advertisement
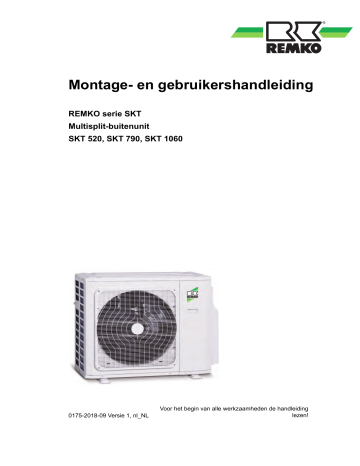
Montage- en gebruikershandleiding
REMKO serie SKT
Multisplit-buitenunit
SKT 520, SKT 790, SKT 1060
0175-2018-09 Versie 1, nl_NL
Voor het begin van alle werkzaamheden de handleiding lezen!
Vóór het in bedrijf nemen / gebruik van dit apparaat deze installatiehandleiding zorgvuldig lezen!!
Deze handleiding maakt deel uit van het apparaat en dient steeds in directe nabijheid van de opstellocatie resp. bij het apparaat bewaard te worden.
Wijzigingen voorbehouden; we aanvaarden geen aansprakelijkheid voor drukfouten en vergissingen!
Montage- en gebruikershandleiding (vertaling van het origineel)
Inhoudsopgave
3
REMKO serie SKT
4
1 Veiligheids- en gebruiksinstructies
1.1 Algemene veiligheidsvoorschriften
Lees de handleiding voor het eerste gebruik van het apparaat zorgvuldig door. Deze bevat nuttige tips, instructies en waarschuwingen voor de veiligheid van personen en goederen. Het niet opvolgen van de gebruikshandleiding kan gevaar voor personen, het milieu, de installatie en tot het verlies van mogelijke aansprakelijkheid leiden.
Bewaar deze gebruikshandleiding en het koelmiddelgegevensblad in de buurt van het apparaat.
1.2 Markering van instructies
Deze paragraaf geeft een samenvatting van alle belangrijke veiligheidsaspecten voor een optimale persoonlijke bescherming en voor een veilig en storingvrij bedrijf.
De in deze handleiding gegeven instructies en veiligheidsvoorschriften dienen opgevolgd te worden, zodat ongelukken, persoonlijk letsel en beschadigingen worden vermeden. Direct aan de apparaten aangebrachte instructies dienen absoluut te worden opgevolgd en in goed leesbare toestand te worden gehouden.
Veiligheidsvoorschriften zijn in deze handleiding gemarkeerd door bepaalde symbolen. Verder beginnen de veiligheidsvoorschriften met bepaalde signaalwoorden die de aard van de risico's aangeven.
GEVAAR!
Bij het aanraken van spanningvoerende delen bestaat direct levensgevaar door een stroomstoot. Beschadiging van de isolatie of van componenten kan levensgevaarlijk zijn.
GEVAAR!
Deze combinatie van symbool en signaalwoord wijst op een direct gevaarlijke situatie die de dood of zwaar letsel tot gevolg heeft, als deze situatie niet wordt gemeden.
WAARSCHUWING!
Deze combinatie van symbool en signaalwoord wijst op een mogelijk gevaarlijke situatie die de dood of zwaar letsel tot gevolg kan hebben, als deze situatie niet wordt gemeden.
VOORZICHTIG!
Deze combinatie van symbool en signaalwoord wijst op een mogelijk gevaarlijke situatie die gering of licht letsel tot gevolg kan hebben en die materiële schade of aantasting van het milieu kan veroorzaken, als deze situatie niet wordt gemeden.
AANWIJZING!
Deze combinatie van symbool en signaalwoord wijst op een mogelijk gevaarlijke situatie die materiële schade of aantasting van het milieu kan veroorzaken, als deze situatie niet wordt gemeden.
Met dit symbool wordt gewezen op nuttige tips, adviezen en informatie over hoe een efficiënt en storingsvrij bedrijf gewaarborgd kan worden.
1.3 Kwalificaties van het personeel
Het personeel voor de inbedrijfstelling, bediening, het onderhoud, de inspectie en de montage dient over de betreffende kwalificaties voor deze werkzaamheden te beschikken.
1.4 Gevaren bij het niet-opvolgen van de veiligheidsvoorschriften
Het niet opvolgen van de veiligheidsvoorschriften kan zowel gevaar voor personen opleveren als voor het milieu en voor apparatuur. Het nietopvolgen van de veiligheidsvoorschriften kan leiden tot het verlies van iedere aanspraak op schadevergoeding.
In detail kan het niet-opvolgen van de voorschriften bijvoorbeeld de volgende risico's opleveren:
5
6
REMKO serie SKT n Het uitvallen van belangrijke functies van de apparatuur.
n Het feit dat voorgeschreven methodes betreffende normaal en technisch onderhoud niet werken.
n Het in gevaar brengen van personen door elektrische en mechanische effecten.
1.5 Veiligheidsbewust werken
De in deze handleiding vermelde veiligheidsinstructies, de bestaande nationale voorschriften ter voorkoming van ongevallen evenals eventuele interne arbeids-, bedrijfs- en veiligheidsvoorschriften van het bedrijf moeten in acht worden genomen.
1.6 Veiligheidsvoorschriften voor de exploitant
De veiligheid van de apparaten en componenten is alleen gegarandeerd bij het bedoeld gebruik en in volledig gemonteerde toestand.
n Het plaatsen, installeren en onderhouden van de apparaten en componenten mag alleen gebeuren door vakpersoneel.
n Eventueel aanwezige aanraakbescherming
(rooster) voor bewegende delen mag niet worden verwijderd bij een apparaat dat in bedrijf is.
n De bediening van apparaten of componenten met zichtbare defecten of beschadigingen is verboden.
n Het aanraken van bepaalde onderdelen of componenten van de apparaten kan brandwonden of letsel veroorzaken.
n De apparaten of componenten mogen niet worden blootgesteld aan mechanische belasting, extreme vochtigheid of extreme temperaturen.
n Ruimten waarin koudemiddel kan lekken voldoende te laden en te ventileren. Anders bestaat er gevaar voor verstikking.
n Alle delen van de behuizing en openingen, bijv.
luchtin- en uitgangen, moeten vrij zijn van vreemde voorwerpen, vloeistoffen of gassen.
n De apparatuur dient tenminste eenmaal jaarlijks door een deskundige gecontroleerd te worden. Visuele controles en reinigingswerkzaamheden mogen in spanningsloze toestand door de gebruiker uitgevoerd worden.
1.7 Veiligheidsvoorschriften voor montage-, onderhouds- en inspectiewerkzaamheden
n Bij het installeren, het repareren, het onderhouden of het reinigen van de apparaten moeten geschikte maatregelen worden genomen om de van de apparaten uitgaande gevaren voor personen te voorkomen.
n Het opstellen, aansluiten en gebruik van de apparaten en componenten moet volgens de gebruiks- en bedrijfsomstandigheden uit de gebruikshandleiding en de geldende lokale voorschriften gebeuren.
n Men dient zich aan de regionale verordeningen en wetten te houden, zoals de wet op de waterhuishouding.
n De elektrische voeding moet worden aangepast aan de eisen van de apparaten.
n De apparaten mogen uitsluitend op die punten worden bevestigd die de fabrikant hiervoor heeft voorzien. De apparaten mogen uitsluitend aan constructies of wanden of op vloeren worden bevestigd of geplaatst die deze belasting kunnen dragen.
n Apparaten voor mobiel gebruik moeten veilig en verticaal op een geschikte ondergrond opgesteld worden. Apparaten voor stationair bedrijf mogen alleen in vast geïnstalleerde toestand gebruikt worden.
n De apparaten en componenten mogen niet worden gebruikt op plaatsen met verhoogd risico op beschadigingen. De minimale vrije ruimte moet worden aangehouden.
n De apparaten en componenten moeten voldoende veiligheidsafstand hebben ten opzichte van ontvlambare, explosieve, brandbare, agressieve en vervuilde zones en atmosferen.
n Veiligheidsinrichtingen moeten niet worden gewijzigd of omzeild.
1.8 Zelfstandige ombouw en veranderingen
Het ombouwen of wijzigen van de apparaten of componenten is niet toegestaan en kan storingen veroorzaken. De veiligheidsvoorzieningen mogen niet worden veranderd of overbrugd. De originele reserveonderdelen en door de fabrikant geautoriseerde accessoires zijn afgestemd op de vereiste veiligheid. Het toepassen van andere onderdelen kan leiden tot het vervallen van de aansprakelijkheid voor gevolgen daarvan.
1.9 Bedoeld gebruik
De apparaten mogen afhankelijk van de uitvoering en uitrusting uitsluitend worden toegepast als airconditioning om het bedrijfsmedium lucht binnen een gesloten ruimte te koelen resp. verwarmen.
Ander of verdergaand gebruik geldt als niet bedoeld gebruik. Voor de hieruit voortvloeiende schade is de fabrikant / leverancier van de machine niet aansprakelijk. Het risico wordt uitsluitend door de gebruiker gedragen. Bij het bedoeld gebruik hoort ook het opvolgen van de bedieningsen installatie-instructies en het aanhouden van de onderhoudsbepalingen.
De in de technische specificaties opgegeven grenswaarden mogen in geen geval worden overschreden.
1.10 Garantie
Voorwaarde voor eventuele aanspraken op garantie is, dat de inkoper of zijn afnemer tegelijk met de verkoop en het in gebruik nemen, de bij het apparaat meegeleverde "Garantieoorkonde" volledig ingevuld naar REMKO GmbH & Co. KG teruggestuurd heeft. De garantievoorwaarden zijn opgenomen in de "Algemene verkoop- en leveringsvoorwaarden". Daarnaast kunnen alleen tussen de bij de overeenkomst betrokken partijen speciale afspraken gemaakt worden. Neem daarom eerst contact op met uw directe handelspartner.
1.11 Transport en verpakking
De apparaten worden in een stevige transportverpakking geleverd. Controleer het apparaat direct bij de levering en noteer eventuele schade of ontbrekende onderdelen op de pakbon en informeer de transporteur en uw leverancier. Bij klachten achteraf wordt geen garantie verleend.
WAARSCHUWING!
Plastic folie en tassen etc. zijn gevaarlijk speelgoed voor kinderen!
Daarom:
- Verpakkingsmateriaal kan niet worden onzorgvuldig.
- Verpakking mag niet toegankelijk zijn voor kinderen!
1.12 Milieubescherming en recycling
Afvoeren van de verpakking
Alle producten worden voor het transport zorgvuldig verpakt in milieuvriendelijke materialen.
Lever een waardevolle bijdrage aan de vermindering van afval en het recyclen van grondstoffen en lever het verpakkingsmateriaal alleen in bij de daarvoor aangewezen inzamelplaatsen.
Afvoeren van de apparaten en componenten
Bij de productie van de apparaten en componenten worden uitsluitend recyclebare materialen gebruikt. Draag bij aan de bescherming van het milieu, door er voor te zorgen dat apparaten of componenten (bijv. batterijen) niet in het huisvuil komen maar alleen op milieuvriendelijke wijze volgens de plaatselijk geldende voorschriften, bijv.
door een erkend afvalverwerkingsbedrijf en recycling of via een inzamelpunt worden verwerkt.
7
8
REMKO serie SKT
2 Technische gegevens
2.1 Apparaatgegevens
Serie
Werking
Nominaal koelvermogen 1)
Energie-efficiëntieklasse SEER
Energieverbruik, jaarlijks, Q
CE
3)
Energie-efficiëntieklasse koelen
Nominaal verwarmingsvermogen 2)
Energie-efficiëntieklasse SCOP 4)
Energieverbruik, jaarlijks, Q
HE
3) 4)
Energie-efficiëntieklasse verwarmen
Voedingsspanning
El. nominaal opgenomen verm. koelen 1)
El. nominaal opgenomen vermogen verwarmen 2)
Opgenomen elektr. vermogen max.
