- Computers & electronics
- Networking
- Gateways/controllers
- ELPRO Technologies Pty
- O9PE2900AA1
- User manual
ELPRO Technologies Pty O9PE2900AA1 900MHz FREQUENCY HOPPING SPREAD SPECTRUM TRANSCEIVER User Manual
Add to My manuals58 Pages
advertisement
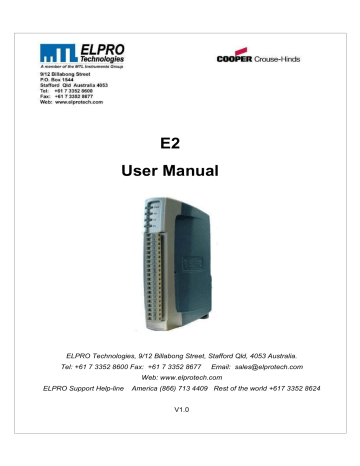
E2
User Manual
ELPRO Technologies, 9/12 Billabong Street, Stafford Qld, 4053 Australia.
Tel: +61 7 3352 8600 Fax: +61 7 3352 8677 Email: [email protected]
Web: www.elprotech.com
ELPRO Support Help-line America (866) 713 4409 Rest of the world +617 3352 8624
V1.0
E2 Wireless I/O Page 1
Page 2 E2 Wireless I/O
Thank you for your selection of the E2 Modem. We trust it will give you many years of valuable service.
ATTENTION!
Incorrect termination of supply wires may cause internal damage and will void warranty. To ensure your E2 module enjoys a long life, double check ALL your connections with the user manual before turning the power on.
CAUTION:
To comply with FCC RF Exposure requirements in section 1.1310 of the FCC Rules, antennas used with this device must be installed to provide a separation distance of at least 20 cm from all persons to satisfy RF exposure compliance.
All equipment must be properly grounded for safe operations. All equipment should be serviced only by a qualified technician
Do Not: operate the transmitter when someone is within 20 cm of the antenna operate the transmitter unless all RF connectors are secure and any open connectors are properly terminated operate the equipment near electrical blasting caps or in an explosive atmosphere
SAFETY Notice:
Exposure to RF energy is an important safety consideration. The FCC has adopted a safety standard for human exposure to radio frequency electromagnetic energy emitted by
FCC regulated equipment as a result of its actions in Docket 93-62 and OET Bulletin 65
Edition 97-01.
E2 Wireless I/O Page 3
FCC Notice:
This device complies with Part 15.247 of the FCC Rules.
Operation is subject to the following two conditions:
This device may not cause harmful interference and
This device must accept any interference received, including interference that may cause undesired operation.
This device must be operated as supplied by ELPRO. Any changes or modifications made to the device without the written consent of ELPRO may void the user’s authority to operate the device.
This device must be installed by professional installers in compliance with 47 CFR Part 15
Subpart C Section 15.204 and 15.205, who will be responsible for maintaining EIRP no greater than 36 dBm in accordance with 47 CFR Part 15 Subpart C Section 15.247
(b)(2)(4).
In accordance with 47 CFR Part 15 Subpart C Section 15.204 only the following antenna/coax cable kits can be used.
Manufacturer Model Kit Net
•
Part 15 –This device has been tested and found to comply with the limits for a Class
A digital device, pursuant to Part15 of the FCC rules (Code of Federal Regulations
47CFR Part 15). Operation is subject to the condition that this device does not cause harmful interference.
•
Notice Any changes or modifications not expressly approved by ELPRO could void the user’s authority to operate this equipment.
This Device should only be connected to PCs that are covered by either FCC DoC or are
FCC certified.
Page 4 E2 Wireless I/O
IMPORTANT Notice:
ELPRO products are designed to be used in industrial environments, by experienced industrial engineering personnel with adequate knowledge of safety design considerations.
ELPRO radio products are used on unprotected license-free radio bands with radio noise and interference. The products are designed to operate in the presence of noise and interference, however in an extreme case, radio noise and interference could cause product operation delays or operation failure. Like all industrial electronic products,
ELPRO products can fail in a variety of modes due to misuse, age, or malfunction. We recommend that users and designers design systems using design techniques intended to prevent personal injury or damage during product operation, and provide failure tolerant systems to prevent personal injury or damage in the event of product failure. Designers must warn users of the equipment or systems if adequate protection against failure has not been included in the system design. Designers must include this Important Notice in operating procedures and system manuals.
These products should not be used in non-industrial applications, or life-support systems, without consulting ELPRO first.
•
A radio license is not required in some countries, provided the module is installed using the aerial and equipment configuration described in the E2 Installation Guide.
Check with your local distributor for further information on regulations.
•
Operation is authorized by the radio frequency regulatory authority in your country on a non-protection basis. Although all care is taken in the design of these units, there is no responsibility taken for sources of external interference. Systems should be designed to be tolerant of these operational delays.
•
To avoid the risk of electrocution, the aerial, aerial cable, serial cables and all terminals of the E2 module should be electrically protected. To provide maximum surge and lightning protection, the module should be connected to a suitable earth and the aerial, aerial cable, serial cables and the module should be installed as recommended in the Installation Guide
•
To avoid accidents during maintenance or adjustment of remotely controlled equipment, all equipment should be first disconnected from the E2 module during these adjustments. Equipment should carry clear markings to indicate remote or automatic operation. E.g. "This equipment is remotely controlled and may start without warning. Isolate at the switchboard before attempting adjustments."
•
The E2 module is not suitable for use in explosive environments without additional protection.
•
The E2 Operates unlicensed Radio frequencies and proprietary protocols to communicate over the radio. Nevertheless, If your system is not adequately secured, third parties may be able to gain access to your data or gain control of your equipment via the radio link. Before deploying a system make sure you have considered the security aspects of your installation carefully.
E2 Wireless I/O Page 5
Limited Lifetime Warranty, Disclaimer and Limitation of
Remedies
ELPRO products are warranted to be free from manufacturing defects for the “serviceable lifetime” of the product. The “serviceable lifetime” is limited to the availability of electronic components. If the serviceable life is reached in less than three years following the original purchase from ELPRO, ELPRO will replace the product with an equivalent product if an equivalent product is available.
This warranty does not extend to:
•
Failures caused by the operation of the equipment outside the particular product's specification, or
•
Use of the module not in accordance with this User Manual, or
•
Abuse, misuse, neglect or damage by external causes, or
•
Repairs, alterations, or modifications undertaken other than by an authorized Service
Agent.
ELPRO liability under this warranty is limited to the replacement or repair of the product.
This warranty is in lieu of and exclusive of all other warranties. This warranty does not indemnify the purchaser of products for any consequential claim for damages or loss of operations or profits and ELPRO is not liable for any consequential damages or loss of operations or profits resulting from the use of these products. ELPRO is not liable for damages, losses, costs, injury or harm incurred as a consequence of any representations, warranties or conditions made by ELPRO or its representatives or by any other party, except as expressed solely in this document.
