advertisement
▼
Scroll to page 2
of
37
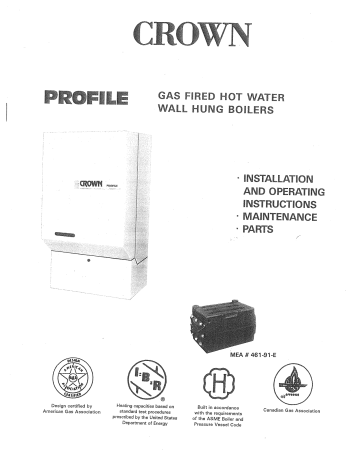
PROFILE Design certified by American Gas Association Heating capacities based on standard test procedures prescribed by the United States Department of Energy MEA 4 461-91-E Г 049770000 Built in accordance with the requirements of the ASME Boiler and Pressure Vessel Code Canadian Gas Association Table of Contents SECTION PAGE I. Product Description eee eee eters eset eee 1 ЦП. Boiler Ratings and Specifications ......................xerrieeri eno reee error R RR RER 1 Ш. Before Starting Installation ....................e.e.ee0imiee RR RD ear eee aora 3 IV. When Your Shipment Arrives ...............e.eeereririrerroor io ree e ae eee eee es 3 У. Locating Boiler .....................xieieeeiioera eee. enoucanvarerooooocarecconeronencarerrara recreo 3 VI. Hanging Boiler .......................eereeeciicer e ee ronca eee eee eee eee 5 Vil. Water System Piping ..................... +++... iii. imei rare ano e erre ecerereane coreo. 8 VII. Completing Boiler Assembly .......................... eeiinnancooo een ea naaa cane cecar en eras 9 1X. Gas Piping ....................e.eeeeiireeenercca reee reee. enorerorecarenerarerenroc ne canene 10 X. Electrical Wiring .......................00eeee in e e enero rerrranee ara canne 11 XI. Start-up and Check-out ....................eeeeeeeere eee eee eee. 16 XII. Maintenance ...................eeeeenneer E EEE necevaoranencacanoneaananeo o ere raocececanoroeen. 18 XII. Troubleshooting ........................... een ree DD ener encerrar ecc 19 27 28 Crown PF series boilers are direct vent gas fired wall mounted boilers designed for hot water space heating only. The PF incorporates a one piece cast iron heat exchanger. All air for combustion is obtained from outdoors via the opening between two concentric tubes. Flue gases are exhausted to the outdoors via the inner of the two concentric tubes. There is no communication of air between the boiler and the indoor space, making this boiler ideal for tightly insulated construction and other applications where an adequate source of clean indoor combustion air cannot be guaranteed. TABLE 1: BOILER RATINGS & CAPACITIES T AGA Heath Water U ippi das ВТО, pay Fair Lo te PF-50 Natural or LP 50,000 42,000 37,000 82.1 190 PF-65 Natural or LP 65,000 55,000 48,000 83.0 190 PF-82 Natural or LP 82,000 68,000 59,000 82.6 190 USA - For altitudes above 2,000 ft. ratings should be reduced at the rate of 4% for each 1,000 ft. above sea level, Heating capacity is based upon DOE (Department of Energy) test procedure. CANADA - For Altitudes above 2000 feet - Consult Factory FIG la: FRONT VIEW SIDE VENTED FIGURE 1b: Side View Rear Vented 2-112 + Relief Valve | — 15 L * f И Gauge = L 1— 13/8 7-314 7 Return k++ 2.3/4 5 | ) Supply | = IS Lo! = | JB | 3-11/32 N DN NS NY Г Г N Ab SV 39 NS | RS N S | S — RS NN NN DT NN + — Gas Pipe NS ¥ Gas Pipe 1 LON F—— 16-3/4~——— Sa 5-5/16 F——— 18-3/4 a All dimensions + 1/8" TABLE 2: TABLE 3: VENT RESTRICTIONS TAPPINGS (Inches NPT) (inches) Supply 3/4 *Female Return 3/4 *Female L Gas 1/2 Female Standard Length ond min. 5-3/8 * With factory supplied fittings. Boiler is also shipped max.: 21-1/16 with (2) 3/4" NPT x 1" Female sweat adaptors Optional | Long Tube Water Content (All Sizes) 1.72 US Gallon min. 5-3/8 max. 78 TABLE 4: Minimum Clearances (inches) [E een reneoceaoen eee ooo raro ecorcoco nene eoearerecoraroeaooeae 1 Front (to door or removable obstruction)............ e... eee ao are e or eaararaa aaieióa, 1 Front (to non-removable obstuction) .......................... prreenercao ancora rea aereo reee. 24 BOOM E rene eeeaaee ee a aa 1-1/4 Casing TOP™ «ooovveiiiiii eee ier in ae ee 9 Vent Terminal to Closest Construction (Horizontal) ee 96 * Relief valve must have sufficient clearance to ceiling so as to allow the relief valve lever to be fully raised. The above | top clearance will allow this with the factory supplied piping installed according to these instructions. | 1) Be sure that boiler is of correct size and gas type (Natural or LP) required. 2) Read this installation manual completely. 3) Be sure that the planned installation 1s in accor- dance with all local codes. In the absence of any local codes, install this boiler in accordance with the National Fuel Gas Code Z223.1-1988. Where required by the authority having jurisdiction the installation must conform to the Standard for Controls and Safety Devices for Automatically Fired Boiler (ANSI/ASME CSD-1). In Canada follow the Canadian Installation Codes for Gas Burning Equipment (CAN/CGA B149.1 and .2) as well as the Canadian Electrical Code, Part I CSA C22.1. This boiler is shipped in two cartons as follows: Carton A: Main assembly including casing, heat exchanger, burner control system and control cover. V. 1) Observe the vent tube length constraints outlined in Table 2. 2) Observe the minimum clearance from the boiler casing to other construction outlined in Table 4. Note that these minimum clearances will automatically be held if the minimum clearances to the bracket shown in Figure 2 are observed. 3) Vent terminal must be located no closer than: 712" from any opening through which exhaust could enter building. #12" above grade level. Y Tft. above a public walkway. y 4ft. horizontally to either side of electric meters, gas meters, regulators, and relief equipment. Fi e Ys Carton B: (Carton B is the same for all size boilers) 4) 5) 6) / Door + Fan assembly + Boiler hanging bracket v Vent components / Relief valve and tridicator Y Relief valve tee / Installation manual / Fan assembly mounting screws 7 Wall hanging bracket mounting hardware Silicone Sealant Be certain that all of the above components are present before starting installation. Where-ever possible vent terminal should be located on the side of the structure facing away from the prevailing wind. This boiler is designed to operate with winds on the vent terminal of up to 40 mph. Reliable operation at wind speeds above 40 mph cannot be guaranteed. | Flue gases contain corrosive products which can condense on, and damage, construction near the vent terminal. For this reason avoid placing vent terminal under overhangs if at all possible. Vent terminal cannot be extended beyond outside wall. Wall must be capable of supporting boiler. damage, injury, or death. This boiler weighs approximately 200 lbs. installed. Failure to properly support it could result in property 1. FIGURE 2: HANGING BRACKET MINIMUM CLEARANCES NAL LLAMAN O" 8-7/16 ele OF TT - ` О A I EL > o oO > 9 2 | 18-5/8 УХУ Х УХУ Install mounting plate making sure it is both level & plumb: a) Wood framed walls- Boiler mounting plate is b) provided with 2 sets of holes on 16 inch centers for installation on a standard studded wall. If it is not possible to line these holes up with the studs, additional 3/8 holes may be located in the mounting plate. Once the mounting plate holes are located over studs, mark hole locations on wall. Drill pilot holes and mount hanging bracket using 5/16 x 2 lag screws and 5/16 washers provided. When drilling holes make sure that they are in center of stud. Masonary walls- After locating boiler mounting plate mark hole locations. Drill pilot hole and drive in 5/16 lag shields provided. Secure boiler mounting plate to wall using 5/16 x 2 lag screws and 5/16 washers provided. 