advertisement
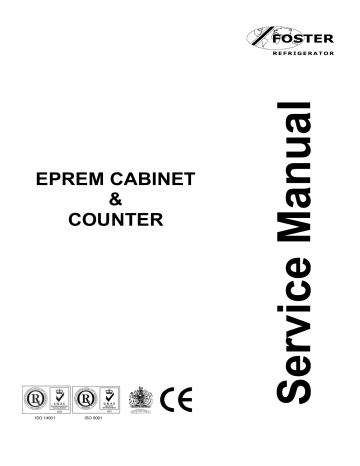
EPREM CABINET
&
COUNTER
ISO 14001 ISO 9001
Contents
Environmental Management Policy
Disposal Requirements
Cabinet description
Controller Operation
Operating Modes
Fuzzy Logic
Defrost Operation
Alarms & warnings
Service Adjustments
Parameters Cabinets & Counters
Technical Data
Wiring Diagrams
1
1
2
2 to 4
4
5 to 6
5
6 to 7
11 to13
14 to 18
7 to 8
9 to10
Environmental Management Policy for Service Manuals and Duets.
Product Support and Installation Contractors
Foster Refrigerator recognises that its activities, products and services can have an adverse impact upon the environment.
The organisation is committed to implementing systems and controls to manage, reduce and eliminate its adverse environmental impacts wherever possible, and has formulated an Environmental Policy outlining our core aims. A copy of the Environmental Policy is available to all contractors and suppliers upon request.
The organisation is committed to working with suppliers and contractors where their activities have the potential to impact upon the environment. To achieve the aims stated in the Environmental Policy we require that all suppliers and contractors operate in compliance with the law and are committed to best practice in environmental management.
Product Support and Installation contractors are required to:
1. Ensure that wherever possible waste is removed from the client’s site, where arrangements are in place all waste should be returned to Foster Refrigerator’s premises. In certain circumstances waste may be disposed of on the clients site; if permission is given, if the client has arrangements in place for the type of waste.
2. If arranging for the disposal of your waste, handle, store and dispose of it in such a way as to prevent its escape into the environment, harm to human health, and to ensure the compliance with the environmental law.
Guidance is available from the Environment Agency on how to comply with the waste management ‘duty of care’.
3. The following waste must be stored of separately from other wastes, as they are hazardous to the environment: refrigerants, polyurethane foam, oils.
4. When arranging for disposal of waste, ensure a waste transfer note or consignment note is completed as appropriate. Ensure that all waste is correctly described on the waste note and include the appropriate six-digit code from the European Waste Catalogue. Your waste contractor or Foster can provide further information if necessary.
5. Ensure that all waste is removed by a registered waste carrier, a carrier in possession of a waste management licence, or a carrier holding an appropriate exemption. Ensure the person receiving the waste at its ultimate destination is in receipt of a waste management licence or valid exemption.
6. Handle and store refrigerants in such a way as to prevent their emission to atmosphere, and ensure they are disposed of safely and in accordance with environmental law.
7. Make arrangements to ensure all staff who handle refrigerants do so at a level of competence consistent with the City Guilds 2078 Handling Refrigerants qualification or equivalent qualification.
8. Ensure all liquid substances are securely stored to prevent leaks and spill, and are not disposed of to storm drains, foul drain, surface water to soil.
DISPOSAL REQUIREMENTS
If not disposed of properly all refrigerators have components that can be harmful to the environment. All old refrigerators must be disposed of by appropriately registered and licensed waste contractors, and in accordance with national laws and regulations.
1
Cabinet Description
EPrem cabinets.
The Pro range consists of a choice of capacities and temperature ranges in the full gastronorm format (650 x 530 shelf) and the non gastronorm (530x 550 shelf) formats.
The cabinets are manufactured as a one piece foam shell with easy clean stainless steel exterior
The cabinets conform to current legislation and exceed the Montreal protocol using zero ODP refrigerants and insulation with Hydrocarbon refrigerant as an option.
There are 3 temperature options exceeding Climate Class 5 operation up to 43°c ambient.
Temperature is controlled by a LAE microprocessor control with digital temperature display.
The standard refrigeration system is integral with an air-cooled condensing unit with the refrigerant distribution into the evaporator controlled by capillary.
Remote systems are available as an option with the refrigerant distribution into the evaporator controlled by expansion valve.
The cooled air is circulated through the evaporator, via the fan into the storage area.
Easy removable plug box and lid.
Coated coils prevent corrosion and prolong refrigeration life.
Removable thermal break giving easy access to the door frame heater.
Easy to read temperature display with wipe clean finish.
Wide magnetic gasket giving a positive door seal
.
EPrem counters.
The Pro range consists of a choice of capacities and temperature ranges in the full gastronorm format (650 x 530 shelf) and the non gastronorm (530x 550 shelf) formats.
The cabinets are manufactured as a one piece foam shell with easy clean stainless steel exterior
The cabinets conform to current legislation and exceed the Montreal protocol using zero ODP refrigerants and insulation with Hydrocarbon refrigerant as an option.
