GRAUPNER S1038 Manual
Add to My manuals32 Pages
GRAUPNER S1038 is an AIO Copter Flight Control with copter firmware Q06. It has an operating voltage of (2.5) 3.6 ... 15.2 V and a frequency range of 2400 ... 2483.5 MHz. It has a current consumption of approximately 70 mA and a temperature range of -15 … +70°C. Its dimensions are approximately 36 x 36 x 10 mm and it weighs approximately 9g. It is suitable for use with remote controlled copter models without passengers. Some of its possible use cases include:
- Controlling the flight of a copter model
- Adjusting the flight parameters of a copter model
- Monitoring the telemetry data of a copter model
advertisement
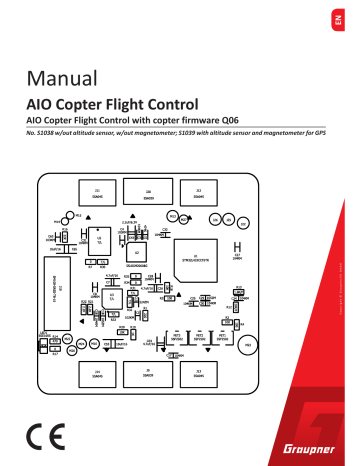
Manual
AIO Copter Flight Control
AIO Copter Flight Control with copter firmware Q06
No. S1038 w/out altitude sensor, w/out magnetometer; S1039 with altitude sensor and magnetometer for GPS
2 / 32 S1035_Falcon_12_Q06_V1sh
Index
Introduction ......................................................................................
4
Service centre ...................................................................................
4
Intended use ....................................................................................
5
Target group .................................................................................
5
Package content ................................................................................
5
Technical data ...................................................................................
6
Symbol description ...........................................................................
6
Safety notes ......................................................................................
6
For your safety by handling the transmitter and the receiver .......
7
For your safety by handling the batteries ......................................
8
Installing the AIO FC: ........................................................................
9
Connecting the RC components of the copter ...............................
9
Connection socket J10 "Telemetry/Update/Waypoints" ............
9
Connection socket J9 "FPV transmitter"......................................
9
Connection socket J11-J14 "RGB-LEDs" ......................................
9 connection socket J28 or Pin lines "ESC" .....................................
9
Connection socket J11-J14 "RGB-LEDs" ......................................
9
Connection socket J27 "CAM POWER“ ........................................
9 binding .............................................................................................
12
Transmitter presettings ..................................................................
13
Flight mode ...................................................................................
13
Auto-flip function on channel 6 ....................................................
16
"Telemetry" menu ..........................................................................
16
SETTING & DATA VIEW ..................................................................
16
Receiver display .........................................................................
16
ROLL/NICK Display .....................................................................
18
YAW Display ................................................................................
19
MULTIC. AUTOPILOT (only by S1039 with GPS #33602) ...........
20
MULTIC. AUTOPILOT (only by S1039 with GPS #33602) ...........
21
BASIC Display ..............................................................................
22
AXIS ASSIGNMENT .....................................................................
26
Care and maintenance ...................................................................
28
Warranty .........................................................................................
28
S1035_Falcon_12_Q06_V1sh 3 / 32
Introduction
Thank you very much for purchasing a Graupner AIO FC .
Read this manual carefully to achieve the best results with your HoTT system and first of all to safely control your models. If you experience any trouble during operation, take the instructions to help or ask your dealer or Graupner Service Centre.
Due to technical changes, the information may be changed in this manual without prior notice. Be always updated by checking periodically on our website, www.graupner.de
to be always uptodate with the products and firmwares.
This product complies with national and European legal requirements.
To maintain this condition and to ensure safe operation, you must read and follow this user manual and all the safety notes before using the product and you have to respect those notes also for future use!
Note
This manual is part of that product. It contains important information concerning operation and handling. Keep these instructions for future reference and give it to third person in case you gave the product.
Service centre
Graupner Central Service
Graupner/SJ GmbH
Henriettenstraße 96
D-73230 Kirchheim/Teck
Graupner USA
3941 Park Dr Suite 20-571
El Dorado Hills, CA 95762
Servicehotline
(+49) (0)7021/722-130
Monday - Thursday:
9:15 am - 4:00 pm
Friday:
9:15 am - 1:00 pm
Website: www.graupnerusa.com
Phone: +1 855-572-4746
Email:[email protected]
Graupner in Internet For the service centers outside Germany please refer to our web site www.graupner.de.
4 / 32 S1035_Falcon_12_Q06_V1sh
Intended use
Target group
Package content
The AIO FC should only be used for the purpose specified by the manufacturer for operation of remote controlled copter models without passengers. Any other type of use is impermissible and may cause significant property damage and/or personal injury. No warranty or liability is therefore offered for any improper use not covered by these provisions.
In addition, it is explicitly pointed out that you must inform yourself about the laws and regulations applicable at your respective starting point before starting the remote control operation. Such conditions may differ from state to state, but this must be followed in every case.
Notes
•
• In general, it should not be forbidden to fly over airfields, factories, nature reserves, built-up areas, etc.
• Where designated no-fly zones are located, and which in no way affect them, it can be determined, for example, using the "Air-
Map" app.
Read through this entire manual before you attempt to install or use the receiver.
The item is not a toy. It is not suitable for children under 14. The installation and operation of the receiver must be performed by experienced modellers. If you do not have sufficient knowledge about dealing with radio-controlled models, please contact an experienced modeller or a model club.
• S1038 or S1039 AIO Copter Flight Control
• Manual
S1035_Falcon_12_Q06_V1sh 5 / 32
Technical data
Antenna
Operating voltage
Frequency range
Modulation
1x 145 mm, of which the last 30 mm active
(2.5) 3.6 ... 15,2 V
2400 ... 2483.5 MHz
2.4 GHz FHSS
Current consumption approx.
