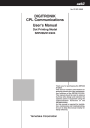
advertisement
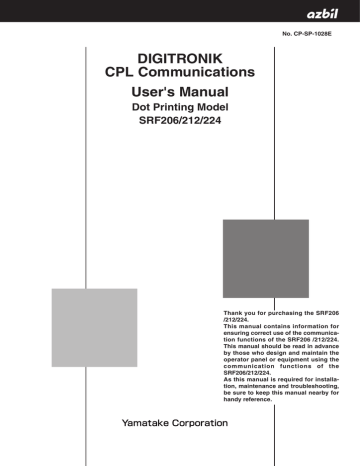
DIGITRONIK
CPL Communications
User's Manual
Dot Printing Model
SRF206/212/224
No. CP-SP-1028E
Thank you for purchasing the SRF206
/212/224.
This manual contains information for ensuring correct use of the communication functions of the SRF206 /212/224.
This manual should be read in advance by those who design and maintain the operator panel or equipment using the communication functions of the
SRF206/212/224.
As this manual is required for installation, maintenance and troubleshooting, be sure to keep this manual nearby for handy reference.
RESTRICTIONS ON USE
This product has been designed, developed and manufactured for general-purpose application in machinery and equipment. Accordingly, when used in the applications outlined below, special care should be taken to implement a fail-safe and/or redundant design concept as well as a periodic maintenance program.
• Safety devices for plant worker protection
• Start/stop control devices for transportation and material handling machines
• Aeronautical/aerospace machines
• Control devices for nuclear reactors
Never use this product in applications where human safety may be put at risk.
IMPORTANT
Writing to EEPROM address is guaranteed only up to 100,000 times.
NOTICE
Be sure that the user receives this manual before the product is used.
Copying or duplicating this user’s manual in part or in whole is forbidden. The information and specifications in this manual are subject to change without notice.
Considerable effort has been made to ensure that this manual is free from inaccuracies and omissions. If you should find an error or omission, please contact Yamatake Corporation.
In no event is Yamatake Corporation liable to anyone for any indirect, special or consequential damages as a result of using this product.
©1998 Yamatake Corporation ALL RIGHTS RESERVED
The DIGITRONIK
TM is a trademark of Yamatake Corporation in Japan.
SAFETY PRECAUTIONS
■ About Icons
The safety precautions described in this manual are indicated by various icons.
Please be sure you read and understand the icons and their meanings described below before reading the rest of the manual.
Safety precautions are intended to ensure the safe and correct use of this product, to prevent injury to the operator and others, and to prevent damage to property. Be sure to observe these safety precautions.
WARNING
CAUTION
Warnings are indicated when mishandling this product might result in death or serious injury.
Cautions are indicated when mishandling this product might result in minor injury to the user, or only physical damage to the product.
■ Examples
Use caution when handling the product.
The indicated action is prohibited.
Be sure to follow the indicated instructions.
i
WARNING
Ground the FG (Frame Ground) terminal to a terminal resistance of
100Ω or less before you connect the SRF206/212/224 to the input circuit
or control circuit.
Failure to do so might cause electric shock or fire.
Be sure to turn the source power OFF before wiring the
SRF206/212/224.
Failure to do so might cause electric shock.
Do not touch power terminals and other electrically charged parts.
Doing so might cause electric shock.
Do not disassemble the SRF206/212/224.
Doing so might cause electric shock or faulty operation.
CAUTION
Wire the SRF206/212/224 according to predetermined standards. Also wire the SRF206/212/224 using specified power leads according to recognized installation methods.
Failure to do might cause electric shock, fire or faulty operation.
Use the SRF206/212/224 within the operating ranges recommended in the specifications (temperature, humidity, voltage, vibration, shock, atmosphere, etc.). Failure to do so might cause faulty operation.
Do not allow lead scraps, chips or water to enter the SRF206/212/224.
Doing so might cause fire or faulty operation.
Tighten the terminal screws to the specification torque.
Incomplete tightening might cause electric shock or fire.
Do not use unused terminals on the SRF206/212/224 as relay terminals.
Doing so might cause electric shock or fire.
We recommend attaching the terminal covers after wiring the
SRF206/212/224.
Failure to do so might cause electric shock.
ii
The Role of This Manual
In all, 2 manuals have been prepared for the SRF206/212/224. Read the manual according to your specific requirements.
The following lists all the manuals that accompany the SRF206/212/224 and gives a brief outline of the manual:
If you do not have the required manual, contact Yamatake Corporation or your dealer.
Dot Printing Model Smart Recorder SRF206/212/224
Installation/Operation Manual No.CP-SP-1027E
This manual is required reading for those who use the SRF206/212/224, those who design hardware for integrating the SRF206/212/224 into operator control panels, those who carry out maintenance, and those who operate instruments in which the SRF206/212/224 is integrated. It outlines the hardware configuration, product features and the other products used in combination with the SRF206/212/224.
It also describes how to install and wire the SRF206/212/224 for integrating into instruments, method of operation, maintenance and inspection, troubleshooting, and hardware specifications.
DIGITRONIK CPL Communications Dot Printing Model
SRF206/212/224 Manual No.CP-SP-1028E
This manual.
This manual is required reading for those who use the CPL communication functions of the SRF206/212/224.
It briefly describes CPL communications, how to wire the SRF206/212/224, communication procedures, communication data for the SRF206/212/224, troubleshooting and communication specifications.
iii
Organization of This User's Manual
This manual is organized as follows:
Chapter 1. COMMUNICATION FUNCTIONS
This chapter lists communication functions and model numbers of the
SRF206/212/224.
Chapter 2. WIRING
This chapter describes RS-232C and RS-485 wiring methods to make a communication link between the
SRF206/212/224 and other instruments.
Chapter 3. SETTINGS
This chapter describes
SRF206/212/224 communication settings.
Chapter 4. COMMUNICATION PROCEDURE
This chapter describes communication procedures, message configuration, data read/write and signal timing operations.
Chapter 5. COMMUNICATION DATA TABLE
This chapter provides various data tables for communications on the
SRF206/212/224
.
Chapter 6. MAINTENANCE AND TROUBLESHOOTING
This chapter describes checkpoints to diagnose failures in
SRF206/212/224 communications.
Chapter 7. SPECIFICATIONS
This chapter lists communication specifications for the
SRF206/212/224
.
Appendix
The appendix provides code tables and network configurations using the
CMC10L
RS-232C/RS485 converter.
iv
Contents
SAFETY PRECAUTIONS
Unpacking
The Role of This Manual
Organization of This User's Manual
Conventions Used in This Manual
Chapter 1.
COMMUNICATION FUNCTIONS
Chapter 2.
WIRING
2-1 RS-232C Connection
• • • • • • • • • • • • • • • • • • • • • • • • • • • • • • • • • • • • • • • • • • • • • • • • • • • • • • •
2-1
2-2 RS-485 Connection
• • • • • • • • • • • • • • • • • • • • • • • • • • • • • • • • • • • • • • • • • • • • • • • • • • • • • • • •
2-3
■
Connection with 5-wire system
• • • • • • • • • • • • • • • • • • • • • • • • • • • • • • • • • • • • • • • •
2-3
■
3-wire system used together
• • • • • • • • • • • • • • • • • • • • • • • • • • • • • • • • • • • • • • • • • • •
2-4
2-3 RS-232C Models
• • • • • • • • • • • • • • • • • • • • • • • • • • • • • • • • • • • • • • • • • • • • • • • • • • • • • • • • • • •
2-5
2-4 RS-485 Models
• • • • • • • • • • • • • • • • • • • • • • • • • • • • • • • • • • • • • • • • • • • • • • • • • • • • • • • • • • • • •
2-6
Chapter 3.
SETTINGS
3-1 Communication Setup Items
• • • • • • • • • • • • • • • • • • • • • • • • • • • • • • • • • • • • • • • • • • • • • • •
3-1
■
System Setup
• • • • • • • • • • • • • • • • • • • • • • • • • • • • • • • • • • • • • • • • • • • • • • • • • • • • • • • • • •
3-1
3-2 Initial Setup
• • • • • • • • • • • • • • • • • • • • • • • • • • • • • • • • • • • • • • • • • • • • • • • • • • • • • • • • • • • • • • • •
3-2
■
Station Address
• • • • • • • • • • • • • • • • • • • • • • • • • • • • • • • • • • • • • • • • • • • • • • • • • • • • • • • •
3-2
■
Transmission Rate and Data Format
• • • • • • • • • • • • • • • • • • • • • • • • • • • • • • • • • • •
3-2
Chapter 4.
COMMUNICATION PROCEDURE
4-1 Outline of Communication Procedure and Messages
• • • • • • • • • • • • • • • • • • • • • •
4-1
■
Communication Procedure
• • • • • • • • • • • • • • • • • • • • • • • • • • • • • • • • • • • • • • • • • • • •
4-1
■
Message Configuration
• • • • • • • • • • • • • • • • • • • • • • • • • • • • • • • • • • • • • • • • • • • • • • • •
4-1
■
Examples
• • • • • • • • • • • • • • • • • • • • • • • • • • • • • • • • • • • • • • • • • • • • • • • • • • • • • • • • • • • • • •
4-2
■
Data Address Concept
• • • • • • • • • • • • • • • • • • • • • • • • • • • • • • • • • • • • • • • • • • • • • • • • •
4-2
4-2 Data Link Layer
• • • • • • • • • • • • • • • • • • • • • • • • • • • • • • • • • • • • • • • • • • • • • • • • • • • • • • • • • • • •
4-3
■
Description
• • • • • • • • • • • • • • • • • • • • • • • • • • • • • • • • • • • • • • • • • • • • • • • • • • • • • • • • • • • • •
4-3
4-3 Application Layer
• • • • • • • • • • • • • • • • • • • • • • • • • • • • • • • • • • • • • • • • • • • • • • • • • • • • • • • • • •
4-6
■
Outline
• • • • • • • • • • • • • • • • • • • • • • • • • • • • • • • • • • • • • • • • • • • • • • • • • • • • • • • • • • • • • • • • •
4-6
4-4 Data Read
• • • • • • • • • • • • • • • • • • • • • • • • • • • • • • • • • • • • • • • • • • • • • • • • • • • • • • • • • • • • • • • • • •
4-7
■
Description of Read Instruction
• • • • • • • • • • • • • • • • • • • • • • • • • • • • • • • • • • • • • • • •
4-7
■
Read Response
• • • • • • • • • • • • • • • • • • • • • • • • • • • • • • • • • • • • • • • • • • • • • • • • • • • • • • • •
4-8
■
Decimal Numeric Expression (numeric data)
• • • • • • • • • • • • • • • • • • • • • • • • • •
4-9
4-5 Data Write
• • • • • • • • • • • • • • • • • • • • • • • • • • • • • • • • • • • • • • • • • • • • • • • • • • • • • • • • • • • • • • • •
4-10
■
Description of Write Instruction
• • • • • • • • • • • • • • • • • • • • • • • • • • • • • • • • • • • • • •
4-10
■
Write Response
• • • • • • • • • • • • • • • • • • • • • • • • • • • • • • • • • • • • • • • • • • • • • • • • • • • • • • •
4-11
v
4-6 Termination Code Table
• • • • • • • • • • • • • • • • • • • • • • • • • • • • • • • • • • • • • • • • • • • • • • • • • •
4-12
■
Normal and Abnormal Termination
• • • • • • • • • • • • • • • • • • • • • • • • • • • • • • • • • • •
4-12
4-7 Timing Specifications
• • • • • • • • • • • • • • • • • • • • • • • • • • • • • • • • • • • • • • • • • • • • • • • • • • • •
4-13
■
Timing Specifications for Instruction and Response Messages
• • • • • •
4-13
■
RS-485 Driver Control Timing Specifications
• • • • • • • • • • • • • • • • • • • • • • • • •
4-13
Chapter 5.
COMMUNICATION DATA TABLE
5-1 Basic Communication Data Processing
• • • • • • • • • • • • • • • • • • • • • • • • • • • • • • • • • • •
5-1
■
Communication Data Types and Formats
• • • • • • • • • • • • • • • • • • • • • • • • • • • • • •
5-1
■
Communication Data Storage Memory
• • • • • • • • • • • • • • • • • • • • • • • • • • • • • • • • •
5-1
■
Data Address
• • • • • • • • • • • • • • • • • • • • • • • • • • • • • • • • • • • • • • • • • • • • • • • • • • • • • • • • • •
5-2
■
Data Read/Write Count
• • • • • • • • • • • • • • • • • • • • • • • • • • • • • • • • • • • • • • • • • • • • • • • • •
5-2
■
Data Unit and Decimal Point Position
• • • • • • • • • • • • • • • • • • • • • • • • • • • • • • • • • •
5-2
5-2 Communication Data Table
• • • • • • • • • • • • • • • • • • • • • • • • • • • • • • • • • • • • • • • • • • • • • • • •
5-3
■
Control Data
• • • • • • • • • • • • • • • • • • • • • • • • • • • • • • • • • • • • • • • • • • • • • • • • • • • • • • • • • • •
5-3
■
Process Data Area
• • • • • • • • • • • • • • • • • • • • • • • • • • • • • • • • • • • • • • • • • • • • • • • • • • • • •
5-6
■
Event Data
• • • • • • • • • • • • • • • • • • • • • • • • • • • • • • • • • • • • • • • • • • • • • • • • • • • • • • • • • • • • •
5-7
■
Digital I/O Area (data area)
• • • • • • • • • • • • • • • • • • • • • • • • • • • • • • • • • • • • • • • • • • • •
5-8
■
Common Data Area (common setup items)
• • • • • • • • • • • • • • • • • • • • • • • • • •
5-10
■
Common Data Area (schedule demand printing)
• • • • • • • • • • • • • • • • • • • •
5-12
■
Common Data Area (messages)
• • • • • • • • • • • • • • • • • • • • • • • • • • • • • • • • • • • • •
5-13
■
Common Data Area (digital input)
• • • • • • • • • • • • • • • • • • • • • • • • • • • • • • • • • • •
5-14
■
Common Data Area (digital output)
• • • • • • • • • • • • • • • • • • • • • • • • • • • • • • • • • •
5-15
■
Common Data Area (user functions)
• • • • • • • • • • • • • • • • • • • • • • • • • • • • • • • • •
5-16
■
Common Data Area (copy)
• • • • • • • • • • • • • • • • • • • • • • • • • • • • • • • • • • • • • • • • • • •
5-17
■
Common Data Area (extended setup)
• • • • • • • • • • • • • • • • • • • • • • • • • • • • • • • •
5-17
■
Segment Table Area
• • • • • • • • • • • • • • • • • • • • • • • • • • • • • • • • • • • • • • • • • • • • • • • • • •
5-18
■
Channel-independent (range)
• • • • • • • • • • • • • • • • • • • • • • • • • • • • • • • • • • • • • • • •
5-21
■
Channel-independent (calculation)
• • • • • • • • • • • • • • • • • • • • • • • • • • • • • • • • • •
5-23
■
Channel-independent (scale)
• • • • • • • • • • • • • • • • • • • • • • • • • • • • • • • • • • • • • • • •
5-24
■
Channel-independent (event)
• • • • • • • • • • • • • • • • • • • • • • • • • • • • • • • • • • • • • • • •
5-25
■
Communication Data Area
• • • • • • • • • • • • • • • • • • • • • • • • • • • • • • • • • • • • • • • • • • • •
5-26
■
Bitmap Data
• • • • • • • • • • • • • • • • • • • • • • • • • • • • • • • • • • • • • • • • • • • • • • • • • • • • • • • • • • •
5-27
■
Range Code Tables
• • • • • • • • • • • • • • • • • • • • • • • • • • • • • • • • • • • • • • • • • • • • • • • • • • •
5-30
Chapter 6.