2) Because of the large variety of different materials used in wall construction, as well as the varying condition of older construction, it is ultimately the installer's responsibility to ensure that the above methods of attach- ment are suitable to the particular wall at the installation site. a) Vent tube opening ELA - Lay outa 3 3/4" dia. hole in the center of boiler mounting plate vent opening. Cut out through wall being careful to keep hole straight. Side Vent Only |- Using horizontal center marks on mounting plate opening, extend a level line around corner. Lay out a vertical center line 5-1/4" in from corner (Fig. 3). Lay out a 4" dia. hole on this center line. Cut out being careful to keep hole straight. Vent tube preparation - Measure the wall thickness from its outside face to the inside face of the mounting plate (Fig. 4a). Add 2-3/8 inches to this dimension. Measure the total length from the flanged end of the vent tubes and cut squarely. | Cutting Side Vent Tube Only the vent hole from the outside wall face to the vertical center line of the boiler mounting plate (Fig. 4b). Subtract 7-1/4 inches from this dimension. Measure this length from the flanged end of the vent tube and cut square- - Measure through ly. Slip rope sealing ring over vent tube and up to flange. NOTE It is easier to cut the vent tubes if the vent terminal is temporarily placed on the end of the vent tube. The terminal can be held on with tape and will sup- port the inner vent tube, resulting in a squarer cut. 11 FIGURE 3A: SIDE VENT HOLE LAYOUT Mounting Plate «gg io x au HA Appendix À. This boiler is supplied with a factory designed vent system intended ONLY for use with itself. Do not attempt to connect other PF series boilers or any other appliances to this vent system. Do not attempt to use any vent components not specified by Crown Boiler Co. for use on this boiler. If you are removing an old appliance connected to a common venting system on this job site, see Apply a bead of silicone here | FIGURE 3b: VENT TERMINAL REAR VIEW b) Using the tape provided, wrap the vent tube where it could come in contact with mortar. с) Apply a bead of silicone (provided by Crown) around the LD. of the vent terminal where it fits over the inner vent tube (Fig. 3b). The vent terminal flue exhaust grill is designed to discharge flue gases at an angle. Slip the vent terminal onto the vent tube and rotate it to a position so that the flue gases will be directed away from any inside corners, overhangs, or other obstructions near the terminal after it is installed. Secure the vent terminal to the vent tube with the screws provided. MAKE SURE THAT A GOOD SEAL EXISTS BETWEEN THE VENT TERMINAL AND INNER VENT TUBE BEFORE PROCEEDING FURTHER. -Install the rubber gasket provided in the boiler mounting plate. Push the vent tube through this gasket and through the wall until the flange 1s against the mounting plate. d) |Side Vented Boilers On ly |-Install the vent collar provided in the vent tube opening. Drill holes through the mounting ears and attach with the screws provided. Push vent through wall until vent terminal is through sealing collar. Bend the 4 tabs on the flue sealing collar inwards to retain the rope sealing ring. Push the vent through the wall until the flange is clear of the mounting plate. CUT LENGTH = L_ + 2-3/8 INCHES FIGURE 4A: CUTTING REAR VENT TUBE a ; FIGURE 4B: CUTTING SIDE VENT TUBE MOUNTING PLATE © Cut Length = L, —7-1/4 | — b) 3) b) с) Boiler preparation Move vent cover plate to match vent tube position (right or rear). Place vent cover removed over remaining opening. This step is not necessary for a left side vented boiler as cover plates are correctly configured for this as shipped. Note: Flue elbow may be temporarily removed to gain access to the vent cover wing nuts. Install 3/4 side outlet tee provided on supply pipe with the run of the tee in the verticle. Install the relief valve provided on the top tapping (Fig. 5). Hanging the boiler This boiler is heavy. Two people are required to safely lift boiler onto mounting plate. Lean boiler against wall directly under mounting bracket. Two people are required to lift unit. Lift boiler and place hook on the rear of the boiler into the slot on the wall mounting plate (Fig. 6). Remove control cover. Center boiler hook in slot in the sideways direction. Check that boiler is plumb and attach boiler to wall with #10 x 1-1/4" screws and 3/16" Top of Boiler FIGURE 5: SUPPLY PIPING Relief Valve 3/4 Side Outlet Tee ° 1/4 х 3/4 Bushing _Gauge washers through lower mounting feet (Fig. 7). Back of Boiler 4 FIGURE 6: HANGING BOILER Before mounting the fan assembly and casing door, complete all water piping in accordance with the following section, pressurize the system, and check the system for leaks. Pay careful attention to the following areas as they will not be visible later on: a) Supply and return joints inside casing (by the flue collector) b) 3/4" drain nipple and cap (lower left corner of heat exchanger) c) Clean out covers on heat exchanger. Fix any leaks found in these areas before attempting to operate boiler. LA | | oT | [© Ш t e г Е Q | | 7 | Feet. This edge plumb. DS Lower r Mounting FIGURE 7: SUPPORT LEGS EE NOTE Although the threaded water piping supplied with this boiler is 3/4" NPT, installations using PF82's may require some 1" piping in order to get adequate water flow through the system. For this reason 3/4" NPT x 1" female sweat adapters are provided and should be installed as close to the 3/4" boiler piping as possible if 1" piping 1s required. For more information'on proper pipe sizing consult Hydronics Institute publication #200. 1) For safe, reliable operation, the system this boiler 2) is connected to must have the following components. e Temperature- pressure gauge (Provided by Crown) e/Properly sized circulator 9% Properly sized expansion tank Y Connection to fresh water for filling (automatic fill preferred) 4 Relief valve (provided by Crown and installed in Part IV, step F part 2). 