Page 6
TABLE OF CONTENTS
E2 Wireless I/O
1 CHAPTER 1 – INTRODUCTION.........................................................................................8
1.1 Overview.........................................................................................................................................................8
1.2 Module Structure .........................................................................................................................................10
1.3 Getting Started .............................................................................................................................................11
2 CHAPTER 2 – INSTALLATION ........................................................................................12
2.1 General..........................................................................................................................................................12
2.2 Power/Supply ...............................................................................................................................................12
2.3 Radio .............................................................................................................................................................13
900 MHz Spread Spectrum radio ....................................................................................................................13
Meshing capability ...........................................................................................................................................14
2.4 Antenna.........................................................................................................................................................15
Dipole and Collinear antennas. .......................................................................................................................17
Yagi antennas..................................................................................................................................................17
2.5 Connections .................................................................................................................................................18
Ethernet port....................................................................................................................................................18
USB Device Port for configuration...................................................................................................................18
RS-232 port .....................................................................................................................................................18
RS-485 port with Modbus Support. .................................................................................................................19
“Factory Boot” switch.......................................................................................................................................20
USB Host port..................................................................................................................................................20
Dipswitch “Bank”..............................................................................................................................................20
Front panel connections ..................................................................................................................................21
Digital Inputs....................................................................................................................................................21
Pulsed Inputs..................................................................................................................................................22
Digital Outputs (Pulsed Outputs) .....................................................................................................................22
Digital Outputs (Pulsed Outputs) .....................................................................................................................23
Analog Inputs...................................................................................................................................................24
Floating Differential Analog Inputs (AIN 1 & 2 only) ........................................................................................24
Single Ended Current Inputs (AIN 3 & 4 only) .................................................................................................25
Single Ended Voltage Inputs ...........................................................................................................................25
Analog Outputs................................................................................................................................................26
3 CHAPTER 3 – OPERATION .............................................................................................27
3.1 Overview.......................................................................................................................................................27
3.2 Indications ....................................................................................................................................................27
Front Panel Indications....................................................................................................................................27
I/O Indications..................................................................................................................................................28
Ethernet Indications.........................................................................................................................................28
3.3 System Design Tips.....................................................................................................................................29
System Dynamics............................................................................................................................................29
3.4 WIBMesh.......................................................................................................................................................30
E2 Wireless I/O Page 7
4 CHAPTER 4 – CONFIGURATION ....................................................................................31
4.1 First time.......................................................................................................................................................31
Default Configuration.......................................................................................................................................31
Accessing Configuration for the first time........................................................................................................31
4.2 Network Configuration ................................................................................................................................34
4.3 Radio Settings..............................................................................................................................................35
4.4 WIBMesh Configuration ......................................................................................................................37
4.5 WIBMesh Mappings.....................................................................................................................................38
Write Mappings ...............................................................................................................................................38
Read Mappings ...............................................................................................................................................39
Gather/Scatter Write Mappings .......................................................................................................................40
4.6 Serial Configuration ....................................................................................................................................42
Modbus TCP to RTU Gateway ........................................................................................................................42
4.7 I/O Configuration .........................................................................................................................................44
Analog Inputs...................................................................................................................................................44
Analog Outputs................................................................................................................................................45
Digital Input......................................................................................................................................................46
Digital Output...................................................................................................................................................46
Pulsed Inputs...................................................................................................................................................46
4.8 Module Information .....................................................................................................................................47
4.9 System Tools ...............................................................................................................................................48
Reading Configuration File ..............................................................................................................................48
Writing Configuration File ................................................................................................................................48
Firmware Upgrade...........................................................................................................................................48
4.10 Address Map ..............................................................................................................................................48
Standard E2 I/O (Basic Local I/O with no expansion modules).......................................................................49
CHAPTER 5 – DIAGNOSTICS ............................................................................................51
5.1
IO Diagnostics.......................................................................................................................................51
5.2
Diagnostic Information.........................................................................................................................52
Connectivity .....................................................................................................................................................52
Statistics ..........................................................................................................................................................52
5 APPENDIX A.....................................................................................................................54
6 Appendix A I/O Store ...............................................................................................................................54
“Output Coils” ..................................................................................................................................................54
“Input Bits” .......................................................................................................................................................54
“Input Registers” ..............................................................................................................................................55
“Holding Registers”..........................................................................................................................................56
Page 8
1
Chapter 1 – Introduction
1.1
E2 Wireless I/O
Overview
The E2 range of I/O modules has been designed to provide standard “off-the-shelf” telemetry functions, for an economic price. Telemetry is the transmission of data or signals over a long distance via radio or twisted-pair wire cable.
Although the E2 Series is intended to be simple in its application, it provides many sophisticated features, which will be explained in the following chapters.
This manual should be read carefully to ensure that the modules are configured and installed to give reliable performance.
The E2 telemetry module replaces the earlier 105 and 905 E-series modules. It provides on-board I/O via a front mounting 20-way connector and has provision for extra expansion modules (ELPRO 115S or MODBUS devices) to be connected using a standard RS485 serial connection.
The module can monitor the following types of signals
•
Digital on/off signals - Contact Closure or Switch
•
Analog continuously variable signals – Tank level, Motor speed, temperature, etc
•
Pulsed signal - Frequency signal – Metering, accumulated total, rainfall, etc
•
Internal Signals – Supply voltage, Supply failure, battery status, etc.
The modules monitor the input signals and transmit the values by radio or Ethernet cabling to another module or modules that have been configured to receive this information.
The E2 radio has been designed to meet the requirements of unlicensed operation for remote monitoring and control of equipment. A radio licence is not required for the E2 in many countries.
The E2 product will seamlessly operate with existing 905U wireless I/O modules the E3 products, which use the same basic hardware but extend the functionality with additional interfaces including an LCD and multiple radio functionality.
The E2 operates on unlicensed radio channels in the 902-915MHz bands.
Input signals that are connected to the module are transmitted and appear as output signals on other modules. A transmission occurs whenever a "change-of-state" occurs on an input signal. A "change-of-state" of a digital or an internal digital input is a change from "off" to "on" or vice-versa. A "change-of-state" for an analog input, internal analog input or pulse input rate is a change in value of the signal of 3% (configurable from 0.8 to 75 %).
In addition to change-of-state messages, update messages are automatically transmitted on a configurable time basis. This update ensures the integrity of the system.
E2 Wireless I/O Page 9
Pulse inputs counts are accumulated and the total count is transmitted regularly according to the configured update time.
The E2 modules transmit the input/output data using radio or Ethernet. The data frame includes the "address" of the transmitting module and the receiving module, so that each transmitted message is acted on only by the correct receiving unit. Each message includes error checking to ensure that no corruption of the data frame has occurred due to noise or interference. The module with the correct receiving "address" will acknowledge the message with a return transmission (acknowledgement). If the original module does not receive a correct acknowledgement, it will retry up to five times before setting the communications fail status of that path. In critical paths, this status can be reflected on an output on the module for alert purposes. The module will continue to try to establish communications and retry, each time an update or change-of-state occurs.
A system can be a complex network or a simple pair of modules. An easy-to-use configuration procedure allows the user to specify any output destination for each input.
Two versions of the E2 are available. The Legacy version provides for operation with existing ELPRO wireless I/O devices (905 series and 105 series modules) The second version provides enhanced features, including IP addressing, allowing thousands of modules to exist in a system, and allowing Automatic routing of messages through repeater stations.
Each E2 radio in a system may have up to 24 expansion I/O modules (ELPRO 115S) connected by RS485 twisted pair. Any input signal at any module may be configured to appear at any output on any module in the entire system.
Modules can be used as repeaters to re-transmit messages on to the destination module. Repeaters can repeat messages on the radio channel or from the radio channel to the serial channel (and serial to radio). Using Legacy protocol, up to five repeater addresses may be configured for each input-to-output link. The meshing protocol will automatically select other stations to act as repeaters as required.
The units may be configured by using a web browser connected to the Ethernet port or using supplied system configuration software connected to the Module’s USB port. The default configuration and software configuration is defined in Section 4 Configuration.
Page 10
1.2
E2 Wireless I/O
Module Structure
The E2 is made up of a number of basic sections, which all interface with a central
Input and output storage area (I/O Store).
The I/O Data Store provides storage for I/O data as well as providing services to other processes in the system. The I/O Store provides eight different blocks of data - two containing input and output bit data, two containing input and output word data, two containing long-word type data and two containing floating-point data. The two files of each type in turn support inputs and outputs on the local machine, and data storage for the gateway function of the machine. These files are mapped into the address map as described below. There are other register values within the database that can be used for system management - these will be discussed later in this manual.
The Radio Interface allows the E2 to communicate with other modules within the system using a proprietary radio protocol called “WIB-Net”. Messages from other E2 modules are received by the radio port and used to update the input values in the I/O
Data Store. The WIB-Net protocol is an extremely efficient protocol for radio communications. Radio messages can be sent using exception reporting - that is, when there is a change of an input signal - or by read/write messages. Each message will be comprised of multiple I/O values termed as a “block” of I/O). There are also update messages, which are sent for integrity purposes. Messages include error checking, with the destination address sending a return acknowledgment. Up to five attempts are made to transmit the message if an acknowledgment is not received. The WIB-Net protocol is designed to provide reliable radio communications on an open license-free radio channel.
The On-Board I/O in the form of - 8 discrete I/O, 2 single ended analog inputs, 2 differential analog inputs and 2 current sourcing analog outputs. Each discrete I/O is either a discrete input (voltage free contact input) or discrete output (transistor output).
Each I/O point is linked to separate I/O registers within the I/O Data Store.
E2 Wireless I/O Page 11
There are also a number of Internal I/O that can be accessed from the I/O Data Store.
These inputs can be used to interpret the status of a single modules or the entire system
•
Supply voltage status – If the primary supply fails, this status is set on.
•
Low battery voltage – Monitors the internal battery charger to trickle charge a back-up battery. If the battery voltage is low, this status is set.
•
Battery voltage – The actual value of the connected battery voltage.
•
Loop Supply – Monitors the +24V DC ALS supply, used for powering analog loops
•
Expansion Module Volts – Monitors the Supply voltage of the connected expansion modules
•
RSSI – Will indicate the radio signal level for the selectable address.
•
Comms Fail – Will indicate a Communications fail for the selected address.
(either Fail to RX or Fail to TX)
Lastly, the Expansion port, which enables 115S expansion I/O modules to be added to the module. Expansion module I/O is dynamically added to the I/O of the E2 by adding an offset to the address.
