Landis McKay Stitcher 77 Operator Instructions Manual
Add to my manuals
18 Pages
Landis McKay Stitcher 77 is a simple, precisely manufactured machine for repairing and resoling women's shoes. It features easy threading, adjustable stitch length, and the ability to stitch various shoe types, including welt, McKay, turn, and cement shoes. Its durable construction and high-quality materials ensure low maintenance and operating costs.
advertisement
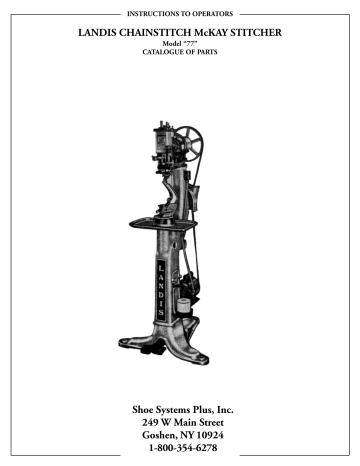
INSTRUCTIONS TO OPERATORS
LANDIS CHAINSTITCH McKAY STITCHER
Model “77”
CATALOGUE OF PARTS
Shoe Systems Plus, Inc.
249 W Main Street
Goshen, NY 10924
1-800-354-6278
MODEL “77” CHAINSTITCH
INTRODUCTION
The Landis Model “77” Chainstitch McKay Stitcher is the result of many years of experience in the design and manufacture of shoe machinery, and has been especially designed to fit the needs of the shoe rebuilder of today and to enable him to increase his business through the repair or resoling of ladies’ shoes.
The Model “77” McKay Stitcher is simple in design, constructed of the finest materials and manufactured with unusual accuracy, which is conductive to low cost of operation and low upkeep. In order to get the benefit of the features of this Stitcher the only necessary contribution by the operator is reasonable care in preparing and fitting up his work. If this is done in a first-class manner, excellent results will be obtained.
When sewing on the Model “77” McKay Stitcher no anxiety need be felt on the part of the operator should small trifles arise at times, which can be eliminated by consulting the following instructions which will enable you to care for your machine properly and keep it in perfect adjustment. For your particular benefit, it is desired that you familiarize yourself as much as possible with the operation of the machine.
The following instructions will be of considerable assistance towards helping you in maintaining, adjusting and operating your machine. Remember that the Model “77” McKay Stitcher is a quality built machine, as are all Landis Machines. Clean it, oil it, and it will render you perfect service.
The Fayscott Landis Machine Corp. will continue to manufacture the Model “77” McKay Stitcher as a Landis Product and we reserve the right to make changes or improvements at any time, without thereby incurring any obligation either to install the same on machinery or equipment previously sold, or install the old part, which has been changed, improved or omitted in new machines or equipment subsequently sold. Prices and equipment subject to change without notice.
FAYSCOTT LANDIS MACHINE CORP.
-1-
GENERAL INSTRUCTIONS
Keep your machine well oiled. Use a good grade of Oil. We recommend Landis Stitcher Oil.
Always use a good grade of Liquid Wax. We recommend Landis Yellow Label-Al-Liquid Wax for McKay
Stitchers.
All Model “77” McKay Stitchers are carefully adjusted at the factory by experts who are competent on these machines, and they are shipped to you ready for operation.
All parts are of the highest grade material possible to purchase for their purpose and are inspected to insure interchangeability so that all repair parts fit into place without fitting or difficulty.
How To Order Parts for Quick Delivery
1. Give the complete part number of the part needed and quantity.
2. Give the Model and Serial Number of your machine.
3. Write your name and address as plainly as possible.
4. Prices of parts do not include postage or insurance. This is extra. Parts are usually shipped parcel post insured.
5. Prices are subject to change without notice.
NOTE: When mailing parts to Factory - be sure to write your name and address plainly on the package. Also write your name and address on your letter explaining why goods are being sent to the factory.
SETTING UP MACHINE
After the Model “77” McKay Stitcher is uncrated and placed in position where it will be used, place motor extension cord plug in electric light socket and machine will be ready to operate.
Machines are carefully oiled before leaving the factory, but should also be oiled carefully before operating.
-2-
LANDIS “77”
THREADING THE WAX POT AND HORN
Put spool of thread on Thread Holder. Put Thread up through first hold in Thread Unwinder Rod and wrap thread half way around Rod and up through second hole in rear of Thread Unwinder Rod. Bring
Thread up through Horn Spindle, by using the long straight Thread Hook furnished. To do this remove
Wax Pot and push Thread Hook down in small hole found below the Wax Pot to the bottom of Horn
Spindle, loop Thread around barb of Thread Hook and pull up through hole, then replace the Wax Pot.
Place Thread in Tension and over Thread Roll to Wax
Pot, down through Lower Wax Pot Roll, then up through Wax Pot Stripper, through Thread Guide
Pin and under Horn Thread Roll and up Horn to small hole in Whirl. A small curved Thread Hook will be found in the supply package. (See Figure
No. 1).
LIQUID WAX - CLEANING WAX POT
Stir Liquid Wax thoroughly before putting it in Wax
Pot. Use “thinner” to thin wax when too thick or heavy. Order Landis Yellow Label Machine Cleaner
& Wax Thinner available in pint and quart cans.
CAUTION: Do not put oil in wax pot.
Remove Wax Pot at least once a week and clean thoroughly with kerosene or coal oil. Keep thread rolls free from old or dried wax. (See Figure No. 1).
SIZE OF THREAD AND NEEDLE
In general practice a No. 33 Needle and 4 Cord right twist Thread will usually be found satisfactory.
