- Home
- Domestic appliances
- Large home appliances
- Water heaters & boilers
- Crown Boiler
- Raptor
- Product Manual
advertisement
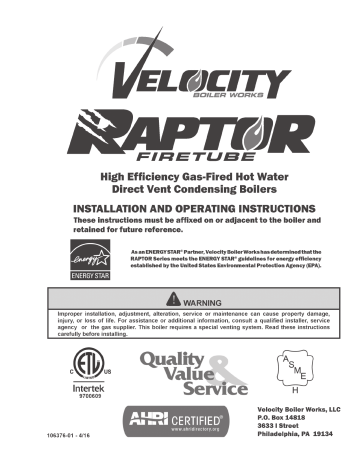
1
IMPORTANT INFORMATION - READ CAREFULLY
NOTE: The equipment shall be installed in accordance with those installation regulations enforced in the area where the installation is to be made. These regulations shall be carefully followed in all cases. Authorities having jurisdiction shall be consulted before installations are made.
All wiring on boilers installed in the USA shall be made in accordance with the National Electrical Code and/or local regulations.
All wiring on boilers installed in Canada shall be made in accordance with the Canadian Electrical Code and/or local regulations.
The City of New York requires a Licensed Master Plumber supervise the installation of this product.
The Massachusetts Board of Plumbers and Gas Fitters has approved the Raptor™ Series boiler. See the Massachusetts Board of Plumbers and Gas Fitters website, http://license.reg.state.ma.us/pubLic/pl_products/pb_pre_form.asp for the latest Approval
Code or ask your local Sales Representative.
The Commonwealth of Massachusetts requires this product to be installed by a Licensed Plumber or Gas Fitter.
The following terms are used throughout this manual to bring attention to the presence of hazards of various risk levels, or to important information concerning product life.
DANGER
Indicates an imminently hazardous situation which, if not avoided, will result in death, serious injury or substantial property damage.
WARNING
Indicates a potentially hazardous situation which, if not avoided, could result in death, serious injury or substantial property damage.
CAUTION
Indicates a potentially hazardous situation which, if not avoided, may result in moderate or minor injury or property damage.
NOTICE
Indicates special instructions on installation, operation, or maintenance which are important but not related to personal injury hazards.
DANGER
Explosion Hazard. DO NOT store or use gasoline or other flammable vapors or liquids in the vicinity of this or any other appliance.
If you smell gas vapors, NO NOT try to operate any appliance - DO NOT touch any electrical switch or use any phone in the building. Immediately, call the gas supplier from a remotely located phone. Follow the gas supplier’s instructions or if the supplier is unavailable, contact the fire department.
2
WARNING
This boiler must only be serviced and repaired by skilled and experienced service technicians.
If any controls are replaced, they must be replaced with identical models.
Read, understand and follow all the instructions and warnings contained in all the sections of this manual.
If any electrical wires are disconnected during service, clearly label the wires and assure that the wires are reconnected properly.
Never jump out or bypass any safety or operating control or component of this boiler.
Assure that all safety and operating controls and components are operating properly before placing the boiler back in service.
Annually inspect all vent gaskets and replace any exhibiting damage or deterioration.
WARNING
Asphyxiation Hazard. Fire Hazard. Explosion Hazard. This boiler requires regular maintenance and service to operate safely. Follow the instructions contained in this manual.
WARNING
Asphyxiation Hazard. This boiler requires regular maintenance and service to operate safely. Follow the instructions contained in this manual.
Improper installation, adjustment, alteration, service or maintenance can cause property damage, personal injury or loss of life. Read and understand the entire manual before attempting installation, start-up operation, or service. Installation and service must be performed only by an experienced, skilled, and knowledgeable installer or service agency.
This boiler must be properly vented.
This boiler needs fresh air for safe operation and must be installed so there are provisions for adequate combustion and ventilation air.
Asphyxiation Hazard. The interior of the venting system must be inspected and cleaned before the start of the heating season and should be inspected periodically throughout the heating season for any obstructions. A clean and unobstructed venting system is necessary to allow noxious fumes that could cause injury or loss of life to vent safely and will contribute toward maintaining the boiler’s efficiency.
Installation is not complete unless a safety relief valve is installed in the supply piping. - See the
System Piping Section of this manual for details.
This boiler is supplied with safety devices which may cause the boiler to shut down and not re-start without service. If damage due to frozen pipes is a possibility, the heating system should not be left unattended in cold weather; or appropriate safeguards and alarms should be installed on the heating system to prevent damage if the boiler is inoperative.
Burn Hazard. This boiler contains very hot water under high pressure. Do not unscrew any pipe fittings nor attempt to disconnect any components of this boiler without positively assuring the water is cool and has no pressure. Always wear protective clothing and equipment when installing, starting up or servicing this boiler to prevent scald injuries. Do not rely on the pressure and temperature gauges to determine the temperature and pressure of the boiler. This boiler contains components which become very hot when the boiler is operating. Do not touch any components unless they are cool.
Respiratory Hazard. Boiler materials of construction, products of combustion and the fuel contain alumina, silica, heavy metals, carbon monoxide, nitrogen oxides, aldehydes and/or other toxic or harmful substances which can cause death or serious injury and which are known to the state of
California to cause cancer, birth defects and other reproductive harm. Always use proper safety clothing, respirators and equipment when servicing or working nearby the appliance.
Failure to follow all instructions in the proper order can cause personal injury or death. Read all instructions, including all those contained in component manufacturers manuals which are provided with the boiler before installing, starting up, operating, maintaining or servicing.
All cover plates, enclosures and guards must be in place at all times.
DANGER
Explosion Hazard. Electrical Shock Hazard. Burn Hazard. This boiler uses flammable gas, high voltage electricity, moving parts, and very hot water under high pressure. Assure that all gas and electric power supplies are off and that the water temperature is cool before attempting any disassembly or service.
Do not attempt any service work if gas is present in the air in the vicinity of the boiler. Never modify, remove or tamper with any control device.
3
4
Special Installation Requirements for Massachusetts
A. For all sidewall horizontally vented gas fueled equipment installed in every dwelling, building or structure used in whole or in part for residential purposes and where the sidewall exhaust vent termination is less than seven (7) ft. above grade, the following requirements shall be satisfied:
1. If there is no carbon monoxide detector with an alarm already installed in compliance with the most current edition of
NFPA 720, NFPA 70 and the Massachusetts State Building Code in the residential unit served by the sidewall horizontally vented gas fueled equipment, a battery operated carbon monoxide detector with an alarm shall be installed in compliance with the most current edition of NFPA 720, NFPA 70 and the Massachusetts State Building Code.
2. In addition to the above requirements, if there is not one already present, a carbon monoxide detector with an alarm and a battery back-up shall be installed and located in accordance with the installation requirements supplied with the detector on the floor level where the gas equipment is installed. The carbon monoxide detector with an alarm shall comply with 527 CMR, ANSI/UL 2034 Standards or CSA 6.19 and the most current edition of NFPA 720. In the event that the requirements of this subdivision can not be met at the time of the completion of the installation of the equipment, the installer shall have a period of thirty (30) days to comply with this requirement; provided, however, that during said thirty (30) day period, a battery operated carbon monoxide detector with an alarm shall be installed in compliance with the most current edition of NFPA 720, NFPA 70 and the Massachusetts State Building Code. In the event that the sidewall horizontally vented gas fueled equipment is installed in a crawl space or an attic, the carbon monoxide detector may be installed on the next adjacent habitable floor level. Such detector may be a battery operated carbon monoxide detector with an alarm and shall be installed in compliance with the most current edition of NFPA 720, NFPA 70 and the
Massachusetts State Building Code.
3. A metal or plastic identification plate shall be permanently mounted to the exterior of the building at a minimum height of eight (8) ft. above grade directly in line with the exhaust vent terminal for the horizontally vented gas fueled heating appliance or equipment. The sign shall read, in print size no less than one-half (1/2) inch in size, “GAS VENT
DIRECTLY BELOW. KEEP CLEAR OF ALL OBSTRUCTIONS”.
4. A final inspection by the state or local gas inspector of the sidewall horizontally vented equipment shall not be performed until proof is provided that the state or local electrical inspector having jurisdiction has granted a permit for installation of carbon monoxide detectors and alarms as required above.
B. EXEMPTIONS: The following equipment is exempt from 248 CMR 5.08(2)(a) 1 through 4:
1. The equipment listed in Chapter 10 entitled “Equipment Not Required To Be Vented” in the most current edition of NFPA
54 as adopted by the Board; and
2. Product Approved sidewall horizontally vented gas fueled equipment installed in a room or structure separate from the dwelling, building or structure used in whole or in part for residential purposes.
C. When the manufacturer of Product Approved sidewall horizontally vented gas equipment provides a venting system design or venting system components with the equipment, the instructions for installation of the equipment and the venting system shall include:
1. A complete parts list for the venting system design or venting system; and
2. Detailed instructions for the installation of the venting system design or the venting system components.
D. When the manufacturer of a Product Approved sidewall horizontally vented gas fueled equipment does not provide the parts for venting flue gases, but identifies “special venting systems”, the following shall be satisfied:
1. The referenced “special venting system” instructions shall be included with the appliance or equipment installation instructions; and
2. The “special venting systems” shall be Product Approved by the Board, and the instructions for that system shall include a parts list and detailed installation instructions.
E. A copy of all installation instructions for all Product Approved sidewall horizontally vented gas fueled equipment, all venting instructions, all parts lists for venting instructions, and/or all venting design instructions shall remain with the appliance or equipment at the completion of the installation.
WARNINGS FOR THE HOMEOWNER
FOLLOW ALL INSTRUCTIONS and warnings printed in this manual and posted on the boiler.
MAINTAIN THE BOILER. To keep your boiler safe and efficient, have a service technician maintain this boiler as specified in Service and Maintenance
Instructions.
IF YOU ARE NOT QUALIFIED to install or service boilers, do not install or service this one.
THE BOILER MAY LEAK WATER at the end of its useful life. Be sure to protect walls, carpets, and valuables from water that could leak from the boiler.
PROTECT YOUR HOME IN FREEZING
WEATHER. A power outage, safety lockout, or component failure will prevent your boiler from lighting. In winter, your pipes may freeze and cause extensive property damage. Do not leave the heating system unattended during cold weather unless alarms or other safeguards are in place to prevent such damage.
DO NOT BLOCK AIR FLOW into or around the boiler. Insufficient air may cause the boiler to produce carbon monoxide or start a fire.
KEEP FLAMMABLE LIQUIDS AWAY from the boiler, including paint, solvents, and gasoline.
The boiler may ignite the vapors from the liquids causing explosion or fire.
KEEP CHILDREN AND PETS away from hot surfaces of the boiler, boiler piping, vent piping and vent terminals.
CARBON MONOXIDE (CO) is an odorless, deadly gas that may be introduced into your home by any malfunctioning fuel-burning product or vent system failure. Consider installing CO alarms near bedrooms in all levels of the building to warn you and your family of potential CO exposure.
WARNINGS FOR THE INSTALLER
READ THIS ENTIRE MANUAL before attempting installation, start-up, or service. Improper installation, adjustment, alteration, service, or maintenance may cause serious property damage, personal injury, or death.
DO NOT DISCONNECT PIPE FITTINGS on the boiler or in the heating system without first verifying that the system is cool and free of pressure and that your clothing will protect you from a release of hot water or steam. Do not rely solely on the boiler’s temperature and pressure gage when making this judgment.
USE PROPER PERSONAL PROTECTION
EQUIPMENT when servicing or working near the boiler. Materials of construction, flue products, and fuel contain alumina, silica, heavy metals, carbon monoxide, nitrogen oxides, and/or other toxic or harmful substances that can are hazardous to health and life and that are known to the State of
California to cause cancer, birth defects, and other reproductive harm.
INSTALL ALL GUARDS, cover plates, and enclosures before operating the boiler.
SIZE THE BOILER PROPERLY relative to the design heat load or, if using domestic hot water priority, the peak hot water load, whichever is larger. A grossly oversized boiler will cycle excessively and this will lead to premature failure of the boiler and its components. Our warranty does not apply to damage from excessive cycling.
ADHERE TO ALL LOCAL CODE
REQUIREMENTS. Contact your local code inspector prior to installation. In the absence of a local code, adhere to the National Fuel Gas
Code ANSI Z223.1/NFPA 54 or CAN/CSA B149.1,
Natural Gas and Propane Installation Code.
ALL WIRING must comply with the National
Electrical Code ANSI/NFPA 70 (in the USA) or the
Canadian Electrical Code CSA C22.1 (in Canada)
and any local regulations.
5
6
Table of Contents
I. Product Description
II. Specifications
III. Before Installing
IV. Locating The Boiler
V. Mounting The Boiler
VI. Air For Ventilation
VII. Venting
A. Vent System Design
B. Design Requirements Unique to Horizontal Twin Pipe Venting Systems
C. Design Requirements Unique to Vertical Venting Systems
D. Design Requirements Unique to Split Vent Systems
E. Assembly of CPVC/PVC Vent Systems
F. Assembly of DuraVent PolyPro Vent Systems
G. Assembly of Selkirk Polyflue Vent Systems
H. Assembly of Centrotherm InnoFlue Vent Systems
I. Condensate Trap and Drain
J. Removing An Existing Boiler From Common Chimney
VIII. Gas Piping
IX. System Piping
A. General System Piping Precaution
B. Standard Piping Installation Requirements
C. Near Boiler Piping Design
D. Piping For Special Situations
X. Wiring
XI. Start-Up and Checkout
XII. Operation
XIII. Service and Maintenance
XIV. Troubleshooting
XV. Repair Parts
Appendix A: LP Gas Conversion Instructions
Appendix B: Instructions for High Altitude Installation
Above 4,500 ft.
Appendix C: RPTR155C Combi Instruction Manual
Appendix D: Special Requirements For Side-Wall
Vented Appliances In The Commonwealth
of Massachusetts
156
160
170
82
91
98
125
65
67
67
68
70
81
132
138
152
9
10
7
7
12
15
36
43
50
55
16
16
22
28
59
62
64
I. Product Description
This boiler is a stainless steel gas fired condensing boiler designed for use in forced hot water heating systems requiring supply water temperatures of 180°F or less. It is designed for installation on a wall. This boiler may be vented vertically or horizontally with combustion air supplied from outdoors. It is not designed for use in gravity hot water systems or systems containing significant amounts of dissolved oxygen.
Models RPTR085 through 270 provide central space heating and/or indirect domestic hot water (DHW) heating.
Model RPTR155C provides economical tankless domestic hot water (DHW) heating in addition to central space heating.
II. Specifications
A
DIMENSIONS
85-155 MBH 155 MBH COMBI 205-270 MBH
20" 23" 21"
19 13
16
"
VENT
CONNECTION
RELIEF
VALVE
TEMPERATURE/
PRESSURE GAUGE
ALTERNATE
SUPPLY/OUTLET
WATER CONNECTION
ALTERNATE
RETURN/INLET
WATER CONNECTION
AIR INTAKE
CONNECTION
SERVICE
ACCESS
PANEL
CONTROL
PANEL
33 5
16
"
"A"
INSIDE
OF WALL
GAS
CONNECTION
CONDENSATE
CONNECTION
CONDENSATE
TRAP CLEANOUT
RETURN/INLET
WATER CONNECTION
DRAIN
VALVE
Figure 2.1: General Configuration
OUTSIDE
OF WALL
SUPPLY/OUTLET
WATER CONNECTION
7
Supply Sensor
Flue
Temperature
Sensor
II. Specifications (continued)
Combustion Air Blower
Gas Valve
Air Proving Switch
Flue/Inlet Switch
Manual Gas
Shutoff Valve
Return Sensor
Transformer
High Voltage Fuse
High Voltage
PCB
Front Door and
Control Panel
Removed
Front Door Removed
Figure 2.2: Boiler Internal Component Locations
Programmed
Display
24 V Fuse
Low Voltage
PCB
Table 2.3: Specifications
Model *
RPTR085
RPTR110
RPTR155
RPTR155C
RPTR205
Maximum
Input
(MBH)
85
110
155
155
205
Minimum
Input
(MBH)
D.O.E.
Heating
Capacity
(MBH)
17
22
31
31
41
79
102
145
145
190
AHRI Net
Rating *
(MBH)
69
89
126
126
165
AFUE
95
95
95
95
95
Water
Volume
(Gallon)
2.6
2.5
3.0
3.0
5.1
Heating Water
Connection
Size (Copper
Sweat)
Gas
Connection
Size
(NPT)
1"
1"
1"
1"
1¼"
1/2"
1/2"
1/2"
1/2"
1/2"
Approx.
Net
Weight
(lb.)
110
115
120
140
135
Maximum
Allowable
Working
Pressure
(PSI)
30
30
30
30
80
RPTR270 270 54 251 218 95 4.6
1¼" 1/2" 145 80
* The Net AHRI Water Ratings shown are based on a piping and pickup allowance of 1.15. The manufacturer should be consulted before selecting a boiler for installations having unusual piping and pickup requirements, such as intermittent system operation, extensive piping systems, etc.
8
II. Specifications (continued)
Table 2.4: Vent Lengths
Model
Size
Nominal
Vent/Intake Size
(in)
2
Min Vent Length
(in)
Max Vent
Length (ft)
85
110
155
205
3
2
3
3
3
36
36
36
36
36
36
60
135
60
135
135
135
270 3 36
See Section VII “Venting” for additional requirements and details.
135
Approx.
Derate at Max Vent
(%)
7.6
3.7
9.7
4.2
7.2
9.7
11.3
III. Before Installing
1. Safe, reliable operation of this boiler depends upon installation by a professional heating contractor in strict accordance with this manual and the requirements of the authority having jurisdiction.
• In the absence of an authority having jurisdiction, installation must be in accordance with this manual
and the National Fuel Gas Code, ANSI Z223.1. In Canada, installation must be in accordance with the B149.1
Installation Code.
• Where required by the authority having jurisdiction, this installation must conform to the Standard for Controls
and Safety Devices for Automatically Fired Boilers (ANSI/ASME CSD-1).
2. Read Section VII “Venting” to verify that the maximum combustion air and exhaust pipe lengths will not be exceeded in the planned installation. Also verify that the vent terminal can be located in accordance with Section VII “Venting”.
3. Make sure that the boiler is correctly sized:
• For heating systems employing convection radiation (baseboard or radiators), use an industry accepted sizing method such as the I=B=R Guide RHH published by the Air-Conditioning, Heating and Refrigeration Institute
(AHRI).
• For new radiant heating systems, refer to the radiant tubing manufacturer’s boiler sizing guidelines.
• For system which includes an indirect water heater, make sure the boiler has the output called for by the indirect water heater manufacturer’s instructions.
4. All boilers are shipped from the factory configured for 0 - 4,500 ft. altitude. Use sea level input rate for 0 - 2,000 ft. Boiler will automatically derate approximately 1.7% per 1,000 ft. from 2,000 ft. to 4,500 ft. For high altitude installation above 4,500 ft., see Appendix B.
5. All boilers are shipped from the factory configured for use with natural gas. They may be converted for use with LP gas (“propane”) using a combustion analyzer in accordance with the instructions in Appendix A.
9
III. Before Installing (continued)
DANGER
• Do not attempt to operate this boiler on LP gas without converting it in accordance with the instructions shown in Appendix A.
• Do not attempt to convert this boiler to LP gas without the use of a combustion analyzer.
• Failure to follow the conversion instructions in Appendix A will result in operation of the boiler at unsafe Carbon Monoxide (CO) levels and may result in personal injury or loss of life. Improper conversion may also result in unreliable operation, resulting in property damage.
• Before attempting to operate this boiler at altitudes above 4,500 ft., follow instructions shown in
Appendix B of this manual.
NOTICE
This product must be installed by a licensed plumber or gas fitter when installed within the
Commonwealth of Massachusetts. See Appendix D for additional important information about installing this product within the Commonwealth of Massachusetts.
IV. Locating the Boiler
1. Observe the minimum clearances shown in Figure 4.1. These clearances apply to combustible construction as well as non-combustible walls, floors, ceilings and doors.
2. Note the recommended service clearances in Figure 4.1. These service clearances are recommended, but may be reduced to the combustible clearances provided:
a. Access to the front of the boiler is provided through a door.
b. Access is provided to the condensate trap located beneath the boiler.
Note that servicing the boiler will become increasingly difficult as these service clearances are reduced.
3. Observe the following clearances from piping to combustible construction:
Non-concentric vent (exhaust): ¼"
Air intake piping: 0"
Hot water piping: ¼"
4. The relief valve and gauge must be installed in the location shown in Figure 2.1 and must be in the same space as the
boiler.
5. The boiler should be located so as to minimize the length of the vent system.
6. The combustion air piping must terminate where outdoor air is available for combustion and away from areas that will contaminate combustion air. Avoid areas near chemical products containing chlorine, chloride based salts, chloro/fluoro carbons, paint removers, cleaning solvents and detergents.
10
1
2
"
IV. Locating the Boiler (continued)
SERVICE
ACCESS
PANEL
FRONT VIEW PROVIDE ACCESS TO THIS AREA
FOR INSPECTION AND CLEANOUT
OF CONDENSATE TRAP
*RIGHT SIDE CLEARANCE MAY BE REDUCED TO 1/2"
HOWEVER RELIEF VALVE MUST REMAIN IN SAME
SPACE AS BOILER.
Figure 4.1: Minimum Clearances To Combustible Construction
11
12
V. Mounting The Boiler
A. Wall Mounting
CAUTION
• Two people are required to safely lift this boiler onto the wall mounting hook.
• Make sure that wall mounting hook is anchored to a structure capable of supporting the weight of the boiler and attached piping when filled with water. Jurisdictions in areas subject to earthquakes may have special requirements for supporting this boiler. These local requirements take precedence over the requirements shown below.
1. If the boiler is installed on a framed wall, minimum acceptable framing is 2 x 4 studs on 16" centers. The boiler mounting holes are on 16" centers for installation between two studs at the standard spacing. In cases where the boiler cannot be centered between the studs, or where the studs are spaced closer than 16" apart, the boiler may be anchored to ¾" plywood or horizontal 2 x 4’s anchored to the studs.
2. 5/16" x 2" lag screws and washers are provided for mounting this boiler. These lag screws are intended for mounting the boiler directly onto studs covered with ½" sheathing. When the boiler is attached to other types of construction, such as masonry, use fasteners capable of supporting the weight of the boiler and attached piping in accordance with good construction practice and applicable local codes.
3. Make sure that the surface to which the boiler is mounted is plumb.
4. Before mounting the boiler, make sure that wall selected does not have any framing or other construction that will interfere with the vent pipe penetration.
5. Once a suitable location has been selected for the boiler, and any needed modifications have been made to the wall, use
Figure 5.1 to locate holes “A” and “B”. Make sure that the horizontal centerline of these holes is level. Holes “C” and
“D” may also be drilled at this time or after the boiler is hung on the wall. If the 5/16" x 2" lag screws are used, drill
3/16" pilot holes.
6. The wall mounting hook is used to secure the boiler to the shipping pallet. Remove this hook from the pallet and secure to the wall using the 5/16" x 2" lag screws and washers, or other suitable anchors as appropriate (Figure 5.2).
Make sure the hook is level.
7. Hang the boiler on the wall hook as shown in Figure 5.2.
8. If not already done in Step (5) locate and drill holes “C” and “D” using the obround slots in the bottom mounting flange. Secure the bottom flange to the wall using the 5/16" x 2" lag screws, or other fasteners as appropriate (Figure
5.2).
9. Verify that the front of the boiler is plumb. If it is not, install washers at holes “C” and “D” between the bottom mounting flange and the wall to adjust.
V. Mounting The Boiler (continued)
Figure 5.1 Wall Layout / Mounting Hole Location
13
V. Mounting The Boiler (continued)
14
Figure 5.2 Boiler Mounting Bracket Installation / Boiler Wall Mounting
VI . Air for Ventilation
WARNING
Outdoor combustion air must be piped to the air intake. Never pipe combustion air from areas containing contaminates such as swimming pools and laundry room exhaust vents. Contaminated combustion air will damage the boiler and may cause property damage, personal injury or loss of life.
Air for combustion must always be obtained directly from outdoors. See Section VII “Venting” for intake piping.
Adequate air for ventilation will be present if the clearances specified in this manual are maintained. If this boiler is installed in a room with other appliances, provide adequate air for combustion and/or ventilation air in accordance with the manufacturer’s installation manual or applicable code.
15
VII. Venting
WARNING
Asphyxiation Hazard. Failure to vent this boiler in accordance with these instructions could cause products of combustion to enter the building resulting in severe property damage, personal injury or death.
Do not interchange vent systems or materials unless otherwise specified.
The use of thermal insulation covering vent pipe and fittings is prohibited.
Do not use a barometric damper, draft hood or vent damper with this boiler.
When using the CPVC/PVC vent option, the use of CPVC is required when venting in vertical or horizontal chase ways.
Do not locate vent termination where exposed to prevailing winds. Moisture and ice may form on surface around vent termination. To prevent deterioration, surface must be in good repair (sealed, painted, etc.).
Do not locate air intake vent termination where chlorines, chlorofluorocarbons (CFC’s), petroleum distillates, detergents, volatile vapors or other chemicals are present. Severe boiler corrosion and failure will result.
The use of cellular core PVC (ASTM F891), cellular core CPVC or Radel (polyphenolsulfone) is prohibited.
Do not locate vent termination under a deck.
Do not reduce specified diameters of vent and combustion air piping.
When installing vent pipe through chimney, as a chase, no other appliance can be vented into the chimney.
Do not allow low spots in the vent where condensate may pool.
DANGER
Failure to follow this warning could result in asphyxiation and/or carbon monoxide poisoning. Correct venting material and installation is required for proper vent operation. PVC Vent Systems must include at least 30 inches of CPVC and one CPVC elbow between the boiler and PVC vent piping. See this Section, VII.
Venting for complete information.
A. Vent System Design
There are three basic ways to vent this boiler:
• Horizontal (“Side Wall”) Twin Pipe Venting (Figure 7.0a) - Vent system exits the building through an outside wall.
Combustion air and flue gas are routed between the boiler and the terminal(s) using separate pipes for at least part of the way. A summary of Horizontal Twin Pipe venting options is shown in Table 7.5.
• Vertical Twin Pipe Venting (Figure 7.0b) - Vent system exits the building through a roof. Combustion air and flue gas are routed between the boiler and the terminal(s) using separate pipes for at least part of the way. A summary of Vertical
Twin Pipe venting options is shown in Table 7.13
• Split Venting (Figure 7.0c) - Exhaust system exits the building through a roof, and combustion air is drawn from a terminal mounted on the side wall. A summary of split venting options is shown in Table 7.21
All of these systems are considered “direct vent” because the air for combustion is drawn directly from the outdoors into the boiler. One of the vent option columns in Tables 7.5, 7.13, 7.21 must match the planned vent and air intake system exactly.
Design details applying to all vent systems are shown in this section. Observe all design requirements in this section, as well as those unique to the type of system being installed:
• B - Design Requirements Unique to Horizontal Twin Pipe Vent Systems
• C - Design Requirements Unique to Vertical Twin Pipe Vent Systems
• D - Design Requirements Unique to Split Vent Systems
16
VII. Venting A. Vent System Design (continued)
Figure 7.0a: Horizontal Twin Pipe
Figure 7.0b: Vertical Twin Pipe
Figure 7.0c: Split Venting
17
VII. Venting A. Vent System Design (continued)
1. Listed Vent Systems and Materials – The following materials and vent systems may be used to vent this boiler:
• CPVC – Use only CPVC listed to ASTM F441. In Canada, this pipe must also be listed to ULC S636.
• PVC – PVC may be used only as permitted in this manual. All PVC must be listed to ASTM D2665. At least 30" of
CPVC pipe, and at least one CPVC elbow, must be installed between the boiler’s vent connection and the PVC pipe. Use of foam core PVC is not permitted for venting. PVC vent pipe may not be used to vent this boiler in Canada.
• DuraVent PolyPro - ULC S636 listed PolyPropylene special gas vent system.
• Selkirk Polyflue - ULC S636 listed PolyPropylene special gas vent system.
• Centrotherm InnoFlue SW - ULC S636 listed PolyPropylene special gas vent system.
• Use PVC and/or CPVC for the air intake system. PVC may be used for all air intake piping between the intake terminal and the boiler.
• When CPVC and/or PVC pipe is used, it must be joined using primer and cement that is listed for use with the pipe material being joined (PVC, CPVC, or CPVC to PVC).
2. Maximum Vent and Air Intake Lengths - The maximum length of the vent air intake piping depends upon the vent option selected and the boiler size. See Tables 7.5, 7.13 or 7.21
for the maximum vent lengths. These maximum lengths apply to both the vent and intake piping (e.g. Option 1 may have up to 60ft of intake and 60ft of vent piping). For all vent systems, the lengths shown in Tables 7.5, 7.13 and 7.21 are in addition to the first 90° elbow. If more elbows are desired, the maximum allowable vent length must be reduced by the amount shown in Table 7.1 for each additional elbow used.
Termination fittings are never counted.
It is recommended that all field supplied PVC or CPVC elbows be “1/4 Bend” (Sanitary 90° El) or “Long Sweep 1/4
Bend” type elbows (Figure 7.2). In this manual “sanitary” and “long sweep” elbows are treated as having the same equivalent length.
Example:
A 3" twin pipe horizontal CPVC/PVC vent system is planned for a horizontally vented 155MBH model which has the following components in the vent system:
• 1 ft CPVC Straight Pipe
• 90 CPVC Elbow (short bend)
• 1-1/2 ft CPVC Straight Pipe
• Coupling
• 10 ft PVC Straight Pipe
• 90 PVC Elbow (Sanitary Elbow Design)
• 15 ft PVC Straight Pipe
• PVC Coupling Terminal
The Vent Option #2 column in Table 7.5 describes a horizontal direct vent system using 3" CPVC and PVC pipe. From this column, we see that the boiler may have a vent length of up to 135ft. The first CPVC 90 degree elbow is not considered. From
Table 7.1, we see that the equivalent length of the 90 PVC elbow is 4ft and that the equivalent length of the coupling is 0ft.
The total equivalent length of the planned venting system is therefore:
1ft (Straight CPVC) + 0ft (first short bend CPVC 90 Elbow) + 1.5ft (Straight CPVC) + 0ft (Coupling) + 10ft (Straight PVC)
+ 4ft (PVC 90 Sanitary Elbow) + 15ft (Straight PVC) + 0ft (Coupling Terminal) = 31.5ft.
Since Table 7.1 shows a maximum allowable vent length of 135ft, the planned vent system length is acceptable
The flex venting used on some of the Vertical Twin Pipe and Split Vent Options also reduces the maximum allowable vent length. See Sections VII-C or VII-D for details.
NOTICE
Do not exceed maximum vent/combustion air system length. Refer to Tables 7.1 and 7.13 in this section for maximum vent/combustion air system length.
Use only vent and combustion air terminals and terminal locations shown in Tables 7.5, 7.13, and
7.21 and related Figures in this section.
18
VII. Venting A. Vent System Design (continued)
3. Minimum Vent and Air Intake Lengths - Observe the minimum vent lengths shown in Tables 7.5, 7.13 and 7.21.
4. Clearances to Combustibles - Maintain the following clearances from the vent system to combustible construction:
• Vent - 1/4" (also observe clearances through both combustible and non-combustible walls - see 9 below)
• Air Intake - 0"
• Concentric Portion of Concentric Terminals - 0"
5. Pitch of Horizontal Vent Piping - Pitch all horizontal vent piping so that any condensate which forms in the piping will run towards the boiler.
• Pitch CPVC/PVC vent piping 1/4" per foot.
• Pitch PolyPropylene vent piping 5/8" per foot.
Les chaudières de catégories I, II et IV doivent présenter des tronçons horizontaux dont la pente montante est d’au moins
5/8 po par pied (52 mm/m) entre la chaudière et l’évent.
Table 7.1: Vent/ Air Intake Fitting Equivalent Length
CPVC/PVC Fitting
2" 90° Elbow (“Sanitary Bend”)
3" 90° Elbow (“Sanitary Bend”)
2" 90° Elbow (“Short Bend” )
3" 90° Elbow (“Short Bend”)
2" 45° Elbow
3" 45° Elbow
2" Coupling
3" Coupling
Equivalent Length (ft)
2.6
4.0
6.0
10.0
1.5
2.0
0.0
0.0
PolyPro, Polyflue or InnoFlue
Vent Fitting
2" 90° Elbow
3" 90° Elbow
2" 45° Elbow
3" 45° Elbow
Equivalent Length (ft)
4.5
8.7
2.5
4.6
Figure 7.2: CPVC and PVC Elbows
19
VII. Venting A. Vent System Design (continued)
7. Supporting Pipe - Vertical and horizontal sections of pipe must be properly supported. Maximum support spacing is as follows:
• Support CPVC/PVC horizontally and vertically every 4 feet.
• Support DuraVent PolyPro horizontally near the female end of each straight section of pipe and vertically every 10 feet.
• Support Centrotherm InnoFlue horizontally every 39 inches with additional supports at elbows and vertically every 78".
• Support 2" Selkirk Polyflue horizontally every 30". Support 3" Polyflue horizontally every 39". Support vertical runs of both 2" and 3" Polyflue every 16 ft.
Les instructions d´installation du système d´évacuation doivent préciser que les sections horizontales doivent être supportées pour prévenir le fléchissement. Les méthodes et les intervalles de support doivent être spécifiés. Les instructions divent aussi indiquer les renseignements suivants:
• les chaudières de catégories II et IV doivent être installées de façon à empêcher l´accumulation de condensat: et
• si nécessaire, les chaudières de catégories II et IV doivent être pourvues de dispositifs d´évacuation du condensat.
8. Allowing for Thermal Expansion -
• For CPVC/PVC pipe design the vent system to allow 3/8" of thermal expansion for every 10ft of CPVC/PVC pipe.
The boiler will always act as an anchor to one end of the vent system. If at all possible, select and install hangers and wall thimbles so that the vent system can expand towards the terminal. When a straight run of pipe exceeds 20ft and must be restrained at both ends, an offset or expansion loop must be provided ( Figures 7.3a, 7.3b). When a straight horizontal run of pipe exceeds 20ft and is restrained at one end with an elbow at the other, avoid putting a hanger or guide less than “Y” inches from the elbow in the adjoining straight section (Figure 7.3c). Thermal expansion fittings are not permitted.
• When properly assembled expansion of PolyPro, Polyflue and InnoFlue vent systems is accommodated at the joints. See
Part VII-F, G & H of this manual for details.
9. Running PVC Vent Pipe Inside Enclosures and Through Walls - PVC vent pipe must be installed in a manner that permits adequate air circulation around the outside of the pipe:
• Do not enclose PVC venting - Use CPVC in enclosed spaces, even if PVC is installed upstream.
• PVC venting may not be used to penetrate combustible or non-combustible walls unless all of the following conditions are met: a. The wall penetration is at least 66 inches from the boiler as measured along the vent.
b. The wall is 12" thick or less c. An airspace of at least that shown in Figure 7.4 is maintained around the OD of the vent.
If any of these conditions cannot be met, use CPVC for the wall penetration.
10. Vent Manufacturer’s Instructions – The vent system manufacturer may have additional vent system design requirements.
Read and follow the vent manufacturer’s instructions in addition to those shown here. Where a conflict arises between the two sets of instructions, the more restrictive requirements shall govern.
20
VII. Venting A. Vent System Design (continued)
Figure 7.3a
Figure 7.3b
Figure 7.3c
Figure 7.3: Expansion Loops for CPVC/PVC Pipe
Figure 7.4: Wall Penetration Clearances for PVC Vent Pipe
21
VII. Venting B. Design Requirements Unique to Horizontal Twin Pipe Venting Systems (continued)
B. Design Requirements Unique to Horizontal Twin Pipe Venting Systems
Table 7.5 summarizes all horizontal twin pipe vent options. Illustrations of horizontal twin pipe vent systems are shown in
Figures 7.6 – 7.10. In addition to the requirements in Part VII-A, observe the following design requirements:
1. Permitted Terminals for Horizontal Venting:
Terminal Option A: Fittings (Acceptable for Vent Options 1-8) – Vent terminates in a plain end (coupling for PVC, bell end for PolyPro, Polyflue and plain end pipe for InnoFlue). Intake terminates in a PVC 90 sweep elbow pointing down.
Outer edge of both terminals must be within 10" of the wall surface (Figures 7.6, 7.9). The section of DuraVent PolyPro,
Centrotherm InnoFlue or Selkirk Polyflue exposed to the outdoors must be UV resistant.
Use of rodent screens is generally recommended for both terminations. Two rodent screens suitable for 3" PVC terminals are installed as shown in Figure 7.27. If 2" CPVC is used, these screens can be cut to fit into the smaller fittings. Rodent screens
(“bird guards”) for PolyPro, InnoFlue and Polyflue are as follows:
Size/Vent System Rodent Screen (“Bird Guard”)
2" PolyPro
3" PolyPro
2" Polyflue
DuraVent # 2PPS-BG
DuraVent # 3PPS-BG
Selkirk # 2PF-HVST
3" Polyflue
2" InnoFlue
3" InnoFlue
Selkirk # 3PV-HVST
Centrotherm # IASPP02
Centrotherm # IASPP03
If necessary to achieve required clearance above grade, CPVC or CPVC/PVC vent systems may be terminated using fittings on snorkels as shown in Figure 7.12. When this is done, the equivalent length of all pipe on the exterior of the building, except for the terminal fittings themselves, must be counted when calculating the equivalent length. The maximum vertical run of the snorkel is 7 feet. Brace both the vent and inlet piping if required. PolyPro, InnoFlue and Polyflue may not be snorkeled.
