advertisement
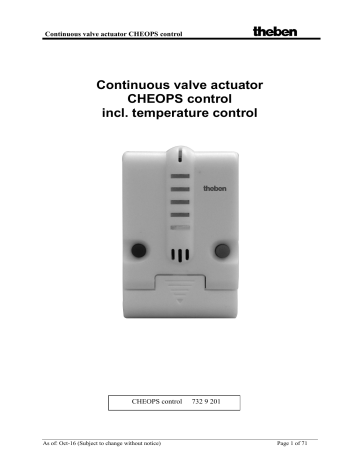
Continuous valve actuator CHEOPS control theben
Continuous valve actuator
CHEOPS control incl. temperature control
CHEOPS control 732 9 201
As of: Oct-16 (Subject to change without notice) Page 1 of 71
Continuous valve actuator CHEOPS control theben
Contents
Strategy 2, Automatic (only for devices from software version 63/ 61 drive) ..... 43
Strategy 3, with defined valve stroke. (Only for devices from software version
Incremental set point temperature adjustment via keys ....................................... 51
Incremental set point temperature adjustment via Object 6 ................................. 51
Direct set point temperature adjustment via Object 1 .......................................... 51
As of: Oct-16 (Subject to change without notice) Page 2 of 71
Continuous valve actuator CHEOPS control theben
As of: Oct-16 (Subject to change without notice) Page 3 of 71
Continuous valve actuator CHEOPS control theben
1 Functional characteristics
The Cheops control drive actuator is both a continuous EIB room temperature controller and an actuator, i.e. Cheops control measures the current room temperature (actual value) and controls the radiator valve, in order to achieve the desired room temperature (set point value).
The valve position can be transferred on the bus. If a room accommodates several radiators, these can be equipped with “Cheops drive” actuators and actuated by Cheops control.
In addition to the heating system, Cheops control can also control a cooling system.
In order to simply adapt to the set point values in respect of living comfort and energy saving,
Cheops control has 4 operating modes:
•
Comfort
•
Standby
•
Night mode
•
Frost protection mode
A set point value is assigned to each operating mode.
Comfort mode is used when the room is occupied
In Standby mode, the set point value is reduced slightly. This operating mode is used when the room is not occupied but is expected to be shortly.
In Night mode, the set point value is drastically reduced, since the room is not expected to be occupied for several hours.
In Frost protection mode, the room is controlled to a temperature that eliminates the risk of damage to the radiators through freezing at low outdoor temperatures:
This can be desirable for 2 reasons:
- The room is not occupied for several days.
- A window has been opened and no further heating is required for the time being.
The operating modes are usually controlled by a timer.
For optimum control, however, presence indicator and/or presence button and window contacts are recommended.
See also Chapter headed " Determining the current set point value ".
As of: Oct-16 (Subject to change without notice) Page 4 of 71
Continuous valve actuator CHEOPS control theben
1.1 Operation
For operation and display functions, Cheops control is fitted with 5 LEDs, a blue and a red button. The top 3 LEDs are red, the bottom 2 LEDs are blue.
The LEDs show the set point temperature, i.e. the desired room temperature.
The middle LED illuminates when the temperature determined by the Basic set point value
has been reached.
The 2 buttons can be used to adapt the set point value to suit the individual requirements of
the room user.
Pushing the red button increases the set point value by one programmed increment , this is
possible twice from the basic set point value (middle LED).
Pushing the blue button reduces the set point value by increments.
If Cheops control is not in comfort mode, or if the set point value has already been decreased by 2 increments from the basic set point value, the bottom LED illuminates.
This indicates to the room user that the set point value cannot be further decreased.
When the red button is pushed, Cheops control automatically finds the correct function that increases the set point value - this depends on the operating mode prior to the button being pushed:
Table 1
Operating mode prior to pushing the red button
Comfort mode
Standby
Night and frost protection
Effect of pushing the red button
Set point value increased by one increment
Switches to comfort operating mode by setting the presence object - without time limit
Switches to comfort operating mode by setting the presence object – for set time and comfort extension
(see "Comfort extension in night mode" on the
" Operating mode " parameter page)
In comfort mode, the set point value can now be changed in increments as usual.
If the blue button is pressed until the bottom blue LED illuminates, the presence object is reset and the original operating mode is restored.
As of: Oct-16 (Subject to change without notice) Page 5 of 71
Continuous valve actuator CHEOPS control theben
1.2 Benefits of Cheops Control
•
Continuous P/PI room temperature control
•
Heating mode + actuation of a cooling system via the EIB
•
Alternative actuation of a second heating step with switching or continuous actuating
value
•
2 buttons for set point offset (up to +/- 3K)
•
Infinite valve adjustment through continuous actuating value
•
Internal temperature measurement possible via either EIB or an external temperature sensor
•
Valve position or set point value offset readout
•
Emergency program on actual value failure
•
Establishing the maximum actuating value
•
Valve protection program
•
External interface for window and presence contacts
•
•
Precise adjustment to each valve
•
Operation with both standard and inverted valves
•
Site function for operation without application
•
Large valve stroke enables adjustment to almost all valves
•
Simple assembly with any valve adapter
1.2.1 Special features
•
If the room temperature is measured via an external sensor or received via an object, Cheops control can start an emergency program if the sensor or temperature transmitter fails.
•
Determining the maximum actuating value (= maximum position)
To adapt the forward flow temperature, Cheops drive can send an acknowledgement to the heating boiler regarding the current power requirement.
This can reduce its temperature if the requirement drops.
•
Window and presence contact inputs
Cheops drive has 2 external inputs, one for a presence contact and one for a window contact. These inputs can be used as an actuator for frost protection or comfort mode.
As of: Oct-16 (Subject to change without notice) Page 6 of 71
Continuous valve actuator CHEOPS control theben
1.3 Hardware versions
There are 2 hardware versions of Cheops, up to 2008 and from 2008 , with some different features.
The version up to 2008 (left) has two circuit boards mounted at right-angles to each other.
The version from 2008 (right) only has one circuit board.
The different features of the two versions are indicated in this manual by "up to 2008" and "from 2008".
Distributed software (firmware) versions (displayed by the LEDs see Reading the software version number ):
Devices up to 2008
V110
V121
Devices from 2008
V44 since March 2008
V63 since December 2008
As of: Oct-16 (Subject to change without notice) Page 7 of 71
Continuous valve actuator CHEOPS control theben
1.4 Differences
Devices up to 2008
•
Only one calibration strategy
•
The former positions are adopted after reset
(small calibration)
•
Valve protection every 24 hours if there is no change in actuating value.
•
Site function always active (25% after adjustment)
•
Error code in $1FB
•
Continuous light with known errors
From 2008: Version V 44
•
New calibration strategy: End position via force with fixed stroke.
•
Cheops always performs two calibration runs and compares the results
•
Site function is fully deleted after the first download.
•
No more error codes
•
Changed LED display during calibration run
•
Corrective measures are automatically started in the event of an error.
From 2008: from V63 / V61 drive
•
New calibration strategy:
Starting point as position, end point via force.
•
Valve protection only every 7 days
•
Calibration strategy code filed in address in $1FB (N.B.:
Number can look like the earlier error codes).
As of: Oct-16 (Subject to change without notice) Page 8 of 71
Continuous valve actuator CHEOPS control theben
2 Technical data
2.1 General
Voltage supply:
Permitted working temperature:
Bus voltage
0°C ...+ 50°C
Runtime: < 20s / mm
Controlling torque:
Max. control stroke:
> 120 N
7.5 mm (linear movement)
Detection of valve limit stops: Automatic
Linearisation of characteristic valve curve: Possible via software
Protection class: III
Protection rating:
Dimensions:
Adapter rings suitable for:
EN 60529: IP 21
HxWxD 82 x 50 x 65 (mm)
Danfoss RA, Heimeier, MNG,
Schlösser from 3/93, Honeywell, Braukmann,
Dumser (Distributor), Reich (Distributor),
Landis + Gyr, Oventrop, Herb, Onda
Typical power consumption Motor off: < 5 mA
Motor on, seal not pressed: 10 mA
Motor on, seal pressed: 12..15 mA
(depending on force)
As of: Oct-16 (Subject to change without notice) Page 9 of 71
Continuous valve actuator CHEOPS control theben
3 The "CHEOPS control V1.2"
Application Program
3.1 Selection in the product database
Manufacturer Theben AG
Product family Valve actuators
Product type Valve actuator with controller
Program name Cheops control V1.2
Download the application from: http://www.theben.de
3.2 Parameter pages
Table 2
Function
Description
Selection of control functions, standard and user-defined settings
Valve characteristics, fine setting of valve parameters, special characteristic valve curves, valve protection
Set point value after loading the application, values for night/frost mode, dead zone, additional step etc.
Own characteristic curve of valve
Function of LEDs and buttons
Selection, calibration, emergency program on failure
Heating parameters, controller type, actuating value limits etc.
Cooling parameters, controller type etc.
Presence and window status considered.
Operating mode after download
Configure inputs for window / presence contact and actual value
Control parameters, hysteresis reduction, bandwidth etc.
Prof. parameters for valves with known characteristic curve
Parameters for high-end linear valve
linear characteristic valve curve
As of: Oct-16 (Subject to change without notice) Page 10 of 71
Continuous valve actuator CHEOPS control theben
3.3 Communication objects
3.3.1 Object characteristics
Cheops control features 12 communication objects.
