advertisement
▼
Scroll to page 2
of 818
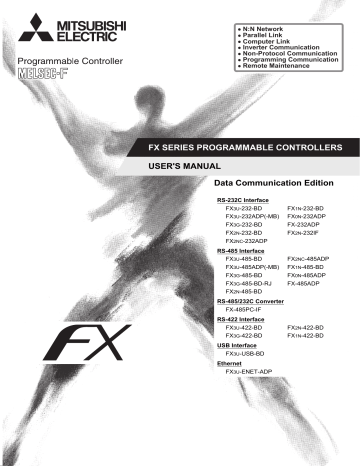
N:N Network Parallel Link Computer Link Inverter Communication Non-Protocol Communication Programming Communication Remote Maintenance FX SERIES PROGRAMMABLE CONTROLLERS USER'S MANUAL Data Communication Edition RS-232C Interface FX3U-232-BD FX3U-232ADP(-MB) FX3G-232-BD FX2N-232-BD FX2NC-232ADP FX1N-232-BD FX0N-232ADP FX-232ADP FX2N-232IF RS-485 Interface FX3U-485-BD FX3U-485ADP(-MB) FX3G-485-BD FX3G-485-BD-RJ FX2N-485-BD FX2NC-485ADP FX1N-485-BD FX0N-485ADP FX-485ADP RS-485/232C Converter FX-485PC-IF RS-422 Interface FX3U-422-BD FX3G-422-BD USB Interface FX3U-USB-BD Ethernet FX3U-ENET-ADP FX2N-422-BD FX1N-422-BD Safety Precaution (Read these precautions before use.) Before installation, operation, maintenance or inspection of this product, thoroughly read through and understand this manual and all of the associated manuals. Also, take care to handle the module properly and safely. This manual classifies the safety precautions into two categories: and . Indicates that incorrect handling may cause hazardous conditions, resulting in death or severe injury. Indicates that incorrect handling may cause hazardous conditions, resulting in medium or slight personal injury or physical damage. Depending on the circumstances, procedures indicated by may also cause severe injury. It is important to follow all precautions for personal safety. Store this manual in a safe place so that it can be taken out and read whenever necessary. Always forward it to the end user. 1. DESIGN PRECAUTIONS • Make sure to have the following safety circuits outside of the PLC to ensure safe system operation even during external power supply problems or PLC failure. Otherwise, malfunctions may cause serious accidents. 1) Most importantly, have the following: an emergency stop circuit, a protection circuit, an interlock circuit for opposite movements (such as normal vs. reverse rotation), and an interlock circuit (to prevent damage to the equipment at the upper and lower positioning limits). 2) Note that when the PLC CPU detects an error, such as a watchdog timer error, during self-diagnosis, all outputs are turned off. Also, when an error that cannot be detected by the PLC CPU occurs in an input/output control block, output control may be disabled. External circuits and mechanisms should be designed to ensure safe machinery operation in such a case. 3) Note that the output current of the service power supply for sensors varies depending on the model and the absence/presence of extension blocks. If an overload occurs, the voltage automatically drops, inputs in the PLC are disabled, and all outputs are turned off. External circuits and mechanisms should be designed to ensure safe machinery operation in such a case. 4) Note that when an error occurs in a relay, triac or transistor output device, the output could be held either on or off. For output signals that may lead to serious accidents, external circuits and mechanisms should be designed to ensure safe machinery operation in such a case. • To maintain the safety of the programmable controller system against unauthorized access from external devices via the network, take appropriate measures. To maintain the safety against unauthorized access via the Internet, take measures such as installing a firewall. • Do not bundle the control line together with or lay it close to the main circuit or power line. As a guideline, lay the control line at least 100mm (3.94") or more away from the main circuit or power line. Noise may cause malfunctions. • Install module so that excessive force will not be applied to the built-in programming port, power connectors, I/O connectors, communication connectors, or communication cables. Failure to do so may result in wire damage/breakage or PLC failure. (1) Safety Precaution (Read these precautions before use.) 2. WIRING PRECAUTIONS • Make sure to cut off all phases of the power supply externally before attempting installation or wiring work. Failure to do so may cause electric shock or damage to the product. • Make sure to attach the terminal cover, offered as an accessory, before turning on the power or initiating operation after installation or wiring work. Failure to do so may cause electric shock. • Make sure to observe the following precautions in order to prevent any damage to the machinery or accidents due to abnormal data written to the PLC under the influence of noise: 1) Do not bundle the main circuit line together with or lay it close to the main circuit, high-voltage line or load line. Otherwise, noise disturbance and/or surge induction are likely to take place. As a guideline, lay the control line at least 100mm (3.94") or more away from the main circuit or high-voltage lines. 2) Ground the shield wire or shield of the shielded cable at one point on the PLC. However, do not use common grounding with heavy electrical systems. • Make sure to properly wire the terminal block in accordance with the following precautions. Failure to do so may cause electric shock, equipment failures, a short-circuit, wire breakage, malfunctions, or damage to the product. - The disposal size of the cable end should follow the dimensions described in the manual. - Tightening torque should follow the specifications in the manual. - Tighten the screws using a Phillips-head screwdriver No.2 (shaft diameter 6mm (0.24") or less). Make sure that the screwdriver does not touch the partition part of the terminal block. • Make sure to properly wire to the terminal block (European type) in accordance with the following precautions. Failure to do so may cause electric shock, equipment failures, a short-circuit, wire breakage, malfunctions, or damage to the product. - The disposal size of the cable end should follow the dimensions described in the manual. - Tightening torque should follow the specifications in the manual. - Twist the end of strand wire and make sure that there are no loose wires. - Do not solder-plate the electric wire ends. - Do not connect more than the specified number of wires or electric wires of unspecified size. - Affix the electric wires so that neither the terminal block nor the connected parts are directly stressed. 3. STARTUP AND MAINTENANCE PRECAUTIONS • Do not touch any terminal while the PLC's power is on. Doing so may cause electric shock or malfunctions. • Before cleaning or retightening terminals, cut off all phases of the power supply externally. Failure to do so may cause electric shock. • Before modifying or disrupting the program in operation or running the PLC, carefully read through this manual and the associated manuals and ensure the safety of the operation. An operation error may damage the machinery or cause accidents. • Do not change the program in the PLC from two or more peripheral equipment devices at the same time. (i.e. from a programming tool and a GOT) Doing so may cause destruction or malfunction of the PLC program. • Do not disassemble or modify the PLC. Doing so may cause fire, equipment failures, or malfunctions. For repair, contact your local Mitsubishi Electric representative. • Turn off the power to the PLC before connecting or disconnecting any extension cable. Failure to do so may cause equipment failures or malfunctions. • Turn of the power to the PLC before attaching or detaching the peripheral devices, expansion boards, special adapters, and expansion memory cassette. Failure to do so may cause equipment failures or malfunctions. (2) FX Series PLC User's Manual - Data Communication Edition FX Series Programmable Controllers User's Manual [Data Communication Edition] Manual number JY997D16901 Manual revision P Date 11/2017 Foreword This manual explains the "serial communication" provided for MELSEC-F FX Series Programmable Controllers and should be read and understood before attempting to install or use the unit. Store this manual in a safe place so that you can take it out and read it whenever necessary. Always forward it to the end user. This manual confers no industrial property rights or any rights of any other kind, nor does it confer any patent licenses. Mitsubishi Electric Corporation cannot be held responsible for any problems involving industrial property rights which may occur as a result of using the contents noted in this manual. © 2005 MITSUBISHI ELECTRIC CORPORATION 1 FX Series PLC User's Manual - Data Communication Edition Outline Precautions • This manual provides information for the use of the FX Series Programmable Controllers. The manual has been written to be used by trained and competent personnel. The definition of such a person or persons is as follows: 1) Any engineer who is responsible for the planning, design and construction of automatic equipment using the product associated with this manual should be of a competent nature, trained and qualified to the local and national standards required to fulfill that role. These engineers should be fully aware of all aspects of safety aspects regarding to automated equipment. 2) Any commissioning or maintenance engineer must be of a competent nature, trained and qualified to the local and national standards required to fulfill the job. These engineers should also be trained in the use and maintenance of the completed product. This includes being familiar with all associated manuals and documentation for the product. All maintenance should be carried out in accordance with established safety practices. 3) All operators of the completed equipment should be trained to use that product in a safe and coordinated manner in compliance with established safety practices. The operators should also be familiar with documentation that is connected with the actual operation of the completed equipment. Note: The term 'completed equipment' refers to a third party constructed device that contains or uses the product associated with this manual • This product has been manufactured as a general-purpose part for general industries, and has not been designed or manufactured to be incorporated in a device or system used in purposes related to human life. • Before using the product for special purposes such as nuclear power, electric power, aerospace, medicine or passenger movement vehicles, consult with Mitsubishi Electric. • This product has been manufactured under strict quality control. However when installing the product where major accidents or losses could occur if the product fails, install appropriate backup or failsafe functions into the system. • When combining this product with other products, please confirm the standards and codes of regulation to which the user should follow. Moreover, please confirm the compatibility of this product with the system, machines, and apparatuses to be used. • If there is doubt at any stage during installation of the product, always consult a professional electrical engineer who is qualified and trained in the local and national standards. If there is doubt about the operation or use, please consult your local Mitsubishi Electric representative. • Since the examples within this manual, technical bulletin, catalog, etc. are used as reference; please use it after confirming the function and safety of the equipment and system. Mitsubishi Electric will not accept responsibility for actual use of the product based on these illustrative examples. • The content, specification etc. of this manual may be changed for improvement without notice. • The information in this manual has been carefully checked and is believed to be accurate; however, if you notice any doubtful point, error, etc., please contact your local Mitsubishi Electric representative. Registration • Microsoft, Windows, Windows NT and Windows Vista are either registered trademarks or trademarks of Microsoft Corporation in the United States and/or other countries. • MODBUS is the registered trademark of Schneider Electric SA. • Ethernet is a trademark of Xerox Corporation. • PC-9800 is the registered trademark of NEC Corporation. • Anywire and ANYWIREASLINK is a trademark of Anywire Corporation. • LONWORKS is a registered trademark of Echelon Corporation in the United States and/or other countries. • DeviceNet is a trademark of ODVA (Open DeviceNet Vender Association, Inc.). • Phillips is a registered trademark of Phillips Screw Company. • Short Mail are trademarks or registered trademarks of NTT DOCOMO, INC. • The company name and the product name to be described in this manual are the registered trademarks or trademarks of each company. 2 FX Series PLC User's Manual - Data Communication Edition Table of Contents Table of Contents SAFETY PRECAUTIONS .................................................................................................. (1) A.Common Items 1. Introduction A-1 1.1 Communication Types .................................................................................................................A-1 1.2 Outline and Features of Communication Types...........................................................................A-3 1.2.1 CC-Link Network ..........................................................................................................................A-3 1.2.2 Ethernet communication...............................................................................................................A-6 1.2.3 N:N Network .................................................................................................................................A-7 1.2.4 Parallel Link ..................................................................................................................................A-8 1.2.5 Computer Link ..............................................................................................................................A-9 1.2.6 Inverter Communication .............................................................................................................A-10 1.2.7 Non-protocol Communication .....................................................................................................A-11 1.2.8 MODBUS Communication..........................................................................................................A-12 1.2.9 Programming Communication ....................................................................................................A-13 1.2.10 Remote Maintenance ...............................................................................................................A-16 1.2.11 CC-Link/LT Network .................................................................................................................A-17 1.2.12 AnyWireASLINK .......................................................................................................................A-18 1.2.13 AS-i system ..............................................................................................................................A-19 1.2.14 Internet Mail Sending................................................................................................................A-20 1.2.15 Short Mail Sending ...................................................................................................................A-21 2. Communication Types and Communication Equipment A-23 2.1 Relationship between Equipment and Communication Types...................................................A-23 2.2 Communication Equipment Applicability Map ............................................................................A-24 2.2.1 2.2.2 2.2.3 2.2.4 2.2.5 2.2.6 2.2.7 2.2.8 FX3U and FX3UC (D, DS, DSS) PLCs........................................................................................A-24 FX3UC-32MT-LT(-2) PLCs .........................................................................................................A-28 FX3G and FX3GC PLCs..............................................................................................................A-30 FX3S PLC ...................................................................................................................................A-32 FX2N and FX2NC PLCs ..............................................................................................................A-34 FX1S, FX1N, and FX1NC PLCs...................................................................................................A-36 FX0N PLCs .................................................................................................................................A-38 FX1, FX2(FX), FX2C, FX0 and FX0S PLCs (reference)..............................................................A-38 2.3 Combination of Communication Equipment (Block Diagram) ....................................................A-40 2.3.1 How to look at combination pages..............................................................................................A-40 2.3.2 For FX3U Series .........................................................................................................................A-41 2.3.3 For FX3UC(D, DS, DSS) Series..................................................................................................A-43 2.3.4 For FX3UC-32MT-LT(-2) ............................................................................................................A-45 2.3.5 For FX3G Series .........................................................................................................................A-47 2.3.6 For FX3GC Series.......................................................................................................................A-50 2.3.7 For FX3S Series .........................................................................................................................A-52 2.3.8 For FX2N Series .........................................................................................................................A-53 2.3.9 For FX2NC Series .......................................................................................................................A-55 2.3.10 For FX1N Series .......................................................................................................................A-57 2.3.11 For FX1NC Series .....................................................................................................................A-59 2.3.12 For FX1S Series .......................................................................................................................A-61 2.3.13 For FX0N Series .......................................................................................................................A-62 2.3.14 For FX2(FX) and FX2C Series (reference) ...............................................................................A-64 3 FX Series PLC User's Manual - Data Communication Edition Table of Contents 3. Outline of Communication Setting in the FX Series A-65 3.1 Setting Method ...........................................................................................................................A-65 3.2 Communication Setting Using Parameter Method (GX Works2) ...............................................A-67 3.2.1 Operating procedure...................................................................................................................A-67 3.2.2 Correspondence between parameter setting and each communication type.............................A-68 3.3 Communication Setting in Parameter Method (FXGP/WIN) ......................................................A-69 3.3.1 Operating procedure...................................................................................................................A-69 3.3.2 Correspondence between parameter setting and each communication type.............................A-71 3.4 Extension of Ports (For FX3G, FX3GC, FX3U, FX3UC) ..............................................................A-72 3.4.1 Extension of Port (For FX3G, FX3GC PLC) ................................................................................A-72 3.4.2 Extension of Port (For FX3U, FX3UC PLC).................................................................................A-74 3.4.3 Limitation when ch1 and ch2 are used at the same time ...........................................................A-75 4. Version Number A-76 4.1 Manufacturer's serial number check method .............................................................................A-76 4.1.1 Checking the nameplate.............................................................................................................A-76 4.1.2 Checking the front of the product ...............................................................................................A-77 4.2 Version check.............................................................................................................................A-77 5. Introduction of Manuals (Type, Reading Method and Acquisition Method) A-78 5.1 Rank and Use Method of This Manual.......................................................................................A-78 5.2 Introduction of Related Manuals ................................................................................................A-79 5.2.1 5.2.2 5.2.3 5.2.4 Manual for communication types in FX PLCs.............................................................................A-79 Manuals related to FX PLCs.......................................................................................................A-79 Communication equipment (option)............................................................................................A-82 Related options for communication ............................................................................................A-84 6. Abbreviations, Generic Names and Terms Used in This Manual 4 A-85 FX Series PLC User's Manual - Data Communication Edition Table of Contents B. N:N Network 1. Outline B-3 1.1 Outline of System.........................................................................................................................B-3 1.2 Procedures Before Operation ......................................................................................................B-4 1.3 Communication Type Applicability in PLC ...................................................................................B-5 1.3.1 1.3.2 1.3.3 1.3.4 Applicable versions.......................................................................................................................B-5 Version check ...............................................................................................................................B-5 How to look at the manufacturer's serial number .........................................................................B-5 Products whose production was stopped .....................................................................................B-5 1.4 Programming Tool Applicability....................................................................................................B-6 1.4.1 For applicable versions.................................................................................................................B-6 1.4.2 For non-applicable versions (setting an alternative model) ..........................................................B-8 2. Specifications B-9 2.1 Communication Specifications (Reference) .................................................................................B-9 2.2 Link Specifications .....................................................................................................................B-10 2.2.1 Link patterns and number of link points in each FX Series ........................................................B-10 2.2.2 Link time .....................................................................................................................................B-11 3. System Configuration and Equipment Selection B-12 3.1 System Configuration.................................................................................................................B-12 3.2 Applicable FX PLC and Communication Equipment..................................................................B-13 4. Wiring B-18 4.1 Wiring Procedure .......................................................................................................................B-18 4.2 Selecting Cables and Terminal Resistors ..................................................................................B-19 4.2.1 4.2.2 4.2.3 4.2.4 Twisted pair cable.......................................................................................................................B-19 10BASE-T cable .........................................................................................................................B-19 Connecting cables ......................................................................................................................B-20 Connecting terminal resistors .....................................................................................................B-22 4.3 Connection Diagram ..................................................................................................................B-23 4.4 Grounding ..................................................................................................................................B-25 5. Communication Setting (Initialization) in FX Programmable Controller B-26 5.1 Check Procedure .......................................................................................................................B-26 5.2 Communication Setting Using Parameter Method (GX Works2) ...............................................B-27 5.2.1 Operating procedure...................................................................................................................B-27 5.3 Communication Settings Using Parameter Method (FXGP/WIN) ..............................................B-28 5.3.1 Operating procedure...................................................................................................................B-28 6. Test Run (Communication Test) B-29 6.1 Test Procedure...........................................................................................................................B-29 6.2 Creating Programs for the Communication Testing ...................................................................B-31 6.2.1 Creating a program for the master station..................................................................................B-31 6.2.2 Creating a program for each slave station..................................................................................B-32 5 FX Series PLC User's Manual - Data Communication Edition Table of Contents 7. Creating Programs 7.1 7.2 7.3 7.4 B-33 Checking Contents of Related Devices......................................................................................B-33 Creating Programs for Master Station (Station No. 0) ...............................................................B-35 Creating Programs for Slave Station (Station No. "n")...............................................................B-38 Cautions on Program Creation...................................................................................................B-40 8. Practical Program Examples B-41 8.1 Practical Example 1 (Pattern 2) .................................................................................................B-41 8.1.1 8.1.2 8.1.3 8.1.4 8.1.5 8.1.6 System configuration example ...................................................................................................B-41 Contents of operations and corresponding program numbers ...................................................B-41 Setting contents..........................................................................................................................B-42 Setting program for master station .............................................................................................B-42 Setting program for slave station (No. 1)....................................................................................B-44 Setting program for slave station (No. 2)....................................................................................B-46 9. Troubleshooting 9.1 9.2 9.3 9.4 9.5 9.6 B-48 Checking FX PLC Version Applicability .....................................................................................B-48 Checking Communication Status Based on LED Indication ......................................................B-48 Checking Installation and Wiring................................................................................................B-48 Checking Sequence Program ....................................................................................................B-48 Checking Setting Contents and Errors.......................................................................................B-50 Checking Absence/Presence of Data Transfer Errors ...............................................................B-50 9.6.1 Check while data transfer sequence is being executed .............................................................B-50 9.6.2 Checking data transfer sequence errors ....................................................................................B-51 9.6.3 Checking error codes .................................................................................................................B-51 10. Related Data B-54 10.1 Related Device List ..................................................................................................................B-54 10.1.1 For FX1N, FX1NC, FX2N, FX2NC, FX3S, FX3G, FX3GC, FX3U and FX3UC PLCs....................B-54 10.1.2 For FX0N and FX1S PLCs ........................................................................................................B-58 10.2 Details of Related Devices .......................................................................................................B-60 10.2.1 Parameter setting [M8038] .......................................................................................................B-60 10.2.2 Channel setting [M8179]...........................................................................................................B-60 10.2.3 Serial communication error [M8063 and M8438]......................................................................B-60 10.2.4 Data transfer sequence error [M8138 to M8190] [M504 to M511]............................................B-61 10.2.5 Data transfer sequence ON [M8191] [M503]............................................................................B-61 10.2.6 Serial communication error code [D8063 and D8438]..............................................................B-61 10.2.7 Corresponding station number settings status [D8173]............................................................B-62 10.2.8 Slave station quantity setting status [D8174]............................................................................B-62 10.2.9 Refresh range setting status [D8175] .......................................................................................B-62 10.2.10 Station number settings [D8176] ............................................................................................B-62 10.2.11 Slave station quantity setting [D8177] ....................................................................................B-63 10.2.12 Refresh range setting [D8178]................................................................................................B-63 10.2.13 Number of retries [D8179] ......................................................................................................B-64 10.2.14 Monitoring time setting [D8180]..............................................................................................B-64 10.2.15 Present link scan time [D8201] [D201] ...................................................................................B-64 10.2.16 Maximum link scan time [D8202] [D202] ................................................................................B-65 10.2.17 Data transfer sequence error count [D8203 to D8210] [D203 to D210] .................................B-65 10.2.18 Data transfer error code [D8211 to D8218] [D211 to D218] ...................................................B-66 10.2.19 Operation mode display [D8419 and D8439] .........................................................................B-67 6 FX Series PLC User's Manual - Data Communication Edition Table of Contents C. Parallel Link 1. Outline C-3 1.1 Outline of System........................................................................................................................ C-3 1.2 Procedures Before Operation ..................................................................................................... C-4 1.3 Communication Type Applicability in PLC .................................................................................. C-5 1.3.1 Applicable versions...................................................................................................................... C-5 1.3.2 Version check .............................................................................................................................. C-5 1.3.3 Products whose production was stopped .................................................................................... C-5 1.4 Programming Tool Applicability................................................................................................... C-6 1.4.1 For applicable versions................................................................................................................ C-6 1.4.2 For non-applicable versions (setting an alternative model) ......................................................... C-8 2. Specifications C-9 2.1 Communication Specifications (Reference) ................................................................................ C-9 2.2 Link Specifications .................................................................................................................... C-10 2.2.1 PLC communication type applicability status ............................................................................ C-10 2.2.2 Link time .................................................................................................................................... C-10 2.3 Link Device Numbers and Number of Points ............................................................................ C-11 2.3.1 For FX0N, FX1S and FX3S Series ............................................................................................. C-11 2.3.2 For FX2(FX), FX2C, FX1N, FX1NC, FX2N, FX2NC, FX3G, FX3GC, FX3U and FX3UC Series.... C-12 3. System Configuration and Selection C-13 3.1 System Configuration................................................................................................................ C-13 3.1.1 Rule for connection.................................................................................................................... C-13 3.2 Configuration of Each Group..................................................................................................... C-14 3.3 Applicable FX PLC and Communication Equipment................................................................. C-18 4. Wiring C-24 4.1 Wiring Procedure ...................................................................................................................... C-24 4.2 Selecting Cables and Terminal Resistors ................................................................................. C-25 4.2.1 4.2.2 4.2.3 4.2.4 4.2.5 Twisted pair cable...................................................................................................................... C-25 10BASE-T cable ........................................................................................................................ C-25 Connecting cables ..................................................................................................................... C-26 Optical fiber cable...................................................................................................................... C-27 Connecting terminal resistors .................................................................................................... C-28 4.3 Connection Diagram ................................................................................................................. C-29 4.3.1 For FX3S, FX3G, FX3GC, FX3U and FX3UC PLCs .................................................................... C-29 4.3.2 For FX1S, FX1N, FX1NC, FX2N and FX2NC PLCs .................................................................... C-30 4.3.3 For FX2(FX) and FX2C PLCs .................................................................................................... C-31 4.4 Grounding ................................................................................................................................. C-31 5. Communication Setting (Initialization) in FX Programmable Controller C-32 5.1 Check Procedure ...................................................................................................................... C-32 5.2 Communication Setting Using Parameter Method (GX Works2) .............................................. C-33 5.2.1 Operating procedure.................................................................................................................. C-33 5.3 Communication Setting Using Parameter Method (FXGP/WIN)............................................... C-34 5.3.1 Operating procedure.................................................................................................................. C-34 7 FX Series PLC User's Manual - Data Communication Edition Table of Contents 6. Test Run (Communication Test) C-35 6.1 Test Procedure.......................................................................................................................... C-35 6.2 Creating Programs for the Communication Test....................................................................... C-36 6.2.1 For FX2(FX), FX2C, FX1N, FX1NC, FX2N, FX2NC, FX3G, FX3GC, FX3U or FX3UC Series....... C-36 6.2.2 For FX0N, FX1S or FX3S Series ................................................................................................ C-37 7. Creating Programs C-38 7.1 Regular Parallel Link Mode ....................................................................................................... C-38 7.1.1 Checking contents of related devices........................................................................................ C-38 7.1.2 Creating programs for master station ........................................................................................ C-40 7.1.3 Creating programs for slave station........................................................................................... C-41 7.2 High Speed Parallel Link Mode................................................................................................. C-42 7.2.1 Checking contents of related devices........................................................................................ C-42 7.2.2 Creating programs for master station ........................................................................................ C-44 7.2.3 Creating programs for slave station........................................................................................... C-45 7.3 Cautions on Program Creation.................................................................................................. C-46 8. Practical Program Examples C-47 8.1 Practical Example 1 (Regular Parallel Link Mode).................................................................... C-47 8.1.1 8.1.2 8.1.3 8.1.4 System configuration example .................................................................................................. C-47 Setting contents......................................................................................................................... C-47 Program for master station ........................................................................................................ C-48 Program for slave station........................................................................................................... C-48 9. Troubleshooting 9.1 9.2 9.3 9.4 9.5 C-49 Checking FX PLC Version Applicability .................................................................................... C-49 Checking Communication Status Based on LED Indication ..................................................... C-49 Checking Installation and Wiring............................................................................................... C-49 Checking Sequence Program ................................................................................................... C-49 Checking Absence/Presence of Errors ..................................................................................... C-51 10. Related Data C-52 10.1 Related Device List ................................................................................................................. C-52 10.2 Details of Related Devices ...................................................................................................... C-53 10.2.1 Parallel link master station declare [M8070]............................................................................ C-53 10.2.2 Channel setting [M8178].......................................................................................................... C-53 10.2.3 Parallel link slave station declare [M8071] .............................................................................. C-53 10.2.4 High-speed parallel link mode [M8162] ................................................................................... C-53 10.2.5 Parallel link ON [M8072].......................................................................................................... C-54 10.2.6 Parallel link setting error [M8073] ............................................................................................ C-54 10.2.7 Serial communication error [M8063 and M8438]..................................................................... C-54 10.2.8 Error judgement time setting [D8070]...................................................................................... C-54 10.2.9 Serial communication error code [D8063 and D8438]............................................................. C-55 10.2.10 Operation mode display [D8419 and D8439] ........................................................................ C-55 8 FX Series PLC User's Manual - Data Communication Edition Table of Contents D. Computer Link 1. Outline D-3 1.1 Outline of System........................................................................................................................ D-3 1.2 Procedures Before Operation ..................................................................................................... D-4 1.3 Communication Type Applicability in PLC .................................................................................. D-5 1.3.1 1.3.2 1.3.3 1.3.4 Applicable versions...................................................................................................................... D-5 Version check .............................................................................................................................. D-5 How to look at the manufacturer's serial number ........................................................................ D-5 Products whose production was stopped .................................................................................... D-5 1.4 Programming Tool Applicability................................................................................................... D-6 1.4.1 For applicable versions................................................................................................................ D-6 1.4.2 For non-applicable versions (setting an alternative model) ......................................................... D-8 2. Specifications D-9 2.1 Communication Specifications (Reference) ................................................................................ D-9 2.2 Link Specifications .................................................................................................................... D-10 2.2.1 Applicable commands and number of device points ................................................................. D-10 2.2.2 Applicable device ranges........................................................................................................... D-11 2.2.3 Link time .................................................................................................................................... D-13 3. System Configuration and Equipment Selection D-14 3.1 System Configuration................................................................................................................ D-14 3.2 Applicable FX PLC and Communication Equipment................................................................. D-15 3.2.1 For communication in accordance with RS-232C ..................................................................... D-15 3.2.2 For communication in accordance with RS-485 ........................................................................ D-21 4. Wiring D-27 4.1 Wiring Procedure ...................................................................................................................... D-28 4.2 Selecting Connection Method ................................................................................................... D-29 4.2.1 For communication in accordance with RS-232C (1-to-1 connection) ...................................... D-29 4.2.2 For communication in accordance with RS-485 (RS-422) (1-to-N connection)......................... D-29 4.3 Selecting Cables and Terminal Resistors (RS-485).................................................................. D-30 4.3.1 4.3.2 4.3.3 4.3.4 Twisted pair cable...................................................................................................................... D-30 10BASE-T cable ........................................................................................................................ D-30 Connecting cables ..................................................................................................................... D-31 Connecting terminal resistors .................................................................................................... D-33 4.4 Connection Diagram for RS-232C ............................................................................................ D-34 4.4.1 Connection diagram between FX PLC and personal computer ................................................ D-34 4.4.2 Connection diagram between FX-485PC-IF and personal computer........................................ D-34 4.5 Connection Diagram for RS-485 and RS-422........................................................................... D-35 4.5.1 One-pair wiring .......................................................................................................................... D-35 4.5.2 Two-pair wiring .......................................................................................................................... D-37 4.5.3 Switching of 1 pair / 2 paired wiring (FX3G-485-BD-RJ) ........................................................... D-39 4.6 Grounding ................................................................................................................................ D-39 9 FX Series PLC User's Manual - Data Communication Edition Table of Contents 5. Communication Setting in FX Programmable Controller D-40 5.1 Communication Setting Methods .............................................................................................. D-40 5.2 Communication Setting Using Parameter Method (GX Works2) .............................................. D-41 5.2.1 Operating procedure.................................................................................................................. D-41 5.3 Communication Settings Using Parameter Method (FXGP/WIN) ............................................. D-43 5.3.1 Operating procedure.................................................................................................................. D-43 6. Control Procedures and Setting Methods D-45 6.1 Data Flow by Link...................................................................................................................... D-45 6.2 Important Points in Computer Link............................................................................................ D-46 6.2.1 Operations of PLC caused by data transfer .............................................................................. D-46 6.3 How to Understand Control Procedure ..................................................................................... D-47 6.4 Basic Formats of Dedicated Protocol........................................................................................ D-47 6.4.1 6.4.2 6.4.3 6.4.4 Control procedure format 1........................................................................................................ D-48 Control procedure format 4........................................................................................................ D-49 Contents of set items in each control procedure (protocol) ....................................................... D-50 Time-out time setting ................................................................................................................. D-53 6.5 Transfer Sequence Time Chart and Communication Time....................................................... D-54 6.5.1 When computer reads data from PLC ....................................................................................... D-54 6.5.2 When computer writes data to PLC........................................................................................... D-54 6.5.3 Transfer time in transfer sequence............................................................................................ D-55 6.6 Transfer Data in Character Area ............................................................................................... D-56 6.6.1 When bit device memory is read or written ............................................................................... D-56 6.6.2 When word device memory is read or written ........................................................................... D-57 7. Commands D-58 7.1 BR Command [Reads Device Memory in 1-Bit Units]............................................................... D-59 7.2 WR Command [Reads Device Memory in 1-Word Units] ......................................................... D-60 7.3 QR Command [Reads Device Memory in 1-Word Units] .......................................................... D-62 7.4 BW Command [Writes Device Memory in 1-Bit Units] .............................................................. D-64 7.5 WW Command [Writes Device Memory in 1-Word Units]......................................................... D-65 7.6 QW Command [Writes Device Memory in 1-Word Units] ......................................................... D-67 7.7 BT Command [Tests Device Memory in 1-Bit Units (by Writing Arbitrarily)] ............................. D-69 7.8 WT Command [Tests Device Memory in 1-Word Units (by Writing Arbitrarily)]........................ D-70 7.9 QT Command [Tests Device Memory in 1-Word Units (by Writing Arbitrarily)] ........................ D-72 7.10 RR/RS Command [Remotely Sets PLC to RUN/STOP Mode] ............................................... D-73 7.10.1 Contents of remote control to set RUN or STOP mode........................................................... D-73 7.10.2 Condition validating remote control to set RUN or STOP mode.............................................. D-73 7.10.3 Remote control specification method and specification examples .......................................... D-74 7.11 PC Command [Reads PLC Model Name]............................................................................... D-75 7.11.1 PLC model name (CPU) and read contents ............................................................................ D-75 7.11.2 Control procedure specification method and specification example........................................ D-75 7.12 GW Command [Offers Global Function] ................................................................................. D-77 7.12.1 Contents of control .................................................................................................................. D-77 7.12.2 Global function control procedure specification method and specification example ............... D-77 7.13 On-demand Function .............................................................................................................. D-78 7.13.1 Special data registers and special auxiliary relays used in on-demand function..................... D-78 7.13.2 Control procedures in on-demand function ............................................................................. D-80 7.13.3 On-demand function specification method and specification examples .................................. D-82 7.14 TT Command [Loop-back Test] .............................................................................................. D-85 10 FX Series PLC User's Manual - Data Communication Edition Table of Contents 8. Troubleshooting 8.1 8.2 8.3 8.4 8.5 D-86 Checking FX PLC Version Applicability .................................................................................... D-86 Checking Communication Status Based on LED Indication ..................................................... D-86 Checking Installation and Wiring............................................................................................... D-86 Checking Sequence Program ................................................................................................... D-86 Checking Error Codes............................................................................................................... D-88 8.5.1 Error codes when NAK is sent................................................................................................... D-88 8.5.2 Error codes in PLC .................................................................................................................... D-89 9. Related Data D-90 9.1 Related Device List ................................................................................................................... D-90 9.2 Details of Related Devices ........................................................................................................ D-92 9.2.1 Serial communication error [M8063 and M8438]....................................................................... D-92 9.2.2 Communication setting keep [M8120] ....................................................................................... D-92 9.2.3 Global function ON [M8126 and M8426] ................................................................................... D-92 9.2.4 On-demand send processing [M8127 and M8427] ................................................................... D-92 9.2.5 On-demand error flag [M8128 and M8428] ............................................................................... D-93 9.2.6 On-demand data word/byte changeover [M8129 and M8429] .................................................. D-93 9.2.7 Serial communication error code [D8063 and D8438]............................................................... D-93 9.2.8 Communication format setting [D8120 and D8420]................................................................... D-94 9.2.9 Station number settings [D8121 and D8421]............................................................................. D-95 9.2.10 On-demand data head device number specification [D8127 and D8427] ............................... D-96 9.2.11 On-demand data quantity specification [D8128 and D8428] ................................................... D-96 9.2.12 Time-out time setting [D8129 and D8429]............................................................................... D-97 9.2.13 Operation mode display [D8419 and D8439] .......................................................................... D-97 9.3 Communication Setting Method Using Sequence Program...................................................... D-98 9.3.1 Setting procedure ...................................................................................................................... D-98 9.3.2 Caution on communication setting using sequence program.................................................... D-98 9.4 ASCII Code Table ..................................................................................................................... D-99 11 FX Series PLC User's Manual - Data Communication Edition Table of Contents E. Inverter Communication 1. Outline E-3 1.1 Outline of System.........................................................................................................................E-3 1.2 Procedures Before Operation ......................................................................................................E-4 1.3 Communication Type Applicability in PLC ...................................................................................E-5 1.3.1 For applicable versions.................................................................................................................E-5 1.3.2 Version check ...............................................................................................................................E-5 1.3.3 How to look at the manufacturer's serial number .........................................................................E-5 1.4 Programming Tool Applicability....................................................................................................E-6 1.4.1 For applicable versions.................................................................................................................E-6 1.4.2 For non-applicable versions (setting an alternative model) ..........................................................E-7 2. Specifications E-8 2.1 Communication Specifications (Reference) .................................................................................E-8 2.2 Connectable Mitsubishi Electric General-purpose Inverters ........................................................E-8 2.3 Link Specifications .......................................................................................................................E-9 2.3.1 When monitoring inverter operations (PLC inverter)................................................................E-9 2.3.2 When controlling inverter operations (PLC inverter) ................................................................E-9 2.3.3 Parameters (PLC inverter).......................................................................................................E-9 2.4 Execution Times in Inverter Communication Instructions ..........................................................E-10 2.4.1 Outline ........................................................................................................................................E-10 2.4.2 Calculation method.....................................................................................................................E-12 2.4.3 Calculation example ...................................................................................................................E-14 3. System Configuration and Selection E-16 3.1 System Configuration.................................................................................................................E-16 3.2 Applicable FX PLC and Communication Equipment..................................................................E-18 4. Wiring E-23 4.1 Wiring Procedure .......................................................................................................................E-24 4.2 Selecting Cables and Connection Devices ................................................................................E-25 4.2.1 4.2.2 4.2.3 4.2.4 S500, E500, A500, F500, V500, D700 and E700 Series (PU connector) ..................................E-25 A500, F500 and V500 Series (FR-A5NR) ..................................................................................E-26 F800, A800, F700 and A700 Series (built-in RS-485 terminal) ..................................................E-27 E700 Series (FR-E7TR) .............................................................................................................E-28 4.3 Connection Cables.....................................................................................................................E-29 4.3.1 10BASE-T cable .........................................................................................................................E-29 4.3.2 Twisted pair cable (recommended) ............................................................................................E-29 4.3.3 Connecting cables ......................................................................................................................E-30 4.4 4.5 4.6 4.7 4.8 Connection Devices (RJ45 Connector and Distributor) .............................................................E-31 Connecting Terminal Resistors ..................................................................................................E-32 Wiring a Shielding Wire (Class-D grounding).............................................................................E-33 Connector in Inverter..................................................................................................................E-34 Connection Diagram ..................................................................................................................E-36 4.8.1 4.8.2 4.8.3 4.8.4 4.8.5 4.8.6 For S500, E500, A500, F500 , V500 and D700 Series (PU connector) .....................................E-36 For A500, F500 and V500 Series (FR-A5NR) ...........................................................................E-38 For E700 Series (PU connector) ................................................................................................E-39 For E700 Series (FR-E7TR) .......................................................................................................E-43 For F800, A800, F700 and A700 Series (built-in RS-485 terminal)............................................E-46 Switching of 1 pair / 2 paired wiring (FX3G-485-BD-RJ) ............................................................E-47 4.9 Grounding ..................................................................................................................................E-47 12 FX Series PLC User's Manual - Data Communication Edition Table of Contents 5. Communication Setting in Inverter E-48 5.1 Communication Port and Applicable Parameters ......................................................................E-48 5.2 S500 Series (When Connected to RS-485 Port)........................................................................E-50 5.2.1 Contents of parameter setting ....................................................................................................E-50 5.2.2 Parameter setting method (reference)........................................................................................E-51 5.3 E500 Series (When Connected to PU Port)...............................................................................E-53 5.3.1 Contents of parameter setting ....................................................................................................E-53 5.3.2 Parameter setting method (reference)........................................................................................E-54 5.4 V500, F500 and A500 Series (Connection to PU Port)..............................................................E-56 5.4.1 Contents of parameter setting ....................................................................................................E-56 5.4.2 Parameter setting method (reference)........................................................................................E-57 5.5 V500, F500 and A500 Series (Connection to FR-A5NR)...........................................................E-59 5.5.1 Contents of parameter setting ....................................................................................................E-59 5.5.2 Parameter setting method (reference)........................................................................................E-59 5.6 E700, D700 Series (when PU port, FR-E7TR is connected) .....................................................E-60 5.6.1 Contents of parameter setting ....................................................................................................E-60 5.6.2 Parameter setting method (reference)........................................................................................E-62 5.7 F700 and A700 Series (when built-in RS-485 terminal is connected)........................................E-64 5.7.1 Contents of parameter setting ....................................................................................................E-64 5.7.2 Parameter setting method (reference)........................................................................................E-65 5.8 F800 and A800 Series (when built-in RS-485 terminal is connected)........................................E-67 5.8.1 Contents of parameter setting ....................................................................................................E-67 5.8.2 Parameter setting method (reference)........................................................................................E-68 5.9 Cautions on Setting....................................................................................................................E-69 6. Communication Setting in FX Programmable Controller E-70 6.1 Parameter Assigning Method.....................................................................................................E-70 6.2 Communication Setting Using Parameter Method (GX Works2) ...............................................E-71 6.2.1 Operating procedure...................................................................................................................E-71 6.3 Communication Setting Using Parameter Method (FXGP/WIN)................................................E-73 6.3.1 Operating procedure...................................................................................................................E-73 7. Creating Programs (FX2N, FX2NC) E-75 7.1 Checking Contents of Related Devices......................................................................................E-75 7.2 Common Items in Inverter Communication Instructions ............................................................E-76 7.2.1 7.2.2 7.2.3 7.2.4 Inverter communication types (EXTR K10 to K13).....................................................................E-76 Function and operation...............................................................................................................E-76 Instruction completion and error flag operation ..........................................................................E-78 Cautions on programming ..........................................................................................................E-80 7.3 Inverter Operation Monitoring Instruction (PLCInverter) [EXTR K10].....................................E-81 7.3.1 Function and operation...............................................................................................................E-81 7.3.2 Inverter instruction codes ...........................................................................................................E-81 7.4 Inverter Operation Control Instruction (PLCInverter) [EXTR K11]..........................................E-82 7.4.1 Function and operation...............................................................................................................E-82 7.4.2 Inverter instruction codes ...........................................................................................................E-82 7.5 Inverter Parameter Reading Instruction (PLCInverter) [EXTR K12] .......................................E-83 7.5.1 Function and operation...............................................................................................................E-83 7.5.2 Inverter parameter number.........................................................................................................E-83 7.5.3 Program example of "second parameter specification code" .....................................................E-83 7.6 Inverter Parameter Writing Instruction (PLCInverter) [EXTR K13] .........................................E-84 7.6.1 Function and operation...............................................................................................................E-84 7.6.2 Inverter parameter number.........................................................................................................E-84 7.6.3 Program example of "second parameter specification code" .....................................................E-84 13 FX Series PLC User's Manual - Data Communication Edition Table of Contents 7.7 Second Parameter Specification Codes ....................................................................................E-85 7.7.1 S500 Series ................................................................................................................................E-85 7.7.2 E500 Series ................................................................................................................................E-85 7.7.3 A500 Series ................................................................................................................................E-86 8. Practical Program Examples (FX2N, FX2NC) E-87 8.1 Practical Example 1 ...................................................................................................................E-87 8.1.1 System configuration example ...................................................................................................E-87 8.1.2 Contents of operation .................................................................................................................E-87 8.1.3 Program example .......................................................................................................................E-88 8.2 Practical Example 2 ...................................................................................................................E-91 8.2.1 System configuration example ...................................................................................................E-91 8.2.2 Contents of operation .................................................................................................................E-91 8.2.3 Program example .......................................................................................................................E-92 9. Creating Programs (FX3S, FX3G, FX3GC, FX3U, FX3UC) E-96 9.1 Differences between FX2N, FX2NC and FX3S, FX3G, FX3GC, FX3U, FX3UC ...........................E-96 9.2 Contents of Related Devices......................................................................................................E-97 9.3 Common Items in Inverter Communication Instructions ............................................................E-98 9.3.1 9.3.2 9.3.3 9.3.4 Inverter communication types (IVCK to IVMC)...........................................................................E-98 Function and operation...............................................................................................................E-98 Instruction completion and error flag operation ........................................................................E-100 Cautions on programming ........................................................................................................E-102 9.4 Inverter Operation Monitoring Instruction (PLCInverter) [FNC270 / IVCK]...........................E-104 9.4.1 Function and operation.............................................................................................................E-104 9.4.2 Inverter instruction codes .........................................................................................................E-104 9.5 Inverter Operation Control Instruction (PLCInverter) [FNC271 / IVDR]................................E-105 9.5.1 Function and operation.............................................................................................................E-105 9.5.2 Inverter instruction codes .........................................................................................................E-105 9.6 Inverter Parameter Reading (PLCInverter) [FNC272 / IVRD]...............................................E-106 9.6.1 Function and operation.............................................................................................................E-106 9.6.2 Inverter instruction codes .........................................................................................................E-106 9.6.3 Program example of "second parameter specification code" ...................................................E-106 9.7 Inverter Parameter Writing (PLCInverter) [FNC273 / IVWR] ................................................E-108 9.7.1 Function and operation.............................................................................................................E-108 9.7.2 Inverter instruction codes .........................................................................................................E-108 9.7.3 Program example of "second parameter specification code" ...................................................E-108 9.8 Inverter Parameter Batch Writing (PLCInverter) [FNC274 / IVBWR] ...................................E-109 9.8.1 Function and operation.............................................................................................................E-109 9.9 Controls Operations and Monitors Operations of an Inverter with a Single Command(PLCInverter)[FNC275 / IVMC]............................................................................E-110 9.9.1 Function and operation.............................................................................................................E-110 9.9.2 Applicable inverters ..................................................................................................................E-111 9.9.3 Applicable programming tool ....................................................................................................E-111 9.10 Second Parameter Specification Codes ................................................................................E-112 9.10.1 S500 Series ............................................................................................................................E-112 9.10.2 E500 Series ............................................................................................................................E-112 9.10.3 A500 Series ............................................................................................................................E-113 9.10.4 F500 Series ............................................................................................................................E-114 9.10.5 V500 Series ............................................................................................................................E-114 9.10.6 F700 Series ............................................................................................................................E-114 9.10.7 A700 Series ............................................................................................................................E-115 9.10.8 E700 and D700 Series ...........................................................................................................E-116 9.10.9 F800 Series ............................................................................................................................E-117 9.10.10 A800 Series ..........................................................................................................................E-118 14 FX Series PLC User's Manual - Data Communication Edition Table of Contents 10. Practical Program Examples (FX3S, FX3G, FX3GC, FX3U, FX3UC) E-119 10.1 Practical Example 1 ...............................................................................................................E-119 10.1.1 System configuration example ...............................................................................................E-119 10.1.2 Contents of operation .............................................................................................................E-119 10.1.3 Program example ...................................................................................................................E-120 10.2 Practical Example 2 ...............................................................................................................E-125 10.2.1 System configuration example ...............................................................................................E-125 10.2.2 Contents of operation .............................................................................................................E-125 10.2.3 Program example ...................................................................................................................E-126 11. Troubleshooting 11.1 11.2 11.3 11.4 E-134 Checking FX PLC Version Applicability (FX2N and FX2NC Series) .......................................E-134 Checking Communication Status Based on LED Indication ..................................................E-134 Checking Installation ..............................................................................................................E-134 Checking Sequence Program ................................................................................................E-134 11.4.1 Checking inverter operation status .........................................................................................E-135 11.5 Checking Absence/Presence of Errors ..................................................................................E-136 11.6 Error Codes............................................................................................................................E-136 12. Related Data E-139 12.1 Related Device List (FX2N, FX2NC) .......................................................................................E-139 12.2 Details of Related Devices (FX2N, FX2NC)............................................................................E-140 12.2.1 Instruction execution complete [M8029] .................................................................................E-140 12.2.2 Extension ROM cassette check [M8104]................................................................................E-140 12.2.3 Communication port busy [M8155].........................................................................................E-140 12.2.4 Communication error or parameter error [M8156]..................................................................E-140 12.2.5 Communication error latch [M8157] .......................................................................................E-141 12.2.6 Extension ROM cassette type code [D8104]..........................................................................E-141 12.2.7 Extension ROM cassette version [D8105]..............................................................................E-141 12.2.8 Inverter response waiting time [D8154] ..................................................................................E-141 12.2.9 Step number of instruction using communication port [D8155] ..............................................E-141 12.2.10 Error code [D8156] ...............................................................................................................E-142 12.2.11 Error occurrence step number latch [D8157]........................................................................E-143 12.3 Related Device List (FX3S, FX3G, FX3GC, FX3U, FX3UC) ....................................................E-144 12.4 Details of Related Devices (FX3S, FX3G, FX3GC, FX3U, FX3UC) .........................................E-145 12.4.1 Instruction execution complete [M8029] .................................................................................E-145 12.4.2 Serial communication error [M8063 and M8438]....................................................................E-145 12.4.3 Inverter communication ON [M8151 and M8156]...................................................................E-145 12.4.4 Inverter communication error [M8152, M8153, M8157 and M8158].......................................E-146 12.4.5 IVBWR instruction error [M8154 and M8159] (only in FX3U and FX3UC PLCs) ....................E-146 12.4.6 Serial communication error code [D8063 and D8438]............................................................E-146 12.4.7 Inverter response waiting time [D8150 and D8155] ...............................................................E-146 12.4.8 Step number of instruction using communication port [D8151 and D8156] ...........................E-147 12.4.9 Inverter communication error code [D8152 and D8157].........................................................E-147 12.4.10 Inverter communication error occurrence step [D8153 and D8158].....................................E-150 12.4.11 IVBWR instruction error parameter number [D8154 and D8159] (only in FX3U and FX3UC PLCs)...........................................................................................E-150 12.4.12 Operation mode display [D8419 and D8439] .......................................................................E-150 12.5 FREQROL Inverter Parameter List ........................................................................................E-151 12.5.1 12.5.2 12.5.3 12.5.4 Parameters in V500, F500, A500, E500, and S500 Series ....................................................E-151 Parameters in F700, A700, E700 and D700 Series ...............................................................E-173 Parameters in F800 and A800 Series ....................................................................................E-190 Communication parameters ...................................................................................................E-208 15 FX Series PLC User's Manual - Data Communication Edition Table of Contents F.Non-Protocol Communication (RS/RS2 Instruction) 1. Outline F-3 1.1 Outline of System.........................................................................................................................F-3 1.2 Procedures Before Operation ......................................................................................................F-7 1.3 Communication Type Applicability in PLC ...................................................................................F-8 1.3.1 1.3.2 1.3.3 1.3.4 Applicable versions.......................................................................................................................F-8 Version check ...............................................................................................................................F-8 How to look at the manufacturer's serial number .........................................................................F-8 Products whose production was stopped .....................................................................................F-8 1.4 Programming Tool Applicability....................................................................................................F-9 1.4.1 For applicable versions.................................................................................................................F-9 1.4.2 For non-applicable versions (setting an alternative model) ........................................................F-11 2. Specifications F-12 2.1 Communication Specifications (Reference) ...............................................................................F-12 2.2 Data Communication Specifications ..........................................................................................F-13 2.2.1 Communication type applicability in PLC ...................................................................................F-13 2.3 Number of Transfer Data ...........................................................................................................F-14 3. System Configuration and Selection F-15 3.1 System Configuration.................................................................................................................F-15 3.2 Applicable FX PLC and Communication Equipment..................................................................F-16 3.2.1 For communication in accordance with RS-232C ......................................................................F-16 3.2.2 For communication in accordance with RS-485 .........................................................................F-22 4. Wiring F-27 4.1 Wiring Procedure .......................................................................................................................F-27 4.2 Selecting Cables and Terminal Resistors ..................................................................................F-28 4.2.1 4.2.2 4.2.3 4.2.4 4.2.5 When using ch0 in FX3G, FX3GC PLC .......................................................................................F-28 Twisted pair cable.......................................................................................................................F-28 10BASE-T cable .........................................................................................................................F-29 Connecting cables ......................................................................................................................F-30 Connecting terminal resistors .....................................................................................................F-32 4.3 Connection Diagram ..................................................................................................................F-33 4.3.1 Connector pin arrangement in communication equipment operating in accordance with RS-232C .............................................................................................................................F-33 4.3.2 Wiring for communication in accordance with RS-232C ............................................................F-33 4.3.3 Wiring for communication in accordance with RS-485 ...............................................................F-35 4.4 Grounding ..................................................................................................................................F-39 5. Communication Setting in FX Programmable Controller F-40 5.1 Communication Setting Method Mechanism..............................................................................F-40 5.2 Communication Setting Using Parameter Method (GX Works2) ...............................................F-41 5.2.1 Operating procedure...................................................................................................................F-41 5.3 Communication Setting Using Parameter Method (FXGP/WIN)................................................F-43 5.3.1 Operating procedure...................................................................................................................F-43 16 FX Series PLC User's Manual - Data Communication Edition Table of Contents 6. Creating Programs (RS Instruction) F-45 6.1 Checking Contents of Related Devices......................................................................................F-45 6.2 How to Use RS Instruction .........................................................................................................F-46 6.2.1 6.2.2 6.2.3 6.2.4 6.2.5 Applicable frames .......................................................................................................................F-46 Function and operation...............................................................................................................F-47 Send/receive data and amount of data.......................................................................................F-48 Operation when data is sent.......................................................................................................F-50 Operation when data is received ................................................................................................F-50 6.3 Operation of Control Line ...........................................................................................................F-52 6.3.1 FX2N (before Ver. 2.00), FX2(FX), FX2C, FX0N, FX1S, FX1N and FX1NC PLCs .......................F-52 6.3.2 FX2N (Ver. 2.00 or later), FX2NC, FX3S, FX3G, FX3GC, FX3U and FX3UC PLCs......................F-54 6.4 Important Points in Creating Programs ......................................................................................F-56 6.5 Communication Error .................................................................................................................F-56 7. Practical Program Example (RS Instruction) F-57 7.1 Example of Printing Using RS Instruction (Using RS-232C Connection)...................................F-57 8. Creating Programs (RS2 Instruction) F-59 8.1 Checking Contents of Related Devices......................................................................................F-59 8.2 How to Use RS2 Instruction .......................................................................................................F-62 8.2.1 8.2.2 8.2.3 8.2.4 8.2.5 8.2.6 Applicable frames .......................................................................................................................F-63 Function and operation...............................................................................................................F-65 Send/receive data and amount of data.......................................................................................F-66 Operation when data is sent.......................................................................................................F-68 Operation when data is received ................................................................................................F-68 Sum check code .........................................................................................................................F-71 8.3 Operation of Control Line ...........................................................................................................F-72 8.4 Important Points in Creating Programs ......................................................................................F-75 8.5 Communication Error .................................................................................................................F-75 9. Practical Program Example (RS2 Instruction) F-76 9.1 Example of Printing Using RS2 Instruction (Using RS-232C Connection).................................F-76 10. When Combined with Another Communication F-78 10.1 Other Communication Type Used Together ............................................................................F-78 10.2 When Combined with Programming Communication ..............................................................F-79 10.2.1 For FX2N and FX2NC PLCs......................................................................................................F-79 10.2.2 For FX3S, FX3G, FX3GC, FX3U and FX3UC PLCs ...................................................................F-80 10.3 10.4 10.5 10.6 When Combined with Computer Link Communication.............................................................F-81 When Combined with Programming Communication ..............................................................F-82 Using RS2 Instruction and Computer Link Communication Together......................................F-83 Communication Setting Method Using Sequence Program.....................................................F-84 10.6.1 Communication setting for RS instruction ................................................................................F-84 10.6.2 Communication setting for RS2 instruction ..............................................................................F-86 17 FX Series PLC User's Manual - Data Communication Edition Table of Contents 11. Troubleshooting 11.1 11.2 11.3 11.4 F-87 Checking FX PLC Version Applicability ...................................................................................F-87 Checking Communication Status Based on LED Indication ....................................................F-87 Checking Installation ................................................................................................................F-87 Checking Sequence Program ..................................................................................................F-88 11.4.1 Checking communication port settings (in FX3S, FX3G, FX3GC, FX3U and FX3UC PLCs)......F-89 11.5 Checking the Absence/Presence of Errors ..............................................................................F-89 12. Related Data F-90 12.1 Related Device List (RS Instruction) ........................................................................................F-90 12.2 Details of related devices (RS instruction) ...............................................................................F-91 12.2.1 Serial communication error [M8063].........................................................................................F-91 12.2.2 Communication setting keep [M8120] ......................................................................................F-91 12.2.3 Sending wait flag [M8121] ........................................................................................................F-91 12.2.4 Sending request [M8122] .........................................................................................................F-91 12.2.5 Receiving complete flag [M8123] .............................................................................................F-92 12.2.6 Carrier detection flag [M8124] ..................................................................................................F-92 12.2.7 Time-out check flag [M8129] ....................................................................................................F-92 12.2.8 Serial communication error code [D8063] ................................................................................F-93 12.2.9 Communication format setting [D8120] ....................................................................................F-94 12.2.10 Remaining amount of data to be sent [D8122] .......................................................................F-94 12.2.11 Amount of data already received [D8123] ..............................................................................F-95 12.2.12 Header [D8124] ......................................................................................................................F-95 12.2.13 Terminator [D8125].................................................................................................................F-95 12.2.14 Time-out time setting time [D8129].........................................................................................F-95 12.2.15 Communication parameter display [D8405] ...........................................................................F-95 12.2.16 Operation mode display [D8419] ............................................................................................F-96 12.3 Related Devices (RS2 Instruction) ...........................................................................................F-96 12.4 Details of Related Devices (RS2 Instruction) ...........................................................................F-97 12.4.1 Serial communication error [M8062, M8063 and M8438].........................................................F-97 12.4.2 Sending wait flag [M8371, M8401 and M8421] ........................................................................F-98 12.4.3 Sending request [M8372, M8402 and M8422] .........................................................................F-98 12.4.4 Receiving complete flag [M8373, M8403 and M8423] .............................................................F-98 12.4.5 Carrier detection flag [M8404 and M8424] ...............................................................................F-99 12.4.6 Data set ready (DSR) flag [M8405 and M8425] .......................................................................F-99 12.4.7 Time-out check flag [M8379, M8409 and M8429] ....................................................................F-99 12.4.8 Serial communication error code [D8062, D8063 and D8438] ...............................................F-100 12.4.9 Communication format setting [D8370, D8400 and D8420] ...................................................F-101 12.4.10 Amount of remaining send data [D8372, D8402 and D8422]...............................................F-102 12.4.11 Amount of data already received [D8373, D8403 and D8423] .............................................F-102 12.4.12 Communication parameter display [D8405 and D8425].......................................................F-102 12.4.13 Time-out time setting [D8379, D8409 and D8429] ...............................................................F-102 12.4.14 Header [D8380, D8381, D8410, D8411, D8430 and D8431] ...............................................F-103 12.4.15 Terminator [D8382, D8383, D8412, D8413, D8432 and D8433]..........................................F-103 12.4.16 Receiving sum (receive data) [D8384, D8414 and D8434] ..................................................F-104 12.4.17 Receiving sum (calculation result) [D8385, D8415 and D8435] ...........................................F-104 12.4.18 Sending sum [D8386, D8416 and D8436]............................................................................F-104 12.4.19 Operation mode display [D8389, D8419 and D8439]...........................................................F-105 12.5 ASCII Code Table ..................................................................................................................F-106 18 FX Series PLC User's Manual - Data Communication Edition Table of Contents G.Non-Protocol Communication (FX2N-232IF) 1. Outline G-3 1.1 Features ...................................................................................................................................... G-3 1.2 Procedures Before Operation ..................................................................................................... G-4 1.3 Communication Type Applicability in PLC .................................................................................. G-5 1.3.1 Applicable versions...................................................................................................................... G-5 1.3.2 Products whose production was stopped .................................................................................... G-5 1.4 Programming Tool Applicability................................................................................................... G-6 1.4.1 For applicable versions................................................................................................................ G-6 1.4.2 For non-applicable versions (setting an alternative model) ......................................................... G-7 2. Specification G-8 2.1 Communication Specifications .................................................................................................... G-8 3. System Configuration and Selection G-9 3.1 System Configuration.................................................................................................................. G-9 3.2 Applicable FX PLC and Communication Equipment................................................................... G-9 3.3 Connection to PLC .................................................................................................................... G-10 4. Wiring G-12 4.1 Pin Arrangement ....................................................................................................................... G-12 4.2 Connection to External Equipment with Terminal Specifications (without Control Line)........... G-12 4.3 Connection to External Equipment with Terminal Specifications (with Control Line)................ G-13 4.3.1 Standard RS-232C mode .......................................................................................................... G-13 4.3.2 Interlink connection mode.......................................................................................................... G-13 4.4 Connection to External Equipment with Modem Specifications ................................................ G-13 19 FX Series PLC User's Manual - Data Communication Edition Table of Contents 5. Creating Programs G-14 5.1 Outline of Communication between FX PLC and 232IF ........................................................... G-14 5.1.1 For FROM and TO instructions ................................................................................................. G-14 5.1.2 For direct specification of buffer memory (U\G) .................................................................. G-14 5.2 FROM and TO Instructions ....................................................................................................... G-15 5.2.1 FROM instruction....................................................................................................................... G-15 5.2.2 TO instruction ............................................................................................................................ G-16 5.3 Direct Specification of Buffer Memory (U\G)....................................................................... G-17 5.4 Buffer Memory (BFM)................................................................................................................ G-18 5.4.1 Buffer memory list...................................................................................................................... G-18 5.4.2 Communication format <BFM #0>............................................................................................. G-20 5.4.3 Command <BFM #1> ................................................................................................................ G-24 5.4.4 Maximum number of receivable bytes <BFM #2> ..................................................................... G-25 5.4.5 Receiving timeout time <BFM #3> ............................................................................................ G-25 5.4.6 Sending header <BFM #5 (highest-order 2 bytes) and BFM #4 (lowest-order 2 bytes)>.......... G-25 5.4.7 Sending terminator <BFM #7 (highest-order 2 bytes) and BFM #6 (lowest-order 2 bytes)>..... G-25 5.4.8 Receiving header <BFM #9 (highest-order 2 bytes) and BFM #8 (lowest-order 2 bytes)> ....... G-25 5.4.9 Receiving terminator <BFM #11 (highest-order 2 bytes) and BFM #10 (lowest-order 2 bytes)>... G-26 5.4.10 Receiving suspension waiting time <BFM #12>...................................................................... G-26 5.4.11 Amount of remaining send data <BFM #13>........................................................................... G-26 5.4.12 Amount of received data buffers <BFM #14>.......................................................................... G-26 5.4.13 Sending sum result <BFM #15> .............................................................................................. G-27 5.4.14 Receiving sum result <BFM #16> ........................................................................................... G-27 5.4.15 Time from CS ON to sending start <BFM #20>....................................................................... G-27 5.4.16 Time from actual sending completion to RS OFF <BFM #21>................................................ G-27 5.4.17 Status <BFM #28>................................................................................................................... G-28 5.4.18 Error code <BFM #29> ............................................................................................................ G-29 5.4.19 Model code <BFM #30> .......................................................................................................... G-29 5.4.20 Number of bytes to be sent <BFM #1000>.............................................................................. G-29 5.4.21 Send data buffer <BFM #1001 to 1256> ................................................................................. G-29 5.4.22 Number of received bytes <BFM #2000>................................................................................ G-29 5.4.23 Receive data buffer <BFM #2001 to 2256>............................................................................. G-29 5.4.24 Preliminary receive data buffer for interlink connection mode <BFM #2257 to 2271> ............ G-29 5.5 Operation of Control Line .......................................................................................................... G-30 5.5.1 When control line is not provided [BFM #0, (b9, b8) = (0, 0)].................................................... G-30 5.5.2 When control line is in standard RS-232C mode [BFM #0, (b9, b8) = (0, 1)] ............................ G-31 5.5.3 When control line is in RS-232C interlink mode [BFM #0, (b9, b8) = (1, 1)].............................. G-32 6. Practical Program Examples G-33 6.1 Example of Sending/Receiving 16-Bit Buffer Length Data........................................................ G-33 6.2 Sending/Receiving 8-Bit Buffer Length Data............................................................................. G-37 7. Troubleshooting G-41 7.1 Check Items .............................................................................................................................. G-41 7.2 Error Codes............................................................................................................................... G-41 20 FX Series PLC User's Manual - Data Communication Edition Table of Contents H.Programming Communication 1. Outline H-3 1.1 Outline of System........................................................................................................................ H-3 1.2 Procedures Before Operation ..................................................................................................... H-4 1.3 Communication Type Applicability in PLC .................................................................................. H-5 1.3.1 Applicable PLC ............................................................................................................................ H-5 1.3.2 Products whose production was stopped .................................................................................... H-5 1.4 Programming Tool Applicability................................................................................................... H-6 1.4.1 For applicable versions................................................................................................................ H-6 1.4.2 For non-applicable versions (setting an alternative model) ......................................................... H-8 2. System Configuration and Selection H-9 2.1 System Configuration.................................................................................................................. H-9 2.1.1 2.1.2 2.1.3 2.1.4 For communication equipment operating in accordance with RS-422 ........................................ H-9 For communication equipment operating in accordance with RS-232C.................................... H-10 For communication equipment operating in accordance with USB ........................................... H-10 For Ethernet adapter ................................................................................................................. H-11 2.2 Applicable FX PLC and Communication Equipment................................................................. H-12 2.3 Caution on Selection ................................................................................................................. H-23 2.3.1 When using 422BD.................................................................................................................... H-23 2.3.2 When using 232BD or 232ADP ................................................................................................. H-24 2.3.3 Other cautions ........................................................................................................................... H-24 3. Selecting Connection Cables H-25 3.1 Connection Procedure .............................................................................................................. H-25 3.2 Connector Shape in Each Product............................................................................................ H-26 3.3 Combinations of Connection Cables......................................................................................... H-27 3.3.1 Handy programming panel ........................................................................................................ H-27 3.3.2 Personal computer .................................................................................................................... H-28 4. Connection Cables and Interfaces H-32 4.1 Simplified Tables....................................................................................................................... H-32 4.1.1 Cable connector shape correspondence table .......................................................................... H-32 4.1.2 Cable combination simplified table ............................................................................................ H-33 4.2 Cable Connection Diagrams ..................................................................................................... H-35 4.2.1 Personal computer connection cable - No. A ............................................................................ H-35 4.2.2 Connector conversion cable (commercial product) - No. B ....................................................... H-37 4.2.3 FX-10P/FX-20P/FX-30P connection cable - No. C.................................................................... H-37 5. Communication Setting (Initialization) in FX Programmable Controller H-38 5.1 Check Procedure ...................................................................................................................... H-38 5.2 Communication Setting Using Parameter Method (GX Works2) .............................................. H-39 5.2.1 Operating procedure.................................................................................................................. H-39 5.3 Communication Setting Using Parameter Method (FXGP/WIN)............................................... H-40 5.3.1 Operating procedure.................................................................................................................. H-40 21 FX Series PLC User's Manual - Data Communication Edition Table of Contents 6. Connection Setting for Personal Computer H-41 6.1 Connection Setting (GX Works2) .............................................................................................. H-41 6.1.1 Setting RS-232C or USB, communication port, and transmission speed.................................. H-42 6.1.2 Setting for using GOT transparent function ............................................................................... H-44 6.1.3 Setting communication time check and number of retries......................................................... H-45 6.2 Connection Setting (FXGP/WIN)............................................................................................... H-46 6.2.1 Setting communication port and transmission speed ................................................................ H-46 6.3 Communication Test (GX Works2) ........................................................................................... H-47 7. Troubleshooting 7.1 7.2 7.3 7.4 7.5 7.6 7.7 7.8 7.9 22 H-48 Checking PLC Version Applicability .......................................................................................... H-48 Checking Programming Tool Applicability................................................................................. H-48 Checking Communication Status Based on LED Indication ..................................................... H-48 Checking Installation ................................................................................................................. H-48 Checking Parameters in PLC.................................................................................................... H-48 Checking Sequence Program ................................................................................................... H-48 Checking Programming Tool Setting ........................................................................................ H-50 Checking Absence/Presence of Errors ..................................................................................... H-50 Operation mode display [D8419 and D8439] (FX3S, FX3G, FX3GC, FX3U, FX3UC) ................ H-51 FX Series PLC User's Manual - Data Communication Edition Table of Contents I.Remote Maintenance 1. Outline I-3 1.1 Outline of System.......................................................................................................................... I-3 1.1.1 Maintenance for programs in PLC................................................................................................. I-3 1.1.2 File transfer between personal computers (supported only by FXGP/WIN).................................. I-4 1.2 Procedures Before Operation ....................................................................................................... I-5 1.3 Communication Type Applicability in PLC .................................................................................... I-6 1.3.1 Applicable versions........................................................................................................................ I-6 1.3.2 Version check ................................................................................................................................ I-6 1.3.3 Products whose production was stopped ...................................................................................... I-6 1.4 Programming Tool Applicability..................................................................................................... I-7 1.4.1 Programming tool for setting modem connected to PLC............................................................... I-7 1.4.2 Programming software for remote maintenance ......................................................................... I-11 1.4.3 Cautions on using FXGP/WIN ..................................................................................................... I-12 2. Specifications I-13 2.1 Communication Specifications (Reference) ................................................................................ I-13 3. System Configuration and Selection I-14 3.1 System Configuration.................................................................................................................. I-14 3.2 Setting Applicable FX PLC and Communication Equipment....................................................... I-15 3.3 Selecting Modem ........................................................................................................................ I-20 3.3.1 List of modems whose operations are confirmed ........................................................................ I-21 4. Wiring I-23 4.1 Wiring Procedure ........................................................................................................................ I-23 4.2 Connection Diagram ................................................................................................................... I-24 5. How to Setup Modems on the PLC Side I-25 5.1 Setting Using GX Works2 ........................................................................................................... I-25 5.1.1 Setting communication by way of RS-232C port ......................................................................... I-25 5.1.2 Modem initialization setting using parameter method ................................................................. I-27 5.1.3 Setting AT command for unregistered modem............................................................................ I-29 5.2 Setting Using FXGP/WIN ............................................................................................................ I-33 5.2.1 Setting communication by way of RS-232C port ......................................................................... I-33 5.2.2 Modem initialization setting using parameter method ................................................................. I-34 5.2.3 Setting AT command for unregistered modem............................................................................ I-35 5.3 Cautions on Use.......................................................................................................................... I-37 6. How to Setup Modems on the PC Side for Remote Access I-38 6.1 Setting Using GX Works2 ........................................................................................................... I-38 6.1.1 Registering AT command for connected modem ........................................................................ I-38 6.1.2 Creating telephone directory (if necessary)................................................................................. I-40 6.2 Setting Using FXGP/WIN ............................................................................................................ I-42 6.2.1 Registering AT command for connected modem ........................................................................ I-42 6.2.2 Registering line connection destination ....................................................................................... I-45 23 FX Series PLC User's Manual - Data Communication Edition Table of Contents 7. Connecting Line I-46 7.1 Preparing for Connection of PLC ................................................................................................ I-46 7.2 Line Connection Procedure......................................................................................................... I-47 7.2.1 For GX Works2............................................................................................................................ I-47 7.2.2 For FXGP/WIN ............................................................................................................................ I-51 8. Troubleshooting 8.1 8.2 8.3 8.4 8.5 8.6 I-54 Checking FX PLC Applicability.................................................................................................... I-54 Checking Programming Tool Applicability................................................................................... I-54 Checking Communication Status Based on LED Indication ....................................................... I-54 Checking Installation ................................................................................................................... I-54 Checking Modem Specifications ................................................................................................. I-55 Checking Setting in PLC ............................................................................................................. I-55 8.6.1 Checking parameters in PLC....................................................................................................... I-55 8.6.2 Checking AT command setting.................................................................................................... I-56 8.6.3 Checking sequence program....................................................................................................... I-57 8.7 Checking Programming Tool Setting .......................................................................................... I-58 8.8 Checking Absence/Presence of Errors ....................................................................................... I-58 8.9 Operation mode display [D8419 and D8439] (FX3S, FX3G, FX3GC, FX3U, FX3UC) .................. I-59 9. Related Information I-60 9.1 ASCII Code Table ....................................................................................................................... I-60 Appendix A: Discontinued models 24 Apx.