advertisement
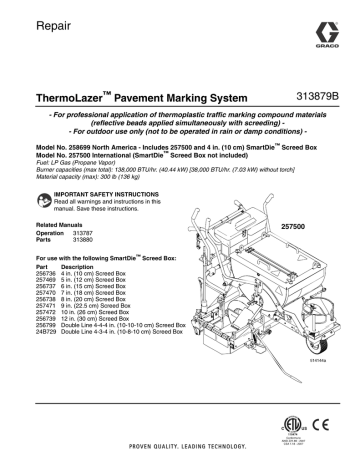
Repair
ThermoLazer
™
Pavement Marking System 313879B
- For professional application of thermoplastic traffic marking compound materials
(reflective beads applied simultaneously with screeding) -
- For outdoor use only (not to be operated in rain or damp conditions) -
Model No. 258699 North America - Includes 257500 and 4 in. (10 cm) SmartDie
™
Screed Box
Model No. 257500 International (SmartDie
™
Screed Box not included)
Fuel: LP Gas (Propane Vapor)
Burner capacities (max total): 138,000 BTU/hr. (40.44 kW) [38,000 BTU/hr. (7.03 kW) without torch]
Material capacity (max): 300 lb (136 kg)
IMPORTANT SAFETY INSTRUCTIONS
Read all warnings and instructions in this manual. Save these instructions.
Related Manuals
Operation 313787
Parts 313880
For use with the following SmartDie
™
Screed Box:
Part Description
256736 4 in. (10 cm) Screed Box
257469 5 in. (12 cm) Screed Box
256737 6 in. (15 cm) Screed Box
257470 7 in. (18 cm) Screed Box
256738 8 in. (20 cm) Screed Box
257471 9 in. (22.5 cm) Screed Box
257472 10 in. (26 cm) Screed Box
256739 12 in. (30 cm) Screed Box
256799 Double Line 4-4-4 in. (10-10-10 cm) Screed Box
24B729 Double Line 4-3-4 in. (10-8-10 cm) Screed Box
257500
ti14144a
Table of Contents
Table of Contents
Table of Contents . . . . . . . . . . . . . . . . . . . . . . . . . . 2
Warnings . . . . . . . . . . . . . . . . . . . . . . . . . . . . . . . . . 3
Kettle Temperature Control, and
Kettle Thermopile Diagnosis . . . . . . . . . . . . . . 5
Kettle Temperature Control Calibration . . . . . . . . . 6
Temperature Control Replacement . . . . . . . . . . . . 6
Thermometer Replacement . . . . . . . . . . . . . . . . . . 6
Kettle Thermometer Calibration . . . . . . . . . . . . . . . 7
Adjust Kettle Pilot Ignitor Electrode Gap . . . . . . . 7
Thermopile Replacement . . . . . . . . . . . . . . . . . . . . 8
Adjust Gas Pressure to Kettle Burners . . . . . . . . 11
Adjust Kettle Pilot Burner Flame . . . . . . . . . . . . . 12
Adjust Kettle Main Burners Flame . . . . . . . . . . . . 12
Cleaning Kettle Main Burner Gas Lines . . . . . . . . 13
Cleaning Kettle Pilot Burner Gas Lines . . . . . . . . 13
Replacing Screed Box Spring . . . . . . . . . . . . . . . . 14
Securing Bead Dispenser Wheel . . . . . . . . . . . . . 15
Linkage Rod Adjustment . . . . . . . . . . . . . . . . . . . . 15
Screed Box/Bead Dispenser Box Actuator . . . . . 15
Adjusting Screed Box Pivot Arm . . . . . . . . . . . . . 16
Troubleshooting . . . . . . . . . . . . . . . . . . . . . . . . . . . 17
Technical Data . . . . . . . . . . . . . . . . . . . . . . . . . . . . 23
Graco Standard Warranty . . . . . . . . . . . . . . . . . . . 24
Graco Information . . . . . . . . . . . . . . . . . . . . . . . . . 24
2 313879B
Warnings
Warnings
The following are general warnings related to the safe setup, use, grounding, maintenance and repair of this equipment. In the text of this manual, the exclamation point symbol alerts you to a warning and the hazard symbol refers to specific risks. Refer back to these General Warnings pages. Additional procedure-specific warnings will be included where applicable.
Warnings
FIRE AND EXPLOSION HAZARD
Flammable fumes and liquids, such as propane gas, gasoline and combustible fuel, in work area can ignite or explode. To help prevent fire and explosion:
• Do not use equipment unless fully trained and qualified.
• Do not allow open containers of flammables within 25 ft (7.6 m) of equipment. Do not operate equipment within 10 ft (3 m) of any structure, combustible material, or other gas cylinders.