Objects 2, 3, 4, 5, 6 and 8 can assume various functions, depending on the configuration
Table 3
No. Function
0
1
Define set point temperature Basic set point value shift set point temperature
Transmit actual value
2
Input actual value
Object name Type Response
2 byte Receive
EIS5
Manual shift of set point value 2 byte
EIS5
Actual value
2 byte
EIS5
Send /
Receive
Send
Receive
Pre-selection of operating
3 mode
1 = night, 0 = standby
Input for presence signal
4
1 = comfort
Input of window state
5
1 = frost protection
1 = decrease/0 = increase
Pre-selection of operating mode
Night < - > Standby
Presence
Comfort
Window state
Frost/heat protection adjustment of set point temperature maximum actuating value
1 byte
KNX Receive
1 bit
1 bit
Send / receive
1 bit Receive
1 bit Send / receive
1 bit Receive
1 bit Receive
Calculates maximum
6 actuating value
0 .. 100%
10 Transmit
11 Heating/cooling
Actual valve position
7 Current actuating value heating actuating value heating
8
Actuating value in cooling mode
Switching actuating value actuating value cooling
Actuating value of additional heating
Continuous actuating value Actuating value of additional heating
9 Transmit Current set point value
Current operating mode
Switchover
1 byte
EIS6
1 byte
EIS6
1 byte
EIS6
Send / receive
Send
Send
1 byte
EIS6
Send
1 bit Send
1 byte
EIS6
2 byte
EIS5
Send
Send
1 byte
KNX
Send
1 bit Receive
As of: Oct-16 (Subject to change without notice) Page 11 of 71
Continuous valve actuator CHEOPS control theben
3.3.2 Object description
•
Object 0 "Basic set point value"
The Basic set point value is first specified via the application at start-up and stored in the
"Basic set point value" object.
It can then be re-specified at any time via Object 0.
If the bus voltage fails, this object is backed up and the last value is restored when the bus voltage returns.
•
Object 1 " Manual shift of set point value "
The object sends and receives a temperature differential in EIS 5 format. The desired room
temperature (current set point value) can be adjusted from the Basic set point value by this
differential.
The following applies in comfort operation (heating): current set point value (Obj. 9 = Basic set point value (Obj. 0) + manual set point value offset
(Obj. 1)
This value can be changed in increments by pressing the buttons on the device or via
Object 6. The value thus changed is then sent.
It is, however, possible to send the set point value offset directly to this object, this set point value offset is then indicated on the LEDs.
Values outside the programmed range are not taken into consideration.
The offset always relates to the basic set point value that is either configured or programmed
via 0 and not the current set point value.
•
Object 2 "Actual value"
Table 4
Selection: Input for actual value Function
Internal sensor Sends the temperature currently being measured by the
External sensor (Interface E2) sensor (if sending through configuration is permitted)
Actual value object Receives the current room temperature from an external
EIB temperature sensor via the bus
As of: Oct-16 (Subject to change without notice) Page 12 of 71
Continuous valve actuator CHEOPS control theben
•
Object 3 "Pre-selection of operating mode" / "Night <-> Standby"
The function of this object depends on the "Objects for determining operating mode"
parameter on the " Operating mode " parameter page.
Table 5
Objects for determining the operating mode
window, window status
Function
With this setting, the object is a 1 byte object. One of 4 operating modes can be directly activated.
1 = comfort, 2 = standby, 3 = night,
4 = frost protection (heat protection)
The details in brackets relate to the cooling operation
With this setting, the object is a 1 bit object. Night or standby operating mode can be activated.
0=standby 1=night
* If a different value from 1...4 is sent to object 3, then operating mode 1 = comfort is adopted
•
Object 4 "Presence / comfort"
The function of this object depends on the "Objects for determining operating mode"
parameter on the " Operating mode " parameter page.
Table 6
Objects for determining the operating mode
window, window status
Function
The status of a presence indicator (e.g. sensor, movement indicator) can be received via this object.
A 1 on this object activates the comfort operating mode.
If a presence indicator is connected to Interface E2 ,
its status is sent via this object to the bus.
A 1 on this object activates the comfort operating mode.
This operating mode takes priority over night and standby operation.
Comfort operation is deactivated by sending an 0 to the object.
As of: Oct-16 (Subject to change without notice) Page 13 of 71
Continuous valve actuator CHEOPS control theben
•
Object 5 "Window state" / "Frost/heat protection"
The function of this object depends on the "Objects for determining operating mode"
parameter on the " Operating mode " parameter page.
Table 7
Objects for determining the operating mode
window, window status
Function
The status of a window contact can be received via this object.
A 1 on this object activates the frost / heat protection operating mode.
If a window contact is connected to Interface E1 , its
status is sent via this object to the bus.
A 1 on this object activates the frost protection operating mode.
During the cooling operation, the heat protection mode is activated.
The frost/heat protection operating mode takes top priority.
•
Object 6 „"adjustment of set point temperature" / "maximum actuating value" /
"Actual valve position"
The function of this object depends on the "Function of Object 6" on the " Device setting "
parameter page.
The frost/heat protection mode remains until it is cleared again by a 0.
Table 8
Function of Object 6 Function
A 0 on the object results in an increase in the set point value and is equivalent to pressing the red button.
A 1 on the object results in a decrease in the set point value and is equivalent to pressing the blue button.
The increment is set on the "Operation" parameter page. The achieved offset can be reported by
As of: Oct-16 (Subject to change without notice) Page 14 of 71
Continuous valve actuator CHEOPS control theben
Continued:
Function of Object 6
Determine the maximum actuating value
Sends the actual valve position
Function
This object has 2 functions here:
1.
Receives actuating values from the other actuators (other rooms), in order to be able to compare them with its own.
2.
Sends its own actuating value to the heating boiler, if it is higher than the others.
(See also: Determining maximum actuating value)
Sends the current valve position (0..100%).
This function can be enabled (e.g. diagnosis) as and when required.
This function is not required for normal operation.
•
Object 7 "Current actuating value, heating"
This object is present only when selected on the " Heating control " page as follows.
The current actuating value (0…100%) can then be sent to other continuous actuators (Cheops drive) in the same room/control circuit.
If you wish to read out Object 7 via the bus, Object 8 must not be present ("Used control
functions" on the " Settings " parameter page set to "Heating control only"). The
"Read" flag must be set.
If you wish to read out Object 8 via the bus, this parameter must be set to "Not present".
•
Object 8 "actuating value cooling"/"Actuating value of additional heating"
The function of this object depends on the "Input for actual value" parameter on the " Settings "
parameter page.
Table 9
Used control functions
Heating and cooling
2-step heating with switching additional step
2-step heating with continuous additional step
Function
Sends the cooling actuating value to control a cooling ceiling, fan coil unit etc.
Sends the switching command to control the additional step (on/off)
Sends the continuous actuating value to control the additional step (0…100%)
As of: Oct-16 (Subject to change without notice) Page 15 of 71
Continuous valve actuator CHEOPS control theben
Note:
In the "Heating control" setting, the object is not available because neither the cooling function nor the additional step are present.
If you wish to read out Object 8 via the bus, Object 7 must be hidden (see above) and the
"Read" flag must be set.
•
Object 9 "Current set point value"
This object sends the Current set point temperature as a EIS 5 telegram (2 bytes) on the bus.
The send response can be set on the "Heating control" parameter page.
•
Object 10 "Current operating mode"
This object sends the current operating mode as a 1 byte value.
The send response can be set on the "Operating mode" parameter page.
The operating modes are coded as follows:
Table 10
Value Operating mode
1 Comfort
2
3
Standby
Night
4 Frost protection/heat protection
•
Object 11 "Switchover"
This object is available if an automatic switching between heating and cooling is not required.
The setting is made on the " Cooling control " parameter page
The cooling operation is forced via a 1 and the heating operation via a 0.
As of: Oct-16 (Subject to change without notice) Page 16 of 71
Continuous valve actuator CHEOPS control theben
3.4 Parameters
3.4.1 Settings
Table 11
Designation
Control
Values
Standard
User-defined
Control functions
Operation
Operating mode
Heating control only
Heating and cooling
additional step
2-step heating with continuous
additional step
Standard
User-defined
Standard
User-defined
Meaning
For simple applications
For specific setting of the control parameters and special applications such as heating/cooling or
User-defined control:
Heating operation only
A cooling unit can also be controlled via the bus (Object
8)
A main step (typically floor heating) and an additional step (On/Off) can be controlled.
A main step (typically floor heating) and an additional step (radiator) can be controlled.
Default setting
Opens the parameter page
Default settings
Opens the parameter page
As of: Oct-16 (Subject to change without notice) Page 17 of 71
Continuous valve actuator CHEOPS control theben
Continued:
Designation
Device settings
Function of external interface
Values
Standard
User-defined
None
E1: Window contact, E2:
Presence
E1: Window contact, E2: Actual value
E1: Window contact, E2: None
Meaning
Default settings
Opens the parameter page
Specifies whether the external interface is occupied by window presence contact or an external temperature sensor is connected.
Note:
IF E2 is declared as actual value input, the "Input for actual value" selection cannot be changed on the "Actual value" parameter page.
As of: Oct-16 (Subject to change without notice) Page 18 of 71
Continuous valve actuator CHEOPS control theben
3.4.2 Set point values
Table 12
Designation
Basic set point value after download of application
Reduction in standby operating mode at heating
Values
18 °C, 19 °C, 20 °C,
21 °C , 22 °C, 23 °C,
24 °C, 25 °C
0,5 K, 1 K, 1,5 K
2 K , 2.5 K, 3 K
3,5 K, 4 K
Reduction in night operating mode at heating
3 K, 4 K, 5 K
6 K, 7 K, 8 K
Set point value for frost protection mode
Transmission of current set point values
3 °C, 4 °C, 5 °C
6°C , 7 °C, 8 °C
9 °C, 10 °C
No cyclical transmission
Every 2 min
Every 3 min
Every 5 min
Every 10 min
Every 15 min
Every 20 min
Every 30 min
Every 45 min
Every 60 min
Meaning
Output set point value for the
temperature control.