1.3 Getting Started
Most applications for the E2 require little configuration. The E2 has many sophisticated features, however if you do not require these features, this section will allow you to configure the units quickly.
First, read Section 2, “Installation”, which will go through the power supply connections and Antenna/coax connections.
Power the E2 and make an Ethernet connection to your PC (refer to section 3.2
“Configuration for the first time”)
Set the E2 address settings as per section 3.2 “Configuration for the first time”
Save the configuration - the E2 is now ready to use.
Before installing the E2, bench test the system as it is a lot easier to fault find problems when the equipment is all together, rather than scattered in multiple locations.
There are other configuration settings, which may or may not improve the operation of the system. For details on these settings, refer to “Chapter 4 – Configuration”.
Page 12
2
Chapter 2 – Installation
2.1
E2 Wireless I/O
General
All E2 Series modules will be housed in a plastic enclosure with DIN rail mounting, providing options for up to 20 I/O points, and separate power & communications connectors. The enclosure measures 170 x 150 x 33 mm including connectors. The antenna protrudes from the top
2.2 Power/Supply
The E2 power supply is of switch-mode design and will accept a 15 - 30 volt DC power source connected to the “Sup + & Sup -” terminals.
•
Note: AC supply requires external rectifier board and Solar requires and External regulator for charging of battery.
Power Supply rating will depend a whether the module has expansion I/O modules connected and if a backup battery is being used.
External “Sealed Lead
Acid” battery if required POWER SUPPLY
_
+
GND
Allow 500mA for the radio, 200mA for the module 1 Amp if expansion I/O modules (115S) connected and 1 Amp if a battery is connected and requires
BAT +
SUP -
SUP + charging.
15-30V DC Supply
E.g. If no battery or expansion I/O modules are connected then the minimum current requirement will be 700mA @13,8V.
If I/O modules are connected and a backup battery is required then the minimum current requirement will be approximately 2.7Amps @13.8V.
The power supply should be CSA Certified Class 2 approved for normal operation and if being used in Class 1 Div 2 explosive areas, the power supply must be approved for this area.
Automatic charging of a 13.8V Sealed Lead-Acid battery connected to the “BAT+” and
“GND” terminals at up to 1A.
E2 Wireless I/O Page 13
The power supply input and battery charging are hosted on a 4-way terminal on the bottom edge of the module labeled “Power Supply”.
To allow increased I/O Capacity, a second 4-way terminal labeled “Expansion I/O” provides a +12 Volt supply and RS485 communications for any 115S serial expansion
I/O modules.
Up to three 115S-11, one 115S-12, or one 115S-13 may be powered by the Expansion
I/O Power Connection
The onboard power supply provides up to 1 Amp for battery charging, and up to 1 Amp to supply I/O modules.
E2 Expansion
B A
I/O
+ B
115S- XX
A + B
115S- XX
A +
2.3 Radio
The following radio variants are available in the E2 dependent on the country of operation.
900 MHz Spread Spectrum radio
The radio operates in the 902-928 MHz ISM band and uses frequency hopped spread spectrum modulation, which is a method of transmitting radio signals by rapidly switching the carrier among many frequency channels, using a pseudorandom sequence known to both transmitter and receiver.
There are eight different pseudo random sequences known as “Hops sets”. Each Hop set uses 50 channels and steps through these channels after every transmission.
The receiver is continually scanning all 50 channels and when a valid data packet is heard it locks on to the channel and receives the data.
A spread-spectrum transmission offers some advantages over a fixed-frequency transmission. These are - Spread-spectrum signals are more resistant to narrowband interference, they are difficult to intercept or eavesdropper because of the pseudorandom transmission sequences and transmissions can share a frequency band with other types of conventional transmissions with minimal interference.
Page 14 E2 Wireless I/O
Meshing capability
The ELPRO WIBMesh protocol is based on the “Ad hoc On Demand Distance Vector”
(AODV) routing algorithm which is a routing protocol designed for ad hoc networks.
AODV is capable of unicast and multicast routing and is an on demand algorithm, meaning that it builds and maintains these routes only as long as they are needed by the source devices.
The Protocol creates a table, which shows the connection routes to other device in the system. The Protocol uses sequence numbers to ensure the routes are kept as current as possible. It is loop-free, self-starting, and can scale to a large numbers of nodes.
See section 3.4 “WIBMesh” for more details on configuration.
E2 Wireless I/O
2.4
Page 15
Antenna
The E2 module will operate reliably over large distances. The distance, which may be reliably achieved, will vary with each application - depending on the type and location of antennas, the degree of radio interference, and obstructions (such as hills or trees) to the radio path.
Typical reliable distances are detailed below however longer distances can be achieved if antennas are mounted in elevated locations – such as on a hill or on a radio mast.
Using the 900 MHz spread Spectrum radio the distances achievable will be:
USA/Canada 15 miles
Australia/NZ 12 km
6dB net gain antenna configuration permitted (4W ERP)
Unity gain antenna configuration (1W ERP)
To achieve the maximum transmission distance, the antennas should be raised above intermediate obstructions so the radio path is true “line of sight”. Because of the curvature of the earth, the antennas will need to be elevated at least 15 feet (5 metres) above ground for paths greater than 3 miles (5 km). The modules will operate reliably with some obstruction of the radio path, although the reliable distance will be reduced.
Obstructions, which are close to either antenna, will have more of a blocking effect than obstructions in the middle of the radio path. For example, a group of trees around the antenna is a larger obstruction than a group of trees further away from the antenna.
The E2 module provides a range of test features, including displaying the radio signal strength. Line-of-sight paths are only necessary to obtain the maximum range.
Obstructions will reduce the range however, but may not prevent a reliable path. A larger amount of obstruction can be tolerated for shorter distances. For very short distances, it is possible to mount the antennas inside buildings. An obstructed path requires testing to determine if the path will be reliable - refer the section 6 of this manual. Where it is not possible to achieve reliable communications between two modules, then a third module may be used to receive the message and re-transmit it.
This module is referred to as a repeater. This module may also have input/output (I/O) signals connected to it and form part of the I/O network - refer to Chapter 4
Configuration of this manual.
An antenna should be connected to the module via 50 ohm coaxial cable (e.g. RG58,
RG213, Cellfoil, etc) terminated with a male SMA coaxial connector. The higher the antenna is mounted, the greater the transmission range will be, however as the length of coaxial cable increases so do cable losses. For use on unlicensed frequency channels, there are several types of antennas suitable for use. It is important antennas are chosen carefully to avoid contravening the maximum power limit on the unlicensed channel - if in doubt refer to an authorised service provider.
The net gain of an antenna/cable configuration is the gain of the antenna (in dBi) less the loss in the coaxial cable (in dB).
Page 16 E2 Wireless I/O
At 900MHz the maximum net gain of the antenna/cable configuration permitted is
Max. (dB)
Europe 0
At 900MHz the gains and losses of typical antennas are
Antenna
Dipole with integral 15’ cable
5dBi Collinear (3dBd)
0
5
8dBi Collinear
6 element Yagi
9 element Yagi
(6dBd) 8
10
12
Cable type
RG58
Loss (dB per 30 ft / 10 m)
-5
RG213 -2.5
Cellfoil -3
The net gain of the antenna/cable configuration is determined by adding the antenna gain and the cable loss. For example, a 6 element Yagi with 70 feet (20 metres) of
Cellfoil has a net gain of 4dB (10dB – 6dB).
Connections between the antenna and coaxial cable should be carefully taped to prevent ingress of moisture. Moisture ingress in the coaxial cable is a common cause for problems with radio systems, as it greatly increases the radio losses. We recommend that the connection be taped, firstly with a layer of PVC
Tape, then with a vulcanising tape such as “3M 23 tape”, and finally with another layer of PVC UV
Stabilised insulating tape. The first layer of tape allows the joint to be easily inspected when trouble shooting as the vulcanising seal can be easily removed.
Where antennas are mounted on elevated masts, the masts should be effectively earthed to avoid lightning surges. For high lightning risk areas, surge suppression devices between the module and the antenna are recommended. If the antenna is not
E2 Wireless I/O Page 17 already shielded from lightning strike by an adjacent earthed structure, a lightning rod may be installed above the antenna to provide shielding.
Dipole and Collinear antennas.
A collinear antenna transmits the same amount of radio power in all directions - as such they are easy to install and use. The dipole antenna with integral 15 ‘cable does not require any additional coaxial cable; however a cable must be used with the collinear antennas.
Collinear and dipole antennas should be mounted vertically, preferably 1 wavelength
(dependent on frequency) away from a wall or mast to obtain maximum range.
Yagi antennas.
A Yagi antenna provides high gain in the forward direction, but lower gain in other directions. This may be used to compensate for coaxial cable loss for installations with marginal radio path.
The Yagi gain also acts on the receiver, so adding Yagi antennas at both ends of a link provides a double improvement.
