Snap-On MUSCLE MIG SYSTEM MM350XL Owner's Manual
Add to My manuals28 Pages
Snap-On MUSCLE MIG SYSTEM MM350XL is a professional-grade welding system designed for light to heavy metal fabrication. It offers precise control over welding voltage and wire feed speed, enabling users to tackle various welding tasks with ease. The system's versatility allows welding of steel, stainless steel, aluminum, bronze, flux-cored, and gasless flux-cored wires, making it suitable for a wide range of projects.
advertisement
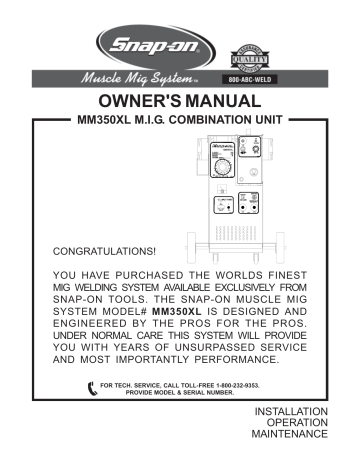
OWNER'S MANUAL
MM350XL M.I.G. COMBINATION UNIT
CONGRATULATIONS!
YOU HAVE PURCHASED THE WORLDS FINEST
MIG WELDING SYSTEM AVAILABLE EXCLUSIVELY FROM
SNAP-ON TOOLS. THE SNAP-ON MUSCLE MIG
SYSTEM MODEL#
MM350XL
IS DESIGNED AND
ENGINEERED BY THE PROS FOR THE PROS.
UNDER NORMAL CARE THIS SYSTEM WILL PROVIDE
YOU WITH YEARS OF UNSURPASSED SERVICE
AND MOST IMPORTANTLY PERFORMANCE.
FOR TECH. SERVICE, CALL TOLL-FREE 1-800-232-9353.
PROVIDE MODEL & SERIAL NUMBER.
INSTALLATION
OPERATION
MAINTENANCE
SAFETY - WELDERS
DANGER
• Electric welding causes ultraviolet rays and weld spatter.
Bystanders will be exposed to ultraviolet rays and weld spatter.
Wear welding helmet with appropriate shade lens while using electric welders.
Do not allow bystanders while welding.
Wear safety shield and protective clothing (user and bystanders).
Read and follow instructions.
Ultraviolet rays will burn eyes; weld spatter can cause injury.
WARNING
• Materials can cause sparks or flying metal when heated which can cause fire.
Wear safety shield and protective clothing (user and bystanders).
Sparks, fire and flying metal can cause injury.
SAFETY - WELDERS
WARNING
• Electrical shock can result from absence of grounding prong.
Do not remove or bypass the grounding prong in any electrical plug.
Electrical shock can cause injury.
WARNING
• Smoke, fumes and gases are created by the welding process.
Use only in well ventilated area.
Avoid breathing smoke, fumes and gases.
Smoke, fumes and gases can cause injury.
WARNING
• Welded surface can be hot and cause burns and injury.
2
MANUFACTURER’S LIMITED WARRANTY
This equipment is warranted against defects in materials and workmanship for a period of two years from the date of purchase.
EXCEPTION: THE MIG TORCH IS WARRANTED FOR A PERIOD OF 30 DAYS FROM THE DATE OF
PURCHASE.
Should the equipment become defective for such reason, the Manufacturer will repair it without charge, if it is returned to the Manufacturer’s factory, freight prepaid. This warranty does not cover: (1) failure due to normal wear and tear; (2) consumable parts, such as, but not limited to, torch contact tips, gas cups and insulating bushings; (3) damage by accident, force majeure, improper use, neglect, unauthorized repair or alteration; (4) anyone other than the original purchaser.
THIS LIMITED WARRANTY IS IN LIEU OF ALL OTHER WARRANTIES, EXPRESS OR IMPLIED. THE
MANUFACTURER SHALL NOT BE LIABLE FOR ANY INJURY TO PERSONS, INCLUDING DEATH; OR LOSS
OR DAMAGE TO ANY PROPERTY, DIRECT OR CONSEQUENTIAL, INCLUDING, BUT NOT LIMITED TO,
LOSS OF USE, ARISING OUT OF THE USE, OR THE INABILITY TO USE, THE PRODUCT. THE USER
ASSUMES ALL RISK AND LIABILITY WHATSOEVER IN CONNECTION WITH THE USE OF THE PRODUCT,
AND BEFORE DOING SO, SHALL DETERMINE ITS SUITABILITY FOR HIS INTENDED USE, AND SHALL
ASCERTAIN THE PROPER METHOD OF USING IT.
SOME STATES DO NOT ALLOW LIMITATIONS ON HOW LONG AN IMPLIED WARRANTY LASTS, OR
THE EXCLUSIONS OR LIMITATIONS OF INCIDENTAL OR CONSEQUENTIAL DAMAGES. SO THE ABOVE
LIMITATIONS OR EXCLUSIONS MAY NOT APPLY TO YOU. THIS WARRANTY GIVES YOU SPECIFIC
LEGAL RIGHTS, AND YOU MAY HAVE OTHER RIGHTS WHICH MAY VARY FROM STATE TO STATE.
TABLE OF CONTENTS
SAFETY PRECAUTIONS ............................................................. 2
INTRODUCTION ........................................................................... 4
DESCRIPTION, SPECIFICATIONS .............................................. 5
CHECK LIST (CONTENTS) .......................................................... 6
INSTALLATION & ELECTRICAL REQUIREMENTS ................... 7
OPERATION ............................................................................... 12
WELDING .................................................................................... 14
MAINTENANCE........................................................................... 16
TROUBLE SHOOTING CHART.................................................. 18
WIRE FEED CALIBRATION ....................................................... 22
CONNECTING FLEXTIG OR SPOOL GUN ............................... 23
LINER INSTALLATION ............................................................... 24
PARTS BREAKDOWN - MIG TORCH ........................................ 25
PARAMETER CHART ................................................................. 25
OPTIONS - FLEXTIG OR SPOOL GUN ..................................... 27
3
INTRODUCTION
The Snap-on Tools MM350XL is a combination welding power source, remote feed unit, MIG torch and accessory package, which is designed to meet the requirements of the light to heavy metal fabrication industries. The MM350XL produces fusion welds by the Gas Metal
Arc Welding process (GMAW or MIG), on steel and aluminum up to "1/2" thick, using .023" through 1/16" steel wire and .023" through 3/64" aluminum wire with the optional
MHG5-B spool gun. (optional liners and drive rolls must be purchased to cover all given wire types and
sizes). Heavier sections can be easily welded using slightly different techniques.
The number of controls on the unit have been reduced to assist inexperienced operators to learn MIG welding. This facilitates rapid set up for welding various thicknesses of material requiring various heat inputs. The VOLTAGE control adjusts the welding voltage and the WIRE FEED control adjusts the speed of the wire feed motor.
