through the groove, then around the horn of bobbin case 3 and fi nally into the recess of latch 2.
● Adjust the bobbin thread tension by turning screw 4.
35
Preparation
9
.04
Threading the needle / adjusting the needle thread tension
36
3
2
1
Fig. 9 - 04
● Switch on the machine.
● Lower the presser foot 1 and open thread trapper 2.
● Thread the needle thread as shown in the above illustration.
● Adjust the needle thread tension by turning knurled screw 3.
● Start the sewing cycle or
● Move the machine to its basic position.
9
.05
Preparation
Selecting the program number
When changing to a different seam program, please make sure that the part set
(folder, pocket plate and sewing jig) correspond to the new seam program.
If the wrong combination of parts and seam program is used, the machine may be damaged seriously!
● Switch on the machine.
● Call up the program number input menu.
● Select the desired program number (0 – 9999) using the number block.
● Confi rm the selection and quit the selection menu.
Description of the other functions
Clear
This function sets the value at "0".
Arrow keys
These functions increase or reduce the value.
Esc
This function stops the input without taking over the value entered.
Sequence selection
This function opens the menu for selecting or confi guring the sequence, see Chapter 9.06
Selecting / confi guring the sequence.
Parts program
This function opens the menu for entering the parts program number.
37
Preparation
9
.06
9
.06.01
Selecting / confi guring a sequence
Selecting a sequence
Instead of selecting a program number, it is also possible to select a corresponding sequence, providing that individual seam programs have been allocated to a sequence, see
Chapter 9.06.02 Confi guring a sequence
● Switch on the machine.
● Call up the menu for entering the program number.
● Call up the menu for entering the sequence.
● Select the desired sequence number (0 – 9) using the number block.
● Confi rm the selection and quit the selection menu.
Description of the other functions
Clear
This function sets the value at "0".
Arrow keys
These functions increase or reduce the value.
Esc
This function stops the input without taking over the value entered.
Program selection
This function opens the menu for selecting a program, see Chapter 9.05 Selecting a program number.
Parts program
This function opens the menu for entering the parts program number.
38
9
.06.02
Preparation
Confi guring a sequence
Up to 4 seam programs can be allocated to a sequence. Each seam programs is allocated to a parts program. During sewing, the seam programs of a selected sequence appear as a function on the display with the parts program, and can be selected directly.
● Call up the menu for entering the sequence and select the desired sequence number without leaving the selection menu, see 9.06.01 Selecting a sequence.
● Call up the sequence programming function.
● Confi gure the sequence from existing seam programs by entering the program numbers on the number block.
● The cursor in the window shows, which seam program has been taken out of the group, or at which position a new seam program has been inserted. The cursor is moved with the arrow keys.
● If applicable, insert (INS) the seam program or parts program at the current cursor position, or delete (DEL) the marked seam program from the sequence.
● Conclude the sequence programming function.
To enable, for example, quicker access to up to 4 different seam programs, the function for automatic switching to the next seam program of a sequence function can be switched off with parameter "112", see Chapter 13.10.02 List of parameters.
39
Preparation
9
.07
Slide confi guration
Different slide confi gurations can be allocated to the program stations (1 – 4) with parameters "116" to "119". Individual programs can also be allocated to slide confi gurations with parameter "115".
● Switch on the machine.
● Call up the input menu.
● Call up the parameter input function.
● Select parameters "115" to "119" and alter the values accordingly, see Chapter 13.10.02
List of parameters.
● Quit the parameter input function.
40
9
.08
9
.08.01
Preparation
Jig monitor
(optional)
To make it possible to monitor the jig, the sewing jig is given a code using magnets which the control can recognize via an additional device. This is a means of preventing pairing a sewing program with the wrong sewing jig which could cause the needle to break.
If the machine is equipped with this optional device, the JIG MONITOR function must be activated, and a jig code must be entered in the sewing program in order to use the jig monitor.
Activating jig monitor
● Switch on the machine.
● Call up the input menu.
● Call up the parameter input function.
● Select parameter "108" and set the value at "1", see Chapter 13.10.02 List of parameters.
● Quit the parameter input function.
41
Preparation
9
.08.02
Determining the jig code
2
1
Fig. 9 - 05
The jig code is entered in the sewing program as a number value (0-99).
The code is created on the jig as a binary number by arranging up to eight magnets 1 in a particular way on carrier 2.
Bit assignment
Example: decimal number ( 3 5 ) is equal to the binary combination ( 1 1 0 0 1 0 1 0 ) tens place ( 3 ) ones place ( 5 )
Ones place
Tens place
0
1
4
5
2
3
8
9
6
7
Bit 0
Bit 4 free magnet free magnet free magnet free magnet free magnet
Bit 1
Bit 5 free free magnet magnet free free magnet magnet free free
Bit 2
Bit 6 free free free free magnet magnet magnet magnet free free
Bit 3
Bit 7 free free free free free free free free magnet magnet
42
9
.09
Setting the bobbin thread stitch counter
● Switch on the machine.
● Call up the menu for entering the number of bobbin thread stitches.
Preparation
● Enter the number of stitches on the number block.
● Conclude the input.
After sewing the number of bobbin thread stitches, the machine stops automatically for changing the bobbin.
Description of the other functions
Clear (on number block)
This function sets the input value at "0".
Arrow keys
These functions increase or reduce the value.
Esc
This function stops the input without taking over the value entered.
Clear (in foot text)
This function sets the bobbin thread counter (number of stitches sewn) at "0".
43
Preparation
9
.10
Changing the part set
The seam program, parts program and parts (folding set, pocket plates and sewing jig) must match and always be used together!
If the wrong combination of parts and seam program is used, the machine may be damaged seriously!
6
7
5
1
3
Fig. 9 - 06
● Switch on the machine.
● Call up the input menu.
● Call up "changing the part set" function.
4
2
44
● Loosen screws 1 and 2, and remove both sewing jig 3 and pocket plate 4.
● Insert a new pocket plate and a matching sewing jig.
● Tighten screws 1 and 2.
● Confi rm change of pocket plat and sewing jig.
Preparation
● Unscrew the compressed air supply 5.
● Loosen screw 6 and remove folder set 7.
● Insert the folder set which matches the pocket plate and the sewing jig, tighten screw 6 and screw the compressed air supply 5 back on.
● Conclude the part set change.
● Move to the basic position, the machine is ready for operation.
Select the matching program number to the part set!
Incorrect combinations can cause severe damage to the machine!
45
Preparation
9
.11
Loading the pre-cut parts
46
Fig. 9 - 07
● Switch on the machine.
● Place the pre-cut parts on the loading table or slide them onto the pocket plate and align them.
The insertion and alignment of the pre-cut parts depends on the selected menu combination, see Parameter 113 and 114 in Chapter 13.10.02.
Menu combination: "Basic position pocket plate front/plain-materialfabric on"
● Slide the pre-cut pocket part onto the pocket plate according to Fig. 9-07.
Menu combination: "Basic position pocket plate back/plain-fabric on"
● Actuate the loading function switch twice pocket plate moves forward.
● Slide the pre-cut pocket part onto the pocket plate according to Fig. 9-07.
Menu combination: "Basic position pocket plate front/plain-materialfabric off"
● Slide the pre-cut pocket part onto the pocket plate according to Fig. 9-07.
● Activate the inserting function switch - the pocket plate is lowered.
● Activate the inserting function switch to raise the pocket plate so that the trousers cutting can be aligned.
● Activate the inserting function switch to lower the pocket plate again.
Menu combination: "Basic position pocket plate back/plain-fabric off"
● Actuate the loading function switch to move the pocket plate forward.
● Slide the pocket cutting onto the pocket plate according to Fig. 9-07.
● Actuate the loading function switch twice: the pocket plate is lowered and raised slightly to allow positioning of the pre-cut trouser part.
Sewing
10 Sewing
The machine may only be operated by appropriately instructed personnel! The operating staff must make sure that only authorized persons are in the danger area of the machine!
In particular for the production, in addition to the input mode, see Chapter 11 Input, the sewing mode is available. Here, depending on the program selection and the machine status, all relevant functions and settings for the production are shown on the display. Automatic operation is standard, but it is possible to switch to manual operation when setting up and checking operating sequences.
Before production the following conditions must be fulfi lled:
● All safety devices must be attached and all covers closed see, Chapter 1.06 Danger warnings.
● The machine must be properly installed and commissioned in accordance with Chapter
8 Installation and commissioning.
● All setting-up work must have been carried out, see Chapter 9 Setting-up.
● Switch on the machine
● Select either automatic or manual sewing. The current operating mode is shown as an inverse symbol.
47
Sewing
10
.01
Automatic sewing mode
● Switch on the machine.
● Select the automatic sewing mode.
48
● Insert and align the pre-cut parts, see Chapter 9.11 Inserting the pre-cut parts.
● Start the program cycle with the double start keys, see Chapter 7.04 Double start keys.
Description of the functions
Program number selection
This function opens the menu for entering the program number. The current program number is shown in the symbol together with the appropriate parts program number.
Standard stitch length
This function opens the menu for entering the standard stitch length. The current stitch length is shown in the symbol.
Maximum speed
This function opens the menu for entering the maximum speed. The current maximum speed is shown in the symbol.
Input menu
This function is used to call up the "input mode" see Chapter 11 Input.
Daily piece counter
Here the day number of pieces is indicated.
Automatic / manual sewing
This function is used to switch between automatic and manual sewing. The appropriate symbol of the current operating mode is shown respectively.
Bobbin thread stitch counter
This function opens the menu for entering and resetting the number of stitches for the bobbin thread, see Chapter 9.09 Setting the bobbin thread stitch counter.
Jig up/down
This function is used to raise or lower the jig.
10
.02
Sewing
Sewing foot up/down
This function is used to raise or lower the sewing foot. In addition the thread trapper is opened or closed.
Bobbin change
This function makes it possible to change the bobbin.
Stacker up/down
This function is used to open or close the stacker.
Basic position
This function is used to move the jig guide, sewing station and jig drive unit to the basic position.
Stop (only during the program cycle)
This function is used to stop the entire program cycle, see Chapter 10.04 Program interruption.
Manual sewing mode
● Switch on the machine.
● Call up the manual sewing mode.
Description of the functions
Program number selection
This function opens the menu for entering the program number. The current program number is shown in the symbol together with the appropriate parts program number.
Standard stitch length
This function opens the menu for entering the standard stitch length. The current stitch length is shown in the symbol.
Maximum speed
This function opens the menu for entering the maximum speed. The current maximum speed is shown in the symbol.
Input menu
This function is used to call up the "input mode" see Chapter 11 Input.
49
Sewing
Daily piece counter
Here the day number of pieces is indicated.
Automatic / manual sewing
This function is used to switch between automatic and manual sewing. The appropriate symbol of the current operating mode is shown respectively.
Bobbin thread stitch counter
This function opens the menu for entering and resetting the number of stitches for the bobbin thread, see Chapter 9.09 Setting the bobbin thread stitch counter.
Jig up/down
This function is used to raise or lower the jig.
Sewing foot up/down
This function is used to raise or lower the sewing foot. In addition the thread trapper is opened or closed.
Stand height adjustment
This function opens a menu for adjusting the stand height (only when the machine is in its basic position).
Bobbin change
This function makes it possible to change the bobbin.
Stacker up/down
This function is used to open or close the stacker.
Sewing start
This function is used to start the sewing operation.
Basic position
This function is used to move the machine to the basic position.
Tacting backwards
This function is used to move backwards in sections in the seam pattern tact for tact. The seam cycle is sewn automatically, if the function is pressed longer.
Tacting forwards
This function is used to move forwards in sections in the seam pattern tact for tact. The seam cycle is sewn automatically, if the function is pressed longer.
Single step (after pressing the double start keys)
This function is used to move the folder and jig feed tact for tact.
50
10
.03
Sewing
Sewing with sequences
To sew with sequences, parameter "114" must be set at value "1", see Chapter
13.10.02 List of parameters.
● Switch on the machine.
● Select the desired sequence, see Chapter 9.06.01 Selecting a sequence.
● Insert the pre-cut parts.
● Start the program cycle by pressing the double start keys, see Chapter 7.04 Double start keys.
Description of the functions
Program number selection
This function opens the menu for entering the program number. The current program number is shown in the symbol. If the function for moving automatically to the next sequence is activated, the sequence symbol is shown as inverse.
Standard stitch length
This function opens the menu for entering the standard stitch length. The current stitch length is shown in the symbol.
Maximum speed
This function opens the menu for entering the maximum speed. The current maximum speed is shown in the symbol.
Input menu
This function is used to call up the "input mode" see Chapter 11 Input.
Individual program
This function depends on the setting of parameter "112" (moving automatically to next sequence), see Chapter 13.10.02 List of parameters.
If the function for moving automatically to the next sequence is activated (value "I", this) function is used to show the symbol for the next individual program to be sewn as inverse.
If the function for moving automatically to the next sequence is deactivated (value "0",) this function is used for the quick selection of the highlighted seam programs.
Daily piece counter
Here the day number of pieces is indicated.
51
Sewing
10
.04
Bobbin thread stitch counter
This function opens the menu for entering and resetting the number of stitches for the bobbin thread, see Chapter 9.09 Setting the bobbin thread stitch counter.
Automatic / manual sewing
This function is used to switch between automatic and manual sewing. The appropriate symbol of the current operating mode is shown respectively.
Jig up/down
This function is used to raise or lower the jig.
Sewing foot up/down
This function is used to raise or lower the sewing foot. In addition the thread trapper is opened or closed.