Yagi antennas are directional. That is, they have positive gain to the front of the antenna, but negative gain in other directions.
Hence, Yagi antennas should be installed with the central beam horizontal and must be pointed exactly in the direction of transmission to benefit from the gain of the antenna. The Yagi antennas may be installed with the elements in a vertical plane (vertically polarised) or in a horizontal plane
(horizontally polarised). For a two-station installation, with both modules using Yagi antennas, horizontal polarisation is recommended. If there are more than two stations transmitting to a common station, then the Yagi
Page 18 E2 Wireless I/O antennas should have vertical polarisation, and the common (or “central” station should have a collinear (non-directional) antenna.
Also, note that Yagi antennas normally have a drain hole on the folded element - the drain hole should be located on the bottom of the installed antenna.
2.5 Connections
Bottom panel connections
Ethernet port
The E2 modules provides a standard RJ-45 Ethernet port compliant to IEEE 802.3
10/100 BaseT. This port provides full access to the module, including configuration, diagnostics, log file download and firmware upload, of both the local and remote units.
Additionally the Ethernet port can provide network connectivity for locally connected third-party devices with Ethernet functionality.
USB Device Port for configuration
The E2 module also provides a USB-device (USB-B) connector. This connector provides configuration of the device and remote configuration access to other devices in the radio network.
RS-232 port
The E2 module provides an RS-232 serial port, which support operations at data rates up to 115,200 baud. This port supports MODBUS as well as “serial device server”, bringing modem functionality to the E-Series products.
The RS-232 port is provided by an RJ-45 connector wired as a DCE according to EIA-
562.
E2 Wireless I/O
RJ-45 Signal
Name
1
2
3
4
5
6
7
8
RI
DCD
DTR
GND
RXD
TXD
CTS
RTS
Required
Y
Y
Signal name
Ring Indicator
Data Carrier Detect
Data Terminal Ready
Receive Data (from Modem)
Page 19
Clear to Send
Request to Send
RS-485 port with Modbus Support.
The E2 module provides an RS-485 serial port, which support operations at data rates up to 115,200 baud. This port Supports MODBUS functionality, as well as functionality as “serial device server”, bringing modem functionality to the E-Series products
The RS-485 port is provided by two screw terminals. On-board termination of the RS-
485 circuit is built-in.
Side Access Configuration Panel
On the side of the module is a small access cover that hides a “Factory Boot” switch, a
USB Host port and a small bank of dipswitches that are used for Analog input voltage/current selection, External Boot and Default configuration settings.
Page 20 E2 Wireless I/O
“Factory Boot” switch
The “Factory Boot” switch is used to allow restoration of the firmware to a module that has become non-functional. This switch should not normally be used, except if advised by ELPRO support.
USB Host port
This port is a USB Host (Master port), which allows interface with a USB storage device for data logging and for Firmware update to the module.
Dipswitch “Bank”
The Dipswitches are used to select a number of functions within the module; the table below indicates switch positions.
DIP Off On Setting
1
2
3
4
AIN3 Voltage I/P
AIN3 Voltage I/P
AIN4 Voltage I/P
AIN4 Voltage I/P
AIN3 Current I/P
AIN3 Current I/P
AIN4 Current I/P
AIN4 Current I/P
ON
1 2 3 4 5 6
ON
1 2 3 4 5 6
ON
1 2 3 4 5 6
ON
1 2 3 4 5 6
5
6
Hardware Watchdog
Disabled
User Configuration
Active
Hardware Watchdog
Enabled
Default Configuration
Active
ON
1 2 3 4 5 6
ON
1 2 3 4 5 6
Dipswitches – 1 to 4 select if analog inputs 3 and 4 will be measuring Current or
Voltage. Set switches 1 and 2 OFF to measure voltage (0-5V) on Analog input 3. Set switches ON to measure current on Analog input 3 (4-20mA). Set switches 3 and 4 OFF
E2 Wireless I/O Page 21 to measure voltage on Analog input 4. Set switches ON to measure current on Analog input 4.
Dipswitch 5 – Factory use only. This switch should be set to ON to enable the hardware watchdog protection feature.
Dipswitch 6 – When set to ON, the module will boot up with a known factory default including a default IP address for Ethernet connection. (Refer to section 4.1)
Front panel connections
The E2 front panel provides connections for eight Digital Input /Output (DIO1-8), two
“Floating” 16 bit, 0.1% accuracy differential analog inputs, two single ended 12 bit, 0.1% accuracy analog inputs, two 15 bit, 0.1% accuracy current sourcing analog outputs and connection terminals for Common and +24V Analog Loop Supply.
Digital Inputs
Each digital I/O channel on the E2 can act as either an input or an output. The input/output direction is automatically determined by the connections and configuration of the I/O.
If you have an I/O channel wired as an input but operate the channel as an output. No electrical damage will occur however, the I/O system will not operate correctly.
Discrete Input / Output Used as input
E2 Module Inputs
V+
V+
If operating the channel as an output and performing a “read inputs” on this location it will indicate the status of the output.
Voltage Free Contact
DIO1
DIO2
Digital inputs signals share the same terminals as the Digital output signals, marked DIO1-8 on the E2 module.
Transistor
Switch Device
A digital input is activated by connecting the input terminal to EARTH or
Common, either by voltage-free contact or by a transistor switch.
Common V-
Page 22 E2 Wireless I/O
Pulsed Inputs
The E2 supports 8 digital signals, of which inputs 1-4 can be used as pulsed inputs.
The maximum pulse frequency is 50 KHz for Input 1 & 2 and 10 KHz for Input 3 & 4.
Digital/Pulsed inputs are suitable for voltage-free contacts, or NPN-transistor switch devices.
Pulsed Inputs
E2 Module Inputs
V+
V+
DIO1
DIO2
Transistor
Switch Device
Common
V-
E2 Wireless I/O Page 23
Digital Outputs (Pulsed Outputs)
Digital outputs are open-collector transistors and are able to switch loads up to 30VDC,
200mA.
The 8 digital outputs share the same terminals as the digital input. These terminals are marked DIO1-8.
When active, the digital outputs provide a transistor switch to EARTH (Common).
To connect a digital output, refer to the diagram across. A bypass diode is recommended to protect against switching surges for inductive loads such as relay coils.
The digital channels DIO1-8 on the E2 module can be used as pulse outputs with a maximum output frequency of 10KHz.
As well as indicating the Digital Output status (on / off), the LEDs can also indicate a
Fail Safe status by flashing the Output LED. This feature can be utilised by configuring a Fail Safe time and status on the “I/O Configuration” web page as shown below.
The output will reflect the status on the input which is done using a
Change of State message and an update message. We use these update messages to establish if the
Output has not been updated and can then trigger the Fail Safe State.
The output expects to receive an update message at a regular interval and if it fails to receive this message after the said time can then activate the Fail Safe State. The Fail Safe
Time is the time the output needs to count down before activating the Fail
Safe state.
The recommend time configured should be a little more than twice the update time of the input that is mapped to it.
This is because the countdown is restarted whenever it received an update so if we send two updates and fail to receive both we can then put the output into a Failsafe state.
Page 24 E2 Wireless I/O
The Failsafe state if ticked (ON) will indicate with the LED being on and briefly flicking off.
The Failsafe state if un-ticked (OFF) will indicate with the LED being off and briefly flicking on.
Analog Inputs
The E2 provides two floating differential analog inputs and two grounded single-ended analog inputs.
Analog Input 1 & 2 can be configured to measurement current (0-20 mA) or Voltage (0-
25V).
Analog input 3 & 4 can be configured to measure current (0-20mA) or voltage (0-5V).
An internal 24V analog loop supply (ALS) provides power for any current loops with a maximum current limit of 175mA.
The LEDs have an analog diagnostic function and will indicate the status of the input.
If the current is less than 3.0 mA the LED will be off and if greater than 20.5mA the LED will be on (Depending on scaling).
The LED will flicker with the duty cycle relative to the analog reading in this range. (Note by default there is a 5 second delay on the input because of the Filter)
LEDs beside AI1+, AI2+ flash according to current on these inputs. LEDs beside AI1- and AI2- flash according to the voltage on the Analog inputs.
Floating Differential Analog Inputs (AIN 1 & 2 only)
Differential mode current inputs should be used when measuring a current loop, which cannot be connected to earth or ground. This allows the input to be connected anywhere in the current loop.
Common mode voltage can be up to
27VDC.
The diagram across indicates how to connect Loop powered or externally powered devices to the E2 Differential
Inputs.
E2 Wireless I/O
Single Ended Current Inputs (AIN 3 & 4 only)
Single-ended current input mode is useful if the sensor loop is grounded to the E2 module.
Devices can be powered externally from the 24V Analog Loop Supply supplied internally within the module.