There are 3 temperature options exceeding Climate Class 5 operation up to 43°c ambient.
Temperature is controlled by a LAE microprocessor control with digital temperature display.
The standard refrigeration system is integral with an air-cooled condensing unit with the refrigerant distribution into the evaporator controlled by capillary.
Remote systems are available as an option with the refrigerant distribution into the evaporator controlled by expansion valve.
The cooled air is circulated through the evaporator, via the fan into the storage area.
Easy accessible condensing unit fitted on slides for ease of servicing.
Coated coils prevent corrosion and prolong refrigeration life.
Removable thermal break giving easy access to the door frame heater.
Easy to read temperature display with wipe clean finish.
Wide magnetic gasket giving a positive door seal.
Controller Operation
FEPC controller (00-556122)
The controller has two displays, the right hand display gives temperature readout and the left hand will display fault codes, error codes and other information.
The controller connects to the power switching unit using a ten way and sixteen way ribbon cable.
Temperature Display symbols
Compressor: LED illuminated beneath the symbol indicates the compressor in operation.
Fan/s: LED illuminated beneath the symbol indicates the fan/s in operation.
Defrost: LED illuminated beneath the symbol indicates defrost in operation.
There is a circular reed switch fitted at the bottom of the facia panel that corresponds with a magnet at the top of the door to stop the evaporator fan when the door is opened (not fitted on heated or fish cabinets).
Door switch kit part number is 16240122.
2
Basic User Functions
Button 1 Button 2
Set Unit to Standby
Button 4 Button 3
Press any button (1, 2, 3 or 4)
Press button 1 (Off)
All relay outputs fall low. Display will show
Set Unit to Run
Press button 4
System will restart
Check Set Point (Low Temperature Band)
Press any button (1, 2, 3 or 4)
Press button 3. (Temp)
Press button 1(-) or 2 (+) to raise or lower the set point.
Press button 4 (<<) to exit to ‘User Main Menu)
View Ancillary Temperatures (If relevant Probes are fitted)
Press any button (1, 2, 3 or 4)
Press button 4 for ‘Service’ menu.
Press button 1 for ‘Info’ menu.
Use buttons 1 ( ) and 2 ( ) to view temperatures
(Text Air Evaporator Condenser Food Tlo
Thi Text )
Tlo indicates the lowest temperature the machine has achieved.
Thi indicates the highest temperature the machine has achieved.
This information is useful when checking on the possible cause of iced up evaporators.
(If the relevant probe is not fitted display shows ---)
Press button 4 (<<) to exit to ‘User Main Menu)
Basic ‘User’ Adjustments
Increase Set Point. (High Point of Temperature Band)
Press any button (1, 2, 3 or 4)
Press button 3 for ‘Temp. Set’ menu.
Use button 2 (+) to adjust setting to required value.
Press button 3 (OK) to save and exit.
Press button 4 (<<) to exit without saving.
Display will return to ‘User Main Menu’.
Note: Maximum value is dependant upon Maximum Temperature Set-Point parameter setting.
3
Decrease Set Point. (Low Point of Temperature Band).
Press any button (1, 2, 3 or 4)
Press button 3 for ‘Temp. Set’ menu.
Use button 1 (-) to adjust setting to required value.
Press button 3 (OK) to save and exit.
Press button 4 (<<) to exit without saving.
Display will return to ‘User Main Menu’
Note: Minimum value is dependant upon Minimum Temperature Set-Point parameter setting.
Initiate Manual Defrost
Press any button (1, 2, 3 or 4)
Press button 2 for ‘Defrost’ initiation.
A defrost and Recovery Program will occur.
On completion unit will return to normal operation.
Note: Not available on Heated (Xt.) variants
Change Display Text Language
Press any button (1, 2, 3 or 4)
Press button 4 for ‘Service’ menu.
Press button 1 for ‘Info’ menu.
Press button 3 for ‘Text’ menu.
Use buttons 1 (-) and 2 (+) to select language.
Press button 3 (OK) to save and exit.
Press button 4 (<<) to exit without saving
Display will return to ‘User Main Menu’
Energy
Operating Modes
Normal Operation
When mains power is initially applied the LCM text display will show the start up message: (including the software version and the base model operating range), for a period of three seconds, during which time the controller performs a ‘self check’. The LED temperature display will not illuminate during this time. After 3 seconds the text will then extinguish and the LED display will show the temperature measured by Probe 1 (T1) - the internal air temperature probe. The function LED’s will also illuminate to show which output relays are energised. Therefore, if the measured temperature is not within the pre-set temperature range the controller will activate the condensing or heating system. All timings (i.e. defrost intervals) will be taken from power up.
The evaporator coil temperature, measured by Probe 2 (T2) may be temporarily viewed by entering the ‘Supervisor
Main Menu’ and pressing button1 (Info); (this facility is only available if the evaporator probe is selected by virtue of model or as an addition in the parameters). The Condenser Coil and Food Probe temperature may also be viewed from this menu if they are fitted by scrolling through the menu using button 1 ( ) and 2 ( ). If no buttons are pressed for a period of one (1) minute the ICM display will be extinguished.
