advertisement
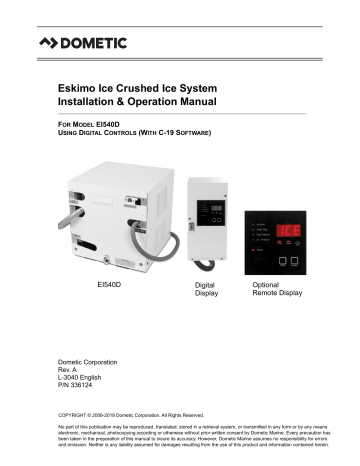
Eskimo Ice Crushed Ice System
Installation & Operation Manual
F
OR
M
ODEL
EI540D
U
SING
D
IGITAL
C
ONTROLS
(W
ITH
C-19 S
OFTWARE
)
EI540D
Digital
Display
Optional
Remote Display
Dometic Corporation
Rev. A
L-3040 English
P/N 336124
COPYRIGHT © 2008-2019 Dometic Corporation. All Rights Reserved.
No part of this publication may be reproduced, translated, stored in a retrieval system, or transmitted in any form or by any means electronic, mechanical, photocopying,recording or otherwise without prior written consent by Dometic Marine. Every precaution has been taken in the preparation of this manual to insure its accuracy. However, Dometic Marine assumes no responsibility for errors and omission. Neither is any liability assumed for damages resulting from the use of this product and information contained herein.
Table of Contents
INTRODUCTION . . . . . . . . . . . . . . . . . . . . . . . . . . . . . . . 1
W
ARNINGS AND
N
OTICES
. . . . . . . . . . . . . . . . . . . . . . 1
I
CE
M
AKING AND
R
EFRIGERATION
B
ASICS
. . . . . . . . . . 2
How Ice Is Made . . . . . . . . . . . . . . . . . . . . . . . . 2
The Refrigeration Process . . . . . . . . . . . . . . . . 2
T
HE
E
FFECT OF
T
EMPERATURE
O
N
I
CE
P
RODUCTION
. 3
Water Temperatures . . . . . . . . . . . . . . . . . . . . . 3
Air Temperature . . . . . . . . . . . . . . . . . . . . . . . . 3
C
OMPONENTS OF THE
I
CE
M
AKER
. . . . . . . . . . . . . . . 4
Ice-Making Unit . . . . . . . . . . . . . . . . . . . . . . . . . 4
Control Box . . . . . . . . . . . . . . . . . . . . . . . . . . . . 4
Ice-Storage Box . . . . . . . . . . . . . . . . . . . . . . . . 5
Seawater System . . . . . . . . . . . . . . . . . . . . . . . 5
Freshwater Supply . . . . . . . . . . . . . . . . . . . . . . 5
Refrigerant Charge . . . . . . . . . . . . . . . . . . . . . . 5
Thermal Expansion Valve (TXV) . . . . . . . . . . . . 5
INSTALLATION PROCEDURES . . . . . . . . . . . . . . . . . . 6
C
HOOSING THE
C
ORRECT
E
QUIPMENT
V
OLTAGE
. . . . . 6
I
NSTALLING THE
U
NIT
. . . . . . . . . . . . . . . . . . . . . . . . . 6
Selecting the Site . . . . . . . . . . . . . . . . . . . . . . . 6
Mounting the Unit . . . . . . . . . . . . . . . . . . . . . . . 6
Installing Condensate Drainage . . . . . . . . . . . . 6
Installing Ice-Delivery Hose . . . . . . . . . . . . . . . 7
Installing the Ice-Level Sensor . . . . . . . . . . . . . 8
Installing the Feedwater System . . . . . . . . . . . . 8
Installing the Seawater Cooling System . . . . . . 9
Installing the Remote Digital Display . . . . . . . 13
Mandatory System Start-Up Test . . . . . . . . . . 13
OPERATION . . . . . . . . . . . . . . . . . . . . . . . . . . . . . . . . . 14
T
HE
D
IGITAL
C
ONTROL
. . . . . . . . . . . . . . . . . . . . . . . 14
B
ASIC
F
UNCTIONS
. . . . . . . . . . . . . . . . . . . . . . . . . . 15
Applying Power . . . . . . . . . . . . . . . . . . . . . . . . 15
On/Off . . . . . . . . . . . . . . . . . . . . . . . . . . . . . . . 15
Ice Bin Sensor . . . . . . . . . . . . . . . . . . . . . . . . 15
Operational LEDs . . . . . . . . . . . . . . . . . . . . . . 15
Operational Information . . . . . . . . . . . . . . . . . 15
Fault History . . . . . . . . . . . . . . . . . . . . . . . . . . 15
F
AULTS
- E
VENTS
T
HAT
I
NTERRUPT
I
CE
P
RODUCTION
15
FULL – Ice Bin Full . . . . . . . . . . . . . . . . . . . . . 15
H20 – Potable Water Switch . . . . . . . . . . . . . . 15
HPF – High Pressure Refrigerant . . . . . . . . . . 15
LAC – Low AC line voltage . . . . . . . . . . . . . . . 16
LPF – Low Pressure Refrigerant . . . . . . . . . . 16
OCA – Over Current Auger and Ice Delivery
Problem . . . . . . . . . . . . . . . . . . . . . . . . . . . . . 16
OCC – Overload Current Compressor . . . . . . 16
SPt – Auger Spout Blockage . . . . . . . . . . . . . 16
UCA – Under Current Auger . . . . . . . . . . . . . . 16
UCC – Under Current Compressor . . . . . . . . . 16
T
HE
C
YCLE OF
O
PERATION
. . . . . . . . . . . . . . . . . . . 17
PROGRAMMABLE PARAMETERS FOR SOFTWARE 18
P
ROGRAM
P
ARAMETER
D
ESCRIPTIONS
. . . . . . . . . . . 18
P
ROGRAM
P
ARAMETER
D
EFAULT
S
ETTINGS
. . . . . . . 18
STARTING THE SYSTEM . . . . . . . . . . . . . . . . . . . . . . 19
S
TART
-
UP
C
HECK
L
IST
. . . . . . . . . . . . . . . . . . . . . . . 19
S
TART
-
UP
P
ROCEDURE
. . . . . . . . . . . . . . . . . . . . . . . 19
SYSTEM SHUTDOWN . . . . . . . . . . . . . . . . . . . . . . . . . 19
T
EMPORARY
S
HUTDOWN
. . . . . . . . . . . . . . . . . . . . . . 19
S
USTAINED
S
HUTDOWN
. . . . . . . . . . . . . . . . . . . . . . 19
S
YSTEM
R
ESTART
/R
ESET
. . . . . . . . . . . . . . . . . . . . . 19
SERVICING THE SYSTEM . . . . . . . . . . . . . . . . . . . . . . 20
R
EFRIGERANT
. . . . . . . . . . . . . . . . . . . . . . . . . . . . . . 20
R-404A T
OOLS
. . . . . . . . . . . . . . . . . . . . . . . . . . . . 20
T
HERMAL
E
XPANSION
V
ALVE
(TXV) . . . . . . . . . . . . . 20
R
ECHARGING THE
S
YSTEM
. . . . . . . . . . . . . . . . . . . . 20
System Shutdown . . . . . . . . . . . . . . . . . . . . . . 20
Evacuate Refrigerant . . . . . . . . . . . . . . . . . . . . 20
Charging the System . . . . . . . . . . . . . . . . . . . . 20
OWNER MAINTENANCE . . . . . . . . . . . . . . . . . . . . . . . 21
S
EAWATER
S
YSTEM
. . . . . . . . . . . . . . . . . . . . . . . . . 21
F
RESH
W
ATER
F
ILTER AND
Y S
TRAINER
. . . . . . . . . . 21
E
VAPORATOR
C
LEANING
. . . . . . . . . . . . . . . . . . . . . . 21
A
UGER
M
OTOR AND
G
EARBOX
. . . . . . . . . . . . . . . . . 21
C
OMPRESSOR
. . . . . . . . . . . . . . . . . . . . . . . . . . . . . 22
R
EFRIGERANT
G
AS
. . . . . . . . . . . . . . . . . . . . . . . . . . 22
W
ATER
R
ESERVOIR
. . . . . . . . . . . . . . . . . . . . . . . . . 22
F
EEDWATER
F
ILTER AND
Y S
TRAINER
. . . . . . . . . . . . 22
W
INTERIZING THE
S
YSTEM
. . . . . . . . . . . . . . . . . . . . 22
TROUBLESHOOTING GUIDE . . . . . . . . . . . . . . . . . . . 22
TECHNICAL ASSISTANCE . . . . . . . . . . . . . . . . . . . . . 23
LIMITED WARRANTY . . . . . . . . . . . . . . . . . . . . . . . . . 23
DIAGRAMS . . . . . . . . . . . . . . . . . . . . . . . . . . . . . . . . . . 24
S
YSTEM
C
ONNECTION
. . . . . . . . . . . . . . . . . . . . . . . 24
E
LECTRICAL
W
IRING
F
OR
115V 60 H
Z
M
ODELS
. . . . 25
E
LECTRICAL
W
IRING
F
OR
230V 60 H
Z
M
ODELS
&
220V 50 H
Z
M
ODELS
. . . . . . . . . . . . . . . . . . . . . . . . 26
L-3040 ENGLISH
Eskimo Ice Installation & Operation Manual
INTRODUCTION
INTRODUCTION
This manual provides installation and operation information for the EI540D self-contained Eskimo Ice System using digital controls (software level C-19).
