- No category
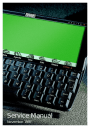
advertisement
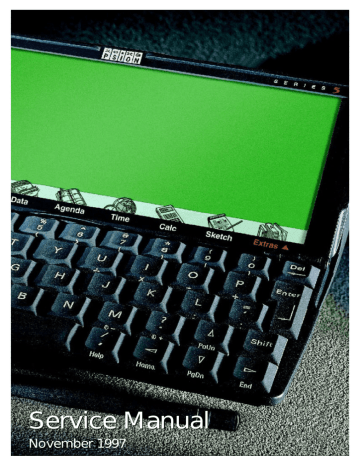
Company Confidential
PSION Computers PLC
Confidentiality & Service Support
Series 5 Service Manual
The Series 5 Service Manual will not be made available as bound and printed copy. It will be made available exclusively as an Adobe Acrobat PDF file. This manual is available as a viewable, printable and downloadable file from the Psion Computers closed World-wide
Web site.
All information published on the Psion Computers closed World-wide Web site must be treated as confidential, unless it is explicitly marked as ‘public domain’. Do not give your password, your user name, or even the address of the web site to anyone without written permission from Psion Computers PLC.
Series 5 Spare Parts Catalogue
This manual lists the Series 5 Spare Parts Kits available. A detailed catalogue of Series 5
Spare parts is also available as a viewable, printable and downloadable file from the Psion
Computers closed World-wide Web site.
Series 5 Service Engineering Information Updates
Engineering Updates will be issued to official Psion Computers Service Centres when necessary. All future Updates will be distributed through the Psion Computers closed Worldwide Web site.
© Copyright Psion Computers PLC 1997
All rights reserved. This Manual and the data referred to herein are copyrighted works of Psion Computers PLC, London,
England, UK. Reproduction in whole or in part, including utilisation in machines capable of reproduction or retrieval, without the express written permission of Psion Computers PLC is prohibited. Reverse Engineering is prohibited.
The information in this document is subject to change without notice.
Psion and the Psion logo are registered trademarks, Psion Series 5 is a trademark of Psion Computers PLC, and EPOC32 is a registered trademark of Psion Software PLC.
Psion Computers PLC acknowledges that some names referred to are registered trade marks.
Company Confidential
PSION Computers PLC
Contents
........................................................................................ 3
..............................................................................................5
- Introduction
- LCD Assembly
- Keyboard Assembly
- Hinge Cover Assembly
- Base Assembly
- PCB/ROM Board Assembly
- PCB/Chassis Assembly
- Final Assembly
- Introduction
- Generic Spares Kit
- LCD Spares Kit
- Language Specific Spares Kits
- PCB Spares Kits
........................................................................14
- Introduction
- Tools Required
- Disassembly Procedure
....................................................................................25
- Overview
- System Power Connections - Saftey Critical Information
- Modes of Operation
- Menu Options Explained
- System Set-Up
- Test Procedure Set-Up
- Test Sequence
- Explanation of Test Procedure
- Fail Ticket Codes
- Connector Circuit Diagram
Company Confidential
PSION Computers PLC
Introduction
The Series 5 is a revolutionary handheld computer which enables the functionality of desktop applications in a handheld form. It combines innovative design and new technology, incorporates a full VGA width back-lit screen, a pen for navigation and a patented touch-type keyboard. The 32 bit Series 5 features a windows-style interface and PsiWin V.2 (Windows 95/Nt4.0) connectivity software to provide total integration and compatibility with office and home computer systems.
There are two models in the new range, a 4MB and 8MB variant both supplied with an industry-standard
CompactFlash™ card slot which allows users to add additional memory. The screen resolution is the largest on a handheld device and allows users to view full page width documents, email messages and
Web pages without horizontal scrolling.
The Series 5 uses a powerful 32 bit open operating system standard, EPOC32 developed by Psion Software and the ARM RISC 7100 processor, providing a high level of processing power while preserving battery life. EPOC32 is optimised for low-power, portable machines and is equally at home in a smartphone, mobile network computer or handheld computer. There are now three different handhelds in the
Psion range, the Series 5, the Series 3c and Siena, each offering a different level of functionality at a different price point.
The purpose of this service manual is to give an overview of the service procedures that may need to be performed on the Psion Series 5 by either a third party user or a registered Psion service centre. It has been designed to be used by the service and repair technicians who have the responsibility of maintaining the products.
The Series 5 uses both conventional component and high-density surface mount component technology which requires specialist servicing techniques. It is also the first Psion product to use the EPOC 32 operating system, based around the ERA architecture running on the ARM 7100 CPU. We therefore recommend that repairs are carried out at a circuit board level, rather than at component level. We also encourage service centres to carry a stock of spare parts to allow immediate servicing of Series 5 components should they need to be replaced. Details of the Series 5 spare parts kits can be found in the Spare
Parts Catalogue and in the Spare Parts section of this document.
Although a final test unit is not essential to service a Series 5 effectively, it is recommended. The final test unit is used within Psion during the manufacturing process to run a final check on the assembly. When a Series 5 is connected to the final test unit test code is downloaded into the machine via the comms interface. The test program can then be run to exercise the LCD, digitiser, keyboard, membrane, Memory Disks, switches, comms door, Irda, speaker and microphone. Operating, idle and standby current consumption can also be measured. This can be extremely valuable to investigate or diagnose a reported problem. In addition, once a repair has been completed, a full test can be run to ensure that the repair has been carried out correctly and that no other fault
has been introduced during the servicing procedure. - See Final Test section for more information.
Company Confidential
PSION Computers PLC
Approvals
FCC Logo - This shows that the product complies with the requirements for shipping products to the
USA. The product has been tested to show compliance with USA Federal Communications Commission requirements as detailed in US Government handbook CFR Part 15. This document covers the requirements for digital devices designed for use in residential and commercial environments (known as Class B devices). A further requirement of the US regs is to display the model number (4/8MB) and the words ‘Tested to Comply with FCC Standards for Home or Office Use’. The Canadian Requirements are covered by displaying the wording ‘This Class B Device complies with Canadian ICE regulations. Tested to comply with FCC standards for home or office use.” (The French translation “Cet apparareil CL B se conforme au reglement sur le materiel brouilleur du Canada”). They show the product complies with the Industry Canada requirements specified in the Canadian Interference Causing Equipment (ICE) regs. These are currently met by testing the product to ICE-003 (currently identical to USA CFR 15 Class B).
IR Logo - This shows that the Series 5 complies with the requirements of the Infrared Data Association standards, and indicates that data may be transferred to other products that display this logo.
CE Logo - This shows the product complies with the requirements for shipping to any country within the European Union and indicates that the Series 5 complies with both the EMC and Low Voltage
Directives. The EMC Directive ensures that the product complies with the emissions requirements of
EN55022 Class B, and the Immunity requirements of EN50082-1. The latter document covers static testing to +8kV, radiated RF testing and surviving 1kV Electrical Fast Transients into the mains adapter inputs. The Low Voltage Directive ensures the product complies with the requirements of the European safety standard for Information Technology Equipment - EN60950.
EPOC 32 is the built-in, highly optimized, C++, multi-tasking, 32-bit operating system of the Series
5, which includes a fully featured suite of Personal Information Management, productivity and communications applications. The platform is entirely modular and supports embedded graphics and voice as well as pen and keyboard input. The real-time performance of EPOC32 allows it to run telephony protocol stacks and makes it suitable for communications enabled devices.
CompactFlash (CF) is an ultra-small removable data storage system. CF provides complete PCMCIA-
ATA functionality and compatibility and has built-in, industry-standard compatibility as the 50-pin CF cartridge can be easily slipped into a passive 68 pin Type II adapter card that fully meets PCMCIA electrical and mechanical interface specifications. CF is widely used in digital cameras, cellular phones, personal digital assistants and personal communicators.