Bobbin change
This function makes it possible to change the bobbin.
Stacker up/down
This function is used to open or close the stacker.
Basic position
This function is used to move the machine to the basic position.
Stop (only during the program cycle)
This function is used to stop the entire program cycle, see Chapter 10.04 Program interruption.
Program interruption
The program cycle can be interrupted by operating the „stop“ function on the control panel or by pressing the stop keys.
By pressing this button the folder goes in home position.
52
If the machine is stopped in this way, the sewing station and the folder are not in their basic position!
● Continue the program cycle by operating the appropriate function or
● Press the double start keys, see Chapter 7.04 Double start keys.
10
.05
Sewing
Error messages
If a malfunction occurs, an error code appears on the display. An error message may be caused by incorrect operation, machine defects, as well as by overload conditions.
(For a description of the error codes see Chapter 14.02 Description of the error codes).
Errors when connecting outputs
If an error occurs when connecting an output, the output concerned is shown with the desired switching state (0) or (I).
In this case (0) means the output should be disconnected and (I) means that the output should be connected.
In the next line the cause leading to the error is displayed.
The target state for maintaining undisturbed operation is shown in brackets.
In the following example the output Y1.1 is to be connected.
Requirement: E1.1 must be set at (1).
Pocket plate forwards
Pocket plate at front
Target state
Pocket plate forwards
Target state
Pocket plate at front
● Check E1.1 and eliminate error.
● Acknowledge elimination of the error..
53
Input
11 Input
In addition to the functions for entering or editing seam programs, in the input mode there are functions for displaying information, for program management, for machine confi guration and settings (country settings and rights of access ), as well as for supporting service and adjustment work.
In the input mode the machine start function is blocked to avoid an unintentional start-up of the machine.
11
.01
Overview of the functions in the input mode
● Switch on the machine.
● Call up the input mode.
Description of the functions
Conclude input
This function is used to conclude the input, and the machines changes to the sewing mode.
Seam program input
This function is used to call up the menu for entering or editing seam programs, see Chapter
11.02 Creating / editing seam programs.
Program management
This function is used to manage the data from the machine memory and CD-Card, see
Chapter 11.04 Program management.
Parameter settings
This function is used to call up the menu for altering parameter settings, see Chapter 13.10
Parameter settings.
54
Info
This function opens a menu for displaying the following information:
- current software status of the machine
- current fi rmware status of the machine
- current fi rmware status of the control panel
- day piece counter
- operating hours counter
- production hours counter
The day piece counter can be reset with the "Clear" function.
Input
Country settings
This function opens a menu for selecting the language shown on the control panel, see
Chapter 8.07 Selecting the language.
Rights of access
This function opens a menu for fi xing the rights of access, see Chapter 11.05 Rights of access.
Stepping motors / reference points
This function opens a menu for moving the stepping motors, and for moving to reference points with the "test" function.
Changing part set
This menu opens a menu for changing the part set, see Chapter 9.10 Changing part set.
Sewing motor
This function opens a menu for testing and adjusting the sewing motor, see Chapter 13.09
Sewing motor settings.
Service menu
This function is used to call up the menu for selecting various service functions, see Chapter
13.08 Service menu.
55
Input
11
.02
Creating / editing seam programs
● Switch on the machine.
● Call up the input mode.
● Call up the seam program input function.
● Lower the jig.
● Confi rm operation.
● Reinsert the desired program number or select the desired program.
● Confi rm the seam number selection.
56
Description of the functions
Input menu
This function ends the programming operation and opens the basic input menu, see Chapter
11.01 Overview of the functions in the input mode.
Input
Conclude input
This function is used to conclude the input, and the machine changes into the sewing mode.
Mark block start
This function is used to defi ne the start of a block, see Chapter 11.02.01 Block functions.
Mark block end
This function is used to defi ne the end of a block, see Chapter 11.02.01 Block functions.
Block functions
This function opens a menu for entering block functions, see Chapter 11.02.01 Block functions.
Image functions
This function opens a menu for entering image functions, see Chapter 11.02.02 Image functions.
Coordinate reference points
This function is used to set the coordinates on the display at "0", in this way creating a new reference point.
Edit
After selecting this function, the current section can be edited.
Insert
This function is used to insert functions or blocks, see Chapter 11.02.03 Inserting functions.
Delete
This function is used to delete the current section.
Sewing foot up/down
This function is used to raise or lower the sewing foot. In addition the thread trapper is opened or closed.
Search
With this function the sewing head is raised and the carriage can be moved near the desired seam pattern point with appropriate direction symbols. After the position has been confi rmed, the machine moves towards the nearest point of the seam pattern.
Tacting forwards
This function is used to move forwards in sections in the seam pattern tact for tact. The seam cycle is sewn automatically, if the function is pressed longer.
Tacting backwards
This function is used to move backwards in sections in the seam pattern tact for tact. The seam cycle is sewn automatically, if the function is pressed longer.
57
Input
11
.02.01
Block functions
● Switch on the machine.
● Call up the input mode.
● Call up the seam program input function.
● Defi ne block start and block end
After a desired point in the program has been selected with the tacting through the program function, it is possible to defi ne the block start with the "mark block start" function.
The block marking must be concluded by defi ning a block end. To do so, tact through the program till reaching the desired point and then operate the "mark block end" function.
When tacking through the program, the marked block can be recognised by the inverse symbol of the section number.
● Call up the block functions.
58
Description of the functions
Conclude input
This function is used to conclude the input, and the machine changes into the sewing mode.
Enlargement factor X-axis
This function is used to enlarge or reduce the block in the X-direction.
Enlargement factor Y-axis
This function is used to enlarge or reduce the block in the Y-direction.
Mirror
This function is used to mirror the block. Mirroring takes place on the straight line, which runs parallel to the Y-axis and through the block start point.
Turn
This function is used to turn the block. The block is turned around the block start point in an anti-clockwise direction.
Input
Shift block
After this function has been selected, a new point must be approached with the jig drive.
With the enter function, this point is taken over and the block shifted.
Delete
When this function is selected, the block is deleted.
Enter
Conclude the block function input and carry out block manipulation.
59
Input
11
.02.02
Image functions
● Switch on the machine.
● Call up the input mode.
● Call up the seam program input function.
● Call up image functions.
60
Description of the functions
Conclude input
This function is used to conclude the input, and the machine changes into the sewing mode.
Enlargement factor X-axis
This function is used to enlarge or reduce the image in the X-direction. The operation is concluded by selecting the point of symmetry either with the number keys or with the control keys.
Enlargement factor Y-axis
This function is used to enlarge or reduce the image in the Y-direction. The operation is concluded by selecting the point of symmetry either with the number keys or with the control keys.
Mirror
This function is used to mirror the image. The operation is concluded by selecting the point of symmetry either with the number keys or with the control keys.
Turn
This function is used to turn the image. The image is turned in an anti-clockwise direction.
The operation is concluded by selecting the point of symmetry either with the number keys or with the control keys.
Shift image
After this function has been selected, a new point must be approached with the jig drive.
With the enter function, this point is taken over and the image is shifted from the current position to the end of the program.
Input
Point of symmetry using number keys
The point of symmetry is defi ned by entering the coordinates with number keys.
Point of symmetry using control keys
With this function the point of symmetry is approached (entered) by pressing the appropriate direction symbols.
61
Input
11
.02.03
Inserting functions
● Switch on the machine.
● Call up the input mode.
● Call up the seam program input function.
● Call up "insert" functions.
62
Description of the functions
Conclude input (in status bar)
This function is used to conclude the input, and the machine changes into the sewing mode.
Straight line
A straight line is a direct connection between two points.
To enter a straight line, a stitch length must be defi ned.
Single stitch
A single stitch or feed motion is entered without taking the stitch length into consideration.
The single stitch or feed motion can be max. 6 mm.
Fast motion
The fast motion function is used for the quick motion of the jig drive. Both axes are moved independently from each other to the end point as quickly as possible. The resulting distance moved is therefore not a straight line (watch out for obstacles on the jig). If the path has to be exact, it is necessary to work with a straight line or curve without start sewing.
Curve check points
It is possible to enter any number of check points. The control unit calculates the course of the curve, taking the stitch length into consideration. Check points do not necessarily have to be end points. A stitch length must be defi ned. The greater the number of check points entered, the more exact the course of the curve.
Curve end
This function changes a curve check point into a curve end point.
Input
Circle
To enter a circle, three points are necessary. The fi rst point is automatically the starting points. The two missing points still have to be entered. A stitch length must be defi ned.
Circular arc
For the circular arc the same applies as for the circle, whereby the last point defi nes the end of the circular arc.
Start sewing
This function is used to start sewing. All following sections are sewn until the thread trimming function is selected.
or
Thread trimming
The thread is cut. The start sewing function must have been activated previously.
Standard stitch length
This function is used to defi ne the stitch length, which will be used predominantly in the program. During sewing the standard stitch will be displayed in the status bar and can be altered on the machine with the stitch alteration function, without changing into the programming mode.
Stitch length
A stitch length is defi ned for a certain seam sector.
This stitch length is not displayed in the status bar during sewing and can only be altered in the programming mode.
Stitch width
This function carries out a zig-zag motion with the jig drive on the base line. Here the stitch length indicates the feed motion along the base line from needle penetration to needle penetration and must be selected accordingly. The stitch width is carried out vertically to the base line. The position of the zig-zag to the base line must also be defi ned. If the stitch width function is to be switched off, the width must be entered as 0.0.
Other functions
This function is used for the selection of more functions, see Chapter 11.02.04 Other functions.
Insert block
This function is used to insert a marked block after the current position.
63
Input
11
.02.04
Other functions
● Switch on the machine.
● Call up the input mode.
● Call up the seam program input function.
● Call up "insert" functions.
● Call up other functions.
64
Description of the functions
Conclude input (in status bar)
This function is used to conclude the input, and the machine changes into the sewing mode.
Programmable outputs
The corresponding outputs (1 to 2) are activated with the menu.
Secondary thread tension (depending on machine status)
This function is used to open or close the secondary thread tension.
Zig-zag seam (depending on machine status)
If sewing with a straight seam has been selected, this function is used to select sewing with zig-zag.
Straight seam (depending on machine status)
If sewing with zig-zag has been selected, this function is used to select sewing with a straight seam.
Wide variable sewing slit (depending on machine status)
If the narrow variable sewing slit has been selected, this function is used to select the wide variable sewing slit.
Narrow variable sewing slit (depending on machine status)
If the wide variable sewing slit has been selected, this function is used to select the narrow variable sewing slit.
Input
Wait for input (inputs 1 to 2)
The processing of the program is stopped until the appropriate input (1 to 2) has reached the selected level.
Wait for time
The processing of the program is stopped until the programmed time has elapsed.
Speed
A speed is entered permanently in the program.
Reduced speed (depending on machine status)
This function is used to sew at a reduced speed or to switch off the reduced speed.
Programmed stop
A stop is programmed in the program.
Processing is continued by calling up the "start" function.
Flap stop
This function is used to defi ne the fl ap stop. The fl ap program is processed from this point on.
Adjustment parameters
This function is used to adjust the activation or deactivation of various functions. The number of stitches is entered for activating or deactivating the corresponding function sooner or later.
Esc
Conclude input without taking over the inputs.
65
Input
11
.03
Seam programming example
The following example describes the seam program input. A drawing with the corresponding coordinate values serves as a programming guideline, see following illustration.
For the use of the seam program, the sewing jig and the corresponding part set must match.
122 mm
6,4 mm x+
Schablonennullpunkt y+ xy-
61 mm
● Switch on the machine.
● Call up the input mode.
● Call up the seam program input function.
● If necessary, enter appropriate code number.
66
● Lower jig.
● Confi rm operation.
● Enter desired program number (e.g. "115") to create a new seam program.
Input
● Confi rm program number selection
● Tact forwards.
● Call up section editing function.
● Enter jig code (e.g. "99").
● Confi rm input.
67
Input
● Tact forwards.
● Call up jig with obstacles with the "edit" function.
● Tact forwards.
68
● Call up the "Esc" function, to change the starting point.
Input
● Move to the starting point with the corresponding direction symbols.
● Save the setting.
● Call up the "insert" function.
● Call up the "start sewing" function
.
69
Input
● Call up the "standard stitch length" function.
● Enter the value for the standard stitch length, e.g. 3.40 mm.
● Confi rm input
.
● Call up the "straight line" function to insert a straight line.
● Move to the end point of the straight line with the corresponding direction symbols.
70
● Save the setting.
● Conclude straight line input.
● Call up other functions.
Input
● Call up the "zig-zag seam" function.
● Call up the "stitch length" function.
● Enter the value for the stitch length, e.g. 0.23 mm.
● Confi rm input.
● Call up the "straight line" function to insert a straight line.
● Move to the end point of the straight line with the corresponding direction symbols.
● Save the setting.
71
Input
● Conclude straight line input.
● Call up other functions.
● Call up "straight seam" function
.
● Call up "standard stitch length" function
.
72
Input
● Call up the "straight line" function to insert a straight line.
● Move to the end point of the straight line with the corresponding direction symbols.
● Save the setting.
● Use the corresponding direction symbols to move to the next straight line end point.
● Save the setting.
● Use the corresponding direction symbols to move to the next straight line end point.
● Save the setting.
● Use the corresponding direction symbols to move to the next straight line end point.
● Save the setting.
73
Input
● Conclude the straight line input.
● Call up other functions.
● Call up the "zig-zag seam" function
.
