advertisement
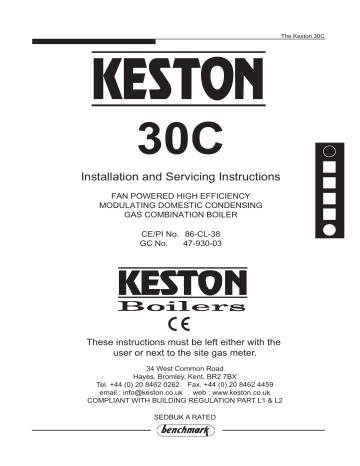
30C
Installation and Servicing Instructions
FAN POWERED HIGH EFFICIENCY
MODULATING DOMESTIC CONDENSING
GAS COMBINATION BOILER
CE/PI No. 86-CL-38
GC No. 47-930-03
The Keston 30C
These instructions must be left either with the user or next to the site gas meter.
34 West Common Road
Hayes, Bromley, Kent, BR2 7BX
Tel. +44 (0) 20 8462 0262 Fax. +44 (0) 20 8462 4459 email : [email protected] web : www.keston.co.uk
COMPLIANT WITH BUILDING REGULATION PART L1 & L2
SEDBUK A RATED
2 Keston 30C - Installation and Servicing
NOTEs FOR ThE INsTALLER
FOR ANy TEChNICAL qUERIEs pLEsE RINg ThE KEsTON
INsTALLER/TEChNICAL hELpLINE : 0208 462 0262
NOTE. BOILER REsET pROCEDURE -
To reset boiler, turn mode knob to reset position and immediately turn knob back to required setting.
The boiler will repeat the ignition sequence.
DOCUMENT AMENDMENTs
Relevant Installation changes implemented in this book from Mod Level ............................ A03 (June 2010)
Keston reserve the right to vary specification without notice
Keston 30C - Installation and Servicing 3
gENERAL
Table 1 - general Data
Keston 30C
Gas supply
Gas Supply Connection
Injector Size
Inlet Connection
Outlet Connection
Flow Connection
Return Connection
Flue Terminal Diameter
Average Flue Temp-Mass Flow Rate
Maximum Working Pressure (Sealed Systems)
Maximum Domestic Hot Water Inlet Pressure
Minimum Domestic Hot Water Inlet Pressure*
Electrical Supply
Power Consumption
Fuse Rating
Water content
Packaged Weight
Maximum Installation Weight
Boiler Casing Size
(mm)
Domestic Hot Water
Domestic Hot Water
Central Heating
Central Heating mm (in)
(DHW) bar (lb/in 2 ) bar (lb/in 2 )
bar (lb/in 2 )
W
Central Heating litre (gal) kg (lb)
Height
Width
Depth kg (lb) mm (in) mm (in) mm (in)
*Required for maximum flow rate. Boiler operates down to 2 l/min DHW delivery
30
2H - G20 - 20mbar
15mm copper compression
4.65
15mm copper compression
15mm copper compression
22mm copper compression
22mm copper compression
50 (nominal)
68 o C - 13g/s
2.5 (36.3)
10.0 (145)
1.3 (18.9)
230 V ~ 50 Hz.
152
External : 3A Internal : T4H HRC L250 V
1.2 (0.26)
37.8 (83.3)
32.8 (72.3)
700 (27.5)
395 (15.5)
278 (11)
Table 2 - performance Data - Central heating
Boiler Input :
Boiler Input ‘Q’ Nett CV
Gas Consumption
Gross CV kW
(Btu/h) kW
(Btu/h) l/s
(ft 3 /h)
Max.
24.3
(82,900)
27.0
(92,000)
0.698
(89)
Boiler Output :
Non Condensing
70 o C Mean Water temp.
Condensing
40 o C Mean Water temp.
Seasonal efficiency*
NOx Classification kW
(Btu/h) kW
(Btu/h)
(SEDBUK)
24.2
(82,600)
25.6
(87,400)
Band A
6.1
(20,700)
6.4
CLASS 5
(21,800)
(91.1%)
Min.
6.1
(20,700)
6.7
(23,000)
0.173
(22)
Table 3 - performance Data - Domestic hot Water
Maximum DHW Input :
Nett CV
Gas Consumption
Maximum
DHW Output
DHW Flow Rate at 35°C temp. rise.
DHW Specific Rate
Gross CV kW
(Btu/h) kW
(Btu/h) l/s
(ft 3 /h) kW
(Btu/h) l/min
(gpm) l/min
(gpm)
30
30.4
(103,600)
33.7
(115,000)
0.871
(111)
30.3
(103,300)
12.4
(2.8)
14.5
(3.2)
* The value is used in the UK Government’s Standard Assessment Procedure (SAP) for energy rating of dwellings. The test data from which it has been calculated have been certified by a notified body.
Note. Gas consumption is calculated using a calorific value of 38.7 MJ/m or 34.9 MJ/m 3 (935 Btu/ft 3
3 (1038 Btu/ft 3 ) gross
) nett
Key to symbols
pMs = Maximum operating pressure of water
To obtain the gas consumption at a different calorific value:
a. For l/s - divide the gross heat input
(kW) by the gross C.V. of the gas (MJ/m 3 )
b. For ft 3 /h - divide the gross heat input (Btu/h) by the gross C.V. of the gas (Btu/ft 3 )
I
C
13
C
33
C
53
= A room sealed appliance designed for connection via ducts to a horizontal or vertical terminal, which admits fresh air to the burner and discharges the products of combustion to the outside through orifices which, in this case, are concentric. The fan is up stream of the combustion chamber.
2h
= An appliance designed for use on 2nd Family gas, Group H only.
c. For m 3 /h - multiply l/s by 3.6.
4 Keston 30C - Installation and Servicing
KEsTON 30C
Natural gas only
Boiler size g.C. Appliance No.
(Benchmark No.)
30 47-930-03 pI No.
86 CL 38 gENERAL
CONTENTs
Benchmark Commissioning Checklist ..................... 75
Boiler Clearances ......................................................... 9
Boiler Exploded Diagram ...................................... 13,14
Condensate Drain ............................................. 9, 20, 46
Electrical Connections ............................................... 31
Electrical supply ........................................................... 8
Fault Finding .......................................................... 64-72
Flue Fitting ............................................................ 17, 18
gas safety Regulations ............................................... 7
gas supply .................................................................... 8
Installation .............................................................. 15-43
pump ........................................................................... 59
safe handling ................................................................ 6
servicing ................................................................ 44-63
short List of parts ...................................................... 73
Thermostatic Radiator Valves ..................................... 8
Water and systems .......................................... 8, 10-12
Water Connections ............................................... 28, 29
Water Treatment ........................................................ 12
Wiring Diagram ........................................................... 37
30C
For GB, to comply with Building Regulations Part L1 (Part 6 in Scotland) the boiler should be fitted in accordance with the manufacturer’s instructions. Self-certification that the boiler has been installed to comply with Building Regulations can be demonstrated by completing and signing the Benchmark Commissioning Checklist.
Before installing this boiler, read the Code of Practice sheet at the rear of this book.
BENChMARK COMMIssIONINg ChECKLIsT DETAILs
B
oiler page
Make and model ......................................................... 5
Appliance serial no. on data badge .......... Front Cover
SEDBUK No. % .......................................................... 4
Controls
Time and temperature control to heating ................. 32
Time and temperature control to hot water ............. 32
Heating zone valves ................................................n/a
TRV’s.......................................................................... 8
Auto bypass ............................................................... 8
Boiler interlock ............................................................ 8
For .................................................................... all boilers
Flushing to BS.7593 .................................................12
Inhibitor .................................................................... 12
Central heating mode
Heat input ...................................................to be calculated page
Burner operating pressure ...................................... n/a
Central heating flow temp. ...........measure and record
Central heating return temp. ........measure and record
For combination boilers only
Scale reducer ........................................................... 12
Hot water mode
Heat input ............................................to be calculated
Max. operating burner pressure .............................. n/a
Max. operating water pressure ........ measure & record
Cold water inlet temp ...................... measure & record
Hot water outlet temp. ..................... measure & record
Water flow rate at max. setting ........ measure & record
For condensing boilers only
Condensate drain ..................................................... 26
For all boilers: complete, sign & hand over to customer
For assistance see Technical Helpline on the back page
NOTE TO ThE INsTALLER: COMpLETE
ThE BENChMARK COMMIssIONINg
ChECKLIsT AND LEAVE ThEsE
INsTRUCTIONs WITh AppLIANCE
Keston 30C - Installation and Servicing 5
gENERAL
INTRODUCTION
The Keston 30C boiler is a wall mounted, full sequence, automatic spark ignition, low water content, fanned flue, high efficiency, condensing, combination gas boiler.
Note. Due to the high efficiency of the boiler a plume of water vapour will form at the terminal during operation.
Central heating (CH) output is fully modulating with a range of 6.1 to 24.2kW (20,700 to 82,600 Btu/h)
Instantaneous domestic hot water (DHW) output is also fully modulating with a maximum of 30.3kW (103,300 Btu/h)
The boiler is supplied fully assembled with DHW plate heat exchanger, diverter valve, circulating pump, pressure gauge, safety valve and CH expansion vessel.
Variable CH and DHW temperature controls are fitted on the user control and the boiler features a DHW preheat facility.
-
-
The boiler includes as standard:
- Automatic bypass
Boiler frost protection
Daily pump and diverter valve exercise.
The boiler casing is of white painted mild steel.
The boiler temperature controls are visible located in the control panel on the front of the boiler.
The heat exchanger is manufactured from cast aluminium.
The boiler is suitable for connection to fully pumped, sealed heating systems ONLY. Adequate arrangements for completely draining the system by provision of drain cocks MUST be provided in the installation pipework.
Pipework from the boiler is routed downwards.
This boiler may require 2 or more operatives to move it to its installation site, remove it from its packaging base and during movement into its installation location. Manoeuvring the boiler may include the use of a sack truck and involve lifting, pushing and pulling.
Caution should be exercised during these operations.
Operatives should be knowledgeable in handling techniques when performing these tasks and the following precautions should be considered:
• Grip the boiler at the base.
• Be physically capable.
• Use personal protective equipment as appropriate, e.g. gloves, safety footwear.
During all manoeuvres and handling actions, every attempt should be made to ensure the following unless unavoidable and/or the weight is light.
• Keep back straight.
• Avoid twisting at the waist.
• Avoid upper body/top heavy bending.
• Always grip with the palm of the hand.
• Use designated hand holds.
• Keep load as close to the body as possible.
• Always use assistance if required.
OpTIONAL ExTRA KITs
• Telescopic Concentric Flue B pack
• Electronic Timer (7 day) kit
• RF Electronic programmable Room Thermostat kit
• stand Off kit
OpERATION
With no demand for CH, the boiler fires only when DHW is drawn off, or periodically for a few seconds without any DHW draw-off, in order to maintain the DHW calorifier in a heated condition. This only occurs if pre-heat knob is in the ‘ON’ period.
When there is a demand for CH, the heating system is supplied at the selected temperature of between 30
DHW draw-off of 12.4 l/min at 35 o o C and 80 o C, until DHW is drawn off. The full output from the boiler is then directed via the diverter valve to the plate heat exchanger to supply a nominal
C temperature rise.
The DHW draw off rate specified above is the nominal that the boiler flow regulator will give. Due to system variations and seasonal temperature fluctuations DHW flow rates/temperature rise will vary, requiring adjustment at the draw off tap.
At low DHW draw-off rate the maximum temperature is limited to
64 o C by the modulating gas control.
The boiler features a comprehensive diagnostic system which gives detailed information on the boiler status when operating, and performance of key components to aid commissioning and fault finding.
sAFE hANDLINg
6 Keston 30C - Installation and Servicing
gENERAL sAFETy
Current gas safety (installation and use) regulations or rules in force:
The appliance is suitable only for installation in GB and IE and should be installed in accordance with the rules in force.
In GB, the installation must be carried out by a Gas Safe
Registered Engineer. It must be carried out in accordance with the relevant requirements of the:
• Gas Safety (Installation and Use) Regulations
• The appropriate Building Regulations either The Building
Regulations, The Building Regulations (Scotland), Building
Regulations (Northern Ireland).
• The Water Fittings Regulations or Water byelaws in Scotland.
• The Current I.E.E. Wiring Regulations.
Where no specific instructions are given, reference should be made to the relevant British Standard Code of Practice.
In IE, the installation must be carried out by a Registered Gas
Installer (RGII) and installed in accordance with the current edition of I.S.813 “Domestic Gas Installations”, the current Building
Regulations and reference should be made to the current ETCI rules for electrical installation.
Detailed recommendations are contained in the following British
Standard Codes of Practice:
Bs. 5440:1 Flues (for gas appliances of rated input not exceeding 70 kW).
Bs. 5440:2 Ventilation (for gas appliances of rated input not exceeding 70 kW).
BsEN. 12828:2003 Heating Systems in buildings: Design for water based heating systems.
BsEN 12831:2003 Heating Systems in buildings: Method for calculation of the design heat load.
BsEN 14336:2004 Heating Systems in buildings: Installation and commissioning of water based heating systems.
Bs. 5546
Bs. 6798
Installation of gas hot water supplies for domestic purposes (2nd Family Gases)
Installation of gas fired hot water boilers of rated input not exceeding 70 kW.
Bs. 6891 Low pressure installation pipes.
health & safety Document No. 635.
The Electricity at Work Regulations, 1989.
The manufacturer’s notes must NOT be taken, in any way, as overriding statutory obligations.
IMpORTANT. These appliances are CE certificated for safety and performance. It is, therefore, important that no external control devices, e.g. flue dampers, economisers etc., are directly connected to these appliances unless covered by these Installation and Servicing Instructions or as otherwise recommended by Keston in writing. If in doubt please enquire.
Any direct connection of a control device not approved by Keston could invalidate the certification and the normal appliance warranty. It could also infringe the Gas Safety Regulations and the above regulations.
sAFE hANDLINg OF sUBsTANCEs
No asbestos, mercury or CFCs are included in any part of the boiler or its manufacture.
LOCATION OF BOILER
Keston 30C - Installation and Servicing
The boiler must be installed on a flat and vertical internal wall, capable of adequately supporting the weight of the boiler and any ancillary equipment.
The boiler may be fitted on a combustible wall and insulation between the wall and the boiler is not necessary, unless required by the local authority.
For electrical safety reasons there must be no access available from the back of the boiler.
The boiler must not be fitted outside.
Timber Framed Buildings
If the boiler is to be fitted in a timber framed building it should be fitted in accordance with the Institute of Gas Engineering document
IGE/UP/7:1998.
Bathroom Installations
This appliance is rated Ip20.
The boiler may be installed in any room or internal space, although particular attention is drawn to the requirements of the current
IEE (BS.7671) Wiring Regulations and the electrical provisions of the building regulations applicable in Scotland, with respect to the installation of the boiler in a room or internal space containing a bath or shower. For IE reference should be made to the current
ETCI rules for electrical installations and I.S. 813:2002.
If the appliance is to be installed in a room containing a bath or shower then, providing water jets are not going to be used for cleaning purposes (as in communal baths/showers), the appliance must be installed beyond Zone 2, as detailed in BS.7671.
Compartment Installations
A compartment used to enclose the boiler should be designed and
Ceiling
2.25m
Zone 1
Zone 0
0.6m
Recessed window
Zone 2
3G8913a constructed specially for this purpose.
An existing cupboard or compartment may be used, provided that it is modified for the purpose.
In both cases, details of essential features of cupboard / compartment design, including airing cupboard installation, are to conform to the following:
• BS 6798 (No cupboard ventilation is required - see ‘Air Supply’ for details).
• The position selected for installation MUST allow adequate space for servicing in front of the boiler.
• For the minimum clearances required for safety and subsequent service, see the wall mounting template and
Frame 1. In addition, sufficient space may be required to allow lifting access to the wall mounting plate.
• The boiler must be installed on a fire resistant surface.
gAs sUppLy
The local gas supplier should be consulted, at the installation
7
gENERAL
planning stage, in order to establish the availability of an adequate supply of gas. An existing service pipe must NOT be used without prior consultation with the local gas supplier.
However, if the system employs thermostatic radiator valves on all radiators, or two port valves, then a bypass circuit must be fitted with an automatic bypass valve to ensure a flow of water should all valves be in the closed position.
The boiler MUST be installed on a gas supply with a governed meter only.
A gas meter can only be connected by the local gas supplier or by a Gas Safe Registered Engineer. In IE by a Registered Gas
Installer (RGII).
An existing meter should be checked, preferably by the gas supplier, to ensure that the meter is adequate to deal with the rate of gas supply required.