Figure 1
S-531
-3-
LANDIS “77”
TO SET NEEDLE
Turn machine until Needle Bar is at its lowest position. Adjust needle until it projects slightly below bottom of whirl. The Needle should be set so that the Whirl lays the thread in the barb groove of the Needle as it revolves around the Needle, much on the order of the Looper on the
Curved Needle Stitcher. (See figure No. 2).
Figure No. 2
PLACING THE FEED POINT
Place Feed Point S-191 so that it extends 3/64” below bottom of
Presser Foot S-130 when Feed Socket S-190 is at its lowest point.
(See figure No. 3).
Figure No. 3
S-130
S-190
S-191
NEEDLE BAR FRICTION
For more friction, turn Adjusting Screw (in top of Main Head) to the right; for less friction, turn screw left.
This Friction Screw is adjusted at the factory and requires little attention. It is used to hold Needle Bar in place when Latch is released. A few drops of oil should be placed in Oil Hole each day.
CAST-OFF FRICTION
The Cast-Off Friction is adjusted at the factory so the Cast-Off Block can be moved up and down with the fingers without moving the Cast-Off Rod. For more friction, turn Adjusting Screw in Cast-Off Friction
Holder to right; for less friction, turn Screw to left. A few drops of oil should be placed in Oil Hole each day.
-4-
S-97
S-96
S-93
S-95
S-92
Figure No. 4
LANDIS “77”
SETTING THE CAST-OFF
The adjustment of the Cast-Off S-95 is important. The Cast-Off Point must be set low enough to completely cover the barb of the Needle S-
92 as the Needle pulls the thread up.
To adjust Cast-Off up or down, loosen Cast-Off Screw S-97, raising or lowering the Cast-Off to the desired position, and afterward tightening the screw. (See figure 4).
The correct relation of the Cast-Off to the Needle is that it just clears the side of the Needle. To test this relation, raise and lower the Cast-
Off repeatedly by lifting on Cast-Off Block, S-96. If too close, the
Cast-Off will spring the Needle sideways. To correct this, spring the
Cast-Off a little away from the Needle. Pliers will be found in the supply package for this purpose. Should the Cast-Off be too far from the Needle, remove the Needle, spring the Cast-Off in as much as necessary.
TO REMOVE AND REPLACE CAST-OFF: Loosen Cast-Off Set Screw
(S-97). Loosen and take off Needle Clamp Collar S-93, remove Cast-
Off. To replace Cast-Off, insert Cast-Off in Cast-Off Block, tighten
Set Screw and replace Needle Clamp Collar. (See figure No. 4).
ADJUSTMENTS FOR ELIMINATING THE SKIPPING OF STITCHES
See that the following are in proper adjustment:
Timing of Whirl (See Page 8)
Setting of Needle (See Page 4)
Setting of Cast-Off (See Page 5)
S-256
S-259
LENGTH OF STITCH - ADJUSTMENT OF FEED
The usual practice is to use about 4-3/4 stitches per inch. Should you desire to sew more or less stitches per inch, loosen the Hexagon Screw S-260 on Feed Cam S-255. Turn Adjusting Screw S-
259 on Movable Cam S-256 in for more stitches per inch and out for less stitches per inch. After adjustment is made, press
Movable Cam and Feed Cam together and tighten Hexagon
Screw. (See figure No. 5).
Figure No. 5
S-255
S-260
-5-
LANDIS “77”
CAUTION:
Before mounting the sole on a shoe, it will be well to find and pull out two to four staples, which will be found near the beginning of the toe curvature, where the upper puckers worst. These staples were put in to hold the sole before the first McKay sewing. These staples will interfere with sewing and may even break the needle. They are generally a little outside the row of lasting tacks.
STITCHING SHOES
Shoes are stitched in the same order as on your other stitching machine; that is to say, the shoe is put on the horn with the heel to the left and the stitches started in the shank, stitching up and around the toe, turning the heel of the shoe from left to right, with the heel towards the operator, then sewing down the opposite side of the shoe to the shank with the heel on the right. You will find this procedure extremely easy.
With the different types of shoes, namely Welt, McKay and Turn, it will be found necessary to stitch at different distances from the edges of the inner sole.
On McKays, the usual practice is to stitch along the old line of stitching if the make-up of the shoe enables the line of stitching to catch the upper.
In stitching the Turn shoe, it is desirable to stitch outside of the inside channel of the turn shoe in order to catch the upper.
In stitching the Welt shoe, it is desirable to stitch as close to the edge of the inner sole as the Horn will permit. The same applies to the stitching of cement shoes.
It might be well to mention the fact that often on McKay shoes the uppers are not drawn or lasted as close to the shank as they should be, in which case it would be good practice to sew a little outside the regular line of stitching to catch the upper.
NOTE: With the channel cut the proper distance from the edge, this difference of stitching from the edge of the inner sole can be accomplished by simply tipping the shoe up in back or down in front, as the case may require, much on the order of the Straight Needle Stitcher. The tipping of the shoe has the desired effect of setting the stitches in on the insole or out as may be desired.
Ordinarily the stitching is accomplished by simply holding the shoe in its place on the horn and the presser foot in the groove, letting the machine feed the shoe around.
-6-
LANDIS “77”
As for sewing the channel, and the general handling of stitching, you will find the Model
“77” McKay Stitcher without doubt the easiest simplest machine to operate and you will find it extremely so in sewing in the channel and around the toe. There is such a marked difference between this and other machines that it is quite noticeable.
After stitching, cut the front thread of the needle loop, the thread nearest you, close to the work, raise the presser foot and remove the shoe. (See figure No. 6).
Cut Outer Thread
When Sewing Is Finished
Figure No. 6
ALOFT WORK
ALOFT STITCHING is easily accomplished with the Aloft Channel Groover which is easy to operate, the channel operation requiring but a second or two, and when properly done, it permits of practically closing the grooved channel over the thread. (See figure No. 7).
