advertisement
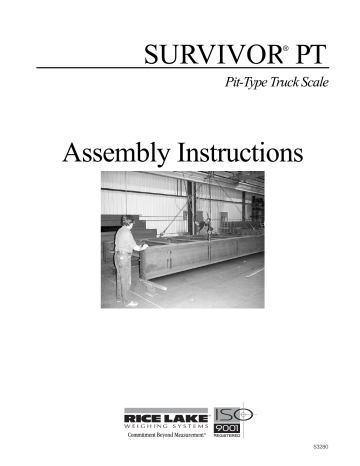
SURVIVOR ® PT
Pit-Type Truck Scale
Assembly Instructions
53280
Survivor ® PT Pit-Type Truck Scale Assembly Instructions
Contents
Introduction.............................................................................................................................................. 1
1.0 Installation ................................................................................................................................... 1
1.1 Foundation Slab Cure Period . . . . . . . . . . . . . . . . . . . . . . . . . . . . . . . . . . . . . . . . . . . . . . . . . . . . . . . 1
1.2 Assembly Time Estimates . . . . . . . . . . . . . . . . . . . . . . . . . . . . . . . . . . . . . . . . . . . . . . . . . . . . . . . . . 1
1.3 Recommended Tools and Equipment . . . . . . . . . . . . . . . . . . . . . . . . . . . . . . . . . . . . . . . . . . . . . . . . 2
1.4 Lifting and Handling . . . . . . . . . . . . . . . . . . . . . . . . . . . . . . . . . . . . . . . . . . . . . . . . . . . . . . . . . . . . . . 2
1.5 Temporary Setting Blocks . . . . . . . . . . . . . . . . . . . . . . . . . . . . . . . . . . . . . . . . . . . . . . . . . . . . . . . . . 2
2.0 Assemble Deck Modules ............................................................................................................. 3
2.1 Place End Module A . . . . . . . . . . . . . . . . . . . . . . . . . . . . . . . . . . . . . . . . . . . . . . . . . . . . . . . . . . . . . 3
2.2 Place and Attach Center Module . . . . . . . . . . . . . . . . . . . . . . . . . . . . . . . . . . . . . . . . . . . . . . . . . . . . 3
2.3 Install Outriggers and Deck Coping . . . . . . . . . . . . . . . . . . . . . . . . . . . . . . . . . . . . . . . . . . . . . . . . . . 4
2.4 Level Module Assembly . . . . . . . . . . . . . . . . . . . . . . . . . . . . . . . . . . . . . . . . . . . . . . . . . . . . . . . . . . . 5
3.0 Load Cell Mount Installation........................................................................................................ 6
3.1 Attach Upper Mount Chair . . . . . . . . . . . . . . . . . . . . . . . . . . . . . . . . . . . . . . . . . . . . . . . . . . . . . . . . . 6
3.2 Prepare Baseplate and Mount Installation . . . . . . . . . . . . . . . . . . . . . . . . . . . . . . . . . . . . . . . . . . . . . 6
3.3 Raise Mount into Final Position . . . . . . . . . . . . . . . . . . . . . . . . . . . . . . . . . . . . . . . . . . . . . . . . . . . . . 6
3.4 Attach Flexible Conduit Sections . . . . . . . . . . . . . . . . . . . . . . . . . . . . . . . . . . . . . . . . . . . . . . . . . . . . 7
3.4.1 Attach Grounding Strap . . . . . . . . . . . . . . . . . . . . . . . . . . . . . . . . . . . . . . . . . . . . . . . . . . . . . . . . . . . . 7
3.4.2 Install Lower Module Assembly Bolts . . . . . . . . . . . . . . . . . . . . . . . . . . . . . . . . . . . . . . . . . . . . . . . . . . 7
3.5 Install Anchor Bolts and Grout . . . . . . . . . . . . . . . . . . . . . . . . . . . . . . . . . . . . . . . . . . . . . . . . . . . . . . 7
3.6 Install Support Bars, Corrugated Metal, and Deck Rebar . . . . . . . . . . . . . . . . . . . . . . . . . . . . . . . . . . 8
3.6.1 Corrugated Metal Sheeting . . . . . . . . . . . . . . . . . . . . . . . . . . . . . . . . . . . . . . . . . . . . . . . . . . . . . . . . . . 8
3.7 Deck Rebar . . . . . . . . . . . . . . . . . . . . . . . . . . . . . . . . . . . . . . . . . . . . . . . . . . . . . . . . . . . . . . . . . . . . 8
4.0 Pour and Finish Concrete Deck ................................................................................................... 9
4.1 Optional Equipment . . . . . . . . . . . . . . . . . . . . . . . . . . . . . . . . . . . . . . . . . . . . . . . . . . . . . . . . . . . . . 10
5.0 Install Cabling in Conduit .......................................................................................................... 11
5.1 Load Cells to Junction Box . . . . . . . . . . . . . . . . . . . . . . . . . . . . . . . . . . . . . . . . . . . . . . . . . . . . . . . 11
5.2 Junction Box to Indicator . . . . . . . . . . . . . . . . . . . . . . . . . . . . . . . . . . . . . . . . . . . . . . . . . . . . . . . . . 11
5.3 Indicator to Peripherals . . . . . . . . . . . . . . . . . . . . . . . . . . . . . . . . . . . . . . . . . . . . . . . . . . . . . . . . . . 11
5.4 Single-Point Ground Conductor. . . . . . . . . . . . . . . . . . . . . . . . . . . . . . . . . . . . . . . . . . . . . . . . . . . . 11
5.5 Junction Box Connections. . . . . . . . . . . . . . . . . . . . . . . . . . . . . . . . . . . . . . . . . . . . . . . . . . . . . . . . 11
5.6 Electrical Ground Connections. . . . . . . . . . . . . . . . . . . . . . . . . . . . . . . . . . . . . . . . . . . . . . . . . . . . . 12
5.7 Install Transient Protection . . . . . . . . . . . . . . . . . . . . . . . . . . . . . . . . . . . . . . . . . . . . . . . . . . . . . . . . 13
6.0 Trimming and Calibration .......................................................................................................... 15
6.1 Overview and Equipment Required . . . . . . . . . . . . . . . . . . . . . . . . . . . . . . . . . . . . . . . . . . . . . . . . . 15
6.2 Trimming Individual Cells . . . . . . . . . . . . . . . . . . . . . . . . . . . . . . . . . . . . . . . . . . . . . . . . . . . . . . . . . 15
6.3 Trimming Paired Sections . . . . . . . . . . . . . . . . . . . . . . . . . . . . . . . . . . . . . . . . . . . . . . . . . . . . . . . . 16
6.4 Calibration with Test Weights. . . . . . . . . . . . . . . . . . . . . . . . . . . . . . . . . . . . . . . . . . . . . . . . . . . . . . 17
7.0 Load Cell Replacement.............................................................................................................. 18
7.1 Overview . . . . . . . . . . . . . . . . . . . . . . . . . . . . . . . . . . . . . . . . . . . . . . . . . . . . . . . . . . . . . . . . . . . . . 18
7.2 Replacement Procedure . . . . . . . . . . . . . . . . . . . . . . . . . . . . . . . . . . . . . . . . . . . . . . . . . . . . . . . . . 18
8.0 Vehicle Scale Limited Warranty ................................................................................................ 19
Technical training s eminar s are available through Rice Lake Weighing Sy s tem s .
