advertisement
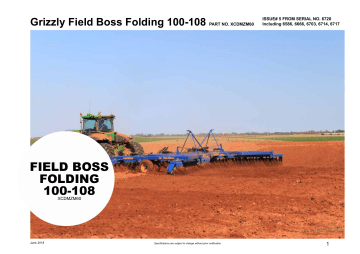
Grizzly Field Boss Folding 100-108
PART NO. XCDMZM60
ISSUE# 5 FROM SERIAL NO. 6720
Including 6586, 6666, 6703, 6714, 6717
FIELD BOSS
FOLDING
100-108
XCDMZM60
June 2018 Specifications are subject to change without prior notification
1
Contents
1. Foreword
page
3
4
3. The Right Machine
6. Safe Instructions
7. Warranty Policy
8. Specifications
11. Storage
12. Lubrication and Maintenance
18
20
25
34
14. Maintenance Record
9
11
6
7
14
35
43
68
69
2
Specifications are subject to change without prior notification
From serial number 6714
Including 6586, 6666, 6703
Foreword
Materials in this manual may not be reproduced in any form without permission in part or in whole, this manual may not be copied reproduced, translated, or reduced to any electronic medium or machine readable form without express written permission of the publishers.
While the publishers have taken all reasonable precautions to ensure the accuracy of information contained in this manual, it is a condition of use of this manual that the publishers do not assume any responsibility or liability for any loss or damage which may result from any inaccuracy or omission in the manual, or from the use of the information contained herein; and the publishers make no warranties expressed or implied, with respect to any of the materials contained herein.
Publishers:
Grizzly Engineering Pty Ltd
2 McAllister Road
Swan Hill VIC 3585
AUSTRALIA www.grizzlyag.com.au
Congratulations on your purchase of a Grizzly
Field Boss Folding Wing, proudly designed and manufactured in Australia to the highest level of quality and performance.
Your Grizzly disc plough has been designed to give you the best possible performance and serviceability over a wide range of conditions and applications.
This booklet is provided to help you obtain the best results from your machine.
The extent to which your machine performs to its potential will depend upon:
1) That it is the correct machine for the task.
2) That it is used in conjunction with a tractor of the correct specification.
3) That it is delivered in first class mechanical order, and is properly prepared for work.
4) That it is used correctly with understanding of the various limitations and tolerances as explained by your Grizzly Dealer, and in this booklet.
5) That it is serviced and maintained regularly as outlined in this booklet.
If you are uncertain of any aspect of your machine’s performance, please refer to the
appropriate sections of this booklet, your
Grizzly Dealer or, if necessary, to Grizzly
Engineering Pty Ltd.
June 2018
PATENT PROTECTED
Specifications are subject to change without prior notification
3
2 Welcome to Grizzly
Company Profile
Australia’s largest manufacturer and exporter of Disc ploughs, Grizzly Engineering Pty
Ltd is an Australian owned and operated manufacturing company based at Swan Hill in
Victoria.
Like many other Australian icons of ingenuity, the Grizzly plough was founded on need.
The Grizzly name was established in the early 1980’s by country people with the will to construct a better offset disc plough.
In 1983, a unique three gang, tandem offset disc design was patented and released. This innovative Grizzly plough provided complete ploughing out (no unworked ridges), less working draught, elimination of side draught and longer disc life. Other new features, at that time, included self phasing wheel lift and improved scrapers.
Grizzly’s broad range of versatile ploughs suit a wide variety of agricultural applications.
Sizes vary from 1.4 metres to 15.6 metres working width.
Grizzly also manufacture Bankers,
Renovators, and a large range of subsoil and row crop Rippers from 1 tine.
Advantages of Grizzly technology include lower power requirements, significant fuel savings, reduced stress on components, reduced maintenance costs, and greater operator control allowing effortless adjustments for better performance.
The Grizzly product has earned a reputation of uncompromising strength, performance and reliability.
4
Each model is designed with inbuilt durability, and accuracy, Efficiency and easy operation for sustainable farming practices.
Continued investment into research and development plays a key role in the success of the company’s product range
The company has a very successful and loyal dealer network throughout Australia.
All dealers are backed by Grizzly training, technical support and rapid delivery parts replacement anywhere in Australia.
Specifications are subject to change without prior notification
This manual includes safety, assembly, setting up and operating instructions, as well as lubrication, maintenance and problem solving instructions, warranty guidelines and assembly drawing and parts for the Field Boss range of machines.
Some components explained in this manual may not be installed on your machine.
Replacement manuals are obtainable from your Grizzly dealer.
Factory and Head Office located in Swan Hill Victoria Australia
From serial number 6714
Including 6586, 6666, 6703
2 Welcome to Grizzly
Considerable practical research and continued improvements have been developed into all Grizzly products for the best possible performance and durability.
This manual is designed to help you have a better understanding of your machine and to attain the best possible results from it. We are grateful for the feedback we have received over the years. We look forward to continued constructive comment from new owners and operators of Grizzly equipment.
The terms “left hand side” (LHS) and “right hand side” (RHS), when used in reference to the machine, mean viewed from behind.
Above: The serial number plate is located at the front of the main frame.
Product Identification
The plough’s Serial Number Plate is located at the front of the main frame. If damage occurs to this Serial Number Plate, serial numbers are also stamped into the frame under the
Serial Number Plate for identification.
This plate shows:
- The Grizzly name.
- The machine’s model number .
- The machine’s serial number.
- Patent numbers.
Precise product identification is important and must be used when seeking parts and service for the Plough, namely:
1 The model number and serial number.
2 The part number and description.
(Refer to the Parts section of this Manual).
For quick reference, we suggest writing your
Field Boss Folding’s model number and serial number in the space below:
LEFT RIGHT
Model No: .......................................................
Serial No: ........................................................
June 2018 Specifications are subject to change without prior notification
5
3 The Right Machine
The Field Boss is a tandem offset disc plough designed for both primary and secondary tillage operations. Its ability to be adjusted and used for both primary and secondary cultivation adds versatility, and extends the overall application of this machine.
Grizzly tandem offset disc ploughs can be adjusted to leave a level finish, and can handle large amounts of trash. The Field
Boss can be used to incorporate stubbles, weeds, regrowth and chemicals into soils.
The benefits of stubble retention and incorporation for good soil management are well known. As a general rule, the earlier the discing operation is performed after harvest and/or rain, the better the result of stubble incorporation with more complete bacterial breakdown at the time of sowing.
The ability to incorporate a wide variety of stubble and weed types in one pass means a saving of time and money. The Grizzly tandem offset disc plough is a minimum tillage machine which will be of most value to your farm program when used with due consideration to soil condition, soil types and the task to be performed. When working lighter soils, attention should be paid to the timing of workings, amount of trash cover and future program for the soil in question. Long fallows in light soils should be avoided.
We trust that your Grizzly Field Boss will play an important part in your farming program for many years to come.
6
Specifications are subject to change without prior notification
From serial number 6714
Including 6586, 6666, 6703
June 2018 Specifications are subject to change without prior notification
7
4 Pre-Delivery Checklist
Specifications and Options Check pull tongue, discs, etc, ensure the machine has the correct options fitted as per order.
Grease Machine All grease points must be greased before operation. See Section 12 for details of how to grease machine ensure all grease points function properly.
Scrapers Check scraper adjustment. See section 10 for instructions.
Level Machine Check the machine is level (See Section 9).
Tyre Pressure Check tyre pressures (See Section 8).
Wheel Nuts Check wheel nut torque (See Section 8).
Hydraulic Hoses and Fittings Check for operation and leaks, inspect hoses and ensure hoses are not able to rub on moving parts. Check hoses to tractor are routed correctly.
Comments
Decals and Paint Check all decals are in correct location and in good condition, inspect paint and touch up as required (See Section 13 for decal locations).
Tighten Bolts Check bolts. See Section 8 for Torque Chart.
Tighten Hydraulic Fittings
All checks done and correct
8
Tighten all Hydraulic Fittings.
Name Sign
Specifications are subject to change without prior notification
Date____/____/____
From serial number 6714
Including 6586, 6666, 6703
June 2018
warranty registration
9
Specifications are subject to change without prior notification
10
back of warranty rego
From serial number 6714
Including 6586, 6666, 6703
Specifications are subject to change without prior notification
6 Safe Use Instructions
Safety & Damage Warnings
The terms WARNING, CAUTION and
IMPORTANT are used throughout this manual and on the machine to stress the importance of personal safety, potential machinery damage and useful operating information.
The term description and usage is shown below.
DANGER!
This is issued where there is a hazardous situation which will result in serious injury or death, if instructions are not followed.
WARNING!
Indicates a hazardous situation which if not avoided could result in death or serious injury.
SAFETY DECAL EXAMPLES...
IMPORTANT!
The note refers to significant, practical information which should not be overlooked
CAUTION!
The caution forewarns of a hazardous situation which may cause injury if instructions are not followed.
• PD000005
• PD000106
Specifications are subject to change without prior notification June 2018
• PD000108
• PD000046
• PD000151
11
6 Safe Use Instructions
Safety is the Operator’s
Responsibility
It is the dealer’s responsibility to explain the capabilities, safe use and service requirements of the Implement. The dealer will demonstrate the safe operation of the machine according to Grizzly’s instructions; which are in this manual.
2) Have Training with Actual
Operation
• Operator training must consist of a demonstration and verbal instruction.
This training is given by your dealer or
Factory representative, before or when the machine is delivered.
The Operator’s Manual delivered with the plough gives operating information as well as routine maintenance and service procedures.
It is a part of the Grizzly machine and must always be stored on the machine, in the document holder provided.
• In signing the installation and warranty form when taking delivery of the machine, the owner understands and undertakes responsibility for further training of any new operators of the machine.
• New operators must start in an area without bystanders and use all the controls until they can operate the machine safely.
Safe Operation Needs a
Qualified Operator
Qualified Operators Must Do the
Following:
1) Understand the Written Instructions,
Rules and Regulations
The written instructions from Grizzly are included in the Machine’s Operation &
Maintenance Manual. Check the rules and regulations for your location. These rules may include any Federal and State safety requirements.
12
3) Know The Work Conditions
• Operators must know any prohibited uses or work areas. They need to know about excessive slopes and rough terrain.
• Operators must know the local road transport regulations, and understand the dangers and requirements of transporting wide equipment.
• Always wear protective clothing when maintaining or servicing the machine, disc self sharpen, wear gloves.
Specifications are subject to change without prior notification
• Operators must not use drugs or alcoholic drinks which impair their alertness or coordination while working. Operators who are taking prescription drugs must get medical advice to determine if they can safely operate a machine.
From serial number 6714
Including 6586, 6666, 6703
6 Safe Use Instructions
WARNING!
Read these safety instructions before allowing any person to operate the machine.
y
Take care when hitching to tractor, never stand between tractor and machine.
y
Never leave the machine in a raised position when not in use. Accidental release of control levers or hydraulic hose failure will cause implement to drop down. This can cause serious injury or death to someone near or under the machine.
y
Do not transport at speeds in excess of 30 kph . Transporting at faster speeds may result in loss of implement control and serious damage or injury. Speed must be reduced when travelling on uneven ground or inclined terrain. Do not transport a fully loaded commodity cart on public roads.
y
Do not transport with a vehicle with a gross mass less than that of the
Machine. Use a tractor large enough to maintain control. Latch brakes together.
June 2018 y
Never allow anyone to ride on the implement in work or transport!
Dangers of riding on a disc implement are extreme and can cause serious injury and death.
y
Do not make any adjustments to a machine until all people who may be close to the machine are considered safe from any potential danger which may result from adjustment.
y
Do not use your hands to clear discs.
Discs can be very sharp and cause serious injury.
y
Use hazard warning lamps and signs as required when transporting the disc plough on public roads.
y
Use a Safety chain and adapter parts with a strength rating greater than the weight of the plough.
y
Do not remove any safety decals from the implement. If any safety decals are removed or damaged they must be replaced in accordance with this manual
Specifications are subject to change without prior notification y
Use due care when adjusting or maintaining any aspect of the machine.
Failure to do so may result in serious injury.
y
When undertaking maintenance on the plough, the operator must ensure that the tractor is turned off and hydraulics lowered, or pinned up. y
Before moving the machine , the operator must make sure the area is well clear and sound the horn as a warning before moving.
y
If operated incorrectly the plough can cause serious injury or death.
y
Avoid High Pressure Fluids, leaking hydraulic fluid can penetrate the skin, If skin is penetrated seek medical advice immediately. Relieve pressure before disconnecting any hydraulic fittings, y
An oversize Agricultural vehicle must not carry a load when travelling on public roads.
13
7 Warranty Policy
Grizzly Engineering Pty. Ltd. (Grizzly) warrants to its Authorised Dealer, who in turn, warrants to the original purchaser (Owner) that each new Grizzly product, part or accessory will be free from proven defects in material and workmanship for twelve (12) months after delivery and installation by an
Authorised Grizzly Dealer, according to the conditions outlined.
This warranty does not cover damages resulting from abuse, accidents, alterations, normal wear or failure to maintain or use the Grizzly product with due care.
During the warranty period, the Authorised Grizzly Dealer shall repair or replace, at Grizzly’s option, without charge for parts and labour any part of the
Grizzly product which fails during normal use and operation because of defects in material or workmanship. The Owner must provide the Authorised
Dealer with prompt written notice of the defect (within 14 days of its occurrence), and allow reasonable time for replacement or repair. The Authorised
Dealer must provide Grizzly written notice and photos if required, within 14 days of receiving notice of the defect by the customer.
Grizzly (at its option) may request failed parts to be returned to the factory. Any travel time of a service technician and/or transportation of the Grizzly product to the Authorised Servicing Dealer for warranty work is the responsibility of the Owner.
This warranty is in lieu of all other warranties (except those of title), expressed or implied, and there are no warranties of merchantability or fitness for a particular purpose. In no event shall the Authorised selling Dealer or Grizzly be liable for downtime expenses, loss of machine use, loss of crops, loss of profits, injury or damage arising from accident, direct or indirect loss, or other incidental, consequential or special damages.
Conditions of Warranty
1) The warranty is not transferable to any third party or subsequent purchaser, unless approved with Grizzly Management.
2) The Installation & Warranty Registration Form (see page 6) must be filled in and returned to Grizzly by the Dealer within seven (7) days of delivery and installation of the unit. By signing the Installation & Warranty Registration Form, the owner acknowledges full responsibility for the safe operation of the Plough and undertakes to fully train any person that might operate the machine. Only when the Installation and Warranty
Registration is completed and returned , can Grizzly fulfil all warranty obligations.
3) Components and conditions not covered by warranty include:
• Abuse Failure resulting from neglect, such as improper operation, lack of required maintenance or continued use of a
machine after the discovery of a defect which results in greater damage to the unit.
• Environmental Conditions Deteriorated or failed components such as hydraulic hoses, seals, valves or connections damaged by corrosive
materials, dirt, sand, excessive heat or moisture.
Warranty determination for these types of failures will be made by Grizzly only after inspection of failed
components.
• Normal Wear Normal wear and consumable items such as oils and lubricants, nuts, bolts, washers, grease caps, spanners,
jacks, bearing housing, axles, poppet valves or seal kits for hydraulic cylinders, seals, discs, axles, tyres, machine
adjustment and periodic service. These are considered to be normal wear items and are not warranted.
• Maintenance Component failure caused by non performance of scheduled maintenance such as correct lubrication and maintenance, tightening or replacement of bolts, nuts, fittings, shields and covers.
14
Specifications are subject to change without prior notification
From serial number 6714
Including 6586, 6666, 6703
7 Warranty Policy
• Damage Damage or machine failure caused by carelessness or accidental damage, improper operation, inappropriate transportation or
storage of the machine, parts or attachments.
• Alterations Any unauthorised alteration, modification, attachments or unauthorized repairs to the Grizzly disc plough, parts or attachments.
Written approval must be obtained from Grizzly for any such items to maintain warranty.
• Replacement Parts The labour or expenses involved in any of the following replacements or service tasks is the responsibility of the owner:
& Service Work (1) Replacement of faulty discs. (2) Gang bearing replacement. (3) Wheel bearing replacement.
(4) Adjustments (refer to manual). (5) Spring adjustment or replacement. (6) Scraper adjustment or replacement.
(7) Periodic service work. Grizzly and its Dealers are not responsible or liable for any such expenses
• Clean-up Time Grizzly does not pay for cleaning the machine, parts, accessories or work area before or after the warranty repair. Clean-up time is affected primarily by the application or conditions in which the unit is operated and maintained. Since clean-up time can be so
variable, cleaning time should be considered a customer expense.