THE MIG PROCESS
AS APPLIED TO THE MM350XL
The MIG process uses a bare, consumable electrode in the form of spooled wire, which is fed by a controllable speed feed unit through the cable and torch to the weld. The emerging wire and the weld are shielded by a stream of
CO2, Argon, or a mixture of the two, which prevents oxidation of the molten weld puddle. The gas shield enables high quality welds to be made without the use of flux, eliminating the need for slag or flux removal after the weld is completed.
WIRE SPOOL
FEED
ROLLS
MIG
TORCH
POWER SOURCE
SHIELDING GAS
+
REVERSE
POLARITY
(STD.)
_
WORK
FIG. 1. SCHEMATIC OF M.I.G. PROCESS
The consumable electrode wire is melted and transferred to the weld puddle by any of three arc modes; short arc transfer, globular transfer, or spray arc transfer. The
MM350XL is capable of performing all modes.
SHORT ARC OR DIP TRANSFER
Short arc transfer occurs at 12 to
22 arc volts (voltage while welding), depending on wire size. Welding commences as the arc is struck and a weld pool is formed. The tip of the electrode wire dips into the pool and causes a short circuit.
The short circuit current flow causes a rapid temperature rise in the electrode wire and the end of the wire is melted off. An arc is immediately formed between the tip of the wire and the weld pool, maintaining the electrical circuit and producing sufficient heat to keep the weld pool fluid. The electrode continues to feed and again dips into the pool.
ELEC-
TRODE
WORK
FIG. 2. SHORT ARC TRANSFER
4
SHORT ARC OR DIP TRANSFER (Cont.)
This sequence of events is repeated up to 200 times per second.
Short arc transfer is suitable for positional welding. The heat input to the workpiece is kept to a minimum which limits distortion and makes possible the welding of thin sheet material.
GLOBULAR TRANSFER
Globular transfer occurs at the intermediate range of 22 to 24 arc volts, depending on wire size. As the name implies, the transfer takes place in the form of irregularly shaped globules. Globular transfer is useful in cases where a lower heat input than that of true spray is required.
ELECTRODE
WORK
ELECTRODE
WORK
GAS NOZZLE
SHIELDING GAS
FIG. 3. GLOBULAR TRANSFER
SPRAY TRANSFER
Spray transfer occurs at 22 to 32 arc volts, depending on wire size.
The length of the arc is held constant by the voltage available.
The higher voltage and current causes the electrode wire to melt off before touching the workpiece.
The molten metal crosses the gap to the workpiece in a spray form.
Spray transfer is used in the downhand position and provides higher deposition rates than short arc transfer or globular transfer.
GAS NOZZLE
SHIELDING GAS
DESCRIPTION
The MM350XL consists of a combination MIG welding power source and remote feed unit, a MIG torch with twelve foot cable, a fifteen foot feeder control cable, a twenty-five foot work cable with clamp, a twenty foot power input cable, a gas regulator - flowmeter, a torch accessory kit, built-in storage compartment and a dual cylinder rack and industrial wheel kit.
Welder controls are simple and clearly marked. The output voltage is controlled by a twelve position tap switch, providing 4 TIG and 8
MIG voltage selections. Wire feed speed is controlled by the wire speed potentiometer on the front of the feed unit.
SPECIFICATIONS
PART NUMBER: MM350XL
INPUT POWER REQUIREMENTS:
Voltage
Phase
208/230 single phase
Frequency
Current
50/60 hertz
46/42
DUTY CYCLE - OUTPUT POWER:
@ 100% - 300 Amps
@ 60% - 350 Amps
DUTY CYCLE TIME PERIOD:
10 minutes
OPEN CIRCUIT VOLTAGE:
18 - 42 volts DC
ARC VOLTAGE:
WELD CURRENT RANGE:
12 - 32 volts DC
30 - 350 amps
REMOTE FEED UNIT
Input Voltage 28 VAC
Wire Feed Speed Range: 50-800 IPM
FIG. 4. SPRAY TRANSFER
(continued on following page)
5
SPECIFICATIONS (Cont.)
WIRE TYPES: mild steel, stainless steel, aluminum, bronze, flux cored, flux cored - gasless
Recommended (for steel) ER70S-6
WIRE SIZES: .023" - 1/16" steel,
3/64 - 1/16" aluminum,
(.023" - 3/64" alum. w/spool gun)
.030" - .035" bronze,
.035" - .045" flux cored
(gas shielded or gasless)
Recommended Size: Aluminum
Others
.035
.035
SHIELDING GASES:
For Steel CO2 or Argon/CO2 mix
Recommended (for steel) 75% Argon/
25% CO2
For Aluminum, Bronze
For Stainless Steel
100% Argon
98% Argon/2% Oxygen
For Flux cored CO2 or
Argon/CO2 mix
DIMENSIONS:
Height
Width
Depth
Weight
35-3/4 in.(90.8 cm.)
27-1/4 in.(69.2 cm.)
34-1/2 in.(87.7 cm.)
275 lbs.(124.9 kg.)
TORCH SPECIFICATIONS
NECK ANGLE:
LEAD LENGTH:
60 degrees
12 feet
OVERALL LENGTH: 12 feet
COOLING METHOD: gas (air)
RATING - DUTY CYCLE:
With Argon/CO2 gas 250 amps @ 100%
With CO2 gas 300 amps @ 100%
CHECK LIST
THE SNAP-ON TOOLS MM350XL INCLUDES
THE FOLLOWING:
1- Combination Power Source/Remote
Feed Unit.
1- Dual Cylinder Rack & Industrial
Wheel Kit.
1- FCA-15X 15 foot Feeder Control
Cable assy.
1- 35XL12 12 foot MIG Torch with adjustable nozzle.
1- 20CP-3M 20 foot Power Input
Cable.
1- SN-178X521 25 foot Work Cable and 500 amp clamp.
1- 350LPK Parts Kit.
1- GR-FM Gas Regulator/Flowmeter.
1- ER70S-6-35-3, Sample Spool of
.035 Steel Wire.
1- 8IN-A 8 inch Reel Adapter.
ITEMS REQUIRED FOR MIG WELDING
WHICH ARE NOT PROVIDED WITH THE
MM350XL
1. Full cover welding helmet with proper colored lens (shade 9 to
11 depending on operator’s preference).
2. Proper shielding gas and cylinder.
3. Leather welding gloves.
4. Electrical power and matching electrical plug.
THE MM350XL REQUIRES A 208
OR 230 VOLT, SINGLE PHASE,
AC, 60 AMP CIRCUIT
5. Other personal protective equipment which may vary to match the welding being performed.
6
INSTALLATION
POSITIONING THE UNIT
Locate the unit adjacent to the welding area and position it so there is adequate clearance all around for ventilation and maintenance.
CONTACTOR SWITCH
CONNECT "208"
WIRE FOR
OPERATION ON
208 VOLT INPUT
WARNING
• Smoke, fumes and gases are created by the welding process.
Use only in well ventilated area.
Avoid breathing smoke, fumes and gases.
Smoke, fumes and gases can cause injury.