• Shut off all burners when adding fuel to equipment.
• Close the tank shut-off valve immediately if you smell propane gas; extinguish all open flames. If gas odor continues, keep away from equipment and immediately call the fire department.
• Follow lighting instructions for the burner and torch.
• Do not heat thermoplastic traffic marking compound material above 450° F (232° C)
• Fire extinguisher equipment shall be present and working.
• Keep work area free of debris, including solvent, rags and gasoline.
EQUIPMENT MISUSE HAZARD
Misuse can cause death or serious injury.
• Do not leave equipment unattended.
• Keep children and animals away from work area.
• Do not exceed the maximum working pressure or temperature rating of the lowest rated system component. See Technical Data in all equipment manuals.
• Check equipment daily. Repair or replace worn or damaged parts immediately with genuine manufacturer’s replacement parts only.
• Do not alter or modify equipment.
• Use equipment only for its intended purpose. Call your Graco distributor for information.
• Do not fill material beyond maximum capacity.
• Route gas lines, hoses, wires and cables away from traffic areas, sharp edges, moving parts, and hot surfaces.
• Do not kink or overbend gas lines.
• Do not override or defeat safety devices.
• Do not operate the unit when fatigued or under the influence of drugs or alcohol.
BURN HAZARD
Equipment surfaces and fluid that is heated can become very hot during operation. To avoid severe burns:
• Do not touch hot fluid or equipment.
• Wait until equipment and material has cooled completely.
CARBON MONOXIDE HAZARD
Exhaust contains poisonous carbon monoxide, which is colorless and odorless. Breathing carbon monoxide can cause death. Do not operate in an enclosed area.
313879B 3
Warnings
Warnings
TOXIC FLUID OR FUMES HAZARD
Toxic fluids or fumes can cause serious injury or death if splashed in the eyes or on skin, inhaled, or swallowed.
• Read MSDS to know the specific hazards of the materials you are using.
PERSONAL PROTECTIVE EQUIPMENT
You must wear appropriate protective equipment when operating, servicing, or when in the operating area of the equipment to help protect you from serious injury, including eye injury, inhalation of toxic fumes, burns, and hearing loss. This equipment includes but is not limited to:
• Clothing and respirator as recommended by the fluid, material, and solvent manufacturer.
• Gloves, shoes, overalls, face shield, hat, etc. rated for elevated temperatures of at least 500° F
(260° C).
4 313879B
Kettle Gas Safety Valve, Kettle Temperature Control, and Kettle Thermopile Diagnosis
Kettle Gas Safety Valve,
Kettle Temperature Control, and
Kettle Thermopile Diagnosis
Terminal Connections
3
TH
TP
TH
The gas safety valve, temperature control and thermopile can be checked by using a millivolt meter. Before checking, make certain all electrical connections are clean and tight.
1
TP
Connect millivolt meter to appropriate terminals (see
Terminal Connections).
ti14524a
2
Step
1
2
Part(s) to Be
Checked
Terminal
Connections
Status of
Temperature
Control
Contacts
Gas safety valve
Temperature control
2 and 3
1 and 2
Closed
Closed
Desired
Meter
Reading Diagnosis
Greater than
100 mV
If mV reading > 100 mV and the automatic valve (main burners) does not come on, replace the gas safety valve.
If mV reading < 100mV, proceed with diagnostic steps 2 and 3.
Less than
80 mV
If reading > 80 mV:
• Clean and tighten electrical connections at temperature control and gas safety valve.
• Check valve to make sure wires are in good condition. Replace as required.
• Rapidly change temperature setting on temperature control to see if cycling cleans the contacts.
3 Gas safety valve magnet and thermopile
1 and 2 Open Greater than
325 mV
If the preceding fails to give mV reading < 80 mV, replace temperature control.
If mV reading < 325 mV:
• Clean and tighten all electrical connections.
• Adjust pilot burner to increase millivolt output (see
If the preceding fails to give mV reading > 325 mV, replace thermopile.
Check valve magnet after obtaining correct mV output for thermopile:
• Ignite pilot burner only and allow the mV reading to stabilize.
• Shut pilot burner (turn gas safety valve knob OFF).
Note the mV reading where magnet drops out.
If magnet unlocks at mV reading < 120 mV, the magnet is
OK. NOTE: When magnet unlocks a click can be heard and mV reading may fluctuate slightly.
313879B 5
6
Kettle Temperature Control Calibration
Kettle Temperature Control Calibration
6.
If the temperature control setting is lower than the remote calibrated temperature setting on temperature probe, turn adjusting screw clockwise. Every
1/4 in. turn will change temperature 35° F (19.4° C).
To Check Kettle Temperature Control Calibration:
1.
Move Thermolazer
™
to an area with no wind.
2.
