- Home
- Do-It-Yourself tools
- Garden tools
- Air compressors
- Graco
- 307879R, 15:1 Ratio Fire-Ball Undercoater Pumps
- User's manual
advertisement
▼
Scroll to page 2
of 10
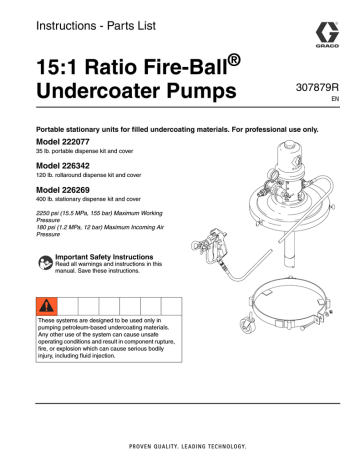
Instructions - Parts List 15:1 Ratio Fire-Ball® Undercoater Pumps 307879R Portable stationary units for filled undercoating materials. For professional use only. Model 222077 35 lb. portable dispense kit and cover Model 226342 120 lb. rollaround dispense kit and cover Model 226269 400 lb. stationary dispense kit and cover 2250 psi (15.5 MPa, 155 bar) Maximum Working Pressure 180 psi (1.2 MPa, 12 bar) Maximum Incoming Air Pressure Important Safety Instructions Read all warnings and instructions in this manual. Save these instructions. These systems are designed to be used only in pumping petroleum-based undercoating materials. Any other use of the system can cause unsafe operating conditions and result in component rupture, fire, or explosion which can cause serious bodily injury, including fluid injection. EN Warnings Warnings The following warnings are for the setup, use, grounding, maintenance, and repair of this equipment. The exclamation point symbol alerts you to a general warning and the hazard symbols refer to procedure-specific risks. When these symbols appear in the body of this manual or on warning labels, refer back to these Warnings. Product-specific hazard symbols and warnings not covered in this section may appear throughout the body of this manual where applicable. WARNING FIRE AND EXPLOSION HAZARD When flammable fluids are present in the work area, such as gasoline and windshield wiper fluid, be aware that flammable fumes can ignite or explode. To help prevent fire and explosion: • Use equipment only in well ventilated area. • Eliminate all ignition sources, such as cigarettes and portable electric lamps. • Keep work area free of debris, including rags and spilled or open containers of solvent and gasoline. • Do not plug or unplug power cords or turn lights on or off when flammable fumes are present. • Ground all equipment in the work area. • Use only grounded hoses. • Stop operation immediately if static sparking occurs or you feel a shock. Do not use equipment until you identify and correct the problem. • Keep a working fire extinguisher in the work area. SKIN INJECTION HAZARD High-pressure fluid from dispensing device, hose leaks, or ruptured components will pierce skin. This may look like just a cut, but it is a serious injury that can result in amputation. Get immediate surgical treatment. • Do not point dispensing device at anyone or at any part of the body. • Do not put your hand over the fluid outlet. • Do not stop or deflect leaks with your hand, body, glove, or rag. • Follow the Pressure Relief Procedure when you stop dispensing and before cleaning, checking, or servicing equipment. • Tighten all fluid connections before operating the equipment. • Check hoses and couplings daily. Replace worn or damaged parts immediately. 2 307879R Warnings WARNING EQUIPMENT MISUSE HAZARD Misuse can cause death or serious injury. • Do not operate the unit when fatigued or under the influence of drugs or alcohol. • Do not exceed the maximum working pressure or temperature rating of the lowest rated system component. See Technical Data in all equipment manuals. • Use fluids and solvents that are compatible with equipment wetted parts. See Technical Data in all equipment manuals. Read fluid and solvent manufacturer’s warnings. For complete information about your material, request MSDS from distributor or retailer. • Turn off all equipment and follow the Pressure Relief Procedure when equipment is not in use. • Check equipment daily. Repair or replace worn or damaged parts immediately with genuine manufacturer’s replacement parts only. • Do not alter or modify equipment. Alterations or modifications may void agency approvals and create safety hazards. • Make sure all equipment is rated and approved for the environment in which you are using it. • Use equipment only for its intended purpose. Call your distributor for information. • Route hoses and cables away from traffic areas, sharp edges, moving parts, and hot surfaces. • Do not kink or over bend hoses or use hoses to pull equipment. • Keep children and animals away from work area. • Comply with all applicable safety regulations. TOXIC FLUID OR FUMES HAZARD Toxic fluids or fumes can cause serious injury or death if splashed in the eyes or on skin, inhaled, or swallowed. • Read MSDSs to know the specific hazards of the fluids you are using. • Store hazardous fluid in approved containers, and dispose of it according to applicable guidelines. PERSONAL PROTECTIVE