Electrical Isolation
If mains power is removed from the controller with the unit operational, the entire system will cease and the relay outputs will fall low, the LCM and LED displays will be extinguished. When mains power is re-established the controller will carry out the initial self-test routine and then the system will re-start and carry on in the ‘Normal
Operating Mode’. However, if the controller is set to ‘Stand-by’ mode when the mains fails or is removed, on reconnection the controller will return to the ‘Stand-by’ mode.
4
Fuzzy Logic.
These are settings that maintain the temperature of the cabinet in a more energy efficient manner.
It works by controlling the evaporator fan/s, defrost and temperature in high usage times by transferring the operation to a second set of control parameters.
When the cabinet is first switched On the economy settings control the operation of the temperature and will remain at those settings until the controller, by monitoring the door opening frequency and the air and evaporator temperatures, identifies a higher usage and switches over to the ‘2 SET MODE’ (2nd parameter set management).
When the machine is used at a lower level the economy settings are activated the cabinet temperature is allowed to rise to the setting ‘TEMP SET 1’ setpoint 1. This is set to a higher temperature setting to allow the air temperature to rise without having much of an impact on the product temperature.
In addition the fan/s will modulate as set in ‘FAN RUN TM’ evaporator fan on and off as set in ‘FAN OFF TM’.
With the fans controller in this way they will generate less heat into the cabinet therefore reduce the requirement of the condensing system.
Fan Operation.
The evaporator fan/s will run normally when the compressor is running but will commence cycling off and on as determined in parameter ‘FAN OFF TM’ fan off and fan run ‘FAN RUN TM’.
The fans will run without the compressor during timed off cycle defrost but will not run during hot gas or electric defrost.
For models that don’t have door switches fitted, i.e. counters, the fuzzy logic will not function as the controller is unable to monitor door opening factors.
NOTE:
The ECM evaporator fan motor has a low heat output motor and it should be noted that when the power is switched off stops rotating straight away.
Auto Defrost operation.
The defrost frequency is determined by the usage of the machine.
In the economy mode it may not perform a defrost as by monitoring the air temperature, evaporator temperature and door opening factor it may decide that there is insufficient ice build up on the evaporator so defrosting is not required.
The parameter ‘DFR/24H’ defrost frequency / 24 H determines how many defrost in a 24 hour period. The cabinet will perform at least 1 defrost per day and if the setting is 3 it has the potential to initiate up to 2 additional defrost whilst in the economy mode.
Should the cabinet experience constant usage the controller will switch automatically to the second parameter settings which could under circumstances of heavy usage initiate up to the amount defrosts per day as set in parameter ‘DEF 24/H 2’.
The second parameter settings ‘2 Set Mode’ will now be active,
It is important to note that during the first few days of operation the defrosting frequency may be at regular intervals but these will reduce as the controller monitors the operation.
NOTE: for cabinets and counters without door switches the amount of defrosts per day will be as set in the parameters ‘Defrost/Day1’ and ‘Defrost/Day2’.
The defrost operation is displayed as follows:
Defrost Initiated
The LED temperature display is extinguished, although the function indicators will remain illuminated
(dependant upon the type of defrost). The LCM text display will show ‘Defrost On’ and the time elapsed clock will start. The defrost will continue until either the Defrost termination temperature or time is reached, at which time the defrost relay will be de-energised. The drain down time will commence during which no relays will be energised, the drain down time is determined by parameter ‘Drain Time’, allowing for the melt water to drain from the evaporator. On completion the condensing unit will start but the evaporator fan/s will not, this is the ‘Fan Delay Period’
Fan Delay
This period is to allow the evaporator to cool before the evaporator fans restart (this does not apply to ‘Off
Cycle’ defrost type. This prevents any warm air remaining from the defrost being distributed throughout the product. During the fan delay period (determined by the parameter ‘FAN DLY TP’ ) the LED temperature display remains extinguished, although the condenser function will be illuminated. The ICM text display will show ‘Defrost On’ and the time elapsed clock will continue. The fan delay period will continue until the temperature, determined by the fan delay temperature parameter ‘FAN DLY TP’, has been achieved. The evaporator fans will restart and the unit will enter the recovery period.
5
Temperature Recovery Period
This period allows the unit to cool the load back to the normal operating temperature range following defrost.
The internal air temperature may have risen out of the normal temperature ranges during the defrost period due to the doors being opened for loading/unloading or a slight transfer of warm air from the evaporator to the air temperature probe. During the temperature recovery period, which is a fixed 5 minute period after the evaporator fans restart, the LCM text display will change to show ‘Temp. Recovery’ with the time elapsed clock continuing. During the first two minutes of the temperature recovery period the LED temperature display will only show the function indicators, however for the final three minutes of the temperature recovery period the internal air temperature will also be shown.
Normal Operating Mode
Five minutes after the evaporator fans have restarted the LCM text display will be extinguished and the unit will enter the normal operating mode and defrost will be completed.