ELECTRICAL SUPPLY
FRONT OF
MACHINE
CONNECT
"230" WIRE FOR
OPERATION ON
230 VOLT INPUT.
WARNING
• Electrical shock can result from absence of grounding prong.
Do not remove or bypass the grounding prong in any electrical plug.
Electrical shock can cause injury.
Ensure that there is a
208 or 230 volt, single phase, 60 amp
electrical supply within easy reach of the unit. The input cable supplied is 20 feet long.Attach a suitable plug making sure the green wire is attached to the ground terminal of the wall plug
. All wiring should be performed by a qualified electrician.
230V INPUT SELECTION
1. Factory selected no change is needed.
208V INPUT SELECTION
1. Remove the left side panel.
FIG. 5. INPUT VOLTAGE SELECTIONS
2. Locate the contactor switch, which is mounted on top of the main power transformer(See Figure 5).
CAUTION
MAKE SURE POWER SOURCE IS
UNPLUGGED BEFORE MAKING IN-
PUT SELECTION CHANGE-OVER.
3. Attached to the power source’s contactor are two (2) two position plugs which allows easy selection of input voltages of either 208 or 230 volts.
4. Remove both plugs labeled 230V and connect the two (2) plugs labeled 208V.
5. Reattach the left side panel of the machine. Voltage input selection is now complete.
7
(continued on following page)
INSTALLING THE FEEDER CONTROL CABLE
ASSEMBLY
1. Uncoil the cable assembly.
GAS HOSE
CURRENT
CABLE
GAS
FITTING
CONTROL
PLUG
(FEMALE
PINS)
CURRENT
LUG
FEED
CABLE
ASSEMBLY
CONTROL
CABLE CONTROL
PLUG
(MALE
PINS)
POWER
PLUG
FIG. 6. FCA-15X FEEDER CABLE ASSEMBLY
2. Insert the current lug through the hole on the front of the feed unit and with the proper size wrench fasten it to the input current stud, located on the back side of the drive bracket.
3. With the proper size wrench attach the gas fitting to the gas terminal (located on the front of the feed unit).
4. Connect the control plug (female pins)onto the control receptacle (INPUT) and tighten (located on the front of the feed unit).
5. Plug the power plug into the positive (+) terminal(located on the front of the welding machine).
6. Connect the control plug (male pins) onto the control receptacle (OUTPUT)and tighten (located on the front of the welding machine).
TO CONTROL
RECEPTACLE
(OUTPUT)
TO (+)
TERMINAL
(STANDARD)
WELDING
MACHINE
TO GAS
TERMINAL
FEED
UNIT
TO
CONTROL
RECEP-
TACLE
(INPUT)
CABLE
HOLE
TO CURRENT
STUD
DRIVE
BRACKET
INPUT
CURRENT
STUD
FIG. 7. CABLE CONNECTION TO FEED UNIT
FIG. 8. CABLE CONNECTION TO
WELDING MACHINE
SHIELDING GAS CONNECTIONS
1. Place a cylinder of the appropriate shielding gas in the rack at the rear of the machine and secure it with the chain provided.
8
2. Rapidly open and close the cylinder valve. This will purge dust and foreign matter from the valve.
CAUTION
Take care to point the valve outlet away from yourself or other people, as escaping high pressure gas may be dangerous.
FLOW TUBE
INDICATES
FLOW RATE
IN C.F.H.
GAUGE -
INDICATES
TANK
PRESSURE
4. Fit the gas hose from the welding machine to the regulator outlet fitting and tighten it with a wrench. Open the cylinder valve.
When welding steel, the gas flow rate is 30 CFH.
NOTE
The MM350XL must be turned
"ON" and the MIG torch trigger depressed, before the gas flow rate can be adjusted.
TORCH CONNECTION
1. Open the access door of the Feed unit to its fullest extent.
NOTE
Prior to inserting the MIG torch into the torch panel mount, apply anti-spatter spray to the "O" rings.
GAS FLOW
ADJUSTING
KNOB
OUTLET
FITTING
TO
WELDING
MACHINE
INLET
FITTING
TO
TANK
2. Back out the thumb screw located on the drive bracket inside the machine. Insert the MIG torch into the torch panel mount and
TIGHTEN THE THUMB SCREW SE-
CURELY.
WARNING
SEVERE DAMAGE TO THIS
PRODUCT MAY RESULT.
TIGHTEN THUMB SCREW BE-
FORE EACH USE.
FIG. 9. GAS FLOW ADJUSTMENT
3. Attach the gas regulator - flowmeter supplied with this unit, to the cylinder valve using a suitable wrench.
NOTE
If this unit is to be used with 100% CO2 shielding gas, an optional gas regulator coupler is required.
MIG
TORCH
TORCH
PANEL
MOUNT
"O"
RINGS
PRESSURE
ROLL
INLET
GUIDE
THUMB
SCREW
DRIVE
ROLL
DRIVE
BRACKET
FIG. 10. TORCH CONNECTION
9
FITTING AND THREADING THE ELEC-
TRODE WIRE - ALWAYS USE ER70S-6
WELDING WIRE WHEN WELDING STEEL.
1. Remove the wire spool clip from the spool hub.
2. Unpack the spool of welding wire from its protective packaging.
3. Place the spool of ER70S-6 welding wire onto the hub. The wire is fed off the bottom of the spool.
CAUTION
Look for wire protruding from the center of the spool. The protruding wire is electrically HOT during welding and must not touch the machine.
6. Make sure the double v-groove drive roll is installed to match the wire size. To change the wire size setting, remove the drive roll, turn it over and reinstall it on the shaft.
"B" SIDE FACING IN FOR
.030" - .035" STEEL WIRES
"C" SIDE FACING IN FOR
.040" - .045" STEEL WIRES
PRESSURE
ROLL ARM
SPOOL
CLIP
SPOOL
HUB
DRIVE
ROLL
INLET
GUIDES
ELECTRODE
(MIG WIRE)
FIG. 11. FITTING AND THREADING THE ELECTRODE
4. Replace the spool clip on the hub.
5. Unlatch the pressure roll arm and swing it open.
FIG. 12. DOUBLE GROOVE DRIVE ROLL
7. Release the wire from the spool and trim off the kinked end with wire cutters. The wire must be straight when it enters the inlet guide.
8. Thread the electrode wire through the inlet guide, over the feed roll and into the liner.
Ensure that the wire locates in the feed roll groove. Do not allow the wire on the spool to loosen.
9. Close and relatch the pressure roll arm.
10. Stretch the torch cable straight out in front of the machine making sure there are no kinks.
Remove the nozzle and contact tip from the torch.
10
11.Turn on the circuit breaker on the front of the machine. The cooling fan will start and the
"ON" indicator light will illuminate. Set the MIG/TIG VOLTAGE control switch to "MIG 3" and the
WIRE SPEED control to "5". Pull the trigger on the MIG torch.
The wire feed system will start and wire will be fed through the cable liner and torch. If the wire does not feed, or appears to slip, tighten the pressure roll arm adjusting nut. Feed the wire until it protrudes from the front of the torch approximately six inches.