Terminal Option B: Ipex Low Profile Terminal (Acceptable for Vent Options 1,2) – This terminal is shown in Figure 7.7. If the terminal is oriented vertically (alternate orientation shown in Fig 7.7) the exhaust opening must be on the top as shown.
See Part VII-E of this manual and the Ipex instructions provided with the terminal, for installation details.
Terminal Option C: Diversitech “Low Profile” Terminal (Acceptable for Vent Options 1,2) – This terminal is shown in Figure
7.7. If the terminal is oriented vertically (alternate orientation shown in Fig 7.7) the exhaust opening must be on the top as shown. See Part VII-E of this manual and the Diversitech instructions provided with the terminal, for installation details.
Terminal Option D: Ipex FGV Concentric Terminal (Acceptable for Vent Options 1,2) - This terminal is shown in Figure 7.8 and may be used with CPVC/PVC vent systems. This terminal is available in various lengths and in both PVC and CPVC.
Terminals acceptable for use with these vent options are as follows:
Ipex PN
196005
196105
196125
196006
196106
196116
197107
197117
FGV Concentric Terminal Description
2 x 16" PVC
2 x 28" PVC
2 x 40" PVC
3 x 20" PVC
3 x 32" PVC
3 x 44" PVC
3 x 32" CPVC
3 x 44" CPVC
See Part VII-E of this manual and the Ipex instructions provided with the terminal, for installation details.
Terminal Option E: Diversitech Concentric Terminal (Acceptable for Vent Options 1,2) - This terminal is shown in Figure 7.8 and may be used with CPVC/PVC vent systems. See Part VII-E of this manual and the Diversitech instructions provided with the terminal, for installation details.
Terminal Option F: DuraVent PolyPro Concentric Terminal (Acceptable for Vent Options 3,4) - This terminal is shown in
Figure 7.10 and may be used with DuraVent 2" or 3" PolyPro vent systems. See Part VII-F of this manual and the DuraVent instructions provided with the terminal, for installation details.
22
'
VII. Venting B. Design Requirements Unique to Horizontal Twin Pipe Venting Systems (continued)
Table 7.5: Summary of Horizontal Twin Pipe Venting Options
Vent Option
Illustrated in Figure
Pipe
Penetration through
Structure
Vent
Intake
1
7.6, 7.7,
7.8
Wall
Wall
2
7.6, 7.7,
7.8
Wall
Wall
3 4
7.9, 7.10 7.9, 7.10
Wall
Wall
Wall
Wall
Material
Vent
CPVC/
PVC
(Note 2)
CPVC/
PVC
(Note 2)
DuraVent
PolyPro
(Rigid)
DuraVent
PolyPro
(Rigid)
5
7.9
Wall
Wall
Selkirk
Polyflue
6
7.9
Wall
Wall
Selkirk
Polyflue
Nominal
Diameter
Intake
Vent
Intake
Min Equivalent Vent Length:
85
110
155
PVC
2"
2"
30"
30"
Model Sizes
205
Not
Permitted
270
Max Equivalent Vent Length (Note 1):
85 60ft
60ft
Model Sizes
110
155
205
270
Not
Permitted
Terminal
Option A
(Fittings)
Vent
Intake
Terminal Option B
(Ipex Low Profile)
Terminal Option C
(Diversitech HVENT)
Terminal Option D
(Ipex FGV Concentric)
Terminal Option E
(Diversitech CVENT)
Terminal Option F
(DuraVent Horizontal
Concentric)
Coupling w/screen
(Note 3)
Elbow w/screen
(Note 3)
Ipex #
196984
PVC
3"
3"
30"
30"
30"
30"
30"
135ft
135ft
135ft
135ft
135ft
Coupling w/screen
(Note 3)
Elbow w/screen
(Note 3)
Ipex
#196985
HVENT-2 HVENT-3
Ipex
196105
Ipex
196006
CVENT-2 CVENT-3
Not
Permitted
PVC
2"
2"
30"
30"
Not
Permitted
30"
30"
30"
30"
30"
60ft
60ft
Not
Permitted
2PPS-12B or
2PPS-36B w/screen
135ft
135ft
135ft
135ft
135ft
3PPS-12B or
3PPS-36B w/screen
60ft
60ft
Not
Permitted
2PF-10UV or
2PF-39UV w/screen
135ft
135ft
135ft
135ft
135ft
3PF-10UV or
3PF-39UV w/screen
Elbow w/screen
Not
Permitted
Not
Permitted
Not
Permitted
Not
Permitted
PVC
3"
3"
30"
30"
30"
30"
30"
Elbow w/screen
Not
Permitted
Not
Permitted
Not
Permitted
Not
Permitted
Not
Permitted 2PPS-HK 3PPS-HK
PVC
2"
2"
30"
30"
Not
Permitted
Elbow w/screen
Not
Permitted
Not
Permitted
Not
Permitted
Not
Permitted
Not
Permitted
PVC
3"
3"
Elbow w/screen
Not
Permitted
Not
Permitted
Not
Permitted
Not
Permitted
Not
Permitted
7
7.9
Wall
Wall
Centrotherm
InnoFlue
SW
PVC
2"
2"
30"
30"
Not
Permitted
60ft
60ft
Not
Permitted
ISEP02 or
ISEP0239 w/screen
Elbow w/screen
Not
Permitted
Not
Permitted
Not
Permitted
Not
Permitted
Not
Permitted
8
7.9
Wall
Wall
Centrotherm
InnoFlue
SW
PVC
3"
3"
30"
30"
30"
30"
30"
135ft
135ft
135ft
135ft
135ft
ISEP03 or
ISEP0339 w/screen
Elbow w/screen
Not
Permitted
Not
Permitted
Not
Permitted
Not
Permitted
Not
Permitted
Notes:
1. Max vent lengths shown also apply to the intake. For example, Vent Option #1 may have up to 60ft of vent pipe and also up to
60 ft of intake pipe.
2. At least 30" of CPVC pipe, and at least one CPVC elbow, must be installed between the boiler's vent connection and PVC pipe.
Downstream vent pipe can be PVC except as noted in text.
3. PVC Terminal coupling and inlet elbow may be offset on snorkels as shown in Figure 7.12.
23
VII. Venting B. Design Requirements Unique to Horizontal Twin Pipe Venting Systems (continued)
2. Horizontal Vent and Air Intake Terminal Location - Observe the following limitations on the vent terminal location (also see
Figure 7.11). When locating a concentric terminal, observe the limitations outlined below for “vent terminals”.
• Vent terminal must be at least 1 foot from any door, window, or gravity inlet into the building.
• When Terminal Option A (fittings) are used, maintain the correct clearance and orientation between the intake and exhaust terminals. If possible, locate vent and combustion air terminals on the same wall to prevent nuisance shutdowns. If not, boiler may be installed with roof vent terminal and sidewall combustion air terminal (see Paragraph
D). When installed on the same wall, locate exhaust vent terminal at same height or higher than combustion air intake terminal. Horizontal separation: Recommended: 36", Minimum: 12", Maximum: none. Minimum horizontal separation of 12" is required regardless of vertical separation.
• The bottom of all terminals must be at least 12" above the normal snow line. In no case should they be less than 12" above grade level.
• The bottom of the vent terminal must be at least 7 feet above a public walkway.
• Do not install the vent terminal directly over windows or doors.
• The bottom of the vent terminal must be at least 3 feet above any forced air inlet located within 10 feet.
• USA Only: A clearance of at least 4 feet horizontally must be maintained between the vent terminal and gas meters, electric meters, regulators, and relief equipment. Do not install vent terminal over this equipment. In Canada, refer to
B149.1 Installation Code for clearance to meters, regulators and relief equipment.
• Do not locate the vent terminal under decks or similar structures.
• Top of terminal must be at least 24" below ventilated eves, soffits and other overhangs. In no case may the overhang depth exceed 48". Where permitted by the authority having jurisdiction and local experience, the terminal may be located closer to unventilated soffits. For the minimum vertical separation which depends upon the depth of the soffit, see Figure 7.11.
• Vent terminal must be at least 6 feet from an inside corner.
• Under certain conditions, water in the flue gas may condense, and possibly freeze, on objects around the vent terminal including on the structure itself. If these objects are subject to damage by flue gas condensate, they should be moved or protected.
• Install the vent and air intake terminals on a wall away from the prevailing wind. Reliable operation of this boiler cannot be guaranteed if these terminals are subjected to winds in excess of 40 mph.
• Air intake terminal must not terminate in areas that might contain combustion air contaminates, such as near swimming pools. See WARNING on page 15.
CPVC VENT PIPE
(FIRST 30" + ELBOW)
PVC VENT PIPE
PITCH VENT PIPE 1
4
" PER
FOOT TOWARDS BOILER
PVC AIR
INTAKE PIPE
TRIM PLATE - PROVIDE
FOR EXPANSION AND
CLEARANCE THROUGH
WALL AS NEEDED
BOILER ROOM
PITCH INTAKE AWAY FROM
BOILER IF POSSIBLE
RECOMMEND EXHAUST MIN.
12" ABOVE INTAKE. MAY
REDUCE TO 0" IF NEEDED.
TRIM
COLLAR
EXHAUST TERMINAL
WITH RODENT SCREEN
INLET TERMINAL WITH
RODENT SCREEN
ALTERNATE INLET
TERMINAL LOCATION
BUILDING EXTERIOR
24
Figure 7.6: Horizontal CPVC/PVC Venting, (Vent Options #1 & 2, Terminal Option A)
VII. Venting B. Design Requirements Unique to Horizontal Twin Pipe Venting Systems (continued)
Figure 7.7: Horizontal CPVC/PVC Venting with Low Profile Terminal,
(Vent Options #1 & 2, Terminal Options B & C)
Figure 7.8: Horizontal CPVC/PVC Venting with Concentric Vent Terminal,
(Vent Options #1 & 2, Terminal Options D & E)
25
VII. Venting B. Design Requirements Unique to Horizontal Twin Pipe Venting Systems (continued)
Figure 7.9: Duravent PolyPro, Selkirk, Polyflue or Centrotherm InnoFlue Horizontal Venting
(Vent Option #3 - 8, Terminal Option A)
26
Figure 7.10: Duravent PolyPro Horizontal Venting with Concentric Terminal,
(Vent Options #3 & 4, Terminal Option F)
VII. Venting B. Design Requirements Unique to Horizontal Twin Pipe Venting Systems (continued)
27
VII. Venting C. Design Requirements Unique to Vertical Venting Systems (continued)
Figure 7.12: Snorkel Terminal Configuration (CPVC/PVC Vent Systems Only)
C. Design Requirements Unique to Vertical Venting Systems
Table 7.13a summarizes all vertical twin pipe vent options. Table 7.13.b summarizes vent options in which an abandoned
B-vent chimney is used both as a chase for the vent pipe and as a conduit for combustion air.
In addition to the requirements in Part VII-A, observe the following design requirements:
1. Permitted Terminals for Vertical Venting
Terminal Option H: Fittings (Acceptable for Vent Options 10-17) – Vent terminates in a plain end (coupling for PVC, bell end for PolyPro, Polyflue and plain end pipe for InnoFlue). Intake terminates in a PVC 180 elbow pointing down (two sweep
90’s may be substituted). Observe the clearances from the roof, and normal snow line on the roof, shown in Figures 7.15 and
7.17. The section of PolyPro, Polyflue or InnoFlue exposed to the outdoors must be UV resistant.
Use of rodent screens is generally recommended for both terminations. Two rodent screens suitable for 3" PVC terminals are installed as shown in Figure 7.28. If 2" CPVC is used, these screens can be cut to fit into the smaller fittings. Rodent screens (“bird guards”) for PolyPro, Polyflue and InnoFlue are as follows:
Size/Vent System Rodent Screen (“Bird Guard”)
2" PolyPro
3" PolyPro
2" Polyflue
3" Polyflue
2" InnoFlue
3" InnoFlue
DuraVent # 2PPS-BG
DuraVent # 3PPS-BG
Selkirk # 2PF-HVST
Selkirk # 3PV-HVST
Centrotherm # IASPP02
Centrotherm # IASPP03
Terminal Option I: Ipex FGV Concentric Terminal (Acceptable for Vent Options 10 & 11) - This terminal is shown in Figure
7.16 and may be used with CPVC/PVC vent systems. Use a compatible roof flashing and storm collar in accordance with the Ipex instructions for this terminal. This terminal is available in various lengths and in both PVC and CPVC. Terminals acceptable for use with these vent options are as follows:
Ipex PN
196005
196105
196125
196006
196106
196116
197107
197117
FGV Concentric Terminal Description
2 x 16" PVC
2 x 28" PVC
2 x 40" PVC
3 x 20" PVC
3 x 32" PVC
3 x 44" PVC
3 x 32" CPVC
3 x 44" CPVC
See Part VII-E of this manual and the Ipex instructions provided with the terminal, for installation details.
28
VII. Venting C. Design Requirements Unique to Vertical Venting Systems (continued)
Table 7.13a: Summary of Vertical Twin Pipe Venting Options
Option
Illustrated in Figure
Pipe
Penetration through
Structure
Vent
Intake
10
7.15, 717 7.15, 7.17 7.17, 7.18 7.17, 7.18
Roof
Roof
11
Roof
Roof
12
Roof
Roof
13
Roof
Roof
Material
Vent
CPVC/
PVC
(Note 2)
Nominal
Diameter
Intake
Vent
Intake
Min Equivalent Vent Length:
PVC
2"
2"
Model Sizes
85
110
155
205
30"
30"
Not
Permitted
270
Max Equivalent Vent Length (Note 1):
Model Sizes
85
110
155
205
270
60ft
60ft
Not
Permitted
Terminal Option H
(Fittings)
Vent
Coupling w/Screen
CPVC/
PVC
(Note 2)
PVC
3"
3"
30"
30"
30"
30"
30"
DuraVent
PolyPro
(Rigid)
PVC
2"
2"
30"
30"
Not
Permitted
DuraVent
PolyPro
(Rigid)
PVC
3"
3"
30"
30"
30"
30"
30"
14
7.17
Roof
Roof
Selkirk
Polyflue
PVC
2"
2"
30"
30"
Not
Permitted
15
7.17
Roof
Roof
Selkirk
Polyflue
PVC
3"
3"
30"
30"
30"
30"
30"
16
7.17
Roof
Roof
Centrotherm
InnoFlue
SW
PVC
2"
2"
30"
30"
Not
Permitted
17
7.17
Roof
Roof
Centrotherm
InnoFlue
SW
PVC
3"
3"
30"
30"
30"
30"
30"
135ft
135ft
135ft
135ft
135ft
Coupling w/Screen
60ft
60ft
Not
Permitted
2PPS-12B or
2PPS-36B w/Screen
135ft
135ft
135ft
135ft
135ft
3PPS-12B or
3PPS-36B w/Screen
60ft
60ft
Not
Permitted
2PF-10UV or
2PF-39UV w/Screen
135ft
135ft
135ft
135ft
135ft
3PF-10UV or
3PF-39UV w/Screen
60ft
60ft
Not
Permitted
135ft
135ft
135ft
135ft
135ft
ISEP02 or
ISEP0239 w/Screen
ISEP03 or
ISEP0339 w/Screen
Terminal Option I
(Ipex FGV Concentric)
Terminal Option J
(Diversitech CVENT
Concentric)
Terminal Option K
(DuraVent Vertical
Concentric)
Ipex
196105
(Note 3)
180 Elbow w/Screen
Ipex
196006
(Note 3)
180 Elbow w/Screen
Not
Permitted
CVENT-2 CVENT-3
Not
Permitted
180 Elbow w/Screen
Not
Permitted
Not
Permitted
180 Elbow w/Screen
Not
Permitted
Not
Permitted
Not
Permitted
Not
Permitted
2PPS-VK 3PPS-VK
Not
Permitted
180 Elbow w/Screen
180 Elbow w/Screen
180 Elbow w/Screen
Not
Permitted
Not
Permitted
Not
Permitted
Not
Permitted
Not
Permitted
Not
Permitted
Not
Permitted
Not
Permitted
Not
Permitted
Notes:
1. Max vent lengths shown also apply to the intake. For example, Vent Option #1 may have up to 60ft of vent pipe and also up to 60 ft of
intake pipe.
2. At least 30" of CPVC pipe, and at least one CPVC elbow, must be installed between the boiler's vent connection and PVC pipe.
Downstream vent pipe can be PVC except as noted in text.
3. Ipex FGV Concentric Terminal available in various lengths and also CPVC (see text).
All vertical terminals require compatible roof flashing and storm collars.
29
VII. Venting C. Design Requirements Unique to Vertical Venting Systems (continued)
Table 7.13b: Summary of Vertical “B-Vent Air Chase” Vent Options
(B-Vent Chase MUST Be Sealed)
Option
Illustrated in Figure
Pipe Penetration
Through Structure
Vent
Intake
18
7.19
Roof
Roof
19
7.19
Roof
Roof
20
7.20
Roof
Roof
Material
Vent
Nominal Diameter
Intake
Vent
Intake
Min B Vent ID
Min Equivalent Vent Length:
85
110
Model Sizes 155
205
270
Max Equivalent Vent Length (Note 1):
85
110
Model Sizes 155
205
270
DuraVent
PolyPro (Rigid/
Flex)
B Vent/PVC
2"
2" or 3"
5"
30"
30"
Not Permitted
60ft
60ft
Not Permitted
Vent Manufacturer’s PN for Flex
Termination/Components Required
2PPS-VFT
2PPS-BV*
2PPS-FLEX**
DuraVent
PolyPro (Rigid/
Flex)
B Vent/PVC
3"
3"
6"
Centrotherm
InnoFlue SW/
Flex
B Vent/PVC
2"
2" or 3"
5"
30"
30"
30"
30"
30"
135ft
135ft
135ft
135ft
135ft
3PPS-VFT
3PPS-BV*
3PPS-FLEX**
30"
30"
Not Permitted
60ft
60ft
Not Permitted
IFBK02****
IAWP02B
21
7.20
Roof
Roof
Centrotherm
InnoFlue
SW/Flex
B Vent/PVC
3"
3"
6"
30"
30"
30"
30"
30"
135ft
135ft
135ft
135ft
135ft
IFBK03****
IAWP03B
* Specify size of B vent (e.g. 2PPS-BV
** Specify length in feet.
6 is for use with 6" B vent)
**** Specify Flex length and B-vent diameter (e.g. IFBK02 2505 includes 25ft of flex and used with 5" B vent)
Note 1: Max vent lengths shown also apply to the intake. Flex vent reduces the maximum allowable vent length.
See equivalent lengths for flex vent shown in Table 7.14 and sizing example on page 32.
NOTICE
Vertical venting and combustion air roof penetrations (where applicable) require the use of roof flashing and storm collar, which are not supplied with the boiler, to prevent moisture from entering the structure.
30
VII. Venting C. Design Requirements Unique to Vertical Venting Systems (continued)
Terminal Option J: Diversitech Concentric Terminal (Acceptable for Vent Options 10 & 11) - This terminal is shown in
Figure 7.16 and may be used with CPVC/PVC vent systems. See Part VII-E of this manual and the Diversitech instructions provided with the terminal, for installation details.
Terminal Option K: DuraVent PolyPro Concentric Terminal (Acceptable for Vent Options 12, 13) - This terminal is shown in Figure 7.18 and may be used with DuraVent 2" or 3" PolyPro vent systems. Use a compatible DuraVent roof flashing and storm collar in accordance with the DuraVent instructions for this terminal See Part VII-F of this manual and the DuraVent instructions provided with the terminal, for installation details.
2. Vertical Vent and Air Intake Location – Observe the following clearances from roof mounted terminals:
• Bottom of air intake opening must be at least 12" above the normal snow line anticipated on the roof.
• Exhaust opening must be at least 2ft above any portion of the roof or structure located within horizontally within 10ft.
• For terminal option H, maintain at least 12" of vertical separation between the exhaust and intake opening as shown in
Figure 7.15 and 7.17.
3. Requirements for B-Vent Air Chase Options – Observe the following additional requirements when using an abandoned
B-vent chimney as an air chase as described in Options #18-21. Also refer to Figures 7.19 & 7.20.
• B vent must be clean and in good condition.
• Use of flex PolyPropylene outside of B-vent chimney is not permitted.
• All joints and seams in the B-vent must be sealed with RTV. If these seams are not accessible, vent options 18-21 cannot be used while complying with the National Fuel Gas Code (as an alternative, the B-vent chimney can be used as a chase for the vent pipe while combustion air is piped from an outside wall - see Part VII-D for additional details).
• All venting is PolyPropylene supplied by the vent manufacturer shown in Table 7.13b. The portion of this venting within the B–vent is flexible.
• All flex pipe must be installed vertically. Up to two offsets (four bends) may be made in the vertical run of flex pipe.
Bends used to make these offsets may not exceed 45 degrees.
• Because the flex pipe is corrugated, it has a higher pressure drop than the rigid pipe used elsewhere in the vent system.
Equivalent lengths for flex venting are shown in Table 7.14. Reduce the maximum allowable vent length shown in Table
7.13b by this equivalent length for each foot of flex pipe used, as well as for each elbow in addition to the first. The termination is not counted. If offsets (described above) are present, the equivalent length of the bends in these offsets can also be ignored.
Example: A 110MBH model is to be installed as using Vent Option 18 as shown in Figure 7.19. The following components are used:
Vent:
2" DuraVent Poly-Pro (Rigid) – 4ft
2" DuraVent Poly-Pro Flex – 20ft
Poly-Pro elbows – 2
DuraVent 2PPS-VFT Terminal (exhaust side)
Intake:
2" PVC – 6ft
2" PVC Sweep 90 – 3
Turn in B vent Tee
Straight B-vent (5" or larger) containing flex vent – 20ft
DuraVent 2PPS-VFT Terminal (intake side)
Vent Equivalent length – First elbow is ignored. The terminal is also ignored. From Table 7.14, the equivalent length of 2"
DuraVent Poly-Pro Flex is 2.0ft. From Table 7.1 the equivalent length of the second 90 elbow is 4.5ft. The equivalent length of the vent system is therefore:
4 + 4.5 + (20 x 2.0) = 48.5ft.
Since Vent Option 18 shows a max vent length of 60ft, the planned vent length of OK.
Intake Equivalent length - First elbow and the turn in the B vent tee are ignored, leaving two sweep 90 elbows that must be counted. From Table 7.1, the equivalent length of each of these elbows is 2.6ft. From Table 7.14 the equivalent length of the
B vent containing flex is 1.0ft. Equivalent length of the intake system is therefore:
(2 x 2.6) +6 +(20 x 1.0) = 31.2ft.
Since this is less than 60ft, the planned intake length is OK.
31
VII. Venting C. Design Requirements Unique to Vertical Venting Systems (continued)
Table 7.14: Equivalent Length of Flex Pipe
Flex Vent (1 ft):
2" DuraVent PolyPro Flex
2" Centrotherm InnoFlue Flex
2" Selkirk Polyflue
3" DuraVent PolyPro Flex
3" Centrotherm InnoFlue Flex
3" Selkirk Polyflue
B-Vent Air Chase (1ft):
2" Flex Vent in 5" (or larger) B-Vent
3" Flex Vent in 6" (or larger) B-Vent
Note: Up to four 45 degree bends may be made in flex pipe or air chase.
These bends are not counted when figuring equivalent length.
Equivalent Length (ft)
2.0 ft
2.0 ft
2.0 ft
2.0 ft
2.3 ft
2.3 ft
1.0 ft
1.0 ft
32
VII. Venting C. Design Requirements Unique to Vertical Venting Systems (continued)
Figure 7.15: Vertical CPVC/PVC Venting (Vent Options 10 & 11, Terminal Option H)
Figure 7.16: Vertical CPVC/PVC Venting with IPEX Concentric Vent Terminal
(Vent Options #10 & 11, Terminal Option I, J)
33
VII. Venting C. Design Requirements Unique to Vertical Venting Systems (continued)
Figure 7.17: Duravent PolyPro, Selkirk Polyflue or Centrotherm InnoFlue Vertical Single Wall PP Venting
(Vent Options #12-17, Terminal Option H)
34
Figure 7.18: Duravent PolyPro Vertical Venting with Concentric Terminal
(Vent Options #12 & 13, Terminal Option J)
VII. Venting C. Design Requirements Unique to Vertical Venting Systems (continued)
Figure 7.19: Duravent PolyPro B-Vent Air Chase System (Vent Options #18 & 19)
Figure 7.20: Centrotherm InnoFlue B-Vent Air Chase System (Vent Options #20 & 21)
35
VII. Venting D. Design Requirements Unique to Split Vent Systems (continued)
D. Design Requirements Unique to Split Vent Systems
Table 7.21 summarizes all split vent options. Illustrations of split vent systems are shown in Figures 7.22, 7.23, and 7.24. In addition to the requirements in Part VII-A, observe the following design requirements:
1. Permitted Terminals for Split Venting:
Rigid Vent Systems (Vent Options 25-32) – Vent terminates in a plain end (coupling for PVC, bell end for PolyPro, Polyflue, and plain end pipe for InnoFlue). Intake terminates in a PVC 90 sweep elbow pointing down. The section of PolyPro,
Polyflue or InnoFlue exposed to the outdoors must be UV resistant.
Use of a rodent screen is generally recommended for the vent termination. A rodent screen suitable for 3" PVC terminals is installed under the termination coupling as shown in Figure 7.27. If 2" CPVC is used, this screen can be cut to fit into the smaller fitting. Rodent screens (“bird guards”) for PolyPro, Polyflue and InnoFlue are as follows:
Size/Vent System
2" PolyPro
3" PolyPro
2" Polyflue
3" Polyflue
2" InnoFlue
3" InnoFlue
Rodent Screen (“Bird Guard”)
DuraVent # 2PPS-BG
DuraVent # 3PPS-BG
Selkirk #2PF-HVST
Selkirk #3PF-HVST
Centrotherm # IASPP02
Centrotherm # IASPP03
Flex Vent Terminals (Options 33-38) – The flex vent kits shown for options 33-38 include vent terminals that must be installed in accordance with the vent manufacturer’s instructions. Different terminals are used for Masonry and B-vent chimney chases.
Air Intake Terminals (Vent Options 25-38) - All split venting options shown in Tables 7.21 terminate in a PVC 90 sweep elbow pointing down. Use of a rodent screen is generally recommended for the intake termination. A rodent screen suitable for 3" PVC terminals is installed under the intake termination elbow coupling as shown in Figure 7.27. If 2" CPVC is used, this screen can be cut to fit into the smaller fitting.
2. Vent Terminal Location – Observe the following clearances from roof mounted vent terminals (also see Figures 7.22, 7.23, or
7.24):
• Bottom of terminal must be at least 12" above the normal snow line anticipated on the roof.
• Exhaust opening must be at least 2ft above any portion of the roof or structure located within horizontally within 10ft.
3. Horizontal Air Intake Terminal Location - Observe the following limitations on the intake terminal location (also see Figures
7.22, 7.23, or 7.24):
• The bottom of all terminals must be at least 12" above the normal snow line. In no case should they be less than 12" above grade level.
• If possible, install the intake terminal on a wall away from the prevailing wind. Reliable operation of this boiler cannot be guaranteed if the intake terminal is subjected to winds in excess of 40 mph.
• Air intake terminal must not terminate in areas that might contain combustion air contaminates, such as near swimming pools. See WARNING on page 15.
4. Use of abandoned chimneys as a vent chase (Options 33-38) – Vent options 33-38 permit flexible PolyPropylene venting to be routed to the roof using an abandoned masonry or B- vent chimney. In these applications combustion air is drawn horizontally from a wall terminal. See Figure 7.23 or 7.24. When using one of these vent options, observe the following
requirements:
• When a masonry chimney containing multiple flues is used as a chase, ALL flues must be abandoned (Figure 7.26).
• Masonry or B vent chimney used as a chase must be structurally sound.
• Use of flex PolyPropylene outside of a masonry or B-vent chimney is not permitted unless allowed by the vent manufacturer and permitted by local codes.
• All venting is PolyPropylene supplied by the vent manufacturer shown in Table 7.21. The portion of this venting within the masonry or B–vent chimney is flexible.
• All flex pipe must be installed vertically. Up to two offsets (four bends) may be made in the vertical run of flex pipe.
Bends used to make these offsets may not exceed 45 degrees (Figure 7.25).
• Because the flex pipe is corrugated, it has a higher pressure drop than the rigid pipe used elsewhere in the vent system.
Equivalent lengths for flex venting are shown in Table 7.14. Reduce the maximum allowable vent length shown in
Table 7.21 by this equivalent length for each foot of flex pipe used, as well as for each elbow in addition to the first. The first elbow and termination are not counted. If offsets (described above) are present, the equivalent length of the bends in these offsets can also be ignored.
36
VII. Venting D. Design Requirements Unique to Split Vent Systems (continued)
Example: A 110MBH model is to be installed as using Vent Option 34 in a masonry chimney as shown in Figure 7.23. The following components are used:
Vent:
3" DuraVent Poly-Pro (Rigid) – 4ft
3" DuraVent Poly-Pro Flex – 30ft
Poly-Pro elbows – 2 (one at base of chimney and one above boiler)
DuraVent 3PPS-FK Terminal
Intake:
3" PVC – 6ft
3" PVC Sweep 90 – 2 (one above the boiler and one as an intake terminal)
Vent Equivalent length – First elbow is ignored. The terminal is also ignored. From Table 7.14, the equivalent length of 3"
DuraVent Poly-Pro Flex is 2.0ft. From Table 7.1 the equivalent length of the second 90 elbow is 8.7ft. The equivalent length of the vent system is therefore:
4 + 8.7 + (30 x 2.0) = 72.7ft.
Since Vent Option 34 shows a max vent length of 135ft, the planned vent length of OK.
Intake Equivalent length - First elbow and termination elbow are ignored, leaving just the straight pipe. Equivalent length of
the intake system is therefore 6ft. Since this is less than 135ft, the planned intake length is OK.
WARNING
• Flex Vent Options may only be used in unused chimneys.
• When a Masonry chimney is used as a chase, ALL flues in that chimney must be unused.
Failure to observe the above requirements could cause flue gas to enter the building, resulting in
severe property damage, personal injury or loss of life.
37
VII. Venting D. Design Requirements Unique to Split Vent Systems (continued)
Table 7.21: Summary of Split Vent System Options
Option #
Illustrated in Figure
Pipe Penetration
Through Structure
Vent
Intake
25
7.22
Roof
Wall
Material
Vent
CPVC/PVC
(Note 2)
Intake
Vent
Nominal Diameter
Intake
Min Equivalent Vent Length:
85
Model Sizes
110
155
205
PVC
2"
2" or 3"
30"
30"
Not Permitted
270
Max Equivalent Vent Length (Note 1):
85
Model Sizes
110
155
205
60ft
60ft
Not Permitted
270
Rigid Vent Terminals
Vent
Intake
Coupling w/Screen
90 Elbow w/Screen
Flex Termination
& Components
(Masonry Chimney
Chase) (Note 3)
Vent
Intake
26
7.22
Roof
Wall
CPVC/PVC
(Note 2)
PVC
3"
3"
30"
30"
30"
30"
30"
135ft
135ft
135ft
135ft
135ft
Coupling w/Screen
90 Elbow w/Screen
27
7.22
Roof
Wall
DuraVent
PolyPro
(Ridged)
PVC
2"
2" or 3"
30"
30"
Not Permitted
28
7.22
Roof
Wall
DuraVent
PolyPro
(Ridged)
PVC
3"
3"
30
7.22
Roof
Wall
Selkirk
Polyflue
PVC
3"
3"
30"
30"
30"
30"
30"
60ft
60ft
Not Permitted
2PPS-12B or
2PPS-36B w/Screen
90 Elbow w/Screen
135ft
135ft
135ft
135ft
135ft
3PPS-12B or
3PPS-36B w/Screen
90 Elbow w/Screen
60ft
60ft
Not Permitted
2PF-10UV or
2PF-39UV w/Screen
90 Elbow w/Screen
135ft
135ft
135ft
135ft
135ft
3PF-10UV or
3PF-39UV w/Screen
90 Elbow w/Screen
Not Permitted
30"
30"
30"
30"
30"
29
7.22
Roof
Wall
Selkirk
Polyflue
PVC
2"
2" or 3"
30"
30"
Not Permitted
Flex Termination
& Components
(B-Vent Chimney
Chase)
Vent
Not Permitted
Intake
Note 1: Max vent lengths shown also apply to the intake. Flex vent reduces the maximum allowable vent length.
See equivalent lengths for flex vent shown in Table 7.14 and sizing example on page 32.
Note 2: At least 30" of CPVC pipe, and at least one CPVC elbow, must be installed between the boiler's vent connection and
PVC pipe.
Note 3: If masonry chimney contains flues in addition to that being used for chase, ALL must be unused.
Note 4: See Polyflue installation manual for gaskets, spacers and other required vent components.
All vertical terminals require compatible roof flashing and storm collars.
38
31
7.22
32
7.22
33
7.23, 7.24
34
7.23, 7.24
35
7.23, 7.24
36
7.23, 7.24
37
7.23, 7.24
Roof
Wall
Centrotherm
InnoFlue SW
PVC
2"
Roof
Wall
Centrotherm
InnoFlue
SW
PVC
3"
2" or 3" 3"
Min Equivalent Vent Length:
30" 30"
30" 30" 30"
Not
Permitted
30"
30"
Not
Permitted
36"
Max Equivalent Vent Length (Note 1):
60ft 135ft 60ft
60ft
Not
Permitted
135ft
135ft
135ft
Roof
Wall
DuraVent
PolyPro
(Rigid/Flex)
PVC
2"
2" or 3"
30"
60ft
Not
Permitted
Roof
Wall
DuraVent
PolyPro
(Rigid/Flex)
PVC
3"
3"
30"
30"
30"
30"
30"
135ft
135ft
135ft
135ft
Roof
Wall
Selkirk Polyflue
(Rigid/Flex)
PVC
2"
2" or 3"
30"
30"
Not Permitted
60ft
60ft
Not Permitted
Roof
Wall
Selkirk Polyflue
(Rigid/Flex)
PVC
3"
3"
30"
30"
30"
30"
30"
135ft
135ft
135ft
135ft
Roof
Wall
Centrotherm
InnoFlue
(Rigid/Flex)
PVC
2"
2" or 3"
30"
30"
Not Permitted
60ft
60ft
Not Permitted
135ft 135ft 135ft
ISEP02 or
ISEP0239 w/
Screen
90 Elbow w/
Screen
ISEP03 or
ISEP0339 w/Screen
90 Elbow w/
Screen
Not Permitted
Not Permitted
Not Permitted
2PPS-FK
2PPS-
FLEX**
90 Elbow w/Screen
2PPS-VFT
2PPS-BF*
2PPS-
FLEX**
90 Elbow w/
Screen
3PPS-FK
3PPS-
FLEX**
90 Elbow w/Screen
3PPS-VFT
3PPS-BF*
3PPS-
FLEX**
90 Elbow w/
Screen
2PF-FLEX-KIT
2PF-FLEX
90 Elbow w/Screen
2PF-10UV or
2PF-39UV w
Screen
2PF-BVSC
(Note 4)
90 Elbow w/Screen
* Specify size of B vent (e.g. 2PPS-BV 6 is for use with 6" B vent).
3PF-FLEX-KIT
3PF-FLEX
90 Elbow w/Screen
3PF-10UV or
3PF-39UV w
Screen
3PF-BVSC
(Note 4)
90 Elbow w/Screen
IFCK02**
90 Elbow w/Screen
IFBK02****
90 Elbow w/Screen
** Specify length in feet.
**** Specify Flex length and B vent diameter (e.g. IFBK02 2505 includes 25ft of flex and used with 5" B vent).
38
7.23, 7.24
Roof
Wall
Centrotherm
InnoFlue
(Rigid/Flex)
PVC
3"
3"
30"
30"
30"
30"
30"
135ft
135ft
135ft
135ft
135ft
IFCK03**
90 Elbow w/Screen
IFBK03****
90 Elbow w/Screen
Note 1: Max vent lengths shown also apply to the intake. Flex vent reduces the maximum allowable vent length.
See equivalent lengths for flex vent shown in Table 7.14 and sizing example on page 32.
Note 2: At least 30" of CPVC pipe, and at least one CPVC elbow, must be installed between the boiler's vent connection and
PVC pipe.
Note 3: If masonry chimney contains flues in addition to that being used for chase, ALL must be unused.
Note 4: See Polyflue installation manual for gaskets, spacers and other required vent components
All vertical terminals require compatible roof flashing and storm collars.
