- Computers & electronics
- TVs & monitors
- Flat panel accessories
- STIEBEL ELTRON
- SBP 100
- Operating instructions
advertisement
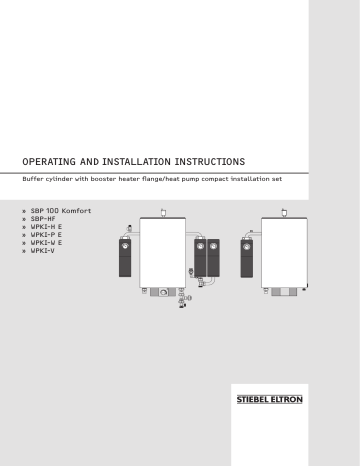
Operating and installatiOn instructiOns
Buffer cylinder with booster heater flange/heat pump compact installation set
» SBP 100 Komfort » WpKi-W e
20 0 40 60 °C 80 100 120 20 40 0 60 80 °C 100 120 20 40 60 °C 0 80 100 120 bar
65°C
2
Inhalt 1 Operating instructions 2 Installation instructions SBP 100 Komfort 3 3 Installation instructions SBF-HF 3 5 4 Installation instructions WPKI-H E, WPKI-P E, WPKI-W E 5 Installation instructions WPKI-H E and WPKI-V 6 Specification 12 Warranty 13 Environment and recycling 6 10 13 4 5 2 9
350
6 10
45 °
3
510 Dimensions in mm
1 7 8
350 45 °
10
510 Dimensions in mm
1 Operating instructions
for users and contractors
Safety Intended use
The sealed wall mounted cylinder with 100 l capacity acts as buffer cylinder for heat pumps.
Observe the application limits listed in the chapter „Specification / Data table“.
The appliance is intended for domestic use, i.e. it can be used safely by untrained persons. The appliance can also be used in a non-domestic environment, e.g. in a small business, as long as it is used in the same way.
Any other use beyond that described shall be deemed inappropriate. Observation of these instructions and of instructions for any accessories used is also part of the correct use of this appliance. Subject to the relevant system, observe the installation instructions of the components of which the system comprises.
WARNING Injury The appliance may be used by children aged 8 and up and persons with reduced physical, sensory or mental capabilities or a lack of experience provided that they are supervised or they have been instructed on how to use the appliance safely and have understood the resulting risks. Children must never play with the appliance. Children must never clean the appliance or perform user maintenance unless they are supervised.
Equipment description
A buffer cylinder is recommended to ensure trouble-free heat pump operation. In addition, they are designed to separate both heat pump and heating circuit volume flows.
Equipment layout
There are four G 1 ¼” equipment connections at the back of the cylinder, which are matched to the WPKI- .... heat pump compact installation set. A G 1/2” connection is provided at the top of the equipment for the air vent valve supplied with the cylinder.
At the bottom of the equipment, an aperture is provided for the electric booster heater.
2 Installation instructions SBP 100 Komfort
for heating contractors
Safety
Only a qualified contractor should carry out installation, commissioning, maintenance and repair of the appliance.
General safety instructions
We guarantee trouble-free function and operational reliability only if the original accessories and spare parts intended for the appliance are used.
Instructions, standards and regulations Observe all applicable national and regional regulations and instructions.
Transport and packaging
This wall mounted cylinder can be transported vertically or horizontally.
To prevent cylinder damage, remove the packaging only at the place of installation.
Place of installation
The installation location should be protected from frost. If the system is not in use at times when a frost is likely, drain the cylinder and all connected systems to prevent damage.
The room must be at least 2.2 m high.
Ensure that the wall at the installation location is capable of bearing the full weight of the cylinder. Install the cylinder vertically, as shown in and .
Cylinder installation
Prior to fitting the cylinder to the wall, insert the connector with the sensor well for the return temperature sensor into the cylinder body -10 and -10.
It is recommended that the components in the WPKl set and the respective circulation pump are fitted to the cylinder and hand tightened before the installation.
Fit the heat pump compact installation set with circulation pumps (see page 6 section 3 “Installation instructions for accessories WPKI-P, WPKI-H, WPKI-W” and page 11 section 4 “Installation instructions for accessory WPKI-V”.