It is the responsibility of the Gas Installer to size the gas
Installer to size the gas installation pipework in accordance with
BS6891:2005. Whilst the principle of the 1:1 gas valve ensures the Keston 30C is able to deliver its full output at inlet pressures as low as 14mb, other gas appliances in the property may not be as tolerant. When operating pressures are found to be below the minimum meter outlet of 19mb these should be checked to ensure this is adequate for correct and safe operation.
ELECTRICAL sUppLy
Warning.
This appliance must be earthed.
Wiring external to the appliance MUST be in accordance with the current I.E.E. (BS.7671) Wiring Regulations and any local regulations which apply. For IE reference should be made to the current ETCI rules for electrical installations.
The mains supply to the boiler and system wiring centre shall be through one common fused double pole isolator and for new heating systems, and where practical replacement boiler installations, the isolator shall be situated adjacent to the appliance.
CONDENsATE DRAIN
Refer to Frames 15, 25 & 48
Allowing for the acceptable pressure loss of 1mb across the installation pipework, it can be assumed that a minimum permitted operating pressure of 18mb will be delivered to the inlet of the appliance. (Reference BS 6400-1 Clause 6.2 Pressure
Absorption).
The integral appliance isolation valve and boiler pipework could further reduce the operating pressure by up to 1.5mb when measured at the inlet test point on the appliance gas valve.
Therefore it has been identified that an operating pressure as low as 16.5mbar could be measured at the appliance inlet pressure test point on the gas valve.
A condensate drain is provided on the boiler. This drain must be connected to a drainage point on site. All pipework and fittings in the condensate drainage system MUST be made of plastic - no other materials may be used.
IMpORTANT.
Any external runs must be in accordance with BS 6798.
The drain outlet on the boiler is sized for standard 21.5mm (3/4”) overflow pipe. It is a universal fitting to allow use of different brands of pipework.
IMpORTANT.
Installation pipes must be fitted in accordance with BS.6891. In IE refer to IS.813:2002.
The complete installation MUST be tested for gas tightness and purged as described in the above code.
WATER CIRCULATION sysTEM
IMpORTANT.
A minimum length of 1 metre of copper pipe MUST be fitted to both flow and return connections from the boiler before connection to any plastic piping.
The central heating system should be in accordance with BS.6798 and, in addition, for smallbore and microbore systems, BS.5449.
WATER TREATMENT - see Frame 5
BOILER CONTROL INTERLOCKs
Central heating systems controls should be installed to ensure the boiler is switched off when there is no demand for heating, in compliance with Building Regulations.
Heating systems utilising full thermostatic radiator valve control of temperature in individual rooms should also be fitted with a room thermostat controlling the temperature in a space served by radiators not fitted with such a valve.
When thermostatic radiator valves are used, the space heating temperature control over a living / dining area or hallway having a heating requirement of at least 10% of the minimum boiler heat output should be achieved using a room thermostat, whilst other rooms are individually controlled by thermostatic radiator valves.
8 Keston 30C - Installation and Servicing
gENERAL
1 BOILER DIMENsIONs, sERVICEs & CLEARANCEs
The boiler connections are made on the boiler connection tails.
Refer to Frames 27-30.
The following minimum clearances must be maintained for operation and servicing.
Additional space will be required for installation, depending upon site conditions.
all dimensions in mm
2.5
2.5
from case
395
30mm
Minimum Top Clearance
Air Flue
700
395
400
100
*
43 65 57 38 39 65
Gas Inlet
Front clearance
The minimum front clearance when built in to a cupboard is 5mm from the cupboard door but 450mm overall clearance is still required, with the cupboard door open, to allow for servicing.
*
Bottom clearance
Bottom clearance after installation can be reduced to 5mm.
This must be obtained with an easily removable panel, to enable the consumer to view the system pressure gauge, and to provide the 100mm clearance required for servicing.
Keston 30C - Installation and Servicing 9
gENERAL
2 sysTEM REqUIREMENTs - Central heating
Notes
a. The method of filling, refilling, topping up or flushing sealed primary hot water circuits from the mains via a temporary hose connection is only allowed if acceptable to the local water authority.
b. Antifreeze fluid, corrosion and scale inhibitor fluids suitable for use with boilers having aluminium heat exchangers may be used in the central heating system.
safety valve setting
Vessel charge pressure bar bar
system pre-charge pressure bar system volume
(litres)
25
50
75
100
125
150
175
190
200
250
300
For other system volumes multiply by the factor access
3.1
4.7
6.3
7.8
9.4
10.9
11.9
12.5
15.6
18.8
3.0
0.5 to 0.75
None 1.0
Expansion vessel volume (litres)
1.6
1.8
3.7
5.5
7.4
9.2
11.0
12.9
14.0
14.7
18.4
22.1
general
1. The installation must comply with all relevant national and local regulations.
2. The installation should be designed to work with flow temperatures of up to 86 o C.
3. All components of the system must be suitable for a working pressure of 3 bar and temperature of 110 minimised. o C. Extra care should be taken in making all connections so that the risk of leakage is
The following components are incorporated within the appliance:
a. Circulating pump.
b. Safety valve, with a non-adjustable preset lift pressure of 3 bar.
c. Pressure gauge, covering a range of 0 to 4 bar.
d. An 8-litre expansion vessel, with an initial charge pressure of 0.75 bar.
4. ‘Make-up’ Water. Provision must be made for replacing water loss from the system, either :
a. From a manually filled ‘make-up’ vessel with a readily visible water level. The vessel should be mounted at least 150mm above the highest point of the system and be connected through a non-return valve to the system, fitted at least
150mm below the ‘make-up’ vessel on the return side of the radiators. or
b. Where access to a ‘make-up’ vessel would be difficult, by pre-pressurisation of the system.
The maximum cold water capacity of the system should not exceed 143 litres, if not pressurized. However, if the system is to be pressurized, the efficiency of the expansion vessel will be reduced and a larger vessel
(or smaller system volume) may be necessary. If the capacity of the vessel is not considered sufficient for this, or for any other reason, an additional vessel MUST be installed on the RETURN to the boiler.
Guidance on vessel sizing is given in Table above.
Water Flow Rate and pressure Loss
Max CH Output
Water flow rate
Temperature Differential
Head available for system kW
(Btu/h) l/min
(gal/min) o C
( o F) m.w.g.
(ft.w.g.)
0.063
24.2
(82,600)
17.3
(3.8)
20
(36)
3.4
(11.1)
0.074
5. Filling
The system may be filled by the following method:
Where the mains pressure is excessive a pressure reducing valve must be used to facilitate filling.
a. Thoroughly flush out the whole system with cold water.
b. Fill and vent the system until the pressure gauge registers 1bar and examine for leaks. Refer to Frame
33 for filling detail.
c. Check the operation of the safety valve by raising the water pressure until the valve lifts. This should occur within 0.3bar of the preset lift pressure.
d. Release water from the system until the
minimum system design pressure is reached;
1.0 bar if the system is to be pre-pressurised.
10 continued . . . . . .
Keston 30C - Installation and Servicing
gENERAL
3 sysTEM REqUIREMENTs - Ch (continued) and hot Water
DOMEsTIC hOT WATER
1. The domestic hot water service must be in accordance with
BS 5546 and BS 6700.
2. Refer to Table 1 for minimum and maximum working pressures. In areas of low mains water pressures the domestic hot water regulator may be removed from the DHW flow turbine cartridge. Refer to Frame 76. The boiler will require the flow rate to be set to obtain a temperature rise of
35 o C at the tap furthest from the boiler.
3. The boiler is suitable for connection to most types of washing machine and dishwasher appliances.
4. When connecting to suitable showers, ensure that:
a. The cold inlet to the boiler is fitted with an approved antivacuum or syphon non-return valve.
b. Hot and cold water supplies to the shower are of equal pressure.
5. hard Water Areas
Where the water hardness exceeds 200mg/litre, it is recommended that a proprietary scale reducing device is fitted into the boiler cold supply within the requirements of the local water company.
IMpORTANT
Provision MUST be made to accommodate the expansion of
DHW contained within the appliance, if a non-return valve is fitted to the DHW inlet, or a water meter with a non-return valve is installed.
4 sysTEM BALANCINg
The boiler does not normally need a bypass but at least some radiators on the heating circuit, of load of at least 10% of the minimum boiler output, must be provided with twin lockshield valves so that this minimum heating load is always available. See note regarding thermostatic radiator valves on page 8.
Note. Systems incorporating zone valves which could completely cut off the flow through the system must also include a bypass.
BALANCINg
1. Set the programmer to ON.
Close the manual or thermostatic valves on all radiators, leaving the twin lockshield valves (on the radiators referred to above) in the OPEN position.
Turn up the room thermostat and adjust the lockshield valve to give an uninterrupted flow through the radiator.
These valves should now be left as set.
2. Open all manual or thermostatic radiator valves and adjust the lockshield valves on the remaining radiators, to give around 20 o C temperature drop at each radiator.
3. Adjust the room thermostat and programmer to NORMAL settings.
Keston 30C - Installation and Servicing 11
gENERAL
5 WATER TREATMENT
CENTRAL hEATINg
The Keston 30C boiler has an ALUMINIUM alloy heat exchanger.
IMpORTANT.
The application of any other treatment to this product may render the guarantee of Keston Invalid.
Keston recommend Water Treatment in accordance with the
Benchmark Guidance Notes on Water Treatment in Central
Heating Systems.
In hard water areas where mains water can exceed 200ppm
Total Hardness (as defined by BS 7593:2006 Table 2) a scale reducing device should be fitted into the boiler cold supply within the requirements of the local water company. The use of artificially softened water, however, is not permitted.
Keston recommend the use of Fernox Quantomat, Sentinel
Combiguard and Calmag CalPhos I scale reducing devices, which must be used in accordance with the manufacturers’ instructions.
For further information contact:
If water treatment is used Keston recommend only the use of
FERNOx, MBI or SENTINEL X100 manufacturers’ instructions. inhibitors and associated water treatment products, which must be used in accordance with the
Notes.
1. It is most important that the correct concentration of the water treatment products is maintained in accordance with the manufacturers’ instructions.
2. If the boiler is installed in an existing system any unsuitable additives MUST be removed by thorough cleansing. BS
7593:2006 details the steps necessary to clean a domestic heating system.
3. In hard water areas, treatment to prevent lime scale may be necessary - however the use of artificially softened water is
NOT permitted.
4. Under no circumstances should the boiler be fired before the system has been thoroughly flushed.
DOMEsTIC hOT WATER
Fernox Manufacturing Co. Ltd
Cookson Electronics
Forsyth Road
Sheerwater
Woking
Surrey GU21 5RZ
+44 (0) 1799 521133
Sentinel Performance Solutions
The Heath Business & Technical Park
Runcorn
Cheshire WA7 4QX
Tel: 0800 389 4670 www.sentinel-solutions.net
Salamander Engineering Ltd
The Heath Business & Technical Park
Runcorn
Cheshire WA7 4QX
Tel: 0800 389 4670
Calmag Ltd.
Unit 4-6, Crown Works
Bradford Road
Sandbeds, Keighley
West Yorkshire BD20 5LN
Tel: +44 (0) 1535 210 320
12 Keston 30C - Installation and Servicing
INsTALLATION
6 BOILER AssEMBLy - Exploded View Legend
Note that item numbers are linked to the spares list
104 CH RETURN VALVE
105 CH FLOW VALVE
106 DHW INLET & OUTLET
107 FILLING LOOP
108 PUMP HEAD
110 AIR VENT PUMP
111 DIVERTER VALVE HEAD
112 DIVERTE R VALVE CARTDRIGE
113 PRESSURE RELIEF VALVE
114 PIPE - PRV OUTLET
115 PIPE - FLOW
116 PIPE - RETURN
117 PIPE - EXPANSION VESSEL
118 EXPANSION VESSEL
119 RETURN GROUP MANIFOLD
120 FLOW GROUP MANIFOLD
121 PLATE HEAT EXCHANGER
127 FLOW SENSOR HALL EFFECT
128 FLOW TURBINE CARTRIDGE
131 WATER PRESSURE TRANSDUCER
135 PRESSURE GAUGE
203 GAS COCK
204 PIPE - GAS INLET
205 GAS VALVE
206 PIPE - GAS INJECTOR
211 INJECTOR ASSEMBLY
214 VENTURI
215 FAN
217 BURNER
218 GASKET - BURNER
219 SUMP CLEAN OUT COVER
223 FLUE MANIFOLD
224 FLUE MANIFOLD TOP
227 CLAMP RETAINING FLUE TURRET
228 HOSE CONDENSATE INTERNAL
229 SIPHON TRAP
230 SIPHON TRAP CAP & SEAL
231 CONDENSATE OUTLET CONNECTION
233 FLUE SENSING NIPPLE
301 CONTROLS BOX FIXINGS HINGE & SPRING
302 PRIMARY PCB
303 CUI BOARD
304 CONTROL THERMISTOR (FLOW / RETURN)
306 ELECTRODE IGNITION
307 ELECTRODE DETECTION
308 IGNITER UNIT
309 THERMISTOR NO FLOW
313 IGNITION LEAD
314 CONTROL BOX LENS
324 CONTROLS BOX LID
325 CONTROL BOX FRONT
326 PROGRAMMER INSERT
401 HEAT ENGINE
503 WALL MOUNTING BRACKET
504 FRONT PANEL
505 FASCIA
506 BRACKET - GAS VALVE
507 BRACKET - EXPANSION VESSEL
136 SAFETY VALVE DRAIN PIPE
512 DROP DOWN DOOR
332 FLUE THERMOSTAT
Keston 30C - Installation and Servicing 13
INsTALLATION
7 BOILER AssEMBLy - Exploded View
14
505
504
227
233
224
503
211
304
214
206
512
313
215
308
30C
309
217
306
205
204
223
218
401
507
118
506
115
332
219
304
303
307
116
301
229
230
228 112
231
121
120
127
128
131
136
113
119
111
105
108
110
106
203
106
104
117
114
324
135
314
326
325
302
107
3G10313a
Keston 30C - Installation and Servicing
INsTALLATION
8 UNpACKINg
The boiler is supplied fully assembled in Pack 1, together with the flue pack for flue lengths up to 450mm.
Unpack and check the contents.
A
B
pack 1 Contents
A Boiler
B Hardware Pack Box
C Wall Mounting Plate
D These Installation Instructions
(includes Warranty/Guarantee)
E Wall Mounting Template
(located on internal protective
packaging)
F Turret Clamp
G Safety Valve Drain Pipe
H Weather Compensator
C
D F
H
G
E
30C
3G10376
HARDWARE PACK CONTENTS
Gas Valve Pack
1. Pipe - Gas Inlet
2. Washer - Gas (blue)
3. Gas Cock
Filling Loop Pack
1. 3/8" Fibre washer (x4)
2. Valve (double check valve) fitting
3. Valve - Filling Loop
4. Plastic Chain (x2)
5. Filling Loop
6. 3/8" Blanking Rubber Washer (x2)
Return Valve Pack
1. Pipe CH Return
2. Washer CH
3. Valve Return
DHW Pack
1. Pipe DHW Outlet
2. Valve - Return DHW
3. Washer DHW (x2)
4. Pipe DHW Inlet
5. Nut 1/2"
Accessory Pack
1. Screw (x2)
2. Wallplug (x2)
Flow Valve Pack
1. Pipe CH Flow
2. Washer CH
3. Valve Flow (with gauge)
Gas Valve Pack
Filling Loop
1
1
6
4
2
2
Return Valve Pack
1
2
3
3
3
5
Keston 30C - Installation and Servicing
DHW Pack
1
2
3
4
3
Accessory Pack
1
2
5
Flow Valve Pack
1
2
3
3G9687 continued . . . . .
15
8 UNpACKINg....CONT’D
Flue pack Contents
INsTALLATION
1. 3 x elbows
2. 2 x 450mm pipe
3. 3 x 100mm pipe
1 2 3
4. Flue Adaptor
5. Air Spigot
6. 2 x Terminals
4
5
6
16 Keston 30C - Installation and Servicing
INsTALLATION
9 FLUE sysTEM
Note. When installing a replacement boiler a new flue system must be used. Do not re-use the existing boiler flue installation.
DEsIgN
Individual air supply and flue outlet pipes are used as standard, although a concentric flue kit is available as an optional extra.
The material used for flue outlet &/or air inlet must be mupVC (pVC-C) to Bs 5255 and/or BsEN 1566-1 and BsEN
1329 of an internal diameter of 51mm. (i.e. nominal 50mm diameter mupVC solvent weld waste pipe).
Marley mupVC (pVC-C) solvent Weld Waste system
(50mm) and polypipe system 2000 mupVC (pVC-C) solvent weld waste (50mm) are the only systems approved for this application.