Option #
Illustrated in Figure
Pipe Penetration
Through Structure
Vent
Intake
25
7.22
Roof
Wall
Material
Vent
CPVC/PVC
(Note 2)
Intake
Vent
Nominal Diameter
Intake
Min Equivalent Vent Length:
85
Model Sizes
110
155
205
PVC
2"
2" or 3"
30"
30"
Not Permitted
270
Max Equivalent Vent Length (Note 1):
85
Model Sizes
110
155
205
60ft
60ft
Not Permitted
270
Rigid Vent Terminals
Vent
Intake
Coupling w/Screen
90 Elbow w/Screen
Flex Termination
& Components
(Masonry Chimney
Chase) (Note 3)
Vent
Intake
26
7.22
Roof
Wall
CPVC/PVC
(Note 2)
PVC
3"
3"
30"
30"
30"
30"
30"
Not Permitted
27
7.22
Roof
Wall
DuraVent
PolyPro
(Ridged)
PVC
2"
2" or 3"
30"
30"
135ft
135ft
135ft
135ft
135ft
Coupling w/Screen
90 Elbow w/Screen
28
7.22
Roof
Wall
DuraVent
PolyPro
(Ridged)
PVC
3"
3"
30"
30"
30"
30"
30"
29
7.22
Roof
Wall
Selkirk
Polyflue
PVC
2"
2" or 3"
30"
30"
Not Permitted
60ft
60ft
Not Permitted
2PPS-12B or
2PPS-36B w/Screen
90 Elbow w/Screen
135ft
135ft
135ft
135ft
135ft
3PPS-12B or
3PPS-36B w/Screen
90 Elbow w/Screen
60ft
60ft
Not Permitted
2PF-10UV or
2PF-39UV w/Screen
90 Elbow w/Screen
135ft
135ft
135ft
135ft
135ft
3PF-10UV or
3PF-39UV w/Screen
90 Elbow w/Screen
30
7.22
Roof
Wall
Selkirk
Polyflue
PVC
3"
3"
30"
30"
30"
30"
30"
Not Permitted
Flex Termination
& Components
(B-Vent Chimney
Chase)
Vent
Not Permitted
Intake
Note 1: Max vent lengths shown also apply to the intake. Flex vent reduces the maximum allowable vent length.
See equivalent lengths for flex vent shown in Table 7.14 and sizing example on page 32.
Note 2: At least 30" of CPVC pipe, and at least one CPVC elbow, must be installed between the boiler's vent connection and
PVC pipe.
Note 3: If masonry chimney contains flues in addition to that being used for chase, ALL must be unused.
Note 4: See Polyflue installation manual for gaskets, spacers and other required vent components.
All vertical terminals require compatible roof flashing and storm collars.
VII. Venting D. Design Requirements Unique to Split Vent Systems (continued)
Table 7.21: Summary of Split Vent System Options (continued)
31
7.22
32
7.22
33
7.23, 7.24
34
7.23, 7.24
35
7.23, 7.24
36
7.23, 7.24
37
7.23, 7.24
Roof
Wall
Centrotherm
InnoFlue SW
PVC
2"
Roof
Wall
Centrotherm
InnoFlue
SW
PVC
3"
2" or 3" 3"
Min Equivalent Vent Length:
30" 30"
30" 30" 30"
Not
Permitted
30"
30"
Not
Permitted
36"
Max Equivalent Vent Length (Note 1):
60ft 135ft 60ft
60ft
Not
Permitted
135ft
135ft
135ft
Roof
Wall
DuraVent
PolyPro
(Rigid/Flex)
PVC
2"
2" or 3"
30"
60ft
Not
Permitted
Roof
Wall
DuraVent
PolyPro
(Rigid/Flex)
PVC
3"
3"
30"
30"
30"
30"
30"
135ft
135ft
135ft
135ft
Roof
Wall
Selkirk Polyflue
(Rigid/Flex)
PVC
2"
2" or 3"
30"
30"
Not Permitted
60ft
60ft
Not Permitted
Roof
Wall
Selkirk Polyflue
(Rigid/Flex)
PVC
3"
3"
30"
30"
30"
30"
30"
135ft
135ft
135ft
135ft
Roof
Wall
Centrotherm
InnoFlue
(Rigid/Flex)
PVC
2"
2" or 3"
30"
30"
Not Permitted
60ft
60ft
Not Permitted
135ft 135ft 135ft
ISEP02 or
ISEP0239 w/
Screen
90 Elbow w/
Screen
ISEP03 or
ISEP0339 w/Screen
90 Elbow w/
Screen
Not Permitted
Not Permitted
Not Permitted
2PPS-FK
2PPS-
FLEX**
90 Elbow w/Screen
2PPS-VFT
2PPS-BF*
2PPS-
FLEX**
90 Elbow w/
Screen
3PPS-FK
3PPS-
FLEX**
90 Elbow w/Screen
3PPS-VFT
3PPS-BF*
3PPS-
FLEX**
90 Elbow w/
Screen
2PF-FLEX-KIT
2PF-FLEX
90 Elbow w/Screen
2PF-10UV or
2PF-39UV w
Screen
2PF-BVSC
(Note 4)
90 Elbow w/Screen
* Specify size of B vent (e.g. 2PPS-BV 6 is for use with 6" B vent).
3PF-FLEX-KIT
3PF-FLEX
90 Elbow w/Screen
3PF-10UV or
3PF-39UV w
Screen
3PF-BVSC
(Note 4)
90 Elbow w/Screen
IFCK02**
90 Elbow w/Screen
IFBK02****
90 Elbow w/Screen
** Specify length in feet.
**** Specify Flex length and B vent diameter (e.g. IFBK02 2505 includes 25ft of flex and used with 5" B vent).
38
7.23, 7.24
Roof
Wall
Centrotherm
InnoFlue
(Rigid/Flex)
PVC
3"
3"
30"
30"
30"
30"
30"
135ft
135ft
135ft
135ft
135ft
IFCK03**
90 Elbow w/Screen
IFBK03****
90 Elbow w/Screen
Note 1: Max vent lengths shown also apply to the intake. Flex vent reduces the maximum allowable vent length.
See equivalent lengths for flex vent shown in Table 7.14 and sizing example on page 32.
Note 2: At least 30" of CPVC pipe, and at least one CPVC elbow, must be installed between the boiler's vent connection and
PVC pipe.
Note 3: If masonry chimney contains flues in addition to that being used for chase, ALL must be unused.
Note 4: See Polyflue installation manual for gaskets, spacers and other required vent components
All vertical terminals require compatible roof flashing and storm collars.
39
VII. Venting D. Design Requirements Unique to Split Vent Systems (continued)
Figure 7.22: Split Rigid Vent System (Vent Options 25-32)
40
Figure 7.23: Split Vent System (Flex in B-Vent Chase) Vent Options 33-38)
VII. Venting D. Design Requirements Unique to Split Vent Systems (continued)
Figure 7.24: Split Vent System (Flex in Abandoned Masonry Chimney) (Vent Options 33-38)
41
VII. Venting D. Design Requirements Unique to Split Vent Systems (continued)
DANGER
Venting of Other Appliances (Or Fireplace) into Chase or Adjacent Flues
Prohibited!
42
Figure 7.25: Masonry Chimney Chase Requirements
VII. Venting E. Assembly of CPVC/PVC Vent Systems (continued)
E. Assembly of CPVC/PVC Vent Systems
DANGER
Failure to follow this warning could result in asphyxiation and/or carbon monoxide poisoning. Correct venting material and installation is required for proper vent operation. PVC Vent Systems must include at least 30 inches of CPVC and one CPVC elbow between the boiler and PVC vent piping. See this Section, VII. Venting for complete information.
Use CPVC vent components within any interior space where air cannot circulate freely, including through vertical or horizontal chase ways, inside a stud wall, in closets and through wall penetrations.
WARNING
Asphyxiation Hazard. Failure to follow these instructions could cause products of combustion to enter the building, resulting in severe property damage, personal injury or death.
The use of cellular core PVC (ASTM F891), cellular core CPVC or Radel (polyphenolsulfone is prohibited.
All condensate that forms in the vent must be able to drain back to the boiler.
Never leave the boiler in operation without the gas sample cap in place (Figure 7.26).
1. Assemble the vent system, starting at the boiler: a. If 3" PVC is to be used for venting, at least one 3" CPVC elbow and at least one 30" straight section of CPVC must be used before transitioning to PVC. If necessary the 30" straight section of CPVC may be cut in any location and the CPVC elbow inserted between the two resulting segments. 3" PVC Sidewall Vent Kit, P/N 107039-02, is available and includes
30" CPVC starter and elbow, PVC terminations, and screens. b. When cutting CPVC or PVC pipe, use a miter saw or a saw designed to cut PVC pipe. Use a miter box or other method to cut pipe squarely. De-burr both the inside and outside of the cut end. c. Dry fit all vent components before assembly. d. The vent adaptor has two different inside diameters. The larger (upper) inside diameter accepts 3" CPVC pipe and is used in this application (the smaller, lower, inside diameter accepts 3" nominal PolyPro, Polyflue or InnoFlue). Lubricate the upper gasket in the vent adaptor with water and insert the first piece of 3" CPVC into the vent adaptor until it bottoms out.
Tighten clamp on vent adapter to secure vent pipe.
e. If 2" CPVC is to be used for the vent system, reduce the first piece of 3" CPVC installed in Step (b) to 2" CPVC using a
CPVC reducing coupling or elbow. Otherwise assemble the 3" CPVC elbow and the remainder of the 30" CPVC piping before transitioning to PVC. If 3" PVC is used, the first piece of PVC will either be connected to the CPVC elbow or the end of a section of CPVC vent pipe. In the latter case, a PVC coupling may be used to connect the first piece of PVC to the last piece of CPVC. 2" PVC Sidewall Vent Kit, P/N 107039-01, is available and includes 30" CPVC starter and elbow,
2" x 3" reducing bushings, PVC terminations, and screens.
f. Clean all CPVC and PVC components with the appropriate primer before cementing. Cement the vent system together, starting at the boiler and following the instructions provided on the cans of cement and primer. Use a field supplied cement and primer that is listed for use with the materials being joined (CPVC and/or PVC). The following, or its equivalent, may be used to join CPVC to PVC:
• IPS Corporation #P-70 Primer
• IPS Corporation #790 Multi-Purpose Solvent Cement
Always use primer on both the pipe and fitting before applying the cement. Assemble the pipe in accordance with the instructions on the cans of primer and cement. g. Assemble the rest of the vent system, being sure to pitch horizontal sections back towards the boiler 1/4"/ft. Support the vent at intervals not exceeding 4ft.
43
VII. Venting E. Assembly of CPVC/PVC Vent Systems (continued)
Figure 7.26: Vent Connections and Flue Gas Sample Cap Location h. Maintain the clearances from the vent pipe outlined in Part VII-A of this manual. If exiting the exterior wall using PVC pipe, use half of an appropriately sized wall thimble (or a sheet metal plate) on the exterior of the building, to provide a weather tight seal while maintaining the proper clearance in the wall penetration. Seal the joint between the pipe and the wall plate using RTV applied on the exterior side of the wall. This sealant must not restrain the expansion of the vent pipe.
2. Installation of Air Intake System - Start assembly of the PVC air intake system at the boiler. Assembly of the air intake system is done in the same manner as the vent system except as follows: a. Drill a 7/32" clearance hole into the front side of the air intake adapter. Insert the first piece of PVC air intake pipe into the air intake connection and drill a 1/8" tap hole into the PVC which lines up with the 7/32" clearance hole and secure them together with a #10 x 1" sheet metal screw. Seal the joint between the intake pipe and the adaptor with
RTV.
b. All intake piping may be PVC.
c. There is a 0" minimum clearance between the air intake piping and all types of construction.
d. To the extent possible, pitch horizontal air intake piping towards the outdoors.
3. Installation of Horizontal Fitting Terminals (Terminal Option A): a. See Figure 7.27 for proper orientation of twin pipe horizontal terminals. Outer edge of both terminals must be within 10" from wall surface. (Figure 7.6) b. If desired, the terminals can be attached to the end of the vent and/or intake pipes with field supplied stainless steel screws so that they can be later removed for cleaning and inspection. If this is done, drill a clearance hole in the coupling or elbow and a tap hole in the end of the vent/intake pipes to accept these screws.
c. If these terminals are installed on snorkels, assemble the snorkels as shown in Figure 7.12. Brace the vertical run of piping on the building exterior as required.
44
VII. Venting E. Assembly of CPVC/PVC Vent Systems (continued)
Figure 7.27: Installation of Standard Horizontal Terminals
Figure 7.28: Installation of Standard Vertical Terminals
45
VII. Venting E. Assembly of CPVC/PVC Vent Systems (continued)
4. Installation of Vertical Fitting Terminals (Terminal Option H): a. See Figure 7.28
for the proper orientation of twin pipe vertical terminals. b. The coupling is used to secure the rodent screen to the end of the vent pipe. c. A 180° bend (or two 90° elbows) are installed on the top of the air intake pipe. If two 90° elbows are used, the rodent screen provided can be installed between them (Figure 7.28). If a 180° bend is used, install the rodent screen in the open side of the bend, using a ring made of PVC pipe. If desired, the termination fittings can be attached to the end of the vent and/or intake pipes with field supplied stainless steel screws so that they can be later removed for cleaning and inspection.
If this is done, drill a clearance hole in these fittings and a tap hole in the end of the vent/intake pipes to accept these screws. d. Use roof flashings and storm collars to prevent moisture from entering the building. Seal the roof flashing to the roof using generally accepted practice for the type of roof on the installation. Apply RTV to seal the storm collars to the vent and intake pipes.
5. Installation of IPEX low profile vent terminal (Terminal Option B) - See Figure 7.29: a. Cut two holes in wall to accommodate the size PVC pipe being used. The distance between hole centers is 5.6".
b. Slide both vent and intake air pipes through the holes and cement them to the base of the vent termination kit using a primer and cement listed for use with PVC.
c. Fasten the vent base to the wall using the supplied screws and anchors. The anchors require the drilling of a 3/16" hole x
1-3/16" deep. Locate the holes using the vent base as a template.
d. Screw the vent cap to the vent base using the supplied screws.
e. Once the vent termination and pipes are secure seal the wall penetrations from the interior using a weather resistant RTV sealant.
6. Installation of Diversitech Low Profile Terminal (Terminal Option C) – See Figure 7.30: a. Use vent plate as a guide to locate the openings for the vent and air intake pipes, as well as to locate the holes for the mounting screws. b. Drill two 3-1/8 holes through the wall for the vent and intake pipes.
c. Drill four 3/16 holes for the mounting screws.
d. Install the vent and intake pipe sections passing through the wall. Cut the pipes so that they protrude the following distances from the surface on which the vent plate will be mounted:
• Vent: Between 1-3/4 and 2-1/4"
• Intake: Between ¼ and 1" e. Seal pipe penetrations in wall with RTV (silicone sealant).
f. Mount the vent plate using the #8 x 2" screws and anchors provided with this kit.
g. Seal the vent plate to the wall with RTV.
h. Apply a bead of RTV around the OD of the vent pipe near its end.
i. Slide the vent cap over the vent pipe and secure to the wall plate with the #8 x 2" screws provided.
7. Installation of IPEX FGV or Diversitech CVENT Concentric Vent Terminal (Terminal Options D,E,I & J) - This terminal may be used for either horizontal or vertical venting. See Figure 7.32 for horizontal installation or Figure 7.33 for vertical installation. When PVC is used for venting the 30" CPVC straight section and CPVC elbow supplied must be used prior to connection of the vent system to this terminal. If the vent system is too short to permit this, use the IPEX FGV CPVC terminal: a. For horizontal installations at the planned location cut a round hole in the exterior wall 1/2" larger than the “C” dimension indicated on Figure 7.31 for the size terminal being used. (See Part VII-B of this manual for permitted terminal locations).
46
WARNING
Asphyxiation Hazard. CPVC/PVC vent piping and fittings rely on glued joints for proper sealing.
Follow all manufacturer instructions and warnings when preparing pipe ends for joining and using the primer and the cement.
When PVC is used with the concentric vent kit, at least one 30" CPVC straight section and at least one
CPVC elbow must be used prior to connection of the vent system to this terminal. If the vent system is too short to permit this, use an FGV CPVC terminal.
Do not operate boiler without the rain cap in place.
Method of securing and sealing terminals to the outside wall must not restrain the expansion of vent pipe.
VII. Venting E. Assembly of CPVC/PVC Vent Systems (continued)
Figure 7.29: Installation of IPEX Low Profile Terminal Through Sidewall
Figure 7.30: Installation of Diversitech Low Profile Terminal Through Sidewall
47
VII. Venting E. Assembly of CPVC/PVC Vent Systems (continued)
Figure 7.31: Cutting IPEX and Diversitech Concentric Vent Terminals
48
Figure 7.32: Installation of IPEX and Diversitech Concentric Terminal through Sidewall
VII. Venting E. Assembly of CPVC/PVC Vent Systems (continued)
Figure 7.33: Installation of IPEX and Diversitech Concentric Terminal Through Roof b. For vertical installations, cut a hole in the roof large enough to clear the concentric terminal at the location of the terminal
(see Part VII-C of this manual for permitted terminal locations).
c. If desired, the terminal can be shortened. See Figure 7.31 for specific information on making the terminal kit shorter based on the kit size being used. Cut the pipe squarely and de-burr both the OD and ID of the cut edges.
d. Cement the inner pipe section of PVC pipe supplied with this kit to the Wye fitting using a primer and cement listed for use with PVC.
e. Cement the outer pipe to the Wye, being careful, to keep the inner and outer pipes concentric.
f. Slip the partially assembled terminal through the wall or ceiling from the inside and for horizontal installations orient so that the side outlet on the Wye is on or above the horizontal plane.
g. For horizontal installations, seal the gap between the OD of the “outer pipe” and the exterior side of the wall with RTV sealant.
h. Cement the rain cap onto the inner pipe. If desired, the rain cap can be attached to the inner pipe with the supplied stainless steel screw and nut so that it can be later removed for cleaning and inspection. If this is done, drill a 3/16" clearance hole in the rain cap and inner pipe in the location shown on Figure 7.31 for the size terminal kit being used and affix screw and nut. Do not overtighten. A field supplied rodent screen may also installed on the end of the rain cap. i. For vertical installations, use a roof flashing and storm collar to prevent moisture from entering the building. Seal the roof flashing to the roof using generally accepted practice for the type of roof on the installation. Install the storm collar after verifying that the bottom of the rain cap will be at least 12" above the normal snow line. Apply RTV to seal the storm collars to the terminal.
49
VII. Venting F. Assembly of DuraVent PolyPro Vent Systems (continued)
F. Assembly of DuraVent PolyPro Vent Systems
1. This boiler has been approved for use with the DuraVent PolyPro single wall PolyPropylene vent system to be provided by the installer.
WARNING
Asphyxiation Hazard. Follow these instructions and the installation instructions included by the original PolyPropylene venting component manufacturers, M&G/DuraVent. Failure to do so could cause products of combustion to enter the building, resulting in severe property damage, personal injury or death. Where a conflict arises between M&G/DuraVent instructions and these instructions, the more restrictive instructions shall govern.
Do not mix vent components or joining methods for listed manufacturers.
Examine all components for possible shipping damage prior to installation.
All condensate that forms in the vent must be able to drain back to the boiler.
2. Assemble the vent system, starting at the boiler: a. The vent adaptor has two different inside diameters. The smaller, lower, inside diameter accepts 3" nominal PolyPro
(Figure 7.26). Lubricate the upper gasket in the vent adaptor with soapy water and insert the first piece of 3" PolyPro into the adaptor until it bottoms out. Tighten clamp on vent adapter to secure vent pipe.
b. If 2" PolyPro is to be used for the vent system, reduce the first piece of 3" PolyPro installed in Step (a) to 2" using
DuraVent #3PPS-R2. Otherwise assemble the next piece of 3" PolyPro. c. For each joint, verify that the gasket is evenly seated in the bell (female) end of the pipe. Lubricate this gasket with water.
Slide a locking band over the male end of the pipe to be joined as shown in Figure 7.34. Push the male end of the next section of pipe into the bell until it bottoms out, then back out 1/4-5/8" to provide room for thermal expansion. Push barb on locking band over the bell end of the first section of pipe as shown in Figure 7.34. d. Assemble the rest of the vent system per the manufacturer’s installation instructions, being sure to pitch horizontal sections back towards the boiler 5/8" per ft. e. Support each horizontal pipe section with a minimum of one wall strap each and at intervals not exceeding 4ft.
50
Figure 7.34: PolyPro Locking Band Installation
VII. Venting F. Assembly of DuraVent PolyPro Vent Systems (continued)
3. Installation of Air Intake System - Start assembly of the PVC air intake system at the boiler. Assembly of the air intake system is done in the same manner as the vent system except as follows: a. Drill a 7/32" clearance hole into the front side of the air intake adapter. Insert the first piece of PVC air intake pipe into the air intake connection and drill a 1/8" tap hole into the PVC which lines up with the 7/32" clearance hole and secure them together with a #10 x 1" sheet metal screw. Seal the joint between the intake pipe and the adaptor with RTV.
b. All intake piping may be PVC.
c. There is a 0" minimum clearance between the air intake piping and all types of construction.
d. To the extent possible, pitch horizontal air intake piping towards the outside.
WARNING
Asphyxiation Hazard. Vent systems made by M&G/DuraVent rely on gaskets for proper sealing. When these vent system is used, take the following precautions:
• Make sure that gasket is in position and undamaged in the female end of the pipe.
• Make sure that both the male and female pipes are free of damage prior to assembly.
• Only cut vent pipe as permitted by the vent manufacturer in accordance with their instructions. When
pipe is cut, the cut end must be square and carefully de-burred prior to assembly.
• Use locking band clamps at all vent pipe joints.
• Do not use anything other than soapy water to lubricate gaskets.
NOTICE
The venting system must be free to expand and contract and supported in accordance with the installation instructions included by the original PolyPropylene venting component manufacturer, M&G/DuraVent.
PolyPropylene pipe sections must be disengaged 1/4 to 5/8 in. (6 mm to 16 mm) per joint to allow for thermal expansion.
4. Installation of Horizontal Fitting Terminals (Terminal Option A): a. See Figure 7.35 for proper orientation of twin pipe horizontal terminals. Outer edge of exhaust coupling must be 10" or less from the wall surface. (Figure 7.9) b. Remove the gasket from the end of the integral exhaust coupling and insert DuraVent Bird Guard #2PPS-BG or #3PPS-
BG in it’s place.
c. Add PVC intake per instructions from Part VII-F.
5. Installation of Vertical Fitting Terminals (Terminal Option H): a. See Figure 7.36
for the proper orientation of twin pipe vertical terminals. b. Remove the gasket from the end of the integral exhaust coupling and insert the installer supplied rodent screen in it’s place. c. A 180° bend (or two 90° elbows) are installed on the top of the air intake pipe. If two 90° elbows are used, the rodent screen provided can be installed between them (Figure 7.36). If a 180° bend is used, install the rodent screen in the open side of the bend, using a ring made of PVC pipe. If desired, the termination fittings can be attached to the end of the intake pipes with field supplied stainless steel screws so that they can be later removed for cleaning and inspection. If this is done, drill a clearance hole in these fittings and a tap hole in the end of the intake pipes to accept these screws. d. Use roof flashings and storm collars to prevent moisture from entering the building. Seal the roof flashing to the roof using generally accepted practice for the type of roof on the installation. Apply RTV to seal the storm collars to the vent and intake pipes.
51
VII. Venting F. Assembly of DuraVent PolyPro Vent Systems (continued)
Figure 7.35: Installation of Duravent PolyPro UV Resistant Single Wall Horizontal Terminal
52
Figure 7.36: Installation of Duravent PolyPro UV Resistant Single Wall Vertical Terminal
VII. Venting F. Assembly of DuraVent PolyPro Vent Systems (continued)
6. Installation of DuraVent PolyPro Horizontal Concentric Vent Terminal (Terminal Option D) -
Install PolyPro Horizontal Concentric Termination Kit #2PPS-HK or #3PPS-HK (Figure 7.38) as follows: a. At the planned location cut a 4-1/8" round hole for the 2" terminal or a 5-1/8" round hole for the 3" terminal in the exterior wall. (See Part VII-A of this manual for permitted terminal locations).
b. If desired, the terminal can be shortened. Mark the desired location of the cut on the outer pipe no closer than 2" from the edge of the tab on the interior wall plate. Prior to cutting outer pipe measure dimension ‘A’ of the inner pipe as shown in
Figure 7.37 and maintain this dimension after cutting the outer pipe. All cuts must be square and de-burred.
c. Attach the exterior wall plate and seal all around with weather resistant RTV.
d. Slide the cap through the exterior wall plate and hole from the outside of the building and orient the termination so the air intake slots face down. The cap must be installed level or sloped 1/8" per foot away from the appliance.
e. Seal the termination to the exterior wall plate with weather resistant RTV.
f. Slide the interior wall plate over the termination and attach to the wall from inside the room.
g. Attach the interior wall plate to the termination with the provided hardware.
h. Install gaskets into co-linear adapter.
i. Attach co-linear adapter to horizontal termination and orient so that the side outlet on the adapter is on or above the horizontal plane.
7. Vertical Installations using PolyPro Vertical Concentric Termination Kit #2PPS-VK or #3PPS-VK (Figure 7.39): a. Cut a hole in the roof large enough to clear the concentric terminal at the location of the terminal (see Part VII-A of this manual for permitted terminal locations).
b. Use a roof flashing and storm collar to prevent moisture from entering the building. See Figure 7.39 for the model number of the flashing to be used depending on the type of roof. Seal the roof flashing to the roof using generally accepted practice for the type of roof on the installation. c. Slide the vertical termination into the flashing from above until seated on the flashing.
d. Plumb the termination and mount the support bracket to the structure.
e. Install gaskets into co-linear adapter.
f. Attach co-linear adapter to vertical termination.
Figure 7.37: Cutting Duravent PolyPro Horizontal Concentric Vent Terminal
53
VII. Venting F. Assembly of DuraVent PolyPro Vent Systems (continued)
Figure 7.38: Installation of Duravent PolyPro Concentric Vent Terminal Through Sidewall
54
Figure 7.39: Installation of Duravent PolyPro Concentric Terminal Through Roof
VII. Venting F. Assembly of DuraVent PolyPro Vent Systems (continued)
8. Installations using PolyPro-flex (Vent Options 18,19,33,34):
WARNING
Asphyxiation Hazard. When using PolyPro flex, observe the following precautions:
• PolyPro flex may be damaged by handling at low temperatures. Do not bend, uncoil, or attempt to install
if it has been stored at a temperature below 42°F without allowing it to warm to a higher temperature
first.
• Do not bend PolyPro flex more than 45°.
• Instructions below reference the DuraVent PolyPro Flex instruction manual. Not all vent
configurations shown in the DuraVent manual are approved for use with this boiler.
Refer to DuraVent PolyPro flex Instructions for assembly of all flex components including the chimney cap and the adaptor to rigid PolyPro at the base of the masonry or B vent chimney. In addition, observe the following requirements: a. Refer to the appropriate Vent option in Tables 7.13b or 7.21 for a list of the principle flex components required. Rigid vent pipe by the same manufacturer will also be required for the run from the boiler to the base of chimney. b. Masonry chimneys cannot be used for an air chase c. B vent chimneys can only be used for an air chase (Vent options 18, 19) if the B vent has the minimum size shown in
Table 7.13b and is fully accessible for sealing of all joints and seams.
d. When Vent Option 18 or 19 is used, install a Tee on the base of the B-vent that is the same size as the B- Vent chimney.
Install the PolyPro Lower B–Vent adaptor in the base of this Tee as described in the DuraVent PolyPro Flex instructions.
Connection of the PVC air intake pipe to the side outlet of the tee is made using a cap and a PVC socket x male thread
adaptor (2" or 3", depending on the Vent Option). Cut a clearance hole in the cap for the male threads. Secure the
adaptor to the cap using a 2" or 3" electrical conduit lock nut. Seal all joints with RTV.
G. Assembly of Selkirk Polyflue Vent Systems
WARNING
Asphyxiation Hazard. When using PolyPro flex, observe the following precautions:
• PolyPro flex may be damaged by handling at low temperatures. Do not bend, uncoil, or attempt to install
if it has been stored at a temperature below 42°F without allowing it to warm to a higher temperature
first.
• Do not bend PolyPro flex more than 45°.
• Instructions below reference the DuraVent PolyPro Flex instruction manual. Not all vent
configurations shown in the DuraVent manual are approved for use with this boiler.
1. This boiler has been approved for use with the Selkirk Polyflue single wall PolyPropylene vent system to be provided by the installer.
2. Assemble the vent system, starting at the boiler: a. The vent adaptor has two different inside diameters. The smaller, lower, inside diameter accepts 3" nominal Polyflue
(Figure 7.26). Lubricate the upper gasket in the vent adaptor with mild soapy water and insert the first piece of 3"
Polyflue into the adaptor until it bottoms out. Tighten clamp on vent adapter to secure vent pipe.
b. If 2" Polyflue is to be used for the vent system, reduce the first piece of 3" Polyflue installed in Step (a) to 2" using
Selkirk #3PF-3R2. Otherwise assemble the next piece of 3" Polyflue.
c. For each joint, verify that the gasket is evenly seated in the bell (female) end of the pipe. Lubricate this gasket with mild soapy water. Slide a Pipe Locking Band over the male end of the pipe to be joined as shown in Figure 7.40. Push the male end of the next section of pipe into the bell until it bottoms out, then back out 1/8—1/4" to provide room for thermal expansion. Slide pipe locking band over the female end of the connections and tighten both hose clamps. d. Assemble the rest of the vent system per the manufacturer’s installation instructions, being sure to pitch horizontal sections back towards the boiler 5/8" per ft.
55
VII. Venting G. Assembly of Selkirk Polyflue Vent Systems (continued) e. Support each pipe section as described in Polyflue manual at intervals not exceeding the following:
Pipe size
2"
Horizontal
30in
3" 39in
Vertical
16ft
16ft
3. Installation of Air Intake System - Start assembly of the PVC air intake system at the boiler. Assembly of the air intake system is done in the same manner as the vent system except as follows: a. Drill a 7/32" clearance hole into the front side of the air intake adapter. Insert the first piece of PVC air intake pipe into the air intake connection and drill a 1/8" tap hole into the PVC which lines up with the 7/32" clearance hole and secure them together with a #10 x 1" sheet metal screw. Seal the joint between the intake pipe and the adaptor with RTV.
b. All intake piping may be PVC. There is a 0" minimum clearance between the air intake piping and all types of construction.
c. To the extent possible, pitch horizontal air intake piping towards the outside.
4. Installation of Horizontal Fitting Terminals (Terminal Option A): a. See Figure 7.41 for proper orientation of twin pipe horizontal terminals. Outer edge of exhaust coupling must be 10" or less from the wall surface. (Figure 7.9) b. Remove the gasket from the end of the integral exhaust coupling and insert Selkirk #2PF-HVST or #3PFHVST in its place.
c. Add PVC intake per instructions from Part VII-F.
5. Installation of Vertical Fitting Terminals (Terminal Option H): a. See Figure 7.42 for the proper orientation of twin pipe vertical terminals.
b. Remove the gasket from the end of the integral exhaust coupling and insert Selkirk #2PF-HVST or #3PFHVST in its place.
c. A 180° bend (or two 90° elbows) are installed on the top of the air intake pipe. If two 90° elbows are used, the rodent screen provided can be installed between them (Figure 7.42). If a 180° bend is used, install the rodent screen in the open side of the bend, using a ring made of PVC pipe. If desired, the termination fittings can be attached to the end of the intake pipes with field supplied stainless steel screws so that they can be later removed for cleaning and inspection. If this is done, drill a clearance hole in these fittings and a tap hole in the end of the intake pipes to accept these screws.
d. Use roof flashings and storm collars to prevent moisture from entering the building. Seal the roof flashing to the roof using generally accepted practice for the type of roof on the installation. Apply RTV to seal the storm collars to the vent and intake pipes.
WARNING
Asphyxiation Hazard. Selkirk Polyflue vent systems rely on gaskets for proper sealing. When this vent system is used, take the following precautions:
• Make sure that gasket is in position and undamaged in the female end of the pipe.
• Make sure that both the male and female pipes are free of damage prior to assembly.
• Only cut vent pipe as permitted by the vent manufacturer in accordance with their Instructions. When
pipe is cut, the cut end must be square and carefully de-burred prior to assembly.
• Use pipe locking bands at all vent pipe joints.
NOTICE
The venting system must be free to expand and contract and supported in accordance with the installation instructions included by the original PolyPropylene venting component manufacturer, Selkirk.
PolyPropylene pipe sections must be disengaged 1/8 to 1/4 in. (3mm to 6mm) per joint to allow for thermal expansion.
56
VII. Venting G. Assembly of Selkirk Polyflue Vent Systems (continued)
6. Installations using flexible Polyflue (Vent Options 35,36):
WARNING
Asphyxiation Hazard. When using Polyflue flex, observe the following precautions:
• Polyflue flex may be damaged by handling at low temperatures. Do not bend, uncoil or attempt to
install if it has been stored at a temperature below 42°F without allowing it to warm to a higher
temperature first.
• Do not bend Polyflue flex more than 45°.
• Instructions below reference the Selkirk Polyflue instruction manual. Not all vent configurations shown
in the Selkirk vent manual are approved for use with this boiler.
Refer to Selkirk Polyflue Instructions for assembly of all flex components including the chimney cap and the adaptor to rigid Polyflue at the base of the masonry or B vent chimney. In addition, observe the following requirements: a. Refer to the appropriate Vent option in Table 7.21 for a list of the principle flex components required. Rigid vent pipe by the same manufacturer will also be required for the run from the boiler to the base of the chimney. b. Polyflue may not be used in air chase applications.
Figure 7.40: Polyflue Pipe Locking Band Installation
57
VII. Venting G. Assembly of Selkirk Polyflue Vent Systems (continued)
Figure 7.41: Installation of Selkirk Polyflue UV Resistant Single Wall Horizontal Terminal
58
Figure 7.42: Installation of Selkirk Polyflue UV Resistant Single Wall Vertical Terminal
VII. Venting H. Assembly of Centrotherm InnoFlue Vent Systems
H. Assembly of Centrotherm InnoFlue Vent Systems
1.
This boiler has been approved for use with the Centrotherm InnoFlue single wall PolyPropylene vent system to be provided by the installer.
WARNING
Asphyxiation Hazard. Follow these instructions and the installation instructions included by the original PolyPropylene venting component manufacturers, Centrotherm. Failure to do so could cause products of combustion to enter the building, resulting in severe property damage, personal injury or death. Where a conflict arises between Centrotherm instructions and these instructions, the more restrictive instructions shall govern.
Do not mix vent components or joining methods for listed manufacturers.
Examine all components for possible shipping damage prior to installation.
All condensate that forms in the vent must be able to drain back to the boiler.
2. Assemble the vent system, starting at the boiler: a. The vent adaptor has two different inside diameters. The smaller, lower, inside diameter accepts 3" nominal InnoFlue
(Figure 7.26). Lubricate the upper gasket in the vent adaptor with water and insert the first piece of 3" InnoFlue into the adaptor until it bottoms out. Tighten Clamp on vent adapter to secure vent pipe.
b. If 2" InnoFlue is to be used for the vent system, reduce the first piece of 3" InnoFlue installed in Step (a) to 2" using
Centrotherm # ISRD0302. Otherwise assemble the next piece of 3" InnoFlue. c. For each joint, verify that the gasket is evenly seated in the bell (female) end of the pipe. Lubricate this gasket with
Centrocerin # IACE50. Slide a connector ring over the male end of the pipe to be joined as shown in Figure 7.43. Push the male end of the next section of pipe into the bell until it bottoms out, then back out 1/4" to provide room for thermal expansion. Push hook on connecting ring over the bell end of the first section of pipe as shown in Figure 7.43. d. Assemble the rest of the vent system per the manufacturer’s installation instructions, being sure to pitch horizontal sections back towards the boiler 5/8"/ft. e. Support each horizontal pipe section with a minimum of one wall strap each and at intervals not exceeding 39in.
Figure 7.43: InnoFlue Connector Ring Installation
59
VII. Venting H. Assembly of Centrotherm InnoFlue Vent Systems
3. Installation of Air Intake System - Start assembly of the PVC air intake system at the boiler. Assembly of the air intake system is done in the same manner as the vent system except as follows: a. Drill a 7/32" clearance hole into the front side of the air intake adapter. Insert the first piece of PVC air intake pipe into the air intake connection and drill a 1/8" tap hole into the PVC which lines up with the 7/32" clearance hole and secure them together with a #10 x 1" sheet metal screw. Seal the joint between the intake pipe and the adaptor with RTV.
b. All intake piping may be PVC.
c. There is a 0" minimum clearance between the air intake piping and all types of construction.
d. To the extent possible, pitch horizontal air intake piping towards the outside.
WARNING
Asphyxiation Hazard. Vent systems made by Centrotherm rely on gaskets for proper sealing. When this vent system is used, take the following precautions:
• Make sure that gasket is in position and undamaged in the female end of the pipe.
