advertisement
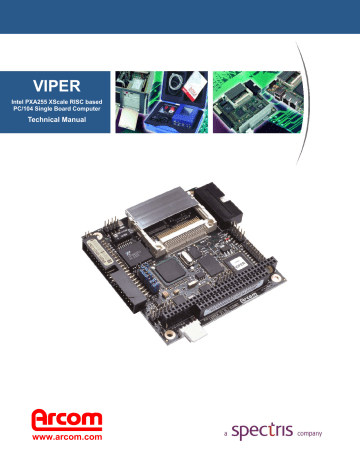
VIPER
VIPER
Intel PXA255 XScale RISC based
PC/104 Single Board Computer
Technical Manual
Contents
www.arcom.com
VIPER Contents
Definitions
Arcom is the trading name for Arcom Control Systems Inc and Arcom Control Systems Ltd.
Disclaimer
The information in this manual has been carefully checked and is believed to be accurate. Arcom assumes no responsibility for any infringements of patents or other rights of third parties, which may result from its use.
Arcom assumes no responsibility for any inaccuracies that may be contained in this document. Arcom makes no commitment to update or keep current the information contained in this manual.
Arcom reserves the right to make improvements to this document and /or product at any time and without notice.
Warranty
This product is supplied with a full 3 year warranty. Product warranty covers failure caused by any manufacturing defects.
Arcom will make all reasonable effort to repair the product or replace it with an identical variant. Arcom reserves the right to replace the returned product with an alternative variant or an equivalent fit, form and functional product. Delivery charges will apply to all returned products. Please go to www.arcom.com/support for information about Product Return Forms.
Trademarks
ARM and StrongARM are registered trademarks of ARM Ltd.
Intel and XScale are trademarks or registered trademarks of Intel Corporation or its subsidiaries in the United States and other countries.
Windows CE .NET is a trademark of the Microsoft Corporation.
CompactFlash is the registered trademark of SanDisk Corp.
Linux is a registered trademark of Linus Torvalds.
RedBoot and Red Hat
TM
is a registered trademark of Red Hat Inc.
VxWorks is a register trademark of Wind River.
Bluetooth is a registered trademark of Bluetooth SIG, Inc.
All other trademarks recognized .
Revision History
Manual PCB Date
Issue A
Issue B
Issue C
Issue D
Issue E
Issue F
Issue G
Issue H
V1 Issue 3
V1 Issue 3
V1 Issue 4
V1 Issue 5
V1 Issue 6
V1 Issue 6
V1 Issue 6
V1 Issue 6
26 th
June 2003
8 th
14
July 2003 th
August 2003
14
11 th th
October 2003
December 2003
11 th
February 2004
14 th May 2004
15 th
July 2004
© 2004 Arcom.
Arcom is a subsidiary of Spectris plc.
For contact details, see page
Comments
First full release of Manual
Minor editorial changes
Content update
Minor changes
Update for new PCB Issue
Minor changes
Major technical information enhancements, updated layout
Minor changes
Arcom operates a company-wide quality management system, which has been certified by the
British Standards Institution (BSI) as compliant with ISO9001:2000
VIPER Contents
Contents
VIPER Introduction
Introduction
The VIPER is an ultra low power PC/104 compatible single board computer based on the Intel 400MHz PXA255 XScale processor. The PXA255 is an implementation of the
Intel XScale micro architecture combined with a comprehensive set of integrated peripherals including, a flat panel graphics controller, DMA controller, interrupt controller, real time clock and multiple serial ports. The VIPER board offers a wide range of features making it ideal for power sensitive embedded communications and multimedia applications.
The board is available in the following standard variants:
• VIPER-400-M64-F32: Intel XScale TM PXA255 400MHz microprocessor, 64MByte
SDRAM, 32MByte FLASH.
• VIPER-400-M64-F16: Intel XScale TM PXA255 400MHz microprocessor, 64MByte
SDRAM, 16MByte FLASH.
• VIPER-400-M64-F32-I: Intel XScale TM PXA255 400MHz microprocessor, 64MByte
SDRAM, 32MByte FLASH, Industrial temperature range.
• VIPER-400-M64-F16-I: Intel XScale TM PXA255 400MHz microprocessor, 64MByte
SDRAM, 16MByte FLASH, Industrial temperature range.
For alternative memory configurations, please contact Arcom.
© 2004 Arcom Issue H
4
VIPER
VIPER ‘at a glance’
Introduction
Five Serial Ports 10/100BaseTX
© 2004 Arcom Issue H
5
VIPER Introduction
VIPER features
Microprocessor
• Intel XScale TM PXA255 400MHz RISC processor
Cache
• 32K data cache, 32K instruction cache, 2K mini data cache
System memory
• Up to 64MByte un-buffered 3.3V SDRAM
Silicon disk
•
•
•
•
Up to 32MByte Intel Strata FLASH (with FLASH access LED)
1MByte Bootloader FLASH EPROM (with FLASH access LED)
256KByte SRAM (with external battery backup)
Type I/II CompactFLASH (CF+) socket
Video
•
•
•
•
TFT/STN (3.3V or 5V – factory fit) flat panel graphics controller
Up to 800X600 resolution
8/16bpp
Backlight Control
Audio
•
•
National Semiconductor A AC’97 CODEC (16bit) and LM4880 Power Amp
Line IN, Line OUT, Microphone and 250mW per channel amplified output
Serial ports
•
•
•
5 x 16550 compatible high-speed UARTs
4 x RS232 and 1 x RS422/485 Interfaces
2 x channels with 128Byte Tx/Rx FIFO
USB host interface
•
•
Two USB 1.1 compliant interfaces
Short circuit protection and 500mA current limit protection
Network support
•
•
SMSC LAN91C111 10/100BaseTX Ethernet controller
One 10/100BaseTX NIC port
© 2004 Arcom Issue H
6
VIPER Introduction
Real Time Clock (RTC)
•
•
Battery backed RTC (external battery)
± 1minute/month accuracy, at 25°C.
Watchdog
• Adjustable timeout of 271ns to 19 minutes, 25 seconds
General Purpose I/O (GPIO)
• 8 x 5V tolerant Inputs
• 8 x 3.3V Outputs (5V tolerant)
User configuration
• 1 user-configurable jumper
Expansion
• PC/104 expansion bus - 8/16 bit ISA bus compatible interface
JTAG port
•
•
Download data to FLASH memory
Debug and connection to In-Circuit Emulator (ICE)
Power
•
•
Typically 2W from a single 5V supply
Power Management features allowing current requirements to be as low as
107mA ±5mA (535mW ±25mW).
Size
• PC/104 compatible footprint 3.8” x 3.6” (96mm x 91mm)
© 2004 Arcom Issue H
7
VIPER Introduction
VIPER support products
The VIPER is supported by the following products:
• VIPER-UPS (Uninterruptible Power Supply)
The VIPER-UPS serves as a 5V DC power supply and battery back up system for the VIPER. The UPS accepts between 10 – 36 VDC (10-25VAC) input and generates the +5V supply for the VIPER. In addition to this, it includes an intelligent battery charger/switch capable of using either the onboard 500mAHr NiMH battery or an external sealed lead acid rechargeable battery. For further details, see www.arcom.com/products/icp/pc104/processors/viper_UPS.htm.
• VIPER-ICE (Industrial Compact Enclosure)
The VIPER-ICE is a simple low cost aluminum enclosure, which provides easy connection to all on board features. The enclosure includes the VIPER-UPS and optionally a color Q-VGA (320x240) TFT flat panel display and analog touch screen.
• VIPER-FPIF1 (Flat Panel Interface)
The VIPER-FPIF1 is a simple board that enables easy connection between the
VIPER and an LCD flat panel. See section VIPER-FPIF1 details , page 33
for further details. Contact Arcom (see
Appendix A – Contacting Arcom , page 72 ) for
purchasing information.
© 2004 Arcom Issue H
8
VIPER Introduction
Handling your board safely
Anti-static handling
This board contains CMOS devices that could be damaged in the event of static electricity discharged through them. At all times, please observe anti-static precautions when handling the board. This includes storing the board in appropriate anti-static packaging and wearing a wrist strap when handling the board.
Packaging
Please ensure that should a board need to be returned to Arcom, it is adequately packed, preferably in the original packing material.
Electromagnetic compatibility (EMC)
The VIPER is classified as a component with regard to the European Community EMC regulations and it is the users responsibility to ensure that systems using the board are compliant with the appropriate EMC standards.
© 2004 Arcom Issue H
9
VIPER Introduction
Conventions
Symbols
The following symbols are used in this guide:
Symbol Explanation
Note - information that requires your attention.
Tip - a handy hint that may provide a useful alternative or save time.
Caution – proceeding with a course of action may damage your equipment or result in loss of data.
A
B
A
B
Jumper fitted on pin A.
Jumper fitted on pin B.
Jumper is fitted.
Jumper is not fitted.
Tables
With tables such as that shown below, the white cells show information relevant to the subject being discussed. Grey cells are not relevant in the current context.
Byte lane
Bit
Field
Reset
Most Significant Byte Least Significant Byte
15 14 13 12 11 10 9 8 7 6 5 4 3 2 1 0
- - - - - - - - - - - - -
RETRIG AUTO_ R_DIS
X X X X X X X X 0 0 0 0 0 0 0 0
Relevant information
© 2004 Arcom Issue H
10
VIPER Getting started
Getting started
Depending on the Development Kit purchased, a Quickstart Manual is provided for
Windows CE .NET, embedded Linux, or VxWorks to enable users to set-up and start using the board. Please read the relevant manual and follow the steps defining the setup of the board. Once you have completed this task you will have a working VIPER system and can start adding further peripherals enabling development to begin.
This section provides a guide to setting up and using of some of the features of the
VIPER. For more detailed information on any aspect of the board see
Detailed hardware description , page 13 .
Using the VIPER
Using the CompactFLASH™ socket
The VIPER is fitted with a Type I/II CompactFLASH socket mounted on the topside of the board. The socket is connected to Slot 0 of the PXA255 PC Card interface. It supports 3.3V Type I and II CompactFLASH cards, for both memory and IO. The VIPER supports hot swap changeover of the cards and notification of card insertion.
RedBoot supports ATA type CompactFLASH cards. Files can be read providing the card is formatted with an EXT2 file system. Eboot cannot boot from CompactFlash.
5V CompactFLASH is not supported.
The CompactFLASH card can only be inserted one way into the socket. The correct orientation is for the top of the card, i.e. with the normal printed side face down to the PCB.
Using the serial interfaces (RS232/422/485)
The five serial port interfaces on the VIPER are fully 16550 compatible. Connection to the serial ports is made via a 40-way boxed header. The pin assignment of this header has been arranged to enable 9-way IDC D-Sub plugs to be connected directly to the
cable. See the section PL4 – COMS ports , page 63 , for pin assignment and connector
details.
A suitable cable for COM1 is provided as part of the Development Kit. The D-Sub connector on this cable is compatible with the standard 9-way connector on a desktop computer.
© 2004 Arcom Issue H
11
VIPER Getting started
Using the audio features
There are four audio interfaces supported on the VIPER: amp out, line out, line in and microphone. The line in, line out and amp interfaces support stereo signals and the microphone provides a mono input. The amplified output is suitable for driving an 8 Ω load with a maximum power output of 250mW per channel. Connections are routed to
PL6 - see the sections
PL6 – Audio connector (page 65 ) for further
connector details.
Using the USB ports
The standard USB connector is a 4-way socket, which provides power and data signals to the USB peripheral. The 10-way header PL7 has been designed to be compatible with PC expansion brackets that support two USB sockets. See the sections
PL7 – USB connector (page 65 ) for further details.
Using the Ethernet interface
The SMSC LAN91C111 10/100BaseTX Ethernet controller is configured by the
RedBoot bootloader for embedded Linux or VxWorks, and by Windows CE .NET once it has booted. Connection is made via connector PL1. A second connector PL2 provides
activity and link status outputs for control LED's. See the sections 10/100BaseTX
PL1 – 10/100BaseTX Ethernet connector (page 61 ) and PL2 –
Ethernet status LED's connector (page 61 ) for further details.
Using the PC/104 expansion bus
PC/104 modules can be used with the VIPER to add extra functionality to the system.
This interface supports 8/16 bit ISA bus style peripherals.
Arcom has a wide range of PC/104 modules, which are compatible with the VIPER.
These include modules for digital I/O, analog I/O, motion control, video capture, CAN bus, serial interfaces, etc. Please contact the Arcom sales team if a particular interface you require does not appear to be available as these modules are in continuous
development. Contact details are provided in Appendix A – Contacting Arcom , page 72 .
In order to use a PC/104 board with the VIPER it should be plugged into PL11 for 8-bit cards and PL11/PL12 for 8/16-bit cards. See the sections
and
PL11 & PL12 – PC/104 connectors (page 67 ) for further details.
