advertisement
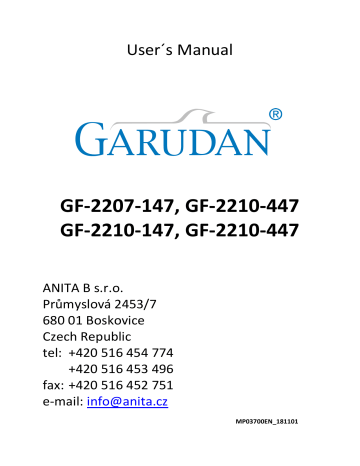
User´s Manual
GF-2207-147, GF-2210-447
GF-2210-147, GF-2210-447
ANITA B s.r.o.
Průmyslová 2453/7
680 01 Boskovice
Czech Republic tel: +420 516 454 774
+420 516 453 496 fax: +420 516 452 751 e-mail:
[email protected]
MP03700EN_181101
© ANITA
VERSION CREATED ON APPROVED BY
MP03700EN_181101 01. 11. 2018 Jakub Lžičař www.garudan.cz
All rights reserved.
Property of Anita B s.r.o. and protected by copyright. The use of this content without written permission is prohibited.
Copyright © Anita B s r.o. (2018)
MP03700EN_181101 2
© ANITA
Content
Safety Instrictions ....................................................................................................................... 4
1. Names of Major Parts ............................................................................................................. 7
2. Machine Specifications ........................................................................................................... 8
3. Optional Parts ......................................................................................................................... 9
4. Installation ............................................................................................................................ 10
5. Preparation Before Sewing .................................................................................................. 17
6. Sewing .................................................................................................................................. 23
7. Thread Tension ..................................................................................................................... 24
8. Cleaning ................................................................................................................................ 26
9. Standard adjustments .......................................................................................................... 27
10. Replacing Gauge Parts (Changing the Needle Width) ........................................................ 44
11. Installing Optional Parts ..................................................................................................... 48
12. Troubleshooting Guide ....................................................................................................... 52 www.garudan.cz
MP03700EN_181101 3
© ANITA
SAFETY INSTRICTIONS
Safety indications end their meanings:
This instruction manual and the indications and symbols that are used on the machine itself are provided in order to ensure safe operation of this machine and to prevent accidents and injury to other people. The meanings of these indications and symbols are given below.
The instructions which follow this term indicate situations where failure to follow the instructions could cause injury when using the machine or physical damage to equipment and surroundings.
CAUTION
Symbol:
This symbol ( ) indicates something that you should be careful of. The picture triangle indicates the nature of the caution that must be taken.
This symbol indicates something that you must not do.
This symbol indicates something that you must d nature of the thing that must be
(For example, the symbol at left means you
. The picture inside the circle indicates the
(For example, the symbol at left means you must make the ground connection
Notes on safety:
CAUTION
INSTALLATION
Machine installation should only be
All cords should be secured at least www.garudan.cz
electrician for any electrical work that may need to be done.
The sewing machine weighs more than
55kg. The installation should be carded out by two or more people.
Do not connect the power cord until installation is complete, machine may operate if the treadle is which could result in injury.
Be sure to connect the ground. If the ground connection is not secure, run the risk of re shocks could occur.
Be sure to wear protective goggles and dling the lubricating oil, so that no oil gets into your eyes or onto your skin, otherwise inflammation can result.
Furthermore, do not drink the oil under circumstances as it can cause vomiting and diarrhea.
Keep the oil out of the reach of children.
MP03700EN_181101 4
© ANITA
CAUTION
SEWING
This sewing machine should only be the necessary training in safe use beforehand.
by operators who have received raining in safe use
The sewing machine should not be used for any applications other than sewing.
ithout these devices attached. Injury may result.
Attach all safety devices before using sewing machine. If the machine is used.
Without these devices attached. Injury may
Turn off the power switch at the following times. The motor will keep turning even after the power is switched off as a result of the motor s inertia.
Wait until the motor stops fully before work.
Turn off the power switch at the times. The motor will keep after the power is of the motor s inertia. motor stops fully before starting press any objects against the machine sewing, as this may result in injury or damage to the machine.
If an error occurs in maching, or if abnormal noises or smells are noticed, immediately turn off the power
When threading the needle. bobbin.
When not using the machine and when leaving the maching unattended.
Then contact your nearest dealer or a Qualified technician.
If the machine develops a problem contact your nearest dealer or a qualified
Technician
CLEANING
carrying out cleaning. The motor will keep turning even after the power is switched off as a result of the motor s inertia.
Wait out it the motor stops fully before starting work. The machine may operate if the treadle is pressed by mistake, operate if the treadle is gloves when handling the lubricating oil, that no oil gets into your eyes or skin, otherwise inflammation can
, do not drink oil under any circumstances, as it can cause vomiting and diarrhea. Keep the oil out of the reach of children.
. Keep the oil out of the reach of www.garudan.cz
MP03700EN_181101 5
© ANITA
3.
2.
Maintenance and inspection machine should only be carried out by a qualified technician.
Ask you dealer or a qualified electrician to carry out any maintenance and the electrical system. off the power switch and the power cord from the following thime. operate if the which could result motor will keep turning is switched off as a result
Wait until the motor stops fully before staring work.
When carrying out inspection adjust maintenance. adjustment and
If the power switch need to be left on extremely care full to observe all safety precautions. carrying out some adjustment, be care full to observe all safety damage to the machine may result.
lubrication, do not touch such as the rotary hook, needle bar with your finger or paper nor push them with other objects. Otherwise may result.
Use only the proper replacement pads as specified by our company.
If any safety devices have been be absolutely sure to re-install original positions and
Correctly before using
When replacing consumable par rts such as the rotary hook.