• Make sure that both the male and female pipes are free of damage prior to assembly.
• Only cut vent pipe as permitted by the vent manufacturer in accordance with their instructions. When
pipe is cut, the cut end must be square and carefully de-burred prior to assembly.
• Use connector rings at all vent pipe joints.
NOTICE
The venting system must be free to expand and contract and supported in accordance with the installation instructions included by the original PolyPropylene venting component manufacturer, Centrotherm.
PolyPropylene pipe sections must be disengaged 1/4 in. (6mm) per joint to allow for thermal expansion.
4. Installation of Horizontal Fitting Terminals (Terminal Option A): a. See Figure 7.44 for proper orientation of twin pipe horizontal terminals. Outer edge of end pipe must be 10" or less from the wall surface. (Figure 7.5) b. Use plain end UV stabilized Centrotherm 2" pipe # ISEP02 or ISEP0239 or 3" pipe # ISEP03 or ISEP0339 and insert
Centrotherm Bird Screen #IASPP02 or #IASPP03 in the end of the pipe.
c. Add PVC intake per instructions from Part VII-F.
5. Installation of Vertical Fitting Terminals (Terminal Option H): a. See Figure 7.45
for the proper orientation of twin pipe vertical terminals. b. Use plain end UV stabilized Centrotherm 2" pipe # ISEP02 or ISEP0239 or 3" pipe # ISEP03 or ISEP0339 and insert
Centrotherm Bird Screen #IASPP02 or #IASPP03 in the end of the pipe. c. A 180° bend (or two 90° elbows) are installed on the top of the air intake pipe. If two 90° elbows are used, the rodent screen provided can be installed between them (Figure 7.45). If a 180° bend is used, install the rodent screen in the open side of the bend, using a ring made of PVC pipe. If desired, the termination fittings can be attached to the end of the intake pipes with field supplied stainless steel screws so that they can be later removed for cleaning and inspection. If this is done, drill a clearance hole in these fittings and a tap hole in the end of the intake pipes to accept these screws. d. Use roof flashings and storm collars to prevent moisture from entering the building. Seal the roof flashing to the roof using generally accepted practice for the type of roof on the installation. Apply RTV to seal the storm collars to the vent and intake pipes.
60
VII. Venting H. Assembly of Centrotherm InnoFlue Vent Systems
Figure 7.44: Installation of Centrotherm InnoFlue UV Stabilized Single Wall Horizontal Terminal
Figure 7.45: Installation of Centrotherm InnoFlue UV Stabilized Single Wall Vertical Terminal
61
VII. Venting H. Assembly of Centrotherm InnoFlue Vent Systems
6. Installations using InnoFlue Flex (Vent Options 20,21,37,38):
WARNING
Asphyxiation Hazard. When using InnoFlue Flex, observe the following precautions:
• InnoFlue Flex may be damaged by handling at low temperatures. Do not bend, uncoil or attempt to
install if it has been stored at a temperature below 42°F without allowing it to warm to a higher
temperature first.
• Do not bend InnoFlue Flex more than 45°.
• Instructions below reference the Centrotherm InnoFlue instruction manual. Not all vent configurations
shown in the Centrotherm manual are approved for use with this boiler.
Refer to Centrotherm InnoFlue Instructions for assembly of all flex components including the chimney cap and the adaptor to rigid InnoFlue at the base of the masonry or B vent chimney. In addition, observe the following requirements: a. Refer to the appropriate Vent option in Tables 7.13b or 7.21 for a list of the principle flex components required. Rigid vent pipe by the same manufacturer will also be required for the run from the boiler to the base of chimney.
b. Masonry chimneys cannot be used for an air chase c. B vent chimneys can only be used for an air chase (Vent options 20, 21) if the B vent has the minimum size shown in
Table 7.13b and is fully accessible for sealing of all joints and seams.
d. When Vent Options 20, 21 are used, install a Tee of the same size at the base of the vent. Route the smooth section of
InnoFlue Flex (3") or Flex Adaptor (2") through a cap in the base of this Tee. Use a Centrotherm IAWP2P or IAWP03B wall plate and RTV to seal this penetration. Install the Base Support using the Base support bracket as described in the
InnoFlue installation manual.
Connection of the PVC air intake pipe to the side outlet of the tee is made using a cap and a PVC socket x male thread adaptor (2" or 3", depending on the Vent Option). Cut a clearance hole in the cap for the male threads. Secure the adaptor to the cap using a 2" or 3" electrical conduit lock nut. Seal all joints with RTV.
I. Condensate Trap and Drain Line
All condensate which forms in the boiler or vent system passes through the heat exchanger and out of a bottom drain port which is connected to the field-installed condensate trap. This trap allows condensate to drain from the heat exchanger while retaining flue gases in the boiler. This trap is an integral part of the boiler but must be connected to a drain pipe as shown in
Figure 7.46
.
A length of corrugated tubing is supplied with the boiler and is connected to the trap as shown in Figure 7.46. Note the following when disposing of the condensate:
1. Attach condensate trap to heat exchanger condensate drain. Slide inlet nut followed by inlet gasket onto heat exchanger drain. Then tighten inlet nut onto trap body. Nut and gasket must be secure to create a seal.
2. Attach condensate trap bracket to bottom of boiler using provided screws.
3. Ensure vent plug is removed from trap to improve condensate drainage.
4. If the corrugated condensate drain line must be extended, construct the extension from PVC or CP VC pipe.
Insert the hose provided with the boiler into the end of the extension as shown in Figure 7.46.
5. Condensate is slightly acidic. Do not use metallic pipe or fittings in the condensate drain line. Do not route the drain line through areas that could be damaged by leaking condensate.
6. Some jurisdictions may require that the condensate be neutralized before being disposed of. Dispose of condensate in accordance with local codes.
7. Do not route, or terminate, the condensate drain line in areas subjected to freezing temperatures.
62
VII. Venting I. Condensate Trap and Drain Line (continued)
8. If the point of condensate disposal is above the trap, it will be necessary to use a condensate pump to move the condensate to the drain. In such cases, select a condensate pump that is approved for use with condensing boilers. If overflow from this pump would result in property damage, select a pump with an overflow switch and use this switch to shut down the boiler.
Alternatively, if heat is a necessity, use the overflow switch to trigger an alarm.
9. Do not attempt to move the trap from the location shown in Figure 7.46.
Do not attempt to substitute another trap for the one provided with the boiler.
WARNING
Asphyxiation Hazard. Failure to install the condensate drain in accordance with the above instructions could cause flue gas to enter the building, resulting in personal injury or death.
NOTICE
Boiler condensate is corrosive. Route condensate drain line in a manner such that any condensate leakage will not cause property damage.
Some jurisdictions may require that condensate be neutralized prior to disposal.
Use materials approved by the authority having jurisdiction.
BOILER JACKET
CONDENSATE DRAIN
INLET NUT
INLET GASKET
VENT
CORRUGATED
DRAIN TUBE
Figure 7.46
: Condensate Trap Installation
#8-18 THREAD FORMING
SCREW (1/4" LONG)
63
VII. Venting J. Removing an Existing Boiler From a Common Chimney (continued)
J. Removing an Existing Boiler From a Common Chimney
This section only applies if this boiler is replacing an existing boiler that is being removed from a common chimney.
In some cases, when an existing boiler is removed from a common chimney, the common venting system may be too large for the remaining appliances. At the time of removal of an existing boiler, the following steps shall be followed with each appliance remaining connected to the common venting system placed in operation, while the other appliances remaining connected to the common venting system are not in operation.
(a) Seal any unused openings in the common venting system.
(b) Visually inspect the venting system for proper size and horizontal pitch and determine there is no blockage or restriction, leakage, corrosion and other deficiencies which could cause an unsafe condition.
(c) Insofar as practical, close all building doors and windows and all doors between the space in which all the appliances remaining connected to the common venting system are located and other spaces of the building. Turn on clothes dryers and any appliance not connected to the common venting system. Turn on any exhaust fans, such as range hoods and bathroom exhausts, so they will operate at maximum speed. Do not operate a summer exhaust fan. Close fireplace dampers.
(d) Place in operation the appliance being inspected. Follow the operating instructions. Adjust thermostat so the appliance will operate continuously.
(e) Test for spillage at the draft hood relief opening after 5 minutes of main burner operation. Use the flame of a match or candle, or smoke from a cigarette, cigar, or pipe.
(f) After it has been determined that each appliance remaining connected to the common venting system properly vents when tested as outlined above, return doors, windows, exhaust fans, fireplace dampers and any other gas-burning appliances to their previous condition of use.
(g) Any improper operation of the common venting system should be corrected so the installation conforms with the National
Fuel Gas Code, ANSI Z223.1. When re-sizing any portion of the common venting system, the common venting system should be re sized to approach the minimum size as determined using the appropriate tables in Part 11 of the National Fuel
Gas Code, ANSI Z223.1.
WARNING
Never common vent this boiler with other appliances.
Au moment du retrait d’une chaudière existante, les mesures suivantes doivent être prises pour chaque appareil toujours raccordé au système d’evacuation commun et qui fonctionne alors que d’autres appareils toujours raccordés au système d’évacuation ne fonctionnent pas:
(a) Sceller toutes les ouvertures non utilisées du système d’évacuation.
(b) Inspecter de façon visuelle le système d’évcuation pour déterminer la grosseur et l’inclinaison horizontale qui conviennent et s’assurer que le système est exempt d’obstruction, d’étranglement, de fuite, de corrosion et autres défaillances qui pourraient présenter des risques.
(c) Dans la mesure du possible, fermer toutes les portes et les fenêtres du bâtiment et toutes les portes entre l’espace où les appareils toujours raccordés au système d’évacuation sont installés et les autres espaces du bâtiment. Mettre en marche les sécheuses, tous les appareils non raccordés au système d’évacuation commun et tous les ventilateurs d’extraction comme les hottes de cuisinière et les ventilateurs des salles de bain. S’assurer que ces ventilateurs fonctionnent à la vitesse maximale.
Ne pas faire fonctionner les ventilateurs d’été. Fermer les registres des cheminées.
(d) Mettre l’appareil inspecté en marche. Suivre les instructions d’allumage. Régler le thermostat de façon que l’appareil fonctionne de façon continue.
(e) Faire fonctionner le brùleur principal pendant 5 min ensuite, déterminer si le coupe-tirage déborde à l’ouverture de décharge.
Utiliser la flamme d’une allumette ou d’une chandelle ou la fumée d’une cigarette, d’un cigare ou d’une pipe.
(f) Une fois qu’il a été déterminé, selon la méthode indiquée ci-dessus, que chaque appareil raccordé au système d’évacuation
est mis à l’air libre de façon adéquate. Remettre les portes et les fenêtres, les ventilateurs, les registres de cheminées et les appareils au gaz à leur position originale.
(g) Tout mauvais fonctionnement du système d’évacuation commun devrat être corrigé de façon que l’installation soit conforme au National Fuel Gas Code, ANSI Z223.1/NFPA 54 et (ou) aux codes d’installation CAN/CSA-B149.1. Si la grosseur d’une section du système d’évacuation doit être modifiée, le système devrait être modifié pour respecter les valeurs minimales des tableaux pertinents de l’appendice F du National Fuel Gas Code, ANSI Z223.1/NFPA 54 et (ou) des codes d’installation
CAN/CSA-B149.1.
64
VIII. Gas Piping
WARNING
Explosion Hazard. Failure to properly pipe gas supply to boiler may result in improper operation or leaks of flammable gas.
Gas supply to boiler and system must be absolutely shut off prior to installing or servicing boiler gas piping.
Always assure gas piping is absolutely leak free and of the proper size and type for the connected load.
Use a thread compound compatible with liquefied petroleum gas. Failure to use proper thread compounds on all gas connectors may result in leaks of flammable gas.
If inlet pressure is above 1/2 psig (3.4 kPa) an additional gas pressure regulator is required. Consult gas supplier.
Size corrugated stainless steel tubing (CSST) to ensure proper capacity and minimize flow restrictions.
Gas piping to the boiler must be sized to deliver adequate gas for the boiler to fire at the nameplate input at an inlet pressure between the minimum and maximum values shown in Table 8.2. When sizing, also consider other existing and expected future gas utilization equipment (i.e. water heater, cooking equipment). For more information on gas line sizing, consult the utility or the National Fuel Gas Code, NFPA 54/ANSI Z223.1, and/or CAN/CSA B149.1 Natural
Gas and Propane Installation Code.
Figure 8.1 shows typical gas piping connection to the boiler. A sediment trap must be installed upstream of all gas controls. Install the factory provided manual shut-off valve outside the jacket with a ground joint union as shown.
All above ground gas piping upstream from manual shut-off valve must be electrically continuous and bonded to a grounding electrode. Refer to National Electrical Code, NFPA 70.
The boiler and its gas connection must be leak tested before placing the boiler in operation. When doing this, the boiler and its individual shut-off must be disconnected from the rest of the system during any pressure testing of that system at pressures in excess of 1/2 psi (3.5kPa). When pressure testing the gas system at pressures of 1/2 psi (3.5kPa) or less, isolate the boiler from the gas supply system by closing its individual manual shut-off valve. Locate leaks using approved combustible gas non-corrosive leak detector solution.
DANGER
Explosion Hazard. Do not use matches, candles, open flames or other ignition source to check for leaks.
WARNING
If gas pressure in the building is above ½ psig (3.4 kPa), an additional gas pressure regulator is required.
Using one additional regulator for multiple gas appliances may result in unsafe boiler operation. The additional regulator must be able to properly regulate gas pressure at the input of the smallest appliance.
If the regulator can not do this, two or more additional regulators are required. Consult regulator manufacturer and/or local gas supplier for instructions and equipment ratings.
65
VIII. Gas Piping (continued)
CAUTION
Support the weight of the gas line piping independently from the boiler gas connection fitting located on the bottom of the boiler.
If an additional regulator is used to reduce boiler inlet pressure below 1/2 psig (3.4 kPa) it must be at least 6 to 10 ft. upstream of the boiler.
It is very important that the gas line is properly purged by the gas supplier or utility company.
INTERNAL
FACTORY SUPPLIED
MANUAL SHUT-OFF VALVE
GAS SUPPLY
VENT, COMBUSTION AIR,
SUPPLY AND RETURN PIPING
OMITTED FOR CLARITY
TEE
66
CAP
3" MIN. DRIP LEG
GROUND
JOINT
UNION
FRONT VIEW
Figure 8.1: Gas Connection to Boiler
Table 8.2: Minimum and Maximum Inlet Pressures
Model Size Max. (Natural & LP), in. wc
85 14.0
110
155
205
270
14.0
14.0
14.0
14.0
Min. (Natural), in. wc
4.0
4.0
4.0
4.0
4.0
Min. (LP), in. wc
8.0
8.0
8.0
8.0
8.0
IX. System Piping
A. General System Piping Precautions
WARNING
Failure to properly pipe boiler may result in improper operation and damage to boiler or structure.
Install boiler so that the gas ignition system components are protected from water (dripping, spraying, rain, etc.) during boiler operation and service (circulator replacement, etc.).
Oxygen contamination of boiler water will cause corrosion of iron and steel boiler components and can lead to boiler failure. Warranty does not cover problems caused by oxygen contamination of boiler water or scale (lime) build-up caused by frequent addition of water.
WATER QUALITY AND BOILER WATER ADDITIVES
IMPORTANT NOTE
The heat exchanger used in this boiler is made from stainless steel. Once filled with system water, it will be subjected to the effects of corrosion, as well as fouling from any debris introduced from the system. Take the following precautions to minimize the chance of severe heat exchanger damage caused by corrosion and/or overheating:
1 Flush the system before connecting the boiler - In a replacement installation, flushing the system will remove impurities, such as sediment, solder flux, metal shavings, and traces of old boiler additives. Even if the system is new, do not omit this step – new systems will contain flux and may even contain some of the other impurities listed above. Flush the system completely and repeat if necessary to completely remove these contaminants. If necessary, a cleaning agent may be used to assist in system cleaning. See Section XI “Start-up and Check-out” for recommended cleaners.
2. Make sure that the system is tight - This is the single most important guideline. Tap water contains dissolved oxygen which causes corrosion. In a tight system, this oxygen comes out of solution and is quickly removed from the system through the automatic air vent. The system then remains essentially free of oxygen. If the system is not tight, however, frequent additions of make-up water can expose the heat exchanger to oxygen on a continuous basis. In addition, frequent additions of hard make-up water can cause calcium deposits to collect in the heat exchanger, causing severe damage. To minimize additions of make-up water:
• Inspect the system thoroughly for leaks before placing it in service.
• If the system includes underground piping, or other piping in which a leak might go undetected, consider isolating the boiler from the system with a heat exchanger.
• Make sure that the expansion tank is properly sized and in good condition. If it is not, the relief valve may open frequently, resulting in regular additions of make-up water.
• If an automatic fill valve is installed, installation of a water meter in the fill line is strongly recommended so that routine additions of make-up water can be detected and their cause corrected.
3. Non-Metallic Tubing - Even if the system is tight, oxygen can be introduced into the system through some types of non-metallic tubing used in radiant or snow melt systems. Other nonmetallic tubing is equipped with an oxygen barrier to prevent migration of oxygen into the water. If the boiler is to be installed in a system containing non-metallic tubing without an oxygen barrier, it must be isolated from the boiler with a heat exchanger as shown in Figure 9.10.
4. Water Chemistry, Antifreeze, and Boiler Water Additives – Improper boiler water chemistry can cause the heat exchanger damage described above, as well as deterioration of seals. Observe the water chemistry requirements shown in Section XI “Start-up and Check-out”.
67
IX. System Piping (continued)
B. Standard Piping Installation Requirements
Observe the following requirements when installing the boiler piping:
1) Relief Valve (Required) – The relief valve is shipped loose and must be installed in the location shown in Figure 9.1.
ASME Section IV currently requires that this relief valve be installed above the heat exchanger as shown. Pipe the outlet of the relief valve to a location where water or stream will not create a hazard or cause property damage if the valve opens. The end of the discharge pipe must terminate in unthreaded pipe. If the relief valve discharge is not piped to a drain, it must terminate at least 6" above the floor. Do not run the discharge piping through an area that is prone to freezing. The termination of the relief valve must be in an area where it is not likely to become plugged by
debris.
The relief valve supplied with the boiler is set to open at 30 psi. If it is replaced, the replacement must have a setting less than or equal to the maximum allowable working pressure (MAWP) shown on the ASME data plate located on front of heat exchanger.
DANGER
Explosion / Scald Hazard.
Pipe relief valve discharge to a location where the potential of severe burns is eliminated.
Do not install a relief valve having a setting greater than the MAWP shown on the rating plate.
Do not install a valve in the relief valve discharge line.
Do not install relief valve in a location other than that specified by the factory.
Do not plug the relief valve discharge.
2) Gauge (Required) - Indicates supply water pressure and temperature. This gauge is shipped loose. Install it as shown in Figure 9.1.
3) Circulator (required) – A boiler loop circulator is required to maintain flow through boiler. Usually at least one additional circulator (not supplied) will be required for the system to work properly. See next section for
68
4) Expansion Tank (required) – If this boiler is replacing an existing boiler with no other changes in the system, the old expansion tank can generally be reused. If the expansion tank must be replaced, consult the expansion tank manufacturer’s literature for proper sizing.
5) Fill Valve (required) – Either a manual or automatic fill valve may be used, but a manual valve is preferred because it eliminates unmonitored additions of make-up water to the system. The ideal location for the fill valve is at the
6) Automatic Air Vent (required) – At least one automatic air vent is required. Manual air vents will usually be required in other parts of the system to remove air during initial fill.
7) Manual Reset High Limit (required by some codes) - This control is required by ASME CSD-1 and some other codes. Install the high limit in the boiler supply piping just above the boiler with no intervening valves. Set the manual reset high limit to 200°F. Wire the limit per Figure 10.3 in Section X “Wiring”.
8) Isolation Valves (recommended) - Isolation valves are useful when the boiler must be drained, as they will eliminate having to drain and refill the entire system.
9) Strainer (recommended) – Install a Y Strainer, or other suitable strainer, to prevent any system debris from entering the boiler and fouling the water passages. Note that some strainers have a significant pressure drop, which may impact the ability of the boiler pump to obtain the required flow. See Paragraph B of this section for additional
information.
10) Drain Valve (required) – Install the drain valve supplied as shown in Figure 9.1.
11) Low Water Cut-off (may be required by local jurisdiction).
A Low Water Cut-off Kit (P/N 105591-01 or 100592-01) is available that plugs into the low voltage wire harness
(refer to Section X “Wiring”). Alternatively, use Hydrolevel Safgard 1100, Taco LTR Series, or equivalent. Install the low water cut-off in the tee provided inside boiler cabinet. See Figure 9.2 for LWCO location.
IX. System Piping (continued)
CAUTION
Do not reverse supply/inlet and return/outlet piping. Reverse piping will cause premature heat exchanger failure. Positively assure supply/inlet and return/outlet pipes are properly connected as shown in this manual.
NOTICE
For combi model RPTR155C, only the inlet bottom/outlet bottom piping configuration may be used. Refer to Appendix C for combi piping.
INLET BOTTOM/OUTLET BOTTOM
Automatic Air Vent
Relief Valve
Copper Piping
Cap
INLET BOTTOM/OUTLET TOP
Automatic Air Vent
Copper Piping
Cap
Relief Valve
Ball Valve
Supply/
Outlet
Temperature/
Pressure
Gauge
Ball Valve
Drain Valve
Return/
Inlet
Supply/
Outlet
Temperature/
Pressure
Gauge
INLET TOP/OUTLET BOTTOM
Automatic Air Vent
Relief Valve Ball Valve
Return/
Inlet
Copper Piping
Cap
Ball Valve Drain Valve
Return/
Inlet
INLET TOP/OUTLET TOP
Automatic Air Vent
Relief Valve
Temperature/
Pressure
Gauge
Ball Valve
Ball Valve
Supply/
Outlet
Return/
Inlet
Ball Valve
Supply/
Outlet
Drain Valve
Temperature/
Pressure
Gauge
Copper Piping
Cap
Drain Valve
Figure 9.1: Near Boiler Piping
69
K2 FT/ RAPTOR
U.S. Boiler Co., Inc.
1:8 1 OF 1
K2 FT/ RAPTOR
U.S. Boiler Co., Inc.
1:8 1 OF 1
1
K2 FT/ RAPTOR
U.S. Boiler Co., Inc.
1:8 1 OF 1
K2 FT/ RAPTOR
U.S. Boiler Co., Inc.
1:6 1 OF 1
1
11
1
IX. System Piping (continued)
Install Optional
Low Water Cutoff
Figure 9.2: LWCO Location
C. Near Boiler Piping Design
Proper operation of this boiler requires that the water flow rate through it remain within the limits shown in Table 9.3 any time the boiler is firing. At flow rates below the minimum shown, the boiler’s temperature rise limit function may prevent the boiler from firing. Flow rates through the boiler in excess of the maximum shown in Table 9.3 can result in excessive noise or erosion damage to piping
There are two basic methods that can be used to pipe this boiler into the system. Method #1 (primary-secondary piping) is always preferred. Additional information on hydronic system design can be found in the I=B=R Guide RHH published by the Air-Conditioning, Heating and Refrigeration Institute (AHRI).
Table 9.3: Flow Limitations
Boiler
Model
RPTR085
RPTR110
RPTR155
RPTR155C
RPTR205
RPTR270
Min. Pipe
Size (in.)
1
1
1
1
1¼
1¼
∆T = 35°F
Min.
Flow
(GPM)
Boiler
Head Loss
(ft)
4.5
0.5
5.8
8.2
8.2
10.9
14.3
0.8
1.3
3.5
0.8
1.4
Flow
(GPM)
∆T = 30°F
Boiler
Head Loss
(ft)
5.3
0.6
6.8
9.6
9.6
12.7
16.7
1.0
1.8
4.8
1.0
1.8
Flow
(GPM)
∆T = 25°F
Boiler
Head Loss
(ft)
6.3
0.9
8.2
11.5
11.5
15.3
20.1
1.3
2.5
7.1
1.4
2.5
∆T = 20°F
Max.
Flow
(GPM)
Boiler
Head Loss
(ft)
7.9
1.2
10.2
14.4
14.4
19.1
25.1
2.0
3.7
11.2
2.0
3.8
70
IX. System Piping (continued)
Method 1: Primary/Secondary Piping (Strongly Recommended)
This method can be used in heat-only applications as shown in Figure 9.7a or 9.8a or with an indirect water heater as shown in Figure 9.7b, 9.7c, 9.8b, 9.8c. In this system, the flow rate through the boiler (“secondary loop”) is completely independent of the flow rate through the system (“primary loop”). Use the following guidelines to ensure that the boiler will have the required flow shown in Table 9.3 regardless of the flow in the heating system.
1) System Loop Piping - Size the system circulator and piping to obtain the design flow rate through the heating system as you would on any other heating system. All piping between the expansion tank and secondary connection tees must be at least 1". In order to keep the flow rates in the system and boiler loops independent of each other, provide at least
8 diameters of straight pipe upstream of the first tee and 4 diameters downstream of the second tee. Keep the distance between the expansion tank and the first secondary tee as short as practical.
Figure 9.4: Boiler Head Loss
71
72
Boiler & Piping Head Loss
Flow (GPM)
Flow (GPM)
Loss (ft)
Flow (GPM)
Loss (ft)
Minimum Pipe Size
Boiler Model
Flow (GPM)
Loss (ft)
Boiler & Piping Head Loss
Flow (GPM)
Boiler & Piping Head Loss
Flow (GPM)
Pipe Size (in.)
Boiler Model
Boiler & Piping Head Loss
Flow (GPM)
15-58FC, Spd. 1 15-58FC, Spd. 2 15-58FC, Spd. 3 26-99FC, Spd. 2 26-99FC, Spd. 1 26-99FC, Spd. 2
Boiler & Piping Head Loss
Flow (GPM)
IX. System Piping (continued)
3) Indirect Water Heater Loop Piping – If an indirect water heater is used, install it as shown in Figure 9.7b, 9.7c, 9.8b, 9.8c.
Refer to the indirect water heater installation manual for the proper sizing the indirect water heater loop pump and piping.
4) Hydraulic Separators – Hydraulic separators serve the same purpose as the closely spaced tees connecting the boiler and system loops. They also generally provide effective connection points for automatic air elimination devices and an expansion tank. These separators are available from several sources and may be used in place of the closely spaced tees.
Select a hydraulic separator having 1" or larger boiler connections that is designed for the boiler flow rates shown in Table
9.3.
Table 9.6: Fitting and Valve Equivalent Length
Fitting or Valve
Description
90° Elbow
Copper Fitting and Sweat Valve
Equivalent Length (Ft)
1
2.5
Copper Pipe or Valve Size
1¼ 1½
3.0
4.0
2
5.5
45° Elbow
Tee (through flow)
Tee (Branch flow)
Diverter Tee (typical)
Gate Valve
Globe Valve
1.0
0.5
4.5
23.5
0.3
25.0
1.2
0.6
5.5
25.0
0.4
36.0
1.5
0.8
7.0
23.0
0.5
46.0
Angle Valve
Ball Valve (standard port)
5.3
4.3
7.8
7.0
9.4
6.6
12.5
14.0
Ball Valve (full port)
Y-Strainer *
Swing Check Valve
Flow-Check Valve
(typical)
Butterfly Valve
1.9
7.0
4.5
54.0
2.7
1.4
5.5
74.0
2.0
2.2
6.5
57.0
2.7
1.3
9.0
177.0
4.5
* Based on Cv of 20. Pressure drop through strainers varies widely. 7 ft. equivalent+ length may be assumed for strainers having a published Cv greater than 10.
2.0
1.0
9.0
23.0
0.7
56.0
NOTE: Table 9.3 is provided as reference to assist in piping design and specifies equivalent
length of typical piping fittings and valves.
73
74
Drain Valve Full Port Isolation Valves Secondary Unions Not Required; Optional Location Shown
From System
Header Temperature Sensor (When Used)
Cold Water Line
Hydraulic Separator May Be Substituted
As Close As Possible To Downstream Tee)
Flow Check Optional Full Port Isolation Valves
Backflow Preventer
Heating System Circulator
Optional Zone Valve Controlled System
Optional Full Port Isolation
From System
Hydraulic Separator May Be Substituted
As Close As Possible To Downstream Tee)
Full Port Isolation Valves Secondary Unions Not Required; Optional Locations Shown
Indirect Circulator
Full Port Isolation
Indirect Supply
Indirect Return
Backflow Preventer
Cold Water Line
Heating System Circulator
Optional Zone Valve Controlled System
Optional Full Port Isolation
Optional Full Port Isolation
75
76
Full Port Isolation Valves Secondary Unions Not Required; Optional Location Shown
Full Port Isolation Valve
From System
Cold Water Line
Backflow Preventer
Indirect Supply Indirect Return
Indirect Domestic Water Heater (IWH)
Hydraulic Separator May Be Substituted
As Close As Possible To Downstream Tee)
Flow Check
Full Port Isolation
Optional Full Port Isolation
Optional Full Port Isolation
Heating System Circulator
Optional Zone Valve Controlled System
Secondary Unions Not Required; Optional Locations Shown
Relief Valve
From System
Hydraulic Separator May Be Substituted
As Close As Possible To Downstream Tee)
Boiler Circulator
Full Port Isolation
Header Temperature Sensor (When Used)
Cold Water Line
Drain Valve
Valve Backflow Preventer
Heating System Circulator
Optional Full Port Isolation Valves
Optional Full Port Isolation
77
78
From System
Secondary Unions Not Required; Optional Locations Shown
Full Port Isolation Valves
Flow Check
Indirect Circulator
Backflow Preventer Cold Water Line
Full Port Isolation
Fill Valve
Indirect Supply
Indirect Return
Indirect Domestic Water Heater (IWH)
Hydraulic Separator May Be Substituted
As Close As Possible To Downstream Tee)
Flow Check
Optional Full Port Isolation
Optional Full Port Isolation
Heating System Circulator
Optional Zone Valve Controlled System
Drain Valve
Full Port Isolation Valves
Boiler Circulator
From System
Secondary Unions Not Required; Optional Locations Shown
Full Port Isolation
Hydraulic Separator May Be Substituted
As Close As Possible To Downstream Tee)
Flow Check
Full Port Isolation
Cold Water Line
Backflow Preventer
Flow Check
Indirect Supply
Indirect Return Indirect Domestic Water Heater (IWH)
Heating System Circulator
Optional Zone Valve Controlled System
Optional Full Port Isolation
Optional Full Port Isolation
79
IX. System Piping (continued)
Method 2: Direct Connection to Heating System (Generally NOT Recommended)
In some cases it may be possible to connect this boiler directly to the heating system as is done with conventional boilers
(Figure 9.9). If this is done, the flow rate through the boiler will equal the flow rate through the system. The flow rate through the system must therefore always remain within the limits shown in Table 9.3. For this reason, the pressure drop through the entire system must be known.
This method is generally not recommended because it is often very difficult to accurately calculate the pressure drop through the system. In replacement installations, it may be impossible to get an accurate measurement of the amount of piping and number of fittings in the system. In addition, if the system is zoned, the system flow may drop well below the minimum required when only one zone is calling for heat.
The one advantage to this method is its installation simplicity. It may make sense to use this method when the boiler is to be installed with a new single zone system having a low-pressure drop.
Calculation of the system pressure drop must be performed by someone having familiarity with pressure drop calculations, such as an HVAC engineer.
NOTICE
Where it is not possible to install a separate boiler loop, the system circulator must be sized to ensure that the flow through the boiler stays within the defined parameters to prevent overheating when the boiler is fired at it’s full rated input. Install a flow meter to measure the flow, or fire the boiler at full rate and ensure the boiler delta T does not exceed 35°F (19°C).
To
Convection
System
From
Convection
System
Balancing
Valve
Y-Strainer
(Recommended)
System
Circulator
Flow Check
(Can Be Incorporated
With System Circulator)
Relief
Valve
80
Air Separator
& Air Vent
Fill
Valve
Backflow
Preventer
Cold
Water
Line
Expansion Tank
Drain Valve
Full Port
Isolation
Valves
Temperature/Pressure
Gauge
Secondary Unions Not
Required; Optional
Location Shown
Figure 9.9: Piping Method #2: Direct Connection of Boiler to Heating System
1
IX. System Piping (continued)
D. Piping for Special Situations
1) corrosion damage to a this boiler. Some examples include:
• Radiant systems that employ tubing without an oxygen barrier.
• Systems with routine additions of fresh water.
• Systems which are open to the atmosphere.
If the boiler is to be used in such a system, it must be separated from the oxygenated water being heated with a heat exchanger as shown in Figure 9.10. Consult the heat exchanger manufacturer for proper heat heat exchanger, such as the pump and expansion tank, must be designed for use in oxygenated water.
exchanger sizing as well as flow and temperature requirements. All components on the oxygenated side of the
Piping with a Chiller - If the boiler is used in conjunction with a chiller, pipe the boiler and chiller in parallel.
Use isolation valves to prevent chilled water from entering the boiler.
Air Handlers - Where the boiler is connected to air handlers through which refrigerated air passes, use flow control valves in the boiler piping or other automatic means to prevent gravity circulation during the cooling
cycle.
Do Not Exceed
12"
From Oxygenated
System
7
8
5
6
1
2
Boiler (Right Side View)
Isolation Valve
3 Swing Check Valve
4 Central Heating Primary Circulator
Plate Heat Exchanger
Air Separator
Automatic Air Vent
Expansion Tank
9 Automatic Fill Valve
10 Cold Water Line
11 Relief Valve
12 Relied Valve Discharge Piping
13 Drain Valve
14 Primary/Secondary Connection
13
Figure 9.10: Isolation of the Boiler from Oxygenated Water with a Plate Heat Exchanger
81
X. Wiring
DANGER
Electrical Shock Hazard. Positively assure all electrical connections are unpowered before attempting installation or service of electrical components or connections of the boiler or building. Lock out all electrical boxes with padlock once power is turned off.
WARNING
All wiring and grounding must be done in accordance with the authority having jurisdiction or, in the absence of such requirements, with the National Electrical Code /NFPA 70). In
Canada, all wiring and grounding must be done in accordance with the Canadian Electrical
Code, Part 1 (CSA C22.1 - latest edition).
Failure to properly wire electrical connections to the boiler may result in serious physical harm.
Electrical power may be suppled from more than one circuit. Make sure all power is off before attempting any electrical work.
Each boiler must be protected with a properly sized over-current device.
Never jump out or make inoperative any safety or operating controls.
The wiring diagrams contained in this manual are for reference purposes only. Each boiler is shipped with a wiring diagram attached to the front door. Refer to this diagram and the wiring diagram of any controls used with the boiler. Read, understand and follow all wiring instructions supplied with the controls.
NOTICE
This boiler is equipped with a listed high water temperature limit function. This limit provides boiler shutdown in the event the boiler water temperature exceeds the set point of the limit control. Certain Local
Codes require an additional water temperature limit. If necessary, install an additional water temperature limit such as a Honeywell L4006 Aquastat. Wire as indicated in Figure 10.3.
Figure 10.1 shows the location of both the high voltage and low voltage printed circuit boards with terminal strips for field wiring. Remove front door to access the PCB’s.
1) Line Voltage (120 VAC) Field Connections – See Figure 10.2 for line voltage connections. Provide a dedicated circuit for the boiler of 15A or greater. A service switch is recommended and is required by many local codes. Locate this switch in accordance with local codes or, in the absence of any, in a location where it can be safely accessed in an emergency involving the boiler. All 120VAC connections to the boiler itself are made on the terminal strip on the high voltage PCB located on the left side if the wiring compartment. 120VAC connections on the terminal strip are:
•
•
•
•
•
•
•
•
120VAC Hot
120VAC Neutral Ground
System Pump Hot
System Pump Neutral
DHW Pump Hot
DHW Pump Neutral
Boiler Pump Hot
Boiler Pump Neutral
82
X. Wiring (continued)
The use of the pump outputs are as follows: a) System Pump - Pumps water through the radiation. This pump is hydraulically separated from the boiler pump, either by closely spaced tees, or by a hydraulic separator. The system pump is always on when the system is responding to a call for CH. Depending on the DHW configuration, it may also be on during a call for DHW. b) DHW Pump (“IWH Circulator”) - Pumps water directly through the indirect water heater.
c) Boiler Pump - Pumps water through the boiler. Boiler pump is always on when the system is responding to a call for CH. Depending on the DHW configuration, boiler pump may be turned off when system is responding to a call for DHW.
Maximum combined current draw for all circulators is 6.3 FLA. See Section XII “Operation” for information on setting
up the pump operation.