The Aloft Presser Foot should be inserted when stitching aloft. This Presser Foot can be used for any other type of channel work. You will find aloft stitching extremely simple.
THREAD
It is highly important that a good grade of right twist thread be used, and should you experience difficulty in breaking thread, examine and test your thread.
SIZES OF THREAD AND NEEDLES
For all ordinary purposes, it has been found that No. 33 needle and 4 cord right twist thread is very satisfactory. Should it be desired to use a different size needle and thread, the chart below will show the sizes of needles to be used with different sizes of thread.
NEEDLE SIZES
THREAD USED WITH
We recommend needles and right twist thread as follows:
33 34 35 36
4 cord 5 cord 6 cord 7 cord
-7-
For More
Tension
Turn
For Less
Tension
Turn
S-583
Thread
Figure No. 8
LANDIS “77”
THREAD TENSION
To increase the Tension, turn Tension Thumb Nut S-583 to the right, and to decrease, turn to the left. (See figure No. 8).
WAX STRIPPER ADJUSTMENT
To replace Wax Stripper S-573, remove
Stripper Screw S-574 and take out old
Stripper, insert new Stripper and replace
Stripper Screw. (See figure No. 9).
Thread
S-574
S-573
CAUTION: Do not tighten rubber stripper too tight as this tends to increase tension.
Figure No. 9
TO REMOVE WHIRL
Remove the Horn Cap S-503 by taking out two Fastening Screws, S-504 and S-505, so that the Horn Tip
S-502 can be raised enough to allow removal of Whirl.
(See figure No. 10).
S-505
S-504
S-503
S-502
Set thread hole in whirl in line with mark on horn tip. The outer edge of pinion tooth in mesh, is even with top of whirl.
Figure No. 10
S-507
TO REPLACE AND TIME WHIRL
Care must be taken to see that the Whirl S-507 is correctly timed. Two settings of the machine are necessary. 1st - Revolve the machine by hand until the arrow on the Feed Cam S-255 coincides with the Arrow on the Main Head (See figure No. 5). 2nd - Set the
Horn at the left until the marks on the Horn and Horn
Table coincide. (See figure No. 11).
With these settings arranged, insert the Whirl so that the small hole in Whirl coincides with mark on Horn
Tip (See figure No. 10). Push the Horn Tip down, replace Horn Cap and fasten securely with two Screws.
Set Horn So That Lines Meet
Figure No. 11
-8-
LANDIS “77”
TO CHANGE PINION
Take out the two Fastening Screws S-504 and S-505, remove Horn
Tip S-502 and Horn Cap S-503; the Pinion S-508 may now be lifted out and replaced with a new one.
Be sure that the new Pinion meshes with the Whirl S-507 properly. (See cut for Pinion Adjustment).
Replace the Horn Tip and Whirl. Be sure Whirl is correctly timed as previously described. Replace Horn Cap and fasten with two Screws. (See figure No. 12).
S-504
S-505
S-503
S-507
S-502
Keep smooth at all times
ADJUSTING PINION
To adjust Pinion S-508, remove Horn Rear Curved Plate S-555, which will permit access to Pinion Adjusting Screw S-510.
TOP OF
HORN
S-508
S-501
Figure No. 12
To raise Pinion turn Adjusting Screw to the right; to lower Pinion, turn Adjusting Screw to the left. Pinion and Whirl teeth should mesh, and turn freely. (See figure No. 13).
Horn S-501
HORN CAP
The top of the Horn Cap should be kept smooth at all times, also the hole should be dressed out smooth with emery cloth if at any time it is nicked or burred.
Hole for Screw
S-556
Hole for Cover Plate
S-555 in Back of Horn
If not perfectly smooth, the thread may catch on sharp edges and strand. (See figure No. 12).
To Adjust Pinion S-508 Up,
Turn Screw S-510 to Right
ALIGNMENT OF HORN
The Horn is lined up at the factory. Should the occasion arise at any time for re-alignment, it can be accomplished by the following procedure:
To Adjust Pinion S-508 Down,
Turn Screw S-510 to Left
Figure No. 13
Loosen four Screws S-531 under Horn Table slightly, which will permit tapping the Horn to correct alignment. Tap into a central position so that hole in Horn Cap runs true. After firmly tightening Horn Holding Screws, you can check the position by putting needle down into the Whirl and see that it does not rub on the side of the hole in Whirl. (See figure No. 14).
When Horn is Centrally
Located, the Whirl Will
Not Rub Needle CLEANING HORN
IMPORTANT: Take off Horn Cap S-503 each day after you are finished sewing and clean Whirl, Pinion and Rollers with kerosene. Your machine will be ready for work the next day and this will eliminate any difficulty from hard and gummed wax.
Figure No. 14
On the LANDIS McKay Stitcher Model “77” the Horn is separated in three parts to provide easy cleaning and threading.