El. nominaal opgenomen stroom koelen 1)
El. nominaal stroomopname verwarmen 2)
Stroomopname max.
Koudemiddelaansluiting inspuitleiding
Koudemiddelaansluiting zuigleiding
Bedrijfsdruk, max.
Werkbereik koelen
Werkbereik verwarmen
Luchtverplaatsing, max.
Beschermingsgraad
Geluidsniveau max.
Geluidsdrukniveau 5)
Koudemiddel 6)
Koudemiddel, basishoeveelheid kW kWh kW kWh
V/
Ph/Hz kW kW kW
A kPa
°C
°C m³/u
IP dB (A) dB (A)
A
A
Inch
(mm)
Inch
(mm) kg
SKT 520 AT SKT 790 AT SKT 1060 AT
Inverter multisplit-buitenunits voor koelen en verwarmen
5,2 a)
(2,1-5,3)
6,3 a)
7,9
6,6 b)
(2,1-7,9) b)
10,6 c)
(21,1-10,6)
7,6 c)
289 a) 419 b) 488 c)
A++ a)
4,7 a)
(2,1-5,6)
4,0 a)
1645
A+
A++
2056
A+ b)
5,9 b)
(2,3-8,2)
4,0 b)
A++ c)
9,3 c)
(2,1-11,1)
3,8 c)
3426
A
230/1~/50
1,75
1,50
2,30
7,6
6,7
12
2,47
2,27
3,30
10,7
9,8
16
1/4 (6,35)
3,89
3,00
4,60
16,9
13,0
21,5
3 x 3/8 + 1 x 1/2
(9,52+12,70)
2100
65
57
1,7
3,8 (9,52)
4200 / 1500
-15 tot +50
-15 tot +24
3500
24
68
60
R410A
2,1
5500
68
64
3
Serie
Co
2
equivalent
Koudemiddel, extra hoeveelheid >5m
Aantal binnenunits, max.
Koudemiddelleiding, lengte pro IT, max.
Koudemiddelleiding, lengte totaal, max.
Koudemiddelleiding, hoogte, max., AT boven
Koudemiddelleiding, hoogte, max., AT onder
Afmetingen
Hoogte
Breedte
Diepte
Gewicht
EDV-nr.
t g/m m m m m mm
SKT 520 AT
3,55
2
20
30
554
SKT 790 AT
4,34
30
3
25
45
10
15
702
SKT 1060 AT
6,26
4
30
60
810 mm mm kg
800
333
36,0
1640521
845
363
52,7
1640791
946
410
70,0
1641060
1) Luchtinlaattemperatuur TK 27 °C / FK 19 °C, buitentemperatuur TK 35 °C, FK 24 °C, max. luchtverplaatsing, 5m leidinglengte
2) Luchtinlaattemperatuur TK 20 °C, buitentemperatuur TK 7 °C, FK 6 °C, max. luchtverplaatsing, 5 m leidinglengte
3) De opgegeven waarde is gebaseerd op resultaten van de genormeerde keuring. Het werkelijk verbruik is afhankelijk van het gebruik en van de gebruikslocatie van het apparaat.
4) De opgegeven waarde is gebaseerd op de gemiddelde verwarmingsperiode (average)
5) Afstand 1 m vrije ruimte: Opgegeven waarden zijn maximale waarden
6) Bevat broeikasgas volgens Kyoto-protocol, GWP 2088 (zie voor meer informatie hoofdstuk "Koudemiddel bijvullen").
In combinatie met a) 2 x SKT 260 IT b) 3 x SKT 260 IT c) 4 x SKT 260 IT
9
REMKO serie SKT
2.2 Apparaatafmetingen
A C
E
B
D
Afb. 1: Afmetingen
Wijzigingen in de afmetingen en de constructie, door de technische vooruitgang, voorbehouden.
SKT 520
SKT 790
SKT 1060
(Alle gegevens in mm)
A
800
845
946
B
554
702
810
C
333
363
410
D
514
540
673
E
340
350
403
10
2.3 Capaciteitscurven verwarmen en koelen
Verwarmingsvermogen SKT 520
6,50
6,00
5,50
5,00
4,50
4,00
3,50
3,00
2,50
2,00
1,50
1,00
0,50
0,00
-15 -7 -5
A
0
[°C]
7
2
1
3
12
Afb. 2: Capaciteitscurve verwarmen SKT 520 (gegevens bij ruimtetemperatuur 20 °C)
A: Buitentemperatuur
1: COP
2: Verwarmingsvermogen in kW
3: Opgenomen vermogen in kW
Buitentemperatuur in °C
Verwarmingsvermogen in kW
Opgenomen vermogen in kW
COP
Koelvermogen SKT 520
-15
3,04
1,30
2,33
-7
3,21
1,32
2,43
-5
3,46
1,35
2,56
0
4,05
1,41
2,88
7
5,57
1,54
3,61
6,50
6,00
5,50
5,00
4,50
4,00
3,50
3,00
2,50
2,00
1,50
1,00
0,50
0,00
21
2
1
3
25 30
A
35
[°C]
40
Afb. 3: Vermogenscurves koelen SKT 520 (Gegevens bij ruimtetemperatuur FK27°/TK19 °C)
A: Buitentemperatuur
1: EER
2: Koelvermogen in kW
3: Opgenomen vermogen in kW
Buitentemperatuur in °C
Koelvermogen in kW
Opgenomen vermogen in kW
EER
21
5,10
1,36
3,74
25
5,44
1,47
3,70
30
5,48
1,60
3,42
35
5,28
1,75
3,02
40
4,53
1,78
2,55
12
6,34
1,57
4,04
11
REMKO serie SKT
Verwarmingsvermogen SKT 790
6,00
5,50
5,00
4,50
4,00
3,50
3,00
2,50
2,00
1,50
1,00
0,50
0,00
10,00
9,50
9,00
8,50
8,00
7,50
7,00
6,50
-15
2
1
3
-7 -5
A
0
[°C]
7 12
Afb. 4: Capaciteitscurve verwarmen SKT 790 (gegevens bij ruimtetemperatuur 20 °C)
A: Buitentemperatuur
1: COP
2: Verwarmingsvermogen in kW
3: Opgenomen vermogen in kW
Buitentemperatuur in °C
Verwarmingsvermogen in kW
Opgenomen vermogen in kW
COP
-15
4,48
1,92
2,34
-7
4,73
1,94
2,43
-5
5,10
1,99
2,56
0
5,97
2,07
2,88
7
8,21
2,27
3,61
Koelvermogen SKT 790
9,00
8,50
8,00
7,50
7,00
6,50
6,00
5,50
5,00
4,50
4,00
3,50
3,00
2,50
2,00
1,50
1,00
0,50
0,00
21
2
1
3
25 30
A
35
[°C]
40
Afb. 5: Vermogenscurves koelen SKT 790 (Gegevens bij ruimtetemperatuur FK27°/TK19 °C)
A: Buitentemperatuur
1: EER
2: Koelvermogen in kW
3: Opgenomen vermogen in kW
Buitentemperatuur in °C
Koelvermogen in kW
Opgenomen vermogen in kW
EER
21
7,64
1,92
3,98
25
8,14
2,07
3,93
30
8,22
2,26
3,64
35
7,91
2,47
3,21
40
6,79
2,50
2,71
12
9,34
2,31
4,05
12
Verwarmingsvermogen SKT 1060
13,50
13,00
12,50
12,00
11,50
11,00
10,50
10,00
9,50
9,00
8,50
8,00
7,50
7,00
6,50
6,00
5,50
5,00
4,50
4,00
3,50
3,00
2,50
2,00
1,50
1,00
0,50
0,00
-15
2
1
3
-7 -5
A
0
[°C]
7 12
Afb. 6: Capaciteitscurve verwarmen SKT 1060 (gegevens bij ruimtetemperatuur 20 °C)
A: Buitentemperatuur
1: COP
2: Verwarmingsvermogen in kW
3: Opgenomen vermogen in kW
Buitentemperatuur in °C
Verwarmingsvermogen in kW
Opgenomen vermogen in kW
COP
-15
6,08
2,53
2,40
-7
6,42
2,57
2,50
-5
6,92
2,63
2,64
0
8,10
2,74
2,96
7
11,14
3,00
3,71
12
12,68
3,05
4,16
Koelvermogen SKT 1060
7,50
7,00
6,50
6,00
5,50
5,00
4,50
4,00
3,50
3,00
2,50
2,00
1,50
1,00
0,50
0,00
12,00
11,50
11,00
10,50
10,00
9,50
9,00
8,50
8,00
21
2
3
1
25 30
A
35
[°C]
40
Afb. 7: Vermogenscurves koelen SKT 1060 (Gegevens bij ruimtetemperatuur FK27°/TK19 °C)
A: Buitentemperatuur
1: EER
2: Koelvermogen in kW
3: Opgenomen vermogen in kW
Buitentemperatuur in °C
Koelvermogen in kW
Opgenomen vermogen in kW
EER
21
10,19
3,03
3,36
25
10,86
3,27
3,32
30
10,96
3,56
3,08
35
10,55
3,89
2,71
40
9,05
3,95
2,29
13
REMKO serie SKT
3 Opbouw en werking
3.1 Beschrijving van het apparaat
De buitenunit dient tijdens koelbedrijf voor het afgeven van de door de binnenunit uit de te koelen ruimte opgenomen warmte aan de buitenlucht. Bij verwarmingsbedrijf kan de door de buitenunit opgenomen warmte via de binnenunit worden afgegeven aan de lucht in de te verwarmen ruimte.
In beide bedrijfsmodi wordt het door de compressor te leveren capaciteit exact aangepast aan de vraag en wordt de insteltemperatuur met minimale temperatuurschommelingen geregeld. Door deze "inverter-techniek" wordt, ten opzichte van conventionele splitsystemen, energie bespaard en wordt het geproduceerde geluidsniveau teruggebracht tot een zeer beperkte waarde. De buitenunit kan buiten of onder bepaalde voorwaarden binnen worden gemonteerd. De binnenunit is ontworpen voor gebruik binnen, bovenaan de wand. De bediening gebeurt via een infrarood-afstandsbediening. De buitenunit bestaat uit een kringloop met compressor, een condensor in lamellenuitvoering, drie elektronische expansiekleppen en een condensorventilator. De buitenunit is te combineren met REMKO-binnenunits van de serie SKT 260 IT met de juiste koelcapaciteit. De besturing van de koudekringloop van de buitenunit gebeurt via de regeling van de binnenunits. Voor het gebruik van het apparaat bij lage buitentemperaturen is een thermische condensordrukregeling als winterregeling voor de besturing van het toerental van de condensorventilator ingebouwd.
Vloerconsoles, wandconsoles en koudemiddelleidingen zijn verkrijgbaar als accessoires.
2
1
3
5
4
TCE
TCE
TCE
TCE
10
11
12
13
6
7
8
9
Afb. 8: Schema koudekringloop binnenunit
1: Condensor
2: Condensorventilator
3: Keerklep
4: Compressor
5: Regelorgaan capillaire buis
6: Aansluitklep zuigleiding A
7: Aansluitklep zuigleiding B
8: Aansluitklep zuigleiding C
9: Aansluitklep zuigleiding D
10: Inspuitleiding A
11: Inspuitleiding B
12: Inspuitleiding C
13: Inspuitleiding D
14
Ba Bb
1a 1b
3
Bc
3
Bd
1c
9
8
7
1d
3 3
A
4
9
8
7 6
2
5
Afb. 9: Systeemopbouw SKT 1060 AT
A: Buiten
Ba-d: Binnen
1a-d: Binnenunits
2:
3:
4:
Buitenunit
Condensleiding
Condensorventilator
5:
6:
7:
8:
9:
Netaansluiting
Afsluitkranen
Zuigleidingen
Inspuitleidingen
Stuurleidingen
De verbinding tussen binnenunit (binnenzone Ba, Bb, Bc, Bd, Be) en buitenunit (aansluiting circuit A, B, C, D, E) van de buitenunit wordt met koudemiddelleidingen alsook een stuurleiding vervaardigd.