Warning labels: appear on the sewing machine
Please follow the instructions on the labels at all times when using the machine. If the labels have been removed or are difficult to read please contact your nearest dealer
1. the machine
Any problems in machine operation which result from unauthorized modifications to the machine will not be covered by the warranty
The following warning labels appear on the sewing machine
Please follow the instructions on the labels at all times when using the machine. If the labels have been removed or are difficult to read please contact you www.garudan.cz
Moving parts may cause injury Operate with safety devices
Turn off main switch be fore threading, changing bobbin and needle, cleaning etc.
Be sure to connect the ground. If the ground connection is not secure you run the risk of receiving a serious electric shock.
Direction of operation
MP03700EN_181101 6
© ANITA
1. NAMES OF MAJOR PARTS
www.garudan.cz
① Face plate ② Bobbin winder
⑥ Reverse Stitching lever ⑦
④ Machine pulley
Stitch length dial ⑧
⑤
Needle plate
Belt cover
⑪ Thread pillar
Safety device
⑨ Finger guard ⑩ Thread take-up cover
MP03700EN_181101 7
© ANITA
2. MACHINE SPECIFICATIONS
GF-2207-147 – Twin needle needle feed lock stitcher
GF-2210-147 – Twin needle needle feed split needle bar lock stitcher
GF-2207-147
Application
L
Thin material
M
Mediumthick material
4.000
4 mm
H
Thick material
L
Mediumthick material
GF-2210-147
M
Thick material
H
VERY thick material
3.000
5 mm
Sewing speed (spm)
Max, stitch length
Presser foot height
Presser foot lifter
Knee lifter
Feed dog height
Needle
DPX5
#9-#14
Needle feed mechanism YES
DPX5
#11-#16
7 mm
13 mm
DPX5
1 mm
#14-#22
DPX5
#11-#16
YES
DPX5
#14-#22
DPX5
#16-#23
Single needle stop mechanism
Application
L
Medium-thick material
NO
Thick material Thick material
NO
GF-2207-447 – Twin needle needle feed lock stitcher with large hook
GF-2210-447 – Twin needle needle feed split needle bar lock stitcher with large hook
GF-2207-447 GF-2210-447
M M
Sewing speed (spm) 3.000
H
VERY thick material
Max, stitch length
Presser foot height
Presser foot lifter
Knee lifter
Feed dog height
Needle
7 mm www.garudan.cz
DPX5
#11-#16
DPX5
#14-#22
1 mm
DPX5
#11-#16
DPX5
#14-#22
YES Needle feed mechanism
Single needle stop mechanism
NO YES
DPX5
#16-#23
MP03700EN_181101 8
© ANITA
3. OPTIONAL PARTS
Upper thread tension assembly:
The following types of upper thread tension assembly are available for use with different thread take-up spring types and different thread tension spring strengths.
Part code
B4-177B
Thread tension spring type Thread take-up spring strength
Standard
B4-177B(A)
B4-177B(B)
Weak
Very weak
Double
*Standard part at time of shipment GF-2207-147, GF-2210-147, GF-2207-447 and GF-2210-447.
(Reference)
Tension spring force (when spring height 12mm)
Standard
Weak
Approx.49N (Approx.5kgf)
Approx.17.64N (Approx.1.8kgf)
Very weak Approx.2.94N (Approx.0.3kgf) www.garudan.cz
MP03700EN_181101 9
© ANITA
4. INSTALLATION
CAUTION tallation should only be carried out by a qualified technician.
Contact your dealer or a qualified electrician for any electrical work done.
The sewing machine weighs approximately 55kg. The installation approximately 55kg. The installation should be carried out two or more
people.
Do not connect the power cord until installation is complete. The machine may operate if the treadle is depressed h could in injury.
Use both hands to hold the machine
head when tilting it back or returning
it to its original position. If only one hand is used, the weight of the machine head may cause your hand to slip, and your hand may get
caught. up location:
* Do not set up this sewing machine near other equipment such as televisions, radios or cordless telephones, otherwise such equipment may be affected by electronic interference from the sewing machine.
* The sewing machine should be plugged directly into an AC wall outlet. Operation problems may result if extension cords are used.
Carrying the machine: www.garudan.cz
shown in the illustration.
* Hold the motor cover(A)by hand also so that the pulley does not rotate.
Tilting back the machine head:
* Hold section (B) with your foot so that the does not move, and then push the arm with both hands to tilt back the machine head.
MP03700EN_181101 10
© ANITA
Returning the machine head to the upright position:
1. Clear away any tools, etc. Which may be near the table holes. etc. Which may be near the table
2. While holding the face plate with your return the machine head to the upright position with your right hand.
Installing the oil pan:
(1)
(2)
Head cushions (left) (2pcs)
Head cushions (right) (2pcs)
(3) Oil pan
(4) Oiler www.garudan.cz
(1) Rubber cushions (2pcs)
(2)
(3)
Nails (4pcs)
Knee lifter
MP03700EN_181101 11
© ANITA
Installing the machine head:
1.
Insert the knee lifter complying bar ① .
2.
Insert the two hinges the machine bed.
② into the holes in
3.
Clamp the hinges ② onto the rubber
Cushions ③ in the work table, and then place the machine head onto the head cushions are on top of the oil pan corners.
④ which
4.
Tap the pillow ⑤ into the table hole.
NOTE: Tap the pillow securely into the table hole. If the pillow is not pushed in as far as it will go the machine head will not be sufficiently stable when it is tilted back.
Remarks: The support pin must be installed reliably, otherwise there is danger when the machines is turned over.
www.garudan.cz
1.
Place the knee lifter assembly ① onto the knee lifter bar ② on the oil pan, and then secure if by tightening the bolt ③ .
