- Computers & electronics
- Telecom & navigation
- Mobile phones
- Car kits
- Gast
- Oil-less Piston Vacuum Pumps & Compressors
- Owner's manual
Gast Oil-less Piston Vacuum Pumps & Compressors Owner's Manual
Add to my manuals
16 Pages
Gast Oil-less Piston Vacuum Pumps & Compressors are durable and reliable devices designed to handle clean, dry air in various applications. With their oil-less operation, these pumps require minimal maintenance and eliminate the need for lubrication, reducing operating costs. Suitable for both vacuum and pressure applications, they offer versatility and can be used in industries such as medical, dental, packaging, and environmental.
advertisement
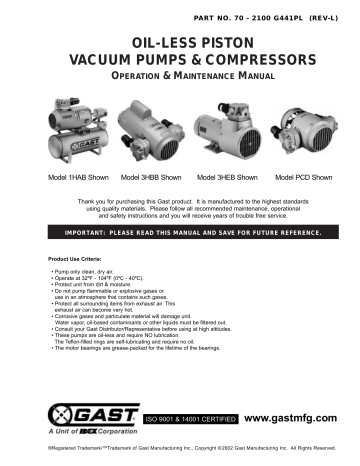
PART NO. 70 - 2100 G441PL (REV-L)
OIL-LESS PISTON
VACUUM PUMPS & COMPRESSORS
O
PERATION
& M
AINTENANCE
M
ANUAL
Model 1HAB Shown Model 3HBB Shown Model 3HEB Shown Model PCD Shown
Thank you for purchasing this Gast product. It is manufactured to the highest standards using quality materials. Please follow all recommended maintenance, operational and safety instructions and you will receive years of trouble free service.
IMPORTANT: PLEASE READ THIS MANUAL AND SAVE FOR FUTURE REFERENCE.
Product Use Criteria:
• Pump only clean, dry air.
• Operate at 32ºF - 104ºF (0ºC - 40ºC).
• Protect unit from dirt & moisture.
• Do not pump flammable or explosive gases or use in an atmosphere that contains such gases.
• Protect all surrounding items from exhaust air. This exhaust air can become very hot.
• Corrosive gases and particulate material will damage unit.
Water vapor, oil-based contaminants or other liquids must be filtered out.
• Consult your Gast Distributor/Representative before using at high altitudes.
• These pumps are oil-less and require NO lubrication.
The Teflon-filled rings are self-lubricating and require no oil.
• The motor bearings are grease-packed for the lifetime of the bearings.
ISO 9001 & 14001 CERTIFIED
www.gastmfg.com
®Registered Trademark/™Trademark of Gast Manufacturing Inc., Copyright © 2002 Gast Manufacturing Inc. All Rights Reserved.
Your safety and the safety of others is extremely important.
We have provided many important safety messages in this manual and on your product. Always read and obey all safety messages.
This is the safety alert symbol. This symbol alerts you to hazards that can kill or hurt you and others. The safety alert symbol and the words
“DANGER” and “WARNING” will precede all safety messages. These words mean:
DANGER
You will be killed or seriously injured if you don’t follow instructions.
WARNING
You can be killed or seriously injured if you don’t follow instructions.
All safety messages will identify the hazard, tell you how to reduce the chance of injury, and tell you what can happen if the safety instructions are not followed.
INSTALLATION
WARNING
c
Electrical Shock Hazard
Disconnect electrical power at the circuit breaker or fuse box before installing this product.
Install this product where it will not come into contact with water or other liquids.
Install this product where it will be weather protected.
Electrically ground this product.
Failure to follow these instructions can result in death, fire or electrical shock.
Correct installation is your responsibility. Make sure you have the proper installation conditions and that installation clearances do not block air flow.
Lift the unit by the motor shell, motor foot or flywheel (depending upon model design). Do Not lift unit by shroud, filters or mufflers. These parts are not designed to support the weight of the unit.
Blocking air flow over the product in any way can cause the product to overheat.
Install safety guards as required to prevent potential injury hazards or damage to surrounding objects.
Mounting
This product can be installed in any orientation.
Mounting the product to a stable, rigid operation surface and using shock mounts will reduce noise and vibration.
Plumbing
Remove plugs from the IN and OUT ports. Connect with pipe and fittings that are the same size or larger than the product’s threaded ports. Be sure to connect the intake and exhaust plumbing to the correct inlet and outlet ports. Ports will not support plumbing.
Accessories
If unit will be used in a system where it will be required to start against any system of back pressure, a positive sealing, one-way check valve should be installed in the air line between system and unit. This check valve is included with all tank mounted compressor units.
The product’s intake and exhaust filters will provide adequate filtration in most applications. Check filters periodically and replace when necessary. Please consult your Gast Distributor/Representative for additional filter recommendations.
Install relief valves and gauges at inlet or outlet, or both, to monitor performance. Check valves may be required to prevent back streaming through the unit.
