advertisement
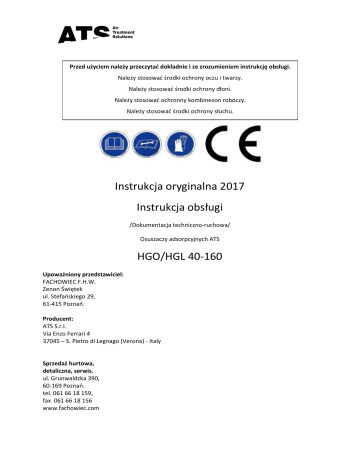
Przed użyciem należy przeczytać dokładnie i ze zrozumieniem instrukcję obsługi.
Należy stosować środki ochrony oczu i twarzy.
Należy stosować środki ochrony dłoni.
Należy stosować ochronny kombinezon roboczy.
Należy stosować środki ochrony słuchu.
Instrukcja oryginalna 2017
Instrukcja obsługi
/Dokumentacja techniczno-ruchowa/
Osuszaczy adsorpcyjnych ATS
HGO/HGL 40-160
Upoważniony przedstawiciel:
FACHOWIEC F.H.W.
Zenon Świętek ul. Stefańskiego 29,
61-415 Poznań.
Producent:
ATS S.r.l.
Via Enzo Ferrari 4
37045 – S. Pietro di Legnago (Verona) - Italy
Sprzedaż hurtowa, detaliczna, serwis. ul. Grunwaldzka 390,
60-169 Poznań. tel. 061 66 18 159, fax 061 66 18 156 www.fachowiec.com
DEKLARACJA ZGODNOŚCI
ATS S.r.l.
Via Enzo Ferrari 4
37045 - S. Pietro di Legnago (Verona) - Italy tel. +39 0442 629219 fax +39 0442 629126 e-mail: [email protected]
http://www.atsairsolutions.com/ deklaruje z pełną odpowiedzialnością, że jednostka, do której deklaracja się odnosi, jest zgodna z Dyrektywą 2014/68/EU dla urządzeń ciśnieniowych; to samo dotyczy poniższych przepisów:
Stosowane procedury oceny zgodności
Moduł A2
Stosowane standardy i specyfikacje techniczne
Inne zastosowane Dyrektywy EC
Zaangażowane jednostki notyfikowane
Nadzór nad systemem QS
Badania / inspekcje / testy podczas produkcji:
Załączone certyfikaty
Certyfikat badania EU-Design nr:
Certyfikat badania EU-Type nr:
Certyfikat zgodności UE nr:
Opis:
Typ, numer seryjny
Rok produkcji
OSUSZACZ POWIETRZA
……………….
2017
Oznaczenie komory
Max dopuszczalne ciśnienie PS:
Max/min dopuszczalna temperatura TS:
Objętość
Ciśnienie próbne PT:
Data testu ciśnienia:
3 - 16
+50 / +2
14,98
22,88
………….
Medium zastosowane do testu ciśnienia:
Grupa płynu:
1
POWIETRZE
POWIETRZE (GRUPA 2)
/
/
SIST EN 13445:2014
Dyrektywa niskonapięciowa (LVD) 2014/35/EU
Kompatybilność elektromagnetyczna (EMC) 2014/30/EU
Moduł A2
INSTITUT ZA VARILSTVO D.O.O. / jednostka certyfik ująca nr: 2042
IZV-PED-CD-A2-830-01-1701 bar
°C
L bar
Name / Surname
Fabio Massaro
Position
Managing Director
Date
……..
Signature
Spis treści:
1.
Informacje ogólne
1.1.
Zasada działania
1.2.
Zasady bezpieczeństwa
2.
Opis techniczny
2.1.
Praca osuszacza
2.2.
Obieg powietrza
3.
Instalacja
3.1.
Przyjęcie towaru i transport
3.2.
Miejsce instalacji
3.3.
Układ instalacji
3.4.
Podłączenie do sieci elektrycznej
3.5.
Układ rurociągowy
3.6.
Filtry przed i za osuszaczem
4.
Uruchomienie
4.1.
Przed uruchomieniem
4.2.
Uruchomienie
5.
Działanie osuszacza
5.1.
Panel sterowania
5.2.
Standardowe programy pracy
5.3.
Ustawienia
6.
Konserwacja, rozwiązywanie problemów, części zamienne, demontaż
6.1.
Kontrola i konserwacja
6.2.
Rozwiązywanie problemów
6.3.
Demontaż osuszacza
LISTA ZAŁĄCZNIKÓW:
A.
Modele osuszacza i warunki pracy
B.
Schemat przepływu powietrza
C.
Wymiary osuszacza
D.
Schemat elektryczny
E.
Widok rozstrzelony
F.
Części zamienne
1.
Informacje ogólne
1.1.
Zasada działania
Osuszacz absorpcyjny to urządzenie ciśnieniowe przeznaczone do usuwania wilgoci ze sprężonego powietrza.
Składa się z dwóch identycznych zbiorników ciśnieniowych, wypełnionych:
Tlenkiem glinu Al
2
O
3
(modele HGO),
Sitem molekularnym (modele HGL).
Tlenek glinu jest adsorpcyjym środkiem osuszającym, który wiąże się z wilgocią. Sito molekularne jest środkiem adsorpcyjnym, który wiąże się z mniejszymi cząsteczkami pary wodnej, co jest niemożliwe w przypadku zastosowania tlenku glinu.
Kolumny są połączone dwoma aluminiowymi blokami. Na dolnym bloku znajdują się cztery zawory i jeden tłumik hałasu.
Zawory wpuszczają powietrze do kolumn w celu wysuszenia powietrza w jednym ze zbiorników i regeneracji tlenku glinu w drugim.
1.2.
Zasady bezpieczeństwa
Objaśnienie symboli
Urządzenie zostało zaprojektowane i wyprodukowane zgodnie z europejską dyrektywą bezpieczeństwa i ochrony zdrowia. W związku z tym każda instalacja, użytkowanie i czynności konserwacyjne muszą być wykonywane z poszanowaniem wytycznych zawartych w niniejszej instrukcji.