Turn temperature control to 400° F (204° C).
3.
Agitate material for 4 to 5 minutes.
4.
After control has reached steady state temperature and burners do not cycle more than once per minute, insert remote calibrated temperature probe in material and directly adjacent kettle temperature control probe.
5.
Compare temperature of remote calibrated temperature probe to temperature setting on temperature control. ti14523a
7.
If the temperature control setting is higher than the remote calibrated temperature probe, turn adjusting screw counterclockwise--every 1/4 in. turn will change temperature 35° F (19.4° C).
8.
Recheck calibration by turning temperature control to 410° F (210° C) and repeat steps 3-7.
Temperature Control Replacement
When replacing temperature control, keep in mind that the temperature probe is an integral part of the assembly. Do not make any sharp bends in the capillary tubing.
Bends should be 0.25 in. (0.64 cm) in radius or greater.
Be sure to seal capillary tubing with high temperature mortar at kettle outlet.
ti14557a
Thermometer Replacement
Thermometer can not be removed from ThermoLazer
™ without damaging thermometer probe. If probe end is frozen in material, heat material and remove until material level is lower than thermometer probe.
313879B
Kettle Thermometer Calibration
Kettle Thermometer Calibration
6.
If kettle thermometer is lower than the remote calibrated temperature probe, turn adjusting screw counterclockwise.
Adjusting Screw
To Check Kettle Thermometer Calibration:
1.
Move ThermoLazer
™
to an area with no wind.
2.
Turn temperature control to 400° F (204° C).
3.
Agitate material for 4 to 5 minutes.
4.
After control has reached steady state temperature and burners do not cycle more than once per minute, insert remote calibrated temperature probe in material and directly adjacent kettle temperature control probe.
5.
Compare temperature of remote calibrated temperature probe to thermometer.
RESET ti14525a
7.
If the kettle thermometer is higher than the remote calibrated temperature probe, turn adjusting screw clockwise.
Adjust Kettle Pilot Ignitor Electrode Gap
1.
Loosen screw (231).
2.
Rotate ignitor electrode (7) until gap of .17 to .20 in.
(.43 to .51 cm) is achieved.
3.
Retighten screw (231).
.17 to .20 in.
7 ti14519a
313879B 7
Thermopile Replacement
Thermopile Replacement
Removal
1.
Shut off gas valve on LP-tank and disconnect hose.
6.
Pull thermopile wire out of gas safety valve enclosure (28).
ti4128a
2.
Remove gas safety valve enclosure back cover.
28
7.
Cut wire tie.
ti14854a
3.
Remove cover (252) from gas safety valve enclosure (28).
28
252 ti14852a
4.
Disconnect thermopile wires from gas safety valve
(13).
13 ti14851a
8.
Disconnect gas pilot line (76) at gas pilot coupling
(171).
171
76 ti14856a
9.
Remove gas pilot mounting plate (18).
18 ti14853a
5.
Remove wire grommet (209) from gas safety valve enclosure (28).
10. Remove thermopile (7).
ti14857a
7
28 ti14855a
209 ti14858a
8 313879B
Thermopile Replacement
Installation
1.
Replace thermopile (7).
7
7.
Connect thermopile wires to gas safety valve (13).
See Parts manual 313880 for additional details.
13 ti14862a
2.
Replace gas pilot mounting plate (18).
ti14866a
8.
Replace cover (252) on gas safety valve enclosure
(28).
18 ti14863a
3.
Connect gas pilot line (76) at gas pilot coupling
(171).
171
252
76 ti14861a
4.
Guide thermopile wire into gas safety valve enclosure (28).
28 ti14867a
9.
Replace gas safety enclosure back cover.
28 ti14864a
10. Reconnect hose and turn LP-gas tank valve ON.
5.
Zip-tie wires together.
ti14127a
6.
Replace wire grommet (209) on gas safety valve enclosure (28).
28 ti14865a
209
313879B 9
Adjust Gas Pressure to Kettle Burners
Adjust Gas Pressure to Kettle Burners
1.
Shut off kettle gas safety valve (CC).
2.
Turn kettle temperature control knob (AA) to 0
(“OFF”).
3.
Remove kettle gas safety valve 1/8-27 NPT pipe plug.
4.
Screw 0 to 30 in. w.c. (0 to 7.47 cb) calibrated gas pressure gauge or manometer into kettle gas safety valve outlet.
5.
Ignite kettle gas pilot burner.
6.
Turn kettle gas safety knob (CC) to ON.
7.
Turn kettle temperature control to 250° F (121° C).
8.
Record gas pressure at kettle gas safety valve outlet. Gas pressure should read 11 in. w.c. (2.74 cb).
9.
Remove adjusting screw cap.
