Haier JC-298G Service manual
Add to my manuals
27 Pages
Haier JC-298G is a freestanding wine cellar with a 298L capacity, designed to preserve the flavors of your wine collection. It features adjustable temperature settings from 6°C to 18°C, allowing you to customize the storage conditions for different types of wine. The active carbon deodorization system helps to remove unwanted odors, while the interior fan ensures well-proportioned temperature distribution throughout the cellar. With its ability to hold up to 120 bottles, the Haier JC-298G is an ideal choice for wine enthusiasts looking for a reliable and efficient storage solution.
advertisement
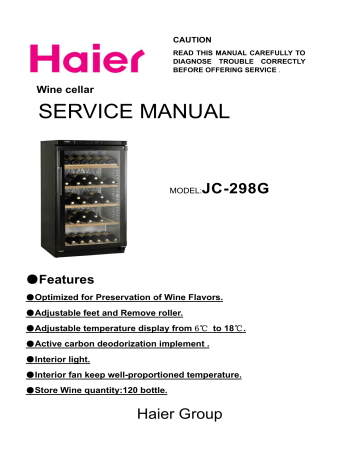
CAUTION
READ THIS MANUAL CAREFULLY TO
DIAGNOSE TROUBLE CORRECTLY
BEFORE OFFERING SERVICE
.
Wine cellar
SERVICE MANUAL
MODEL:
JC-298G
●
Features
●
Optimized for Preservation of Wine Flavors.
●
Adjustable feet and Remove roller.
●
Adjustable temperature display from 6℃ to 18℃.
●
Active carbon deodorization implement .
●
Interior light.
●
Interior fan keep well-proportioned temperature.
●
Store Wine quantity:120 bottle.
Haier Group
Contents
1. Content s……………………………………………………………………….……1
2. Safety cautions…..…………………………………………………………………3
3. S pecifications……………………………………………………………………....5
4. Inst allation and accessory parts………………………………………….….......7
5. Part s identifications ………………………………………………. ……………..9
5.1 Control panel……….……………………………………………………........9
5.2 Connectting wires……………………………………………………….......10
5.3 F
ix the power wire and ballast
………………………………………... 11
5.4
The compressor……
……………………………………………………... 12
5.5
Fix the door…….
………………………………………………………….12
6. Control panel principle…………………………………………………………...13
7. System flow chart…………………………………………………………………14
8. System flow scenograph…………………………………………………………15
9. Circuit diagram….………………………………………………………………...16
10.1 Brief principle diagram……………………………………………………..16
10.2 Connect diagram……………………………………………………………17
10.3 Control panel diagram……………………………………………………..18
10.4 Display board diagram…………………………………………………......19
10. Normal problems………………………………………………………………….20
11. Trouble shooting………………………………………………………………….23
11.1 Compressor does’t start………… ……… ……………………………...23
11.2 poor cooling……………………… ……… ……………………………....24
12. Failure code display……………………………………………….......25
1
2
Safety Precautions
Read all of the instructions before using this appliance. When using this appliance, always exercise basic safety precautions, including the following:
1. Use this appliance only for its intended purpose as described in this uses and care guide.
2. This Wine cellar must be properly installed in accordance with the installation section. Instructions before it is used, See grounding instructions in the installation section.
3. Never unplug your Wine cellar by puling on the power cord, Always grasp the plug firmly and pull straight out from the outlet.
4. Repair or replace immediately, all electric service cords that have become frayed or otherwise damaged, Do not use a cord that shows cracks or abrasion damage along its length, the plug or the connector end.
5. Unplug your Wine cellar before cleaning or before making any repairs, Note: If for any reason this product requires service, we strongly, recommend that a certified technician perform the service.
6. If your old Wine cellar is not being used, we recommend that you remove the door and leave the shelves in place; this will reduce the possibility of danger to children.
7.
This Wine cellar should not be recessed or built-in an enclosed
Cabinet. It is designed for freestanding installation only
8. Do not operate your Wine cellar in the presence of explosive fumes.
9. Do not damage the refrigerant circuit.
10.Do not use any electrical device or any sharp instrument in defrosting your Wine cellar.
3
4
Specifications
WINE CELLAR
1.
Model JC-298G
Photo
Commercial brand
Product description
Type of Appliance (FS= freestanding BI= built-in)
Energy efficiency class
Climate class (N= + 18-32 °C T=+ 18-43 °C)
Freezer compartment / Star rating
Approvals (VDE / TÜV / IMQ / NF / ÖVE / DEMKO etc.)
Certifications ( CE / ISO 9001/2)
EAN codes
2.
