HTP EFT-399PU Use and Care Manual
Add to my manuals
8 Pages
HTP EFT-399PU is a gas-fired boiler designed to provide efficient and reliable heating for residential and commercial applications. With a maximum heating capacity of 399,000 BTU, it is suitable for large spaces and can be used for both hydronic and space heating systems. The boiler features a fully modulating burner that automatically adjusts the heat output based on demand, maximizing energy efficiency and reducing operating costs. It also boasts a compact design and quiet operation, making it an ideal choice for installation in tight spaces or near living areas.
advertisement
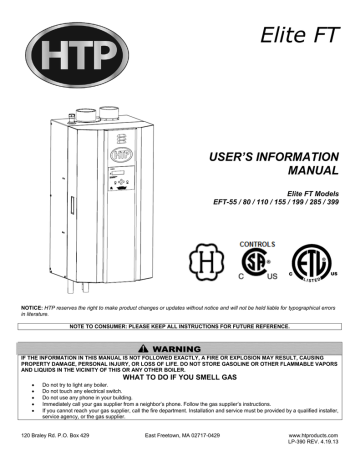
Elite FT
USER ’S INFORMATION
MANUAL
Elite FT Models
EFT-55 / 80 / 110 / 155 / 199 / 285 / 399
NOTICE: HTP reserves the right to make product changes or updates without notice and will not be held liable for typographical errors in literature.
NOTE TO CONSUMER: PLEASE KEEP ALL INSTRUCTIONS FOR FUTURE REFERENCE.
IF THE INFORMATION IN THIS MANUAL IS NOT FOLLOWED EXACTLY, A FIRE OR EXPLOSION MAY RESULT, CAUSING
PROPERTY DAMAGE, PERSONAL INJURY, OR LOSS OF LIFE. DO NOT STORE GASOLINE OR OTHER FLAMMABLE VAPORS
AND LIQUIDS IN THE VICINITY OF THIS OR ANY OTHER BOILER.
Do not try to light any boiler.
Do not touch any electrical switch.
WHAT TO DO IF YOU SMELL GAS
Do not use any phone in your building.
Immediately call your gas supplier from a neighbor’s phone. Follow the gas supplier’s instructions.
If you cannot reach your gas supplier, call the fire department. Installation and service must be provided by a qualified installer, service agency, or the gas supplier.
120 Braley Rd. P.O. Box 429 East Freetown, MA 02717-0429 www.htproducts.com
LP-390 REV. 4.19.13
2
3
The following defined terms are used throughout this manual to bring attention to the presence of hazards of various risk
levels, or to important product information.
DANGER indicates an imminently hazardous situation which, if not avoided, will result in death or serious injury.
WARNING indicates a potentially hazardous situation which, if not avoided, could result in death or serious injury.
CAUTION indicates a potentially hazardous situation which, if not avoided, may result in minor or moderate injury.
CAUTION used without the safety alert symbol indicates a potentially hazardous situation which, if not avoided, may result in property damage.
NOTICE
NOTICE is used to address practices not related to personal injury.
4
TABLE OF CONTENTS
PART 1 – PRODUCT AND SAFETY INFORMATION
USER
– Have this boiler serviced/inspected by a qualified service technician annually.
FAILURE TO ADHERE TO THE GUIDELINES IN THIS MANUAL CAN RESULT IN SUBSTANTIAL PROPERTY DAMAGE, SEVERE
PERSONAL INJURY, OR DEATH.
The combustion chamber insulation in this product contains ceramic fiber material. Ceramic fibers can be converted to cristobalite in very high temperature applications. The International Agency for Research on Cancer (IARC) has concluded, “Crystalline silica inhaled in the form of quartz or cristobalite from occupational sources is carcinogenic to humans (Group 1).” DO NOT, UNDER ANY
CIRCUMSTANCES, OPEN THE COMBUSTION CHAMBER OF THIS BOILER! The combustion chamber of this boiler may be opened by a qualified service technician ONLY. FAILURE TO FOLLOW THESE INSTRUCTIONS CAN RESULT IN SUBSTANTIAL
PROPERTY DAMAGE, SEVERE PERSONAL INJURY, OR DEATH.
A. BOILER OPERATION
Do not block flow of the boiler exhaust vent or intake pipe.
Should overheating occur, or gas supply fail to shut off, do not turn off or disconnect electrical supply to the circulator. Instead, shut off the gas supply at a location external to the boiler following the instructions on page 2.
Do not use this boiler if any part has been under water. Immediately call a qualified service technician to inspect the boiler and replace any part of the control system or gas control that has been under water.
B. PRIMARY WATER
Do not attempt to clean the heating system. Call a qualified service technician for service.
If you notice any leaks, immediately call a qualified service technician. Leaks in boiler or piping must be repaired at once.