• Transportation Warranty does not cover transportation or insurance costs for ploughs or other equipment needing repair or replacement of war
& Insurance Costs ranted components. Nor does it cover any freight or insurance costs in obtaining new parts or returning old parts to Grizzly for
inspection purposes.
• Travel Time Travel time required for warranty repairs is the responsibility of the Owner.
• Diagnostic Time Warranty does not cover time required to diagnose a warranty problem. Diagnostic time is affected greatly by the training and
expertise of the technician employed to do the job. With proper training of service personnel, diagnostic time should be at a minimum. Grizzly expects that Dealers will assign a well trained and proficient technician to handle any warranty repairs.
• Non-Genuine Parts Use of parts other than Grizzly parts for repair of warranted parts will automatically negate any warranty. Warranted components
must be replaced with genuine Grizzly repair parts.
• Unauthorised Repairs by an unauthorised agent will automatically forfeit any warranty. Warranty repairs must be carried out by an Authorised
Grizzly Dealer.
4 Special Warranty Considerations apply in respect to the following: a) Tyres: Tyres are covered by the tyre manufacturer’s warranty. Claims for tyre faults must follow Grizzly’s normal claim procedures.
b) Hydraulics: Hydraulics are covered by the hydraulics manufacturer’s warranty. Claims for hydraulic faults must follow Grizzly’s normal claim
procedures.
c) Discs: Discs are covered by the discs manufacturer’s warranty. Claims for disc faults must follow Grizzly’s normal claim procedures.
d) Scrapers: Wear on scraper leading edges is normal. Scrapers are only covered under warranty in the event of breakage.
Our goods come with guarantees that cannot be excluded under the Australian Consumer Law. You are entitled to a replacement or refund for a major failure and compensation for any other reasonably foreseeable loss or damage. You are also entitled to have the goods repaired or replaced if the goods fail to be of acceptable quality and the failure does not amount to a major failure within our 12 months machine warranty period.
June 2018 Specifications are subject to change without prior notification
15
Disc Warranty Guidelines
Types of Disc Failure Most Often
Encountered
The first two illustrations (1 & 2) show typical material failures where a credit may be allowable.
The illustrations (3 a, b, c & 4) show examples of disc damage through misuse - where credits will not be allowed.
IMPORTANT!
All warranty claims must be submitted in accordance with the
Grizzly Warranty Policy. Credit for disc failure will be given only when the failure is the result of sub-standard or faulty materials.
In many cases disc failure is the result of misuse and credit will not be given.
IMPORTANT!
Discs worn 50mm (2”) below the original diameter will not be eligible for warranty claims.
Any instance where discs have been reworked, welded or reprocessed in any way since leaving the factory, will void all warranty.
16
Covered by Warranty
1 Straight Line Breaks
A straight line break resulting from defective material.
Covered by Warranty
2 Laminated or Split Discs
Laminating of material resulting in splits or layering of the discs is the result of defective material from the steel mill. This steel defect is often beyond the disc manufacturer’s control because it is not possible to identifiy the problem before the failure occurs.
IMPORTANT!
If the dish shape is deformed, credit will not be allowed.
Specifications are subject to change without prior notification
From serial number 6714
Including 6586, 6666, 6703
Disc Warranty Guidelines
Not Covered by Warranty
3 Irregular Breaks or Fractures
Irregular breaks or fractures (where the cracks are not in a straight line) resulting from use in abnormal conditions such as excessive or large stones, tree stumps, frozen ground, etc.
Not Covered by Warranty Not Covered by Warranty
4 Chipped, Bent or Broken Edges
Chipped, bent or broken edges resulting from use in abnormal ground conditions.
June 2018
Not Covered by Warranty
Specifications are subject to change without prior notification
Not Covered by Warranty
17
8 Specifications
FIELD BOSS
Folding Wing st January 2019
MODEL FW072 FW076 FW080 FW084 FW092 FW100 FW108
RRP EXCL GST
INCL GST PRICE
$120,810
$132,891
$124,800
$137,280
$127,700
$140,470
$129,800
$142,780
$135,960
$149,556
$151,84
$167,024
$157,190
$172,909
43 st January 2019
FIELD BOSS FOLDING WING
OPTIONAL SPECIFICATIONS
PRICE EXCLUDES 10% GST INCL GST IN ITALICS
OPTION DESCRIPTON PRICE
Draught kW
Requirements
(hp)
Hectares per hour@ 8 kph
Disc Spacing
Total Weight kg approx
Weight per disc kg
Weight with fillable wing beams kg
Weight per disc
(kg)
Cutting Width
@21 Degrees
Transport
Width
Transport
Height
No. of Bearings
156-186
(210-250)
6.4
8700
120
9000
125
164+
(220+)
6.4
9000
118
9300
122
8.55m
(28)
5.46m
(17’11”)
4m
(13’4”)
170+
(230+)
7.1
9350
117
9750
122
9.1m
(29’6”)
5.46 m
(17’11”)
4.3m
(14’1”)
178+
(240+)
7.45
230mm (9”)
9700
115
10000
119
9.5m
(31’)
5.46 m
(17’11”)
4.5m
(14’9”)
40
186+
(250+)
8.2
10100
110
10400
113
10.4m
(34’)
5.46m
(17’11”)
5m
(16’5”)
240+
(300+)
8.9
11400
114
11800
118
11.3m
(37’)
6.26m
(20’6”)
5m
(16’5”)
242+
(325+)
9.6
11880
110
12200
113
12.2m
(40’)
6.26m
(20’6”)
5.4m
(17’9”)
48
“Road” Tyre Options
For machines doing frequent road travel
NOTE:
Discs
Recommended disc configuration is 8mm on front with 6mm on rear, this allows for a more even wearing of the discs.
Fluted discs and larger scalloped discs can experience delays in supply. Alw ays confirm availability before placing the order
Upgrade to 8 x (305/70R 19.5)
Scalloped 660mm x 8mm (26” x 5/16”)
Adds extra 5kgs per disc
Scalloped 710mm x 6mm (28” x ¼”)
Adds extra 3kgs per disc
Scalloped 710mm x 8mm (28” x 5/16”)
Adds extra 8kgs per disc
Fluted 710mm x 6mm (28” x ¼”)
Adds extra 4kgs per disc
$2,500
$2,750
$45 per disc
$49.50
$45 per disc
$49.50
$85 per disc
$93.50
$75.00 per disc
$82.50
Tyres Size
Stub Axle Size
Main Frame
Size
Scrapers
Gang Bearings
8.2m
(26’7”)
5.46m
(17’11”)
3.8m
(12’8”)
32
8 x (13.0/65 – 18) 16PR - See Options
75mm
200 x 100 x 9.00mm RHS - See Options
Grizzly Floppy ‘T’ Bar Scrapers - Pat No. 602879, Reg. Design No 95931
38mm x 100mm Self Aligning Greasable 2 year warranty
Pull Tongues
NOTE: CAT Sizes explained on Page 23
“OVERSIZE” Sign and tow hitch
Rear Tow Hitch
Spare Wheel Bracket
Fluted 710mm x 8mm (28” x 5/16”)
Adds extra 10kgs per disc
Fixed Pull – CAT 2, 3, 5
Articulated Pull CAT 2, 3, 4, 5
“OVERSIZE” sign and implement tow hitch.
Add tail lights and indicators
Heavy duty tow hitch. Bolts on to back of machine.
Bolt on spare wheel bracket and wheel.
$110 per disc
$121
NO CHARGE
$600
$660
$800
$880
$200
$220
$500
$550
See price on page 23
Gang Angles
Gang Axles &
Bolts
Gang Frame
Size
Spool Size
Pull Assembly
Hydraulics - Lift
Hydraulics -
Wings
Pitch Control
2 x (4” x 48”)
19/21/23 degrees
38mm (1 ½”) Square / 6 x 20mm tie bolts
250mm x 150mm x 6.0mm RHS
220mm Heavy Wall Pipe
SHS 150mm x 150mm x 9mm Reinforced / Pull Tongue Fixed CAT 4 - See Options
(5”x12”, 4¾”x12”, 4½”x12, 4¼”x12”) (5 ½ ”x12”, 5”x12”, 4½”x12”, 4¼”x12”)
2 x (5” x 48”)
3”x 8” hydraulic pitch control with Dual Spring Assembly
Bolt on Filler Discs
(per pair)
Heavy Frame
Adjustable 20” Scalloped filler disc on outside of gang for fine tuning finish
Additional to standard filler discs
Upgrade Mainframe and Wing frame on FW072 – FW108 to 200 x 100 x 12.5mm
(FW100 and FW108 must also have the road tyre option)
Adds approx. 1000kgs
$800
$880
$9,500
$10,450
Disc Size 660mm x 6mm (26" x ¼”) Scalloped Discs – See Options
Filler Disc Size Two 4 notch 550mm x 6mm Filler Discs – See Options
Copyright 2019
*prices and specifications are subject to change without prior notice / Weights indicated are with most common options
18
Copyright 2019
*prices and specifications are subject to change without prior notice / Weights indicated are with most common options
Specifications are subject to change without prior notification
From serial number 6714
Including 6586, 6666, 6703
8 Specifications
Size Nm ft/lb
M20 240 180
M24 425 310
M30 750 553
Bolt Torque Chart
Integrated Management System
WI 09J TORQUE CHART
HYD ¾" JIC 53 39
Size Nm ft/lb
M5
M6
M8
4.2
3.7
7.6
6.7
18.5 16.4
M10 37.0 32.7
M12 64.7 57.2
M16
M20
M24
M30
160 141
312 277
538 476
750 664
Size Nm ft/lb
M5
M6
M8
6.7
5.9
10.9
9.7
26.9 23.8
M10 52.9 46.8
M12 91.6
81
M16
M20
M24
M30
227 201
444 393
750 664
750 664
Work Instruction
Size Nm ft/lb
1/2"
M18
M20
125 92
475 350
570 420
Size Nm ft/lb
M16
M20
122 91
270 200
M20 HT
PC 10.9
420 310
June 2018
Current Tyre
Size
Model Ply Pressure kpa psi
11.5/80 - 15.3
BKT 13.0/65 – 18
56-64
FieldBoss
72-108
FieldBoss
14
16
496
670
72
97
305/70R 19.5
72-108
FieldBoss
N/A 690
Reference: 'Thomas Warburton - Pocket Fastener Guide' Page 49
100
20%
Rev 8 / 20 May 19
Specifications are subject to change without prior notification
Q:\Quality_System\Work Instructions & Safe Work Procedures\WI Work Instructions\WI 09J TORQUE CHART
19
1
9 Assembly Instructions
9:1 Loading / Unloading
3. Assemble disc gang assemblies to the main frame.
9:2 Fitting Wing Gangs
9:3 Setting Pull Height
9:4 Setting Tongue Height
9:5 Tow Bar
Follow the assembly instructions below: a) Position the disc gang assemblies 1, 2 and
3 on the ground to assimilate their correct position under the main frame. See Section
13.
b) Use 75mm x 75mm (3” x 3”) timber blocks on either side of the discs to chock the discs and stop the disc gangs moving or rolling away.
9:1 Loading / Unloading
The Field Boss Folding Wing is delivered in a flat pack configuration. It requires a level floor area or ground site, the use of a crane, three adjustable stands, a tape measure and various spanners to assemble the machine.
1. Unpack the flat pack.
Using a crane, unstack the flat pack and place the components in a convenient place on the floor or ground. Use a plan view of the machine shown in the operator’s manual under plough frame assemblies (see Parts
Section) to familiarise yourself with location of machine sections. The plough comes with a tool kit which should be stored in the plough’s tool box when not in use.
2. Assemble the main frame.
Align the two sections of the main frame (or centre frame) while on the ground and bolt them together. Fully tighten all the frame bolts.
20
Specifications are subject to change without prior notification
Sling Points
From serial number 6714
Including 6586, 6666, 6703
9 Assembly Instructions c) Using adjustable stands with 1 tonne load bearing capacity, stand the disc gang beams up and position gangs as closely as possible to their position under the main frame.
To help position gangs accurately, a tape measure should be used to measure and locate the exact distance of hole positions between disc gangs. These can be quickly measured from the main frame. Fit all gangs to No 2 gang angle position.
d) Use the crane to lift and position the main frame over the top of disc gang assemblies 1,
2 and 3, and fit pivot bolts.
e) Align holes and bolt the disc gang assemblies to the main frame. Fully tighten gang to frame bolts.
June 2018
4. Fit axles to the main frame wheel arms.
Fit axles to the main frame wheel arms and fully tighten axle bolts. See Section 13.
5. Fit wheels to the main frame axles.
Fit wheels to the main frame axles and fully tighten wheel studs.
6 Assemble the hitch pull onto the main frame.
a) Align the main pull frame and fit the two pins.
b) Fit the lock-up bar - using the pin attachment on the pull frame and two threaded bolts on the main frame. The two threaded bolts on the main frame must be fitted using Loctite (see instructions in the box).
Specifications are subject to change without prior notification c) Fit the two pins to hold the hitch pull in the lock-up position.
7 Fit the Hydraulic Pitch Control Assembly
Fit the Pitch Control Ram using the pin attachment on the pull frame, and the pitch control swivel assembly to the main frame using two threaded bolts. These two threaded bolts must be fitted using Loctite (see instructions in the box).
Important: The two threaded bolts used to attach the pitch control swivel assembly must be fitted using Loctite supplied in the kit.
There is a choice of two hole locations for the pitch control swivel assembly. Use the top hole location for most soil conditions.
21
9 Assembly Instructions
9:2 Fitting Wing Gangs
With the machine on flat hard ground, sitting on the discs, fold the wing frames up and fit wing lock pins.
Check the setting of the centre frame gangs, these should be all on the same setting usually setting 2.
Place the 4 wing gangs in position as shown, use timber blocks to hold the gangs in alignment with centre frame gangs, and a stand (NJIG488) on the scraper side of each gang to hold the gangs up.
Place the wing gangs as close as possible to the centre frame gangs.
<--------- 8 TO 15mm GAP
Lower the wings down onto the disc gang assemblies, align holes and bolt the disc gang frame’s to the wing frame.
LEFT
GANG 3
STAND
GANG 7
STAND
RIGHT
GANG 1
STAND
GANG 5
STAND
Position and locate the disc gang assemblies
1 & 5 for the right wing, and disc gang assemblies 3 & 7 for the left wing.
Before fully tightening the gang to frame bolts ensure that:
Wings are level with centre frame.
Wing disc gangs are fully in-line with main frame disc gangs, and are all on the same setting.
The gap between the block on the wing gangs and the centre gangs is no less than 8mm and no more than 15mm.
Disc spacing between the outer disc of centre frame gangs and inner disc of the wing gangs are the same on all 4 wings.
Tighten gang to frame bolts (380ft.lbs.).
For working flat level ground, or irrigation country, the wings should be as close as possible, 8 to 10mm.
For working undulating or crabhole country the gap between the centre frame and wings should be around 20mm.
22
Specifications are subject to change without prior notification
From serial number 6714
Including 6586, 6666, 6703
9 Assembly Instructions
9:3 Pull Height 9:4 Pull Tongue Height
The Field Boss Folding Wing pull features hydraulic pitch control and level lift for precision operation. However the pull and the pitch control mechanism must be set up to work in the optimum position so that full adjustment is available to the operator.
Too much tension will prohibit the ability of the disc gangs to float over undulations, and make it difficult to get a level finish.
When the plough is working at the required depth, the optimum position of the pull is level, or sloping slightly up towards the tractor.
After adjusting the pull height it may be necessary to move the tongue up or down to achieve a level pull. To set the correct working position of the pull, follow the instructions below:
1. Choose a level site for the plough and tractor for adjusting the pull tongue.
2. Lower the plough so that the discs are resting on the ground, and the wheels are resting on the ground .
3. Disconnect the pull from the tractor, using the Pitch control hydraulics raise the pull to clear the tractor, move the tractor forward so that the tractor drawbar clears the pull.
4. Raise / lower the pull so that is is sloping slightly down towards the tractor.
5. Remove the pull tongue and replace at the height of the tractor draw bar tighten the bolts to 274 ft/lbs.
6. Reconnect the tractor.
Test at working depth the pull should be sloping slightly up towards the tractor.
Pull Tongue adjustment
IMPORTANT!
The initial setting up of your plough behind a tractor is critical to its correct performance.
June 2018 Specifications are subject to change without prior notification
IMPORTANT!
When ever a different tractor is used with the plough, it is absolutely essential to check the pull height is correctly adjusted.
Failure to adjust the pull height correctly may adversely affect ploughing performance.
23
9 Assembly Instructions
9:5 Tow Bar
The Field Boss Folding Wing has a optional
CAT 2 tow bar this is designed for towing harrows, trailer or fuel cart, or any light load.