The following pipes and fittings are approved:
Polypipe System 2000 muPVC solvent Weld Waste System
(50mm)
poly pipe Code
MU 301
MU 313
4m length muPVC wastepipe 5/225
50mm x 45 deg muPVC obtuse bend
MU 314
MU 310
MU 316
50mm x 92.5 deg muPVC swept bend
50mm muPVC straigh coupling
50mm x 92.5 deg muPVC swept pipe
Marley muPVC solvent Weld Waste System (50mm)
Marley Code
KP 304
KP32
50mm x 4m double spigot pipe
50mm x 45 deg bend
KSC3
KB3
KT3
50mm straight coupling
50mm x 88.5 deg bend
50mm swept tee
Both the 50mm flue outlet terminal and the 50mm air inlet terminal are supplied with the flue pack and are illustrated in
Fig. 1 and must be used in ALL installations. (Both terminals are identical).
Fig.1
MAxIMUM LENgThs
The maximum lengths of both air inlet pipe and flue outlet pipe, when no bends are used, are as detailed in fig.2b.
However, each bend used has an equivalent length that must be deducted from the maximum straight length stated in fig. 2b.
Knuckle bends must not be fitted.
A 92.5º swept elbow is equivalent to 1.0m straight length. A 45º bend is equivalent to 0.5m straight length.
It is possible to have variable flue and air lengths as detailed below.
Fig. 2b
Maximum Combined Flue & Air Intake Lengths
Total Flue & Air Intake 22m
(does not include allowance for elbow on top of boiler)
Example (assuming 50mm muPVC flue and air pipework)
Air inlet uses two 92.5º swept elbows. Hence, maximum length permissible (i.e. a+b in fig. 2a) = 22m - 1m - 1m = 20m.
Flue outlet uses one 92.5º swept elbow. Hence, maximum length permissible (i.e. c+d in fig. 2a)= 22m - 1m = 21m).
But maximum total flue and air intake must not exceed 19m in the examples above.
Boiler Output Vs Flue Length
Due to the resistance presented by extended flue length a slight reduction in maximum boiler output will occur where combined flue and air lengths in excess of 16.0m (50mm muPVC) are used. In such cases the boiler output will be reduced by 1.0% per additional metre.
When the flue and air terminals are located within 500mm of each other ensure that the air terminal is pointing towards the ground using a 90º bend and one of the 100mm sections of pipe provided within the flue pack.
FLUE c d
Fig.2a
KESTON 30C
AIR b a
Keston 30C - Installation and Servicing 17
INsTALLATION
09 FLUE sysTEM.... CONT’D sLOpE
‘Horizontal’ flue outlet pipework MUST slope at least 2 degrees
(32mm per metre run) downwards towards the boiler. Pipework can be vertical. Only swept elbows can be used.
Air inlet pipework can be truly horizontal or vertical, or sloping in a downward direction towards the boiler but in each case rain, etc., must be prevented from entering the pipe. There must be no troughs in any of the pipework, whether it be air inlet or flue outlet.
Due to the low temperature of the flue gases further condensate will form within the flue system. Drain points, with suitable traps, must therefore be incorporated within the flue system at the base of the vertical flue sections in excess of 6m, for 50mm muPVC pipe flue systems. These additional condensate drains must be run to discharge. Such drain points can be formed using standard muPVC fittings. Refer to fig. 3.
Fig.3
Dimensions (mm)
A Below, above or beside openable window, air brick, etc.
B Below gutters, soil pipes, drain pipes.
C Below eaves.
D Below balconies or car port roof (lowest point).
E From vertical drain or soil pipes.
F From internal or external corner or to a boundary alongside the terminal. *
G Above ground or balcony or roof.
H From surface or boundary facing a terminal. *
I From terminal facing a terminal.
J From opening in a car port.(not recommended)
K Vertically from terminal on same wall.
L Horizontally from terminal on same wall.
Flue
Terminal
300
75
200
200
75
200
300
600
1,200
1,200
1,500
300
Air
Inlet
50
75
50
50
50
50
100
100
1,200
100
1,500
300
*The dimensions given in the table above may need to be increased to avoid wall staining and nuisance depending on site conditions.
CLEARANCEs FROM WALL
Flue outlet and air inlet terminations must be at least 40mm from the wall face.
To Boiler
Tee Fitting
6 in min.
DIsTANCE BETWEEN FLUE OUTLET & AIR
INLET
There is no maximum - the terminations must not be on opposite sides of the dwelling but can be in areas of unequal pressure.
A minimum clearance of at least 500mm must be left between the terminations otherwise a 90º elbow MUsT be fitted to air inlet and pointed towards the ground. The absolute minimum clearance between the flue and air terminals is 100mm.
TERMINATIONs
Air inlet terminals must be facing horizontally or downwards to prevent entry of rain into the terminal and positioned to ensure only fresh air is drawn into the boiler. The air terminal must be located outside of the building. Flue terminals must be positioned so that flue products are not drawn into the air inlet. Site specific wind conditions should be considered to achieve this. Drawing of combustion air directly from a ventilated boiler room invalidates the heat exchanger warranty.
The flue outlet terminal is designed to face outwards and must not be directed in the region of the air inlet. The flue terminal and air inlet terminal can be located on different, but not opposing wall faces.
The two terminals are subject to the requirements of BS 5440 Pt
1 for clearances from features of the building although some can be decreased to the values indicated.
The Keston 30C, as with any condensing boiler, will generate a condensate “plume” from the flue terminal in all weather conditions. Consideration must therefore be given to the effect of this “plume” when selecting a location for the flue terminal. It is the responsibility of the installer to ensure the selected terminal location does not cause nuisance.
If either the air inlet or flue outlet terminate at a height of less than 2.0 m above ground level, the terminal must be protected by a suitable guard. The K6 terminal guard (with plastic coating), manufactured by Tower Flue Components Ltd is suitable for this purpose.
gENERAL INsTALLATIONs
All parts of the system must be constructed in accordance with
BS 5440 Part 1, except where specifically mentioned in these instructions.
All pipework must be adequately supported.
All joints other than approved push-on or plastic compression connectors must be made and sealed with solvent cement suitable for muPVC pipes and conforming to BS 6209: 1982.
Consideration must be given to Corgi/Gas Safe bulletin TB200/
TB008 regarding flues in voids.
The boiler casing must always be correctly fitted to the boiler when leaving the appliance operational.
External wall faces and any internal faces of cavity walls must be good.
Rubber collars are available for flue and air terminals to finish the external wall face around the terminals (Part No C.08.00.07.0).
AIR sUppLy
The Keston 30C is a room sealed appliance and therefore does not require purpose provided ventilation to the boiler room for combustion air.
COMpARTMENT INsTALLATION
Due to the low casing temperatures generated by the boiler, no compartment ventilation is required. However, the cupboard or compartment must not be used for storage.
18 Keston 30C - Installation and Servicing
INsTALLATION
10 INsTALLINg ThE BOILER
Installation of the boiler is straightforward but consideration must be given to access to allow flue and air pipes to be pushed through walls and ceilings. The order in which the components are installed will depend upon particular site conditions, but in general it will be easiest and most accurate to install the boiler and then build up the flue outlet and air inlet pipes to the terminal - this is the sequence described.
11 WALL MOUNTINg TEMpLATE
The wall mounting template is located on the internal protective packaging.
Note.
The template shows the positions of the fixing holes and the position of the air and flue connections. Care MUST be taken to ensure the correct holes are drilled.
1. Tape template into the selected position. Ensure squareness by hanging a plumbline as shown.
2. Mark onto the wall the following:
a The wall mounting plate screw positions (choose one from each group).
b The position of the air and flue when exiting straight out of the wall where the boiler is mounted.
Note. Mark the centre of the hole as well as the circumference.
3. Remove the template from the wall.
3G10378
12 pREpARINg ThE WALL
IMpORTANT.
Ensure that, during the cutting operation, masonry falling outside of the building does not cause damage or personal injury.
1. Cut the flue and air holes (preferably with 60mm core bore tool) ensuring the holes are square to the wall.
2. Drill 2 holes with a 7.5mm / 8mm masonry drill and insert the plastic plugs, provided, for the wall mounting plate.
3. Locate 2 No.14 x 50mm screws in the wall mounting plate
(one at each side, in any of the 3 holes provided at each side) and screw home.
Rear flue only
60mm diameter holes
X
Section through wall
Note. Check all of the hole positions before drilling.
Keston 30C - Installation and Servicing 19
INsTALLATION
13 FITTINg ThE WALL MOUNTINg pLATE 14 MOUNTINg ThE BOILER
Screw the wall mounting plate to the wall using 2 wall plugs
(previously fitted) with the 2 screws provided.
Choose one of the 2 sets of slots in left and right bank.
Ensuring that at least one of the screws is fitted into a top slot.
1. Ensure the plastic plugs are removed from both the CH and DHW connections before mounting the boiler.
2. Lift the boiler onto the wall mounting plate (refer to the
Introduction section for safe handling advice), locating it over the two tabs.
Example of fixing esp9496
20
15 CONDENsATE DRAIN
Ensure that the siphon is full of water before commissioning the boiler. Refer to Frame 26.
The routing of the drain must be made to allow a minimum fall of 1 in 20 away from the boiler, throughout its length.
The drainage pipework must be arranged so that obstruction (e.g. through freezing) of external drainage pipe does not give rise to spillage within the dwelling.
IMpORTANT.
All pipework and fittings in the condensate drain system must be made of plastic. No other materials may be used.
The drain outlet on the boiler is standard 21.5mm overflow pipe and is suitable for either push fit or solvent weld applications. This size must not be reduced in any part of its length.
The boiler includes as standard, a 75mm condensate trap.
The condensate trap also includes a siphon to reduce the possibility of freezing in the drain outlet.
If external condensate pipe is used then the pipe should be 32mm nominal diameter. Consideration should be given to insulating external condensate pipe runs.
30C
Keston 30C - Installation and Servicing
16 AssEMBLy pRACTICE
Remove all plastic debris and burrs when installing air intake piping. Plastic fillings caused by cutting muPVC pipe must not be allowed to be drawn into the combustion air blower. Prevent dust entering the air intake when cutting on building sites. Blower failure which is determined to be caused by plastic filings or other debris will not be covered by guarantee.
INsTALLINg FLUE AND AIR pIpEs
INsTALLATION
Important - When installing the boiler on an existing system a new flue and air intake system MUST also be installed. You
MUsT NOT re-use existing flue or air pipework components.
• Remove the flue adaptor and air spigot from the flue pack supplied with the boiler.
• Remove boiler front panel - Frame 45
•
Remove air intake blanking plate by unscrewing 4 x M5 screws and put to one side, leaving sponge gasket in place.
• Fix air spigot to boiler using the 4 M5 screws, see diag. below. Ensure sponge gasket is in place and not damaged.
•
Insert the flue adaptor into the flue manifold on the top of the boiler ad secure using the clamp provided in the packaging box, see diagram below.
•
Measure, cut and check the air and flue pipes to pass to the exit from the wall(s) or ceiling.
• Always thoroughly deburr all pipes and most important, remove shavings from within the pipe.
•
Assemble, using solvent weld cement, the pipework from the boiler connections to the exit from the first wall/ ceiling, (remount the boiler if removed). When pushing pipe through walls, ensure grit and dust is not allowed to enter the pipe.
Ensure pipes are fully engaged into sockets and solvent welded with no leaks.
•
Using the same methods drill any further holes (always covering existing pipework), cut and assemble the pipework.
• From outside, complete the two terminations - See
Frame 9 Flue System and make good all holes. (Wall sealing collars are available to make good hole areas on the wall face (part number C.08.0.00.07.0).
•
support any pipes whose route could be displaced either of its own accord or by accident. Any horizontal run over 1m or vertical runs of any length must always be supported. Brackets should be placed at intervals of approximately 1m. Brackets should be loose enough on the pipe to allow thermal expansion and contraction movement.
•
Flue pipework through walls MUsT be sleeved to allow thermal expansion and contraction movement.
• Check all connections for security and re-seal any joints using solvent cement where soundness may be in doubt.
Note. It is equally important to seal the air inlet with solvent cement as the flue outlet pipe joints.
Keston 30C - Installation and Servicing
Retaining Clip
(assembled)
21
INsTALLATION
17 DETERMININg ThE FLUE LENgTh AND FLUE pACKs REqUIRED FOR
CONCENTRIC OpTION KIT
Where a concentric flue option is chosen the following instruction should be followed and the standard flue in flue box omitted.
IMpORTANT. The boiler MUST be installed in a vertical position
Only use Keston concentric flue pipe and fittings.
FLUE KITs
pack B - telescopic supplied as an optional extra
Concentric Flue screw Retaining Kit - optional kit for mechanical fixing of flue joints.
Finishing Kit - Supplied as an optional extra.
Refer to ‘Flue Extension Ducts’
Dimension x - Wall thickness.
Dimension L - Wall thickness plus boiler spacing.
Dimension s - Optional stand-off frame depth 45mm.
MaXiMUM HOriZOnTaL FLUE LEngTH = 575MM
MiniMUM HOriZOnTaL FLUE LEngTHs - TELEscOpic TErMinaL = 350MM
(centre Line of turret to outside of wall terminal)
1. If the telescopic B pack is used, they may be mounted horizontally.
The 1.5 degrees is taken care of by the inclination of the flue within the air pipe.
2. Only use water as a lubricant during assembly.
Total Flue length dimension
(measuring from CL of turret to outside wall)
Rear flue
dim. x+155
Side flue
dim. L+197
Up to 575 mm Up to 575 mm
REAR FLUE
155 + S = 200mm
155 mm
165mm
Minimum Top
Clearance
155 + S = 200mm sIDE FLUE
Wall Thickness X
197mm 197mm
Side flue length L
Wall Thickness X
22
Note: All other clearances as per Twin Flue Application (see Frame1)
Keston 30C - Installation and Servicing
INsTALLATION
18 TERMINAL WALL sEAL AssEMBLy / pOsITIONINg - CONCENTRIC FLUE OpTION
Prior to fitting the flue, the rubber terminal wall seal provided in the flue pack MUST be fitted to the flue terminal as shown below in Figure 1.
Once the flue is installed it is IMPORTANT that the rubber terminal wall seal is pressed against the outside wall to create an adequate seal between the flue and wall as shown in
Figure 2.
FIgURE 1 FIgURE 2
Wall Seal Lip
Step
Rubber
Terminal
Wall Seal
Ensure lip of wall seal is positioned over step on plastic nose of flue terminal
(note, seal is cut away for clarity) isfu9783
19 FLUE AssEMBLy - CONCENTRIC FLUE OpTION - Exploded View
:
An optional flue duct extension kit is required for wall thicknesses greater than
side 378mm
Rear 420mm
LEgEND
1. Duct assembly.
2. Flue turret.
3. Turret clamp.
3
2
1
TOP
3G10379
The flue terminal MUST be fitted with the ‘TOP’ uppermost to allow the correct fit.
Keston 30C - Installation and Servicing 23
INsTALLATION
20 WALL MOUNTINg TEMpLATE - CONCENTRIC FLUE OpTION
The wall mounting template is located on the internal protective packaging.
Note.
The template shows the positions of the fixing holes and the position of the air and flue connections. Care MUST be taken to ensure the correct holes are drilled.
1. Tape template into the selected position. Ensure squareness by hanging a plumbline as shown.
2. Mark onto the wall the following:
a The wall mounting plate screw positions (choose one from each group).
b The position of the air and flue when exiting straight out of the wall where the boiler is mounted.
Note. Mark the centre of the hole as well as the circumference.
3. Remove the template from the wall.
3G10378
21 pREpARINg ThE WALL - CONCENTRIC FLUE OpTION
IMpORTANT.
Ensure that, during the cutting operation, masonry falling outside of the building does not cause damage or personal injury.
1. Cut the flue hole (preferrably with 5” core bore tool for concentric), ensuring that the hole is square to the wall.
Both wall faces immediately round the cut hole should be flat.
2. Drill 2 holes with a 7.5mm / 8mm masonry drill and insert the plastic plugs, provided, for the wall mounting plate.
3. Locate 2 No.14 x 50mm screws in the wall mounting plate
(one at each side, in any of the 3 holes provided at each side) and screw home.
X
Section through wall
Rear flue only
5" diameter hole
Side flue only
5" diameter hole
Note.
Check all of the hole positions before drilling.
24 Keston 30C - Installation and Servicing
INsTALLATION
22 sETTINg ThE FLUE - REAR - CONCENTRIC FLUE OpTION
TELEscOpic FLUE - Wall thickness of 195mm to 420mm
Notes.
a. If the stand-off frame is used it is essential to add 45mm to ‘X’ the measured wall thickness when marking the flue (this will allow for the fitted frame).