MAINTENANCE AND TROUBLESHOOTING
■
Check Items in Case Communication is Disabled
• • • • • • • • • • • • • • • • • • • • • •
6-1
Chapter 7.
SPECIFICATIONS
■
RS-232C Specifications
• • • • • • • • • • • • • • • • • • • • • • • • • • • • • • • • • • • • • • • • • • • • • • • •
7-1
■
RS-485 Specifications
• • • • • • • • • • • • • • • • • • • • • • • • • • • • • • • • • • • • • • • • • • • • • • • • • •
7-1
vi
APPENDIX
■
Code Table
• • • • • • • • • • • • • • • • • • • • • • • • • • • • • • • • • • • • • • • • • • • • • • • • • • • • • • • • •
App.-1
■
SRF Character Code Table
• • • • • • • • • • • • • • • • • • • • • • • • • • • • • • • • • • • • • • • • •
App.-2
■
Connection With CMC10L
• • • • • • • • • • • • • • • • • • • • • • • • • • • • • • • • • • • • • • • • • •
App.-3
Conventions Used in This Manual
The following conventions are used in this manual:
Handling Precaution
: Handling Precautions indicate items that the user should pay attention to when handling the xxx.
Note
: Notes indicate useful information that the user might benefit by knowing.
(1), (2), (3) : The numbers with the parenthesis indicate steps in a sequence or indicate corresponding parts in an explanation.
vii
Chapter 1.
COMMUNICATION FUNCTIONS
• On a system operating on the RS-232C interface, a master station (a host computer, usually a PC) is connected to the instrument in a point-to-point configuration. At this time, only one instrument can communicate with the master station using a preset station address.
• On a system operating on the RS-485 interface, up to 31 instruments (see * 1) can be connected to a master station. Station addresses are then used to identify other stations for communication.
• The communication protocol and format conform to the RS-232C and RS-485 interfaces.
•
When the following procedure is established during communication, instrument data can be read or written:
1. The master station (host computer) transmits a request message to the slave station.
2. The master station receives a response message from the slave station.
•
The master station issues two types of requests to a slave station: read and write.
•
The type of read/write data can be optionally selected with a data address.
• CPL (Controller Peripheral Link) Communications isYamatake host communication protocol.
RS-232C connection example RS-485 connection example RS-485 connection example
Master station Master station
Master station
RS-232C
RS-232C
RS-232C/RS-485 converter
RS-485 (5-wire system)
RS-232C
CMC10L001A000
*2
RS-485 (35-wire system)
Slave station
Slave station
Slave station
Connection between master station and slave station
Connection between master station and slave station
• The high-performance communication controller CMC10L is available for conversion between the RS-232C and
RS-485 interfaces.
* 1 : When the master station is an MA500 DIM or CMC10L , it can be connected to up to 16 slave stations.
*
2 : The communication adapter
CMC10L is an RS-232C/RS-485 converter available from Yamatake .
1-1
Chapter 2.
WIRING
2 - 1 RS-232C Connection
WARNING
Ground the FG (Frame Ground) terminal to a terminal resistance of
100Ω or less before you connect the SRF206/212/224 to the input circuit
or control circuit.
Failure to do so might cause electric shock or fire.
Be sure to turn the source power OFF before wiring the SRF206/212/224.
Failure to do so might cause electric shock.
Do not touch power terminals or other electrically charged parts.
Doing so might cause electric shock.
CAUTION
Wire the SRF206/212/224 according to predetermined standards. Also wire the SRF206/212/224 using specified power leads according to recognized installation methods.
Failure to do might cause electric shock, fire or faulty operation.
Do not allow lead scraps, chips or water to enter the SRF206/212/224.
Doing so might cause fire or faulty operation.
Tighten the terminal screws to the specification torque.
Incomplete tightening might cause electric shock or fire.
Do not use unused terminals on the SRF206/212/224 as relay terminals.
Doing so might cause electric shock or fire.
We recommend attaching the terminal covers after wiring the
SRF206/212/224.
Failure to do so might cause electric shock.
An SRF206/212/224 supporting an RS-232C communication function is wired for communication as shown below.
•
Communication with the master station in a point-to-point configuration
The SRF206/212/224 is provided with three communication terminals (RD,
SD and SG). Data may not be output unless the other terminals of the master station RS-232C interface are short-circuited as shown in figure on the next page.
Usually, the pin array of the RS-232C connector of a PC is as shown in the figure on the next page (terminal mode). The locations of pins SD and RD, RS and CS and DR and ER may be reversed (MODEM mode), but this is rare.
Check the RS-232C pin array in the host computer instruction manual.
2-1
Chapter 2. WIRING
RD
SD
SG
RS
CS
DR
CD
ER
8
6
5
7
2
3
1
4
SD
RD
SG
Host computer (master station)
DIGITRONIK control (slave station)
Example of connection using
Yamatake CBL232FNZ02
Note
Cable model No.
: CBL232FNZ02
(2m cable for RS-232C, 9pin D-Sub socket↔contact-crimptype terminal lug)
● RS-232C connector signals
9 pins
Pin No. JIS Code Name
5
6
3
4
1
2
7
8
CD
RD
SD
ER
SG
DR
RS
CS
DCD
RxD
TxD
DTR
GND
DSR
RTS
CTS
Signal Direction
Host-station
←
←
→
→
←
→
←
2-2
Chapter 2. WIRING
2 - 2 RS-485 Connection
■ Connection with 5-wire system
The following is an example of a system connection of a DIGITRONIK control supporting the RS-485 communication function using the 5-wire system:
Terminating resistor
Terminating resistor
DIGITRONIK control or
5-wire system(slave station)
SDA
SDB
RDA
RDB
SG
FG
Shielded cable
Master station
RDA
RDB
SDA
SDB
SG
FG Shielded cable
DIGITRONIK control or
5-wire system(slave station)
SDA
SDB
RDA
RDB
SG
FG
Shielded cable
Terminating resistor
Terminating resistor
DIGITRONIK control or
5-wire system(slave station)
SDA
SDB
RDA
RDB
SG
FG
Connect a terminating resistor of 150Ω±5%, 1/2W min. to the instrument at each end of the transmission line. Connect only one end of the shielded wire to the frame ground.
Other 3-wire system DIGITRONIK units of Yamatake can be used on the same communication line. Conduct the wiring shown at the item "
■ 3-wire system used together" on next page.
Handling Precautions
Be sure to connect SG terminals each other. Failure to do so might cause unstable communications.
2-3
Chapter 2. WIRING
■ 3-wire system used together
An SRF206/212/224 supporting the RS-485 communication function can also be used in a 3-wire system. The following is an example of such a connection:
Terminating resistor
DIGITRONIK control or
5-wire system (slave station)
SDA
*
*
SDB
RDA
RDB
SG
FG
Master station
RDA
RDB
SDA
SDB
SG
*
*
FG
Shielded cable
Shielded cable
3-wire system (slave station)
DA
DB
Shielded cable
Terminating resistor
SG
FG
DIGITRONIK control or
5-wire system (slave station)
SDA
*
*
SDB
RDA
RDB
SG
FG
Connect one terminating resistor of 150Ω±5%, 1/2W min. to the instrument at each end of the transmission line. Connect only one end of the shielded wire to the frame ground.
(*) must be wired externally.
On 3-wire system, the CMC10L001A000 of Yamatake can be used as a coverter for master station.
See, "
■ Connection with CMC10L" (Page App.-3) for details.
Handling Precautions
Be sure to connect SG terminals each other. Failure to do so might cause unstable communications.
2-4
Chapter 2. WIRING
2 - 3 RS-232C Models
The communication terminal array of an RS-232C model supporting the communication function is as follows:
1
2
3
N
1
2
3
4
5
6
7
8
9
10
11
14
15
12
13
16
17
18
19
20
21
24
25
22
23
26
27
28
29
30
Communication terminals
Option unit 1
RS-232C
(Yamatake CPL communications)
SD
RD
SG
9
10
19
20
29
30
Connection example :
RD
SD
SG
RS
CS
DR
CD
ER
2
3
5
7
8
6
1
4
SD
RD
SG
Host computer (master station)
DIGITRONIK control (slave station)
Note
Cable model No. :
CBL232FNZ02
(2m cable for RS-232C, 9pin D-Sub socket contact-crimptype terminal lug)
2-5
Chapter 2. WIRING
2 - 4 RS-485 Models
The communication terminal array of an RS-485 model supporting the communication function is as follows:
Connection example:
1
2
3
RS-485
N
3
4
5
6
1
2
7
8
9
10
25
26
23
24
21
22
27
28
29
30
15
16
13
14
11
12
17
18
19
20
Option unit 1
(Yamatake CPL communications)
SDA
SDB
SG
Terminating resistor
Terminating resistor
Communication terminals
Shielded cable
Master station
RDA
RDB
SDA
SDB
SG
FG
DIGITRONIK control (slave station)
SDA
SDB
RDA
RDB
SG
FG
Shielded cable
DIGITRONIK control (slave station)
SDA
SDB
RDA
RDB
SG
FG
9
10
19
20
29
30
(internally connected at terminal)
RDB
RDA
Shielded cable
Terminating resistor
Terminating resistor
DIGITRONIK control (slave station)
SDA
SDB
RDA
RDB
SG
FG
Connect a terminating resistor of 150
Ω±5%, 1/2W min. to the station at each end of the transmission line. Connect only one end of the shielded wire to the frame ground.
2-6
Chapter 3.
SETTINGS
3 - 1 Communication Setup Items
■
System Setup
Communication setup items are displayed in system setup screen Nos. “ ”, “ ” and “ ”.
These setup items are not displayed on models that do not support the communications option.
DATA
LOCK
EVNT
COPY
SPD
CLK
SYS
RNG SCL
CH
EVNT
Display No.
Description
Configuration lock
List printing ON/OFF
Menu level
Recording format
Recorder ID No.
Recording time ON/OFF
Scale recording ON/OFF
Recording color selection
Communication access rights
Station address
Communications method
Extended menu entry
Setup Details
Communication access rights : “1” read only
“2” read/write
Station address
Communication method
: “0 to 127”. Communication is inhibited when set to “0”.
: “1” 4800bps, 8bits, even parity, 1 stop bit
“2” 4800bps, 8bits, no parity, 2 stop bits
“3” 9600bps, 8bits, even parity, 1 stop bit
“4” 9600bps, 8bits, no parity, 2 stop bits
3-1
Chapter 3. SETTINGS
3 - 2 Initial Setup
Before starting communication, set up the communication conditions for the SRF206/212/224 and master station.
■
Station Address
Set a decimal numeric within the range “0” to “127” to system setup screen No.
“ ” on the SRF206/212/224 .
Slave stations connected in a multi-drop configuration on the same transmission line in an RS-485 system must have unique addresses.
The default address is “0”.
Since the communication function is not activated at address “0”, be sure to set a value other than “0” to execute communication.
■
Transmission Rate and Data Format
Set a decimal numeric within the range “1” to “4” to system setup screen No. “ ” on the SRF206/212/224 .
Use the same transmission rate and data format as on the master station. The default is “1”.
1: 4800bps, 8bits, even parity, 1 stop bit
2: 4800bps, 8bits, no parity, 2 stop bits
3: 9600bps, 8bits, even parity, 1 stop bit
4: 9600bps, 8bits, no parity, 2 stop bits
3-2
Chapter 4.
COMMUNICATION PROCEDURE
4 - 1 Outline of Communication Procedure and Messages
This chapter outlines communication procedures and the concept behind message configuration.
■
Communication Procedure
The following is a simple breakdown of the communication procedure:
1. The master station transmits an instruction message to a slave station to specify a station for communication.
2. The slave station processes the instruction message, and executes read and write operations.
3. The slave station transmits a response message according to the contents of processing.
4. The master station receives the response message and executes processing.
■
Message Configuration
A message consists of two layers as shown below. Both the instruction message from a master station and the response message from a slave station take this form.
●
Data link layer
•
This layer contains the basic information required for communication.
•
It also contains message destination and check information.
● Application layer
• This layer is where data read and write operations are executed.
• The content of this layer varies according to the purpose of the operation.
The figure below shows the individual layers.
Application layer
Data link layer
A total of 31 stations
Instruction message from master station
Response message from slave station
Slave stations
Master station
The driver of the data link layer knows:
¥ Destination (station address)
¥ Load check sheet (checksum)
Application layer
Data link layer
The load (data) of the application layer changes every time according to the purpose of the operation.