4 One automatic air vent and sufficient manual vents to purge all air from the system. (Automatic vent supplied by Crown) Some of these components are available in a package designed for use with this boiler. See your Crown dealer for specifications. This boiler is supplied with an automatic air vent, 3/4" Tee, and a 3/4" x 1/8" bushing so that the air vent may be mounted at the boiler return. If this is done, the Tee is screwed on to the male connection on the right top of the boiler with its run in the vertical. The bushing and air vent are then installed on the top of this Tee and the return connection is made on the side of this Tee. If you are installing the boiler with a low water cut-off on the supply as shown in Fig. 8b, install an air vent by the low water cut-off regardless of whether one is installed on the retum. AT LEAST ONE AUTOMATIC AIR VENT MUST BE PROVIDED ON EITHER THE SUPPLY OR RETURN ON THE TOP OF THIS BOILER. 4) 3) 6} 7) 8) If the boiler is to be installed above the radiation, a low- water cut-off must be installed in the system. The best location for this is the supply piping above the boiler. Locate this low water cut-off and an automatic air vent in a cross as shown in Fig, 8b. This boiler is designed for use in a closed system. Excessive feeding of fresh water through boiler will destroy the heat exchanger. If boiler is to be used in conjuction with a water chiller, a means must be provided to prevent the chilled medium from entering the boiler. Install shut-off valves as shown in Figure 8a. If the boiler is to be connected to heating coils located in air handling units where they may be exposed to refrigerated air circulation, flow control valves or other automatic means must be used to prevent gravity circulation during the cooling cycle. If any part of the heating system is subject to freezing temperatures, antifreeze should be used to protect the system from damage. A non toxic antifreeze must be used. Consult antifreeze manufacturer for proper ratio of antifreeze to water. Pipe relief valve to nearby drain or other location ~ Where hot water discharge will not cause injury or damage. Leave a 6" inch gap between the relief valve pipe termination and the drain pipe or closest obstruction. Termination of relief valve must be unthreaded. Do not pipe relief valve pipe to outdoors or other potentially freezing location. | i For Heating: Open B.D Close A,C For Cooling: Open A, C Close B,D "FIGURE 8a: TYPICAL CHILLER PIPING 3/4 x 1/8 Bushing T И IL Г) Automatic Air Vent Relief Valve Discharge - Probe _/ Boiler L.W.C.O. 3/4 Cross To System FIGURE 8b: TYPICAL LOW WATER CUT OFF PIPING 9) Zoning- Many different ways of zoning systems exist and the details of such are beyond the scope of this manual. The following points should however be kept in mind. ¢ If this boiler is to be used with an indirect water heater it may be desirable to install the boiler with a 3 way zone valve so that all boiler water is diverted to the water heater during a call for domestic water. This “priority zoning’ can also be done using 2 way zone valves, or circulators, and a SPDT switching system. «/ If circulators are used for zoning, a flow check should be installed on the opposite end of the zone from the circulator to prevent gravity, or other unwanted circulation. 1) Slide vent tube towards boiler and engage the flange studs in the casing. 2) Secure vent tube to casing with the four 5mm wing nuts provided. - If not already done, remove the four wing nuts securing the flue elbow to the flue collector, leaving the silicone pressure tubes attached. Insert the flue elbow into the inner vent tube and reinstall wing nuts. Using the silicone supplied, carefully seal the joint between the flue elbow and the inner vent tube. 3) | Side Vent Only | - If not already done, remove the four wing nuts securing the flue elbow to the flue collector, leaving the silicone pressure tubes attached. Insert the flue elbow into the aluminum flue elbow extension provided in the parts bag. Insert the flue elbow and extension into the inner vent tube and reinstall wing nuts. Using the silicone supplied, carefully seal the joints between the flue elbow, elbow extension, and inner vent tube. NOTE It is important NOT to apply the silicone to the above mentioned joints until AFTER the elbow and extension (if used) are installed. If silicone is applied to the male side of these joints prior to inserting them, it will be extremely difficult to break the joints if the flue collector must be removed for servicing. 4) Mount fan assembly to boiler with the seven 5mm screws provided. Plug fan wires into fan plug on boiler (Fig. 11). 5) Install casing door, making sure that a good seal exists around the joint between this door and the casing. 6) Seal vent terminal to outside wall with 400 F. silicone 7) Install wall plate provided to cover any damage to the wall around the vent terminal. Exhaust Tube / Elbow Extension oe venting PT Silicone ‚Р e > | FIGURE 9: ELBOW COMPONENTS pt ar it ie 7 Flue Elbow Silicone FIGURE 10: FLUE ELBOW INSTALLA E (SIDE VENT SHOWN) FIGURE 11: FAN INSTALLATION Smm x 15mm Dog Point Screw (7 Required) OF > Sr - | Fan Plug I | NOTE It 1s easier to make the electrical connections in the junction box prior to installing gas piping. 1) Observe the following when making gas connection. y Use only ungalvanized steel pipe and black malable iron fittings unless other materials are permitted by the authority having jurisdiction over local gas piping. ¢ Use a pipe dope suitable for use with Natural & LP gas regardless of the fuel used. Apply dope to male threads only, keeping first 3 threads free of dope. 10 ¢ Use only ground joint unions. ¢ Install a drip leg to prevent sediment from reaching the gas valve (Fig. 12). ¢’ Install a manual main shut-off valve. Where codes require place this outside the control cover (Fig. 12). Y Install a union in an accessible location so that gas train may be removed from boiler if needed for servicing (Fig. 12). &” Make sure gas piping is properly sized for the installation. Consult authority having jurisdiction over this (usually the gas company) or in the absence of such an authority, ASNI-7223.1-1988. A YT TA e 1 Wd | Do not use an open flame to check for leaks. 