It may not be legal to tow impliments along public roads, check local road rules before using this hitch on roads.
Tow bar
24
Specifications are subject to change without prior notification
IMPORTANT!
Always use a torque wrench on wheel nuts and gang bolts.
Overtightening will damage threads.
From serial number 6714
Including 6586, 6666, 6703
10 Operating Instructions
10:1 Before using the machine
10:2 Connecting the tractor
10:1 Read the safety instructions
10:3 Preparing the Field Boss
Folding for transport
Before using the machine ensure anyone operating the machine is familiar with the contents of this manual, the pre-delivery check has been done and all operators have been trained in the safe use of this machine.
10:4 Choosing and setting gang angles
10:2 Connecting to the tractor
10:5 Ploughing techniques
10:6 Depth control
10:7 Hydraulic pitch control
10:8 Changing from work to
transport
WARNING!
Do not transport with a vehicle with a gross mass less than that of the plough. Check local road regulations.
Use beacons flags and signs as required.
Always ensure gangs are locked securely for transport.
With the tractor close enough to the machine, connect the hydraulic hoses (ensure quick release couplings are clean) The hoses with the red band are the wheel lift system, the hoses with the blue band are for the pitch control. The hoses with the green band are for the wing fold.
Using the pitch control raise the pull to the tractor height, back the tractor up and fit the drawbar pin.
Check the hoses to ensure the hoses from the tractor to the machine can’t be damaged.
If the hoses are too long they may need to be shortened, or reversed through the stand as shown.
Fit suitably rated safety chains (not supplied with the machine) to the bracket under the pull.
June 2018 Specifications are subject to change without prior notification
Hoses reversed through holder, out of harms way
Hoses hanging too close to draw bar pin
25
10 Operating Instructions
10:3 Preparing the Field Boss
Folding Wing for Transport.
Folding Wings for Transport
To fold the wings for transport, follow these instructions:
1 Raise the plough off the ground with the lift circuit.
2 Fold the wings up until they rest in the wing cradles. Make sure every body is well clear of the machine when folding the wings up.
3 Lock both wings into their cradles with the pins provided.
Wing Locking Pin
Pin the Lock-Up Bar for Transport
The plough’s lock-up bar (located under the pitch control) must be pinned to provide a rigid hitch for transport. This involves inserting two pins into the transport lock-up bar. To do this:
1. Fully raise the plough on the wheel lift circuit.
2. Using the Pitch Control cyclinder, level the machine by eye from the tractor.
3. Remove both lower and upper pins from lock-up slides and pin either slide, which allows machine to be at the closest level.
4. Adjust the cylinder so that the second slide can be fitted and pinned. Ensure the pin is locked.
Lock Up Bar in Transport Position
26
Specifications are subject to change without prior notification
Travel Pin
Fit Travel Pins for Transport
Before the plough is transported, it is essential that the travel pins are placed on the wheel lift cylinders.
1. Fully raise the plough off the ground.
2. Next fit and secure the travel pins (stored in the plough toolbox) to the wheel lift cylinders.
3. When both travel pins are fitted, keep the pressure in the lines so weight is on the cylinders not on the travel pins.
WARNING!
Always stay out from underneath a Field Boss Folding Wing unless it is resting firmly on the ground or supported with transport pins.
From serial number 6714
Including 6586, 6666, 6703
10 Operating Instructions
IMPORTANT!
ALWAYS USE AS LITTLE SET AS
POSSIBLE TO ACHIEVE YOUR REQUIRED
PLOUGHING DEPTH.
The most common mistakes made in operating tandem offset disc ploughs are:
1 Wheels not touching the ground when working.
2 Too much set (gang angle) for the job.
3 Levelling adjustment springs are too tight.
4 Failure to read and follow instructions in the operator’s manual.
5 Operating at a speed greater then the conditions and application allow for.
10:4 Choosing the Correct
Gang Angle for your
Application
The reasons for this are:
1. Less power (kW (hp) is required to pull the plough. At minimum settings there is less soil carried on the face of each disc. This means there is less soil movement and significantly less draught than at greater gang angle settings.
2. Minimum settings maximise your cutting width.
3. Discs tend to last longer.
4. If obstacles are encountered, discs have a better chance of rolling over them.
5. A greater percentage of straw is left on the soil surface to protect the soil from wind and water erosion.
6. A faster speed maybe achieved.
Most Grizzly offset disc ploughs do the majority of their work on the middle settings.
It is important that all gangs are adjusted to the same setting, otherwise forces within the machine will be unbalanced.
IMPORTANT!
Take care and ensure that all gangs are given the same setting number and that all gangs are fully aligned. Misalignment or wrong settings will result is poor ploughing performance.
Remove the bolt and pin from each gang
Specifications are subject to change without prior notification June 2018
Changing Gang Angles
Gang angles on the plough can be altered to suit varying soil and working conditions.
To alter gang angle follow these instructions:
To change the centre frame gangs:
1. Loosen the M24 pivot bolt and loosen the
M20 bolts on the slots on the outside of the frame and completly remove the M20 bolts located in the gang setting holes.
2. Raise the frame on the wheels using hydraulics and slide gangs using a crow bar or similar.
3. Move the gang to the desired setting and torque bolts to specified torque.
To change the wing gangs:
1. Loosen all M20 bolts located on slots and completely remove the M20 bolt located in the setting hole.
2. Raise the frame on the wheels using hydraulics and slide gangs using a crow bar or similar.
3. Move the gang to the desired setting and torque bolts to specified torque ensuring the correct distance between wing gangs and centre frame gangs. See Section 9:2.
27
10 Operating Instructions
SETTING 1 (19 degree Gang Angle)
This is the best setting to use in the following situations: a) Peaty country, soil that flows readily, soft soils.
b) Initial working in root bound pasture.
c) Wet or sticky conditions.
d) Secondary working, fallowing.
e) Provide for lowest draft requirements.
f) Where there is greater likelihood of encountering hidden objects, stumps, rocks etc.
SETTING 2 (21 degree Gang Angle)
This is a general purpose setting. Often machines are never changed from this setting.
Setting 2 is recommended: a) In sticky, puggy or rubbery ground, better penetration can often be achieved on 2 rather than using setting 3.
b) Used to achieve good cut out, but still ensure a fine tilth and level finish.
c) For leaving a predominance of stubble on top of worked country.
d) For general ploughing when ground is
IMPORTANT!
All gangs must be set on the same setting, otherwise forces within the machine will be unbalanced.
Failure to set gangs on the same setting will result in inferior ploughing performance.
tighter.
e) Where greater penetration is required.
f) Where more vigorous cultivation is required or it is desired to bury more of the surface cover.
SETTING 3 (23 degree Gang Angle)
The most vigorous setting 3 is only recommended: a) To obtain maximum depth in hard bed conditions.
b) To chip weeds or increase cut out at shallower working depths.
c) To enable working in the tightest conditions.
Setting 3 has advantages in some conditions/ applications as outlined above. However, it should be noted that:
1) This setting is not suitable for: i) Working wet or sticky ground as the discs will tend to throw the soil, and the trash handling ability of the machine is compromised.
ii) Working in stumps or stones as obstacles are struck at a greater angle which puts greater strain on the discs and the frame, making them more susceptible to damage.
iii) Secondary working, since the soil is moved the most, it is more difficult to achieve the desired level finish. The machine may produce ridges on this setting. Setting 1 or 2 will be much more satisfactory.
2) This setting is more likely to bring the ground up lumpy or cloddy and may cause ridging.
28
Specifications are subject to change without prior notification
3) The machine is in its narrowest working width on this setting.
4) Discs continually used on this setting tend to wear blunt which to some extent reduces the cutting and penetrating ability of the machine.
The most common mistakes made in operating tandem offset disc ploughs are:
1. Wheels not touching the ground when working.
2. Too much set (gang angle) for the job.
3. Levelling adjustment springs are too tight.
4. Failure to read and follow instructions in the operator’s manual.
5. Travelling too fast for the conditions.
IMPORTANT!
It is best practice to use the minimum possible set to achieve the desired result.
From serial number 6714
Including 6586, 6666, 6703
10 Operating Instructions
10:5 Ploughing Techniques 10:5:3 Ploughing Patterns
10:5:1 Turning at Headlands
The plough must always be raised from the ground when turning sharply at headlands.
When turning at the end of a run it is necessary to lift discs clear of the ground to avoid uneven working and ridging as well as damage to the plough.
Also when turning sharply make sure the plough pull does not contact rear tractor tyres.
10:5:2 Operating Speed
Your plough is fitted with rear filler discs on each side at the rear of the machine.
This allows for working in any direction, whether ploughing perimeters, headlands or diagonally.
10:5:4 Ploughing Soft Ground
Ploughing soft ground requires less set/gang angle, and reduced speed, when ploughing deeper than 100 mm (4”) deep more gang angle may be required to achieve the depth, depending on the size and concavity of the discs.
The optimum speed for the machine will be determined by the conditions and the task being performed.
Operating speed is generally about 7-8kph (4-
5mph).
Secondary working or working deeper in soft soils or peaty loam soils will require a reduction in speed, to as low as 4-5 kph.
IMPORTANT!
Generally, most conditions will allow you to get the required depth on the first pass.
Setting 1-2 is usually the most appropriate setting, it may be necessary to work some country twice to achieve the desired results.
Sometimes full depth can be achieved in the first pass on Setting 3, but with the result of leaving large, hard to break clods and boulders.
If the plough is not lifted from the ground and obstacles such as rocks and stumps are encountered while working through a corner, disc & machine damage may result because of the very square angle at which the disc strikes an obstruction.
10:5:5 Ploughing hard ground or
in large clods
June 2018 Specifications are subject to change without prior notification
10:5:6 Stumps and Rocks
A disc plough is primarily a rolling, chopping machine.This means that: a) The faster the disc is going, the soil is thrown further, resulting in ridges and gutters.
b) When stumps, rocks, etc are encountered, the disc which strikes the obstacle must either break it, cut it or lift the machine over it. Discs are not designed to remove stumps.
c) The less set and less speed that can be used the better because: i) The disc will have a better chance to cut the obstacle. More set creates a greater bulldozing and less cutting effect.
ii) There are less twisting and tearing forces acting on the disc. This gives the disc a better chance to roll over obstacles and minimises the chance of disc damage.
iii) Using less speed and minimal gang settings also exerts less strain on frame components and bearings.
Minimal set and speed will maximise the cutting width, and reduce the load on the tractor, reducing fuel consumption.
IMPORTANT!
Always use less set on discs and lower speed when operating in stumps and/or rocks. Damage caused by misuse in rocks and/or stumps is not covered by warranty.
29
10 Operating Instructions
10:5: 7 Working in Moist
IMPORTANT!
If the lead disc overlaps too little
(less than 9” [one disc]), then soil cut-out will not be complete. If the lead disc overlaps too much (more than 9” [one disc]), then a line or gutter may be left in the ploughed ground.
Your Grizzly features revolutionary Floppy T
Bar Scrapers which enable it to operate in conditions in which ploughs with conventional scrapers would fail.
However there are limitations to the performance of any disc plough. There are various adjustments which can be made to assist the performance of your plough in trying conditions (refer Gang Angle Selection in previous section).
There may be times when your plough will block. In these situations, it will be necessary to wait until conditions are more suitable.
10:5: 8
Prevously Worked
Identify the mark left by the filler disc (outside rear disc) from a previous round which is a guide for placement of the leading disc (on either side).
The lead disc should be cutting (one disc) in from the filler disc mark.
The filler disc mark must be ploughed out by the leading disc for cut-out to be complete.
IMPORTANT!
Always lift the plough out of work when turning sharply on headlands.
Failure to lift the plough while turning will cause uneven working and ridging in the soil and may also cause excessive forces and damage to the plough. Also when turning sharply make sure the plough pull does not contact rear tractor tyres, otherwise damage may occur.
30
IMPORTANT!
When working at excessive speed in dry conditions, premature disc wear may occur.
Specifications are subject to change without prior notification
From serial number 6714
Including 6586, 6666, 6703
10 Operating Instructions
10:6 Operating the Plough with
Depth Control Stops
Adjustable depth stops can be fitted to the master cylinder (the right side of the machine) for accurate depth settings when operating.
Proper care must be taken when altering depth stops.
When adjusting depth stops:
• Make sure the plate grooves are clean and free of dirt to ensure proper meshing of grooves.
• Two depth stop plates must be fitted to one cylinder, there is no advantage fitting depth stop plates to two cylinders or more.
• Grooves must be properly aligned so that both plates contact the cylinder end equally. Inaccurate alignment will cause damage to the depth stops and/or cylinders. This is not covered by warranty.
June 2018
Depth Stops
When adjusting depth stops make sure groove and plates are clean and properly aligned, use loctite
243 on bolts.
Specifications are subject to change without prior notification
IMPORTANT!
Depth control stops can be damaged if they are incorrectly fitted.
Depth stops must be fitted to the right hand cylinder only and aligned to contact the cylinder evenly.
31
10 Operating Instructions
10:7 Hydraulic pitch control
The Grizzly hydraulic pitch control allows the operator to adjust the relative level of the front and rear gangs to maintain the best possible level finish.
The pitch control springs supply enough rigidity to allow easy hydraulic adjustment to give control of furrows or ridges left in the centre of the worked ground.
They should also be flexible enough to allow the plough frame to rise over undulations.
Adjusting the pitch control.:
With the hydraulic pitch control cylinder adjusted to around mid position (ram extended halfway), and the machine level, work the machine in typical working soil conditions at required working depth for 50 meters.
After stopping the machine, note the quality of the ploughed finish, the ploughed ground should be level across the width of the machine.
Adjust if the following occurs:
IMPORTANT!
a) A hollow exists in the centre of ploughed work.
If a furrow exists in the centre of ploughed work, adjust the hydraulic pitch control ram to raise the front and lower the rear of the machine.
If the swivel assembly is removed for service, always use Loctite stud lock to secure the bolts. Tighten to
450ft/lb .
b) A ridge in the centre of ploughed work.
If a ridge appears, it will be necessary to adjust the hydraulic pitch control ram to raise the rear and lower the front of the machine.
Loctite bolts use high strength loctite
32
• Top Springs
The top springs should show 30mm of the thread above the lock nut.
To adjust the top springs: a) Lower the plough onto the ground and extend the hydraulic pitch control cylinder to relieve pressure on top springs.
b) Loosen the lock nut and adjust so that there is 30mm of thread extend through the lock nut.
c) Tighten the lock nut.
Specifications are subject to change without prior notification
Correctly adjusted the top springs have 30mm of thread extending through the lock nut.
From serial number 6714
Including 6586, 6666, 6703
10 Operating Instructions
10:8 Changing from work to
Transport
1. Fold the wings and fit pins.
Preparation of the plough for transport involves three steps:
1. Fold the wings and fit pins
2. Ensure the pitch lock pins are fitted.
To fold the wings for transport, follow these instructions:
1. Raise the plough off the ground with the lift circuit.
2. Fold the wings up until they rest in the wing cradles. Make sure every body is well clear of the machine when folding the wings up.
3. Lock both wings into their cradles with the pins provided.
3. Fit the travel pins to the wheel lift assembly.
2. Ensure the pitch lock pins are fitted.
4. Check safety equipment
The plough’s lock-up bar (located under the pitch control) must be pinned to provide a rigid hitch for transport. This involves inserting two pins into the transport lock-up bar.
WARNING!
Do not exceed 30 km/h when towing the plough
IMPORTANT!
Always ensure the transport lock-up is properly fitted to pitch control, and travel pins are fitted to the wheel lift.
To do this:
1. Fully raise the plough on the wheel lift circuit.
2. Using the Pitch Control cyclinder, level the machine by eye from the tractor.
3. Remove both lower and upper pins from lock-up slides and pin either slide, which allows machine to be at the closest level.
4. Adjust the cylinder so that the second slide can be fitted and pinned. Ensure the pin is locked.
June 2018 Specifications are subject to change without prior notification
Pitch lock pin, for transport only.
Remove when working
2. Fit the travel pins to the wheel lift assembly.
Before the plough is transported, it is essential that the travel pins are placed on the wheel lift cylinders.
1. Fully raise the plough off the ground.
2. Next fit and secure the travel pins (stored in the plough toolbox) to the wheel lift cylinders. When both travel pins are fitted, keep the pressure in the lines so weight is on the cyllinders not on the travel pins.
33
11 Storage
Wash the machine
To properly check the machine it must be clean. After washing lower the machine on to the discs and raise the wheels.
This will protect the ram shafts and make it possible to check the wheel bearings.