4-1
Chapter 4. COMMUNICATION PROCEDURE
■ Examples
Messages have the following structure:
● Read instruction
・Instruction message
STX 0 1 0 0 X R S , 1 0 0 1 W , 2 ETX 9 A CR LF
Data link layer Application layer Data link layer
・Response message
STX 0 1 0 0 X 0 0 , 0 , 4 2 ETX 9 4 CR LF
Data link layer Application layer Data link layer
● Write instruction
・Instruction message
STX 0 1 0 0 X W S , 1 0 0 1 W , 5 8 ETX 5 A CR LF
Data link layer Data link layer Application layer
・Response message
STX 0 1 0 0 X 0 0 ETX 8 2 CR LF
Data link layer
Application layer
Data link layer
The following sections describe in detail the data link layer and application layer:
■ Data Address Concept
The SRF206/212/224 uses “data addresses” to read and write data. Data addresses allow data to be written and read to and from a corresponding address for the data.
Data A
Data B
Data C
:
501W
502W
503W
:
See Chapter 5. “COMMUNICATION DATA TABLE” for information on the relationship between data and address.
4-2
Chapter 4. COMMUNICATION PROCEDURE
4 - 2 Data Link Layer
■
Description
• The data link layer contains eight types of basic message transmission information.
• The instruction message and response message have the same structure in the data link layer.
STX
Station address
Subaddress
Device ID code
The underlined SRF200 parameters ( ) are set to fixed values.
ETX
Checksum
CR
LF
02H 30H 41H 30H 30H 58H 52H 53H 2CH 31H 30H 30H 31H 57H 2CH 32H 03H 38H 41H 0DH 0AH
STX 0 A 0 0 X R S , 1 0 0 1 W , 2 ETX 8 A CR LF
Data link layer Application layer Data link layer
The following describes each function of the data link layer:
●
STX (Start of TeXt)
◆ Role
: Indicates the beginning of a message.
Description • Fixed at 02H.
• When the instrument receives an STX, it is identified as the first character of a new instruction message regardless of location with a message.
●
Station address
◆ Role
: Specifies the destination station, and allows communication with the specified station.
Description • If “0” is set as the station address, the communication function is stopped.
So, to enable communication be sure to set an address value of
“1” or more.
• Two hexadecimal characters. For details, see the example.
• See
Chapter 3. “SETTINGS”
for information on station address settings.
Example : When the station address of the other instrument is “10”:
1. 10 (decimal) = 0AH (hexadecimal)
2. This can be converted into character codes:
0 = 30H, A = 41H
3. “0A” (30H, 41H) calculated in example 2 is used as the station address.
Handling Precautions
Note that the function of the station address differs entirely from that of the data address of the application layer.
●
Subaddress
Description
:
The subaddress is meaningless on the SRF206/212/224 .
Be sure to set a subaddress of “00” (30H, 30H) that has the same format as the station address.
●
Device ID code
Description
:
Only character codes “X” (58H) or “x” (78H) can be set on the
SRF206/212/224 .
4-3
Chapter 4. COMMUNICATION PROCEDURE
●
ETX (End of TeXt)
◆ Role
: Indicates the end of the application layer.
Description : Fixed at 03H.
●
Checksum
◆ Role
: A value to be used to check whether or not a message has been corrupted by an error (such as noise) during communication.
Description
•
Two hexadecimal characters.
•
This function operates as follows:
1. Add one byte each to the character codes of the message from
STX to ETX.
2. Derive the two’s complement of the result of this addition.
3. Convert the result into character codes.
Example : The instruction message on the preceding page is used in the following example:
1. Add one byte each to the character codes from STX to ETX.
The lower-order one byte of the calculation result is 76H.
2. The result of two’s complement addition is 8AH.
3. 85H is converted into character codes and used as the checksum value. The result is “8A”, (38H) and (41H).
See the station address example (on the preceding page) for information on character code conversion.
Handling Precautions
The checksum in the instruction message can be omitted, but no checksum is then included in the response message. The checksum function should not be omitted to ensure proper message reception and transmission.
4-4
Chapter 4. COMMUNICATION PROCEDURE
●
CR and LF (Carriage Return/Line Feed)
◆ Role
: Indicates the end of a message.
Description • “CR” is (0DH), and “LF” is (0AH).
• Be sure to use CR and LF in pair.
Handling Precautions
● If any of the following errors occur in the data link layer, the instrument respond:
• The communication conditions for both stations do not match (different transmission speeds or the occurrence of a parity error).
• The address of the transmitting station differs from the station address for the receiving station.
• The station address is “00”.
• STX, ETX, CR and LF are not placed at the specified positions.
• The device ID code is neither “X” nor “x”.
• The station address, subaddress or checksum is not two charactersdoes not long.
• The calculation result of the checksum does not match the checksum of the message.
• Non-specified characters are included in the message.
● The data link layer contains a response message which is identical to the instruction message except for the checksum function.
● Use upper-case characters “A” to “F” in the hexadecimal numerics for the station address and checksum.
4-5
Chapter 4. COMMUNICATION PROCEDURE
4 - 3
■
Outline
Application Layer
• The application layer contains instructions, data, data count and termination code.
• In the application layer, the instruction message and response message have a different structure.
• There are two types of instruction messages: read instructions and write instructions. Each of these instruction messages have their own responses.
• A termination code indicates how an instruction message has been processed.
Application layer Instruction message
Read instruction
Instruction code (RS)
Leading data address
Read data count
Write instruction Instruction code (WS)
Leading data address
Write data
Response message
Read response
Write response
Termination code
Read data
Termination code
4-6
Chapter 4. COMMUNICATION PROCEDURE
4 - 4 Data Read
■
Description of Read Instruction
• This instruction permits the contents of continuous data addresses starting from the specified leading read data address to be read in one message.
• The application layer of a read instruction consists of the following three types of data:
Read instruction code
Leading read data address
Read data count
02H 30H 31H 30H 30H 58H 52H 53H 2CH 31H 30H 30H 31H 57H 2CH 32H 03H 39H 41H 0DH 0AH
STX 0 1 0 0 X R S , 1 0 0 1 W , 2 ETX 9 A CR LF
Data link layer Application layer Data link layer
• Individual data items are delimited by a comma “,” (character code 2CH).
• An upper-case character code is used for each numeric or character in the application layer.
• A decimal number is used for each numeric.
• Additional “0”s or spaces cannot be added to each data item.
Example : The underlined portion of “RS,01001W,2” is not allowed
Example incorrect.
: The underlined portions of “RS, 1001W,02” are not allowed
Example incorrect.
: The above example shows that two-data items are read from
1001W as one message.
●
Read instruction code (RS)
◆ Role
: A read command
Description : Two “RS” (52H, 53H) characters
●
Leading read data address
◆ Role
: Specifies the leading read data address.
Description
•
See
Chapter 5. “COMMUNICATION DATA TABLE”
for information on the relationship between data addresses and read data.
•
Be sure to append the numeric representing the data address with
“W” (57H).
●
Read data count
◆ Role
: Specifies how many data items are read continuously, starting with the specified data address.
Handling Precautions
See Chapter 5.“COMMUNICATION DATA TABLE” for information on the upper limit of the read data count.
4-7
Chapter 4. COMMUNICATION PROCEDURE
■
Read Response
●
Termination Code
◆ Role
: When the message in the data link layer is correct, a response message is sent back according to the contents of the instruction message.
Description : All data in the application layer is expressed in decimal character code.
◆ Role
: A numeric which specifies how the instruction message has been processed by the instrument.
Different values are set according to the processing result.
Description : The response message must include a termination code. The termination codes are classified as follows:
Termination code Normal
Warning
* The termination code is a
2-digit decimal.
Abnormal
●
Normal response/warning response
◆ Role
: Sends back the read data.
Description : Information in the application layer
•
Termination code : See
4-6 “Termination Code Table”
for information on
•
Read data termination codes.
: Only the specified number of data items are input.
: The decimal point is removed from a numeric when it is entered.
Example : “55.6” is converted to “556” when entered.
: Individual data items are delimited by a comma “,”(2CH).
: The range and number of digits of each data item depend upon the read data.
Example : A normal response (when two data items are read properly)
Termination code (00 = normal)
Read data
02H 30H 31H 30H 30H 58H 30H 30H 2CH 31H 32H 33H 2CH 38H 37H 30H 03H 46H 35H 0DH 0AH
STX 0 1 0 0 X 0 0 , 1 2 3 , 8 7 0 ETX F 5 CR LF
Data link layer Application layer Data link layer
Example : A warning response (❈❈ indicates the warning code numeric.)
Termination code (
❈❈
= warning)
Read data
02H 30H 31H 30H 30H 58H
❈
H
❈
H 2CH 30H 2CH 38H 37H 30H 03H ??H ??H 0DH 0AH
STX 0 1 0 0 X
❈ ❈
, 0 , 8 7 0 ETX ?
?
CR LF
Data link layer Application layer Data link layer
4-8
Chapter 4. COMMUNICATION PROCEDURE
●
Abnormal response
◆ Role
: Indicates that there is an abnormality in an instruction message, which contains no data and cannot be normally read.
Description : Information in the application layer
Termination code : Indicates an abnormality type.
: See
4-6 “Termination Code Table”
for details.
Example : An abnormal response
Termination code
(
❈❈
= error)
02H 30H 31H 30H 30H 58H
❈
H
❈
H 03H ??H ??H 0DH 0AH
STX 0 1 0 0 X
❈ ❈
ETX ??
??
CR LF
Data link layer Application layer Data link layer
■
Decimal Numeric Expression (numeric data)
◆ Role
: All the numerics, read count, write value (see the description of the WS command) and read data in the data address follow the rules given below.
(1) When a numeric is negative, prefix the numeric with a minus sign “-” (2DH).
Example : “-123” (2DH, 31H, 32H, 33H)
(2) When a numeric is “0”, use one “0”.
Example : “0” (30H)
Example : “00” (30H, 30H) is not allowed.
(3) When a numeric is positive, never prefix the numeric with a plus sign “+”.
(4) Never add additional “0”s or spaces before a numeric.
Example : “0123” (30H, 31H, 32H, 33H) is not allowed.
Example : “ 123” (20H, 31H, 32H, 33H) is not allowed.
4-9
Chapter 4. COMMUNICATION PROCEDURE
4 - 5 Data Write
■
Description of Write Instruction
• This instruction permits the contents of continuous data addresses starting with the specified leading write data address to be simultaneously written in one message.
• The application layer of a write instruction consists of the following three types of data:
Write instruction code
Leading write data address
Write data (1st data item)
Write data (2nd data item)
02H 30H 31H 30H 30H 58H 57H 53H 2CH 31H 30H 30H 31H 57H 2CH 32H 2CH 36H 35H
STX 0 1 0 0 X W S , 1 0 0 1 W , 2 ,
6
5
Data link layer Application layer
03H 46H 45H 0DH 0AH
ETX F E CR LF
Data link layer
•
Individual data items are delimited with a comma “,” (character code 2CH).
•
The write data count need not be specified.
• An upper-case character code is used for each numeric or character in the application layer.
•
A decimal number is used for each numeric.
•
Additional “0”s (30H) or spaces cannot be added to each data item.
Example
Example
Example
: The underlined portion of “WS,01001W,2” is not allowed.
: The underlined portions of “WS, 1001W,02” are not allowed.
: The above example shows that “2” and “65” are written at address 1001W and 1002W in one message.
●
Write instruction code (WS)
◆ Role
: A write command
Description : Two “WS” (57H, 53H) characters
●
Leading write data address
◆ Role
: Specifies the leading write data address.
•
See
Chapter 5. “COMMUNICATION DATA TABLE”
for information on the relationship between data addresses and write data.
•
Be sure to append the numeric representing the data address with
“W” (57H).
●
Write data
◆ Role
: Data to be written to continuous addresses starting with the specified data address.
Description
•
The range of a numeric to be written differs according to each data address.
• Individual data are delimited by a comma “,” (2CH).
•
The data address at which the corresponding data is written is incremented by 1 sequentially, starting with the leading data address (see the example given on the preceding page).
• The number of data item which can be written in one message is limited. See
Chapter 5. “COMMUNICATION DATA
TABLE”
for details.
4-10
Chapter 4. COMMUNICATION PROCEDURE
■
Write Response
◆ Role
: When the message in the data link layer is correct, only the termination code is sent back.
Description : The termination codes are classified as follows:
Termination code Normal
Warning
* The termination code is a
2-digit decimal.
Abnormal
●
Normal response/warning response
◆ Role
: Returns how the write instruction message has been processed.
Only a normal termination code or warning termination code is returned.
Description : Information in the application layer
Termination code : A numeric specifying how the instruction message has been processed by the instrument.
Example : Normal response (when all data items are correctly written)
Termination code (00 = normal)
02H 30H 31H 30H 30H 58H 30H 30H 03H 38H 32H 0DH 0AH
STX 0 1 0 0 X 0 0 ETX 8 2 CR LF
Data link layer Application layer Data link layer
Example : A warning response (❈❈ indicates the warning code numeric.)
Termination code (
❈❈
= warning)
02H 30H 31H 30H 30H 58H ??H ??H 03H ??H ??H 0DH 0AH
STX 0 1 0 0 X
❈ ❈
ETX ?
?
CR LF
Data link layer Application layer Data link layer
●
Abnormal response
◆ Role
: Only the abnormal termination code is returned.
Description : Information in the application layer
Termination code : Indicates that there is an abnormality in the instruction message, and that write processing cannot be executed.
See
4-6 “Termination Code Table”
for details.
Example : An abnormal response (❈❈ indicates an abnormal response.)
Termination code (
❈❈
= error)
02H 30H 31H 30H 30H 58H
❈
H
❈
H 03H ??H ??H 0DH 0AH
STX 0 1 0 0 X
❈ ❈
ETX ?
?
CR LF
Data link layer Application layer Data link layer
4-11
Chapter 4. COMMUNICATION PROCEDURE
4 - 6 Termination Code Table
■
Normal and Abnormal Termination
Type
Normal
Abnormal
Abnormal
Abnormal
Abnormal
Abnormal
Abnormal
Warning
Response
Code
00
99
40
41
42
43
44
46
Description
Normal termination
Command error
Format error
Data item number error
Address range error
Numeric abnormality error
Numeric value range abnormal error
Write inhibit status error
Warning
Warning
Warning
81
30
31
Write inhibit data error
Instrument control error
Write busy error
Reason for Occurrence Read Data
Command has been processed normally.