Example: with a basic set point value of 21 o
and a
2K reduction in heating operation, Cheops control controls at a set point value of
21 – 2 = 19°C
By what value should the temperature be reduced in night mode?
Preset temperature for frost protection operation in heating mode
(Heat protection operation applies in cooling mode).
How often should the
currently valid Set point value
be sent?
Send only at a change.
Send cyclically
As of: Oct-16 (Subject to change without notice) Page 19 of 71
Continuous valve actuator CHEOPS control theben
Continued:
Designation Values Meaning
Parameters for heating / cooling operation
Dead zone between heating and cooling
1 K, 1,5 K, 2 K,
2,5 K, 3 K, 3,5 K
Specifies the interval between set point value in heating and
4 K, 4,5 K, 5,5 K
6 K cooling operations.
Example with set point value
Cheops will only start cooling when the temperature
≥
Set point value + Dead zone is, i.e. 21°C + 2K = 23°C.
Increase in standby mode at cooling
0,5 K, 1 K, 1,5 K
2 K , 2.5 K, 3 K
3,5 K, 4 K
The temperature is increased in standby mode during cooling operation
See increase in standby mode Increase in night mode at cooling
Set point value for heat protection at cooling
3 K, 4 K, 5 K
6 K, 7 K, 8 K
42 °C (no heat protection)
29 °C, 30 °C, 31 °C
32 °C, 33 °C, 34 °C
35 °C
The heat protection represents the maximum permitted temperature for the controlled room. It performs the same function on cooling as frost protection mode on heating, e.g. saves energy while prohibiting non-permitted temperatures
Important:
In principle, Cheops control will not allow a set point value above 42 o
C (even via bus set point value definition)
As of: Oct-16 (Subject to change without notice) Page 20 of 71
Continuous valve actuator CHEOPS control theben
Continued:
Designation
Current set point value in comfort mode
Differential between main step and additional step
Values
Transmit mean value between heating and cooling
Transmit actual temperature setpoint
(Heating < > Cooling)
Meaning
Feedback of current set point value via the bus:
Same value in comfort operation mode during both heating and cooling operation, i.e.:
dead zone sent, to prevent room users becoming irritated.
Example with basic set point value of 21°C and dead zone of 2K:
Mean value= 21°+1K =22°C
Although control takes place at 21 o
C and/or 23°C
The set point value actually being controlled is always sent.
Example with basic set point value of 21°C and dead zone of 2K:
During heating and cooling,
21°C and basic set point value
+ dead zone are sent respectively (21°C + 2K =
23°C)
1 K , 1,5 K, 2 K,
2.5 K, 3 K, 3.5 K,
4 K
Specifies the negative interval between the current set point value and the set point value of the additional step.
Example with basic set point value of 21°C and 1K differential:
Main step controls using the basic set point value and the additional step controls using the basic set point value – 1K
= 20°C
As of: Oct-16 (Subject to change without notice) Page 21 of 71
Continuous valve actuator CHEOPS control theben
3.4.3 Actual value
Table 13
Designation
Input of actual value
Temperature offset for internal sensor
(in 0,1K, -64...63)
Values
Internal sensor object Actual value
Manual input -64.. 63
Transmission of actual value at change
Does not send by 0,2 K, 0,3 K by 0.5 K , 0.7 K by 1 K, 1.5 K
2 K
Meaning
Cheops control can obtain its actual value from three sources. Selection can be made from 2 such sources: fitted sensor bus (Object 2).
An external sensor can be selected via the "Function of external interface" parameter
page. In this case, there is no option to select between internal sensor and actual value object.
Positive or negative correction of measured temperature in 1/10 K increments
Example: Cheops sends
20.3°C. A room temperature of 21.,0°C is measured using a calibrated thermometer. In order to increase the temperature of Cheops to 21
°C, an "7" (i.e. 7 x 0.1K) must be entered.
Cheops sends 21.3°C. 20.5°C is measured. In order to reduce the temperature of
Cheops to 20.5 °C, an "-8" (i.e. -8 x 0.1K) must be entered.
Is the current room temperature to be sent?
If so, from which minimum change should this be sent again?
This setting keeps the bus load as low as possible.
As of: Oct-16 (Subject to change without notice) Page 22 of 71
Continuous valve actuator CHEOPS control theben
Continued:
Designation Values
Transmission of actual value no cyclical transmission
Every 2 min
Every 3 min
Every 5 min
Every 10 min
Every 15 min
Every 20 min
Every 30 min
Every 45 min
Every 60 min
Temperature offset for
64...63)
Position in case of failure of actual value or sensor
Meaning
How often should the values be sent, regardless of the temperature changes?
Parameters for external sensors
Manual input -64.. 63 See above, Temperature offset for internal sensor
0%
10%
20%
30%
40%
50%
60%
70%
80%
90%
100%
Continued control with internal sensor
Cheops control continuously monitors the function of the external sensor when selected.
If the line to this sensor is interrupted or short-circuited,
Cheops control can either assume a fixed position
(emergency program) or switch to an integrated sensor until the fault is cleared.
As of: Oct-16 (Subject to change without notice) Page 23 of 71
Continuous valve actuator CHEOPS control theben
3.4.4 Heating control
Table 14
Designation Values
Setting of control parameters Via type of system
User-defined
Type of system
Minimum actuating value in heating mode
Behaviour at minimum actuating value underflow
(heating mode)
0%, 5%, 10%
15%, 20%, 25%
30%, 40%
0%
0 % = 0 % otherwise min. actuating value
Object “actuating value heating”
Transmission of actuating value heating
Radiator heating floor heating available not available
At change by 1%
At change by 2 %
At change by 3 %
At change by 5 %
At change by 7 %
At change by 10 %
At change by 15 %
Meaning
Standard application
Prof. application Self-
PI control with:
Integrated time = 150 minutes
Bandwidth = 4 k
Integrated time = 210 minutes
Bandwidth = 6 k
Smallest permitted actuating value (Exception: actuating
value of 0% is always used)
Run to 0% as soon as the defined min. actuating value is underrun.
Runs to the min. actuating value as long as the value is greater than 0% and smaller or equivalent to the min. actuating value.
However, if a actuating value of 0% is required (set point temperature reached), Cheops control returns to 0%.
The heating actuating value is not to be sent on the bus
(Object 8 can be read).
The heating actuating value is required to control other actuators (Cheops drive).
After how many % change* in the actuating value is the new value to be sent.
Small values increase control accuracy but also the bus load.
As of: Oct-16 (Subject to change without notice) Page 24 of 71
Continuous valve actuator CHEOPS control theben
Continued:
Designation
Transmission of actuating value heating
Proportional band of heating control
Integral action time constant of heating controller
Values no cyclical transmission
Every 2 min
Every 3 min
Every 5 min
Every 10 min
Every 15 min
Every 20 min
Every 30 min
Every 45 min
Every 60 min
User-defined parameters
2 K , 2.5 K, 3 K
3,5 K, 4 K, 4,5 K
5 K, 5,5 K, 6 K
6.5 K, 7 K, 7.5 K
8 K, 8.5 K
Only proportional controller
30 min, 45 min, 60 min
75 min, 90 min, 105 min
120 min, 135 min, 150 min
165 min, 180 min, 195 min
210 min, 225 min
Meaning
How often is the current heating actuating value to be send, regardless of changes?
Prof. setting to adapt the control response to the room. see Appendix
For PI control only:
The integrated time determines the reaction time of the control.
For radiators, times of approx.
150 min and for floor heating, longer times of approx. 210 min are recommended.
These times can be adapted to suit particular circumstances.
If the heating is overdimensioned and therefore too fast, shorter values should be used. Conversely, underdimensioned heating (slow) benefits from longer integrated times.
*Change since last sending
As of: Oct-16 (Subject to change without notice) Page 25 of 71
Continuous valve actuator CHEOPS control theben
3.4.5 Cooling control
Table 15
Designation Values
Setting of control parameters Via type of system
User-defined
Type of system
Cooling ceiling
Fan Coil Unit
Transmission of actuating value cooling
Switch over between heating and cooling
On change by 1%
On change by 2 %
On change by 3 %
On change by 5 %
On change by 7 %
On change by 10 %
On change by 15 %
Automatically via object
Meaning
Standard application
Prof. application Self-
PI control with:
Integrated time = 90 minutes
Bandwidth = 4 k
Integrated time = 180 minutes
Bandwidth = 4 k
After how many % change* in the actuating value is the new value to be sent.
Small values increase control accuracy but also the bus load.
Cheops control automatically switches to cooling mode when the actual temperature is above the threshold: set point value + dead zone.
Cooling mode can be activated only on the bus side
Cooling mode remains off for as long as this object is reset
(=0).
Proportional band of cooling controller
User-defined parameters
2 K, 2,5 K, 3 K
3,5 K, 4 K , 4,5 K
5 K, 5,5 K, 6 K
6.5 K, 7 K, 7.5 K
8 K, 8.5 K
Prof. setting to adapt the
room.
Large values cause finer changes to the actuating values with the same control deviation and a more precise control than smaller values.
