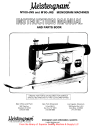
advertisement
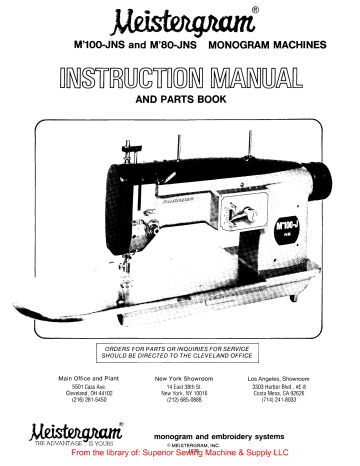
M'100-JNS and M'SO-JNS MONOGRAM MACHINES
AND PARTS BOOK
ORDERS FOR PARTS OR INQUIRIES FOR SERVICE
SHOULD BE DIRECTED TO THE CLEVELAND OFFICE
Main Office and Plant
5501 Cass Ave.
Cleveland, OH 441 02
(216) 281-5450
New York Showroom
14 East 38th St.
New York, NY 10016
(212) 685-0888
Los Angeles, Showroom
3303 Harbor Blvd., #E-8
Costa Mesa, CA 92626
(714) 241-8033
monogram and embroidery systems
© MEISTERGRAM, INC.
From the library of: Superior Sewing Machine & Supply LLC
TABLE OF CONTENTS
Section I Page No.
M'1 00-JNS Machine Complete .................................... .
M'100-JNS and M'80-JNS Machine Head ........................... .
Threading Machine and Needles .................................. .
Bobbin Winder Assembly and Adjustment .......................... .
Thread Types, Adjusting Upper Thread Tension,
Tension Take-up Spring ....................................... .
Bobbin Case Threading and Adjustment ............................ .
Stitch Width Control and Adjustment ............................... .
Presser Foot Assembly and Adjustment ............................ .
Motor and Clutch Assembly ...................................... .
Cleaning and Oiling Machine Head ................................ .
Timing the Hook and Needle ...................................... .
Adjusting Zigzag Mechanism ..................................... .
M'100-JNS Pantograph Parts:
Hoop Arm Assembly .......................................... . 13
Upper Pantograph Assembly ................................... . 14
Lower Pantograph Assembly ................................... . 14
Template Holder Assembly . . . . . . . . . . . . . . . . . . . . . . . . . . . . . . . . . . . . . . 14
Pantograph Instruction . . . . . . . . . . . . . . . . . . . . . . . . . . . . . . . 15, 16, 17 & 18
7
8
9
10
11
12
5
6
1
2
3
4
Section II (see front page of this section for contents)
Instructions as to monogramming and basic operation of equipment, working with different types of material and garments, cause and correction of common operating problems.
Section Ill (see front page of this section for contents)
Detailed parts listing for internal components of the M'80-JNS and M'100-JNS monogram machine head.
M' 80-JNS with Supply Cabinet and Panels
M' 100-JNS with Panels
From the library of: Superior Sewing Machine & Supply LLC
~~~v eJ
(: ~ ~ \
1AV
~v ~·v ~V~'IfA~
M'100-JNS MACHINE COMPLETE
PANELs NOT sHowN)
INSTRUCTION MANUAL
Pantograph Lid
Thread Stand
Light Fixture
Combination
Monogram
Machine
Sewing
Head
Upper
Pantograph
Assembly
Bobbin
Winder
Assembly
Knee
Lever
Assembly
Motor and Light
Switch
From the library of: Superior Sewing Machine & Supply LLC
l!~Y ~)I
(
·~~
1 1
~~~ ?~~'!J~~
M'100-JNS and M'80-JNS MACHINE HEAD PARTS
INSTRUCTION
Thread Stand/Light Fixture
Presser Bar
~
2-Hole
Thread Guide
I
4-Hole
Thread Guide
~
/ T h r e a d Guide For Light Fixture
Tension
Thread Guide
Bobbin
Winder
Assembly
From the library of: Superior Sewing Machine & Supply LLC
6. Up to and through thread take-up lever.
_l~l~
'],
( ,' ~ /) ,;',/ '/! / V ~,V ~VJ0f~
~NSTRUCTION
MANUAL
THREADING MACHINE
2. Through three-holed thread guide starting with top hole
.c1nd working down, back to front.
1. Bring thread from the
:hread cone up through thread
:;uide located on lamo stand.
~hen through the 4-hole thread guide pm located on top of head, then through the 2-hole
:hread gu1de.
7. Down through tension thread guide.
8. Through lower thread guide.
3. Draw thread down the front of the machine around and under from right to left between the tension discs.
5. Under tension thread guide and through upper thread guide.
Scarf
NEEDLES
NEEDLES
It is very important that the proper type needle be used with your M'80-JNS or
M'1 00-JNS machine. These needles are readily available from Meistergram in the following sizes: (The numbers in parentheses are the metric equivalent) #7 (60),
#9 (65), #1 0 (70), #11 (75), #12 (80}, #14 (90).
The size of the needle is stamped on the shank of each needle.
Sizes 10 or 11 will work well on almost all types and thicknesses of material. For thin or sheer material a size 7 or 9 may provide better results: for very thick material a size 12 or 14 may be required. However, when switching to these extreme size needles it may be necessary to re-time the machine. (see section on Timing)
Inserting Needle
1) Turn balance wheel forward until needle bar is at it's highest point. Loosen screw on needle bar and insert needle as far up as it will go.
2) Be sure needle eye and long groove are facing forward toward operator. The scarf should be facing toward the back.
3) Be sure needle is not bent, blunt or rough. Do not use needle size any larger than necessary for the material being monogrammed.
From the library of: Superior Sewing Machine & Supply LLC
3
17.~/ ,~~ /V ~r; r;.Vr;l!J~~
INSTRUCTION MANUAL
BOBBIN WINDER ASSEMBLY
Be sure to use only Meistergram Mercerized Cotton
Thread tor the bobbin. Do not use Meisterlon Rayon.
THREADING THE BOBBIN WINDER
1) Place cone of cotton thread on right hand side of thread stand. Bring thread up thrqugh right hand hole ofT-Bar thread guide on Lamp, then down and through top of bobbin winder thread guide. and then around and under tension discs as shown in Fig. #1.
2) Pull thread over to bobbin winder, insert bobbin onto shaft and wind thre·ad around clockwise several times. Push trip latch forward as in Fig. 2. Bobbin will wind automatically while machine is running and will shut off when fulL
Correctly wound Bobbm
ADJUSTING BOBBIN WINDER
Too Much on Left Side Too Much on Right Side
4
If too much thread is on the left side of the bobbin, loosen screw on regulator base and move to right; if too much thread is on the right side, move to left as shown in Fig. #1.
The amount of thread wound on the bobbin is controlled by the trip latch in Fig. 2. This can be adjusted by turning screw on trip latch to increase or decrease the amount of thread on bobbin. The amount of thread on the bobbin should be slightly iess than the diameter of the bobbin, If thread is rn excess of the size of the bobbin it will not rotate within the bobbin case.
Tightening the tension nut, Fig. # 1, will wind the thread tighter on the bobbin. In this way your bobbin will hold more thread and be firmer,
From the library of: Superior Sewing Machine & Supply LLC
;·v1eisterion Silk-like
Rayon - approx.
5,500 yds.
THREAD
Meistergram threads are orepared exclusively for use with our high speed monogram machines and are color fast. Refer to Thread
Color Cards for selection and be sure to specify "Meistergram
Gatton" or "Meisterlon Rayon" when ordering.
Too Thread- use either cotton or rayon. Bobbin Thread- use
onlv cotton. Fer finer appearance use same color cotton thread in bobbin to match the top thread being used.
;,1eisteraram Mercerized
Cotton~ approx.
12,000 yds.
ADJUSTING UPPER THREAD TENSION:
Correct Tension
)p Too Loose or
""'ottom Too Tight
Top Too Tight or
)ttom Too Loose
The upper thread tension and bobbin tension can be set independently of each other and are very important for producing proper stitch (see section on Bobbin Tension and Case). Tensions should be set so that on the back of the monogram, the bobbin stitch is about 1f3 of the width of the top zigzag stitch.
Tension on the top thread can be adjusted by turning the tension nut (A) in Fig. 1. Tension may be adjusted for variances in thread and material being embroidered. If tension is
too tight it may cause thread breakage, puckering of material, the bobbin will be too wide on the back or the bobbin may pull up and show through the top of the material. If tension is too loose, thread may loop on top or bottom of material, embroidery will not lay smoothly and very little bobbin will show on back of monogram.
To check tension, thread the machine through the tension assembly and take-up lever. Then pull on thread by hand to feel the amount of tension and adjust accordingly.
Take-up lever should be at its highest position when doing this.
TENSION TAKE-UP SPRING
(often referred to as check spring or thread controller spring)
Extending from behind the tension discs is a hooked spring called the tension take-up spring. This spring provides tension on the top thread until the needle has carried it down to the material. It may be necessary to adjust the tension of the take-up to lighter tension on thinner material j and tighter tension on thicker material.
I
I
~~~~n
1(1 \
Ill /-;~ ]
TAKE-UP SPRING
/~-
1
I/ / /
~~
/LIGHTER
Insert screwdriver into tension stud and turn slightly as shown in Fig. 2.
This will wind the spring tighter or make it looser and you can determine the amount of spring pressure by pushing it with your finger. If tension is too loose, thread will loop up under material or on top. if too tight it may cause the stitches to skip. j '
FIG. 2
CHANGING THE TAKE-UP SPRING:
If the take-up spring breaks or becomes too worn to operate properly then the spring should be replaced. First, loosen set screw in the head located to the right on the tension assembly and remove the assembly.
Adjusting Top
Tension Nut
FIG. 1
From the library of: Superior Sewing Machine & Supply LLC
5
BOBBIN CASE
Raise needle bar to highest position. To remove the bobbin case, tilt back the machine head or reach under the machine. Open latch on case and remove both the case and bobbin.
When the latch is open, the bobbin will be held in the case; when latch is released bobbin drops out.
TENSION
ADJUSTING SCREW
BOBBIN CASE
THREADING BOBBIN CASE:
1. Place bobbin into case as shown.
4. Tension on the bobbin case can be adjusted by turning tension screw.
Tension should be set so that slight amount of pull is required to release thread.
I
2. Guide thread into slot on top of case.
6
3. Pull thread under tension spring and wind around pig-tail thread guide.
5. Replacing Bobbin Case:
Raise needle bar to highest position, hold latch on case open to retain the bobbin, tilt bacK machine head or reach underneath with bobbin case and insert on shaft in the hook assembly. Release latch and press bobbin case into position so that you hear a distinct
"click". If you do not hear click, remove case and insert again. Be sure that several inches of bobbin thread are hanging free from bobbin case.
NOTE: Make sure bobbin case is free of dirt and oil. Use only cotton thread in the bobbin. Do not use rayon.
From the library of: Superior Sewing Machine & Supply LLC
I ,
~...,.~"'-"11~'~( ·~~ ~~ ~~ ~~~~~~
INSTRUCTION MANUAL
ADJUSTING THE STITCH WIDTH
KN~E LEVER ASSEMBLY
KNEE LEVER
ROD
---~
1. The stitch width can be regulated by the knee lever underneath the table of the machine.
3. From the sitting position, make certain the knee lever contacts the right knee or a spot most comfortable to the operator by adjusting the knee lever rod.
4. Located on the front of the machine head is the zigzag width scale, with two regulating knobs.
These two knobs can be used to set your minimum and maximum width of stitch desired.