Undefined command has been received.
CPL application error
Too many or too few read data items
Write address contains access inhibit flag.
Write data whose value is not within range
-32768 to +32767 is included.
Write data other than the specified value is included.
The write command was received in a write inhibit status.
Write address contains a read-only address or an address relating to an unmounted channel.
A nonexecutable control command has been received.
The write command was received during writing on the instrument.
Present
Not present
Not present
Not present
—
—
—
—
—
—
—
* A “nonexecutable control command” is a control command that cannot be executed depending to the operating status of the recorder such as a feed request issued during printing.
* When two or more errors occur simultaneously, the response code having the higher priority is returned first.
4-12
Chapter 4. COMMUNICATION PROCEDURE
4 - 7 Timing Specifications
■ Timing Specifications for Instruction and Response Messages
When a slave station is connected with the master station directly via the RS-232C interface, the following precautions regarding the transmission timing of instruction messages from the master station and response messages from the slave station should be observed:
● Response time-out
The maximum response time from the end of the instruction message transmission by the master station until when the master station receives a response message from the slave station is one second ((1) in figure). So, the response time-out should be set to one second.
Generally, when a response time-out occurs, the instruction message is resent.
For details, see Chapter 6. “COMMUNICATION PROGRAM FOR MASTER
STATION.”
● Transmission start time
A wait time of 10ms or more is required before the master station starts to transmit the next instruction message (to the same slave station or a different slave station) after the end of receiving a response message ((2) in figure).
RS-485 3-wire system
(1) (2)
Transmission line
Instruction message
Response message
Instruction message
Response message
RS-485 5-wire system and RS-232C
(1) (2)
Master station, transmission line
Slave station, transmission line
Instruction message
Response message
Instruction message
Response message
(1) End of master station transmission - Transmission start time of slave station = 1s max.
(2) End of slave station transmission - Transmission start time of master station = 10ms min.
■ RS-485 Driver Control Timing Specifications
When the transmission/reception on the RS-485 3-wire system is directly controlled by the master station, care should be paid to the following timing:
(1) (4)
Master station
Driver control
(enable)
(disable)
Transmission line
Effective data
(instruction message)
Slave station
Driver control (disable)
(2)
Effective data
(response message)
(enable)
(3)
End of master station transmission
End of slave station transmission
(1) End of master station transmission - Driver disable time = 500 s max.
(2) End of slave station reception - Driver enable time = 1ms min.
(3) End of slave station transmission - Driver disable time = 10ms max.
(4) End of master station reception - Driver enable time = 10ms min.
4-13
Chapter 5.
COMMUNICATION DATA TABLE
5 - 1 Basic Communication Data Processing
■
Communication Data Types and Formats
●
Types of communication data
There are two types of communication data:
●
Run status: Data indicating the run status (PV, event, etc.) of the instrument.
●
Configuration: Data (event setting values, etc.) for setting the instrument status.
●
Format of communication data
Communication data is classified into the following formats:
●
Numeric data: Data indicating a numeric value (PV, etc.).
●
Bit data: Data where each bit is significant (alarms, etc.). Bit data must
●
Text data: be composed by transmission and decomposed by reception.
Data indicating text.
Text data (unit, tag name, etc.) must be converted according to the character code table.
For details on character data, see ■
SRF Character Code
Table (App.-2)
.
IMPORTANT
Writing to EEPROM addresses is guaranteed only up to 100,000 times.
■
Communication Data Storage Memory
●
Memory type
The communication data handled on the
SRF206/212/224
(excluding some data items such as time data) is stored in the following two types of memory:
•
• RAM:
EEPROM:
Stored data is cleared when the power is turned OFF. However data can be written to this memory any number of times.
Stored data is retained even when the power is turned OFF, whereas data write operations are limited to a total of 100,000 times owing to device characteristics.
When data is written to RAM by communications on the
SRF206/212/224
, the data is also automatically written to EEPROM excluding control data and other data items.
●
Communication memory devices
Data is transferred automatically between RAM and EEPROM as required. For this reason, there is no need to be conscious of these two types of memory.
5-1
Chapter 5. COMMUNICATION DATA TABLE
■ Data Address
The data addresses are allocated as in the table below.
Communication Data
Control data
Process data
Event data
Digital I/O
Common data
Segment table data
Channel data
Communication data
Address
300 to 399
400 to 449
450 to 499
500 to 599
600 to 999
1000 to 1099 nn00 to nn99 *
3500 to 3999
* Address “nn” is a value obtained by adding “10” to channels “1” to “24”.
For example, “nn” becomes “11” in the case of channel 1.
■ Data Read/Write Count
The number of data items that can be read and written continuously in a single communication operation is determined within a range in which the command frame length is less than 256bytes.
Data in the continuous data that does not exist due to differences in model Nos. is handled as follows:
• Reading: “0” is read as dummy data (warning response is returned).
• Writing: Data is not written (warning response is returned).
Handling Precautions
Command frames up to 256bytes in length sometimes cannot be handled depending on the hardware and software of the master station in use. (For example, N88 BASIC can handle only up to 255bytes.) If this happens, limit the command frame length to match the limitations of the master station.
■ Data Unit and Decimal Point Position
Read/write data is not appended with a decimal point.
The unit and decimal point position is determined for each data item.
For details on the data unit and decimal point position, see the SRF206/212/224
Installation/Operation Manual.
Example:
Let’s assume that the data to be read and written is numeric data “105”. The data unit and decimal point position is automatically determined by the data address and instrument setup items.
So, the numeric data “105” can have various meaning such as 10.5% and 105°C depending on the data address to be read and written.
5-2
Chapter 5. COMMUNICATION DATA TABLE
5 - 2 Communication Data Table
The address and read/write (R/W) enable status of each data item to be determined are shown in the table below.
Meaning of R/W column symbol
« R/W enabled
X R/W disabled
■
Control Data
Item
Address
R W Meaning of Data
Recording start/stop 300 X
«
Starts/stops recording.
0: Stop recording
1: Start recording
• If “1” is written before a complete recording stop status (wire dot head is at home position) after “0” is written, response code 30 is returned.
• If a write is carried out during chart feeding, response code 30 is returned.
• If “1” is written during printing, the recording standby status is entered, and recording is resumed when printing ends.
If “1” is written during recording standby, response code 30 is returned.
• An error response is not returned even if “1” is written in a recording start status.
Demand printing start/stop 301 X
«
Starts/stops demand printing.
0: Stop demand printing
1: Start demand printing
• If “1” is written during printing or chart feeding, response code 30 is returned.
List printing start/stop 302 X
«
Starts/stops list printing.
0: Stop list printing
1: Start specified list printing
2: Start range/scale settings printing
3: Start event and DI/DO settings printing
4: Start MSG, S.DMD, UF and communications settings printing
5: Start segment table settings printing
6: Start all list printing
7: Start communications list printing
• If “1” to “7” is written during printing, chart feeding or recording, response code 30 is returned.
Chart feed 303 X
«
Feeds chart by about 40mm.
0: Feed OFF
1: Starts chart feed
• Chart feed automatically stops when chart is fed 40mm.
• Chart feed does not stop even if “0” is written during feeding.
• If “1” is written during printing, chart feeding and recording, response code 30 is returned.
• When the feed key on the instrument body is manipulated during chart feeding by this command, feed stops when the key is released.
Start message printing 304 X
« Prints eight messages
0: Printing OFF
1 to 8: Starts printing of No.1 to No.8 messages.
• Printing does not stop even if “0” is written during message printing.
• If “1” is written with the message print buffer full, response code 30 is returned.
Chart feed speed/scale selection 305 X
«
Switches chart feed speed/scale.
1: No.1 chart feed speed/No.1 scale
2: No.2 chart feed speed/No.2 scale
• The scale is switched according to the channel whose scale switching method is preset to contact input/communications.
• When the power is turned OFF, this item is reset to 1 (No.1 chart feed speed/No.1 scale).
5-3
Chapter 5. COMMUNICATION DATA TABLE
Item
Address
R W Meaning of Data
Reset integrating calculation 306 X
«
Clears integrating calculation or F value calculation
Bitmap data No.1 (see page 5-27)
0 to 63
• If “0” is written, the reset status stays as it is, and integrating calculation is not started unless “1” is written.
• The initial status after the power is turned ON is “0” (reset).
• If one of internal DI, external DI or communications is continuing when a DI function is set to integrating calculation reset, the integrating calculation is continued. (Integrating calculation is reset by all reset.)
Clear batch counter 307 X
« Clears the batch count to “0”
0: Continues count.
1: Clears count.
• If “1” is written, the count status is automatically returned to after it is cleared.
• By clearing the batch counter, the batch count value is cleared to “0”.
• If the batch count value is read before start of recording immediately after the batch counter is cleared, “0” is read.
• The counter is incremented by “1” when recording is started. So, batch count “0” is never printed by recording printing.
Recording status 310
«
X
Reads recording status.
0: Recording stopped
1: Recording in progress
• When recording is stopped during movement of the wire dot head, “0” is read even if a complete recording status is not entered.
Demand printing status 311
«
X
Reads the demand printing status.
0: Demand printing stopped
1: Demand printing in progress
• When printing is stopped during movement of the wire dot head, “0” is read even if a complete printing status is not entered.
List printing status 312
«
X
Chart feed status
Message print status
Chart feed speed/ scale selection status
Integrating calculation status
313
314
315
316
«
«
«
«
X
X
X
X
Reads the list printing status.
0: Stop list printing
1: Specified list printing
2: Range/scale settings printing
3: Event and DI/DO settings printing
4: MSG, S.DMD, UF and communications settings printing
5: Segment table settings printing
6: All list printing
7: Communications list printing
Reads the chart feed status.
0: Chart feed stopped
1: Chart feed in progress
Reads the message printing status.
0: Message printing stopped
1 to 8: No.1 to No.8 message printing in progress
Reads the currently selected chart feed speed.
1: No.1 chart feed speed/No.1 scale
2: No.2 chart feed speed/No.2 scale
Reads integrating calculation or F value calculation
Bitmap data No.2 (see page 5-27)
0 to 16191
• Bits b0 to b5 indicate the status of integrating calculation reset (306W) that is written by communications.
Integrating calculation sometimes is continued by DI even these bits are in a reset status.
• Bits b8 to b13 indicate the status of the actual integrating calculation.
These become “1” when one of communications, internal DI and external DI.
5-4
Chapter 5. COMMUNICATION DATA TABLE
Item
Address
R W Meaning of Data
Batch count value 317
«
X
Reads the current batch count value.
0 to 99
• By clearing the batch counter, the batch count value is cleared to “0”.
• If the batch count value is read before the start of recording, immediately after the batch counter is cleared,
“0” is read.
• The counter is incremented by “1” when recording is started. So, batch count “0” is never printed by recording printing.
Binary count value
Instrument alarm status
Basic catalog No. information
Option information
318
380
397
398
«
«
«
«
X
X
X
X
Reads the binary count value.
0 to 99
Reads the information of alarms that occur on the instrument.
Bitmap data No.3 (see page 5-27)
-32768 to +32767
Reads the basic catalog No. information of the instrument.
206: 6-dot model
212: 12-dot model
224: 24-dot model
Reads options that can be operated on the instrument.
Bitmap data No.4 (see page 5-28)
0 to 254
• Optional functions that can be operated on the instrument may vary from the currently mounted optional functions.
Software information 399
«
X
Reads the software version.
100h onwards
The software version is expressed in Hexadecimal.
For example: Version 1.13 = 113h,
Version 0.25 = 25h
5-5
Chapter 5. COMMUNICATION DATA TABLE
■ Process Data Area
Item
Address
R W Meaning of Data
Event status summary 400
401
❍
X
Reads the summary of the event occurrence status of channels 1 to 24.
Bitmap data No.5 (see page 5-28)
-32768 to +32767
Bitmap data No.6 (see page 5-28)
0 to 256
• Even if one of the upper and lower limit events of events No.1 to No.4 occurs, the assigned bit becomes “1”.
PV value (channel 1)
PV value (channel 2)
PV value (channel 3)
PV value (channel 4)
PV value (channel 5)
PV value (channel 6)
PV value (channel 7)
PV value (channel 8)
PV value (channel 9)
PV value (channel 10)
PV value (channel 11)
PV value (channel 12)
PV value (channel 13)
PV value (channel 14)
PV value (channel 15)
PV value (channel 16)
PV value (channel 17)
PV value (channel 18)
PV value (channel 19)
PV value (channel 20)
PV value (channel 21)
PV value (channel 22)
PV value (channel 23)
PV value (channel 24)
411
412
413
414
415
416
417
418
419
420
421
422
423
424
425
426
427
428
429
430
431
432
433
434
❍
❍
❍
❍
❍
❍
❍
❍
❍
❍
❍
❍
❍
❍
❍
❍
❍
❍
❍
❍
❍
❍
❍
❍
X
X
X
X
X
X
X
X
X
X
X
X
X
X
X
X
X
X
X
X
X
X
X
X
Reads the PV values of channels 1 to 24.
-32767: Recording mode OFF
-32768: Relative humidity calculation error
-20000: Minus-side overload or overflow
-19999 to +29999: Normal input
30000: Plus-side overload or overflow
32767: Non-measured data
• The PV value after calculation is read when the calculation has been set.
• In the case of the ON/OFF range, 0 = OFF and 1 = ON.
• For details on the decimal point in linear scale ranging, refer to the engineering range decimal point (page 5-
21).
Note
: The content of the event status summary in the process data area
(address 400W) is same as the event status summary in the event data
(address 450W). And the content of the event status summary in the process data area (address 401W) is same as the event status summary in the event data (address 451W).
5-6
Chapter 5. COMMUNICATION DATA TABLE
■ Event Data
Item
Address
R W Meaning of Data
Event status summary 450
451
❍
X Reads the summary of the event occurrence status of channels 1 to 24.
Bitmap data No.5 (see page 5-28)
-32768 to +32767
Bitmap data No.6 (see page 5-28)
0 to 256
• Even if one of the upper and lower limit events of events No.1 to No.4 occurs, the assigned bit becomes “1”.