Before powering up the system, check that the jumper settings on the card for I/O address and IRQ settings do not conflict with any devices on the VIPER. The ISA interface on the VIPER does not support DMA. See the section
page
25 , for details about PC/104 interrupt use.
The VIPER provides +5V to a PC/104 add-on-board via the PL11 and PL12 connectors.
If a PC/104 add-on-board requires a +12V supply, then +12V must be supplied to the
VIPER Power Connector PL16 pin 4. If –12V or –5V are required, these must be supplied directly to the PC/104 add-on board.
The VIPER is available with non-stack through connectors by special order. Contact
Arcom (see
Appendix A – Contacting Arcom , page 72 ) for more details.
© 2004 Arcom Issue H
12
VIPER Detailed hardware description
Detailed hardware description
The following section provides a detailed description of the functions provided by the
VIPER. This information may be required during development after you have started adding extra peripherals or are starting to use some of the embedded features.
VIPER block diagram
The diagram below illustrates the functional organization of the VIPER PC/104 SBC.
VIPER
COM 1 RS232
Transceiver
COM 2&3 RS232
Transceiver
14.318MHz
X3
Clock
Generation
1.8432MHz
6MHz
8MHz
14.318MHz
24.576MHz
25MHz
X2 3.6864MHz
PL4
COM 4 RS232
Transceiver Control
DUART
RTC X1 32.768kHz
PL1
&
PL2
COM5 RS422/485
Transceiver
10/100 baseTX
Transformer LAN91C111 Control
Power
Amp
AMP R+L
Serial
EEPROM
64MB
SDRAM
1MB
Bootloader
FLASH
16 or 32MB
Silicon Disk
AC'97
Signals
BLKEN &
LCDEN
AC'97
Codec
LCD Signals
LINE IN R+L
LINE OUT R+L
MIC IN
PL6
Dual
MOSFET
LCDEN
BLKSAFE &
LCDSAFE
PL3
PXA255
256kB
SRAM
Reg
POSBIAS /
NEGBIAS
PL7
5V USB Power
Switch
USB1 & 2
USB Host
Controller
Control Jumper Configuration
PL17
&
LK1
PL9
IN[0:7] / OUT[0:7] Buffers and
Transceivers
Control
JTAG
PL10
PL11
&
PL12
PC/104 Address & Data
PC/104 Control
Buffers and
Transceivers
CPLD
3.3V
Voltage
Monitor
3.3V
1.06-1.29V
3.3V
Triple Reg
VBAT_IN
5V
PL16
PL5
CF Address & Data
CF Control
3.3V
Buffers and
Transceivers
CF Power
Switch
CF_SWITCH
Control Micropower
DAC
1.8V
Reg
© 2004 Arcom Issue H
13
VIPER Detailed hardware description
VIPER address map
-
CS5
CS5
-
CS5
CS5
-
CS4
-
CS3
-
CS2
-
CS1
-
CS0
PXA255 chip Bus/register width Description
-
NA
NA
-
CS5
-
CS5
NA
NA
-
NA
- 0xA4000000 – 0xFFFFFFFF -
SDCS0 0xA0000000 – 0xA3FFFFFC 32-bit
-
NA
0x4C000000 – 0x9FFFFFFF
0x48000000 – 0x4BFFFFFF
-
32-bit
0x44000000 – 0x47FFFFFF
0x40000000 – 0x43FFFFFF
0x3C200400 – 0x3FFFFFFF
0x3C000000 – 0x3C1FFFFF
32-bit
32-bit
-
16-bit
0x30000400 – 0x3BFFFFFF
0x30000000 – 0x300003FF
-
16-bit
0x20000000 – 0x2FFFFFFF 32-bit
0x14840000 – 0x1FFFFFFF -
0x14800000 – 0x1483FFFF 8-bit
0x14500001 – 0x47FFFFFF -
0x14500000 – 0x14500000 8-bit
0x14300020 – 0x144FFFFF -
0x14300010 – 0x1430001F
0x14300000 – 0x1430000F
0x14100002 – 0x14100003
0x14100000 – 0x14100001
0x10000000 – 0x10000002
0x0C000004 – 0x0FFFFFFF
0x08000300 – 0x0800030E
0x06000000 – 0x080002FF
0x04000000 – 0x05FFFFFE
0x00100000 – 0x03FFFFFF
0x00000000 – 0x000FFFFE
8-bit
8-bit
0x14100004 – 0x142FFFFF -
8-bit
8-bit
0x10000004 – 0x140FFFFF -
32-bit
-
0x0C000000 – 0x0C000002 16-bit
0x08000310 – 0x0BFFFFFF -
16-bit
-
16-bit
-
16-bit
Reserved
SDRAM, IC2&3
Reserved
Memory Control Registers 1
LCD Control Registers 1
PXA255 Peripherals 1
Reserved
PC/104 Memory Space
Reserved
PC/104 I/O Space
CompactFLASH, PL5
Reserved
Reserved
General Purpose Input, PL9
Reserved
Reserved
PC104I Register (see page 26 )
Reserved
Ethernet Data port
Reserved
USB Host Controller
Reserved
Ethernet I/O Space
Reserved
FLASH Memory / Silicon Disk
Reserved
Bootloader FLASH
1 Details of the internal registers are in the Intel Developer Manual on the Development Kit CD.
© 2004 Arcom Issue H
14
VIPER Detailed hardware description
Translations made by the MMU
For details of translations made by the MMU by Redboot for embedded Linux, please refer to VIPER embedded Linux Quickstart Manual.
For details of translations made by the MMU by Redboot for VxWorks, please refer to
VIPER VxWorks Quickstart and Technical Manual
For details of translations made by the MMU for Windows CE .NET, please check the
Windows CE .NET documentation for more information about memory mapping. One source of this information is on the msdn website under Windows CE .NET Memory
Architecture .
© 2004 Arcom Issue H
15
VIPER Detailed hardware description
PXA255 processor
The PXA255 is a low power ARM (version 5TE) instruction set compliant RISC processor. The PXA255 does not include a floating-point unit. The device does, however, contain a DSP co-processor to enhance multimedia applications.
The 400MHz PXA255 is driven by a 3.6864 MHz clock, which generates all the highspeed clocks within the device. The default run mode frequency is 400MHz for embedded Linux, VxWorks and Windows CE .NET. Currently embedded Linux and
VxWorks supports changing the operating frequency and Windows CE .NET will provide support shortly. Please refer to the relevant operating system technical manual to select an alternative operating frequency.
The processor has two supply inputs: I/O and core generated on the VIPER from the main +5V supply input. The I/O supply is powered from +3.3V, and the core is powered from a +1.06 to +1.3V adjustable supply. See the section
Processor power management , page 55 , for operation details.
The PXA255 has an integrated Memory and CompactFlash Controller with 100 MHz
Memory Bus, 32 KB data and 32 KB instruction caches and 2 KB Mini data cache for streaming data.
The PXA255 provides up to 85 GPIO pins, many of these have been configured for alternative functions like the AC’97 and PC card / CompactFLASH interfaces. Details of these pin configurations are provided in the section
page
The PXA255 also has the following features that can be used on the VIPER:
• Peripheral Control Module:
- 16 channel configurable DMA controller.
- Integrated LCD controller with unique DMA for fast color screen support.
- Serial ports including AC’97, three UARTs, and enhanced USB end point interface.
• System Control Module:
- General-purpose interruptible I/O ports.
- Watchdog.
- Power management controller.
- Two on-chip oscillators.
The PXA255 processor is packaged in a 256-pin PBGA, which is attached to the board during the assembly process.
The PXA255 processor is a low power device and does not require a heat sink for temperatures up to 70 ° C (85 ° C for the industrial variant).
© 2004 Arcom Issue H
16
VIPER Detailed hardware description
PXA255 GPIO pin assignments
The following table summarizes the use of the 85 PXA255 GPIO pins, their direction, alternate function and active level.
For embedded Linux the GPIO pins are setup by Redboot. Under VxWorks and
Windows CE .NET, they are setup by themselves and not by the bootloader.
Key:
Active Function active level or edge.
Sleep Pin state during sleep mode (all Hi-Z states are to ‘1’ during sleep).
GPIO
No AF Signal Name Dir Active Sleep Function
0 0 ETHER_INT Input
1 0 PC/104_IRQ Input See
2 0 USB_IRQ page
Input
(page
3 0 UART_INT1 Input
4 0 UART_INT2 Input
Input
Input
COM 5 Interrupt
COM 4 Interrupt
Input NA Input User
LK2
6 0 PSU_DATA Output 0 Microprocessor
Voltage DAC Data
8 0 CF_RDY
9 0 BLKEN
10 0 LCDEN
11 0 PSU_CLK
12 0 SHDN
13 0 EN1#
Input NA
Output High
Output High
Input
0
0
Reserved
Input NA Input CompactFLASH
Ready/nBusy
(page
page
LCD Backlight Enable
(page
LCD Logic Supply
Enable
(page
Output
Output High
Output Low
0
1
0
Voltage DAC Clock
Processor power management (page 55 )
COM 1, 2, 3 & 4 UART
Shutdown
COM 1, 2, 3 & 4 UART
Enable
(page
© 2004 Arcom Issue H
17
VIPER Detailed hardware description
GPIO
No AF Signal Name Dir Active Sleep Function
14 0 FLASH_
STATUS
Input NA Input Bootloader
Status,
Ready / nBusy
(page
FLASH memory/silicon disk (page
15 2 CS1
16 2 PWM0
17 2 PWM1
18 1 ARDY
Output Low Hi-Z Chip Select 1
(page
Output See inverter datasheet
On/Off or variable if
PWM
Output NA 0
Input Low Input 10/100 Ethernet PHY
Ready
(page
-
Processor power management (page 55 )
19 0 PSU_nCS_LD Output Low 0
Voltage DAC Chip
Select
20 0 OUT0
21 0 OUT1
22 0 OUT2
23 0 OUT3
24 0 OUT4
25 0 OUT5
26 0 OUT6
27 0 OUT7
Output
User
Config
Input BITCLK
Input NA Input SDATA_IN0
30 2 AC97_OUT Output NA
31 2 AC97_SYNC Output
0
0
SDATA_OUT
SYNC
(page
-
33 2 CPLDCS Output Low Hi-Z Chip Select 5
(page
(page
© 2004 Arcom Issue H
18
VIPER Detailed hardware description
GPIO
No AF Signal Name Dir Active Sleep Function
34 1 RXD1
35 1 CTS1
36 1 DCD1
37 1 DSR1
38 1 RI1
39 2 TXD1
40 2 DTR1
41 2 RTS1
42 1 RXD2
43 2 TXD2
44 1 CTS2
45 2 RTS2
46 2 RXD3
47 1 TXD3
48 2 CB_POE
Input NA
Input NA
Input NA
Input COM1 Receive Data
Input COM1 Clear To Send
Input COM1 Data Carrier
Detect
Input NA
Input NA
Output NA
Output NA
Output NA
Input NA
Output NA
Input NA
Input COM1 Data Sender
Ready
Input COM1 Ring Indicator
0
0 COM1 Data Terminal
Ready
0 COM1 Request To
Send
Input COM2 Receive Data
0
Input COM2 Clear To Send
Output NA 0 COM2 Request To
Send
Input COM3 Receive Data Input NA
Output NA 0
Output Low Hi-Z Socket 0 & 1 Output
Enable
(page
49 2 CB_PWE
50 2 CB_PIOR
51 2 CB_PIOW
52 2 CB_PCE1
Output Low Hi-Z Socket 0 & 1 Write
Enable
Output Low Hi-Z Socket 0 & 1 I/O Read
Output Low Hi-Z Socket 0 & 1 I/O Write
Output Low Hi-Z Socket 0 & 1 Low Byte
Enable
53 2 CB_PCE2 Output Low Hi-Z Socket 0 & 1 High
Byte Enable
54 2 CB_PKTSEL Output NA 0 PSKTSEL 0 = Socket
0 Select / 1 = Socket 1
Select
55 2 CB_PREG Output Low 0 PREG
56 1 Input PWAIT
57 1 CB_PIOIS16 Input Low Input IOIS16
-
-
-
-
© 2004 Arcom Issue H
19
VIPER Detailed hardware description
GPIO
No AF Signal Name Dir Active Sleep Function
58 2 LCD_D0
59 2 LCD_D1
60 2 LCD_D2
61 2 LCD_D3
62 2 LCD_D4
63 2 LCD_D5
64 2 LCD_D6
65 2 LCD_D7
66 2 LCD_D8
67 2 LCD_D9
68 2 LCD_D10
69 2 LCD_D11
70 2 LCD_D12
Output NA
Output NA
Output NA
Output NA
Output NA
Output NA
Output NA
Output NA
Output NA
Output NA
Output NA
Output NA
Output NA
71 2 LCD_D13
72 2 LCD_D14
Output NA
Output NA
73 2 LCD_D15 Output NA
74 2 LCD_FCLK Output NA
75 2 LCD_LCLK
76 2 LCD_PCLK
77 2 LCD_BIAS
78 2 ETHERCS2
79 2 USBCS
80 2 ETHERCS1
Output NA
Output NA
Output NA
Output Low
Output Low
Output Low
0
0
0
0
0
0
0
0
0
0
0
0
0
0
0
0
0
LCD Data Bit 0
LCD Data Bit 1
LCD Data Bit 2
LCD Data Bit 3
LCD Data Bit 4
LCD Data Bit 5
LCD Data Bit 6
LCD Data Bit 7
LCD Data Bit 8
LCD Data Bit 9
LCD Data Bit 10
LCD Data Bit 11
LCD Data Bit 12
(page
LCD Data Bit 13
LCD Data Bit 14
LCD Data Bit 15
LCD Frame Clock (STN)
Vertical Sync (TFT)
0
0
0
LCD Line Clock (STN) /
Horizontal Sync (TFT)
LCD Pixel Clock
(STN) / Clock (TFT)
LCD Bias (STN) / Date
Enable (TFT)
Hi-Z Chip Select 2
Hi-Z Chip Select 3
Hi-Z Chip Select 4
(page
Input NA Input SDRAM
Detection 0 = 64MB,
1 = 16MB
82 0 CF_SWITCH Output High 0 CompactFLASH
Power Switch Enable
-
and
(page
83 0 RTC_IO
84 0 RTC_CLK
Bidirectional
Output 0
© 2004 Arcom Issue H
20
VIPER Detailed hardware description
Real Time Clock
There are two RTCs on the VIPER: Under embedded Linux and VxWorks the internal
RTC of the PXA255 should only be used for power management events, and an external Dallas DS1307 RTC should be used to keep the time and date. Under
Windows CE .NET the time and date stamps are copied from the external RTC to the internal RTC of the PXA255, to run the RTC internally.
