advertisement
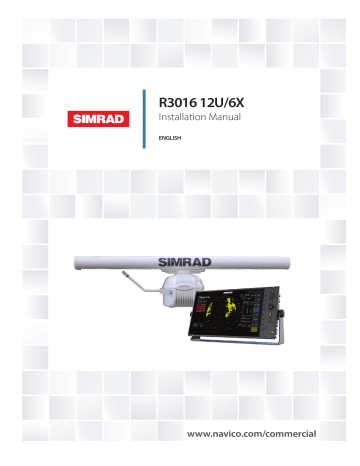
R3016 12U/6X
Installation Manual
ENGLISH
www.navico.com/commercial
Preface
Disclaimer
As Navico is continuously improving this product, we retain the right to make changes to the product at any time which may not be reflected in this version of the manual. Please contact your nearest distributor if you require any further assistance.
It is the owner’s sole responsibility to install and use the equipment in a manner that will not cause accidents, personal injury or property damage. The user of this product is solely responsible for observing maritime safety practices.
NAVICO HOLDING AS AND ITS SUBSIDIARIES, BRANCHES AND AFFILIATES DISCLAIM ALL LIABILITY FOR ANY USE OF THIS PRODUCT IN A WAY THAT MAY CAUSE ACCIDENTS, DAMAGE OR THAT MAY VIOLATE THE LAW.
This manual represents the product as at the time of printing. Navico Holding AS and its subsidiaries, branches and affiliates reserve the right to make changes to specifications without notice.
Governing Language
This statement, any instruction manuals, user guides and other information relating to the product (Documentation) may be translated to, or has been translated from, another language (Translation). In the event of any conflict between any Translation of the Documentation, the English language version of the Documentation will be the official version of the Documentation.
Copyright
Copyright © 2016 Navico Holding AS.
Warranty
The warranty card is supplied as a separate document.
In case of any queries, refer to the brand website of your display or system: www.navico.com/ commercial.
•
Regulatory statements
This equipment is intended for use in international waters as well as coastal sea areas administrated by member states pursuant to international conventions.
The R3016 12U/6X Radar system complies with: the Navigation requirements of Marine equipment directive (MED) 96/98/EC, and the last modification by directive 2015/559/EU, Annex A.1. item 4.36, Radar equipment for CAT 3 vessels.
The relevant Declaration of Conformity is available on the product's section on the following website: www.navico.com/commercial.
Wheelmark
The Marine Equipment Directive 96/98/EC (MED) applies to all ships for which safety certificates are issued by - or on behalf of - member states pursuant to international conventions. This applies to all new ships, to existing ships not previously carrying such equipment, and to ships having their equipment replaced. This means that all system components covered by annex A1 must be type-approved accordingly and must carry the Wheelmark, which is a symbol of conformity with the Marine Equipment Directive.
Navico has no responsibility for incorrect installation or use of the equipment. It is essential for the person in charge of the installation to be familiar with the relevant requirements as well as with the contents of the manuals, which covers correct installation and use.
Preface | R3016 12U/6X Installation manual 3
4
About this manual
This manual is a reference guide for installing the R3016 12U/6X radar system. The manual is written for the professional radar and marine electronics technicians, and assumes some prior knowledge and skills relevant to the type of work to be carried out.
The latest available manual version can be downloaded from the website: www.navico.com/ commercial.
Safety precautions
Safety precautions described in this section are applicable to the radar system. They are general safety precautions that are not related to any specific procedure, and they might therefore not appear elsewhere in this manual. They are recommended precautions that personnel must understand and apply during operation and maintenance of the system.
You are obliged to read these operating instructions prior to operation, and to adhere to the operating instructions in order to prevent possible danger. Prevention of danger includes that operator personnel are trained and authorized for safe operation of the equipment. We assume no liability for damage due to improper operation which could have been prevented.
The system must only be operated by persons who have passed the relevant mandatory training on the respective systems and applications. Only reading these operating instructions cannot replace such training. Persons authorized to operate, maintain and troubleshoot the system are instructed and trained by Simrad. Persons operating or servicing this radar system must be familiar with the general safety regulations and specific safety systems, and they must have passed all required training. They must have read the relevant operating instructions and manuals before starting to work.
Have these operating instructions always at hand on all relevant locations, and ensure that copies are available to all operators. Operating personnel must at all times follow all safety regulations.
During normal operation, the unit can be quickly disconnected from the main power line by turning OFF the relevant circuit breaker located on the electric switchboard.
Do not replace components or make adjustments inside the unit when the voltage supply is turned ON. Always remove power and discharge to ground a circuit before touching it.
Under no circumstances should any person initiate servicing or repairing the unit except in the presence of a qualified person.
Ensure unobstructed access to all operator panels, controls, and relevant switchgear cabinets in order to enable instant response to alarms.
Whenever it is necessary to disconnect the waveguide from a radar transmitter for maintenance purpose, the transmitter output should be terminated with a matched load. If this is not possible, care should be taken. Do not stand in front of an open-ended waveguide from which power is being radiated.
Ú
Note:
Main power is always present on the terminal board unless the main break from the power distribution panel of the vessel is turned off.
Warning: Never look down a waveguide from which power is being radiated!
Warnings High voltage
Radar equipment includes high voltage that can cause injury or loss of life. Danger exists only when the units are opened, exposing internal circuits, as when servicing the equipment.
This radar has been carefully designed to protect personnel from possible injury from high voltages. Although every effort has been made to eliminate danger to personnel, no responsibility is accepted for any injury or loss of life suffered in connection with this equipment.
Preface | R3016 12U/6X Installation manual
Radio frequency radiation
Harmful effects (particularly to the eyes) may be caused by exposure of any part of the human body to high power radio frequency radiation.
Hazard distances are given in the following table:
Configuration
12 kW Transceiver + 6 ft. antenna
Distance 100 W/m 2 point (m) Distance 50 W/m 2 point (m)
0.05
Distance 10 W/m 2 point (m)
0.9
The system is however designed to always disable the microwave radiation when the antenna is not rotating.