2) Low Voltage Field Connections – Low voltage field connections on the low voltage PCB are shown in Figure 10.3 and are listed from top to bottom:
• Heat T’Stat - 24VAC heating thermostat (R - 24V “Hot”)
• Heat T’Stat - 24VAC heating thermostat (W - Energized or Call for Heat)
• Heat T’Stat - 24VAC heating thermostat (C - 24V Common)
• DHW T’Stat - 24VAC domestic hot water thermostat (1)
• DHW T’Stat - 24VAC domestic hot water thermostat (2)
• External Limit - Field supplied low voltage safety limit contacts (1)
• External Limit - Field supplied low voltage safety limit contacts (2)
• Alarm Contact (1)
• Alarm Contact (2)
• Outdoor Sensor - Tasseron TSA00AA Outdoor Temperature Sensor (1)
• Outdoor Sensor - Tasseron TSA00AA Outdoor Temperature Sensor (2)
• Header Sensor - Optional Honeywell 32003971-003 Sensor (1)
• Header Sensor - Optional Honeywell 32003971-003 Sensor (2)
• EnviraCOM Device (D)
• EnviraCOM Device (R)
• EnviraCOM Device (C)
• MODBUS - (A)
• MODBUS - (B)
• MODBUS - (-V)
LOW
VOLTAGE
PCB
HIGH
VOLTAGE
PCB
Figure 10.1: Location of High and Low Voltage Printed Circuit Boards (PCB)
83
X. Wiring (continued)
120 VAC Connections
Pump Fuse
Spare Pump Fuse
Boiler
Pump
DHW
Pump
System
Pump
120 V Line
BOILER
PUMP
OVERCURRENT
PROTECTION/
DISCONNECT
Figure 10.2: High Voltage PCB Terminal Connections
DHW
PUMP
SYSTEM
PUMP
120VAC/60HZ
POWER
SUPPLY
84
EnviraCOM THERMOSTAT
(Optional - Replaces
Heating Thermostat)
(By Others) Spare
Fuse
Low Voltage Connections
Fuse F1 250 V 1.6A Slow-Blow 5x20mm
EnviraCOM
C
R
D
MODBUS
Boiler-To-Boiler
Communication Network
V-
B
A
Heat
T'stat
DHW
T'stat
1
External
Limit
Alarm
Header
Sensor
Outdoor
Sensor
1
REMOVE THIS JUMPER IF
EXTERNAL LIMIT IS USED
Figure 10.3: Low Voltage PCB Terminal Connections
TO MODBUS DEVICE
(if used)
X. Wiring (continued)
With the exception of the alarm contacts, external power must not be applied to any of the low voltage terminals - doing so may damage the boiler control. Also note the following: a) External Limit - The external limit terminals are intended for use with a field supplied safety device, such as a manual reset high limit. When an external limit is used, the jumper between these two terminals must be removed. Failure to remove this jumper will render the external safety devices ineffective.
b) Alarm Contacts - These contacts close when the boiler enters a “hard” lockout (lockout requiring manual reset). They may be used as an input to a building alarm system. Contact rating is 24VAC, 0.63FLA. Do not use for line voltage applications.
c) EnviraCOM - Used to connect EnviraCOM thermostat or other EnviraCOM device approved by the boiler manufacturer for use with this boiler. A Honeywell EnviraCOM connection is also located as labeled on the boiler control itself.
d) Outdoor Sensor - Use only the Tasseron TSA00AA (10 KOhms) outdoor sensor supplied with the boiler. When this sensor is connected and enabled, the boiler will adjust the target supply water temperature downwards as the outdoor air temperature increases. This sensor should be located on the outside of the structure in an area where it will sense the average air temperature around the house. Avoid placing this sensor in areas where it may be covered with ice or snow.
In general, locations where the sensor will pick up direct radiation from the sun should also be avoided. Avoid placing the sensor near potential sources of electrical noise such as transformers, power lines, and fluorescent lighting. Wire the sensor to the boiler using 22 gauge or larger wire. As with the sensor itself, the sensor wiring should be routed away from sources of electrical noise. Where it is impossible to avoid such noise sources, wire the sensor using a 2 conductor, UL
Type CM, AWM Style 2092 shielded cable. Connect one end of the shielding on this cable to ground. See Section XII
“Operation” for information on enabling the outdoor reset sensor. e) Header Sensor - When this sensor is installed and enabled, the boiler will attempt to maintain the target water temperature in the header rather than in the supply. Where the system flow rate varies widely, the use of a header sensor allows the temperature of the water being sent to the radiation to be more accurately controlled. Use sensor
P/N 103104-01 (Honeywell 32003971-003) with 1/2" NPT immersion well, P/N 80160456. Installation of this sensor in a well, as opposed to on the surface of the header, is highly recommended. Alternatively use 1/2" NPT direct immersion sensor, P/N 101935-01. Locate this sensor immediately downstream of the second primary-secondary Tee (Figure 10.4).
Use of a direct immersion sensor is also acceptable. The sensor wiring should be routed away from sources of electrical noise. Where it is impossible to avoid such noise sources, wire the sensor using a 2 conductor, UL Type CM, AWM
Style 2092, 300Volt 60°C shielded cable. Connect one end of the shielding on this cable to ground. See Section XII
“Operation” for information on enabling the header sensor. f) MODBUS - Boiler-To-Boiler communication network is used for multiple boiler (“Lead-Lag”) installations. See the multiple boiler installation supplement for additional information.
CAUTION
When making low voltage connections, make sure that no external power source is present in the thermostat or limit circuits. If such a power source is present, it could destroy the boiler’s control.
One example of an external power source that could be inadvertently connected to the low voltage connections is a transformer in the old thermostat wiring.
Do not attempt to use EnviraCOM connections for any purpose not explicitly permitted by the boiler manufacturer. Attempting to do so may result in unreliable operation and/or damage to controls.
85
From System
86
Downstream Primary/Secondary Tee
Header Temperature Sensor (Honeywell 32003971-003)
DETAIL B SCALE 1 : 4
As Close As Possible To Downstream Tee Well Should Extend Into Header Flow As Far As Possible. Use Extension
Heating Circulators
X. Wiring (continued)
Figure 10.5: Internal Wiring Ladder Diagram
87
88
BK - BLACK BL - BLUE BR - BROWN GR - GREEN GY - GRAY OR - ORANGE PI - PINK RD - RED VI - VIOLET WH - WHITE YE - YELLOW R/G - RED W/GRAY TRACKER B/G - BLUE W/GRAY TRACKER P/G - PINK W/GRAY TRACKER Y/G - YELLOW W/GRAY TRACKER V/G - VIOLET W/GRAY TRACKER
LOW VOLTAGE FACTORY WIRING, MINIMUM SIZE 20 AWG TYPE TEW/AWM STRANDED WIRE, 105°C LINE VOLTAGE FACTORY WIRING, SIZE 18 AWG TYPE TEW/AWM STRANDED WIRE, 105°C
DHW FLOW SWITCH (155
89
X. Wiring (continued)
HEATING THERMOSTATS
24 VAC
POWER
TACO SR504
(OR EQUIVALENT)
ZONE 1 ZONE 2 ZONE 3 ZONE 4
PRIORITY OFF
ZONE 4
PRIORITY
ON
OFF
FOUR ZONE SWITCHING RELAY
WITH OPTIONAL PRIORITY
POWER
ZONE 1
ZONE 2
ZONE 3
ZONE 4
120V RELAY
X X
END
SWITCH
ZC ZR
ZONE 1 ZONE 2 ZONE 3 ZONE 4
120 VOLT CIRCULATORS
POWER
INPUT
FUSE 1 AMP
90
REMOVE
JUMPER
120 VAC Connections
Pump Fuse
Spare Pump Fuse
Spare
Fuse
Low Voltage Connections
Fuse F1 250 V 1.6A Slow-Blow 5x20mm
EnviraCOM
MODBUS
Boiler-To-Boiler
Communication Network
V-
B
A
Boiler
Pump
DHW
Pump
System
Pump
120 V Line
N
120V
L
Heat
T'stat
DHW
T'stat
External
Limit
Alarm
DHW
CIRCULATOR
HIGH VOLTAGE PCB
DHW
AQUASTAT
LOW VOLTAGE PCB
***USE SAME POWER SOURCE FOR ALL CONTROLS AND
ENSURE POLARITY TO ALL CONTROL DEVICES IS CORRECT
Header
Sensor
Outdoor
Sensor
XI. Start-Up and Checkout
WARNING
Completely read, understand and follow all instructions in this manual before attempting start-up.
NOTICE
Safe lighting and other performance criteria were met with the gas train assembly provided on the boiler when the boiler underwent the test specified in ANSI Z21.13.
Use the following procedure for initial start-up of the boiler:
1) Verify that the venting, water piping, gas piping and electrical system are installed properly.
2) Confirm all electrical, water and gas supplies are turned off at the source and that vent is clear of obstructions.
3) Confirm that all manual shut-off gas valves between the boiler and gas source are closed.
4) If not already done, flush the system to remove sediment, flux, and traces of boiler additives.
5) Fill the boiler and hydronic system with water meeting the following requirements below (also see the NOTICE on the next page):
• pH between 6.5 and 9.5
• Hardness less than 7 grains/gallon
• Chlorides less than 200 ppm
• Iron level less than 0.5 ppm
• Copper level less than 0.1 ppm
• Pressurize the system to at least 14.5 psi at the boiler
WARNING
Burn Hazard. The maximum operating pressure of this boiler is 30 psig (210 kPa) or 80 psig (340 kPa), depending on the model and safety relief valve option selected. Never exceed the maximum allowable working pressure on the heat exchanger ASME plate.
6) Bleed air from the heat exchanger and piping system.
7) Check all gas piping for leaks and purge piping sections that are filled with air. Refer to the National Fuel Gas Code for additional information on testing and purging gas lines.
DANGER
Explosion Hazard. Do not use matches, candles, open flames or other ignition source to check for leaks.
Make sure that the area around the boiler is clear and free from combustible materials, gasoline and other flammable vapors and liquids.
8) Confirm vent system is complete and free of obstructions before attempting to fire boiler.
9) Inspect all wiring for loose, uninsulated or miswired connections.
10) If the boiler is to be converted to LP Gas (propane), convert as described in Appendix A. If boiler is operating at elevations above 4,500 ft., see Appendix B of this manual for setup instructions.
91
XI. Start-Up and Checkout (continued)
DANGER
Asphyxiation Hazard. Failure to properly convert this boiler for use on LP Gas (propane) can cause unreliable operation at elevated carbon monoxide (CO) levels, resulting in personal injury or death.
NOTICE
To minimize the risk of premature heat exchanger failure, observe the following water chemistry requirements:
1) Minimize the introduction of make-up water, dissolved oxygen, and contaminants into the boiler by following
the installation guidelines shown in the “Water Quality and Boiler Water Additives Note” on Page 67.
2) Make sure the system is filled with water meeting the following criteria:
• pH between 6.6 and 8.5
• Chloride level less than 125PPM. If fill water is drawn from a system containing a water softener, test a
sample of the fill water to confirm that this criteria is met.
• Hardness less than 7 grains/gallon.
• Iron level less than 0.5PPM.
• Copper level less than 0.1PPM.
3) Avoid the use of petroleum based boiler additives. These can attack seals in both the boiler and system.
4) If freeze protection is required, use the following or its equivalent:
• Fernox Alphi -11 (inhibited Propylene Glycol). Velocity Boiler Works Part # 101146-01 is for a 5 gallon
bucket.
• Sentinel ® X500 Inhibited Antifreeze (combined antifreeze and inhibitor)
Refer to the antifreeze manufacturer’s instructions for required dosage. In general these products are a blend of glycol (for freeze protection) and inhibitors (to protect the glycol from attacking metallic system components).
Do not add any more antifreeze than is necessary to protect the system from freeze damage. Many of these products require annual testing of the system water to ensure that the inhibitors are still active; consult the manufacturer’s instructions for maintenance requirements. Allowance must be made for the additional expansion of the glycol solution.
5) For system cleaning, use the following or its equivalent:
• Fernox Cleaner F3
• Sentinel ® X400 System Restorer (For Older Closed Loop Hydronic Heating Systems)
• Sentinel ® X300 System Cleaner (For New Heating Systems)
• Sentinel ® X100 Inhibitor (For Protecting Closed Loop Hydronic Heating Systems Against Lime scale And
Corrosion)
Refer To the instructions supplied with the cleaner for proper dosage and use.
Fernox products are available from Alent plc Consumer Products Division, 4100 6th Avenue, Altoona PA.
(972) 547 6002 ([email protected]).
Sentinel ® products are available from Douglas Products and Packaging, 1550 E. Old 210 Highway, Liberty, MO
64068, Tel:(877) 567-2560 (Toll Free) and/or selected HVAC distributors.
WARNING
Poison Hazard. Use only inhibited propylene glycol solutions specifically formulated for hydronic systems.
Do not use ethylene glycol, which is toxic and can attack gaskets and seals used in hydronic systems. Use of ethylene glycol could result in property damage, personal injury or death.
92
XI. Start-Up and Checkout (continued)
11) Start the boiler using the operating instructions on page 97 . With the boiler powered up, and with no call for heat, the display should look like Figure 11.1a. Once a call for heat is present, it will look like Figure 11.1b.
12) The boiler should attempt to fire approximately 30 seconds after a call for heat appears. With the front door removed from the boiler, this try for ignition will appear as an audible spark (lasting approximately 4 seconds) and an audible click from the gas valve. Upon initial start-up, the gas train will be filled with air. Even if the gas line has been completely purged of air, it may take several tries for ignition before a flame is established. If the boiler does not light after four tries for ignition, it will enter a “soft lockout” and will wait for one hour before attempting another ignition sequence. This soft lockout can be reset by interrupting power to the boiler for a few seconds. Once a flame has been established for the first time, subsequent calls for burner operation should result in a flame on the first try.
13) If there is a problem that appears before the first try for ignition, or if the boiler fails to light after four tries for ignition, the blinking red screen with “HELP” highlighted on the Home screen ( Figure 11.1c
). Touching this “HELP” button will take the user to the Diagnostics menu where the cause of the problem can usually be found by pressing the flashing button on each successive screen. For more information, see Section XII “Operation”.
14) Inspect the flame visible through the window. On high fire the flame should be stable and mostly blue (Figure 11.2). No yellow tipping should be present; however, intermittent flecks of yellow and orange in the flame are normal.
15) Check the inlet gas pressure. Verify that the inlet gas pressure is between the upper and lower limits shown on the rating plate with all gas appliances on and off.
16) Perform a combustion test. Boilers are equipped with a screw cap in the vent adapter. Be sure to replace this cap when combustion testing is complete. Check CO locked into high or low fire as follows:
2
(or O
2
) and CO at both high and low fire. The boiler may be temporarily a) Fire the boiler through any call for heat.
b) From the Home Screen, press “ADJUST” to enter the adjust menu.
c) Press “ADJUST”.
d) Press “LOGIN”. e) Press “000”. f) Enter the password “086”.
g) Press return arrow to close the keypad.
h) Press “SAVE”.
i) Press “ADJUST”.
j) Press “MANUAL CONTROL”.
k) Press “HIGH” or “LOW” as appropriate.
To return the boiler to automatic modulation, press AUTO FIRE. Note: If the Auto Fire button is not pressed, boiler will remain in manual fire for around 10 minutes. After 10 minutes boiler automatically returns to automatic modulation.
At both high and low fire, CO readings should be less than 200 PPM air free. Typical CO
Table 11.4. Final readings should be taken with all doors and covers in place.
2
and O
2 readings are shown in
If throttle screw is very far out of adjustment, boiler may not start or it may not be possible to achieve acceptable combustion readings. In this case, shut down boiler. Fully close throttle screw and reopen to number of turns shown in Table
11.5. Follow operating instructions to restart boiler. Use a combustion analyzer to verify combustion readings, and adjust throttle screw as needed to achieve readings per Table 11.4.
17) Perform a check of the ignition safety shut-off device. With the burner firing, carefully unplug the orange flame rod wire at the flame rod using a pair of insulated pliers. The burner should shut off immediately.
18) Test any external limits or other controls in accordance with the manufacturer’s instructions.
19) Refer to the Operation Manual to set-up the control for the system in which the boiler is installed. Some common set-up tasks include:
• Setting the CH and DHW temperature set-points (as shipped, both setpoints are set to 180°F).
• Selecting the type of indirect water heater (if any) and location of DHW pumps.
• Defining the system pump operation.
20) Adjust the heating and indirect water heater thermostats to their final set points.
93
94
XI. Start-Up and Checkout (continued)
Figure 11.1a: Home Screen at Power-Up (No Call for Heat)
Figure 11.1b: Home Screen on Heat Demand
Figure 11.1c: Home Screen with Active Fault
Figure 11.2: Burner Flame
XI. Start-Up and Checkout (continued)
WARNING
Asphyxiation Hazard. Each boiler is tested at the factory and adjustments to the air fuel mixture are normally not necessary when operating on natural gas at sea level. Consult the factory before attempting to make any such adjustments. Improper gas valve or mixture adjustments could result in property damage, personal injury or loss of life due to carbon monoxide (CO) poisoning.
WARNING
Asphyxiation Hazard. The outlet pressure for the gas valve has been factory set and requires no field adjustment. This setting is satisfactory for both natural gas and propane. Attempting to adjust the outlet pressure may result in damage to the gas valve and cause property damage, personal injury or loss of life. due to carbon monoxide (CO) poisoning.
Offset Regulator
- Do Not Adjust
Outlet Tap Gas Inlet
Inlet Tap
Gas Outlet
Throttle Screw
Tube to Air
Proving Switch
Figure 11.3: Gas Valve Detail
95
XI. Start-Up and Checkout (continued)
WARNING
All combustion performance numbers MUST be verified with a combustion analyzer. Failure to do so will result in substantial property damage, severe personal injury or death.
Table 11.4: Acceptable Combustion Readings for Natural Gas (0-4,500 ft.)
Model
Size
85
110
155
205
270
%CO
2
8.7 - 10.5
8.7 - 10.5
8.7 - 10.5
8.7 - 10.5
8.7 - 10.5
%O
2
2.5 - 5.6
2.5 - 5.6
2.5 - 5.6
2.5 - 5.6
2.5 - 5.6
Max. CO
Air Free
COAF readings must be less than
200 ppm.
Table 11.5: Starting Number of Throttle Turns for Natural Gas
Model
Size
85
110
155
205
270
No. Counter-clockwise Turns
(From Fully Closed)
4½
4½
6½
6¼
2½
NOTICE
This boiler has a limited warranty, a copy of which is included with this boiler. It is the responsibility of the installing contractor to see that all controls are correctly installed and are operating properly when the installation is complete.
96
XI. Start-Up and Checkout (continued)
Operating Instructions
97
XII. Operation
A. Overview
1. B1020 Controller
The B1020 Controller (Control) contains features and capabilities which help improve heating system operation, and efficiency. By including unique capabilities, the Control can do more, with less field wiring, and fewer aftermarket controls and components
– improving the operation of both new and replacement boiler installations.
2. Advanced Touch Screen Display
IMPORTANT
This boiler is equipped with a feature that saves energy by reducing the boiler water temperature as the heating load decreases. This feature is equipped with an override which is provided primarily to permit the use of an external energy management system that serves the same function.
THIS OVERRIDE MUST NOT BE USED UNLESS AT LEAST ONE OF THE FOLLOWING
CONDITIONS IS TRUE:
• An external energy management system is installed that reduces the boiler water temperature as the heating load decreases.
• This boiler is not used for any space heating.
• This boiler is part of a modular or multiple boiler system having a total input of
300,000 BTU/hr or greater.
• This boiler is equipped with a tankless coil.
Home Screen
Boiler status and setup selections are available from an easy to use, LCD Touch Screen Display. In the event of a fault condition the user is guided by “blinking” touch buttons to Help screens that describe the problem.
Operation evaluation and problem-solving is enhanced by historical capability including graphic trends, lockout history records as well as boiler and circulator cycle counts and run time hours.
3. Advanced Modulating Control
The Control modulates the boiler input by varying the fan speed. As the fan speed increases, so does the amount of fuel gas drawn into the blower. As a result, a fairly constant air-fuel ratio is maintained across all inputs. The Control determines the input needed by looking at both current and recent differences between the measured temperature and the setpoint temperature.
As the measured temperature approaches the setpoint temperature, the fan will slow down and the input will drop. The Control also utilizes boiler return water and flue gas temperatures to adjust fan speed.
4. Built-in Safety Control
The Control includes safety controls designed to ensure safe and reliable operation. In addition to flame safety controls the Control includes supply water temperature, differential water temperature, and stack temperature safety limits and stepped modulation responses.
Boiler modulation is adjusted when required to help avoid loss of boiler operation due to exceeding limits.
Additionally, the Control accepts the field installation of optional auxiliary safety limits.
5. Outdoor Air Reset
When selected the modulation rate setpoint is automatically adjusted based on outside air temperature, time of day and length of demand (boost) settings.
Outdoor air “reset” setpoint saves fuel by adjusting the water temperature of a heating boiler lower as the outside air temperature increases.
6. Warm Weather Shutdown (WWSD)
Some boilers are used primarily for heating buildings, and the boilers can be automatically shutdown when the outdoor air temperature is warm. When outside air temperature is above the WWSD setpoint, this function will shut down the boiler, boiler and system pump.
7. Energy Management System (EMS) Interface
A factory configured RS485 Modbus interface is available for Energy Management System (EMS) monitoring when not used for Multiple Boiler
Sequencer Peer-To-Peer Network. Consult factory for points list or if this interface must be used in addition to the boiler Peer-to-Peer Network.
8. Circulator Control
The Control may be used to sequence the domestic hot water, boiler and system circulators. Service rated relay outputs are wired to a line voltage terminal block for easy field connection. Simple parameter selections allow all three pumps to respond properly to various hydronic piping arrangements including either a boiler or primary piped indirect water heater. Circulators may
98
XII. Operation (continued) be configured to provide the functionality of a two zone zone panel. The system and DHW pump outputs may be configured as one heating and one domestic or two heating zones. Circulators are automatically run for a 20 second exercise period after not being used for longer than 7 days. Circulator exercise helps prevent pump rotor seizing.
9. Multiple Boiler Sequencer Peer-To-Peer
Network
The Control includes state-of-the-art modulating lead-lag sequencer for up to eight (8) boilers capable of auto rotation, outdoor reset and peer-to-peer communication. The peer-peer network is truly “plug and play”. Communication is activated by simply connecting a RJ45 ethernet cable between boilers.
The Control provides precise boiler coordination by sequencing boilers based on both header water temperature and boiler modulation rate. For example, the lead boiler can be configured to start a lag boiler after operating at 50% modulation rate for longer than an adjustable time. The boilers are modulated in “unison” (parallel) modulation rate to ensure even heat distribution.
B. Supply Water Temperature Regulation
1. Priority Demand
The Control accepts a call for heat (demand) from multiple places and responds according to it’s
“Priority”. When more than 1 demand is present the higher priority demand is used to determine active boiler settings. For example, when Domestic Hot
Water (DHW) has priority the setpoint, “Diff Above”,
“Diff Below” and pump settings are taken from DHW selections. Active “Priority” is displayed on the “Boiler
Status” screen.
2. Setpoint Purpose
The Control starts and stops the boiler and modulates the boiler input from minimum (MBH) to maximum
(MBH) in order to heat water up to the active setpoint.
The setpoint is determined by the priority (Central
Heat or Domestic Hot Water) and as described in the following paragraphs.
3. Central Heat Setpoint
Upon a Central Heat call for heat the setpoint is either the user entered Central Heat Setpoint, or is automatically adjusted by Outdoor Air Reset or, an
Energy Management System (EMS) supplied setpoint.
4. Auxiliary Heat Setpoint
Auxiliary Heat is a second heating demand that may be used to serve either lower temperature radiation or warmer heat demands such as fan coils. Upon an
Auxiliary Heat call for heat the setpoint is either the user entered Auxiliary Heat Setpoint or is automatically adjusted as Outdoor Air Reset
.
Table 12.1: Order of Priority
Boiler Responding to:
1st
2nd
3rd
Sequencer
Control
Domestic Hot
Water
The boiler is connected to the peerto-peer network. The boiler accepts demand from the Sequencer Master.
DHW call for heat is on and selected as the priority demand. DHW is always higher priority than Central Heat. It also has higher priority than the Sequencer
Control when DHW priority is “enabled” and “Boiler Piped” IWH is selected.
Central Heat Central Heat call for heat is on and there is no DHW demand or DHW priority time has expired.
4th Auxiliary Heat Auxiliary Heat call for heat is on and there is no Central Heat or DHW demand. (NOTE: May be user selected to be higher priority than
5th Frost
Protection
Central Heat.)
Frost Protection is active and there is no other call for heat. Frost protection will be a higher priority than Sequencer
6th
7th
Warm
Weather
Shutdown
(WWSD)
Standby
Control if the Sequence Master has no active call for heat.
WWSD is active and the boiler will not respond to central heat demands.
DHW demand is not blocked by
WWSD.
There is no demand detected.
5. Outdoor Air Reset
If an outdoor temperature sensor is connected to the boiler and Outdoor Reset is enabled, the Central
Heat setpoint will automatically adjust downwards as the outdoor temperature increases. When the water temperature is properly matched to heating needs there is minimal chance of room air temperature overshoot.
Excessive heat is not sent to the room heating elements by “overheated” (supply water temperature maintained too high a setting) water. Reset control saves energy by reducing room over heating, reducing boiler temperature & increasing combustion efficiency and, reducing standby losses as a boiler and system piping cool down to ambient following room over heating.
6. Boost Time
When the Central Heat Setpoint is decreased by Outdoor
Air Reset settings the Boost function can be enabled to increase the setpoint in the event that central heat demand is not satisfied for longer than the Boost Time minutes. The Boost feature increases the operating temperature setpoint by 10°F (5.6°C) every 20 minutes
(field adjustable) the central heat demand is not satisfied.
This process will continue until heat demand is satisfied
(indoor air is at desired temperature), or the central heat setpoint is reached. Once the heat demand is satisfied,
99
the operating setpoint reverts to the value determined by the Outdoor Air Reset settings. If Boost Time is zero, then the boost function is not used.
7. Domestic Hot Water (DHW) Setpoint
Upon a DHW call for heat the setpoint is the user entered
DHW setpoint . The optimal value of this setpoint is established based on the requirements of the indirect water heater.
8. Domestic Hot Water Priority (DHWP)
When domestic hot water priority is selected and there is a DHW call for heat, the system pump will be turned off (when “System Pump Run Pump for” parameter is set for “Central Heat Optional Priority”) and the DHW pump will be turned on. Additionally, if outdoor reset is active, the active setpoint is adjusted to the DHW Setpoint. Priority protection is provided to ensure central heat supply in the case of excessively long DHW call for heat.
C. Boiler Protection Features
1. Supply Water Temperature High Limit
The control is equipped with internal operating control and high limit features. The control monitors a dual element temperature sensor that is mounted in the supply water manifold and provides UL353 and UL1998 internal safety algorithms. If supply water temperature increases above the active setpoint plus diff above, default 190°F (87.7°C) the boiler is cycled off. If the temperature exceeds 210°F (98.9°C), a manual reset hard lockout results. If the boiler is responding to the internal Multiple Boiler Control Sequencer, Header
Sensor or an External EMS demand and the supply water temperature increases above 190°F (87.7°C) the control begins to reduce the blower maximum speed setting and if the temperature increases to 200°F (93°C) a forced recycle results. Additionally, if the supply temperature rises faster than the degrees Fahrenheit per second limit a soft lockout is activated.
2. High Differential Temperature Limit
The Control monitors the temperature difference between the return and supply sensors. If this difference exceeds 52°F (29°C) the control begins to reduce the maximum blower speed. If temperature difference exceeds 62°F (34°C) a forced boiler recycle results.
The unit will restart automatically once the temperature difference has decreased and the minimum off time has expired. If the temperature difference remains above
72°F (40°C) for longer than 3 minutes a manual reset hard lockout results.
XII. Operation (continued)
3. Return Temperature Higher Than Supply
Temperature (Inversion Limit)
The Control monitors the supply and return temperature sensors. If the return water temperature exceeds the supply water temperature for longer than a limit time delay the Control shuts down the boiler and delays restart. If the inverted temperature is detected more than five times the boiler manual reset Hard Lockout is set. This condition is the result of incorrectly attaching the supply and return piping.
4. External Limit
An external limit control can be installed on the low voltage terminal strip. Be sure to remove the jumper when adding an external limit control to the system. If the external limit opens, the boiler will shut down and an open limit indication and error code are provided.
If the limit installed is a manual reset type, it will need to be reset before the boiler will operate.
5. Boiler Mounted Limit Devices
The control monitors individual limit devices: External
Limit, Optional Low Water Cut-Off (LWCO) and
Blocked Flue/Inlet Switch. If any of these limits open the boiler will shut down and an open limit indication is provided. Additionally, the control monitors an air proving switch. During the boiler start sequence the control requires the air proving switch to be in the
“open” position before the blower starts and in the
“closed” position after the blower starts. If the air proving switch is not in the required position the start sequence is halted or the boiler is shut down and the open limit indication is provided. The air proving switch is only required to be closed during pre-purge.
It is normal for the air proving switch to be open during run mode.
6. Stack High Limit
The Control monitors the flue gas temperature sensor located in the vent connector. If the flue temperature exceeds 194°F (90°C), the control begins to reduce the maximum blower speed. If the flue temperature exceeds
204°F (96°C), a forced boiler recycle results. If the flue temperature exceeds 214°F (101°C), the control activates a manual reset Hard Lockout.
7. Ignition Failure
The Control monitors ignition using a burner mounted flame sensor. In the event of an ignition failure, the control retries 5 times and then goes into soft lockout for one hour.
8. Central Heating System Frost Protection
When enabled, Frost Protection starts the boiler and system pump and fires the boiler when low outside air and low supply water temperatures are sensed. The
Control provides the following control action when frost protection is enabled:
100
Table 12.2: Frost Protection
Device
Started
Boiler Pump
Boiler
Start
Temperatures
Outside Air < 0°F (-18°C)
Supply Water < 45°F (7.2°C)
Stop
Temperatures
Outside Air > 4°F (-16°C)
Supply Water > 50°F (10°C)
Supply Water < 38°F (3.3°C) Supply Water > 50°F (10°C)
FROST PROTECTION NOTE
The Control helps provide freeze protection for the boiler water. Boiler flue gas condensate drain is not protected from freezing. Since the Control only controls the system and boiler circulators individual zones are not protected. It is recommended that the boiler be installed in a location that is not exposed to freezing temperatures.
D. Multiple Boiler Control Sequencer
1. “Plug & Play” Multiple Boiler Control
Sequencer
When multiple boilers are installed, the Control’s
Sequencer may be used to coordinate and optimize the operation of up to eight (8) boilers. Boilers are connected into a “network” by simply “plugging in” standard ethernet cables into each boiler’s “Boiler-To-
Boiler Communication” RJ45 connection.
2. Sequencer Master
A single Control is parameter selected to be the
Sequencer Master. The call for heat, outdoor and header sensors, and common pumps are wired to the
Sequencer Master “enabled” Control.
3. Lead/Slave Sequencing & Equalized Run Time
One boiler is a “Lead” boiler and the remaining networked boilers are “Slaves”. When demand is increasing, the Lead boiler is the first to start and the
Slave boilers are started in sequential order (1,2,3,…) until the demand is satisfied. When demand is decreasing, the boilers are stopped in reverse order with the Lead boiler stopped last (…,3,2,1). To equalize the run time the sequencer automatically rotates the
Lead boiler after 24 hours of run time.
4. Improved Availability
The following features help improve the heat availability:
a. Backup Header Sensor: In the event of a header sensor failure the lead boiler’s supply sensor is used by the Sequence Master to control firing rate. This feature allows continued coordinated sequencer control even after a header sensor failure.
b. “Stand Alone” Operation Upon Sequence Master
Failure: If the Sequence Master Control is powered down or disabled or if communication is lost between boilers, individual boilers may be setup to automatically resume control as a “stand alone” boiler.
XII. Operation (continued)
c. Slave Boiler Rate Adjustment: Each slave boiler continues to monitor supply, return and flue gas temperatures and modifies the Sequence Master’s firing rate demand to help avoid individual boiler faults, minimize boiler cycling and provide heat to the building efficiently.
d. Slave Boiler Status Monitoring: The Sequence
Master monitors slave boiler lockout status and automatically skip over disabled boilers when starting a new slave boiler.
5. Customized Sequences
Normally, boilers are started and stopped in numerical order. However, custom sequences may be established to optimize the heat delivery. For example, in order to minimize boiler cycling, a large boiler may be selected to run first during winter months and then selected to run last for the remainder of the year.
6. Multiple Demands
The Sequence Master responds to Central Heat,
Auxiliary Heat, DHW and frost protection demands similar to the stand alone boiler. For example, when selected and DHW priority is active, the sequence master uses DHW setpoint, “Diff Above”, “Diff Below” and pump settings.
7. Shared or Isolated DHW Demand
When the Indirect Water Heater (IWH) parameter is set to “Primary Piped” the Sequence Master sequences all required boilers to satisfy the DHW setpoint. When
“Boiler Piped” is selected only the individual slave boiler, with the wired DHW demand and pump, fires to satisfy the DHW setpoint.
8. DHW Two boiler Start
When the Indirect Water Heater (IWH) parameter is set to “Primary Piped” and the DHW Two Boiler Start parameter is set to “Enabled” two boilers are started without delay in response to a DHW call for heat.
This feature allows rapid recovery of large IWH’s and multiple IWH’s.
9. Optimized Boiler Modulation
Boiler firing rate is managed to increase smoothly as boilers are started. For example, when a second boiler is started the initial firing rate is 100%/2 or 50%, when the third boiler is started the firing rate starts at
200%/3 or 66%. After the initial start, the Sequence
Master develops a unison firing rate demand based on it’s setpoint and sensed header temperature.
10. Innovative Condensing Boiler Control
During low loads, the Sequence Master limits firing rates to a “Base Load Common Rate” to ensure modulating condensing boiler peak operating efficiency. Lower firing rates boost efficiency by helping increase the amount of flue gas water vapor condensation. The
101
XII. Operation (continued)
Control maintains a “Base Load Common Rate” until the last lag boiler is started. At this point, the “Base
Load Common Rate” is released to allow boilers to modulated as required to meet heat load.
11. Advanced Boiler Sequencing
After there is a Call For Heat input, both header water temperature and boiler firing rate percent are used to start and stop the networked boilers. The control starts and stops boilers when the water temperature is outside the user selected “Diff Above” and “Diff Below” settings.
Also, in order to minimize temperature deviations, the control adjusts the number of boilers running based on the firing rate. This combination allows the boilers to anticipate slow load changes before they disrupt water temperature yet still respond quickly to sudden load changes. These special sequencer features help reduce energy wasting system temperature swings and the resulting unnecessary boiler cycling.
12. Stop All Boilers
All boilers are stopped without delay if the Call for
Heat input is removed or if the header temperature is higher than 195°F (90.6°C) (field adjustable).
102
E. Multiple Boiler Control Sequencer
1. Normal Operation
XII. Operation (continued)
Table 12.3: Boiler Sequence of Operation
Status Screen Display
Priority:
Standby
Status:
Standby
Description
(burner Off, circulator(s) Off)
Boiler is not firing and there is no call for heat, priority equals standby. The boiler is ready to respond to a call for heat.
Priority:
Central Heat
Status:
Standby
(burner Off, circulator(s) On)
Boiler is not firing. There is a Central Heat call for heat and the Supply temperature is greater than setpoint minus the “Diff Below”.
Priority:
Central Heat
Status:
Prepurge
Priority:
Central Heat
Status:
Direct ignition
Priority:
Central Heat
Status:
Running
When supply temperature drops burner demand continues with following Status shown:
Safe Startup:
Drive purge:
Flame circuit is tested.
The blower is driven to the fan purge speed.
Prepurge: After the blower reaches the fan purge speed setting the 10
second combustion chamber purge is conducted.
After purge time is complete the following Status is shown:
Drive light-off: The blower is driven to light-off rate.
Pre-Ignition Test: After the blower reaches light-off rate a safety relay test is
conducted.
Pre-ignition: Spark is energized and it is confirmed that no flame is present
Direct Ignition: Spark and Main fuel valve are energized.
(burner On, circulator(s) On)
After flame is proven the sequence continues with run stabilization and low fire hold time. Once the field adjustable low fire hold time is completed normal boiler operation begins, modulation rate depending on temperature and setpoint selections.
Priority:
Domestic
Hot Water
Status:
Running
If the Central Heat call for heat is active and a Domestic Hot Water (DHW) call for heat received the DHW demand becomes the “priority” and the modulation rate, setpoint, “Diff Above” and “Diff Below” are based on DHW settings.
Priority:
Standby
Status:
Post-purge
Priority:
Standby
Status:
Standby
Delay
Priority:
Standby
Status:
Lockout
(burner Off, circulator(s) Off)
If there is no call for heat the main fuel valve is closed and the blower is driven to the fan post-purge speed. After the blower reaches the fan post-purge speed setting the combustion chamber purge is conducted.
Standby delay status is entered when a delay is needed before allowing the burner control to be available. Select “Help” button from the “Home Screen” to determine the cause of the Standby Delay.
A lockout status is entered to prevent the boiler from running due to a detected problem. Select “Help” button from the “Home Screen” to determine the cause of the Lockout. The last 5 Lockouts are recorded in the Lockout History.