2) Testing gas pipi b) The boiler and its individual shut-off valve must be ВЕН PTS disconnected from the gas supply piping system a) Gas piping must be tested for leaks immediately during any pressure testing of that system at test after turning on gas to the boiler. To do this pressures greater than 1/2 psi. pray the pip ing with & soap suds solution. Forming c) The individual shut-off valve of the boiler must be matter small. at once 7 ’ closed during any pressure test of the gas supply - piping system at pressures less than or equal to 1/2 psi. FIGURE 12: TYPICAL GAS PIPING o- Gas Valve Ground Joint Union Gas Cock 1) Wiring must be in accordance with all codes. In the 3) Boiler system must be connected to its own 15 amp 2) absence of any codes, boiler must be wired and grounded in accordance with the National Electric code (ANSI/NFPA 70-1990). High voltage connections - Four high voltage pigtails are located in the utility box to the left of the gas valve. These are: Black- “Hot” to boiler White- ““Neutral”” for boiler and circulator Red- “Hot” for circulator Green- Equipment ground 11 circuit. À remote emergency shut-off switch should be installed ahead of all other boiler controls. If the boiler is in a closet, install the emergency switch just outside the closet. Bring a cable or cables into the utility box along the gas line so that they will be in the control cover's ‘‘“U”’ slot when the cover is installed. Make connections inside utility box and install utility box cover. If a circulator with an amp draw of more than 12 amps is used a contactor is required. 4) Low voltage connections - Remove the two 8-32 x 1/2 screws from the control tray and swing it down (Fig. 13a, 13b). The low voltage terminal strip is in the forward left corner. Terminals are as follows: T,T- Connect to thermostat , zone valve, end switch, or other dry contacts which are intended to start the boiler upon closing (Fig. 14b). 1,2- Auxilary 24VAC power source for 3 way motorized zone valve or other device requiring less than 15.6 VA of power. 5) IMPORTANT If terminals 1 & 2 are connected to a device drawing more than 0.65 AMPS the boiler transformer may be destroyed. Make 24 volt connections by running low voltage wiring from the low voltage terminal strip through the clips on the left edge of the control tray. These wires can then be ‘routed out of the boiler either along the gas pipe or through metal conduit installed in the 7/8" knock-out to the left of the control tray. Zone wiring- Fig. l4c, d, and e show common zone wiring for 3 way domestic water zone valves, 2 way zone valves, and circulator zoning respectively. (See Gas Valve Figure 15 Detail) High Limit Control Tray (See Figure 13b Detail) FIGURE 13A: GENERAL CONTROL LAY-OUT | Lift tray off rear hooks to remove 12 FIGURE 13B: CONTROL TRAY TOP VIEW Wiring Hamesses omitted for clarity High voltage terminal strip Pressure Switch Negative Pressure 58670 Ignition Module Connector ‘Thermostat Cable Clip Transformer Low Voltage ~~ Terminal Strip | | Circulator Relay Fan/Latch Relay FIGURE 14A: 115 VOLT WIRING - FOR USE WITH FIGURES 14B, C, D Emergency L.W.C.O. i Contacts (If used | Switch ( ) n Black Lead — о о— со — H A White Lead N | Gnd HD n RedLead G С " AE EE ree i | Н Circulator 1 O hi — A ol en | Wire Nut Field Wiring 24 Volt Transformer Factory Wiring (Fig. 14D only) FIGURE 14B: 24 VOLT WIRING - SINGLE ZONE Low Voltage Terminal Strip O 2 O 1 О OT О OT 24 Volt Heat Anticipator Setting = 1.0 Thermostat 13 FIGURE 14C: 24 VOLT WIRING - PRIORITY ZONING OF AN INDIRECT WATER HEATER WITH A 3 WAY ZONE VALVE Orange Flair- Superior LW.H. Aquastat 2 UWO 14002 Yellow 3 3 Way Zone Valve 1 Blue T Blue T Low Voltage Terminal Strip Pipe: АВ - To Retum A - From 1.W.H. B - From Heating Radiation 24V Heating Thermostat Set Heat Anticipator to 1.0 ELL V8043F ZONE VALVES FIGURE 14D: 24 VOLT WIRING - ZONING WITH HONEYW | Low Voltage 11 Terminal Strip 24 Volt 24 Volt O 2 Thermostat Thermostat _ _ O 1 O T O T Set Heat Anticipators | | to 0.32 5 y y End Switch End Switch | | | TH-TR TH TR TH-TR TH TR T° | RTT RR О Transformer (24V connections Shown) 14 0F'0 01 siojedpnuy 9H 195 JOYE AO) Q | — dmg ¡euTuna] IBENOA MOT Ny | L -09 Ó ! 5 er Ко О 1 o 7 © TZ S ¢ 1 eE LO Y SP8U | Y Su 20 N9ImMÁSUON NEMÁJUON I L LI I 1 7 D SIDA a LT LT JEISOULIOULL ART я JEJSOULIOUL AFZ US) N JeJSOULIOUT, ATZ (pesnioN) pou V A HUM 4 : _00 0 pag y (posn Jy) sean) UNIMS OIM Adue81our (Paioads osimJOyLQ SsajUfN sIJOA SL | BULIM |v) ONINOZ HOILVTINOHID - DNIHIM LIOA SLL ONV bZ 371 JYNDIA 15 „= « XI. START-UP 1) Fill the boiler system with water and purge of all air. 2) Fire boiler: Turn on electrical power from remote Pressurize to desired operating pressure (typically disconnect switch. 15ps1). | NOTE Safe lighting and other performance criteria were met with gas manifold and control Never attempt to fill a hot empty boiler. assembly provided on this boiler when the boiler underwent the tests specified in ANSI 221, 135-1991. if you do not follow these instructions exactly, a fire or explosion may result causing property damage, personal injury or loss of life. A. This appliance is equipped with an ignition device ° If you cannot reach your gas supplier, call the which automatically lights the pilot. Do not try to fire department. light the pilot by hand. C. Use only your hand to push in or turn the gas B. BEFORE OPERATING smell all around the control knob. Never use tools. If the knob will appliance area for gas. Be sure to smell next to not push in or turn by hand, don't try to repair it, the floor because some gas is heavier than air and call a qualified service technician. Force or will settle on the floor. attempted repair may result in a fire or explosion. WHAT TO DO IF YOU SMELL GAS D. Do not use this appliance if any part has been Do not try to light any appliance. under water. Immediately call a qualified service Do not touch any electric switch; do not use any technician to inspect the appliance and to replace phone in your building. immediately call your gas supplier from a neighbor's phone. Follow the gas supplier's instructi any part of the control system and any gas control which has been under water. . . . 5. Remove control access panel. i 1. STOP! Read the safety information above on this 6. Push in gas control knob slightly and turn label. , clockwise to "OFF." 2. Set the thermostat to lowest setting. - NOTE: Knob cannot be turned to "OFF" unless 3. Turn off all electric power to the appliance. knob is pushed in slightly. Do not force. 4. This appliance is equipped with an ignition device 7 Wait five (5) minutes to clear out any gas. | which automatically lights the pilot. Do not try you then smell gas, STOP! Follow "B" in the to light the pilot by hand. safety information above on this label. If you | don't smell gas, go to next step. 8. Turn gas control knob counterclockwise to "ON" 3. Replace control access panel. 