-1 FX Series PLC User's Manual - Data Communication Edition Common Items 1 Introduction 1.1 Communication Types A Common Items 1. Introduction 1.1 Communication Types C Reference subsection Function Application N:N Network Computer link MODBUS communication Application Function Application Function Application Data acquisition and centralized control. Communicates with and controls Mitsubishi Electric inverter FREQROL. Operation monitoring, writing of control values, referencing and changing parameters, etc. Enables MODBUS communication with MODBUS-compatible equipment in accordance with RS-232C or RS-485. Line control in the decentralized or centralized method. Application Function Application Receives and sends data from/to various pieces of equipment with an RS-232C or RS-485 interface in non-protocol procedures. Data reception and sending from/to a personal computer, bar code reader, printer and other various measuring instruments. Application Application 1.2.7 Adds RS-232C, RS-422, USB and Ethernet ports in addition to the provided RS-422 port in PLCs. Simultaneously connection of two display units, programming tools, etc. 1.2.9 Connects with a PLC located in a remote location through a modem and telephone line to enable program transfer and remote monitoring access. Maintenance of sequence programs in FX PLCs. 1.2.10 H I Apx.A A-1 Discontinued models Function Reference subsection G Remote Maintenance Remote maintenance Function 1.2.2 Reference subsection Sequence program Programming communication 1.2.8 Programming Communication Connects the FX PLC to a high-order system such as personal computer or workstation via Ethernet (100BASE-TX or 10BASE-T) using TCP/IP or UDP/IP communication protocol. Line control in the decentralized or centralized method and information transfer from/to the host network. General-purpose serial communication Non-protocol communication 1.2.6 F Non-Protocol Communication (FX2N-232IF) Ethernet 1.2.5 Reference subsection Ethernet communication Function 1.2.4 E Non-Protocol Communication (RS/RS2 Instruction) Inverter communication Function 1.2.3 D Inverter Communication Parallel link Function Application Function Application Line control in the decentralized or centralized method and information transfer from/to the host network. Easily enables data link between FX PLCs. Line control in the decentralized or centralized method. Easily enables data link between FX PLCs. Line control in the decentralized or centralized method. Connects a personal computer or another computer as the master station, and connects FX PLCs as slave stations. Protocols in a computer support computer link protocol formats 1 and 4. 1.2.1 Computer Link CC-Link • Connects FX PLCs as remote device stations to the CC-Link system whose master station is a MELSEC A/QnA PLC. • Connects FX PLCs as remote device stations and intelligent device stations to the CC-Link system whose master station is a MELSEC Q PLC. • Constructs a CC-Link system whose master station is an FX PLC. Parallel Link The table below shows the communication types supported by the FX Series. Link B N:N Network This manual explains the communication types supported by FX PLCs. This chapter explains the serial communication (in accordance with RS-232C, RS-485/RS-422), various link communication types, etc. and states the applicable FX PLCs. FX Series PLC User's Manual - Data Communication Edition Common Items 1 Introduction 1.1 Communication Types Reference subsection I/O link CC-Link/LT (built in FX3UC-32MTLT(-2)) AnyWireASLINK Function Constructs a CC-Link/LT system whose master station is an FX PLC. Application Wire-conserving network inside control panel and unit. Function Application AS-i system Function Application MELSEC I/O link Function Application Constructs an AnyWireASLINK system whose master station is an FX PLC. Wire-conserving network inside control panel and unit. Constructs an AS-i (Actuator Sensor Interface) system whose master block is an FX PLC. Wire-conserving network inside control panel and unit. Installs remote I/O units near I/O equipment in remote locations to conserve wiring. ON/OFF control of I/O equipment in a remote location. Internet mail Application Short mail A-2 Function Application 1.2.12 1.2.13 — Reference subsection Electronic mail sending Function 1.2.11 Sends internet mail to personal computers and cellular phones using the RS-232C communication in PLCs. Monitoring of unmanned facilities, facilities located in remote locations and facilities inside factories. Sends short mails to cellular phones in the NTT DoCoMo network. Notice of material shortage, error contents, operating time, etc. 1.2.14 1.2.15 FX Series PLC User's Manual - Data Communication Edition 1 Introduction Common Items A Outline and Features of Communication Types Common Items 1.2 1.2 Outline and Features of Communication Types This section outlines the communication types supported by FX PLCs. 1.2.1 CC-Link Network B 1. Outline C Parallel Link 1) When the master station is an A/QnA PLC ACPU, QnACPU Master station D Terminal resistor Computer Link Terminal resistor FXCPU Remote device station Remote I/O for CC-Link Inverter, AC servo, etc. Sensor, solenoid valve, etc. E Inverter Communication • • Number of connectable units : 64 maximum Total extension distance : 1200 m (3937' 0") 2) When the master station is a Q PLC F Master station Non-Protocol Communication (RS/RS2 Instruction) QCPU Terminal resistor G Terminal resistor Intelligent device station FXCPU Remote I/O for CC-Link Inverter, AC servo, etc. Sensor, solenoid valve, etc. H Number of connectable units : 64 maximum Total extension distance : 1200 m (3937' 0") Programming Communication • • Remote device station Non-Protocol Communication (FX2N-232IF) FXCPU N:N Network For details, refer to the FX2N-16CCL-M USER’S MANUAL. For details, refer to the FX3U-16CCL-M USER’S MANUAL. For details, refer to the FX2N-32CCL USER’S MANUAL. For details, refer to the FX3U-64CCL USER’S MANUAL. I Remote Maintenance Apx.A Discontinued models A-3 FX Series PLC User's Manual - Data Communication Edition 1 Introduction Common Items 1.2 Outline and Features of Communication Types 3) When the master station is an FX2N-16CCL-M Master station FX2N-16CCL-M FXCPU Terminal resistor Remote device station FXCPU Terminal resistor Sensor, solenoid valve, etc. Inverter, AC servo, etc. Remote I/O for CC-Link Number of connectable units : Remote I/O station : Remote device station • Total extension distance : 1200 m (3937' 0") • 7 maximum 8 maximum 4) When the master station is an FX3U-16CCL-M Master station FX3U-16CCL-M FXCPU Terminal resistor Terminal resistor Intelligent device station FXCPU FXCPU Remote device station Remote I/O for CC-Link Inverter, AC servo, etc. Sensor, solenoid valve, etc. • Number of connectable units : Remote I/O station : Remote device station + Intelligent device station* 1 • Total extension distance : 1200 m (3937' 0") *1. 8 maximum 8 maximum Local stations can not be connected. 2. Applicable PLCs :Applicable (If applicable versions of main units are limited, they are described inside ( ).) —:Not applicable FX2(FX), FX0N FX1S FX2C PLC FX1NC FX2N, FX2NC FX3S FX3G, FX3GC FX3U, FX3UC FX2N16CCL-M — — — (Ver. 1.10 or later) (Ver. 2.20 or later) — FX3U16CCL-M — — — — — — — *2 *2 (Ver. 2.20 or later) FX Series FX2Nremote device station 32CCL connectivity — — — FX Series intelligent device station connectivity — — — — — — — FX Series master station connectivity *2. *3. FX3U64CCL *3 *3 (Ver. 2.20 or later) FX3G and FX3GC PLCs Ver. 2.00 or later, or FX3U and FX3UC PLCs Ver. 3.10 or later support the access function to other FX Series PLC main units connected to FX3U-64CCL. The table below shows versions of GX Works2 and GX Developer that support the access function to other FX Series PLC main units via CC-Link. PLC connected through A-4 FX1N GX Developer QCPU(Q mode) QCPU(Q mode) GX Works2 FXCPU*2 + FX3U-16CCL-M PLC main unit accessed FX3G FX3GC FX3U Ver. 8.78G or later — Ver. 8.72A or later Ver. 1.08J or later Ver. 1.77F or later Ver. 1.08J or later FX3UC Ver. 8.72A or later Ver. 1.08J or later Ver. 1.87R or later Ver. 1.87R or later Ver. 1.73B or later Ver. 1.73B or later FX Series PLC User's Manual - Data Communication Edition Common Items 1 Introduction 1.2 Outline and Features of Communication Types A Equipment operating in accordance with the CC-Link standard 4. Function 5. Applications Decentralized or centralized control of the line, reception and sending of information from/to the host network, etc. 6. Detailed information on CC-Link C Parallel Link For details on CC-Link and connectable equipment, refer to the CC-Link Partner Association's homepage or catalogues (issued by the CC-Link Partner Association). CC-Link Partner Association's homepage: http://www.cc-link.org/ B N:N Network Master station allows connection of remote device station, remote I/O station (inverters, AC servos, sensors, solenoid valves, etc.) supporting the CC-Link network to achieve data link. FX PLCs are classified as master stations, remote device stations or intelligent device stations. Common Items 3. Communication targets D Computer Link E Inverter Communication F Non-Protocol Communication (RS/RS2 Instruction) G Non-Protocol Communication (FX2N-232IF) H Programming Communication I Remote Maintenance Apx.A Discontinued models A-5 FX Series PLC User's Manual - Data Communication Edition 1 Introduction Common Items 1.2.2 1.2 Outline and Features of Communication Types Ethernet communication For details, refer to FX3U-ENET-ADP User’s Manual. 1. Outline Network Range (Only within LAN) Router Hub SNTP server FX3U-ENET-ADP Local station External device External device GX Works2 2. Applicable PLCs :Applicable (If applicable versions of main units are limited, they are described inside ( ).) —:Not applicable PLC FX2(FX),FX2C FX0N FX1S,FX1N,FX1NC FX2N,FX2NC FX3S Communication applicability — — — — *1 *1. FX3G, FX3GC FX3U, FX3UC (Ver. 2.00 or later) (Ver. 3.10 or later) The FX3U-ENET-ADP Ver. 1.20 or later is applicable to the FX3S PLC. 3. Applicable software Use the following version when setting the FX3U-ENET-ADP or connecting using MELSOFT: Product name GX Works2 *2. Model name SWDNC-GXW2-E Applicability Ver. 1.73B or later*2 Ver. 1.492N or later supports the FX3S PLC. Ver. 1.87R or later supports the FX3G, FX3GC PLCs. Caution Setting and others are disabled when using nonapplicable versions. 4. Communication targets Ethernet-compatible equipment 5. Function The FX3U-ENET-ADP can connect FX3S, FX3G, FX3GC, FX3U, FX3UC Series PLCs to a high-order system such as personal computer via Ethernet (100BASE-TX or 10BASE-T) using TCP/IP or UDP communication protocol. 6. Applications 1) Collects and changes the PLC data. (Communication using the MELSEC communication protocol) 2) Reads, writes and verifies programs, and monitors and tests device values in the main unit remotely. (Communicates with GX Works2 via Ethernet through MELSOFT connection.) 3) Executes monitoring remotely using a web browser. (The data monitoring function enables monitoring the information and device values in the main unit and FX3U-ENET-ADP using a web browser.) A-6 FX Series PLC User's Manual - Data Communication Edition 1 Introduction Common Items A N:N Network Refer to the "N:N Network" section. 1. Outline B FX CPU Station No. 7 Terminal resistor N:N Network FX CPU Station No. 1 RS-485 RS-485 RS-485 Terminal resistor FX CPU Station No. 0 Number of connectable FX PLCs : 8 maximum (station Nos. 0 to 7) Total extension distance : 500 m (1640' 5") [50 m (164' 0") when 485BD is connected] C M1448 to M1511 D70 to D77 Station No. 7 M1000 to M1063 D0 to D7 M1064 to M1127 D10 to D17 D Computer Link Station No. 1 M1000 to M1063 D0 to D7 M1064 to M1127 D10 to D17 Parallel Link For FX3U PLC (pattern 2) Station No. 0 M1000 to M1063 D0 to D7 M1064 to M1127 D10 to D17 M1448 to M1511 D70 to D77 Common Items 1.2.3 1.2 Outline and Features of Communication Types M1448 to M1511 D70 to D77 E :Applicable (If applicable versions of main units are limited, they are described inside ( ).) —:Not applicable FX2(FX),FX2C FX0N FX1S,FX1N, FX1NC FX2N FX2NC FX3S FX3G, FX3GC FX3U, FX3UC Communication applicability — (Ver. 2.00 or later) (Ver. 2.00 or later) 3. Communication targets Between FX0N, FX1S, FX1N, FX1NC, FX2N, FX2NC, FX3S, FX3G, FX3GC, FX3U and FX3UC Series PLCs F Non-Protocol Communication (RS/RS2 Instruction) PLC Inverter Communication 2. Applicable PLCs G 4. Function 5. Applications H Programming Communication By this network, data link can be achieved in a small-scale system, and the machine information can be transferred between machines. Non-Protocol Communication (FX2N-232IF) This network allows up to eight connected FX PLCs to automatically transfer data among the connected PLCs. In the network, data can be transferred among PLCs for devices determined in the refresh range, and those devices can be monitored by every PLC. I Remote Maintenance Apx.A Discontinued models A-7 FX Series PLC User's Manual - Data Communication Edition 1 Introduction Common Items 1.2.4 1.2 Outline and Features of Communication Types Parallel Link Refer to the "Parallel Link" section. 1. Outline RS-485 RS-485 Terminal resistor FX CPU Master station FX CPU Slave station Terminal resistor Slave station M800 to M899 D490 to D499 M900 to M999 D500 to D509 Master station M800 to M899 D490 to D499 M900 to M999 D500 to D509 100 bit devices (M) and 10 word devices (D) Number of connectable FX PLCs: 2 Total extension distance: 500 m (1640' 5") [50 m (164' 0") when 485BD is connected]*1 *1. The distance is different for the FX2-40AW/AP. 2. Applicable PLCs :Applicable (If applicable versions of main units are limited, they are described inside ( ).) —:Not applicable PLC FX2(FX),FX2C FX0N FX1S,FX1N, FX1NC FX2N FX2NC FX3S FX3G, FX3GC FX3U, FX3UC Communication applicability (Ver. 1.20 or later) (Ver. 1.04 or later) 3. Communication targets Between FX2(FX), FX2C, FX0N, FX1S, FX1N, FX1NC, FX2N, FX2NC, FX3S, FX3G, FX3GC, FX3U and FX3UC Series PLCs 4. Function This network automatically transfers data for 100 bit devices (M) and 10 data registers (D) between two PLCs of the same series. Between PLCs in the FX0N, FX1S or FX3S Series, data can be transferred for 50 bit devices (M) and 10 data registers (D). 5. Applications Information can be transferred between two FX PLCs. (It is recommended to use the N:N Network when connecting two PLCs of the same series among the FX1S, FX1N, FX1NC, FX2N, FX2NC, FX3S, FX3G, FX3GC, FX3U and FX3UC Series. N:N Network functionality supports linking of up to eight FX PLC units, therefore it offers excellent future expandability options.) A-8 FX Series PLC User's Manual - Data Communication Edition 1 Introduction Common Items A Computer Link Refer to the "Computer Link" section. 1. Outline 1) 1-to-N connection (RS-485) FXCPU ACPU RS-485 FXCPU RS-485 RS-485 Terminal RS-232C resistor Terminal resistor RS-485 Personal computer B N:N Network A computer link Common Items 1.2.5 1.2 Outline and Features of Communication Types C FX-485PC-IF 2) 1-to-1 connection (RS-232C) Parallel Link Number of connectable FX/A PLCs : 16 maximum Total extension distance : 500 m (1640' 5") [50 m (164' 0") when 485BD is connected] D Computer Link RS-232C FXCPU Personal computer E 2. Applicable PLCs :Applicable (If applicable versions of main units are limited, they are described inside ( ).) —:Not applicable FX2(FX),FX2C FX0N FX1S,FX1N, FX1NC FX2N FX2NC FX3S FX3G, FX3GC FX3U, FX3UC Communication applicability (Ver. 3.30 or later) (Ver. 1.20 or later) (Ver. 1.06 or later) F Non-Protocol Communication (RS/RS2 Instruction) PLC Inverter Communication Number of connectable FX PLCs : 1 Total extension distance : 15 m (49' 2") G 3. Communication targets 4. Function This link allows connection of up to sixteen FX or A (including A1FX CPU) PLCs to a personal computer for data transfer when the personal computer directly specifies devices in the connected PLCs. Non-Protocol Communication (FX2N-232IF) Between FX2(FX), FX2C, FX0N, FX1S, FX1N, FX1NC, FX2N, FX2NC, FX3S, FX3G, FX3GC, FX3U, FX3UC Series PLCs, A Series PLCs and personal computers H Programming Communication 5. Applications By this link, production, inventory, etc. can be controlled. I Remote Maintenance Apx.A Discontinued models A-9 FX Series PLC User's Manual - Data Communication Edition 1 Introduction Common Items 1.2.6 1.2 Outline and Features of Communication Types Inverter Communication Refer to the "Inverter Communication" section. 1. Outline RS-485 FXCPU Terminal resistor Inverter Inverter Inverter Terminal resistor Number of connectable inverters : 8 maximum Total extension distance : 500 m (1640' 5") [50 m (164' 0") when 485BD is connected] 2. Applicable PLCs :Applicable —:Not applicable PLC Communication applicability FX2(FX),FX2C FX0N FX1S,FX1N,FX1NC FX2N, FX2NC FX3S FX3G, FX3GC FX3U, FX3UC — — — 3. Communication targets 1) For FX2N or FX2NC PLC FREQROL Series (S500, E500 and A500) inverters 2) For FX3S, FX3G, FX3GC, FX3U or FX3UC PLC FREQROL Series (S500, E500, A500, F500, V500, D700, E700, A700, F700, A800 and F800) inverters The table below shows PLC versions applicable to each inverter. PLC FREQROL-S500/ E500/A500 FX2N, FX2NC Ver. 3.00 or later FREQROL-F500/ V500 FREQROL-F700/ A700 FREQROL-D700/ E700 FREQROL-A800/ F800 — FX3S Ver. 1.00 or later Ver.1.10 or later FX3G Ver. 1.10 or later Ver.2.22 or later Ver. 1.40 or later FX3GC FX3U FX3UC Ver. 2.20 or later Ver. 1.00 or later Ver. 2.20 or later Ver.2.22 or later Ver. 2.32 or later Ver.3.11 or later Ver. 2.32 or later Ver.3.11 or later 4. Function This communication allows the connection of inverters (computer link) in accordance with RS-485 to control operations and change parameters. 5. Applications Operations with up to eight inverters can be controlled from a PLC. A-10 FX Series PLC User's Manual - Data Communication Edition 1 Introduction Common Items A Non-protocol Communication Refer to the "Non-protocol Communication (RS/RS2 instruction)" section. Refer to the "Non-protocol Communication (FX2N-232IF)" section. 1. Outline C 15 m (49' 2") maximum Printer FXCPU Parallel Link Bar code reader Printer N:N Network Bar code reader 500 m (1640' 5") maximum [50 m (164' 0") when 485BD is connected] RS-232C Personal computer B RS-422/ RS-485 Personal computer FXCPU D 15m (49' 2") maximum Printer *1 FXCPU FX-422CAB0 Standard built-in port (RS-422) Available only in FX3G, FX3GC PLC. 2. Applicable PLCs :Applicable (If applicable versions of main units are limited, they are described inside ( ).) —:Not applicable PLC FX2(FX),FX2C FX0N FX1S,FX1N,FX1NC FX2N FX2NC FX3S FX3G, FX3GC FX3U, FX3UC Communication applicability (Ver. 3.00 or later) (Ver. 1.20 or later) (Ver. 1.06 or later) PLC FX2(FX),FX2C FX0N Communication applicability — — FX1S,FX1N,FX1NC FX2N,FX2NC — — FX3G, FX3GC FX3U, FX3UC FX3S FX3G, FX3GC FX3U, FX3UC — — 3) Non-protocol communication (FX2N-232IF) PLC FX2(FX),FX2C FX0N Communication applicability — — FX1S,FX1N,FX1NC FX2N,FX2NC — Bar code readers, printers, personal computers (micro computer boards), measuring instruments, etc. 4. Function This communication allows non-protocol serial communication between equipment with an RS-232C or RS422/RS-485 interface. Communication with a bar code reader, printer, personal computer (micro computer board), measuring instrument, etc. A-11 Apx.A Discontinued models 5. Applications I Remote Maintenance 3. Communication targets H Programming Communication FX3S G Non-Protocol Communication (FX2N-232IF) 2) Non-protocol communication (RS2 instruction) F Non-Protocol Communication (RS/RS2 Instruction) 1) Non-protocol communication (RS instruction) E Inverter Communication *1. Bar code reader FX-232AWC-H FX-232AWC FX-232AW Computer Link RS-232C RS-422 Converter Personal computer Common Items 1.2.7 1.2 Outline and Features of Communication Types FX Series PLC User's Manual - Data Communication Edition 1 Introduction Common Items 1.2.8 1.2 Outline and Features of Communication Types MODBUS Communication For details, refer to FX3S/FX3G/FX3GC/FX3U/FX3UC User's Manual - MODBUS Serial Communication Edition. 1. Outline 1) In the case of the RS-485 FXCPU slave No.1 ••••••••••••••• RS-485 RS-485 RS-485 Terminal resistor FXCPU master FXCPU slave No.32 Terminal resistor • Number of connectable units: Master 1 : Slave 32 maximum • Total extension distance : 500 m (1640’5”) maximum 2) In the case of the RS-232C RS-232C RS-232C FXCPU master FXCPU slave • Number of connectable units: Master 1 : Slave 1 • Total extension distance : 15 m (49’2”) maximum 2. Applicable PLCs :Applicable (If applicable versions of main units are limited, they are described inside ( ).) —:Not applicable PLC FX2(FX),FX2C FX0N FX1S,FX1N,FX1NC FX2N,FX2NC FX3S FX3G FX3GC FX3U, FX3UC Communication applicability — — — — (Ver. 1.30 or later) (Ver. 2.40 or later) 3. Communication targets MODBUS-compatible equipment 4. Function This function enables MODBUS communication with MODBUS-compatible equipment in accordance with RS-232C or RS-485. 5. Applications Line control in the decentralized or centralized method. A-12 FX Series PLC User's Manual - Data Communication Edition 1 Introduction Common Items A Programming Communication Refer to the "Programming Communication" section. 1. Outline B 1) Standard built-in port in accordance with RS422 (programming tool or personal computer) N:N Network Programming tool Cable RS-422 C FX-10P(-E)/FX-20P(-E)/FX-30P, etc. Cable RS-232C FX-232AWC-H FX-232AWC FX-232AW RS-232CRS-422 converter FXCPU Cable D Standard built-in port (RS-422) Computer Link Personal computer Parallel Link Programming tool FX-USB-AW USB Cable USBRS-422 converter Programming tool F Cable RS-422 Non-Protocol Communication (RS/RS2 Instruction) FX-10P(-E)/FX-20P(-E)/FX-30P, etc. Cable RS-232CRS-422 converter Personal computer Cable FXCPU G Non-Protocol Communication (FX2N-232IF) RS-232C FX-232AWC-H FX-232AWC FX-232AW RS-422 Programming tool FX-USB-AW USB Cable H Programming Communication USBRS-422 converter 3) Communication equipment operating in accordance with RS-232C (personal computer) Programming tool I FXCPU Remote Maintenance RS-232C RS-232C Cable Personal computer 4) Standard built-in port in accordance with USB (personal computer) Programming tool Apx.A Discontinued models FXCPU USB E Inverter Communication 2) Communication equipment operating in accordance with RS-422 (programming tool or personal computer) Personal computer Common Items 1.2.9 1.2 Outline and Features of Communication Types Cable USB Standard built-in port A-13 FX Series PLC User's Manual - Data Communication Edition 1 Introduction Common Items 1.2 Outline and Features of Communication Types 5) Communication equipment operating in accordance with USB (personal computer) Programming tool USB FXCPU Cable USB Personal computer 6) Ethernet adapter (personal computer) Cable FXCPU FXCPU Cable Ethernet adapter Ethernet Cable Ethernet adapter Programming tool Hub Personal computer A-14 FX Series PLC User's Manual - Data Communication Edition 1 Introduction Common Items 1.2 Outline and Features of Communication Types A :Applicable (If applicable versions of main units are limited, they are described inside ( ).) —:Not applicable PLC Standard built-in port in accordance with RS-422 Communication equipment operating in accordance with RS-422(-BD) — — — — (-BD) — — — — (ADP) — — Standard built-in port in accordance with USB — — — — — — Communication equipment operating in accordance with USB(-BD)*1 — — — — — — Ethernet adapter — — — — — — FX3S FX3G FX3GC FX3U FX3UC (D, DS, DSS) FX3UC (LT, LT-2) Standard built-in port in accordance with RS-422 Communication equipment operating in accordance with RS-422(-BD) — — (-BD) — — (ADP) — — — — — — — *2 (Ver. 2.00 or later) (Ver. 3.10 or later) (Ver. 3.10 or later) Communication equipment operating in accordance with RS-232C PLC Communication equipment operating in accordance with RS-232C Standard built-in port in accordance with USB Communication equipment operating in accordance with USB(-BD)*1 Ethernet adapter *1. When using USB communication with a model that does not support USB communication equipment (-BD), use the FX-USB-AW. However, FX2(FX) and FX2C PLCs do not support the FX-USB-AW. Use the standard built-in port in accordance with USB in the FX3S, FX3G and FX3GC PLCs. C D E F G H Programming Communication *2. (Ver. 2.00 or (Ver. 3.10 later) or later) B Computer Link FX2NC Parallel Link FX2N N:N Network FX1NC Non-Protocol Communication (FX2N-232IF) FX1S, FX1N Non-Protocol Communication (RS/RS2 Instruction) FX0N Inverter Communication FX2(FX), FX2C Common Items 2. Applicable PLCs The FX3U-ENET-ADP Ver. 1.20 or later is applicable to the FX3S PLC. 3. Communication targets Personal computer and programming tool 4. Function 5. Applications 1) Programs can be changed and monitored using a personal computer or programming tool. 2) A personal computer (for changing programs) can be directly connected in accordance with RS-232C. A-15 Apx.A Discontinued models 3) While the standard programming connector built in an FX PLC is used for connecting a display unit, a personal computer or programming tool can be connected at the same time for monitoring and transferring data. I Remote Maintenance This communication allows connection of a personal computer or programming tool to a standard port built in a PLC or optional connector to execute sequence programs. FX Series PLC User's Manual - Data Communication Edition 1 Introduction Common Items 1.2 Outline and Features of Communication Types 1.2.10 Remote Maintenance Refer to the "Remote Maintenance" section. 1. Outline 1) Remote access (GX Works2, GX Developer or FXGP/WIN) Programming tool RS-232C Line (such as general subscriber's telephone line) Modem Personal computer FXCPU Modem 2) File transfer (FXGP/WIN) Programming tool Programming tool Line (such as general subscriber's telephone line) Modem Personal computer Modem Personal computer 2. Applicable PLCs :Applicable (If applicable versions of main units are limited, they are described inside ( ).) —:Not applicable PLC FX2(FX),FX2C FX0N FX1S,FX1N,FX1NC FX2N, FX2NC FX3S FX3G, FX3GC FX3U, FX3UC Communication applicability — — 3. Communication target Personal computer (GX Works2, GX Developer or FXGP/WIN) 4. Function This communication allows connection between a modem on the PLC side and a modem on the personal computer side through a line (cellular phone or general subscriber’s telephone line) for PLC monitoring or transferring from the personal computer. The FXGP/WIN allows transfer of file data between personal computers. 5. Applications By this communication, programs in a PLC located in a remote location can be changed and maintained. A-16 FX Series PLC User's Manual - Data Communication Edition 1 Introduction Common Items 1.2 Outline and Features of Communication Types A For FX3UC-32MT-LT(-2) built-in CC-Link/LT master, refer to FX3UC Hardware Edition. For the FX2N-64CL-M, refer to FX2N-64CL-M USER’S MANUAL (Detailed Volume). 1. Outline B Master N:N Network Main line length FXCPU Terminal resistor Terminal resistor Remote I/O Remote I/O Remote I/O Remote I/O C Parallel Link Remote I/O Common Items 1.2.11 CC-Link/LT Network Branch line length Remote I/O D Computer Link Number of connectable units : 64 (stations) Total extension length : 500 m (1640' 5") (main line length) 2. Applicable PLCs :Applicable (If applicable versions of main units are limited, they are described inside ( ).) —:Not applicable FX2(FX),FX2C FX0N FX1S FX1N,FX1NC Communication applicability — — — FX2N, FX3S FX2NC — FX3G, FX3GC FX3U, FX3UC 3. Communication target Inverter Communication PLC E F Equipment operating in accordance with the CC-Link/LT network standard This network allows remote control of I/O information for sensors, lamps, etc. Input (X) numbers and output (Y) numbers can be handled, and I/O points can be assigned continuously even if 2-point or 4-point type remote I/O units are being used. Non-Protocol Communication (RS/RS2 Instruction) 4. Function G 5. Applications 6. Detailed information on CC-Link/LT For product information on CC-Link, refer to the CC-Link Partner Association's homepage or catalogues (issued by the CC-Link Partner Association). CC-Link Partner Association's homepage: http://www.cc-link.org/ Non-Protocol Communication (FX2N-232IF) Wire conservation for inputs and outputs. H Programming Communication I Remote Maintenance Apx.A Discontinued models A-17 FX Series PLC User's Manual - Data Communication Edition 1 Introduction Common Items 1.2 Outline and Features of Communication Types 1.2.12 AnyWireASLINK For details, refer to the FX3U-128ASL-M User's Manual. 1. Outline Terminating unit FXCPU AnyWireASLINK master Slave module Slave module Slave module Slave module Number of connectable units : 128 maximum Total extension distance : 200 m (656′ 2″) The FX3U-128ASL-M AnyWireASLINK master block is jointly developed and manufactured by Mitsubishi Electric and Anywire Corporation. 2. Applicable PLCs :Applicable (If applicable versions of main units are limited, they are described inside ( ).) —:Not applicable PLC FX2(FX), FX2C FX0N FX1S FX1N, FX1NC FX2N, FX2NC FX3S FX3G, FX3GC FX3U, FX3UC Communication applicability — — — — — — (Ver. 2.20 or later) 3. Communication targets Slave modules for AnyWireASLINK 4. Function This network allows remote control of I/O information for sensors and LED. 5. Applications Wire conservation for inputs and outputs. A-18 FX Series PLC User's Manual - Data Communication Edition 1 Introduction Common Items 1.2 Outline and Features of Communication Types A For details, refer to the FX2N-32ASI-M User's Manual. 1. Outline B AS-i flat cable N:N Network AS-i master FXCPU Slave Repeater Slave AS-i power supply Slave C Slave Parallel Link AS-i power supply Number of connectable units : 31 slave units Total extension distance : 100 m (328' 1") [300 m (984' 3") maximum when two repeaters are connected] Terminal resistors are not required. D :Applicable (If applicable versions of main units are limited, they are described inside ( ).) —:Not applicable FX2(FX),FX2C FX0N FX1S Communication applicability — — FX1N,FX1NC FX2N FX2NC FX3S *1 — FX3G, FX3U, FX3GC FX3UC — FX2NC-MT-D/UL and FX2NC-M-DSS(-T-DS) PLCs are not applicable. E Inverter Communication PLC Computer Link 2. Applicable PLCs *1. Common Items 1.2.13 AS-i system F 3. Communication targets 4. Function This network allows remote control of I/O information for sensors and actuators (slave units). The automatic address assignment function enables easy replacement of a slave unit when it has failed. Non-Protocol Communication (RS/RS2 Instruction) Slave units (sensors and actuators) for AS-i G 5. Applications Non-Protocol Communication (FX2N-232IF) Wire conservation for inputs and outputs. H Programming Communication I Remote Maintenance Apx.A Discontinued models A-19 FX Series PLC User's Manual - Data Communication Edition 1 Introduction Common Items 1.2 Outline and Features of Communication Types 1.2.14 Internet Mail Sending For the detains, refer to the FX-232DOPA USERS MANUAL. (Only Japanese manual is available for this product.) 1. Outline FX-232DOPA RS-232C DoPa Mobile Ark 9601D FXCPU Antenna Provider In accordance with DoPa Internet Cellular phone Personal computer 2. Applicable PLCs :Applicable (If applicable versions of main units are limited, they are described inside ( ).) —:Not applicable PLC FX2(FX),FX2C FX0N FX1S FX1N,FX1NC FX2N, FX2NC FX3S FX3G, FX3GC FX3U, FX3UC Communication applicability — — — — 3. Communication targets Personal computer and cellular phone which can receive internet mails 4. Function This setting sends an electronic mail from a PLC to notify the facility operation status, etc. to a personal computer or cellular phone which can receive electronic mails. This function is applicable through dial-up connection to a mail server using a combination of FX-232DOPA and DoPa Mobile Ark9601D by NTT DoCoMo. 5. Applications Monitoring of unmanned facilities, monitoring of facilities located in distant places, monitoring of facilities inside factories and distribution of logging data A-20 FX Series PLC User's Manual - Data Communication Edition 1 Introduction Common Items 1.2 Outline and Features of Communication Types A For details, refer to the FX1S/FX1N/FX2N/FX1NC/FX2NC PLC PROGRAMMING MANUAL. (Only the Japanese Manual is available.) 1. Outline B N:N Network RS-232C Line (such as general subscriber's NTT DoCoMo telephone line) Short Mail Center FXCPU Common Items 1.2.15 Short Mail Sending Modem C Parallel Link Cellular phone 2. Applicable PLCs PLC Communication applicability FX2(FX), FX1N, FX0N FX1S FX2C FX1NC — — — — FX2N FX2NC FX3S (Ver. 3.00 or later) (Ver. 3.00 or later) — FX3G, FX3U, FX3GC FX3UC — — D Computer Link :Applicable (If applicable versions of main units are limited, they are described inside ( ).) —:Not applicable E Cellular phones by NTT DoCoMo with a contract for i-mode or short mail 4. Function This function sends a short mail from a PLC to notify the facility operation status, etc. to a cellular phone by NTT DoCoMo which can receive short mails. This function is applicable through connection in a line to a Short Mail Center of NTT DoCoMo. Monitoring of unmanned facilities, monitoring of facilities located in distant places and monitoring of facilities in factories F Non-Protocol Communication (RS/RS2 Instruction) 5. Applications Inverter Communication 3. Communication targets G Non-Protocol Communication (FX2N-232IF) H Programming Communication I Remote Maintenance Apx.A Discontinued models A-21 FX Series PLC User's Manual - Data Communication Edition Common Items 1.2 Outline and Features of Communication Types MEMO A-22 1 Introduction FX Series PLC User's Manual - Data Communication Edition Common Items 2 Communication Types and Communication Equipment 2.1 Relationship between Equipment and Communication Types A Communication Types and Communication Equipment 2.1 Relationship between Equipment and Communication Types C Built-in port Parallel Link The figure below shows the relationship between communication equipment and communication types: Communication adapter B N:N Network This chapter explains which communication types are supported by serial ports of communication equipment and connectors of networks. For the communication equipment required in the system configuration, refer to a description later. Refer to "2.3 Combination of Communication Equipment (Block Diagram)". Common Items 2. I/O link Link N:N Network Parallel link Computer link Inverter communication MODBUS communication Ethernet communication Ethernet General-purpose serial communication Non-protocol communication (RS/RS2 instruction) Sequence program Programming communication D Computer Link CC-Link/LT (built in for FX3UC-32MT-LT(-2)) General-purpose serial communication Non-protocol communication (RS2 instruction) E Sequence program Inverter Communication Programming communication Remote maintenance Electronic mail sending F Non-Protocol Communication (RS/RS2 Instruction) Internet mail Short mail Communication types G Expansion board Link Non-Protocol Communication (FX2N-232IF) FX PLC main unit Special function equipment H N:N Network Parallel link Computer link Inverter communication General-purpose serial communication Sequence program Programming communication Remote maintenance Electronic mail sending Non-protocol communication (FX2N-232IF) I I/O link ● ● CC-Link/LT AnyWireASLINK AS-i system MELSEC I/O LINK Electronic mail sending Apx.A ● Internet mail Discontinued models Internet mail Short mail CC-Link General-purpose serial communication Remote Maintenance Non-protocol communication (RS/RS2 instruction) Programming Communication Link A-23 FX Series PLC User's Manual - Data Communication Edition 2 Communication Types and Communication Equipment Common Items 2.2 2.2 Communication Equipment Applicability Map Communication Equipment Applicability Map The table below shows the communication types applicable in each FX Series and includes the supporting communication equipment. The communication types can be used when a built-in port or piece of communication equipment is connected, but some of them may not be applicable at the same time. 2.2.1 PLC FX3U and FX3UC (D, DS, DSS) PLCs Communication equipment Communication specifications Manual name (Obtain manuals if necessary.) FX3U-USB-BD Data Link CC-Link Product manual FX3U-232ADP(-MB) — — — RS-232C — — — — *5 FX2N-232IF FX3U-485-BD FX3U-485ADP(-MB)*1 FX3U-422-BD FX3U PLC Standard built-in port RS-485 RS-422 FX2N-16CCL-M *2 FX3U-16CCL-M *3*4 FX2N-32CCL FX3U-128ASL-M — FX3U-ENET-ADP*1 — *6. *7. *8. *9. A-24 — — — — *6 — — — *5 — *5 *5 *6 — — — — — — — — — — — — *5. — — FX2N-16LNK-M *3. *4. — — FX2N-32ASI-M *1. *2. — FX3U-64CCL FX2N-64CL-M MODBUS Communication Edition This manual USB FX3U-232-BD *1 N:N Parallel Computer Inverter MODBUS Network link link communication communication The expansion board is required to connect the FX3U PLC. The FX2N-16CCL-M cannot be used at the same time with the FX3U-16CCL-M, FX3U-128ASL-M and/ or FX2N-32ASI-M. The FX3U-16CCL-M cannot be used at the same time with the FX2N-16CCL-M and/or FX2N-32ASI-M. The FX3U-16CCL-M can be used at the same time with the FX3U-128ASL-M when CC-Link parameters are set using network parameters. Two channels cannot be set at the same time in N:N Network and parallel link. N:N Network and parallel link cannot be used together. Only the FX3U-485ADP-MB and FX3U-232ADP-MB support MODBUS communication. The FX3U-128ASL-M cannot be used at the same time with the FX2N-16CCL-M and/or FX2N-32ASI-M. The FX2N-32ASI-M cannot be used at the same time with the FX3U-16CCL-M, FX3U-128ASL-M and/ or FX2N-16CCL-M. Two channels cannot be set at the same time in remote maintenance. FX Series PLC User's Manual - Data Communication Edition 2 Communication Types and Communication Equipment Common Items 2.2 Communication Equipment Applicability Map A Common Items B Non-protocol communication Product manual This manual CC-Link/ LT AnyWire ASLINK AS-i system Sequence program Mail sending MELSECRemote Internet mail Programming I/O LINK maintenance sending Product manual FX-232DOPA User's Manual This manual — — — *9 *9 — — — — — — — — — — — — — — — — — — — — — — — — — — — — — — — — — — — — — — *4*7 — — — — — — — — — — — — — *8 E F Non-Protocol Communication (RS/RS2 Instruction) — Inverter Communication — D Computer Link C Parallel Link Ethernet Wire-reducing network N:N Network Ethernet General-purpose communication communication — G Non-Protocol Communication (FX2N-232IF) H Programming Communication I Remote Maintenance Apx.A Discontinued models A-25 FX Series PLC User's Manual - Data Communication Edition 2 Communication Types and Communication Equipment Common Items PLC 2.2 Communication Equipment Applicability Map Communication equipment Communication specifications Manual name (Obtain manuals if necessary.) FX3U-232ADP(-MB) FX2N-232IF*1 RS-485 Standard built-in port RS-422 FX2N-16CCL-M*1 FX2N-32ASI-M Product manual *8. *9. — *6 — — — — — *6 — — — *5 *5 — — — — — — *6. *7. — *3*4 FX3U-ENET-ADP *5. — — — *3. *4. MODBUS Communication Edition This manual FX2N-16LNK-M*1 *1. *2. A-26 *1 N:N Parallel Computer Inverter MODBUS Network link link communication communication *2 FX3UC FX3U-16CCL-M*1 (D,DS, *1 DSS) FX2N-32CCL PLC FX3U-64CCL*1 FX3U-128ASL-M*1 CC-Link RS-232C FX3U-485ADP(-MB) FX2N-64CL-M*1 Data Link The FX2NC-CNV-IF or FX3UC-1PS-5V is required to connect to the FX3UC PLC. The FX2N-16CCL-M cannot be used at the same time with the FX3U-16CCL-M, FX3U-128ASL-M and/ or FX2N-32ASI-M. The FX3U-16CCL-M cannot be used at the same time with the FX2N-16CCL-M and/or FX2N-32ASI-M. The FX3U-16CCL-M can be used at the same time with the FX3U-128ASL-M when CC-Link parameters are set using network parameters. Two channels cannot be set at the same time in N:N Network and parallel link. N:N Network and parallel link cannot be used together. Only the FX3U-485ADP-MB and FX3U-232ADP-MB support MODBUS communication. The FX3U-128ASL-M cannot be used at the same time with the FX2N-16CCL-M and/or FX2N-32ASI-M. The FX2N-32ASI-M cannot be used at the same time with the FX3U-16CCL-M, FX3U-128ASL-M and/ or FX2N-16CCL-M. Two channels cannot be set at the same time in remote maintenance. FX Series PLC User's Manual - Data Communication Edition 2 Communication Types and Communication Equipment Common Items 2.2 Communication Equipment Applicability Map A Ethernet Non-protocol communication Product manual This manual Wire-reducing network CC-Link/ LT AnyWire ASLINK AS-i system Sequence program Mail sending MELSECRemote Internet mail Programming I/O LINK maintenance sending Product manual *9 — — — — — — — — — — — — — — — — — — — — — — — — — — — — — — — — *4*7 — — *8 — — — — — — — — — — — D Computer Link — C Parallel Link — B N:N Network FX-232DOPA User's Manual This manual Common Items Ethernet General-purpose communication communication — E Inverter Communication F Non-Protocol Communication (RS/RS2 Instruction) G Non-Protocol Communication (FX2N-232IF) H Programming Communication I Remote Maintenance Apx.A Discontinued models A-27 FX Series PLC User's Manual - Data Communication Edition 2 Communication Types and Communication Equipment Common Items 2.2.2 PLC 2.2 Communication Equipment Applicability Map FX3UC-32MT-LT(-2) PLCs Communication equipment Communication specifications Manual name (Obtain manuals if necessary.) FX3U-USB-BD Data Link CC-Link Product manual USB FX3U-232-BD FX3U-232ADP(-MB)*1 RS-232C FX2N-232IF*2 FX3U-485-BD FX3U-485ADP(-MB)*1 FX3U-422-BD Standard built-in port FX3UC32MT- FX2N-16CCL-M*2 LT(-2) FX3U-16CCL-M*2 PLC FX2N-32CCL*2 FX3U-64CCL RS-485 RS-422 MODBUS Communication Edition This manual — — — — — — — — — — — — *7 — — — — — *6 *6 — *6 *6 *7 — — — — — — — — — — *3 *4*5 *2 FX2N-64CL-M*2 N:N Parallel Computer Inverter MODBUS Network link link communication communication — — Built-in type CC-Link/ LT master — FX3U-128ASL-M*2 — FX2N-32ASI-M*2 — FX3U-ENET-ADP*1 — *1. The expansion board is required to connect the FX3UC-32MT-LT(-2) PLC. *2. The FX2NC-CNV-IF or FX3UC-IPS-5V is required to connect the FX3UC-32MT-LT(-2) PLC. *3. The FX2N-16CCL-M cannot be used at the same time with the FX3U-16CCL-M, FX3U-128ASL-M and/ or FX2N-32ASI-M. *4. The FX3U-16CCL-M cannot be used at the same time with the FX2N-16CCL-M and/or FX2N-32ASI-M. *5. The FX3U-16CCL-M can be used at the same time with the FX3U-128ASL-M when CC-Link parameters are set using network parameters. *6. Two channels cannot be set at the same time in N:N Network and parallel link. N:N Network and parallel link cannot be used together. *7. Only the FX3U-485ADP-MB and FX3U-232ADP-MB support MODBUS communication. *8. For the FX2N-64CL-M, refer to FX2N-64CL-M User's Manual. For FX3UC built-in CC-Link/LT master, refer to FX3UC Hardware Edition. *9. The FX3U-128ASL-M cannot be used at the same time with the FX2N-16CCL-M and/or FX2N-32ASI-M. *10. The FX2N-32ASI-M cannot be used at the same time with the FX3U-16CCL-M, FX3U-128ASL-M and/ or FX2N-16CCL-M. *11. Two channels cannot be set at the same time in remote maintenance. A-28 FX Series PLC User's Manual - Data Communication Edition 2 Communication Types and Communication Equipment Common Items 2.2 Communication Equipment Applicability Map A Non-protocol communication Product manual This manual CC-Link/ LT AnyWire ASLINK AS-i system Sequence program Mail sending MELSECRemote Internet mail Programming I/OLINK maintenance sending Product manual FX-232DOPA User's Manual This manual — — *11 *11 — — — — — — — — — — — — — — — — — — — — — — — — — — — — — — — — — — — — — *8 — — — — — *5*9 — — — — — — — — F — Non-Protocol Communication (RS/RS2 Instruction) — *10 E Inverter Communication — *8 D Computer Link — C Parallel Link — B N:N Network Ethernet Wire-reducing network Common Items Ethernet General-purpose communication communication G Non-Protocol Communication (FX2N-232IF) H Programming Communication I Remote Maintenance Apx.A Discontinued models A-29 FX Series PLC User's Manual - Data Communication Edition 2 Communication Types and Communication Equipment Common Items 2.2.3 PLC 2.2 Communication Equipment Applicability Map FX3G and FX3GC PLCs Communication equipment Communication specifications Manual name (Obtain manuals if necessary.) Standard built-in port FX3G-232-BD FX3U-232ADP(-MB)*1 Data Link CC-Link Product manual USB RS-232C FX3G-485-BD FX3G-485-BD-RJ RS-485 FX3U-485ADP(-MB)*1 FX3G PLC FX3G-422-BD Standard built-in port RS-422 FX2N-16CCL-M FX2N-32CCL — — — — — — — — — — — — *6 *5 *5 — *5 *5 — *5 *5 * 6 — — — — — — — — — — *2 — FX2N-64CL-M — FX3U-128ASL-M — FX3U-ENET-ADP*1 — Standard built-in port USB — — — — — FX3U-232ADP(-MB) RS-232C — — — * 6 FX3U-485ADP(-MB) RS-485 *5 *5 * 6 Standard built-in port RS-422 — — — — — FX2N-16CCL-M*10 *2 FX3GC FX3U-16CCL-M*10 PLC FX2N-32CCL*10 FX3U-64CCL*10 *3*4 — FX2N-64CL-M*10 — FX3U-128ASL-M*10 — FX3U-ENET-ADP — *1. The FX3G-CNV-ADP is required to connect the FX3G PLC. *2. The FX2N-16CCL-M cannot be used at the same time with the FX3U-16CCL-M and/or FX3U-128ASL-M. *3. The FX3U-16CCL-M cannot be used at the same time with the FX2N-16CCL-M. *4. The FX3U-16CCL-M can be used at the same time with the FX3U-128ASL-M when CC-Link parameters are set using network parameters. *5. Two channels cannot be set at the same time in N:N Network and parallel link. N:N Network and parallel link cannot be used together. *6. Only the FX3U-485ADP-MB and FX3U-232ADP-MB support MODBUS communication. *7. Only the RS2 instruction is supported. *8. The FX3U-128ASL-M cannot be used at the same time with the FX2N-16CCL-M. *9. Two channels cannot be set at the same time in remote maintenance. *10. The FX2NC-CNV-IF or FX3UC-1PS-5V is required to connect the FX3GC PLC. A-30 MODBUS Communication Edition This manual *3*4 FX3U-16CCL-M FX3U-64CCL N:N Parallel Computer Inverter MODBUS Network link link communication communication FX Series PLC User's Manual - Data Communication Edition 2 Communication Types and Communication Equipment Common Items 2.2 Communication Equipment Applicability Map A Non-protocol communication Product manual This manual CC-Link/ LT AnyWire ASLINK AS-i system Sequence program Mail sending MELSECRemote Internet mail Programming I/O LINK maintenance sending Product manual FX-232DOPA User's Manual This manual — — — — *9 — — — — — — — — — — — — *7 — — — — — — — — — — — — — — — — — — — — — — — — — — — *4*8 — — — — — — E — — *9 — — — — — — *7 — — — — — — — — — — — — — — — — — — — — — — — — — *4*8 — — — — — — G Non-Protocol Communication (FX2N-232IF) — F Non-Protocol Communication (RS/RS2 Instruction) — Inverter Communication — D Computer Link — C Parallel Link *9 B N:N Network Ethernet Wire-reducing network Common Items Ethernet General-purpose communication communication H Programming Communication I Remote Maintenance Apx.A Discontinued models A-31 FX Series PLC User's Manual - Data Communication Edition 2 Communication Types and Communication Equipment Common Items 2.2.4 PLC 2.2 Communication Equipment Applicability Map FX3S PLC Communication equipment Communication specifications Manual name (Obtain manuals if necessary.) Standard built-in port FX3G-232-BD FX3U-232ADP(-MB)*1 FX3S PLC CC-Link FX3G-485-BD-RJ USB RS-232C RS-485 FX3U-485ADP(-MB)*1 Standard built-in port FX3U-ENET-ADP*1 RS-422 — N:N Parallel Computer Inverter MODBUS Network link link communication communication Product manual FX3G-485-BD FX3G-422-BD A-32 Data Link MODBUS Communication Edition This manual — — — — — — — — — — — — * 2 — — * 2 — — — — — — — — — — — *1. The FX3S-CNV-ADP is required to connect the FX3S PLC. *2. Only the FX3U-485ADP-MB and FX3U-232ADP-MB support MODBUS communication. FX Series PLC User's Manual - Data Communication Edition 2 Communication Types and Communication Equipment Common Items 2.2 Communication Equipment Applicability Map A Non-protocol communication Product manual This manual Mail sending MELSEC-I/O Remote Internet mail Programming LINK maintenance sending Product manual FX-232DOPA User's Manual This manual — — — — — — — — — — — — — — — — — — — — — C D Computer Link — B Parallel Link CC-Link/LT AS-i system Sequence program N:N Network Ethernet Wire-reducing network Common Items Ethernet General-purpose communication communication — E Inverter Communication F Non-Protocol Communication (RS/RS2 Instruction) G Non-Protocol Communication (FX2N-232IF) H Programming Communication I Remote Maintenance Apx.A Discontinued models A-33 FX Series PLC User's Manual - Data Communication Edition 2 Communication Types and Communication Equipment Common Items 2.2.5 PLC 2.2 Communication Equipment Applicability Map FX2N and FX2NC PLCs Communication equipment Communication specifications Manual name (Obtain manuals if necessary.) Link CC-Link Product manual Computer link Inverter communication This manual — — — FX2NC-232ADP*1 — — — — — *3 — — — — — RS-232C FX2N-232IF FX2N-485-BD FX2NC-485ADP*1 RS-485 FX0N-485ADP*1 FX2N-422-BD — — — — — — — — Standard built-in port RS-422 FX2N-16CCL-M *2 FX2N-32CCL FX2N-64CL-M — — FX2N-32ASI-M — FX2N-16LNK-M — FX2NC-232ADP FX0N-232ADP RS-232C FX2N-232IF*4 FX2NC-485ADP FX0N-485ADP FX2NC Standard built-in port PLC FX2N-16CCL-M*4 RS-485 RS-422 FX2N-64CL-M*4 — — — — — *3 — — — — — — — — — *2 FX2N-32CCL*4 A-34 Parallel link FX2N-232-BD FX0N-232ADP*1 FX2N PLC N:N Network — — FX2N-32ASI-M*4 — FX2N-16LNK-M*4 — *1. The FX2N-CNV-BD is required to connect the FX2N PLC. *2. The FX2N-16CCL-M cannot be used at the same time with the FX2N-32ASI-M. *3. It is recommended to use a connector or thin type FX2NC-232ADP (9-pin D-Sub). *4. The FX2NC-CNV-IF is required to connect the FX2NC PLC. *5. The FX2NC-MT-D/UL and FX2NC-M-DSS(-T-DS) does not support this connection. FX Series PLC User's Manual - Data Communication Edition 2 Communication Types and Communication Equipment Common Items 2.2 Communication Equipment Applicability Map A Non-protocol communication I/O link CC-Link/ LT Mail sending MELSEC-I/O Remote Internet mail Programming LINK maintenance sending Product manual This manual Short mail sending FX-232DOPA User's Manual FX1S, FX1N, FX2N, FX1NC, FX2NC Programming Manual *3 *3 *3 *3 *3 — — — — — — — — — — — — — — — — — — — — — — — — — — — — — — — *2 — — — E *3 *3 *3 *3 — — — — — — — — — — — — — — — — — — — — — — — *2*5 — — — F G Non-Protocol Communication (FX2N-232IF) — Non-Protocol Communication (RS/RS2 Instruction) *3 Inverter Communication — D Computer Link C Parallel Link B N:N Network This manual AS-i system Sequence program Common Items General-purpose communication H Programming Communication I Remote Maintenance Apx.A Discontinued models A-35 FX Series PLC User's Manual - Data Communication Edition 2 Communication Types and Communication Equipment Common Items 2.2.6 PLC 2.2 Communication Equipment Applicability Map FX1S, FX1N, and FX1NC PLCs Communication equipment Communication specifications Manual name (Obtain manuals if necessary.) Link CC-Link Inverter communication This manual — — — FX2NC-232ADP*1 — — — — — *2 — RS-232C FX1N-485-BD — FX2NC-485ADP*1 — — — — — — — — — — FX1N-232-BD — — — FX2NC-232ADP*1 — — — FX0N-232ADP*1 — — *2 — FX1N-485-BD — — — FX1N-422-BD Standard built-in port FX2NC-485ADP*1 RS-485 RS-422 RS-232C RS-485 FX0N-485ADP*1 FX1N-422-BD Standard built-in port RS-422 FX2N-32CCL FX2N-64CL-M — — — FX2NC-485ADP FX0N-485ADP Standard built-in port FX1NC PLC FX2N-16CCL-M*4 RS-232C RS-485 RS-422 — — — — — — — — *2 — — — — — — — FX2N-16LNK-M*4 — — FX2N-32ASI-M*4 — — *3 FX2N-32CCL*4 FX2N-64CL-M*4 — — — FX2N-16LNK-M FX0N-232ADP — — FX2N-32ASI-M FX2NC-232ADP — *3 FX2N-16CCL-M A-36 Computer link FX1N-232-BD FX0N-485ADP*1 FX1N PLC Parallel link Product manual FX0N-232ADP*1 FX1S PLC N:N Network *1. The FX1N-CNV-BD is required to connect the FX1S or FX1N PLC. *2. It is recommended to use a connector or thin type FX2NC-232ADP (9-pin D-Sub). *3. The FX2N-16CCL-M cannot be used at the same time with the FX2N-32ASI-M. *4. The FX2NC-CNV-IF is required to connect the FX1NC PLC. FX Series PLC User's Manual - Data Communication Edition 2 Communication Types and Communication Equipment Common Items 2.2 Communication Equipment Applicability Map A CC-Link/LT This manual AS-i system Sequence program MELSEC-I/O LINK Programming Product manual Remote maintenance Mail sending Internet mail sending B FX-232DOPA User's Manual This manual *2 *2 *2 — — — — — — — — — — — — *2 *2 *2 — — — — — — — — — — — — — — — — — — — — — *3 — — — *2 *2 *2 — — — — — — — — — — — — — — — — *3 — — — H Programming Communication — G *2 Non-Protocol Communication (FX2N-232IF) F Non-Protocol Communication (RS/RS2 Instruction) — — E Inverter Communication — D Computer Link — — Parallel Link — *2 C *2 N:N Network Non-protocol communication I/O link Common Items General-purpose communication — I Remote Maintenance Apx.A Discontinued models A-37 FX Series PLC User's Manual - Data Communication Edition 2 Communication Types and Communication Equipment Common Items 2.2.7 PLC 2.2 Communication Equipment Applicability Map FX0N PLCs Communication equipment Communication specifications Manual name (Obtain manuals if necessary.) FX2NC-232ADP FX0N-232ADP FX2NC-485ADP FX0N-485ADP FX0N PLC Standard built-in port PLC Parallel link RS-422 FX2N-16CCL-M — Computer link Inverter communication This manual — RS-485 — N:N Network Product manual RS-232C — *1 — — — — — — — — — — — FX2N-32ASI-M — FX2N-16LNK-M — *1. It is recommended to use a connector or thin type FX2NC-232ADP (9-pin D-Sub). *2. Only Japanese manual is available for this product. FX1, FX2(FX), FX2C, FX0 and FX0S PLCs (reference) Communication equipment Communication specifications Manual name (Obtain manuals if necessary.) FX1 PLC CC-Link FX2N-32CCL FX2N-64CL-M 2.2.8 Link Standard built-in port FX-232ADP FX2(FX) FX-485ADP PLC FX-40AW FX2C FX-40AP PLC Link CC-Link N:N Network Parallel link Product manual Computer link Inverter communication This manual RS-422 — — — — RS-232C — — — RS-485 — — — — — — — Optical communication — — — Standard built-in port RS-422 — — — — FX0 PLC Standard built-in port RS-422 — — — — FX0S PLC Standard built-in port RS-422 — — — — *1. A-38 Only Japanese manual is available for this product. FX Series PLC User's Manual - Data Communication Edition 2 Communication Types and Communication Equipment Common Items 2.2 Communication Equipment Applicability Map A CC-Link/LT This manual AS-i system Sequence program MELSEC-I/O LINK Programming Product manual Remote maintenance Mail sending Internet mail sending B FX-232DOPA User's Manual*2 This manual — — — *1 — — — — — — — — — — — — — — — — — — — — — — — D Computer Link — C Parallel Link N:N Network Non-protocol communication I/O link Common Items General-purpose communication E Inverter Communication Non-protocol communication This manual I/O link CC-Link/LT AS-i system Sequence program MELSEC-I/O LINK Programming Product manual Remote maintenance Mail sending Internet mail sending FX-232DOPA User's Manual*1 This manual F Non-Protocol Communication (RS/RS2 Instruction) General-purpose communication — — — — — — — — — — — — — — — — — H — — — — — — — — — Programming Communication Non-Protocol Communication (FX2N-232IF) G — I Remote Maintenance Apx.A Discontinued models A-39 FX Series PLC User's Manual - Data Communication Edition Common Items 2.3 2 Communication Types and Communication Equipment 2.3 Combination of Communication Equipment (Block Diagram) Combination of Communication Equipment (Block Diagram) The block diagram below shows combinations of optional communication equipment applicable in each FX Series. 2.3.1 How to look at combination pages FX Series name Communication equipment connection type Applicable communication type FX1N Series A B FX PLC main unit mounting position For special function units/blocks C , refer to the next page. C A , B and C indicate the mounting position. B (For the mounting procedure, refer to the respective communication equipment manual.) RS-485 European terminal block FX1N-485-BD B N:N Network A Parallel link Selection example European terminal block FX1N-CNV-BD FX2NC-485ADP Computer link Non-protocol communication A M3 terminal block FX0N-485ADP B RS-422 One line can be selected. Connection condition 8-pin MINI-DIN, female Programming communication FX1N-422-BD B A European terminal block FX1N-CNV-BD FX2NC-485ADP Non-protocol communication A M3 terminal block FX0N-485ADP B RS-232C 9-pin D-Sub, male FX1N-232-BD B Computer link A Non-protocol communication 9-pin D-Sub, male FX1N-CNV-BD FX2NC-232ADP Remote maintenance A 25-pin D-Sub, female FX0N-232ADP A-40 Programming communication FX Series PLC User's Manual - Data Communication Edition 2 Communication Types and Communication Equipment Common Items A For FX3U Series Common Items 2.3.2 2.3 Combination of Communication Equipment (Block Diagram) FX3U Series A For special function units/blocks C refer to the next page. C B B N:N Network A , B , and C indicate the mounting position. (For the mounting procedure, refer to the respective communication equipment manual.) Either FX3UB ch1 232ADP(-MB), FX3U-485ADP(-MB) or FX3U-ENET-ADP can be selected. European terminal N:N Network block Parallel link A ch2 Computer link FX3U-485-BD European terminal Non-protocol block communication B A ch1 Inverter communication FX3U-485ADP(-MB) European terminal MODBUS *1 block communication RDA RS-485 RD RDB SDA SD SDB SG B Parallel Link FX3U-CNV-BD C D FX3U-485ADP(-MB) RS-422 8-pin MINI-DIN, female Computer Link ch1 Programming communication FX3U-422-BD E ch1 B Inverter Communication RDA RD RDB SDA SD SDB SG A ch2 FX3U-485-BD B A European terminal block ch1 B RS-232C communication F European terminal block FX3U-485ADP(-MB) ch1 G RD A ch2 FX3U-232-BD B communication 9-pin D-Sub, male A ch1 USB communication*1 communication Remote maintenance H Programming Communication 9-pin D-Sub, male FX3U-232-BD MODBUS Programming FX3U-232ADP(-MB) B Computer link Non-protocol Non-Protocol Communication (FX2N-232IF) 9-pin D-Sub, male SD FX3U-232ADP(-MB) ch1 USB Mini-B connector Programming I Modular jack Ethernet Programming Apx.A RD SD B A A ch2 ch1 Ethernet FX3U-ENET-ADP communication Discontinued models FX3U-ENET-ADP FX3U-CNV-BD communication Remote Maintenance FX3U-USB-BD *1. Non-protocol Non-Protocol Communication (RS/RS2 Instruction) FX3U-485ADP(-MB) FX3U-CNV-BD European terminal block Modular jack Only the FX3U-485ADP-MB and FX3U-232ADP-MB support MODBUS communication. A-41 FX Series PLC User's Manual - Data Communication Edition 2 Communication Types and Communication Equipment Common Items 2.3 Combination of Communication Equipment (Block Diagram) FX3U Series A B C A , B , and C indicate the mounting position. (For the mounting procedure, refer to the respective communication equipment manual.) For special adapters with communication type A and communication expansion boards B , refer to the previous page. For master station FX 2N-16CCL-M CC-Link E R R O R M3/M3.5 terminal block*4 FX 3U -16CCL-M*1*2 FX 2N -16CCL-M *3 For remote device station M3 terminal block CC-Link FX2N-32CCL For intelligent device station M3 terminal block Up to 8 units can be selected. FX3U-64CCL*2 POW ER SD RD 9-pin D-Sub, male Non-protocol communication FX2N-232IF Dedicated connector CC-Link/LT FX2N-64CL-M European terminal block AnyWireASLINK FX 3U-128ASL-M*2*5 U ASI ASI ACTIVE POWE R ADDRESS/ ERROR FX2N-32ASI-M MOD E SE T M3 terminal block AS-i system M3 terminal block PRJ MODE PRG ENABLE FROM/ TO CONFIG ERR FX2N-32ASI-M*6 MELSEC-I/O LINK FX2N-16LNK-M *1. *2. *3. The FX3U-16CCL-M cannot be used at the same time with the FX2N-16CCL-M and/or the FX2N-32ASI-M. Only one unit can be connected to the main unit. The FX2N-16CCL-M cannot be used at the same time with the FX3U-16CCL-M, FX3U-128ASL-M and/or the FX2N-32ASI-M. *4. The terminal screw size is "M3" in the FX3U-16CCL-M. The terminal screw size is "M3.5" in the FX2N-16CCL-M. *5. The FX3U-128ASL-M cannot be used at the same time with the FX2N-16CCL-M and/or FX2N-32ASI-M. *6. The FX2N-32ASI-M cannot be used at the same time with the FX3U-16CCL-M, FX3U-128ASL-M and/or the FX2N-16CCL-M. Only one station can be used for the whole system. Limitation in the number of connectable units Connected special function units/blocks operate using the 24V DC or 5V DC power supply of the PLC. Therefore, the total current consumption larger than the plc current capacity reduces the number of connectable units. For details, refer to the respective FX PLC manual. A-42 FX Series PLC User's Manual - Data Communication Edition Common Items 2.3 Combination of Communication Equipment (Block Diagram) A For FX3UC(D, DS, DSS) Series Common Items 2.3.3 2 Communication Types and Communication Equipment FX3UC(D, DS, DSS) Series A For special function units/blocks B , refer to the next page. B ch2 European terminal block FX3U-485ADP (-MB) FX3U-485ADP (-MB) A ch1 N:N Network Parallel link Computer link Non-protocol communication Inverter communication MODBUS communication*1 Inverter Communication ch2 European terminal block FX3U-485ADP (-MB) D E European terminal block A C Computer Link RS-422 Parallel Link A N:N Network RS-485 B A and B indicate the mounting position. (For the mounting procedure, refer to the respective communication equipment manual.) Either FX3U232ADP(-MB), FX3U-485ADP(-MB) or FX3U-ENET-ADP A ch1 can be selected. European terminal block Non-protocol communication F Non-Protocol Communication (RS/RS2 Instruction) FX3U-485ADP (-MB) G A ch1 9-pin D-Sub, male ch2 9-pin D-Sub, male FX3U-232ADP (-MB) communication MODBUS *1 communication Programming communication Remote maintenance FX3U-232ADP (-MB) A I Remote Maintenance A ch2 ch1 Modular jack Ethernet Programming Ethernet FX3U-ENET-ADP communication FX3U-ENET-ADP *1. Only the FX3U-485ADP-MB and FX3U-232ADP-MB support MODBUS communication. A-43 Apx.A Discontinued models Modular jack H Programming Communication A Computer link Non-protocol Non-Protocol Communication (FX2N-232IF) RS-232C FX Series PLC User's Manual - Data Communication Edition 2 Communication Types and Communication Equipment Common Items 2.3 Combination of Communication Equipment (Block Diagram) FX3UC(D, DS, DSS) Series A and B indicate the mounting position. (For the mounting procedure, refer to the respective communication equipment manual.) A B For special adapters with communication type A , refer to the previous page. For master station FX 2N -16CCL-M M3/M3.5 terminal block*4 CC-Link E R R O R FX2NC-CNV-IF FX3U-16CCL-M*1*2 FX 2N -16CCL-M*3 For remote device station FX3UC-1PS-5V M3 terminal block CC-Link FX2N-32CCL For intelligent device station M3 terminal block Up to 8 units can be selected. FX3U-64CCL*2 POWER SD RD 9-pin D-Sub, male Non-protocol communication FX2N-232IF Dedicated connector CC-Link/LT FX2N-64CL-M European terminal block AnyWireASLINK FX 3U-128ASL-M*2*5 U ASI ASI ACTIVE POWE R ADDRESS/ ERROR FX2N-32ASI-M MOD E SE T M3 terminal block AS-i system M3 terminal block PRJ MODE PRG ENABLE FROM/ TO CONFIG ERR FX2N-32ASI-M*6 MELSEC-I/O LINK FX2N-16LNK-M *1. *2. *3. *4. *5. *6. The FX3U-16CCL-M cannot be used at the same time with the FX2N-16CCL-M and/or the FX2N-32ASI-M. Only one unit can be connected to the main unit. The FX2N-16CCL-M cannot be used at the same time with the FX3U-16CCL-M, FX3U-128ASL-M and/or the FX2N-32ASI-M. The terminal screw size is "M3" in the FX3U-16CCL-M. The terminal screw size is "M3.5" in the FX2N-16CCL-M. The FX3U-128ASL-M cannot be used at the same time with the FX2N-16CCL-M and/or FX2N-32ASI-M. The FX2N-32ASI-M cannot be used at the same time with the FX3U-16CCL-M, FX3U-128ASL-M and/or the FX2N-16CCL-M. Only one station can be used for the whole system. Limitation in the number of connectable units Connected special function units/blocks operate using the 24V DC or 5V DC power supply of the PLC. Accordingly, when the total current consumption is larger than the current capacity of the PLC, it is necessary to add the power block FX3UC-1PS-5V. For details, refer to the respective FX PLC manual. A-44 FX Series PLC User's Manual - Data Communication Edition 2 Communication Types and Communication Equipment Common Items A For FX3UC-32MT-LT(-2) Common Items 2.3.4 2.3 Combination of Communication Equipment (Block Diagram) FX3UC-32MT-LT(-2) A For special function units/blocks C , refer to the next page. C B B A , B and C indicate the mounting position. (For the mounting procedure, refer to the respective communication equipment manual.) RDA RS-485 RD RDB SDA SD SDB SG A FX3U-485-BD A European terminal block ch1 FX3U-485ADP(-MB) FX3U-CNV-BD N:N Network Parallel link Computer link Non-protocol communication Inverter communication MODBUS *1 communication D FX3U-485ADP(-MB) ch1 RS-422 8-pin MINI-DIN, female Programming communication FX3U-422-BD B E ch1 RDB SDA SDB SG A ch2 FX3U-485-BD B European terminal block A European terminal block FX3U-485ADP(-MB) ch1 RD SD A B A USB 9-pin D-Sub, male MODBUS communication Programming communication 9-pin D-Sub, male Remote maintenance FX3U-232ADP(-MB) ch1 Programming I B A Modular jack Ethernet Programming Apx.A ch2 ch1 Ethernet FX3U-ENET-ADP communication Modular jack Only the FX3U-485ADP-MB and FX3U-232ADP-MB support MODBUS communication. A-45 Discontinued models FX3U-ENET-ADP FX3U-CNV-BD communication Remote Maintenance A FX3U-USB-BD H USB Mini-B connector RD SD *1. communication*1 G Programming Communication B Computer link Non-protocol ch1 FX3U-232ADP(-MB) FX3U-CNV-BD 9-pin D-Sub, male ch2 FX3U-232-BD F Non-Protocol Communication (FX2N-232IF) RS-232C communication Non-Protocol Communication (RS/RS2 Instruction) B Non-protocol ch1 FX3U-485ADP(-MB) FX3U-CNV-BD European terminal block Inverter Communication RDA RD SD C Computer Link B European terminal block Parallel Link B ch2 European terminal block N:N Network Either FX3U232ADP(-MB), FX3U-485ADP(-MB) or FX3U-ENET-ADP can be selected. ch1 B FX Series PLC User's Manual - Data Communication Edition 2 Communication Types and Communication Equipment Common Items 2.3 Combination of Communication Equipment (Block Diagram) FX3UC-32MT-LT(-2) A B C A , B and C indicate the mounting position. (For the mounting procedure, refer to the respective communication equipment manual.) For special adapters with communication type A and communication expansion boards B , refer to the previous page. FX 2N -16CCL-M For master station M3/M3.5 terminal block* 4 CC-Link E R R O R FX2NC-CNV-IF 3 1 2 FX3U -16CCL-M* * FX 2N-16CCL-M* For remote device station FX3UC-1PS-5V M3 terminal block CC-Link FX2N-32CCL Up to 7 units can be selected. For intelligent device station M3 terminal block *2 FX3U-64CCL POWER SD RD 9-pin D-Sub, male For FX3UC-32MT-LT(-2) built-in. FX2N-232IF Non-protocol communication Dedicated connector Dedicated connector CC-Link/LT FX2N-64CL-M European terminal block AnyWireASLINK FX 3U-128ASL-M*2*5 U ASI ASI ACTIVE POWE R ADDRESS/ ERROR FX2N-32ASI-M MOD E SE T M3 terminal block AS-i system PRJ MODE PRG ENABLE FROM/ TO CONFIG ERR FX2N-32ASI-M*6 *1. *2. *3. The FX3U-16CCL-M cannot be used at the same time with the FX2N-16CCL-M and/or the FX2N-32ASI-M. Only one unit can be connected to the main unit. The FX2N-16CCL-M cannot be used at the same time with the FX3U-16CCL-M, FX3U-128ASL-M and/or the FX2N-32ASI-M. *4. The terminal screw size is "M3" in the FX3U-16CCL-M. The terminal screw size is "M3.5" in the FX2N-16CCL-M. *5. The FX3U-128ASL-M cannot be used at the same time with the FX2N-16CCL-M and/or FX2N-32ASI-M. *6. The FX2N-32ASI-M cannot be used at the same time with the FX3U-16CCL-M, FX3U-128ASL-M and/or the FX2N-16CCL-M. Only one station can be used for the whole system. Limitation in the number of connectable units Connected special function units/blocks operate using the 24V DC or 5V DC power supply of the PLC. Accordingly, when the total current consumption is larger than the current capacity of the PLC, it is necessary to add the power block FX3UC-1PS-5V. For details, refer to the respective FX PLC manual. A-46 FX Series PLC User's Manual - Data Communication Edition Common Items 2.3 Combination of Communication Equipment (Block Diagram) A For FX3G Series Common Items 2.3.5 2 Communication Types and Communication Equipment 1. FX3G Series (14-point, 24-point type) A B B For special function units/blocks C , refer to the this section 3. C N:N Network A , B and C indicate the mounting position. (For the mounting procedure, refer to the respective communication equipment manual.) B ch1 RS-485 European terminal block B ● Parallel link ● Computer link ch1 RJ45 connector A ch1 B ● MODBUS communication*1 FX3U-485ADP(-MB) ch1 RS-422 ● Programming communication FX3G-422-BD B ch1 European terminal block ● Non-protocol communication FX3G-485-BD-RJ B A G ch1 B FX3U-485ADP(-MB) ● Computer link ch1 RS-232C FX3G-232-BD B ● MODBUS communication*1 A ch1 9-pin D-sub, male FX3U-232ADP(-MB) B A ch1 Ethernet *1. ● Remote maintenance ● Ethernet Modular jack FX3U-ENET-ADP ● Programming communication ● Programming communication H I Remote Maintenance FX3G-CNV-ADP FX3G-CNV-ADP ● Non-protocol communication Programming Communication 9-pin D-sub, male Non-Protocol Communication (FX2N-232IF) European terminal block FX3G-CNV-ADP Non-Protocol Communication (RS/RS2 Instruction) ch1 RJ45 connector E F FX3G-485-BD B D Inverter Communication 8-pin MINI-DIN, female C Computer Link European terminal block FX3G-CNV-ADP ● Non-protocol communication ● Inverter communication FX3G-485-BD-RJ B ● N:N Network Parallel Link FX3G-485-BD Apx.A Only the FX3U-485ADP-MB and FX3U-232ADP-MB support MODBUS communication. Discontinued models A-47 FX Series PLC User's Manual - Data Communication Edition 2 Communication Types and Communication Equipment Common Items 2.3 Combination of Communication Equipment (Block Diagram) 2. FX3G Series (40-point, 60-point type) B A C For special function units/blocks D D, refer to the this section 3. A , B , C and indicate the mounting position. (For the mounting procedure, refer to the respective communication equipment manual.) B Only either A or C can be used as ch2. ch1 RS-485 European terminal block FX3G-485-BD B ch1 C ch2 European terminal block FX3G-485-BD-RJ A ch2 C A ch1 FX3U-485ADP(-MB) B ch1 FX3G-422-BD B Either FX3U232ADP(-MB) or FX3U-485ADP (-MB) can be selected. ch1 FX3G-485-BD B B ch2 A FX3G-422-BD ch1 FX3U-485ADP(-MB) A-48 Non-protocol communication FX3U-485ADP(-MB) A ch1 FX3U-232ADP(-MB) A ch1 A ch2 *1 FX3U-232ADP(-MB) A ch2 *1 Ethernet FX3G-CNV-ADP communication European terminal block ch2 FX3G-232-BD B Programming European terminal block European terminal block C FX3G-CNV-ADP 8-pin MINI-DIN, female ch2 ch1 B communication*2 European terminal block 8-pin MINI-DIN, female *1 FX3G-485-BD-RJ FX3G-CNV-ADP MODBUS RJ45 connector A RS-232C C ch1 B Non-protocol European terminal block FX3U-485ADP(-MB) RS-422 Computer link communication RJ45 connector FX3G-485-BD-RJ Parallel link Inverter ch2 *1 N:N Network communication FX3G-485-BD B FX3G-CNV-ADP RJ45 connector FX3U-ENET-ADP FX3U-ENET-ADP FX3G-232-BD 9-pin D-Sub, male Computer link MODBUS communication*2 9-pin D-Sub, male Non-protocol 9-pin D-Sub, male Programming 9-pin D-Sub, male Remote Modular jack Modular jack communication communication maintenance Ethernet Programming communication *1. Ch2 is not available when the FX3G-8AV-BD, FX3G-4EX-BD or FX3G-2EYT-BD is used. *2. Only the FX3U-485ADP-MB and FX3U-232ADP-MB support MODBUS communication. FX Series PLC User's Manual - Data Communication Edition Common Items 2 Communication Types and Communication Equipment 2.3 Combination of Communication Equipment (Block Diagram) A , , and indicate the mounting position. (For the mounting procedure, refer to the respective communication equipment manual. For special adapters with communication type and communication expansion board , , refer to this section 1,2. CC-Link E R R O R B N:N Network FX2N-16CCL-M For master station M3/M3.5 terminal block*4 C Parallel Link FX3U-16CCL-M*1*2 FX2N-16CCL-M *3 For remote device station Up to 8 units can be selected Common Items 3. FX3G Series (Special unit/special block diagram) M3 terminal block ● CC-Link D Computer Link FX2N-32CCL For intelligent device station M3 terminal block E *2 Dedicated connector Inverter Communication FX3U-64CCL ● CC-Link/LT F European terminal block Non-Protocol Communication (RS/RS2 Instruction) FX2N-64CL-M AnyWireASLINK G FX 3U-128ASL-M*2*5 The FX3U-16CCL-M cannot be used at the same time with the FX2N-16CCL-M. *2. Only one unit can be connected to the main unit. *3. The FX2N-16CCL-M cannot be used at the same time with the FX3U-16CCL-M and/or FX3U-128ASL-M. *4. The terminal screw size is "M3" in the FX3U-16CCL-M. The terminal screw size is "M3.5" in the FX2N-16CCL-M. *5. The FX3U-128ASL-M cannot be used at the same time with the FX2N-16CCL-M. Non-Protocol Communication (FX2N-232IF) *1. H Programming Communication Limitation in the number of connectable units Connected special function units/blocks operate using the 24V DC or 5V DC power supply of the PLC. Accordingly, the number of connectable units depends on the system configuration. For details, refer to the respective FX PLC manual. I Remote Maintenance Apx.A Discontinued models A-49 FX Series PLC User's Manual - Data Communication Edition 2 Communication Types and Communication Equipment Common Items 2.3.6 2.3 Combination of Communication Equipment (Block Diagram) For FX3GC Series FX3GC Series A For special function units/blocks B , refer to the next page. B A and B indicate the mounting position. (For the mounting procedure, refer to the respective communication equipment manual.) Either FX3U232ADP(-MB), FX3U-485ADP(-MB) A ch1 or FX3U-ENET-ADP N:N Network RS-485 European can be selected. Parallel link terminal block Computer link A Non-protocol ch2 communication FX3U-485ADP(-MB) European Inverter terminal block communication MODBUS *1 communication FX3U-485ADP(-MB) A ch1 RS-422 European terminal block FX3U-485ADP(-MB) A ch2 Non-protocol communication European terminal block FX3U-485ADP(-MB) A Computer link Non-protocol ch1 communication RS-232C 9-pin D-Sub, male FX3U-232ADP(-MB) A ch2 9-pin D-Sub, male MODBUS communication*1 Programming communication Remote maintenance FX3U-232ADP(-MB) A ch2 Modular jack A ch1 FX3U-ENET-ADP Ethernet Modular jack ● Ethernet ● Programming communication FX3U-ENET-ADP *1. A-50 Only the FX3U-485ADP-MB and FX3U-232ADP-MB support MODBUS communication. FX Series PLC User's Manual - Data Communication Edition 2 Communication Types and Communication Equipment Common Items 2.3 Combination of Communication Equipment (Block Diagram) A A Common Items FX3GC Series A and B indicate the mounting position. (For the mounting procedure, refer to the respective communication equipment manual.) B B For special adapters with communication type A , refer to the previous page. B FX2N-16CCL-M CC-Link FX2NC-CNV-IF FX3U-16CCL-M*1*2 B B For master station M3/M3.5 terminal block*4 C FX2N-16CCL-M *3 For remote device station Parallel Link M3 terminal block CC-Link D Computer Link Up to 8 units can be selected. E R R O R FX3UC-1PS-5V N:N Network B FX2N-32CCL B For intelligent device station M3 terminal block E FX3U-64CCL B Dedicated connector CC-Link/LT B European terminal block AnyWireASLINK G FX 3U-128ASL-M*2*5 The FX3U-16CCL-M cannot be used at the same time with the FX2N-16CCL-M. *2. Only one unit can be connected to the main unit. *3. The FX2N-16CCL-M cannot be used at the same time with the FX3U-16CCL-M and/or FX3U-128ASL-M. *4. The terminal screw size is "M3" in the FX3U-16CCL-M. The terminal screw size is "M3.5" in the FX2N-16CCL-M. *5. The FX3U-128ASL-M cannot be used at the same time with the FX2N-16CCL-M. Non-Protocol Communication (FX2N-232IF) *1. F Non-Protocol Communication (RS/RS2 Instruction) FX2N-64CL-M Inverter Communication *2 H Programming Communication Limitation in the number of connectable units Connected special function units/blocks operate using the 24V DC or 5V DC power supply of the PLC. Accordingly, when the total current consumption is larger than the current capacity of the PLC, it is necessary to add the power block FX3UC-1PS-5V. For details, refer to the respective FX PLC manual. I Remote Maintenance Apx.A Discontinued models A-51 FX Series PLC User's Manual - Data Communication Edition Common Items 2.3.7 2 Communication Types and Communication Equipment 2.3 Combination of Communication Equipment (Block Diagram) For FX3S Series FX3S Series A C B For special function units/blocks C are not connectable. A , B and C indicate the mounting position. (For the mounting procedure, refer to the respective communication equipment manual.) B RS-485 European terminal block FX3G-485-BD B RJ45 connector FX3G-485-BD-RJ B A N:N Network Parallel link Computer link Non-protocol communication Inverter communication MODBUS *1 communication European terminal block FX3S-CNV-ADP FX3U-485ADP(-MB) B RS-422 8-pin MINI-DIN, female ● Programming communication FX3G-422-BD B European terminal block FX3G-485-BD B RJ45 connector Non-protocol communication FX3G-485-BD-RJ B A European terminal block FX3S-CNV-ADP FX3U-485ADP(-MB) B RS-232C 9-pin D-Sub,male communication*1 A Programming 9-pin D-Sub,male FX3S-CNV-ADP FX3U-232ADP(-MB) B A Ethernet *1. A-52 communication Remote maintenance ● Ethernet Modular jack FX3S-CNV-ADP communication MODBUS FX3G-232-BD B Computer link Non-protocol ● Programming communication FX3U-ENET-ADP Only the FX3U-485ADP-MB and FX3U-232ADP-MB support MODBUS communication. FX Series PLC User's Manual - Data Communication Edition 2 Communication Types and Communication Equipment Common Items A For FX2N Series Common Items FX2N Series A B D B For special function units/blocks C , refer to the next page. C B RS-485 European terminal block B A European terminal block FX2N-CNV-BD FX2NC-485ADP A ● ● ● ● N:N Network Parallel link Computer link Non-protocol communication ● Inverter communication D FX0N-485ADP Essential when inverter communication is used. B FX2N-ROM-E1 RS-422 ● Programming communication FX2N-422-BD B F European terminal block ● Non-protocol A communication European terminal block G Non-Protocol Communication (FX2N-232IF) A FX2N-CNV-BD FX2NC-485ADP M3 terminal block B H FX0N-485ADP RS-232C FX2N-232-BD ● Computer link ● Non-protocol A communication A FX2N-CNV-BD FX2NC-232ADP communication ● Programming ● Remote 25-pin D-Sub, female maintenance ● Short mail sending Apx.A D Discontinued models FX0N-232ADP FX2N-ROM-E1 I Remote Maintenance 9-pin D-Sub, male Programming Communication 9-pin D-Sub, male B Non-Protocol Communication (RS/RS2 Instruction) FX2N-485-BD B E Inverter Communication 8-pin MINI-DIN, female D Computer Link M3 terminal block C Parallel Link FX2N-485-BD N:N Network A , B , C and D indicate the mounting position. (For the mounting procedure, refer to the respective communication equipment manual.) One line can be selected. 2.3.8 2.3 Combination of Communication Equipment (Block Diagram) Essential when the short mail sending is used A-53 FX Series PLC User's Manual - Data Communication Edition Common Items 2 Communication Types and Communication Equipment 2.3 Combination of Communication Equipment (Block Diagram) FX2N Series A B D A , B , C and D indicate the mounting position. (For the mounting procedure, refer to the respective communication equipment manual.) C For special adapters with communication type A , communication expansion board B and function extension memory cassettes D , refer to the previous page. C For master station FX2N-16CCL-M M3.5 terminal block CC-Link E R R O R FX2N-16CCL-M*1 CC-Link C For remote device station M3 terminal block FX2N-32CCL Up to 8 units can be selected. C POWER SD RD 9-pin D-Sub, male Non-protocol communication FX2N-232IF C Dedicated connector CC-Link/LT M3 terminal block AS-i system M3 terminal block MELSEC-I/O LINK FX2N-64CL-M C U ASI ASI ACTIVE POWE R ADDRESS/ ERROR FX2N -32ASI-M MOD E SE T PRJ MODE PRG ENABLE FROM/ TO CONFIG ERR FX2N-32ASI-M*2 C FX2N-16LNK-M *1. The FX2N-16CCL-M cannot be used at the same time with the FX2N-32ASI-M. *2. The FX2N-32ASI-M cannot be used at the same time with the FX2N-16CCL-M. Limitation in the number of connectable units Connected special function units/blocks operate using the 24V DC or 5V DC power supply of the PLC. Therefore, the total current consumption larger than the PLC current capacity reduces the number of connectable units. For details, refer to the respective FX PLC manual. A-54 FX Series PLC User's Manual - Data Communication Edition Common Items 2.3 Combination of Communication Equipment (Block Diagram) A For FX2NC Series Common Items FX2NC Series A D For special function units/blocks C , refer to the next page. C B A RS-485 European terminal block C M3 terminal block D Essential when inverter communication is used D Computer Link FX0N-485ADP N:N Network Parallel link Computer link Non-protocol communication Inverter communication Parallel Link FX2NC-485ADP A N:N Network A , C and D indicate the mounting position. (For the mounting procedure, refer to the respective communication equipment manual.) E Inverter Communication FX2NC-ROM-CE1 A RS-422 European terminal block FX2NC-485ADP F Non-protocol communication A M3 terminal block G Non-Protocol Communication (FX2N-232IF) FX0N-485ADP A RS-232C Non-Protocol Communication (RS/RS2 Instruction) One line can be selected. 2.3.9 2 Communication Types and Communication Equipment 9-pin D-Sub, male H A 25-pin D-Sub, male D Essential when the short mail sending is used I Remote Maintenance FX0N-232ADP Computer link Non-protocol communication Programming communication Short mail sending Programming Communication FX2NC-232ADP Apx.A Discontinued models FX2NC-ROM-CE1 A-55 FX Series PLC User's Manual - Data Communication Edition Common Items 2 Communication Types and Communication Equipment 2.3 Combination of Communication Equipment (Block Diagram) FX2NC Series A D A , C and D indicate the mounting position. (For the mounting procedure, refer to the respective communication equipment manual.) C For special adapters with communication type A and function extension memory boards D , refer to the previous page. C C For master station FX2N-16CCL-M CC-Link M3.5 terminal block E R R O R FX2NC-CNV-IF FX2N-16CCL-M*1 C CC-Link For remote device station M3 terminal block FX2N-32CCL Up to 4 units can be selected. C POWER SD RD 9-pin D-Sub, male Non-protocol communication FX2N-232IF C Dedicated connector CC-Link/LT M3 terminal block AS-i system M3 terminal block MELSEC-I/O LINK FX2N-64CL-M C U ASI ASI ACTIVE POWE R ADDRESS/ ERROR FX 2N-32ASI-M MOD E SE T PRJ MODE PRG ENABLE FROM/ TO CONFIG ERR FX2N-32ASI-M*2*3 C FX2N-16LNK-M *1. The FX2N-16CCL-M cannot be used at the same time with the FX2N-32ASI-M. *2. The FX2N-32ASI-M cannot be used at the same time with the FX2N-16CCL-M. *3. The FX2NC-MT-D/UL and FX2NC-M-DSS(-T-DS) are not supported. Limitation in the number of connectable units Connected special function units/blocks operate using the 24V DC or 5V DC power supply of the PLC. Therefore, the total current consumption larger than the plc current capacity reduces the number of connectable units. For details, refer to the respective FX PLC manual. A-56 FX Series PLC User's Manual - Data Communication Edition 2 Communication Types and Communication Equipment Common Items 2.3 Combination of Communication Equipment (Block Diagram) A Common Items 2.3.10 For FX1N Series FX1N Series A B For special function units/blocks C , refer to the next page. C B N:N Network A , B and C indicate the mounting position. (For the mounting procedure, refer to the respective communication equipment manual.) B RS-485 European terminal block B A European terminal block FX2NC-485ADP N:N Network Parallel link Computer link Non-protocol communication D A M3 terminal block B ● Programming communication FX1N-422-BD F European terminal block FX1N-485-BD B A ● Non-protocol FX1N-CNV-BD FX2NC-485ADP communication A M3 terminal block H Programming Communication B FX0N-485ADP RS-232C 9-pin D-Sub, male FX1N-232-BD ● Computer link ● Non-protocol A communication 9-pin D-Sub, male ● Programming communication FX1N-CNV-BD FX2NC-232ADP I Remote Maintenance B G Non-Protocol Communication (FX2N-232IF) European terminal block Non-Protocol Communication (RS/RS2 Instruction) One line can be selected. B E Inverter Communication FX0N-485ADP 8-pin MINI-DIN, female RS-422 C Computer Link FX1N-CNV-BD ● ● ● ● Parallel Link FX1N-485-BD ● Remote A maintenance Apx.A Discontinued models 25-pin D-Sub, female FX0N-232ADP A-57 FX Series PLC User's Manual - Data Communication Edition Common Items 2 Communication Types and Communication Equipment 2.3 Combination of Communication Equipment (Block Diagram) FX1N Series A B C A , B and C indicate the mounting position. (For the mounting procedure, refer to the respective communication equipment manual.) For special adapters with communication type A and communication expansion boards B , refer to the previous page. C For master station FX2N-16CCL-M CC-Link M3.5 terminal block E R R O R FX2N-16CCL-M*1 CC-Link C Up to 8 units can be selected. For remote device station M3 terminal block FX2N-32CCL C Dedicated connector CC-Link/LT M3 terminal block AS-i system M3 terminal block MELSEC-I/O LINK FX2N-64CL-M C U ASI ASI ACTIVE POWE R ADDRESS/ ERROR FX2N -32ASI-M MOD E SE T PRJ MODE PRG ENABLE FROM/ TO CONFIG ERR FX2N-32ASI-M*2 C FX2N-16LNK-M *1. The FX2N-16CCL-M cannot be used at the same time with the FX2N-32ASI-M. *2. The FX2N-32ASI-M cannot be used at the same time with the FX2N-16CCL-M. Limitation in the number of connectable units Connected special function units/blocks operate using the 24V DC or 5V DC power supply of the PLC. Accordingly, the number of connectable units depends on the system configuration. For details, refer to the respective FX PLC manual. A-58 FX Series PLC User's Manual - Data Communication Edition Common Items 2 Communication Types and Communication Equipment 2.3 Combination of Communication Equipment (Block Diagram) A Common Items 2.3.11 For FX1NC Series FX1NC Series A B For special function units/blocks C , refer to the next page. C A RS-485 European terminal block FX2NC-485ADP A M3 terminal block D Computer Link FX0N-485ADP European terminal block FX2NC-485ADP E Non-protocol communication A M3 terminal block F Non-Protocol Communication (RS/RS2 Instruction) FX0N-485ADP A RS-232C 9-pin D-Sub, male A 25-pin D-Sub, female Computer link Non-protocol communication Programming communication Remote maintenance G Non-Protocol Communication (FX2N-232IF) FX2NC-232ADP Inverter Communication One line can be selected. A RS-422 C Parallel Link N:N Network Parallel link Computer link Non-protocol communication N:N Network A and C indicate the mounting position. (For the mounting procedure, refer to the respective communication equipment manual.) H Programming Communication FX0N-232ADP I Remote Maintenance Apx.A Discontinued models A-59 FX Series PLC User's Manual - Data Communication Edition Common Items 2 Communication Types and Communication Equipment 2.3 Combination of Communication Equipment (Block Diagram) FX1NC Series A A and C indicate the mounting position. (For the mounting procedure, refer to the respective communication equipment manual.) C For special adapters with communication type A , refer to the previous page. C C For master station FX2N-16CCL-M CC-Link M3.5 terminal block E R R O R FX2NC-CNV-IF FX2N-16CCL-M*1 CC-Link C Up to 2 units can be selected. For remote device station M3 terminal block FX2N-32CCL C Dedicated connector CC-Link/LT M3 terminal block AS-i system M3 terminal block MELSEC-I/O LINK FX2N-64CL-M C U ASI ASI ACTIVE POWE R ADDRESS/ ERROR FX2N-32ASI-M MOD E SE T PRJ MODE PRG ENABLE FROM/ TO CONFIG ERR FX2N-32ASI-M*2 C FX2N-16LNK-M *1. The FX2N-16CCL-M cannot be used at the same time with the FX2N-32ASI-M. *2. The FX2N-32ASI-M cannot be used at the same time with the FX2N-16CCL-M. Limitation in the number of connectable units Connected special function units/blocks operate using the 24V DC or 5V DC power supply of the PLC. Accordingly, the number of connectable units depends on the system configuration. For details, refer to the respective FX PLC manual. A-60 FX Series PLC User's Manual - Data Communication Edition 2 Communication Types and Communication Equipment Common Items 2.3 Combination of Communication Equipment (Block Diagram) A Common Items 2.3.12 For FX1S Series FX1S Series A B C special units/blocks are not connectable. C B N:N Network A , B and C indicate the mounting position. (For the mounting procedure, refer to the respective communication equipment manual.) B RS-485 European terminal block B A European terminal block FX2NC-485ADP N:N Network Parallel link Computer link Non-protocol communication D A M3 terminal block B ● Programming communication FX1N-422-BD F European terminal block FX1N-485-BD B A ● Non-protocol FX1N-CNV-BD FX2NC-485ADP communication A M3 terminal block B H Programming Communication FX0N-485ADP RS-232C 9-pin D-Sub, male FX1N-232-BD ● Computer link ● Non-protocol A communication 9-pin D-Sub, male communication ● Remote A FX1N-CNV-BD ● Programming I Remote Maintenance B G Non-Protocol Communication (FX2N-232IF) European terminal block Non-Protocol Communication (RS/RS2 Instruction) One line can be selected. B E Inverter Communication FX0N-485ADP 8-pin MINI-DIN, female RS-422 C Computer Link FX1N-CNV-BD ● ● ● ● Parallel Link FX1N-485-BD maintenance FX2NC-232ADP Apx.A Discontinued models 25-pin D-Sub, female FX0N-232ADP A-61 FX Series PLC User's Manual - Data Communication Edition Common Items 2 Communication Types and Communication Equipment 2.3 Combination of Communication Equipment (Block Diagram) 2.3.13 For FX0N Series FX0N Series A For special function units/blocks C , refer to the next page. C A and C indicate the mounting position. (For the mounting procedure, refer to the respective communication equipment manual.) A RS-485 European terminal block N:N Network Parallel link Computer link Non-protocol communication FX2NC-485ADP A M3 terminal block FX0N-485ADP One line can be selected. A RS-422 European terminal block FX2NC-485ADP Non-protocol communication A M3 terminal block FX0N-485ADP A RS-232C 9-pin D-Sub, male Computer link Non-protocol communication FX2NC-232ADP A 25-pin D-Sub, female FX0N-232ADP A-62 FX Series PLC User's Manual - Data Communication Edition Common Items 2 Communication Types and Communication Equipment 2.3 Combination of Communication Equipment (Block Diagram) A A C A and C indicate the mounting position. (For the mounting procedure, refer to the respective communication equipment manual.) B N:N Network For special adapters with communication type A , refer to the previous page. C M3 terminal block CC-Link C AS-i system D MELSEC-I/O LINK E Parallel Link FX2N-32CCL C U ASI ASI ACTIVE POWE R ADDRESS/ ERROR M3 terminal block FX 2N -32ASI-M MOD E SE T PRJ MODE PRG ENABLE FROM/ TO CONFIG ERR Computer Link Up to 4 units can be selected. For remote device station Common Items FX0N Series FX2N-32ASI-M C M3 terminal block Inverter Communication FX2N-16LNK-M F Non-Protocol Communication (RS/RS2 Instruction) Limitation in the number of connectable units Connected special function units/blocks operate using the 24V DC or 5V DC power supply of the PLC. Therefore, the total current consumption larger than the plc current capacity reduces the number of connectable units. For details, refer to the respective FX PLC manual. G Non-Protocol Communication (FX2N-232IF) H Programming Communication I Remote Maintenance Apx.A Discontinued models A-63 FX Series PLC User's Manual - Data Communication Edition Common Items 2 Communication Types and Communication Equipment 2.3 Combination of Communication Equipment (Block Diagram) 2.3.14 For FX2(FX) and FX2C Series (reference) FX2(FX),FX2C Series A indicate the mounting position. (For the mounting procedure, refer to the respective communication equipment manual.) A A RS-485 M3.5 terminal block Computer link 25-pin D-Sub, female Computer link Non-protocol communication FX-485ADP One line can be selected. A RS-232C FX-232ADP A Dedicated M3.5 terminal block Parallel link Connector for optical fiber Parallel link FX2-40AW A Dedicated FX2-40AP A-64 FX Series PLC User's Manual - Data Communication Edition 3 Outline of Communication Setting in the FX Series Common Items 3.1 Setting Method A Common Items 3. Outline of Communication Setting in the FX Series • Computer link • Inverter communication B N:N Network This chapter describes which communication parameters can be changed for the following communication types, and provides methods on how to change them. • Non-protocol communication (RS/RS2 instruction) C • Internet mail sending Setting Method The following two communication setting methods are available for FX PLCs. Either method can be used, but the method using parameters is recommended. 1) Specify the settings using parameters in the programming tool Register the settings in parameters, transfer it to the PLC and turn the PLC's power OFF and then ON. (This method is not available in FX2(FX), FX2C, and FX0N PLCs.) (This method is not available for ch0 in FX3G, FX3GC PLCs.) Caution Regardless of the method chosen above, a PLC operates the same way. If both methods are selected, priority is given to the method using parameters. FX Series FX2(FX),FX2C FX0N FX1S FX1N,FX1NC FX2N,FX2NC FX3S FX3G,FX3GC FX3U,FX3UC Parameter method — — *1 Program method *1. Only ch1 and ch2 are available. PLC memory Parameter area Program area [MOV H D8120] Written by program [MOV K D8121] [MOV K D8129] In FX3S, FX3G, FX3GC, FX3U and FX3UC Program method [MOV H D8370] [MOV K D8379] [MOV H D8400] [MOV K D8409] [MOV H D8420] [MOV K D8421] [MOV K D8429] Written by program Written by program Written by program H In FX3S, FX3G, FX3GC, FX3U and FX3UC ch0 RS2 instruction D8370 Communication format D8379 Time-out time setting ch1 RS2 instruction D8400 Communication format D8409 Time-out time setting Ch0 is available only in the FX3G, FX3GC PLC. The setting method using parameter cannot be used for ch0. Only ch1 is available in the FX3S PLC. ch2 Computer link RS instruction Inverter communication Programming communication D8420 Communication format D8421 Station number settings D8429 Time-out time setting I Remote Maintenance Sequence program for set values ch1 Computer link RS instruction Inverter communication Programming communication D8120 Communication format D8121 Station number settings D8129 Time-out time setting Programming Communication Parameter method Transferred when power is turned ON G Non-Protocol Communication (FX2N-232IF) 3. Setting flow Setting window F Non-Protocol Communication (RS/RS2 Instruction) 2. Communication setting method availability in each FX PLC E Inverter Communication 2) Directly specify the settings in a sequence program Prepare a sequence program which sets the communication format, station number and time-out time setting, and then transfer the program to the PLC. D Computer Link 1. Setting methods Parallel Link 3.1 Apx.A Discontinued models When both methods are selected at the same time, priority is given to the contents set using the parameter method. A-65 FX Series PLC User's Manual - Data Communication Edition Common Items 3 Outline of Communication Setting in the FX Series 3.1 Setting Method 4. Time at which the settings become valid 1) Specifying the settings using parameters in the programming tool: When the PLC power is turned ON, the contents of the parameters are automatically transferred to the PLC. As soon as the parameters are transferred to the PLC, the settings become valid. 2) Directly specifying the settings in a sequence program: To enable the settings, write data after turning the PLC mode to RUN from STOP, and then reboot the PLC's power. A-66 FX Series PLC User's Manual - Data Communication Edition Common Items 3.2 Communication Setting Using Parameter Method (GX Works2) A Communication Setting Using Parameter Method (GX Works2) 3.2.1 Operating procedure With GX Works2 open, follow the steps in this section for activating the serial communication setting method. Opening the parameter setting window In the project view area of the navigation window, double-click [Parameter] [PLC Parameter]. If the navigation window is not displayed, select [View] [Docking Window] [Navigation] from the menu bar. C Parallel Link 1 B N:N Network Communication settings may be changed by the parameter method with GX Works2, GX Developer, FXGP/WIN for Windows and FX-30P handy programming panel. This section describes how to change parameters with GX Works2. For details on FXGP/WIN operating procedure, refer to section 3.3. For details on GX Developer operating procedure, refer to GX Developer Operating Manual. For details on FX-30P operating procedure, refer to FX-30P Operation Manual. Common Items 3.2 3 Outline of Communication Setting in the FX Series D Computer Link E Inverter Communication 2 Setting the serial communication (parameters) F Non-Protocol Communication (RS/RS2 Instruction) Click the [PLC System(2)] tab on the dialog box. When using programming communication, parallel link, N:N Network or remote maintenance, do not check the "Operate Communication Setting" box. When using computer link, inverter communication or non-protocol communication (RS/RS2 instruction) function, check the "Operate Communication Setting" box, and then set each item. Click [End]. G Non-Protocol Communication (FX2N-232IF) H Programming Communication I Remote Maintenance 3 Writing parameters to the PLC A-67 Apx.A Discontinued models Select [Online] [Write to PLC] from the menu bar, click [Parameter + Program], and then click [Execute]. FX Series PLC User's Manual - Data Communication Edition 3 Outline of Communication Setting in the FX Series Common Items 3.2.2 3.2 Communication Setting Using Parameter Method (GX Works2) Correspondence between parameter setting and each communication type Even — 1-bit *1 19200 9600 4800 2400 1200 600 300 — — — — — — — — — — — — — — — — — — RS-485 — Invalid — — — — Sum check Invalid/valid — — — Transmission control procedure Format 1 — — — Header Invalid/valid Terminator Invalid/valid Control cable Invalid/valid Hardware type Regular/ RS-232C Control mode — — — Format 4 — — — Station number settings 00 to 0F — — — Time-out time setting 1 to 255 — — — — — B C D E F Reference page *1. Only available for FX3S, FX3G, FX3GC, FX3U and FX3UC PLCs. Remote maintenance — This communication is not executed in this setting. Programming communication AS-i system Odd This communication is not executed in this setting. None This communication is not executed in this setting. AnyWireASLINK — This communication is not executed in this setting. This communication is not executed in this setting. This communication is not executed in this setting. 7-bit 8-bit CC-Link/LT network — This communication is not executed in this setting. — This communication is not executed in this setting. Internet mail sending Short mail sending Non-protocol communication (FX2N-232IF) Non-protocol communication (RS/RS2 instruction) RS RS2 Inverter communication Computer link — 38400 A-68 Parallel link Dedicated protocol 2-bit Transmission speed (bps) N:N Network This communication is not executed in this setting. Stop bit This communication is not executed in this setting. Parity — This communication is not executed in this setting. Data length Non-protocol communication This communication is not executed in this setting. Protocol Ethernet communication Contents CC-Link network Set item MODBUS communication The table below shows the communication types and set items which can be set using parameters: G — — — — — H Remarks Not selectable I FX Series PLC User's Manual - Data Communication Edition Common Items 3.3 Communication Setting in Parameter Method (FXGP/WIN) A Communication Setting in Parameter Method (FXGP/WIN) 3.3.1 Operating procedure 1 Adjusting serial setting (parameter) Select [Option] [Serial setting (parameter)] from the toolbar. The following dialog appears according to absence/presence of parameter settings. C Parallel Link This subsection explains the serial communication setting method. Suppose that FXGP/WIN is already started up. B N:N Network Communication settings may be changed by the parameter method with GX Works2, GX Developer, FXGP/WIN for Windows and FX-30P handy programming panel. This section describes how to change parameters with FXGP/WIN. Ch0 and Ch 2 cannot be set using FXGP/WIN. For details on GX Works2 operating procedure, refer to section 3.2. For details on GX Developer operating procedure, refer to GX Developer Operating Manual. For details on FX-30P operating procedure, refer to FX-30P Operation Manual. Common Items 3.3 3 Outline of Communication Setting in the FX Series D E Inverter Communication There is no communication setting. When using the programming communication, parallel link, N:N Network or remote maintenance, click the [No] button. When using computer link, inverter communication, or non-protocol communication (RS instruction) function, click the [Yes] button. Computer Link 1. When there are no parameter settings F Non-Protocol Communication (RS/RS2 Instruction) G Non-Protocol Communication (FX2N-232IF) H Programming Communication I Remote Maintenance Apx.A Discontinued models A-69 FX Series PLC User's Manual - Data Communication Edition Common Items 3 Outline of Communication Setting in the FX Series 3.3 Communication Setting in Parameter Method (FXGP/WIN) 2. When there are already parameter settings There is communication setting. Confirm the setting contents. When using programming communication, parallel link, N:N Network or remote maintenance, click the [Clear] button. A-70 FX Series PLC User's Manual - Data Communication Edition 3 Outline of Communication Setting in the FX Series Common Items A Correspondence between parameter setting and each communication type Common Items 9600 4800 2400 1200 300 Header Invalid/valid Terminator Invalid/valid Control cable Invalid/valid RS-485 — — — — — — — — — — — — — — — — — — — Invalid — — — — Sum check Invalid/valid — — — Transmission control procedure Format 1 — — — Format 4 — — — Station number settings 00 to 0F — — — Time-out time setting 1 to 255 — — Reference page Remote maintenance Programming communication AS-i system AnyWireASLINK — — — B C D E F G — — — — — H H Not selectable I Remote Maintenance Control mode G Programming Communication Regular/RS-232C — F Non-Protocol Communication (FX2N-232IF) 600 — Non-Protocol Communication (RS/RS2 Instruction) 19200 This communication is not executed in this setting. — This communication is not executed in this setting. This communication is not executed in this setting. — E This communication is not executed in this setting. CC-Link/LT network Internet mail sending Odd This communication is not executed in this setting. None This communication is not executed in this setting. This communication is not executed in this setting. Short mail sending Non-protocol communication (FX2N-232IF) Non-protocol communication (RS instruction) Inverter communication Computer link — 2-bit Hardware type Parallel link 8-bit Even Baud rate (bps) N:N Network 7-bit This communication is not executed in this setting. — This communication is not executed in this setting. — — 1-bit Stop bit Ethernet communication Dedicated protocol This communication is not executed in this setting. D Inverter Communication Parity — This communication is not executed in this setting. Data length Non-protocol communication C Computer Link Protocol Remarks Parallel Link CC-Link network Contents B N:N Network Set item MODBUS communication The table below shows the communication types and items which can be set using parameters: This communication is not executed in this setting. 3.3.2 3.3 Communication Setting in Parameter Method (FXGP/WIN) I Apx.A Discontinued models A-71 FX Series PLC User's Manual - Data Communication Edition Common Items 3.4 3 Outline of Communication Setting in the FX Series 3.4 Extension of Ports (For FX3G, FX3GC, FX3U, FX3UC) Extension of Ports (For FX3G, FX3GC, FX3U, FX3UC) In FX3G, FX3GC, FX3U and FX3UC PLCs, up to two communication port channels can be connected using a communication expansion board and communication special adapter. Point • Only one channel can be connected to the FX3G PLC (14-point and 24-point type). • The standard built-in port (RS-422) can be used as ch0 when the non-protocol communication function (RS2 instruction) is used in the FX3G, FX3GC PLC. Refer to the "Non-protocol Communication (RS/RS2 instruction)" section. • When a CF card special adapter is connected to the PLC, it is handled in the same way as a communication special adapter, and occupies one communication port channel. For details, refer to FX3U-CF-ADP User’s Manual. • When a FX3U-8AV-BD, FX3G-8AV-BD, FX3G-4EX-BD or FX3G-2EYT-BD is connected to the PLC, it is handled in the same way as a communication expansion board, and occupies one communication port channel. • When the FX3U-ENET-ADP is used, one communication port is occupied. Only one FX3U-ENET-ADP unit can be connected at the last stage (left end) of the main unit and special adapters. For details, refer to FX3U-ENET-ADP User’s Manual. 3.4.1 Extension of Port (For FX3G, FX3GC PLC) 1. For FX3G PLC (40-point, 60-point type) The communication expansion board connected to the option connector 1 or the first communication special adapter works as ch1, and the communication expansion board connected to the option connector 2 or the second communication special adapter works as ch2. When using two communication special adapters • When using a communication expansion board and a communication special adapter together Communication Communication special adapter special adapter (ch2) *1 (ch1) Communication Communication special adapter expansion board (ch1) FX3G-CNV-ADP (ch2) Analog special Standard built-in port (RS-422) adapter (ch0) *1. FX3G-CNV-ADP Analog special Standard built-in port (RS-422) (ch0) adapter Ch2 is not available when the FX3G-8AV-BD, FX3G-4EX-BD or FX3G-2EYT-BD is used. • When using one communication expansion board Communication expansion board (ch2) Communication expansion board (ch1) Standard built-in port (RS-422) (ch0) A-72 Standard built-in port (RS-422) (ch0) FX Series PLC User's Manual - Data Communication Edition Common Items 3 Outline of Communication Setting in the FX Series 3.4 Extension of Ports (For FX3G, FX3GC, FX3U, FX3UC) A Common Items • When using two communication expansion board Communication Communication expansion board expansion board (ch2) (ch1) B N:N Network Standard built-in port (RS-422) (ch0) 2. For FX3G PLC (14-point, 24-point type) Communication special adapter FX3G-CNV-ADP (ch1) Communication expansion board (ch1) C Parallel Link One communication port channel can be connected to the FX3G PLC main unit (14-point and 24-point type). It is not allowed to connect two communication special adapters. D Computer Link E Standard built-in port (RS-422) (ch0) Standard built-in port (RS-422) (ch0) Inverter Communication Analog special adapter 3. For FX3GC PLC F Non-Protocol Communication (RS/RS2 Instruction) Communication Communication special adapter special adapter (ch1) (ch2) Standard built-in port (RS-422) (ch0) G Non-Protocol Communication (FX2N-232IF) Analog special adapter H Programming Communication I Remote Maintenance Apx.A Discontinued models A-73 FX Series PLC User's Manual - Data Communication Edition 3 Outline of Communication Setting in the FX Series Common Items 3.4.2 3.4 Extension of Ports (For FX3G, FX3GC, FX3U, FX3UC) Extension of Port (For FX3U, FX3UC PLC) When a communication expansion board and communication special adapter are used, the board is handled as ch 1 and the adapter is handled as ch 2. When connecting two communication special adapters using the FX3U-CNV-BD*1, the one closer to the main unit is handled as ch 1 and the farther one is handled as ch 2. When a FX3U-8AV-BD or CF card special adapter is used, however, it occupies one communication port channel. *1. When using the FX3UC(D, DS, DSS) PLC, the FX3U-CNV-BD is not required. 1. For FX3U PLC • When using a communication expansion board and a communication special adapter together Communication Communication special adapter expansion board (ch2) (ch1) FX 3U -4AD-ADP P O WE R FX 3U -4AD-ADP FX 3 U -4AD-ADP FX 3U -4AD-ADP P O WE R P O WE R When using two communication special adapters FX 3U -4AD-ADP P O WE R Communication special adapter (ch1) Communication special adapter (ch2) FX 3U -4AD-ADP FX 3U -4AD-ADP P O WE R P O WE R FX3U-CNV-BD FX 3U -4AD-ADP P O WE R P O WE R RDA RD RDB SDA SD SDB SG Analog special adapter *2. High speed input/output special adapter*2 High speed input/output special adapter*2 Analog special adapter When using high speed special input/output adapters, make sure to connect them to the PLC main unit first before connecting communication special adapters, CF card special adapter and analog special adapters. 2. For FX3UC(D,DS,DSS) PLC Communication special adapter (ch2) FX3U-4AD-ADP Analog special adapter FX3U-4AD-ADP FX3U-4AD-ADP POWER POWER POWER Communication special adapter (ch1) FX3U-4AD-ADP POWER 3. For FX3UC-32MT-LT(-2) PLC • When using a communication expansion board and a communication special adapter together Communication special adapter Analog (ch2) special adapter FX3U-4AD-ADP POWER FX3U-4AD-ADP FX3U-4AD-ADP FX3U-4AD-ADP POWER POWER Communication special adapter (ch2) FX3U-4AD-ADP POWER POWER RDA RD RDB SDA SD SDB SG A-74 Communication expansion board (ch1) When using two communication special adapters Analog special adapter FX3U-4AD-ADP FX3U-4AD-ADP POWER POWER Communication special adapter (ch1) FX3U-CNV-BD FX3U-4AD-ADP POWER FX Series PLC User's Manual - Data Communication Edition 3 Outline of Communication Setting in the FX Series Common Items A Limitation when ch1 and ch2 are used at the same time Communication channel: ch2 C Communication channel: ch1 Parallel Link RD A RD RD B SD A SD SD B SG Communication special adapter Expansion board Expansion board FX3G/FX3GC/FX3U/FX3UC PLC : Applicable, : Not applicable Communication setting for ch1 N:N Network Parallel link Computer link E F Inverter communication Non-protocol communication *1 (RS instruction) Non-protocol communication (RS2 instruction) Programming communication Remote *2 maintenance (Example 1) (Example 2) G Non-Protocol Communication (FX2N-232IF) Communication setting for ch2 Non-protocol Non-protocol Inverter Programming Remote communication communication communication communication maintenance (RS instruction) (RS2 instruction) Non-Protocol Communication (RS/RS2 Instruction) MODBUS communication Computer link Inverter Communication MODBUS communication N:N Network Parallel link D Computer Link Communication special adapter B N:N Network When using ch1 and ch2 at the same time, available communication type combinations are limited. For details, refer to the table below. When a CF card special adapter, FX3U-8AV-BD, FX3G-8AV-BD, FX3G-4EX-BD, FX3G-2EYT-BD or the FX3UENET-ADP is used, one communication port (1ch) is occupied. However, the occupied communication port does not apply any restrictions to the combination of communication functions when ch1 and ch2 are used at the same time. Common Items 3.4.3 3.4 Extension of Ports (For FX3G, FX3GC, FX3U, FX3UC) H Ch2 cannot be set for non-protocol communication (RS instruction). *2. When using remote maintenance on ch2, use GX Works2 or GX Developer. For applicable versions of GX Works2 and GX Developer, refer to I. Remote Maintenance Subsection 1.4.1 or 1.4.2. Example 1: When "parallel link" is set for ch1, the "N:N Network" cannot be set for ch2. Example 2: When "computer link" is set for ch1, the "N:N Network" can be set for ch2. Programming Communication *1. I Remote Maintenance Apx.A Discontinued models A-75 FX Series PLC User's Manual - Data Communication Edition 4 Version Number Common Items 4. 4.1 4.1 Manufacturer's serial number check method Version Number Manufacturer's serial number check method The year and month of production of the PLC main unit can be checked on the nameplate, and "LOT" indicated on the front of the product. 4.1.1 Checking the nameplate The year and month of production of the PLC main unit can be checked from the manufacturer's serial number "S/N" indicated on the label adhered to the right side of the product. Example nameplate (manufacture's serial number : 1010001) Right side * Actual product nameplate differs from the example shown above. <Product during December, 2009 or earlier> 9 Z 0 0 0 <Product from January, 2010> 1 Control number Month (Example: Dec.): 1 to 9 = January to September, X = October, Y = November, Z = December Year (Example: 2009): Last digit of year A-76 1 0 1 0 0 0 1 Control number Month (Example: Jan.): 1 to 9 = January to September, X = October, Y = November, Z = December Year (Example: 2010): Last two digit of year FX Series PLC User's Manual - Data Communication Edition 4 Version Number Common Items A Checking the front of the product The year and month of production of the PLC main unit can be checked from the manufacturer's serial number "LOT" on the front (at the bottom) of the product. The "LOT" indication is provided only with the following PLC main units. Main unit "LOT" indication adoption time March 2013 and later (From first product) FX3G Series PLC October 2008 and later FX3GC Series PLC January 2012 and later (From first product) FX3U Series PLC January 2009 and later FX3UC Series PLC January 2009 and later B N:N Network FX3S Series PLC Common Items 4.1.2 4.2 Version check C Parallel Link Example: FX3U-48MR/ES D Computer Link <Product during December, 2009 or earlier> 9 <Product from January, 2010> Z 1 Month (Example: Jan.): 1 to 9 = January to September, X = October, Y = November, Z = December Year (Example: 2010): Last two digit of year Version check The PLC version can be checked by reading the last three digits of device D8001. D8001 4 2 5 G 1 Non-Protocol Communication (FX2N-232IF) PLC type and version 2 F Non-Protocol Communication (RS/RS2 Instruction) 4.2 E 1 Inverter Communication Month (Example: Dec.): 1 to 9 = January to September, X = October, Y = November, Z = December Year (Example: 2009): Last digit of year 0 Version information (Example: Ver. 2.51) PLC type (Example: 24 = FX2N, FX2NC, FX3U or FX3UC Series) H Programming Communication I Remote Maintenance Apx.A Discontinued models A-77 FX Series PLC User's Manual - Data Communication Edition 5 Introduction of Manuals (Type, Reading Method and Acquisition Method) Common Items 5. 