70 mA
Temperature range -15 … +70°C
Dimensions approx.
36 x 36 x 10 mm
Weight approx.
9 g
Symbol description
!
Always observe the information indicated by these warning signs.
Particularly those which are additionally marked with the words
CAUTION or WARNING .
The signal word WARNING indicates the potential for serious injury, the signal word CAUTION indicates possibility of lighter injuries.
The signal word Note indicates potential malfunctions.
Attention indicates potential damages to objects.
Safety notes
!
These safety instructions are intended not only to protect the product, but also for your own and other people’s safety. Therefore please read this section very carefully before using the product!
• Do not leave the packaging material lying around, this could be a dangerous toy for children.
• Persons, including children, with reduced physical, sensory or mental capabilities, or lack of experience or knowledge, or not capable to use safely the receiver must not use the receiver without supervision or instruction by a responsible person.
• Operation and use of radio-controlled models needs to be learnt!
If you have never driven such a model, then start extra carefully and make sure to be familiar with the reactions of the model to the remote control commands. Proceed responsibly.
6 / 32 S1035_Falcon_12_Q06_V1sh
• First, always perform a range and function test on the ground (to do so, hold your model tight), before you use your model. Repeat the test with running motor and with short throttle bursts.
• Only use the components and spare parts that we recommend.
Always use matching, original Graupner plug-in connections of the same design and material.
• Make sure that all of the plug-in connections are tight. When disconnecting the plug-in connections, do not pull the cables.
• Protect the AIO FC from dust, dirt, moisture and foreign parts. Do not expose it to vibrations or to extreme heath or cold. The models may only be operated remotely in normal outside temperatures such as from -10°C to +55°C.
• Always use all your HoTT components only with the latest firmware version.
• If you have questions which cannot be answered by the operating manual, please contact us or another expert in the field.
For your safety by handling the transmitter and the receiver
!
WARNING
Also while programming the transmitter, make sure that a connected motor cannot accidentally start. Disconnect the fuel supply or drive battery beforehand.
!
CAUTION
Avoid every kind of short-circuit in all sockets of the transmitter!
Risk of fire! Use only the suitable connectors. In no case the electronic component of the transmitter or of the receiver may be changed or modified. Due to licensing reasons, any reconstruction and/or modification of the product is prohibited.
Note
During transport protect the model and the transmitter from damages.
S1035_Falcon_12_Q06_V1sh 7 / 32
For your safety by handling the batteries
!
CAUTION
• Protect the batteries from dust, dirt, moisture, heat and vibrations. Only use in dry locations.
• Do not use any damaged battery.
• Batteries may not be heated, burned, short-circuited.
• If handled improperly, there is a danger of fire, explosion, irritation and burns.
• Leaked electrolyte is caustic and should not be touched or come into contact with your eyes. In case of emergency, rinse with a large quantity of water and consult a Med. Doctor.
• Stock the batteries in dry and fresh conditions.
• Dispose of the battery in the proper disposal centers.
8 / 32 S1035_Falcon_12_Q06_V1sh
Installing the AIO FC:
The AIO FC must be mounted with its lower surface parallel to the chassis using the rubber buffers and M3 screws.
The AIO FC must be protected against dust, splash water, etc. in the model. But do not pack your AIO FC too airtight so that it does not overheat during operation and the height sensor on the S1039 can work properly.
The cables may not be wound around antenna or run next to it. Make sure that the cables cannot shift to lie directly adjacent to antenna during flight.
In the case of carbon fibre chassis, at least the last 35 mm of the antennas shall be routed outside.
Connecting the RC components of the copter
Insert the connection cable of the ESCs of the copter, which must be connected to the receiver, with the black or brown cable upwards into the connector strip of the receiver, as shown in the illustration on the left. The polarity of the plug-in system cannot be reversed. Do not apply force. The servo connections of the Graupner -HoTT receiver are numbered. Only use speed controllers that are multishot capable to connect the motors.
Connection socket J10 "Telemetry/Update/Waypoints"
If required, the optional GPS module #33602 can be connected to the socket labelled "J10". In addition, the receiver updates are performed on this socket.
Connection socket J9 "FPV transmitter"
If necessary, the FPV transmitter # is connected to the socket labelled
"J9".
Connection socket J11-J14 "RGB-LEDs"
If required, the optional RGB LED PCBs are connected to sockets labelled "J11-J14".
connection socket J28 or Pin lines "ESC"
The 4in1 ESC 7242.4 is connected to the sockets labelled "J?". The
4in1 ESCs # S3087 or # S3088 are connected to the double row pin headers J23 / 24.
Connection socket J11-J14 "RGB-LEDs"
If required, the optional RGB LED PCBs are connected to sockets labelled "J11-J14".
Connection socket J27 "CAM POWER“
The FPV camera is connected to this socket
S1035_Falcon_12_Q06_V1sh 9 / 32
10 / 32 S1035_Falcon_12_Q06_V1sh
S1035_Falcon_12_Q06_V1sh 11 / 32
binding
To establish a connection with the transmitter, the Graupner HoTT receiver must first be "bound" to at least one model memory in "its"
Graupner HoTT transmitter. This process is generally called "binding". However, the available methods to be used are not always the same, so the following step-by-step instructions apply only to binding a HoTT AIO FC to any transmitter:
Binding step-by-step
• If the AIO FC is already bound to a specific transmitter and this binding should be maintained, the transmitter should ideally be switched on before the receiver. At the latest, however, within approximately 15 seconds from the moment when the receiver is switched on, the red LED of the receiver is constantly on.