EQUIPMENT Wear appropriate protective equipment when in the work area to help prevent serious injury, including eye injury, hearing loss, inhalation of toxic fumes, and burns. This protective equipment includes but is not limited to: • Protective eyewear, and hearing protection. • Respirators, protective clothing, and gloves as recommended by the fluid and solvent manufacturer 307879R 3 Installation Installation Grounding The equipment must be grounded to reduce the risk of static sparking and electric shock. Electric or static sparking can cause fumes to ignite or explode. Improper grounding can cause electric shock. Grounding provides an escape wire for the electric current. To ground the pump: Remove the ground screw (Z) and insert through the eye of the ring at the end of the ground wire (Y). Fasten the ground screw back onto the pump and tighten securely. Connect the other end of the groundw ire to a true earth ground. See FIG. 1. To order a ground wire and clamp, order Part No. 222011. Z Pump or sprayer: If using an electrical sprayer, plug the power supply cord or extension cord, each equipped with an undamaged three-prong plug, into a properly grounded outlet. Do not use an adapter. All extensions cords much have three wires and be rated for 15 amps. If using another type of sprayer or pump, ground it by connecting a grounding wire (12 ga minimum) from the pump or sprayer’s grounding lug to a true earth ground. Fluid hoses: SUe only electrically conductive hoses with a maximum of 500 ft. (150 m) combined hose length to ensure grounding continuity. FIG. 1 Assembling the Unit • Refer to the appropriate parts drawings on pages 7 9 to assemble your unit. Use thread sealant on all male connections, except at swivels. • For models 222077 and 226269: Remove the cover from the supply drum and install the pump and cover. Tighten the cover with thumbscrews • For model 226342 only: Assemble the dolly. Place the opened drumo n the dolly. Tighten the nut onto the carriage bolt to secure the drum. Air compressor or hydraulic power supply: Follow local code. Spray gun : Obtain grounding through connection to a properly grounded fluid hose and sprayer or pump. Supply container: Follow local code. Object being sprayed: Follow local code. Y All solvent pails used when flushing: Follow local code. Use only conductive metal pails, which are conductive. DO not place the pail on a non-conductive surface, such as paper or cardboard, which interrupts the grounding continuity. To maintain grounding continuity when flushing or relieving pressure: always hold a metal part of the spray gun firmly to the side of a grounded metal pail, then trigger the gun. 4 307879R Installation Typical Installation Air Line and Accessories This typical installation is only a guide for selecting and installing a system. It is not an actual system design. Contact your Graco distributor for assistance in designing a system to suit your needs. NOTE: Install the air line accessories in the order shown in FIG. 2. D 1. Install a pump runaway valve (G) to shut off the air to the pump if the pump accelerates beyond the pre-adjusted setting. A pump that runs too fast can be seriously damaged. 2. Install an air line lubricator (F) for automatic air motor lubrication. 3. Install the air regulator (C) to control pump speed and pressure. J G E F C 4. On the main air supply line from the compressor, install an air line filter (E) to remove harmful dirt and contaminants from your compressed air supply. B NOTICE H A Do not hand air accessories directly on the air inlet. The fittings are not strong enough to support accessories and may cause one or more to break. Provide a bracket on which to mount accessories. FIG. 2 Key: A B C D E F G H J Fluid Dispense Line Pump Ground Wire Air Regulator Main Air Supply Line Air Filter Pump Lubricator Pump Runaway Vavle Fluid Drain Valve Bleed-type Master Air Valve 307879R 5 Operation Operation Pressure Relief Procedure Follow the Pressure Relief Procedure whenever you see this symbol. This equipment stays pressurized until pressure is manually relieved. To help prevent serious injury from pressurized fluid, such as skin injection, splashing fluid and moving parts, follow the Pressure Relief Procedure when you stop spraying and before cleaning, checking, or servicing the equipment. 2. Open the master air valve from the compressor. 3. For the pump that is connected, trigger the dispense valve into a grounded metal waste container, making metal-to-metal contact between the container and valve. Open the bleed-type master air valve and open the pump air regulator slowly, just until the pump is running. When the pump is primed and all the air has been pushed out of the lines, release the trigger. 