103
XII. Operation E. Boiler Sequence Of Operation (continued)
2. Using The Display
The Control includes a touch screen LCD display. The user monitors and adjusts boiler operation by selecting screen navigation “buttons” and symbols. The “Home Screen” and menu selections are shown below. When no selection is made, while viewing any screen, the display reverts to the “Home Screen” after 4 minutes. The “Home Screen” provides boiler temperature, firing rate in BTU/hr, boiler status, efficiency information and page links.
(Figure 12.6) (Figure 12.8) (Figure 14.1)
Figure 12.4: Home Screen Details
(Figure 12.9)
104
Figure 12.5: Screen Navigation
XII. Operation E. Boiler Sequence Of Operation (continued)
3. Status Screens
Boiler Status screens are the primary boiler monitoring screens. The user may simply “walk” though boiler operation by repeatedly selecting the right or left “arrow” symbol. These screens are accessed by selected the “Status” button from the “Home” screen.
Figure 12.6: Status Screens
Figure 12.7: Boiler Status Screen Definitions
105
106
XII. Operation E. Boiler Sequence Of Operation (continued)
1. Status Screens (continued)
Bargraph Screen
The bargraph screen presents measured values for easy comparison.
Pumping is a major part of any hydronic system. This screen provides the status of the boiler’s demand to connected pumps as well as the status of Frost
Protection and pump Exercise functions.
This screen provides the status of the boilers five (5) possible heat demands.
When demand is off the Control has not detected the call-for-heat. This screen allows the user to determine which demands are present when more than one demand is present.
Cycles and Hours
Boiler cycles and hours are used to monitor the boilers overall compatibility to the heating load.
Excessive cycling compared to run time may be an indication of pumping, boiler sizing or adjustment issues.
XII. Operation E. Boiler Sequence Of Operation (continued)
4. Detail Screens
Detail screens are accessed by selecting the “Detail” button from the “Home” screen. These screens provide in depth operating parameter status such as “On Point”, “Off Point” and “Setpoint Source” information. Demand-specific details are provided for Central Heat, Auxiliary Heat, Domestic Hot Water and the Sequence Master demands and outdoor air reset. Sequencer screens are only shown when the Sequence Master is enabled.
Figure 12.8: Detail Screen Overview
5. Multiple Boiler Sequencer Screens
When the Sequence Master is enabled the following screen is
available
:
The Sequencer Status screen is selected by “pressing” “Status” button from the “Home” screen when Sequence Master is enabled.
Header:
measured header water temperature is the temperature being used to start, stop and fire boiler when there is a call-forheat.
<
Rate
Network:
Sequencer
Supply
Setpoint
Priority:
132 F
180 F
100%
Lead
2
1 ,2 ,3 ,4 ,5 ,6 ,7 ,8
>
Domestic Hot Water
Setpoint:
active setpoint temperature is the result of Outdoor Air Reset,
Setback and Domestic Hot Water
(DHW) selections.
Networked Boiler Status:
Provides connected, start sequence and firing rate status information for all connected boiler addresses. The boiler number is underlined if the boiler is running and blinks if the boiler has the start sequence in progress. For example the status for boiler address 1 is provided as follows:
1 - Boiler 1 is connected to the network
1 - “Blinking underline” - boiler 1 is starting
1 - “Solid underline” - boiler 1 is running
Lead Boiler:
Upon power up the lowest numbered boiler becomes the lead boiler. The lead boiler is the first to start and last to stop. The lead boiler is automatically rotated after
24 hours of run time.
Additionally, the lead is rotated if there is a lead boiler fault.
Rate:
The rate % value is equal to the Sequence Master demand to the slave boilers.
Priority:
Sequencer Priority available are: Standby (no call for heat is present), Central
Heat, Auxiliary Heat,
Domestic Hot Water, Frost
Protection or Warm
Weather Shutdown.
107
XII. Operation (continued)
F. Changing Adjustable Parameters
1. Entering Adjust Mode
The Control is factory programmed to include basic modulating boiler functionality. These settings are password protected to discourage unauthorized or accidental changes to settings. User login is required to view or adjust these settings:
- Press the “Adjust” button on the
“Home”screen.
- Press the “Adjust” button on the Adjust
Mode screen or Press “Service Contact” for service provider contact information.
- Press “Login” button to access password screen.
- Press 5-digit display to open a keypad.
Enter the password (Installer Password is 86) and press the return arrow to close the keypad. Press the “Save” button.
- Press the “Adjust” button to enter
Adjustment mode.
For Service Contact:
CONTRACTOR NAME
ADDRESS LINE 1
ADDRESS LINE 2
PHONE NUMBER
Password required to
Get past here
Installer Password =
86
Enter Password
086
1
6
2
7
3
8
4
9
5
0
ES
C
B
S
CL
R
After entering the password press
To return to password screen
Adjust Mode
Warning!
Improper settings or service create risk of property damage, injury or death.
Contractor Adjust
Login to Access
Adjustment Mode
Access Level: Installer
Login Adjust
Enter Pasword
000
Press Save to enter password
Save Adjust
After password is Saved
These buttons access
Adjust mode screens
Figure 12.9: Adjust Mode Screens
2. Adjusting Parameters
Editing parameters is accomplished as follows:
108
XII. Operation F. Changing Adjustable Parameters (continued)
2. Adjusting Parameters (continued)
The following pages describe the Control’s adjustable parameters. Parameters are presented in the order they appear on the Control’s Display, from top to bottom and, left to right. From the “Home” screen select the Adjust button to access the adjustment mode screens show below (if required, refer to the previous page to review how to enter Adjustment mode):
“Press”
Factory
System
Setup button to access the following parameters:
Range /
Choices
Parameter and Description
Setting
Fahrenheit
Wired
0
Enabled
Disabled
70°F
Fahrenheit,
Celsius
Not Installed,
Wired
Wireless
-100 to 100 tenths of degree
Enable/Disable
Enable/Disable
0-100°F
Temperature Units
The Temperature Units parameter determines whether temperature is represented in units of Fahrenheit or Celsius degrees.
Outdoor Sensor Source
Not Installed Outdoor Sensor is not connected to the boiler, the sensor is not monitored for faults.
Wired Outdoor Sensor is installed directly on the boiler terminal Strip.
Wireless Outdoor sensor is installed and wireless.
Outdoor Air Sensor Calibration
Outdoor Air Sensor Calibration offset allows a single point calibration. Using a reliable source (reference) for outdoor temperature measure outdoor air temperature. Set the offset equal to the difference between the controller reading and the reference. The result will be the Control’s measurement matching the reference reading.
Frost Protection
Disable Frost Protection is not used.
Enable Boiler and system circulators start and boiler fires when low outside air, supply and return
temperatures are sensed.
Warm Weather Shutdown Enable
Disable Warm Weather Shutdown (WWSD) is not used.
Enable The boiler and pumps will not be allowed to start in response to a central heat call for heat if
the outside temperature is greater than the WWSD setpoint. WWSD is initiated as soon as
outside air temperature is above WWSD Setpoint. The control does not require call for heat
to be satisfied. The boiler will still start in response to a Domestic Hot Water call for heat.
Warm Weather Shutdown Setpoint
The Warm Weather Shutdown (WWSD) Setpoint used to shutdown the boiler when enabled by the
“WWSD Enable” parameter.
109
XII. Operation F. Changing Adjustable Parameters (continued)
2. Adjusting Parameters (continued)
WARNING
Asphyxiation Hazard. Boiler type is factory set and must match the boiler model. Only change the boiler type setting if you are installing a new or replacement Control. The boiler type setting determines minimum and maximum blower speeds. Incorrect boiler type can cause hazardous burner conditions and improper operation that may result in PROPERTY LOSS, PHYSICAL INJURY OR DEATH.
“Press”
Factory
Setting
Range /
Choices
SeeTable
12.10
100%
100%
100%
See Table
12.10
4000 RPM button to access the following parameters:
Parameter and Description
See Table
12.10
Minimum to
Maximum
Heat Rate
Minimum to
Maximum
Heat Rate
Minimum to
Maximum
Heat Rate
Minimum
to Maximum
3500 - 4000
RPM
Boiler Type
Boiler Size Setup
To verify the boiler size selection, a qualified technician should do the following:
1. Check boiler’s label for actual boiler size.
2. Set “Boiler Type” to match actual boiler size.
3. Select “Confirm”.
The Boiler Type parameter changes multiple, minimum and maximum modulation settings. This parameter is intended to allow a user to set the parameters in a spare part Control to a particular boiler type. When changing the “Boiler Type” be sure to select “ENTER” and “NEXT” until all parameters are entered as shown by the “complete” indication.
Central Heat Maximum Expected Heat Rate
This parameter defines the highest modulation rate the Control will go to during a central heat call for heat. If the rated input of the installed home radiation is less than the maximum output of the boiler, change the Central Heat Maximum Expected Heat Rate (fan speed) setting to limit the boiler output accordingly.
Domestic Hot Water (DHW) Max Expected Heat Rate
This parameter defines the highest modulation rate the Control will go to during a Domestic Hot
Water call for heat. If the rated input of the indirect water heater is less than the maximum output of the boiler, change the DHW Maximum Expected Heat Rate (fan speed) setting to limit the boiler output accordingly.
Auxiliary Maximum Expected Heat Rate
This parameter defines the highest modulation rate the Control will go to during the auxiliary heat call for heat. If the rated input of the Auxiliary Heat Zones is less than the maximum output of the boiler, change the Auxiliary Heat Maximum Expected Heat Rate (fan speed) setting to limit the boiler output accordingly.
Minimum Modulation
This parameter is the lowest modulation rate the Control will go to during any call for heat.
Lightoff Rate
This is the blower speed during ignition and flame stabilization periods.
110
XII. Operation F. Changing Adjustable Parameters (continued)
Control Repair Part Kit
Altitude
Model
Maximum Heat Rate (RPM)
Minimum Heat rate (RPM)
Model
Maximum Heat Rate (RPM)
Minimum Heat rate (RPM)
Altitude
Model
Maximum Heat Rate (RPM)
Minimum Heat rate (RPM)
Model
Maximum Heat Rate (RPM)
Minimum Heat rate (RPM)
Model
Maximum Heat Rate (RPM)
Minimum Heat rate (RPM)
Model
Maximum Heat Rate (RPM)
Minimum Heat rate (RPM)
Altitude
Model
Maximum Heat Rate (RPM)
Minimum Heat rate (RPM)
Model
Maximum Heat Rate (RPM)
Minimum Heat rate (RPM)
Altitude
Model
Maximum Heat Rate (RPM)
Minimum Heat rate (RPM)
Model
Maximum Heat Rate (RPM)
Minimum Heat rate (RPM)
Table 12.10: Parameters Changed Using the Boiler Type Parameter Selections:
107097-01
0 - 4,500 Ft.
RPTR-085-04 RPTR-110-04 RPTR-155-04 RPTR-205-04 RPTR-270-04
5400
1400
5300
1400
5400
1400
RPTRC-155-04
5400
6000
1500
6700
1700
1400
4,501 - 6, 000 ft
RPTR-085-46 RPTR-110-46 RPTR-155N-46 RPTR-205N-46 RPTR-270N-46
6100
1600
6450
1600
6500 7500 7000
1600 1700 1800
RPTR-155P-46 RPTR-205P-46 RPTR-270P-46
6900
1600
RPTRC-155N-46
8100
1750
8500
2000
6500
1600
RPTRC-155P-46
6900
6900
1700
1600
6,001 - 7,800 Ft.
RPTR-085N-67 RPTR-110-67 RPTR-155-67 RPTR-205N-67 RPTR-270N-67
6500 7100 6800 6750
1700
RPTR-085P-67
7000
1600 1600 1700
RPTRC-155-67 RPTR-205P-67 RPTR-270P-67
7100 7200 6950
1700 1600
7,801 - 10,100 Ft.
1700 1750
RPTR-085-70 RPTR-110-70 RPTR-155-70 RPTR-205-70 RPTR-270N-70
7200
1800
7200
1800
7100
1700
RPTRC-155-70
7100
1700
6800
1600
6450
1700
RPTR-270P-70
6650
1700
111
XII. Operation F. Changing Adjustable Parameters (continued)
“Press”
Central Heat,
Optional Priority
Any Demand
Primary
Loop Pipe
IWH
button to access the following parameters:
Factory Setting Range / Choices
Never,
Any Demand,
Central Heat,
No Priority,
Central Heat,
Optional Priority
Central Heat Only,
Optional Priority:
Never
Any Demand,
Header Sensor
Demand,
CH, Off for DHW
Never,
Primary Loop
Piped IWH
Boiler Piped IWH
Auxiliary Heat
Loop:
Parameter and Description
System Pump run pump for:
Activates the system pump output according to selected function.
Never: Pump is disabled and not shown on status screen.
Any Demand: Pump Runs during any call for heat.
Central Heat, No Priority: Pump Runs during central heat, auxiliary heat and frost
protection call for heat. Pump does not start for a DHW call for
heat and continues to run during Domestic Hot Water Priority.
Central heat, Optional
Priority: Pump Runs during central heat, auxiliary heat and frost
protection call for heat. Pump does not start for a DHW call for
heat and will be forced off if there is a DHW call for heat and
Domestic Hot Water Priority is active.
Central Heat Only,
Optional Priority: Pump runs during central heat and frost protection call for heat.
Pump does not start for Auxiliary Heat or DHW call for heat.
The pump will be forced off when DHW priority is active. This
option allows the system pump output to be used as a zone
pump.
Boiler Pump run pump for:
Activates the boiler pump output according to selected function.
Never: Pump is disabled and not shown on status screen.
Any Demand: Pump Runs during any call for heat.
Header Sensor Demand: Pump Runs when boiler is firing and when there is DHW
demand. Selected when Header Sensor is selected as
modulation sensor and boiler is a stand alone boiler.
CH, Off for DHW: Pump runs during central heat, auxiliary heat and frost
protection call for heat and will be forced off if there is a DHW
call for heat and DHW priority is active.
Domestic Pump run pump for:
Activates the Domestic pump output according to selected function.
Never: Pump is disabled and not shown on status screen.
Primary Loop Piped IWH: Pump Runs during domestic hot water call for
heat. Domestic Hot Water Priority enable/disable
does not affect pump operation.
Boiler Piped IWH: Pump runs during DHW demand. Pump is forced off during
central heat demand when 1) DHW priority is disabled or 2)
DHW priority is enabled and DHW demand has remained on for
longer than Priority Time.
Auxiliary Heat Loop: Pump runs during Auxiliary Heat and frost protection call for
heat. Pump does not start for Central Heat or DHW call for
heat. The pump will be forced off when DHW priority is active.
This allows the DHW pump output to be used as a zone pump.
112
XII. Operation F. Changing Adjustable Parameters (continued)
Example Pump Parameter selections:
Single boiler with no Indirect Water Heater
A.
B.
C.
At least eight pipe diameters upstream of first tee.
At least 18" (~46 cm) of straight pipe for Conventional Air Scoop.
Hydraulic Separator
For Tees
Close Nipple
(Locate Header Sensor
Air Separator
& Air Vent
Expansion Tank
To
System
Flow
Check
Optional
Full Port
Heating
Circulators
Full Port
Isolation
Valves
Fill Valve
Backflow
Preventer
To
System
System
Circulator
System
Valves
A
C
B
Header Temperature
Sensor
(When Used)
Boiler Circulator
Water
Line
Relief Valve
Parameter Selection:
System pump = “Central Heat,
Optional Priority”
Boiler pump = “any demand”
DHW pump = “never”
Full Port
Isolation
Valves
Secondary Unions Not
Location Shown
Explanation:
This piping arrangement only services central heat. When there is any demand both boiler and system pumps turn on.
CAUTION: It is the installers responsibility
to select boiler piping configurations that provide
the proper flow rates and performance for the
boiler.
Single boiler Indirect Water Heater (IWH)Piped to Primary, Optional Domestic Hot Water Priority.
A.
B.
C.
At least eight pipe diameters upstream of first tee.
No further apart than 12" (~30 cm) or four pipe diameters, whichever is smaller.
At least 18" (~46 cm) of straight pipe for Conventional Air Scoop.
From
System
To
System
Optional
Full Port
Isolation
Valves
Heating
Circulators
Optional
Full Port
Isolation
Valves
To System
System
Zone
Valves
Flow
Check
Hydraulic Separator
May Be Substituted
For Tees
(Locate Header Sensor
To Downstream Tee)
Sensor
(When Used)
Air Separator
& Air Vent
Fill Valve
Full Port
Valve
System
Circulator
Flow
Check
Y-Strainer
(Recommended)
C
Indirect
Supply
B
A
Backflow
Preventer
Water
Line
Full Port
Valve
Relief Valve
Drain Valve
Isolation
Valves
Boiler Circulator
Required; Optional
Location Shown
Parameter Selections:
System Pump = “Central Heat,
Optional Priority”
Boiler Pump = “any demand”
DHW Pump = “Primary Loop Piped IWH”
DHW Priority Enable is optional
Explanation:
This piping arrangement permits the system pump to run or not run when there is a domestic hot water call for heat.
Domestic hot water priority is optional. It is permissible for the domestic and system pumps to run at the same time. The boiler pump must run for every call for heat.
CAUTION: It is the installers responsibility
to select boiler piping configurations that provide
the proper flow rates and performance for the boiler
and indirect water heater.
Optional Zone Valve
Controlled System
Indirect Domestic
(IWH)
113
1
1
XII. Operation F. Changing Adjustable Parameters (continued)
Example Pump Parameter selections (continued):
Single Boiler with Supply Piped IWH, System and DHW Wired to Master
C.
No further apart than 12" (~30 cm) or four pipe diameters, whichever is smaller.
At least 18" (~46 cm) of straight pipe for Conventional Air Scoop.
Y-Strainer
(Recommended)
Hydraulic Separator
For Tees
A
C
B
Flow Check
(Locate Header Sensor
To Downstream Tee)
Expansion Tank
Boiler Circulator
Isolation
Valves
Full Port
Valves
Preventer
Cold
B
Relief Valve
Drain Valve
Isolation
Valves
Secondary Unions Not
Locations Shown
Flow Check
Parameter Selections:
System Pump = “Central Heat,
Optional Priority”
Boiler Pump = “any demand”
DHW Pump = “Primary Loop Piped IWH”
DHW Priority Enable is optional
Explanation:
When call for Domestic Hot Water is received the DHW pump is turned on and the boiler pump is turned on. This piping arrangement permits the system pump to run or not run when there is a domestic hot water call for heat. Domestic hot water priority is optional.
It is permissible for the domestic and system pumps to run at the same time. The boiler pump must run for every call for heat.
Zone
Valves
Indirect
Return
Water Heater
(IWH)
CAUTION: It is the installers responsibility
to select boiler piping configurations that provide
the proper flow rates and performance for the boiler
and indirect water heater.
114
1
XII. Operation F. Changing Adjustable Parameters (continued)
Example Pump Parameter selections (continued):
Multiple boilers IWH Piped to Primary, Optional Domestic Hot Water Priority
Sequencer Master
(Boiler 1)
Boiler 2
Wiring locations:
Thermostat
DHW call for heat
System pump
DHW pump
X
X
X
X
Boiler Pump X
Sequencer Master Parameter Selections:
Sequencer Master Enabled
Indirect Water
Heater
“Primary Piped”
Pump Parameter Selections:
System Pump =
Central Heat,
Optional Priority
X
Never
Boiler Pump = Any demand
Any demand
DHW Pump =
Primary Loop
Piped IWH
Never
Explanation:
This piping arrangement permits the system pump to run or not run when there is a domestic hot water call for heat. Domestic hot water priority is optional. It is permissible for the domestic and system pumps to run at the same time. The boiler pump must run for every call for heat.
Multiple Boilers, IWH piped to primary, system pump required to run for any call for heat
Sequencer Master
(Boiler 1)
Wiring locations:
Thermostat
DHW call for heat
System pump
DHW pump
X
X
X
X
Boiler Pump X
Sequencer Master Parameter Selections:
Sequencer Master Enabled
Indirect Water
Heater
“Primary Piped”
Pump Parameter Selections:
System Pump = Any demand
Boiler 2
X
Never
Boiler Pump =
DHW Pump =
Any demand
Primary Loop
Piped IWH
Any demand
Never
Explanation:
This piping arrangement requires the system pump to be running for any calls for heat. Also the boiler pump must run for any call for heat.
115
“Press”
XII. Operation F. Changing Adjustable Parameters (continued)
button to access the following parameters:
Factory Setting
Contractor Name
Address Line 1
Address Line 2
Phone
Range / Choices
User defined
User defined
User defined
User defined
Parameter and Description
Contractor Name
Contractor Address Line 1
Contractor Address Line 2
Contractor Phone
“Press” button to access the following screen:
The Manual Speed Control speed screen allows the technician to set firing rate at low or high speed for combustion testing.
116
XII. Operation F. Changing Adjustable Parameters (continued)
“Press” button to access the following parameters:
Factory
Setting Range / Choices
180°F
(82.2°C)
60°F to 190°F
(16°C to 87.8°C)
10°F
(5.6°C)
5°F
(2.8°C)
2°F to 25°F
(1.1°C to 14°C)
2°F to 25°F
(1.1°C to 14°C)
Parameter and Description
Central Heat Setpoint
Target temperature for the central heat priority. Value also used by the outdoor air reset function.
Central Heat Diff Above
The boiler stops when the water temperature rises ‘Diff Above’ degrees above the setpoint.
NOTE
Never set the Diff Above such that the Setpoint plus the ‘Diff Above’ is greater than 200°F. the result may be nuisance manual reset hard lockouts. For example, if the setpoint is 180°F, the maximum ‘Diff Above’ is 20°F. Further, if the setpoint is 190°F, the maximum ‘Diff Above’ is 10°F.
Central Heat Diff Below
The boiler starts when the water temperature drops ‘Diff Below’ degrees below the setpoint.
3
120 seconds 0 to 300 seconds
Supply
Sensor
1 to 5
Supply Sensor,
Header Sensor
Response Speed
This parameter adjusts the Central Heat temperature controller Proportion Integral Derivative
(PID) values. Higher values cause a larger firing rate change for each degree of temperature change. If set too high firing rate “overshoots” required value, increases to high fire causing the temperature to exceed the “Diff Above” setpoint and cycle the boiler unnecessarily. Lower values cause a smaller firing rate change for each degree of temperature change. If set too low, the firing rate response will be sluggish and temperature will wander away from setpoint.
Low Fire Hold Time
“Low Fire Hold Time” is the number of seconds the control will wait at low fire modulation rate before being released to modulate. After ignition and flame stabilization periods the firing rate is held at low fire for “Low Fire Hold Time”. This delay allows heat to travel out to the system and provide system feedback prior to the control modulating firing rate.
Modulation Sensor
Heat Demand may respond to the boiler’s Supply Temperature or Header Temperature sensors.
When Header Sensor is selected the boiler is fired in response to the sensor wired to Header
Sensor Low Voltage Terminal Block Terminals.
117
XII. Operation F. Changing Adjustable Parameters (continued)
“Press”
Factory
Setting button to access the following parameters:
Range / Choices Parameter and Description
180°F
(82.2°C)
60°F to 190°F
(16°C to 87.8°C)
Auxiliary Heat Setpoint
Target temperature for the Auxiliary Heat priority. Value also used by the outdoor air reset
function.
10°F
(5.6°C)
5°F
(2.8°C)
3
Disable
DHW
Demand
Supply
Sensor
2°F to 25°F
(1.1°C to 14°C)
2°F to 25°F
(1.1°C to 14°C)
1 to 5
Disable, Enable
Auxiliary Heat,
DHW Demand
Supply Sensor,
Header Sensor
Auxiliary Heat Diff Above
The boiler stops when the water temperature rises ‘Diff Above’ degrees above the setpoint.
NOTE
Never set the Diff Above such that the Setpoint plus the ‘Diff Above’ is greater than 200°F. the result may be nuisance manual reset hard lockouts. For example, if the setpoint is 180°F, the maximum ‘Diff Above’ is 20°F. Further, if the setpoint is 190°F, the maximum ‘Diff Above’ is 10°F.
Auxiliary Heat Diff Below
The boiler starts when the water temperature drops ‘Diff Below’ degrees below the setpoint.
Response Speed
This parameter adjusts the Auxiliary Heat temperature controller Proportion Integral Derivative
(PID) values. Higher values cause a larger firing rate change for each degree of temperature change. If set too high firing rate “overshoots” required value, increases to high fire causing the temperature to exceed the “Diff Above” setpoint and cycle the boiler unnecessarily. Lower values cause a smaller firing rate change for each degree of temperature change. If set too low, the firing rate response will be sluggish and temperature will wander away from setpoint.
Auxiliary Priority Over Central Heat
This parameter allows the Auxiliary Heat demand to be higher or lower priority than Central Heat demand. When both demands are active at the same time the Control uses the Setpoint, Diff
Above and Diff Below for the demand that has priority.
Disabled Auxiliary Heat is lower priority than Central Heat demand.
Enable Auxiliary Heat is higher priority than Central Heat demand.
DHW Terminal Use
The Control’s “DHW Temp Switch” input terminal may be used as a Domestic Hot Water (DHW) demand or Auxiliary Heat demand. When the “DHW Terminal Use” is set to Auxiliary Heat a contact closure sensed at the DHW terminal will cause an Auxiliary Heat to call for heat.
DHW Demand: DHW Heat demand may be wired to DHW Terminal.
Auxiliary Heat: Auxiliary Heat demand may be wired to DHW Terminal.
Modulation Sensor
Heat Demand may respond to the boiler’s Supply Temperature or Header Temperature sensors.
When Header Sensor is selected the boiler is fired in response to the sensor wired to Header
Sensor Low Voltage Terminal Block Terminals.
118
XII. Operation F. Changing Adjustable Parameters (continued)
“Press” button to access the following parameters:
Factory
Setting Range / Choices
Parameter and Description
170°F
(76.7°C)
60°F to 190°F
(16°C to 87.8°C)
Domestic Hot Water Setpoint
The Domestic Hot Water (DHW) Setpoint parameter is used to create a minimum boiler water temperature setpoint that is used when DHW heat demand is “on”.
When the DHW heat demand is not “on” (the contact is open or not wired) this setpoint is ignored.
10°F
(5.6°C)
5°F
(2.8°C)
3
2°F to 25°F
(1.1°C to 14°C)
2°F to 25°F
(1.1°C to 14°C)
1 to 5
Domestic Hot Water Diff Above
The boiler stops when the water temperature rises ‘Diff Above’ degrees above the setpoint.
Domestic Hot Water Diff Below
The boiler starts when the water temperature drops ‘Diff Below’ degrees below the setpoint.
Response Speed
This parameter adjusts the Domestic Hot Water temperature controller Proportion Integral
Derivative (PID) values. Higher values cause a larger firing rate change for each degree of temperature change. If set too high firing rate “overshoots” required value, increases to high fire causing the temperature to exceed the “Diff Above” setpoint and cycle the boiler unnecessarily.
Lower values cause a smaller firing rate change for each degree of temperature change. If set too low, the firing rate response will be sluggish and temperature will wander away from setpoint.
10 seconds 0 to 300 seconds
Enable
60
DHW
Demand
Enable Disable
30 to 120
Minutes
Auxiliary Heat,
DHW Demand
Low Fire Hold Time
“Low Fire Hold Time” is the number of seconds the control will wait at low fire modulation rate before being released to modulate. After ignition and flame stabilization periods the firing rate is held at low fire for “Low Fire Hold Time”. This delay allows heat to travel out to the indirect water heater and provide feedback prior to the control modulating firing rate.
Domestic Hot Water Priority (DHWP)
When Domestic Hot Water Priority is Enabled and Domestic Hot Water (DHW) heat demand is
“on” the DHW demand will take “Priority” over home heating demand. When the System and
Boiler pumps are configured as “Central Heat (off DHW priority)” or “Central Heat, Optional
Priority” then they will be forced “off” during DHW Priority. Priority protection time is provided to end DHWP in the event of a failed or excessive long DHW demand.
Priority Time
When DHWP is Enabled the Priority Time Parameter appears and is adjustable.
DHW Terminal Use
The Control’s “DHW Temp Switch” input terminal may be used as a Domestic Hot Water (DHW) demand or Auxiliary Heat demand. When the “DHW Terminal Use” is set to Auxiliary Heat a contact closure sensed at the DHW terminal will cause an Auxiliary Heat to call for heat.
DHW Demand: DHW Heat demand may be wired to DHW Terminal.
Auxiliary Heat: Auxiliary Heat demand may be wired to DHW Terminal.
119
XII. Operation F. Changing Adjustable Parameters (continued)
“Press”
Factory
Setting
Enabled
0°F
(-18°C)
70°F
(21.1°C)
110°F
(43.3°C)
130°F
(54.4°C)
20 Minutes button to access the following parameters:
Range / Choices Parameter and Description
Enable Disable
-40°F to 100°F
(-40°C to 37.8°C)
32°F to 100°F
(0°C to 37.8°C)
70°F to 190°F
(21.1°C to 87.8°C)
80°F to 190°F
(26.7°C to 87.8°C)
0-1800 Seconds
(0-30 Minutes)
Central Heat Outdoor Reset Enable
If an outdoor sensor is installed and Outdoor Reset is Enabled, the boiler will automatically adjust the heating zone set point temperature based on the outdoor reset curve in Figure
8. The maximum set point is defined by the Central Heat Setpoint [factory set to 180°F
(82.2°C)] when the outdoor temperature is 0°F (-18°C) or below. The minimum set point temperature shown is 130°F (54.4°C) [adjustable as low as 80°F (26.7°C)] when the outdoor temperature is 50°F (10°C) or above. As the outdoor temperature falls the supply water target temperature increases. For example, if the outdoor air temperature is 30°F,
(-1.1°C) the set point temperature for the supply water is 150°F (65.6°C).
Disable Do Not Calculate setpoint based on outdoor temperature
Enable Calculate the temperature setpoint based on outdoor temperature using a reset
curve defined by Low Outdoor Temp, High Outdoor Temp, Low Boiler Water
Temp, Min Boiler Temp and Central Heat Setpoint and Boost Time parameters.
Central Heat Low Outdoor Temperature
The Low Outdoor Temperature parameter is also called “Outdoor Design Temperature”.
This parameter is the outdoor temperature used in the heat loss calculation. It is typically set to the coldest outdoor temperature.
Central Heat High Outdoor Temperature
The High Outdoor Temperature parameter is the outdoor temperature at which the Low
Boiler Water Temperature is supplied. This parameter is typically set to the desired building temperature.
Central Heat Low Boiler Water Temperature
The Low Boiler Water Temperature parameter is the operating setpoint when the High
Outdoor Temperature is measured. If the home feels cool during warm outdoor conditions, the Low Boiler Water Temperature parameter should be increased.
Minimum Boiler Temperature (Central Heat and Auxiliary Heat)
The Minimum Boiler Temperature parameter sets a low limit for the Reset setpoint. Set this parameter to the lowest supply water temperature that will provide enough heat for the type radiation used to function properly. Always consider the type of radiation when adjusting this parameter.
Central Heat Boost Time
When the Central Heat Setpoint is decreased by Outdoor Reset settings, the Boost Time parameter is used to increase the operating setpoint when the home heat demand is not satisfied after the Boost Time setting is exceeded. When heat demand has been “on” continuously for longer than the Boost Time parameter the operating setpoint is increased by 10°F (5.6°C). The highest operating setpoint from Boost Time is current Central Heat
Setpoint. A setting of 0 seconds disables this feature. Boost is not used when Sequence
Master is enabled.
120
XII. Operation F. Changing Adjustable Parameters (continued)
“Press”
Factory
Setting
Enabled
0°F
(-18°C)
70°F
(21.1°C)
110°F
(43.3°C)
20 Minutes button to access the following parameters:
Range / Choices
Enable Disable
-40°F to 100°F
(-40°C to 37.8°C)
32°F to 100°F
(0°C to 37.8°C)
70°F to 190°F
(21.1°C to 87.8°C)
0-1800 Seconds
(0-30 Minutes)
Parameter and Description
Auxiliary Heat Outdoor Reset Enable
If an outdoor sensor is installed and Outdoor Reset is Enabled, the boiler will automatically adjust the heating zone set point temperature based on the outdoor reset curve in Figure
8. The maximum set point is defined by the Central Heat Setpoint [factory set to 180°F
(82.2°C)] when the outdoor temperature is 0°F (-18°C) or below. The minimum set point temperature shown is 130°F (54.4°C) [adjustable as low as 80°F (26.7°C)] when the outdoor temperature is 50°F (10°C) or above. As the outdoor temperature falls the supply water target temperature increases. For example, if the outdoor air temperature is 30°F,
(-1.1°C) the set point temperature for the supply water is 150°F (65.6°C).
Disable Do Not Calculate setpoint based on outdoor temperature
Enable Calculate the temperature setpoint based on outdoor temperature using a reset
curve defined by Low Outdoor Temp, High Outdoor Temp, Low Boiler Water
Temp, Min Boiler Temp and Central Heat Setpoint and Boost Time parameters.
Auxiliary Heat Low Outdoor Temperature
The Low Outdoor Temperature parameter is also called “Outdoor Design Temperature”.
This parameter is the outdoor temperature used in the heat loss calculation. It is typically set to the coldest outdoor temperature.
Auxiliary Heat High Outdoor Temperature
The High Outdoor Temperature parameter is the outdoor temperature at which the Low
Boiler Water Temperature is supplied. This parameter is typically set to the desired building temperature.
Auxiliary Heat Low Boiler Water Temperature
The Low Boiler Water Temperature parameter is the operating setpoint when the High
Outdoor Temperature is measured. If the home feels cool during warm outdoor conditions, the Low Boiler Water Temperature parameter should be increased.
Auxiliary Heat Boost Time
When the Auxiliary Heat Setpoint is decreased by Outdoor Reset settings, the Boost Time parameter is used to increase the operating setpoint when the home heat demand is not satisfied after the Boost Time setting is exceeded. When heat demand has been “on” continuously for longer than the Boost Time parameter the operating setpoint is increased by 10°F (5.6°C). The highest operating setpoint from Boost Time is current Auxiliary Heat
Setpoint. A setting of 0 seconds disables this feature.
121
XII. Operation F. Changing Adjustable Parameters (continued)
Central Heat
Setpoint
180°F to 190°F
(82.2°C to 87.8°C)
160°F to 190°F
(71.1°C to 87.8°C)
Fan Coil
Figure 12.11: Outdoor Reset Curve
Heating Element Type
Central Heat
Setpoint
100°F to 140°F
(37.8°C to 60°C)
Heating Element Type
In Slab Radiant High
Mass Radiant
Convection
Baseboard
Fin Tube
Convective
130°F to 160°F
(54.4°C to 71.1°C)
Staple-up Radiant
Low Mass Radiant
130°F to 160°F
(54.4°C to 71.1°C)
Radiant
Baseboard
140°F to 160°F
(60°C to 71.1°C)
Radiators
122
XII. Operation F. Changing Adjustable Parameters (continued)
“Press”
Factory
Setting
Range / Choices button to access the following parameters:
Parameter and Description
Disable
Boiler
Piped
Disabled
180 Secs 120 - 1200 Secs
195°F
(90.6°C)
70%
3
Enable,
Disable
Boiler Piped,
Primary Piped
Enable,
Disable
Central Heat
Setpoint,
195°F (90.6°C)
50% - 100%
1-5
Master Enable/Disable
The Sequencer Master Enable/Disable is used to “turn on” the Multiple Boiler Controller.
Warning! enable ONLY one Sequence Master.
Indirect Water Heater (IWH)
Boiler Piped Sequencer to respond to an Isolated DHW demand that is piped to a single
boiler. The individual boiler goes on “Leave” from the Sequencer Master and
goes to DHW Service.
Primary Piped The Sequence Master responds to the DHW Call For Heat. This allows one or
more boilers to provide heat to the IWH.
DHW Two Boiler Start
The Sequencer to immediately start two boilers for a DHW call for heat. Used when DHW is the largest demand. Only visible when primary piped IWH is selected.
Boiler Start Delay
Slave boiler time delay after header temperature has dropped below the setpoint minus “Diff below” setpoint. Longer time delay will prevent nuisance starts due to short temperature swings.
Stop All Boilers Setpoint
When this temperature is reached all boilers are stopped. This setpoint allows the Sequencer to respond to rapid load increases.
Base Load Common Rate
To maximize condensing boiler efficiency, the firing rate is limited to an adjustable value. Boilers are kept at or below this firing rate as long as the boilers can handle the load. After last available boiler has started, the modulation rate limit is released up to 100%.
Response Speed
This parameter adjusts the Sequence Master temperature controller Proportion Integral Derivative
(PID) values. Higher values cause a larger firing rate change for each degree of temperature change. If set too high firing rate “overshoots” required value, increases to high fire causing the temperature to exceed the “Diff Above” setpoint and cycle the boiler unnecessarily. Lower values cause a smaller firing rate change for each degree of temperature change. If set too low, the firing rate response will be sluggish and temperature will wander away from setpoint.
“Press”
Factory
Setting
button to access the following parameters:
Range / Choices Parameter and Description
None
Normal
1-8
Use Boiler First,
Normal,
Use Boiler Last
Boiler Address
Each boiler must be given a unique address. When “Normal” slave selection order is used, the boiler address is used by the Master Sequencer as the boiler start order. The boiler address is also the Modbus Address when a Energy Management System is connected.
