Chandler 406RB-1 Instruction Manual
Add to my manuals
50 Pages
Chandler 406RB-1 is a single-needle, lockstitch, industrial sewing machine with a walking foot. It is designed for sewing medium to heavy-weight materials such as leather, canvas, and denim. The machine has a maximum sewing speed of 2,000 stitches per minute and a stitch length range of 0.5 to 5 mm. It is also equipped with a built-in LED light and an automatic thread trimmer.
advertisement
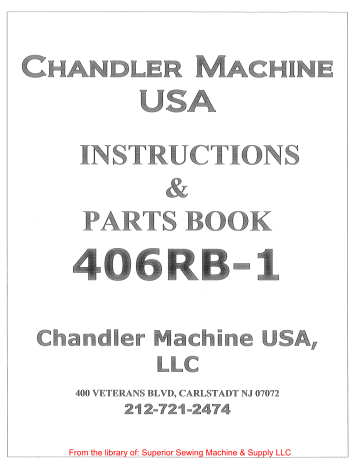
I
400 VETERANS BLVD, CARLSTADT NJ 07072
From the library of: Superior Sewing Machine & Supply LLC
From the library of: Superior Sewing Machine & Supply LLC
u
From the library of: Superior Sewing Machine & Supply LLC
From the library of: Superior Sewing Machine & Supply LLC
CONTENTS
1. MAIN PARTS NAMES································································· .................................................................. -1
2. SPECIFICATIONS··········································································································································1
3. WORK TABLE AND MOTOR ........................................................................................................................ 2
4. INSTALLATION·············································································································································3
4-1: Installing the rubber hinge and the corner rubber···· ........ ··········· .... ·· .. ····· .. ··· .. ················ .... · .. ·· .... ······· .. ·· .... ·· ·3
4-2. Installing the oil pan··· ...... · ... ·· .. ······ .... ········· ..... ·············· ..... ··· .. ··················· ...... · .. ··· ... ·············· ... · .. ········· ·3
4--3. Installing the machine head··············· ... ······ .. ················· .. · .. ······················ .. ·· .. ··· .. · .... ··· .. ················ .. · .. · .. ···· ·3
4-4. installing the spool pin ... ······· .... ···· ... · ..... ··················· .. ···· ... ··· .. ··· .. ·············· ..... ····· .. ······ .. ·· .. ·················· .... -4
4-5. installing the knee lifter assembly·············································································································· -4
4-6. Installing the belt······ .. ···· .. ··· .. ·············· .. ················ .. · .. ····················· .. ·· .. ················································ ·5
4-7. Installing the bobbin winder .. ··················· .. · .. ·············································· .. ····································· .. ··· ·5
4-8. Installing the belt guard{L)· · · · · · · · · · · · · · · · · · · · · · · · · · · · · · · · · · · · · · · · · · · · · · · · · · · · · · · · · · · · · · · · · · · · · · · · · · · · · · · · · · · · · · · · · · · · · · · · · · · · · · · · · · · · · · · · · · · · · · · ·6
4-9. Installing the thread stand············ .. ············· .. ················ .. ·········· .. ····· .. ······················ .. ··············· .. ·········· .. ·6
4-1 0. Lubrication··················································· · · · · · · · · · · · · · · · · · · · · · · · · · · · · · · · · · · · · · · · · · · · · · · · · · · · · · · · · · · · · · · · · · · · · · · · · · · · · · · · · · · · · · · · 7
4-11. Checking the machine pulley rotating direction·· .. ··············· .. ·· ... · .. ··· .. ·············· .. ······ ...... ··· .. ·········· .. ·· .. ········· ·8
5-1. Installing the needle···· .. ·· .. ·· .. ········ .... · .. ·· .. ··· .. ··· ...... ···· ...... ······· .. ···· .. ···· ...... ··· .. ···· .... ·· ...... ···· .. ··················· ·9
5-2. Removing the bobbin case············ ........ ················· .. ····························· .... ······································· .... ···· ·9
5-3. Winding the lower thread················- ....................................................................................................... 10
5-4. Installing the bobbin case· .. · .. ········································ .... ··········· .. ··············· .. ······································· ·1 0
5-5. Threading the upper thread············································· .................. ················································ ······11
5-6. Adjusting the stitch length································· .. ········································ ··························· .. ················11
6. SEWING······················································································································································12
6-1. Sewing················································································································································12
6--2. Backtacking·························································-······· ......................................................................... 12
7 .THREAD TENSION···································· ........ ·········· ...... ·········································································· ·13
7-1. Adjusting the thread tension·· ..... ················ ......... ·········· ..... ··························································· ..... ····· ·13
7-2. Adjusting the presser foot pressure····················· ..................... ···························································· ···13
8.STANDARD ADJUSTMENTS········································ .. ··············································································14
8-1. Adjusting the thread controller spring··················· .. ································ .. ··············································· .. ·14
8-2. Adjusting the height of the feed dog· ..... ········· ...... ······························ ... ········· ... ···································· ···15
8-3. Adjusting the feed dog position (longitudinal)···· .. ··········································································· ···· .. ······15
8-4. Adjusting the positions of the needle and needle hole of the feed dog·················· ... ··············· ... ·········:.· ...... ·· ·16
8-5. Adjusting the timing the needle with feed ................................................................................................... 18
8-6. Adjusting the height of the needle bar····································································································· ·18
8-7. Adjusting the timing between the needle and hook ...................................................................................... -19
8-8. Adjusting the clearance between rotary hook and opener (thread release finger)··············································· ·20
8--9. Adjusting the clearance between feed forked connection and feed fork collar·················································· ·21
8--10. Adjusting the height of the presser feet····················:··························· ..... ··········································· ···21 s-·11. Adjusting the presser foot movement amount······························································· ............... ··· ·········22
8-12. Adjusting the timing of the vibrating presser foot ... ······· .. ···· .. ····································································· ·23
8-13. Adjusting the L0d regulator···········································-·············· ........................................................ 24
9.SAFETY CLUTCH MECHANISM···· .............................................................................................................. 25
From the library of: Superior Sewing Machine & Supply LLC
1. MAIN PARTS NAMES
2.SPECIFICATIONS
1" MAIN
Feed regulating dial
Vibrating presser foot
~lifting presser foot Safety clutch mechanism
<Rear of machine> materials--very thick materials
3.WORK TABLE AND MOTOR
3.WORK TABLE AND MOTOR
Work Table
• When using a table made by another manufacturer, drill holes in the table as shown in the figure below.
• The top of the table should be 40 mm in thickness and should be strong enough to hold the weight and withstand the vibration of the sewing machine.
Thread stand hole
Work table processing diagram Head
Motor mounting holes
!<:nee lifter installation position
14
A-A cross section B-B cross section
Oil pan installation position
15.5mm
Work Table
• All cords which are connected to the motor should be secured at least 25 mm away from any moving parts. Furthermore, do not excessively bend the cords or secure them too firmly with staples, otherwise them is the danger that fire or electric shocks could occur.
<Motor>
• Sek;ct UiG correct motor from those listecl in the table. f{,:Jfor to the instruction manual for the motor for details on installing and using the motor.
<M0tor pulley and V-belt>
Select the correct motor pulley and V-belt by referring to the table to suit the power frequency of your area.
• Install the correct belt guard which to the motor being used.