Fit the wall mounting panel or mounting brackets to the respective wall and hook the cylinder into one or the other fitting.
Observe the gap between the heat pump and the cylinder .
Select fixing materials in accordance with the wall construction/condition.
Fit the air vent valve into the top of the cylinder -1 .
1 Air vent valve 2 G 1 ¼” flow connector heat pump compact installation set 3 G 1 ¼” return connector heat pump compact installation set 4 G 1 ¼” heating flow connector 5 G 1 ¼” heating return connector 6 Type plate SBP 100 7 Cleaning aperture 8 Fill & drain valve 9 Panel 10 Connector with sensor well for return temperature sensor
Special accessories Heat pump compact installation sets
The heat pump compact installation sets WPKI-P, WPKI-H, WPKI-W and WPKI-V are components of the heat pump system and are specifically designed for the SBP 100 buffer cylinder.
Keep these instructions safely and pass them on to any new user, should the equipment change hands. Let your contractor check their content in conjunction with any maintenance or repair work.
Water connection
For connector allocation, see equipment layout.
Implement the water connections in accordance with the installation drawings in the heat pump installation instructions.
For filling, venting and draining the system, open the non-return valves of the heat pump compact installation set, i.e. set them to . Then return them into position . The setting screw of the WPKI-H non-return valve is located behind the thermometer.
Commissioning
(only by a qualified contractor)
1. Fill and vent the cylinder.
2. Check the safety valve function.
Maintenance
Regularly vent the safety valve until water streams from it. Close the safety valve after checking.
3
8 4 11 13 1 2 3 1 12 8 9 10 7 6 5 4 1 2 High limit safety cut-out 600 78.5
710 Controller 110 20 0 40 80 100 120
3 Installation instructions SBF-HF
for heating contractors
Installing the electric booster heater
SBP-HF Part no. 074252 Instructions and regulations – DIN VDE 100 – DIN VDE 0701 – Regulations of your local electricity supply company – The equipment type plate The wall mounted cylinder with electric booster heater is only designed for a permanently connected power supply in conjunction with the knock-out cable entry.
The equipment must be able to be separated from the mains supply, for example by fuses, which disconnect all poles with at least 3 mm contact separation.
Fitting the booster heater flange: – Open the control chamber lid ( ).
– When retrofitting the heater: Drain the water from the cylinder, release the pipe fittings and remove the equipment from the wall.
– Remove the drain valve (to be re-used).
– Remove the flange plate. The semi-shells, pressure plate and insulating plate will be re-used.
– Install the booster heater flange into the cylinder ( ), use new gaskets, push on the insulating plate, position the pressure plate inside the recess ( -12) of the plastic casing, and tighten 10 screws ( -4) with 8 Nm.
– Fit the drain valve ( -2) with a new flange gasket and tighten with 20 Nm.
Fit the wiring set: – Fit the component support with 3 screws ( -1).
– Fit the terminals ( -5 and 6).
– Secure the earth strap with a self-tapping screw (M5) ( -9) on the cylinder tab ( -10).
– Secure the straps in the strap holders ( -8).
– Insert the controller bulbs into the sensor pipe ( -11) until the limiter clicks into place ( – Push the red plug onto the booster heater flange.
).
Mount the cylinder on the wall.
Install the heat pump compact installation set WPKI-...
Fill the cylinder or the complete system with water.
Power supply preparation 250 mm Route the power supply cable through the PG21 fitting of the strain relief ( diagram (see wiring diagram -7) and connect in accordance with the connection ) at the terminal strip ( -5).
Remove the knock-out in the strain relief ( -7) for the control cable from the heat pump manager, and route the control cable via the PG11 fitting into the cylinder. Connect the control cable at the terminal strip ( -6) at terminals 8-9.
Control chamber cover – Remove the adhesive cover strip.
– Affix a new adhesive cover strip and push firmly down.
– Affix the wiring diagram pad to the interior of the control chamber cover.
– Undo the controller screws ( selector (to be re-used later).
secure with 4 screws.
undone screws.