10. Turn on all electric power to the appliance. 11. Set thermostat to desired setting. 12. If the appliance will not operate, follow the instructions “To Turn Off Gas To Appliance" and call your service technician or gas supplier. Gas Control Knob Shown in "ON" Position 16 3) Check-out a) Ignition system safety check- Fire boiler and carefully disconnect ignition cable from the S8670E. Main and burner flame should immediately extinguish. If it does not, consult the gas utility or Crown representative. Do not leave In operation. If main flame extinguishes, turn off power to the boiler and reconnect spark cable. Boiler may then be restarted b) High limit check- Set the high limit to the desired setting (180° F is typical for baseboard or standing radiation). Raise or temporarily jump the thermostat so as to run the boiler until the water temperature reaches the limit setting. At the water temperature + 10°F the burners should shut down and the circulator continue to operate. ¢) Thermostat check and adjustment - Lower thermostat to point shown on thermostat thermometer and make sure that the burners and circulator shut-off at approximately this setting. Set thermostat heat anticipator. On a zoned system this step must be done for each thermostat. d) Main burner check-out- Main burner flame should be mostly blue in color and well defined (Fig. 17). No yellow should be present although orange flecks may intermittently appear. If yellow is present in the flame: ¢# Check the manifold pressure at the gas valve. This should be: 4.0 in w.c. for Natural gas 8.0 in w.c. for LP Gas y Check gas orifice size against parts list in the back of this manual. Check for burrs or score marks in orifice opening. If the boiler is natural gas fired, the input may alternately be checked by clocking the gas meter. The input is then approximately: BTU/hr input= (1000 BTU/fE3) x (4Cu. ft clocked) x {3600 Shr.) (4 Seconds clocked) ¢ Check the orifice and burner venturi for any foreign matter. e Check to make sure that the flue orifice and air intake orifice are of the correct size. ¢ Check that there is no recirculation of flue gases into combustion air system. y Check casing for combustion air leakage. Manifold Pressure Regulator FIGURE 15: GAS VALVE PV, MV/PV, and MV ” Electrical Corrections — 1/8” Manifold Pressure Tap 1/8" Line Pressure Tap — Ground Correction Pilot Tube Connection Manual Gas Control Knob Pilot adjustment > (Actual adjustment located under this screw) 1. Set the thermostat to lowest setting. 2. Turn off all electric power to the appliance if service is to be performed. 3. Remove control access panel. TO TURN OFF GAS TO APPLIANCE 4. Push in gas control knob slightly and turn 5. Replace control access panel to "OFF." Do not force. clockwise -—a 17 $) Pilot check-out- Pilot should be blue, stable, and completely cover the gap between the electrode and grounding strap (Fig. 18). If necessary, it may be adjusted by removing the cover screw shown in Fig. 15. Using a 1/8" flat bladed screw driver, turn the pilot adjusting screw clockwise to lower the pilot and counter clockwise to raise it. Casing seal check — With the boiler operating run your hand around the casing door joint and all other joints and seals to make sure no air is leaking from these areas. Low Water Cut-off Check-out — Check the low water cut off for proper operation at the intervals specified by the low water cut-off manufacturer. Consult the low water cut-off manufacturer's instructions for the proper manner in which to do this. FIGURE 16: PILOT FLAME „= Possible Yellow or Orange Tip Blue Flame FIGURE 17: MAIN FLAME CHARACTERISTICS Completely Blue Flame -OK Blue Flames, Yellow Tips -Orange-Yellow Tipping normal on LP Excessive tipping may indicate lack of adequate air (See part 3d) Lifting Flame % - Slight lifting is normal on start-up Excessive lifting after several minutes of operation may indicate excessive manifold pressure. Yellow Flames -Unacceptable - See part 3d AINTENANCE In order to ensure safe reliable operation the follow- ing maintenance procedures should be performed by a qualified serviceman on an annual basis. 1) Check flue passages for cleanliness - Remove control cover, casing cover, fan assembly, and 18 fire door. Remove the flue elbow, flue collector, and baffles (if used). Place a light in the combustion chamber. Using a mirror (held at a 45° angle over the top of heat exchanger) examine the flue passages. Remove any visible deposits from the flue ways with a small flue brush. In order to prevent such deposits from falling onto burners place a piece of cardboard on top of burner assembly before brushing out flue collector. 2) |) b) с) d) À rapid accumulation of soot in a gas boiler 1s indicative of a hazardous condition. The cause of such sooting should be located and corrected (See section X part 3d) Shine a light down both the inlet and exhaust tubes (this may have to be done from the vent terminal end). Inspect both air intake and vent tubes for foreign objects or deterioration of tubes. Also inspect vent terminal for blockage. Clean and repair as necessary Sequence of normal operation (Reference Fig. 18, Fig. 19). Upon a call for heat thermostat terminals are made, energizing relay coil 1K. This closes contacts 1K 1 which energizes circulator. If the high limit contacts are made, and the C-NC pressure switch contacts are made, current flows through the 2K relay coil. This energizes the combustion fan via contacts 2K2 and simultaneously provides an alternate route to coil 2K around th C-NC contacts via contacts 2K1. | The purpose of this ““latch”” system is to provide a check, before attempting to start the burners, that the pressure switch is not stuck in the “pressure OK” position. The fan moves air through the boiler providing a pressure differential across the pressure sensing tubes in the flue elbow. If a pressure differential of at least a 1.74 +£0.07" w.c. is present, the C-NC contacts will break and the C-NO contacts will make. This energizes the Honeywell S8670-based intermittent ignifton system. Upon begin energized, the S8670 module waits for a 30 second prepurge period to pass before attempt- ing to light the pilot. At the end of this time, an ignition spark 1s started and 24VAC is applied to the pilot valve in the VR8204 (terminals PV-MV/PV). à 6 ES uy 5 3) 4) 5) e) g) 19 After cleaning and inspecting heat exchanger and vent tubes, reassemble flue collector, flue elbow, and fan assembly, replacing any deteriorated gaskets. Burner assembly should be inspected for foreign matter in