Cour s e de s cription s and date s can be viewed at www.ricelake.com
or obtained by calling 715-234-9171 and a s king for the training department
© 2007 Rice Lake Weighing Systems. All rights reserved. Printed in the United States of America.
Specifications subject to change without notice.
February 2007
ii Survivor
®
PT Pit-Type Truck Scale Assembly Instructions
Introduction
This manual is intended for use by technicians responsible for installing and servicing the PT
Pit-Type series truck scale. You will find that the PT
Pit-Type truck scale has been designed so that your on-site installation time is reduced as much as possible. A well-organized, experienced installation crew should be able to install a typical 70’x 11’ truck scale in one day.
NOTE: This booklet covers the PT Pit-Type truck scale installations. Use these instructions as general installation guidelines unless the engineering drawings furnished with your scale differ from the instruction in this booklet.
Engineering drawings furnished with your scale always take priority over these general installation guidelines.
Refer to the engineering drawings furnished with the scale for all component numbering sequences.
A u t h o r i z e d d i s t r i b u t o r s a n d t h e i r employees can view or download this manual from the Rice Lake Weighing
S y s t e m s d i s t r i b u t o r s i t e a t www.ricelake.com
.
1.0
Installation
The modular sections of the SURVIVOR
®
PT Pit-Type truck scale are shipped pre-assembled and ready to be placed into position on temporary setting blocks using a crane capable of handling 10,000 lbs. The individual modules are bolted together and the deck is leveled in final position flush with the top of the pit. Mounts are shipped pre-assembled with load cells, adapters, and flexible conduit sections attached. Mounts are installed to the level of the deck, then anchored and grouted to the foundation. Cabling is run in conduit and electronic equipment connected to finish the installation.
The general assembly order is summarized below:
1. Set deck modules into position on setting blocks and bolt deck modules together.
2. Install outriggers and deck channel coping.
3. Place deck into final position even with top of pit.
4. Assemble mounts with load cells to the deck unit; remove setting blocks.
5. Install mount anchor bolts and grout beneath mount plates.
6. Install corrugated sheet metal, rebar and pour concrete.
7. Run cabling through conduit; make electrical connections.
8. Connect indicator and peripheral devices.
9. Calibrate scale.
1.1
Foundation Slab Cure Period
Standard concrete reaches full strength after a 28-day cure. Note that the concrete foundation must cure in a moist state for at least seven days (three days for high-early concrete). At seven days, standard concrete is approximately 75% of its maximum strength and can handle moderate loads. Loading of a slab before it reaches
75% of maximum strength may damage the foundation.
1.2
Assembly Time Estimates
When scheduling installation for a typical three-section, 70' truck scale, plan for a two-hour minimum crane rental to position the sections.
A two-man crew, aided by a crane operator, can unload modules from the truck, place them into position and bolt them together in one to two hours. Mount and load cell installation requires approximately two hours. All electrical wiring and final connections can normally be completed the same day.
Note: These estimated times may vary.
Installation 1
1.3
Recommended Tools and Equipment
The following is a list of recommended tools and equipment necessary to assemble and install the SURVIVOR
®
PT Pit-Type truck scale:
• One heavy duty crane, equipped with chains or cables, for module placement;
• Rotary hammer drill (3/4");
• Drill with 5/16" socket for installing sheet metal screws through corrugated sheeting;
• Carbide masonry bit (3/4" x 30");
• Two low-profile, four-ton hydraulic jacks;
• Setting blocks (12-1/4") and shims to total
13-3/4" height;
• Torque wrench (800 ft-lb);
• Socket wrenches to 1-5/8" (drive compatible with torque wrench);
• Box end wrenches to 1-1/2";
• Open end wrench set (7/16"-3/4");
• Four-foot bubble or construction level
(transit);
• Small torpedo level;
• Spacers for deck-to-pit wall alignment;
• Hammers, maul, pry bar;
• Hand tools for pulling and connecting electrical wiring and sheet metal cutting and trimming.
1.4
Lifting and Handling
The top module can be lifted using four chains attached to the four lift lugs provided with the scale. Once the first module is removed from the truck and is placed on the setting blocks, the four lift lugs can be removed and used for lifting and positioning the other modules.
NOTE: Rice Lake Weighing S ystems will credit the customer for the return of the four lift lugs.
Please call for an RMA number.
1.5
Temporary Setting Blocks
Most installers use 12-1/4" temporary setting blocks for initial module positioning and to aid in installing deck module bolts. When an end module is placed into position on the setting blocks, the top of the module will be
6-1/3" below the top of the pit. The outriggers and deck coping are assembled before the load cells mounts are installed and will bring the top of the scale to approximately 1/3" below the top of the pit. Shims are added during final leveling to raise the deck surface the last 1/3".
23.92"
6.33"
NOTES:
Figure 1-1. Setting Block Diagram.
• Please refer to the construction prints included with the SURVIVOR
® PT
Pit-Type truck scale to confirm all foundation and scale dimensions.
• Do not place the setting blocks in the location on the piers where the load cell mounts are to be placed.
42.5"
2 Survivor
®
PT Pit-Type Truck Scale Assembly Instructions
2.0 Assemble Deck Modules
The modules are designated either as an end module or a center module. All two-module scales will have two end modules, while longer scales will have two end modules and one or more center module (see diagram below).
adjustments in module alignment, but it is easier to leave the second module attached to the crane for making small alignment changes.
5. Install the three top bolts, washers and nuts on the inside of the beam. Install the bolts, washers and nuts on the opposite beam using six bolts, washers and nuts. Tighten only finger tight.