10. Turn adjusting screw (148) clockwise to increase gas pressure (counterclockwise to decrease gas pressure).
11. Install adjusting screw cap.
12. Turn kettle temperature control knob (AA) to 0
(“OFF”).
13. Shut off kettle gas safety valve (CC).
14. Remove gas pressure measuring device.
15. Add LP-gas pipe sealant to 1/8-27 NPT pipe plug
(156) and install in kettle gas safety valve.
CC ti14518a ti14521a
148
156
10 313879B
Adjust Kettle Pilot Burner Flame
Adjust Kettle Pilot Burner Flame
1.
Ignite kettle gas pilot burner.
2.
Record pilot burner flame height and color. Flame should be 2 to 3 in. (5 to 7 cm) high and blue-orange in color.
3.
Remove flame adjusting screw cap.
4.
Turn adjusting screw clockwise to decrease flame height (counterclockwise to increase flame height).
5.
Install flame adjusting screw cap.
ti14522a
2 to 3 in.
ti14413a
Adjust Kettle Main Burners Flame
1.
Ignite kettle gas pilot burner.
2.
Turn kettle gas safety valve (CC) to ON.
3.
Turn kettle temperature control knob (AA) to 250° F
(121° C).
4.
Record pilot burner flame height and color. Flame should be 1 to 2 in. (3 to 5 cm) high and blue-orange in color.
5.
Record burner venturi gap. Gap should be .17 to .20 in. (4 to 5 mm).
6.
Loosen air shutter jam nut and adjust air shutter to obtain correct gap.
7.
Lock air shutter jam nut. Use thread sealant for a more secure locking.
313879B
.17 to .20 in.
ti14525a
1 to 2 in.
11
Cleaning Kettle Main Burner Gas Lines
Cleaning Kettle Main Burner Gas Lines
1.
Disconnect gas tubing line (49) from gas tube fitting tee (165).
2.
Force air into gas tubing line (49). Insert rubber hose over gas tubing tee and force air into tubing at
30 psi (2.1 bar).
3.
Reconnect gas tubing line (49) to gas tube fitting tee
(165).
165 ti14558a
49
Cleaning Kettle Pilot Burner Gas Lines
1.
Disconnect gas tubing line (186) from gas tubing line (118).
2.
Force air into gas tubing line (118). Insert rubber hose over gas tubing tee and force air at 30 psi
(2.1 bar).
3.
Reconnect gas tubing line (186) to gas tubing tee
(118).
118
186
12 ti14559a
313879B
Replacing Screed Box Spring
1.
Position replacement spring as shown below and slide into spring guard.
3.
Set screed box on its side.
Replacing Screed Box Spring ti14551a
2.
Push spring up through guard and loop end around guard pin until spring sits in groove.
ti14553a
4.
Loop open end of spring and guard over first pin on screed box. Then push spring guard up and over second pin on screed box.
ti14549a ti14550a ti14552a
313879B 13
Securing Bead Dispenser Wheel
Securing Bead Dispenser Wheel
To properly dispense beads, drive wheel (27) must be in direct contact with tire (89). If drive wheel (27) becomes loose and/or starts to slip, use allen wrench to tighten set screw (211).
NOTE: To ensure proper contact between drive wheel
(27) and tire (89), make sure air pressure is always at 60 psi (4.14 bar).
89
211 ti14564a 27
Linkage Rod Adjustment
Adjustments can be made to linkage rods by removing clevis cotter hairpin (268), clevis (179) pin, loosening nuts (128), and then turning clevis as required to lengthen or shorten rod connectors.
To ensure proper application of beads and thermoplastic, make sure screed box linkage rod (182) measures
16.875 in. (42.8 cm). Be sure to measure where nut
(128) meets clevis (179) when checking for proper linkage rod length.
2.
If the wheel does not cause the ThermoLazer tire to rotate both forward and backwards, loosen nuts
(128), clevis cotter hair pin, clevis pin, and rotate the clevis (179) one turn counterclockwise.
179
128
16.875 in.
182 ti14565a
Adjust the bead box linkage rod (181) so bead box drive is touching ThermoLazer tire when screed box is in down (but not open) position. A slight downward force on the bead box linkage should be required when inserting the clevis pin through the clevis deployment bar.
1.
With screed box in down (but not open) position, rotate the bead box wheel by hand.
3.
Reconnect clevis to deployment bar and again rotate bead box wheel to see if adjustments cause
ThermoLazer to move forward and backwards.
4.
Continue to rotate clevis 1/2 turn counterclockwise until rotating bead box wheel causes ThermoLazer to move forward and backwards.