74
● Call up the "stitch length" function.
● Enter the value for the stitch length, e.g. 0.23 mm.
● Confi rm input.
Input
● Call up the "straight line" function to insert a straight line.
● Move to the end point of the straight line with the corresponding direction symbols.
● Save the setting.
● Conclude straight line input.
● Call up other functions.
● Call up "straight seam" function.
● Switch on the thread trimming function.
75
Input
● Conclude the seam program input (function in status bar).
To be able to sew with the newly-created or edited seam program, the stitch generation must be carried out. Incomplete or incorrect programs also can be ended with the "Esc" function without stitch generation. In this case, when the seam program is called up in the sewing mode, an appropriate error message will appear.
● Carry out the stitch generation.
● Move to the basic position.
● After entering the appropriate program number, the created seam program can be selected and processed.
To begin with tact through a newly-created or corrected seam program on the machine, to make sure that it matches the jig!
76
11
.04
Input
Program management
The program management function is used to manage seam programs as well as confi guration and machine data. Files can be selected from the machine memory or from a SD-Card and be copied or deleted.
● Switch on the machine.
● Call up the input mode.
● Call up the program management function.
Both data carriers with the corresponding fi les appear on the display:
- Machine memory ("C:\DATEN\") is currently selected
- SD-Card ( ) is currently inserted
The data carrier is selected by touching the appropriate box, and the content of the appropriate data carrier is also updated. The selected drive is shown as a invers symbol, the selectet fi les are shown blue.
Seam programs are fi led at a different level to that for the confi guration and machine data, in order to avoid the confi guration and machine data being processed by mistake.
77
Input
Description of the functions
Input mode
This function is used to change to the initial state of the input mode.
Update drives
This function is used to update (upload) the drives.
Conclude input
This function is used to conclude the input and change to the sewing mode.
Data selection
With these functions the desired fi les are marked in the current drive. Individual fi les are selected with the arrow keys. In combination with the lock key (*) several fi les can be selected at one time with the arrow keys.
Copy
This function is used to copy the fi les selected from the current data carrier onto the second data carrier.
Delete
This function is used to delete the selected fi les.
MDAD/KONF
This function is used to call up the level for the confi guration and machine data. The current settings and the machine confi guration are stored in the fi les "MDAT3588" and "KONF3588.
BIN". In this way the machine data can be copied on to a CD-Card as a backup, or several machines with the same designation can be confi gured quickly by reading in the machine data.
Format
This function is used to format the CD-Card inserted.
In the course of the formatting operation, all data on the CD-Card is deleted!
78
11
.05
Input
Rights of access
The functions, which can be selected on the control panel, are ordered by code numbers and can be protected from unauthorized access. For this purpose the control unit differentiates between three user groups (User 1, 2 and 3), which are all assigned a corresponding
PIN. If a function is selected, to which the user does not have access, the user is requested to enter a PIN. After the corresponding PIN has been entered, the selected function is executed. In addition to the 3 user groups, the control unit also recognises the so-called "super user". The super user is equipped with a key switch and has access to all functions, and is also authorised to defi ne the rights of access.
● Insert the key switch and switch on the machine.
● Call up the input mode.
● Call up the menu for entering rights of access.
Description of the functions
Input mode
This function is used to change from the initial state to the input mode.
Conclude input
This function is used to conclude the input and change to the sewing mode.
Enter PIN
With this function it is possible to defi ne an individual PIN for each user.
Function selection
This function is used to select the code number for the functions to be blocked or authorised.
Locking/releasing
These functions are used to lock or release the function for the appropriate user.
79
Input
Allocation of the code numbers
Function
Program number selection
Enter stitch length
Enter speed
Input
Create program
Program management
Parameter settings
Parameter group 100
General settings
Parameter group 200
Seam parameters
Parameter group 300
Sewing motor positions
Parameter group 400
Times
Parameter group 500
Counters
Parameter group 600
Info
Reset day piece counter
Reset bobbin thread stitch counter
Clear operating hours counter
Clear production hours counter
Country settings
Rights of access
Service
Carry out a cold start
Symbol
Code number
User 1
Standard setting
User 2 User 3
0
1
2
3
4
5
6
7
-
-
-
8
9
-
-
10
11
12
16
23
24
21
22
19
20
17
18
80
Function
Machine confi guration
Load software
Set contrast control panel
Thread trimming cycle
Needle position
Set zero points
Input
Symbol
Code number
Standard setting
User 1 User 2 User 3
25
26
27
28
29
30
81
12
12
.01
Care and maintenance
Care and maintenance intervals
Care and maintenance
Clean the entire machine ...........................................................................................weekly
Clean the hook compartment ................................................................. several times daily
Clean needle area ................................................................................... several times daily
Check oil level for sewing head lubrication ..................................................daily before use
Lubricate needle bar frame eccentric ..........................................................every 2 months
Lubricate jig guides ......................................................................................every 2 months
Lubricating the pocket plate guide ...............................................................every 2 months
Clean the blower air fi lter .................................................................................... as required
Check air pressure .......................................................................................daily before use
Clean air fi lter of the air fi lter/lubricator unit ........................................................ as required
These maintenance intervals are calculated for the average running time of a single-shift operation. If the machine is operated more often, shorter intervals are recommended.
83
Care and maintenance
12
.02
Cleaning the machine
The required cleaning cycle for the sewing machine is dependent on the following factors:
● Single or multi-shift operation
● Accumulation of dust from the various fabrics
Thus, appropriate cleaning instructions can only be determined on an individual basis for each machine.
1
1
Fig. 12 - 01
To avoid operation disturbances, we recommend the following cleaning work for a machine in single shift operation:
● Clean the hook compartment and the needle area of the sewing head several times daily.
● Clean the entire machine at least once a week.
Procedure:
● Switch on the machine.
● Call up manual sewing.
● Call up the "bobbin change" function.
● After cleaning press double start keys 1 at the same time.
84
12
.03
Cleaning the hook
1
3
Care and maintenance
5 mm
1
● Unscrew screws 1.
● Remove hook gib 2.
● Turn handwheel until the tip of the bobbin case 3 penetrates the hook race groove by approx. 5 mm.
● Remove the bobbin case 3.
● Clean the hook race.
● Reinsert bobbin case 3.
● Screw on hook gib 2.
● Press double-start keys.
Fig. 12 - 02
2
1
12
.04
Cleaning the blower air fi lter
● Remove cover 1.
● Take out fi lter element and clean with compressed air.
● Insert the clean fi lter element and replace cover 1.
1
Fig. 12 - 03
85
Care and maintenance
12
.05
Checking/adjusting the air pressure
1
0.4
0.2
0
+ -
0.6
0.8
1
2
● Before operating the machine, always check the air pressure on gauge1.
● Gauge 1 must show a pressure of 6 bar.
● If necessary adjust to this reading.
● To do so, pull knob 2 upwards and turn it so that the gauge shows a pressure of
6 bar.
3
Fig. 12 - 06
Bar
4,5
5
6
Confi guration of the pressure controller:
● Turn screw 3 until the green arrow points to 4.5 bar.
The machine is automatically switched off if a pressure of < 4.5 bar is reached, and can be automatically reactivated, once pressure reaches a value > 5.0 bar.
134-010
MPa
= 0,45
= 0,5
= 0,6 psi
= 65
= 73
= 87
12
.06
Cleaning the air fi lter of the air-fi lter/lubricator
2
1
Fig. 12 - 07
0.4
0.2
0
+ -
0.6
0.8
1
Switch the machine off!
Disconnect the air hose at the air-fi lter/lubricator.
134-011
To drain water bowl 1:
● Water bowl 1 drains itself automatically when the compressed-air hose is disconnected from the air-fi lter/lubricator.
Cleaning fi lter 2:
● Unscrew water bowl 1.
● Take out fi lter 2.
● Clean fi lter 2 with compressed air or isopropyl alcohol (part No. 95-665 735-91).
● Screw in fi lter 2 and screw on water bowl 1.
86
12
.07
Care and maintenance
Checking the oil level of the sewing head lubrication
● The oil level in drum 1 must be checked daily before use of the machine.
● The oil level must be between the upper and lower markings of drum 1.
● When necessary, pour oil through hole 2.
2
Only use oil with a viscosity of
22.0 mm
2
/s at 40° C and a density of 0.865 g/cm 3 at 15°C!
1
● Before the machine is fi rst operated or whenever the machine has been at a standstill for a longer period of time, also add a few drops of oil to the hook race.
Fig. 12 - 06
We recommend PFAFF sewing-machine oil, part
No. 280-1-120 144.
12
.08
Lubricating the needle bar frame eccentric
1
2
Switch off the machine and ensure that it cannot be switched on accidentally!
Turn off compressed air!
Only use Isofl ex Topas L32, high-performance grease, part
No. 280-1-120 210.
● Unscrew the cover on the reverse side of the sewing head.
● Grease eccentric 1 via grease nipple 2 using a grease gun every 2 months for single-shift operation and monthly for double-shift operation.
● Screw on cover.
Fig. 12 - 07
87
Care and maintenance
12
.09
Lubricating sewing jig feed
3
1
2
Fig. 12 - 08
Switch off the machine and ensure that it cannot be switched on accidentally!
Danger due to unintentional starting of the machine!
Only use Isofl ex Topas L32, high-performance grease, part No. 280-1-120 210.
● Unscrew the cover of the sewing jig feed.
● Grease the guides via grease nipple 1, 2 and 3 using a grease gun every 2 months for single-shift operation and monthly for double-shift operation.
● Screw on cover.
88
12
.10
Lubricating the pocket plate guide
1
Care and maintenance
Switch off the machine and ensure that it cannot be switched on accidentally!
Danger due to unintentional starting of the machine!
Only use Isofl ex Topas L32, high-performance grease, part
No. 280-1-120 210.
● Grease the guide at grease nipple 1 using a grease gun every two months for single-shift operation and monthly for twoshift operation.
Fig. 12 - 09
89
Adjustment
13 Adjustment
Please observe all notes from Chapter 1 Safety!
In particular care must be taken to see that all protective devices are refi tted properly after adjustment, see Chapter 1.06 Danger warnings!
13
.01
Notes on adjustment
All following adjustments are based on a fully assembled machine and may only be carried out by expert staff trained for this purpose.
Machine covers, which have to be removed and replaced to carry out checks and adjustments, are not mentioned in the text.
The order of the following chapters corresponds to the most logical work sequence for machines which have to be completely adjusted. If only specifi c individual work steps are carried out, both the preceding and following chapters must be observed.
Screws, nuts indicated in brackets ( ) are fastenings for machine parts, which must be loosened before adjustment and tightened again afterwards.
Unless stated otherwise, during all adjustment work the machine must be disconnected from the electric and pneumatic power supply!
Danger of injury if the machine is started accidentally!
13
.02
Tools, gauges and other accessories for adjusting
● 1 set of screwdrivers with blade widths from 2 to 10 mm
● 1 set of wrenches with jaw widths from 6 to 22 mm
● 1 set of Allan keys from 1.5 to 6 mm
● 1 universal screwdriver with interchangeable blades
● 1 metal ruler
● 1 adjustment pin (zero point adjustment)
● 1 adjustment gauge (for adjustments to sewing head), part no. 61-775 913-15
● 1 adjustment gauge (for adjustments to sewing head), part no. 61-778 162-15
● 1 adjustment gauge (for adjustments to feed)
● 1 needle rise gauge, part no. 61-111 600-01
● 1 adjustable clamp, part no. 08-880 137 00
13
.03
Abbreviations t.d.c. = top dead centre b.d.c. = bottom dead centre
90
13
.04
Adjustment
Removing/inserting sewing head
Turn off compressed air!
Switch off main switch and ensure that it cannot be turned back on accidentally.
1
7
4
3
5
2
6
Fig. 13 - 01
● To remove the sewing head, remove the protective cover 1 (screws 2).
● Remove the cover plate 3 (screws 4; 6 screws altogether)
● Unplug pneumatic power supply 5 and electrical power supply 6.
● Unhook catch 7 and fold down sewing head.
● Remove V-belt from belt pulley on motor.
● Lift sewing head and remove from its bracket.
● Remove the ground cable of the sewing head.
● To insert the sewing head, carry out the steps above in reverse.
91
Adjustment
13
.05
Adjusting the sewing head
13
.05.01
Spacing between sewing head and bedplate
Requirement
When the sewing head is lowered, the distance from the lower edge of the shaft 1 to the bedplate must be 132.8 mm.
4
3
1
1
2
Fig. 13 - 02
● Check the distance between the shaft 1 and the bedplate using adjustment gauge 2
(part no. 61-775 913-15).
● If required, turn plunger 3 (nut 4) according to the requirement.
92
13
.05.02
Sewing head position in relation to the bedplate
Adjustment
Requirement
When the sewing head is lowered, after the screws 3 have been loosened, the presser bar 4 must pass exactly through the corresponding hole in the adjustment gauge 1.
3
3
4
1
5
4
2
1
5
Fig. 13 - 03
● Unscrew needle plate and screw on adjustment gauge 1 (part no. 61-778 162-15).
● Unscrew presser 2.
● Loosen screws 3 and guide presser bar 4 into the hole in the adjustment gauge 1.
● If required, move sewing head (screws 5) according to the requirement.
● Move presser bar 4 back to its original position and tighten screws 3 lightly.
Adjustment gauge 1 remains screwed on for further adjustments.
The precise adjustment of the presser bar 4 is described in chapter 13.05.21
Presser height.