Jakiekolwiek działania instalacyjne lub konserwacyjne, wymagające dostępu do wewnętrznych części osuszacza muszą być wykonywane przez wykwalifikowany personel.
Producent nie ponosi odpowiedzialności w przypadku innych lub niezgodnych zastosowań osuszacza z przewidzianymi w instrukcji.
2.
Opis techniczny
2.1.
Praca osuszacza
Osuszacz pracuje w sposób całkowicie zautomatyzowany. Wymaga jedynie minimum uwagi użytkownika i konserwacji. Każda sekwencja pracy jest programowana przez płytę główną lub mechaniczny wyłącznik czasowy.
Standardowy osuszacz pracuje w cyklu 9-minutowym, w którym 4,5 minuty to suszenie, 4 minuty regeneracja i 30 sekund zwiększanie ciśnienia.
2.2.
Obieg powietrza
Osuszacz jest przeznaczony do osuszania sprężonego powietrza. Każde zastosowanie urządzenia inne niż opisane w załączniku A wymaga autoryzacji producenta.
3.
Instalacja
3.1.
Przyjęcie towaru i transport
W momencie przyjęcia przesyłki, kupujący musi szczegółowo sprawdzić osuszacz w celu weryfikacji jego kompletności i obecności wszystkich elementów zawartych w dokumentacji.
W przypadku brakujących lub zniszczonych części, ewentualne roszczenia należy kierować do naszej siedziby lub do najbliższego sprzedawcy, w terminie nie dłuższym niż
8 dni od dnia dostawy.
Konieczne jest utrzymywanie osuszacza zawsze w pionowej pozycji, zgodnie z symbolami zamieszczonymi na opakowaniu. W przypadku ewentualnego przemieszczania osuszacza należy używać do podnoszenia urządzeń adekwatnych do jego wagi.
Po umieszczeniu urządzenia w miejscu instalacji należy zdjąć opakowanie. Zaleca się przechowywanie oryginalnego opakowania przynajmniej do końca okresu gwarancyjnego osuszacza. Należy pamiętać o utylizacji różnych materiałów zgodnie z obowiązującymi przepisami prawa.
Nie należy usuwać paneli podczas transportu osuszacza oraz umieszczania go w miejscu docelowym.
Osuszacz, gdy jest nieużywany, może być przechowywany w swoim opakowaniu, w miejscu wolnym od kurzu, w maksymalnej temperaturze 50°C i wilgotności właściwej nie przekraczającej 90%. W przypadku, gdy czas przechowywania przekroczy 12 miesięcy, prosimy skontaktować się z producentem.
3.2.
Miejsce instalacji
Podczas przygotowywania odpowiedniego miejsca do instalacji osuszacza prosimy wziąć pod uwagę następujące wymagania:
Osuszacz musi być chroniony przed czynnikami atmosferycznymi i nie może być eksponowany na działanie promieni słonecznych.
Podstawa do osadzenia osuszacza musi być płaska i zdolna do utrzymania wagi urządzenia.
Miejsce musi być suche, czyste, bez wewnętrznej recyrkulacji powietrza (zaleca się wydmuchanie ciepłego powietrza na zewnątrz z miejsca instalacji).
Należy zachować odpowiedni prześwit dookoła osuszacza w celu umożliwienia odpowiedniego chłodzenia urządzenia oraz ułatwienia czynności kontrolnych i konserwacyjnych.
Wprowadzane powietrze musi być wolne od dymu oraz łatwopalnych oparów, które mogłyby prowadzić do eksplozji bądź ryzyka zapalenia.
3.3.
Układ instalacji
Przed przystąpieniem do jakichkolwiek działań związanych z instalacją należy upewnić się, że:
Żadna z części systemu nie jest pod ciśnieniem,
Żadna z części systemu nie jest podłączona do sieci elektrycznej
Połączenia rurowe są odpowiednich rozmiarów i odpowiednio zlokalizowane w celu uniknięcia działania zewnętrznych sił na osuszacz,
Osuszacz jest stabilnie przymocowany do podłoża,
Osuszacz jest poprzedzony filtrem o dokładności filtracji min. 0,01 mg/m3.
W celu zredukowania problemu wibracji zaleca się stosowanie elastycznych rur.
UWAGA!
Niewłaściwa instalacja może unieważnić gwarancję!
3.4.
Podłączenie do sieci elektrycznej
UWAGA – wysokie napięcie!
NALEŻY ZASTOSOWAĆ PROCEDURY PRAWIDŁOWEGO POSTĘPOWANIA W PRZYPADKU PORAŻENIA
PRĄDEM ELEKTRYCZNYM.
Podłączenie do sieci elektrycznej musi być przeprowadzone przez wykwalifikowany personel, a systemy bezpieczeństwa muszą być zgodne z lokalnymi zasadami i prawem.
Przed podłączeniem urządzenia do sieci elektrycznej należy sprawdzić, czy napięcie i częstotliwość prądu dostępne w sieci są zgodne z danymi umieszczonymi na tabliczce znamionowej osuszacza. W przypadku napięcia dozwolone są odchylenia na poziomie ±5%.
Osuszacz ma zainstalowany przewód elektryczny.
Gniazdo elektryczne musi być wyposażone w bezpiecznik. Przekrój zasilających przewodów elektrycznych musi być dobrany przez wykwalifikowany personel, zgodnie z obowiązującymi zasadami i ze zużyciem osuszacza (wartości nominalne podane na tabliczce znamionowej osuszacza).
Podłącz osuszacz po upewnieniu się, że napięcie nominalne i częstotliwość są stałe i odpowiadają nominalnym wartościom urządzenia. Użytkownik musi zapewnić instalację z adekwatną izolacją i uziemieniem, zgodnymi z lokalnie obowiązującymi zasadami.
3.5.