4. If you have more than one pump, repear this procedure for each pump. 1. Engage the gun trigger. NOTE: When the pump is primed, and with sufficient air supplied, the pump starts when the dispenseing valve is opened and shuts off when it is closed. 2. Shut off the power supply to the pump and open any air bleed valves in the system. 5. Set air pressure to each pump at the lowest pressure needed to get the desired results. 3. Disengage the gun trigger stop. 6. Set the air pressure to each pump at the lowest pressured needed to get desired results. 4. Hold a metal part of the gun girmly to the side of a grounded metal pail, and trigger the gun to relieve pressure. 5. Engage the gun trigger to stop. 6. Open the fluid drain valve, and have a container ready to catch the drainage. 7. Leave the drain valve open until you are ready to use the system again. NOTE: If you suspect the gun, hose, or sprayy tip is completely clogged, or that pressure has not been fully relieved after following the steps above, very slowly loosen the tip guard retaining nut, outlet accessory nut, or hose end coupling, and relieve pressure gradually, then loosen completely and clear the tip or hose. Start-up: Single or Multiple Pump Systems The maximum workng pressure of each pump in the system may not be the same size. To reduce the disk of over-pressurizing any part of your syste, be sure you know the maximum working pressure rating of each pump and its connected components. Never exceed the maximum working pressure of the lowest rated component connected to a particular pump. To determine the fluid output pressure using the air regulator reading, multiply the ratio of the pump by the air pressure shown on the regulator gauge. For example: 10:(1) ratio x 100 psi air = 1000 psi fluid output 10:(1) ratio x 0.7 MPa air = 7MPa fluid output 10:(1) ratio x 7 bar air = 70 bar fluid output Limit the air to the pump so that no air line or fluid line component or accessory is over-pressurized. 1. Close the air regulators and bleed-type master air valves to all by one pump. 6 307879R Operation NOTICE Never allow a pump to run dry of fluid being pumped. A dry pump quickly accelerates to a high speed, possibly damaging itsself, and it may get very hot. NOTE: A pump runaway valve can be installed on the air line to automaticaly shut off the pump if it starts to run too fast. See page 5. 7. Read and follow the instructions supplied with each component. 8. Whenever you shut off the system always follow the Pressure Relief Procedure on page 6. Parts 1 112 111 107 109 101 106 113 102 110 3d 3c 108 114 103 3a 3b Model 222077 35 lb. Pail Size Unit Ref. 1 Part 206405 2 3 3a 3b 3c 3d 222079 222058 206522 100220 100916 100922 307879R Description Qty. PUMP, 15:1 Ratio Fire-Ball, See 1 306531 for parts DISPENSE KIT 1 COVER, includes items 3a through 3d 1 COVER, pail 1 THUMBSCREW 3 LOCKWASHER 2 CAPSCREW 2 Dispense Kit 222079 Ref. 101 Part 109075 102 103 106 107 108 109 110 111 112 113 114 114558 239663 156971 10965 234237 156849 104984 210657 100940 169971 155570 Description Qty. AIR REGULATOR, see 308167 for 1 parts COUPLER, quick disconnect 1 SWIVEL, see 306861 for parts 1 NIPPLE, 1/4 npt 1 HOSE, fluid, cpld 1 SPRAY GUN, see 309092 for parts 1 NIPPLE, 3/8 npt 1 TEE, pipe, 1/4 npt 1 BALL VALVE, see 306861 for parts 1 ELBOW, street, 1/4 npt 1 FITTING, pin 1 UNION, swivel, 1/4 npsm (f) x 1/4 npt (f) 1 7 Operation Model 226342 120 lb. Drum Size Unit with Dolly 1 3 2 4e 4c 4b 4a 4d Ref. 1 2 3 4 4a 4b 4c 4d 4e 8 Part Description Qty. 206669 PUMP, 15:1 Fire-Ball, See 306531 1 for parts 222079 DISPENSE KIT, see page 7 1 204574 COVER, see 306345 for parts 1 204144 BASE, dolly, includes 4a through 4e 1 100023 WASHER, flat 5/16” 1 100307 NUT, full hex, 3/8-16 1 101851 CASTER, wheel, 2 1/2” dia 4 102971 BOLT, carriage, 3/8-16 x 3” 1 205419 CLAMP, dolly 1 307879R Operation 112 1 111 109 107 101 110 106 108 113 102 114 103 3 Model 226269 400 lb Stationary Drum Size Unit Ref. 1 2 3 Part Description Qty. 206700 PUMP, 15:1 Fire-Ball, See 306531 1 for parts 222082 DISPENSE KIT, see page 1 200326 COVER, drum 1 307879R Dispense Kit 222082 Ref. 101 102 103 106 107 108 109 110 111 112 113 114 Part Description Qty. 109075 AIR REGULATOR, See 308167 for 1 parts 114558 COUPLER, quick disconnect 1 239663 SWIVEL, see 306861 for parts 1 156971 NIPPLE, 1/4 npt 1 109167 HOSE, fluid, cpld 1 234237 SPRAY GUN, See 309092 for parts 1 156849 NIPPLE, 3/8 npt 1 104984 TEE, pipe, 1/4 npt 1 210657 BALL VALVE, See 306861 for parts 1 100840 ELBOW, street 1/4 npt 1 169971 FITTING, pin 1 155570 UNION, swivel, 1/4 npsm (f) x 1/4 1 npt (f) 9 Graco Standard Warranty Graco warrants all equipment