As of: Oct-16 (Subject to change without notice) Page 26 of 71
Continuous valve actuator CHEOPS control theben
Continued:
Designation
Integral time of the cooling controller
Values
Pure P control
30 min, 45 min, 60 min
75 min, 90 min , 105 min
120 min, 135 min, 150 min
165 min, 180 min, 195 min
210 min, 225 min
Meaning see Appendix
For PI control only:
The integrated time determines the reaction time of the control.
These times can be adapted to suit particular circumstances.
If the cooling system is overdimensioned and therefore too fast, shorter values should be used. Conversely, underdimensioned cooling (slow) benefits from longer integrated times.
*Change since last sending
As of: Oct-16 (Subject to change without notice) Page 27 of 71
Continuous valve actuator CHEOPS control theben
3.4.6 Additional heating step
See also Appendix: 2-step heating
Table 16
Designation
Hysteresis
Values
0,3 K
0,5 K
0,7 K
1 K
1.5 K
Feedback of hysteresis controlled with switch point
Cyclical transmission of additional heating system
None
0,1 K/min
0,2 K/min
0.3 K/min
Meaning
off point (set point value) and the re-switch on point (Set point value – hysteresis).
The hysteresis prevents constant switch on/off.
The feedback causes a gradual decrease in the
This increases control accuracy.
The hysteresis is equivalent to the programmed value for each switch-off and is gradually reduced by the feedback process. The hysteresis can reduce to 0 over prolonged periods of switch-off.
At the next switch-on, it is reset to the configured value.
How often should the switching status of the additional step be sent?
No cyclical transmission
Every 2 min
Every 3 min
Every 5 min
Every 10 min
Every 15 min
Every 20 min
Every 30 min
Every 45 min
Every 60 min
As of: Oct-16 (Subject to change without notice) Page 28 of 71
Continuous valve actuator CHEOPS control theben
Continued:
Designation
Proportional band of additional heating system
Values Meaning
Parameters for continuous additional step
2 K, 2,5 K, 3 K
3,5 K, 4 K , 4,5 K
Prof. setting to adapt the control response to the room.
5 K, 5,5 K, 6 K
6.5 K, 7 K, 7.5 K
8 K, 8.5 K
Large values cause finer changes to the actuating values with the same control
Transmission of actuating value of additional heating system
On change by 1%
On change by 2 %
On change by 3 %
On change by 5 %
On change by 7 %
On change by 10 %
On change by 15 % deviation and a more precise control than smaller values.
After how many % change* in the actuating value is the new value to be sent.
Small values increase control accuracy but also the bus load.
*Change since last sending
As of: Oct-16 (Subject to change without notice) Page 29 of 71
Continuous valve actuator CHEOPS control theben
3.4.7 Operation
Table 17
Designation
Function of LEDs
Values
None
Indication of set point value shift
Fixed indication of position
Time-limited display of set point val. shift
Enabled
Disabled
Meaning
The LEDs are always off
The middle LED illuminates if no offset has been entered.
The remainder indicate an
upward or downward offset increment
The 5 LEDs show the current valve position as follows
(from bottom to top):
All OFF: Position 0%
1st LED: Position > 0…20%
2nd LED: Position >
20..00,40%
3rd LED: Position >
40..00,60%
4th LED: Position >
60..00,80%
5th LED: Position >
80..0.100%
The current set point value offset is displayed for 10s after a key is pressed.
Otherwise, all LEDs remain off.
The keys can be operated.
Hint: Pushing both keys at the same time displays the current valve position on the LEDs
(see above, fixed position display).
Safeguards against undesired operation
As of: Oct-16 (Subject to change without notice) Page 30 of 71
Continuous valve actuator CHEOPS control theben
Continued:
Designation
Maximum shift of set point value
Values
+/-1 K (1 push button stroke corresponds to 0,5 K)
+/-2 K (1 push button stroke corresponds to 1,0 K)
+/-3 K (1 push button stroke corresponds to 1,5 K)
+/-4 K (1 push button stroke corresponds to 2,0 K)
+/-5 K (1 push button stroke corresponds to 2.5 K)
Meaning
What is the max. amount by which the the set point value
is the change at each increment/key pressure?
As of: Oct-16 (Subject to change without notice) Page 31 of 71
Continuous valve actuator CHEOPS control theben
3.4.8 Operating mode
Table 18
Designation
Objects to select operating mode
Operating mode after download of application
Type of presence sensor
Values
presence, window state
Frost protection
Night reduction
Standby
Comfort
Presence detector
Push button
Comfort extension during night operation
(with presence key)
Comfort mode extension via red push button in night mode
None
30 min
1 hour
1,5 hours
2 hours
2,5 hours
3 hours
3.5 hours
Meaning
Cheops control can also respond to window and presence contact.
Conventional setting
Operating mode after start-up or re-programming.
The presence sensor activates comfort mode
Comfort mode as long as presence is detected
1.
The presence object is reset on change of operating mode definition object
(Object 3).
2.
If the presence object is set during night operation, it is reset after the configured comfort extension finishes (see below).
Party switching: enables the red key or presence key to switch
Cheops control from night to comfort mode for a certain period.
As of: Oct-16 (Subject to change without notice) Page 32 of 71
Continuous valve actuator CHEOPS control theben
Continued:
Designation
Transmission of current operating mode
Values
No cyclical transmission
Every 2 min
Every 3 min
Every 5 min
Every 10 min
Every 15 min
Every 20 min
Every 30 min
Every 45 min
Every 60 min
Meaning
How often should the current operating mode be sent?
As of: Oct-16 (Subject to change without notice) Page 33 of 71
Continuous valve actuator CHEOPS control theben
3.4.9 Device settings
Table 19
Designation
Direction of control action of valve
Strategy for identifying valve
Values
Normal (closed with pushed tappet)
Inverted, (open with pushed tappet)
Standard
Automatic
Meaning
For all standard valves
Adjustment to inverted valves
Standard identification for most valve models.
With defined valve stroke
Only for devices from software V63.
The valve is closed with a pre-defined force (see below,
"Closing force for" parameter).
The 0 % position is checked at the valve with every run and the “100 % open” position is measured at the valve.
Only for devices from software V63.
The 0 % position is checked at the valve with every run and the
100 % (open) position is established from the set stroke.
As of: Oct-16 (Subject to change without notice) Page 34 of 71
Continuous valve actuator CHEOPS control theben
Continuation:
Designation
Additional pressing of rubber seal in 1/100mm
Closing force for
Closing force for
Values
0..79
Strategy = Standard
(Default = 20 )
Application
The set value determines the additional pressing in 1/100 mm.
This allows the valve to be further closed by a set path if, due to the characteristics of the rubber seal, it fails to close completely.
Caution: In order to avoid seal damage, the value should be increased by max. 10 increments.
Setting:
1 is equivalent to 1/100mm
10 is equivalent to 0.1 mm
20 is equivalent to 0.2 mm etc.
See appendix: Valves and valve seals
Strategy = Automatic (from SW V63)
Standard valves
Valves with high spring tension
This parameter determines the closing force for the 0 % position
Strategy = With defined valve stroke (from SW V63)
Standard valves
Valves with high spring tension
See above.
Valve stroke
Valve protection
2 mm, 3 mm , 4 mm,
5 mm, 6 mm active inactive
The traverse from the 0% to the 100 % position are set manually.
This function prevents the valve from stopping if it is not actuated for a prolonged period.
The valve protection program
(if active) is always run if after 24 hrs the control variable has not changed.
In this case, the valve is completely opened and then closed.
This procedure is not indicated on the LEDs.
As of: Oct-16 (Subject to change without notice) Page 35 of 71
Continuous valve actuator CHEOPS control theben
Continuation:
Designation
Type of valve seal
Characteristic curve of valve
Designation
Valve protection*
Values
Valve with Standard seal
Valve with hard seal
Valve with soft seal
Valve with medium-soft seal
Typical characteristic curve
Values
Active
Inactive
drive to new valve position Position always accurate
At change of actuating value >1
%
At change of actuating value >2
%
At change of actuating value >3
%
At change of actuating value >5
%
At change of actuating value >7
%
At change of actuating value >10
%
At change of actuating value >15
%
Application
This parameter should be changed only if the valve does not open with low actuating values.
For all standard valve types
For special valves with known characteristic curves or for special applications
For high-quality valves that have flows proportional to the path of the valve tappet.
Meaning
This function prevents the valve from stopping if it is not actuated for a prolonged period.
The valve protection program
(if active) is always run if after 24 hrs the actuating value has not changed.
In this case, the valve is completely opened and then closed.
This procedure is not indicated on the LEDs.
The valve is re-positioned each time the actuating value is changed.
The valve is never repositioned until the actuating value has changed from the last position by more than the set value. Enables frequent, small positioning increments to be suppressed
Important:
Too high a value can affect the temperature control.
As of: Oct-16 (Subject to change without notice) Page 36 of 71
Continuous valve actuator CHEOPS control theben
Continuation:
Designation
Function of Object 6
Values
Increase or decrease set point value
Determines maximum actuating value
Sends the actual valve position
Designation
Transmission of maximum actuating value
Transmission of actual valve position
Values when internal actuating value is higher than the received
Every 2 min
Every 3 min
Every 5 min
Every 10 min
Every 15 min
Every 20 min
Every 30 min
Every 45 min
Every 60 min
Does not send
At change of 1%
At change of 2 %
At change of 3 %
At change of 5 %
At change of 7 %
At change of 10 %
At change of 15 %
Application
Change set point value in increments via Object 6
Object 6 Determining the maximum actuating actuating value
Object 6 sends the current valve position during the tappet movement.