Event status (channel 1)
Event status (channel 2)
Event status (channel 3)
Event status (channel 4)
Event status (channel 5)
Event status (channel 6)
Event status (channel 7)
Event status (channel 8)
Event status (channel 9)
Event status (channel 10)
Event status (channel 11)
Event status (channel 12)
Event status (channel 13)
Event status (channel 14)
Event status (channel 15)
Event status (channel 16)
Event status (channel 17)
Event status (channel 18)
Event status (channel 19)
Event status (channel 20)
Event status (channel 21)
Event status (channel 22)
Event status (channel 23)
Event status (channel 24)
461
462
463
464
465
466
467
468
469
470
471
472
473
474
475
476
477
478
479
480
481
482
483
484
❍
❍
❍
❍
❍
❍
❍
❍
❍
❍
❍
❍
❍
❍
❍
❍
❍
❍
❍
❍
❍
❍
❍
❍
X
X
X
X
X
X
X
X
X
X
X
X
X
X
X
X
X
X
X
X
X
X
X
X
Reads the event occurrence status of channels 1 to 24.
Bitmap data No.7 (see page 5-29)
If the upper limit event or the lower limit event of
No.1 to No.4 of each channel occurs, the assigned bit becomes ''1''.
Note
: The content of the event status summary in the process data area
(address 400W) is same as the event status summary in the event data
(address 450W). And the content of the event status summary in the process data area (address 401W) is same as the event status summary in the event data (address 451W).
5-7
Chapter 5. COMMUNICATION DATA TABLE
■
Digital I/O Area (data area)
Item
External switch input status summary
No.1 external switch input
No.2 external switch input
No.3 external switch input
No.4 external switch input
No.5 external switch input
No.6 external switch input
No.7 external switch input
No.8 external switch input
No.9 external switch input
No.10 external switch input
No.11 external switch input
No.12 external switch input
Internal contact input status summary
No.1 internal contact input
No.2 internal contact input
No.3 internal contact input
No.4 internal contact input
No.5 internal contact input
No.6 internal contact input
No.7 internal contact input
No.8 internal contact input
No.9 internal contact input
No.10 internal contact input
No.11 internal contact input
No.12 internal contact input
«
«
«
«
«
«
«
«
«
«
«
«
«
Address
500
R W
«
X
508
509
510
511
512
520
501
502
503
504
505
506
507
X
X
X
X
X
X
X
X
X
X
X
X
X
Meaning of Data
Reads the summary of No.1 to No.12 external switch input status.
Bitmap data No.8 (see page 5-29)
0 to 4095
Reads the status of No.1 to No.12 external switch input status.
0: OFF
1: ON
Reads the summary of No.1 to No.12 internal switch input status.
Bitmap data No.8 (see page 5-29)
0 to 4095
Reads the No.1 to No.12 internal contact input status.
0: OFF
1: ON
«
«
«
«
«
«
«
«
«
«
«
«
526
527
528
529
530
531
532
521
522
523
524
525
X
X
X
X
X
X
X
X
X
X
X
X
5-8
Chapter 5. COMMUNICATION DATA TABLE
No.1 relay output
No.2 relay output
No.3 relay output
No.4 relay output
No.5 relay output
No.6 relay output
No.7 relay output
No.8 relay output
No.9 relay output
No.10 relay output
No.11 relay output
No.12 relay output
Open collector output status summary
No.1 open collector output
No.2 open collector output
No.3 open collector output
No.4 open collector output
No.5 open collector output
No.6 open collector output
No.7 open collector output
No.8 open collector output
No.9 open collector output
No.10 open collector output
No.11 open collector output
No.12 open collector output
Item
Relay output status summary
566
567
568
569
570
571
572
561
562
563
564
565
«
«
«
«
«
«
«
«
«
«
«
«
«
Address
540
R W
«
X
548
549
550
551
552
560
541
542
543
544
545
546
547
X
X
X
X
X
X
X
X
X
X
X
X
X
Meaning of Data
Reads the summary of the No.1 to No.12 relay output status.
Bitmap data No.8 (see page 5-29)
0 to 4095
Reads the No.1 to No.12 relay output status.
0: OFF
1: ON
Reads the summary of the No.1 to No.12 open collector output status.
Bitmap data No.8 (see page 5-29)
0 to 4095
Reads the No.1 to No.12 open collector output status.
0: OFF
1: ON
«
«
«
«
«
«
«
«
«
«
«
«
X
X
X
X
X
X
X
X
X
X
X
X
5-9
Chapter 5. COMMUNICATION DATA TABLE
■
Common Data Area (common setup items)
Item
Address
R W Meaning of Data
No.1 chart feed speed
No.2 chart feed speed
Fixed date interval timer
Fixed time interval timer (h)
600
601
602
603
«
«
«
«
«
«
«
«
Sets and reads the No.1 chart feed speed.
1 to 480 (mm/h)
Sets and reads the No.2 chart feed speed.
1 to 480 (mm/h)
Sets and reads the fixed date interval timer.
1: 10min
2: 20min
3: 30min
4: 1h
5: 2h
6: 3h
7: 6h
8: 12h
9: 24h
Sets and reads the fixed time interval timer.
H: 0 to 23
Min: 0 to 59
Fixed time interval timer (min) 604
« «
The possible setting range is 00:05 to 23:59.
If an attempt is made to set less than 5min, a numerical value range error (response code 44) is returned.
Clock: Year 605
« «
Sets and reads the clock date and time.
Year: 0 to 99
Clock: Month
Clock: Day
606
607
«
«
«
«
Month: 1 to 12
Day: 1 to 31
Clock: H
Clock: Min
608
609
«
«
«
«
H:
Min:
0 to 23
0 to 59
• Non-existent dates (e.g. February 30th) cannot be set.
• If an attempt is made to set a non-existent date, a numerical value range error (response code 44) is returned.
• If “0” to “89” is written, the year becomes 2000 onwards, and if “90” to “98” is written, the year becomes 1990 onwards.
Configuration lock 610
« «
Menu level
Recording format
Recorder ID No.
611
612
613
«
«
«
«
«
«
Reads the setting inhibited (lock), setting permitted
(unlock) and configuration lock setup on the SRF display setup unit.
0: Unlock
1: Lock
Sets and reads the menu level.
0: Level 0 displayed
1: Levels 0 and 1 displayed
2: All items displayed
Sets and reads the recording format.
1: Trend
2: Trend + tabulation
3: Trend + schedule demand
4: Fixed interval tabulation
5: Fixed time tabulation
Writes and reads the recorder ID No.
0 to 99
5-10
Chapter 5. COMMUNICATION DATA TABLE
Item
Address
R W Meaning of Data
Recording time ON/OFF
Scale recording ON/OFF
Recording color selection
Communications access rights
614
615
616
617
«
«
«
«
«
«
«
X
Sets and reads recording time ON/OFF.
0: OFF
1: ON
Sets and reads scale recording ON/OFF.
0: OFF
1: ON
Selects and reads the recording color.
1: Standard type
2: DIN type
Reads the communications access rights when the area is accessed by CPL communications.
1: Read only
2: Read/Write
• Only during reading, writing is not possible even on write-accessible areas.
• Even during reading and writing, writing is not possible on only read-accessible areas, and reading is not possible on only write-accessible areas.
Station address
618
«
X
Reads the communications address used in CPL communications.
0 to 127
• When “0” is set, CPL communications is not possible.
Communications method
619
«
X
Reads the communications method for CPL communications.
1: 4800bps, even parity, 1 stop bit
2: 4800bps, no parity, 2 stop bits
3: 9600bps, even parity, 1 stop bit
4: 9600bps, no parity, 2 stop bits
5-11
Chapter 5. COMMUNICATION DATA TABLE
■
Common Data Area (schedule demand printing)
Item
Address
R W Meaning of Data
Time setup ON/OFF
630
635
636
637
638
631
632
633
634
« « Sets and reads the No.1 to No.8 time setup used in schedule demand printing.
0: OFF
1: No.1 time setup ON (enabled)
2: No.1 and No.2 time setup ON (enabled)
3: No.1 to No.3 time setup ON (enabled)
4: No.1 to No.4 time setup ON (enabled)
5: No.1 to No.5 time setup ON (enabled)
6: No.1 to No.6 time setup ON (enabled)
7: No.1 to No.7 time setup ON (enabled)
8: No.1 to No.8 time setup ON (enabled)
Sets and reads the time when schedule demand printing is carried out.
h: 0 to 23 min: 0 to 59
No.1 time setup: h
No.1 time setup: min
No.2 time setup: h
No.2 time setup: min
No.3 time setup: h
No.3 time setup: min
No.4 time setup: h
No.4 time setup: min
« «
No.5 time setup: h
No.5 time setup: min
No.6 time setup: h
No.6 time setup: min
639
640
641
642
No.7 time setup: h
No.7 time setup: min
No.8 time setup: h
No.8 time setup: min
643
644
645
646
• If the time setup is not set to ON by 630W, demand printing is not carried out at the set time.
5-12
Chapter 5. COMMUNICATION DATA TABLE
■
Common Data Area (messages)
Item
No.1 message
(1st character) to (12th character)
No.2 message
(1st character) to (12th character)
No.3 message
(1st character) to (12th character)
No.4 message
(1st character) to (12th character)
No.5 message
(1st character) to (12th character)
No.6 message
(1st character) to (12th character)
No.7 message
(1st character) to (12th character)
No.8 message
(1st character) to (12th character)
Address
R W
650 to 661
« «
662 to 673
674 to 685
686 to 697
698 to 709
710 to 721
722 to 733
734 to 745
Meaning of Data
Character codes by which 12 characters used for printing messages are set and read
Refer to Appendix, SRF Character Codes.
5-13
Chapter 5. COMMUNICATION DATA TABLE
■
Common Data Area (digital input)
Item
No.1 external switch input
Address
751
R W
« «
No.2 external switch input
No.3 external switch input
No.4 external switch input
No.5 external switch input
No.6 external switch input
No.7 external switch input
No.8 external switch input
No.9 external switch input
No.10 external switch input
No.11 external switch input
No.12 external switch input
752
753
754
755
756
757
758
759
760
761
762
Meaning of Data
Sets and reads the No.1 to No.12 external switch inputs.
0: Function setup OFF
1: Recording ON/OFF (all channels unconditionally)
2: Print on demand
3: Print all lists
4: Print specified lists
5: Chart feed
6: Print communications list
7: Chart feed speed/scale selection
8: Clear batch counter
11 to 16: Clear integrating calculation No.1 to No.6
21 to 28: Print No.1 to No.8 messages
31: Recording ON/OFF (channels 1 to 3)
32: Recording ON/OFF (channels 4 to 6)
33: Recording ON/OFF (channels 7 to 9)
34: Recording ON/OFF (channels 10 to 12)
35: Recording ON/OFF (channels 13 to 18)
36: Recording ON/OFF (channels 19 to 24)
40: BIN code input (bit 0)
41: BIN code input (bit 1)
42: BIN code input (bits 2)
43: BIN code input (bits 3)
44: BIN code input (bits 4)
45: BIN code input (bits 5)
• Channels in which the scale is selected by digital inputs is set by the scale switching method for each channel.
No.1 internal contact input
771
« «
No.2 internal contact input
No.3 internal contact input
No.4 internal contact input
No.5 internal contact input
No.6 internal contact input
No.7 internal contact input
No.8 internal contact input
No.9 internal contact input
No.10 internal contact input
No.11 internal contact input
No.12 internal contact input
772
773
774
775
776
777
778
779
780
781
782
Sets and reads the No.1 to No.12 internal switch inputs.
0: Function setup OFF
1: Recording ON/OFF (all channels unconditionally)
2: Print on demand
3: Print all lists
4: Print specified lists
5: Chart feed
6: Print communications list
7: Chart feed speed/scale selection
8: Clear batch counter
11 to 16: Clear integrating calculation No.1 to No.6
21 to 28: Print No.1 to No.8 messages
31: Recording ON/OFF (channels 1 to 3)
32: Recording ON/OFF (channels 4 to 6)
33: Recording ON/OFF (channels 7 to 9)
34: Recording ON/OFF (channels 10 to 12)
35: Recording ON/OFF (channels 13 to 18)
36: Recording ON/OFF (channels 19 to 24)
40: BIN code input (bit 0)
41: BIN code input (bit 1)
42: BIN code input (bits 2)
43: BIN code input (bits 3)
44: BIN code input (bits 4)
45: BIN code input (bits 5)
• Channels in which the scale is selected by digital inputs is set by the scale switching method for each channel.
5-14
Chapter 5. COMMUNICATION DATA TABLE
■
Common Data Area (digital output)
Item
No.1 relay output
No.2 relay output
No.3 relay output
No.4 relay output
No.5 relay output
No.6 relay output
No.7 relay output
No.8 relay output
No.9 relay output
No.10 relay output
No.11 relay output
No.12 relay output
No.1 open collector output
No.2 open collector output
No.3 open collector output
No.4 open collector output
No.5 open collector output
No.6 open collector output
No.7 open collector output
No.8 open collector output
No.9 open collector output
No.10 open collector output
No.11 open collector output
No.12 open collector output
Address
811
812
821
822
807
808
809
810
801
802
803
804
805
806
827
828
829
830
823
824
825
826
831
832
R W
« «
« «
Meaning of Data
Sets and reads the No.1 to No.12 relay outputs.
0: OR action/excitation/non-hold
1: OR action/excitation/hold
2: OR action/non-excitation/non-hold
3: OR action/non-excitation/hold
4: AND action/excitation/non-hold
5: AND action/excitation/hold
6: AND action/non-excitation/non-hold
7: AND action/non-excitation/hold
8: OR action/excitation/non-hold/event re-output
9: OR action/non-excitation/non-hold/event reoutput
Sets and reads the No.1 to No.12 open collector outputs.