– Push the temperature selector ( -2) from the support and remove the temperature – Position the control chamber cover and – Secure the controller to the control chamber cover with the previously -3) onto the controller axis.
65°C
– Affix the rating plate of the booster heater flange set on the l.h. side of the casing ( -13) and tick the selected output.
Install the safety valve into the heating flow.
The safety valve must not be able to be closed towards the cylinder. The blow-off aperture of the safety valve must remain open towards the atmosphere. When using the heat pump compact installation set WPKI-H, the safety valve can be inserted into the threaded hole provided for this purpose in the upper pipe bend ( ).
Before and after fitting the control chamber cover, the contractor must carry out the following checks in accordance with DIN VDE 0701 [or local regulations] after fitting the electric booster heater:
Visual inspection of: – The condition and security of the control chamber cover, the adhesive strip and the temperature selector.
– Connecting cables. – Strain relief and cable routing.
– Cable routing.
– Positioning of the capillary tubes from the temperature controller and the temperature limiter.
Check the earth connection Check the ionisation resistance Check the system for leaks Check the safety valve function Check the safety labels Function check Check the heating up and the first switching of the temperature controller.
5
6
4 Installation instructions WPKI-H E, WPKI-P E, WPKI-W E in conjunction with the WPF....M, heat pumps
for heating contractors
4.1 General information WPKI-H E
Weight:
WPKI-P E
Weight:
WPKI-W E
Weight:
Part no. 233098
approx. 3.5 kg
Part no. 233097
approx. 5.1 kg
Part no. 233099
approx. 3.8 kg The heat pump compact installation sets WPKI-P E , WPKI-H E, WPKI-W E and WPKI-V are components of the heat pump system and are specifically designed for the SBP 100 buffer cylinder in conjunction with the WPF...M heat pumps.
These heat pump compact installation sets offer contractors a clear and easy to manage connection of the SBP buffer cylinder to the heat pump, the heating system and the DHW cylinder.
Required special accessories
Circulation pumps UP 25 7.0 E UP 25 7.5 E UP 25/1-7 E Part no.
232942 232943 231187
4.2 Assembly
These sets are supplied as prepared assemblies.
All pre-assembled parts are factory sealed.
It is recommended that the set components and the respective circulation pump (see accessories) are fitted to the cylinder and hand tightened before the installation.
Tighten the fittings once all components have been connected to the cylinder, have been aligned and secured with the wall retainers.
An Allen key (SW 5) is required to open and close the ball shut-off valves in the heat pump return.
Circulation pumps Observe the flow direction when fit ting the circulation pump.
HE circulation pumps should never be switched directly. Use an external relay with a breaking capacity of at least 10 A/250 V AC or our relay set WPM-RBS.
For the circulation pump rating curve, see page 13.
4.2.1 WPKI-H E
The WPKI-H E set comprises all necessary components for connecting the heating system to the SBP 100 buffer cylinder.
Heating flow 1 Connection bend G 1 ¼” with safety valve connector 2 Wall retainer 3 Ball shut-off valve G 1” 4 Handle with inserted thermometer 5 Connector G 1” with ball shut-off valve Heating return 6 Connector G 1 ¼” 7 Connector G 1” with ball shut-off valve 8 EPS insulation pieces Assembly according to Fig. and .
Shorten the threaded wall retainer rod subject to the distance to the wall, at which the cylinder was mounted .
It must not be possible to shut-off the safety valve against the heat source.
Fit the heating flow ( return (
-b)
.
-a)
and the heating
4.2.2 WPKI-P E
The WPKI-P E set comprises all necessary components for connecting the heat pump to the SBP 100 buffer cylinder: Heat pump flow 1 Connection bend G 1 ¼” 2 Wall retainer 3 Ball shut-off valve with non-return valve 4 Handle with inserted thermometer 5 Ball shut-off valve 6 Connector G 1 ¼” 7 Safety valve with pressure gauge Heat pump return 8 Connector G 1 ¼” with sensor well for return temperature sensor 9 Ball shut-off valve 10 Connector G 1 ¼” with connection for fill & drain valve and expansion vessel 11 EPS insulation pieces Assembly according to Fig. , and .