This setting is most suitable for diagnostic operations
Meaning
Object 6 will only send if all other actuators have a smaller actuating value
Object 6 sends its actuating value cyclically and starts a new calibration
Sends the new valve position as soon as it has changed since the last sending by the configured amount.
At the end of positioning, the achieved value is sent regardless of the configured interval.
As of: Oct-16 (Subject to change without notice) Page 37 of 71
Continuous valve actuator CHEOPS control theben
3.4.10 External interface
See also "External interface" Appendix
Table 20
Designation
Type of connected window contact
Values
Window open = contact closed,
Window open = contact open
Transmission of window state
Type of connected presence contact
Transmission of presence status
No transmission
Only in case of change at change and cyclically with actual operating mode
Present = contact closed,
Present = contact open
No transmission
Only in case of change at change and cyclically with actual operating mode
Meaning
Enables both NC and NO contacts to be used
If several contacts are present, these must be switched in parallel
If several contacts are present, these must be switched in series
Is the status of the connected window contact to be sent to the bus?
Same cycle time as for sending current operating mode
Enables both NC and NO contacts to be used
Is the status of the connected presence contact to be sent to the bus?
Same cycle time as for sending current operating mode
As of: Oct-16 (Subject to change without notice) Page 38 of 71
Continuous valve actuator CHEOPS control theben
3.4.11 Linear characteristic valve curve
This setting should be used only for valves described exclusively as linear.
Note: The values can be shown but not changed in this table.
Table 21
Designation
Valve position in % for 10% volume flow (1..99)
Valve position in % for 20 % volume flow (1..99)
Valve position in % for 30 % volume flow (1..99)
Valve position in % for 40 % volume flow (1..99)
Valve position in % for 50 % volume flow (1..99)
Valve position in % for 60 % volume flow (1..99)
Valve position in % for 70 % volume flow (1..99)
Valve position in % for 80 % volume flow (1..99)
Valve position in % for 90 % volume flow (1..99)
60
70
40
50
80
90
Values
10
20
30
Meaning
At 10% valve stroke, a volumetric flow of 10% is reached, at 20%, a volumetric flow of 20% is reached etc.
As of: Oct-16 (Subject to change without notice) Page 39 of 71
Continuous valve actuator CHEOPS control theben
3.4.12 Own characteristic valve curve
Prof. setting for special valves.
This parameter appears only when an internal characteristic valve curve has been selected from the "Unit settings" page.
The actuator response can be accurately adjusted using the characteristic valve curve
(manufacturer’s documentation).
This parameter enables the Cheops control to be adjusted on a valve at 9 points of the characteristic curve (10%.....90%). A certain flow is reached for each point at a certain % of the valve stroke.
Table 22
Designation
Valve position in % for 10% volume flow (1..99)
Values
1..99 ( 10 )
Valve position in % for 20 % volume flow (1..99)
Valve position in % for 30 % volume flow (1..99)
Valve position in % for 40 % volume flow (1..99)
Valve position in % for 50 % volume flow (1..99)
Valve position in % for 60 % volume flow (1..99)
Valve position in % for 70 % volume flow (1..99)
Valve position in % for 80 % volume flow (1..99)
Valve position in % for 90 % volume flow (1..99)
1..99 ( 20 )
1..99 ( 30 )
1..99 ( 40 )
1..99 ( 50 )
1..99 ( 60 )
1..99 ( 70 )
1..99 ( 80 )
1..99 ( 90 )
Meaning
At what % valve stroke is a volumetric flow of 10% reached?
At what % valve stroke is a volumetric flow of 20% reached?
At what % valve stroke is a volumetric flow of 30% reached?
At what % valve stroke is a volumetric flow of 40% reached?
At what % valve stroke is a volumetric flow of 50% reached?
At what % valve stroke is a volumetric flow of 60% reached?
At what % valve stroke is a volumetric flow of 70% reached?
At what % valve stroke is a volumetric flow of 80% reached?
At what % valve stroke is a volumetric flow of 90% reached?
The values in brackets indicate a linear valve.
As of: Oct-16 (Subject to change without notice) Page 40 of 71
Continuous valve actuator CHEOPS control theben
Diagram 1 shows a characteristic valve curve, as occurs frequently in practice.
In this characteristic curve, a 30% flow occurs at a valve stroke as low as 10%. At a valve stroke of 50%, the flow is over 80%.
Diagram 1
Example of a characteristic curve
100%
80%
60%
40%
20%
0%
0% 20% 40% 60% 80% 100%
Valve position
A linear characteristic curve as shown in Diagram 2 would be ideal for the control.
A non-linear characteristic curve can be linearised by inputting an own characteristic curve.
To do this, the valve position (stroke) at 10, 20.....90% is taken from Diagram 1 and "internal characteristic curve" entered into the parameter page.
Diagram 2
Linear characteristic curve
100%
90%
80%
70%
60%
50%
40%
30%
20%
10%
0%
0% 20% 40% 60%
Valve position
80% 100%
As of: Oct-16 (Subject to change without notice) Page 41 of 71
Continuous valve actuator CHEOPS control theben
4 Start-up
IMPORTANT INFORMATION.
•
During maintenance work on the radiator, the actuator is always dismounted and the valve securely closed by an alternative method
(original protective cap etc…). The valve could be unexpectedly opened, potentially causing water damage, through either the control or the valve protector.
•
Cheops must already be mounted on the valve when the application is downloaded, otherwise no adaptation can take place.
4.1 Installation
First, the unit is mounted onto the valve using the correct adapter ring.
The bus voltage can then be applied.
This automatically starts the adaption process.
When does the adjustment process occur?
Automatic adjustment occurs for the first time after the bus voltage is applied in the Site function , and afterwards each time the application is downloaded.
A new calibration run is performed at regular intervals after reset and during the course of the heating phase.
In order to correct the changes of the Valve characteristics over the course of time (aging of the rubber seal), the valve is automatically remeasured on a regular basis.
NOTE:
•
If an adjusted device is mounted on a different valve, the adjustment process must be repeated by downloading the application.
•
The previously stored positions are deleted after a download.
The calibration run is performed twice on account of the plausibility test.
As of: Oct-16 (Subject to change without notice) Page 42 of 71
Continuous valve actuator CHEOPS control theben
4.2 Calibration strategies
2 additional calibration strategies from software V63.
The aim is to enable adjustment to maximum number of different valves.
The selection of the calibration strategy is made via input in the " Strategy for identifying valve " parameter (Device settings).
4.2.1 Strategy 1, standard
The valve is measured during a calibration run (e.g. after reset) and the "valve open" and
"valve closed" positions are stored. The calibration run is performed twice after download and the resulting values compared for plausibility. The calibration run is performed until two successive matching value pairs have been measured. These values are then stored and the positions used for future runs. The measured values are compared with the stored values during the calibration run so that the process is only performed once for plausibility.
4.2.2 Strategy 2, Automatic (only for devices from software version 63/
61 drive)
With this option, only the "Open" valve position is calculated during the calibration run. In order to close the valve, the actuator pushes out the tappet until the set force is exerted on the valve. The following closing forces are available:
Closing force for Closing force
Standard valves approx. 100 N
Valves with high spring tension approx. 120 N
It is always recommended to use the "normal valve" setting first as this is completely sufficient for most valves.
The "Valve with high spring tension" setting should only be tried if you cannot close the valve. This enables the current consumption to be increased to 15 mA during the pressing of the rubber seal.
As of: Oct-16 (Subject to change without notice) Page 43 of 71
Continuous valve actuator CHEOPS control theben
4.2.3 Strategy 3, with defined valve stroke. (Only for devices from software version 63)
With this option, only the Open position of the valve is calculated by working back from a set path from the closing position. In order to close the valve, the actuator pushes out the tappet until the set force is exerted on the valve (closing force for standard valves/valves with high spring tension).
This calibration strategy is primarily to be used if the actuator tappet touches the valve tappet, even if it is completely withdrawn, and measurements cannot be performed.
With a completely unknown valve, the 3 mm with closing force for standard valves value is a usable starting value.
It is always recommended to use the closing force for standard valves first.
This setting is completely suitable for most valves.
The Valve with high spring tension setting should only be tried if you cannot close the valve.
This enables the current consumption to be increased to 15 mA during the pressing of the rubber seal.
The sequence light comes on if this calibration method fails three times.
As of: Oct-16 (Subject to change without notice) Page 44 of 71
Continuous valve actuator CHEOPS control theben
4.2.4 LED display during calibration run
LEDs
4
Version up to 2008 Version from 2008
3
2
Flashes as long as the spindle is in its maximum inner position
1
0
4
3
2
Flashes until the 100 % position has been found
Flashes while valve is scanned
1
0
4
3
Flashes until the 0 % position has been found
Flashes during position calculation (can be very brief)
2
1
0
“Settings” parameter page:
Applied control functions = Heating and cooling
“Set point values” parameter page:
Base set point value after loading the application = 21 °C
Dead zone between heating and cooling = 2 K
Increase in standby mode (during cooling) = 2 K
“Operation” parameter page
Maximum set point offset = +/-2 K (equivalent to 1.0 K keystroke)
The blue key is pressed once, i.e. the set point value is decreased by 1 K.
As of: Oct-16 (Subject to change without notice) Page 45 of 71
Continuous valve actuator CHEOPS control theben
4.3 Site function
While the unit remains in the delivered condition, i.e. no further applications have been downloaded, Cheops control functions in field mode.
This function enables Cheops control to be used immediately on site with basic functions.