X-Ray radiation
This radar system does not generate X-ray radiation.
Trademarks
Simrad ® is used by license from Kongsberg.
NMEA ® and NMEA 2000 ® are registered trademarks of the National Marine Electronics Association.
SD ™ and microSD ™ are trademarks or registered trademarks of SD-3C, LLC in the United States, other countries or both.
Preface | R3016 12U/6X Installation manual 5
6
Contents
7
7 7 8
Introduction
R3016 12U/6X Radar system System components
9
9 9 10
Connector layouts
Up-mast transceiver connectors R3016 Сontrol unit connectors
R3000 power supply unit connectors
11 Installation overview
11
12 12 13 13
Obstructions and blind sectors Transceiver height implications
Mounting location Tools required
14 Hardware mounting
14
Install the up-mast transceiver
15 16 18 21
Install the R3000 power supply unit
Adding the heater system (optional)
22 Wiring
22
22 22 23 23 24 25 25 26 26 27 29 29
System overview diagram Up-mast transceiver cables
Up-mast transceiver grounding Connection at the up-mast transceiver
Transceiver power supply connection
Power supply diagnostics Control unit power and alarm output connection
Connection of Ethernet cable to control unit Sensor connection
SI80 connection VDR connection
31 Technical specifications
35 Spare parts
36 Accessories
37 Dimensional drawings
37
Up-mast transceiver and antennas
37 38 38 38
R3016 Control unit SI80 Signal Interface unit Antenna rotating diameter
39 Technical drawings
39
Contents | R3016 12U/6X Installation manual
1 + _
Introduction
• • •
R3016 12U/6X Radar system
The R3016 12U/6X Radar system is a type approved radar system conforming to the International Maritime Organization (IMO) requirements for vessels that are subject to SOLAS regulations.
The system consists of: R3016 Control unit 12kW up-mast transceiver with 6ft. antenna R3000 Power supply unit • • • • • The radar assists in safe navigation and in avoiding collision by providing an indication, in relation to own ship, of the position of other surface craft, obstructions and hazards, navigation objects and shorelines. For this purpose, the radar provides the integration and display of radar video, target tracking information, positional data derived from own ship’s position and geo-referenced data.
To be able to provide consistent data, the R3016 12U/6X Radar system is designed to be integrated using serial interfaces with other electronic equipment normally present in a vessel bridge: Gyro-compass or transmitting heading device (HDG) Speed and Distance Measuring Equipment (SDME) Electronic Position Fixing System (EPFS) Automatic Identification System (AIS) Bridge Alert Management system (BAM) The R3016 12U/6X Radar system is a Category 3 type approved system, approved only in the configuration specified in the certificate. The type approval certificates are available at the product web site: www.navico.com/commercial.
System components The R3016 Control unit
The R3016 Control unit includes 3 main components: a processor, a monitor and a keypad.
The processor is made of a dual core CPU that integrates information coming from the transceiver and the external sensors.
The monitor is a non-touch monitor type approved for Category 3 Radar use.
The keypad is the main control device for the system. The system cursor is controlled by the directional pad, while several options are provided to activate radar functionalities and navigate menus during operation.
The R3016 Control unit is fitted with an SD card reader used for updating the software and for transferring data from the system.
The control unit is directly linked with the transceiver using a dedicated signal cable (15, 30 or 65 m length).
The up-mast radar sensor
The up-mast radar sensor comprises two main parts: a 6 foot antenna and a 12 kW transceiver.
The antenna is a 6 foot X-band antenna, fixed to the transceiver unit with 4 bolts.
The transceiver is the system radio transmitter and receiver, measuring the radar echo received from the pulse transmission. The transceiver includes a processing unit that eliminates unwanted echoes or noise, and transfers digitized video data to the control unit.
On the back of the unit there is a safety switch and 3 connectors: Signal connector, Main power connector, and a connector for the optional Heater kit.
Introduction | R3016 12U/6X Installation manual 7
8 POWER
The R3000 Power supply unit
System nominal input is 24 VDC. The power supply unit converts the available 24 VDC power source up to the transceiver's operating voltage. The transceiver input voltage is higher to minimize the effect of voltage drop due to cable length.
Output power cables are available in 15, 30 and 65 m lengths.
• • •
The Heater kit
The optional Heater kit is used when installing the heater in the transceiver. The heater warms up the radar transceiver to ensure safe start-up and operation. The main components of the Heater kit are: the R3000 Power supply unit - provides the additional output required to drive heater element the Heater upgrade kit - all the parts that are to be included in the transceiver unit the cable - connects the R3000 Power supply unit to the transceiver heater power connector Power cables for connection between R3000 Power supply unit and Heater kit are available in 15, 30 and 65 m lengths.
SI80 Signal Interface unit
The optional SI80 Signal Interface unit is used to provide an additional IEC 61162-2 port.
Connection to the R3016 Control unit is made via NMEA 2000. The SI80 provides power and termination for the backbone.
R3016 12U/6X manuals
The following documentation is delivered with the R3016 12U/6X Radar system:
R3016 12U/6X Operator manual (988-10911-00n)
User descriptions of the radar and of the features included in the system.
Intended audience: System operator.
R2009/R3016 Quick Guide (988-10951-00n)
Graphical document describing the keys and the main functions.
Intended audience: System operator.
R3016 12U/6X Installation and System wiring manual (988-10912-00n)
Mechanical installation and wiring, technical specifications and mechanical drawings for all system components.
Intended audience: Shipyard installation personnel.
R3016 12U/6X Configuration and maintenance manual (988-10913-00n)
System setup/configuration, commissioning, trouble shooting, maintenance procedures, replacement procedures for replaceable parts and spare parts listing.
Intended audience: Installation and service engineers.
R3016 Control unit Mounting template (988-10917-00n)
1:1 cut-out template with dimensions.
Ú
Note:
The last digit in the part numbers is the document's revision code. The latest version of all documents can be downloaded from the product website on www.navico.com/commercial.