15
REMKO serie SKT
3.2 Combinaties
Binnenunit
De volgende binnenunit SKT 260 IT kan met de buitenunits SKT 520-1060 AT worden gecombineerd.
4 Bediening
De bediening van de compressor in de buitenunit gebeurt via de regeling van de stuurprint in de buitenunit. Daarom moet het hoofdstuk "Regeling" uit de gebruikshandleiding van de buitenunit worden opgevolgd.
Help mee bij het besparen van energie tijdens standby! Wordt het apparaat, de installatie of de component niet gebruikt, raden we het onderbreken van de voedingsspanning aan. Componenten met een veiligheidsfunctie zijn uitgesloten van onze aanbeveling!
Afb. 10: Binnenunit
De volgende combinaties van de buitenunits kunnen worden geselecteerd:
SKT 520 - Combinatie met 2 binnenunits
Combinatie
1
Binnenunits
2,6 kW ll
Vervolg op de volgende pagina.
SKT 790 - Combinatie met 3 binnenunits
Combinatie
1
Binnenunits
2,6 kW lll
SKT 1060 - Combinatie met 4 binnenunits
Combinatie
1
Binnenunits
2,6 kW llll
16
5 Montageaanwijzingen voor het vakpersoneel
5.1 Belangrijke aanwijzingen voor het installeren
Markeer de koudemiddelleidingen (inspuit- en zuigleiding) evenals de bijbehorende elektrische besturingsleiding van elke binnenunit met een letter. Sluit de leidingen alleen aan op de aansluitingen die bij elkaar horen.
n Is de enkele lengte van de koudemiddelleiding langer dan 5 meter, moet koudemiddel bijgevuld worden. De hoeveelheid bij te vullen koudemiddel kunt u vinden in het hoofdstuk "Koudemiddel bijvullen".
n Gebruik alleen de meegeleverde wartelmoeren voor de koudemiddelleidingen en verwijder deze pas vlak voor het aansluiten van de koudemiddelleidingen.
n Voer alle elektrische aansluitingen uit volgens de geldende DIN- en VDE-bepalingen.
n Sluit de elektrische leidingen altijd volgens de voorschriften aan op de elektrische aansluitklemmen. Anders kan brand ontstaan.
n Voor de inbedrijfstelling van de totale installatie moeten de gebruikshandleidingen van de binnenunit en de buitenunit worden opgevolgd.
n Breng het apparaat in de originele verpakking zo dicht mogelijk bij de montagelocatie. Zo vermijdt u transportschade.
n Controleer de inhoud van de verpakking op volledigheid en op zichtbare transportschade.
Meld eventuele schade onmiddellijk aan uw leverancier en de transporteur.
n Til het apparaat op aan de hoeken en niet aan de koudemiddel- of condensaansluitingen.
n De koelmiddelleidingen (aanvoer- en afzuigleiding), ventielen en de verbindingen moeten dampdiffusiedicht worden geïsoleerd. Eventueel moet ook de condensleiding worden geïsoleerd.
n Kies een montageplaats, die een vrije luchttoeen -afvoer waarborgt (zie de paragraaf "Minimale vrije ruimte").
n Installeer het apparaat niet in de onmiddellijke nabijheid van apparaten met een sterke warmtestraling. De montage in de buurt van warmtebronnen vermindert de capaciteit van het apparaat.
n Open de afsluitkranen van de koudemiddelleidingen pas na het afronden van alle installatiewerkzaamheden.
n Sluit open koudemiddelleidingen tegen het binnendringen van vocht met geschikte doppen, resp. plakband en knik of druk niet op de koudemiddelleidingen.
n Vermijd onnodig buigen. Zo wordt het drukverlies in de koudemiddelleidingen geminimaliseerd en wordt de vrije retour van de compressorolie gewaarborgd.
n Neem bijzondere voorzorgsmaatregelen voor de olieretour, als de buitenunit hoger dan de binnenunit is geplaatst (zie de paragraaf
"Maatregelen olieretour").
AANWIJZING!
Let beslist op de juiste combinaties en aansluitposities van elektrische- en koudemiddelleidingen! De aansluitingen van de individuele kringlopen mogen niet onderling verwisseld worden. Een verwisseling van de besturings- en koudemiddelleidingen kan fatale gevolgen hebben (schade aan de compressor)!
De inbedrijfstelling van de individuele circuits moet na elkaar gebeuren.
AANWIJZING!
Afhankelijk van de koelcapaciteit van de buitenunit en de binnenunit zijn verschillende koudemiddelleidingen noodzakelijk.
5.2 Wanddoorvoeren
n Er moet een wanddoorbreking worden gemaakt met een diameter van minimaal 70 mm en met minimaal 10 mm verval van binnen naar buiten.
n Om beschadigingen aan de leiding te voorkomen, moet de doorbraak aan de binnenkant worden bekleed of bijv. worden voorzien van een PVC-buis (zie afbeelding).
n Vanwege de brandveiligheid dient de muur van de wanddoorvoer na de montage met een geschikt afdichtmiddel worden afgesloten.
Gebruik geen cement- of kalkhoudende materialen!
17
REMKO serie SKT
1 2 5
3 4
Afb. 11: Wanddoorbraak
1: Vloeistofleiding
2: Besturingskabel
3: Condensleiding
4: Zuigleiding
5: PVC-buis
5.3 Montagemateriaal
De buitenunit wordt met behulp van 4 bouten via een wandframe tegen de wand of op een vloerconsole aan de vloer bevestigd.
Regen
Het apparaat bij vloer- of dakopstelling met min. 10 cm bodemvrijheid monteren. Hiervoor is er een vloerconsole verkrijgbaar.
Zon
De condensor van de buitenunit is een module die warmte afgeeft. Instraling van de zon verhoogt de temperatuur van de lamellen en vermindert daardoor de warmteafvoer van de lamellenwarmtewisselaar. De buitenunit moet indien mogelijk aan de noordzijde van het betreffende gebouw worden geplaatst. Indien mogelijk moeten er bouwkundige voorzieningen worden aangebracht die voor schaduw zorgen. Dit kan door een klein afdak gebeuren. De uitgaande warme luchtstroom mag door de maatregelen echter niet worden beïnvloed.
Wind
Als het apparaat op een winderige plaats wordt geïnstalleerd, let er dan op dat uitstromende warme lucht met de hoofdwindrichting mee wordt afgevoerd. Als dit niet mogelijk is, moeten bouwkundige voorzieningen worden aangebracht ter bescherming tegen wind. Let er op, dat de windbescherming de luchttoevoer van het apparaat niet beïnvloedt. Extra stabilisatie is raadzaam. Dat kan bijv. met kabels of andere constructies worden gerealiseerd.
WAARSCHUWING!
Gebruik uitsluitend voor de toepassing geschikt bevestigingsmateriaal.
5.4 Keuze van de installatielocatie
Binnenunit
De binnenunit is voor horizontale montage aan de wand boven deuren ontworpen. Deze kan ook bovenaan de wand (min. 1,75 m boven de vloer) worden geplaatst.
Buitenunit
De buitenunit is ontworpen voor een horizontaal staande positie buiten. De opstellocatie van het apparaat moet horizontaal, vlak en stevig zijn.
Bovendien moet het apparaat worden vastgezet zodat het niet kan kantelen. De buitenunit kan zowel buiten als binnen een gebouw worden geplaatst. Bij de buitenmontage moet u rekening houden met de volgende aanwijzingen ter bescherming van het apparaat tegen weersinvloeden.
1
Afb. 12: Windbescherming
1: Wind
Sneeuw
In gebieden met sterke sneeuwval moet het apparaat bij voorkeur tegen een wand worden geïnstalleerd. De montage dient dan min. 20 cm boven de te verwachten sneeuwhoogte te gebeuren, om het binnendringen van sneeuw in de buitenunit te verhinderen. Een wandconsole is leverbaar als accessoire.
18
20 cm
1
Afb. 13: Minimale afstand tot sneeuw
1: Sneeuw
3
2
W
Opstelling binnen een gebouw n Zorg voor voldoende warmteafvoer als het apparaat in een kelder, op het dak, in een aangrenzende ruimte of in hallen wordt geplaatst
n Installeer een extra ventilator, met hetzelfde luchtdebiet als de in die ruimte op te stellen buitenunit, die de eventuele drukverliezen in de
luchtkanalen kan compenseren (Afb. 14).
n Houd u zich aan de statische en andere bouwtechnische voorschriften en bepalingen in verband met het gebouw en zorg eventueel voor geluidsdemping.
K
3
1
Afb. 14: Opstelling binnen een gebouw
K: Koude verse lucht
W: Warme lucht
1: Buitenunit
2: Extra ventilator
3: Lichtschacht
19
REMKO serie SKT
5.5 Minimale vrije ruimte
De minimale vrije ruimte is nodig voor onderhoudsen reparatiewerkzaamheden en voor een optimale luchtverdeling.
E 1
5.6 Olieretourmaatregelen
Als de buitenunit hoger dan de binnenunit wordt geplaatst, moeten geschikte maatregelen voor de olieretour worden getroffen. Dit gebeurt meestal door het maken van een olie-sifon, die om de
7 meter stijging moet worden geïnstalleerd.
A
D
A
B
2
Afb. 15: Minimale vrije ruimte buitenunit
1: Luchtinlaat
2: Luchtuitlaat
B
C
A
D
E
Alle gegevens in mm
SKT 520-1060
100
1200
600
150
600
C
1
B
2
Afb. 16: Olieretourmaatregelen
A: Buitenunit
B: Binnenunit
1: Olie-sifon in de zuigleiding naar de buitenunit
1 x elke 7 stijgende meter, radius: 50 mm
2: Max. 10 m
20
6 Installatie
6.1 Aansluiting van de koudemiddelleidingen
De gebouwaansluiting van de koudemiddelleidingen gebeurt aan de achterkant van de apparaten.
Eventueel moet op de binnenunit een verloopnippel naar een grotere of kleinere diameter worden geïnstalleerd. Deze verloopnippels worden standaard meegeleverd met de binnenunit. Na de montage moeten de verbindingen dampdiffusiedicht worden geïsoleerd.
AANWIJZING!
Het installeren mag alleen door geautoriseerd vakpersoneel worden uitgevoerd.
AANWIJZING!
Het apparaat is vanuit de fabriek gevuld met gedroogde stikstof voor lekdichtheidscontrole.
De onder druk staande stikstof ontsnapt bij het losdraaien van de wartelmoeren.
AANWIJZING!
Er mag alleen gereedschap worden gebruikt, dat geschikt is voor gebruik in de koeltechniek
(bijv.: buigtang, pijpsnijder, ontbramer en felsgereedschap) koelmiddelbuizen mogen niet worden afgezaagd.
AANWIJZING!
Bij alle werkzaamheden dient te worden uitgesloten dat vuil, spaanders, water enz. in de koelmiddelleidingen terechtkomt!
De volgende aanwijzingen hebben betrekking op het installeren van de koudekringloop en de montage van de binnen- en buitenunit.
1.
De vereiste leidingdiameters kunt u vinden in de tabel "Technische gegevens".
2.
Installeer de binnenunit en sluit de koudemiddelleiding aan volgens de gebruikshandleiding van de binnenunit.
3.
Installeer de buitenunit met het wandframe resp. met de vloerconsole aan statisch geschikte delen van het gebouw (montageaanwijzingen van de consoles opvolgen).
4.
Zorg dat geen geluid wordt overgedragen naar delen van het gebouw. Contactgeluiden kunnen door trillingsdempers worden verminderd!
5.
Leg de koudemiddelleidingen van de binnennaar de buitenunit. Zorg voor een voldoende bevestiging en neem evt. maatregelen tegen voor de olieretour!
6.
Verwijder de vanuit de fabriek gemonteerde beschermdoppen evenals de wartelmoeren van de aansluitingen en gebruik deze tijdens de montage.
7.
Zorg voor het maken van de felsranden aan de leidinguiteinden dat de wartelmoeren aanwezig zijn op de leidingen.