5.1 Rank and Use Method of This Manual Introduction of Manuals (Type, Reading Method and Acquisition Method) This chapter specifies the manuals related to PLC main units for each communication type. 5.1 Rank and Use Method of This Manual When communication equipment is connected, an FX PLC can offer various communication options. PLC Wiring and installation of PLC • HARDWARE MANUAL, HANDY MANUAL (which is supplied with each product) Supplied with • User's Manual Separate manual (for FX3S, FX3G, FX3GC, FX3U and FX3UC) Sequence program • PROGRAMMING MANUAL Separate manual Communication equipment Installation and name of each part • INSTALLATION MANUAL (which is supplied with each product) Supplied with Manuals supplied with each communication equipment are shown at the section 5.2. This information is provided for convenience to offer the terminal layout, external dimensions, etc., and may not be up-to-date. Communication types N:N Network Parallel link Computer link Non-protocol Inverter Other communication communication communication How to use each communication type This • User's Manual manual Communication Control Edition Separate manual This manual specifies the setting method, cable connection, program examples and troubleshooting for each communication type. A-78 FX Series PLC User's Manual - Data Communication Edition 5 Introduction of Manuals (Type, Reading Method and Acquisition Method) Common Items A Introduction of Related Manuals This section shows major manuals required to use the communication types in this manual. Manuals for PLC main units and manuals for communication equipment are classified separately. "Separate manual" shown in the "Included/separate manual" column indicates that the manual is supplied separately. "Included" indicates that the manual is included with each product. Manual for communication types in FX PLCs Included/separate document Contents JY997D16901 Separate manual (this manual) Describes the contents of communication types supported by FX Series PLCs. FX3S/FX3G/FX3GC/FX3U/FX3UC Series User's Manual JY997D26201 - MODBUS Serial Communication Edition Separate manual Explains the MODBUS serial communication network in FX3S/FX3G/FX3GC/FX3U/FX3UC PLCs. Manual name Manual number C Manuals for data communication Manuals related to FX PLCs For instructions used in sequence programs, refer to the PROGRAMMING MANUAL. For hardware specifications and wiring of the PLC, refer to the HANDY MANUAL or USERS MANUAL. Manual number Included/separate document Contents Manuals for PLC main unit FX3U Series For detailed explanation, refer to the FX3U Series User's Manual - Hardware Edition. JY997D50301 Included FX3U Series User's Manual - Hardware Edition JY997D16501 Separate manual I/O specifications, wiring and installation of the PLC main unit FX3U extracted from the FX3U Series User's Manual - Hardware Edition. Details about the hardware including I/O specifications, wiring, installation and maintenance of the FX3U PLC main unit. FX3UC Series For detailed explanation, refer to the FX3UC Series User's Manual - Hardware Edition. JY997D50501 I/O specifications, wiring and installation of the PLC main unit FX3UC-32MT-LT-2 extracted from the FX3UC Series User's Manual - Hardware Edition. FX3UC-32MT-LT-2 Series Hardware Manual JY997D31601 Included FX3UC Series User's Manual - Hardware Edition JY997D28701 Separate manual Details about the hardware including I/O specifications, wiring, installation and maintenance of the FX3UC PLC main unit. FX3G Series I For detailed explanation, refer to the FX3G Series User’s Manual - Hardware Edition. JY997D46001 Included FX3G Series User's Manual - Hardware Edition JY997D31301 Separate manual I/O specifications, wiring and installation of the PLC main unit FX3G extracted from the FX3G Series User's Manual - Hardware Edition. Details about the hardware including I/O specifications, wiring, installation and maintenance of the FX3G PLC main unit. Remote Maintenance FX3G Series Hardware Manual H Programming Communication Included G Non-Protocol Communication (FX2N-232IF) FX3UC(D, DS, DSS) Series Hardware Manual I/O specifications, wiring and installation of the PLC main unit FX3UC (D, DS, DSS) extracted from the FX3UC Series User's Manual - Hardware Edition. F Non-Protocol Communication (RS/RS2 Instruction) FX3U Series Hardware Manual E Inverter Communication Manual name D Computer Link 5.2.2 Parallel Link FX Series User’s Manual Data Communication Edition B N:N Network 5.2.1 Common Items 5.2 5.2 Introduction of Related Manuals Apx.A Discontinued models A-79 FX Series PLC User's Manual - Data Communication Edition 5 Introduction of Manuals (Type, Reading Method and Acquisition Method) Common Items Manual name 5.2 Introduction of Related Manuals Manual number Included/separate document Contents FX3GC Series For detailed explanation, refer to the FX3GC Series User's Manual - Hardware Edition. FX3GC Series Hardware Manual JY997D45201 Included FX3GC Series User's Manual - Hardware Edition JY997D45401 Separate manual I/O specifications, wiring and installation of the PLC main unit FX3GC extracted from the FX3GC Series User's Manual - Hardware Edition. Details about the hardware including I/O specifications, wiring, installation and maintenance of the FX3GC PLC main unit. FX3S Series For detailed explanation, refer to the FX3S Series User’s Manual - Hardware Edition. FX3S Series Hardware Manual JY997D48301 Included I/O specifications, wiring and installation of the PLC main unit FX3S extracted from the FX3S Series User's Manual - Hardware Edition. I/O specifications, built-in analog specifications, wiring and installation of the PLC main unit FX3S-30M/E-2AD extracted from the FX3S Series User's Manual - Hardware Edition. FX3S-30M/E-2AD Hardware Manual JY997D51701 Included FX3S Series User's Manual - Hardware Edition JY997D48601 Separate manual JY992D66301 Included Describes the contents of the FX2N PLC hardware including the specifications, wiring and installation procedure. FX2NC (DSS, DS) Series HARDWARE MANUAL JY992D76401 Included Describes the contents of the FX2NC(DSS, DS) PLC hardware including the specifications, wiring and installation procedure. FX2NC (D/UL) Series HARDWARE MANUAL JY992D87201 Included Describes the contents of the FX2NC(D/UL) PLC hardware including the specifications, wiring and installation procedure. JY992D89301 Included Describes the contents of the FX1N PLC hardware including the specifications, wiring and installation procedure. JY992D92101 Included Describes the contents of the FX1NC PLC hardware including the specifications, wiring and installation procedure. JY992D83901 Included Describes the contents of the FX1S PLC hardware including the specifications, wiring and installation procedure. JY992D47501 Included Describes the contents of the FX0N PLC hardware including the specifications, wiring and installation procedure. JY992D47401 Included Describes the contents of the FX PLC hardware including the specifications, wiring and installation procedure. JY992D59001 Included Describes the contents of the FX2C PLC hardware including the specifications, wiring and installation procedure. Details about the hardware including I/O specifications, wiring, installation and maintenance of the FX3S PLC main unit. FX2N Series FX2N Series HARDWARE MANUAL FX2NC Series FX1N Series FX1N Series HARDWARE MANUAL FX1NC Series*1 FX1NC Series HANDY MANUAL FX1S Series FX1S Series HARDWARE MANUAL FX0N Series FX0N Series HARDWARE MANUAL FX2(FX) Series FX Series HARDWARE MANUAL FX2C Series*2 FX2C Series HANDY MANUAL *1. FX1NC Series PLC Manual is available only in Japanese. *2. FX2C Series PLC Manual is available only in Japanese. A-80 FX Series PLC User's Manual - Data Communication Edition 5 Introduction of Manuals (Type, Reading Method and Acquisition Method) Common Items 5.2 Introduction of Related Manuals A Manual number Included/separate document Contents Manuals for programming FX1S, FX1N, FX2N, FX1NC, FX2NC PROGRAMMING MANUAL JY992D88101 Separate manual Explains instructions applicable in the FX1S, FX1N, FX2N, FX1NC and FX2NC PLCs. FX0, FX0S, FX0N, FX1, FX2, FX2C JY992D48301 PROGRAMMING MANUAL Separate manual Explains instructions available in the FX0, FX0S, FX0N, FX1, FX2, FX2C PLCs. MELSEC-Q/L/F Structured Programming Manual (Fundamentals) SH080782 Separate manual Programming methods, specifications, functions, etc. required to create structured programs FXCPU Structured Programming Manual [Device & Common] JY997D26001 Separate manual Devices, parameters, etc. provided in structured projects of GX Works2 FXCPU Structured Programming Manual [Basic & Applied Instruction] JY997D34701 Separate manual Sequence instructions provided in structured projects of GX Works2 FXCPU Structured Programming Manual [Application Functions] JY997D34801 Separate manual Application functions provided in structured projects of GX Works2 B C D Computer Link Explains basic instructions and applied instructions available in the FX3S/FX3G/FX3GC/ FX3U/FX3UC PLC. Parallel Link Separate manual N:N Network FX3S/FX3G/FX3GC/FX3U/FX3UC Programming Manual - Basic & JY997D16601 Applied Instruction Edition Common Items Manual name E Inverter Communication F Non-Protocol Communication (RS/RS2 Instruction) G Non-Protocol Communication (FX2N-232IF) H Programming Communication I Remote Maintenance Apx.A Discontinued models A-81 FX Series PLC User's Manual - Data Communication Edition 5 Introduction of Manuals (Type, Reading Method and Acquisition Method) Common Items 5.2.3 5.2 Introduction of Related Manuals Communication equipment (option) The table below specifies the manuals for communication equipment operating in accordance with RS-232C, RS-422, RS-485 or USB and for the Ethernet adapter. Manual name Manual number Included/separate document Contents Included Describes the contents of the RS-232C communication expansion board, FX3U-232-BD hardware including the specifications and installation procedure. Included Describes the contents of the RS-232C communication expansion board, FX3G-232-BD hardware including the specifications and installation procedure. Included Describes the contents of the RS-232C communication expansion board, FX2N-232-BD hardware including the specifications and installation procedure. Included Describes the contents of the RS-232C communication expansion board, FX1N-232-BD hardware including the specifications and installation procedure. Included Describes the contents of the RS-232C communication special adapter, FX3U-232ADP hardware including the specifications and installation procedure. Included Describes the contents of the RS-232C communication special adapter, FX3U-232ADP-MB hardware including the specifications and installation procedure. Included Describes the contents of the RS-232C communication special adapter, FX2NC-232ADP hardware including the specifications and installation procedure. Included Describes the contents of the RS-232C communication special adapter, FX0N-232ADP hardware including the specifications and installation procedure. Included Describes the contents of the RS-232C communication special adapter, FX-232ADP hardware including the specifications and installation procedure. Included Describes the contents of the RS-232C communication special extension block, FX2N232IF hardware including the specifications and installation procedure. For communication in accordance with RS-232C FX3U-232-BD INSTALLATION MANUAL FX3G-232-BD INSTALLATION MANUAL FX2N-232-BD USER'S GUIDE FX1N-232-BD USER'S GUIDE FX3U-232ADP INSTALLATION MANUAL FX3U-232ADP-MB INSTALLATION MANUAL FX2NC-232ADP INSTALLATION MANUAL FX0N-232ADP INSTALLATION MANUAL FX-232ADP USER'S GUIDE FX2N-232IF HARDWARE MANUAL JY997D12901 JY997D32001 JY992D63201 JY992D84401 JY997D13701 JY997D26401 JY997D01101 JY992D51201 JY992D48801 JY992D73501 For communication in accordance with RS-422 FX3U-422-BD INSTALLATION MANUAL JY997D13101 Included Describes the contents of the RS-422 communication expansion board, FX3U-422-BD hardware including the specifications and installation procedure. FX3G-422-BD INSTALLATION MANUAL JY997D32101 Included Describes the contents of the RS-422 communication expansion board, FX3G-422-BD hardware including the specifications and installation procedure. FX2N-422-BD USER'S GUIDE JY992D66101 Included Describes the contents of the RS-422 communication expansion board, FX2N-422-BD hardware including the specifications and installation procedure. A-82 FX Series PLC User's Manual - Data Communication Edition 5 Introduction of Manuals (Type, Reading Method and Acquisition Method) Common Items 5.2 Introduction of Related Manuals A FX1N-422-BD USER'S MANUAL Manual number JY992D84101 Included/separate document Contents Included Describes the contents of the RS-422 communication expansion board, FX1N-422-BD hardware including the specifications and installation procedure. For communication in accordance with RS-485(422) JY997D13001 Included Describes the contents of the RS-485 communication special expansion board, FX3U-485-BD hardware including the specifications and installation procedure. FX3G-485-BD INSTALLATION MANUAL JY997D32201 Included Describes the contents of the RS-485 communication special expansion board, FX3G-485-BD hardware including the specifications and installation procedure. JY997D51501 Included FX2N-485-BD HARDWARE MANUAL JY992D73401 Included Describes the contents of the RS-485 communication expansion board, FX2N-485-BD including the specifications and installation procedure. JY992D84201 Included FX3U-485ADP INSTALLATION MANUAL JY997D13801 Included Describes the contents of the RS-485 communication special adapter, FX3U-485ADP hardware including the specifications and installation procedure. FX2NC-485ADP INSTALLATION MANUAL JY997D01201 Included Describes the contents of the RS-485 communication special adapter, FX2NC-485ADP hardware including the specifications and installation procedure. Included Describes the contents of the RS-485 communication special adapter, FX0N-485ADP hardware including the specifications and installation procedure. Included Describes the contents of the USB communication expansion board, FX3U-USB-BD hardware including the specifications and installation procedure. Describes the contents of the Ethernet communication special adapter, FX3U-ENET-ADP hardware including the specifications and installation procedure. FX0N-485ADP INSTALLATION MANUAL JY992D53101 For communication in accordance with USB FX3U-USB-BD USER'S MANUAL JY997D13501 For communication in accordance with Ethernet JY997D47401 Included FX3U-ENET-ADP USER'S MANUAL JY997D45801 Separate manual G H Programming Communication FX3U-ENET-ADP INSTALLATION MANUAL F Non-Protocol Communication (FX2N-232IF) Included Non-Protocol Communication (RS/RS2 Instruction) JY997D26301 E Inverter Communication FX3U-485ADP-MB INSTALLATION MANUAL Describes the contents of the RS-485 communication special adapter, FX3U-485ADP-MB hardware including the specifications and installation procedure. D Computer Link FX1N-485-BD USER'S GUIDE Describes the contents of the RS-485 communication expansion board, FX1N-485-BD hardware including the specifications and installation procedure. C Parallel Link FX3G-485-BD-RJ INSTALLATION MANUAL Describes the contents of the RS-485 communication special expansion board, FX3G-485-BD-RJ hardware including the specifications and installation procedure. B N:N Network FX3U-485-BD INSTALLATION MANUAL Common Items Manual name Describes FX3U-ENET-ADP Ethernet communication special adapter details. I Remote Maintenance Apx.A Discontinued models A-83 FX Series PLC User's Manual - Data Communication Edition 5 Introduction of Manuals (Type, Reading Method and Acquisition Method) Common Items 5.2.4 5.2 Introduction of Related Manuals Related options for communication The table below specifies the manuals for products required to use communication equipment (options) above in the system configuration. Manual name Manual number Included/separate document Contents Connector conversion board FX3U-CNV-BD INSTALLATION MANUAL JY997D13601 Included Describes the contents of the FX3U-CNV-BD special adapter connection board hardware including the installation procedure. FX2N-CNV-BD JY992D63601 Included Describes the contents of the FX2N-CNV-BD special adapter connection board hardware including the installation procedure. FX1N-CNV-BD JY992D84701 Included Describes the contents of the FX1N-CNV-BD special adapter connection board hardware including the installation procedure. FX3G-CNV-ADP INSTALLATION MANUAL JY997D32301 Included Describes the contents of the FX3G-CNV-ADP special adapter connection conversion adapter hardware including the installation procedure FX3S-CNV-ADP INSTALLATION MANUAL JY997D48801 Included Describes the contents of the FX3S-CNV-ADP special adapter connection conversion adapter hardware including the installation procedure Connector conversion adapter RS-485/RS-232C converter for computer link communication FX-485-PC-IF-SET HARDWARE MANUAL JY992D81801 Included Describes the contents of the FX-485-PC-IF-SET interface unit hardware including the specifications and installation procedure. JY997D34201 Included Describes the contents of the FX-30P Handy Programming Panel hardware including the specifications and installation procedure. Separate manual Describes the contents of the FX-30P Handy Programming Panel hardware including the specifications and installation procedure as well as programming operations. FX-30P FX-30P INSTALLATION MANUAL FX-30P OPERATION MANUAL A-84 JY997D34401 FX Series PLC User's Manual - Data Communication Edition 6 Abbreviations, Generic Names and Terms Used in This Manual Common Items 5.2 Introduction of Related Manuals A Abbreviations, Generic Names and Terms Used in This Manual 1. Programmable controllers Name C FX PLC or FX CPU Generic name of FX1, FX2(FX), FX2C, FX0, FX0S, FX0N, FX1S, FX1N, FX1NC, FX2N, FX2NC, FX3S, FX3G, FX3GC, FX3U and FX3UC Series PLCs FX3U Series Generic name of FX3U Series PLCs FX3UC Series Generic name of FX3U Series PLC main units D Generic name of FX3UC Series PLCs Computer Link FX3UC PLC or main unit Generic name of FX3UC Series PLC main units FX3G Series FX3G PLC or main unit FX3GC Series Generic name of FX3G Series PLCs Generic name of FX3G Series PLC main units Generic name of FX3GC Series PLCs E FX3GC PLC or main unit Generic name of FX3GC Series PLC main units FX3S PLC or main unit FX2N Series FX2N PLC or main unit FX2NC Series Generic name of FX3S Series PLCs Inverter Communication FX3S Series Generic name of FX3S Series PLC main units Generic name of FX2N Series PLCs Generic name of FX2N Series PLC main units Generic name of FX2NC Series PLCs FX2NC-M(-T) PLC FX2NC-16MR-T, FX2NC-16MT, FX2NC-32MT, FX2NC-64MT, and FX2NC-96MT FX2NC-MT-D/UL PLC FX2NC-16MT-D/UL, FX2NC-32MT-D/UL, FX2NC-64MT-D/UL, and FX2NC-96MT-D/UL FX2NC-M-DSS (-T-DS) PLC FX2NC-16MR-T-DS, FX2NC-16MT-DSS, FX2NC-32MT-DSS, FX2NC-64MT-DSS, and FX2NC-96MT-DSS FX1N PLC or main unit FX1NC Series FX1NC PLC or main unit FX1S PLC or main unit FX0N Series FX0N PLC or main unit FX0 Series FX0S PLC or main unit FX2(FX) Series FX2C Series FX2C PLC or main unit Generic name of FX1S Series PLCs Generic name of FX1S Series PLC main units Generic name of FX0N Series PLCs Generic name of FX0N Series PLC main units I Generic name of FX0 Series PLCs Generic name of FX0 Series PLC main units Generic name of FX0S Series PLCs Generic name of FX0S Series PLC main units Generic name of FX2(FX) Series PLCs Apx.A Generic name of FX2(FX) Series PLC main units Discontinued models FX2(FX) PLC or main unit H Generic name of FX1NC Series PLC main units Only Japanese manual is available for this product. Remote Maintenance FX0 PLC or main unit FX0S Series Generic name of FX1N Series PLC main units Generic name of FX1NC Series PLCs G Programming Communication FX1S Series Generic name of FX1N Series PLCs F Non-Protocol Communication (FX2N-232IF) Generic name of FX2NC-M(-T), FX2NC-MT-D/UL, and FX2NC-M-DSS(-T-DS) Series PLC main units Non-Protocol Communication (RS/RS2 Instruction) FX2NC PLC or main unit FX1N Series Parallel Link Programmable controllers FX3U PLC or main unit B N:N Network The table below shows abbreviations, generic names and terms used in this manual. Abbreviation/ generic name Common Items 6. Generic name of FX2C Series PLCs Generic name of FX2C Series PLC main units A-85 FX Series PLC User's Manual - Data Communication Edition 6 Abbreviations, Generic Names and Terms Used in This Manual Common Items 5.2 Introduction of Related Manuals Abbreviation/ generic name FX1 Series FX1 PLC or main unit Q PLC Name Generic name of FX1 Series PLCs Generic name of FX1 Series PLC main units Only Japanese manual is available for this product. Generic name of CPU units QCPU (Q mode) and QCPU (A mode) QCPU (Q mode) Generic name of CPU units Q00JCPU, Q00CPU, Q01CPU, Q02CPU, Q02HCPU, Q06HCPU, Q12HCPU, and Q25HCPU QCPU (A mode) Generic name of CPU units Q02CPU-A, Q02HCPU-A, and Q06HCPU-A QnA PLC Generic name of CPU units QnACPU (large type) and QnACPU (small type) QnACPU (large type) Generic name of CPU units Q2ACPU, Q2ACPU-S1, Q3ACPU, Q4ACPU, and Q4ARCPU QnACPU (small type) Generic name of CPU units Q2ASCPU, Q2ASCPU-S1, Q2ASHCPU, and Q2ASHCPU-S1 A PLC Generic name of CPU units ACPU (large type), ACPU (small type), and A1FXCPU ACPU (large type) Generic name of CPU units AnUCPU, AnACPU, AnNCPU, and A0J2(H)CPU ACPU (small type) Generic name of CPU units A2US(H)CPU, AnS(H)CPU, and A1SJ(H)CPU A1FXCPU Generic name of CPU unit A1FXCPU 2. Expansion boards and special adapters Abbreviation/ generic name Name Expansion board Expansion board Generic name of input/output expansion board, communication expansion boards, special adapter connection boards, analog expansion boards and analog potentiometer expansion boards Input/output expansion board Generic name of input/output expansion board 4EX-BD FX3G-4EX-BD 2EYT-BD FX3G-2EYT-BD Communication expansion board or communication board Generic name of communication expansion boards 232BD FX3U-232-BD, FX3G-232-BD, FX2N-232-BD, and FX1N-232-BD 422BD FX3U-422-BD, FX3G-422-BD, FX2N-422-BD, and FX1N-422-BD 485BD FX3U-485-BD, FX3G-485-BD, FX3G-485-BD-RJ, FX2N-485-BD, and FX1N-485-BD USBBD FX3U-USB-BD Analog expansion board Generic name of analog expansion board 2AD-BD FX3G-2AD-BD 1DA-BD FX3G-1DA-BD Analog potentiometer expansion board 8AV-BD Generic name of analog potentiometer expansion board FX3U-8AV-BD, FX3G-8AV-BD Special adapter connection board or connector Generic name of CNVBD conversion board CNVBD FX3U-CNV-BD, FX2N-CNV-BD, and FX1N-CNV-BD Special adapters A-86 Special adapter Generic name of high speed input/output special adapters, CF card special adapter, communication special adapters and analog special adapters High speed input/output special adapter Generic name of high speed input special adapters and high speed output special adapters 2HSY-ADP FX3U-2HSY-ADP 4HSX-ADP FX3U-4HSX-ADP FX Series PLC User's Manual - Data Communication Edition 6 Abbreviations, Generic Names and Terms Used in This Manual Common Items 5.2 Introduction of Related Manuals A CF card special adapter CF-ADP Name Generic name of CF card special adapter FX3U-CF-ADP B Generic name of communication special adapters 232ADP FX3U-232ADP(-MB), FX2NC-232ADP, FX0N-232ADP, and FX-232ADP 485ADP FX3U-485ADP(-MB), FX2NC-485ADP, FX0N-485ADP, and FX-485ADP ENET-ADP FX3U-ENET-ADP N:N Network Communication special adapter or communication adapter Common Items Abbreviation/ generic name C Special adapters CNVADP Parallel Link Special adapter connection conversion adapter or Generic name of CNVADP connection conversion adapter FX3G-CNV-ADP, FX3S-CNV-ADP D 3. Extension equipment Name Extension equipment Extension equipment Special function unit 232IF Generic name of special function units Generic name of special function block Generic name of FX2N-232IF 4. Networks Abbreviation/ generic name F Name Generic name of CC-Link master station and CC-Link remote device stations and CC-Link intelligent device stations CC-Link master (station) Generic name of CC-Link master station with model name FX2N-16CCL-M or FX3U-16CCL-M CC-Link remote station Generic name of remote I/O stations and remote device stations G Generic name of CC-Link/LT master station, CC-Link/LT remote I/O stations, power supply adapters, and dedicated power supplies Generic name of built-in type CC-Link/LT master and (additional) CC-Link/LT master Built-in type CC-Link/LT master Generic name of built-in type CC-Link/LT master built in to the FX3UC-32MT-LT(-2) (Additional) CC-Link/LT master Generic name of CC-Link/LT master station with model name FX2N-64CL-M Power supply adapter Generic name of units connecting the power supply to the CC-Link/LT system Dedicated power supply Generic name of power supplies connected to the CC-Link/LT system I Generic name of AnyWireASLINK master station with model name FX3U-128ASL-M AS-i system AS-i master Generic name of AS-i system master station with model name FX2N-32ASI-M MESEC I/O LINK MELSEC I/O LINK master Generic name of MELSEC I/O LINK master station with model name FX2N-16LNK-M Apx.A Discontinued models Ethernet Ethernet adapter Remote Maintenance AnyWire AnyWireASLINK master H Programming Communication CC-Link/LT master Non-Protocol Communication (FX2N-232IF) CC-Link intelligent device Generic name of CC-Link intelligent device station with model name FX3U-64CCL station CC-Link/LT equipment Non-Protocol Communication (RS/RS2 Instruction) Open field networks CC-Link and CC-Link/LT CC-Link equipment E Inverter Communication Special function block Generic name of extension blocks, powered extension units, special function blocks and special function units Computer Link Abbreviation/ generic name Generic name of Ethernet communication special adapter with model name FX3U-ENET-ADP A-87 FX Series PLC User's Manual - Data Communication Edition 6 Abbreviations, Generic Names and Terms Used in This Manual Common Items 5.2 Introduction of Related Manuals 5. Peripheral equipment Abbreviation/ generic name Name Peripheral equipment Peripheral equipment Generic name of programming software, handy programming panels, and display units Programming tools Programming tool Generic name of programming software and handy programming panels Programming software Generic name of programming software GX Works2 Generic name of programming software packages SWDNC-GXW2-J and SWDNC-GXW2-E GX Developer Generic name of programming software packages SWD5C-GPPW-J and SWD5C-GPPW-E FXGP/WIN Generic name of programming software packages FX-PCS/WIN and FX-PCS/WIN-E Handy programming panel (HPP) Generic name of FX-30P, FX-20P(-E)-SET0, FX-20P(-E), FX-10P-SET0 and FX-10P(-E) Display units GOT1000 Series Generic name of GT16, GT15, GT14, GT11 and GT10 GOT-900 Series Generic name of GOT-A900 and GOT-F900 Series GOT-A900 Series Generic name of GOT-A900 Series GOT-F900 Series Generic name of GOT-F900 Series Internet mail sending tools Mail sending units FX-232DOPA Generic name of FX-232DOPA mail sending units FX-232DOPA mail sending main units Only Japanese manual is available for this product. These products can only be used in Japan. 6. Others Abbreviation/ generic name Name Inverters FREQROL inverter Generic name of Mitsubishi Electric F800, A800, F700, A700, E700, D700, V500, F500, A500, E500, and S500 Series inverters Communication Communication equipment Generic name of communication equipment operating in accordance with RS-232C, communication equipment operating in accordance with RS-422, communication equipment operating in accordance with RS-485, communication equipment operating in accordance with USB, and communication equipment operating in accordance with Ethernet Communication equipment operating in accordance with RS232C Generic name of 232BD, 232ADP, and 232IF Communication equipment operating in accordance with RS-422 Generic name of 422BD Communication equipment operating in accordance with RS-485 Generic name of 485BD and 485ADP Communication equipment operating in accordance with USB Generic name of USB BD Communication equipment operating in Generic name of special adapter connectable to the Ethernet accordance with Ethernet A-88 FX Series PLC User's Manual - Data Communication Edition 6 Abbreviations, Generic Names and Terms Used in This Manual Common Items 5.2 Introduction of Related Manuals A Name Personal computers Personal computer Personal computers supporting Windows in which GX Works2, GX Developer or FXGP/WIN is installed Refer to the manual for each software product for supported Windows versions. Windows 95 Abbreviation of Microsoft Windows 95 Windows 98 Abbreviation of Microsoft Windows 98 Windows Me Abbreviation of Microsoft Windows Millennium Edition Windows NT4.0 Abbreviation of Microsoft Windows NT4.0 Workstation Windows 2000 Abbreviation of Microsoft Windows 2000 Professional Windows XP Abbreviation of Microsoft Windows XP Professional and Microsoft Windows XP Home Edition Windows Vista Abbreviation of Microsoft Windows Vista Ultimate Operating System Microsoft Windows Vista Enterprise Operating System Microsoft Windows Vista Business Operating System Microsoft Windows Vista Home Premium Operating System Microsoft Windows Vista Home Basic Operating System Windows 7 Abbreviation of Microsoft Windows7 Enterprise Operating System Microsoft Windows7 Ultimate Operating System Microsoft Windows7 Professional Operating System Microsoft Windows7 Home Premium Operating System Microsoft Windows7 Starter Operating System Windows 8 Abbreviation of Microsoft Windows 8 Operating System Microsoft Windows 8 Pro Operating System Microsoft Windows 8 Enterprise Operating System Windows 8.1 Abbreviation of Microsoft Windows 8.1 Operating System Microsoft Windows 8.1 Pro Operating System Microsoft Windows 8.1 Enterprise Operating System Windows 10 Microsoft Windows 10 Home Operating System Microsoft Windows 10 Pro Operating System Microsoft Windows 10 Enterprise Operating System Microsoft Windows 10 Education Operating System B N:N Network Windows Generic name of Windows 95, Windows 98, Windows Me, Windows NT4.0, Windows 2000, Windows XP, Windows Vista, Windows 7, Windows 8, Windows 8.1 and Windows 10 Common Items Abbreviation/ generic name C Parallel Link D Computer Link E Inverter Communication F Non-Protocol Communication (RS/RS2 Instruction) G Non-Protocol Communication (FX2N-232IF) H Programming Communication I Remote Maintenance Apx.A Discontinued models A-89 FX Series PLC User's Manual - Data Communication Edition Common Items 5.2 Introduction of Related Manuals MEMO A-90 6 Abbreviations, Generic Names and Terms Used in This Manual FX Series PLC User's Manual - Data Communication Edition N:N Network A Common Items B N:N Network FX Series Programmable Controllers C Parallel Link User's Manual [Data Communication Edition] B. N:N Network D Computer Link E Inverter Communication F Non-Protocol Communication (RS/RS2 Instruction) G Non-Protocol Communication (FX2N-232IF) H Programming Communication Foreword I © 2005 MITSUBISHI ELECTRIC CORPORATION B-1 Apx.A Discontinued models This manual confers no industrial property rights or any rights of any other kind, nor does it confer any patent licenses. Mitsubishi Electric Corporation cannot be held responsible for any problems involving industrial property rights which may occur as a result of using the contents noted in this manual. Remote Maintenance This manual explains the "N:N Network" provided for the MELSEC-F FX Series Programmable Controllers and should be read and understood before attempting to install or use the unit. Store this manual in a safe place so that you can take it out and read it whenever necessary. Always forward it to the end user. FX Series PLC User's Manual - Data Communication Edition N:N Network B-2 FX Series PLC User's Manual - Data Communication Edition 1 Outline N:N Network 1.1 Outline of System A Common Items 1. Outline B This chapter explains the N:N Network. N:N Network Outline of System The N:N Network allows connection of up to eight FX PLCs via mutually linked devices through communication in accordance with RS-485. 2) Data link is automatically updated among a maximum of eight FX PLCs. 3) The available total extension distance is 500 m (1640' 5") maximum (when only the 485ADP is used in the configuration). 8 units 500 m (1640' 5") [50 m (164' 0") when 485BD is included] FX PLC Slave station No. 1 For the specifications, refer to Chapter 2. FX PLC Slave station No. 2 ....... + + To check applicable PLC models, refer to Section 1.3. + Communication equipment operating in accordance with RS-485 Communication equipment operating in accordance with ....... RS-485 F For selection, refer to Chapter 3. For wiring, ....... refer to Chapter 4. D70 to D77 ....... The number of linked devices can be selected among three patterns. For details, refer to Chapter 2. ... Bit devices M1000 to M1063 M1064 to M1127 M1128 to M1191 M1448 to M1511 Word devices D0 to D7 D10 to D17 D20 to D27 The link information can be monitored in the master station and all slave stations. ... ... M1448 to M1511 Word devices D0 to D7 D10 to D17 D20 to D27 Transfer direction G H Programming Communication D70 to D77 Bit devices M1000 to M1063 M1064 to M1127 M1128 to M1191 ... ... M1448 to M1511 Word devices D0 to D7 D10 to D17 D20 to D27 Transfer direction Non-Protocol Communication (FX2N-232IF) Bit devices M1000 to M1063 M1064 to M1127 M1128 to M1191 Non-Protocol Communication (RS/RS2 Instruction) Communication equipment operating in accordance with RS-485 E Inverter Communication FX PLC Master station ....... Number of linked units ....... Total extension distance D Computer Link Important points and reference chapter/section System C Parallel Link 1) One of three patterns can be selected according to the number of devices to be linked (except FX0N and FX1S PLCs). ... 1.1 D70 to D77 The figure above shows the maximum number of linked devices. There are differences in the specifications and limitations depending on the selected link pattern and FX Series. I Remote Maintenance Apx.A Discontinued models B-3 FX Series PLC User's Manual - Data Communication Edition N:N Network 1.2 1 Outline 1.2 Procedures Before Operation Procedures Before Operation The flow chart below shows the N:N Network setting procedures up until data link: N:N Network Refer to Chapter 1. Outline Refer to Chapter 2. Check communication specifications. Refer to Chapter 3. Determine system configuration and selection. Outline of system • Applicable PLC versions • Applicable programming tools Communication specifications • Number of link points and time • Number of system devices System configuration • Select communication equipment. Refer to Chapter 4. Perform wiring. Wiring procedure • One-pair wiring using twisted cables • Wiring example Programming tool Connect PLC.*1 Refer to Chapter 5. Perform PLC communication setting (initialization). Turn ON power. Refer to Chapter 6. Perform test run (communication test and judgement method). Serial communication setting in PLC • Communication setting is not required. (Check only unset items.) Communication test • Create test programs. Refer to Chapter 7. Create programs. Based on SD/RD lamp lighting status and contents of error check devices, verify that communication is normally executed. Communication parameter setting programs • Basic program • Error indication program example • Detailed explanation of setting devices If there is abnormality, refer to the troubleshooting (Chapter 9). Refer to Chapter 8. Practical program examples Program examples of pattern 2 are shown. *1 For the method to connect a programming tool to a PLC, refer to the "Programming Communication" section in this manual or the respective programming tool manual. For details on operating procedures, refer to the respective programming tool manual. B-4 FX Series PLC User's Manual - Data Communication Edition 1 Outline N:N Network 1.3 Communication Type Applicability in PLC Communication Type Applicability in PLC 1.3.1 Applicable versions Common Items 1.3 A PLC FX3U Series FX3GC Series Parallel Link FX2NC Series FX2N Series (Ver. 2.00 or later)*1 FX1NC Series FX1N Series FX1S Series D The link device range is limited. *1 The link device range is limited. FX0S Series — N:N Network option is not provided. FX0 Series — N:N Network option is not provided. — N:N Network option is not provided. FX2(FX) Series — N:N Network option is not provided. FX1 Series — N:N Network option is not provided. E Applicable in products manufactured in October, 1997 and later (manufacturer’s serial No.: 7X**** and later). The PLC version can be checked by reading the last three digits of device D8001. For a detailed description of the version check, refer to A. Common Items Section 4.2. How to look at the manufacturer's serial number The year and month of production of the PLC main unit can be checked on the nameplate, and "LOT" indicated on the front of the product. For a detailed description of the How to look at the manufacturer's serial number, refer to A. Common Items Section 4.1. Products whose production was stopped Production was stopped for some models of MELSEC-F Series PLCs and programming tools described in this manual. For models whose production was stopped, refer to Appendix A. To see the latest available products, refer to the general catalog. H Programming Communication 1.3.4 G Non-Protocol Communication (FX2N-232IF) 1.3.3 F Non-Protocol Communication (RS/RS2 Instruction) Version check Inverter Communication FX2C Series *1. Computer Link FX3G Series (Ver. 2.00 or later) Remarks C FX3S Series FX0N Series 1.3.2 Applicability (applicable version) FX3UC Series B N:N Network The communication type is applicable in the following versions. :Applicable (If applicable versions of main units are limited, they are described inside ( ).) —:Not applicable I Remote Maintenance Apx.A Discontinued models B-5 FX Series PLC User's Manual - Data Communication Edition 1 Outline N:N Network 1.4 Programming Tool Applicability 1.4 Programming Tool Applicability 1.4.1 For applicable versions The programming tool is applicable for each FX Series from the following version: 1. English versions Product name Model name Applicable version Remarks FX3U and FX3UC PLCs GX Works2 SWDNC-GXW2-E Ver. 1.08J or later GX Developer SWD5C(F)-GPPW-E Ver. 8.18U or later FX-30P - Ver. 1.00 or later GOT1000 Series display units Refer to manuals of GOT1000 Series display units for applicable models and versions supporting the list editor function. FX3G PLC GX Works2 SWDNC-GXW2-E Ver. 1.08J or later GX Developer SWD5C(F)-GPPW-E Ver. 8.72A or later FX-30P - Ver. 1.00 or later GOT1000 Series display units Refer to manuals of GOT1000 Series display units for applicable models and versions supporting the list editor function. FX3GC PLC GX Works2 SWDNC-GXW2-E FX-30P Ver. 1.77F or later Ver. 1.30 or later GOT1000 Series display units - Refer to manuals of GOT1000 Series display units for applicable models and versions supporting the list editor function. FX3S PLC GX Works2 SWDNC-GXW2-E FX-30P GOT1000 Series display units Ver. 1.492N or later - Ver. 1.50 or later - Refer to manuals of GOT1000 Series display units for applicable models and versions supporting the list editor function. FX2N and FX2NC PLCs GX Works2 SWDNC-GXW2-E Ver. 1.08J or later GX Developer SWD5C(F)-GPPW-E SW2 A or later FX-PCS/WIN-E SW0PC-FXGP/WIN-E Ver. 1.00 or later FX-30P Ver. 1.00 or later FX-20P-E(-SET0) FX-20P-MFXC-E Ver. 3.00 or later FX-10P-E Ver. 3.00 or later GOT-F900 Series display units F940WGOT-TWD-E F940GOT-*WD-E F940GOT-*BD-H-E F940GOT-*BD-RH-E GOT1000 Series display units - F940WGOT-TWD-E (Ver. 1.00 or later) F940GOT-LWD-E, F940GOT-SWD-E (Ver. 1.00 or later) F940GOT-LBD-H-E, F940GOT-SBD-H-E (Ver. 1.00 or later) F940GOT-LBD-RH-E, F940GOT-SBD-RH-E (Ver. 1.00 or later) Refer to manuals of GOT1000 Series display units for applicable models and versions supporting the list editor function. FX1S, FX1N and FX1NC PLCs B-6 GX Works2 SWDNC-GXW2-E GX Developer SWD5C(F)-GPPW-E FX-PCS/WIN-E SW0PC-FXGP/WIN-E Ver. 1.08J or later SW5 A or later Ver. 3.00 or later FX-30P Ver. 1.00 or later FX-20P-E(-SET0) FX-20P-MFXD-E Ver. 4.00 or later FX-10P-E Ver. 4.00 or later - FX Series PLC User's Manual - Data Communication Edition 1 Outline N:N Network 1.4 Programming Tool Applicability A Model name Remarks F940WGOT-TWD-E (Ver. 1.00 or later) F940GOT-LWD-E, F940GOT-SWD-E (Ver. 1.00 or later) F940GOT-LBD-H-E, F940GOT-SBD-H-E (Ver. 1.00 or later) F940GOT-LBD-RH-E, F940GOT-SBD-RH-E (Ver. 1.00 or later) Refer to manuals of GOT1000 Series display units for applicable models and versions supporting the list editor function. 2. Japanese versions Product name Model name Applicable version Remarks C FX3U and FX3UC PLCs SWDNC-GXW2-J Ver. 1.07H or later GX Developer SWD5C(F)-GPPW-J Ver. 8.13P or later FX-30P Parallel Link GX Works2 - Ver. 1.00 or later GOT1000 Series display units Refer to manuals of GOT1000 Series display units for applicable models and versions supporting the list editor function. SWDNC-GXW2-J Ver. 1.07H or later GX Developer SWD5C(F)-GPPW-J Ver. 8.72A or later FX-30P - Ver. 1.00 or later GOT1000 Series display units Refer to manuals of GOT1000 Series display units for applicable models and versions supporting the list editor function. SWDNC-GXW2-J FX-30P Ver. 1.77F or later Ver. 1.30 or later GOT1000 Series display units - Refer to manuals of GOT1000 Series display units for applicable models and versions supporting the list editor function. SWDNC-GXW2-J FX-30P Ver. 1.492N or later Ver. 1.50 or later GOT1000 Series display units - Refer to manuals of GOT1000 Series display units for applicable models and versions supporting the list editor function. GX Works2 SWDNC-GXW2-J GX Developer SWD5C(F)-GPPW-J FX-PCS/WIN SW0PC-FXGP/WIN Ver. 2.00 or later FX-PCS-KIT/98 SW1PC-FXGP/98(-3,-5) Ver. 4.00 or later FX-PCS/98-3 SW1PC-FXGP/98-3 Ver. 4.00 or later FX-PCS-KIT/V-3 SW1PC-FXGP/V3 Ver. 2.00 or later FX-A7PHP-KIT Ver. 1.07H or later SW1RX-GPPFX Ver. 3.00 or later SW2 A or later FX-20P(-SET0) FX-20P-MFXC Ver. 4.00 or later FX-10P(-SET0) Ver. 3.00 or later GOT-F900 Series display units F940WGOT-TWD F940GOT-*WD F940GOT-*BD-H F940GOT-*BD-RH I F940WGOT-TWD (Ver. 1.00 or later) F940GOT-LWD, F940GOT-SWD (Ver. 1.00 or later) F940GOT-LBD-H, F940GOT-SBD-H (Ver. 1.00 or later) F940GOT-LBD-RH, F940GOT-SBD-RH (Ver. 1.00 or later) Apx.A Refer to manuals of GOT1000 Series display units for applicable models and versions supporting the list editor function. B-7 Discontinued models GOT1000 Series display units - Remote Maintenance Ver. 1.00 or later H Programming Communication FX-30P G Non-Protocol Communication (FX2N-232IF) FX2N and FX2NC PLCs F Non-Protocol Communication (RS/RS2 Instruction) FX3S PLC GX Works2 E Inverter Communication FX3GC PLC GX Works2 D Computer Link FX3G PLC GX Works2 B N:N Network GOT1000 Series display units Applicable version Common Items Product name GOT-F900 Series display units F940WGOT-TWD-E F940GOT-*WD-E F940GOT-*BD-H-E F940GOT-*BD-RH-E FX Series PLC User's Manual - Data Communication Edition 1 Outline N:N Network 1.4 Programming Tool Applicability Product name Model name Applicable version Remarks FX1S, FX1N and FX1NC PLCs GX Works2 SWDNC-GXW2-J GX Developer SWD5C(F)-GPPW-J FX-PCS/WIN SW0PC-FXGP/WIN Ver. 4.00 or later FX-PCS/98-3 SW1PC-FXGP/98-3 Ver. 5.00 or later SW5 A or later FX-30P Ver. 1.00 or later FX-20P(-SET0) FX-20P-MFXD Ver. 5.00 or later FX-10P(-SET0) Ver. 4.00 or later GOT-F900 Series display units F940WGOT-TWD F940GOT-*WD F940GOT-*BD-H F940GOT-*BD-RH - F940WGOT-TWD (Ver. 1.00 or later) F940GOT-LWD, F940GOT-SWD (Ver. 1.00 or later) F940GOT-LBD-H, F940GOT-SBD-H (Ver. 1.00 or later) F940GOT-LBD-RH, F940GOT-SBD-RH (Ver. 1.00 or later) Refer to manuals of GOT1000 Series display units for applicable models and versions supporting the list editor function. GOT1000 Series display units 1.4.2 Ver. 1.07H or later For non-applicable versions (setting an alternative model) Even programming tool not applicable to a PLC can create programs when an alternative model is set. In this case, however, programming is enabled only in the function ranges provided for the alternative PLC model such as instructions and program size. Model to be programmed Priority: High Low Model to be set FX3UC Series FX3UC FX2N FX2(FX) FX3U Series FX3UC, FX3U FX2N FX2(FX) FX3GC Series FX3G, FX3GC FX1N *1 FX2N*1 FX3G Series FX3G FX1N*1 FX2N*1 FX3S Series FX3S FX3G FX1N*1 FX2NC, FX2N FX2(FX) FX2N FX2(FX) FX1NC Series FX1NC, FX1N FX2N FX2(FX) FX1N Series FX1N FX2N FX2(FX) FX1S Series FX1S FX2(FX) FX0N Series FX0N FX2(FX) FX0S Series FX0S FX2(FX) FX0 Series FX0 FX2(FX) FX2C Series FX2C, FX2(FX) FX2(FX) FX2NC Series FX2N Series FX2(FX) Series FX1 Series *1. FX2(FX) FX1 "FX2N" is selected when the FX-10P(-E) is used. Point In the FX3S PLC, set the memory capacity for PLC parameters to 4,000 steps or less. B-8 FX Series PLC User's Manual - Data Communication Edition 2 Specifications N:N Network 2.1 Communication Specifications (Reference) A Common Items 2. Specifications B This chapter explains the communication specifications and performance. N:N Network 2.1 Communication Specifications (Reference) Communication is executed according to the (fixed) specifications shown in the table below. Specification items such as baud rate cannot be changed. Number of connectable units Transmission standard Maximum total extension distance Control procedure Communication method Baud rate Remarks 8 maximum RS-485 standard 500 m (1640' 5") or less [50 m (164' 0") or less when 485BD is included in system] Distance varies depending on communication equipment type. N:N Network — Half-duplex, bidirectional communication E 38400 bps Inverter Communication Start bit Character Data bit format Parity bit Fixed Stop bit Header F Fixed Control line — Sum check Fixed Non-Protocol Communication (RS/RS2 Instruction) Terminator D Computer Link Protocol type Specifications Parallel Link Item C G Non-Protocol Communication (FX2N-232IF) H Programming Communication I Remote Maintenance Apx.A Discontinued models B-9 FX Series PLC User's Manual - Data Communication Edition 2 Specifications N:N Network 2.2 Link Specifications 2.2 Link Specifications 2.2.1 Link patterns and number of link points in each FX Series The number of occupied link points varies depending on the number of slave stations used. For example, when three slave stations are connected in "Pattern 1", M1000 to M1223 and D0 to D33 are occupied, and unoccupied devices can be used as general devices for control. (Link devices for unconnected slave stations can be used as general devices for control, but it is recommended to leave them in the unoccupied status if slave stations may be added in the future.) : Applicable —: Not applicable Pattern 0 Pattern 1 Pattern 2 FX3U, FX3UC Series PLC Series FX3G, FX3GC Series FX3S Series FX2N, FX2NC Series FX1N, FX1NC Series FX1S Series — — FX0N Series — — Pattern 0 Slave stations B-10 Pattern 2 Word device (D) Bit device (M) Word device (D) Bit device (M) Word device (D) 0 4 in each station 32 in each station 4 in each station 64 in each station 8 in each station Station No. 0 — D 0 to D 3 M1000 to M1031 D 0 to D 3 M1000 to M1063 D 0 to D 7 Station No. 1 — D10 to D13 M1064 to M1095 D10 to D13 M1064 to M1127 D10 to D17 Station No. 2 — D20 to D23 M1128 to M1159 D20 to D23 M1128 to M1191 D20 to D27 Station No. 3 — D30 to D33 M1192 to M1223 D30 to D33 M1192 to M1255 D30 to D37 Station No. 4 — D40 to D43 M1256 to M1287 D40 to D43 M1256 to M1319 D40 to D47 Station No. 5 — D50 to D53 M1320 to M1351 D50 to D53 M1320 to M1383 D50 to D57 Station No. 6 — D60 to D63 M1384 to M1415 D60 to D63 M1384 to M1447 D60 to D67 Station No. 7 — D70 to D73 M1448 to M1479 D70 to D73 M1448 to M1511 D70 to D77 Station No. Master station Pattern 1 Bit device (M) FX Series PLC User's Manual - Data Communication Edition 2 Specifications N:N Network A Link time The link time indicates the cycle time in which link devices are updated. The link time varies depending on the number of linked units (master station and slave stations) and the number of linked devices as shown in the table below. Unit: ms Pattern 1 Pattern 2 32 bit-devices 4 word-devices 64 bit-devices 8 word-devices 2 18 22 34 3 26 32 50 4 33 42 66 5 41 52 83 6 49 62 99 7 57 72 115 8 65 82 131 C Parallel Link Pattern 0 0 bit-devices 4 word-devices B N:N Network Number of linked stations Common Items 2.2.2 2.2 Link Specifications D Computer Link E Inverter Communication F Non-Protocol Communication (RS/RS2 Instruction) G Non-Protocol Communication (FX2N-232IF) H Programming Communication I Remote Maintenance Apx.A Discontinued models B-11 FX Series PLC User's Manual - Data Communication Edition 3 System Configuration and Equipment Selection N:N Network 3. 3.1 System Configuration System Configuration and Equipment Selection This chapter explains the configuration of the communication equipment operating in accordance with RS485 and the system selection required by FX PLCs. 3.1 System Configuration This section outlines the system configuration required to use the N:N Network. Connect (optional) equipment operating in accordance with RS-485 to the FX PLC main unit. 1 , 2 , 3 and 4 indicate the communication equipment combination patterns. Important point in selection Total extension distance + This is the communication board built into the PLC, reducing the installation area. 50 m (164' 0") + Attach the special adapter connection board to the main unit, and then attach the communication adapter to the left side of the main unit. 500 m (1640' 5") + Attach the connector conversion adapter to the main unit, and then attach the communication adapter to the left side of the main unit. 500 m (1640' 5") + Attach the communication adapter to the left side of the main unit. 500 m (1640' 5") Communication equipment operating in accordance with RS-485 FX PLC 1 Communication board 2 + Communication Special adapter connection adapter board 3 + Communication adapter Connector conversion adapter 4 Communication adapter For communication equipment combinations for each FX Series, refer to the next page. B-12 FX Series PLC User's Manual - Data Communication Edition 3 System Configuration and Equipment Selection N:N Network A Applicable FX PLC and Communication Equipment FX Series Total extension distance Communication equipment (option) Check C Parallel Link 500 m (1640' 5") FX0N FX2NC-485ADP FX0N-485ADP (European terminal block) D (Terminal block) Computer Link 50 m (164' 0") FX1N-485-BD E (European terminal block) FX1N-CNV-BD + FX2NC-485ADP FX1N-CNV-BD 500 m (1640' 5") F FX0N-485ADP (Terminal block) Non-Protocol Communication (RS/RS2 Instruction) (European terminal block) Inverter Communication + FX1S 50 m (164' 0") G FX1N-485-BD + FX2NC-485ADP (European terminal block) FX1N-CNV-BD 500 m (1640' 5") H Programming Communication FX1N-CNV-BD + Non-Protocol Communication (FX2N-232IF) (European terminal block) FX1N FX0N-485ADP (Terminal block) I 500 m (1640' 5") Apx.A Remote Maintenance 50 m (164' 0") FX2N-485-BD + FX2N FX2NC-485ADP (European terminal block) + Discontinued models FX2N-CNV-BD B N:N Network Select a (optional) communication equipment combination, and put a check mark in the "Check" column. During selection, pay attention to the following: - In the table below, only the external dimensions are different between the units shown in "FX2NC-485ADP/ FX0N-485ADP". Select either one. - In the table below, only the cable is different between the units shown in "FX3G-485-BD/FX3G-485-BDRJ". Select either one. - N:N Network is not provided for the FX1, FX2(FX), FX2C, FX0 and FX0S PLCs. Common Items 3.2 3.2 Applicable FX PLC and Communication Equipment FX2N-CNV-BD FX0N-485ADP (Terminal block) B-13 FX Series PLC User's Manual - Data Communication Edition 3 System Configuration and Equipment Selection N:N Network 3.2 Applicable FX PLC and Communication Equipment FX Series Communication equipment (option) Total extension distance 50 m (164' 0") FX3G-485-BD (European terminal block) FX3G-485-BD-RJ (RJ45 connector) + FX3S 500 m (1640' 5") FX3S-CNV-ADP FX3U-485ADP(-MB) (European terminal block) 50 m (164' 0") FX3G-485-BD (European terminal block) FX3G-485-BD-RJ (RJ45 connector) FX3G (14-point, 24-point type) 500 m (1640' 5") FX3G-CNV-ADP FX3U-485ADP(-MB) (European terminal block) When using channel 1 (ch 1) ch1 ch1 50 m (164' 0") FX3G-485-BD (European terminal block) FX3G-485-BD-RJ (RJ45 connector) The communication equipment works as ch1 when connected to the option connector 1. FX3G (40-point, 60-point type) ch1 500 m (1640' 5") FX3G-CNV-ADP B-14 FX3U-485ADP(-MB) (European terminal block) Check FX Series PLC User's Manual - Data Communication Edition 3 System Configuration and Equipment Selection N:N Network 3.2 Applicable FX PLC and Communication Equipment A Communication equipment (option) Total extension distance Check When using channel 2 (ch 2) ch2 ch2 B N:N Network 50 m (164' 0") FX3G-485-BD (European terminal block) FX3G-485-BD-RJ (RJ45 connector) C The communication equipment works as ch2 when connected to the option connector 2. ch2 FX3U-ADP(-MB) FX3U-485ADP(-MB) (Where represents (European terminal block) 232 and 485). D 500 m (1640' 5") Computer Link FX3G-CNV-ADP Parallel Link ch1 FX3G (40-point, 60-point type) Ch2 is not available when the FX3G-8AV-BD, FX3G-4EX-BD or FX3G-2EYT-BD is connected to the option connector 2. E Inverter Communication When using channel 1 (ch 1) ch1 RD A 50 m (164' 0") RD RD B SD A SD SD B SG F Non-Protocol Communication (RS/RS2 Instruction) FX3U-485-BD (European terminal block) ch1 FX3U G 500 m (1640' 5") Non-Protocol Communication (FX2N-232IF) + FX3U-CNV-BD Common Items FX Series FX3U-485ADP(-MB) (European terminal block) H Programming Communication I Remote Maintenance Apx.A Discontinued models B-15 FX Series PLC User's Manual - Data Communication Edition 3 System Configuration and Equipment Selection N:N Network 3.2 Applicable FX PLC and Communication Equipment FX Series Total extension distance Communication equipment (option) When using channel 2 (ch 2) ch1 ch2 + RD SD FX3U--BD (Where represents 232, 422, 485, USB and 8AV). 500 m (1640' 5") FX3U-485ADP(-MB) (European terminal block) When a FX3U-8AV-BD is used, it occupies one communication port channel. ch1 ch2 FX3U + + FX3U-CNV-BD FX3U-232ADP(-MB), FX3U-485ADP(-MB) (European terminal block) FX3U-485ADP(-MB), FX3U-CF-ADP When a FX3U-CF-ADP is used, it occupies one communication port channel. 500 m (1640' 5") 500 m (1640' 5") FX1NC FX2NC-485ADP (European terminal block) FX0N-485ADP (Terminal block) 500 m (1640' 5") FX2NC FX2NC-485ADP (European terminal block) FX0N-485ADP (Terminal block) When using channel 1 (ch 1) ch1 500 m (1640' 5") FX3U-485ADP(-MB) (European terminal block) When using channel 2 (ch 2) ch1 FX3GC + FX3U-ADP(-MB) (Where represents 232 and 485). B-16 ch2 500 m (1640' 5") FX3U-485ADP(-MB) (European terminal block) Check FX Series PLC User's Manual - Data Communication Edition 3 System Configuration and Equipment Selection N:N Network 3.2 Applicable FX PLC and Communication Equipment A Total extension distance Communication equipment (option) Check When using channel 1 (ch 1) ch1 Common Items FX Series B N:N Network 500 m (1640' 5") FX3U-485ADP(-MB) (European terminal block) C When using channel 2 (ch 2) ch1 FX3UC (D, DS, DSS) Parallel Link ch2 + 500 m (1640' 5") D Computer Link FX3U-232ADP(-MB), FX3U-485ADP(-MB) (European terminal block) FX3U-485ADP(-MB), FX3U-CF-ADP When a FX3U-CF-ADP is used, it occupies one communication port channel. When using channel 1 (ch 1) E ch1 Inverter Communication RD A 50 m (164' 0") RD RD B SD A SD SD B SG FX3U-485-BD F (European terminal block) + FX3U-CNV-BD Non-Protocol Communication (RS/RS2 Instruction) ch1 500 m (1640' 5") G FX3U-485ADP(-MB) Non-Protocol Communication (FX2N-232IF) (European terminal block) When using channel 2 (ch 2) ch1 + RD SD FX3U--BD (Where represents 232, 422, 485, USB and 8AV). H 500 m (1640' 5") Programming Communication FX3UC-32MT-LT (-2) ch2 FX3U-485ADP(-MB) (European terminal block) When a FX3U-8AV-BD is used, it occupies one communication port channel. + I ch2 + Remote Maintenance ch1 500 m (1640' 5") Apx.A Discontinued models FX3U-CNV-BD FX3U-232ADP(-MB), FX3U-485ADP(-MB) (European terminal block) FX3U-485ADP(-MB), FX3U-CF-ADP When a FX3U-CF-ADP is used, it occupies one communication port channel. B-17 FX Series PLC User's Manual - Data Communication Edition 4 Wiring N:N Network 4. 4.1 Wiring Procedure Wiring This chapter explains the wiring. WIRING PRECAUTIONS • Make sure to cut off all phases of the power supply externally before attempting installation or wiring work. Failure to do so may cause electric shock or damage to the product. • Make sure to attach the terminal cover, offered as an accessory, before turning on the power or initiating operation after installation or wiring work. Failure to do so may cause electric shock. WIRING PRECAUTIONS • Make sure to observe the following precautions in order to prevent any damage to the machinery or accidents due to abnormal data written to the PLC under the influence of noise: 1) Do not bundle the main circuit line together with or lay it close to the main circuit, high-voltage line or load line. Otherwise, noise disturbance and/or surge induction are likely to take place. As a guideline, lay the control line at least 100mm (3.94") or more away from the main circuit or high-voltage lines. 2) Ground the shield wire or shield of the shielded cable at one point on the PLC. However, do not use common grounding with heavy electrical systems. • Make sure to properly wire the terminal block in accordance with the following precautions. Failure to do so may cause electric shock, equipment failures, a short-circuit, wire breakage, malfunctions, or damage to the product. - The disposal size of the cable end should follow the dimensions described in the manual. - Tightening torque should follow the specifications in the manual. - Tighten the screws using a Phillips-head screwdriver No.2 (shaft diameter 6mm (0.24") or less). Make sure that the screwdriver does not touch the partition part of the terminal block. • Make sure to properly wire to the terminal block (European type) in accordance with the following precautions. Failure to do so may cause electric shock, equipment failures, a short-circuit, wire breakage, malfunctions, or damage to the product. - The disposal size of the cable end should follow the dimensions described in the manual. - Tightening torque should follow the specifications in the manual. - Twist the end of strand wire and make sure that there are no loose wires. - Do not solder-plate the electric wire ends. - Do not connect more than the specified number of wires or electric wires of unspecified size. - Affix the electric wires so that neither the terminal block nor the connected parts are directly stressed. 4.1 1 Wiring Procedure Preparing for wiring Prepare cables and terminal resistors required for wiring. 2 3 4 For details, refer to Section 4.2. Turning OFF the power to the PLC Before starting any wiring work, make sure that the PLC power is OFF. Connecting the power supply (FX0N-485ADP only) Connect the power supply to the 24V DC power terminal. Wiring communication equipment Connect communication equipment operating in accordance with RS-485. For details, refer to Section 4.3. B-18 FX Series PLC User's Manual - Data Communication Edition N:N Network 4.2 Selecting Cables and Terminal Resistors A Selecting Cables and Terminal Resistors Common Items 4.2 4 Wiring Select cables using the procedure described below. 4.2.1 Twisted pair cable B 1. Recommended cables Manufacturer Model name Showa Holdings Co., Ltd. The Furukawa Electric Co., Ltd. Three-pair cable of 0.2 mm2 SPEV(SB)-0.5-2P Two-pair cable of 0.5 mm2 KMPEV-SB CWS-178 0.2SQ 2P Two-pair cable of 0.2 mm2 KMPEV-SB CWS-178 0.5SQ 2P Two-pair cable of 0.5 mm2 DPEV SB 0.3 3P Three-pair cable of 0.3 mm2 DPEV SB 0.5 3P Three-pair cable of 0.5 mm2 D-KPEV-SB 0.2 3P Three-pair cable of 0.2 mm2 D-KPEV-SB 0.5 3P Three-pair cable of 0.5 mm2 IPEV-SB 2P 0.3 mm2 Two-pair cable of 0.3 mm2 IPEV-SB 2P 0.5 mm2 Two-pair cable of 0.5 mm2 D E Inverter Communication Fujikura Ltd. SPEV(SB)-MPC-0.2 3P Computer Link Sumitomo Electric Industries, Ltd. Two-pair cable of 0.2 mm2 Parallel Link Mitsubishi Cable Industries, Ltd. C Remarks SPEV(SB)-0.2-2P N:N Network Use shielded twisted pair cables for connecting communication equipment operating in accordance with RS485. The table below shows recommended model names and manufacturers of cables used for wiring. 2. Cable structural drawing (reference) F Pair Non-Protocol Communication (RS/RS2 Instruction) Shield G 4.2.2 Non-Protocol Communication (FX2N-232IF) Two-pair cable structural drawing example Three-pair cable structural drawing example 10BASE-T cable 1. Selection procedure when purchasing 1) Cable type : 10BASE-T cable (Category 3 or higher) 2) Connection specifications : Straight type 3) Connector H Programming Communication 10BASE-T cables used in LAN wiring for a personal computer can be connected to FX3G-485-BD-RJ. I : RJ45 connector (Connector with metal frame is used) Pay attention to the following point when purchasing commercial cables. • Use shielded cables. Make sure to connect the shield to the metal frame of the connector, and perform class D grounding. Remote Maintenance 2. Cautions on using commercial cables Apx.A Discontinued models B-19 FX Series PLC User's Manual - Data Communication Edition 4 Wiring N:N Network 4.2.3 4.2 Selecting Cables and Terminal Resistors Connecting cables 1. European type terminal block The FX3G-485-BD-RJ terminal block is used for grounding. The other options use shielded twisted pair cables for connecting communication equipment operating in accordance with RS-485. The table below shows applicable cables and tightening torques. Cable size when Cable size when one cable is two cables are connected connected FX3U-485-BD FX3G-485-BD FX3U-485ADP (-MB) AWG22 to AWG20 AWG22 Bar terminal with Insulating sleeve (cable size) Tightening torque Applicable 0.22 to 0.25 (AWG22 to AWG20) N·m Tool size A B 0.4 (0.01") 2.5 (0.09") FX3G-485-BDRJ AWG20 to AWG16 Not applicable 0.5 to 0.6 N·m 0.6 (0.03") 3.5 (0.14") FX2N-485-BD FX1N-485-BD AWG26 to AWG16 Not applicable 0.5 to 0.6 N·m 0.6 (0.03") 3.5 (0.14") Not applicable 0.4 to 0.5 N·m 0.6 (0.03") 3.5 (0.14") FX2NC-485ADP AWG26 to AWG16 AWG26 to AWG20 Do not tighten terminal screws with a torque outside the above-mentioned range. Failure to do so may cause equipment failures or malfunctions. With regard to the cable end treatment, use a stranded cable or solid cable as it is, or use a bar terminal with insulating sleeve. FX3G-485-BD-RJ, FX2N-485-BD, FX1N-485-BD and FX2NC-485ADP cannot use a bar terminal with insulating sleeve. • When using a stranded cable or solid cable as it is - Twist the end of a stranded cable so that wires do not get barbed. - Do not plate the end of the cable. FX3G-485-BD, FX3U-485-BD, FX3U-485ADP(-MB) FX3G-485-BD-RJ, FX2N-485-BD, FX1N-485-BD Approx. 9 mm (0.35") Approx. 6 mm (0.23") FX2NC-485ADP • When using a bar terminal with insulating sleeve Because it is difficult to insert a cable into an insulating sleeve depending on the thickness of the cable sheath, select the proper cable according to the outline drawing. <Reference> Manufacturer Model name Caulking tool Phoenix Contact Co., Ltd. AI 0.5-8WH CRIMPFOX 6*1 (or CRIMPFOX 6T-F*2) *1. *2. B-20 Old model name : CRIMPFOX ZA 3 Old model name : CRIMPFOX UD 6 Approx. 8 mm (0.31") Insulating sleeve Contact area (Crimp area) 8 mm (0.31") 2.6 mm (0.1") 14 mm (0.55") FX Series PLC User's Manual - Data Communication Edition 4 Wiring N:N Network 4.2 Selecting Cables and Terminal Resistors A Select a screwdriver with a straight tip. A If the diameter of screwdriver grip is too small, tightening torque will not be able to be achieved. To achieve the appropriate tightening torque shown in the previous page, use the following screwdriver or an appropriate replacement (grip diameter: approximately 25mm (0.98")). For size A and size B, refer to the table above. B B N:N Network Note <Reference> FX3U-485-BD, FX3G-485-BD, FX3U-485ADP(-MB) Phoenix Contact Co., Ltd. C Model name Parallel Link Manufacturer SZS 0.4 2.5 FX3G-485-BD-RJ, FX2N-485-BD, FX1N-485-BD, FX2NC-485ADP Manufacturer Phoenix Contact Co., Ltd. Model name D SZF 1-0.6 3.5 Computer Link 2. Terminal block In the FX0N-485ADP and FX-485ADP, the terminal screw size is "M3". Make sure to use a crimp-style terminal with the following sizes. Make sure that the tightening torque is 0.5 to 0.8 N·m. Do not tighten terminal screws with a torque outside the above-mentioned range. Failure to do so may cause equipment failures or malfunctions. E Inverter Communication • When wiring one cable to one terminal 6.2mm(0.24") or less Terminal Crimp screw terminal F Non-Protocol Communication (RS/RS2 Instruction) 6.2mm(0.24") or less 3.2(0.13") 3.2(0.13") Terminal G 6.3mm(0.25") or more Terminal Crimp screw terminal H 3.2(0.13") Programming Communication 6.2mm(0.24") or less 3.2(0.13") Non-Protocol Communication (FX2N-232IF) • When wiring two cables to one terminal 6.2mm(0.24") or less Common Items • Tool When tightening a terminal on the European terminal block, use a small commercial straight shape screwdriver whose tip is shown in the figure to the right. Terminal 6.3mm(0.25") or more I Remote Maintenance Apx.A Discontinued models B-21 FX Series PLC User's Manual - Data Communication Edition N:N Network 4.2.4 4 Wiring 4.2 Selecting Cables and Terminal Resistors Connecting terminal resistors Make sure to provide a terminal resistor at the end of each line. In the case of one-pair wiring, connect a terminal resistor to the RDA-RDB signal terminal of the communication equipment. Brown 1. Terminal resistor type Use two terminal resistors of 110 , 1/2 W. Among the terminal resistors supplied with the communication equipment, select ones with the color codes shown to the right. Precision 1 1 1 =110 (101) 2. When using the FX3U-485-BD, FX3G-485-BD, FX3G-485-BD-RJ or FX3U-485ADP(-MB) The FX3U-485-BD, FX3G-485-BD, FX3G-485-BD-RJ and FX3U-485ADP(-MB) have built-in terminal resistors. Set the terminal resistor selector switch accordingly. • FX3U-485-BD • FX3U-485ADP(-MB) Terminal resistor selector switch 330 OPEN 110 Terminal resistor selector switch • FX3G-485-BD Remove the upper terminal block before changing over the switch in the FX3G-485-BD. Removal: Loosen the terminal block mounting screws, and remove the terminal block. Installation: Attach the terminal block, and tighten the terminal block mounting screws. Tightening torque: 0.4 to 0.5 N•m Do not tighten terminal screws with a torque outside the above-mentioned range. Failure to do so may cause equipment failures or malfunctions. For installation and removal of the terminal block, use the recommended tool shown below or a tool having straight tip (such as screwdriver) as shown in the right figure. <Reference> Manufacturer Model name SZS 0.4 2.5 Phoenix Contact Co., Ltd. Terminal resistor selector switch Terminal block mounting screws • FX3G-485-BD-RJ Terminal resistor selector switch B-22 Select a screwdriver with a straight tip. 0.4mm (0.01") 2.5mm (0.09") FX Series PLC User's Manual - Data Communication Edition 4 Wiring N:N Network A Connection Diagram Common Items 4.3 4.3 Connection Diagram Use one-pair wiring for an N:N Network. Terminal resistor: 110 B FX2NC-485ADP SDA (TXD+) SDA (TXD+) SDA (TXD+) SDA (TXD+) SDB (TXD-) SDB (TXD-) SDB (TXD-) SDB (TXD-) RDA (RXD+) RDA (RXD+) RDA (RXD+) RDA (RXD+) RDB (RXD-) RDB (RXD-) RDB (RXD-) RDB (RXD-) SG LINK SG SG *3 D SG Class-D grounding (resistance: 100 or less)*1 C Computer Link FG*2 Terminal resistor: 110 Parallel Link *3 FX0N-485ADP FX3U-485-BD FX3G-485-BD FX2N-485-BD FX1N-485-BD FX3U-485ADP(-MB) N:N Network FX3U-485-BD FX3G-485-BD FX2N-485-BD FX1N-485-BD FX3U-485ADP(-MB) Class-D grounding (resistance: 100 or less)*1 *1 Make sure to perform Class-D grounding on the shield of a twisted pair cable connected to the FX2N-485-BD, FX1N-485-BD, FX3U-485-BD, FX3G-485-BD, FX2NC-485ADP or FX3U-485ADP(-MB). E Inverter Communication *2 Make sure to connect the FG terminal to the (grounding) terminal in the PLC requiring Class-D grounding. If the grounding terminal is not provided in the PLC, perform Class-D grounding directly. *3 Make sure to provide a terminal resistor at the end of each line. The FX3U-485-BD, FX3G-485-BD and FX3U-485ADP(-MB) have a built-in terminal resistor. Set the terminal resistor selector switch accordingly. The FX0N-485ADP, FX2NC-485ADP, FX2N-485-BD and FX1N-485-BD are supplied together with terminal resistors. F Non-Protocol Communication (RS/RS2 Instruction) G Non-Protocol Communication (FX2N-232IF) H Programming Communication I Remote Maintenance Apx.A Discontinued models B-23 FX Series PLC User's Manual - Data Communication Edition 4 Wiring N:N Network 4.3 Connection Diagram • FX3G-485-BD-RJ FX3G-485-BD-RJ 5 4 3 6 1 2 Terminal 7 resistor *2 8 Connector metal frame Distributor (BMJ-8) RDA RDB SDA SDB SG 5 4 3 6 1 2 7 8 5 4 3 6 1 2 7 8 *1 Connector metal frame SG SDB SDA RDB RDA SG SDB SDA RDB RDA Connector metal frame 5 4 3 6 1 2 7 8 FX3G-485-BD-RJ (Terminal resistor selector switch: Open) *1 5 RDA 4 RDB 3 SDA 6 SDB 1 SG 2 Terminal 7 resistor *2 8 Connector metal frame Class-D grounding *1 *1 5 4 3 6 1 2 7 8 (Terminal resistor selector switch: 110Ω)*2 5 4 3 6 1 2 7 8 Class-D Class-D grounding grounding Class-D grounding *1. 5 4 3 6 1 2 7 8 5 4 3 6 1 2 7 8 *1 FX3G-485-BD-RJ Distributor (BMJ-8) 5 4 3 6 1 2 7 8 Class-D grounding (Terminal resistor selector switch: 110Ω)*2 FX3G-485-BD-RJ (Terminal resistor selector switch: Open) Use shielded cables, and make sure to perform class D grounding on the shield. When using the terminal block to connect ground, wire the ground wire only to either one of two poles of the terminal block. *2. Make sure to provide a terminal resistor at the end of each line. Set the terminal resistor selector switch accordingly. Prepare the following devices if necessary. Product name Model name TM11AP-88P Distributor BMJ-8 BMJ-8-28N (No internal connection of the No. 2 and 8 pin) HACHIKO ELECTRIC CO., LTD. (Do not use a plug with terminal resistor) The FX3G-485-BD-RJ has a built-in wiring circuit switch. Set the wiring circuit switch to 1 pair. Wiring circuit switch B-24 Manufacturer RJ45 connector HIROSE ELECTRIC CO., LTD. FX Series PLC User's Manual - Data Communication Edition 4 Wiring N:N Network A Grounding Common Items 4.4 4.4 Grounding Grounding should be performed as stated below. • The grounding resistance should be 100 or less. PLC Other equipment Other equipment Shared grounding Good condition PLC Other equipment C Common grounding Not allowed Parallel Link Independent grounding Best condition PLC B N:N Network • Independent grounding should be performed for best results. When independent grounding can not be performed, perform "shared grounding" as shown in the following figure. For details, refer to the Hardware Edition of each series. • The grounding wire size should be AWG 14 (2 mm2) or larger. • The grounding point should be close to the PLC, and all grounding wires should be as short as possible. D Computer Link E Inverter Communication F Non-Protocol Communication (RS/RS2 Instruction) G Non-Protocol Communication (FX2N-232IF) H Programming Communication I Remote Maintenance Apx.A Discontinued models B-25 FX Series PLC User's Manual - Data Communication Edition 5 Communication Setting (Initialization) in FX Programmable Controller N:N Network 5. 5.1 Check Procedure Communication Setting (Initialization) in FX Programmable Controller The communication setting is not required in FX PLCs for the N:N network. Using the following procedure, verify that the communication setting is not specified for another communication type and verify that the setting is correct. When using this communication function in ch1 in an FX3S, FX3G, FX3GC, FX3U or FX3UC PLC, check D8120 and D8400 using the following procedure. When using this communication function in ch2 in an FX3G, FX3GC, FX3U or FX3UC PLC, check D8420 using the following procedure. In other PLCs, use D8120 for verification. 5.1 1 Check Procedure Monitoring D8120 (D8400, D8420) Turn ON the power to the PLC while it is in STOP mode, and monitor D8120 (D8400, D8420). 1. When the value of D8120 (D8400, D8420) is "0" The communication setting is not provided. 2. When the value of D8120 (D8400, D8420) is any value other than "0" The communication setting is provided. 2 Checking absence/presence of parameter setting Check for the absence/presence using the GX Works2, GX Developer, FXGP/WIN or FX-30P. 1) GX Works2 operating procedure (For details, refer to Section 5.2.) 2) FXGP/WIN operating procedure (For details, refer to Section 5.3.) For details on GX Developer operating procedure, refer to GX Developer Operating Manual. For details on FX-30P operating procedure, refer to FX-30P Operation Manual. 3 Checking absence/presence of sequence program setting Check whether or not a write instruction is programmed for D8120 (D8400, D8420). 1. When such an instruction is programmed Program example: (for D8120) Change the program as shown below, and then change the PLC mode from STOP to RUN. M8002 Initial pulse FNC 12 MOV H23F6 D8120 Program example The value varies depending on the communication setting. M8002 Initial pulse FNC 12 MOV H0000 D8120 Changed program 2. When such an instruction is not programmed Proceed to the next step. 4 B-26 Monitoring D8120 (D8400, D8420) again, and confirming that its value is "0" FX Series PLC User's Manual - Data Communication Edition N:N Network 5.2 Communication Setting Using Parameter Method (GX Works2) A Communication Setting Using Parameter Method (GX Works2) 5.2.1 Operating procedure C This subsection explains the serial communication setting method. Suppose that GX Works2 is already started up. Opening the parameter setting window In the project view area of the navigation window, double-click [Parameter] [PLC Parameter]. If the navigation window is not displayed, select [View] [Docking Window] [Navigation] from the menu bar. Parallel Link 1 B N:N Network Communication setting may be changed using the parameter method with GX Works2, GX Developer, FXGP/WIN for Windows and FX-30P handy programming panel. This section describes how to change parameters with GX Works2. For details on FXGP/WIN operating procedure, refer to section 5.3. For details on GX Developer operating procedure, refer to GX Developer Operating Manual. For details on FX-30P operating procedure, refer to FX-30P Operation Manual. Common Items 5.2 5 Communication Setting (Initialization) in FX Programmable Controller D Computer Link E Inverter Communication F Setting the serial communication (parameters) Non-Protocol Communication (RS/RS2 Instruction) 2 Select a channel to be used, and click the [PLC System(2)] tab on the dialog box. Make sure that the "Operate Communication Setting" check box is clear. If a check mark is there, clear it. Click [End]. G Non-Protocol Communication (FX2N-232IF) H Programming Communication I Remote Maintenance 3 Writing parameters and program to the PLC Apx.A B-27 Discontinued models Select [Online] [Write to PLC] from the menu bar, click [Parameter + Program], and then click [Execute]. FX Series PLC User's Manual - Data Communication Edition N:N Network 5.3 5 Communication Setting (Initialization) in FX Programmable Controller 5.3 Communication Settings Using Parameter Method (FXGP/WIN) Communication Settings Using Parameter Method (FXGP/WIN) Communication setting may be changed using the parameter method with GX Works2, GX Developer, FXGP/WIN for Windows and FX-30P handy programming panel. This section describes how to change parameters with FXGP/WIN. Ch2 cannot be set using FXGP/WIN. For details on GX Works2 operating procedure, refer to section 5.2. For details on GX Developer operating procedure, refer to GX Developer Operating Manual. For details on FX-30P operating procedure, refer to FX-30P Operation Manual. 5.3.1 Operating procedure This subsection explains the serial communication setting method. Suppose that FXGP/WIN is already started up. 1 Adjusting serial setting (parameter) Double-click [Option] [Serial setting (parameter)] from the toolbar. The following dialog box appears according to absence/presence of parameter settings. 1. When there are no parameter settings The dialog box shown below appears to indicate that there are no communication settings. Click the [No] button. In this case, the next step is not required. 2. When there are already parameter settings The dialog box shown below appears to indicate that there are communication settings. Click the [Clear] button to delete the communication settings from parameters. Transfer parameters to the PLC using the following step. 2 Writing a sequence program (parameters) to the PLC Select [PLC] [Transfers] [Write] from the toolbar, and click [OK] button. B-28 FX Series PLC User's Manual - Data Communication Edition 6 Test Run (Communication Test) N:N Network 6.1 Test Procedure A Common Items 6. Test Run (Communication Test) 6.1 C Parallel Link 1 Test Procedure B N:N Network This chapter explains the communication test procedures for the N:N Network. It is recommended to first wire the master station and slave stations, initialize communication settings in the FX PLCs, and then execute the communication test using the following procedure to confirm proper operation. Creating programs for the communication test Create new programs for the communication test for the master station and slave stations. For program examples, refer to Section 6.2. Computer Link 2 Transferring the program to each PLC Turn ON the power to each PLC, and transfer the program. 3 Validating the communication setting E When the PLC is in RUN mode, set it to STOP mode once, and then set it to RUN mode again. Or turn OFF the power of the master station and all slave stations in communication, and then turn ON the power of these stations at the same time. Inverter Communication 4 Confirming flashing of the communication status indicator lamps (SD and RD) F Confirming the link of the master station Set the inputs X000 to X003 to ON or OFF. Slave station No. 1 Slave station No. 2 G Non-Protocol Communication (FX2N-232IF) Set the PLC inputs (X000 to X003) to ON or OFF in the master station, and confirm that the outputs (Y000 to Y003) turn ON or OFF in each slave station. Non-Protocol Communication (RS/RS2 Instruction) Confirm that the built-in SD and RD lamps of the communication equipment are flashing. If they are off, take proper action while referring to the troubleshooting procedures described later. 5 D H Confirm that the inputs in the master station turn ON or OFF according to the outputs Y000 to Y003. I Remote Maintenance Confirm that the inputs in the master station turn ON or OFF according to the outputs Y000 to Y003. Programming Communication Master station Apx.A Discontinued models B-29 FX Series PLC User's Manual - Data Communication Edition 6 Test Run (Communication Test) N:N Network 6 6.1 Test Procedure Confirming the link of slave stations Set the PLC inputs (X000 to X003) to ON or OFF in each slave station, and confirm that the outputs (Y004 to Y007, Y010 to Y013, Y014 to Y017... Y030 to Y033) turn ON or OFF in each slave station. Set the inputs X000 to X003 to ON or OFF. Master station Confirm that the inputs (X000 to X003) in the slave station No. 1 turn ON or OFF according to the outputs (Y004 to Y007) respectively. Confirm that the inputs (X000 to X003) in the slave station No. 2 turn ON or OFF according to the outputs (Y010 to Y013) respectively. Set the inputs X000 to X003 to ON or OFF. Slave station No. 1 Slave station No. 2 Confirm that the inputs (X000 to X003) in the slave station No. 2 turn ON or OFF according to the outputs (Y010 to Y013) respectively. Confirm that the inputs (X000 to X003) in the slave station No. 1 turn ON or OFF according to the outputs (Y004 to Y007) respectively. If unable to establish link, refer to "Chapter 9. Troubleshooting". Assignment of inputs and outputs (link devices) The table below shows devices used in the test programs shown later: Station No. B-30 Input (X) Link device Output (Y) 0 Master station X000 to X003 D0 Y000 to Y003 1 Slave station No. 1 X000 to X003 D10 Y004 to Y007 2 Slave station No. 2 X000 to X003 D20 Y010 to Y013 3 Slave station No. 3 X000 to X003 D30 Y014 to Y017 4 Slave station No. 4 X000 to X003 D40 Y020 to Y023 5 Slave station No. 5 X000 to X003 D50 Y024 to Y027 6 Slave station No. 6 X000 to X003 D60 Y030 to Y033 7 Slave station No. 7 X000 to X003 D70 Y034 to Y037 FX Series PLC User's Manual - Data Communication Edition N:N Network 6.2 Creating Programs for the Communication Testing A Creating Programs for the Communication Testing Common Items 6.2 6 Test Run (Communication Test) Create the programs shown below for the master station and each slave station. (In the communication test, set the refresh range to pattern 0.) 6.2.1 B Creating a program for the master station M8038 0 FNC 12 MOV K0 D8176 C FNC 12 MOV K0 D8178 FNC 12 MOV K3 D8179 FNC 12 MOV K5 D8180 M8000 34 K1X000 D0 FNC 12 MOV D10 K1Y004 FNC 12 MOV D20 K1Y010 D70 K1Y034 Step for writing information from the master station (master station → slave station) The contents of X000 to X003 in the master station are transferred to outputs (Y) in this slave station. Steps for reading information from a slave station (slave station → master station) By using link devices, read information from all slave stations. The table below shows the link devices to be used: Slave station No. 1 2 3 4 5 6 7 Link device D10 D20 D30 D40 D50 D60 D70 Output (Y) Y004 to Y007 Y010 to Y013 Y014 to Y017 Y020 to Y023 Y024 to Y027 Y030 to Y033 Y034 to Y037 Specify device numbers for the connected slave stations. F G H Programming Communication FNC 12 MOV When using ch1, this step is not required. When using ch2, program "OUT M8179". (Only in the FX3G, FX3GC, FX3U and FX3UC) Non-Protocol Communication (FX2N-232IF) FNC 12 MOV E Non-Protocol Communication (RS/RS2 Instruction) 28 D Computer Link D8177 Parallel Link K2 Set the number of slave stations to D8177. The setting range is from K1 to K7. Inverter Communication FNC 12 MOV M8179 M8000 N:N Network Create the program shown below for the communication test. (This program is not required during actual operation.) I Remote Maintenance END Caution 2) In the circuit from step 34, create a program for link devices (MOV instruction) for all connected slave stations. B-31 Apx.A Discontinued models 1) When using a PLC (such as an FX1S and FX3S Series PLC) with a small number of outputs, transfer information from slave stations to auxiliary relays (M), etc., and then monitor the auxiliary relays using a programming tool. (Example: Change "K1Y004" to "K1M4".) FX Series PLC User's Manual - Data Communication Edition 6 Test Run (Communication Test) N:N Network 6.2.2 6.2 Creating Programs for the Communication Testing Creating a program for each slave station Create the program shown below for the communication test. (This program is not required during actual operation.) Determine the station number of each slave station, and then transfer a program corresponding to the station number to each slave station. Assign station numbers from "1" in the ascending order. (Use one station number only once. Do not skip station numbers.) M8038 0 M8000 8 FNC 12 MOV FNC 12 MOV K1 D8176 Set the slave station number to D8176. The setting range is from K1 to K7. M8179 When using ch1, this step is not required. When using ch2, program "OUT M8179". (Only in the FX3G, FX3GC, FX3U and FX3UC) K1X000 D10 Specify the link device number for this slave station. M8000 14 FNC 12 MOV D0 K1Y000 FNC 12 MOV D20 K1Y010 FNC 12 MOV D30 K1Y014 FNC 12 MOV D70 K1Y034 Step for writing information from a slave station (slave station → master station) Transfer the contents of X000 to X003 in this slave station to a link device. The link device varies depending on the station number. The table below shows the link devices to be used: Slave station No. Link device Output (Y) 1 D10 Y004 to Y007 2 D20 Y010 to Y013 3 D30 Y014 to Y017 4 D40 Y020 to Y023 5 D50 Y024 to Y027 6 D60 Y030 to Y033 7 D70 Y034 to Y037 Step for reading information from the master station (master station → slave station) The contents of X000 to X003 in the master station are transferred to outputs (Y) in this slave station. Steps for reading information from another slave station (another slave stations → this slave station) By using link devices, read information from all other slave stations. The table below shows the link devices to be used: Slave station No. 1 2 3 4 5 6 7 Link device D10 D20 D30 D40 D50 D60 D70 Output (Y) Y004 to Y007 Y010 to Y013 Y014 to Y017 Y020 to Y023 Y024 to Y027 Y030 to Y033 Y034 to Y037 Specify link device numbers for other slave stations. (Do not specify the device number (D10) for this slave station.) END Caution 1) When using a PLC (such as an FX1S and FX3S Series PLC) with a small number of outputs, transfer information from slave stations to auxiliary relays (M), etc., and then monitor the auxiliary relays using a programming tool. (Example: Change "K1Y004" to "K1M4".) 2) In the circuit from step 14, specify link devices for other slave stations. B-32 FX Series PLC User's Manual - Data Communication Edition 7 Creating Programs N:N Network 7.1 Checking Contents of Related Devices A Common Items 7. Creating Programs 7.1 Checking Contents of Related Devices C 1. Devices for setting the N:N Network These devices are used for setting the N:N Network. Setting these devices is essential for using N:N Network. Name Description Set value Parallel Link The tables below show the devices used by the N:N Network. Device B N:N Network This chapter explains how to set the N:N Network and how to create programs. In N:N Network, pattern 0, 1 or 2 can be set according to the refresh range value. The number of used devices varies depending on the pattern. In N:N Network using (including) the FX0N or FX1S Series, only pattern 0 is applicable. D This device is a flag for setting communication parameters, and is used to check for absence/presence of N:N Network program also. Do not set this device to ON in the sequence program. M8179 Channel setting Set the channel of the communication port to be used (in the FX3G, FX3GC, FX3U and FX3UC). When "OUT M8179" program does not exist: ch 1 When "OUT M8179" program exists: ch 2 D8176 Station number settings Set the station number used in the N:N Network. Master station: 0, slave station: 1 to 7 [Initial value: 0] 0 to 7 Slave station quantity setting Set the total number of slave stations. This setting is not required in PLCs working as slave stations. [Initial value: 7] Inverter Communication D8177 1 to 7 F D8178 Refresh range setting Select the desired pattern of device points used for communication. This setting is not required in PLCs working as slave stations. [Initial value: 0] Only pattern 0 is applicable when a FX0N or FX1S Series is included. 0 to 2 Non-Protocol Communication (RS/RS2 Instruction) D8179 Number of retries When a response is not given even after communication is repeated the specified number of times, it is regarded as an error. Errors in other stations can be checked. This setting is not required in PLCs working as slave stations. [Initial value: 3] 0 to 10 D8180 Monitoring time Set the time (50 to 2550 ms) for communication error in 10 ms units. This setting is not required in PLCs working as slave stations. [Initial value: 5] 5 to 255 Computer Link Parameter setting M8038 E G Non-Protocol Communication (FX2N-232IF) H Programming Communication I Remote Maintenance Apx.A Discontinued models B-33 FX Series PLC User's Manual - Data Communication Edition 7 Creating Programs N:N Network 7.1 Checking Contents of Related Devices 2. Devices for determining errors in the N:N Network These devices are used for determining errors in the N:N Network. Use them to output link errors to the outside and interlock sequence programs. Different devices are used between the FX0N/FX1S Series and the FX1N/FX1NC/FX2N/FX2NC/FX3S/FX3G/ FX3GC/FX3U/FX3UC Series. Use devices according to the PLCs used. Device FX0N, FX1S FX1N, FX1NC, FX2N, FX2NC, FX3S, FX3G, FX3GC, FX3U, FX3UC M504 M8183 M505 to M511*1 M8184 to M8190*2 M503 M8191 Name Description Master station data This device turns ON when a data transfer transfer sequence sequence error occurs in the master station. error Slave station data transfer sequence error This device turns ON when a data transfer sequence error occurs in a slave station. Data transfer sequence ON This device remains ON while the N:N Network is operating. *1. Station No. 1: M505, Station No. 2: M506, Station No. 3: M507... Station No. 7: M511 *2. Station No. 1: M8184, Station No. 2: M8185, Station No. 3: M8186... Station No. 7: M8190 3. Link devices These devices are used for sending and receiving information among the PLCs. The device numbers used and number of devices vary depending on the station number set in D8176 (station number settings) and the pattern set in D8178 (refresh range setting). 1) In the case of pattern 0 0 (master station) 1 2 3 4 5 6 7 D0 to D3 D10 to D13 D20 to D23 D30 to D33 D40 to D43 D50 to D53 D60 to D63 D70 to D73 0 (master station) 1 2 3 4 5 6 7 Bit devices (32 points for each station) M1000 to M1031 M1064 to M1095 M1128 to M1159 M1192 to M1223 M1256 to M1287 M1320 to M1351 M1384 to M1415 M1448 to M1479 Word device (4 points for each station) D0 to D3 D10 to D13 D20 to D23 D30 to D33 D40 to D43 D50 to D53 D60 to D63 D70 to D73 0 (master station) 1 2 3 4 5 6 7 Bit devices (64 points for each station) M1000 to M1063 M1064 to M1127 M1128 to M1191 M1192 to M1255 M1256 to M1319 M1320 to M1383 M1384 to M1447 M1448 to M1511 Word device (8 points for each station) D0 to D7 D10 to D17 D20 to D27 D30 to D37 D40 to D47 D50 to D57 D60 to D67 D70 to D77 Station No. Word device (4 points for each station) 2) In the case of pattern 1 Station No. 3) In the case of pattern 2 Station No. Caution When creating a program, do not change the information in devices used by other stations. If such information is changed, other stations will not operate normally. B-34 FX Series PLC User's Manual - Data Communication Edition 7 Creating Programs N:N Network A Creating Programs for Master Station (Station No. 0) Common Items 7.2 7.2 Creating Programs for Master Station (Station No. 0) Create programs for the master station. Arbitrarily create programs for reading and writing link devices. Program for setting the N:N Network FNC 12 MOV K2 D8177 FNC 12 MOV K1 D8178 FNC 12 MOV K3 D8179 K5 D8180 Channel setting D Number of retries: 3 (3 times) Set the number of retrying communication after a link error is detected. [Setting range: 0 to 10] E Monitoring time: 5 (50 ms) Set the time by which communication error is determined. [Setting range: 5 to 255] Set the communication port to be used. When using ch1, this step is not required. When using ch2, program "OUT M8179". (in the FX3G, FX3GC, FX3U and FX3UC) F Non-Protocol Communication (RS/RS2 Instruction) M8179 Refresh range setting: 1 (pattern 1) Set the pattern of devices used in communication. [Setting range: 0 to 2] (Only pattern 0 is applicable in the FX0N or FX1S Series.) Cautions on setting up the N:N Network • When setting up the N:N Network in a program using Structured Ladder or FBD programming, connect the ENO output to the EN input for the MOV instruction. <Program example> H Parameter setting K5 EN s MOV ENO d D8180 K2 D8177 K1 MOV EN ENO s d D8178 K3 MOV EN ENO s d D8179 I • When setting up the N:N Network in a program using ST programming, use the MOV instruction as shown in the following program example. <Program example> MOV(MOV(MOV(MOV(MOV(M8038, K0, D8176), K2, D8177), K1, D8178), K3, D8179), K5, D8180); Remote Maintenance D8176 MOV EN ENO s d Programming Communication K0 MOV EN ENO s d G Non-Protocol Communication (FX2N-232IF) Note the following cautions when creating a program using Structured Ladder, FBD or ST programming in the FX1S, FX1N, FX1NC, FX2N or FX2NC PLC. M8038 Inverter Communication FNC 12 MOV C Slave station quantity setting: 2 (2 slave stations) Set the number of connected slave stations. [Setting range: 1 to 7] Computer Link D8176 Parallel Link K0 B N:N Network 0 Parameter setting M8038 FNC 12 MOV Make sure to start the program for setting the N:N Network from step 0. Station number setting: 0 (master station) Station number "0" indicates the master station. Apx.A Discontinued models B-35 FX Series PLC User's Manual - Data Communication Edition N:N Network 7 Creating Programs 7.2 Creating Programs for Master Station (Station No. 0) Program for indicating link errors Station No. 1 Data transfer sequence error M8184 This program is required to indicate the N:N Network status. Y000 When a link error occurs in the station No. 1, Y000 is set to ON. Y001 When a link error occurs in the station No. 2, Y001 is set to ON. • Create this step for each connected slave station. Note that the devices to be used are different depending on the PLC Series. For FX0N and FX1S Series: M505 to M511 (station No. 1 to station No. 7) For any series other than FX0N and FX1S Series: M8184 to M8190 (station No. 1 to station No. 7) Y010 While the N:N Network is executed, Y010 remains ON. • Note that the devices to be used are different depending on the PLC Series. For FX0N and FX1S Series: M503 For any series other than FX0N and FX1S Series: M8191 Station No. 2 Data transfer sequence error M8185 Data transfer sequence ON M8191 Program for writing link devices (master station → slave station) M1000 This program is required to write information from the master station to each slave station. The information from X000 is written to M1000 (link device). M1001 The information from X002 is written to M1001 (link device). M1002 The information from M10 is written to M1002 (link device). X000 X002 M10 M8000 Station No. 1 Data transfer sequence error M8184 FNC 12 MOV K4M100 K4M1010 FNC 12 MOV D100 D0 The information from M100 to M115 is written to M1010 to M1025 (link devices). The information from D100 is written to D0 (link device). * In pattern 0, bit devices are not applicable. Use word devices only. Program for reading link devices (master station ← slave station) M1064 M0 This program is required to read information from each slave station to the master station. Monitor link errors in each slave station, and read them. The information from M1064 (link device) is read to M0. M1065 Y011 The information from M1065 (link device) is read to Y011. M15 The information from M1066 (link device) is read to M15. M1066 B-36 FNC 12 MOV K4M1070 K4Y020 The information from M1070 to M1085 (link devices) is read to Y020 to Y037. FNC 12 MOV D10 D110 The information from D10 (link device) is read to D110. FX Series PLC User's Manual - Data Communication Edition N:N Network 7 Creating Programs 7.2 Creating Programs for Master Station (Station No. 0) A Common Items Station No. 2 Data transfer sequence error M8185 M1128 M1 B Y012 The information from M1129 (link device) is read to Y012. M18 The information from M1130 (link device) is read to M18. M1130 K4M1140 K4M20 The information from M1140 to M1155 (link devices) is read to M20 to M35. FNC 12 MOV D20 D200 The information from D20 (link device) is read to D200. C Parallel Link FNC 12 MOV N:N Network M1129 The information from M1128 (link device) is read to M1. D Computer Link For details on link devices, refer to Section 7.1. For cautions on program creation, refer to Section 7.4. E Inverter Communication F Non-Protocol Communication (RS/RS2 Instruction) G Non-Protocol Communication (FX2N-232IF) H Programming Communication I Remote Maintenance Apx.A Discontinued models B-37 FX Series PLC User's Manual - Data Communication Edition N:N Network 7.3 7 Creating Programs 7.3 Creating Programs for Slave Station (Station No. "n") Creating Programs for Slave Station (Station No. "n") Create programs for the slave stations. Arbitrarily create programs for reading and writing link devices. Program for setting the N:N Network 0 Make sure to start the program for setting the N:N Network from step 0. Parameter setting M8038 FNC 12 MOV K1 D8176 Station number setting: 1 (slave station) Set the station number of each slave station. Only set the station number for the slave station; Other settings are not required. Channel setting M8179 Set the communication port to be used (in the FX3G, FX3GC, FX3U and FX3UC). When using ch1, this step is not required. When using ch2, program "OUT M8179". Program for indicating link errors Station No. 0 Data transfer sequence error M8183 This program is required to indicate the N:N Network status. Y000 When a link error occurs in station No. 0, Y000 is set to ON. Y001 When a link error occurs in station No. 2, Y001 is set to ON. • Create this step for each connected slave station. Note that the devices to be used are different depending on the PLC Series. For FX0N and FX1S Series: M504 to M511 (station No. 0 to station No. 7) For any series other than FX 0N and FX1S Series: M8183 to M8190 (station No. 0 to station No. 7) Station No. 2 Data transfer sequence error M8185 Data transfer sequence ON M8191 Y010 While the N:N Network is executed, Y010 remains ON. • Note that the devices to be used are different depending on the PLC Series. For FX0N and FX1S Series: M503 For any series other than FX 0N and FX1S Series: M8191 Program for writing link devices (slave station → master or slave station) This program is required to write information from a slave station to the master station or another slave station. X000 M1064 The information from X000 is written to M1064 (link device). M1065 The information from X002 is written to M1065 (link device). M1066 The information from M10 is written to M1066 (link device). X002 M10 M8000 FNC 12 MOV K4M100 K4M1070 The information from M100 to M115 is written to M1070 to M1085 (link devices). FNC 12 MOV D100 D10 The information from D100 is written to D10 (link device). * In pattern 0, bit devices are not available. Use word devices only. B-38 FX Series PLC User's Manual - Data Communication Edition N:N Network 7 Creating Programs 7.3 Creating Programs for Slave Station (Station No. "n") A M1000 M0 The information from M1000 (link device) is read to M0. M1001 The information from M1001 (link device) is read to Y011. M15 The information from M1002 (link device) is read to M15. M1002 K4Y020 The information from M1010 to M1025 (link devices) is read to Y020 to Y037. FNC 12 MOV D0 D110 The information from D0 (link device) is read to D110. D Computer Link K4M1010 E M1128 M1 M1129 The information from D1128 (link device) is read to M1. The information from D1129 (link device) is read to Y012. M18 The information from D1130 (link device) is read to M18. M1130 F Non-Protocol Communication (RS/RS2 Instruction) Y012 Inverter Communication Station No. 2 Data transfer sequence error M8185 FNC 12 MOV C Parallel Link Y011 B N:N Network Station No. 0 Data transfer sequence error M8183 This program is required to read information from the master station or another slave station to a slave station. Monitor link errors in each slave station, and read them. Common Items Program for reading link devices (slave station master or slave station) FNC 12 MOV K4M1140 K4M20 The information from M1140 to M1155 (link devices) is read to M20 to M35. G FNC 12 MOV D20 D200 The information from D20 (link device) is read to D200. Non-Protocol Communication (FX2N-232IF) H Programming Communication For details on link devices, refer to Section 7.1. For cautions on program creation, refer to Section 7.4. I Remote Maintenance Apx.A Discontinued models B-39 FX Series PLC User's Manual - Data Communication Edition N:N Network 7.4 7 Creating Programs 7.4 Cautions on Program Creation Cautions on Program Creation 1. Effect on the operation cycle When the N:N Network is used, the operation cycle in each PLC becomes longer by about 10% regardless of the number of linked stations and adopted communication patterns. 2. Program for setting the N:N Network 1) Make sure to create a program for setting the N:N Network from step 0 using M8038 (drive contact). Otherwise, the N:N Network is disabled. 2) Do not set M8038 to ON using a program or programming tool. 3) Set station numbers consecutively. If a station number that is used twice or more is skipped, link will not be achieved normally. 4) Pay close attention when setting up the N:N Network for the master station in a program using Structured Ladder, FBD or ST programming in the FX1S, FX1N, FX1NC, FX2N or FX2NC PLC. For details, refer to Section 7.2. 3. Program for reading link devices Do not change the contents of link devices at other stations. 1) When a link error (data transfer sequence error) occurs, the link device information is held in the status just before occurrence of the link error. Create a fail-safe program which does not cause abnormality even if a link error occurs. 4. Cautions on using FX0N/FX1S PLCs 1) Link pattern when FX0N/FX1S PLCs are used or included When FX0N/FX1S PLCs are included in the system, make sure to set pattern 0 in D8178 (refresh range setting). If any other pattern is set, data transfer error occurs in all FX0N/FX1S PLCs included in the system, and the link time becomes longer. 2) When user devices are occupied as system devices In FX0N/FX1S PLCs, M503 to M511 and D201 to D255 are handled as devices dedicated to the N:N Network, and cannot be handled as general devices any more. Do not set these devices to ON or OFF using a user program, display unit or programming tool. If these devices are set to ON or OFF, the N:N Network may malfunction. 5. Cautions on using FX3G/FX3GC/FX3U/FX3UC PLCs 1) Only ch 1 or ch 2 can be set in the N:N Network. 2) Do not use the N:N Network and parallel link at the same time. (For example, it is not allowed to use ch1 for the N:N Network and use ch2 for parallel link.) 6. Link device update timing Link device update in N:N network is executed in the interrupt processing. Because the interrupt processing is generated asynchronously from operations of the sequence program, it may be performed during ladder operation. B-40 FX Series PLC User's Manual - Data Communication Edition 8 Practical Program Examples N:N Network 8.1 Practical Example 1 (Pattern 2) A Common Items 8. Practical Program Examples B This chapter shows practical programs. N:N Network 8.1 Practical Example 1 (Pattern 2) This program example adopts pattern 2 which uses the maximum number of link devices. When an FX0N or FX1S PLC is included, however, only pattern 0 is applicable. Parallel Link 8.1.1 C System configuration example The example below shows a system configuration in which three FX PLCs are linked. FX2N PLC FX2N PLC FX2N PLC D FX2N-485-BD Computer Link FX2N-485-BD FX2N-485-BD E Station No. 1 (slave station) Inverter Communication Station No. 0 (master station) Station No. 2 (slave station) - Refresh range: 64-bit devices and 8 word devices (pattern 2) - Number of retries: 5 - Monitoring time: 70 ms Contents of operations and corresponding program numbers The program examples shown later execute the data processing shown in the table below. The operation No. corresponds to the operation [1] (for example) indicated in the programs shown later. Operation No. Data source Data change destination and contents Master station Inputs X000 to X003 (M1000 to M1003) Slave station No. 1 Outputs Y010 to Y013 [2] Slave station No. 1 Inputs X000 to X003 (M1064 to M1067) Master station [3] Slave station No. 2 Inputs X000 to X003 (M1128 to M1131) Master station Data register D1 Slave station No. 1 Set value of counter C1 Slave station No. 2 Outputs Y010 to Y013 Outputs Y014 to Y017 H Slave station No. 2 Outputs Y014 to Y017 Programming Communication Outputs Y020 to Y023 Slave station No. 1 Outputs Y020 to Y023 Word device link [4] [6] [7] Master station Data register D2 I Output Y005 Slave station No. 2 Set value of counter C2 Slave station No. 2 Contact of counter C2 (M1140) Master station Output Y006 Slave station No. 1 Data register D10 Master station Slave station No. 1 (D10) + Slave station No. 2 (D20) is stored to D3. Slave station No. 1 Master station (D0) + Slave station No. 2 (D20) is stored to D11. Slave station No. 2 Master station (D0) + Slave station No. 1 (D10) is stored to D21. Slave station No. 2 Data register D20 Master station Data register D0 Slave station No. 2 Data register D20 Master station Data register D0 Slave station No. 1 Data register D10 B-41 Apx.A Discontinued models [8] Slave station No. 1 Contact of counter C1 (M1070) Master station Remote Maintenance [5] Master station G Non-Protocol Communication (FX2N-232IF) Bit device link [1] Non-Protocol Communication (RS/RS2 Instruction) 8.1.2 F FX Series PLC User's Manual - Data Communication Edition 8 Practical Program Examples N:N Network 8.1.3 8.1 Practical Example 1 (Pattern 2) Setting contents The program examples shown later adopt the following communication parameters: 8.1.4 System device Master station Station No. 1 Station No. 2 D8176 K0 K1 K2 Station number settings Contents D8177 K2 — — Total number of slave stations: 2 D8178 K2 — — Refresh range: Pattern 2 D8179 K5 — — Number of retries: 5 D8180 K7 — — Monitoring time: 70 ms Setting program for master station For the master station setting program, refer to the program shown below. The program shown below consists of three blocks, "parameter setting program", "error indication program" and "operation program". 1. Parameter setting program Make sure to start from step 0. 0 Parameter setting M8038 FNC 12 MOV K 0 D8176 Station number settings: 0 (master station) FNC 12 MOV K 2 D8177 Slave station quantity setting: 2 (2 slave stations) FNC 12 MOV K 2 D8178 Refresh range setting: 2 (pattern 2) FNC 12 MOV K 5 D8179 Number of retries setting: 5 (5 times) FNC 12 MOV K 7 D8180 Monitoring time setting: 7 (70 ms) Caution Pay close attention when setting up the N:N Network for the master station in a program using Structured Ladder, FBD or ST programming in the FX1S, FX1N, FX1NC, FX2N or FX2NC PLC. For details, refer to Section 7.2. 2. Error indication program Because the master station does not recognize errors within itself (the master station), programs for errors within itself are not required. Data transfer sequence error in slave station No. 1 M8184 Y001 Data transfer sequence error in slave station No. 2 M8185 Y002 Data transfer sequence ON M8191 Y003 B-42 FX Series PLC User's Manual - Data Communication Edition 8 Practical Program Examples N:N Network 8.1 Practical Example 1 (Pattern 2) A RUN monitor M8000 MOV K1X000 K1M1000 Common Items 3. Operation program Operation [1] B Data transfer sequence error in slave station No. 1 MOV K1M1064 K1Y014 Operation [2] MOV K1M1128 K1Y020 Operation [3] N:N Network M8184 Data transfer sequence error in slave station No. 2 M8185 C Parallel Link Data transfer sequence error in slave station No. 1 M8184 MOV K 10 D 1 D Operation [4] M1070 Computer Link C1 contact of slave station No. 1 Y005 Data transfer sequence error in slave station No. 2 M8185 K 10 Operation [5] C2 contact of slave station No. 2 M1140 Data transfer sequence error in slave station No. 2 M8184 M8185 Y006 F ADD D 20 D 3 Operation [6] MOV K 10 D 0 Operation [7] Operation [8] G Non-Protocol Communication (FX2N-232IF) D 10 Non-Protocol Communication (RS/RS2 Instruction) Data transfer sequence error in slave station No. 1 E D 2 Inverter Communication MOV END H Programming Communication I Remote Maintenance Apx.A Discontinued models B-43 FX Series PLC User's Manual - Data Communication Edition N:N Network 8.1.5 8 Practical Program Examples 8.1 Practical Example 1 (Pattern 2) Setting program for slave station (No. 1) For the slave station setting program, refer to the program shown below. The program shown below consists of three blocks, "parameter setting program", "error indication program" and "operation program". 1. Parameter setting program Make sure to start from step 0. 0 Parameter setting M8038 FNC 12 MOV K 1 D8176 Station number settings: 1 (slave station No. 1) 2. Error indication program Because slave station No. 1 does not recognize errors within itself (slave station No. 1), programs for errors within itself are not required. Data transfer sequence error in master station M8183 Y000 Data transfer sequence error in slave station No. 2 M8185 Y002 Data transfer sequence ON M8191 Y003 B-44 FX Series PLC User's Manual - Data Communication Edition 8 Practical Program Examples N:N Network 8.1 Practical Example 1 (Pattern 2) A Common Items 3. Operation program Counter reset X001 RST C 1 B K1M1000 K1Y010 Operation [1] MOV K1X000 K1M1064 Operation [2] MOV K1M1128 K1Y020 Operation [3] C Parallel Link MOV N:N Network Master station Data transfer sequence error M8183 Data transfer sequence error in slave station No. 2 M8185 D Computer Link Counter input X000 C1 D1 C1 Y005 Y006 Operation [5] K 10 D 10 Operation [6] Operation [8] D 0 D 20 D 11 Operation [7] F Non-Protocol Communication (RS/RS2 Instruction) MOV Inverter Communication ADD E M1070 Data transfer sequence error in slave Slave station No. 2 station No. 2 C2 contact M8185 M1140 Data transfer sequence error in slave station No. 2 M8185 Operation [4] G Non-Protocol Communication (FX2N-232IF) END H Programming Communication I Remote Maintenance Apx.A Discontinued models B-45 FX Series PLC User's Manual - Data Communication Edition N:N Network 8.1.6 8 Practical Program Examples 8.1 Practical Example 1 (Pattern 2) Setting program for slave station (No. 2) For the slave station setting program, refer to the program shown below. The program shown below consists of three blocks, "parameter setting program", "error indication program" and "operation program". 1. Parameter setting program Make sure to start from step 0. 0 Parameter setting M8038 FNC 12 MOV K 2 D8176 Station number settings: 2 (slave station No. 2) 2. Error indication program Because slave station No. 2 does not recognize errors within itself (slave station No. 2), programs for errors within itself are not required. Data transfer sequence error in master station M8183 Y000 Data transfer sequence error in slave station No. 1 M8184 Y002 Data transfer sequence ON M8191 Y003 B-46 FX Series PLC User's Manual - Data Communication Edition 8 Practical Program Examples N:N Network 8.1 Practical Example 1 (Pattern 2) A Common Items 3. Operation program Counter reset X001 RST C 2 B MOV K1M1000 K1Y010 Operation [1] MOV K1M1064 K1Y014 Operation [2] MOV K1X000 K1M1128 Operation [3] Data transfer sequence error in slave station No. 1 M8184 C Parallel Link D Slave Station No. 1 C1 contact M1070 Y005 Computer Link Data transfer sequence error in slave station No. 1 M8184 N:N Network Master station Data transfer sequence error M8183 Operation [4] Counter input X000 E Inverter Communication C2 D2 C2 Y006 Operation [5] F MOV K 10 D 20 Data transfer sequence error in slave station No. 1 M8184 Non-Protocol Communication (RS/RS2 Instruction) M1140 Operation [6] Operation [7] G D 0 D 10 D 21 Non-Protocol Communication (FX2N-232IF) ADD Operation [8] H END Programming Communication I Remote Maintenance Apx.A Discontinued models B-47 FX Series PLC User's Manual - Data Communication Edition N:N Network 9. 9 Troubleshooting 9.1 Checking FX PLC Version Applicability Troubleshooting This chapter explains troubleshooting. 9.1 Checking FX PLC Version Applicability Verify that the FX Series PLC main unit is an applicable version. For the version applicability check, refer to Section 1.3. 9.2 Checking Communication Status Based on LED Indication Check the status of the "RD" and "SD" indicator LEDs provided in the optional equipment. LED status RD SD Flashing Flashing Flashing Off Off Flashing Off Off Operation status Data is being sent or received. Data is received, but is not sent. Data is sent, but is not received. Data is not sent nor received. While the N:N Network is executed normally, both LEDs flash brightly. If they do not flash, check the wiring and the communication setting in the master and slave stations. 9.3 Checking Installation and Wiring 1. Mounting status If the communication equipment is not securely connected to the PLC, communication is not possible. For mounting method, refer to the respective communication equipment manual. 2. Power supply (For FX0N-485ADP) The FX0N-485ADP requires a driving power supply. Verify that the power supply is correctly provided. 3. Wiring Verify that the wiring to all communication equipment is correct. If the communication equipment is wired incorrectly, communication is not possible. For wiring method check, refer to Chapter 4. 9.4 Checking Sequence Program 1. Communication setting in the sequence program Verify that the parallel link is not set. Using both the parallel link and the N:N Network at the same time is not allowed. Verify that the communication format (D8120, D8400 and D8420) is set correctly. Communication is not possible if a communication port is set twice or more. After changing any setting, make sure to reboot the PLC's power. For communication setting, refer to Chapter 5. 2. Communication setting using parameters Verify that the communication settings using parameters are suitable for use. Do not set parameters for the N:N Network. If the communication settings are not suitable for use, communication will not function correctly. After changing the setting, make sure to reboot the PLC’s power. For the communication setting, refer to Chapter 5. B-48 FX Series PLC User's Manual - Data Communication Edition N:N Network 9 Troubleshooting 9.4 Checking Sequence Program A Verify that the same channel is not used in the Ethernet port setting. Do not set the channel used in N:N network. After changing the setting, make sure to reboot the PLC's power. 4. N:N network and MODBUS communication (in FX3S, FX3G, FX3GC, FX3U and FX3UC PLCs) C 5. Presence of VRRD and VRSC instructions Parallel Link 1) Except FX3G, FX3U and FX3UC PLCs Verify that the VRRD and VRSC instructions are not used in the program. If these instructions are used, delete them, reboot the PLC’s power. 2) In FX3G PLC - In the case of the 14 points and 24-point type Verify that the VRRD and VRSC instructions are not used in the program. If these instructions are used, delete them, reboot the PLC's power. - In the case of the 40 points and 60-point type Verify that the VRRD and VRSC instructions are not used in the program. If these instructions are used in the program, the communication function is not available in ch2. Use ch1, or delete these instructions. After deleting these instructions, reboot the PLC's power. D Computer Link E Inverter Communication 3) In FX3U and FX3UC PLCs Verify that the VRRD and VRSC instructions are not used in the program. If these instructions are used in the program, the communication function is not available in ch1. Use ch2, or delete these instructions. After deleting these instructions, reboot the PLC's power. F Non-Protocol Communication (RS/RS2 Instruction) 6. Presence of RS instruction (except FX3S, FX3G, FX3GC, FX3U and FX3UC PLCs) Verify that the RS instruction is not used in the program. If this instruction is used, delete it, reboot the PLC's power. 7. Presence of RS and RS2 instructions (in FX3S, FX3G, FX3GC, FX3U and FX3UC PLCs) Verify that the RS and RS2 instructions are not being used for the same channel. If these instructions are used for the same channel, delete them, reboot the PLC’s power. G Non-Protocol Communication (FX2N-232IF) 8. Presence of EXTR instruction (in FX2N and FX2NC PLCs) Verify that the EXTR instruction is not used in the program. If this instruction is used, delete it, then reboot the PLC’s power. 9. Presence of IVCK, IVDR, IVRD, IVWR, IVBWR*1, and IVMC instructions (in FX3S, FX3G, FX3GC, FX3U and FX3UC PLCs) H Only available for FX3U and FX3UC PLCs. Programming Communication Verify that the IVCK, IVDR, IVRD, IVWR, IVBWR and IVMC instructions are not being used for the same channel. If these instructions are used for the same channel, delete them, reboot the PLC’s power. *1. B N:N Network If N:N network and MODBUS communication are set in a same channel, N:N network is executed, but MODBUS communication is ignored. In this case, the error "Communication port is occupied in another communication, (Error code 203)" is stored in D8402/D8422 for the corresponding channel in the PLC. For details of MODBUS communication errors and error devices, refer to the FX3S/FX3G/FX3GC/ FX3U/FX3UC Series User's Manual - MODBUS Serial Communication Edition. Common Items 3. Ethernet port setting (in FX3S, FX3G, FX3GC, FX3U and FX3UC PLCs) I 10.Presence of ADPRW instructions (in FX3S, FX3G, FX3GC, FX3U and FX3UC PLCs) 11.Presence of FLCRT, FLDEL, FLWR, FLRD, FLCMD, and FLSTRD instructions (in FX3U and FX3UC PLCs) B-49 Apx.A Discontinued models Verify that the FLCRT, FLDEL, FLWR, FLRD, FLCMD and FLSTRD instructions are not being used for the same channel. If these instructions are used for the same channel, delete them, reboot the PLC’s power. Remote Maintenance Verify that the ADPRW instructions are not being used for the same channel. If these instructions are used for the same channel, delete them, and reboot the PLC’s power. FX Series PLC User's Manual - Data Communication Edition 9 Troubleshooting N:N Network 9.5 9.5 Checking Setting Contents and Errors Checking Setting Contents and Errors 1. Checking the setting contents Verify that the N:N Network is set correctly. Each FX PLC has devices for checking the setting. Verify that the correct contents are stored in the devices shown in the table below. Device Name Description D8173 Station number settings status Provided to check the station number. D8174 Slave station quantity setting status Provided to check the number of slave stations. D8175 Refresh range setting status Provided to check the refresh range. If the correct contents are not stored in the devices above, check the sequence program. 2. Checking setting errors 1) Error flags If the parameter setting includes an error, the serial communication error flag turns ON. Verify that the devices shown in the table below are ON. Device Name Description M8063 Turns ON when abnormality occurs during serial communication Serial communication error 1 (ch 1) using ch 1. M8438 Serial communication error 2 (ch 2) Turns ON when abnormality occurs during serial communication using ch 2. When using the N:N Network on ch 1, check M8063. When using the N:N Network on ch 2, check M8438. 2) Error codes When the serial communication error flag turns ON, the error code is stored in the device specified in the table below. Device D8063 D8438 Name Error code Serial communication error code 1 (ch 1) Serial communication error code 2 (ch 2) Description 6308 N:N Network parameter setting error 6309 N:N Network setting error 3808 N:N Network parameter setting error 3809 N:N Network setting error Caution The serial communication error flags and serial communication error codes are not cleared even when communication is restored. Serial communication errors are cleared in FX3S, FX3G, FX3GC, FX3U and FX3UC PLCs when the power is turned off and on. Serial communication errors are cleared in other PLCs when the mode is switched from STOP to RUN. 9.6 Checking Absence/Presence of Data Transfer Errors Verify that link errors have not occurred in the master station and slave stations. Link errors can be checked using the flags specified below. 9.6.1 Check while data transfer sequence is being executed While the N:N Network is being executed, the data transfer sequence ON flag remains ON. Verify that the device specified in the table below is ON. FX Series B-50 Device FX1N, FX1NC, FX2N, FX2NC, FX3S, FX3G, FX3GC, FX3U, FX3UC M8191 FX0N, FX1S M503 Name Data transfer sequence ON flag Description Remains ON while data transfer is being executed. FX Series PLC User's Manual - Data Communication Edition N:N Network 9.6 Checking Absence/Presence of Data Transfer Errors A Checking data transfer sequence errors When a link error occurs in the master station or slave station, the data transfer sequence error flag turns ON. The data transfer sequence error flag varies depending on the FX Series and station number. Refer to the table below. Slave station No. 1 Slave station No. 2 Slave station No. 3 Slave station No. 4 Slave station No. 5 Slave station No. 6 Slave station No. 7 FX1N, FX1NC, FX2N, FX2NC, FX3S, FX3G, FX3GC, FX3U, FX3UC M8183 M8184 M8185 M8186 M8187 M8188 M8189 M8190 FX0N, FX1S M504 M505 M506 M507 M508 M509 M510 M511 Checking error codes When a data transfer sequence error occurs, the corresponding data transfer sequence error flag turns ON, and the error code is stored in the corresponding data register. For error codes, refer to the next page. The data register used to store the data transfer error code varies depending on the FX Series and station number. Refer to the table below. Slave station No. 1 Slave station No. 2 Slave station No. 3 Slave station No. 4 Slave station No. 5 Slave station No. 6 Slave station No. 7 FX1N, FX1NC, FX2N, FX2NC, FX3S, FX3G, FX3GC, FX3U, FX3UC D8211 D8212 D8213 D8214 D8215 D8216 D8217 D8218 FX0N, FX1S D211 D212 D213 D214 D215 D216 D217 D218 The data register for storing the data transfer error code stores the corresponding error code. When a data transfer sequence error occurs, refer to the error code list shown below, and confirm the check points. Error code Error name Contents of error Check point G 01H Monitoring timeout L M Slave station did not respond to the Wiring and power sending request from the master station supply within the monitoring time. 02H Station number error L M An unexpected slave station responded Station number to the sending request by the master settings station. 03H Counter error L M The counter value included in the parameter data is different from the Wiring counter value given by a slave station. 04H Message format error L M, L Wiring, power The message given by the slave station supply and station is incorrect. number settings 11H Monitoring timeout M L The master station did not give a sending Wiring and power request to the next slave station within supply the monitoring timer. Remote Maintenance 14H Message format error M L Wiring, power The message from the master station is supply and station incorrect. number settings Apx.A 21H Slave station no response error L L*1 Wiring, power The specified slave station does not exist. supply and station number settings Discontinued models Non-Protocol Communication (FX2N-232IF) Station Station in which which error detected occurred error F Non-Protocol Communication (RS/RS2 Instruction) 2. Error code list E Inverter Communication Master station FX Series D Computer Link 1. Error storing device C Parallel Link 9.6.3 B N:N Network Master station FX Series Common Items 9.6.2 9 Troubleshooting Programming Communication B-51 H I FX Series PLC User's Manual - Data Communication Edition N:N Network 9 Troubleshooting 9.6 Checking Absence/Presence of Data Transfer Errors Error code Error name Station Station in which which error detected occurred error Contents of error 22H Station number error L L*1 An unexpected slave station responded Station number to the sending request by the master settings station. 23H Counter error L L*1 The counter value included in the parameter data is different from the Wiring counter value given by a slave station. 31H Parameter not received L L*2 Before parameters had been received, Wiring and power sending request was received from the supply master station. M: Master station, L: Slave station B-52 Check point *1. Any slave station other than the slave station in which error occurred *2. Station in which error occurred 9.6 Checking Absence/Presence of Data Transfer Errors N:N Network 9 Troubleshooting FX Series PLC User's Manual - Data Communication Edition A Common Items MEMO B N:N Network C Parallel Link D Computer Link E Inverter Communication F Non-Protocol Communication (RS/RS2 Instruction) G Non-Protocol Communication (FX2N-232IF) H Programming Communication I Remote Maintenance Apx.A Discontinued models B-53 FX Series PLC User's Manual - Data Communication Edition 10 Related Data N:N Network 10.1 Related Device List 10. Related Data 10.1 Related Device List 10.1.1 For FX1N, FX1NC, FX2N, FX2NC, FX3S, FX3G, FX3GC, FX3U and FX3UC PLCs 1. Bit devices Device number Name Description Initial value Detection R/W Devices for communication setting M8038 Parameter setting Communication parameter setting flag — M, L R M8179 Channel setting Sets the communication port channel to be used (in the FX3G, FX3GC, FX3U and FX3UC). — M, L R/W Devices for checking communication status M8063 Serial communication Turns ON when abnormality occurs in serial error 1 (ch 1) communication using ch 1. — M, L R M8438 Turns ON when abnormality occurs in serial Serial communication communication using ch 2 (in the FX3G, FX3GC, error 2 (ch 2) FX3U and FX3UC). — M, L R M8183 Data transfer sequence error Turns ON when a data transfer sequence error occurs in the master station. — L R M8184 to M8190 Data transfer sequence error Turns ON when a data transfer sequence error occurs in a slave station. However, data transfer sequence errors within the slave station itself cannot be detected. — M, L R Data transfer sequence ON Remains ON while data transfer is being executed. — M, L R M8191 R R/W M L B-54 : Read only (used as a contact in program) : Read or Write : Master station (station No. 0) : Slave station (station No. 1 to 7) FX Series PLC User's Manual - Data Communication Edition 10 Related Data N:N Network 10.1 Related Device List A Common Items B N:N Network C Slave station No. 3 Slave station No. 4 Slave station No. 5 Slave station No. 6 Slave station No. 7 — M8184 M8185 M8186 M8187 M8188 M8189 M8190 D Computer Link Slave station No. 2 Parallel Link Slave station No. 1 E Inverter Communication Master station F Non-Protocol Communication (RS/RS2 Instruction) G Non-Protocol Communication (FX2N-232IF) H Programming Communication I Remote Maintenance Apx.A Discontinued models B-55 FX Series PLC User's Manual - Data Communication Edition 10 Related Data N:N Network 10.1 Related Device List 2. Word devices (data registers) Device number Name Description Initial value Detection R/W Devices for checking D8173 Corresponding station number settings status Provided to check the station number. — M, L R D8174 Slave station quantity setting status Provided to check the number of slave stations. — M, L R D8175 Refresh range setting status Provided to check the refresh range. — M, L R D8063 Serial communication error code 1 (ch 1) Stores the serial communication error code for ch 1. — M, L R D8419 Operation mode display (ch 1) Stores the communication type being used by ch 1. (in the FX3S, FX3G, FX3GC, FX3U and FX3UC) — M, L R D8438 Serial communication error code 2 (ch 2) Stores the serial communication error code for ch 2. (in the FX3G, FX3GC, FX3U and FX3UC) — M, L R D8439 Operation mode display (ch 2) Stores the communication type being used by ch 2. (in the FX3G, FX3GC, FX3U and FX3UC) — M, L R Devices for communication setting D8176 Corresponding station number settings Provided to set the station number. 