Motor Control
It is your responsibility to contact a qualified electrician and assure that the electrical installation is adequate and in conformance with all national and local codes and ordinances. Grounding is required.
Determine the correct overload setting required to protect the motor (see motor starter manufacturer’s recommendations). Select fuses, motor protective switches or thermal protective switches to provide protection. Fuses act as short circuit protection for the motor, not as protection against overload. Incoming line fuses must be able to withstand the motor’s starting current. Motor starters with thermal magnetic overload or circuit breakers protect motor from overload or reduced voltage conditions.
The wiring diagram supplied with the product provides required electrical information. Check that power source is correct to properly operate the dual-voltage motors.
Electrical Connection
WARNING
c
Electrical Shock Hazard
This product must be properly grounded.
Do not modify the plug provided. If it will not fit the outlet, have the proper outlet installed by a qualified electrician.
If repair or replacement of the cord or plug is necessary, do not connect the grounding wire to either flat blade terminal. The wire with insulation that is green or green with yellow stripes is the grounding wire.
Check the condition of the power supply wiring.
Do not permanently connect this product to wiring that is not in good condition or is inadequate for the requirements of this product.
Failure to follow these instructions can result in death, fire or electrical shock.
Model with a power supply cord:
This product must be grounded. For either 120-volt or
220/240-volt circuits connect power supply cord grounding plug to a matching grounded outlet. Do not use an adapter. (See diagram.)
In the event of an electrical short circuit, grounding reduces the risk of electric shock by providing an escape wire for the electric current. This product may be equipped with a power supply cord having a grounding wire with an appropriate grounding plug.
The plug must be plugged into an outlet that is properly installed and grounded in accordance with all local codes and ordinances.
Check with a qualified electrician or serviceman if the grounding instructions are not completely understood, or if you are not sure whether the product is properly grounded. Do not modify the plug provided. If it will not fit the outlet, have the proper outlet installed by a qualified electrician.
Grounded Plug
Grounding Pin
120-volt grounded connectors shown. 220/240-volt grounded connectors will differ in shape.
Grounded Outlet
Model that is permanently wired:
This product must be connected to a grounded, metallic, permanent wiring system, or an equipment grounding terminal or lead on the product.
Power supply wiring must conform to all required safety codes and be installed by a qualified person. Check that supply voltage agrees with that listed on product nameplate.
Extension cords:
Use only a 3-wire extension cord that has a 3-blade grounding plug. Connect extension cord plug to a matching 3-slot receptacle. Do not use an adapter.
Make sure your extension cord is in good condition.
Check that the gage wire of the extension cord is the correct size wire to carry the current this product will draw.
An undersized cord is a potential fire hazard, and will cause a drop in line voltage resulting in loss of power causing the product to overheat. The following table indicates the correct size cord for length required and the ampere rating listed on the product nameplate.
If in doubt, use the next heavier gage cord. The smaller the gage number, the heavier the wire gage.
Minimum gage for extension cords
Amps Volts
120v
240v
Length of cord in feet
25 50 100 150 200 250 300 400 500
50 100 200 300 400 500 600 800 1000
0-2
2-3
3-4
4-5
5-6
6-8
8-10
10-12
12-14
14-16
16-18
18-20
18 18 18 16 16 14 14 12 12
18 18 16 14 14 12 12 10 10
18 18 16 14 12 12 10 10 8
18 18 14 12 12 10 10 8 8
18 16 14 12 10 10 8
18 16 12 10 10 8 6
18 14 12 10 8
16 14 10 8 8
16 12 10 8 6
8
6
6 6
6
6
8
6
6
4
4
4
4
8
6
2
16 12 10 8
14 12 8 8
14 12 8 6
6
6
6
6
4
4
4
4
4
4
2
2
2
2
2
OPERATION
WARNING
Injury Hazard
Install proper safety guards as needed.
Keep fingers and objects away from openings and rotating parts.
When provided, motor terminal covers must be in place for safe operation.
Product surfaces become very hot during operation, allow product surfaces to cool before handling.
Air stream from product may contain solid or liquid material that can result in eye or skin damage, wear proper eye protection.
Wear hearing protection. Sound level from motor may exceed 70 dBA.
Failure to follow these instructions can result in burns, eye injury or other serious injury.
It is your responsibility to operate this product at recommended pressures or vacuum duties and room ambient temperatures. Do not start against a vacuum or pressure load. Do not remove relief valve head while unit is operating.
Start Up
If motor fail to start or slows down significantly under load, shut off and disconnect from power supply. Check that voltage is correct for motor and that motor is turning in the proper direction. If the motor is turning in the wrong direction, it will overheat.
MAINTENANCE
WARNING
c
Electrical Shock Hazard
Disconnect electrical power supply cord before performing maintenance on this product.
If product is hard wired into system, disconnect electrical power at the circuit breaker or fuse box before performing maintenance on this product.