Układ rurociągowy
Aby zapewnić możliwość serwisowania i konserwacji osuszacza zaleca się stosowanie trójzaworowego układu obejścia .
3.6.
Filtry przed i za osuszaczem
Filtry przed osuszaczem chronią go przed zanieczyszczeniem olejem, wodą, kamieniem itd., w celu wydłużenia żywotności osuszacza.
Konieczne jest zastosowanie automatycznego spustu kondensatu w filtrze.
Aby ulepszyć działanie osuszacza zaleca się zainstalowanie przed nim kompletnego zestawu filtrów.
Za osuszaczem zaleca się stosowanie filtra o dokładności 1µ w celu wyeliminowania proszku z tlenku glinu.
4.
Uruchomienie
4.1.
Przed uruchomieniem
Przed uruchomieniem osuszacza należy upewnić się, że wszystkie parametry robocze odpowiadają danym nominalnym (dostępnym na liście w załączniku)
Osuszacz jest przetestowany i gotowy do normalnej pracy, nie wymaga żadnej kalibracji.
Niemniej jednak konieczne jest sprawdzenie prawidłowego działania osuszacza w pierwszych godzinach pracy.
4.2.
Uruchomienie
Po podłączeniu urządzenia do instalacji rurociągowej oraz elektrycznej należy postępować zgodnie z poniższymi wskazówkami:
POWOLI zwiększać ciśnienie w osuszaczu aż do osiągnięcia ciśnienia roboczego.
Zasilić obwód elektryczny. Osuszacz uruchomi się automatycznie. Osuszacz może wymagać do 24 godzin pracy do osiągnięcia normalnego punktu rosy. W związku z tym wskaźniki i/lub alarmy nie powinny być do tego czasu brane pod uwagę.
Po rozruchu może pojawić się pylenie, które w późniejszym czasie zmaleje.
ON / OFF:
Osuszacz powinien uruchamiać się automatycznie po podłączeniu zasilacza. Jeśli osuszacz nie uruchomi się automatycznie, należy postępować według procedur:
- nacisnąć przycisk w celu uruchomienia osuszacza,
- nacisnąć przycisk w celu wyłączenia osuszacza.
Kiedy osuszacz jest wyłączony, na wyświetlaczu jest widoczna migająca dioda LED1 (patrz rozdział
5.1)
UWAGA
PODCZAS PIERWSZEGO ROZRUCHU NALEŻY SPRAWDZIĆ PRACĘ OSUSZACZA PRZEZ JEDEN LUB DWA
CYKLE. ZWŁASZCZA PODCZAS ZMIANY KOLUMN. NALEŻY ZWERYFIKOWAĆ, CZY SYSTEM DZIAŁA WE
WŁAŚCIWEJ KOLEJNOŚCI I SEKWENCJI. JEŚLI OSUSZACZ NIE FUNKCJONUJE PRAWIDŁOWO
SKONTAKTUJ SIĘ ZE SPRZEDAWCĄ.
5.
Działanie osuszacza
5.1.
Panel sterowania
LED
LED 1
LED 2
LED 3
LED 4
LED 5
LED 6
OPIS
Wł. / wył. kolumna 2
Zalecany serwis konieczny serwis kolumna 1 alarm
NIE ŚWIECI
Urządzenie nie podłączone do prądu
MRUGA
Tryb czuwania
W kolumnie 2 jest zwiększane ciśnienie / kolumna 1 osusza
Serwis będzie wkrótce potrzebny
Konieczny serwis
W kolumnie 1 jest zwiększane ciśnienie / kolumna 2 osusza
Ostrzeżenie o wysokim punkcie rosy
ŚWIECI
Urządzenie pracuje
Kolumna 2 osusza / kolumna 1 regeneruje się
Kolumna 1 osusza / kolumna 2 regeneruje się
Specyfikacja techniczna:
zasilanie: 230VAC, 50-60Hz, ±10%,
wyjścia: przekaźnik 5 pinowy, 230VAC, 5A
ochrona IP: IP65 (tylko panel przedni)
certyfikat: CE
temperatura przechowywania: -40, +50°C
temperatura pracy: 0, +40°C
5.2.
Standardowe programy pracy
Modele HGO i HGL mają trzy różne programy pracy.
1.
Czasowa kontrola sekwencji (standard): osuszacz jest kontrolowany czasowo. Każda faza robocza jest kontrolowana przez jeden z parametrów panelu sterowania. Użytkownik końcowy może zmienić wartość w oparciu o tabele w rozdziale 5.3.
2.
Kontrola punktu rosy (energooszczędny): osuszacz pracuje w trybie energooszczędnym, połączony z czujnikiem punktu rosy. Panel sterowania jest zaprogramowany do pracy z dwoma różnymi rodzajami czujników. Osuszacz ustawi automatycznie czas pracy ale wymagana wartość temperatury punktu rosy może być ustawiona na panelu sterowania.
3.
Zdalne sterowanie (specjalne zastosowanie) ta specjalna opcja jest używana do oszczędzania energii przy zastosowaniach specjalnych, gdy -40°C nie jest wymagane.
Osuszacz utrzyma stałe sekwencje ale będzie się włączał i wyłączał w zależności od zewnętrznego styku podłączonego do sterownika.
5.3.
Ustawienia
Aby ustawić osuszacz należy go włączyć.
Aby wejść w menu ustawień lub z niego wyjść naciśnij przycisk
Gdy wyświetlacz pokaże pierwsze P1 ustaw jego wartość na 03. przez 3 sekundy.
Aby przewinąć w dół menu trzymaj wciśnięty przycisk
Aby zmieniać wartość używaj przycisków „w górę” i „w dół”
W celu zatwierdzenia zmiany trzymaj przycisk przez 3 sekundy. Wyświetlacz będzie pokazywał SA.
Aby wrócić do ustawień fabrycznych trzymaj przyciski „w górę” i „w dół” wciśnięte jednocześnie przez 3 sekundy. Wyświetlacz będzie pokazywał dF.