NOTE: Do not install the bottom bolt at this time.
END CENTER END
Figure 2-1. Center and end modules.
In a three module scale, the end module is the first to be positioned on setting blocks followed by the center module. The last module to be assembled is an end module. Scales with more than threee modules will have additional center modules installed. As an example, a 100' scale would have two end modules and three center modules.
2.1 Place End Module A
Place one 12-1/4" temporary setting block on the top of each pier and position them so that they will not interfere with the installation of the load cell mounts.
The scale module should be 3/4" away from the bulkhead ramp and 3/4" from each pit wall side (see figure on right). By using the 12-1/4" blocks, the top of the main beam will be approximately 6-1/3" below the top of the pit.
2.2 Place and Attach Center Module
NOTE: To assist in easy assembly of the center module, make sure that both modules have direct end-to-end surface contact.
1. Place four 12-1/4" setting blocks on top of the piers in the center sections.
2. Position and place the center module on the setting blocks, making sure that both the end module and center module end plates are aligned.
3. Check that the module is centered side-to-side in the pit.
NOTE: At the installer’s discretion, install the center section with the J-box on the near side to the scale house.
4. When both modules are aligned, insert the top three 1-1/8" bolts with flat washers, lock washers and nuts on the outside of the beam.
(Leave out the bottom bolt to facilitate load cell mount installation).
NOTES:
• Tighten bolts and nuts finger tight until all modules are in place.
• A long pry bar can be used to make small
Figure 2-2. Top bolts, washers, and nuts installed.
6. If required, place and install any additional center modules in a similar manner.
7. Install the remaining end module on four setting blocks ensuring the end beams are aligned with and in direct surface contact with the center module.
Figure 2-3. Module installation.
8. Center the module side-to-side and check that the end of the main beam is 3/4" from the end of the concrete pit wall. Install and tighten the three top bolts on each beam (inside and outside) finger tight as in the previous operation.
NOTE: Do not install the bottom bolt at this time.
Assemble Deck Modules 3
9. To reduce the on-site crane operating time, the manhole frame (shown in photograph on right) can be installed at this time. It is recommended to locate the frame in a central location close to the J box as shown in the diagram below.
Manhole Frame
(24" square)
Figure 2-4. Manhole frame.
NOTES: Before installing the manhole frame, remove a section of the corrugation support bar in the location where the manhole frame is to be installed. Additional manholes are available as options. Consult with local weights and measures officials for any state restrictions or access in the state being installed.
O S HA may have restrictions on pit access. Consult with customer’s safety engineers for details.
To Scale House Corrugation Support Bar
(remove material as needed to install manhole frame)
Junction Box
Suggested Location of Manhole
Top View
Figure 2-5. Optimal manhole frame location.
2 . 3 I n s t a l l O u t r i g g e r s a n d D e c k
Coping
1. Install the outriggers on each module section
(as shown on below) using the 3/4" x 2-1/2" bolts, washers and nuts at the locations shown on the drawing. Torque all bolts to 260 ft-lb.
NOTE: To compensate for irregularities in pit dimensions, 1/2" shims are provided with the truck scale kit assembly. These shims are to be inserted (if required) between the coping attach points and the module frame assembly.
5. Repeat procedure for the opposite side.
Recheck module assembly to see if it is centered side-to-side in the pit.
1/2" Shims Installed
Here if Required
Outrigger
Figure 2-6. Outrigger location
2. Position an L-shaped deck coping on top of the outriggers and secure it to the module frame using the 1/2" x 2" bolts, nuts and washers.
3. Assemble the center section deck coping to the end channels using four 2-1/2" bolts, washers and nuts.
4. Attach the third module deck coping to the center section and to the end of the module assembly.
Figure 2-7. Optional shim placement
As an optional recommended procedure, and to make the module deck coping more rigid, each deck coping may be tack welded to the outrigger at each contact location. It should be noted that during the concrete pour the deck coping may bow outward towards the pit walls. To maintain a 3/4" gap between the deck coping and the side of the pit, it is recommended that temporary spacers (3/4" bolts or shim stock) be used
4 Survivor
®
PT Pit-Type Truck Scale Assembly Instructions
between the deck coping and the pit wall. Remove spacers after the concrete has set and before the scale is put into service.
NOTE: Install the 3/4" bolts or shim stock and space at equal intervals between the deck coping and the pit wall coping before welding as shown in the drawing on the right.
2.4 Level Module Assembly
Using a suitable jack and shims, raise each module section so that the top of the deck coping is level with the top of the pit. After raising module assembly, re-check module alignment to make sure that the top is level and centered side-to-side in the pit.
Assemble Deck Modules 5
3.0 Load Cell Mount Installation
Load cell mounts, complete with load cells and conduit adapters, have been assembled at the factory to save on-site installation time. Load cell mount installation consists of sliding the complete unit into place beneath the deck, raising the mount with the leveling screws to the deck, and connecting the grounding strap.
When installing load cell mounts, start at one corner of the module assembly and install the remaining load cell mounts on that side. Likewise, when the load cell mounts are installed on the other side, start with the corner of the module assembly.
The lower mounts assemblies come complete with load cells installed, so complete any necessary welding on the scale before installing mounts.
NOTE: Remove load cell mount from packing box and file printed load cell Certification of Conformance (CC) in a safe place for future reference.
3.1 Attach Upper Mount Chair
1. Attach the upper chair to the bottom of the module assembly by using four 3/4" bolts with washers making sure that the 1/4" hole for ground strap installation is toward the center of the scale module. retightening load cell bolts, torque to 70 to 80 ft-lb. The 90 degree fitting on the flexible conduit attached to a load cell can rotate 180 d e g r e e s t o a l l o w f o r c o r r e c t c o n d u i t placement.
4. Set the mount assembly on the concrete pier directly in front of its final position. Carefully slide the mount into position under the upper chair.
3.3 Raise Mount into Final Position
1. Turn the leveling screws to raise the mount until the link is centered in the chair bearing and lightly touching.
2. Level the plate in both directions.
3. When the baseplate is directly under the chair, the link will be hanging vertical when centered in the chair (see figure on left).
Approximately 1/4" of the link should protrude (see figure below) beyond each side of the chair.
Figure 3-1. Upper chair bolts installed.
2. Torque upper chair bolts to 260 ft-lb.
3.2 Prepare Baseplate and Mount
Installation
1. Turn the four levelling screws through the baseplate so approximately 1/2" extends beyond the bottom surface.
2. Each load cell mount comes equipped with a
90-degree threaded LB conduit adapter.