0 M, L R/W D8177 Slave station quantity setting Provided to set the number of slave stations used in communication. 7 M R/W D8178 Refresh range setting Provided to set the refresh range. 0 M R/W D8179 Number of retries Provided to set the number of retry times. 3 M R/W D8180 Monitoring time Provided to set the no-response monitoring time. 5 M R/W — M R Devices for checking communication status D8201 Present link scan time D8202 Maximum link scan time Maximum value of the network cycle time — M R D8203 Data transfer sequence error count Amount of data sequence errors that occurred in the master station — L R D8204 to D8210 Data transfer sequence error count Amount of data sequence errors that occurred in a slave station. However, data sequence errors occurring within the slave station itself cannot be counted. — M, L R D8211 Data transmission error code Stores the error code for the master station. — L R D8212 to D8218 Data transmission error code Stores the error code for a slave station. However, data sequence errors occurring within the slave station itself cannot be counted. — M, L R R R/W M L B-56 Current value of the network cycle time : Read only : Read or Write : Master station (station No. 0) : Slave station (station No. 1 to 7) FX Series PLC User's Manual - Data Communication Edition 10 Related Data N:N Network 10.1 Related Device List A Slave station No. 1 Slave station No. 2 Slave station No. 3 Slave station No. 4 Slave station No. 5 Slave station No. 6 Slave station No. 7 Computer Link — — — — — — — E — — — — — — — — — — — — — — — — — — — — — Inverter Communication Common Items Master station — — — — — — — F — — — — — — — — D8204 D8205 D8206 D8207 D8208 D8209 D8210 — — — — — — — D8212 D8213 D8214 D8215 D8216 D8217 D8218 B N:N Network C Parallel Link D Non-Protocol Communication (RS/RS2 Instruction) G Non-Protocol Communication (FX2N-232IF) H Programming Communication I Remote Maintenance Apx.A Discontinued models B-57 FX Series PLC User's Manual - Data Communication Edition 10 Related Data N:N Network 10.1 Related Device List 10.1.2 For FX0N and FX1S PLCs 1. Bit devices Device number Initial value Detection R/W — M, L R Turns ON when a data transfer sequence error occurs in the master station. — L R Turns ON when a data transfer sequence error occurs in a slave station. M505 to M511 Data transfer sequence error However, data transfer sequence errors within the slave station itself cannot be detected. — M, L R Remains ON while data transfer is being executed. — M, L R Initial value Detection R/W — M, L R Name Description Devices for communication setting M8038 Parameter setting Communication parameter setting flag Devices for checking communication status M504 M503 Data transfer sequence error Data transfer sequence ON R: Read only (used as a contact in program) M: Master station (station No. 0) L: Slave station (station No. 1 to 7) 2. Word devices (data registers) Device number Name Description Devices for checking D8173 Corresponding station number settings status D8174 Slave station quantity setting Provided to check the number of slave status stations. — M, L R D8175 Refresh range setting status Provided to check the refresh range. — M, L R Provided to check the station number. Devices for communication setting D8176 Corresponding station number settings Provided to set the station number. 0 M, L R/W D8177 Slave station quantity setting Provided to set the number of slave stations used in communication. 7 M R/W D8178 Refresh range setting Provided to set the refresh range. 0 M R/W D8179 Number of retries Provided to set the number of retries. 3 M R/W D8180 Monitoring time Provided to set the no-response monitoring time. 5 M R/W Devices for checking communication status D201 Present link scan time Stores the current value of the network cycle time. — M R D202 Maximum link scan time Stores the maximum value of the network cycle time. — M R D203 Data transfer sequence error Stores the amount of data sequence errors count that occurred in the master station. — L R Amount of data sequence errors that Data transfer sequence error occurred in a slave station. D204 to D210 However, data sequence errors that occurred count within the slave station itself cannot be counted. — M, L R D211 Data transmission error code Stores the error code for the master station. — L R Stores the error code for a slave station. D212 to D218 Data transmission error code However, data sequence errors that occurred within the slave station itself cannot be counted. — M, L R D219 to D255 Not applicable — — — Provided for the internal processing. R: Read only R/W: Read or Write M: Master station (station No. 0) L: Slave station (station No. 1 to 7) B-58 FX Series PLC User's Manual - Data Communication Edition 10 Related Data N:N Network 10.1 Related Device List A Slave station Slave station Slave station Slave station Slave station Slave station Slave station No. 1 No. 2 No. 3 No. 4 No. 5 No. 6 No. 7 — B N:N Network Common Items Master station C M505 M506 M507 M508 M509 M510 M511 Parallel Link D Slave station Slave station Slave station Slave station Slave station Slave station Slave station No. 1 No. 2 No. 3 No. 4 No. 5 No. 6 No. 7 — — — — — — — — — — — — — — — — — — — — — — — — — — — — — — — — — — — — — — — — — — — D204 D205 D206 D207 D208 D209 D210 — — — — — — — D212 D213 D214 D215 D216 D217 D218 — — — — — — — — F G H I Remote Maintenance Programming Communication Non-Protocol Communication (FX2N-232IF) Non-Protocol Communication (RS/RS2 Instruction) E Inverter Communication Computer Link Master station Apx.A Discontinued models B-59 FX Series PLC User's Manual - Data Communication Edition N:N Network 10.2 10 Related Data 10.2 Details of Related Devices Details of Related Devices The devices described below are used in the N:N Network. 10.2.1 Parameter setting [M8038] This device works as the communication parameter setting flag. 1. Stations requiring program setting Setting is required for the master station and slave stations. 2. Detailed contents "LD M8038" provided in step 0 starts the parameter setting, and the last instruction in this circuit block finishes the setting. (This sequence program is not executed in every scan cycle.) 3. Cautions on use Do not set this device to ON using a program or programming tool. 10.2.2 Channel setting [M8179] This device works as the channel setting flag (in the FX3G, FX3GC, FX3U and FX3UC). 1. Stations requiring program setting Setting is required for the master station and slave stations. 2. Detailed contents When using ch 2 as the communication port, set this device to ON in the sequence program. When using ch 1, the sequence program is not required. 10.2.3 Serial communication error [M8063 and M8438] These devices turn ON when an error is included in the parameters used to set the N:N Network. (M8438 is available in the FX3G, FX3GC, FX3U and FX3UC.) 1. Stations requiring program setting Setting is required for the master station and slave stations to check the communication status. 2. Detailed contents M8063 turns ON when an error is included in the parameters used to set N:N Network using ch 1. M8438 turns ON when an error is included in the parameters used to set N:N Network using ch 2. 3. Cautions on use Do not set these devices to ON using a program or programming tool. Serial communication errors are not cleared even when communication is restored. Serial communication errors are cleared in FX3S, FX3G, FX3GC, FX3U and FX3UC PLCs when the power is turned off and on. Serial communication errors are cleared in other PLCs when the mode is switched from STOP to RUN. B-60 FX Series PLC User's Manual - Data Communication Edition 10 Related Data N:N Network 10.2 Details of Related Devices A These devices turn ON when a data transfer sequence error occurs in the master station or a slave station. 1. Stations requiring program setting Setting is required for the master station and slave stations. However, setting for the station itself is not required. B A used device varies depending on the FX Series. Slave station No. 1 Slave station No. 2 Slave station No. 3 Slave station No. 4 Slave station No. 5 Slave station No. 6 Slave station No. 7 FX1N, FX1NC, FX2N, FX2NC, FX3S, FX3G, FX3GC, FX3U, FX3UC M8183 M8184 M8185 M8186 M8187 M8188 M8189 M8190 FX0N, FX1S M504 M505 M506 M507 M508 M509 M510 M511 3. Cautions on use D Computer Link Data transfer sequence errors in a station itself cannot be detected. Do not set these devices to ON using a program or programming tool. 10.2.5 Data transfer sequence ON [M8191] [M503] This device remains ON while data transfer is being from or to in the master station or slave station. E 1. Stations requiring program setting Inverter Communication Setting is required for the master station and slave stations. 2. Detailed contents The device used varies depending on the FX Series. FX Series Data transfer sequence ON M8191 FX0N, FX1S M503 F Non-Protocol Communication (RS/RS2 Instruction) FX1N, FX1NC, FX2N, FX2NC, FX3S, FX3G, FX3GC, FX3U, FX3UC C Parallel Link Master station N:N Network 2. Detailed contents FX Series Common Items 10.2.4 Data transfer sequence error [M8138 to M8190] [M504 to M511] 3. Cautions on use G Do not set this device to ON using a program or programming tool. These devices store the serial communication error code (D8438 is available in the FX3G, FX3GC, FX3U and FX3UC). H 1. Stations requiring program setting Programming Communication Setting is required for the master station and slave stations to check the error code. 2. Detailed contents The following error code is stored when a serial communication error occurs. Error code ch2 D8063 D8438 6308 3808 N:N Network parameter setting error 6309 3809 N:N Network setting error I Description Remote Maintenance ch1 Non-Protocol Communication (FX2N-232IF) 10.2.6 Serial communication error code [D8063 and D8438] 3. Cautions on use B-61 Apx.A Discontinued models Serial communication errors are not cleared even after communication has recovered its normal status. Serial communication errors are cleared in FX3S, FX3G, FX3GC, FX3U and FX3UC PLCs when the power is turned off and on. Serial communication errors are cleared in other PLCs when the mode is switched from STOP to RUN. FX Series PLC User's Manual - Data Communication Edition 10 Related Data N:N Network 10.2 Details of Related Devices 10.2.7 Corresponding station number settings status [D8173] This device is used to check the station’s own station number settings status. 1. Stations requiring program setting Setting is required for the master station and slave stations to check the setting status. 2. Detailed contents The contents stored in the corresponding station number settings device D8176 are stored in D8173. 3. Cautions on use Do not change the preset numeric value using a program or programming tool. 10.2.8 Slave station quantity setting status [D8174] Use this device to check the number of slave stations set in the master station. 1. Stations requiring program setting Setting is required for the master station and slave stations to check the setting status. 2. Detailed contents The contents stored in the slave station quantity setting device D8177 in the master station are stored in D8174. 3. Cautions on use Do not change a preset numeric value using a program or programming tool. 10.2.9 Refresh range setting status [D8175] Use this device to check the refresh range set in the master station. 1. Stations requiring program setting Setting is required for the master station and slave stations to check the setting status. 2. Detailed contents The contents stored in the refresh range setting device D8178 in the master station are stored in D8175. 3. Cautions on use Do not change a preset numeric value using a program or programming tool. 10.2.10 Station number settings [D8176] Set a value ranging from 0 to 7 to the special data register D8176 (initial value: 0). 1. Stations requiring program setting The master and slave stations require program setting. 2. Detailed contents Set value 0 1 to 7 B-62 Description Master station Slave station number Examples: "1" Station No. 1, "5" Station No. 5 FX Series PLC User's Manual - Data Communication Edition 10 Related Data N:N Network 10.2 Details of Related Devices A Common Items 10.2.11 Slave station quantity setting [D8177] Set a value ranging from 1 to 7 to the special data register D8177 (initial value: 7). 1. Stations requiring program setting B The master station requires program setting, and slave stations do not require program setting. Set value Description Set value 4 Description Not applicable Four slave stations are connected. 1 One slave station is connected. 5 Five slave stations are connected. 2 Two slave stations are connected. 6 Six slave stations are connected. 3 Three slave stations are connected. 7 Seven slave stations are connected. 10.2.12 Refresh range setting [D8178] D Set a value ranging from 0 to 2 to the special data register D8178 (initial value: 0). Computer Link 1. Stations requiring program setting The master station requires program setting, and slave stations do not require program setting. 2. Pattern applicability in FX PLC E Pattern (set value) Pattern 0 (0) Pattern 1 (1) Pattern 2 (2) FX0N PLC Not applicable Not applicable FX1S PLC Not applicable Not applicable FX1N, FX1NC PLC FX2N, FX2NC PLC FX3S PLC FX3G, FX3GC PLC FX3U, FX3UC PLC Inverter Communication FX Series F Non-Protocol Communication (RS/RS2 Instruction) 3. Number and assignment of link devices Pattern 2 Bit device (M) Word device (D) Bit device (M) Word device (D) Bit device (M) Word device (D) H 0 4 in each station 32 in each station 4 in each station 64 in each station 8 in each station Programming Communication Station No. Pattern 1 G Non-Protocol Communication (FX2N-232IF) The number of link devices varies depending on the selected pattern, but the head device number remains the same. It is recommended to leave unused numbers in the unused status to enable pattern change in the future. Pattern 0 C Parallel Link 0 N:N Network 2. Detailed contents — D 0 to D 3 M1000 to M1031 D 0 to D 3 M1000 to M1063 D 0 to D 7 1 — D10 to D13 M1064 to M1095 D10 to D13 M1064 to M1127 D10 to D17 2 — D20 to D23 M1128 to M1159 D20 to D23 M1128 to M1191 D20 to D27 3 — D30 to D33 M1192 to M1223 D30 to D33 M1192 to M1255 D30 to D37 4 — D40 to D43 M1256 to M1287 D40 to D43 M1256 to M1319 D40 to D47 5 — D50 to D53 M1320 to M1351 D50 to D53 M1320 to M1383 D50 to D57 6 — D60 to D63 M1384 to M1415 D60 to D63 M1384 to M1447 D60 to D67 7 — D70 to D73 M1448 to M1479 D70 to D73 M1448 to M1511 D70 to D77 I Remote Maintenance 0 Apx.A Discontinued models B-63 FX Series PLC User's Manual - Data Communication Edition N:N Network 10 Related Data 10.2 Details of Related Devices 4. Cautions on use 1) Cautions on using FX0N and FX1S PLCs When FX0N and/or FX1S PLCs are included in the system, make sure to set the refresh range to pattern 0. If any other pattern is selected, data transfer error will occur in all FX0N and FX1S PLCs included in the system, and the link time will become longer. 2) Occupied devices The devices used in each pattern are occupied for the N:N Network in all stations. Make sure that such devices are not used in general programs. 10.2.13 Number of retries [D8179] Set a value ranging from 0 to 10 to the special data register D8179 (initial value: 3). 1. Stations requiring program setting The master station requires program setting, and slave stations do not require program setting. 2. Detailed contents When any response is not given after the specified number of retries, the irresponsive station is regarded as having a data transfer sequence error by other stations. 10.2.14 Monitoring time setting [D8180] Set a vale ranging from 5 to 255 to the special data register D8180 in "10 ms" units (initial value: 5 [50 ms]). 1. Stations requiring program setting The master station requires program setting, and slave stations do not require program setting. 2. Detailed contents If data transfer between the master station and a slave station requires time longer than the monitoring time set here, the master station or slave station is regarded as abnormal. 10.2.15 Present link scan time [D8201] [D201] This device stores the current value of the network cycle in the N:N Network (unit: 10 ms). 1. Stations requiring program setting The master station requires program setting. 2. Detailed contents The device used varies depending on the FX Series. FX Series Data transfer sequence ON FX1N, FX1NC, FX2N, FX2NC, FX3S, FX3G, FX3GC, FX3U, FX3UC D8201 FX0N, FX1S D201 3. Cautions on use Do not change the preset numeric value using a program or programming tool. B-64 FX Series PLC User's Manual - Data Communication Edition 10 Related Data N:N Network 10.2 Details of Related Devices A Common Items 10.2.16 Maximum link scan time [D8202] [D202] This device stores the maximum value of the network cycle in the N:N Network (unit: 10 ms). 1. Stations requiring program setting B The master station requires program setting. N:N Network 2. Detailed contents The device used varies depending on the FX Series. FX Series Data transfer sequence ON D8202 FX0N, FX1S D202 C Parallel Link FX1N, FX1NC, FX2N, FX2NC, FX3S, FX3G, FX3GC, FX3U, FX3UC 3. Cautions on use Do not change the preset numeric value using a program or programming tool. D These devices store the amount of data transfer sequence errors that occurred in the master station and slave stations. 1. Stations requiring program setting E Inverter Communication The master and slave stations require program setting. However, setting for the station itself is not required. 2. Detailed contents The device used varies depending on the FX Series. Slave station No. 1 Slave station No. 2 Slave station No. 3 Slave station No. 4 Slave station No. 5 Slave station No. 6 Slave station No. 7 FX1N, FX1NC, FX2N, FX2NC, FX3S, FX3G, FX3GC, FX3U, FX3UC D8203 D8204 D8205 D8206 D8207 D8208 D8209 D8210 FX0N, FX1S D203 D204 D205 D206 D207 D208 D209 D210 G Non-Protocol Communication (FX2N-232IF) 3. Cautions on use F Non-Protocol Communication (RS/RS2 Instruction) Master station FX Series Computer Link 10.2.17 Data transfer sequence error count [D8203 to D8210] [D203 to D210] Data transfer sequence errors that occurred within the station itself cannot be detected. Do not change a preset numeric value using the program or programming tool. H Programming Communication I Remote Maintenance Apx.A Discontinued models B-65 FX Series PLC User's Manual - Data Communication Edition 10 Related Data N:N Network 10.2 Details of Related Devices 10.2.18 Data transfer error code [D8211 to D8218] [D211 to D218] These devices store the error code in the master station and slave stations. 1. Stations requiring program setting The master station requires program setting. However, this setting for the station itself is not required. 2. Detailed contents 1) The device used varies depending on the FX Series. FX Series Master station Slave station No. 1 Slave station No. 2 Slave station No. 3 Slave station No. 4 Slave station No. 5 Slave station No. 6 Slave station No. 7 FX1N, FX1NC, FX2N, FX2NC, FX3S, FX3G, FX3GC, FX3U, FX3UC D8211 D8212 D8213 D8214 D8215 D8216 D8217 D8218 FX0N, FX1S D211 D212 D213 D214 D215 D216 D217 D218 2) Error code list Error code Error name Station Station in which which error detected occurred error Contents of error 01H Monitoring timeout L M Slave station did not respond to the Wiring and power sending request from the master station supply within the monitoring time. 02H Station number error L M An unexpected slave station responded Station number to the sending request by the master settings station. 03H Counter error L M The counter value included in the parameter data is different from the Wiring counter value given by a slave station. 04H Message format error L M, L Wiring, power The message given by the slave station supply and station is incorrect. number settings 11H Monitoring timeout M L The master station did not give a sending Wiring and power request to the next slave station within supply the monitoring timer. 14H Message format error M L Wiring, power The message from the master station is supply and station incorrect. number settings 21H Slave station no response error L L*1 Wiring, power The specified slave station does not exist. supply and station number settings 22H Station number error L L*1 An unexpected slave station responded Station number to the sending request by the master settings station. 23H Counter error L L*1 The counter value included in the parameter data is different from the Wiring counter value given by a slave station. 31H Parameter not received L L*2 Before parameters had been received, Wiring and power sending request was received from the supply master station. M: Master station, L: Slave station *1. Any slave station other than the slave station in which error occurred *2. Station in which error occurred 3. Cautions on use Data transfer sequence errors that occurred within the station itself cannot be detected. Do not change the preset numeric value using a program or programming tool. B-66 Check point FX Series PLC User's Manual - Data Communication Edition 10 Related Data N:N Network 10.2 Details of Related Devices A These devices store the communication type being used. (in the FX3S, FX3G, FX3GC, FX3U and FX3UC) 1. Detailed contents The table below shows the contents of the communication type codes. Code B N:N Network These devices store the code of the communication type currently being used in the communication port. When communication port ch1 is used, D8419 stores the communication type. When communication port ch2 is used, D8439 stores the communication type. Common Items 10.2.19 Operation mode display [D8419 and D8439] Description Programming communication 1 PP modem mode 2 Protocol dedicated to computer link 3 N:N Network RS instruction 5 RS2 instruction 6 Parallel link 7 Inverter instruction 8 Variable analog potentiometer expansion board is used. 9 MODBUS communication CF-ADP 11 ENET-ADP 12 Input/output expansion board is used. E Inverter Communication 10 D Computer Link 4 C Parallel Link 0 F Non-Protocol Communication (RS/RS2 Instruction) G Non-Protocol Communication (FX2N-232IF) H Programming Communication I Remote Maintenance Apx.A Discontinued models B-67 FX Series PLC User's Manual - Data Communication Edition N:N Network 10.2 Details of Related Devices MEMO B-68 10 Related Data FX Series PLC User's Manual - Data Communication Edition Parallel Link A Common Items B N:N Network FX Series Programmable Controllers C Parallel Link User's Manual [Data Communication Edition] C. Parallel Link D Computer Link E Inverter Communication F Non-Protocol Communication (RS/RS2 Instruction) G Non-Protocol Communication (FX2N-232IF) H Programming Communication Foreword I © 2005 MITSUBISHI ELECTRIC CORPORATION C-1 Apx.A Discontinued models This manual confers no industrial property rights or any rights of any other kind, nor does it confer any patent licenses. Mitsubishi Electric Corporation cannot be held responsible for any problems involving industrial property rights which may occur as a result of using the contents noted in this manual. Remote Maintenance This manual explains "parallel link" provided for the MELSEC-F FX Series Programmable Controllers and should be read and understood before attempting to install or use the unit. Store this manual in a safe place so that you can take it out and read it whenever necessary. Always forward it to the end user. FX Series PLC User's Manual - Data Communication Edition Parallel Link C-2 FX Series PLC User's Manual - Data Communication Edition 1 Outline Parallel Link 1.1 Outline of System A Common Items 1. Outline B This chapter explains the parallel link. N:N Network 1.1 Outline of System The parallel link allows connection between two FX PLCs of the same series to mutually link devices. 2) Data link is automatically updated between up to two FX PLCs. 3) The total extension distance is 500 m (1640' 5") maximum (when only the 485ADPs are used except, when the 485BDs are used with FX2(FX)/FX2C PLCs). 2 units 500 m (1640' 5") [50 m (164' 0") when 485BD is used] FX PLC ....... Number of linked units ....... Total extension distance E For specifications, refer to Chapter 2. FX PLC Inverter Communication To check applicable ....... PLC models, refer to Section 1.3. + + Communication equipment operating in accordance with RS-485 Master station Bit devices ....... For selection, refer to Chapter 3. ....... For wiring, refer to Chapter 4. F Non-Protocol Communication (RS/RS2 Instruction) Communication equipment operating in accordance with RS-485 Slave station Transfer direction Bit devices M900 to M999 M900 to M999 Word devices Word devices D490 to D499 D490 to D499 D500 to D509 D500 to D509 devices can be selected among two patterns. For details, refer to Chapter 2. G H The figure above shows the maximum number of linked devices. There are differences in the specifications and limitation depending on the selected link pattern and FX Series. Programming Communication M800 to M899 ....... The number of linked Non-Protocol Communication (FX2N-232IF) M800 to M899 D Computer Link Important points and reference chapter/section System C Parallel Link 1) According to the number of devices to be linked, either pattern can be selected between the regular mode and the high speed mode. I Remote Maintenance Apx.A Discontinued models C-3 FX Series PLC User's Manual - Data Communication Edition Parallel Link 1.2 1 Outline 1.2 Procedures Before Operation Procedures Before Operation The flow chart below shows the Parallel Link setting procedures up until data link: Parallel link Refer to Chapter 1. Outline Refer to Chapter 2. Check communication specifications. Refer to Chapter 3. Determine system configuration and selection. Outline of system • Applicable PLC versions • Applicable programming tools Communication specifications • Number of link points and link time • Number of system devices System configuration • Select communication equipment. Refer to Chapter 4. Perform wiring. Wiring procedure • Wiring using twisted cables • Wiring example Programming tool Connect PLC*1 Refer to Chapter 5. Perform PLC communication setting (initialization). Turn ON power. PLC serial communication setting • Communication setting is not required. (Check only unset items.) Refer to Chapter 6. Perform test run (communication test). Communication test • Create test programs. Refer to Chapter 7. Create programs. Based on SD/RD lamp lighting status and contents of error check devices, verify that communication is being executed normally. Communication parameter setting programs • Basic program • Error indication program example • Detailed explanation of setting devices If there are problems, refer to the troubleshooting (Chapter 9). Refer to Chapter 8. Practical program examples Program examples in the regular parallel link mode are shown. *1 For the programming tool to PLC connection procedure, refer to the "Programming Communication" section in this manual or the respective programming tool manual. For details on operating procedures, refer to the respective programming tool manual. C-4 FX Series PLC User's Manual - Data Communication Edition 1 Outline Parallel Link 1.3 Communication Type Applicability in PLC Communication Type Applicability in PLC 1.3.1 Applicable versions Common Items 1.3 A PLC FX3U Series FX3GC Series (Ver. 1.04 or later) FX1NC Series FX1N Series The link device range is limited. D FX1S Series The link device range is limited. FX0N Series (Ver. 1.20 or later) The link device range is limited. Computer Link FX2NC Series FX2N Series C Parallel Link FX3G Series FX3S Series Remarks FX0S Series — Parallel link is not provided. FX0 Series — Parallel link is not provided. FX2C Series The high-speed link mode is supported in Ver. 3.07 and later. FX2(FX) Series The high-speed link mode is supported in Ver. 3.07 and later. FX1 Series — Parallel link is not provided. F Non-Protocol Communication (RS/RS2 Instruction) Version check The PLC version can be checked by reading the last three digits of device D8001. For a detailed description of the version check, refer to A. Common Items Section 4.2. 1.3.3 E Inverter Communication 1.3.2 Applicability (applicable version) FX3UC Series B N:N Network The communication types are applicable in the following versions. : Applicable (If applicable versions of main units are limited, they are described inside ( ).) —: Not applicable G Products whose production was stopped Non-Protocol Communication (FX2N-232IF) Production was stopped for some models of MELSEC-F Series PLCs and programming tools described in this manual. For models whose production was stopped, refer to Appendix A. To see the latest available products, refer to the general catalog. H Programming Communication I Remote Maintenance Apx.A Discontinued models C-5 FX Series PLC User's Manual - Data Communication Edition 1 Outline Parallel Link 1.4 Programming Tool Applicability 1.4 Programming Tool Applicability 1.4.1 For applicable versions The programming tool is applicable of main units for each FX Series from the following version: 1. English versions Product name Model name Applicable version Remarks FX3U and FX3UC PLCs GX Works2 SWDNC-GXW2-E Ver. 1.08J or later GX Developer SWD5C(F)-GPPW-E Ver. 8.18U or later FX-30P - Ver. 1.00 or later GOT1000 Series display units Refer to manuals of GOT1000 Series display units for applicable models and versions supporting the list editor function. FX3G PLC GX Works2 SWDNC-GXW2-E Ver. 1.08J or later GX Developer SWD5C(F)-GPPW-E Ver. 8.72A or later FX-30P - Ver. 1.00 or later GOT1000 Series display units Refer to manuals of GOT1000 Series display units for applicable models and versions supporting the list editor function. FX3GC PLC GX Works2 SWDNC-GXW2-E FX-30P Ver. 1.77F or later Ver. 1.30 or later GOT1000 Series display units - Refer to manuals of GOT1000 Series display units for applicable models and versions supporting the list editor function. FX3S PLC GX Works2 SWDNC-GXW2-E FX-30P Ver. 1.492N or later Ver. 1.50 or later GOT1000 Series display units - Refer to manuals of GOT1000 Series display units for applicable models and versions supporting the list editor function. FX2N and FX2NC PLCs GX Works2 SWDNC-GXW2-E Ver. 1.08J or later GX Developer SWD5C(F)-GPPW-E SW2 A or later FX-PCS/WIN-E SW0PC-FXGP/WIN-E Ver. 1.00 or later FX-30P Ver. 1.00 or later FX-20P-E(-SET0) FX-20P-MFXC-E Ver. 3.00 or later FX-10P-E Ver. 3.00 or later GOT-F900 Series display units F940WGOT-TWD-E F940GOT-*WD-E F940GOT-*BD-H-E F940GOT-*BD-RH-E GOT1000 Series display units - F940WGOT-TWD-E (Ver. 1.00 or later) F940GOT-LWD-E, F940GOT-SWD-E (Ver. 1.00 or later) F940GOT-LBD-H-E, F940GOT-SBD-H-E (Ver. 1.00 or later) F940GOT-LBD-RH-E, F940GOT-SBD-RH-E (Ver. 1.00 or later) Refer to manuals of GOT1000 Series display units for applicable models and versions supporting the list editor function. FX1S, FX1N and FX1NC PLCs GX Works2 C-6 SWDNC-GXW2-E Ver. 1.08J or later GX Developer SWD5C(F)-GPPW-E SW5 A or later FX-PCS/WIN-E SW0PC-FXGP/WIN-E Ver. 3.00 or later FX-30P Ver. 1.00 or later FX-20P-E(-SET0) FX-20P-MFXD-E Ver. 4.00 or later FX-10P-E Ver. 4.00 or later - FX Series PLC User's Manual - Data Communication Edition 1 Outline Parallel Link 1.4 Programming Tool Applicability A Model name Remarks F940WGOT-TWD-E (Ver. 1.00 or later) F940GOT-LWD-E, F940GOT-SWD-E (Ver. 1.00 or later) F940GOT-LBD-H-E, F940GOT-SBD-H-E (Ver. 1.00 or later) F940GOT-LBD-RH-E, F940GOT-SBD-RH-E (Ver. 1.00 or later) Refer to manuals of GOT1000 Series display units for applicable models and versions supporting the list editor function. 2. Japanese versions Product name Model name Applicable version Remarks C FX3U and FX3UC PLCs SWDNC-GXW2-J Ver. 1.07H or later GX Developer SWD5C(F)-GPPW-J Ver. 8.13P or later FX-30P Parallel Link GX Works2 - Ver. 1.00 or later GOT1000 Series display units Refer to manuals of GOT1000 Series display units for applicable models and versions supporting the list editor function. SWDNC-GXW2-J Ver. 1.07H or later GX Developer SWD5C(F)-GPPW-J Ver. 8.72A or later FX-30P - Ver. 1.00 or later GOT1000 Series display units Refer to manuals of GOT1000 Series display units for applicable models and versions supporting the list editor function. SWDNC-GXW2-J FX-30P Ver. 1.77F or later Ver. 1.30 or later GOT1000 Series display units - Refer to manuals of GOT1000 Series display units for applicable models and versions supporting the list editor function. SWDNC-GXW2-J FX-30P Ver. 1.492N or later Ver. 1.50 or later GOT1000 Series display units - Refer to manuals of GOT1000 Series display units for applicable models and versions supporting the list editor function. GX Works2 SWDNC-GXW2-J GX Developer SWD5C(F)-GPPW-J FX-PCS/WIN SW0PC-FXGP/WIN Ver. 2.00 or later FX-PCS-KIT/98 SW1PC-FXGP/98(-3,-5) Ver. 4.00 or later FX-PCS/98-3 SW1PC-FXGP/98-3 Ver. 4.00 or later FX-PCS-KIT/V-3 SW1PC-FXGP/V3 Ver. 2.00 or later FX-A7PHP-KIT Ver. 1.07H or later SW1RX-GPPFX Ver. 3.00 or later SW2 A or later FX-20P(-SET0) FX-20P-MFXC Ver. 4.00 or later FX-10P(-SET0) Ver. 3.00 or later GOT-F900 Series display units F940WGOT-TWD F940GOT-*WD F940GOT-*BD-H F940GOT-*BD-RH I F940WGOT-TWD (Ver. 1.00 or later) F940GOT-LWD, F940GOT-SWD (Ver. 1.00 or later) F940GOT-LBD-H, F940GOT-SBD-H (Ver. 1.00 or later) F940GOT-LBD-RH, F940GOT-SBD-RH (Ver. 1.00 or later) Apx.A Refer to manuals of GOT1000 Series display units for applicable models and versions supporting the list editor function. C-7 Discontinued models GOT1000 Series display units - Remote Maintenance Ver. 1.00 or later H Programming Communication FX-30P G Non-Protocol Communication (FX2N-232IF) FX2N and FX2NC PLCs F Non-Protocol Communication (RS/RS2 Instruction) FX3S PLC GX Works2 E Inverter Communication FX3GC PLC GX Works2 D Computer Link FX3G PLC GX Works2 B N:N Network GOT1000 Series display units Applicable version Common Items Product name GOT-F900 Series display units F940WGOT-TWD-E F940GOT-*WD-E F940GOT-*BD-H-E F940GOT-*BD-RH-E FX Series PLC User's Manual - Data Communication Edition 1 Outline Parallel Link 1.4 Programming Tool Applicability Product name Model name Applicable version Remarks FX1S, FX1N and FX1NC PLCs GX Works2 SWDNC-GXW2-J GX Developer SWD5C(F)-GPPW-J FX-PCS/WIN SW0PC-FXGP/WIN Ver. 4.00 or later FX-PCS/98-3 SW1PC-FXGP/98-3 Ver. 5.00 or later SW5 A or later FX-30P Ver. 1.00 or later FX-20P(-SET0) FX-20P-MFXD Ver. 5.00 or later FX-10P(-SET0) Ver. 4.00 or later GOT-F900 Series display units F940WGOT-TWD F940GOT-*WD F940GOT-*BD-H F940GOT-*BD-RH - F940WGOT-TWD (Ver. 1.00 or later) F940GOT-LWD, F940GOT-SWD (Ver. 1.00 or later) F940GOT-LBD-H, F940GOT-SBD-H (Ver. 1.00 or later) F940GOT-LBD-RH, F940GOT-SBD-RH (Ver. 1.00 or later) Refer to manuals of GOT1000 Series display units for applicable models and versions supporting the list editor function. GOT1000 Series display units 1.4.2 Ver. 1.07H or later For non-applicable versions (setting an alternative model) Even programming tool not applicable to a PLC can create programs when an alternative model is set. In this case, however, programming is enabled only in the function ranges provided for the alternative PLC model such as instructions and program size. Model to be programmed Priority: High Low Model to be set FX3UC Series FX3UC FX2N FX2(FX) FX3U Series FX3UC, FX3U FX2N FX3GC Series FX3G, FX3GC FX3G Series FX3S Series FX2(FX) FX1N *1 FX2N*1 FX3G FX1N*1 FX2N*1 FX3S FX3G FX1N*1 FX2NC Series FX2NC, FX2N FX2(FX) FX2N Series FX2N FX2(FX) FX1NC Series FX1NC, FX1N FX2N FX2(FX) FX1N Series FX1N FX2N FX2(FX) FX1S Series FX1S FX2(FX) FX0N Series FX0N FX2(FX) FX0S Series FX0S FX2(FX) FX0 Series FX0 FX2(FX) FX2C Series FX2C, FX2(FX) FX2(FX) FX2(FX) Series FX1 Series *1. FX2(FX) FX1 "FX2N" is selected when the FX-10P(-E) is used. Point In the FX3S PLC, set the memory capacity for PLC parameters to 4,000 steps or less. C-8 FX Series PLC User's Manual - Data Communication Edition 2 Specifications Parallel Link 2.1 Communication Specifications (Reference) A Common Items 2. Specifications B This chapter explains the communication specifications and performance of the parallel link. N:N Network 2.1 Communication Specifications (Reference) The parallel link is executed using the (fixed) communication specifications shown in the table below. Specification items such as baud rate cannot be changed. Number of connectable units Transmission standard Protocol type Control procedure FX3UC, FX3U, FX3GC, FX3G, FX3S PLCs Baud rate FX2NC, FX2N, FX1NC, FX1N, FX1S, FX0N, FX2C, FX2(FX) PLCs 2 maximum (1:1) RS-485 or RS-422 standard 500 m (1640' 5") or less D [50 m (164' 0")or less when 485BD is included in system] Wire link: 10 m (32' 9") or less Optical fiber: 50 m (164' 0") or less Wire link: FX2-40AW Optical fiber: FX2-40AP Parallel link — E Half-duplex, bidirectional communication Inverter Communication Communication method C Remarks 115200bps 19200bps Start bit F Fixed Non-Protocol Communication (RS/RS2 Instruction) Character Data bit format Parity bit Stop bit Header Terminator Computer Link FX3UC, FX3U, FX3GC, FX3G, FX3S, Maximum FX2NC, FX2N, FX1NC, FX1N, FX1S, FX0N total PLCs extension distance FX2(FX), FX2C PLCs Specifications Parallel Link Item Fixed — Sum check Fixed G Non-Protocol Communication (FX2N-232IF) Control line H Programming Communication I Remote Maintenance Apx.A Discontinued models C-9 FX Series PLC User's Manual - Data Communication Edition 2 Specifications Parallel Link 2.2 Link Specifications 2.2 Link Specifications 2.2.1 PLC communication type applicability status : Applicable (If applicable versions of main units are limited, they are described inside ( ).) —: Not applicable Regular parallel link mode applicability (applicable version) High speed parallel link mode applicability (applicable version) FX3UC Series FX3U Series PLC FX3GC Series FX3G Series FX3S Series FX2NC Series FX2N Series (Ver. 1.04 or later) (Ver. 1.04 or later) FX1NC Series FX1N Series Series (Ver. 1.20 or later) (Ver. 1.20 or later) FX1S FX0N Series 2.2.2 FX0S Series — — FX0 Series — — FX2C Series (Ver. 3.07 or later) FX2(FX) Series (Ver. 3.07 or later) Link time The link time indicates the cycle time in which link devices are updated. The link time varies depending on the link mode as shown in the tables below. 1. For FX3S, FX3G, FX3GC, FX3U and FX3UC Series Link mode Time Regular parallel link mode 15 ms + Master station operation cycle (ms) + Slave station operation cycle (ms) High speed parallel link mode 5 ms + Master station operation cycle (ms) + Slave station operation cycle (ms) 2. For FX2(FX), FX2C, FX0N, FX1S, FX1N, FX1NC, FX2N and FX2NC Series Link mode C-10 Time Regular parallel link mode 70 ms + Master station operation cycle (ms) + Slave station operation cycle (ms) High speed parallel link mode 20 ms + Master station operation cycle (ms) + Slave station operation cycle (ms) FX Series PLC User's Manual - Data Communication Edition 2 Specifications Parallel Link 2.3 Link Device Numbers and Number of Points Link Device Numbers and Number of Points 2.3.1 For FX0N, FX1S and FX3S Series Mode B High speed parallel link mode Bit device (M) Word device (D) Bit device (M) Word device (D) Type 50 in each station 10 in each station 0 2 in each station Master station M400 to M449 D230 to D239 — D230, D231 Slave station M450 to M499 D240 to D249 — D240, D241 FX0N, FX1S, FX3S FX0N, FX1S, FX3S M400 to M449 M450 to M499 RUN monitor M8070 D240 to D249 Automatic update M400 to M449 D M450 to M499 D230 to D239 D240 to D249 M8000 RUN monitor Master station Slave station For the slave station, set M8071 to ON. 2. High speed parallel link mode FX0N, FX1S, FX3S M8000 D230, D231 D230, D231 RUN monitor M8070 RUN monitor Master station M8162 M8071 D240, D241 Automatic update For the master station, set M8070 and M8162 to ON. Slave station M8162 High speed parallel link mode For the slave station, set M8071 and M8162 to ON. G Non-Protocol Communication (FX2N-232IF) High speed parallel link mode D240, D241 F Non-Protocol Communication (RS/RS2 Instruction) M8000 FX0N, FX1S, FX3S E Inverter Communication For the master station, set M8070 to ON. M8071 Computer Link D230 to D239 M8000 Automatic update C Parallel Link 1. Regular parallel link mode N:N Network Regular parallel link mode Common Items 2.3 A H Programming Communication I Remote Maintenance Apx.A Discontinued models C-11 FX Series PLC User's Manual - Data Communication Edition 2 Specifications Parallel Link 2.3.2 2.3 Link Device Numbers and Number of Points For FX2(FX), FX2C, FX1N, FX1NC, FX2N, FX2NC, FX3G, FX3GC, FX3U and FX3UC Series Regular parallel link mode Mode Bit device (M) Word device (D) High speed parallel link mode Bit device (M) Word device (D) Type 100 in each station 10 in each station 0 2 in each station Master station M800 to M899 D490 to D499 — D490, D491 Slave station M900 to M999 D500 to D509 — D500, D501 1. Regular parallel link mode FX2(FX), FX2C, FX1N, FX1NC, FX2N, FX2NC, FX3G, FX3GC, FX3U, FX3UC M900 to M999 D490 to D499 M8000 RUN monitor M800 to M899 M8070 D500 to D509 Automatic update Automatic update FX2(FX), FX2C, FX1N, FX1NC, FX2N, FX2NC, FX3G, FX3GC, FX3U, FX3UC M800 to M899 M900 to M999 D490 to D499 D500 to D509 M8000 RUN monitor Master station For the master station, set M8070 to ON. M8071 Slave station For the slave station, set M8071 to ON. 2. High speed parallel link mode FX2(FX), FX2C, FX1N, FX1NC, FX2N, FX2NC, FX3G, FX3GC, FX3U, FX3UC M8000 M8070 RUN Master station monitor M8162 M8000 D490, D491 RUN monitor M8071 D490, D491 D500, D501 Automatic update High speed parallel link mode For the master station, set M8070 and M8162 to ON. C-12 FX2(FX), FX2C, FX1N, FX1NC, FX2N, FX2NC, FX3G, FX3GC, FX3U, FX3UC D500, D501 Slave station M8162 High speed parallel link mode For the slave station, set M8071 and M8162 to ON. FX Series PLC User's Manual - Data Communication Edition 3 System Configuration and Selection Parallel Link 3.1 System Configuration A Common Items 3. System Configuration and Selection 3.1 System Configuration 3.1.1 Rule for connection C Parallel Link This section outlines the system configuration required to use the parallel link. Add (optional) communication equipment operating in accordance with RS-485 to an FX PLC main unit. B N:N Network This chapter explains the configuration of communication equipment operating in accordance with RS-485 and the system selection required by FX PLCs. When using the parallel link, PLCs in the same group can be connected as shown in the table below. Group D PLC Series FX3U and FX3UC Series FX3G and FX3GC Series 3 FX3S Series FX2N and FX2NC Series FX1N and FX1NC Series 6 FX1S Series 7 FX0N Series 8 FX2(FX) and FX2C Series E Inverter Communication 4 5 Computer Link 1 2 F Non-Protocol Communication (RS/RS2 Instruction) G Non-Protocol Communication (FX2N-232IF) H Programming Communication I Remote Maintenance Apx.A Discontinued models C-13 FX Series PLC User's Manual - Data Communication Edition 3 System Configuration and Selection Parallel Link 3.2 Configuration of Each Group 3.2 Configuration of Each Group 1 , 2 and 3 indicate the communication equipment combination patterns. 1. Group 1 (FX3U and FX3UC PLCs) Communication equipment operating in accordance with RS-485 FX PLC Important point in selection Total extension distance 1 RDA RD + RDB SDA SD SDB SG Communication board FX3U Series This is the communication board built into the PLC, reducing the installation area. 50 m (164' 0") Attach the expansion board to the main unit, and then attach the communication adapter to the left side of the main unit. 500 m (1640' 5") Attach the communication adapter to the left side of the main unit. 500 m (1640' 5") RDA RD + RDB SDA SD SDB SG Communication board FX3UC-32MT-LT(-2) 2 + Communication adapter + Expansion board + Communication adapter FX3U Series + Expansion board FX3UC-32MT-LT(-2) 3 + Communication adapter FX3UC Series (D, DS, DSS) For communication equipment combinations for each FX Series, refer to the next section. C-14 FX Series PLC User's Manual - Data Communication Edition 3 System Configuration and Selection Parallel Link 3.2 Configuration of Each Group A Communication equipment operating in accordance with RS-485 FX PLC Important point in selection Total extension distance 1 Communication board 50 m (164' 0") FX3G Series B N:N Network This is the communication board built into the PLC, reducing the installation area. + Common Items 2. Group 2 (FX3G and FX3GC PLCs) C + Attach the connector conversion adapter to the main unit, and then attach the communication adapter to the left side of the main unit. + Communication Connector adapter conversion adapter 500 m (1640' 5") D FX3G Series Attach the communication adapter to the left side of the main unit. 500 m (1640' 5") For communication equipment combinations for each FX Series, refer to the next section. F Communication equipment operating in accordance with RS-485 FX PLC Important point in selection Total extension distance 1 Communication board 50 m (164' 0") FX3S Series Attach the connector conversion adapter to the main unit, and then attach the communication adapter to the left side of the main unit. + Communication Connector adapter conversion adapter H 500 m (1640' 5") FX3S Series Programming Communication 2 G Non-Protocol Communication (FX2N-232IF) This is the communication board built into the PLC, reducing the installation area. + Non-Protocol Communication (RS/RS2 Instruction) 3. Group 3 (FX3S PLC) + E Inverter Communication FX3GC Series Communication adapter Computer Link 3 + Parallel Link 2 I Remote Maintenance For communication equipment combinations for each FX Series, refer to the next section. Apx.A Discontinued models C-15 FX Series PLC User's Manual - Data Communication Edition 3 System Configuration and Selection Parallel Link 3.2 Configuration of Each Group 4. Group 4 (FX2N and FX2NC PLCs) Communication equipment operating in accordance with RS-485 FX PLC Important point in selection Total extension distance 1 This is the communication board built into the PLC, reducing the installation area. + Communication board FX2N Series 2 + Communication adapter 50 m (164' 0") + Special adapter connection board Attach the special adapter connection board to the main unit, and then attach the communication adapter to the left side of the main unit. 500 m (1640' 5") Attach the communication adapter to the left side of the main unit. 500 m (1640' 5") FX2N Series 3 + Communication adapter FX2NC Series For communication equipment combinations for each FX Series, refer to the next section. 5. Group 5 (FX1N and FX1NC PLCs) Communication equipment operating in accordance with RS-485 FX PLC 1 + Communication board Total extension distance This is the communication board built into the PLC, reducing the installation area. 50 m (164' 0") Attach the special adapter connection board to the main unit, and then attach the communication adapter to the left side of the main unit. 500 m (1640' 5") Attach the communication adapter to the left side of the main unit. 500 m (1640' 5") FX1N Series 2 + Important point in selection + Communication Special adapter adapter connection board FX1N Series 3 + Communication adapter FX1NC Series For communication equipment combinations for each FX Series, refer to the next section. C-16 FX Series PLC User's Manual - Data Communication Edition 3 System Configuration and Selection Parallel Link 3.2 Configuration of Each Group A Communication equipment operating in accordance with RS-485 FX PLC 1 + This is the communication board built into the PLC, reducing the installation area. 50 m (164' 0") B Attach the special adapter connection board to the main unit, and then attach the communication adapter to the left side of the main unit. 500 m (1640' 5") C FX1S Series 2 + Total extension distance + Parallel Link Communication Special adapter adapter connection board N:N Network Communication board Important point in selection Common Items 6. Group 6 (FX1S PLC) FX1S Series For communication equipment combinations for each FX Series, refer to the next section. D Communication equipment operating in accordance with RS-485 FX PLC Total extension distance Attach the communication adapter to the left side of the main unit. 500 m (1640' 5") 1 + FX0N Series Communication adapter For communication equipment combinations for each FX Series, refer to the next section. Communication equipment using optical fiber or in accordance with RS-485 FX PLC 1 Communication adapter Attach the communication adapter to the left side of the main unit. Perform wiring using optical fiber cables. 50 m (164' 0") FX2(FX)/FX2C Series 2 10 m (32' 9") FX2(FX)/FX2C Series For communication equipment combinations for each FX Series, refer to the next section. G H Programming Communication Attach the communication adapter to the left side of the main unit. Perform wiring using twisted pair cables. + Communication adapter Total extension distance Non-Protocol Communication (FX2N-232IF) + Important point in selection F Non-Protocol Communication (RS/RS2 Instruction) 8. Group 8 (FX2(FX) and FX2C PLCs) E Inverter Communication Important point in selection Computer Link 7. Group 7 (FX0N PLC) I Remote Maintenance Apx.A Discontinued models C-17 FX Series PLC User's Manual - Data Communication Edition 3 System Configuration and Selection Parallel Link 3.3 3.3 Applicable FX PLC and Communication Equipment Applicable FX PLC and Communication Equipment Select a (optional) communication equipment combination, and put a check mark in the "Check" column. During selection, pay attention to the following: - In the table below, only the external dimensions are different between the units shown in "FX2NC-485ADP/ FX0N-485ADP". Select either one. - In the table below, only the cable is different between the units shown in "FX3G-485-BD/FX3G-485-BDRJ". Select either one. - The parallel link is not provided for the FX1, FX0 and FX0S PLCs. FX Series Total extension distance Communication equipment (option) 500 m (1640' 5") FX0N FX2NC-485ADP FX0N-485ADP (European terminal block) (Terminal block) 50 m (164' 0") FX1N-485-BD (European terminal block) + FX1S FX1N-CNV-BD + FX2NC-485ADP (European terminal block) FX1N-CNV-BD 500 m (1640' 5") FX0N-485ADP (Terminal block) 50 m (164' 0") FX1N-485-BD (European terminal block) + FX1N FX1N-CNV-BD + FX2NC-485ADP (European terminal block) FX1N-CNV-BD 500 m (1640' 5") FX0N-485ADP (Terminal block) 50 m (164' 0") FX2N-485-BD + FX2N FX2N-CNV-BD C-18 FX2NC-485ADP (European terminal block) + FX2N-CNV-BD FX0N-485ADP (Terminal block) 500 m (1640' 5") Check FX Series PLC User's Manual - Data Communication Edition 3 System Configuration and Selection Parallel Link 3.3 Applicable FX PLC and Communication Equipment A Communication equipment (option) Total extension distance Check B 50 m (164' 0") FX3G-485-BD-RJ (RJ45 connector) + FX3S N:N Network FX3G-485-BD (European terminal block) Common Items FX Series C Parallel Link 500 m (1640' 5") FX3S-CNV-ADP FX3U-485ADP(-MB) (European terminal block) D FX3G-485-BD (European terminal block) Computer Link 50 m (164' 0") FX3G-485-BD-RJ (RJ45 connector) E Inverter Communication FX3G (14-point, 24-point type) 500 m (1640' 5") FX3G-CNV-ADP FX3U-485ADP(-MB) (European terminal block) F ch1 Non-Protocol Communication (RS/RS2 Instruction) When using channel 1 (ch 1) ch1 G 50 m (164' 0") FX3G-485-BD-RJ (RJ45 connector) The communication equipment works as ch1 when connected to the option connector 1. H ch1 Programming Communication FX3G (40-point, 60-point type) Non-Protocol Communication (FX2N-232IF) FX3G-485-BD (European terminal block) 500 m (1640' 5") FX3G-CNV-ADP FX3U-485ADP(-MB) (European terminal block) I Remote Maintenance Apx.A Discontinued models C-19 FX Series PLC User's Manual - Data Communication Edition 3 System Configuration and Selection Parallel Link 3.3 Applicable FX PLC and Communication Equipment FX Series Communication equipment (option) Total extension distance When using channel 2 (ch 2) ch2 ch2 50 m (164' 0") FX3G-485-BD (European terminal block) FX3G-485-BD-RJ (RJ45 connector) The communication equipment works as ch2 when connected to the option connector 2. ch1 FX3G (40-point, 60-point type) ch2 500 m (1640' 5") FX3G-CNV-ADP FX3U- ADP(-MB) (Where represents 232 and 485). FX3U-485ADP(-MB) (European terminal block) Ch2 is not available when the FX3G-8AV-BD, FX3G-4EX-BD or FX3G-2EYT-BD is connected to the option connector 2. When using channel 1 (ch 1) ch1 RD A 50 m (164' 0") RD RD B SD A SD SD B SG FX3U-485-BD (European terminal block) ch1 FX3U + FX3U-CNV-BD C-20 FX3U-485ADP(-MB) (European terminal block) 500 m (1640' 5") Check FX Series PLC User's Manual - Data Communication Edition 3 System Configuration and Selection Parallel Link 3.3 Applicable FX PLC and Communication Equipment A Total extension distance Communication equipment (option) Check When using channel 2 (ch 2) ch1 ch2 B SD FX3U--BD (Where represents 232, 422, 485, USB and 8AV). N:N Network + RD 500 m (1640' 5") FX3U-485ADP(-MB) (European terminal block) C Parallel Link When a FX3U-8AV-BD is used, it occupies one communication port channel. ch1 ch2 FX3U + + FX3U-232ADP(-MB), FX3U-485ADP(-MB) (European terminal block) FX3U-485ADP(-MB), FX3U-CF-ADP When a FX3U-CF-ADP is used, it occupies one communication port channel. D 500 m (1640' 5") Computer Link FX3U-CNV-BD E Inverter Communication 500 m (1640' 5") FX1NC FX2NC-485ADP (European terminal block) F FX0N-485ADP (Terminal block) Non-Protocol Communication (RS/RS2 Instruction) 500 m (1640' 5") (European terminal block) G FX0N-485ADP Non-Protocol Communication (FX2N-232IF) FX2NC FX2NC-485ADP (Terminal block) When using channel 1 (ch 1) ch1 H Programming Communication 500 m (1640' 5") FX3U-485ADP(-MB) (European terminal block) I When using channel 2 (ch 2) FX3GC ch2 + 500 m (1640' 5") Apx.A FX3U-485ADP(-MB) (European terminal block) Discontinued models FX3U-ADP(-MB) (Where represents 232 and 485). Remote Maintenance ch1 Common Items FX Series C-21 FX Series PLC User's Manual - Data Communication Edition 3 System Configuration and Selection Parallel Link 3.3 Applicable FX PLC and Communication Equipment FX Series Total extension distance Communication equipment (option) When using channel 1 (ch 1) ch1 500 m (1640' 5") FX3U-485ADP(-MB) (European terminal block) When using channel 2 (ch 2) ch2 ch1 FX3UC (D, DS, DSS) + 500 m (1640' 5") FX3U-232ADP(-MB), FX3U-485ADP(-MB) (European terminal block) FX3U-485ADP(-MB), FX3U-CF-ADP When a FX3U-CF-ADP is used, it occupies one communication port channel. When using channel 1 (ch 1) ch1 RD A 50 m (164' 0") RD RD B SD A SD SD B SG FX3U-485-BD (European terminal block) ch1 + FX3U-CNV-BD 500 m (1640' 5") FX3U-485ADP(-MB) (European terminal block) When using channel 2 (ch 2) ch1 ch2 + RD FX3UC-32MT-LT (-2) SD FX3U--BD (Where represents 232, 422, 485, USB and 8AV). 500 m (1640' 5") FX3U-485ADP(-MB) (European terminal block) When a FX3U-8AV-BD is used, it occupies one communication port channel. ch1 + ch2 + FX3U-232ADP(-MB), FX3U-485ADP(-MB) (European terminal block) FX3U-485ADP(-MB), FX3U-CF-ADP When a FX3U-CF-ADP is used, it occupies one communication port channel. FX3U-CNV-BD C-22 500 m (1640' 5") Check FX Series PLC User's Manual - Data Communication Edition Parallel Link 3 System Configuration and Selection 3.3 Applicable FX PLC and Communication Equipment A Communication equipment (option) Total extension distance Check Common Items FX Series B N:N Network 50 m (164' 0") FX2-40AP (for optical fiber) C Parallel Link FX2(FX) 10 m (32' 9") FX2-40AW (for wire link) D Computer Link 50 m (164' 0") FX2-40AP (for optical fiber) Inverter Communication FX2C E 10 m (32' 9") F Non-Protocol Communication (RS/RS2 Instruction) FX2-40AW (for wire link) G Non-Protocol Communication (FX2N-232IF) H Programming Communication I Remote Maintenance Apx.A Discontinued models C-23 FX Series PLC User's Manual - Data Communication Edition 4 Wiring Parallel Link 4. 4.1 Wiring Procedure Wiring This chapter explains the wiring. WIRING PRECAUTIONS • Make sure to cut off all phases of the power supply externally before attempting installation or wiring work. Failure to do so may cause electric shock or damage to the product. • Make sure to attach the terminal cover, offered as an accessory, before turning on the power or initiating operation after installation or wiring work. Failure to do so may cause electric shock. WIRING PRECAUTIONS • Make sure to observe the following precautions in order to prevent any damage to the machinery or accidents due to abnormal data written to the PLC under the influence of noise: 1) Do not bundle the main circuit line together with or lay it close to the main circuit, high-voltage line or load line. Otherwise, noise disturbance and/or surge induction are likely to take place. As a guideline, lay the control line at least 100mm (3.94") or more away from the main circuit or high-voltage lines. 2) Ground the shield wire or shield of the shielded cable at one point on the PLC. However, do not use common grounding with heavy electrical systems. • Make sure to properly wire the terminal block in accordance with the following precautions. Failure to do so may cause electric shock, equipment failures, a short-circuit, wire breakage, malfunctions, or damage to the product. - The disposal size of the cable end should follow the dimensions described in the manual. - Tightening torque should follow the specifications in the manual. - Tighten the screws using a Phillips-head screwdriver No.2 (shaft diameter 6mm (0.24") or less). Make sure that the screwdriver does not touch the partition part of the terminal block. • Make sure to properly wire to the terminal block (European type) in accordance with the following precautions. Failure to do so may cause electric shock, equipment failures, a short-circuit, wire breakage, malfunctions, or damage to the product. - The disposal size of the cable end should follow the dimensions described in the manual. - Tightening torque should follow the specifications in the manual. - Twist the end of strand wire and make sure that there are no loose wires. - Do not solder-plate the electric wire ends. - Do not connect more than the specified number of wires or electric wires of unspecified size. - Affix the electric wires so that neither the terminal block nor the connected parts are directly stressed. 4.1 1 Wiring Procedure Preparing for wiring Prepare cables and terminal resistors required for wiring. 2 3 4 For details, refer to Section 4.2. Turning OFF the power to the PLC Before starting any wiring work, make sure that the power to the PLC is OFF. Connecting the power supply (FX0N-485ADP only) Connect the power supply to the 24V DC power terminal. Wiring communication equipment Connect communication equipment operating in accordance with RS-485. For details, refer to Section 4.3. C-24 FX Series PLC User's Manual - Data Communication Edition Parallel Link 4.2 Selecting Cables and Terminal Resistors A Selecting Cables and Terminal Resistors Common Items 4.2 4 Wiring Select cables using the procedure described below. 4.2.1 Twisted pair cable B 1. Recommended cables Manufacturer Model name Showa Holdings Co., Ltd. The Furukawa Electric Co., Ltd. Three-pair cable of 0.2 mm2 SPEV(SB)-0.5-2P Two-pair cable of 0.5 mm2 KMPEV-SB CWS-178 0.2SQ 2P Two-pair cable of 0.2 mm2 KMPEV-SB CWS-178 0.5SQ 2P Two-pair cable of 0.5 mm2 DPEV SB 0.3 3P Three-pair cable of 0.3 mm2 DPEV SB 0.5 3P Three-pair cable of 0.5 mm2 D-KPEV-SB 0.2 3P Three-pair cable of 0.2 mm2 D-KPEV-SB 0.5 3P Three-pair cable of 0.5 mm2 IPEV-SB 2P 0.3 mm2 Two-pair cable of 0.3 mm2 IPEV-SB 2P 0.5 mm2 Two-pair cable of 0.5 mm2 D E Inverter Communication Fujikura Ltd. SPEV(SB)-MPC-0.2 3P Computer Link Sumitomo Electric Industries, Ltd. Two-pair cable of 0.2 mm2 Parallel Link Mitsubishi Cable Industries, Ltd. C Remarks SPEV(SB)-0.2-2P 2. Cable structural drawing (reference) F Pair G Three-pair cable structural drawing example Non-Protocol Communication (FX2N-232IF) 4.2.2 Non-Protocol Communication (RS/RS2 Instruction) Shield Two-pair cable structural drawing example 10BASE-T cable 10BASE-T cables used in LAN wiring for a personal computer can be connected to FX3G-485-BD-RJ. 1) Cable type : 10BASE-T cable (Category 3 or higher) 2) Connection specifications : One-pair wiring: Straight type Two-pair wiring: Cross type (Use a cross cable with the following connection) 5 4 3 6 1 2 7 8 I Remote Maintenance 5 4 3 6 1 2 7 8 H Programming Communication 1. Selection procedure when purchasing 3) Connector N:N Network Use shielded twisted pair cables for connecting communication equipment operating in accordance with RS485. The table below shows recommended model names and manufacturers of cables used for wiring. : RJ45 connector (Connector with metal frame is used) Apx.A Pay attention to the following point when purchasing commercial cables. • Use shielded cables. Make sure to connect the shield to the metal frame of the connector, and perform class D grounding. C-25 Discontinued models 2. Cautions on using commercial cables FX Series PLC User's Manual - Data Communication Edition 4 Wiring Parallel Link 4.2.3 4.2 Selecting Cables and Terminal Resistors Connecting cables 1. European type terminal block The FX3G-485-BD-RJ terminal block is used for grounding. The other options use shielded twisted pair cables for connecting communication equipment operating in accordance with RS-485. The table below shows applicable cables and tightening torques. Cable size when Cable size when one cable is two cables are connected connected FX3U-485-BD FX3G-485-BD FX3U-485ADP (-MB) AWG22 to AWG20 AWG22 Bar terminal with Insulating sleeve (cable size) Tightening torque Applicable 0.22 to 0.25 (AWG22 to AWG20) N·m Tool size A B 0.4 (0.01") 2.5 (0.09") FX3G-485-BDRJ AWG20 to AWG16 Not applicable 0.5 to 0.6 N·m 0.6 (0.03") 3.5 (0.14") FX2N-485-BD FX1N-485-BD AWG26 to AWG16 Not applicable 0.5 to 0.6 N·m 0.6 (0.03") 3.5 (0.14") Not applicable 0.4 to 0.5 N·m 0.6 (0.03") 3.5 (0.14") FX2NC-485ADP AWG26 to AWG16 AWG26 to AWG20 Do not tighten terminal screws with a torque outside the above-mentioned range. Failure to do so may cause equipment failures or malfunctions. With regard to the cable end treatment, use a stranded cable or solid cable as it is, or use a bar terminal with insulating sleeve. FX3G-485-BD-RJ, FX2N-485-BD, FX1N-485-BD and FX2NC-485ADP cannot use a bar terminal with insulating sleeve. • When using a stranded cable or solid cable as it is - Twist the end of a stranded cable so that wires do not get barbed. - Do not plate the end of the cable. FX3G-485-BD, FX3U-485-BD, FX3U-485ADP(-MB) FX3G-485-BD-RJ, FX2N-485-BD, FX1N-485-BD Approx. 9 mm (0.35") Approx. 6 mm (0.23") FX2NC-485ADP • When using a bar terminal with insulating sleeve Because it is difficult to insert a cable into an insulating sleeve depending on the thickness of the cable sheath, select the proper cable according to the outline drawing. <Reference> Manufacturer Model name Caulking tool Phoenix Contact Co., Ltd. AI 0.5-8WH CRIMPFOX 6*1 (or CRIMPFOX 6T-F*2) *1. *2. C-26 Old model name : CRIMPFOX ZA 3 Old model name : CRIMPFOX UD 6 Approx. 8 mm (0.31") Insulating sleeve Contact area (Crimp area) 8 mm (0.31") 2.6 mm (0.1") 14 mm (0.55") FX Series PLC User's Manual - Data Communication Edition 4 Wiring Parallel Link 4.2 Selecting Cables and Terminal Resistors A Select a screwdriver with a straight tip. Note A If the diameter of screwdriver grip is too small, tightening torque will not be able to be achieved. To achieve the appropriate tightening torque shown in the previous page, use the following screwdriver or an appropriate replacement (grip diameter: approximately 25mm (0.98")). <Reference> FX3U-485-BD, FX3G-485-BD, FX3U-485ADP(-MB) For size A and size B, refer to the table above. B B N:N Network Manufacturer C Model name Parallel Link SZS 0.4 2.5 Phoenix Contact Co., Ltd. FX3G-485-BD-RJ, FX2N-485-BD, FX1N-485-BD, FX2NC-485ADP Manufacturer Model name SZF 1-0.6 3.5 Phoenix Contact Co., Ltd. D Computer Link 2. Terminal block In the FX0N-485ADP and FX-485ADP, the terminal screw size is "M3". Make sure to use a crimp-style terminal with the following sizes. Make sure that the tightening torque is 0.5 to 0.8 N·m. Do not tighten terminal screws with a torque outside the above-mentioned range. Failure to do so may cause equipment failures or malfunctions. E 3.2(0.13") Inverter Communication • When wiring one cable to one terminal 6.2mm(0.24") or less Terminal Crimp screw terminal F 3.2(0.13") 6.2mm(0.24") or less Non-Protocol Communication (RS/RS2 Instruction) Terminal • When wiring two cables to one terminal 3.2(0.13") 6.2mm(0.24") or less G 3.2(0.13") Terminal H 6.3mm(0.25") or more Programming Communication 4.2.4 Terminal Crimp screw terminal Non-Protocol Communication (FX2N-232IF) 6.3mm(0.25") or more 6.2mm(0.24") or less Optical fiber cable Two optical fiber cables are required. I 1. Cable types Length Remarks F-OFC-M10 10 m (32' 9") Optical connector CA9104AP manufactured by Hitachi is already connected. F-OFC-M30 30 m (98' 5") Optical connector CA9104AP manufactured by Hitachi is already connected. F-OFC-M50 50 m (164' 0") Optical connector CA9104AP manufactured by Hitachi is already connected. Remote Maintenance Cable Common Items • Tool When tightening a terminal on the European terminal block, use a small commercial straight shape screwdriver whose tip is shown in the figure to the right. Apx.A Separate the optical connector from strong electric cables as much as possible. Connect devices with the smallest load to the output terminals Y000 to Y003 which are located near the optical connector. C-27 Discontinued models 2. Cautions on wiring FX Series PLC User's Manual - Data Communication Edition Parallel Link 4.2.5 4 Wiring 4.2 Selecting Cables and Terminal Resistors Connecting terminal resistors In the case of one-pair wiring, connect a terminal resistor to the RDA-RDB signal terminal of the communication equipment. In the case of two-pair wiring, connect a terminal resistor to the RDA-RDB signal terminal and SDA-SDB terminal of the communication equipment. Brown 1. Terminal resistor type In the case of one-pair wiring, use two terminal resistors of 110 , 1/2 W. In the case of two-pair wiring, use four terminal resistors of 330 , 1/4 W. Among the terminal resistors supplied with the communication equipment, select ones with the color codes shown to the right. 1 1 1 =110 (101) Orange Brown Precision 2. When using the FX3U-485-BD, FX3G-485-BD, FX3G-485-BD-RJ or FX3U-485ADP(-MB) The FX3U-485-BD, FX3G-485-BD, FX3G-485-BD-RJ and FX3U-485ADP(-MB) have built-in terminal resistors. Set the terminal resistor selector switch accordingly. • FX3U-485-BD • FX3U-485ADP(-MB) Terminal resistor selector switch Precision 3 3 1 =330 (101) 330 OPEN 110 Terminal resistor selector switch • FX3G-485-BD Remove the upper terminal block before changing over the switch in the FX3G-485-BD. Removal: Loosen the terminal block mounting screws, and remove the terminal block. Installation: Attach the terminal block, and tighten the terminal block mounting screws. Tightening torque: 0.4 to 0.5 N•m Do not tighten terminal screws with a torque outside the above-mentioned range. Failure to do so may cause equipment failures or malfunctions. For installation and removal of the terminal block, use the recommended tool shown below or a tool having straight tip (such as screwdriver) as shown in the right figure. <Reference> Manufacturer Model name Phoenix Contact Co., Ltd. SZS 0.4 2.5 Select a screwdriver with a straight tip. 0.4mm (0.01") Terminal resistor selector switch Terminal block mounting screws • FX3G-485-BD-RJ Terminal resistor selector switch C-28 2.5mm (0.09") FX Series PLC User's Manual - Data Communication Edition 4 Wiring Parallel Link 4.3 Connection Diagram A Connection Diagram 4.3.1 For FX3S, FX3G, FX3GC, FX3U and FX3UC PLCs Common Items 4.3 B FX3U-485-BD, FX3G-485-BD FX3G-485-BD-RJ*1 FX3U-485ADP(-MB) SDA (TXD+) *2 FX3U-485-BD, FX3G-485-BD FX3G-485-BD-RJ*1 FX3U-485ADP(-MB) SDA (TXD+) C SDB Terminal (TXD-) resistor RDA (RXD+) RDB (RXD-) RDB (RXD-) SG SG 110 *2 D Computer Link RDA (RXD+) Parallel Link Terminal SDB resistor (TXD-) 110 N:N Network 1. In the case of one-pair wiring Class-D grounding (resistance: 100 or less)*3 *2. The FX3U-485-BD, FX3G-485-BD, FX3G-485-BD-RJ and FX3U-485ADP(-MB) have a built-in terminal resistor. Set the terminal resistor selector switch to 110 . *3. Make sure to perform Class-D grounding on the shield of a twisted pair cable connected to the FX3U-485-BD, FX3G-485-BD or FX3U-485ADP(-MB). 2. In the case of two-pair wiring FX3U-485-BD, FX3G-485-BD FX3G-485-BD-RJ *4 FX3U-485ADP(-MB) SDB (TXD-) SDB (TXD-) RDA (RXD+) RDA (RXD+) *5 RDB Terminal (RXD-) resistor 330 2 SG G *5 H Programming Communication SDA (TXD+) *5 RDB (RXD-) Terminal SG F Non-Protocol Communication (FX2N-232IF) *5 FX3U-485-BD, FX3G-485-BD FX3G-485-BD-RJ *4 FX3U-485ADP(-MB) SDA (TXD+) E Non-Protocol Communication (RS/RS2 Instruction) Inside FX3G-485-BD-RJ, SDA and RDA are connected and SDB and RDB are connected respectively when 1-pair wiring is adopted. Signals are not connected to pins Nos. 4 and 5 of the RJ45 connector. For cables of FX3G-485-BD-RJ, refer to Subsection 4.2.2. Make sure to perform class D grounding on the shield of connected cables. Inverter Communication *1. resistor 330 2 I Remote Maintenance Class-D grounding (resistance: 100 or less)*6 For cables of FX3G-485-BD-RJ, refer to Subsection 4.2.2. Make sure to perform class D grounding on the shield of connected cables. *5. The FX3U-485-BD, FX3G-485-BD, FX3G-485-BD-RJ and FX3U-485ADP(-MB) have a built-in terminal resistor. Set the terminal resistor selector switch to 330 . *6. Make sure to perform Class-D grounding on the shield of a twisted pair cable connected to the FX3U-485-BD, FX3G-485-BD or FX3U-485ADP(-MB). Apx.A Discontinued models *4. C-29 FX Series PLC User's Manual - Data Communication Edition 4 Wiring Parallel Link 4.3 Connection Diagram 3. Switching of 1 pair / 2 paired wiring (FX3G-485-BD-RJ) The FX3G-485-BD-RJ has a built-in wiring circuit switch. Set the wiring circuit switch to 1 pair / 2 pair. Wiring circuit switch 4.3.2 For FX1S, FX1N, FX1NC, FX2N and FX2NC PLCs 1. In the case of one-pair wiring FX2N-485-BD FX2NC-485ADP FX1N-485-BD FX0N-485ADP Terminal resistor 110 FX2N-485-BD FX0N-485ADP FX1N-485-BD FX2NC-485ADP SDA (TXD+) SDA (TXD+) SDA (TXD+) SDA (TXD+) SDA (TXD+) SDA (TXD+) SDB (TXD-) SDB (TXD-) SDB (TXD-) SDB (TXD-) SDB (TXD-) SDB (TXD-) RDA (RXD+) RDA (RXD+) RDA (RXD+) RDA (RXD+) RDA (RXD+) RDA (RXD+) RDB (RXD-) RDB (RXD-) RDB (RXD-) RDB (RXD-) RDB (RXD-) RDB (RXD-) SG LINK SG LINK SG SG FG FG*2 SG SG Class-D grounding (resistance: 100 or less)*1 C-30 *1. Make sure to perform Class-D grounding on the shield of a twisted pair cable connected to the FX2N-485-BD, FX1N-485-BD or FX2NC-485ADP. *2. Make sure to connect the FG terminal to the (grounding) terminal in the PLC requiring Class-D grounding. If the grounding terminal is not provided in the PLC, perform Class-D grounding directly. Terminal resistor 110 FX Series PLC User's Manual - Data Communication Edition 4 Wiring Parallel Link 4.4 Grounding A FX2N-485-BD FX2NC-485ADP FX1N-485-BD FX0N-485ADP FX2N-485-BD FX0N-485ADP FX1N-485-BD FX2NC-485ADP SDA (TXD+) SDA (TXD+) SDA (TXD+) SDA (TXD+) SDB (TXD-) SDB (TXD-) SDB (TXD-) SDB (TXD-) SDB (TXD-) SDB (TXD-) RDA (RXD+) RDA (RXD+) RDA (RXD+) RDA (RXD+) RDA (RXD+) RDA (RXD+) RDB (RXD-) RDB (RXD-) RDB (RXD-) RDB (RXD-) RDB (RXD-) RDB (RXD-) SG LINK SG LINK SG SG FG FG*2 Terminal resistor 330 2 SG B Terminal resistor 330 2 C Parallel Link SDA (TXD+) N:N Network SDA (TXD+) Common Items 2. In the case of two-pair wiring SG D Computer Link Class-D grounding (resistance: 100 or less)*1 Make sure to perform Class-D grounding on the shield of a twisted pair cable connected to the FX2N-485-BD, FX1N-485-BD or FX2NC-485ADP. *2. Make sure to connect the FG terminal to the (grounding) terminal in the PLC requiring Class-D grounding. If the grounding terminal is not provided in the PLC, perform Class-D grounding directly. For FX2(FX) and FX2C PLCs FX2-40AP FX2-40AW FX2-40AP SA SA T R SB SB R T SG*1 SG*1 F Non-Protocol Communication (RS/RS2 Instruction) FX2-40AW G Non-Protocol Communication (FX2N-232IF) *1. 4.4 E Inverter Communication 4.3.3 *1. Connect the SG terminal to the SG terminal in each PLC (main unit). Grounding H • The grounding resistance should be 100 or less. • Independent grounding should be performed for best results. When independent grounding can not be performed, perform "shared grounding" as shown in the following figure. For details, refer to the Hardware Edition of each series. Other equipment Independent grounding Best condition PLC Other equipment Shared grounding Good condition PLC Other equipment I Remote Maintenance PLC Programming Communication Grounding should be performed as stated below. Common grounding Not allowed Apx.A • The grounding wire size should be AWG 14 (2 mm2) or larger. C-31 Discontinued models • The grounding point should be close to the PLC, and all grounding wires should be as short as possible. FX Series PLC User's Manual - Data Communication Edition 5 Communication Setting (Initialization) in FX Programmable Controller Parallel Link 5. 5.1 Check Procedure Communication Setting (Initialization) in FX Programmable Controller The communication setting is not required in FX PLCs for parallel link. If the communication setting is already provided for another communication type or for checking the existing communication setting, perform the following procedure. When using this communication function in ch1 in an FX3S, FX3G, FX3GC, FX3U or FX3UC PLC, check D8120 and D8400 using the following procedure. When using this communication function in ch2 in an FX3G, FX3GC, FX3U or FX3UC PLC, check D8420 using the following procedure. In other PLCs, use D8120 for verification. 5.1 1 Check Procedure Monitoring D8120 (D8400, D8420) Turn ON the power to the PLC while it is in STOP mode, and monitor D8120 (D8400, D8420). 1. When the value of D8120 (D8400, D8420) is "0" The communication setting is not provided. 2. When the value of D8120 (D8400, D8420) is any value other than "0" The communication setting is provided. 2 Checking absence/presence of parameter setting Check absence/presence using the GX Works2, GX Developer, FXGP/WIN or FX-30P. 1) GX Works2 operating procedure (For details, refer to Section 5.2.) 2) FXGP/WIN operating procedure (For details, refer to Section 5.3.) For details on GX Developer operating procedure, refer to GX Developer Operating Manual. For details on FX-30P operating procedure, refer to FX-30P Operation Manual. 3 Checking absence/presence of sequence program setting Check whether or not a write instruction is programmed for D8120 (D8400, D8420). 1. When such an instruction is programmed Program example: (for D8120) Change the program as shown below, and then change the PLC mode from STOP to RUN. M8002 Initial pulse FNC 12 MOV H23F6 D8120 Program example The value varies depending on the communication setting. M8002 Initial pulse FNC 12 MOV H0000 D8120 Changed program 2. When such an instruction is not programmed Proceed to the next step. 4 C-32 Monitoring D8120 (D8400, D8420) again, and confirming that its value is "0" FX Series PLC User's Manual - Data Communication Edition Parallel Link 5.2 Communication Setting Using Parameter Method (GX Works2) A Communication Setting Using Parameter Method (GX Works2) 5.2.1 Operating procedure C Opening the parameter setting window In the project view area of the navigation window, double-click [Parameter] [PLC Parameter]. If the navigation window is not displayed, select [View] [Docking Window] [Navigation] from the menu bar. Parallel Link This subsection explains the serial communication setting method. Suppose that GX Works2 is already started up. 1 B N:N Network Communication settings may be changed using the parameter method with GX Works2, GX Developer, FXGP/WIN for Windows and FX-30P handy programming panel. This section describes how to change parameters with GX Works2. For details on FXGP/WIN operating procedure, refer to section 5.3. For details on GX Developer operating procedure, refer to GX Developer Operating Manual. For details on FX-30P operating procedure, refer to FX-30P Operation Manual. Common Items 5.2 5 Communication Setting (Initialization) in FX Programmable Controller D Computer Link E Inverter Communication F Setting the serial communication (parameters) Click the [PLC System(2)] tab in the dialog box. Select a channel to be used, and make sure that the "Operate Communication Setting" box is cleared. If a check mark is there, clear it. Click [End]. Non-Protocol Communication (RS/RS2 Instruction) 2 G Non-Protocol Communication (FX2N-232IF) H Programming Communication I Remote Maintenance 3 Writing parameters and program to the PLC Apx.A C-33 Discontinued models Select [Online] [Write to PLC] from the menu bar, click [Parameter + Program], and then click [Execute]. FX Series PLC User's Manual - Data Communication Edition Parallel Link 5.3 5 Communication Setting (Initialization) in FX Programmable Controller 5.3 Communication Setting Using Parameter Method (FXGP/WIN) Communication Setting Using Parameter Method (FXGP/WIN) Communication settings may be changed using the parameter method with GX Works2, GX Developer, FXGP/WIN for Windows and FX-30P handy programming panel. This section describes how to change parameters with FXGP/WIN. Ch2 cannot be set using FXGP/WIN. For details on GX Works2 operating procedure, refer to section 5.2. For details on GX Developer operating procedure, refer to GX Developer Operating Manual. For details on FX-30P operating procedure, refer to FX-30P Operation Manual. 5.3.1 Operating procedure This subsection explains the serial communication setting method. Suppose that FXGP/WIN is already started up. 1 Adjusting serial setting (parameter) Double-click [Option] [Serial setting (parameter)] from the toolbar. The following dialog box appears according to absence/presence of parameter settings. 1. When there are no parameter settings The dialog box shown below appears to indicate that there are no communication settings. Click the [No] button. In this case, the next step is not required. 2. When there are already parameter settings The dialog box shown below appears to indicate that there are communication settings. Click the [Clear] button to delete the communication settings from parameters. Transfer parameters to the PLC using the following step. 2 Writing a sequence program (parameters) to the PLC Select [PLC] [Transfers] [Write] from the toolbar, and click [OK] button. C-34 FX Series PLC User's Manual - Data Communication Edition 6 Test Run (Communication Test) Parallel Link 6.1 Test Procedure A Common Items 6. Test Run (Communication Test) 6.1 C Parallel Link 1 Test Procedure B N:N Network This chapter explains the communication test procedures for the parallel link. It is recommended to wire the master station and slave station, initialize communication settings in the FX PLCs, and then execute the communication test using the following procedure to confirm the proper operation. Creating programs for the communication test Create new programs for the communication test for the master station and slave station. For program examples, refer to Section 6.2. Computer Link 2 Transferring the program to each PLC Turn ON the power to each PLC, and transfer the program. 3 Validating the communication setting E When the PLC is in RUN mode, set it to STOP mode once, and then set it to RUN mode again. Or turn OFF the power of the master station and slave station, and then turn ON the power to both stations at the same time. Inverter Communication 4 Confirming flashing of the communication status indicator lamps (SD and RD) F Confirming the link of the master station Set the inputs X000 to X003 to ON or OFF. Slave station H Programming Communication Master station G Non-Protocol Communication (FX2N-232IF) Set the PLC inputs (X000 to X003) to ON or OFF in the master station, and confirm that the outputs (Y000 to Y003) turn ON or OFF in the slave station. Non-Protocol Communication (RS/RS2 Instruction) Confirm that the built-in SD and RD lamps of the communication equipment are flashing. If they are off, take proper action while referring to the troubleshooting procedures described later. 5 D Confirm that the outputs Y000 to Y003 of the slave station turn ON or OFF according to the inputs of the master station. I Remote Maintenance Apx.A Discontinued models C-35 FX Series PLC User's Manual - Data Communication Edition Parallel Link 6 6 Test Run (Communication Test) 6.2 Creating Programs for the Communication Test Confirming the link of the slave station Set the PLC inputs (X000 to X003) to ON or OFF in the slave station, and confirm that the outputs (Y000 to Y003) turn ON or OFF in the master station. Set the inputs X000 to X003 to ON or OFF. Master station Confirm that the outputs Y000 to Y003 of the slave station turn ON or OFF according to the inputs of the master station. Slave station If unable to establish link, refer to "9. Troubleshooting". 6.2 Creating Programs for the Communication Test Create the programs shown below for the master station and slave station. 6.2.1 For FX2(FX), FX2C, FX1N, FX1NC, FX2N, FX2NC, FX3G, FX3GC, FX3U or FX3UC Series 1. Program for communication test (for the master station) Create the program shown below for the communication test. (This program is not required during actual operation.) M8000 M8070 0 MOV K500 D8070 M8000 M8178 8 M8000 11 22 C-36 MOV K1X000 K1M800 MOV K1M900 K1Y000 END (In the FX3G, FX3GC, FX3U and FX3UC) This step is not required when using ch 1. When using ch 2, set M8178 to ON. FX Series PLC User's Manual - Data Communication Edition Parallel Link 6 Test Run (Communication Test) 6.2 Creating Programs for the Communication Test A Create the program shown below for the communication test. (This program is not required during actual operation.) M8000 M8071 0 K500 D8070 M8000 M8178 8 B N:N Network MOV (In the FX3G, FX3GC, FX3U and FX3UC) This step is not required when using ch 1. When using ch 2, set M8178 to ON. C M8000 MOV K1X000 K1M900 MOV K1M800 K1Y000 END 22 D Computer Link 6.2.2 Parallel Link 11 For FX0N, FX1S or FX3S Series 1. Master station communication test program M8000 M8070 MOV K500 D8070 MOV K1X000 K1M400 MOV K1M450 K1Y000 F M8000 Non-Protocol Communication (RS/RS2 Instruction) 8 G END 19 Create the program shown below for the communication test. (This program is not required during actual operation.) M8000 MOV K500 D8070 MOV K1X000 K1M450 MOV K1M400 K1Y000 M8000 8 I Remote Maintenance 19 H Programming Communication M8071 Non-Protocol Communication (FX2N-232IF) 2. Slave station communication test program 0 E Inverter Communication Create the program shown below for the communication test. (This program is not required during actual operation.) 0 Common Items 2. Program for communication test (for the slave station) END Apx.A Discontinued models C-37 FX Series PLC User's Manual - Data Communication Edition Parallel Link 7. 7 Creating Programs 7.1 Regular Parallel Link Mode Creating Programs The parallel link has two modes, regular parallel link mode and high speed parallel link mode. Program settings and the number of device to be used are different in each mode. When connecting FX PLCs in the parallel link, use the same mode in both PLCs. 7.1 Regular Parallel Link Mode This section explains the program setting method in the regular parallel link mode. 7.1.1 Checking contents of related devices The tables below show devices used in the parallel link. 1. Devices for setting the parallel link These devices are used for setting the parallel link. The setting of these devices is essential to use the parallel link. Device Name Description M8070 Parallel link master station declare Set this device to ON when linking a PLC as the master station. M8071 Parallel link slave station setting Set this device to ON when linking a PLC as the slave station. M8178 Channel setting Set the channel of communication port to be used (in the FX3G, FX3GC, FX3U and FX3UC). When this device is OFF: ch1 When this device is ON: ch2 D8070 Error judgement time (ms) Set the time for judging error in the parallel link data communication. [Initial value: 500] 2. Devices for judging errors in the parallel link These devices are used for judging errors in the parallel link. Use them to output link errors to the outside and interlock sequence programs. Device C-38 Name Description M8072 Parallel link ON This device remains ON while the parallel link is executed. M8073 Master/slave station setting error This device turns ON when there is an error in the setting of the master station or slave station. M8063 Link error This device turns ON when a communication error occurs. FX Series PLC User's Manual - Data Communication Edition Parallel Link 7 Creating Programs 7.1 Regular Parallel Link Mode A Device Number of devices Bit device M800 to M899 100 Word device D490 to D499 10 Description The devices in the slave station are automatically updated to the status of devices in the master station. Device Number of devices Bit device M400 to M449 50 Word device D230 to D239 10 Description The devices in the slave station are automatically updated to the status of devices in the master station. Bit device M900 to M999 100 Word device D500 to D509 10 Description The devices in the master station are automatically updated to the status of devices in the slave station. F b) For FX0N, FX1S or FX3S Series Number of devices Bit device M450 to M499 50 Word device D240 to D249 10 Description The devices in the master station are automatically updated to the status of devices in the slave station. Non-Protocol Communication (RS/RS2 Instruction) Device E Inverter Communication Number of devices D Computer Link 2) Sending devices for the slave station These devices are used for sending the information from the slave station to the master station. To prevent malfunctions, do not change the setting of these devices in the master station. The device numbers used and number of devices vary depending on the PLC type. For applicable devices, refer to the tables below. a) For FX2(FX), FX2C, FX1N, FX1NC, FX2N, FX2NC, FX3G, FX3GC, FX3U or FX3UC Series Device C Parallel Link b) For FX0N, FX1S or FX3S Series B N:N Network 1) Sending devices for the master station These devices are used for sending the information from the master station to the slave station. To prevent malfunctions, do not change the setting of these devices in the slave station. The device numbers used and number of devices vary depending on the PLC type. For applicable devices, refer to the tables below. a) For FX2(FX), FX2C, FX1N, FX1NC, FX2N, FX2NC, FX3G, FX3GC, FX3U or FX3UC Series Common Items 3. Link devices G Non-Protocol Communication (FX2N-232IF) H Programming Communication I Remote Maintenance Apx.A Discontinued models C-39 FX Series PLC User's Manual - Data Communication Edition Parallel Link 7.1.2 7 Creating Programs 7.1 Regular Parallel Link Mode Creating programs for master station Create programs for the master station. RUN monitor M8000 Master station setting M8070 Channel setting M8178 Parallel link ON M8072 Program for setting the master station M8070 is set to ON to set a PLC as the master station. (In the FX3G, FX3GC, FX3U and FX3UC) When using ch 1, this step is not required. When using ch 2, set M8178 to ON". Program for indicating link errors Y010 Master/ slave station setting error When the parallel link is interrupted or the setting is defective, Y10 is set to ON. M8073 RUN monitor M8000 FNC 12 MOV Program for writing link devices (master station → slave station) K1X000 Link device X010 C0 The information on X000 to X003 is written to link devices. • For PLC series other than the FX0N, FX1S or FX3S: M800 to M899 • For FX0N, FX1S or FX3S Series: M400 to M449 K100 FNC 12 MOV C0 Link device The current value of C0 is written to link devices. • For PLC series other than the FX0N, FX1S or FX3S: D490 to D499 • For FX0N, FX1S or FX3S Series: D230 to D239 RUN monitor M8000 FNC 12 MOV FNC 12 MOV Program for reading link devices (slave station → master station) Link device Link device K1Y000 D10 X010 C1 D10 C-40 The information on link devices is read to Y000 to Y003. • For PLC series other than the FX0N, FX1S or FX3S: M900 to M999 • For FX0N, FX1S or FX3S Series: M450 to M499 The current value of link devices is read to D10, and it is made the setting value of C1. • For PLC series other than the FX0N, FX1S or FX3S: D500 to D509 • For FX0N, FX1S or FX3S Series: D240 to D249 FX Series PLC User's Manual - Data Communication Edition Parallel Link 7.1 Regular Parallel Link Mode A Creating programs for slave station Common Items 7.1.3 7 Creating Programs Create programs for the slave station. RUN monitor M8000 Slave station setting M8071 M8178 (In the FX3G, FX3GC, FX3U and FX3UC) When using ch 1, this step is not required. When using ch 2, set M8178 to ON". C Program for indicating link errors Y010 Master/ slave station setting error When the parallel link is interrupted or the setting is defective, Y10 is set to ON. M8073 D FNC 12 MOV Program for writing link devices (slave station → master station) K1X000 Link device X010 K100 FNC 12 MOV C0 Link device The current value of C0 is written to link devices. FNC 12 MOV Link device Link device K1Y000 D10 X010 C1 The information on link devices is read to Y000 to Y003. • For PLC series other than the FX0N, FX1S or FX3S: M800 to M899 • For FX0N, FX1S or FX3S Series: M400 to M449 The current value of link devices is read to D10, and it is made the setting value of C1. • For PLC series other than the FX0N, FX1S or FX3S: D490 to D499 • For FX0N, FX1S or FX3S Series: D230 to D239 H Programming Communication D10 G Non-Protocol Communication (FX2N-232IF) FNC 12 MOV Program for reading link devices (master station → slave station) F Non-Protocol Communication (RS/RS2 Instruction) • For PLC series other than the FX0N, FX1S or FX3S : D500 to D509 • For FX0N, FX1S or FX3S Series: D240 to D249 RUN monitor M8000 E Inverter Communication C0 The information on X000 to X003 is written to link devices. • For PLC series other than the FX0N, FX1S or FX3S: M900 to M999 • For FX0N, FX1S or FX3S Series: M450 to M499 Computer Link RUN monitor M8000 Parallel Link Parallel link ON M8072 B N:N Network Channel setting Program for setting the slave station M8071 is set to ON to set a PLC as the slave station. I Remote Maintenance Apx.A Discontinued models C-41 FX Series PLC User's Manual - Data Communication Edition 7 Creating Programs Parallel Link 7.2 7.2 High Speed Parallel Link Mode High Speed Parallel Link Mode This section explains the program setting method in the high speed parallel link mode. 7.2.1 Checking contents of related devices The tables below show devices used in the parallel link. 1. Devices for setting the parallel link These devices are used for setting the parallel link. Setting of these devices is essential in using the parallel link. Device Name Description M8070 Parallel link master station declare Set this device to ON when linking a PLC as the master station. M8071 Parallel link slave station declare Set this device to ON when linking a PLC as the slave station. M8162 High speed parallel link mode Set this device to ON when using the high speed parallel link mode. M8178 Channel setting Set the channel of communication port to be used (in the FX3G, FX3GC, FX3U and FX3UC). When this device is OFF: ch1 When this device is ON: ch2 D8070 Error judgement time (ms) Set the time for judging error in the parallel link data communication. [Initial value: 500] 2. Devices for judging errors in the parallel link These devices are used for judging errors in the parallel link. Use them to output link errors to the outside and interlock sequence programs. Device Name Description M8072 Parallel link ON This device remains ON while the parallel link is executed. M8073 Master/slave station setting error This device turns ON when there is an error in the setting of the master station or slave station. M8063 Link error This device turns ON when a communication error occurs. 3. Link devices 1) Sending devices for the master station These devices are used for sending the information from the master station to the slave station. To prevent malfunctions, do not change the setting of these devices in the slave station. The device numbers used and number of devices vary depending on the PLC type. For applicable devices, refer to the tables below. a) For FX2(FX), FX2C, FX1N, FX1NC, FX2N, FX2NC, FX3G, FX3GC, FX3U or FX3UC Series Device Word device D490, D491 Number of devices Description 2 The devices in the slave station are automatically updated to the status of devices in the master station. Number of devices Description 2 The devices in the slave station are automatically updated to the status of devices in the master station. b) For FX0N, FX1S or FX3S Series Device Word device C-42 D230, D231 FX Series PLC User's Manual - Data Communication Edition Parallel Link 7 Creating Programs 7.2 High Speed Parallel Link Mode Word device D500, D501 Number of devices Description 2 The devices in the master station are automatically updated to the status of devices in the slave station. C b) For FX0N, FX1S or FX3S Series Word device D240, D241 Number of devices Description 2 The devices in the master station are automatically updated to the status of devices in the slave station. Parallel Link Device B N:N Network Device A Common Items 2) Sending devices for the slave station These devices are used for sending the information from the slave station to the master station. To prevent malfunctions, do not change the setting of these devices in the master station. The device numbers used and number of devices vary depending on the PLC type. For applicable devices, refer to the tables below. a) For FX2(FX), FX2C, FX1N, FX1NC, FX2N, FX2NC, FX3G, FX3GC, FX3U or FX3UC Series D Computer Link E Inverter Communication F Non-Protocol Communication (RS/RS2 Instruction) G Non-Protocol Communication (FX2N-232IF) H Programming Communication I Remote Maintenance Apx.A Discontinued models C-43 FX Series PLC User's Manual - Data Communication Edition Parallel Link 7.2.2 7 Creating Programs 7.2 High Speed Parallel Link Mode Creating programs for master station Create programs for the master station. RUN monitor M8000 Master station setting M8070 Program for setting the master station M8070 is set to ON to set a PLC as the master station. High speed parallel link mode M8162 Channel setting M8178 Parallel link ON M8072 M8162 is set to ON to set the high speed parallel link mode. (In the FX3G, FX3GC, FX3U and FX3UC) When using ch 1, this step is not required. When using ch 2, set M8178 to ON". Program for indicating link errors Y010 Master/ slave station setting error When the parallel link is interrupted or the setting is defective, Y10 is set to ON. M8073 RUN monitor M8000 FNC 12 MOV Program for writing link devices (master station → slave station) K1X000 Link device X010 C0 The information on X000 to X003 is written to link devices. • For PLC series other than the FX0N, FX1S or FX3S: D490 and D491 • For FX0N, FX1S or FX3S Series: D230 and D231 K100 FNC 12 MOV C0 Link device The current value of C0 is written to link devices. • For PLC series other than the FX0N, FX1S or FX3S : D490 and D491 • For FX0N, FX1S or FX3S Series: D230 and D231 RUN monitor M8000 FNC 12 MOV FNC 12 MOV Program for reading link devices (slave station → master station) Link device Link device K1Y000 D10 X010 C1 D10 C-44 The information on link devices is read to Y000 to Y003. • For PLC series other than the FX0N, FX1S or FX3S: D500 and D501 • For FX0N, FX1S or FX3S Series: D240 and D241 The current value of link devices is read to D10, and it is made the setting value of C1. • For PLC series other than the FX0N, FX1S or FX3S: D500 and D501 • For FX0N, FX1S or FX3S Series: D240 and D241 FX Series PLC User's Manual - Data Communication Edition Parallel Link 7.2 High Speed Parallel Link Mode A Creating programs for slave station Common Items 7.2.3 7 Creating Programs Create programs for the slave station. RUN monitor M8000 Slave station setting M8071 Program for setting the slave station M8071 is set to ON to set a PLC as the slave station. M8162 Channel setting Parallel link ON M8072 C (In the FX3G, FX3GC, FX3U and FX3UC) When using ch 1, this step is not required. When using ch 2, set M8178 to ON". Parallel Link M8178 M8162 is set to ON to set the high speed parallel link mode. Program for indicating link errors Y010 When the parallel link is interrupted or the setting is defective, Y10 is set to ON. M8073 RUN monitor M8000 K1X000 Link device C0 The information on X000 to X003 is written to link devices. • For PLC series other than the FX0N, FX1S or FX3S: D500 and D501 • For FX0N, FX1S or FX3S Series: D240 and D241 F K100 C0 Link device The current value of C0 is written to link devices. • For PLC series other than the FX0N, FX1S or FX3S: D500 and D501 • For FX0N, FX1S or FX3S Series: D240 and D241 Link device K1Y000 D10 X010 C1 The information on link devices is read to Y000 to Y003. • For PLC series other than the FX0N, FX1S or FX3S: D490 and D491 • For FX0N, FX1S or FX3S Series: D230 and D231 The current value of link devices is read to D10, and it is made the setting value of C1. • For PLC series other than the FX0N, FX1S or FX3S: D490 and D491 • For FX0N, FX1S or FX3S Series: D230 and D231 D10 H Programming Communication FNC 12 MOV Link device G Non-Protocol Communication (FX2N-232IF) FNC 12 MOV Program for reading link devices (master station → slave station) Non-Protocol Communication (RS/RS2 Instruction) FNC 12 MOV E Inverter Communication FNC 12 MOV Program for writing link devices (slave station → master station) X010 RUN monitor M8000 D Computer Link Master/ slave station setting error N:N Network High speed parallel link mode B I Remote Maintenance Apx.A Discontinued models C-45 FX Series PLC User's Manual - Data Communication Edition Parallel Link 7.3 7 Creating Programs 7.3 Cautions on Program Creation Cautions on Program Creation 1. Program for reading link devices 1) Do not change the contents of link devices for the other station. 2) When a link error occurs, the link device information remains the same as the status just before the error. Create a fail-safe program which does not cause abnormality even if a link error occurs. 2. Cautions on using FX3G, FX3GC, FX3U, FX3UC PLCs 1) Only ch1 or ch2 can be set in the parallel link. 2) Do not use the N:N Network and the parallel link at the same time. (For example, it is not allowed to use ch1 for the N:N Network and simultaneously use ch2 for the parallel link.) C-46 FX Series PLC User's Manual - Data Communication Edition Parallel Link 8 Practical Program Examples 8.1 Practical Example 1 (Regular Parallel Link Mode) A Common Items 8. Practical Program Examples B This chapter shows practical programs examples. N:N Network 8.1 Practical Example 1 (Regular Parallel Link Mode) When many link devices are required, use the regular parallel link mode. C System configuration example Parallel Link 8.1.1 The example below shows a system configuration in which two FX2N PLCs are linked. FX2N PLC FX2N PLC D Master station Slave station Computer Link FX2N-485-BD E Inverter Communication FX2N-485-BD - Link range: 100-bit devices and 10-word devices (regular parallel link mode) - Error judgement time: 500 ms 8.1.2 Setting contents F Device Non-Protocol Communication (RS/RS2 Instruction) The program examples shown later adopt the following communication parameters: Description Parallel link master station setting M8071 Parallel link slave station setting D8070 Communication error judgement time G Non-Protocol Communication (FX2N-232IF) M8070 H Programming Communication I Remote Maintenance Apx.A Discontinued models C-47 FX Series PLC User's Manual - Data Communication Edition 8 Practical Program Examples Parallel Link 8.1.3 8.1 Practical Example 1 (Regular Parallel Link Mode) Program for master station For the master station, refer to the program shown below. RUN monitor M8000 RUN monitor M8000 FNC 20 ADD M8070 FNC 12 MOV K2X000 K2M800 D0 FNC 12 MOV D2 D490 K2M900 K2Y000 X010 T0 The ON/OFF status of inputs X000 to X007 in the master station is output to Y000 to Y007 in the slave station. When the calculation result (D0 + D2) in the master station is moved to D490 of the slave station. The ON/OFF status of M0 to M7 in the slave station is output to Y000 to Y007 in the master station. The value of D10 in the slave station is stored to the timer setting (T0) in the master station. D500 8.1.4 Program for slave station For the slave station, refer to the program shown below. RUN monitor M8000 RUN monitor M8000 FNC 10 CMP M8071 FNC 12 MOV D490 K2M800 K2Y000 K100 M10 X010 C-48 M10 The ON/OFF status of inputs X000 to X007 in the master station is output to Y000 to Y007 in the slave station. When the calculation result (D0 + D2) in the master station is 100 or less, Y010 is set to ON in the slave station. Y010 FNC 12 MOV K2M0 K2M900 FNC 12 MOV D10 D500 The ON/OFF status of M0 to M7 in the slave station is output to Y000 to Y007 in the master station. The value of D10 in the slave station stored to the timer setting (T0) in the master station. FX Series PLC User's Manual - Data Communication Edition Parallel Link 9 Troubleshooting 9.1 Checking FX PLC Version Applicability A Common Items 9. Troubleshooting B This chapter explains troubleshooting. N:N Network 9.1 Checking FX PLC Version Applicability Verify that the FX PLC main unit is an applicable version. For the version applicability check, refer to Section 1.3. Parallel Link 9.2 Checking Communication Status Based on LED Indication Check the status of the "RD" and "SD" indicator LEDs provided in the optional equipment. LED status D RD SD Flashing Flashing Off Data is received, but is not sent. Off Flashing Data is sent, but is not received. Off Off Computer Link Operation status Flashing Data is being sent or received. E Data is not sent or received. Inverter Communication While the parallel link is executed normally, both LEDs flash brightly. If they do not flash, check the wiring and the communication setting in the master and slave stations. 9.3 Checking Installation and Wiring F If the communication equipment is not securely connected to the PLC, communication is not possible. For the mounting method, refer to the respective communication equipment manual. 2. Power supply (for FX0N-485ADP) The FX0N-485ADP requires a driving power supply. Verify that the power supply is correctly provided. Verify that the wiring to all communication equipment is correct. If the communication equipment is wired incorrectly, communication is not possible. For wiring method check, refer to Chapter 4. G Non-Protocol Communication (FX2N-232IF) 3. Wiring Non-Protocol Communication (RS/RS2 Instruction) 1. Mounting status H Checking Sequence Program 1. Communication setting in the sequence program 2. Communication setting using parameters C-49 Apx.A Discontinued models Verify that the communication settings using parameters are suitable for use. If the communication settings are not suitable for the purpose of use, communication will not function correctly. After changing any setting, make sure to reboot the PLC’s power. For communication setting, refer to Chapter 5. I Remote Maintenance Verify that N:N Network (D8173 to D8180) is not set. Using both the parallel link and N:N Network at the same time is not allowed. Verify that the communication format (D8120, D8400 and D8420) is set correctly. Communication is not possible if a communication port is set twice or more. After changing any setting, make sure to cycle power to the PLC. For communication setting, refer to Chapter 5. Programming Communication 9.4 C FX Series PLC User's Manual - Data Communication Edition Parallel Link 9 Troubleshooting 9.4 Checking Sequence Program 3. Ethernet port setting (in FX3S, FX3G, FX3GC, FX3U and FX3UC PLCs) Verify that the same channel is not used in the Ethernet port setting. Do not set the channel used in parallel link. After changing the setting, make sure to reboot the PLC's power. 4. Presence of VRRD and VRSC instructions 1) Except FX3G, FX3U and FX3UC PLCs Verify that the VRRD and VRSC instructions are not used in the program. If these instructions are used, delete them, reboot the PLC’s power. 2) In FX3G PLC - In the case of the 14 points and 24-point type Verify that the VRRD and VRSC instructions are not used in the program. If these instructions are used, delete them, reboot the PLC's power. - In the case of the 40 points and 60-point type Verify that the VRRD and VRSC instructions are not used in the program. If these instructions are used in the program, the communication function is not available in ch2. Use ch1, or delete these instructions. After deleting these instructions, reboot the PLC's power. 3) In FX3U and FX3UC PLCs Verify that the VRRD and VRSC instructions are not used in the program. If these instructions are used in the program, the communication function is not available in ch1. Use ch2, or delete these instructions. After deleting these instructions, reboot the PLC's power. 5. Presence of RS instruction (except FX3S, FX3G, FX3GC, FX3U and FX3UC PLCs) Verify that the RS instruction is not used in the program. If this instruction is used, delete it, reboot the PLC’s power. 6. Presence of RS and RS2 instructions (in FX3S, FX3G, FX3GC, FX3U and FX3UC PLCs) Verify that the RS and RS2 instructions are not being used for the same channel. If these instructions are used for the same channel, delete them, reboot the PLC’s power. 7. Presence of EXTR instruction (in FX2N and FX2NC PLCs) Verify that the EXTR instruction is not used in the program. If this instruction is used, delete it, then reboot the PLC’s power. 8. Presence of IVCK, IVDR, IVRD, IVWR, IVBWR*1, and IVMC instructions (in FX3S, FX3G, FX3GC, FX3U and FX3UC PLCs) Verify that the IVCK, IVDR, IVRD, IVWR, IVBWR and IVMC instructions are not being used for the same channel. If these instructions are used for the same channel, delete them, reboot the PLC’s power. *1. Only available for FX3U and FX3UC PLCs. 9. Presence of ADPRW instructions (in FX3S, FX3G, FX3GC, FX3U and FX3UC PLCs) Verify that the ADPRW instructions are not being used for the same channel. If these instructions are used for the same channel, delete them, and reboot the PLC’s power. 10.Presence of FLCRT, FLDEL, FLWR, FLRD, FLCMD, and FLSTRD instructions (in FX3U and FX3UC PLCs) Verify that the FLCRT, FLDEL, FLWR, FLRD, FLCMD and FLSTRD instructions are not being used for the same channel. If these instructions are used for the same channel, delete them, reboot the PLC’s power. C-50 FX Series PLC User's Manual - Data Communication Edition 9 Troubleshooting Parallel Link A Checking Absence/Presence of Errors Verify that errors have not occurred in the master station and slave station. Errors can be checked using the flags shown below. B 1. Checking the device M8072 2. Checking the device M8073 If the parallel link is not set correctly, M8073 turns ON. If M8073 is ON, verify that the master station and slave station are set correctly in sequence programs. 3. Devices for checking link errors No error 6312 Character error in parallel link 6313 Sum check error in parallel link 6314 Format error in parallel link 0000 No error 3812 Character error in parallel link 3813 Sum check error in parallel link 3814 Format error in parallel link Action E Verify that the parallel link setting programs are set correctly. Check the wiring also. Caution G Non-Protocol Communication (FX2N-232IF) The devices for checking link errors are not cleared even after communication errors are reset. Serial communication errors are cleared in FX3S, FX3G, FX3GC, FX3U and FX3UC PLCs when the power is turned off and on. Serial communication errors are cleared in other PLCs when the mode is switched from STOP to RUN. F Non-Protocol Communication (RS/RS2 Instruction) D8438 (in FX3G, FX3GC, FX3U and FX3UC) Description 0000 Inverter Communication D8063 Error code D Computer Link 2) Checking the error code When a communication error occurs in parallel link using ch 1, the error code is stored in D8063. When a communication error occurs in parallel link using ch 2, the error code is stored in D8438. The table below shows the details of error codes. C Parallel Link 1) Checking the error flags M8063 and M8438 (in the FX3G, FX3GC, FX3U and FX3UC) If a communication error occurs in the parallel link, the serial communication error flag turns ON. When ch1 is used, M8063 turns ON. When ch2 is used in the FX3G, FX3GC, FX3U and FX3UC, M8438 turns ON. When the serial communication error flag turns ON, the error code is stored in D8063 or D8438. N:N Network While the parallel link is established, M8072 remains ON. If M8072 is OFF, an error has occurred in the parallel link setting or communication. Device Common Items 9.5 9.5 Checking Absence/Presence of Errors H Programming Communication I Remote Maintenance Apx.A Discontinued models C-51 FX Series PLC User's Manual - Data Communication Edition 10 Related Data Parallel Link 10.1 Related Device List 10. Related Data 10.1 Related Device List 1. Bit devices Device number Name Initial DetecR/W value tion Description Devices for communication setting M8070 Parallel link master station setting M8071 Parallel link slave station setting M8162 M8178 Links a PLC as the master station when it turns ON. M W Links a PLC as the slave station when it turns ON. L W High speed parallel link mode Turns ON when two-word device communication mode is selected. M, L W Channel setting Sets the communication port to be used. (in the FX3G, FX3GC, FX3U and FX3UC) OFF: ch1, ON: ch2 M, L W Devices for checking communication status M8072 Parallel link ON Remains ON while the parallel link is being executed. M, L R M8073 Parallel link setting error Turns ON when an error is included in the setting contents of the master station or slave station. M, L R M, L R M, L R M8063 Serial communication Turns ON when an error error 1 (ch 1) communication using ch 1. occurs in serial M8438 Turns ON when an error occurs in serial Serial communication communication using ch 2. (in the FX3G, FX3GC, FX3U error 2 (ch 2) and FX3UC) R: Read only (used as a contact in program) W: Write only M: Master station L: Slave station 2. Word devices (data registers) Device number Name Initial DetecR/W value tion Description Devices for communication setting D8070 Error judgement time Sets the error judgement time communication in the parallel link. for data 500 M, L W Devices for checking communication status D8063 Serial communication Stores the error code when an error occurs in serial communication using ch 1. error code 1 (ch 1) 0000 M, L R D8438 Stores the error code when an error occurs in serial Serial communication communication using ch 2. (in the FX3G, FX3GC, FX3U error code 2 (ch 2) and FX3UC) 0000 M, L R Devices for checking D8419 Operation mode display (ch 1) Stores the communication type being used by ch 1. (in the FX3S, FX3G, FX3GC, FX3U and FX3UC) — M, L R D8439 Operation mode display (ch 2) Stores the communication type being used by ch 2. (in the FX3G, FX3GC, FX3U and FX3UC) — M, L R R: Read only W: Write only M: Master station L: Slave station C-52 FX Series PLC User's Manual - Data Communication Edition 10 Related Data Parallel Link A Details of Related Devices Common Items 10.2 10.2 Details of Related Devices The devices described below are used in parallel link. 10.2.1 Parallel link master station declare [M8070] B N:N Network When this device is set to ON, the PLC is handled as the master station in the parallel link. 1. Applicable stations The master station requires program setting. 2. Detailed contents C Parallel Link In the FX PLC to be handled as the master station, set M8070 to "normally ON" using M8000. 3. Cautions on use Set this device to ON in a sequence program. 10.2.2 Channel setting [M8178] D Computer Link This device works as the channel setting flag (in the FX3G, FX3GC, FX3U and FX3UC). 1. Applicable stations The master and slave station require program setting. 2. Detailed contents E Inverter Communication When using ch 2 as the communication port, set this device to ON in the sequence program. When using ch 1, the sequence program is not required. 10.2.3 Parallel link slave station declare [M8071] When this device is set to ON, the PLC is handled as the slave station in the started communication. F Non-Protocol Communication (RS/RS2 Instruction) 1. Applicable stations The slave station requires program setting. 2. Detailed contents In the FX PLC to be handled as a slave station, set M8071 to "normally ON" using M8000. G 3. Cautions on use Non-Protocol Communication (FX2N-232IF) Set this device to ON using a sequence program. 10.2.4 High-speed parallel link mode [M8162] When M8162 turns OFF, the regular parallel link mode is selected. When M8162 turns ON, the high-speed parallel link mode is selected. Programming Communication 1. Applicable stations The master and slave station require program setting. 2. Detailed contents I The table below shows the number of link devices. Regular parallel link mode High-speed parallel link mode Word device (D) Bit device (M) Word device (D) 100 in each station 10 in each station 0 2 in each station FX0N, FX1S, FX3S 50 in each station 10 in each station 0 2 in each station 3. Cautions on use Set this device to ON using a sequence program. C-53 Apx.A Discontinued models Bit device (M) FX2(FX), FX2C, FX1N, FX1NC, FX2N, FX2NC, FX3G, FX3GC, FX3U, FX3UC Remote Maintenance PLC H FX Series PLC User's Manual - Data Communication Edition Parallel Link 10 Related Data 10.2 Details of Related Devices 10.2.5 Parallel link ON [M8072] This device is provided to verify that the parallel link is being executed. 1. Applicable stations The master and slave station may check parallel link status. 2. Detailed contents M8072 remains ON while the parallel link is being executed normally, and remains OFF while the parallel link is not being executed normally. 10.2.6 Parallel link setting error [M8073] This device is provided to verify that the setting is correct in the master station and slave station in the parallel link. 1. Applicable stations The master and slave station may check parallel link status. 2. Detailed contents M8073 remains OFF when the setting is correct in the master station or slave station, and turns ON when the setting is incorrect. 10.2.7 Serial communication error [M8063 and M8438] These devices are provided to check communication errors. (M8438 is available only in the FX3G, FX3GC, FX3U and FX3UC.) 1. Applicable stations The master and slave station may check parallel link status. 2. Detailed contents M8063 turns ON when an error occurs using parallel link on ch 1. When M8063 turns ON, the error code is stored in D8063. M8438 turns ON when an error occurs using parallel link on ch 2. When M8438 turns ON, the error code is stored in D8438. 3. Cautions on use Do not set these devices to ON using a program or programming tool. Serial communication errors are not cleared even when communication is restored. Serial communication errors are cleared in FX3S, FX3G, FX3GC, FX3U and FX3UC PLCs when the power is turned off and on. Serial communication errors are cleared in other PLCs when the mode is switched from STOP to RUN. 10.2.8 Error judgement time setting [D8070] This device is provided to set the error judgment time (initial value: 500 ms). 1. Applicable stations The master and slave station may check parallel link status. 2. Detailed contents When data transmission requires more time than the time set here, it is regarded as error. 