Attention
As soon as the LED starts to flash, the AIO FC is in bind mode.
From this point on there is the risk that the AIO FC unintentionally binds to a transmitter, which is casually in bind mode at the same time, whereupon the model can run uncontrolled at any time. The distance between transmitter and AIO FC should be at least 0.5 m, otherwise the receiver of the AIO FC can be overdriven.
• If the AIO FC is unbound or it should be bound to another transmitter or only the model memory has to be changed than the previous one, proceed as follows:
1. Prepare the transmitter or model memory to be bound according to the instructions for binding.
2. Switch on the copter power supply.
3. The LED of the AIO FC lights constantly red.
4. Approximately 15 seconds after the AIO FC is switched on, its red LED starts to flash, indicating that the AIO FC is now in bind mode.
5. Start the transmitter-side binding according to the instructions of the transmitter.
6. If the red LED of the AIO FC goes out within about three seconds, the binding process has been completed successfully.
7. Your transmitter/AIO FC combination is ready for operation.
8. If the LED on the AIO FC remains still red, the "binding" has failed. Change the positions of the associated antennas and try the entire procedure again.
12 / 32 S1035_Falcon_12_Q06_V1sh
Transmitter presettings
Depending on the bandwidth of the model type selection of the transmitter used, either the model type "Copter" or alternatively a
"Fixed-wing model" should be selected. Some of the current HoTT transmitters are even shipped with preconfigured model memory.
According to the transmitter instructions, the appropriate control mode and, if necessary, "motor front / rear" must be set. Usually
"backwards" so that the channel 1 indicator in the servo display indicates -100% in the "motor off" position of the "motor / pitch control stick".
Flight mode
1
3
5
7
E5
E6
E7
E8
3 free free free
+100% +100%
+100% +100%
+100% +100%
+100% +100% trv +
0%
0%
+
–100%
0%
2
4
6
8
0%
+100%
0%
0%
S1038: Flight mode has to be set to channel 5. To do this, program a
2-way switch in the "Control settings" menu on Channel 5 as follows:
S1039: Flight mode has to be set to channel 5. To do this, according to the transmitter instructions, program a 3-way switch in the »Transmitter setting« menu on channel 5 as follows on the next page:
Attitude mode
The stick movements acts directly proportionally to Roll and Nick. In the attitude mode, the maximum inclination angle is limited to approx. 50° at 100% of the stick travel.
The attitude mode is active as long as the bar of channel 5 is on the left of +49% in the »Servo display«.
(The -100% shown on the left are based on the switch programming above.)
Flight mode suggested for beginners.
E5
E6
E7
E8
3 free free free
+100% +100%
+100% +100%
+100% +100%
+100% +100% trv +
1
3
5
7
0%
0%
+
+100%
0%
6
8
2
4
0%
+100%
0%
0%
Rate mode
In this mode, the rate is determined by the rash of the stick without inclination limit. In this aerobatic mode rolls and loops are possible.
The rate mode is active as soon as the bar of channel 5 in the display
»Servo Display« is +50% or higher.
(The -100% shown on the left are based on the switch programming above.)
Not suitable for beginners.
S1035_Falcon_12_Q06_V1sh 13 / 32
E5
E6
E7
E8
3
SW6/7 free free
+100% +100%
+100% +125%
+100% +100%
+100% +100%
Trvl +
1
3
5
7
0%
0%
+
+100%
0%
2
4
6
8
0%
+100%
0%
0%
E5
E6
E7
E8
SW4/5
SW6/7
3 free
+100% +100%
+100% +100%
+100% +100%
+100% +100%
Trvl +
1
3
5
7
0%
0%
+
+100%
0%
6
8
2
4
0%
+100%
0%
0%
Only S1038:
C5 = 0% (Attitude mode) and C6 = 125% = Auto-flip mode
C5 = 0% (Attitude mode) and C6 = 100% = switching between the
FPV transmitter channels, only when the motors are switched off.
Only S1039 and only with GPS 33602: Autopilot mode
C5 = -100% and C6 = 0% = Autopilot mode (with GPS), control of the copter speed. Neutral stick position means GPS position and altitude hold.
If you start in autopilot mode, the height is maintained at the middle of the stick (0%).
If you start in Rate or Attitude mode and then switch to the autopilot mode, the throttle position when switching the mode is the stick position at which the altitude is maintained.
C5 = -100% and C6 = -100% = Come back home to the start point
(with GPS)
C5 = -100% and C6 = +100% = Departure from previously programmed waypoints (in preparation)
E5
E6
E7
E8
SW4/5
SW6/7
3 free
+100% +100%
+100% +100%
+100% +100%
+100% +100%
Trvl +
1
3
5
7
0%
0%
+
+100%
0%
6
8
2
4
0%
+100%
0%
0%
Note
When the GPS is connected, the copter only allows the motors to be switched on if 6 GPS satellites or more are found.
While searching for GPS satellites, an HD camera should be off. If more than 8 satellites have been found, the HD camera can be switched on. Check if there are more than 6 satellites in the GPS Copter telemetry display. The Autopilot and Come back home mode only work in the configuration of how the compass was calibrated (eg with HD camera on. If you change the airfield, the compass should be recalibrated.
Only S1039: Carefree GPS mode
C5 = -100% and C6 = 0%, so as C7 = +100% = Carefree control mode
In Carefree control mode, the flight direction is saved when activated, even if the Copter is then rotated by yaw command.
This facilitates the control of the copter in difficult visibility conditions.
C5 = -100% and C6 = 0%, so as C7 -100%....+50% = normal control mode
14 / 32 S1035_Falcon_12_Q06_V1sh
FAIL SAFE
Pos hold
1 2 3 4 5 6 7 8
Delay 0.25s
STO
Mod.Name
Control mode
Motor on CH1
M.Stop
Timers
ALPHA 110
1 idle rear
–125% +100% 1
0:00 –––
M1
M2
M3
M4
M5
S 5
??