1. Measure and note wall thickness X. Refer to Frame 17.
2. Add 75mm to dimension X and set telescopic flue length as indicated in drawing.
3. Using a 3.5mm drill bit, drill one hole in outer air duct taking care not to pierce plastic inner flue.
4. Fix to length using self tappers provided.
5. Seal outer air duct using the tape provided.
Drill hole
X + 75
Adhere sealing tape
Measurement to be taken from this point nm8944
23 sETTINg ThE FLUE - sIDE - CONCENTRIC FLUE OpTION
TELEscOpic FLUE - Wall thickness of 150mm to 375mm
1. Measure and note wall thickness X. Refer to Frame 17.
2. Measure distance from side of boiler to inside of wall and add to wall thickness X=L. Refer to Frame 17.
3. Add 115mm to dimension L and set telescopic flue length as indicated in drawing.
4. Using a 3.5mm drill bit, drill one hole in outer air duct taking care not to pierce plastic inner flue.
5. Fix to length using self tappers provided.
6. Seal outer air duct using the tape provided.
Drill hole
L + 115
Adhere sealing tape
Measurement to be taken from this point nm8945
Keston 30C - Installation and Servicing 25
INsTALLATION
24 CONDENsATE pIpE TERMINATION CONFIgURATIONs
notes: aLL EXTErnaL pipE rUns MUsT BE in accOrDancE WiTH Bs 6798
1. INTERNAL TO sINK WAsTE
UpsTREAM OF sINK WAsTE TRAp
BOILER cla7771a
DRAIN
Open end of pipe direct into gulley below grating but above water level
Ground Level
2. INTERNAL CONNECTION TO sOIL AND VENT sTACK
* Make connection to SVP using a solvent welded saddle
BOILER esp8882
3. TERMINATION TO sOAK AWAy
External wall
BOILER cla7774
Termination to Soak away minimum
500mm
Ground Level
4. TERMINATION TO DRAIN / gULLy
External wall
BOILER cla7775
DRAIN
Open end of pipe direct into gulley below grating but above water level
Ground Level
26 Keston 30C - Installation and Servicing
INsTALLATION
25 CONNECTINg ThE CONCENTRIC FLUE OpTION TO ThE BOILER
Notes.
• Before fitting the flue turret fill the condensate trap within the boiler by pouring a cupful of water into the flue outlet (shown
below). Take care to ensure that the water is only poured into the flue outlet, and does not spill into the boiler casing.
• During assembly check that flue seals do not become dislodged.
nOTE. siDE FLUE
Select flue orientation before inserting turret into boiler manifold.
DO NOT twist the turret once inserted.
1. Ensure front panel is removed.
2. Locate the flue into the turret.
3. Insert the flue assembly through the prepared hole in the wall. Push through and pull back to seal against outside wall face.
4. Locate the flue turret into the flue manifold and secure by applying downward pressure.
5. Engage the clamp in its slide mechanism and push it horizontally backwards
6. Locate BOTH plastic pegs BEFORE the front retaining clip is fully located.
Note - Flues over 1 metre long
It is recommended that a support bracket is fitted for every 1 metre of extension pipe used and a bracket should be used at every joint, to ensure pipes are held at the correct angle.
4
3G9847a
2
3G9847b
3
3G10380
5
3G9847d
Keston 30C - Installation and Servicing
Flue Outlet
6
Retaining Clip
(assembled)
3G10381
3G9847e
Plastic Pegs
(assembled)
27
INsTALLATION
26 WATER CONNECTIONs - Ch
NOTEs.
Ensure all boss blanking plugs are removed before connecting hardware. Each valve must be fitted to the correct boss as shown in the picture.
Ensure each union is fitted with fibre seals provided.
Do not subject any of the isolating valves to heat as the seals may be damaged.
1. Connect the CH flow service valve and copper tail provided in
CH Flow
1
.
the hardware pack to the threaded boss connection provided at the lower rear of the boiler.
2. Connect the CH return valve (black handle) and copper tail.
3. If connecting the boiler to heating loads in excess of
60,000 Btu/h, connecting flow and return heating system pipework must be sided in 28mm diameter at the point of pipe connection to the boiler tails. Use 22mm x 28mm pipe adaptors as appropriate.
CH
Return
2
Black
Handle
Yellow
Handle
Blue
Handle
Note that all isolation handles are shown in the open position.
Black
Handle
Black
Handle
3G9849a
28
27 WATER CONNECTIONs - DhW
1. Fit the DHW inlet service valve (blue handle) and copper tail to the threaded boss connection ensuring the seal provided is correctly located.
2. Fit DHW outlet pipe tail to DHW outlet connection, ensuring the seal provided is correctly located.
3. Fit the filling loop provided between the DHW inlet valve and the CH return valve.
CH Flow
DHW
Outlet
2
DHW
Inlet
1
CH
Return
Black
Handle
Yellow
Handle
Blue
Handle
Note that all isolation handles are shown in the open position.
3G9849b
3
Filling
Loop
Black
Handle
Black
Handle
Keston 30C - Installation and Servicing
INsTALLATION
28 gAs CONNECTION
IMpORTANT. The gas service cock is sealed with a non-metallic blue fibre washer, which must not be overheated when making capillary connections. Refer to Frame 1 for details of the position of the gas connection.
For additional gas supply information refer to “Gas Supply” on page 8.
Gas
Supply
Black
Handle
Yellow
Handle
Note that all isolation handles are shown in the open position.
Gas Pressure
Test Point
Blue
Handle
3G9849c
Black
Handle
Black
Handle
29 sAFETy VALVE DRAIN
The safety valve connection, located at the bottom right-hand side of the boiler, comprises a 15mm diameter stub pipe.
The discharge pipe should be positioned so that the discharge of water or steam cannot create a hazard to the occupants of the premises or damage the electrical components and wiring.
A purpose made safety valve drain pipe is provided with the boiler to allow safe discharge through a wall to the outside of the building. This is particularly relevant to ‘high rise’ installations but can be used for all installations.
3G9849d
Black
Handle
Yellow
Handle
Note that all isolation handles are shown in the open position.
Blue
Handle
Black
Handle
Black
Handle
Safety
Drain
Valve
Safety Valve
Drain Connection
15mm elbow or fittings
(not supplied)
Keston 30C - Installation and Servicing
Safety Valve
Drain Pipe
29
INsTALLATION
30 FILLINg
IMpORTANT - when filling:
When filling, there may be a slight water leak from the air vent therefore electrical connections should be protected.
Note. The domestic hot water flow rate is automatically regulated to a maximum of
12.4 l/m (2.8 gpm).
1. Ensure Filling Loop is connected
2. Ensure dust cap on auto air vent is slackened off (refer to
Frame 68).
3. Check all isolation handles are in the open position
3G9849d
Black
Handle
Yellow
Handle
Blue
Handle
Note that isolation handles are shown in the OPEN position on this picture.
Black
Handle
Black
Handle
Safety
Drain
Valve
30
4. Once pressure gauge dial reads between 1 - 1.5 bar turn the filling loop isolation valves back to the closed position.
3G9862
Black
Handle
Yellow
Handle
Blue
Handles
Blue
Handle
Black
Handle
Black
Handle
Safety
Drain
Valve
Black
Handle
Black
Handle
3G9865
5. Disconnect filling loop at the LH side, ensuring washer is retained and screw on cap.
Note. Fully open all DHW taps and ensure water is flowing freely. Once satisfied close all taps.
Keston 30C - Installation and Servicing
31 ELECTRICAL CONNECTIONs
INsTALLATION
Warning. This appliance MUST be earthed.
A mains supply of 230Vac ~ 50 Hz is required.
The fuse rating should be 3A. All external controls and wiring must be suitable for mains voltage.
Wiring external to the boiler MUST be in accordance with the current I.E.E. (BS.7671) Wiring Regulations and any local regulations.
Wiring should be 3 core PVC insulated cable, not less than
0.75mm
2 (24 x 0.2mm), and to BS 6500 Table 16. For IE reference should be made to the current ETCI rules for electrical installations.
Connection must be made in a way that allows complete isolation of the electrical supply such as a double pole switch having a 3mm (1/8”) contact separation in both poles. The means of isolation must be accessible to the user after installation.
32 INTERNAL WIRINg
The Keston 30C boiler comes pre-fitted with 1.8m of mains cable. This must be connected to a permanent live supply and NOT switched by thermostats/programmers. For installers wishing to change this cable refer to Frame 33.
The Keston 30C boiler comes pre-fitted with a link wire between the room thermostat/Timer connections on the terminal strip. This creates a permanent call for heat and must be removed when adding a room thermostat/ programmer.
The terminal block cover carries two spare fuses for the main PCB.
To add thermostat/programmer:
1. Isolate the mains supply to the boiler.
2. Remove the front panel. Refer to Frame 44.
3. Swing the control box down into the servicing position.
Refer to Frame 50.
4. Route incoming cables through the grommets in bottom panel (note, grommets are ‘blind’ and will require puncturing) and secure using clamps and screws provided in hardware pack.
5. Pull off rubber terminal block cover.
6. Connect wires to terminal block, as shown below
7. Re-assemble in reverse order.
Spare PCB fuses
Keston 30C - Installation and Servicing continued . . . .
31
INsTALLATION
32 INTERNAL WIRINg.... CONT’D
Keston offer 2 kits as follows:
(see individual kits for installation instructions)
Electronic Timer (7 day) kit - 7 day electronic CH timer fits into the control box of the boiler. This can be fitted in conjunction with a room thermostat. Features English language installation help messages.
DIAGRAM A
Internal Timer or
Programmable Room Stat
L
N
ROOM
STAT/
TIMER
FROST
STAT
( OPTIONAL )
N
Room
Stat or
Prog.
Room
Stat
Optional
Frost Stat
(1) ROOM ThERMOsTAT WITh INTERNAL BOILER TIMER OR
(2) pROgRAMMABLE ROOM ThERMOsTAT
1. Remove link wire between room stat/timer terminals.
2. Connect room stat across terminals as shown in diagram A
3. If room stat has a neutral connection, connect this to terminal
N (load) in the fused spur.
DIAGRAM B
External
Timer
L
N
ROOM
STAT/
TIMER
FROST
STAT
( OPTIONAL )
N
Room
Stat
ROOM ThERMOsTAT + TIMER
1. Remove link wire between room stat/timer terminals.
2. Connect room stat and programmer in series as shown in diagram B.
3. If room stat has a neutral connection, connect this to terminal N (load) in the fused spur.
FROsT ThERMOsTAT
If parts of the system are vulnerable to freezing or the programmer is likely to be left off during cold weather, a frost stat should be fitted in conjunction with a pipe thermostat.
1. Position the frost thermostat in a suitable position, i.e. area vulnerable to freezing.
2. Connect frost stat across terminals marked frost stat shown in diagrams A &
B.
32
DIAGRAM C
Weather Compensation Kit
L
N
ROOM
STAT/
TIMER
FROST
STAT
( OPTIONAL )
OpenTherm
Harness
Weather
Compensation
Timer
Outside
Sensor
WEAThER COMpENsATION KIT
The two wires from the weather compensation kit (outside sensor), must be connected into the two right hand terminals as shown in diagram C.
Keston 30C - Installation and Servicing
INsTALLATION
33 REpLACINg pRE-FITTED MAINs CABLE
If it is necessary to use an alternative mains cable to the one pre-fitted then use the following guide.
Replacement wiring should comply with notes in Frame 31.
1. Isolate the mains supply to the boiler.
2. Remove the front panel. Refer to Frame 44.
3. Swing the control box down into the service position. Refer to frame
50.
4. Remove the live, neutral and earth wires from the terminal block.
5. Loosen the cable clamp and withdraw the mains cable.
6. Route replacement cable back through the cable clamp and grommet and re-tighten to provide cord anchorage.
7. Connect the live, neutral and earth wires to the terminal strip.
When making the mains electrical connections to the boiler it is important that the wires are prepared in such a way that the earth conductor is longer than the current carrying conductors, such that if the cord anchorage should slip, the current carrying conductors become taut before the earthing conductor.
8. Swing the control box back up into the operating position and re-fit the front panel ensuring a good seal is made.
4
5
34 FITTINg ThE WEAThER COMpENsATION KIT - sUppLIED As sTANDARD
This kit provides the facility to apply outside air temperature control to the boiler water flow temperature which provides energy savings. The outside sensor provided measures outside air temperature and sends a signal to the boiler, which adjusts the maximum boiler flow temperature in response. If outside air temperature is greater than the system design temperature, the boiler flow temperature is reduced providing running cost savings. The boiler will operate in the condensing mode more frequently increasing savings.
Once the sensor is fitted it is automatically detected.
The sensor operation may be configured by adjustment of the boiler operating parameters, if necessary.
Kit Contents
A. Outside Air Sensor
A
3G10011
Keston 30C - Installation and Servicing 33
1.
2.
3.
4.
5.
INsTALLATION
35 FITTINg ThE KIT
Note. A timer should be fitted to the system so that CH will be switched off when appropriate.
Fitting the sensor
The air sensor should be located on an external wall of the building to be heated. Fix the sensor to a north/north-east facing wall to avoid direct radiation from the sun. The air sensor should be located to avoid any heating effect from the boiler flue.
To fix the air sensor to the wall, unscrew the sensor box plastic cover and screw/plug the sensor body to the wall.
Wire a twin core 0.5mm
2 cable from the sensor to the boiler through an RH grommet located on the underside of the boiler. Cable length between sensor and boiler should be no greater than 20m. Note that this connection is safety extra low voltage. It is not necessary for the person carrying out the wiring to be approved to Part P of the Building Regulations.
Avoid running this cable alongside mains voltage cables.
Wiring the Weather Compensation Kit to the Keston 30C.
Isolate the electricity supply to the boiler.
Remove the boiler front panel (refer to boiler installation instructions).
Hinge down the control box.
Connect the sensor wiring into the RHS of the 4 way terminal block and secure with a cable clamp.
Re-assemble in reverse order.
4
34 Keston 30C - Installation and Servicing
INsTALLATION
36 Ch OpERATION
The On and Off time control of central heating should be controlled by a separate timer. This can be a standard unit or either of the options available from Keston 30C range.
During programmed On times the Central Heating Radiator Flow Temperature is controlled by the boiler relative to the Outside
Temperature as shown in the following diagram.
The Room temperature can be adjusted using the Central Heating Temperature Control Knob on the boiler as follows.
Essentially rotating the knob clockwise increases the room temperature and rotating the knob anti-clockwise decreases the room temperature.
If the Central Heating Temperature Control Knob is rotated fully clockwise then for an Outside Temperature of 15°C a Flow
Temperature of 40°C will be provided. For an Outside Temperature of 0°C a Flow Temperature of 78°C will be provided with the relationship varying lineally in between these 2 points (line on the graph 2.5)
If the Central Heating Temperature Control Knob is in its mid position then for an Outside Temperature of 15°C a Flow
Temperature of 36°C will be provided. For an Outside Temperature of 0°C a Flow Temperature of 65°C will be provided with the relationship varying lineally in between these 2 points (line on the graph between 1.6 and 1.8)
If the Central Heating Temperature Control Knob is rotated fully anti-clockwise then for an Outside Temperature of 15°C a Flow
Temperature of 30°C will be provided. For an Outside Temperature of 0°C a Flow Temperature of 44°C will be provided with the relationship varying lineally in between these 2 points (line on the graph 1.0)
Keston 30C - Installation and Servicing 35
INsTALLATION
37 ExTERNAL ELECTRICAL CONTROLs
Wiring External to the Boiler
The fuse rating should be 3A.
Wiring external to the boiler MUST be in accordance with the current I.E.E. (BS.7671) Wiring Regulations and any local regulations.
Frost protection
If parts of the pipework run outside the house or if the boiler will be left off for more than a day or so then a frost thermostat should be wired into the system.
This is usually done at the programmer, in which case the programmer selector switches are set to OFF and all the other controls MUST be left in the running position.
The frost thermostat should be sited in a cold place but where it can sense heat from the system.
Note. If the boiler is installed in a garage it may be necessary to fit a pipe thermostat, preferably on the return pipework.
Earths are not shown for clarity but must never be omitted.
Programmable Room Stat
Programmable
Room
Stat
Optional
Frost Stat
Mains In
Room Stat
L N
Frost Stat
Use of General Live for Room Stat
Room
Stat
Optional
Frost Stat
Mains In
Room Stat
L N
Frost Stat
3G9990a
36
OpenTherm programmable Room Temperature Control
Note. These terminals MUST ONLY be connected to an
OpenTherm Controller, (such as the Keston Chronothern Room
Controller (c.17.4.21.00.0). Connecting any other device / control wiring may destroy the primary PCB.