Key features
Gross capacity
Total net capacity
Freezing capacity
Energy consumption
Defrosting ( H=manual A=automatic) Fridge/Freez
Frost free system
Defrost water outlet
Air circulating ventilator
Kind of coolant (R134a/R600a)
Foaming components
3.
Technical data
Voltage / frequency
Input power / mains fuse minimum
Length of cable / incl. plug
Temperature range (from>to) Fridge / Freez
Features: (DI N 8950 resp. 8953)
Energy consumption (EN 153) per l 100
Energy consumption (EN 153) per l 100
Cooling system: K=Compressor / A=Absorbtion
Max noise level
4.
Aesthetics
Colours
(see L):
Top
Cabinet
Door Glass
Door Frame l l kg/24 h kWh/year
Ye
Haier
WINE CELLAR
FS
/
ST
/
VDE
CE
693026532226(2 )
298
292
0.72
262.8
A
/
s
Yes
R600a
CP-IP
V/Hz
W /A
220-240 V~/ 50
160W/1.10A cm 200/205
°C 6~18 kWh/year 262.8 kWh/24 h dbA
0.72
K
42
Black
Gray Black
Intransparent
Black
Fascia panel / Handle (w / b / g / s)
Inside door/-drawers (w =white t=transpar.)
Door:
F= Flat / R= Rounded / S= Streamline
Hinged (r =right l =left) / reversible)
Deco frame: panel thikness till: mm
Compartments number / adjustable
Lock
Shelves:
Number
Number of bottles (total)
Type ( gr=grill/g=glass/p=plastic)
Colour of shelves
Adjustable
Drawers:
Number
Crisper:
Salad crisper(s) transparent / white
5.
Equipment & Accessories
Control Panel:
Control panel interior / exterior
Thermometer interior / exterior
Control lamps green / yellow / red
Over temperature ALARM LED / acoustic
Adjustable thermostat
Fast freeze switch
Interior light
Adjustable feet front / rear n°
Castors front / rear
Wall spacer grid /-distance holder / Flush back
6.
Product dimensions
Unit dimensions H / W / D
Depth with open door
Net weight
7.
Packing dimensions & loadability
Packing dimensions H / W / D
Gross weight
40 ' Container load
40 ' HC Container load
8.
Recycling symbols
Carton weight in g
Polystyrene weight in g
Polyethylene foil weight in g
Wood weight in kg
9.
Service
Users instruction (languages)
Max. failure rate ( during first 12 Months) n°.
Ex
_
W cm cm cm kg kg kg
- kg cm 134x kg pcs pcs
%
11 front rear
10/10/10
128*66.5*67
132
69.0
73 x74
77.0
96
96
D / F / I / GB
-
Black
- / -
S r / reversible
90
-/ adjustable
Yes
6
120
w ood:6
Wood
YES
0
-/-
Exterior terior
/ acoustic
Yes
5
6
Installation and Accessory Parts
Unpacking Your Wine cellar
1.Remove all p ackaging m aterial; this includes the foam base and all adhesi ve tape holding the Wine cellar accessories inside and outside.
2.Inspect and rem ove any remains of p acking, t ape or printed material s before powering on the Wine cellar.
Adjusting Your Wine cellar
1.Your Wine cellar is designed for freest anding installation only. It should not be recessed or built-in.
2.Place the Wine cellar on a floor strong enough to support it fully loaded.
3.When moving the Wine cellar , never tilt it more than a 45-degree angle. Thi s could damage the compressor and the sealed system.
4.If the Wine cellar is tilted let it st and in an upright position for at least 24 hours prior to plugging. This is to allow the refrigerant to settle.
·
Proper Air Circulation
z
To assure your W ine cellar works at the maximum efficiency it was desi gned for, you should install it in a location where there is proper air circulation, z
Plumbing and electrical connections. z
The following are recommended clearances around the Wine cellar:
Sides…………..0.8”(20mm)
Top. ……………6.3”(630mm)
Back…………..4”(100mm)
·Do not over fill wine cellar for proper internal air circulation.
Electrical Requirement
z
Make sure there is a suit able power Outlet (220~240V) with proper grounding to power the wine cellar. z
Make sure there is ef fective grounding for the wine cell ar, this is a dangerous practice since it provides no ef fective grounding for the freezer and may result in shock hazard.
Install Limitations
z
Do not inst all your wine cell ar in any location not properl y insulated or heated e.g. garage etc, your wine cellar was not designed to operate i n temperature settings below 32· Fahrenheit. z
Select a suit able location for the wi ne cellar on a hard even surfaces away from direct sunlight or heat source e.g. radiator s, baseboard heaters, cooki ng appliances etc, Any floor unevenness should be corrected.