C. FREEZE PROTECTION FLUIDS
Hydronic systems that use glycol as heat transfer fluid must be serviced periodically. Glycol can break down over time, become acidic, and attack gaskets and seals in boilers. This can result in property damage, severe personal injury, or death.
Each glycol manufacturer has different recommendations for testing and replacement. Do not test glycol quality yourself. Have your qualified service technician check glycol quality during annual servicing. If you are unsure when your glycol was last tested, call a qualified service technician to test and replace glycol, if necessary.
5
PART 2 – COMBUSTION AIR – CONTAMINATION PREVENTION
Do not operate the boiler if its combustion air intake is located in or near one of the areas or in the vicinity of products listed in Table 1.
These areas will always contain hazardous contaminates that can form strong acids while passing through the burner and vent system.
These acids will corrode the boiler ’s heat exchanger, burner components and vent system, resulting in flue gas spillage and/or water leakage, possible substantial property damage, severe personal injury, or death. If the boiler combustion air intake is located in any area likely to cause or contain contamination, or if products which would contaminate the air cannot be removed, the intake must be repiped and terminated to another location.
DO NOT re-pipe ventilation system on your own. Call a qualified service provider for assistance.
PRODUCTS TO AVOID
Spray cans containing fluorocarbons
Permanent wave solutions
Chlorinated waxes/cleaners
Chlorine-based swimming pool chemicals
AREAS LIKELY TO HAVE CONTAMINANTS
Dry cleaning/laundry areas and establishments
Swimming pools
Metal fabrication plants
Beauty shops
Calcium chloride used for thawing
Sodium chloride used for water softening
Refrigerant leaks
Paint or varnish removers
Hydrochloric or Muriatic acid
Cements and glues
Antistatic fabric softeners used in clothes dryers
Refrigeration repair shops
Photo processing plants
Auto body shops
Plastic manufacturing plants
Furniture refinishing areas and establishments
New building construction
Remodeling areas
Chlorine-type bleaches, laundry detergents, and cleaning solvents Garages and workshops
Adhesives used to fasten building products
Table 1
PART 3 – MAINTENANCE SCHEDULE
A. SERVICE TECHNICIAN
The following maintenance should be performed by a qualified service technician annually:
General
Attend to any reported problems.
Inspect the interior of the boiler jacket area; clean and vacuum if necessary.
Clean the condensate trap and fill with fresh water.
If applicable, check the condensate neutralizer and ensure it is full of condensate neutralizing marble chips.
Check for leaks: Water, gas, flue and condensate.
Verify exhaust vent and intake piping are in good condition and sealed tight.
Check exhaust vent and intake pipe bracing. Ensure bracing is undamaged and in good condition.
Check boiler water pressure, piping and expansion tank.
Check control settings.
Check ignition electrode. Sand off any white oxide. Clean and reposition.
Check ignition and ground wiring.
Check all control wiring and connections.
Check burner flame pattern (stable and uniform).
Additional Items if Combustion or Performance is Poor
Clean heat exchanger and flue ways.
Remove burner assembly and clean burner head using compressed air only.
Once the maintenance items are completed, the service technician should review service with the owner.
B. OWNER MAINTENANCE
Periodically
Check area around the boiler.
6
Check and remove any blockage from the outdoor exhaust vent and intake pipe terminations. DO NOT perform this maintenance if exhaust vent and intake pipe terminations are in difficult to reach locations.
Check the temperature/pressure gauge.
Monthly
Check exhaust vent and intake piping.
Check exhaust vent and intake pipe bracing. Ensure bracing is undamaged and in good condition.
Check the pressure relief valve.
Check the condensate drain system.
If applicable, check the condensate neutralizer and ensure it is full of condensate neutralizing marble chips.
Every 6 Months
Check boiler piping and gas supply piping for corrosion or signs of potential leakage.
PART 4 – MAINTENANCE PROCEDURES
The boiler must be inspected and serviced annually, preferably at the start of the heating season, by a qualified service technician. In addition, the maintenance and care of the boiler as outlined in this manual must be performed by the user/owner to assure maximum efficiency and reliability. Follow the maintenance procedures given throughout this manual. Failure to perform the service and maintenance or follow the directions in this manual could damage the boiler or system components, resulting in substantial property damage, severe personal injury, or death.
A. DAILY MAINTENANCE
Check the Surrounding Area
from the area surrounding the boiler and the vicinity of the combustion air intake. If contaminates are found:
Remove products immediately from area.
If contaminates have been there for an extended period, call a qualified service technician to inspect the boiler for possible damage from acid corrosion.
If products cannot be removed, immediately call a qualified service technician to re-pipe the combustion air intake piping away from the contaminated areas.
Combustible/Flammable Materials
Do not store combustible materials, gasoline, or other flammable vapors or liquids near the boiler. If found, remove these materials immediately.