Introduction | R3016 12U/6X Installation manual
2
Connector layouts
Up-mast transceiver connectors
The R3000 power supply unit converts ships 24 V to 50 V required by the up-mast transceiver.
1 2 3 4 5 1 2 3 4 5 5-pin power connector
Provides power to transceiver
RJ45 Ethernet socket
Provides radar and 2-way communication over a digital connection
Heater power connector (optional - shown not installed)
Provides power to a heater element
Safety switch
Used to disconnect power to transceiver circuits (excludes heater)
Ground terminal post
Mandatory grounding connection point for connection to vessel ground
R3016 Сontrol unit connectors
ETHERNET HDMI NMEA2000 POWER NMEA0183 NMEA0183 1 2 3 4 5 6 5 6 1 2 3 4 Ethernet
Radar data input and communication with transceiver
HDMI
Provides video output to voyage data recorder (VDR)
NMEA 2000
Connection for SI80 expands NMEA 0183 I/O
Power
24 VDC power input and system failure alarm output
NMEA 0183 (Serial 1)
2 x Inputs + 1 x Output
NMEA 0183 (Serial 2)
2 x Inputs + 1 x Output
Connector layouts | R3016 12U/6X Installation manual 9
R3000 power supply unit connectors
POWER STATUS J2 PWR OUT OFF ON PWR IN
1 2 3 8 9 4 5 6 7 1 2 3 4 5 6 7 8 9 Negative output
Negative return to transceiver
Positive output
50 VDC output is used to supply transceiver or heater kit
J2
Power cable shield connection point
ON/OFF supply switch
Disables output from supply
Negative input
Negative return for power input
Positive input
24 VDC power input
Fuse
Protects supply from output overcurrent
Power LED
Indicates state of the power supply input
Status LED
Indicates state of power input Ú
Note:
The drawing shows the power supply front cover removed for terminal access.
10 Connector layouts | R3016 12U/6X Installation manual
3
Installation overview
The information provided by radar is of vital importance to skippers and the safe navigation of ships. Special care should be taken to ensure correct installation of the radar, in order to ensure the performance of the radar system is not compromised. Interference, either by reflecting structures or other RF transmitters, may significantly impair radar performance by creating blind sectors, clutter on the radar display or generation of false targets. All hardware should be mounted with appropriate gauge and number of fasteners, and structure radar is mounted to should be determined to be fit for purpose, capable of supporting the radar in any weather or sea state.
Interference
Other radar
Do not install the radar transceiver on the same beam plane as other radar – provide at least 45 degrees vertical separation. Use sector blanking as required to eliminate interference from same frequency radar on vessel.
A
TX 45 12.5
12.5
45 STBY
B A B
R3016 12U/6X radar sensor Other radar The following shows suggested minimum vertical separation for different radar combinations, where radars are installed one above the other:
A A
TX 12.5
12.5
TX 2 m (6 ft) 3 m (9.8 ft) STBY STBY
C B A
TX 12.5
12.5
2 m (6 ft) STBY 12.5
12.5
A B C D D
R3016 12U/6X radar sensor Pulse compression radar Broadband radar Other pulse radar
Installation overview | R3016 12U/6X Installation manual 11
12 Other RF sources
The radar antenna should be installed at a safe distance from interfering high-power energy sources and other transmitting and receiving radio antennas.
Sensitive equipment
Some electronics such as GPS and electronic heading sensors may be particularly sensitive to radar emissions. Follow the manufacturers guide on suitable separation distances. Avoid having such equipment directly in the beam of the radar.
Obstructions and blind sectors
The antenna should be mounted clear of any structure that may cause signal reflections and resultant blind sectors. Large flat metallic structures perpendicular to the radar generally cause the worst reflections, and should be avoided.
Railings
The underside of the radar antenna should be a minimum of 50 cm above any safety rail.
Swing diameter
Ensure all obstructions are clear of the rotation of the antenna (see
"Up-mast transceiver and antennas"
on page 37). To avoid the antenna coming in contact with other installed objects
while it is rotating, ensure that there is at least 200 mm between the swing circle (turning radius) and the other installed objects.
Blind sectors
It should be kept to a minimum, and not occur in an area of the horizon from right ahead to 22.5° abaft the beam to either side. Any two blind sectors separated by 3° or less should be treated as one combined blind sector. Individual blind sectors of more than 5°, or a total of blind sectors of more than 20°, should not occur in the remaining area abaft the aforementioned area. For radar installations with two radar systems, where possible, the antennas should be placed in such a way as to minimize the blind sectors.
Distance to water surface
For all radar systems and where practical, a line of sight from the radar antenna to the bow of the ship should hit the surface of the sea at no more than 500 m or twice the ship length, depending which value is smaller. This goes for all load and trim conditions.
l < 2l < 500 m
Transceiver height implications
The following table indicates the effect of mounting height of antenna on the distance before the beam hits the water.
Height (m) Distance (m) 1 4.7
2 9.4
3 14.1
4 18.8
5 23.5
7.5
35.3
10 47.0
Height (m) 15 Distance (m) 70.6
20 94.1
25 117.6
30 141.1
40 188.2
50 235.2
Installation overview | R3016 12U/6X Installation manual
Height impact
The radar antenna should be located in an elevated position to permit maximum target visibility, but no higher than necessary to achieve this as sea clutter worsens and short range performance is compromised with increase of height. On smaller vessels excessive height may also have a negative impact on vessel stability.
Mounting location
Up-mast transceiver
Safe service access should be provided using service platforms where necessary, having a minimum size of 1 m 2 at a suitable height and with a safety rail of suitable height.
The design of the mounting platform for the up-mast transceiver should take into account the vibration requirements defined by IEC 60945.
The platform that is being mounted to should be level when vessel is loaded and underway at typical cruise speed.
Ú
Note:
When working at height, ensure appropriate safety harness and lanyard is used.