2.
Adjust the knee lifter.
1) Lower the presser foot ④ by using the presser bar lifter ⑤ .
2) Loosen rage nut ⑥ .
3) Turn the screw ⑧ to adjust so that the amount of play in the knee lifter ⑦ is approximately 2mm when the knee lifter plate ① is gently pressed.
4) Securely tighten the nut ⑥ .
5) Loosen the nut ⑨ .
MP03700EN_181101 12
© ANITA
Installation:
6) Turn the screw ⑩ until the distance between the end of the screw ⑩ approximately 8mm.
and the knee lifter ⑦ is
7) Turn the screw ⑩ to adjust so that the presser foot
⑤ is at the desired position within a distance of 13mm of the needle plate when the knee lifter pressed.
⑨ plate is fully
8) After adjustment is completes, securely tighten the nut ⑨ .
1.
Control box
1) Control box
2) Bolts (5pcs)
3) Spring washers (5pcs)
4) Washer (5 purchase)
2.
Connecting rod
5) Nut
6) Connecting rod www.garudan.cz
3.
Power switch
1) Power switch
2) Screw (2pcs)
MP03700EN_181101 13
© ANITA
DANGER ing areas where high voltages are present can result in severe injury.
CAUTION
Contact your dealer or a qualified electrician for any electrical work that ma
to be done.
Do not connect the power cord until installation is complete. The machine may operate if the treadle is depressed by mistake, which could in injury.
Be sure to connect the ground. If the ground connection is not secure, you run a
high risk of receiving a serious electric shock, and problems with correct operation
may also occur.
Connecting the cords: www.garudan.cz
MP03700EN_181101 14
© ANITA
Installing the cotton stand:
Assemble the cotton stand ① while referring to the cotton stand instruction manual, and then install the cotton stand to the far right comer of ① the work table.
Lubrication:
The sewing machine should always be lubricated and the oil supply replenished before it is used for the first time, and also after long periods of no-use.
Use only the lubricating oil
Lubricating via the oil cover (every 6 months) www.garudan.cz
(Semi dry specifications)
Pour lubricating oil into the oil cover
(1) about as often as grease is applied.
1.
Tilt back the machine head
2.
Pour lubricating oil into the oil cover (1) until the oil level reaches the reference line (2)
3.
Return the machine head to its normal position.
MP03700EN_181101 15
© ANITA
Checking the machine pulley rotating direction:
If the lubricating oil level drops below the bottom reference line (2) of the oil gauge window (1) be sure to add more oil.
1.
Insert the power cord plug into the wall outlet, and then turn on the power switch.
2.
Depress the treadle and check that the direction of the machine pulley matches the direction of the arrow ①
* If the direction of rotary is reversed,
. change the direction of rotation to the correct to the correct direction while referring to the instruction manual for the www.garudan.cz
MP03700EN_181101 16
© ANITA
5. PREPARATION BEFORE SEWING
Installing the needle:
GF-2207-147, GF-2207-447 GF-2210-147, GF-2210-447
1.
Turn the machine pulley to move the needle bar to its highest position.
2.
Loosen the screws, hold the needles with their long groove fasting inward, insert them all the way into the needle bars, and re-tighten the screws.
Remove the bobbin or cap: www.garudan.cz
1. Raise the needles ① to the highest positions, and open the slide plates the right and left.
② by moving them to
2. Pull the rotary hook latches ③ upward, and then remove the bobbin ④ .
1. Raise the needle ① to this highest positions, and open the slide plates the right and left.
② by moving them to
2. After lifting up the rotary hook latch ③ , life the corner of the cap to moving the cap ④ .
MP03700EN_181101 17
© ANITA
Winding the lower thread:
1. Turn on the power switch.
2. Place the bobbin ① into the bobbin winder shaft ② .
3. Wind the thread several times around the bobbin ① in the direction indicated by the arrow.
4. Push down the bobbin presser arm ③ .
5. Raise the presser foot with presser lifter.
6. Depress the treadle. Lower thread winding will then start.
7. Once winding of the lower thread is completed, the bobbin presser arm automatically.
③ will return
* If the thread cannot be wound on evenly, loosen the screw ④ and move the bobbin winder guide
⑤ to the side where there is less thread.
* Turn the adjustment screw bobbin winding amount.
⑥ to adjust the
- To increase the winding amount: Tighten the screw.
- To decrease the winding amount: Loosen the screw.
Note: The amount of thread wound onto the bobbin should be a maximum of 80% of the bobbin capacity.
www.garudan.cz
MP03700EN_181101 18
© ANITA
Installing the bobbin or cap:
Installing the bobbin (GF-2207-147, GF-2207-447)
1. Turn the machine pulley to raise the needle
① to its highest position.
2. Insert the bobbin ② into the rotate hook
③ so that the winding direction is as shown in the illustration.
3. Return the rotary hook latch original position.
④ to its
4. Turn the machine pulley to rotary the rotary hook ③ until the tension spring ⑤ is visible.
5. Pass the thread through slit A in the rotary hook and then pass it at under through tension spring ⑤ .
6. Pull out the thread to length of approximately 50 mm.
7. Close the slide plates.
Installing the cap (GF-2210-147, GF-2210-447) www.garudan.cz
② so that the
2. Thread the thread by one of the following methods in accordance with the shape of the cap being used.
1) Pass the thread through slot “A” and under the tension spring ③ .
2) Pass the thread through slot “B” and “C” and then through the thread-loosening-prevention spring.
3) Pass the thread through the thread hole and pull out about 50mm.