??
??
??
??
??
??
??
Type from to
1 =
MIX 1 S
Trv+100%+100%
Offset +100%
5
STO SEL
Fail-Safe settings
We recommend to set Channel 1 and Channel 5 to "Pos" according to the transmitter instructions and to put the pitch control stick in the motor OFF position before storing the fail-safe settings and to set the attitude / rate mode switch to the "Attitude mode" position so that the attitude mode is active in fail-safe situations and the motors stop. When using the # S1039 AIO FC with GPS, it is recommended to set C1 on Hold and C5 and 6 on Pos, in the Come back home position, so that the copter will fly back to the starting position if there is a loss of signal. Please note that when the signal is received again, the set mode will become active again and the pilot will have to take again the control.
Throttle Cut
For safety reasons, a motor stop switch must always be programmed on the transmitter side according to the transmitter instructions.
Only when this is placed into the appropriate position, an undesired start of the motors is reliably prevented.
But in order to be able to switch off the motors also in the Acro 3D mode, another mixer has to be programmed. Namely, if the copter is operated in the acro 3D mode with the rate mode enabled, the motor stop function would not shut off the motors, but set them to
"full power backwards". To prevent this, the mixer must be programmed in such a way that switching the motor stop switch to the motor OFF position also switches to the attitude mode, in which the stop of all motors is ensured.
Programming step-by-step
9. Program a linear mixer of "S => 5" according to the transmitter instructions.
10. Assign to this mixer the same switch with the same switching direction, which switches to the attitude mode.
11. Change to the setting page of the mixer.
12. Set the "travel" symmetrically to +100%.
13. Change to the line "Offset".
14. Now either set the offset value manually to +100% or set the motor stop switch to "motor ON" and then push the ENT key. In both cases, however, the adjacent picture must arise.
S1035_Falcon_12_Q06_V1sh 15 / 32
Auto-flip function on channel 6
E5
E6
E7
E8
3
SW6/7 free free
+100% +100%
+100% +125%
+100% +100%
+100% +100%
Trvl +
If the copter is in attitude mode, the automatic flip function can easily trigger a flip of the copter.
The auto-flip function is activated via a key switch assigned to channel 6. This has to be programmed on channel 6 in the "Control setting" menu of the transmitter and then, with the button held down, the asymmetrical travel must be set to +125%.
If this button is pressed, the servo position of channel 6 exceeds the value of 111% and the autoflip function is thus "armed" for 5 seconds. As soon as the roll or pitch control stick is moved over more than 50% of the stick travel within this time, the copter will automatically flip in that direction.
Note
After the flip, position deviations in the range <10 ° are possible.
"Telemetry" menu
SETTING & DATA VIEW
TELEMETRY
SETTING & DATA VIEW
SENSOR
DISPLAY RF STATUS
SELECT ANNOUNCE
RX DATA ON
ALARM SETTINGS
The basic handling of the "Telemetry" menu is described in the respective transmitter instructions or the instructions of the Smart-
Box. By way of derogation, only in certain receivers the menu structure is summarized under the generic term "setting & data view".
These instructions also provide information on how to access this menu. Change accordingly to the first setting page of the AIO FC .
Note
The setting values shown in the following display illustrations always show the standard values.
Receiver display
RECEIVER Q.06
LANGUAGE: English
ALARM VOLT: 3.8V
ALARM TEMP: 70°C
Altitude max: 100m
PERIOD: 20ms
Video chennel R3
ALARM Capac. 400mAh
LANGUAGE
In the "Language" line you can set the display language in the receiver menu.
The choices are: German, English, French, Italian, Spanish
ALARM VOLT
If the receiver voltage falls below the set value, a low-voltage warning is generated by the transmitter in the form of a "sound-declining alarm tone" or the "receiver voltage" speech output message.
16 / 32 S1035_Falcon_12_Q06_V1sh
S1035_Falcon_12_Q06_V1sh
ALARM TEMP
If the receiver temperature exceeds the set temperature, a warning is generated by the transmitter in the form of a "3-step sound-climbing alarm tone" or the "receiver temperature" speech output message.
Max. altitude
If the copter exceeds the set max. height, the transmitter will warn you with "max. height "or, by transmitters without speech output, with a corresponding tone sequence.
only with S1039: In autopilot mode, the altitude is limited to the set altitude.
PERIOD
currently no function
Note
Changing the cycle time is only necessary when installing servos for additional functions.
Video channel:
If the video transmitter # 16570.123 is connected to the connector
J9, then the video channel can be set via this menu item.
only with S1038: The video channel can also be switched on by pressing the C6 (+ 100%) for 2 seconds. This is only possible when the motors are switched off.
ALARM Capac.
If the used battery capacity exceeds the set value, a warning message "Capacity" is output in the transmitter or a corresponding sequence of tones by transmitters without voice output. In this case you should return to the starting point or, if this is no longer possible, land safely.
17 / 32
ROLL/NICK Display
MULTICOPTER RO/NI
ROLL/NICK P 50
ROLL/NICK D 50
DAMPING 40
ROLL FACTOR % 95
POWER2SENS. 80
R/N DYNAMIC 70
––ATTITUDE MODE––
ROLL/NICK I 80
AGILITY 3
––RATE MODE––
R/N RATE I 40
RATE 70
The control is based on the PID principle, where the "P" stands for
"proportional", the "I" for "integral" and the "D" for "digital". In short
...
... the deviation from the setpoint proportional to the manipulated variable has an effect at the P value.