3. Cautions on use Set the error judgment time for the master station to a value twice or more the scan time in the slave station. If the error judgment time is less than twice the scan time, a serial communication error may occur. C-54 FX Series PLC User's Manual - Data Communication Edition 10 Related Data Parallel Link 10.2 Details of Related Devices A These devices store the serial communication error code. (D8438 is available only in the FX3G, FX3GC, FX3U and FX3UC.) 1. Applicable stations B N:N Network The master and slave station may check the serial communication error code. 2. Detailed contents The table below shows the details of error codes. Device Error code D8438 (ch 2) No error 6312 Character error in parallel link 6313 Sum check error in parallel link 6314 Format error in parallel link 0000 No error Character error in parallel link 3813 Sum check error in parallel link 3814 Format error in parallel link C Verify that the parallel link setting programs are correct, and check the wiring also. 3. Cautions on use 10.2.10 Operation mode display [D8419 and D8439] 1. Detailed contents These devices store the code of the communication type currently being used in the communication port. When communication port ch1 is used, D8419 stores the communication type. When communication port ch2 is used, D8439 stores the communication type. Code Description Programming communication 1 PP modem mode 2 Protocol dedicated to computer link 3 N:N Network RS instruction 5 RS2 instruction 6 Parallel link 7 Inverter instruction 8 Variable analog potentiometer expansion board is used. 9 MODBUS communication 10 CF-ADP 11 ENET-ADP 12 Input/output expansion board is used. I Remote Maintenance 4 H Programming Communication 0 G Non-Protocol Communication (FX2N-232IF) The table below shows the contents of the communication type codes. F Non-Protocol Communication (RS/RS2 Instruction) These devices store the communication type being used. (in the FX3S, FX3G, FX3GC, FX3U and FX3UC) E Inverter Communication Do not set this device to ON using a program or programming tool. Serial communication errors code are not cleared even when communication is restored. Serial communication errors are cleared in FX3S, FX3G, FX3GC, FX3U and FX3UC PLCs when the power is turned off and on. Serial communication errors are cleared in other PLCs when the mode is switched from STOP to RUN. D Computer Link 3812 Action Parallel Link D8063 (ch 1) Description 0000 Common Items 10.2.9 Serial communication error code [D8063 and D8438] Apx.A Discontinued models C-55 FX Series PLC User's Manual - Data Communication Edition Parallel Link 10.2 Details of Related Devices MEMO C-56 10 Related Data FX Series PLC User's Manual - Data Communication Edition Computer Link A Common Items B N:N Network FX Series Programmable Controllers C Parallel Link User's Manual [Data Communication Edition] D. Computer Link D Computer Link E Inverter Communication F Non-Protocol Communication (RS/RS2 Instruction) G Non-Protocol Communication (FX2N-232IF) H Programming Communication Foreword I © 2005 MITSUBISHI ELECTRIC CORPORATION D-1 Apx.A Discontinued models This manual confers no industrial property rights or any rights of any other kind, nor does it confer any patent licenses. Mitsubishi Electric Corporation cannot be held responsible for any problems involving industrial property rights which may occur as a result of using the contents noted in this manual. Remote Maintenance This manual explains "computer link" provided for the MELSEC-F FX Series Programmable Controllers and should be read and understood before attempting to install or use the unit. Store this manual in a safe place so that you can take it out and read it whenever necessary. Always forward it to the end user. FX Series PLC User's Manual - Data Communication Edition Computer Link D-2 FX Series PLC User's Manual - Data Communication Edition 1 Outline Computer Link 1.1 Outline of System A Common Items 1. Outline B This chapter explains computer link. N:N Network 1.1 Outline of System Computer link allows connection of up to sixteen FX PLCs and A PLCs to a personal computer working as the master station to link data. 2) Applicable computer link protocols are the same as dedicated supported computer link protocols units in the A Series PLC. (But the supported formats and commands are limited.) Important points and reference chapter/section System In the case of RS-485 ....... Number of linked units ....... Total extension distance 500 m (1640' 5") [50 m (164' 0") when 485BD is used] Personal computer FX PLC Station No. 0 (00H) FX PLC Station No. 15 (0FH) FX-485PC-IF E + Communication equipment operating in accordance with RS-485 For selection, refer to Chapter 3. ....... For wiring, refer to Chapter 4. F Non-Protocol Communication (RS/RS2 Instruction) ....... In the case of RS-232C 15 m (49' 2") G FX PLC Station No. 0 (00H) Non-Protocol Communication (FX2N-232IF) Personal computer Inverter Communication + Communication equipment operating in accordance with RS-485 For the specifications, refer to Chapter 2. To check applicable PLC ....... models, refer to Section 1.3. ... D Computer Link 16 units C Parallel Link 1) Up to sixteen PLCs can be connected in computer link. H + Programming Communication Communication equipment operating in accordance with RS-232C I The number of devices handled all at once varies depending on the command and the types of devices. Remote Maintenance Apx.A Discontinued models D-3 FX Series PLC User's Manual - Data Communication Edition 1 Outline Computer Link 1.2 1.2 Procedures Before Operation Procedures Before Operation The flow chart below shows the Computer Link setting procedures up until data link. Computer link Refer to Chapter 1. Outline Refer to Chapter 2. Check communication specifications. Refer to Chapter 3. Determine system configuration and selection. Outline of system • Applicable PLC versions • Applicable programming tools Communication specifications • Link time • Number of devices System configuration • Select communication equipment. Refer to Chapter 4. Perform wiring. Wiring procedure • Wiring example Programming tool Connect PLC*1 Refer to Chapter 5. Perform PLC communication setting. PLC serial communication setting • Communication setting Refer to Chapter 6. Computer link Refer to Chapter 7. Commands Based on SD/RD lamp lighting status and contents of error check devices, verify that communication is being executed normally. Computer link • Dedicated protocol format • Transfer sequence time chart and communication time Commands • Applicable command list • Specification method • On-demand function If there are problems, refer to the troubleshooting (Chapter 8). *1 For the programming tool to PLC connection procedure, refer to the "Programming Communication" section in this manual or the respective programming tool manual. For details on operating procedures, refer to the respective programming tool manual. D-4 FX Series PLC User's Manual - Data Communication Edition 1 Outline Computer Link 1.3 Communication Type Applicability in PLC Communication Type Applicability in PLC 1.3.1 Applicable versions Common Items 1.3 A PLC FX3U Series FX3GC Series FX2N Series (Ver. 1.06 or later) FX1NC Series FX1N Series FX1S Series FX0N Series (Ver. 1.20 or later) C The version can be checked by monitoring D8001. The version can be checked by monitoring D8001. — Computer link is not provided. FX0 Series — Computer link is not provided. FX2C Series (Ver. 3.30 or later)*1 FX2(FX) Series (Ver. 3.30 or later)*1 *1. E Computer link is not provided. Applicable in products manufactured in June, 1996 and later (manufacturer’s serial No.: 66**** and later). The PLC version can be checked by reading the last three digits of device D8001. For a detailed description of the version check, refer to A. Common Items Section 4.2. How to look at the manufacturer's serial number The year and month of production of the PLC main unit can be checked on the nameplate, and "LOT" indicated on the front of the product. For a detailed description of the How to look at the manufacturer's serial number, refer to A. Common Items Section 4.1. Products whose production was stopped Production was stopped for some models of MELSEC-F Series PLCs and programming tools described in this manual. For models whose production was stopped, refer to Appendix A. To see the latest available products, refer to the general catalog. H Programming Communication 1.3.4 G Non-Protocol Communication (FX2N-232IF) 1.3.3 F Non-Protocol Communication (RS/RS2 Instruction) Version check Inverter Communication FX0S Series — D Computer Link FX2NC Series Remarks Parallel Link FX3G Series FX3S Series FX1 Series 1.3.2 Applicability (applicable version) FX3UC Series B N:N Network The communication type is applicable in the following versions. : Applicable (If applicable versions of main units are limited, they are described inside ( ).) —: Not applicable I Remote Maintenance Apx.A Discontinued models D-5 FX Series PLC User's Manual - Data Communication Edition 1 Outline Computer Link 1.4 Programming Tool Applicability 1.4 Programming Tool Applicability 1.4.1 For applicable versions The programming tool is applicable for each FX Series from the following version shown: 1. English versions Product name Model name Applicable version Remarks FX3U and FX3UC PLCs GX Works2 SWDNC-GXW2-E Ver. 1.08J or later GX Developer SWD5C(F)-GPPW-E Ver. 8.18U or later FX-30P - Ver. 1.00 or later GOT1000 Series display units Refer to manuals of GOT1000 Series display units for applicable models and versions supporting the list editor function. FX3G PLC GX Works2 SWDNC-GXW2-E Ver. 1.08J or later GX Developer SWD5C(F)-GPPW-E Ver. 8.72A or later FX-30P - Ver. 1.00 or later GOT1000 Series display units Refer to manuals of GOT1000 Series display units for applicable models and versions supporting the list editor function. FX3GC PLC GX Works2 SWDNC-GXW2-E FX-30PSWDNC-GXW2-E GOT1000 Series display units Ver. 1.77F or later Ver. 1.30 or later - Refer to manuals of GOT1000 Series display units for applicable models and versions supporting the list editor function. FX3S PLC GX Works2 SWDNC-GXW2-E FX-30P Ver. 1.492N or later Ver. 1.50 or later GOT1000 Series display units - Refer to manuals of GOT1000 Series display units for applicable models and versions supporting the list editor function. FX2N and FX2NC PLCs GX Works2 SWDNC-GXW2-E Ver. 1.08J or later GX Developer SWD5C(F)-GPPW-E SW2 A or later FX-PCS/WIN-E SW0PC-FXGP/WIN-E Ver. 1.00 or later FX-30P Ver. 1.00 or later FX-20P-E(-SET0) FX-20P-MFXC-E Ver. 3.00 or later FX-10P-E Ver. 3.00 or later GOT-F900 Series display units F940WGOT-TWD-E F940GOT-*WD-E F940GOT-*BD-H-E F940GOT-*BD-RH-E GOT1000 Series display units - F940WGOT-TWD-E (Ver. 1.00 or later) F940GOT-LWD-E, F940GOT-SWD-E (Ver. 1.00 or later) F940GOT-LBD-H-E, F940GOT-SBD-H-E (Ver. 1.00 or later) F940GOT-LBD-RH-E, F940GOT-SBD-RH-E (Ver. 1.00 or later) Refer to manuals of GOT1000 Series display units for applicable models and versions supporting the list editor function. FX1S, FX1N and FX1NC PLCs GX Works2 D-6 SWDNC-GXW2-E Ver. 1.08J or later GX Developer SWD5C(F)-GPPW-E SW5 A or later FX-PCS/WIN-E SW0PC-FXGP/WIN-E Ver. 3.00 or later FX-30P Ver. 1.00 or later FX-20P-E(-SET0) FX-20P-MFXD-E Ver. 4.00 or later FX-10P-E Ver. 4.00 or later - FX Series PLC User's Manual - Data Communication Edition 1 Outline Computer Link 1.4 Programming Tool Applicability A Model name Remarks F940WGOT-TWD-E (Ver. 1.00 or later) F940GOT-LWD-E, F940GOT-SWD-E (Ver. 1.00 or later) F940GOT-LBD-H-E, F940GOT-SBD-H-E (Ver. 1.00 or later) F940GOT-LBD-RH-E, F940GOT-SBD-RH-E (Ver. 1.00 or later) Refer to manuals of GOT1000 Series display units for applicable models and versions supporting the list editor function. 2. Japanese versions Product name Model name Applicable version Remarks C FX3U and FX3UC PLCs SWDNC-GXW2-J Ver. 1.07H or later GX Developer SWD5C(F)-GPPW-J Ver. 8.13P or later FX-30P Parallel Link GX Works2 - Ver. 1.00 or later GOT1000 Series display units Refer to manuals of GOT1000 Series display units for applicable models and versions supporting the list editor function. GX Works2 SWDNC-GXW2-J Ver. 1.07H or later SWD5C(F)-GPPW-J Ver. 8.72A or later FX-30P - Ver. 1.00 or later GOT1000 Series display units Refer to manuals of GOT1000 Series display units for applicable models and versions supporting the list editor function. SWDNC-GXW2-J FX-30P Ver. 1.77F or later Ver. 1.30 or later GOT1000 Series display units - Refer to manuals of GOT1000 Series display units for applicable models and versions supporting the list editor function. GX Works2 SWDNC-GXW2-J FX-30P Ver. 1.492N or later Ver. 1.50 or later GOT1000 Series display units - Refer to manuals of GOT1000 Series display units for applicable models and versions supporting the list editor function. GX Works2 SWDNC-GXW2-J Ver. 1.07H or later SWD5C(F)-GPPW-J FX-PCS/WIN SW0PC-FXGP/WIN Ver. 2.00 or later SW2 A or later FX-PCS-KIT/98 SW1PC-FXGP/98(-3,-5) Ver. 4.00 or later FX-PCS/98-3 SW1PC-FXGP/98-3 Ver. 4.00 or later FX-PCS-KIT/V-3 SW1PC-FXGP/V3 Ver. 2.00 or later FX-A7PHP-KIT SW1RX-GPPFX Ver. 3.00 or later Ver. 1.00 or later FX-20P(-SET0) FX-20P-MFXC Ver. 4.00 or later FX-10P(-SET0) Ver. 3.00 or later GOT-F900 Series display units F940WGOT-TWD F940GOT-*WD F940GOT-*BD-H F940GOT-*BD-RH I F940WGOT-TWD (Ver. 1.00 or later) F940GOT-LWD, F940GOT-SWD (Ver. 1.00 or later) F940GOT-LBD-H, F940GOT-SBD-H (Ver. 1.00 or later) F940GOT-LBD-RH, F940GOT-SBD-RH (Ver. 1.00 or later) Apx.A Refer to manuals of GOT1000 Series display units for applicable models and versions supporting the list editor function. D-7 Discontinued models GOT1000 Series display units - Remote Maintenance FX-30P H Programming Communication GX Developer G Non-Protocol Communication (FX2N-232IF) FX2N and FX2NC PLCs F Non-Protocol Communication (RS/RS2 Instruction) FX3S PLC E Inverter Communication FX3GC PLC GX Works2 D Computer Link FX3G PLC GX Developer B N:N Network GOT1000 Series display units Applicable version Common Items Product name GOT-F900 Series display units F940WGOT-TWD-E F940GOT-*WD-E F940GOT-*BD-H-E F940GOT-*BD-RH-E FX Series PLC User's Manual - Data Communication Edition 1 Outline Computer Link 1.4 Programming Tool Applicability Product name Model name Applicable version Remarks FX1S, FX1N and FX1NC PLCs GX Works2 SWDNC-GXW2-J Ver. 1.07H or later GX Developer SWD5C(F)-GPPW-J FX-PCS/WIN SW0PC-FXGP/WIN Ver. 4.00 or later FX-PCS/98-3 SW1PC-FXGP/98-3 Ver. 5.00 or later FX-30P Ver. 1.00 or later FX-20P(-SET0) FX-20P-MFXD Ver. 5.00 or later FX-10P(-SET0) Ver. 4.00 or later GOT-F900 Series display units F940WGOT-TWD F940GOT-*WD F940GOT-*BD-H F940GOT-*BD-RH - F940WGOT-TWD (Ver. 1.00 or later) F940GOT-LWD, F940GOT-SWD (Ver. 1.00 or later) F940GOT-LBD-H, F940GOT-SBD-H (Ver. 1.00 or later) F940GOT-LBD-RH, F940GOT-SBD-RH (Ver. 1.00 or later) Refer to manuals of GOT1000 Series display units for applicable models and versions supporting the list editor function. GOT1000 Series display units 1.4.2 SW5 A or later For non-applicable versions (setting an alternative model) Even programming tool not applicable to a PLC can create programs when an alternative model is set. In this case, however, programming is enabled only in the function ranges provided for the alternative PLC model such as instructions and program size. Model to be programmed Priority: High Low Model to be set FX3UC Series FX3UC FX2N FX2(FX) FX3U Series FX3U, FX3UC FX2N FX2(FX) FX3GC Series FX3G, FX3GC FX1N*1 FX2N*1 FX3G Series FX3G FX1N*1 FX2N*1 FX3S Series FX3S FX3G FX1N*1 FX2NC Series FX2NC, FX2N FX2(FX) FX2N Series FX2N FX2(FX) FX1NC Series FX1NC, FX1N FX2N FX2(FX) FX1N Series FX1N FX2N FX2(FX) FX1S Series FX1S FX2(FX) FX0N Series FX0N FX2(FX) FX0S Series FX0S FX2(FX) FX0 Series FX0 FX2(FX) FX2C Series FX2C, FX2(FX) FX2(FX) FX2(FX) Series FX1 Series *1. FX2(FX) FX1 "FX2N" is selected when the FX-10P(-E) is used. Point In the FX3S PLC, set the memory capacity for PLC parameters to 4,000 steps or less. D-8 FX Series PLC User's Manual - Data Communication Edition 2 Specifications Computer Link 2.1 Communication Specifications (Reference) A Common Items 2. Specifications B This chapter explains the communication specifications and performance. N:N Network 2.1 Communication Specifications (Reference) Communication is executed within the specifications shown in the table below. The baud rate, etc. can be changed in the parameter settings of a programming tool or in a sequence program. Number of connectable units Transmission standard Protocol type Control procedure Communication method 16 maximum RS-485 or RS-232C standard RS-485: 500 m (1640' 5") or less [50 m (164' 0") or less when 485BD is included in system] RS-232C: 15 m (49' 2") or less Computer link (dedicated protocol) Distance varies depending on communication equipment type. Formats 1 and 4 are applicable. — Half-duplex, bidirectional communication 38400 Start bit Character Data bit format Parity bit Stop bit Inverter Communication *1 bps Fixed 7 or 8-bit None, odd or even F 1 or 2-bit Fixed Terminator Fixed Control line Fixed Sum check Provided or not provided Non-Protocol Communication (RS/RS2 Instruction) Header D E 300, 600, 1200, 2400, 4800, 9600, 19200 or Baud rate *1. Remarks Computer Link Maximum total extension distance Specifications Parallel Link Item C FX3U and FX3UC Series PLC Ver. 2.41 or later, and FX3S, FX3G, FX3GC Series PLC is applicable. G Non-Protocol Communication (FX2N-232IF) H Programming Communication I Remote Maintenance Apx.A Discontinued models D-9 FX Series PLC User's Manual - Data Communication Edition 2 Specifications Computer Link 2.2 Link Specifications 2.2 Link Specifications 2.2.1 Applicable commands and number of device points Number of points processed in one-time update Command Name Symbol Unit: Bit Batch reading WR 57H, 52H Device memory BW *1 BT WT 51H, 57H 42H, 54H 57H, 54H Unit: Word PLC QT*1 51H, 54H 54 FX2(FX), FX3S, FX2C, FX3G, FX3GC, FX1N, FX1NC, FX3U, FX3UC FX2N, FX2NC 256 256 13 words 32 words 32 words 208 points 512 points 512 points Read word devices in 1 point units. 13*4 64*2 64*2 Reads bit devices in 16 point units. — — 32 words 512 points Read word devices in 1 point units. — — 64*2 46 160 160 Writes bit devices in 16 point units. 10 words 10 words 10 words 160 points 160 points 160 points Writes word devices in 1 point units. 11*5 64*2 64*2 Writes bit devices in 16 point units. — — 10 words 160 points Writes word devices in 1 point units. — — 64*2 Specifies bit devices arbitrarily in 1 point units, and sets or resets them. 10 20 20 Specifies bit devices arbitrarily in 16 point units, and sets or resets them. 6 words 96 points Specifies word devices arbitrarily in 1 point units, and writes them. 6*3 10*3 10*3 Specifies bit devices arbitrarily in 16 point units, and sets or resets them. — — 10 words 160 points Specifies word devices arbitrarily in 1 point units, and writes them. — — 10*3 — — — 1 1 1 Remote RUN RR Remote STOP RS 52H, 52H Requests remote RUN or remote 52H, 53H STOP to PLC. PLC model name reading PC 50H, 43H Reads PLC model name. GW Turns global signal ON or OFF 47H, 57H (M8126 in FX Series) in all PLCs connected in computer link. Global 10 words 10 words 160 points 160 points On-demand — — Maximum Maximum Maximum quantity quantity quantity Set the sending request flag to ON in specified in specified in specified in PLC (only when 1-to-1 connection is sequence sequence sequence adopted in system configuration). program: program: program: 64 words 64 words 13 words Loop-back test TT 54H, 54H Returns received characters back to 25 254 254 the computer as they are. characters characters characters *1. *2. *3. *4. *5. D-10 Reads bit devices in 16 point units. 42H, 57H Writes bit devices in 1 point units. WW 57H, 57H QW Test (random writing) 51H, 52H Unit: Word Unit: Bit FX0N, FX1S 42H, 52H Reads bit devices in 1 point units. Unit: Word Unit: Bit Contents of processing BR QR*1 Batch writing ASCII code Available only in FX3S, FX3G, FX3GC, FX3U and FX3UC PLCs. 32 points when 32-bit counters (C200 to C255) are specified. 32-bit counters (C200 to C255) are not applicable. 6 points when 32-bit counters (C200 to C255) are specified. 5 points when 32-bit counters (C200 to C255) are specified. FX Series PLC User's Manual - Data Communication Edition 2 Specifications Computer Link A Applicable device ranges Common Items 2.2.2 2.2 Link Specifications The tables below show devices and device number ranges applicable for the device memory access. • Construct each of the BR, BW, BT, WR, WW, and WT commands in five characters. Device + Device number 4 characters 3 characters for timer or counter • Construct each of the QR, QW, and QT commands in seven characters. Device + Device number = 7 characters C 6 characters 5 characters for timer or counter Parallel Link 1 character 2 characters for timer or counter 1. Bit devices FX PLCs do not support timer coils (TC) and counter coils (CC). Device number range (character) FX1S Input relay (X) X0000 to X0337 — Y0000 to Y0015 Y0000 Y0000 Y0000 to to to Y0267 Y0177 Y0177 — M0000 M0000 to M0511 M0000 to M1535 to M3071 — S0000 to S0127 S0000 to S0999 — TS000 to TS063 — TS000 to TS255 — CS000 to CS031 CS235 to CS254 CS000 to CS255 — — — E — — — — — — — — — — — — — — — — — Octal M008000 to M008511 TS000 to TS000 to TS000 to Decimal TS137 TS319 TS511 TS00000 TS00000 TS00000 to to to TS00137 TS00319 TS00511 CS000 to CS031 CS000 to CS255 CS200 to CS255 CS00000 to CS00031 CS00000 to CS00255 CS00200 to CS00255 F G H I — — — — — D-11 Apx.A Discontinued models — Remote Maintenance CS000 to CS031 CS235 to Counter CS255 contact (C) M8000 to M8255 X0000 X0000 X0000 to to to X0017 X0177 X0377 X000000 X000000 X000000 to to to X000017 X000177 X000377 Y0000 Y0000 Y0000 to to to Y0015 Y0177 Y0377 Y000000 Y000000 Y000000 to to to Y000015 Y000177 Y000377 M0000 to M0000 to M7679 M1535 M000000 M000000 to to M007679 M001535 S0000 to S0000 to S4095 S0255 S000000 S000000 to to S004095 S000255 M8000 to M8511 D Programming Communication Special M8000 to M8254 auxiliary relay (M) Timer contact (T) Y0000 to Y0337 FX3S FX3U, FX3UC Non-Protocol Communication (FX2N-232IF) State relay (S) X0000 X0000 X0000 to to to X0267 X0177 X0177 FX0N FX3G, FX3GC Non-Protocol Communication (RS/RS2 Instruction) Auxiliary relay (M) FX2N, FX2NC Inverter Communication Output relay (Y) X0000 to X0017 FX2(FX), FX1N, FX2C FX1NC Available Device commands number expression BR, WR, QR, Decimal/ BW, WW, QW, Octal BT WT QT Computer Link Device B N:N Network 1 character 2 characters for timer or counter = 5 characters FX Series PLC User's Manual - Data Communication Edition 2 Specifications Computer Link 2.2 Link Specifications 2. Word devices Device number range (character) Device FX1S Timer current value (T) FX0N TN000 to TN063 FX2(FX), FX1N, FX2C FX1NC FX2N, FX2NC TN000 to TN255 — CN000 to CN031 CN235 Counter to current CN255 value (C) CN000 to CN031 CN235 to CN254 CN000 to CN255 — Data register (D) File register (D) RAM file register (D) Extension register (R) Special data register (D) *1. D0000 to D0255 D0000 to D0999 D0000 to D7999 — — D1000 to D2499 D1000 to D2999 FX3S FX3G, FX3GC FX3U, FX3UC TN000 TN000 TN000 to to to TN137 TN319 TN511 TN00000 TN00000 TN00000 to to to TN00137 TN00319 TN00511 CN000 to CN031 CN000 to CN255 CN200 to CN255 CN00000 to CN00031 CN00000 to CN00200 CN00255 to CN00255 D0000 to D0000 to D7999 D2999 Decimal D000000 D000000 to to D007999 D002999 — — *1 — — *1 — — — — — — — — — — D8000 to D8511 — D008000 to D008511 — — — — D6000 to D7999 — — — — D8000 to D8255 D8000 to D8255 — Available Device commands number expression BR, WR, QR, Decimal/ BW, WW, QW, Octal BT WT QT R0000 to R9999 R000000 R000000 to to R023999 R032767 — The WT and QT commands do not support 32-bit counters (C200 to C255). Caution 1) When using bit devices in a command requiring specification in 1-word units, make sure that the head device number is a multiple of "8". 2) Special auxiliary relays and special data registers are classified into ones for read only, write only and ones for system only. If data is written to any range in which writing is not allowed, an error may occur in the PLC. For details on special auxiliary relays and special data registers, refer to the manual of the PLC. 3) In FX1S, FX1N, FX1NC, FX2N, FX2NC, FX3S, FX3G, FX3GC, FX3U and FX3UC PLCs, the PLCs cannot access the program area (in the built-in RAM, memory cassette and built-in EEPROM) when users set file registers (D). In FX 3U and FX3UC PLCs, extension registers (R) cannot access extension file registers (ER) in a mounted memory cassette. In FX3G, FX3GC PLCs, extension registers (R) cannot access extension file registers (ER). D-12 FX Series PLC User's Manual - Data Communication Edition 2 Specifications Computer Link A Link time Common Items 2.2.3 2.2 Link Specifications 1. Data transfer Data transfer Data transfer B Interval time Time to read continuous word devices (timers, counters or data registers) in one station = (21*1 + 4 Number of read points*2) Time to send or receive 1 character (ms) + Interval time + Maximum scan time (special data register D8012) in PLC 3 + Message waiting time *1. The number of points is counted in 1-word units. 3. Time to send or receive one character The table below shows the time required to send or receive one character when the start bit is 1-bit, the data length is 7-bit, the parity is 1-bit, and the stop bit is 1-bit. 38400*3 0.26 F Number of stations <When the transmission speed is 19200 bps> Unit : sec Number of stations 1 8 16 Number of data points 1 8 16 10 0.3 1.9 3.7 10 0.2 1.6 3.2 32 0.4 2.6 5.2 32 0.3 2.0 3.9 64 0.5 3.7 7.3 64 0.4 2.5 5.0 *3. Available only in FX3S, FX3G, FX3GC, FX3U and FX3UC PLCs. *4. The message waiting time is "0" when the RS-485 interface and two-pair wiring are used. The message waiting time is "0" also when the RS-232C interface is used. When one-pair wiring is adopted, a message waiting time of 70 to 150 ms is required for each transfer. Add this message waiting time. Apx.A Discontinued models *5. I Remote Maintenance When the types of read or written devices increase, "Data transfer time shown in above table Number of device types" is required. When the number of read or written points exceeds "64"*5, the transfer time increase. Accordingly, for achieving efficient data transfer, it is recommended to decrease the number of types of transferred devices and use as many continuous device numbers as possible. H Programming Communication Number of data points G Non-Protocol Communication (FX2N-232IF) The tables below show the data transfer times depending on the number of continuously read or written word devices at the transmission speeds of 9600 bps and 19200 bps when the message waiting time is 0 ms*4, the maximum scan time is 20 ms, and the interval time is 100 ms. <When the transmission speed is 9600 bps> Unit : sec E Non-Protocol Communication (RS/RS2 Instruction) Time to send or receive 1 character (ms) 33.34 16.67 8.34 4.17 2.08 1.04 0.52 Inverter Communication Transmission speed (baud rate) (bps) 300 600 1200 2400 4800 9600 19200 D Computer Link *2. This is the number of characters when the protocol format 1 is used and the sum check is not provided. When the protocol format 4 is used, add "4" to this value. When the sum check is provided, add "4" to this value also. C Parallel Link Time to write continuous word devices (timers, counters or data registers) in one station = (20*1 + 4 Number of written points*2) Time to send or receive 1 character (ms) + Interval time + Maximum scan time (special data register D8012) in PLC + Message waiting time N:N Network 2. Data transfer time The maximum number of points is as follows for the FX0N and FX1S PLCs: Maximum number of read points : 13 Maximum number of written points: 11 D-13 FX Series PLC User's Manual - Data Communication Edition 3 System Configuration and Equipment Selection Computer Link 3. 3.1 System Configuration System Configuration and Equipment Selection This chapter explains the system configuration and communication equipment selection operating in accordance with RS-485 or RS-232C required by FX PLCs. 3.1 System Configuration This section outlines the system configuration required to use computer link. Connect (optional) equipment operating in accordance with RS-485 or RS-232C to the FX PLC main unit. 1 , 2 , 3 and 4 indicate the communication equipment combination patterns. Communication equipment operating in accordance with RS-485 or RS-232C Important point in selection Total extension distance + This is the communication board built into the PLC, reducing the installation area. RS-485: 50 m (164' 0") RS-232C: 15 m (49' 2") + Attach the special adapter connection board to the main unit, and then attach the communication adapter to the left side of the main unit. RS-485: 500 m (1640' 5") RS-232C: 15 m (49' 2") + Attach the connector conversion adapter to the main unit, and then attach the communication adapter to the left of the main unit. RS-485: 500 m (1640' 5") RS-232C: 15 m (49' 2") + Attach the communication adapter to the left side of the main unit. RS-485: 500 m (1640' 5") RS-232C: 15 m (49' 2") FX PLC 1 Communication board 2 + Communication adapter Special adapter connection board 3 + Communication adapter Connector conversion adapter 4 Communication adapter For communication equipment combinations for each FX Series, refer to the next page. D-14 FX Series PLC User's Manual - Data Communication Edition 3 System Configuration and Equipment Selection Computer Link A Applicable FX PLC and Communication Equipment For communication in accordance with RS-232C FX Series Communication equipment (option) Total extension distance Check C Parallel Link 3.2.1 B N:N Network Select a (optional) communication equipment combination, and put a check mark in the "Check" column. During selection, pay attention to the following: - In the table below, only the external dimensions are different between the units shown in "FX2NC-485ADP/ FX0N-485ADP". Select either one. - In the table below, only the outside dimensions and D-SUB connector shape are different between units shown in "FX2NC-232ADP/FX0N-232ADP". Select either one. - In the table below, only the cable is different between the units shown in "FX3G-485-BD/FX3G-485-BDRJ". Select either one. - Computer link is not provided for the FX1, FX0 or FX0S PLCs. Common Items 3.2 3.2 Applicable FX PLC and Communication Equipment D Computer Link 15 m (49' 2") FX0N FX2NC-232ADP (9-pin D-Sub, male) FX0N-232ADP (25-pin D-Sub, female) E Inverter Communication 15 m (49' 2") FX1N-232-BD (9-pin D-Sub, male) + + FX1N-CNV-BD FX2NC-232ADP FX1N-CNV-BD (9-pin D-Sub, male) Non-Protocol Communication (RS/RS2 Instruction) FX1S F 15 m (49' 2") G FX0N-232ADP (25-pin D-Sub, female) Non-Protocol Communication (FX2N-232IF) 15 m (49' 2") FX1N-232-BD H (9-pin D-Sub, male) + (9-pin D-Sub, male) 15 m (49' 2") I FX0N-232ADP Remote Maintenance FX1N-CNV-BD FX2NC-232ADP FX1N-CNV-BD + Programming Communication FX1N (25-pin D-Sub, female) Apx.A Discontinued models D-15 FX Series PLC User's Manual - Data Communication Edition 3 System Configuration and Equipment Selection Computer Link 3.2 Applicable FX PLC and Communication Equipment FX Series Communication equipment (option) Total extension distance 15 m (49' 2") FX2N-232-BD (9-pin D-Sub, male) FX2N + + FX2N-CNV-BD FX2NC-232ADP (9-pin D-Sub, male) FX2N-CNV-BD 15 m (49' 2") FX0N-232ADP (25-pin D-Sub, female) 15 m (49' 2") FX3G-232-BD (9-pin D-Sub, male) + FX3S FX3S-CNV-ADP 15 m (49' 2") FX3U-232ADP(-MB) (9-pin D-Sub, male) 15 m (49' 2") FX3G-232-BD (9-pin D-Sub, male) FX3G (14-point, 24-point type) 15 m (49' 2") FX3G-CNV-ADP D-16 FX3U-232ADP(-MB) (9-pin D-Sub, male) Check FX Series PLC User's Manual - Data Communication Edition Computer Link 3 System Configuration and Equipment Selection 3.2 Applicable FX PLC and Communication Equipment A Communication equipment (option) Total extension distance Check When using channel 1 (ch 1) ch1 Common Items FX Series B N:N Network 15 m (49' 2") FX3G-232-BD (9-pin D-Sub, male) C The communication equipment works as ch1 when connected to the option connector 1. Parallel Link 15 m (49' 2") Computer Link FX3G-CNV-ADP D FX3U-232ADP(-MB) (9-pin D-Sub, male) When using channel 2 (ch 2) E Inverter Communication FX3G (40-point, 60-point type) 15 m (49' 2") FX3G-232-BD (9-pin D-Sub, male) F FX3U- ADP(-MB) (Where represents 232 and 485). FX3U-232ADP(-MB) (9-pin D-Sub, male) G 15 m (49' 2") Non-Protocol Communication (FX2N-232IF) FX3G-CNV-ADP Non-Protocol Communication (RS/RS2 Instruction) The communication equipment works as ch2 when connected to the option connector 2. Ch2 is not available when the FX3G-8AV-BD, FX3G-4EX-BD or FX3G-2EYT-BD is connected to the option connector 2. H Programming Communication I Remote Maintenance Apx.A Discontinued models D-17 FX Series PLC User's Manual - Data Communication Edition 3 System Configuration and Equipment Selection Computer Link 3.2 Applicable FX PLC and Communication Equipment FX Series Total extension distance Communication equipment (option) When using channel 1 (ch 1) ch1 15 m (49' 2") RD SD FX3U-232-BD (9-pin D-Sub, male) ch1 + FX3U-CNV-BD 15 m (49' 2") FX3U-232ADP(-MB) (9-pin D-Sub, male) When using channel 2 (ch 2) ch1 ch2 + RD FX3U SD FX3U--BD (Where represents 232, 422, 485, USB and 8AV) 15 m (49' 2") FX3U-232ADP(-MB) (9-pin D-Sub, male) When a FX3U-8AV-BD is used, it occupies one communication port channel. ch1 + ch2 + FX3U-CNV-BD FX3U-232ADP(-MB), FX3U-485ADP(-MB) (European terminal block) FX3U-485ADP(-MB), FX3U-CF-ADP When a FX3U-CF-ADP is used, it occupies one communication port channel. 15 m (49' 2") 15 m (49' 2") FX1NC FX2NC-232ADP (9-pin D-Sub, male) FX0N-232ADP (25-pin D-Sub, female) 15 m (49' 2") FX2NC D-18 FX2NC-232ADP (9-pin D-Sub, male) FX0N-232ADP (25-pin D-Sub, female) Check FX Series PLC User's Manual - Data Communication Edition 3 System Configuration and Equipment Selection Computer Link 3.2 Applicable FX PLC and Communication Equipment A Communication equipment (option) Total extension distance Check When using channel 1 (ch 1) ch1 Common Items FX Series B N:N Network 15 m (49' 2") FX3U-232ADP(-MB) (9-pin D-Sub, male) C When using channel 2 (ch 2) ch2 Parallel Link ch1 FX3GC + 15 m (49' 2") D FX3U-232ADP(-MB) FX3U-232ADP(-MB), FX3U-485ADP(-MB) Computer Link (9-pin D-Sub, male) When using channel 1 (ch 1) ch1 E Inverter Communication 15 m (49' 2") FX3U-232ADP(-MB) (9-pin D-Sub, male) When using channel 2 (ch 2) ch1 + 15 m (49' 2") G FX3U-232ADP(-MB) (9-pin D-Sub, male) Non-Protocol Communication (FX2N-232IF) FX3U-232ADP(-MB), FX3U-485ADP(-MB), FX3U-CF-ADP Non-Protocol Communication (RS/RS2 Instruction) FX3UC (D, DS, DSS) F ch2 When a FX3U-CF-ADP is used, it occupies one communication port channel. H Programming Communication I Remote Maintenance Apx.A Discontinued models D-19 FX Series PLC User's Manual - Data Communication Edition 3 System Configuration and Equipment Selection Computer Link 3.2 Applicable FX PLC and Communication Equipment FX Series Total extension distance Communication equipment (option) When using channel 1 (ch 1) ch1 15 m (49' 2") RD SD FX3U-232-BD (9-pin D-Sub, male) ch1 + FX3U-CNV-BD 15 m (49' 2") FX3U-232ADP(-MB) (9-pin D-Sub, male) When using channel 2 (ch 2) ch1 ch2 + RD FX3UC-32MT-LT (-2) SD FX3U--BD (Where represents 232, 422, 485, USB and 8AV) 15 m (49' 2") FX3U-232ADP(-MB) (9-pin D-Sub, male) When a FX3U-8AV-BD is used, it occupies one communication port channel. ch1 + ch2 + 15 m (49' 2") FX3U-232ADP(-MB), FX3U-232ADP(-MB) (9-pin D-Sub, male) FX3U-485ADP(-MB), FX3U-CF-ADP When a FX3U-CF-ADP is used, it occupies one communication port channel. FX3U-CNV-BD 15 m (49' 2") FX2(FX) FX-232ADP (25-pin D-Sub, female) 15 m (49' 2") FX2C D-20 FX-232ADP (25-pin D-Sub, female) Check FX Series PLC User's Manual - Data Communication Edition 3 System Configuration and Equipment Selection Computer Link A For communication in accordance with RS-485 FX Series Total extension distance Communication equipment (option) Check Common Items 3.2.2 3.2 Applicable FX PLC and Communication Equipment B N:N Network 500 m (1640' 5") FX0N FX2NC-485ADP FX0N-485ADP (European terminal block) (Terminal block) C Parallel Link 50 m (164' 0") FX1N-485-BD (European terminal block) D FX1N-CNV-BD + FX2NC-485ADP (European terminal block) FX1N-CNV-BD Computer Link + FX1S 500 m (1640' 5") E FX0N-485ADP (Terminal block) Inverter Communication 50 m (164' 0") FX1N-485-BD F (European terminal block) FX2NC-485ADP (European terminal block) FX1N-CNV-BD 500 m (1640' 5") G FX0N-485ADP Non-Protocol Communication (FX2N-232IF) FX1N-CNV-BD + Non-Protocol Communication (RS/RS2 Instruction) + FX1N (Terminal block) 50 m (164' 0") H + FX2N FX2NC-485ADP (European terminal block) 500 m (1640' 5") I FX2N-CNV-BD FX0N-485ADP Remote Maintenance FX2N-CNV-BD + Programming Communication FX2N-485-BD (Terminal block) Apx.A Discontinued models D-21 FX Series PLC User's Manual - Data Communication Edition 3 System Configuration and Equipment Selection Computer Link 3.2 Applicable FX PLC and Communication Equipment FX Series Communication equipment (option) Total extension distance 50 m (164' 0") FX3G-485-BD (European terminal block) FX3G-485-BD-RJ (RJ45 connector) + FX3S 500 m (1640' 5") FX3S-CNV-ADP FX3U-485ADP(-MB) (European terminal block) 50 m (164' 0") FX3G-485-BD (European terminal block) FX3G-485-BD-RJ (RJ45 connector) FX3G (14-point, 24-point type) 500 m (1640' 5") FX3G-CNV-ADP FX3U-485ADP(-MB) (European terminal block) When using channel 1 (ch 1) 50 m (164' 0") FX3G-485-BD (European terminal block) FX3G-485-BD-RJ (RJ45 connector) The communication equipment works as ch1 when connected to the option connector 1. FX3G (40-point, 60-point type) 500 m (1640' 5") FX3G-CNV-ADP D-22 FX3U-485ADP(-MB) (European terminal block) Check FX Series PLC User's Manual - Data Communication Edition 3 System Configuration and Equipment Selection Computer Link 3.2 Applicable FX PLC and Communication Equipment A Communication equipment (option) Total extension distance Check When using channel 2 (ch 2) Common Items FX Series B N:N Network 50 m (164' 0") FX3G-485-BD (European terminal block) FX3G-485-BD-RJ (RJ45 connector) C The communication equipment works as ch2 when connected to the option connector 2. Parallel Link FX3G (40-point, 60-point type) FX3U- ADP(-MB) FX3U-485ADP(-MB) (Where represents (European terminal block) 232 and 485). Computer Link FX3G-CNV-ADP D 500 m (1640' 5") Ch2 is not available when the FX3G-8AV-BD, FX3G-4EX-BD or FX3G-2EYT-BD is connected to the option connector 2. E Inverter Communication When using channel 1 (ch 1) ch1 RD A 50 m (164' 0") RD RD B SD A SD SD B SG F Non-Protocol Communication (RS/RS2 Instruction) FX3U-485-BD (European terminal block) ch1 FX3U FX3U-CNV-BD G 500 m (1640' 5") Non-Protocol Communication (FX2N-232IF) + FX3U-485ADP(-MB) (European terminal block) H Programming Communication I Remote Maintenance Apx.A Discontinued models D-23 FX Series PLC User's Manual - Data Communication Edition 3 System Configuration and Equipment Selection Computer Link 3.2 Applicable FX PLC and Communication Equipment FX Series Total extension distance Communication equipment (option) When using channel 2 (ch 2) ch1 ch2 + RD SD FX3U--BD (Where represents 232, 422, 485, USB and 8AV). 500 m (1640' 5") FX3U-485ADP(-MB) (European terminal block) When a FX3U-8AV-BD is used, it occupies one communication port channel. ch1 FX3U ch2 + FX3U-CNV-BD + FX3U-232ADP(-MB), FX3U-485ADP(-MB), FX3U-CF-ADP 500 m (1640' 5") FX3U-485ADP(-MB) (European terminal block) When a FX3U-CF-ADP is used, it occupies one communication port channel. 500 m (1640' 5") FX1NC FX2NC-485ADP (European terminal block) FX0N-485ADP (Terminal block) 500 m (1640' 5") FX2NC FX2NC-485ADP (European terminal block) FX0N-485ADP (Terminal block) When using channel 1 (ch 1) ch1 500 m (1640' 5") FX3U-485ADP(-MB) (European terminal block) When using channel 2 (ch 2) ch1 FX3GC + FX3U- ADP(-MB) (Where represents 232 and 485). D-24 ch2 500 m (1640' 5") FX3U-485ADP(-MB) (European terminal block) Check FX Series PLC User's Manual - Data Communication Edition 3 System Configuration and Equipment Selection Computer Link 3.2 Applicable FX PLC and Communication Equipment A Total extension distance Communication equipment (option) Check When using channel 1 (ch 1) ch1 Common Items FX Series B N:N Network 500 m (1640' 5") FX3U-485ADP(-MB) (European terminal block) C When using channel 2 (ch 2) ch2 FX3UC (D, DS, DSS) Parallel Link ch1 + 500 m (1640' 5") D Computer Link FX3U-232ADP(-MB), FX3U-485ADP(-MB) (European terminal block) FX3U-485ADP(-MB), FX3U-CF-ADP When a FX3U-CF-ADP is used, it occupies one communication port channel. When using channel 1 (ch 1) E ch1 Inverter Communication RD A 50 m (164' 0") RD RD B SD A SD SD B SG FX3U-485-BD F (European terminal block) + FX3U-CNV-BD Non-Protocol Communication (RS/RS2 Instruction) ch1 500 m (1640' 5") G FX3U-485ADP(-MB) Non-Protocol Communication (FX2N-232IF) (European terminal block) When using channel 2 (ch 2) ch1 + RD SD FX3U--BD (Where represents 232, 422, 485, USB and 8AV). H 500 m (1640' 5") Programming Communication FX3UC-32MT-LT (-2) ch2 FX3U-485ADP(-MB) (European terminal block) When a FX3U-8AV-BD is used, it occupies one communication port channel. + I ch2 + Remote Maintenance ch1 500 m (1640' 5") Apx.A FX3U-CNV-BD Discontinued models FX3U-232ADP(-MB), FX3U-485ADP(-MB) (European terminal block) FX3U-485ADP(-MB), FX3U-CF-ADP When a FX3U-CF-ADP is used, it occupies one communication port channel. D-25 FX Series PLC User's Manual - Data Communication Edition 3 System Configuration and Equipment Selection Computer Link 3.2 Applicable FX PLC and Communication Equipment FX Series Communication equipment (option) Total extension distance 500 m (1640' 5") FX2 FX-485ADP (Terminal block) 500 m (1640' 5") FX2C D-26 FX-485ADP (Terminal block) Check FX Series PLC User's Manual - Data Communication Edition Computer Link 4 Wiring 3.2 Applicable FX PLC and Communication Equipment A Common Items 4. Wiring B This chapter explains the wiring. N:N Network WIRING PRECAUTIONS WIRING PRECAUTIONS C Parallel Link • Make sure to cut off all phases of the power supply externally before attempting installation or wiring work. Failure to do so may cause electric shock or damage to the product. • Make sure to attach the terminal cover, offered as an accessory, before turning on the power or initiating operation after installation or wiring work. Failure to do so may cause electric shock. D Computer Link E Inverter Communication F Non-Protocol Communication (RS/RS2 Instruction) G Non-Protocol Communication (FX2N-232IF) • Make sure to observe the following precautions in order to prevent any damage to the machinery or accidents due to abnormal data written to the PLC under the influence of noise: 1) Do not bundle the main circuit line together with or lay it close to the main circuit, high-voltage line or load line. Otherwise, noise disturbance and/or surge induction are likely to take place. As a guideline, lay the control line at least 100mm (3.94") or more away from the main circuit or high-voltage lines. 2) Ground the shield wire or shield of the shielded cable at one point on the PLC. However, do not use common grounding with heavy electrical systems. • Make sure to properly wire the terminal block in accordance with the following precautions. Failure to do so may cause electric shock, equipment failures, a short-circuit, wire breakage, malfunctions, or damage to the product. - The disposal size of the cable end should follow the dimensions described in the manual. - Tightening torque should follow the specifications in the manual. - Tighten the screws using a Phillips-head screwdriver No.2 (shaft diameter 6mm (0.24") or less). Make sure that the screwdriver does not touch the partition part of the terminal block. • Make sure to properly wire to the terminal block (European type) in accordance with the following precautions. Failure to do so may cause electric shock, equipment failures, a short-circuit, wire breakage, malfunctions, or damage to the product. - The disposal size of the cable end should follow the dimensions described in the manual. - Tightening torque should follow the specifications in the manual. - Twist the end of strand wire and make sure that there are no loose wires. - Do not solder-plate the electric wire ends. - Do not connect more than the specified number of wires or electric wires of unspecified size. - Affix the electric wires so that neither the terminal block nor the connected parts are directly stressed. H Programming Communication I Remote Maintenance Apx.A Discontinued models D-27 FX Series PLC User's Manual - Data Communication Edition 4 Wiring Computer Link 4.1 1 4.1 Wiring Procedure Wiring Procedure Selecting the connection method Select the wiring method suitable to the application. For details, refer to Section 4.2. 2 Preparing for wiring Prepare cables and terminal resistors required for wiring. For details, refer to Section 4.3. 3 Turning OFF the PLC power Before starting any wiring work, make sure that the PLC power is OFF. 4 Connecting the power supply (FX0N-485ADP only) Connect the power supply to the 24V DC power terminal. 5 Wiring communication equipment Connect communication equipment operating in accordance with RS-485 or RS-232C. For communication in accordance with RS-232C, refer to Section 4.4. For communication in accordance with RS-485, refer to Section 4.5. D-28 FX Series PLC User's Manual - Data Communication Edition 4 Wiring Computer Link A Selecting Connection Method 4.2.1 For communication in accordance with RS-232C (1-to-1 connection) With communication in accordance with RS-232C, 1-to-1 connection is applicable. Make sure that the total extension distance is 15 m (49' 2") or less. FX PLC C Parallel Link Personal computer B N:N Network When using computer link, communication can be achieved in accordance with RS-232C or RS-485 (422). In FX3G, FX3GC, FX3U and FX3UC PLCs, computer link is applicable in up to two channels at the same time. In such a case, communication can be achieved in accordance with RS-232C on both channels, in accordance with RS-485 on both channels, or in accordance with RS-232C on one channel and RS-485 on the other channel. Common Items 4.2 4.2 Selecting Connection Method D + Computer Link Communication equipment operating in accordance with RS-232C 15 m (49' 2") or less E For communication in accordance with RS-485 (RS-422) (1-to-N connection) With communication in accordance with RS-485 (RS-422), up to 16 PLCs can be connected. Make sure that the total extension distance is 500 m (1640' 5") or less [50 m (164' 0") or less when 485BD is included]. Personal computer FX PLC Station No. 0 ... + + Communication equipment operating in accordance with RS-485 Communication equipment operating in accordance with RS-485 G One-pair wiring and two-pair wiring are applicable for communication in accordance with RS-485 (RS-422). The wiring method is determined for each application. Refer to the table below, and perform suitable wiring. Computer link Two-pair wiring When the message waiting time*2 should be 70 ms or less — When the message waiting time*2 may be more than 70 ms *3 When the on-demand function is used — *1. When computer link is added to an existing system, adopt the wiring method used in the existing system. *2. For the message waiting time, refer to Subsection 6.4.3. *3. "Echo transfer" is generated when the FX-485PC-IF is used in the one-pair wiring. Take proper countermeasures in the computer so that the echo transfer can be ignored. I Remote Maintenance : Recommended wiring method, : Applicable wiring method, —: Non-applicable wiring method H Programming Communication *1 One-pair wiring Non-Protocol Communication (FX2N-232IF) FX-485PC-IF F FX PLC Station No. 15 Non-Protocol Communication (RS/RS2 Instruction) RS-232C/RS-485 communication converter Inverter Communication 4.2.2 Apx.A Discontinued models D-29 FX Series PLC User's Manual - Data Communication Edition Computer Link 4.3 4 Wiring 4.3 Selecting Cables and Terminal Resistors (RS-485) Selecting Cables and Terminal Resistors (RS-485) Select cables using the procedure described below. 4.3.1 Twisted pair cable Use shielded twisted pair cables for connecting communication equipment operating in accordance with RS485. The table below shows recommended model names and manufacturers of cables used in wiring. 1. Recommended cables Manufacturer Model name Mitsubishi Cable Industries, Ltd. Showa Holdings Co., Ltd. Sumitomo Electric Industries, Ltd. The Furukawa Electric Co., Ltd. Fujikura Ltd. Remarks SPEV(SB)-0.2-2P Two-pair cable of 0.2 mm2 SPEV(SB)-MPC-0.2 3P Three-pair cable of 0.2 mm2 SPEV(SB)-0.5-2P Two-pair cable of 0.5 mm2 KMPEV-SB CWS-178 0.2SQ 2P Two-pair cable of 0.2 mm2 KMPEV-SB CWS-178 0.5SQ 2P Two-pair cable of 0.5 mm2 DPEV SB 0.3 3P Three-pair cable of 0.3 mm2 DPEV SB 0.5 3P Three-pair cable of 0.5 mm2 D-KPEV-SB 0.2 3P Three-pair cable of 0.2 mm2 D-KPEV-SB 0.5 3P Three-pair cable of 0.5 mm2 IPEV-SB 2P 0.3 mm2 Two-pair cable of 0.3 mm2 IPEV-SB 2P 0.5 mm2 Two-pair cable of 0.5 mm2 2. Cable structural drawing (reference) Pair Shield Two-pair cable structural drawing example 4.3.2 Three-pair cable structural drawing example 10BASE-T cable 10BASE-T cables used in LAN wiring for a personal computer can be connected to FX3G-485-BD-RJ. 1. Selection procedure when purchasing 1) Cable type : 10BASE-T cable (Category 3 or higher) 2) Connection specifications : Straight type 3) Connector : RJ45 connector (Connector with metal frame is used) 2. Cautions on using commercial cables Pay attention to the following point when purchasing commercial cables. • Use shielded cables. Make sure to connect the shield to the metal frame of the connector, and perform class D grounding. D-30 FX Series PLC User's Manual - Data Communication Edition 4 Wiring Computer Link A Connecting cables 1. European type terminal block Cable size when Cable size when one cable is two cables are connected connected AWG22 to AWG20 AWG22 Tightening torque Applicable 0.22 to 0.25 (AWG22 to AWG20) N·m Tool size A B 0.4 (0.01") 2.5 (0.09") AWG20 to AWG16 Not applicable 0.5 to 0.6 N·m 0.6 (0.03") 3.5 (0.14") FX2N-485-BD FX1N-485-BD AWG26 to AWG16 Not applicable 0.5 to 0.6 N·m 0.6 (0.03") 3.5 (0.14") Not applicable 0.4 to 0.5 N·m 0.6 (0.03") 3.5 (0.14") FX2NC-485ADP AWG26 to AWG16 AWG26 to AWG20 • When using a stranded cable or solid cable as it is - Twist the end of a stranded cable so that wires do not get barbed. - Do not plate the end of the cable. FX3G-485-BD-RJ, FX2N-485-BD, FX1N-485-BD Approx. 9 mm (0.35") Approx. 6 mm (0.23") Model name Caulking tool Phoenix Contact Co., Ltd. AI 0.5-8WH CRIMPFOX 6*1 (or CRIMPFOX 6T-F*2) Insulating sleeve Contact area (Crimp area) 8 mm (0.31") 2.6 mm (0.1") H 14 mm (0.55") Programming Communication Manufacturer G Approx. 8 mm (0.31") Non-Protocol Communication (FX2N-232IF) • When using a bar terminal with insulating sleeve Because it is difficult to insert a cable into an insulating sleeve depending on the thickness of the cable sheath, select the proper cable according to the outline drawing. <Reference> *1. *2. F FX2NC-485ADP Non-Protocol Communication (RS/RS2 Instruction) FX3G-485-BD, FX3U-485-BD, FX3U-485ADP(-MB) E Inverter Communication Do not tighten terminal screws with a torque outside the above-mentioned range. Failure to do so may cause equipment failures or malfunctions. With regard to the cable end treatment, use a stranded cable or solid cable as it is, or use a bar terminal with insulating sleeve. FX3G-485-BD-RJ, FX2N-485-BD, FX1N-485-BD and FX2NC-485ADP cannot use a bar terminal with insulating sleeve. D Computer Link FX3G-485-BDRJ C Parallel Link FX3U-485-BD FX3G-485-BD FX3U-485ADP (-MB) Bar terminal with Insulating sleeve (cable size) B N:N Network The FX3G-485-BD-RJ terminal block is used for grounding. The other options use shielded twisted pair cables for connecting communication equipment operating in accordance with RS-485. The table below shows applicable cables and tightening torques. Common Items 4.3.3 4.3 Selecting Cables and Terminal Resistors (RS-485) Old model name : CRIMPFOX ZA 3 Old model name : CRIMPFOX UD 6 I Remote Maintenance Apx.A Discontinued models D-31 FX Series PLC User's Manual - Data Communication Edition 4 Wiring Computer Link 4.3 Selecting Cables and Terminal Resistors (RS-485) • Tool When tightening a terminal on the European terminal block, use a small commercial straight shape screwdriver whose tip is shown in the figure to the right. Select a screwdriver with a straight tip. Note A If the diameter of screwdriver grip is too small, tightening torque will not be able to be achieved. To achieve the appropriate tightening torque shown in the previous page, use the following screwdriver or an appropriate replacement (grip diameter: approximately 25mm (0.98")). For size A and size B, refer to the table above. <Reference> FX3U-485-BD, FX3G-485-BD, FX3U-485ADP(-MB) Manufacturer Phoenix Contact Co., Ltd. Model name SZS 0.4 2.5 FX3G-485-BD-RJ, FX2N-485-BD, FX1N-485-BD, FX2NC-485ADP Manufacturer Phoenix Contact Co., Ltd. Model name SZF 1-0.6 3.5 2. Terminal block In the FX0N-485ADP and FX-485ADP, the terminal screw size is "M3". Make sure to use a crimp-style terminal with the following sizes. Make sure that the tightening torque is 0.5 to 0.8 N·m. Do not tighten terminal screws with a torque outside the above-mentioned range. Failure to do so may cause equipment failures or malfunctions. • When wiring one cable to one terminal 6.2mm(0.24") or less 6.2mm(0.24") or less 3.2(0.13") Terminal Crimp screw terminal 3.2(0.13") Terminal • When wiring two cables to one terminal 6.2mm(0.24") or less 6.2mm(0.24") or less D-32 3.2(0.13") 6.3mm(0.25") or more Terminal Crimp screw terminal 3.2(0.13") Terminal 6.3mm(0.25") or more B FX Series PLC User's Manual - Data Communication Edition Computer Link A Connecting terminal resistors Make sure to provide a terminal resistor at the end of each line. In the case of one-pair wiring, connect a terminal resistor to the RDA-RDB signal terminal of the communication equipment. In the case of two-pair wiring, connect a terminal resistor to the RDA-RDB signal terminal and SDA-SDB terminal of the communication equipment. Brown Orange Brown Precision 3 3 1 =330 (101) The FX3U-485-BD, FX3G-485-BD, FX3G-485-BD-RJ and FX3U-485ADP(-MB) have built-in terminal resistors. Set the terminal resistor selector switch accordingly. • FX3U-485ADP(-MB) • FX3U-485-BD 330 OPEN 110 D Terminal resistor selector switch E Manufacturer Select a screwdriver with a straight tip. Model name 0.4mm (0.01") 2.5mm (0.09") G Non-Protocol Communication (FX2N-232IF) SZS 0.4 2.5 Phoenix Contact Co., Ltd. F Non-Protocol Communication (RS/RS2 Instruction) Removal: Loosen the terminal block mounting screws, and remove the terminal block. Installation: Attach the terminal block, and tighten the terminal block mounting screws. Tightening torque: 0.4 to 0.5 N•m Do not tighten terminal screws with a torque outside the above-mentioned range. Failure to do so may cause equipment failures or malfunctions. Inverter Communication • FX3G-485-BD Remove the upper terminal block before changing over the switch in the FX3G-485-BD. For installation and removal of the terminal block, use the recommended tool shown below or a tool having straight tip (such as screwdriver) as shown in the right figure. <Reference> Computer Link Terminal resistor selector switch C Parallel Link 2. When using the FX3U-485-BD, FX3G-485-BD, FX3G-485-BD-RJ or FX3U-485ADP(-MB) B N:N Network 1 1 1 =110 (101) 1. Terminal resistor type In the case of one-pair wiring, use two terminal resistors of 110 , 1/2 W. In the case of two-pair wiring, use four terminal resistors of 330 , 1/4 W. Among the terminal resistors supplied with the communication equipment, select ones with the color codes shown to the right. Precision Common Items 4.3.4 4 Wiring 4.3 Selecting Cables and Terminal Resistors (RS-485) H Terminal resistor selector switch Programming Communication I Terminal block mounting screws Remote Maintenance • FX3G-485-BD-RJ Terminal resistor selector switch Apx.A Discontinued models D-33 FX Series PLC User's Manual - Data Communication Edition 4 Wiring Computer Link 4.4 4.4 Connection Diagram for RS-232C Connection Diagram for RS-232C Representative wiring examples are shown in this section. When pin numbers in the external equipment are different, wire the pins as shown below. 4.4.1 Connection diagram between FX PLC and personal computer External equipment operating in accordance with RS-232C PLC side Name FX3U-232-BD FX3G-232-BD FX2N-232-BD FX1N-232-BD FX3U-232ADP(-MB) 1 Name FG When CS and RS are used Name 9-pin 25-pin D-Sub D-Sub 1 FG When DR and ER are used 9-pin 25-pin D-Sub D-Sub 1 RD(RXD) 2 3 RD(RXD) 2 3 RD(RXD) 2 3 SD(TXD) 3 2 SD(TXD) 3 2 SD(TXD) 3 2 ER(DTR) 4 20 RS(RTS) 7 4 ER(DTR) 4 20 SG(GND) 5 7 SG(GND) 5 7 SG(GND) 5 7 DR(DSR) 6 6 CS(CTS) 8 5 DR(DSR) 6 6 Connection diagram between FX-485PC-IF and personal computer 485PC-IF D-34 FX0N232ADP FX-232ADP FG 4.4.2 FX2NC232ADP Personal computer Signal name Pin No. Signal name SD (TXD) 2 SD (TXD) RD (RXD) 3 RD (RXD) RS (RTS) 4 RS (RTS) CS (CTS) 5 CS (CTS) DR (DSR) 6 DR (DSR) SG (GND) 7 SG (GND) ER (DTR) 20 ER (DTR) FX Series PLC User's Manual - Data Communication Edition 4 Wiring Computer Link 4.5 Connection Diagram for RS-485 and RS-422 Connection Diagram for RS-485 and RS-422 4.5.1 One-pair wiring *3 B FX2NC-485ADP SDA (TXD+) SDA (TXD+) SDA (TXD+) SDB (TXD-) SDB (TXD-) SDB (TXD-) SDB (TXD-) RDA (RXD+) RDA (RXD+) RDA (RXD+) RDA (RXD+) RDB (RXD-) RDB (RXD-) RDB (RXD-) RDB (RXD-) LINK SG LINK SG SG FG*2 Class-D grounding (resistance: 100 or less)*1 Class-D grounding (resistance: 100 or less)*1 Terminal resistor: 110 *3 C D Computer Link SDA (TXD+) Parallel Link Terminal resistor: 110 FX0N-485ADP FX3U-485-BD FX3G-485-BD FX2N-485-BD FX1N-485-BD FX3U-485ADP(-MB) N:N Network Communication equipment operating in accordance with RS-485 Common Items 4.5 A SG *1. Make sure to perform Class-D grounding on the shield of a twisted pair cable connected to the FX2N-485-BD, FX1N-485-BD, FX3G-485-BD, FX3U-485-BD, FX2NC-485ADP or FX3U-485ADP(-MB). *2. Make sure to connect the FG terminal to the (grounding) terminal in the PLC requiring Class-D grounding. If the grounding terminal is not provided in the PLC, perform Class-D grounding directly. *3. Make sure to provide a terminal resistor at the end of each line. • The FX3U-485-BD, FX3G-485-BD and FX3U-485ADP(-MB) have a built-in terminal resistor. Set the terminal resistor selector switch accordingly • The FX0N-485ADP, FX2NC-485ADP, FX2N-485-BD and FX1N-485-BD are supplied together with terminal resistors. E Inverter Communication F Non-Protocol Communication (RS/RS2 Instruction) G Non-Protocol Communication (FX2N-232IF) H Programming Communication I Remote Maintenance Apx.A Discontinued models D-35 FX Series PLC User's Manual - Data Communication Edition 4 Wiring Computer Link 4.5 Connection Diagram for RS-485 and RS-422 • FX3G-485-BD-RJ Communication equipment operating in accordance with RS-485 SDA (TXD+) Terminal SDB resistor (TXD-) 110Ω RDA *2 (RXD+) RDB (RXD-) LINK SG Distributor (BMJ-8) 5 4 3 6 1 2 7 8 5 4 3 6 1 2 7 8 5 4 3 6 1 2 7 8 Class-D grounding Class-D Class-D grounding grounding Connector metal frame 5 4 3 6 1 2 7 8 FX3G-485-BD-RJ (Terminal resistor selector switch: Open) *1. *1 *1 SG SDB SDA RDB RDA SG SDB SDA RDB RDA Connector metal frame 5 4 3 6 1 2 7 8 5 4 3 6 1 2 7 8 5 4 3 6 1 2 7 8 *1 *1 FX3G-485-BD-RJ Distributor (BMJ-8) 5 4 3 6 1 2 7 8 Class-D grounding *1 5 RDA 4 RDB 3 SDA 6 SDB 1 SG 2 Terminal 7 resistor *2 8 Connector metal frame Class-D grounding (Terminal resistor selector switch: 110Ω)*2 FX3G-485-BD-RJ (Terminal resistor selector switch: Open) Use shielded cables, and make sure to perform class D grounding on the shield. When using the terminal block to connect ground of FX3G-485-BD-RJ, wire the ground wire only to either one of two poles of the terminal block. *2. Make sure to provide a terminal resistor at the end of each line. Set the FX3G-485-BD-RJ terminal resistor selector switch accordingly. Prepare the following devices if necessary. Product name D-36 Model name Manufacturer RJ45 connector TM11AP-88P HIROSE ELECTRIC CO., LTD. Distributor BMJ-8 BMJ-8-28N (No internal connection of the No. 2 and 8 pin) HACHIKO ELECTRIC CO., LTD. (Do not use a plug with terminal resistor) FX Series PLC User's Manual - Data Communication Edition 4 Wiring Computer Link A Two-pair wiring *3 Terminal resistor: 330 ×2 FX2NC-485ADP SDA (TXD+) SDB (TXD-) SDB (TXD-) SDB (TXD-) SDB (TXD-) RDA (RXD+) RDA (RXD+) RDA (RXD+) RDA (RXD+) RDB (RXD-) RDB (RXD-) RDB (RXD-) RDB (RXD-) LINK SG LINK SG SG FG*2 Class-D grounding (resistance: 100 or less)*1 Class-D grounding (resistance: 100 or less)*1 *3 B C *3 Terminal resistor: 330 ×2 Parallel Link *3 FX0N-485ADP SDA (TXD+) FX3U-485-BD FX3G-485-BD FX2N-485-BD FX1N-485-BD FX3U-485ADP(-MB) SDA (TXD+) N:N Network Communication equipment operating in accordance with RS-485/RS-422 SDA (TXD+) Common Items 4.5.2 4.5 Connection Diagram for RS-485 and RS-422 D SG Computer Link *1. Make sure to perform Class-D grounding on the shield of a twisted pair cable connected to the FX2N-485-BD, FX1N-485-BD, FX3G-485-BD, FX3U-485-BD, FX2NC-485ADP or FX3U-485ADP(-MB). *2. Make sure to connect the FG terminal to the (grounding) terminal in the PLC requiring Class-D grounding. If the grounding terminal is not provided in the PLC, perform Class-D grounding directly. *3. Make sure to provide a terminal resistor at the end of each line. • The FX3U-485-BD, FX3G-485-BD and FX3U-485ADP(-MB) have a built-in terminal resistor. Set the terminal resistor selector switch accordingly. • The FX0N-485ADP, FX2NC-485ADP, FX2N-485-BD and FX1N-485-BD are supplied together with terminal resistors. E Inverter Communication F Non-Protocol Communication (RS/RS2 Instruction) G Non-Protocol Communication (FX2N-232IF) H Programming Communication I Remote Maintenance Apx.A Discontinued models D-37 FX Series PLC User's Manual - Data Communication Edition 4 Wiring Computer Link 4.5 Connection Diagram for RS-485 and RS-422 • FX3G-485-BD-RJ Communication equipment operating in accordance with RS-485/RS-422 Distributor (BMJ-8) SDA 5 (TXD+) 4 SDB *2 3 (TXD-) 6 RDA (RXD+) 1 RDB *2 2 Terminal (RXD-) 7 resistor LINK 8 330Ω SG ×2 5 4 3 6 1 2 7 8 Class-D grounding 5 4 3 6 1 2 7 8 Class-D Class-D grounding grounding *1 *1 Connector metal frame 5 4 3 6 1 2 7 8 FX3G-485-BD-RJ (Terminal resistor selector switch: Open) *1. 5 4 3 6 1 2 7 8 SG SDB SDA RDB RDA SG SDB SDA RDB RDA Connector metal frame 5 4 3 6 1 2 7 8 5 4 3 6 1 2 7 8 5 4 3 6 1 2 7 8 *1 *1 FX3G-485-BD-RJ Distributor (BMJ-8) Class-D grounding *1 RDA 5 4 RDB 3 SDA 6 SDB 1 SG Terminal 2 resistor 7 *2 Terminal 8 resistor Connector metal frame Class-D grounding (Terminal resistor selector switch: 330Ω)*2 FX3G-485-BD-RJ (Terminal resistor selector switch: Open) Use shielded cables, and make sure to perform class D grounding on the shield. When using the terminal block to connect ground of FX3G-485-BD-RJ, wire the ground wire only to either one of two poles of the terminal block. *2. Make sure to provide a terminal resistor at the end of each line. Set the FX3G-485-BD-RJ terminal resistor selector switch accordingly. Prepare the following devices if necessary. Product name D-38 Model name Manufacturer RJ45 connector TM11AP-88P Distributor BMJ-8 BMJ-8-28N (No internal connection of the No. 2 and 8 pin) HACHIKO ELECTRIC CO., LTD. (Do not use a plug with terminal resistor) HIROSE ELECTRIC CO., LTD. FX Series PLC User's Manual - Data Communication Edition 4 Wiring Computer Link A Switching of 1 pair / 2 paired wiring (FX3G-485-BD-RJ) Common Items 4.5.3 4.6 Grounding The FX3G-485-BD-RJ has a built-in wiring circuit switch. Set the wiring circuit switch to 1 pair / 2 pair. B N:N Network Wiring circuit switch C Parallel Link 4.6 Grounding D Grounding should be performed as stated below. • Independent grounding should be performed for best results. When independent grounding can not be performed, perform "shared grounding" as shown in the following figure. For details, refer to the Hardware Edition of each series. Other equipment Independent grounding Best condition PLC Other equipment Shared grounding Good condition PLC Other equipment E Inverter Communication PLC Computer Link • The grounding resistance should be 100 or less. Common grounding Not allowed • The grounding wire size should be AWG 14 (2 mm2) or larger. F Non-Protocol Communication (RS/RS2 Instruction) • The grounding point should be close to the PLC, and all grounding wires should be as short as possible. G Non-Protocol Communication (FX2N-232IF) H Programming Communication I Remote Maintenance Apx.A Discontinued models D-39 FX Series PLC User's Manual - Data Communication Edition 5 Communication Setting in FX Programmable Controller Computer Link 5. 5.1 Communication Setting Methods Communication Setting in FX Programmable Controller This chapter explains the communication setting method types and setting methods for computer link. 5.1 Communication Setting Methods This section explains the communication setting methods and setting procedures in FX PLCs. 1. Setting method types 1) Specifying the setting using parameters in the sequence programming software: Register the setting as parameters by executing communication setting on the personal computer screen using the sequence programming software, and transfer them to a PLC. (This method using parameters is not available for FX2(FX), FX2C, or FX0N PLCs.) 2) Specifying the setting by writing data to special data registers: Create a sequence program specifying the communication format, station number settings and time-out time setting, and then transfer the sequence program to a PLC. Caution A PLC operates in the same way regardless of the selected method shown above. If both methods are selected, priority is given to the method using parameters. 2. Communication setting method applicability for each FX Series FX Series Specification using parameters Specification using special data registers FX1S, FX1N, FX1N, FX2N, FX2NC, FX3S, FX3G(ch1), FX3GC(ch1), FX3U(ch1), FX3UC(ch1) (Recommended) FX3G(ch2), FX3GC(ch2), FX3U(ch2), FX3UC(ch2) — FX2(FX), FX2C, FX0N — For the detailed contents of special data registers, refer to Section 9.2. Setting data write method to special data registers, refer to Section 9.3. 3. Setting data flow PLC memory Setting window Parameter area Parameter method Transferred when power is turned ON Program area [MOV H D8120] [MOV H D8121] [MOV K D8129] Written by program ch1: Computer link D8120 Communication format D8121 Station number settings D8129 Time-out time setting In FX3G, FX3GC, FX3U and FX3UC ch2: Computer link Sequence program for set values Program method D8420 Communication format D8421 Station number settings D8429 Time-out time setting When both methods are used at the same time, priority is given to the contents set in the parameter method. D-40 FX Series PLC User's Manual - Data Communication Edition Computer Link 5 Communication Setting in FX Programmable Controller 5.2 Communication Setting Using Parameter Method (GX Works2) A Caution 5.2 Communication settings may be changed via the parameter method with GX Works2, GX Developer, FXGP/WIN for Windows and FX-30P handy programming panel. This section describes how to change parameters with GX Works2. For details on FXGP/WIN operating procedure, refer to section 5.3. For details on GX Developer operating procedure, refer to GX Developer Operating Manual. For details on FX-30P operating procedure, refer to FX-30P Operation Manual. D Operating procedure E Inverter Communication This subsection explains the serial communication setting method. Suppose that GX Works2 is already started up. 1 Computer Link 5.2.1 Communication Setting Using Parameter Method (GX Works2) C Parallel Link Since the special data registers (D8120, D8121, D8129) is a battery backed area in the case of the FX2N, FX2NC, FX3U and FX3UC series, a value cannot be normally saved when the battery is discharge (or after a battery error occurs). Therefore, keep in mind that a computer link setting may not be possible in this case. B N:N Network 1) When specifying the setting using parameters: When the PLC power is turned ON, the parameters set using the parameter setting window in the sequence programming software are automatically transferred to the PLC. As soon as the parameters are transferred to the PLC, the setting becomes valid. After the program (parameters) are transferred to the PLC, it is necessary to reboot the PLC’s power. 2) When specifying the setting by writing data to special data registers: Set the PLC mode from STOP to RUN, write the required data, reboot the PLC’s power. As soon as the PLC power is turned ON, the setting becomes valid. Common Items 4. Time at which the settings become valid Opening the parameter setting window F Non-Protocol Communication (RS/RS2 Instruction) In the project view area of the navigation window, double-click [Parameter] [PLC Parameter]. If the navigation window is not displayed, select [View] [Docking Window] [Navigation] from the menu bar. G Non-Protocol Communication (FX2N-232IF) H Programming Communication I Remote Maintenance Apx.A Discontinued models D-41 FX Series PLC User's Manual - Data Communication Edition Computer Link 2 5 Communication Setting in FX Programmable Controller 5.2 Communication Setting Using Parameter Method (GX Works2) Setting the serial communication (parameters) Click the [PLC System(2)] tab on the dialog box. 3 Setting the serial communication (parameters) Select a channel and check the box labeled "Operate Communication Setting" box, then adjust the parameters for that channel. Click [End]. Adjust the settings on the personal computer to match those set here. 4 Writing parameters to the PLC Select [Online] [Write to PLC] from the menu bar, click [Parameter + Program], and then click [Execute]. D-42 FX Series PLC User's Manual - Data Communication Edition Computer Link A Communication Settings Using Parameter Method (FXGP/WIN) 5.3.1 Operating procedure 1 Displaying the serial setting (parameter) Select [Option] [Serial setting (parameter)] from the toolbar. The following dialog box appears according to absence/presence of parameter setting. C Parallel Link This subsection explains the serial communication setting method. Suppose that FXGP/WIN is already started up. B N:N Network Communication settings may be changed by the parameter method with GX Works2, GX Developer, FXGP/WIN for Windows and FX-30P handy programming panel. This section describes how to change parameters with FXGP/WIN. Ch2 cannot be set using FXGP/WIN. For details on GX Works2 operating procedure, refer to section 5.2. For details on GX Developer operating procedure, refer to GX Developer Operating Manual. For details on FX-30P operating procedure, refer to FX-30P Operation Manual. Common Items 5.3 5 Communication Setting in FX Programmable Controller 5.3 Communication Settings Using Parameter Method (FXGP/WIN) D Computer Link 1. When there are no parameter settings There are no communication settings. Click the [Yes] button. E Inverter Communication F Non-Protocol Communication (RS/RS2 Instruction) G Non-Protocol Communication (FX2N-232IF) H Programming Communication I Remote Maintenance Apx.A Discontinued models D-43 FX Series PLC User's Manual - Data Communication Edition Computer Link 5 Communication Setting in FX Programmable Controller 5.3 Communication Settings Using Parameter Method (FXGP/WIN) 2. When there are already parameter settings The existing communication setting contents are displayed. 2 Adjusting serial setting (parameter) Execute the communication setting as shown below. Adjust the settings on the personal computer to match those set here. 3 Writing a sequence program (parameters) to the PLC Select [PLC] [Transfers] [Write] from the toolbar, and click [OK] button. D-44 FX Series PLC User's Manual - Data Communication Edition 6 Control Procedures and Setting Methods Computer Link 6.1 Data Flow by Link A Control Procedures and Setting Methods B Data Flow by Link The figures below show images of data flow achieved when data is read from or written to a PLC CPU and the status is controlled. In the case of communication in accordance with RS-232C, ignore "485PC-IF" and regard "485ADP" as "232ADP". [10] [11] 485PC-IF RS-485 [3] 485ADP PLC CPU [4] [9] Various data [8] [7] [12] Response [13] [14] Device memory information (read) PLC CPU information (read) [5] Read [6] Data Interface for signal conversion Sequence program OS*1 Device memory, etc. E Inverter Communication 2. When the computer writes data to the PLC Computer OS*1 RS-232C [2] Command, data, etc. 485PC-IF [1] Request RS-485 [3] 485ADP PLC CPU [4] Sequence program OS*1 [6] [7] Device memory information (written) PLC CPU information (written) [5] Write Device memory, etc. G Non-Protocol Communication (FX2N-232IF) 3. When the PLC sends data to the computer (on-demand function) [4] Data OS*1 Sequence program [2] [3] Data Read [1] Sending request Device + memory, etc. Data writing The OS (standing for "Operating System") indicates the software used to efficiently operate the resources including the CPUs, memories, terminals, files, and networks using user programs, etc. H I Remote Maintenance *1. On-demand data RS-485 [5] PLC CPU Programming Communication [7] Write 485ADP 485PC-IF RS-232C [6] Data OS*1 F Non-Protocol Communication (RS/RS2 Instruction) [8] Response Computer D Computer Link [1] Request OS*1 RS-232C [2] Command C Parallel Link 1. When the computer reads data from the PLC Computer N:N Network 6.1 Common Items 6. Apx.A Discontinued models D-45 FX Series PLC User's Manual - Data Communication Edition 6 Control Procedures and Setting Methods Computer Link 6.2 6.2 Important Points in Computer Link Important Points in Computer Link This section explains important points to be understood before creating programs for computer link. 6.2.1 Operations of PLC caused by data transfer The PLC operations and scan time using computer link are as described below. 1. While the PLC is in RUN mode For requests from the computer, the PLC executes access for one request during each END processing. Sending and receiving are executed as interrupts. Accordingly, when sending and receiving are executed, the scan time is longer by about 10%. The scan time can be checked in D8010 to D8012 in the PLC. 2. Condition in which the transfer sequence in the PLC is initialized The transfer sequence in the PLC is initialized in the following cases: - When the power is turned ON - When regular sending/receiving is completed - When the control code "EOT" or "CL" is received in each format - When the control code "NAK" is sent - When the time-out time setting is detected For details on the time-out time setting, refer to Subsection 6.4.4. 3. Occurrence of framing error in the computer When a commercial interface in accordance with RS-485 is used in the computer, a framing error may occur while nothing is sent from the PLC to the computer depending on the interface in the computer. To cope with this nonconformity, let the computer ignore any data until the PLC sends STX, ACK or NAK. 4. Response of "NAK" from the PLC When an error is detected, the PLC sends NAK to the computer. 5. Command sending from the computer When sending commands from the computer to the PLC, wait for the interval times in the following table or more after the PLC finishes receiving data in response to the previous command, and then send the next command. PLC Interval times FX3U, FX3UC 300 s FX2N, FX2NC, FX3S, FX3G, FX3GC 100 s FX2(FX), FX2C, FX0N, FX1S, FX1N, FX1NC two scan times D-46 FX Series PLC User's Manual - Data Communication Edition 6 Control Procedures and Setting Methods Computer Link A How to Understand Control Procedure This section explains how to understand the transfer data shown in the later description of each function. 1. When the computer reads data from the PLC (computer PLC) E N Q A C K Data S T X PLC side N:N Network Computer side B C A Data Data C B A E N Q Data A C K PLC side E Data Basic Formats of Dedicated Protocol Control code CR LF Sum check code Character Message waiting time Command PLC number *1. Whether or not the sum check code is added can be specified using a parameter. *2. Whether or not the control code is added can be specified by selecting the protocol type. H I Remote Maintenance Station number *2 Programming Communication Control code *1 G Non-Protocol Communication (FX2N-232IF) There are two types of control procedures in dedicated protocols. CR and LF are not added to each block in format 1. CR and LF are added to each block in format 4. (The format names are the same as those used in the computer link units for A Series PLCs.) This section explains the contents of control procedures and the contents of each item specified in the control procedures in each format. The basic format of control procedures (protocols) is as shown below: For details, refer to Subsections 6.4.1 and 6.4.2. F Non-Protocol Communication (RS/RS2 Instruction) [1] Part A indicates transfer from the computer to the PLC. [2] Part B indicates transfer from the PLC to the computer. [3] Create a program in the computer so that each data is transferred in turn from the left to the right, and that the data is transferred in the order "A B" as a whole. (Example: In the part A, data is transferred in turn from the right starting from "ENQ".) Inverter Communication B 6.4 D Computer Link 2. When the computer writes data to the PLC (computer PLC) Parallel Link [1] Parts A and C indicate transfer from the computer to the PLC. [2] Part B indicates transfer from the PLC to the computer. [3] Create a program in the computer so that each data is transferred in turn from the left to the right, and that the data is transferred in the order "A B C" as a whole. (Example: In the part A, data is transferred in turn from the right starting from "ENQ".) Computer side Common Items 6.3 6.3 How to Understand Control Procedure Apx.A Discontinued models D-47 FX Series PLC User's Manual - Data Communication Edition 6 Control Procedures and Setting Methods Computer Link 6.4.1 6.4 Basic Formats of Dedicated Protocol Control procedure format 1 The table below shows the control procedure for format 1. PLC No. A C K or or E Character area B T X Sum check code PLC No. S T X N A K Station No. PLC No. A C K Station No. PLC No. Station No. PLC No. * Error code PLC side Station No. Character area A Sum check code Message wait time Command PLC No. When computer reads data from PLC E N Computer side Q Station No. * PLC No. Transfer order N A K Station No. Control procedure (protocol) Station No. Description When computer writes data to PLC PLC side Transfer order Character area C Sum check code Message wait time Command PLC No. E N Computer side Q Station No. * N A K Remarks Error code or 1) The sum check code is added only when "sum check code provided" is selected. The sum check code is not added when "sum check code not provided" is selected. 2) When "sum check code provided" is selected, the sum check is executed only to the character areas marked with "*" in the figure above. 3) The contents of "Character area A", "Character area B" and "Character area C" vary depending on the contents of transfer, but do not vary depending on the control procedure format. For details on character contents, refer to "7. Commands". D-48 FX Series PLC User's Manual - Data Communication Edition 6 Control Procedures and Setting Methods Computer Link A Control procedure format 4 Common Items The table below shows the control procedure for format 4. PLC No. or A C K C L or X RF C L RF D PLC No. Station No. * C L RF C L RF A C K PLC No. Sum check code Message wait time Command Transfer order Character area C Station No. PLC side E Inverter Communication C L F RF Non-Protocol Communication (RS/RS2 Instruction) When computer writes data to PLC PLC No. * E N Computer side Q Error code PLC No. N A K Station No. or C L RF G 1) The sum check code is added only when "sum check code provided" is selected. The sum check code is not added when "sum check code not provided" is selected. 2) When "sum check code provided" is selected, the sum check is executed only to the character areas marked with "*" in the figure above. 3) The contents of "Character area A", "Character area B" and "Character area C" vary depending on the contents of transfer, but do not vary depending on the control procedure format. For details on character contents, refer to "7. Commands". Non-Protocol Communication (FX2N-232IF) Remarks C Computer Link N A K E Character area B T Sum check code S T X Error code PLC side PLC No. RF Station No. Character area A Sum check code Message wait time Command PLC No. C L RF B Parallel Link When computer reads data from PLC E N Computer side Q Station No. * PLC No. Transfer order C L N:N Network N A K Station No. Control procedure (protocol) Station No. Description Station No. 6.4.2 6.4 Basic Formats of Dedicated Protocol H Programming Communication I Remote Maintenance Apx.A Discontinued models D-49 FX Series PLC User's Manual - Data Communication Edition 6 Control Procedures and Setting Methods Computer Link 6.4.3 6.4 Basic Formats of Dedicated Protocol Contents of set items in each control procedure (protocol) This subsection explains the contents of the data used in each control procedure. 1. Control codes The table below shows control codes. Signal name Code STX 02H Start of Text Description ETX 03H End of Text CL 0CH Clear EOT 04H End of Transmission CR 0DH Carriage Return NAK 15H Negative Acknowledge ENQ 05H Enquiry ACK 06H Acknowledge Signal name Code LF 0AH Description Line Feed 1) When the PLC receives ENQ or ACK, it initializes the transfer sequence and begins receiving. 2) When the PLC receives EOT or CL as shown below, it initializes the transfer sequence. At this time, the PLC gives no response. For format 1 For format 4 E O T EC L O T RF or or C CC L Computer side L Computer side L R F PLC side PLC side 3) In FX3S, FX3G, FX3GC, FX3U and FX3UC PLCs, a waiting time of 2 scan times or more is required from sending of the EOT/CL code from the computer to sending of the next message. 2. Station number The station number indicates a number provided in each PLC to determine to which PLC the computer accesses. The station number is specified in hexadecimal. • In FX Series PLCs, set the station number using parameters. The setting range is from 00H to 0FH. • For the station number setting method in A Series PLCs, refer to the respective A Series PLC manual. Computer FX Series 485PC-IF FX Series 485 ADP Station No. 0 (00H) 485 ADP Station No. 1 (01H) FX Series 485 ADP Station No. 2 (02H) FX Series 485 ADP Station No. 15 (0FH) In FX2(FX), FX2C and FX0N PLCs, set a value to D8121. M8002 Initial pulse MOV H0 D8121 For details on the program, refer to Section 9.3. Cautions on setting station numbers 1) Do not overlap station numbers. If the same number is set for two or more stations, the transfer data is destroyed and normal communication is not possible. 2) It is not necessary to set consecutive station numbers as shown in the setting example above. Any station numbers in the setting range (00H to 0FH) are applicable. (Examples: Station numbers may be set arbitrarily. Some station numbers may be skipped.) D-50 FX Series PLC User's Manual - Data Communication Edition Computer Link 6 Control Procedures and Setting Methods 6.4 Basic Formats of Dedicated Protocol A 4. Command A command specifies the contents of access executed by the computer to a PLC. A command is converted into a two-digit ASCII code. For an explanation of commands, refer to Chapter 7. Example: When the message waiting time is set to 100 ms Message waiting time (100 ms) E Inverter Communication "A" Computer side PLC side The waiting time should be the interval times in the following table or more. Interval times FX3U, FX3UC 300 s FX2N, FX2NC, FX3S, FX3G, FX3GC 100 s F Non-Protocol Communication (RS/RS2 Instruction) Sending is started 100 ms or later. PLC D Computer Link The message waiting time should be specified because some computers require more time before receiving additional data. Set the waiting time according to the specifications of each computer. Set the waiting time within the range from 0 to 150 ms in 10-ms units. 10 ms is handled as "1H", and a value ranging from "0H (0)" to "FH (15)" is converted into a one-digit ASCII code. When executing communication using the 485PC-IF in a 1-to-N system adopting the one-pair wiring, make sure to set the message waiting time to 70 ms (7) or more. When the scan time of a PLC in the system exceeds 70 ms, set the message waiting time to the maximum scan time or higher. C Parallel Link 5. Message waiting time B N:N Network The PLC number is used to identify a PLC to be accessed when computer link is combined with the MELSECNET (II) or MELSECNET/B in A Series PLCs. The PLC number of each FX Series PLC is fixed to "FFH", and converted into two-digit ASCII code. When the on-demand function is used, however, the PLC number is automatically changed to "FEH" by the PLC. For the PLC number of an A Series PLC used together with the MELSECNET (II) or MELSECNET/B, refer to the respective A Series PLC manual. Common Items 3. PLC number G Non-Protocol Communication (FX2N-232IF) FX2(FX), FX2C, FX0N, FX1S, FX1N, FX1NC two scan times H Programming Communication I Remote Maintenance Apx.A Discontinued models D-51 FX Series PLC User's Manual - Data Communication Edition 6 Control Procedures and Setting Methods Computer Link 6.4 Basic Formats of Dedicated Protocol 6. Sum check code The sum check code indicates a two-digit ASCII code converted from the least significant byte (8-bit) of the sum check target data added as hexadecimal data. Using the FX PLC parameters, set whether or not the sum check code is added in the message. - When "sum check code provided" is selected, the sum check code is added in the message during sending. During receiving, the sum check code is compared with the value calculated from the received data to check the received data. - When "sum check code not provided" is selected, the sum check code is not added, so the received data is not checked either. A calculation example of the sum check code is shown below. Example: When the station number "0", PLC number "FF", command "BR (device memory batch read)", message waiting time "30 ms" and data "ABCD" are transferred in format 1, the sum check code value is as shown below: Computer side E Station No. N Q 00 PLC No. FF Com- Mes- Character area Sum mand sage check wait code time A B C D BR BD 3 05H 30H 30H 46H 46H 42H 52H 33H 41H 42H 43H 44H 42H 44H PLC side 30H+30H+46H+46H+42H+52H+33H+41H+42H+43H+44H=2BDH Total from "station number" to "character area" D-52 Last two digits S T X 00 FF 02H 30H 30H 46H 46H 30 ms (Message waiting time) ... FX Series PLC User's Manual - Data Communication Edition 6 Control Procedures and Setting Methods Computer Link A Time-out time setting When the receiving of data from the computer is interrupted and is not restarted within the preset time (timeout time setting), the PLC regards the situation as a timeout error and initializes the transfer sequence. 1. Time-out time setting range 1) Details of setting range Setting range in parameter Setting range in sequence program (D8129 (ch1) and D8429 (ch2)) Not applicable 1 to 3276 (10 to 32760 ms) Not applicable 1 to 255 (10 to 2550 ms) FX1S, FX1N, FX1NC 1 to 255 (10 to 2550 ms) 1 to 255 (10 to 2550 ms) FX2N, FX2NC, FX3S 1 to 255 (10 to 2550 ms) 1 to 3276 (10 to 32760 ms) FX3G, FX3GC, FX3U, FX3UC ch1 1 to 255 (10 to 2550 ms) 1 to 3276 (10 to 32760 ms) ch2 1 to 3276 (10 to 32760 ms) Not applicable D Computer Link FX2(FX), FX2C FX0N When the set value is "0", it is handled as "100 ms". E Inverter Communication 2) Example of setting program When setting the time-out time setting to 60 ms M8002 MOV K6 C Parallel Link FX Series B N:N Network The time-out time setting can be set using parameters or sequence program. In the FX2(FX), FX2C and FX0N Series, however, the parameter setting method is not applicable. When setting the time-out time setting in a sequence program, write a value for ch1 to D8129, and a value for ch2 (in the FX3G, FX3GC, FX3U and FX3UC Series) to D8429 (unit: 10 ms). However, D8429 (ch2) cannot be set in sequence programs. The setting range is different between the parameter method and the sequence program method. Common Items 6.4.4 6.4 Basic Formats of Dedicated Protocol D8129 Initial pulse For details on the program, refer to Section 9.3. F The time-out time setting is not updated until the next character data is received. Set a time to receive a character according to the transmission speed (baud rate). For one character (12-bit), the minimum set value of the time-out time setting is as shown below: Non-Protocol Communication (RS/RS2 Instruction) 2. Caution on programming Baud rate (bps) Time-out time setting (minimum set value) 40 50 ms (5) 600 20 30 ms (3) 1200 10 20 ms (2) 5 10 ms (1) 4800 2.5 10 ms (1) 9600 1.25 10 ms (1) 19200 0.625 10 ms (1) 38400 0.312 10 ms (1) H Programming Communication 2400 G Non-Protocol Communication (FX2N-232IF) Time to receive one character (ms) 300 I Remote Maintenance Apx.A Discontinued models D-53 FX Series PLC User's Manual - Data Communication Edition 6 Control Procedures and Setting Methods Computer Link 6.5 6.5 Transfer Sequence Time Chart and Communication Time Transfer Sequence Time Chart and Communication Time This section explains the communication time chart between the computer and the PLC. As shown in the figures below, communication between the computer and the PLC is always executed after "END". The scan time is extended by the communication time. 6.5.1 When computer reads data from PLC E N Q Computer A C K Waiting time (TW) Interface T3 T4 Reading processing S T X PLC T0 T1 T5 It should be the interval times in the following table or more. This time is "0" when the message waiting time is not set or when the waiting time is shorter than the communication time with the CPU. T2 Sequence program END Step 0 Step 0 Step 0 END END END The PLC watches the time elapse. When it reaches the transmission time, the PLC starts the transmission. If not, the PLC evaluate the time elapse in the END process of the next step. PLC Interval times FX3U, FX3UC 300 s FX2N, FX2NC, FX3S, FX3G, FX3GC 100 s FX2(FX), FX2C, FX0N, FX1S, FX1N, FX1NC two scan times 6.5.2 When computer writes data to PLC Computer E N Q Waiting time (TW) T3 Interface Writing processing Data is written. PLC T0 This time is "0" when the message waiting time is not set or when the waiting time is shorter than the communication time with the CPU. T1 T2 Sequence program END D-54 Step 0 END Step 0 END Step 0 END FX Series PLC User's Manual - Data Communication Edition 6 Control Procedures and Setting Methods Computer Link A Transfer time in transfer sequence This subsection explains how to calculate the approximate time after the computer starts data transfer and the PLC gives a response until all communication is completed. For the contents of T0 to T5, refer to the previous page. 1. When the computer reads data from the PLC 1 Number of bits in one character (1 + 7 (8) + 0 (1) + 1 (2)) Baud rate Number of characters Data length (7 or 8) Parity bit (0 or 1) Stop bit (1 or 2) 2. When the computer writes data to the PLC Communication time = T0 + (T1 + Longer time between T2 and TW) + T3 T0, T3 = E Start bit Data length (7 or 8) Parity bit (0 or 1) Stop bit (1 or 2) F Non-Protocol Communication (RS/RS2 Instruction) T1: Maximum one scan time (Because data is written to the PLC during the END processing while the PLC is in RUN mode, writing requires up to one scan time depending on the sending timing. Writing requires about 1 ms while the PLC is in STOP mode.) T2: END processing time in the PLC executing data transfer TW: Message waiting time Inverter Communication 1 Number of bits in one character (1 + 7 (8) + 0 (1) + 1 (2)) Baud rate Number of characters D Computer Link T1: Maximum one scan time (Because data is read from the PLC during the END processing while the PLC is in RUN mode, reading requires up to one scan time depending on the sending timing. Reading requires about 1 ms while the PLC is in STOP mode.) T2: END processing time in the PLC executing data transfer T4: Scan time or longer (In the case of wiring in the 1-to-N configuration, T4 should be longer than the time-out time setting (D8129) extended by one scan time.) TW: Message waiting time C Parallel Link Start bit B N:N Network Communication time = T0 + (T1 + Longer time between T2 and TW) + T3 + T4 + T5 T0, T3, T5 = Common Items 6.5.3 6.5 Transfer Sequence Time Chart and Communication Time G Non-Protocol Communication (FX2N-232IF) H Programming Communication I Remote Maintenance Apx.A Discontinued models D-55 FX Series PLC User's Manual - Data Communication Edition 6 Control Procedures and Setting Methods Computer Link 6.6 6.6 Transfer Data in Character Area Transfer Data in Character Area This section explains the transfer data in the character area sent and received between the computer and a PLC using each command. The transfer data explained below is handled as the character area B in reading and the character area C in writing. For character areas, refer to Subsections 6.4.1 and 6.4.2. 6.6.1 When bit device memory is read or written The bit device memory is handled in 1-bit (1-point) units or in 1-word (16-point) units. The transfer data in each case is explained below. 1) In 1-bit (1-point) units When the bit device memory is handled in 1-bit (1-point) units, a specified number of devices starting from the specified head device are expressed in turn from the left end in "1 (31H)" for the ON status or "0 (30H)" for the OFF status. Example: When indicating the ON/OFF status of five devices starting from M10 Number of devices Head device M 0 0 1 0 0 5 1 0 1 0 1 4DH 30H 30H 31H 30H 30H 35H 31H 30H 31H 30H 31H Indicates that M14 is ON. Indicates that M13 is OFF. Indicates that M12 is ON. Indicates that M11 is OFF. Indicates that M10 is ON. 2) In 1-word (16-point)" units When the bit device memory is handled in 1-word (16-point) units, one word is expressed in 4-bit units in turn from the most significant bit in hexadecimal. Example: When indicating the ON/OFF status of 32 devices starting from M16 Because devices are handled in 16 point units, the number of device is "02". Number of devices Head device M 0 0 1 6 0 2 Data A B 1 Data 2 3 4 C D 4DH 30H 30H 31H 36H 30H 32H 41H 42H 31H 32H 33H 34H 43H 44H A B 1 2 3 4 C D b15 b14 b13 b12 b11 b10 b9 b8 b7 b6 b5 b4 b3 b2 b1 b0 b15 b14 b13 b12 b11 b10 b9 b8 b7 b6 b5 b4 b3 b2 b1 b0 1 0 1 0 1 0 1 1 0 0 0 1 0 0 1 0 0 0 1 1 0 1 0 0 1 1 0 0 1 1 0 1 M M M M M M M M M M M M M M M M M M M M M M M M M M M M M M M M 31 30 29 28 27 26 25 24 23 22 21 20 19 18 17 16 47 46 45 44 43 42 41 40 39 38 37 36 35 34 33 32 D-56 FX Series PLC User's Manual - Data Communication Edition 6 Control Procedures and Setting Methods Computer Link A When word device memory is read or written In the case of word device memory, one word is expressed in 4-bit units in turn from the most significant bit in hexadecimal. B Example 1: When indicating the contents stored in the data registers D350 and D351 D 0 3 5 0 0 2 Data 5 6 A Data B 1 7 0 N:N Network Number of devices Head device F 44H 30H 33H 35H 30H 30H 32H 35H 36H 41H 42H 31H 37H 30H 46H 5 6 A B 1 7 0 C F Parallel Link b15 b14 b13 b12 b11 b10 b9 b8 b7 b6 b5 b4 b3 b2 b1 b0 b15 b14 b13 b12 b11 b10 b9 b8 b7 b6 b5 b4 b3 b2 b1 b0 0 1 0 1 0 1 1 0 1 0 1 0 1 0 1 1 0 0 0 1 0 1 1 1 0 0 0 0 1 1 1 1 Indicates that D350 stores "56ABH ("22187" in decimal)". Indicates that D351 stores "170FH ("5903" in decimal)". Number of devices Head device C N 2 0 0 0 1 Data 1 2 3 D *1 Computer Link Example 2: When indicating the contents stored in the 32-bit counter C200 Data 4 5 6 7 8 44H 4EH 32H 30H 30H 30H 31H 31H 32H 33H 34H 35H 36H 37H 38H 2 3 4 5 6 E 7 8 Inverter Communication 1 b15 b14 b13 b12 b11 b10 b9 b8 b7 b6 b5 b4 b3 b2 b1 b0 b15 b14 b13 b12 b11 b10 b9 b8 b7 b6 b5 b4 b3 b2 b1 b0 0 0 0 1 0 0 1 0 0 0 1 1 0 1 0 0 0 1 0 1 0 1 1 0 0 1 1 1 1 0 0 0 F Indicates that C200 stores "12345678H ("305,419,896" in decimal)". Non-Protocol Communication (RS/RS2 Instruction) *1. Common Items 6.6.2 6.6 Transfer Data in Character Area For indicating the current value of C200, use "CN200". G Non-Protocol Communication (FX2N-232IF) H Programming Communication I Remote Maintenance Apx.A Discontinued models D-57 FX Series PLC User's Manual - Data Communication Edition 7 Commands Computer Link 7. 6.6 Transfer Data in Character Area Commands This chapter explains specification methods and specification examples of commands in dedicated protocols used in computer link communication type. For control procedures in dedicated protocols, refer to "6. Control Procedures and Setting Methods". The table below shows a reference section for each command. Applicable PLC Command D-58 Contents of processing FX3S, FX3G, FX3GC, FX3U, FX3UC FX2(FX), FX2C, FX0N, FX1S, FX1N, FX1NC, FX2N, FX2NC Reference section BR Reads bit devices in 1-point units. 7.1 WR Reads bit devices in 16-point units, or word devices in 1-point units. 7.2 QR Reads bit devices in 16-point units, or word devices in 1-point units. — 7.3 BW Writes bit devices in 1-point units. 7.4 WW Writes bit devices in 16-point units, or word devices in 1-point units. 7.5 QW Writes bit devices in 16-point units, or word devices in 1-point units. — 7.6 BT Specifies bit devices arbitrarily in 1-point units, and sets or resets them (forcibly sets them to ON or OFF). 7.7 WT Specifies bit devices arbitrarily in 16-point units, and sets or resets them (forcibly sets them to ON or OFF). Or specifies word devices arbitrarily in 1-point units, and writes data to them. 7.8 QT Specifies bit devices arbitrarily in 16-point units, and sets or resets them (forcibly sets them to ON or OFF). Or specifies word devices arbitrarily in 1-point units, and writes data to them. — 7.9 RR Sets a PLC to RUN mode in remote control. RS Sets a PLC to STOP mode in remote control. PC Reads the PLC model name code. 7.11 GW Turns the global function ON or OFF in all linked PLCs. 7.12 — Offers the on-demand function (by which a PLC gives a sending request), and does not offer any command. 7.13 TT Returns received characters back to the computer as they are. 7.14 7.10 FX Series PLC User's Manual - Data Communication Edition 7 Commands Computer Link A BR Command [Reads Device Memory in 1-Bit Units] This section explains the control procedure specification method and specification example when the bit device memory is read all at once. B 1. Specification method S T X * E T X PLC No. A C K Sum check code Read device range specification PLC No. PLC side Station No. Head device (5 characters) Sum check code Message wait time PLC No. Station No. BR "0 (30H)" indicates the OFF status. "1 (31H)" indicates the ON status. Station No. Number of device points (2 characters (hexadecimal) 1) Specify the device point range while satisfying the following conditions: - 1 Number of device points 256*1 (Use "00H" to specify 256 points.) - Head device number + Number of device points -1 Maximum device number *1. 54 in the FX0N and FX1S Series 2. Specification example Computer side PLC side E N 0 5 F F B R A X 0 0 4 0 0 5 4 7 Q This range is regarded as the sum check target. 05H 30H 35H 46H 46H 42H 52H 41H 58H 30H 30H 34H 30H 30H 35H 34H 37H 06H 30H 35H 46H 46H G S E T 0 5 F F 0 1 1 0 1 T 0 5 X X 02H 30H 35H 46H 46H 30H 31H 31H 30H 31H 03H 30H 35H The message wait time is specified in 10-ms units within the range from 0 to 150 ms, and expressed in hexadecimal within the range from 0 to FH. For example, "100 ms" is expressed as "A". I Remote Maintenance Point H Programming Communication Indicates that X044 is ON. Indicates that X043 is OFF. Indicates that X042 is ON. Indicates that X041 is ON. Indicates that X040 is OFF. Non-Protocol Communication (FX2N-232IF) This range is regarded as the sum check target. A C 0 5 F F K F Non-Protocol Communication (RS/RS2 Instruction) When reading the contents of five devices X040 to X044 in the PLC whose station number is 5 (while the message waiting time is set to 100 ms) (When X040 and X043 are OFF and X041, X042 and X044 are ON) E Inverter Communication 2) Express the station number, PLC number, number of device points and sum check code in hexadecimal. D Computer Link Character area B * Data on specified number of device points (Characters of specified number of device points) C Parallel Link E N Computer side Q N:N Network The specification method in the control procedure format 1 is shown below: Batch read command (unit: bit) Character area A Common Items 7.1 7.1 BR Command [Reads Device Memory in 1-Bit Units] Apx.A Discontinued models D-59 FX Series PLC User's Manual - Data Communication Edition 7 Commands Computer Link 7.2 7.2 WR Command [Reads Device Memory in 1-Word Units] WR Command [Reads Device Memory in 1-Word Units] This section explains the control procedure specification method and specification examples when the word device memory is read all at once or when the bit device memory is read (in 16-point units) all at once. 1. Specification method The specification method in the control procedure format 1 is shown below: S T X Read device range specification E T X * A C K Sum check code PLC side PLC No. One device uses 4 characters. Four digits (hexadecimal) express one word data. Station No. Head device (5 characters) Station No. Sum check code WR Message wait time PLC No. Station No. E N Q Computer side PLC No. Number of device points (2 characters (hexadecimal) Batch read command (unit: word) Character area A Character area B * Data on specified number of device points (Characters of specified number of device points) 1) Specify the device point range while satisfying the following conditions: - 1 Number of device points 64*1 (32*1 in case of bit devices) - Head device number + Number of device points ("Number of devices 16" in case of bit devices) -1 Maximum device number - When 32-bit devices (CN200 to CN255) are read, one device point is handled as two word data. Accordingly, up to 32 device points*2 can be specified. 2) Express the station number, PLC number, number of device points and sum check code in hexadecimal. *1. Up to 13 device points in the FX0N and FX1S Series *2. Up to 6 device points in the FX0N and FX1S Series 2. Specification examples Example 1: When reading the contents of thirty-two devices from X040 to X077 in the PLC whose station number is 5 (while the message waiting time is set to 0 ms) Computer side E N 0 5 F F W R 0 X 0 0 4 0 0 2 4 8 Q 05H 30H 35H 46H 46H 57H 52H 30H 58H 30H 30H 34H 30H 30H 32H 34H 38H PLC side This range is regarded as the sum check target. A C 0 5 F F K This range is regarded as the sum check target. 06H 30H 35H 46H 46H S T 0 5 F F X E A B C D T 0 8 X 1 2 3 4 02H 30H 35H 46H 46H 31H 32H 33H 34H 41H 42H 43H 44H 03H 30H 38H 1 2 3 4 A B C D 0 0 0 1 0 0 1 0 0 0 1 1 0 1 0 0 1 0 1 0 1 0 1 1 1 1 0 0 1 1 0 1 X 0 5 7 D-60 X 0 5 2 X 0 5 1 X 0 5 0 X 0 4 7 X 0 4 3 X 0 4 2 X 0 4 1 X 0 4 0 X 0 7 7 X 0 7 2 X 0 7 1 X 0 7 0 X 0 6 7 X 0 6 3 X 0 6 2 X 0 6 1 X 0 6 0 FX Series PLC User's Manual - Data Communication Edition 7 Commands Computer Link 7.2 WR Command [Reads Device Memory in 1-Word Units] A The WR command handles data in 1-word units. When reading thirty-two devices from X040 to X077, specify the number of device points as "02" (One point specifies 16 devices.) Example 2: When reading the present value of two devices from T123 and T124 in the PLC whose station number is 5 (while the message waiting time is set to 0 ms) PLC side This range is regarded as the sum check target. 05H 30H 35H 46H 46H 57H 52H 30H 54H 4EH 31H 32H 33H 30H 32H 36H 34H This range is regarded as the sum check target. S T 0 5 F F X 7 B C 9 1 2 3 4 E T B 3 X 06H 30H 35H 46H 46H Indicates that the current value of T123 is "7BC9H (hexadecimal) (which is "31689" in decimal). Indicates that the current value of T124 is "1234H (hexadecimal) (which is "4660" in decimal). C Parallel Link 02H 30H 35H 46H 46H 37H 42H 43H 39H 31H 32H 33H 34H 03H 42H 33H A C 0 5 F F K B N:N Network Computer side E N 0 5 F F W R 0 T N 1 2 3 0 2 6 4 Q Common Items Point D Computer Link E Inverter Communication F Non-Protocol Communication (RS/RS2 Instruction) G Non-Protocol Communication (FX2N-232IF) H Programming Communication I Remote Maintenance Apx.A Discontinued models D-61 FX Series PLC User's Manual - Data Communication Edition 7 Commands Computer Link 7.3 7.3 QR Command [Reads Device Memory in 1-Word Units] QR Command [Reads Device Memory in 1-Word Units] This section explains the control procedure specification method and specification examples when the word device memory is read all at once or when the bit device memory is read (in 16-point units) all at once. This command is available only in FX3S, FX3G, FX3GC, FX3U and FX3UC PLCs. 1. Specification method The specification method in the control procedure format 1 is shown below: Batch read command (unit: word) Number of device points (2 characters (hexadecimal) S T X Read device range specification Data on E specified number of T device points X PLC No. Station No. Sum check code K PLC No. PLC side One device uses 4 characters. Four digits (hexadecimal) A express one data word . C Station No. Head device (7 characters) Sum check code QR Message wait time PLC No. E N Computer side Q Station No. Character area A Character area B 1) Specify the device point range while satisfying the following conditions: - 1 Number of device points 64 (32 for bit devices) - Head device number + Number of device points ("Number of devices 16" for bit devices) -1 Maximum device number - When 32-bit devices (CN00200 to CN00255) are read, one device point is handled as two word data. Accordingly, up to 32 device points can be specified. 2) Express the station number, PLC number, number of device points and sum check code in hexadecimal. 2. Specification examples (For FX3U and FX3UC PLCs) Example 1: When reading the contents of thirty-two devices from X040 to X077 in the PLC whose station number is 5 (while the message waiting time is set to 0 ms) Computer side E N 0 5 F F Q R 0 X 0 0 0 0 4 0 0 2 A 2 Q 05H 30H 35H 46H 46H 51H 52H 30H 58H 30H 30H 30H 30H 34H 30H 30H 32H 41H 32H PLC side This range is regarded as the sum check target. A C 0 5 F F K This range is regarded as the sum check target. 06H 30H 35H 46H 46H S T 0 5 F F X 1 2 3 4 E A B C D T C 8 X 02H 30H 35H 46H 46H 31H 32H 33H 34H 41H 42H 43H 44H 03H 43H 38H 1 2 3 4 A B C D 0 0 0 1 0 0 1 0 0 0 1 1 0 1 0 0 1 0 1 0 1 0 1 1 1 1 0 0 1 1 0 1 X 0 5 7 D-62 X 0 5 0 X 0 4 7 X 0 4 1 X 0 4 0 X 0 7 7 X 0 7 0 X 0 6 7 X 0 6 1 X 0 6 0 FX Series PLC User's Manual - Data Communication Edition 7 Commands Computer Link 7.3 QR Command [Reads Device Memory in 1-Word Units] Computer side B 05H 30H 35H 46H 46H 51H 52H 30H 52H 30H 33H 30H 30H 30H 30H 30H 32H 39H 42H N:N Network PLC side E N 0 5 F F Q R 0 R 0 3 0 0 0 0 0 2 9 B Q This range is regarded as the sum check target. A C 0 5 F F K This range is regarded as the sum check target. 06H 30H 35H 46H 46H 7 B C 9 1 2 3 4 C E T B 3 X Parallel Link S T 0 5 F F X A Common Items Example 2: When reading the contents of two devices from R30000 to R30001 in the PLC whose station number is 5 (while the message waiting time is set to 0 ms) 02H 30H 35H 46H 46H 37H 42H 43H 39H 31H 32H 33H 34H 03H 42H 33H Indicates that the value of R30000 is "7BC9H" (hexadecimal) (which is "31689" in decimal). Indicates that the value of R30001 is "1234H" (hexadecimal) (which is "4660" in decimal). D Computer Link E Inverter Communication F Non-Protocol Communication (RS/RS2 Instruction) G Non-Protocol Communication (FX2N-232IF) H Programming Communication I Remote Maintenance Apx.A Discontinued models D-63 FX Series PLC User's Manual - Data Communication Edition 7 Commands Computer Link 7.4 7.4 BW Command [Writes Device Memory in 1-Bit Units] BW Command [Writes Device Memory in 1-Bit Units] This section explains the control procedure specification method and shows a specification example when the bit device memory is written all at once. 1. Specification method The specification method in the control procedure format 1 is shown below: Number of device points Character area A (2 characters (hexadecimal) PLC side Written device range specification "0 (30H)" indicates the OFF status. "1 (31H)" indicates the ON status. A C K PLC No. * Station No. Head device (5 characters) Sum check code BW Message wait time PLC No. E N Q Computer side Station No. Batch write command (unit: bit) * Data on specified number of device points (Characters of specified number of device points) 1) Specify the device point range while satisfying the following conditions: - 1 Number of device points 160*1 - Head device number + Number of device points -1 Maximum device number 2) Express the station number, PLC number, number of device points and sum check code in hexadecimal respectively. *1. 46 in the FX0N and FX1S Series 2. Specification example When writing data to five devices from M903 to M907 in the PLC whose station number is 0 (while the message waiting time is set to 0 ms) This range is regarded as the sum check target. Computer side PLC side D-64 E N 0 0 F F B W 0 M 0 9 0 3 0 5 0 1 1 0 1 2 6 Q 05H 30H 30H 46H 46H 42H 57H 30H 4DH 30H 39H 30H 33H 30H 35H 30H 31H 31H 30H 31H 32H 36H Specifies to turn M903 OFF. Specifies to turn M904 ON. Specifies to turn M905 ON. Specifies to turn M906 OFF. Specifies to turn M907 ON. A C 0 0 F F K 06H 30H 30H 46H 46H FX Series PLC User's Manual - Data Communication Edition 7 Commands Computer Link A WW Command [Writes Device Memory in 1-Word Units] This section explains the control procedure specification method and shows a specification examples when the word device memory is written all at once or when the bit device memory is written (in 16-point units) all at once. The specification method in the control procedure format 1 is shown below: C PLC side A C K Written device range specification PLC No. * Station No. Head device (5 characters) Sum check code Message wait time Station No. W W Number of device points (2 characters (hexadecimal) Character area C Parallel Link E N Q Computer side PLC No. Batch write command (unit: word) D Computer Link One device uses 4 characters. Four digits (hexadecimal) express one data word. * Data on specified number of device points (Characters of specified number of device points) 1) Specify the device point range while satisfying the following conditions: 2) Express the station number, PLC number, number of device points and sum check code in hexadecimal. *2. Up to 5 device points in the FX0N and FX1S Series 2. Specification examples Example 1: When writing data to thirty-two devices from M640 to M671 in the PLC whose station number is 0 (while the message waiting time is set to 0 ms) Computer side 2 3 4 7 A B 9 6 0 5 05H 30H 30H 46H 46H 57H 57H 30H 4DH 30H 36H 34H 30H 30H 32H 32H 33H 34H 37H 41H 42H 39H 36H 30H 35H PLC side A C 0 0 F F K This range is regarded as the sum check target. H 3 4 7 A B 9 Programming Communication 06H 30H 30H 46H 46H 2 6 0 0 1 0 0 0 1 1 0 1 0 0 0 1 1 1 1 0 1 0 1 0 1 1 1 0 0 1 0 1 1 0 M 6 5 4 M 6 5 3 M 6 4 3 M 6 4 2 M 6 4 1 M 6 4 0 M 6 7 1 M 6 7 0 M 6 6 9 M 6 5 9 M 6 5 8 M 6 5 7 I M 6 5 6 Remote Maintenance M 6 5 5 G Non-Protocol Communication (FX2N-232IF) E N 0 0 F F W W 0 M 0 6 4 0 0 2 Q F Non-Protocol Communication (RS/RS2 Instruction) Up to 11 device points in the FX0N and FX1S Series E Inverter Communication - 1 Number of device points 64*1 (10 in case of bit devices) - Head device number + Number of device points ("Number of devices x 16" in case of bit devices) -1 Maximum device number - When 32-bit devices (CN200 to CN255) are written, one device point is handled as two word data. Accordingly, up to 32 device points*2 can be specified. *1. B N:N Network 1. Specification method Common Items 7.5 7.5 WW Command [Writes Device Memory in 1-Word Units] Point The WW command handles data in 1-word units. When writing data to thirty-two devices from M640 to M671, specify the number of device points as "02" (One point specifies 16 devices.) Apx.A Discontinued models D-65 FX Series PLC User's Manual - Data Communication Edition 7 Commands Computer Link 7.5 WW Command [Writes Device Memory in 1-Word Units] Example 2: When writing data to two devices D0 and D1 in the PLC whose station number is 0 (while the message waiting time is set to 0 ms) Computer side E N 0 0 F F W W 0 D 0 0 0 0 0 2 Q 1 2 3 4 A C D 7 F 9 05H 30H 30H 46H 46H 57H 57H 30H 44H 30H 30H 30H 30H 30H 32H 31H 32H 33H 34H 41H 43H 44H 37H 46H 39H PLC side This range is regarded as the sum check target. A C 0 0 F F K 06H 30H 30H 46H 46H Indicates that "1234H (hexadecimal) (which is "4660" in decimal) is written to D0. Indicates that "ACD7H (hexadecimal) (which is "-21289" in decimal) is written to D1. D-66 FX Series PLC User's Manual - Data Communication Edition 7 Commands Computer Link A QW Command [Writes Device Memory in 1-Word Units] This section explains the control procedure specification method and shows a specification examples when the word device memory is written all at once or when the bit device memory is written (in 16-point units) all at once. This command is available only in FX3S, FX3G, FX3GC, FX3U and FX3UC PLCs. The specification method in the control procedure format 1 is shown below: Number of device points (2 characters (hexadecimal) C A C K Written device range specification PLC No. PLC side Station No. Data on specified number of device points Head device (7 characters) Sum check code Message wait time PLC No. QW Parallel Link Station No. Character area C E N Computer side Q D 2) Express the station number, PLC number, number of device points and sum check code in hexadecimal. 2. Specification examples (For FX3U and FX3UC PLCs) E N 0 5 F F Q W 0 M 0 0 0 6 4 0 0 2 2 3 4 7 A B 9 6 6 4 Q G 05H 30H 35H 46H 46H 51H 57H 30H 4DH 30H 30H 30H 36H 34H 30H 30H 32H 32H 33H 34H 37H 41H 42H 39H 36H 36H 34H A C 0 5 F F K This range is regarded as the sum check target. Non-Protocol Communication (FX2N-232IF) PLC side 06H 30H 35H 46H 46H 2 3 4 7 A B 9 6 H M 6 4 8 M 6 4 7 M 6 4 1 M 6 4 0 M 6 7 1 M 6 6 4 M 6 6 3 M 6 5 7 Programming Communication 0 0 1 0 0 0 1 1 0 1 0 0 0 1 1 1 1 0 1 0 1 0 1 1 1 0 0 1 0 1 1 0 M 6 5 6 F Non-Protocol Communication (RS/RS2 Instruction) Example 1: When writing data to thirty-two devices from M640 to M671 in the PLC whose station number is 5 (while the message waiting time is set to 0 ms) E Inverter Communication 1) Specify the device point range while satisfying the following conditions: - 1 Number of device points 64 (10 in case of bit devices) - Head device number + Number of device points ("Number of devices 16" in case of bit devices) -1 Maximum device number - When 32-bit devices (CN00200 to CN00255) are written, one device point is handled as two word data. Accordingly, up to 32 device points can be specified. Computer Link One device uses 4 characters. Four digits (hexadecimal) express one data word. Computer side B N:N Network 1. Specification method Batch write command (unit: word) Common Items 7.6 7.6 QW Command [Writes Device Memory in 1-Word Units] M 6 5 6 I Remote Maintenance Apx.A Discontinued models D-67 FX Series PLC User's Manual - Data Communication Edition Computer Link 7 Commands 7.6 QW Command [Writes Device Memory in 1-Word Units] Example 2: When writing data to two devices from R30000 to R30001 in the PLC whose station number is 5 (while the message waiting time is set to 0 ms) Computer side E N 0 5 F F Q W 0 R 0 3 0 0 0 0 0 2 7 B C 9 1 2 3 4 5 F Q 05H 30H 35H 46H 46H 51H 57H 30H 52H 30H 33H 30H 30H 30H 30H 30H 32H 37H 42H 43H 39H 31H 32H 33H 34H 35H 46H PLC side This range is regarded as the sum check target. A C 0 5 F F K 06H 30H 35H 46H 46H Indicates that "7BC9H (hexadecimal) (which is "31689" in decimal) is written to R30000. Indicates that "1234H (hexadecimal) (which is "4660" in decimal) is written to R30001. D-68 FX Series PLC User's Manual - Data Communication Edition Computer Link BT Command [Tests Device Memory in 1-Bit Units (by Writing Arbitrarily)] This section explains the control procedure specification method and shows a specification example when the bit device memory is specified arbitrarily and written all at once. B 1. Specification method PLC No. A C K 1 character "0 (30H)" indicates reset (setting to OFF). "1 (31H)" indicates set (setting to ON). * Number of device points (2 characters (hexadecimal)) 1) Specify the device point range while satisfying the following conditions: - 1 Number of device points 20*1 2) Express the station number, PLC number, number of device points and sum check code in hexadecimal. 2. Specification example When writing data for setting M50 to ON, S100 to OFF and Y001 to ON in the PLC whose station number is 5 (while the message waiting time is set to 0 ms) F This range is regarded as the sum check target. Computer side 05H 30H 35H 46H 46H 42H 54H 30H 30H 33H 4DH 30H 30H 35H 30H 31H 53H 30H 31H 30H 30H 30H 59H 30H 30H 30H 31H 31H 45H 43H PLC side Set (ON) 06H 30H 35H 46H 46H G Non-Protocol Communication (FX2N-232IF) A C 0 5 F F K Non-Protocol Communication (RS/RS2 Instruction) E N 0 5 F F B T 0 0 3 M 0 0 5 0 1 S 0 1 0 0 0 Y 0 0 0 1 1 E C Q Reset (OFF) E Inverter Communication 10 in the FX0N and FX1S Series Set (ON) D Computer Link Point *1. Parallel Link PLC side C Station No. Device (5 characters) Sum check code Device (5 characters) Set or reset * Character area A Set or reset BT Message wait time PLC No. Station No. Computer side E N Q N:N Network The specification method in the control procedure format 1 is shown below: Test (write arbitrarily) command (unit: bit) A Common Items 7.7 7 Commands 7.7 BT Command [Tests Device Memory in 1-Bit Units (by Writing Arbitrarily)] H Programming Communication I Remote Maintenance Apx.A Discontinued models D-69 FX Series PLC User's Manual - Data Communication Edition Computer Link 7.8 7 Commands 7.8 WT Command [Tests Device Memory in 1-Word Units (by Writing Arbitrarily)] WT Command [Tests Device Memory in 1-Word Units (by Writing Arbitrarily)] This section explains the control procedure specification method and shows a specification example when the word device memory and bit device memory (in 16-point units) are specified arbitrarily and written all at once. Word devices and bit devices (in 16-point units) can be specified together. However, the WT command cannot handle 32-bit word devices C200 to C255 (CN200 to CN255). 1. Specification method The specification method in the control procedure format 1 is shown below: WT Message wait time PLC No. Computer side E N Q Station No. Test (write arbitrarily) command (unit: word) Number of device points (2 characters (hexadecimal)) Character area A Device Data (5 characters) (4 characters) Device Data (5 characters) (4 characters) PLC side One device uses 4 characters. Four digits (hexadecimal) express one data word. PLC No. A C K Station No. Sum check code When specifying bit devices, specify the head device. 1) Specify the device point range while satisfying the following conditions: - 1 Number of device points 10*1 (in unit of 10*1 in case of bit devices (One unit indicates 16 points.)) 2) Express the station number, PLC number, number of device points and sum check code in hexadecimal. 3) The WT command cannot handle 32-bit word devices C200 to C255 (CN200 to CN255). *1. D-70 6 in the FX0N and FX1S Series FX Series PLC User's Manual - Data Communication Edition Computer Link 7 Commands 7.8 WT Command [Tests Device Memory in 1-Word Units (by Writing Arbitrarily)] A When writing data for setting the current value of D500 to "1234H", Y100 to Y117 to "BCA9H" and the current value of C100 to "64H" in the PLC whose station number is 5 (while the message waiting time is set to 0 ms) This range is regarded as the sum check target. B E N 0 5 F F W T 0 0 3 D 0 5 0 0 1 2 3 4 Y 0 1 0 0 B C A 9 Q N:N Network Computer side 05H 30H 35H 46H 46H 57H 54H 30H 30H 33H 44H 30H 35H 30H 30H 31H 32H 33H 34H 59H 30H 31H 30H 30H 42H 43H 41H 39H PLC side B This range is regarded as the sum check target. A 9 C Parallel Link Indicates that "1234H (which is "4660" in decimal)" is written to D500. C 1 0 1 1 1 1 0 0 1 0 1 0 1 0 0 1 Y 1 1 7 Y 1 1 6 Y 1 1 5 Y 1 1 4 Y 1 1 3 Y 1 1 2 Y 1 1 1 Y 1 1 0 Y 1 0 7 Y 1 0 6 Y 1 0 5 Y 1 0 4 Y 1 0 3 Y 1 0 2 Y 1 0 1 Y 1 0 0 D Computer Link Each bit is reset (OFF) in the case of "0", and set (ON) in the case of "0". C N 1 0 0 0 0 6 4 0 7 43H 4EH 31H 30H 30H 30H 30H 36H 34H 30H 37H A C 0 5 F F K E 06H 30H 30H 46H 46H Inverter Communication Indicates that "64H (which is "100" in decimal)" is written to the current value of C100. Common Items 2. Specification example F Non-Protocol Communication (RS/RS2 Instruction) G Non-Protocol Communication (FX2N-232IF) H Programming Communication I Remote Maintenance Apx.A Discontinued models D-71 FX Series PLC User's Manual - Data Communication Edition Computer Link 7.9 7 Commands 7.9 QT Command [Tests Device Memory in 1-Word Units (by Writing Arbitrarily)] QT Command [Tests Device Memory in 1-Word Units (by Writing Arbitrarily)] This section explains the control procedure specification method and shows a specification example when the word device memory and bit device memory (in 16-point units) are specified arbitrarily and written all at once. Word devices and bit devices (in 16-point units) can be specified together. However, the QT command cannot handle 32-bit word devices C200 to C255 (CN00200 to CN00255). This command is available only in FX3S, FX3G, FX3GC, FX3U and FX3UC PLCs. 1. Specification method The specification method in the control procedure format 1 is shown below: Message wait time Number of device points (2 characters) PLC No. QT Station No. PLC No. Computer side E N Q Station No. Command for test (by writing arbitrarily in 1-word units) Character area A Data on devices (4 characters) Device (7 characters) Device (7 characters) Data on devices (4 characters) Sum check code PLC side A C K 1) Specify the device point range while satisfying the following conditions: - 1 Number of device points 10 (in unit of 10 in case of bit devices (One unit indicates 16 points.)) 2) Express the station number, PLC number, number of device points and sum check code in hexadecimal. 3) Word devices and bit devices (in 16-point units) can be specified together. 4) The QT command cannot handle 32-bit word devices C200 to C255 (CN00200 to CN00255). 