Power Motor motor
2,000 spm
50 HZ Motor pulley 55 41 inches
60HZ Motor pulley 45 41 inches
4. INSTALLATION
4. INSTALLATION
o
The sewing machine should only be installed by a qualified technician.
• Ask your dealer or a qualified electrician for any electrical work that may need to be done.
· The sewing machine weights more than 29 kg.
The installation should be carried out by two or more people. o
Do not connect the power cord until installation is complete, otherwise the m8chine will oper8te ifthe treadle is prEJSSt)cl by mistake, v;hich could result in injury.
Be sure to connect the ground. If the ground connection is not secure, serious electric shocks will result.
• Install the belt guard to the machine head.
4-1. Installing the rubber hinge and the corner rubber
1. Install the rubber hinge (1) on the table with nails
(2 (Two places)
2. Install the corner rubber Q) at the four corners of the table with nails
4~2.
Installing the oil pan
Fit oil pan with 4 nails into the opening in the table, and secure it
(Refer to the work table processing diagram on page 2.)
4-3. Installing the machine head
1. Insert the two bed hinge connections
CD into the holes in the machine bed.
2. Fitthe bed hinge connection to the rubber hinge and then place the machine head onto the corner rubber
3. Tap the head rest into the table hole.
NOTE: Tap the head rest securely into the table hole. If the head rest is not pushed in as far as it will go, the machine head will not be sufficiently stable when it is tilted back.
4. INSTALLATION
4~4.
Installing the spool pin.
Insert the spool pin
CD into the installation hole, and screw it in tightly.
4-5. Installing the knee lifter assembly
1. Assemble the knee lifter assembly as shown in the illustration.
NOTE:Make sure that the knee lifter stopper
fZ:;
is facing in the correct direction.
2. Install the knee lifter assembly
CD on the back of the table with 4 screws (Refer to the work table processing diagram on page 2.)
3. Adjust the knee lifter.
1) Lower the presser foot @ by using the presser bar lifter®.
2) Loosen bolts @.(1) and
(til
3) Adjust the position of the thrusting bar complete
® so that the clearance between its curved section and the very bottom of the roller @ is approximately 2 mm when the knee pad (9) is at the stop position.
4) Securely tighten bolts and
G) Press the knee pad to mise the presser foot mm; then move the knee lifter stopper
!f by 14
:z in the direction of the arrow so that it is against the installation bracket projection @,securely tighten the bolt@.
4. INSTALLATION
ling
thH
belt
1. Remove the screw (1) and romove the belt guard upper cover
2. Tilt back the rnachine head, and then place the belt onto the motor pulley and the machine pulley.
3. Turn the nut to adjust so that there is 15-20 mm of deflection in the belt Q) when it is pressed with a finQer with a force of 9.8 N (1 kgf).
4. Insert the belt guard upper cover into the belt guard from above the pulley, and then tighten it vvith the screw
4-7. Installing the bobbin winder
1. Push down the bobbin set lever as tar as it will go.
2. Place the bobbin winder pulley so that it pushes the belt by approximately 5 mrn, and then place the bobbin winder @ so that it is parallel with the belt hole in the work table.
3. Install the bobbin winder@ to the work table with the two screws @.
4. Pull the bobbin set lever
GJ back and check that there is approximately 5 mm of clearance between the bobbin winder pulley (2) and the belt®.
From the library of: Superior Sewing Machine & Supply LLC
4. INSTALLATION
4~8.
Installing the belt guard (L)
1. Tilt back the machine head, and then remove the V-belt from the motor pulley.
2. While tilting the machine forward, insert belt guard(L)
G) into the belt guard (2) from underneath, and let it rest there.
3. Place the V-belt back onto the pulley.
4. Install belt guard (L) G) with the two screws @ so that there is no clearance between the belt guard (2) and belt guard (L) G) (position@), and so that the reverse lever @ and the belt guard (2) are not touching
(positions @ and
©).
4-9. Installing the thread stand
Assemble the thread stand as shown in the illustration, and then install it to the work table.
* Securely tighten the nut
CD
so that the thread stand does not move.
From the library of: Superior Sewing Machine & Supply LLC
4. INSTALLATION
4-" 10. Lubrication
• Do not connect the power cord until lubrication has been completed, otherwise the machine may operate ifthe treadle is pressed by mistake, which could result in injury.
• Be sure to vvear protective goggles and gloves when handling the lubricating oil, so that no oil gets into your eyes or onto your skin, otherwise inflammation can result
Furthermore, do not drink the oil under any circumstances, as it can cause vomiting and diarrhoea. Keep the oil out of the reach of children.
The sewing machine should always be lubricated and the oil supply replenished before it is used for the first time, and also after long periods of non-use.
Use only the lubricating oil.
• Add 1-2 drops of oil in the places indicated by the arrows.
Add oil to other sliding parts also, while being careful to avoid oil leaks.
Oiling must be done at least twice daily in continuous use.
4. INSTALLATION
II For oiling to hook
Remove the oil plug
CD and pour oil until the oil surface reaches to the red line of the oil indicator \2). After pouring oil, tighten the oil plug
CD securely.
Oiling adjustment to hook
Loosen the nut®. adjust oiling by adjusting screw@. To increase oil flow, loosen the adjusting screw@, to decrease oil flow, tighten the screw@. After oiling adjustments completed, tighten the nut® securely.
Do not touch any of the moving parts or place any objects against the machine while sewing, as this may result in personal injury or damage to the machine.
1. lnsertthe power cord plug into the wall outlet and then turn on the power switch.
2. Depress the treadle and check that the direction of rotation of the machine pulley matches the direction of the arrow
CD.
* If the direction of rotation is reversed, change the direction of rotation to the correct direction while referring to the instruction manual for the motor.
5. PREPARATION BEFORE SEWING
5. PR PARATION BEFOR SEWING
5-1 . Installing the needle
• Turn off the power switch before installing the needle. The motor will keep turning even after the switched off as a result of the motor's inertia. Wait until the motor stops fully before starting machine may operate if the treadle is pressed by mistake, which could result in injury.
1. Turn the machine pulley toward you to move the needle bar to its highest position.
2. Loosen the screw(!).
3. Holding the needle (2) with its long groove facing left insert all the way into the needle bar.
4. Tighten the screw
CD.
Long groove~
5-2. R£~moving the bobbin case
• Turn off the power supply before removing the bobbin case. The motor will keep turning even after the power is switched off as a result of the motor's inertia. Wait until the motor stops fully before starting work. The machine may operate if the treadle is pressed by mistake, which could result in injury.
1. Open the bed slide.
2. Pull the latch
CD of the bobbin case upward and then remove the bobbin case.
3. The bobbin (2) will come out when the latch
CD is released.
2
5. PREPARATION BEFORE SEWING
5~3.
Winding the lower thread
• Do not touch any of the moving parts or place any objects against the machine while winding the lower as this may result in personal injury or damage to the machine.
1. Turn on the power switch.
2. Place the bobbinG:· onto the bobbin winder shaft
3. Wind the thread several times around the bobbin
<1· in the direction indicated the arrow.
4. Push down the bobbin set lever Q).
5. Raise the presser foot with the presser bar lifter.
6. Depress the treadle. Lower thread winding will then start.
7. Once .winding of the lower thread is completed, the bobbin set lever® will return automatically.
* If the thread cannot be wound on evenly, loosen the screw@_~ and move the bobbin winder bracket to the side where there is less thread.