A defrost can be initiated manually if required. The procedure for this is detailed in the ‘User Functions’ section, but the defrost operation and display will be the same as for an automatic defrost. Should a manual defrost be initiated the automatic defrost clock will be reset, and therefore subsequent defrosts will follow at the normal time interval.
Alarms and Warnings
Door Opening Warning
Display shows door open warning. The controller siren sounds, but can be muted by pressing any button. The display will continue until cancelled by shutting the door. If the door open warning is muted and the door is left open the warning will eventually become a temperature related problem and then the appropriated alarm would be generated. The door alarm will sound after the period determined from the ‘Door Stop’ plus the ‘Door Alarm’ parameters. This will occur if the ‘Door Switch’ parameter is set to ‘Yes’
High Temperature Alarm
This alarm occurs if the internal temperature rises above the set point plus the hysteresis value, plus the high alarm temperature differential for the time determined by the alarm delay period. If this alarm occurs, the LCM display will flash the above alarm message. The alarm siren will sound but can be muted for a period of one hour by pressing any button. The LCM display will continue to flash throughout this alarm. The LED display will show the internal air temperature and the function icons. If the temperature has not returned to within the operating limits after one hour the alarm will resound for one minute. This process will continue until automatically cancelled by the system returning to its normal operating temperatures.
Low Temperature Alarm
This alarm occurs if the internal temperature falls below the set point minus the low alarm temperature differential for the time determined by the alarm delay period. If this alarm occurs, the LCM display will flash the above alarm message. The alarm siren will sound but can be muted for a period of one hour by pressing any button. The LCM display will continue to flash throughout this alarm. The LED display will show the internal air temperature and the function icons. If the temperature has not returned to within the operating limits after one hour the alarm will resound for one minute. This process will continue until automatically cancelled by the system returning to its normal operating temperatures.
Air Temperature Probe Failure
The display will flash ‘Probe 1’, as shown above, indicating an air probe (T1) failure; it is not possible to display the temperature with a probe 1 fault. The alarm will sound but can be temporarily muted by pressing any button. The siren will resound after one hour for one minute if the fault has not been rectified. During this period the unit will continue to operate, as determined by the ‘Comp.Cycle’ parameter, but will have a reduced performance as the compressor ON and OFF function will be on a timed basis. It is not possible to view the air or food temperature when this fault occurs. The alarm message will continue to be displayed until the fault has been rectified and then cleared by entering the ‘Basic User Functions’ and deleting the alarm message.
Evaporator Temperature Probe Failure
The display will flash ‘Probe 2’, as shown above, indicating an evaporator probe (T2) failure. The alarm will sound but can be temporarily muted by pressing any button. The siren will resound after one hour for one minute if the fault has not been rectified. During this period the unit will continue to operate but this failure will have an effect on the defrost, termination on a timed basis and not temperature, and therefore effect efficiency if unfixed, The alarm message will continue to be displayed until the fault has been rectified and will then automatically reset and the unit will function normally
6
Note.
The condenser probe is no longer fitted as in previous model.
The ‘Condenser Clean’ and ‘Service Due’ warnings will not be displayed as the parameters are set to ‘0’ and therefore switched off.
The diagnostics is no longer incorporated as in previous models so functions SF010, SF020 and SF030 will not be displayed.
Service Adjustments
The controller has three ‘Service’ modes – the Output Relay Test function, the Model Selection Function and the individual Parameter adjustments. These features are accessible only from the ‘Service Main Menu’.
Service Main Menu.
Press any button (1, 2, 3 or 4)
Press button 4 ‘Service’ for the ‘Service Menu’.
Press button 3 ‘Settings’ for the ‘Settings Menu’.
Press button 2 ‘+’ to advance the code number to ‘131’ if you go beyond the number press button 1 ‘-‘ to lower to the correct number.
Press button 3 ‘OK’ to enter the ‘Service Main Menu’.
To exit the ‘Service Main Menu’ and return to the ‘User Main Menu’ press button 4 ‘<<’. If no further buttons are pressed for one minute the controller will revert to the normal operating mode.
Out-Put Relay Test
Whilst in the ‘Service Main Menu’ press button 1 ‘Test’ all relays will de-energise and the screen opposite will be displayed.
To test relay 1 ‘Condensing Unit Relay’ press button 1.
Relay 1 will energise.
To test relay 2 ‘Evaporator Fan Relay’ press button 2.
Relay 2 will energise.
To test relay 3 ‘Defrost System Relay’ press button 3.
Relay 3 will energise.
To test all three relay outputs press buttons 1, 2 and 3 together. All three relays will energise.
To exit the ‘Output Relay Test Menu’ and return to the ‘User Main Menu’ press button 4 ‘<<’. If no further buttons are pressed for one minute the controller will revert to the normal operating mode.