⑤
3. Turn the machine pulley to raise the needle to its highest position.
4. Insert the cap ② into the rotary hook.
5. Push latch ⑦ of the rotary hook flat.
6. Close the bed slide.
MP03700EN_181101 19
© ANITA
Thread the Upper thread:
Turn the machine pulley and raise the thread take-up laver before threading the upper thread. This will make threading easier and it will prevent the thread from coming out at the sewing start.
Thread the left-side thread first.
The position of the finger guard is adjustable, be sure to lower it once threading has been completed.
www.garudan.cz
MP03700EN_181101 20
© ANITA
Adjusting the stitch length:
GF-2207-147, GF-2207-447
GF-2210-147, GF-2210-447
Turn the stitch length dial clockwise or counter clockwise that the desired stitch length is at the uppermost position on the dial.
The larger the number, the longer the stitch longer will be.
Corner sewing method:
NOTE: If using this machine in place of a single-needle machine, remove the needle which is not being used. In such cases, do not use the procedures given below to stop the unused needle bar from moving, otherwise damage to the machine may result.
To stop needle bars (right and left)
Operate the stop lever after the needle has penetrated the material and has moving.
Do not sew at speeds of over 1000 spm while one of the needle bars been stopped.
www.garudan.cz
To stop operation of the left needle bar: Move the stop lever ① to the “ L“ position.
MP03700EN_181101 21
© ANITA
Number of stitches: quick-reference guide
To stop operation of the right needle bar:
Move the stop lever ① to the R position.
To resume twin-needle sewing:
Press the push lever then return to its original position automatically.
⑦.
The stop lever ① will
6.35 mm:
www.garudan.cz
Determine the sewing pitch from the chart below to make beautiful corner stitching.
The number of stitches of the outer needle varies according to the combination of sewing angle and sewing pitch.
[Example]
For a sewing angle of 40°, and a sewing pitch of 2.9 mm, the number of stitches becomes 6.
MP03700EN_181101 22
© ANITA
6. SEWING
Sewing:
1. While holding the two upper threads with your fingers, turn the machine pulley by hand toward you until the lower threads come out onto the feed dog.
2. Pull the lower thread toward you and check that they pull out smoothly.
3. Turn on the power switch.
Back tacking (GF-2207-147, GF-2207-447, GF-2210-147, GF-2210-447):
4. Depress the treadle to start sewing.
When the reverse stitching lever is pushed, the cloth feed direction will www.garudan.cz
to its original position, the feed direction will change back to normal.
MP03700EN_181101 23
© ANITA
7. THREAD TENSION
Adjusting the thread tension:
Good even stitches
Upper thread tension too weak or lower thread tension too strong.
Upper thread tension too strong or lower thread tension too weak.
Lower thread tension www.garudan.cz
adjusted by turning the lower thread tension adjustment Screw ① .
MP03700EN_181101 24
© ANITA
Upper thread tension
After the lower thread tension has adjusted, adjust the upper thread tension so that a good, even stitch is obtained.
1. Lower the presser foot.
2. Adjust by turning the thread tension nut
Adjusting the presser foot pressure:
The presser foot pressure should be as weak as possible, but strong enough so that the www.garudan.cz
the presser foot pressure.
① .
② to adjust
3. Tighten the adjustment nut ① .
② .
Use
Presser foot pressure
For thin material 29.4N (3kgf)
For
Medium thick material
For thick material
39.2N (3kgf)
49N (5kgf)
Adjustment screw height
21 mm
21 mm
18 mm
18 mm
16 mm
16 mm
MP03700EN_181101 25
© ANITA
8. CLEANING
The following cleaning operations should be carried out each day in order to maintain the performance of this machine and to ensure a long service life. Furthermore, if the sewing machine has not been used for along period of time, carry out the following clearing procedures before using it again.
Cleaning the rotary hook
1. Turn the machine pulley to raise the needle to its highest position.
2. Open the left and slide plates.
3. Remove the bobbin or the cap.
4. Remove all thread scraps from inside the rotary hook.
5. Replace the bobbin or the cap.
Lubrication:
Lubrication the sewing machine according to the procedure on page . www.garudan.cz
1. Check that the upper threads have been threaded correctly. (Refer to page )
2. Check that the end of the needle is not broken.
* If the end of the needle is broken, the needle should be replaced.
3. Lower the finger guard
4. Carry out a lest sewing.
④ .
MP03700EN_181101 26
© ANITA
9. STANDARD ADJUSTMENTS
Adjusting of the feed dog height:
1. Turn the pulley until the feed dog
① rises to the highest position.
2. Tilt back the machine head.
3. Loosen Screw ② and raise or lower the feed dog holder ③ so that the feed dog ① will raise to about
1.0mm above the needle plate.
4. Tighten the screw ④ .
Adjusting the presser foot height: www.garudan.cz
① and then loosen
3. Raise the presser foot ④ with the presser foot lifter ⑦ .
② .
4. Loosen the screw ⑤ and then move the needle bar up hoe down to adjust so that the presser foot ④ is approximately 7mm above the top of the needle plate. Note: Be careful not to rotate the needle bar ⑥ .
5. Tighten the screw ⑤ .
6. Adjust the presser foot pressure by turning the presser foot adjustment screw ② , and then tighten the nut ① .
(Refer to page 24)
MP03700EN_181101 27
Adjusting the thread tension spring:
© ANITA
Thread take-up spring tension
The standard tension for thread take-up spring L ① and thread take-up spring R is 0.147-0.343N(15 - 35g)for both
② spring.(Thread take-up spring L
1. Open the face plate.
① )
2. Loosen the screw ⑤ .
3. Loosen the knob ⑥ , and then rum the thread tension stud tension.
⑦ to adjust the
4. Tighten the screw ⑤ , and then tighten the knob ⑥ . (Thread take-up sprig R ② )
1. Loosen the set screw ⑧ .
2. Loosen the knob ⑥ and then turn the adjustment knob ⑨ to adjust the tension.
3. Tighten the screw ⑧ , and then tighten the knob ⑥ . www.garudan.cz
MP03700EN_181101 28
© ANITA
Operating range of thread take-up spring
The standard operating range for thread take-up spring L ① and thread take-up spring R ② is 5-10mm for both springs.