* Turn the adjustment screw @j to adjust the bobbin winding amount.
To increase the winding amount: Tighten the screw.
To decrease the wincing amount: Loosen the screw.
Note:The amount of thread wound onto the bobbin should be a maximum of 80% of the bobbin capacity.
Thread winding amount
5~4.
Installing the bobbin case
• Turn off the power supply before installing the bobbin case. The motor will keep turning even after the power is switched off as a result of the motor's inertia. Wait until the motor stops fully before starting work. The machine may operate if the treadle is pressed by mistake, which could result in injury.
1. While holding the bobbin so that the thread winds to the right, insert the bobbin into the bobbin case.
2. Pass the thread through the slot tension spring \21. and under the
3. Pull the thread cut through the hole in the end of the tension spring (2:.
4. Check that the bobbin turns clockwise when the thread is pulled.
5. Hold the latch ;.3; on the bobbin case and insert the bobbin case into the rotary hook.
6. Close the bed slide.
From the library of: Superior Sewing Machine & Supply LLC
5. PREPARATION BEFORE SEWING
5-5.
Threading the upper thread
CAUTION
• Turn off the power supply before installing the bobbin case. The motor will keep turning even after the power is switched off as a result of the motor's inertia. Wait until the motor stops fully before starting work. The machine may operate if the treadle is pressed by mistake, which could result in injury.
Turn the machine pulley and raise the thread take up lever
G:· before threading the upper thread. This will make threading easier and it will prevent the thread from coming out at the sewing start.
5-6.
Adjusting the stitch length
Stitch length can be set by turning the feed regulating dial
Ci·.
Numeric figures on the dial
i.l'
show the stitch length in mm. The desired numeric figure on the dial should be set at just above, while depressing the revers lever slightly.
6. SEWING
6.
" Attach all devices bofor:1 attached, injury rnay result.
" Turn off the powe; switch at the times. The motor will turning evon after the; pnvver is sv\'itchcd off JS a result of the motor's inertia. Wait until the rnmor slops fully before vvork. The rnachine rnayoperate if the treadle is by mistake, which could msult in injury.
When threading the needle
When replacing the needle and bobbin
When not using the machine and when leaving the machine unattended
• Do not touch any of the moving parts or place any objects against the machine while sewing, as this may personal injury or damage to the machine. rnachir18. If the rnachine is used vvlthout these devices
6~1.
Sewing
1. While holding the upper thread with your fingers, turn the machine pulley by hand toward you until the lower thread comes out onto the feed dog.
2. Pull the lower thread toward you and check that it pulls out smoothly,
3. Turn on the power switch.
4. Depress the treadle to start sewing,
Lower thread
6~2.
Backtacking
When the reverse lever is pushed, the material feed direction will be reversed, and when it is returned to its original position, the feed direction will change back to normal.
7. THREAD TENSION
7. THREAD TENSION
7
~
Upper thread
Lower thread
Good even stitches
Upper thread tension too weak or lower thread tension too strong
Upper thread tension too strong or lower thread tension too weak
II Upper thread tension
The tension of the upper thread is adjusted using the tension thumb nut G).
To increase the tension of the upper thread, ·~urn the tension thumb nut (f1 to the right. To decrease tension, turn the tension thumb nut <}1 to the left.
Lower thread
7
~2.Adjusting
the presser foot pressure
- - - - - - - - - .
II Lower thread tension
CAUTION
Turn off the power switch before removing or inserting the bobbin case.
The motor will keep turning even after the power is switched off as a result of the motor's inertia. Wait until the motor stops fully before starting work. The machine may operate if the treadle is pressed by rl'istake, which could result in injury.
Adjust by turning the thread tension nut (2J until the bobbin case will not drop by its own weight while the thread end coming out of the bobbin case is held.
Adjust the presser foot pressure to lower as much as possible so that the presser foot can properly hold down material by turning the screw (f•.
8. STANDARD ADJUSTMENTS
8. STAN ADJUSTMENTS
Maintenance and inspection of the sewing machine should only be carried out by qualified personnel.
Ask your dealer or a qualified electrician to carry out any maintenar.ce and inspection of the electrical systern.
If any safety devices have been rernoved,be sure to m-install them to their original positions and check that they operate correctly before using the machine.
8-1. Adjusting the thread controller spring
power cord from the wall outlet at the times, otherwise the machine may operate if treadle is by mistake, which could in injury. However, the motor will keep even after the power is switched off as a the motor's inertia. Wait until the fully before starting work.
When carrying out inspection, maintenance
When replacing consumable parts rotary hook
If the power switch needs to be left on carrying out some adjustment. be careful to observe all safety precautions.
Operating range of spring
The standard operating range for spring
CD is 5-1 Omm.
1. Loosen the screw
\2·,
and then turn the thread con troller spring stop ~ to adjust the operating range.
• For more operating range, move the spring stop ~~?! to the right.
• For less operating range, move the spring stop Qi to the left.
2. Tighten the screw (2_:.
Tension of the spring
The standard tension for spring is 0.39-0.78 N (40-80g).
1. Loosen the tension thumb nut \4; and screw@.
2. Turn the tension stud (§l to adjust the tension.
To increase the spring tension, slightly turn the tension stud ®!counterclockwise.
To decrease the tension, turn the stud clockwise.
3. After adjustment, tighten the tension thumb nut 0\) and screw\!?).
8. STANDARD ADJUSTMENT~;
8~2.
Adjusting the height of the feed dog
The maximum height of the feed dog from the surface of the needle plate (2) is normally 1 mm. To adjust the height of the feed dog:
1. Tilt the machine head away from you. Turn the pulley to raise the feed dog to its highest position.
2, Loosen the screw~.
3. Raise or lower the feed dog
CD
as necessary,
4. Tighten the screw Q ..
8~3.
AdjUsting the feed dog position (longitudinal)
31.5mm
1. Change the feed amount to the smallest possible setting.
2. Turn the pulley to raise the feed dog position. to its highest
3. Tilt the machine head away from you.
4. Loosen the screw (2), and then move the feed rock shaft crank
~' to adjust so that there is a distance of
32.1 mm from the edge of the needle plate to the center of the needle hole on the feed dog (1•.
5. Securely tighten the screw
CZ·.
3. WORK TABLE AND fvlOTOR
3.
VVmk Table
When using a table made manufacturer, drill holes in the table 21s shown in the
The top of ihe table should be 40 mn1 in thickness and should bG strong below. to hold the vibration of the sewing machine. and withstand the
Thread
15.5mm
., ., .
"'""' cross section
Oil pan installation position
8. STANDARD ADJUSTMENTS
3~4.
Adjusting the Positions of the needle and needle hole of the feed dog
Turning the pulley to lower the needle bar slowly, check whether the needle descends to the center of the needle hole of the feed dog or not.