Failure to follow these instructions can result in death, fire or electrical shock.
WARNING
Injury Hazard
Product surfaces become very hot during operation, allow product surfaces to cool before handling.
Air stream from product may contain solid or liquid material that can result in eye or skin damage, wear proper eye protection.
Failure to follow these instructions can result in burns, eye injury or other serious injury.
It is your responsibility to:
• Regularly inspect and make necessary repairs to product in order to maintain proper operation.
• Make sure that pressure and vacuum is released from product before starting maintenance.
If unit is operated at maximum duties in a fairly clean,
65ºF - 75ºF (18ºC - 24ºC) ambient environment with
35% relative humidity, complete first inspection and maintenance after 4000 hours of operation. Earlier maintenance may be required depending upon the environment.
Check intake and exhaust filters after first 500 hours of operation. Clean filters and determine how frequently filters should be checked during future operation. This one procedure will help assure the product’s performance and service life.
Check the thickness of the rider ring. It should measure greater than .055”. Change all rings if thickness measures .055” or less.
1. Disconnect electrical power supply to unit.
2. Vent all air lines.
3. Remove filter cover.
4. Check filter felt. Replace felt if it is covered with contamination or shows signs of increasing differential pressure.
5. Reinstall felt and filter cover.
Check that all external accessories such as relief valves and gauges are attached and are not damaged before re-operating product.
Pressure or Vacuum Tank Systems
Check the air filter cartridge. A dirty filter restricts air flow and causes unit to run hotter resulting in longer operating cycles.
Check the air receiver for moisture regularly. The humidity in the environment will determine how quickly moisture will accumulate and need to be drained.
Clean the pump and motor regularly. Dirt and film buildup on the outer shell affects the unit’s ability to dissipate heat.
SHUTDOWN PROCEDURES
It is your responsibility to follow proper shutdown procedures to prevent product damage.
NEVER ADD OIL TO THIS OIL-LESS PUMP.
Proper shutdown procedures must be followed to prevent pump damage. Failure to do so may result in premature pump failure. Gast Manufacturing Oil-Less
Piston Vacuum Pumps and Compressors are constructed of ferrous metals or aluminum which are subject to rust and corrosion when pumping condensable vapors such as water. Follow the steps below to assure correct storage and shutdown between operating periods.
1. Disconnect plumbing.
2. Operate product for at least 5 minutes without plumbing.
3. Run at maximum vacuum for 10 - 15 minutes.
4. Repeat step 2.
5. Disconnect power supply.
6. Plug open ports to prevent dirt or other contaminants from entering product.
SERVICE KIT INSTALLATION
WARNING
c
Electrical Shock Hazard
Disconnect electrical power supply cord before installing Service Kit.
If product is hard wired into system, disconnect electrical power at the circuit breaker or fuse box before installing Service Kit.
Vent all air lines to release pressure or vacuum.
Failure to follow these instructions can result in death, fire or electrical shock.
Gast will NOT guarantee field-rebuilt product performance. For performance guarantee, the product must be returned to a Gast Authorized
Service Facility.
Service Kit contents vary. Most contain head and cylinder gaskets, valves, piston rings and seals, rider rings and felt filters.
1. Disconnect electrical power to pump.
2. Disconnect air supply and vent all air lines to release pressure or vacuum.
3. Remove shroud, cylinder head and valve components.
4. Remove cylinder and rings.
5. Clean all parts with water or non-petroleum based solvent such as Gast AH255B Solvent. Do Not use kerosene or ANY other combustible solvents.
6. Install piston seals, piston rings and rider rings on piston. Locate ring joints approximately opposite each other.
7. Use cylinder screws with washers to attach cylinder to bracket. Tighten screws only until they are finger tight.
8. Move pistons to top dead center position. Adjust each cylinder flush with top of piston.
9. Torque cylinder screws to 150-160 in. lbs.
10. Replace valve components in original order.
11. Install cylinder head and head screws. The exhaust ports have been marked on the cylinder heads by omitting the ends of two of the fins. Do not tighten screws at this time.
12 Install manifold nuts and seals on manifold. Insert into cylinder head and manifold.
13. Torque head screws to 150-160 in. lbs.
14. Turn fan by hand to check that rod assembly is not hitting head. If rod hits head, loosen cylinders and adjust.
15. Install manifold and tighten manifold nut one-quarter to one-half turn beyond finger tight.
16. Operate unit for 10 minutes. Tighten screws again.
17. Install fan shroud.
Check that all external accessories such as relief valves and gauges are attached to cover and are not damaged before re-operating product.
If pump still does not produce proper vacuum or pressure, send unit to a Gast Authorized Service Facility for repair.