1. Loosen the left and right screws ③ and then turn the left and right thread take-up spring stoppers ④ to adjust the operating range.
2. Tighten the screws ③ . www.garudan.cz
Thread take-up spring operation timing
The standard operation take-up spring L ① and thread take-up spring R ② is the middle position within the operating range of the thread take-up spring guide ⑩ ,
1. Loosen the screw ⑪
2. Loosen the knob the tension.
⑥ , and then turn the left and right thread take-up spring guided ⑩ to adjust
3. Tighten the screw ⑪ ,and then tighten the knob ⑥ .
MP03700EN_181101 29
© ANITA
Adjusting the needle and rotary hook timing:
Needle rotary hook point gap
1. Tilt back the machine head.
2. Loosen screws Ⓐ , Ⓑ , Ⓒ .
3. Move the rotary hook base ① left or right so that the clearance
to the between the needle and the rotary hook tip ③ is 1-3mm.
4. Then turn the adjusting screw 6 to adjust so that the clearance between the needle ②
0.05mm.
and the rotary hook tip 3 is
5. After adjusting, securely tighten screws Ⓐ , Ⓑ , and Ⓒ .
Needle bar height and lift amount www.garudan.cz
3. Tilt screw ⑨ and move rotary hook ⑦ so that the clearance between the rotary
⑦ hook and needle plate is 1.3mm.
NOTE: Loosen screw
Rotary hook.
⑨ , Rotary hook will cause the position of the needle and
4. Tighten screw ⑨ .
MP03700EN_181101 30
© ANITA
Clearance between rotary hook and opener
1. Loosen the setscrew ⑪ and move the opener ① to the left or right to adjust so that the clearance between the rotary hook ⑦ and the opener ⑩ is
0.2mm when the opener direction of the arrow.
⑩ is pulled as far as it will go in the
2. Tighten the set screw ⑪ .
Needle bar height and lift amount
[GF-2207-147, GF-2207-447]
Needle bar height
1. Change the stitch length to the smallest possible setting.
2. Open the face plate.
3. Turn the machine pulley to move the needle bar ⑫ to its lowest position. ⓐ Reference line
⑫ at the top of the needle bar must be aligned with the lower edge of the needle bar supporter
⑬ at this time. www.garudan.cz
⑭ and move
⑫ up and down to
5. Tighten the Screw ⑭ .
6. Turn the machine pulley and check that the needle goes into the middle of the needle hole in the feed fog.
MP03700EN_181101 31
© ANITA
[GF-2207-147, GF-2207-447]
Needle bar lift amount
Stitch Length
F
2 mm
GF-2207-147
(L)
2 mm
M
3 mm
(L)
GF-2210-447
3 mm
M
Needle bar height (H) 2.4 mm 2.4 mm 2.4 mm
7. Remove the needle plate.
8. Remove the feed dog.
9. Set the stitch length to either 2 (appros 2mm) or 3 (appros 3mm)on the scale, depending on the model and specifications of the machine(Refer to the table).
10. Turn the machine pulley to raise the needle bar table below for the value for H).
⑫ by Hmm from its lowest Position (refer to the
11. The reference line ⓑ on the needle bar ⑫ will be aligned with the lower edge of the needle bar supporter ⑬ . The rotary hook tip ⑮ must be aligned with the center of the needle at this time.
12. Tilt back the machine head, loosen the three screws with the center of the needle.
⑯ , and then align the rotary hook tip ⑯
13. Tighten the screws ⑯ .
14. The distance from the upper edge of the needle hole to the rotary hook tip ⑮ must be 1-1.5mm when the rotary hook tip
15. Install the feed dog.
⑮ is aligned with the center of the needle.
16. Install the needle plate.
www.garudan.cz
32 MP03700EN_181101
© ANITA
(L)
GF-2210-147
M H (L)
GF-2210-447
M H
Stitch length
Needle bar height (H)
1. Remove the needle plate.
2. Remove the feed dog.
3. Set the stitch length to eighter 2(approx. 2mm) on 3(approx. 3mm) or the scale, depending on the model and specifications of the machine (refer to the table).
4. Turn the machine pulley to raise the needle bar by Hmm from its lowest position (refer to the table for the value for H).
2 mm
2.4 mm
2 mm
2.4 mm
The reference line ⓑ oh the needle bar ⑫ will be aligned with the lower edge of the needle bar supporter.
The rotary hook tip ⑮ must be aligned with the center of the needle at this time.
5. Till back the machine head, loosen the three screws the center of the needle.
⑯ , and then align the rotary hook tip with
6. Tighten the screws ⑯ . www.garudan.cz
when the rotary hook tip is aligned with the center of the needle.
⑮ must be 1-1.5mm
8. Loosen the set screw is 1 - 1.5mm.
⑰ to adjust so that the upper edge of the needle hole to the rotary hook, tip
9. Turn the screw ⑲ to adjust so that the distance from the upper edge of the hole of the needle hole to the rotary hook tip ⑮ is.
10. After adjustment is completed, insert the needle bar clamp ⑱ into the hole of the needle bar bar ⑫ as it will go, and check that the distance is 1 - 1.5mm.
Secure it by tightening the set screw
11. Install the feed dog.
12. Install the needle plate.
⑰ .
MP03700EN_181101 33
© ANITA
Adjusting the rotary hook lubrication amount:
CAUTION
Be careful not to touch your fingers or the lubrication amount check sheet against moving
parts such as the rotary hook or the feed mechanism when checking the amount of oil hook, otherwise injury may result.