If the needle does not enter into the center of the hole:
1. Remove the cover and loosen the screw 12.· slightly.
2. Holding the needle bar rock frame ;Ji move it as may be required to get the correct position to the feeder.
3. Tighten the screw ((2 and close the cover.
Needle
-eclle hole ter
-Feed dog
8. STANDARD ADJUSTMENTS
I
A
J'
t' timing tl1e needle with
Adjusting the height of the neeclle
It is important that the tirning relationship between the needle on its downward stroke and the · feed dog movement is maintained at all tirnes. When the scart of the needle on the downward stroke reaches the top start When procedure to change the rhe feed dog moven1ent must use the following
1. Clla:1ge the feed amoum to the largest possible setting.
2. Loosen the screw for cover and the screw for oil resc-::voir Q, and then l"ernove the cover plate and the oil reservoir
3. Normally put the arrow mark '~i of the earn on the V ditch of arm shaft
4. Turn the machine pulley to the needle at 1 mm up from its lowest point.
5. And, pushing the reverse lever up and down, turn the cam and set this atthe point both the needle and the feed dog rest
6. After positioning completed, tighten the each screw securely.
When the needle bar
G.• is at its highest point, normally the measurement between the surface of the needle plate and the upper end of the needle eye is 22.3mm.
1. Loosen the screw \2' and move the setting posi tion of the needle bar 0 to get the correct posi tion.
2. Tighten the screw
<Needle bar highest point>
Needle plata
8. STANDARD ADJUSTMENTS
8-7. Adjusting the timing between the needie and the hook
After setting the needle bar height, set stitch length to minimum, turn the machine pulley toward you until the needle bar reaches its lowest point. Continue turning and allow the needle bar to raise about 2mm while on its upward stroke. With needle bar in this position, the point of the sewing hook should be at the center of the needle, and normally, the measurement between the hook point and the upper end of the needle eye should be 2.4mm, further the clearance between the hook point and the needle hollow should be about 0.02 to 0.1 mm.
*If they are not measured as above, perform the adjustments below.
II Adjusting the timing
1. Loosen the three set screws d '·
2. Turn the hook shaft (2; to align the hook point with the center of the needle.
3. Tighten the three set screws timing of the sewing hook. and re-check the
Adjusting the clearance
1. Loosen the two screws Q· slightly.
2. Move the hook to the right or to the left as may require.
*
Please note one of the two screws (,3) is placed on the V ditch of hook shaft. Therefore, keep the screw on V ditch during adjustment.
3. Tighten the two screws ~;.
8. STANDARD ADJUSTMENTS
8-~~8.
Adjusting t11e Clearance between rotary hook and opener
(Thread release finger)
The opener facilitates the passage of the needle thread loop by slightly nudging the inner hook creating a slight rotating movement of it. This movement at that very instant opens a clearance gap between the notch of the inner hook and the tab of the hook retainer permitting the needle thread loop to be drawn easily through the gap.
0
L~
BCiearance between the opener and projection of hook.
1 . Loosen the screw (1).
2. Adjust the clearance between projection of hook and the opener ~' by means of movernent of thread releasing shaft bushing @ to the right or to the left as may be required. The standard clearance between the two parts is 0.7-0.9mm.
3. Tighten the screw securely.
B Position of the opener cam:
Place the one of screws I_Q) which is indicated by "S" 01~ V ditch of the hook shaft.
B Adjustment of operation:
1. Turn the machine pulley until the opener
'.3: presses the projection of hook ~) extremely on its travel.
2. Press the opener
(:1· to the projection of hook (2: and make the right side clearance between the notch on the bobbin case holder and tab the hook retainer (§;
0.4-0.6mm.
This adjustment can be done by loosening the screw
3. Tighten the screw J_l securely.
8. STANDARD ADJUSTMENTS
8~9.
Adjusting the cleare.nce between feed forked connection and feed fork collar
Incorrect clearance between the fork of feed forked connection and feed fork collar
<2'
will bring irregular stitch lenoth or overheating, etc.
1. Remove the cover plate
·:3; and the oil reservoir~~'"
2. To increase the clearance, loosen the nut CQ; and turn the nut ,(2; to left or counter-·clockwise.
This adjustment should be done with turning the machine pulley toward you to get correct clearance.
3. Upon completion of adjustment, tighten the screw and screw (9).
8-,1 0. Adjusting the height of the presser feet
The standard height for the lifting presser foot ~) is 8.5 mm when the presser foot has been raised by the presser bar lifter(!.).
1. Loosen the screw,<~, raise the presser bar lifter (L;, and then loosen the set screw~~).
2. Move the lifting presser foot (2) up or down to adjust its height.
3. Tighten the screw@.
4. Tighten the screw (,_1) to adjust the presser foot pressure. (Refer to page 13.)
NOTE: If the height of the lifting presser foot is changed, the movement amount of the presser foot·~) and vibrating presser foot 0 will
Adjust the amount of movement of The vibrating presser foot ~ so that it matches the movement of the lifting presser foot (Refer to page 21.)
8. STANDARD ADJUSTMENTS
Movement amount for lifting presser foot
Movement amount for vibrating presser foot
Vibrating presser foot and lifting presser foot (ZJ move up and down alternately.
Normally, vibrating presser foot and lifting presser foot (::;' operate to the same height in their vertical motions.
• The maximum height of vibrating presser foot lifting presser foot (2; is 5.0 mm. and
If changing the movement amounts of both the lifting presser foot and vibrating presser foot simultaneously, use method (A); if increasing the movement amount for only one (thereby decreasing the movement of the other). use method (8).
Method (A): Simultaneous adjustment of the movement amount for both the lifting presser foot and vi brating presser foot
1. Loosen nut (3).
2. Move nut '~J up or down as suitable to the work.
(Raise the nut for increasing motion; or lower it for decreasing motion.)
3. Tighten the nut Q\
4 Method (B): Adjustment of the movement amount for the vibrating presser foot
1. Loosen the vibrating presser bar screw @:, and lower the presser bar lifter •J;ii.
2. While holding the vibrating presser foot
G , loosen the bolt 1§.: and then move the presser foot up or down as necGssary.
3. 1-\ftt1r the vibrating presser foot
4. Tighten the vibrating presser bar screvv
8. STANDAHD ADJUSTMENTS
8--1 Adjusting the timing of the vibrating presser foot
<When the needle lowers>
Check the vibrating presser foot timing as follows:
1. Lower the presser bar lifter lever, then turn the pulley toward you. At this time, tne vibrating presser foot should reach the feed dog before the needle eye does.
2. When the needle is raised, make sure the vibrating presser foot is still holding the material firmly. If the vibrating presser foot rises while the needle is still penetrating to the material, it may cause skipped stitches, etc.
Feed dog
<When the needle raises>
I l
I \
'-;-~~~~,
~~\ lifting presser foot\--~
\
\
'-.._
Needle
Feed dog
If the timing is not correct after you make these adjustments:
1. Loosen the two screws G_. ..
2. To synchronize the timing of the vibrating presser foot, turn the cam C:Z).
3. Tighten the screws():.
8. STANDARD ADJUSTMENTS
8·~
13, Adjusting the feed regulator
If the stitch length of forward and reverse are not same, make adjustment of feed regulator.
1. Remove the arm rear cover plate
2. Turn the cover plate \{;;), loosen the screw holding upward the reverse lever. with
3. When the mark of feed regulator and feed regulator rod <5J are alignment, stitch length of forward and reverse will be same.
4. Turn feed regulator rod 0 to the arrow "X" , stitch length of reverse is bigger and stitch length of forward is smoller.
5. Turn feed regulator rod (g) to the arrow "Y" ,stitch length of reverse is smoller and stitch length of forward is bigger.
6. After adjustment,tigthen the screw
·JJ.
9. SAFETY CLUCH MECHANISM
9.