It is best to set the top knob for maximum width desired and leave the lower knob on "0". Start sewing with no stitch width and then push the knee lever up to the maximum width knob so indicator stops. When
2.
The farther you push your knee to the right the finished monogramming, bring the width back to "0" wider will be the width of stitch. and run several stitches into material to lock the stitch.
From the library of: Superior Sewing Machine & Supply LLC
7
PRESSER FOOT ASSEMBLY
2~ Presser Bar Lifting---
Stud Holder
ADJUSTING THE PRESSER FOOT
The "jumping" presser foot is an exclusive design found only on Meistergram monogram machines. The presser foot action is coordinated with the movement of the needle bar so that the foot applies pressure to the material during stitching and then releases pressure to allow movement of the material after the needle has risen clear of the materiaL
5. Presser Bar Spring
8
6. Guide Bracket
To adjust the presser foot, turn the balance wheel forward so that the needle has gone into the material and then has just come out of the material on the upward stroke. At this point, loosen the screw holding the presser toot and posit1on the foot so that it is lightly pressing down on the material. Tighten the screw. The presser foot should be adjusted when embroidering different thicknesses of material. Oniy slight pressure is required to hold the material as the needle passes up through it. If too much pressure is used the foot will bang on the work plate. The foot can be raised up and thus disconnected from the action of the needle movement by lifting the lever on the back of the head. However, you should not operate the machine with the foot in this position as the screw on the needle bar may hit the foot and bend it. If you wish to operate the machine with the presser bar up, remove the presser foot.
From the library of: Superior Sewing Machine & Supply LLC
CLUTCH MOTOR ASSEMBLY
The sewing head is driven by a belt connected to the clutch motor.
The clutch has been adjusted to provide the operator with the ability to run the machine slowly or a full speed depending on the pressure applied to the foot treadle.
The position of the foot treadle can be changed for mdividual comfort by aajustiog the clamp on the pitman rod (refer to photo on pg. 1 ).
The motor and clutch have been permanently sealed and do not require any oiling.
2
By pressing down on the foot treadle with your heel, brake inside the clutch is engaged and will prevent the motor and clutch from operating. It is a good habit to always "heel down" on the treadle when threading or changing the needle so as to prevent accidentally hitting your fingers with the needle. Also, you can remove your root from the treadle when doing any of the above operations which put your fingers in close proximity of the needle.
When you remove your foot from the treadle the brake is automatically engaged and the machine will stop sewing. By tightening the brake adjustment nut, the brake w11l engage faster. By loosening the nut, the brake will take longer to engage. It is very seldom that you will have to make any adjustment to this nut.
The position of the motor can be raised or lowered by loosening the two nuts on the large adjusting screw. This can be done if the belt becomes loose and by lowering the motor you then tighten the belt. Be sure that these two nuts are tightly secured to prevent vibration.
Should you have reason to remove the motor plug, be sure that it is re-plugged in exactly the same manner. lf the plug is turned up-side-down the motor will run backwards and the machine will not sew.
Pulley
Pulley
Guard
From the library of: Superior Sewing Machine & Supply LLC
9
CLEANING AND OILING
Like any other piece of machinery it is very important to keep the head and ail moving parts cleaned and lubricated. located under the top cover of the machine are two separate oil reservoirs. When you first receive your machine, remove the top cover and then remove the cover plates of the reservoirs. Saturate the felt pads in each reservoir with oil and replace the covers. In future oilings it will only be necessary to fill the reservoirs by oiling through the hole in the top cover.
Located on the head you will find various other oil holes. Oil holes are also located under the work plate. You should oil each of these holes at least twice a week to keep your machine running smoothly. If the machine is being used continuously put a few drops of oil in all oil holes every day.
Oil machine at the end of the day and allow to sit over night. Place a piece of cloth over slot on work plate to prevent oil from running into bobbin. Before sewing, wipe excess oil from needle bar and presser bar. Run machine without thread for several minutes. Then sew off machine with cotton thread which will absorb oil in the hook. If oil has accumulated in the hook, thread will bunch up on back of material. Excess oil in the hook should be wiped out.
Get in the habit of cleaning the head every day.
Loosen the head clamp located on the table and tilt back machine. With small brush, clean around the hook assembly and shaft making sure to remove lint and thread. Even a small piece of thread caught in the hook can jam the machine. Be sure to clean and oil the hook often.
Once a week remove the top cover plate and the face plate. Oil where indicated in photos below. Also, turn balance wheel by hand and oil all moving parts very lightly.
With a piece of cloth. remove excess oil that may have accumulated in the bottom of the head.
Be sure to remove any thread that may have accumulated around the take-up lever assembly.
Meistergram Cotton thread will produce lint rapidly so be sure to clean around the needle bar and hook often.
10
Put one or two drops of oil in grooves
on
side of hook assembly each day.
For Efficient Operation of Your Machine Use Meistergram
Sewing Machine Oil.
From the library of: Superior Sewing Machine & Supply LLC
FIG. A
TIMING THE HOOK AND NEEDLE
FIG. B
0.1- 0. OSmm
NEEDLE EYE
FIG. E
0
A common problem that can develop with the sewing operation of the machine is a result of the hook and needle being out of time causing the stitches to skip and thread or needles to break.
These machines are equipped with a full rotary hook which picks up the thread from the needle and passes it completely around the bobbin case allowing time for the tension take..:up spring to draw up the stitch while the hook is making the second revolution.
Stitching problems may be a result of improper or faulty thread, bent, blunt or wrong size needles, needles in backwards or not far enough up into the needle bar, faulty take-up spring, lack of or too much oil in the hook, faulty bobbin case or hook, poorly wound bobbin, nicks or scratches on thread guides or hook, material resting too high off the work plate or presser foot incorrectly adjusted.
Before attempting to re-time the machine, check the above items first.
TIMIN G PR OCEDURE
(turn off machine motor before proceeding and
: press down on foot treadle to release the brake)
1) First remove large work plate. Use a new needle, size #1 0 or #11 and insert properly all the way up into needle bar, with long groove in needle facing toward you.
2) Turn balance wheel toward you so the needle is going straight up and down with no width or sideways movement and check to see if the needle is entering the small throat plate at the center of the slot. (if the width indicator is on "0" but your needle is still zigzaging, refer to page 12 for instructions on "Adjusting
ZigZag Mechanism" before proceeding any further).
3) If needle is not entering in the center of the throat plate, correct by turning eccentric stud, fig. C, to center needle.
4) Raise needle to highest position by turning balance wheel toward you. Remove throat plate and turn balance wheel toward you so that red dot on machine head is lined up with red dot on balance wheel. (fig. A). At this point the needle bar is at its lowest position. The needle should be as low as possible without hitting the flat part of the bobbin case. To adjust, loosen the needle bar set screw, fig. C, and raise or lower needle bar as necessary. To check height of needle, press knee lever so indicator is at approximately #11 or #12 on the width scale. Turn balance wheel toward you so that needle goes all the way down on the left hand side of the zigzag. You will then be able to see how close the needle is to the flat part of the bobbin case, fig. D, and if necessary re-adjust the height of the needle bar as described above.
5) Next, with the needle going straight up and down, with no zigzag width, turn balance wheel toward you to line up red dot on machine head with green dot on balance wheel. (fig. B). At this position, the point of the hook should be at the center of the needle and very close to the needle without touching it. (fig. E & F).
6) If the point of the hook is not at the center of the needle or too far from the needle to pick up the thread, it is necessary to change the position of the hook so it lines up properly with the needle. You will note three screws behind the hook which hold it onto the shaft. First loosen the 2 outer screws, then loosen the middle screw enough to turn the hook left or right and to move it forward or backward so that the hook point can be positioned properly as in fig. E & F. Then tighten the three screws securely.
7) Now that the timing is completed it should be checked to see if it is proper. Push the knee lever so the stitch width is at #11 and turn the balance wheel toward you so that the needle is rising on the left hand side of the zigzag ·and meets the point of the hook. At this position the point of the hook should be just above the eye of the needle and close to the needle without touching it, as in fig. E & F.
8) If the timing appears to be correct, replace the throat plate and sew on the machine to be sure it is timed properly. If when sewing the stitches still "skip" or if your examination in #7 above shows that the timing is incorrect, then repeat steps #4, 5 & 6 to re-time the machine. Remember, if the needle bar is too high or the hook point is too far from the needle, the machine will skip stitches.
9) It may take several adustments of the hook and needle bar to achieve the proper timing. In some cases it is necessary to set the hook a little to the right of the needle, which "slows" the hook, or to set the hook a little to the left of the needle, which makes the hook "fast" in order to achieve proper timing. However, this should not be done until you have tried the proper timing sequence as outlined above.
From the library of: Superior Sewing Machine & Supply LLC 11
ADJUSTING THE ZIGZAG STITCH WIDTH MECHANISM
(refer to page 7 in this manual and page 3 of Section 3 in Parts List)
The machine is designed so that the stitch can be regulated by pressing the knee lever. In this manner the stitch can be as narrow as the thread itself when the indicator is on "0" or adjusted up to about V2" when the indicator is on "12".
If the zigzag mechanism is not operating properly check for these problems and solutions:
1) Without pressing the knee lever the needle is still making a zigzag stitch refer to page 7 in this manual and check for the following: bottom indicator knob is not at lowest position ... return spring on knee lever assembly is dis-engaged or weak . . . the I ifter on knee lever assembly is set too high and is pushing up the lifter in the machine head
... the knee lever rod is loose or in the wrong position.
If the above do not correct the problem, remove the top cover of the machine head and refer to Section 3 of the Parts Manual for the following directions: a. make sure that the two springs #335 and #332 are attached to the machine head as indicated. b. check I ifting rod #367 to be sure it is not bent and it is moving freely. c. check zigzag regulator #346 to be sure it is not loose.
To do this, remove rear oil reservoir #132 from head, remove end screw #350, loosen two screws #348 and loosen bushing screw #345. To reach #345, push knee lever which will then expose the screw. The end of regulator #346 is now exposed in the indicator
#347. Use a screwdriver with a large blade and turn regulator #346 to the right to tighten. Tighten bushing screw #345, then tighten the two screws #348 with indicator on "0". Put a piece of paper under needle and turn balance wheel forward by hand, without pushing on knee lever. Needle should go up and down in same hole in paper without making any zigzag. d. if the needle continues to zigzag, loosen the screws
#357 on connector #356. Tap the connector I ightly to the left, tighten one of the screws and check the needle in and out of the paper. If the zigzag continues, adjust the connector a I ittle more to the left or right as required and then tighten the screws.
2) Indicator will not go all the way up the scale a. Check the knee lever rod to see if it is positioned properly so as not to hit the table top or the desk ledge preventing full movement. b. the lifter on the knee lever assembly is set too low and preventing full movement of the knee lever. The lifter should be about Va" below lifting rod roller
#371, when indicator is at "0". c. check lifting crank #359 by loosening two screws
#360 and position crank at lowest position and tighten the screws.
3) Indicator is not at "0" when needle is sewing straight up and down. loosen 2 screws #348 position indicator at "0".