Orient the adapter so that the cable will point toward the inside of the scale when mounted.
NOTE: Each mount must be oriented so the cable exit from the load cell is facing the interior of the module to which it will be attached. The correct orientation will place the flexible conduit section on the load cell near the rigid conduit attached to the weighbridge.
3. If a load cell must be reversed to achieve correct orientation, remove a load cell and reverse its direction in the field. When
Figure 3-2. Final mount position.
LINK
4. If adjustment is necessary, tap baseplate edges lightly with a hammer to slide the entire mount sideways
.
UPPER CHAIR
LOAD CELL
1/4" PROTRUSION
LEVELING SCREW
BASEPLATE
1/2"
Figure 3-3. Load Cell Mount Parts.
6 Survivor
®
PT Pit-Type Truck Scale Assembly Instructions
3.4 Attach Flexible Conduit Sections
A 30" section of flexible conduit (shown in the photo below) is included on each load cell.One end is threaded for mating with the LB connector at the load cell. The other end adapts to 3/4" galvanized rigid conduit.
1. Use an industrial hammer drill with a 3/4" carbide masonry bit at least 36" long to drill anchor bolt holes. This long bit allows the drill body to clear the siderail so the hole can be drilled nearly vertical. Hold the bit as close to vertical as possible and drill a 3/4" hole at least 6" into the concrete pier beneath each anchor bolt slot on both sides of the baseplate.
2. Place a washer and nut on each anchor bolt.
Use a 24" long driver pipe with an inside diameter slightly larger than the 3/4" bolt
(shown in the illustration below) to drive anchors into the drilled holes until the washer is solid against the baseplate.
NOTE: Do not apply excessive force to the anchor bolt.
Bending of the baseplate could occur.
Figure 3-4. Flexible conduit.
NOTE: Flexible conduit may also be plastic-coated metal (flex conduit).
3.4.1 Attach Grounding Strap
1. Remove the 1/4-20 hex bolt with washer in the upper chair. Use this bolt to attach the braided grounding strap to the upper chair as shown below.
Grounding Strap
Attachment
Point
NOTE: Do not drive anchor bolt without driver pipe.
Figure 3-6. Drive anchors into drilled holes.
Grouting
1. Erect temporary dams around each baseplate and inject 9000 psi non-shrinking, epoxy/ cement grout.
2. Take care not to leave air voids; the baseplate must have even support from continuous grout contact.
NOTE: After the grout has hardened, tighten anchor bolt nuts until the heads expand and the bolts are solidly anchored.
Figure 3-5. Grounding Strap Location.
2. Attach lower end of grounding strap to either one of the two holes in the baseplate.
3.4.2 Install Lower Module Assembly Bolts
Upon completing the load cell mount installation, the lower module assembly bolts can be installed at each location. Torque all module assembly bolts to 800 ft-lb.
3.5 Install Anchor Bolts and Grout
Anchor Bolts
Each mount requires two anchor bolts to prevent lateral motion. Two 7" x 3/4" anchor bolts with expansion heads are supplied with the scale for each load cell. The anchor bolts are installed in holes in each module pier.
Figure 3-7. Grout example.
Load Cell Mount Installation 7
3.6 Install Support Bars, Corrugated
Metal, and Deck Rebar
3.6.1 Corrugated Metal Sheeting
To s up p o r t t h e c o n c r e t e d e c k p o u r, 2 6 - g a u g e galvanized corrugated metal sheeting (15/16" by 3-3/
4" wide corrugations) is installed on the main frame assembly. The panels are installed perpendicular to the cross beams and rest on the cantilever support channels, the main beams, and the frame cross beams.
1. Install the sheet metal starting below the
Nelson studs along one side of the frame.
2. Form the sheet metal to the contour of the frame assembly and overlap adjoining panels a minimum of 15" or four full corrugations.
CHANNEL
CANTILEVER SUPPORT
NELSON STUD
CORRUGATED METAL
CROSS BEAM
MINIMUM OVERLAP
NOTES:
• S ecure the corrugated metal sheet to the manhole frame by installing 12 sheet metal screws (or tack weld) around base of manhole frame.
• When pouring concrete, make sure that concrete is poured over the overlap not into the overlap.
3.7 Deck Rebar
Concrete deck reinforcing consists of installing #5 rebar on 12" centers at the locations shown on the drawing along with using standard construction practices.
NOTE: At the installer’s discretion, rebar may or may not be tied together.
The first (bottom) layer of rebar installation consist of positioning 6'-3" rebars perpendicular to the main beams and on 1-1/2" chairs (bolsters) located on top of the corrugated sheet metal. On top of this rebar layer, a second layer (70' rebar) is installed perpendicular to the first layer and parallel to the main beam.
The third layer will be the 2' rebar placed on chairs.
On top of these will be another layer of 70' rebar running the length of the frame assembly.
The final two layers will require installing 9'-4' rebar on the appropriate chairs. On this will be the top layer of 70' rebar.
MAIN BEAM
(DRAWING NOT TO SCALE)
Figure 3-8. Installation of Support Bars, Corrugated
Metal, and Deck Rebar.
Panels must fit closely to the vertical webs of all support beams to prevent concrete runout during the deck pour.
3. Trim sheet metal as needed for clearance around any vertical gussets in the support beams and around the manhole on the cross beams. The photograph below shows the metal sheeting used on a EZ-SR truck scale installation.
Figure 3-9. Metal sheeting example.
8 Survivor
®
PT Pit-Type Truck Scale Assembly Instructions
4.0 Pour and Finish Concrete Deck
With a concrete crew of three experienced workers, a 70' by 10' scale can be poured and finished in approximately three hours. Access to only one side of the scale is necessary as most concrete trucks carry extension chutes at least
16' long. If possible, order concrete in front-unloading trucks. The truck will be moving slowly while filling; the improved driver-visibility with front-unloading makes that process faster and more accurate.
To protect against unsightly concrete splatters on the top of the support channels, mask off the top of the channel with tape or use 4 to 6 mil plastic to cover the top surface.
Position the unloading chute at the near left side of the scale and begin filling having the truck move slowly to the right.
To ensure concrete flowing evenly into the frame and encasing all Nelson studs and rebar, a concrete vibrator is highly recommended. These units are available for rent at most construction equipment rental sources. They work very quickly to level concrete, settle out surface stones, and leave a stone-free layer at the top surface to make finishing easier.