14 313879B
Screed Box/Bead Dispenser Box Actuator
Screed Box/Bead Dispenser Box Actuator
If the screed box/bead dispenser box actuator does not remain in the “down and locked” position, adjust the
3/4-16 lock nut by turning clockwise 1/4 to 1/2 turn or until the actuator does not freely rotate.
ti14604a
Adjusting Screed Box Pivot Arm
If the SmartDie
™
screed box jumps up when setting the box in the down-and-locked position, check linkage rod
If the SmartDie
™
screed box continues to jump up after adjusting linkage rods, move the screed box pivot arm spring to the next hole.
1.
Unhook top of box pivot arm spring.
3.
Move bottom of box pivot arm spring to desired hole and reconnect. Moving the spring in will decrease tension, while moving the spring out will increase tension.
ti14629a
4.
Reconnect top of box pivot arm spring.
ti14627a
2.
Unhook bottom of box pivot arm spring.
313879B ti14628a ti14630a
Repeat moving pivot arm spring until SmartDie
™
screed box stops jumping up when setting box in the down-and-locked position.
If moving pivot arm spring does not stop the SmartDie
™ screed box from jumping up when setting box in down-and-locked position, replace pivot arm spring.
15
Troubleshooting
Troubleshooting
Problem Cause Solution
Kettle pilot burner does not ignite or does not remain ignited
Low or empty LP-gas tank
Gas supply hose not connected to tank
LP-gas tank shut-off valve closed
Manual gas shut-off valve closed
Gas lines leaking or disconnected
Replace with full tank.
Connect gas supply hose.
Open LP-gas tank shut-off valve.
Open manual gas shut-off valve.
Check for gas leaks. Connect and tighten fittings.
Turn knob to “PILOT” position and fully push in (see Operation manual).
See Operation manual.
Kettle gas safety valve knob not in correct position
Not providing adequate time for thermopile to heat up
Kettle pilot igniter has weak battery
Kettle pilot electrode gap incorrect
Incorrect flame length and/or gas pressure
Strong wind blowing flame out
Burner and/or gas lines plugged
Replace part (see Parts manual).
Adjust flame and pressure (see Repair manual).
Move ThermoLazer
™
out of strong winds.
Make sure burner view ports are closed.
Unplug holes and lines. Isolate all gas regulators if clearing line with forced air (see
Kettle gas safety valve not functioning correctly
Thermopile not functioning correctly
Kettle pilot electrode ground wire not correctly connected
Kettle pilot electrode lead wire has a short
Kettle pilot igniter not functioning correctly
Kettle burner regulator not functioning correctly
Replace part if it fails diagnostic test (see
Replace part if it fails diagnostic test (see
Clean connections and retighten. Replace ground wire if damaged.
Replace part (see Parts manual).
Replace part (see Parts manual).
Replace part (see Parts manual).
16 313879B
Troubleshooting
Problem
Kettle main burners do not ignite or are not burning correctly
Cause
Kettle gas safety valve knob not at correct position
Kettle temperature control dial set at a lower temperature than material temperature
Kettle gas safety valve not functioning correctly
Burner and/or gas lines plugged
Solution
Turn knob to ON position (see Operation manual).
Turn kettle temperature control dial to temperature 25° F (13.9° C) higher than material temperature.
See Repair manual and replace part if it fails diagnostic testing.
Unplug holes and lines. Isolate all gas regulators if clearing line with forced air (see
Replace part (see Parts manual).
Kettle temperature control not functioning correctly
Gas lines have been disconnected
Incorrect flame length and/or gas pressure
Kettle gas safety valve knob not at correct position
Connect and tighten hose fittings. Check for gas leaks.
Adjust flame and pressure (see page 11).
Replace part (see Parts manual).
Kettle main burners do not shut off
Kettle temperature control dial is not turned to a setting lower than material temperature
Turn kettle temperature control dial to a setting 25° F (13.9° C) (minimum) lower than material temperature.
Replace part (see Parts manual).
Kettle temperature control not functioning correctly
Kettle gas safety valve not functioning correctly
Replace part if it fails diagnostic testing
Kettle main burner does not turn on
Kettle temperature control dial is not turned to a setting higher than material temperature
Turn kettle temperature control dial to a setting 25° F (13.9° C) (minimum) higher than material temperature.
Replace part (see Parts manual).
Thermometer not matching material temperature in kettle
Kettle temperature control not functioning correctly
Kettle gas safety valve not functioning correctly
Material has not reached temperature control set point
Material not fully obligated
Cool or windy ambient conditions
Replace part if it fails diagnostic test (see
Allow time for material to reach operating temperature.
Agitate material.
Move ThermoLazer
™
out of cool windy conditions. Discharge material and check thermometer.
Thermometer calibrated incorrectly
Kettle temperature control calibrated incorrectly
Thermometer not functioning correctly
Kettle temperature control not functioning correctly
Kettle gas safety valve not functioning correctly
Incorrect flame length and/or gas pressure
Calibrate thermometer (see page 7).