Grease and check
Greasing the machine after washing will purge any water from pins etc. (See Section 12 for more details).
Check bearings, pivots, pins etc. for wear.
Check discs and scrapers.
Retract all cylinders to protect shafts from rusting, this will ensure there is no weight left on the tyres.
Order parts
This is a good time to forward order any replacement parts you will need for next year,
Some components are imported and may have long delivery times.
When ordering parts quote the serial number of the machine, this is on the identification plate located on the front of the machine, and the part number of the parts from the parts section of this manual.
34
Specifications are subject to change without prior notification
From serial number 6714
Including 6586, 6666, 6703
12 Lubrication and Maintenance
12:1 Greasing
12:2 Before Use
12:3 Tightening Gang Bolts
12:4 Gang Bearings
12:5 Replacing Discs
12:6 Scrapers
12:7 Tyres
12:8 Wheel Bearings
12:9 Hydraulics
June 2018 Specifications are subject to change without prior notification
35
12 Lubrication and Maintenance
12:1 Greasing
There are several grease points on the Field
Boss Folding Wing. These should be greased at the start of every season, then as indicated, and again after cleaning the machine at the end of season.
figure g3 Wheel hubs 4 point weekly figure g6 Wheel lift cylinders 2 points each weekly figure g1 Pull tongue 3 points weekly figure g4 Pitch control points weekly (FW072-
FW108) figure g7 Wing Pivot 2 points per side as required figure g2 Wheel pivots 2 points per gang as required
36 figure g5 Disc gang bearings daily 1 point per hub
Specifications are subject to change without prior notification
From serial number 6714
Including 6586, 6666, 6703
12 Lubrication and Maintenance
12:2 Before Use
Ensure the pre-delivery checks have been done. See Section 4.
Routine Service Procedures
Proper servicing and maintenance schedules must be carried out to gain the best performance and longest life of the plough and its components.
After 4 Hours Use
Tighten gang bolts, and wheel nuts to specified torque (See Torque Table in Section
8).
Check that scraper adjustment allows scrapers to move up to ½” (12mm) from disc spool, ensure the scrapers are not dragging on the spools or discs, this will cause premature wear.
Check over the machine, ensure there are no loose bolts, visually check disc bearings and dust covers.
After 10 Hours Use
Check all items of the 4 hour service.
12:3 Tighten Gang Bolts
Check gang axle and gang bolts.
Gang bolts may need to be retightened more regularly in some conditions, check the gang bolts often in the first week, loose blots will cause damage to housings, bolts, spools, and discs.
It is the operators responsibility to ensure bolts are kept tight, this type of damage is not covered by warranty.
Tighten to the specified torque (section 8) do not overtighten.
After 40 hours use
The gang bolts should be tightened periodically thereafter.
When working in stump or rocky conditions check more frequently - continual checking at least every 4 hours is recommended.
IMPORTANT!
Use a torque wrench, do not over tighten bolts.
June 2018 Specifications are subject to change without prior notification
WARNING!
Whenever transporting the plough on roads, check the wheel nuts
570Nm.
WARNING!
It may be necessary to tighten gang bolts at the hours specified when the plough is new because the disc and spool take time to
“bed in”. If this is not done, gang bolts may become loose and can cause considerable damage to bolts, spools and discs. Such wear or damage is not covered by warranty.
37
12 Lubrication and Maintenance
12:4 Gang Bearings
When disc gang bearings are unservicable it is neccessary to remove the gang assembly and replace the bearing.
Follow the procedures below:
1. Remove the scrapers from the bank of discs where the failed bearing is.
2. Clean the housing and area surrounding the bearing to be replaced.
3. With the discs resting on the ground, remove the two 16mm axle locator bolts holding the gang axle to the gang frame.
4. Lift the plough up about 250mm, ensure the bank of discs is free from the gang frame, if it doesn’t drop out, ensure
6. Clean the bearing and housing, to check if the bearing is serviceable or not, grip the inner race and apply pressure in and out and feel for movement, if there is noticeable movement, the bearing will need to be replaced.
7. Place the end of the gang axle into the bearing to be removed and twist bearing in the direction of the slots in the bearing housing, as far as it will go.
WARNING!
6 BOLT DISCS 28" SCALLOPED - 1 1/2"
housing and remove it through the slot.
Replacing disc bearings involves moving and handling very heavy disc gangs and components.
When moving, disassembling, reassembling and refitting discs
& disc gangs, take all protective precautions necessary to avoid injury by sharp discs, heavy components, jamming or crushing.
Never push against a disc with your foot or arm.
Failure to do this may lead to serious injury.
9. Thoroughly clean the housing, paying particular attention to the grease groove.
Check for damage and replace if needed.
10. Insert the new bearing into the bearing housing, making sure to align the grease hole of the bearing and the grease groove of the bearing housing.
6 BOLT DISCS 28" SCALLOPED - 1 1/2"
BEARING
Place the end of the gang axle into the bearing to be removed.
L:\Inventor\Parts\GG-\GGF036NESDS.idw
axle locator bolt everybody is clear and carefully bump the discs with a crow bar, which will separate the disc gang from the gang frame. Roll the gang assembly out from under the plough.
5. Remove the dust covers and spacer washers and slide the gang axle out.
38
L:\Inventor\Parts\GG-\GGF036NESDS.idw
Twist bearing with the axle, in the direction of
Specifications are subject to change without prior notification
Use a soft mallet and drift to knock the bearing into right angled position to remove it.
From serial number 6714
Including 6586, 6666, 6703
L:\Inventor\TEMPLATES\parts book.idw
C ( 1 : 8 ) L:\Inventor\Parts\GG-\GGF036NESDS.idw
C
E ( 1 : 7 )
E
G ( 1 : 8 )
6 BOLT DISCS 28" SCALLOPED - 1 1/2"
BEARING 12 Lubrication and Maintenance loose in the housing, the housing will need to be replaced. (See 12.8).
12. Ensure both bearings are aligned correctly, grease the bearings and ensure they grease properly, Replace the gang axle and reassemble, dust covers, spacers and spring. Be sure to use a spacer washer under each dust cover and on the thrust end and a spring on the lead end. The dust cover hole must be facing downwards to allow dirt to fall out.
6 BOLT DISCS 28" SCALLOPED - 1 1/2"
BEARING
11. Partially twist the bearing into the housing by hand, notice how tight the bearing is in the housing, the bearing should require a mallet to tap it around far enough to complete the alignment of the bearing in the housing, using the gang axle. If the bearing can be aligned by hand, or is
13. Roll gang to its position under the plough.
BEARING
FMEUGP00 (SPACER)
BNTAA000 (DUST COVER)
FMEUGP00 (SPACER)
FMEUGP00 (SPACER)
BNTAA000 (DUST COVER)
FHDSA035 (SPRING)
L:\Inventor\Parts\GG-\GGF036NESDS.idw
HOLE
GROOVE
F
When installing the new bearing, make sure the grease hole of the bearing & the grease groove of the bearing housing are aligned.
June 2018
ALIGN NOTCHES
Spacer and dust cover detail
L:\Inventor\Parts\CG-\GGF036NESDS-1.idw
IMPORTANT!
When inserting the new bearing, make sure the grease hole of the outer bearing casing (which is offset from centre) will align with the grease groove in the bearing housing when the bearing is fully fitted. If it is not aligned you will not be able to get grease into the bearing.
Specifications are subject to change without prior notification
WARNING!
When moving and refitting disc gangs to & from the gang frames, always stay out from underneath a plough unless it is resting on the ground or supported with stands or blocks when raised.
Failure of hydraulic systems or jacks can cause the plough to drop, pinning or crushing personnel and causing serious injury.
12:5 Replace discs
When discs become worn or damaged it is necessary to remove individual disc gang assemblies from the plough and replace the worn or damaged discs.
While discs are being replaced it is an excellent time to check the bearings, dust covers and gang axle bolts and replace if required.
Replacing discs involves moving heavy and sharp components, when replacing discs or bearings ensure all safe work practices are used to avoid injury. A crane will be required to lift most components.
IMPORTANT!
Disc bearings can be changed without removing the bearing housing. The bearing housing will only be removed when discs are being replaced.
39
G
12 Lubrication and Maintenance
1. Repeat the steps 1 to 6 from 12.4 to remove the scrapers and bank of discs. In a clean area, disassemble the discs in the following manner.
2. Remove the dust covers, spacers, spring, and gang axle.
3. Mark each disc spool clearly so that the concave and convex ends of each spool can be identified for reassembly (See picture).
4. On a flat hard surface stand the bank of discs up on the bolt heads, a support part number NJIG714, is available from your
Grizzly Dealer as a spare part.
5. Remove the gang tie bolt nuts Dismantle the assembly of discs and spools by lifting the components up, a crane will be required for the larger discs.
6. Reassemble the disc gang, making sure the concave end of each spool is fitted to the convex side of a disc, and the convex end of each spool fitted to the concave side of a disc.
7. Use the support (NJIG714) to sit the bearing housing on to keep the gang bolts in position, ensure scalloped discs don’t have the notches in the same line.
8. Apply a small amount of anti-seize to the threads of the gang bolts, attach washers and new nuts to the gang bolts. Evenly tighten the gang bolts in sequence 1, 2,
3, 4, 5 & 6 (shown right) so that the discs
LEAD HOUS I NG
THRUST HOUSING
6
1
4
3
5
2
FLAT WASHER
CONCA V E MARKING
NJIG714 and spools bed together properly. Tighten
6 bolt systems to 200ftlb for PC. 8.8 20mm bolts or 310ft/lb for PC. 10.9 20mm bolts
(See Section 8).
9. Replace the gang axle and reassemble using new dust covers, spacers, and springs as required. Check the parts drawing for the spacer and spring locations. The dust cover hole is facing down to allow dirt to fall out.
10. Roll gang to its position under the plough making sure all safety precautions are taken to avoid injury.
11. Lower the plough to re-attach the gang axle making sure all safety precautions are taken to avoid injury. It is important to secure the lead end of the gang axle first and fully compress the dust cover spring.
Check the spring tension. The spring should be compressed to a length of 10-
12mm. Use spacer washers to minimise end play. Allow 12mm movement.
12. Replace the two axle bolts and nuts, and tighten. See Section 9 (use new bolts and nuts).
13. Replace the gang scrapers and tighten bolts, don’t over tighten scraper bolts, ensure the scraper can move freely, adjust the scrapers to 10mm-12mm from the spool.
40
Specifications are subject to change without prior notification
From serial number 6714
Including 6586, 6666, 6703
A
12 Lubrication and Maintenance
12:7 Tyres
Check the tyre pressure.
Uneven tyre pressure can cause the machine to plough unevenly. See Section 8.
12:6 Scrapers
Check the scrapers regularly, the scrapers should move freely from the spool to 12mm away, The side movement should be kept to a minimum by tightening the scraper pivot bolt.
Don’t overtighten the pivot bolt, this will lock the scraper, this will result in the scraper not functioning correctly. To adjust the scraper loosen the lock nut at the top of the scraper, adjust the adjuster bolt as required , to achieve 8mm - 12mm cleatance between the scraper and spool, tighten the lock nut.
12:8 Wheel Bearings
Check wheel bearings, with the wheels in the air spin the wheel, check for bearing noise, heat, and movement in the bearing. If there is excessive movement the bearing will need to be adjusted.
To adjust the wheel bearing preload.
1. Raise the wheels (using hydraulics).
2. Remove the cap screws from the cap and remove the cap from the hub.
3. Remove the cotter pin.
4. Tighten the nut while turning the hub.
When there is a tight bind on the bearing, the parts are seated correctly, approx
150ft/lbs.
5. Back the nut off 1/6 to 1/4 of a turn or sufficiently to allow .005mm to .02mm end play.
Note: Failure to back off adjusting nut could cause bearing to run hot and fail.
6. Replace the cotter pin.
7. Replace the cap (use flange sealant).
IMPORTANT!
Having a gap of over 12mm may cause damage to the gang beam and adjuster bolt. Ensure correct gap is maintained.
June 2018 Specifications are subject to change without prior notification
41
12 Lubrication and Maintenance
12:9 Hydraulics
The Field Boss Folding Wing Series utilises separate hydraulic circuits for wheel lift and pitch control. With proper care and maintenance these hydraulics will provide reliable and long life operations.
The first and foremost consideration in maintaining hydraulics in good working condition is to be meticulous about keeping your hydraulic circuits clean and free from contaminants.
Avoid dirty oils and contaminants at all costs.
They will damage hydraulic componentry and cause functional problems.
When transporting the plough, always use the travel bars (provided with the plough) on wheel lift cylinders. The travel bars are essential to prevent excessive loading on cylinder components when transporting.
Phasing Cylinders
When storing the plough overnight or for longer periods, make sure the phasing cylinders are left fully closed to protect shafts and avoid unnecessary seal damage, OR alternatively, coat the shafts with CRC or equivalent to protect them while the rams are extended.
42
Specifications are subject to change without prior notification
WARNING!
Ensure pressure in the retract line does not exceed 2000psi.
From serial number 6714
Including 6586, 6666, 6703
13 Parts
ASSEMBLY KIT-FIELD BOSS 100-108 9mm
30 46 3 41 11 8 69 48 7 50 14
GSGV0002
52
7
19
27
44
45
42
16
53
25
28
22
15
L:\Inventor\Parts\GS-\GSGV0002.idw
June 2018 Specifications are subject to change without prior notification
59
58
60
53
25
33
38
1
24
47
62
43
K ( 1 : 6 )
K
13
14
15
16
10
11
12
17
18
19
20
21
22
23
24
7
8
9
5
6
1
2
3
4
ASSEMBLY KIT-FIELD BOSS 100-108 9mm
ITEM QTY PART NO.
DESCRIPTION ITEM QTY PART NO.
DESCRIPTION
2 ATS404
2 ATS423
8 BMAAA000
10 BMCAA000
4 BVA5278
4 BVBEA06X
2 CABSE130
1 CGBEE003A
1 CHAGH000
1 CHCUG000
3 FABEA020
8 FABEA025
22 FABEA045
2 FABEA080
8 FABGA050
4 FABGA075
2 FABHA040
4 FABHA065
8 FABJA080
2 FABKA047B
2 FABKA047BB
3 FABKA075
4 FEABA008
11 FFBEA000
HITCH PIN, 3/4
S74 CAT 1 TOP LINK PIN
GREASE NIPPLE 1/4" UNF
GREASE NIPPLE 1/8 BSP
DU THRUST WASHER
DX BUSH 50 x 55(40mm)
DEPTH GAUGE
TOOL BOX LID 3mm
DISC LOCK SPANNER<10mm DISC
PLATE 12mm.S/A SPANNER 57mmA/F
BOLT M8 X 20
BOLT M 8 X 25
BOLT M8 X 45
BOLT M 8 X80
BOLT M12 X 50 PC 8.8
BOLT M12 X 75 PC 8.8
BOLT M16 X 40 PC 8.8
BOLT M16 X 65 PC 8.8
BOLT M20 X 80 pc 8.8 COARSE
BOLT M24x47 34mm SHANK zinc
BOLT KIT- PITCH CONTROL SWIVEL
BOLT M24 X 75
HAMMER DRIVER SCREW
NYLOC NUT M8 P TYPE
34
35
36
37
31
32
33
25
26
27
28
29
30
41
42
43
38
39
40
44
45
46
47
48
12 FFBGA000
4 FFBHA000
8 FFBJA000
3 FFBKA000
2 FFDYA000
48 FFFJA030
NYLOC NUT M12 P TYPE
NUT NYLOC M16 P TYPE PC8 ZINC
NYLOC NUT M20 P TYPE 2.5
NYLOC NUT M24 P TYPE
1 1/2 - 6 BSW THIN NUT (BLACK)
WHEEL NUT 18mm - (30mm AF)
2 FFGYA065
2 FGBKA135C
2 FGBSA191
2 FGBSA250
4 FGBUA128
4 FHURA280
1 FKAEA000
4 FKAKA000
4 FKBDA000
SPRING ASSY NUT (38.1) 100mm
LOCKUP PIN 1" (130)
TRANSPORT LOCK PIN
PULL PIN 40mm (247)
WING PIVOT PIN - FIELD BOSS
Spring 280 x 17 x 68 11 coils
LYNCH PIN 6mm
2 FMAMGK00
11 FMCEE000
24 FMCGE000
8 FMCHE000
LYNCH PIN 7/16" strong clip!