Use the following procedure to check the amount of oil being supplied to the rotary hook when replacing the rotary hook or when changing the sewing speed.
Guide to lubrication adjustment
1. Tilt back the machine head.
to within 9-14 mm.
Checking the lubrication amount
1. Turn off the power switch.
2. Remove the thread from all points from the thread take-up to the needle.
2. Remove the thread from all points from the thread and the bobbin.
4. Use the lifting lever to lift the presser foot.
5. Turn on the power switch.
6. Run the machine at the normal sewing speed for approximately 1minute without sewing any owing the same start/stop pattern as when actually sewing).
7. Place the lubrication amount check sheet (2) to the left of the rotary hook (the right side is the right side of the rotary hook), and hold it in place while running the www.garudan.cz
8. Check the amount of oil which has spattered onto the sheet.
ype of paper can be used as the lubrication amount check sheet (2).)
Adjusting the lubrication amount
1. Tilt back the machine head.
2. Turn the adjusting screw (1) to adjust the lubrication lf the rotary hook adjusting screw (1) is turned counterclockwise, the lubrication amount becomes lf the rotary hook adjusting screw (1) is turned clockwise, the lubrication amount becomes smaller.
Check the lubrication amount again according to the procedure given in "Checking the lubrication amount"
Turn the adjusting screw (1) and check the lubrication amount repeatedly until the lubrication
4. Check the lubrication amount again after the sewing machine has be approximately two hours.
MP03700EN_181101 34
© ANITA
Adjusting of the needle and feed timing:
1. Remove the needle.
2. Remove the belt cover.
3. Tilt the machine head back and remove the timing belt ① .
4. Turn the machine pulley until the A mark is aligned with the red dot.
5. While holding the upper shaft so that it won't move align the mark in the lower belt pulley ② with the reference line in the arm bed and attach the timing belt machine pulley.
7. Replace the belt cover.
① .
6. Check the position of the A mark on the
8. Install the needle.
www.garudan.cz
MP03700EN_181101 35
Checking the lubrication amount:
© ANITA
After turning the lubrication adjustment screw to adjust the lubrication amount operate the machine for 5-10 minutes before checking the lubrication amount.
1. Remove the needle.
2. Remove the bobbin or the cap.
3. Turn on the power.
4. Insert a piece of white paper into the left side of the rotary hook (into the right side for the right rotary hook) and depress the treadle fully to operate the machine at maximum speed for approximately 10 seconds.
5. Stop the machine and check the amount of oil shown is scattered on the paper. (The adjustment is good if the amount of oil shown at left is scattered during approximately 10 seconds.) www.garudan.cz
MP03700EN_181101 36
© ANITA
Thread Wiper Adjustment:
1. Stop the machine while needle bar is at its highest position.
2. Turn off the power switch.
3. Set the stitch length to 2 on the scale.
Adjusting the forward and back position
4. Loosen the screws ② and move the solenoid ③ up and down to adjust so that the tips of the thread wiper ① are
0.3-0.5mm forward of the thread wiper
① is pressed by hand as shown in the illustration.
5. Secure tighten the screw.
Adjusting the vertical position
The tip of the thread wiper will travel as indicated by the dotted lines.
6. Loosen the screws ④ and move the thread wiper ① to the left and right to adjust so that the tips of the thread wiper
① are 0.3-0.5mm to the Inside of the needle center lines.
7. Securely tighten the screw ④ .
Adjusting the return position. www.garudan.cz
37 MP03700EN_181101
MP03700EN_181101
© ANITA
8. Loosen the screws ⑥ and raise or lower the Stopper ⑦ until the clearance between the tip of thread wiper ① and the presser bar
⑤ is about 3mm when the thread wiper ① returns to is original position.
9. Securely tighten the screws ⑥ . 1f the clearance is too little, the thread wiper may not be able to hook the threads
① depending on the kind of thread. Set the thread wiper ① as close to the needles as possible, provided that the threads will positively pass through the work.
Also check that the needle set screws will not contact the thread wiper.
10. Loosen the screw ④ and turn the thread wiper supporter ⑤ to adjust so that the clearance between the tip of the needle and the thread wiper ① is 0.5-1 mm when the thread wiper ① is pressed by hand as shown in the illustration. www.garudan.cz
④ . After adjustment, carry out a test sewing to check that the thread wiper operates correctly.
38
© ANITA
Movable and Fixed Knife Adjustment:
Removing to movable and fixed knives
1. Remove the needles and raise the presser foot.
2. Loosen the screws ① and ② , and then remove the needle plate ③ .
3. Remove the holed screws ④ and remove the movable knife ⑤ .
4. Remove the screws ⑥ and remove the fixed knife ⑦ .
Sharpening the fixed knife
If the knives become blunt, sharpen the fixed knives as shown.
The moving knife cannot be sharpened with an ordinary whetstone.
If it becomes blunt, replace it with a new one.
www.garudan.cz
39 MP03700EN_181101
© ANITA
Installing the movable and fixed knives
1. Turn the machine pulley by hand until the ooedres are pulled the way in the arrow direction.
2. Lightly secure the movable knife with screw.
Install the movable knife on the top of the bobbin thread clamp spring.
3. Press down on the top of the movable knife and slide the movable knife (Firmly tighten screw so that the gap between the tip of the movable knife and the rotary hook position bracket is 0.05 to
0.2mm)
4. Tilt back the machine head.
5. Loosen the screws ⑪ .
6. Move the movable knife with your finger so that they are at the positions shown in the illustration.
7. Tighten the screw ⑪ .
www.garudan.cz
MP03700EN_181101 40
© ANITA
Tension Release:
If the thread slips out of the needle hole after thread cutting, or if the tension disc remain open, adjust as follows.