The ice produced by this system is not potable and should not be ingested.
Do not eat, chew, suck, swallow, or put the ice into drinks. The ice produced by this system is intended solely for the refrigeration purposes of freshly caught fish stored in a fish box.
W
ARNINGS AND
N
OTICES
DANGER
This equipment is not ignition protected per CFR 183.410 and may not be installed in areas that may be exposed to flammable gas.
DANGER
The equipment referenced in this manual operates on 115 or 230 volts AC. Such voltages can be lethal, therefore proper care must be taking during installation, operation, and servicing to prevent injury or loss of life.
DANGER
The equipment referenced in this manual operates with compressed refrigerant at high pressures. Proper care must be taken during installation, operation, and servicing to prevent injury or loss of life due to improper procedures.
WARNING
Never install the unit in the bow of a boat
.
It must be installed on the transom, in the aft, or in a machinery space that does not require ignition protection that is as far aft of midship as possible.
WARNING
This manual contains essential safety information concerning the safe and proper installation, operation, and maintenance of your ice making system. It is very important that you read and understand the contents of this manual thoroughly before installing or using the equipment. You should keep this manual on your boat for future reference. Failure to follow Dometic approved installation, start-up, operation, and troubleshooting procedures will void the warranty. If there are any statements in this manual that you do not understand, refer to the back cover of this manual for technical support options.
WARNING
The ice produced by this system is not potable and should not be ingested. Do not eat, chew, suck, swallow, or put the ice into drinks. The ice produced by this system is intended solely for the refrigeration purposes of freshly caught fish stored in a fish box.
NOTICE
Some equipment may be shipped with specific installation sheets or wiring diagrams that may supercede the information located in this manual. Dometic reserves the right to update or change any information located herein at any time and without prior notice.
NOTICE
Your ice-making system uses the environmentally safe refrigerant R-404A. Federal law forbids the intentional release of any refrigerant gas into the environment. Make certain that any field service is performed by a specialist with the proper equipment to prevent loss of refrigerant during servicing.
L-3040 ENGLISH 1
INTRODUCTION
Eskimo Ice Installation & Operation Manual
I
CE
M
AKING AND
R
EFRIGERATION
B
ASICS
Figure 1: Ice-Making Process
H
OW
I
CE
I
S
M
ADE
Fresh water is applied to the interior wall of the evaporator shell.
Using a refrigeration process, heat is removed from the fresh water in order to freeze it.
As the water freezes onto the wall of the evaporator shell, the auger scrapes it off and into a discharge port. The ice shavings are then compressed and pushed into the ice transport tube which runs to the ice-collection bin. See Figure 1.
T
HE
R
EFRIGERATION
P
ROCESS
The basic principle of an ice machine system is that a liquid refrigerant absorbs heat as it turns into a gaseous state
(evaporates) and releases heat as it turns back into a liquid state (condenses). The system consists of five main components:
•
Evaporator
- Absorbs heat from the fresh water in the evaporator shell causing the fresh water to freeze.
•
Auger
- Scrapes the frozen fresh water from the interior sides of the evaporator shell and extrudes it into the discharge hose.
•
Condenser
- Releases heat into the system’s circulating seawater and turns the refrigerant gas back into a liquid.
•
Compressor
- Drives the refrigerant through the loop.
•
Metering Device
- Meters the flow of refrigerant to the evaporator.
The ice maker’s refrigerant compound has a very low boiling point. It flows in a closed loop between an evaporator and a condenser, alternately absorbing and releasing heat. This process removes the heat from the fresh water in the evaporator/ auger assembly and causes the fresh water to freeze on the inside of the evaporator wall. The heat absorbed by the refrigerant is transferred to the seawater.
A water pump circulates seawater through the inner tube in the condenser coil which cools the refrigerant in the outer tube and condenses it from a gas into a liquid. The heat from the refrigerant is exchanged to the seawater and discharged overboard.
The liquid refrigerant is then pumped through the evaporator coil and the cycle repeats. See Figure 2.
2 L-3040 ENGLISH
Eskimo Ice Installation & Operation Manual
Figure 2: Refrigeration System Diagram
INTRODUCTION
T
HE
E
FFECT OF
T
EMPERATURE
O
N
I
CE
P
RODUCTION
W
ATER
T
EMPERATURES
Seawater and freshwater temperatures affect the ice machine’s efficiency and capacity. The system is most efficient when the seawater and fresh water temperatures are 55-80°F (13-27°C). The ideal temperature for both is 70°F (21.1°C). See Figure 3.
High Temperatures
- As water temperatures approach 90°F (32°C) and above, the water’s ability to absorb heat diminishes, so the capacity of the system decreases. Also, when seawater temperature increases above 90°F (32°C), the system could sustain a high-pressure shutdown to protect the compressor.
Low Temperatures
- As water temperatures approach 45°F (7.2°C) and below, the water’s ability to provide heat exchange diminishes, so the capacity of the system decreases. Also, as the water temperature decreases, the system could sustain a lowpressure shutdown to protect the compressor.
CAUTION
Extreme care should be taken in operating any unit below seawater temperatures of 45°F (7.2°C). The seawater could freeze in the condenser tubing, possibly causing it to burst, which is not covered by the warranty.
A
IR
T
EMPERATURE
The Effect of Ambient Air Temperature
The ambient air temperature affects the ice machine’s efficiency and capacity, but not as significantly as the water temperatures. The system is most efficient when the ambient air temperature is 55-80°F (13-27°C). At temperatures above and below this range, ice production will decrease. See Figure 3.
L-3040 ENGLISH 3
INTRODUCTION
Figure 3: Ice Production and Temperature Graph
Eskimo Ice Installation & Operation Manual
C
OMPONENTS OF THE
I
CE
M
AKER
I
CE
-M
AKING
U
NIT
The ice-making unit has an R-404A compressor, seawater-cooled condenser, a filter/drier, and an accumulator. The auger assembly contains the evaporator barrel, auger rotor, gearbox, motor, water reservoir, and expansion device.
The freshwater delivered to it is converted to ice which exits the system via an ice-delivery hose routed properly to a storage box up to 35 feet (10.6m) away. See Figure 4 on page 7.
The unit is pre-charged with refrigerant from the factory. The unit has plug-and-play electrical connections for the ice-level sensor and the optional remote display.
C
ONTROL
B
OX
The ice-making unit has an electrical control box with digital display that can be mounted on the unit or remotely mounted up to
7’ (2.1m) away.
The control box (Figure 11, page 14) contains the system function switches, digital display, and system indicator lights. It lets you control all system operations and provides visual indications of system activity, such as whether the system is running or has a fault. If a fault condition is detected, the system shuts down automatically. The control panel lets you restart the system after a sustained fault. See the “The Digital Control” on page 14 for further operating instructions.