-9-
S-320
S-21
S-22
S-26
S-32
S-256
S-25
S-630
S-260
S-307
S-255 S-259
S-301
S-305
S-174
S-318
S-326
S-327
S-45
S-44
S-104
S-85
S-84
S-81
S-105
S-82
S-86
S-98
S-642
S-93
S-644
S-40
S-79
S-314
S-313
S-41
S-306
S-302
S-48
S-36
S-37
S-38
S-42
S-62
S-64
S-65
S-63
S-308
S-70
S-61
S-60
S-71
S-128
S-150
S-77
S-76
S-75
S-94
S-95
S-97
S-39
S-97
S-117
S-99
S-109
S-96
S-116
S-198
S-172
S-171
S-170
S-197
S-152 S-151
S-136
S-166
S-140
S-139 S-137
S-160
S-186
S-199
S-196
S-130
S-202
S-205
S-190
S-191
S-188
S-131
S-206
S-141
S-205
S-192
-10-
S-361
S-363
S-365
S-366
S-347
S-347
S-342
S-346
S-343
S-341
S-354 S-345 S-357
S-227
S-226
S-181
S-228
S-175
S-179
S-222
S-176
S-177
S-220
S-230
S-221
S-146
S-242 S-250
S-246
S-247
S-239
S-155
S-214
S-215
S-380
S-385
S-386
S-397
S-395
S-390
S-391
-11-
S-571
S-566 S-574
S-508
S-578
S-582
S-513
S-560
S-583
S-518
S-572
S-575
S-507
S-627
S-630
S-545
S-504
S-564
S-556
S-534
S-638
S-639
S-633
S-631
S-632
S-726
S-11
S-10
S-12
S-13
S-710
S-732
S-736
S-725
S-727
S-728
S-692
S-415
-12-
P AR
77-S-71
77-S-75
77-S-76
77-S-77
77-S-79
77-S-81
77-S-82
77-S-83
77-S-84
77-S-85
77-S-86
77-S-87
77-S-88
77-S-93
77-S-94
77-S-95
77-S-96
77-S-97
77-S-98
77-S-99
77-S-104
77-S-105
77-S-106
77-S-109
77-S-61
77-S-62
77-S-63
77-S-64
77-S-65
77-S-66
77-S-68
77-S-69
77-S-70
77-S-41-1
77-S-41A
77-S-42
77-S-43
77-S-44
77-S-45
77-S-46
77-S-47
77-S-48
77-S-49
77-S-50
77-S-60
77-S-1
77-S-2
77-S-2A
77-S-3
77-S-5
77-S-6
77-S-7
77-S-10
77-S-11
77-S-12
77-S-13
77-S-21
77-S-22
77-S-23
77-S-24
77-S-25
77-S-25A
77-S-26
77-S-27
77-S-29
77-S-30
77-S-31
77-S-32
77-S-36
77-S-37
77-S-38
77-S-39
77-S-40
1
1
1
1
1
1
1
1
1
1
1
1
1
1
1
1
1
1
1
1
1
1
1
1
1
2
2
1
1
1
1
1
1
2
1
1
1
1
1
1
1
1
1
1
1
1
1
1
1
4
1
1
1
2
3
1
1
1
1
1
1
1
2
4
2
1
1
1
1
1
1
1
1
LIST OF PARTS - MODEL “77” MCKAY STITCHER
P AR T
NAME OF P AR T
Main Head
Main Head Fastening Screw (Short)
Main Head Fastening Screw (Long)
Main Head Fastening Screw Washer
Main Head Rear Cover
Main Head Rear Cover Screw
Main Head Rear Cover Lock Washer
Main Head Front Cover
Main Head Front Cover Fulcrum
Main Head Front Cover Set Screw
Main Head Front Cover Spring
Cam Shaft
Cam Shaft Key
Cam Set Screw
Needle Bar Driving Cam Set Screw
Miter Gear
Miter Gear Set Screw
Hand Wheel
Hand Wheel Set Screw
Needle Bar Driving Cam Assembly,
Includes 77-S-30 and 77-S-31
Needle Bar Driving Cam
Needle Bar Driving Stud
Needle Bar Driving Cam Roll
Needle Bar Cam
Needle Bar Cam Post
Needle Bar Cam Post Screw
Needle Bar Cam Bumper Washer
Needle Bar Latch Holder Assembly,
Includes 77-S-43, 77-S-46 and 77-S-50
Needle Bar Latch
Needle Bar Latch Pin
Needle Bar Latch Spring
Needle Bar Latch Holder
Needle Bar Latch Holder Set Screw
Needle Bar Latch Holder Nut
Needle Bar Latch Stud
Needle Bar Latch Spring Pin
Needle Bar Latch Stud Collar
Needle Bar Latch Stud Collar Set Screw
Needle Bar Latch Stud Taper Pin
Thread Measure Cam
Thread Measure Cam Set Screw
Thread Measure Cam Stud
Thread Measure Cam Block
Thread Measure Cam Spring
Thread Measure Cam Spring Screw
Thread Measure Cam Block Set Screw
Thread Measure Presser Bar Block
Thread Measure Presser Bar Dowel
Thread Measure Presser Bar Adjusting
Screw
Thread Measure Presser Bar Nut
Needle Bar Friction Spring
Needle Bar Friction Fibre
Needle Bar Friction Screw
Needle Bar, assembled
Needle Bar Guide
Needle Bar Guide Post Clamp Screw
Needle Bar Guide Dowel
Needle Bar Guide Stop Screw
Needle Bar Guide Stop Nut
Needle Bar Guide Post
Needle Bar Guide Post Nut
Needle Bar Guide Post Lock Washer
Needle Clamp Collar
Needle Clamp Collar Screw
Cast Off
Cast Off Holder
Cast Off Holder Set Screw
Cast Off Spring
Cast Off Spring Screw
Cast Off Guide
Cast Off Guide Clamp Screw
Cast Off Guide Pin
Cast Off Rod Assembly, Includes77-S-99,
77-S-110, 77-S-111 and 77-S-112
1
1
1
1
1
1
2
1
1
1
1
1
1
1
1
1
1
1
1
1
1
1
1
1
2
1
1
1
1
1
1
1
77-S-177
77-S-178
77-S-179
77-S-180
77-S-181
77-S-186
77-S-187
77-S-188
77-S-190
77-S-191
77-S-191A
77-S-192
77-S-196
77-S-197
77-S-198
77-S-199
77-S-202
77-S-205
77-S-206
77-S-214
77-S-161
77-S-162
77-S-163
77-S-164
77-S-165
77-S-166
77-S-170
77-S-171
77-S-172
77-S-174
77-S-175
77-S-176
1
1
2
2
1
1
1
1
1
1
1
1
1
1
2
1
1
4
1
1
1
1
1
1
1
1
1
1
1
1
1
2
1
1
1
3
77-S-110
77-S-111
77-S-112
77-S-116