The Dip Switches are used to determine if the inputs will be current or voltage. .
Dip Switches 1 & 2 are used for or
Analog 3 and Dip Switches 3 & 4 are used for Analog 4
For Current set both Dip Switches to the “On” position, for Voltage set both to “Off”
Refer below for Dipswitch settings when both analog inputs 3&4 are used for current
ON
1 2 3 4 5 6
Single Ended Voltage Inputs
All analog inputs can be setup to read voltage.
If using Analog input 1 & 2 connect the voltage source across the positive terminal of the input and Common.
If using Analog input 3 & 4 then connect across the input terminal and Common.
Note: default scaling gives 0-10V for 4-20mA output
If using Analog input 3 & 4 for Voltage set both Dip Switches to the “Off” position,
Analog input 1 &2 do not require switch setup.
DIP switch settings used for voltage
ON
1 2 3 4 5 6
Page 25
Page 26
Analog Outputs
The E2 module provides two 0 - 24 mA DC analog outputs for connecting to instrument indicators for the display of remote analog measurements.
The E2 Analog outputs are a sourcing output and should be connected from the analog output terminal through the device or indicator to Common. See diagram for connections.
The LEDs function as a primitive level indicator depending on current -
Dim for 4mA and Bright for 20mA
E2 Wireless I/O
E2 Wireless I/O
3
Chapter 3 – Operation
3.1
Page 27
Overview
The E2 range of I/O modules has been designed to provide standard “off-the-shelf” telemetry functions, for an economic price. Telemetry is the transmission of data or signals over a long distance via radio or twisted-pair wire cable.
3.2 Indications
When power is initially connected to the module it will go through an internal diagnostics check where it will perform some internal setup and diagnostics checks to determine if the module is operating correctly. These checks will take approximately 90 seconds.
The table below indicates the correct LED indications.
Front Panel Indications
LED
Indicator
Condition
PWR
PWR
PWR
Meaning
Fast Flash System Boot – Stage 1
SLOW Flash System Boot – Stage 2
232
232
485
485
GREEN
RED
Receiving RS232 data
Transmitting RS232 data
GREEN
RED
Receiving RS485 data
Transmitting RS485 data
Page 28 E2 Wireless I/O
I/O Indications
LED
Indicator
Condition Meaning
DIO 1-8
DIO 1-8
DIO 1-8
ORANGE
FLASHING ORANGE
– Mostly On
FLASHING ORANGE
– Mostly Off
ORANGE
ORANGE
Digital input ON
Update Failure – Failsafe state On
Update Failure – Failsafe state Off
AI 1 & 2 #1
AI 1 & 2 #2
AI 1 & 2
AI3 & 4
FLASHING ORANGE
ORANGE
Analog input current indication
Analog input voltage indication
Duty cycle relative to the analog reading
Slow =4mA, Fast=20mA
Analog input current / voltage indication
AO1 & 2 ORANGE Analog output current indication
LED’s display the status of each of the eight digital inputs (If the LED is lit then the input is on).
If the DIO are used as outputs then the LEDs will, display the status of each of the digital output (If the LED is lit then the output is on).
Two LEDs exist for each Differential analog input (Channel 1 & 2). The first is used to indicate the set point and the second whether the analogue input is reading zero or negative.
For each of the single ended analog channels, the LED indicates when the analogue input loop is in loop mode.
The two lowest Analog output LEDs are in series with the analog Output and will indicate the output current. (Dim for 4mA Bright for 20mA).
Ethernet Indications
On the end plate, the ethernet socket incorporates two LED’s These LEDs indicating the Ethernet status
100M – GREEN LED indicates presence of a 100 Mbit /s
Ethernet connection, with a 10 Mbit /s connection the LED will be off.
LINK – ORANGE indicates an Ethernet connection and LED briefly flashed off with ethernet activity.
E2 Wireless I/O
3.3
System Dynamics
Page 29
System Design Tips
Page 30
3.4
E2 Wireless I/O
WIBMesh
The ELPRO WIBMesh protocol is based on the “Ad hoc On-demand Distance Vector”
(AODV) routing algorithm which is a routing protocol designed for ad hoc networks.
AODV is capable of unicast (single addressed message) and multicast (Broadcast to all) routing and is an “on-demand” protocol, meaning that it builds and maintains these routes only as long as they are needed by the source devices. Another words the network is silent until a connection is needed. The Protocol creates a table, which shows the connection routes to other device in the system and uses sequence numbers to ensure the routes are kept as current as possible.
When a module in a network needs to make a connection to another module it broadcasts a request for connection. Other modules forward this message, and record the module address that they heard it from, creating a table of temporary routes back to the starting module. If a module receives a message and it already has an existing route to it, it will send a message backwards through the temporary route to the requesting module.
Each request for a route has a sequence number. Modules use this sequence number so that they do not repeat route requests that they have already passed on. Another such feature is that the route requests have a "time to live" number that limits how many times they can be retransmitted. Another such feature is that if a route request fails, another route request may not be sent until twice as much time has passed as the timeout of the previous route request.
The original starting module then begins using the route that has the least number of hops. Unused entries in the routing tables are recycled after a time.
When a link fails, a routing error is passed back to a transmitting node, and the process repeats.
E2 Wireless I/O
4
Chapter 4 – Configuration
4.1
Page 31
First time
The E2 has a built-in web server, containing web pages for analyzing and modifying the module’s configuration. The configuration can be accessed using Microsoft® Internet
Explorer.
Default Configuration
The default factory configuration of the E2 is
IP address192.168.0.1XX, where XX is the last two digits of the serial number (the default IP address is shown on the printed label on the back of the module) netmask 255.255.255.0
Username is “user” and the default password is “user”
The E2 will temporarily load some factory-default settings if powered up with the #6 dipswitch under the side configuration panel switched on. When in SETUP mode, wireless operation is disabled. The previous configuration remains stored in non-volatile memory and will only change if a configuration parameter is modified and the change saved.
Do not forget to set the switch back to the OFF position and re-cycle the power at the conclusion of the configuration for normal operation otherwise, it will continue to boot into the default IP address.
Accessing Configuration for the first time
The Default IP address is in the range 192.168.0.XXX and so will require a PC on this network or be able to change the network settings to access the module configuration.
This is the procedure for changing A PC network settings. methods for accessing the configuration for the first time.
You will need a “straight-through” Ethernet cable between the PC Ethernet port and the E2. The factory default Ethernet address for the E2 is 192.168.0.1XX where XX are the last two digits of the serial number
(check the label on the back of the module).
Connect the Ethernet cable between unit and the PC configuring the module.
Page 32 E2 Wireless I/O
Open the side configuration panel and set the #6 Dipswitch to ON Switch to the ON position. This will always start the E2 with Ethernet IP address 192.168.0.1XX, subnet mask 255.255.255.0, gateway IP 192.168.0.1 and the radio disabled. Do not forget to set the switch back to the OFF position and restart the module at the conclusion of configuration.
Power up the E2 module.
Open “Network Settings” on your PC under Control Panel. The following description is for Windows XP - earlier Windows operating systems have similar settings.
Open “Properties” of Local Area Connection.
Select Internet Protocol (TCP/IP) and click on Properties.
On the General tab enter IP address 192.168.0.1, Subnet mask 255.255.255.0 and press “OK”
Open Internet Explorer and ensure that settings will allow you to connect to the IP address selected. If the PC uses a proxy server, ensure that Internet Explorer will bypass the Proxy Server for local addresses.
This option may be modified by opening Tools -> Internet
Options -> Connections Tab -> LAN Settings->Proxy
Server -> bypass proxy for local addresses.
Enter the default IP address for the E2 https://192.168.0.1XX where XX is the last two digits of the serial number.
Enter the username “user” and default password “user”.
E2 Wireless I/O Page 33
Figure 1 – Welcome Webpage
To resume normal configured operation when Configuration is complete, switch Factory
Default dip-switch on the E2 to RUN and cycle power.
Note: Security Certificates. Configuration of the E2 uses an encrypted link (https). The security certificate used by the E2 is issued by ELPRO and matches the IP address
192.168.0.100.
When you first connect to the E2, your web browser will issue a warning that ELPRO is not a trusted authority. Ignore this warning and proceed to the configuration web page.
To avoid seeing this warning in future, you can install the certificate into your browser.
Internet Explorer 7 has an additional address check on security certificates. Unless the
E2 has the address 192.168.0.100, when you first connect to the E2, Internet Explorer
7 will issue a warning about mismatched security certificate address. You can turn off this behaviour in IE7 by selecting
“Tools > Internet Options > Advanced > Security > Warn about certificate address mismatch*”
Page 34
4.2
E2 Wireless I/O
Network Configuration
You can view or modify Ethernet network parameters by selecting the “Network” menu.