After vibrating to approximate level, screed the concrete to the level of the top of the support channels with a 2x4 board cut to length
With the deck level and floated, finish with either a magnesium float or steel trowel for a neat deck line level with the top of the support beams and top of the pit.
When the entire frame has been floated with a magnesium float and has set enough for finishing, use a radius edger to finish the metal/concrete joint.
For a non-skid surface, use a stiff bristle broom for a brushed finish when the concrete has set enough for final finishing. It is recommended that a non-skid surface be applied for all northern tier states.
Pour and Finish Concrete Deck 9
Curing the Completed Concrete Deck
The concrete deck must be maintained in a moist state for at least seven days for a satisfactory cure. If the top surface of the deck is allowed to dry during this time, the finished surface will be prone to unsightly spalling and be weakened from surface cracking.
A moist surface can be maintained by covering the entire deck with a continuous 4 to 6 mil sheet of polyethylene plastic turned up and dammed at the ends and kept filled with 1" of water. Alternately, an epoxy-based concrete curing solution can be sprayed or rolled onto the deck surface immediately after final finishing and while the concrete surface is still moist. As the epoxy curing solution will also seal in concrete stains on the exposed support beams, clean off stains with a damp sponge before applying the curing solution to the deck. Epoxy-based concrete curing products are available at contractor-supply companies. Do not use the petroleum-based or paraffin-based waterproofing agents specifically advertised for wood decks and concrete patios. These products are not curing agents, and will allow the deck surface to rapidly dry.
4.1 Optional Equipment
The following is a brief summary of the optional Survivor SR-PT equipment available from RLWS.
Eighteen Inch Main Beam Module
An 18" main beam module is available from RLWS as an option. Use of this option will require increasing the pit pillar height approximately 6". Refer to the appropriate drawing for exact pit dimensions. This option should only be used in states where there is a requirement for a minimum of 48" clearance below the main I-beam flange. (Steel weight is increased approximately 1/3 when selecting this option.)
10 Survivor
®
PT Pit-Type Truck Scale Assembly Instructions
5.0 Install Cabling in Conduit
5.1 Load Cells to Junction Box
To Scale House
Load Cells (8 locations)
Junction Box
Conduit Runs (typical)
Bottom View
Figure 5-1. Load Cell Cable to Junction Box.
Each load cell is equipped with 60' of load cell cable, sufficient to reach a centrally-located junction box on standard scales. A watertight conduit adapter and a 30" section of 3/4" flexible conduit is supplied for both ends of each load cell cable located at the load cell and at the junction box. Main conduit runs between these 30" flexible end sections are 3/4" galvanized metal conduit already installed on the deck as shown above.
NOTE: If using a single center module, some of the conduit runs are not used. These conduit runs are used when more than one center module is installed.
5.2 Junction Box to Indicator 5.4 Single-Point Ground Conductor
A 60' section of 6-wire homerun cable is supplied. It is to be run in 3/4" galvanized metal conduit from the junction box to the indicator. A 30" flexible conduit section and watertight conduit connector is provided where this cable exits the junction box. Galvanized metal conduit must be obtained locally.
NOTE: S cales over 70 feet in length have two or three J boxes. Refer to blueprint package provided with scale for details.
A bare 10-gauge solid wire is run from the scale frame to the grounding lug on the junction box, then underground to the main AC power earth ground. If the optional DC transient protection board is installed, the ground conductor should also be connected to the transient protection board’s ground lug. Consult with y o u r p o w e r u t i l i t y f o r l o c a l r e s t r i c t i o n s o r requirements for utility ground rod connections.
5.3 Indicator to Peripherals
All 3/4" metal conduit for cabling from the indicator to remote displays and other peripheral devices must be obtained locally. Conduit runs may be buried in a trench or secured above ground. Use separate conduit runs for AC power and DC data lines to avoid interference. As a general guideline, run AC and DC cables in separate trenches if possible. When DC data cables must run in the same trench as AC power lines, separate cables as much as possible.
5.5 Junction Box Connections
Each JB8SPT junction box is large enough to hold the summing board, transient protection devices, desiccant package, and extra load cell cable coiled inside the enclosure.
In a single-platform scale, the single junction box location is determined by the length of the load cell cables and the four mounting studs on the outside main beams. Both A and B modules are equipped with m o u n t i n g s t u d s . I n a m u l t i - a x l e s c a l e w i t h independent sections, each section requires its own junction box to sum the load cell signals from that section.
Install Cabling in Conduit 11
A summing card mounted within the junction box is used to make all cable terminal connections. All terminal pin functions are clearly marked.
A 10-gauge bare ground wire is run from one of the junction box mounting studs to the ground lug of the junction box as shown in the figure below. The ground lug on the bottom of the junction box is connected to a buried ground cable from the AC power ground terminal or ground rod, thus grounding the scale frame to the same single-point ground point as the AC power for the indicator.
Ground Lug
Located in
J-box Pocket
10 ga. bare ground wire to DC protection ground before indicator
Figure 5-2. J-Box Grounding.
Before final closure, add an industrial corrosion inhibitor and desiccant (RLWS Industrial Corrosion Inhibitor,
PN 16037) to the junction box enclosure. This desiccant protects an enclosure up to 5 ft
3
from internal corrosion for approximately 1 year.
NOTE: Make sure that the 10 gauge ground wire makes connection to bare metal.
5.6 Electrical Ground Connections
Improper grounding systems on outdoor truck scales often cause corrupted data as a result from ground-loop current flows. Improper grounding systems may also invite possible lightning strikes and cause damage to costly electronic systems. Always attempt to establish a single-point grounding system.
When establishing a ground system for the scale installation, do not install more than one ground rod for each scale location. Separate earth grounds do not share the same zero reference as the existing earth ground for the AC power system. The difference in electrical potential invites ground-loop current flow between the separate grounds, often corrupting serial data, such as RS-232, which depends on a stable zero reference.
In addition, a separate earth ground system at the scale can actually invite lightning or power surge damage:
• A minor powerline surge in the scale house electrical supply should immediately be shunted to ground. If a separate ground system exists at the scale with a lower potential than the main ground, the surge may travel to the scale ground rod, damaging load cells on its way.
• A lightning ground strike may instantly raise the zero potential of a ground rod at the scale location while leaving the scale house ground rod unaffected. A lightning surge takes the easiest path to the lower-potential ground: through the scale wiring and back to the scale house ground, therefore possibly damaging the indicator on its way.
12 Survivor
®
PT Pit-Type Truck Scale Assembly Instructions
The best grounding system for the scale is the same grounding system used for the incoming AC power system.