RAM PIN CLIP
1" FLAT WASHER (ZINC COATED)
M8 WASHER 5/16"F436 HARD ZYP
M12 WASHER 1/2" type 1HARD ZYP
M16 WASHER 5/8" F436 HARD ZYP
8 FMDJNJ00
8 FSAA2001
SQUARE WASHER M20 X 50 X 8
20mm BOLT HEAD LOCK
1 GBG100-108-W-5L 9mm100-108 LEFT FIELD BOSS WING
1 GBG100-108-W-5R 9mm100-108 RIGHT FIELD BOSS WING
1 GCG100-108-5 FIELD BOSS 100 / 108 FRAME
ITEM QTY
49
50
51
PART NO.
1 GDFE0000
1 GDFE0008
1 GHPF0002-4
2 GKUA0001P
1 GSFM0002S
1 GSFM0008
2 MDAYA014
2 MGGFA075P
1 PAAGA300
3 PD000053
3 PD000054
3 PD000061
1 PD000082
1 PDAEF004
1 TDAPC000
1 TDASC000
1 TDFHA000
1 TDFSA000
1 TDGAA200
1 TDGAC000
1 XBCDOC235
1 XCDMZM00
1 XIDP
1 GKFE0000
70
71
78
67
68
69
64
65
66
61
62
63
52
53
54
55
56
57
58
59
60
8
64 63 57 67 69 37
10 66 65 9 41 68 24 11
GSGV0002
DESCRIPTION
LOCKUP SLIDER- PAINTED
LOCK UP ASSEMBLY (1175mm)
HYDRAULIC KIT F BOSS 100-108 9mm
FRAME
SWIVEL ASSY PITCH CONTROL
BOLT KIT - FIELD BOSS SPLIT
BOLT KIT - FIELD BOSS WING GANG
PIN RETAINER BUSH
SLIDER ASSEMBLY- PITCH LOCK
GRIZZLY BLUE SPRAY CAN 300gram
Decal "0"
Decal:"1" GOLD 100mm x 55mm
Decal "8"
SHUT THE GATE SIGN
DECAL KIT 100-112 FIELD BOSS
SOCKET 24mm.3/4" DRIVE
SOCKET 30mm.3/4" DRIVE
19mm COMBINATION SPANNER
30mm COMBINATION SPANNER
3/4" DRIVE 200mm EXTENSION
L HANDLE 3/4" DRIVE
DOCUMENT HOLDER
FIELD BOSS FOLDING MANUAL
ENGRAVE ID PLATE
PARKING JACK - HEAVY-DUTY
L:\Inventor\Parts\GS-\GSGV0002.idw
44
Specifications are subject to change without prior notification
TOOL BOX
From serial number 6714
Including 6586, 6666, 6703
J ( 1 : 10 )
G
G ( 1 : 3 )
J
ASSEMBLY KIT-FIELD BOSS 100-108 9mm
18 26 43
35 6
53 12 4 52 49 7 56 31 36
GSGV0002
29 20 13
H ( 1 : 18 )
L:\Inventor\Parts\GS-\GSGV0002.idw
June 2018
5 4 43 18
WING HINGE
COMPONENTS
50 14
62
78
40
39
32
50
56
2
55
17
34
4
71
23
8
Specifications are subject to change without prior notification
45
H
FIELD BOSS 100 / 108 FRAME
A
L:\Inventor\Parts\GC-\GCG100-108-5-1.idw
46
12
GCG100-108-5
A ( 0.05 : 1 )
4
13
14
1
5
8
2 5
1
10
6
11
3
9
7
Specifications are subject to change without prior notification
10
11
12
13
14
7
8
9
ITEM
1
2
3
4
5
6
1
1
1
8
4
8
QTY
4
2
8
1
1
1
1
2
PART NO.
BDMZA000
CCACA301
FABKA050
FFBJA000
FKDXA004
FMCMG000
GJGA0013A
GJGA0014A
GJHB01L
GJHB01R
GNAKG100L
GNAKG100R
MDAEA650
WMNAA740
DESCRIPTION
GE70 RADIAL SPHERICAL PLAIN BEARING
2mm SPACER WHEEL LEG - 70mm id
BOLT M24 X 50
NYLOC NUT M20 P TYPE 2.5
Internal Circlip 105mm Dia
M24 WASHER F436 HARD ZYP
LEFT WHEEL LEG - 108 FIELD BOSS
RIGHT WHEEL LEG - 108 FIELD BOSS
LEFT INSIDE WHEEL LEG PLATE
RIGHT INSIDE WHEEL LEG PLATE
LEFT WING SUPPORT F/B 100/108
RIGHT WING SUPPORT F/B 100/108
ROUND 16mm (650mm) depth point
H70 HUB AND STUB DUAL
From serial number 6714
Including 6586, 6666, 6703
BOLT KIT - FIELD BOSS SPLIT
7
6 5
2
3
4
1
E
7
E ( 1 : 5 )
F
L:\Inventor\Parts\GS-\GSGV0002.idw
June 2018
GSFM0002S
6 5
1 6
F ( 1 : 5 )
6 5 1
Specifications are subject to change without prior notification
4
5
6
7
ITEM
1
2
3
12
36
36
4
QTY
36
12
12
PART NO.
FFBJA000
FABGA065
FFBGA000
FMCGE000
FMCJG000
FABJA065
MAEMA250P
DESCRIPTION
NYLOC NUT M20 P TYPE 2.5
BOLT M12 X 65 PC 8.8
NYLOC NUT M12 P TYPE
M12 WASHER 1/2" type 1HARD ZYP
M20 WASHER 3/4" F436 HARD
BOLT M20 X 65 pc 10.9 COARSE
PULL STAY JOINER
47
BOLT KIT - FIELD BOSS WING GANG
GSFM0008
L:\Inventor\Parts\GS-\GSGV0002.idw
48
Specifications are subject to change without prior notification
4
1
3
2
FSAAFF08 GANG TO FRAME BOLT KIT 1 UNIT
ITEM
1
2
3
4
QTY
16
16
16
16
PART NO.
FABJA080
FFBJA000
FMDJNJ00
FSAA2001
DESCRIPTION
BOLT M20 X 80 pc 8.8 COARSE
NYLOC NUT M20 P TYPE 2.5
SQUARE WASHER M20 X 50 X 8
20mm BOLT HEAD LOCK
From serial number 6714
Including 6586, 6666, 6703
TWIN PITCH CONTROL
3.4.1
USE HIGH STRENGTH LOCTITE
3.4.2
3.4.3
3.3
3.4.6
3.4.5
3.4.4
GDFGL006
3.1
L:\Inventor\Parts\GD-\GDFGL006.idw
June 2018
3
3.2
2
1
POS
1
2
3
3.1
3.2
3.3
3.4
3.4.1
3.4.2
3.4.3
3.4.4
3.4.5
3.4.6
QTY
1
1
1
1
1
2
1
1
1
1
1
1
1
PART NO
FEBFA020
GNJJ0007
HYP300/08 NC
FKBDA000
FGHKA080
HLFED200
HKEB0001
HKBS ORING022-90
HKBS ORING232-90
HKBS ORING041-70
HKAS/520-881510
HKAS 520-4458700
HKBS 81-1377630
DESCRIPTION
GRUB SCREW M10X1.5 x (20mm)
TWIN PITCH BAR - FIELD BOSS
HYD. CYL3"x8" 1" PIN 2"ROD
RAM PIN CLIP
1" RAM PIN
PTE ROD 8" x 2" (1.5" UNF)
PTE S/KIT SLM 3.0" X 2.0" ROD HALLITE 81
O RING BS 022 90 DURO
O RING BS 232 90 DURO
O RING BS 041 70 DURO
ROD WIPER "520" 2.0"X2.5"X.25
ROD SEAL "605"2.0"X2.375"X.25
PISTON SEAL 3.0" HALLITE "81"
Specifications are subject to change without prior notification
49
H70 HUB AND STUB DUAL
To assemble and adjust the setting of this hub:
NOTE: CLEAN THREAD BEFORE ASSEMBLING, IF
YOU ARE ASSEMBLING A NEW AXLE USING 1-
1
2
"
UNF DIE NUT, CLEAN ALL OTHER COMPONENTS.
Step 1: Clean and prime the seal #1.3 and seal ring
#6 Fit seal to seal ring using Loctite 480, allow to dry before proceeding.
Step 2: F it bearing cups #1.1 and #1.2 into the hub, place bearing cone #1.1 into the hub.
Step 3: Fit the seal and seal ring to axle, ensure this does not rotate on axle, use loctite 680 if required.
Step 4: Fit the hub to the axle, then fit the bearing cone #1.2, washer #5, and nut #3.
Step 5: Tighten the nut while turning the hub.
When there is a tight bind on the bearing, the parts are seated correctly, approx 150ft/lbs.
Step 6: Back the nut off 1/6 to 1/4 of a turn or sufficiently to allow .005mm to .02mm end play.
Note: Failure to back off adjusting nut could cause bearing to run hot and fail.
Step 7: Insert the split pin #1.4 as shown, trim the s tr aight leg, bend the other over the axle end.
Step 8: Fit the cap #9 using loctite 515 flange sealant on the faces, and tighten the 4 M6 #4 cap screws 16nm(12ft/lbs).
Step 9: Grease with a grease gun using CASTROL
BTX or similar until grease is visible through rear seal.
4 seal detail ( 1:2 )
9
3
5
1.2
L:\Inventor\Parts\WM-\WMNAA740.idw
50
8
2
1.1
7
1.3
WMNAA740 seal detail
A-A ( 1:15 )
1.4
POS
1.4
2
3
4
1
1.1
1.2
1.3
7
8
5
6
9
QTY
1
12
2
6
1
1
2
1
1
2
2
2
2
PART NO
BAMAA001
BBMAA000
BCMAA000
BNRBA010
FKCFA080
FDBJA001
FFCUA000
FJBEA020
FMAUKP00
MFRNA015
WBMBA740
WJMAA000
WKMBA000
Specifications are subject to change without prior notification
DESCRIPTION
H70 BEARING KIT
BEARING - H70 INNER (32213)
BEARING FOR H70 OUTER (32210)
H70 TRIPPLE LIP SEAL
Split Pin 6 X 80
WHEEL STUD 18 X 55 (PC10.9-12.9)
1 1/2"UNF CASTELLATED NUT
8 X 20 SOCKET HEAD CAP SCREW
WASHER 41 X 70 X 4
SEAL SPACER
H70 DUAL WELDED STUB MAINSTREAM
H70 HUB
H70 CAP
From serial number 6714
Including 6586, 6666, 6703
C
553
C
BOLT ON DISC 24 x 6 filler
GDADA024
L:\Inventor\Parts\GD-\GDADA024.idw
June 2018
6
2
2
5
4
3
8
3
4
1
7
Specifications are subject to change without prior notification
POS
7
8
5
6
3
4
1
2
QTY
1
1
4
4
2
2
1
4
PART NO
D24DSB03
FABGA030
FABHA040
FABHA045
FFBHA000
FMCGE000
GNANA01A
MACGA255A
DESCRIPTION
24" x 1/4"(610x6)4 bolt scalloped
12 X 30 1.75 BOLT
BOLT M16 X 40 PC 8.8
16 X 45 2mm BOLT
NUT NYLOC M16 P TYPE PC8 ZINC
M12 WASHER 1/2" type 1HARD ZYP
STUB AXLE - BOLT ON DISC
H30 DUST CAP COVER(40 x 6 X 255mm)
51
FIELDBOSS and TINY 230 DISC SET
3
15 2
2 6 16
15
9 16 10 16 10 16 10 1 1 14 12 15
3
13
L:\Inventor\Fieldboss\gang 4d,28x6s filler.idw
52
11
Note: When disc thickness changes the spool length must also change.
POS PART NO DESCRIPTION
1 BGB100B1
2 BHB100B1
3 BNTAA000
4 D22CSB04
5 D22CSB05 DISC 22"x6mm 4FILLER 6BOLT
6 D24CSB05/*** 24" X 1/4" (610 X 6) 6 BOLT FILLER
7 D24DSB02
8 D24DWB01
9 D26DSB26-*** DISC 26" X 6mm SCALLOPED 6 BOLT
9 D26DWB02
9 D26ESB02
9 D26EWB02
9 D26FSB02
1 1/2" 6 BOLT HOUSING (lead) BEARING FITTED
1 1/2" 6 BOLT HOUSING (thrust) BEARING FITTED
DUST COVER -1 1/2" (38mm) AXLE
DISC 22"x5mm 10 SCALLOPED 6BLT
DISC 24"x6mm 10SCALLOPED 6BLT
DISC 24" x 6 mm FLUTED 6BOLTS
DISC 26 x 6mm FLUTED 6 BOLTS
DISC 26"x8mm 10SCALLOPED 6BLT
DISC 26 x 8mm FLUTED 6 BOLT
DISC 26"x10mm,10 SCALLOPED 6BT
10 D28DSB08/*** DISC 28"x6mm SCALLOPED 6BLT
10 D28DWB01
10 D28ESB01
DISC 28"x6mm FLUTED 6 BOLT
DISC 28"x8mm 10SCALLOPED 6BLT
POS PART NO
10 D28EWB01
10 D28FSB02
10 D28FW01
10 D2SESB02
11 FAAJA550
11 FAAJA790
11 FAAJB020
11 FAAJB260
11 FAAJB490
12 FFBJA003
13 FHDSA035
14 FMCJG000
15 FMEUGP00
16 MEGRA226
16 MEGRA228
16 MEGRA230
Specifications are subject to change without prior notification
DESCRIPTION
DISC 28"X 8mm FLUTED 6 BOLT
DISC 28"x10mm 10SCALLOPED 6BLT
DISC 28"x 10mm FLUTED 6 BOLT
DISC 26 X 8 SCALLOPED 6 BOLT
M20 BOLT - 3 DISC 230 (550mm)
M20 BOLT - 4 DISC 230 (785mm)
M20 BOLT - 5 DISC 230 (1025mm)
M20 BOLT - 6 DISC 230(1255mm)
M20 BOLT - 7 DISC 9" (1490mm)
M20 CONE LOCK NUT CLASS 10
1 1/2" CONICAL SPRING
M20 WASHER 3/4" F436 HARD
4mm SPACER 40 SQUARE
SPOOL 219 (225mm) 10mm DISC
SPOOL 219 (227mm) 8mm DISC
SPOOL 219mm (229mm) 6mm DISC
From serial number 6714
Including 6586, 6666, 6703
ARTICULATED PULLS
80 THRU
90
73 THRU
90
GPEBF00C CONSTRUCTION TONGUE
75mm PIN (PAINTED GOLD)
GPCATA5C
CONSTRUCTION ARTIC
PULL ASSY
GPEBF000 CAT 5
ARTICULATED TONGUE
GPCATA5 CAT 5
ARTICULATED PULL ASSY.
54 THRU
82
41 THRU
GPDBF000 CAT 4
ARTICULATED TONGUE
GPCATA4 CAT 4
ARTICULATED PULL ASSY.
82
34 THRU
GPCBF000 CAT 3
ARTICULATED TONGUE
GPCATA3 CAT 3
ARTICULATED PULL ASSY.
GPBBF000 CAT 1-2
ARTICULATED TONGUE
GPCATA1-2 CAT 1-2
ARTICULATED PULL ASSY.
62
L:\Inventor\Parts\GP-\GPALL.idw
June 2018
10
Specifications are subject to change without prior notification
9
8
6
2
POS
9
10
7
8
5
6
3
4
1
2
QTY
10
1
8
1
1
2
6
2
2
1
PART NO
BMCAA000
CCDDA002
FABJA075
FABJA080
FFBJA000
FHKDC091
FMCJG000
FYBCC000
GPCBF000
GPFAB000
DESCRIPTION
GREASE NIPPLE 1/8 BSP
SPRING RETAINER
BOLT M20 X 75 pc 8.8 COARSE
BOLT M20 X 80 pc 8.8 COARSE
NYLOC NUT M20 P TYPE 2.5
EXTENSION SPRING 98 X 25 X 3.15
M20 WASHER 3/4" F436 HARD
8mm D SHACKLE
CAT 3 FLOPPY SWIVEL TONGUE
ARTIC. PULL SIDE PLATE ASSY
FIT SEAL BACKWARDS TO ALLOW GREASE TO PASS.