referenced in this document which is manufactured by Graco and bearing its name to be free from defects in material and workmanship on the date of sale to the original purchaser for use. With the exception of any special, extended, or limited warranty published by Graco, Graco will, for a period of twelve months from the date of sale, repair or replace any part of the equipment determined by Graco to be defective. This warranty applies only when the equipment is installed, operated and maintained in accordance with Graco’s written recommendations. This warranty does not cover, and Graco shall not be liable for general wear and tear, or any malfunction, damage or wear caused by faulty installation, misapplication, abrasion, corrosion, inadequate or improper maintenance, negligence, accident, tampering, or substitution of non-Graco component parts. Nor shall Graco be liable for malfunction, damage or wear caused by the incompatibility of Graco equipment with structures, accessories, equipment or materials not supplied by Graco, or the improper design, manufacture, installation, operation or maintenance of structures, accessories, equipment or materials not supplied by Graco. This warranty is conditioned upon the prepaid return of the equipment claimed to be defective to an authorized Graco distributor for verification of the claimed defect. If the claimed defect is verified, Graco will repair or replace free of charge any defective parts. The equipment will be returned to the original purchaser transportation prepaid. If inspection of the equipment does not disclose any defect in material or workmanship, repairs will be made at a reasonable charge, which charges may include the costs of parts, labor, and transportation. THIS WARRANTY IS EXCLUSIVE, AND IS IN LIEU OF ANY OTHER WARRANTIES, EXPRESS OR IMPLIED, INCLUDING BUT NOT LIMITED TO WARRANTY OF MERCHANTABILITY OR WARRANTY OF FITNESS FOR A PARTICULAR PURPOSE. Graco’s sole obligation and buyer’s sole remedy for any breach of warranty shall be as set forth above. The buyer agrees that no other remedy (including, but not limited to, incidental or consequential damages for lost profits, lost sales, injury to person or property, or any other incidental or consequential loss) shall be available. Any action for breach of warranty must be brought within two (2) years of the date of sale. GRACO MAKES NO WARRANTY, AND DISCLAIMS ALL IMPLIED WARRANTIES OF MERCHANTABILITY AND FITNESS FOR A PARTICULAR PURPOSE, IN CONNECTION WITH ACCESSORIES, EQUIPMENT, MATERIALS OR COMPONENTS SOLD BUT NOT MANUFACTURED BY GRACO. These items sold, but not manufactured by Graco (such as electric motors, switches, hose, etc.), are subject to the warranty, if any, of their manufacturer. Graco will provide purchaser with reasonable assistance in making any claim for breach of these warranties. In no event will Graco be liable for indirect, incidental, special or consequential damages resulting from Graco supplying equipment hereunder, or the furnishing, performance, or use of any products or other goods sold hereto, whether due to a breach of contract, breach of warranty, the negligence of Graco, or otherwise. FOR GRACO CANADA CUSTOMERS The Parties acknowledge that they have required that the present document, as well as all documents, notices and legal proceedings entered into, given or instituted pursuant hereto or relating directly or indirectly hereto, be drawn up in English. Les parties reconnaissent avoir convenu que la rédaction du présente document sera en Anglais, ainsi que tous documents, avis et procédures judiciaires exécutés, donnés ou intentés, à la suite de ou en rapport, directement ou indirectement, avec les procédures concernées. Graco Information For the latest information about Graco products, visit www.graco.com. TO PLACE AN ORDER, contact your Graco distributor or call to identify the nearest distributor. Phone: 612-623-6928 or Toll Free: 1-800-533-9655, Fax: 612-378-3590. All written and visual data contained in this document reflects the latest product information available at the time of publication. Graco reserves the right to make changes at any time without notice. For patent information, see www.graco.com/patents. Original instructions. This manual contains English. MM 307879 Graco Headquarters: Minneapolis International Offices: Belgium, China, Japan, Korea GRACO INC. AND SUBSIDIARIES • P.O. BOX 1441 • MINNEAPOLIS MN 55440-1441 • USA Copyright 1998, Graco Inc. All Graco manufacturing locations are registered to ISO 9001. www.graco.com Revised January 2013
advertisement
* Your assessment is very important for improving the workof artificial intelligence, which forms the content of this project