8.
Bewerk de verlegde koudemiddelleidingen
zoals hierna afgebeeld (Afb. 17 en Afb. 18).
9.
Controleer of de felsrand een correcte vorm
10.
Maak nu de verbinding van de koudemiddelleidingen met de aansluiting met de hand, om te waarborgen dat ze goed zitten.
11.
Bevestig de schroefkoppelingen nu definitief net 2 steeksleutels met een geschikte sleutelwijdte. De schroefkoppeling tijdens het vastdraaien met een steeksleutel tegen-
12.
Gebruik alleen voor het temperatuurbereik geschikte en diffusiedichte isolatieslangen.
13.
Let bij de montage op de buigradius van de koudemiddelleidingen en buig een leiding nooit tweemaal op dezelfde plaats. Hierdoor kan de leiding bros worden en scheuren.
14.
Voorzie ten slotte de geïnstalleerde koudemiddelleidingen, inclusief koppelingen, van een geschikte warmte-isolatie.
15.
Ga bij het aansluiten van alle overige koudemiddelleidingen bij de afsluitkleppen te werk zoals hierboven beschreven.
21
REMKO serie SKT
Markeer de koudemiddelleidingen (inspuit- en zuigleiding) evenals de bijbehorende elektrische besturingsleiding van elke binnenunit met een letter. Sluit de leidingen alleen aan op de aansluitingen die bij elkaar horen.
1
AANWIJZING!
Let beslist op de juiste combinaties en aansluitposities van elektrische- en koudemiddelleidingen! De aansluitingen van de individuele kringlopen mogen niet onderling verwisseld worden. Een verwisseling van de besturings- en koudemiddelleidingen kan fatale gevolgen hebben (schade aan de compressor)!
De inbedrijfstelling van de individuele circuits moet na elkaar gebeuren.
Afb. 18: Omfelsen van de koudemiddelleiding
1: Felsgereedschap
1
2
Afb. 17: Ontbramen van de koudemiddelleiding
1: Koudemiddelleiding
2: Ontbramer
Afb. 19: Correcte felsvorm
22
1
AANWIJZING!
Er moet een vacuüm van min. 20 mbar abs.
worden bereikt!
2
Afb. 20: Schroefkoppelingen aanhalen
1: Vastdraaien met de eerste steeksleutel
2: Tegenhouden met de tweede steeksleutel
Aanhaalmoment in Nm Pijpdiameter in inches
1/4"
3/8"
1/2"
5/8"
3/4"
15-20
33-40
50-60
65-75
95-105
6.2 Controle op lekkages
Zodra alle aansluitingen gemaakt zijn, wordt het manometerstation als volgt aangesloten op de schraderkleppen, indien aanwezig: rood = kleine klep = hogedruk blauw = grote klep = zuigdruk
Na het maken van alle aansluitingen wordt de lektest met droge stikstof uitgevoerd.
Voor het controleren op lekkages lekzoekspray spuiten op alle aansluitingen. Zijn bellen te zien, is de aansluiting niet correct uitgevoerd. Draai dan de schroefkoppelingen strakker aan of maak eventueel een nieuwe felsrand aan de leiding.
Na succesvolle lektest, de overdruk uit de koudemiddelleidingen ontlasten en een vacuümpomp met een absolute onderdruk van min. 10 mbar aansluiten, om te zorgen voor een vacuüm in de leidingen. Bovendien wordt zo het aanwezige vocht uit de leidingen verwijderd.
De tijdsduur voor het verkrijgen van het vacuüm is afhankelijk van het leidingvolume van de binnenunit en de lengte van de koudemiddelleidingen, de procedure duurt echter minimaal 60 minuten .
Zodra de vreemde gassen en het vocht volledig uit het systeem verwijderd zijn, de kleppen van het manometerstation sluiten en de kleppen van de buitenunit openen, zoals beschreven is in het hoofdstuk "Inbedrijfstelling".
6.3 Extra instructies voor het aansluiten van de koudemiddelleidingen
n Bij het combineren van de buitenunit met meerdere binnenunits kan de procedure voor het aansluiten van de koudemiddelleidingen afwijken. Monteer de bij de buitenunit meegeleverde verloopnippels op de buitenunit.
n Is de enkele lengte van de verbindingsleiding groter dan 5 m, moet bij het in bedrijf nemen van de installatie koudemiddel worden bijgevuld (zie hoofdstuk "Koudemiddel bijvullen").
23
REMKO serie SKT
6.4 Koudemiddel bijvullen
Het apparaat beschikt over een basisvulling met koudemiddel. Daarnaast moet bij koudemiddelleidingen van meer dan 5 meter enkele lengte per koudekringloop een extra vulhoeveelheid volgens de hiernaast opgenomen tabel worden bijgevuld:
SKT 520-1060 AT
Tot en met
5 m
0 g/m vanaf 5m
30 g/m
VOORZICHTIG!
Draag bij de omgang met koudemiddelen altijd de betreffende beschermende kleding.
GEVAAR!
Let er op dat het gebruikte koudemiddel altijd in vloeibare vorm wordt bijgevuld!
AANWIJZING!
De vulhoeveelheid van het koudemiddel moet gecontroleerd worden op basis van de oververhitting.
AANWIJZING!
Lekkage van koudemiddel draagt bij aan de klimaatverandering. Koudemiddelen met een geringer broeikaseffect dragen bij een lekkage minder bij aan de opwarming van de aarde dan degene met een hoger broeikaseffect.
Dit apparaat bevat koudemiddel met een broeikaseffect van 2088. Hierdoor heeft een lekkage van 1 kg van dit koudemiddel een 2088 keer grotere invloed op de opwarming van de aarde dan 1 kg CO
2
, over een periode van 100 jaar.
Geen werkzaamheden aan het koudecircuit uitvoeren of het apparaat demonteren in onderdelen - altijd de hulp inroepen van vakpersoneel.
7 Condensaataansluiting en gewaarborgde afvoer
Condensaansluiting
Door de dauwpuntonderschrijding bij de lamellencondensor, ontstaat er tijdens verwarmingsbedrijf condens. Onder het apparaat moet een condensopvangbak worden gemonteerd die het condenswater kan afvoeren.
n De in het gebouw gemonteerde condensleiding moet gelegd worden met een verval van min.
2%. Monteer eventueel dampdiffusiedichte isolatie.
n Bij gebruik van het apparaat bij een buitentemperatuur onder 4 °C, moet de condensleiding vorstvrij worden gelegd. Daarnaast moeten de onderzijde van de bekleding van de behuizing en de condensopvangbak vorstvrij worden gehouden, om een doorlopende afvoer van condens te waarborgen. Monteer eventueel een lintverwarming langs de leiding n Na het leggen controleren op een vrije afvoer van het condens en zorgen voor een permanente lekdichtheid.
Gewaarborgde afvoer bij lekkages
Regionale voorschriften of wetten betreffende het milieu, bijv. wetgeving betreffende de waterhuishouding (WHG), kunnen bepalingen bevatten dat ongecontroleerde afvoer bij lekken voorkomen dient te worden, zodat uittredende koelmachineolie of potentieel gevaarlijke koelmiddelen veilig afgevoerd kunnen worden.
AANWIJZING!
Bij een condensaatafvoer via een kanaal moet conform DIN EN 1717 gegarandeerd zijn, dat aanwezige belastingen betreffende afvalwater
(bacteriën, schimmels, virussen) niet in het aangesloten apparaat terechtkomen.
24
8 Elektrische aansluiting
8.1 Algemene informatie en veiligheidsinstructies
Bij de apparaten MVT moet een netvoedingsaansluitleiding en de meegeleverde 4-aderige stuurleiding van de binnenunit naar de buitenunit verlegd worden.
Wij adviseren stuurleidingen met een leidingdoorsnede van minimaal 1,5 mm² te gebruiken.
GEVAAR!
Het elektrische installeren moet gebeuren door een gespecialiseerd bedrijf. De montage van de elektrische aansluiting moet spanningsloos gebeuren.
AANWIJZING!
De elektrische aansluiting van de apparaten moet worden uitgevoerd volgens de plaatselijke voorschriften op een bijzonder voedingspunt met aardlekschakelaar en moet daarom door een elektricien worden.
We raden aan de besturingsleidingen als afgeschermde leiding uit te voeren.
8.2 Aansluiten van de buitenunit
Vóór u begint met het aansluiten moet u de volgende aanwijzingen opvolgen: n De schakelkast moet in de buurt van de buitenunit geïnstalleerd worden. Wij adviseren een hoofd- resp. reparatieschakelaar te plaatsen
(afb. 9).
n De stroomtoevoer van de binnenunit verloopt via de verbindingsleiding van de buitenunit.
n De elektrische zekering van de installatie moet gebeuren volgens de technische gegevens.
Noodzakelijke doorsneden aanhouden!
n Wordt de buitenunit op een dak gemonteerd, moet ervoor worden gezorgd dat deze tegen blikseminslag wordt beschermd.
n Markeer de elektrische stuurleiding en de daarbij horende koudemiddelleidingen van elke binnenunit met dezelfde letter (A t/m D).
n Sluit de leidingen alleen aan op de aansluitingen die gemarkeerd zijn met dezelfde letters. Een verwisseling van de stuur- en koudemiddelleidingen kan fatale gevolgen hebben, zoals schade aan de compressor!
Voor het aansluiten van de leiding als volgt te werk gaan:
1.
Verwijder de zijwand aan de kant van de aansluiting.
2.
Kies de doorsnede van de aansluitleiding volgens de voorschriften.
3.
Voer de beide leidingen door de beschermring van de vaste aansluitplaat.
4.
Steek de stuurleiding in de betreffende klem.
Let op de juiste toewijzing van de circuits.
5.
Veranker de leiding in de trekontlasting en het apparaat weer samenbouwen.
Bij enkele binnenunits zijn extra sensorleidingen resp. stuurleidingen noodzakelijk.
Controleer of alle elektrische stekker- en klemverbindingen goed vastzitten en goed contact maken, eventueel aandraaien.
25
REMKO serie SKT
5 4
Afb. 21: Aansluiten van de buitenunit
3
1 2
Afb. 22: Elektrische aansluiting van de leiding op het voorbeeld van SKT 790 AT
1: Netaansluiting
2: Trekontlasting
3: Stuurleiding binnenunit A
4: Stuurleiding binnenunit C
5: Stuurleiding binnenunit B
26
8.3 Elektrisch aansluitschema
SKT AT in combinatie met de binnenunits SKT 260 IT
SKT 520 AT SKT 790 AT
N
1
S(A)
1
S(B)
1
S(C)
SKT 1060 AT
1
S(D)
1
1
1 2 (N) S
A
Afb. 23: Elektrisch aansluitschema
1: Netaansluiting
A: SKT 260 IT
1
1 2 (N) S
A
1
1 2 (N) S
A
1
1 2 (N) S
A
27
REMKO serie SKT
8.4 Elektrische schakelschema
Overzichtsschema SKT 520 AT
A
1
B
3
4
5
AT
L(B) N(B) S(B)
IT
6 7 8 2 9
Afb. 24: Overzichtsschema SKT 520 AT
A: Besturingsprintplaat
B: Inverterprintplaat
AT: Netaansluiting buitenunit 230V / 1~ / 50Hz
IT: Aansluiting binnenunit 1-2
1: Compressor
2: Condensor ventilatormotor
3: 4-wegklep
4: Carterverwarming
5: Verwarming condensaatreservoir
6: Temperatuursensor condensoruitlaat T3
7: Temperatuursensor condensorinlaat T4
8: Temperatuursensor heetgasleiding TP
9: Expansiekleppen
10: Temperatuursensoren zuigleiding
9
10
28
Overzichtsschema SKT 790 ATR
9 10
13
B
A
2
3 1
AT IT 4 5 6
Afb. 25: Overzichtsschema SKT 790 AT
A: Besturingsprintplaat
B: Inverterprintplaat
AT: Netaansluiting buitenunit 230V / 1~ / 50Hz
IT: Aansluiting binnenunit 1-3
1: Compressor
2: Condensor ventilatormotor
3: Transformator
4: 4-wegklep
5: Carterverwarming
6: Verwarming condensaatreservoir
7: Temperatuursensor condensoruitlaat T3
8: Temperatuursensor condensorinlaat T4
9: Hogedruksensor
10: Lagedruksensor
11: Temperatuursensor heetgasleiding TP
12: Expansiekleppen
13: Temperatuursensoren zuigleiding
8
7
11
12
29
REMKO serie SKT
Overzichtsschema SKT 1060 AT
2
1
11
13
B
7
8
9
10
5
6
4
A 12
3
Afb. 26: Overzichtsschema SKT 1060 AT
A: Besturingsprintplaat
B: Inverterprintplaat
C: Com-printplaat
AT: Netaansluiting buitenunit 230V / 1~ / 50Hz
IT: Aansluiting binnenunit 1-4
1: Compressor
2: Condensor ventilatormotor
3: Transformator
4: 4-wegklep
AT IT
5: Carterverwarming
6: Verwarming condensaatreservoir
7: Temperatuursensor condensoruitlaat T3
8: Temperatuursensor condensorinlaat T4
9: Hogedruksensor
10: Lagedruksensor
11: Temperatuursensor heetgasleiding TP
12: Expansiekleppen
13: Temperatuursensoren zuigleiding
C
30
9 Vóór de inbedrijfstelling
Na succesvolle lekdichtheidscontrole moet de vacuümpomp via het manometerstation worden aangesloten op de klepaansluitingen van de buitenunit (zie hoofdstuk "Lekdichtheidscontrole") en moet daarna worden gezorgd voor een vacuüm.