·
Initial Setup
1.Operating Your Wine cellar
Once the wine cel lar is in i ts proper place, pl ug it in an electrical outl et having
220~240 volts.
Set the temperature, the temperature is adjust able from 6 ℃ to 18℃. After using the wine cellar for 5 hours set the wi ne cellar to your desired setting. Place wine inside the wine cellar.
2.Wine Storage shelves
7
8
Your Freezer has 5 removable even shelves and 1 removable catercorner shelf. It allows you to store wine more accessibly or you can remove it if not needed.
3.Defrosting and cleaning The Wine cellar
·
Defrost whenever the frost becomes 1/ 4” thick. Never use a sharp or metallic instrument to remove the frost as it may damage the cooling coils.(A punctured coil will void the warranty)
·
Unplug the power pin, then take out stored wine and place in a safety place.
Defrosting usually takes a few hours. To defrost faster keep the freezer door open.
·
When frost buildup has melted, wipe water of f with a dry cloth. Replace the electrical plug in the electrical outlet.
·
Reset the temperature control to the desired setting.
Parts identifications
Control panel
Fan and evaporator clapboard
Handle
Glass door
Adjustable feet
1. Control panel
a.
Firstly, loosen the philip screw on the top
b.
Hold the control panel, meanwhile push
Hinge, the door should open for 135°when the wiring harness button with your loosening the right side philip screw. thumb to take the control wire apart.
9
10
c.
One side of the signal wire was connecting
d.
The socket of sensor wire is connecting with the control panel, the other side was connecting with the display panel, please refer to
with the middle of the display panel. Take it
apart firstly, note that you should unplug it softly
in order to protect the plug.
the signal wire to take it apart. e.
When changing the control panel, you should push the button to pull out of the control panel. Do never pull it wildly without pushing the button. That will break it. f.
The disply panel is fixed on the plastic panel with three philip screws, you should regulate the philip screw properly to make the button on the disply panel sensitive.
On the right side of the picture is fan switch, you can connect it directly with the wire without thinking of the direction, but remember to push the button on the wire when you take it apart from the fan switch.
2.Connectting wires
a.
On the picture is the connection of the control
b.
On the left top of the back of the cabinet and connect wire.
is box cover, take it apart you will find
the Cord stopper cover.
c.
When you take the box cover apart, as on the picture, the blue one is lamp wire, connecting with the connect wire and ballast wire. The red one is fan wire, connecting with the control wire.
The white one is connect wire, connecting with heater wire.
3.Fix the power wire and ballast
a.
Take the Wire Seat apart first to loosen the Power wire。 b.Then take the Ballast cover apart c. The Power and control wire in the Ballast cover is fixed in the slot with accesso ry. In the picture is the plug connecting the contro l wire and power wire. The black one is ballast wire, spring out from the Cord stopper cover. d.Take the Philip screw ap art from the ballas ,then you can t ake the ballas ap art. When assembling it ,please fix the below screw first. e.
The ballast wire has locked oneself port , When changing it, you can use a thin steel bar insert in the faucet and then pull the wire out, when fix the wire again you need to use the other two faucet, the used ones is broken for it is one-off.
11
12
4.The compressor
a.
The assemble step of the compressor accessory
b.
There is buckle on the Water box is showing on the picture. The earth wire is connecting to to fix on the compressor, and the compressor, the live wire and zero wire is connected also some anti-shock material to the compressor power panel, rotate the plastic bolt to fix between them. the wire. The compressor power panel is one whole part.
5.Fix the door
a.
Pull the bottom Hinge cover out flatly. b.
The bottom Hinge is fixed with four bolts, you should use a M6 sleeve to unfix it, then you can take the door out.
Control panel principle
Brief description of control panel principle about :JC-298G
1.
Adjustable temperature display
: While you are entering the temperature by pressing the temperature buttons about 3 seconds, the set temperature will flash on the display.
To reduce the temperature, press the bottom button “▼”.
To increase the temperature, press the top button “▲”.
2.The small yellow lamp is the LAMP switch. When the lamp is on, the Interior light will run
3.The small red lamp is the ALARM lamp. When the lamp is on, the alarm will be on.
13
14
System Flow Chart
The refrigeration system of direct cooling single-system cooler belongs to the category of a singletemperature and single-control refrigerating system with one evaporators and is controlled by a single temperature control.
System flow scenograph
15
16
Circuit diagram
1. Brief principle diagram
M
M1
Notes:
1. If the wine cellar has been placed in a horizontal or tilted position for any period of time wait 24 hours before plugging the unit in.