When prompted for username and password, enter “user” as the username, and “user” as the password in the password field (This is the factory default – See section 4.8
“Module Information” to change). If you have forgotten the IP address or password, the
Factory Default switch may be used to access the existing configuration. Refer to section above for this procedure.
The Network Configuration page allows configuration of parameters related to the wired and wireless Ethernet interfaces. In general, IP address selection will be dependant upon the connected wired Ethernet device(s) – before connecting to an existing LAN consult the network administrator.
Device Mode
Default Gateway This is the address that the device will use to forward messages to remote hosts that are not connected to any of the local bridged network (Ethernet or Wireless). This is only required if the wired LAN has a Gateway unit which connects to devices beyond the LAN - for example, Internet access. If there is no Gateway on the LAN, set to the same address as the “Ethernet IP Address” below.
Obtain IP Address
Automatically
Checking this item enables DHCP client on the E2. A DHCP client requests its IP address from a DHCP server, which assigns the IP Address automatically. Default is unchecked.
Ethernet Interface
MAC Address This is the unique hardware address of the E2 and is assigned in the Factory. The E2 has two MAC addresses, one for each interface (Ethernet and Wireless) The Ethernet
MAC is the primary MAC Address.
IP Address The IP address of the E2 on its wired (Ethernet Interface) port and wireless (Wireless Interface) port. This should be set to the IP address you require. If the device mode is set to bridge, then the wired and wireless ports will have the same
IP address.
IP Subnet Mask The IP network mask of the E2 on its wired (Ethernet
Interface) port and wireless (Wireless Interface) port. This should be set to appropriate subnet mask for your system
(Typically 255.255.255.0).
E2 Wireless I/O
Radio Interface
Page 35
IP Address
Save Changes
The IP address of the E2 on its wired (Ethernet Interface) port and wireless (Wireless Interface) port. This should be set to the IP address you require. If the device mode is set to bridge, then the wired and wireless ports will have the same
IP address.
IP Subnet Mask The IP network mask of the E2 on its wired (Ethernet
Interface) port and wireless (Wireless Interface) port. This should be set to appropriate subnet mask for your system
(Typically 255.255.255.0).
Save changes to non-volatile memory. The module will need to be restarted before the changes take effect.
Save Changes and
Reset.
Save settings to non-volatile memory, and reboot E2. Once the module has completed the reboot sequence, all changes are in effect.
4.3
The E2 can be configured for different radio transmission rates. A reduction in rate increases the reliable range (transmission distance). The factory-default data rate settings are suitable for the majority of applications and should only be modified by experienced users.
The E2 allows for configurable fixed or fallback radio transmission Data Rates. When a fixed rate is configured, the radio transmission rate is never altered, even under extremely poor conditions. The fallback rates allow a maximum rate to be configured whilst enabling the unit to automatically reduce the rate when transmit errors occur.
When a radio transmission is unsuccessful, the E2 will automatically drop to the next lowest data rate and enter probation. If subsequent transmissions are successful at the lower rate, the E2 will attempt to increase to the next highest rate when probation has ended. When a station connects to an access point the two devices negotiate a data rate based which is within configured range of radio data rates for both devices. If there is no common data rate, then the devices will not be able to connect.
Select the “Radio” Menu to change the following configuration parameters. If a change is made, you need to select “Save Changes” to retain the changes. Changes will not take effect until the unit is reset.
Page 36 E2 Wireless I/O
Transmit Power
Level
Transmit Data Rate
Channel
Save Changes
Save Changes and
Reset.
Radio Settings
This allows adjustment of the radio power. Do not set the radio power above the allowed setting for your country You can reduce the power for short range applications, or to allow the use of high gain transmitter antennas while still complying with the emission requirements of your country.
See “Appendix D” for dBm to mW conversion
•
The radio baud rate in Mega (million) bits per second
(Mbps) for point to point radio transmissions. The default value is Auto. Select a fixed rate to force the radio to use the selected rate. Select a fallback rate to allow the radio to select a lower rate if there are communications problems. Normally an Access point is configured with either auto or a fallback data rate to allow clients to connect with different data rates.
Select available channel, frequency and bandwidth from drop down list. Australia only has 1 channel available
(Channel 41).
Radio Channels 1 to 11 may be configured at the Access
Point. Default radio channel is set to 3.
Save changes to non-volatile memory. The module will need to be restarted before the changes take effect.
Save settings to non-volatile memory, and reboot E2. Once the module has completed the reboot sequence, all changes are in effect.
E2 Wireless I/O
4.4
Page 37
The “TX Attempts for Acknowledged messages” is now many times the configured module will attempt to communicate a message to another module (message reties).
After failing to communicate the module will be flagged as being in comms fail.
Every time it tries to communicate to the remote module, it will reduce the number of attempts down to one as it has been flagged as being in Comms fail.
If communications is restored the module will go back to transmitting the number of time configured in “Tx Attempts for Acknowledged messages”.
The “TX count for unacknowledged messages” is the number of times it transmit the same data message. It is used if the E2 has been setup as a transmit only module
(similar to the older Elpro 905U-K or 505U-K modules)
Being a Transmit only module there is no communication handshake between modules so transmitting the same message a number of times gives a greater reliability in communications.
Page 38
4.5
E2 Wireless I/O
Selecting WIBMesh Mappings from the right hand side of the main menu will show the I/O
Configuration screen.
This is where you configure Read, Write and
Gather/Scatter mappings as well as any Sensitivity
Blocks.
Write Mappings
Add or delete mapping by using the buttons then select “Save and Activate Changes”.
Block Write Mapping
Destination IP This is the IP address that you wish to write the I/O to.
Ack Selecting this box will mean the mapping will be acknowledged
Invert
Update Period
This will allow the mapping to be inverted. E.g. if the digital input is on and inverted then the output will be off and visa versa. Applies to all the I/O in the mapping and can only be used with Words and Bits, No Floating Point or Long values
This is the period that the mappings are sent as an update or check signal.
Update Offset
COS Delay
Allows an offset to be configured for each mapping. Used to stagger the transmissions so on start-up the module does not try to send all mapping at the same time. Default it will be 0 however the normal would be around 10 minutes
You can enter a delay period such that the message is delayed from sending for the configured time. Used to hold off the transmissions to allow more COS (Change of State) messages to be added to the mapping.
E2 Wireless I/O Page 39
COS Enabled
COS Resets Update
Timer
Force Reg
Fail Reg
Can enable or disable the COS message. If disabled messages would only be sent on the update period.
Enabling this timer will mean If a COS is received in between update messages it will reset the Update timer, meaning it will not receive another update until the further Update period has passed.- used to reduce the amount of radio traffic
Register location that when written to will force the Write
Mapping to be sent. E.g. External device can initiate the transmissions.
Register location that will indicate a failure to communicate with the remote Destination Address configured
First Local Reg Starting Local address that values will be written to.
First Remote Reg Starting Remote address that the values will read from.
Reg Count Total number of register values (consecutive)
Save Changes
Save Changes and
Reset.
Save changes to non-volatile memory. The module will need to be restarted before the changes take effect.
Save settings to non-volatile memory, and reboot E2. Once the module has completed the reboot sequence, all changes are in effect.
Read Mappings
Destination IP
Invert
Update Period
Block Read Mapping
This is the Module IP address that you wish to read I/O from.
This will allow the mapping to be inverted. E.g. if the digital input is on and inverted then the output will be off and visa versa. Applies to all the I/O in the mapping and can only be used with Words and Bits, No Floating Point or Long values
This is the period that the mappings are sent as an update or check signal.
Page 40 E2 Wireless I/O
Update Offset
Response Timeout
Force Reg
Fail Reg
First Local Reg
First Remote Reg
Reg Count
Save Changes
Save Changes and
Reset.
Allows an offset to configured for each mapping. Used to stagger the transmissions so on start-up the module does not try to read all mapping at the same time. Default it will be 0 however the normal would be around 10 minutes
Time before a response Failure is registered
Register location that when written to will force the Read
Mapping to be sent. E.g. External device can initiate the transmissions.
Register location that will indicate a failure to communicate with the remote Destination Address configured
Starting Local address that values will be written to.
Starting Remote address that the values will read from.
Total number of register values (consecutive)
Save changes to non-volatile memory. The module will need to be restarted before the changes take effect.
Save settings to non-volatile memory, and reboot E2. Once the module has completed the reboot sequence, all changes are in effect.
Gather/Scatter Write Mappings
Destination IP
Ack
Invert
Update Period
Gather/Scatter Write Mapping
This is the Module IP address that you wish to read I/O from.
Selecting this box will mean the mapping will be acknowledged
This will allow the mapping to be inverted. E.g. if the digital input is on and inverted then the output will be off and visa versa. Applies to all the I/O in the mapping and can only be used with Words and Bits, No Floating Point or Long values
This is the period that the mappings are sent as an update or check signal.