3. ZIGZAG WIDTH REGULATING MECHANISM COMPONENTS & PRESSER BAR ASSEMBLY
365
! c?ro
361
.357
~·
368
~
370
•
367
311
12 l--33 3
From the library of: Superior Sewing Machine & Supply LLC
M'100-JNS PANTOGRAPH PARTS AND INSTRUCTIONS
The M'1 00-JNS Monogram machine operates on the same principle as an engraving machine and has two sets of connected
"pantographs". The detailed parts of the tracing mechanism are as follows:
1)
HOOP ARM ASSEMBLY (HA)
HA-1
Hoop Arm Block
HA-2
T-Bar
HA-5
Hoop Connecting
Block
HA-8
Hoop Block
With Hoop
HA-9
Metal
Outside
Hoop
HA-10 HA-11
Wooden Hoop Thumb
Inside
Hoop
Screw With
Retaining Ring
From the library of: Superior Sewing Machine & Supply LLC 13
PANTOGRAPH ASSEMBLY
~UPPERPANTOGRAPHASSEMBLY(U~
UP 3- Side Sliding Bloc
UP 4- Ear Block
UP 7- Hoop Arm
Connecting Bracket
UP 1 -Center Sliding Block UP 6 - Vertical Rod
UP 8- Screws for UP 2
LP 6 -
3) LOWER PANTOGRAPH ASSEMBLY (LP)
LP 2- Vertical
Sliding Block
LP 3- Vertical
Pantograph Arm
4) TEMPLATE HOLDER ASSEMBLY
LP 4 - Horizontal
Sliding Block
LP 8- Handle
LP 9- Stylus Thumb S
4- Side Template Guide
14
TH 1 -Base Plate TH 2- Top Template Guide TH 3- Bottom Template Guide
From the library of: Superior Sewing Machine & Supply LLC
INSTRUCTIONS
M'100-J PANTOGRAPH ASSEMBLIES refer to pages 12 & 13
1) HOOP ARM ASSEMBLY (HA)
Install Hoop Arm Assembly by attaching HA 1 to UP 7 with thumb screw HA 3.
The Hoop Arm provides adjustment in three different directions: a) by loosening screw HA 3, the assembly can be adjusted up or down for various thicknesses of material. Set the hoop arm so that the block on the hoop, HA 8, is slightly above the work plate when the material is in the hoop. If the hoop arm is too low, the block will drag on the plate. If too high, the material will be too far above the plate and not allow for proper stitching. b) by loosening thumb screw HA 4, the T-bar can be adjusted from side to side or left to right.
This enables you to center your work in the hoop, or in a particular area, adjust spacing between letters and to make monograms vertically or diagonally. Loosening also enables you to position the hoop so that it lies flat on the plate and is not tilted toward the front or back. c) by loosening thumb screw HA 6, the hoop can be adjusted from front to back which enables you to place the monograms where desired. This thumb screw also enables you to remove and attach the hoop to the clamp.
BE SURE THAT ALL SCREWS ARE SECURED FIRMLY TO PREVENT
DISTORTED MONOGRAMS AND IMPROPER OPERATION
2) UPPER PANTOGRAPH ASSEMBLY (UP)
The Upper Pantograph acts as a supporting assembly between the Lower Pantograph and the Hoop
Arm Assembly. It's smooth sliding action is possible by two sets of rods and bearing-loaded blocks.
The Hoop Arm Assembly is to be connected to the UP on part UP 7.
The Lower Pantograph is to be connected to the UP on the part UP 2, the connecting lock.
From the library of: Superior Sewing Machine & Supply LLC
15
16
There are two sliding blocks,
UP
3, and into each block is inserted the ends of the vertical rods,
UP
6. These rods are secured into the sliding blocks by two set screws, located on the bottom of each block.
These set screws must be secure to keep the vertical rods from moving and causing distortion or double lines in the monogram. Be sure to check these screws, to make sure they have not loosened, with the small allen wrench included in your tool kit.
Keep both sets of rods cleaned and lightly oiled.
3) LOWER PANTOGRAPH ASSEMBLY (LP):
The Lower Pantograph Assembly (LP). which is attached to the Desk Ledge, acts as the tracing mechanism and governs the movement of the hoop under the needle to form the monogram. By' adjusting the vertical and horizontal blocks on the arms of the LP, the movement of the LP is reduced and results in smaller monograms. This is an exclusive feature of the M'100-JNS.
The LP is designed to be adjusted to produce five different sizes from one size template letter.
(Photo A) These different sizes are expressed in ratios or fractions of:
1 : 1
3/4
1/2
1/3
1/4
The template size is the actual size of the letter engraved on the templates, not the size of the blank.
To determine the size of the letter which will be produced, divide the size of the letter on the blank by the desired ratio setting. For instance, a 2" letter divided by the setting 1/2 will result ia a 1" letter. Or, refer to the chart below: (Fig. B)
~
Fig. B
4"
3"
1:1
lEULL SIZE
4"
TEMPLATE
LETTER
SIZE
Ratio Settings
3
/4
SIZE
3"
1f2
SIZE
2" lfl
1
/4
_S_IZE SIZE
11//'
111
311
21//' 11/r;" 1" %11
2"
211
11/c/' 1
II
1/'211
1" 111
%" 1f'2''
%"
1 I
13
11
1/4''
From the library of: Superior Sewing Machine & Supply LLC
(Lower Pantograph Assembly continued)
You will find these ratio settings marked on the adjustable connecting plate ( LP 1), the vertical arm ( LP 3), and the horizonta I arm ( LP 5).
To produce different size letters from one template, you must change the ratio settings on the machine. Follow these steps in the order listed:
(Photo C Pg. 18)
1) Under the lid on the table top is the Upper Pantograph Assembly. Attached to the large center sliding block (UP 1) is the Connecting Lock (UP 2). This lock is connected to the
Adjustable Connecting Plate (LP 1 ). Hold the plate with one hand and turn the lock handle counter-clockwise,toward the back of the machine, to loosen the lock. Then, push the lock over toward the left, out of the adjustable plate.
(PhotoDPg.18)
2) Grasp the connecting plate with the left hand, and move to the desired setting, while holding the horizontal arm ( LP 5) stationary with the right hand. The adjustable plate is attached to the vertical sliding block ( LP 2). This block will move along the arm and lock at each ratio setting. The front edge of the vertical block should be lined up with the ratio setting desired, which is stamped on the vertical arm.
(Photo E Pg. 1 8)
3) Grasp the horizontal pantograph arm (LP 5} at both ends and push horizontally, to the left or right, so that the desired ratio setting lines up with the right hand side of the horizontal block ( LP 4). The horizontal arm has the same ratio settings as the vertical arm.
{Photo C Pg. 18)
4) Bring the connecting lock over to the adjustable plate and insert lock into same ratio setting slot as the two arms are set at. Tighten lock very securely, by turning clockwise, toward front of the machine.
IMPORTANT:
Be sure that the horizontal arm, vertical arm and connecting lock are all located at the same ratio setting. If one of these three settings are not the same it will result in a distorted monogram.
Be sure the connecting lock is secured tightly to prevent movement of the plate, when locked, or this will also cause distortion of the monogram. The plate should swing freely when not connected to the lock.
The movement of the vertical and horizontal sliding blocks is governed by spring pressure on a pin inside each block ( LP 2 and LP 4). These pins have been set at the factory prior to shipment, however, if the blocks are too tight to move easily or too loose during monogramming, adjust the set screws with the large allen wrench in the tool kit.
Be sure that all parts of the Lower Pantograph are kept clean and lightly oiled.
From the library of: Superior Sewing Machine & Supply LLC
17
4) TEMPLATE HOLDER ASSEMBL V: (TH)
The adjustable Template Holder is designed to hold various styles and sizes of templates and locks them in position with two large guides at top and bottom and four small side guides.
The screws should be tightened enough to secure the templates from moving but undue pressure should not be required to loosen them.
A series of holes are provided for the screws for the large guides which will enable you to place the guides to accommodate various size templates. It is not necessary to remove screws; just loosen and slide the guides back and replace templates.
Templates: These are made of a very tough bakelite and will provide long life. For smooth movement of the stylus, use graphite or soft lead pencil in all grooves on template or stylus will drag.
(Photo C) (Photo D)
(Photo E)
18
From the library of: Superior Sewing Machine & Supply LLC
MEISTERGRAM INSTRUCTION MANUAL
SECTION II
This section contains information on basic operation of the machine, working with different garments and material, general guidelines and techniques, as well as common problems which may occur and how to correct them.
Part 1) How to start monogramming with the M'1 00-JNS.
Part 2) Monogram Guidelines and Techniques, Different
Garments and Materials.
Part 3) Cause and Correction of Common Problems.
In these instructions you will note references made to various page numbers. These pages are in Section I of the manual or in the detailed Parts List, Section Ill.
IMPORT ANT: if you have not had personal instruction on the machine, please read this section entirely before starting to monogram. A complete understanding of the entire process is necessary before you start.
INSTRUCTION: If you have any questions regarding the operation of the machine or wish to schedule a visit from one of our instructors, please contact:
Instruction Dept.
Meistergram
310 Lakeside Ave., W.
Cleveland, Ohio 44113
(216) 621-8731
P~1one calls for Instruction or Service, orders for parts and supplies can be taken Monday through Friday from 9:00am to 5:00pm.
COLLECT PHONE CALLS WILL NOT
BE ACCEPTED
When calling for Instruction or Service, please have your manual at hand so reference to the proper sections or parts can be made.
From the library of: Superior Sewing Machine & Supply LLC
SECTION II- PART #1
Introduction:
This section deals with a step-by-step explanation of how to actually monogram with the M'100 machine. We have shown in detai I the various elements necessary to begin operation and become proficient with the machine.
Be sure to read this section entirely before proceeding.
Also, you should have read Section I entirely and have become familiar with the mechanics of the equipment before proceeding with Section II.
Naturally, it is impossible to include every single bit of information or experience in working with the machine but these guidelines will give you a good basic understanding on which to build your own technique.
Remember also, in many cases there are no hard and fast rules as to the way in which something must be done. If you develop your own methods or technique in certain areas that you like better, by all means use it. By studying this manual and with a short amount of practice you should be well on your way to becoming a proficient monogram operator.
A. Inserting Material Into Hoop
Using the 8" or 1 0" hoop, insert a piece of the practice cloth or felt as shown in photo 1. Lay hoop on flat surface and press in the wooden hoop. Adjust the hoop thumb screw and pull excess material around the outside of the hoop so that the material is tight in the hoop.
The hoop thumb screw has a small retaining ring and as you turn the screw to open the hoop, the ring pushes against the hoop to open it. Adjust the hoop opening to approximate the material being inserted and then tighten or loosen as required. When removing the material it is not necessary to loosen the screw. Pressing the material or wooden hoop from underneath will allow you to "pop" the material out of the metal hoop without loosening the screw.
Be sure to apply a few drops of oil to the hoop screws so they move easily.
Index of Part #1:
A. Inserting Material Into Hoop
B. Attaching Presser Foot
C. Pulling Up Bobbin Thread
D. Testing Free-Hand
E. Marking The Material
F. Adjusting Hoop Arm Height
G. Inserting Templates & Adjusting Holder
H. Centering Material and Templates
I. Setting Stylus to Trace Templates
J. Sitting Properly at Machine
K. Check List Before Starting to Monogram
L. Locking Stitch at Beginning of Monogram
M. Outlining and Filling in Letter
N. Adjusting the Stitch Width
0. Sewing Sideways
P. Locking Monogram
Q. Speed of Machine & Hand Movement
R. Moving to Another Letter
S. Templates-How to Follow & Where to Start
T. Working In Different Ratio Settings
U. Clipping Threads
V. Free-Hand Monogramming
The wooden hoop should be pushed down through the metal hoop about Va ", as shown in photo 2. This will prevent the metal hoop and thumb screw from hitting the work plate and will bring the material into closer contact with the actual sewing surface of the machine.
Be sure the material is tight in the hoop. If the material is loose the machine may not sew properly and may also cause the material to pucker, break thread, etc.