0: OR action/excitation/non-hold
1: OR action/excitation/hold
2: OR action/non-excitation/non-hold
3: OR action/non-excitation/hold
4: AND action/excitation/non-hold
5: AND action/excitation/hold
6: AND action/non-excitation/non-hold
7: AND action/non-excitation/hold
8: OR action/excitation/non-hold/event re-output
9: OR action/non-excitation/non-hold/event reoutput
5-15
Chapter 5. COMMUNICATION DATA TABLE
■
Common Data Area (user functions)
Item
Address
R W Meaning of Data
User function 1 key basic registration
User function 1 assignment 1
User function 1 assignment 2
User function 1 assignment 3
User function 1 assignment 4
User function 1 assignment 5
User function 1 assignment 6
User function 1 assignment 7
User function 1 assignment 8
850
851
852
853
854
855
856
857
858
« «
Sets and reads the basic registration of the user function 1 key.
0: OFF
1: Output to internal contact input No.1
2: Call up setup items
Sets and reads the user function 1 key.
Value obtained by adding the following cardinal numbers to the screen No. of the setup to be registered as “0”.
Setup 0: No assignment
Setup Item Cardinal Number
Event • • • • • • • • • • • • • • • • • • • • 1nn00
Chart feed speed • • • • • • • • • • • • • 1000
Date/time • • • • • • • • • • • • • • • • • • 1500
System • • • • • • • • • • • • • • • • • • • • 2000
Range • • • • • • • • • • • • • • • • • • • 2nn00
(Calculation setup is range setup + 5000)
Scale • • • • • • • • • • • • • • • • • • • • 3nn00
Copy • • • • • • • • • • • • • • • • • • • • • 6500
Schedule demand • • • • • • • • • • • • 2500
Message • • • • • • • • • • • • • • • • • • 3000
Extended • • • • • • • • • • • • • • • • • • 3500
External switch input • • • • • • • • • • 4000
Internal contact input • • • • • • • • • • 4100
Relay output • • • • • • • • • • • • • • • • 4200
Open collector output • • • • • • • • • • 4300
Segment 1 X-axis • • • • • • • • • • • • 5000
Segment 1 Y-axis • • • • • • • • • • • • 5100
Segment 2 X-axis • • • • • • • • • • • • 5200
Segment 2 Y-axis • • • • • • • • • • • • 5300
Segment 3 X-axis • • • • • • • • • • • • 5400
Segment 3 Y-axis • • • • • • • • • • • • 5500
User function 2 key basic registration
860
« «
“nn” indicates the channel No.
Values converted to decimal from hexadecimal are used for the screen No.
Sets and reads the basic registration of the user function 2 key.
0: OFF
1: Output to internal contact input No.2
2: Call up setup items
User function 2 assignment 1
861
« «
Same as user function 1 assignment
User function 2 assignment 2
862
User function 2 assignment 3
863
User function 2 assignment 4
864
User function 2 assignment 5
865
User function 2 assignment 6
866
User function 2 assignment 7
867
User function 2 assignment 8
868
The calculation setup cardinal number is the value obtained by adding “5000” to the range setup cardinal number.
5-16
Chapter 5. COMMUNICATION DATA TABLE
■
Common Data Area (copy)
Item
Address
R W Meaning of Data
Copy source channel
Copy destination channel lower limit
900
901
«
«
«
«
Sets and reads the copy source channel in channel data copying.
1 to number of channels
Sets and reads the copy destination channel lower limit in channel data copying.
1 to (902W) value
• When 901W and 902W are written simultaneously by a single write command, the 902W data to be written simultaneously is written normally, if it is greater than the 901W data to be written, even if the 901W data to be written is greater than the 902W data before it is written.
For example, when 901W=1 and 902W=2, 901W=3/902W=4 can be written simultaneously.
Copy destination channel upper limit
902
« «
Copy execution
903
« «
Sets and reads the copy destination channel upper limit in channel data copying.
(901W) value to number of channels
Executes copying and reads the copy state.
0: Execution OFF/end copy
1: Copy all data
2: Copy range, calculation and scale data
3: Copy event data
4: Copy tag data
5: Copy engineering unit data
• When writing to EEPROM is started by copy execution, the response is returned before writing is completed.
If the command (even other than the copy execution command) for writing to EEPROM is received before writing is completed, response code 31 is returned.
• When a read is carried out, “0” is always read.
Accordingly, read does not become an error response. However, it is meaningless.
• When addresses 900W to 903W contain erroneous data, not all data from 900W to 903W is written, and an error is returned.
• The data (0 to 5) to be written to 903W is not written to EPPROM. However, the data to be copied is written to
EEPROM.
• When the values of the upper and lower limits of the copy destination channel are inverted, a numerical value range error (response code 44) is returned.
■
Common Data Area (extended setup)
Item
Initial printing ON/OFF
Count function switching
Date type selection
Address
910
911
912
R W
« «
« «
« «
Meaning of Data
Switches initial printing (printing of various parameters carried out when recording is started)
ON/OFF.
0: OFF 1: ON
Switches the type of count to be printed.
0: Batch count 1: BIN code
Selects the format of the date to be printed.
0: JP (YY, MM, DD) 1: US (MM, DD, YY)
2: EU (DD, MM, YY)
• JP (Japanese format): The date is printed out as “1997/09/29”
• US (American format): The date is printed out as “SEP,29,'97”.
• EU (European format): The date is printed out as “29,09,1997”.
Atmosphere
913
« «
Thermal resistance
Reference contact compensation
914
915
«
«
«
«
Sets and reads the atmospheric pressure of the parameters used for calculating the relative humidity.
670 to 1330 (hPa)
Sets and reads the resistance of the parameters used for calculating the F value.
10 to 200
Sets reference contact compensation inside the instrument.
0: Internally OFF 1: Internally ON
5-17
Chapter 5. COMMUNICATION DATA TABLE
■
Segment Table Area
Item
Address
R W Meaning of Data
Segment table 1 X-axis point 01
Segment table 1 X-axis point 02
1000
1001
« « Sets and reads the break points in the segment table.
Segment table 1 X-axis point 03
Segment table 1 X-axis point 04
1002
-1000 to +11000
-1000 means -10.00%, and 11000 means 110.00%.
Segment table 1 X-axis point 05
Segment table 1 X-axis point 06
Segment table 1 X-axis point 07
Segment table 1 X-axis point 08
Segment table 1 X-axis point 09
Segment table 1 X-axis point 10
Segment table 1 X-axis point 11
Segment table 1 X-axis point 12
Segment table 1 X-axis point 13
Segment table 1 X-axis point 14
Segment table 1 X-axis point 15
1003
1004
1005
1006
1007
1008
1009
1010
1011
1012
1013
1014
• Writing is possible even if the segment table is not used (nn19W=0).
Segment table 1 Y-axis point 01
Segment table 1 Y-axis point 02
Segment table 1 Y-axis point 03
Segment table 1 Y-axis point 04
Segment table 1 Y-axis point 05
Segment table 1 Y-axis point 06
Segment table 1 Y-axis point 07
1015
« «
1016
1017
1018
1019
1020
1021
1022
Sets and reads the break points in the segment table.
-1000 to +11000
-1000 means -10.00%, and 11000 means 110.00%.
Segment table 1 Y-axis point 08
Segment table 1 Y-axis point 09
Segment table 1 Y-axis point 10
Segment table 1 Y-axis point 11
Segment table 1 Y-axis point 12
Segment table 1 Y-axis point 13
Segment table 1 Y-axis point 14
Segment table 1 Y-axis point 15
1023
1024
1025
1026
1027
1028
1029
• Writing is possible even if the segment table is not used (nn19W=0).
5-18
Chapter 5. COMMUNICATION DATA TABLE
Item
Address
R W Meaning of Data
Segment table 2 X-axis point 01
1030
« «
Sets and reads the break points in the segment table.
Segment table 2 X-axis point 02
1031
Segment table 2 X-axis point 03
1032
-1000 to +11000
-1000 means -10.00%, and 11000 means 110.00%.
Segment table 2 X-axis point 04
1033
Segment table 2 X-axis point 05
1034
Segment table 2 X-axis point 06
1035
Segment table 2 X-axis point 07
1036
Segment table 2 X-axis point 08
1037
Segment table 2 X-axis point 09
1038
Segment table 2 X-axis point 10
1039
Segment table 2 X-axis point 11
1040
Segment table 2 X-axis point 12
1041
Segment table 2 X-axis point 13
1042
Segment table 2 X-axis point 14
1043
Segment table 2 X-axis point 15
1044
• Writing is possible even if the segment table is not used (nn19W=0).
Segment table 2 Y-axis point 01
Segment table 2 Y-axis point 02
Segment table 2 Y-axis point 03
Segment table 2 Y-axis point 04
1045
« «
1046
1047
1048
Sets and reads the break points in the segment table.
-1000 to +11000
-1000 means -10.00%, and 11000 means 110.00%.
Segment table 2 Y-axis point 05
Segment table 2 Y-axis point 06
Segment table 2 Y-axis point 07
Segment table 2 Y-axis point 08
1049
1050
1051
1052
Segment table 2 Y-axis point 09
Segment table 2 Y-axis point 10
Segment table 2 Y-axis point 11
Segment table 2 Y-axis point 12
1053
1054
1055
1056
Segment table 2 Y-axis point 13
Segment table 2 Y-axis point 14
1057
1058
Segment table 2 Y-axis point 15
1059
• Writing is possible even if the segment table is not used (nn19W=0).
5-19
Chapter 5. COMMUNICATION DATA TABLE
Item
Address
R W Meaning of Data
Segment table 3 X-axis point 01
1060
« «
Sets and reads the break points in the segment table.
Segment table 3 X-axis point 02
1061
Segment table 3 X-axis point 03
1062
-1000 to +11000
-1000 means -10.00%, and 11000 means 110.00%.
Segment table 3 X-axis point 04
1063
Segment table 3 X-axis point 05
1064
Segment table 3 X-axis point 06
1065
Segment table 3 X-axis point 07
1066
Segment table 3 X-axis point 08
1067
Segment table 3 X-axis point 09
1068
Segment table 3 X-axis point 10
1069
Segment table 3 X-axis point 11
1070
Segment table 3 X-axis point 12
1071
Segment table 3 X-axis point 13
1072
Segment table 3 X-axis point 14
1073
Segment table 3 X-axis point 15
1074
• Writing is possible even if the segment table is not used (nn19W=0).
Segment table 3 Y-axis point 01
Segment table 3 Y-axis point 02
Segment table 3 Y-axis point 03
Segment table 3 Y-axis point 04
1075
1076
1077
1078
1079
« «
Sets and reads the break points in the segment table.
-1000 to +11000
-1000 means -10.00%, and 11000 means 110.00%.
Segment table 3 Y-axis point 05
Segment table 3 Y-axis point 06
Segment table 3 Y-axis point 07
Segment table 3 Y-axis point 08
1080
1081
1082
1083 Segment table 3 Y-axis point 09
Segment table 3 Y-axis point 10
Segment table 3 Y-axis point 11
Segment table 3 Y-axis point 12
1084
1085
1086
1087 Segment table 3 Y-axis point 13
Segment table 3 Y-axis point 14
Segment table 3 Y-axis point 15
1088
1089
• Writing is possible even if the segment table is not used (nn19W=0).
5-20
Chapter 5. COMMUNICATION DATA TABLE
■ Channel Data (range)
Address “nn” is a value obtained by adding “10” to channels “1” to “24”.
For example, “nn” becomes “11” in the case of channel 1.
Range code
Item
Recording mode
Address nn00
❍ nn01
R
❍
W
❍
❍
Meaning of Data
Sets and reads the recording mode.
0: OFF
1: Display
2: Display + recording
3: Digital input-dependent
Sets and reads the range codes to be used.
See Range Code Table (page 5-30).
• If the range code is written, the following are initialized to their defaults: measurement range decimal point/lower limit/upper limit, engineering range decimal point/lower limit/upper limit, PV bias value, No.1 and
No.2 scale lower limit/upper limit, scale switching method, auto-switching point and auto-switching differential.
• When the range code is set to the communications input B or ON/OFF, a sub-code number is required.
Sub-code No.
nn02
❍ ❍
If set for ON/OFF input range;
Sets and reads the sub-code No.
See table for “Digital data acquisition point address” (page 5-31).
If set for communications input B;
Sets and reads the sub-code No.
See table for “PV data acquisition point address“ (page 5-31).
• Settings are enabled only in the case of the communications input B or ON/OFF input range.
Burnout nn03
❍ ❍
Sets and reads operation at burnout.
0: OFF
1: UP
2: DOWN
Measurement range decimal point nn04
❍
X Reads the measurement range decimal point.
0: No digits past the decimal point XXXXX
1: 1 digit past the decimal point
2: 2 digits past the decimal point
XXXX.X
XXX.XX
3: 3 digits past the decimal point
4: 4 digits past the decimal point
XX.XXX
X.XXXX
Measurement range lower limit nn05
❍ ❍
Sets and reads the measurement range lower limit.
-19999 to +29999
• Set the measurement range lower limit so that it is smaller than the measurement range upper limit.
• When the range code is changed, settings are initialized to their defaults.
• For details on the decimal point, refer to the measurement range decimal point (address: nn04W).
Measurement range upper limit nn06
❍ ❍
Sets and reads the measurement range upper limit.
-19999 to +29999
• Set the measurement range lower limit so that it is smaller than the measurement range upper limit.
• When the measurement range lower limit is set so that it is equal to or greater than the measurement range upper limit, a numerical value range error (response code 44) is returned.
• When the range code is changed, settings are initialized to their defaults.
• For details on the decimal point, refer to the measurement range decimal point (address: nn04W).
5-21
Chapter 5. COMMUNICATION DATA TABLE
Item
Address
R W Meaning of Data
Engineering range decimal point nn07
« «
Sets and reads the engineering range decimal point.
0: No digits past the decimal point XXXXX
1: 1 digit past the decimal point XXXX.X
2: 2 digits past the decimal point
3: 3 digits past the decimal point
4: 4 digits past the decimal point
XXX.XX
XX.XXX
X.XXXX
• If the scaling is not linear the range code setting is disabled.
• When the range code is changed, settings are initialized to their defaults.
Engineering range lower limit nn08
« « Sets and reads the engineering range lower limit.
-19999 to +29999
• For details on the decimal point, refer to the engineering range decimal point (address: nn07W).
• When the range code is changed, settings are initialized to their defaults.
Engineering range upper limit nn09
« « Sets and reads the engineering range upper limit.
-19999 to +29999
• For details on the decimal point, refer to the engineering range decimal point (address: nn07W).