The ARM7100 is a high-integration, application specific microcontroller which meets the needs of next generation electronic organizers and PDA’s providing the combination of features and performance to cope with the increasing software demands of friendlier user interfaces, increased functionality and advanced communication protocols. The ARM7100 is the microcontroller component of the unique hardware and software open architecture employed by the Series 5.
Company Confidential
PSION Computers PLC
Circuit Description
The electronic design for the Psion Series 5 handheld computer product is the first to make use of the
ERA architecture based around the ARM7100 cpu. The product hardware supports optional DRAM builds of 4 and 8 Mbytes, and features a 640x240 monochrome display, a button operated dictaphone function, a pen activated digitised screen, full travel keyboard switches and a Compact Flash (Memory
Disk) socket. TheSeries 5 electronics are made up of a main PCB and a ROM daughter PCB.
Circuit Diagram:
MAIN PCB
4MB or 8MB
SRDRAM
DAUGHTER
ROM - 6MB
Daughter PCB
32 BIT BUS 32 BIT BUS
CODEC
MICROPHONE
6V DC IN
PSU
7.68M
EIGER
ARM 7100
32.768K
16Bit
ASIC 12
PCMCIA I/F
SPEAKER
CF SLOT
2x ALKALINE
MAIN
BATTERIES
LITHIUM
BACK UP
3.3V
IrDA RS232
DICTAPHONE
SWITCH
QWERTY
KEYBOARD
640x240 LCD
DIGITISER
BACKLIGHT
CPU, DRAM and POR Generator
The Series 5 cpu (IC1) is the ARM 7100 device, which integrates an ARM7100 32 bit RISC core with
Psion specific peripherals. Its main clock input frequency is 3.6864 MHz (+/- 50 ppm), provided by crystal X2 working in fundamental mode. This signal is internally multiplied up in frequency by a factor of 5, to 18.432 MHz (54.2535 ns). An expansion clock of this frequency is available as an output from the ARM 7100, and is used on Series 5 by the Compact Flash interface device, ASIC12 (IC2).
Company Confidential
PSION Computers PLC
Circuit Description
A Power-On-Reset (cold reset) signal to the ARM 7100 is provided by a Ricoh RN5VLR20AA open drain FET output, voltage detector device, IC4. The ARM 7100 is reset during power-on by IC4, which detects when VDD crosses a set point voltage. This threshold voltage is set to 2.0 V ± 2.5% (2.0V ±
50mV). An RC circuit stretches the low state signal , to allow sufficient time for the ARM 7100 to reset.
Power-On-Reset erases all data held in volatile storage, and is an indication that all power has been lost and subsequently re-applied.
A User Reset (warm reset) signal is available on Series 5 via a switch. The switch forms part of the
Lithium backup battery negative contact, and would normally be accessible to the user only by opening the backup battery case cover and using a pointed instrument. The user reset signal is normally held inactive high by a pull up resistor, R1. A small value capacitor, C113, provides a measure of noise bypass in order to protect the system from inadvertent resets during ESD events and other electrically noisy periods. Operating this switch vectors the CPU to a warm restart and all user data should be recovered in this process.
Keyboard Interface
The Series 5 keyboard contains a total of 53 keys, organised in a conventional QWERTY arrangement.
The implementation is a departure from the S3a family of products, and features a separate keyboard switch matrix assembly which slides out as the LCD screen is opened. The electrical connection between the keyboard and the main Series 5 PCB is achieved by means of a 22 way Flat Flexi Cable (only
20 ways are used for keys), fitted to a 22 way ZIF connector. The outside pins on the flexi are the grounded to allow a for a ground ring on the keyboard membrane to improve ESD protection.
LCD and Digitiser Interface
The LCD screen supplied on Series 5 is a 640 by 240 pixel passive matrix module, normally white pixels. All the data, clock and synchronisation signals are provided by the ARM 7100 device. A separate passive resistive digitiser module consisting of a glass lower plate and a hardened plastic top plate is assembled over the LCD screen. Resistive ink is printed on the inside of the digitiser faces and four electrical connections provide the means for sensing resistance across the x- and y- axes. The electrically conductive internal faces of the digitiser are kept apart by means of very small bumps manufactured into the plastic member. A 22 way Flat Flexi Cable carries the electrical interface to the Series 5 main PCB.
LCD and VLD PSU
The LCD module requires a number of power/voltage rails, which have to be enabled and disabled in a defined sequence, in order to ensure that at no time no residual DC is presented across the LCD panels.
This DC would cause drift in the liquid crystal and eventually would irreversibly damage its light polarisation characteristics.
The logic supply to the LCD module, VLL, is supplied from a normal drive port output, as the required current is only around 2mA maximum. The main high voltage supply to the LCD module is generated by an ARM 7100 controlled boost switched mode power supply, with a 4 bit DAC acting as a variable resistor in the feedback path.
Company Confidential
PSION Computers PLC
Exploded Views
Introduction
The following exploded diagrams show the construction of the sub-assemblies that comprise the Series
5. The structure of the diagrams attempts to reflect the assembly stages employed at the point of manufacture. Descriptions for each component are also given along with the relative part numbers. You can access each subassembly directly by clicking on the icon next to the relevant title below:
LCD Assembly
Keyboard Assembly
Hinge Cover Assembly
Base Assembly
PCB/ROM Board Assembly
PCB/Chassis Assembly
Final Assembly
LCD Assembly
LCD Conductive Label
p/no: 6205-0058-01
Digitiser
p/no: 2902-0002
LCM/DIG Zebra
p/no: 8705-0006-01
LCD Side Bar Label
p/no: 6205-0016-01
Dig/LCD Clamp
p/no: 8206-0002-01
LCD Icon Label
p/no: 6205-0009-01
LCD Inner Mldg
p/no: 2902-0013-01
LCM 640 x 240 B/W 3V TAB Tranfl
p/no: 2902-0006-01
Backlight Assy.
p/no: 2902-0007-01
LCD Compression Spacer
p/no: 8105-0042-01
LCD Flexi Cover Label
p/no: 6205-0060-01
Mldg LCD Outer Coated
p/no: 2902-0014-01
Company Confidential
PSION Computers PLC
Exploded Views
Keyboard Assembly
Mldg Keycaps Numeric x 12
p/no: 8105-0009-01
Mldg Keycaps Alpha x 38
p/no: 8105-0008-01
Mldg Keycaps Tab x 1
p/no: 8105-0010-01
Mldg Keycaps Spacebar x 1
p/no: 8105-0011-01
Key Mat
p/no: 8705-0001-01
Company Confidential
PSION Computers PLC
Exploded Views
Mldg Keycaps Enter x 1
p/no: 8105-0014-01
Keyboard Membrane
p/no: 7900-0007-01
Key Frame Shield
p/no: 6205-0057-01
Enter Key Torsion Wire
p/no: 8405-0006-01
Space Bar Torsion Wire
p/no: 8405-0005-01
Mldg Keycap Fixed
p/no: 8105-0029-01
Light Guide - Power
p/no: 8105-0032-01
LCD/KBD Hinge Pin x 2
p/no: 8305-0001
Keyframe Mldg Coated
p/no: 2902-0011-01
Keyframe Approvals Label
4MB p/no: 6205-0002-01
8MB p/no: 6205-0053-01
Hinge Cover Assembly
Mldg Battery Door
p/no: 8105-0004-01
Battery Foam x 2
p/no: 8705-0010-02
Company Confidential
PSION Computers PLC
Exploded Views
Mldg IR Window
p/no: 8105-0026-01
Mldg COMMS Door
p/no: 8105-0021-01
Mldg Hinge Cover Coated
p/no: 2902-0012-01
Base Assembly
Mldg Base Coated
p/no: 2902-0009-01
Company Confidential
PSION Computers PLC
Exploded Views
Mldg Dictaphone Door
p/no: 8105-0043-01
Light Pipe Record
p/no: 8105-0036-01
Mldg Pen Ejector
p/no: 8105-0022-01
Pen Eject Spring
p/no: 8405-0011-01
Mldg Rubber Foot x 4
p/no: 8705-0008-01
Mldg Record Button
p/no: 8105-0044-01
Mldg Stop Button
p/no: 8105-0046-01
Mldg Play Button
p/no: 8105-0045-01
PCB/ROM Board Assembly
ROM Board 01
3 x Flash Devices
Company Confidential
PSION Computers PLC
Exploded Views
ROM Board 02
1 x ROM Device
1 x Flash Device
ROM Board 03
2 x ROM Devices
Main PCB Assy.