SPECIFIC PROBLEMS AND REMEDIES
Unit stalls after vacuum or pressure starts building up in receiver:
1. Disconnect electrical power supply from unit.
2. Check that voltage from power source matches that listed on nameplate.
3. Check wiring connections against diagram on nameplate. Single voltage motors will operate only at designated voltage.
Motor will not start:
1. Disconnect electrical power supply from unit.
2. Check that voltage from power source matches that listed on nameplate.
3. Check wiring connections against diagram on nameplate. Single voltage motors will operate only at designated voltage.
4. Reconnect electrical supply to unit. Check that power is on. If extension cord is used, check that it is the correct size and length to adequately supply power to the unit.
5. If unit will still not operate, contact your Gast
Distributor/Representative or a Gast Authorized
Service Facility.
Motor starts at 0 PSI but will not start under pressure:
1. Replace the check valve.
2. Wait for the thermal overload switch to reset before attempting to operate.
3. If unit will not restart, the thermal overload switch may need to be replaced. If there isn’t a thermal overload switch, the motor may be damaged and requires service.
Motor starts intermittently:
1. Disconnect electrical power supply from unit.
2. Check points in the pressure or vacuum switch for wear or dirt.
3. Check for dirt buildup or uneven wear.
4. Replace parts as required.
Unit cycles On-Off more often than when first installed:
1. Check air receiver and drain water that has accumulated.
Unit or motor is running more often than when first installed:
1. Check system for air leaks. If new or different pneumatic equipment has been added, the air requirements may have changed.
2. Check and clean filters.
3. Check for buildup of foreign material on head.
4. Check valves and rings for wear and damage.
Air receiver loses pressure:
1. Check for system leaks through pipes, fittings and seals.
2. Inspect the check valve to see if it is allowing air pressure to leak back into unit.
3. Pressure pumps will have bubbles around head assembly during operation. Stop operating the pump for a few minutes and check for air leaks at pump.
4. Vacuum systems should have the check valve removed and inspected for dirt buildup. It may be necessary to need an AV460 filter installed prior to tank to eliminate contaminants.
A leak is located at the unit:
1. Vent all pressure from inside the air receiver until gauge reads 0 PSI.
2. Inspect check valve for dirt buildup, wear and proper operation.
3. Replace check valve if necessary.
PARTS & ORDERING INFORMATION
Please reference the exploded view on the opposite page for the following model and parts table.
1HAA / 1HAB SERIES
REF DESCRIPTION QTY 1HAA 1HAB 1HAE 1LAA 1VAF 2HAH 2LAF 3HEB 3HEE 3LEM
15
16
17
18
1
2
∆
3
INLET FILTER ASSEMBLY
FELT
SAFETY VALVE
4
5
∆
6
∆
7
8
∆
9
∆
CYLINDER HEAD
HEAD GASKET
OUTLET VALVE
PLATE VALVE
INLET VALVE
CYLINDER GASKET
10 CYLINDER
11
∆
PISTON RING
12
∆
PISTON SEAL
13
∆
RIDER RING
14 PISTON ROD ASSEMBLY
1
1
1
1
1
1
1
1
1
1
2
2
1
1
***
***
COUNTER WEIGHT
FLAT KEY
FAN
SHROUD
TANK ASSEMBLY
SERVICE KIT
1
1
1
1
1
1
B300A
B344A
B300A
B344A
B300A
B344A
B300A
B344A
B300A
B344A
AS100E AS100G AS100G AS100C –
AF508 AF508 AF508 AF508 AF508
AF518
AF531
AF529
AF530
AF518
AF531
AF529
AF530
AF518
AF531
AF529
AF530
AF518
AF531
AF529
AF530
AF518
AF531
AF529
AF530
B300A
B344A
B300F
B344A
B300F
B344A
B300F
B344A
B300F
B344A
AS100G AS100C AS100G AS100G AS100C
AF508 AF508 AH691 AH691 AH691
AF518
AF531
AF529
AF530
AF518
AF531
AF529
AF530
AF520A AF520A AF520A
AF545
AK779
AF544
AF545
AK779
AF544
AF545
AK779
AF544
AF519A AF519A AF519A AF519A AF519A AF519A AF519A AF521
AF510 AF510 AF510 AF510 AF510 AF510 AF510 AF509
AF527
AF526
AF527
AF526
AF527
AF526
AF527
AF526
AF527
AF526
AF527
AF526
AF527
AF526
AF541
AF540
AF533
AF534
–
K264
AF533
AF534
AF599
K264
AF533
AF534
–
K264
AF533
AF534
AF599AA-1
K264
AF533
AF534
–
K264
AF547
AF534
AF599
K264
AF547
AF534
–
K264
AF547
AT343
–
K514A
AF521
AF509
AF541
AF540
AF521
AF509
AF541
AF540
AF594 AF594 AF594 AF594 AF594 AF594 AF594 AF595 AF595 AF595
AF560A AF560B AF560E AF560A AF560F AF560H AF560F AK893B AK893E AK893M
AF517A AF517B AF517E AF517A AF517D AF517C AF517D AT780B AK780E AK780A
AF524 AF524 AF524 AF524 AF524 AF524 AF524 AB136 AB136 AB136
AF547
AT343
–
K514A
AF547
AT343
–
K514A
Model 1HAB shown.