the venturi and blade holes. Any such matter should be blown out with compressed air or vacuumed out. Once burner has been inspected the fire door may be reinstalled. Fan motor 1s equipped with ball bearings, and should not be lubricated. Reassemble casing cover, and control cover. Perform checks outlined in Section X. Upon establishment of a pilot flame, AC current coming up the ignition cable is rectified to a DC current by the pilot flame. This signal passes from the pilot grounding strap through the frame of the boiler to the ground screw in the utility box. It then travels to the ‘“Grd’’ terminal on the S8670 via the green wire. | If the S8670 senses a current greater than 1.2uA DC it deenergizes the spark and energizes the main valve on the VR8204 gas valve (Terminals MV-MV/PV). If the pilot flame is not detected by the S8670 after a 90 second trial for ignition, it will deenergize the pilot valve and spark. It will then wait 5 minutes and try to establish pilot again. During this time the fan and circulator will continue to operate. If no pilot is ever detected, this cycle will continue indefinitely. After the main flame is established, the pilot will continue to burn. Both main and pilot flames will continue to burn until the thermostat or high limit opens. When either device opens the 2K relay coil is deenergized and the system returns to its original status. If the high limit opens, only the 2K coil is opened. The 1K coil remains energized, keeping the circulator running until the call for heat is satisfied. 2) a) b) The following four pages contain a troubleshooting chart for use in locating and solving control problems. To use it do the following: Go to the start box on the next page and follow the instructions contained in that box. Follow the line out of that box into diamond which asks "does the circulator start.” If the circulator is operating follow the path leaving this diamond to the right (the "Y" for yes path). If it is not operating leave the diamond by the bottom ("N" for no path). Continue in this manner, following the boxed instructions and answering the questions in diamonds, until you come to a box with a list of possible causes denoted with asterisks (*). One of these causes is probably behind the problem being experienced. If you rule out all the causes in a particular box, first retrace the path taken to get to this box and make sure that all questions have been accurately answered. If you arrive at the same box, check the wiring against the connections diagram in Fig. 19. If all wiring is in accordance with this diagram, contact a Crown representative for further assistance. IMPORTANT Although the causes listed in the boxes above are in no particular order, all controls are factory tested at least once in the assembly process and A DEFECTIVE CONTROL IS GENERALLY THE LEAST LIKELY CAUSE. If you suspect you have a defective control, double check your path through the trouble- shooting chart before you replace it. It is also important to remember that THE LIKELIHOOD OF COMING ACROSS TWO IDENTICAL DEFECTIVE CONTROLS IN A ROW IS ALMOST NIL. If this seems to be happening, chances are that either there is nothing wrong with the control or it is being damaged by some other problem (a short burning out a transformer, for example). 20 Start: Turn off emergency switch, turn it back on, and make sure that thermostat is calling for heat. Is 110 volts present across 1 & 3 В on transformer? ~~ * Loose connection between transformer and low voltage terminal strip. * Defective transformer. Does ” Does combustion © Circulator rd Is 24 volts > Present between 1 & 2 on low voltage Disconnect thermostat or zone valve end switch connections from T & T on low voltage terminal strip. TEMPORARILY jump T & T together. > fanoperate? 7 Is 115 volts present between transformer terminal Q 43 and on fan latch > relay terminal 452 7 Does | < circulator № * Loose connection between transformer and house fuse box. * Open fuse or circuit breaker. Is 24 volts present across * Loose electrical connection in gray or brown wiring. > circulator relay? 7 * Loose connection in 110 volt circulator wiring. * "Frozen" or defective circulator. * Defective circulator relay, * Loose connection in black and white fan leads. * Loose connection in pin connectors between control tray and fan. * Defective Fan. * Field thermostat wiring is not calling for heat. Check for bad electrical connection. Consult thermostat or zone valve instructions. . 21 * Pressure switch C and NC terminals are not "made." Possible cause of this are: a) Kinked pressure sensing tubes. b) Condensate or blockage in pressure sensing tubes. с) Defective pressure switch. Di will not "retry” until 5 minutes has Wait 30 seconds. Note: If fan has been running more than 120 seconds continuously, the ignition system may be "locked out.” If this has happened the ignition system ~~" Does spark > ee DSK Start at po 7 passed from the time of lockout. Next Page Instead of waiting 5 minutes for this to occur, the ignition system may be “reset” by turning the 115 volt power to the boiler off and back on. The ignition spark should then start after approximately 30 seconds. Disconnect yellow and brown leads from S8670E. Connect a volt meter to these leads. Is 24 Volts = present between — = terminals 13 and 8 on fan/latch relay? Is 24 volts < present across » * Loose connection in wiring Y or pin connector between high limit and control tray. * Boiler is off on high limit. * High limit is defective. * Make sure that S8670E is not "locked out.” * Inspect spark cable for poor connection or broken insulation. * Inspect pilot for cracked porcelain or misoriented electrode/grounding strap. * Defective 58670E. “154 Vois SN present between terminals 13 = and 14 on , > fanflatch relay? ~ * Defective fan/latch relay or relay base. ls at least 1.7" w.c. of pressure present between „the pressure switch hose , connections? 