A. If the thread slips out of the needle hole (The tension release lever is not working properly during thread cutting)
1. Press the thread trimming solenoid sewing machine pulley.
① and turn the
2. The tension disc ④ tension release lever
should be open 0.8mm when the
② roller reaches the top of the tension release cam ③ .
3. Make sure the tension disc is open when the tension release lever ② roller is at the top of the tension release cam ③ , and closed when the lever roller is on the lever.
B. If the tension disc remain open.
1. Make sure the tension release lever ② is returned.
2. Make sure the return spring ⑥ is not disengaged.
Check the above and adjust with nut ⑤ as necessary.
If adjustment is not possible, replace the tension release wire ⑦ .
www.garudan.cz
41 MP03700EN_181101
© ANITA
Synchronizer Adjustment:
Needle up position stop adjustment
1. Turn on the power.
2. Stop the machine while the needle bar is at its highest position.
3. The pulley reference line should be visible in the windows stopped.
① of the belt cover when the machine is
Check that the distance from the top of the need le plate to the bosom of the needle clamp is 39-
42mm at this time.
<Adjustment method>
1. Turn the machine pulley until the A mark is in line with the red dot.
2. Turn the glisten parcel turned on.
② until the guild light is
3. Turn the glisten parcel ② a little, make sure the
A mark is in line with the red dot, when the needle is up stop position. www.garudan.cz
2. Press the treadle, and then release the treadle to neutral.
3. Make sure the gap from the top of the needle plate to the bosom of the needle clamp is approximately 16mm.
MP03700EN_181101 42
© ANITA
Thread trimmer timing adjustment:
Thread Trimmer Timing Adjustment
1. Remove the needles.
2. Hold the thread trimming solenoid ① depressed and turn the sewing machine pulley in its normal direction of rotation until the pulley become hard to turn(the movable knife will begin to move).
3. The T mark on the machine pulley scale must be in line with the red dot on the machine head.
(The permissible deviation of the T mark from the center of the red dot is 2mm)
Upper and Lower Shaft Timing Adjustment
[GF-2207-147, GF-2210-447, GF-2207-447,
GF-2210-447]
1. Remove the timing belt in line with the red dot.
② .
2. Turn the machine pulley until the T mark is
3. With the thread trimming solenoid ① depressed turn the lower belt wheel in the arrow direction until it is hard to turn.
4. Keep the machine pulley and lower belt wheel ③ still and put the timing belt ② on.
* Never loosen the screw ④ .
www.garudan.cz
MP03700EN_181101 43
© ANITA
10. REPLACING GAUGE PARTS (CHANGING THE NEEDLE WIDTH)
How to change gauges
1. Turn the machine pulley to move the needle bar to its highest position.
2. Remove the needle ① .
3. Remove the slide plate ② .
4. Remove the needle clamp ③ .
5. Raise the presser foot by using the presser foot lifter ④ .
6. Remove the presser foot ⑤ .
7. Remove the needle plate ⑥ .
8. Remove the feet dog ⑦ .
9. Tilt back the machine head.
www.garudan.cz
MP03700EN_181101 44
© ANITA
MP03700EN_181101
Adjust the rotary hook base
Make the following adjustment when replacing the current gauge with one wider, the feed dog cannot be installed if this adjustment is not made.
Loosen screw Ⓐ , Ⓑ , Ⓒ and shift the rotary hook base right or left.
Installation
1. Attach the needle clamp. www.garudan.cz
1) Turn the machine pulley and check that the needle goes into the middle of the needle hole in the feed dog.
2) Loosen ② and align the needles so that the needles will fall in the centers of the needle holes in the feed dog.
45
© ANITA
4. Check the needle bar height.
Turn the machine pulley to move the needle bar the its lowest position and adjust so that reference line is aligned as shown in the machine head.
5. Tilt back the machine head.
6. Adjust the clearance between the needle ③ and the rotary hook tip
④ .
1) Loosen screws Ⓐ , Ⓑ , Ⓒ .
2) Move the rotary hook base ⑤ to the left or right so that the clearance between the needle ③ and the rotary hook tip ④ is 1-3mm.
3) Tighten screw C, and then turn the adjusting screw ⑥ to adjust so that the clearance between the needle
③ and the rotary hook tip ④ is
0.05mm.
After adjusting, securely tighten screws and Ⓐ , Ⓑ , Ⓒ .
www.garudan.cz
MP03700EN_181101 46
© ANITA
7. Adjust the needle bar lift amount.
1) Set the stitch length to eight 2
(approx. 2 mm) or 3 (approx3ram) on the scale, depending on the model and specifications of the machine.
(Refer to the table on page 17.)
2) Turn the machine pulley to move the needle ⓑ or to its lowest position and adjust so that reference line b is aligned as shown in the illustration.
Check that the rotary hook tip ④ is aligned with the center of the needle and that the distance from the upper edge of the needle hole to the rotary hook up ④ is 1-1.5mm at this time.
(Refer to pages 33 and 34 for the adjustment procedures.)