10
53
FIXED PULL TONGUES
74
85
6
1
70
2
4
5
58
7
5
80
12
50
15
15
10
2
4
1
48
30
POS
1
2
QTY
10
GPBAA500 / GPCATF5
CAT 5 FIXED PULL ASSY
PART NO
FABJA070
DESCRIPTION
BOLT M20 X 70 pc
10.9 COARSE
10 FFBJA000 NYLOC NUT M20 P
TYPE 2.5
3
4
5
1
20
1
FKDYA000
FMCJG000
6 1
L:\Inventor\Parts\GP-\GPALL.idw
CIRCLIP 95mm
M20 WASHER 3/4"
F436 HARD
GPBAA04-5 CAT 4-5 FIXED PULL
TONGUE
MDBUA085 CAT 5 PULL BUSH
POS
1
2
3
4
5
7
QTY
10
GPBAA005 / GPCATF4
CAT 4 FIXED PULL ASSY
PART NO
FABJA070
DESCRIPTION
BOLT M20 X 70 pc
10.9 COARSE
10
1
20
1
1
FFBJA000
FKDYA000
FMCJG000
GPBAA04-5
NYLOC NUT M20 P
TYPE 2.5
CIRCLIP 95mm
M20 WASHER 3/4"
F436 HARD
CAT 4-5 FIXED PULL
TONGUE
MDDTA068A CAT 4 PULL BUSH
POS
8
9
10
2
11
4
12
QTY
2
1
8
8
1
16
1
GPBAA400 / GPCAT3F
CAT 3 FIXED PULL ASSY
PART NO
CCCZH000
CGCTU000
FABJA065
FFBJA000
FKDZA003
FMCJG000
MDDRA067
A
DESCRIPTION
PULL TONGE S/PLATES
PLATE 50mm PULL
TONGUE
BOLT M20 X 65 pc 10.9
COARSE
NYLOC NUT M20 P
TYPE 2.5
CIRCLIP 85mm
M20 WASHER 3/4" F436
HARD
CAT 3 HARDENED BUSH
GPBAA007 / GPCATF1-2
CAT 0 FIXED PULL ASSY
POS
8
QTY
2
PART NO
CCCZH000
13
10
2
14
15
1
4
4
1
1
CGCTP001
FABJA065
FFBJA000
FKDZA060
MDDRA049 a
DESCRIPTION
PULL TONGE
S/PLATES
CAT 0- 3 FIXED
PULL TONGUE
BOLT M20 X 65 pc 10.9
COARSE
NYLOC NUT
M20 P TYPE 2.5
CIRCLIP 60mm
CAT 0 PULL
BUSH
54
Specifications are subject to change without prior notification
From serial number 6714
Including 6586, 6666, 6703
108 Folding Field Boss Gangs 6mm RHS
ITEM QTY PART NO.
DESCRIPTION ITEM QTY PART NO.
DESCRIPTION
4
4.1
4.2
4.3
1
2
3
5
5.1
86 FABHA065
86 FFBHA000
43 GFXAA200
43 GFXBA200
1 MCCHA200
1 FFAFA000
1 FEBFA040
BOLT M16 X 65 PC 8.8
NUT NYLOC M16 P TYPE PC8 ZINC
SCRAPER - LEFT
SCRAPER - RIGHT
SCRAPER PAD (50x6x200)
M10 Hex Nut ZINC AS1112
BOLT M10 X 35
1 GRGU100-108-2 100 TO 108 PLATE GANG 2
2 MJAMB181A AXLE 1 1/2"(1181) 5 DISC- 230
6
6.1
7
1 GRGU100-108-4 100 TO 108 PLATE GANG 4
4 MJAMB181A AXLE 1 1/2"(1181) 5 DISC- 230
1 GRGU100-108-6 100 TO 108 PLATE GANG 6
7.1
8
2 MJAMB181A
1 GRGU108-1
8.1
26 MAEJA080A
8.2
11 FABHA090
8.3
11 FFBHA000
8.4
3 MJAMA944A
AXLE 1 1/2"(1181) 5 DISC- 230
108 PLATE GANG 1
SCRAPER LUG FLAT 65 X 10 (80mm)
BOLT M16 X 90 PC 10.9 Z/P H/T~
NUT NYLOC M16 P TYPE PC8 ZINC
AXLE 1 1/2"(946) 4 DISC-230
8.4
ITEM QTY
8.5
1
PART NO.
MJAMB181A
9
9.1
1 GRGU108-3
1 MJAMB181A
9.2
10
3 MJAMA944A
1 GRGU108-5
10.1
2 MJAMA944A
10.2
2 MJAMB181A
11 1 GRGU108-7
11.1
2 MJAMB181A
11.2
2 MJAMA944A
8.5
8.3
5.1
5.1
8.4
8.4
GRGU108
DESCRIPTION
AXLE 1 1/2"(1181) 5 DISC- 230
108 PLATE GANG 3
AXLE 1 1/2"(1181) 5 DISC- 230
AXLE 1 1/2"(946) 4 DISC-230
108 PLATE GANG 5
AXLE 1 1/2"(946) 4 DISC-230
AXLE 1 1/2"(1181) 5 DISC- 230
108 PLATE GANG 7
AXLE 1 1/2"(1181) 5 DISC- 230
AXLE 1 1/2"(946) 4 DISC-230
8.2
B
9.1
9.2
9.2
1
3
2
2
4.2
4.3
9.2
8 1
9
6.1
6.1
6.1
5
4
6.1
10.1
7
6
10.1
4.1
10.2
10.2
11
B ( 1 : 8 )
7.1
10
7.1
11.2
11.2
11.1
L:\Inventor\Parts\GR-\GRGU108.idw
June 2018
11.1
Specifications are subject to change without prior notification
55
A ( 1 : 63 )
B
4.2
4.3
5
5.1
3
4
1
2
4.1
108 Folding Field Boss Gangs 9mm
ITEM QTY PART NO.
DESCRIPTION ITEM QTY PART NO.
86 FABHA065
86 FFBHA000
43 GFXAA200
43 GFXBA200
1 FEBFA040
1 FFAFA000
1 MCCHA200
1 GRGU100-108-2-9
2 MJAMB181A
BOLT M16 X 65 PC 8.8
NUT NYLOC M16 P TYPE PC8 ZINC
SCRAPER - LEFT
SCRAPER - RIGHT
BOLT M10 X 35
M10 Hex Nut ZINC AS1112
SCRAPER PAD (50x6x200)
GANG 2-9mm 100-112 FIIELD BOSS
AXLE 1 1/2"(1181) 5 DISC- 230
8.1
8.2
8.3
8.4
6
6.1
7
7.1
8
1 GRGU100-108-4-9
4 MJAMB181A
1 GRGU100-108-6-9
2 MJAMB181A
1 GRGU108-1-9
11 FABHA090
11 FFBHA000
26 MAEJA080A
3 MJAMA944A
DESCRIPTION
GANG 4 - 100-112 FIELD BOSS
AXLE 1 1/2"(1181) 5 DISC- 230
GANG 6 - 100-112 FIELD BOSS
AXLE 1 1/2"(1181) 5 DISC- 230
GANG 1-9mm 108 FIELD BOSS
BOLT M16 X 90 PC 10.9 Z/P H/T~
NUT NYLOC M16 P TYPE PC8 ZINC
SCRAPER LUG FLAT 65 X 10 (80mm)
AXLE 1 1/2"(946) 4 DISC-230
ITEM QTY
10.1
10.2
11
11.1
11.2
8.5
9
9.1
9.2
10
PART NO.
1 MJAMB181A
1 GRGU108-3-9
3 MJAMA944A
1 MJAMB181A
1 GRGU108-5-9
2 MJAMA944A
2 MJAMB181A
1 GRGU108-7-9
2 MJAMA944A
2 MJAMB181A
8.4
8.5
5.1
5.1
8.4
8.4
9.2
B
9.1
3
9.1
9.1
6.1
6.1
6.1
5
8
4.1
2
1
4
8.1
8.2
8.3
GRGU108-9
DESCRIPTION
AXLE 1 1/2"(1181) 5 DISC- 230
GANG 3-9mm 108 FIELD BOSS
AXLE 1 1/2"(946) 4 DISC-230
AXLE 1 1/2"(1181) 5 DISC- 230
GANG 5-9mm 108 FIELD BOSS
AXLE 1 1/2"(946) 4 DISC-230
AXLE 1 1/2"(1181) 5 DISC- 230
GANG 7-9mm 108 FIELD BOSS
AXLE 1 1/2"(946) 4 DISC-230
AXLE 1 1/2"(1181) 5 DISC- 230
4.2
9
6.1
7
6
10.1
4.3
10.1
10.2
11
7.1
3
7.1
4
10.2
B ( 1 : 10 )
10 11.1
11.1
11.2
11.2
L:\Inventor\Parts\GR-\GRGU108-9.idw
56
Specifications are subject to change without prior notification
From serial number 6714
Including 6586, 6666, 6703
A ( 1 : 65 )
B
POS
13
14
15
16
9
10
11
12
7
8
5
6
3
4
1
2
HYDRAULIC KIT F BOSS 100-108 9mm FRAME
QTY
1
2
2
1
1
1
1
1
2
1
1
1
1
1
1
1
PART NO
GDFGL006
HFALL50-BA
HGCZA350A
HGCZB500A
HGCZB600A
HGCZC800A
HGCZC800B
HGCZD500Q
HGCZD600A
HGCZD700Q
HGCZE500A
HGCZF200A
HGCZG900Q
HGCZH100A
HGCZK000A
HHAAAA77
DESCRIPTION
TWIN PITCH CONTROL
RETRACT LINE RELIEF VALVE KIT
HYD HOSE 3/8" E26 (350)
HYD HOSE 3/8" E26 (1500)
HYD HOSE 3/8" E26 (1600)
HYD HOSE 3/8" E26 (2800)
HYD HOSE 3/8" E26 (2800) QR 1/2"BSP FEMALE 3/4UNO MALE
HYD HOSE 3/8" E26 (3500) QR 3/4" JIC FEMALE 3/4UNO MALE
HYD HOSE 3/8" E26 (3600)
HYD HOSE 3/8" E26 (3700) QR 3/4" JIC FEMALE 3/4UNO MALE
HYD HOSE 3/8" E26 (4500)
HYD HOSE 3/8" E26 (5200)
HYD HOSE 3/8" E26 (6900) QR 3/4" JIC FEMALE 3/4UNO MALE
HYD HOSE 3/8" E26 (7100)
HYD HOSE 3/8" E26 (11000)
TEE 3/4JICM 3/4JICM 3/4JICM S19-121212
POS
29
30
31
32
25
26
27
28
21
22
23
24
17
18
19
20
QTY
1
1
1
1
1
2
1
1
32
1
26
1
3
3
8
6
PART NO
GHPF0002-4
DESCRIPTION
HHABAM07
HHABAM07A
HHZWUA07B
HHZWUA07R
HJBCA000
HJBEA000
HJBFA000
HMDEA004
HXEAF000
HXEBF000
HXECF000
HYP500/48
HZP425/12D
HZP450/12D
ELBOW 3/4 JICM 3/4 UN O MALE
ELBOW RESTRICTOR3/4 JICM 3/4 UN O
HYD Coupling COVER BLUE
HYD Coupling COVER RED
20mm DOUBLE HOSE CLAMP SHELL
STACKING BOLT RCD-3BS
TOP PLATE DOUBLE FOR GROUP 3
DEPTH STOP - CAPTIVE PAIR
HEAT SHRINK RED - WHEEL LIFT
HEAT SHRINK GREEN - FOLD
HEAT SHRINK BLUE- PITCH CONTROL
HYD. CYLINDER 5" x 48" 2" Rod
HYD CYL.4.25"x12" D/S 1.38"rod
HYD. CYL. 4.5 X 12 DS 1.5"
HZP500/12D55 HYD. CYLINDER 5 X 12 DS 55 ROD
HZP550/12D HYD. CYLINDER 5.5 X 12 DS 2.25" ROD
18
17 15 30 11 17
28
18
6
4
28
5
17
11
17
18 3 16
12
13
31
15
17
29
14
17
L:\Inventor\Parts\GH-\GHPF0002-4.idw
June 2018
18
17
16
13
17
32 12 9 10 18
21
Specifications are subject to change without prior notification
18
1
8
2
A
13
7
10
13 7 8
A ( 1 : 10 )
20
19
57
HYDRAULIC KIT F BOSS 100-108 9mm FRAME
POS QTY PART NO DESCRIPTION
3 1 HGCZA350A
4 1 HGCZB500A
HYD HOSE 3/8" E26 (350)
HYD HOSE 3/8" E26 (1500)
5 1 HGCZB600A HYD HOSE 3/8" E26 (1600)
6 1 HGCZC800A HYD HOSE 3/8" E26 (2800)
7 2 HGCZC800B HYD HOSE 3/8" E26 (2800) QR 1/2"BSP FEMALE 3/4UNO MALE
8 1 HGCZD500Q HYD HOSE 3/8" E26 (3500) QR 3/4" JIC FEMALE 3/4UNO MALE
9 1 HGCZD600A HYD HOSE 3/8" E26 (3600)
10 1 HGCZD700Q HYD HOSE 3/8" E26 (3700) QR 3/4" JIC FEMALE 3/4UNO MALE
11 1 HGCZE500A
12 1 HGCZF200A
HYD HOSE 3/8" E26 (4500)
HYD HOSE 3/8" E26 (5200)
13 2 HGCZG900Q HYD HOSE 3/8" E26 (6900) QR 3/4" JIC FEMALE 3/4UNO MALE
14 1 HGCZH100A HYD HOSE 3/8" E26 (7100)
15 1 HGCZK000A HYD HOSE 3/8" E26 (11000)
7
13
8
7
13
10
7
7
14 9
8 10
9
11
15
15
12
11
13
3
13
12
5
L:\Inventor\Parts\GH-\GHPF0002-4.idw
58
6
Specifications are subject to change without prior notification
4
15
14
From serial number 6714
Including 6586, 6666, 6703
HYD. CYLINDER 5 X 12 DS 55 ROD
2
6
3
8
4
7.5
7.4
7.3
7.2
7.6
7.1
7.7
1
ITEM
7.2
7.3
7.4
7.5
7.6
7.7
8
5
6
7
7.1
3
4
1
2
QTY
1
1
2
1
1
1
1
1
1
2
2
2
2
1
1
PART NO.
HLFEG550
HMCBA001
BMAAA006
FABDA016
FGHPA072
FKBDA000
HKPB0002
HKBS 81-6594330
HKBS ORING248-70
HKBS/ORINGBU248
HKAS 605-4306100
HKAS 831-4531400
HKB ORING049-70
HKAS/ORING030-90
MDAEA006
HZP500-12D55
DESCRIPTION
PTE ROD 12" x 55mm(1.75" UNF)
CLEVIS 1.25"PIN 1.75"UNF
STRAIGHT GREASE NIPPLE 6mm
SET SCREW 6 X 15
PIN 1 1/4" ANTI ROT. GREASABLE
RAM PIN CLIP
PTE S/KIT SHP 5.0" X 55mm ROD
PISTON SEAL 4.0" HALLITE "81"
O RING BS 248 70 DURO - 5"
BACK UP FOR O RING BS 24 - 5"
ROD SEAL "605" 55 X 65 X 10
ROD WIPER TYPE 831 55mm ROD 65
O RING BS 049 70 DURO - 5"
O RING BS 030 90 DURO - 2"
HEADED BUSH
L:\Inventor\Parts\GH-\GHPF0002-4.idw
June 2018 Specifications are subject to change without prior notification
59
HYD. CYLINDER 5.5 X 12 DS 2.25" ROD
3
7
5.7
5.6
5.4
5.3
5.5
5.1
5.2
1
8
2
6
5.7
6
7
8
5.3
5.4
5.5
5.6
ITEM
1
2
3
4
5
5.1
5.2
1
2
1
1
1
1
1
1
1
1
2
1
QTY
2
2
2
PART NO.