... the existing control deviation is continuously summed up at the I value and then acts on the manipulated variable via the I value.
... the differential component only takes into account the speed of the control deviation and then acts on the control accordingly via the
D component.
ROLL/NICK P
This parameter determines the tilting behaviour of the copter during the maximum climb.
In order to prevent tilting at full climbing power in the end, this parameter must be increased in steps of 5 until a medium-fast tilting occurs. Subsequently, this value is to be adjusted in individual steps until the tilting has disappeared.
ROLL/NICK D
This parameter determines the tilting behaviour of the roll / pitch function of the copter.
As described above, this parameter must be adjusted until the Multicopter engages exactly over Roll and Nick. A too high value leads to very rapid oscillations.
DAMPING
The damping factor should be set as low as possible, but as high as necessary, so that the PID control can operate optimally. To prevent oscillations or tilting, the damping should be <30. To dampen motor or prop vibration and prevent motor noise, higher values may be needed. These can be adjusted at the beginning in steps of 10 and then finer.
ROLL FACTOR %
Set the Roll setting as percent value of the overall gain. For symmetrical copters, the value should normally be left at 100. If, because of its gravity centre, the Copter is more agile on the Roll axis than on the Nick axis, then you can change here the roll factor. In the Graupner
ALPHA RACE 250 Q this value is set about 65%.
POWER 2SENS.
Very strong drives can lead to oscillating at full throttle. This parameter allows you to set a kind of gyro suppression. Higher values result in an increased suppression towards full throttle.
18 / 32 S1035_Falcon_12_Q06_V1sh
R/N DYNAMIC
Higher dynamic values provide a more direct feel for the flight (3D flight 50 ... 100), lower dynamic values for smoother flight recordings, rounder freestyle flying and races (30 ... 50).
–– ATTITUDE MODE ––
ROLL/NICK I
Set the I component of the Attitude mode. At too low values of Copter tilts slowly. If it stops after a roll or pitch command and “oscillates”, the value must be reduced.
AGILITY
This value determines how fast a change of position is made.
–– RATE MODE ––
R/N RATE I
Sets the I component of the rotation in rate mode. At too low values of Copter tilts slowly. If it stops after a roll or pitch command and
“oscillates”, the value must be reduced.
RATE
This value sets the maximum potential rate in Rate mode.
YAW Display
MULTICOPTER YAW
YAW P 40
YAW I 25
YAW D 40
RATE 70
YAW DYNAMIC 75
The general comments on PID control in the description of the roll / pitch display are also applicable here.
YAW P
The P factor is responsible for the snap to yaw. Higher values result in a faster stop. At too high P-values the copter starts to “swing”. In such cases, the value must be reduced again.
YAW I
The I-factor ensures constant rotations. Start with low values and only increase them until the rotations are constant. Too high value cause an oscillation when you stop. Eventually, the motors can start rotating and thus cause unwanted rising.
S1035_Falcon_12_Q06_V1sh 19 / 32
YAW D
The D-factor affects the stopping behaviour in Yaw. In most Copters a hard D action is necessary. The D component must be set as low as possible, since it affects the whole system.
RATE
For beginners we recommend a rate of about 50. For racers and freestyle pilots we recommend a value between 50 and 70.
YAW DYNAMIC
Higher dynamic values provide a more direct feel for the flight (3D flight 80 ... 100), lower dynamic values for smoother flight recordings, rounder freestyle flying and races (30 ... 80).
MULTIC. AUTOPILOT (only by S1039 with GPS #33602)
MULTIC. AUTOPILOT
ALTITUDE HOLD P 20
ALTITUDE HOLD I 25
ALTITUDE HOLD D 30
ALTITUDE HOLD II 5
POS HOLD P 45
POS HOLD I 5
POS HOLD D 10
POS HOLD II 5
RETURN ALTITUDE 25
ALTITUDE HOLD P
(Factory setting: 20)
The altitude hold P value compensates the climb and descent rate and must be adjusted so that it is compensated as well as possible.
The copter must under no circumstances swing around the desired height, otherwise the value must be reduced.
ALTITUDE HOLD I
(Factory setting: 25)
The altitude hold I value compensates for the height difference and must be set so that it is compensated as well as possible. The copter must under no circumstances swing around the desired height, otherwise the value must be reduced.
ALTITUDE HOLD D
(Factory setting: 30)
The altitude hold D value compensates the acceleration (wind gusts) in the height direction and it must be adjusted so that it is compensated as well as possible.
ALTITUDE HOLD II
(Factory setting: 5)
The altitude hold II value compensates for the time-integrated height difference, so that the desired height is kept as good as possible. This does not usually have to be adjusted.
POS HOLD P
(Factory setting: 45)
20 / 32 S1035_Falcon_12_Q06_V1sh
MULTIC. AUTOPILOT
ALTITUDE HOLD P 20
ALTITUDE HOLD I 25
ALTITUDE HOLD D 30
ALTITUDE HOLD II 5
POS HOLD P 45
POS HOLD I 5
POS HOLD D 10
POS HOLD II 5
RETURN ALTITUDE 25
YAW D
The D-factor affects the stopping behaviour in Yaw. In most Copters a hard D action is necessary. The D component must be set as low as possible, since it affects the whole system.
RATE
For beginners we recommend a rate of about 50. For racers and freestyle pilots we recommend a value between 50 and 70.
YAW DYNAMIC
Higher dynamic values provide a more direct feel for the flight (3D flight 80 ... 100), lower dynamic values for smoother flight recordings, rounder freestyle flying and races (30 ... 80).