The accuracy of the DS1307 RTC is based on the operation of the 32.768KHz watch crystal. Its calibration tolerance is ±20ppm, which provides an accuracy of +/-1 minute per month if the board is in an ambient environment of +25°C. When the board is
° operated outside this temperature then the accuracy may be degraded by -0.035ppm/
C² ±10% typical. The watch crystal’s accuracy will age by ±3ppm max in the first year, then ±1ppm max in the year after, and logarithmically decreasing in subsequent years.
The following PXA255 GPIO pins are used to emulate the I²C interface to the DS1307
RTC:
PXA255 Pin
GPIO84
Function
Clock (100MHz max)
GPIO83 Data
The DS1307 RTC also contains 64Bytes of RAM, which can be used for any user data that needs to be recoverable on power-up.
To ensure the DS1307 RTC doesn’t lose track of the date and time when the 5V supply is powered-down, an external battery must be fitted. See the section
Battery backup , page 51 , for details.
© 2004 Arcom Issue H
21
VIPER Detailed hardware description
Watchdog timer
The PXA255 contains an internal watchdog timer, which can be used to protect against erroneous software. Timeout periods can be adjusted from 271ns to 19 minutes 25 seconds. When a timeout occurs the board is reset. On reset the watchdog timer is disabled until enabled again by software.
For further details see the Arcom operating system Technical Manual and the Intel
PXA255 developer’s manual on the Development Kit CD.
© 2004 Arcom Issue H
22
VIPER Detailed hardware description
Memory
The VIPER has four types of memory fitted:
•
•
•
•
1MByte of bootloader FLASH containing Redboot to boot embedded Linux or
VxWorks, or Eboot to boot Windows CE .NET.
A resident FLASH disk containing the OS and application images.
SDRAM for system memory.
256KBytes of Static RAM (SRAM).
Bootloader FLASH
A 1MByte Bottom Boot FLASH EPROM device, arranged as 512Kbit x 16, is used as the bootloader FLASH. It holds Redboot (for embedded Linux or VxWorks) or Eboot (for
Windows CE .NET), together with configuration information. When the microprocessor comes out of reset it boots the relevant bootloader from here, which in turn boots up the
OS from the FLASH memory/silicon disk. Whenever the Bootloader FLASH memory is accessed the FLASH access LED illuminates.
FLASH memory/silicon disk
The VIPER supports 16MBytes or 32MBytes of Intel StrataFLASH memory for the OS and application images. The FLASH memory is arranged as 64Mbit x 16-bits (16MByte device) or as 128Mbit x 16-bits (32MByte device) respectively.
The FLASH memory array is divided into equally sized symmetrical blocks that are
64-Kword in size. A 128Mbit device contains 128 blocks, and 256Mbit device contains
256 blocks. Flash cells within a block are organized by rows and columns. A block contains 512 rows by 128 words. The words on a row are divided into 16 eight-word groups.
The PXA255 GPIO14 pin is connected to the FLASH memory status output. This pin can be used to generate an interrupt to indicate the completion of a CFI command.
Whenever the FLASH memory is accessed the FLASH access LED illuminates.
SDRAM interface
There are two memory configurations supported by the VIPER: 16MBytes or 64MBytes of SDRAM located in Bank 0. The SDRAM is configured as 4MBytes x 32-bits
(16MBytes) or 16MBytes x 32-bits (64MBytes), by 2 devices with 4 internal banks of
1MBytes or 4MBytes x 16-bits.
These are surface mount devices soldered to the board and cannot be upgraded.
RedBoot (embedded Linux and VxWorks) automatically detects the amount of memory fitted to the board, and configures the SDRAM controller accordingly. For Windows CE
.NET applications the SDRAM memory will always be 64MBytes.
The SDRAM controller supports running the memory at frequencies between 50MHz and 99.5MHz (default). This can be configured to achieve the optimum balance between power consumption and performance.
© 2004 Arcom Issue H
23
VIPER Detailed hardware description
Static RAM
The VIPER has a 256KByte SRAM device fitted, arranged as 256Kbit x 8-bits. Access to the device is on 16-bit boundaries, whereby the least significant byte is the SRAM data and the 8-bits of the most significant byte are don’t care bits. The reason for this is that the PXA255 is not designed to interface to 8-bit peripherals. This arrangement is summarized in the following data bus table:
Most Significant Byte Least Significant Byte
D15 D14 D13 D12 D11 D10 D9 D8 D7 D6 D5 D4 D3 D2 D1 D0
Don’t Care SRAM Data
The data in the SRAM can be made non-volatile by fitting an external battery to power the device in the event of power loss on the main VIPER 5V supply. See the section
Battery backup page 51 for details.
CompactFLASH
The CompactFLASH connector PL5 is interfaced to Slot 0 of the PXA255 PC card controller, and appears in PC card memory space socket 0.
This is a hot swappable 3.3V interface, controlled by the detection of a falling edge on
GPIO32 when a CompactFLASH card has been inserted. On detection set GPIO82 to logic ‘1’ to enable the 3.3V supply to the CompactFLASH connector. The
CompactFLASH (RDY/nBSY) signal interrupts on GPIO8.
0x2C000000 – 0x2FFFFFFF
0x28000000 – 0x2BFFFFFF
0x24000000 – 0x27FFFFFF
0x20000000 – 0x23FFFFFF
Socket 0 Common Memory Space
Socket 0 Attribute Memory Space
Reserved
Socket 0 I/O Space
© 2004 Arcom Issue H
24
VIPER Detailed hardware description
Interrupt assignments
Internal interrupts
For details on the PXA255 interrupt controller and internal peripheral interrupts please see the Intel PXA255 developer’s manual on the Development Kit CD.
External interrupts
The following table lists the PXA255 signal pins used for generating external interrupts.
PXA255 Pin Peripheral
GPIO0 Ethernet
GPIO1 PC/104 interrupt controller
GPIO2 USB
GPIO3 COM5
GPIO4 COM4
GPIO8
GPIO14
GPIO32
CompactFLASH RDY/nBSY
FLASH (OS)
CompactFLASH card detect
Active
See
Ready =
Ready =
, Busy =
, Busy =
© 2004 Arcom Issue H
25
VIPER Detailed hardware description
PC/104 interrupts
The PC/104 interrupts are logically OR’ed together so that any interrupt generated on the PC/104 interface generates an interrupt input on GPIO1.
The PC/104 interrupting source can be identified by reading the PC104I register located at offset 0x100000 from CS5 (0x14000000). The register indicates the status of the interrupt lines at the time the register is read. The relevant interrupt has its corresponding bit set to ‘1’. The PXA255 is not designed to interface to 8-bit peripherals, so only the least significant byte from the word contains the data.
PC/104 interrupt register [PC104I]
Byte lane
Bit
Most Significant Byte Least Significant Byte
15 14 13 12 11 10 9 8 7 6 5 4 3 2 1 0
Field
Reset
R/W
-
X
-
-
X
-
-
X
-
-
X
-
-
X
-
-
X
-
-
X
-
-
X
-
IRQ12 IRQ11 IRQ10 IRQ7 IRQ6 IRQ5 IRQ4 IRQ3
0 0 0 0 0 0 0 0
R/W
Address 0x14100000
PC/104 interrupts IRQ9, IRQ14 and IRQ15 are not used by the VIPER, please use an alternate interrupt source from the table above.
The ICR Register located at offset 0x100002 from CS5 (0x14000000) must be set-up correctly for the OS running. The PC/104 interrupts are signaled and handled slightly differently between embedded Linux / VxWorks and Windows CE .NET.
See the following relevant subsections for specific PC/104 details for the target OS.
Interrupt configuration and reset register [ICR]
Byte lane
Bit
Most Significant Byte Least Significant Byte
15 14 13 12 11 10 9 8 7 6 5 4 3 2 1 0
Field - - - - - - - - - - - - -
R_DIS AUTO_
Reset
R/W
X
-
X
-
X
-
X
-
X
-
X
-
X
-
X
-
0 0 0 0
W
0 0 0 0
Address 0x14100002
© 2004 Arcom Issue H
26
VIPER Detailed hardware description
ICR Bit Functions
Bit Name
0 RETRIG
0 No interrupt retrigger (embedded Linux and VxWorks).
1 Interrupt retrigger (Windows CE .NET).
0 No auto clear interrupt / Toggle GPIO1 on new interrupt.
1 AUTO_CLR
1
Auto clear interrupt / Low to high transition on GPIO1 on
First Interrupt.
0
2 R_DIS
Keep set as 0 under normal operating conditions. See the section
for details.
1
3 - 7 - X No function.
PC/104 interrupts under embedded Linux and VxWorks
Leave the ICR register set to its default value, so that a new interrupt causes the microprocessor PC/104 interrupt pin GPIO1 to be toggled for every new interrupt on a different PC/104 interrupt source. Ensure the GPIO1 input is set up in a level triggered mode. The retrigger interrupt function is not required for embedded Linux or VxWorks.
The following diagram gives an example of how the PC/104 interrupt on GPIO1 behaves over time when the ICR AUTO_CLR bit is set to ‘0’:
GPIO1
1 st
IRQ on IRQ7
1 st
IRQ on IRQ5
1 st
IRQ on IRQ12
1 st
IRQ on IRQ7 serviced
2 nd
IRQ on IRQ7
Time
Once the VIPER microprocessor has serviced a PC/104 interrupt, clear the corresponding bit in the PC104I register by writing ‘1’ to it.
© 2004 Arcom Issue H
27
VIPER Detailed hardware description
PC/104 interrupts under Windows CE .NET
Write 0x2 to the ICR Register so that the first PC/104 interrupt source causes the
PXA255 PC/104 interrupt pin GPIO1 to receive a low to high transition. When the first
PC/104 interrupt occurs the Interrupt service routine will start polling through the
PC/104 interrupt sources in the PC104I register. The first bit it sees set to a ‘1’, sets a semaphore to make a program run to service the corresponding interrupt.
Once this program has serviced the interrupt the interrupting source returns its interrupt output to the inactive state (‘0’) if it hasn’t requested another interrupt whilst the microprocessor serviced the last interrupt. Once this happens the corresponding bit in the PC104I register shall be automatically cleared. Each PC/104 board requesting an interrupt shall keep its interrupt in the active state (‘1’) until the interrupt has been serviced by the microprocessor. When there are no interrupts outstanding the level of the PC/104 interrupt on GPIO1 shall automatically return to logic ‘0’. If it is still ‘1’ then there are interrupts outstanding, which would have occurred during the servicing of the last interrupt.
To capture any interrupts that could have occurred whilst the last interrupt was serviced, the retrigger interrupt bit in the ICR register is set to ‘1’ to retrigger a low to high transition on GPIO1 to restart the interrupt polling mechanism if there are any outstanding interrupts.