The set point temperature can be selected directly on the device using the red (+) and blue (-) keys.
There are 5 set point temperature values available. The selected temperature is indicated on the LEDs as follows.
22°C
20°C
18°C
16°C
5°C
This enables Cheops control to automatically control the room temperature during the period between assembly and start-up by an EIB specialist.
The ETS database can be found on our download page: http://www.theben.de/downloads.htm
.
As of: Oct-16 (Subject to change without notice) Page 46 of 71
Continuous valve actuator CHEOPS control theben
5 Appendix
5.1 Determining the current set point value
The current set point value can be adapted in line with certain requirements by selecting the operating mode.
The operating mode can be specified by Objects 3…5.
There are two methods available:
5.1.1 New operating modes
If on the parameter page “operating mode”, new operating mode is selected by the " Objects to select operating mode" parameter, the current operating mode can be defined as follows:
Table 23
Pre-selected operating mode Object 3
Presence
Object 4
Window status
Object 5
Current operating mode Object 10
Any
Any
Comfort
Standby
Any
1
0
0
1
0
0
0
Frost/heat protection
Comfort
Comfort
Standby
Night 0
Frost/heat protection 0
0
0
Night
Frost/heat protection
Typical application: In the mornings Object 3 activates "Standby" or "Comfort" mode and in the evenings "Night" mode via a timer (e.g. TR 648).
During holiday periods, Object 3 also selects frost / heat protection via another channel of the timer.
Object 4 is connected to a presence indicator. If a presence is detected, Cheops control switches to Comfort mode (see Table).
Object 5 is connected to a window contact. As soon as a window is opened, Cheops control switches to frost protection mode.
As of: Oct-16 (Subject to change without notice) Page 47 of 71
Continuous valve actuator CHEOPS control theben
5.1.2 Old operating modes
If on the parameter page, old operating mode is selected by the " Objects to select operating mode" parameter, the current operating mode can be defined as follows:
Table 24
Night
Object 3
Comfort
Object 4
Frost / heat protection
Object 5
Current operating mode Object 10
Any
Any
Standby
Night
Any
1
0
0
1
0
0
0
Frost/heat protection
Comfort
Standby
Night
Typical application: In the mornings "Standby" mode and in the evenings "Night" mode is activated via a timer.
During holiday periods, Object 5 selects frost / heat protection via another channel on the timer.
Object 4 is connected to a presence indicator. If a presence is detected, Cheops control switches to Comfort mode (see Table).
Object 5 is connected to a window contact. As soon as a window is opened, Cheops control switches to frost protection mode.
The old method has two advantages over the new method:
1.
To switch from Comfort to Night operating mode, 2 telegrams (2 timer channels if necessary) are required.
Object 4 must be set to 0 and object 3 to 1.
2.
If during periods when "Frost / heat protection" is selected via the timer, the window is opened and then closed again, the "Frost / heat protection" mode is cleared.
As of: Oct-16 (Subject to change without notice) Page 48 of 71
Continuous valve actuator CHEOPS control theben
5.1.3 Set point value calculations
Assuming the current operating mode, the current set point value of Cheops control is calculated as follows:
A distinction is drawn between whether heating or cooling operation is currently required.
5.1.3.1
In heating operation
Table 25: Current set point value on heating
Operating mode Current set point value
Comfort
Basic set point value + set point value offset
Standby
Night
Frost/heat protection
Basic set point value + set point value offset – reduction in standby mode
Basic set point value + set point value offset – reduction in night mode
Programmed set point value for frost protection mode
Example:
Heating in comfort mode.
"Set point values" parameter page
"Operation" parameter page
The set point value has previously been increased by one step using the red key (1 keystroke)
Calculation:
Current set point value = basic set point value + set point value offset
= 21°C + 1K
= 22°C
If operation is switched to standby mode, the current set point value is calculated as follows:
Current set point value = basic set point value + set point value offset - reduction in standby mode
= 21°C +1K -2K
= 20°C
As of: Oct-16 (Subject to change without notice) Page 49 of 71
Continuous valve actuator CHEOPS control theben
5.1.3.2
In cooling operation
Table 26: Current set point value on cooling
Operating mode
Comfort
Current set point value
Standby
Night
Basic set point value + set point value offset + dead zone
Basic set point value + set point value offset + dead zone + increase in standby mode
Basic set point value + set point value offset + dead zone + increase in night mode
Programmed set point value for heat protection mode Frost/heat protection
Example:
Cooling in comfort mode.
The room temperature is too high and Cheops control has switched to cooling operation
Calculation:
Current set point value = basic set point value + set point value offset + dead zone
= 21°C -1K +2K
= 22°C
Changing to standby mode causes a further increase in the set point value (energy saving) and gives rise to the following set point value.
Set point value = basic set point value + set point value offset + dead zone + increase in
standby mode
= 21°C - 1K + 2K + 2K
= 24°C
5.2 Set point value offset
The current set point value on Cheops control can be adapted in 3 ways:
• step by step by the red (+) and the blue (-) key
• in increments via Object 5 " adjustment of set point temperature "
• directly via Object 1 " Manual shift of set point value "
The differential between the set point value offset and the Basic set point value is sent by
Object 1 at each change (e.g. -1.00).
The offset limits are specified on the "Operation" parameter page by the "Maximum set point value offset" parameter and apply for all 3 types of set point value offset.
As of: Oct-16 (Subject to change without notice) Page 50 of 71
Continuous valve actuator CHEOPS control theben
This parameter indicates the maximum permitted offset and the increment per keystroke (or per activation of Object 6).
5.2.1 Incremental set point temperature adjustment via keys
Each time the blue key is pressed, the set point value is decreased by one increment.
Each time the red key is pressed, the set point value is decreased by one increment.
When the max. permitted offset is reached, further keystrokes have no effect.
5.2.2 Incremental set point temperature adjustment via Object 6
Each time a 1 is sent to Object 6, the set point value is decreased by one increment.
Each time a 0 is sent to Object 6, the set point value is increased by one increment.
When the max. permitted offset is reached, further send actions have no effect.
5.2.3 Direct set point temperature adjustment via Object 1
In this case, the set point value is changed by sending the desired offset to Object 1.
This involves the differential (may be preceded by a minus sign) being sent in EIS5 format.
The offset always relates to the programmed and not to the current set point value.
Example – Basic set point value 21°C:
If a value of 2.00 is sent to Object 1, the new set point value is calculated as follows:
21°C + 2,00K = 23.00°C.
To then bring the set point value to 22°C, the differential is resent to the programmed basic set point value (here 21°C), in this case 1.00K (21°C+1.00K=22°C)
5.3 External interface
The external interface consists of inputs E1 and E2.
Both inputs are routed through the Cheops connection line.
The use of these inputs (presence sensor or actual value) is specified on the " Settings "
parameter page.
The inputs themselves are configured on the "External interface" parameter page.
As of: Oct-16 (Subject to change without notice) Page 51 of 71
Continuous valve actuator CHEOPS control theben
5.3.1 Connections
Table 27
Name
BUS
E1
E2
Colour
Black (-)
Red (+)
Yellow
Green
White
Brown
Function
EIB bus line
Binary input for window contacts(e)
Binary input for presence indicator, presence key or analogue input for external temperature sensor
5.3.2 Input E1
E1 is used exclusively for window contacts (if present).
The window contacts can be connected to E1 directly and without additional supply voltage.
On the "External interface" parameter page, the Type of connected window contact
(Opener/closer) can be set.
When the "Open" window position is detected, Cheops control switches to frost operating mode.
As of: Oct-16 (Subject to change without notice) Page 52 of 71
Continuous valve actuator CHEOPS control theben
5.3.3 Input E2
•
E2 as binary input:
A presence indicator, switch or key can be directly connected here
If a presence indicator ( or switch) is used, the period of comfort mode is determined by the indicator, i.e. comfort mode remains in force for as long as presence is indicated.
If a presence key is used, operation switches without time limit from standby to comfort mode when presence is indicated.
If presence is indicated during night operation, comfort mode is activated for a limited time.
Because the presence key is often not reset when the room is vacated, the presence input is automatically reset when the defined operating mode is changed, so that a night reduction, for example, can take place.
The selection between key and indicator is made on the "Operating mode" parameter page.
The type of presence contact can be set on the "External interface" parameter page.
•
E2 as analogue input for an external sensor
With this configuration, all settings are made on the "Actual value" parameter side.
An external sensor (Order No. 907 0 191) is connected to E2.
The maximum permitted line length is 10m.
Important:
If E2 is declared as actual value input, the "Input for actual value" selection cannot be changed on the "Actual value" parameter page.
As of: Oct-16 (Subject to change without notice) Page 53 of 71
Continuous valve actuator CHEOPS control theben
5.4 Monitoring the actual value
5.4.1 Application
Case 1: A sensor is connected to interface E2.
Its connection line could be inadvertently interrupted or short-circuited, e.g. during building or renovation work.
Case 2: The temperature is determined by a different EIB device and sent to Cheops control.
This external temperature transmitter could fail (bus line short circuited etc…) and not longer be able to perform its function, for a short time or permanently.
Because control is not possible if the actual value fails, this value must be monitored.
5.4.2 Principle
If an external sensor is connected to E2, it is constantly monitored for short-circuit or line break.
If the temperature is received via Object 2, Cheops control can monitor whether new actual value telegrams are received at regular intervals.
In both cases, either an emergency program can be started or further control can be handled by the internal sensor, should the actual value fail.