PCB Corner Label
p/no: 6205-0059-01
Company Confidential
PSION Computers PLC
Exploded Views
PCB/Chassis Assembly
Hinge Wire Staple x2
p/no: 8405-0011-01
Hinge Wire RH
p/no: 8405-0013-01
Speaker Flexi Assy.
p/no: 2902-0005-01
Hinge Wire LH
p/no: 8405-0012-01
Speaker Gasket
p/no: 8705-0009-02
Pivot Arm Pin x 2
p/no: 8305-0002-01
CPU Chassis
p/no: 2902-0010-01
Chassis Protective Label
p/no: 6205-0072-01
PCB Assembly
Final Assembly
LCD Assembly
Key Frame Assembly
LCD/Kbd. Hinge Pin x 2
Chassis Assembly
Pivot Arm Pin x 2
Main PCB Assy.
Fixing Screws
Hinge Cover Assy.
Slim Base Assy.
Company Confidential
PSION Computers PLC
Exploded Views
Company Confidential
PSION Computers PLC
Spares Kits
Introduction
The following spares are offered to service centres enabling thorough and complete service and repair work. They have been subdivided into relevant groups to differentiate between generic kits that supply parts for the servicing of all Series 5’s and the language and option specific kits which deal with the localised servicing requirements. The spares kits are detailed in the separate Series 5 Spare Parts Catalogue, which is available from Psion Computers.
Part Number Description
1908-0003-01 S5 Spares Kit LCD Assembly
1908-0004-01 S5 Spares Kit Base Assembly
1908-0005-01 S5 Spares Kit Chassis Assembly
1908-0006-01 S5 Spares Kit Hinge Cover Assembly
1908-0007-01 S5 Spares Kit Labels 4M - UK/USA
1908-0008-01 S5 Spares Kit Labels 8M - UK/USA
1908-0009-01 S5 Spares Kit Labels 4M - German
1908-0010-01 S5 Spares Kit Labels 8M - German
1908-0011-01 S5 Spares Kit Labels 4M - French
1908-0012-01 S5 Spares Kit Labels 8M - French
1908-0013-01 S5 Spares Kit Keyboard Assembly - UK
1908-0014-01 S5 Spares Kit Keyboard Assembly - USA
1908-0015-01 S5 Spares Kit Keyboard Assembly - German
1908-0016-01 S5 Spares Kit Keyboard Assembly - French
1908-0017-01 S5 Spares Kit Main PCB 4M - UK
1908-0018-01 S5 Spares Kit Main PCB 8M - UK
1908-0019-01 S5 Spares Kit Main PCB 4M - USA
1908-0020-01 S5 Spares Kit Main PCB 8M - USA
1908-0021-01 S5 Spares Kit Main PCB 4M - German
1908-0022-01 S5 Spares Kit Main PCB 8M - German
1908-0023-01 S5 Spares Kit Main PCB 4M - French
1908-0024-01 S5 Spares Kit Main PCB 8M - French
1908-0025-01 S5 Spares Kit ROM PCB - UK
1908-0026-01 S5 Spares Kit ROM PCB - USA
1908-0027-01 S5 Spares Kit ROM PCB - German
1908-0028-01 S5 Spares Kit ROM PCB - French
1908-0029-01 S5 Spares Kit Tamper Proof Label
Company Confidential
PSION Computers PLC
Dissasembling the Series 5
Introduction
This section deals with the disassembly of the Psion Series 5. The procedure has been structured around the spare parts that are offered assembled as kits which are referenced in the previous section. As such a
Series 5 can be disassembled quickly into specific sub-assemblies allowing the accurate replacement of faulty components. The design of the Series 5 promotes simple servicing procedures and it can be dismantled quickly using only a small number of tools. We recommend that servicing is carried out at board level and not at component level, and as such this disassembly procedure explains servicing in line with the spares kits detailed in this manual.
The Series 5 hand-held computer contains CMOS devices that may be damaged by electrostatic discharge (ESD). The following steps to minimise ESD must be taken before the unit is dismantled.
To prevent any damage that could result if the unit or its parts are not handled properly, observe the following precautions during any handling procedures:
• Minimise all handling of static-sensitive components and assemblies.
• Transport and store static-sensitive components and assemblies in their original containers or in antistatic bags.
• Label accordingly any package that contains static-sensitive components or assemblies.
• Discharge static electricity from the body by wearing a grounded antistatic wrist strap while handling these components. Servicing static-sensitive components or assemblies should be done only at a static-free work station by qualified service technicians. Increasing the humidity in the work area minimises static electricity problems.
• Do not allow anything that can generate or hold a static charge on the work station surface.
• Pick up components by their bodies, never by their leads.
• Do not slide components over any surface.
• Avoid handling components in areas with a floor or work-surface covering that can generate static charge.
Before commencing the disassembly procedure be sure to remove any batteries including the lithium dry cell. To remove the lithium dry cell open the battery door to expose the it and use the stylus to release the cell from its location. The stylus should be inserted beneath the cell next to the voltage details in the base moulding. (Refer to the User Guide for further instructions) Do not use a metallic tool to do this as it may short the cell.
Caution: Danger of explosion if lithium battery is incorrectly replaced.
Replace only with the same or equivalent type of lithium battery and dispose of used batteries as recommended in the Series 5 User Guide
When removing the internal workings from the case, care should be taken not to damage the LCD module. Do not bend the module, as the circuit board is prone to fracturing. If the LCD breaks, be careful not to get any liquid crystal in your mouth or eyes. In the event of any liquid crystal getting on skin or clothes, wash off immediately with soap and plenty of water. Do not remove both the lithium dry cell and main
Company Confidential
PSION Computers PLC
Dissasembling the Series 5
batteries without first ensuring that the data contained in The Series 5’s internal memory has first been backed up. Removal of both the battery sources, without previously attaching an external power supply, will erase all information stored on the internal memory.
Ensure that all case mouldings are disassembled and stored together as they are finished as assemblies and as such small colour variations may appear between batches. Always replace the entire case set if one moulding is damaged in any way.
Tools Required
Tool
Screwdriver
Pliers
Hinge Pin Removal
Snips
Description
2.5 x 35mm
Micro Shear
Type
Phillips
Disassembly Procedure
Once the Series 5 has had all batteries and any Memory Disks removed the first stage of disassembly is to remove the slim base assembly. First remove the stylus then remove the 3 case screws from the base moulding which are located as shown in the following photograph. (The “Warranty Void if Removed” label will be destroyed during this procedure). Once the screws have been removed the Base moulding
Remove fixing screws
Remove stylus
Remove lithium battery
can be lifted off the main assembly. First ensure that the Memory Disk and lithium battery doors are open as this will free locating clips between the PCB and the base moulding. The moulding should then be eased upwards from its front edge to disengage it from the hinge moulding. Ensure that the moulding in lifted clear without damaging any of the locating details along the bottom edge of the base moulding.