Part 1
Page
1
From the library of: Superior Sewing Machine & Supply LLC
B. Attaching the Presser Foot
As in photo 3, attach the presser foot and adjust to the proper height for the material, referring to pg. 8 in the manual.
0
C. Pulling Up the Bobbin Thread
With both the machine and bobbin case completely threaded, place the hoop holding the material under the needle. Turn the balance wheel toward you, holding onto the top thread and with the presser foot down. Keep turning the wheel until the needle comes up out of the material to its highest position and pull gently on the top thread. This will bring up your bobbin thread as shown in
photo 4. Pull out about 6" of top and bottom thread.
This procedure is only necessary when the bobbin thread is loose or unattached to the material. Thus, when you are finished monogramming one letter and wish to move to the next letter it is not necessary to pull up the bobbin thread since it is already attached to the material.
D. Testing Free-hand
Before actually embroidering a monogram it is a good idea to get a feel of the machine and the stitching operation. This can be done by running the machine and guiding the material free-hand, as shown in photo 5. To start, hold both threads, with the presser foot down as in photo 4, press the foot treadle and the knee lever while holding onto the hoop. The hoop should not be attached to the machine at this time. just guide it around free-hand. During this exercise, vary the speed of the machine as well as the knee lever. Run the machine fast and slow, varying the knee lever from thin to thick. Try moving your hands slowly so that the stitches are very close together and also try to come back and sew over previous stitching. (Further along in this
Section is more detail on how to do actual free-hand monogramming with stencils. l
E. Marking the Material
Once you are familiar with the feel of the machine you can go on to embroider a monogram using the templates.
In preparation for this and when monogramming most
From the library of: Superior Sewing Machine & Supply LLC
Part 1
Page 2
garments it is necessary to mark the item to be monogrammed. This marking will enable you to place the monogram in the proper location on the garment as well as to place the garment into the hoop so that it is straight.
First, lay out a piece of practice cloth on a flat surface and insert two pins so that they cross vertically and horizontally. The intersection of these two pins should coincide with the spot where the center of the middle letter of the monogram is to be located. Lay the material over the metal hoop. Make sure that the hoop is straight by lining it up with the edge of the pantograph lid. The intersection of the two pins should be in the center of the hoop and this can be checked by visually lining up the pins with the red marks on the metal hoop. Next, insert the wood hoop, checking to be sure that the red marks on the wood hoop match the red marks on the metal hoop, as well as line up with the pins as photo 6. Tighten the thumb screw and be sure the material is tight in the hoop and that the pins are centered both vertically and horizontally.
Practice this procedure several times so you become familiar with it. With experience. you may only use one pin or even a chalk dot mark. Often. operators are able to insert the merchandise without marking at all as they become very familiar from handling a great many garments.
Additional information as to marking specific garments and the location for monograms is contained in Part #2 of this section.
F. Adjusting Hoop Arm Height
After marking and centering the material in the hoop, attach the hoop to the Hoop Arm Assembly, as described on page 15, and shown in photo 7. Adjust the height 9f the hoop arm, up or down, as required for thickness of the material to be embroidered. Other adjustments for the hoop arm are described in proper sequence later on in the manual.
G. Inserting Templates and Adjusting Holder
Select three template letters to be embroidered. Open and adjust the template holder as described on page 18 and shown on page 14 and photo 8. The guides on the template holder are adjustable to hold a wide variety of templates.
Place the templates approximately in the center of the template holder assembly and tighten the screws for the guides so the templates are held firmly in place without moving. When using a new set of templates it is advisable to go through all the letters with a pencil. The graphite from the lead will allow the stylus to move easily through the template when monogramming. The top and bottom guides have three sets of holes each so that the guides can be opened to hold larger templates or brought closer together for smaller templates.
Part 1
Page 3
H. Centering Material and Templates
Set the Lower Pantograph at the 1 :1 ratio as described and shown on pages 16, 17 and 18. Insert the stylus into the
Lower Pantograph Arm and move the arm so the stylus is over the center of the middle letter. To center the mark on the material with the center of the templates, as shown in
photo 9, loosen the thumb screw holding the stylus so that the stylus is resting in the center of the middle letter. Lift the arm slightly and tighten the thumb screw. This pressure will hold the stylus in place. Then loosen the thumb screws
HA 4 and HA 6, shown on page 13 and described on page
15, and move the hoop so that the pins are under the needle while the stylus is at the center of the template. Refer also to photo 7 for movement of hoop. When the mark in the material is centered under the needle and matches the center of the templates, loosen sty I us thumb screw and raise the stylus above the level of the templates. You now should check to see if the template letters will fit into the hoop you have selected.
Raise the needle to the highest position and lower the presser foot. Move the arm and stylus to the extreme left and right side of the letters as well as the top and bottom of the letters. You should be able to fit the three letters into the hoop completely without the presser foot hitting the wood hoop insert. If there is not enough room you must use a larger hoop or adjust the ratio to produce smaller letters.
In some cases, you may have to re-position the garment into the hoop.
From the library of: Superior Sewing Machine & Supply LLC
Grasp handle as shown in photo 10, with arms raised above the template holder. This will allow you to move your arms and wrists freely. Practice tracing the letters without running the sewing machine so that you get the feeling of following the templates. A slow, steady movement is what you want to achieve. Trace forward and backward over the letters.
I. Setting Stylus to Trace Templates
When your lettering will fit into the hoop, loosen the stylus thumb screw and let stylus fall into groove in center template letter and tighten thumb screw. In this manner the stylus will move easily through the template without getting stuck where the lines cross.
If your stylus is down in the groove too tightly you will find that it will drag as you are tracing the templates and get stuck at the point where two grooves intersect. If the stylus is too high you will find that it frequently will come out of the groove and thus make an improper monogram.
Therefore, your stylus should be resting slightly higher than the bottom of the groove. A slight downward pressure with your hands will keep the stylus in the track of the groove and allow you to pass easily through the point where the grooves intersect (see illustrations 1.
Correct Height of Stylus
Stylus too
Low
Side View of Template
Stylus too
High
From the library of: Superior Sewing Machine & Supply LLC
Part 1
Page 4
J. Sitting Properly at Machine
Finally, position yourself at the machine with your left foot on the treadle and your right leg against the knee lever assembly, as shown in photo 11, and with your right foot on the floor. This will allow you the flexibility to control the speed of the machine with one foot and control the stitch width with the other leg.
It is advisable to have an adjustable chair, such as available from Meistergram, so that the legs and backrest can be changed according to the operator, particularly so she can sit high enough to see the stitching in the hoop.
K. Check List Before Starting to Monogram:
• the material is marked for the center of the middle letter location
• material is tight in the hoop
• hoop is attached to hoop arm assembly and adjusted for height
• presser foot is set for thickness of material
• templates are secured in template holder
• lower pantograph is set at desired ratio
• mark on material is under needle and centered with middle of templates
! all hoop arm screws are tight
• the template letters will fit into the hoop
• sty I us is set properly into template
• presser foot is lowered and bobbin thread is pulled up
L. Locking Stitch at Beginning
Holding on to both threads, turn balance wheel forward several times and lock several stitches in at the point at which you want to start monogramming. Then you will not have to hold onto the thread and it will be attached to the material. Press the knee lever slightly with your right leg and with your left foot press down on the foot treadle to activate the machine. Start moving your hands to trace the templates with the sty I us.
M. Outlining and Filling In the Letter
Go over the letter once at a moderate speed and a medium stitch width while watching the stylus and template. This will give you an outline of the letter on the material, photo 12. Then, go back over the letter a second time, moving your hands slowly and running the machine fast. During this second pass over the letter do not look at the template but watch the actual sewing so that you can lay the stitches close together to fill in the embroidery,
photo 12. Also, make your stitch width slightly wider the second time over the letter. With some practice, you will be able to do most of your templates without looking at them as you become familiar with their pattern. If you do not watch the stitching operation you will tend to develop gaps in the letters and improper width of the letters.
N. Adjusting the Stitch Width
It is important to use the knee lever to adjust the width of your stitch while monogramming. By learning this technique at the beginning you will become accustomed to it and it will enable you to produce beautiful embroidery with a thick and thin effect. Page 7 contains information on setting the stitch regulating knobs. The photo 13 illustrates a letter embroidered by using the knee lever to adjust the stitch width and a letter embroidered using the same stitch width all the way through. For certain types of lettering, like the various block styles, you will want to set the maximum stitch knob and hold your knee at that position. But, for most lettering of a script style you will want to vary your knee to achieve a thick and thin effect. Because the machine will zigzag sideways you will automatically achieve a narrow stitch when sewing across a horizontal portion of a letter. But when going up the vertical part of the letter you can vary the stitch width a great deal. A general rule of thumb for thickness is that the main part of the letter will be thick as compared to the ends or minor parts of the letter which will be thinner in comparison and tapered.
With practice, many operators can embroider a complete monogram and vary the width of the lettering without setting the knobs. You will become accustomed to this after you have worked with the various template letters and will be able to make the necessary thick and thin effect by
"eye." However, until you achieve this proficiency, start by setting the maximum knob at a desired setting for the style and size template you are using. For practice, use
Part 1
Page 5 From the library of: Superior Sewing Machine & Supply LLC
a 3" or 4" script letter. Set the maximum knob at #6 on the indicator with the M'1 00-JNS model. Go over the letter once making it thin at the beginning and thick in the middle parts. Then thinning out at the end of the letters. When doing the letter the first time to get your out! ine push your knee only up to #5 for the thickest part of your letter. Then, when you go back over the letter the second time, fill in the stitching and make your width slightly wider than the out! in e. When you come to the main part or thickest part of the letter, push your knee up to #6. Practice this technique with different styles of lettering, sizes and ratio settings so you can establish your pattern for adjusting the stitch width.
Try making large extremes in the stitch width, just for practice, so you get the feel of what can be done with the knee lever and the different effects you can achieve by changing the stitch width.
A I ittle attention and practice with the stitch width adjustment will set your embroidery above the ordinary!
0. Sewing Sideways
Because the machine zigzags sideways, more stitching will tend to be made in the horizontal portions of the letters, such as the top and bottom of curves and various parts of block letters. When moving through these parts of the letters you should move your hands slightly faster and decrease the width slightly to avoid building up the stitching too much. Then resume normal speed to fill in the vertical parts of the letter as desired.
P. Locking a Monogram
It is recommended to sew several stitches, with the needle going straight up and down, both at the beginning and end of the letter to "lock" in the monogram. Therefore, it is advisable not to use the minimum knob of stitch width regulator. If you use both knobs to hold the indicator at a particular setting you will not be able to bring the indicator back down to "0" to run in a few stitches to lock the monogram. You then run the risk of the finished letter unraveling from the material because it is not locked in place. If you use the knee lever as recommended in paragraph N you will be able to start your embroidery with no stitch width to lock in several stitches and finish your embroidery by bringing the knee lever back to "0" to lock in several stitches at the end.
Q. Speed of Machine and Hand Movement
The speed at which you run the machine and move your hands is important to achieving smooth, good looking embroidery. Your objective is to have the stitches close together to give a "satin" appearance. In most cases you will want to run the machine at high speed and move your hands slowly to fill in the stitching. The slower you run the machine the slower you must move your hands. When you want to stop the machine, press down with your heel on the foot treadle which will apply the brake to the motor and the machine will stop. With practice you will be able to run the machine at various speeds depending on the pressure you apply to the foot treadle. The same applies to your hand movement. At first you will have lumps at various points in your monogram and in other parts you will have open spaces. By moving your stylus smoothly through the template and practicing with the speed of the machine you can achieve a smooth, satin stitch to your embroidery.