BMAAA006
FABDA016
FGHPA072
FKBDA000
HKRB0000
HKBS 53-65944101
HKAS/ORING030-90
HKBS ORING252-70
HKBS ORINGBU252
HKBS ORING160-70
HKAS 513-8838710
HKAS 520-8881610
HLFEG550
HMCBA001
MDAEA006
HZP550-12D
DESCRIPTION
STRAIGHT GREASE NIPPLE 6mm
SET SCREW 6 X 15
PIN 1 1/4" ANTI ROT. GREASABLE
RAM PIN CLIP
PTE S/KIT SHP STD 5.5" X 2.25"
PISTON SEAL 5.5" HALLITE "53"
O RING BS 030 90 DURO - 2"
O RING BS 252 70 DURO
BACK UP FOR O RING BS 252
O RING BS 160 70 DURO
ROD SEAL "513"2.25"X2.75"X.375
ROD WIPER "520"2.25"X2.75X.25
PTE ROD 12" x 55mm(1.75" UNF)
CLEVIS 1.25"PIN 1.75"UNF
HEADED BUSH
L:\Inventor\Parts\GH-\GHPF0002-4.idw
60
Specifications are subject to change without prior notification
From serial number 6714
Including 6586, 6666, 6703
5
PTE 100-108 F/BOSS RAM KIT 12mm
15
11
GHPF0002-5
L:\Inventor\Parts\GH-\GHPF0002-5.idw
June 2018
4
6
5
11
12
8
13
2
7
3
3
14
14
12
13
7
10
9
15
9
POS
4
5
2
3
6
7
8
9
10
11
12
13
14
15
PART NO
HFALL50-BA
HGCZA350A
HGCZB500A
HGCZB600A
HGCZC800A
HGCZC800B
HGCZD500Q
HGCZD600A
HGCZD700Q
HGCZE500A
HGCZF900A
HGCZG600A
HGCZG900Q
HGCZK600A
DESCRIPTION
RETRACT LINE RELIEF VALVE KIT
HYD HOSE 3/8" E26 (350)
HYD HOSE 3/8" E26 (1500)
HYD HOSE 3/8" E26 (1600)
HYD HOSE 3/8" E26 (2800)
HYD HOSE 3/8" E26 (2800) QR 1/2"BSP
FEMALE 3/4UNO MALE
HYD HOSE 3/8" E26 (3500) QR 3/4" JIC
FEMALE 3/4UNO MALE
HYD HOSE 3/8" E26 (3600)
HYD HOSE 3/8" E26 (3700) QR 3/4" JIC
FEMALE 3/4UNO MALE
HYD HOSE 3/8" E26 (4500)
HYD HOSE 3/8" E26 (5900) 3/4JIC
FEMALE 3/4JIC FEMALE
HYD HOSE 3/8" E26 (6600)
HYD HOSE 3/8" E26 (6900) QR 3/4" JIC
FEMALE 3/4UNO MALE
HYD HOSE 3/8" E26 (11600)
Specifications are subject to change without prior notification signed ________________ __ / __ / __
1
2
1
1
1
1
1
1
QTY
1
1
1
1
1
2
CHECKED
61
PTE 100-108 F/BOSS RAM KIT 12mm
13
14
15
16
9
10
11
12
7
8
5
6
3
4
1
2
POS QTY PART NO DESCRIPTION
1 GDFGL006 TWIN PITCH CONTROL
1 HFALL50-BA RETRACT LINE RELIEF VALVE KIT
1 HGCZA350A HYD HOSE 3/8" E26 (350)
1 HGCZB500A HYD HOSE 3/8" E26 (1500)
1 HGCZB600A HYD HOSE 3/8" E26 (1600)
1 HGCZC800A HYD HOSE 3/8" E26 (2800)
2 HGCZC800B HYD HOSE 3/8" E26 (2800) QR 1/2"BSP FEMALE 3/4UNO MALE
1 HGCZD500Q HYD HOSE 3/8" E26 (3500) QR 3/4" JIC FEMALE 3/4UNO MALE
1 HGCZD600A HYD HOSE 3/8" E26 (3600)
1 HGCZD700Q HYD HOSE 3/8" E26 (3700) QR 3/4" JIC FEMALE 3/4UNO MALE
1 HGCZE500A HYD HOSE 3/8" E26 (4500)
1 HGCZF900A HYD HOSE 3/8" E26 (5900) 3/4JIC FEMALE 3/4JIC FEMALE
1 HGCZG600A HYD HOSE 3/8" E26 (6600)
2 HGCZG900Q HYD HOSE 3/8" E26 (6900) QR 3/4" JIC FEMALE 3/4UNO MALE
1 HGCZK600A HYD HOSE 3/8" E26 (11600)
2 HHAAAA77 TEE 3/4JICM 3/4JICM 3/4JICM S19-121212
GHPF0002-5
POS QTY PART NO DESCRIPTION
28
29
30
31
32
24
25
26
27
17
18
19
20
8 HHABAM07 ELBOW 3/4 JICM 3/4 UN ORING MALE
7 HHABAM07A ELBOW RESTRICTOR3/4 JICM 3/4 UN O
3 HHZWUA07B HYD Coupling COVER BLUE
3 HHZWUA07R HYD Coupling COVER RED
21 32 HJBCA000
22 1 HJBEA000
23 26 HJBFA000
1 HMDEA004
1 HXEAF000
1 HXEBF000
1 HXECF000
20mm DOUBLE HOSE CLAMP SHELL
STACKING BOLT RCD-3BS
TOP PLATE DOUBLE FOR GROUP 3
DEPTH STOP - CAPTIVE PAIR
HEAT SHRINK RED - WHEEL LIFT
HEAT SHRINK GREEN - FOLD
HEAT SHRINK BLUE- PITCH CONTROL
HYD. CYLINDER 5" x 48" 2" Rod 2 HYP500/48
1 HZP425/12D HYD CYL.4.25"x12" D/S 1.38"rod
1 HZP450/12D HYD. CYL. 4.5 X 12 DS 1.5"
1 HZP500/12D55 HYD. CYLINDER 5 X 12 DS 55 ROD
1 HZP550/12D HYD. CYLINDER 5.5 X 12 DS 2.25" ROD
13
15
32
29
12
28
5
4
6
28
9
3
14
14
12
5
11
1
10
7
31
15
30
8
7
2
11
L:\Inventor\Parts\GH-\GHPF0002-5.idw
62
Specifications are subject to change without prior notification
From serial number 6714
Including 6586, 6666, 6703
RETRACT LINE RELIEF VALVE KIT
TO THE BASE END OF THE MASTER CYLINDER
SET TO 1000 PSI MAX.
GAUGE
TO THE ROD END OF THE SMALLEST CYLINDER
TO THE TRACTOR 9
1
7 8
2
3
10
4
5
L:\Inventor\Parts\GH-\GHPF0002-5.idw
June 2018
HFALL50-BA
5
9
8
6
2
11
7
3
10
9
Specifications are subject to change without prior notification
ITEM
5
6
7
3
4
1
2
QTY
2
1
2
2
1
1
2
8
9
10
11
2
1
2
3
PART NO.
HHAABA07
HHACAA01
HHACAA02
HHACAA03
HHACAA06
HHACAS07
HHACBF12
HHBCS2312
HHBEM000
HHKY0000
HHMWA008
DESCRIPTION
TEE 3/4JICF 3/4JICM 3/4JICM
1/2" BSPP RETAINING RING 36B-08
1/2" BSPP O RING ROD-BP08
1/2" BSPP NUT
BULKHEAD 1/2" BSP
TEST POINT ADAPTOR 3/4 JIC - M16
STRAIGHT 1/2BSPTM 3/4 JICF SWIVEL
(S71-0812)
ELBOW 45DEG JIC -12-12
STRAIGHT 3/4 JIC M 1/2 BSPP ORING M
IN LINE HYDRAULIC FILTER
INLINE RELIEF VALVE 1/2" BSP
63
HYD CYL.4.25"x12" D/S 1.38"rod
7
3
1
9
2
4
5.2
5.4
5.5
5.6
5.1
5.3
6
8
6
7
8
9
5.4
5.5
5.6
5.1
5.2
5.3
ITEM
1
4
5
2
3
1
1
1
1
1
1
2
1
1
1
QTY
2
2
1
2
2
PART NO.
BMAAA006
FABDA016
FGHPA072
FKBDA000
HKKB0SLP
HKBS
53-0082211
HKAS
520-8881110
HKBS
ORING119.90
HKAS
513-8835110
HKBS
ORING242-90
HKBS
ORING046-70
HLFEG138
HMCBA000
HNZA0000
MDAEA006
HZP425-12D
DESCRIPTION
STRAIGHT GREASE NIPPLE
6mm
SET SCREW 6 X 15
PIN 1 1/4" ANTI ROT.
GREASABLE
RAM PIN CLIP
PTE S/KIT SLP4.25" X 1.38"
ROD
PISTON SEAL 4.25" HALLITE
"53"
ROD
WIPER"520"1.375"X1.75"X.18
O RING BS 119 90 DURO
ROD SEAL
"513"1.375"X1.75"X.37
O RING BS 242 90 DURO
O RING BS 046 70 DURO
PTE ROD 12" x 1.375"(1.25"UNF)
CLEVIS 1.25" PIN 1.25"UNF D/S
PHASING VALVE FOR PTE
CYINDER
HEADED BUSH
L:\Inventor\Parts\GH-\GHPF0002-5.idw
64
Specifications are subject to change without prior notification
From serial number 6714
Including 6586, 6666, 6703
HYD. CYL. 4.5 X 12 DS 1.5"
7
3
1
4
2
9
5.3
5.2
5.4
5.5
5.1
5.6
6
ITEM
3
4
1
2
5
5.1
QTY
2
2
2
2
1
1
5.2
5.3
5.4
5.5
5.6
6
7
8
1
1
1
1
1
1
1
1
PART NO.
BMAAA006
FABDA016
FGHPA072
FKBDA000
HKMB0SLP
HKBS/81-659423
0
HKAS
513-8835410
HKAS/520-88812
10
HKBS
ORING244-90
HKBS
ORING047-70
HKBS
ORING121-90
HLFEG150
HMCBA000
HNZA0000
9 2 MDAEA006
HZP450-12D
DESCRIPTION
STRAIGHT GREASE NIPPLE 6mm
SET SCREW 6 X 15
PIN 1 1/4" ANTI ROT. GREASABLE
RAM PIN CLIP
PTE S/KIT SLP 4.5" X 1.5" ROD
PISTON SEAL 4.5" HALLITE "81"
ROD SEAL "513"1.5"X1.875"X.375
ROD WIPER"520"1.5"X1.875"X .18
O RING BS 244 90 DURO
O RING BS 047 70 DURO
O RING BS 121 90 DURO
PTE ROD 12" x 1.5" (1.25"UNF)
CLEVIS 1.25" PIN 1.25"UNF D/S
PHASING VALVE FOR PTE
CYINDER
HEADED BUSH
8
L:\Inventor\Parts\GH-\GHPF0002-5.idw
June 2018 Specifications are subject to change without prior notification
65
1
2
3
5
6
7
10
11
12
13
HYDRAULIC KIT F BOSS 100-112 12mm
FRAME - WING LOCK VALVES
ITEM QTY PART NO.
DESCRIPTION ITEM QTY PART NO.
DESCRIPTION
8
9
1 GDFGL006
1 HFALL50-BA
2 HGCZA350A
2 HGCZB500A
2 HGCZC800B
1 HGCZD500Q
1 HGCZD600A
1 HGCZD700Q
1 HGCZE500A
1 HGCZF900A
1 HGCZG600A
2 HGCZG900Q
TWIN PITCH CONTROL
RETRACT LINE RELIEF VALVE KIT
HYD HOSE 3/8" E26 (350)
HYD HOSE 3/8" E26 (1500)
HYD HOSE 3/8" E26 (2800) QR 1/2"BSP
FEMALE 3/4UNO MALE
HYD HOSE 3/8" E26 (3500) QR 3/4" JIC
FEMALE 3/4UNO MALE
HYD HOSE 3/8" E26 (3600)
HYD HOSE 3/8" E26 (3700) QR 3/4" JIC
FEMALE 3/4UNO MALE
HYD HOSE 3/8" E26 (4500)
HYD HOSE 3/8" E26 (5900)
HYD HOSE 3/8" E26 (6600)
HYD HOSE 3/8" E26 (6900) QR
17
18
19
20
14
15
16
21
22
23
24
25
1 HGCZK600A
2 HGGDB222
2 HHAAAA77
2 HHABAA07
12 HHABAM07
2 HHABAM07A
2 HHACBF12
6 HHBEM000
2 HHHWBB07
3 HHZWUA07B
3 HHZWUA07R
32 HJBCA000
HYD HOSE 3/8" E26 (11600)
HYDRAULIC TUBE 3/8" - 3/4"JIC (1222)
TEE 3/4JICM 3/4JICM 3/4JICM S19-121212
ELBOW 3/4J.I.CM. 3/4JICF (S15-1212)
ELBOW 3/4 JICM 3/4 UN O MALE
ELBOW RESTRICTOR3/4 JICM 3/4 UN O
STRAIGHT 1/2BSPTM 3/4 JICF SWIVEL
STRAIGHT 3/4 JIC M 1/2 BSPP ORING M
DUAL COUNTERBALANCE VALVE
HYD Coupling COVER BLUE
HYD Coupling COVER RED
20mm DOUBLE HOSE CLAMP SHELL
21
32
33
18
15
22 22 15
GHPF0002-5B
33
34
35
36
ITEM QTY
26 1
PART NO.
HJBEA000
27
28
29
30
31
32
26 HJBFA000
1
1
1
1
HMDEA004
HXEAF000
HXEBF000
HXECF000
DESCRIPTION
STACKING BOLT RCD-3BS
TOP PLATE DOUBLE FOR GROUP 3
DEPTH STOP - CAPTIVE PAIR
HEAT SHRINK RED - WHEEL LIFT
HEAT SHRINK GREEN - FOLD
2 HYP500/48
1
1
HZP425/12D
HZP450/12D
HEAT SHRINK BLUE- PITCH CONTROL
HYD. CYLINDER 5" x 48" 2" Rod
HYD CYL.4.25"x12" D/S 1.38"rod
HYD. CYL. 4.5 X 12 DS 1.5"
1 HZP500/12D55 HYD. CYLINDER 5 X 12 DS 55 ROD
1 HZP550/12D HYD. CYLINDER 5.5 X 12 DS 2.25" ROD
18
32
17
28
33
36
16
21
1
35
6
9
2
7
34
6
L:\Inventor\Parts\GH-\GHPF0002-5B.idw
66
Specifications are subject to change without prior notification
From serial number 6714
Including 6586, 6666, 6703
HYDRAULIC KIT F BOSS 100-112 12mm
FRAME - WING LOCK VALVES
14
10
GHPF0002-5B
L:\Inventor\Parts\GH-\GHPF0002-5B.idw
June 2018
10
11
15
7
12
6 5 13
15
5
3
13
11
8
9
8
6
12
14
ITEM
9
7
6
10
11
14
15
3
5
8
13
12
2
1
1
1
2
2
2
2
1
1
QTY
1
1
PART NO.
HGCZD700Q
HGCZD500Q
HGCZC800B
HGCZE500A
HGCZF900A
HGCZK600A
HGCZD600A
HGCZG900Q
HGCZG600A
HGGDB222
HGCZA350A
HGCZB500A
Specifications are subject to change without prior notification
DESCRIPTION
HYD HOSE 3/8" E26 (3700) QR 3/4" JIC FEMALE 3/4UNO MALE
HYD HOSE 3/8" E26 (3500) QR 3/4" JIC FEMALE 3/4UNO MALE
HYD HOSE 3/8" E26 (2800) QR 1/2"BSP FEMALE 3/4UNO MALE
HYD HOSE 3/8" E26 (4500)
HYD HOSE 3/8" E26 (5900)
HYD HOSE 3/8" E26 (11600)
HYD HOSE 3/8" E26 (3600)
HYD HOSE 3/8" E26 (6900) QR
HYD HOSE 3/8" E26 (6600)
HYDRAULIC TUBE 3/8" - 3/4"JIC (1222)
HYD HOSE 3/8" E26 (350)
HYD HOSE 3/8" E26 (1500)
67
5
6
14
DECAL KIT 100-112 FIELD BOSS
14 7 2 8 14 13 12 11 14
3
4
L:\Inventor\Parts\PA-\PDAEF004.idw
68
PDAEF004
5
14
1
4
15
14
1
4
14
4
6
10
14
3
5
6
14
3
14
6
7
4
5
8
ITEM QTY
1
2
3
2
1
3
4
3
3
1
1
PART NO.
PD000005
PD000046
PD000070
PD000074
PD000076
PD000079
PD000080
PD000081
DESCRIPTION
DECAL WARNING Stand Clear
DECAL Warning do not exceed 30 Kph
DECAL "FIELD BOSS"
DECAL 1 2 3 (30 X 130)
321 gang angle
DECAL GRIZZLY 100mm x 757mm
GRIZZLY DECAL 50mm
DECAL "CAUTION REMOVE TRANSPORT LOCKS"
ITEM QTY
9
10
1
1
11
12
13
14
15
PART NO.
PD000089
PD000090
1
1
1
PD000108
PD000151
PD000152
12 PD000GR40
1 PDAA0000
Specifications are subject to change without prior notification
DESCRIPTION
Decal "Quality assured company"
DEPTH STOP SIDE PLATE FITTING
INSTRUCTIONS
DECAL INJECTION HAZARD
DECAL WARNING HAZARDOUS
DECAL OPERATING INSTRUCTION. TRAILING
GREASE EVERY 40 HRS DECAL
ID PLATE
From serial number 6714
Including 6586, 6666, 6703
15 MAINTENANCE RECORD CHART
DATE PART NUMBER
1
17
18
15
16
19
13
14
11
12
8
9
6
7
10
4
5
2
3
June 2018 Specifications are subject to change without prior notification
NOTE
69
16 Problem Solving
PROBLEM
One side digging deeper than the other.
