- Computers & electronics
- Telecom & navigation
- Mobile phones
- Car kits
- Jacobsen
- JHR33001
- Owner's manual
advertisement
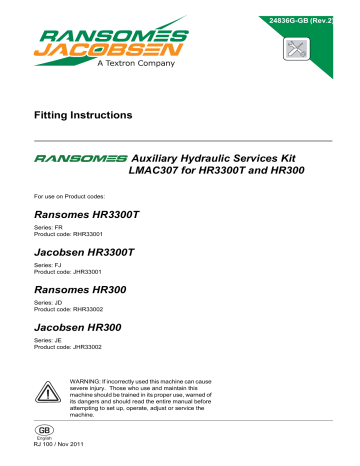
24836G-GB (Rev.2)
Fitting Instructions
Auxiliary Hydraulic Services Kit
LMAC307 for HR3300T and HR300
For use on Product codes:
Ransomes HR3300T
Series: FR
Product code: RHR33001
Jacobsen HR3300T
Series: FJ
Product code: JHR33001
Ransomes HR300
Series: JD
Product code: RHR33002
Jacobsen HR300
Series: JE
Product code: JHR33002
WARNING: If incorrectly used this machine can cause severe injury. Those who use and maintain this machine should be trained in its proper use, warned of its dangers and should read the entire manual before attempting to set up, operate, adjust or service the machine.
RJ 100 / Nov 2011
©
2011, Ransomes Jacobsen Limited. All Rights Reserved
1 CONTENTS
FITTING INSTRUCTIONS - LMAC307
2.3
2.3.2
3.1
3.2
4.1
4.2
4.4
4.5
4.6
GUIDELINES FOR THE DISPOSAL OF SCRAP PRODUCTS .......... 5
END OF SERVICE LIFE ..................................................................... 5
OPERATING INSTRUCTIONS ........................................................... 6
SAFETY SIGNS .................................................................................. 6
PREPARATION .................................................................................. 8
DESCRIPTION ................................................................................... 8
MACHINE PREPARATION ................................................................. 9
INSTALLATION OF VALVE ................................................................ 9
REPLACEMENT OF FUSE ............................................................... 11
PARTS LIST
LMAC307 KIT-AUXILIARY HYDRAULIC SERVICES ....................... 12
GB-3
2 INTRODUCTION
FITTING INSTRUCTIONS - LMAC307
2.1 IMPORTANT
IMPORTANT: This is a precision machine and the service obtained from it depends on the way it is operated and maintained.
This SAFETY AND OPERATORS MANUAL should be regarded as part of the machine. Suppliers of both new and second-hand machines are advised to retain documentary evidence that this manual was provided with the machine.
This machine is designed solely for use in customary grass cutting operations. Use in any other way is considered as contrary to the intended use. Compliance with and strict adherence to the conditions of operation, service and repair as specified by the manufacturer, also constitute essential elements of the intended use.
Before attempting to operate this machine, ALL operators MUST read through this manual and make themselves thoroughly conversant with Safety Instructions, controls, lubrication and maintenance.
Accident prevention regulations, all other generally recognized regulations on safety and occupational medicine, and all road traffic regulations shall be observed at all times.
Any arbitrary modifications carried out on this machine may relieve the manufacturer of liability for any resulting damage or injury.
It is important that during the life of the machine wearing and replaceable parts are disposed of in an environmentally responsible way using the resources available in the country where it is used. There are guidelines in this manual for the eventual decommissioning of the mower once it has no further use. Hardware provided.
A Maximum front axle load in Kg (for machines being driven on the highway)
B Gross weight (mass) in Kg
C Maximum rear axle load in Kg (for machines being driven on the highway)
D Power in Kw
E Date code
F Machine type (Designation)
J Serial number
West Road
Ransomes Europark
Ipswich IP3 9TT
England
A B
C D
E
Kg Kg Kg Kw
F
H
G
J
GB-4
2 INTRODUCTION
FITTING INSTRUCTIONS - LMAC307
2.3
GUIDELINES FOR THE DISPOSAL OF
SCRAP PRODUCTS
2.3.1 DURING SERVICE LIFE
Used oil, oil filters and engine coolant are hazardous materials and should be handled in a safe and environmentally responsible way.
In the event of a fluid leak, contain the spill to prevent it entering the ground or drainage system. Local legislation will dictate how such spills are to treated.
Following the maintenance procedures laid out in this manual will ensure that the impact the machine has on the local environment is controlled.
When it has been identified that a turf care product has no further functional value and requires disposal, the following actions should be taken.