93
Adjustment
13
.05.03
Upper and lower toothed belt guards
Requirement
The upper and lower toothed belt guards must be positioned as close as possible over the toothed belt sprockets without touching them.
2
1
1
4
3
Fig. 13 - 04
● Move the upper 1 (screw 2) and lower toothed belt guards 3 (screws 4) at the underside of the sewing head according to the requirement.
Carry out the adjustment carefully!
Otherwise, when the sewing head is raised up, the toothed belt could disengage!
94
Adjustment
13
.05.04
Counterweight
Requirement
In needle bar position BDC the largest eccentricity of the counterweight 1 must be at the top.
1 2
1
Fig. 13 - 05
● Move needle bar to BDC.
● Turn counterweight 1 (screws 2) according to the requirement.
95
Adjustment
13
.05.05
Preadjusting the needle height
Requirement
At needle bar position TDC, the distance between the needle point and the adjustment gauge must be approx. 22 mm.
2
1
22 mm
Fig. 13 - 06
● Move needle bar 1 (screws 2) without twisting it according to the requirement.
96
Adjustment
13
.05.06
Zero stitch
Requirement
When the cylinder plunger 1 is fully extended (straight stitch position), the crank 2 must not carry out any movement when the handwheel is turned.
4
2 3 1
Fig. 13 - 07
● Pull out cylinder plunger 1 fully.
● Turn crank 2 (screw 3) according to the requirement.
In order to better recognize the movement of the crank, insert an Allan key into screw 4.
97
Adjustment
13
.05.07
Centering the needle in the needle hole
Requirement
When the cylinder plunger 5 is fully extended (straight stitch position), adjustment pin 1 must fi t precisely into the corresponding adjustment hole of the adjustment gauge 8.
4
3
6
7
2
5
1
Fig. 13 - 08
● Insert adjustment pin 1 into the needle bar and screw tight.
● Loosen screws 2, 3 and 4.
● Pull out cylinder plunger 5 until it stops.
● Move needle bar frame 6 according to the requirement.
● Turn shaft 7 according to the requirement.
● Tighten screws 2, 3 and 4.
● Unscrew adjustment gauge 8 (part no. 61-778 162-15) and adjustment pin 1.
8
98
Adjustment
13
.05.08
Zigzag stitch movement
Requirement
When the needle is in TDC, the needle bar 1 must not carry out any movement when the lever 4 is operated.
1
2 3
4
Fig. 13 - 09
● Bring needle bar 1 to TDC.
● Turn eccentric 2 (screw 3), without twisting it, according to the requirement.
99
Adjustment
13
.05.09
Needle bar rise, hook-to-needle clearance, needle height and needle guard
Requirement
In straight stitch position and with the needle bar 2.4 past BDC,
1. the hook point must be at the middle of the needle; the distance between the needle and the hook point must be from 0.05 to 0.1 mm.
2. the top edge of the needle eye must be 1.0 mm below the hook point, and
3. the needle guard 4 must touch the needle lightly.
4
6
0,05 - 0,1 mm
7
3
1
2
2
Fig. 13 - 10
● Set the stitch length control to straight stitch position.
● Loosen the fastening screws of the bevel gear 1 and screws 2.
● Move the needle bar to BDC.
● In this position, slide the 2.4 mm thick feeler gauge of the needle bar rise gauge closely under the needle bar bearing.
● Move adjustable clamp (part no. 08-880 137 00) against feeler gauge as far as possible and screw it onto the needle bar.
● Remove the feeler gauge and turn the handwheel 3 in the direction of the arrow until the adjustable clamp is resting on the needle bar.
100
Adjustment
● Unscrew the hook gib and remove the bobbin case.
● Position the hook point at the center of the needle and move the hook bearing according to requirement 1. Make sure that the needle is not pressed against by the needle guard 4.
● Tighten screws 2.
● Taking the backlash of the toothed gear into account, tighten the fastening screws of the bevel gear 1.
● If required, move the needle bar (screw 5) without twisting it according to requirement
2.
● Turn eccentric 6 (screw 7) according to requirement 3.
● Insert bobbin case and screw on hook gib.
101
Adjustment
13
.05.10
Bobbin case opener stroke
Requirement
1. The front edges of the retaining spring 1 and the retaining trip 7 must be fl ush with each other.
2. When the bobbin case opener 5 is at its rear point of reversal, the distance between the bobbin case base 6 and the retaining spring 1 must be equal to the thread thickness.
4
3
5
1
1
7
2
6 thread thic kness
6
Fig. 13 - 11
● Align the retaining spring 1 (screw 2) according to requirement 2.
● Move shaft 3 (screw 4) according to requirement 1.
102
Adjustment
13
.05.11
Counter presser lifting stroke
Requirement
At needle bar position BDC, the counter presser 3 must be positioned at its top point of reversal.
1
2
2
Fig. 13 - 12
● Move needle bar to BDC.
● Turn eccentric 1 (screws 2) according to the requirement.
3
103
Adjustment
13
.05.12
Counter presser height
Requirement
When the needle bar is at BDC, the top edge of the counter presser 6 must be 1 mm over the closed hook compartment cover 3.
104
3
6
Fig. 13 - 13
● Position lever 1 (nut 2) at its lower stop (see arrow).
● Fit hook compartment cover 3 and turn bracket 4 (screw 5) according to the requirement.
Adjustment
13
.05.13
Counter presser position
Requirement
In straight stitch position, when the needle penetrates, it must be centered in the needle hole of the counter presser 2.
2
3
2
3
Fig. 13 - 14
● Pull out plunger 1 until it stops (straight stitch position).
● Adjust the counter presser 2 (screws 3) according to the requirement.
1
105
Adjustment
13
.05.14
Zigzag stitch width
Requirement
At the maximum zigzag stitch width, the needle must not strike against the edge of the counter presser.
1
2
Fig. 13 - 15
● Turn screw 1 (nut 2) according to the requirement.
By turning screw 1, the bartack width can be adjusted.
106
Adjustment
13
.05.15
Resting position of the roller lever / radial position of the control cam
Requirement
1. When the plunger 1 is retracted, there must be a distance of 0.1 mm between the outer edge of the control cam 6 and the roller of the roller lever 5.
2. When the thread trimmer is switched on beforehand, the control cam 6 must have just brought the roller lever 5, in TDC take-up lever, to its resting position.
7
6
3
4
0,1 mm
4
2
5
1
8
6
5
9
Fig. 13 - 16
● Retract the plunger 1 in cylinder 2 until it stops.
● Move the cylinder carrier 3 (screws 4) according to requirement 1.
● Bring the take-up lever to BDC and push the roller lever 5 into the control cam 6 by hand.
● By turning the handwheel 7 in the direction of the arrow, bring the take-up lever to TDC and check requirement 2.
● If required, turn the control cam 6 (screws 8) according to requirement 2.
On plunger 1, the thread should be approx. 1 mm above the lock nut 9.
107
Adjustment
13
.05.16
Thread catcher height
Requirement
The lower edge of the thread catcher 3 must be positioned at a distance of 0.8 mm above the bobbin case 4.
3
4
2
6
1
7
8
3
108
4
5
Fig. 13 - 17
● Loosen screws 1 and 2.
● Position the thread catcher 3 above the bobbin case 4.
● Move the thread catcher 3 (screw 5) according to the requirement.
● Determine the vertical play of shaft 6, move retaining collar 7 against bearing housing 8 and tighten screw 2.
Screw 1 remains slightly unscrewed for further adjustments.
Adjustment
13
.05.17
Thread catcher position and knife height
Requirement
When the thread trimmer is in resting position,
1. the front edges of the thread catcher 3 and the knife 5 must be fl ush with each other.
2. the upper edges of the thread catcher 3 and the knife 5 must be even.
3
5
6
6
5
2
1
4
Fig. 13 - 18
● Bring the needle bar to BDC.
● Move roller lever 1 against control cam 2 by hand.
● Turn the thread catcher 3 according to requirement 1.
● Tighten screw 4.
● Check the knife height according to requirement 2.
To adjust the height, disassemble knife 5 (screws 6) and insert shim
(part no. 91-141 402-05) according to the requirement.
To align the knife see chapter 13.05.18 Knife pressure.
109
Adjustment
13
.05.18
Knife pressure
Requirement
When the point of the thread catcher 4 is 6 mm in front of the front edge of the knife 4, the cutting edge of the knife must lightly press against the thread catcher 4.
6
6
4
5
6 mm
3
2
1
Fig. 13 - 19
● Bring the take-up lever to BDC.
● Press the roller lever 1 into the control cam 2.
● Turn the handwheel 3 in the direction of the arrow until the thread catcher 4 is approx. 4 mm in front of the knife 4.
● Move the knife 5 (screws 6) according to the requirement.
● Check requirement 1 from chapter 13.05.17 Thread catcher position and knife height.
110
13
.05.19
Bobbin thread clamp spring
Requirement
The clamp spring 1 must
1. not be pressed down during the movement of the thread catcher.
2. clamp the bobbin thread reliably after it is cut
3. not obstruct insertion and removal of the bobbin case.
Adjustment
1
3
2
2
Fig. 13 - 20
● Bring the thread trimmer to resting position.
● Move the clamp spring 1 (screws 2) so that the clamp lips are as close as possible to the inside wall and to the front edge of the thread catcher 3.
● Adjust the height by bending the clamp spring 1 so that between the upper side of clamp spring 1 and the lower side of the thread catcher 3 there is a distance of approx. 0.1 mm.
111
Adjustment
13
.05.20
Manual cutting test
Requirement
1. When it is moving forward, the thread catcher 1 must not push along the bobbin thread 3 in front of it.
2. At the front point of reversal of the thread catcher 1, the bobbin thread 3 must lie approx. 2 mm behind the lug of the thread catcher 1.
3. At the end of the cutting operation, the needle and bobbin threads must be cut perfectly. The bobbin thread 3 must be clamped.
2
1
3
1
2 mm
3
112
Fig. 13 - 21
● Carry out the cutting operation manually.
● Check requirement 1. If necessary, readjust the thread catcher 1 according to chapter
13.05.16 Thread catcher height.
● Check requirement 2. If necessary, readjust the thread catcher 1 according to chapter
13.05.17 Thread catcher position and knife height.
● Check requirement 3. If necessary, readjust the bobbin thread clamp spring 2 according to chapter 13.05.19 Bobbin thread clamp spring.
Adjustment
13
.05.21
Presser height
Requirement
1. When the take-up lever is at TDC, the needle point must not extend under the presser 1 when the presser 1 is raised.
2. The presser 1 must be aligned laterally so that the sewing thread is blown out from under the presser 1 when the sewing jig is moved into position.
2
4
4
1
1
3
1
Fig. 13 - 22
● Screw on presser 1.
● Bring the take-up lever 2 to TDC.
● Move the presser bar 3 (screws 4) according to requirement 1 and/or turn according to requirement 2.
113
Adjustment
13
.05.22
Bobbin winder
Requirement
1. When the bobbin winder is switched on, the bobbin winder spindle must move securely with the winder.
2. When the bobbin winder is switched off, friction wheel 5 must not be driven by drive wheel 1.
3. The bobbin winder must switch off automatically when the bobbin has been fi lled approx. 1 mm from the edge.
2
1 5
114
4
3
Fig. 13 - 23
● Move drive wheel 1 (screws 2) according to requirements 1 and 2.
● Move pin 3 (screw 4) according to requirement 3.
13
.05.23
Needle thread tension release
Adjustment
Requirement
For the tension release, the distance between the tension disks must be 0.5 mm.
0,5 mm
Fig. 13 - 24
● Turn screw 1 (nut 2) according to the requirement.
2
1
115
Adjustment
13
.05.24
Thread check spring and slack thread regulator
Requirement
1. The stroke of thread check spring 7 must be completed when the needle point penetrates the material (travel of the spring approx. 7 mm).
2. When the thread loop is at its largest when going round the hook, the thread check spring 7 must be lifted slightly above support 1.
6
1
7
3
2
5
116
Fig. 13 -25
● Position rest 1 (screw 2) according to Requirement 1.
● To adjust the spring tension, turn screw 3 (screw 4).
● Position thread regulator 5 (screw 6 ) according to Requirement 2.
For technical reasons, it may be necessary to deviate from the travel of the spring and/or the spring tension indicated here.
13
.05.25
Sewing head lifting cylinder
Requirement
The up and down movement of the sewing head must be uniform.
Adjustment
4
6
2
Fig. 13 - 26
● Insert the sewing head and connect. (See chapter 13.04 Removing/inserting sewing head).
● Adjust the speed (screw 1) and shock absorbing action (screw 2) of the upwards movement of the sewing head, and the speed (screw 3) and shock absorbing action (screw 4) of the downwards movement of the sewing head according to the requirement.
The pressure for the downward movement can be regulated with screw 5
(standard setting 4.5 bar).
When adjusting the shock absorbing action, make sure that the cylinder 6 moves as far as it can go especially for the downward movement of the sewing head!
117
1
3
5
Adjustment
13
.05.26
Hook lubrication
Requirement
When the machine is running, after approx. 10 seconds a fi ne line of oil must form on a paper strip 2 held next to the hook.
1
3
4
2
118
Fig. 13 - 27
● Unscrew the hook compartment cover.
● Remove the cover from sensor 1 with metal gauge.
● Switch on the machine.
● Call up the input menu.
● Call up the "sewing motor adjustment" function, see Chapter 13.09 Sewing motor adjustments.
● Set the speed at 2000 min
-1 .
When the sewing motor is running, do not reach into the needle area!
Danger of injury by the moving parts!