See Repair manual and replace part if it can not be calibrated. See Parts manual
313880.
Replace part (see Parts manual).
Replace part (see Parts manual).
Replace part if it fails diagnostic test (see
Adjust flame and pressure (see page 11).
313879B 17
Troubleshooting
Problem Cause Solution
SmartDie
™
screed box
IR burner does not ignite, does not remain ignited, or can not change heat output
Torch does not ignite
PaddleMax
™ handle is hard to move
ControlFlow
ControlFlow
agitator
gate valve difficult to open or close
™
™ valve leaking
gate
Empty LP-gas tank
LP-gas tank shut-off valve closed
Gas supply hose not connected to tank
Gas lines leaking or disconnected
Replace with full tank.
Open LP-gas tank shut-off valve.
Connect gas supply hose.
Check for gas leaks. Connect and tighten fittings.
See Operation manual.
Not allowing time for IR burner thermocouple to sense heat
IR burner regulator/flow control valve not functioning correctly
Replace part (see Parts manual).
Replace part (see Parts manual).
IR burner safety shut-off valve not functioning correctly
IR burner thermocouple not functioning correctly
Empty LP-gas tank
LP-gas tank shut-off valve closed
Torch manual gas shut-off valve closed
Gas supply hose not connected to tank
Gas lines leaking or disconnected
Replace part (see Parts manual).
Replace with full tank.
Open LP-gas tank shut-off valve.
Open manual shut-off valve.
Connect gas supply hose.
Torch assembly not functioning correctly
Material is cold
Check for gas leaks. Connect and tighten fittings.
Replace part (see Parts manual).
Allow time for material to reach operating temperature
Replace bushings (see Parts manual).
Bushings are worn
Linkage ball rod ends need lubrication
Foreign material lodged between agitator and kettle
Cold material temperature
Gate sticking in guides
Add grease
Remove material in kettle and CARE-
FULLY dislodge and remove foreign material.
Heat material to operating temperature.
Make sure thermometer is free to move.
Check for excess material in guides. Apply heat as required and remove excess material. Add grease to lubricate guides.
Bushings are worn
Gate not completely closed
Foreign material lodged in gate opening
Replace bushings (see Parts manual).
Close gate completely.
CAREFULLY dislodge and remove foreign material.
18 313879B
Troubleshooting
Problem Cause Solution
SmartDie leaking
™
screed box
Foreign material in screed box discharge opening
Dirty screed box
Spring broken
Incorrect deployment rod linkage length
Incorrectly adjusted SmartDie
™
screed box/bead dispenser box actuator
Worn screed box gate
Worn screed box trough
CAREFULLY dislodge and remove foreign material.
CAREFULLY clean box. All moving parts need to be free of debris.
Excessive material buildup when starting and stopping extruding
Beads not discharging or discharging unevenly
Beads not discharging at required flow rate
Screed box not adjusted to ground
Screed box open when ThermoLazer
™
is stationary
Foreign material in screed box discharge opening
Dirty screed box
Low bead level in bead hopper
Bead dispenser doors closed
Bead dispenser drive wheel not engaged
Replace gate (see Parts manual 313880).
Replace trough (see Parts manual
313880).
See Operation manual.
Synchronize ThermoLazer box motion.
CAREFULLY dislodge and remove foreign material.
™
and screed
CAREFULLY clean box. All moving parts need to be free of debris.
Fill bead hopper.
Open doors as required to obtain desired flow pattern width.
Secure bead dispenser wheel (see page
Bead dispenser drive wheel slipping
Tighten. Check air pressure (see page 14).
Debris in discharge opening of bead dispenser Remove debris.
Remove debris.
Debris on ThermoLazer
™
tire or bead dispenser wheel
Moisture in beads Remove wet beads. Dry hopper, bead hoses and bead dispenser. Fill hopper with dry beads.
Rotate flow rate lever to correct position.
Bead dispenser flow rate lever not correctly set
Bead dispenser drive wheel slipping Tighten wheel and check tire pressure
Bead dispenser doors not fully open
Moisture in beads
Open door fully.
Remove wet beads. Dry hopper, bead hoses and bead dispenser. Fill hopper with dry beads.
Moisture on road surface
Rough road surface
Bead Dispenser low on material
Allow road surface moisture to dry.
Smooth road surface.
Add material to Bead Hopper.
313879B 19
Troubleshooting
Applying Material
Problem Cause Solution
Ragged line edges when extruding Dirty screed box
Cold material temperatures
Marking speed too fast
Material thickness too think
CAREFULLY clean box. Discharge opening and die plate runners need to be free of debris.
Heat material as required.