If the thread is with the rotary stop the lovver shaft and lot the safcNV clutch flelease the clutch mechanisrn as rnentionFJcl below. the clutch mecl1anisrn the rotary hook c1nd opmatcs to
Turn off the power switch before clutch rnechanisrn, The motor v,;ill the povver is switched off as a result the motor's inertia. Wait until the motor stops fully before
T!1o machine may operate if the treadle is mistake, which could result in injury. vvork.
1. Remove the thread, etc. entangled with the rotary hook.
NOTE: Do not use a sharp-edged tool to clean the hook, as doing so may damage the hook.
2. Slowly turn the machine pulley while pressing push button and the safety clutch mechanism returns to the original position.
Adjustment of spring tension of safety clutch
If the safety clutch should become necessary to adjust spring tension, use the following procedure:
1. Depress the button in the bed plate of the machine with your left hand. At the same time, turn the machine pulley strongly so that the safety clutch disengages.
2. Tilt back the machine head. Hold the safety clutch (left) and turn the safety clutch (right) until you can see the screw 0 through the hole
3. To strengthen the tension of spring turn the screw to the right, while to lighten the tension, turn the screw to the left.
4. Upon completion of adjustment, depress the button
At the same time, turn the machine pulley until the safety clutch re-engages.
THREAD LATE
13
2
f--··
34
35
36
37
30
31
32
33
23
24
25
26
19
20
21
22
27
28
29
42
43
44
45
38
39
40
41
46
47
J
4
,.
6
7
8
9
!0
II
12
13
14
15
16
17
NO.
I
']
PAHT
-~
'-----·~
B!9451
BR09~
Bl0700
Kl052
B10551 nl9452
B8040
Bl5054
I
Bl0683
Bl95JO
Bl0759-A
Bl0760
B 1942 i C·--A
I
Bl9421
Bl951l
Bl079l
B10690
B8100
B\9518
Bl5062
BI80S5
Bl9501
B18030-S
B6031·-02
B18032C
B6034
B6035
B18495
B37254
B19455
B10703
Bl2384
Bl0709
B30046
Bl9531
Bl9532
Bi9533
B28206
B!95l3
BI0793
Bl0678
Bl9422
B19512
Bl0689
Bl0694
BBI18319
Bl9534
NO.
~-
I
!
I
2
1
2
1
1
1
1
1
1
2
1
I
I
1
J
I
I
I
1
1
1
1
I
I
2 l
1
I
I l l
2
] l
I l l
I l
I l l l l l
PARTS NA:vtE
··-
FACE PLATE
SCHEW 9/64
X
40
P0:11Tl0\J PfN
SCHE\V 9/64 x 40 L:o:4.5
OlLGUAHD
T.\KE~UP LF:VEH CO\'EH
SCBE\'i' 9/M x 40 L"'8.0
TllHF\D GUIDE: (UPPER)
I
TIWEAD GUIDE (MIDDLE)
I
I
SCHEW 9/61 x 40 L"'6.5
Tl!HEAD GiJtDE (LOWEH)
I THHEAD GUIDE FELT
TENSIO~~ BHACKET COMPLETE
TENSION BHACKET
TENSION STUD
TENSION BHACKET PIN
THHEADDISC
TENSION HELEASE WASHER
TENSION SPRING
TENSION THUMB NUT STOPPER
TENSION THUMB NUT
TENSION RELEASE PLUNGEH
TENSION HELEASE LEVER
SCH.EW 9/64 X 40
THREAD CONTROLLEH STUD
THH.EAD CONTROLLEH SPHING
THREAD CONTH.OLLEH DISC
SCHEW 3/32 x 56 L=6.0
TENSION THUMB NUT
THHEAD CO NTH OLLER SPRING STOP
SCREW 9/64 x 40 L=6.5
SCH.EW 11164 x 40 Loo=l4.0
THREAD HETAINEB
SCREW 11/64 x 40 L=8.5
TENSION RELEASE LEVEH ROD
NEEDLE PLATE
SCHEW 11164 x 40 b::8.5
BED SLIDE COMPLETE
BED SLIDE SPRING
SCREW 3/32 x 56 L=2.7
EDGE GUIDE PLATE
SCHEW M4 x 0.7 L=8.0
AH.M CAP
WASHER
SCHEW 3/16 x 32
SPOOL PIN SCHEW 7/32 x 32
EARTH WIRE SCREW M4 x 0.7 L=4.0
'
-----~-----~
-
30
31
32
33
34
35
36
41
42
43
44
37
38
39
40
45
46
47
NO.
4
5
6
7
8
9
10
25
26
27
28
19
20
21
22
23
24
15
16
17
18
11
12
13
14
1
2
3
29
ARM SHAFT, THREAD
TAKE~-U
PAHT NO.
B19415
Bl0563
Bl8006
BI7R6
BI0725
B18486
B19508
B18008
BI0579
Bl0725
Bl9508
B23637
Bl9503-A
BI9503-B
BI9503-·C
B8009
Bl0724
B 18003C
1310527
Bl8003
I\!0528
Bl5026
BI0728
Bl9504
BI0724 fll0726
B10523
B19418
B19417
Bl9414
Bl9416
Bl9521
B!0827
B19528C
B23637
BJ7041
B10723
Bl70l7C
1317018
Bl7019
BJ7015C
BJ7016
Bl7013
Bl0579
Bl3081
Bl8470
Bl0576
Bl0579
B19505
2
1 j
I
I l
I
1
1
I l j l
1
.Qty
1 l l
I
I
1 l
I
I l
1
I l
I
2
I
2 l
1
1 l l
2
I
I
I l
I
2 l
1
1
I
1
I
1
R
PAHTS NAME
SCREW 15/64 x 28 L= 7.5
OILING WICK
TIJHEAD TAKE-UP LEVER COMPLETE
TAKE-UP LEVEH HINGED STUD
THREAD TAKE-UP LEVEH
NEEDLE BAH CONNECTING LINK
TAKE-UP LEVEH DRIVING STUD i
OILING WICK
I
OIL PACKING STOP SCREW 5/16
X
28 L=6.0
OILING \VICK
OILING WICK
NEEDLE BAH CONNECTING LINK STUD
scrmw
1/4 x 28 L=4.5
SCREW 114 x 28 L=6.5
NEEDLE BAR CRANK
SET SCREW 114 x 28 L=l4.0
POSITION SCREW l/4 x 28 L=20.0
WASHER
ARM SHAFT BUSHING (FRONT)
SCREW 15/64 x 28 L=12.0
OILING FELT
LIFTING ECCENTRIC
SCREW 114 x 40 L:~5.5
AHM SHAFT BUSHING (MIDDLE)
SCHEW 15/64 x 28 L=20.0
OILING FELT
ARM SHAFT BUSHING COLLAR
SCHEW l/4 x 28 L=7.5
AHM SHAFT (STANDAHD MACHINE)
AHM SHAFT (lR" MACHINE)
ARM SHAFT (25 " MACHINE)
FEED LIFTING CAM
SCREW 1/4 x 40 L"'7.5
FEED DHIVING ECCENTHIC COMPLETE
SCHEW 1/4 x 28 L=7.5
OILING FELT
OILING FELT HETAINEH
AHM SHAFT GEAH (SPIHAL) COMPLETE
POSITION SCREW 114 x 40 L=8.0
SET SCREW 1/4 x 40 L:::7.5
GEAH COVEH COMPLETE (UPPEH)
SET SCHEW 9/64 x 40 L= 10.0
AHM SHAFT BUSHING (REAR)
SCREW 15/64 x 28 L=20.0
OILING FELT
BALANCE WHEEL
POSITION SCHEW 15/64 x 28 L=21.0
SET SCREW 15/64 x 28 L=20.0
SCHEW 3/32 x 28 L= 11.0
NEED
BAR ROCK FRAM
48
49
50
51
52
44
45
46
47
NO.