The diagram below explains how the PC/104 interrupt on GPIO1 behaves over time when the ICR AUTO_CLR bit is set to ‘1’:
Highest
Priority
IRQ3
IRQ4
IRQ5
IRQ6
IRQ7
IRQ10
IRQ11
Lowest
Priority
IRQ12
1.12µs
GPIO
1
1 st
IRQ received
(IRQ service routine started)
2 nd
IRQ received whilst last IRQ is being serviced
1 st
IRQ serviced
(GPIO1 doesn’t go low)
Set RETRIG bit in ICR register to ‘1’ to retrigger interrupt on GPIO1 if there are any outstanding
IRQ service routine started
2 nd
IRQ serviced (GPIO1 goes low because there are no outstanding
Set RETRIG bit in ICR register to ‘1’ to retrigger interrupt on GPIO1 if there are any outstanding
Time
© 2004 Arcom Issue H
28
VIPER Detailed hardware description
Flat panel display support
The Intel PXA255 processor contains an integrated LCD display controller that permits
1, 2, and 4-bit gray-scale, and 8 or 16-bit color pixels. A 256-byte palette RAM provides flexible color mapping capabilities. The LCD display controller supports active (TFT) and passive (STN) LCD displays.
The PXA255 can drive displays with a resolution up to 800x600, but as there is a unified memory structure, the bandwidth to the application decreases significantly. If the application makes significant use of memory, such as when video is on screen, you may also experience FIFO under-run to the LCD causing the frames rates to drop or display image disruption. Reducing the frame rate to the slowest speed possible gives the maximum bandwidth to the application. The display quality for an 800x600 resolution
LCD is dependant on the compromises that can be made between the LCD refresh rate and the application.
A full explanation of the graphics controller operation can be found in the PXA255 data sheets included on the support CD.
The flat panel data and control signals are routed to PL3. See the section
PL3 – LCD connector , page 62 , for pin assignment and part number details.
The VIPER-FPIF1 allows the user to easily wire-up a new panel using pin and crimp style connectors. Contact Arcom (see
Appendix A – Contacting Arcom , page 72 ) for
purchasing information.
A list of proven Flat Panel displays are included on the VIPER product page .
Click on the Flat Panel Display Options tab for up-to-date details.
The following tables provide a cross-reference between the flat panel data signals and their function when configured for different displays.
TFT panel data bit mapping to the VIPER
Panel data bus bit
FPD 15
FPD 14
FPD 13
18-bit TFT
R5
R4
R3
12-bit TFT
R3
R2
R1
9-bit TFT
R2
R1
R0
FPD 12
FPD 11
R2
R1
R0
NA
NA
NA
GND R0 NA NA
FPD 10 G5 G3 G2
FPD 9 G4 G2 G1
© 2004 Arcom Issue H
29
VIPER Detailed hardware description
Panel data bus bit
FPD 8
FPD 7
FPD 6
FPD 5
FPD 4
FPD 3
FPD 2
18-bit TFT
G3
G2
G1
G0
B5
B4
B3
12-bit TFT
G1
G0
NA
NA
B3
B2
B1
9-bit TFT
G0
NA
NA
NA
B2
B1
B0
FPD 1
FPD 0
B2
B1
B0
NA
NA
NA
GND B0 NA NA
The PXA255 cannot directly interface to 18-bit displays, as its color palette RAM has 5 bits of red, 6 bits of green, and 5 bits of blue, since the human eye can distinguish more shades of green than of red or blue.
STN panel data bit mapping to the VIPER
FPD 9
FPD 8
FPD 7
FPD 6
FPD 5
FPD 4
FPD 3
FPD 2
FPD 1
FPD 0
Panel data bus Bit
FPD 15
FPD 14
FPD 13
FPD 12
FPD 11
FPD 10
Dual scan color STN Single scan color STN Dual scan mono STN
DL6(G)
DL6(R)
NA
NA
NA
NA
DL5(B)
DL4(G)
DL3(R)
DL2(B)
NA
NA
NA
NA
NA
NA
NA
NA
DL1(G)
DL0(R)
DU7(G)
DU6(R)
DU5(B)
DU4(G)
DU3(R)
DU2(B)
DU1(G)
DU0(R)
NA
NA
D7(G)
D6(R)
D5(B)
D4(G)
D3(R)
D2(B)
D1(G)
D0(R)
NA
NA
DL3
DL2
DL1
DL0
DU3
DU2
DU1
DU0
© 2004 Arcom Issue H
30
VIPER Detailed hardware description
Below is a table covering the clock signals required for passive and active type displays:
VIPER
LCLK
FCLK
Active display signal (TFT)
PCLK Clock
Horizontal Sync
Vertical Sync
Passive display signal (STN)
Line Clock
Frame Clock
Bias
The display signals are +3.3V compatible; the VIPER contains power control circuitry for the flat panel logic supply and backlight supply. The flat panel logic is supplied with a switched 3.3V (default) or 5V supply while the backlight is supplied with a switched 5V supply for the inverter.
There is no on-board protection for these switched supplies! Care must be taken during power up/down to ensure the panel is not damaged due to the input signals being incorrectly configured.
Typically the power up sequence is as follows (please check the datasheet for the particular panel in use):
1. Enable display VCC
2. Enable flat panel interface
Power down is in reverse order.
LCD backlight enable
The PXA255 GPIO9 pin controls the LCD Inverter supply voltage for the backlight.
When GPIO9 is set to logic ‘1’, the backlight supply BLKSAFE is supplied with 5V
(turned on). The BLKEN signal on PL3 is the un-buffered GPIO9 signal. See the section
PL3 – LCD connector , page 62 , for PL3 pin assignment, connector and mating
connector details.
If you want to use a 12V backlight inverter, then the switched 5V supply on
BLKSAFE or the control signal BLKEN can be used to control an external 12V supply to the inverter.
© 2004 Arcom Issue H
31
VIPER Detailed hardware description
LCD logic supply enable
The PXA255 GPIO10 pin controls the supply voltage for the LCD Logic. When GPIO10 is set to logic ‘1’, the LCD supply LCDSAFE is supplied with 3.3V (turned on). See the section
PL3 – LCD connector , page 62 , for PL3 pin assignment, connector and mating
connector details.
This may be factory configured (using a surface mount resistor) to supply 5V. If the flat panel logic is powered from 5V, it must be compatible with 3.3V signaling.
LCD backlight brightness control
The control of the backlight brightness is dependant upon the type of backlight inverter used in the display. Some inverters have a ‘DIM’ function, which uses a logic level to choose between two levels of intensity. If this is the case then GPIO16 (Alternative
Function 0) is used to set this. Other inverters have an input suitable for a pulse-width modulated signal; in this case GPIO16 should be configured as PWM0 (Alternative
Function 2).
STN BIAS voltage
The VIPER provides a negative and a positive bias voltage for STN type displays. The negative and positive bias voltages are set to –22V and +22.5V respectively. Pin connections for these can be found in the section
PL3 – LCD connector , page 62 .
Please contact Arcom for details of other bias voltages. Contact details are provided in
Appendix A – Contacting Arcom , page 72 .
Do not exceed 20mA load current.
© 2004 Arcom Issue H
32
VIPER Detailed hardware description
VIPER-FPIF1 details
The VIPER-FPIF1 allows easy connection between the VIPER and a TFT or STN LCD flat panel display.
The connectors on the following pages are shown in the same orientation as the picture above.
Connector Function
LK1 TFT Clock Delay Selection
PL1
PL2
Connects to the VIPER
Generic LCD Connector
PL3
PL4
PL5
Direct connection to a NEC NL3224BC35-20 5.5inch 320x240 TFT Display
Connects to Backlight Inverter
STN Bias Voltages
© 2004 Arcom Issue H
33
VIPER Detailed hardware description
VIPER-FPIF1 Connectors
LK1 – TFT Clock Delay Selection
It has been found that some TFT displays require a delay on the clock, if this is required fit the jumper in position A, if not then fit in position B.
A B
PL1 – VIPER LCD cable connector
Connector: Oupiin 3215-40GSB , 40-way, 1.27mm (0.05”) x 2.54mm (0.1”) straightboxed header.
Mating connector: Oupiin 1203-40GB.
Pin Signal Name
1 BLKEN#
3 GND
5 NEGBIAS
Pin Signal Name
2 BLKSAFE
4 GND
6 LCDSAFE
7 GPIO16/PWM0 8 POSBIAS
9 GND
11 BLUE_DATA0
13 BLUE_DATA2
12 BLUE_DATA1
14 BLUE_DATA3
15 GND
17 BLUE_DATA4
16 GND
18 GREEN_DATA0
19 GREEN_DATA1 20 GREEN_DATA2
21 GND 22 GND
23 GREEN_DATA3 24 GREEN_DATA4
25 GREEN_DATA5 26 FPD11
27 GND
29 FPD12
28 GND
30 FPD13
31 FPD14
33 GND
35 FCLK
37 GND
39 PCLK
32 FPD15
34 GND
36 BIAS / DE
38 GND
40 LCLK
© 2004 Arcom Issue H
34
VIPER Detailed hardware description
PL2 – Generic LCD connector
Connector: Taicom TI34BHS , 34-way, 2.54mm (0.1”) x 2.54mm (0.1”) straight-boxed header.
Mating connector: Fujitsu FCN-723-B034/2.
Mating connector crimps: Fujitsu FCN-723J-AU/Q . (As it is possible to connect a crimp type connector to PL2, a wide range of LCD displays can be connected with a custom cable.)
Pin Signal Name
1 GND
Pin Signal Name
2 BLUE_DATA0
3 BLUE_DATA1 4 BLUE_DATA2
5 GND 6 BLUE_DATA3
7 BLUE_DATA4 8 GREEN_DATA0
11 GREEN_DATA2 12 GREEN_DATA3
13 GREEN_DATA4 14 GREEN_DATA5
15 GND
17 RED_DATA0
16 GND
18 RED_DATA1
19 RED_DATA2
21 RED_DATA3
23 GND
25 GND
20 GND
22 RED_DATA4
24 PCLK
26 LCDSAFE
27 LCDSAFE
29 FCLK
31 BKLSAFE
33 NC
28 LCLK
30 GND
32 LBIAS
34 BKLEN#
© 2004 Arcom Issue H
35
VIPER Detailed hardware description
PL3 – Direct connection to a NEC NL3224BC35-20 5.5inch 320x240 TFT display
Connector: Oupiin 2345-33TD2 .
Mating Cable: Eunsung 0.5x33x190xAx0.035x0.3x5x5x10x10.
Pin Signal Name
1 PCLK
2 LCLK
3 FCLK
4 FCLK
5 GND
6 GND
7 RED_DATA0
8 RED_DATA1
9 RED_DATA2
10 RED_DATA3
11 RED_DATA4
12 GND
Pin Signal Name
23 BLUE_DATA2
27 LBIAS
28 LCDSAFE
29 LCDSAFE
13 GREEN_DATA0 30 GND
14 GREEN_DATA1 31 GND
15 GREEN_DATA2 32 GND
16 GREEN_DATA3 33 GND
17 GREEN_DATA4
© 2004 Arcom Issue H
36
VIPER
PL4 – Backlight inverter connector
Connector: Framatome 76384-407 .
Mating Connector: Framatome 65240-007 .
1 GND
2 PWM0
3 BKLEN#
4 GND
5 GND
6 BKLSAFE
7 BKLSAFE
PL5 – STN Bias connector
Connector: Framatome 76384-404 .
Mating Connector: Framatome 65240-004 .
1 NEGBIAS
2 GND
3 GND
4 POSBIAS
Detailed hardware description
© 2004 Arcom Issue H
37
VIPER Detailed hardware description
Audio
A National Semiconductor LM4548A AC’97 audio CODEC is used to support the audio features of the VIPER. Audio inputs supported by the LM4548A are stereo line in and a mono microphone input.
The LM4548A provides a stereo line out that can also be amplified by a National
Semiconductor LM4880 250mW per channel power amplifier, suitable for driving an 8 Ω load. The LM4548A AC’97 codec may be turned off if it is not required. See the section
Audio power management , page 58 , for details.
Connection to the VIPER Audio features is via header PL6. See the table below for pin assignments and the section
PL6 – Audio connector , page 65 , for connector and mating
connector details.
Signal levels (max)
Microphone
10 MIC
7 Audio ground reference.
1Vrms input
Line in
Line out
2
6
4
1
5
3
Line input left
Line input right
Audio ground reference
Line output left
Line output right
Audio ground reference
1Vrms input
1Vrms output
Amp out
12 Audio ground reference
1.79Vpeak output,
1.26Vrms output (8 Ω load)
223mW
© 2004 Arcom Issue H
38
VIPER Detailed hardware description
General purpose I/O
Eight general-purpose input lines and eight general-purpose output lines are provided on connector PL9.
To read from IN[0:7], read the least significant byte from offset 0x500000 of CS5
(0x14500000) to sample the 8 inputs from PL9.