77-S-117
77-S-118
77-S-119
77-S-120
77-S-128
77-S-129
77-S-130
77-S-130B
77-S-131
77-S-133
77-S-134
77-S-136
77-S-137
77-S-138
77-S-139
77-S-140
77-S-141
77-S-142
77-S-143
77-S-146
77-S-147
77-S-150
77-S-151
77-S-152
77-S-154
77-S-154A
77-S-155
77-S-156
77-S-157
77-S-158
77-S-159
77-S-160
NAME OF P AR
Cast Off Rod
Cast Off Rod Collar
Cast Off Rod Collar Pin
Cast Off Friction Holder
Cast Off Friction Holder Gib Screw
Cast Off Friction Spring
Cast Off Friction Fibre
Cast Off Friction Screw
Presser Bar Assembly,
Includes 77-S-68, 77-S-69 and 77-S-129
Presser Bar
Presser Foot
Two Prong Presser Foot
Presser Foot Screw
Presser Bar Holder
Presser Bar Holder Pin
Presser Bar Guide
Presser Bar Guide Clamp Screw
Presser Bar Guide Dowel
Presser Bar Guide Stop Screw
Presser Bar Guide Stop Nut
Presser Bar Guide Post
Presser Bar Guide Post Nut
Presser Bar Guide Post Lock Washer
Lift Lever
Lift Lever Screw
Presser Bar Spring
Presser Bar Spring Collar
Presser Bar Spring Collar Set Screw
Lift Lever Rod
Lift Lever Rod Retaining Pin
Lift Lever Rod Nut
Lift Lever Rod Washer
Lift Lever Rod Stud
Lift Lever Rod Stud Lock Washer
Lift Lever Rod Stud Nut
Lifting Dog Assembly,
Includes 77-S-161, 77-S-162 and 77-S-163
Presser Foot Lifting Dog Block
Presser Foot Lifting Dog Tail
Presser Foot Lifting Dog
Fulcrum Pin
Presser Foot Lifting Dog Block
Spring
Presser Foot Lifting Dog Block
Spring Screw
Presser Foot Lifting Dog Spring
Lifting Dog Trip Pin
Lifting Dog Trip Pin Set Screw
Lifting Dog Trip Pin Set Screw Rod
Presser Foot Lift Cam
Presser Foot Lifting Lever
Presser Foot Lifting Lever Adjusting
Screw
Presser Foot Lifting Lever Adjusting
Screw Nut
Presser Foot Lifting Lever Spring Pin
Presser Foot Lifting Lever Cam Roll
Presser Foot Lifting Lever Cam Stud
Presser Foot Lifting Lever Cam Nut
Feed Socket Cam Block
Feed Socket Cam Block Dowel
Feed Socket Cam Block Fastening
Screw
Feed Socket
Feed Point (Regular)
Feed Point (Aloft)
Feed Point Screw
Feed Socket Collar
Feed Socket Collar Set Screw
Feed Socket Spring
Feed Socket Spring Fastening Screw
Feed Socket Cam Plate
Feed Socket Cam Plate Dowel Screw
Feed Socket Cam Plate Dowel
Feed Lever Connecting Link
-13-
P AR T
77-S-239
77-S-240
77-S-241
77-S-242
77-S-243
77-S-244
77-S-246
77-S-247
77-S-248
77-S-249
77-S-250
77-S-215
77-S-220
77-S-221
77-S-222
77-S-223
77-S-226
77-S-227
77-S-228
77-S-229
77-S-230
77-S-231
77-S-231A
77-S-255
77-S-256
77-S-257
77-S-258
77-S-259
77-S-260
77-S-261
77-S-301
77-S-302
77-S-304
77-S-305
77-S-306
77-S-307
77-S-308
77-S-311
77-S-312
77-S-313
77-S-314
77-S-318
77-S-319
77-S-320
77-S-321
77-S-322
77-S-323
77-S-324
77-S-325
77-S-326
77-S-326A
77-S-326B
77-S-327
77-S-327A
77-S-327B
77-S-336
77-S-337
77-S-340
77-S-341
77-S-342
77-S-343
77-S-344
77-S-345
77-S-346
1
1
1
1
1
1
1
1
2
2
2
1
1
4
4
1
1
2
1
1
1
1
1
1
1
1
1
1
1
1
1
1
1
1
1
2
1
1
1
2
1
1
1
1
1
1
1
1
1
1
1
1
1
1
1
1
1
2
1
1
1
1
1
1
LIST OF PARTS - MODEL “77” MCKAY STITCHER
P AR T
NAME OF P AR T
Feed Lever Connecting Link Stud
Feed Lever
Feed Lever Clamp Screw
Feed Lever Set Screw
Feed Lever Dowel
Feed Lever Spring
Feed Lever Spring Collar
Feed Lever Spring Collar Set Screw
Feed Lever Shaft
Feed Lever Shaft Bushing
Feed Lever Shaft Bushing Clamp
Adjusting Bushing for Feed Lever Shaft
Bush. Clamp Screw
Feed Cam Lever Assembly, Includes
77-S-229, 77-S-240 and 77-S-241
Feed Cam Lever
Feed Cam Lever Dowel Pin
Feed Cam Lever Cam Roll
Feed Cam Lever Cam Stud
Feed Cam Lever Cam Stud Nut
Feed Cam Lever Oil Wiper
Feed Cam Lever Oil Wiper Plate
Feed Cam Lever Oil Wiper Screw
Feed Cam Lever Oil Wiper Nut
Feed Cam Lever Oil Wiper Fastening
Screw
Feed Cam
Feed Cam Plate Assembly, Includes
77-S-257 and 77-S-258
Feed Cam Plate
Feed Cam Plate Block
Feed Cam Plate Adjusting Screw
Feed Cam Plate Clamp Screw
Feed Cam Plate Dowel
Clutch Sleeve
Clutch Sleeve Set Screw
Clutch Sleeve Plunger Pin
Clutch Sleeve Stop
Clutch Sleeve Plunger
Clutch Sleeve Plunger Pin
Clutch Sleeve Plunger Spring
Clutch Sleeve Plunger Fibre Stop
Clutch Sleeve Plunger Stop Stud
Clutch Sleeve Plunger Stop Bar
Clutch Sleeve Plunger Stop Bar Screw
Clutch Pulley Assembly, Includes 77-S-319,
77-S-320, 77-S-321, 77-S-322, 77-S-323,
77-S-324, 77-S-325, 77-S-326 and 77-S-327
Clutch Pulley (10 1/2” Diam.)