4 L-3040 ENGLISH
Eskimo Ice Installation & Operation Manual
INTRODUCTION
I
CE
-S
TORAGE
B
OX
The ice-storage box is the destination point where the ice will accummulate via the ice-delivery hose. An ice-level sensor installed in the storage box halts ice production when the box is full.
The ice-storage box should be able to hold water and have at least 2" (51mm) of insulation to keep the ice frozen as long as possible. It is helpful to install a drain in the box at the end opposite from the ice input. To improve ice-production performance, keep the drain plugged to prevent cold air and cold water from escaping the storage box.
S
EAWATER
S
YSTEM
Seawater is pumped into the ice-making unit to efficiently cool the hot refrigerant via a cupronickel coaxial tube design. The condensing unit may be connected to its own single-station pump or to a larger, multi-station pump via a pump relay box.
The seawater system (Figure 7, page 10) consists of a thru-hull fitting, seacock, strainer, seawater pump, seawater hose, and overboard discharge. There must be water flow of at least 2 GPM / 7.6 LPM (maximum 2.75 GPM / 10.4 LPM) or coil erosion can occur.
F
RESHWATER
S
UPPLY
Use the 1/4" SAE male flare fitting on the auger unit to supply freshwater for ice making. Provide water with pressure of at least
15 PSI. An in-line water filter (included in kit) is
mandatory
to comply with Dometic Warranty Regulations, to help prevent clogging of the needle valve in the water reservoir, and to help keep the auger walls from fouling with mineral deposits which will cause premature failure of water seals and bearings. See “Fresh Water Filter and Y Strainer” on page 21 for maintenance instructions.
R
EFRIGERANT
C
HARGE
The unit is pre-charged with the correct amount of R-404A refrigerant. If service is required, see data plate for correct charge amount.
T
HERMAL
E
XPANSION
V
ALVE
(TXV)
The TXV is used as the expansion valve of the refrigerant system. It allows high-pressure liquid to become low-pressure liquid and start the refrigeration process. The simple and reliable TXV provides a load-modulated system pressure over a wide range of ambient and seawater temperatures. The TXV
is not
adjustable.
L-3040 ENGLISH 5
6
INSTALLATION PROCEDURES
Eskimo Ice Installation & Operation Manual
INSTALLATION PROCEDURES
This section covers the installation procedures for your ice-making system.
Read the manual completely before attempting to install any equipment.
C
HOOSING THE
C
ORRECT
E
QUIPMENT
V
OLTAGE
Know the frequency and voltage provided where your ice-making system will be used and select the appropriate 60 Hz or 50 Hz model.
Do not operate a 60Hz unit on 50Hz power or a 50Hz unit on 60Hz power, as this will cause damage and void the warranty.
The voltage rating of a unit is a nominal rating. The voltage in a given location may be higher or lower by as much as 10% and the system will still operate correctly. For example, in a 60 Hz environment you may see 110 VAC to 120 VAC, or 208 VAC to
240 VAC. In a 50 Hz environment common voltages range from 220 VAC to 240 VAC.
I
NSTALLING THE
U
NIT
S
ELECTING THE
S
ITE
Never install the unit in the bow of the boat.
Dometic ice-making units are designed to be installed in any convenient location on the transom, in the aft, or in a machinery space that does not require ignition protection that is as far aft of midship as possible. The unit can be located in living areas if necessary. Some considerations:
• This equipment is not ignition protected per CFR 183.410 and may not be installed in areas that may be exposed to flammable gas.
• The unit will produce condensation, so the drip pan is necessary.
• The unit is water cooled and does not need direct ventallation, but do not install in a sealed space.
• The space around the unit may be insulated to reduce noise if necessary.
Site Location Check List
• Location is aft of midship.
Never install the unit in the bow of the boat.
• Location is not exposed to flammable gas.
• Location provides adequate space for access to refrigerant, seawater, and electrical connections.
• Location provides accessibility for service and maintenance.
• Location is away from direct spray, from engine air intakes, and from water washdown.
• Mounting space is a flat, horizontal surface.
M
OUNTING THE
U
NIT
1.
Do not remove any covers, caps, or fittings that may expose any wiring or refrigerant until you are ready for those steps of the installation.
2.
On a flat, horizontal surface, orient the unit so the refrigerant, seawater, and electrical connections are accessible and use the 4 provided hold-down clips to secure it.
3.
If you decide to remotely mount the control box, be sure it is away from direct spray, from engine air intakes, and from water washdown.
4.
If pump wires need to be extended by butt connections, make sure they are tightly crimped and heat shrunk.
5.
AC power source must be installed and grounded/bonded in accordance with ABYC standards.
6.
Connect control wires to terminal strip with ring terminals.
I
NSTALLING
C
ONDENSATE
D
RAINAGE
The condensate drain pan is 2.0” (51mm) high with one drain location. During conditions of high humidity, condensate may be produced at a rate of approximately one-half gallon (1.9 liter) per hour. With this in mind, it is important to route condensate drains downward to a sump pump. It is not recommended to route condensate drains to the bilge.
After the condensate drain installation is complete, test the installation by pouring one quart (liter) of water into the pan and checking for good flow.
L-3040 ENGLISH
Eskimo Ice Installation & Operation Manual
INSTALLATION PROCEDURES
I
NSTALLING
I
CE
-D
ELIVERY
H
OSE
Planning the Route
The maximum length of the ice-delivery hose is 35 feet (10.6 m) under ideal conditions.
The best hose routing provides a level but slightly upward rise from the ice maker to the ice-storage box, with very few bends.
No bend should be tighter than a radius of 18" (458mm). Refer to Figure 4 below to see:
•
Best Routing
- A continuous uphill route of travel from the ice maker.
•
Good Routing
- A continuous route of travel from the ice maker, with only one high spot.
•
Acceptable Routing
- A route of travel from the ice maker which includes one low spot and two high spots.
Figure 4: Routing of Ice-Delivery Hose
Mount the ice-delivery hose as high as possible in the ice-storage box.
Figure 5: Heat & Stretch
Auger End of Hose
Procedure
1.
The hose delivery location should be as high as possible
in the icestorage box and facilitate the best hose route from the auger (as described above and shown in Figure 4).
2.
Install the proper thru-hull in the ice-storage box using the supplied fitting. The thru-hull must be large enough for the 3/4" (19.1mm) ice-delivery hose.
NOTE:
In cases where the EI540D is replacing an existing older Eskimo Ice system that used a larger fitting and hose, it might be possible to insert the newer, smaller hose inside the existing hose and use the existing icedischarge thru-hull.
3.
Insulate the full length of hose with 1-1/8" (29mm) ID, 3/4" (19mm) thick wall insul-tube, minimum.
4.
Double clamp thru-hull end so the hose will not get pulled out. In addition, PVC glue may also be used at the thru-hull end.
5.
The hose at the auger end must be stretched in order to fit over the auger spout: Heat 1.75” (45mm) of the hose end in hot water (160°F / 71°C) or with a heat gun to soften, then stretch it by inserting and rotating pliers inside the tube. See
Figure 5, page 7.
L-3040 ENGLISH 7
INSTALLATION PROCEDURES
Eskimo Ice Installation & Operation Manual
6.
The EI540D now REQUIRES a Constant Torque Hose Clamp to secure the ice delivery hose to the auger spout.
It is supplied with the machine and attached to the Auger spout with a black wire tie. The clamp must be installed behind the 8 protruding dimples on the auger ice spout. The use of another type of clamp will void the warranty and liability of ice overflow and damage if the hose comes off while producing ice. Secure hose end with constant torque hose clamp to auger spout.
It is CRITICAL that you check the integrity of this hose connection when you perform the system start-up test.
(See “Mandatory System Start-Up Test” on page 13.)
7.
Securely strap hose to bulkhead every 12” (30.5cm), keeping in mind that the hose will be much heavier once filled with ice. Be careful not to kink, flatten, oval or crush hose, because any obstructions will prevent free flow of ice.
I
NSTALLING THE
I
CE
-L
EVEL
S
ENSOR
To prevent overflow, this sensor stops ice production when the ice in the storage box reaches the level of the sensor. Use
Figure 6 below to determine placement for the ice-level sensor at the storage box location. The EI540D will not operate without the ice-level photo sensor installed.