2. Specification example When writing data for setting the current value of R12000 to "1234H" and Y100 to Y117 to "BCA9H" in the PLC whose station number is 5 (while the message waiting time is set to 0 ms) This range is regarded as the sum check target. Computer side E N 0 5 F F Q T 0 0 2 R 0 1 2 0 0 0 1 2 3 4 Q 05H 30H 35H 46H 46H 51H 57H 30H 30H 32H 52H 30H 31H 32H 30H 30H 30H 31H 32H 33H 34H PLC side This range is regarded as the sum check target. Y 0 0 0 1 0 0 B C A 9 E 3 59H 30H 30H 30H 31H 30H 30H 42H 43H 41H 39H 45H 33H A C 0 5 F F K B C A 06H 30H 35H 46H 46H 9 1 0 1 1 1 1 0 0 1 0 1 0 1 0 0 1 Y 1 1 7 D-72 Y 1 1 0 Y 1 0 7 Y 1 0 1 Y 1 0 0 FX Series PLC User's Manual - Data Communication Edition Computer Link A RR/RS Command [Remotely Sets PLC to RUN/STOP Mode] This section explains the control procedure specification method and shows a specification example when the computer remotely sets the PLC mode to RUN or STOP. B 7.10.1 Contents of remote control to set RUN or STOP mode Remote control to set to STOP mode E NO Inverter Communication YES Special auxiliary relay M8037 is set to ON. D Computer Link • Remote STOP mode control When the RS command (which sets remote STOP mode in control) is executed in the computer, the PLC executes the following processing. If the RS command is executed while the PLC is in STOP mode, the PLC status does not change, and the PLC returns the remote error code (18H) to the computer. C Parallel Link • Remote RUN mode control When the RR command (which sets remote RUN mode in control) is executed in the computer, the PLC sets M8035 and M8036 to activate the forced RUN mode. If the RR command is executed while the PLC is in RUN mode, however, the PLC status does not change, and the PLC returns the remote error code (18H) to the computer. N:N Network When the computer executes remote control of the PLC mode to RUN or STOP, the forced RUN mode is activated in the PLC, and the special auxiliary relays M8035, M8036 and M8037 are controlled as follows: Forced RUN mode Common Items 7.10 7 Commands 7.10 RR/RS Command [Remotely Sets PLC to RUN/STOP Mode] PLC returns remote error code (18H) to computer, and PLC status does not change. F Non-Protocol Communication (RS/RS2 Instruction) Special auxiliary relays M8035, M8036 and M8037 are set to OFF. PLC switches to STOP mode. G • Remote STOP mode control The PLC is in RUN mode (forced RUN mode) without using the RUN terminal or built-in RUN/STOP selector switch. When the PLC power is turned OFF and then ON after the RR command is executed by the computer, all of the special auxiliary relays M8035, M8036 and M8037 are set to OFF. As a result, the PLC switches to STOP mode. I Remote Maintenance Point H Programming Communication • Remote RUN mode control The PLC is in STOP mode. (The built-in RUN/STOP selector switch is set to STOP.) (In an FX2(FX) or FX2C PLC, the RUN terminal in the PLC is OFF, and the built-in RUN/STOP selector switch is set to STOP.) Non-Protocol Communication (FX2N-232IF) 7.10.2 Condition validating remote control to set RUN or STOP mode Apx.A Discontinued models D-73 FX Series PLC User's Manual - Data Communication Edition 7 Commands Computer Link 7.10 RR/RS Command [Remotely Sets PLC to RUN/STOP Mode] 7.10.3 Remote control specification method and specification examples This subsection explains the control procedure specification method and specification examples when remote RUN or STOP mode control is executed. 1. Specification method The specification method in the control procedure format 1 is shown below: A C K PLC No. PLC side Station No. Sum check code RR or RS Message wait time Station No. Computer side E N Q PLC No. RR command to remotely set the PLC to the RUN mode RS command to remotely set the PLC to the STOP mode Express the station number, PLC number, number of device points and sum check code in hexadecimal respectively. 2. Specification examples Example 1: When remotely setting the PLC whose station number is 5 to RUN mode (while the message waiting time is set to 0 ms) This range is regarded as the sum check target. Computer side E N 0 5 F F R R 0 C 5 Q 05H 30H 35H 46H 46H 52H 52H 30H 43H 35H PLC side A C 0 5 F F K 06H 30H 35H 46H 46H Example 2: When remotely setting the PLC whose station number is 0 to STOP mode (while the message waiting time is set to 0 ms) This range is regarded as the sum check target. Computer side PLC side E N 0 0 F F R S 0 C 1 Q 05H 30H 30H 46H 46H 52H 53H 30H 43H 31H A C 0 0 F F K 06H 30H 30H 46H 46H D-74 FX Series PLC User's Manual - Data Communication Edition 7 Commands Computer Link A PC Command [Reads PLC Model Name] This section explains the control procedure specification method and specification example when the model name of a PLC linked to the computer is read. B 7.11.1 PLC model name (CPU) and read contents Model name code (hexadecimal) PLC model name (CPU) 8DH A2CCPU 9AH FX0N 8EH A2USCPU 82H FX1S F2H A2CPU-S1, A2USCPU-S1 83H C FX1N, FX1NC 9EH A3CPU, A3NCPU A3H FX2N, FX2NC 9DH A3ACPU 94H FX3S F5H A3HCPU, A3MCPU A4H FX3G, FX3GC F4H A3UCPU 84H FX3U, FX3UC F3H A4UCPU 85H A0J2HCPU 98H A52GCPU 9AH A1CPU, A1NCPU A1H A73CPU A3H A1SCPU, A1SJCPU 98H A7LMS-F A3H D AJ72P25/R25 ABH 92H AJ72LP25/BR15 8BH A2ACPU-S1 93H 7.11.2 Control procedure specification method and specification example 1. Specification method Non-Protocol Communication (RS/RS2 Instruction) PLC model name (2 characters) E T X PLC No. G Sum check code PLC No. S T X Station No. Character area B Station No. Sum check code Message wait time PLC No. A C K Non-Protocol Communication (FX2N-232IF) PLC side Station No. PC command to read the PLC model name Computer side E F The specification method for control procedure format 1 is shown below: PC Computer Link A2H Inverter Communication A2CPU(-S1), A2NCPU(-S1), A2SCPU A2ACPU E N Q Parallel Link FX2(FX), FX2C N:N Network Model name code (hexadecimal) PLC model name (CPU) Common Items 7.11 7.11 PC Command [Reads PLC Model Name] Express the station number, PLC number, number of device points and sum check code in hexadecimal respectively. H Programming Communication I Remote Maintenance Apx.A Discontinued models D-75 FX Series PLC User's Manual - Data Communication Edition Computer Link 7 Commands 7.11 PC Command [Reads PLC Model Name] 2. Specification example When reading the model name of the PLC whose station number is 15 (while the message waiting time is set to 0 ms) This range is regarded as the sum check target. Computer side PLC side E N 0 F F F P C 0 C 5 Q This range is regarded as the sum check target. 05H 30H 46H 46H 46H 50H 43H 30H 43H 35H A C 0 F F F K 06H 30H 46H 46H 46H S E T 0 F F F 8 D T 8 1 X X 02H 30H 46H 46H 46H 38H 44H 03H 38H 31H The example above indicates that the model name of the target PLC is the FX2(FX) or FX2C Series. D-76 FX Series PLC User's Manual - Data Communication Edition Computer Link A GW Command [Offers Global Function] 7.12.1 Contents of control • In the control procedure, specify the station number "FFH" so that all stations are handled as targets. If any value other than "FFH" is specified, a special auxiliary relay is set to ON or OFF only in a station with the specified station number. • When the PLC power is turned OFF or when the PLC is set to STOP mode, the special auxiliary relay M8126 or M8426 is set to OFF and the processing request in the global function is cleared. 7.12.2 Global function control procedure specification method and specification example 1. Specification method The specification method in the control procedure format 1 is shown below: Factor number (1 character) PLC side Sum check code Message wait time PLC No. GW F Character area A Non-Protocol Communication (RS/RS2 Instruction) E N Q Computer side Station No. GW command to execute the global command When the data value is "1 (31H)", M8126 or M8426 is set to ON. When the data value is "0 (30H)", M8126 or M8426 is set to OFF. 2. Specification example When setting to ON the special auxiliary relay M8126 of M8426 in all FX PLCs (In all of A Series PLCs in computer link, however, Xn2 is set to ON.) H Programming Communication This range is regarded as the sum check target. E N F F F F G W 0 1 1 7 Q I 05H 46H 46H 46H 46H 47H 57H 30H 31H 31H 37H Indicates that the special auxiliary relay M8126 or M8426 is set to ON in target stations. Remote Maintenance PLC side G Non-Protocol Communication (FX2N-232IF) Express the station number, PLC number, number of device points and sum check code in hexadecimal respectively. Computer side E Inverter Communication This subsection explains the control procedure specification method and specification example when the global function is executed from the computer. D Computer Link • In this function, PLCs do not give any response to the GW command from the computer. C Parallel Link The global function sets a special auxiliary relay to ON or OFF in all FX Series PLCs linked to the computer. M8126 is set to ON or OFF in PLCs except the FX3G, FX3GC, FX3U and FX3UC Series. In FX3G, FX3GC, FX3U and FX3UC PLCs, M8126 is set to ON or OFF in computer link using ch1, and M8426 is set to ON or OFF in computer link using ch2. In A Series PLCs, Xn2 is set to ON or OFF for all PLCs linked to the computer. B N:N Network The global function executed in the computer sets a special auxiliary relay to ON or OFF in all PLCs linked to the computer in the multi-drop link method. For A Series PLCs, however, refer to the respective A Series PLC manual. This section explains the control procedure specification method and specification example when the global function is used. Common Items 7.12 7 Commands 7.12 GW Command [Offers Global Function] Specify "FFH" for handling all stations as targets. When handling only one station as a target, specify the station number (ranging from 00 to 0F) of the target station. Apx.A Discontinued models D-77 FX Series PLC User's Manual - Data Communication Edition 7 Commands Computer Link 7.13 7.13 On-demand Function On-demand Function When there is data to be sent from a PLC to the computer, the on-demand function can specify the data register area storing the data to be sent, and let the PLC start sending. When data is sent between the computer and a PLC, only the computer can start data transmission. When there is emergency data to be sent from a PLC to the computer, the on-demand function is applicable to let the PLC begin sending data to the computer. PLC Sequence program D8127 D8128 Head device number (n) Data length (m) Computer D(n) D(n+m-1) Point This function is applicable when the computer and the PLC CPU have the 1-to-1 configuration. 7.13.1 Special data registers and special auxiliary relays used in on-demand function The tables below show the special data registers and special auxiliary relays used in the on-demand function. 1. In all PLCs except FX3G, FX3GC, FX3U and FX3UC PLCs and when ch1 is used in FX3G, FX3GC, FX3U and FX3UC PLCs Device Name On-demand send M8127*1 processing Remains ON while the on-demand function is being executed. ON: On-demand data is being sent. OFF: Sending of on-demand data is completed. M8128 On-demand error flag Turns ON when an error is included in a specified value to be sent in the ondemand function. ON: Error is included. OFF: Error is not included. M8129 On-demand byte/word changeover Specifies the unit (byte or word) of data handled in the on-demand function. ON: Unit = Byte (8-bit) OFF: Unit = Word (16-bit) D8127 On-demand head device number specification Sets the head data register device number containing the data to be sent using the on-demand function in a sequence program. D8128 On-demand data quantity specification Sets the amount of data to be sent using the on-demand function in a sequence program. *1. D-78 Description FX0N, FX1S, FX1N and FX1NC PLCs do not support this device. FX Series PLC User's Manual - Data Communication Edition 7 Commands Computer Link 7.13 On-demand Function A Common Items 2. When ch2 is used in FX3G, FX3GC, FX3U and FX3UC PLCs Description M8427 On-demand send processing Remains ON while the on-demand function is being executed. ON: On-demand data is being sent. OFF: Sending of on-demand data is completed. M8428 On-demand error flag Turns ON when an error is included in a specified value to be sent in the ondemand function. ON: Error is included. OFF: Error is not included. M8429 On-demand byte/word changeover Specifies the unit (byte or word) of data handled in the on-demand function. ON: Unit = Byte (8-bit) OFF: Unit = Word (16-bit) D8427 On-demand head device number specification Sets the head data register device number containing the data to be sent using the on-demand function in a sequence program. D8428 On-demand data quantity specification Sets the amount of data to be sent using the on-demand function in a sequence program. B C Parallel Link Name N:N Network Device D • The on-demand send processing signal (M8127 or M8427) turns ON when the PLC gives a request to send data to the computer, and turns OFF when sending of the specified data is completed. Use this signal for interlock to prevent giving two or more on-demand requests at the same time. • While the on-demand send processing signal is ON, the PLC cannot receive commands sent from the computer. Computer Link Point E Inverter Communication • Amount of on-demand data and number of data registers used for sending according to the unit specification (word or byte) When the specified unit is a word: The amount of on-demand data is equivalent to the number of data registers to be sent. F Example: When the amount of on-demand data is "5", the number of data registers for sending is "3". Non-Protocol Communication (RS/RS2 Instruction) When the specified unit is a byte: Two on-demand data units use one data register for sending. G Non-Protocol Communication (FX2N-232IF) H Programming Communication I Remote Maintenance Apx.A Discontinued models D-79 FX Series PLC User's Manual - Data Communication Edition 7 Commands Computer Link 7.13 On-demand Function 7.13.2 Control procedures in on-demand function This subsection explains the control procedures for the on-demand function. When using ch2 in an FX3G, FX3GC, FX3U or FX3UC Series PLC, exchange special auxiliary relays (M) and special data registers (D) according to the table below. All PLCs except FX3G, FX3GC, FX3U and FX3UC PLCs FX3G, FX3GC, FX3U and FX3UC PLCs (ch1) FX3G, FX3GC, FX3U and FX3UC PLCs (ch2) M8127*1 M8427 M8128 M8129 *1. M8428 M8429 D8127 D8427 D8128 D8428 FX0N, FX1S, FX1N and FX1NC PLCs do not support this device. 1) Control procedure in the PLC Sending of on-demand data Checks unit (word or byte) of data to be sent ........ It is checked whether M8129 is ON or OFF. ON: Unit = byte (8-bit) OFF: Unit = word (16-bit) Writes data to be sent to data registers ........ Data to be sent is written to data registers. Resets on-demand error ........ The on-demand error flag M8128 turns OFF. (While M8128 is ON, the on-demand function is disabled.) Starts on-demand function ........ The head device (data register) number storing the ondemand data is written to D8127, and the amount of data is written to D8128. When a request is accepted, M8127 is set to ON. When sending is complete, M8127 turns OFF. Checks for sending error When there is error When there is no error Sending is completed D-80 ........ If the on-demand error flag M8128 is ON, it means that data was not sent due to an error in the specified value to be sent. FX Series PLC User's Manual - Data Communication Edition 7 Commands Computer Link 7.13 On-demand Function A Common Items 2) Control procedure in the computer Receiving of on-demand data "FE", the received data should be processed as on-demand data. Data processing C Parallel Link Completion of receiving 3) Time chart when the on-demand function is requested While the computer is sending data E N Q D A C K [2] On-demand data [3] PLC side Computer Link Computer side E Inverter Communication S T X On-demand send processing M8127 [1] F Writes data to be sent and amount of data to be sent. PLC [3] H S T X [1] I [2] Remote Maintenance On-demand send processing M8127 PLC A C K Programming Communication PLC side On-demand data G Non-Protocol Communication (FX2N-232IF) While the computer is receiving data E N Q Non-Protocol Communication (RS/RS2 Instruction) [1] As soon as an on-demand request is given, the on-demand send processing signal M8127 turns ON. [2] After receiving of command data (ENQ ~) from the computer is completed, the PLC sends on-demand data. [3] After the sending of on-demand data is complete, the PLC sends response data (STX ~) to the command data (ENQ ~). Computer side B N:N Network Judges whether receive data is ........ To the on-demand data, the PLC adds "FE" as the PLC on-demand data or data given number. Only when the PLC number of the received data is by command execution. Writes data to be sent and amount of data to be sent. D-81 Apx.A Discontinued models [1] As soon as an on-demand request is given, the on-demand send processing signal M8127 turns ON. [2] After the sending of response data (STX ~) to the command data (ENQ ~) from the computer is completed, the PLC sends on-demand data. [3] After the receiving of on-demand data is complete, the computer sends response data (ACK ~) to the sending of the response data (STX ~) from the PLC. FX Series PLC User's Manual - Data Communication Edition 7 Commands Computer Link 7.13 On-demand Function 7.13.3 On-demand function specification method and specification examples This subsection explains the on-demand function specification method and specification examples. When using ch2 in an FX3G, FX3GC, FX3U or FX3UC Series PLC, exchange special auxiliary relays (M) and special data registers (D) according to the table below. All PLCs except FX3G, FX3GC, FX3U and FX3UC PLCs FX3G, FX3GC, FX3U and FX3UC PLCs (ch1) FX3G, FX3GC, FX3U and FX3UC PLCs (ch2) M8127*1 M8427 M8128 M8428 M8129 *1. M8429 D8127 D8427 D8128 D8428 FX0N, FX1S, FX1N and FX1NC PLCs do not support this device. 1. Specification method The specification method in the control procedure format 1 is shown below: Added by PLC On-demand send processing M8127 PLC Writes data to be sent and amount of data to be sent. ON Data to be sent E T X Sum check code S T X PLC No. PLC side Station No. Computer side OFF Write the head device number (data register) storing the data to be sent to the special data register D8127. Write the amount of data to the special data register D8218. 1) Specify the data quantity specification range while satisfying the following condition: - Amount of data 40H (= 64 in decimal) 2) The PLC adds "FE" as the PLC number. 3) Express the station number, PLC number, number of device points and sum check code in hexadecimal. IMPORTANT Do not use the on-demand function when the system configuration is not 1-to-1 type. If the on-demand function is used in the multi-drop link system in which the computer and PLC CPUs have the 1-to-N configuration, the transfer data and on-demand send data in the control procedure format 1 or 4 are destroyed, and normal data sending is not possible. D-82 FX Series PLC User's Manual - Data Communication Edition 7 Commands Computer Link 7.13 On-demand Function A When sending the data stored in the data registers D100 and D101 by a trigger from a sequence program (when the station number is 0 and the data unit to be sent is set to "word") The PLC number "FE" is automatically added by the PLC. Computer side PLC side 1 2 3 4 5 6 7 8 B E T 9 2 X N:N Network S T 0 0 F E X 02H 30H 30H 46H 45H 31H 32H 33H 34H 35H 36H 37H 38H 03H 39H 32H M8127 On-demand command [1] D8127 D8128 100 2 C M8128 ON/OFF M8129 OFF [2] D100 D101 1234H 5678H It turns ON when an error is included in the specified value for sending. Data is sent in 4-bit units starting from highest-order bits. D Computer Link Sequence program example 0 3 40 M8127 M8127 M8128 M8127 M8128 M0 MOV H1234 D100 MOV H5678 D101 RST M8128 RST Y000 RST Y001 MOV K100 D8127 MOV K2 D8128 SET Y000 SET Y001 E ........ Data to be sent is set. The on-demand error flag is reset. ........ (The on-demand function is disabled while M8128 is ON.) F The head device number storing the data to be ........ sent and the amount of data are specified, and the on-demand function is started up. ........ On-demand error is checked for, and the check result is output. END M8128 G Non-Protocol Communication (FX2N-232IF) 37 M0 PLS ........ The data unit is set to "word" value. The startup command is the pulse operation ........ type. Non-Protocol Communication (RS/RS2 Instruction) 33 M8129 M8002 Inverter Communication 7 M8000 X000 Parallel Link PLC Writes data to be sent and amount of data to be sent. Common Items 2. Specification example 1 H OFF: Data is sent normally. Programming Communication ON: Data is not sent because an error occurred. I Remote Maintenance Apx.A Discontinued models D-83 FX Series PLC User's Manual - Data Communication Edition 7 Commands Computer Link 7.13 On-demand Function 3. Specification example 2 When sending the data stored in the data registers D100 and D101 by a trigger from a sequence program (when the station number is 0 and the data unit to be sent is set to "byte") The PLC number "FE" is automatically added by the PLC. Computer side PLC side S T 0 0 F E X 3 4 1 2 7 8 5 6 E T 9 2 X 02H 30H 30H 46H 45H 31H 32H 33H 34H 37H 38H 35H 36H 03H 39H 32H M8127 PLC Writes data to be sent and amount of data to be sent. On-demand command [1] D8127 D8128 100 4 M8128 ON/OFF M8129 ON [2] D100 D101 1234H 5678H It turns ON when an error is included in the specified value for sending. Data is sent in 4-bit units, in the order "lowest-order 8-bit highest-order 8-bit". Sequence program example 0 3 7 33 37 40 M8000 M8129 X000 M8002 M0 M8127 M8127 M8128 M8127 M8128 PLS M0 MOV H1234 D100 MOV H5678 D101 RST M8128 RST Y000 RST Y001 MOV K100 D8127 MOV K4 D8128 SET Y000 SET Y001 ........ The data unit is set to "byte" value. ........ The startup command is the pulse operation type. ........ Data to be sent is set. The on-demand error flag is reset. ........ (The on-demand function is disabled while M8128 is ON.) The head device number storing the data to be sent ........ and the amount of data are specified, and the ondemand function is started up. ........ On-demand error is checked for, and the check result is output. END M8128 OFF: Data is sent normally. ON: Data is not sent because an error occurred. D-84 FX Series PLC User's Manual - Data Communication Edition 7 Commands Computer Link A TT Command [Loop-back Test] The loop-back test function checks whether or not communication between the computer and a PLC is normal. This section explains the control procedure specification method and specification example when the loopback test function is used. The specification method in the control procedure format 1 is shown below: Data (Data for character length) E T X Sum check code Character length S T X 2 characters (hexadecimal) PLC No. PLC side C 2 characters (hexadecimal) Station No. Data (Data for character length) Sum check code Character length Message wait time PLC No. TT Character area A Parallel Link E N Q Computer side Station No. Loop-back test command D Character area B 2) Express the station number, PLC number, number of device points and sum check code in hexadecimal respectively. When executing the loop-back test to the PLC whose station number is 0 using the data "ABCDE" (while the message waiting time is set to 0 ms) This range is regarded as the sum check target. F E N 0 0 F F T T 0 0 5 A B C D E 7 8 Q Non-Protocol Communication (RS/RS2 Instruction) PLC side E Inverter Communication 2. Specification example Computer Link 1) Specify the character length specification range while satisfying the following condition: - 1 Character length 254 Computer side B N:N Network 1. Specification method Common Items 7.14 7.14 TT Command [Loop-back Test] This range is regarded as the sum check target. 05H 30H 30H 46H 46H 54H 54H 30H 30H 35H 41H 42H 43H 44H 45H 37H 38H S E T 0 0 F F 0 5 A B C D E T A 3 X X G Non-Protocol Communication (FX2N-232IF) 02H 30H 30H 46H 46H 30H 35H 41H 42H 43H 44H 45H 03H 41H 33H Both data should be equivalent. H Programming Communication I Remote Maintenance Apx.A Discontinued models D-85 FX Series PLC User's Manual - Data Communication Edition Computer Link 8. 8 Troubleshooting 8.1 Checking FX PLC Version Applicability Troubleshooting This chapter explains troubleshooting. 8.1 Checking FX PLC Version Applicability Verify that the FX PLC main unit is an applicable version. For the version applicability check, refer to Section 1.3. 8.2 Checking Communication Status Based on LED Indication Check the status of the "RD(RXD)" and "SD(TXD)" indicator LEDs provided in the optional equipment. LED status Operation status RD(RXD) SD(TXD) Flashing Flashing Flashing Off Data is received, but is not sent. Off Flashing Data is sent, but is not received. Off Off Data is being sent or received. Data is not sent or received. While computer link is executed normally, both LEDs flash brightly. If they do not flash, check the wiring, station number settings and communication setting. 8.3 Checking Installation and Wiring 1. Mounting status If the communication equipment is not securely connected to the PLC, communication is not possible. For mounting method, refer to the respective communication equipment manual. 2. Power supply (for FX0N-485ADP) The FX0N-485ADP requires a driving power supply. Verify that the power supply is provided correctly. 3. Wiring Verify that the wiring to all communication equipment is correct. If the communication equipment is wired incorrectly, communication is not possible. For wiring method check, refer to Chapter 4. 8.4 Checking Sequence Program 1. Communication setting in the sequence program Verify that the parallel link and N:N Network are not set. Verify that the communication format (D8120, D8400 and D8420) is set correctly. Communication is not possible if a communication port is set twice or more. After changing any setting, make sure to reboot the PLC’s power. 2. Communication setting using parameters Verify that the communication settings using parameters is suitable to the purpose of use. If the communication settings are not suitable to the purpose of use, communication will not function correctly. After changing any setting, make sure to reboot the PLC’s power. 3. Ethernet port setting (in FX3S, FX3G, FX3GC, FX3U and FX3UC PLCs) Verify that the same channel is not used in the Ethernet port setting. Do not set the channel used in computer link. After changing the setting, make sure to reboot the PLC's power. D-86 FX Series PLC User's Manual - Data Communication Edition Computer Link 8 Troubleshooting 8.4 Checking Sequence Program A Common Items 4. Presence of VRRD and VRSC instructions 1) Except FX3G, FX3U and FX3UC PLCs Verify that the VRRD and VRSC instructions are not used in the program. If these instructions are used, delete them, reboot the PLC’s power. 2) In FX3G PLC - In the case of the 14 points and 24-point type Verify that the VRRD and VRSC instructions are not used in the program. If these instructions are used, delete them, reboot the PLC's power. - In the case of the 40 points and 60-point type Verify that the VRRD and VRSC instructions are not used in the program. If these instructions are used in the program, the communication function is not available in ch2. Use ch1, or delete these instructions. After deleting these instructions, reboot the PLC's power. B N:N Network C Parallel Link 3) In FX3U and FX3UC PLCs Verify that the VRRD and VRSC instructions are not used in the program. If these instructions are used in the program, the communication function is not available in ch1. Use ch2, or delete these instructions. After deleting these instructions, reboot the PLC's power. D Computer Link 5. Presence of RS instruction (except FX3S, FX3G, FX3GC, FX3U and FX3UC PLCs) Verify that the RS instruction is not used in the program. If this instruction is used, delete it, reboot the PLC’s power. 6. Presence of RS and RS2 instructions (in FX3S, FX3G, FX3GC, FX3U and FX3UC PLCs) E Inverter Communication Verify that the RS and RS2 instructions are not being used for the same channel. If these instructions are used for the same channel, delete them, reboot the PLC’s power. 7. Presence of EXTR instruction (in FX2N and FX2NC PLCs) Verify that the EXTR instruction is not used in the program. If this instruction is used, delete it, then reboot the PLC’s power. F Verify that the IVCK, IVDR, IVRD, IVWR, IVBWR and IVMC instructions are not being used for the same channel. If these instructions are used for the same channel, delete them, reboot the PLC’s power. *1. Only available for FX3U and FX3UC PLCs. Non-Protocol Communication (RS/RS2 Instruction) 8. Presence of IVCK, IVDR, IVRD, IVWR, IVBWR*1, and IVMC instructions (in FX3S, FX3G, FX3GC, FX3U and FX3UC PLCs) G Verify that the ADPRW instructions are not being used for the same channel. If these instructions are used for the same channel, delete them, and reboot the PLC’s power. 10.Presence of FLCRT, FLDEL, FLWR, FLRD, FLCMD, and FLSTRD instructions (in FX3U and FX3UC PLCs) H Programming Communication Verify that the FLCRT, FLDEL, FLWR, FLRD, FLCMD and FLSTRD instructions are not being used for the same channel. If these instructions are used for the same channel, delete them, reboot the PLC’s power. Non-Protocol Communication (FX2N-232IF) 9. Presence of ADPRW instructions (in FX3S, FX3G, FX3GC, FX3U and FX3UC PLCs) I Remote Maintenance Apx.A Discontinued models D-87 FX Series PLC User's Manual - Data Communication Edition Computer Link 8 Troubleshooting 8.5 Checking Error Codes 8.5 Checking Error Codes 8.5.1 Error codes when NAK is sent The table below shows error codes and contents of errors when NAK is sent in communication between the computer and a PLC. As an error code, a two-digit ASCII code (hexadecimal) within the range from 00H to FFH is sent. When two or more errors occur at the same time, priority is given to the error code with the smallest number, and the error code with the smallest number is sent. When any error shown below occurs, the entire transfer sequence is initialized. Error code list Error code (hexadecimal) Contents of error Sum check error has occurred. The sum check code included in the received data is different from the sum value calculated from the received data. Action Check the data sent from the computer and the contents of the sum check. Modify either one, and then execute communication again. 02H Sum check error 03H The communication protocol is 1) Check the contents of parameters abnormal. and the contents of control A control procedure set using procedure. Modify either contents, parameters was ignored, and a different and then execute communication control procedure was adopted in again. Protocol error communication. Or the adopted control 2) Refer to the command list shown in procedure was partially different from the Chapter 7, modify the specified preset control procedure. Or a command command etc., and then execute specified in the preset control procedure communication again. does not exist. 06H Character area error An error occurred in the character area A, B or C. Or a specified command does 1) Check the contents of the character areas A, B and C, modify the not exist. contents if necessary, and then 1) The control procedure set using execute communication again. parameters is different. 2) Refer to "2.2.2 Applicable device 2) A specified device number does not ranges", modify the number of exist in the target PLC. characters used to specify the device 3) A device number is not set with the number, and then execute specified number of characters (5 or communication again. 7 characters). 07H Character error Check the data to be written to the ASCII code data to be written to a device device, modify it if necessary, and then is not hexadecimal. execute communication again. 0AH 10H 18H D-88 Error item A station with the corresponding PLC number does not exist. Check the PLC number included in the message, modify it if necessary, and then execute communication again. The PLC number should be "FFH" in all FX Series PLCs. PLC number error A station with the corresponding PLC number does not exist. Check the PLC number included in the message, modify it if necessary, and then execute communication again. The PLC number should be "FFH" in all FX Series PLCs. Remote control error Remote control to set the RUN or STOP mode is disabled. Set the PLC mode to RUN or STOP The RUN or STOP mode is determined using the forced RUN mode. in the PLC hardware (by using the RUN/ STOP selector switch, etc.). PLC number error FX Series PLC User's Manual - Data Communication Edition Computer Link A Error codes in PLC Device The transfer data is abnormal. Check the transfer specifications set using parameters, and execute communication again. 6305 Command error When the station number was FF, any command other than "GW" was received. Check the specified command, modify it if necessary, and then execute communication again. 6306 Monitoring timeout The received message was insufficient. Because normal message was not received within the time-out time setting, the transfer sequence was initialized. The message is insufficient. Check the transfer program in the computer, modify it if necessary, and then execute communication again. 3801 Parity, overrun or framing error The transfer data is abnormal. Check the transfer specifications set using parameters, and execute communication again. 3805 Command error When the station number was FF, any command other than "GW" was received. Check the specified command, modify it if necessary, and then execute communication again. Monitoring timeout The received message was insufficient. Because normal message was not received within the time-out time setting the transfer sequence was initialized. The message is insufficient. Check the transfer program in the computer, modify it if necessary, and then execute communication again. 3806 E F G Non-Protocol Communication (FX2N-232IF) Serial communication errors and serial communication error code are not cleared even when communication is restored. Serial communication errors are cleared in FX3S, FX3G, FX3GC, FX3U and FX3UC PLCs when the power is turned off and on. Serial communication errors are cleared in other PLCs when the mode is switched from STOP to RUN. D Computer Link Parity, overrun or framing error Non-Protocol Communication (RS/RS2 Instruction) 6301 Action Inverter Communication D8438 (ch2) Error item Parallel Link D8063 (ch1) C Error code Contents of error B N:N Network When an error is included in a message sent from the computer to a PLC, an error occurs in the PLC. When such an error occurs, the serial communication error flag turns ON. When PLCs other then FX3G, FX3GC, FX3U and FX3UC PLCs are used or when ch1 is used in an FX3G, FX3GC, FX3U or FX3UC PLC, the special auxiliary relay M8063 turns ON as an error flag. When ch2 is used in an FX3G, FX3GC, FX3U or FX3UC PLC, the special auxiliary relay M8438 turns ON as an error flag. When a serial communication error occurs, the error code is stored in D8063 if M8063 turns ON, or stored in D8438 if M8438 turns ON. The error code list is shown below: Common Items 8.5.2 8 Troubleshooting 8.5 Checking Error Codes H Programming Communication I Remote Maintenance Apx.A Discontinued models D-89 FX Series PLC User's Manual - Data Communication Edition 9 Related Data Computer Link 9. 9.1 9.1 Related Device List Related Data Related Device List 1. Bit devices Device Name Description R/W M8063 Serial communication error 1 Turns ON when an error occurs in serial communication using ch 1. R M8120 Communication setting keep Keeps the communication setting status (for FX0N PLCs). Global function ON Turns ON or OFF when the global command (GW) is received from the computer (for ch 1). R On-demand send processing Remains ON while the on-demand function is being executed (for ch 1). ON: On-demand data is being sent. OFF: Sending of on-demand data is completed. R M8128 On-demand error flag Turns ON when an error is included in a specified value for data sending used in the on-demand function (for ch 1). R M8129 On-demand data byte/word switch Specifies the unit (byte or word) of data handled in the ondemand function (for ch 1). ON: Unit = Byte (8-bit) OFF: Unit = Word (16-bit) R/W M8426 Global function ON Turns ON or OFF when the global command (GW) is received from the computer (for ch 2). R M8427 On-demand send processing Remains ON while the on-demand function is being executed (for ch 2). ON: On-demand data is being sent. OFF: Sending of on-demand data is completed. R M8428 On-demand error flag Turns ON when an error is included in a specified value for data sending used in the on-demand function (for ch 2). R M8429 On-demand data byte/word switch Specifies the data unit (byte or word) handled in the ondemand function (for ch 2). ON: Unit = Byte (8-bit) OFF: Unit = Word (16-bit) M8438 Serial communication error 2 Turns ON when an error occurs in serial communication using ch 2. M8126 M8127 *1 R: Read only R/W: Read or Write *1. D-90 FX0N, FX1S, FX1N and FX1NC PLCs do not support this device. R/W R/W R FX Series PLC User's Manual - Data Communication Edition 9 Related Data Computer Link 9.1 Related Device List A Device Name Description R/W Stores the error code when an error occurs in serial communication (for ch 1). D8120 Communication format setting Sets the communication format (for ch 1). R/W D8121 Station number settings Sets the station number in computer link (for ch 1). R/W D8127 On-demand data head device number specification Sets the head data register device number containing the data to be sent using the on-demand function (for ch 1). R/W D8128 On-demand data quantity specification Sets the amount of data to be sent using the on-demand function (for ch 1). R/W D8129 Time-out time setting Sets the evaluation time for error when the receiving of data from the computer is interrupted (for ch 1). R/W D8063 R Communication format setting Sets the communication format (for ch 2). R/W R D8421 Station number settings Sets the station number in computer link (for ch 2). R/W D8427 On-demand data head device number specification Sets the head data register device number containing the data to be sent using the on-demand function (for ch 2). R/W D8428 On-demand data quantity specification Sets the amount of data to be sent using the on-demand function (for ch 2). R/W D8429 Time-out time setting Sets the evaluation time for error when the receiving of data from the computer is interrupted (for ch 2). R/W D8438 Serial communication error code 2 Stores the error code when an error occurs in serial communication (for ch 2). D8439 Operation mode display (ch 2) Stores the communication type being used (for ch 2). R R D Computer Link Operation mode display (ch 1) Stores the communication type being used (for ch 1). D8420 C Parallel Link D8419 B N:N Network Serial communication error code 1 Common Items 2. Word devices E Inverter Communication R: Read only R/W: Read or Write F Non-Protocol Communication (RS/RS2 Instruction) G Non-Protocol Communication (FX2N-232IF) H Programming Communication I Remote Maintenance Apx.A Discontinued models D-91 FX Series PLC User's Manual - Data Communication Edition Computer Link 9.2 9 Related Data 9.2 Details of Related Devices Details of Related Devices The devices described below are used for computer link. 9.2.1 Serial communication error [M8063 and M8438] These devices turn ON when an error occurs during serial communication. 1. Detailed contents These devices work as the serial communication error flags. In all PLCs except FX3G, FX3GC, FX3U and FX3UC PLCs using the communication port, M8063 turns ON. For FX3G, FX3GC, FX3U and FX3UC PLCs using the communication port ch1, M8063 turns ON. In FX3G, FX3GC, FX3U and FX3UC PLCs using the communication port ch2, M8438 turns ON. When serial communication error flags turn ON, a corresponding error code is stored in D8063 and D8438. 2. Cautions on use Serial communication errors code are not cleared even when communication is restored. Serial communication errors are cleared in FX3S, FX3G, FX3GC, FX3U and FX3UC PLCs when the power is turned off and on. Serial communication errors are cleared in other PLCs when the mode is switched from STOP to RUN. 9.2.2 Communication setting keep [M8120] Set this device to ON in a sequence program so that the communication setting is kept (for FX0N PLCs). 1. Detailed contents In an FX0N PLC, set M8120 to ON in a sequence program so that the communication format setting and station number settings are kept. 2. Cautions on use In an FX0N PLC, the communication setting status is kept only when M8120 is set to ON. In any PLC other than FX0N PLCs, setting of M8120 is not required. 9.2.3 Global function ON [M8126 and M8426] These devices turn ON/OFF when the PLC receives the global command (GW) from personal computers. 1. Detailed contents When the computer sends the global command, the global ON flag turns ON or OFF in all connected stations. In all PLCs except FX3G, FX3GC, FX3U and FX3UC PLCs using the communication port, M8126 turns ON or OFF. For FX3G, FX3GC, FX3U and FX3UC PLCs using the communication port ch1, M8126 turns ON or OFF. In FX3G, FX3GC, FX3U and FX3UC PLCs using the communication port ch2, M8426 turns ON or OFF. 2. Cautions on use The global ON flag turns OFF from ON when the PLC power is turned OFF or when the PLC mode is changed to STOP. 9.2.4 On-demand send processing [M8127 and M8427] These devices remain ON while the on-demand function is being executed. 1. Detailed contents When a PLC gives data sending request using the on-demand function, the on-demand send processing flag turns ON. In FX2(FX), FX2C, FX2N, FX2NC and FX3S PLCs and in FX3G, FX3GC, FX3U and FX3UC PLCs using the communication port ch1, M8127 turns ON/OFF. In FX3G, FX3GC, FX3U and FX3UC PLCs using the communication port ch2, M8427 turns ON/OFF. 2. Cautions on use Use these devices for interlock to prevent generation of two or more on-demand requests at the same time. D-92 FX Series PLC User's Manual - Data Communication Edition 9 Related Data Computer Link A On-demand error flag [M8128 and M8428] These devices turn ON when an error is included in a specified value for data sending used with the ondemand function. 1. Detailed contents 2. Cautions on use C Parallel Link While the on-demand error flag is ON, data sending is disabled for the on-demand function. When sending data from a PLC using the on-demand function, set to OFF the on-demand error flag. 9.2.6 B N:N Network When the amount of on-demand data is incorrect, the on-demand error flag turns ON. In all PLCs except FX3G, FX3GC, FX3U and FX3UC PLCs using the communication port, M8128 turns ON. For FX3G, FX3GC, FX3U and FX3UC PLCs using the communication port ch1, M8128 turns ON. In FX3G, FX3GC, FX3U and FX3UC PLCs using the communication port ch2, M8428 turns ON. Common Items 9.2.5 9.2 Details of Related Devices On-demand data word/byte changeover [M8129 and M8429] These devices specify the unit (word or byte) of on-demand data. D 1. Detailed contents Computer Link Use this device to specify the data unit sent using the on-demand function. Set these devices to ON to specify "byte" (8-bit). Set these devices to OFF to specify "word" (16-bit). In all PLCs except FX3G, FX3GC, FX3U and FX3UC PLCs using the communication port, use M8129. For FX3G, FX3GC, FX3U and FX3UC PLCs using the communication port ch1, use M8129. In FX3G, FX3GC, FX3U and FX3UC PLCs using the communication port ch2, use M8429. E 2. Cautions on use 9.2.7 F Serial communication error code [D8063 and D8438] 1. Detailed contents Parity, overrun or framing error The transfer data is abnormal. 6305 Command error When the station number was FF, any command other than "GW" was received. 6306 Monitoring timeout The received message was insufficient. Because normal message was not received within the time-out time setting, the transfer sequence was initialized. 3801 Parity, overrun or framing error The transfer data is abnormal. 3805 Command error When the station number was FF, any command other than "GW" was received. Monitoring timeout The received message was insufficient. Because normal message was not received within the time-out time setting, the transfer sequence was initialized. 3806 D-93 H I Apx.A Discontinued models 6301 Contents of error Remote Maintenance D8438 (ch2) Error item Programming Communication D8063 (ch1) Error code G Non-Protocol Communication (FX2N-232IF) When the serial communication error flag (M8063 or M8438) turns ON, a corresponding error code is stored in these devices. In all PLCs except FX3G, FX3GC, FX3U and FX3UC PLCs using the communication port, an error code is stored in D8063. For FX3G, FX3GC, FX3U and FX3UC PLCs using the communication port ch1, an error code is stored in D8063. In FX3G, FX3GC, FX3U and FX3UC PLCs using the communication port ch2, an error code is stored in D8438. The error code list is shown below: Non-Protocol Communication (RS/RS2 Instruction) These devices store the error codes during serial communication. Device Inverter Communication When the unit is set to "word", the amount of on-demand data units is equivalent to the number of data registers for sending. When the unit is set to "byte", two on-demand data units use one data register for sending. Example: When the amount of on-demand data is "5", the amount of data registers for sending is "3". FX Series PLC User's Manual - Data Communication Edition 9 Related Data Computer Link 9.2 Details of Related Devices 2. Cautions on use Error codes are not cleared even after communication recovers its normal status. Serial communication errors are cleared in FX3S, FX3G, FX3GC, FX3U and FX3UC PLCs when the power is turned off and on. Serial communication errors are cleared in other PLCs when the mode is switched from STOP to RUN. 9.2.8 Communication format setting [D8120 and D8420] These devices set the serial communication format. 1. Detailed contents These devices set the serial communication format. In FX1S, FX1N, FX1NC, FX2N, FX2NC, FX3S, FX3G, FX3GC, FX3U and FX3UC PLCs, the contents set in parameters are transferred to these devices when the power is turned ON. In FX2(FX), FX2C and FX0N PLCs, set the communication format using a sequence program, and then turn ON the power. In all PLCs except FX3G, FX3GC, FX3U and FX3UC PLCs using communication port ch1, use D8120. Set the communication format using parameters when using the communication port ch2 in FX3G, FX3GC, FX3U and FX3UC PLCs. Use D8420 for confirmation. The tables below show the setting details. • Contents of D8120 Bit No. Name b0 Data length b1 b2 Parity b3 Stop bit b4 b5 b6 b7 Baud rate (bps) Contents 0 (bit = OFF) 1 (bit = ON) 7-bit 8-bit b2, b1 (0, 0): Not provided (0, 1): Odd (1, 1): Even 1-bit b7, b6, b5, b4 (0, 1, 1, 1): 4800 (1, 0, 0, 0): 9600 (1, 0, 0, 1): 19200 (0, 1, 1, 0): 2400 (1, 0, 1, 0): 38400*1 b8 Header Not provided Provided (D8124) Initial value: STX (02H) b9 Terminator Not provided Provided (D8125) Initial value: ETX (03H) b10 b11 Control line Computer link b11, b10 (0, 0): RS-485/RS-422 interface (1, 0): RS-232C interface b12 *1. D-94 2-bit b7, b6, b5, b4 (0, 0, 1, 1): 300 (0, 1, 0, 0): 600 (0, 1, 0, 1): 1200 Not applicable b13 Sum check Not added Added b14 Protocol Not used Used b15 Control procedure Format 1 Format 4 This setting is available only in FX3S, FX3G, FX3GC, FX3U and FX3UC PLCs. FX Series PLC User's Manual - Data Communication Edition 9 Related Data Computer Link 9.2 Details of Related Devices A Bit No. Name b0 Data length Parity b3 Stop bit Baud rate (bps) 1 (bit = ON) 7-bit 8-bit b2, b1 (0, 0): Not provided (0, 1): Odd (1, 1): Even B 1-bit b7, b6, b5, b4 (0, 0, 1, 1): 300 (0, 1, 0, 0): 600 (0, 1, 0, 1): 1200 (0, 1, 1, 0): 2400 2-bit b7, b6, b5, b4 (0, 1, 1, 1): 4800 (1, 0, 0, 0): 9600 (1, 0, 0, 1): 19200 (1, 0, 1, 0): 38400 C b8 Header Not provided Provided b9 Terminator Not provided Provided b10 b11 b12 Control line b13 Sum check Not added Added b14 Protocol Not used Used b15 Control procedure Format 1 Format 4 b12, b11, b10 (0, 0, 0): RS-485/RS-422 interface (0, 1, 0): RS-232C interface D Computer Link Computer link Parallel Link b4 b5 b6 b7 Contents 0 (bit = OFF) N:N Network b1 b2 Common Items • Contents of D8420 E 9.2.9 Station number settings [D8121 and D8421] F Non-Protocol Communication (RS/RS2 Instruction) Do not use both the parameters and communication format setting devices (D8120 or D8420) at the same time. If the communication format is set using both methods at the same time, priority is given to the setting using parameters. When setting the communication format device (D8120) in an FX0N PLC, set the communication setting latched (battery backed) device (M8120) to ON. When using computer link, make sure to set the header (b8) and terminator (b9) to "not provided". And set the protocol (b14) to "used". If the communication format is set using the special data register, the setting becomes valid when the power is turned ON after the setting is written to the special data register. Inverter Communication 2. Cautions on use G 1. Detailed contents Do not use both the parameters and station number settings device (D8121) at the same time. If the station number is set using both methods at the same time, priority is given to the setting using a parameter. When setting the station number settings device (D8121) in an FX0N PLC, set the communication setting latched (battery backed) device (M8120) to ON. I Remote Maintenance 2. Cautions on use H Programming Communication Set the station number of each PLC used in computer link. The applicable setting range is from 0 to 15 (from H00 to H0F). In FX1S, FX1N, FX1NC, FX2N, FX2NC, FX3S, FX3G, FX3GC, FX3U and FX3UC PLCs, the contents set using parameters are stored when the power is turned ON. In FX2(FX), FX2C and FX0N PLCs, set the station number using a sequence program, and then turn ON the power. In all PLCs except FX3G, FX3GC, FX3U and FX3UC PLCs and in FX3G, FX3GC, FX3U and FX3UC PLCs using communication port ch1, use D8121. Set the station number using parameters when using the communication port ch2 in FX3G, FX3GC, FX3U and FX3UC PLCs. Use D8421 for confirmation. Non-Protocol Communication (FX2N-232IF) These devices set the station number in computer link. Apx.A Discontinued models D-95 FX Series PLC User's Manual - Data Communication Edition Computer Link 9 Related Data 9.2 Details of Related Devices 9.2.10 On-demand data head device number specification [D8127 and D8427] These devices set the head data register device number containing the data to be sent using the on-demand function in a sequence program. 1. Detailed contents These devices set the head data register device number containing the data to be sent using the on-demand function. In all PLCs except FX3G, FX3GC, FX3U and FX3UC PLCs and in FX3G, FX3GC, FX3U and FX3UC PLCs using the communication port, use D8127. For FX3G, FX3GC, FX3U and FX3UC PLCs using the communication port ch1, use D8127. In FX3G, FX3GC, FX3U and FX3UC PLCs using the communication port ch2, use D8427. If there is an error in the set data, the on-demand error flag (M8128 or M8428) turns ON. 2. Cautions on use When setting the on-demand data head device number specification device (D8127 or D8427), set the flag using the pulse operation type. While the on-demand send processing flag (M8127 or M8427) is ON, do not write data. 9.2.11 On-demand data quantity specification [D8128 and D8428] These devices set the amount of data to be sent from a PLC using the on-demand function in a sequence program. 1. Detailed contents These devices set the amount of data to be sent using the on-demand function. Set the amount of data 64 or less. In all PLCs except FX3G, FX3GC, FX3U and FX3UC PLCs using the communication port, use D8128. For FX3G, FX3GC, FX3U and FX3UC PLCs using the communication port ch1, use D8128. In FX3G, FX3GC, FX3U and FX3UC PLCs using the communication port ch2, use D8428. If an error is included in the set data, the on-demand error flag (M8128 or M8428) turns ON. 2. Cautions on use When setting the on-demand data quantity specification device (D8128 or D8428), set the flag using the pulse operation type. While the on-demand send processing flag (M8127 or M8427) is ON, do not write data. D-96 FX Series PLC User's Manual - Data Communication Edition 9 Related Data Computer Link 9.2 Details of Related Devices A These devices set the evaluation time for error when receiving of data from the computer is interrupted. 1. Detailed contents Setting range 1 to 255 (10 to 2550 ms) (When "0" is set, it is handled as "100 ms".) FX2(FX), FX2C, FX2N, FX2NC, 1 to 3276 (10 to 32760 ms) (When "0" is set, it is handled as "100 ms".) FX3S, FX3G, FX3GC, FX3U, FX3UC D 2. Cautions on use These devices store the communication type being used. (in the FX3S, FX3G, FX3GC, FX3U and FX3UC) 1. Detailed contents The table below shows the contents of the communication type codes. G Description Programming communication PP modem mode 2 Protocol dedicated to computer link 3 N:N Network 4 RS instruction 5 RS2 instruction 6 Parallel link 7 Inverter instruction 8 Variable analog potentiometer expansion board is used. MODBUS communication CF-ADP 11 ENET-ADP 12 Input/output expansion board is used. I Remote Maintenance 9 10 H Programming Communication 1 Non-Protocol Communication (FX2N-232IF) 0 F Non-Protocol Communication (RS/RS2 Instruction) These devices store the code of the communication type currently being used in the communication port. When communication port ch1 is used, D8419 stores the communication type. When communication port ch2 is used, D8439 stores the communication type. E Inverter Communication 9.2.13 Operation mode display [D8419 and D8439] Computer Link Do not set the time-out time setting parameter and the time-out time (D8129) at the same time. The priority is given to the parameter setting. When setting the time-out time setting device (D8129) in an FX0N PLC, set the communication setting latched (battery backed) device (M8120) to ON. Make sure that the time-out time setting is not shorter than the time required to receive one character at the set baud rate. Code C Parallel Link FX Series FX0N, FX1S, FX1N, FX1NC B N:N Network These devices set the error evaluation time in 10-ms units used when the receiving of data from the computer is interrupted. In all PLCs except FX3G, FX3GC, FX3U and FX3UC PLCs using the communication port, use D8129. For FX3G, FX3GC, FX3U and FX3UC PLCs using the communication port ch1, use D8129. Set the time-out time setting using parameters when using the communication port ch2 in FX3G, FX3GC, FX3U and FX3UC PLCs. Use D8429 for confirmation. The table below shows the setting range. Common Items 9.2.12 Time-out time setting [D8129 and D8429] Apx.A Discontinued models D-97 FX Series PLC User's Manual - Data Communication Edition 9 Related Data Computer Link 9.3 9.3 Communication Setting Method Using Sequence Program Communication Setting Method Using Sequence Program When adjusting the communication setting using a sequence program, transfer values to D8120 (communication format), D8121 (station number settings) and D8129 (time-out time setting), and then turn the power ON. This section explains the communication setting method using a sequence program. 9.3.1 Setting procedure Perform the following procedure to set the communication using a sequence program. 1 Creating a program using a programming tool Create the program shown below using a programming tool. M8000 M8002 Initial pulse M8120 This step is required only in FX0N PLC. FNC 12 MOV H6082 D8120 The communication format is set. FNC 12 MOV H0 D8121 The station number is set. FNC 12 MOV K1 D8129 The time-out time setting is set. For details on these devices, refer to Section 9.2. 2 Writing the sequence program to the PLC Transfer the created program to the PLC. 3 Setting the PLC mode to RUN Set the PLC to RUN mode, and execute the program. 4 Turning the PLC power OFF and then ON Turn OFF the PLC power, and then turn it to ON so that the communication setting becomes valid. 9.3.2 Caution on communication setting using sequence program 1) Do not set the communication using a sequence program and parameters at the same time. If the communication is set using both methods at the same time, priority is given to the setting using parameters. 2) Since the special data registers (D8120, D8121, D8129) is a battery backed area in the case of the FX2N, FX2NC, FX3U and FX3UC series, a value cannot be normally saved when the battery is discharge (or after a battery error occurs). Therefore, keep in mind that a computer link setting may not be possible in this case. D-98 FX Series PLC User's Manual - Data Communication Edition Computer Link A ASCII Code Table Common Items 9.4 9 Related Data 9.4 ASCII Code Table <ASCII code table (8-bit code expressed in hexadecimal)> The ASCII codes A1H to DFH indicate Japanese characters. B N:N Network C Parallel Link D Computer Link E Inverter Communication *1. \ (ASCII CODE:5C) symbol is displayed as " " in Japanese. F Non-Protocol Communication (RS/RS2 Instruction) G Non-Protocol Communication (FX2N-232IF) H Programming Communication I Remote Maintenance Apx.A Discontinued models D-99 FX Series PLC User's Manual - Data Communication Edition Computer Link MEMO D-100 9 Related Data 9.4 ASCII Code Table FX Series PLC User's Manual - Data Communication Edition Inverter Communication A Common Items B N:N Network FX Series Programmable Controllers C Parallel Link User's Manual [Data Communication Edition] E. Inverter Communication D Computer Link E Inverter Communication F Non-Protocol Communication (RS/RS2 Instruction) G Non-Protocol Communication (FX2N-232IF) H Programming Communication Foreword I © 2005 MITSUBISHI ELECTRIC CORPORATION E-1 Apx.A Discontinued models This manual confers no industrial property rights or any rights of any other kind, nor does it confer any patent licenses. Mitsubishi Electric Corporation cannot be held responsible for any problems involving industrial property rights which may occur as a result of using the contents noted in this manual. Remote Maintenance This manual explains "inverter communication" provided for the MELSEC-F FX Series Programmable Controllers and should be read and understood before attempting to install or use the unit. Store this manual in a safe place so that you can take it out and read it whenever necessary. Always forward it to the end user. FX Series PLC User's Manual - Data Communication Edition Inverter Communication E-2 FX Series PLC User's Manual - Data Communication Edition 1 Outline Inverter Communication 1.1 Outline of System A Common Items 1. Outline B This chapter explains inverter communication. N:N Network 1.1 Outline of System 1) Mitsubishi Electric general-purpose inverters FREQROL F800, A800, F700, A700, E700, D700, V500, F500, A500, E500 and S500 (containing the communication type) Series can be linked. (FX2N and FX2NC PLCs support only the A500, E500, and S500 (containing the communication function) Series inverters.) 3) The total extension distance is 500m (1640' 5") maximum (for the system configured with 485ADP only). Important points and reference chapter/paragraph System FX PLC Inverter Inverter + + + G Built-in PU port For selection, in accordance ....... refer to Chapter 3. with RS-485 Non-Protocol Communication (FX2N-232IF) Built-in PU port in accordance with RS-485 For the communication setting of inverters, refer to Chapter 5. wiring, ....... For refer to Chapter 4. Master station Station No. 1 F Non-Protocol Communication (RS/RS2 Instruction) ....... To check available PLC models, refer to Section 1.3. ...... Communication equipment operating in accordance with RS-485 E ....... Number of linked units ....... Total extension distance For the specifications, refer to Chapter 2. Inverter Communication Up to eight inverters 500m (1640' 5") [50m (164' 0") when 485BD is included] D Computer Link 2) Inverter operations can be monitored, various command can be given to inverters, and parameters can be read or written in inverters. C Parallel Link Inverter communication allows connection between an FX PLC and up to eight inverters to monitor operations of inverters, give various commands to inverters and read and write inverter parameters through communication via RS-485 . Station No. n H Inverter operations, reading/writing parameters, and monitor output can be performed with the PLC function by writing a prepared sequence program to the inverter. The inverter PLC function differs from the inverter communication function. Programming Communication Point I Remote Maintenance Apx.A Discontinued models E-3 FX Series PLC User's Manual - Data Communication Edition 1 Outline Inverter Communication 1.2 1.2 Procedures Before Operation Procedures Before Operation The flow chart below shows the Inverter Communication setting and sequence programs creation procedures up until data link: Inverter Communication Refer to Chapter 1 Outline Refer to Chapter 2 Check communication specifications Refer to Chapter 3 Determine system configuration and selection Outline of system • Available PLC versions • Available programming tools Communication specifications • Applicable inverters • Operation commands and parameters • Execution time in inverter communication System configuration • Select communication equipment Refer to Chapter 4 Perform wiring Refer to Chapter 5 Set inverter communication Refer to Chapter 6 Perform PLC communication setting Wiring procedure • Selection of cables and connection equipment • Wiring example Parameter communication Programming tool Connect PLC*1 Refer to Chapter 7, 9 Create programs Based on SD/RD lamp lighting status and contents of error check devices, verify that communication is being executed normally. If there are problems, refer to the troubleshooting (Chapter 11). Programs for FX2N, FX2NC Series (Chapter 7) • Common items • Basic programs Programs for FX3S, FX3G, FX3GC, FX3U, FX3UC Series (Chapter 9) • Common items • Basic programs Refer to Chapter 8, 10 Practical program examples *1. E-4 Program examples for FX2N, FX2NC Series (Chapter 8) • Basic programs Program examples for FX3S, FX3G, FX3GC, FX3U, FX3UC Series (Chapter 10) • Basic programs For the programming tool to PLC connection procedure, refer to the "Programming Communication" section in this manual or the respective programming tool manual. For details on operation method, refer to the respective programming tool manual. FX Series PLC User's Manual - Data Communication Edition 1 Outline Inverter Communication 1.3 Communication Type Applicability in PLC Communication Type Applicability in PLC 1.3.1 For applicable versions Common Items 1.3 A The communication types are applicable for the following versions. PLC Applicability *1 FX3U Series *1 FX3GC Series *1 FX3G Series *1 FX3S Series *1 FX2NC Series *1 FX2N Series *1 A500, E500 and S500 Series inverters can be connected. — Inverter communication is not provided. — Inverter communication is not provided. FX1S Series — Inverter communication is not provided. FX0N Series — Inverter communication is not provided. — Inverter communication is not provided. FX0 Series — Inverter communication is not provided. FX2C Series — Inverter communication is not provided. FX2(FX) Series — Inverter communication is not provided. FX1 Series — Inverter communication is not provided. E F The table below shows PLC versions applicable to each inverter. Ver.1.00 or later Ver.2.20 or later Ver.2.20 or later FX3U Ver.2.32 or later Ver.3.11 or later Ver.2.32 or later Ver.3.11 or later Ver.1.40 or later Ver.2.22 or later FX3G Ver.1.10 or later Ver.2.22 or later FX3S Ver.1.00 or later Ver.1.10 or later FX2N, FX2NC Ver.3.00 or later — G Non-Protocol Communication (FX2N-232IF) FX3GC Non-Protocol Communication (RS/RS2 Instruction) FREQROL-S500/ FREQROL-F500/ FREQROL-F700/ FREQROL-D700/ FREQROL-A800/ E500/A500 V500 A700 E700 F800 FX3UC D Inverter Communication FX0S Series C Computer Link FX1NC Series PLC Version check H The PLC version can be checked by reading the last three digits of device D8001. For a detailed description of the version check, refer to A. Common Items Section 4.2. Programming Communication 1.3.3 F800, A800, F700, A700, E700, D700, V500, F500, A500, E500 and S500 Series inverters can be connected. FX1N Series *1. 1.3.2 Remarks Parallel Link FX3UC Series B N:N Network : Applicable —: Not applicable How to look at the manufacturer's serial number I Remote Maintenance The year and month of production of the PLC main unit can be checked on the nameplate, and "LOT" indicated on the front of the product. For a detailed description of the How to look at the manufacturer's serial number, refer to A. Common Items Section 4.1. Apx.A Discontinued models E-5 FX Series PLC User's Manual - Data Communication Edition 1 Outline Inverter Communication 1.4 Programming Tool Applicability 1.4 Programming Tool Applicability 1.4.1 For applicable versions The programming tool is applicable for each FX Series from the version shown: 1. English versions Product name Model name Applicable version Remarks FX3U and FX3UC PLCs GX Works2 SWDNC-GXW2-E Ver. 1.08J or later The IVMC instruction is supported in Ver. 1.48A or later. GX Developer SWD5C(F)-GPPW-E Ver. 8.18U or later The IVMC instruction is not supported. Ver. 1.00 or later The IVMC instruction is supported in Ver. 1.20 or later. FX-30P GOT1000 Series display units Refer to manuals of GOT1000 Series display units for applicable models and versions supporting the list editor function. FX3G PLC GX Works2 SWDNC-GXW2-E Ver. 1.08J or later The IVMC instruction is supported in Ver. 1.62Q or later. GX Developer SWD5C(F)-GPPW-E Ver. 8.72A or later The IVMC instruction is not supported. Ver. 1.00 or later The IVMC instruction is supported in Ver. 1.50 or later. FX-30P GOT1000 Series display units Refer to manuals of GOT1000 Series display units for applicable models and versions supporting the list editor function. FX3GC PLC GX Works2 SWDNC-GXW2-E FX-30P GOT1000 Series display units Ver. 1.77F or later - Ver. 1.30 or later The IVMC instruction is supported in Ver. 1.50 or later. Refer to manuals of GOT1000 Series display units for applicable models and versions supporting the list editor function. FX3S PLC GX Works2 SWDNC-GXW2-E FX-30P Ver. 1.492N or later Ver. 1.50 or later GOT1000 Series display units - Refer to manuals of GOT1000 Series display units for applicable models and versions supporting the list editor function. FX2N and FX2NC PLCs GX Works2 SWDNC-GXW2-E GX Developer SWD5C(F)-GPPW-E SW7 A or later FX-PCS/WIN-E SW0PC-FXGP/WIN-E Ver. 3.10 or later FX-30P Ver. 1.00 or later FX-20P-E(-SET0) FX-20P-MFXD-E Ver. 4.10 or later FX-10P-E Ver. 4.10 or later GOT-F900 Series display units F940WGOT-TWD-E F940GOT-*WD-E F940GOT-*BD-H-E F940GOT-*BD-RH-E GOT1000 Series display units E-6 Ver. 1.08J or later The versions shown on supporting EXTR instruction are applicable. the left F940WGOT-TWD-E (Ver. 1.30 or later) F940GOT-LWD-E, F940GOT-SWD-E (Ver. 6.30 or later) F940GOT-LBD-H-E, F940GOT-SBD-H-E (Ver. 6.30 or later) F940GOT-LBD-RH-E, F940GOT-SBD-RH-E (Ver. 6.30 or later) Refer to manuals of GOT1000 Series display units for applicable models and versions supporting the list editor function. FX Series PLC User's Manual - Data Communication Edition 1 Outline Inverter Communication 1.4 Programming Tool Applicability A Product name Model name Applicable version Remarks FX3U and FX3UC PLCs SWDNC-GXW2-J Ver. 1.07H or later The IVMC instruction is supported in Ver. 1.45X or later. GX Developer SWD5C(F)-GPPW-J Ver. 8.13P or later The IVMC instruction is not supported. Ver. 1.00 or later The IVMC instruction is supported in Ver. 1.20 or later. FX-30P GOT1000 Series display units Refer to manuals of GOT1000 Series display units for applicable models and versions supporting the list editor function. FX3G PLC SWDNC-GXW2-J Ver. 1.07H or later GX Developer SWD5C(F)-GPPW-J Ver. 8.72A or later The IVMC instruction is not supported. Ver. 1.00 or later The IVMC instruction is supported in Ver. 1.50 or later. FX-30P Refer to manuals of GOT1000 Series display units for applicable models and versions supporting the list editor function. FX3GC PLC GX Works2 SWDNC-GXW2-J FX-30P - Ver. 1.30 or later The IVMC instruction is supported in Ver. 1.50 or later. Refer to manuals of GOT1000 Series display units for applicable models and versions supporting the list editor function. FX3S PLC GX Works2 SWDNC-GXW2-J FX-30P Ver. 1.492N or later - Ver. 1.50 or later GOT1000 Series display units FX2N and FX2NC PLCs GX Works2 SWDNC-GXW2-J GX Developer SWD5C(F)-GPPW-J FX-PCS/WIN SW0PC-FXGP/WIN SW7 A or later Ver. 4.20 or later Ver. 1.00 or later FX-20P(-SET0) FX-20P-MFXD Ver. 5.10 or later FX-10P(-SET0) Ver. 4.10 or later the left G F940WGOT-TWD (Ver. 1.30 or later) F940GOT-LWD, F940GOT-SWD (Ver. 6.30 or later) F940GOT-LBD-H, F940GOT-SBD-H (Ver. 6.30 or later) F940GOT-LBD-RH, F940GOT-SBD-RH (Ver. 6.30 or later) H Refer to manuals of GOT1000 Series display units for applicable models and versions supporting the list editor function. Programming Communication GOT1000 Series display units The versions shown on supporting EXTR instruction are applicable. Non-Protocol Communication (FX2N-232IF) FX-30P GOT-F900 Series display units F940WGOT-TWD F940GOT-*WD F940GOT-*BD-H F940GOT-*BD-RH 1.4.2 Ver. 1.07H or later F Non-Protocol Communication (RS/RS2 Instruction) Refer to manuals of GOT1000 Series display units for applicable models and versions supporting the list editor function. E Inverter Communication GOT1000 Series display units Ver. 1.77F or later D Computer Link GOT1000 Series display units C Parallel Link GX Works2 The IVMC instruction is supported in Ver. 1.56J or later. B N:N Network GX Works2 Common Items 2. Japanese versions I For non-applicable versions (setting an alternative model) Remote Maintenance In FX2N, FX2NC, FX3G, FX3U and FX3UC PLCs, it is not possible to create programs using programming tools of inapplicable versions. Select "FX3G" in model selection when creating programs using a programming tool whose version is not applicable to the FX3S and FX3GC PLC. Apx.A Discontinued models Point In the FX3S PLC, set the memory capacity for PLC parameters to 4,000 steps or less. E-7 FX Series PLC User's Manual - Data Communication Edition 2 Specifications Inverter Communication 2. 2.1 Communication Specifications (Reference) Specifications This chapter explains the communication specifications and performance. 2.1 Communication Specifications (Reference) Item Specifications Number of connectable units 8 maximum Transmission standard Remarks RS-485 standard Maximum total extension distance 500 m (1640' 5") or less when 485ADP is used 50 m (164' 0") or less when 485BD is used Protocol type Inverter computer link Control procedure Asynchronous system Communication method Distance varies depending on communication equipment type. Link startup mode Half-duplex, bidirectional communication 4800, 9600, 19200 or 38400*1 bps Baud rate Any one can be selected. ASCII Character format *1. 2.2 Start bit — Data bit 7-bit Parity bit Even Stop bit 1-bit FX3U and FX3UC Series PLC Ver. 2.41 or later, and FX3S, FX3G, FX3GC Series PLC is applicable. Connectable Mitsubishi Electric General-purpose Inverters Series E-8 Built-in PU connector FR-A5NR (option) Remarks Only models containing the RS-485 communication type can be connected. FREQROL-S500 — FREQROL-E500 — FREQROL-A500 FREQROL-F500 FREQROL-V500 Only available for FX3S, FX3G, FX3GC, FX3U and FX3UC PLCs. Series Built-in PU connector Built-in RS-485 terminal Remarks FREQROL-A700 — FREQROL-F700 — FREQROL-A800 — FREQROL-F800 — Only available for FX3S, FX3G, FX3GC FX3U and FX3UC PLCs. Series Built-in PU connector FR-E7TR (option) Remarks FREQROL-D700 — FREQROL-E700 Only available for FX3S, FX3G, FX3GC, FX3U and FX3UC PLCs. FX Series PLC User's Manual - Data Communication Edition 2 Specifications Inverter Communication A Link Specifications Common Items 2.3 2.3 Link Specifications The tables below show applicable parameters and operation commands. 2.3.1 When monitoring inverter operations (PLC inverter) Read contents V500, F500, A500 E500 S500 H70 Output current H71 Output voltage — H72 Special monitor — — H73 Special monitor selection number — — H74 Alarm definition H75 Alarm definition H76 Alarm definition — H77 Alarm definition — H79 Inverter status monitor (extended) — — — H7A Inverter status monitor H6E Set frequency (EEPROM) H6D Set frequency (RAM) H7F Link parameter expansion setting H6C Second parameter changing Refer to Subsection 9.4.2 When controlling inverter operations (PLC inverter) D E F F800, A800, F700, A700, E700, D700 V500 F500, A500 E500, S500 Operation mode HF3 Special monitor selection number — HF9 Run command (expansion) — — — HFA Run command Set frequency (EEPROM) Set frequency (RAM) HFD Inverter reset HF4 Alarm definition all clear — HFC All parameter all clear HFC User clear — — — HFF Link parameter expansion setting H Programming Communication HEE HED G Non-Protocol Communication (FX2N-232IF) HFB Non-Protocol Communication (RS/RS2 Instruction) Applicable inverter Written contents C Computer Link Output frequency [number of rotations] Parallel Link Operation mode H6F Inverter Communication H7B Instruction code (hexadecimal) 2.3.3 F800, A800, F700, A700, E700, D700 N:N Network Applicable inverter Instruction code (hexadecimal) 2.3.2 B I Parameters (PLC inverter) Remote Maintenance For inverter parameters which can be changed (read and written), refer to "12. Related Detailed Data" later. Apx.A Discontinued models E-9 FX Series PLC User's Manual - Data Communication Edition 2 Specifications Inverter Communication 2.4 Execution Times in Inverter Communication Instructions 2.4 Execution Times in Inverter Communication Instructions 2.4.1 Outline The period of time after one inverter communication instruction is driven until communication with the inverter is completed (M8029 turns ON) is regarded as the required time for the inverter communication instruction as shown in the figure below. X0 SET M0 M0 Inverter communication instruction M8029 RST M0 M0 M8029 Tinv T1 T2 First time sending/receiving in a single instruction T3 Second time sending/receiving in a single instruction "n"th time sending/receiving in a single instruction Communication preparation processing Communication termination processing T4 Inverter waiting time T6[n]*1 T5 T7[n]*1 T8[n]*1 T9[n]*1 The request message is being sent Inverter data check time The response message is being received *1. E-10 The time required for the "n"th time sending/receiving in a single instruction. FX Series PLC User's Manual - Data Communication Edition Inverter Communication 2 Specifications 2.4 Execution Times in Inverter Communication Instructions Inverter communication instruction IVWR 1 IVCK 1 Change of the 2nd parameter is unnecessary 2 Change of the 2nd parameter is necessary*2 3 Change of the 2nd parameter is unnecessary 2 Change of the 2nd parameter is necessary*2 3 Number of times of communication S2 IVMC C 2 + Number of parameters *2 requiring change of the 2nd parameter 1 D For parameters requiring change of the 2nd parameter, refer to section 9.10. Computer Link *2. S2 B Parallel Link IVBWR IVDR N:N Network IVRD Number of times of sending/receiving in per instruction A Common Items Some inverter communication instructions execute several times of sending/receiving in a single instruction. The following table shows the number of times of sending/receiving in each communication instruction. E Inverter Communication F Non-Protocol Communication (RS/RS2 Instruction) G Non-Protocol Communication (FX2N-232IF) H Programming Communication I Remote Maintenance Apx.A Discontinued models E-11 FX Series PLC User's Manual - Data Communication Edition 2 Specifications Inverter Communication 2.4.2 2.4 Execution Times in Inverter Communication Instructions Calculation method Calculate the required time "Tinv" for inverter communication instruction in units of "ms" as follows. "INT(n)" in the calculation formula indicates an integer obtained by truncating decimal places of "n". 1. Length of 1 character In inverter communication, the communication setting is as shown in following table. The length of 1 character is as shown in the following calculation expression. Length of 1 character = Start bit + Data length + Parity bit + Stop bit = 10[bit] Name Set value bit Start bit - 1 Data length 7 7 Parity bit Even number 1 Stop bit 1 1 Total 10 2. Execution times in inverter communication instructions Execution times in inverter communication instructions is as shown in the following calculation expression. Tinv = T1 + T2 + T3 T1 = 1[ms] T2 = {n(T4+T5)}+T6[n][ms] Sending and receiving frequency T6[1]+T6[2]+T6[3]+ T3 = 1[ms] Calculate "T4", "T5" and "T6 [n]" as shown in the following table. Communication time T4 = ( INT ( T5 = 1[ms] T6[n] T7[n]+T9[n] T8[n] E-12 Calculation method 15 ) + 1) Scan time Scan time • For Scan time < T7[n]+T8[n]+T9[n] T7[n]+T8[n]+T9[n] = ( INT ( ) + 1) Scan time Scan time • For Scan time T7[n]+T8[n]+T9[n] T7[n]+T8[n]+T9[n] = ( INT ( ) + 2) Scan time Scan time ={( 1 Number of sending and Length of )( ) } 1000 receiving characters*1 1 character Communication speed [bps] = Data check time in inverters*4 FX Series PLC User's Manual - Data Communication Edition 2 Specifications Inverter Communication Inverter communication instruction IVDR IVMC Third Sending Receiving Total Sending Receiving Total Sending Receiving Total Change of the 2nd parameter is unnecessary. 11 4 15 9 11 20 - - - Change of the 2nd parameter is necessary. 11 4 15 11 4 15 9 11 20 HF3, HFA, HFF 11 4 15 - - - - - - HFD 13 *3 13 - - - - - - Other than above 13 4 17 - - - - - - H73, H7A, H7F, H6C 9 9 18 - - - - - - Other than above 9 11 20 - - - - - - Change of the 2nd parameter is unnecessary. 11 4 15 13 4 17 - - - Change of the 2nd parameter is necessary. 11 4 15 11 4 15 13 4 17 Change of the 2nd parameter is unnecessary. 11 4 15 13 4 17 - - - Change of the 2nd parameter is necessary. 11 4 15 11 4 15 13 4 17 19 19 38 - - - - - - - 0 S2 . The inverter gives no response because the inverter is being reset. The PLC waits for 2.2 s until reset of the inverter is completed, and then completes execution of the inverter communication instruction. *4. Refer to the following table for the data check time in inverters. Make sure to refer to the manual of the inverter used, and confirm the data check time for the communication command used. D E F G Item Data check time Various monitors, operation command, set frequency (RAM) <12ms Parameters read/write, set frequency (EEPROM) <30ms Parameter all clear/all clear <5s H Reset instruction No response (The PLC waits for 2.2 s until reset of the inverter is completed, and then completes execution of the inverter communication instruction.) Programming Communication Non-Protocol Communication (FX2N-232IF) *3. C Non-Protocol Communication (RS/RS2 Instruction) Indicates the number of sent/received characters required to write 1 parameter. The IVBWR instruction executes parameter writing by the number of times of communication B Inverter Communication IVBWR*2 Second Computer Link IVWR First Parallel Link IVCK Parameter/ instruction code N:N Network IVRD *2. A Refer to the following table for the number of sent/received characters. Common Items *1. 2.4 Execution Times in Inverter Communication Instructions I Remote Maintenance The IVWR, IVRD and IVBWR instructions automatically change expansion parameters and the 2nd parameter. The data check time for the last (2nd or 3rd) sending/receiving in the IVWR and IVRD instructions and the data check time for the last sending/receiving of each parameter writing in the IVBWR instruction correspond to parameter reading/writing (< 30 ms). The data check time for sending and receiving (expansion parameter change and 2nd parameter change) other than the above correspond to various monitors (< 12 ms). Apx.A Discontinued models E-13 FX Series PLC User's Manual - Data Communication Edition Inverter Communication 2.4.3 2 Specifications 2.4 Execution Times in Inverter Communication Instructions Calculation example This is a calculation example for the following communication settings and scan time when communicating with an inverter. Communication speed = 19200[bps] Length of 1 character = 10[bit] Scan time = 10[ms] 1. Calculation example 1 Calculation of required time when Pr. 3 is read by the IVRD instruction Tinv = T1 + T2 + T3 = 114[ms] T1 = 1[ms], T3 = 1[ms] Calculate "T2" as follows because Pr.3 does not require change of the 2nd parameter. T2 = 2(T4+T5) + T6[1] + T6[2] = 2(20+1) + 20 + 50 = 112[ms] Sending and receiving frequency The first sending and receiving The second sending and receiving ) + 1 ) 10 = 20[ms] T4 = ( INT( 15 10 T5 = 1[ms] T7[1] + T8[1] + T9[1] T6[1] = ( INT( ) + 1 ) 10 = ( INT( 19.8 ) + 1 ) 10 = 20[ms] 10 10 T7[1] + T8[1] + T9[1] = 7.8 + 12 = 19.8[ms] T7[1] + T9[1] = ( ( T8[1] = 12[ms] T6[2] = ( INT( 1 ) (11+4) 10 ) 1000 = 7.8[ms] 19200 T7[2] + T8[2] + T9[2] ) + 1 ) 10 = ( INT( 40.4 ) + 1 ) 10 = 50[ms] 10 10 T7[2] + T8[2] + T9[2] = 10.4 + 30 = 40.4[ms] T7[2] + T9[2] = ( ( 1 ) (9+11) 10 ) 1000 = 10.4[ms] 19200 T8[2] = 30[ms] Tinv = T1 + T2 + T3 = 1+112+1 = 114[ms] 2. Calculation example 2 Calculation of required time when Pr.902 is read by the IVRD instruction Tinv = T1 + T2 + T3 = 155[ms] T1 = 1[ms], T3 = 1[ms] Calculate "T2" as follows because Pr.902 requires change of the 2nd parameter. T2 = 3(T4+T5) + T6[1] + T6[2] + T6[3] = 3(20+1) + 20 + 20 + 50 = 153[ms] Sending and receiving frequency The first sending and receiving The second sending and receiving ) + 1 ) 10 = 20[ms] T4 = ( INT( 15 10 The third sending and receiving T5 = 1[ms] T7[1] + T8[1] + T9[1] T6[1] = ( INT( ) + 1 ) 10 = ( INT( 19.8 ) + 1 ) 10 = 20[ms] 10 10 T7[1] + T8[1] + T9[1] = 7.8 + 12 = 19.8[ms] T7[1] + T9[1] = ( ( T8[1] = 12[ms] T6[2] = ( INT( 1 ) (11+4) 10 ) 1000 = 7.8[ms] 19200 T7[2] + T8[2] + T9[2] ) + 1 ) 10 = ( INT( 19.8 ) + 1 ) 10 = 20[ms] 10 10 T7[2] + T8[2] + T9[2] = 7.8 + 12 = 19.8[ms] T7[2] + T9[2] = ( ( T8[2] = 12[ms] T6[3] = ( INT( 1 ) (11+4) 10 ) 1000 = 7.8[ms] 19200 T7[3] + T8[3] + T9[3] ) + 1 ) 10 = ( INT( 40.4 ) + 1 ) 10 = 50[ms] 10 10 T7[3] + T8[3] + T9[3] = 10.4 + 30 = 40.4[ms] T7[3] + T9[3] = ( ( 1 ) (9+11) 10 ) 1000 = 10.4[ms] 19200 T8[3] = 30[ms] Tinv = T1 + T2 + T3 = 1+153+1 = 155[ms] E-14 FX Series PLC User's Manual - Data Communication Edition 2 Specifications Inverter Communication 2.4 Execution Times in Inverter Communication Instructions A Calculation of required time when Pr. 10 to Pr. 14 [ S2 = 5] are written by the IVBWR instruction Tinv = T1 + T2 + T3 = 512[ms] T1 = 1[ms], T3 = 1[ms] Calculate "T2" as follows because Pr.10 to Pr. 14 do not require change of the 2nd parameter and the time required for writing is same in each parameter. S2 C ) + 1 ) 10 = 20[ms] T4 = ( INT( 15 10 Parallel Link T5 = 1[ms] T7[1] + T8[1] + T9[1] T6[1] = ( INT( ) + 1 ) 10 = ( INT( 19.8 ) + 1 ) 10 = 20[ms] 10 10 T7[1] + T8[1] + T9[1] = 7.8 + 12 = 19.8[ms] T8[1] = 12[ms] 1 ) (11+4) 10 ) 1000 = 7.8[ms] 19200 D Computer Link T7[2] + T8[2] + T9[2] ) + 1 ) 10 = ( INT( 38.9 ) + 1 ) 10 = 40[ms] T6[2] = ( INT( 10 10 T7[2] + T8[2] + T9[2] = 8.9 + 30 = 38.9[ms] T7[2] + T9[2] = ( ( T8[2] = 30[ms] B N:N Network T2 = ( 2 (T4+T5) + T6[1]+T6[2] ) + ( 2 (T4+T5) + T6[3]+T6[4] ) + Time required to write Pr. 10 Time required to write Pr. 11 = 5 ( 2 (T4+T5) + T6[1]+T6[2] ) = 5 ( 2 (20+1) + 20 + 40 ) = 510[ms] T7[1] + T9[1] = ( ( Common Items 3. Calculation example 3 1 ) (13+4) 10 ) 1000 = 8.9[ms] 19200 E Tinv = T1 + T2 + T3 = 1+510+1 = 512[ms] Inverter Communication F Non-Protocol Communication (RS/RS2 Instruction) G Non-Protocol Communication (FX2N-232IF) H Programming Communication I Remote Maintenance Apx.A Discontinued models E-15 FX Series PLC User's Manual - Data Communication Edition 3 System Configuration and Selection Inverter Communication 3. 3.1 System Configuration System Configuration and Selection This chapter explains the system configuration and communication equipment selection operating in accordance with RS-485 required by FX PLCs. 3.1 System Configuration This section outlines the system configuration required to use inverter communication. Connect (optional) equipment operating in accordance with RS-485 to the FX PLC main unit. 1 , 2 , 3 , 4 , 5 , 6 , 7 and 8 indicate the communication equipment combination patterns. Communication equipment operating in accordance with RS-485 FX PLC 1 Important point in selection This is the communication board built into the PLC, reducing the installation area. + Total extension distance 50 m (164' 0") FX2N PLC Communication board Function extension memory cassette (only for FX2N PLC) 2 + + Communication Special adapter connection board adapter FX2N PLC Attach the special adapter connection board to the main unit, and then attach the communication adapter to the left side of the main unit. 500 m (1640' 5") Attach the communication adapter to the left side of the main unit. 500 m (1640' 5") Because the communication board can be built in to the PLC, the installation area does not change 50 m (164' 0") Function extension memory cassette (only for FX2N PLC) 3 + FX2NC PLC Communication adapter Function extension memory board (only for FX2NC PLC) 4 RD A RD RD B SD A SD SD B + SG Communication board FX3U PLC RD A RD RD B SD A SD SD B + SG Communication board E-16 FX3UC-32MT-LT(-2) FX Series PLC User's Manual - Data Communication Edition 3 System Configuration and Selection Inverter Communication 3.1 System Configuration A FX PLC Important point in selection Total extension distance 5 + + FX3U PLC Expansion board Attach the expansion board to the main unit, and then attach the communication adapter to the left side of the main unit. 500 m (1640' 5") + + Expansion board C Parallel Link Communication adapter B N:N Network Communication adapter Common Items Communication equipment operating in accordance with RS-485 FX3UC-32MT-LT(-2) D 6 FX3GC, FX3UC(D, DS, DSS) Communication adapter E Because the communication board can be built in to the PLC, the installation area does not change. + F FX3S, FX3G PLC + + Connector conversion adapter FX3S, FX3G PLC G Non-Protocol Communication (FX2N-232IF) Attach the connector conversion adapter 500 m to the main unit, and then attach the (1640' 5") communication adapter to the left side of the main unit. 8 Non-Protocol Communication (RS/RS2 Instruction) Communication board 50 m (164' 0") Inverter Communication 7 Communication adapter 500 m (1640' 5") Computer Link Attach the communication adapter to the left side of the main unit. + H Programming Communication For communication equipment combinations for each FX Series, refer to the next section. I Remote Maintenance Apx.A Discontinued models E-17 FX Series PLC User's Manual - Data Communication Edition 3 System Configuration and Selection Inverter Communication 3.2 3.2 Applicable FX PLC and Communication Equipment Applicable FX PLC and Communication Equipment Select a (optional) communication equipment combination, and put a check mark in the "Check" column. During selection, pay attention to the following: - In the table below, only the external dimensions are different between the units shown in "FX2NC-485ADP/ FX0N-485ADP". Select either one. - In the table below, only the cable is different between the units shown in "FX3G-485-BD/FX3G-485-BDRJ". Select either one. - Inverter communication is not provided for the FX1, FX2(FX), FX2C, FX0, FX0S, FX0N, FX1S, FX1N and FX1NC PLCs. FX Series Communication equipment (option) Total extension Check distance 50 m (164' 0") FX2N-485-BD FX2N + + FX2N-ROM-E1 (Function extension memory cassette) FX2N-CNV-BD + FX2NC-485ADP (European terminal block) 500 m (1640' 5") FX2N-CNV-BD FX0N-485ADP (Terminal block) 50 m (164' 0") FX3G-485-BD (European terminal block) FX3G-485-BD-RJ (RJ45 connector) + FX3S 500 m (1640' 5") FX3S-CNV-ADP FX3U-485ADP(-MB) (European terminal block) 50 m (164' 0") FX3G-485-BD (European terminal block) FX3G-485-BD-RJ (RJ45 connector) FX3G (14-point, 24-point type) 500 m (1640' 5") FX3G-CNV-ADP E-18 FX3U-485ADP(-MB) (European terminal block) FX Series PLC User's Manual - Data Communication Edition 3 System Configuration and Selection Inverter Communication 3.2 Applicable FX PLC and Communication Equipment A Communication equipment (option) Total extension Check distance When using channel 1 (ch 1) Common Items FX Series B N:N Network 50 m (164' 0") FX3G-485-BD (European terminal block) FX3G-485-BD-RJ (RJ45 connector) C Parallel Link The communication equipment works as ch1 when connected to the option connector 1. 500 m (1640' 5") Computer Link FX3G-CNV-ADP D FX3U-485ADP(-MB) (European terminal block) When using channel 2 (ch 2) E Inverter Communication FX3G (40-point, 60-point type) 50 m (164' 0") FX3G-485-BD (European terminal block) FX3G-485-BD-RJ (RJ45 connector) F Non-Protocol Communication (RS/RS2 Instruction) The communication equipment works as ch2 when connected to the option connector 2. G Non-Protocol Communication (FX2N-232IF) 500 m (1640' 5") FX3G-CNV-ADP FX3U- ADP(-MB) (Where represents 232 and 485). FX3U-485ADP(-MB) (European terminal block) H Programming Communication Ch2 is not available when the FX3G-8AV-BD, FX3G-4EX-BD or FX3G-2EYT-BD is connected to the option connector 2. I Remote Maintenance Apx.A Discontinued models E-19 FX Series PLC User's Manual - Data Communication Edition 3 System Configuration and Selection Inverter Communication FX Series 3.2 Applicable FX PLC and Communication Equipment Total extension Check distance Communication equipment (option) When using channel 1 (ch 1) ch1 RD A 50 m (164' 0") RD RD B SD A SD SD B SG FX3U-485-BD (European terminal block) ch1 + FX3U-CNV-BD 500 m (1640' 5") FX3U-485ADP(-MB) (European terminal block) When using channel 2 (ch 2) ch1 ch2 + RD FX3U SD FX3U--BD (Where represents 232, 422, 485, USB and 8AV). 500 m (1640' 5") FX3U-485ADP(-MB) (European terminal block) When a FX3U-8AV-BD is used, it occupies one communication port channel. ch1 + FX3U-CNV-BD FX3U-232ADP(-MB), FX3U-485ADP(-MB), FX3U-CF-ADP ch2 + 500 m (1640' 5") FX3U-485ADP(-MB) (European terminal block) When a FX3U-CF-ADP is used, it occupies one communication port channel. FX2NC 500 m (1640' 5") + FX2NC-485ADP (European terminal block) FX2NC-ROM-CE1 (Function extension memory board) E-20 FX0N-485ADP (Terminal block) FX Series PLC User's Manual - Data Communication Edition 3 System Configuration and Selection Inverter Communication 3.2 Applicable FX PLC and Communication Equipment A Communication equipment (option) Total extension Check distance When using channel 1 (ch 1) ch1 B N:N Network 500 m (1640' 5") FX3U-485ADP(-MB) C (European terminal block) ch1 Parallel Link When using channel 2 (ch 2) ch2 FX3GC + 500 m (1640' 5") D Computer Link FX3U-485ADP(-MB) FX3U- ADP(-MB) (Where represents 232 and 485). (European terminal block) When using channel 1 (ch 1) E ch1 Inverter Communication 500 m (1640' 5") FX3U-485ADP(-MB) F (European terminal block) ch1 ch2 + (Where represents 232 and 485). G 500 m (1640' 5") Non-Protocol Communication (FX2N-232IF) FX3U-ADP(-MB) Non-Protocol Communication (RS/RS2 Instruction) When using channel 2 (ch 2) FX3UC (D, DS, DSS) Common Items FX Series FX3U-485ADP(-MB) (European terminal block) When a FX3U-CF-ADP is used, it occupies one communication port channel. H Programming Communication I Remote Maintenance Apx.A Discontinued models E-21 FX Series PLC User's Manual - Data Communication Edition 3 System Configuration and Selection Inverter Communication FX Series 3.2 Applicable FX PLC and Communication Equipment Total extension Check distance Communication equipment (option) When using channel 1 (ch 1) ch1 RD A 50 m (164' 0") RD RD B SD A SD SD B SG FX3U-485-BD (European terminal block) ch1 + FX3U-CNV-BD 500 m (1640' 5") FX3U-485ADP(-MB) (European terminal block) When using channel 2 (ch 2) ch1 ch2 + RD FX3UC-32MT-LT(-2) SD FX3U--BD (Where represents 232, 422, 485, USB and 8AV). 500 m (1640' 5") FX3U-485ADP(-MB) (European terminal block) When a FX3U-8AV-BD is used, it occupies one communication port channel. ch1 + FX3U-CNV-BD FX3U-232ADP(-MB), FX3U-485ADP(-MB), FX3U-CF-ADP ch2 + 500 m (1640' 5") FX3U-485ADP(-MB) (European terminal block) When a FX3U-CF-ADP is used, it occupies one communication port channel. E-22 FX Series PLC User's Manual - Data Communication Edition Inverter Communication 4 Wiring 3.2 Applicable FX PLC and Communication Equipment A Common Items 4. Wiring B This chapter explains the wiring. N:N Network WIRING PRECAUTIONS C Parallel Link • Make sure to cut off all phases of the power supply externally before attempting installation or wiring work. Failure to do so may cause electric shock or damage to the product. • Make sure to attach the terminal cover, offered as an accessory, before turning on the power or initiating operation after installation or wiring work. Failure to do so may cause electric shock. D WIRING PRECAUTIONS Computer Link E Inverter Communication F Non-Protocol Communication (RS/RS2 Instruction) G Non-Protocol Communication (FX2N-232IF) • Make sure to observe the following precautions in order to prevent any damage to the machinery or accidents due to abnormal data written to the PLC under the influence of noise: 1) Do not bundle the main circuit line together with or lay it close to the main circuit, high-voltage line or load line. Otherwise, noise disturbance and/or surge induction are likely to take place. As a guideline, lay the control line at least 100mm (3.94") or more away from the main circuit or high-voltage lines. 2) Ground the shield wire or shield of the shielded cable at one point on the PLC. However, do not use common grounding with heavy electrical systems. • Make sure to properly wire the terminal block in accordance with the following precautions. Failure to do so may cause electric shock, equipment failures, a short-circuit, wire breakage, malfunctions, or damage to the product. - The disposal size of the cable end should follow the dimensions described in the manual. - Tightening torque should follow the specifications in the manual. - Tighten the screws using a Phillips-head screwdriver No.2 (shaft diameter 6mm (0.24") or less). Make sure that the screwdriver does not touch the partition part of the terminal block. • Make sure to properly wire to the terminal block (European type) in accordance with the following precautions. Failure to do so may cause electric shock, equipment failures, a short-circuit, wire breakage, malfunctions, or damage to the product. - The disposal size of the cable end should follow the dimensions described in the manual. - Tightening torque should follow the specifications in the manual. - Twist the end of strand wire and make sure that there are no loose wires. - Do not solder-plate the electric wire ends. - Do not connect more than the specified number of wires or electric wires of unspecified size. - Affix the electric wires so that neither the terminal block nor the connected parts are directly stressed. H Programming Communication I Remote Maintenance Apx.A Discontinued models E-23 FX Series PLC User's Manual - Data Communication Edition 4 Wiring Inverter Communication 4.1 1 4.1 Wiring Procedure Wiring Procedure Confirming the connection method Confirm the inverter connection method. For details, refer to Section 4.2. 2 Preparing for wiring Prepare cables, distributors and terminal resistors required for wiring. For connection cables, refer to Section 4.3. For distributors, refer to Section 4.4. For terminal resistors, refer to Section 4.5. 3 Turning OFF the PLC power Before starting any wiring work, make sure that the PLC power is OFF. 4 Connecting the power supply (FX0N-485ADP only) Connect the power supply to the 24V DC power terminal. 5 Wiring communication equipment Connect communication equipment with communication port of inverters (PU port, built-in terminal for RS-485, FR-A5NR, FR-7TR). For details, refer to Section 4.8. 6 Connecting terminal resistors Connect terminal resistors to the communication equipment of the PLC and the RDA-RDB signal terminal in the last inverter. For details, refer to Section 4.5. 7 Wiring a shielding wire (Class-D grounding) When using a twisted pair cable, wire a shielding wire. For details, refer to Section 4.6. E-24 FX Series PLC User's Manual - Data Communication Edition 4 Wiring Inverter Communication A Selecting Cables and Connection Devices When connecting equipment operating in accordance with RS-485, use the following connection method with 10BASE-T or shielded twisted pair cables. 4.2.1 Non-stranded cable (10BASE-T cable for LAN) Terminal resistor (Which is supplied with or built in the communication equipment for the FX PLC side, and should be arranged by the user for the inverter side) S500, E500, A500, F500, V500, D700 and E700 Series (PU connector) C Parallel Link 1. In the case of 1-to-1 connection When a distributor is not used When a distributor is used 10BASE-T cable Terminal resistor RS-485 connector (PU connector) Terminal resistor 10BASE-T cable 10BASE-T cable E Terminal resistor Use a distributor because a terminal resistor cannot be connected to the inverter. Inverter Communication RS-485 connector (PU connector) 2. In the case of 1-to-N connection F When a distributor is used 10BASE-T cable 10BASE-T cable Distributor 10BASE-T cable 10BASE-T cable Distributor Terminal resistor 10BASE-T cable RS-485 connector PU connector H Programming Communication *1. PU connector G Non-Protocol Communication (FX2N-232IF) 10BASE-T cable Terminal resistor Non-Protocol Communication (RS/RS2 Instruction) Distributor *1 D Computer Link Distributor *1 B N:N Network PU connector (RJ45 connector) Common Items 4.2 4.2 Selecting Cables and Connection Devices When using FX3G-485-BD-RJ, use the PU connector (RJ45 connector) for connection. I Remote Maintenance Apx.A Discontinued models E-25 FX Series PLC User's Manual - Data Communication Edition 4 Wiring Inverter Communication 4.2.2 4.2 Selecting Cables and Connection Devices A500, F500 and V500 Series (FR-A5NR) 1. In the case of 1-to-1 connection When a distributor is not used FR-A5NR Twisted pair cable Terminal resistor Terminal resistor 2. In the case of 1-to-N connection When a distributor is not used Twisted pair cable Twisted pair cable Terminal resistor Twisted pair cable Terminal resistor E-26 FR-A5NR FR-A5NR FR-A5NR FX Series PLC User's Manual - Data Communication Edition 4 Wiring Inverter Communication A F800, A800, F700 and A700 Series (built-in RS-485 terminal) Common Items 4.2.3 4.2 Selecting Cables and Connection Devices 1. In the case of 1-to-1 connection Set the terminal resistor switch in the inverter to "100 ". B N:N Network Built-in RS-485 terminal C Parallel Link Twisted pair cable 2. In the case of 1-to-N connection Set the terminal resistor switch in the last inverter to "100 ". D Twisted pair cable Computer Link Twisted pair cable E Twisted pair cable Built-in RS-485 terminal Inverter Communication Built-in RS-485 terminal Built-in RS-485 terminal F Non-Protocol Communication (RS/RS2 Instruction) G Non-Protocol Communication (FX2N-232IF) H Programming Communication I Remote Maintenance Apx.A Discontinued models E-27 FX Series PLC User's Manual - Data Communication Edition 4 Wiring Inverter Communication 4.2.4 4.2 Selecting Cables and Connection Devices E700 Series (FR-E7TR) 1. In the case of 1-to-1 connection When a distributor is not used FR-E7TR Twisted pair cable Terminal resistor 2. In the case of 1-to-N connection When a distributor is not used Twisted pair cable Terminal resistor E-28 Twisted pair cable Twisted pair cable FR-E7TR FR-E7TR FR-E7TR FX Series PLC User's Manual - Data Communication Edition 4 Wiring Inverter Communication Connection Cables 4.3.1 10BASE-T cable A Common Items 4.3 4.3 Connection Cables B 10BASE-T cables used in LAN wiring for a personal computer can be connected. N:N Network 1. Selection procedure when purchasing 1) Cable type : 10BASE-T cable (Category 3 or 5) 2) Connection specifications : Straight type 3) Connector : RJ45 connector C Parallel Link 2. Cautions on using commercial cables Pay attention to the following point when purchasing commercial cables. • 5V DC is output to the PU connector in the inverters for supplying power to the PU. It is necessary to cut pins No. 2 and 8 of commercial cables to prevent wiring to pins No. 2 and 8. (It is recommended to use the distributor BMJ-8-28N). Twisted pair cable (recommended) Computer Link 4.3.2 D The table below shows recommended model names and manufacturers of cables used in wiring. Use commercial three-pair type twisted pair cables of 0.3 mm2 or more. E 1. Recommended cable list Sumitomo Electric Industries, Ltd. The Furukawa Electric Co., Ltd. Model name Inverter Communication Manufacturer Remarks DPEV SB 0.3 3P Three-pair cable of 0.3 mm2 DPEV SB 0.5 3P Three-pair cable of 0.5 mm2 D-KPEV-SB 0.5 3P Three-pair cable of 0.5 mm2 F Non-Protocol Communication (RS/RS2 Instruction) 2. Cable structural drawing (reference) G Non-Protocol Communication (FX2N-232IF) Three-pair cable structural drawing example H Programming Communication 3. Point of contact For details on cables such as specifications and price, contact each cable manufacturer. I Remote Maintenance Apx.A Discontinued models E-29 FX Series PLC User's Manual - Data Communication Edition 4 Wiring Inverter Communication 4.3.3 4.3 Connection Cables Connecting cables 1. European type terminal block The FX3G-485-BD-RJ terminal block is used for grounding. The other options use shielded twisted pair cables for connecting communication equipment operating in accordance with RS-485. The table below shows applicable cables and tightening torques. Cable size when Cable size when one cable is two cables are connected connected FX3U-485-BD FX3G-485-BD FX3U-485ADP (-MB) AWG22 to AWG20 Bar terminal with Insulating sleeve (cable size) Applicable 0.22 to 0.25 (AWG22 to AWG20) N·m AWG22 Tool size Tightening torque A B 0.4 (0.01") 2.5 (0.09") FX3G-485-BDRJ AWG20 to AWG16 Not applicable 0.5 to 0.6 N·m 0.6 (0.03") 3.5 (0.14") FX2N-485-BD AWG26 to AWG16 Not applicable 0.5 to 0.6 N·m 0.6 (0.03") 3.5 (0.14") Not applicable 0.4 to 0.5 N·m 0.6 (0.03") 3.5 (0.14") FX2NC-485ADP AWG26 to AWG16 AWG26 to AWG20 Do not tighten terminal screws with a torque outside the above-mentioned range. Failure to do so may cause equipment failures or malfunctions. With regard to the cable end treatment, use a stranded cable or solid cable as it is, or use a bar terminal with insulating sleeve. FX3G-485-BD-RJ, FX2N-485-BD and FX2NC-485ADP cannot use a bar terminal with insulating sleeve. • When using a stranded cable or solid cable as it is - Twist the end of a stranded cable so that wires do not get barbed. - Do not plate the end of the cable. FX3G-485-BD, FX3U-485-BD, FX3U-485ADP(-MB) FX3G-485-BD-RJ, FX2N-485-BD Approx. 9 mm (0.35") FX2NC-485ADP Approx. 6 mm (0.23") Approx. 8 mm (0.31") • When using a bar terminal with insulating sleeve Insulating sleeve Contact area (Crimp area) Because it is difficult to insert a cable into an insulating sleeve depending on the thickness of the cable sheath, select the proper cable according to the outline drawing. 8 mm (0.31") <Reference> 2.6 mm 14 mm Manufacturer Model name Caulking tool Phoenix Contact Co., Ltd. AI 0.5-8WH CRIMPFOX 6*1 (or CRIMPFOX 6T-F*2) *1. *2. E-30 Old model name : CRIMPFOX ZA 3 Old model name : CRIMPFOX UD 6 (0.1") (0.55") FX Series PLC User's Manual - Data Communication Edition 4 Wiring Inverter Communication 4.4 Connection Devices (RJ45 Connector and Distributor) A Select a screwdriver with a straight tip. A If the diameter of screwdriver grip is too small, tightening torque will not be able to be achieved. To achieve the appropriate tightening torque shown in the previous page, use the following screwdriver or an appropriate replacement (grip diameter: approximately 25mm (0.98")). <Reference> FX3U-485-BD, FX3G-485-BD, FX3U-485ADP(-MB) For size A and size B, refer to the table above. Phoenix Contact Co., Ltd. C Model name Parallel Link Manufacturer B B N:N Network Note SZS 0.4 2.5 FX3G-485-BD-RJ, FX2N-485-BD, FX2NC-485ADP Manufacturer Phoenix Contact Co., Ltd. Model name D SZF 1-0.6 3.5 Computer Link 2. Terminal block In the FX0N-485ADP, the terminal screw size is "M3". Make sure to use a crimp-style terminal with the following sizes. Make sure that the tightening torque is 0.5 to 0.8 N·m. Do not tighten terminal screws with a torque outside the above-mentioned range. Failure to do so may cause equipment failures or malfunctions. E Inverter Communication • When wiring one cable to one terminal 3.2(0.13") 6.2mm(0.24") or less Terminal Crimp screw terminal F Non-Protocol Communication (RS/RS2 Instruction) 3.2(0.13") 6.2mm(0.24") or less Terminal • When wiring two cables to one terminal 3.2(0.13") 6.3mm(0.25") or more 3.2(0.13") 6.2mm(0.24") or less H Terminal 6.3mm(0.25") or more Programming Communication 4.4 G Terminal Crimp screw terminal Non-Protocol Communication (FX2N-232IF) 6.2mm(0.24") or less Connection Devices (RJ45 Connector and Distributor) I Model name Remote Maintenance Prepare the following devices if necessary. Product name Common Items • Tool When tightening a terminal on the European terminal block, use a small commercial straight shape screwdriver whose tip is shown in the figure to the right. Manufacturer 5-554720-3 Distributor BMJ-8 BMJ-8-28N (No internal connection of the No. 2 HACHIKO ELECTRIC CO., LTD. and 8 pin) (Do not use a plug with terminal resistor) Tyco Electronics Japan G.K. Apx.A Discontinued models RJ45 connector E-31 FX Series PLC User's Manual - Data Communication Edition 4 Wiring Inverter Communication 4.5 4.5 Connecting Terminal Resistors Connecting Terminal Resistors Connect a terminal resistor to both the communication equipment of the FX PLC and the RDA-RDB signal terminal in the last inverter. For details on connection, refer to each wiring diagram. 1. Terminal resistor types Prepare the following two types of terminal resistors. Among the terminal resistors supplied with the communication equipment, select ones with the color codes shown to the right. 1) On the FX PLC side, use a terminal resistor of 110 , 1/2 W supplied together with the communication equipment operating in accordance with RS-485. Brown Precision 1 1 1 =110 (101) Brown Black Brown Precision 2) On the inverter side (PU connector except FR-A5NR, FR-E7TR), use a terminal resistor of 100 , 1/2 W (not supplied). 3) On the inverter side (FR-A5NR), use a terminal resistor chip (supplied together with the FR-A5NR). 1 0 1 =100 (101) 4) On the inverter side (FR-E7TR), use the terminal resistor switch. 2. Connecting a terminal resistor to the FX PLC Connect a terminal resistor between the RDA and RDB terminals of the communication equipment. 3. When using the FX3U-485-BD, FX3G-485-BD, FX3G-485-BD-RJ or FX3U-485ADP(-MB) The FX3G-485-BD, FX3U-485-BD, FX3G-485-BD-RJ and FX3U-485ADP(-MB) have built-in terminal resistors. Set the terminal resistor selector switch accordingly. • FX3U-485-BD • FX3U-485ADP(-MB) Terminal resistor selector switch 330 OPEN 110 Terminal resistor selector switch • FX3G-485-BD Remove the upper terminal block before changing over the switch in the FX3G-485-BD. Removal: Loosen the terminal block mounting screws, and remove the terminal block. Installation: Attach the terminal block, and tighten the terminal block mounting screws. Tightening torque : 0.4 to 0.5 N•m Do not tighten terminal screws with a torque outside the above-mentioned range. Failure to do so may cause equipment failures or malfunctions. For installation and removal of the terminal block, use the recommended tool shown below or a tool having straight tip (such as Select a screwdriver screwdriver) as shown in the right figure. with a <Reference> straight tip. Manufacturer Phoenix Contact Co., Ltd. Model name SZS 0.4 2.5 Terminal resistor selector switch Terminal block mounting screws E-32 0.4mm (0.01") 2.5mm (0.09") FX Series PLC User's Manual - Data Communication Edition Inverter Communication 4 Wiring 4.6 Wiring a Shielding Wire (Class-D grounding) A Common Items • FX3G-485-BD-RJ Terminal resistor selector switch B N:N Network 4. Connecting a terminal resistor to the inverter 1) When the PU connector or RS-485 connector (S500 Series) is used - Connect a terminal resistor between pin No. 3 (RDA) and pin No. 6 (RDB). - Connect a distributor to the PU terminal because terminal resistors cannot be connected. - Connect a terminal resistor only to the inverter located furthest away from the FX PLC. C Parallel Link Communication may be affected by noise echo depending on the transmission speed and transmission distance. When communication is hindered by noise echo, connect a terminal resistor to the inverter. D 3) When the FR-E7TR is used in connection A terminal resistor is built into the FR-E7TR. Set the terminal resistor switch in the E700 Series inverter located at the end to "100". Computer Link 2) When the FR-A5NR is used in connection - Connect a terminal resistor chip (which is supplied together with the FR-A5NR) between the RDB and RDR terminals in the most distant inverter. E Inverter Communication Terminal resistor switch F 100 H Programming Communication Wiring a Shielding Wire (Class-D grounding) Connect the FG FG terminal is provided in the communication equipment terminal to the (grounding) terminal of the PLC requiring Class-D grounding. Apx.A terminal is not provided in the communication equipment Discontinued models 2. When the FG I Remote Maintenance Perform Class-D grounding only to one side of a cable according to the absence/presence of the grounding terminal. For details on connection, refer to each wiring diagram. 1. When the G Non-Protocol Communication (FX2N-232IF) OPEN Terminal resistor switch 4.6 Non-Protocol Communication (RS/RS2 Instruction) 4) When the inverter built-in RS-485 terminal is used A terminal resistor is built into the RS-485 terminal. Set the terminal resistor switch in the F700/A700 Series inverter located at the end to "100". Perform Class-D grounding directly to the shielding wire of the cable. E-33 FX Series PLC User's Manual - Data Communication Edition 4 Wiring Inverter Communication 4.7 4.7 Connector in Inverter Connector in Inverter 1. In the case of PU port connector Pin No. Signal name 8 P5S 7 SG 6 RDB 5 SDA 4 SDB 3 RDA 2 P5S 1 SG Remarks When seen from inverter front (receptacle side) Not used (8) (1) Modular jack Not used The pins Nos. 2 and 8 (P5S) are provided for the power supply of the operation panel or parameter unit. Do not wire them into inverter communication. 2. In the case of computer link using the FR-A5NR Attach the FR-5NR to an A500, F500 or V500 Series inverter. Terminal block Screw size: M3 SDA SDB RDA RDB RDR SG A B C Terminal symbol Connect them to PLC communication equipment operating in accordance with RS-485. For details, refer to the instruction manual of the FR-A5NR. 3. In the case of computer link using the FR-E7TR Attach the FR-E7TR to an E700 Series inverter. Terminal block Connect them to PLC communication equipment operating in accordance with RS-485. For details, refer to the instruction manual of the FR-E7TR. E-34 FX Series PLC User's Manual - Data Communication Edition 4 Wiring Inverter Communication 4.7 Connector in Inverter A Common Items 4. In the case of built-in RS-485 terminal F800, A800, F700 and A700 Series inverters are equipped with a built-in RS-485 terminal. Terminal symbol B N:N Network Connect them to the communication equipment operating in accordance with RS-485 of the PLC. European terminal block C Parallel Link For details, refer to the instruction respective inverter manual. D Computer Link E Inverter Communication F Non-Protocol Communication (RS/RS2 Instruction) G Non-Protocol Communication (FX2N-232IF) H Programming Communication I Remote Maintenance Apx.A Discontinued models E-35 FX Series PLC User's Manual - Data Communication Edition 4 Wiring Inverter Communication 4.8 Connection Diagram 4.8 Connection Diagram 4.8.1 For S500, E500, A500, F500 , V500 and D700 Series (PU connector) 1. When one inverter is connected Terminal resistor: 110 • FX3U-485-BD, FX3G-485-BD and FX3U-485ADP(-MB): Set the built-in selector switch. • FX2N-485-BD and FX2NC-485ADP: Connect a terminal resistor (supplied) between the RDA and RDB terminals. FX3U-485-BD FX3G-485-BD FX2N-485-BD FX2NC-485ADP FX0N-485ADP FX3U-485ADP(-MB) RDA RDB SDA SDB 24V LINK DC 50mA SG 24+ 24G FG Distributor RDA RDB SDA SDB SG Class-D grounding 10BASE-T cable PLC 5 4 3 6 1 Connect a terminal resistor of 100 , 1/2 W (not supplied). 5 4 3 6 1 When seen from inverter front (receptacle side) 54361 8 PU (RS-485) S S R R connector DDDD S A B A BG 1 Inverter 54361 Modular jack • FX3G-485-BD-RJ FX3G-485-BD-RJ 5 4 3 6 1 2 Terminal 7 resistor 8 Connector metal frame RDA RDB SDA SDB SG PLC E-36 5 4 3 6 1 2 7 8 5 4 3 6 1 2 7 8 5 4 3 6 1 2 7 8 PU(RJ45) connector 5 4 3 6 1 2 7 8 SG RDB RDA SDB SDA (Terminal resistor selector switch: 110Ω) (Wiring circuit switch: 2 pair) Distributor (BMJ-8-28N) Inverter Connect a terminal resistor of 100 Ω, 1/2 W (not supplied). FX Series PLC User's Manual - Data Communication Edition 4 Wiring Inverter Communication 4.8 Connection Diagram A Terminal resistor: 110 • FX3U-485-BD, FX3G-485-BD and FX3U-485ADP(-MB): Set the built-in selector switch. • FX2N-485-BD and FX2NC-485ADP: Connect a terminal resistor (supplied) between the RDA and RDB terminals. RDA RDB SDA SDB SG Class-D grounding 10BASE-T cable PLC 5 4 3 6 1 Distributor 5 4 3 6 1 5 4 3 6 1 Distributor 5 4 3 6 1 5 4 3 6 1 5 4 3 6 1 54361 54361 54361 PU (RS-485) S S R R S connector D D D D G PU (RS-485) S S R R S connector D D D D G PU (RS-485) S S R R S connector D D D D G 54361 54361 Inverter ABAB Inverter ABAB ... Inverter C Parallel Link RDA RDB SDA SDB 24V LINK DC 50mA SG 24+ 24G FG Distributor ABAB D 54361 Computer Link For the pin arrangement in the connector, refer to the connection diagram for one inverter. • FX3G-485-BD-RJ Connect a terminal resistor of 100 Ω, 1/2 W (not supplied) to the most distant inverter. 5 4 3 6 1 2 7 8 PU(RJ45) connector 5 4 3 6 1 2 7 8 PU(RJ45) connector F 5 4 3 6 1 2 7 8 G 5 4 3 6 1 2 7 8 H Programming Communication Inverter 5 4 3 6 1 2 7 8 Non-Protocol Communication (FX2N-232IF) 5 4 3 6 1 2 7 8 SG RDB RDA SDB SDA PLC 5 4 3 6 1 2 7 8 SG RDB RDA SDB SDA (Terminal resistor selector switch: 110Ω) (Wiring circuit switch: 2 pair) 5 4 3 6 1 2 7 8 Distributor (BMJ-8-28N) Non-Protocol Communication (RS/RS2 Instruction) 5 4 3 6 1 2 Terminal 7 resistor 8 Connector metal frame RDA RDB SDA SDB SG Distributor (BMJ-8-28N) E Inverter Communication FX3G-485-BD-RJ B N:N Network FX3U-485-BD FX3G-485-BD FX2N-485-BD FX2NC-485ADP FX0N-485ADP FX3U-485ADP(-MB) Connect a terminal resistor of 100 , 1/2 W (not supplied) to the most distant inverter. Common Items 2. When two or more (up to eight) inverters are connected Inverter I Remote Maintenance Apx.A Discontinued models E-37 FX Series PLC User's Manual - Data Communication Edition 4 Wiring Inverter Communication 4.8.2 4.8 Connection Diagram For A500, F500 and V500 Series (FR-A5NR) 1. When one inverter is connected FX3U-485-BD FX3G-485-BD FX2N-485-BD FX2NC-485ADP FX0N-485ADP FX3U-485ADP(-MB) RDA RDB SDA SDB 24V DC LINK 50mA SG 24+ 24G FG Class-D grounding RDA RDB SDA SDB SG Terminal resistor: 110 • FX3U-485-BD, FX3G-485-BD and FX3U-485ADP(-MB): Set the built-in selector switch. • FX2N-485-BD and FX2NC-485ADP: Connect a terminal resistor (supplied) between the RDA and RDB terminals. Twisted pair cable (0.3mm2or more) Connect the terminal resistor connection piece. 0.3mm2 or more SS S DD G AB Terminal arrangement RRR DDD A BR Terminal block Screw size: M3 FR-A5NR Inverter PLC SDA SDB RDA RDB RDR Terminal symbol SG A B C Connect them to the communication unit of the PLC. 2. When two or more (up to eight) inverters are connected FX3U-485-BD FX3G-485-BD FX2N-485-BD FX2NC-485ADP FX0N-485ADP FX3U-485ADP(-MB) RDA RDB SDA SDB 24V LINK DC 50mA SG 24+ 24G FG Class-D grounding RDA RDB SDA SDB SG Terminal resistor: 110 • FX3U-485-BD, FX3G-485-BD and FX3U-485ADP(-MB): Set the built-in selector switch. • FX2N-485-BD and FX2NC-485ADP: Connect a terminal resistor (supplied) between the RDA and RDB terminals. 