Model Selection Function
The ‘Model Selection Function’ allows the controller to be set during manufacturing, or replacement, to the most appropriate model range with the accompanying default setting values. There are eleven temperature default models which are:- HIGH TEMP-D (High Temperature with Door Switch), HIGH TEMP (High Temperature without
Door Switch), LOW TEMP-GD (Low Temperature with Hot Gas Defrost and Door Switch), LOW TEMP-G (Low
Temperature with Hot Gas Defrost without Door Switch), LOW TEMP-ED (Low Temperature with Electric Defrost and Door Switch), LOW TEMP-E (Low Temperature with Electric Defrost without Door Switch), MEAT TEMP-GD
(Meat Temperature with Hot Gas Defrost and Door Switch), MEAT TEMP-G (Meat Temperature with Hot Gas
Defrost without Door Switch), FISH TEMP. (Fish Temperature without door switch), WINE TEMP. (Wine
Temperature with door switch), HEATED CAB. (Heated Temperature without door switch).
All controllers arrive from the manufacturer with the HIGH TEMP-D settings if any other setting is required the following procedure should be followed.
7
From ‘Service Main Menu’ depress button 2 ‘Model’
Use button 1(-) or button 2(+) to select required model
(in this case wine)
Once the model has been selected depress button 3 (OK) to confirm.
Once confirmed the controller will reset parameter values and return to the ‘Service Main Menu’.
If during the model selection button 4(<<) is pressed, the controller will revert to the ‘Service Main Menu’ without making any changes. Similarly if no buttons are pressed for a period of one minute the controller will revert to the
‘Normal Operating Mode’ without saving any of the changes.
NOTE: When the model change mode is entered any previously made changes to the parameters will be lost and will revert to the default parameters.
Parameter Adjustment
The individual Parameter Adjustment allows the controller’s standard settings to be adjusted to suit particular requirements. This allows adjustment for specific customer, engineer requirement or to overcome an operating problem.
If any parameters require adjusting; for example if the standard number of defrosts in the economy or heavy duty settings (2) requires to be increased the following procedure should be followed.
From ‘Service Main Menu’ depress button 2 ‘Model’
Use button 2 ( ) to scroll through to the required parameter heading.
If the require parameter is missed use button 1( ) to scroll backwards through the parameters.
Select ‘Defrost/ Day 1’ for the economy settings defrost or ‘Defrost/Day 2’ for the
Defrost/Day 1 heavy duty settings.
Depress button 3 (Set) to enable adjustment of the parameter value.
Use button 1 (-) or 2 (+) to adjust the value to the required setting.
In this case 6.
Defrost/Day 2
Defrost/Day 2
4
Defrost/Day 2
6
Depress button 3 (OK) to save the new value. Controller updates settings and the display shows the next parameter heading
If no further changes are required press button 4 to return to the ‘Service Main
Menu’.
If during the model selection button 4(<<) is pressed, the controller will revert to the ‘Service Main Menu’ without making any changes. Similarly if no buttons are pressed for a period of one minute the controller will revert to the