Vóór de eerste inbedrijfstelling van het apparaat en na ingrepen in de koudekringloop moeten de volgende controles worden uitgevoerd en in het inbedrijfstellingsprotocol worden gedocumenteerd: n Controle van alle koudemiddelleidingen en kleppen met lekzoekspray of zeepwater op lekdichtheid.
n Controle van de koudemiddelleidingen en de isolatie op beschadigingen.
n Controleer de elektrische verbinding tussen binnen- en buitenunit op de juiste polariteit.
n Controleer alle bevestigingen, ophangingen etc. op correcte houding en correct niveau.
10 Inbedrijfstelling
AANWIJZING!
De inbedrijfstelling mag alleen door speciaal geschoold vakpersoneel en volgens de certificeringseisen worden uitgevoerd en moet worden gedocumenteerd. Voor de inbedrijfstelling van de totale installatie moeten de gebruikshandleidingen van de binnenunit en de buitenunit worden opgevolgd.
Nadat alle onderdelen zijn aangesloten en getest, kan de installatie in bedrijf worden genomen. Voor een correcte werking moet voor de overdracht aan de exploitant een functiecontrole worden uitgevoerd, om eventuele onregelmatigheden tijdens bedrijf te kunnen constateren.
Deze controle is afhankelijk van de gemonteerde binnenunit. In de gebruikshandleiding van de in bedrijf te nemen binnenunit is de werkwijze vastgelegd.
AANWIJZING!
Let beslist op de juiste combinaties en aansluitposities van elektrische- en koudemiddelleidingen! De aansluitingen van de individuele kringlopen mogen niet onderling verwisseld worden. Een verwisseling van de besturings- en koudemiddelleidingen kan fatale gevolgen hebben (schade aan de compressor)!
De inbedrijfstelling van de individuele circuits moet na elkaar gebeuren.
Functiecontrole en proefdraaien
Controleer de volgende punten: n Lekdichtheid van de koudemiddelleidingen.
n Gelijkmatige loop van compressor en ventilator.
n Afgifte van koude lucht aan binnenunit en verwarmde lucht aan buitenunit in koelbedrijf.
n Functiecontrole van de binnenunit en het correcte verloop van alle programma's.
n Controle van de oppervlaktetemperatuur van de zuigleiding en bepaling van de verdamperoververhitting. Houd voor een temperatuurmeting de thermometer op de zuigleiding en trek van de gemeten temperatuur, de op manometer afgelezen kookpunttemperatuur af.
n De gemeten temperaturen in het inbedrijfstellingsprotocol noteren.
31
REMKO serie SKT
Werkingstest van de bedrijfsmodus koelen
1.
Neem de afsluitdopen van de kleppen.
2.
Begin de inbedrijfstelling, door de afsluiters van de buitenunit kort te openen, tot de manometer een druk van ca. 2 bar aangeeft.
3.
Controleer de lekdichtheid van alle gemaakte aansluitingen met lekzoekspray en geschikte lekzoekapparatuur.
4.
Heeft u geen lekkages gevonden, draai dan de afsluiters met een zeskantsleutel linksom tot de aanslag open. Zijn lekkages geconstateerd, moet het koudemiddel worden afgezogen en de defecte aansluiting opnieuw tot stand worden gebracht. Het opnieuw tot stand brengen van een vacuüm en een droging is daarbij verplicht!
5.
Schakel de aanwezige hoofdschakelaar resp.
de zekering in.
6.
Stel de instelwaarde op de binnenunit met de afstandsbediening in op een lagere waarde dan de actuele ruimtetemperatuur.
Door de inschakelvertraging loopt de compressor pas enkele minuten later aan.
7.
Schakel het binnentoestel in de koelmodus.
8.
Controleer tijdens het proefdraaien alle regel-, besturings- en veiligheidsinrichtingen op werking en correcte instellingen.
9.
Controleer de apparaatbesturing van de binnenunit op basis van de in de bedieningshandleiding beschreven functies (timer, temperatuurinstellingen en alle modusinstellingen).
Controleer zoals in het volgende hoofdstuk "Functiecontrole en testrun" beschreven de individuele bedrijfsparameters met behulp van de display op de buitenunit en noteer deze in het inbedrijfstellingsrapport.
10.
Meet de oververhitting, buiten-, binnen-, uitgangs- en verdampingstemperaturen en vermeld de meetgegevens in het inbedrijfstellingsprotocol.
11.
Verwijder de manometer.
12.
Ga bij alle andere koudecircuits te werk zoals eerder beschreven.
Afsluitende maatregelen n Stel de insteltemperatuur in op de gewenste waarde met de afstandsbediening.
n Monteer alle gedemonteerde onderdelen.
n Leg de werking van de installatie uit aan de gebruiker.
AANWIJZING!
Controleer na elke ingreep in de koudekringloop de afsluitkleppen en de afsluitdoppen op lekkages. Gebruik eventueel geschikt afdichtmateriaal.
Beschrijving van de sensor
T1 Temperatuursensor ruimtetemperatuur binnenunit
T2 Temperatuursensor ruimtetemperatuur condensor midden
T2B Temperatuursensor zuigleiding (in de buitenunit geïntegreerd)
T3 Temperatuursensor condensoruitgang
T4 Temperatuursensor luchtinlaat condensor
T5 Temperatuursensor heetgasleiding compressor
Ts Instelwaarde
Display van de buitenunit
Op de besturingsprintplaat van de buitenunit vindt u het digitale display. Met dit display kan de actuele bedrijfsmodus worden weergegeven.
n In stand-by geeft het display "- -" weer n Als de compressor draait, geeft het display de actuele bedrijfsfrequentie weer.
n Bij ontdooien geeft het display “dF” weer of afwisselend "df" en de actuele compressorfrequentie (elke 0,5 sec.) n Als de compressor in de functie Voorverwarmen staat, geeft het display “PH” weer of afwisselend "PH" en de actuele compressorfrequentie (elke 0,5 sec.) n Als de olieretourfunctie van het systeem actief is, geeft het display "RO" weer of schakelt afwisselend tussen "RO" en de actuele compressorfrequentie (elke 0,5 sec.) n Als door lage buitentemperaturen de winterregeling actief is, geeft het display "LC" weer of afwisselend de compressorfrequentie en "LC"
(elke 0,5 sec.)
32
n In "Force Cool Mode – geforceerde besturing", geeft het display "FC" of afwisselend "FC" en de actuele compressorfrequentie (elke 0,5 sec.) n Als binnen 15 minuten de compressor in een onjuist frequentiebereik komt, wordt deze uitgeschakeld en geeft het apparaat "E6" weer n Als een storing is opgetreden, wordt de storing gecodeerd weergegeven. Zie tabel "Storingsweergave buitenunit"
1
Afb. 27: Check-knop op de printplaat van de buitenunit
1: Check-knop
Bedrijfsmodi opvragen
Op de besturingsprintplaat in de buitenunit bevindt zich een "Check"-toets SW1. Door het indrukken van deze toets kunnen de verschillende bedrijfsmodi worden opgevraagd. Door herhaaldelijk indrukken komt u in de verschillende parameterniveaus (zie onderstaande tabel):
Pos. Display
0
1
2
Standaardaanduiding
Aantal gedetecteerde binnenunits
Bedrijfsmodus (gecodeerd)
Beschrijving
Actuele compressorfrequentie of storingsweergave
Actuele waarde
Stand-by:0, Circulatiemodus:1, Koelmodus:2,
Verwarmingsmodus:3 Geforceerde modus voor testdoeleinden:4 Ontdooien:5
3 Aansluitleiding binnenunit A
4
5
6
Aansluiting binnenmodule B
Aansluiting binnenmodule C
Aansluiting binnenmodule D
Het vermogen wordt in PS weergegeven. Als er geen apparaat is aangesloten of wordt gedetecteerd, geeft het display het volgende weer:
“――” (2,0 kW=0.8 PS, 2,6kW=1,0 PS, 3,5 kW=1.2 PS, 5kW=1.5 PS)
7 Aansluiting binnenmodule E
8 Vermogenscapaciteit binnenunit A
9 Vermogenscapaciteit binnenunit B
10 Vermogenscapaciteit binnenunit C
11 Vermogenscapaciteit binnenunit D
12 Vermogenscapaciteit binnenunit E
13 Totale vermogenscapaciteit van alle binnenunits
14 Actuele frequentieaanvraag afhankelijk van de totale vermogenscapaciteit
15 Frequentielimiet
16 Frequentie die moet worden overgedragen aan de verdichter
Actuele waarde* PS 2,0 kW=0.8 PS, 2,6kW=1,0
PS, 3,5 kW=1.2 PS, 5kW=1.5 PS)
33
REMKO serie SKT
Weer voortzetten
Pos. Display
17 Temperatuur zuigleiding binnenunit A (T
2B
A)
18 Temperatuur zuigleiding binnenunit B (T
2B
B)
19 Temperatuur zuigleiding binnenunit C (T
2B
C)
20 Temperatuur zuigleiding binnenunit D (T
2B
D)
21 Temperatuur zuigleiding binnenunit E (T
2B
E)
22 Ruimtetemperatuur binnenunit A (T
1
A)
23 Ruimtetemperatuur binnenunit B (T
1
B)
24 Ruimtetemperatuur binnenunit C (T
1
C)
25 Ruimtetemperatuur binnenunit D (T
1
D)
26 Ruimtetemperatuur binnenunit E (T
1
E)
27 Temperatuur condensor binnenunit A (T
2
A)
28 Temperatuur condensor binnenunit B (T
2
B)
29 Temperatuur condensor binnenunit C (T
2
C)
30 Temperatuur condensor binnenunit D (T
2
D)
31 Temperatuur condensor binnenunit E (T
2
E)
32 Temperatuur condensoruitlaat (T3)
33 Temperatuur luchtinlaat condensor (T4)
Beschrijving
Actuele waarde Is de temperatuur lager dan
-9 °C geeft het display "-9". Is de temperatuur hoger dan 70 °C, geeft het display "70" weer.
Als er geen binnenunit is aangesloten, geeft het display het volgende weer: "――"
Actuele waarde Is de temperatuur lager dan
0 °C geeft het display "0". Is de temperatuur hoger dan 70 °C, geeft het display "70" weer.
Als er geen binnenunit is aangesloten, geeft het display het volgende weer: "――"
Actuele waarde Is de temperatuur lager dan
-9 °C geeft het display "-9". Is de temperatuur hoger dan 70 °C, geeft het display "70" weer.