TABELA PARAMETRÓW
Parametr Domyślnie
P1
P2
P3
P4
P5
3
24
-39
0
0
Min
1
6
-80
0
0
Max Skok co: Jednostka
99 1 10*s Wartość
36 1 10*s
Uwagi
Wartość suszenia i oczyszczania, wyrażana w dziesiątkach sekund, np. 24=240 sekund
Zadana wartość temperatury.
+20
3
1
1
1
1
°C
Znak minusa jest zastąpiony migającą kropką (39. Oznacza -
39)
Wybór programu pracy; należy wybrać go podczas pracy osuszacza.
0= Czasowa kontrola sekwencji
1= Kontrola punktu rosy typ 1
2= Kontrola punktu rosy typ 2
3= Zdalne sterowanie
Rodzaj zdalnego sterowania:
0= kontakt normalnie otwarty
1=kontakt normalnie zamknięty
Jak ustawić sterownik w czasowej kontroli sekwencji
Jeżeli rzeczywisty przepływ powietrza przez osuszacz jest niższy niż nominalny, użytkownik końcowy może zredukować oczyszczanie powietrza zmieniając parametr P1. Nie należy zmieniać parametru P2 bez zgody producenta.
Wartość parametru P1
Rzeczywisty przepływ [%]
3 domyślnie
100/85
6/9
85/70
9/18
70/50
Aby obliczyć przepływ rzeczywisty [%] należy zastosować współczynniki korekcyjne dla ciśnienia roboczego i temperatury wejściowej.
Współczynnik korekcyjny ciśnienia roboczego:
Ciśnienie [bar] 4
Współczynnik P 0,63
5
0,75
6
0,88
Współczynnik korekcyjny temperatury wejściowej:
7
1
8
1,14
9
1,25
10
1,39
Temperatura [°C] 25
Współczynnik T 1
30
1
35
1
40
0,97
45
0,88
Przepływ rzeczywisty [%] = Max przepływ rzeczywisty / skorygowany przepływ nominalny
50
0,73
Skorygowany przepływ nominalny = przepływ nominalny x współczynnik P x współczynnik T
6.
Konserwacja, rozwiązywanie problemów, części zamienne, demontaż
6.1.
Kontrola i konserwacja
Wtyczki
Ze względów bezpieczeństwa należy sprawdzać wtyczki zainstalowane w osuszaczu co 6 miesięcy.
Upewnij się, że żadne z wtyczek nie są narażone na działanie wody (deszcz, para, wilgoć). W przypadku pojawienia się korozji na wtyczkach prosimy o kontakt z producentem.
OSTRZEŻENIE
Konserwacja osuszacza może być przeprowadzana tylko przez wykwalifikowany personel!
Przed przystąpieniem do jakichkolwiek czynności konserwacyjnych należy pamiętać, że:
-żadna część systemu nie znajduje się pod wysokim ciśnieniem,
-żadna część systemu nie znajduje się pod napięciem elektrycznym
Po dwóch latach pracy, lub gdy dioda „konieczny serwis” zaczyna mrugać, należy:
- Wymienić osuszający tlenek glinu,
-Wymienić wszystkie O-ringi w osuszaczu,
-Wymienić membrany zaworów elektromagnetycznych,
-Wymienić tłumiki hałasu.
ZAWÓR BEZPIECZEŃSTWA:
Po dwóch latach pracy należy sprawdzić zawór bezpieczeństwa.
Po długim okresie pracy osuszacza zawór bezpieczeństwa musi być sprawdzony i zatwierdzony przez notyfikowaną jednostkę zgodnie z przepisami dotyczącymi bezpieczeństwa.
6.2.
Rozwiązywanie problemów
Rozwiązywanie problemów i ewentualny nadzór i/lub czynności konserwacyjne muszą być wykonywane przez wykwalifikowany personel.
PROBLEM
Osuszacz nie utrzymuje ciśnienia
Osuszacz nie oczyszcza się
Osuszacz zmniejsza ciśnienie zbyt gwałtownie
Ciśnienie w regenerującej się kolumnie jest wysokie
(powyżej 1 bara)
Osuszacz nie zmienia kolumn pomiędzy osuszaniem a regeneracją
Nadmierny spadek ciśnienia w osuszaczu
Zbyt wysoki punkt rosy
PRZYCZYNA PROBLEMU
Wina zaworu między kolumnami
Zawór między kolumnami nie otwiera się
Tłumik jest zatkany
Woda dostaje się do rotora osuszacz
Środek osuszający zanieczyszczony olejem
DZIAŁANIE NAPRAWCZE
Sprawdź zawór płuczący między kolumnami; Sprawdź sekwencjonowanie czasowe
Sprawdź zawór elektromagnetyczny. Napraw lub, w razie konieczności, wymień.
Patrz: Procedura wymiana tłumika
Zawór między kolumnami nie zamyka się
Sprawdź zawór elektromagnetyczny. Napraw lub, w razie konieczności, wymień.
Patrz: Procedura wymiana tłumika Tłumik jest zatkany
Wyjściowy zawór zwrotny nie zamyka się
Wyczyść i/lub wymień
Sprawdź napięcie wyjściowe
Zasilanie nie jest podłączone
Zawór elektromagnetyczny jest niesprawny zaworu elektromagnetycznego
Sprawdź napięcie wejściowe zaworu elektromagnetycznego
Włącznik czasowy jest wyłączony Sprawdź panel sterowania
Nadmierny przepływ
Zbyt niskie ciśnienie wejściowe
Zbyt wysoka temperatura wejściowa powietrza
Sprawdź wartość przepływu
Sprawdź źródło ciśnienia
Sprawdź chłodnicę lub sprężarkę
Sprawdź separator wody, filtr wstępny i wymień środek osuszający, jeśli to konieczne
Zainstaluj odpowiedni filtr wstępny i wymień środek osuszający, jeśli to konieczne
Nie wystarczająca szybkość oczyszczania
Sprawdź tłumik
6.3.