‘Normal Operating Mode’ without saving any of the changes.
8
Scale
Min Temp 1
Max Temp 1
Temp. Set 1
Temp. Hyst 1
Minimum setpoint [ I ]
Maximum setpoint [ I ]
Setpoint [ I ]
Thermostat hysteresis [ I ] run failure stop failure
Eprem Controller Default Parameter Values
LT
GAS
LT ‘G’
No DS
LT
ELE
LT ‘E’
No DS
MT
GAS
MT ‘G’
No DS
Fish Wine Heated
-40
Min
Temp 1
Min
Temp 1
-10
Max
Temp 1
1 ºC 1 1 -21 -21 -21 -21 -2 -2 -1 8 83
100 3 ºC 3 3 -19 -19 -19 -19 0 0 1 12 91
Max
Temp 1
10
2
3
ºC
ºC
2
3
2 -19 -19 -19 -19 -1 -1 0 10 87
3 3 3 3 3 2 2 2 2 -3
Defr. Type Defrost type
-40 40 20 ºC 20 20 20 20 20 20 20 20 20
1 120 20 min 20 20 20 20 20 20 20 20 20
OFF/ ELE/ GAS OFF flag OFF OFF GAS GAS ELE ELE GAS GAS OFF OFF OFF
Fan in Def
Fan Tm Con
0 60 10 min 10 10 10 10 10 10 10 10 10
No Yes Yes flag Yes Yes No No No No No No Yes Yes Yes Fan activity during defrost
Fan temperature maximum 3 3
Evaporator fan timed control No Yes Yes flag Yes Yes Yes Yes Yes Yes Yes Yes No Yes No
0 180 15 sec. 15 15 15 15 15 15 15 15 15
-12 0 -5 ºC -5 -5 -5 -5 -5 -5 -5 -5 -5
0 120 90 min 90 90 90 90 90 90 90 90 90
9
Con Hi Op
Condenser high temp. alarm operation
0 75 60 ºC 60 60 60 60 60 60 60 60 60
NON; ALR; STP NON flag NON NON NON NON NON NON NON NON NON
Eco Sense
2 Set Mode
Min.Temp. 2
Max. Temp. 2
Temp. Set 2
Sensitivity function eco / heavy duty 1 5 3 flag 3 3 3 3 3 3 3 3 3
2nd parameter set switching mode
Minimum 2nd temp. set
NON; HDD
-40 11SH
HDD
1 flag
ºC
HDD
1
HDD
1
HDD
-21
HDD
-21
HDD
-21
HDD
-21
HDD
-2
HDD
-2
NON
1
NON
1
NON
1
Maximum 2nd temp. set
Effective 2nd temperature set point
Temp. Hyst 2 Hysteresis 2nd temperature set
Fan Tm Con 2 Evap. fan timed control in mode 2
11SL
11SL
-10
NO
100
11SH
10
3
1
3
ºC
ºC
ºC
3
1
3
3
1
3
-21
-21
3
-21
-21
3
-21
-21
3
-21
-21
3
0
-2
2
0
-2
2
3
1
3
3
1
3
3
1
3
Defrost/Day 2
Door Switch
Door Stop
Defrost Frequency / 24h in mode 2
Door switch enabling
Compressor stop delay from door opening
0
NO
24
YES
4
YES
1/24h flag
4
YES
4
NO
4
YES
4
NO
4
YES
4
NO
4
YES
4
NO
4 4
YES YES
4
YES
Air T1
Evap. Probe T2 (evap.) probe enabling o/s T2 offset
Cond. Probe T3 (cond.) probe enabling o/s T3 offset
Food Probe T4 (Food) probe enabling
NO
NO
NO
YES
YES
YES
NO
NO
NO flag NO NO YES YES YES YES YES YES NO NO NO flag
Temp Dly Delay for min./max. temp storage 1 30 5 min 5 5 5 5 5 5 5 5 5 5 5
0 250 200 flag 200 200 200 200 200 200 200 200 200
10
TECHNICAL DATA FPRO CABINETS
Model
EPREM S 400H
EPREM S 400L
EPREM S 400F
EPREM G 500H
EPREM G 500L
EPREM G 600H
EPREM G 600M
EPREM G 600L
EPREM G 600F
EPREM G 1100H
EPREM G 1100L
EPREM G 1350H
EPREM G 1350M
EPREM G 1350L
EPREM G 1350F
EPREM G 300/300 HL
EPREM B 600H
EPREM B 600L
EPREM S 450H
EPREM S 450L
EPREM G 550H
EPREM G 550L
EPREM S 1000H
EPREM S 1000L
Gas
R134A
R404A
R134A
R404A
R134A
R404A
R134A
R404A
R134A
R404A
R134A
R404A
R134A
R134A
R404A
R134A
R134A
R404A
R134A
R134A
R404A
R134A
R134A
R404A
R134a
Gas Charge
380 grms
360 grms
270 grms
380 grms
360 grms
380 grms
380 grms
360 grms
270 grms
450 grms
660 grms
450 grms
450 grms
660 grms
360 grms
320 grms
300 grms
380 grms
360 grms
320 grms
300 grms
350 grms
325grms
450grms
450grms
Compressor Capillary
FR7.5GX
SC15CLX
FR7.5GX
FR7.5GX
SC15CLX
FR7.5GX
FR7.5GX
SC15CLX
FR7.5GX
SC15GX
CAJ2446Z-SE
SC15GX