Clutch Pulley Driving Dog
Clutch Pulley Pipe Plug
Clutch Pulley Plate
Clutch Pulley Plate Gasket
Clutch Pulley Plate Screw
Clutch Pulley Wool Yarn
Clutch Pulley Set Collar
Hand Wheel Set Collar (Regular)
Hand Wheel Set Collar (For Repairs)
Clutch Pulley Set Collar Set Screw
Hand Wheel Set Collar Set Screw (Regular)
Hand Wheel Set Collar Retaining Screw
(For Repairs)
Clutch Pulley Round Belt
Motor Belt
Clutch Throw Out Lever Assembly,
Includes 77-S-341, 77-S-342, 77-S-343,
77-S-344, 77-S-345, 77-S-346, 77-S-347 and
77-S-348
Clutch Throw Out Lever
Clutch Throw Out Lever Wedge
Clutch Throw Out Lever Wedge Screw
Clutch Throw Out Lever Wedge Dowel
Clutch Throw Out Lever Bumper
Clutch Throw Out Lever Plate
1
1
2
1
1
1
1
1
1
1
1
1
1
1
1
1
2
1
1
1
1
1
1
2
1
3
1
2
2
1
1
1
1
1
1
1
2
1
1
3
3
77-S-381
77-S-382
77-S-383
77-S-384
77-S-385
77-S-386
77-S-387
77-S-390
77-S-390A
77-S-390B
77-S-390C
77-S-390D
77-S-391
77-S-392
77-S-394
77-S-395
77-S-396
77-S-397A
77-S-398
77-S-404
77-S-405
77-S-409
77-S-410
77-S-411
77-S-412
77-S-415
77-S-416
77-S-501
77-S-502
77-S-503
77-S-504
77-S-505
77-S-506
77-S-507
77-S-508
77-S-509
77-S-510
77-S-511
77-S-512
77-S-512A
77-S-513
77-S-347
77-S-348
77-S-354
77-S-355
77-S-356
77-S-357
77-S-360
77-S-361
77-S-362
77-S-363
77-S-364
77-S-365
77-S-365A
77-S-366
77-S-380
1
1
1
1
1
1
1
1
1
1
1
1
1
1
1
NAME OF P AR
Clutch Throw Out Lever Plate Screw
Clutch Throw Out Lever Plate Lock
Washer
Clutch Throw Out Lever Shaft
Clutch Throw Out Lever Shaft Set
Screw
Clutch Throw Out Lever Shaft Collar
Clutch Throw Out Lever Shaft Collar
Set Screw
Clutch Idler Pulley Assembly,
Includes 77-S-361 and 77-S-362
Clutch Idler Pulley
Clutch Idler Pulley Needle Bearing
Clutch Idler Pulley Screw
Clutch Idler Pulley Screw Nut
Clutch Idler Pulley Lever
Clutch Idler Pulley Screw Nut Lock
Washer
Clutch Idler Pulley Lever Spring
Lower Clutch Pulley Assembly,
Includes 77-S-381, 77-S-382,
77-S-383 and 77-S-387
Lower Clutch Pulley
Lower Clutch Stationary “V” Pulley
Lower Clutch Stationary Pulley Screw
Lower Clutch Sliding “V” Pulley
Lower Clutch Pulley Key
Lower Clutch Pulley Fibre Washer
Lower Clutch Stationary Pulley Screw
Lock Washer
Lower Clutch Yoke
Lower Clutch Yoke Spacing Washer
(1/8”)
Lower Clutch Yoke Spacing Washer
(3/16”)
Lower Clutch Yoke Set Collar
Lower Clutch Yoke Set Collar Set
Screw
Lower Clutch Yoke Adjusting Screw
Lower Clutch Yoke Adjusting Screw
Nut
Lower Clutch Yoke Bracket Lock
Washer
Lower Clutch Yoke Bracket
Lower Clutch Yoke Bracket Fastening
Screw
Lower Clutch Yoke Shaft (New Style)
Lower Clutch Yoke Shaft Set Screw
Lower Clutch Yoke Finger
Lower Clutch Yoke Finger Set Screw
Lower Clutch Shaft
Lower Clutch Shaft Oil Cup
Lower Clutch Shaft Oil Wick
Lower Clutch Shaft Set Screw
Lower Clutch Belt Guard
Lower Clutch Belt Guard Set Screw
Horn
Horn Tip
Horn Tip Cap
Horn Tip Cap Upper Screw
Horn Tip Cap Lower Screw
Horn Tip Cap Lower Screw Insert
Horn Whirl
Horn Pinion Shaft
Horn Pinion Shaft Sleeve
Horn Pinion Shaft Adjusting Screw
Horn Pinion Shaft Bushing
Horn Hollow Hex Set Screw (Lower
Shaft)
Horn Hollow Hex Set Screw (Pinion
Shaft)
Horn Pinion Shaft Sleeve Assembly,
Includes 77-S-509, 77-S-510, 77-S-511,
77-S-514 and 77-S-515
-14-
P AR T
77-S-514
77-S-515
77-S-518
77-S-519
77-S-520
77-S-521
77-S-530
77-S-531
77-S-532
77-S-533
77-S-534
77-S-535
77-S-537
77-S-545
77-S-593
77-S-594
77-S-595
77-S-601
77-S-602
77-S-603
77-S-605
77-S-610
77-S-611
77-S-612
77-S-616
77-S-617
77-S-620
77-S-621
77-S-578
77-S-579
77-S-580
77-S-581