2.The alarm will sound when the appliance is switched on for the first time and when the appliance is warm. Press the Alarm button to switch it off. The temperature display will also flash until set temperature is reached.
3.The appliance has been tested and is supplied set for normal operation of 12°C.
2.Connect diagram
17
3. Control panel diagram
1/2W
2
GND
18
4. Display board diagram
A
B
C
D
1
B
A
R39220
R40220
P3
R8 4.7K
2SA1037AK
+5V
P2
R7 4.7K
+5V
2SA1037AK
+5V
3
4
1
2
IC2
A0
A1
A2
VSS
VCC
TEST
SCL
SDA
AT24C01A
8
7
6
5
R21
10K
R22
10K
SCL
SDA
CN3
1
2
3
4
5267-4A
+5V
GND
TX
RX
+5V
C4
R25
10K R32
1K
104
R35
100
CN2
LC
2
1
5267-2A
+5V
R28
4.7K
1
R30 2K
R36
100
C5
104
2 3 4
+5V
R1
2K
R23
10K
R37
560
C1
XT1
4.9152MHZ
22
R26
10M
1
C2
22
C0 +5V
2
3
4
104
7
8
5
6
OSC1
OSC2
A1/KB1
VDD
A2/KB2
A3/KB3
B7/AD7
B6/AD6
P1
2SA1037AK
R2
2K
R24
10K
RST
C3
104
2
GND
+5V
C
HEAT
LAMP
CN1
3
4
1
2
5
5267-5A
R6 10K
R34
10k
MC68HC908JL8CFA
IC1
R38
10k
R31
10K
R3 2K
R4 2K
R5 2K
E1
16V/220U
+5V
R9 4.7K
P4
2SA1037AK
F
R41220
G
R42 220
LED3 LED2
A
P5
2SA1037AK
R10 4.7K
+5V
D5/T1C1
D2/AD9
A4/KB4
D3/AD8
B0/AD0
B1/AD1
D1/AD10
B2/AD2
24
23
22
21
20
19
18
17
+5V
R33
220
BUZZ1
PS1740P02C
P6
2SA1037AK
R11
4.7K
P7
2SA1037AK
R12
4.7K
P8
2SA1037AK
R13
4.7K
P9
2SA1037AK
R14
4.7K
R19
2K
+5V
D
220 R43
H
R44
220
+5V
+5V
+5V
+5V
E
R45
220
R46
220
C
N1
2SC2412K
LED1
TOT-5371
B
R15
4.7K
N3
2SC2412K
R16
4.7K
N2
2SC2412K
R17
4.7K
R18
4.7K
N4
2SC2412K
D4
RLS4148
D3
RLS4148
D2
RLS4148
D1
RLS4148
+5V
SW4 SW3 SW2 SW1
R20
10K
C
D
R29 4.7K
3 4
Normal peoblems
Problems Reasons
Compress or can not be started
1. Fuse is broken
2. The cont act of plug, socket, and cable is not good. Cable broken.
3. The volt age is too low , 10- 15% less than rated voltage
4. The knob of temperature controller is at “rest” position.
5. The temperature controller is out of order.
6. S tarting relay or thermal protection unit is out of order or broken.
7. Wire broken of motor st arting coil or operation coil.
8. The compressor motor is burned or rot ator and st ator are blocked to dead.
9. There is leakage of high-pressure gas valve or the shaft is embraced to dead.
Compress or st arts too frequent, operation time too long, but temperatu re drop in wine cellar is too slow
1. The point of sensor was moved.
2. The temperature controller is out of order.
3. The environment temperature is too high, humidity too high, airflow is impeded.
4. The frost layer at the evaporator is too thick.
5. The refrigerant is insufficient or leakage.
6. Compressor efficiency is reduced.
7. The drying filter is blocked.
Compress or runs without stop, temperatu re in freezer is too low
1. The point of sensor was moved.
2.The temperature sensing probe of controller is not placed well, and causes maladjustment
3.Compressor efficiency reduced.
Removing methods
1. Check if there is short circuit and solve it, if not, change cap able fuse
2. Check and connect tightly , or change.
3. Use till volt age rises to rated value or attach a stabilizer.
4. Rot ate the knob to wanted position for suitable temperature.
5. Change the controller.
6. Change starting relay or thermal protection unit.
7. Measure using R ×1 position of avometer, if ther e is wire broken, change compressor.
8. Change compressor.
9. Change compressor.
1 Check the point of sensor,and move it to original place.
2.Change the temperature controller.
3.Put the wine cellar to suitable place and make air circulate well.
4Remove frost regularly.
5.Check or supplement refrigerant.
6.Change compressor.
7.Change new drying filter.
1.Check the point of sensor,and move it to original place.