Company Confidential
PSION Computers PLC
Dissasembling the Series 5
The Daughter PCB can now be removed if necessary. Certain intermittent faults can be caused by dry or faulty joints on the daughter PCB so quick replacement can be undertaken at this stage of disassembly to ascertain if this is the cause of the fault. The daughter PCB can be removed by unclipping the connec-
Unclip retaining socket
tor and easing the PCB out of its socket. Take care not to bend the PCB during this procedure as it is prone to fracture. When replacing the daughter PCB ensure that the replacement is of the same OS build number and language as the PCB that is being removed. This can be checked in the system screen on the
Series 5 by pressing ‘Control+H’.
The hinge cover moulding should now be removed. This can be done by inserting a blunt pointed instrument (such as a spare Series 5 stylus) into the centre of the hinge moulding and gently levering the moulding out of its locating clips on the chassis as shown in the photograph below. Note that the battery housing door needs to be closed to facilitate the removal of the hinge cover moulding assembly.
The hinge moulding assembly contains the battery door, RS232 door and IrdA window mouldings.
Each of these can be snapped out of place and replaced if necessary. The battery cover moulding has a small amount of silicone based lubricant applied on the running surface at both ends during manufacture to enhance the rotating movement the door performs in use. Replacement doors should therefore have such a lubricant applied.
Unclip Hinge
Moulding
Company Confidential
PSION Computers PLC
Dissasembling the Series 5
The Main PCB can now be removed. First unscrew the 3 retaining screws and the disconnect the Speaker
Flexi and the Backlight flexi as shown in the following photographs:
Retainig Screws
Unclip Speaker
Flexi
Unclip Backlight
Flexi
Lift the PCB up to expose the LCD (orange) and Keyboard (blue) flexi connectors. These should be removed from their respective LIF sockets on the main PCB. This process can be made simpler by placing the Series 5 assembly onto the edge of a slightly raised surface, such as a book, which will allow the PCB to be lowered once it is in position, thus giving more slack to the flexi connectors.
Unclip LCD and Keyboard flexi connectors
The Main PCB can now be replaced if necessary. When replacing the PCB ensure that the same RAM size is present on the replacement PCB and ensure that the damaged PCB is stored in an anti-static bag.
Company Confidential
PSION Computers PLC
Dissasembling the Series 5
The Chassis and LCD/Keyboard assembly should now be separated. The hinge pins that hold the two assemblies together can be removed by using the hinge pin removal tool supplied as part of the generic spare parts kit. Insert the tool into the hinge pins and remove by flexing the tool and pulling the pins out of the LCD outer moulding. Take care not to damage the painted finish on the LCD outer moulding whilst removing the hinge pins.
Remove hinge pins
The LCD/Keyboard assembly can now be slid off the chassis moulding as shown in the photograph below.
Slide LCD/Keyframe assembly off chassis moulding
Company Confidential
PSION Computers PLC
Dissasembling the Series 5
The LCD and Keyboard assemblies can now be separated. The LCD inner moulding must be cut to expose the LCD hinge pin before removal can take place. Using the micro shear pliers remove the necessary section of the LCD inner moulding, ensuring that the hinge pin is sufficiently exposed to allow a pair of pliers sufficient purchase space to grip the hinge pin for final removal.
Cut away shaded section of hinge
Using the pliers, grab the exposed hinge pin and push it out of the end of the hinge assembly.
Hinge pin
Company Confidential
PSION Computers PLC
Dissasembling the Series 5
Lever the remainder of the hinge pin out of the hinge assembly, taking care not to damage the painted surfaces of the keyframe and LCD outer mouldings.
Hinge pin
The LCD and keyboard assemblies can now be separated. Replacement keyboards are supplied as complete assemblies. Ensure that the replacement keyboard assembly is of the same language as the keyboard being replaced. The LCD assembly can be removed from the LCD outer moulding by carefully sliding the digitiser/LCD assembly out of the moulding. Grip the LCD as shown in the diagram below and ensure that the digitiser/LCD assembly remains level as it is removed, as the assembly will not slide out of the moulding if it at all out of line. Ensure that the same LCD outer moulding is used during reassembly (if it is undamaged) to ensure that no colour differences exist between mouldings.
Slide out LCD/Digitiser assembly
It is recommended that the supplied digitiser/
LCD assembly is used to replace a faulty LCD or digistiser as both the LCD conductive strip and the Digi/LCM clamp are placed at the factory using accurate equipment as they are difficult to fit precisely. It is also good practise to check that the backlight has not been damaged whilst the LCD assembly is broken down as this part is of delicate construction and is prone to damage during servicing.
Company Confidential
PSION Computers PLC
Dissasembling the Series 5
The LCD/digitiser assembly can now be removed and replaced if necessary. The assembly of the digitiser and LCD is very fragile and is supported by the LCD inner moulding. To separate these three components the outer apps label and conductive strip must first be removed. Carefully peel the conductive label away from one corner and lift it off the digitiser surface as shown in the photograph below. The outer apps label will be removed also.
Peel off conductive strip
Remove the LCM clamp by levering one edge of it away from the LCD inner moulding. Ensure that the flexi connectors are not damaged during removal.
Hinge LCM clamp away
Company Confidential
PSION Computers PLC
Dissasembling the Series 5
Remove the digitiser ensuring that the inner surface is kept free of dust and finger prints. It can now be replaced if necessary. The LCM/digitiser contact will become exposed when the digitiser is removed ensure that it is undamaged when removed from the contacts on the digitiser flexi. Lift the digitiser flexi clear from the two locating pins on the LCD inner moulding as shown in the photograph below and separate the LCD from the assembly. The LCD can now be replaced if necessary.
The Series 5 is now fully disassembled.
Digitiser flexi
Company Confidential
PSION Computers PLC
Reassembly Instructions
Reassembly is essentially a reversal of the disassembly procedure. However, take note of the following points.
• Exercise caution whilst re-inserting the FFC’s into the ZIF sockets. Inserting FFC’s into the connectors at an angle can cause short or open circuits. Ensure that the bends in the FFC’s are retained to ensure correct alignment of all components on the main PCB.
• Replace any labels that have been removed in the disassembly procedure with new labels. Do not attempt to re-fit labels that have previously been removed from the Series 5.
• Extreme caution is required when replacing the LCD assembly in the outer moulding. If the screen is not wholly centered it is very easy to damage the LCD or digitiser.
As the digitiser and LCD assemblies are reassembled ensure that no dust or finger prints are present between the two interior surfaces. Ensure that the assembly is held as shown in the following photograph as the drivers that run along the bottom edge of the LCD are very fragile and can be broken very easily.
When replacing the base moulding as part of the final stage of disassembly, ensure that the pen eject mechanism has not become dislodged. The spring that operates the pen eject can drop out if care is not taken whilst replacing the base assembly.
Pen eject mechanism
Company Confidential
PSION Computers PLC
Reassembly Instructions
When replacing both the main PCB and the slim base assembly ensure that the Series 5 is open as shown. This will ensure that the switches that operate the machine on/off and door opening warnings will not be fouled as the base is replaced.
Ensure that the Memory Disk and lithium doors on the base assembly are also open. To replace the slim base assembly align along the bottom edge of the Series 5 assembly, ensuring that the dictaphone buttons have located and lever the moulding down into place. The base should snap into place along the back edge where it meets the hinge moulding assembly. Ensure that the base is located correctly before re-screwing it down using the 3 case screws. These case screws should not be over tightened as they purchase into the chassis moulding and can strip easily.