Control and display
The orientation of the R3016 Control unit should be such that the user is looking ahead. The lookout’s view should not be obscured, and any ambient light should cause minimum degradation on the display screen in accordance with MSC/Circ.982.
• • • • • • •
Tools required
The following list covers the basic tools that are essential to installation of this system: Torx screwdriver, T20 (performance monitor arm) Philips screwdriver #1 (control unit flush mounting) Philips screwdriver #2 (power supply + SI80 + heater kit) Posi screwdriver #3 (control unit bracket fasteners) Combination wrench, 13 mm (antenna bolts) Combination wrench, 19 mm (transceiver mounting nuts) Hex key wrench, offset type, 6 mm (cover) Ú
Note:
Power supply machine screw nuts are not provided. Technicians can choose the screws and proper tools.
• • • • • The following tools are not essential, but likely to be required: Jigsaw (wood and metal blades) (cut-out for controller flush mounting) Router + bits (cut-out for controller flush mounting) Cordless drill Drill bit set 16 mm drill bit (needed for NMEA 2000 plugs) Ú
Note:
In case the heater system is included, additional tools are required. Refer to
Installation overview | R3016 12U/6X Installation manual 13
4
Hardware mounting
Install the up-mast transceiver
The up-mast transceiver must be mounted with the cable connectors pointed aft. Ensure there is adequate space for the housing to open fully backwards. There should also be sufficient space behind the up-mast transceiver in order to easily access the plugs and safety switch at back of housing.
524 mm (20.6”) 458 mm (18.0”) 634 mm (25”) >200 mm (7.9”) >141mm (7.4”) 93 mm (3.7”) 178 mm (7.0”) Securely mount the up-mast transceiver prior to fitting the antenna.
14
Ú Ú
Note:
The waveguide protection cover on the up-mast transceiver must not be removed until immediately prior to antenna fitment.
Note:
While the up-mast transceiver is fitted with mounting studs to cater for common installation scenarios, it may be required to fit different studs or bolts to suit the specific requirements of the installation. The supplied studs are M12, and allow mounting to a surface no more than 30mm thick. Any replacement hardware should allow for a wound in depth of at least 2x the diameter of the bolt or stud (e.g. >24mm). Use a good quality isolating or anti-seize compound on the thread, to prevent electrolysis.
Fasteners should be of 316L stainless and property class 70 or better (bolt heads will be marked accordingly), or similar strength high tensile steel with a permanent protective coating system applied.
Hardware mounting | R3016 12U/6X Installation manual
Fitting the performance monitor arm
Attach the PM arm to the up-mast transceiver housing using the supplied T20 fasteners. The arm should be oriented to point upwards. Ensure the gasket ring is fitted between the housing and the base of the arm.
All electrical connections are made when the performance arm is attached to the up-mast transceiver – it is not necessary to complete any further connections inside the up-mast transceiver enclosure.
Fitting the control unit
The control unit may be mounted using either the supplied dash top bracket, or flush mounted in to the ships control console. A suitable position will not obscure the view out of the bridge windows, and will be oriented to minimize direct sunlight reflection off the screen. The screen should be mounted no more than 0.75m from either the standing or seated position of the operator. All keypad controls must be easily accessible.
U-bracket mounting
1.
Place the bracket in the desired mounting location. Ensure that the chosen location has enough height to accommodate the unit fitted in the bracket, and allows tilting of the unit. Also adequate space is required on both sides to allow tightening and loosening of the knobs.
2.
Mark the screw locations using the bracket as a template, and drill pilot holes. Use fasteners suited to the mounting surface material. If the material is too thin for self tappers, reinforce it, or mount the bracket with machine screws and large washers. Use only 304 or 316 stainless steel fasteners.
3.
4.
5.
Screw down the bracket.
Using the screws provided in the gimbal kit, fasten the gimbals to the unit.
Mount the unit to the bracket using the knobs. Hand tighten only. The ratchet teeth in the bracket and display case ensure a positive grip and prevent the unit changing from the desired angle.
6.
Fix the bracket straps.
Hardware mounting | R3016 12U/6X Installation manual 15
3 4 5 6
Panel mounting
The screws and gasket used for panel mounting are included in the box. For mounting instructions, refer to the Panel mounting template.
Install the R3000 power supply unit
The power supply should ideally be installed in an area that is dry, cool, and free of excessive vibration.
Cooling requirements
The power supply must be installed in an area that offers sufficient cooling, and that is not subject to temperatures is excess of 55 °C. Ideally the area should be actively ventilated to ensure a consistent operating temperature. The power supply must be installed on a vertical surface, with the cables exiting downwards. Where area of installation is poorly ventilated, provide space around all sides of the power supply, per the following diagram;
16 Hardware mounting | R3016 12U/6X Installation manual
500 mm 200 mm
POWER STATUS
200 mm 500 mm
Grounding wire
The R3000 power supply unit has a chassis ground terminal on the underside of the case. The chassis ground is DC isolated from power to eliminate the risk of electrolytic corrosion.
It is recommended that the power supply unit ground is connected to the vessels bonded ground or a non-bonded RF ground at the closest possible location, using 12 AWG wire (or thicker):
Fastening in place
The power supply unit is supplied with different fasteners to suit most mounting materials.
Self-tapping wood screws with washers and nuts (x4) for wood, fiberglass, or soft plastics, and machine screws (x4) for harder surfaces such as aluminum, and those too thin for self tapping screws. The self-tapping screws are 6G x 45mm (1.75”), so will extend in to mounting surface approximately 30mm (1.2”). The machine screws are 60mm (2.4”)”, so mounting surface should be no more than 40mm (1.6”) thick.
Drill bit sizes for the self-tappers and machine screws are 2.5mm and 4.5mm respectively.
Hardware mounting | R3016 12U/6X Installation manual 17
18
Adding the heater system (optional)
An optional heater can be installed to ensure transceiver reliable operation down to -40 °C.
The heater kit consists of an R3000 power supply, and the heater components and fasteners for inside the transceiver. The heater power cable must be ordered separately in a length suited to the installation. The power cable is the same type as used for powering the transceiver.