• When the range code is changed, settings are initialized to their defaults.
PV filter nn10
« «
Sets and reads the PV filter.
0 to 15
• Settings are disabled in the case of the communications input range and ON/OFF input range.
PV bias nn11
« « Sets and reads the PV bias.
-19999 to +29999
• Settings are disabled in the case of the communications input range and ON/OFF input range.
• When the range code is changed, settings are initialized to their defaults.
5-22
Chapter 5. COMMUNICATION DATA TABLE
■ Channel Data (calculation)
Address “nn” is a value obtained by adding “10” to channels “1” to “24”.
For example, “nn” becomes “11” in the case of channel 1.
Item
Address
R W Meaning of Data
Input calculation type nn15
❍ ❍
Sets and reads the input calculation type.
0: OFF (PV value)
1: Channel A - channel B
2: Fixed value - current channel
3: Current channel - fixed value
4: Integrating calculation
5: F value calculation
6: Relative humidity calculation
• When the input calculation type is changed, calculation parameters 1 to 3 are initialized to their defaults.
Calculation parameter 1 nn16
❍ ❍
Sets and reads calculation parameter 1.
• When input calculation type is set to “1”:
1 to number of channels: Ach of inter-channel deviation
• When input calculation type is set to “2”:
-19999 to +29999:fixed value of fixed value deviation
• When input calculation type is set to “3”:
-19999 to +29999:fixed value of fixed value deviation
• When input calculation type is set to “4”:
0: Integrating unit set to “s”
1: Integrating unit set to “min”
2: Integrating unit set to “h”
• When input calculation type is set to “5”:
0 to 2000: Value 10 times the standard reference temperature of F value calculation
(Example: “121.1°C” becomes “1211”.)
• When input calculation type is set to “6”:
1 to number of channels: dry-bulb temperature input channel
• This setting is disabled when the input calculation type is set to OFF.
In this case, the numerical value range is in error if a value other than “0” is written.
• When the input calculation type is changed, the settings are initialized to their defaults.
Calculation parameter 2 nn17
❍ ❍
Sets and reads the calculation parameter 2.
• When input calculation type is set to “1”:
1 to number of channels: Bch of inter-channel deviation
• When input calculation type is set to “4”:
1 to 6: reset number of integrating calculation
• When input calculation type is set to “5”:
1 to 6: reset number of F value calculation
• When input calculation type is set to “6”:
0: Large wind speed (2.5m/s or more)
1: Medium wind speed (0.5 to 2.5m/s)
2: Small wind speed (0.5m/s or less)
• This setting is disabled when the input calculation type is set to OFF or fixed value deviation.
In this case, the numerical value range is in error if a value other than “0” is written.
• When the input calculation type is changed, the settings are initialized to their defaults.
Calculation parameter 3 nn18
❍ ❍
Sets and reads integrating parameter 3.
0 to 10: Integration weighting
• This setting is disabled when the input calculation type is set to other than integrating type.
In this case, “0” to “10” can be written.
• When the input calculation type is changed, the settings are initialized to their defaults.
Segment table use nn19
❍ ❍
Sets and reads segment table use.
0: Use disabled
1: Use segment table 1
2: Use segment table 2
3: Use segment table 3
5-23
Chapter 5. COMMUNICATION DATA TABLE
■ Channel Data (scale)
Address “nn” is a value obtained by adding “10” to channels “1” to “24”.
For example, “nn” becomes “11” in the case of channel 1.
Item
No.1 scale lower limit
Address
R nn20
❍
W
❍
Meaning of Data
Sets and reads the No.1 scale lower limit value.
-19999 to +29999
• When the range code is changed, settings are initialized to their defaults.
• For details on the decimal point, refer to the engineering range decimal point (address: nn07W).
No.1 scale upper limit nn21
❍ ❍
Sets and reads the No.1 scale upper limit value.
-19999 to +29999
• When the range code is changed, settings are initialized to their defaults.
• For details on the decimal point, refer to the engineering range decimal point (address: nn07W).
Scale switching method nn22
❍ ❍
Sets and reads the scale switching method
0: OFF
1: Automatic
2: External switch input, internal contact input or
CPL communications
• When the range code is changed, settings are initialized to their defaults.
No.2 scale lower limit nn23
❍ ❍
Sets and reads the No.2 scale lower limit value.
-19999 to +29999
• When the range code is changed, settings are initialized to their defaults.
• For details on the decimal point, refer to the engineering range decimal point (address: nn07W).
No.2 scale upper limit nn24
❍ ❍
Sets and reads the No.2 scale upper limit value.
-19999 to +29999
• When the range code is changed, settings are initialized to their defaults.
• For details on the decimal point, refer to the engineering range decimal point (address: nn07W).
Auto-switching point nn25
❍ ❍
Sets and reads the auto-switching point.
-19999 to +29999
• When the range code is changed, settings are initialized to their defaults.
Settings are not initialized even if the scale switching method is changed.
• For details on the decimal point, refer to the engineering range decimal point (address: nn07W)
Auto-switching differential nn26
❍ ❍
Sets and reads the auto-switching differential.
0 to 29999
• When the range code is changed, settings are initialized to their defaults.
Settings are not initialized even if the scale switching method is changed.
• For details on the decimal point, refer to the engineering range decimal point (address: nn07W)
Scale selection status nn27
❍ ❍
Reads the scale selection status.
1: No.1 scale
2: No.2 scale
5-24
Chapter 5. COMMUNICATION DATA TABLE
■ Channel Data (event)
●
●
Address “nn” is a value obtained by adding “10” to channels “1” to “24”.
For example, “nn” becomes “11” in the case of channel 1.
For details on the decimal point, refer to the engineering range decimal point
(address: nn07W).
Item
No.1 event setting value
No.2 event setting value
No.3 event setting value
No.4 event setting value
No.1 event type selection
No.2 event type selection
No.3 event type selection
No.4 event type selection
Address nn40 nn41 nn42 nn43 nn44 nn45 nn46 nn47
❍
R W
❍ ❍
❍
Meaning of Data
Sets and reads the No.1 to No.4 event setting values.
-19999 to +29999
Sets and reads the No.1 to No.4 event type selection.
0: OFF
1: LOW
2: HIGH
❍ ❍
No.1 event differential
No.2 event differential
No.3 event differential
No.4 event differential
No.1 event recording ON/OFF
No.2 event recording ON/OFF
No.3 event recording ON/OFF
No.4 event recording ON/OFF
No.1 event output destination nn48 nn49 nn50 nn51 nn52 nn53 nn54 nn55 nn56
❍
❍
❍
❍
Sets and reads the No.1 to No.4 event differential value.
0 to 29999
Sets and reads the No.1 to No.4 event recording
ON/OFF.
0: OFF
1: ON
No.2 event output destination
No.3 event output destination nn57 nn58
Sets and reads the No.1 to No.4 event output destination.
0: OFF
1 to 12: No.1 to No.12 relay output
13 to 24: No.1 to No.12 open collector output
25 to 36: No.1 to No.12 internal contact input
No.4 event output destination nn59
Tag (1st character) to (12th character)
❍ ❍
Engineering unit (1st character) to
(6th character) nn60 to nn71 nn80 to nn85
❍ ❍
Writes and reads the tag character string (12 characters).
Refer to Appendix, SRF Character Codes.
Writes and reads the engineering unit string (6 characters).
Refer to Appendix, SRF Character Codes.
5-25
Chapter 5. COMMUNICATION DATA TABLE
■
Communication Data Area
Item
Address
R W Meaning of Data
Communications PV value
(communications input A
*1 communications input B
*2
) or
3500
« « to
3523
Writes and reads the communications PV value.
-19999 to +29999
• The communications PV value becomes “not fixed” when the power is turned ON again.
Communication list 1st line
(1st character) to (85th character)
Communication list 2nd line
(1st character) to (85th character)
Communication list 3rd line
(1st character) to (85th character)
3600 to
3684
3700 to
3784
3800 to
3884
«
«
«
«
«
«
Writes and reads the printed characters on the 1st and 3rd lines of the communications list.
Refer to Appendix, SRF Character Codes.
• The 1st to the 3rd line are printed together.
• If a complete line is not all characters (20H, 84H to 8FH, A0H), that line is not printed, and the next line is printed pushed up.
*1 Communications input A
Range code PV data acquisition point address
(CPL address)
80
81
82
83
84
85
86
87
3500W
3501W
3502W
3503W
3504W
3505W
3506W
3507W
*2 Communications input B
Range code Sub-code PV data acquisition
No.
point address
(CPL address)
88
2
3
0
1
4
5
6
9
10
7
8
11
3500W
3501W
3502W
3503W
3504W
3505W
3506W
3507W
3508W
3509W
3510W
3511W
See "
■
Range code tables" (Page 5-30) for details.
Range code Sub-code PV data acquisition
No.
point address
(CPL address)
88
12
13
14
15
16
17
18
19
20
21
22
23
3512W
3513W
3514W
3515W
3516W
3517W
3518W
3519W
3520W
3521W
3522W
3523W
5-26
Chapter 5. COMMUNICATION DATA TABLE
■
Bitmap Data
No.1
Clear integrating calculation (address: 306W) b5 b4 b3 b2 b1 b0
16 15 14 13 12 11 10 9 8 7 6 5 4 3 2 1
1 : Clear integrating calculation No.1
2 : Clear integrating calculation No.2
3 : Clear integrating calculation No.3
4 : Clear integrating calculation No.4
5 : Clear integrating calculation No.5
6 : Clear integrating calculation No.6
7 to 16 : —
No.2
Integrating calculation status (address: 316W) b13 b12 b11 b10 b9 b8 b5 b4 b3 b2 b1 b0
16 15 14 13 12 11 10 9 8 7 6 5 4 3 2 1
1 : 0 to 5 : Clear integration by communications No.1
2 : 0 to 5 : Clear integration by communications No.2
3 : 0 to 5 : Clear integration by communications No.3
4 : 0 to 5 : Clear integration by communications No.4
5 : 0 to 5 : Clear integration by communications No.5
6 : 0 to 5 : Clear integration by communications No.6
7, 8: —
9 : Clear integration by DI and communications No.1
10 : Clear integration by DI and communications No.2
11 : Clear integration by DI and communications No.3
12 : Clear integration by DI and communications No.4
13 : Clear integration by DI and communications No.5
14 : Clear integration by DI and communications No.6
15, 16: —
No.3
Instrument alarm information (address: 380W) b15 b14 b13 b12 b11 b10 b9 b8 b6 b5 b4 b3 b2 b0
16 15 14 13 12 11 10 9 8 7 6 5 4 3 2 1
1 : ROM diagnosis
2 : —
3 : EEPROM diagnosis
4 : Calibration data diagnosis
5 : Configuration data diagnosis
6 : Auto-zero input diagnosis
7 : Reference voltage diagnosis
8 : —
9 : Reference contact temperature diagnosis
10 : Model No. information diagnosis
11 : A/D converter diagnosis
12 : Printer position diagnosis
13 : Ribbon position diagnosis
14 : Mode selection pin diagnosis
15 : Clock backup battery diagnosis
16 : Processing cycle diagnosis
5-27
Chapter 5. COMMUNICATION DATA TABLE
No.4
Option information (address: 398W) b7 b6 b5 b4 b3 b2 b1 b0
16 15 14 13 12 11 10 9 8 7 6 5 4 3 2 1
1 : RS-485 communication
2 : RS-232C communication
3 : No.1 to No.4 external switch input
4 : No.5 to No.8 external switch input
5 : No.9 to No.12 external switch input
6 : No.1 to No.6 relay output
7 : No.7 to No.12 relay output
8 : No.1 to No.12 open collector output
9 to 16 : —
No.5
Event status summary (address: 400, 450W) b15 b14 b13 b12 b11 b10 b9 b8 b7 b6 b5 b4 b3 b2 b1 b0
16 15 14 13 12 11 10 9 8 7 6 5 4 3 2 1
1 : Channel 1
2 : Channel 2
3 : Channel 3
4 : Channel 4
5 : Channel 5
6 : Channel 6
7 : Channel 7
8 : Channel 8
9 : Channel 9
10 : Channel 10
11 : Channel 11
12 : Channel 12
13 : Channel 13
14 : Channel 14
15 : Channel 15
16 : Channel 16
No.6
Event status summary (address: 401, 451W) b23 b22 b21 b20 b19 b18 b17 b16
16 15 14 13 12 11 10 9 8 7 6 5 4 3 2 1
1 : Channel 17
2 : Channel 18
3 : Channel 19
4 : Channel 20
5 : Channel 21
6 : Channel 22
7 : Channel 23
8 : Channel 24
9 to 16 : —
5-28
Chapter 5. COMMUNICATION DATA TABLE
No.7
Event status (address: 461 to 484W) b7 b6 b5 b4 b3 b2 b1 b0
16 15 14 13 12 11 10 9 8 7 6 5 4 3 2 1
1 : No.1 lower-limit event status
2 : No.1 upper-limit event status
3 : No.2 lower-limit event status
4 : No.2 upper-limit event status
5 : No.3 lower-limit event status
6 : No.3 upper-limit event status
7 : No.4 lower-limit event status
8 : No.4 upper-limit event status
9 to 16 : —
No.8
External switch input status summary (address: 500W)
Internal contact input status summary (address: 520W)
Relay output status summary (address: 540W)
Open collector output status summary (address: 560W) b11 b10 b9 b8 b7 b6 b5 b4 b3 b2 b1 b0
16 15 14 13 12 11 10 9 8 7 6 5 4 3 2 1
7
8
9
10
11
12
13 to 16
5
6
3
4
1
2
External Switch Input
Status Summary
No.1 external switch input
No.2 external switch input
No.3 external switch input
No.4 external switch input
No.5 external switch input
No.6 external switch input
No.7 external switch input
No.8 external switch input
No.9 external switch input
No.10 external switch input
No.11 external switch input
No.12 external switch input
Internal Contact Input
Status Summary
No.1 internal switch input
No.2 internal switch input
No.3 internal switch input
No.4 internal switch input
No.5 internal switch input
No.6 internal switch input
No.7 internal switch input
No.8 internal switch input
No.9 internal switch input
No.10 internal switch input
No.11 internal switch input
No.12 internal switch input
—
Relay Output
Status Summary
No.1 relay output
No.2 relay output
No.3 relay output
No.4 relay output
No.5 relay output
No.6 relay output
No.7 relay output
No.8 relay output
No.9 relay output
No.10 relay output
No.11 relay output
No.12 relay output
Open Collector Output
Status Summary
No.1 open collector output
No.2 open collector output
No.3 open collector output
No.4 open collector output
No.5 open collector output
No.6 open collector output
No.7 open collector output
No.8 open collector output
No.9 open collector output
No.10 open collector output
No.11 open collector output
No.12 open collector output
5-29
Chapter 5. COMMUNICATION DATA TABLE
■
Range Code Tables
Input Type
DC voltage
Linear scaling range
DC voltage
Input voltage direct-reading range
*1
Thermocouple
Resistance temperature detector
Communications input A *2
Communications input B *2
ON/OFF *3 mV
V mV
V
T
N
WRe0-26
WRe5-26
PR40-20
PL II
Ni-Ni•Mo
Pt100
E
J
B
K
R
S
JPt100
JPt50
Ni508
No sub-code setting required
Sub-code setting required
—
Range Code
27/57
28/58
29/59
30/60
31/61
32/62
40/70
41/71
16
20/50
21/51
22/52
23/53
24/54
25/55
26/56
42/72
43/73
80 to 87
88
90
12
13
14
15
05
06
10
11
00
01
02
03
04
Measurement Range
-20.00 to +20.00
-40.00 to +40.00
-60.00 to +60.00
-200.0 to +200.0
-2.000 to +2.000
-5.000 to +5.000
0.000 to 10.000
-20.00 to +20.00
-40.00 to +40.00
-60.00 to +60.00
-200.0 to +200.0
-2.000 to +2.000
-5.000 to +5.000
0.000 to 10.000
0.0 to 1760.0°C
0.0 to 1760.0°C
0.0 to 1820.0°C
-200.0 to +1370.0°C
-220.0 to +800.0°C
-200.0 to +1100.0°C
-200.0 to +400.0°C
0.0 to 1300.0°C
0.0 to 2320.0°C
0.0 to 2320.0°C
0.0 to 1880.0°C
0.0 to 1290.0°C
0.0 to 1200.0°C
-200.0 to +650.0°C
-200.0 to +550.0°C
-200.0 to +550.0°C
-50.0 to +150.0°C
32 to 3308°F
-328 to +2498°F
-328 to +1472°F
-328 to +2012°F
-328 to +752°F
32 to 2372°F
32 to 4208°F
32 to 4208°F
32 to 3416°F
32 to 2354°F
32 to 2192°F
-328.0 to +1202.0°F
-328.0 to +1022.0°F
-328.0 to +1022.0°F
-58.0 to +302.0°F
-19999 to +29999
-19999 to +29999
32 to 3200°F
32 to 3200°F
*1 Voltage value can be read directly without linear scaling.