CAUTION
Keep hands and face away from the front of the torch and do not allow the wire to contact ground. The wire is electrically HOT when the torch trigger is actuated.
14.For steel welding only, spray anti-spatter compound inside the nozzle and on the outside of the contact tip.
WIRE FEED PRESSURE ROLL ADJUST-
MENT
The wire feed pressure roll is adjusted at the factory, prior to delivery. It may be necessary to readjust the setting as components
"seat in" or when changing to a different diameter wire. To check for proper roll pressure, hold the torch in one hand and pinch the wire between two fingers of the other gloved hand. Pull the torch trigger. If the wire continues to feed when firm pressure is applied to the wire, the pressure roll adjusting nut should be backed off until the feed rolls start to slip. If the wire will not feed with very little pressure applied, the pressure roll adjusting nut should be tightened.
12.Install the contact tip over the protruding wire and tighten it firmly using a proper size wrench. Make sure the tip is the correct size for the wire being used.
13.Install the nozzle on the torch.
For steel, the contact tip should be flush or stick out up to 1/16 inch beyond the end of the nozzle. Using wire cutters, trim off the wire so the stickout is approximately 1/4 inch for steel.
PRESSURE ROLL
ADJUSTING NUT
PRESSURE
ROLL ARM
PRESSURE
ROLL
DRIVE
ROLL
1/4"
STICK-OUT
FIG. 13. WIRE STICKOUT
FIG. 14. PRESSURE ROLL ADJUSTMENT
(continued on following page)
11
FITTING AND THREADING THE ELEC-
TRODE WIRE (Cont.)
WIRE SPOOL DRAG ADJUSTMENT
The center bolt of the Spool Hub
Assembly is used for drag adjustment.
1. If there is too much drag, causing excessive slippage, reduce the drag by turning the c e n t e r a d j u s t m e n t b o l t ,
counter-clockwise.
2. If there is not enough drag, causing the wire spool to override and the wire to tangle, increase the drag by turning the center adjustment bolt, clock-
wise.
CENTER
"ADJUSTMENT"
BOLT
SPOOL HUB
ASSEMBLY
FIG. 15. WIRE SPOOL DRAG ADJUSTMENT
WORK (GROUND) CABLE
Uncoil the work (ground) cable and plug it into the negative (-) terminal on the machine.
OPERATION
The following operating instructions and detailed setup procedures enable an operator without previous experience to produce quality fusion welds. It is recommended that an operator without prior experience with this equipment, first practice on scrap metal of the same type and thickness as the material to be welded.
OPERATING SEQUENCE
1. Make sure that the pieces of metal to be welded are free of grease, dirt, paint and scale.
Use a wire brush to remove paint and scale. Paint must be completely removed to bare metal.
Grease and oil could burn and cause a fire or safety hazard.
Failure to clean the metal properly will result in erratic and porous welds.
2. Install the unit as directed in the installation instructions and make sure the work clamp is firmly attached to a cleaned area on the workpiece to be welded.
3. Open the shielding gas cylinder valve. Press the torch trigger and listen for gas flow.
CAUTION
The welding wire will feed when the trigger is actuated. Take care that the wire is not directed to hit yourself or anything that is common to the work cable on the welder.
12
PROCESS SELECTION
The following controls are located on the front of the MM350XL.
A.
CONTROL
RECEP-
TACLE
(INPUT)
B.
STORAGE
COMPART-
MENT
G.
GAS
TERMINAL
H.
OCV/GAS
PURGE
I.
WIRE
SPEED
E. CIRCUIT BREAKER
Primary power switch and overload protection device.
F. "ON" INDICATOR LIGHT
Illuminates when the circuit breaker on the machine is "ON".
G. GAS TERMINAL
Single terminal connection for gas from welding machine.
H. OCV/GAS PURGE
Operates the gas solenoid to purge the lines of impurities prior to welding. Pressing the switch also causes open circuit voltage to be registered on the power source voltmeter.
CAUTION
Torch is electrically HOT when switch is actuated.
C.
MIG/TIG
VOLTAGE
SWITCH
D.
VOLT-
METER
E.
CIRCUIT
BREAKER
F.
"ON"
INDICATOR
LIGHT
J.
TORCH
PANEL
MOUNT
K.
CONTROL
RECEPTACLE
(OUTPUT)
L.
(+)POSITIVE
TERMINAL
M.
(-)NEGATIVE
TERMINAL
FIGURE 16. FRONT PANEL
A. CONTROL RECEPTACLE (INPUT)
Input receptacle for wire feed voltage, trigger circuit and wire speed control from welding machine.
B. STORAGE COMPARTMENT
Compartment for tools and the
350LPK parts kit.
C. MIG/TIG VOLTAGE SWITCH
Twelve position switch provides
"4" TIG (requires optional FLEX
TIG) and "8" MIG voltage settings.
D. VOLTMETER
Indicates open circuit voltage when torch trigger switch is activated and arc (welding) voltage during welding.
I. WIRE SPEED
Potentiometer controls speed of wire drive motor to give wire speed of 50 to 800 inches per minute.
J. TORCH PANEL MOUNT
Combination current output, contactor switch connection, gas supply connection, and wire feed output in a single unit.
K. CONTROL RECEPTACLE (OUTPUT)
Output receptacle for wire feed voltage, trigger circuit and wire speed control out to the remote feed unit.
L. (+)POSITIVE TERMINAL
Positive output terminal from the welder DC power source. The
Power plug is inserted into this terminal for standard welding operation. The work cable can be plugged into this terminal for straight polarity welding on very light sheet metal, or for using flux cored gasless wire.
(continued on following page)
13
PROCESS SELECTION (cont.)
M. (-)NEGATIVE TERMINAL
Negative output terminal. The work cable is plugged into this terminal during standard welding operation. The Power plug can be inserted into this terminal for straight polarity welding on very light sheet metal, or for using flux cored gasless wire.
WELDING
DANGER
• Electric welding causes ultraviolet rays and weld spatter.
Bystanders will be exposed to ultraviolet rays and weld spatter.
Wear welding helmet with appropriate shade lens while using electric welders.
Do not allow bystanders while welding.
Wear safety shield and protective clothing (user and bystanders).
Read and follow instructions.
Ultraviolet rays will burn eyes; weld spatter can cause injury.
Optimum control settings will vary according to the thickness of the metal, the type of joint, operator preference, etc. Best results can be obtained through experience with the welding machine or by making trial welds. Select some sample material of the same type and thickness as the material to be welded. Set the welding controls(using the parameter chart located on the door of the feed unit or on page 25) for optimum results using the sample material thickness and wire size being used as a starting point, weld until experience is gained using the unit.
CONTINUOUS WELDING ON
STEEL
1. Trim the electrode wire to leave approximately 1/4 inch stickout beyond the end of the contact tip and install the welding nozzle.
The contact tip should be flush or stick out up to 1/16 inch beyond the end of the nozzle.
WARNING
• Materials can cause sparks or flying metal when heated which can cause fire.
Wear safety shield and protective clothing (user and bystanders).
Sparks, fire and flying metal can cause injury.