Some operators have a tendency to move their hands quickly all the time and so they must go over the letter several times to fill it in. Other operators like to move their hands very slowly and can finish a monogram by going over the letter only once. In most cases it will be a comb ination of fast and slow hand movement depending on the size of the letter, material being embroidered, etc. With some practice you will find the speed that best suits your technique. The machine does operate very well at high speed and you should not hesitate to run it fast.
R. Moving to Another Letter
When you have finished monogramming one letter and wish to move to the next letter, follow these steps. Turn bal~~ce wheel forward until the take-up lever is at highest pos1t1on and then turn balance wheel backward about % of a turn so take-up lever comes down to lowest position.
This action will provide several inches of slack thread at the front of the machine head. Next, lift the tracing arm slightly and move the stylus to the next letter and insert into groove on template. Put one or two stitches into material and you are now ready to embroider the next letter. It is important to have some slack thread otherwise you may break the thread when moving from one letter to the next.
Another method of getting slack thread rather than turning the balance wheel is to simply pull a little thread through the upper tension assembly with your finger. The amount of slack thread required depends on how far you are moving from one letter to another.
S. Templates-How to Follow and Where to Start
Following the templates and determining where to start on different letters and different styles may at first appear to be confusing. However, with a I ittle practice you will be able to follow each letter, no matter of style or size, quickly and efficiently. The key to this is to visualize the pattern in which you want to follow each letter. It is not necessary to start at the beginning point of any letter. In some cases it is debatable as to which point is actually the starting point! You can start in the middle or end of a letter if you desire. The important point is to look at the letter and decide which is the most efficient way in which you should travel to cover the letter. In some parts of the letter you may have to retrace your movements and go over part of the letter twice, and in other areas you will only go over it once. Sew quickly over the parts of the letter that have to be sewn twice to prevent the thread from building up. Once you have become familiar with various letters you will not give this any thought but be able to do it automatically.
T. Working in Different Ratio Settings
The ratio settings at which you have set the Lower
Pantograph will have a determination as to the speed at which you will run the machine and the width of the stitch.
Refer to page 16 regarding the Lower Pantograph and various ratio settings. For example, if you are set at 1 :1 and trace a 4" template letter, then the material will also move
4". However, when you set the ratio at V4 and trace the same 4" letter the material only moves 1 ".
In view of the above you cannot move your hands and run the machine at the same speed in all ratio settings otherwise you will get too much stitching at the lower ratios and not enough in the larger ratios.
Therefore, you should move your hands faster in the smaller ratio settings so the stitching does not pile up or you should run the machine slower. In the larger ratio settings you should run the machine faster and move your hands slower.
Practice with different styles and sizes of lettering at various ratio settings so you can get the feel of the technique. Also, as the letters get smaller in size they get closer together so you will have to adjust your stitch width accordingly. For some styles you may want to put spacers
From the library of: Superior Sewing Machine & Supply LLC
Part 1
Page 6
between the letters in the smaller ratio settings so they will not be so close together.
U. Clipping Threads
When you finish monogramming you need to clip the loose threads and connecting threads between the letters, as well as the bobbin thread on the bottom of the material.
Use the curved applique scissors or smaller curved trimming scissors for this purpose. They allow you to get close to the monogram and the material while only cutting the desired· thread. The thread is easier to cut and makes a better appearance if you pull the thread slightly while cutting it. The longer the thread, the easier it is to trim.
When going from one letter to the next you may want to start monogramming at a point that will give you a longer piece of thread to cut than if you moved to a close point between letters and then had to struggle with a short piece of thread.
V. Free-hand Monogramming
The M'1 00 model is not a "free-hand" or a "manual" machine since the operator follows a distinct groove in the template. Free-hand monogramming implies that the operator is forming the letters or design by the free movement of her hands. This type of work can be done on the
M'1 00 instead of using the templates. It is also done on the M '80 type machines which can only be used for free-h-and embroidery.
To use the M'1 00 for free-hand work, first remove the hoop arm assembly. Next, position the lower pantograph over to one side and lower the stylus into one of the holes on the template holder so that the pantograph will be held in position and kept out of the operator's way.
Most free-hand operators will use some sort of guide in order to do lettering and this is usually in the form of a stencil. Also required are chalk and a dauber to transfer the stencil outline onto the material. This is illustrated in
photo 14. Various stencil styles and sizes, as well as chalk and daubers are available from Meistergram.
The material is then placed into the hoop and the operator guides the hoop by hand under the needle, using her knee to adjust the stitch width and sewing over the stencilled outline of the letter, photo 15.
In addition to stencils, the operator can draw the lettering on the material or even pin a piece of paper with lettering directly onto the material. In some cases, experienced operators can do free-hand monogramming without any stencil or drawing. However, this takes a great deal of skill and practice.
To practice free-hand work, draw some curved and straight lines on cloth and practice sewing over these lines, using your stitch width. The objective is to be able to go over each I ine several times, widening your stitch each time, yet achieving a smooth even line. When using a template this is easy but when doing it free-hand it takes a lot of practice to become skilled.
Many operators can go from using the templates to doing free-hand work since the hand movement required for following the templates is the same for moving the hoop by hand.
Another means of using the M'1 00 for free-hand work is to use the lower pantograph but without any templates.
In this case you would attach the hoop holding the material to the hoop arm assembly. Remove the stylus and hold onto the lower pantograph to guide the hoop under the needle. This works best if you set the ratio setting at V2.
Free-hand monogramming can be very rewarding and creative but takes a great deal of practice, patience and coordination. The results depend entirely on the ability of the operator but open many new embroidery techniques and applications.
®
®
Part 1
Page 7
7
-
From the library of: Superior Sewing Machine & Supply LLC
SECTION II-PART #2
Introduction:
In this part you will find information pertaining to:
A. Backing Materials
B. Thread and Thread Lubricants
C. Bobbins
D. Needle Sizes and Types
E. Hoop Sizes and When to Use
F. Placement of Monograms on Various Garments
G. Staggering Monograms Diagonally and Vertically
H. Correcting Mistakes
I. Production Work
J. Organization of Monogram Department
As in the previous sections we are presenting guidelines that have proven successful in many monogram operations.
After working on various garments and gaining experience and practice you will develop your own methods and techniques which best suit you and your particular operation.
Nylon backing is available in three colors from Meistergram white, red and black. Use the white nylon on light colored fabrics, the red on medium shades and the black on dark shades.
CD
A. Backing Material
Some garments and fabrics can not be embroidered without the use of "backing" material behind them. Meistergram has available the following types of backing materials:
Nylon
Grip Backing
Paper
Generally speaking, backing material is used with all knit or stretch fabrics as well as with thin or sheer fabrics. When usmg backing be sure that the piece of backing material is larger than the hoop which will be used. The garment and the backing must be placed in the hoop together so that the backing extends over the sides of the hoop.
Nylon Backing
Photo 1 illustrates a sweater being placed in a hoop with nylon backing extending over the hoop. For the purposes of the picture only we have shown a large amount of backing.
When using the backing it need only extend about 2" all around the hoop.
Nylon backing is used on knit and stretch fabrics. Without the use of the nylon the knit fabric will not hold the stitch and will actually be forced down into the slot in the sewing plate. Earlier we talked about the material to be monogrammed being tight in the hoop. Knit fabrics, by themselves, can not be made tight since they stretch. Therefore, a firm backing is required with these types of fabrics.
To use the nylon backing, cut a piece slightly larger than the hoop to be used and place underneath the garment.
Press in the wood hoop and then pull the nylon backing around the hoop so that the nylon is tight. You may also pull gently on the knit fabric so that it is not loose. Do not pull the knit too much or you will stretch it out of shape.
After monogramming, cut away the nylon leaving a small margin around the monogram.
Grip Backing
This is a pelion-like material with a high fiber count that will provide some of the stability of nylon but can be torn away like paper. It should be used in the same manner as the nylon but it is not strong enough for some knit or stretch material. It is well suited for providing body behind thin materials such as coat linings, nylon jackets, blouses, sheets, etc. It will help to eliminate or reduce puckering in some cases. You may want to use the grip backing in combination with the nylon for some knits that have a great deal of stretch or are characterized by large, open weave.
Paper
Various Backing Paper is available from Meistergram as follows:
No. 20 Heavy Tissue
No. 30 Light Tissue
No. 10 Stamping Paper
Paper does not have to be put in the hoop with the material, but rather slid under the hoop between the garment and the work plate of the sewing machine head.
The paper will give thin or sheer fabrics extra weight and body, such as shirts, handkerchiefs, napkins, lingerie, sheets, etc. When finished with the monogram all paper can be torn away and will not show through the front of the garment.
Paper can also be used under the garment which may be rough on the back as it will allow it to move smoothly on the work plate.
The No. 20 Tissue should be used on the heavier garments and the No. 30 on lighter material.
No. 10 Stamping Paper is used primarily for applying either stencil! ing or drawing designs on and then pinning onto the garment for free-hand monogramming. This paper can also be used as a backing material.
From the library of: Superior Sewing Machine & Supply LLC
Part 2
Page 1
An additional use of the paper is for the top material rather than as a backing. This is usefu I on terry cloth and velours in which it is difficult to cover up the pile on the material. For this you would put the paper on top of the material and insert into the hoop. Outline your monogram one time and then pull away the excess paper. Go over your monogram and finish stitching. The paper will cover up the pile of the material and will prevent small pieces from protruding through the stitches.
Important- paper used as a backing has a tendency to shred during the sewing operation. Small pieces of paper can get caught in the hook and jam the machine. Be sure to clean away all excess pieces of paper around the hook assembly if using paper as a backing.
B. Thread and Thread Lubricants
There are many types of sewing thread on the market today, both for industrial and home sewing applications.
However, each type of thread has different characteristics such as twist, content, size, etc. It is important to use the correct thread with your Meistergram machine for proper results.
Two types of thread available from Meistergram are as follows:
Meistergram Mercerized Cotton -solid colors
Meistergram H/D Rayon -solid colors, varigated, metallic
These threads are all color fast and boil fast. Under normal conditions they can be used on a wide range of garments and materials, withstand laundry and dry cleaning processes and provide many years of beautiful embroidery.
Generally, the Mercerized Cotton thread is used on cotton fabrics or in instances where the embroidery will be subject to a great deal of wear. Use only the cotton thread as the bobbin thread. Do not use the rayon thread for winding bobbins.
The rayon thread has a high sheen and silk-like appearance,
It adds distinction to coat linings, jackets, sweaters, purses, etc.
Rayon thread should not be used in the bobbin.
However, you may use the rayon or cotton interchangably on all types of garments depending on the tastes of you and your customers.
Lubricants
Some material, particularly vinyl and heavy canvas, may require a lubricant on the thread to prevent breaking and other common sewing problems. These resu It from the needle getting too hot due to the friction caused from the material in question. Non-staining silicone lubricant is available from
Meistergram. It can be sprayed onto the cone of thread, on the needle and the material or applied with a lubricating box attached to the top of the sewing machine head.
Thread lubricant is particularly useful with rayon thread.
C. Bobbins and Bobbin Thread
Refer to page 4 of Section I regarding how to wind the bobbin correctly. Be sure to only use Meistergram mercerized cotton thread in the bobbin. Do not use the rayon.
The bobbins supplied by Meistergram are specially made and you will note that the sides of the bobbin curve inward slightly. This is to prevent the needle from hitting the edge of the bobbin. If the wrong type of bobbin is used it may result in burs or nicks on the edge of the bobbin and needle and this will interfere with the sewing operation of the machine.