Slave Selection Order
“Use Boiler First”; places the Slave in the lead permanently.
“Normal”; firing order follows boiler number (1,2,3,..) order.
“Use Boiler Last”; places the slave last in the firing order.
123
XII. Operation F. Changing Adjustable Parameters (continued)
“Press” button to access the following parameters:
Factory
Setting
Local
Range /
Choices
Local,
4-20mA
Parameter and Description
Central Heat Modulation Source
This parameter enables the 4-20mA input to control firing rate and the thermostat input to control boiler on/off demand directly without using the internal setpoint. The 4-20mA selection is used to enable a remote multiple boiler controller:
Local: 4-20mA Input on Control Terminals J8-6 and J10-8 is ignored.
4-20mA 4-20mA Input on Control Terminals J8-6 and J10-8 is used to control firing Rate %
directly.
Modbus Modbus input used to control firing Rate % directly.
Central Heat Setpoint Source
Sets the remote (Energy Management System) control mode as follows:
Local
130°F
(54.4°C)
180°F
(82.2°C)
Local,
4-20mA
80°F (26.7°C) -
Central Heat
Setpoint
80°F (26.7°C) -
Central Heat
Setpoint
Local: Local setpoint and modulation rate is used. 4-20mA input on Control Terminals J8-6 and
J10-8 is ignored.
4-20mA 4-20mA Input on Control Terminals J8-6 and J10-8 is used as the temperature setpoint.
The following two parameters may be used to adjust the signal range.
Modbus Modbus is used as the temperature setpoint.
Central Heat 4-20mAdc Setup, 4 mA Water Temperature*
Sets the Central Heat Temperature Setpoint corresponding to 4mA for signal input on Control
Terminals J8-6 and J10-8. Current below 4mA is considered invalid, (failed or incorrect wired input).
Central Heat 4-20mAdc Setup, 20 mA Water Temperature*
Sets the Central Heat Temperature Setpoint corresponding to 20mA for signal input on Control
Terminals J8-6 and J10-8. Current above 20mA is considered invalid, (failed or incorrect wired input).
Central Heat Demand Source
Local
Local,
Modbus
This parameter enables a Modbus input to be take the place of the Heating Thermostat Input:
Local Local Heating Thermostat input is used for Central Heat demand.
Modbus Modbus input is used for Central Heat demand.
* Only visible when Central Heat Setpoint Source is set to 4-20mA.
124
XIII. Service and Maintenance
Important Product Safety Information
Refractory Ceramic Fiber Product
Warning:
The Repair Parts list designates parts that contain refractory ceramic fibers
(RCF). RCF has been classified as a possible human carcinogen. When exposed to temperatures above 1805°F, such as during direct flame contact,
RCF changes into crystalline silica, a known carcinogen. When disturbed as a result of servicing or repair, these substances become airborne and, if inhaled, may be hazardous to your health.
AVOID Breathing Fiber Particulates and Dust
Precautionary Measures:
Do not remove or replace RCF parts or attempt any service or repair work involving RCF without wearing the following protective gear:
1. A National Institute for Occupational Safety and Health (NIOSH) approved respirator
2. Long sleeved, loose fitting clothing
3. Gloves
4. Eye Protection
• Take steps to assure adequate ventilation.
• Wash all exposed body areas gently with soap and water after contact.
• Wash work clothes separately from other laundry and rinse washing machine after use to avoid contaminating other clothes.
• Discard used RCF components by sealing in an airtight plastic bag. RCF and crystalline silica are not classified as hazardous wastes in the United
States and Canada.
First Aid Procedures:
• If contact with eyes: Flush with water for at least 15 minutes. Seek immediate medical attention if irritation persists.
• If contact with skin: Wash affected area gently with soap and water.
Seek immediate medical attention if irritation persists.
• If breathing difficulty develops: Leave the area and move to a location with clean fresh air. Seek immediate medical attention if breathing difficulties persist.
• Ingestion: Do not induce vomiting. Drink plenty of water. Seek immediate medical attention.
125
XIII. Service and Maintenance (continued)
WARNING
Asphyxiation Hazard. Fire Hazard. Explosion Hazard. This boiler requires regular maintenance and service to operate safely. Follow the instructions contained in this manual.
Improper installation, adjustment, alteration, service or maintenance can cause property damage, personal injury or loss of life. Read and understand the entire manual before attempting installation, start-up operation, or service. Installation and service must be performed only by an experienced, skilled, and knowledgeable installer or service agency.
DANGER
Explosion Hazard. Electrical Shock Hazard. Burn Hazard. This boiler uses flammable gas, high voltage electricity, moving parts, and very hot water under high pressure. Assure that all gas and electric power supplies are off and that the water temperature is cool before attempting any disassembly or service.
Do not attempt any service work if gas is present in the air in the vicinity of the boiler. Never modify, remove or tamper with any control device.
126
WARNING
This boiler must only be serviced and repaired by skilled and experienced service technicians.
If any controls are replaced, they must be replaced with identical models.
Read, understand and follow all the instructions and warnings contained in all the sections of this manual.
If any electrical wires are disconnected during service, clearly label the wires and assure that the wires are reconnected properly.
Never jump out or bypass any safety or operating control or component of this boiler.
Assure that all safety and operating controls and components are operating properly before placing the boiler back in service.
Annually inspect all vent gaskets and replace any exhibiting damage or deterioration.
Burn Hazard. This boiler contains very hot water under pressure. Do not unscrew any pipe fittings nor attempt to disconnect any components of this boiler without positively assuring the water is cool and has no pressure. Always wear protective clothing and equipment when installing, starting up or servicing this boiler to prevent scald injuries. Do not rely on the pressure and temperature gauges to determine the temperature and pressure of the boiler. This boiler contains components which become very hot when the boiler is operating. Do not touch any components unless they are cool.
Respiratory Hazard. Boiler materials of construction, products of combustion and the fuel contain alumina, silica, heavy metals, carbon monoxide, nitrogen oxides, aldehydes and/or other toxic or harmful substances which can cause death or serious injury and which are known to the state of
California to cause cancer, birth defects and other reproductive harm. Always use proper safety clothing, respirators and equipment when servicing or working nearby the appliance.
Failure to follow all instructions in the proper order can cause personal injury or death. Read all instructions, including all those contained in component manufacturers manuals which are provided with the boiler before installing, starting up, operating, maintaining or servicing.
All cover plates, enclosures and guards must be in place at all times.
XIII. Service and Maintenance (continued)
NOTICE
Warranty does not cover boiler damage or malfunction if the following steps are not performed at the intervals specified.
1) Continuously:
a. flammable vapors and liquids.
Keep the area around the combustion air inlet terminal free from contaminates.
c.
2) Monthly Inspections:
Inspect the vent piping and outside air intake piping to verify they are open, unobstructed and free from leakage or deterioration. Call the service technician to make repairs if needed.
Inspect the condensate drain system to verify it is leak tight, open and unobstructed. Call the service technician if the condensate drain system requires maintenance.
Inspect the water and gas lines to verify they are free from leaks. Call the service technician to make
repairs
NOTICE
Water leaks can cause severe corrosion damage to the boiler or other system components. Immediately repair any leaks found.
4) Annual Inspections and Service: In addition to the inspections listed above, the following should be performed by a service technician once every year.
Follow the procedure for turning the boiler off found in the Operating Instructions, Section XI “Start-
up
b.
c.
Checkout”.
Turn off all power to the boiler.
Inspect the wiring to verify the conductors are in good condition and attached securely.
CAUTION / ATTENTION
Electrical Shock Hazard. Label all wires prior to disconnection when servicing controls. Wiring errors can cause improper and dangerous operation. Verify proper operation after servicing.
Au moment de l´entretien des commandes, étiquetez tous les fils avant de les débrancher. Les erreurs de câblage peuvent nuire au bon fonctionnement et être dangereuses. S´assurer que l´appareil fonctionne adéquatement une fois k´entretien terminé.
Verify that the gas shutoff shown in Figure 8.1 is closed.
Disconnect the flexible gas line at the gas valve flare connection (Figure 13.1).
WARNING
Fire Hazard. Explosion Hazard. Always use a back-up wrench on the flare connection when making or breaking this connection as shown in Figure 13.1. Failure to do so can cause adjacent threaded connections to loosen or damage to the gas valve. Check all internal gas piping for leaks any time it is disconnected or disturbed during servicing.
Unplug the electrical connection to the gas valve.
Disconnect the air proving switch tube from the gas valve outlet tap.
Unplug the power and speed control cables from the blower.
127
XIII. Service and Maintenance (continued)
Flexible Gas line
Connection
When disconnecting flexible gas line, to prevent damage to gas valve
Figure 13.1: Disconnecting Flexible Gas Line
Flame Sensor
Igniter
128
Figure 13.2: Igniter and Flame Sensor Location
K2 FT/ RAPTOR
U.S. Boiler Co., Inc.
---
1:2 1 OF 1
K2 FT/ RAPTOR
U.S. Boiler Co., Inc.
---
1:2 1 OF 1
1
1
XIII. Service and Maintenance (continued)
i. Unplug the igniter, ground, and flame sensor wires from the ignition electrode and the flame sensor (Figure 13.2).
j. gas valve assembly from the heat exchanger, being careful not to damage the refractory insulation on the inside of the door (see Refractory Warning on page 125) or the electrodes.
k. chamber may be brushed with a nonabrasive, nonmetallic brush. Do not use cleaning agents, solvents, acid or alkali products of any type to clean the heat exchanger .
l.
ports.
m. Inspect igniter electrode and flame sensor for deposits. Clean any found with steel wool. Do not use sand paper or Emory cloth for this cleaning. Inspect the ceramic portion of both of these parts for cracks and replace if any are found. Verify that the igniter gap is within the range shown in Figure 13.3.
n. Inspect the blower gas valve assembly, looking for dust, lint, or other debris that may have been drawn into this assembly. Excessive deposits may be vacuumed out.
Inspect all rubber and plastic components on the blower/gas valve assembly, looking for deterioration. Replace blower and/or gas valve if deterioration is found.
Inspect and clean the condensate trap. Place a bucket under the condensate cleanout cap on the bottom of the
boiler to catch water in the trap. Unscrew the cap. Flush any debris found in the trap with water – do not use other cleaning agents. Reassemble the trap as shown in Figure 13.4.
WARNING
Asphyxiation Hazard. Do not operate the boiler without the float in place. Doing so could result in flue gas leakage into the indoors resulting in personal injury or death from Carbon Monoxide (CO) poisoning.
NOTICE
Attempting to clean the heat exchanger or trap with anything other than water could result in condensate backup, causing the boiler to shut-down.
CAUTION
Do not over tighten fire door mounting nuts. Doing so could break the fire door mounting studs. If any of these studs are damaged, the heat exchanger must be replaced. Use of a short 10 mm box wrench will reduce the risk of damaging these studs.
Inspect the vent system to verify that:
• All gaskets and joints between the boiler heat exchanger and terminal are leak tight.
• All supports are intact and vent system is properly pitched
• All pipe is in good condition. Look for damage such as cracks, heat distortion, discoloration, and embrittlement.
If any such damage is found, the pipe must be replaced and the cause of the damage identified and corrected.
• Vent/Intake terminals are in good condition, free from blockages, and still correctly located relative to doors,
• There is no gasoline, flammable liquids/vapors, or halogen based products stored in the vicinity of the vent or inlet terminals. Also verify that there are no chemical products containing chlorine, chloride based salts, chlorofluorocarbons, paint removers, cleaning solvents, or detergents stored near the air intake terminal.
129
XIII. Service and Maintenance (continued)
0.177in±0.02
4.5mm±0.5
Figure 13.3: Igniter Gap
BOILER JACKET
CONDENSATE DRAIN
#10-32 SHCS
130
CONDENSATE TRAP
COLLAR
CONDENSATE TRAP
CLEAN OUT CAP
GASKET FOR CLEAN OUT CAP
CLEAN OUT CAP NUT
Figure 13.4: Condensate Trap Exploded Parts View
INLET NUT
INLET GASKET
VENT
OUTLET NUT
CORRUGATED
DRAIN TUBE
CONDENSATE TRAP
BRACKET
#10 SPLIT LOCK
WASHER
#10-32 HEX NUT
#8-18 THREAD FORMING
SCREW (1/4" LONG)
XIII. Service and Maintenance (continued)
Refer Section VII “Venting” to re-assemble any vent system components that are disassembled during this inspection and for details on supporting, pitching, and terminating the vent system.
Reconnect any wiring which has been disconnected.
Inspect the hydronic system. Look for leaks and repair any found. If system contains antifreeze, or other additives, test and/or maintain them as directed by the additive manufacturer. Refer to Section XI “Start-up and Checkout” for important information on boiler water and the use of boiler water additives.
u. Inspect air vent(s) in hydronic piping. Ensure vents are unobstructed and properly functioning.
CAUTION
If burner comes on with no flow through the boiler. Turn the boiler off immediately. Failure to do so could cause severe heat exchanger damage.
Follow ALL instructions in Section XI “Start-up and Checkout” to place the boiler back in service, including the performance of a combustion test.
Outdoor Air Temperature Sensor
Temperature versus Resistance
(P/N 102946-01)
(10kOhm NTC Sensor)
78
80
90
100
110
120
60
70
76
10
20
30
40
50
Outdoor Temperature
°F °C
-20
-10
0
-28.9
-23.3
-17.8
-12.2
-6.7
-1.1
4.4
10.0
15.6
21.1
24.4
25.6
26.7
32.2
37.8
43.3
48.9
Ohms of
Resistance
14356
11578
10210
9795
9398
7672
6301
5203
4317
106926
80485
61246
47092
36519
28558
22537
17926
Supply, Return and Stack Temperature Sensor and Header Temperature Sensor
(P/N 101935-01 or 103104-01)
Temperature versus Resistance
(10kOhm NTC Sensor), Beta of 3950
°F
Temperature
°C
122
140
158
176
194
212
248
32
50
68
77
86
104
50
60
70
80
90
100
120
25
30
40
0
10
20
Ohms of
Resistance
3602
2488
1752
1256
916
697
386
32648
19898
12492
10000
8057
5327
131
XIV. Troubleshooting
WARNING
Electrical Shock Hazard. Turn off power to boiler before working on wiring.
A. Troubleshooting problems where no error code is displayed.
Condition
Boiler not responding to call for heat, “Status” and
“Priority” show “Standby”.
Boiler not responding to a call for heat, “Status” shows “Standby” and “Priority” shows Central Heat or Domestic Hot Water.
Possible Cause
Boiler is not seeing call for heat. Check thermostat or zone wiring for loose connection, miswiring, or defective thermostat/zone control.
Boiler is not firing, temperature is greater than setpoint. Water flow through boiler primary loop non-existent or too low.
Boiler Running but System or Boiler Circulator is not running
Home is cold during mild weather days
Home is cold during cold weather days
• Check wiring for loose connection, miswiring.
• When there is a Domestic Hot Water Heat Request the System or Boiler pumps will be
forced “off” when there “Run Pump for” parameter is set to “Central heat, off DHW
demand” or “Central Heat, Optional Priority”. This has been set to allow all of the heat
to be provided for fast indirect water heater recovery. After one hour of “priority
protection” or the end of the Domestic Hot Water Heat Request the system and boiler
pumps will be free to run.
• Increase Low Boiler Water Temperature parameter 5°F (2.8°C) per day.
• Increase High Boiler Water Temperature parameter 5°F (2.8°C) per day
B. Display Faults:
Faults are investigated by selecting the “Help” button from the “Home” screen. When a fault is active the “Help” button flashes and the home screen turns a red color. Continue to select flashing buttons to be directed to the Fault cause.
Figure 14.1: Help Menu
Figure 14.1: Help Menu
Indication
Display Completely Dark
Fan off, LWCO lights off, no green power light on Control
Display Completely Dark, Fan running
Blinking Green power light on Control
Condition
No 120Vac Power at Boiler
No 24Vac
Power to Control
Control
Fault
Display Completely Dark but Boiler fires No 5 Vdc
Power to Display
**00FF or **ERFF Display lost
Communication with Control
ER0011
ER0012
Adjustment
Mode Password
Timeout
Control Failed
Possible Cause
Check breaker and wiring between breaker panel and boiler.
- Blown high voltage fuse, Replacement Fuse Kit, part number 105349-01.
- Loose 120Vac connection wiring between boiler J-Box and transformer
- Loose 24 Vac connection wiring between transformer and Control.
- Blown low voltage fuse, Replacement Fuse Kit, part number 105349-01.
- The green light is connected to internal power supply. The power supply
is repeatedly starting and stopping (not normal) making the light flash. The
microprocessors are not running.
- Try disconnecting all terminals except 24VAC to power the Control. The
green light should be steady. If it is not, then the control is defective. If steady,
start plugging in all the connectors while watching the green light.
When faulty wiring reconnected, green light will begin to flash.
- Loose 5 Vdc connection wiring between display and Control
- Defective Display or Control.
- Loose or defective display harness
- Defective Display
- Defective Control
- The Control and Display are NOT defective. The password has timed out.
Simply cycle power to the Display to restore operation.
- Defective Control. Replace Sage.
132
XIV. Troubleshooting (continued)
C. Help Screen Faults
Indication Condition
Sequencer
Setup
Boiler Size
Setup
Sequencer
Setup
Fault
Boiler
Size
Fault
Possible Cause
This alarm is active if the slave boiler has lost communication with the Sequence
Master. Check the following:
- RJ 45 peer-to-peer network disconnected
- Sequencer Master was Enabled and then Disabled
- Master’s Boiler has been powered down.
- To clear fault restore communication or cycle power
WARNING!
Boiler size setting may not match actual boiler size.
The Boiler size setting determines min, max and light-off blower speeds. Incorrect boiler size can cause hazardous burner conditions and improper operation that may result in PROPERTY LOSS, PHYSICAL INJURY, OR DEATH.
Refer to page 110 for boiler size setting instructions.
D. Help Screen Diagnostic Features
Indication Possible Cause
Lockout History is stored in a first-in, first-out basis. Each History file is stored with boiler run hour of when the lockout occurred.
The “When happened” and “Current” provide:
- “Current” is the run hour and status the boiler just finished.
- “When happened” is the run hour and status when the lockout occurred.
For Service Contact:
CONTRACTOR NAME
CONTRACTOR ADDRESS 1
CONTRACTOR ADDRESS 2
PHONE NUMBER
The user is given the contact information of the responsible service provider. Refer to page 116 for data entry instructions.
133
134
E. Active Fault Screen Faults
XIV. Troubleshooting (continued)
Indication
Limit String Status
Sensor Status
Rate Limit
EMS Status
Condition
Limit String
Fault
Sensor Fault
Rate Limit
Energy
Management
System Fault
Possible Cause
The Limit String Status screen shows the safety limit status. A contact icon, either
“open” or “closed”, graphically represents each safety limit. The “closed” contact icon is steady; the “open” contact icon is blinking. For example, the screen shown to the left illustrates a “closed” external limit contact and an “open’ LWCO contact.
NOTE: Since the limit string items are wired in series, all limits downstream of the
“open” limit will also appear on the screen as “open” (blinking) icons regardless of whether or not they are actually open. The Air Proving Switch is wired independent to all other limits. The Air Proving Switch is only required to be closed during boiler prepurge. It is normal for it to be open during run mode.
The Sensor Status screen shows the status of all sensors. Possible states include:
None: Feature requiring this sensor has not been selected.
Normal: Sensor is working normally.
Shorted: Sensor is shorted or is defective.
Open: There is a break in the wiring between the Control and the sensor or the
sensor is defective
Out of Range: Sensor is defective or is being subjected to electrical noise.
Unreliable: Sensor is defective or is being subjected to electrical noise.
When a sensor fails “opened” or “shorted” the value is changed to reverse video
(background black and value white) “024” or “768” respectively to indicate that there is a fault with the sensor.
The following messages appear when the firing rate is limited or reduced to help avoid a lockout or save energy.
Refer to Hard Lockout section for corrective actions
- High Stack Temperature Limit
- High Supply Temperature Limit
- High Differential Temperature Limit
The following messages appear as part of normal start and stop sequences:
- Minimum Modulation (normal start/stop sequence)
- Low Fire Hold Rate: Low fire hold rate is a normal start-up rate hold used to help
ensure system temperature feedback prior to release to modulation. Low Fire
Hold Time may be adjusted. Refer to the “Changing Adjustable Parameters”,
Paragraph F, for additional information.
- Maximum Expected Heat Rate: Maximum Expected Heat Rate limit is a normal
start-up rate hold used to save energy. This limit helps reduce extra cycles
and save energy. Boiler is free to modulate up to the sum of the active zones and
domestic hot water expected heat rates. Each zone heat rate is adjustable and
may be modified under the modulation menu. Refer to the “Changing Adjustable
Parameters”, Paragraph F, for additional information.
The Energy Management System (EMS) fault screen provides input fault status. When an input is shown as “Not Selected” it is not required for this application or has not yet been selected. These options are selected under the “Energy Management” Adjust mode menu.
Modbus Input Failure If a modus input is selected and out of range or not present
a “535” value is shown reverse video (background black and
value white). To fix the problem check the input source and
check that the input is properly connected.
4-20mA Input Failure Failure status for the 4-20mA input is the same as shown
under Sensor Fault.
XIV. Troubleshooting (continued)
F. Troubleshooting problems where a Soft Lockout Code is displayed.
When a soft lockout occurs, the boiler will shut down, the display will turn red and the “Help” button will “blink”. Select the “blinking” “Help” button to determine the cause of the soft lockout. The boiler will automatically restart once the condition that caused the lockout is corrected.
Soft Lockout Codes Displayed
Lockout
Number
7
Return sensor
(10 KOhms) fault
8
Supply sensor
(10 KOhms) fault
10
Stack sensor
(10 KOhms) fault
Condition
2
Boiler Safety Limit
Open
Boiler Safety Limit wired to terminals J6-1 or
3 OPEN:
• External Limit.
• Optional LWCO
3
Boiler Safety Limit
Open
Blocked Flue/Inlet Switch wired to terminals
J5-1 OPEN
Shorted or open return temperature sensor.
Shorted or open supply temperature sensor.
Possible Cause
External Limit:
• Water temperature is higher than External Limit setting. See “Hard
Lockout 4” for additional information.
• External device not used and jumper not installed.
• External Limit device is defective.
• Loose wiring to limit device
Optional Low Water Cut Off (LWCO)
• If yellow light on LWCO is on, system is low on water. Ensure air vent
is unobstructed and properly functioning as a blocked air vent can result
in low water indication.
• If neither yellow or green light on LWCO is on, check LWCO harness.
• Blocked Flue/Inlet Switch contact open - check for blocked flue/air intake.
NOTE
Blocked Flue/Inlet Switch Special Note
Before a call for heat the air pressure switch is closed. When there is a call for heat with a blocked vent the air pressure switch will open (due to excessive pressure of the blower against a blocked flue pipe) after the blower starts. The control stops the start sequence and stops the blower. After the blower stops the pressure switch re-closes and the cycle continues. The displays shows the cause of trip for only the time the pressure switch is open.
• Shorted or mis-wired return sensor wiring.
• Defective return sensor.
• Shorted or mis-wired supply sensor wiring.
• Defective supply sensor.
11
Ignition failure
Shorted or open flue gas (stack) temperature sensor.
• Shorted or mis-wired flue temperature sensor wiring.
• Defective flue temperature sensor.
Flame failure after 5 tries to restart. Flame rod not detecting flame.
• Condensate trap plugged.
• No gas pressure.
• Gas pressure under minimum value shown on rating plate.
• Gas line not completely purged of air.
• Defective Electrode.
• Loose burner ground connection.
• Defective Ignition Cable.
• Defective gas valve (check for 24 Vac at harness during trial for ignition
before replacing valve).
• Air-fuel mixture out of adjustment - consult factory.
• Defective or fouled electrode.
• Plugged drain line in trap.
135
XIV. Troubleshooting (continued)
Soft Lockout Codes Displayed (continued)
Lockout
Number
13
Flame rod shorted to ground
14
Differential
Temperature inlet/ outlet high
15
Return temp higher than supply
16
Supply temp has risen too quickly
Condition
• Flame rod shorted to ground
• Condensate Trap plugged.
Temperature rise between supply and return is too high.
The Control is reading a return sensor temperature higher than the supply sensor temperature. Condition must be present for at least 75 seconds for this error code to appear.
Supply water temperature has risen too quickly.
17
Normal waiting for blower speed to match purge and
Normal waiting for blower speed to match purge and light-off setpoint. light-off setpoint.
27
Undefined Fault Undefined Fault
Possible Cause
• Shorted or mis-wired flame rode wiring.
• Defective flame rod.
• Plugged drain line in trap.
• Inadequate boiler water flow. Verify that circulator is operating and that
circulator and piping are sized per Water Piping and Trim Section of this
manual.
• Flow through boiler reversed. Verify correct piping and circulator
orientation.
• No boiler water flow. Verify that system is purged of air and that appropriate
valves are open.
• Sensor wiring reversed.
• Supply or return sensor defective.
• See possible causes for “Hard Lockout 4”.
• Inadequate boiler water flow.
• Verify that circulator is operating and that circulator and piping are sized
per Water Piping and Trim Section of this manual.
28 or 53
Air Proving Switch
Failed to Close
Air Proving Switch Failed to Close
54
Air Proving Switch
Failed to Open
Air Proving Switch Failed to Open
• Consult Factory.
The air proving switch has failed to close;
• Check switch, check switch connection and wiring.
• Blocked vent, blocked inlet, blocked or disconnected air switch tube,
blocked heat exchanger or burner.
• Something is blocking air/flue gas flow through boiler
The air proving switch has failed closed, check switch is operating properly.
The air proving switch is “Closed” when it should be “Open”. The air proving switch is checked for proper function before the blower is started and the start sequence is allowed to continue. If the air switch is closed before the blower is started (when there is no air flow) first a soft lockout is initiated and then a manual reset hard lockout results. The possible cause of the air proving switch to be closed or fail to open is as follows:
• The air proving switch is jumpered.
• The air proving switch is defective.
• The blower is running before the start sequence starts the blower. This
can be caused by a loss of communication between the blower and
Control. The blower goes to high speed when there is no communication
between the Control and the blower. Possible cause of loss of
communication is a defective wiring harness, blower or Control.
136
XIV. Troubleshooting (continued)
G. Troubleshooting problems where a Hard Lockout Code is displayed.
When a hard lockout occurs, the boiler will shut down, the display will turn red and the “Help” button will “blink”. Select the “blinking” “Help” button to determine the cause of the Hard Lockout. Once the condition that caused the lockout is corrected, the boiler will need to be manually reset using the Reset button on the “Active Fault” display or located on the Control.
Alarm Output Contact
The Control includes an alarm output contact located on the low voltage terminal board. The alarm contact closes when the
Control goes into a manual reset Hard Lockout. The list of Hard Lockouts is shown below.
Hard Lockout Codes Displayed
Lockout Number
4
Supply high limit
6
Stack High limit
12
Flame detected out of sequence
18
Light off rate proving failed
19
Purge rate proving failed
20
Invalid Safety Parameters
21
Invalid Modulation Parameter
22
Safety data verification needed
23
24VAC voltage low/high
Condition
Control supply sensor detected temperatures in excess of 210°F.
Control Flue gas (Stack) sensor detected temperatures in excess of
214°F (101°C).
A flame signal was present when there should be no flame.
• Condensate trap plugged.
Blower is not running at Light-off rate when it should or blower speed signal not being detected by Control.
Blower is not running at Purge rate when it should or blower speed signal not being detected by Control.
Unacceptable Control Safety related parameter detected.
Unacceptable Control Modulation related parameter detected.
Safety related parameter change has been detected and a verification has not been completed.
Possible Cause
• Heating load at time of error was far below the minimum firing
rate of the boiler.
• Defective system circulator or no flow in primary loop.
• Defective boiler circulator, no flow or insufficient flow in boiler loop.
• Control system miswired so that the boiler operation is
permitted when no zones are calling.
• Heat exchanger needs to be cleaned.
• Boiler over-fired.
• Air-fuel mixture out of adjustment - consult factory.
• Defective gas valve - make sure inlet pressure is below
maximum on rating plate before replacing valve.
• Plugged drain line in trap.
• Loose connection in 120 VAC blower wiring.
• Loose or miswired blower speed harness.
• Defective blower
• Loose connection in 120 VAC blower wiring.
• Loose or miswired blower speed harness.
• Defective blower
Safety Parameter verification required. Contact factory.
Reset the control.
Safety related Control parameter has been changed and verification has not been performed.
Control 24Vac control power is high or low.
• Loose connection in 24Vac VAC power wiring.
• Loose or miswired 24Vac harness.
• Miswired wiring harness causing power supply short to ground.
• Defective transformer.
• Transformer frequency, voltage and VA do not meet
specifications.
Power detected at fuel valve output when fuel valve should be off.
• Reset the control. If problem reoccurs, replace the Control.
24
Fuel Valve Error
25
Hardware Fault
26
Internal Fault
27
Undefined Fault
54
Air Proving Switch
Failed to Open
Internal control failure.
Internal control failure.
Undefined Fault
Air Proving Switch Failed to Open
• Reset the control. If problem reoccurs, replace the Control.
• Reset the control. If problem reoccurs, replace the Control.
• Reset the Control. If problem reoccurs, replace the Control.
See Soft Lockout 54.
137
XV. Repair Parts
The following parts may be obtained from any Velocity Boiler Works distributor. To find the closest
Velocity Boiler Works distributor, consult the area Velocity Boiler Works representative or the factory at:
Velocity Boiler Works
Customer Service
P.O. Box 14818
Philadelphia, PA 19134 www.velocityboilerworkscom
1H 1G
Space Heating Models:
• RPTR085
• RPTR110
• RPTR155
• RPTR205
• RPTR270
1K
1F
1E
1R
1D
1W 1J
1C
1M
1B 1L
1U 1Q
1A
1V
1I
1U
1P
1N
1O
1S
138
1T
XV.
Repair Parts (continued)
Key
No. Description
Space Heating Models Heat Exchanger & Piping Repair Parts
RPTR085 RPTR110
Part Number (Qty)
RPTR155 RPTR205 RPTR270
Contact Velocity Boiler Works. Provide boiler serial number.
1A Heat Exchanger
1B Burner Repair Kit (includes burner and screws)
1C
Burner Screw, Socket Head Cap Screw, M4 x 6mm,
316SS
1D Burner Plate Insulation
106986-01 106986-02 106986-03
101064-01 (3)
106969-01
101064-01 (4)
106969-02
106986-04
101064-01 (5)
106969-03
1E
1F
1G
Burner Plate Repair Kit (includes burner plate and insulation)
Burner Plate Flange Locknut, Serrated, M6 x 1.0,
Zinc Plated Steel
Flame Sensor Repair Kit (includes electrode, gasket and hardware)
106985-01
101724-01 (4)
106985-02
105798-01
106985-03
101724-01 (5)
1H
Igniter Repair Kit (includes electrode, gasket and hardware)
1I Heat Exchanger Flue Gasket Repair Kit
1J Flue Pipe Repair Kit (includes pipe and gasket)
1K Flue Pipe Gasket Repair Kit
1L Silicone Tubing Repair Kit
1M Flue/Inlet Switch Repair Kit
1N Condensate Trap Repair Kit
1O Return Sensor Repair Kit
1P Flue Gas / Blocked Drain Sensor Repair Kit
1Q Supply Sensor Repair Kit
1R 30 PSI Relief Valve
1S 3/4" NPT Drain Valve
1T Temperature & Pressure Gauge Repair Kit
1U Water Gasket Repair Kit (includes 2 gaskets)
1V
Supply Pipe Assembly Repair Kit (includes pipe assembly, gasket and jacket grommets)
107000-01
106998-01
106988-01
106995-01
106977-01
103005-02
106999-01
106989-01
105857-01
106990-01
106991-01
106993-01
106994-01
81660319
806603061
105894-01
107000-02
106998-02
106988-02
106996-01
106977-02
106997-01 106997-02
139
Combi Domestic Hot Water and Space Heating Model:
• RPTR155C
XV.
Repair Parts (continued)
2H 2F
2R
2K
2G
2J
2V
2U
2Q
2A
2BB
2W 2U
2S
2Z
2X
2AA 2P
2I
2BB
2Y
2T
2EE
2II
2FF
2GG
2GG 2HH
2GG
2Z
2GG
2O
2N
2CC
2DD
2GG
140
2E
2D
2C
2B
2M
2L
XV.
Repair Parts (continued)
Key
No.
2A
Description
Heat Exchanger
155 MBH Combi Heat Exchanger and Piping Repair Parts
Part Number (Qty)
RPTR155C
Contact Velocity Boiler Works.
Provide boiler serial number.
Burner Repair Kit (includes burner and screws) 106986-03
2F
2G
2H
2I
2J
2B
2C
2D
2E
Burner Screw, Socket Head Cap Screw, M4 x 6mm, 316SS
Burner Plate Insulation
Burner Plate Repair Kit (includes burner plate and insulation)
Burner Plate Flange Locknut, Serrated, M6 x 1.0, Zinc Plated Steel
Flame Sensor Repair Kit (includes electrode, gasket and hardware)
Igniter Repair Kit (includes electrode, gasket and hardware)
Heat Exchanger Flue Gasket Repair Kit
Flue Pipe Repair Kit (includes pipe and gasket)
2K
2L
Flue Pipe Gasket Repair Kit
Silicone Tubing Repair Kit
2M Flue/Inlet Switch Repair Kit
2N Condensate Trap Repair Kit
2O Return Sensor Repair Kit
2P Flue Gas / Blocked Drain Sensor Repair Kit
2Q Supply Sensor Repair Kit
2R 30 PSI Relief Valve
2S 3/4" NPT Drain Valve
2T Temperature & Pressure Gauge Repair Kit
2U Water Gasket Repair Kit (supply and return pipes, includes 2 gaskets)
2V
2W
Supply Pipe Assembly Repair Kit (includes pipe assembly, zone valve body, gasket and jacket grommet)
Return Pipe Assembly Repair Kit (includes pipe assembly, gasket and jacket grommet)
2X Zone Valve Actuator
2Y Circulator to Flat Plate Pipe Assembly Repair Kit (includes gasket)
2Z
Water Gasket Repair Kit (top flat plate heat exchanger connections, includes 2 gaskets)
2AA DHW Circulator, Taco 007 (includes circulator and gaskets)
2BB Circulator Flange Kit (includes 2 flanges and hardware)
2CC
Flat Plate Heat Exchanger Repair Kit (includes heat exchanger, water gaskets and jacket gasket)
2DD Flat Plate Heat Exchanger to Mixing Valve Repair Pipe Assembly (includes gaskets)
2EE DHW to Mixing Valve / Flat Plate Repair Pipe Assembly (includes gaskets)
2FF Mixing Valve to DHW Repair Pipe Assembly (includes gaskets)
2GG
Water Gasket Repair Kit (bottom flat plate heat exchanger connections and mixing valve, includes 5 gaskets)
2HH Thermostatic Mixing Valve
2II Flow Switch not shown DHW Circulator and Zone Valve Repair Harness
101064-01 (4)
106969-02
106985-02
101724-01 (5)
105798-01
103005-02
107000-01
106998-01
106999-01
106989-01
105857-01
106990-01
106991-01
106993-01
106994-01
81660319
806603061
105894-01
106995-01
106977-03
106978-01
106847-01
106979-01
106996-01
106943-01
105149-01
106984-01
106980-01
106981-01
106982-01
106488-01
106342-01
106343-01
107004-01
141
3D
All Models
XV. Repair Parts (continued)
3H
3I
3O
3G
3E
3P
3L 3R 3Q
3J
3K
3F 3M
3C
3A
3B
3N
142
XV.
Repair Parts (continued)
Key
No. Description
All Models Blower and Gas Train Repair Parts
RPTR085 RPTR110
Part Number (Qty)
RPTR155 &
RPTR155C
RPTR205 RPTR270
107001-01 107001-02 107001-03
3B Blower Outlet Gasket Repair Kit
3C Blower Control Harness Repair Kit (4 wire harness)
3D Blower Power Harness Repair Kit (3 wire harness)
3E
Venturi Repair Kit (includes venturi, cork gasket, gas valve o-ring and hardware)
3F Venturi Cork Gasket
106029-01
107002-01
107003-01
107005-01 107005-02 107005-03 107005-04 107005-05
3H Gas Valve 90° Inlet Flange Repair Kit
3I Gas Valve Flange Adapter, 5/8" OD Flare x 1/2" NPT
3J Gas Valve Wire Harness Repair Kit
3K Gas Flex Tube Repair Kit
3L Gas Shutoff Valve Repair Kit
3M Gas Pipe, 1/2" Sch.40 x 22" Long, Carbon Steel
106082-01
107006-01
107007-01
106363-01
107008-01
107009-01
107010-01
106158-01
107011-01
3P Attenuator Pipe Assembly Repair Kit
3Q Air Proving Switch Repair Kit
3R Silicone Tubing Repair Kit
107013-01
105087-01 107015-01
107012-01
107014-01 107013-01
107015-02
106989-01
143
144
• RPTR085 • RPTR1 • RPTR155 • RPTR205 • RPTR270
XV.