Adjustment
● Run the sewing motor for 2 – 3 minutes.
● With the motor running, hold a strip of paper 2 next to the hook and check the requirement.
● If necessary, adjust the oil supply with screw 3.
● Switch the machine off and screw on the hook compartment cover.
The wick used for lubricating the front parts must always be impregnated with oil. However, oil must not drip onto the bedplate!
● If necessary, regulate the amount of oil with screw 4.
119
Adjustment
13
.06
Adjusting the folding, feed and stacker devices
13
.06.01
Aligning the sewing jig
Requirement
The lowered sewing jig must lie evenly and lightly on the table top at both the folding and the sewing stations, and hold the workpiece securely.
4
Y
5 5
1
X
X
Y
2
3
Fig. 13 - 28
● Loosen screws 1 on both sides of the machine.
● Align the sewing jig by turning screws 2 (nuts 3) on both sides of the machine so that it is parallel to the table top in the x-direction.
● Tighten screws 1.
● Align the sewing jig by moving the carrier 4 (screws 5 on both sides of the machine) so that it is parallel to the table top in the y-direction.
120
13
.06.02
Height of the pocket plate guide
Requirement
The lowered pocket plate must be parallel to the top edge of the table.
Adjustment
2
3
5
4
1 1
6
Fig. 13 - 29
● Check the requirement using a metal ruler.
● Loosen screws 1 and 2.
● Adjust the height of the guide 3 with screw 4 (nut 5) according to the requirement.
● Turn the plunger (lock nut) of cylinder 6 until the guide 3 is parallel to the table top.
● Tighten screws 1 and 2.
121
Adjustment
13
.06.03
Aligning the pocket plate arm
Requirement
The lowered pocket plate 4 should be resting evenly on the table top.
122
1
3
1
3
2
2
Fig. 13 - 30
● Loosen screws 1.
● Turn screws 2 (nuts 3) according to the requirement.
● Tighten screws 1.
Re-check the height of the pocket plate Chap. 13.06.02.
13
.06.04
Aligning the pocket plate guide
Adjustment
Requirement
Guide 7 must be positioned perpendicular to guide 8 of the sewing jig feed.
90°
8
7
2
1
1
Fig. 13 - 31
● Switch on the machine.
● Bring the machine into the basic position.
● Taschenblech entnehmen und Taschenblech-Lehre 1 einsetzen.
● Call up "folder position", see Chapter 8.09 Checking / adjusting the zero points.
● Mittels Absteckstift 2 die Regel überprüfen.
● Druckluft abnehmen.
123
Adjustment
90°
8
7
4
4
6
5
1
Fig. 13 - 32
● Slide pocket plate gauge 1 to the back and mark front position.
● Loosen screws 3 and 4.
● Turn screw 5 (nut 6) according to the requirement.
3
3
1
2
124
Adjustment
13
.06.05
Front pocket plate position
Requirement
When the folder is positioned at zero point, the adjustment holes of the pocket plate and the sewing jig must be aligned.
2
1
3
3
Fig. 13 - 33
● Switch on the machine.
● Bring the machine into the basic position.
● Remove the pocket plate and insert the pocket plate gauge 1.
● Call up "folder position", see Chapter 8.09 Checking / adjusting the zero points.
● Set the value for the y-axis to „0".
● Check the requirement using the adjustment pin 1.
● Change the value for the x-axis according to the requirement via the control panel and store.
● Move the pocket plate arm 2 (screws 3) according to the requirement.
125
Adjustment
13
.06.06
Monitoring the sewing jig feed
Requirement
1. It should not be possible to move sewing jig 5 beyond its zero point in y-direction, and not more than 5 mm down or more than the value of measurement x up.
2. Initiator 3 should be positioned 0.2 mm below cam switch 1.
PFAFF 3588-05/020: X = 260 mm
PFAFF 3588-15/020: X = 290 mm
2
2
1
4
4
3 x
0
5 mm
5
Fig. 13 - 34
● Move the switch vane 1 (screws 2) according to requirement 1.
● Move the proximity switch 3 (screw 4) according to requirement 2.
126
Adjustment
13
.06.07
Positioning the edge folding unit
Requirement
When the edge folding unit and pocket plate are lowered
1. Folder arm 4 must be parallel with pocket plate arm 3 and the table top.
2. The pins in folder arm 4 and the bushes 2 in pocket plate gauge 1 must be aligned, and
3. there must be a clearance of 19 mm between folder arm 4 and pocket plate gauge.
4. The folder arm must rest lightly on the table top and hold the workpiece securely.
4
2 2
3 4
1
Fig. 13 - 35
● Remove pocket plate and edge folder
● Insert pocket plate gauge 1 and bushes 2.
● Switch on the machine.
● Call up manual sewing.
● Press the double start buttons.
● Operate the "single step" function, until pocket plate arm 3 and folder arm 4 have been lowered.
● Loosen screw 5.
127
Adjustment
2
4
2
1
3 4
6
5
5
5
5
6
8
7
Fig. 13 - 36
● Carry out the adjustment in accordance with requirements 1 and 2 by twisting and moving folder arm 4 and by twisting screws 6.
● Tighten screws 5.
● Turn shock absorber 7 (nut 8) according to requirement 3.
● Remove pocket plate gauge 1 and fi t the folding unit.
● Apply Tesamoll (adhesive tape) to the edge folder frame to fulfi l requirement 4.
128
Adjustment
13
.06.08
Aligning the die
Requirement
When the folder is lowered and the pocket plate is raised at the same time,
1. the bottom edges of the die’s 1 strips must be at a distance of approx. the thickness of the fabric under the underside of the pocket plate.
2. and they must be positioned on all sides at the same distance of 0.3 to 1 mm (depending on the fabric) to the pocket plate edges.
4
4
4
3
3
2
3
2
2
1
Fig. 13 - 37
● Align the bottom edges of the die’s 1 strips with the underside of the pocket plate via screws 2 (nuts 3).
● Turn damper 9 (nut 10) - see Fig. 13-37 - according to requirement 1.
● Align die 1 (screws 4) according to requirement 2.
129
Adjustment
13
.06.09
Control sequence of the folder plates
Pocket style
1. Switching position
2. Switching position
3. Switching position
4. Switching position a + b c + d e f + g a + b c + d + e f g + h a + b c + d e f a + b c + d + e f g a + b c + d e f + g
130
Fig. 13 - 38
The control sequence and the number of folder plates (and the number of switching positions) depends on the pocket style. The folder installation shown in
Fig. 13-38 is for the third pocket style.
For other pocket styles, refer to the above table for the cylinders corresponding to the relevant switching positions.
Adjustment
13
.06.10
Position of folder plates
Requirement
1. The front edges of the folder plates 1 must be parallel to the die 4.
2. In the initial position, the folder plates 1 must be positioned on all sides approx.
0.1 mm under the lower edges of the strips of the die 4.
2
2
4
3
3
3
1
1
3
3
1
3
3
1
3
1
2
2
2
2
2
2
Fig. 13 - 39
● Remove the folder.
● Align folder plate 1 (screws 2) according to requirement 1.
● Insert the folder plates 1 one after another according to the control sequence (see chapter 13.06.09 Control sequence of the folder plates) and align according to requirement
2 (screws 3).
● Remount the folder.
131
Adjustment
13
.06.11
Position of corner folders
Requirement
1. In folder position, the corner folders 4 must be parallel under the slanted side of the folder plate and overlap by 1 to 2 mm.
2. The corner folders 4 must be positioned 1 to 2 mm under the folder plates depending on the fabric thickness.
5
3
4
1 - 2 mm
5
4
1
2
5
4
4
132
Fig. 13 - 40
● Preadjust the clamps 1 (screws 2) according to requirement 1.
● For the fi nal adjustment, turn stop screws 3 according to requirement 1.
● Adjust the corner folders 4 (screws 5) according to requirement 2.
13
.06.12
Aligning the seam in relation to the pocket
Requirement
The seam is to be at the same distance on all sides to the pocket edge.
Adjustment
Fig. 13 - 41
● Switch on the machine.
● Using parameters "608" and "609" adjust the seam in accordance with the requirement, see Chapter 13.10 Parameter settings.
● Switch off the machine.
133
Adjustment
13
.06.13
Seam backtack distance
Requirement
The distance between the seam backtack and the pocket opening is to be approx. 1 mm.
1
2
2
2
2
1
Fig. 13 - 42
● Adjust stops 1 (screws 2) on the pocket plate according to the requirement.
134
Adjustment
13
.06.14
Stacking device
Requirement
When it is in operating position, the stacking device 2 must hold the workpiece with the least amount of pressure possible.
4
2
0
6
8
100
150
10
50
0
200
250
1
12
14
1
2
Fig. 13 - 43
● Adjust the pressure at pressure reducing valve 1 according to the requirement.
To carry out the adjustments, the outputs Y 52 and Y 51 must be switched, see
Kapitel 13.08 Servicemenu.
135
Adjustment
13
.06.15
Aligning the feed rollers
Requirement
The lowered feed follers 4 must rest lightly and evenly on the table top, and be positioned parallel to the front edge of the table.
4
4
1
2
1
3
1
2
1
Fig. 13 - 44
● Turn screws 1 (loosen screws 2 slightly) and the plunger of the cylinder 3 according to the requirement.
136
13
.07
Shaping folder plates
13
.07.01
New installation / self-manufacture of folder plates
Adjustment
c g e
2 f h d c
3 e f d c
1, 4 d c
5 d f
30°
30° g f g e e
Fig. 13 - 45
● Make and/or install the folder plates according to Fig. 13-45.
When newly installing or making the folder plates, make sure that they lie behind the corners of the pocket plate by at least the amount of the fabric thickness on the marked spots.
For the fi fth pocket style, the folder plates e, f and g must be additionally slanted by 30°.
137
Adjustment
13
.07.02
Slanting the lateral folder plates
Do not begin with this work process until the adjustments in chapters 13.06.12
Aligning the seam in relation to the pocket and 13.06.13 Seam backtack distance have been carried out!
1 - 2 mm
30°
1 1
1 - 2 mm
30°
138
2
Fig. 13 - 46
● With the folder plates fully extended, transfer the front edges of the stops 1 and the outer edge of the pocket plate 2 to the lateral folder plate.
● Trace slanted edge of 30°.
● Work the folder plate up to 1 - 2 mm before the trace.
● Round off the edges of the folder plate and polish.
13
.08
Adjustment
Service menu
The status of the digital and analog inputs is displayed in the service menu. The outputs can be set or reset manually. In addition it is also possible to call up functions for carrying out a cold start, for loading the operating program and for setting the control panel.
● Switch on the machine.
● Call up the input mode.
● Call up the service menu.
Explanation of the functions
Input mode
This function is used to change to the initial state of the input mode.
Conclude input
This function is used to conclude the input and change into the sewing mode.
Can-nodes
This function is used to select the required Can-node. The currently selected Can-node is shown as an inverse symbol.
Special outputs
This function is used to set or reset special outputs.
Plus/minus keys
These functions are used to set (+) or reset (-) the selected output.
Arrow keys
These functions are used to select the desired outputs.
Cold start
This function is used to carry out a cold start, see Chapter 13.08.01 Cold start.
Loading the operating program
This function is used to load the machine operating program, see Chapter 13.08.02 Loading/ updating the operating program.
139
Adjustment
Control panel settings
This function is used to call up a menu for changing the display contrast and for switching the key tone on or off, see Chapter 8.08 Setting the control panel.
Adjusting the zero points
This function is used to call up a menu for setting the zero points, see Chapter 8.09 Adjusting the zero points.
13
.08.01
Coldstart
When a cold start is carried out, all newly created or edited programs, as well as all altered parameter settings are deleted!
The machine memory is deleted or set back to the status at the time of delivery.
● Switch on the machine and call up the input mode.
● Call up the service menu.
● Call up the cold start function.
140
● Confi rm that a cold start is to be carried out.
Explanation of further functions
Input mode
This function is used to change to the initial state of the input mode.
Service menu
This function is used to return to the service menu, see Chapter 13.08 Service menu.
Conclude input
This function is used to conclude the input and change into the sewing mode.
Esc
The input is interrupted.
Adjustment
13
.08.02
Loading / updating the operating program
To boot a new machine software, a sd-card with the needed fi les has to be plugged in the sd-slot of the control panel.
During the loading of the operating program all data in the machine memory is deleted!
● Switch on the machine and push the button "FORCE UPDATE".
● Start the bootsequence with the key "ENTER".
Install update 79-001 103-80/003 for the machine KL3588?
Installing the update, Please wait....
- COPYING 3588.EXE FROM SD-CARD
TO C:\UPDATE\3588.EXE
● To install the software, push the key "NEXT".
Update successfully copied.
Press NEXT to install the update in control box and start the application
141
Adjustment
13
.09
Sewing motor adjustments
● Switch on the machine.
● Call up the input mode.
● Call up the "sewing motor adjustments".
Description of the functions
Conclude input
This function is used to conclude the input and change to the sewing mode.
Speed adjustment
This function is used to increase or reduce the set speed.
Start
This function is used to start the motor running.
Stop
This function is used to stop the motor running.
Thread trimming cycle
This function is used to run the thread trimming cycle.
Needle position
The present set position of the needle is displayed.
To adjust the needle bar position to t.d.c., bring the needle bar into the appropriate position by turning the balance wheel, and then operate the "POS" function to take over this position.
142
13
.10
Adjustment
Parameter settings
All parameters, which can be altered, are shown in the list of parameters, see Chapter
13.10.02 List of parameters. A description of how to select parameters and alter the values is given below.
13
.10.01
Selecting and altering parameters.