7 * Pressure sensing tubes are reversed. Make sure that the connections with red rings are connected together and go to the left ("red") pressure switch connection. * Pressure sensing tubes are reversed. * Kinked pressure sensing tube. * Condensate or blockage in pressure sensing tubes. * Leaky pressure sensing tube. * Flue orifice missing. * Blockage in vent tubes. * Loose or missing casing door. * Sooted heat exchanger. * Damaged or missing gaskets under fan. * Defective fan. Make sure that the connections with red rings are connected together and go to the left ("red") pressure switch connection. * Defective pressure switch. From Previous Page Does spark > shut off after Disconnect blue and white leads from the PV and MV/PV terminals on the 58670E ignition module, Connect a volt meter to these terminals. MAKE SURE THAT MODULE IS NOT LOCKED OUT WHILE METER IS READ. IF MODULE IS NOT LOCKED OUT A SPARK WILL BE PRESENT AT THE PILOT. fat не Is 24 volts present between PV and MV/PV WHILE SPARK IS PRESENT AT PILOT? * Bad electrical connection between 58670E and gas valve in blue or white wires. * Closed manual gas valve. * Gas lines not purged of air. * Plugged or leaking pilot line. * Damaged pilot assembly. * Defective gas valve. | * Defective S8670E. Does main flame come on? Disconnect the ground lead from the 44 (GND) terminal on the S8670E. Connect a DC micro-amp meter between the ground lead and the #4 connection. Disconnect the red lead from the MV terminal on the S8670E module. Connect a volt meter between the MV terminal and the #4 terminal on the TRANSFORMER. pln ~~" Isatleast © Se 1.2 pA DC present ™ WHILE PILOT IS BURNING? A0 1824 volts present between these terminals? Ar) * Defective S8670F * Bad connection in red wire between 58670E and gas valve, * Blockage in main burner orifice or manifold piping. * Defective gas valve. * Bad connection in spark cable. * Poor ground connection between pilot assembly and 58670E (part of the ground path is through the frame of the boiler). * Damaged pilot assembly * Improper pilot flame (lame should look like that shown in Fig. 16, page 17). * Defective S8670E., 23 PRA. zara Does the ° 7 burner shut =, down before the water temperature reaches the high limit setting + 15° ~~ Does burner ‘ and circulator shut ~. degrees while the thermostat 7 Ns still calling for heat? rd * High limit bulb is not bottomed out in its well. * High limit capillary tube is kinked or broken. * Gray and blue leads to high limit are electrically touching (probably due to damaged insulation and/or bent quick-connects). * Defective high limit. down at the end x. of a call > É Does Burner “a and circulator shut a down when the field wi-ing is disconnected = from the boiler > ™~ T&T terminals? ~~ er ЕЕ ty i) ыы Pr NE ooo END * Field wiring is still calling for heat. Make sure that all wiring is per the zone valve and/or thermostat manufacturer's instructions. Also look for a “short” in the leads going to the T & T terminals. * Boiler wiring not in accordance with Figs. 18 and 19 of this manual. * Blue or gray leads in direct electrical contact with pink lead or terminal #5 of transformer. * Contacts in circulator or fan/latch relay welded together. * Other problem internal to the boiler - consult a Crown representative immediately. 24 FIGURE 18: BOILER LADDER DIAGRAM N 120 VAC H | || o © © 1K1 Circulator Circulator Contacts [| LE 2K2 Fan Fan Contacts Transformer Room 1K Thermostat Circulator Relay Ignition System C / 2K High | | Fan/Latch Relay Limit Pressure Coil Switch | ti 2K1 Latch Contacts © O 1 2 24 VAC Auxiliary Power Supply Factory Wiring NOTE: System is shown in the deenergized position with thermostat open and high limit closed. Field Wiring umm 1930 Je 1 Fuero MONA Ari ong u2a153 pay MUM Pera UMOIG ued Ad AD 19 ЛЯ Jd OF INMV SdAL DS0L DMYV 91 Surseo UT speay uey 107 Hu, adÁr 2007 IMY 81 ‘95 paoedal aq ¿sur arm Áue y 10323UU07 UL] 1240-55017) —— UoISeg .7/T SENS og... [eun], MaS UOISEH 06 F/T SIM Z A UOISe „06 .P/T “За JON] UIMS ornssaid Tq || ON oO | > A9ULIOJSUBT, | ON X OFLLV Ua {7 7 € dmg feunuro ad M IÍLNOA MOT AD e I HS 2750 OL al AD qe OL | Xd +0 Or \ 19 Ta O or x VOON "OC Xa a Aeray Ya 1? YE TOO! yee JT aNo a Tl Did = = M >| 1 Si AD с a Ta = “Tw Los Г MP Eg 10pauu09 E L | 107190 + AN 3 = MT UST “id e Md M AIAN BATRA Seq) y TE} Ad TI S| AND § M M Y | STA | | i Al AFC |. . _ | а. eds AN ding Teururay, a8ejoA YSIH | O 0 О| = | oT = 7 © T M} Xe 5 L | $ 9 о—— Y с Y M ; M Mg Ma 103uu05 UL] WVHOVIA SNCILOINNOD H3IH0od 61 3SUNDH xog uonoun( Ad Ad — 26 The following information is provided to assist the installer who is permanently removing a gas fired appliance from a common venting system. It is provided for informational purposes only and is not directly relevant to the installation of a PF series boiler. NEVER ATTEMPT TO CONNECT A PF BOILER INTO A CHIMNE At the time of removal of an existing (a) boiler, the following steps shall be followed with each appliance remaining connected to the common venting system placed in operation, while the other appliances remaining connected to the common venting system are not in (e) operation. (a) (5) (©) Seal any unused openings in the common venting system. Visually inspect the venting system for (1) proper size and horizontal pitch and determine there is no blockage or restriction, leakage, corrosion and other deficiencies which could cause an unsafe condition. Insofar as is practical, close all building doors and windows and all doors between the space in which the appliances (5) remaining connected to the common venting system are located and other spaces of the building. Turn on clothes dryers and any appliance not connected to the common venting system. Turn on any exhaust fans, such as range hoods and bathroom exhausts, so they will operate at maximum speed. Do not operate a summer exhaust fan. Close fireplace dampers. Place in operation the appliance being inspected. Follow the lighting instructions. Adjust thermostat so appliance will operate continuously. Test for spillage at the draft hood relief opening after 5 minutes of main burner operation. Use the flame of a match or candle, or smoke from a cigarette, cigar or pipe. After it has been determined that each appliance remaining connected to the common venting system properly vents when tested as outlined above, return doors, windows, exhaust fans, fireplace dampers and any other gas-burning appliance to their previous conditions of use.” Any improper operation of the common venting system should be corrected so the installation conforms with the National Fuel Gas Code, ANSI 7223.1-1988. When resizing any portion of the common venting system, the common venting system should be resized to approach the minimum size as determined using the appropriate tables in Appendix G in the National Fuel Gas Code, ANSI Z223.1- 1988. 27 | PARTS Tf ED 5 à E g/d Y à FE o a By wil dd FE EF Y IMPORTANT 1) This boiler uses a mixture of metric and english threaded fasteners. These fasteners are specified in the following parts lists ("M5" and "5 millimeter" are the same thread diameter). All specified metric fasteners are available through Crown Distributors and may also be found in some hardware or auto supply stores. 