Test the photo sensor for correct operation to avoid machine damage and avoid ice overflow. See “Mandatory System Start-Up
Test” on page 13.
1.
The sensor must be located 2.5” (64mm) minimum to 3” (76mm) maximum to the left or right side of the ice-delivery hole. Drill a 23/32" (19mm) hole for sensor.
2.
Use the 2 lock nuts provided to secure sensor into the hole.
3.
Use marine-grade sealant around the hole if desired. (Remember that the unit may have to be removed at some time.)
4.
Route the cable to the ice maker’s electrical box and plug the end into the ice-bin sensor socket. See the appropriate electrical wiring diagram in this manual for the voltage model you are using.
NOTE wiring changes from earlier Eskimo Ice models:
The wiring has changed in the electrical box for the ice sensor. There are 4 wires in the sensor harness: white, black, blue and brown. The signal wire in the center position of the ice-level sensor plug is now a white wire, not black as before. The white wire was previously cut off at the grey insulation. Now the black is cut off and the white is used. Note the photo sensor can be used for old as well as new. It is just dependent how it is wired.
Figure 6: Location of Ice-Level Sensor (front view)
Mount the ice-delivery hose as high as possible in the ice-storage box.
8
I
NSTALLING THE
F
EEDWATER
S
YSTEM
Feedwater for the unit should be fresh water supplied by the boat’s potable water system. The water reservoir has a float switch to ensure the unit does not operate without a water supply.
L-3040 ENGLISH
Eskimo Ice Installation & Operation Manual
INSTALLATION PROCEDURES
Requirements
• Supplied feedwater must have a pressure of at least 15 PSI.
• The water system must be able to supply at least 4 GPH when the ice maker is operating.
• Install the in-line filter (supplied in kit) just prior to the unit to remove sediment which may clog the needle valve in the water reservoir.
• Dometic recommends installing a shut-off valve in the feedwater line between the source and the filter to facilitate filter changes.
WARNING
Use of saltwater as feedwater will damage auger components and evaporator barrel and will void the warranty.
WARNING
Failure to install and use the water filter included with the installation kit will void the warranty.
Note, if unit is purchased separately you must also purchase the water filter to maintain warranty.
Procedure
1.
Run copper tubing or equivalent from the freshwater source to the in-line water filter.
2.
Run copper tubing or equivalent from the water filter to the water input, and connect with the supplied 1/4" SAE male flare connection on the unit.
3.
Ensure there are no leaks in the field-installed portion of the system.
Water Quality and Filters
No water from a municipality is “pure” feedwater, but water from a vessel’s onboard water maker comes close. The feedwater problem is that water contains suspended and dissolved feedwater solids. Pure water freezes first, leaving the feedwater solids to increase in concentration in the unfrozen feedwater. Solids also bond to the evaporator wall during feedwater freezing, forming scale. Eventually, built-up scale will shorten machine life.
A Dometic-supplied filter for use with ice makers must always be used, otherwise the warranty will be void. Replace the filter at least twice yearly, or more often if the machine is used frequently. While filters help clean the water, a 6-month cleaning of the evaporator barrel is required. See “Evaporator Cleaning” on page 21 of the “OWNER MAINTENANCE” section.
Using
saltwater
to make ice is
not
approved by Dometic. Saltwater is very corrosive, and it contains many more dissolved and suspended solids than freshwater. If you want a brine solution for your catch, we suggest sprinkling salt over the ice in the storage box. USE OF SALTWATER AS FEEDWATER IN ANY DOMETIC ICE MAKER WILL CAUSE SEVERE DAMAGE AND
VOID THE WARRANTY!
I
NSTALLING THE
S
EAWATER
C
OOLING
S
YSTEM
Self-Draining System
A poorly plumbed seawater system is the most common installation problem. When water flow is lost, not only will the ice maker cease to produce ice, but the pump could be damaged from running without water flow.
When using a centrifugal seawater pump, it is imperative that the seawater piping be routed continually uphill from the thru-hull to the condenser, then smoothly up or down to the overboard discharge without any dips or loops, and with only one high point in the system. This type of routing is called self-draining because all water will drain out of the piping if the boat is taken out of the water.
If air gets into the system, which can happen in heavy seas or with a sharp turn, it can become trapped in the pump. Because centrifugal pumps cannot pump air, water flow is lost. A self-draining system, however, allows air in the piping to rise naturally through the pump and be expelled. It also makes winterizing the system much easier. Figure 7, page 10 shows a properly plumbed system and some common mistakes.
L-3040 ENGLISH 9
INSTALLATION PROCEDURES
Figure 7: Seawater Piping Recommendations
Eskimo Ice Installation & Operation Manual
10
Thru-Hull Inlet Fitting
A separate thru-hull fitting must be installed for each seawater pump. Do not attempt to draw water from the thru-hull fitting of an engine, generator, or other device.
Install a scoop-type thru-hull fitting:
1.
Drill a properly sized hole for the thru-hull fitting as far below the water line and as close to the keel as possible.
2.
Make sure the scoop of the thru-hull fitting faces the bow.
3.
Bed the scoop with marine sealant designed for underwater use, and tighten the nut onto the thru-hull to secure it.
Seacock
The seacock must be accessible and easy to close in case of emergency or to clean the strainer.
1.
Install a full-flow seacock directly onto the thru-hull fitting.
2.
Use threaded-seal tape to seal the threads.
Seawater Piping
• Only use reinforced marine-grade hose or other suitable piping (PVC, CPVC, cupronickel, or stainless steel).
• Double clamp all hose connections.
• Use only plastic, bronze, or stainless steel fittings (do not use brass).
• Avoid loops or dips in all hose runs.
• Make sure enough hose is used to allow for future removal of components.
L-3040 ENGLISH
Eskimo Ice Installation & Operation Manual
INSTALLATION PROCEDURES
• Use the correct size hose, fittings, and components: 5/8” seawater hose, 3/4” inlet. Note that the pump inlet piping
(including thru-hull and strainer) may need to be larger than the outlet pipe size. Do not use pump connections to determine hose size.
• The "pump inlet" recommended pipe size includes all fittings and hose up to the pump connection (thru-hull, seacock, strainer, hose, manifold). The "pump discharge" recommended pipe size includes all fittings and hose from the pump discharge up to the overboard discharge, and should be a minimum of 5/8”.
Strainer
A seawater strainer must be installed between the seacock and the pump, and should be situated to provide easy access for cleaning. The strainer must be located vertically above the seacock and below the pump so any air that gets into the strainer can get out.
1.
Mount the strainer to a bulkhead so it is properly supported before connecting hoses.
2.
Make sure the water flow through the strainer is in the correct direction. Some strainers have an arrow that shows correct flow direction.
3.
Run appropriate seawater piping from the seacock to the strainer, and use threaded-seal tape on pipe threads.
Seawater Pump
Required Flow Rate
The Dometic EI540D ice maker requires at least 2 GPM / 7.6 LPM (or 120 GPH / 454.2 LPH) up to a maximum of 3.5 GPM /
13.2 LPM (or 210 GPH / 792 LPH) of seawater flow for rated performance.
Centrifugal Pumps
Centrifugal pumps are not self-priming, and must be mounted so they are below the heeled waterline in any given operating condition. The pump should be accessible for future service.
1.
Mount the pump so the outlet is directed upward. If you are using the Dometic pump, other mounting orientations are acceptable as shown in Figure 8, and the head on these pumps can be rotated to allow mounting on a vertical bulkhead.
2.
Run appropriate seawater piping from the strainer to the pump, and use threaded-seal tape on pipe threads.
Self-Priming Pumps
Self-priming pumps are available if a centrifugal pump cannot be mounted below the waterline.
Figure 8: Dometic Pump Head Orientation
Correct Orientations
Incorrect Orientations
Manifolds
If a pump serves multiple units, a seawater manifold is needed to supply water to all units. This can be as simple as a tee for two units, or a custom manifold for seven to eight units.
It is very important to consider manifold orientation so that all units get their required flow. See Figure 9 on page 12 for proper orientation tips. Verify the manifold still provides the required flow rate for the ice maker.
A manifold can also be used on the outlets of multiple ice makers when using a single overboard discharge.