● Switch on the machine and call up the input mode.
● Call up the parameter input function.
● Select the parameter separately by group (hundred fi gure) and parameter within the function group.
● Alter the value of the selected parameter.
● Quit parameter input function.
143
Adjustment
13
.10.02
List of parameters
100 101 Bobbin thread monitor
(0 = off; 1 = counter; 2 = sensor; 3 = sensor +stop)
102 Needle thread monitor
(0 = off; 1 = on)
103 Fade-out stitches needle thread monitor. The number of stitches, during which the needle thread monitor is not activated during sewing, is changed.
104 Fade-out stitches bobbin thread monitor. The number of stitches, during which the bobbin thread monitor is not activated during sewing, is changed.
105 Reaction time needle thread monitor. The sensitivity of the needle thread monitor is altered (1 = quickest reaction, max. sensitivity)
106 Retracing stitches
The number of stitches which are automatically retraced after a needle thread error, is changed.
107 Sewing
(0 = off; 1 = on)
108 Jig monitoring
(0 = off; 1 = on)
109 Intermediate stop
0 = off;
1 = 1st stop after folder lowered;
2 = 2nd stop after folding operation;
3 = 1st and 2nd stop
Press the double start keys to continue operation.
110 Alternate folding
(0 = off; 1 = on)
111 Continuous carriage feed
(0 = off; 1 = on)
112 Automatic switching to next sequence
(0 = off; 1 = on)
0 - 3
0 -1
0 – 99
0 – 99
1 - 9
0 - 99
0 - 1
0 - 1
0 - 3
0 - 1
0 - 1
0 - 1
1
1
5
5
1
15
1
0
0
0
0
1
144
Adjustment
100
113 Uni-material
This parameter changes the function of the loading switch
0 = reverse suction air and ventilate pocket plate
1 = reverse suction air
2 = reverse ventilation pocket plate, 1st position: ventilated
3 = reverse ventilation pocket plate, 1st position: down
114 Basic position pocket plate
0 = forwards; 1 = back
115 Slide confi guration
Y9 = value 8
Y8 = value 4
Y7 = value 2
Y6 = value 1
Calculate sum of valves to be switched.(e.g.: Switch valves Y9 and Y7 -> 8 + 2 = 10)
116 Slide confi guration Program station 1
Y9 = value 8
Y8 = value 4
Y7 = value 2
Y6 = value 1
Calculate sum of valves to be switched.
(e.g.: Switch valves Y8 and Y6 -> 4 + 1 = 5)
117 Slide confi guration Program station 2
Y9 = value 8
Y8 = value 4
Y7 = value 2
Y6 = value 1
Calculate sum of valves to be switched.
(e.g.: Switch valves Y9 and Y6 -> 8 + 1= 9)
118 Slide confi guration Program station 3
Y9 = value 8
Y8 = value 4
Y7 = value 2
Y6 = value 1
Calculate sum of valves to be switched.
(e.g.: Switch valves Y7 and Y6 -> 2 + 1 = 3)
0 - 3
0 - 1
0 - 15
0 - 15
0 - 15
0 - 15
0
0
15
15
15
15
145
Adjustment
146
100
119 Slide confi guration Program station 4
Y9 = value 8
Y8 = value 4
Y7 = value 2
Y6 = value 1
Calculate sum of valves to be switched.
(e.g.: Switch valves Y9 and Y8 -> 8 + 4 = 12)
120 Tilt sewing head
0 = off; 1 = on
121 Folding version
0 = standard
1 = version 1 (only pre-cut part is moved to sewing station)
2 = version 2 (pre-cut part and pocket are moved to sewing station without folding)
3 = version 3, pre-folded pockets
4 = version 4, as standard but for round pockets
122 Jig version
0 = standard
1 = fl ap version 1 (fl ap completed)
2 = fl ap version 2 (fl ap open)
3 = variable sewing slit
4 = cargo
123 Stop in case of undervoltage
0 = off; 1 = on
124 Reverse needle positioning
0 = off; 1 = on
200 201 Tilting sewing head
0 = not fi tted; 1 = fi tted
202 Hook
0 = horizontal hook; 1 = vertical hook
203 Jig monitor
0 = not fi tted; 1 = fi tted
204 Height adjustment
0 = not fi tted; 1 = fi tted
205 Cargo unit
0 = not fi tted; 1 = fi tted
209
Machine typ
0 = Standard (with P200 and QE5542)
1 = Standard (with MMC 1002 and QE5540)
0 - 15 15
0 - 1
0 - 4
0 - 4 0
0 - 1
0 -1
0 -1
0 - 1
0 - 1
0 - 1
0 - 1
0 - 1
0
0
0
0
1
0
0
0
0
Adjustment
300
301 NIS (carriage start) [°], see Chap. 13.10.03
302 Take-up lever tdc [°]
303 Thread trimming on [° ]
Point at which impulse for thread trimming is given to thread trimming valve is changed (° = degrees after tdc needle bar).
305 Thread trimming off [° ]
400
500
306
401
501
Open thread tension
Time for label clamp closed [0.01 s]
Reduced speed
80 – 150
70 – 90
110
75
160 – 360 200
Parameter
303 / 302
5 - 20
10 – 256
345
15
20
200 – 4000 3600
502 Cutting speed (positioning speed)
503 Speed for slow start stitches
504 Slow start stitches
Number of stitches, which are to be sewn at reduced speed when sewing starts, is changed
505 Delay stitches zig-zag on
This parameter is used to enter the number of stitches after which the "zig-zag on" command is given later, see Chapter 13.10.04 Delay zig-zag on/off
506 Delay stitches zig-zag off
This parameter is used to enter the number of stitches after which the "zig-zag off" command is given later, see Chapter 13.10.04 Delay zig-zag on/off
600
601 Direction of slow rolling stacker
0 = backwards: 1 = forwards
602 Slow rolling time stacker [0.01 s]
This parameter is used to enter the time for the slow rolling motion of the stacker roller, see Chapter
13.10.05 Stacker rolling time
50 - 250
200 - 700
0 – 99
0 - 99
0 - 99
0 - 1
0 - 999
200
700
2
3
3
1
50
603 Quick rolling time stacker [0.01 s]
This parameter is used to enter the time for the quick rolling motion of the stacker roller, see Chapter
13.10.05 Stacker rolling time
0 - 999 35
147
Adjustment
600 604 Delay time for stacker frame back [0.01s]
The parameter is used to enter the delay time between stacker roller roll slowly and stacker frame back.
605 Time for folder slide back [0.01s]
The parameter is used to enter the delay time for the folder slide.The time should be set so that the folder does not move up until the folder plate is in its rear end position.
606 Time for pocket plate open [0.01s]
The parameter is used to enter the delay time between pocket plate back and pocket plate open. If the time selected is 0.00 s, the pocket plate opens when the end switch pocket plate back (E1.2) is activated.
607 Speed feed unit [%]
The parameter is used to enter the speed of the sewing jig feed unit from the folding to the sewing station.
608 Seam correction X [0.01 mm]
This parameter is used to change the position of the seam on the pocket in x-direction.
609 Seam correction Y [0.01 mm]
This parameter is used to change the position of the seam on the pocket in y-direction.
610 Stacker cycle
0 = standard
1 = short part
2 = off (basic position retracted)
3 = off (basic position extended)
0 - 999
0 - 999
0 - 999
20 - 100
-20 - +20
-20 - +20
0 - 3
0
30
50
100
0
0
0
148
13
.10.03
Carriage start
(NIS)
This function changes the time for starting the motors of the jig drive
(º = degree after t.d.c. needle bar).
Adjustment
Needle at t.d.c.
0°
Needle leaves the material, carriage start at approx. 270°
Needle pierces the material, carriage stops, command for carriage start is given at approx. 110°
Needle in material, continuous area of
180°
The command for the carriage start is given when the needle pierces the material. The carriage, however, starts half a revolution later (180º), when the needle leaves the material.
Under certain circumstances the stitch formation can be infl uenced by the setting.
149
Adjustment
13
.10.04
Zig-zag delay on/off
Due to the delay of the valve and cylinder, output of the commands for DELAY
ZIGZAG ON and OFF must be delayed as a function of the speed.
Zick-Zack on
Zick-Zack off
Delay correct
Delay too short, increase stitch count
Delay too long, decrease stitch count
Fig. 13 - 47
Delay correct
Fig. 13 - 48
Delay too short, increase stitch count
Delay too long, decrease stitch count
13
.10.05
Stacker rolling time stacker frame workpiece slow rolling time, correct rolling direction
Fig. 13 - 49 slow rolling time, change rolling direction if necessary
150
14 Control
14
.01
Basic setting / Diagnosis / Pin assignment
14
.01.01
Basic control unit A20
Control unit
In the factory, the basic control unit is equipped with the necessary operating and ramp software. This may only be replaced by appropriately trained personnel.
Pin locations
Key for booting the software
X5, SM-axis 1
X6, SM-axis 2
X7, SM-axis 3
X11, Main drive
Index
Thread monitor
5 V CPU,
Si 2A/T
24 V, max. 5 A
Periphery, Si,3 A/T
Mains connection
X4, Com2
X3, Com1
X8 CAN-Bus
1
8 V/AC, Si 0,5 A/T
Network, Si 1.25 A/T
151
Control unit
Operation indicators/Voltage supply
LEDs for various operating voltages are provided on top of the device (see sticker on the device).
These LEDs are for + 12V, + 15.1V and + 24V.
Fuses
2,0 AT / 5V / CPU
6,3 AT / 24V / Periphery
0,5 AT / 16V / Control panel
1,25 AT / 230V / Main
Pin assignment
X3 (COM1) and X4 (COM2)
PIN
1
2
3
4
5
Signal
Vterm1
RxD
TxD bridged to PIN 6
GND
PIN
6
7
8
9
Signal gedrückt an PIN 6
RTS
CTS
Vterm2
X5 or X3 (Sewing motor)
6
7
8
PIN
1
2
3
4
5
Signal
Puls + direction +
Fkt1 +
Fkt2 +
Vex +
Inp2 +
Inp1 +
X8 (CAN-Bus)
PIN
1
2
3
4
5
Signal
DoRi +
GND
PIN
9
10
11
12
13
14
15
PIN
6
7
8
9
Signal
Puls direction -
Fkt1 -
Fkt2 -
Vex -
Inp2 -
Inp1 -
Signal
DoRi -
GND
152
X11 (Main drive)
8
9
10
11
12
13
4
5
6
7
PIN
1
2
3
Signal
Puls + direction +
Fkt1 +
Fkt2 +
Vex +
Inp2 +
Inp1 +
R1_A
R1_B
R2_A
R2_B
GND
21
22
23
24
25
26
17
18
19
20
PIN
14
15
16
Control unit
Signal
A_A
A_B
B_A
B_B
I_A
I_B
GND
A_OC
B_OC
I_OC
V2
GND
Vex
14
.01.02
Sewing drive A22
Before leaving the factory, the sewing drive controller is equipped with the necessary operating software. This software may only be replaced by appropriate specialist personnel.
The LED Power on indicates if (the sewing drive) is ready to operate. There are no diagnostic functions and fuses available. If error messages occur in the machine display, please refer to chapter 14.02.04
Sewing motor errors.
X1 or X7 (Synchronizer)
PIN
1
2
3
4
5
Signal
FA
FB
SM
ADTC1
+ 5V
PIN
6
7
8
9
Signal
GND
X2 (Commutating signal generator)
PIN
3
4
5
1
2
Signal
ADTC2
+ 5V
PIN
6
7
8
9
Signal
KA
KB
KC
GND
153
Control unit
X3 (Interface)
8
9
10
11
12
13
4
5
6
7
PIN
1
2
3
X1 or X14 (motor)
Signal
PE
U
V
W
Signal
GND
TxD
RxD
TxD\
RxD\
GND
REF1
REF1\
REF2
REF2\
GND
21
22
23
24
25
26
17
18
19
20
PIN
14
15
16
Signal
A
A\
B
B\
Index
Index\
154
14
.01.03
Stepping motor drive A21
The stepping motor controller has the following initial setting:
DIP switch
OFF ON
*
*
*
*
Step no.: 1000
Step no.:
Current reduction active
Enable
Control unit
Rotary switch
B
Position B ==> phase current 5.4 A
For information on the status indications via LED please refer to chapter 14.02.05 Errors – Stepping motor drive.
Pin assignment
X5 (Stepping motor 1) or X6 Stepping motor 2)
PIN
1
7
8
5
6
2
3
4
Signal
Pulse +
Direction +
Current contro +
Ready +
PIN
9
10
11
12
13
13
15
Signal
Pulse -
Direction -
Current contro -
Ready -
155
Control unit
14
.01.04
Stacker motor drive
Before leaving the factory, the stacker motor drive has been set and/or programmed to meet the requirements of this machine. It may only be replaced by a programmed drive.
Operation controls
LED H1 (yellow) off
LED H2 (green) off on off
Discription
Power off, no function
Power on, after approx
0,5s of self-test ready for operation drive has been started off on on on fl ashes off overload protection active see chapter 14.02.06Errors -
Stacker drive
156
14
.01.05
AC-Line-Controller
The AC-Line-Controller is set in the factory to the requirements of this machine.
An exchange is only permissible after prior adjustments.