2.Adjust to suitable position, normally contact tightly with evaporator cover.
3.Change compressor.
Compressor buzzes and cannot be started, thermal protection unit jump repeatedly.
After short time of operation, over load protection unit cuts off
Too much noise when compressor runs
Electricity leakage of wine c ellar body, you will feel tingle when touching by hand
1. Voltage is too low.
2. Starting relay out of order.
3. The st arting coil of st arting motor is broken.
4. Compressor does not run.
1. Supplement a st abilizer, adjust to rated value.
2. Change starting relay.
3. Change compressor.
4.The shaft and piston in the compressor is blocked, please change.
1. The voltage is too high.
2. Over load protection unit is not good, it jumps earlier.
3. Starter contacting point is adhered.
4. There is short circuit in compressor.
5. There is mechanical problem in the compressor.
6. Temperature around compressor is too high.
1. The floor is loose.
2. The wine cellar body is not stable and in level.
3. When compressor runs, friction between tubes and wine cellar body causes resonance.
4. Compressor fix ing screw is loose.
5. The vibration absorption cushion for comp ressor fixing is too tight, or too loose or ageing.
6. Compressor inside noise is too big or vibration absorption suspending spring is broken.
1. Wine cellar body has not been connected to the ground.
2. The compressor terminal contacts body shell and causes short circuit.
3.When the component s of electrical system get wet, insulation ability is dropped, electricity leaks.
1. Supplement a st abilizer and adjust its value to rated.
2. Change over load protection unit.
3. Change starting relay.
4. Change compressor.
5. Change compressor.
6.Increase heat radiation space.
1. Reinforce the floor.
2. Make the wine cellar body stable.
3. Move the tube a little away to avoid friction.
4. Make the screw tight.
5. Adjust the degree of tight or loose of vibration absorption cushion, or change cushion.
6. Change compressor.
1. Make the ground connection as stipulated.
2. Change compressor.
3. Check carefully step by step, if insulation is seriously damaged, please change; remove wet p arts and put them into drying box to make them dry.
1
2
Electricit y leakage of temperat ure controlle r
Tempera ture controlle r out of order
The probe of temperat ure sensing tube doesn’t contact evaporat or well
1. The service time is too long.
2. The environment is too dirty.
3. Humidity is too high.
1. There is leakage of temperature sensing medium.
2. Damage of cam of cont point spring, etc. acting
It has not been mounted to position or changed during transportation.
1. Change temperature controller.
2. Use brush to remove dust.
3. Make the temperature dry and control the environment humidity.
Change temperature controller.
Mount it again.
Trouble shooting
1.Compressor does’t st art
3
4
2.Poor cooling
Poor cooling
Check the diaplay temperature nomber whether it is setted at 18°C
Y
Whether the rear side and the top is too close to the wall
Y
Whether the cellar is under sunlight directly
Y
Whether the cellar is near thermal source
Y
Whether the room temperature is too hoot or not
Y
Whether the condenser is blocked by cloth pieces or paper or dirt or not
Y
Whether the glass door has been closed well
Y
Whether the glass door door seal bar is too dirty or sealed well
N
N
N
N
Avoid these matters which will affect heat radiation of condenser and reduce refrigeration ability
Frequent opening and extended opening of glass door will reduce refrigeration ability
N
Change to lower
Remove dirt and put on a little talcum power
Failure code display
Error indicator
Description and reason Solutions
F1
Sensor A is failure (broken circuit or open circuit).
Red indicator is light with buzzing.
Check sensor A and it’s connecting status, replace sensor if necessary.
F2
Sensor B is failure (broken circuit or open circuit).
Red indicator is light with buzzing.
Check sensor B and it’s connecting status, replace sensor if necessary.
F3
F4
When the sensor A and sensor B are all failure (broken circuit or open light with buzzing. Compressor enter into protection mode (stop cooling).
Check sensor A and sensor B and circuit), it shows “F3”. Red indicator is their connecting status, replace sensor if necessary.
Continuous compressor running time is more than 3 hours, and Sensor B felt the inner temperature change is within 1 ℃. Compressor enter into protection mode (stop cooling).
Check if sensor B and it’s connecting status is failure, check cooling system.
REMARK:
Buzzing sound can hear when “F1” or “F2” or “F3” or “F4” appears on the display panel. Press the ”ALARM” button can remove the buzzing sound.
advertisement
* Your assessment is very important for improving the workof artificial intelligence, which forms the content of this project
Key Features
- Freestanding 150 bottle(s) Number of temperature zones: 1
- Number of shelves: 5
- 42 dB
- 288 kWh
- Interior light
Related manuals
advertisement