Occasionally, a bobbin will become bent or out of shape and
Part 2
Page 2 From the library of: Superior Sewing Machine & Supply LLC therefore not turn properly in the bobbin case; this too will cause problems.
It is a good idea at all times to have an empty bobbin on the bobbin winder and a cone of thread for winding new bobbins. You can also wind bobbins in advance using different colors of thread. If you do not have bobbins wound in advance you will find it very time consuming to stop in the middle of your embroidery to wind a bobbin.
Be very careful that the loose end of the thread from the cone used for winding the bobbin does not lay near the machine belt or slot in the table for the machine belt. This loose end may be pulled by the belt down onto the pulley and shaft. Before you realize this has happened several thousand yards of thread will be wrapped around the pulley!
Therefore, keep the loose end attached to an empty bobbin or laying well over the back or side of the machine.
Most embroidery can be done using only one color of bobbin thread regardless of the color of the top thread.
However, if you are concerned that the bobbin thread will get pulled up onto the top of the garment or if you prefer a nicer looking effect on the back of the monogram then you should use a bobbin thread that is either the same color or similar shade as the top thread. For instance, white bobbin with light colors and black bobbin with dark colors.
A tight tension on the bobbin winder assembly will allow you to wind more thread onto the bobbin and therefore you will have to change the bobbin less often.
D. Needles Sizes and Types
There are thousands of different sewing machine needles on the market and they are made for specific classes of machines. In most cases they can not be interchanged from one machine to another without causing problems.
On page 3 of Section I we discussed various needle sizes that are available from Meistergram. This particular type needle must be used with your machine. When tested at the factory the machine is sewn-off with a No. 10 and No. 11 needle. These two sizes of needles will allow you to embroider almost everything without any difficulty.
The smaller size needles, No. 7 and No. 9 can be used on sheer and lightweight fabrics. The larger needles, No. 12 and
No. 14 can be used on heavy weights such as canvas, heavy pile and vinyl.
However, when switching to a much smaller or much larger needle it may be necessary to re-time the machine in order for the needle to work properly without skipping stitches.
Ball point needles are available in some sizes and can be used for embroidering on knits. Wedge point needles are available for vinyl and leather. However, there is not a great advantage to these needles and experience has proven that the regular No. 10 and No. 11 needles work just as well on the above items.
When ever possible you should test the various needles on the particular item to be embroidered to find the on~ best suited.
E. Hoop Sizes and When to Use
Referring to the Meistergram Supply List you will note the metal hoops for the M'1 00 type machines. These are available in a ringe of sizes from 2" up to 12".
As a general rule you should use a hoop size no larger than necessary for the size lettering or embroidery you are doing. As an example, you would not use a 1 0" hoop to
embroider several 1" letters. The hoop used should accomodate the lettering and the presser foot when it is in the down pos1t1on. That is why you should move the tracing arm around the perimeter of your lettering before starting to monogram to be sure that it fits into the hoop.
With some practice and experience you will quickly recognize which size hoop you will require for a given style and size of lettering.
The inside wooden hoop insert, when it is new, has a waxlike finish on it which provides extra gripping strength. However, at first this may leave a slight residue on the garment.
Some operators remove this coating with a light sand paper.
Other operators prefer to wrap the wood insert with a seam binding. However, in most cases the hoops are used as they are.
On some fabrics with a very high pile, such as velour robes, the hoop may leave an impression on the material.
Some of this is due to the hoop being too tight. In most cases, however, the ring mark will disappear on its own or it can be brushed out after the monogram is completed. Some operators will put a piece of paper on top of the garment or another piece of material around the hoop ring to prevent ring marks on difficult fabrics.
Regular wooden hoops are also available for use in doing free-hand work. These can not be attached to the machine like the metal hoops. The metal hoops can also be used for free-hand work.
It is always a good idea to have several wood hoop inserts on hand for your metal hoops in case one should break.
Besides the hoops, Meistergram has available and can make special clamping devices and gauges for particular products. These are very useful as it eliminates the need for hooping, particularly when embroidering a great many of the same item.
II
•
F. Placement of Monogram on Various Garments- Photo 2
The position in which monogram or name is placed on a garment is subject to many variables such as customer preference, size and style of garment, size and style of monogram, degree of difficulty in working with the garment, etc.
We have, however, provided guide I ines for placement on the most popular types of garments. Please note that these measurements are approximate and represent the center of the entire monogram.
You will find many placements of your own that will develop from working with different garments and customer requests. Generally speaking, most monograms will be placed on the left side of the garment in the area where a breast pocket would be. On flat goods the monogram will normally be centered on the merchandise at some determined distance from the edge.
Do not hesitate to create your own placements on any merchandise or to alter the following suggestions as to position.
1. Shirt Pockets: %"to%" below top center of pocket
To use the 2" shirt pocket hoop, first remove the presser foot from the machine. Mark the center of the pocket with a pin or by folding the pocket. Insert the 2" hoop into pocket so that top edge of pocket is even with top red lines on the hoop and so that the hoop extension is out of pocket, as shown in photo 3. Insert black plastic hoop so red I ines on both hoops match. Turn and fold back body of shirt away from the shirt pocket so that only the back of the pocket will rest on work plate. Attach hoop to hoop arm assembly and proceed with small monogram.
2. Shirt Cuffs: measure 1" from center of cuff toward the button hole with bottom of letters%" to%" above cuff edge. This will place the monogram in the top center of wrist.
From the library of: Superior Sewing Machine & Supply LLC
Part 2
Page 3
3. Ties: 2" to 2Y:!" up from bottom of tip or 1 0" to 11" up from tip if tie is to be worn with vest.
4. Men's Wear: Robes, Sweaters, Jackets, Sport Shirts,
Pajamas, etc. 7" to 10" down from left shoulder seam and 4" to 6" over from center front.
5. Ladies Wear: Robes, Sweaters, Blouses, Jackets,
Pajamas, etc. 4" to 6" down from left shoulder seam and 3" to 5" over from center.
6. Children's Wear: similar to above only on smaller scale.
7. Towels: the correct placement of the monogram on a towel is the opposite side and opposite end from the label, as follows: bottom of monogram should be centered
Bath Sheet 3" above border or 4" above hem
Bath T owe I
Hand Towel
2" above border or 4" above hem
1 Y:!" above border or 2" above hem
Fingertip Towel 1" above border or 1 Y2" above hem
Wash Cloth 1" above border or 1 Y:!" above hem
8. Sheets: bottom of monogram should be centered 2" above wide hem I ine on top side of sheets
9. Pillow Cases: bottom of monogram should be centered 1 Y:!" above hem I ine
When working with unusual merchandise or items out of the ordinary you will generally find that the easiest place in which to place the monogram usually is the best place to put the monogram!!
G. Staggering Monogram Diagonally and Vertrcally
Most styles of templates fit into the template holder straight across in a horizontal position. However, they can be staggered in several positions as explained below. Since this requires adjustment to the hoop arm, please refer to the following pages: page 13, Section I Hoop Arm Assembly page 15, Section I page 3, Section II, Part I
Hoop Arm Assembly
Adjusting Hoop Arm Height
The T-bar has odd numbers on the horizontal portion and even numbers on the vertical portion. In order to stagger the letters as illustrated in photo 4 of the sweater, you must always embroider the center letter of the monogram first. When you move your stylus over to the letter on the right you must then loosen thumb screw HA 6 and move the hoop away from you which will place the right hand letter lower than the center letter. Prior to moving the hoop, note the number on the vertical scale that corresponds with the front edge of the hoop block clamp, HA 7. This will be your reference point. For example, the hoop block clamp is at number 10 on the vertical scale. Before moving the clamp to lower the right hand letter you must decide how much lower you want the letter to be. Generally, the top of the right hand letter should be at the middle of the center letter or at the bottom of the center letter. Move your stylus to the top of the right hand letter, lock it in position, loosen thumb screw HA 6 and then move the hoop so that the needle is at
Part 2
Page 4 the desired location. Tighten the thumb screw and note how many numbers you have moved from your reference point, number 10. For our example you moved four spaces to number 14. After embroidering the right hand letter, move the stylus over to the left and letter, loosen the thumb screw and move the hoop block clamp to number 6 on the scale.
The left hand letter will then be located in the same relative position to the center letter as the right hand letter since you moved four spaces up and four spaces down from the reference point, number 10.
The distance between marks on the vertical and horizontal scales is %of an inch. The amount of space that you will move depends on the size of the letters and the style.
Another manner in which to stagger the letters without adjusting the hoop arm is to use small hand magnets. These are available from Meistregram and allow you to place the templates into the holder in staggered position instead of straight across. The magnets will hold the templates in position at points where the guides on the template holder will not be able to reach.
To monogram letters vertically, i. e., one on top of the other, requires adjustment to both the thumb screws HA 4 and
HA 6. The same basic procedure is used as for diagonal positioning. First embroider the center letter. Move to the right letter and adjust hoop from reference point so that the top of the right hand letter is below bottom of center letter. Then
From the library of: Superior Sewing Machine & Supply LLC
find reference point on horizontal scale of T-bar and adjust so that top of right hand letter is under the center letter.
Using the same spacing from both reference points you will be able to place the left hand letter on top of the center letter.
With small to medium size templates you may be able to place them into the template holder in a vertical position and use the magnets to help hold in the templates in place. This will enable you to do vertical work without adjusting the hoop arm assembly.
H. Correcting Mistakes
Occasionally you will embroider the wrong letter on a garment or your stylus will come out of the template and an incorrect line will be embroidered.
To remove such errors use the monogram ripper, razor blade, or sharp, fine point scissors and cut the bobbin thread on the back of the monogram. Then using tweezers pull out the bobbin thread and the top thread. If you have gone over the monogram several times this may have to be repeated twice to get out all of the thread.
Usually little or no marking will be left on the material when the thread is removed, but this depends on the type of material embroidered.
I. Production Work
When your monogram service experiences a great deal of work, proper organization will enable you to achieve higher productivity. Some steps to follow for this are:
1. have extra sets of hoops so that garments can be hooped ahead of time by an assistant
2. have an assistant trim the garments and prepare the next garment, pick the proper templates and thread so that the monogrammer will not have to take her time for these duties
3. arrange monogram orders by color of thread to be used and/or by style of template so these do not have to be changed as often
4. arrange orders by type of garment so operators can run through a particular batch of orders without having to adjust the machine or hoops
Other steps can be taken and may vary depending on the type of item being embroidered. A better means of organization usually develops after having some experience with the machine.
J. Organization of Monogram Department
An important ingredient for the success of any business endeavor is organization and this can not be stressed enough.
The proper layout of your monogram department and procedures will enable you to operate profitably and efficiently.
Here are some important considerations in the organization of your department.
1. decide which colors and styles and sizes of monograms will be available to your customers
2. establish prices for each style of monogram and size that you will be offering
3. establish separate wholesale prices for certain accounts
4. have samples of the colors and styles available for your customers to see
5. use order forms for each order, with a receipt for the customer, a receipt for the operator, as well as an office copy
6. set aside a certain area for incoming garments to be monogrammed and a separate area for finished goods
7. keep your department clean
8. keep all supplies such as thread, templates, hoops, needles and other accessories on peg board, marked drawers, shelves or boxes within easy reach of the operator
9. watch your inventory of supplies, such as thread and needles, and establish re-order points so that you do not run out of needed materials in the middle of an order
10. review your thread colors and monograms styles often so that your customers can be presented with new selections
These are but a few ideas to consider when setting up your department, and again, many others will be evident to you once you begin your operation. The main point to consider is to be sure and give thought to the flow of garments through your department so that your monogramming will be done as efficiently as possible.