Shorten the threaded wall retainer rod subject to the distance to the wall, at which the cylinder was mounted .
It must not be possible to shut-off the safety valve against the heat source.
Connect the expansion vessel and the fill & drain valve at the connector provided (
-e
).
Fit the heat pump flow ( pump return (
-c
).
-d
) and the heat
4.2.3 WPKI-W E
The WPKI-W E set comprises all necessary components for connecting a DHW cylinder.
DHW flow 1 Connector G 1” with ball shut-off valve and non-return valve 2 Handle with inserted thermometer 3 Ball shut-off valve 4 Connection bend 5 Connector G 1 ¼” for installing the heat pump flow DHW return 6 Connection G 1 ¼” for installing the heat pump return.
7 EPS insulation pieces Assembly according to Fig. and .
Install the tee with shut-off valve ( the heat pump return.
-1
) into Fit the heat pump flow ( return (
-c -d
), the heat pump ) and the cylinder return (
-f
).
Connect the expansion vessel and the fill & drain valve at the connector provided (
-e
).
3 4
20 0 40 80 100 120
1 WPKI-H E 2 5 6 7 1 2 WPKI-W E
20 40 0 60 °C 80 100 120
7 8 11 10 8 9 2 WPKI-P E 1
40 20 0 80 100 120
3 4 7
Wall retainer
1 0 bar 2 3 4
6 5 3
830 mm
5 4 6
7
8
2.
WPKI-H E 1.
20 40 0 80 100 120
Wall retainer
1.
WPKI-P E 2.
20 40 0 80 100 120 20 40 60 °C 0 80 100 120
a b c e d 1.
40 20 0 80 100 120 20 40 0 80 100 120
WPKI-W E 2.
1 c e f d
Connection diagram SBP 100 mit WPF....M
9
5 Installation instructions WPKI-H E, WPKI-V in conjunction with the WPF heat pump
for the installer 5.1 General information WPKI-H E
Weight:
Part no. 233098
approx. 3.5 kg
WPKI-V
Weight:
Part no. 074347
approx. 3.0 kg The heat pump compact installation sets WPKI-H and WPKI-V are components of the heat pump system and are specifically designed for the SBP 100 buffer cylinder in conjunction with the WPF heat pump.
These heat pump compact installation sets offer contractors a clear and easy to manage connection of the SBP buffer cylinder to the heat pump and the heating system.
Required special accessories
Circulation pumps UP 25 7.0 E UP 25 7.5 E UP 25/1-7 E Part no.
232942 232943 231187
5.2 Assembly
These set are supplied as prepared assemblies.
All pre-assembled parts are factory sealed.
It is recommended that the set components and, in case of the WPKl-H E, the respective circulation pump are fitted to the cylinder and hand tightened before the installation.
Tighten the fittings once all components have been connected to the cylinder, have been aligned and secured with the wall retainer (only WPKI-H E).
5.2.1 WPKI-H E
The WPKI-H E set comprises all necessary components for connecting the heating system to the SBP 100 buffer cylinder.
Heating flow 1 Connection bend G 1 ¼” with safety valve connector 2 Wall retainer 3 Ball shut-off valve G 1” 4 Handle with inserted thermometer 5 Connector G 1” with ball shut-off valve Heating return 6 Connector G 1 ¼” 7 Connector G 1” with ball shut-off valve 8 EPS insulation pieces Assembly according to Fig. and .
Shorten the threaded wall retainer rod subject to the distance to the wall, at which the cylin der was mounted .
Fit the heating flow ( return (
-b)
.
-a)
and the heating An Allen key (SW 5) is required to open and close the ball shut-off valve in the heating return.
Circulation pumps Observe the flow direction when fit ting the circulation pump.
HE circulation pumps should never be switched directly. Use an external relay with a breaking capacity of at least 10 A/250 V AC or our relay set WPM-RBS.
For the circulation pump rating curve, see page 13.