E2 Wireless I/O Page 41
Update Offset
COS Delay
COS Enabled
COS Resets Update
Timer
Allows an offset to configured for each mapping. Used to stagger the transmissions so on start-up the module does not try to send all mapping at the same time. Default it will be 0 however the normal would be around 10 minutes
You can enter a delay period such that the message is delayed from sending for the configured time. Used to hold off the transmissions to allow more COS messages to be added to the mapping.
Can enable or disable the COS messaged. If disabled messages would only be sent on the update period.
Enabling this timer will mean If a COS is received in between any updates it will reset the Update timer, meaning it will not receive another update until the further Update period has passed.- used to reduce the amount of radio traffic
Force Reg
Fail Reg
Register location that when written to will force the Write
Mapping to be sent. E.g. External device can initiate the transmissions.
Register location that will indicate a failure to communicate with the remote Destination Address configured
Reg Count
Total number of register values (consecutive)
L1 & R2 – L32 & R32
Local and Remote pairs indicating up to 32 scattered local I/O registers can be mapped to 32 remote I/O registers
Save Changes
Save changes to non-volatile memory. The module will need to be restarted before the changes take effect.
Save Changes and
Reset.
Save settings to non-volatile memory, and reboot E2. Once the module has completed the reboot sequence, all changes are in effect.
Page 42
4.6
E2 Wireless I/O
Serial Configuration
The E2 has an RS-232, and RS-485 port for serial communications. These ports may be used to connect external Modbus RTU devices via the Modbus TCP to RTU
Gateway.
Modbus TCP to RTU Gateway
The Modbus TCP to RTU Gateway allows an Ethernet Modbus/TCP Client (Master) to communicate with a serial Modbus RTU Slave. The E2 makes this possible by internally performing the necessary protocol conversion. The conversion is always performed by the E2, which is directly connected to the Modbus serial device (i.e. only this module needs to have Modbus TCP to RTU Gateway enabled).
The example below demonstrates how a Modbus/TCP Client (Master) can connect to one or more Modbus RTU (i.e serial) Slaves. In this example the E2 Access Point is configured with the “RS232 Modbus/TCP to RTU Gateway” enabled.
Once enabled, the gateway converts the Modbus/TCP queries received from the
Master into Modbus RTU queries and forwards these over the RS232 port to the Slave.
When the serial response to the query arrives from the Slave, it is converted to a
Modbus/TCP response and forwarded via the network to the Modbus/TCP Master. If no response was received serially by the E2 within the configured Response Timeout, the
E2 will initiate a number of retries specified by the configured Maximum Request
Retries.
The Modbus TCP to RTU Gateway may be configured to operate on either the RS-232 or RS-485 port.
E2 Wireless I/O
RS232 / RS485 Serial Port Configuration
RS232 Port
Page 43
Select the desired functionality. Select either Serial Gateway or Modbus TCP to RTU
Data Rate
The serial data rate desired. Serial data rates available range from 110bps to a maximum of 230,400bps.
Data Format
The data format desired. All the standard data formats are supported.
Flow Control
Selects CTS/RTS or None
RS232 / RS485 Modbus TCP / RTU Converter
Pauses Between
Requests
Enter the delay between serial request retries in milliseconds
Response Timeout
Enter the serial response timeout in milliseconds – a serial retry will be sent if a response is not received within this timeout.
Connection Timeout
Enter the TCP connection timeout in seconds – if no
Modbus/TCP data is received within this timeout then the TCP connection will be dropped. Set this field to zero for no timeout.
Maximum Request
Retries
Maximum
Connections
Enter the maximum number of request retries performed serially.
Enter the maximum number of simultaneous TCP connections to the server allowed.
Page 44
4.7
E2 Wireless I/O
I/O Configuration
Analog Inputs
The following configuration parameters are available on the E2 Analog inputs
Name – Can re-name the inputs or use the default, up to 30 characters including spaces.
Zero / Span – These variables will change the Scale of the Analog Inputs.
Filter (sec) – The Filter time is the time for the analog to reach 63% of its settled value on a step change. By default the Pulsed inputs are not filtered.
Setpoints – All of the analogs have an Upper and a Lower setpoint, which can be used as an indicator locally or remotely. The internal setpoint status must be mapped to an output for this option to have effect.
The setpoints operate with a deadband or a windowed function depending on what values are entered in each setpoint location. Setpoint values are in whatever the raw input is , i.e. AI 1-4 will be mA, AI5-12 will be Volts and AI13-16 will be in Hertz.
•
Upper setpoint: Positive indicates deadband function, Negative indicates windowed function.
•
Lower Setpoint: Positive indicates normal function, Negative indicates inverted function.
E2 Wireless I/O Page 45
Deadband - If the Analog Input is less than the Lower Set point, the set-point status will be active (on, “1”) and remain active until the Analog Input is greater than the Upper Set
Point, the set-point status will be reset (off, “0”). Note that the Upper Set Point must always be higher than the Lower Set Point.
Windowed – The Upper and Lower sets are used to setup a “window” within the analog range. If the analog value is inside of this window, the setpoint will be active (on, “1”), and if the analog value is outside of this window, the setpoint will be reset (off, “0”)
Inverted - If the Upper and Lower setpoint values are entered as negative numbers the inverse of the “Deadband” and “Windowed” will occur, i.e. The function is exactly the same however the setpoint logic will be inverted. (If setpoint was on, inverted will be off)
Analog Outputs
Name – Can re-name the outputs or use the default, up to 30 characters including spaces.
Zero / Span – These variables will change the Scale of the Analog Outputs.
Failsafe Time (sec) – The Fail Safe Time is the time the output needs to count down before activating the failsafe state. Receiving an update or a COS message will reset the Fail Safe Timer back to its starting value. If the Fail Safe Timer gets down to zero then the output will be set to the Fail Safe state (mA)
It is recommend this Fail Safe Time be configured for a little more than twice the update time of the input that is mapped to it, that way the output will reset if it fails to receive two update messages.
Failsafe Time (sec) – The value that you wish the output the reset to.
Page 46 E2 Wireless I/O
Digital Input
Name – Can re-name the inputs or use the default, up to 30 characters including spaces.
Debounce Time (sec) – Debounce is the time which an input must stay stable before the module decides that a change of state has occurred. If a digital input changes (on - off) and changes again (off - on) in less than the debounce time, then the module will ignore both changes. Default debounce time is .5 seconds.
Digital Output
Pulsed Inputs
E2 Wireless I/O
4.8
Page 47
This configuration page is primarily for information purposes. With the exception of the password, the information entered here is displayed on the home configuration webpage of the E2.
Username
Password
Device Name
Owner
Contact
Description
Location
Configuration of Username. This is the username used to access the configuration on the E2. Take care to remember this username if you change it as it will be needed to access the E2 in future.
Configuration of Password. This is the password used to access the configuration on the E2. Take care to remember this password if you change it as it will be needed to access the module in future.
A text field if you wish to label the particular E2.
A text field for owner name.
A text field for owner phone number, email address etc.
A text field used for a description of the purpose of the unit.
A text field used to describe the location of the E2.
Page 48
4.9
E2 Wireless I/O
This screen is where you can log system instructions, etc to the screen and from there you can save to a file.
This screen also is where any uploading and saving of the configuration is done.
Reading Configuration File
Reads the module configuration into an XML file for saving.
Writing Configuration File
Allows you to load an XML configuration file into the module and then reset
Firmware Upgrade
This option allows the module firmware to be updated by loading a special firmware file into the module and then performing a reset. The module will then go through a boot routine and loads the new firmware.
4.10
The I/O data store provides storage of all I/O data in the system. The data store provides services to other processes, and is configured indirectly by the other processes making use of it’s services.
The I/O Store provides eight different “data files”. Two bit files, two word files, two longword files and two floating point files. The two files of each type in turn support inputs and outputs on the local machine, and data storage for the gateway function of the machine.
E2 Wireless I/O
These files are mapped into the address map as described below.
Store name Type Size
Page 49
Address
ain word inputs (16-bit)
2500 (bits)
2500 (words)
10001
30001
0001
0008
10001
10008
10009
10020
30001
30004
30005
30006
30007
30008 pin real_ain pot long inputs (32-bit) float inputs (32-bit) long outputs (32-bit)
20 (longwords)
20 (floats)
20 (longwords)
36001
38001
46001 real_aot float outputs (32-bit) 20 (floats) 48001
The E2 provides an address map, which maps the internal register files to addresses.
Addresses are common for ELPRO protocol and for Modbus Protocol. The table also details the internal IO Store name for each of the address ranges.
The following table shows the basic onboard I/O available in a standard E2 module with no expansion I/O connected. For a more detailed I/O map (showing the full register range), see Appendix A at the end of the manual.