2.3.2 END OF SERVICE LIFE
These guidelines should be used in conjunction with applicable Health, Safety and Environmental legislation and use of approved local facilities for waste disposal and recycling.
• Position the machine in a suitable location for any necessary lifting equipment to be used.
•
•
Use appropriate tools and Personal Protective Equipment (PPE) and take guidance from the technical manuals applicable to the machine.
Remove and store appropriately:
1. Batteries
2. Fuel residue
3. Engine coolant
4. Oils
• Disassemble the structure of the machine referring to the technical manuals where appropriate. Special attention should be made for dealing with ‘stored energy’ within pressurised elements of the machine or tensioned springs.
•
•
•
Any items that still have a useful service life as second hand components or can be re-serviced should be separated and returned to the relevant centre.
Other worn out items should be separated into material groups for recycling and disposal consistent with available facilities.
More common separation types are as follows:
• Steel
• Non ferrous metals
• Aluminium
• Brass
• Copper
•Plastics
•Identifiable
• Recyclable
• Non recyclable
• Not identified
• Rubber
• Electrical & Electronic Components
Items that cannot be separated economically into different material groups should be added to the ‘General waste’ area.
• Do not incinerate waste.
Finally update machinery records to indicate that the machine has been taken out of service and scrapped. Provide this serial number to Jacobsen
Warranty department to close off relevant records.
GB-5
3 SAFETY INSTRUCTIONS
FITTING INSTRUCTIONS - LMAC307
This safety symbol indicates important safety messages in this manual. When you see this symbol, be alert to the possibility of injury, carefully read the message that follows, and inform other operators.
3.1 OPERATING INSTRUCTIONS
• Ensure that the instructions in this book are
• read and fully understood.
No person should be allowed to operate this
• machine unless they are fully acquainted with all the controls and the safety procedures.
Never allow children or people unfamiliar with these instructions to use this machine. Local regulations may restrict the age of the operator.
3.2 SAFETY SIGNS
• It is essential all safety labels are kept legible, if they are missing or illegible they must be replaced. If any part of the machine is replaced and it originally carried a safety label, a new label must be affixed to the replacement part. New safety labels are obtainable from Ransomes dealers.
•
•
•
•
•
•
•
•
MAINTENANCE & CLEANING
Stop the engine and make sure all moving parts are stationary.
Apply brakes and disengage all drives.
Read all the appropriate servicing instructions.
Use only the replacement parts supplied by the original manufacturer.
When adjusting the cutting cylinders take care not to get hands and feet trapped when rotating cylinders.
Make sure that other people are not touching any cutting units, as rotation of one cylinder can cause the others to rotate.
To reduce the fire hazard, keep the engine, silencer and battery compartments free of grass, leaves or excessive grease.
Replace worn or damaged parts for safety.
GB-6
•
•
•
•
•
•
•
•
•
•
•
•
•
•
•
•
•
When working underneath lifted parts or machines, make sure adequate support Is provided.
Do not dismantle the machine without releasing or restraining forces which can cause parts to move suddenly.
Do not alter engine speed above maximum quoted in Engine Specification. Do not change the engine governor settings or overspeed the engine. Operating the engine at excessive speed may increase the hazard of personal injury.
When refuelling, STOP THE ENGINE, DO
NOT SMOKE. Add fuel before starting the engine, never add fuel while the engine is running.
Use a funnel when pouring fuel from a can into the tank.
Do not fill the fuel tank beyond the bottom of the filler neck.
Replace all fuel tank and container caps securely.
Store fuel in containers specifically designed for this purpose.
Refuel outdoors only and do not smoke while refuelling.
If fuel is spilled, do not attempt to start the engine but move the machine away from the area of spillage and avoid creating any source of ignition until fuel vapours have dissipated.
Allow the engine to cool before storing in any enclosure.
Never store the equipment with fuel in the tank inside a building where fumes may reach an open flame or spark.
If the fuel tank has to be drained, this should be done outdoors.
Do not spill fuel onto hot components.
When servicing batteries, DO NOT SMOKE, and keep naked lights away.
Do not place any metal objects across the terminals.
When Pressure Washing the Mower. Turn the engine off and remove the starter key.
If the engine has been running, it should be allowed to cool sufficiently to prevent damage to the block and exhaust manifold. Never force water into any electrical components,
3 SAFETY INSTRUCTIONS
the air cleaner or exhaust muffler as water could enter the engine cylinder and cause damage.
DANGER:
Indicates an imminently hazardous situation which, if not avoided, WILL result in death or serious injury.