Heater kit parts
5 3 6 2 7 1 8 4 1 2 3 4 5 6 7 8
Heater element Connector (female) for temperature sensor In-line fuse holder (10 A SB fuse) External waterproof socket Thermo-conductive gel Temperature sensor 2 x hex pan screws M4 2 x hex pan head screws M3 • • •
Tools required
The following list covers the basic tools that are essential to installation the heater kit: Screwdriver Torx - T20 Screwdriver Torx - T10 Hex key – 6 mm
Install the heater R3000 power supply unit
As the heater power supply housing is identical to the transceiver power supply unit, use the
"Install the R3000 power supply unit"
Hardware mounting | R3016 12U/6X Installation manual
Install heater kit in transceiver housing
Ensure the radar system is shut down, and a warning sign has been placed at the controller.
When at the up-mast transceiver set the safety switch in the (power) OFF position.
Remove the two pan head screws securing the blanking plate found between the Ethernet port and the safety switch on the rear of the up-mast transceiver.
Pass the heater elements, spade connectors, and fuse holder through the hole, from outside to the inside.
Secure the plug body to the transceiver housing with existing fasteners.
Inside the up-mast transceiver identify the temperature sensor and heater element mounting locations by referring to the following diagram. Route the Heater kit loom along the dotted line shown. Ensure no part of the cable has enough slack to risk coming in to contact with moving parts like the main gear wheel.
Secure the temperature sensor with two supplied M3 pan head screws, and slide on the blue spade connectors. Insert the heater elements into the mounting holes and secure them in place using supplied M4 pan head screws.
Hardware mounting | R3016 12U/6X Installation manual 19
1 2 3 7 8 6 4 5 20 1 2 3 4 5 6 7 8 Temperature sensor mounting screw holes
Pan head screws are inserted here to retain the sensor
Lower heater element mounting hole
Lower element is directly inserted into this hole
Lower heater element retaining screw hole
Pan head screw is inserted here to retain the element
Upper heater element mounting hole
Upper element is directly inserted into this hole
Upper heater element retaining screw hole
Pan head screw is inserted here to retain the element
PCB mounted cable clip
Pass a heater loom through this clip
Mounting foot
Cable a tie loom to this point
Heater loom route
Follows a route of existing cables. Ensure the loom is secured to the existing loom at regular intervals using cable ties. Pass the loom through any cable clip that is used to support existing cables.
Hardware mounting | R3016 12U/6X Installation manual
Install the SI80
The SI80 is delivered with an Installation Guide (SI80_IG_988-10475-00n). See the guide for installation instructions.
Hardware mounting | R3016 12U/6X Installation manual 21
22 5
Wiring
• • • • • • • •
General precautions
Check all ground connections. During the hardware installation they must be completed before power and communication cabling.
Create drips loops where cable connects to product, to prevent water collecting on device connectors.
Cables should be kept as short as possible, to minimize chance of interference and voltage drop.
All cables between antenna and radar system units should be routed as directly as possible, consistent with consideration for other equipment, in order to reduce electromagnetic interference effects.
Cables should not be installed close to high-power or high frequency conducting cables, such as radar or radio-transmitter lines, large DC motor cables. Where cables intersect, try to stay at right angles (90°) to minimize inductance of noise.
Only use suitable waterproof connectors when joining cables.
If a cable being pulled through a concealed area requires excessive force to finish pulling through the remaining cable, consider rerouting cable via an alternative route – otherwise cable conductors may get broken, the cable sheath & insulation may be damaged, or the same damage may be done to adjacent cables, which may cause a fire.
System overview diagram
VDR
POWER STATUS ETHERNET HDMI NMEA2000 POWER NMEA0183 NMEA0183 POWER STATUS
SDME TRACK DATA READER EPFS AIS BAM GYRO • • •
Up-mast transceiver cables
It is advised to run the cables starting at the up-mast transceiver location, working towards the power supply and control unit console: Gravity feeding of cables in radar tower conduit is naturally easier, especially where no draw wire is available.
The Ethernet plug is smaller at console end: 20mm plug diameter vs 36 mm plug.
The power cable is un-terminated at the POWER SUPPLY end, whereas up-mast transceiver end has 36 mm plug.
Ú
Note:
Minimum bend radius of the Ethernet cable is 100 mm. Do not subject the cable to tighter bends, as distortion of the cable can degrade the cables performance, and at worst may break conductors due to fatigue.
Wiring | R3016 12U/6X Installation manual
Up-mast transceiver grounding
Connect a tinned copper cable (>25 mm 2 ) between the ground terminal on the up-mast transceiver and the radar mast, using crimped or soldered ring terminals at either end. Cable should be kept to minimum necessary length. Ensure it is fastened using a suitable stainless bolt and lock nut or spring washer. Self-tapping screws should not be used. Good electrical connection is essential - ensure paint or other isolating coatings on surface are properly removed around area of bolt and ring terminal contact with mast. After fitting, apply a suitable anti-corrosive coating to the assembly.
Ú Ú
Note:
Radar mast should be a good conductor (i.e. metal), and be bonded to rest of ships ground. If not, earth cable should be run to nearest grounded structure.
Note:
Earth strap is ideally braided tinned copper, but tinned power cable is also suitable.
Connection at the up-mast transceiver
The plugs for Ethernet and power should only be connected when the earth strap is already in place.
Before inserting plugs, ensure the safety switch is set to the OFF position as marked on switch.
All three connectors are keyed, so plug orientation cannot be done incorrectly. Ensure the retainer clip is fully engaged after insertion.
4 3 1 2 1
Retention clip
Wiring | R3016 12U/6X Installation manual 23
2 3 4
Power plug (5-pin in armored housing) Ethernet plug (RJ45 in armored housing) Earth strap Ú
Note:
Coil the Ethernet cable to form two loops, and clip on the supplied ferrite choke.