SC15GX
CAJ2446Z-SE
SC12GX
FR7.5GX
SC15CLX
FR7.5GX
SC15CLX
FR7.5GX
SC15CLX
FR7.5GX
SC21CLX
GP16TB
CAJ2446Z-SE
3.0m x 0.042
3.0m x 0.047
3.0m x 0.054
3.0m x 0.042
3.0m x 0.047
3.0m x 0.042
3.0m x 0.042
3.0m x 0.047
3.0m x 0.054
3.0m x 0.054
3.0m x 0.054
3.0m x 0.054
3.0m x 0.054
3.0m x 0.054
2.5m x 0.054
3.0m x 0.042
3.0m x 0.042
3.0m x 0.042
3.0m x 0.047
3.0m x 0.042
3.0m x 0.042
3.0m x 0.042
3.0m x 0.054
3.0m x 0.054
3.0m x 0.054
Technical Data Pro Counter
Defrost Type
Timed Off Cycle
Hot Gas
Timed Off Cycle
Timed Off Cycle
Hot Gas
Timed Off Cycle
Hot Gas
Hot Gas
Timed Off Cycle
Timed Off Cycle
Hot Gas
Timed Off Cycle
Hot Gas
Hot Gas
Timed Off Cycle
Timed Off Cycle
Electric
Timed Off Cycle
Hot Gas
Timed Off Cycle
Electric
Timed Off Cycle
Electric
Timed Off Cycle
Electric
Voltage
230-1-50
230-1-50
230-1-50
230-1-50
230-1-50
230-1-50
230-1-50
230-1-50
230-1-50
230-1-50
230-1-50
230-1-50
230-1-50
230-1-50
230-1-50
230-1-50
230-1-50
230-1-50
230-1-50
230-1-50
230-1-50
230-1-50
230-1-50
230-1-50
230-1-50
Power
Consumption kW/48hrs
4.2 (indicative)
6.2 (indicative)
3.8 (indicative)
4.1 (indicative)
6.2 (indicative)
3.71(tested)
5.4 (indicative)
14.81(tested)
4.8 (indicative)
7.6 (indicative)
9.0 (indicative)
6.52 (tested)
10 (indicative)
28.76 (tested)
13.16 (indicative)
10.2 (indicative)
3.71(tested)
14.81(tested)
10.0 (indicative)
6.2 (indicative)
4.1 (indicative)
6.8 (indicative)
7.6 (indicative)
9.0 (indicative)
Fuse
Rating
Model Gas Gas Charge Compressor Capillary Defrost Type Voltage
Power
Consumption kW/48hrs
3.3 (tested)
Fuse
Rating
EPREM 1/2H
EPREM 1/2M
EPREM 1/2L
EPREM 1/3H
EPREM 1/3M
EPREM 1/3L
EPREM 1/4H
EPREM 1/4M
EPREM 1/4L
EPREM 2/2H
EPREM 2/2M
EPREM 2/2L
EPREM 2/3H
EPREM 2/3M
EPREM 2/3L
R134A
R134A
R404A
R134A
R134A
R404A
R134A
R134A
R404A
R134A
R134A
R404A
R134A
R134A
R404A
360 grms
360 grms
335 grms
315 grms
315 grms
360 grms
370 grms
370 grms
375 grms
365 grms
365 grms
360 grms
380 grms
380 grms
380 grms
FR7.5GX
FR7.5GX
SC 15CLX
FR7.5GX
FR7.5GX
SC 15CLX
SC12GX
SC12GX
SC 21CLX
FR7.5GX
FR7.5GX
SC 15CLX
SC12GX
SC12GX
SC 21CLX
3m X 0.042
3m X 0.042
3m X 0.042
3m X 0.042
3m X 0.042
3M X 0.042
3M X 0.054
3M X 0.054
3m X 0.054
3m X 0.042
3m X 0.042
3.0 X 0.042
3m X 0.054
3m X 0.054
3m X 0.054
Timed Off Cycle
Hot Gas
Hot Gas
Timed Off Cycle
Hot Gas
Hot Gas
Timed Off Cycle
Hot Gas
Hot Gas
Timed Off Cycle
Hot Gas
Hot Gas
Timed Off Cycle
Hot Gas
Hot Gas
230/50/1
230/50/1
230/50/1
230/50/1
230/50/1
230/50/1
230/50/1
230/50/1
230/50/1
230/50/1
230/50/1
230/50/1
230/50/1
230/50/1
230/50/1
3.3 (indicative)
6.4 (indicative)
4.7 (indicative)
4.7 (indicative)
23.9 (indicative)
5.2 (indicative)
5.2 (indicative)
23.9 (indicative)
3.8 (indicative)
5.6 (indicative)
23.9 (indicative)
11.0 (indicative)
12.4 (indicative)
16.8 (indicative)
Note: The Power Consumption values referred to as tested are to the ECA test standard. Actual power consumption will be greatly affected by ambient temperature,
13 Amp
13 Amp
13 Amp
13 Amp
13 Amp
13 Amp
13 Amp
13 Amp
13 Amp
13 Amp
13 Amp
13 Amp
13 Amp
13 Amp
13 Amp
13 Amp
13 Amp
13 Amp
13 Amp
13 Amp
13 Amp
13 Amp
13 Amp
13 Amp
13 Amp
13 Amp
13 Amp
13 Amp
13 Amp
13 Amp
13 Amp
13 Amp
13 Amp
13 Amp
13 Amp
13 Amp
13 Amp
13 amp
13 Amp
11
loading, usage and cabinet maintenance.