NOZZLE
CONTACT TIP
(FLUSH TO
1/16" STICKOUT)
ELECTRODE WIRE
(1/4" STICKOUT)
WARNING
• Welded surface can be hot and cause burns and injury.
FIG. 17. NOZZLE ADJUSTMENT
FOR WELDING STEEL
14
2. Spray the inside of the nozzle and the outside of the contact tip with anti-spatter compound.
3. Locate the torch over the joint to be welded with the contact tip approximately 3/4 inch from the work surface.
4. Use a welding helmet with a shade
9 to 11 filter lens, depending on operator preference.
NOTE
When welding steel, the ideal position for holding the torch is inclined approximately 30 degrees towards the direction of travel. This allows the arc to be seen easily, resulting in greater control of the weld pool. Most right-handed weldors move from left to right.
This method, known as forehand welding, provides a gas shield for the cooling weld puddle and helps in obtaining an oxidation free weld deposit.
30 DEGREES
DIRECTION
OF TRAVEL
SHIELDING
GAS
WORK
FIG. 18. TORCH POSITION FOR WELDING STEEL
- RIGHTHANDED WELDOR
5. Squeeze the torch trigger. The wire will feed and an arc will be established. As the weld is deposited, move the torch slowly along the weld seam at a constant speed, while maintaining a constant arc length and a constant tip-to-work distance.
BURN BACK
OPERATING HINTS
In the event the welding wire burns back into the contact tip:
1. Remove the nozzle from the torch.
2. Unscrew the contact tip from the gas diffuser using a pair of pliers as the tip will be very hot.
3. Free the wire from the contact tip and clean the end of the tip so the new wire will slide smoothly through the hole. DO
NOT use a drill or reamer to clean the hole as they will enlarge it and cause an erratic arc. Replace the contact tip if it is badly damaged.
4. Install the contact tip in the torch and tighten it firmly with an appropriate wrench.
5. Reinstall the torch nozzle.
6. If the wire continues to burn back, check for erratic wire feed, or speed up the wire by increasing the WIRE SPEED control setting or reducing the
VOLTAGE control setting.
(continued on following page)
15
OPERATING HINTS (Cont.)
SPATTER
Before beginning to weld and periodically during welding, the torch nozzle must be removed and the spatter (small globules of melted metal) cleared from the inside of the nozzle and the outside of the contact tip and the gas diffuser.
Spatter buildup between the contact tip and the nozzle can cause a short circuit and consequently, failure of the torch or welding machine.
The frequent use of anti-spatter spray will help prevent the adherence of spatter to the torch components.
NOTE
DO NOT use any anti-spatter spray when welding stainless steel.
Restricted gas flow, holding the torch too far from the work piece, and the use of CO2 gas rather than
75% Argon - 25% CO2 will increase the spatter levels.
MAINTENANCE
To ensure that this equipment maintains its operating efficiency, the following maintenance schedule and procedures are recommended. These routines should be performed regularly by the operator.
REGULARLY - Usage and shop conditions determine frequency.
1. Remove and clean the torch nozzle and contact tip. The use of anti-spatter compound will reduce the adherence of spatter and makes its removal easier.
2. Blow out the torch liner prior to the installation of each new spool of wire. The contact tip and gas diffuser must be removed, but it is not necessary to remove the liner.
3. If the torch cable assembly is bent severely, a kink may develop in the steel liner. This can cause wire feeding problems so a new liner should be installed.
16
WEEKLY
1. Remove dirt and dust from the wire feed compartment. Use low pressure dry compressed air.
2. Remove dirt and metal deposits from the grooves in the feed roll. If the grooves are badly worn, the feed roll should be replaced. If the pressure roll does not turn freely, it should be replaced.
3. Check all gas fittings for leaks. Tighten or repair as required.
EVERY SIX MONTHS
1. Disconnect the welder from its main power supply.
2. Remove the machine’s side panels.
3. Using low pressure dry compressed air, remove dust and dirt from all components.
4. Check for loose or frayed wiring. Particularly check welding current wire connections.
5. Replace torch liner if necessary.
RECOMMENDED
CUSTOMER SPARE PARTS
The Snap-on Tools MM350XL is a machine of proven design and reliability. Following is a list of consumable items recommended as spare parts for this unit.
contact tips ....... M3-T30, etc.
gas nozzles .............. M6-C62 nozzle insulators .......... M6-B gas diffusers .............. M6-D steel liner(.020-.030) .. M123L-B steel liner(.035-.045) .. M124L-N steel liner(.062) ....... M126L-G drive roll (.020-.035) .. 20-35DR drive roll (.045-5/64) . 45-564DR
In the event of the failure of any part of this equipment, contact your Snap-On Tools representative for replacement parts and service.
When ordering parts from Snap-On
Tools Corporation, order numbers should be preceded by "CKS".
WARNING
•
DO NOT lift the unit when a gas cylinder is installed or attached.
•
DO NOT weld on any item that has a common electrical ground.
•
DO NOT operate the unit with the side panels removed. Overheating will occur.
•
DO NOT weld upon the case of the welding machine.
•
ONLY a qualified electrician should perform work inside the welding machine.
•
ALWAYS wear protective clothing, leather gloves and a full cover welding hood while welding.
•
DO NOT weld in a closed in area.
Proper ventilation is a necessity, or a fresh air supplied hood should be worn.
•
WHEN welding near combustibles, a helper or "watcher" should stand by with a fire extinguisher or other fire protective device.
•
NEVER weld on a closed vessel or one that has contained combustibles.
IF IN DOUBT - DON’T DO IT!
BE SAFE - DON’T BE SORRY!
17
TROUBLE SHOOTING
(SYMBOL*)
FOR TECH. SERVICE, CALL TOLL-FREE 1-800-232-9353
The Trouble Shooting Chart is a guide in identifying and correcting possible troubles which may occur when operating this equipment.
FAULT POSSIBLE CAUSE REMEDY
EQUIPMENT MALFUNCTION
No main power, MM350XL switch is "OFF".
(CB1)
Turn switch "on".
fan does not Wall breaker is "tripped".
Reset wall breaker.
operate,
"on" indicator
"Open" circuit breaker on MM350XL.
(CB1)
Reset or replace breaker.
light is off.
Loose or broken connection Tighten or repair in power input circuit.
connection.
Main power on, MIG torch unplugged.
torch Faulty trigger switch.
(S1)
Plug in MIG torch.
Replace micro switch.
trigger activated,
Fault in torch cable.
Check torch cable for continuity.
no response.
Loose or broken connection Check or repair on wiring harness.
(PLG2) connections.
Wire feed motor unplugged.
Plug in motor.
(RC5)
Faulty control transformer.
Check for 28VAC output.
(T3)
Main power on, Pressure roll arm unlatched. Latch arm & add tension.
torch "Slippage" at drive rolls.
Increase drive roll trigger activated, Wire path restricted.
tension. See page 11.
Clean path or replace no wire feed but contactor 5 amp mini breaker is operates & gas flows.
tripped.