77-S-582
77-S-583
77-S-584
77-S-586
77-S-587
77-S-588
77-S-590
77-S-591
77-S-592
77-S-546
77-S-547
77-S-549
77-S-550
77-S-551
77-S-552
77-S-553
77-S-556
77-S-557
77-S-558
77-S-560
77-S-561
77-S-562
77-S-562A
77-S-563-1
77-S-566-1
77-S-567
77-S-568
77-S-571
77-S-572
77-S-573
77-S-574
77-S-575
77-S-576
77-S-622
77-S-623
77-S-624
LIST OF PARTS - MODEL “77” MCKAY STITCHER
P AR T
1
2
1
3
4
1
1
1
1
2
1
1
1
1
1
2
1
4
1
1
14
1
1
2
4
2
2
1
1
1
1
2
1
1
1
1
1
1
1
1
1
1
1
1
1
1
1
1
1
1
1
1
1
1
1
1
1
1
4
1
1
1
1
1
1
2
1
1
NAME OF P AR T
Horn Center Bevel Gear
Horn Center Bevel Gear Taper Pin
Horn Lower Shaft Assembly, Includes
77-S-514, 77-S-515, 77-S-519, 77-S-520 and 77-S-521
Horn Lower Shaft
Horn Lower Shaft Bushing
Horn Lower Shaft Bevel Gear
Horn Spring Oiler
Horn Fastening Screw
Horn Thread Guard Plate
Horn Thread Roll
Horn Thread Roll Pin
Horn Thread Guide Pin
Horn Spindle Bearing Oiler
Horn Front Cover Assembly, Includes
77-S-546, 77-S-547, 77-S-549, 77-S-550,
77-S-551 and 77-S-552
Horn Front Cover
Horn Front Cover Pin
Horn Front Cover Knob
Horn Front Cover Latch
Horn Front Cover Lock Washer
Horn Front Cover Dowel
Horn Rear Cover
Horn Rear Cover Screw
Horn Rear Lower Cover
Horn Rear Lower Cover Screw
Horn Wax Pot Assembled Complete
Wax Pot Only
Wax Pot Stud (Right)
Wax Pot Stud (Left) Cotter Pin
Wax Pot Stud (Left) With Hole
Horn Wax Pot Lid
Horn Wax Pot Lid Hinge
Horn Wax Pot Lid Stop Screw
Horn Wax Pot Thread Roll
Horn Wax Pot Thread Roll Pin
Horn Wax Pot Stripper
Horn Wax Pot Stripper Screw
Horn Wax Pot Thread Guide Pin
Horn Wax Pot Thread Roll Thread
Guide Pin
Thread Tension Lever
Thread Tension Plate
Thread Tension Lever Dowel
Thread Tension Stud
Thread Tension Spring
Thread Tension Thumb Nut
Thread Tension Washer
Horn Wax Pot Plug
Horn Wax Pot Stripper Screw
Horn Wax Pot Stripper Plunger
Table
Table Fastening Screw (Long)
Table Fastening Screw (Short)
Table Fastening Screw Nut
Table Fastening Screw Lock Washer
Table Rubber Bushing
Horn Spindle Bearing
Horn Spindle Bearing Dowel Pin
Horn Spindle Bearing Fastening Screw
Horn Spindle Bearing Lock Washer
Horn Spindle
Horn Spindle Dowel
Horn Spindle Oil Tube
Horn Spindle Thrust Disc
Horn Spindle Thrust Bearing Retainer
Steel Balls
Horn Spindle Hollow Shaft Assembly,
Includes 77-S-622, 77-S-623 and 77-S-624
Horn Spindle Hollow Shaft
Horn Spindle Hollow Shaft Upper Gear
Horn Spindle Hollow Shaft Upper Gear
Key
NAME OF P AR
Horn Spindle Hollow Shaft Spacer
Horn Spindle Hollow Shaft Washer
Horn Spindle Hollow Shaft Lower
Gear
Drive Shaft Miter Gear
Drive Shaft Center Bevel Gear
Drive Shaft Center Bevel Pinion
Gear Ball Point Set Screw
Drive Shaft Gear Guard
Drive Shaft Gear Guard Screw
Drive Shaft Gear Guard Lock Washer
Vertical Drive Shaft Thrust Collar
Vertical Drive Shaft Thrust Collar
Set Screw
Vertical Drive Shaft
Vertical Drive Shaft Lower Bushing
Vertical Drive Shaft Upper Bushing
Vertical Drive Shaft Upper Bushing
Oil Wick
Vertical Drive Shaft Upper Bushing
Set Screw
Vertical Drive Shaft Upper Bushing Nut
Horizontal Drive Shaft
Horizontal Drive Shaft Bracket (Rear)
Horizontal Drive Shaft Bracket (Front)
Horizontal Drive Bracket Rod
Horizontal Drive Bracket Rod Pin
Column
Tripod
Tripod Fastening Screw
Tripod Fastening Screw Washer
Tripod Fastening Screw Lock Washer
Clutch Pedal
Presser Foot Pedal
Pedal Fulcrum
Pedal Fulcrum Set Screw
Presser Foot Pedal Spring
Clutch Pedal Yoke
Clutch Pedal Pin
Clutch Pedal Yoke Cotter Pin
Clutch Pedal Yoke Nut
Clutch Pedal Yoke Screw
Clutch Throw Out Rod