WARNING:
Indicates a potentially hazardous situation which, if not avoided, COULD result in death or serious injury.
CAUTION:
Indicates a potentially hazardous situation which, if not avoided, MAY result in minor or moderate injury and property damage. It may also be used to alert against unsafe practices.
IMPORTANT:
Transport speed is for highway use only. Never select transport speed on grass areas or uneven or unsurfaced roads or tracks.
FITTING INSTRUCTIONS - LMAC307
GB-7
4 FITTING INSTRUCTIONS
FITTING INSTRUCTIONS - LMAC307
4.1 PREPARATION
CAUTION: Read the rotary mower’s manual and become familiar with the rotary mower, the controls and proper use of the equipment.
Stay alert for potential hazards and follow all safety precautions. Read all instructions completely and make sure you understand them before proceeding with the assembly
1. Park the rotary mower on a flat and level surface, fully lower the implements to the ground, engage parking brake, stop the engine and remove key from ignition switch.
2. Wait for all movement to stop before making any adjustments or modifications.
3.
Take this opportunity to thoroughly inspect the equipment and perform other maintenance.
The “Right” and “Left”, “Front” and “Rear” of the machine are referenced from the operator’s right and left when seated in the operator’s seat facing the direction of forward travel.
4.2 DESCRIPTION
The following instruction details the process of installing the Auxiliary Hydraulic Services Kit.
4.2.1 HR3300T
This kit activates functions C & D (double Axis) of the control joystick, enabling the ability to ‘slew’ an attachment fitted to the machine in a clockwise or anticlockwise direction (viewed from above), for example when a rotary brush or snow blade is fitted.
C Used to slew the rotary brush or snow blade in a clockwise direction.
D Used to slew the rotary brush or snow blade in an anticlockwise direction.
When the joystick is moved to position C oil flows to port B on the valve, and when the joystick is moved to position D it flows to port A.
Maximum flow available : 9 l/min
Maximum pressure available : 125 bar (1800 psi)
4.2.2 HR300
This kit adds a switch to the instrument panel enabling the ability to ‘slew’ an attachment (i.e. a rotary brush or snow blade) fitted to the machine in a clockwise or anticlockwise direction (viewed from above).
C Used to slew the rotary brush or snow blade in a clockwise direction.
D Used to slew the rotary brush or snow blade in an anticlockwise direction.
When the machine is shipped from the factory the joystick (HR3300T) or switch lever (HR300) is configured to operate in 2 directions (single Axis) A & B, for use with a rotary cutter deck.
A One touch lowers the lift arms.
B Raise the lift arms. (Needs to be held at position
B for lifting arms into transport position).
K Joystick (HR3300T), Switch Lever (HR300)
K
HR3300T
D C
C
When the switch is moved to position C oil flows to port B on the valve, and when the switch is moved to position D it flows to port A.
A
B
K
HR300
D
Maximum flow available : 9 l/min
Maximum pressure available : 125 bar (1800 psi)
A
B
GB-8
4 FITTING INSTRUCTIONS
4.3 VALVE PREPARATION
Assemble the valve, bracket and hydraulic fittings as shown on the diagram in the parts list section.
Leave the hydraulic fittings loose to allow for adjustment once the assembly is on the machine. Do not insert the screws for attaching the bracket to the operators platform at this stage.
4.4 MACHINE PREPARATION
1.
Remove any attachments (for example a deck) from the front of the machine to provide access to the underside of the operators platform.
2.
Remove the hydraulic hose connected to the
‘SP’ port on the Lift Valve and feed it back under the operators platform (See Fig. 1).
4.5 INSTALLATION OF VALVE
1.
Attach the hose removed from the Lift Valve to port ‘P’ on the new valve (see the parts list section for location of port ‘P’).
FOR HR3300T
2a. Locate the two Ø 7 holes in the stiffening ribs underneath the operators platform. There should be one hole in each (See Fig. 2a).
Note these holes are not available on machines with serial numbers FR000322 & FY000312 and below and therefore will need to be drilled in the position shown opposite (See Fig. 3).
FOR HR300
2b. Locate the four Ø 9 holes in the stiffening ribs underneath the operators platform. There should be two holes in each (See Fig. 2b).
FITTING INSTRUCTIONS - LMAC307
Fig. 1
Fig. 3
SP
Fig. 2a
Fig. 2b
GB-9
4 FITTING INSTRUCTIONS
FOR HR3300T
3a. Attach the valve and bracket to the stiffening ribs in the orientation shown in Fig. 4a using the two M6 x 25 screws and the M6 washers provided in the kit.