MULTIC. AUTOPILOT (only by S1039 with GPS #33602)
MULTIC. AUTOPILOT
ALTITUDE HOLD P 20
ALTITUDE HOLD I 25
ALTITUDE HOLD D 30
ALTITUDE HOLD II 5
POS HOLD P 45
POS HOLD I 5
POS HOLD D 10
POS HOLD II 5
RETURN ALTITUDE 25
ALTITUDE HOLD P
(Factory setting: 20)
The altitude hold P value compensates the climb and descent rate and must be adjusted so that it is compensated as well as possible.
The copter must under no circumstances swing around the desired height, otherwise the value must be reduced.
ALTITUDE HOLD I
(Factory setting: 25)
The altitude hold I value compensates for the height difference and must be set so that it is compensated as well as possible. The copter must under no circumstances swing around the desired height, otherwise the value must be reduced.
ALTITUDE HOLD D
(Factory setting: 30)
The altitude hold D value compensates the acceleration (wind gusts) in the height direction and it must be adjusted so that it is compensated as well as possible.
ALTITUDE HOLD II
(Factory setting: 5)
The altitude hold II value compensates for the time-integrated height difference, so that the desired height is kept as good as possible. This does not usually have to be adjusted.
POS HOLD P
(Factory setting: 45)
The POS HOLD P value compensates for the position speed and must be set to compensate as well as possible. The copter must never circling or overshooting the GPS target position, otherwise the value must be reduced.
POS HOLD I
(Factory setting: 5)
The POS HOLD I value compensates for the position difference and must be set to compensate as well as possible. Under no circumstances the copter should oscillate around the GPS target position, otherwise the value must be reduced or the compass calibration and voltage calibration have to be repeated.
POS HOLD D
(Factory setting: 10)
The POS HOLD D value compensates the acceleration (wind gusts) of the GOS position and it must be adjusted so that it is compensated as well as possible.
MULTIC. AUTOPILOT (only by S1039 with GPS #33602)
MULTIC. AUTOPILOT
ALTITUDE HOLD P 20
ALTITUDE HOLD I 25
ALTITUDE HOLD D 30
ALTITUDE HOLD II 5
POS HOLD P 45
POS HOLD I 5
POS HOLD D 10
POS HOLD II 5
RETURN ALTITUDE 25
POS HOLD II
(Factory setting: 50)
Currently without effect.
The POS HOLD II value compensates for the distance difference integrated on time so that the position setpoint is kept as good as possible. This does not usually have to be adjusted.
RETURN FLIGHT ALTITUDE
(Factory setting: 25)
Determines the return altitude at Coming Home in meters.
S1035_Falcon_12_Q06_V1sh 21 / 32
BASIC Display
MULTICOPTER BASE
TYPE QUADRO XI
ESC S3087
MODE ACRO 3D
MINPOWER % 5
FREESTYLE MIN
CALIBR.COMPASS No
CALIBR.CURRENT No
TYPE
The "Type" line defines the basic configuration of the copter. The following selections are available:
QUADRO X QUADRO XI (invers)
1 2 1 2
4
QUADRO +
3 4 3
1
4 2
3
Connect the speed controllers of the motors to the receiver following the proper scheme. The represented motor direction is referred to the copter seen from the top.
ESC
S3087, S3088, 7242.4
The 4in1 controllers have a built-in power shunt. For correct current indication, the current connection of the 4in1 controller must be connected to the S1038 / S1039 and the corresponding 4in1 controller must be selected.
CONTROLLER SETTING
To initialize the controller, the signal of the motor / pitch control stick of the transmitter is transmitted directly to the speed controller of the copter.
MODE
CONTROLLER SETTING
To initialize the controller, the signal of the motor / pitch control stick of the transmitter is transmitted directly to the speed controller of the copter.
22 / 32 S1035_Falcon_12_Q06_V1sh
NORMAL
This setting must be used for copters with speed controller without reverse of the direction of rotation.
ACRO 3D
This setting is reserved for copters whose speed controllers are equipped with direction reverse.
Note
For safety reason the " Type " and " Mode " changes take effect after switching off and on the receiver system.
Throttle travel
Rate mode
Throttle travel
Attitude mode
M1
M2
M3
M4
M5
S 5
C1 C1
??
??
??
??
??
??
Type from zu to
1 =
3 =
MIX 2 C1 C1
Trvl –30% 0%
Offset 0%
SYM ASY
!
positive full linear
Min. linear negative full linear up to full
Motor Min.
CAUTION
Since the power control operates differently in the rate mode, see figure on the left, the motors may start rotating more or less when switching from the attitude mode to the rate mode, depending on the current position of the pitch stick. Therefore always mount the propellers immediately before starting the flight operation and start and land exclusively in "attitude mode".
During prolonged extreme aerobatics of the copter in Acro 3D mode (e.g. , sequence> 1min), the receiver may lose its attitude information and, as a result, the copter may move to an undesired position when switching to attitude mode. In this situation, the copter should be in the Rate mode and either it is left quiet for about 30 seconds or it is landed for a short time, so that the receiver can readjust the position information again.
Note
If the motors do not stop completely in the attitude mode, so that the position control is still active and can also serve as a rescue mode in an emergency, this can be remedied with the aid of a mixer:
Mixer programming step by step
15. Program a same-channel mixer "1 => 1" according to the transmitter instructions.
16. Assign to this mixer the same switch with the same switching direction, which switches to the attitude mode.
17. Leave this switch in the ON position.
18. Change to the setting page of the mixer.
19. Change through "ASY" to the setting field of the "Travel" line.
20. Set the value in the active value field of the "Travel" line to -30%.
S1035_Falcon_12_Q06_V1sh 23 / 32
MULTICOPTER BASE
TYPE QUADRO XI
ESC S3087
MODE ACRO 3D
MINPOWER % 5
FREESTYLE MIN
CALIBR.COMPASS No
CALIBR.CURRENT No
In the idle position of the throttle / pitch stick, the bar of channel
1 in the "servo display" should now be at about -66%.