TECHNICAL DATA FPRO R290 CABINETS
Model
EPREM S 400H
EPREM S 400L
EPREM G 500H
EPREM G 500L
EPREM G 600H
EPREM G 600M
EPREM G 600L
EPREM G 600F
EPREM G 1100H
EPREM G 1100L
EPREM G 1350H
EPREM G 1350M
EPREM G 1350L
EPREM B 600H
EPREM B 600L
Gas
R290
R290
R290
R290
R290
R290
R290
R290
R290
R290
R290
R290
R290
R290
R290
Gas Charge
160 grms
150 grms
160 grms
150 grms
160 grms
160 grms
150 grms
160 grms
200 grms
220 grms
200 grms
200 grms
220 grms
160 grms
150 grms
Compressor Capillary Defrost Type
TL5CNX
SC15CNX
TL5CNX
SC15CNX
TL5CNX
TL5CNX
SC15CNX
NL7CNX
SC12CNX
MX23FB
SC12CNX
SC12CNX
MX23FB
TL5CNX
SC15CNX
2.8m x 0.042
3.0m x 0.042
2.8m x 0.042
3.0m x 0.042
2.8m x 0.042
2.8m x 0.042
3.0m x 0.047
3.0m x 0.054
3.0m x 0.054
3.0m x 0.054
3.0m x 0.054
3.0m x 0.054
3.0m x 0.054
2.8m x 0.042
3.0m x 0.047
Technical Data Pro R290 Counter
Timed Off Cycle
Hot Gas
Timed Off Cycle
Hot Gas
Timed Off Cycle
Hot Gas
Hot Gas
Timed Off Cycle
Timed Off Cycle
Hot Gas
Timed Off Cycle
Hot Gas
Hot Gas
Timed Off Cycle
Hot Gas
Voltage
230-1-50
230-1-50
230-1-50
230-1-50
230-1-50
230-1-50
230-1-50
230-1-50
230-1-50
230-1-50
230-1-50
230-1-50
230-1-50
230-1-50
230-1-50
Power
Consumption kW/48hrs
4.2 (indicative)
6.2 (indicative)
3.8 (indicative)
13.4 (indicative)
3.8 (tested)
5.4 (indicative)
13.4 (tested)
4.8 (indicative)
7.6 (indicative)
9.0 (indicative)
5.66 (tested)
9.0 (indicative)
25.1 (tested)
3.8 (tested)
13.4 (tested)
Fuse
Rating
Model
EPREM 1/2H
EPREM 1/2M
EPREM 1/2L
EPREM 1/3H
EPREM 1/3M
EPREM 1/3L
EPREM 1/4H
EPREM 1/4M
EPREM 2/2H
EPREM 2/2M
EPREM 2/2L
EPREM 2/3H
Gas
R290
R290
R290
R290
R290
R290
R290
R290
R290
R290
R290
R290
Gas Charge
160 grms
160 grms
160 grms
160 grms
160 grms
160 grms
165 grms
165 grms
160 grms
160 grms
160 grms
160 grms
Compressor
TL5CNX
TL5CNX
SC15CNX
TL5CNX
FR7.5GX
SC15CNX
SC12CNX
SC12CNX
TL5CNX
FR7.5GX
SC15CNX
SC12CNX
Capillary
3m X 0.042
3m X 0.042
3m X 0.042
3m X 0.042
3m X 0.042
3M X 0.042
3M X 0.054
3M X 0.054
3m X 0.042
3m X 0.042
3.0 X 0.042
3m X 0.054
Defrost Type
Timed Off Cycle
Hot Gas
Hot Gas
Timed Off Cycle
Hot Gas
Hot Gas
Timed Off Cycle
Hot Gas
Timed Off Cycle
Hot Gas
Hot Gas
Timed Off Cycle
Voltage
230/50/1
230/50/1
230/50/1
230/50/1
230/50/1
230/50/1
230/50/1
230/50/1
230/50/1
230/50/1
230/50/1
230/50/1
Power
Consumption kW/48hrs
3.2 (tested)
3.2 (indicative)
6.4 (indicative)
4.3 (indicative)
4.7 (indicative)
22.8 (indicative)
5.2 (indicative)
5.2 (indicative)
3.8 (indicative)
5.6 (indicative)
22.8 (indicative)
11.0 (indicative)
Fuse
Rating
Note: The Power Consumption values referred to as tested are to the ECA test standard. Actual power consumption will be greatly affected by ambient temperature, loading, usage and cabinet maintenance.
12
13 Amp
13 Amp
13 Amp
13 Amp
13 Amp
13 Amp
13 Amp
13 Amp
13 Amp
13 Amp
13 Amp
13 Amp
13 Amp
13 Amp
13 Amp
13 Amp
13 Amp
13 Amp
13 Amp
13 Amp
13 Amp
13 Amp
13 Amp
13 Amp
13 Amp
13 Amp
13 Amp
Energy Saving Features
NOTE : The energy consumption will be increased by maintenance issues for example: - blocked condenser, poor door seal, increased ambient temperature and high usage.
The refrigeration systems have a solenoid valve fitted in the discharge line between the condenser and the drier. The solenoid valve is controlled by the temperature controller along with the condensing unit and condenser fan. The reason it is fitted is to reduce the power consumption each time the compressor starts. This is achieved by reducing the refrigerant migration into the evaporator therefore reducing the amperage when the compressor starts.
The ECM evaporator fan motor has a low heat output motor and it should be noted that when the power is switched off stops rotating straight away.
Single Section Plug Box Single Section Plug Box
Discharge Line
Solenoid Valve
Position
Hot Gas
Solenoid Valve
Position
Hot Gas
Solenoid Valve
Position
Discharge Line
Solenoid Valve
Position
13
Wiring Diagrams
14
15
16
17
18
Foster European Operations
France
Foster Refrigerator France SA
Tel: (33) 01 34 30 22 22. Fax: (33) 01 30 37 68 74.
Email: [email protected]
Germany
Foster Refrigerator Gmbh,
Tel: (49) 781 990 7840. Fax (49) 781 990 7844.
Email: [email protected]
Foster Refrigerator
Oldmedow Road
Kings Lynn
Norfolk
PE30 4JU
Tel: 01553 691122
Fax: 01553 691447
Website: www.fosterrefrigerator.co.uk
Email: [email protected]
a Division of ‘ITW (UK) Ltd’
EPREM /SM/ 11/08
19
advertisement
* Your assessment is very important for improving the workof artificial intelligence, which forms the content of this project