5.4.3 Practice
The response is defined as follows on the "Actual value" parameter page:
•
External sensor on E2
Emergency program (0…100%) or internal measurement:
As of: Oct-16 (Subject to change without notice) Page 54 of 71
Continuous valve actuator CHEOPS control theben
•
Receive actual value via Object 2
First the monitoring period must be defined.
This should be at least double the cycle time of the temperature transmitter (e.g. if the temperature is sent to Cheops control every 5 minutes, the monitoring period must be at least
10 minutes).
The response to the actual value failure can then be programmed as above.
Emergency program (0…100%) or internal measurement:
Important recommendation:
Rooms can cool down dramatically when the outdoor temperature is low. This may cause radiators to freeze. To prevent this from happening, you must not select a too low position in the emergency program.
A value of
≥
30% is recommended.
As of: Oct-16 (Subject to change without notice) Page 55 of 71
Continuous valve actuator CHEOPS control theben
5.5 Valves and valve seals
5.5.1 Valve structure
Valve seat
Tappet
Rubber seal
5.5.2 Valves and valve seals
When idle, i.e. tappet not actuated, the tappet is pushed outwards by the spring and the valve opens (100% with normal effect).
When the tappet is pushed, the rubber seal is pressed into the valve seat and the valve closes
(0% position with normal effect).
The valve does not close immediately on touching the valve seat, depending on the characteristics, the existing tappet may have to move onwards until the valve is fully closed.
This response depends on the hardness, shape, aging or damage to the valve seal.
To correct the influence of this parameter, Cheops allows an additional pressing of the valve
seal to be entered (see also Troubleshooting ).
Caution: In order to avoid seal damage, the value should be increased by max. 10 increments.
As of: Oct-16 (Subject to change without notice) Page 56 of 71
Continuous valve actuator CHEOPS control theben
5.6 Limit of actuating value
To control the temperature, Cheops control sets an actuating value of between 0% and 100%.
For practical reasons, it is not usually necessary to use the entire bandwidth of between 0% and 100%).
5.6.1 Minimum actuating value
The unpleasant whistling noise that some valves can generate at low actuating value, can be avoided by specifying a minimum actuating value.
If, for instance, this response is determined at below 8%, a minimum actuating value of 10% is specified.
On receipt of a actuating value below the specified limit value, Cheops control can respond in one of 2 ways ("Response on under-running the minimum actuating value in heating operation"):
•
Either move to immediately to 0% ("0%")
• or stop at the position of the minimum actuating value and do not close valve completely until actuating value 0% is received (0%=0% otherwise minimum actuating value)
As of: Oct-16 (Subject to change without notice) Page 57 of 71
Continuous valve actuator CHEOPS control theben
5.7 Determine the maximum actuating value
5.7.1 Application
If within a system all valve actuators are only slightly open, e.g. one at 5%, one at 12%, another at 7% etc., the heating boiler can reduce its output because only a small amount of heating energy is required.
In order to guarantee this, the heating boiler requires the following information:
How high is the actuating value in the room, which currently exhibits the greatest heat requirement?
With Cheops valve actuators, this task is handled by the "Maximum position" function.
5.7.2 Principle
The actuating values are constantly compared between all participants (Cheops valve actuators). Those participant with a higher actuating value than the one received may send it, those with a smaller one may not.
In order to accelerate the process, the greater the difference between its own and the received actuating value, the greater the speed at which the valve actuator sends.
Thus, the valve actuator with the highest actuating value sends first and beats the remainders.
5.7.3 Practice
The actuating value comparison takes place via Object 3 ("Maximum position") where for each valve actuator, a common group address for the maximum position is placed on
Object 3.
In order to start the actuating value comparison between the participants, one (and only one) participant must send a value to this group address cyclically.
This task can be handled by either boiler or valve actuator.
If it is the boiler, it must send the smallest possible value, i.e. 0%.
If it is a Cheops valve actuator, the parameter " Transmission of object
"Max. actuating value"(for boiler control)" on parameter page " Security and forced mode” must be set to any cycle time.
This valve actuator then regularly sends its own actuating value and the others can respond accordingly.
Irrespective of which participants act as initiator, the "Transm. of object “max. actuating value” (for heating system)" must be set to the default value for all other valve actuators, see
Figure:
As of: Oct-16 (Subject to change without notice) Page 58 of 71
Continuous valve actuator CHEOPS control theben
5.8 2-step heating
A 2-step heating system consists of a slow main step and a fast additional step.
Typically, Cheops control is plugged into the floor heating system (main step) and the radiators are controlled as the additional step.
Cheops controls the two steps in parallel, the additional step being controlled at a lower set point value.
The differential between main and additional step is defined on the "Set point value" parameter page.
Cheops drive valve actuators can be used as a continuous additional step (recommended).
Thermal valve actuators (Order No. 907 0 248) or possibly an electrical additional heater can
be used as a switching additional step.
As of: Oct-16 (Subject to change without notice) Page 59 of 71
Continuous valve actuator CHEOPS control theben
5.9 Temperature control
5.9.1 Introduction
Cheops Control can be used as a P or a PI controller, although the PI control is always preferred.
With the proportional control (P control), the actuating value is rigidly adjusted to the temperature differential.
The proportional integral control (PI control) is far more flexible, i.e. controls more quickly and more accurately.
To explain the function of both temperature controls, the following example compares the room to be heated with a vessel.
The filling level of the vessel denotes the room temperature.
The water supply denotes the radiator output.
The heat loss from the room is illustrated by a drain.
In our example, the maximum supply volume is 4 litres per minute and also denotes the maximum radiator output.
This maximum output is achieved with an actuating value of 100%.
Accordingly, at an actuating value of 50%, only half the water volume, i.e. 2 litres per minute would flow into our vessel.
The bandwidth is 4l.
This means that the controller will send an actuating value of 100% while the actual value is smaller than or equal to (211 – 41) 171.
Function:
•
Desired filling quantity:
21 litres (= set point value)
•
From when should the supply flow gradually be reduced in order to avoid an overflow? :
4l below the desired filling volume, i.e. at 21l – 41 = 171 (=bandwidth)
•
Original filling volume
15l (=actual value)
•
The losses amount to 1l/minute
As of: Oct-16 (Subject to change without notice) Page 60 of 71
Continuous valve actuator CHEOPS control theben
5.9.2 Response of the P-control
21l
17l
15l
Max. 4l/Min.
Bandwidth
Set point value
Actual value
Losses
1l/Min
A filling volume of 15l gives rise to a control deviation of 211 – 151 = 61
Because our actual value lies outside the bandwidth, the control will control the flow at 100% i.e. at 4l / minute
The supply quantity (actuating value) is calculated from the control deviation
(set point value – actual value) and the bandwidth.
Actuating value = (control deviation / bandwidth) x 100
The table below shows the response and therefore also the limits of the P-control
Filling level Actuating value Supply Losses Increase in filling
15l 100% 4 l/min level
3 l/min
19l
20l
50%
25%
2 l/min
1 l/min
1 l/min 1 l/min
0 l/min
The last line indicates that the filling level cannot increase any further, because the flow allows only the same amount of water to flow in as can flow out through loss.
The result is a permanent control deviation of 11 and the set point value can never be reached.
If the loss was 1l higher, the permanent control deviation would increase by the same amount and the filling level would never exceed the 19l mark.
As of: Oct-16 (Subject to change without notice) Page 61 of 71
Continuous valve actuator CHEOPS control theben
P-control as temperature control
The P-control behaves during heating control as shown in the previous example.
The set point temperature (21 o
C) can never quite be reached.
The permanent control deviation increases as the heat loss increases and as the ambient temperature decreases.
5.9.3 Response of the PI-control
Unlike the pure P-control, the PI-control works dynamically.
With this type of control, the actuating value will not remain unchanged, even at constant deviation.
In the first instant, the PI-control sends the same actuating value as the P-control, although the longer the set point value is not reached, the more this value increases.
This increases is time-controlled over the integration time.
With this calculation method, the actuating value does not change if the set point value and the actual value are the same.
Our example, therefore, shows equivalent in and outflow.
Notes on temperature control:
Effective control depends on agreement of bandwidth and integration time with the room to be heated.
The bandwidth influences the increment of the actuating value change:
Large bandwidth = finer increment on actuating value change.
The integration time influences the response time to temperature changes:
Long integration time = slow response.
Poor agreement can result in either the set point value being exceeded (overshoot) or the control taking too long to reach the set point value.
Usually, the best results are achieved with the standard settings or the settings via system type.
Standard settings:
Control by system type
As of: Oct-16 (Subject to change without notice) Page 62 of 71
Continuous valve actuator CHEOPS control theben
6 Troubleshooting
Caution: Error codes are only available in the version up to 2008.
Table 28
Response Error code
Potential cause Remedy
82
84
All LEDs flash as continuous light from bottom to top, i.e. valve adaption was unsuccessful
81
81
81
83
No valve
Valve tappet is already touched, although the spindle of the valve actuator is fully returned.
Plug unit onto valve and reload application
Use other valve adapter.
Please contact our Customer
Service.
When the spindle is returned, the valve tappet must be at least 3/10 mm away from the
spindle (see below, Check adapter ring).
Check whether tappet sits correctly, if so, replace valve.
Valve tappet cannot be moved, even with maximum force
(120N).
Following start-up, valve actuator with valve was mounted onto a different valve
Re-download the application, valve actuator is then automatically adapted and must be readapted.
Valve seal too heavily pressed Cancel additional pressing of rubber seal
Valve jams Check valve
As of: Oct-16 (Subject to change without notice) Page 63 of 71
Continuous valve actuator CHEOPS control theben
Table 29: General, for every hard and software version.