I
1
3
4
5
6
7
H
9 lO
15
16
17
18
19
20
11
12
13
14
21
22
23
24
25
26
27
28
37
38
39
40
41
42
43
33
34
35
36
29
30
31
32
,N
PART NO.
BI0557
B19509
Bl0556
Bl072R
Bl0728
I
Bi95l7 l l "'_,, . ;\ i
I
1
.\Yy
Jn47U
BI9412C
Bl7104
Bl9515
Bl9516
Bl9514
Bl0514
B19420
Bl9419
Bl0775
B12136
B10774
Bl7114
Bl8485
B37215
Bl704l
Bl00446
Bl 1876C lll 1877
Bll876
Bl0581
Bl7048-A
B17048-B
Bl7048-C
B6026-02
Bl9409
Bl8017
BI80J8
Bl9408
B34722
B34721
B8100
Bl0728
B34712
B1761l
B37134
Bl9426
Bl9429
B34723
B37134
B30078
Bl9413
B6035
RB140553
Bl0533
BNOI22
I
Qty l l l l
I i i
!
1
1
1 l
2
2 l
1
1 l l
!
I
1
I
I
I l
I
1
1
I l
I
I
1
1
I
I
2
I
I
I
I
I l
1
I
2 l
I
I
I l
I
PARTS NAME
LIFTING BELL CRANK Ui\K
LlFTlNC BELL C!L\i\K
PI\ESSEH BAH CO\\;E(~TINC LE\K
OILING \VICK
I ~,~~: 1 ~~ ;~~~~
.J/, 0 X
.,.,
,_o Led 6.0
VJ 'W; TL\r· l'H'•'''"FH B' P '•'XTE'''""0·' 1
.!_'\
F!U·.s:;F:l{ BAH EXTENSION SPHlNG
YfBlL\TlNG PHESSEH BAR
VlBH -\TfNG PHESSEH FOOT COi\lPLF:TE
PINCH SCREW 11/64 x 40 L"'6.0
HINGE SCREW 1/4 x 28
NUT 114 x 28
LIFTING ROCK SHAFT
LIFTING ROCK SHAFT BUSHING
PINCH SCREW 1/4 x 28 L=l6.0
CONNECTING CRANK
HINGE SCREW 7/32 x 32
WASHER
CONNECTING COLLAR
NUT7/32 x 32
LIFTING ECCENTRIC CONNECTION
WASHER
OILING FELT
SCREW 15/64 x 28 L=8.8
HINGE STUD
NEEDLE BAR ROOK FHAME
PINCH SCREW M4 x 0.7 L=lO.O
NEEDLE BAH CONNECTING STUD
OILING WICK
POSITION BHACKET
SCHEW M4 x 0.7 L= 10.0
WASHEH
NEEDLE BAR
SCREW 3/32 x 56 L=2.7
SCHEW 1/8 x 40 L=4.5
NEEDLE BAH THREAD GUIDE
NEEDLE DP x 17 #22
SLIDE BLOCK COMPLETE
SLIDE BLOCK
HINGE SCREW 7/32 x 32
SCREW 7/32 x 32 L=7.0
ARM SHAFT (STANDARD MACHINE)
ARM SHAFT (18" MACHINE)
ARM SHAFT (25 " MACHINE)
NUT9/32 x 28
CONNECTION
CONNECTION ROD
HINGE SCREW 9/32 x 28
PINCH SCHEW 1/4 x 28 L=-17.5
VIBRATING PRESSER BAR BLOCK
VIBRATING PRESSER BAR BLOCK GUIDE
SCREW 9/64 x 40 L=6.5
OILING WICK
PRESS R BAR,LIFTING PRESS R FOOT
((?~/
37
I
36
/ 3 4 7\
\
33
8
32 \ ~&
16
34
35
36
37
30
31
32
33
24
25
26
27
28
29
20
21
22
23
I
RESS
NO.
6
7
8
9
10
11
I
2
3
4
5
12
13
14
15
16
17
I8
19
BAR, LIFTING PR
PART NO.
B8043
B6729
B9406
B0538
B5999
B8478
B9518
B4828
B8479
B0547
B0546-A
B0659
B9405
B8085
B8477
B0796
B8483
B9403
B18080-A
Bl8080-B
B18080-C
B0548-A
B9408
B5111
B6026
B9519
B9404
B384
B359-A
B360
B808!
B8862
B0539-A
B4717
B4718
B4719
B6287
B0601
134720
Qty
1 l
2
I
I
I
I l l
I l l
2
·2
2
I
2
I l
I
1
1
1
1
1
I
I
I
I
I
1
I
1
1 i
2
1
I
I
RFOOT
PARTS NAME
SCREW M6 xI L=IO.O
PnESSEH BAH POSITION GUIDE
SCHEW 15/64 x 18 L=1 1.0
PHESSEH BAH BUSHING (UPPEH)
SCHEW M6 x 1 L=6.0
PHESSEH BAH POSITION GUIDE BHACKET
PINCH SCREW 11/64 x 40 1=:14.0
SCREW 1 lt64 x 40
PRESSER BAR LIFTING BRACKET
SPRING
'f!i:NSION HELEASE SLIDE
PRESSER BAll LJFTEll
HINGE SCHEW 3116 x 32
SCREW 11/64 x 40 L=8.5
PRESSER BAH
LIFTING PHESSEH FOOT
SCREW 9/64 x 40 L=9.0
HINGE SCREW 114 x 28
ARM SHAFT (STANDARD MACHINE)
ARM SHAFT (18 " MACHINE)
ARM SHAFT (25 " MACHINE)
BRACKET GUIDE BLOCK
PINCH SCREW 1/4 x 28 L=l7.5
PIN
PRESSER BAR SPRING
PRESSER BAH SPRING REGULATING SCREW 1/4 x 28
PH.ESSER BAR SPHING SUI'POHT SCHEW 1/4 x 28
HINGE SCHEW 15/64 x 28
LIFTING LEVEn CONNECTING ROD JOINT
NUT3/16x 32
LIFTING LEVER CONNECTING HOD
KNEE LIFTEH BELL CRANK COMPLETE
PHESSEH BAH BUSHING (LOWER)
LIFTING BELL CHANK GUIDE COLLAR
LIFTING BELL CHANK GUIDE BLOCK
LIFTING BELL CHANK CUIDE PLATE
WASIIEH
SCHE\\T M5 x 0.8 bc!O.O
SCHEW M6 x l L=12.0
'
-
~
,
-
-·"""
'
MECHANISM
NO.
~---~--
1
2
3
4
5
6
7
MECHANISM
PART NO.