From the library of: Superior Sewing Machine & Supply LLC
Part 2
Page 5
PART3
CAUSE AND CORRECTION OF
COMMON PROBLEMS
THE NEEDLE BREAKS
Cause of the trouble:
The operator pulls the fabric during sewing and needle hits work plate and bends or breaks.
Some portions of the fabric are too hard or too thick, the needle bends or breaks
What to do about it:
Operator must coordinate hand movement of the material with speed of the machine.
Sew slowly over such areas of material. If necessary use a heavier needle.
The needle has a blunt point and cannot penetrate the fabric.
Replace with new needle. (See page no. 3.)
Needle is held too loosely in needle bar.
The needle is bent and strikes slot in work plate or hits the hook.
The needle is set too low and hits the bobbin case.
Throat plate is not held firmly in place and needle is hitting it.
Presser foot is in raised position and needle is hitting side of foot.
Upper thread is too heavy for the needle in use.
Needle bends and breaks.
Upper thread has knots which can not pass through eye of needle.
The presser foot is not exerting enough pressure while sewing heavy fabrics or vinyl.
Insert new needle and tighten properly.
Replace needle and check height of needle bar and timing of hook.(See page no. 11.)
Replace needle and check height of needle bar and timing of hook. (See page no. 11.)
Remove large work plate and secure throat plate properly.
Either lower the presser foot or remove from presser bar.
Replace needle with correct size or change size of upper thread.
Change thread.
Loosen screw on presser foot and adjust downward for more pressure as needle is coming out of material. (See page no. 8.)
Needle is still in fabric while operator tries to move hoop for next letter or to remove hoop.
The Thread Take-up Spring is not adjusted correctly. It exerts too much pull on the upper thread at the moment the needle enters the fabric. The needle bends and strikes the slot in the plate or hook and breaks.
The point of the hook is too close to the needle.
Needle must always be raised to highest point before removing hoop or moving to next letter.
Adjust the Thread Take-up Spring so that the loop of the spring has finished its upward motion at the moment the needle enters the fabric. (See page no. 5.)
There is no slack thread or not enough slack thread when moving hoop to next letter.
Adjust the clearance between the hook and needle.
(See section on Timing, page no. 11.)
Pull a slight amount of thread thru the tension assembly so that when moving hoop to next letter, thread will not pull and bend the needle.
From the library of: Superior Sewing Machine & Supply LLC
Part 3
Page 1
LOOPS OR KNOTS ON TOP SURFACE OF FABRIC
The upper thread lies flat on the top surface of the fabric and the lower bobbin thread appears in the top stitch.
Cause of the trouble:
The tension of the upper thread is too tight or the tension of the bobbin thread is too weak.
What to do about it:
Loosen the tension on the top thread or tighten the tension on the bobbin until both are correctly balanced. (See pages no. 5 and 6.)
The tension spring on the bobbin case is bent out of shape providing insufficient tension on the lower thread.
Lint, dirt or pieces of thread have accumulated underneath the tension spring on the bobbin case.
Rust or rough spots between the upper tension discs.
Thread has slipped out from underneath tension spring on bobbin case or thread guide on bobbin case.
Try to correct the deformed spring by re-shaping or replace bobbin case.
Remove and clean spring and bobbin case. Replace and adjust correctly. (See page no. 6.)
Remove tension discs and clean and polish. If badly worn, replace. (See page no. 5.)
Be sure bobbin thread is completely under the lip of tension spring on bobbin case and thread guide.
(See page no. 6.)
LOOPS OR KNOTS ON THE UNDERSIDE OF THE FABRIC
The lower bobbin thread lies flat on the underside of the fabric and the upper thread appears on the bottom in the form of loops or knots.
Cause of the trouble:
The tension of the upper thread is too weak or the tension of the bobbin thread is too tight.
What to do about it:
Tighten the top tension or loosen the bobbin tension until correctly balanced. (See pages no. 5 and 6.)
There is dirt, lint or pieces of thread between the top tension discs.
The head of the tension adjusting screw on the bobbin case protrudes and catches the top thread.
The point of the needle is bent.
The bobbin is not evenly wound and unwinds irregularly.
Take apart the upper tension, clean the discs, replace and adjust. (See page no. 5.)
Adjust this screw correctly or if necessary smooth the head of the screw with fine emery cloth, or replace screw. (See page no. 6.)
Replace needle.
Replace the bobbin with one that is properly wound.
Check bobbin winder for proper operation and alignment. (See page no. 4.)
Replace defective bobbin. The bobbin is damaged or bent and does not revolve freely and evenly.
Bobbin case has lint, dirt or pieces of thread which prevent bobbin from revolving freely.
The needle is not timed correctly in relation to the hook.
There is insufficient clearance between the bobbin case holder portion of the hook and bobbin case holder position bracket.
Clean bobbin case thoroughly.
See section on "Timing". (See page no. 11.)
Either move hook assembly back or move the bobbin case holder position bracket to allow room for thread to pass. (See pages no. 10 and 11.)
Part 3
Page 2 From the library of: Superior Sewing Machine & Supply LLC
(Loops or Knots on Underside of Fabric- Cont'd.)
What to do about it: Cause of the trouble:
The upper thread gets caught somewhere below the work plate.
The Thread Take-up Spring is not adjusted correctly and/or is not working properly.
Examine hook, bobbin case, position bracket and slots in plates for rough spots which may catch the thread. Eliminate these spots with fine emery cloth.
Adjust the Thread Take-up Spring until it has the correct tension and its upward movement is just finished at the moment the needle enters the fabric.
(See page no. 5.)
NEEDLE THREAD BREAKS
What to do about it: Cause of the trouble:
The tension of the upper thread is too tight. Loosen upper thread tension. (See page no. 5.)
The machine is not threaded properly. Check threading of machine. Make sure thread is not wrapped around any of the thread guides or is being obstructed. (See page no. 3.)
Loosen top tension or replace thread. Thread may have weakened from improper storage or be of poor quality. May also have knots which can not pass through eye of needle.
The needle has a rough eye or sharp eye, is not straight or has a blunt point.
Needle is inserted wrong.
Insert a new needle.
Be sure long groove on needle is facing front and needle is all the way up into needle bar. (See page no.
3.)
Replace bobbin.
See section on "Timing". (See page no.
11.)
The bobbin is bent, wound too full or unevenly.
The needle is too high and hook cannot catch the loop of the thread.
The latch on the bobbin case does not close entirely and catches upper thread, breaking it.
Lint or dirt have accumulated in the circular groove on top of the center post of the hook on which the bobbin case is placed. This prevents the latch from closing which will catch the thread.
Too little clearance between bobbin case holder and position bracket. Upper thread gets caught.
Clean bobbin case and replace if necessary with a new one.
Remove lint or dirt from circular groove on center post, clean around the bobbin case holder area.
Move hook back or move back position bracket to allow thread to pass. (See pages no.
10
and
11.)
Smooth off with fine emery cloth and polish with crocus cloth.
Rough spots on edges of the portion of the bobbin case holder and position bracket which engage each other.
The Thread Take-up Spring, behind the tension discs, is not adjusted correctly and does not take up the slack of the thread. The needle pierces and breaks the thread
Adjust the Thread Take-up Spring so there is no thread under the point of the needle when it is about to enter the fabric. (See page no. 5.)
From the library of: Superior Sewing Machine & Supply LLC
Part 3
Page 3
Cause of the trouble:
The tension of the Thread Take-up Spring is too tight or too weak.
Take-up Spring is bent, out of shape or worn, or broken.
(Needle Thread Breaks - Cont'd.)
What to do about it:
Loosen or tighten tension of the spring accordingly.
(See page no. 5.)
If possible, reform spring or replace with new one.
The point of the hook has burrs, rough spots or edges which cut the upper thread. The point of the hook may be worn, blunt, or damaged.
Smooth off defective areas with fine emery cloth and polish with crocus cloth. All portions of the hook must be smooth. If the point of the hook is broken, replace entire hook.
Adjust the screw properly or smooth off any rough spots so the thread can pass freely. (See page no. 6.)
The head of the small screw used for adjusting the tension on the bobbin case protrudes too much beyond the tension spring and catches the thread.
The top surface of the bobbin case is damaged and has burrs or rough spots which catch the thread and break it.
The Hook is not timed correctly in relation to the needle.
Smooth off rough spots with fine emery cloth and polish with crocus cloth.
See Section on "Timing:'. (See page no. 11.)
Some parts along which the upper thread passes have become rough or sharp and may possess deep grooves.
The needle is too close to the slot in the work plate or throat plate.
With fine emery cloth or cord remove rough spots on thread guides tension discs, take-up spring, takeup lever, slot in work and throat plate, etc.
The needle is too close to the hook and rubs against the point of the hook.
Sometimes the fabric to be sewn causes thread breakage.
Too much oil or lack of oil in the hook assembly.
The upper thread is of the wrong twist causing the thread to unravel.
Check to see of needle is bent. If not, check alignment of both plates and re-adjust or buff slots in plates to allow more room.
Check to see if the needle is bent. If needle is straight, move hook back slightly away from the needle. See section on "Timing". Point of Hook should be as close as possible without touching the needle. (See page no. 11.)
It may be necessary to re-adjust thread tension, takeup spring tension and timing.
Light amount of oil is necessary for free movement of hook. See section on "Cleaning and Oiling".
(See page no.
1 0.)
Use Meistergram Mercerized Cotton or Meisterlon
Rayon which are designed for monogram purposes.
Part 3
Page 4 From the library of: Superior Sewing Machine & Supply LLC
BOBBIN THREAD BREAKS
What to do about it: Cause of the trouble:
The tension of the lower thread is too tight. Loosen the tension spring on the bobbin case by means of the small screw. There should be a slight amount of drag on the thread when pulled through the bobbin case and it should move freely. (See page no. 6.)
The bobbin is wound too fully and can not revolve freely in the bobbin case.
Remove some of the thread and check bobbin winder assembly. Adjust trip latch so less thread is wound on bobbin. (See page no. 4.)
The thread on the bobbin is wound too loose or unevenly; it is piled up at certain spots or crisscrossed.
Lint or dirt have accumulated in the bobbin case preventing free movement.
Check bobbin winder assembly and adjust properly.
See section on "Bobbin Winder and Bobbin". (See page no. 4.)
Remove bobbin case and bobbin and clean thoroughly.
Replace bobbin. The bobbin bent or out of shape. Edges of the bobbin are rough, sharp or have nicks.
Lint, dirt or piece of thread is lodged under tension spring of bobbin case.
Spring on bobbin case latch is worn preventing latch from closing properly.
Wrong thread or defective thread is being used in the bobbin.
Remove bobbin case tension spring and clean.
Replace bobbin case.
There are rough spots, sharp edges or burrs on the bobbin case or slots in the plates which break the thread.
Use only Meistergram Mercerized Cotton Thread in the bobbin, do not use Meisterlon Rayon for the bobbin. Replace with correct thread.
Examine all parts along which the lower thread passes.
Smooth off any defective portions with fine emery cloth.
Cause of the trouble:
The machine is not threaded correctly.
SKIPPING STITCHES
What to do about it:
Check to see if thread is running properly from spool to needle. Refer to section on "Threading". (See page no. 3.)
An incorrect needle is being used; needle is incorrectly inserted, bent or blunt.
Insufficient pressure from the Presser Foot.
Replace needle; refer to section on "Needles". (See page no. 3.)