Ground left uneven.
a) Rams need rephasing.
b) Ploughing Shallow.
CAUSE
Ploughing with a large % of weight on wheels.
REMEDY a) Hold tractor control lever in fully open position on the lift side for 30 seconds.
b) Sometimes a large amount of set is required to
Ploughing with a large % of weight on wheels. be able to plough shallow and still plough every thing out.
c) Ploughing with too much set (especially secondary working).
c) Reduce set.
a) Machine travelling too fast.
b) Machine performing secondary work with too much set.
a) Forces each side of the machine uneven gangs not all on same set.
a) Slow down until soil pattern on worked ground is level.
b) Place all gangs on setting one. Rework.
a) Check setting.
b) Paddock has a ridge in it.
b) Plough down centre of the ridge.
Machine predominantly hangs to one side.
c) Tyre pressure uneven.
d) Rams not rephased.
c) Check tyre pressures. See Section 8.
d) Rephase as explained previously.
e) Ploughing with too much set (especially secondary working smaller machines) in free flowing soil.
f) Ploughing on side of hill.
Rib of unploughed ground in the middle of the work area.
Cutting edges out of adjustment.
a) Travelling too fast.
e) Reduce set to 1, reduce speed until seedbed is level.
f) Reduce Set.
Contact Grizzly Dealer.
a) Slow down.
Machine bouncing.
b) Tyre pressure too great.
c) Too much set for conditions.
b) Check tyre pressure. See Section 8.
c) Reduce set and/or slow down.
70 d) Not enough weight (or all of 5 above).
Specifications are subject to change without prior notification d) Add oil to outside wing beams (for extra weight).
From serial number 6714
Including 6586, 6666, 6703
16 Problem Solving
Folding machine wings ploughing deeper than centre section.
Straw or cotton wrapping around the edge of the disc.
Ridge left in the middle of the work.
Hollow or gutter left in the middle of the work.
a) Hydraulic rams out of phase.
b) Tyre pressure lower on wings.
a) Ground wet or soft.
a) Refer rephasing earlier.
b) Check tyre pressures. See Section 8.
a) Wait till condition more suitable. Can sometimes be helped by ploughing deeper.
b) Too much set and disc is bulldozing material. Scallop disc (straw tends to wrap in the scallop of the disc because it has nothing to cut against).
b) Reduce set, plough deeper.
a) Too much soil travelling through the rear discs.
b) Going too fast.
c) Front discs worn more then the rear discs.
a) Close-up the pitch control ram to reduce the soil flow through the rear discs.
b) Slow down.
a) Not enough soil travelling through the rear discs.
b) Going too fast.
c) Replace with new discs.
a) Extend the pitch control ram to increase the soil flow through the rear discs.
b) Slow down.
a) Working in wet conditions and dirt causes extra wear. a) Wait until soil conditions improve.
Excessive wear of disc spools.
(Please note: Some wear is normal) b) Scrapers set too close to spools.
b) Adjust scrapers to be approximately 10-12mm away.
Excessive scraper noise only detected when machine is working.
c) Scraper pivot bolt too tight.
Scraper pads move against the “back” of discs when under load.
c) Loosen pivot bolt nut to all scraper arms to move more freely.
Remove scraper and straighten it so that it does not contact disc. Alternatively, adjust by levering with a crowbar or similar tool.
June 2018 Specifications are subject to change without prior notification
71
PHASING PROBLEMS
Creeping
Air in the hydraulic system
A. Hose vibrating/squealing
B. Control valve shuddering
C. Lag in cylinder movement
D. Creeping when load is applied
By-passing of the piston
A. Both cylinder move together until Master is on depth stop then Slave stops
B. Both cylinders creep, Master cylinder stops when it hits the depth stop but the slave continues
Check valve or Tractor valve leaking
Master cylinder piston by-passing (1)
C. Master cylinder retracts but the slave extends slightly
Master cylinder piston by-passing (2)
D. Master cylinder stationary but not on depth stop, Slave creeps in
Slave cylinder piston by-passing
Cylinder moving at different rates
72
Cylinders connected the wrong way around
They should be connected in series so that the rod end of the larger cylinder is connected to the base of the smaller cylinder
Specifications are subject to change without prior notification
From serial number 6714
Including 6586, 6666, 6703
Bleeding
1. Ensure oil is clean and couplings are clean
2. If depth stops are fitted to the cylinders they should be adjusted so that the cylinder can be fully retracted before commencing the bleeding operation
3. Ensure oil level is topped up. Low oil levels and/or foaming oil is a common cause of unsuccessful bleeding
4. CAUTION!
During bleeding operation the master cylinder will fully extend before the next cylinder extends (otherwise injury may occur)
5. If equipment is likely to be damaged due to this motion then the ends of the cylinders must be disconnected and positioned so that the rods can move in and out freely
6. Purge all the air from the system by fully stroking the rams in both directions. Allow the oil to flow through the cylinders for about 2 minutes at each end of the stroke
7. In most cases the tractor should be run at idle only
8. Cylinder bleed better in extension with the rod ends up
9. Cylinder bleed better in retraction with the rod ends down
10. Horizontal cylinders bleed better if the valve is at the top
11. The system can be considered to be correctly bled when all the cylinders move together without any lag between them and there is no creep when load is applied to the cylinders
12. Other signs of air in the system can be hoses vibrating / squealing or the control handle shuddering
13. Minute air bubbles dissolved in the oil will not be totally eliminated until the oil is allowed to stand for 12 hours approx., then ultimate phasing performance will result
Re-phasing
• After initial bleeding the cylinders will only require occasional re-phasing during operation. This is done by fully extending the rams until all cylinders have reached the end of their stroke.
• There is a difference between bleeding and re-phasing. Bleeding is removing air from the circuit, re-phasing is synchronising the cylinders. Stop the re-phasing operation as soon as the cylinders have reached the end of the stroke.
• Holding the cylinders at the end of the stroke and allowing oil to flow for no reason will cause premature wear of the phasing valves.
• Cylinders should not require re-bleeding unless air has entered the system due to low oil level, or removing hoses/cylinders etc.
Fault Finding
If the system is free from air and the cylinders still creep, raise the machine and mark each rod with a "Nikko" pen a known distance (say
10mm) from the wiper or face of gland. Measure the movement of each cylinder rod to determine which cylinder is moving the most (Do not rely on the movement of the machine as this can give a false indication).
June 2018 Specifications are subject to change without prior notification
73
Master cylinder bypass
When all cylinders creep and the Master cylinder hits the depth stop but the Slave continues to creep.
Third cylinder bypass
When the Master cylinder lowers onto depth stop and the Second cylinder also stops but cylinder 3 creep down while cylinder 4 creep outward slightly.
Second cylinder bypass Fourth cylinder bypass
When the Master cylinder lowers onto depth stop and the Second cylinder continues to creep but the cylinder 3 & 4 creep outward slightly.
74
When the Master cylinder lowers onto depth stop and the Second and Third cylinders also stops but cylinder 4 creep down.
Specifications are subject to change without prior notification
From serial number 6714
Including 6586, 6666, 6703
Grizzly can make your work easier!
BANKER / CHANNELLER
The Banker/Channeller is designed specifically for water-tight bank and channel formation.
Applications include irrigation channels, flood irrigation, embankments, tree plantation rows, elevated seed bed preparation, salt reduction programs, contour farming, erosion control, levee banks and ect. Banker/Channeller’s linkage is compatible with quick hitch systems.
The machine is available in 10 up to 14 discs, with a wide or narrow frame.
WHEEL TRACK RENOVATOR
Grizzly’s very successful Wheel Track
Renovator is designed to fill wheel depressions and gutters left from
Controlled Traffic Farming, Self Propelled
Sprayers and situations where wheel tracks are an issue.
The machine can be set up for 2m or 3m centres (or adjusted to be anywhere in between thanks to the Grizzly Tension
Clamp System) and is capable of filling gutters 350mm (14”) deep in one pass.
No hassles!!!
BANKER / HILLER
Built to form small water tight contour banks on lower horsepower tractors. Help prevent erosion from water run off.
Ideal for forming small banks for tree planting in orchards and tree plantations.
The machine is available with 3 discs per side and is width adjustable.
June 2018 Specifications are subject to change without prior notification
75
GRADER BLADE
The Grader Blade is perfect for many varied applications from professional road maintenance crews to maintaining farm roads and tracks. The Grader Blade is an extremely robust blade with the most features on the market.
It can be optioned up so there is 4 way hydraulic movement. If hydraulic banks are in short supply on the tractor you can get optional Electronic over hydraulic diverter which allows you to operate all 4 sets of hydraulics from just 2 sets in the tractor cab.
Available in 1.8, 2.4 & 3 mtr models.
DEEP DIGGER
The Deep Digger breaks up hardpan and compacted soils. By opening the subsoil, compacted ground can be rejuvenated, allowing better drainage, root growth and mineral osmosis.
The Deep Digger is available in both linkage and trailing designs. Heavy
Duty tines are set in a characteristic “V” formation for quick and easy penetration and draft reduction.
All tines can be removed to a non-working position if wide tine spacing or a narrower width is desirable.
The machine is available in sizes 1 up to
15 tines.
GM44 LITTLE JACK RIPPER
The Little Jack machine is a medium duty machine with an easy to change shear pin breakout system. Little Jack is most at home doing general ripping and pasture renovation, and with its optional coulters it can leave a pasture paddock looking like its barely been touched.
Little Jack offers a heavy duty head stock and uses the same heavy duty tines as the bigger Jack Machine. These standar features ensure that this medium duty machine has maximum strenth and durability for it’s size.
76
Specifications are subject to change without prior notification
From serial number 6714
Including 6586, 6666, 6703
GM77 JACK RIPPER
The minimum tillage point on both Jack and Little Jack Rippers are replaceable as are the shin guards and can have the optional hard facing done at the factory.
Standard minimum underframe clearance of 700mm means a superior trash flow and a greater maximum depth.
Grizzly’s unique Tension Clamp System is the secret to its superior strength in tough going conditions.
BEDFORMER
The Grizzly Bed Former is designed to be able to form beds on varying bed widths in both irrigation and dryland farming situations when drainage in high rainfall areas is critical.
The machine can be used in cultivated or uncultivated soil depending on conditions and performance of the machine. In some conditions the area to be formed into beds will need to be cultivated to ensure beds are formed in the best manner.
If you are working where rocks or underground obstacles may be present then a hydraulic breakout machine should be used and care should be taken when using the machine.
VINI - DISC
Highly versatile medium linkage tandem offsets suitable for vineyard, orchard and small farm cultivation.
Renowned for ground breaking technology in large scale cultivation equipment,
Grizzly brings the same engineering expertise to our medium duty linkage systems. Ideal for small acreage, where maneuverability is of prime importance.
Typical applications include viticulture, orchards, small farms, market gardens, and other specialized circumstances.
The machine is available in 12 and up to
20 discs.
June 2018 Specifications are subject to change without prior notification
77
LINKAGE-HEAVY
The Linkage Heavy offset features a heavy frame construction. This model particularly suits conditions requiring extra strength and penetration such as fire break maintenance and deep working in hard soil types.
The machine is available in 16 up to 40 discs.
GRUMPY
Medium duty tandem offset for general farm use on small to medium sized farms.
Narrow transport width (9’ 6”) allowing machine to pass through any gate and transport on public roads.
With extra strong frame and all features of Grizzly’s heavier models, the Grumpy is effective for pasture renovation, seed bed preparation and general tillage applications.
The machine is available is sizes 28 up to
40 discs.
THE OFFSET
The Offset is Grizzly’s only 2-gang disc plough. Available in a medium duty machine, the Offset range features proven Grizzly features as well as the option of hydraulically adjustable gangs.
The Offset comes with standard hydraulic pitch control that has the ability to control depth on the front and rear gangs.
Adjustments can be made on the move and has the added benefit of helping to keep the machine tracking straight. By putting more or less force on the rear gangs, the pitch control keeps you on track.
The machine is available in sizes 24 up to
36 discs.
78
Specifications are subject to change without prior notification
From serial number 6714
Including 6586, 6666, 6703
HEAVY
The original Grizzly Heavy duty disc that is still a favourite of many farmers and contractors. Its simple, heavy, robust design and its ability to take a 32” disc, makes it a very attractive choice for farmers wanting strength, weight and of course a great job out the back of the machine.
SANDGROPER
Light to medium duty, broad acre machine.
Ideally suited to sandy soil conditions.
Uses proven, reliable features of the heavy duty Grizzly range.
The Sandgroper is the accurate and versatile solution for incorporating stubble, green-manure or killing weeds.
Advantages include depth consistency, lower horsepower requirements, significant fuel savings and minimized stress on components, resulting in less wear and reduced maintenance costs.
The machine is available in sizes 72 (8.7 metres) up to 108 (11.9 metres) discs.
FIELD BOSS FIXED FRAME
The Field Boss features heavy construction for long lasting strength and excellent penetration in tight and heavy soils. By eliminating power-draining side draft, the Field Boss requires less horsepower, making it less punishing on tractors and very cost effective to operate.
The Field Boss is equipped with a great range of setting options and Grizzly patented features making it a flexible, accurate and easy to operate with an ideal finish every time.
The machine is available in sizes 24 up to
48 discs.
June 2018 Specifications are subject to change without prior notification
79
FIELD BOSS FOLDING WING
The Field Boss features heavy construction for long lasting strength and excellent penetration in tight and heavy soils.
By eliminating power-draining side draft,
The Field Boss requires less horsepower, making it less punishing on tractors and very cost effective to operate.
The Field Boss is particularly effective for uneven and undulating ground due to the independent flotation of the centre frame and wings.
The machine is available in sizes 56 (6.2 metres) up to 108 (12 metres) discs.
FIELD MASTER
The new Field Master is the lasted award winning machine from Grizzly.
With it’s 2.5mtr transport width that allows transport through narrow gates and roads and it’s hydraulic gang shift which gives smooth, reliable and easy transport to working position.
Grizzly have maintained the use of it’s legendary tried, tested and proven running gear. However adding the hydraulic gang shift makes this the perfect machine for farmers on the move or contractor’s that require a fast transition from transport to working position and back again in seconds without having to get out of the tractor.
The Grizzly Field Master in the answer to all those cultivation problems you have.
EAST / WEST COASTER
The East Coaster’s fully floating gang design, engineered to automatically conform to the natural contour of the ground. Gangs may be liquid filled for extra penetration. Operating adjustments are effortless requiring no tools or personal strain.
Quick, easy opening and closing between transport and working modes is hydraulically performed with minimal operator input.
The East Coaster is packed with advanced features and is available in sizes 108 (12 metres) up to 136 (15.1 metres) discs, with disc sizes available from 26” to 28”.
80
Specifications are subject to change without prior notification
From serial number 6714
Including 6586, 6666, 6703
TINY RANGE
The TINY 230 is the starting point in the
TINY range of Heavy Duty Disc ploughs.
The heavy frame construction is ideal for
Heavy Duty work such as cotton, land clearing and getting into hard to penetrate soils. The TINY 230 has 230mm disc spacings and up to 32” x 10mm scalloped discs and uses the proven bearing design found in the Field Boss and other
Heavy Duty Grizzly ploughs. The narrow spacings also make it ideal at cutting out at shallower depths and with plenty of flotation available with optional tyres it can perform primary and secondary tillage needs.
The TINY 290 takes things to the next level in weight and robust design. Made using a full frame and gangs of 16mm thick RHS. The 290mm spacings and either 32” x 10mm discs or optional 36” x
1/2 “ discs allow for deep penetration and handling the toughest country. Often used for cutting out tree regrowth or controlling tough woody regrowth and renovating buffel grass country. The TINY is also used for mixing of lime and clay deep into acidic or non-wetting soils with great success.
The TINY 390 is the ultimate in heavy machines – offering up to a massive
400kg of weight per disc with its 390mm disc spacings and 36” x ½” discs. Ideal for heavy duty mixing jobs at maximum depths or for breaking into hard soil conditions.
The TINY 460 is fitted with 42” discs and is designed for use where deep working is required. Deep mixing of all soil types
300mm and deeper as well as getting a cut out of tree roots. This machine it truly impressive to see and owners of these machines are truly impressed with its performance. Break open country in a way you thought couldn’t be done.
All the TINY range folds down to an amazing 3.5m road transport.
June 2018 Specifications are subject to change without prior notification
81
advertisement
* Your assessment is very important for improving the workof artificial intelligence, which forms the content of this project
Related manuals
advertisement