Default setting
Potentiometer
UL (upper limit)
LL (lower limit) off Delay
Value
260V
195V
Min
Operation displays
LED H1 (green) off on on
LED H1 (red) off off on
Discription line off, no function machine functional,
voltage outside the set range machine functional,
voltage within the set range
14
.02
Description of the error messages
14
.02.01
General errors
Display Description
Control unit
ERROR: 3
ERROR: 4
ERROR: 5
ERROR: 6
ERROR: 7
ERROR: 8
ERROR: 10
ERROR: 11
ERROR: 12
ERROR: OPERATING
DATA CHECK SUM (COLD
START CARRIED OUT)
NEW OPERATING SOFT-
WARE (COLD START CAR-
RIED OUT)
COLD START CARRIED
OUT
ERROR: 15
ERROR: 101
ERROR: 102
(#node no.)(status)
ERROR: 103
ERROR: 104
ERROR: 105
ERROR: 201 (#sewing motor error)
ERROR: 210
ERROR: 211
ERROR: 212
ERROR: 213
ERROR: 214
ERROR: 215
ERROR: 216
ERROR: 217
ERROR: 219
ERROR: 220
ERROR: 221
ERROR: 240 (cause)
ERROR: 241 (cause)
Error in allocation EMS memory
C167 not reacting
Boot fi le (c167boot.bin) cannot be opened
Error in fl ash-programming
Error when opening a fi le
Battery
CAN-error (reset)
CAN-error (no. of nodes)
Communication main drive
Operating data check sum
New operating software
Cold start
Main drive changed
C167-error
CAN-error, status = Bit1 - node inactive,
Bit 8 - short circuit
End stage (SmX)
End stage (SmY)
Error compressed air
Sewing motor error (see Chapter 14.02.04 Sewing motor errors)
Command byte of NM-interface not free,command could not be given
Coordinates outside sewing area
Stitch length too long (> 6 mm)
Carraige initiators not found
Remove material
Ramp not completed
Insert material
No jig inserted, program number could not be read
Wrong jig
Wrong jig code
No carriage start (NIS)
Move to starting point blocked
Move to Home blocked
157
Control unit
Display
ERROR: 242 (cause)
ERROR: 243 (cause)
ERROR: 244 (cause)
ERROR: 245 (cause)
ERROR: 246 (cause)
ERROR: 247 (cause)
ERROR: 248 (cause)
ERROR: 249 (cause)
ERROR: 250 (cause)
AC
ERROR: 261
ERROR:301
ERROR: 302
ERROR: 303
ERROR: 305
ERROR: 306
ERROR: 308
ERROR: 310
ERROR: 311
ERROR: 312
ERROR: 313
ERROR: 314
ERROR: 315
ERROR: 316
ERROR: 317
ERROR: 318
ERROR: 319
ERROR: 320
ERROR: 321
ERROR: 322
ERROR: 323
ERROR: 324
ERROR: 325
ERROR: 326
ERROR: 327
ERROR: 328
ERROR: 329
ERROR: 330
(#Stitch generation error)
(#Section number)
ERROR: 331 Stitch too large (> 6 mm)
Description
Move to folder blocked
Move from folder to mach. zero point blocked
Move from folder to stacker point blocked
Move to stacker point blocked
Tacting blocked
Moving in sewing program blocked
Shifting to fl ap slit blocked
Move from stacker point to mach. zero point blocked
Sewing blocked
Undervoltage (error 255)
Bobbin thread error
Carriage position invalid
Needle position (carriage) invalid
Folder position invalid
Confi guration invalid
Needle position (t.d.c.) invalid
Machine not in basic position
File not on source
Source reading error, fi le cannot be opened
Target writing error, fi le cannot be opened
Source reading error
Target writing error
File confi guration cannot be opened
Error when opening MDAT-fi le
Writing error in MDAT-fi le
Machine data identifi cation incorrect
Reading error in MDAT-fi le
Prog. with incorrect machine class
Prog. with incorrect machine version
Prog. with incorrect data set version
Incorrect program number
No carriage start, NIS
Memory overfl ow when writing fi le to fl ash
Flash writing error
Image leaves sewing area
Block not marked or incorrectly marked
Program too large
Conversion error
158
Display
ERROR: 332
ERROR: 341
(#sewing motor error)
ERROR: 342
(# program number)
ERROR: 343
(# program number)
ERROR: 344
(# program number)
ERROR: 345
(# program number)
ERROR: 401
ERROR: 402
ERROR: 403
ERROR: 501
ERROR: 502
14
.02.02
CAN-errors
Error byte bit7 bit6 bit5 bit4 bit3 bit2 bit1 bit0
Description
-
-
End stage error (short circuit)
Receive status (waiting for input object)
Transmit status (transmit output object)
Transmit status
Node time out
Node active
Control unit
Description
Check-point not permitted
Sewing motor error,
(see Chapter 14.02.04 Sewing motor errors)
Program incomplete
Program too large
Program does not exist
Flash reading error or program defective
Text fi le cannot be opened
Error when reading text fi le
Error in allocation of storage space for texts
Error when opening fi le "pikto.hex" or "vorlagen.hex"
No acknowledgement from control panel
159
Control unit
16
17
18
19
10
11
12
13
14
15
20
21
22
23
24
5
6
3
4
7
8
9
29
30
31
25
26
27
28
14
.02.03
Stitch generation error
Display
1
2
Description
Incorrect machine identifi cation
Section "jig type" or section "obstacle" missing or on wrong place
Increment too large
Program end without thread trimming
Impermissible stitch length data
Incorrect element in geometrical data set
Quick motion although machine is sewing
Impermissible stitch length data
Impermissible stitch length data
Circle check-point = circle end point
Division by zero
Impermissible stitch length data
No coordinates section before curve check-point
Sewing area limit exceeded
Curve without end point
Mach. function buffer overfl ow
Start sewing command in loading point program
Incorrect curve check-point
Incorrect curve check-point
Incorrect curve check-point
Incorrect curve check-point
Stitch length not initialised
Loading point program not ended
Stitch width command in loading point program
Impermissible value for section stitch direction
Cutting command, although thread cut
Start sewing command, although machine sewing
Cutting command in sewing-off-area
Sewing-off command, although thread cut
Cutting command directly after start sewing command
Start bartack too long
160
Control unit
14
.02.04
Sewing motor errors
Display
1
2
3
4
30h (48)
31h (49)
32h (50)
33h (51)
34h (52)
35h (53)
36h (54)
37h (55)
38h (56)
39h (57)
3Ah (58)
3Bh: (59)
3Ch: (60)
3Dh: (61)
3Eh: (62)
3Fh: (63)
40h - 4Fh -
50h: (80)
51h: (81)
52h: (82)
53h: (83)
54h: (84)
55h: (85)
56h: (86)
57h: (87)
58h: (88)
59h: (89)
5Ah: (90)
5Bh: (91)
5Ch - 69h -
6Ah: (106)
6Bh: (107)
6Ch: (108)
6Dh: (109)
6Eh: (110)
6Fh: (111)
70h: (112)
71h - FFh -
Description
Transmission error
Timeout serial interface
Check sum error in incoming data
Timeout command
Timeout-slave expired (command string incomplete)
Incorrect command code
Framing or parity error
Check sum incorrect
Incorrect date request
No parameter programmable (motor operation)
Parameter does not exist
Incorrect parameter value
EEPROM being programmed
Incorrect machine speed
Incorrect position
Path for guided positioning too short
Reset of position counter not possible (motor running)
Turning to tdc after mains on not permitted
System mark not recognised
Target position < 3 incr. away from count position
Network control (failure of 2 network half waves)
Error power electronics during initialization
Short circuit in motor
Mains voltage off recognized
Error power electronics in operation
No increments
Motor blocked
Commutation transmitter connector missing
Increment transmitter connector missing
Fault in motor running (target speed not reached)
-
Regulating algorithm blocked
EEPROM not programmable
EEPROM missing
-
Master reset carried out
Residual path for path-controlled, guided delay ramp too short
Slave has received 5 successive garbled messages
Time-out over
161
Control unit
14
.02.05
Errors – Stepping motor drive
If problems occur with the stepping motor drive during the operation, an error might have occurred in the stepping motor controller.
The error message is indicated by LEDs on the stepping motor controller.
LED
01 ROT. ERROR
06 READY
07 FAULT
08 TEMP
09 OVER-VOLT
10 LOW-VOLT
09 + 10
Meaning goes out when
- the motor blocks
- the stepping motor amplifi er is not ready
- the Enable input is not activated
- a breakage has occurred in the supply and/or blocking detection
line is lit up when
- the amplifi er is driven correctly
- the supplied voltage is in the rated range lights up if a short-circuit occurs between two motor phases lights up if the temperature at the cooling device is too high (>75ºC) lights up if there is an over-voltage (>400 V) during braking lights up if there is a low voltage (< 200 V) are lit if the Enable input is not activated
162
Control unit
14
.02.06
Errors - Stacker drive
If problems occur with the stacker drive during operation, an error might have occurred in the motor drive.
In this case, a fl ashing LED on the motor controller indicates the error.
Correction/
Comment
H1(yellow) Condition/
fl ashes cause
once
|_________|_________
twice
| |________| |________ low voltage
three times
| | |_______| | |_______
I > 180% I
N
short-circuit
four times
| | | |______| | | |______ acts as generator processor error on again (Reset) power off automatic reset power off due to overcurrent overcurrent or motor check drive
fi ve times
| | | | |_____| | | | |_____
six times
| | | | | |____| | | | | |____
converter
seven times
| | | | | | |___| | | | | | |___
eight times
| | | | | | | |__| | | | | | | |__ temperature too high
nine times
| | | | | | | | |_| | | | | | | | |_
I*t power off motor
I*t power off frequency motor temperature too high frequency converter check mounting conditions
Error in the EEPROM switch the mains off and back fl ashes until UZK <65V, check drive/motor cable check mains, motor overloaded, frequency converter overloaded, check bridge X5/10-11 frequency converter overloaded, switch mains off and on
163
Control unit
14
.03
List of outputs and inputs
14
.03.01
CAN-Nodes 1
Output
OUT9
OUT10
OUT11
OUT12
OUT13
OUT14
OUT15
OUT16
OUT1
OUT2
OUT3
OUT4
OUT5
OUT6
OUT7
OUT8
Term
Y5U2
Y6
Y7
Y8
Y9
Y10
Y35U1
Y35U2
Y1U1
Y1U2
Y2U1
Y2U2
Y3
K4
K20
Y5U1
Function
Pocket plate forwards
Pocket plate backwards
Pocket plate up
Pocket plate down
Pocket plate ventilation on
Stamp solenoid on
Pocket plate solenoid on
Folder up
Folder down
Corner slide forwards
Folder slide 1 forwards
Folder slide 2 forwards
Folder slide 3 forwards
Suction air on
Jig up
Jig down
Input
IN8
IN9
IN10
IN11
IN12
IN13
IN14
IN15
IN16
IN1
IN2
IN3
IN4
IN5
IN6
IN7
Term
E1U1
E1U2
E2U2
Function
Pocket plate at front
Pocket plate at back
Pocket plate down
E5U1
E5U2
TSAUG
TDOPP1
TDOPP2
E35U1
E35U2
PRESS
FKEY
TSSTOP
AC_OK
Folder up
Folder down
Key suction
Double start key 1
Double start key 2
Jig up
Jig down
Compressed air ok
Key (for secured functions)
Separate stop key
Undervoltage monitoring
Remark
Impulse valve
Impulse valve
Impulse valve
Impulse valve
Valve
Solenoid
Solenoid
Impulse valve
Impulse valve
Valve
Valve
Valve
Valve
Valve
Impulse valve
Impulse valve
164
Control unit
14
.03.02
CAN-Nodes 2
Output
OUT1
OUT2
OUT3
OUT4
OUT5
OUT6
OUT7
Term
Y30
Y31U1
Y31U2
K32
Y34
Y36
Y37
OUT8
OUT9
OUT10
OUT11
OUT12
OUT13
OUT14
OUT15
OUT15
OUT16
Y38
Y50
Y51
Y52
Y33
OUT1
OUT2
Y39
Y39U2
Y39U1
Funktion
Sewing foot down, thread clamp open
Raise sewing head
Lower sewing head
Thread tension on
Blower needle cooling on
Zig-zag on (prog. Outlet 3)
Secondary thread tension on
(prog. Outlet 5) ready made fl aps
Roller down
Clamp strap open
Stacker frame back
Thread trimming on
Programmable outlet 1
Programmable outlet 2
Bobbin cover open (with vertical hook)
Bedplate up (with horizontal hook)
Bedplate down (with horizontal hook
Remark
Valve
Impulse valve
Impulse valve
Solenoid
Valve
Valve
Valve
Valve
Valve
Valve
Valve
Valve
Dig. Signal
Dig. signal
Valve
Impulse valve
Impulse valve
Input
IN5
IN6
IN7
IN8
IN1
IN2
IN3
IN4
IN9
IN10
IN11
IN12
IN13
IN14
IN15
IN16
Term
E30
E31U1
E31U2
THERR
IN1
IN2
E39U2
E39U1
E50U1
E50U2
Function
Sewing foot raised
Sewing head raised
Sewing head lowered
Needle thread error
Programmable inlet 1
Programmable inlet 2
Bedplate up (with horizontal hook)
Bedplate down (with horizontal hook)
Bobbin cover closed (with vertical hook)
Roller down
Roller up
E52
SM1LI-
MIT
SM2LI-
MIT
E62
Stacker frame back
Zero position SM1
Zero position SM2
Defl ector down (cargo)
165
Control unit
14
.03.03
CAN-Nodes 3
Output
OUT1
OUT2
Term
Y11
OUT3
OUT4
OUT5
OUT6
OUT7
OUT8
OUT9
OUT10
OUT11
OUT12
OUT13
OUT14
OUT15
OUT16
Funktion Remark
Y12U1
Y12U2
Y40
STR
STL
S1IND
S2IND
K53
Y60
Y61
Y62
Label holding jig open
(with manual label feed)
Swing folder slide 3 (with folder slide 4)
Flap position off or var. sewing slit narrow
Flap position on or var. sewing slit wide
Valve
Impulse valve
Impulse valve
BOBRES Reset for bobbin thread monitor
Hook lubrication on
Start stacker motor clockwise rot.