See section on "Presser Foot" and adjust properly.
(See page no. 8.)
Excessive oil on the hook or thread.
The thread take-up spring is not adjusted correctly.
Clean off hook assembly, bobbin case, needle bar, presser bar and foot.
Correct tension and/or position of spring. See section on "Tension Take-up Spring". (See page no. 5.)
Part 3
Page 5
From the library of: Superior Sewing Machine & Supply LLC
(Skipping Stitches - Cont'd.)
Cause of the trouble:
The machine is out of time. Hook is too early or too late in meeting the needle, needle is too high, hook is too far from the needle.
What to do about it:
Re-time machine. See section on "Timing". Often results from breaking a needle which may move the needle bar up slightly putting the machine out of time. (See page no. 11.)
The point of the hook is blunt, damaged or broken.
The type of fabric being monogrammed makes the formation of the loop of the thread difficult, especially in knits, vinyls, open weave materials, etc.
Upper thread is not of the correct twist. Unravels and forms improper loop which is not picked up by the hook.
Replace the hook assembly.
Try using various types of backing material. Adjust upper thread tension, take-up spring tension, presser foot and re-time if necessary.
Use Meistergram thread, specifically designed for monogramming.
MACHINE TURNS HEAVILY OR JAMS
(Refer to Detailed Parts List- Yellow Pages)
Cause of the trouble:
Sewing thread is wedged between the balance wheel and the arm of the machine.
The belt, running from the clutch to the balance wheel, is too tight.
Dirt, lint, piece of thread is wedged between the bobbin case holder and rotary hook of the hook assembly.
Bearings of the machine are tight due to rust, lack of oil or use of improper oil.
Clutch assembly bearing requires lubrication.
Internal parts require lubrication, are out of alignment, etc.
Motor may be defective or burnt out.
Thread is wrapped around take-up lever assembly inside machine.
What to do about it:
Remove balance wheel and eliminate thread. Often caused by leaving loose end of thread hanging from thread guide on Lamp.
Replace belt. Proper length belt will provide enough tension without slipping.
This can often be worked out by saturating the hook with oil, removing the belt, and working the balance wheel back and forth to wear out any foreign material in the hook. Or, disassemble the hook and clean thoroughly.
Clean out bearings and lubricate with good sewing machine oil. Do not use thick oil or vegetable oils.
Place oil on sleeve and shaft of clutch assembly. (See page no. 9.)
Remove top cover plate on head and refering to Parts
List, oil all moving parts and checking for areas that may be binding.
Replace motor.
Caused by running machine without sewing but with loose thread in take-up lever. This is drawn into the machine and gets tangled. Saturate take-up assembly and work back and forth by turning wheel, using needle or pin to get thread out.
Part 3
-Page 6
From the library of: Superior Sewing Machine & Supply LLC
Cause of the trouble:
The machine is not sufficiently oiled.
MACHINE RUNS NOISILY
What to do about it:
Presser foot is too low and is hitting plate.
Hoop is too low and banging on work plate.
Flag on top of presser bar is not riding correctly on cam on take-up lever.
Presser bar lifting bracket is set too low and hitting presser bar lever.
Machine is set too low in table, work plate is vibrating.
Clutch is out of alignment.
There is too much space between the bobbin case holder and position bracket.
Oil the machine wherever lubrication is required.
See section on "Oiling and Cleaning". (See page no.
10.)
Loosen screw on presser bar and raise foot slightly.
Raise hoop arm assembly slightly.
With needle at lowest position, loosen set screw on flag and push down so that small bar extending from flag is riding on cam on take-up lever. (See page no. 8.)
With needle at lowest position, insert screwdriver between bracket and lever, loosen screw on bracket, raise slightly and tighten. (See page no. 8.)
Raise machine slightly in each corner so work plate is above the table top.
Loosen screw holding motor disc and re-position disc so there is only a slight amount of space between motor disc and clutch disc. Cork on discs may be worn and should be replaced. (See page no. 9.)
Move hook or bracket closer, allowing enough space for thread to pass. If these parts are worn then replace.
Needle is too low and is hitting bobbin case. Raise the height of the needle bar, if needle is inserted correctly. Then check for proper timing.
(See page no.
11.)
From the library of: Superior Sewing Machine & Supply LLC
Part 3
Page 7
SECTION Ill
DETAILED PARTS LIST FOR SEWING HEAD MECHANISM
The detailed parts list applies to both the M'80JNS and M'100JNS sewing machine heads.
It is divided into the following sections:
1. Main Frame & Miscellaneous Cover Components
2. Needle Bar & Hook Drive Shaft Components
3. Zig Zag Width Regulating Mechanism Components & Presser Bar Assembly
Detail pertaining to other operating parts of the machines, such as the Pantograph System, etc. are found elsewhere in the manual.
Ordering Parts: All orders for parts should be sent to:
Meistergram
310 Lakeside Ave., W.
Cleveland, Ohio 44113
Phone Calls for Service, orders for parts, or questions pertaining to service and operation of equipment should be made to Meistergram in Cleveland,
(216) 621-8731
Service calls can be taken Monday through Friday from 9:00 a.m. to 5:00 p.m.
Please ask for either service or order department.
COLLECT PHONE CALLS CAN NOT BE ACCEPTED
WHEN CALLING THE SERVICE DEPARTMENT, PLEASE HAVE YOUR MANUAL
AT HAND SO REFERENCE TO THE PROPER PARTS CAN BE VERIFIED.
From the library of: Superior Sewing Machine & Supply LLC
1. MAIN FRAME & MISCELLANEOUS COVER COMPONENTS i71 70]
I
106
Part No.
109
110
111
112
113
114
115
101
102
103
104
105
106
107
108
11 6
117
118
Description
Arm bed
Top cover
... Screw
Face plate
... Screw
Arm side cover (large)
... Screw
Arm side cover (small)
... Screw
Needle plate
Needle thread guide pin (4 hole)
Needle thread guide pin (2 hole)
Three hole thread eyelet
... Screw
Arm thread guide (upper)
(lower)
... Screw
Tension post thread guide
... Screw
Amt. Req.
1
2
1
2
1
2
2
1
2
2
Part No.
129
130
131
132
133
134
135
136
137
119
120
121
122
123
124
125
126
127
128
Description
Tension post socket
... Screw
Tension post
... Screw
Take up spring
Tension disk
Tension release washer
Tension spring
Tension nut
Reservoir (front) oil wick
.. Oil pad
. cover plate
... Screw
Oil reservoir (rear)
... Screw
... Oil wick
... Oil pad
... Cover plate
... Screw
From the library of: Superior Sewing Machine & Supply LLC
Amt. Req.
2
1
2
1
2
1
1
2
2. NEEDLE BAR & HOOK
201-
203-
210
2 ~-226
2~
I~243
247
~ j!'~254
~55
52 256
258
282
28J
284
Part No.
220
221
222
223
224
225
226
227
214
215
216
217
218
219
201
202
203
204
205
206
207
208
209
210
211
212
213
Description
Needle bar frame
... Hinge pin
... Screw
Needle bar
Needle bar connecting stud
... Bushing
... Washer
... Screw
Needle bar set screw
Needle bar connecting link
... Screw
... Adjusting screw
... Needle bar frame guide pin
... Screw
Needle
Needle screw
Take-up lever link hinge pin
... Screw
Take up lever w /cam
Needle bar crank
... Screw (large)
... Screw (small)
Counter weight
... Screw (large)
... Screw (small)
Needle bar connecting link guide plate
Needle connecting link guide plate screw (upper)
Amt. Req.
237
238
239
240
241
242
243
244
245
246
247
228
229
230
231
232
233
234
235
236
248
249
250
251
252
253
254
255
Part No. Description
... Screw (lower)
Arm shaft
... Bushing (front)
... Screw
... Collar
... Screw
Needle vibration pinion (spiral)
... Screw
Arm shaft (horizontal) level gear
... Screw
Arm shaft bushing (rear)
... Screw
Hand wheel
... Screw
... Positioning screw
Gear and pinion case
... Screw
Pinion
... Screw
Upright shaft
... Bushing (upper)
... Screw
... Bushing (lower)
... Screw
... Miter gear
... Screw
Miter gear case
... Screw
Amt. Req.
1
2
2
1
2
1
2
1
2
1
2
1
2
CONTINUED ON OTHER SIDE From the library of: Superior Sewing Machine & Supply LLC
2. NEEDLE BAR & HOOK DRIVE SHAFT COMPONENTS
~242
44
WfDm;
l 219 243 t
~247
:1'~r-254
~255
52 256
258
282
283
Part No.
256
257
258
259
260
261
262
263
264
265
266
267
268
269
Description
... Oil plug screw
Hook drive shaft
Hook drive shaft miter gear
... Screw
... Bushing (right)
... Screw
... Thrust collar
... Screw
... Bushing (left)
... Screw
... Helical gear (right)
... Screw
Helical gear (left)
... Screw
Amt. Req.
1
2
1
2
2
1
2
Part No.
279
280
281
282
283
284
270
271
272
273
274
275
276
277
278
Description
Helical gear cover
... Screw
Hook shaft
... Bushing (front)
... Screw
... Thrust collar
... Screw
... Bushing (rear)
... Screw
Hook
... Screw
Bobbin case posit1on finger
... Screw
Bobbin
Bobbin case
Amt. Req.
1
2
1
3
From the library of: Superior Sewing Machine & Supply LLC
3. ZIGZAG WIDTH REGULATING MECHANISM COMPONENTS & PRESSER BAR ASSEMBLY
I
. 370
306
356
367
311 j1.a-J72
~371
351 i fl-313
~
J14
Part No.
312
313
314
315
316
317
318
319
320
321
322
323
324
301
302
303
304
305
306
307
308
309
310
311
325
326
327
328
329
330
331
332
333
334
335
336
Description Amt. Req. Part No. Description
Presser bar lifting stud for cam
... Screw
Presser bar lifting stud holder
Presser bar
... Screw
1
2
1
2
337
338
339
340
341
Zig-zag regulator
... Screw
... Slide block
... Stud
... Nut
Presser bar lifter screw
Presser spring
Presser bar lifter lever
... Screw
Presser bar guide bracket
... Screw
Presser bar lifter lever releasing bracket
Presser foot
342
343
344
345
346
347
348
349
350
... Holder
... Screw
Zig-zag regulator bushing
... Screw
Zig-zag regulator
Indicator
... Screw
... Washer
... Screw ... End screw
Eccentric stud
... Screw
Needle vibrating cam shaft
... Collar (rear)
... Screw
... Bushing (rear)
1
2
351
352
353
354
355
356
357
Zig-zag indicator plate
... Screw
... Stopper
... Washer
... Nut
Zig-zag connector
... Screw
... Collar (front)
... Screw
... Bevel gear (large)
... Screw
Needle vibrating cam
... Screw
Cam shaft bushing (front)
... Screw
1
1
2
1
2
358
359
360
361
362
363
364
365
366
367
... Screw
Lifting crank shaft
Lifting crank
... Screw
Indicator stop lever
... Screw
... Bracket
... Screw
... Adjusting screw
... End screw
Needle bar frame pitman
... Nut
Lifting rod
... Spring (small) 368 ... Cotter pin
... Screw 369 ... Stabilize plate
... Spring hook 370 .. Screw
Lifting spring 371 Lifting rod roller
From the library of: Superior Sewing Machine & Supply LLC
Amt. Req.
2
1
4
2
2
2
1
2
~
1
2
advertisement
* Your assessment is very important for improving the workof artificial intelligence, which forms the content of this project