5.2.2 WPKI-V
The WPKI-V set DHW cylinder.
comprises all necessary components for connecting the WPF heat pump to the SBP 100 buffer cylinder and the Heat pump flow 1 Connector G 1 ¼” with ball shut-off valve 2 Non-return valve 3 Connector G 1 ¼” Heat pump return 4 Connector G 1 ¼” with sensor well for re turn temperature sensor 5 Ball shut-off valve 6 Connector G 1 ¼” with connection for fill & drain valve and expansion vessel Assembly according to Fig. and .
Connect the expansion vessel and the fill & drain valve at the connector provided (
-c
).
( Fit the heat pump flow ( return (
-e
), the heat pump
-d
) and the cylinder return
-f
).
An Allen key (SW 5) is required to open and close the ball shut-off valve in the heating return.
10
3 4
20 0 40 80 100 120
1 WPKI-H E 2 6 5 7 8 WPKI-H E 2.
1.
40 20 0 80 100 120
WPKI-V 5 6 4 WPKI-V 1 2 3
Wall retainer
415 mm
c d f e a b
11
Connection diagram
SBP 100 with WPF 5....13
6. Specification Data table
Application limits Max. permissible pressure Test pressure Max. permissible temperature Hydraulic data Rated capacity Energy data Standby energy consumption/24 h at 65 °C Dimensions Height Width Depth Weights Weight (wet) Weight (dry) Connections Heat pump connection Heating connection Air vent valve connection 12 mm mm mm kg kg MPa MPa °C kWh l SBP 100 Komfort 185443 0.3
0.45
95 100 0.9
955 510 510 142.5 42.5
G 1 1/4 A G 1 1/4 A G 1/2
Circulation pump rating curves
7 6 5 2 1 4 3 0 0 Δp-c 232942 UP 25 7.0 E max.
0,5 1,0 1,5 2,0 2,5 3,0 max.
40 20 0 0 0,5 1,0 X = Delivery flow rate in m 3 /h Y = Pump head in m Z = Power consumption in W 1,5 2,0 2,5 3,0 7 6 5 4 3 2 1 0 0 Δp-c max.
232943 UP 25 7.5 E 0,5 1,0 1,5 2,0 2,5 3,0 4,0 5,0 max.
40 20 0 0 0,5 1,0 1,5 2,0 2,5 3,0 4,0 5,0 X = Delivery flow rate in m 3 /h Y = Pump head in m Z = Power consumption in W 75 50 1 0 3 2 8 7 6 5 4 25 0 6 m max 5 m 4 m 3 m 2 m min 1 m 1 2 6 m 5 m 4 m 3 m 2 m 1 m min 1 2 X = Delivery flow rate in m 3 /h Y = Pump head in m Z = Power consumption in W 231187 UP 25/1-7E 3 4 5 3 4 5
Warranty
The warranty conditions of our German companies do not apply to appliances acquired outside of Germany. In countries where our subsidiaries sell our products, it is increasingly the case that warranties can only be issued by those subsidiaries. Such warranties are only granted if the subsidiary has issued its own terms of warranty. No other warranty will be granted.
We shall not provide any warranty for appliances acquired in countries where we have no subsidiary to sell our products. This will not affect warranties issued by any importers.
Environment and recycling
We would ask you to help protect the environment. After use, dispose of the various materials in accordance with national regulations.