Start stacker motor anti-clockwise rot.
Stacker motor frequency 1
Stacker motor frequency 2
Stand height adjustment on
Swing in defl ector (cargo)
Defl ector forwards (cargo)
Defl ector down (cargo)
Dig. Signal
Valve
Dig. Signal
Dig. Signal
Dig. Signal
Dig. Signal
Relay
Valve
Valve
Valve
Input
IN9
IN10
IN11
IN12
IN13
IN14
IN14
IN15
IN16
IN5
IN6
IN7
IN8
IN1
IN2
IN3
IN4
Term jigcode jigcode jigcode jigcode jigcode jigcode jigcode jigcode
BOBERR
Funktion
Jig code bit 0
Jig code bit 1
Jig code bit 2
Jig code bit 3
Jig code bit 4
Jig code bit 5
Jig code bit 6
Jig code bit 7
Bobbin thread error
ETINKL
E14
E12U2
E12U1
E54U1
E54U2
Label in clamp, man. label feed
Jig with obstacles
Flap pos. switched off or sewing slit wide
Flap position activated (for fl ap version 2)
Stand up
Stand down
166
14
.03.04
Special outputs
Term
S1
S2
S3
S4
S5
Funktion
Stacker motor forwards slowly
Stacker motor backwards slowly
Stacker motor forwards quickly
Stand up
Stand down
Control unit
Remark
14
.04
Boot key
1
This work may only be carried out by properly instructed personnel!
Do not touch any live parts!
Danger to life through electric voltage!
167
Pneumatics-switch diagram
Version 26.05.99
95-775 774-95
Part 1
The control elements and valves are in the machine‘s basic position.Main switch -ON, compressed air -ON
168
95-775 774-95
Part 2 Version 26.03.99
Pneumatics-switch diagram
169
Pneumatics-switch diagram
Version 04.11.15
95-775 774-95
Part 3
170
95-775 774-95
Part 4 Version 26.03.99
Pneumatics-switch diagram
171
Pneumatics-switch diagram
Version 26.05.99
95-775 774-95
Part 5
172
95-775 774-95
Part 6 Version 26.03.99
Pneumatics-switch diagram
173
Pneumatics-switch diagram
Version 19.05.06
95-778 520-95
174
14 Stromlaufpläne
Reference list
A60
K4
K32
K53
K54
Z1
E1
T1
C1
Q1
A21
A22
A23
A24
A11
A12
A13
A20
A25
A26
M1
M2
M3
M4
M5
M6
M7
A42+A43
Reference list for circuit diagrams
Stepping motor 1
Stepping motor 2
Sewing motor
Stacker motor
Height-adjustment motor
Suction motor
Ventilator control cabinet
CAN node 1
CAN node 2
CAN node 3
Controller BS 3
Stepping motors end phase (dual output amplifi er)
Sewing motor, end phase
Synchronizer
Needle thread monitor, monitoring results
Needle thread monitor, sensor
Control panel
Stepping motors end phase (two individual output amplifi ers)
Rotary switch motor current, setting B = 5.4.A
Description of LEDs
1 DC bus live
2 Operational, power amplifi er authorised, motor live
3 Short circuit between 2 motor phases or against protective earth
4 Static = excessive power amplifi er temperature,
blinking = excessive motor temperature
5 Overvoltage (DC bus > 420VDC)
6 Undervoltage (DC bus > 180VDC)
7 Error message on rotation monitoring
8 Encoder connected and operational
5+6 Power amplifi er deactivated, motor currentless
3 - 6 Frequency too high at signal point
Frequency converter
Stamp solenoid
Thread tension is released
Switching relay, height adjustment / stacker
Voltage supervision relay
Line fi lter
Sewing lamp
Transformer for sewing lamp
Capacitor for M6 (-4/01)
On/off switch
175
Inputs
E39.2
E50.1
E50.2
E52
E54.1
E54.2
E62 in1 in2 sm1limit sm2limit tdopp1 tdopp2 tsaug press fkey tsstop therr boberr eterr etrdy etinkl jigcode
E14
E30
E31.1
E31.2
E35.1
E35.2
E39
E39.1
E1.1
E1.2
E2.2
E5.1
E5.2
E12.2
E13
Pocket plate at front
Pocket plate at rear
Pocket plate down
Folder up
Folder down
Flap position off / sewing slit wide
Linkage monitoring
Jig with obstacles
Presser foot up
Sewing head lifted
Sewing head lowered
Jig up
Jig down
Bobbin cover closed
Bedplate down
Bedplate up
Roller down
Roller up
Stacker frame at front
Frame up
Frame down
Defl ector down
Programmable input 1
Programmable input 2
Neutral position SM1
Neutral position SM2
Double-start key 1
Double-start key 2
Suction key (foot switch)
Air pressure OK
Key (for secured functions)
Separate stop key
Needle thread disturbance
Bobbin thread disturbance
Label feed error
Label feed completed
Label in clamp
Jig code
176
X33
X34
X35
X36
X37
X38
X39
X29
X30
X31
X32
X25
X26
X27
X28
X40
X41
X42
X43
X21
X22
X23
X24
X17
X18
X19
X20
X1
X10
X11
X12
X13
X15
X16
Distribution strip 230 V and 24 V
Neutral position SM1
Neutral position SM2
Feed roller down (stacker)
Feed roller up (stacker)
Central electric plug sewing head
E31.1 (sewing head lifted)
E31.2 (sewing head lowered)
K32 (Thread tension is released) tdopp1 and tdopp2 (double-start keys)
E54.1 and E54.2 (frame up/down)
Foot switch - suction key (tsaug )
M6 (suction motor)
M5 (height adjustment)
E1.1 (folder)
E1.2 (folder)
E2.2 (folder)
E4.1 (folder)
E4.2 (folder)
E5.1 (folder)
E5.2 (folder)
E39 (bobbin cover opens)
Rotor position
Sewing motor
Press (air fi lter/lubricator unit)
Linkage monitoring
Key for secured function (fkey (
E13 (linkage monitoring)
Separate stop key
E35.2 jig down
E35.1 jig up
Label in clamp (etinkl )
E12.2 Flap positioning / variable sewing slit
E12.2 Flap positioning / variable sewing slit
Connections
177
Outputs
Y1.1
Y1.2
Y2.1
Y2.2
Y3
Pocket plate at front
Pocket plate at back
Pocket plate on
Pocket plate off
Pocket plate ventilation on
Y6
Y7
Y8
Y9
K32
K33
Y33
Y34
Y36
Y37
Y38
Y39
Y11
Y12.1
Y12.2
Y30
Y31.1
Y31.2
Y39.2
Corner folder at front
Edge folder 1 at front
Edge folder 2 at front
Edge folder 3 at front
No pressure on label retaining clamp, or it is open
Flap positioning on / var. sewing slit narrow
Flap positioning off / var. sewing slit wide
Presser foot up / Thread trapper up
Raise head (arm)
Lower head (arm)
Thread tension release on (Thread tens. up)
Thread cutting on (vertical hook system)
Thread cutting on (horizontal hook system)
Air blast / needle cooling on
Zigzag on (programmable output 3)
Secondary thread tension (prog. output 4)
Ready made fl aps or cargo slide
Bobbin cover open
Bedplate on (tilt)
Y51
Y52
K53
Clamp strap on
Stacker stand at front
Frame height adjustment on
A60.5
A60.6
A60.3
A60.4
A60.6
A60.7
A60.10
LUST-converter "S1 ind"
LUST-converter "S2 ind"
Peter-converter "STR"
Peter-converter "STL"
Peter-converter "S1 ind"
Peter-converter "S2 ind"
Peter-converter "GND"
178
91-191 367-95
Version
Terminals X 1
179
Cirguit diagrams
Version
91-191 570-95
Part 1
180
91-191 570-95
Part 1a Version
Cirguit diagrams
181
Cirguit diagrams
Version
91-191 570-95
Part 2
182
91-191 570-95
Part 2a Version
Cirguit diagrams
183
Cirguit diagrams
Version
91-191 570-95
Part 3
184
91-191 570-95
Part 4 Version
Cirguit diagrams
185
Cirguit diagrams
Version
91-191 570-95
Part 5
186
91-191 570-95
Part 6
Version
Cirguit diagrams
187
Cirguit diagrams
Version
91-191 570-95
Part 7
188
91-191 570-95
Part 8 Version
Cirguit diagrams
189
PFAFF Industriesysteme und Maschinen AG
Hans-Geiger-Str. 12 - IG Nord
D-67661 Kaiserslautern
Phone: +49 - 6301 3205 - 0
Fax: +49 - 6301 3205 1386
E-mail: [email protected]
Printed in Germany
advertisement
Related manuals
advertisement
Table of contents
- 7 General notes on safety
- 8 Important notes for the user
- 9 Notes for operating and technical staff
- 12 Specifi cations
- 13 Disposal of Machine
- 14 Transportation, packing and storage
- 14 Transportation to customer‘s premises
- 14 Transportation inside the customer‘s premises
- 14 Disposal of packing materials
- 15 Explanation of symbols
- 18 Switch for the loading function
- 21 Mounting and commissioning the machine
- 22 Removing the transit support bracket
- 22 Mounting the spool holder
- 24 Switching the machine on/off
- 25 Selecting the language
- 26 Adjusting the control panel
- 27 Checking / adjusting the zero points
- 33 Inserting the needle
- 34 Winding the bobbin thread, adjusting the thread tension
- 35 Changing the bobbin / adjusting the bobbin thread tension
- 36 Threading the needle / adjusting the needle thread tension
- 37 Selecting the program number
- 38 Selecting / confi guring a sequence
- 38 Selecting a sequence
- 39 .06.02 Confi guring a sequence
- 41 Jig monitor (optional)
- 41 Activating jig monitor
- 42 Determining the jig code
- 43 Setting the bobbin thread stitch counter
- 44 Changing the part set
- 46 Loading the pre-cut parts
- 48 Automatic sewing mode
- 49 Manual sewing mode
- 51 Sewing with sequences
- 54 Overview of the functions in the input mode
- 56 Creating / editing seam programs
- 66 Seam programming example
- 79 Rights of access
- 83 Care and maintenance
- 83 Care and maintenance intervals
- 84 Cleaning the machine
- 85 Cleaning the hook
- 85 Cleaning the blower air fi lter
- 86 Cleaning the air fi lter of the air-fi lter/lubricator
- 86 Checking/adjusting the air pressure
- 87 Checking the oil level of the sewing head lubrication
- 87 Lubricating the needle bar frame eccentric
- 88 Lubricating sewing jig feed
- 89 Lubricating the pocket plate guide
- 90 Notes on adjustment
- 90 Tools, gauges and other accessories for adjusting
- 91 Removing/inserting sewing head
- 92 Adjusting the sewing head
- 92 Spacing between sewing head and bedplate
- 93 Sewing head position in relation to the bedplate
- 94 Upper and lower toothed belt guards
- 96 Preadjusting the needle height
- 98 Centering the needle in the needle hole
- 99 Zigzag stitch movement
- 100 Needle bar rise, hook-to-needle clearance, needle height and needle guard
- 102 Bobbin case opener stroke
- 103 Counter presser lifting stroke
- 104 Counter presser height
- 105 Counter presser position
- 106 Zigzag stitch width
- 107 Resting position of the roller lever / radial position of the control cam
- 108 Thread catcher height
- 109 Thread catcher position and knife height
- 111 Bobbin thread clamp spring
- 112 Manual cutting test
- 115 Needle thread tension release
- 116 Thread check spring and slack thread regulator
- 117 Sewing head lifting cylinder
- 120 Adjusting the folding, feed and stacker devices
- 120 Aligning the sewing jig
- 121 Height of the pocket plate guide
- 122 Aligning the pocket plate arm
- 123 Aligning the pocket plate guide
- 125 Front pocket plate position
- 126 Monitoring the sewing jig feed
- 127 Positioning the edge folding unit
- 129 Aligning the die
- 130 Control sequence of the folder plates
- 131 Position of folder plates
- 132 Position of corner folders
- 133 Aligning the seam in relation to the pocket
- 134 Seam backtack distance
- 136 Aligning the feed rollers
- 137 Shaping folder plates
- 137 New installation / self-manufacture of folder plates
- 138 Slanting the lateral folder plates
- 141 Loading / updating the operating program
- 142 Sewing motor adjustments
- 143 Selecting and altering parameters
- 144 List of parameters
- 149 Carriage start (NIS)
- 150 Zig-zag delay on/off
- 150 Stacker rolling time
- 151 Basic setting / Diagnosis / Pin assignment
- 151 Basic control unit A
- 155 Stepping motor drive A
- 156 Stacker motor drive
- 157 Description of the error messages
- 160 Stitch generation error
- 161 Sewing motor errors
- 162 Errors – Stepping motor drive
- 163 Errors - Stacker drive
- 164 List of outputs and inputs