Slow Thermolazer
™
speed.
Slow Thermolazer
™
speed and keep screed box filled.
Rough material surface when extruding
Overheated material
Moisture on road surface
Rough road surface
Screed box low on material
Reduce heat.
Allow road surface moisture to dry.
Smooth road surface.
Add material to screed box.
EXAMPLES:
Correct line application will produce a full straight line with sharp edges; correct color, thickness and width; a firm bond to the surface; and have uniform reflectivity.
ti14507a
Insufficient adhesion (material bulges at beginning of line)
• Material temperature too low
• Thermolazer
™
speed too fast
• Debris on road
• Surface temperature too cold
Rough and bumpy line
Gas bubbles in line ti14508a
• Debris on surface
• Crust from overheated material
• Debris caught in die ti14509a
• Material not covering road high spot
• Moisture or solvent on surface
• Material is overheated
• Raise material temperature
• Decrease speed of
Thermolazer
™
• Clear debris from road
• Wait for temperature of surface to raise
• Clear debris from surface
• Lower material temperature
• Clean debris from die
• Adjust screed box line thickness
• Remove solvent from surface
• Lower temperature of material ti14510a
20 313879B
Troubleshooting
Problem
Ragged edges and gaps in line ti14511a
Cause
• Material temperature is too low
• Thermolazer
™
speed is too fast
Solution
• Raise material temperature
• Wait for change in ambient conditions to remove moisture
• Reduce Thermolazer
™
speed
Swollen rounded line • Material temperature is too high • Lower material temperature
Material shadows on sides ti14512a
• Uneven road surface
• Die is not evenly riding on substrate
• Apply to even road surfaces
• Remove debris from screed box lever rod
• Inspect/replace damaged screed box lever rod/lever arm ti14513a
Line is wavy ti14514a
• Strong road surface camber • Apply so camber does not influence application
• Incorrect Thermolazer
™
operation
• Use correct application methods
(for example, try locking swivel wheel)
Cracks in line • Cracks in road surface
• Temperature stress from overheating
• Material applied too cold
•
•
Repair cracks
Lower temperature in material ti14515a
Rough edges and lines in surface
• Material applied too thin
• Increase material temperature
• Slow Thermolazer
™
speed to apply thicker material
• Raise material temperature • Material temperature is too low
• Material is overheated or scorched • Lower material temperature
• Moisture in road surface • Wait until road surface is dry ti14516a
Jagged line ends; material drips between lines
• Die does not fully close
• Debris caught in die
• Worn die gate
• Worn die trough ti14517a
• Broken spring
•
•
•
•
•
Clean die
Clear debris from die
Replace die gate
Replace die trough
Replace spring
313879B 21
Technical Data
Technical Data
Fuel:
Gas supply pressure (maximum):
Kettle burner inlet pressure:
IR burner inlet pressure:
Liquefied petroleum gas (LP-gas) (propane vapor)
250 psi (17.24 bar)
11 in. w.c. (2.7 kPa)
12 psi (.83 bar)
Torch inlet pressure: 18 psi (1.24 bar)
Kettle main burner heating capacity (maximum): Two (2) burners; each burner rated at 10,100 btu/hr (2.96 kW)
Kettle pilot burner heating capacity (maximum): 3800 btu/hr (1.11 kW)
IR burner heating capacity (maximum): 14,000 btu/hr (4.10 kW)
Torch heating capacity (maximum):
Kettle holding capacity (maximum):
Kettle Temperature (maximum):
Kettle Temperature (operating):
Tire pressure (rear wheels):
Tire pressure (swivel wheel):
Battery (Kettle Pilot Burner Igniter):
Bead Hopper Capacity (maximum):
100,000 btu/hr (29.31 kW)
300 lb (136 kg) (thermoplastic traffic marking compound materials)
450° F (232° C)
380° - 420° F (193° - 216° C) 60 psi (4.14 bar)
60 psi (4.14 bar)
45 psi (3.10 bar)
AA (1.5 V)
80 lb (36.3 kg) Type II glass bead
Dimensions
Weight:
Length:
Height:
Width:
295 lb (134 kg)
72 in. (1.83 m)
51 in. (1.30 m)
48 in. (1.22 m)
22 313879B
Graco Standard Warranty
Graco Standard Warranty
Graco warrants all equipment referenced in this document which is manufactured by Graco and bearing its name to be free from defects in material and workmanship on the date of sale to the original purchaser for use. With the exception of any special, extended, or limited warranty published by Graco, Graco will, for a period of twelve months from the date of sale, repair or replace any part of the equipment determined by
Graco to be defective. This warranty applies only when the equipment is installed, operated and maintained in accordance with Graco’s written recommendations.