Response
Valve does not close when actuating value is 0%
Potential cause
Valve seal is insufficient for pressing onto the valve seat
Valve opens only with an unexpectedly large actuating value
Valve seal is damaged
Existing valve seal is too soft
Valve does not move to positions below or above a certain value
No LED display and no automatic adaption after reset
Error message with ETS device info / Application program:
Run state
Halted
Minimum or maximum actuating value parameter(s) have been changed
Device was unloaded with
ETS software
Device was unloaded with
ETS software
Remedy
Enter additional pressing of rubber seal.
Caution: Increase parameter by max. increments of 10.
OR (from 2008):
Choose another calibration strategy .
Replace valve.
Adapt parameter type of valve seal.
Valve opens only with actuating values over:
5%
⇒
Standard valve seal
10%
⇒
medium-soft seal
20%
⇒
select soft seal
Check minimum and maximum actuating value parameters
Reload individual address
+ application program
Reload individual address
+ application program
6.1 Display current valve position
The current valve position can be viewed by simultaneously the blue and red buttons.
Position:
80..100%
60..80%
40..60%
20..40%
1..20%
As of: Oct-16 (Subject to change without notice) Page 64 of 71
Continuous valve actuator CHEOPS control theben
6.2 Read-out error code
Important:
The error code was replaced (from 2008) by the calibration strategy code.
Up to 2008:
If the valve causes an error message and the LEDs flash as continuous light, Cheops generates an error code.
This remains in the BCU memory and can (start-up/test) be read-out using the ETS software.
1.
Select device in the project and click on Test / Device memory viewer menu item
2.
Enter memory area 1FB, deselect RAM and EEPROM
3.
Click the button
As of: Oct-16 (Subject to change without notice) Page 65 of 71
Continuous valve actuator CHEOPS control theben
4.
The error code appears in the results window
ERROR CODE
Table 30
Code Name
00 No error
81 Overload switch-off
(overcurrent)
82 Valve not found
83 Valve does not move
84 Stroke too short
As of: Oct-16 (Subject to change without notice) Page 66 of 71
Continuous valve actuator CHEOPS control theben
6.3 Checking end position
The end positions stored during the adaption process can be read out in exactly the same way as the error numbers using the ETS software.
The internal stop position (spindle inserted, valve open) is stored in Hex-format under the address $1FC and the external stop position under $1FD.
After downloading the application, these values are reset (i.e. $1FC = 00 and $1FD = FF).
The found stop positions are stored here following successful adaption.
If both addresses show 00 after adaption, the adaption is deemed to have been unsuccessful.
To determine the stop positions in millimetres, the values are converted into decimal and divided by 20.
Example calculation:
Table 31
Position Valve Addres s
Hexadecimal
Value
Internal stop
External stop
Open $1FC
Close d
$1FD
24
61
The stroke is calculated from the two values as follows:
Stroke = external stop - internal stop
In our example:
Stroke = 4.85 – 1.8 mm = 3.05 mm
Limit values for successful adaption
The following values must be respected:
Equivalent to decimal value
36
97
Table 32
Internal stop
Dimension Hex value
≥
0,3mm
≥
6
External stop
Dimension Hex value
≤
7,5mm
≤
96
Result decimal value/20 =
1,8 mm
4,85 mm
Stroke
Dimension Hex value
≥
1.2mm
≥
18
As of: Oct-16 (Subject to change without notice) Page 67 of 71
Continuous valve actuator CHEOPS control theben
6.4 Checking adapter ring
The maximum dimension between top edge of adapter ring and end of tappet is 4.7 mm.
If this dimension is over-run, an alternative adapter ring must be used.
Max. 4,7mm
6.5 Reading the software version number
Cheops displays the current software version via LEDs.
After reset, this is displayed as a binary number in three stages.
•
Stage 1: Full display: All LEDs = ON
•
Stage 2: LED 0 is ON and the upper 4 Bits are shown
(= Hi-Nibble, value: see table)
•
Stage 3: LED 0 is ON and the lower 4 Bits are displayed (= Lo-Nibble).
•
The values of the individual LEDs are displayed as follows
LEDs Value
4 8 (=2
3
)
3 4 (=2
2
)
2
1
2 (=2
1
)
1 (=2
0
)
0 none
The number is produced from the sum of the values of the illuminated
LEDs 1..4.
LED 0 is not counted.
As of: Oct-16 (Subject to change without notice) Page 68 of 71
Continuous valve actuator CHEOPS control theben
6.5.1 Examples of different versions
Devices from 2008
Example 1
Version 044
= $2C
(1 circuit board)
Example 2
Version 061
= $3D
(1 circuit board)
Example 3
Version 063
= $3F
(1 circuit board)
Example 4
Version
(2 circuit boards)
Stage 1 = All LEDs ON
Devices up to 2008
110
= $6E
Example 5
Version 121
= $79
(2 circuit boards)
4 4 4 4 4
3
2
1
0
3
2
1
0
2
1
0
4
3
4
3
2
1
0
00101100
= $2C
3
2
1
0
4
3
2
1
0
4
3
2
1
0
00111101
= $3D
3
2
1
0
Stage 2 = Hi-Nibble
4
3
2
1
0
Stage 3 = Lo-Nibble
4
3
2
1
0
00111111
= $3F
3
2
1
0
2
1
0
4
3
4
3
2
1
0
01101110
= $6E
2
1
0
4
3
4
3
2
1
0
01111001
= $79
As of: Oct-16 (Subject to change without notice) Page 69 of 71
Continuous valve actuator CHEOPS control theben
7 Glossary
7.1 Basic set point value
The basic set point value is the standard temperature for comfort mode and the reference temperature for reduction in standby and night modes.
After reset (bus returned), the last used basic set point value is restored.
7.2 Hysteresis
On Cheops control, the hysteresis determines how far the temperature should drop below the set point value before the control switches on the additional step again.
Example with set point value (additional step) 20 o
C, hysteresis 0.5 K and starting temperature
19 o
C.
The additional step is switched on and does not switch off again until the set point value (20 o
) is reached.
The temperature falls and the additional step does not switch on again until 20°C-0.5K= 19.5° is reached.
Without hysteresis, the controller would switch on and off continuously provided the temperature is within the set point value range.
7.3 Continuous and switching control
With a continuous actuating value, the valve is brought to any position between 0% and
100%. This achieves in a pleasant and precise control.
A switching control has only 2 statuses, On or Off, i.e. in our case, valve fully open or fully closed.
As of: Oct-16 (Subject to change without notice) Page 70 of 71
Continuous valve actuator CHEOPS control theben
7.4 Dead zone
The dead zone is a buffer area between heating and cooling operation.
Neither heating nor cooling takes place within this dead zone.
If Cheops control switches to cooling operation, the set point value is increased internally by the amount of the dead zone.
Without this buffer zone, the system would switch continuously between heating and cooling.
As soon as the set point value had been under-run, the heating would activate and when the set point value would be achieved, cooling were to be started immediately and the temperature would fall to below the set point value and switch on the heating again.
7.5 Valve stroke
Mechanical path that is between the two end positions, i.e. 0% (valve closed) and 100%
(valve fully open) covered (see Valve arrangement diagram ).
As of: Oct-16 (Subject to change without notice) Page 71 of 71
advertisement
* Your assessment is very important for improving the workof artificial intelligence, which forms the content of this project
Related manuals
advertisement
Table of contents
- 4 Functional characteristics
- 5 Operation
- 6 Benefits of Cheops Control
- 6 Special features
- 7 Hardware versions
- 8 Differences
- 9 Technical data
- 9 General
- 10 The "CHEOPS control V1.2" Application Program
- 10 Selection in the product database
- 10 Parameter pages
- 11 Communication objects
- 11 Object characteristics
- 12 Object description
- 17 Parameters
- 17 Settings
- 19 Set point values
- 22 Actual value
- 24 Heating control
- 26 Cooling control
- 28 Additional heating step
- 30 Operation
- 32 Operating mode
- 34 Device settings
- 38 External interface
- 39 Linear characteristic valve curve
- 40 Own characteristic valve curve
- 42 Start-up
- 42 Installation
- 43 Calibration strategies
- 43 Strategy 1, standard
- 43 Strategy 2, Automatic (only for devices from software version 63/ 61 drive)
- 45 LED display during calibration run
- 46 Site function
- 47 Appendix
- 47 Determining the current set point value
- 47 New operating modes
- 48 Old operating modes
- 49 Set point value calculations
- 50 Set point value offset
- 51 Incremental set point temperature adjustment via keys
- 51 Incremental set point temperature adjustment via Object
- 51 Direct set point temperature adjustment via Object
- 51 External interface
- 52 Connections
- 52 Input E
- 54 Monitoring the actual value
- 54 Application
- 54 Principle
- 54 Practice
- 56 Valves and valve seals
- 56 Valve structure
- 56 Valves and valve seals
- 57 Limit of actuating value
- 57 Minimum actuating value
- 58 Determine the maximum actuating value
- 58 Application
- 58 Principle
- 58 Practice
- 59 2-step heating
- 60 Temperature control
- 60 Introduction
- 61 Response of the P-control
- 62 Response of the PI-control
- 63 Troubleshooting
- 64 Display current valve position
- 65 Read-out error code
- 67 Checking end position
- 68 Checking adapter ring
- 68 Reading the software version number
- 70 Glossary
- 70 Basic set point value
- 70 Hysteresis
- 70 Continuous and switching control
- 71 Dead zone
- 71 Valve stroke