~---·~~
B8523
131021
B7095
138539
B8540
B0599
Bl412
B8490
B8489
B009
B8492
130066
B8488
B8489
B009
B802l
B7041
B0723
B8493
B8018
Bl05
B8065
B849l
139508
139525
B8122
138121
B211
B8014
137207
Bl05
139527
138015
13105
138702
B009
B9526
B9535
139529
B9530
B0230
B8031
B009
B8065
B8694
B8696
Bl094
Bl8061-A
B18061-B
Bl8061-C
8
9
10
44
45
46
47
48
40
41
42
43
33
34
35
36
37
38
39
29
30
31
32
23
24
25
26
27
28
15
16
17
18
19
20
21
22
11
12
13
14
Qty
1
1
1
1
1
1 l
1
I
1
1
1
1
1
1
1
1
I
1
1
2
2
1
1
2
1
1
1
1
1
1
1
1
1
1
1
1 l
1
1
1
1
1
1
1
2
I
I
1
1
PARTS NAME
--~----~---~-~~--~-~--
FEED ROCK SHAFT BUSHING (FHONT)
SCREW 15/64 x 28 L=7.5
PINCH SCREW M5 x 0.8 L=d4.0
FEED ROCK SHAFT BASE
FEED BASE SUPPORTING PIN
"E" RING
AflM SHAFT (STANDAHD MACHINE)
ARM SHAl•T (18
II
MACHINE)
AHM SHAFT (25
11
MACHINE)
FEED HOCK SHAFT BUSHING (BACK)
SCHEW 15/64 x 28 L=7.5
FEED BASE
FEED BAR SLIDE BLOCK
SLIDE BLOCK PIN
WASHER
SCREW 3/10 x 32 L=5.0
FEED DOG
SCREW 1/8 x 40 L=6.0
FEED FOHKED CONNECTION
HINGE SCREW M3 x 0.5
NUT l\13
X
0.5(SMALL)
HINGE SCHEW 9/32 x 28
FEED CONNECTING LINK
NUT9/32 x 28
FEED ROCK SHAFT CRANK (BACK)
HINGE SCREW 9/32 x 28
NUT9/32 x28
PINCH SCHEW M6 x 1 L=18.0
"E" lUNG
HJNGE SCREW M6 x 1
WASHER
WASHER
NUTM6x 1
RETAINING lUNG
FEED LIFTING ROCK SHAFT BUSHING(FHONT)
SCREW 15/64 x 28 L=7.5
FEED LIFTING CRANK (FRONT)
PINCH SCHEW M5 x 0.8 L=12.0
FEED LIFTING HOCK SHAFT
FEED LIFTING BOCK SHAFT BUSHING (BACK)
SCHEW 15/64 x 28 L=7.5
CHANK CONNECTING HOD
OIUNGFELT
RETAINEB
FEED LIFTING CH.ANK(BACK)
HINGE SCHEW 9/32 x 28
NUT9/32 x 28
PINCH SCHEW M5 x 0.8 L=l4.0
LLVriNG SHAFT COLLAR
SCREW 1/4 x 40 L=5.5
'
I
-
NO.
8
9
10
Jl
12
13
14
15
16
1
2
3
4
5
6
7
26
27
28
29
22
23
24
25
30
31
17
!8
19
20
21
PART NO.
1319546
1318494
1317057
131392
Bl9552
1330066
1350174
1319523
B18496
1313142746
1319!522
1313145502
1313100328
1318420
1319543
1337509
1319542C
1319542
1319524
1337134
Bl7209
138105
1318506
B18721C
1318507
1318515
1318516
137033
1318574
1319544
1310845
14
12-~~
11
Qty
1
1
1
1
1
4
2
1
1
1
1
1
1
1
1
1
1
1
1
1
1
1
1
1
1
1
1
1
I
1
2
PARTS NAME
FEED HEGULATOH COMPLETE
FEED REGULATOH
FEED HEGULATOR HOD
PINCH SCHEW M4 x 0.7 L=10.0
FEED REGULATOR SCHEW 9/32 x 28
NUT9/32x 28
REVEHSE LEVEH SHAFT CRANK
REVEHSE BLOCK COMPLETE
SCHEW 15/64 x 28
REVERSE LEVEH SPHING
SPRING RETAINER
SCREW 9/64 x 40 L=10.8
REVERSE LEVER SHAFT
REVERSE LEVER
PINCH SCREW 15/64 x 28 1.=18.0
FEED HEGULATING BASE
FEED HEGULATING SUPPOHT STUD
WASHER
SCREW 11/64 x 40 L-=6.5
SCHEW 11164 x 28 L= 11.5
SCHEW M5 x 0.8 L=12.0
POSITION PIN
FEED REGULATING SCREW
FEED HEGULATING DIAL
WASHER
SCREW 3/16 x 32 L=20.0
PIN
SPRING
ORING
ARM SIDE COVER
SCREW MS x 0.8 L=6.0
---~---
ARM SHAFT(UPRIGHT),LOWER SHAFT
51
16
/til
54
bc~·,•c.
NO.
32
33
34
35
36
37
38
17
18
19
20
13
14
15
16
7
8
9
10
11
12
21
22
23
24
25
26
27
2R
29
30
31
1
2
1
·'
4A
4B
5
/
0
44
45
46
47
48
49
50
51
52
53
39
40
41
42
43
54
55
PAHT NO.
B8009
B18047
Bl7019
Bll\056
Bll\046
BIROS!
Bl804R
Bl8049
Bl8050
Bl7019
B18057-A
Bl8057-B
Bl8057-C
B8009
Bl7028C
Bl7022
B17023C
B17022
B17026
B10579
B19553
Bl7020
B17026
Bl0579
B19554
Bl7021C
Bl7022
B30750
Bl8058C
B18059
Bl8039
Bl8040
BI8041
Bl8042
B8009
B18043
B30066
B18053
B18054
810674
1318052
B19508
B1R038-A
Bl8096
Bl8034
Bi8033C
Bl8033-07
Bl8033-08
]}18035
B6025
B18090
B8009
Bll069
Bl8044
B8009
Bl8351
B0148-B
BJ8089
"'"-"'--
-
I
Qty
1
1
1
1
1
1
1
1
1
2
1
1
1
1
1
2
1
1
1
3
1 l
1
1
1
1
1
1
1
1
1
1
1
1
1
1
1
1
1
2
1
1
1
2
1
2
1
2
1
1
1
3
1
1
1
1
1
1
PARTS NAME
BOBBIN CASE COMPLETE
BOBBIN
HOTATING BOOK COMPLETE
POSITION SCHEW 11/84 x 40 L=8.9
SET SCilEW 11/64 x 40 L=7.3
IIOOK SUPPORTING PLATE
SCREW 1!164 x 40 L=l2.0
HOOK SHAFT BUSHING (F'lWNT)
SCREW 15/64 x 28 L=7.5
OlLlNG FELT
HOOK SHAFT C:\:V!