Repair Parts (continued)
Key
No. Description
Space Heating Models Jacket Repair Parts
Part Number (Qty)
RPTR085 RPTR110 RPTR155 RPTR205 RPTR270
4B Door Latch Catch
4C Door Grounding Latch (includes catch and keeper)
4D Control Panel Frame Assembly w / Gaskets
4E Jacket Screw, 8-18 x 1/2" Long, type B
4F Gas Train Support Bracket
4G Gas Pipe Clamp
4I Door Latch Keeper
4J Water Pipe Grommet
4K
Vent Connector Repair Kit (includes connector, gaskets and hardware)
4L
Air Intake Connector Repair Kit (includes connector, gasket and locknut)
4M Air Intake Shield
4N Right Side Panel Assembly w / Gaskets
107016-02
106145-01 (4)
106093-01
106577-01
105368-01
106331-01
106162-01
80860700
106139-01 (4)
106146-01 (4)
107034-01
106295-01
107017-01
106389-01
103252-01 (4)
106296-01
4P Condensate Drain Grommet
4Q Wall Hanging Bracket
4R Bottom Securing Bracket
4S Wall Mounting Screw, 5/16" x 2" Lag Screw
107018-01
106139-01
102869-01
105520-01
101043-01 (5)
145
146
XV.
Repair Parts (continued)
Key
No. Description
155 MBH Combi Jacket Repair Parts
Part Number (Qty)
RPTR155C
5B Door Latch Catch
5C Door Grounding Latch (includes catch and keeper)
5D Control Panel Frame Assembly w / Gaskets
5E Jacket Screw, 8-18 x 1/2" Long, type B
5F Gas Train Support Bracket
5G Gas Pipe Clamp
5I Door Latch Keeper
5J Water Pipe Grommet
5K
Vent Connector Repair Kit (includes connector, gaskets and hardware)
5L
Air Intake Connector Repair Kit (includes connector, gasket and locknut)
5M Air Intake Shield
5N Right Side Panel Assembly w / Gaskets
5P Condensate Drain Grommet
5Q Wall Hanging Bracket
5R Bottom Securing Bracket
5S Wall Mounting Screw, 5/16" x 2" Lag Screw
5T Pump Support Bracket
107016-02
106145-01 (4)
106093-01
106577-01
105368-01
106720-01
106162-01
80860700
106146-01 (2)
106139-01 (3)
107034-01
107017-01
106389-01
106715-01
107018-01
106139-01
102869-01
105520-01
101043-01 (5)
106972-01
147
148
XV.
Repair Parts (continued)
All Models Control Panel Repair Parts
Part Number (Qty)
Key No. Description
6A
6B
6C
6D
6E
6F
6G
6H
6I
6J
6K
6L
6M
6N not shown
Control Panel
Transformer Repair Kit
Jacket Screw, 8 -18 x 1/2" Long, Type B
Door Latch Keeper
High Voltage PCB Repair Kit (includes PCB, fuses and screws
High Voltage PCB Cover
Repair Programmed Control
Control Foot Gasket
Low Voltage PCB Repair Kit (includes PCB, fuse and screws)
PCB and Latch Keeper Screw, 8 -32 x 3/8" Long,
Machine Screw
Wire Harness Tie Gasket
User Interface Inner Plastic Trim
Programmed Display Repair Kit (includes display and hardware)
Ground Screw, 8 -32 x 3/8" Long, Thread Forming
High Voltage and Low Voltage Fuse Kit
RPTR085 RPTR110 RPTR155 &
106290-01
106034-01
105368-01
106146-01 (2)
107020-01
106934-01
107097-01
105109-01 (4)
107035-01
106538-01 (12)
105110-01 (4)
106380-01
107100-01
102200-01
105856-01
RPTR205 RPTR270
149
7A 7D 7F
XV.
Repair Parts (continued)
7H 7G 7E
7C 7B
Key
No. Description
7B 2" x 30" Sched. 40 CPVC Pipe
7C 2" CPVC 90 Elbow
7D 2" PVC 90 Elbow Intake Termination
7E 2" PVC Coupling Vent Termination
7F 2" SS Termination Screen
7G 2" x 3" CPVC Reducing Bushing
7H 2" x 3" PVC Reducing Bushing
2" CPVC/PVC Sidewall Vent Components
RPTR085 RPTR110
Part Number (Qty)
RPTR155 &
RPTR155C
RPTR205 RPTR270
107039-01 Not Permitted
106612-01
106610-01
106618-01
101870-01
102191-04 (2)
106611-01
106619-01
Not Permitted
Not Permitted
Not Permitted
Not Permitted
Not Permitted
Not Permitted
Not Permitted
Key
No. Description
7B 3" x 30" Schedule 40 CPVC Pipe
7C 3" CPVC 90 Elbow
7D 3" PVC 90 Elbow Intake Termination
7E 3" PVC Coupling Vent Termination
7F 3" SS Termination Screen
3" CPVC/PVC Sidewall Vent Components
RPTR085 RPTR110
Part Number (Qty)
RPTR155 &
RPTR155C
RPTR205 RPTR270
107039-02
102193-01
102192-01
105293-01
105292-01
102191-01 (2)
150
XV.
Repair Parts (continued)
8A
8B
8C
8D 8E
8F
8G
Key
No. Description
All Models Wire Harness Repair Parts
Part Number (Qty)
RPTR205 RPTR270
8A Low Voltage / Communication Harness Repair Kit
8B High Voltage Harness Repair Kit
8C Ignition Cable Harness Repair Kit
8D Blower Control Harness Repair Kit (4 wire harness)
8E Blower Power Harness Repair Kit (3 wire harness)
8F DHW to Circulator and Zone Valve Harness Repair Kit
8G Gas Valve Harness Repair Kit not shown LWCO Jumper Repair Kit not shown Outdoor Temperature Sensor (not shown) not shown Header Sensor
RPTR155C
107036-01
107037-01
107038-01
107002-01
107003-01
107004-01
107008-01
105908-01
102946-01
103104-01
151
Appendix A: Instructions for Conversion of this Boiler for use with LP Gas
DANGER
These instructions include a procedure for adjusting the air-fuel mixture on this boiler. This procedure requires a combustion analyzer to measure the CO2 (or Oxygen) and Carbon Monoxide (CO) levels in flue gas. Adjusting the air-fuel mixture without a proper combustion analyzer could result in unreliable boiler operation, personal injury, or death due to carbon monoxide poisoning.
WARNING
This conversion kit shall be installed by a qualified service agency in accordance with the manufacturer’s instructions and all applicable codes and requirements of the authority having jurisdiction. If the information in these instructions is not followed exactly, a fire, an explosion or production of carbon monoxide may result causing property damage, personal injury, or loss of life. The qualified service agency is responsible for proper installation of this kit. The installation is not proper and complete until the operation of the converted appliance is checked as specified in the manufacturer’s instructions supplied with the kit.
CAUTION
The gas supply shall be shut off prior to disconnecting the electrical power, before proceeding with the conversion.
152
To convert this boiler for use on LP gas, perform the following steps:
1) If not already done, install the boiler in accordance with this manual, following all instructions in
Section XI “Start-up and Check-out” up to Step 10.
2) Install provided LP gas orifice per Table A. Orifice installation is shown in Figure A.1. Boiler sizes
205 and 270 require field installation of factory supplied orifice and adjustment of throttle screw for conversion to LP gas. Boiler sizes 85, 110, and
155, require only adjustment of throttle screw for conversion to LP gas.
Table A: LP Gas (Propane) Orifice Sizes
(Field Installed)
Boiler Size
85
110
155
205
270
LP Gas Orifice
Dia.
not used not used not used
0.224 in.
0.224 in.
LP ORIFICE
(SIZES 205-270 MBH ONLY)
O-RING
Figure A.1: LP Orifice Installation
Appendix A - (continued)
3) Before attempting to start the boiler turn the throttle (Figure A.3) clockwise until it stops (several full turns).
4) Turn throttle counter-clockwise the exact number of turns shown in Table A.4.
WARNING
The pressure regulator has been factory set using precision instruments and must never be adjusted in the field. The gas valve outlet pressure is the same for both natural gas and propane. Make sure that all adjustments are made with the throttle, not the pressure regulator. Attempting to adjust the pressure regulator will result in damage to the gas valve and may cause property damage, personal injury or loss of life.
WARNING
The throttle adjustments shown in Table A.4 are approximate. The final throttle setting must be found using a combustion analyzer. Leaving the boiler in operation with a CO level in excess of 200PPM air-free could result in injury or death from carbon monoxide poisoning.
5) Attempt to start the boiler using the operating instructions located on Page 97. If the boiler does not light on the first try for ignition, allow to boiler to make at least four more attempts to light. If boiler still does not light, turn the throttle counter-clockwise in 1/8 turn increments, allowing the boiler to make at least four tries for ignition at each setting, until the boiler lights.
6) After the burner lights, force the burner to high fire by entering the Adjust Menu and then High Fire Hold as described in
Section XI “Start-up and Checkout”. Allow the boiler to operate for approximately 5 minutes before taking combustion readings. Note: after 10 minutes, the boiler is automatically released from high fire hold.
153
Appendix A - (continued)
Offset Regulator
- Do Not Adjust
Outlet Tap Gas Inlet
Figure A.3: Gas Valve Detail
Table A.4: Starting Number of Throttle Turns for Conversion to LP Gas
Model
Size
85
110
155
205
270
# Counter-clockwise Turns
(From Fully Closed)
2½
2½
3
4½
2¼
Inlet Tap
Gas Outlet
Throttle Screw
Tube to Air
Proving Switch
WARNING
All combustion performance numbers MUST be verified with a combustion analyzer. Failure to do so will result in substantial property damage, severe personal injury or death.
154
Appendix A - (continued)
7) Perform a combustion test, sampling flue products from the tap in the front of the vent adaptor.
8) While the burner is at high fire adjust the throttle as needed to obtain the CO
2
(or O
2
) settings shown in the Table A.5:
• To reduce the CO
2
(increase the O
• To increase the CO
2
(reduce the O
2
) turn the throttle clockwise
2
) turn the throttle counter-clockwise
Make adjustments in increments of 1/8 to 1/4 turn and allow the boiler at least a minute to respond to each adjustment before making another. In general, the CO level will be at its lowest somewhere in the CO
2
range shown in this table.
Table A.5: Acceptable Combustion Readings for LP Operation (0 - 4,500 ft)
Model
Size
85
110
155
205
270
%CO
2
9.5 - 11.0
9.5 - 11.0
9.5 - 11.0
9.5 - 11.0
9.5 - 11.0
%O
2
4.2 - 6.5
4.2 - 6.5
4.2 - 6.5
4.2 - 6.5
4.2 - 6.5
Max. CO
Air Free
COAF readings must be less than
200 ppm.
9) Verify that the gas inlet pressure is between 8.0 and 14.0 inches w.c. with all gas appliances (including the converted boiler) both on and off.
10) A sheet of yellow labels is provided in the envelope with this manual for boilers converted from natural to LP gas. Select the model from this sheet of labels and apply them as follows:
• Apply the “Rating Plate Label” adjacent to the rating plate.
• Apply the “Gas Valve Label” to a conspicuous area on the gas valve.
• Apply the “Boiler Conversion Label” to a conspicuous surface on, or adjacent to, the outer boiler jacket. Fill in the
date of the conversion and the name and address of the company making the conversion with a permanent marker.
11) Refer to the Section XI “Start-up and Checkout” and perform any checks not already completed.
155
Appendix B: Instructions for High Altitude Installations Above 4,500 ft.
These instructions apply only to the following altitude ranges: 4501 ft.- 6000 ft., 6001 ft.- 7800 ft., 7801 ft.- 10,100 ft.
These instructions contain specific information to setup your boiler to ensure proper operation.
WARNING
LP Conversions - boiler setup from factory is configured for use with natural gas installed from 0 - 4,500 ft. above sea level only. For conversion to LP at altitude above 4,500 ft., please follow these specific instructions before converting for use with LP. If the information in these instructions is not followed exactly, a fire, an explosion or production of carbon monoxide may result causing property damage, personal injury or loss of life. The qualified service agency is responsible for proper installation of this boiler for use with LP gas. The installation is not proper and complete until the operation of the converted appliance is checked as specified in the manufacturer’s instructions supplied.
DANGER
These instructions include a procedure for adjusting the air-fuel mixture on this boiler. This procedure requires a combustion analyzer to measure the CO
2
(or Oxygen) and Carbon Monoxide (CO) levels in flue gas. Adjusting the air-fuel mixture without a proper combustion analyzer could result in unreliable boiler operation, personal injury, or death due to carbon monoxide poisoning.
WARNING
Failure to setup the boiler in accordance with these instructions could result in high amount of Carbon
Monoxide to be produced which could result in death, serious injury, and/or reduced component life.
Adjusting Boiler Type (must be completed first)
Select the correct boiler size and altitude range using the touch screen display as follows:
1. Check boiler’s label for actual boiler size.
2. Confirm installation altitude
3. Power up the boiler. The display will show the
Home screen.
4. Press “Adjust” button on the Home screen.
5. Press “Adjust” button on the Adjust Mode screen.
6. Press “Login” button to access Password screen.
7. Press 5-digit display to open a keypad. Enter the
password “86” and press the return arrow to close keypad. Press “Save” button.
8. Press “Adjust” button to enter Adjustment Mode.
9. Press “Modulation Setup” menu button.
10. Press “Adjust” button on the Boiler Type screen.
11. Use the ↓ ↑ arrow buttons to select the correct size, fuel and altitude of your boiler. Press the (Check with Circle) button to enter your selection.
12. Press “Enter” button until display stops blinking, press next and repeat until “Completed” is displayed.
13. Press X to exit.
156
Altitude Start-up Instructions for Natural Gas and
LP
1. Confirm boiler size, type and installed altitude prior to startup. Install boiler in accordance with the
Installation manual included with boiler.
2. Instructions Unique to LP Boilers: Follow Appendix
A to complete LP conversion before proceeding.
Final settings for high altitude installations are shown for CO
2
and CO(Air-Free) Maximum in
Table B.3. Set the throttle screw to its preliminary setting for LP (see Table B.5).
3. Start boiler as described in boiler Installation manual and lock boiler in high fire (See XI. Startup and Checklist). If boiler does not light, turn throttle screw in 1/8 turn increments in a counterclockwise direction until boiler fires. Do not stop here, follow
Steps 4-7.
Verify that the gas inlet pressure is between the following limits with all gas appliances (including the converted boiler) both on and off:
• Natural Gas: 4.0 - 14.0 inches w.c.
• LP Gas: 8.0 - 14.0 inches w.c.
If inlet pressure is not within limits, adjust before preforming high altitude setup procedure.
Appendix B - (continued)
4. After 5 minutes of operation check CO
2
and CO
(Air-Free) and ensure it is within the limits outlined in Table B.3. Air-Free Carbon Monoxide in Flue Gas must be less than 200 ppm during all operation. If
CO(Air-Free) and CO
2 only.
is within these limits, move to Step 6 and check fan speed at high fire operation
5. If CO
2
is outside the range outlined in Table B.3, adjust throttle screw such that the CO
2
falls in this range while boiler is locked manually in high fire.
Turning throttle screw counter-clockwise increases the CO
2
, while clockwise rotation leans the mixture, reducing the CO
2
. Once CO
2
is within the limits in
Table B.3, check CO (Air-Free) again to ensure it is below 200 ppm. If CO (Air-Free) is above 200 ppm turn throttle screw clockwise in 1/8 turn increments until CO (Air-Free) is below 200 ppm, while ensuring CO
B.3. If CO
2
remains in the range specified in Table
(Air-Free) is still above 200 ppm, reduce fan speed in 100 rpm increments until CO (Air-Free) is less than 200 ppm.
6. Start boiler five times at the above settings to ensure boiler lights off without delay and without noise.
Check CO
CO
2
2
and CO (Air-Free) to ensure that the
is within the range specified in Table B.3 and
CO (Air-Free) is below 200 ppm. Be sure to replace the screw cap in the vent adapter when combustion testing is complete.
7. Lock boiler in low fire. Ensure CO are within limits. If CO
2
2
and CO
is not, adjust offset on gas valve at minimum input rate to bring into specification.
8. Verify that the gas inlet pressure is between the following limits with all gas appliances (including the converted boiler) both on and off:
• Natural Gas: 4.0 - 14.0 inches w.c.
• LP Gas: 8.0 - 14.0 inches w.c.
If inlet pressure is not within limits, adjust before performing high altitude setup procedure.
Offset Regulator
- Do Not Adjust
Outlet Tap Gas Inlet
Figure B.1: Gas Valve Detail (High Altitude Only)
Inlet Tap
Gas Outlet
Throttle Screw
Tube to Air
Proving Switch
157
158
Appendix B - (continued)
Table B.2: Altitude Adjustments (Above 4500 ft. only)
Altitude Model Fuel
RPTR085
RPTR110
RPTR155 & RPTR155C
RPTR205
RPTR205
NG / LP
NG / LP
NG /LP
NG
LP
NG RPTR270
RPTR270
RPTR085
RPTR110
RPTR110
RPTR155 & RPTR155C
RPTR155 & RPTR155C
LP
NG / LP
NG
LP
NG
LP
6001 ft. to 7,800 ft.
RPTR205
RPTR270
RPTR085
NG / LP
NG / LP
NG / LP
RPTR110
RPTR110
RPTR155 & RPTR155C
NG
LP
NG
RPTR155 & RPTR155C
RPTR205
RPTR205
RPTR270
LP
NG
LP
NG / LP
De-rate’s per 1000 ft. are approximate
Based on minimum vent length
(0 - 2000 ft. is Sea Level Input Rate, 2000 - 4500 ft. derate 1.7% / 1000 ft.)
Table B.3: Acceptable Combustion Readings (Above 4500 ft.)
Altitude
6001 ft. to 7,800 ft.
7,801 ft. to 10,100
Model
RPTR085
RPTR110
RPTR155
RPTR205
RPTR270
RPTR085
RPTR110
RPTR155
RPTR205
RPTR270
RPTR085
RPTR110
RPTR155
RPTR205
RPTR270
Natural Gas CO
2
9.5 - 9.9
(%)
9.5 - 9.8
9.5 - 9.7
9.5 - 9.7
9.4 - 9.5
9.5 - 9.8
9.5 - 9.7
9.5 - 9.6
9.5 - 9.6
9.5 - 9.6
9.5 - 9.6
9.5
9.5
9.5
9.0 - 9.1
LP Gas CO
2
(%)
10.0 - 10.7
10.0 - 10.4
10.0 - 10.4
9.5 - 10.3
10.0 - 10.3
10.0 - 10.2
10.0 - 10.1
10.0 - 10.2
10.0
10.0 - 10.4
10.0 - 10.4
10.0 - 10.1
10.0 - 10.1
10.0 - 10.1
10.0
Percentage derate
(Approx. per 1000 feet)
0.0%
0.0%
0.0%
1.6%
0.0%
3.8%
0.0%
0.0%
0.0%
0.7%
0.0%
0.5%
1.9%
3.1%
0.2%
0.5%
0.8%
0.9%
1.2%
2.0%
2.6%
3.4%
Max. CO Air Free
COAF readings must be less than 200 ppm.
Appendix B - (continued)
Table B.4: Fan Speeds Tested
Model
RPTR085
RPTR110
RPTR155 &
RPTR155C
RPTR205
RPTR270
Fuel
NG
LP
NG
LP
NG
LP
NG
LP
NG
LP
4501-
6000 ft.
6100
6100
6450
6450
6500
6900
7500
8100
7000
8500
HF Target FS (RPM)
6001-
7800 ft.
7801-
10,100 ft.
6650 7200
7000
6900
6900
7100
7100
6800
7200
6750
6950
7200
7200
7200
7100
7100
6800
6800
6450
6650
4501-
6000 ft.
1600
1600
1600
1600
1600
1600
1700
1750
1800
2000
LF Target FS (RPM)
6001-
7800 ft.
7801-
10,100 ft.
1700 1800
1700
1700
1700
1600
1600
1600
1700
1700
1750
1800
1800
1800
1700
1700
1600
1600
1700
1700
Table B.5: Starting Number of Throttle Turns for
Conversion to LP Gas
Model Size
85
110
155
205
270
No. Counter-Clockwise Turns
(From Fully Closed)
2½
2½
3
4½
2¼
Table B.6: LP Gas (Propane) Orifice Sizes
(Field Installed)
Model Size
85
110
155
205
270
LP Gas Orifice
Dia.
not used not used not used
0.224 in.
0.224 in.
WARNING
All combustion performance numbers MUST be verified with a combustion analyzer. Failure to do so will result in substantial property damage, severe personal injury or death.
159
Appendix C: RPTR155C Combi Instruction Manual
I – Product Description
The RPTR155C provides economical, reliable, tank-less domestic hot water (DHW) production in addition to central space heating provided by the Raptor high efficiency boiler.
II – Domestic Hot Water Basic Operation
The RPTR155C Combi provides central heat through a high efficiency stainless steel heat exchanger and DHW through a flat plate heat exchanger. DHW is activated by a flow switch. Water temperatures are regulated by the boiler controls and a thermostatic mixing valve.
III – Specifications
RPTR155C Boiler Input Rate: 155MBH
Compatible Boiler Control: B1020 or higher
Thermostatic Mixing Valve:
Adjustable 70°F (21°C) — 145°F (63°C).
ASSE 1017 Certified
Minimum Flow to Operate: 0.5 gpm (2
l
/min)
Lead Content: Components comply with SDWA Section 1417,
Jan. 4, 2014 version.
RPTR155C Performance
DHW Output @ 70°F (39°C) T.rise: 4.0 gpm (15.1
l
/min)
DHW Output @ 77°F (43°C) T.rise: 3.65 gpm (13.8
l
/min)
160
Appendix C - (continued)
IMPORTANT INFORMATION - READ CAREFULLY
NOTE: The equipment shall be installed in accordance with those installation regulations enforced in the area where the installation is to be made. These regulations shall be carefully followed in all cases. Authorities having jurisdiction shall be consulted before installations are made.
All wiring on boilers installed in the USA shall be made in accordance with the National Electrical Code and/or local regulations.
161
Appendix C - (continued)
DANGER
Electrical Shock Hazard. Positively assure all electrical connections are unpowered before attempting installation or service of electrical components or connections of the boiler or building. Lock out all electrical boxes with padlock once power is turned off.
Water temperature above 120°F (49°C) can cause serious injury. Mixing valve temperature setting should be done by a licensed contractor per local code requirements. To ensure correct temperature control, use the water thermometer at faucet outlet.
WARNING
Improper installation, adjustment, alteration, service or maintenance can cause property damage, personal injury or loss of life. Read and understand the entire Raptor boiler manual before attempting installation, start-up operation, or service. Installation and service must be performed only by an experienced, skilled, and knowledgeable installer or service agency.
Failure to properly install, adjust, service or pipe this Combi may result in improper operation causing damage to the boiler and structure and personal injury. All work should be done in accordance with current manufacturer instructions and local codes.
NOTICE
Hard water conditions may result in scale deposits in Combi components. Hard water will significantly shorten the life of these parts. Water conditioning is recommended for water hardness greater than
200 ppm.
Domestic Hot Water output capacity in gpm changes with varying domestic inlet water
temperatures.
Domestic Hot Water components must comply with SDWA Section 1417, Jan. 4, 2014 version.
Do not use ethylene glycol or chemicals that are not explicitly permitted by the boiler installation instructions. See the “Start-Up and Checkout” section of these instructions for important information on water chemistry requirements.
162
DANGER
Explosion/Scald Hazard.
Pipe relief valve discharge to a location where the potential of severe burns is eliminated.
Do not install relief valve having a setting greater than the MAWP shown on the rating plate.
Do not install a valve in the relief valve discharge line.
Do not install relief valve in a location other than that specified by the factory.
Do not plug the relief valve discharge.
Appendix C - (continued)
IV – Introduction
1. Parts Included: 3 copper pipe assemblies, thermostatic mixing valve, flow switch, and miscellaneous parts bag.
2. Install boiler per installation instructions. Attach supply and return piping at bottom of jacket (See Figure C.1).
3. Install 30psi relief and air vent at top of boiler shown in Figure C.2. Please note there is no top and bottom supply/return connection available on combi 155 boiler, only bottom supply and return piping.
4. Install DHW piping included in miscellaneous parts carton. See pages 165 and 166 for DHW pipe assembly. Correctly pipe domestic side in/out connections using check valve, relief valve, and expansion tank as described in Figure C.2.
5. Complete wiring and system connections. See page 166.
6. Adjust mixing valve. See page 167.
Figure C.1: Combi Piping Assembly Outside of Jacket
163
Appendix C - (continued)
V – Piping Diagram
A.
B.
C.
At least eight pipe diameters upstream of first tee.
No further apart than 12" (~30 cm) or four pipe diameters, whichever is smaller.
At least 18" (~46 cm) of straight pipe for Conventional Air Scoop.
Y-Strainer
(Recommended)
Hydrolic Separator
May Be Substituted
For Tees
Close Nipple
(Locate Header Sensor
As Close As Possible
To Downstream Tee)
To
System
Flow Check
Optional
Full Port
Isoltaion
Valves
Air Separator
& Air Vent
Optional
Full Port
Isoltaion
Valves
To
System
System
Circulator
Fill Valve
Backflow
Preventer
Cold
Water
Line
C
From
System
B
A
Header
Temperature
Sensor
Domestic
Cold Water
In
Domestic
Hot Water
Out
Boiler
Circulator
Flow Check
Optional
Full Port
Isolation
Valves
Relief
Valve
(**)
System
Zone
Valves
Relief
Valve
(*)
A
Drain Valves
Optional Zone Valve
Controlled System
Temperature and Pressure
Gauge (*)
Secondary Unions Not
Required; Optional
Location Shown
Full Port
Valves
Y-Strainer Notes:
- Refer to preceding sections of this manual for additional piping and water
quality requirements.
- Relief valve (supplied by installer) in DHW piping marked (**) is to be
installed as required by local codes.
- Provide supports for relief valve and system piping to minimize load
placed on the Combi piping connections.
- Components marked (*) are supplied with the boiler. All other components
are supplied by installer.
Figure C.2: Domestic and Space Heating Piping Diagram for RPTR155C
Flow
Switch (*) Mixing
Valve (*)
DETAIL A
SCALE 1 : 3
164
CAUTION
Application of excessive heat during sweating to repair piping could damage union gaskets or brazed joints on Combi piping.
It is the installers responsibility to select piping configurations that will provide the proper flow rates through the system.
Appendix C - (continued)
Tools Needed:
• 1/2 inch open-end wrench
• Flat Head screwdriver
• Phillips head screwdriver, Standard and small
• Small flat-head screwdriver
• Pliers
• Adjustable wrench
• Electric drill with extension
VI – General Installation Instructions
All connections in this kit require gaskets (included) and thread sealant (installer supplied).
Pipe assemblies are packed with hand-tight, pre-assembled unions. Remove these unions before re-attaching
them with gaskets at final connections.
VII - Preparation
Connections to gas, electrical power and building heating system water piping should be completed using the instructions and warnings in preceding sections of this manual.
1. Review all local codes to assure installation compliance.
2. Confirm that all electrical, water and gas supplies are shut off at sources.
3. Unpack and identify all parts. Retain all instructions.
IX – DHW Section (on bench)
4. Unpack mixing valve and gather three remaining pipe assemblies. Identify hot water inlet, (H) cold water inlet (C ) and mixed water outlet connections on mixing valve.
(See Figure C.3) Install copper elbow hot water inlet pipe (smallest pipe) to mixing valve. Shortest side should attach to side connection marked “H” on mixing valve. Hand-tighten. Ensure gaskets from kit are properly installed.
Attach side branch of cold water inlet pipe to “C” connection on mixing valve. Hand-tighten.
Figure C.3: DHW Assembly Diagram
WARNING
Technicians must install, a boiler safety relief valve (SRV) per the preceding sections of this manual. These
Combi instructions offer an alternate SRV location. SRV components are supplied with the boiler.
165
Appendix C - (continued)
5. Install short pipe to mix end of mixing valve. Install flow switch to mixed water outlet pipe. Ensure that flow direction arrow points away from mixing valve.
NOTICE
Proper installation of the flow switch is required for the boiler to fire and produce domestic hot water.
6. Attach remaining long, L-shaped mixed water outlet pipe to mixed water outlet connection of mixing valve. Hand- tighten.
X - DHW Section (at boiler)
7. Remove two 3/4" unions from DHW pipe section and add thread sealant. Attach and tighten them to flat plate heat exchanger at bottom of jacket.
8. Square up installation and tighten all unions. Ensure gaskets are properly installed.
9. Install remaining domestic piping per Figure C.2 ensuring that check valve, relief valve, and expansion tank are installed on domestic side per local codes.
XI – Electrical
WARNING
Turn off all power before proceeding.
10. Remove door from boiler. Identify low voltage PCB on right side of compartment.
11. Remove a knockout near “DHW T’Stat” connection.
Install a knockout strain relief.
12. Thread two wire leads from flow switch through strain relief and connect them to either of the two
“DHW T’Stat” terminals. See wiring schematic in
"Wiring Section” of this manual.
CAUTION
Safety relief valve, expansion tank and flow check valves for DHW are not supplied with this Combi.
Consult local codes to determine if required.
XII – System Readiness (Consult preceding sections in this manual for boiler connections)
13. Fill system. Bleed air from main heat exchanger through top, left manual air vent.
14. Connect gas line and condensate line per preceding sections in this manual.
15. Connect near boiler heating system water lines per diagram Figure C.2. Follow general piping instructions in the "System
Piping” Section of this manual.
16. Installing isolation valves and drain valves on DHW inlet and outlet is recommended to permit flat plate heat exchanger to be flushed periodically.
17. Connect to incoming domestic cold water and building domestic hot water systems. Refer to Figure C.2.
166
Appendix C - (continued)
WARNING
To complete service and place boiler back into operation, follow “Start-up and Checkout” Section in this manual.
XIII – Boiler Control Set-up
18. Turn on boiler power
19. From boiler home screen, select “Adjust” and login.
20. Select “Domestic Hot Water” menu.
21. Priority time may be adjusted between 30 and 60 minutes.
DANGER
Water temperature above 120°F (49°C) can cause serious injury. Mixing valve temperature setting should be done by a licensed contractor per local code requirements. To ensure correct temperature control, use the water thermometer at faucet outlet.
XIV – Mixing Valve Set-up
23. Set and operate mixing valve per manufacturer instructions. If instructions are lost, download a new copy from manufacturer’s website (customer.
honeywell.com) before proceeding.
24. Measure water temperature using a thermometer or the thermostrip provided with mixing valve.
25. Loosen hand-wheel screw, lift hand-wheel and turn to the desired temperature as indicated on thermostrip.
26. Re-position hand-wheel and re-tighten screw.
35
167
Appendix C - (continued)
XV – Troubleshooting
Enough Hot
Water Flow?
Yes
No Check to see if hot water flowrate is greater than 0.54 gpm.
Boiler
Running?
No
DHW priority on?
Yes
No In DHW settings, enable priority.
Flow switch installed correctly?
Yes
No
Arrow on flow switch should point in direction of flow.
(from mix valve to sweat connection)
Flow switch wired correctly?
No
Check connections on low voltage PCB.
Check for continuity between flow switch leads (with flow turned on). If no continuity replace flow switch.
XVI – Service, Maintenance and Inspection
• Monthly – Inspect all water and gas lines for leaks. Contact technician for service.
• Annual – Use thermometer to verify proper mixing valve operation.
• Annual –
WARNING
Follow boiler shut down procedure in the preceding Sections of this manual before cleaning.
Flush DHW loop to remove scaling. Vinegar can be used to remove scaling.
• Periodic – Consult mixing valve manual for maintenance instructions.
XVII – Flat Plate Heat Exchanger Replacement
1. Unscrew control panel assembly from front and tilt back ensuring wire harness connections are removed to avoid damaging them. Unscrew top and bottom flat plate heat exchanger connections including bottom fasteners. Loosen
“S” pipe attached to circulator to facilitate remove of flat plate.
2. Pull Flat Plate Heat Exchanger from boiler. Install new heat exchanger in reverse ensuring gaskets are installed. For replacement gaskets, see Section XV 'Repair Parts'.
3. Connect Wire Harness and Re-Install Control Panel ensuring no wires are pinched between panel and front frame.
168
Appendix C - (continued)
XVIII - Domestic Actuator Replacement
1. Switch power supplies OFF. Disconnect electrical leads, carefully noting the position and color of each lead.
2. Please the manual operating level in the manual open position.
3. Remove actuator by depressing locking button and lifting straight up.
4. To Install: Line up motor coupling to slot in shaft of body and fit the head onto the valve body, ensuring it seats correctly.
5. Snap actuator onto body by pressing down.
6. Wire connection to harness. Ensure actuator is set to AUTO mode.
7. Inspect the actuator installation and the valve body to ensure it is operating properly.
169
Appendix D: Special Requirements For Side-Wall Vented Appliances In The
Commonwealth of Massachusetts
170
IMPORTANT
The Commonwealth of Massachusetts requires compliance with regulation 248 CMR 4.00 and 5.00 for installation of side-wall vented gas appliances as follows:
(a) For all side wall horizontally vented gas fueled equipment installed in every dwelling, building or structure used in whole or in part for residential purposes, including those owned or operated by the Commonwealth and where the side wall exhaust vent termination is less than seven (7) ft. above finished grade in the area of the venting, including but not limited to decks and porches, the following requirements shall be satisfied:
1. INSTALLATION OF CARBON MONOXIDE DETECTORS. At the time of installation of the side wall horizontal vented gas fueled equipment, the installing plumber or gas fitter shall observe that a hard wired carbon monoxide detector with an alarm and battery back-up is installed on the floor level where the gas equipment is to be installed.
In addition, the installing plumber or gas fitter shall observe that a battery operated or hard wired carbon monoxide detector with an alarm is installed on each additional level of the dwelling, building or structure served by the side wall horizontal vented gas fueled equipment. It shall be the responsibility of the property owner to secure the services of qualified licensed professionals for the installation of hard wired carbon monoxide detectors.
a. In the event that the side wall horizontally vented gas fueled equipment is installed in a crawl space or an attic, the hard wired carbon monoxide detector with alarm and battery back-up may be installed on the next adjacent floor level.
b. In the event that the requirements of this subdivision can not be met at the time of completion of installation, the owner shall have a period of thirty (30) days to comply with the above requirements; provided, however, that during said thirty (30) day period, a battery operated carbon monoxide detector with an alarm shall be
installed.
2. APPROVED CARBON MONOXIDE DETECTORS. Each carbon monoxide detector as required in accordance with the above provisions shall comply with NFPA 720 and be ANSI/UL 2034 listed and IAS certified.
3. SIGNAGE. A metal or plastic identification plate shall be permanently mounted to the exterior of the building at a minimum height of eight (8) ft. above grade directly in line with the exhaust vent terminal for the horizontally vented gas fueled heating appliance or equipment. The sign shall read, in print size no less than one-half (1/2) inch in size, “GAS VENT DIRECTLY BELOW. KEEP CLEAR OF ALL OBSTRUCTIONS”.
4. INSPECTION. The state or local gas inspector of the side wall horizontally vented gas fueled equipment shall not approve the installation unless, upon inspection, the inspector observes carbon monoxide detectors and signage installed in accordance with the provisions of 248 CMR 5.08(2)(a)1 through 4.
(b) EXEMPTIONS: The following equipment is exempt from 248 CMR 5.08(2)(a)1 through 4:
1. The equipment listed in Chapter 10 entitled “Equipment Not Required To Be Vented” in the most current edition of NFPA 54 as adopted by the Board; and
2. Product Approved side wall horizontally vented gas fueled equipment installed in a room or structure separate from the dwelling, building or structure used in whole or in part for residential purposes.
(c) MANUFACTURER REQUIREMENTS - GAS EQUIPMENT VENTING SYSTEM PROVIDED. When the manufacturer of Product Approved side wall horizontally vented gas equipment provides a venting system design or venting system components with the equipment, the instructions provided by the manufacturer for installation of the equipment and the venting system shall include:
Appendix D - (continued)
1. Detailed instructions for the installation of the venting system design or the venting system components; and
2. A complete parts list for the venting system design or venting system.
(d) MANUFACTURER REQUIREMENTS - GAS EQUIPMENT VENTING SYSTEM NOT PROVIDED. When the manufacturer of a Product Approved side wall horizontally vented gas fueled equipment does not provide the parts for venting the flue gases, but identifies “special venting systems”, the following requirements shall be satisfied by the manufacturer:
1. The referenced “special venting system” instructions shall be included with the appliance or equipment installation instructions; and
2. The “special venting systems” shall be Product Approved by the Board, and the instructions for that system shall include a parts list and detailed installation instructions.
(e) A copy of all installation instructions for all Product Approved side wall horizontally vented gas fueled equipment, all venting instructions, all parts lists for venting instructions, and/or all venting design instructions shall remain with the appliance or equipment at the completion of the installation.
171
172
advertisement
* Your assessment is very important for improving the workof artificial intelligence, which forms the content of this project
Related manuals
advertisement