Clutch Throw Out Rod Spring
Clutch Throw Out rod Clamp with
Screws
Clutch Throw Out Rod Clamp Set
Screw
Column Door
Column Door Hinge Pin
Column Door Hinge
Column Door Hinge Screw
Column Door Knob
Column Door Knob Screw
Column Door Knob Nut
Column Door Assembled Complete
Thread Holder Cup
Thread Holder Cup Fastening Screw
Thread Holder Cup Fastening Screw
Nut
Thread Holder
Thread Holder Wood Screw
Thread Unwinder Bracket
Thread Unwinder Bracket Screw
Motor Extension Cord Complete
Wire Terminals (Copper)
2” Diam. Motor Pulley
Motor Pulley Set Screw
Motor Base
Motor Fastening Screw
Motor Fastening Screw Washer
Motor Fastening Screw Nut
Motor Base Fulcrum Set Screw
Motor Switch
Motor Switch Fastening Screw
77-S-703
77-S-710
77-S-711
77-S-712
77-S-713
77-S-715
77-S-716
77-S-717
77-S-722
77-S-725
77-S-726
77-S-726A
77-S-727
77-S-728
77-S-740
77-S-741
77-S-764
77-S-768
77-S-770
77-S-770A
77-S-777
77-S-778
77-S-778A
77-S-778B
77-S-781
77-S-795
77-S-795B
77-S-644
77-S-645
77-S-654
77-S-655-1
77-S-656
77-S-659
77-S-660
77-S-680
77-S-681
77-S-682
77-S-683
77-S-684
77-S-688
77-S-689
77-S-690
77-S-691
77-S-692
77-S-693
77-S-694
77-S-695
77-S-696
77-S-696A
77-S-700
77-S-701
77-S-702
77-S-625
77-S-626
77-S-627
77-S-630
77-S-631
77-S-632
77-S-633
77-S-635
77-S-636
77-S-637
77-S-638
77-S-639
77-S-640
77-S-641
77-S-642
77-S-643
2
4
1
1
1
1
1
2
2
1
2
2
1
4
4
2
1
1
1
2
4
1
1
1
1
1
1
1
4
2
2
1
2
2
1
1
1
1
1
4
4
1
2
1
4
1
1
4
1
1
1
1
1
1
1
1
1
2
1
1
6
1
1
1
1
1
1
1
-15-
P AR T
77-S-796
77-S-850
77-S-852
77-S-855
77-S-856
77-S-861
1
1
1
1
1
1
LIST OF PARTS - MODEL “77” MCKAY STITCHER
P AR T
NAME OF P AR T
Motor Switch Rod
1/4” Hollow Hex Wrench
3” Screw Driver
1/4” Square Socket Wrench
3/16” Hollow Hex “L” Wrench
Oil Can
77-S-863
77-S-864
77-S-865
77-S-870
77-S-871
1
1
2
1
1
NAME OF P AR
Threading Wire - Straight
Threading Wire - Bent
Can Liquid Wax
Model Name Plate
Model Name Plate Drive
Screw
HC53
HC54
HC58
HC62
HC63
HC67
HC68
HC69
HC73
HC77
P AR
HC50
HC50A
CHAMPION AND LANDIS COMBINATION HAND CHANNELER AND GROOVER
P AR
4
3
1
1
1
2
1
1
1
1
NAME OF P AR T
Right Hand Channeler & Groover
Complete with Sharpening Stone
Left Hand Channeler & Groover
Complete with Sharpening Stone
PARTS
Hand Channeler Frame
Hand Groover Frame
Hand Channeler Knife
Semi-English Knife
Groover Knife
Edge Gauge
Edge Gauge Screw
Edge Gauge Washer
Hand Channeler Handle
Sharpening Stone
MX-1R
MX-1L
X-6R
X-6L
X-5R
X-5L
X-4R
X-4L
NAME OF P AR
McKay Lip Channeler - Right
Hand Complete
McKay Lip Channeler - Left
Hand Complete
McKay Lip Channeler Knife - Right
Hand
McKay Lip Channeler Knife - Left
Hand
LANDIS HAND GROOVERS
McKay Groover - Right Hand
Complete
McKay Groover - Left Hand
Complete
McKay Groover Knife - Right Hand
McKay Groover Knife - Left Hand
ILLUSTRATION OF CHAMPION COMBINATION HAND CHANNELER AND GROOVER
Champion Combination
Hand Channeler and
Has an Adjustable Gauge. Groove can be cut in channel where desired.
Groover
Quickly adjusted for cutting channel any margin from the edge of sole or to make thin or thick lip.
-16-
advertisement
* Your assessment is very important for improving the workof artificial intelligence, which forms the content of this project
Key Features
- Capable of sewing on ladies' shoes
- Simple design for ease of use
- Constructed of the finest materials for durability
- Manufactured with precision for low maintenance and operating costs
- Adjustable needle bar friction for optimal performance
- Cast-off friction is factory-adjusted for convenience