1. Isolate the mains supply to the boiler.
2. Remove the front panel. Refer to Frame 44.
3. Swing the control box down into the servicing position. Refer to Frame 50.
4. Remove the control box cover. Refer to Frame 62, no’s 3 and 4.
5. Unclip the 3 way in-line connector containing 2 purple wires and 2 red wires.
6. Connect this 3 way connector to the 3 way connector containing 2 purple wires wired from the 4 way terminal block.
7. Connect the two wires from the OpenTherm Programmable
Room Temperature Control to the two LH connections of the terminal block as shown.
8. Re-assemble in reverse order.
5 6
Keston 30C -
7
Installation and Servicing
38 WIRINg DIAgRAM
Fused at 4A
INsTALLATION
Internal T imer High
Chassis Earth
Diverter V
Gas Valve
Keston 30C - Installation and Servicing
Flame Sensor Electrode
Internal T imer Low
Service Connector ater Flow
Pressure Sensor
Exchanger Thermistor
37
38
INsTALLATION
39 COMMIssIONINg AND TEsTINg
A. Electrical Installation
1. Checks to ensure electrical safety should be carried out by a competent person.
2. ALWAYS carry out the preliminary electrical system checks, i.e. earth continuity, polarity, resistance to earth and short circuit, using a suitable test meter.
B. gas Installation
1. The whole of the gas installation, including the meter, should be inspected and tested for tightness and purged in accordance with the recommendations of BS. 6891.
In IE refer to IS.813:2002.
2. Purge air from the gas installation by the approved methods only.
Warning.
Whilst effecting the required gas tightness test and purging air from the gas installation, open all windows and doors, extinguish naked lights and DO nOT sMOkE.
gENERAL
please note: The combustion for this appliance has been checked, adjusted and preset at the factory for operation on the gas type defined on the appliance data plate. No measurement of the combustion is necessary. DO NOT adjust the air/gas ratio valve.
Having checked:
- That the boiler has been installed in accordance with these instructions.
- The integrity of the flue system and the flue seals, as described in the Flue Installation section.
Proceed to put the boiler into operation as follows:
ChECK ThE OpERATIONAL (WORKINg) gAs
INLET pREssURE
DHW Outlet
opening hot tap to maximum flow.
Gas Supply
With the boiler operating in the maximum rate condition check that the operational
(working) gas pressure at
Black
Handle
Supply” on page 8.
Yellow
Handle
DHW Inlet
Ensure that this inlet pressure can be obtained with all other gas appliances in the property working.
Gas Pressure
Test Point
Blue
Handle
CH Return
3G9927a
Black
Handle
Safety
Drain
Valve
Keston 30C - Installation and Servicing
40 INITIAL LIghTINg
Legend
A. Pre-heat On/off
B. DHW temperature control
C. CH temperature control
D. Off/Summer/Winter/Reset Control
E. Boiler Status
F. Burner ‘on’ indicator
g. CH Flow Isolating Valve
h. Pressure Gauge
J. Gas Inlet Pressure Test Point
K. Gas Service Cock
L. DHW Inlet Valve
M. CH Return Isolating Valve
N. DHW Outlet
H
INsTALLATION
A B E F
G
N
K
J
C
L
M
D
1. Check that the system has been filled and that the boiler is not airlocked. Ensure the automatic air vent cap is open. Refer to
Frame 30.
Note.
It is important the burner is not operated before the system is fully vented of air. If it is necessary to operate the appliance pump to assist venting of the air this must be done with the gas service cock turned off.
2. Refit the boiler front panel. Refer to Frame 44.
3. Check that the drain cock is closed and that the CH and DHW isolating valves (M, L and G) are OPEN.
4. Check that the electrical supply is OFF.
5. Check that the boiler mode control knob (D) is off.
6. Check that the gas service cock (K) is OPEN.
7. Slacken the screw in the inlet pressure test point (J) and connect a gas pressure gauge via a flexible tube.
8. Switch the electricity supply ON and check all external controls are calling for heat.
3G9863
11. With the boiler firing, set the DHW Temp Control knob (B) to maximum and fully open a DHW tap.
The boiler will continue to run and the display (E) will show “Hot Water” - “Temperature XX
Efficiency”.
o c” - “High
12. Ensure that with the boiler operating the dynamic gas pressure is able to obtain maximum output. Refer to Table
2.
IMpORTANT
The gas input to the burner is regulated by the gas valve according to the air flow produced by the fan. It is NOT user-adjustable. Any interference to sealed settings on the gas valve will adversely affect operation and render our warranty void.
For additional gas supply information refer to “Gas Supply” on page 8
13. Turn off the DHW tap.
CENTRAL hEATINg
9. Set the CH temp control (C) to max and turn the mode control knob (D) to , ensure the timer/room stat are on. The boiler control will now go through its ignition sequence until the burner is established.
10. If the boiler does not light the following messages will be displayed in rotation “ignition Lockout” - “1 check other gas appliances” - “2 Reset boiler” - “3 Contact
installer”. After 5 attempts the boiler will lock out and carry on displaying the messages. Reset the boiler (refer to Frame
40B). The boiler will repeat its ignition sequence. If reset occurs 5 times within 15 minutes then “Too many resets” will be shown. If power is removed this will be reset.
When the burner is established the BLUE ‘Burner On’ neon
(F) will be illuminated, the LCD will display “central Heating” and “Radiator Temp XX o c”.
DOMEsTIC hOT WATER
Note. The temperature displayed “XXºC” is that measured at that moment, not the set temperature.
Note. The boiler incorporates a fan overrun cycle which MUST NOT be prematurely interrupted by isolation of the mains electricity supply.
Keston 30C - Installation and Servicing continued. . . . .
39
40
INsTALLATION
40 INITIAL LIghTINg . . . . CONT’D
ThE DIspLAy
The user control has one neon and one display to inform the user about the status. The display will show the status of the boiler.
The neon will show the status of the flame. If no flame is detected the neon is off. When the flame is detected the neon will be lit permanently.
The display scrolls through a maximum of 3 messages under any operational condition as shown below.
Notes: Boiler frost protection - boiler fires if temperature is below 5º C.
The temperatures shown below are for illustration purposes only. The measured temperatures will be shown on the boiler.
DIspLAy FUNCTIONs IN NORMAL OpERATION
NORMAL OPERATION MESSAGE 1
Mode knob in standby position and no heat demand
Mode knob in summer position and no heat demand
Mode knob in winter position and no heat demand
Domestic hot water operation
Standby mode
Summer mode
Winter mode
Hot water
MESSAGE 2
For hot water turn mode knob clockwise
For central heating turn mode knob clockwise
Timer or room stat off
Temperature 64ºC
MESSAGE 3
For central heating turn mode knob clockwise twice
High efficiency
Central heating operation
Pre-heat operation
Boiler frost protection
Pump overrun
Fan post-purge
Central heating
Pre heat
Boiler frost protection
Pump overrun
Fan post-purge
Radiator Temp 80ºC
Temperature 59ºC
Temperature 5ºC
High efficiency
High efficiency
High efficiency
Note. High efficiency will not be shown for central heating operation if the central heating flow temperature knob is set to greater than 73ºC.
DIspLAy FUNCTIONs - sETTINgs ChANgED
NORMAL OPERATION MESSAGE 1
Pre-heat knob moved to off position Pre heat off
Pre-heat knob moved to on position
DHW temperature knob moved
CH temperature knob moved
Pre heat on
64ºC DHW temp
80ºC CH temp
Mode knob moved to standby position
Mode knob moved to summer position
Mode knob moved to winter position
Mode knob moved to reset position
Standby mode
Summer mode
Winter mode
Reset
MESSAGE 2
Hot water temperature 64ºC
Maximum radiator temperature 80ºC
Central heating off
Central heating off
Central heating on
MESSAGE 3
May not be achieved for high flow rates in winter
Hot water off
Hot water on
Hot water on
Keston 30C - Installation and Servicing
INsTALLATION
40 INITIAL LIghTINg . . . . CONT’D
INsTALLER MODE
Installer Mode is entered as follows:
1. Turn the DHW temperature control knob full anti-clockwise.
2. Turn the CH flow temperature control knob full anti-clockwise.
3. Turn and hold the mode knob in the reset position for more than 5 secs and then turn it to the Winter or Summer position.
The boiler will display “Installer mode”.
If no faults have occurred the boiler will display “no faults”.
If any faults have occurred a list of faults up to a maximum of 10 including the type of fault and how long ago it occurred will be shown in the following format.
MESSAGE 1
LIST OF FAULTS
Fault 1 (latest fault)
Fault 2
Fault 3
The boiler will then display the current values of flow temperature, return temperature, domestic hot water temperature, DHW flow rate and diverter valve position in the following format:
MESSAGE 1
CURRENT VALUES
Flow temp 80ºC
Return temp 60ºC
DHW temp 64ºC
DHW flow rate 8 l/min
Diverter valve DHW position
MESSAGE 2
Low water pressure
No water flow lockout
Overheat lockout
MESSAGE 3
2 days ago
78 days ago
384 days ago
Note.
If you would like to hold one of the values on the display to watch its behaviour then turn the reset knob to the reset position while it is displayed and hold it there.
Finally the display will operate in one of two modes. If there is a fault then more extensive corrective actions will be shown than are usually displayed for the end user. If there is not a fault then the information displayed for current operating states will also be more extensive than is usually displayed for the end-user (pre-purge, ignition and post purge for example).
Installer mode automatically ends after 10 mins or by moving the mode knob to the standby position.
40B REsET pROCEDURE
To reset boiler, turn the mode control knob (D) to reset position and immediately turn knob back to required setting. The boiler will repeat the ignition sequence.
A B E
Legend
A. Pre-heat On/off
B. DHW temperature control
C. CH temperature control
F C D
D. Off/Summer/Winter/Reset Control
E. Boiler Status
F. Burner ‘on’ indicator
Keston 30C - Installation and Servicing 41
INsTALLATION
41 gENERAL ChECKs
Make the following checks for correct operation in:
DOMEsTIC hOT WATER (DhW) MODE
1. Fully open all DHW taps in turn and ensure that water flows freely and that the mode knob is either in summer or winter position. The boiler will display
“Hot Water” - “Temperature XX o
Efficiency”
c” - “High
where the temperature shown is the current Domestic Hot
Water temperature.
When the burner is lit the light above the display will be on.
2. Close all taps except the furthest one from the boiler and check that the boiler is firing at maximum rate.
This is factory set to give a DHW temperature rise of approximately 35
“operation”.
o C at the flow rate stated on page 6 under
3. Reduce the DHW draw-off rate to about 3 l/min (0.7gpm) and check that the boiler modulates to deliver DHW at approximately 64 o C (with the DHW temperature control knob set to maximum).
4. Close the DHW tap and check that the main burner extinguishes. The pump should overrun for 60 seconds during which the boiler will display “Pump overrun”. The fan will then continue to run for a further 3 minutes during which the boiler will display “Fan post purge” after which the boiler will display one of the following “Standby mode”
- “Summer mode” - “Winter Mode” depending on the position of the mode knob.
Note. On systems in excess of 2 bar inlet pressure a water pressure governor may be required to prevent water noise.
Ch & DhW MODE
1. Ensure the CH controls are calling for heat and that the boiler mode knob is in the winter position and the CH flow temperature control knob is in the maximum position. The
Boiler will display
“Central Heating” - “Radiator Temp XXC”
where the temperature shown is the current flow temperature.
When the burner is lit the light above the display will be on.
2. Fully open the DHW tap and check that hot water is delivered.
The boiler will display “Hot water” - Temperature XX
- High Efficiency” o c”
3. Gas Rate
Check the boiler gas rate when the boiler is at full DHW output. Check at the gas meter, with no other appliance in use. Refer to Tables 2 and 3 for gas rates.
4. Close the DHW tap. The burner should remain on and the boiler will display “Central heating” - “Radiator temp
XXc”.
5. Set the central heating external controls to off. The burner will go off and the fan and pump continue to run for 4 minutes.
The boiler will display “Pump overrun” after which the boiler will display one of the following: “Standby mode”
- “Summer mode” - “Winter mode” depending on the position of the mode knob.
6. Check the correct operation of the timer (if fitted) and all other system controls. Operate each control separately and check that the main burner responds.
Note. The temperature displayed “XXºC” is that measured at that moment, not the set temperature.
42
WATER CIRCULATION sysTEM
1. With the system COLD, check that the initial pressure is correct to the system design requirements.
For pre-pressurised systems, this should be 1.0 bar.
2. With the system HOT, examine all water connections for soundness. The system pressure will increase with temperature rise but should not exceed 2.5 bar.
3. With the system still hot, turn off the gas, water and electricity supplies to the boiler and drain down to complete the flushing process.
Note: A flushing solution should be used during the flushing procedure. Flushing solutions: Fernox
Superfloc, Sentinel X300 (new systems) or X400
(existing systems). Refer to Frame 5.
4. Refill and vent the system, add inhibitor (see Frame
5), clear all air locks and again check for water soundness.
5. Reset the system initial pressure to the design requirement.
6. Balance the system. Refer to Frame 4.
7. Check the condensate drain for leaks and check that it is discharging correctly.
8. Finally, set the controls to the User’s requirements.
Notes.
1. If the pump has not operated in the last 24 hours it will run briefly to prevent seizure
2. If the diverter valve has not operated in the last 24 hours it will be operated briefly to prevent seizure. These two operations will not occur at the same time.
WATER TEMpERATUREs
Temperatures can be selected using the CH and DHW thermostats.
Knob setting
Max
Min
Ch Flow Temp DhW Outlet Temp o C ( o F)
80 (176)
30 (86) o C ( o F)
64 (147)
40 (104)
Keston 30C - Installation and Servicing
INsTALLATION
42 hANDINg OVER
After completing the installation and commissioning of the system the installer should hand over to the householder by the following actions:
1. Make the householder aware that the user instructions are located in the pocket in the drop down door and explain his/her responsibilities under the relevant national regulations.
2. Explain and demonstrate the lighting and shutting down procedures.
3. The operation of the boiler and the use and adjustment of all system controls should be fully explained to the householder, to ensure the greatest possible fuel economy consistent with the household requirements of both heating and hot water consumption.
Advise the User of the precautions necessary to prevent damage to the system and to the building, in the event of the system remaining inoperative during frosty conditions.
4. Explain the function and the use of the boiler heating and domestic hot water controls.
Explain that due to system variations and seasonal temperature fluctuations DHW flow rates/temperature rise will vary, requiring adjustment at the draw off tap. It is therefore necessary to draw the users attention to the section in the Users Instructions titled “Control of Water
Temperature” and the following statement:
“Additionally, the temperature can be controlled by the user via the draw-off tap: the lower the rate the
higher the temperature, and vice versa”.
5. Explain the function of the boiler fault mode.
Emphasise that if a fault is indicated, the boiler should be turned off and a Gas Safe Registered Engineer consulted.
In IE contact a Registered Gas Installer (RGII).
6. Explain and demonstrate the function of time and temperature controls, radiator valves etc., for the economic use of the system.
7. If a timer is fitted draw attention to the timer Users
Instructions and hand them to the householder.
8. Loss of system water pressure
Explain that the dial underneath the boiler indicates the central heating system pressure and that if the normal COLD pressure of the system is seen to decrease over a period of time then a water leak is indicated. Explain the re-pressurising procedure and if unable to re-pressurise or if the pressure continues to drop a registered local heating installer should be consulted.
9. Explain boiler reset procedure (refer to Frame 41B).
10. After installation and commissioning please complete the Commissioning Checklist before handover to the customer. For IE, its is necessary to complete a “Declaration of Conformity” to indicate compliance to I.S.
813:2002.
IMpORTANT
11. A comprehensive service should be carried out ANNUALLY.
Stress the importance of regular servicing by a Gas Safe
Registered Engineer. In IE servicing work must be carried out by a Registered Gas Installer (RGII).
12. Inform the householder of the guarantee form and the requirement to register it to receive the full benefit of the warranty.
Keston 30C - Installation and Servicing 43
44
sERVICINg
43 sERVICINg sChEDULE
For the very latest copy of literature for specification & maintenance practices, visit our website www.keston.co.uk, where you will be able to download the relevant information.
Warning. Always turn OFF the gas supply at the gas service cock, and switch OFF and disconnect the electricity supply to the appliance before servicing.
Combustion testing must be carried out by a competent person using a combustion analyser conforming to Bs7927.