(CB2)
Wire feed circuit board needs calibrated.
torch liner.
Reset or replace breaker.
Calibrate wire feed circuit board. See page 22.
Replace circuit board.
Defective wire feed circuit board.
(PC1)
Faulty wire feed motor or connection.
(M)
Repair or replace faulty item.
Check motor on a
12VDC battery.
Faulty motor relay.
(CR1)
Sand points or replace relay.
Loose or broken connection.
Tighten or repair connection.
(SYMBOL*) - USE THIS IDENTIFIER, ALONG WITH THE SCHEMATIC DIAGRAM FOUND IN THE SERVICE
MANUAL, FOR TROUBLE-SHOOTING PURPOSES.
18
TROUBLE SHOOTING (Cont.)
(SYMBOL*)
FOR TECH. SERVICE, CALL 1-800-232-9353
FAULT POSSIBLE CAUSE
EQUIPMENT MALFUNCTION (Cont.)
REMEDY
Main power on, Loose torch thumb screw.
torch Broken or loose connection.
Tighten thumb screw.
Check cables for trigger activated, continuity.
Repair or tighten no welding current, but Unplugged or faulty power gas flows & wire feeds.
contactor switch.
(W) connections.
Plug in or replace switch.
208/230V selector wires off. Reattach wire.
(W)
"Opened" thermal switch.
(TP1 & TP2)
Faulty diodes.
(D1-D8)
Allow unit to cool, then retry.
Check diodes. See page
21.
Main power on, No shielding gas torch - tank empty.
trigger activated,
Loose or broken connections.
no gas flow, Faulty Gas solenoid but contactor valve.
(GS) operates & wire feeds.
Clogged gas flow path.
FAULTY WELDS
"Jerky" or
"slipping" wire feed.
Replace tank.
Tighten or repair connections.
Repair or replace valve.
Locate & clean clog.
Worn , kinked or dirty torch Clean or replace liner.
liner.
Wire spool turns too hard.
Lubricate spool shaft.
Set drag adjustment.
Worn double v-groove drive Replace drive roll.
roll.
Weak pressure roll spring.
Replace spring.
Worn or dirty contact tip.
Replace contact tip.
Worn inlet guide(s).
Sticking pressure roll.
Clean or replace guides.
Replace pressure roll.
Feed roll tension incorrect. Adjust feed roll tension. See page 11.
(continued on following page)
19
TROUBLE SHOOTING (Cont.)
(SYMBOL*)
FOR TECH. SERVICE, CALL TOLL-FREE 1-800-232-9353
FAULT
"Birdnesting"
(Wire wrapping around drive rolls)
"Cold" weld puddle.
POSSIBLE CAUSE
FAULTY WELDS (Cont.)
REMEDY
Excessive feed roll tension. Reduce tension. See page
11.
Poor alignment.
Make sure wire is properly aligned
Oversize contact tip.
across roller.
Replace contact tip with correct size.
Incorrect machine settings.
Increase heat & wire speed.
Incorrect shielding gas.
Excessive wire stick-out.
Replace with proper gas.
Hold torch closer to
Poor connections.
Faulty diode.
(D1-D8) work.
Check and tighten all connections.
Test diodes, replace faulty diode(s). See page 21.
Heavy spatter.
Incorrect machine settings.
Increase heat, decrease wire feed speed.
Incorrect shielding gas.
Excessive wire stick-out.
Replace with proper gas.
Hold torch closer to work.
Porous welds.
No shielding gas.
Not enough gas flow.
Contaminated wire.
Faulty gas solenoid.
Turn on gas.
Check hoses for leaks, make sure cylinder is not empty. Increase flow rate.
Change wire.
Replace solenoid.
(GS)
Incorrect electrode wire.
Use correct wire.
Contaminated base material.
Clean or etch base material.
(SYMBOL*) - USE THIS IDENTIFIER, ALONG WITH THE SCHEMATIC DIAGRAM FOUND IN THE SERVICE
MANUAL, FOR TROUBLE-SHOOTING PURPOSES.
20
TESTING AND REPLACING DIODES
Silicon diodes have proven to be highly reliable. However, weld spatter build-up in the torch can short out and cause diode overload and consequent failure. The following information is provided as a guide should a failure be suspected.
Silicon diodes exhibit two main fault conditions:
3. If all the diodes check out satisfactorily with the Volt-
Ohm Meter, a load check must be made. This is easily accomplished using a twelve volt battery and a twelve volt headlight bulb connected as shown.
Again test for electrical current flow in both directions.
The bulb should light in one (1) direction only - not both.
CAUTION
NEVER use a "megger" or a high voltage device to test a diode.
1. "Open Circuit" - causes a reduction in welder output.
2. "Short Circuit" - causes the circuit breaker to trip.
DIODE
12 VOLT
HEADLIGHT
BULB
12 VOLT
BAT-
TERY
+ -
If a fault is suspected, the diode may be tested as follows:
1. Remove the top connection of each diode to be tested.
2. Using a Volt-Ohm Meter set on
RX1K, check for continuity through the diode in both directions. If there is no continuity in either direction, the diode is in "open circuit" condition and must be replaced. If there is continuity in both directions, the diode is in "short circuit" condition and must be replaced. If there is continuity in one direction only, the diode is functioning properly.
DIODE
12 VOLT
HEADLIGHT
BULB
12 VOLT
BAT-
TERY
+ -
FIG. 19. DIODE LOAD CHECK CONNECTION
DIAGRAM - TEST FOR FLOW IN BOTH
DIRECTIONS
4. When replacing diodes, it is very important that a heat conductive compound (Radio Shack
#276-1372) be used where the diode makes contact with the aluminum heat sink. Do not grease the threads on the diode.
21
WIRE FEED CALIBRATION
Due to INPUT LINE VOLTAGE variations supplied to the welding machine. The WIRE FEED SPEED should be checked for proper operation.
TO CHECK
1. Remove any tension on the drive roll.
2. Turn the wire speed dial (on the front of the machine) to "0".
3. Activate the torch trigger.
4. The bottom drive roll should rotate very slowly(non-jerky).
5. If this proves to be true, no adjustment is required.
IF ADJUSTMENT IS REQUIRED
1. Remove the left hand side panel from the base unit.
2. Locate the printed circuit board mounted at the back of the machine.
3. Referring to Figure 20, locate the trim resistor, this is located in the upper right hand corner of the wire feed PC board.
4. Turn the wire speed dial (on the front of the machine) to "0".
5. Remove any tension on the drive roll.
TRIM
RESISTOR
FIGURE 20. WIRE FEED PC BOARD
6. Activate the torch trigger.
7. Rotate the trim resistor, back and forth, until the bottom drive roll moves.
8. Calibrate so the bottom drive roll rotates very slowly (nonjerky).
9. If calibrated correctly the wire speed dial (on the front of the machine) should affect the speed of the drive roll from "0" thru
"10".
10. Adjustment is now complete!
22
CONNECTING THE FLEXTIG
CHANGING FROM STANDARD MIG OPERA-
TION TO FLEXTIG OPERATION
1. Unplug the feeder control cable plug from the control receptacle
(OUTPUT)on the welder.