L-3040 ENGLISH 11
INSTALLATION PROCEDURES
Eskimo Ice Installation & Operation Manual
Figure 9: Seawater Manifold Orientation
Pump Relay
The pump relay (if needed) is generally located in the engine room or mechanical space near the seawater pump, but can be mounted anywhere that is convenient and accessible. It must be in a dry location, away from water spray, with some room for heat dissipation.
Choose your pump relay based on the number of units that will operate off one pump. Choose each trigger to reflect the voltage of the unit it serves. The polarity of the signal from the unit does not matter to the trigger, but the voltage is very important.
Connection to Ice Maker
Connect a hose from water discharge of pump to water inlet on the condensing coil.
Overboard Discharge
Connect a hose from the water outlet of the condensing coil to the overboard discharge. The overboard discharge should be located 1” to 2”
(25-50mm) above the waterline. This facilitates visual confirmation of water flow and also keeps it close to the waterline to minimize splashing.
If the overboard discharge is located below the waterline a valve must be installed per ABYC guidelines.
Note: In some applications a Sea Chest might impede water flow depending on the water volume other devices discharge into the common overboard. Proper water flow must be confirmed to ensure proper operation of ice maker if a Sea Chest is used.
Bonding
Bond all metallic parts (thru-hull, valves, strainer, manifolds, etc.) that are in contact with seawater to the vessel’s bonding system in accordance with ABYC standards. Items should only be bonded or grounded once. If an item is in contact with an electrically grounded part (pump, seawater condenser) then it should not be bonded again.
12 L-3040 ENGLISH
Eskimo Ice Installation & Operation Manual
INSTALLATION PROCEDURES
I
NSTALLING THE
R
EMOTE
D
IGITAL
D
ISPLAY
For easier operation accessibility, an optional remote digital display may be installed wherever desired, however, it can not be exposed to saltwater spray. The remote display requires a cable that must be ordered separately, and is available in lengths up to 100’ (30.5m).
Figure 10: Cutout Dimensions
For Digital Display
1.
Find a convenient location that is protected from saltwater spray.
2.
Cut out a square hole that is 3-3/16” x 3-3/16” (82 x 82 mm). See
Figure 10 to prepare the mounting space.
3.
Route the display’s cable to control box and plug into the mating
8-pin male RJ45 connector.
4.
Mount the remote display into the cutout.
5.
If you are relocating the existing display, cover the hole on the back of the box.
Cutout Dimensions
3-3/16”
(82mm)
M
ANDATORY
S
YSTEM
S
TART
-U
P
T
EST
It is
CRITICAL
that you test the durability of the hose connections, the icelevel sensor, and the amp-sensing feature during the installation process:
1.
Run the machine to start producing ice. See “OPERATION” on page 14.
2.
Block the output end of the ice delivery hose and run the system until the machine shuts down with the OCA code to confirm the overload feature.
3-3/16”
(82 mm)
Note: Image shown is not to scale.
3.
Check to see that the unit displays the
OCA code
indicating an ice-hose clog, restriction, actual auger motor overload, possible motor problem, or internal gear problem. The amp-sensing feature of the control monitors the amp draw of the auger unit and shuts down and locks out when an overload is sensed. The
115V auger locks out at 2.6 amps; the 230V/60Hz and 220V/50Hz augers lock out at 1.3 amps.
NOTE:
The Spout fault code of earlier models is no longer used since there is no spout switch on this unit.
NOTE:
If an OCA has occurred and you remove the immediate obstruction, such as ice piled up in front of the discharge, and then reset the unit, a second OCA might occur if a sufficient amount of time has not elapsed to allow ice to melt in the auger or where ice might be compacted in the hose on a long run.
4.
Check the hose connection at the auger end. It is CRITICAL to make sure that the ice delivery hose did not come off the auger spout or move in any way. If there is a problem, refer to “Installing Ice-Delivery Hose” on page 7 and make the hose secure then retest.
5.
Reset the system and resume ice production to test the photo sensor for correct operation to avoid machine damage and avoid ice overflow. When ice blocks the sensor the unit should stop producing ice, and this should occur before the collection bin overflows.
L-3040 ENGLISH 13
OPERATION
Eskimo Ice Installation & Operation Manual
OPERATION
This section of the manual provides the essential information for safe operation for all Dometic ice makers. If you encounter any operational problems, refer to the back cover of this manual for technical support options.
WARNING
Failure to install and use the water filter included with the installation kit will void the warranty.
Note, if unit is purchased separately you must also purchase the water filter to maintain warranty.
T
HE
D
IGITAL
C
ONTROL
The control system is programmed to operate the unit within assigned parameters. It uses sensors, timers, and counters to protect system components from failure due to loss of fresh water, loss of seawater, ice clogs, low refrigerant charge, high pressure, low pressure, or auger-motor start failures.
To prevent overflow, a sensor also controls system operation based on ice level in the ice-storage box. The control panel shows system function and failure mode, if one occurs. See “Faults - Events That Interrupt Ice Production” on page 15 for details.
The digital control display panel is also the user interface for programming system parameters. See “PROGRAMMABLE
PARAMETERS FOR SOFTWARE” on page 18 for more information.
If the optional remote digital display panel is installed, the system can be operated from either control location—the display panel by the unit or at the remote location.
See Figure 11 and Table 1 on page 14 to identify all parts of the control.
Figure 11: Control Panel
11
10
9
8
7
1
2
14
6 5 4 3
Table 1: Digital Control - Diagram Legend
1
2
3
4
5
6
Digital display
Ice Bin Full indicator
Function button
Auger indicator
Power button (on/off)
Compressor indicator
7
8
9
10
11
Power indicator
Low Pressure fault light
High Pressure fault light
Water Flow fault light (for freshwater feed)
Not used on this model
L-3040 ENGLISH
Eskimo Ice Installation & Operation Manual
OPERATION
B
ASIC
F
UNCTIONS
A
PPLYING
P
OWER
When power is first applied, the display will light all LED’s for 2 seconds, then go blank for 1 second, then show software revision for 2 seconds. The unit will then go to the last state it was in before power was disconnected. The power LED will remain lit anytime power is applied.
O
N
/O
FF
Press the On/Off button to toggle between Off and ICE production. dLY will appear in the display and the unit will begin a startup routine. ICE will appear in the display when production begins.
I
CE
B
IN
S
ENSOR
When the ice-storage box is full, the unit will stop ice production and the display will show FULL. If the ice bin sensor is not installed, the unit will not operate and the display will continue to show FULL.
O
PERATIONAL
LED
S
Ice Flow, Water Flow, High Pressure, and Low Pressure are trouble lights on the display and will light if a fault occurs and a fault code will be displayed. Comp and Auger are status lights and show operation of these systems. FULL is also a status light that is on whenever the ice-storage box is full.
O
PERATIONAL
I
NFORMATION
Compressor current, Auger current, and AC voltage can be viewed while the unit is in operation. Simultaneously press and release the On/Off and Function buttons. CA will appear in the display and after 5 seconds, a value indicating the compressor current in amps will show. Press Function to change to AA and auger current in amps will display. Press Function again and AC line voltage will display. Press the On/Off button to exit from this feature.
F
AULT
H
ISTORY
History of faults that occur can be viewed from the off setting. Press and hold the On/Off button for 3 seconds. This will enter the fault history log. The display will indicate H 1. Press the function button to scroll through the events recorded in the log. The unit will record up to 16 events. While viewing, the display will alternate between the fault mnemonic and the event number. To exit the history mode, press the On/Off button. The unit will also exit the history log in 30 seconds if no key is pressed. Faults are recorded in the order they occur, most recent to oldest.
F
AULTS
- E
VENTS
T
HAT
I
NTERRUPT
I
CE
P
RODUCTION
If trouble occurs during operation the fault codes defined below will be displayed. Trouble LEDs will be lit for
High Pressure,
Low Pressure, Water Flow,
and
Ice Flow
. The unit will restart once the fault is cleared or repaired.
Lockout
- Excessive faults will result in the code flashing on the display called a lockout. A lockout may be cleared by pressing the On/Off button to turn the unit off then on again, by pressing the reset switch or pressing the function button.