The 120 VAC power source used to power the indicator is connected to an existing earth ground rod system at the scale house or other building where the indicator is located. This consist of a double ground rod system of two 5/
8" x 8' copper rods driven 8' deep at the service entrance where the local utility company brings their lines into the building. The local utility company can test the resistance of the existing ground rods with a clamp-on megohmeter to measure resistance. A reading of 3¾ or less is acceptable as a ground. If the test determines that the grounding system is inadequate, the utility company can suggest methods to improve the system. It is crucial that the scale owner authorize and make the recommended improvements to assure an adequate electrical ground. Do not connect the scale to the AC power supply until the grounding system is adequate.
Each load cell grounding strap is securely fastened to the top and bottom plates of each load cell mount. The grounding strap is designed to channel power surges on the deck around—rather than through—the load cell to ground. All ground connections must be properly torqued and rechecked at regular service intervals. After connecting to bare metal apply a thick coating of anti-oxidant grease on all ground connections to prevent corrosion.
A separate grounding system conductor must extend uninterrupted from the main service panel ground to the scale to protect load cells and scale wiring from lightning and other transient damage. As a minimum requirement for ground wire installation, the conductor must be at least a 10-gauge unsheathed copper wire. Run the bare ground wire conductor intact from the AC power ground rod to the scale in a separate trench.
Bring the wire up from the trench near the junction box and attach it to the ground lug of the junction box. Use a short piece of 10-gauge wire to ground the scale frame by running a ground wire from the junction box ground lug to a junction box mounting bolt on the scale frame.
5.7 Install Transient Protection
An two-year lightning protection package comes standard on all SURVIVOR
®
PT Pit-Type truck scales. This package is designed to protect the AC and DC portions of the system. The package includes:
• A DC transient protection board mounted within the junction box. This DC transient protector can accommodate up to eight load cells and will help protect serial communication lines. Scales with more than eight load cells require a DC transient protection board in each junction box.
• A self-contained DC transient protection unit in the homerun cable at the indicator.
• A 10-gauge bare ground conductor cable. This conductor cable, to be buried underground, runs from the scale frame to the junction box DC transient board, to the indicator DC transient board, and finally to the
AC power ground lug.
• A 120 VAC uninterruptable power supply/surge protector in the AC line before the indicator.
NOTE: Transient protection for additional peripheral devices (except some boards) is not included in the standard transient protection package. Call the Rice Lake Weighing S ystems S ales Department at (715) 234-9171 for additional transient protection for these devices.
Install Cabling in Conduit 13
+SI
-SI
+EX
-EX
SHD
+SI
-SI
+EX
-EX
SHD
J3
J4
J7
TRIM
TRIM
TRIM
R17
R18
R19
R21
R22
R23
R14
R26
R40
JP7
+SI
-SI
JP8
+EX
-EX
SHD
R20
JP10
JP9
+SI
-SI
+EX
-EX
SHD
J5
J2
+SI
J1 TRIM
TRIM
TRIM
R4
R5
R6
R8
R9
R10
R1
R13
R27
JP2
JP5
JP3
JP4
R7
L2
L1
L4
L3
Assembly
PN Rev.
ARC
EXPANSION/J9
SHD
+SI
-SI
+SEN
+EX
-SEN
-EX
INDICATOR/J10
SHD
+SI
+SI
-SI
+EX
-EX
SHD
+SI
-SI
+EX
-EX
SHD
J8
R43
R44
R45
R47
R48
R49
JP
JP
TRIM R52
CONNECT BOTH SHUNTS
TO APPLY SIGNAL
JP17
JP20
JP18
JP19
-SI
+EX
-EX R31
R32
R30
JP12
JP13
SHD
+SI
R46
-SI
R34
R35
R36 +EX
-EX
SHD
JP15
J6 JP
JP
TRIM R39
DISCONNECT BOTH SHUNTS
TO REMOVE SIGNAL
JP14
R33
ARGND
CUT TRACE TO ISOLATE SENSE LINE
Transient Board Connectors JMP/POS JMP/NEG
-SI
+SEN
+EX
-SEN
-EX
2005
Grounding Lug
JB8SPT
Junction Box
With Transient Protection
RLWS PN 91783
TP-232
DC Transient Protection
RLWS PN 33185
UJB-3T6
DC Transient Protection
RLWS PN 21134
SOLA S2K
AC Transient Protection
RLWS PN 80928
AC Outlet
TP-232
DC Transient Protection
RLWS PN 33185
AC Outlet
SOLA S2K
AC Transient Protection
RLWS PN 80928
AC Power
Supply
#10 Copper
Ground Wire
Serial
Communication
Homerun
Cable
Load Cell
Cable
Power Company Ground Rod
*Always verify that installed wiring is properly grounded
Figure 5-3. Single-Point Grounding Diagram.
14 Survivor
®
PT Pit-Type Truck Scale Assembly Instructions
6.0 Trimming and Calibration
6.1 Overview and Equipment Required
Load Cell Trimming
Individual load cell signal trimming (equalizing the signal output from each load cell) must be done first along each side of the scale so all cells on a side have equal signal output. Adjustments are somewhat interactive, so each side should be done at least twice.
Once that is done, load cell pairs —one from each side—are trimmed as paired sections until each sectional output is equal. Adjustments to each section should also be done at least twice.
1st – Trim Side 1 Cells (1, 2, 3, 4)
1 2 3 4
3rd – Trim Sections
(1, 8; 2, 7; 3, 6; 4, 5)
Weight
Cart
5 8 7 6
2nd – Trim Side 2 Cells (5, 6, 7, 8)
Figure 6-1. Load Cell Trimming Diagram.
Equipment Required
Both of these trimming operations can be done using only a weight cart parked in various locations on the scale. Final verification of equal output trimming, however, will require test weights to be placed on the deck in various locations.
6.2 Trimming Individual Cells
1. Connect all load cells to the summing board terminals in the junction box.
2. Connect the main interface cable from the junction box to the indicator.
3. Power up the indicator.
4. Turn all load cell potentiometers (individual and section) in the junction box clockwise until a clicking noise is heard when you continue turning. This eliminates any initial resistance so all signals are at full strength.
You’re now ready to do individual signal trimming .
Side 1
The first objective is to adjust individual load cells along one side of the scale for equal signal output w h e n e q u a l w e i g h t i s p u t o n t h o s e c e l l s . F o r convenience, that side of the scale will be referred to as Side 1. The trimming weight you will use will be the loaded weight cart.