To ensure the continued safe and efficient operation of the appliance it is recommended that it is checked at regular intervals and serviced as necessary. The frequency of servicing will depend upon the installation condition and usage but should be carried out at least annually.
It is the law that any service work must be carried out by a Gas Safe Registered Engineer. In IE service work must be carried out by a Registered Gas Installer (RGII).
INspECTION
1. Light the boiler and carry out a pre-service check, noting any operational faults.
2. Check the flue terminal (and terminal guard if fitted) is undamaged and clear of any obstruction.
gENERAL
please note: During routine servicing, and after any maintenance or change of part of the combustion circuit, the following must be checked:
- The integrity of the flue system and the flue seals,
3. Check all water and gas joints for signs of leakage. Remake any suspect joints ensuring a gas tightness check is carried out if applicable and the water system is correctly refilled, vented and re-pressurised.
CLEANINg pROCEDURE
Note. In order to carry out either servicing or replacement of components the boiler front panel must be removed. Refer to
Frame 44.
1. Clean the main burner. Refer to frame 46.
2. Clean the heat exchanger & condensate trap/siphon. Refer to
Frames 47 & 48.
- The integrity of the boiler combustion circuit and the relevant seals
- The operational (working) gas inlet pressure at maximum rate.
- The gas rate
- The combustion performance.
COMpETENCE TO CARRy OUT ThE ChECK
OF COMBUsTION pERFORMANCE
please note: BS 6798:2009 Specification for installation and maintenance of gas-fired boilers of rated input not exceeding 70kW net advises that:
3. Check the main injector for blockage or damage. Refer to Frame
45.
4. Check that the flue terminal is unobstructed and that the flue system is sealed correctly.
- The person carrying out a combustion measurement should have been assessed as competent in the use of a flue gas analyser and the interpretation of the results.
ALSO IF THE DHW FLOW RATE IS IN QUESTION :-
5. Check the DHW filter for blockage. Refer to Frame 74.
The cleaning procedures are covered more fully in Frames 45-50 and
MUST be carried out in sequence.
- The flue gas analyser used should be one meeting the requirements of BS7927 or BS-EN50379-3 and be calibrated in accordance with the analyser manufacturers requirements, and
IMpORTANT.
6. After completing the servicing or exchange of components always test for gas tightness.
7. When work is complete the front panel MUST be correctly refitted, ensuring that a good seal is made.
- Competence can be demonstrated by satisfactory completion of the CPA1 ACS assessment, which covers the use of electronic portable combustion gas analysers in accordance with BS7967, Parts 1 to 4.
Do nOT OpEraTE the boiler if the front panel is not fitted.
8. If, for any reason, the condensate trap/siphon has been removed ensure the trap is refilled with water before reassembling.
9. Check the gas consumption.
10. Check combustion by connecting the flue gas analyser to the flue gas sampling point as shown in the diagram and measure CO &
CO
2
.
If the CO/CO
2 ratio is greater than 0.004 AND the integrity of the complete flue system and combustion circuit seals have been verified and the inlet gas pressure (and gas rate) have been verified, then contact Keston.
11. Complete the service section in the Benchmark Commissioning
Checklist.
Keston 30C - Installation and Servicing
sERVICINg
44 BOILER FRONT pANEL REMOVAL / REpLACEMENT
REMOVAL
1. Loosen the two screws retaining the front panel.
2. Pull the two spring clips down to disengage and pull panel forward and upward and remove.
REpLACEMENT
3. Hook the panel onto the top retaining clips.
4. Push the panel until the 2 bottom spring clips engage ensuring the 4 control knobs line up with the holes in the front panel.
5. Re-tighten the two retaining screws.
3
1
2 view from bottom of boiler
Flue sampling point for concentric flue only view from top of boiler
45 FAN AND VENTURI AssEMBLy REMOVAL AND CLEANINg
1. Disconnect the electrical leads from the fan.
2. Undo the gas pipe union connection to the injector housing.
3. Remove the extended nut on the fan mounting bracket.
4. Lift off fan and venturi assembly.
5. Inspect the injector for blockage or damage.
6. Inspect fan outlet sealing gasket and replace if necessary.
3
5
Injector
2
1
Keston 30C - Installation and Servicing 45
46
sERVICINg
46 BURNER REMOVAL AND CLEANINg
1. Ensure the sump is fully drained
2. Undo the two screws and remove the sump cover retaining the lower flue manifold.
3. Lift the manifold to clear the bottom sealing gasket and remove manifold.
4. Remove the 2 burner front fixing screws and loosen the 2 rear extended nuts by at least ten turns.
5. Lift off the burner from the combustion chamber. To facilitate the removal angle the burner as shown.
IMpORTANT
The burner head is a ceramic plaque construction. Care must be taken to ensure that the burner is not placed down upon
its face as this may cause damage to the ceramic.
6. Brush off any deposits that may be on the ceramic with a
SOFT brush.
7. Inspect the sealing gasket around the burner for any signs of damage. Replace as necessary.
2
5
3
4
4
47 CLEANINg ThE CONDENsATE TRAp/sIphON
1. Remove the cleaning plug taking care with any residual condense.
2. Pull off the rubber pipe noting the position and flush out any deposits with clean water.
3. Replace the cleaning plug and refill the siphon with water.
4. Replace the rubber pipe connector with the twin wall seal fitted to the condensate siphon.
2
4
1
2
3G9690
Keston 30C - Installation and Servicing
sERVICINg
48 CLEANINg ThE hEAT ExChANgER
note: Ensure the condensate trap/siphon
is fully drained before cleaning. Refer to
Frame 61.
1. Remove ignition and flame detection electrodes. Refer to Frames 56 & 57.
2. It is advisable to replace the sump cover prior to the water flush process.
3. Thoroughly flush the heat exchanger by pouring water into the top of the combustion chamber ensuring the full top area is covered.
4. Remove the sump cover and clean loose deposits from the sump.
5. Inspect the ignition and detection electrodes. Ensure that they are clean and in good condition - replace if necessary.
6. Re-fit the ignition and flame detection electrodes, ensuring that both earth tabs are fitted to ignition electrode.
7. Check that the ignition and detection gaps are correct. Refer to Frames 56 & 57.
1
Ignition Electrode
3
Flame Detection
49 REAssEMBLy
Reassemble the boiler in the following order:
1. Ensure that the condensate trap/siphon is full of water.
2. Refit the burner ensuring the sealing gasket is correctly positioned and free from damage (tighten the 4 fixing screws in the sequence shown below).
3. Refit the fan / venturi assembly ensuring the retaining tabs are correctly positioned and the sealing gasket is correctly positioned and free from damage.
4. Reconnect the fan electrical leads.
5. Remove the sump cover and refit the lower flue manifold as shown.
6. Refit the sump cover.
7. Refit the boiler front panel.
IMpORTANT. Ensure that the boiler front panel is correctly fitted and that a good seal is made.
8. Swing the control box back into its working position and secure.
9. Turn on the gas supply at the gas service cock.
10. Reconnect the electrical supply.
4
2
5
1
3
Keston 30C - Installation and Servicing 47
sERVICINg
50 REpLACEMENT OF COMpONENTs
gENERAL
When replacing ANy component
1. Isolate the electricity supply.
2. Turn off the gas supply.
3. Remove the boiler front panel. Refer to Frame 44.
4. Release the retaining clip and swing the control box down into its servicing position.
After replacing ANY component check operation of the boiler, including gas tightness, gas rate and combustion test.
IMpORTANT.
When work is complete, the front panel must be correctly refitted - ensuring that a good seal is made.
Notes.
1. In order to assist fault finding, the control panel has an LED diagnostic display. The key to boiler fault
conditions is shown in Frame 80.
2. In order to replace components in Frames 66-78 it is necessary to drain the boiler. Refer to Frame 65.
4
48
ThE BOILER MUsT NOT BE OpERATED WIThOUT ThE FRONT pANEL FITTED
51 FAN REpLACEMENT
1. Refer to Frame 50.
2. Disconnect the electrical leads from the fan.
3. Undo the gas pipe union connection to the injector housing.
4. Remove the extended nut retaining the fan mounting bracket.
5. Lift and remove the fan and venturi assembly.
6. Remove the screw and twist venturi anticlockwise to remove venturi assembly, noting the orientation of the venturi in relation to the fan body.
7. Transfer the venturi assembly to the new fan, replacing the ‘o’ ring if evidence of damage or deterioration is visible.
8. Fit the new fan / venturi assembly ensuring the retaining tabs are correctly positioned and the fan outlet sealing gasket is correctly positioned and free from damage. Refit the extended nut.
9. Reassemble the boiler in reverse order, taking care not to overtighten the screw on the fan mounting bracket.
10. Check the operation of the boiler. Refer to
Frames 40 & 41.
4
8
3
6
Retaining Tabs
2
Keston 30C - Installation and Servicing
sERVICINg
52 BURNER INJECTOR REpLACEMENT
4 1. Refer to Frame 50.
2. Disconnect the electrical leads from the fan.
3. Undo the gas pipe union connection to the injector housing.
4. Loosen the screw retaining the fan mounting bracket.
5. Lift and remove the fan and venturi assembly.
6. Remove the 2 injector housing screws.
7. Withdraw the injector housing.
8. Fit the new injector housing complete with injector.
9. Reassemble in reverse order, ensuring that the new gas seal supplied is located correctly in the injector housing.
10. Check operation of the boiler. Refer to Frames 40
& 41.
6
3
2
53 BURNER REpLACEMENT
1. See Frame 46.
2. Refer to Frame 50.
3. Disconnect 2 flag terminals from the flue thermostat.
4. Undo the two screws and remove the sump cover.
5. Lift the manifold to clear the bottom sealing gasket and remove manifold.
6. Remove the 2 front fixing screws and loosen the 2 rear extended nuts.
7. Lift off the burner from the combustion chamber. To facilitate the removal angle the burner as shown.
8. Fit the new burner, replacing any damaged or deteriorating sealing gasket.
9. Reassemble in reverse order. Refer to Frame 49.
10. Check the operation of the boiler. Refer to Frames 40 &
41.
7
4
5
6
6
Keston 30C - Installation and Servicing
4
49
sERVICINg
54 CONTROL ThERMIsTOR & RETURN ThERMIsTOR RENEWAL
1. Refer to Frame 50.
2. Unclip the control thermistor from the flow pipe and withdraw it from the boiler.
3. Unclip the return thermistor from the return pipe and withdraw it from the boiler.
4. Disconnect the electrical leads from the thermistors.
5. Reconnect the electrical leads to the new thermistors and reassemble in reverse order, ensuring that the thermistors are securely fitted to the pipes on the thermistor locator tabs as shown.
6. Check the operation of the boiler. Refer to Frames 40 & 41.
5
2
Thermistor Locator Tab
(with thermistor fitted)
3
55 FLUE ThERMOsTAT REpLACEMENT
1. Refer to Frame 50.
2. Undo the two screws and remove the sump cover plate.
3. Disconnect the two flag terminals from the flue thermostat.
4. Lift the manifold to clear the bottom
.
sealing gasket and remove manifold.
5. Unscrew the two M3.5 screws that connect the thermostat to the manifold.
6. Replace thermostat with new part and then refit the two screws, remembering to fit rubber gasket and sealing clamp.
Flue Thermostat
50 Keston 30C - Installation and Servicing
sERVICINg
56 IgNITION ELECTRODE REpLACEMENT
1. Refer to Frame 50.
2. Remove the burner. Refer to Frame 53.
3. Unplug the ignition lead from the electrode.
4. Remove the earth lead from the ignition electrode.
5. Remove the 2 screws holding the ignition electrode to the combustion chamber.
6. Remove the electrode.
7. Fit the new ignition electrode, using the new gasket supplied. Check dimensions as shown.
8. Reassemble in reverse order.
9. Check the operation of the boiler. Refer to Frames
40 & 41.
Ignition Electrode
Spark Gap
3.5mm
Str aig ht ed ge
3mm
57 FLAME DETECTION ELECTRODE REpLACEMENT
1. Refer to Frame 50.
2. Remove the burner. Refer to Frame 53.
3. Unplug the flame detection lead from the electrode.
4. Remove the 2 screws retaining the detection electrode.
5. Remove the electrode.
6. Fit the new flame detection electrode, using the new gasket supplied.
7. Reassemble in reverse order.
8. Check the operation of the boiler. Refer to
Frames 40 & 41.
Str aig ht ed ge
Flame Detection Electrode
12.5mm
Keston 30C - Installation and Servicing 51
sERVICINg
58 spARK gENERATOR REpLACEMENT
1. Refer to Frame 50.
2. Disconnect the leads from the spark generator.
3. Remove the M5 screws securing the spark generator to the boiler chassis.
4. Fit the new spark generator and reassemble in reverse order ensuring the two earth leads are correctly replaced.
5. Check operation of the boiler. Refer to Frames 40 & 41.
2
Spark Generator
4 3
2
3
59 gAs CONTROL VALVE REpLACEMENT
1. Refer to Frame 50.
2. Unplug the electrical plug connection from the gas control valve and disconnect the earth wire.
3. Undo the union nut on the outlet of the gas control valve.
4. Undo the gas inlet pipe union at the inlet to the gas control valve.
5. Loosen the back nut retaining the valve to the bracket and withdraw the valve forwards.
6. Fit the new gas control valve ensuring the two sealing washers are in place and reconnect gas and electrical connections.
7. Check operation of the boiler. Refer to Frames
40 & 41.
4
2
52
3
5
Keston 30C - Installation and Servicing
sERVICINg
60 DIVERTER VALVE ACTUATOR REpLACEMENT
1. Refer to Frame 50.
2. Remove the electrical plug.
3. Using a suitable tool pull out the retaining clip and lift the diverter head from the brass body.
4. Fit new actuator head and reassemble in reverse order.
6. Check operation of the boiler. Refer to
Frames 40 & 41.
Diverter Valve Actuator
Retaining Clip
61 CONDENsATE TRAp/sIphON REpLACEMENT
1. Refer to Frame 50.
Note: Ensure condensate trap is fully drained before removal.
2. Pull off the rubber pipe at the sump drain.
3. Disconnect the condensate pipe.
4. Remove the cleaning plug
5. Turn the siphon clockwise to disengage and lift to remove.
6. Reassemble in reverse order.
7. When reassembling ensure the trap is full of water.
8. Check operation of the boiler. Refer to Frames 40 &
41.
5 drain
2
Siphon
4
3
Keston 30C - Installation and Servicing
3G9690
53
sERVICINg
62 MAIN pCB REpLACEMENT
Note. Fit the earth strap provided with the PCB to your wrist and secure to a suitable earth on the boiler chassis.
1. Refer to Frame 50.
2. Note the control knob positions.
3. Remove the 2 screws retaining the control box cover.
4. Carefully lift the 4 retaining clips and remove control box cover.
5. Unplug all lead connections to the PCB including the ribbon cable (to facilitate ribbon cable removal, ease side clips apart and pull upwards), also where applicable, push the small plastic clip with an electrical screwdriver to facilitate plug removal.
6. Spring out the two side retaining clips and pull the PCB upwards to clear the 4 corner retaining posts.
7. Take the new Primary PCB and attach the appropriate Boiler
Chip Card (BCC).
Note. Ensure the correct orientation of BCC by placing
“TOP” side up as shown.
8. Re-connect all plug connections.
9. Reassemble in reverse order.
10. Turn power back on to the boiler, after a few moments the display will start alternating between “c” and “0”. Turn the reset knob fully clockwise and when the display shows “ - ” turn the knob fully anti-clockwise IMMEDIATELY.
Finally move the knob into the required position (Standby,
Summer or Winter).
11. Check operation of the boiler. Refer to Frames 40 & 41.
4
54
5
Plastic
Clip
Ribbon Cable Connection
5
3
6
7
Keston 30C - Installation and Servicing
sERVICINg
63 UsER CONTROL pCB REpLACEMENT
Note. Fit the earth strap provided with the PCB to your wrist and a suitable earth on the boiler chassis.
1. Refer to Frame 50.
2. Remove the main PCB, refer to Frame 62.
3. Unclip the PCB and lift to clear the mounting posts.
4. Fit the new PCB ensuring the 4 potentiometer spindles line up with the control knobs which must be in a vertical position.
5. Reassemble in reverse order.
6. Check operation of the boiler. Refer to Frames
40 & 41.
4
PCB
3
Potentiometer spindle
Control Knobs (to be in vertical position)
64 DhW FLOW TURBINE sENsOR REpLACEMENT
1. Refer to Frame 50.
2. Remove condensate trap/siphon. Refer to Frame 61.
3. Lift off the flow turbine sensor plastic retaining clip.
4. Unplug the electrical connection and transfer to new turbine sensor.
5. Reassemble in reverse order.
6. Check operation of the boiler. Refer to
Frames 40 & 41.