When the Series 5 is fully reassembled check that the colour of each of the mouldings tie up and that no colour differences exist between mouldings.
It is important to note that the Series 5 can occasionally experience a software crash which can be rectified by enacting a soft reset - see User Guide. However it is possible that a crash can be caused by an intermittent hardware fault, and therefore it is advisable to fully test any unit that has experienced a crash. Faults such as failure to read links, power supplies or batteries can be caused by the peripherals themselves and these faults should be determined only using a Series 5 that is known to work. Some brands of batteries are shorter in length than the European average and as such can give poor contact, which can result in the unit giving incorrect low battery warnings. Also, rechargeable batteries have a very low usage time and as such can give the false impression that the Series 5 is draining them too quickly.
Company Confidential
PSION Computers PLC
Final Test Procedure
This section outlines the Final Test procedure for the Series 5 hand-held computer. The test equipment requirements to perform the final test procedure are outlined in the following table:
Qty.
Description
1 Final Test Unit
1 Mains lead
1 Fail Ticket printer and lead
1 DC Jack and Dummy Battery Lead
1 Series 5 Expansion Lead
1 Test Compact Flash
1 Lithium battery
Part No.
1910-0001-01 n/a n/a
2903-0002-01
2903-0003-01 n/a
4900-0053
The Final Test Unit is suitable for working with supplies in the range 90-130 / 180-260 VAC 47-
63Hz without adjustment.
Fail Ticket Printer
Unit Under Test
Final Test Box
LCD Display
Company Confidential
PSION Computers PLC
Final Test Procedure
System Power Connections - Safety Critical Information
The Series 5 Final Test System is designated as conforming to Class 1 insulation standards and as such
MUST BE MAINS EARTHED.
The unit is supplied with a moulded IEC 320 Mains Cord with local variant mains plug fitted. This cord must be used for mains connection and be maintained in good condition. Should this cord show wear through the insulation, cutting damage or other fault, the power should be removed and the cord replaced with a suitable replacement available from Psion Computers PLC as a spare part.
If the IEC 320 Mains Cord is to be used with a local variant power socket with only two conductors
(Live & Neutral), then a separate earth connection MUST be made to the M6 earth stud fitted to the rear of the main case. The Earth Connection Cable must be adequate to carry at least 25A at 250v. The other end of the earth cable must be connected by a suitable clamp to a mains earth point within the building
(not a water pipe or other similar fitting). Connection resistance at 25A should be less than or equal to
0.1R. This earth connection is a safety critical feature, in event of uncertainty, consult a qualified electrician.
Typical standard connection to 3 pin mains socket using moulded IEC320 mains lead supplied with the system:
3-Pin Mains
Socket
Typical 2-conductor mains connection showing separate earth connection between ground stake/earth point in building and M6 stud on rear of case:
2-Pin Mains
Socket
Moulded IEC
Lead
Graound Stake/Building
Earth Point
Earth Cable
M6 Stud
Company Confidential
PSION Computers PLC
Final Test Procedure
Separate Earth Lead Connection Detail:
KEY
1) M6 NUT
2) EXTERNALLY SERRATED M6 WASHER
3) M6 PLAIN WASHER
4) M6 RING TERMINAL
5) M6 STUD ON REAR OF CHASSIS
1 2 1 3
4
2 5
Modes of Operation
There are two modes of operation that the Final Test box programme can provide. Supervisor Mode allows various setup and test parameters to be chosen. Run Mode allows an operator to connect a Series
5 unit to the tester and to perform the chosen tests which are prompted by various messages on the Final
Test box display and the Unit Under Test (UUT) display.
It is also possible to Reprogramme the Final Test box which can be done by connection with an IBM compatible PC running the DOS utility ‘INTERSVR.EXE’ which is available for DOS version 3.3 or later. This allows two PC’s to be connected together with one acting as a server to the other. The units may be connected by either the parallel or serial ports providing the cables are as described by the
‘INTERLNK’ utility, (see the DOS HELP INTERLNK.EXE utility). The PC must be switched on and be running ‘INTERSVR.EXE’ and have a disk image file loaded in a directory as follows:
C:\TC486\REPRO.IMG
When the Final Test box is switched on it will detect the presence of the attached PC and use it as a server. This will be seen on the PC’s screen as it’s drives are allocated to the Final Test box. After a few seconds it will begin reading the disk image file ‘REPRO.IMG’ which will be indicated by a flashing legend in the bottom left hand corner of the PC’s screen as follows:
READING
When the
READING legend has stopped flashing wait for a couple of seconds and perform the following procedure: Wait for a couple of seconds. Turn off the Final Test Box. Disconnect the Interlink cable.
Turn the Final Test Box back on.
The test box should now reboot and display the following screen:
NO BUILD
OPTION SET
Company Confidential
PSION Computers PLC
Final Test Procedure
It is now necessary to enter the “Supervisor Mode” and set up the Final Test Box as required. Turning the key switch clockwise puts the Final Test Unit into a “Supervisory Setup Mode”. The display will then show the following:
1/9-MAIN V1.10F
BUILD OPTION
‘1/9’ indicates that this is the first option available from a total of 9. Pressing the down arrow button will move to the second option, and then to the third and so on. Pressing the up arrow button will move back through the option screens. ‘Main’ indicates that this is the main option menu and not a subset. ‘V1.10F’ indicates the version of the software running on the Final Test box.
‘BUILD OPTION’ is the description of the first menu option. An option can be selected by pressing the green ‘ACCEPT’ button. This will then take the supervisor to the next menu level. The first row will display the number of options available and a title description. The second row will display the currently accepted option. Pressing the blue ‘UP’ or ‘DOWN’ buttons will move the displayed options appropriately. Once the desired configuration is displayed, the ‘ACCEPT’ button should be pressed, and the display will then return to the Main menu selection. The supervisor may ignore any changes by pressing the red ‘BACK’ button, which will return the supervisor to the previous menu level without changing anything.
The various options currently available are as follows:
Menu Option
BUILD OPTION
MOD. LEVEL
DIAGNOSTIC
FAIL TICKET
PASS TICKET
CYCLE MODE
RESULT LOG
SYSTEM SETUP
VERSIONS
SET ROM BOARD
PROG. EEPROM
Default Setting
See text
See text
DISABLED
ENABLED
DISABLED
DISABLED
DISABLED
See text n/a
See text
See text
Description
Sets, by Psion part number, the chosen machine build being tested.
A variable that can be incremented from A to Z that is added into the
Series 5 unit’s serial number.
If enabled, pauses the test sequence after specific tests to show additional test result data on the Final Test box display.
To enable the printing of fail tickets.
To enable the printing of pass tickets. Not yet implemented.
If enabled, puts the unit into a 100 cycle mode. Only the tests without operator intervention are performed.
Outputs some test result data onto COM2 port at 9600, 8N1 Baud.
Enables setting of the Test Box date, time, unit number and printer type.
Shows current versions of the source code, limits file, build file and sequence file being used by the final test box.
To configure the type of system memory used in the Series 5 unit.
To enable programming the serial E2PROM on the Series 5 unit.
Final Test Procedure
If the supervisor wishes to ignore any change they have made at any point, then the red ‘BACK’ button should be pushed which will ignore all previous key presses and take the supervisor back to the previous menu level.
To permanently save the options selected the supervisor must either enter the
‘BUILD OPTION’ menu and ‘ACCEPT’ the desired part number, or enter the ‘SYSTEM SETUP’ and
‘ACCEPT’ the ‘SAVE SETTINGS’ option. If this is not done then the options which have been changed will be lost when the unit is powered off.