Demontaż osuszacza
W przypadku, gdy osuszacz musi być zdemontowany, musi być podzielony na jednorodne grupy materiałów.
CZĘŚĆ
Wzmocnienia i obudowa
Kompresor chłodniczy
Glinka
Bloki dolne i górne
Zawory zwrotne
Rury
Zawór bezpieczeństwa
Zawór elektromagnetyczny
Panel sterowania
Przewody elektryczne
Części elektryczne
MATERIAŁ
Stal węglowa, farba epoksydowa
Stal, miedź, aluminium, olej
Tlenek glinu
Aluminium
Stal nierdzewna
Wytłaczane aluminium
Mosiądz, stal
Mosiądz, stal
Miedź, PCV
Miedź, PCV
PCV, Miedź, Mosiądz
Zalecamy zastosowanie się do zasad bezpieczeństwa dotyczących segregacji każdego rodzaju materiałów. Płyn chłodzący zawiera kropelki oleju smarującego, uwolnione przez kompresor chłodniczy. Nie należy pozbywać się tego płynu w środowisku. Płyn musi być usunięty z osuszacza za pomocą odpowiednich urządzeń i dostarczony do punktu odbioru, gdzie zostanie przetworzony w sposób umożliwiający jego ponowne użycie.
LISTA ZAŁĄCZNIKÓW
A.
Modele osuszacza i warunki pracy
Wejście/Wyjście
DN m3/h scfm
HGO 40
3/4” DN20
40
23,5
HGO 80
3/4” DN20
80
47
Model
HGO 120
3/4” DN20
120
70
Wejście/Wyjście
DN m3/h scfm
HGL 40
3/4” DN20
30
18
HGL 80
3/4” DN20
60
35
Model
HGL 120
3/4” DN20
90
53
HGO 160
3/4” DN20
160
94,1
HGL 160
3/4” DN20
120
71
Temperatura punktu rosy HGO
Temperatura punktu rosy HGL
Ciśnienie próbne
Minimalne ciśnienie robocze
Maksymalne ciśnienie robocze
Ciśnienie zaworu bezpieczeństwa
Napięcie zasilania
Przeznaczenie urządzenia*
-40°C
-70°C
22,8 bar
3 bar
16 bar
16,1 bar
230 V
Osuszanie sprężonego powietrza do użytku przemysłowego
Grupa materiałowa
Minimalna temperatura wejściowa
Maksymalna temperatura wejściowa
Minimalna temperatura otoczenia
Powietrza (grupa 2)
+2°C
+50°C
+5°C
Maksymalna temperatura otoczenia
*Osuszacz musi znajdować się w suchym miejscu, wolnym od kurzu i pyłu
+40°C
B.
Schemat przepływu powietrza
C.
Wymiary osuszacza
MODEL
A
B
C
F
G
D
E
*WYMIARY [mm]
165
190
610
60
40
630
400
470
80
1030
400
470
165
190
1010
60
120
1430
400
470
165
190
1410
60
160
1730
400
470
165
190
1710
60
D.
Schemat elektryczny
E.
Widok rozstrzelony
F.
Części zamienne
Części zamienna
Zestaw do wymiany środka suszącego do HGO 40
Zestaw do wymiany środka suszącego do HGO 80
Zestaw do wymiany środka suszącego do HGO 120
Zestaw do wymiany środka suszącego do HGO 160
Kryza HGO-HGL 40
Kryza HGO-HGL 80
Kryza HGO-HGL 120
NRV
EMVM
EMVS
EMVC
O
M
Kryza HGO-HGL 160
Zawór zwrotny
Membrana zaworu elektromagnetycznego
Sprężyna zaworu elektromagnetycznego
Cewka zaworu elektromagnetycznego
Zestaw O-ringów
Tłumik
C
PG
SV
Sterownik
Wskaźnik ciśnienia
Zawór bezpieczeństwa
HGO.K0040
HGO.K0080
HGO.K0120
HGO.K0160
0BI.610005
0BI.610006
0BI.610007
0BI.610008
0BI.610013
0BI.610014
0BI.610015
0BI.610016
0BI.610017
0BI.540013
0BI.590005
0BI.540007
0BI.540006
DESICCANT
DRYER
Instruction and Maintenance Manual
HGO 40-160
HGL 40-160
DECLARATION OF
CONFORMITY
ATS S.r.l.
Via Enzo Ferrari 4
37045 - S. Pietro di Legnago (Verona) - Italy tel. +39 0442 629219 fax +39 0442 629126 e-mail: [email protected]
http://www.atsairsolutions.com/ declares under its own responsibility that the unit to which this declaration relates is in conformity with Pressure Equipment Directive 2014/68/EU as well as the following regulations:
Applied conformity assessment procedures: Modulo A2
Applied standards and technical specifications:
Other applied EC-Directives:
Engaged notified bodies
Surveillance of the QS-System:
SIST EN 13445:2014
Low Voltage (LVD) 2014/35/EU
Electromagnetic Compatibility (EMC) 2014/30/EU
Modulo A2
Examination / inspections / test during manufacturing:
INSTITUT ZA VARILSTVO D.O.O. / certification body no.: 2042
Certificates which are included
EU-Design Examination Certificate No.:
EU-Type Examination Certificate No.:
/
/
EU-Certificate of conformity No.: IZV-PED-CD-A2-830-01-1701
Description: AIR DRYER
Type-, serial-, identification-No:
……………….
Year of manufacturing: 2017
Chamber designation: 1
Name / Surname
Fabio Massaro
Position
Managing Director max. allowable pressure PS: allowable max./min. temperature TS:
Volume
3 - 16
+50 / +2
14,98 bar
°C
L
Date
……..
Signature
Test pressure PT:
Pressure test date:
22,88
………….