FULL – I
CE
B
IN
F
ULL
If the ice bin sensor is blocked for more than 15 continuous seconds, the unit will stop ice production and the display will show
FULL. If the ice bin sensor is not installed, the unit will not operate and the display will continue to show FULL.
H20 – P
OTABLE
W
ATER
S
WITCH
If the potable water switch is open during production for 15 seconds, the display will show H20 fault and the Water Flow LED will light. The auger will continue to run for the duration of the auger delay. Ice production will stop and the switch must be closed for operation to restart. H20 Fault can be caused by lack of fresh water flow, clogged main filter or a clogged Y Strainer.
NOTE
If HPF or H20 appears steady on the display (not flashing) on initial start up, this may be due to an open switch, defective water-level switch, empty reservoir, or clog. This can also occur from an open switch or wiring to the switch.
HPF – H
IGH
P
RESSURE
R
EFRIGERANT
If the High Pressure Refrigerant Switch is open during production for ~500ms, the display will show HPF fault and the High
Pressure LED will light. The compressor delay is then activated for restart. The auger will continue to run for the duration of the auger delay. At the end of the compressor delay the unit will show dLY beginning the restart routine. The compressor delay begins from the moment the switch is opened. The maximum number of faults that can occur in 30 minutes is set for three by
L-3040 ENGLISH 15
OPERATION
Eskimo Ice Installation & Operation Manual
default. HPF can be caused by lack of seawater flow due to a dirty strainer, pump being airlocked or seawater lines in need of maintenance.
LAC – L
OW
AC
LINE VOLTAGE
If the line voltage to unit is less than value selected in the programmable parameter for 5 minutes continuously the unit will stop operation. The compressor delay is started and the unit will restart at the end of the delay if the voltage is greater than the value selected in the programmable parameter. Parameter default is set to off.
LPF – L
OW
P
RESSURE
R
EFRIGERANT
If the Low Pressure Refrigerant Switch is open during production for 60 seconds, the display will show LPF fault and the Low
Pressure LED will light. The compressor delay is then activated for restart. The auger will continue to run for the duration of the auger delay. At the end of the compressor delay the unit will show dLY beginning the restart routine. This switch is checked at the start of a cycle and during operation. The compressor delay begins from the moment the switch is opened. Three faults in a
30 minute period will result in a lockout. LPF can be caused by, Low refrigerant levels, Seawater below 50°, or faulty low pressure switch.
OCA – O
VER
C
URRENT
A
UGER AND
I
CE
D
ELIVERY
P
ROBLEM
If the auger current exceeds 1.3 amps for 230VAC or 2.6 amps for 115VAC equipment for ~500ms the unit will stop all operation and lockout. For Eskimo Ice models without a spout switch, the system relies on the amp reading of the auger motor to detect an ice clog and/or ice delivery problem along with an overload and/or bad auger motor. 115VAC systems must see 2.6 amps for
1 second to trip the OCA; 230VAC/60Hz and 220VAC/50Hz systems must see 1.3 amps for 1 second to trip OCA.
OCC – O
VERLOAD
C
URRENT
C
OMPRESSOR
If the compressor current exceeds 18 amps for 230VAC or 36 amps for 115VAC equipment for ~500 ms the unit will stop the compressor. Auger operation will continue for the duration of the auger delay then stop and lock out.
SPt – A
UGER
S
POUT
B
LOCKAGE
Not applicable with the EI540D.
UCA – U
NDER
C
URRENT
A
UGER
If the auger current is less than the default value .5 amps for 1 second the unit will stop all operation and lock out. UCA fault can be caused by over voltage, open wire or open thermal overload.
NOTE
If you experience erratic behavior such as reoccurring nuisance faults or erratic display behavior reboot the system by shutting off at breaker for 30 seconds and powering back up. This should clear any glitches caused by power surge, spikes or brown outs.
UCC – U
NDER
C
URRENT
C
OMPRESSOR
If the compressor current is less than the default value of 5 amps (115 volt) or 2 amps (230 volt) for ~500 ms the unit will stop operation and lock out. The auger will continue to run for the duration of the auger delay. UCC fault can be caused by over voltage or open wire.
16 L-3040 ENGLISH
Eskimo Ice Installation & Operation Manual
T
HE
C
YCLE OF
O
PERATION
Figure 12: Typical Operation Cycle For Making Ice
OPERATION
L-3040 ENGLISH
Refer to list of faults in this manual to see which faults automatically reset once the particular switch resets, and which faults must be cleared manually.
17
PROGRAMMABLE PARAMETERS FOR SOFTWARE
Eskimo Ice Installation & Operation Manual
PROGRAMMABLE PARAMETERS FOR SOFTWARE
The programmable parameters with their factory defaults described in this section. Table on page 18 contains the parameter codes along with their permitted values and default settings. Parameters P1 / t-1 through t-5 are user adjustable parameters.
Checking Software Revision Level
To confirm software revision, first turn off power to unit. Then, observe when power is reapplied: The display will light all LEDs for 2 seconds, the display will go blank for 1 second, then the display will show the software revision (C-19) for 2 seconds.
Entering And Using Program Mode
• While in the Off mode, enter program mode (P) by pressing and holding both the
On/Off
and
Function
buttons for 5 seconds.
• Then, to enter the (T) programming mode to make changes, push and hold the
RESET SWITCH
on the control box for
15 seconds until the
t-1
appears.
• Use the
On/Off
button to advance through parameters. Use the
Function
button to select the parameter value desired.
• Exit the program mode either by pressing and releasing both the
On/Off
and
Function
buttons or by waiting 60 seconds.
P
ROGRAM
P
ARAMETER
D
ESCRIPTIONS
P-1: t-1: High Pressure Restart Delay -
This sets the start compressor restart delay after a high refrigerant pressure fault is cleared. The default setting is 0 and can be set from 0-30 minutes. Default "0" for off is mainly used for sport fishing where backing down can cause an airlock. Only use for continuous nuisance trips.
t-2: Low AC Line Voltage -
This option can be set to detect low AC line voltage. Low AC line voltage condition must exist for 5 minutes for a shtudown to occur. Default setting is off and can be set from 75 to 100 (for 115VAC) or 175 to 200 (for 230VAC).
t-3: CAN ID -
Used to set CAN bus ID. The range is from 1-254.
t-4: CAN Group ID -
Used to set CAN bus group ID. The range is from 1-254.
t-5: Reset Programmable Parameters -
Resets all programmable parameters to factory defaults. Set this setting to 1 and unit will reset all values. Setting will change back to 0 on exit of the programming mode or by pressing the On/Off button to scroll through parameters.
NOTE
Changes to technical parameters not listed above should be performed by an authorized service dealer. Please refer to the back cover of this manual for technical support options.
P
ROGRAM
P
ARAMETER
D
EFAULT
S
ETTINGS
Table 2 shows the default setting of each programmable parameter.
Table 2: Programmable Parameters - Values and Defaults
t-3 t-4 t-5
Number
P-1 t-1 t-2
Description
High Pressure Restart Delay
Low AC Line Voltage
CAN ID
CAN Group ID
Reset Programmable Parameters
0
Default
5
0 off n/a
0 - 30 minutes
Value Range
75-100 or 175-200
1-254
1-254
0 = No, 1 = Yes
18 L-3040 ENGLISH
Eskimo Ice Installation & Operation Manual
STARTING THE SYSTEM
STARTING THE SYSTEM
S
TART
-
UP
C
HECK
L
IST
Before you start the system:
• Confirm freshwater supply is on.
• Confirm freshwater filter is installed.
• Confirm that electrical connections are correct and tight.
• Confirm that the circuit breaker is of the correct size.
• Confirm the ice-level sensor is mounted securely, the cable is routed safely, and the sensor is functioning properly.
• Confirm all units are mounted securely.
• Confirm seawater connections have correct flow direction and all connections are tight.
• Confirm there are no loops or dips in the seawater system.
• Confirm all metallic parts are bonded correctly.
• Confirm frequently accessed parts are easily accessible (i.e., control panel, filters, CPV, refrigerant ports, etc.).
• Confirm ice-delivery hose is securely fastened and has insulation and drain hole, if needed.