Als er geen binnenunit is aangesloten, geeft het display het volgende weer: "――"
34 Heetgastemperatuur condensoruitlaat (T5)
35 Stroomopname
36 Actuele netspanning
37 Openingsgraden inspuitklep A
38 Openingsgraden inspuitklep B
39 Openingsgraden inspuitklep C
40 Openingsgraden inspuitklep D
41 Openingsgraden inspuitklep E
42 Frequentielimiet
43 Gemiddelde waarde sensor T2
44 Actueel toerental ventilatormotor condensor
45 Laatste foutmelding
De weergegeven waarde ligt tussen 30-129 °C.
Als de temperatuur lager is dan 30 °C, geeft het display "30" weer. Als de temperatuur hoger is dan 99 °C, geeft het display de waarde zonder
"1" weer. Als het display bijv "0.5" toont, wordt
105 °C gemeten.
De weergegeven waarde is een hexadecimaal cijfer. Geeft het display bijv. de waarde "Cd" weer, is de gemeten waarde 205.
Actuele waarde X 4. Als de waarde hoger is dan 99, geeft het display de 2e en 3e positie van de waarde weer. Geeft het display bijv.
"2.0" weer, zijn de openingsgraden 120x4=480 stappen.)
Geen toepassing
(Som T2 van alle binnenunits)/(Aantal aangesloten binnenunits) (in de koelmodus: T2B, in de verwarmingsmodus: T2)
UIT:0, Hoog:1, Medium:2, Laag hoog:3 Laag medium 4, Laag laag:5
00 betekent geen foutmelding opgetreden
34
(3) Koelvermogen - Verwarmingscapacit. AT/IT
Display
7
8
5
6
9
10
3
4
1
2
Koelvermogen (kW)
2,0-2,5
2,0-2,5
3,0-3,8
4,5-5,0
5,0
5,5-6,1
6,1-7,0
7,0-7,5
7,5-8,0
>8,0
Verwarmingsvermogen (kW)
2,0-2,5
2,0-2,5
3,0-3,8
4,5-5,0
5,5-6,1
6,1-7,0
6,1-7,0
7,0-7,5
7,5-8,0
>8,0
(6) Temperatuur sensor heetgas
Display
10
11
12
13
14
15
16
Temperatuur (°C)
35-40
40-45
45-50
50-55
55-60
60-65
65-70
(5) Temperatuursensor luchtinlaat
Display
15
20
25
30
35
40
45
50
55
60
65
70
Temperatuur (°C)
-7,5
-5,0
-2,5
0
2,5
5,0
7,5
10,0
12,5
15,0
17,5
20,0
Display
75
80
85
90
95
99
Temperatuur (°C)
22,5
25,0
27,5
30,0
32,5
34,5
(7) Stroomopname buitenunit
76
78
80
82
67
68
70
72
Display
44
46
54
55
58
62
66
84
88
92
94
Stroomopname (A)
6,0
6,2
7,4
7,6
7,8
8,0
8,6
10,0
10,2
10,4
10,6
8,8
9,0
9,2
9,5
11,0
11,6
12,0
12,2
35
REMKO serie SKT
11 Verhelpen van storingen, foutanalyse en klantenservice
11.1 Verhelpen van storingen en klantenservice
De apparaten en componenten worden volgens de modernste methodes gefabriceerd, en meervoudig op feilloze werking gecontroleerd. Ontstaan desondanks toch storingen, controleer dan de werking volgens de onderstaande lijst. Bij installaties met binnen- en buitenunit moet eveneens het hoofdstuk "Verhelpen van storingen en service" uit beide bedieningshandleidingen worden opgevolgd. Als alle controles zijn uitgevoerd en het apparaat nog steeds niet probleemloos werkt, licht dan uw gespecialiseerd bedrijf in!
Functiestoring
Storing
Het apparaat start niet of schakelt zelfstandig uit
De unit werkt met verminderd resp.
zonder koelvermogen.
Mogelijke oorzaken
Stroomuitval, onderspanning,
Netzekering defect / hoofdschakelaar uitgeschakeld
Netkabel beschadigd
Wachttijd na het inschakelen te kort
Gebruikstemperatuurbereik onder-/overschreden
Tijdelijke over- resp.
onderspanning
Uitschakelcontact van de externe condenspomp geopend
Vervangen van de koudemiddelleidingen
Vervangen van de elektrische besturingsleidingen
Controle
Werken alle andere elektrische bedrijfsmiddelen?
Oplossing
Spanning controleren ev.
wachten op herinschakelen
Werken alle lichtinstallaties?
Werken alle andere elektr.
bedrijfsmiddelen?
Kon een herstart worden uitgevoerd na ca. 5 minuten?
Werken de ventilatoren van de units?
Laten controleren door een erkend vakbedrijf
Staat de externe condenspomp van de binnenunit op "Storing"?
Zijn de inspuitleidingen en zuigleidingen van de kringlopen A, B en C op de juiste manier aangesloten?
Netzekering vervangen, hoofdschakelaar inschakelen
Laten repareren door een vakbedrijf
Langere wachttijden inplannen
Houd rekening met het temperatuurbereik
Uitschakelen en herinschakelen van de installatie
Afvoer van de condenspomp reinigen, pomp laten vervangen
Laten verhelpen door een erkend vakbedrijf
Zijn de stuurleidingen van de koudemiddelleidingen van de circuits A, B en C op de juiste manier aangesloten?
Vreemde voorwerpen in de luchtinlaat- en luchtuitstroomzones?
Laten verhelpen door een erkend vakbedrijf
Reinig de lamellen. Luchtweerstand verminderen.
Luchtinlaat en / of luchtuitlaatopening worden door vreemde objecten geblokkeerd.
Warmte-/resp. windbelasting is toegenomen.
Is er een bouwkundige / gebruiksmatige wijziging?
Geen warmteafgifte mogelijk.
Werkt de ventilator van de buitenunit?
Lekkage in koudekringloop Is er een sterke rijpvorming zichtbaar op de grote afsluitklep?
Uitzetten van de warmte-/ windbelasting door overeenkomstige maatregelen.
Ventilator / winterregeling controleren.
Laten repareren door een vakbedrijf.
36
Functiestoring (vervolg)
Storing
De zuigleiding en / of de vloeistofafscheider van de compressor zijn bevroren
Mogelijke oorzaken
Warmtebelasting is toegenomen
Controle
Werkt de buitenunit in duurbedrijf?
Oplossing
Warmtebelasting verminderen, evt. extra apparaat installeren / bevroren onderdelen isoleren
Storingsweergave printplaat buitenunit
P1
P2
P3
P4
F2
F3
F4
F5
Aanduiding Beschrijving van de fout
E0 EEPROM-fout buitenunit
E2
E3
Communicatiefout tussen binnen- en buitenunit
Communicatiefout tussen inverter-printplaat en besturingsprintplaat
E4
E5
E8
F1
Temperatuursensor luchtinlaat buitendeel defect
Over- resp. onderspanningsfout
Toerentalregeling condensatorventilator zonder functie
Temperatuursensor zuigleiding binnenunit A defect
P5
P6
LP
Temperatuursensor zuigleiding binnenunit B defect
Temperatuursensor zuigleiding binnenunit C defect
Temperatuursensor zuigleiding binnenunit D defect
Temperatuursensor zuigleiding binnenunit E defect
Hogedrukstoring
Lagedrukstoring
Stroomopname compressor te hoog
Temperatuursensor heetgasleiding defect
Overtemperatuur condensor
Veiligheidsuitschakeling inverter-printplaat
Omgevingstemperatuur te laag
Opmerking
Na het verhelpen van de storing blijft de storingsmelding gedurende 30 seconden bestaan (uitzondering
E2 en E3).
37
REMKO serie SKT
11.2 Storingsanalyse buitenunit
Fout E0: EEPROM-fout buitenunit
Spanning uitschakelen, 2 minuten later weer inschakelen.
Is de fout nog aanwezig?
JA
Vervang de besturingsprintplaat.
Fout E3: Communicatiefout tussen inverter-printplaat en besturingsprintplaat
Printplaat geeft E3 weer
De besturingsprintplaat kan niet communiceren met de inverter-printplaat
JA Brandt er nog een LED van de inverter-printplaat?
NEE
JA
Elektrische verbinding tussen inverterprintplaat en de besturingsprintplaat controleren. Is dit correct uitgevoerd?
NEE
Verbinding corrigeren. Is de fout nog aanwezig?
NEE
Inverter-printplaat vervangen. Is het probleem verholpen?
NEE
Besturingsprintplaat vervangen. Is het probleem verholpen?
NEE
NEE
JA
JA
De installatie is weer bedrijfsklaar.
Volledige E-box vervangen
38
Fout E5: Over- resp. onderspanningsfout
JA
Over- resp. onderspanningsbeveiliging is aangesproken.
Controleer de spanning van de netaansluiting op de klemmen L en N van de buitenunit. Ligt deze op 220 en 240 V?
JA
Controleer de spanning tussen de klemmen P en N op de inverter-printplaat?
Ligt de gemeten waarde tussen 277-356 VDC (SKT
520 AT), resp. 277-410
VDC (grotere modules)
NEE
Gelijkrichter vervangen. Is de fout opgelost?
NEE
Inverter-printplaat vervangen. Werkt het apparaat normaal?
NEE
Besturingsprintplaat vervangen.
NEE
JA
JA
Netaansluiting corrigeren
Probleem verholpen.
39
4
5
6
2
3
Klem
1
40
REMKO serie SKT
Fout E8: Toerentalregeling condensatorventilator zonder functie
Besturingsprintplaat vervangen.
Spanning uitschakelen, 2 minuten later weer inschakelen. Is de fout nog aanwezig?
JA
Spanning uitschakelen, condensorventilator met de hand draaien. Loopt deze soepel?
JA
Elektrische verbindingsleidingen naar de motor controleren. Zijn deze correct uitgevoerd?
JA
NEE
Controleer de uitgangsspanning van de besturingsprintplaat (zie Bijlage).
Is er sprake van spanning op de uitgang?
JA
NEE Ventilatormotor vervangen.
NEE Het apparaat werkt normaal.
NEE Oorzaak vaststellen en probleem verhelpen.
NEE
Verbindingen vervangen.
Controleer de gelijkstroommotor (besturingsunit is in de motor geïntegreerd)
Meet de spanning tussen de klemmen 1-3 en 4-3 van de stekker als het apparaat zich in stand-by bevindt.
Controleer de gemeten spanning aan de hand van de onderstaande tabel. Als de gegevens niet overeenstemmen moet de besturingsprintplaat worden vervangen.
1 2 3 4 5 6
Kleur
Rood
---
Zwart
Wit
Geel
Blauw
Spanning
140V~380V
---
0V
13,5-16,5V
0~6,5V
15V
Fout P1: Hogedrukstoring (bij grotere modules)
Hogedrukstoring P1 is geactiveerd.
Is de elektrische verbinding tussen de hogedruksensor en de besturingsprintplaat juist?
JA
Controleer of de hogedruksensor defect is.
NEE
Apparaat uitschakelen.
Koudemiddelhoeveelheid aanpassen.
JA
JA
Haal de stekker uit de hogedruksensor en meet de weerstand. De waarde moet 0 zijn.
JA
Is de buitentemperatuur hoger dan 50 °C?
NEE
Wordt voldoende lucht via de condensor geleid?
JA
Loopt de ventilatormotor van de condensator goed?
JA
Controleer de koudemiddelvulhoeveelheid. Is de installatie te vol gevuld?
NEE
Besturingsprintplaat vervangen.
NEE
NEE
Hogedruksensor vervangen.
Condensor reinigen.
NEE Zie Probleemoplossing voor
Fout E8
41
REMKO serie SKT
Fout P2: Lagedrukstoring
Lagedruksensor is geactiveerd. Fout P2 is geactiveerd.
Is de elektrische verbinding tussen de lagedruksensor en de besturingsprintplaat juist?