Air Contaminates
If allowed to contaminate combustion air, products containing chlorine or fluorine will produce acidic condensate that will cause
If any of these contaminates are in the room where the boiler is located, or combustion air is taken from one of the areas listed, the contaminates must be removed immediately or the intake pipe must be relocated to another area.
Check Exhaust Vent and Intake Pipe Terminations
Verify that the boiler exhaust vent and intake pipe terminations are clean and free of obstructions. Remove any debris on the exhaust vent or intake pipe openings. If removing the debris does not allow the boiler to operate correctly, contact your qualified service technician to inspect the boiler and the vent system.
Check Temperature Display and Pressure Gauge
Ensure the pressure reading on the gauge does not exceed 25 psig. Higher pressure readings may indicate a problem with the expansion tank.
Ensure the temperature on the LED display panel does not exceed 180 o
F. Higher temperature readings may indicate a problem with the thermostat operating controls.
Contact a qualified service technician if problem persists.
B. MONTHLY MAINTENANCE
Check Exhaust Vent and Intake Piping
Visually inspect the exhaust vent for any signs of blockage, leakage, or deterioration of the piping. Inspect the exhaust vent bracing.
Ensure bracing is undamaged and in good condition. Notify a qualified service technician immediately if any problems are found.
7
Failure to inspect the venting system and have it repaired by a qualified service technician can result in vent system failure, causing severe personal injury or death.
Visually inspect the intake piping for any signs of blockage. Inspect the entire length of the intake pipe to ensure piping is intact and all joints are properly sealed. Inspect the intake pipe bracing. Ensure bracing is undamaged and in good condition. Notify a qualified service technician if any problems are found.
Check Pressure Relief Valve
Visually inspect the primary pressure relief valve and discharge pipe for signs of weeping or leakage.
If the pressure relief valve often weeps, the expansion tank may not be operating properly. Immediately contact a qualified service technician to inspect the boiler and system.
Check Exhaust Vent Condensate Drain System
While the boiler is running, check the discharge end of the condensate drain tubing. Ensure no flue gas is leaking from the condensate drain tubing by holding your fingers near the opening.
If you notice flue gas leaking from the opening, this indicates a dry condensate drain trap. If problem persists, contact a qualified service technician to inspect the boiler and condensate line and refill the condensate trap.
If applicable, check the condensate neutralizer and ensure it is full of condensate neutralizing marble chips.
C. 6 MONTH MAINTENANCE
Check Primary and Gas Piping
Remove the boiler cover and perform a gas leak inspection following Operating Instructions, page 2, this manual. If gas odor or leak is detected, follow procedures on page 2. Call a qualified service technician.
Visually inspect for leaks around the internal boiler water connections and around the heat exchanger. Visually inspect the external system piping, circulators, and system components and fittings. Immediately call a qualified service technician to repair any leaks.
Have leaks fixed at once by a qualified service technician. Failure to comply could result in substantial property damage, severe personal injury, or death.
Operate Pressure Relief Valve
Before proceeding, verify that the relief valve outlet has been piped to a safe place of discharge, avoiding any possibility of scalding from hot water.
To avoid water damage or scalding due to relief valve operation, a discharge line must be connected to the valve outlet and directed to a safe place of disposal. This discharge line must be installed by a qualified service technician or heating/plumbing installer in accordance with the boiler installation manual. The discharge line must be terminated so as to eliminate possibility of severe burns or property damage should the valve discharge.
Read the temperature and pressure gauge to ensure the system is pressurized. Minimum is 10 psi. Maximum is 25 psi. Lift the relief valve top lever slightly, allowing water to relieve through the valve and discharge piping.
If water flows freely, release the lever and allow the valve to seat. Watch the end of the relief valve discharge pipe to ensure that the valve does not weep after the line has had time to drain. If the valve weeps, lift the lever again to attempt to clean the valve seat. If the valve does not properly seat and continues to weep, contact a qualified service technician to inspect the valve and system.
If water does not flow from the valve when you completely lift the lever, the valve or discharge line may be blocked.
Immediately shut the boiler down per instructions on page 2 and call a qualified service technician to inspect the valve and system.
MAINTENANCE NOTES
8
LP-390 Rev. 4.19.13
advertisement
* Your assessment is very important for improving the workof artificial intelligence, which forms the content of this project
Related manuals
advertisement
Table of contents
- 4 – PRODUCT AND SAFETY INFORMATION
- 4 A. BOILER OPERATION
- 4 B. PRIMARY WATER
- 4 C. FREEZE PROTECTION FLUIDS
- 5 – COMBUSTION AIR – CONTAMINATION PREVENTION
- 5 – MAINTENANCE SCHEDULE
- 5 A. SERVICE TECHNICIAN
- 5 B. OWNER MAINTENANCE
- 6 – MAINTENANCE PROCEDURES
- 6 A. DAILY MAINTENANCE
- 6 B. MONTHLY MAINTENANCE
- 7 C. 6 MONTH MAINTENANCE