2. Unplug the feeder gas and current cable/power plug and the work cable from the welders front panel.
3. Plug the FLEXTIG torch power cable into the negative (-) weld terminal and plug the work cable into the positive (+) weld terminal. This provides straight polarity current as required for
TIG welding.
4. Plug the FLEXTIG torch switch cord into the welder control receptacle (OUTPUT).
5. Attach the FLEXTIG torch gas hose directly to the gas regulator/flowmeter and adjust the flow to 20 C.F.H.
NOTE
Pure Argon is the shielding gas to be used for TIG welding.
6. Follow the operating instructions in the F L E X T I G m a n u a l
(Form WC5229).
7. To change back to standard MIG operation, reverse the procedure.
CONNECTING THE MHG5-B
SPOOL GUN
CHANGING FROM STANDARD MIG OPERA-
TION TO SPOOL GUN OPERATION
1. Unplug the feeder control cable plug from the control receptacle
(OUTPUT) of the welder.
2. Plug the MHG5-B spool gun control cable plug into the welder control receptacle (OUTPUT).
3. Remove the feeder gas and current cable/power plug from the welders positive (+) weld terminal.
4. Plug the MHG5-B gun cable fitting into the welder positive
(+) weld terminal.
NOTE
Make sure the welder primary gas hose and regulator/flowmeter are connected to a cylinder of the proper shielding gas - 100%
Argon for aluminum and 98%
Argon + 2% O2 for stainless steel and 75% Argon + 25%
CO2 for steel welding.
5. Follow the operating instructions in the MHG5-B manual (Form
WC5268).
6. To change back to standard MIG operation, reverse the procedure.
23
M.I.G. TORCH LINER INSTALLATION
(steel only)
The MIG torch liner provided with the MM350XL is designed for wire diameters from .035 thru .045. If smaller or larger wire diameters are to be fed and or there is a problem (i.e. clog, kink, etc.), a liner change is required.
Following is a step by step guide to aid in liner removal and installation.
NOTE
When removing the welding wire from the MIG torch, care should be taken to avoid the wire from uncoiling from the wire spool.
REMOVING OLD LINER
1.
Remove torch assembly from the welding machine.
2.
Place torch assembly on a flat surface, making sure torch is laying straight as possible.
3.
Remove nozzle, bushing insulator, contact tip and gas diffuser from the front end of the torch assembly.
4.
Loosen set screw located on the connector end of the torch assembly (see FIG. 22).
5.
Grip the liner and gas seal firmly, then pull. The liner should easily slide from torch assembly.
INSTALLING NEW LINER
1.
Remove the new liner from the package.
2.
Uncoil liner and lay the liner parallel next to the MIG torch assembly.
3.
Adjust the liner stickout length to 3/4" as shown in FIG. 21.
GAS SEAL 3/4"
LINER
STICKOUT
FIG. 21. - LINER STICKOUT
4.
Install the new liner into the
MIG torch assembly, until gas seal seats flush with the connector plug.
5.
Tighten set screw. (Do not overtighten), refer to FIG. 22.
SET SCREW
3/4"
CONNECTOR
PLUG
FIG. 22. - TORCH CONNECTOR END
6.
Following the diagram in FIG.
23, measure out 1 5/8"+ from the neck assembly and cut off the protruding liner.
7.
Debur the cutoff end of the liner to insure unobstructed wire feed.
1 5/8+"
NECK
ASSEMBLY
PROTRUDING
LINER
FIG. 23. - TORCH FRONT END
8.
Install the gas diffuser and contact tip of proper wire size, tighten with a wrench.
9.
Install the bushing insulator onto the gas diffuser.
10.
Install the TWIST-ON adjustable nozzle and twist the nozzle during the installation. Turn to
Page 14 for correct nozzle adjustment.
24
CONSUMABLE PARTS BREAKDOWN - 35XL SERIES M.I.G. TORCH
XL STYLE FRONT END - STANDARD
WIRE SIZE
.020 - .025 inch
.030 inch
035 inch
.040 - .047 inch
CONTACT TIP
M3-T25
M3-T30
M3-T35
M3-T45
(1-7/16" length)
GAS DIFFUSER
M6-D
NOZZLE
M6-C62
(5/8" I.D.)
INSULATOR
M6-B
(includes rings)
LINERS FOR STEEL WELDING
WIRE
SIZE
TORCH
LENGTH
.020-.030 inch 10 feet
12 feet
ORDER NUMBER
LINER W/SEAL SEAL ONLY
M103L-B
M123L-B
M3LS-B (Blue)
10 feet
.035-.045 inch 12 feet
15 feet
1/16 inch
10 feet
12 feet
15 feet
M104L-N
M124L-N
M154L-N
M106L-G
M126L-G
M156L-G
M4LS-N (Natural)
M6LS-G (Green)
MATERIAL
CARBON
STEEL
SHIELDING GAS
TYPE FLOW
75%
ARGON
25%
CO2
Guide For Setting Welder - Adjust For Best Results
GAS METAL ARC (MIG) PROCESS - DCEP (REVERSE POLARITY)
Note: Settings are approximate and may vary. Adjust for best results.
25
CFH
(Min.)
WELDING WIRE
TYPE SIZE
ER70S-6
.030"
.035"
.045"
MIG WIRE AMPS
THICKNESS VOLTAGE SPEED OUTPUT
18 Ga.(.048") 1 1/2 80
16 Ga.(.060")
14 Ga.(.075")
12 Ga.(.105")
1/8"
2
3
3
4
3/4
2
3
4
90
110
120
135
3/16"
1/4"
14 Ga.(.075")
12 Ga.(.105")
1/8"
3/16"
1/4"
5/16"
5
5
2
3
3
4
4
5
6 1/2
8
1
2
2 1/2
3 1/2
4
6 1/2
150
160
110
115
120
140
150
160
3/8"
1/8"
3/16"
1/4"
5/16"
3/8"
1/2"
4
5
6
3
4
6
3
7 1/2
2
3
3
4
5
7 1/2
190
150
200
210
220
240
260
1/16" z Optional Drive Roller and Liner are required.
25
PARTS BREAKDOWN - 35XL SERIES MIG TORCH (Cont.)
M3-402 M3-402
PART NO. DESCRIPTION (SYMBOL)
TORCH NECK GROUP
M3-101B ..... TORCH NECK *
M3-112 ....... NECK INSULATOR
M3-119 ....... LOCK SCREW - SWITCH HOUSING
M3-120 ....... FERRULE *
M3X-401
TORCH NECK GROUP
M3-200B ..... SWITCH ASSEMBLY
CONSISTING OF:
M3-201B ..... SWITCH HOUSING
M3-202 ....... SWITCH (S1)
M3-203 ....... SWITCH SCREW (2 REQUIRED)
M3-211 ....... TRIGGER - WITH ADJUSTING SCREW
M3-212 ....... TRIGGER ADJUSTING SCREW (ONLY)
M3-213 ....... TRIGGER PIN
M3-214 ....... TRIGGER SPRING
M3-101B*
M3-112
M3-119 M3-120*
QUICK CONNECTOR GROUP
M3-120 ....... FERRULE *
M3-301A ..... CONNECTOR HOUSING
M3-305A ..... CONNECTOR STEM *
M3-306 ....... CONNECTOR PLUG
- WITH SETSCREW & O-RINGS
M3-307 ....... SETSCREW (ONLY)
M3-308 ....... O-RING (ONLY) (2 REQUIRED)
M3-309 ....... TERMINAL - CONNECTOR CONTACT
(2 REQUIRED)
M3-310A ..... BOOT / CABLE SUPPORT
SN-807G ....... CABLE COVER
M3-200B ASSEMBLY
M3-405
(2 REQD.)