13
14
Notes
Notes
15
Deutschland
STIEBEL ELTRON GmbH & Co. KG Dr.-Stiebel-Straße 33 | 37603 Holzminden Tel. 05531 702-0 | Fax 05531 702-480 [email protected] www.stiebel-eltron.de
Verkauf Kundendienst
Tel. 05531 702-110 | Fax 05531 702-95108 | [email protected] Tel. 05531 702-111 | Fax 05531 702-95890 | [email protected]
Ersatzteilverkauf
Tel. 05531 702-120 | Fax 05531 702-95335 | [email protected]
Australia
STIEBEL ELTRON Australia Pty. Ltd. 4/8 Rocklea Drive | Port Melbourne VIC 3207 Tel. 03 9645-1833 | Fax 03 9645-4366 [email protected] www.stiebel.com.au
Austria
STIEBEL ELTRON Ges.m.b.H. Eferdinger Str. 73 | 4600 Wels Tel. 07242 47367-0 | Fax 07242 47367-42 [email protected] www.stiebel-eltron.at
Belgium
STIEBEL ELTRON bvba/sprl 't Hofveld 6 - D1 | 1702 Groot-Bijgaarden Tel. 02 42322-22 | Fax 02 42322-12 [email protected] www.stiebel-eltron.be
Czech Republic
STIEBEL ELTRON spol. s r.o. K Hájům 946 | 155 00 Praha 5 - Stodůlky Tel. 251116-111 | Fax 235512-122 [email protected] www.stiebel-eltron.cz
Denmark
Pettinaroli A/S Mandal Allé 21 | 5500 Middelfart Tel. 06341 666-6 | Fax 06341 666-0 [email protected] www.stiebel-eltron.dk
Finland
STIEBEL ELTRON OY Kapinakuja 1 | 04600 Mäntsälä Tel. 020 720-9988 [email protected] www.stiebel-eltron.fi
France
STIEBEL ELTRON SAS 7-9, rue des Selliers B.P 85107 | 57073 Metz-Cédex 3 Tel. 0387 7438-88 | Fax 0387 7468-26 [email protected] www.stiebel-eltron.fr
Hungary
STIEBEL ELTRON Kft. Gyár u. 2 | 2040 Budaörs Tel. 01 250-6055 | Fax 01 368-8097 [email protected] www.stiebel-eltron.hu
Japan
NIHON STIEBEL Co. Ltd. Kowa Kawasaki Nishiguchi Building 8F 66-2 Horikawa-Cho Saiwai-Ku | 212-0013 Kawasaki Tel. 044 540-3200 | Fax 044 540-3210 [email protected] www.nihonstiebel.co.jp
Netherlands
STIEBEL ELTRON Nederland B.V. Daviottenweg 36 5222 BH 's-Hertogenbosch Tel. 073 623-0000 | Fax 073 623-1141 [email protected] www.stiebel-eltron.nl
Poland
STIEBEL ELTRON Polska Sp. z o.o. ul. Działkowa 2 | 02-234 Warszawa Tel. 022 60920-30 | Fax 022 60920-29 [email protected] www.stiebel-eltron.pl
Russia
STIEBEL ELTRON LLC RUSSIA Urzhumskaya street 4, building 2 | 129343 Moscow Tel. 0495 7753889 | Fax 0495 7753887 [email protected] www.stiebel-eltron.ru
4
Irrtum und technische Änderungen vorbehalten! | Subject to errors and technical changes! | Sous réserve d‘erreurs et de modifications techniques! | Onder voorbehoud van vergissingen en technische wijzigingen! | Salvo error o modificación técnica! | Excepto erro ou alteração técnica | Zastrzeżone zmiany techniczne i ewentualne błędy | Omyly a technické změny jsou vyhrazeny! | A muszaki változtatások és tévedések jogát fenntartjuk! | Отсутствие ошибок не гарантируется. Возможны технические изменения.
| Chyby a technické zmeny sú vyhradené! Stand 8845
Slovakia
TATRAMAT - ohrievače vody, s.r.o. Hlavná 1 | 058 01 Poprad Tel. 052 7127-125 | Fax 052 7127-148 [email protected] www.stiebel-eltron.sk
Switzerland
STIEBEL ELTRON AG Industrie West Gass 8 | 5242 Lupfig Tel. 056 4640-500 | Fax 056 4640-501 [email protected] www.stiebel-eltron.ch
Thailand
STIEBEL ELTRON Asia Ltd. 469 Moo 2 Tambol Klong-Jik Amphur Bangpa-In | 13160 Ayutthaya Tel. 035 220088 | Fax 035 221188 [email protected] www.stiebeleltronasia.com
United Kingdom and Ireland
STIEBEL ELTRON UK Ltd. Unit 12 Stadium Court Stadium Road | CH62 3RP Bromborough Tel. 0151 346-2300 | Fax 0151 334-2913 [email protected] www.stiebel-eltron.co.uk
United States of America
STIEBEL ELTRON, Inc. 17 West Street | 01088 West Hatfield MA Tel. 0413 247-3380 | Fax 0413 247-3369 [email protected] www.stiebel-eltron-usa.com
advertisement
Related manuals
advertisement