5-30
*2 The value acquired by CPL communications is handled as a PV input value, and is processed for recording in the same way as in usual processing.
Acquisition point address of the communications input data is set as follows:
Communications input A : If the communications input is used in less than 8 channels, the PV data acquisition point address can be designated by setting the range codes from
"80" through to "87". Sub-code setting is not required.
Range code PV data acquisition point address
(CPL address)
80
81
82
83
84
85
86
87
3500W
3501W
3502W
3503W
3504W
3505W
3506W
3507W
Chapter 5. COMMUNICATION DATA TABLE
Communications input B : The PV data acquisition point address can be set by selecting the range code
" 88 " and setting the sub-code when the communications input is used in more than 9 channels.
Range code Sub-code PV data acquisition
No.
point address
(CPL address)
0 3500W
88
3
4
1
2
5
6
7
3501W
3502W
3503W
3504W
3505W
3506W
3507W
10
11
8
9
3508W
3509W
3510W
3511W
Range code Sub-code PV data acquisition
No.
point address
(CPL address)
12 3512W
88
13
14
15
16
17
18
19
3513W
3514W
3515W
3516W
3517W
3518W
3519W
20
21
22
23
3520W
3521W
3522W
3523W
*3 ON/OFF type digital signal is recorded as an input. The ON/OFF input data acquisition point address is designated by setting the range code "90" and by the following sub-code No.:
Sub-code No.
0
1 to 12
13 to 24
31 to 42
51 to 62
Digital data acquisition point address
OFF
Relay output No.1 to No.12
Open collector output No.1 to No.12
External switch input No.1 to No.12
Internal contact input No.1 to No.12
Supplement
A digital data acquisition point address can be designated regardless of the presence of actual digital input and output. However, the "OFF" status is fixed when a digital input that is not installed is designated.
5-31
Chapter 6.
TROUBLESHOOTING
■
Check Items in Case Communication is Disabled
1. Make sure that the RS-232C and RS-485 connections are correctly wired.
2. Make sure that the communication conditions for the SRF206/212/224 match those of the host computer.
If any one of the below settings between stations differ, communication is disabled.
Settings that can be used on the SRF206/212/224 are underlined.
Transmission speed:
Data length:
Parity:
Stop bit:
4800, 9600bps
8bits
No parity, even parity
1 stop bit, 2 stop bits
3. Make sure that the destination address of the command frame transmitted from the host computer matches the address of the
SRF206/212/224
.
The
SRF206/212/224 default address is “0”. The
SRF206/212/224 will not respond even when the destination address of the command frame is set to “00”
(30H, 30H).
4. Use the upper-case for all characters other than the device ID code (“X” or “x” on the
SRF206/212/224
).
6-1
Chapter 7.
SPECIFICATIONS
■ RS-232C Specifications
Name
Transmission mode
Transmission line
Transmission speed (bps)
Transmission distance
Communications flow
Synchronization
Data format
Error detection
Station address
Network type
Other
Remarks
Unbalanced
3-wire system
1200, 2400, 4800, 9600
15m max.
Half duplex
Start-stop synchronization
8 data bits, 1 stop bit, even parity
8 data bits, 2 stop bits, no parity
Parity check, checksum
0 to 127 (Communication function is inhibited when set to “0”.)
1-to-1
Conforms to RS-232C interface specifications.
■ RS-485 Specifications
Name
Transmission mode
Transmission line
Transmission speed (bps)
Transmission distance
Communications flow
Synchronization
Data format
Error detection
Station address
Network type
Other
Remarks
Balanced
5-wire system/3-wire system
1200, 2400, 4800, 9600
500m max.
(300m when connected with the
MA500DIM and CMC410.)
Half duplex
Start-stop synchronization
8 data bits, 1 stop bit, even parity
8 data bits, 2 stop bits, no parity
Parity check, checksum
0 to 127 (Communication function is inhibited when set to “0”.)
1-to-N (31 units or less, however 16 units or less for MA500 DIM or
CMC410)
Conforms to RS-485 interface specifications.
7-1
APPENDIX
■
Code Table
0
0
1
2 STX
3 ETX
6
7
4
5
8
9
A LF
B
E
F
C
D CR
1 2 3 4 5 6 7
SPACE
0 @ P p
!
1 A Q
`
a
"
2 B R b r q
# 3 C S c s
$
%
4
5
D
E
T
U d e t u
(
& 6 F V f v
'
7 G W g w
8 H X h x
/
) 9 I Y i y
*
+
:
J Z j z
;
K [ k {
,
< L ¥ l
— = M ] m
.
> N ^ n
?
O _ o
}
~
^
The shaded areas ( ) are not used by this communication system. (The codes depend on the station.)
App.-1
APPENDIX
■ SRF Character Code Table
Lower
Bits
Upper
Bits
0
1
2
3
4
5
6
7
8
9
A
B
C
D
E
F
2
,
(44)
—
(45)
.
(46)
/
(47)
(
(40)
)
(41)
*
(42)
+
(43)
$
(36)
%
(37)
&
(38)
´
(39)
(32)
!
(33)
“
(34)
#
(35)
4
L
(76)
M
(77)
N
(78)
O
(79)
H
(72)
I
(73)
J
(74)
K
(75)
D
(68)
E
(69)
F
(70)
G
(71)
@
(64)
A
(65)
B
(66)
C
(67)
3
<
(60)
=
(61)
>
(62)
?
(63)
8
(56)
9
(57)
:
(58)
;
(59)
4
(52)
5
(53)
6
(54)
7
(55)
0
(48)
1
(49)
2
(50)
3
(51)
5 6 7 8 t
(116) u
(117) v
(118) w
(119) p
(112) q
(113) r
(114) s
(115) x
(120) y
(121) z
(122)
Ω
(123) l
(108) m
(109) n
(110) o
(111) h
(104) i
(105) j
(106) k
(107) d
(100) e
(101) f
(102) g
(103)
`
(96) a
(97) b
(98) c
(99)
(124)
µ
(125)
2
(126)
2
(127)
(132)
(133)
(134)
(135)
(136)
(137)
(138)
(139)
(140)
(141)
(142)
(143)
3
(128)
°
(129)
°
(130)
•
(131)
¥
(92)
]
(93)
^
(94)
_
(95)
X
(88)
Y
(89)
Z
(90)
[
(91)
T
(84)
U
(85)
V
(86)
W
(87)
P
(80)
Q
(81)
R
(82)
S
(83)
App.-2
APPENDIX
■
Connection With CMC10L
The
CMC10L001A000 is available as an RS-232C/RS-485 (5-wire system) converter from Yamatake. The following diagram shows an example of wiring, using a straight cable for a host computer in the terminal mode:
Terminating resistor
DIGITRONIK control or
5-wire system (slave station)
SDA
SDB
RDA
*
*
RDB
SG
FG
DA
DB
Shielded cable
RD
SD
2
3
MOD.
2
TER.
MOD.
3
TER.
SG
RS
CS
DR
SG
ER
7
8
6
5
4
CD
1
Host computer
7
8
6
5
4
1
CMC10L
Shielded cable
Shielded cable
Terminating resistor
3-wire system (slave station)
DA
DB
SG
FG
DIGITRONIK control or
5-wire system (slave station)
SDA
SDB
RDA
*
*
RDB
SG
FG
Connect two terminating resistors of 150 Ω±5%, 1/2W min. to the instrument at each end of the transmission line. Connect only one end of the shielded wire to the frame ground.
(*) must be wired externally.
App.-3
APPENDIX
Connect the master station SD to the slave station RD, and the master station RD to the slave station SD.
So, set the MODE switch on the front of the CMC10L as (MODEM/TERMI
NAL) of the host computer RS-232C connector and the type of cable
(crossover/straight) used.
RS-232C
TERMINAL
TERMINAL
MODE
MODE
Cable type MODE switch
Straight
Crossover
Straight
Crossover
MODEM
TERMINAL
TERMINAL
MODEM
● RS-232C cable
Straight: An RS-232C cable with a D-Sub (9-pin) connector at each end where pins with the same number are mutually connected (for example, pin 2 to pin 2, and pin 3 to pin 3).
CD
RD
SD
ER
SG
DR
RS
CS
6
7
8
3
4
5
1
2
6
7
8
3
4
5
1
2
CD
RD
SD
ER
SG
DR
RS
CS
Crossover: An RS-232C cable with a D-Sub (9-pin) connector at each end where different number pins are connected (for example, pin 2 to pin 3, and pin 3 to pin 2).
RD
SD
RS
CS
DR
ER
CD
SG
2
3
7
8
6
4
1
5
2
3
7
8
6
4
1
5
RD
SD
RS
CS
DR
ER
CD
SG
App.-4
APPENDIX
D-Sub (25-pin) ↔D-Sub (9-pin) conversion cable :
An RS-232C cable for conversion between D-Sub (25-pin) and D-Sub (9-pin).
FG
SD
RD
RS
CS
DR
ER
CD
SG
1
2
3
4
5
6
20
8
7
3
8
6
4
2
7
1
5
SD
RD
RS
CS
DR
ER
CD
SG
App.-5
Revision History
Printed Manual Number Edition
Date
Revised pages Description
98-08 CP-SP-1028E 1st Edition
99-11
02-08
08-03
2nd Edition
4-3
4-4
Appendix-2
Communication frame changed from 5 35H to
A 41H.
Checksum Example changed:
7BH→76H, 85H→8AH,
“85”, (38H) and (35H)Æ“8A”, (38H) and (41H)
Character code (124) removed.
3rd Edition
1-4
2-1
2-2
2-3, 2-4
2-5
2-6
4-2
4-12
4-13
5-21
Description of CPL communications changed,
Figure changed.
Description changed, Handling Precautions deleted.
Figure of Example of connection using changed,
Layout of RS-232C connector signals changed.
Section 2-2 RS-485 Connection Overall changed.
Figure of connection example changed,
Cable model No.changed.
Description changed.
Frame of Read instruction, EXT→ETX changed.
Item of Priority deleted.
CMA50 deleted.
Address of Range code "nn00"→"nn01" changed,
Digital signal No.→Sub-code No. changed, description of Digital signal No.chaged,
5-26
5-30, 5-31
Description of communication input B added.
Address of communication PV value 3500 to
3507→3500 to 3523 changed, Description of communication input A and communication input
B added.
Description of communication input A and communication input B added.
Old chapter 6. COMMUNICATION PROGRAM Chapter 6
FOR MASTER STATION deleted, old chapter 7. TROUBLESHOOTING.
Chapter 7
App.-3
Old chapter 8. SPECIFICATIONS.
Description of connection with CMA50→ connection with CMC10L changed.
App.-4, App.-5 Description of RS-232C cable changed.
4th Edition
2-2
2-3, 2-4, 2-6
5-6, 5-7
App.-2
App.-4
Signal table (25 pins, 14 pins) deleted.
Handling Precautions added.
Note and comment added.
Upper bits row and lower bits column corrected.
Assigned signals RD and SD changed.
Advanced Automation Company
1-12-2 Kawana, Fujisawa
Kanagawa 251-8522 Japan
URL: http://www.azbil.com
Printed on recycled paper.
(07)
Specifications are subject to change without notice.
Printed in Japan.
1st Edition: Issued in Aug. 1998(M)
4th Edition: Issued in Mar. 2008(G)
advertisement
* Your assessment is very important for improving the workof artificial intelligence, which forms the content of this project