This warranty does not cover, and Graco shall not be liable for general wear and tear, or any malfunction, damage or wear caused by faulty installation, misapplication, abrasion, corrosion, inadequate or improper maintenance, negligence, accident, tampering, or substitution of non-Graco component parts. Nor shall Graco be liable for malfunction, damage or wear caused by the incompatibility of Graco equipment with structures, accessories, equipment or materials not supplied by Graco, or the improper design, manufacture, installation, operation or maintenance of structures, accessories, equipment or materials not supplied by Graco.
This warranty is conditioned upon the prepaid return of the equipment claimed to be defective to an authorized Graco distributor for verification of the claimed defect. If the claimed defect is verified, Graco will repair or replace free of charge any defective parts. The equipment will be returned to the original purchaser transportation prepaid. If inspection of the equipment does not disclose any defect in material or workmanship, repairs will be made at a reasonable charge, which charges may include the costs of parts, labor, and transportation.
THIS WARRANTY IS EXCLUSIVE, AND IS IN LIEU OF ANY OTHER WARRANTIES, EXPRESS OR IMPLIED, INCLUDING BUT NOT LIMITED
TO WARRANTY OF MERCHANTABILITY OR WARRANTY OF FITNESS FOR A PARTICULAR PURPOSE.
Graco’s sole obligation and buyer’s sole remedy for any breach of warranty shall be as set forth above. The buyer agrees that no other remedy
(including, but not limited to, incidental or consequential damages for lost profits, lost sales, injury to person or property, or any other incidental or consequential loss) shall be available. Any action for breach of warranty must be brought within two (2) years of the date of sale.
GRACO MAKES NO WARRANTY, AND DISCLAIMS ALL IMPLIED WARRANTIES OF MERCHANTABILITY AND FITNESS FOR A
PARTICULAR PURPOSE, IN CONNECTION WITH ACCESSORIES, EQUIPMENT, MATERIALS OR COMPONENTS SOLD BUT NOT
MANUFACTURED BY GRACO. These items sold, but not manufactured by Graco (such as electric motors, switches, hose, etc.), are subject to the warranty, if any, of their manufacturer. Graco will provide purchaser with reasonable assistance in making any claim for breach of these warranties.
In no event will Graco be liable for indirect, incidental, special or consequential damages resulting from Graco supplying equipment hereunder, or the furnishing, performance, or use of any products or other goods sold hereto, whether due to a breach of contract, breach of warranty, the negligence of Graco, or otherwise.
FOR GRACO CANADA CUSTOMERS
The Parties acknowledge that they have required that the present document, as well as all documents, notices and legal proceedings entered into, given or instituted pursuant hereto or relating directly or indirectly hereto, be drawn up in English. Les parties reconnaissent avoir convenu que la rédaction du présente document sera en Anglais, ainsi que tous documents, avis et procédures judiciaires exécutés, donnés ou intentés, à la suite de ou en rapport, directement ou indirectement, avec les procédures concernées.
Graco Information
TO PLACE AN ORDER, contact your Graco distributor or call to identify the nearest distributor.
Toll Free: 1-800-690-2894.
313879B 23
All written and visual data contained in this document reflects the latest product information available at the time of publication.
Graco reserves the right to make changes at any time without notice.
This manual contains English. MM 313879
Graco Headquarters: Minneapolis
International Offices: Belgium, China, Japan, Korea
GRACO INC. P.O. BOX 1441 MINNEAPOLIS, MN 55440-1441
Copyright 2008, Graco Inc. is registered to I.S. EN ISO 9001 www.graco.com
advertisement
* Your assessment is very important for improving the workof artificial intelligence, which forms the content of this project
Related manuals
advertisement
Table of contents
- 2 Table of Contents
- 3 Warnings
- 5 Kettle Gas Safety Valve, Kettle Temperature Control, and Kettle Thermopile Diagnosis
- 6 Kettle Temperature Control Calibration
- 6 Temperature Control Replacement
- 6 Thermometer Replacement
- 7 Kettle Thermometer Calibration
- 7 Adjust Kettle Pilot Ignitor Electrode Gap
- 8 Thermopile Replacement
- 10 Adjust Gas Pressure to Kettle Burners
- 11 Adjust Kettle Pilot Burner Flame
- 11 Adjust Kettle Main Burners Flame
- 12 Cleaning Kettle Main Burner Gas Lines
- 12 Cleaning Kettle Pilot Burner Gas Lines
- 13 Replacing Screed Box Spring
- 14 Securing Bead Dispenser Wheel
- 14 Linkage Rod Adjustment
- 15 Screed Box/Bead Dispenser Box Actuator
- 15 Adjusting Screed Box Pivot Arm
- 16 Troubleshooting
- 22 Technical Data
- 23 Graco Standard Warranty
- 23 Graco Information