8. Return the head to its original position.
9. Attach the needle plate.
10. Attach the presser foot.
www.garudan.cz
MP03700EN_181101 47
© ANITA
11. INSTALLING OPTIONAL PARTS
Replacing the rotary hook:
Removal
1. Turn the machine pulley to move the needle bar to its highest position.
2. Remove the needle ① .
3. Remove the slide plates ② .
4. Raise the presser foot ④ with the presser foot lifter ③ .
5. Remove the needle foot ④ .
6. Remove the needle plate ⑤ .
7. Remove the feed dog ⑥ .
8. Remove the opener ⑦ .
9. Remove the bobbin ⑧ or the cap.
10. Tilt back the machine head.
11. Loosen the three set screws ⑨ .
12. Turn the machine pulley to move the needle bar to its highest position. www.garudan.cz
13. Remove the rotary hook ⑩ .
MP03700EN_181101 48
© ANITA
Installation
1. Insert the new rotary hook into the mounting hole ⑪ .
2. Install the needles ① .
3. While referring to pages 34, adjust so that the rotary hook tip ⑭ is aligned with the center of the needle
① when the needle bar is raised from its lowest potation until reference line ⓑ at the bottom of the needle bar ⑫ is aligned with the lower edge of the needle bar supporter ⑬ tighten ten the three screws ⑨ .
NOTE:
In order to prevent the torque from becoming too high, tighten all three screws fully.
⑨ less than fully, and then turn them all again to tighten them www.garudan.cz
MP03700EN_181101 49
© ANITA
4. Return the machine head to its original position.
5. Install the opener ⑦ .
6. Install the feed dog ⑥ .
⑤ .
④ .
9. Loosen the set screws ⑨ and move the rotary hook ⑩ up and down to adjust so that the clearance between
⑩ and the needle plate ⑤ is 1.3mm.
NOTE Do not turn the rotary hook while the set screws ⑨ are loosened, otherwise change the timing between the needle and the rotary hook.
⑨ .
⑮ and move the that the clearance between the rotary hook ⑩ opener
and the opener pulled as far as it will go in the direction of the arrow.
⑦ to the left or right to adjust 50
⑦ is 0.2mm whe ⑦ is
12. Tighten the set screw ⑮ .
13. Install the slide plates ② .
2 drops of oil to the left and right rotary hook races ⑯ . ubrication amount while referring to page 34 .
www.garudan.cz
MP03700EN_181101 50
© ANITA
Replacing the upper thread tension assembly:
Removal
1. Open the faceplate.
2. Loosen the screw ① .
3. Loosen the screw ② and then remove the upper thread tension assembly ③
Installation
1. Install the new upper thread tension
. assembly ③ and tighten it with the screw
② .
2. Adjust the tension of the thread take-up spring ④ (Refer to page 28)
3. Tighten the screw ①
4. Close the face plate.
. www.garudan.cz
MP03700EN_181101 51
12. TROUBLESHOOTING GUIDE
Be sure the check the following before calling an authorized service station.
Problem
1. Sewing machine pulley doesn’t turn.
Where to check
Is a breaker or fuse blown?
Is the power cord disconnected?
© ANITA
Page
2. Needle thread and bobbin thread break.
3. Seams don´t match.
Is the needle tip bent? Is the needle tip blunt?
If the needle tip is bent or broken, replace the needle.
Is the needle properly installed?
If it is incorrect, install the needle correctly.
Is the machine properly threader?
If it is incorrect, thread the thread correctly.
Is the rotary hook properly lubricated?
If the oil level is below the lower reference line in the oil sight glass, add more oil.
Is dust or thread in the rotary hook?
Clean the rotary hook.
Is the upper thread tension too strong or too weak?
Adjust the upper thread tension.
Is the rotary hook, feed dog or other part damaged?
If they are damaged, smooth them with an oiled grindstone or replace the damaged parts.
www.garudan.cz
Is the presser foot pressure too weak?
Adjust the presser foot pressure.
Is the feed dog too low?
Adjust the feed dog height.
Is the bobbin scratched?
If the bobbing is damaged, smooth it with an oiled grindstone or replace it.
19
20
13
19
19
13
13
14
12
10
MP03700EN_181101 52
© ANITA
Problem
4. Skipped stitches.
5. Poor thread tightening.
6. Broken needles.
Where to check
Is the needle tip bent? Is the needle tip blunt?
If the needle tip is bent or broken, replace the needle.
Is the needle properly installed?
If it is incorrect, install the needle correctly.
Is the machine properly threaded?
If it is incorrect, thread the thread correctly.
Is the presser foot pressure too weak?
Adjust the presser foot pressure.
Is the machine properly threaded?
If it is incorrect, thread the thread correctly.
Is the thread take-up spring operation range too small?
Adjust the operation range of the thread take-up spring.
Is the needle thread tension and bobbin thread tension too low?
Adjust the upper and lower thread tension.
Is the bobbin scratched?
If the bobbin is damaged, smooth it with an oiled grindstone or replace it.
Is the material being pushed with excessive force during sewing?
If the needle tip is bent or broken, replace the needle.
Dose the needle pass the center of the needle hole in the feed dog?
Check the needle down position. If the needle dose not drop into the middle of the needle hole in the feed dog re-install the feed dog.
[GF-2207-147, GF-2207-447] www.garudan.cz
of broken needle sticking in the material. If the needle breaks, search for all places until the whole of the needle is found again.
Caution
If problems 2 to 6 above are not due to the cause on the right, check the needle and feed timing, or the needle and rotary hook timing.
If the above suggestions do not remedy the problem, turn off the power and contact the of purchase.
14
22
17-18
27-28
Page
13
13
14
17
MP03700EN_181101 53
advertisement
* Your assessment is very important for improving the workof artificial intelligence, which forms the content of this project
Related manuals
advertisement
Table of contents
- 4 Safety Instrictions
- 7 1. Names of Major Parts
- 8 2. Machine Specifications
- 9 3. Optional Parts
- 10 4. Installation
- 17 5. Preparation Before Sewing
- 23 6. Sewing
- 24 7. Thread Tension
- 26 8. Cleaning
- 27 9. Standard adjustments
- 44 10. Replacing Gauge Parts (Changing the Needle Width)
- 48 11. Installing Optional Parts
- 52 12. Troubleshooting Guide