S
TART
-
UP
P
ROCEDURE
1.
Turn on the designated circuit breaker for the unit and also the one for the pump if it is on a separate breaker at the boat's electrical panel.
2.
Open the seacock on the pump intake.
3.
Press the On/Off switch on the ice-maker to power-on the unit. It displays “
dly
” to indicate it is in timer-delay mode for up to 255 seconds under normal default parameters before it displays “
ICE
” to indicate that it is in the ice-producing mode.
4.
Confirm water is flowing through the overboard discharge.
5.
Look for ice output within 5 to 10 minutes of system start-up, plus approximately one minute for each foot of hose between storage box and auger unit.
NOTE:
The seawater pump should start automatically whenever the unit is running. Regularly check for seawater flow by observing the overboard discharge. If you do not observe any flow when the system is running, check for obstructions in the seawater cooling system.
SYSTEM SHUTDOWN
T
EMPORARY
S
HUTDOWN
Some system conditions result in a temporary shutdown followed by an automatic restart once the situation is resolved. This is normal behavior, for example when the ice-level sensor detects that the ice-storage box is full.
S
USTAINED
S
HUTDOWN
Some system failures result in a sustained shutdown and are indicated by the appropriate fault code flashing in the digital display. A reset indicates an actual problem, not just a passing event, and the cause should be investigated.
Sustained shutdown in need of reset is caused by any of these events:
• High-pressure switch triggered 3 times within 30 minutes.
• Low-pressure switch triggered 3 times within 30 minutes.
• Auger motor high amps and low amps each time the fault occurs.
• Compressor high amps and low amps each time the fault occurs.
NOTE:
If system needs to be reset more than twice within one day, have the system serviced.
S
YSTEM
R
ESTART
/R
ESET
Use any one of these methods to restart operation:
• Turn the unit off then on at either the main digital control box or the optional remote digital display.
• Press the Reset switch on the unit’s control panel.
• Turn the unit’s circuit breaker off then on.
L-3040 ENGLISH 19
SERVICING THE SYSTEM
Eskimo Ice Installation & Operation Manual
SERVICING THE SYSTEM
This section contains information critical to correct servicing of this Dometic ice-making system. Read and understand all information before beginning. If you have any questions, refer to the back cover of this manual for technical support options.
R
EFRIGERANT
Your Dometic ice-making system contains R-404A refrigerant, an environmentally safe gas. The unit comes pre-charged with the right amount of refrigerant for operation and should not need seasonal recharging. If recharging is necessary, R-404A should be charged in the liquid phase with “Charge-Guard” and weighed in according to data label located on electric box.
R-404A T
OOLS
Use a dedicated R-404A gauge set.
T
HERMAL
E
XPANSION
V
ALVE
(TXV)
One feature of the TXV is that it modulates refrigerant flow according to load and conditions automatically. This enables more consistent ice production over a wide range of conditions.
The TXV comes set from the factory and will not need resetting in the field. If under warranty, call for authorization before tampering with the TXV, otherwise warranty will be voided!
R
ECHARGING THE
S
YSTEM
S
YSTEM
S
HUTDOWN
Optimally, turn the system off 4 to 6 hours prior to servicing to allow refrigerant to reach ambient temperature. This will expedite the recovery of the refrigerant.
E
VACUATE
R
EFRIGERANT
1.
Connect the gauge set to both the high and low side ports. Attach the center line of gauge set to the recovery unit.
2.
Evacuate system per governing EPA regulations.
3.
With the gauge set still connected to both ports, attach the center line of the gauge set to the vacuum pump.
4.
Turn on vacuum pump. Open both high and low manifolds and allow the pump to run so the vacuum reaches 28" HG.
Close gauge-set valves and turn off pump.
5.
Leave the system for 15 minutes then observe the gauges. If any vacuum has been lost, check for leaks, especially at any mechanical fittings.
6.
Repeat the vacuum process until a vacuum of 200 microns or less is achieved, 50 microns is ideal. If the system was open to the environment, allow 12 to 24 hours for evacuation. Close gauge-set valves and turn off pump. If no vacuum is lost, proceed with charging.
NOTE:
If moisture was a problem, refer to Refrigeration Bulletin 02-1 for instructions on clean up. This bulletin is available on the DometicEnviro.com Customer News and Information website under Technical Field Notices 2002: "Control of Moisture in
Refrigeration Systems" (FN#175-I2).
C
HARGING THE
S
YSTEM
1.
Remove line from vacuum pump and connect to a bottle of R-404A. The charge should be weighted in by placing the bottle on a refrigerant scale.
2.
Turn the bottle upside down and purge the charge hose at the gauge set. R-404A should be charged in the liquid phase with “Charge-Guard” and weighed in according to data label located on electric box.
3.
Allow refrigerant to flow in the high side until the correct weighed charge is reached (per data label). Disconnect refrigerant bottle.
4.
Disconnect high-side refrigerant hose, then turn machine on to allow compressor to recover residual liquid in gauge manifold through low-side hose.
20 L-3040 ENGLISH
Eskimo Ice Installation & Operation Manual
OWNER MAINTENANCE
OWNER MAINTENANCE
The periods and procedures given for maintenance and cleaning are guides only and should not to be construed as absolute or invariable. Cleaning frequency will vary depending on local water conditions (hard water, etc.) and the ice volume produced.
S
EAWATER
S
YSTEM
Check the seawater strainer daily and remove any debris. If you are in water where jellyfish or other debris are a problem, it may be necessary to add a strainer on the outside of the thru-hull fitting. Verify that all water connections are tight, and check for water flow from the overboard discharge. The centrifugal pump does not need any routine maintenance.
F
RESH
W
ATER
F
ILTER AND
Y S
TRAINER
Change the filter at least twice per year, or every 1500 gallons, whichever comes first. The correct filter helps prevent clogging of the needle valve and scale buildup within the evaporator chamber. Occasionally check the Y strainer and clean away any debris.
E
VAPORATOR
C
LEANING
Every 6 months the evaporator should be cleaned by an authorized service agency. Under severe conditions of water with high mineral content, your machine may require more frequent cleaning. The following steps should be used:
1.
Shut off feedwater supply to the ice machine.
2.
Disconnect clear tubing from bottom evaporator, and drain all water from the evaporator and water reservoir.
Reconnect the tubing.
3.
Prepare an ice-machine cleaning solution per manufacturer’s directions to make two quarts (1.9L) of cleaner. Follow instructions on bottle for mixing ratio.
4.
Remove cover to the water reservoir.
5.
Slowly pour the cleaning solution into the reservoir until just below overflow.
6.
Allow solution to sit in reservoir for 15 minutes.
7.
Turn the machine to the ON position and allow to make ice (Note: Ice quality may be poor).
8.
Continue pouring cleaning solution into the reservoir, maintaining the level just below overflow, while the machine makes ice.
9.
Continue ice making until all the solution is used and the reservoir is empty.
10. Turn the machine to the OFF position.
11. Disconnect clear tubing from bottom evaporator, and drain all cleaning solution from the evaporator and water reservoir. Reconnect the tubing.
12. Open the fresh water supply to the ice maker and allow reservoir to fill completely to rinse.
13. Disconnect clear tubing from bottom evaporator, and drain all rinse water from the evaporator and water reservoir.
Reconnect the tubing.
14. Repeat the rinsing process another 2 times (3 times total) to purge ice machine of cleaning solution.
15. Turn the machine to the ON position.
16. Let the machine make ice for
AT LEAST 20 minutes
to flush out any remaining cleaning solution.
17. Remove all ice from the ice-storage box; do not use any ice produced during the cleaning or rinsing cycles.
18. Use hot water (if possible) to rinse the ice-storage box thoroughly.
WARNING
Ice-machine cleaners use strong acids. Read and follow all instructions and warnings on the container of the solution you use.
A
UGER
M
OTOR AND
G
EARBOX
The auger motor and gearbox are permanently lubricated and need no maintenance unless leakage or contamination has occurred.
L-3040 ENGLISH 21
TROUBLESHOOTING GUIDE
Eskimo Ice Installation & Operation Manual
C
OMPRESSOR
The compressor has no user-serviceable parts, and is lubricated constantly during operation.