JA
Controleer of de lagedruksensor defect is.
NEE
Verbinding corrigeren.
Apparaat uitschakelen.
JA
Haal de stekker uit de lagedruksensor en meet de weerstand. De waarde moet 0 zijn.
JA
Is de omgevingstemperatuur lager dan +5 °C resp.
-15 °C voor apparaten met winterregeling?
NEE
Controleer of de klep bij hogedruk doorlaat.
JA
Controleer of de ventilatormotor van de binnenunit in koelmodus werkt.
JA
Besturingsprintplaat vervangen. Fout verholpen?
NEE
Vulhoeveelheid koudemiddel controleren. Treedt verlies van het koudemiddel op?
JA
Probleem verholpen.
NEE
NEE
NEE
Lagedruksensor vervangen.
Kleppen openen.
Zie Probleemoplossing
Gebruikshandleiding binnenunit
42
Fout P3: Stroomopname compressor te hoog
Veiligheidsuitschakeling vanwege verhoogd vermogensverbruik van de compressor.
Apparaat uitschakelen.
Condensor reinigen.
Probleem verholpen.
JA
Apparaat spanningsvrij schakelen, aansluitend inschakelen en de totale vermogensverbruik meten.
Ligt deze binnen het aangegeven bereik?
JA
Controleer het koelcircuit. Is deze in orde?
JA
Is de buitentemperatuur hoger dan 50 °C?
NEE
JA
Is het condensor vervuild?
NEE
JA
Besturingsprintplaat vervangen. Werkt het apparaat normaal?
NEE
JA Volledige E-box vervangen.
43
REMKO serie SKT
Fout P4: Temperatuursensor heetgasleiding defect
Heetgastemperatuur bij compressor te hoog
Koudemiddelcircuit op lekkages controleren. Lekkage gevonden?
NEE
JA
Lekkage verholpen en installatie opnieuw in gebruik nemen.
JA Is de heetgastemperatuur hoger dan 115 °C?
NEE
Elektrische verbinding tussen de temperatuursensor heetgasleiding en de besturingsprintplaat controleren. Is dit correct uitgevoerd?
JA
Meet de weerstand van de temperatuursensor van de heetgasleiding. Is deze correct (ze Bijlage)?
JA
Besturingsprintplaat vervangen.
NEE
NEE Elektrische verbinding juist herstellen.
Temperatuursensor vervangen.
44
Fout P5: Overtemperatuur op de condensor
Als de koudemiddeltemperatuur op de condensoruitlaat hoger is dan 65 °C stopt het apparaat. Het apparaat schakelt weer in bij een temperatuur van 52 °C.
Veiligheidsuitschakeling overtemperatuur. Apparaat geeft
P5 weer.
JA
NEE
Elektrische verbinding tussen de temperatuursensor condensoruitlaat en de printplaat controleren. In orde?
NEE
Verbinding juist herstellen.
JA Weerstand van de temperatuursensor controleren (weerstanden, zie tabel). In orde?
JA NEE
Is de koudemiddeltemperatuur op de condensoruitlaat hoger dan 65 °C?
JA
Is de buitentemperatuur hoger dan
50 °C?
NEE
Loopt de ventilator van de condensator conform de voorschriften?
JA
Is het condensor vervuild?
NEE
Koudemiddelvulhoeveelheid correct?
JA
Besturingsprintplaat vervangen
JA
NEE
JA
Apparaat uitschakelen.
Zie Probleemoplossing voor Fout E8
Condensor reinigen.
Temperatuursensor vervangen.
45
REMKO serie SKT
Fout P6: Veiligheidsuitschakeling inverter-printplaat (deel 1)
Veiligheidsuitschakeling inverter-printplaat
Controleer de spanning tussen de klemmen P en N van de inverter-printplaat.
Ligt deze waarde tussen
277-366 VDC (SKT 520 AT) resp. 277-410 VDC (grotere modules)?
JA
Controleer de elektrische verbinding tussen de besturingsprintplaat en de inverter-printplaat. Is deze in orde?
JA
NEE
NEE
Corrigeer de verbinding. Fout opgelost?
Is de aansluiting naar de condensor correct uitgevoerd?
JA
NEE
NEE
Corrigeer de verbinding. Fout opgelost?
Inverter-printplaat vervangen. Werkt het apparaat normaal?
NEE
Loopt de ventilator van de condensator goed?
JA
Besturingsprintplaat vervangen. Werkt het apparaat normaal?
NEE
Compressor vervangen.
Werkt het apparaat normaal?
NEE
NEE
JA
Zie Probleemoplossing voor Fout E8
JA
JA
Zie verder het tweede gedeelte van deze tabel op de volgende pagina!
Probleem verholpen.
46
Fout P6: Veiligheidsuitschakeling inverter-printplaat (deel 2)
Veiligheidsuitschakeling inverter-printplaat
JA
Controleer de spanning tussen de klemmen P en
N van de inverter-printplaat. Ligt deze waarde tussen 277-366 VDC
(SKT 520 AT) resp.
277-410 VDC (grotere modules)?
NEE
Controleer de stroomvoorziening van de netaansluiting. Ligt deze op
208-230 V?
JA
NEE
JA
Corrigeer de netaansluiting. Werkt de installatie normaal?
Zie verder het eerste gedeelte van deze tabel op de vorige pagina!
NEE
Zijn de kabels van de netaansluiting juist geplaatst? Is de nulleider correct?
JA
NEE
Kabel aantrekken. Fout opgelost?
NEE
Zijn alle elektrische verbindingen juist in de E-box aangesloten?
NEE
Elektr. verbinding corrigeren.
JA NEE
Controleer de gelijkrichter op functioneren. Gebruik hiertoe een multimeter en meet de spanning tussen beide klemmen.
De waarde van de weerstand moet 0 zijn.
JA NEE
Controleer de elektrische verbindingen van de gelijkrichter. Zijn deze correct uitgevoerd?
JA
NEE
Gelijkrichter vervangen.
Elektr. verbinding vervangen.
47
REMKO serie SKT
Afzonderlijke componenten controleren
Controle van de temperatuursensoren
Klem de temperatuursensor van de besturingsprintplaat af, meet de weerstand aan de contacten van de stekker.
(zie tabellen
Ä „Weerstandswaarden van de sensoren T1, T2, T3, T4 en T2B“ op pagina 50 en
)
1
Afb. 28: Temperatuursensoren controleren
1: Multimeter
Controleren van de compressor-weerstandswaarde
Controleer de weerstandswaarden met een multimeter.
A
1
A
B
C
B
C
Afb. 29: Meting van de weerstandswaarden
1: Aansluitklem
A: blauw
B: rood
C: zwart
Pos.
blauw-rood
ASN108D22UEZ
1,57Ω (20 °C)
Weerstandswaarde
ASM135D23UFZ
1,75Ω (20 °C)
ATF235D22UMT
0,75Ω (20 °C)
Afb. 30: Meting van de weerstandswaarden met de multimeter
48
Controle van de IPM-printplaat
Schakel het apparaat uit en wacht tot de condensatoren volledig zijn ontladen. Ontkoppel de kabel van de
IPM-printplaat en meet de weerstand tussen P en UVWN, UVW en N.
Normale weerstand Normale weerstand Voltmeter
(+) Rood (-) Zwart
N
U
P
V
W
¥
Meerdere MOhm
Voltmeter
(+) Rood (-) Zwart
U
V
N
W
(+) Rood
¥
Meerdere MOhm
Controleren van de ventilatormotor binnenunit-weerstandswaarden
Controleer de weerstandswaarden met een multimeter.
A
1
A
B
C
B
C
Afb. 31: Meting van de weerstandswaarden
1: Aansluitklem
A: rood
B: zwart
C: wit
Pos.
YKSS-68-4-15-1
(Weilng)
Zwart - Rood 285,8Ω ±8% (20 °C)
Rood - Geel 178,5Ω ±8% (20 °C)
Geel - Blauw 178,5Ω ±8% (20 °C)
Weerstandswaarde
49
REMKO serie SKT
Weerstandswaarden van de sensoren T1, T2, T3, T4 en T2B
K Ohm K Ohm K Ohm K Ohm
50
Weerstandswaarde van de sensor T5
K Ohm K Ohm K Ohm K Ohm
51
REMKO serie SKT
12 Reiniging en onderhoud
Een regelmatige verzorging en het opvolgen van enkele basisvoorwaarden, garandeert een storingsvrij gebruik en een lange levensduur van het apparaat.
Onderhoud n We adviseren een onderhoudsovereenkomst voor een jaarlijkse onderhoudsbeurt met een gespecialiseerd bedrijf af te sluiten.
GEVAAR!
Vóór alle werkzaamheden aan het apparaat moet de netvoeding worden uitgeschakeld en beveiligd tegen onbevoegd herinschakelen!
Verzorging n Houd het apparaat vrij van vuil, begroeiing en andere afzettingen.
n Reinig het apparaat alleen met een vochtige doek. Gebruik geen waterstraal.
n Gebruik geen bijtende, schurende of oplosmiddelhoudende reinigingsmiddelen n Reinig vóór het begin van een langere stilstandperiode de lamellen van de binnen- en buitenunit, terwijl de ventilator draait.
Op deze manier is de bedrijfszekerheid van de installatie altijd gegarandeerd!
AANWIJZING!
Wettelijke voorschriften eisen een jaarlijkse lektest van de koudekringloop in relatie tot de koudemiddelvulhoeveelheid. De controle en het documenteren hiervan moet gebeuren door het betreffende vakpersoneel.
Aard van de werkzaamheden
Controle/Onderhoud/Inspectie
Algemeen
Spanning en stroom controleren
Werking compressor/ventilatoren controleren
Vervuiling condensor
Vulhoeveelheid koudemiddel controleren
Condensafvoer controleren
Isolatie controleren
Bewegende delen controleren
Lektest koudekringloop
1) Zie instructie hierboven
Inbedrijfstelling l l l l l l l l l
Maandelijks l
Halfjaarlijks l l
Jaarlijks l l l l l l 1)
52
13 Uit bedrijf nemen
Tijdelijk uit bedrijf nemen
1.
Laat de binnenunit 2 tot 3 uur in circulatiebedrijf of in koelbedrijf met maximale temperatuurinstelling draaien, zodat de restvochtigheid uit het apparaat wordt verwijderd.
2.
Neem de installatie met de afstandsbediening uit bedrijf.
3.
Schakel de stroomvoorziening van het apparaat uit.
4.
Dek het apparaat indien mogelijk af met een kunststoffolie om deze tegen weersinvloeden te beschermen.
Afdanken van de apparatuur
Het afvoeren van de apparaten en componenten moet volgens de lokaal geldende voorschriften, bijv. door geautoriseerde gespecialiseerde bedrijven op het gebied van afvalverwerking en recycling of inzamelpunten, worden uitgevoerd.
De firma REMKO GmbH & Co. KG of haar vertegenwoordigers verwijzen u graag naar een gespecialiseerd bedrijf bij u in de buurt.
53
REMKO serie SKT
14 Illustratie van het apparaat en onderdelenlijsten
14.1 Apparaatafbeelding SKT 520 AT
8
1 2
19
20
21
12
3
4
15
9
5
11
10
6
22
24
14
13
23
7
18
16
17
25
Afb. 32: Apparaatafbeelding SKT 520 AT
Wijzigingen in de afmetingen en de constructie, door de technische vooruitgang, voorbehouden.
54
14.2 Reserveonderdelenlijst SKT 520 AT
BELANGRIJK!
Voor het waarborgen van een correcte levering van de reserveonderdelen, altijd het apparaattype en het betreffende serienummer (zie typeplaatje) opgeven.
Nr.