*** Item not shown.
∆
Denotes parts included in the Service Kit.
Parts listed are for stock models. For specific OEM models, please consult the factory.
When corresponding or ordering parts, please give complete model and serial numbers.
EXPLODED PRODUCT VIEW – MODEL 1HAB
PARTS & ORDERING INFORMATION
Please reference the exploded view on the opposite page for the following model and parts tables.
1 VBF – 3LBD SERIES
REF DESCRIPTION QTY 1VBF 1VSF 2LBB 2HBB 2HBC 3HBB 3HBE 3LBA 3LBD
1 INLET FILTER ASSEMBLY 1
2
2
∆
3
FELT
SAFETY VALVE
4
5
∆
6
∆
7
8
∆
9
∆
CYLINDER HEAD
HEAD GASKET
OUTLET VALVE
PLATE VALVE
INLET VALVE
CYLINDER GASKET
10 CYLINDER
11
∆
PISTON RING
12
∆
PISTON SEAL
13 PISTON ROD ASSEMBLY
14
∆
RIDER RING
15 FLAT KEY
2
1
2
2
2
2
2
2
2
4
4
2
2
1
16 FAN/FAN ASSEMBLY
17 SHROUD
18
∆
MANIFOLD SLEEVE
*** SERVICE KIT
2
1
1
1
B300A
B300A
B344A
–
AF508
AF518
AF531
AF529
AF530
B344A
–
AF508
AF518
AF531
AF529
AF530
B300A
B344A
AS100C
AF508
AF518
AF531
AF529
AF530
B300A
B344A
AS100G
AF508
AF518
AF531
AF529
AF530
B300A
B344A
AS100G
AF508
AF518
AF531
AF529
AF530
B300A
B344A
AS100G
AF508
AF518
AF531
AF529
AF530
B300A
B344A
AS100G
AF508
AF518
AF531
AF529
AF530
B300A
B344A
AS100C
AF508
AF518
AF531
AF529
AF530
B300A
B344A
AS100C
AF508
AF518
AF531
AF529
AF530
AF519A AF519A AF519A AF519A AF519A AF519A AF519A AF519A AF519A
AF510
AF527
AF510
AF527
AF510
AF527
AF510
AF527
AF510
AF527
AF510
AF527
AF510
AF527
AF510
AF527
AF510
AF527
AF526 AF526 AF526 AF526 AF526 AF526 AF526 AF526 AF526
AF560F AF560F AF560B AF560B AF560C AF560B AF560E AF560A AF560D
AF594
AF524
AF533
AF535
AF594
AF524
AF533
AF535
AF594
AF524
AF533
AF535
AF594
AF524
AF533
AF535
AF594
AF524
AF533
AF535
AF594
AF524
AF533
AF535
AF594
AH984
AF547
AF535
AF594
AF524
AF533
AF535
AF594
AH984
AF547
AF535
AF567A AF567A AF567A AF567A AF567A AF567A AF567A AF567A AF567A
K260 K260 K260 K260 K260 K260 K260 K260 K260
4VCF – 6HCA SERIES
REF DESCRIPTION QTY 4VCF 4VSF 4HCJ 4LCB 4HCC 5LCA 5HCD 5HCE 6HCN 6HCA
1 INLET FILTER ASSEMBLY 1
2
2
∆
3
FELT
SAFETY VALVE
4
5
∆
6
∆
7
8
∆
9
∆
CYLINDER HEAD
HEAD GASKET
OUTLET VALVE
PLATE VALVE
INLET VALVE
CYLINDER GASKET
10 CYLINDER
11
∆
PISTON RING
12
∆
PISTON SEAL
13 PISTON ROD ASSEMBLY
14
∆
RIDER RING
15 KEY
2
1
2
2
2
2
2
2
2
4
4
2
2
1
16 FAN/FAN ASSEMBLY
17 SHROUD
18
∆
MANIFOLD SLEEVE
*** SERVICE KIT
2
1
1
1
B300F
B300F
B344A
–
AF507
B344A
–
AF507
B300A
B344A
AS100G
AF507
B300A
B344A
AS100D
AF507
B300A
B344A
AS100G
AF507
B300F
B344A
AS100E
AF507
B300A
B344A
AS100H
AF507
B300A
B344A
AS100H
AF507
B300F
B344A
AS100H
AF507
B300F
B344A
AS100H
AF507
AF520A AF520A AF520A AF520A AF520A AF520A AF520A AF520A AF520A AF520A
AF545
AF543
AF544
AF521
AF545
AF543
AF544
AF521
AF545
AF543
AF544
AF521
AF545
AF543
AF544
AF521
AF545
AF543
AF544
AF521
AF545
AF543
AF544
AF521
AF545
AF543
AF544
AF521
AF545
AF543
AF544
AF521
AF545
AF543
AF544
AF521
AF545
AF543
AF544
AF521
AF509
AF541
AF509
AF541
AF509
AF541
AF509
AF541
AF509
AF541
AF509
AF541
AF509
AF541
AF509
AF541
AF509
AF541
AF509
AF541
AF540 AF540 AF540 AF540 AF540 AF540 AF540 AF540 AF540 AF540
AF561F AF561F AF561J AF561B AF561C AF561A AF561D AF561E AF561N AF561A
AF595 AF595 AF595 AF595 AF595 AF595 AF595 AF595 AF595 AF595
AB136D AB136D AB136D AB136D AB136D AB136D AB136D AB136D AB136F AB136F
AF547
AF549
AF547
AF549
AF547
AF549
AF547
AF549
AF547
AF549
AF547
AF549
AF547
AF549
AF547
AF549
AF747
AF656
AF747
AF656
AF567A AF567A AF567A AF567A AF567A AF567A AF567A AF567A AF567A AF567A
K263 K263 K263 K263 K263 K263 K263 K263 K263 K263
Model 1VBF shown.