With two loops the cable will pass through the ferrite three times. The loops should be made within about 10cm of the LAN plug inserted in to the transceiver housing. Do not make the loops too tight as this could damage the cable.
Transceiver power supply connection
The power supply converts ship's 24 V to 52 V required by the up-mast transceiver.
Two R3000 power supplies are required for installations utilizing a heater kit. One of the power supplies is used to drive the transceiver, the other powers the heater.
To access the electrical terminals on the power supply, remove the front cover by undoing the six Philips screws on the front of the unit. Lift off the cover, and pull forward the w shaped plastic gasket retainer. Pull out the rubber gaskets.
24
When running cables in to the supply, ensure they pass through the gasket first.
The ship's 24 V DC supply should be connected using appropriate sized cabling to support the maximum current draw (approx. 15 - 20 A under max wind load) without significant voltage drop. It is recommended a minimum of 10mm2 (8 AWG) cable is used when doing short runs. The terminals will accept up to 25mm2 (4 AWG) cable.
4 1 2 3
POWER STATUS PWR OUT OFF ON PWR IN
5
POWER STATUS PWR OUT OFF ON PWR IN
6 7 + Wiring | R3016 12U/6X Installation manual
1 2 3 4 5 6 7
Transceiver power cable (15 m in the example) Ethernet cable Heater power cable (15 m in the example) Transceiver R3000 power supply Fused supply (30 A fuse for each supply with normal action, able to cut 32 VDC) Ship's 24 VDC supply The longer 30 m and 65 m cables have additional cores which require connection to the extra screw terminals, per the diagram below.
PWR OUT PWR OUT PWR OUT
1 2 1 2 3
Wired with 15 m cable Wired with 30 m cable Wired with 65 m cable
3
Power supply diagnostics
There are two LEDs on the front cover of the R3000 power supply unit. They provide basic diagnostic information on the connections: wiring and power supply connection status.
The following table covers the various possible sequences.
LED
STATUS POWER
Color
Green Green OFF Red Red
Pattern
On constant On constant N/A On constant Blinking
Meaning
Output voltage (52 VDC) is available to the transceiver Input supply is good, voltage is within acceptable range • • • • • No supply, or protection fuse is blown R3000 switch set to OFF Output overload Input voltage too high (>45 V DC) Input voltage too low (<17 V DC) Output voltage too high (>60V) • Temperature too high (>125° C) Output overload Ú
Note:
The power supply has an initialization sequence at startup, and will momentarily illuminate the red LED, this is normal behavior.
Control unit power and alarm output connection
The R3016 Control unit power cable has four wires, two of which provide power to the unit, and two for the alarm output.
Wiring | R3016 12U/6X Installation manual 25
ETHERNET HDMI NMEA2000 POWER NMEA0183 NMEA0183 1 2 3 6 4 5 + 7 1 2 3 4 5 6 7
Alert management system Blue wire – alarm output (N/C isolated contact) Yellow wire – alarm output negative return Red wire - positive DC supply (24 VDC system) Black wire - negative DC supply (24 VDC system) Fuse - see table at end of section DC supply
Connection of Ethernet cable to control unit
The Ethernet cable is pre-terminated and is simply plugged directly to the R3016 Control unit's NETWORK connector. Under no circumstance should this cable be plugged into a network hub or any other Ethernet device.
Ú
Note:
Direct connection must be made between the transceiver and controller. Failure to do so would make the system non-compliant.
Sensor connection
Any sensor connected to the R3016 12U/6X system should meet IMO performance standards and be certified. Failure to do so would make the rest of the system non-compliant.
The R3016 control unit supports up to 4 inputs and 2 outputs for sensors. Expansion beyond the supplied 4 inputs and 2 outputs can be achieved by the addition of an SI80 through connection to the control unit’s NMEA 2000 port.
All inputs and outputs can be configured to match the speed of the connected sensors.
Sensor connection overview diagram
The diagrams below show the configuration of a system with 5 inputs using the SI80 for expansion, as well as a system only using the 4 on-board inputs.
26 Wiring | R3016 12U/6X Installation manual
ETHERNET HDMI NMEA2000 POWER NMEA0183 NMEA0183
SDME TRACK DATA READER EPFS AIS
Configuration with BAM
BAM GYRO
ETHERNET HDMI NMEA2000 POWER NMEA0183 NMEA0183
TRACK DATA READER EPFS AIS SDME
Configuration without BAM
GYRO R3016 12U/6X
must
be connected to an External Position Fixing System (EPFS), a gyro compass/heading sensor, and a SDME source via serial line.
Ground stabilization requires an external sensor signal capable of providing an input and an indication of own ship’s speed over ground, for example from an EPFS, SDME or use of stationary tracked reference targets. If a ground-referenced speed log is used for ground stabilization, it must be of dual axis type.
Connections to a BAM device is mandatory if these devices are available on a vessel.
Ú Ú Ú
Note:
The gyro-compass or heading sensor must have an update rate that is adequate for the ship’s rate of turn – the performance should meet or exceed the relevant standards adopted by the IMO (IMO A.424(XI), A.821(19) and MSC.116(73)).
Note:
Analog sensors are not supported on the R3016 12U/6X radar system.
Note:
If more than four inputs are required (i.e. when BAM is connected), an SI80 will
need to be connected to provide additional NMEA 0183 ports. Refer to
Serial ports – color code
The NMEA 0183 labelled ports on the back of the control unit provide four inputs (Listeners) and two outputs (Talkers) for the various IEC 61162 interfaced sensors, including gyro/ heading, speed log, EPFS, SDME, etc.
Wiring | R3016 12U/6X Installation manual 27
28 ETHERNET HDMI NMEA2000 POWER NMEA0183 NMEA0183 1 2 3 4 5 6 Key
1 2 3
Description
Port 1 Listener (twisted pair with screen and drain) Port 2 Listener (twisted pair with screen and drain) Port 1 Talker (1A and 1B twisted pair)
Key
4 5 6
Description
Port 3 Listener (twisted pair with screen and drain) Port 4 Listener (twisted pair with screen and drain) Port 3 Talker (1A and 1B twisted pair) Ú Ú
Note:
The serial cables supplied are identical.