MINPOWER %
The setting is principally used to prevent the motors shut down in flight. Adjust so that the motors are running straight. Under no circumstances unnecessarily high set, this would limit the controller possibilities.
FREESTYLE
The setting basically serves to prevent the I-factor from generating a vibration.
The higher the value, the more I-vibrations are prevented, but also the straight-ahead flight is degraded. Values up to max. 20 recommended.
The adjustment range is from 1 ... 100
MIN = disabled
Alternatively, the effect on the I value can also be adjusted by the transmitter. To do this, a rotary or slider control is assigned to one of the control channels 5 ... 16 and the remaining settings are left at the default values. In the value field of the "Freestyle" line, the corresponding channel is then merely to be selected instead of a fixed value.
Note
If a channel is selected in this line, but no control is assigned in the transmitter or otherwise it influences its neutral position, the value
"50" in parenthesis is predefined.
Only by #S1039: CALIBR. COMPASS
Note
When using an HD camera, it must be turned on when calibrating the compass. Otherwise the autopilot mode and
Come back home mode only work with HD camera switched off. If the autopilot and Come back home functions are used, then the HD camera must be turned on, since the current of the HD camera also affects the compass calibration.
If you change the airfield, the compass should be recalibrated. However, the current calibration does not need to be repeated.
24 / 32 S1035_Falcon_12_Q06_V1sh
MULTICOPTER BASE
MODE ACRO 3D
MINPOWER % 5
FREESTYLE MIN
CALIBR.COMPASS NO
CALIBR.CURRENT NO
CALIBR.POSITION NO
LOGGING 0
Activation of the field with SET or ENT.
Set the field to Yes
Deactivate the field again
Now turn the multicopter north pointing slowly twice in a circle on all axes and then randomly in different directions until No appears.
Then the compass is calibrated.
Only by #S1039: CALIBR. CURRENT
MULTIKOPTER BASE
MODE ACRO 3D
MINPOWER % 5
FREESTYLE MIN
CALIBR.COMPASS NO
CALIBR.CURRENT NO
CALIBR.POSITION NO
LOGGING 0
Note
It is advisable to first determine the throttle hovering position and note it, then swap the propeller and install them in the adjacent motor, so that the copter is sucked to the ground, instead of lifting.
The attitude control is not active in this mode, so the current calibration must be done on the ground.
The copter must not move during calibration. In addition, the sticks
(except the throttle one) must not be moved during calibration.
The current calibration should be done in calm wind conditions, otherwise the current will fluctuate too much and make the calibration more difficult.
Activation of the field with SET or ENT.
Set the field to Yes
Deactivate the field again
When display OFF, the motors must be switched off
If the display changes to Min, then please switch the motors to the
Mingas throttle position.
If the display changes to Hover, then please add "Hovering throttle" until the display changes to "No".
If the copter accidentally or by a control command has rotated on the yaw axis, the calibration must be repeated.
MULTICOPTER BASE
MODE ACRO 3D
MINPOWER % 5
FREESTYLE MIN
CALIBR.COMPASS NO
CALIBR.CURRENT NO
CALIBR.POSITION NO
LOGGING 0
CALIBR. POSITION
With this option, if necessary, the basic calibration of the acceleration sensors can be readjusted, so that the copter hovers with the stick and trim to neutral, in attitude mode, precisely horizontally.
To recalibrate, place the copter on an absolutely horizontal surface and then set the value field to "YES".
As soon as the calibration is completed, the display changes back to
"NO". To accept the calibration that has just been carried out in the non-volatile memory of the receiver, it is essential to push or tap on the ENT key.
S1035_Falcon_12_Q06_V1sh 25 / 32
Only by S1039: LOGGING
Logging 0 displays the Euler angles in the Copter telemetry display and also allows the position display using the Graupner HoTT OSD #
33641 on the FPV screen or in the FPV video goggles.
The other logging functions are exclusively intended for the service.
AXIS ASSIGNMENT
Note
The gyroscope calibration, required each time the copter is switched on, takes place as soon as the copter or its receiver is absolutely quiet. The motors will not start until the calibration is completed.
After approx. 3 seconds in the rest position, several beeps can be heard from all motors. The number of beeps varies depending on the speed controller used. These "wiggles" signal that initialisation has been successful and that calibration is complete.
!
AXIS ASSIGNMENT
NEW SETUP NO
ROLL +0
NICK +0
YAW +0
CAUTION
If the copter is used for long time (>1min) in Acro 3D mode the receiver can loose its position information and the copter can move itself out of control. In this case the copter should be left in the rate mode and hover or land calmly for approx. 30 s, so that the receiver can track the position again.
In this display, the gyros and their effective direction are to be determined.
NEW SETUP
After selecting the line "do setup" and changing the value field to
"yes", assign the axes as follows:
Do setup step by step
1. Push or tap on the ENT key
"NO" is displayed inverted.
2. Change the value field to "YES".
3. Push or tap on the ENT key
4. At the transmitter briefly bring the roll control stick to the right stop.
The display shows the roll axis inverted.
5. Tilt the copter more than 45 degrees to the right.
As soon as the detected axis with the required sign is displayed in
"normal" representation, the axis assignation is completed.
26 / 32 S1035_Falcon_12_Q06_V1sh
S1035_Falcon_12_Q06_V1sh
6. At the transmitter briefly bring the nick control stick to the front stop.
The display shows the nick axis inverted.
7. Tilt the copter more than 45 degrees to the front.
As soon as the detected axis with the required sign is displayed in
"normal" representation, the axis assignation is completed.