SCH.E\V 1~:18·1 28 L=7.5
\VASHEFt
01UNG F.Er:I'
HOOK DRIVING Sll!UT
THHEAD m:LEASING FINGER
SCHEW M5 x 0.8 L=8.0
THHEA!l HELEASING SHAFT
THHEAD RELEASING SHAFT BUSHING
SCHEW 15/64 x 28 L=7.5
THHEAD HELEASING SHAFT FOHK
PINCH SCHEW M5 x 0.8 L=12.0
PUSH BUTfON
PUSH BUTrON SPHING
CLIP
HOOK SHAFT LOCK RATCHET
SCHEW 1/4 x 40 L=5.0
HOOK SHAFT BUSHING (HEAR)
SCHEW 15/64 x 28 L=7.5
SAFETY CLUTCH (LEFT)
SCHEW 1/4 x 40 L=7.5
LOWEHSHAFT
OILING WICK
scrmw
9/32 x 28
SAFETY CLUTCH (HIGHT)
STEEL BALL
SPHING
SCHEW 1/4 x 40 L=7.5
ARM SHAH (STANDAHD MACHINE)
AHM SHAFT (18
11
MACHINE)
ARM SHAFT (25
11
MACHINE)
SCREW 15/64 x 28 L'"7.5
LOWER SHAFT GEAR (SPIHAL) COMPLETE
SET SCREW 1/4 x 40 L=5.0
ARM SHAFT (UPHIGHT) GEAH (LOWEll) (SPIHAL) COMPLE
SET SCHEW 1/4 x 40 L=5.0
OILING FELT
SET SCHEW 15/64 x 28 L=20.0
AHM SHAFT (UPHIGHT) BUSHING (LOWEH)
ARM SHAFT (UPRIGHT)
OILING FELT
SCREW 15/64 x 2R L=20.0
ARM SHAFT (UPIUGHT) BUSHING (UPPEH)
AHM SHAFT (UPHIGHT) GEAH (SPIHAL) COMPLETE
SET SCREW 1/4 x 40 L=5.0
BAND
GEAH COVER (LOWER) (SPIRAL) COMPLETE
PINCH SCREW 15/64 x 28 L=26
~-
LUBRICATION
I
I
G
20
NO.
9
10
11
12
5
6
7
8
13
1·1
15
Ho
I
2
3
4 l7
18
19
20
21
22 n
24
25
26
27
28
29
30
31
32
33
PAl{'!'
Blill08
Bl\069
BI8100
Bl8Hll
B18094 n
18093
1321104
Bl8095
134137
B 18_'15-l
1319545
Bl8353
1115007
1318092
1318091
B20!7l
B-~ 12 t
B30022 ll3!206
1318112
Bll069
1318110
1311069
B2017l
Bl8ll3
Bl8l09
Bl8111
B18l04
1319106
Bll044
B2017!
Ill 1069
B200ri7
NO.
!
Qly
1
1
I l
I l
1
1
I
I
1
1
1
4
1
1
1
1
1
1
I
I l
I l
1
1
1
1
1
1
1
1
--
PAHTS NAME
IWBBERPLUG
SCHEW M4 x 0.7 L=9.5
OILING WICK CLAMP
NUT
OfL TUBE 160Mi\l
OILING FELT
OILING WICK 380Mll!
OILING FELT
HUBBEHPLUG
OIL TUBE 35MM
OILING WICK 2201\Il\1
OIL TUBE 75MM
FEU
OIL
m:srmvom
SCHLW i/8 x 40 L=7.0
I
nt'BBEH PLL;c
OP
.1-u;r
IWBBEil PLUG
OiLING WICK IOO~L\l
OILING FELT
OILTUBI·: 80:111\1
O[L!NC WiCK 180m!
OIL CONTlWLLEH
OIL COSrROLLEH PLATE
SCREW \l/64 x 40 L~7.5
HEGULA Tli\IG SCREW M4 x 0.7 L= !6.0
NUT M-tx0.7
OIL HESERVOIR GASKET
OIL H.ESEHVOIR PLATE
OIL HESERVOIR WINDOW
SCHEW 9/64 x 40 L=10.0
OIL PACKING
SCREW ll/64 x 40
16'----g
18 l
17--Q
ACC SORIES
7
1111~1
17 18 19
~
~
20 21 i
II
~
~ ~
I rm
1
22 23 24
5
/\~ i i i
25
26
27
15
9
17
18
19
20
21
22
23
24
25
26
27
11
12
13
14
1.5
16 f--
ACCESSORIES
NO.
8
9
10
5
6
7
1
2
3
4
PART NO.
Bl9458
B19459
B19460
B19466
B19467
Bl9468
Bl9462
Bl9461
138180
B6054-B
B6054-C
136055
Bll866
Bl1885
136055
B 11887
!36055
B19456
Bl9457
B8132-B
B6057
B8123
B18034
BN0122
Bl0734
B35254
Bl9464
Bl9464-14
B6054-A
~
Qty
1
4
1
1
3
1
1
1
1
1
6
1
1
I
1
1
1
1 l
1 l
1
4
2
2
4
4
4
1
PARTS NAME
ACCESSORIES BAG
VINYL COVER
OIL
BOBBIN
NEEDLE DP x 17 #22
BOBBIN WINDER COMPLETE
SPOOL PIN COMPLETE
KNEE LIFTEH COMPLETE
SCREW
ARM SHAFT (STANDARD MACHINE)
Al\lVI SHAFT (18" MACHJNE) i\HM SHAVr (25" MACHINE)
NAIL
BED I!INGE BUBBEH
BED HINGE CONNECTION
NAIL
RUBBER
Ni\lL
\\'HENCH 2.0 MM
WHENCH 2.5 l\1M
WHENCH 3.0 MM
WRENCH 4.0 MM
WHENCH 5.0 MM
SCHEW DHIVER(LAHCE)
SCREW DBJVEH(MlDDLE)
SCREW DIUVER(SMALL)
DOUBLE IlEAD WRENCH
SPANNER 6 x 7 MM
SCREW DIUVEH(+)
A VAl CHARG
1
14
13- ·
I v
12
1
·--~
3
v-.
·~~
\,
·r--~-14
13
6i---. •-(])
\
5
~18
NO.
9
10
11
6
7
8
1
2
3
4
5
12
13
14
15
16
17
18
19
20
21
PARTS AVAILABLE AT EXTRA CHARG
PART NO.
Bl5098C
Bl5099
B15098
B8100
812418
88100
811142
B17372
B50409
B15121
Bl5122
1311830
1316287
1315081
1310937
Bl0677
B18484
1318469
1337136
1318469-02
B6333
Qty
2
1
1
1
1
1
1
2
1
2
1
2
1
1
1
2
1
1
1
2
1
PARTS NAME
BELT GUARD SET
BELT GUAHD UPPEH COVER
BELTGUAHD
SCREW 9/64 x 40 L=6.5
UPPER COVEll SCHEW 13/64 x 32 L=9.0
SCREW (LOWEH) 9/64 x 40 L=6.5
WASHER
SYNCHRONIZEH SUPPOHT
SYNCHRONIZEH SUPPOHT NUT
AUXILIAHY BELT GUARD (LARGE)
AUXILIARY BELT GUAHD (SMALL)
SCHEW 9/64 x 40 L=o5.0
WASHER
SCHEW
FINGER GUARD
WASHER
SCREW 9/64 x 40 L=1 LO
HOOK SHAFT COVER
SCHEW MS x 0.8 L=lO
HOOK SHAFT COVER (LOWEH)
SCREW 9/64 x 40 L=6.5
'
-
~
-
-43-
From the library of: Superior Sewing Machine & Supply LLC
From the library of: Superior Sewing Machine & Supply LLC
I
400 VETERANS BLVD, CARLSTADT NJ 07072
From the library of: Superior Sewing Machine & Supply LLC
advertisement
* Your assessment is very important for improving the workof artificial intelligence, which forms the content of this project
Key Features
- Walking foot prevents material from shifting during sewing
- Large bobbin capacity for less frequent thread changes
- Built-in LED light illuminates the work area
- Automatic thread trimmer for quick and easy thread cutting
- Knee lifter for easy lifting of the presser foot
- Adjustable stitch length for a variety of sewing applications