R
EFRIGERANT
G
AS
The refrigerant included in the system is adequate for the life of the system and should not need routine or seasonal charging. If the need exists for routine charging, have your dealer look for a refrigerant leak that needs repair.
W
ATER
R
ESERVOIR
If water reservoir is fouled or contaminated, refer to “Evaporator Cleaning” on page 21 and follow that cleaning procedure, as the water reservoir is a window to your evaporator’s condition.
F
EEDWATER
F
ILTER AND
Y S
TRAINER
Change the filter at least twice per year, or every 1500 gallons, whichever comes first. The correct filter helps prevent clogging of the needle valve and scale buildup within the evaporator chamber. Occasionally check the Y strainer and clean away any debris.
W
INTERIZING THE
S
YSTEM
Close the seacock and remove the inlet hose from the condensing unit. Allow all water to drain from the system. Loosen screws on the pump head to allow water to drain from the pump. Cutoff feedwater supply, and drain the unit. Remove water from the water reservoir inside the unit. You may also add non-toxic antifreeze to the water reservoir.
Use a shop wet-vac to remove the water from the evaporator through the ice discharge spout tube, or remove the water tank assembly from the spout and drain it.
TROUBLESHOOTING GUIDE
Before calling for service, review this list. It may save time and expense. This list contains common occurrences that are not a result of defective workmanship or materials.
If you still need service after trying these procedures, call your local dealer or refer to the back cover of this manual for technical support options..
PROBLEM POSSIBLE REASONS & SOLUTIONS
Unit does not operate at all.
1. Power switch in the “Off” position. Press power switch to turn the unit on.
2. Check for tripped breaker or blown fuses.
3. Significantly low voltage to unit.
4. Misconnected or loose plugs or wiring.
High-pressure fault.
(HPF)
1. Check seawater system for clogs, air trap, faulty pump, dirty strainer, or condenser in need of descaling.
2. Faulty pump relay trigger at relay station (if pump is used for more than one unit). Replace trigger.
Low-pressure fault.
(LPF)
Ice-clog.
(OCA)
1. Low refrigerant charge. Have a certified technician check the pressure.
2. Improperly set Thermal Expansion Valve (TXV). If under warranty, call for authorization before adjusting TXV, otherwise warranty will be voided.
1. Check for obstruction at the ice discharge in the ice-storage box.
2. Check for frozen ice-delivery hose.
3. Check routing for dips or kinks in the ice-delivery hose.
4. Check for auger motor failure.
22 L-3040 ENGLISH
Eskimo Ice Installation & Operation Manual
TECHNICAL ASSISTANCE
Feedwater fault.
(H2O)
PROBLEM
Ice delivery volume seems less or slower.
Water leaks.
Display consistently shows
“Full”.
Squeaking or groaning noise coming from evaporator/auger assembly.
Typically heard once per revolution as auger rotates.
Excessive buzzing, grinding noise from evaporator/auger assembly. Usually constant.
Oil in auger assembly drain pan.
POSSIBLE REASONS & SOLUTIONS
1. Check water pressure in boat’s potable water system.
2. Check for a supply valve that has been turned off.
3. Check for a clogged feedwater filter.
4. Check for a cloged Y strainer located on the feedwater line of the unit.
5. Check for a clogged needle valve in the water reservoir.
1. High seawater temperature.
2. High feedwater temperature.
3. Low seawater flow. Check pump and strainer.
4. Drive motor weak. Replace motor.
5. Auger corroded or stained due to water conditions. Clean and/or replace assembly.
6. Inlet water filter or Y-strainer partially clogged. Clean or replace filter. Remove clog.
7. Loss of refrigerant charge. Consult trained technician.
1. Defective water seal. Replace seals.
2. Water level in reservoir too high. Adjust float.
1. Make sure ice sensor is installed in the ice-storage box.
2. Check ice sensor for proper operation.
1. This type of noise is normal during ice production. It is caused by the shearing of extremely hard ice from the evaporator wall. No adjustment is necessary as this is normal.
2. See description of “excessive noise” below to compare.
1. Mineral or scale deposit on auger and evaporator walls. Clean evaporator as described in
“Evaporator Cleaning” on page 21.
2. Low water supply. Check for fouled filter or float valve.
3. Gear-reducer assembly loose on mounts. Tighten the mounts.
4. Gear-motor end-play or worn bearing. Replace worn part.
1. Leaking water seals in the evaporator/auger assembly. Replace seals.
TECHNICAL ASSISTANCE
If you need technical assistance with your Eskimo Ice system, refer to the back cover of this manual for technical support options.
LIMITED WARRANTY
LIMITED WARRANTY AVAILABLE AT WWW.DOMETIC. COM/WARRANTY
IF YOU HAVE QUESTIONS, OR TO OBTAIN A COPY OF THE LIMITED WARRANTY FREE OF CHARGE, CONTACT:
DOMETIC CORPORATION
MARINE CUSTOMER SUPPORT CENTER
2000 NORTH ANDREWS AVENUE
POMPANO BEACH, FLORIDA, USA 33069
1-800-542-2477
L-3040 ENGLISH 23
DIAGRAMS
Eskimo Ice Installation & Operation Manual
Figure 13: Diagram of System Components and Water Flow
24
Figure 14: EI540D Connection Locations
Seawater Out
Fresh Water In
Electrical Box Wire
Ice Outlet
Seawater In
Drain
L-3040 ENGLISH
Eskimo Ice Installation & Operation Manual
E
LECTRICAL
W
IRING
F
OR
115V 60 H
Z
M
ODELS
Figure 15: Wiring Diagram for 115V 60Hz Models
DIAGRAMS
L-3040 ENGLISH 25
DIAGRAMS
Eskimo Ice Installation & Operation Manual
E
LECTRICAL
W
IRING
F
OR
230V 60 H
Z
M
ODELS
& 220V 50 H
Z
M
ODELS
Figure 16: Wiring Diagram for 230V 60Hz Models and 220V 50 Hz Models
26 L-3040 ENGLISH
Mobile living made easy.
YOUR LOCAL
DEALER
dometic.com/dealer
dometic.com
YOUR LOCAL
SUPPORT
dometic.com/contact
YOUR LOCAL
SALES OFFICE
advertisement
* Your assessment is very important for improving the workof artificial intelligence, which forms the content of this project
Related manuals
advertisement
Table of contents
- 3 INTRODUCTION
- 4 How Ice Is Made
- 4 The Refrigeration Process
- 5 Water Temperatures
- 5 Air Temperature
- 6 Ice-Making Unit
- 6 Control Box
- 7 Ice-Storage Box
- 7 Seawater System
- 7 Freshwater Supply
- 7 Refrigerant Charge
- 7 Thermal Expansion Valve (TXV)
- 8 INSTALLATION PROCEDURES
- 8 Selecting the Site
- 8 Mounting the Unit
- 8 Installing Condensate Drainage
- 9 Installing Ice-Delivery Hose
- 10 Installing the Ice-Level Sensor
- 10 Installing the Feedwater System
- 11 Installing the Seawater Cooling System
- 15 Installing the Remote Digital Display
- 15 Mandatory System Start-Up Test
- 16 OPERATION
- 17 Applying Power
- 17 On/Off
- 17 Ice Bin Sensor
- 17 Operational LEDs
- 17 Operational Information
- 17 Fault History
- 17 FULL – Ice Bin Full
- 17 H20 – Potable Water Switch
- 17 HPF – High Pressure Refrigerant
- 18 LAC – Low AC line voltage
- 18 LPF – Low Pressure Refrigerant
- 18 Problem
- 18 OCC – Overload Current Compressor
- 18 SPt – Auger Spout Blockage
- 18 UCA – Under Current Auger
- 18 UCC – Under Current Compressor
- 21 STARTING THE SYSTEM
- 21 SYSTEM SHUTDOWN
- 22 SERVICING THE SYSTEM
- 22 (TXV)
- 22 System Shutdown
- 22 Evacuate Refrigerant
- 22 Charging the System
- 23 OWNER MAINTENANCE
- 24 TROUBLESHOOTING GUIDE
- 25 TECHNICAL ASSISTANCE
- 25 LIMITED WARRANTY
- 26 DIAGRAMS