Keston 30C - Installation and Servicing
4
3
55
sERVICINg
65 DRAININg ThE BOILER
CENTRAL hEATINg CIRCUIT
1. Refer to Frame 50.
2. Close all the CH water isolating valves on the boiler inlet.
3. To drain the primary heat exchanger circuit: Open the drain valve and attach a length of hose to the CH drain point.
4. After replacing any component on the boiler, remove the hose, close the drain valve and open all system isolating valves (re-pressurise as appropriate by re-connecting the filling loop, refer to Frame 30) before proceeding to check operation of the boiler.
5. Disconnect filling loop. Refer to Frame 30.
6. Check operation of the boiler. Refer to Frames 40 & 41.
CH
Flow
Filling Loop
Gas
CH
Circuit
Drain
CH
Return
3G9692b
Filling Loop
DOMEsTIC hOT WATER CIRCUIT
1. Refer to Frame 50.
2. Close all the DHW water isolating valves on the boiler inlet.
3. To drain the domestic hot water circuit: As there is no direct drain for the domestic hot water circuit, depending on the location of the boiler, opening the lowest hot water tap may drain this circuit. However it must be noted that some residual water will be experienced during replacement of components.
4. After replacing any component on the boiler, close tap, close the drain valve and open all system isolating valves (repressurise as appropriate by re-connecting the filling loop, refer to Frame 30) before proceeding to check operation of the boiler.
5. Disconnect filling loop. Refer to Frame 30.
6. Check operation of the boiler. Refer to Frames 40 & 41.
66 pREssURE gAUgE RENEWAL
1. Refer to Frame 50.
2. Drain the heating system. Refer to Frame 65.
3. Unscrew the pressure gauge and discard.
4. Fit new pressure gauge, using suitable jointing compound.
5. Refill the boiler. Refer to Frame 30.
6. Check operation of the boiler. Refer to Frames
40 & 41.
56
DHW
Outlet
Gas DHW
Inlet
CH
Return
3G9692c
Keston 30C -
3G9690
Installation and Servicing
sERVICINg
67 sAFETy RELIEF VALVE RENEWAL
9
1. Refer to Frame 50.
2. Drain the boiler. Refer to Frame 65.
3. Remove the condensate trap/siphon. Refer to
Frame 61.
4. Remove expansion vessel. Refer to Frame 78.
5. Disconnect the electrical connection from the return thermistor.
6. Disconnect the 22mm pipe connection at the rear of the pump outlet.
7. Pull off the clip retaining the pipe to the heat exchanger swing the pipe to clear the pump and remove pipe.
8. Undo the safety valve union connection.
9. Withdraw the clip securing the safety valve.
10. Lift safety valve from boiler.
11. Fit the new safety valve and reassemble in reverse order ensuring the new ‘o’ ring is fitted to the top of the return pipe.
12. Refill boiler. Refer to Frame 30. Check operation of boiler. Refer to Frames 40 & 41.
10
7
5
8
6
68 pUMp AUTOMATIC AIR VENT REpLACEMENT
1. Refer to Frame 50.
2. Drain the boiler. Refer to frame 65.
3. Remove the expansion vessel. Refer to Frame 78.
4. Firstly, increase access area by disconnecting the
22mm pipe connection at top of pump chamber and bottom of heat exchanger and remove pipe Refer to
Frame 67 (no’s 5,6 & 7).
5. The automatic air vent head is retained in the pump body with a bayonet connection. The air vent head and float assembly is removed by turning the head anticlockwise (viewed from above) and pulling upwards.
6. Reassembly is the reverse of the above. Ensure the air vent head ‘o’ ring seal is in place when refitting and the new ‘o’ ring is fitted to the return pipe top connection.
7. Ensure the air vent cap is loose.
8. Refill the boiler. Refer to Frame 30. Check for leaks around the new air vent joint.
9. Check the operation of the boiler. Refer to Frames 40 &
41.
Keston 30C - Installation and Servicing
5
57
58
sERVICINg
69 DhW FLOW TURBINE CARTRIDgE REpLACEMENT
5 1. Refer to Frame 50.
2. Drain the boiler. Refer to Frame 65.
3. Remove condensate trap/siphon. Refer to
Frame 61.
4. Remove the DHW flow turbine sensor. Refer to
Frame 64.
5. Unscrew the top connection to access the internal part.
6. Fit the new turbine cartridge.
7. Refit the turbine flow sensor
8. Reassemble in reverse order.
9. Refill the boiler. Refer to Frame 30.
10. Check operation of the boiler. Refer to
Frames 40 & 41.
4
7
70 DIVERTER VALVE INTERNAL CARTRIDgE REpLACEMENT
FRONT CARTRIDgE REpLACEMENT
1. Refer to Frame 50.
2. Drain the boiler. Refer to Frame 65.
3. Remove the diverter valve head. Refer to Frame 60.
4. Unscrew the top connection to access the internal cartridge.
5. Fit the new valve mechanism ensuring the correct fit of the pin.
6. Reassemble in reverse order.
7. Refill the boiler. Refer to Frame 30.
8. Check operation of the boiler. Refer to
Frames 40 & 41.
REAR CARTRIDgE REpLACEMENT
1. Refer to Frame 50.
2. Drain the boiler. Refer to Frame 65.
3. Remove the diverter valve head. Refer to Frame 60.
4. Remove the flow pipe. Refer to Frame 77 no. 12.
5. Disconnect the CH flow pipe and DHW outlet pipe union connections underneath the boiler. Refer to Frame 65.
6. Remove the plate heat exchanger LH fixing screw. Refer to Frame 71.
7. Remove the screw retaining the brass block to the bottom of the boiler casing and lift the brass block clear of the boiler.
8. Unscrew the rear cartridge connection.
9. Fit the new valve mechanism ensuring the correct fit of the pin.
10. Reassemble in reverse order.
11. Refill the boiler. Refer to Frame 30.
12. Check operation of the boiler. Refer to
Frames 40 & 41.
FRONT CARTRIDgE REAR CARTRIDgE
3
4
9 8
Keston 30C - Installation and Servicing
sERVICINg
71 DhW pLATE hEAT ExChANgER REpLACEMENT
1. Refer to Frame 50.
2. Drain the boiler. Refer to Frame 65.
3. Remove condensate trap/siphon. Refer to Frame 61.
4. Remove the diverter valve actuator. Refer to Frame 60.
5. Remove the 2 allen screws securing the plate heat exchanger to the brass housings.
6. Manoeuvre the plate heat exchanger out of the top LH or centre of the controls area.
7. Fit the new plate heat exchanger, using the new o-rings supplied.
Note. The mounting pins are offset so the correct position can be defined from the location of the holes on the brass mounting.
8. Reassemble in reverse order.
9. Refill the boiler. Refer to Frame 30.
10. Check operation of the boiler. Refer to Frames 40 & 41.
5
72 pUMp hEAD REpLACEMENT
1. Refer to Frame 50.
2. Drain the boiler. Refer to Frame 65.
3. Disconnect the electrical plug from the pump.
4. Remove the 4 Allen screws retaining the pump head.
5. Remove the pump head.
6. Fit the new pump head.
7. Reassemble in reverse order.
8. Refill the boiler. Refer to Frame 30.
9. Check operation of the boiler. Refer to
Frames 40 & 41.
4
3
Keston 30C - Installation and Servicing 59
sERVICINg
73 Ch WATER pREssURE sENsOR REpLACEMENT
1. Refer to Frame 50.
2. Drain the boiler. Refer to Frame 65.
3. Remove condensate trap/siphon. Refer to
Frame 61.
4. Using a suitable tool pull out the retaining clip.
5. Pull the pressure sensor upwards to remove.
6. Unplug the electrical connection and transfer to the new pressure sensor.
7. Push the new pressure sensor onto the rear pump housing and fit retaining clip.
8. Reassemble in reverse order.
9. Refill the boiler. Refer to Frame 30.
10. Check Operation of the boiler. Refer to Frames
40 & 41.
6
4 5
74 DhW FILTER CLEANINg / REpLACEMENT
1. Refer to Frame 50.
2. Isolate the mains cold water supply to the boiler.
3. Drain the boiler DHW circuit. Refer to frame 65.
4. Remove the DHW flow turbine cartridge.
Refer to Frame 69.
5. Unscrew the flow regulator housing.
6. Remove the filter.
7. Clean or replace filter as necessary.
8. Reassemble in reverse order.
9. Refill the boiler. Refer to Frame 30.
10. Check Operation of the boiler. Refer to
Frames 40 & 41.
5 6
60 Keston 30C - Installation and Servicing
sERVICINg
75 DhW FLOW REgULATOR CLEANINg / REpLACEMENT
1. Refer to Frame 50.
2. Isolate the mains cold water supply to the boiler.
3. Drain the boiler DHW circuit. Refer to Frame
65.
4. Remove the DHW flow turbine cartridge.
Refer to Frame 69.
5. Unscrew the flow regulator housing.
6. Inspect the flow regulator for any blockage and remove if necessary.
7. Reassemble in reverse order.
8. Refill the boiler. Refer to Frame 30.
9. Check Operation of the boiler. Refer to
Frames 40 & 41.
5
6
76 NO FLOW ThERMIsTOR REpLACEMENT
1. Refer to Frame 50.
2. Drain down the boiler. Refer to Frame 65.
3. Unplug the electrical lead.
4. Unscrew the thermistor (to facilitate removal a
13mm socket spanner should be used).
5. Fit the new thermistor using the sealing washer provided.
6. Reassemble in the reverse order.
7. Refill the boiler. Refer to Frame 30.
8. Check the operation of the boiler. Refer to Frames
40 & 41.
3
4
Keston 30C - Installation and Servicing 61
sERVICINg
77 hEAT ENgINE RENEWAL
Refer also to Frames 6 & 7 - ‘Boiler Exploded View’
IMpORTANT
Before starting the removal procedure, protect the gas and electrical controls with a waterproof sheet or plastic bag.
1. Refer to Frame 50.
2. Drain the boiler. Refer to Frame 65.
3. Remove the fan / venturi assembly and place on one side.
Refer to frame 51.
4. Remove the burner and place on one side. Refer to Frame
53.
5. Remove the ignition and detection electrodes and diverter actuator head. Refer to Frames 56, 57 and 60.
6. Remove the spark generator. Refer to Frame 58.
7. Remove the gas valve. Refer to Frame 59.
8. Remove the expansion vessel. Refer to Frame 78.
9. Remove the no flow thermistor. Refer to Frame 76.
10. Remove the 2 M5 screws retaining the gas valve mounting bracket and transfer bracket to the new heat exchanger.
11. Undo the inlet pipe union nut and remove the retaining spring clip and remove pipe.
12. Undo the flow pipe union nut and remove pipe.
13. Remove the condensate rubber pipe. Refer to Frame 61, no. 2.
14. Remove the two heat exchanger fixing screws.
15. Remove the Heat exchanger.
16. Reassemble in reverse order, ensuring the heat exchanger
LH retaining bracket is correctly positioned. Replace any new ‘o’ rings supplied with new heat exchanger and replacing gaskets or seals if any sign of damage is evident. When replacing the spring clips located on both the flow and return pipe connections, ensure clip is oriented to correctly match connecting pipe diameters.
17. Ensure the trap/siphon is filled with water. Refer to Frame 61.
18. Refill the boiler. Refer to Frame 30.
19. Check operation of the boiler. Refer to Frames 40 & 41.
14
12
10
11
62 Keston 30C - Installation and Servicing
sERVICINg
78 ExpANsION VEssEL REChARgINg & REpLACEMENT
REChARgINg
1. Refer to Frame 50.
2. Remove the charge point cover.
3. Recharge the tank pressure to 0.75 bar.
4. Re-assemble in reverse order
5. Check operation of the boiler. Refer to Frames 40
& 41.
REpLACEMENT
6. Refer to Frame 50.
7. Drain the boiler CH circuit. Refer to Frame 65.
8. Unscrew the union nut on the vessel water connection pipe.
9. Support the expansion vessel and unscrew the 2 screws from the securing clamp, located on the top of the boiler, and remove. (Note the position of the bracket on the vessel)
3
10. Remove the expansion vessel.
11. Fit the new expansion vessel.
12. Reassemble in reverse order.
13. Refill the boiler. Refer to Frame 30.
14. Check operation of the boiler. Refer to Frames 40
& 41.
9
79 BOILER sEALINg pANEL sEAL REpLACEMENT
1. Refer to Frame 50.
2. Remove the old seal from the casing and thoroughly clean the casing surfaces.
3. Fit the new seal, ensuring the bottom joint provides an air tight seal.
5. Reassemble in reverse order.
6. Check operation of the boiler. Refer to
Frames 40 & 41.
Note. Ensure that the boiler front panel is correctly sealed, compressing the seal to make an airtight joint.
Recharge
Point
Keston 30C - Installation and Servicing 63
FAULT FINDINg
80 FAULT FINDINg ChART MAIN MENU
Note. Boiler status display information is shown in shaded boxes below. Up to six messages will be displayed in rotation.
Overheat lockout 1 Fill system to 1.0 bar 2 Bleed radiators
3 Check radiator valves open 4 Reset boiler 5 Contact installer
Go to Frame 81
Flow Temperature Overheat Lockout
Ignition lockout /
Flue Overheat
1 Check other gas appliances work
2 Reset boiler 3 Contact Installer
Go to Frame 82
Ignition Lockout
No water flow lockout
3 Check radiator valves open
Fill system to 1.0 bar
4 Reset boiler
2 Bleed radiators
5 Contact installer
Too many resets
Fault 8
Low water pressure 1 Fill system to 1.0 bar 2 Bleed radiators 3 Contact installer
Flame loss
Flow thermistor fault
Return thermistor fault
Outside sensor fault
Low mains voltage
PCB Fault
PCB Replaced
No Display
Fan fault
1 Check other gas appliances 2 contact installer
No water flow thermistor fault
Boiler Chip Card Fault
Contact installer
Contact installer
No CH operation but DHW operates OK
No DHW operation but CH operates OK
Contact installer
Contact installer
Contact installer
Contact installer
Contact electricity provider
Contact installer
Reset boiler
Contact installer
Contact installer
Go to Frame 83
No Water Flow Lockout
5 Resets with 15 minutes
Turn power off and on
Go to Frame 84
False Flame Lockout
Go to Frame 85
Low Water Pressure
Go to Frame 86
Flame Loss
Go to Frame 87
Fan Fault
Go to Frame 88
Flow Thermistor Fault
Go to Frame 90
Return Thermistor Fault
Go to Frame 90
Outside sensor fault
Low mains voltage
Contact Electricity Provider
If PCB is a spare check Boiler Chip Card
(BCC) fitted otherwise replace PCB
Reset the boiler
Go to Frame 89
Return Thermistor Fault
Go to Frame 92
BCC Fault
Go to Frame 93
No CH operation but DHW works OK
Go to Frame 94
No DHW but CH operates OK
Go to Frame 95
No Display
64
REsET pROCEDURE - To reset boiler, turn mode knob to reset position and immediately turn knob back to required setting.
Keston 30C - Installation and Servicing
FAULT FINDINg
81 OVERhEAT LOCKOUT - 1 FILL sysTEM TO 1.0 BAR - 2 BLEED RADIATORs -
3 ChECK RADIATOR VALVEs OpEN - 4 REsET BOILER - 5 CONTACT INsTALLER
Is the Boiler and CH System filled with water and all isolation and radiator valves open?
NO Fill and vent the system and open all isolation valves, then reset boiler
YES
Is the Flow/Return Differential across the Boiler in excess of 30°C?
NO
Check the Flow and Return Thermistors (Refer to Frame 54)
YES Check that the Pump is rotating freely. Is the Differential now below 20°C?
NO YES
Replace the Pump, then reset boiler
OK, now reset boiler
REsET pROCEDURE - To reset boiler, turn mode knob to reset position and immediately turn knob back to required setting.
Keston 30C - Installation and Servicing 65
FAULT FINDINg
82 IgNITION LOCKOUT / FLUE OVERhEAT - 1 ChECK OThER gAs AppLIANCEs WORK
- 2 REsET BOILER - 3 CONTACT INsTALLER
If the boiler is reset does the boiler ignite for a short time and then extinguish?
YES
Check the detection electrode and associated harness for: continuity, visual condition and position (Refer to Frame 57).
Check if the condensate pipe is blocked.
Replace as necessary
Check siphon and condensate drain pipe work for blockage and rectify if necessary. Boiler now working OK?
NO
NO
YES
Is the Gas Pressure available at the Boiler Inlet (>18 mbar)?