8. At the transmitter briefly bring the yaw control stick to the right stop.
9. Turn the copter clockwise by more than 45 degrees to the right.
As soon as the detected axis with the required sign is displayed in
"normal" representation, the axis assignation is completed.
The gyros and their operating directions have now been assigned.
Attention
To be on the safe side, the directions of action of the gyroscope settings must be checked.
Check step by step
1. Remove the rotors of the copter.
2. Use the pitch control stick to give approx. 25% "throttle".
All motors run at the same speed.
3. Switch to the attitude mode.
4. Tilt the copter forward.
The front motors must turn faster than back ones.
5. Tilt the copter to one side.
The motors of the side, the "hanging" side must turn faster than those of the opposite, higher side.
‖ If this is not the case, the entire gyro assignment must be repeated.
Firmware update
Updates to the receiver’s firmware are made via the receiver connection 5 using a PC running Windows 7 ... 10. You will also need a
USB interface, No. 7168.6, and adapter lead, No. 33565.1, which are available separately. The adapter cable must be plugged into J10 so that the first pin on the right remains free.
The programs and files required can be found in the Download area for the corresponding products at www.graupner.de
.
Connect the adapter lead to the USB interface. The polarity of the plug-in system cannot be reversed. Note the small chamfers on the sides. Do not use force, the plug should click into place easily.
Connect the other end of the adapter lead to the AIO FC's socket labelled with "J10". The polarity of the plug-in system cannot be reversed. Do not apply force.
27 / 32
The update takes place via the program part "Slowflyer / Gyro
Receiver Downloads" of the program "Firmware_Upgrade_gr_Studio" available under "Links". Please follow the notes of the software.
The further procedure is also described in detail in the manual contained in the data package. You can also download these from the download page of the product at www.graupner.de
.
SIMPLIFIED DECLARATION OF CONFORMITY
Graupner/SJ hereby declares that the AIO FC S1038 and S1039 complies with the Directive 2014/53/EU.
The full text of the EU Declaration of Conformity is available at the following Internet address: www.graupner.de
Notes on environmental protection
If this symbol is on the product, instructions for use or packaging, it indicates that the product may not be disposed with normal household waste once it has reached the end of its service life. It must be turned over to a recycling collection point for electric and electronic apparatus.
Individual markings indicate which materials can be recycled. You make an important contribution to protection of the environment by utilizing facilities for reuse, material recycling or other means of exploiting obsolete equipment.
Batteries must be removed from the unit and disposed of separately at an appropriate collection point. Please inquire if necessary from the local authority for the appropriate disposal site.
Care and maintenance
P
The product does not need any maintenance. Always protect it against dust, dirt and moisture.
Clean the product only with a dry cloth (do not use detergent!) lightly rub.
Warranty certificate
Graupner/SJ GmbH, Henriettenstrassee 96, 73230 Kirchheim/Teck grants from the date of purchase of this product for a period of 24 months. The warranty applies only to the material or operational defects already existing when you purchased the item. Damage due to misuse, wear, overloading, incorrect accessories or improper handling are excluded from the guarantee. The legal rights and claims are not affected by this guarantee.
Please check exactly defects before a claim or send the product, because we have to ask you to pay shipping costs if the item is free from defects.
These operating instruction are exclusively for information purposes and are subject to change without prior notification. The current version can be found on the Internet at www.graupner.de on the relevant product page. In addition, the company Graupner/SJ has no responsibility or liability for any errors or inaccuracies that may appear in construction or operation manuals.
Not liable for printing errors.
S1035_Falcon_12_Q06_V1sh 29 / 32
FCC Warning :
This device complies with Part 15 of the FCC Rules. Operation is subject to the following two conditions
(1) this device may not cause harmful interference, and
(2) this device must accept any interference received, including interference that may cause undesired operation. Changes or modifications not expressly approved by the party responsible for compliance could void the user’s authority to operate the equipment.
Note 1: This equipment has been tested and found to comply with the limits for a Class B digital device, pursuant to part 15 of the FCC Rules. These limits are designed to provide reasonable protection against harmful interference in a residential installation. This equipment generates, uses and can radiate radio frequency energy and, if not installed and used in accordance with the instructions, may cause harmful interference to radio communications. However, there is no guarantee that interference will not occur in a particular installation. If this equipment does cause harmful interference to radio or television reception, which can be determined by turning the equipment off and on, the user is encouraged to try to correct the interference by one or more of the following measures:
—Reorient or relocate the receiving antenna.
—Increase the separation between the equipment and receiver.
—Connect the equipment into an outlet on a circuit different from that to which the receiver is connected.
—Consult the dealer or an experienced radio/TV technician for help.
Note 2: 1.Changes or modifications to this unit not expressly approved by the party responsible for compliance could void the user’s authority to operate the equipment.
2. The minimum separation generally be used is at least 20 cm.
a. The module is limited to OEM installation ONLY. It must be clear that manual is intended for OEM/Integrators only b. OEM integrators are responsible for ensuring that the end-user has no manual instructions to remove or install module.
c. The module is limited to installation in mobile or fixed applications, according to Part
2.1091(b).
d. Separate approval is required for all other operating configurations, including portable configurations with respect to Part 2.1093 and different antenna configurations.
e. Authorized antennas per Part 15.204 (including ant. spec.).
f. Antenna installation requirements, where relevant.
g. According to FCC KDB 996369 D01, please revise the labeling instructions of the finished products to “Contains Transmitter Module FCC ID: SNL-36308010” or “Contains FCC ID:
SNL-36308010” etc.
30 / 32 S1035_Falcon_12_Q06_V1sh
S1035_Falcon_12_Q06_V1sh 31 / 32
32 / 32 S1035_Falcon_12_Q06_V1sh
advertisement
Related manuals
advertisement