*** Item not shown.
∆
Denotes parts included in the Service Kit.
Parts listed are for stock models. For specific OEM models, please consult the factory.
When corresponding or ordering parts, please give complete model and serial numbers.
EXPLODED PRODUCT VIEW – MODEL 1VBF
PARTS & ORDERING INFORMATION
Please reference the exploded views on the next page for the following model and parts tables.
PAB – VAB SERIES
REF DESCRIPTION QTY PAB VAB
1
2
∆
3
FILTER ASSEMBLY
FELT
SAFETY VALVE
4
5
∆
6
∆
7
8
∆
9
∆
CYLINDER HEAD
HEAD GASKET
OUTLET VALVE
PLATE VALVE
INLET VALVE
CYLINDER GASKET
10 CYLINDER
11
∆
PISTON RING
12
∆
PISTON SEAL
13
∆
RIDER RING
14 PISTON ROD ASSEMBLY
15 PULLEY
15A COUNTER WEIGHT
16
17
FLAT KEY
FAN
18
***
SHROUD
SERVICE KIT
1
1
1
1
2
2
1
1
1
1
1
1
1
1
1
1
1
1
1
1
B300A
B344A
B300A
B344A
AS100G –
AF508 AF508
AF518
AF531
AF529
AF530
AF518
AF531
AF529
AF530
AF519A AF519A
AF510 AF510
AF527
AF526
AF527
AF526
AF594 AF594
AF560B AF560B
AB140C AB140C
AF517B AF517B
AF524
AF533
AF534
K264
AF524
AF533
AF534
K264
VBB – PCA-10 SERIES
REF DESCRIPTION QTY VBB VCD PBB PCA-10
16
17
18
19
***
1
2
∆
3
FILTER ASSEMBLY
FELT
SAFETY VALVE
4
5
∆
6
∆
7
8
∆
9
∆
CYLINDER HEAD
HEAD GASKET
OUTLET VALVE
PLATE VALVE
INLET VALVE
CYLINDER GASKET
10 CYLINDER
11
∆
PISTON RING
12
∆
PISTON SEAL
13 PISTON ROD ASSEMBLY
14
∆
RIDER RING
15 PULLEY
FLAT KEY
FAN
SHROUD
MANIFOLD SLEEVE
SERVICE KIT
1
1
2
2
4
4
2
2
2
1
1
1
2
2
2
2
1
2
2
2
B300A
B344A
–
AF508
AF518
AF531
AF529
AF530
B300A
B344A
–
AF507
B300A
B344A
B300F
B344A
AS100G AS100H
AF508 AF507
AF520A AF518
AF545 AF531
AF543
AF544
AF529
AF530
AF520A
AF545
AF543
AF544
AF519A AF521
AF510 AF509
AF527
AF526
AF541
AF540
AF519A AF521
AF510 AF509
AF527
AF526
AF541
AF540
AF560B AF561D AF560B AF561A
AF594 AF595 AF594 AF595
AB140C AK670
AF524 AB136
AB140C
AF524
AK670
AB136
AF533
AF535
AF547
AF549
AF533
AF535
AF661
AF656
AF567A AF567A AF567A AF567A
K260 K263 K260 K263
Models PAB and PBB shown.
** Item not shown.
∆
Denotes parts included in the Service Kit.
Parts listed are for stock models. For specific OEM models, please consult the factory.
When corresponding or ordering parts, please give complete model and serial numbers.
EXPLODED PRODUCT VIEWS – MODEL PAB (TOP) & MODEL PBB (BOTTOM)
PARTS & ORDERING INFORMATION
Please reference the exploded view on the next page for the following model and parts table.