1. Park the cart as close as possible to Side 1 being trimmed with the wheels centered over the end load cell mount (No. 1 in drawing to b e l o w ) . R e c o r d t h e i n d i c a t o r r e a d i n g .
Remember that the scale is still uncalibrated, so the indicator readings are simply raw counts rather than weight units.
1 2 3 4
8 7 6 5
Figure 6-2. Trimming Load Cell Number One .
2. Move the cart directly over mount No. 2 and record that reading. Move the cart directly over mount No. 3 and record that reading.
Trimming and Calibration 15
Move the cart so the wheels are centered directly over mount No. 4 (you may have to turn the weight cart around so all wheels remain on the scale) and record the reading.
1
2 3 4
1 2 3 4
8 7 6 5
Figure 6-3. Trimming Load Cell Numbers 2, 3, and 4.
3. The lowest reading of the four will be your reference cell. You won’t change that cell’s signal. Instead you’ll use the individual cell potentiometers for the other three cells to reduce those signals to match your reference cell. Remember that you turned all pots to full signal (0 resistance) before starting. So you can’t increase the signal from any cell—you can only decrease signal by trimming with the pots.
4. Note that the best trim is always the least trim.
If one of the four readings differs from the others by more than 5% of the displayed counts, there is probably a mechanical problem with that load cell mount causing the large difference. Find it and correct it before going on. Check for binding, an out-of-level or misaligned link, or similar problems with the load cell and mount. Do not try to trim down large signal differences with resistance pots—you’ll only add larger problems for yourself later because of interaction between mounts.
5. Park the loaded weight cart over one of the high-reading cells on Side 1. Turn that cell’s individual potentiometer until the displayed reading equals your recorded reference cell reading. Repeat for the other two high-reading cells on side 1.
6. As adjustments are somewhat interactive, repeat the process in Steps 1 through 5 until all four cells on Side 1 read within 1% of each other.
7.
Side 2.
Move to the Side 2 of the scale. Load each cell in turn with the weight cart and record readings on those four cells in the same way.
The cell which reads the closest to the Side 1 reference cell will be used as your reference cell for trimming the other cells on side 2.
8 6 6 5
Figure 6-4. Trimming Load Cell Number Five.
NOTE: The reference cell on S ide 2 should be the same as the
S ide 1 readings. Move the weight cart over the cell chosen for the S ide 2 reference cell. Adjust the cell’s individual pot to equal the final S ide 1 readings. In the example at left, Cell 8 has been chosen as the S ide 2 reference cell.
8. Reload the other Side 2 cells (5, 6, 7 in the example) in turn with the weight cart and adjust their individual pots so their readings are equal to the Side 2 reference cell (8 in the example).
1
8
2
7
3
6
4
5
Figure 6-5. Trimming Load Cell Number Eight.
9. Repeat Steps 7 through 9 if needed to get all
Side 2 cells reading within 1% of each other and within 1% of the Side 1 reference cell.
6.3 Trimming Paired Sections
Now that you’ve trimmed all individual load cells for equal output, pairs of load cells on opposite sides of the scale must be trimmed for equal sectional output.
This process is called section signal trimming .
1. Park the loaded weight cart in the middle of the scale and directly over an imaginary line connecting an end pair of cells (1 and 8 in the example at right). Record the indicator reading.
1
8
2
7
3
6
4
5
Figure 6-6. Trimming Paired Section 1:8.
16 Survivor
®
PT Pit-Type Truck Scale Assembly Instructions
2. Move the weight cart directly over the next paired cell section (2, 7 in Figure ) and record the indicator reading.
1 2 3 4
6.4 Calibration with Test Weights
The calibration procedure can only be done after all trimming as described above has been completed. A qualified scale technician with a test weight truck and the expertise to access the scale indicator’s Setup or
Calibration mode must perform the calibration procedure.
8 7 6 5
1 2 3 4
Figure 6-7. Trimming Paired Sections 2:7, 3:6, and 4:5 .
Do the same for the last two paired sections
(cells 3, 6 and 4, 5)
.
3. Choose the lowest reading of the four as your reference section, which will not be adjusted.
Using the section potentiometers, reload the other three sections in turn and trim the sections to match the reading of the reference section. Recheck section readings a second time as the adjustment made may be somewhat interactive.
4. As a final verification of the load cell trimming, do a final corner check. Place a
1000 lb. weight on one corner of the platform and record the raw-count reading on the indicator. Move the weight to all the other corners in turn and record those readings. The readings should be within 1% of each other.
8 7 6 5
Figure 6-8. Calibration with Test Weights.
Equipment Required
Truck scales are routinely calibrated using 25% of the capacity weight of the scale. Certified Class F test weights equaling at least 12.5% of the scale’s capacity will be required for calibrating a commercial legal-for-trade truck scale. In addition, some type of weight for a substitution test of an additional 12.5% of the capacity will be required. This can be the test-weight truck, bags of sand, or any convenient items easy to load onto t he scal e. This total calibration weight of 25% of scale capacity (12.5% test weights, 12.5% substitution weight) is required by weights and measures officials for commercial truck scales in most states. Check with your local weights and measures officials for the requirements in your jurisdiction.
I n d u s t r i a l s c a l e s n o t u s e d f o r l e g a l - f o r- t r a d e transactions do not require certified test weights.
We i g h t e q u a l t o 2 5 % o f s c a l e c a p a c i t y i s recommended for calibrating such scales.
S e e H a n d b o o k 4 4 f o r d e t a i l e d c a l i b r a t i o n requirements and procedures.
Trimming and Calibration 17
7.0 Load Cell Replacement
Load cell replacement procedures are included in the following paragraphs.
7.1 Overview 7.2 Replacement Procedure
Load cells are replaced on the Survivor PT Pit-Type truck scale by jacking up the scale deck approximately
1/4" at the location of the load cell mount and removing the upper mount chair, load cell and link as a unit.
After loosening the load cell bolts so they clear the threads in the baseplate columns, the four bolts holding the upper chair to the deck are removed, allowing the chair, load cell and link to be slid out as an assembly. Replace the load cell and reassemble in the reverse order.
If a low-profile hydraulic jack under 7-1/2" in height is not available, a bracket can be ordered from RLWS
(PN 49523) to provide clearance for higher jacks.
Upper
Mount
Chair
Upper Chair Bolts
Link
Figure 7-1. Load cell mount.