Note:
The wiring of sensors which are connected to inputs should be recorded for reference as is required when commissioning the system.
4 4 5 3 3 5 6 2
7 8 1 5 6 2 3 4
Key 7 8
Unit socket
1 Port (left socket) Port (right socket)
Port 2 Port 2 Port 1 Port 1 Port 1 Port 1 Port 1 Port 1 Port 4 Port 4 Port 3 Port 3 Port 3 Port 3 Port 3 Port 3
2 Purpose 1 8
Cable plug
7 Color
Shield Listener B (Rx+) Listener A (Rx-) Shield Common Talker B (Tx+) Talker A (Tx-) Shield Listener A (Rx-) Listener B (Rx+) Drain Green Yellow Drain Black Brown White Drain Yellow Green
6 Wiring | R3016 12U/6X Installation Manual
SI80 connection
The SI80 is connected when a fifth serial port is required. The device is connected to the control unit via NMEA 2000, using Micro-C cables. The NMEA 2000 network must be powered and be terminated at both ends.
ETHERNET HDMI NMEA2000 POWER NMEA0183 NMEA0183
T
2 1 3 + 4 5 6
T
9 7 8 1 2 3 4 5 6 7 8 9
SI80 (connected as end-of-line device on network due to internal terminator) Terminator (on-board selectable) SI80 power cable Fuse DC supply (+24 V DC) Micro-C drop cable (must be <6’, not included) Micro-C backbone (bare ends at SI80) Micro-C T-piece Micro-C terminator plug (not included) Refer to
Installation Guide
supplied with the SI80 for further details, including alternative NMEA 2000 connection, as well as NMEA 0183 input wiring.
Ú Ú Ú
Note:
on page 36 for a list of cables available.
Note:
The SI80 should only be used to connect to the SDME or heading source. Never connect the BAM system via the SI80.
Note:
Do not connect more than one sensor via the SI80. This would make the system non-compliant.
VDR connection
An HDMI video output is provided for interface to a 3 rd party Voyage Data Recorder (VDR).
The output mirrors the screen display, and is at the same resolution. The VDR connected to should accept digital video input, either using DVI or HDMI interface.
Wiring | R3016 12U/6X Installation manual 29
VDR
ETHERNET HDMI NMEA2000 POWER NMEA0183 NMEA0183 1 2 3 1 2 3
Voyage Data Recorder with DVI input DVI connectors DVI – HDMI adaptor cable Ú
Note:
It is not possible for the user to deactivate video output to the VDR port.
30 Wiring | R3016 12U/6X Installation manual
6
Technical specifications
For updated technical specifications, compliance and certifications, refer to the product website.
General Description Standards Type approval
• • • • • • 12 kW X-band pulse radar IMO class 3 with 6 ft end-fed slotted waveguide antenna IMO-Resolution A.278 (VIII), A.694 (17), A.
823 (19), MSC 191 (79), MSC 192 (79) EN 62388 Ed.2.0, 2014 EN 62288 Ed.2.0, 2014 EN 60945 Ed.4.0, 2002 incl. Corr.1, 2008 EN 61162-1 Ed.4.0, 2010 EN 61162-2 Ed.1.0, 1999 Maritime Equipment Directive 96/98/EC, 4.36
Radar Equipment CAT 3
Environmental Temperature
Operating temperature, protected unit -15°C to 55°C (According to IEC 60945 ed.4.0) Operating temperature, exposed unit -25°C to 55°C (According to IEC 60945 ed.
4.0) Operating temperature, exposed unit (heater kit fitted) -40°C to 55°C according to RMRS rules (2-020101-040-E Vol 2 - Environmental Test of Equipment) Storage temperature, exposed unit -25°C to 70°C (According to IEC 60945 ed.
4.0)
Vibration
Storage temperature, exposed unit (heater kit fitted) -60°C to 70°C according to RMRS rules (2-020101-040-E Vol 2 - Environmental Test of Equipment) Damp heat +40°C, 93 % relative humidity 1 cycle (According to IEC 60945 eg. 4.0) According to IEC60945 ed. 4.0
Shock
According to RMRS rules (2-020101-040-E Vol 2 - Environmental Test of Equipment)
IP class
R3016 Control unit IP66
Relative wind velocity
Scanner IP66 Power supply units IP65 100 knots wind tunnel test at 20 RPM (According to IEC 62388)
Power Transceiver up-mast unit
Supply voltage (V DC) 50 Average power (W) 250. (Additional 300W if heater kit is included)
R3016 Control unit
Supply voltage (V DC) 24
Technical specifications | R3016 12U/6X Installation manual 31
32 Power
Average power (W) 20
R3000 Power supply unit
Supply voltage (V DC) 24 Max power (W) 300 330 when used for Heater kit Fuse Rating (A) 30
Heater kit
Warm-up time from cold start-up at -40 °C (heater kit fitted) Fuse rating (for heater loom in transceiver) (A) 3 hours 10
Physical Dimensions Antenna swing circle diameter (cm) Weight
Refer to Dimensional drawings 183 cm (6 feet) Pedestal + Antenna (Kg) 40 (35 kg transceiver + 5 kg antenna) R3016 Control unit (Kg) 4 Power Supply Unit (Kg) 1 Heater loom & connector Trivial
Performance RPM Nominal peak power (KW) Operating frequency (MHz) Pulse length (ns)
20 or 36 (selectable) 12 9410 Short pulse 75 Medium pulse 300 Long pulse 825
PRF (Hz)
Short pulse 3000 Medium pulse 1500
Modulator IF amplifier IF dynamic (dB) IF center frequency (MHz) IF bandwidth (MHz)
Long pulse 750 MOSFET Solid State Logarithmic 95 60 Short pulse 24 Medium pulse 4.8
Horizontal Beam width (deg.) Vertical Beam width (deg.) VSWR
Long pulse 1.8
1.35
22 < 1.20
Technical specifications | R3016 12U/6X Installation manual
Performance Overall noise figure (nominal dB) MDS on long pulse (dBm)