0.3mm2 or more Class D grounding SS S DD G AB PLC Connect the terminal resistor connection piece to the inverter located furthest away from the PLC. Twisted pair cable (0.3mm2 or more) RRR DDD A BR FR-A5NR Inverter SS S DD G AB Class D grounding RRR DDD ABR FR-A5NR Inverter .... SS S DD G AB RRR DDD ABR FR-A5NR Inverter For the pin arrangement of the connector, refer to the connection diagram above for one inverter. E-38 FX Series PLC User's Manual - Data Communication Edition 4 Wiring Inverter Communication A For E700 Series (PU connector) Common Items 4.8.3 4.8 Connection Diagram 1. When one inverter is connected (4-wire type) Terminal resistor: 110 • FX3U-485-BD, FX3G-485-BD, FX3U-485ADP(-MB): Set the built-in selector switch. N:N Network Distributor B Connect a terminal resistor of 100 Ω, 1/2 W (not supplied). C Parallel Link When seen from inverter front (receptacle side) 10BASE-T cable PLC PU (RS-485) connector Inverter D Computer Link Modular jack • FX3G-485-BD-RJ FX3G-485-BD-RJ 5 4 3 6 1 2 7 8 E Connect a terminal resistor of 100 Ω, 1/2 W (not supplied). F Non-Protocol Communication (RS/RS2 Instruction) 5 4 3 6 1 2 7 8 PU(RJ45) connector 5 4 3 6 1 2 7 8 G Non-Protocol Communication (FX2N-232IF) PLC 5 4 3 6 1 2 7 8 SG RDB RDA SDB SDA (Terminal resistor selector switch: 110Ω) (Wiring circuit switch: 2 pair) Distributor (BMJ-8-28N) Inverter Communication 5 4 3 6 1 2 Terminal 7 resistor 8 Connector metal frame RDA RDB SDA SDB SG Inverter H Programming Communication I Remote Maintenance Apx.A Discontinued models E-39 FX Series PLC User's Manual - Data Communication Edition 4 Wiring Inverter Communication 4.8 Connection Diagram 2. When two or more (up to eight) inverters are connected (4-wire type) Terminal resistor: 110 • FX3U-485-BD, FX3G-485-BD, FX3U-485ADP(-MB): Set the built-in selector switch. Distributor Connect a terminal resistor of 100 , 1/2 W (not supplied) to the most distant inverter. Distributor Distributor 10BASE-T cable PU (RS-485) connector PU (RS-485) connector PU (RS-485) connector Inverter Inverter Inverter PLC For the pin arrangement in the connector, refer to the connection diagram for one inverter. • FX3G-485-BD-RJ Connect a terminal resistor of 100 Ω, 1/2 W (not supplied) to the most distant inverter. FX3G-485-BD-RJ 5 4 3 6 1 2 Terminal 7 resistor 8 Connector metal frame RDA RDB SDA SDB SG E-40 5 4 3 6 1 2 7 8 5 4 3 6 1 2 7 8 5 4 3 6 1 2 7 8 PU(RJ45) connector 5 4 3 6 1 2 7 8 Inverter 5 4 3 6 1 2 7 8 5 4 3 6 1 2 7 8 PU(RJ45) connector 5 4 3 6 1 2 7 8 SG RDB RDA SDB SDA PLC 5 4 3 6 1 2 7 8 Distributor (BMJ-8-28N) SG RDB RDA SDB SDA (Terminal resistor selector switch: 110Ω) (Wiring circuit switch: 2 pair) Distributor (BMJ-8-28N) Inverter FX Series PLC User's Manual - Data Communication Edition 4 Wiring Inverter Communication 4.8 Connection Diagram A Common Items 3. When one inverter is connected (2-wire type) Terminal resistor: 110 • FX3U-485-BD, FX3G-485-BD, FX3U-485ADP(-MB): Set the built-in selector switch. Distributor B N:N Network Connect a terminal resistor of 100 , 1/2 W (not supplied). When seen from inverter front (receptacle side) C Parallel Link 10BASE-T cable PU (RS-485) connector Inverter PLC Modular jack D FX3G-485-BD-RJ 5 4 3 6 1 2 7 8 Connect a terminal resistor of 100 Ω, 1/2 W (not supplied). E 5 4 3 6 1 2 7 8 PU(RJ45) connector F Non-Protocol Communication (RS/RS2 Instruction) 5 4 3 6 1 2 7 8 G Non-Protocol Communication (FX2N-232IF) PLC 5 4 3 6 1 2 7 8 SG RDB RDA SDB SDA (Terminal resistor selector switch: 110Ω) (Wiring circuit switch: 1 pair) Distributor (BMJ-8-28N) Inverter Communication 5 4 3 6 1 2 Terminal 7 resistor 8 Connector metal frame RDA RDB SDA SDB SG Computer Link • FX3G-485-BD-RJ Inverter H Programming Communication I Remote Maintenance Apx.A Discontinued models E-41 FX Series PLC User's Manual - Data Communication Edition 4 Wiring Inverter Communication 4.8 Connection Diagram 4. When two or more (up to eight) inverters are connected (2-wire type) Terminal resistor: 110 • FX3U-485-BD, FX3G-485-BD, FX3U-485ADP(-MB): Set the built-in selector switch. Distributor Connect a terminal resistor of 100 , 1/2 W (not supplied) to the most distant inverter. Distributor Distributor 10BASE-T cable PU (RS-485) connector PU (RS-485) connector PU (RS-485) connector Inverter Inverter Inverter PLC For the pin arrangement in the connector, refer to the connection diagram for one inverter. • FX3G-485-BD-RJ Connect a terminal resistor of 100 Ω, 1/2 W (not supplied) to the most distant inverter. FX3G-485-BD-RJ 5 4 3 6 1 2 Terminal 7 resistor 8 Connector metal frame RDA RDB SDA SDB SG E-42 Distributor (BMJ-8-28N) 5 4 3 6 1 2 7 8 5 4 3 6 1 2 7 8 5 4 3 6 1 2 7 8 PU(RJ45) connector 5 4 3 6 1 2 7 8 Inverter 5 4 3 6 1 2 7 8 5 4 3 6 1 2 7 8 PU(RJ45) connector 5 4 3 6 1 2 7 8 SG RDB RDA SDB SDA PLC 5 4 3 6 1 2 7 8 SG RDB RDA SDB SDA (Terminal resistor selector switch: 110Ω) (Wiring circuit switch: 1 pair) Distributor (BMJ-8-28N) Inverter FX Series PLC User's Manual - Data Communication Edition 4 Wiring Inverter Communication A For E700 Series (FR-E7TR) Common Items 4.8.4 4.8 Connection Diagram 1. When one inverter is connected (4-wire type) B N:N Network Terminal resistor: 110 • FX3U-485-BD, FX3G-485-BD, FX3U-485ADP(-MB): Set the built-in selector switch. Twisted pair cable (0.3mm2 or more) C Set the terminal resistor switch to the "100 " side. Parallel Link 0.3mm2 or more Terminal arrangement Terminal block PLC D Computer Link Connect them to PLC communication unit. Inverter 2. When two or more (up to eight) inverters are connected (4-wire type) E Twisted pair cable (0.3mm2 or more) Inverter Communication Terminal resistor: 110 • FX3U-485-BD, FX3G-485-BD, FX3U-485ADP(-MB): Set the built-in selector switch. Set the terminal resistor switch to "100 " in the inverter located furthest away from the PLC. F Non-Protocol Communication (RS/RS2 Instruction) 0.3mm2 or more Class D grounding Inverter Inverter G Non-Protocol Communication (FX2N-232IF) PLC Class D grounding Inverter For the pin arrangement of the connector, refer to the connection diagram above for one inverter. H Programming Communication I Remote Maintenance Apx.A Discontinued models E-43 FX Series PLC User's Manual - Data Communication Edition Inverter Communication 4 Wiring 4.8 Connection Diagram When adopting branches, perform the wiring as shown below: (4-wire type) When connecting a 100 terminal resistor, set the switch to the "100 " side. For crossover wiring of a shielded cable using the terminal SG, set the terminal 2/SG selector switch to the right side (ON) to change over the terminal 2 to the terminal SG. (By this setting, analog inputs to the terminal 2 become invalid.) To next station inverter PLC E-44 FX Series PLC User's Manual - Data Communication Edition 4 Wiring Inverter Communication 4.8 Connection Diagram A Common Items 3. When one inverter is connected (2-wire type) Terminal resistor: 110 • FX3U-485-BD, FX3G-485-BD, FX3U-485ADP(-MB): Set the built-in selector switch. B 0.3mm2 or more N:N Network Twisted pair cable (0.3mm2 or more) Set the terminal resistor switch to the "100 " side. Crossover wiring Terminal arrangement C PLC Parallel Link Terminal block Connect them to PLC communication unit. Inverter D Terminal resistor: 110 • FX3U-485-BD, FX3G-485-BD, FX3U-485ADP(-MB): Set the built-in selector switch. Crossover wiring Crossover wiring Crossover wiring 0.3mm2 or more PLC Inverter F Class D grounding Inverter Non-Protocol Communication (RS/RS2 Instruction) Class D grounding E Inverter Communication Twisted pair cable (0.3mm2 or more) Set the terminal resistor switch to "100 " in the inverter located furthest away from the PLC. Computer Link 4. When two or more (up to eight) inverters are connected (2-wire type) Inverter G Non-Protocol Communication (FX2N-232IF) For the pin arrangement of the connector, refer to the connection diagram above for one inverter. When adopting branches, perform the wiring as shown below: (2-wire type) H To next station inverter I Remote Maintenance For crossover wiring of a shielded cable using the terminal SG, set the terminal 2/SG selector switch to the right side (ON) to change over the terminal 2 to the terminal SG. (By this setting, analog inputs to the terminal 2 become invalid.) Programming Communication When connecting a 100 terminal resistor, set the switch to the "100 " side. Apx.A Discontinued models PLC Perform crossover wiring. E-45 FX Series PLC User's Manual - Data Communication Edition 4 Wiring Inverter Communication 4.8.5 4.8 Connection Diagram For F800, A800, F700 and A700 Series (built-in RS-485 terminal) 1. When one inverter is connected Terminal resistor: 110 - FX3U-485-BD, FX3G-485-BD, FX3U-485ADP(-MB): Set the built-in selector switch. FX3U-485-BD FX3G-485-BD FX3U-485ADP(-MB) Twisted pair cable (0.3mm2 or more) RDA RDB SDA SDB SG Set the terminal resistor switch to the "100" side. 0.3mm2 or more PLC SS S DD G AB 11 Class-D grounding RR DD AB 11 Inverter 2. When two or more (up to eight) inverters are connected Terminal resistor: 110 - FX3U-485-BD, FX3G-485-BD, FX3U-485ADP(-MB): Set the built-in selector switch. FX3U-485-BD FX3G-485-BD FX3U-485ADP(-MB) RDA RDB SDA SDB SG Set the terminal resistor switch to "100" in the inverter located furthest away from the PLC. Twisted pair cable (0.3mm2 or more) 0.3mm2 or more Class-D grounding Class-D grounding Class-D grounding PLC SS SS S D D DD G BA BA 1122 SS SS S DD D D G BA BA 1122 R R RR D D DD S B ABA G 1122 Inverter R R RR D D DD S BA BA G 1122 .... Inverter When adopting branches, perform the wiring as shown below: + - + - Connect them to SDA and SDB in PLC. Connect them to RDA and RDB in PLC. Connect it to SG in PLC. E-46 RXD + - + - RXD TXD + - + - TXD + - + - SG SG SG VCC SG VCC Connect them to RDA1 and RDB1 in next inverter. Connect them to SDA1 and SDB1 in next inverter. Connect it to SG in next inverter. SS S DD G BA 11 RR DD BA 11 Inverter FX Series PLC User's Manual - Data Communication Edition 4 Wiring Inverter Communication A Switching of 1 pair / 2 paired wiring (FX3G-485-BD-RJ) Common Items 4.8.6 4.9 Grounding The FX3G-485-BD-RJ has a built-in wiring circuit switch. Set the wiring circuit switch to 1 pair / 2 pair. B N:N Network Wiring circuit switch C Parallel Link 4.9 Grounding D Grounding should be performed as stated below. • Independent grounding should be performed for best results. When independent grounding can not be performed, perform "shared grounding" as shown in the following figure. For details, refer to the Hardware Edition of each series. Other equipment Independent grounding Best condition PLC Other equipment Shared grounding Good condition PLC Other equipment E Inverter Communication PLC Computer Link • The grounding resistance should be 100 or less. Common grounding Not allowed • The grounding wire size should be AWG 14 (2 mm2) or larger. F Non-Protocol Communication (RS/RS2 Instruction) • The grounding point should be close to the PLC, and all grounding wires should be as short as possible. G Non-Protocol Communication (FX2N-232IF) H Programming Communication I Remote Maintenance Apx.A Discontinued models E-47 FX Series PLC User's Manual - Data Communication Edition 5 Communication Setting in Inverter Inverter Communication 5. 5.1 Communication Port and Applicable Parameters Communication Setting in Inverter Before connecting an inverter to a PLC, set parameters related to communication in the inverter parameter unit (PU) in advance using the procedure described in this chapter. If these parameters are overwritten from the PLC after the inverter is connected, communication will be disabled. If these parameters are changed by mistake, they should be set again. 5.1 Communication Port and Applicable Parameters When connecting an inverter to a PLC, it is necessary to set parameters corresponding to the communication port in advance. S500 Series Remove the surface cover. E500 Series Remove the operation panel. A500, F500 and V500 Series Remove the operation panel. PU connector FR-A5NR PU connector Remove the surface cover RS-485 port (PU connector) F700 and A700 Series Remove the surface cover. E700 Series Open the PU connector cover. PU connector RS-485 terminal D700 Series Remove the surface cover. F800, A800 Series Remove the surface cover. RS-485 terminal PU connector E-48 Remove the surface cover. FR-E7TR FX Series PLC User's Manual - Data Communication Edition Inverter Communication 5 Communication Setting in Inverter 5.1 Communication Port and Applicable Parameters A Model classification Inverter connection destination S500 Series Only models with built-in RS-485 port RS-485 port Parameters applicable in Reference inverter section Pr79, n1 to n12 5.2 5.4 Option FR-A5NR computer link Pr79, Pr331 to Pr342 5.5 Models with built-in PU port PU port Pr79, Pr117 to Pr124 5.4 Option FR-A5NR computer link Pr79, Pr331 to Pr342 5.5 Models with built-in PU port PU port Pr79, Pr117 to Pr124 5.4 Option FR-A5NR computer link Pr79, Pr331 to Pr342 5.5 PU port Pr79, Pr117 to Pr124, Pr340, Pr549 5.6 Pr79, Pr117 to Pr124, Pr.340, Pr549 5.6 A700 Series Models with built-in RS-485 terminal RS-485 terminal Pr79, Pr331 to Pr342, Pr549 5.7 F700 Series Models with built-in RS-485 terminal RS-485 terminal Pr79, Pr331 to Pr342, Pr549 5.7 A800 Series Models with built-in RS-485 terminal RS-485 terminal Pr79, Pr331 to Pr342, Pr549 PN000, PN001, PN030 to PN038, PD000, PD001, PD010, PD011 5.8 F800 Series Models with built-in RS-485 terminal RS-485 terminal Pr79, Pr331 to Pr342, Pr549 PN000, PN001, PN030 to PN038, PD000, PD001, PD010, PD011 5.8 A500 Series F500 Series V500 Series D700 Series Models having built-in PU port E700 Series Models having built-in PU port PU port Option FR-E7TR control terminal option B C D Computer Link 5.3 Pr79, Pr117 to Pr124 Parallel Link Pr79, Pr117 to Pr124 PU port N:N Network PU port Models with built-in PU port E Inverter Communication E500 Series Models with built-in PU port Common Items Model F Non-Protocol Communication (RS/RS2 Instruction) G Non-Protocol Communication (FX2N-232IF) H Programming Communication I Remote Maintenance Apx.A Discontinued models E-49 FX Series PLC User's Manual - Data Communication Edition 5 Communication Setting in Inverter Inverter Communication 5.2 S500 Series (When Connected to RS-485 Port) 5.2 S500 Series (When Connected to RS-485 Port) 5.2.1 Contents of parameter setting 1. Contents of communication setting (essential items) The table below shows parameters which should be set in all cases. Parameter No. Parameter item Set value n1 Communication station number n2 Communication speed n3 Stop bit length n4 n7 n11 00 to 31 Setting contents Up to eight inverters can be connected. 48 4800 bps 96 9600 bps 192 19200 bps (standard) 10 Data length: 7-bit/Stop bit: 1-bit Parity check presence/absence 2 Even parity present Wait time setting --- Set with communication data CR/LF selection 1 With CR, without LF Pr79 Operation mode selection 0 External operation mode is selected when power is turned ON. n10 Link start mode selection 1 Computer link operation n6 Communication check time interval --- Communication check suspension 2. Parameters which should be adjusted between test operation and actual operation Parameter No. n5 Parameter item Number of communication retries Set value Setting contents --- Set the value shown on the left during adjustment, and set a value from 1 to 10 during operation. 3. Others (which should be set if necessary) The table below shows parameters to be considered when using various system configuration and inverters. For the method of use, refer to the respective inverter manual. Parameter No. E-50 Set value Setting contents n12 EEPROM write selection 0 or 1 0: Written to RAM and EEPROM 1: Written to RAM only. Not written to EEPROM n8 Operation command write 0 or 1 0: PLC 1: External n9 Speed command write 0 or 1 0: PLC 1: External Pr37 *1. Parameter item Speed display*1 0 or 0.1 to 999 0: Frequency display, setting 0.1 to 999: Machine speed at 60Hz. This inverter communication function cannot read or write Pr37. Set Pr37 to "0" when setting or monitoring the frequency in the PLC. If any value other than "0" is set and the instruction code HFF is set to "01", the frequency may not be set or monitored normally. FX Series PLC User's Manual - Data Communication Edition 5 Communication Setting in Inverter Inverter Communication A Parameter setting method (reference) Common Items 5.2.2 5.2 S500 Series (When Connected to RS-485 Port) This subsection explains the parameter setting method using the operation panel. For details on the operation panel, refer to the respective inverter manual. B MODE key Changes over the setting mode. C N:N Network 3-digit monitor LED Shows the frequency, parameter number, etc. RUN indicator Lights or flashes during operation. Parallel Link Setting dial Changes the set value of the frequency and parameters. SET key Sets each setting. The operating procedure example below shows a case in which the baud rate is set to 19,200 bps. D Confirming the RUN indicator and the operation mode Computer Link 1 Confirm that the operation is stopped (that the RUN indicator is OFF). 2 Selecting the parameter setting mode E Monitor/frequency setting mode Inverter Communication Press the MODE key, and select the parameter setting mode. Parameter setting mode The last parameter read is displayed. F Setting the set value of Pr. 30 to "1" (This step is not necessary if Pr. 30 is already set to "1".) Non-Protocol Communication (RS/RS2 Instruction) 3 1. Turn the setting dial to display "P30". G Non-Protocol Communication (FX2N-232IF) 2. Press the SET key to read the currently set value. H Programming Communication 3. Turn the setting dial to change the set value to "1". I Remote Maintenance Press the SET key to set "1". Apx.A Discontinued models The set value and parameter number are displayed alternately. When the set value and parameter number are displayed alternately, the setting is completed. E-51 FX Series PLC User's Manual - Data Communication Edition Inverter Communication 4 5 Communication Setting in Inverter 5.2 S500 Series (When Connected to RS-485 Port) Setting the set value of "n2" to "192" ("192" indicates the baud rate of 19200 bps.) Turn the setting dial to display "n2". Press the SET key to read the currently set value. Turn the setting dial to change the set value to "192". Press the SET key to set "192". The set value and parameter number are displayed alternately. When the set value and parameter number are displayed alternately, the setting is completed. 5 E-52 Changing other parameters in the same way as step 4 For details on the parameters to be set, refer to Subsection 5.2.1. FX Series PLC User's Manual - Data Communication Edition 5 Communication Setting in Inverter Inverter Communication 5.3 E500 Series (When Connected to PU Port) E500 Series (When Connected to PU Port) 5.3.1 Contents of parameter setting Common Items 5.3 A B N:N Network 1. Contents of communication setting (essential items) The table below shows parameters which should be set in all cases. Parameter item Set value Pr117 Communication station number 00 to 31 Pr118 Communication speed Pr119 Stop bit / Data length Setting contents Up to eight inverters can be connected. 48 4800 bps 96 9600 bps C 192 19200 bps (standard) 10 Data length: 7-bit/Stop bit: 1-bit 2 Even parity present Parallel Link Parameter No. Pr120 Parity check presence/absence Pr123 Waiting time setting Pr124 CR•LF presence/absence selection 1 With CR, without LF Pr79 Operation mode selection 0 External operation mode is selected when power is turned ON. Pr122 Communication check time interval 9999 D Communication check suspension E Pr121 Parameter item Number of communication retries Set value Setting contents 9999 Set the value shown on the left during adjustment, and set a value from 1 to 10 during operation. 3. Others (which should be set if necessary) Parameter No. Pr37 Pr342 Speed display*1 Frequency setting command selection*2 EEPROM write selection (only in 400 V class) Set value 0 or 0.01 to 9998 0, 1, 9999 0 or 1 Setting contents 0: Frequency display, setting 0.01 to 9998: Machine speed at 60Hz. 0 : The built-in frequency setting knob is valid. 1 : The built-in frequency setting knob is invalid. 9999 : The built-in frequency setting knob is valid when the frequency is set to "0 Hz" by the keys. 0: EEPROM is written. 1: RAM is written. This inverter communication function cannot read or write Pr37. Set Pr37 to "0" when setting or monitoring the frequency in the PLC. If any value other than "0" is set to Pr37 and the instruction code HFF is set to "01", the frequency may not be set or monitored normally (in the 400 V class). (In the 200 V and 100 V classes, the frequency may not be set or monitored normally if any value other than "0" is set to Pr37 without regard to the setting of the instruction code HFF.) *2. When changing the frequency from the PLC, set "1" or "9999". H Programming Communication *1. G Non-Protocol Communication (FX2N-232IF) Pr146 Parameter item F Non-Protocol Communication (RS/RS2 Instruction) The table below shows parameters to be considered when using various system configuration and inverters. For the method of use, refer to the respective inverter manual. Inverter Communication 2. Parameters which should be adjusted between test operation and actual operation Parameter No. Computer Link 9999 Set with communication data I Remote Maintenance Apx.A Discontinued models E-53 FX Series PLC User's Manual - Data Communication Edition 5 Communication Setting in Inverter Inverter Communication 5.3.2 5.3 E500 Series (When Connected to PU Port) Parameter setting method (reference) This subsection explains the parameter setting method using the operation panel. For details on the operation panel, refer to the respective inverter manual. When the cover is closed When the cover is open Display LED 4 digits Displays the frequency, parameter number, etc. Unit indicator Operation status indication The LEDs light and flash according to the mode and operation status. Setting key Sets each setting. UP/DOWN key Change the set value of the frequency and parameters. MODE key Changes over the mode. The operating procedure example below shows a case in which the baud rate is set to 19200 bps. 1 Confirming the RUN indicator and the operation mode indicator Confirm that the operation is stopped (that the RUN indicator is Off). 2 Selecting the parameter setting mode Press the MODE key, and select the parameter setting mode. Monitoring mode *1. 3 Frequency setting mode*1 Parameter setting mode The frequency setting mode is displayed only in the PU operation mode. Reading the parameter (Pr. 118) There are two methods to read the parameter number: • Method to read the parameter number using the UP and DOWN keys Press the UP and DOWN keys, and display the parameter number to be read. E-54 FX Series PLC User's Manual - Data Communication Edition Inverter Communication 5 Communication Setting in Inverter 5.3 E500 Series (When Connected to PU Port) A Common Items • Method to set each digit of the parameter number a) Press the SET key to flash the most significant digit. Set a numeric value using the UP and DOWN keys. B N:N Network b) Press the SET key to flash the middle digit. Set a numeric value using the UP and DOWN keys. C Parallel Link c) Press the SET key to flash the least significant digit. Set a numeric value using the UP and DOWN keys. D Computer Link E Setting the set value of Pr. 118 to "192" ("192" indicates the baud rate of 19200 bps.) 1. Press the SET key to read the currently set value. Change the set value using the UP and DOWN keys. Inverter Communication 4 F Non-Protocol Communication (RS/RS2 Instruction) G 2. Press and hold the SET key for 1.5 seconds to set "192". Non-Protocol Communication (FX2N-232IF) Press and hold it for 1.5 sec. The set value and parameter number are displayed alternately. H Programming Communication 3. Press the SET key to display the next parameter. I 5 Remote Maintenance The parameter number and set value are displayed alternately Change other parameters in the same way as step 3. For details on parameters to be set, refer to Subsection 5.3.1. Apx.A Discontinued models E-55 FX Series PLC User's Manual - Data Communication Edition 5 Communication Setting in Inverter Inverter Communication 5.4 V500, F500 and A500 Series (Connection to PU Port) 5.4 V500, F500 and A500 Series (Connection to PU Port) 5.4.1 Contents of parameter setting 1. Contents of communication setting (essential items) The table below shows parameters which should be set in any case. Parameter No. Parameter item Set value Pr117 Communication station number Pr118 Communication speed Pr119 Stop bit length/data length 00 to 31 Setting contents Up to eight inverters can be connected. 48 4800 bps 96 9600 bps 192 19200 bps (standard) 10 Data length: 7-bit/Stop bit: 1-bit 2 2: Even parity Pr120 Parity check presence/absence Pr123 Waiting time setting Pr124 CR•LF presence/absence selection 1 CR: Provided, LF: Not provided Pr79 Operation mode selection 0 External operation mode is selected when power is turned ON. Pr122 Communication check time interval 9999 9999 Set in communication data Communication check is stopped. 2. Parameters which should be adjusted between test operation and actual operation Parameter No. Pr121 Parameter item Number of communication retries Set value Setting contents 9999 Set the value shown on the left during adjustment, and set a value from 1 to 10 during operation. 3. Others (which should be set if necessary) The table below shows parameters to be considered when using various system configuration and inverters. For the method of use, refer to the respective inverter manual. E-56 Parameter No. Parameter item Set value Pr342 EEPROM write selection 0 or 1 Setting contents 0: EEPROM are written. 1: RAM is written. FX Series PLC User's Manual - Data Communication Edition Inverter Communication 5.4 V500, F500 and A500 Series (Connection to PU Port) A Parameter setting method (reference) Common Items 5.4.2 5 Communication Setting in Inverter This subsection explains the parameter setting method using the operation panel. For details on the operation panel, refer to the respective inverter manual. B N:N Network Display LED4 digit Displays the frequency, parameter number, etc. Operation status indication REV LED flashes during reverse rotation. FWD LED flashes during forward rotation. C Parallel Link Mode key Changes over the mode. UP.down key Change the set value of the frequency and parameters. Set key Sets each setting. D 1 Computer Link The operating procedure example below shows a case in which the baud rate is set to 19200 bps. Confirming the RUN indicator and the operation mode indicator Confirm that the operation is stopped (that both the REV and FWD indicators are Off). E Selecting the parameter setting mode Inverter Communication 2 Press the MODE key, and select the parameter setting mode. Monitor mode Frequency setting mode*1 Parameter setting mode F The frequency setting mode is displayed only during the PU operation mode. G Reading the parameter (Pr. 118) Non-Protocol Communication (FX2N-232IF) 3 Non-Protocol Communication (RS/RS2 Instruction) *1. There are two methods to read the parameter number: • Method to read the parameter number using the UP and DOWN keys Press the UP and DOWN keys, and display the parameter number to be read. H Programming Communication I Remote Maintenance • Method to set each digit of the parameter number a) Press the SET key to flash the most significant digit. Set a numeric value using the UP and DOWN keys. Apx.A Discontinued models E-57 FX Series PLC User's Manual - Data Communication Edition Inverter Communication 5 Communication Setting in Inverter 5.4 V500, F500 and A500 Series (Connection to PU Port) b) Press the SET key to flash the middle digit. Set a numeric value using the UP and DOWN keys. c) Press the SET key to flash the least significant digit. Set a numeric value using the UP and DOWN keys. 4 Setting the set value of Pr. 118 to "192" ("192" indicates the baud rate of 19200 bps.) 1. Press the SET key to read the currently set value. Change the set value using the UP and DOWN keys. 2. Press and hold the SET key for 1.5 seconds to set "192". Press and hold it for 1.5 sec. The set value and parameter number are displayed alternately. 3. Press the SET key to display the next parameter The set value and parameter number are displayed alternately. 5 E-58 Changing other parameters in the same way as step 3 For details on the parameters to be set, refer to Subsection 5.4.1. FX Series PLC User's Manual - Data Communication Edition 5 Communication Setting in Inverter Inverter Communication 5.5 V500, F500 and A500 Series (Connection to FR-A5NR) V500, F500 and A500 Series (Connection to FR-A5NR) 5.5.1 Contents of parameter setting Common Items 5.5 A B The table below shows parameters which should be set in all cases. Parameter No. Parameter item Set value Communication station number Pr332 Communication speed Pr333 Stop bit / Data length 00 to 31 Pr334 Parity check presence/absence Pr337 Waiting time setting Pr341 CR, LF presence/absence selection Setting contents Up to eight inverters can be connected. 48 4800 bps 96 9600 bps (standard) 192 19200 bps 10 Data length: 7-bit/Stop bit: 1-bit 2 9999 C Parallel Link Pr331 2: Even parity Set in communication data D CR: Provided, LF: Not provided 0 External operation mode is selected when power is turned ON. 1 Computer link Computer Link 1 Communication check is stopped. 2. Parameters which should be adjusted between test operation and actual operation E Pr79 Operation mode selection Pr340 Link startup mode selection Pr336 Communication check time interval Pr335 Parameter item 9999 Set value Setting contents 9999 Set the value shown on the left during adjustment, and set a value from 1 to 10 during operation. Number of communication retries 3. Others (which should be set if necessary) Parameter No. Parameter item Set value Setting contents F Pr342 EEPROM write selection 0 or 1 0: EEPROM is written. 1: RAM is written. Pr338 Operation command right 0 or 1 0: PLC 1: Outside G Pr339 Speed command write 0 or 1 0: PLC 1: Outside Non-Protocol Communication (FX2N-232IF) Non-Protocol Communication (RS/RS2 Instruction) The table below shows parameters to be considered when using various system configuration and inverters. For the method of use, refer to the respective inverter manual. Inverter Communication Parameter No. 5.5.2 N:N Network 1. Contents of communication setting (essential items) Parameter setting method (reference) H Programming Communication The parameter setting method is the same as that for the V500, F500 and A500 Series (connection to the PU port). For the parameter setting method, refer to Subsection 5.4.2. I Remote Maintenance Apx.A Discontinued models E-59 FX Series PLC User's Manual - Data Communication Edition 5 Communication Setting in Inverter Inverter Communication 5.6 E700, D700 Series (when PU port, FR-E7TR is connected) 5.6 E700, D700 Series (when PU port, FR-E7TR is connected) 5.6.1 Contents of parameter setting 1. Contents of communication setting (essential items) The table below shows parameters which should be set in all cases. Parameter No. Pr117 Pr118 Pr119 Parameter item PU communication station number PU communication speed PU communication stop bit length Set value 00 to 31 Setting contents Up to eight inverters can be connected. 48 4800 bps 96 9600 bps 192 19200 bps (standard) 384 38400 bps 10 Data length: 7-bit/Stop bit: 1-bit 2 2: Even parity Pr120 PU communication parity check Pr123 PU communication waiting time setting Pr124 PU communication CR/LF presence/ absence selection 1 CR: Provided, LF: Not provided Pr79 Operation mode selection 0 External operation mode is selected when power is turned ON. Pr549 Protocol selection 0 Mitsubishi inverter operation) protocol Pr340 Communication startup mode selection 9999 1 or 10 Set in communication data (computer link 1: Network operation mode 10: Network operation mode Operation mode can be changed between the PU operation mode and network operation mode from the operation panel. 2. Parameters which should be adjusted between test operation and actual operation Parameter No. Pr121 Pr122 Parameter item Number of PU communication retries PU communication check time interval Set value Setting contents 9999 Set the value shown on the left during adjustment, and set a value from 1 to 10 during operation. 9999 Set the value shown on the left during adjustment, and set a proper value in accordance with the system specification during operation. Caution on setting the PU communication check time interval (Pr122) Description During adjustment or when communication with the PLC is not executed periodically E-60 Set value 9999 When communication with the PLC is not executed 0 (Initial Value) Set the communication time in the following cases • When it is necessary to monitor absence of communication for a certain time and stop the inverter in such a case while communication with the PLC is being executed • When it is necessary to stop the motor at the point which the PLC mode is changed from RUN to STOP 0.1 to 999.8 sec FX Series PLC User's Manual - Data Communication Edition 5 Communication Setting in Inverter Inverter Communication 5.6 E700, D700 Series (when PU port, FR-E7TR is connected) A The table below shows parameters to be considered when using various system configuration and inverters. For the method of use, refer to the respective inverter manual. Parameter No. Pr37 Parameter item Speed display*1 Set value Setting contents 0 or 0.01 0: Frequency display, setting to 9998 0.01 to 9998: Machine speed at 60Hz. Built-in potentiometer switching*2 0 or 1 Pr342 Communication EEPROM write selection 0 or 1 0: EEPROM is written. 1: RAM is written. B N:N Network Pr146 0: Built-in frequency setting potentiometer valid 1: Built-in frequency setting potentiometer invalid Common Items 3. Others (which should be set if necessary) C This inverter communication function cannot read or write Pr37. Set Pr37 to "0" when setting or monitoring the frequency in the PLC. If any value other than "0" is set to Pr37 and the instruction code HFF is set to "01", the frequency may not be set or monitored normally. *2. Set Pr146 to "1" when changing the frequency from the PLC. Parallel Link *1. D Computer Link E Inverter Communication F Non-Protocol Communication (RS/RS2 Instruction) G Non-Protocol Communication (FX2N-232IF) H Programming Communication I Remote Maintenance Apx.A Discontinued models E-61 FX Series PLC User's Manual - Data Communication Edition 5 Communication Setting in Inverter Inverter Communication 5.6.2 5.6 E700, D700 Series (when PU port, FR-E7TR is connected) Parameter setting method (reference) This subsection explains the parameter setting method using the operation panel. For details on the operation panel, refer to the respective inverter manual. Operating status display Lit or flicker during inverter operation Monitor (4-digit LED) Show the frequency, parameter number, etc. Setting dial Used to change the frequency setting and parameter values. SET key Determines each setting MODE key Used to change each setting mode The operating procedure example below shows a case in which the baud rate is set to 19200 bps. 1 Confirming the RUN indicator and the operation mode indicator Confirm that the operation is stopped (that the RUN indicator is off). 2 Selecting the parameter setting mode Press the MODE key, and select the parameter setting mode. Monitor/frequency setting mode Parameter setting mode The previously read parameter is displayed. 3 Setting the parameter Pr. 160 to "0" (This step is not required if Pr. 160 is already set to "0".) 1. Turn the setting dial until "Pr. 160" is displayed. 2. Press the SET key to read the current set value. 3. Turn the setting dial, and change the set value to "0". E-62 FX Series PLC User's Manual - Data Communication Edition Inverter Communication 5 Communication Setting in Inverter 5.6 E700, D700 Series (when PU port, FR-E7TR is connected) A Common Items Press the SET key to determine the set value. B The set value and parameter number are displayed alternately. 4 N:N Network The set value and parameter number are displayed alternately, and the setting is completed. Setting the parameter Pr. 118 to "192" ("192" indicates the baud rate of 19200 bps.) C Turn the setting dial until "Pr. 118" is displayed. Parallel Link D Computer Link Press the SET key to read the current set value. E Inverter Communication Turn the setting dial, and change the set value to "192". F Non-Protocol Communication (RS/RS2 Instruction) Press the SET key to determine the set value. G The set value and parameter number are displayed alternately, and the setting is completed. 5 Changing other parameters in the same way as step 4 For details on the parameters to be set, refer to Subsection 5.6.1. Non-Protocol Communication (FX2N-232IF) The set value and parameter number are displayed alternately. H Programming Communication I Remote Maintenance Apx.A Discontinued models E-63 FX Series PLC User's Manual - Data Communication Edition 5 Communication Setting in Inverter Inverter Communication 5.7 F700 and A700 Series (when built-in RS-485 terminal is connected) 5.7 F700 and A700 Series (when built-in RS-485 terminal is connected) 5.7.1 Contents of parameter setting 1. Contents of communication setting (essential items) The table below shows parameters which should be set in all cases. Parameter No. Pr331 Pr332 Parameter item Set value RS-485 communication station 00 to 31 RS-485 communication speed Setting contents Up to eight inverters can be connected. 48 4800 bps 96 9600 bps (standard) 192 19200 bps 384 38400 bps Pr333 RS-485 communication stop bit length 10 Data length: 7-bit/Stop bit: 1-bit Pr334 RS-485 communication selection 2 2: Even parity parity check Pr337 RS-485 communication waiting time setting Pr341 RS-485 communication CR/LF selection 1 CR: Provided, LF: Not provided Pr79 Operation mode selection 0 External operation mode is selected when power is turned ON. Pr340 Communication startup mode selection 1 Computer link Pr336 RS-485 communication check time interval Pr549 Protocol selection 9999 9999 0 Set in communication data Communication check is stopped. Mitsubishi inverter (computer link) protocol 2. Parameters which should be adjusted between test operation and actual operation Parameter No. Parameter item Pr335 RS-485 communication number of retries Set value Setting contents 9999 Set the value shown on the left during adjustment, and set a value from 1 to 10 during operation. 3. Others (which should be set if necessary) The table below shows parameters to be considered when using various system configuration and inverters. For the method of use, refer to the respective inverter manual. Parameter No. E-64 Parameter item Set value Setting contents Pr342 Communication EEPROM write selection 0 or 1 0: EEPROM is written. 1: RAM is written. Pr338 Communication operation command source 0 or 1 0: PLC 1: Outside Pr339 Communication operation command source 0 or 1 0: PLC 1: Outside FX Series PLC User's Manual - Data Communication Edition Inverter Communication 5.7 F700 and A700 Series (when built-in RS-485 terminal is connected) A Parameter setting method (reference) Common Items 5.7.2 5 Communication Setting in Inverter This subsection explains the parameter setting method using the operation panel. For details on the operation panel, refer to the respective inverter manual. Rotation direction indicator FWD: Lit during forward rotation REV: Lit during reverse rotation Setting dial Used to change the frequency setting and parameter values. C Parallel Link MODE key Changes over the mode. SET key Sets each setting. D The operating procedure example below shows a case in which the baud rate is set to 19200 bps. Computer Link 1 Confirming the RUN indicator and the operation mode indicator Confirm that the operation is stopped (that the RUN indicator is off). 2 E Selecting the parameter setting mode Inverter Communication Press the MODE key, and select the parameter setting mode. Monitor/frequency setting mode Parameter setting mode The previously read parameter is displayed. F Non-Protocol Communication (RS/RS2 Instruction) 3 B N:N Network Operation mode indicator NET: Lit to indicate network operation mode Monitor (4-digit LED) shows the frequency, parameter number, etc. Setting the parameter Pr. 160 to "0" (This step is not required if Pr. 160 is already set to "0".) G 1. Turn the setting dial until "Pr. 160" is displayed. Non-Protocol Communication (FX2N-232IF) H 2. Press the SET key to read the current set value. Programming Communication I 3. Turn the setting dial, and change the set value to "0". Remote Maintenance Apx.A Discontinued models E-65 FX Series PLC User's Manual - Data Communication Edition Inverter Communication 5 Communication Setting in Inverter 5.7 F700 and A700 Series (when built-in RS-485 terminal is connected) Press the SET key to determine the set value. The set value and parameter number are displayed alternately. The set value and parameter number are displayed alternately, and the setting is completed. 4 Setting the parameter Pr. 332 to "192" ("192" indicates the baud rate of 19200 bps.) Turn the setting dial until "Pr. 332" is displayed. Press the SET key to read the current set value. Turn the setting dial, and change the set value to "192". Press the SET key to determine the set value. The set value and parameter number are displayed alternately. The set value and parameter number are displayed alternately, and the setting is completed. 5 E-66 Change other parameters in the same way as step 4 For details on the parameters to be set, refer to Subsection 5.7.1. FX Series PLC User's Manual - Data Communication Edition 5 Communication Setting in Inverter Inverter Communication 5.8 F800 and A800 Series (when built-in RS-485 terminal is connected) F800 and A800 Series (when built-in RS-485 terminal is connected) 5.8.1 Contents of parameter setting B N:N Network 1. Contents of communication setting (essential items) The table below shows parameters which should be set in all cases. Parameter Parameter Parameter item No. group Pr331 N030 RS-485 communication station Set value Setting contents 00 to 31 Up to eight inverters can be connected. 4800 bps 96 9600 bps (standard) 192 19200 bps 384 38400 bps RS-485 communication stop bit length/ data length 10 Data length: 7-bit/Stop bit: 1-bit N032 RS-485 communication data length 1 Data length: 7 bits N033 RS-485 communication stop bit length 0 Stop bit: 1 bit Pr334 N034 RS-485 communication parity check selection 2 2: Even parity Pr337 N037 RS-485 communication waiting time setting 9999 Pr341 N038 RS-485 communication CR/LF selection 1 CR: Provided, LF: Not provided Pr79 D000 Operation mode selection 0 External operation mode is selected when power is turned ON. Pr340 D001 Communication startup mode selection 1 Computer link 0 Mitsubishi inverter (computer link) protocol N031 — Pr333 Protocol selection Computer Link N000 D Set in communication data E Parameter Parameter No. group Pr335 N035 RS-485 communication number of retries N036 RS-485 communication check time interval Set value Setting contents 9999 Set the value shown on the left during adjustment, and set a value from 1 to 10 during operation. 9999 Set the value shown on the left during adjustment, and set a value in accordance with the system specification during operation. H 3. Others (which should be set if necessary) Set value Setting contents N001 Communication EEPROM write selection 0 or 1 0: Write to EEPROM and RAM. 1: Write to RAM only. Pr338 D010 Communication operation command source 0 or 1 0: PLC 1: Outside Pr339 D011 Communication operation command source 0 or 1 0: PLC 1: Outside I Remote Maintenance Pr342 Programming Communication The table below shows parameters to be considered when using various system configuration and inverters. For the method of use, refer to the respective inverter manual. Parameter Parameter Parameter item No. group G Non-Protocol Communication (FX2N-232IF) Pr336 Parameter item F Non-Protocol Communication (RS/RS2 Instruction) 2. Parameters which should be adjusted between test operation and actual operation Inverter Communication Pr549 RS-485 communication speed C Parallel Link 48 Pr332 Common Items 5.8 A Apx.A Discontinued models E-67 FX Series PLC User's Manual - Data Communication Edition 5 Communication Setting in Inverter Inverter Communication 5.8.2 5.8 F800 and A800 Series (when built-in RS-485 terminal is connected) Parameter setting method (reference) This subsection explains the parameter setting method using the operation panel. For details on the operation panel, refer to the respective inverter manual. Hz Operation mode indicator NET : Lit to indicate network operation mode PU EXT NET MODE key Changes over the mode. MODE MON PRM P.RUN SET Monitor (5-digit LED) shows the frequency, parameter number, etc. IM PM ESC FWD REV SET key Sets each setting. PU EXT STOP RESET FR-DU08 Rotation direction key FWD: Lit during forward rotation REV : Lit during reverse rotation Setting dial Used to change the frequency setting and parameter values. The operating procedure example below shows a case in which the baud rate is set to 19200 bps. 1 Confirming the RUN indicator and the operation mode indicator Confirm that the operation is stopped (that the P.RUN indicator is off). 2 Selecting the parameter setting mode Press the MODE key, and select the parameter setting mode. Monitor/frequency setting mode Parameter setting mode MODE 3 The previously read parameter is displayed. Setting the parameter Pr. 160 to "0" (This step is not required if Pr. 160 is already set to "0".) 1. Turn the setting dial until "Pr. 160" is displayed. 2. Press the SET key to read the current set value. SET 3. Turn the setting dial, and change the set value to "0". E-68 FX Series PLC User's Manual - Data Communication Edition 5 Communication Setting in Inverter Inverter Communication 5.9 Cautions on Setting A Common Items Press the SET key to determine the set value. SET B The set value and parameter number are displayed alternately. 4 N:N Network The set value and parameter number are displayed alternately, and the setting is completed. Setting the parameter Pr. 332 to "192" ("192" indicates the baud rate of 19200 bps.) C Turn the setting dial until "Pr. 332" is displayed. Parallel Link D Computer Link Press the SET key to read the current set value. SET E Inverter Communication Turn the setting dial, and change the set value to "192". F Non-Protocol Communication (RS/RS2 Instruction) Press the SET key to determine the set value. SET G The set value and parameter number are displayed alternately. 5 For details on the parameters to be set, refer to Subsection 5.8.1. Cautions on Setting 1. Setting of the "communication check time interval" and "RS-485 communication check time interval" During adjustment or when communication with the PLC is not executed periodically When communication with the PLC is not executed Value shown in table 0 0.1 to 999.8 sec E-69 Apx.A Discontinued models Set the communication time in the following cases: When it is necessary to monitor the absence of communication for a certain time and stop the inverter in such a case while communication with the PLC is being executed When it is necessary to stop the motor at the point which the PLC mode is changed from RUN to STOP Set value I Remote Maintenance Description H Programming Communication 5.9 Change other parameters in the same way as step 4 Non-Protocol Communication (FX2N-232IF) The set value and parameter number are displayed alternately, and the setting is completed. FX Series PLC User's Manual - Data Communication Edition 6 Communication Setting in FX Programmable Controller Inverter Communication 6. 6.1 Parameter Assigning Method Communication Setting in FX Programmable Controller This chapter explains the communication setting method for inverter communication. Set non-protocol communication for inverter communication. 6.1 Parameter Assigning Method Use parameters for communication setting in the FX PLC. 1. Parameter assigning method Register the communication setting in the sequence programming software parameters, and transfer the parameters to the PLC. 2. Setting flow PLC memory Setting window Parameter area Parameter method Transferred when power is turned ON Inverter communication using ch1 D8120 Communication format Program area In FX3G, FX3GC, FX3U and FX3UC Inverter communication using ch2 D8420 Communication format E-70 FX Series PLC User's Manual - Data Communication Edition 6 Communication Setting in FX Programmable Controller Inverter Communication A Communication Setting Using Parameter Method (GX Works2) 6.2.1 Operating procedure 1 Opening the parameter setting window D Computer Link In the project view area of the navigation window, double-click [Parameter] [PLC Parameter]. If the navigation window is not displayed, select [View] [Docking Window] [Navigation] from the menu bar. C Parallel Link This subsection explains the serial communication setting method. Suppose that GX Works2 is already started up. B N:N Network Communication settings may be changed via the parameter method with GX Works2, GX Developer, FXGP/WIN for Windows and FX-30P handy programming panel. This section describes how to change parameters with GX Works2. For details on FXGP/WIN operating procedure, refer to section 6.3. For details on GX Developer operating procedure, refer to GX Developer Operating Manual. For details on FX-30P operating procedure, refer to FX-30P Operation Manual. Common Items 6.2 6.2 Communication Setting Using Parameter Method (GX Works2) E Inverter Communication Setting the serial communication (parameters) Non-Protocol Communication (RS/RS2 Instruction) 2 F Click the [PLC System(2)] tab in the FX Parameter window. G Non-Protocol Communication (FX2N-232IF) H Programming Communication I Remote Maintenance Apx.A Discontinued models E-71 FX Series PLC User's Manual - Data Communication Edition 6 Communication Setting in FX Programmable Controller Inverter Communication 3 6.2 Communication Setting Using Parameter Method (GX Works2) Setting the serial communication (parameters) Set the parameters as shown below: [1] [2] [3] [5] [4] [1] Set the channel to be used. (This parameter can be set only in the FX3G, FX3GC, FX3U and FX3UC PLCs.) [2] Check the "Operate Communication Setting" box. [3] Set "Protocol" to "Non-procedural", "Data Length" to "7Bit", "Parity" to "Even", and "Stop Bit" to "1Bit". [4] Set "Transmission Speed" to either "4800", "9600", "19200" or "38400*1", and make sure that the set value here is the same as the set value in the inverters. [5] Ignore these items. *1. This transmission speed is supported only in FX3S, FX3G, FX3GC, FX3U and FX3UC PLCS. Click [End]. 4 Writing parameters and program to the PLC Select [Online] [Write to PLC] from the menu bar, click [Parameter + Program], and then click [Execute]. E-72 FX Series PLC User's Manual - Data Communication Edition Inverter Communication 6.3 Communication Setting Using Parameter Method (FXGP/WIN) A Communication Setting Using Parameter Method (FXGP/WIN) 6.3.1 Operating procedure 1 Displaying serial setting (parameter) Select [Option] [Serial setting (parameter)] from the toolbar. The following dialog box appears according to absence/presence of parameter setting. C Parallel Link This subsection explains the serial communication setting method. Suppose that FXGP/WIN is already started up. B N:N Network Communication settings may be changed via the parameter method with GX Works2, GX Developer, FXGP/WIN for Windows and FX-30P handy programming panel. This section describes how to change parameters with FXGP/WIN. Ch2 cannot be set using FXGP/WIN. For details on GX Works2 operating procedure, refer to section 6.2. For details on GX Developer operating procedure, refer to GX Developer Operating Manual. For details on FX-30P operating procedure, refer to FX-30P Operation Manual. Common Items 6.3 6 Communication Setting in FX Programmable Controller D Computer Link 1. When there are no parameter settings There are no communication settings. Click the [Yes] button. E Inverter Communication F Non-Protocol Communication (RS/RS2 Instruction) G Non-Protocol Communication (FX2N-232IF) H Programming Communication I Remote Maintenance Apx.A Discontinued models E-73 FX Series PLC User's Manual - Data Communication Edition 6 Communication Setting in FX Programmable Controller Inverter Communication 6.3 Communication Setting Using Parameter Method (FXGP/WIN) 2. When there are already parameter settings The existing communication setting contents are displayed. 2 Adjusting serial setting (parameter) Execute the communication setting as shown below. [1] [2] [3] [1] Set "Protocol" to "RS instruction", "Data bits" to "7", "Parity" to "Even", and "Stop bits" to "1". [2] Set "Transfer speed [bps]" to either "4800", "9600" or "19200", and make sure that the set value here is the same as the set value in the inverters. [3] Ignore these items. 3 Writing a sequence program (parameters) to the PLC Select [PLC] [Transfers] [Write] from the toolbar, and click [OK] button. E-74 FX Series PLC User's Manual - Data Communication Edition 7 Creating Programs (FX2N, FX2NC) Inverter Communication 7.1 Checking Contents of Related Devices A Common Items 7. Creating Programs (FX2N, FX2NC) 7.1 Checking Contents of Related Devices C 1. Bit devices Name Description R/W R M8104 Extension ROM cassette check R Remains ON while an extension ROM cassette is attached. R Remains ON while the communication port is used by an EXTR instruction. R Unused M8155 Communication port busy M8156 Communication error Turns ON when a communication error is caused by an EXTR instruction. or parameter error R M8157 Communication error Turns ON when a communication error occurs. latch*1 R F R: Read only (used as a contact in program) Cleared when the PLC mode is changed from STOP to RUN. 2. Word devices Device No. Name Description R/W Stores the extension ROM cassette type code (value: K1). R D8105 Extension ROM cassette version Stores the extension ROM cassette version. (value: K100 = Ver. 1.00). R D8154 Inverter response waiting time Sets the inverter response waiting time. D8155 Step number of instruction using communication port Stores the step number of the EXTR instruction using the communication port. R D8156 Error code*1 Stores an error code when a communication error is caused by an EXTR instruction. R D8157 Error occurrence step number latch*1 Stores the instruction step number in which a communication error has occurred. (Stores K-1 when no error has occurred.) R R/W *1. H I Remote Maintenance R: Read only W: Write only R/W: Read or Write G Programming Communication Extension ROM cassette type code Non-Protocol Communication (FX2N-232IF) D8104 Non-Protocol Communication (RS/RS2 Instruction) *1. E Inverter Communication M8154 D Computer Link M8029 Turns ON when execution of EXTR instruction is completed, and remains Instruction execution ON for 1 scan. complete Turns ON also when execution of instruction is completed if M8156 (communication error or parameter error) turns ON. Parallel Link The tables below show the devices used in inverter communication in FX2N and FX2NC PLCs. Device No. B N:N Network This chapter explains how to create programs which change inverter parameters and give operation commands to inverters. As explanation, a program example is shown for each applied instruction. Cleared when the PLC mode is changed from STOP to RUN. Apx.A Discontinued models E-75 FX Series PLC User's Manual - Data Communication Edition 7 Creating Programs (FX2N, FX2NC) Inverter Communication 7.2 Common Items in Inverter Communication Instructions 7.2 Common Items in Inverter Communication Instructions 7.2.1 Inverter communication types (EXTR K10 to K13) An FX2N and FX2NC PLC and inverter execute communication using EXTR (FNC180) instruction. EXTR instruction can be described in four types of methods, from "EXTR K10" to "EXTR K13", depending on the data communication direction and parameter writing/reading direction. S S1 FNC180 Function Inverter station number EXTR number S2 S3 Inverter instruction code Read/ Write Only EXTR (16-bit type) is applicable. DEXTR (32-bit type), EXTRP (pulse type) and DEXTRP (32-bit pulse type) are not applicable. Instruction EXTR(FNC180) 7.2.2 Function number (S) Read value storage destination or value written to inverter Function Control direction Detailed explanation K10 Monitors inverter operations PLC inverter 7.3 K11 Controls inverter operations PLC inverter 7.4 K12 Reads inverter parameters PLC inverter 7.5 K13 Writes inverter parameters PLC inverter 7.6 Function and operation 1. Communication start timing At the rising edge (OFFON) of the drive condition, the PLC starts communication with an inverter. Even if the drive condition turns OFF during communication with an inverter, the PLC executes communication until the end. When the drive condition is always ON, the PLC executes communication repeatedly. 2. Simultaneous driving of EXTR instructions and communication processing 1) Driving instructions at the same time - Two or more EXTR functions (K10 to K13) can be programmed, and driven at the same time. - When two or more instructions are driven at the same time during communication, the next EXTR instruction in the program is executed after the current communication with an inverter is finished. M8000 RUN monitor FNC180 EXTR FNC180 EXTR (1) M8155 ONOFF M8155 ONOFF (2) M8155 ONOFF FNC180 EXTR E-76 (3) FX Series PLC User's Manual - Data Communication Edition 7 Creating Programs (FX2N, FX2NC) Inverter Communication 7.2 Common Items in Inverter Communication Instructions M1 FNC180 EXTR ......[1] FNC180 EXTR ......[2] C Parallel Link M0 *1 *2 EXTR instruction [1] (Communicating) D 15ms 15ms M1 *2 E 15ms EXTR instruction [1] 15ms EXTR instruction [2] EXTR instruction [1] EXTR instruction [2] *3 EXTR instruction [1] *3 The PLC does not execute the instruction even if M8155 is turned OFF because the drive contact is OFF. *2. When two or more instructions are driven at the same time during communication, the next EXTR instruction is executed after the current instruction is completed. *3. M8155 remains OFF until the next EXTR instruction is driven after execution of the current EXTR instruction is completed. FNC180 EXTR M8029 M0 Command is latched Communication is executed RST M0 Command is reset I Remote Maintenance SET H Programming Communication X001 G Non-Protocol Communication (FX2N-232IF) 2) Cautions on programming When the drive contact for another EXTR instruction is driven by a pulse signal during communication with an inverter, the communication is not executed. When communicating with inverters for two or more items, let the drive contact for the EXTR instruction remain ON until sending is completed. After communication with all inverters is completed, set the drive contact to OFF using the instruction execution complete flag M8029. F Non-Protocol Communication (RS/RS2 Instruction) *1. Inverter Communication EXTR instruction [2] (Communicating) M0 Computer Link 15ms M8155 B N:N Network M0 A Common Items - The PLC waits for 15 ms after acquiring the communication port, and then starts communication using EXTR instructions. Even if the drive condition turns ON, the PLC does not start execution of the EXTR instruction until the communication port busy flag M8155 turns OFF from ON if M8155 was set to ON by another EXTR instruction. The PLC frees the communication port, and then executes EXTR instructions driven in the next step and so on. Instruction execution complete 3. Communication complete flag (M8029) E-77 Apx.A Discontinued models When communication with an inverter is completed, the instruction execution complete flag M8029 turns ON, and remains ON for 1 scan. For details on using M8029 method, refer to program examples shown below. FX Series PLC User's Manual - Data Communication Edition 7 Creating Programs (FX2N, FX2NC) Inverter Communication 7.2.3 7.2 Common Items in Inverter Communication Instructions Instruction completion and error flag operation When two or more EXTR instructions are programmed, the following flags turn ON or OFF according to the execution result of each EXTR instruction. For acquiring the result of each EXTR instruction, make sure to provide these flags just below each EXTR instruction. Device number Description M8029 Instruction execution complete M8156 Communication error or parameter error D8156 Error code 1. Operation of M8029 (instruction execution complete flag) M8029 (instruction execution complete flag) operates as shown below. In the program below, M0 and M2 turn OFF and M1 turn ON when communication is completed. M0 (OFF) M1 (ON) M2 (OFF) Operation of instruction execution complete flag [1] EXTR instruction is not driven. FNC180 EXTR M8029 : OFF M8029 : ON M8029 : OFF [2] EXTR instruction is driven. FNC180 EXTR [3] EXTR instruction is not driven. FNC180 EXTR 2. Operations of M8156 (error flag) and D8156 (error code) M8156 (error flag) and D8156 (error code) operate as shown below. In the program below, a communication error occurs in [1] and [3], and communication is completed normally in [2]. M8000 RUN monitor Operation of communication error flag M8156 : ON M8156 : OFF D8156: K1 Error code is not changed M8156 : ON D8156: K268 Error code is stored [1] Communication error (no response from inverter) FNC180 EXTR Error code status D8156: K1 Error code is stored [2] Normal communication FNC180 EXTR [3] Communication error (data range error) FNC180 EXTR E-78 FX Series PLC User's Manual - Data Communication Edition 7 Creating Programs (FX2N, FX2NC) Inverter Communication 7.2 Common Items in Inverter Communication Instructions A X000 SET M0 SET M50 Common Items 3. Program examples Start command M0 FNC180 EXTR Communication error M8029 FNC 12 MOV X001 D8156 D50 RST M0 SET M1 SET M51 M50 Error in the 1st instruction D50 C Parallel Link Instruction execution complete N:N Network M8156 B D M1 FNC180 EXTR M8156 Communication error Instruction execution complete M51 E Error in the 2nd instruction FNC 12 MOV D8156 D51 RST M1 Inverter Communication M8029 Computer Link Start command D51 F Non-Protocol Communication (RS/RS2 Instruction) G Non-Protocol Communication (FX2N-232IF) H Programming Communication I Remote Maintenance Apx.A Discontinued models E-79 FX Series PLC User's Manual - Data Communication Edition 7 Creating Programs (FX2N, FX2NC) Inverter Communication 7.2.4 7.2 Common Items in Inverter Communication Instructions Cautions on programming 1. Using the EXTR instruction together with another instruction • The EXTR instruction cannot be used together with the RS instruction. • The EXTR instruction cannot be used together with a EXTR K0 instruction. 2. When programming the EXTR instruction in a state of a STL instruction Make sure to let the state relay remain ON until communication with an inverter is completed. If the state relay is set to OFF during communication, the EXTR instruction is stopped in the middle of execution, and another EXTR instruction cannot be started. Program a sequence while observing the following cautions • Add M8029 (instruction execution complete flag) ON condition to the state relay transfer condition, and provide such an interlock that the state relay ON/OFF status does not change during communication with an inverter. If the state changes during communication, communication may not be performed normally. • When resetting many state relays all at once using ZRST (FNC 40) instruction, etc., make sure that the M8155 (communication port busy) OFF condition is established. X000 SET M0 S0 S999 RST M0 Reset input M0 M8155 Communication port busy FNC 40 ZRST State relays S0 to S999 are reset all at once. 3. Using the EXTR instruction in a program flow The EXTR instruction cannot be used in the following program flows Program flow disabling the EXTR instruction Between CJ and P instructions Between FOR and NEXT instructions Between P and SRET instructions Between I and IRET instructions Remarks Conditional jump Repeat Subroutine Interrupt routine 4. Caution on write during RUN 1) Condition in which the EXTR instruction can be written While the PLC is in the STOP status, the EXTR instruction can be written during RUN. 2) Condition in which the EXTR instruction cannot be written The EXTR instruction cannot be written during RUN. If the EXTR instruction is written during RUN while communication or if the EXTR instruction is deleted in RUN mode, communication may be disabled after that. (In such a case, set the PLC to STOP, and then to RUN mode again to initialize the status.) 5. When using the E500 Series Parameters Nos. 922 and 923 in the E500 Series cannot be used in inverter communication. E-80 FX Series PLC User's Manual - Data Communication Edition 7 Creating Programs (FX2N, FX2NC) 7.3 Inverter Operation Monitoring Instruction (PLCInverter) [EXTR K10] Inverter Communication Inverter Operation Monitoring Instruction (PLCInverter) [EXTR K10] EXTR K10 instruction reads the operation status of an inverter to the PLC. 7.3.1 Function and operation B 1. Applicable devices Bit device Word device X Y M T System/ User Digit specification C S KnX KnY KnM KnS T C D Index V Z Constant Pointer Modification S K H S2 D D Computer Link S1 P 2. Program example M0 S1 S2 D K10 K6 H6F D100 Command contact Function number: K10 Inverter station number: 0 to 31 7.3.2 E Inverter Communication FNC180 EXTR S Read value storage destination Inverter instruction code (hexadecimal) F Inverter instruction codes Applicable inverter S2 Read contents Operation mode H6F Output frequency [speed] H70 Output current H71 Output voltage — H72 Special monitor — — H73 Special monitor selection No. — — H74 Alarm definition H75 Alarm definition H76 Alarm definition — H77 Alarm definition — H7A Inverter status monitor H7B Set frequency read (E2PROM) Set frequency read (RAM) H7F Link parameter expansion setting H6C Second parameter changing These codes cannot be specified in S2 in EXTR K10 instruction. They are automatically processed when a "second parameter specification code" is specified in EXTR K12 instruction. E-81 H I Apx.A Discontinued models H6E H6D G Remote Maintenance S500 Programming Communication E500 Non-Protocol Communication (FX2N-232IF) A500 Non-Protocol Communication (RS/RS2 Instruction) The table below shows inverter instruction codes which can be specified in S2 . For the instruction codes, refer to the pages explaining computer link in detail in each inverter manual. Inverter instruction code (hexadecimal) C Parallel Link System/User Others N:N Network When an "instruction code" specified for computer link operation in inverters is specified in EXTR instruction, a value in the inverter is read to D . Operand type Common Items 7.3 A FX Series PLC User's Manual - Data Communication Edition 7 Creating Programs (FX2N, FX2NC) 7.4 Inverter Operation Control Instruction (PLCInverter) [EXTR K11] Inverter Communication 7.4 Inverter Operation Control Instruction (PLCInverter) [EXTR K11] This instruction writes a control value required to operate an inverter from the PLC to the inverter. 7.4.1 Function and operation When an "instruction code" specified for computer link operation in inverters is specified in EXTR instruction, a value specified in S3 is written to the specified item in the inverter. 1. Applicable devices Bit device Operand type Word device System/User X Y M T System/ User Digit specification C Others S KnX KnY KnM KnS T C D Index V Z Constant Pointer Modification S K H S1 S2 S3 P 2. Program example S M0 S1 FNC180 EXTR K11 K6 Command contact Function number: K11 Inverter station number: 0 to 31 7.4.2 S2 S3 HFA K2M50 Value written to inverter Inverter instruction code (hexadecimal) Inverter instruction codes The table below shows inverter instruction codes which can be specified in S2 . For the instruction codes, refer to the pages explaining computer link in detail in each inverter manual. Applicable inverter S2 Read contents Inverter instruction code (hexadecimal) E-82 E500 S500 HFB Operation mode HF3 Special monitor selection No. — — HFA Run command HEE Set frequency write (EEPROM) HED Set frequency write (RAM) Inverter reset HFD*1 *1. A500 HF4 Alarm definition batch clear HFC Parameter all clear HFC User clear — — The instruction code "HFD (inverter reset)" does not request response from the inverter. Accordingly, even if inverter reset is executed to a station number in which an inverter is not connected, error does not occur. It takes about 2.2 seconds to complete execution of inverter reset. FX Series PLC User's Manual - Data Communication Edition 7 Creating Programs (FX2N, FX2NC) 7.5 Inverter Parameter Reading Instruction (PLCInverter) [EXTR K12] Inverter Communication Inverter Parameter Reading Instruction (PLCInverter) [EXTR K12] Common Items 7.5 A This instruction reads a parameter of an inverter to the PLC. 7.5.1 Function and operation B 1. Applicable devices Bit device System/User X Y M T System/ User Digit specification C Others S KnX KnY KnM KnS T C D Index V Z Constant Pointer Modification S K H S2 D D Computer Link S1 P 2. Program example M0 S1 S2 D K12 K6 K7 D150 Command contact Function number: K12 Inverter station number: 0 to 31 7.5.2 E Inverter Communication FNC180 EXTR S Read value storage destination Inverter parameter number (decimal) F Inverter parameter number Non-Protocol Communication (RS/RS2 Instruction) Refer to related data shown later. 7.5.3 Program example of "second parameter specification code" SET M0 H X001 Drive contact FNC180 EXTR S S1 S2 S3 K12 K6 K2201 D100 Programming Communication M0 G Non-Protocol Communication (FX2N-232IF) In the program example shown below, the parameter number 201 (frequency: 201, time: 1201, motor rotation direction: 2201) is read from the A500 inverter whose station number is 6. Read devices: D100 = Motor rotation direction, D101 = Frequency, D102 = Time Read command C Parallel Link Operand type Word device N:N Network When a parameter number of an inverter is specified in EXTR instruction, the value of the parameter in the inverter is read to D . Motor rotation directionD100 Read value storage destination Function number Inverter station number: 0 to 31 Inverter parameter number (decimal) K12 K6 K201 D101 FNC180 EXTR K12 K6 K1201 D102 I FrequencyD101 Remote Maintenance FNC180 EXTR TimeD102 The unit is specified by Pr. 200. Apx.A M8029 M0 Discontinued models RST Execution complete flag E-83 FX Series PLC User's Manual - Data Communication Edition 7 Creating Programs (FX2N, FX2NC) 7.6 Inverter Parameter Writing Instruction (PLCInverter) [EXTR K13] Inverter Communication 7.6 Inverter Parameter Writing Instruction (PLCInverter) [EXTR K13] This instruction writes a value from the PLC to a parameter in an inverter. 7.6.1 Function and operation When a parameter number in an inverter is specified in EXTR instruction, the value of specified item in the inverter. is written to the S3 1. Applicable devices Bit device Operand type Word device System/User X Y M T System/ User Digit specification C Others S KnX KnY KnM KnS T C D Index V Z Constant Pointer Modification S K H S1 S2 S3 P 2. Program example S S1 S2 S3 K13 K6 Command contact Function number: K13 Inverter station number: 0 to 31 K7 D160 M0 7.6.2 FNC180 EXTR Value written to inverter Inverter parameter number (decimal) Inverter parameter number Refer to related data shown later. 7.6.3 Program example of "second parameter specification code" In the program example shown below, data is written from the PLC to parameter number 201 (frequency: 201, time: 1201, motor rotation direction: 2201) in the A500 inverter. X001 Write command M0 Drive contact FNC180 EXTR SET M0 S S1 S2 S3 K13 K6 K2201 H1 Function number: K13 Inverter station number: 0 to 31 Value written to inverter Inverter parameter number (decimal) FNC180 EXTR K13 K6 K201 H14 FNC180 EXTR K13 K6 K1201 H100 RST Execution complete flag Frequency: 20Hz Time: 1:00 The unit is specified by Pr. 200. M8029 E-84 Motor rotation direction: Forward M0 FX Series PLC User's Manual - Data Communication Edition 7 Creating Programs (FX2N, FX2NC) Inverter Communication A Second Parameter Specification Codes 7.7.1 S500 Series 1. Second parameter specification codes for parameter numbers C2 to C7 Name [Value to be specified in S2 in EXTR instruction for parameter No. (decimal)] Frequency setting voltage bias frequency 902 C3 Frequency setting voltage bias 1902 C4 Frequency setting voltage gain 903 C5 Frequency setting current bias frequency 904 C6 Frequency setting current bias 1904 C7 Frequency setting current gain 905 D Computer Link C2 E E500 Series Second parameter specification code Name [Value to be specified in S2 in EXTR instruction for parameter No. (decimal)] Analog (H01) Terminal analog value (H02) 902 Frequency setting voltage bias 902 1902 2902 903 Frequency setting voltage gain 903 1903 2903 904 Frequency setting current bias 904 1904 2904 905 Frequency setting current gain 905 1905 2905 F Non-Protocol Communication (RS/RS2 Instruction) Offset/Gain (H00) Inverter Communication 1. Second parameter specification codes for parameter numbers 902 to 905 Parameter No. Parallel Link 7.7.2 C Second parameter specification code Parameter No. B N:N Network When handling the following parameters in computer link operation, it is necessary to select second parameters. In EXTR K12 and EXTR K13 instructions, when a value shown in the tables below is set to S2 , the extension parameter and second parameter are automatically overwritten, and the parameter values are then read or written. Common Items 7.7 7.7 Second Parameter Specification Codes G Non-Protocol Communication (FX2N-232IF) H Programming Communication I Remote Maintenance Apx.A Discontinued models E-85 FX Series PLC User's Manual - Data Communication Edition 7 Creating Programs (FX2N, FX2NC) Inverter Communication 7.7.3 7.7 Second Parameter Specification Codes A500 Series 1. Second parameter specification codes for parameter numbers 201 to 230 Second parameter specification code Parameter No. [Value to be specified in S2 in EXTR instruction for parameter No. (decimal)] Name Operation frequency read/write Time read/write Rotation direction write/read 201 Program set 1 201 1201 2201 202 Program set 1 202 1202 2202 203 Program set 1 203 1203 2203 204 Program set 1 204 1204 2204 205 Program set 1 205 1205 2205 206 Program set 1 206 1206 2206 207 Program set 1 207 1207 2207 208 Program set 1 208 1208 2208 209 Program set 1 209 1209 2209 210 Program set 1 210 1210 2210 211 Program set 2 211 1211 2211 212 Program set 2 212 1212 2212 213 Program set 2 213 1213 2213 214 Program set 2 214 1214 2214 215 Program set 2 215 1215 2215 216 Program set 2 216 1216 2216 217 Program set 2 217 1217 2217 218 Program set 2 218 1218 2218 219 Program set 2 219 1219 2219 220 Program set 2 220 1220 2220 221 Program set 3 221 1221 2221 222 Program set 3 222 1222 2222 223 Program set 3 223 1223 2223 224 Program set 3 224 1224 2224 225 Program set 3 225 1225 2225 226 Program set 3 226 1226 2226 227 Program set 3 227 1227 2227 228 Program set 3 228 1228 2228 229 Program set 3 229 1229 2229 230 Program set 3 230 1230 2230 2. Second parameter specification codes for parameter numbers 902 to 905 Second parameter specification code Parameter No. E-86 Name [Value to be specified in S2 in EXTR instruction for parameter No. (decimal)] Offset/Gain (H00) Analog (H01) Terminal analog value (H02) 902 Frequency setting voltage bias 902 1902 2902 903 Frequency setting voltage gain 903 1903 2903 904 Frequency setting current bias 904 1904 2904 905 Frequency setting current gain 905 1905 2905 FX Series PLC User's Manual - Data Communication Edition 8 Practical Program Examples (FX2N, FX2NC) Inverter Communication 8.1 Practical Example 1 A Common Items 8. Practical Program Examples (FX2N, FX2NC) B This chapter explains practical programs for inverter communication. N:N Network 8.1 Practical Example 1 This fundamental program example monitors operations of an inverter, controls operations of an inverter and writes parameters to an inverter. Parallel Link 8.1.1 System configuration example An FX PLC is connected to an inverter. FX2N, FX2NC Inverter D Computer Link System memory Terminal resistor E Distributor Contents of operation F Non-Protocol Communication (RS/RS2 Instruction) As an example of operation control, an inverter can be stopped (X000), rotated forward (X001) and rotated reverse (X002). By changing the contents of D10, the speed can be changed. The contents of D10 can be changed from a sequence program or display unit. Inverter Communication 8.1.2 C G Non-Protocol Communication (FX2N-232IF) H Programming Communication I Remote Maintenance Apx.A Discontinued models E-87 FX Series PLC User's Manual - Data Communication Edition 8 Practical Program Examples (FX2N, FX2NC) Inverter Communication 8.1.3 8.1 Practical Example 1 Program example 1. Writing parameters to an inverter while the PLC is in RUN mode M8002 SET Initial pulse The write instruction is driven M10 Driving of write instruction FNC180 EXTR K11 K0 H0FD H9696 The inverter is reset FNC180 EXTR K11 K0 H0FB H0*1 Computer link operation is specified FNC180 EXTR K13 K0 K1 K12000 The maximum frequency is set to "120 Hz" FNC180 EXTR K13 K0 K2 K500 The minimum frequency is set to "5 Hz" FNC180 EXTR K13 K0 K7 K10 The acceleration time is set to "1 s" FNC180 EXTR K13 K0 K8 K10 The deceleration time is set to "1 s" RST M10 M8029 Instruction execute complete *1. M10 The write instruction is driven When using an E500 Series inverter, use "H2" to specify computer link operation. 2. Changing the speed using a sequence program M8000 FNC 12 K6000 MOV P RUN monitor D10 Operation speed M17 FNC 12 K4000 MOV P Command for switching to speed 1 FNC 12 K2000 MOV P Command for switching to speed 2 D10 The operation speed is written as "20 Hz" Operation speed K11 K0 H0ED D10 Operation speed E-88 The operation speed is written as "40 Hz" Operation speed M18 FNC180 EXTR D10 "60 Hz" is written as the initial value at startup The preset frequency is written to the inverter FX Series PLC User's Manual - Data Communication Edition 8 Practical Program Examples (FX2N, FX2NC) Inverter Communication 8.1 Practical Example 1 A X000 SET Operation stop command input H0FA is set to "00H" Operation stop X000 RST Forward Operation stop rotation command input command input X002 M15 B Operation stop is reset by input X001 or X002 N:N Network X001 M15 Common Items 3. Controlling operations of an inverter Operation stop C M15 Operation stop X001 X002 M21 Forward Reverse rotation rotation command input command input X002 X001 M22 D b2 of H0FA is set to ON Reverse rotation command K11 K0 H0FA K2M20 Operation command is written M27 to M20H0FA Computer Link RUN monitor FNC180 EXTR b1 of H0FA is set to ON Forward rotation command Reverse Forward rotation rotation command input command input M8000 Parallel Link Reverse rotation command input E Inverter Communication F Non-Protocol Communication (RS/RS2 Instruction) G Non-Protocol Communication (FX2N-232IF) H Programming Communication I Remote Maintenance Apx.A Discontinued models E-89 FX Series PLC User's Manual - Data Communication Edition 8 Practical Program Examples (FX2N, FX2NC) Inverter Communication 8.1 Practical Example 1 4. Monitoring operations of an inverter M8000 FNC180 EXTR RUN monitor K10 K0 H07A K2M100 Inverter running M100 Y000 Inverter running Indicator lamp, etc. M101 Y001 Forward rotation Indicator lamp, etc. M102 Y002 Reverse rotation Indicator lamp, etc. M103 Y003 Up to frequency Indicator lamp, etc. M104 Contents of status (according to necessity) Y004 Overload is applied Indicator lamp, etc. M106 Y006 Frequency is detected Indicator lamp, etc. M107 Y007 Alarm occurrence Indicator lamp, etc. FNC180 EXTR K10 K0 H06F D50 Frequency monitor value END E-90 Inverter status is read H7AM107 to M100 Output frequency monitor FX Series PLC User's Manual - Data Communication Edition 8 Practical Program Examples (FX2N, FX2NC) Inverter Communication A Practical Example 2 Common Items 8.2 8.2 Practical Example 2 This program executes the same control as practical example 1 shown above. 8.2.1 System configuration example B FX2N, FX2NC N:N Network An FX PLC is connected to an inverter. Inverter C Parallel Link System memory Terminal resistor Distributor 8.2.2 D The differences from practical example 1 are that the inverter status is not read while data is written to an inverter, and that the contents to be written are detected and written to an inverter only when the contents to be written are changed. Because communication between the PLC and the inverter is minimum in this program, the communication time is reduced and the response time is improved. E Computer Link Contents of operation Inverter Communication F Non-Protocol Communication (RS/RS2 Instruction) G Non-Protocol Communication (FX2N-232IF) H Programming Communication I Remote Maintenance Apx.A Discontinued models E-91 FX Series PLC User's Manual - Data Communication Edition 8 Practical Program Examples (FX2N, FX2NC) Inverter Communication 8.2.3 8.2 Practical Example 2 Program example 1. Writing parameters to an inverter while the PLC is in RUN mode M8002 SET Initial pulse M10 The write instruction is driven M10 Driving of write instruction FNC180 EXTR K11 K0 H0FD H9696 FNC180 EXTR K11 K0 H0FB H0*1 FNC180 EXTR K13 K0 K1 K12000 The maximum frequency is set to "120Hz" FNC180 EXTR K13 K0 K2 K500 The minimum frequency is set to "5Hz" FNC180 EXTR K13 K0 K7 K10 The acceleration time is set to "1s" FNC180 EXTR K13 K0 K8 K10 The deceleration time is set to "1s" RST M10 M8029 Instruction execute complete *1. E-92 The inverter is reset Computer link operation is specified The write instruction is driven When using an E500 Series inverter, use "H2" to specify computer link operation. FX Series PLC User's Manual - Data Communication Edition 8 Practical Program Examples (FX2N, FX2NC) Inverter Communication 8.2 Practical Example 2 A M8000 FNC 12 K6000 MOV P RUN monitor D10 Operation speed FNC 12 K4000 MOV P Command for switching to speed 1 FNC 12 K2000 MOV P Command for switching to speed 2 D10 D10 C D80 Operation Operation speed speed is withdrawn SET FNC180 EXTR K11 M11 Change in the operation speed (D10) is detected D Computer Link D80 Operation Operation speed is speed withdrawn The write instruction is driven The operation speed is written as "20 Hz" Parallel Link FNC 12 MOV Initial pulse M11 The operation speed is written as "40 Hz" Operation speed M8002 D10 B Operation speed M18 FNC228 LD<> D10 "60 Hz" is written as the initial value at startup N:N Network M17 Common Items 2. Changing the speed using a sequence program The write instruction is driven K0 H0ED D10 The preset frequency is written to the inverter E M8029 Instruction execute complete RST Inverter Communication Operation speed M11 The write instruction is driven F Non-Protocol Communication (RS/RS2 Instruction) G Non-Protocol Communication (FX2N-232IF) H Programming Communication I Remote Maintenance Apx.A Discontinued models E-93 FX Series PLC User's Manual - Data Communication Edition 8 Practical Program Examples (FX2N, FX2NC) Inverter Communication 8.2 Practical Example 2 3. Controlling operations of an inverter X000 SET M15 Operation stop command input X001 H0FA is set to "00H" Operation stop X000 RST M15 Forward Operation stop rotation command input command input X002 Operation stop is reset by input X001 or X002 Operation stop Reverse rotation command input M15 X001 X002 Operation stop Forward rotation command input X002 Reverse rotation command input X001 Forward rotation command Forward rotation command input Reverse rotation command Reverse rotation command input M8002 M21 M22 FNC 12 K2M20 MOV Initial pulse D81 SET Operation command is withdrawn M12 M8029 Instruction execute complete E-94 Changes in the operation commands (M28 to M20) are detected M12 Driving of write instruction FNC180 EXTR Driving of write instruction b2 of H0FA is set to ON D81 Operation command is withdrawn FNC228 LD<> K2M20 b1 of H0FA is set to ON K11 K0 H0FA K2M20 RST M12 Driving of write instruction Operation commands are written M27 to M20H0FA FX Series PLC User's Manual - Data Communication Edition 8 Practical Program Examples (FX2N, FX2NC) Inverter Communication 8.2 Practical Example 2 A M10 M11 M12 MC N0 M70 Driving of Driving of Driving of write write write instruction instruction instruction While data is not written to an inverter, the status is read. B N:N Network N0 Common Items 4. Monitoring operations of an inverter M70 M8000 FNC180 EXTR RUN monitor K10 K0 H07A K2M100 C Inverter status is read. H07AM107 to M100 M100 Parallel Link Inverter running Y000 Inverter running Indicator lamp, etc. M101 D Forward rotation Computer Link Y001 Indicator lamp, etc. M102 Y002 Reverse rotation E Indicator lamp, etc. Y003 Up to frequency Inverter Communication M103 Contents of status (according to necessity) Indicator lamp, etc. M104 F Y004 Overload is applied M106 Non-Protocol Communication (RS/RS2 Instruction) Indicator lamp, etc. Y006 Frequency is detected Indicator lamp, etc. M107 G Alarm occurrence Non-Protocol Communication (FX2N-232IF) Y007 Indicator lamp, etc. FNC180 EXTR K10 K0 H06F D50 Output frequency monitor H MCR Programming Communication Frequency monitor value N0 END I Remote Maintenance Apx.A Discontinued models E-95 FX Series PLC User's Manual - Data Communication Edition Inverter Communication 9. 9 Creating Programs (FX3S, FX3G, FX3GC, FX3U, FX3UC) 9.1 Differences between FX2N, FX2NC and FX3S, FX3G, FX3GC, FX3U, FX3UC Creating Programs (FX3S, FX3G, FX3GC, FX3U, FX3UC) This chapter explains how to create programs which change parameters of inverters and give operation commands to inverters. As explanation, a program example is shown for each applied instruction. 9.1 Differences between FX2N, FX2NC and FX3S, FX3G, FX3GC, FX3U, FX3UC Instruction devices used in inverter communication are different between FX3S, FX3G, FX3GC, FX3U, FX3UC PLCs and FX2N, FX2NC PLCs. When using a program for FX2N, FX2NC PLCs in FX3S, FX3G, FX3GC, FX3U, FX3UC PLCs, change the devices according to the tables below. 1. Inverter communication instructions Function FX2N,FX2NC FX3S,FX3G,FX3GC,FX3U,FX3UC Monitoring operation of an inverter EXTR(K10) IVCK Controlling operation of an inverter EXTR(K11) IVDR Reading parameters from an inverter EXTR(K12) IVRD Writing parameters to an inverter EXTR(K13) IVWR Writing parameters to an inverter all at once — IVBWR*1 Controls operations and monitors operations of an inverter with a single command — IVMC *1. Only available for FX3U and FX3UC PLCs. 2. Related devices 1) Bit devices Function FX2N,FX2NC FX3S,FX3G,FX3GC,FX3U,FX3UC ch1 ch2 Instruction execution complete M8029 M8029 M8029 Communication error (shared by all communication) M8063*2 M8063*5 M8438*5 M8155 M8151 M8156 Inverter communication error M8156 M8152*3 M8157*3 Inverter communication error latch*3 M8157 M8153 M8158 — M8154*3 M8159*3 Inverter communicating IVBWR instruction error*4 *2. In the FX2N and FX2NC PLCs, M8063 does not turn ON when an inverter communication error occurs. *3. Cleared when the PLC mode is changed from STOP to RUN. *4. The IVBWR instruction is supported only in FX3U and FX3UC PLCs. *5. Cleared when PLC power supply is turned from OFF to ON. 2) Word devices Function ch1 ch2 D8063 D8063*6 D8438*6 Response wait time of inverter communication D8154 D8150*6 D8155*6 Step number of instruction during inverter communication D8155 D8151 D8156 Inverter communication error code*7 D8156 D8152 D8157 Inverter communication error occurrence step*7 D8157 D8153 D8158 IVBWR instruction error parameter E-96 FX3S,FX3G,FX3GC,FX3U,FX3UC Error code (shared by all communication) Operation mode display *6. *7. *8. FX2N,FX2NC number*7*8 — D8154 D8159 — D8419 D8439 Cleared when PLC power supply is turned from OFF to ON. Cleared when the PLC mode is changed from STOP to RUN. The IVBWR instruction is supported only in FX3U and FX3UC PLCs. FX Series PLC User's Manual - Data Communication Edition 9 Creating Programs (FX3S, FX3G, FX3GC, FX3U, FX3UC) Inverter Communication A Contents of Related Devices The tables below show devices used for inverter communication in FX3S, FX3G, FX3GC, FX3U and FX3UC PLCs. B 1. Bit devices Name Turns ON when execution of inverter communication instruction is completed, and remains ON for 1 scan. Turns ON also when execution of instruction is completed if inverter communication error flag (M8152 or M8157) turns ON. R M8063 M8438 Serial communication error*1 Turns ON when an error occurs in any type of communication. R M8151 M8156 Inverter communicating Remains ON while inverter communication is being executed. R M8152 M8157 Inverter communication error*2 Turns ON when an error occurs during communication with an inverter. R M8153 M8158 Inverter communication error latch*2 Turns ON when an error occurs during communication with an inverter. R M8154 M8159 IVBWR instruction error*2, *3 Turns ON when an error is caused by IVBWR instruction. R M8029 Instruction execution complete *2. Cleared when the PLC mode is changed from STOP to RUN. *3. The IVBWR instruction is supported only in FX3U and FX3UC PLCs. Inverter Communication Cleared when PLC power supply is turned from OFF to ON. F 2. Word devices Name ch2 Description D8063 D8438 Error code for serial communication*4 Stores a communication error code. R/W R D8151 D8156 Step number of instruction executing Stores the step number of an instruction during inverter communication inverter communication. R D8152 D8157 Error code for inverter communication*5 Stores an inverter communication error code. R Step where inverter communication Latches a step number in which inverter error occurred*5 communication error has occurred.*7 Error parameter number of IVBWR instruction*5*6 Stores a parameter number in which an IVBWR instruction error has occurred. R Stores the communication type being used. R D8153 D8158 D8154 D8159 D8419 D8439 Operation mode display Sets the response wait time of inverter communication. R/W R R: Read only W: Write only R/W: Read or Write Cleared when PLC power supply is turned from OFF to ON. *5. Cleared when the PLC mode is changed from STOP to RUN. *6. The IVBWR instruction is supported only in FX3U and FX3UC PLCs. *7. Updated only for the first error occurrence, and not for the second error occurrence or later. H I Remote Maintenance *4. G Programming Communication Inverter communication response waiting time*4 Non-Protocol Communication (FX2N-232IF) D8150 D8155 Non-Protocol Communication (RS/RS2 Instruction) Device No. ch1 D E R: Read only (used as a contact in program) *1. C Computer Link R/W Parallel Link Description ch2 N:N Network Device No. ch1 Common Items 9.2 9.2 Contents of Related Devices Apx.A Discontinued models E-97 FX Series PLC User's Manual - Data Communication Edition 9 Creating Programs (FX3S, FX3G, FX3GC, FX3U, FX3UC) Inverter Communication 9.3 Common Items in Inverter Communication Instructions 9.3 Common Items in Inverter Communication Instructions 9.3.1 Inverter communication types (IVCK to IVMC) Execute inverter communication using the following applied instructions. There are six types of applied instructions, "IVCK (FNC270) to IVMC (FNC275)", depending on the data communication direction and parameter reading/writing direction. Inverter communication instruction S1 S2 S3 n Inverter station number Inverter instruction code Read/ Write Used channel Only 16-bit type is applicable. DIVCK (32-bit type), IVCKP (pulse operation type) and DIVCKP (32-bit pulse operation type) are not applicable. Instruction Function Control direction Detailed explanation IVCK(FNC270) Monitors operations of an inverter. PLC inverter 9.4 IVDR(FNC271) Controls operations of an inverter. PLC inverter 9.5 IVRD(FNC272) Reads a parameter from an inverter. PLC inverter 9.6 Writes a parameter to an inverter. PLC inverter 9.7 IVBWR(FNC274) Writes parameters to an inverter all at once. PLC inverter 9.8 IVMC(FNC275) Controls operations and monitors operations of an inverter with a single command PLC inverter 9.9 IVWR(FNC273) *1 *1. 9.3.2 K1:ch1 K2:ch2 Read value storage destination or value written to inverter Only available for FX3U and FX3UC PLCs. Function and operation 1. Communication start timing At the rising edge (OFFON) of the drive condition, the PLC starts communication with an inverter. Even if the drive condition turns OFF during communication with an inverter, the PLC executes communication until the last instruction. When the drive condition is always ON, the PLC executes communication repeatedly. 2. Simultaneous driving of instructions and communication processing 1) Driving instructions at the same time - Two or more IVCK (FNC270) to IVMC (FNC275) instructions can be programmed, and driven at the same time. - When two or more instructions are driven at the same time in the channel used for communication, the latter inverter communication instruction in the program is executed after the current communication with the inverter has finished. M8000 RUN monitor FNC273 IVWR FNC271 IVDR (1) M8151 ONOFF (2) M8151 ONOFF FNC270 IVCK E-98 (3) FX Series PLC User's Manual - Data Communication Edition 9 Creating Programs (FX3S, FX3G, FX3GC, FX3U, FX3UC) Inverter Communication 9.3 Common Items in Inverter Communication Instructions M1 FNC273 IVWR FNC270 IVCK C Parallel Link M0 *2 *1 IVWR instruction (Communicating) D 15ms 15ms M1 *2 E 15ms IVWR 15ms IVCK IVWR IVCK *3 IVWR *3 The PLC does not execute the instruction even if M8151 is turned OFF because the drive contact is OFF. *2. When two or more instructions are driven at the same time during communication, the next inverter communication instruction is executed after the current instruction is completed. *3. M8151 remains OFF until the next inverter communication instruction is driven after execution of the current inverter communication instruction is completed. X001 M8029 Command is latched Communication is executed RST M0 Command is reset H I 3. Communication complete flag (M8029) When communication with an inverter is completed, the instruction execution complete flag M8029 turns ON, and remains ON for 1 scan. For the M8029 use method, refer to program examples shown below. Remote Maintenance Instruction execution complete M0 Programming Communication FNC274 IVCK SET G Non-Protocol Communication (FX2N-232IF) 2) Cautions on programming When communicating with inverters for two or more items, let the drive contact for inverter communication instruction remain ON until sending is completed. After communication with all inverters is completed, set the drive contact to OFF using the instruction execution complete flag M8029. F Non-Protocol Communication (RS/RS2 Instruction) *1. Inverter Communication IVCK instruction (Communicating) M0 Computer Link 15ms M8151 B N:N Network M0 A Common Items - The PLC waits for 15 ms after acquiring the communication port, and then starts communication using inverter communication instructions. Even if the drive condition turns ON, the PLC does not start execution of an inverter communication instruction until the communication port busy flag M8151 turns OFF from ON, if M8151 is already set to ON by another inverter communication instruction. The PLC frees the communication port, and then executes inverter communication instructions driven in the next step and so on. Apx.A Discontinued models E-99 FX Series PLC User's Manual - Data Communication Edition 9 Creating Programs (FX3S, FX3G, FX3GC, FX3U, FX3UC) Inverter Communication 9.3.3 9.3 Common Items in Inverter Communication Instructions Instruction completion and error flag operation When two or more inverter communication instructions are programmed, the following flags turn ON or OFF according to the execution result of each inverter communication instruction. To acquire the result of each inverter communication instruction, make sure to provide these flags just below each inverter communication instruction. Device number ch1 Device number Description ch2 M8029 ch1 Instruction execution complete Description ch2 D8063 D8438 Serial communication error code M8063 M8438 Serial communication error D8152 D8157 Inverter communication error code M8152 M8157 Inverter communication error D8153 D8158 Step in which inverter communication error occurred Inverter communication error M8153 M8158 latch D8154 D8159 IVBWR error parameter number*1 M8154 M8159 IVBWR instruction error*1 The IVBWR instruction is supported only in FX3U and FX3UC PLCs. *1. 1. Operation of M8029 (instruction execution complete flag) The operation of M8029 (instruction execution complete flag) represents the state in which the IVDR instruction is completed while M0, M2 are off and M1 is ON. M0 (OFF) M1 (ON) M2 (OFF) Operation of instruction execution complete flag [1] IVWR instruction is not driven FNC273 IVWR M8029 : OFF M8029 : ON M8029 : OFF [2] IVDR instruction is driven FNC271 IVDR [3] IVCK instruction is not driven FNC270 IVCK 2. Processing of communication errors The following two types of processing are executed for communication errors. The parity error/overrun error/framing error flags (shown in the upper column) turns ON when an error occurs in any type of communication. The error flag shown in the lower column turns ON when an error occurs during communication with an inverter. Bit device ch1 ch2 ch1 ch2 Word device ch1 ch2 M8063 M8438 M8152 M8157 M8153 M8159 ch1 ch2 Description D8063 D8438 ON OFF OFF 6301 3801 Parity error, overrun error or framing error ON ON ON (only at first time) 6320 3820 Any inverter communication error other than those above When inverter communication error flag turns ON, the step number is stored in the inverter communication error occurrence step device (D8153 or D8158). Create the program shown below for each corresponding instruction to check the inverter communication error code (stored in D8152 or D8157). E-100 FX Series PLC User's Manual - Data Communication Edition 9 Creating Programs (FX3S, FX3G, FX3GC, FX3U, FX3UC) Inverter Communication 9.3 Common Items in Inverter Communication Instructions A X000 SET M0 K1 SET M50 Common Items 3. Program example Start command M0 FNC277 IVWR Communication error M8029 Instruction execution complete FNC 12 MOV N:N Network M8152 B M50 Instruction error is checked D50 RST M0 D50 C Parallel Link D8152 D Computer Link E Inverter Communication F Non-Protocol Communication (RS/RS2 Instruction) G Non-Protocol Communication (FX2N-232IF) H Programming Communication I Remote Maintenance Apx.A Discontinued models E-101 FX Series PLC User's Manual - Data Communication Edition 9 Creating Programs (FX3S, FX3G, FX3GC, FX3U, FX3UC) Inverter Communication 9.3.4 9.3 Common Items in Inverter Communication Instructions Cautions on programming 1. Using an inverter communication instruction together with another instruction • An inverter communication instruction using ch1 cannot be used together with a RS instruction. • An inverter communication instruction cannot be used together with a RS2 instruction if the RS2 instruction uses the same channel. 2. When programming an inverter communication instruction in a state of a STL instruction Make sure to let the state relay remain ON until communication with an inverter is completed. Program a sequence while observing the following cautions • Add M8029 (instruction execution complete flag) ON condition to the state relay transfer condition, and provide such interlock that the state relay ON/OFF status does not change during communication with an inverter. If the state changes during communication, communication may not be performed normally. • When resetting many state relays all at once using the ZRST (FNC 40) instruction, etc., make sure that the M8151 or M8156 (communication port busy) condition is OFF. X000 SET M0 S0 S999 RST M0 Reset input M0 M8151 Communication port busy FNC 40 ZRST State relays S0 to S999 are reset all at once. 3. Using an inverter communication instruction in a program flow An inverter communication instruction cannot be used in the following program flows Program flow disabling the inverter communication instruction Between CJ and P instructions Between FOR and NEXT instructions Between P and SRET instructions Between I and IRET instructions Remarks Conditional jump Repeat Subroutine Interrupt routine 4. Caution on writing during RUN 1) Condition in which inverter communication instruction can be written: While the PLC is in the STOP status, inverter communication instruction can be written during RUN. 2) Condition in which inverter communication instruction cannot be written: Inverter communication instruction cannot be written during RUN. If an inverter communication instruction is written during RUN during communication or if an inverter communication instruction is deleted while in RUN, communication may be disabled after that. (In such a case, set the PLC to STOP, and then to RUN mode again to initialize the status.) 5. When using the E500 Series Parameters Nos. 922 and 923 in the E500 Series cannot be used in inverter communication. E-102 FX Series PLC User's Manual - Data Communication Edition 9 Creating Programs (FX3S, FX3G, FX3GC, FX3U, FX3UC) Inverter Communication 9.3 Common Items in Inverter Communication Instructions A The FX PLC executes the first communication, and then retries communication twice (3 time in total). *2. When "display of the number of times of password disable error" is enabled using Pr297 and when a password disable error occurs 5 times, the "reading/writing restriction" cannot be disabled even if the right password is input. For recovery from this status, it is necessary to all-clear all parameters. When the value given as a result of reading Pr297 is "0" to "4", registration of the password is completed normally. F Non-Protocol Communication (RS/RS2 Instruction) *3. E Inverter Communication *1. D Computer Link 2) When registering the password When registering the password in the inverter using an inverter communication instruction, write the password to Pr297, read Pr297, and then confirm that registration of the password is completed normally*3. If writing of the password to Pr297 is not completed normally due to noise, etc., the FX PLC automatically retries writing, and the registered password may be reset by the retry. C Parallel Link Cases in which a password reset error occurs in an inverter communication instruction, and the actual number of times of reset error in such cases - When a wrong password is written to Pr297 due to a password input error When the writing instruction is executed once, a password reset error occurs 3 times. - When the password cannot be written correctly to Pr297 due to noise, etc. A password reset error occurs up to 3 times. B N:N Network 1) When a communication error occurs When a communication error occurs in an inverter communication instruction, the FX PLC automatically retries communication up to 3 times*1. Hence, when a password disable error occurs in the inverter in which "display of the number of times of password disable error"*2 is enabled using Pr297, please note that the number of times of password disable error displayed in accordance with the setting of Pr297 may not be the same as the actual number of times of password input error as described below. Do not execute automatic retry (re-driving of an inverter instruction) using a sequence program when writing data to Pr297. Common Items 6. Cautions when using the password function for inverter G Non-Protocol Communication (FX2N-232IF) H Programming Communication I Remote Maintenance Apx.A Discontinued models E-103 FX Series PLC User's Manual - Data Communication Edition 9 Creating Programs (FX3S, FX3G, FX3GC, FX3U, FX3UC) 9.4 Inverter Operation Monitoring Instruction (PLCInverter) [FNC270 / IVCK] Inverter Communication 9.4 Inverter Operation Monitoring Instruction (PLCInverter) [FNC270 / IVCK] The IVCK instruction reads the operation status of an inverter to the PLC. 9.4.1 Function and operation When an "instruction code" specified for computer link operation in the inverters is specified in the IVCK (FNC270) instruction, a value in the inverter is read to D . 1. Applicable devices Operand Type Bit Devices Word Devices System/User Digit Specification System/User X Y M T C S D.b KnX KnY KnM KnS T C D R Others Special Unit U\G V ConReal CharacPointer stant Number ter String Index Z Modify K H S1 1 2 S2 1 2 1 2 D n E "" P 1: Only available for FX3G, FX3GC, FX3U and FX3UC PLCs. 2: Only available for FX3U and FX3UC PLCs. 2. Program example M0 FNC270 IVCK Command contact S1 S2 D n K6 H6F D100 K1 Communication channel K1:ch1 Read value storage destination K2:ch2 Inverter instruction code (hexadecimal) Inverter station number: 0 to 31 9.4.2 Inverter instruction codes The table below shows inverter instruction codes which can be specified in S2 . Any instruction codes not shown in the table below may cause communication errors. Use only instruction codes shown below. For the instruction codes, refer to the pages explaining computer link in detail in each inverter manual. S2 Inverter Instruction code (hexadecimal) E-104 Applicable inverter F800, A800, F700, V500 F500, A500 A700, E700, D700 H7B Operation mode H6F Output frequency [speed] H70 H71 H72 H73 H74 H75 H76 H77 H79 H7A Output current Output voltage Special monitor Special monitor selection No. Alarm definition Alarm definition Alarm definition Alarm definition Inverter status monitor (expansion) Inverter status monitor H6E Set frequency read (E2PROM) E500 S500 *1 — — — — — — — — — — — *1 *1 H6D Set frequency read (RAM) H7F Link parameter expansion setting These codes cannot be specified in S2 of the IVCK instruction. They are automatically processed when a "second parameter specification code" is specified the Second parameter changing IVRD instruction. H6C *1. Read contents Please write "0" to instruction code HFF (Link parameter expansion setting) just before the IVCK instruction when reading frequency. When "0" is not written, reading of the frequency may not be executed normally. FX Series PLC User's Manual - Data Communication Edition 9 Creating Programs (FX3S, FX3G, FX3GC, FX3U, FX3UC) Inverter Communication 9.5 Inverter Operation Control Instruction (PLCInverter) [FNC271 / IVDR] Inverter Operation Control Instruction (PLCInverter) [FNC271 / IVDR] This instruction writes a control value required to operate an inverter from the PLC to the inverter. 9.5.1 Function and operation 1. Applicable devices Bit Devices System/User Word Devices Digit Specification System/User X Y M T C S D.b KnX KnY KnM KnS T C D R Others Special Unit U\G V ConReal CharacPointer stant Number ter String Index Z Modify K H S1 1 2 S2 1 2 1 2 S3 n E "" P D Computer Link 1: Only available for FX3G, FX3GC, FX3U and FX3UC PLCs. 2: Only available for FX3U and FX3UC PLCs. 2. Program example M0 S2 S3 n K6 HFA K2M50 K1 Communication channel K1:ch1 K2:ch2 Value written to inverter Inverter station number: 0 to 31 Inverter instruction code (hexadecimal) F Inverter instruction codes The table below shows inverter instruction codes which can be specified in S2 . For the instruction codes, refer to the pages explaining computer link in detail in each inverter manual. Applicable inverter S2 Inverter Instruction code (hexadecimal) F500, A500 E500, S500 Operation mode HF3 Special monitor selection No. — HF9 Run command (expansion) — — — HFA Run command HEE Set frequency write (EEPROM) *3 HED Set frequency write (RAM) *3 Inverter reset*2 Alarm definition batch clear — Parameter all clear HFC User clear — — — HFF Link parameter expansion setting E-105 I Apx.A Discontinued models The instruction code "HFD (inverter reset)" does not request a response from the inverter. Accordingly, even if inverter reset is executed to a station number at which an inverter is not connected, error does not occur. It takes about 2.2 seconds to complete execution of inverter reset. When resetting the inverter, please specify H9696 as the operand S3 of the IVDR instruction. Do not use H9966. Please write "0" to instruction code HFF (Link parameter expansion setting) just before the IVDR instruction when writing frequency. When "0" is not written, writing of the frequency may not be executed normally. H Remote Maintenance HF4 HFC G Programming Communication *3. V500 Non-Protocol Communication (FX2N-232IF) *2. F800, A800, F700, A700, E700, D700 HFB HFD*1 *1. Write contents Non-Protocol Communication (RS/RS2 Instruction) 9.5.2 E Inverter Communication Command contact FNC271 IVDR S1 C Parallel Link Operand Type B N:N Network When an "instruction code" specified for computer link operation in the inverters is specified in the IVDR (FNC271) instruction, the value specified in S3 is written to the specified item of the inverter. Common Items 9.5 A FX Series PLC User's Manual - Data Communication Edition 9 Creating Programs (FX3S, FX3G, FX3GC, FX3U, FX3UC) 9.6 Inverter Parameter Reading (PLCInverter) [FNC272 / IVRD] Inverter Communication 9.6 Inverter Parameter Reading (PLCInverter) [FNC272 / IVRD] This instruction reads a parameter of an inverter to the PLC. 9.6.1 Function and operation When a parameter number of an inverter is specified in IVRD (FNC272) instruction, the value of the parameter is read to D . 1. Applicable devices Operand Type Bit Devices System/User Word Devices Digit Specification System/User X Y M T C S D.b KnX KnY KnM KnS T C D R Others Special Unit U\G V ConReal CharacPointer stant Number ter String Index Z Modify K H S1 1 2 S2 1 2 D 1 2 n E "" P 1: Only available for FX3G, FX3GC, FX3U and FX3UC PLCs. 2: Only available for FX3U and FX3UC PLCs. 2. Program example M0 Command contact FNC272 IVRD S1 S2 D n K6 K7 D150 K1 Inverter station number: 0 to 31 9.6.2 Communication channel K1:ch1 K2:ch2 Read value storage destination Inverter parameter number (decimal) Inverter instruction codes Refer to related data shown later. 9.6.3 Program example of "second parameter specification code" For second parameter specification code, refer to Section 9.9. In the program example shown below, the parameters (frequency: 201, time: 1201, motor rotation direction: 2201) are read from the A500 inverter whose station number is 6. E-106 FX Series PLC User's Manual - Data Communication Edition 9 Creating Programs (FX3S, FX3G, FX3GC, FX3U, FX3UC) 9.6 Inverter Parameter Reading (PLCInverter) [FNC272 / IVRD] Inverter Communication A Common Items Read devices: D100 = Motor rotation direction, D101 = Frequency, D102 = Time X001 Read command M0 M0 S1 S2 D n K6 K2201 D100 K1 B Motor rotation directionD100 N:N Network Drive contact FNC272 IVRD SET Communication channel K1:ch1 Read value storage destination Inverter parameter number (decimal) Inverter station number: 0 to 31 K6 K201 D101 K1 FNC272 IVRD K6 K1201 D102 K1 C FrequencyD101 Parallel Link FNC272 IVRD TimeD102 The unit is specified by Pr. 200. M8029 RST D M0 Computer Link Execution complete flag E Inverter Communication F Non-Protocol Communication (RS/RS2 Instruction) G Non-Protocol Communication (FX2N-232IF) H Programming Communication I Remote Maintenance Apx.A Discontinued models E-107 FX Series PLC User's Manual - Data Communication Edition 9 Creating Programs (FX3S, FX3G, FX3GC, FX3U, FX3UC) 9.7 Inverter Parameter Writing (PLCInverter) [FNC273 / IVWR] Inverter Communication 9.7 Inverter Parameter Writing (PLCInverter) [FNC273 / IVWR] This instruction writes a value from the PLC to a parameter in an inverter. 9.7.1 Function and operation When a parameter number in an inverter is specified in IVWR (FNC273) instruction, the value of written to the specified item in the inverter. is S3 1. Applicable devices Operand Type Bit Devices Word Devices System/User Digit Specification System/User X Y M T C S D.b KnX KnY KnM KnS T C D R Others Special Unit U\G V ConReal CharacPointer stant Number ter String Index Z Modify K H S1 1 2 S2 1 2 S3 1 2 n E "" P 1: Only available for FX3G, FX3GC, FX3U and FX3UC PLCs. 2: Only available for FX3U and FX3UC PLCs. 2. Program example M0 Command contact FNC273 IVWR S1 S2 S3 n K6 K7 D160 K1 Communication channel K1:ch1 K2:ch2 Value written to inverter Inverter parameter number (decimal) Inverter station number: 0 to 31 9.7.2 Inverter instruction codes Refer to related data shown later. 9.7.3 Program example of "second parameter specification code" For second parameter specification code, refer to Section 9.9. In the program example shown below, data is written from the PLC to the parameters (frequency: 201, time: 1201, motor rotation direction: 2201) in the A500 inverter. X001 Write command M0 Drive contact SET M0 S1 S2 S3 n K6 K2201 H1 K1 FNC273 IVWR Communication channel K1:ch1 Value written to inverter Inverter parameter number (decimal) Inverter station number: 0 to 31 FNC273 IVWR K6 K201 H14 K1 FNC273 IVWR K6 K1201 H100 K1 RST Execution complete flag Frequency: 20Hz Time: 1:00 The unit is specified by Pr. 200. M8029 E-108 Motor rotation direction: Forward M0 FX Series PLC User's Manual - Data Communication Edition 9 Creating Programs (FX3S, FX3G, FX3GC, FX3U, FX3UC) 9.8 Inverter Parameter Batch Writing (PLCInverter) [FNC274 / IVBWR] Inverter Communication Inverter Parameter Batch Writing (PLCInverter) [FNC274 / IVBWR] Common Items 9.8 A This instruction writes values from the PLC to parameters in an inverter all at once. The IVBWR instruction is supported only in FX3U and FX3UC PLCs. 9.8.1 B Function and operation S3 1. Applicable devices Bit Devices Word Devices System/User Digit Specification System/User X Y M T C S D.b KnX KnY KnM KnS T C D R U\G V ConReal CharacPointer stant Number ter String Index Z Modify K H S2 S3 E "" P D Computer Link S1 n C Others Special Unit 2. Program example FNC274 IVBWR Command contact S2 S3 n K6 K8 D200 K1 Inverter station number: 0 to 31 Number of parameters to be written (decimal) E Inverter Communication M0 S1 Communication channel K1: ch1 K2: ch2 Head device of parameter table written to inverter Parameter No. 1 D201 Value 1 written to parameter S3 +2 D202 Parameter No. 2 S3 +3 D203 Value 2 written to parameter : : : : : : S3 +14 D214 Parameter No. 8 S3 +15 D215 Value 8 written to parameter G S2 Non-Protocol Communication (FX2N-232IF) D200 S3 +1 F Non-Protocol Communication (RS/RS2 Instruction) The following table shows values (two word devices/point) in a specified table which are written to a number of consecutive parameters specified in S2 starting from a word device specified in S3 . S3 Parallel Link Operand Type N:N Network When a parameter number in an inverter is specified in the IVBWR (FNC274) instruction, the values of and later are written to the specified items in the inverter all at once. 2 = Number of occupied word devices H Programming Communication I Remote Maintenance Apx.A Discontinued models E-109 FX Series PLC User's Manual - Data Communication Edition 9.9 Controls Operations and Monitors Operations of an Inverter with a Single Command(PLCInverter)[FNC275 / IVMC] Inverter Communication 9.9 9 Creating Programs (FX3S, FX3G, FX3GC, FX3U, FX3UC) Controls Operations and Monitors Operations of an Inverter with a Single Command(PLCInverter)[FNC275 / IVMC] This instruction writes 2 types of settings (operation command and set frequency) to the inverter, and reads 2 types of data (inverter status monitor, output frequency, etc.) from the inverter at the same time. The following PLC versions support the IVMC instruction. PLC 9.9.1 Applicable version FX3S Ver. 1.00 or later FX3G, FX3GC Ver. 1.40 or later FX3U, FX3UC Ver. 2.70 or later Function and operation 1. Applicable devices Bit Devices Operand Type Word Devices System/User Digit Specification System/User X Y M T C S D.b KnX KnY KnM KnS T C D Others Special Unit R ConReal CharacPointer stant Number ter String Index U\G V Z Modify K H S1 1 2 S2 1 2 S3 1 2 D 1 2 n E "" P 1: Only available for FX3G, FX3GC, FX3U and FX3UC PLCs. 2: Only available for FX3U and FX3UC PLCs. 2. Program example S1 S2 S3 D n D10 D20 K1 M0 FNC275 K0 H0000 IVMC Command contact Inverter station number (K0 to K31) Multiple instructions for inverter: Send/receive data type specification 3. Send/receive data type Channel to be used (K1: ch1, K2: ch2) Head device which stores values to be read from the inverter Head device which stores data to be written to the inverter S2 The table below shows valid send data 1 and 2 and receive data 1 and 2 specified by the send/receive data type S2 . S2 Send/receive data type (HEX) Send data (Write contents to Inverter) Data 1 ( S3 ) H0000 H0001 H0010 H0011 Run command (expansion) Data 2 ( S3 Receive data (Read contents from Inverter) +1) Set frequency (RAM) Set frequency (RAM, EEPROM) Data 1 ( D Data 2 ( D +1) Output frequency (speed) Inverter status monitor (expansion) • Number of occupied devices Two devices are occupied respectively by S3 and Make sure not to use those devices in another control. Special monitor Output frequency (speed) Special monitor Caution E-110 ) D . FX Series PLC User's Manual - Data Communication Edition 9 Creating Programs (FX3S, FX3G, FX3GC, FX3U, FX3UC) 9.9 Controls Operations and Monitors Operations of an Inverter with a Single Command(PLCInverter)[FNC275 / IVMC] Inverter Communication A • If any unspecified value is set in S2 , unexpected data may be written to and read from the inverter, and values of D and D +1 may be updated. 9.9.2 Applicable inverters This instruction is applicable to the following inverters: • FREQROL-A800 (Applicable in all) C Parallel Link • FREQROL-F800 (Applicable in all) • FREQROL-E700 (February 2009 and later) • FREQROL-D700 (Applicable in all) For details, refer to the respective inverter manual. Applicable programming tool The following programming tools support this instruction. 1. English versions Product name Model name Applicable version Remarks E FX3U and FX3UC PLCs SWDNC-GXW2-E Ver. 1.48A or later Ver. 1.20 or later Inverter Communication GX Works2 FX-30P - FX3G PLC GX Works2 SWDNC-GXW2-E FX-30P Ver. 1.62Q or later Ver. 1.50 or later - F SWDNC-GXW2-E FX-30P Ver. 1.77F or later Ver. 1.50 or later - Non-Protocol Communication (RS/RS2 Instruction) FX3GC PLC GX Works2 - G FX3S PLC GX Works2 SWDNC-GXW2-E FX-30P Ver. 1.492N or later Ver. 1.50 or later Non-Protocol Communication (FX2N-232IF) 2. Japanese versions Product name Model name Applicable version Remarks FX3U and FX3UC PLCs GX Works2 SWDNC-GXW2-J Ver. 1.45X or later Ver. 1.20 or later H - Programming Communication FX-30P FX3G PLC GX Works2 SWDNC-GXW2-J FX-30P Ver. 1.56J or later Ver. 1.50 or later - FX3GC PLC GX Works2 SWDNC-GXW2-J Ver. 1.50 or later I - Remote Maintenance FX-30P Ver. 1.77F or later FX3S PLC GX Works2 FX-30P SWDNC-GXW2-J Ver. 1.492N or later Ver. 1.50 or later D Computer Link 9.9.3 B N:N Network • IVMC instruction reads the inverter status at the time of communication with the inverter, and stores the read status to D . Accordingly, the status written by the IVMC instruction can be read by a next or later read instruction (IVCK or IVMC). Common Items • If a device number outside the range due to indexing, etc. is specified in D , the receive data from the inverter is not stored in D . However, values set in S3 and S3 +1 may be written to the inverter. - Apx.A Discontinued models E-111 FX Series PLC User's Manual - Data Communication Edition 9 Creating Programs (FX3S, FX3G, FX3GC, FX3U, FX3UC) Inverter Communication 9.10 9.10 Second Parameter Specification Codes Second Parameter Specification Codes When handling the following parameters in computer link operation, it is necessary to select second parameters. In IVRD, IVWR, and IVBWR*1 instructions, when a value shown in the tables below is set in S2 ( S3 in IVBWR*1 instruction), the extension parameter and second parameter are automatically overwritten, and parameter values are either read or written. *1. The IVBWR instruction is supported only in FX3U and FX3UC PLCs. 9.10.1 S500 Series 1. Second parameter specification codes for parameter numbers C2 to C7 Second parameter specification code Parameter No. Name [(decimal) value to be specified in S2 in IVRD/IVWR instruction for parameter number] C2 Frequency setting voltage bias frequency 902 C3 Frequency setting voltage bias 1902 C4 Frequency setting voltage gain 903 C5 Frequency setting current bias frequency 904 C6 Frequency setting current bias 1904 C7 Frequency setting current gain 905 9.10.2 E500 Series 1. Second parameter specification codes for parameter numbers 902 to 905 Second parameter specification code Parameter No. E-112 Name [(decimal) value to be specified in S2 in IVRD/IVWR instruction for parameter number] Offset/Gain (H00) Analog (H01) Analog value of terminal (H02) 902 Frequency setting voltage bias 902 1902 2902 903 Frequency setting voltage gain 903 1903 2903 904 Frequency setting current bias 904 1904 2904 905 Frequency setting current gain 905 1905 2905 FX Series PLC User's Manual - Data Communication Edition 9 Creating Programs (FX3S, FX3G, FX3GC, FX3U, FX3UC) Inverter Communication 9.10 Second Parameter Specification Codes A 1. Second parameter specification codes for parameter numbers 201 to 230 and 902 to 905 Second parameter specification code Name Operation frequency read/write Time read/write Rotation direction write/read 203 Program set 1 203 1203 2203 204 Program set 1 204 1204 2204 205 Program set 1 205 1205 2205 206 Program set 1 206 1206 2206 207 Program set 1 207 1207 2207 208 Program set 1 208 1208 2208 209 Program set 1 209 1209 2209 210 Program set 1 210 1210 2210 211 Program set 2 211 1211 2211 212 Program set 2 212 1212 2212 213 Program set 2 213 1213 2213 214 Program set 2 214 1214 2214 215 Program set 2 215 1215 2215 216 Program set 2 216 1216 2216 217 Program set 2 217 1217 2217 218 Program set 2 218 1218 2218 219 Program set 2 219 1219 2219 220 Program set 2 220 1220 2220 221 Program set 3 221 1221 2221 222 Program set 3 222 1222 2222 223 Program set 3 223 1223 2223 224 Program set 3 224 1224 2224 225 Program set 3 225 1225 2225 226 Program set 3 226 1226 2226 227 Program set 3 227 1227 2227 228 Program set 3 228 1228 2228 229 Program set 3 229 1229 2229 230 Program set 3 230 1230 2230 C D E F G H 2. Second parameter specification codes for parameter numbers 902 to 905 Second parameter specification code Parameter No. Name [(decimal) value to be specified in S2 in IVRD/IVWR instruction for parameter number] Analog (H01) Analog value of terminal (H02) 902 Frequency setting voltage bias 902 1902 2902 903 Frequency setting voltage gain 903 1903 2903 904 Frequency setting current bias 904 1904 2904 905 Frequency setting current gain 905 1905 2905 I Remote Maintenance Offset/Gain (H00) Programming Communication 2202 Computer Link 2201 1202 Parallel Link 1201 202 Non-Protocol Communication (FX2N-232IF) 201 Program set 1 Non-Protocol Communication (RS/RS2 Instruction) Program set 1 202 Inverter Communication 201 B N:N Network Parameter No. [(decimal) value to be specified in S2 in IVRD/IVWR instruction for parameter number] Common Items 9.10.3 A500 Series Apx.A Discontinued models E-113 FX Series PLC User's Manual - Data Communication Edition 9 Creating Programs (FX3S, FX3G, FX3GC, FX3U, FX3UC) Inverter Communication 9.10 Second Parameter Specification Codes 9.10.4 F500 Series 1. Second parameter specification codes for parameter numbers 902 to 905 Second parameter specification code Parameter No. Name [(decimal) value to be specified in S2 in IVRD/ IVWR instruction for parameter number] Offset/Gain (H00) Analog (H01) Analog value of terminal (H02) 902 Frequency setting voltage bias 902 1902 2902 903 Frequency setting voltage gain 903 1903 2903 904 Frequency setting current bias 904 1904 2904 905 Frequency setting current gain 905 1905 2905 9.10.5 V500 Series 1. Second parameter specification codes for parameter numbers 902 to 905 Second parameter specification code Parameter No. Name [(decimal) value to be specified in S2 in IVRD/ IVWR instruction for parameter number] Offset/Gain (H00) Analog (H01) Analog value of terminal (H02) 902 1902 2902 902 Speed setting No. 2 bias 903 Speed setting No. 2 gain 903 1903 2903 904 Torque command No. 3 bias 904 1904 2904 905 Torque command No. 3 gain 905 1905 2905 917 No.1 terminal bias (speed) 917 1917 2917 918 No.1 terminal gain (speed) 918 1918 2918 919 No.1 terminal bias (torque/magnetic flux) 919 1919 2919 920 No.1 terminal gain (torque/magnetic flux) 920 1920 2920 9.10.6 F700 Series 1. Second parameter specification codes for parameter numbers 125, 126, and C2 to C7 Parameter No. E-114 Second parameter specification code Name [(decimal) value to be specified in S2 in IVRD/IVWR instruction for parameter number] C2 Terminal 2 frequency setting bias frequency 902 C3 Terminal 2 frequency setting bias 1902 125 Terminal 2 frequency setting gain frequency 903 C4 Terminal 2 frequency setting gain 1903 C5 Terminal 4 frequency setting bias frequency 904 C6 Terminal 4 frequency setting bias 1904 126 Terminal 4 frequency setting gain frequency 905 C7 Terminal 4 frequency setting gain 1905 FX Series PLC User's Manual - Data Communication Edition Inverter Communication 9 Creating Programs (FX3S, FX3G, FX3GC, FX3U, FX3UC) 9.10 Second Parameter Specification Codes A 1. Second parameter specification codes for parameter numbers 125, 126, C2 to C7, C12 to C19, and C38 to C41 Second parameter specification code Name [(decimal) value to be specified in S2 in IVRD/IVWR instruction for parameter number] C2 Terminal 2 frequency setting bias frequency 902 C3 Terminal 2 frequency setting bias 1902 125 Terminal 2 frequency setting gain frequency 903 C4 Terminal 2 frequency setting gain 1903 904 Terminal 4 frequency setting bias 1904 126 Terminal 4 frequency setting gain frequency 905 C7 Terminal 4 frequency setting gain 1905 C12 Bias frequency (speed) for terminal No. 1 917 C13 Bias (speed) for terminal No. 1 1917 C14 Gain frequency (speed) for terminal No. 1 918 C15 Gain (speed) for terminal No. 1 1918 Bias command (torque) for terminal No. 1 919 C17 Bias (torque) for terminal No. 1 1919 C18 Gain command (torque) for terminal No. 1 920 C19 Gain (torque) for terminal No. 1 1920 C38 Bias command (torque) for terminal No. 4 932 C39 Bias (torque) for terminal No. 4 1932 C40 Gain command (torque) for terminal No. 4 933 C41 Gain (torque) for terminal No. 4 1933 E Inverter Communication C16 D Computer Link Terminal 4 frequency setting bias frequency C6 C Parallel Link C5 B N:N Network Parameter No. Common Items 9.10.7 A700 Series F Non-Protocol Communication (RS/RS2 Instruction) G Non-Protocol Communication (FX2N-232IF) H Programming Communication I Remote Maintenance Apx.A Discontinued models E-115 FX Series PLC User's Manual - Data Communication Edition Inverter Communication 9 Creating Programs (FX3S, FX3G, FX3GC, FX3U, FX3UC) 9.10 Second Parameter Specification Codes 9.10.8 E700 and D700 Series 1. Second parameter specification codes for parameter numbers 125, 126, C2 to C7 and C22 to C25 Second parameter specification code Parameter No. C2 C3 125 C4 C5 C6 126 C7 E-116 Name [(decimal) value to be specified in S2 in IVRD/ IVWR instruction for parameter number] Terminal 2 frequency setting bias frequency 902 Terminal 2 frequency setting bias 1902 Terminal 2 analog value 2902 (Only the IVRD instruction) Terminal 2 frequency setting gain frequency Terminal 2 frequency setting gain 903 1903 Terminal 2 analog value 2903 (Only the IVRD instruction) Terminal 4 frequency setting bias frequency 904 Terminal 4 frequency setting bias 1904 Terminal 4 analog value 2904 (Only the IVRD instruction) Terminal 4 frequency setting gain frequency Terminal 4 frequency setting gain 905 1905 Terminal 4 analog value 2905 (Only the IVRD instruction) C22 Frequency setting voltage bias frequency (built-in potentiometer) 922 C23 Frequency setting voltage bias (built-in potentiometer) 1922 C24 Frequency setting voltage gain frequency (built-in potentiometer) 923 C25 Frequency setting potentiometer) 1923 voltage gain (built-in FX Series PLC User's Manual - Data Communication Edition Inverter Communication 9 Creating Programs (FX3S, FX3G, FX3GC, FX3U, FX3UC) 9.10 Second Parameter Specification Codes A 1. Second parameter specification codes for parameter numbers Pr125, Pr126, C2 to C19 and C38 to C41 Second parameter specification code Name [(decimal) value to be specified in S2 in IVRD/ IVWR instruction for parameter number] C2 Terminal 2 frequency setting bias frequency 902 Terminal 2 frequency setting bias 1902 Terminal 2 frequency setting gain frequency 903 C4 Terminal 2 frequency setting gain 1903 C5 Terminal 4 frequency setting bias frequency 904 Terminal 4 frequency setting bias 1904 Terminal 4 frequency setting gain frequency 905 C7 Terminal 4 frequency setting gain 1905 C12 Terminal 1 bias frequency (speed) 917 C13 Terminal 1 bias (speed) 1917 918 Terminal 1 gain (speed) 1918 C16 Terminal 1 bias command (torque) 919 C17 Terminal 1 bias (torque) 1919 C18 Terminal 1 gain command (torque) 920 C19 Terminal 1 gain (torque) 1920 C8 Current output bias signal 930 C9 Current output bias current 1930 C10 Current output gain signal 931 C11 Current output gain current 1931 C38 Terminal 4 bias command (torque) 932 C39 Terminal 4 bias (torque) 1932 C40 Terminal 4 gain command (torque) 933 C41 Terminal 4 gain (torque) 1933 PID display bias coefficient 934 C43 PID display bias analog value 1934 C44 PID display gain coefficient 935 C45 PID display gain analog value 1935 F G Non-Protocol Communication (FX2N-232IF) C42 E Non-Protocol Communication (RS/RS2 Instruction) Terminal 1 gain frequency (speed) C15 Inverter Communication C14 D Computer Link C6 126 C Parallel Link C3 125 B N:N Network Parameter No. Common Items 9.10.9 F800 Series H Programming Communication I Remote Maintenance Apx.A Discontinued models E-117 FX Series PLC User's Manual - Data Communication Edition Inverter Communication 9 Creating Programs (FX3S, FX3G, FX3GC, FX3U, FX3UC) 9.10 Second Parameter Specification Codes 9.10.10 A800 Series 1. Second parameter specification codes for parameter numbers Pr125, Pr126, C2 to C19 and C38 to C41 Parameter No. E-118 Second parameter specification code Name [(decimal) value to be specified in S2 in IVRD/ IVWR instruction for parameter number] C2 Terminal 2 frequency setting bias frequency 902 C3 Terminal 2 frequency setting bias 1902 125 Terminal 2 frequency setting gain frequency 903 C4 Terminal 2 frequency setting gain 1903 C5 Terminal 4 frequency setting bias frequency 904 C6 Terminal 4 frequency setting bias 1904 126 Terminal 4 frequency setting gain frequency 905 C7 Terminal 4 frequency setting gain 1905 C12 Terminal 1 bias frequency (speed) 917 C13 Terminal 1 bias (speed) 1917 C14 Terminal 1 gain frequency (speed) 918 C15 Terminal 1 gain (speed) 1918 C16 Terminal 1 bias command (torque) 919 C17 Terminal 1 bias (torque) 1919 C18 Terminal 1 gain command (torque) 920 C19 Terminal 1 gain (torque) 1920 C8 Current output bias signal 930 C9 Current output bias current 1930 C10 Current output gain signal 931 C11 Current output gain current 1931 C38 Terminal 4 bias command (torque) 932 C39 Terminal 4 bias (torque) 1932 C40 Terminal 4 gain command (torque) 933 C41 Terminal 4 gain (torque) 1933 C42 PID display bias coefficient 934 C43 PID display bias analog value 1934 C44 PID display gain coefficient 935 C45 PID display gain analog value 1935 FX Series PLC User's Manual - Data Communication Edition 10 Practical Program Examples (FX3S, FX3G, FX3GC, FX3U, FX3UC) Inverter Communication 10.1 Practical Example 1 A Common Items 10. Practical Program Examples (FX3S, FX3G, FX3GC, FX3U, FX3UC) B N:N Network This chapter explains practical programs for inverter communication. 