Menu Options Explained
BUILD OPTION - When this is selected, (by pressing the green ‘ACCEPT’ button) the following screen will appear:
1/22 - BUILD
2900000301
‘1/22’ indicates that this is the first option available from a total of 22. Pressing the down arrow button will move to the second option etc. ‘BUILD’ indicates that this is the ‘BUILD’ option menu. ‘2900000301’ is the Psion part number, in this case inferring the build for an English 4 Mbyte machine.
Pressing the blue ‘UP’ or ‘DOWN’ button arrows will toggle the display through the available build options, (shown in the following table). When the required build is displayed, press the green ‘ACCEPT’ button. The screen will then show the following for a couple of seconds before returning to the main menu display shown previously:
1/22 - BUILD
SAVING......
Note - When the screen shows that it is saving the options, ALL the current option settings are saved into non-volatile memory and will remain as such until changed again. Hence, it is necessary to enter the ‘BUILD OPTION’ menu and re-’ACCEPT’ to save any other changes. If this is not done then the settings will be lost when the unit is powered off.
Final Test Procedure
The following is a table of the current Psion p/no’s for all the relevant build options:
Part No.
2900-0003-01
2900-0004-01
2900-0009-01
2900-0010-01
2900-0011-01
2900-0012-01
2900-0013-01
2900-0014-01
2900-0015-01
2900-0016-01
2900-0017-01
2900-0018-01
2900-0019-01
2900-0020-01
2900-0021-01
2900-0022-01
2900-0023-01
2900-0024-01
2900-0025-01
2900-0026-01
2900-0027-01
2900-0028-01
RAM - Mbyte
4
8
Language
English
English
4
8
4
8
4
8
4
8
4
8
4
8
8
4
8
4
8
4
8
4
American
American
French
French
German
German
Not Available
Not Available
Italian
Italian
Spanish
Spanish
Swedish
Swedish
Norwegian
Norwegian
Danish
Danish
Finnish
Finnish
Mod. Level
For production purposes, a MOD. LEVEL is set in the Series 5 part number. To change the Modification Level, use the blue UP or DOWN buttons to select the MOD. LEVEL menu option and press the green ACCEPT button. The following display will then appear:
1/26 - MOD.
LEVEL A
Pressing the blue ‘UP’ or ‘DOWN’ buttons will then increment or decrement the Mod. letter, from ‘A’ to
‘Z’. When the required letter is displayed, press the green ‘ACCEPT’ button. The display will then return to the main option menu.
Company Confidential
PSION Computers PLC
Final Test Procedure
Note: Once a unit has passed Final Test, the serial E
2
PROM on the main PCB is locked. If it is re-tested then it must have the same MOD. LEVEL set otherwise it will fail Final Test, producing a Concession Ticket (providing it has passed every other test). For this reason the current
MOD. LEVEL is printed on the fail tickets to ensure that its setting is clear.
System Setup
This allows permanent saving of the set up parameters in Non-Volatile Flash memory and the setting of the current time, date and Final Test unit number, (shown on the back of the final test unit itself). It will also allow the Fail Ticket printer to be set to either the Serial COM1 or Parallel port and for a small printing test to be done. ‘ACCEPT’ing the ‘SYSTEM SETUP’ option will then display the following option:
1/6 - SYSTEM SETUP
SAVE SETTINGS
Pressing the blue ‘UP’ or ‘DOWN’ buttons lets the supervisor chose between setting the system options as displayed in the following chart:
Menu No.
1/6
2/6
3/6
4/6
5/6
6/6
Name Functions
SAVE SETTINGS Saves ALL settings to Non-Volatile Flash memory.
SYSTEM TIME Sets the DOS system time.
SYSTEM DATE Sets the DOS system date.
SYSTEM NUMBER Sets the Final Test Unit number shown on the back of the box.
SYSTEM PRINTER Configures Fail ticket printer to either Parallel or Serial port.
PRINTER TEST Prints a short ASCII test data field to the Fail ticket printer.
When the correct option is displayed, press the green ‘ACCEPT’ button to enter the next menu level. For example, ‘ACCEPT’ing the ‘SYSTEM TIME’ option will then display the following option.
SYSTEM TIME hh:mm:ss
Company Confidential
PSION Computers PLC
Final Test Procedure
If it is incorrect the hour (hh) minute (mm) and second (ss) settings may be changed. An underscore cursor will initially be indicating the hour setting. Pressing the blue ‘UP’ or ‘DOWN’ buttons will increment or decrement the hour accordingly. When the time is displayed correctly press the green
‘ACCEPT’ button and the underscore cursor will move on to the next unit, in this case the minutes - mm.
Repeat for the minutes and second settings. When the seconds (ss) setting is ‘ACCEPT’ed the display will return to the previous menu level and the time will have been set accordingly.
The ‘SYSTEM NUMBER’ should be the same as the number on the rear label. The Printer default setting is the parallel port but it may be changed to the serial port COM1 with a configuration of 9600
Baud, 8N1. If the ‘PRINTER TEST’ option is ‘ACCEPT’ed a simple test data pattern will be printed out to the relevant port.
If the ‘SAVE SETTINGS’ option is ‘ACCEPT’ed then all the configuration settings are saved into nonvolatile memory, in the same way as ‘ACCEPT’ing the Psion part number in the ‘BUILD OPTION’ menu.
Result Log
If this option is enabled the following tests will output a result on the serial port, COM2 at 9600 8N1:
• Stand-by Current
• Vpc measurement
• Measured frequency from the UUT speaker
This can be logged by a terminal to give on line results. The output is ASCII code giving a test description, followed by the result.
Set ROM Board
The unit is required to set into the Series 5 unit’s memory whether it’s system memory is using All
Flash, All ROM or Flash & ROM. This can be done by ‘ACCEPT’ing this menu option. The screen will then display the following option:
1/3-ROM BOARD
ALL FLASH
Pressing the blue ‘UP’ or ‘DOWN’ buttons allows the supervisor to select which memory configuration is being used. When the correct option is displayed, press the green ‘ACCEPT’ button to return to the main menu.
Company Confidential
PSION Computers PLC
Final Test Procedure
Returning To The Main Menu
Pressing the red ‘BACK’ button when on the main option menu will return the screen immediately to option one of that main menu, ie: the ‘BUILD OPTION’ menu. When all the required options have been appropriately set and saved, the Supervisor Key switch is returned to the normal vertical position, (Run
Mode) and the display will show the selected build option to confirm it’s current setup.
Press Start....
2900000301
Explanation of Run Mode
The key switch should be in the vertical position. The Final Test Box is then ready to test a Series 5 and the display will appear as follows:
Press Start....
2900000301
To test a Series 5 follow the Test Procedure Set-Up and then the Test Procedure.
Test Procedure Set-Up
To avoid the possibility of this test equipment malfunctioning it must be used in a benign electromagnetic environment. Strong radiating devices, such as mobile phones, must not be used in the vicinity of the product as they may cause a temporary disturbance. This test equipment must be used in a static-free environment. Such an environment can be provided by using static dissipative surfaces on the test bench below the equipment and ensuring that operators are discharged by means of static wristbands, prior to using the equipment. Static dissipative surfaces and wristbands can be obtained from your local component stockists.
The supervisor must select the correct Psion part number for the batch of units to be tested. It is essential that the set up is correct before testing the units. In particular check the MOD. LEVEL, ROM card type and the Psion Part type.
For each Series 5 to be tested in the batch the operator will perform the following tasks:
• Insert the test CompactFlash card and insert the lithium cell.
Company Confidential
PSION Computers PLC
Final Test Procedure
• Insert the dummy battery module and the DC Jack plug.