VIPER Inputs PXA255 data
IN0 D0
IN1 D1
IN2 D2
IN3 D3
IN4 D4
IN5 D5
IN6 D6
IN7 D7
PXA255
D[0:7]
Transceiver
IN[0:7]
3.3V
10k ohms
PL9
The PXA255 is not designed to interface to 8-bit peripherals, so when the 8-bits of data are read only the least significant byte from the word contains the data.
Data bus
Most Significant Byte Least Significant Byte
D15 D14 D13 D12 D11 D10 D9 D8 D7 D6 D5 D4 D3 D2 D1 D0
Don’t Care IN Data
© 2004 Arcom Issue H
39
VIPER Detailed hardware description
To write to OUT[0:7], write to the following PXA255 processor GPIO lines to drive the outputs.
VIPER Outputs PXA255 GPIO
OUT0 GPIO20
OUT1 GPIO21
OUT2 GPIO22
OUT3 GPIO23
OUT4 GPIO24
OUT5 GPIO25
OUT6 GPIO26
OUT7 GPIO27
PXA255
GPIO[20:27]
Buffer
OUT[0:7]
OUT0B
PL9
The PXA255 GPIO lines must be configured using the registers built into the device to ensure they function correctly. RedBoot configures GPIO20 – GPIO27 as outputs, and sets OUT0 – 2 to logic ‘0’, and OUT3 – 7 as logic ‘1’. Eboot cannot set these up as outputs as it only boots the Windows CE .NET image. Once Windows CE .NET is booted you can simply write to a mapped address. For an example of how to do this under Windows CE .NET please see the Windows CE .NET Technical Manual.
Please note:
•
•
IN0-7 cannot be configured as outputs as they are hardwired as input-only by a buffer.
OUT0-7 cannot be configured as inputs as they are hardwired as output-only by a buffer.
The GPIO lines are programmed using the GPCR0 and the GPSR0 to set the line to ‘0’ or ‘1’ respectively. The registers are 32-bit wide and bits 20-27 relate to GP20-27.
Register Address
GPCR0 0x40E00024
GPSR0 0x40E00018
The general-purpose inputs are 5V tolerant, and the outputs can sink and source up to
24mA @ 3.3V.
OUT0B is an inverted OUT0 signal, and is driven to 5V, which provides compatibility with the VIPER-UPS.
© 2004 Arcom Issue H
40
VIPER Detailed hardware description
The following general purpose IO lines are used by the VIPER-UPS:
Function IO
External Power Fail IN0
Battery Low
UPS Power down
IN1
OUT0B
© 2004 Arcom Issue H
41
VIPER Detailed hardware description
USB interface
There are two USB interfaces on the VIPER. These interfaces have been designed to support the Open Host Controller Interface (OpenHCI).
There are four signal lines associated with each USB channel:
• VBUS
• DPOS
• DNEG
• GND
Their arrangement is summarized in the following illustration:
USB Connector 1
3
4
1
2
VBUS 1
DNEG 1
1
DPOS 1
GND
PL7
2
VBUS 2
DNEG 2
DPOS 2
GND
USB Connector 2
3
4
1
2
(SHIELD) 9 10 (SHIELD)
A USB power control switch controls the power and protects against short-circuit
conditions. See the section USB power management , page 58 , for details of control.
If the USB voltage is short-circuited, or more than 500mA is drawn from either supply, the switch turns off the power supply and automatically protects the device and board.
The VBUS power supply is derived from the VIPER +5V supply.
If you require details for the USB bus, or would like to determine whether particular peripherals are available, see www.usb.org
.
A factory fit option changes USB port 1 from a host interface to a device using the PXA255 USB controller. Please contact Arcom for more details. Contact
details are provided in Appendix A – Contacting Arcom , page 72 .
© 2004 Arcom Issue H
42
VIPER Detailed hardware description
10/100BaseTX Ethernet
An SMSC LAN91C111 Ethernet controller provides a single 10/100BaseTX interface.
The device provides an embedded PHY and MAC, and complies with the IEEE802.3u
10/100BaseTX and IEEE 802.3x Full-duplex Flow Control specifications. Configuration data and MAC information are stored in an external 93C46 EEPROM.
The 10/100base-T magnetics are located on the VIPER. Connection to the VIPER
Ethernet port is via header PL1. See
PL1 – 10/100BaseTX Ethernet connector , page
61 , for pin assignment, connector and mating connector details.
A second header PL2 provides the Activity and Link status LED signals. The output lines sink current when switched on therefore the anode of each LED should be connected to pins 1 and 3 of PL2 and the cathode to the appropriate status line.
The Link LED illuminates when a 10 or 100base-T link is made, and the Activity LED illuminates when there is Tx or Rx activity.
Ethernet breakout board
Arcom can provide an Ethernet breakout board with an RJ45 connector to interface to the VIPER Ethernet connectors PL1 and PL2. The Ethernet breakout board features brackets for panel mounting ease.
The Ethernet Breakout board allows easy connection between the VIPER and a
10/100base-T Ethernet Connection. It is shown below:
The connectors on the following pages are shown in the same orientation as the picture above.
Connector Function
PL1 10/100BaseTX Ethernet Signals
© 2004 Arcom Issue H
43
VIPER Detailed hardware description
Ethernet breakout PL1 Ethernet breakout PL2
Ethernet signal mapping between VIPER and Ethernet breakout connectors
Ethernet breakout PL1 –
2x4-way header
Ethernet breakout PL3 -
RJ45
Pin Signal Name Pin Signal Name
Ethernet breakout PL3
VIPER PL1 – 10/100BaseTX
Ethernet connector
Pin Signal Name
8 LANGND 8 RJ-1 8 LANGND
Ethernet LED signal mapping between VIPER and Ethernet breakout connectors
Ethernet breakout PL2 –
1x 4-way header
VIPER PL2 – Ethernet status
LED's connector
Pin Signal Name Pin Signal Name
2
4
LINK LED-
ACTIVITY LED-
2 LINK (Green)
3 3.3V
4 ACTIVITY (Yellow)
© 2004 Arcom Issue H
44
VIPER Detailed hardware description
Serial COMs ports
There are five high-speed, fully functionally compatible 16550 serial UARTs on the
VIPER. Four of these channels can be used as standard RS232 serial interfaces, and the remaining one (COM5) can be configured as RS422 or RS485.
Port Address
COM1 0x40100000 –
0x40100023
IRQ
Internal
COM2 0x40200000 –
0x40200023
Internal
COM3 0x40700000 –
0x40700023
Internal
COM4 0x14300010 –
0x1430001F
GPIO3
COM5 0x14300000 –
0x1430000F
GPIO4
FIFO Depth
RX / TX Signals
64 / 64 RS232 Rx, Tx, CTS, RTS, RI, DSR,
DCD, DTR
64 / 64 RS232 Rx, Tx, RTS, CTS
64 / 64 RS232 Rx, Tx
128 / 128 RS232 Rx, Tx, CTS, RTS, RI, DSR,
DCD, DTR
128 / 128 RS422 / RS485 Tx, Rx
Please see the Intel Developer’s Manual for details of internal interrupts.
COM1 – RS232 interface
Uses the Full Function UART in the PXA255 (FFUART). The port is buffered to RS232 levels by a 5V transceiver with ±15kV ESD protection, and supports full handshaking and modem control signals. Maximum baud rate on this channel is 230kb/s (this is limited by the transceiver performance). A factory fit option configures COM1 as TTL
Level signals to interface to a modem. Please contact Arcom for details. Contact details
are provided in Appendix A – Contacting Arcom , page 72 .
COM2 – RS232 interface
Uses the Bluetooth UART in the PXA255 (BTUART). The port is buffered to RS232 levels by a 5V transceiver with ±15kV ESD protection, and supports RTS, CTS handshaking only. Maximum baud rate on this channel is 230kb/s (this is limited by the transceiver performance).
© 2004 Arcom Issue H
45
VIPER Detailed hardware description
COM3 – RS232 interface
Uses the Standard UART in the PXA255 (STUART). The port is buffered to RS232 levels by a 5V transceiver with ±15kV ESD protection, but does not support any handshaking (RX / TX only). Maximum baud rate on this channel is 230kb/s (this is limited by the transceiver performance).
COM4 – RS232 interface
Supported on Channel 0 of an external Exar XR16C2852 with 128bytes of Tx and Rx
FIFOs, and buffered to RS232 levels by a 5V transceiver with ±15kV ESD protection.
The maximum baud rate on this channel is 115kb/s.
COM5 – RS422/485 interface
Supported on Channel 1 of an external Exar XR16C2852 with 128bytes of Tx and Rx
FIFOs, and buffered to RS422/485 levels by a 5V transceiver with ±15kV ESD protection, to provide support for RS422 (default) and RS485 (jumper selectable) interfaces. The maximum baud rate on this channel is 115kb/s.
RS422
The RS422 interface provides full-duplex communication. The signals available are
TXA, TXB, RXA, RXB and Ground. The maximum cable length for an RS422 system is
4000ft (1200m) and supports 1 transmitter and up to 10 receivers.
To enable RS422 operation,
LK6 and LK7 should be in position ‘B’. LK4 and LK5 should
be made if the board is at the end of the network. See
RS485/422 configuration – LK4,
LK5, LK6 and LK7 , page 71 , for details.
RS485
This is a half-duplex interface that provides combined TX and RX signals. PL4 pin 5 provides TXB/RXB and pin 6 provides TXA/RXA. A ground connection is also required for this interface. The maximum cable length for this interface is the same as RS422
(4000ft), but RS485 supports up to 32 transmitters and receivers on a single network.
Only one transmitter should be switched on at a time.
The VIPER uses the RTS signal to control transmission. When this signal is at logic ‘1’ the driver is switched off and data can be received from other devices. When the RTS line is at logic ‘0’ the driver is on. Any data that is transmitted from the VIPER is automatically echoed back to the receiver. This enables the serial communications software to detect that all data has been sent and disable the transmitter when required.
should be in position ‘A’ to enable the RS485 interface. The UART used on the VIPER for COM5 has extended features including auto-RTS control for RS485.
This forces the RTS signal to change state (and therefore the direction of the RS485 transceivers) when the last bit of a character has been sent onto the wire. Please refer to the XR16C2852 datasheet on the Development Kit CD.
LK4 and LK5 provide parallel line termination resistors and should be made if the
VIPER is at the end of the network.
© 2004 Arcom Issue H
46
VIPER Detailed hardware description
Typical RS422 and RS485 Connection
RS422 POINT-TO-POINT RS422 MULTI-DROP RS485 MULTI-DROP
Number of Wires
Transmitters Enabled
5 always
Receivers Enabled always
Duplex Mode full
LK6 B
LK7 B
Number of Wires
Transmitters Enabled
5 active RTS
Receivers Enabled always
Duplex Mode full
LK6 B
LK7 B
Number of Wires 3
Transmitters Enabled active RTS
Receivers Enabled always
Duplex Mode half
LK6 A
LK7 A
© 2004 Arcom Issue H
47
VIPER Detailed hardware description
PC/104 interface
The PC/104 interface supports 8/16 bit ISA bus style signals. Add on boards can be used to enhance the functionality of the main board. Arcom has an extensive range of
PC/104 compliant modules and these can be used to quickly add digital I/O, analog I/O, serial ports, video capture devices, PC card interfaces etc. The ISA bus is based on the x86 architecture and is not normally associated with RISC processors. It shall be necessary to modify standard drivers to support any 3 rd party PC/104 modules.
Any PC/104 board plugged in will appear in the PC Card memory space socket 1.
0x3D000000 – 0x3FFFFFFF
0x3C000000 – 0x3CFFFFFF
0x30000400 – 0x3BFFFFFF
0x30000000 – 0x300003FF
Reserved
PC/104 memory space (16MB)
Reserved
PC/104 I/O space (1kB)
The PC/104 bus signals are compatible with the ISA bus electrical timing definitions.
DMA, bus mastering, and shared interrupts are not supported on the VIPER’s PC/104 interface. For details on PC/104 Interrupts please see
The VIPER provides +5V to a PC/104 add-on-board via the PL11 and PL12 connectors.
If a PC/104 add-on-board requires a +12V supply, then +12V must be supplied to the
VIPER power connector PL16 pin 4. If –12V or –5V are required, these must be supplied directly to the PC/104 add-on board.
All signals between the PXA255 and the PC/104 are buffered. When access to the
PC/104 bus is not in use the PXA255 socket 1 and the PC/104 connector are automatically isolated by the buffers transceiver output enables being driven to ‘1’.
© 2004 Arcom Issue H
48
VIPER Detailed hardware description
JTAG and debug access
Debug access to the PXA255 400MHz XScale processor is via the JTAG connector
PL10 and the reset pin of PL17. The EPI Majic MX probe has been used to debug the
PXA255 processor on the VIPER. There are many other debug tools that can be interfaced to the VIPER for access to the JTAG Interface of the Intel XScale PXA255 processor.