Omschrijving
1 Beschermrooster voor condensor
2 Voorplaat condensor
3 Ventilatorblad
4 Ventilatormotor
5 4-wegklep
6 Elektronische inspuitklep
7 Bodemplaat
8 Afdekplaat
9 Compressor
10 Heetgassensor
11 Afsluitklep zuigleiding
12 Zijdeel links
13 Temperatuursensor condensoruitgang
14 Temperatuursensor condensor
15 Condensor
16 Inverterprintplaat
17 Besturingsprintplaat
18 Afdekking koelmiddelaansluitingen
19 Verwarming condensaatreservoir
20 Carterverwarming
21 Houder ventilatormotor
22 Afsluitklep inspuitleiding
23 Scheidingsplaat
24 Zijdeel rechts
25 Serviceklephouder
55
REMKO serie SKT
14.3 Apparaatafbeelding SKT 790 AT
1
19
20
2
3
26
8
21
12
4
15
5
21
11
9
6
22
24
17
25
13
18
14
16
23
7
Afb. 33: Apparaatafbeelding SKT 790 AT
Wijzigingen in de afmetingen en de constructie, door de technische vooruitgang, voorbehouden.
56
14.4 Reserveonderdelenlijst SKT 790 AT
BELANGRIJK!
Voor het waarborgen van een correcte levering van de reserveonderdelen, altijd het apparaattype en het betreffende serienummer (zie typeplaatje) opgeven.
Nr.
Omschrijving
1 Beschermrooster voor condensor
2 Voorplaat condensor
3 Ventilatorblad
4 Ventilatormotor
5 4-wegklep
6 Elektronische inspuitklep
7 Bodemplaat
8 Afdekplaat
9 Compressor
10 Heetgassensor
11 Afsluitklep zuigleiding
12 Zijdeel links
13 Temperatuursensor condensoruitgang
14 Temperatuursensor condensor
15 Condensor
16 Inverterprintplaat
17 Besturingsprintplaat
18 Afdekking koelmiddelaansluitingen
19 Verwarming condensaatreservoir
20 Carterverwarming
21 Houder ventilatormotor
22 Afsluitklep inspuitleiding
23 Scheidingsplaat
24 Zijdeel rechts
25 Serviceklephouder
57
REMKO serie SKT
14.5 Apparaatafbeelding SKT 1060 AT
1
22 23
16
25
24
2
3
28
4
26
6 8
11
7
5
9
27
14
12
10
29
13
15
17
21
19
18
20
Afb. 34: Apparaatafbeelding SKT 1060 AT
Wijzigingen in de afmetingen en de constructie, door de technische vooruitgang, voorbehouden.
58
14.6 Reserveonderdelenlijst SKT 1060 AT
BELANGRIJK!
Voor het waarborgen van een correcte levering van de reserveonderdelen, altijd het apparaattype en het betreffende serienummer (zie typeplaatje) opgeven.
Nr.
Omschrijving
1 Beschermrooster voor condensor
2 Voorplaat condensor
3 Ventilatorblad
4 Ventilatormotor
5 4-wegklep
6 Lagedruksensor
7 Hogedruksensor
8 Elektronische inspuitklep
9 Compressor
10 Vloeistofscheider
11 Afsluitklep zuigleiding
12 Afsluitklep inspuitleiding
13 Temperatuursensor condensoruitgang
14 Temperatuursensor luchtinlaat
15 Temperatuursensor heetgasleiding
16 Condensor
17 Inverterprintplaat
18 Besturingsprintplaat
19 Zijdeel rechts
20 Afdekking koelmiddelaansluitingen
21 Voorplaat condensorruimte
22 Zijdeel links
23 Afdekplaat
24 Carterverwarming
25 Verwarming condensaatreservoir
26 Houder ventilatormotor
27 Bodemplaat
28 Scheidingsplaat
29 Serviceklephouder
59
REMKO serie SKT
15 Index
A
Afvoeren van de apparaten en componenten . . . 7
Afvoeren van de verpakking . . . . . . . . . . . . . . . . 7
Apparaatafbeelding . . . . . . . . . . . . . . . . 54, 56, 58
B
Bedoeld gebruik . . . . . . . . . . . . . . . . . . . . . . . . . 7
C
Capaciteitscurven
Koelen . . . . . . . . . . . . . . . . . . . . . . . 11, 12, 13
Verwarmen . . . . . . . . . . . . . . . . . . . . 11, 12, 13
Combinatiemogelijkheden . . . . . . . . . . . . . . . . . 16
Condensaansluiting . . . . . . . . . . . . . . . . . . . . . . 24
D
Drijfgas volgens Kyoto-protocol . . . . . . . . . . . . . . 9
E
Elektrisch aansluitschema . . . . . . . . . . . . . . . . . 27
Elektrische aansluiting . . . . . . . . . . . . . . . . . . . 25
F
Functiecontrole . . . . . . . . . . . . . . . . . . . . . . . . . 31
G
Garantie . . . . . . . . . . . . . . . . . . . . . . . . . . . . . . . 7
Gelijkstroommotor controleren . . . . . . . . . . . . . 40
Gewaarborgde afvoer bij lekkages . . . . . . . . . . 24
I
Installatielocatie, kiezen . . . . . . . . . . . . . . . . . . 18
K
Keuze van de installatielocatie . . . . . . . . . . . . . 18
Klantendienst . . . . . . . . . . . . . . . . . . . . . . . . . . 36
M
Meting van
compressormotoren . . . . . . . . . . . . . . . . . . . 48
IPM-printplaat . . . . . . . . . . . . . . . . . . . . . . . . 49
Temperatuursensoren . . . . . . . . . . . . . . . . . 48
Ventilatormotor binnenunit . . . . . . . . . . . . . . 49
Milieubescherming . . . . . . . . . . . . . . . . . . . . . . . 7
Minimale vrije ruimte . . . . . . . . . . . . . . . . . . . . . 20
Montagemateriaal . . . . . . . . . . . . . . . . . . . . . . . 18
O
Olieretourmaatregelen . . . . . . . . . . . . . . . . . . . 20
Onderhoud . . . . . . . . . . . . . . . . . . . . . . . . . . . . 52
P
Proefdraaien . . . . . . . . . . . . . . . . . . . . . . . . . . . 31
R
Recycling . . . . . . . . . . . . . . . . . . . . . . . . . . . . . . 7
Reiniging en onderhoud . . . . . . . . . . . . . . . . . . 52
Reserveonderdelen bestellen . . . . . . . . 55, 57, 59
Reserveonderdelenlijst . . . . . . . . . . . . . 55, 57, 59
S
Storingen
Controle . . . . . . . . . . . . . . . . . . . . . . . . . . . . 36
Mogelijke oorzaken . . . . . . . . . . . . . . . . . . . 36
Oplossing . . . . . . . . . . . . . . . . . . . . . . . . . . . 36
Storingsweergave printplaat buitenunit . . . . . . . 37
U
Uit bedrijf nemen
Langdurig . . . . . . . . . . . . . . . . . . . . . . . . . . . 53
Tijdelijk . . . . . . . . . . . . . . . . . . . . . . . . . . . . . 53
V
Veiligheid
Algemene . . . . . . . . . . . . . . . . . . . . . . . . . . . . 5
Gevaren bij het niet-opvolgen van de veilig-
heidsvoorschriften . . . . . . . . . . . . . . . . . . . . . 5
Kwalificaties van het personeel . . . . . . . . . . . 5
Markering van instructies . . . . . . . . . . . . . . . . 5
Veiligheidsbewust werken . . . . . . . . . . . . . . . 6
Veiligheidsvoorschriften voor de exploitant . . . 6
Veiligheidsvoorschriften voor inspectiewerk-
zaamheden . . . . . . . . . . . . . . . . . . . . . . . . . . 6
Veiligheidsvoorschriften voor montage . . . . . . 6
Veiligheidsvoorschriften voor onderhouds . . . 6
Zelfstandige ombouw . . . . . . . . . . . . . . . . . . 6
Zelfstandige vervaardiging van reserveon-
derdelen . . . . . . . . . . . . . . . . . . . . . . . . . . . . 6
Verhelpen van storingen en klantenservice . . . . 36
W
Wanddoorbraak . . . . . . . . . . . . . . . . . . . . . . . . . 18
Weerstandswaarden
Sensor T5 . . . . . . . . . . . . . . . . . . . . . . . . . . 51
Sensoren T1, T2, T3, T4 en T2B . . . . . . . . . 50
Werkingstest van de bedrijfsmodus koelen . . . 32
60
61
REMKO serie SKT
62
REMKO INTERNATIONAL
… en altijd dicht bij u in de buurt!
Maak gebruik van onze ervaring en advies
Het advies
Via onze intensieve training brengen we de vakkennis van onze adviseurs steeds op de nieuwste stand. Dit heeft ons de reputatie opgeleverd, meer te zijn dan een goede, betrouwbare leverancier:
REMKO, een partner, die helpt bij het oplossen van problemen.
De verkoop
REMKO beschikt niet alleen over een goed uitgebouwd netwerk van vertegenwoordigingen in binnen- en buitenland, maar ook over hoog gekwalificeerd vakkundig personeel voor de verkoop.
REMKO-medewerkers in de buitendienst zijn meer dan alleen verkoper: voor alles dienen zij voor onze klanten adviseurs te zijn in de airconditioning- en warmtetechniek.
De servicedienst
Onze apparaten werken nauwkeurig en betrouwbaar.
Als er onverhoopt toch een storing optreedt, dan is de
REMKO servicedienst snel ter plaatse. Ons omvangrijk netwerk van ervaren speciaalzaken waarborgt u altijd een snelle en betrouw-bare service.
REMKO GmbH & Co. KG
Koel- en verwarmingstechniek
Im Seelenkamp 12 D-32791 Lage
Postfach 1827
Telefon
Telefax
Internet
D-32777 Lage
+49 5232 606-0
+49 5232 606-260 [email protected]
www.remko.de
advertisement
* Your assessment is very important for improving the workof artificial intelligence, which forms the content of this project
Related manuals
advertisement
Table of contents
- 5 1.1 Algemene veiligheidsvoorschriften
- 5 1.2 Markering van instructies
- 5 1.3 Kwalificaties van het personeel
- 5 1.4 Gevaren bij het niet-opvolgen van de veiligheidsvoorschriften
- 6 1.5 Veiligheidsbewust werken
- 6 1.6 Veiligheidsvoorschriften voor de exploitant
- 6 1.7 Veiligheidsvoorschriften voor montage-, onderhouds- en inspectiewerkzaamheden
- 6 1.8 Zelfstandige ombouw en veranderingen
- 7 1.9 Bedoeld gebruik
- 7 1.10 Garantie
- 7 1.11 Transport en verpakking
- 7 1.12 Milieubescherming en recycling
- 8 2.1 Apparaatgegevens
- 10 2.2 Apparaatafmetingen
- 11 2.3 Capaciteitscurven verwarmen en koelen
- 14 3.1 Beschrijving van het apparaat
- 16 3.2 Combinaties
- 17 5.1 Belangrijke aanwijzingen voor het installeren
- 17 5.2 Wanddoorvoeren
- 18 5.3 Montagemateriaal
- 18 5.4 Keuze van de installatielocatie
- 20 5.5 Minimale vrije ruimte
- 20 5.6 Olieretourmaatregelen
- 21 6.1 Aansluiting van de koudemiddelleidingen
- 23 6.2 Controle op lekkages
- 23 6.3 Extra instructies voor het aansluiten van de koudemiddelleidingen
- 24 6.4 Koudemiddel bijvullen
- 25 8.1 Algemene informatie en veiligheidsinstructies
- 25 8.2 Aansluiten van de buitenunit
- 27 8.3 Elektrisch aansluitschema
- 28 8.4 Elektrische schakelschema
- 36 11.1 Verhelpen van storingen en klantenservice
- 38 11.2 Storingsanalyse buitenunit
- 54 14.1 Apparaatafbeelding SKT 520 AT
- 55 14.2 Reserveonderdelenlijst SKT 520 AT
- 56 14.3 Apparaatafbeelding SKT 790 AT
- 57 14.4 Reserveonderdelenlijst SKT 790 AT
- 58 14.5 Apparaatafbeelding SKT 1060 AT
- 59 14.6 Reserveonderdelenlijst SKT 1060 AT