Pressure test medium: AIR
Fluid
– fluidgroup:
AIR (GROUP 2) bar
INDEX
1. GENERAL INFORMATION
1.1 Functional description
1.2 Safe use of the dryer
2. TECHNICAL DESCRIPTION
2.1 Operation
2.2 Air circuit
3. INSTALLATION
3.1 Acceptance and transport
3.2 Installation site
3.3 Installation layout
3.4 Connection to the mains
3.5 Piping arrangement
3.6 Prefilter and afterfilter
4. START UP
4.1 Before Start Up
4.2 Start Up
5. OPERATION
5.1 Controller
5.2 Standard operation
5.3 Set up
6. MAINTENANCE, TROUBLESHOOTING, SPARES AND DISMANTLING
6.1 Controls and Maintenance
6.2 Troubleshooting
6.3 Dismantling of the dryer
LIST OF ATTACHMENTS
A Dryer models and operating conditions
B
C
D
E
F
Flow diagram
Dryer dimensions
Wiring diagram
Exploded view
Suggested spares
1. GENERAL INFORMATION
1.1 FUNCTIONAL DESCRIPTION
The desiccant air dryer is a pressure appliance designed to remove humidity from compressed air.
It is made of two identical pressure vessels, which are filled with:
-aluminum oxide Al2O3 (for HGO models)
-molecular sieve + aluminum oxide (for HGL models)
Alumina is an adsorption-drying agent, which binds humidity.
Molecular sieve is an adsorption agent that binds to smaller molecules of water vapour which alumina can’t.
The columns are connected with two aluminium blocks. On the lower block are located four valves and one silencer.
The valves force the air into the columns in order to dry the air in one vessel and regenerate the alumina in the second one.
1.2 USE OF THE MACHINE IN SAFE CONDITIONS
Symbols applied on the dryer and manual
General warning
Danger - high voltage, electrical current
Do not touch electrical hazard
Prohibition of maintenance to unqualified personnel
Danger point Environmental requirements
Mandatory consulting the manual Recyclable materials
This system has been designed and manufactured in compliance with the European safety directive in force, therefore any installation, use and maintenance operations must be performed respecting the instructions contained in this manual.
Any installation, use and maintenance operation requiring to access the internal parts of the dryer must be performed by qualified personnel.
The manufacturer will not be liable in case of uses different or nor complying with those foreseen in this manual.
2. TECHNICAL DESCRIPTION
2.1 OPERATION
The dryer is totally automatic during operation; it needs only a minimum maintenance and care. Each sequence of operations is programmed by a central circuit board or mechanical timer.
Standard dryer operates on a 9-minute cycle with 4,5 minutes drying, 4 minutes regenerating and 30 seconds pressurizing.
2.2 AIR CIRCUIT
The dryer was manufactured in order to dry compressed air; every application of the machine in conditions other than those described in Annex A must be authorized by the manufacturer.
3. INSTALLATION
3.1 ACCEPTANCE AND TRANSPORTATION
At the moment the customer accepts the delivery, he must fully inspect the dryer to verify its integrity and the presence of all the items listed in the shipping documentation.
Eventual claims for missing and/or damaged parts must be addressed directly to our facility or the closest reseller, within 8 (eight) days from the date on which the goods have been received.
It is mandatory to keep the dryer always in vertical position, as indicated by the symbols present on the packaging. For eventual displacements, use adequate devices with reference to the weight of the machine.
Remove the packaging after having positioned the dryer in the installation site. We suggest keep the original packaging at least for the warranty period of the machine.
Anyhow, do not forget to dispose the various materials in compliance with the relevant rules locally in force.
Do not remove any panels during transportation and positioning of dryer.
If not in use, the dryer can be stored in its packaging in a dust free and protected site at a maximum temperature of 50 °C, and a specific humidity non exceeding the 90%.
Should the stocking time exceed 12 months, please contact the manufacturer.
3.2 INSTALLATION SITE
While preparing a proper site for the installation of the dryer, please take into account the following requirements
- The machine must be protected from atmospheric agents and not directly exposed to sun light.
- The seating base must be flat and capable to hold the weight of the machine.
- A clean, dry and without internal air recirculation (we suggest to blow the warm air outside the installation site).
- Make sure to leave sufficient clearance around the dryer in order to allow an adequate cooling of the machine and maintenance/control operations.
The incoming air must be free from smoke or flammable vapours which could lead to explosion or fire risks.
3.3 INSTALLATION LAYOUT
Before attempting any installation operation, make sure that:
- no part of the system is under pressure
- no part of the system is electrically powered
- piping connections are properly sized and located in order to avoid any external force on the dryer
- dryer is firmly secured to the ground
- a filter with a minimum filtration rate of 0.01 mg/m3 has been installed before the dryer
Flexible pipes are recommended to reduce vibration problems.
WARNING!
Incorrect installation may void warranty!
3.4 CONNECTION TO THE MAINS
DANGER - High Voltage is present.
PROPERLY HANDLING PROCEDURES MUST BE USED OF ELECTRICAL
SHOCK.
The connection to the mains, to be carried out by qualified personnel, and the safety systems must comply with local rules and laws.
Before connecting the unit to the electric power, verify that the voltage and the frequency available on the mains correspond to the data reported on the data plate of the dryer. In terms of voltage, a ±5% tolerance is allowed.
The dryer comes with a mains connecting cable already installed.
The mains socket must be provided with a mains magneto-thermal differential breaker and the cross section of the power supply cables must be suitable sized by qualified staff in compliance to rules in force and to the consumption of the dryer (see the nominal values on the data plate of the dryer).
Power the dryer after having checked that the nominal voltage and line frequency are constant and matching the nominal values of the machine. The user must provide the installation with an adequate line protection and a ground terminal complying with the electrical rules locally in force.
3.5 PIPING ARRANGEMENT
To ensure service and maintenance to the dryer, a three-valve bypass system is suggested.
3.6 PREFILTERS and AFTERFILTERS
Prefilters, located before dryer, protect the desiccant bed from contamination by oil, water, pipe scale etc., so to extend the dryer desiccant life.