• Slide up the 15Way expansion cover and connect the 15Way expansion connector.
• Slide back the Dictaphone switch cover.
• Open the Unit Under Test and place on the cradle on the Final Test Unit.
• Ensure the UUT is connected to the Final Test Unit thus:
Final Test Cradle
Dummy Battery
& DC Jack
RS232
PASS FAIL
ABORT
START
Series 5 unit contains:
Lithium Battery + Test Compact Flash
Company Confidential
PSION Computers PLC
Final Test Procedure
Test Sequence
1. Press Start Button - Once the operator has connected the UUT to the cradle, the ‘START’ button can be pressed. This begins the test sequence by loading the test program from the Test CompactFlash into the UUT’s memory. If the sequence fails within the first 6 tests the test will be aborted immediately and a Fail Ticket will be printed. If it fails after these tests, testing will continue to try and diagnose a full fault list which will be printed at the end of the test.
Press Start Button
2. Display Test - The operator will have to determine whether the machine passes three quality tests for the LCD display and one for the backlight operation. An LCD display pattern will be shown followed by a flashing backlight and a minimum and maximum contrast tests. For each of these tests the operator must press the ‘PASS’ or ‘FAIL’ key according to the quality of the display and the status of the backlight.
The operator must check the display for any missing rows or columns in the displayed image or any inconsistencies.
In summary -
• Press ‘PASS’ or ‘FAIL’ button according to quality.
LCD Display Test
Company Confidential
PSION Computers PLC
Final Test Procedure
3. Keys - A keyboard layout will be displayed on the screen. The operator must press each key and as they are detected, the displayed key will change to a lighter contrast. When all the keys have been successfully detected the program will automatically proceed to the next test. If a key should fail to be detected, after a set time the program will continue noting the keys that have failed.
In summary -
• Press each key on UUT.
• If a key fails wait for time-out
Keyboard Test Display
4. Digitiser Operation and Calibration - The operator will be prompted to place the perspex digitiser calibrator over the LCD display. When this has been snugly fitted to the unit, the operator must press the
‘START’ key to enable the test to proceed. A flashing, reducing square will then appear under the bottom left button on the digitiser calibrator perspex. The operator should then repeatedly push and release the button a number of times. The test requires five distinct pushes when a “Success Bleep” noise will be heard and the reducing square will move to the top right button. The operator should repeatedly press the buttons until these indications have successfully occurred. The operator should repeatedly push and release the top right button a number of times until a “Success Bleep” noise is heard. At this point a cross will also appear on the screen which should aline with the two crosses on the perspex calibrator. The operator should then press the ‘PASS’ key.
If when pressing either of the calibrator buttons the digitiser is faulty, a failure “Nhhhhh” noise will be heard and a message written to the UUT screen. The operator should then press the ‘FAIL’ key to continue.
In summary -
• Place perspex digitiser calibrator over LCD screen
• Press ‘START’ key to proceed
• Press and release the bottom left calibrator button a number of times
• If successful press and release the top right calibrator button a number of times
• If successful the cross on the screen should aline with the crosses on the perspex.
• Press ‘PASS’
If the test fails at any point,
• Press ‘FAIL’
Company Confidential
PSION Computers PLC
Final Test Procedure
Digitsier Calibrator
Note: To minimise any possible damage to the digitiser screen, the buttons on the perspex digitiser calibrator should be pushed with one finger while the back of the screen is supported by the other fingers of that hand. If a large force is used it may mark or damage the digitiser or dislodge the unit from the Final Test box.
5. CompactFlash Door switch - The UUT will display a message showing that the CompactFlash door is closed. The operator should pick up the UUT with the case screen still open. The operator should then open the door and see a message appear on the UUT screen showing that it has opened. The operator should then close the door and see a message appear on the UUT screen showing that it has closed. If the unit is faulty, it will fail after a time out period, no intervention is required.
In summary -
• Pick up the UUT with the screen open
• Open the CompactFlash door
• Close the CompactFlash door
Company Confidential
PSION Computers PLC
Final Test Procedure
Note: Hold the unit the correct way up (and not upside down as is displayed) to view the instructions displayed on the screen.
6. Case Open Switch - The operator will be prompted by the display on the Final Test Box to close the
UUT screen and press the ‘PASS’ key to continue the test.
In summary -
• Close the UUT screen
• Press the ‘PASS’ key to continue
Press Pass Key
7. Dictaphone buttons - The operator will be prompted by the display on the Final Test Box to press each of the three dictaphone switches. They should press in and release easily of their own accord. If a switch is sticky or needs help in releasing, it should not be manipulated. Instead let the test fail. The test will ‘FAIL’ if any of the dictaphone switches have not been successfully detected and released within a specified time out period. If the switches are all successfully operated, the program will move on to the next test.
In summary -
• Press and release all three dictaphone buttons
• Wait for Final Test Box display to increment to the next test
Dictaphone Buttons
Company Confidential
PSION Computers PLC
8. Dictaphone Status LED - The operator will be prompted by the display on the Final Test Box to observe whether the Dictaphone Status LED has been lit. If successful the operator should press ‘PASS’, if it is unlit the operator should press ‘FAIL’.
In summary -
• Press ‘PASS’ or ‘FAIL’ button according to operation of LED.
Dicataphone Status
Light
9. Remove Lithium and CompactFlash - The operator will be prompted by the display on the Final
Test Box to remove the Lithium battery and CompactFlash device. As each is removed the Final Test box will clear the displayed message, so that when both have been removed, it moves onto the next test.
10. Final Test Result - If the UUT has successfully passed all the tests, the message ‘PASS’ will be displayed on the UUT and on the display on the Final Test Box. If any test has failed, the message ‘FAIL’ will be displayed on the UUT and on the display on the Final Test Box and a fail ticket will be printed showing the particular failure. Ensure that a fail ticket and the UUT are stored together.
Fail Ticket
11. Power Down - Press the ‘PASS’ key one further time to turn off the power UUT and remove the
Expansion connector from the UUT, and the DC Jack / Battery cables.
- The Final Test procedure is now complete.
Company Confidential
PSION Computers PLC
Explanation of Tests
The Final Test Unit is capable of automatically testing the following features of the Series 5 (Not specifically in this order):
On & Boot-Up Operation - Initially the battery supply voltage is set to 2.50V and the supply current is limited to 65mA to prevent damage to the Unit Under Test. The actual measured supply current must be less than 10mA for testing to proceed. The supply current limit is then increased to 700mA and the
UUT is woken up by toggling its serial DSR line on the expansion connector.
The current is checked to be greater than zero to ensure that the connections are made and the Unit is booting up. The Final Test program is read from the CompactFlash Disk within the UUT establishing communication with the Test Box and asserting its DTR line in response.
The Stand-by Current test is made with the processor asleep and at 2.75 volts. It should be within the values specified in the following table:
Model (Memory Size)
4Mbyte
8Mbyte
Standby Current
1.50mA
2.10mA
DC Jack Supply - A 6V supply (current limited to 500mA) is applied to the DC jack socket of the UUT.
No ground connection is present on this jack, instead a separate circuit tests that the GND connection is present on the jack socket fitted to the UUT. This is done in order that it may detect any fault in the ground return path such as a break in the toroidal input filter, as this would prevent normal operation via this connector.
CompactFlash - This is implied to be operational if the unit boots up into Test Mode. There is no specific checking of all the lines on the connector but for the Unit to boot successfully from CompactFlash requires good conformance. If the UUT boots successfully it will assert its DTR line and will then establish communication with the Final Test box via the expansion connector Tx and Rx lines.