YES
Is approx 215Vdc supply available at the Gas Valve? (* See note)
YES
Unplug gas valve. Is resistance between outside pins 4KΩ (±2)?
YES
Check spark generator and associated harness for: continuity and visual condition. (Refer to
Frame 59) Are these functioning correctly?
YES
Check ignition electrode and associated harness for: continuity, visual condition and position.
(Refer to Frame 56) Are these functioning correctly?
Check flue for obstruction
YES
Clear obstruction
NO
NO
NO
NO
NO
Check gas supply and rectify fault
Check wiring connection from gas valve to PCB for continuity. If the wiring is
OK then replace the PCB
Replace Gas Valve
Replace Spark
Generator and harness as necessary
Replace Ignition
Electrode and associated harness as necessary
NO
Check wiring to thermostat
YES
NO
Check flue temperature always remains below 90ºC
NO
Check if burner is damaged
NO
Replace heat exchanger
YES
YES
Ensure wiring correctly connected
Replace Thermostat
Replace burner
* note: due to the wave form of the rectified voltage, the reading will vary depending on the type of meter used to measure the value. In general terms a reading greater than 150V indicates that the correct voltage is supplied to the gas valve.
REsET pROCEDURE - To reset boiler, turn mode knob to reset position and immediately turn knob back to required setting.
66 Keston 30C - Installation and Servicing
FAULT FINDINg
83 NO WATER FLOW LOCKOUT - 1 FILL sysTEM TO 1.0 BAR - 2 BLEED RADIATORs -
3 ChECK RADIATOR VALVEs OpEN - 4 REsET BOILER - 5 CONTACT INsTALLER
Is the Boiler and CH System filled with water and all isolation and radiator valves open?
YES
Reset the boiler. Is the Flow/Return Differential across the Boiler in excess of 30°C?
NO
Check the No Water Flow Thermistor
(Refer to Frame 76).
Check resistance using a suitable multimeter connected across the thermistor’s terminal pins
At 25
At 60
At 85 o o o
C expect
C expect
C expect
9,700 - 10,300
2,400 - 2,600
1,000 - 1,100
Does the boiler now work OK?
Ohms
Ohms
Ohms
NO
YES
NO
Fill and vent the system and open all isolation valves, reset the boiler
Check pump connection and check that the Pump is rotating freely. Is the
Differential now below 20°C?
NO
Replace the Pump OK
YES
Check the Flow and Return Thermistors
(Refer to Frame 54)
Check resistance using a suitable multimeter connected across the thermistor’s terminal pins
At 25
At 60
At 85 o o o
C expect
C expect
C expect
9,700 - 10,300 Ohms
2,400 - 2,600 Ohms
1,000 - 1,100 Ohms
REsET pROCEDURE - To reset boiler, turn mode knob to reset position and immediately turn knob back to required setting.
84 FAULT 8 - CONTACT INsTALLER (FALsE FLAME LOCKOUT)
Reset the boiler, does Boiler Work OK?
NO
Separate the flame detection electrode in-line connector. Is there continuity between the terminals pins connected to the electrode?
NO
Check routing and integrity of internal boiler wiring.
YES
YES
Check routing and integrity of internal boiler wiring is OK. Check condition of Flame Sense
Electrode and replace if deteriorated.
Replace Flame Detection Electrode
REsET pROCEDURE - To reset boiler, turn mode knob to reset position and immediately turn knob back to required setting.
85 LOW WATER pREssURE - 1 FILL sysTEM TO 1.0 BAR - 2 BLEED RADIATORs -
3 CONTACT INsTALLER
NO Fill and vent the system and open all isolation valves Are the Boiler and CH System filled with water and all isolation and radiator valves open (check pressure gauge is between 1 to 1.5 bar)?
YES
Are connections on water pressure sensor secure?
YES
Replace water pressure sensor
NO
Re-fit connections
Keston 30C - Installation and Servicing 67
FAULT FINDINg
86 FLAME LOss - 1 ChECK OThER gAs AppLIANCEs WORK -
2 CONTACT INsTALLER
Does the boiler ignite for a short time and then extinguish?
NO Is the Gas Pressure available at the Boiler Inlet (18 mbar)?
NO Check gas supply and rectify fault
YES
Check the detection electrode and associated harness for: continuity, visual condition and position (Refer to Frame 57). Check if condensate pipe is blocked. Check if flue is blocked.
Replace as necessary
YES
Is 215Vdc supply available at the
Gas Valve while the flame is on?
(* See note)
YES
Check spark generator and associated harness for: continuity and visual condition. (Refer to
Frame 58) Are these functioning correctly?
YES
NO
NO
Check wiring from gas valve to PCB for continuity.
If the wiring is OK then replace the PCB
Replace Spark Generator and Harness as necessary.
NO
Replace Ignition
Electrode and associated harness as necessary
Check ignition electrode and associated harness for: continuity, visual condition and position.
(Refer to Frame 56) Are these functioning correctly?
YES
Check siphon and condensate drain pipe work for blockage and rectify if necessary. Boiler now working OK?
NO
NO
Replace Gas Valve
Check flue for obstruction
YES
Clear obstruction
NO
Check wiring to thermostat
NO
Check flue temperature always remains below 90ºC
NO
Check if burner is damaged
NO
Replace heat exchanger
YES
YES
YES
Ensure wiring correctly connected
Replace Thermostat
Replace burner
68
* note: due to the wave form of the rectified voltage, the reading will vary depending on the type of meter used to measure the value. In general terms a reading greater than 150V indicates that the correct voltage is supplied to the gas valve.
Keston 30C - Installation and Servicing
FAULT FINDINg
87 FAN FAULT - CONTACT INsTALLER
Does the wiring from the Fan to the PCB have secure connections at both ends and has not deteriorated? Does the wiring have continuity?
YES
NO
Rectify Wiring & connections
NO Is there 230Vac at the Blue and Brown connections to the 3 way connection on the Fan?
YES
Replace PCB
Replace Fan
88 FLOW ThERMIsTOR FAULT - CONTACT INsTALLER
Remove the Flow Thermistor from the CH Flow Pipe and disconnect the wires.
Check the resistance using a suitable multimeter connected across the thermistor’s terminal pins.
At 25 o C expect 9,700 - 10,300 Ohms
At 60
At 85 o o
C expect
C expect
2,400 - 2,600 Ohms
1,000 - 1,100 Ohms
Is the Thermistor value correct?
YES
NO
NO
Fit a new Thermistor
Check and replace wiring as necessary
Is there continuity between the PCB and the Thermistor?
YES
Replace PCB
89 RETURN ThERMIsTOR FAULT - CONTACT INsTALLER
Remove the Return Thermistor from the CH Return
Pipe and disconnect the wires.
Check the resistance using a suitable multimeter connected across the thermistor’s terminal pins.
At 25 o C expect
At 60 o C expect
At 85 o C expect
9,700 - 10,300 Ohms
2,400 - 2,600 Ohms
1,000 - 1,100 Ohms
Is the Thermistor value correct?
NO
Fit a new Thermistor
NO
Check and replace wiring as necessary
YES
Is there continuity between the PCB and the Thermistor?
YES
Replace PCB
Keston 30C - Installation and Servicing 69
FAULT FINDINg
90 OUTsIDE sENsOR FAULT - CONTACT INsTALLER
Is the wiring securely connected at both the boiler and
Outside Sensor?
YES
Disconnect the wires to the outside sensor.
Check the resistance using a suitable multimeter connected across the Outside Sensor’s terminal pins.
At 0 o C expect 31,000 - 35,000 Ohms
At 15 o C expect 15,000 - 16,500 Ohms
At 30 o C expect 7,700 - 8,500 Ohms
Is the Outside Sensor value correct?
YES
Is the wiring securely connected between the incoming terminal block boiler connection of the
Outside Sensor and the PCB?
NO
NO
NO
YES
Securely connect the wiring at both the boiler and Outside Sensor
Fit a new Outside Sensor
Securely connect the wiring at the
Terminal Block and the PCB
Replace PCB
70
91 NO WATER FLOW ThERMIsTOR FAULT - CONTACT INsTALLER
Is the wiring securely connected to the No Water Flow
Thermistor (located in the top of the Heat Exchanger?)
YES
Disconnect the wiring from the No Water Flow Thermistor
Check the resistance using a suitable multimeter connected across the Thermistor’s terminal pins.
At 25 o C expect
At 60 o C expect
At 85 o C expect
9,700 - 10,300
2,400 - 2,600
1,000 - 1,100
Ohms
Ohms
Ohms
Is the Thermistor value correct?
YES
Is the wiring securely connected to the low voltage 11 way connector at the front left hand side of the PCB?
NO
NO
NO
YES
Securely connect the wiring to the No
Water Flow Thermistor
Fit a new Thermistor
Securely connect the wiring to the PCB
Replace PCB
Keston 30C - Installation and Servicing
FAULT FINDINg
92 BOILER ChIp CARD FAULT - CONTACT INsTALLER
NO
Is the correct BCC for the boiler securely inserted into the slot at the front left of the PCB?
(identified by the label on the BCC)
YES
Replace the BCC with a new BCC (that is correct for the boiler). After switching power on and ‘c0’ being shown, reset the boiler. Is ‘c2’ still shown?
YES
Securely attach the BCC for the boiler onto the PCB and after switching power on and ‘c0’ being shown, reset the boiler.
Note. Ensure the correct orientation of BCC by placing “TOP” side up.
Replace PCB
REsET pROCEDURE - To reset boiler, turn mode knob to reset position and immediately turn knob back to required setting.
93 NO Ch OpERATION BUT DhW WORKs OK
NO
Is the mode knob in the Winter position?
YES
Are the Timer and the Room Thermostat switched on?
YES
Are the Radiator Valves Open?
YES
NO
NO
NO
Is there 230Vac at (A)?
YES
Replace the Diverter Valve
Move the mode knob to the Winter position
Switch the Timer and Room Thermostat On
Open the Radiator Valves
There is no Voltage from the Timer/Room Stat. This is not boiler fault. Ensure Voltage is supplied to boiler by rectifying external wiring.
A
Keston 30C - Installation and Servicing 71
FAULT FINDINg
94 NO hW BUT Ch ON
Does the display show “hot water” -
“temperature XXºC” - “high efficiency”?
YES
Are the flow rates correct as per Frame 2.
YES
NO
NO
Is the red neon illuminated on the turbine sensor?
Adjust flow rates to achieve 35º temp rise and check filter fitted in turbine is not blocked with debris.
YES Is hot and cold
NO pipework crossed?
Replace PCB
NO
Is the wiring between the PCB and the diverter valve motor connected?
YES
NO
Check diverter head fully engaged and clip secured onto waterset.
YES
Is diverter stuck in the CH position
YES
Check and replace diverter valve motor head.
Is Boiler DHW OK?
NO
Change diverter Valve cartridge - rear section
NO
Reconnect wiring or replace wiring harness if no continuity.
Re-engage diverter head and secure clip to wateset
Replace PCB
Is the wiring connected between PCB and DHW sensor?
YES
Remove the turbine, and check for debris in the turbine & filter. Replace turbine if necessary. Is
DHW OK?
NO
NO
Replace turbine sensor
Re-connect wiring
72
95 NO DIspLAy
Is there 230Vac to the boiler at L and N?
YES
NO
Is the wiring from the terminal block to the Main PCB connected securely?
YES
NO
Is the ribbon cable from the main PCB to the User
Interface PCB connected securely?
YES
Is ribbon cable damaged?
YES
NO
NO
Replace the
User Interface
PCB
Replace ribbon cable
Supply power to the boiler
Connect the wiring from the terminal block to the
Main PCB securely.
Connect the ribbon from the main PCB to the User
Interface PCB securely
L
N
Keston 30C - Installation and Servicing
shORT LIsT OF pARTs
The following are parts commonly required due to damage or expendability. Their failure or absence is likely to affect safety or performance of this appliance.
When ordering spares please quote:
The list is extracted from the British Gas List of Parts, which contains all available spare parts.
The full list is held by British Gas Services, Keston distributors and merchants.
1. Boiler model
2. Appliance G.C. No.
3. Description.
4. Quantity.
5. Product number.
When replacing any part on this appliance use only spare parts that you can be assured conform to the safety and performance specification that we require. Do not use reconditioned or copy parts that have not been clearly authorised by Keston.
Key No. g.C. part No. Description qty./boiler product Number
303
304
306
307
308
309
313
211
215
217
229
232
302
302B
320
328
403
504
512
332
118
121
127
128
131
135
205
107
108
110
111
112
113
Filling Loop
Pump Head Kit
Automatic Air Vent
Diverter Valve Head
Diverter Valve Cartridges
Pressure Relief Valve
Expansion Vessel
Plate Heat Exchanger
Flow Sensor (Hall Effect)
DHW Flow Turbine
Water Pressure Sensor
Pressure Gauge
Gas Valve kit
Injector & Housing
Fan Kit
Burner
Siphon Trap Kit
Turret Manifold Gasket
Primary PCB
Boiler Chip Card (BCC)
CUI Board
Control Thermistor (Flow/Return)
Ignition Electrode Kit
Detection Electrode Kit
Spark Generator
Thermistor - No Flow
Ignition lead
Detection Lead
Fuse - PCB
Heat Engine Gasket Kit
Front Panel
Front Panel Door
Flue Thermostat
1
1
1
1
1
2
1
1
1
1
1
1
1
1
1
1
1
1
1
1
1
1
1
1
1
1
1
1
1
1
1
1
1
KS301175611
KS301175569
KS301175571
KS301175583
KS301175620
KS301175939
KS301175937
KS301175713
KS301175589
KS301175591
KS301175592
KS301175593
KS301175594
KS301175598
KS301175530
KS301175670
KS301174894
KS301174813
KS301175668
KS301175413
KS301175551
KS301175418
KS301175590
KS301175661
KS301175596
KS301175679
KS301175562
KS301175604
KS301175627
KS301175618
KS301175723
KS301175722
KS301175949
Keston 30C - Installation and Servicing 73
96 shORT LIsT
107 108
shORT LIsT OF pARTs
110
111
121
112
113
118 127
128
131 205
211
135
232
215
217
229
302
303
304
306
74
302B
307
332
320
308
328
309
504
313
403
512
30C
3G9977a
Keston 30C - Installation and Servicing
INSTALLER NOTIFICATION GUIDELINES
A change to Building Regulations (England and Wales) requires the installer to notify when installing a heating appliance, as from 1st April 2005.
76
Install and commission this appliance to manufacturers' instructions
Complete the
Benchmark Checklist
Competent Person's
SELF CERTIFICATION SCHEME
Choose
Buildings Regulations notification route
If you notify via
Gas Safe Register they will then notify the relevant
Local Authority Building
Control (LABC) scheme on members behalf
Gas Safe Register Engineers log on to the engineers section of the website at www.gassaferegister.co.uk
or telephone
0800 408 5577
You must ensure that the notification number issued by
Gas Safe Register is written onto the Benchmark Checklist
Gas Safe Register will record the data and will send a certificate of compliance to the property
BUILDING CONTROL
Contact your relevant
Local Authority
Building Control (LABC) who will arrange an inspection or contact a government approved inspector
LABC will record the data and will issue a certificate of compliance
IT IS A CONDITION OF THE
MANUFACTURERS WARRANTY
THAT THE BENCHMARK
COMMISSIONING CHECKLIST IS
FULLY COMPLETED AND LEFT
WITH THE APPLIANCE
Keston 30C - Installation and Servicing
ThIs pAgE INTENTIONALLy LEFT BLANK
Gas Safe Register ID Number
Gas Safe Register ID Number
Gas Safe Register ID Number
Gas Safe Register ID Number
Gas Safe Register ID Number
Gas Safe Register ID Number
Gas Safe Register ID Number
Gas Safe Register ID Number
Gas Safe Register ID Number
Gas Safe Register ID Number
Gas Safe Register ID Number
Gas Safe Register ID Number
Gas Safe Register ID Number
Gas Safe Register ID Number
Gas Safe Register ID Number
Gas Safe Register ID Number
Gas Safe Register ID Number
Gas Safe Register ID Number
Gas Safe Register ID Number
Gas Safe Register ID Number
Gas Safe Register ID Number
Keston Boilers, 34 West Common Road, Hayes, Bromley, Kent, BR2 7BX.
Telephone: 0208 462 0262 Fax: 0208 462 4459. November 2010 UIN 205531 A04
Keston pursues a policy of continuing improvement i n t h e d e s i g n a n d p e r f o r m a n c e o f i t s p r o d u c t s .
The right is therefore reserved to vary specification without notice.
advertisement
* Your assessment is very important for improving the workof artificial intelligence, which forms the content of this project
Related manuals
advertisement