An automatic drain on the filter is mandatory.
To improve the dryer performance install a complete set of filters upstream of dryer.
A post filter with a filtration rate of 1 micron is recommended to capture the alumina powder.
4. START UP
4.1 BEFORE START UP
Before starting the machine, make sure that all operating parameters correspond to the nominal data (operating parameters in the list attached).
The dryer is supplied already tested and present for normal operation, and it does not require any calibration. Nevertheless, it is necessary to check the operating performances during the first working hours.
4.2 START UP
After all piping and electrical connections have been made, proceed as follows:
SLOWLY pressurize the dryer up to reach full operating pressure.
Energize electrical circuit. The dryer will start automatically.
The dryer may require up to 24 hours of operation to reach normal operating dew points.
Therefore, indicators and/or alarms should not be considered until that time.
After start up, some dusting may occur. This will decrease afterwards.
ON / OFF:
The dryer should start automatically when connected to power supply.
If the dryer does not start automatically, use the procedure below:
-Push button to START the dryer.
-Push button to STOP the dryer.
When the dryer is turned off, the display shows LED1 blinking (see chapter 5.1)
NOTE
AT INITIAL START-UP, CHECK THE DRYER OPERATION FOR ONE OR TWO
CYCLES, ESPECIALLY AT THE TIME OF THE TOWER SHIFT. VERIFY THAT
SYSTEM IS OPERATING IN ITS PROPER ORDER AND
SEQUENCE. IF THE DRYER IS NOT FUNCTIONING PROPERLY, CONTACT
YOU REPRESENTATIVE.
5. OPERATION
5.1 CONTROLLER
ON/ OFF SET
SET
LED1
POWER:
ON
LED2: COLUMN 2
LED3: SERVICE ADVISED
LED6: ALARM
LED5: COLUMN 1
LED4: SERVICE URGENT
<< >>
DOWN UP
LED DESCRIPTION
LED 1 ON/OFF
LED 2 Column 2
LED 3
Service advice
LED 4 Urgent service
LED 5 Column 1
LED 6 Alarm
OFF
Unit is not energised
SPECIFICATIONS
- POWER SUPPLY: 230VAC,50-60HZ ., +/-10%
- OUTPUTS: n° 5 RELAYS , 230VAC, 5A
- IP PROTECTION : IP65 (only front panel)
- CERTIFICATION: CE
- STOCKING TEMPERATURE: 40, +50°C
- OPERATING TEMPERATURE: 0 ,+40°C
5.2 STANDARD OPERATION
BLINKING ON
Unit in standby
Column 2
Repressurizing /
Column 1 Drying
Service will be needed soon
Unit is working
Column 2 Drying /
Column 1
Regenerating
Service is needed
Column 1
Repressurizing /
Column 2 Drying
High dew point alarm
Column 1 Drying /
Column 2
Regenerating
HGO and HGL have 3 different operating modes.
1. TIMED SEQUENCE CONTROL (STANDARD): the dryer is time controlled.
Every working phase is controlled by one of the parameter of the controller.
The end user can change the value based on the table on chapter 5.3.
2. DEW POINT CONTROL (ENERGY SAVING): the dryer works in Energy saving mode connected with a dew point sensor. Controller is programmed to work with 2 different kind of sensors.
Dryer will automatically adjust time of work, but the required dew point value can be adjusted on the controller.
3. REMOTE CONTROL (SPECIAL APPLICATION): this special mode is generally used to save energy in special application when 40 °C is not really required.
The dryer will keep the timed sequence constant but it will switch on and off depending on the external contact connected on controller.
5.3 SET-UP
To set the dryer up, turn it on.
To enter or exit SET MENU press button for 3 seconds.
After that the display will show first P1 , then the default value of P1 03.
To scroll down the menu keep the button
To change the value use “up” and “down” buttons. pressed.
To confirm the change press for 3 seconds. The display will show SA .
To set default parameters keep
“up” and “down” pressed for 3 seconds. The display will show dF .
PARAMETER TABLE
Parameter Default Min. Max. STEP UNIT
REMARKS
P1
P2
P3
P4
3
24
-39
0
1
6
-80
0
99
36
+20
3
1
1
1
1
10*s
Value of repress ration, shown in tens of seconds.
Example 3=30 seconds
10*s
Value of drying and purge, shown in tens of seconds.
Example 24=240 seconds
°C
SETPOINT value; the minus sign is shown by the lowest decimal point blinking (39. means -39)
CONTROL MODE; selects the CONTROL MODE during OPERATING MODE.
P5 0 0 1 1
0=TIMED SEQUENCE CONTROL
1=DEW POINT CONTROL SENSOR TYPE 1
2=DEW POINT CONTROL SENSOR TYPE 2
3=REMOTE CONTROL
Type of REMOTE CONTROL.
0=normally open contact
1=normally closed contact
HOW SET CONTROLLER IN TIMED SEQUENCE CONTROL
If the real flow on the dryer is lower than nominal flow, the end user can reduce the air purge changing parameter P1. Do not change P2 if not agreed with the manufacturer.
P1 3 default 6 / 9 9 / 18
70 / 50 Real Flow % 100 / 85 % 85 / 70 %
To calculate Real Flow % use the follows instructions:
Correction factors for working pressure
Pressure Bar 4 5 6 7
1 Factor P
Temperature
°C
0,63 0,75 0,88
Correction factors for inlet temperature
25 30 35 40
8
1,14
45
9
1,25
50
10
1,39
0,88 0,73 Factor T 1 1 1 0,97
Real Flow % = Max real Flow / Adjusted Nominal Flow
Adjusted Nominal Flow = Nominal Flow x Factor P x Factor T
6. MAINTENANCE, TROUBLESHOOTING, SPARES AND
DISMANTLING
6.1 CONTROLS AND MAINTENANCE
PLUGS
For safety reasons please check the plugs installed on the dryer every 6 months.
Make su re that no plugs are exposed to water (rain, spray…) or moisture.