The tables below detail the pins connections between the VIPER and Majic MX .
Compare PL10 and PL17 pin numbers to match VIPER JTAG connection to the Majic MX connections .
VIPER JTAG Connections
Connector Pin Name Description
1 VCC3 3.3V Supply pin to JTAG debug tool
PL10
3
4
6
GND nTRST
TDI
Not required on VIPER.
PXA255 JTAG interface reset
JTAG test data input to the PXA255
PL17
8
9
TMS
TCK
PXA255 JTAG test mode select
PXA255 JTAG test clock
6 RESETSW reset
- - -
- - Not required on VIPER
- - Not supported by VIPER
© 2004 Arcom Issue H
49
VIPER Detailed hardware description
Majic
MX
Connections
Connector Pin Name Description
JTAG interface voltage reference for
MX
PL10
3
7
6
RTCLK
TDO nSRST
Ground to stop RTCLK from floating.
MX JTAG interface reset
JTAG test data output from the
MX
JTAG test data input to the Majic MX
MX JTAG test mode select
MX JTAG test clock
Open collector system reset
PL17
PLUS passive probe
The Majic MX probe supports industry-standard debugger APIs, such GNU gdb for Linux and Microsoft Platform Builder for Windows CE .NET, which allows you to choose the
EPI debugger or a wide variety of other third party debuggers.
© 2004 Arcom Issue H
50
VIPER Power and power management
Power and power management
Power supplies
The VIPER is designed to operate from a single +5V ±5% (4.75V to +5.25V) supply.
The power connector PL16 has a +12V connection defined, but is not required for the
VIPER under normal operation. It can be used to supply +12V to the PC/104 stack if required. For details of the power connector please see the section
PL16 – Power connector , page 68 .
There are four on board supply voltages derived from the +5V supply. These are +1.06 to +1.3V (microprocessor Core), +1.8V (CPLD Core) and two +3.3V. One of the +3.3V supplies is dedicated for use with the CompactFLASH interface on PL5 and +3.3V flat panels on PL3.
The +5V supply is monitored automatically on-board; if this supply falls below +4.63V the board is reset. When the power supply rises above this threshold voltage the board comes out of reset and reboots itself. The power supply monitor ensures that the board does not hang if the supply voltage fails at any point.
If using the CompactFLASH socket and an LCD display, ensure the total current requirement on 3.3V does not exceed 900mA! Please check the datasheets of the devices you are using, as there is no on-board protection!
Battery backup
An external battery (CR2032 or similar) providing +3.0V to +3.3V can be used as a battery backup for the DS1307 RTC and the SRAM. The external battery supplies power to the battery backup circuit only when there is no +5V supply to the board.
To use an external battery connect its + and - terminals across PL16 pins 3 (VBAT) and
2 (GND) respectively, see
PL16 – Power connector , page 68 .
The table below shows the typical and maximum current load on the external battery.
Device Load on Battery Typical (µA) Maximum (µA)
DS1307 RTC with Clock Out Off
DS1307 RTC with Clock Out On
0.3
0.48
0.5
0.8
Supply Supervisor 0.6 1
Total with RTC Clock Out Off
Total with RTC Clock Out On
1.1
1.28
3.5
3.8
An onboard Schottky diode drops 13mV from VBAT at 25°C. At -40°C this may increase to 170mV and at +85°C decrease below 10mV. The SRAM and
DS1307 minimum voltages are 1.5V and 2V respectively. If the supply falls below these points then the corresponding device may loose data. Please check your battery datasheet for mAh and operating temperature specifications.
© 2004 Arcom Issue H
51
VIPER Power and power management
Power management
The VIPER board supports various power management functions. Under normal conditions the VIPER consumes typically 405mA ±5mA (2025mW ±25mW) once it has finished booting. During the boot process the VIPER consumes up to 470mA, 2350mW.
This is with:
•
•
•
•
The processor running at 400MHz in idle mode.
Its external memory running at 100MHz.
All on board peripherals powered.
No external peripherals powered.
To estimate the power consumption of the VIPER use the following formula:
(VIPER current (norm) - processor current saving
- on board peripheral current saving + external peripheral current) x 5V
Read the following subsections to estimate the power for the processor, on board and external peripheral devices.
Processor power estimations
Take into account the processor operating frequency, core voltage and memory frequency for the application. The figures shown in the table below are when the processor memory frequency is set to 100MHz. Currently embedded Linux and
VxWorks supports changing the operating frequency and Windows CE .NET will provide support shortly. Please refer to the relevant operating system technical manual to select an alternative operating frequency.
Processor Mode Vcore (V)
Current Saving (mA) from 5V when Processor Core is
400MHz 300MHz 200MHz 100MHz Asleep
Active 1.1
Active 1.06 - - -31 ±15 -16 ±21 -
Idle 1.29 0 - - - -
Idle 1.1 - 14 - - -
Sleep 1.06 - - - - 62
Current figures when the microprocessor is active were taken with the following load conditions. Calculating checksums of two files (first file: 1.1MB and second file: 0.5MB), and copying two 256kB files.
© 2004 Arcom Issue H
52
VIPER Power and power management
On board peripheral device power estimations
Use the table below to estimate power savings from on board peripheral devices.
Ethernet
Power down
COM1 – COM5
Sleep Mode
AC’97 Codec shutdown
Current Saving
(mA)
Power Saving
(mW)
Yes Yes - 182 910
External peripheral device power estimations
Take into account any external peripherals by an application, such as:
• USB devices: Keyboard, Memory Stick, and Mouse.
•
•
CompactFLASH socket: CompactFLASH memory, or Microdrive
Flat Panel Display: TFT logic + backlight, STN logic + backlight + bias voltage
The table give examples of addition current / power from external peripheral devices.
32MB Sandisk
CompactFLASH
SDCFB-32-101-80
64MB FlashDio™
USB memory stick
FDU100A
Inserted, (no access)
Reading consistently
Inserted, (no access)
Reading consistently
Additional
Current (mA)
Additional
Power (mW)
1 5
48 240
75
121
NEC 5.5” LCD +
Inverter (as used with VIPER-ICE)
NL3224BC35-20
+ 55PW131
LCD and backlight on 650
LCD on and backlight off 291
375
605
3250
1455
For devices using the 3.3V supply from the CompactFLASH socket and FPD logic supply, use 92% as the regulator efficiency.
© 2004 Arcom Issue H
53
VIPER Power and power management
Power estimate examples
Example 1: VIPER in standby (microprocessor in sleep mode and every power saving option enabled)
In this case, the power consumed by the respective categories is:
• VIPER current (norm) = 405mA ±5mA
• Processor current saving = 62mA
• On board peripheral current saving = 236mA
• External peripheral current = 0mA
Applying the formula shown on page 52, the estimated VIPER current in standby is:
405mA ±5mA - 62mA - 236mA + 0mA
= 107mA ±5mA (535mW ±25mW).
Example 2: VIPER at 400MHz with 100MHz external memory + LCD with backlight on
In this case, the power consumed by the respective categories is:
• VIPER current (norm) = 405mA (tolerance accounted for in CPU current saving)
• Processor current saving = -92 ±15mA
• On board peripheral current saving = 0mA
• External peripheral current = +650mA
Therefore, the estimated current the VIPER is using is:
405mA + 92mA ±15mA - 0mA + 650mA
= 1147mA, ±15mA (5735mW, ±75mW).
© 2004 Arcom Issue H
54
VIPER Power and power management
Processor power management
The power manager in the PXA255 offers the ability to disable the clocks to the different internal peripherals. By default, all clocks are enabled after reset. To reduce power consumption disable the clocks for any unused peripherals.
The clock speed of the processor core, PXbus (the internal bus connecting the microprocessor core and the other blocks of the PXA255), LCD and SDRAM can also be changed to achieve a balance between performance and power consumption. For more details on the internal power manager please see the Intel PXA255 developer’s manual on the Development Kit CD.
To adjust the core voltage, write the values shown in the following table to the LTC1659
DAC. Please see the LTC1659 datasheet and Intel ® PXA255 Processor Electrical,
Mechanical, and Thermal Specification on the Development Kit CD.
DAC Data Hex Value CPU Core Voltage Comment
0x000 1.65V Not recommended to set the VCORE above
1.3V as the power consumption will increase for no performance benefit.
0x325 1.29V
0xDE5
0xFFF
1.1V
1.06V
Typical VCORE for peak voltage range at
400MHz operation.
Maximum VCORE for medium voltage range at 200MHz operation.
Typical VCORE for high voltage range at
300MHz operation.
Typical VCORE for low voltage and medium voltage range, suitable for 100MHz to
200MHz operation.
When the microprocessor is in sleep mode, the CPU core voltage is shutdown.
To communicate with the VCORE DAC, use the following pins to emulate the LTC1659 interface:
GPIO LTC1659 DAC pin Function
GPIO6 Data
GPIO11 Clock
© 2004 Arcom Issue H
55
VIPER Power and power management
Before putting the PXA255 into sleep mode, ensure that the R_DIS bit in the ICR register located at offset 0x100002 from CS5 (0x14100000) is set to ‘1’. The PXA255 is not designed to interface to 8-bit peripherals, so only the least significant byte from the word contains the data.
Interrupt configuration and reset register
Byte lane
Bit
Most Significant Byte Least Significant Byte
15 14 13 12 11 10 9 8 7 6 5 4 3 2 1 0
Field - - - - - - - - - - - - -
R_DIS AUTO_
Reset
R/W
X
-
X
-
X
-
X
-
X
-
X
-
X
-
X
-
0 0 0 0
W
0 0 0 0
Address 0x14100002
ICR bit functions
Bit Name
0
1
RETRIG
AUTO_CLR
2 R_DIS
3 - 7 -
0 No interrupt retrigger (embedded Linux/VxWorks)
1 Interrupt retrigger (Windows CE .NET)
0 No auto clear interrupt / toggle GPIO1 on new interrupt
1 Auto clear interrupt / low pulse for 1.12µS on GPIO1 on new interrupt
0
1
Keep set as 0 under normal operating conditions.
X No function
© 2004 Arcom Issue H
56
VIPER Power and power management
UART power management
COM4 and COM5 are generated from an external Exar XR16C2852 DUART. This device supports a sleep mode with an auto wake up. By enabling this feature the
DUART enters sleep mode when there are no interrupts pending. The part resumes normal operation when any of the following occur:
•
•
•
Receive data start bit.
Change of state on: CTS, DSR, CD, RI
Data is being loaded into transmit FIFO.
If the part is awakened by one of the above conditions, it returns to the sleep mode automatically after the condition has cleared. Please see the XR16C2852 datasheet on the Development Kit CD for information on enabling the sleep mode. Placing the
XR16C2852 into low power mode can reduce the power consumption of the VIPER by
2mA (10mW).
GPIO12 and GPIO13 on the PXA255 can be used to power down the RS232 drivers on the VIPER, to save power. The following table shows the affect of GPIO12 and GPIO13 on the RS232 drivers. Placing the drivers in shutdown mode can reduce the power consumption of the VIPER by up to 57mA (285mW).
Transmitters Receivers
1 X Shutdown High-Z High-Z
CompactFLASH power management
The power supply to the CompactFLASH interface is controlled via software, and supports hot swap card insertion and CompactFLASH power down states. GPIO82 on the PXA255 is used to control the power supply. Setting this line to logic ‘0’ switches off power to the CompactFLASH interface.
Ethernet power management
The network interface supports a power down mode, which shuts down the internal
MAC and PHY blocks of the network controller. Placing the controller into low power mode can reduce the power consumption of the VIPER by up to 123mA (615mW). To power down the PHY write ‘1’ to the power down bit in the MII PHY Register 0, Control
Register. To power down the MAC write ‘1’ to the EPH PowerEN bit in the Bank 1,
Configuration Register. See the LAN91C111 datasheet contained on the Development
Kit CD for further details.
© 2004 Arcom Issue H
57
VIPER Power and power management
USB power management
The USB Host controller supports a USB suspend state. Placing the controller into the
USB suspend state can reduce the power consumption of the VIPER by up to 21mA
(105mW). To suspend the USB, the software must write to the relevant bits in the
HcControl Register (81h). Please see the ISP1160 datasheet contained on the
Development Kit CD.
Audio power management
The audio interface supports the AC’97 low power modes. Shutting down the digital and analog interfaces can reduce consumption by up to 54mA (270mW).
To shut down the AC’97 Codec, the software must write to the relevant bits in the
Powerdown Control / Status Register (26h). Please see the LM4548A datasheet contained on the Development Kit CD.
Wake up events
When the PXA255 processor is placed into sleep mode, a number of different sources can be used to wake the processor. Below is a list of sources, and the related PXA255
GPIO signal.
Source GPIO
Ethernet GPIO0
PC/104 IRQ GPIO1
USB GPIO2
COM5 GPIO3
COM4 GPIO4
RTC Alarm Internal
See section 3.5 in the PXA255 Applications Processor Developers Manual, included in the Development Kit CD.