M3-203
(2 REQD.)
M3-202 M3-211
M3-201B
M3-214
M3X-401....... HANDLE
M3-402 ....... HANDLE SCREW (2 REQUIRED)
M3-405 ....... TERMINAL - TORCH END
(2 REQUIRED)
M3-406 ....... TERMINAL - CONNECTOR END
(2 REQUIRED)
M3-407 ....... HANGING BRACKET
SN-1029 .... LABEL, 35XL SERIES
M2510CBL... 10 FOOT CABLE *
M2512CBL... 12 FOOT CABLE *
M3-212 M3-213
M3-407
M2510CBL*
M2512CBL*
QUICK CONNECTOR GROUP
M3-307
M3-309
(2 REQD.)
M3-308
(2 REQD.)
M3-301A
M3-306
SN-807G
M3-305A*
M3-120*
M3-310A
M3-406
(2 REQD.)
NOTES:
* BECAUSE SPECIAL TOOLS
AND PROCEDURES ARE
REQUIRED TO PROPERLY
INSTALL THE CABLE ON
THE TORCH NECK AND
THE CONNECTOR STEM,
ITEMS WITH THE ASTERICK
ARE AVAILABLE FACTORY
INSTALLED ONLY.
TORCH REBUILD PROGRAM
35XL SERIES TORCHES
CAN BE REBUILT BY THE
FACTORY FOR A NOMINAL
LABOR + PARTS CHARGE.
26
OPTIONS
FLEXTIG
TIG WELD WITH YOUR
SNAP-ON TOOLS MUSCLE MIG SYSTEM
(MM140SL, MM250SL & MM350XL)
The TIG Welding Process is used to produce the highest quality, porosity-free welds. The FLEXTIG adds TIG Welding capabilities to your Snap-on Tools MIG
Welder.
The FLEXTIG is designed for Tungsten-Inert Gas (TIG) welding with Direct
Current, Straight Polarity (DCSP) on steel, stainless steel, chrome-moly, copper or cast iron (18 Ga. minimum plate thickness).
THE FLEXTIG WILL NOT WELD ALUMINUM.
The FLEXTIG consists of a 200 amp, gas cooled torch with built-in gas control valve and remote on-off switch, 12-1/2 or 25 foot cable assembly and accessories required for putting the unit in service.
1 each
1 each
1 each
SPECIFICATIONS
Part Number ........................ FLEXTIG 12 (12-1/2' cable)
FLEXTIG 25 (25' cable)
Torch Rating ....................... 200 Amps, DCSP
Duty Cycle ........................... 100% (reduce duty cycle when operating over 200 amps.)
Cooling Method ................... Gas(100% ARGON)
Shielding Gas
Control Method ............... Gas Valve on Torch
Welding Current
On-Off Control ................ Locking Switch onTorch
1 each
3 each
3 each
2 each
2 each
2 each
6 each
2 each
1 each
3 each
3 each
CONTENTS OF FLEXTIG
TIG Torch with built-in valve
Locking Electric Switch with cord & plug
(installed on torch)
12-1/2 foot Power Cable with Connector
(installed on torch)
15 foot Gas Hose with fitting
(installed on torch)
3C116 Collet - for 1/16" tungsten
3C332 Collet - for 3/32" tungsten
3CB116 Collet Body - for 1/16" tungsten
3CB332 Collet Body - for 3/32" tungsten
3C6 Gas Cup - 3/8" orifice
3C7 Gas Cup - 7/16" orifice
3C8 Gas Cup - 1/2" orifice
300L Long Backcap
1/16" X 3" Tungsten Electrode
3/32" X 3" Tungsten Electrode
MHG5-B
ONE POUND SPOOL GUN
FOR ALUMINUM MIG WELDING
WITH SNAP-ON TOOLS
MUSCLE MIG SYSTEMS
(MM140SL, MM250SL & MM350XL)
The MHG5-B (Motorized Hand Gun System) is a compact, light-in-weight, easy to operate MIG welding system designed for aluminum welding. It will feed .023" Thru 3/64" diameter wire from 4 inch spools. The standard equipment cable is 25 feet in length. 35 foot and 50 foot cables are optional.
The wire speed control knob is built into the gun handle.
With the following options, the MHG5-B can also be used to weld steel or stainless steel (.030"-.035" diameter wire size).
SN-2160K Knurled Drive Roll for .030 - .035" steel wire
M5-T30 Contact tip - for .030" steel wire or M5-T35 Contact tip - for .035" steel wire
SPECIFICATIONS
Part Number ....................... MHG5-B
Gun Rating ......................... 200 Amps @ 100% duty cycle
250 Amps @ 60% duty cycle
Wire Feed Speed Range ... 50 to 850 inches per minute
Cooling Method .................. Air (gas)
1 each
1 each
MHG5-B SYSTEM COMPONENTS
MHG-5 Spool Gun (only)
HGC9-25 Hand Gun Cable Assembly with fittings - 25 feet length
7 each
1 each
1 each
MG-TXX Contact Tip(1 installed in gun)
2 - .030 (MG-T30)
3 - .035 (MG-T35)
2 - 3/64 (MG-T364)
M35-NA62 Nozzle Assembly
(installed on gun)
M35-D Gas Diffuser
(installed on gun)
27
Snap-on is a trademark of Snap-on Technologies, Inc. © 2002 Snap-on Technologies, Inc.
Manufactured in USA for Snap-on x 2801 - 80th Street x Kenosha, WI 53141-1410
ZMM350XL 6/02 (Rev. 2/03)
advertisement
Related manuals
advertisement
Table of contents
- 2 SAFETY PRECAUTIONS
- 4 INTRODUCTION
- 5 DESCRIPTION, SPECIFICATIONS
- 6 CHECK LIST (CONTENTS)
- 7 INSTALLATION & ELECTRICAL REQUIREMENTS
- 12 OPERATION
- 14 WELDING
- 16 MAINTENANCE
- 18 TROUBLE SHOOTING CHART
- 22 WIRE FEED CALIBRATION
- 23 CONNECTING FLEXTIG OR SPOOL GUN
- 24 LINER INSTALLATION
- 25 PARTS BREAKDOWN - MIG TORCH
- 25 PARAMETER CHART
- 27 OPTIONS - FLEXTIG OR SPOOL GUN