2) It is extremely important that the casing and fan seals be maintained (see Part XI, for more information on this). When replacing parts be sure to have silicone sealant and any extra gaskets on hand which might be damaged during the replacement process. 3) All replacement parts {except for screws and other common hardware) must be factory original unless otherwise noted. They must be installed by a qualified serviceman. 4) Replacement parts are available through Crown distributors only. We do not sell direct. 28 CASING AND VENT COMPONENTS KEY # DESCRIPTION CROWN QUANTITY PER BOILER PART # 1 Vent Terminal Mounting Screw Pkg. 10-193 Pkg. C 2 Vent Terminal 10-135 1 3 Wall Plug 10-194 Pkg. B 4 Wall Plug Screw > 10-194 Pkg. B 5 Rope Sealing Ring 10-136 1 6 Vent Tubes, Standard 10-124 6 Vent Tubes, 76 in. 10-195 7 Sealing Collar (side vent only) 10-137 1 8 Casing Door 10-211 1 9 Casing Door Gasket 10-152 1 10 Sight Glass Gasket 10-153 2 11 Sight Glass 10-156 1 12 Sight Glass Retainer 10-154 1 13 6-32 Hex Nut 90-011 3 14 M6 x 15 Casing Door Screws 10-196 2 15 Retainers for Casing Door Screws 10-197 2 16 8-32 x 1/2 Philips Head Machine Screws 90-014 18 17 Utility Box 96-001 1 * Cover for Utility Box 96-002 1 18 Strain Relief Adapter 10-173 1 19 Strain Relief 10-033 1 20 Line Voltage Harness 10-161, 10-032 1 each 21 #10 x 3/16 Sheet Metal Screw 90-007 6 22 Pipe Seal Plate 10-023 2 23 Pipe Seal Gasket 10-024 2 24 M5 Wing Nut 10-019 16 25 Pinhole Grommett 10-026 5 26 Pressure Sensing Tubes 10-020 2 27 Pressure Sensing Tube Grommetts 10-021 4 28 Ignition Wire Grommett 10-021 1 29 Control Cover Bracket 10-036 1 30 1/4-20 Knurled Screw 10-051 1 31 Retainer for (30) 10-052 1 32 Control Cover 10-212 1 33 5/16 x 27 Lag Screw 90-010 6 34 5/16 Flat Washer 90-008 6 35 5/16 “Long” Lag Shield 90-009 6 36 Boiler Mounting Bracket 10-128 1 37 Rear Vent Gasket (rear venting only) 10-129 1 38 Smm x 850mm Rope 10-120 1 39 Casing 10-110 1 40 Retaining Clips 10-043 8 41 M5 x 15 Cap Screw 90-017 2 42 1/4 - 20 x 1/2 Truss Hd. Screw 90-005 4 43 Control Tray Chassis (Metal only) 10-086 1 44 Boiler Hook 10-118 1 45 M8 x 10mm Cap Screw 10-119 2 46 Vent Cover Gasket 10-116 3 47 Vent Cover 10-117 3 48 Support Channels 10-112 2 49 M5 x 12mm Machine Screw 10-115 6 50 Chassis Suppport Bracket 10-027 1 51 1/4-20 x 5/8 Machine Screw 90-015 2 52 1/4-20 Thin Nut 90-004 2 53 #10 x 1 1/4 Sheet Metal Screw 90-018 2 54 3/16 USS Washer 90-020 2 55 #10 Plastic Anchor 90-019 2 29 INNER CASING COMPONENTS KEY # DESCRIPTION CROWN QUANTITY PER BOILER PART # 56 Vent Tube Gasket 10-134 1 57 Elbow Extension (side vent only) 10-142 i 58 Upper Silicone Pressure Sensing Tubing 10-046 2 59 Flue Elbow 10-017 1 61 Flue Elbow Gasket 10-018 1 62 Flue Orifice for: PF 50 10-016 PF 65 10-015 PF 82 10-014 63 Flue Collector 10-013 1 64 Fan Mounting Plate Gasket 10-146 1 65 Fan Mounting Plate 10-144 1 66 M5mmx15mm Dog Point Screw 10-045 15 67 Fan Gasket 10-145 1 68 M8mm Hex Nut 10-009 24 69 3/4 x 8 1/2 Nipple 95-001 2 70 Flue Collector Gasket {12mm x 850mm Rope) 10-199 1 71 Flue Baffle (PF 65 and 82 only) 10-012 1 72 M8mm Thin Hex Nut 10-122 4 73 High Limit Well 10-083 1 74 High Limit Retainer Pin 10-044 1 75 M8 x 32mm Stud 10-121 À 76 Heat Exchanger 10-078 1 77a Heat Exchanger Cover 10-079 2 77b Heat Exchanger Cover Gasket 10-080 2 78 M8 Washer 10-082 16 79 M8x27 Studs 10-081 16 80 “Dart Clip 10-062 2 81 Firedoor Insulation 10-061 1 82 Firedoor Assy, Metal Only 10-200 1 83 Firedoor Sight Glass 10-063 1 Firedoor Assembly Complete 10-215 84 #6 x 1/4 Sheet Metal Screw 90-002 2 85 M8 x 18mm Stud 10-008 4 86 Firebox 10-001 1 87 Side Firebox Insulation 10-002 2 —- Rear Firebox Insulation 10-003 1 88 Cerablanket Strip 10-011 1 89 Left Side Baffle 10-004 1 90 Right Side Baffle 10-005 1 91 M5 Hex Nut 10-010 8 92 Bottom Radiation Shield 10-006 1 93 Radiation Shield Spacers 10-007 4 31 - 68,78 86 38 90 9 76 93 — 773, 77h 79 == © Rely 32 01 BURNER ASSEMBLY KEY DESCRIPTION CROWN QUANTITY PER BOILER PART # 94 Pilot Assembly For Natural Gas (Q345A 2014) 10-066@ 1 For Propane (Q345A 2006) 10-157 1 (Includes key parts 97 or 98) 95 Ignition wire assembly (Honeywell 394803) 10-041 1 96 10-32 x 3/16 Machine Screws 90-007 2 97 Pilot Orifice For Nat Gas Boilers (0.018") 85-002 For LP Gas Boilers (0.012') 85-001 98 Pilot Tube Ferrule (long) 85-003 99 Pilot Tube (1/8 OD) 10-067 1 101 Burner 10-065 1 102 3/8" Gas Valve Elbow (Honeywell 393670) 10-077 1 103 8-32 x 1/2 Screw Part of 10-077 2 104 8-32 x 1-1/4 Screw Part of 10-077 2 105 “O” Ring Part of 10-077 1 106 Main Burner Orifice: PF 50 (#22 Drill) 10-073 1 PF 65 (#17 Drill) 10-072 1 PF 82 (#12 Drill) 10-071 1 PF 50LP (#41 Drill) 10-076 1 PF 65LP (436 Drill) 10-075 1 PF 82LP (432 Drill) 10-074 1 107 Gas Valve Nat Gas (VR8204A-2274 10-068* 1 LP Gas (VR8204A-2282) 10-158 1 108 Pilot Tube Ferrule (Short) 85-004 109 Gas Valve Brace 10-037 1 110 8-32 x 1/4 Truss Hd. Machine Screw 90-016 2 PF50 Burner Assy. Complete 10-201 PF65 Burner Assy. Complete 10-202 PF82 Burner Assy. Complete 10-203 PF50LP Burner Assy. Complete 10-204 PF65LP Burner Assy. Complete 10-205 PF82LP Burner Assy. Complete 10-206 * @ A Honeywell Tradeline Q345A1313 may be used as a replacement for this. If a replacement VR8204A2274 is not available, a VR8204A2241 (used on some Crown ABF's, XE's and JBF's) may be used with the manifold pressure readjusted to 4.0" w.c.. - FAN AND FAN HARDWARE KEY DESCRIPTION CROWN QUANTITY PER BOILER PART # 111 8-32x1 1/2 Screw 90-013 3 112 8-32 Lock Washer 90-003 3 113 Fan 10-143 1 114 Strain Relief 10-148 1 115 Pin Connector Male Shell 10-149 1 116 Pins for Key #115 10-150 2 117 Wire Harness “N” 10-040 1 Fan Asssy. Complete 10-207 CONTROL COMPONENTS KEY DESCRIPTION CROWN QUANTITY PART # PER BOILER 118 High Voltage Terminal Strip 10-095 1 119 58670E1007 a 10-087 + 1 120 Differential Pressure Switch 10-089 1 121 Low Voltage Terminal Strip 10-093 1 122 Marker Strip 10-094 1 123 Honeywell AT140 10-088 1 124 Circulator Relay 10-090 1 125 Fan/Latch Relay Base 10-092 1 126 Fan/Latch Relay 10-091 1 Honeywell 1418982012 High Limit 10-030 1 Control Tray Wire Harnes Sets: High Voltage Wire Harness Set 10-216 1 Low Voltage Wire Harness Set 10-217 1 Gas Valve Wire Harness 10-106 1 Gas Valve Harness Strain Relief 10-108 1 6-32x1/2 Machine Screws for Key #124 90-002 2 Jumpers for Terminal Strips 10-096 3 Control Assy. Complete 10-208 Notes: + NOT interchangable with 58600 modules used on other Crown Boilers. 8-32x1/2 Machine Scews (Key #40) used to attach all controls and devices to tray except for circulator relay. FAN AND FAN HARDWARE CONTROL TRAY TOP VIEW Wiring Harnesses omitted for clarity 118 120 119 40 123 121 124 122 125,126 36
advertisement
Related manuals
advertisement