Load Cell
Bolts
Load Cell
Baseplate
1. Remove the upper bolt and washer holding the ground strap to the upper chair.
2. Disconnect the flexible conduit section from the rigid metal conduit.
3. Disconnect the load cell terminal connections in the junction box. Attach a pull cord to the end of the load cell cable and pull the cable out of the rigid conduit to free the load cell cable from the scale deck. Tie off pull cable so that it will not pull itself back into the conduit.
4. Loosen the two load cell bolts until they disengage from the column threads.
5. Remove the four bolts that hold the upper mount chair to the deck frame.
6. Jack up the scale deck approximately 1/4" at the load cell location. Install blocking for safety.
7. Hold the loosened load cell bolts up to clear the threaded holes in the column and slide the upper chair, load cell and link straight out as an assembly.
8. Set the chair aside until reassembly.
9. Lift the load cell bolts out of the damaged load cell and remove the cell from its link.
10. Remove flexible conduit section from the 90° elbow conduit connector.
11. Remove two small screws on the side of the
90° elbow connector and remove the access plate.
12. ull the cable out the access hole. Remove the
90° elbow connector from the load cell.
13. Install the 90° elbow connector and flexible conduit section on the new load cell.
14. Complete reassembly by following Steps 1 through 9 in reverse order.
15. Use the pull cord to get the new load cell c a b l e b a c k i n t o t h e s u m m i n g b o x f o r connection.
18 Survivor
®
PT Pit-Type Truck Scale Assembly Instructions
8.0 Vehicle Scale Limited Warranty
Rice Lake Weighing Systems (RLWS) warrants that all RLWS brand equipment and systems properly installed by a Distributor will operate in accordance with written specifications as confirmed by the Distributor and accepted by RLWS. All systems and components are warranted against defects in materials and workmanship for
2 years from date of shipment from the manufacturer. Furthermore, the seller warrants the fabricated weighbridge against faulty workmanship and defective materials for 5 years from the date of shipment from the manufacturer.
RLWS warrants that the equipment sold hereunder will conform to the current written specifications authorized by RLWS. RLWS warrants the equipment against faulty workmanship and defective materials. If any equipment fails to conform to these warranties, RLWS will, at its option, repair or replace such goods returned within the warranty period subject to the following:
• Upon discovery by Buyer of such non-conformity, RLWS will be given prompt written notice with a detailed explanation of the alleged deficiencies.
• Individual electronic components returned to RLWS for warranty purposes must be packaged to prevent electrostatic discharge (ESD) damage in shipment. Packaging requirements are listed in a publication,
“Protecting Your Components From Static Damage in Shipment,” available from RLWS Equipment
Return Department.
• Examination of such equipment by RLWS confirms that the non-conformity actually exists, and was not caused by accident, misuse, neglect, alteration, improper installation, improper repair, or improper testing. RLWS shall be the sole judge of all alleged non-conformities.
• Such equipment has not been modified, altered or changed by any person other than RLWS or its duly authorized repair agents.
• RLWS will have a reasonable time to repair or replace the defective equipment. Buyer is responsible for shipping charges both ways.
• Vehicle scale products are eligible for warranty labor and mileage charges with pre-approval by RLWS
Service Department, and only to the limits described in the vehicle scale reimbursement program.
• RLWS will not be liable for the cost of any repairs made by others.
T HESE WARRANTIES EXCLUDE ALL OTHER WARRANTIES , EXPRESSED OR IMPLIED , INCLUDING WITHOUT
LIMITATION WARRANTIES OF MERCHANTABILITY OR FITNESS FOR A PARTICULAR PURPOSE . N EITHER
RLWS NOR DISTRIBUTOR WILL BE LIABLE FOR INCIDENTAL OR CONSEQUENTIAL DAMAGES .
RLWS AND BUYER AGREE THAT RLWS’ SOLE AND EXCLUSIVE LIABILITY HEREUNDER IS LIMITED TO
REPAIR OR REPLACEMENT OF SUCH GOODS . I N ACCEPTING THIS WARRANTY , THE BUYER WAIVES ALL OTHER
CLAIMS TO WARRANTY .
S HOULD THE SELLER BE OTHER THAN RLWS, THE BUYER AGREES TO LOOK ONLY TO THE SELLER FOR
WARRANTY CLAIMS .
No terms, conditions, understanding, or agreements purporting to modify the terms of this warranty shall have any legal effect unless made in writing and signed by a corporate officer of RLWS and the Buyer.
2001 Rice Lake Weighing Systems, Inc. Rice Lake, WI USA. All Rights Reserved.
RICE LAKE WEIGHING SYSTEMS • 230 WEST COLEMAN STREET • RICE LAKE, WISCONSIN 54868 • USA
Vehicle Scale Limited Warranty 19
advertisement
Related manuals
advertisement
Table of contents
- 5 Introduction
- 5 Installation
- 5 1.1 Foundation Slab Cure Period
- 5 1.2 Assembly Time Estimates
- 6 1.3 Recommended Tools and Equipment
- 6 1.4 Lifting and Handling
- 6 1.5 Temporary Setting Blocks
- 7 Assemble Deck Modules
- 7 2.1 Place End Module A
- 7 2.2 Place and Attach Center Module
- 8 2.3 Install Outriggers and Deck Coping
- 9 2.4 Level Module Assembly
- 10 Load Cell Mount Installation
- 10 3.1 Attach Upper Mount Chair
- 10 3.2 Prepare Baseplate and Mount Installation
- 10 3.3 Raise Mount into Final Position
- 11 3.4 Attach Flexible Conduit Sections
- 11 Attach Grounding Strap
- 11 Install Lower Module Assembly Bolts
- 11 3.5 Install Anchor Bolts and Grout
- 12 3.6 Install Support Bars, Corrugated Metal, and Deck Rebar
- 12 Corrugated Metal Sheeting
- 12 3.7 Deck Rebar
- 13 Pour and Finish Concrete Deck
- 14 4.1 Optional Equipment
- 15 Install Cabling in Conduit
- 15 5.2 Junction Box to Indicator
- 15 5.3 Indicator to Peripherals
- 15 5.4 Single-Point Ground Conductor
- 15 5.5 Junction Box Connections
- 16 5.6 Electrical Ground Connections
- 17 5.7 Install Transient Protection
- 19 Trimming and Calibration
- 19 6.1 Overview and Equipment Required
- 19 6.2 Trimming Individual Cells
- 20 6.3 Trimming Paired Sections
- 21 6.4 Calibration with Test Weights
- 22 Load Cell Replacement
- 22 7.1 Overview
- 22 7.2 Replacement Procedure
- 23 8.0 Vehicle Scale Limited Warranty