Standard E2 I/O (Basic Local I/O with no expansion modules)
Address Input / Output Description
Local DIO1 – DIO8 (as Outputs)
Local DIO1 – DIO8 (as inputs)
Setpoint status from Analog inputs 1 through 12. (AI1,2,3,4 Current
Mode), (Internal Supplies), (AI1,2,3,4 Voltage Mode)
Local AI1 – AI4. (Current Mode)
( AI1, AI2 4-20mA diff., AI3, AI4 4-20mA Sink)
Local Supply voltage (8-40V scaling)
Local Battery voltage
Local 24V loop voltage
115S Supply Voltage
Page 50
30009
30012
30013
30016
40001
40002
Local AI1 – AI4. (Voltage Mode)
( AI1, AI2 0-10V, AI3, AI4 0-5V)
Local Pulse rate inputs PI1 – PI4
Local AO1 – AO2
E2 Wireless I/O
E2 Wireless I/O
Chapter 5 – Diagnostics
Page 51
By selecting this option on the main screen will allow some basic reading and writing of the I/O store within the module.
To read a location, enter an address location, e.g. 10001 (for digital Inputs), enter a count (number of consecutive registers) and then press the “Read” button
Below the buttons, you will see the returned address location and values
To Write to outputs , enter the address location, count and value and then press the “Write” button.
You will then see the outputs change to the value you entered.
E.g. Write to Register 1 with a count of 8 and a value of 65535 will turn all the Local
Digital Outputs on.
Page 52 E2 Wireless I/O
Connectivity
The Connectivity webpage displays connections and available networks. The
“Connected Devices” section displays the radio channel, received signal strength, and radio data rate for each Client or Access Point by their MAC Address. The readings shown are based upon the last received data message from the Access Point or Client.
Client stations also display a list of detected Access points (Site Survey), including network name (SSID), channel and maximum data rate.
Note that when updating the Connectivity webpage, it is necessary to hold down the
<ctrl> key while pressing the refresh button. Otherwise, the information will not be updated.
Statistics
The Statistics webpage is used for advanced debugging of E2. This webpage details the state of the E2 and performance information. This page is typically useful to ELPRO technical support personnel in diagnosing problems with the module.
Note that when updating the Statistics webpage, it is necessary to hold down the <ctrl> key while pressing the refresh button. Otherwise, the information will not be updated.
E2 Wireless I/O Page 53
Page 54
5
Appendix A
6
Appendix A
E2 Wireless I/O
I/O Store
“Output Coils”
0001
0008
0009
0020
0021
0040
0041
0500
0501
3000
3001
10000
Local DIO1 – DIO8 (as Outputs) at address 1-8.
Spare
Locally attached 115s modules DIO Outputs
(See 115S detail below)
(space for up to 24 115S modules – 20 registers)
General Purpose Bit Storage – Used for:
•
Staging area for data concentrator
•
Fieldbus storage
•
Force Mapping registers (assigned in Config)
Not Available
“Input Bits”
10001
10008
10009
10020
10021
10040
10041
10500
10501
10595
Local DIO1 – DIO8 (as inputs) at address 1-8.
(115S-11 DIO1-DIO16)
SetPoint status from Analog inputs 1 through 12.
Locally attached 115s modules DIO Inputs
(See 115S detail below)
(space for up to 24 115S modules)
Comm Fail Status to remote with address (location -10500)
E2 Wireless I/O Page 55
10597
10598
10599
10600
10601
12500
12501
30000
Message Buffers Exhausted Alarm Latch
Spare
Spare
Spare
General Purpose Bit Storage – Used for:
•
Staging area for data concentrator
•
Fieldbus storage
Not Available
“Input Registers”
30001
30004
30005
30006
30007
30008
30009
30012
30013
30016
30018
30020
30021
30040
30041
30500
30501
30595
Local AI1 – AI4. (Current Mode)
( AI1, AI2 4-20mA diff., AI3, AI4 4-20mA Sink)
Local Supply voltage (8-40V scaling)
Local Battery voltage
Local 24V loop voltage
115S Supply Voltage
Local AI1 – AI4. (Voltage Mode)
( AI1, AI2 0-10V, AI3, AI4 0-5V)
Local Pulse rate inputs PI1 – PI4
Spare
Locally attached 115smodules
(See 115S detail below)
(space for up to 24 115S modules)
RSSI Level from Neighbour with address (location -30500)
30597
30598
Spare
Spare
Page 56 E2 Wireless I/O
30599
30600
30601
32500
32501
36000
36001
36008
36009
36040
36041
38000
Spare
Spare
General Purpose word Storage – Used for:
•
•
Staging area for data concentrator
Fieldbus
Not Available
Local Pulsed inputs 1-4.B.E Format.
Most significant word at lower / odd address. spare
Not Available storage
38001
Local Analog inputs as floating point values
Modscan Format (Sign + Exponent + Most significant 7 bits of significant at Even / Higher Addressed location. Lower 16 bits of
Significant at lower / Odd addressed location)
(12.3 => 38001=CCCD, 38002=4144)
38032
38033 - 38040 Spare space for floating point values
32501
40000
Not Available
“Holding Registers”
40001
40002
40003
40020
40021
40040
40041
Local AO1 – AO2
Spare
Locally attached 115smodules
(See 115S detail below)
(space for up to 24 115S modules)
E2 Wireless I/O
40500
40501
42500
42501
46000
46001
46008
46009
46040
36041
38000
48001
48004
40005
48040
48041 onwards
General Purpose word Storage – Used for:
•
Staging area for data concentrator
Fieldbus Mappings storage
Not Available
Page 57
Local Pulsed Outputs 1-4. B.E Format. Most significant word at lower / odd address. spare
Not Available
Local Analog outputs as floating point values
Modscan Format (Sign + Exponent + Most significant 7 bits of significant at Even / Higher Addressed location. Lower 16 bits of
Significant at lower / Odd addressed location)
(12.3 => 48001=CCCD, 48002=4144)
Spare space for floating point values
Not Available
advertisement
Related manuals
advertisement
Table of contents
- 9 1 CHAPTER 1 – INTRODUCTION
- 9 1.1 Overview
- 11 1.2 Module Structure
- 12 1.3 Getting Started
- 13 2 CHAPTER 2 – INSTALLATION
- 13 2.1 General
- 13 2.2 Power/Supply
- 14 2.3 Radio
- 14 900 MHz Spread Spectrum radio
- 15 Meshing capability
- 16 2.4 Antenna
- 18 Dipole and Collinear antennas
- 18 Yagi antennas
- 19 2.5 Connections
- 19 Ethernet port
- 19 USB Device Port for configuration
- 19 RS-232 port
- 20 RS-485 port with Modbus Support
- 21 “Factory Boot” switch
- 21 USB Host port
- 21 Dipswitch “Bank
- 22 Front panel connections
- 22 Digital Inputs
- 23 Pulsed Inputs
- 23 Digital Outputs (Pulsed Outputs)
- 25 Analog Inputs
- 25 Floating Differential Analog Inputs (AIN 1 & 2 only)
- 26 Single Ended Current Inputs (AIN 3 & 4 only)
- 26 Single Ended Voltage Inputs
- 27 Analog Outputs
- 28 3 CHAPTER 3 – OPERATION
- 28 3.1 Overview
- 28 3.2 Indications
- 28 Front Panel Indications
- 29 I/O Indications
- 29 Ethernet Indications
- 30 3.3 System Design Tips
- 30 System Dynamics
- 31 3.4 WIBMesh
- 32 4 CHAPTER 4 – CONFIGURATION
- 32 4.1 First time
- 32 Default Configuration
- 32 Accessing Configuration for the first time
- 35 4.2 Network Configuration
- 36 4.3 Radio Settings
- 38 WIBMesh Configuration
- 39 4.5 WIBMesh Mappings
- 39 Write Mappings
- 40 Read Mappings
- 41 Gather/Scatter Write Mappings
- 43 4.6 Serial Configuration
- 43 Modbus TCP to RTU Gateway
- 45 4.7 I/O Configuration
- 45 Analog Inputs
- 46 Analog Outputs
- 47 Digital Input
- 47 Digital Output
- 47 Pulsed Inputs
- 48 4.8 Module Information
- 49 4.9 System Tools
- 49 Reading Configuration File
- 49 Writing Configuration File
- 49 Firmware Upgrade
- 49 4.10 Address Map
- 50 Standard E2 I/O (Basic Local I/O with no expansion modules)
- 52 CHAPTER 5 – DIAGNOSTICS
- 52 IO Diagnostics
- 53 Diagnostic Information
- 53 Connectivity
- 53 Statistics
- 55 5 APPENDIX A
- 55 I/O Store
- 55 “Output Coils
- 55 “Input Bits
- 56 “Input Registers
- 57 “Holding Registers