© 2004 Arcom Issue H
58
VIPER Connectors, LEDs and jumpers
Connectors, LEDs and jumpers
The following diagram shows the location of the connectors, LEDs and jumpers on the
VIPER:
The connectors on the following pages are shown in the same orientation as the picture above, unless otherwise stated.
© 2004 Arcom Issue H
59
VIPER Connectors, LEDs and jumpers
Connectors
There are 12 connectors on the VIPER for accessing external devices.
Connector Function interface
Connector Details in Section
PL1 – 10/100BaseTX Ethernet connector , page 61
PL2
PL3
Ethernet controller status
LED’s
LCD panel interface
PL2 – Ethernet status LED's connector , page 61
PL5 CompactFLASH type I/II
PL6 Audio
PL7 USB
PL9 GPIO
PL10 JTAG
PL11
PL12
64-way PC/104 expansion
40-way PC/104 expansion
PL13
PL16
Factory use only
(no connector fitted)
Power / battery / external reset
PL17 &
LK1
Link header
PL5 – CompactFLASH connector , page 64
PL6 – Audio connector , page 65
PL9 – GPIO connector , page 66
PL10 – JTAG connector , page 66
PL11 & PL12 – PC/104 connectors , page 67
PL11 & PL12 – PC/104 connectors , page 67
-
PL16 – Power connector , page 68
PL17 & LK1 – Jumper header , page 68
© 2004 Arcom Issue H
60
VIPER Connectors, LEDs and jumpers
PL1 – 10/100BaseTX Ethernet connector
Connector: Oupiin 2015-2 X 4 G D, 8-way, 2.54mm (0.1”) x 2.54mm (0.1”) dual row header.
Mating connector: Framatome 71600-008 .
Pin Signal Name
1 TX+ 2 TX-
3 RX+
5 RJ-2
7 RJ-1
4 RJ-2
6 RX-
8 LANGND
PL2 – Ethernet status LED's connector
Connector: Molex 87089-0616, 6-way, 2mm (0.079”) x 2mm (0.079”) pin header.
Mating connector: Molex 51110-0650.
Mating connector crimps (x6): Molex 50394-8100.
Pin Signal Name
1 3.3V 2 Link
3 3.3V
5 NC
4 Activity
6 NC
© 2004 Arcom Issue H
61
VIPER Connectors, LEDs and jumpers
PL3 – LCD connector
Connector: Oupiin 3214-40GRB, 40-way, 1.27mm (0.05”) x 2.54mm (0.1”) right angled boxed header.
Mating connector: Oupiin 1203-40GB.
Pin Signal Name
1 BLKEN# 2 BLKSAFE
3 GND 4 GND
5 NEGBIAS 6 LCDSAFE
9 GND
11 FPD0
13 FPD2
15 GND
17 FPD4
19 FPD6
21 GND
23 FPD8
25 FPD10
27 GND
29 FPD12
31 FPD14
33 GND
35 FCLK
37 GND
39 PCLK
10 GND
12 FPD1
14 FPD3
16 GND
18 FPD5
20 FPD7
22 GND
24 FPD9
26 FPD11
28 GND
30 FPD13
32 FPD15
34 GND
38 GND
40 LCLK
As viewed from the connector pins
© 2004 Arcom Issue H
62
VIPER Connectors, LEDs and jumpers
PL4 – COMS ports
Connector: Oupiin 3014-40GRB, 40-way, 2.54mm (0.1”) x 2.54mm (0.1”) dual row IDC boxed header.
Mating connector: Framatome 71600-040.
Pin Signal Name
1 NC
3 NC
Pin Signal Name
2 NC
4 NC
(TX5+/RX5+ RS485)
7 RX5+ (RS422)
(TX5-/RX5- RS485)
8 RX5- (RS422)
9 GND
11 TX3
13 RX2
15 TX2
10 GND
12 RX3
14 RTS2
16 CTS2
17 GND
19 GND
21 DCD4
23 RX4
25 TX4
27 DTR4
29 GND
31 DCD1
33 RX1
35 TX1
37 DTR1
39 GND
18 GND
20 NC
22 DSR4
24 RTS4
26 CTS4
28 RI4
30 NC
32 DSR1
34 RTS1
36 CTS1
38 RI1
40 NC
As viewed from the connector pins
© 2004 Arcom Issue H
63
VIPER Connectors, LEDs and jumpers
PL5 – CompactFLASH connector
Connector: 3M N7E50-A516HE-50, 50-way CompactFLASH Type II Connector.
Pin Signal Name
26 /CD1
27 D11
28 D12
29 D13
30 D14
31 D15
32 /CE2
Pin Signal Name
1 GND
2 D03
3 D04
4 D05
5 D06
6 D07
7 /CE1
34 /IORD
35 /IOWR
36 /WE
37 RDY/BSY
38 +3.3V
39 GND
8 A10
9 /OE
10 A09
11 A08
12 A07
13 +3.3V
14 A06
40 N/C
41 /RESET
15 A05
16 A04
42 WAIT 17 A03
43 /INPACK 18 A02
44 /REG
45 N/C
46 N/C
47 D08
48 D09
49 D10
50 GND
19 A01
20 A00
21 D00
22 D01
23 D02
24 /IOCS16
25 /CD2
© 2004 Arcom Issue H
64
VIPER Connectors, LEDs and jumpers
PL6 – Audio connector
Connector: Oupiin 2015-2 X 6 G D, 12-way, 2.54mm (0.1”) x 2.54mm (0.1”) dual row header.
Mating connector: Framatome 71600-012 .
Pin Signal Name
1 LEFT IN
3 GND
Pin Signal Name
2 LEFT OUT
4 GND
7 GND
9 GND
11 AMP RIGHT OUT 12 GND
PL7 – USB connector
Connector: Oupiin 2015-2 X 5 G D, 10-way, 2.54mm (0.1”) x 2.54mm (0.1”) dual row header.
Mating connector: Framatome 71600-010 .
Pin Signal Name Pin Signal Name
1 VBUS-1 2 VBUS-2
3 DNEG-1 4 DNEG-2
5 DPOS-1 6 DPOS-2
7 GND 8 GND
9 SHIELD 10 SHIELD
© 2004 Arcom Issue H
65
VIPER Connectors, LEDs and jumpers
PL9 – GPIO connector
Connector: Oupiin 2115-2 X 10 G D N, 20-way, 2mm (0.079”) x 2mm (0.079”) dual row header.
Mating connector: Framatome 69307-020.
Mating connector crimps (x20): Framatome 77138-001 .
Pin Signal Name Pin Signal Name
1 +5V 2 +5V
3 IN0
5 IN2
4 IN1
6 IN3
7 IN4
9 IN6
11 OUT0
13 OUT0_
INVERTED
15 OUT2
17 OUT4
19 OUT6
8 IN5
10 IN7
12 GND
14 OUT1
16 OUT3
18 OUT5
20 OUT7
PL10 – JTAG connector
Connector: Oupiin 2015-2 X 5 G D, 10-way, 2.54mm (0.1”) x 2.54mm (0.1”) dual row header.
Mating connector: Framatome 71600-010 .
Pin Signal Name Pin Signal Name
1 VCC3 2 NC
3 GND
5 NC
4 nTRST
6 TDI
7 TDO
9 TCLK
8 TMS
10 NC
© 2004 Arcom Issue H
66
VIPER Connectors, LEDs and jumpers
PL11 & PL12 – PC/104 connectors
Connectors:
• Astron 25-1201-232-2G, 64-way, 2.54mm (0.1”) x 2.54mm (0.1”) Stackthrough
PC/104 compatible connector (row A & B).
• Astron 25-1201-220-2G, 40-way, 2.54mm (0.1”) x 2.54mm (0.1”) Stackthrough
PC/104 compatible connector (row C & D).
Pin Row D Row C
0 GND GND
1 /MEMCS16 /SBHE
2 /IOCS16 LA23
3 IRQ10 LA22
4 IRQ11
5 IRQ12
LA21
LA20
6 NU (IRQ15) LA19
7 NU (IRQ14) LA18
8 NU (DACK0) LA17
9 NU (DRQ0) /MEMR
10 NU (DACK5) /MEMW
11 NU (DRQ5) D8
16 +5V D13
17 NC (Master) D14
18 GND
19 GND
D15
KEY
Pin Row A
9 D0
11 AEN
15 A16
16 A15
17 A14
18 A13
19 A12
20 A11
21 A10
22 A9
23 A8
24 A7
25 A6
26 A5
27 A4
28 A3
Row B
RSTDRV
+5V
NC
NC
NC
+12V
/SMEMW
/SMEMR
/IOW
/IOR
NU (DACK3)
NU (DRQ3)
NU (DACK1)
NU (DRQ1)
NU (REFSH)
8MHz Clk
IRQ7
IRQ6
IRQ5
IRQ4
IRQ3
NU (DACK2)
BALE
+5V
OSC
GND
GND
© 2004 Arcom Issue H
67
VIPER Connectors, LEDs and jumpers
PL16 – Power connector
Connector: Molex 22-05-7058, 5-way, 2.54mm (0.1") Pitch KK® Header - Right Angle
Friction Lock 7395 series connector.
Mating Connector: Molex 22-01-2055 , 5-way, 2.54mm (0.1") Pitch KK® Crimp Terminal
Housing 2695 series connector.
1 +5V
2 GND
3 VBAT
4 +12V
5 /Reset
VBAT provides connections for a battery backup supply for the 256KByte static
RAM and the Dallas DS1307 64 x 8 Serial Real-Time Clock.
+12V connection defined, but is not required for the VIPER under normal operation. It can be used to supply +12V to the PC/104 stack if required.
A momentary switch (push to make) may be connected across /Reset and
GND. Do not connect the switch across /Reset and +5V or +12V.
PL17 & LK1 – Jumper header
Connector: Oupiin 2015-2 X 8 G D, 16-way, 2.54mm (0.1”) x 2.54mm (0.1”) dual row header.
Ref Pin Signal Name Pin Signal Name
6 RESETSW 5 GND
PL17 4 User Config 1
2 Reserved
3 GND
1 GND
10 RX5/TX5-_120R 9 PL4_RX5/TX5+
8 RX5-_120R 7 PL4_RX5+
LK1
4 RX5+ 3 RX5-
2 PL4_RX5+ 1 PL4_RX5-
© 2004 Arcom Issue H
68
VIPER Connectors, LEDs and jumpers
Status LED’s
There is a single status LED on the VIPER, which indicates FLASH access to the bootloader FLASH or the main FLASH memory / Silicon Disk.
© 2004 Arcom Issue H
69
VIPER Connectors, LEDs and jumpers
Jumpers
There are seven user selectable jumpers on the VIPER, their use is explained below.
Default settings
The default positions of the jumpers is as follows:
PL17
LK1
6
4
2
10
8
6
4
A
2 B
LK6 LK7
LK1 5
LK2
LK3
3
1
LK4 9
LK5
A
7
5
3
B 1
PL17
LK1
Rotate this diagram 90 o
clockwise to match the VIPER picture on page
Reset – LK1
A momentary switch (push to make) may be connected to LK1. When the button is pressed the board goes into a full hardware reset. When the switch is released (open circuit) the board reboots.
User configurable jumper 1 – LK2
This jumper can be used by an application program to signify a configuration setting.
LK2 Description
GPIO7 read as ‘0’.
GPIO7 read as ‘1’.
Default setting:
Reserved – LK3
This jumper is reserved for factory use only.
© 2004 Arcom Issue H
70
VIPER Connectors, LEDs and jumpers
RS485/422 configuration – LK4, LK5, LK6 and LK7
These jumpers are used to enable/disable the RS485 receive buffer and RS485/422 line termination, see
COM5 – RS422/485 interface , page 46 , for more details.
This jumper can be used by an application program to signify a configuration setting.
LK4 Description
(RS485 TX/RX) RS422 TX line termination resistor (120 Ω ) connected.
(RS485 TX/RX) RS422 TX line termination resistor (120 Ω ) disconnected.
LK5 Description
RS422 RX line termination resistor
(120 Ω ) connected.
RS422 RX line termination resistor
(120 Ω ) disconnected.
LK6 & LK7 Description
A
Default setting:
Default setting:
B
A
Default setting:
A
B
RS422 full-duplex.
B
Only fit LK4 and LK5 if the VIPER is at the end of the network.
© 2004 Arcom Issue H
71
VIPER Appendix A – Contacting Arcom
Appendix A – Contacting Arcom
Arcom sales
Arcom’s sales team is always available to assist you in choosing the board that best meets your requirements. Contact your local sales office or hotline.