Note: To boot successfully the CompactFlash door switch must be closed and the CompactFlash Card
(Psion Memory Disk) must be properly inserted. If the door switch is not closed or does not operate, the test program on the CompactFlash Card will not boot. Instead the normal Series 5 operating system will boot which will fail to establish communication with the Final Test box. (If this does happen, a further examination in the normal Series 5 mode can be made to check the operation of the door switch. Select drive D from the System window and then open and close the door to see if the disk has been detected).
LCD and Backlight - Three tests check that the LCD is functioning correctly. A pattern is displayed with different contrast levels to check proper control of the signal lines. Minimum and maximum contrast levels are displayed to reveal any shorts or opens on any lines. Due to the low light level from the backlight, it is turned on and off at a frequency of 0.4Hz to show a variation and confirm operation. In time with the backlight turning on and off , the message on the Final Test box display changes to show
Company Confidential
PSION Computers PLC
the actual status.
Note: A hood may still be necessary to enable backlight to be seen in very bright lighting conditions.
Digitiser Operation and Calibration - To ensure correlation between the position of the digitiser and the LCD, a calibration is performed. This requires two known positions to be hit on the screen and the difference between the expected and actual positions to be calibrated out. These values are stored in nonvolatile memory and form the factory default settings. The calibration can be adjusted by the user through the operating system but that data will be lost if the unit loses all power. A perspex calibrator that fits over the screen produces the two known positions. Each button is pushed five times and the average taken. The positions are checked to be within reasonable limits and the calibration values are calculated.
Keyboard - All the keys are verified to be operating correctly. A keyboard image will appear on the UUT screen and each must press and release properly. As each key is detected it is greyed out on the screen image.
Dictaphone Buttons and Status LED - The Final Test box display will prompt the operator to press and release each dictaphone button to confirm reliable operation. They should work easily not sticking in any position. The Final Test box display will also prompt the operator to confirm that the Status LED is turned on. The operator presses the ‘PASS or FAIL’ button to indicate its performance.
Case Switch and CompactFlash Door Switch - The Case is initially open and then the Final Test box display will prompt the operator to close it, confirming reliable operation. The Final Test box display will prompt the operator to open and close the CompactFlash Door to confirm reliable operation.
Microphone and Speaker - The Unit Under Test produces a tone via its speaker and the Final Test box ensures that the predominant frequency component received is the same as that produced and of a sufficient magnitude. The Final Test box produces a 1KHz tone and the Unit Under Test ensures that the frequency component received by its microphone is the same.
Expansion Connector Test - All the RS232 control lines are checked independently. The ground and shield connections are checked. The Vpc voltage (that supplies the CompactFlash socket) is measured with a small load.
IrDA Test - Independent send and receive packets are checked with codes particular to IrDA specification.
Internal Memory Interface - The internal memory card can be either all Flash devices, all Mask ROM’ed devices or a combination of Masked ROM and Flash. The type of device fitted on the ROM card is checked according to the setup of the Final Test box and an appropriate access speed set. A checksum value of the lower 4Mbyte and upper 2Mbyte devices is performed at the maximum access speed of the memory devices to confirm integrity of both the devices and the connection.
Note: If the connection interface or ROM’s are badly corrupted the UUT will not be able to perform any kind of boot up and run the tests.
Company Confidential
PSION Computers PLC
FAIL Ticket Codes
27
28
29
31
24
25
26
33
50
Ticket Code
01
03
04
06
07
08, 10
09
11
12
13
Diagnostic Check
Too much current
No response
No response
Didn’t respond to wakeup signal DSR
Didn’t boot into Test program, no DTR asserted
Failed Tx, Rx communication
Battery module contacting positive contact
Unit’s battery spring clip present
Honda Connector (DSR), (and see test 04)
Honda Connector (DTR), (and see test 04)
CompactFlash fully inserted
CompactFlash door fully shut and device detected
ROM Board connections
Honda Connector (Tx, Rx)
Lithium reset contact permanently down
Test Program Setup Language, RAM size
Standby current out of limits.
DRAM on PCB
Dry joints, floating inputs.
Shorts caused by metallisation of plastics onto PCB
LCD connector
Backlight connector
Keyboard connector
Keys
Honda Connector (Tx, Rx)
Honda Connector (RTS, DTR, CTS, DSR, DCD)
14
15
16
17
18
19
22
23
IrDA not blocked.
Lithium in socket.
Dry joints on lithium contacts.
DC Jack lead properly inserted
Honda Connector (Vin2+, Ground)
Honda Connector (Shield)
Honda Connector (Vpc)
Unit properly seated, Speaker fitted correctly
Unit properly seated, Microphone fitted
PCB
Change
Re-test, ensuring contact
PCB battery spring
PCB Honda connector
PCB Honda connector
Re-test, ensuring fully home
Plastics cam operator, PCB door switch
PCB ROM Board connector
PCB Honda Connector
Bend contact away from PCB
Wrong unit build
PCB
PCB
Dictaphone Plastics
LCD
Backlight
Keyboard
Keys
PCB Honda connector
PCB Honda connector
PCB IrDA devices
PCB
Lithium contacts
PCB DC Jack socket
PCB Honda connector
PCB Honda connector
PCB Honda connector
Speaker
PCB Microphone
ROM board devices
Case switch is not broken,Stuck open
Digitiser connections
Action of dictaphone buttons
Case switch is not broken,Stuck closed
Dictaphone Status LED
Plastic cam operator of ConpactFlash door
Removed Lithium and CompactFlash
Test Program Setup
Passed all tests, correct build
PCB case switch
Digitiser
Plastics, PCB dictaphone switches
PCB case switch
PCB Status LED
Plastics, PCB C.Flash Door switch
PCB
Wrong unit build
PCB, E2
Company Confidential
PSION Computers PLC
Connector Circuit Diagram
Dummy Battery and DC Jack - External Cable
DH2
D-TYPE HOOD
J3
DB25, Male
22
10
23
11
20
8
21
9
24
12
18
6
19
7
16
4
17
5
1
14
2
15
3
25
13
PPSU_01
PPSU_S1
GND
A2
PPSU_S2
PPSU_O2
Battery Supply (Red) 16/0.2mm
Battery Gnd (Black) 16/0.2mm
Cable to be Braided and with heatshrink terminating each end.
Dummy Battery Cable Length : 42cm
DC Jack Cable Length : 30cm
Breakout DC Jack cable through Braiding 20cm from 25 Way D
DC Jack Gnd check
DC Jack Supply, (Striped wire)
J4
1
Gnd
DUMMY PROTEA BATTERY
Positive
J5
DC JACK CABLE
2
External Honda Cable
DH1
D-TYPE HOOD
J2
DB25, Female
19
7
20
8
16
4
17
5
18
6
1
14
2
15
3
23
11
24
12
25
13
21
9
22
10
/DTR
/CTS
Tx
/RTS
Rx
/DSR
/OUT1
F0
F1
Analogue In 7
Analogue Out B1
Cut Honda MC to MC cable in half and solder into D-type connector.
Note that the shield is the foil around the wires. This should be connected to a wire and soldered into the D-Type.
NB: Colour coding of MC cable may change, please check.
J1
12
13
14
15
10
11
8
9
6
7
3
4
5
1
2
Vin2+
RTS
DTR
TXD
DSR
DCD
CTS
RXD
Vpcc
NC
Vpp
NC
NC
NC
Sgnd
Shield
PROTEA_TEST_LEAD
16
BR1
BRAIDING
HS1
HEATSHRINK ADHESIVE LINED
W1
CABLE WIRE 16/0.2MM
W2
CABLE WIRE 16/0.2MM
advertisement
* Your assessment is very important for improving the workof artificial intelligence, which forms the content of this project
Related manuals
advertisement