5 VDF – 8LDF SERIES
REF DESCRIPTION QTY 5VDF 5VSF 6LCF ** 6HDK 7LDE 7HDD 7HDE 8HDM 8HDN 8LDF
20
20
21
22
***
16
17
18
19
1
2
3
∆
INLET FILTER ASSEMBLY 2
4
FELT
SAFETY VALVE
4
5
∆
6
∆
7
8
∆
9
∆
CYLINDER HEAD
HEAD GASKET
OUTLET VALVE
PLATE VALVE
INLET VALVE
CYLINDER GASKET
10 CYLINDER
11
∆
PISTON RING
12
∆
PISTON SEAL
13 PISTON ROD ASSEMBLY
14
∆
RIDER RING
15 MANIFOLD
2
4
1
4/2 **
B344A
–
AF507
B344A
–
AF507
B344A
AS100D
AF507
B344A
AS100G
AF507
B344A
AS100D
AF507
B344A
AS100G
AF507
B344A
AS100G
AF507
B344A
AS100F
AF507
B344A
AS100G
AF507
B344A
AS100B
AF507
4/2 ** AF520A AF520A AF520A AF520A AF520A AF520A AF520A AF520A AF520A AF520A
4/2 **
4/2 **
4/2 **
4/2 **
4/2 **
8/4 **
8/4 **
4/2 **
4/2 **
1
B300F
AF545
AF543
AF544
AF521
AF509
AF541
AF540
AF561F
AF595
AF659
B300F
AF545
AF543
AF544
AF521
AF509
AF541
AF540
AF561F
AF595
AF659
B300F
AF545
AF543
AF544
AF521
AF509
AF541
AF540
AF561F
AF595
–
B300A
AF545
AF543
AF544
AF521
AF509
AF541
AF540
AF561K
AF595
AF659
B300F
AF545
AF543
AF544
AF521
AF509
AF541
AF540
AF561E
AF595
AF659
B300A
AF545
AF543
AF544
AF521
AF509
AF541
AF540
AF561D
AF595
AF659
B300A
AF545
AF543
AF544
AF521
AF509
AF541
AF540
AF561E
AF595
AF659
B300F
AF545
AF543
AF544
AF521
AF509
AF541
AF540
AF561M
AF595
AF659
B300F
AF545
AF543
AF544
AF521
AF509
AF541
AF540
AF561N
AF595
AF659
B300F
AF545
AF543
AF544
AF521
AF509
AF541
AF540
AF561F
AF595
AF659
SQUARE KEY
FAN ASSEMBLY-CW
SHROUD
2/1 ** AB136F AB136F AB136F AB136F AB136F AB136F AB136F AB136F AB136F AB136F
FAN/FAN ASSEMBLY-CCW 1
1
2/1 **
AF748
AF747
AF656
AF748
AF747
AF656
AF748
AF747
AF656
AF748
AF747
AF656
AF748
AF747
AF656
AF748
AF747
AF656
AF748
AF747
AF656
AF748
AF747
AF656
AF748
AF747
AF656
AF748
AF747
AF656
MANIFOLD SLEEVE
MANIFOLD SLEEVE
TANK ASSEMBLY
MANIFOLD
SERVICE KIT
2
5
– – AF567A –
AF567A AF567A – AF567A
–
AF567A
–
AF567A
–
AF567A
–
AF567A
–
AF567A
–
AF567A
1 – – AF606-1 AF606-1 AF606-1 AF606-1 – AF606-1 AF606-1 –
2/1 ** AF550E AF550E AF550E AF550C AF550D AF550B AF550D AF550A AF550A AF550E
1 K303 K303 K263 K303 K303 K303 K303 K303 K303 K303
Model 5VDF shown.
** 6LCF is a two-cylinder unit. Other models are four-cylinder units.
*** Item not shown.
∆
Denotes parts included in the Service Kit.
Parts listed are for stock models. For specific OEM models, please consult the factory.
When corresponding or ordering parts, please give complete model and serial numbers.
EXPLODED PRODUCT VIEW – MODEL 5VDF
WARRANTY
Gast finished products, when properly installed and operated under normal conditions of use, are warranted by Gast to be free from defects in material and workmanship for a period of twelve (12) months from the date of purchase from
Gast or an authorized Gast Representative or Distributor. In order to obtain performance under this warranty, the buyer must promptly (in no event later than thirty (30) days after discovery of the defect) give written notice of the defect to
Gast Manufacturing Incorporated, PO Box 97, Benton Harbor Michigan USA 49023-0097 or an authorized Service
Center (unless specifically agreed upon in writing signed by both parties or specified in writing as part of a Gast OEM
Quotation). Buyer is responsible for freight charges both to and from Gast in all cases.
This warranty does not apply to electric motors, electrical controls, and gasoline engines not supplied by Gast. Gast’s warranties also do not extend to any goods or parts which have been subjected to misuse, lack of maintenance, neglect, damage by accident or transit damage.