If corrosion appears on plugs please contact the manufacturer.
WARNING
Maintenance on the machine can only be carried out by authorized personnel!
Before attempting any maintenance operation, make sure that:
- no part of the system is under pressure
- no part of the system is electrically powered
AFTER 2 YEARS OF OPERATION OR WHEN LED LIGHT ˝SERVICE URGENT˝
STARTS BLINKING:
- Replace desiccant alumina
- Replace all O-rings on the dryer
- Replace solenoid valve membranes
- Replace mufflers
SAFETY VALVE:
After 2 years of working check the safety valve.
After a long period of operation the safety valve must be checked and approved by a notified body in accordance to safety regulations.
6.2 TROUBLESHOOTING
Troubleshooting and eventual control and/or maintenance operations must be performed by qualified personnel.
PROBLEM
Dryer fails to pressurize
Dryer fails to purge
Dryer depressurizes too rapidly
The pressure in regenerating tower is high
(above 1 bar)
The dryer fails to shift towers from drying to regenerating service
There is an excessive pressure drop in the dryer
Dew point is high
PROBABLE CAUSE CORRECTIVE ACTION
Faulty purge valve Check purge valve
Check timer sequencing
Purge valve does not open Check solenoid valve.
Repair and replace it if necessary
Purge muffler is clogged Refer to muffler replacement procedure
Purge valve does not close Check solenoid valve.
Repair and replace it if necessary
Muffler is clogged Refer to muffler replacement procedure
Clean and/or replace Outlet check valve stays open
There is no input power
Solenoid valve is faulty
Timing on dryer is off
Excessive flow rate
Inlet pressure under design condition
Inlet temperature above design condition
Water entering desiccant bed
Desiccant contaminated by oil
Insufficient purge rate
Check output voltage to solenoid valve
Check input voltage to solenoid valve
Check controller
Check flow rate
Check pressure source
Check aftercooler or check compressor
Check air/moisture separator and prefilter and replace desiccant if necessary
Install suitable prefilter and replace desiccant if necessary
Check muffler
6.3 DISMANTLING OF THE DRYER
If the dryer is to be dismantled, it has to be split into homogeneous groups of materials.
PART
Supports and covers
Refrigeration Compressor
Alumina
Upper and Lower blocks
Non return valves
Pipe
Safety Valve
Solenoid Valve
Controller
Electric cables
Electric parts
MATERIAL
Carbon steel, Epoxy paint
Steel, Copper, Aluminum, Oil
Alumina oxide
Aluminum,
Stainless steel
Extruded Aluminum,
Brass, Steel
Brass, Steel
Copper, PVC
Copper, PVC
PVC, Copper, Brass
We recommend to comply with the safety rules in force for the disposal of each type of material. The chilling fluid contains droplets of lubrication oil released by the refrigerating compressor. Do not dispose this fluid in the environment. It has to be discharged from the dryer with a suitable device and then delivered to a collection centre where it will be processed to make it reusable.
LIST OF
ATTACHMENTS
A. DRYER MODELS AND OPERATING CONDITIONS
INLET/OUTLET
DN m3/h scfm
MODELS
HGO 40 HGO 80 HGO 120 HGO 160
3/4''
DN20
40
3/4''
DN20
80
3/4''
DN20
120
3/4''
DN20
160
23,5 47 70 94,1
Test pressure (PT)
Minimum working pressure
Maximum working pressure
Safety device set pressure
Supply voltage
Intended use*
Product (fluid) group
Minimum inlet temperature
Maximum inlet temperature
Minimum ambient temperature
Maximum ambient temperature
*Dryer must be kept in dry and dust free area
22,8 bar
3 bar
16 bar
16,1 bar
230 V
Drying compressed air for industrial use
Air (fluid group 2)
+2 °C
+50 °C
+5 °C
+40 °C
B. FLOW DIAGRAM
610013
NON RETURN
VALVE
COLUM1
(PG)
PRESSURE
GAUGE
PG 540007
AIR OUTLET
(EMV)
ELECTRO
MAGNETIC
VALVE
1
C. DRYER DIMENSIONS
(EMV)
ELECTRO
MAGNETIC
VALVE
2
(EMV)
ELECTRO
MAGNETIC
VALVE
3
540013
MUFFLER
610014
ELECTRO
610015
VALVE
4
B
E
G
C
MODEL 40 80 120 160
D
A
D
E
B
C
F
G
630 1030 1430 1730
400
470
165
190
400
470
165
190
400
470
165
190
400
470
165
190
610
60
1010
60
1410
60
*DIMENSIONS (mm)
1710
60
D. WIRING DIAGRAM
(EMV)
ELECTROMAGNETIC
VALVE
EMV 1
EMV 2
EMV 3
EMV 4
(C)
CONTROLLER
E. EXPLODED VIEW
NRV
PG
GG
G
C
SV
VV
VV
M EMV
F. SPARE PARTS
SPARE PARTS
DESICCANT REPLACEMENT KIT HGO 40
DESICCANT REPLACEMENT KIT HGO 80
DESICCANT REPLACEMENT KIT HGO 120
DESICCANT REPLACEMENT KIT HGO 160
ORIFICE HGO – HGL 40
ORIFICE HGO
– HGL 80
ORIFICE HGO – HGL 120
ORIFICE HGO
– HGL 160
NRV Non Return Valve
EMVM
EMVS
Electro Magnetic Valve
Membrane
Electro Magnetic Valve
Spring
EMVC
O
M
C
PG
SV
Electro Magnetic Valve
Coil
O-ring Set
Muffler
Controller
Gauge
Safety Valve
HGO.K0040
HGO.K0080
HGO.K0120
HGO.K0160
0BI.610005
0BI.610006
0BI.610007
0BI.610008
0BI.610013
0BI.610014
0BI.610015
0BI.610016
0BI.610017
0BI.540013
0BI.590005
0BI.540007
0BI.540006
advertisement
Related manuals
advertisement