- Computers & electronics
- Telecom & navigation
- Mobile phones
- Car kits
- Festo
- CASB-MT-D3-R7
- Instructions
advertisement
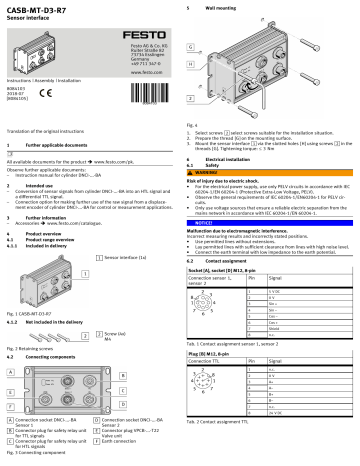
CASB-MT-D3-R7
Sensor interface
5 Wall mounting
Festo AG & Co. KG
Ruiter Straße 82
73734 Esslingen
Germany
+49 711 347-0 www.festo.com
Instructions | Assembly | Installation
8084103
2018-07
[8084105]
8084103
Translation of the original instructions
1 Further applicable documents
All available documents for the product è www.festo.com/pk.
Observe further applicable documents:
– Instruction manual for cylinder DNCI-...-BA
2 Intended use
– Conversion of sensor signals from cylinder DNCI-...-BA into an HTL signal and a differential TTL signal.
– Connection option for making further use of the raw signal from a displacement encoder of cylinder DNCI-...-BA for control or measurement applications.
3 Further information
– Accessories è www.festo.com/catalogue.
4 Product overview
4.1
Product range overview
4.1.1
Included in delivery
1 Sensor interface (1x)
Fig. 1 CASB-MT-D3-R7
4.1.2
Not included in the delivery
Fig. 2 Retaining screws
4.2
Connecting components
2 Screw (4x)
M4
Fig. 4
1. Select screws 2 select screws suitable for the installation situation.
2. Prepare the thread [G] on the mounting surface.
3. Mount the sensor interface 1 via the slotted holes [H] using screws 2 in the threads [G]. Tightening torque: £ 3 Nm
6
6.1
Electrical installation
Safety
WARNING!
Risk of injury due to electric shock.
• For the electrical power supply, use only PELV circuits in accordance with IEC
60204-1/EN 60204-1 (Protective Extra-Low Voltage, PELV).
• Observe the general requirements of IEC 60204-1/EN60204-1 for PELV circuits.
• Only use voltage sources that ensure a reliable electric separation from the mains network in accordance with IEC 60204-1/EN 60204-1.
NOTICE!
Malfunction due to electromagnetic interference.
Incorrect measuring results and incorrectly stated positions.
• Use permitted lines without extensions.
• Lay permitted lines with sufficient clearance from lines with high noise level.
• Connect the earth terminal with low impedance to the earth potential.
6.2
Contact assignment
Socket [A], socket [D] M12, 8-pin
Connection sensor 1, sensor 2
Pin
7
8
5
6
1
2
3
4
Signal
5 V DC
0 V
Sin +
Sin –
Cos –
Cos +
Shield n.c.
Tab. 1 Contact assignment sensor 1, sensor 2
Plug [B] M12, 8-pin
Connection TTL
Tab. 2 Contact assignment TTL
Pin
3
4
5
6
1
2
7
8
Signal n.c.
0 V
A+
A–
B+
B– n.c.
24 V DC
A Connection socket DNCI-...-BA
Sensor 1
B Connector plug for safety relay unit for TTL signals
C Connector plug for safety relay unit for HTL signals
Fig. 3 Connecting component
D Connection socket DNCI-...-BA
Sensor 2
E Connector plug VPCB-...-T22
Valve unit
F Earth connection
Plug [C] M12, 5-pin
Connection HTL
Tab. 3 Contact assignment HTL
Pin
3
4
1
2
5
Signal
A
B
24 V DC
0 V n.c.
Plug [E] M12, 8-pin
Connection VPCB Pin
5
6
7
8
3
4
1
2
Tab. 4 Contact assignment VPCB
6.3
Assembly of electrical connections
1. Use permitted lines:
Signal
5 V DC
0 V
Sin +
Sin –
Cos –
Cos +
Shield n.c.
Connecting component
[A], [D]
[B]
[C]
[E]
Sensor 1, sensor 2
TTL
HTL
VPCB
Line Cable length [m]
Integrated in the displacement encoder of cylinder
DNCI-...-BA
NEBU-M12W8-...
NEBU-M12G5-...
KM12-8GD8GD-2-PU
£ 1.5
£ 10
£ 10
£ 2
Tab. 5 Permitted lines
2. Connect matching plugs to the sockets [A] and [D]. Tightening torque: 0.4 Nm ± 10 %
3. Connect matching sockets to the plugs [B], [C] and [E]. Tightening torque: 0.4 Nm ± 10 %
6.4
Assembling the earthing cable
8 Technical data
CASB-MT-D3-R7
Reverse polarity protection
Output frequency, HTL signal
Output frequency, TTL signal
Nominal operating voltage DC
Requirement on the power supply
Residual ripple
Current consumption with load-free outputs
Current rating per output
CE marking (see declaration of conformity):
è www.festo.com/sp
KC Mark
Degree of protection
Degree of protection
Note on degree of protection
Signal range, HTL signal
High
Low
Signal range, TTL signal
High
Low
Yes
[Hz] £ 450
[Hz] £ 7200
[V] 24
PELV
5 %
[mA] 50
[mA] 50
To EU EMC Directive
1)
[V]
[V]
[V]
[V]
KC EMC
IP65
In assembled state
³ 18
£ 2
³ 2.4
£ 0.4
1) The product is suitable for industrial purposes only. Measures for interference suppression may be required in residential areas.
Tab. 7 Technical data CASB-MT-D3-R7
Fig. 5 Assembling the earthing cable
1. Undo screw [J] and toothed disc [K] from the sensor interface 1 .
2. Place cable lug [L] of the earthing cable between the screw [J] and the toothed disc [K].
3. Tighten the screw [J]. Tightening torque: 1 Nm ± 10 %
7
7.1
Malfunctions
Diagnostics
LED TTL
Off
Off
On
On
Tab. 6 Diagnostics
LED HTL
Off
On
Off
On
Status
24 V DC not present
Valve VPCB not connected
24 V DC not present at HTL
Ready for operation
advertisement
Related manuals
advertisement
Table of contents
- 1 Further applicable documents
- 1 Intended use
- 1 Further information
- 1 Product overview
- 1 Product range overview
- 1 Included in delivery
- 1 Not included in the delivery
- 1 Connecting components
- 1 Wall mounting
- 1 Electrical installation
- 1 Safety
- 1 Contact assignment
- 2 Assembly of electrical connections
- 2 Assembling the earthing cable
- 2 Malfunctions
- 2 Diagnostics
- 2 Technical data