Sales office US
Arcom
7500W 161 st Street
Overland Park
Kansas
66085
USA
Sales office Europe
Arcom
Clifton Road
Cambridge
CB1 7EA
UK
Tel: 01223 411 200
Fax: 01223 410 457
E-mail: [email protected]
Tel:
Fax:
913 549 1000
913 549 1002
E-mail: [email protected]
Full information about all Arcom products is available on our Web site at www.arcom.com
.
While Arcom’s sales team can assist you in making your decision, the final choice of boards or systems is solely and wholly the responsibility of the buyer.
Arcom’s entire liability in respect of the boards or systems is as set out in
Arcom’s standard terms and conditions of sale. If you intend to write your own low level software, you can start with the source code on the disk supplied. This is example code only to illustrate use on Arcom’s products. It has not been commercially tested. No warranty is made in respect of this code and Arcom shall incur no liability whatsoever or howsoever arising from any use made of the code.
Technical support
Arcom has a team of technical support engineers who can provide assistance if you have any problems with your VIPER board.
Technical support US
Tel: 913 549 1010
Fax: 913 549 1001
E-mail: [email protected]
Technical support Europe
Tel: +44 (0)1223 412 428
Fax: +44 (0)1223 403 409
E-mail: [email protected]
© 2004 Arcom Issue H
72
VIPER Appendix B – Specification
Appendix B – Specification
Microprocessor
Memory
Graphics Controller
Intel XScale™ PXA255 processor.
16MByte, 64MByte 3.3V un-buffered SDRAM.
16MByte, 32MByte Intel StrataFLASH.
1MByte Bootloader ROM.
256k SRAM (battery backed off board).
PXA255 Flat panel controller offering resolutions:
• 320 x 240, 8/16 bpp.
•
•
640 x 480, 8/16 bpp.
800 x 600, 8 bpp.
Peripherals Serial:
CompactFLASH: One 50 pin Type I/II CompactFLASH
Socket.
Audio:
USB:
RS232 on COM1, COM2, COM3, & COM4
RS422/485 on COM5.
16-bit AC’97-compliant CODEC, stereo.
Dual channel v1.1 host support (factory fit device option).
Temperature Operating:
-40 o C (-40 o o C (+158 o F) (commercial).
F) to +85 o C (+185 o F) (industrial).
Humidity
Real Time Clock
Software
Power Requirement
10% to 90% RH (non-condensing).
Accuracy +/- 1 minute/month.
RedBoot Bootloader for embedded Linux or VxWorks.
Eboot Bootloader for Windows CE .NET.
5V +/- 5%.
2W typical consumption (without LCD, CF or USB devices fitted).
107mA ±5mA (535mW ±25mW) in standby mode.
Battery Input
Dimensions
2.7v to 3.3v (external).
Typical discharge 2
PC/104 compatible format.
3.775” x 3.550”.
µ A.
Weight 96
MTBF 90,000 hours based on MIL-HDBK-217F using generic failure rates.
© 2004 Arcom Issue H
73
VIPER Appendix C - Mechanical diagram
Appendix C - Mechanical diagram
4.38
95.89
90.80
93.22
88.61
PL4
.00
PL2
A
PL1
Unit of measure = mm ( 1inch = 25.4mm)
Chassis ground mounting positions
5.63
A
Ø3.18 FOUR (A) HOLES
82.55
PL5
PL3
56.36
46.86
34.29
32.84
5.44
21.75
17.24
12.75
7.64
5.08
0.00
PL6
PL17
LK1-1
PL10
PL7
PL9
39.95
16.39
B1
A1
A
PL16
C0
D0
PL11
PL12
C19
D19
A
B32
A32
0.00
.9
.42
When mounting the VIPER use only M3 (metric) or 4-40 (US) screws. The mounting pad is
6.35mm, 0.25” and the hole is 3.175mm, 0.125”, so ensure any washers fitted are smaller than the pad.
Using oversized screws and washers, or tooth locking washers, can cause short circuits and over-voltage conditions.
We recommend that you use a Loctite screw thread lock or a similar product over tooth locking washers
© 2004 Arcom Issue H
74
VIPER Appendix D - Reference information
Appendix D - Reference information
Product information
Product notices, updated drivers, support material, 24hr-online ordering: www.arcom.com
PC/104 Consortium
PC/104 Specifications. Vendor information and available add on products. www.PC/104.org
USB Information
Universal Serial Bus (USB) Specification and product information www.usb.org
CFA (CompactFlash Association)
CF+ and CompactFlash Specification and product information http://www.compactflash.org
Intel
Intel XScale™ PXA255 processor documentation www.intel.com http://www.intel.com/design/pca/prodbref/252780.htm
Standard Microsystems Corporation
SMSC SMC91C111 Ethernet Controller documentation www.smsc.com
Exar Corporation
Exar XR16C2852 DUART with 128Byte FIFO documentation www.exar.com
National Semiconductor Corporation
National Semiconductor LM4548A AC’97 Codec documentation http://www.national.com
© 2004 Arcom Issue H
75
VIPER Appendix D - Reference information
Koninklijke Philips Electronics N.V.
Philips LM4548A AC’97 Codec documentation http://www.philips.com
Maxim Integrated Products Inc.
Maxim DS1307 64 x 8 Serial Real Time Clock documentation http://www.maxim-ic.com
Linear Technology Corporation.
Linear Technology LTC1659 Micropower DAC documentation http://www.linear.com/
© 2004 Arcom Issue H
76
VIPER Appendix E - Acronyms and Abbreviations
Appendix E - Acronyms and Abbreviations
API Application Program(ming) Interface
CFI Common FLASH Interface
CODEC Coder/Decoder
COM
CPLD Complex Programmable Logic Device
CPU
CMOS
DMA
EEPROM
Central Processing Unit (PXA255)
Complementary Metal Oxide Semiconductor
Electrically Erasable and Programmable Read-Only Memory
EMC
EPROM
FFUART
FIFO
Erasable and Programmable Read-Only Memory
Full Function UART
FPIF1
GPIO
Flat Panel Interface
General Purpose Input/Output
ICE In-Circuit-Emulator
IO Input/Output
LED Light Emitting Diode
LCD
LSB
Liquid Crystal Display
Least Significant Bit
NA Not
NC No
NU Not
NiMH Nickel Metal Hydride
OS Operating
PROM Programmable Read-Only Memory
PWM
QVGA
REF DES
RTC
SBC
SDRAM
SRAM
STN
Pulse-Width
Quarter VGA, display resolution 320 x 240 pixels
Reference Designator, Component Identification Number on the PCB
Single Board Computer
Synchronous Dynamic Random Access Memory
Static Random Access Memory
Super Twisted Nematic, technology of passive matrix liquid crystal
TFT
UART
UPS
USB
VAC
VDC
VGA
Thin Film Transistor, a type of LCD flat-panel display screen
Universal Asynchronous Receiver / Transmitter
Uninterruptible Power Supply
Universal Serial Bus
Voltage Direct Current
Video Graphics Adapter, display resolution 640 x 480 pixels
VIPER-Industrial Compact Enclosure
© 2004 Arcom Issue H
77
VIPER
Index
1
10/100 base ethernet · 5
A active display signal · 31 address map · 14 amp · 5 amplifier · 6 anti-static · 9 assignments, GPIO pins · 17 audio · 5, 6, 12, 38 connector · 65 power management · 58
B backlight · 6 brightness · 32 enable · 31 inverter connector · 37 base TX ethernet · 43 battery · 51, 73 battery input · 5 block diagram · 13 board · 4 bootloader · 6, 12
FLASH · 23 breakout board · 43 bus expansion · 12
C cache · 6
CE · 11 clock · 7, 16, 21, 73
CODEC · 6
COM · 5 ports connector · 63
COM1 · 45
COM2 · 45
COM3 · 46
COM4 · 46
© 2004 Arcom Issue H
Index
COM5 · 46, 71
CompactFLASH · 5, 6, 11, 24 connector · 64 power · 57 connector · 59, 60 audio · 65
CompactFLASH · 64
COMS port · 63 ethernet · 61 ethernet status · 61
JTAG · 66
LCD · 62
PC/104 · 67 power · 68
USB · 65 contact details · 72 controller graphics · 73
D dark boot · 70 digital I/O · 5 dimensions · 73 display · 29
E
EMC · 9
EPROM · 6 ethernet · 5, 6, 12, 43 breakout board · 43 connector · 61
LED · 5 power management · 57 expansion bus · 12 external device power · 53 interrupt · 25
F features · 6
FIFO · 6
FLASH · 6
78
VIPER flash access LED · 59
FLASH memory · 23 flat panel · 29 footprint · 7
FPIF · 33
G general purpose I/O · 39
GPIO · 7 pins assignments · 17 graphics controller · 73
H humidity · 73
I
I/O · 5 interface
USB · 42 internal interrupt · 25 interrupt · 25 external · 25 internal · 25
J
JTAG · 5
JTAG connector · 66 jumper · 5, 7, 59, 70 header · 68
L
LAN · 12
LCD · 29, 33 backlight brightness · 32 backlight enable · 31 connector · 62 generic connector · 35 logic supply enable · 32
SBC cable connector · 34
LED · 5, 59, 69
Linux · 11, 12, 16, 23, 26, 27, 52, 56, 73
PC/104 interrupts · 27
LK1 · 59, 60, 68, 70
LK2 · 70
LK3 · 70
LK4 · 71
LK5 · 71
LK6 · 71
LK7 · 71
© 2004 Arcom Issue H
M map, address · 14 mechanical diagram · 74 memory · 6, 23, 73 mic · 5 microphone · 6 microprocessor · 73
MTBF · 73
N network · 6
O on board device power · 53
P passive display signal · 31
PC/104 · 26, 48 consortium · 75 interface · 5
PC/104 interrupts
Linux · 27
Windows CE · 28 peripheral · 73 peripheral control module · 16
PL1 · 59, 60, 61
PL10 · 59, 60, 66
PL11 · 59, 60, 67
PL12 · 59, 60, 67
PL13 · 60
PL16 · 59, 60, 68
PL17 · 59, 60, 68
PL2 · 59, 60, 61
PL3 · 59, 60, 62
PL4 · 59, 60, 63
PL5 · 59, 60, 64
PL6 · 59, 60, 65
PL7 · 59, 60, 65
PL9 · 59, 60 port serial · 6, 45
USB · 6 power · 5, 7, 51, 52, 73 audio · 58
CompactFLASH · 57 connector · 51, 68 ethernet · 57 external device · 53 processor · 52, 55 supply · 51
UART · 57
USB · 58
Index
79
VIPER voltage · 51 processor · 5, 6, 73 power · 52 power management · 55
PXA255 · 16 product information · 75
PXA255 · 16
R
RAM, static · 24 real time clock · 7, 21, 73
RedBoot · 73 reset · 70 resolution · 6
RS232 · 6, 11, 45, 46
RS422 · 6, 11, 46, 71
RS485 · 6, 11, 46, 71
RTC · 7
S
SDRAM · 23 serial port · 5, 6, 11, 45
Silicon Disk · 6, 23 size · 7 software · 73 specification · 73
SRAM · 6 static · 9 static RAM · 24 status LED · 69
STN · 5, 30, 33 bias connector · 37
StrataFLASH · 5 support · 8 technical · 72 system control module · 16 memory · 6
T technical support · 72 temperature · 73
TFT · 5, 6, 29, 33 timer watchdog · 22
U
UART · 6 power management · 57
USB · 5, 6, 12, 75 connector · 65 interface · 42 power management · 58
V video · 6
W wake up events · 58 watchdog · 7 timer · 22 weight · 73
Windows CE · 73
PC/104 · 28
Index
© 2004 Arcom Issue H
80
advertisement
Related manuals
advertisement
Table of contents
- 1 VIPER Technical Manual
- 3 Contents
- 4 Introduction
- 5 VIPER ‘at a glance’
- 6 VIPER features
- 8 VIPER support products
- 9 Handling your board safely
- 10 Conventions
- 11 Getting started
- 11 Using the VIPER
- 13 Detailed hardware description
- 13 VIPER block diagram
- 14 VIPER address map
- 15 Translations made by the MMU
- 16 PXA255 processor
- 17 PXA255 GPIO pin assignments
- 21 Real Time Clock
- 22 Watchdog timer
- 23 Memory
- 25 Interrupt assignments
- 29 Flat panel display support
- 38 Audio
- 39 General purpose I/O
- 42 USB interface
- 43 10/100BaseTX Ethernet
- 45 Serial COMs ports
- 48 PC/104 interface
- 49 JTAG and debug access
- 51 Power and power management
- 51 Power supplies
- 52 Power management
- 59 Connectors, LEDs and jumpers
- 60 Connectors
- 69 Status LED’s
- 70 Jumpers
- 72 Appendix A – Contacting Arcom
- 73 Appendix B – Specification
- 74 Appendix C - Mechanical diagram
- 75 Appendix D - Reference information
- 77 Appendix E - Acronyms and Abbreviations
- 78 Index