< 5 -105
Display features Presentation mode Typical viewing distance (m) Resolution (pixels) Aspect ratio PPI Diameter (mm) Short range
Day or Night 0.75
1366x768 16:9 >180 Available scales (NM) 1/8, 1/4, 1/2, 3/4, 1.5 and 3 Range video resolution (m) 11.25
Azimuth on-screen resolution (Deg) 0.1
Medium range
Available scales (NM) 6 and 12 Range video resolution (m) 45 Azimuth on-screen resolution (Deg) 0.1
Long range
Available scales (NM) 24, 36, 48, 64, 72 Range video resolution (m) 125 Azimuth on-screen resolution (Deg) 0.1
Relative Motion (RM) True Motion (TM) Off-centering
Head Up, Course Up and North Up Course Up and North Up Up to 75% of range scale in use
Cursor
Polar and Geographical coordinates, continuously displayed when cursor is activated
I/O interface Data inputs
Serials 2 x IEC 61162-1 2 x IEC 61162-2 1 x IEC 61162-1 using SI80 (optional) Radar Video Input 1 x Ethernet 100Mbs
Data outputs Alarm output Micro-C connector VDR
Serials 2 x IEC 61162-1 1 x Isolated pair normally closed radar failure contact SI80 connection for IEC 61162-1 expansion (to be used with Speed Log sensor, when BAM is present) HDMI output, same resolution as radar display
Target tracking Acquisition
Manual, up to 20 targets
Technical specifications | R3016 12U/6X Installation manual 33
Target tracking Tracking AIS Presentation Safe checking
Automatic, up to 20 targets Totally 120 target capacity, of which a maximum of 20 can be activated.
AIS overflow mechanism of priority 120 targets in total
Mapping Map drawing Map stabilization Map storage Map adjustments Parallel Index Data readout
Operator compiled maps Up to 32 maps, each may contain up to 120 segments and 32 symbols Selectable colors and line styles Relative Geographic By name Built-In non-volatile memory used SD Card transfer available Translation and rotation allowed Four independent parallel index lines Own ship data Target tracking data AIS target data
Compass safe distance R3016 Control unit 12 kW X-Band SRT transceiver R3000 Power supply unit Safe distance to the standard magnetic compass
0.65 m 1.43 m 0.3 m
Safe distance to the steering magnetic compass
0.43 m 0.87 m 0.24 m
34 Technical specifications | R3016 12U/6X Installation manual
7
Spare parts
For updated technical specifications, compliance, and certifications refer to the product website.
Part number
000-10668-001 000-13252-001 000-10675-001 000-10680-001 000-10683-001 000-10682-001 SP-305274A1-001 000-10678-001 000-10679-001 000-10684-001 000-10681-001 000-10671-001 000-10672-001 000-10674-001 000-13253-001 000-12393-001 000-12399-001
Description
Performance monitor (PM) arm SRT LAN electronic assembly RF detector assembly with LNFE Noise diode Motor SRT gear reducer Performance monitor diode Duplexer circulator Limiter Brushless controller assembly Bearing reader PCB SRT power PCB SRT MOS PCB SRT control PCB Magnetron Serial cable high speed NMEA 0183 8 way (2 m) Front case service pack R3016
Note
Serial cable 000-12401-001 000-12408-001 000-12410-001 000-12412-001 000-12414-001 000-12520-001 Keypad reader kit R3016 SD door kit R3016 Dash mounting kit R3016 Bracket mounting pack R3016 Suncover R3016 Bezel assembly edge R3016 Bonded touch screen replacement Keypad PCB and buttons replacement Card reader door and gasket replacement
Spare parts | R3016 12U/6X Installation manual 35
8
Accessories
Part number
000-12387-001 000-12388-001 000-12389-001 000-12390-001 000-12391-001 000-12392-001 000-12427-001 000-10425-001 000-0127-52 000-0119-88 000-0127-53 000-12386-001
Description
Power cable (15 m) Power cable (30 m) Power cable (65 m) Ethernet cable (15 m) Ethernet cable (30 m) Ethernet cable (65 m) HDMI DVI cable (1.5 m) SI80 SIMRAD signal interface TR-120-KIT Micro-C cable (0.6 m) Micro-C cable (1.8 m) Heater upgrade kit for SRT LAN
Note
For transceiver or heater use For transceiver or heater use For transceiver or heater use For transceiver or heater use For transceiver or heater use For transceiver or heater use NMEA 2000 terminator kit NMEA 2000 cable NMEA 2000 cable Requires separate power cable
36 Accessories | R3016 12U/6X Installation manual
9
Dimensional drawings
Up-mast transceiver and antennas
1800mm (70.8”) 364mm (14.3”)
R3000 Power supply unit
213.0 mm (8.39") 195.0 mm (7.68") 458mm (18.0”) 524mm (20.6”) 146mm (5.7”) 178mm (7.0”) 200mm (7.9”)
POWER STATUS Dimensional drawings | R3016 12U/6X Installation manual 37
R3016 Control unit
505 mm (19.88”) 455 mm (17.91”) 67 mm (2.63”)
+ _
477 mm (18.77”)
SI80 Signal Interface unit
211 mm (8.29") 197 mm (7.77") 185 mm (7.27") 80 mm (3.15") 180 mm (7.08") 48 mm (1.88") 120 mm (4.72”) 60 mm (2.36")
Antenna rotating diameter
38
1830 mm (72.05”)
Dimensional drawings | R3016 12U/6X Installation manual
10
Technical drawings
The System block diagram (992-21511-01A-R3016) is enclosed.
System block diagram
PREWIRED 2 x 000-12393-001 (2 m)
Technical drawings | R3016 12U/6X Installation manual 39
www.navico.com/commercial
advertisement
Related manuals
advertisement