FOR HR300
3b. Attach the valve and bracket to the stiffening ribs in the orientation shown in Fig. 4b using the threaded spacers, M8 x 20 screws and the M8 washers provided in the kit.
Position the hydraulic hoses as necessary and tighten all fittings. Note that it will be necessary to curl the hose that runs from the Lift Valve to the new valve under the operator platform.
4.
Connect the jumper harness in the kit to the solenoid connections on the valve and to the relevant connection on the harness. The connector can be found on the harness in between the Cutter & Brake Valve and the Lift
Valve (See Fig. 5).
FITTING INSTRUCTIONS - LMAC307
Fig. 4a
CUTTER & BRAKE VALVE
Fig. 4b
LIFT VALVE
CONNECTOR
Fig. 5
GB-10
4 FITTING INSTRUCTIONS
4.6 REPLACEMENT OF FUSE
NOTE: this step is only necessary on HR3300T machines with serial numbers of FR000322/FY000312 and below.
1.
Unscrew and remove the four M6x16 Pan.Hd screws plus hardware securing the Instrument
Panel Cover to the Instrument Panel and lift the Cover off. Retain all hardware (See Fig 6).
2.
Locate the Relay/Fuse Mounting Panel.
3.
Replace the 2A Fuse at position 7 with the 5A fuse included in the kit (See Fig. 7).
4.
Replace the Instrument Panel Cover and fasten in place with the M6x16 Pan.Hd screws plus hardware removed in Step 1.
FITTING INSTRUCTIONS - LMAC307
Fig. 6
Fig. 7
GB-11
PARTS MANUAL
LMAC307 KIT-AUXILIARY HYDRAULIC SERVICES
Illustration Number: LMAC307-1
Parts-12
PARTS MANUAL
LMAC307 KIT-AUXILIARY HYDRAULIC SERVICES
ITEM
*
16
17
18
19
20
13
14
15
*
9
10
11
12
6
7
8
*
*
*
*
5
*
*
*
*
1
2
3
4
PART NO.
DESCRIPTION
002591040
4152478
4166700
4173283
4171467
4171468
4171469
4173700
4173701
4173703
4171464
4176920
4177121
4177184
4177201
002218065
1/4" BSP Dowty Seal
Wldmt-Platform
Hose Assembly
Valve
• Solenoid Valve
•• Seal Kit (Solenoid Valve)
• Coil
• Check Valve
•• Seal Kit (Check Valve)
• Relief Valve
•• Seal Kit (Relief Valve)
Hose-Lift Valve 'SP' to Aux Valve 'P'
Harness-Jumper, Aux Hyd Valve
Assembly-Aux Hyd Valve Bracket
Ftg-M/M 1/4 BSPP X 9/16 SAE
• O-Ring
4177202
450009
450172
450377
QRC-1/4"BSPP Female
Bolt-Hex M6 X 70
Scrw-Hex M6 X 25
Nut-Hex M6 Nyloc
450389
450410
Wshr-M6 X 12.5 X 1.8
Wshr-Slw M6
W158006-01 Ftg-M/M 11/16 ORS X 9/16 SAE
158061-01 • O-Ring
002218065
008233156
4211920
450191
450411
4252554
• O-Ring
Fuse-5 Amp
Spacer-Hex M8 x 40
Scrw-Hex M8 x 20
Lockwshr-M8 x 12.75 x 2
Spacer Plate
QTY.
4
8
1
1
8
1
2
1
6
2
2
2
2
2
2
1
1
1
A/R
1
A/R
1
1
A/R
2
1
1
1
2
1
Not included in Kit LMAC307
Not Illustrated
9/16" SAE
11/16" ORFS
9/16" SAE
Not Illustrated
Parts-13
PARTS MANUAL
LMAC307 KIT-AUXILIARY HYDRAULIC SERVICES - FOR HR300 ONLY
Illustration Number: LMAC307-2
Parts-14
PARTS MANUAL
LMAC307 KIT-AUXILIARY HYDRAULIC SERVICES - FOR HR300 ONLY
ITEM
1
2
PART NO.
4262593
4263052
DESCRIPTION
Switch
Decal-Slew Control
QTY.
1
1
Parts-15
Ransomes Jacobsen Limited
West Road, Ransomes Europark, Ipswich,
England, IP3 9TT
English Company Registration No. 1070731 www.ransomesjacobsen.com
Jacobsen, A Textron Company
11108 Quality Drive, Charlotte,
NC 28273, USA
www.Jacobsen.com
advertisement
Related manuals
advertisement