THIS EXPRESS WARRANTY EXCLUDES ALL OTHER WARRANTIES OR REPRESENTATIONS EXPRESSED OR
IMPLIED BY ANY LITERATURE, DATA, OR PERSON. GAST’S MAXIMUM LIABILITY UNDER THIS EXCLUSIVE
REMEDY SHALL NEVER EXCEED THE COST OF THE SUBJECT PRODUCT AND GAST RESERVES THE RIGHT,
AT ITS SOLE DISCRETION, TO REFUND THE PURCHASE PRICE IN LIEU OF REPAIR OR REPLACEMENT.
GAST WILL NOT BE RESPONSIBLE OR LIABLE FOR INDIRECT OR CONSEQUENTIAL DAMAGES OF ANY KIND, however arising, including but not limited to those for use of any products, loss of time, inconvenience, lost profit, labor charges, or other incidental or consequential damages with respect to persons, business, or property, whether as a result of breach of warranty, negligence or otherwise. Notwithstanding any other provision of this warranty, BUYER’S
REMEDY AGAINST GAST FOR GOODS SUPPLIED OR FOR NON-DELIVERED GOODS OR FAILURE TO FURNISH
GOODS, WHETHER OR NOT BASED ON NEGLIGENCE, STRICT LIABILITY OR BREACH OF EXPRESS OR
IMPLIED WARRANTY IS LIMITED SOLELY, AT GAST’S OPTION, TO REPLACEMENT OF OR CURE OF SUCH
NONCONFORMING OR NON-DELIVERED GOODS OR RETURN OF THE PURCHASE PRICE FOR SUCH GOODS
AND IN NO EVENT SHALL EXCEED THE PRICE OR CHARGE FOR SUCH GOODS. GAST EXPRESSLY
DISCLAIMS ANY WARRANTY OF MERCHANTABILITY OR FITNESS FOR A PARTICULAR USE OR PURPOSE WITH
RESPECT TO THE GOODS SOLD. THERE ARE NO WARRANTIES WHICH EXTEND BEYOND THE DESCRIPTIONS
SET FORTH IN THIS WARRANTY, notwithstanding any knowledge of Gast regarding the use or uses intended to be made of goods, proposed changes or additions to goods, or any assistance or suggestions that may have been made by Gast personnel.
Unauthorized extensions of warranties by the customer shall remain the customer’s responsibility.
CUSTOMER IS RESPONSIBLE FOR DETERMINING THE SUITABILITY OF GAST PRODUCTS FOR CUSTOMER’S
USE OR RESALE, OR FOR INCORPORATING THEM INTO OBJECTS OR APPLICATIONS WHICH CUSTOMER
DESIGNS, ASSEMBLES, CONSTRUCTS OR MANUFACTURES.
This warranty can be modified only by authorized Gast personnel by signing a specific, written description of any modifications.
MAINTENANCE RECORD
DATE
PROCEDURE PERFORMED
MAINTENANCE RECORD
DATE PROCEDURE PERFORMED
PART NO. 70 - 2100 G441PL (REV-L)
TROUBLESHOOTING CHART
Low High Pump Motor Excess Reason and remedy
Vacuum Pressure Vacuum Pressure Overheat Overload Noise for problem.
•
•
•
•
At pump
•
•
•
•
•
•
•
Filter dirty. Clean or replace.
Muffler dirty. Clean or replace.
• •
• • •
•
Valves dirty or valves bent.
Clean or replace.
Damaged or worn piston rings.
Repair or replace.
Leaky relief valve.
Inspect and adjust.
• • •
•
•
•
•
•
At pump • •
•
•
•
•
•
Damaged valves.
Replace.
Plugged vacuum/pressure line.
Inspect and repair.
Low voltage, won’t start.
Check power source.
Worn rings/piston hitting cylinder.
Replace.
•
•
•
•
•
•
•
•
•
•
•
•
•
•
•
Cylinder misadjustment.
Realign.
Leaky hose or check valve.
Replace.
Dirt or liquid on top of piston.
Inspect and clean.
Blown head gasket.
Replace.
We have Gast Authorized Repair Facilities throughout the world. For the most up-to-date listing, contact one of our sales offices below:
World Headquarters
P.O. Box 97
2550 Meadowbrook Rd.
Benton Harbor, MI 49023-0097
Ph: 269/926-6171
FAX: 269/925-8288 www.gastmfg.com
European Sales & Service
Headquarters
Beech House Knaves Beech
Business Centre
Loudwater, High Wycombe Bucks,
England HP10 9SD
Tel: +44 1628 551500
Fax: +44 1628 551590 www.gastmfg.com
Gast Hong Kong
Unit 12, 21/F, Block B
New Trade Plaza
6, On Ping Street, Shatin
N. T. Hong Kong
Ph: (852) 2690 1008
Fax: (852) 2690 1012 www.gasthk.com
ISO 9001 & 14001 CERTIFIED
www.gastmfg.com
advertisement
* Your assessment is very important for improving the workof artificial intelligence, which forms the content of this project