10.1 Practical Example 1 An FX PLC (ch 1) is connected to an inverter. FX3S, FX3G, FX3GC, FX3U, FX3UC D Computer Link 10.1.1 System configuration example C Parallel Link This fundamental program example monitors operations of an inverter, controls operations of the inverter and writes parameters to the inverter. Programs can be made simpler and the communication time can be reduced by using the IVMC instruction as long as the PLC and inverter support the IVMC instruction. For details on PLC versions support the IVMC instruction, refer to section 9.9. Refer to "9.9.2 Applicable inverters" for supported inverters. Inverter E Inverter Communication F Terminal resistor Non-Protocol Communication (RS/RS2 Instruction) Distributor 10.1.2 Contents of operation *1. D11 when the IVMC instruction is used G Non-Protocol Communication (FX2N-232IF) As an example of operation control, an inverter can be stopped (X000), rotated forward (X001) and rotated reverse (X002). By changing the contents of D10*1, the speed can be changed. The contents of D10*1 can be changed from a sequence program or display unit. H Programming Communication I Remote Maintenance Apx.A Discontinued models E-119 FX Series PLC User's Manual - Data Communication Edition 10 Practical Program Examples (FX3S, FX3G, FX3GC, FX3U, FX3UC) Inverter Communication 10.1 Practical Example 1 10.1.3 Program example 1. Writing parameters to an inverter while the PLC is in RUN mode M8002 SET Initial pulse M10 The write instruction is driven M10 Driving of write instruction FNC271 IVDR K0 H0FD H9696 K1 The inverter is reset FNC271 IVDR K0 H0FB H0*1 K1 Computer link operation is specified FNC 12 MOV P K1 D200 The maximum frequency (Pr. 1) is specified FNC 12 MOV P K12000 D201 The maximum frequency (Pr. 1) is set to "120 Hz" FNC 12 MOV P K2 D202 The minimum frequency (Pr. 2) is specified FNC 12 MOV P K500 D203 The minimum frequency (Pr. 2) is set to "5 Hz" FNC 12 MOV P K7 D204 The acceleration time (Pr. 7) is specified FNC 12 MOV P K10 D205 The acceleration time (Pr. 7) is set to "1 sec" FNC 12 MOV P K8 D206 The deceleration time (Pr. 8) is specified FNC 12 MOV P K10 D207 The deceleration time (Pr. 8) is set to "1 sec" D200 K1 FNC274 IVBWR*2 K0 K4 M8029 Instruction execute complete *1. *2. E-120 RST The parameters are written all at once D200 to D207 (Pr. 1, Pr. 2, Pr. 7 and Pr. 8) M10 Driving of write instruction When using an E500 Series inverter, use "H2" to specify computer link operation. The FX3S, FX3G and FX3GC PLC does not support the IVBWR instruction. Use the IVWR instruction instead. FX Series PLC User's Manual - Data Communication Edition 10 Practical Program Examples (FX3S, FX3G, FX3GC, FX3U, FX3UC) Inverter Communication 10.1 Practical Example 1 A Common Items 2. Changing the speed using a sequence program • When the IVMC instruction is not used M8000 FNC 12 MOV P RUN monitor K6000 D10 M17 FNC 12 MOV P Command for switching to speed 1 D10 The operation speed "40 Hz" is written Operation speed M18 K2000 D10 C The operation speed "20 Hz" is written Parallel Link FNC 12 MOV P Command for switching to speed 2 FNC271 IVDR K4000 B N:N Network Operation speed "60 Hz" is written as the initial value at startup Operation speed K0 H0ED D10 K1 The preset frequency*1 is written to the inverter *1. For the V500 Series inverter, write "0" to instruction code HFF (Link parameter expansion setting) just before writing the set frequency in the program. E • When the IVMC instruction is used FNC 12 MOV P RUN monitor K6000 D11 Operation speed M17 M18 D11 F The operation speed "40 Hz" is written Operation speed FNC 12 MOV P K2000 D11 The operation speed "20 Hz" is written G Operation speed Non-Protocol Communication (FX2N-232IF) Command for switching to speed 2 K4000 "60 Hz" is written as the initial value at startup Non-Protocol Communication (RS/RS2 Instruction) Command for switching to speed 1 FNC 12 MOV P Inverter Communication M8000 D Computer Link Operation speed H Programming Communication I Remote Maintenance Apx.A Discontinued models E-121 FX Series PLC User's Manual - Data Communication Edition 10 Practical Program Examples (FX3S, FX3G, FX3GC, FX3U, FX3UC) Inverter Communication 10.1 Practical Example 1 3. Controlling operations of an inverter • When the IVMC instruction is not used X000 SET Operation stop command input X001 Forward rotation command input M15 H0FA is set to "00H" Operation stop X000 RST Operation stop command input M15 Operation stop is reset by input X001 or X002 Operation stop X002 Reverse rotation command input M15 X001 Operation Forward stop rotation command input X002 Reverse rotation command input M8000 X002 M21 Reverse rotation command input Forward rotation command X001 M22 Forward rotation command input FNC271 IVDR RUN monitor b1 of H0FA is set to ON b2 of H0FA is set to ON Reverse rotation command K0 H0FA K2M20 K1 Operation command is written M27 to M20H0FA • When the IVMC instruction is used X000 SET Operation stop command input X001 Forward rotation command input M15 H0F9 is set to "0000H" Operation stop X000 RST Operation stop command input M15 Operation stop is reset by input X001 or X002 Operation stop X002 Reverse rotation command input M15 X001 Operation Forward stop rotation command input X002 Reverse rotation command input M8000 RUN monitor E-122 X002 M21 Reverse rotation command input b1 of H0F9 is set to ON Forward rotation command X001 M22 Forward rotation command input b2 of H0F9 is set to ON Reverse rotation command FNC 12 MOV K4M20 D10 Operation command The run command is set to the device for writing. FX Series PLC User's Manual - Data Communication Edition 10 Practical Program Examples (FX3S, FX3G, FX3GC, FX3U, FX3UC) Inverter Communication 10.1 Practical Example 1 A Common Items 4. Monitoring operations of an inverter • When the IVMC instruction is not used M8000 FNC270 IVCK RUN monitor K0 H079*1 K4M100 K1 Inverter status is read H79M115 to M100 B N:N Network M100 Y000 Inverter is operating Indicator lamp, etc. C M101 Forward rotation Parallel Link Y001 Indicator lamp, etc. M102 Y002 Reverse rotation D M103 Y003 Up to frequency Indicator lamp, etc. Contents of status (according to necessity) E M104 Inverter Communication Y004 Overload is applied Indicator lamp, etc. M106 Y006 Frequency is detected F Non-Protocol Communication (RS/RS2 Instruction) Indicator lamp, etc. M107 Y007 Alarm occurrence Indicator lamp, etc. K0 H06F D50 K1 G Output frequency monitor*2 Non-Protocol Communication (FX2N-232IF) FNC270 IVCK Computer Link Indicator lamp, etc. Frequency monitor value END H S500, E500, A500, F500 and V500 Series inverters do not support the command code H79 (Inverter status monitor (extended)). Use the command code H7A (Inverter status monitor). *2. For the V500 Series inverter, write "0" to instruction code HFF (Link parameter expansion setting) just before reading the output frequency monitor in the program. Programming Communication *1. I Remote Maintenance Apx.A Discontinued models E-123 FX Series PLC User's Manual - Data Communication Edition 10 Practical Program Examples (FX3S, FX3G, FX3GC, FX3U, FX3UC) Inverter Communication 10.1 Practical Example 1 • When the IVMC instruction is used M8000 FNC275 IVMC RUN monitor K0 H0000 D10 FNC 12 MOV D20 D20 K1 K4M100 The set frequency (RAM) and run command (expansion) are written. The inverter status monitor (expansion) and output frequency (speed) are read.*1 The inverter status monitor (expansion) is stored in bit devices. M100 Y000 Inverter is operating Indicator lamp, etc. M101 Y001 Forward rotation Indicator lamp, etc. M102 Y002 Reverse rotation Indicator lamp, etc. M103 Y003 Up to frequency Indicator lamp, etc. Contents of status (according to necessity) M104 Y004 Overload is applied Indicator lamp, etc. M106 Y006 Frequency is detected Indicator lamp, etc. M107 Y007 Alarm occurrence Indicator lamp, etc. FNC 12 MOV D21 D50 Output frequency (speed) monitor END *1. E-124 The IVMC instruction reads the inverter status at the time of communication with the inverter, and stores it in D . Accordingly, the inverter status written by the IVMC instruction can be read when the next reading instruction (IVCK, IVMC, etc.) is executed. FX Series PLC User's Manual - Data Communication Edition 10 Practical Program Examples (FX3S, FX3G, FX3GC, FX3U, FX3UC) Inverter Communication A Practical Example 2 This program executes the same control as practical example 1 shown earlier from one communication port (ch1) to two inverters (Station number: 0 and 1). B 10.2.1 System configuration example N:N Network An FX PLC (ch1) is connected to two inverters (Station number: 0 and 1). FX3S, FX3G, FX3GC, FX3U, FX3UC Common Items 10.2 10.2 Practical Example 2 Inverter A (station number 0) Inverter B (station number 1) C Parallel Link D Terminal resistor Computer Link Distributor Distributor 10.2.2 Contents of operation E Differences from the practical example 1 are the following three points: • Status is not being read when a write to inverter command is given. • The PLC only writes when it detects that contents to be written have changed since last being written. Inverter Communication • The PLC executes communication from one communication port to two inverters. F Non-Protocol Communication (RS/RS2 Instruction) G Non-Protocol Communication (FX2N-232IF) H Programming Communication I Remote Maintenance Apx.A Discontinued models E-125 FX Series PLC User's Manual - Data Communication Edition 10 Practical Program Examples (FX3S, FX3G, FX3GC, FX3U, FX3UC) Inverter Communication 10.2 Practical Example 2 10.2.3 Program example 1. Writing parameters to an inverter while the PLC is in RUN mode M8002 Initial pulse FNC 40 ZRST M510 M607 Clearing devices backed up against power interruption FNC 40 ZRST D510 D707 Clearing devices backed up against power interruption SET M10 The write instruction is driven (station number 0) SET The write instruction is driven (station number 1) *Inverter A (station number 0) M10 Driving of write instruction (station number 0) M510 FNC271 IVDR K0 H0FD H9696 K1 FNC271 IVDR K0 H0FB H0*1 K1 FNC 12 MOV P K1 D200 FNC 12 MOV P K12000 D201 FNC 12 MOV P K2 D202 FNC 12 MOV P K500 D203 FNC 12 MOV P K7 D204 The acceleration time (Pr. 7) is specified (station number 0) FNC 12 MOV P K10 D205 The acceleration time (Pr. 7) is set to "1 sec" (station number 0) FNC 12 MOV P K8 D206 The deceleration time (Pr. 8) is specified (station number 0) FNC 12 MOV P K10 D207 The deceleration time (Pr. 8) is set to "1 sec" (station number 0) D200 K1 FNC274 IVBWR*2 K0 K4 M8029 RST Instruction execute complete E-126 M10 Driving of write instruction (station number 0) The inverter is reset (station number 0) Computer link operation is specified (station number 0) The maximum frequency (Pr. 1) is specified (station number 0) The maximum frequency (Pr. 1) is set to "120 Hz" (station number 0) The minimum frequency (Pr. 2) is specified (station number 0) The minimum frequency (Pr. 2) is set to "5 Hz" (station number 0) The parameters are written all at once D200 to D207 (Pr. 1, Pr. 2, Pr. 7 and Pr. 8) (station number 0) FX Series PLC User's Manual - Data Communication Edition 10 Practical Program Examples (FX3S, FX3G, FX3GC, FX3U, FX3UC) Inverter Communication 10.2 Practical Example 2 A Common Items *Inverter B (station number 1) M510 FNC271 IVDR K1 H0FD H9696 K1 FNC271 IVDR K1 H0FB H0*1 K1 FNC 12 MOV P K1 D700 FNC 12 MOV P K12000 D701 FNC 12 MOV P K2 D702 FNC 12 MOV P K500 D703 FNC 12 MOV P K7 D704 The acceleration time (Pr. 7) is specified (station number 1) FNC 12 MOV P K10 D705 The acceleration time (Pr. 7) is set to "1 sec" (station number 1) FNC 12 MOV P K8 D706 The deceleration time (Pr. 8) is specified (station number 1) FNC 12 MOV P K10 D707 The deceleration time (Pr. 8) is set to "1 sec" (station number 1) D700 K1 D The minimum frequency (Pr. 2) is specified (station number 1) The minimum frequency (Pr. 2) is set to "5 Hz" (station number 1) Computer Link RST Instruction execute complete The maximum frequency (Pr. 1) is set to "120 Hz" (station number 1) E F The parameters are written all at once D700 to D707 (Pr. 1, Pr. 2, Pr. 7 and Pr. 8) (station number 1) G Non-Protocol Communication (FX2N-232IF) M8029 Parallel Link K4 C Non-Protocol Communication (RS/RS2 Instruction) K1 The maximum frequency (Pr. 1) is specified (station number 1) Inverter Communication FNC274 IVBWR*2 B The inverter is reset (station number 1) Computer link operation is specified (station number 1) N:N Network Driving of write instruction (station number 1) M510 Driving of write instruction (station number 1) H When using an E500 Series inverter, use "H2" to specify computer link operation. *2. The FX3S, FX3G and FX3GC PLC does not support the IVBWR instruction. Use the IVWR instruction instead. Programming Communication *1. I Remote Maintenance Apx.A Discontinued models E-127 FX Series PLC User's Manual - Data Communication Edition 10 Practical Program Examples (FX3S, FX3G, FX3GC, FX3U, FX3UC) Inverter Communication 10.2 Practical Example 2 2. Changing the speed using a sequence program *Inverter A (station number 0) M8000 FNC 12 K6000 MOV P RUN monitor D10 Operation speed "60 Hz" is written as the initial value at startup. (station number 0) M17 FNC 12 K4000 MOV P Command for switching to speed 1 D10 Operation speed (station number 0) (station number 0) M18 FNC 12 K2000 MOV P Command for switching to speed 2 D10 Operation speed (station number 0) The operation speed is written as "20 Hz" (station number 0) M8002 FNC 12 MOV Initial pulse D10 D80 Operation Operation speed speed is (station withdrawn number 0) (station number 0) FNC228 LD<> The operation speed is written as "40 Hz" D10 D80 SET The write instruction is driven Operation Operation speed speed is withdrawn (station (station number 0) number 0) M11 FNC271 IVDR The write instruction is driven K0 M11 (station number 0) H0ED D10 K1 Operation speed (station number 0) Change in the operation speed (D10) is detected The preset frequency*1 is written to the inverter (station number 0) M8029 Instruction execute complete RST M11 The write instruction is driven (station number 0) *1. E-128 For the V500 Series inverter, write "0" to instruction code HFF (Link parameter expansion setting) just before writing the set frequency in the program. FX Series PLC User's Manual - Data Communication Edition 10 Practical Program Examples (FX3S, FX3G, FX3GC, FX3U, FX3UC) Inverter Communication 10.2 Practical Example 2 A Common Items *Inverter B (station number 1) M8000 FNC 12 K6000 MOV P D510 Operation speed B "60 Hz" is written as the initial value at startup. N:N Network RUN monitor (station number 1) M517 FNC 12 K4000 MOV P Command for switching to speed 1 D510 (station number 1) M518 FNC 12 K2000 MOV P Command for switching to speed 2 D510 Operation speed (station number 1) The operation speed is written as "20 Hz" D FNC 12 MOV Initial pulse D510 Computer Link (station number 1) M8002 D580 Operation Operation speed speed is (station withdrawn D510 D580 SET The write instruction is driven Operation Operation speed speed is withdrawn (station (station number 1) number 1) FNC271 IVDR The write instruction is driven K1 H0ED D510 K1 Operation speed (station number 1) F (station number 1) Non-Protocol Communication (RS/RS2 Instruction) M11 M511 E Change in the operation speed (D510) is detected Inverter Communication number 1) (station number 1) FNC228 LD<> C Parallel Link Operation speed (station number 1) The operation speed is written as "40 Hz" The preset frequency*1 is written to the inverter G (station number 1) Instruction execute complete RST Non-Protocol Communication (FX2N-232IF) M8029 M511 The write instruction is driven H (station number 1) For the V500 Series inverter, write "0" to instruction code HFF (Link parameter expansion setting) just before writing the set frequency in the program. Programming Communication *1. I Remote Maintenance Apx.A Discontinued models E-129 FX Series PLC User's Manual - Data Communication Edition 10 Practical Program Examples (FX3S, FX3G, FX3GC, FX3U, FX3UC) Inverter Communication 10.2 Practical Example 2 3. Controlling operations of an inverter * Inverter A (station number 0) X000 SET M15 Operation stop command input (station number 0) X001 H0FA is set to "00H" Operation stop (station number 0) X000 RST Forward Operation stop rotation command input command (station number 0) input (station number 0) M15 Operation stop (station number 0) Operation stop is reset by input X001 or X002 X002 Reverse rotation command input (station number 0) M15 Operation stop (station number 0) X001 X002 Forward rotation command input (station number 0) X002 M21 Reverse rotation command input (station number 0) Forward rotation command (station number 0) X001 Reverse rotation command input (station number 0) M22 Forward rotation command input (station number 0) FNC 12 D81 MOV K2M20 Operation command is withdrawn (station number 0) Initial pulse D81 SET Operation command is withdrawn (station number 0) M12 Driving of write instruction (station number 0) FNC271 IVDR M8029 Instruction execute complete E-130 b2 of H0FA is set to ON Reverse rotation command (station number 0) M8002 FNC228 LD<> K2M20 b1 of H0FA is set to ON Changes in the operation commands (M27 to M20) are detected M12 Driving of write instruction (station number 0) K0 H0FA K2M20 K1 RST M12 Driving of write instruction (station number 0) Operation commands are written. M27 to M20H0FA FX Series PLC User's Manual - Data Communication Edition 10 Practical Program Examples (FX3S, FX3G, FX3GC, FX3U, FX3UC) Inverter Communication 10.2 Practical Example 2 A Common Items * Inverter B (station number 1) X010 SET M515 Operation stop (command input station number 1) B X010 RST M515 Operation stop (station number 1) Operation stop is reset by input X011 or X012 C Parallel Link Forward Operation stop rotation command input command (station number 1) input (station number 1) N:N Network X011 H0FA is set to "00H" Operation stop (station number 1) X012 Reverse rotation command input (station number 1) M515 (station number 1) X012 Forward rotation command input (station number 1) X012 M521 Reverse rotation command input (station number 1) Forward rotation command (station number 1) X011 M522 Forward rotation command input (station number 1) Reverse rotation command (station number 1) M8002 D581 SET Operation command is withdrawn (station number 1) M8029 Instruction execute complete G Driving of write instruction (station number 1) K1 H0FA K2M520 K1 RST M512 Operation commands are written. M527 to M520H0FA H Programming Communication Driving of write instruction (station number 1) FNC271 IVDR M512 Non-Protocol Communication (FX2N-232IF) M512 F Changes in the operation commands (M527 to M520) are detected Non-Protocol Communication (RS/RS2 Instruction) FNC 12 MOV K2M520 D581 Operation command is withdrawn (station number 1) Initial pulse FNC228 LD<> K2M520 E b2 of H0FA is set to ON Inverter Communication Reverse rotation command input (station number 1) D b1 of H0FA is set to ON Computer Link Operation stop X011 Driving of write instruction (station number 1) I Remote Maintenance Apx.A Discontinued models E-131 FX Series PLC User's Manual - Data Communication Edition 10 Practical Program Examples (FX3S, FX3G, FX3GC, FX3U, FX3UC) Inverter Communication 10.2 Practical Example 2 4. Monitoring operations of an inverter * Inverter A (station number 0) M10 Driving of write instruction (station number 0) N0 M11 Driving of write instruction (station number 0) M12 MC N0 M70 While data is not written to an inverter, the status is read K1 Inverter status is read (station number 0) H79M115 to M100 Driving of write instruction (station number 0) M70 M8000 FNC270 IVCK RUN monitor K0 H079*1 K4M100 Inverter is operating (station number 0) M100 Y000 Inverter running (station number 0) Indicator lamp, etc. M101 Y001 Forward rotation (station number 0) Indicator lamp, etc. M102 Y002 Reverse rotation (station number 0) Indicator lamp, etc. M103 Y003 Up to frequency (station number 0) Indicator lamp, etc. M104 Y004 Overload is applied (station number 0) Indicator lamp, etc. M106 Y006 Frequency is detected (station number 0) Indicator lamp, etc. M107 Y007 Alarm occurrence (station number 0) Indicator lamp, etc. FNC270 IVCK K0 H06F D50 K1 Frequency monitor value (station number 0) MCR E-132 Contents of status (according to necessity) Output frequency monitor *2 (station number 0) N0 *1. S500, E500, A500, F500 and V500 Series inverters do not support the command code H79 (Inverter status monitor (extended)). Use the command code H7A (Inverter status monitor). *2. For the V500 Series inverter, write "0" to instruction code HFF (Link parameter expansion setting) just before reading the output frequency monitor in the program. FX Series PLC User's Manual - Data Communication Edition 10 Practical Program Examples (FX3S, FX3G, FX3GC, FX3U, FX3UC) Inverter Communication 10.2 Practical Example 2 A Common Items * Inverter B (station number 1) M510 N0 Driving of write instruction (station number 1) M512 MC N0 M570 While data is not written to an inverter, the status is read K1 Inverter status is read (station number 1) H79M615 to M600 Driving of write instruction (station number 1) B N:N Network Driving of write instruction (station number 1) M511 M570 M8000 RUN monitor K1 H079*1 K4M600 Inverter is operating (station number 1) M600 C Parallel Link FNC270 IVCK Y010 Inverter running (station number 1) D M601 Computer Link Indicator lamp, etc. Y011 Forward rotation (station number 1) Indicator lamp, etc. M602 E Y012 Reverse rotation (station number 1) M603 Y013 Up to frequency (station number 1) Inverter Communication Indicator lamp, etc. Contents of status (according to necessity) Indicator lamp, etc. M604 F Overload is applied (station number 1) Non-Protocol Communication (RS/RS2 Instruction) Y014 Indicator lamp, etc. M606 Y016 Frequency is detected (station number 1) G M607 Non-Protocol Communication (FX2N-232IF) Indicator lamp, etc. Y017 Alarm occurrence (station number 1) Indicator lamp, etc. FNC270 IVCK K1 H06F D550 K1 MCR Programming Communication Frequency monitor value (station number 1) H Output frequency monitor *2 (station number 1) N0 I *1. S500, E500, A500, F500 and V500 Series inverters do not support the command code H79 (Inverter status monitor (extended)). Use the command code H7A (Inverter status monitor). *2. For the V500 Series inverter, write "0" to instruction code HFF (Link parameter expansion setting) just before reading the output frequency monitor in the program. Remote Maintenance END Apx.A Discontinued models E-133 FX Series PLC User's Manual - Data Communication Edition Inverter Communication 11 Troubleshooting 11.1 Checking FX PLC Version Applicability (FX2N and FX2NC Series) 11. Troubleshooting This chapter explains troubleshooting and error codes. 11.1 Checking FX PLC Version Applicability (FX2N and FX2NC Series) Verify that the FX PLC main unit is an applicable version for inverter communication. For version applicability, refer to Section 1.3. 11.2 Checking Communication Status Based on LED Indication Check the status of the "RD(RXD)" and "SD(TXD)" indicator LEDs provided in the optional equipment. LED status 11.3 Operation status RD SD Flashing Flashing Flashing Off Data is received, but is not sent. Off Flashing Data is sent, but is not received Off Off Data is being sent or received. Data is not sent nor received. Checking Installation 1. Mounting status If the communication equipment is not securely connected to the PLC, communication is not possible. For mounting method, refer to the respective communication equipment manual. 2. Power supply (for FX0N-485ADP) The FX0N-485ADP requires a driving power supply. Verify that the power supply is provided correctly. 3. Wiring Verify that the wiring to all communication equipment is correct. If the communication equipment is wired incorrectly, communication is not possible. For wiring method check, refer to Chapter 4. 11.4 Checking Sequence Program 1. Communication setting in the sequence program Verify that N:N Network (D8173 to D8180) and parallel link (M8070 and M8071) are not set. After changing any setting, make sure to turn OFF the PLC power, and then turn the power ON again. 2. Communication setting using parameters Verify that the communication settings using parameters are correct. If the contents of the parameters do not agree, communication will not function correctly. After changing any parameters, make sure to turn OFF the PLC power, and then turn the power ON again. 3. Ethernet port setting (in FX3S, FX3G, FX3GC, FX3U and FX3UC PLCs) Verify that the same channel is not used in the Ethernet port setting. Do not set the channel used in inverter communication. After changing the setting, make sure to reboot the PLC's power. E-134 FX Series PLC User's Manual - Data Communication Edition Inverter Communication 11 Troubleshooting 11.4 Checking Sequence Program A 1) Except FX3G, FX3U and FX3UC PLCs Verify that the VRRD and VRSC instructions are not used in the program. If these instructions are used, delete them, turn OFF the PLC power, and then turn the power ON again. C Parallel Link 3) In FX3U and FX3UC PLCs Verify that the VRRD and VRSC instructions are not used in the program. If these instructions are used in the program, the communication function is not available in ch1. Use ch2, or delete these instructions. After deleting these instructions, reboot the PLC's power. B N:N Network 2) In FX3G PLC - In the case of the 14 points and 24-point type Verify that the VRRD and VRSC instructions are not used in the program. If these instructions are used, delete them, turn OFF the PLC power, and then turn the power ON again. - In the case of the 40 points and 60-point type Verify that the VRRD and VRSC instructions are not used in the program. If these instructions are used in the program, the communication function is not available in ch2. Use ch1, or delete these instructions. After deleting these instructions, turn OFF the PLC power, and then turn the power ON again. Common Items 4. Presence of VRRD and VRSC instructions D Computer Link 5. Presence of RS instruction (in FX2N and FX2NC PLCs) Verify that the RS instruction is not used in the program. If this instruction is used, delete it, turn OFF the PLC power, and then turn the power ON again. 6. Presence of RS and RS2 instructions (in FX3S, FX3G, FX3GC, FX3U and FX3UC PLCs) 7. Presence of ADPRW instructions (in FX3S, FX3G, FX3GC, FX3U and FX3UC PLCs) Verify that the ADPRW instructions are not being used for the same channel. If these instructions are used for the same channel, delete them, and reboot the PLC’s power. E Inverter Communication Verify that the RS and RS2 instructions are not being used for the same channel. If these instructions are used for the same channel, delete them, turn OFF the PLC power, and then turn the power ON again. F Verify that the FLCRT, FLDEL, FLWR, FLRD, FLCMD and FLSTRD instructions are not being used for the same channel. If these instructions are used for the same channel, delete them, reboot the PLC’s power. G Non-Protocol Communication (FX2N-232IF) 11.4.1 Checking inverter operation status Non-Protocol Communication (RS/RS2 Instruction) 8. Presence of FLCRT, FLDEL, FLWR, FLRD, FLCMD, and FLSTRD instructions (in FX3U and FX3UC PLCs) 1. When the operation mode of an inverter is not changed over to computer link mode 1) Verify that the inverter is set to the external operation mode. H 2) Verify that no signal is being input to the external terminals STF and STR. Programming Communication 3) Verify that the correct operation mode changeover program is being executed. 2. When an inverter cannot be started even in computer link mode 1) Verify that the program for starting the inverter is executed correctly. 2) Verify that the operation command and speed command are set correctly. I 3) Verify that the allowable communication time interval is set correctly. 1) Verify that a communication cable is connected correctly between the PLC and the inverter. (Check for poor contact or wire breakage.) 3) Verify that the allowable communication time interval is set correctly. 4) Verify that terminal resistors are wired correctly. E-135 Apx.A Discontinued models 2) Verify that a sequence program is created so that communication is executed with each inverter within a constant cycle. Set the communication check time interval to a large value, and check the communication status. Remote Maintenance 3. When an inverter is stopped by an alarm during operation due to defective communication FX Series PLC User's Manual - Data Communication Edition 11 Troubleshooting Inverter Communication 11.5 11.5 Checking Absence/Presence of Errors Checking Absence/Presence of Errors Verify that the error flag is not ON. If the error flag is ON, check the error code and take proper countermeasures. For error codes, refer to the next page. 11.6 Error Codes When a communication error occurs, the error flag turns ON, and the error code is stored in the data register. For error codes, refer to the table below. 1. Error storing devices FX Series Error flag Data register for storing error code FX2N,FX2NC M8156 D8156 FX3S,FX3G,FX3GC,FX3U,FX3UC ch1 ch2 ch1 ch2 M8152 M8157 D8152 D8157 2. Error code list Error code (DEC) E-136 Contents of error 0 Normal end 1 Inverter operation (No Errors) Inverter did not give response. 2 Timeout error Sending from inverter was aborted midway. 3 Station number error Unspecified station gave response. 4 Sum check error The sum of data sent back by the inverter did not match. 5 Parameter number specification error In writing or reading a parameter, an improper parameter number was specified. At this time, error code (K6706) is set to D8067. K6706: Out-of-range data value for operand in applied instruction. 6 Communication port occupied by another communication type Because the port is being used for another communication type, it cannot be used for communication with the inverter. At this time, error code (K6762) is set to D8067. K6762: The port specified in inverter communication instruction is being used by another communication type. 7 A value outside the allowable range is set to the station number. Station number At this time, error code (K6706) is set to D8067. outside setting range K6706: Out-of-range data value for operand in applied instruction. 8 Sending timeout error*1 9 Received data error*1 Wrong data was received from the inverter. Sending to the inverter was not completed within the specified time. 256 Inverter sent the error code H0. Computer NAK error The number of retries exceeded the allowable number because of an error in the transfer request data. 257 Parity error 258 Sum check error 259 Protocol error 260 Framing error When errors have occurred consecutively Inverter sent the error code H2. beyond the The sum check code in the computer is different from the sum value allowable calculated from the data received by the inverter. number of Inverter sent the error code H3. retries, inverter Syntax error is included in the data received by the inverter, is brought to an receiving of data was not completed within the specified time, or CR/ alarm stop. LF does not agree with the parameters. Inverter sent the error code H1. The contents are different from the specified parity. Inverter sent the error code H4. The stop bit length is different from the initial set value. FX Series PLC User's Manual - Data Communication Edition Inverter Communication 11 Troubleshooting 11.6 Error Codes A Contents of error Inverter operation 262 Undefined Inverter sent the error code H6. Not defined currently in inverter. Character error Inverter does not accept Inverter sent the error code H7. received data, An unused character (other than 0 to 9, A to F and control codes) but is not was received. brought to an alarm stop. 263 Undefined Inverter sent the error code H8. Not defined currently in inverter. 265 Undefined Inverter sent the error code H9. Not defined currently in inverter. 266 268 Inverter sent the error code HA. A parameter was written in a mode other than computer link mode, Inverter does or while the inverter was operating. not accept received data, Inverter sent the error code HB. Instruction code error. Instruction code error but is not Non-existing instruction code was specified. brought to an Inverter sent the error code HC. Data range error In writing a parameter or operation frequency, data outside the alarm stop. allowable range was specified. Mode error Undefined 270 Undefined Inverter sent the error code HE. Not defined currently in inverter. 271 Undefined Inverter sent the error code HF. Not defined currently in inverter. F G This error code is supported only in FX3S/FX3G/FX3GC/FX3U/FX3UC PLCs. Non-Protocol Communication (FX2N-232IF) *1. E Non-Protocol Communication (RS/RS2 Instruction) 269 Inverter sent the error code HD. Not defined currently in inverter. D Inverter Communication 267 C Computer Link 264 Parallel Link Overrun error B N:N Network 261 When errors have occurred consecutively Inverter sent the error code H5. beyond the Before receiving the completed data in the inverter, the computer allowable sent the next set of data. number of retries, inverter is brought to an alarm stop. Common Items Error code (DEC) H Programming Communication I Remote Maintenance Apx.A Discontinued models E-137 FX Series PLC User's Manual - Data Communication Edition 11 Troubleshooting Inverter Communication 11.6 Error Codes 3. IVMC instruction error codes When errors occur in the send data of the IVMC instruction, the following error codes are stored. It is recommended to check error codes in hexadecimal. Refer to the error code list earlier in this section for other errors. Error code (HEX) IVMC Send Send instruction data2 data1 error error error information information information b15 to b8 b7 to b4 b3 to b0 H00 H0 H0 HA H0 HB HC H02 HA H0 HB E-138 Contents of error Inverter operation No error has occurred in both send data 1 and send data 2. Normal end The inverter sent error code HA to send data 1 of the IVMC instruction. A parameter was written in a mode other than computer link mode or while the inverter was The inverter accepts operating. The inverter did not accept the data corresponding to received data, but was not stopped by alarm. send data 2, and is not The inverter sent error code HB to send data 1 of brought to an alarm the IVMC instruction. stop. Non-existing instruction code was specified. The inverter sent error code HC to send data 1 of the IVMC instruction. Data outside the allowable range was specified. The inverter sent error code HA to send data 2 of the IVMC instruction. A parameter was written in a mode other than computer link mode or while inverter was The inverter accepts operating. The inverter did not accept the data corresponding to received data, but was not stopped by alarm. send data 1, and is not The inverter sent error code HB to send data 2 of brought to an alarm the IVMC instruction. stop. Non-existing instruction code was specified. HC The inverter sent error code HC to send data 2 of the IVMC instruction. Data outside the allowable range was specified. HA to HC The inverter sent error codes to both send data 1 and send data 2 of the IVMC instruction. Refer to the contents of the error of the corresponding error codes of send data 1 and send data 2 for details of error codes. HA to HC The inverter does not accept data corresponding to send data 1 and 2, but is not brought to an alarm stop. FX Series PLC User's Manual - Data Communication Edition 12 Related Data Inverter Communication 12.1 Related Device List (FX2N, FX2NC) A Common Items 12. Related Data B This chapter shows various technical information. N:N Network 12.1 Related Device List (FX2N, FX2NC) The tables below show special auxiliary relays and special data registers used in inverter communication (EXTR K10 to EXTR K13). Device No. Name Description R/W R M8104 Extension ROM cassette check R Remains ON while an extension ROM cassette is attached. R Remains ON while the communication port is used by an EXTR instruction. R Unused M8155 Communication port busy M8156 Communication error Turns ON when a communication error is caused by an EXTR instruction. or parameter error R M8157 Communication error Turns ON when a communication error is caused by an EXTR instruction. latch*1 R R: Read only (used as a contact in program) *1. F Cleared when the PLC mode is changed from STOP to RUN. Name Description R/W Stores the type code of an extension ROM cassette (value: K1). R D8105 Extension ROM cassette version Stores the version of an extension ROM cassette (value: K100 = Ver. 1.00). R D8154 Inverter response waiting time Sets the inverter response waiting time. D8155 Step number of instruction using the communication port Stores the step number of EXTR instruction using the communication port. R D8156 Error code*1 Stores an error code when a communication error is caused by an EXTR instruction. R Stores the instruction step number in which a communication error has occurred. (Stores K-1 when no error has occurred.) R D8157 Error occurrence step number latch*1 R/W H I Remote Maintenance R: Read only W: Write only R/W: Read or Write *1. G Programming Communication Extension ROM cassette type code Non-Protocol Communication (FX2N-232IF) D8104 Non-Protocol Communication (RS/RS2 Instruction) 2. Word devices Device No. E Inverter Communication M8154 D Computer Link M8029 Turns ON when execution of EXTR instruction is completed, and remains Instruction execution ON for 1 scan. complete Turns ON also when execution of instruction is completed if M8156 (communication error or parameter error) turns ON. Parallel Link 1. Bit devices C Cleared when the PLC mode is changed from STOP to RUN. Apx.A Discontinued models E-139 FX Series PLC User's Manual - Data Communication Edition Inverter Communication 12.2 12 Related Data 12.2 Details of Related Devices (FX2N, FX2NC) Details of Related Devices (FX2N, FX2NC) The following devices are special devices used in inverter communication. 12.2.1 Instruction execution complete [M8029] When execution of an inverter communication instruction is completed, this device turns ON. 1. Detailed contents When execution of an inverter communication instruction is completed, M8029 turns ON, and remains ON for 1 scan. When an error occurs in an inverter communication instruction, M8029 turns ON. 2. Cautions on use M8029 is used as the execution complete flag for other instructions (such as positioning instructions). When using M8029, provide the contact just under the instruction whose execution completion is to be checked. 12.2.2 Extension ROM cassette check [M8104] This device remains ON while an extension ROM cassette is attached. 1. Detailed contents M8104 remains ON while an extension ROM cassette is attached. - FX2N . . . . . . FX2N-ROM-E1 - FX2NC . . . . . FX2NC-ROM-CE1 2. Cautions on use While M8104 is OFF, EXTR instructions cannot be used. 12.2.3 Communication port busy [M8155] This device remains ON while the communication port is being used by an EXTR instruction. 1. Detailed contents M8155 remains ON while communication with an inverter is executed by an EXTR instruction. When M8155 turns ON, D8155 stores the step number of an instruction using the communication port. While M8155 is ON, another EXTR instruction cannot be executed. 12.2.4 Communication error or parameter error [M8156] This device turns ON when an error is caused in communication with an inverter by an EXTR instruction. 1. Detailed contents M8156 turns ON when an error is caused in communication with an inverter by an EXTR instruction. When M8156 turns ON, D8156 stores the error code. 2. Cautions on use M8156 is set to OFF by an EXTR instruction located in the next step in the program. When using M8156, provide it just under the EXTR instruction whose error is to be checked. E-140 FX Series PLC User's Manual - Data Communication Edition Inverter Communication 12 Related Data 12.2 Details of Related Devices (FX2N, FX2NC) A Common Items 12.2.5 Communication error latch [M8157] This device turns ON when the communication error flag M8156 turns ON. 1. Detailed contents B N:N Network M8157 turns ON when a communication error occurs and M8156 turns ON. When M8157 turns ON, D8157 stores the step number in which the error has occurred. 2. Cautions on use M8157 remains ON until the PLC mode is changed from STOP to RUN. 12.2.6 Extension ROM cassette type code [D8104] C Parallel Link This device stores the type code of an extension ROM cassette. 1. Detailed contents While the following ROM is attached to an FX PLC, D8104 stores its model code. - FX2N . . . . . . FX2N-ROM-E1 (model code: K1) - FX2NC . . . . . FX2NC-ROM-CE1 (model code: K1) D Computer Link 12.2.7 Extension ROM cassette version [D8105] This device stores the version of an extension ROM cassette. 1. Detailed contents E Inverter Communication While an extension ROM is attached, D8105 stores its version information (K100 = Ver. 1.00). 12.2.8 Inverter response waiting time [D8154] This device sets the response waiting time of an inverter. F 1. Detailed contents Non-Protocol Communication (RS/RS2 Instruction) D8154 sets the response waiting time of an inverter. Set a value within the range from "1 to 32767" (unit: 100 ms) to D8154. When "0" or a negative value is set, it is handled as "100 ms". 12.2.9 Step number of instruction using communication port [D8155] G Non-Protocol Communication (FX2N-232IF) This device stores the step number of an instruction occupying the communication port. 1. Detailed contents D8155 stores the step number of EXTR instruction using the communication port. H Programming Communication I Remote Maintenance Apx.A Discontinued models E-141 FX Series PLC User's Manual - Data Communication Edition Inverter Communication 12 Related Data 12.2 Details of Related Devices (FX2N, FX2NC) 12.2.10 Error code [D8156] This device stores the error code when an error is caused in communication with an inverter by an EXTR instruction. 1. Detailed contents D8156 stores one of the following error codes when an error is caused in communication with an inverter by the EXTR instruction. Error code (DEC) 0 Normal end (no error) 1 Inverter did not give response. 2 Timeout error. This code interlocks with M8156. Sending from inverter was aborted midway through. 3 An unspecified station gave response. 4 The sum of data sent back by the inverter did not match. 5 In writing or reading a parameter, an improper parameter number was specified. At this time, the error code K6706 is set to D8067. 6 Because the port is being used for another communication, it cannot be used for communication with the inverter. At this time, the error code K6762 is set to D8067. 7 A value outside the allowable range is set to the station number. At this time, error code (K6706) is set to D8067. 256 Inverter sent the error code H0. Computer NAK error. An error was included in the transfer request data from the computer beyond the allowable number of retries. 257 Inverter sent the error code H1. Parity error. The contents are different from the specified parity. 258 259 E-142 Contents of error Inverter operation Inverter sent the error code H2. Sum check error. When errors have The sum check code in the computer is different from the sum value calculated from occurred the data received by inverter. consecutively beyond the allowable number Inverter sent the error code H3. Protocol error. Syntax error is included in the data received by the inverter, and the receiving of of retries, inverter is data has not been completed within the specified time, or CR/LF does not agree brought to an alarm stop. with the parameters. 260 Inverter sent the error code H4. Framing error. The stop bit length is different from the initial set value. 261 Inverter sent the error code H5. Overrun error. Before receiving the completed data in the inverter, the computer sent the next set of data. 262 Inverter sent the error code H6. Not defined currently in inverter. 263 Inverter sent the error code H7. Character error. An unused character (other than 0 to 9, A to F and control codes) was received. 264 Inverter sent the error code H8. Not defined currently in inverter. 265 Inverter sent the error code H9. Not defined currently in inverter. Inverter does not accept the received data, but is not brought to an alarm stop. FX Series PLC User's Manual - Data Communication Edition Inverter Communication 12 Related Data 12.2 Details of Related Devices (FX2N, FX2NC) A 266 268 Inverter operation Inverter sent the error code HA. Mode error. A parameter was written in a mode other than computer link mode, or while inverter was operating. Inverter does not accept the received data, but is not stopped by Inverter does not alarm. accept the received data, but is not Inverter sent the error code HB. Instruction code error. brought to an alarm Non-existing instruction code was specified. stop. Inverter sent the error code HC. Data range error. In writing a parameter or operation frequency, data outside the allowable range was specified. Inverter does not accept the received data, but is not stopped by alarm. Inverter sent the error code HD. Not defined currently in inverter. 270 Inverter sent the error code HE. Not defined currently in inverter. 271 Inverter sent the error code HF. Not defined currently in inverter. C Parallel Link 269 B N:N Network 267 Contents of error Common Items Error code (DEC) D Computer Link 12.2.11 Error occurrence step number latch [D8157] This device stores the step number in which the communication error has occurred. E 1. Detailed contents Inverter Communication When M8157 turns ON, D8157 stores the step number in which communication error has occurred. When errors have occurred in two or more instructions, D8157 holds the step number of the instruction in which an error occurred first. When no error has occurred, D8157 stores "-1". F Non-Protocol Communication (RS/RS2 Instruction) G Non-Protocol Communication (FX2N-232IF) H Programming Communication I Remote Maintenance Apx.A Discontinued models E-143 FX Series PLC User's Manual - Data Communication Edition 12 Related Data Inverter Communication 12.3 12.3 Related Device List (FX3S, FX3G, FX3GC, FX3U, FX3UC) Related Device List (FX3S, FX3G, FX3GC, FX3U, FX3UC) The tables below show special auxiliary relays and special data registers used in inverter communication (FNC270 (IVCK) to FNC275 (IVMC)). The FX3G PLC (14-point, 24-point type) and FX3S PLC does not support ch2. 1. Bit devices Device No. Description R/W Turns ON when the execution of inverter communication instruction is completed, and remains ON for 1 scan. Turns ON also when the execution of instruction is completed if inverter communication error flag (M8152 or M8157) turns ON. R M8063 M8438 Serial communication error*1 Turns ON when an error occurs in any type of communication. R M8151 M8156 Inverter communicating Remains ON while inverter communication is being executed. R M8152 M8157 Inverter communication error*2 Turns ON when an error occurs during communication with an inverter. R M8153 M8158 Inverter communication error latch*2 Turns ON when an error occurs during communication with an inverter. R M8154 M8159 IVBWR instruction error*2, *3 Turns ON when an error is caused by IVBWR instruction. R ch1 Name ch2 M8029 Instruction execution complete R: Read only (used as a contact in program) *1. Cleared when PLC power supply is turned from OFF to ON. *2. Cleared when the PLC mode is changed from STOP to RUN. *3. The IVBWR instruction is supported only in FX3U and FX3UC PLCs. 2. Word devices Device No. ch1 Name ch2 Description D8063 D8438 Error code for serial communication*4 Stores a communication error code. R D8150 D8155 Inverter communication response waiting time*4 D8151 D8156 Step number of instruction executing Stores the step number of an instruction executing inverter communication inverter communication. R D8152 D8157 Error code for inverter communication*5 Stores an inverter communication error code. R D8153 D8158 Inverter communication error occurring step latch*5 Latches a step number in which an inverter communication error has occurred.*7 R Error parameter number of IVBWR Stores a parameter number in which an IVBWR instruction error has occurred. R Stores the communication type being used. R D8154 D8159 instruction*5*6 D8419 D8439 Operation mode display Sets the response wait time of inverter communication. R: Read only W: Write only R/W: Read or Write E-144 R/W *4. Cleared when PLC power supply is turned from OFF to ON. *5. Cleared when the PLC mode is changed from STOP to RUN. *6. The IVBWR instruction is supported only in FX3U and FX3UC PLCs. *7. Updated only for the first error occurrence, and not for the second error occurrence or later. R/W FX Series PLC User's Manual - Data Communication Edition Inverter Communication 12.4 Details of Related Devices (FX3S, FX3G, FX3GC, FX3U, FX3UC) A Details of Related Devices (FX3S, FX3G, FX3GC, FX3U, FX3UC) Common Items 12.4 12 Related Data The following devices are special devices used in inverter communications. The FX3G PLC (14-point, 24-point type) and FX3S PLC does not support ch2. B 12.4.1 Instruction execution complete [M8029] N:N Network When execution of an inverter communication instruction is completed, this device turns ON. 1. Detailed contents 2. Cautions on use M8029 is used as the execution complete flag for other instructions (such as positioning instructions). When using M8029, provide the contact just under the instruction whose execution completion is to be checked. C Parallel Link When execution of an inverter communication instruction is completed, M8029 turns ON, and remains ON for 1 scan. When an error occurs in an inverter communication instruction, M8029 turns ON, and remains ON for 1 scan in the same way. D Computer Link 12.4.2 Serial communication error [M8063 and M8438] These devices turn ON when an error occurs during communication with an inverter. 1. Detailed contents F Non-Protocol Communication (RS/RS2 Instruction) 2. Cautions on use E Inverter Communication M8063 or M8438 turns ON when a parity error, overrun error or framing error occurs during communication with inverters or when on inverter communication error occurs. M8063 turns ON when an error occurs during communication using ch1. When M8063 turns ON, D8063 stores the error code. M8438 turns ON when an error occurs during communication using ch2. When M8438 turns ON, D8438 stores the error code. Serial communication errors are not cleared even when communication is restored. Clear them by turning off and on the PLC. 12.4.3 Inverter communication ON [M8151 and M8156] 1. Detailed contents 2. Cautions on use While M8151 or M8156 remains ON, another inverter communication instruction cannot be executed. H Programming Communication M8151 or M8156 remains ON while communication with an inverter is executed by an inverter communication instruction. M8151 remains ON while communication port ch1 is used. While M8151 remains ON, D8151 stores the step number of an instruction using the communication port. M8156 remains ON while communication port ch2 is used. While M8156 remains ON, D8156 stores the step number of an instruction using the communication port. G Non-Protocol Communication (FX2N-232IF) These devices remain ON while the communication port is used by an inverter communication instruction. I Remote Maintenance Apx.A Discontinued models E-145 FX Series PLC User's Manual - Data Communication Edition Inverter Communication 12 Related Data 12.4 Details of Related Devices (FX3S, FX3G, FX3GC, FX3U, FX3UC) 12.4.4 Inverter communication error [M8152, M8153, M8157 and M8158] These devices turn ON when an error occurs in an inverter communication instruction. 1. Detailed contents M8152 or M8157 turn ON when an error occurs in an inverter communication instruction. M8152 turn ON when an error occurs during communication using communication port ch1. When M8152 turn ON, D8152 stores the error code and D8153 stores the error step number. M8157 turn ON when an error occurs during communication using communication port ch2. When M8157 turn ON, D8157 stores the error code and D8158 stores the error step number. To D8152, D8153, D8157 and D8158 are updated only for the first error occurrence, and not for the second error occurrence or later. 2. Cautions on use M8152 and M8157 do not turn OFF even if the communication recovers its normal status. Clear them by switching the PLC mode from STOP to RUN. 12.4.5 IVBWR instruction error [M8154 and M8159] (only in FX3U and FX3UC PLCs) These devices turn ON when an error occurs in IVBWR instruction. 1. Detailed contents M8154 or M8159 turns ON when a parameter number of set value specified in IVBWR instruction is outside the allowable range. M8154 turns ON when an error occurs in IVBWR instruction using communication port ch1. When M8154 turns ON, D8154 stores the rejected parameter number. M8159 turns ON when an error occurs in IVBWR instruction using the communication port ch2. When M8159 turns ON, D8159 stores the rejected parameter number. 2. Cautions on use IVBWR instruction errors are not cleared even when communication is restored. Clear them by turning off and on the PLC. 12.4.6 Serial communication error code [D8063 and D8438] These devices store the error code when the serial communication error flag turns ON. 1. Detailed contents When an error occurs in an inverter communication instruction, D8063 or D8438 stores one of the following error codes. Error code ch1 ch2 Contents D8063 D8438 6301 3801 Parity error, framing error or overrun error 6320 3820 Inverter communication error 2. Cautions on use Serial communication error codes are not cleared even when communication is restored. Clear them by switching the PLC mode from STOP to RUN. 12.4.7 Inverter response waiting time [D8150 and D8155] These devices set the response waiting time of the inverter. 1. Detailed contents Set the response waiting time of an inverter. When using communication port ch1, set a value to D8150. When using communication port ch2, set a value to D8155. Set a value within the range from "1 to 32767" (unit: 100 ms). If "0" or negative value is set, it is handled as "100 ms". E-146 FX Series PLC User's Manual - Data Communication Edition Inverter Communication 12 Related Data 12.4 Details of Related Devices (FX3S, FX3G, FX3GC, FX3U, FX3UC) A Common Items 12.4.8 Step number of instruction using communication port [D8151 and D8156] These devices store the step number of the instruction occupying the communication port. 1. Detailed contents. 2. Cautions on use A decimal value without sign is stored as the step number in D8151 and D8156. C These devices store an error code when a communication error is caused by an inverter communication instruction. 1. Detailed contents • D8152 stores the error code of an error in communication using communication port ch1. • D8157 stores the error code of an error in communication using communication port ch2. D Computer Link Special data registers shown below respectively store inverter communication errors, depending on each communication port. Parallel Link 12.4.9 Inverter communication error code [D8152 and D8157] E 2. Error codes Contents of error 2 Timeout error. This code interlocks with M8156. Sending from inverter was aborted midway through. 3 An unspecified station gave response. 4 The sum of data sent back by the inverter did not match. 5 In writing or reading a parameter, an improper parameter number was specified. At this time, the error code K6706 is set to D8067. 6 Because the port is being used for another communication type, it cannot be used for communication with the inverter. At this time, the error code K6762 is set to D8067. 7 A value outside the allowable range is set to the station number. At this time, error code (K6706) is set to D8067. 8 Sending to the inverter was not completed within the specified time. 9 Wrong data was received from the inverter. F G H Programming Communication Inverter did not give response. Non-Protocol Communication (FX2N-232IF) Normal end (no error) 1 Non-Protocol Communication (RS/RS2 Instruction) 0 Inverter operation Inverter Communication The following error codes are stored. Error code (DEC) B N:N Network D8151 or D8156 stores the step number of the inverter communication instruction using the communication port. D8151 stores the step number using communication port ch1. D8156 stores the step number using communication port ch2. I Remote Maintenance Apx.A Discontinued models E-147 FX Series PLC User's Manual - Data Communication Edition Inverter Communication 12.4 Details of Related Devices (FX3S, FX3G, FX3GC, FX3U, FX3UC) Error code (DEC) Contents of error 256 Inverter sent the error code H0. Computer NAK error. An error was included in the transfer request data from the computer beyond the allowable number of retries. 257 Inverter sent the error code H1. Parity error. The contents are different from the specified parity. 258 259 Inverter sent the error code H4. Framing error. The stop bit length is different from the initial set value. 261 Inverter sent the error code H5. Overrun error. Before receiving the completed data in the inverter, the computer sent the next set of data. 262 Inverter sent the error code H6. Not defined currently in inverter. 263 Inverter sent the error code H7. Character error. An unused character (other than 0 to 9, A to F and control codes) is received. 264 Inverter sent the error code H8. Not defined currently in inverter. 265 Inverter sent the error code H9. Not defined currently in inverter. 267 268 Inverter operation Inverter sent the error code H2. Sum check error. The sum check code in the computer is different from the sum value calculated When errors have occurred consecutively from the data received by the inverter. beyond the allowable Inverter sent the error code H3. Protocol error. number of retries, inverter Syntax error is included in the data received by the inverter, and the receiving of is brought to an alarm data was not completed within the specified time, or CR/LF does not agree with stop. the parameters. 260 266 E-148 12 Related Data Inverter does not accept the received data, but is not brought to an alarm stop. Inverter sent the error code HA. Mode error. A parameter was written in a mode other than computer link mode or while inverter was operating. Inverter does not accept the received data, but is not stopped by alarm. Inverter does not accept the received data, but is Inverter sent the error code HB. Instruction code error. not brought to an alarm Non-existing instruction code was specified. stop. Inverter sent the error code HC. Data range error. In writing a parameter or operation frequency, data outside the allowable range was specified. Inverter does not accept the received data, but is not stopped by alarm. 269 Inverter sent the error code HD. Not defined currently in inverter. 270 Inverter sent the error code HE. Not defined currently in inverter. 271 Inverter sent the error code HF. Not defined currently in inverter. FX Series PLC User's Manual - Data Communication Edition Inverter Communication 12 Related Data 12.4 Details of Related Devices (FX3S, FX3G, FX3GC, FX3U, FX3UC) A Common Items 3. IVMC instruction error codes When errors occur in the send data of the IVMC instruction, the following error codes are stored. It is recommended to check error codes in hexadecimal. Refer to the error code list earlier in this section for other errors. Error code (HEX) B b7 to b4 b3 to b0 H00 H0 H0 HA HB HC HA HB The inverter sent error code HA to send data 1 of the IVMC instruction. A parameter was written in a mode other than computer link mode or while the inverter was The inverter accepts operating. The inverter did not accept the data corresponding to received data, but was not stopped by alarm. send data 2, and is not The inverter sent error code HB to send data 1 of brought to an alarm the IVMC instruction. stop. Non-existing instruction code was specified. The inverter sent error code HC to send data 1 of the IVMC instruction. Data outside the allowable range was specified. The inverter sent error code HA to send data 2 of the IVMC instruction. A parameter was written in a mode other than computer link mode or while inverter was The inverter accepts operating. The inverter did not accept the data corresponding to received data, but was not stopped by alarm. send data 1, and is not The inverter sent error code HB to send data 2 of brought to an alarm the IVMC instruction. stop. Non-existing instruction code was specified. F G The inverter does not The inverter sent error codes to both send data 1 accept data and send data 2 of the IVMC instruction. corresponding to send Refer to the contents of the error of the data 1 and 2, but is not corresponding error codes of send data 1 and brought to an alarm send data 2 for details of error codes. stop. Non-Protocol Communication (FX2N-232IF) HA to HC D E The inverter sent error code HC to send data 2 of the IVMC instruction. Data outside the allowable range was specified. HC HA to HC C Non-Protocol Communication (RS/RS2 Instruction) H0 Inverter Communication H02 No error has occurred in both send data 1 and send data 2. Normal end Computer Link H0 Inverter operation Parallel Link b15 to b8 Contents of error N:N Network IVMC Send Send instruction data2 data1 error error error information information information H Programming Communication I Remote Maintenance Apx.A Discontinued models E-149 FX Series PLC User's Manual - Data Communication Edition 12 Related Data Inverter Communication 12.4 Details of Related Devices (FX3S, FX3G, FX3GC, FX3U, FX3UC) 12.4.10 Inverter communication error occurrence step [D8153 and D8158] These devices store the step number in which an inverter communication error has occurred. 1. Detailed contents D8153 or D8158 stores the step number of the instruction causing an inverter communication error. D8153 stores the step number in which an error has occurred in communication using communication port ch1. D8158 stores the step number in which an error has occurred in communication using communication port ch2. When errors that occurred in two or more instructions, D8153 or D8158 holds the step number in which the error occurred first. When no error has occurred, D8153 or D8158 stores "-1". 2. Cautions on use A decimal value without the sign is stored as the step number in D8153 and D8158. 12.4.11 IVBWR instruction error parameter number [D8154 and D8159] (only in FX3U and FX3UC PLCs) These devices store the parameter number in which an error has occurred when IVBWR instruction error flag "M8154 or M8159" turns ON. 1. Detailed contents D8154 or D8159 stores the parameter number which was not written by IVBWR instruction. D8154 stores the parameter number which was not written in communication using communication port ch1. D8159 stores the parameter number which was not written in communication using communication port ch2. When errors that occurred in two or more IVBWR instructions, D8154 or D8159 holds the parameter number in which the error occurred first. 12.4.12 Operation mode display [D8419 and D8439] These devices store the communication type being used. 1. Detailed contents These devices store the code of the communication type currently being used in the communication port. When communication port ch1 is used, D8419 stores the communication type. When communication port ch2 is used, D8439 stores the communication type. The table below shows the contents of the communication type codes. Code 0 E-150 Description Programming communication 1 PP modem mode 2 Protocol dedicated to computer link 3 N:N Network 4 RS instruction 5 RS2 instruction 6 Parallel link 7 Inverter instruction 8 Variable analog potentiometer expansion board is used. 9 MODBUS communication 10 CF-ADP 11 ENET-ADP 12 Input/output expansion board is used. FX Series PLC User's Manual - Data Communication Edition 12 Related Data Inverter Communication A FREQROL Inverter Parameter List This section shows the list of parameters provided in FREQROL F800, A800, F700, A700, E700, V500, F500, A500, E500 and S500 Series inverters. For details on each function, refer to the respective inverter manual. The following parameters are provided in FREQROL inverters. (For details, make sure to refer to the respective inverter manual.) FREQROL V500 Series FREQROL F500 Series FREQROL A500 Series FREQROL E500 Series FREQROL S500 Series Name Pr No. Name Pr No. Name Pr No. Name 0 Torque boost 0 Torque boost*3 0 Torque boost*3 0 Torque boost*3 1 Maximum speed (simple mode) 1 Maximum frequency 1 Maximum frequency 1 Maximum frequency 1 Maximum frequency 2 Minimum speed (simple mode) 2 Minimum frequency 2 Minimum frequency 2 Minimum frequency 2 Minimum frequency 3 Base frequency 3 Base frequency 3 Base frequency 3 Base frequency*3 3 Base frequency*3 4 Multi-speed setting (high speed) (simple mode) 4 Multi-speed setting (high speed) 4 Multi-speed setting (high speed) 4 Multi-speed setting (high speed) 4 Multi-speed setting (high speed) 5 Multi-speed setting (middle speed) (simple mode) 5 Multi-speed setting (middle speed) 5 Multi-speed setting (middle speed) 5 Multi-speed setting (middle speed) 5 Multi-speed setting (middle speed) 6 Multi-speed setting (low speed) (simple mode) 6 Multi-speed setting (low speed) 6 Multi-speed setting (low speed) 6 Multi-speed setting (low speed) 6 Multi-speed setting (low speed) 7 Acceleration time (simple mode) 7 Acceleration time 7 Acceleration time 7 Acceleration time 7 Acceleration time 8 Deceleration time (simple mode) 8 Deceleration time 8 Deceleration time 8 Deceleration time 8 Deceleration time 9 Electronic thermal O/L relay 9 Electronic thermal O/L relay 9 Electronic thermal O/L relay 9 Electronic thermal O/L relay 9 Electronic thermal O/L relay 10 DC injection brake operation speed 10 DC injection brake operation frequency 10 DC injection brake operation frequency 10 DC injection brake operation frequency 10 DC injection brake operation frequency 11 DC injection brake operation time 11 DC injection brake operation time 11 DC injection brake operation time 11 DC injection brake operation time 11 DC injection brake operation time 12 DC injection brake voltage 12 DC injection brake voltage 12 DC injection brake voltage 12 DC injection brake voltage 12 DC injection brake voltage 13 Starting speed 13 Starting frequency 13 Starting frequency 13 Starting frequency 13 Starting frequency Load pattern Load pattern Load pattern 14 Load pattern selection 14 15 Jog speed setting 15 Jog frequency 15 Jog frequency 15 Jog frequency 15 Jog frequency 16 Jog acceleration/ deceleration time 16 Jog acceleration/ deceleration time 16 Jog acceleration/ deceleration time 16 Jog acceleration/ deceleration time 16 Jog acceleration/ deceleration time 17 MRS input selection 17 MRS input selection 17 MRS input selection 17 RUN key rotation direction selection 18 High speed maximum frequency 18 19 Base frequency voltage 19 Base frequency voltage 19 selection*3 Base frequency voltage*3 14 19 selection*3 High speed maximum frequency Base frequency voltage*3 14 19 selection*3 Base frequency voltage*3 E F G H I Remote Maintenance D Programming Communication Torque boost (manual) Computer Link 0 C Non-Protocol Communication (FX2N-232IF) Standard operation function (V500 Series operation selection functions) Pr No. Non-Protocol Communication (RS/RS2 Instruction) Standard operation functions Name Inverter Communication Basic functions Pr No. Parallel Link Function B N:N Network 12.5.1 Parameters in V500, F500, A500, E500, and S500 Series Common Items 12.5 12.5 FREQROL Inverter Parameter List Apx.A Discontinued models E-151 FX Series PLC User's Manual - Data Communication Edition 12 Related Data Inverter Communication 12.5 FREQROL Inverter Parameter List FREQROL V500 Series FREQROL F500 Series FREQROL A500 Series FREQROL E500 Series FREQROL S500 Series Function Pr No. E-152 Name 20 Acceleration/ deceleration time increment 21 Torque restriction level 20 21 22 Pr No. Name 20 Acceleration/ deceleration reference frequency Acceleration/ deceleration time increment 21 22 Stall prevention operation level Pr No. Name Pr No. Name 20 Acceleration/ deceleration reference frequency 20 Acceleration/ deceleration reference frequency Acceleration/ deceleration time increment 21 Acceleration/ deceleration time increment 21 Stall preventing function selection 22 Stall prevention operation level 22 Stall prevention operation level 22 Stall prevention operation level 23 Stall prevention operation level compensation factor at double speed 23 Stall prevention operation level compensation factor at double speed 23 Stall prevention operation level compensation factor at double speed 23 Stall prevention operation level compensation factor at double speed 24 Multi-speed setting (speed 4) 24 Multi-speed setting (speed 4) 24 Multi-speed setting (speed 4) 24 Multi-speed setting (speed 4) 24 Multi-speed setting (speed 4) 25 Multi-speed setting (speed 5) 25 Multi-speed setting (speed 5) 25 Multi-speed setting (speed 5) 25 Multi-speed setting (speed 5) 25 Multi-speed setting (speed 5) 26 Multi-speed setting (speed 6) 26 Multi-speed setting (speed 6) 26 Multi-speed setting (speed 6) 26 Multi-speed setting (speed 6) 26 Multi-speed setting (speed 6) 27 Multi-speed setting (speed 7) 27 Multi-speed setting (speed 7) 27 Multi-speed setting (speed 7) 27 Multi-speed setting (speed 7) 27 Multi-speed setting (speed 7) 28 Multi-speed input compensation 28 Multi-speed input compensation 28 Multi-speed input compensation 28 Stall preventing operation reduction starting frequency 29 Acceleration/ deceleration pattern 29 Acceleration/ deceleration pattern 29 Acceleration/ deceleration pattern 29 Acceleration/ deceleration pattern 29 Acceleration/ deceleration pattern 30 Regenerative function selection 30 Regenerative function selection 30 Regenerative function selection 30 Regenerative function selection 30 Extended function display selection 31 Speed jump 1A 31 Frequency jump 1A 31 Frequency jump 1A 31 Frequency jump 1A 31 Frequency jump 1A 32 Speed jump 1B 32 Frequency jump 1B 32 Frequency jump 1B 32 Frequency jump 1B 32 Frequency jump 1B 33 Speed jump 2A 33 Frequency jump 2A 33 Frequency jump 2A 33 Frequency jump 2A 33 Frequency jump 2A 34 Speed jump 2B 34 Frequency jump 2B 34 Frequency jump 2B 34 Frequency jump 2B 34 Frequency jump 2B 35 Speed jump 3A 35 Frequency jump 3A 35 Frequency jump 3A 35 Frequency jump 3A 35 Frequency jump 3A 36 Speed jump 3B 36 Frequency jump 3B 36 Frequency jump 3B 36 Frequency jump 3B 36 Frequency jump 3B 37 Speed display 37 Speed display 37 Speed display 37 Speed display*8 37 Speed display*8 38 Automatic torque boost 38 Frequency at 5V (10V) input 38 Frequency setting voltage gain frequency 39 Automatic torque boost operation starting current 39 Frequency at 20mA input 39 Frequency setting current gain frequency 40 Start-time ground fault detection selection Output terminal functions Pr No. Acceleration/ deceleration reference frequency Acceleration/ deceleration reference speed Standard operation function (V500 Series operation selection functions) Name 41 Up-to-speed sensitivity 41 Up-to-frequency sensitivity 41 Up-to-frequency sensitivity 41 Up-to-frequency sensitivity 41 Up-to-frequency sensitivity 42 Speed detection 42 Output frequency detection 42 Output frequency detection 42 Output frequency detection 42 Output frequency detection 43 Speed detection for reverse rotation 43 Output frequency detection for reverse rotation 43 Output frequency detection for reverse rotation 43 Output frequency detection for reverse rotation 43 Output frequency detection for reverse rotation FX Series PLC User's Manual - Data Communication Edition 12 Related Data Inverter Communication 12.5 FREQROL Inverter Parameter List A Function Pr No. Name Pr No. Name Pr No. Name Pr No. Name 44 Second acceleration/ deceleration time 44 Second acceleration/ deceleration time 44 Second acceleration/ deceleration time 44 Second acceleration/ deceleration time 44 Second acceleration/ deceleration time 45 Second deceleration time 45 Second deceleration time 45 Second deceleration time 45 Second deceleration time 45 Second deceleration time 46 Second torque boost 46 47 Second V/F (base frequency) 47 48 Second stall prevention operation current 48 Second stall prevention operation current 49 Second stall prevention operation frequency 49 Second stall prevention operation frequency 50 Second speed detection 50 Second output frequency detection 50 Second output frequency detection 52 DU/PU main display data selection 52 DU/PU main display data selection 52 DU/PU main display data selection 52 53 PU level display data selection 53 PU level display data selection 53 PU level display data selection 54 DA1 terminal function selection 54 FM terminal function selection 54 FM terminal function selection 55 Speed monitoring reference 55 Frequency monitoring reference 55 Frequency monitoring reference 56 Current monitoring reference 56 Current monitoring reference 57 Restart coasting time 57 58 Restart cushion time 59 Remote setting function selection 60 Intelligent mode selection 47 Second V/F (base frequency)*3 Second electronic thermal O/L relay boost*3 D 53 Frequency setting operation selection 54 FM terminal function selection 54 FM (AM) terminal function selection 55 Frequency monitoring reference 55 Frequency monitoring reference 56 Current monitoring reference 56 Current monitoring reference 56 Current monitoring reference Restart coasting time 57 Restart coasting time 57 Restart coasting time 57 Restart coasting time 58 Restart cushion time 58 Restart cushion time 58 Restart cushion time 58 Restart cushion time G 59 Remote setting function selection 59 Remote setting function selection 59 Remote setting function selection 59 Remote setting function selection 60 Intelligent mode selection 60 Intelligent mode selection 60 Shortest acceleration/ deceleration mode 61 Reference I for intelligent mode 61 Reference I for intelligent mode 61 Reference current 62 Reference I for intelligent mode acceleration 62 Reference I for intelligent mode acceleration 62 Reference current for acceleration 63 Reference I for intelligent mode deceleration 63 Reference I for intelligent mode deceleration 63 Reference current for deceleration 64 Starting frequency for elevator mode I 65 Retry selection 65 Retry selection 66 66 Stall prevention operation level reduction starting frequency 66 Stall prevention operation level reduction starting frequency 67 Number of retries at alarm occurrence 67 Number of retries at alarm occurrence 67 Number of retries at alarm occurrence 66 67 Number of retries at alarm occurrence 67 Number of retries at alarm occurrence Retry selection E-153 Apx.A Discontinued models Retry selection F H 65 Stall prevention operation level reduction starting frequency E Remote Maintenance Operation panel/ PU main display data selection C Programming Communication Retry selection (base frequency)*3 Second torque Control panel display data selection 65 48 Second V/F 46 52 Operation selecting functions 47 boost*3 Computer Link (base frequency)*3 Second torque Non-Protocol Communication (FX2N-232IF) Additional function Second V/F 46 Non-Protocol Communication (RS/RS2 Instruction) Restart boost*3 Parallel Link Second torque B Inverter Communication Display functions Name N:N Network Second functions Pr No. Common Items FREQROL V500 Series FREQROL F500 Series FREQROL A500 Series FREQROL E500 Series FREQROL S500 Series FX Series PLC User's Manual - Data Communication Edition 12 Related Data Inverter Communication 12.5 FREQROL Inverter Parameter List FREQROL V500 Series FREQROL F500 Series FREQROL A500 Series FREQROL E500 Series FREQROL S500 Series Function Operation selecting functions Pr No. Name Pr No. Name Pr No. Name Pr No. Name Pr No. Name 68 Retry waiting time 68 Retry waiting time 68 Retry waiting time 68 Retry waiting time 68 Retry waiting time 69 Retry count display erasure 69 Retry count display erasure 69 Retry count display erase 69 Retry count display erasure 69 Retry count display erase 70 Special regenerative brake duty 70 Special regenerative brake duty 70 Special regenerative brake duty 71 Applied motor 71 Applied motor 71 Applied motor 71 Applied motor 71 Applied motor 72 PWM frequency selection (simple mode) 72 PWM frequency selection 72 PWM frequency selection 72 PWM frequency selection 72 PWM frequency selection 73 Speed setting signal 73 0 to 5V/0 to 10V selection 73 0 to 5V/0 to 10V selection 73 0 to 5V/0 to 10V selection 73 0 to 5V/0 to 10V selection 74 Filter time constant 74 Filter time constant 74 Filter time constant 74 Input filter time constant 75 Reset selection/ disconnected PU detection/PU stop selection 75 Reset selection/ disconnected PU detection/PU stop selection 75 Reset selection/ PU stop selection 75 Reset selection/ disconnected PU detection/PU stop selection 75 Reset selection/ disconnected PU detection/PU stop selection 76 Alarm code output selection 76 Alarm code output selection Parameter write disable selection (simple mode) 77 Parameter write disable selection 77 Parameter write disable selection 77 Parameter write disable selection 77 Parameter write disable selection 78 Reverse rotation prevention selection 78 Reverse rotation prevention selection 78 Reverse rotation prevention selection 78 Reverse rotation prevention selection 78 Reverse rotation prevention selection 79 Operation mode selection (simple mode) 79 Operation mode selection 79 Operation mode selection 79 Operation mode selection 79 Operation mode selection 80 Motor capacity 80 Motor capacity 80 Motor capacity 81 Number of motor poles 81 Number of motor poles Motor excitation current (no load current) 82 *1 Motor excitation current*5 82 Motor excitation current 83 Rated motor voltage 83 Rated motor voltage 83 Rated motor voltage 84 Rated motor frequency 84 Rated motor frequency 84 Rated motor frequency 89 Speed control gain 90 91 92 93 94 E-154 77 82 Motor constant Motor constant R1*1 Motor constant R2*1 Motor constant L1*1 Motor constant L2*1 Motor constant X*1 90 91 92 93 94 Motor constant (R1)*5 90 Motor constant (R1) Motor constant (R2)*5 Motor constant (L1)*5 Motor constant (L2)*5 Motor constant (X)*5 95 Online auto tuning selection (simple mode) 95 Online auto tuning selection 96 Auto tuning setting/status 96 Auto tuning setting/status 96 Auto tuning setting/status FX Series PLC User's Manual - Data Communication Edition 12 Related Data Inverter Communication 12.5 FREQROL Inverter Parameter List A Function Pr No. Name Pr No. 100 Name V/F 1 (first frequency) 102 V/F 2 (second frequency) V/F 2 (second 103 frequency voltage) 104 V/F 3 (third frequency) V/F 3 105 (third frequency voltage) V/F 4 (fourth frequency) V/F 4 107 (fourth frequency voltage) 108 V/F 5 (fifth frequency) V/F 1 (first frequency)*3 102 frequency)*3 V/F 2 (second 103 frequency voltage)*3 104 (third frequency)*3 V/F 3 105 (third frequency voltage)*3 106 D frequency)*3 V/F 4 107 (fourth frequency voltage)*3 108 V/F 5 (fifth E frequency)*3 V/F 5 109 (fifth frequency voltage)*3 111 Third deceleration time 111 Third deceleration time 113 F Non-Protocol Communication (RS/RS2 Instruction) Third acceleration /deceleration time V/F 4 (fourth 110 C V/F 3 Third acceleration /deceleration time B V/F 2 (second 110 Name V/F 1 101 (first frequency voltage)*3 112 Third functions Pr No. Inverter Communication V/F 5 109 (fifth frequency voltage) Name Computer Link 106 Pr No. Third torque boost*3 Third V/F (base frequency)*3 Third stall prevention 115 operation frequency H 117 Communication station number 117 Communication station number 117 Communication station number 117 Communication station number 118 Communication speed 118 Communication speed 118 Communication speed 118 Communication speed 119 Stop bit length/ data length 119 Stop bit length/ data length 119 Stop bit length/ data length 119 Stop bit length Parity check 120 presence/ absence Parity check 120 presence/ absence Number of 121 communication retries Number of 121 communication retries Number of 121 communication retries Number of 121 communication retries Communication 122 check time interval Communication 122 check time interval Communication 122 check time interval Communication 122 check time interval Apx.A Discontinued models Parity check 120 presence/ absence I Remote Maintenance Third speed detection Programming Communication Third output 116 frequency detection 116 CommuniParity check cation 120 presence/ functions absence G Non-Protocol Communication (FX2N-232IF) Third stall 114 prevention operation current Parallel Link 5-point flexible V/F characteristics 100 Name N:N Network V/F 1 101 (first frequency voltage) Pr No. Common Items FREQROL V500 Series FREQROL F500 Series FREQROL A500 Series FREQROL E500 Series FREQROL S500 Series E-155 FX Series PLC User's Manual - Data Communication Edition 12 Related Data Inverter Communication 12.5 FREQROL Inverter Parameter List FREQROL V500 Series FREQROL F500 Series FREQROL A500 Series FREQROL E500 Series FREQROL S500 Series Function Pr No. Name Pr No. Name Pr No. Name Pr No. Name Waiting time Waiting time Waiting time Waiting time 123 123 123 123 setting setting setting setting Communication CR and LF CR and LF CR and LF CR and LF functions 124 presence/absence 124 presence/absence 124 presence/absence 124 presence/absence selection selection selection selection PID control Name 128 PID action selection 128 PID action selection 128 PID action selection 128 PID action selection 88 PID action selection 129 PID proportional band 129 PID proportional band 129 PID proportional band 129 PID proportional band 89 PID proportional band PID integral time 130 PID integral time 130 PID integral time 130 PID integral time 130 PID integral time 90 131 Maximum 131 Maximum 131 Maximum 131 Maximum 91 PID maximum 132 Minimum 132 Minimum 132 Minimum 132 Minimum 92 PID minimum PID action set 133 point for PU operation PID action set 133 point for PU operation PID action set 133 point for PU operation PID action set 133 point for PU operation 93 PID action set point for PU operation 94 PID differential time 134 PID differential time 134 PID differential time Commercial power supplyinverter switch135 over sequence output terminal selection Commercial power supplyinverter switchover Pr No. 136 MC switch-over interlock time 134 PID differential time 134 PID differential time Commercial power supplyinverter switch135 over sequence output terminal selection 136 MC switch-over interlock time 137 Start waiting time 137 Start waiting time Commercial power supply138 inverter switchover selection at alarm occurrence Commercial power supply138 inverter switchover selection at alarm occurrence Automatic Automatic inverterinverter139 commercial power 139 commercial power supply switchsupply switchover frequency over frequency Backlash 140 acceleration stopping speed Backlash Backlash 141 acceleration stopping time Backlash 142 deceleration stopping speed Backlash 143 deceleration stopping time 144 Display functions E-156 Speed setting switchover PU display 145 language selection Backlash acceleration 140 stopping Backlash acceleration 140 stopping frequency*2 frequency*2 Backlash 141 acceleration stopping time*2 Backlash 141 acceleration stopping time*2 Backlash deceleration 142 stopping Backlash deceleration 142 stopping frequency*2 Backlash 143 deceleration stopping time*2 144 Speed setting switchover PU display 145 language selection frequency*2 Backlash 143 deceleration stopping time*2 144 Speed setting switchover PU display 145 language selection PU display 145 language selection n13 PU display (145) language FX Series PLC User's Manual - Data Communication Edition 12 Related Data Inverter Communication 12.5 FREQROL Inverter Parameter List A Function Pr No. Name Pr No. Name Stall prevention 148 operation level at 0 V input Stall prevention 148 operation level at 0 V input Stall prevention 149 operation level at 10 V input Stall prevention 149 operation level at 10 V input Output current detection level 151 Output current detection period 152 Zero current detection level 152 153 Zero current detection period 153 Output current detection level 48 Output current detection level 151 Output current detection period 151 Output current detection period 49 Output current detection signal delay time Zero current detection level 152 Zero current detection level 152 Zero current detection level 50 Zero current detection level Zero current detection period 153 Zero current detection period 153 Zero current detection period 51 Zero current detection time RT activated condition Stall prevention 156 operation selection Stall prevention 156 operation selection 157 OL signal waiting time 158 DA2 terminal function selection 158 AM terminal function selection 158 AM terminal function selection Extended function 160 selection (simple mode) 160 User group read selection 160 User group read selection Automatic restart after 162 instantaneous power failure selection Automatic restart after 162 instantaneous power failure selection First cushion time for restart 163 First cushion time for restart 163 First cushion time for restart 164 First cushion voltage for restart 164 First cushion voltage for restart 164 First cushion voltage for restart Restart current restriction level Restart stall 165 prevention operation level Actual operation hour meter clear Stall prevention 156 operation selection 160 F User group read selection G H 170 Watt-hour meter clear 170 Watt-hour meter clear 171 Actual operation hour meter clear 171 Actual operation hour meter clear 171 Actual operation hour meter clear I User group 1 173 registration User group 1 deletion 174 User group 1 deletion 174 User group 1 deletion 175 User group 2 registration 175 User group 2 registration 175 User group 2 registration 176 User group 2 deletion 176 User group 2 deletion 176 User group 2 deletion Apx.A Discontinued models 174 D E Restart stall 165 prevention operation level User group 1 173 registration C Remote Maintenance Automatic restart after 162 instantaneous power failure selection 163 171 RT signal 155 activated condition OL signal output waiting time User group 1 173 registration User functions Voltage reduction selection during 154 stall prevention operation 157 150 OL signal output timer Programming Communication Initial monitor value Output current detection level 157 165 B Non-Protocol Communication (FX2N-232IF) Restart after instantaneous power failure Frequency setting 146 command selection Non-Protocol Communication (RS/RS2 Instruction) Additional function Stall prevention 156 operation selection Name Inverter Communication Sub functions Pr No. 150 Voltage reduction selection during 154 stall prevention operation 155 Name Computer Link 150 Pr No. Parallel Link Current detection Name N:N Network Additional functions Pr No. Common Items FREQROL V500 Series FREQROL F500 Series FREQROL A500 Series FREQROL E500 Series FREQROL S500 Series E-157 FX Series PLC User's Manual - Data Communication Edition 12 Related Data Inverter Communication 12.5 FREQROL Inverter Parameter List FREQROL V500 Series FREQROL F500 Series FREQROL A500 Series FREQROL E500 Series FREQROL S500 Series Function Pr No. Name Pr No. Name Pr No. Name Pr No. Name Pr No. Name 180 DI1 terminal function selection 180 RL terminal function selection 180 RL terminal function selection 180 RL terminal function selection 60 RL terminal function selection 181 DI2 terminal function selection 181 RM terminal function selection 181 RM terminal function selection 181 RM terminal function selection 61 RM terminal function selection 182 DI3 terminal function selection 182 RH terminal function selection 182 RH terminal function selection 182 RH terminal function selection 62 RH terminal function selection 183 DI4 terminal function selection 183 RT terminal function selection 183 RT terminal function selection 183 MRS terminal function selection 184 AU terminal function selection 184 AU terminal function selection JOG terminal function selection 185 JOG terminal function selection 185 186 CS terminal function selection 186 CS terminal function selection Terminal assignment functions 187 STR terminal function selection 63 STR terminal function selection 190 DO1 terminal function selection 190 RUN terminal function selection 190 RUN terminal function selection 190 RUN terminal function selection 64 RUN terminal function selection 191 DO2 terminal function selection 191 SU terminal function selection 191 SU terminal function selection 191 FU terminal function selection 192 DO3 terminal function selection 192 IPF terminal function selection 192 IPF terminal function selection 192 A/B/C terminal function selection 65 A/B/C terminal function selection 193 OL terminal function selection 193 OL terminal function selection 194 FU terminal function selection 194 FU terminal function selection Additional function 195 A/B/C terminal function selection 195 A/B/C terminal function selection 195 A/B/C terminal function selection 199 User's initial value setting 199 User's initial value setting Programmed 200 operation minute/ second selection 201 Program set 1 202 Program set 1 203 Program set 1 204 Program set 1 205 Program set 1 206 Program set 1 207 Program set 1 208 Program set 1 209 Program set 1 Programmed operation 210 Program set 1 211 Program set 2 212 Program set 2 213 Program set 2 214 Program set 2 215 Program set 2 216 Program set 2 217 Program set 2 218 Program set 2 219 Program set 2 220 Program set 2 221 Program set 3 222 Program set 3 223 Program set 3 E-158 FX Series PLC User's Manual - Data Communication Edition 12 Related Data Inverter Communication 12.5 FREQROL Inverter Parameter List A Function Pr No. Name Pr No. Name Pr No. Name Pr No. Name Pr No. Name 224 Program set 3 225 Program set 3 B 226 Program set 3 227 Program set 3 228 Program set 3 229 Program set 3 230 Program set 3 231 Timer setting Multi-speed setting (speed 8) 232 Multi-speed setting (speed 8) 80 Multi-speed setting (speed 8) 233 Multi-speed setting (speed 9) 233 Multi-speed setting (speed 9) 233 Multi-speed setting (speed 9) 81 Multi-speed setting (speed 9) 234 Multi-speed setting (speed 10) 234 Multi-speed Multi-speed 234 setting (speed 10) setting (speed 10) 82 Multi-speed setting (speed 10) 235 Multi-speed setting (speed 11) 235 Multi-speed Multi-speed 235 setting (speed 11) setting (speed 11) 83 Multi-speed setting (speed 11) 236 Multi-speed Multi-speed 236 setting (speed 12) setting (speed 12) 84 Multi-speed setting (speed 12) Multi-speed setting (speed 12) 237 Multi-speed setting (speed 13) 237 Multi-speed Multi-speed 237 setting (speed 13) setting (speed 13) 85 Multi-speed setting (speed 13) 238 Multi-speed setting (speed 14) 238 Multi-speed Multi-speed 238 setting (speed 14) setting (speed 14) 86 Multi-speed setting (speed 14) Multi-speed Multi-speed 239 239 setting (speed 15) setting (speed 15) 87 Multi-speed setting (speed 15) Multi-speed 239 setting (speed 15) 240 Soft-PWM setting 240 Soft-PWM setting 240 Soft-PWM setting 240 Soft-PWM setting 70 Soft-PWM setting Cooling fan 244 operation selection Cooling fan 244 operation selection Cooling fan 244 operation selection Cooling fan 244 operation selection 76 Cooling fan operation selection 245 Rated motor slip 95 Rated motor slip Slip compensation time constant 247 Constant-output region slip compensation selection 97 Constant-output region slip compensation selection 98 Automatic torque boost selection (motor capacity) Earth (ground) 249 fault detection at start*6 99 Motor primary resistance 250 Stop selection 250 Stop selection Output phase 251 failure protection selection Sub functions Stop selecting function Additional functions 250 Stop selection Output phase 251 failure protection selection Output phase 251 failure protection selection Output phase 251 failure protection selection 252 Override bias 252 Override bias 252 Override bias 253 Override gain 253 Override gain 253 Override gain Power failure stop selection Subtraction speed 262 at deceleration start 264 Power-failure deceleration time 1 Power failure stop selection Subtraction 262 frequency at deceleration start Apx.A Subtraction 263 starting frequency 264 I Discontinued models Subtraction 263 starting speed 261 H Remote Maintenance 261 Power failure stop functions G Programming Communication 96 F Non-Protocol Communication (FX2N-232IF) Slip compensation response time E Non-Protocol Communication (RS/RS2 Instruction) 246 D Inverter Communication 236 C Computer Link 232 Parallel Link Multispeed operation Multi-speed 232 setting (speed 8) N:N Network Programmed operation Common Items FREQROL V500 Series FREQROL F500 Series FREQROL A500 Series FREQROL E500 Series FREQROL S500 Series Power-failure deceleration time 1 E-159 FX Series PLC User's Manual - Data Communication Edition 12 Related Data Inverter Communication 12.5 FREQROL Inverter Parameter List FREQROL V500 Series FREQROL F500 Series FREQROL A500 Series FREQROL E500 Series FREQROL S500 Series Function Power failure stop functions Function selection Pr No. Name 265 Power-failure deceleration time 2 Power-failure 266 deceleration time switchover speed Pr No. Name Pr No. Name 265 Power-failure deceleration time 2 Power-failure deceleration time 266 switchover frequency Stop-on-contact/ load torque high 270 speed frequency control selection Pr No. Name Pr No. Name High speed 271 setting maximum current High speed frequency control Stop-oncontact 12-bit digital input E-160 Current averaging range 274 Current averaging filter constant Stop-on-contact exciting current 275 low speed multiplying factor 278 Brake opening speed 278 279 Brake opening current 279 281 282 frequency*4 Brake opening current*4 Brake opening 280 current detection time*4 Brake operation time at start Brake operation speed Brake opening 281 282 Brake operation time at start*4 Brake operation *4 frequency Brake operation Brake operation 283 time at stop 283 Deceleration 284 detection function selection Deceleration 284 detection function selection*4 285 Droop control functions 273 Stop-on-contact 276 PWM carrier frequency Brake opening 280 current detection time Brake sequence function Middle speed 272 setting minimum current time at stop*4 Overspeed 285 detection frequency Overspeed detection speed 286 Droop gain 286 Droop gain Droop filter 287 constant 287 Droop function 288 activation selection Droop filter constant 300 BCD input bias 300 BCD code input bias 300 BCD code input bias 301 BCD input gain 301 BCD code input gain 301 BCD code input gain 302 Binary input bias 302 Binary input bias 302 Binary input bias 303 Binary input gain 303 Binary input gain 303 Binary input gain FX Series PLC User's Manual - Data Communication Edition 12 Related Data Inverter Communication 12.5 FREQROL Inverter Parameter List A Function Name Pr No. Name Pr No. Name Digital input and analog 304 compensation input enable/ disable selection Selection of whether digital input and analog 304 compensation input are enabled or disabled Selection of whether digital input and analog 304 compensation input are enabled or disabled Read timing 305 operation selection Data read timing 305 signal on/off selection Data read timing 305 signal on/off selection Analog output signal selection 306 Analog output signal selection 306 Analog output signal selection 307 Setting for zero analog output 307 Setting for zero analog output 307 Setting for zero analog output Setting for 308 maximum analog output Setting for 308 maximum analog output Name Pr No. Name B C Parallel Link 306 Pr No. Setting for 308 maximum analog output D Analog meter 310 voltage output selection Setting for zero 311 analog meter voltage output Setting for zero 311 analog meter voltage output Setting for zero 311 analog meter voltage output Setting for maximum analog 312 meter voltage output Setting for maximum analog 312 meter voltage output Setting for maximum analog 312 meter voltage output 313 Y0 output selection 313 Y0 output selection 313 Y0 output selection F 314 Y1 output selection 314 Y1 output selection 314 Y1 output selection Non-Protocol Communication (RS/RS2 Instruction) 315 Y2 output selection 315 Y2 output selection 315 Y2 output selection 316 Y3 output selection 316 Y3 output selection 316 Y3 output selection 317 Y4 output selection 317 Y4 output selection 317 Y4 output selection 318 Y5 output selection 318 Y5 output selection 318 Y5 output selection 319 Y6 output selection 319 Y6 output selection 319 Y6 output selection 320 RA1 output selection 320 RA1 output selection 321 RA2 output selection 321 RA2 output selection 321 RA2 output selection 322 RA3 output selection 322 RA3 output selection 322 RA3 output selection Digital input 329 Digital input unit selection Relay output 330 RA output selection 330 RA output selection 331 Communication station number 331 332 Relay output 330 RA output selection Inverter station number 331 Communication station number n1 Communication (331) station number Communication speed 332 Communication speed n2 Communication (332) speed I Stop bit length/ 333 data length Stop bit length/ 333 data length n3 Stop bit length/ (333) data length Parity check yes/ 334 no Parity check yes/ 334 no 335 335 Communication retry count Parity check n4 presence/ (334) absence Number of n5 communication (335) retries E-161 H Apx.A Discontinued models Communication retry count Remote Maintenance Computer 332 Communication speed link Stop bit length/ function 333 data length (S500 Series Parity check communi- 334 presence/ cation absence parameter) Number of 335 communication retries G Programming Communication RA1 output selection Non-Protocol Communication (FX2N-232IF) 320 E Inverter Communication Analog output/ digital output Analog meter 310 voltage output selection Computer Link Analog output Analog output Analog output 309 signal voltage/ 309 signal voltage/ 309 signal voltage/ current switchover current switchover current switchover Analog meter 310 voltage output selection N:N Network 12-bit digital input Pr No. Common Items FREQROL V500 Series FREQROL F500 Series FREQROL A500 Series FREQROL E500 Series FREQROL S500 Series FX Series PLC User's Manual - Data Communication Edition 12 Related Data Inverter Communication 12.5 FREQROL Inverter Parameter List FREQROL V500 Series FREQROL F500 Series FREQROL A500 Series FREQROL E500 Series FREQROL S500 Series Function Pr No. Name Name Pr No. Name Communication 336 check time interval Communication 336 check time interval Communication 336 check time interval Waiting time 337 setting Waiting time 337 setting Waiting time 337 setting Computer Operation link 338 command source function Speed command (S500 339 source Series communiLink startup mode 340 cation selection parameter) CR and LF 341 presence/absence selection DeviceNet communication Pr No. Pr No. Name Operation command write 338 Operation command right 338 Operation command source n8 Operation (338) command write 339 Speed command write 339 Speed command write 339 Speed command source n9 Speed command (339) write 340 Link startup mode selection 340 Link startup mode selection 340 Link startup mode n10 Link start mode (340) selection selection 341 CR and LF yes/no selection 341 CR and LF yes/no selection 2 342 E PROM write selection 2 342 E PROM write selection DeviceNet 345 address (lower) DeviceNet 345 address startup data (lower byte) DeviceNet 345 address startup data (lower byte) DeviceNet 345 address startup data (lower byte) DeviceNet baud 346 rate startup data (lower byte) DeviceNet baud 346 rate startup data (lower byte) DeviceNet baud 346 rate startup data (lower byte) DeviceNet 347 address startup data (higher byte) DeviceNet 347 address startup data (higher byte) DeviceNet baud 348 rate (higher) DeviceNet baud 348 rate startup data (higher byte) DeviceNet baud 348 rate startup data (higher byte) Stop position 350 command selection Stop position 350 command selection DeviceNet 347 address (higher) 351 Communication n6 check time (336) interval 338 2 342 E PROM write selection DeviceNet baud rate (lower) Name n7 Wait time setting (337) 2 342 E PROM write selection 346 Pr No. Orientation switchover speed 351 n11 CR and LF (341) selection n12 E2PROM write (342) selection Orientation switchover speed 352 Creep speed 353 355 DC injection start position 356 Internal stop position command 357 In-position zone 358 Servo torque selection Orientation 359 encoder rotation direction 359 Encoder rotation direction External position 360 command selection 360 12-bit data selection 361 Position shift 361 Position shift Orientation 362 position loop gain 362 Position loop gain E-162 Position loop 354 switchover position Orientation control/ Internal stop encoder 356 position command feedback control/ 357 In-position zone pulse train input Creep switch position 363 Completion signal output delay time FX Series PLC User's Manual - Data Communication Edition 12 Related Data Inverter Communication 12.5 FREQROL Inverter Parameter List A Function Pr No. Pr No. Name Pr No. Name 364 Encoder stop check time 365 Orientation censored limit 366 Reconfirmation time 367 Speed feedback range Pr No. Name Pr No. Name B N:N Network Name 368 Feedback gain Control mode selection Torque 371 characteristic selection D 370 Speed control P gain 373 Speed control I gain 374 Over-speed detection level E 380 Acceleration S pattern 1 380 Acceleration S pattern 1 381 Deceleration S pattern 1 381 Deceleration S pattern 1 F 382 Acceleration S pattern 2 382 Acceleration S pattern 2 383 Deceleration S pattern 2 383 Deceleration S pattern 2 Non-Protocol Communication (RS/RS2 Instruction) 375 Servo lock gain 385 376 Disconnection detection selection Input pulse 384 division scaling factor Speed for zero input pulse 385 Speed for 386 maximum input pulse Frequency for zero input pulse Frequency for 386 maximum input pulse 388 Send time interval at hart beat 388 Send time interval at hart beat 389 Minimum sending time at hart beat 389 Minimum sending time at hart beat Receive time 391 interval at heart beat 392 Event-driven detection width % setting 390 reference frequency Receive time 391 interval at heart beat 392 I Remote Maintenance % setting 390 reference frequency H Initial 387 communication delay time Programming Communication Initial 387 communication delay time G Non-Protocol Communication (FX2N-232IF) Input pulse 384 division scaling factor LONWORKS communication Computer Link 372 Inverter Communication Orientation control/ encoder feedback Over-speed control/ 374 detection level pulse train input C Number of 369 orientation encoder pulse Parallel Link Number of 369 orientation encoder pulse Common Items FREQROL V500 Series FREQROL F500 Series FREQROL A500 Series FREQROL E500 Series FREQROL S500 Series Event-driven detection width Apx.A Discontinued models E-163 FX Series PLC User's Manual - Data Communication Edition 12 Related Data Inverter Communication 12.5 FREQROL Inverter Parameter List FREQROL V500 Series FREQROL F500 Series FREQROL A500 Series FREQROL E500 Series FREQROL S500 Series Function Pr No. 393 Name Pr No. Name Pr No. Name Pr No. Name Pr No. Name Orientation selection Number of 394 machine side gear teeth 395 Number of motor side gear teeth Orientation Orientation speed 396 selection gain (P term) Extension input 397 Orientation speed integral time 398 Orientation speed gain (D term) 399 Orientation deceleration ratio 400 DI11 terminal function selection 401 DI12 terminal function selection 402 DI13 terminal function selection 403 DI14 terminal function selection 404 DI15 terminal function selection 405 DI16 terminal function selection High resolution 406 analog input selection Motor 407 temperature detection filter Extension output 410 DO11 terminal function selection 411 DO12 terminal function selection 412 DO13 terminal function selection Encoder pulse 413 output division ratio Position 419 command source selection Command pulse 420 scaling factor numerator Command pulse 421 scaling factor Positioning denominator control 422 Position loop gain 423 Position feed forward gain Position command 424 acceleration/ deceleration time constant E-164 FX Series PLC User's Manual - Data Communication Edition 12 Related Data Inverter Communication 12.5 FREQROL Inverter Parameter List A Function Pr No. Name Pr No. Name Pr No. Name Pr No. Name Pr No. Name Position feed 425 forward command filter B 427 Excessive level error 428 Command pulse selection 429 Clear signal selection C 432 Pulse train torque command bias 433 Pulse train torque command gain Parallel Link Pulse monitor 430 selection Torque command D Computer Link 434 IP address 1 435 IP address 2 436 IP address 3 437 IP address 4 438 Sub-net mask 1 439 Sub-net mask 2 440 Sub-net mask 3 441 Sub-net mask 4 442 Gateway address 1 443 Gateway address 2 444 Gateway address 3 F 445 Gateway address 4 448 Digital torque command gain 450 Second applied motor G Second motor 451 control method selection 452 Second electronic thermal O/L relay 453 Second motor capacity 454 Number of second motor poles 464 Digital position control sudden stop deceleration time H I First position feed 466 amount upper 4 digits Remote Maintenance First position feed 465 amount lower 4 digits Programming Communication Position control Digital torque command bias Non-Protocol Communication (FX2N-232IF) Motor constant 447 Non-Protocol Communication (RS/RS2 Instruction) 446 Password Torque command E Inverter Communication Position control N:N Network 426 In-position width Positioning control Common Items FREQROL V500 Series FREQROL F500 Series FREQROL A500 Series FREQROL E500 Series FREQROL S500 Series Apx.A Discontinued models Second position 467 feed amount lower 4 digits E-165 FX Series PLC User's Manual - Data Communication Edition 12 Related Data Inverter Communication 12.5 FREQROL Inverter Parameter List FREQROL V500 Series FREQROL F500 Series FREQROL A500 Series FREQROL E500 Series FREQROL S500 Series Function Pr No. Name Pr No. Name Pr No. Name Pr No. Name Pr No. Name Second position 468 feed amount upper 4 digits Third position 469 feed amount lower 4 digits Third position 470 feed amount upper 4 digits Fourth position 471 feed amount lower 4 digits Fourth position 472 feed amount upper 4 digits Fifth position feed 473 amount lower 4 digits Fifth position feed 474 amount upper 4 digits Sixth position feed 475 amount lower 4 digits Sixth position feed 476 amount upper 4 digits Position control Seventh position 477 feed amount lower 4 digits Seventh position 478 feed amount upper 4 digits Eighth position 479 feed amount lower 4 digits Eighth position 480 feed amount upper 4 digits Ninth position 481 feed amount lower 4 digits Ninth position 482 feed amount upper 4 digits Tenth position 483 feed amount lower 4 digits Tenth position 484 feed amount upper 4 digits Eleventh position 485 feed amount lower 4 digits Eleventh position 486 feed amount upper 4 digits Twelfth position 487 feed amount lower 4 digits E-166 FX Series PLC User's Manual - Data Communication Edition 12 Related Data Inverter Communication 12.5 FREQROL Inverter Parameter List A Function Pr No. Name Pr No. Name Pr No. Name Pr No. Name Pr No. Name Twelfth position 488 feed amount upper 4 digits B N:N Network Thirteenth position feed 489 amount lower 4 digits Thirteenth position feed 490 amount upper 4 digits Fourteenth position feed 491 amount lower 4 digits 492 Fourteenth position feed amount upper 4 digits D Fifteenth position 493 feed amount lower 4 digits Computer Link Fifteenth position 494 feed amount upper 4 digits E 495 Remote output selection 496 Remote output data 1 497 Remote output data 2 F Auxiliary motor operation Communication 500 error recognition waiting time Communication 500 error recognition waiting time Motor switch-over selection Communication 501 error occurrence count display Communication 501 error occurrence count display MC switching 502 interlock time Communication 502 error-time stop mode selection Stop mode selection at 502 communication error 503 Start waiting time 503 Auxiliary motor 504 connection-time deceleration time Capacitor life 504 alarm output setting time 500 501 H Programming Communication Capacitor life timer I 506 Output stop detection time 507 Output stop detection level Apx.A Discontinued models Output stop 508 cancel process value level 509 Remote Maintenance Auxiliary motor 505 disconnection-time acceleration time G Non-Protocol Communication (FX2N-232IF) CommuniCommunication cation 500 error recognition (F500 waiting time Series Communication Advanced PID control 501 error occurrence count display functions) Stop mode selection at 502 communication error Non-Protocol Communication (RS/RS2 Instruction) Action selection at SSCNET 499 communication interruption Capacitor life (F500 Series Advanced PID control functions) Inverter Communication Remote output C Parallel Link Position control Common Items FREQROL V500 Series FREQROL F500 Series FREQROL A500 Series FREQROL E500 Series FREQROL S500 Series Auxiliary motor 1 starting frequency E-167 FX Series PLC User's Manual - Data Communication Edition 12 Related Data Inverter Communication 12.5 FREQROL Inverter Parameter List FREQROL V500 Series FREQROL F500 Series FREQROL A500 Series FREQROL E500 Series FREQROL S500 Series Function Capacitor life (F500 Series Advanced PID control functions) Restart after instantaneous power failure Pr No. Name Pr No. Name 510 Auxiliary motor 2 starting frequency 511 Auxiliary motor 3 starting frequency Pr No. Name Pr No. Name Pr No. Name Auxiliary motor 1 512 stopping frequency Auxiliary motor 2 513 stopping frequency Auxiliary motor 3 514 stopping frequency 515 Auxiliary motor start delay time 516 Auxiliary motor start delay time Restart acceleration time 611 Control system 800 selection (simple mode) Torque 801 characteristic selection Operation selecting function 802 Pre-excitation selection 803 Constant output region torque characteristic selection 804 Torque command source selection 805 Torque command source (RAM) Torque command 806 source (RAM, EEPROM) 807 Speed restriction selection 808 Forward rotation speed restriction 809 Reverse rotation speed restriction Torque restriction 810 input method selection Control system function (A500 Series vector control) Torque restriction 812 level (regeneration) Torque restriction 813 level (3rd quadrant) Torque restriction 814 level (4th quadrant) E-168 FX Series PLC User's Manual - Data Communication Edition 12 Related Data Inverter Communication 12.5 FREQROL Inverter Parameter List A Function Pr No. Name 815 Torque restriction level 2 Pr No. Name Pr No. Name Acceleration 816 torque restriction level Deceleration 817 torque restriction level Deceleration 817 torque restriction level 818 Name Pr No. Name B N:N Network Acceleration 816 torque restriction level Pr No. Easy gain tuning response level setting (simple mode) C Parallel Link Easy gain tuning 819 selection (simple mode) 820 Speed control P gain 1 D 822 Speed setting filter 1 823 Speed detection filter 1 824 Torque control P gain 1 825 Torque control integral time 1 826 Torque setting filter 1 827 Torque detection filter 1 828 Model speed control gain 830 Speed control P gain 2 831 Speed control integral time 2 G Speed setting 832 filter 2 Non-Protocol Communication (FX2N-232IF) Computer Link Speed control 821 integral time 1 Torque control P gain 2 835 Torque control integral time 2 836 Torque setting filter 2 837 Torque detection filter 2 840 Torque bias selection F H I 841 Torque bias 1 Torque biases 842 Torque bias 2 843 Torque bias 3 844 Torque bias filter 845 Remote Maintenance 834 Programming Communication Speed detection filter 2 Non-Protocol Communication (RS/RS2 Instruction) 833 E Inverter Communication Control system function (A500 Series vector control) Common Items FREQROL V500 Series FREQROL F500 Series FREQROL A500 Series FREQROL E500 Series FREQROL S500 Series Apx.A Discontinued models Torque bias operation time E-169 FX Series PLC User's Manual - Data Communication Edition 12 Related Data Inverter Communication 12.5 FREQROL Inverter Parameter List FREQROL V500 Series FREQROL F500 Series FREQROL A500 Series FREQROL E500 Series FREQROL S500 Series Function Pr No. Name Pr No. Name Pr No. Name Pr No. Name Pr No. Name Torque bias 846 balance compensation Torque biases 847 Fall-time torque bias No. 3 bias Fall-time torque 848 bias No. 3 gain 849 Analog input offset adjustment 851 Number of encoder pulses 852 Encoder rotation direction 854 Excitation ratio Additional functions 859 Torque current 862 Notch filter frequency 863 Notch filter depth 864 Torque detection Display functions Terminal assignment function Protection functions 865 Low speed detection 866 Torque monitoring reference 867 DA1 output filter No. 1 terminal 868 function assignment 870 Speed deviation level 871 Speed deviation time 873 Speed restriction 874 OLT level setting Operation selecting functions 875 Fault definition 876 Thermal relay protector input Speed feed forward/model 877 adaptive speed control selection Control system functions 878 Speed feed forward filter Speed feed 879 forward torque restriction 880 Load inertia ratio Maintenance functions E-170 881 Speed feed forward gain 890 Maintenance output setting time 891 Maintenance output timer 892 Maintenance output signal clear FX Series PLC User's Manual - Data Communication Edition 12 Related Data Inverter Communication 12.5 FREQROL Inverter Parameter List A Function Pr No. Pr No. Name Pr No. Name Pr No. Name FM terminal calibration DA1 terminal calibration 900 FM terminal calibration 900 FM terminal calibration 900 901 DA2 terminal calibration 901 AM terminal calibration 901 AM terminal calibration Pr No. Name C1 FM (AM) terminal (900 calibration (901)) 902 Frequency setting voltage bias 902 Frequency setting voltage bias 903 Speed setting No. 2 gain 903 Frequency setting voltage gain 903 Frequency setting voltage gain 903 Frequency setting current bias Frequency setting C5 current bias Frequency setting (904) frequency 904 current bias C6 Frequency setting (904) current bias Frequency setting current gain 905 Torque command No. 3 bias 904 905 Torque command No. 3 gain 905 No. 1 terminal bias (speed) 918 No. 1 terminal gain (speed) 904 Frequency setting current gain 905 Frequency setting C7 Frequency setting (905) current gain current gain Parameter set by C8 manufacturer. Do (269) not set. F Non-Protocol Communication (RS/RS2 Instruction) No. 1 terminal 920 gain (torque/ magnetic flux) Built-in frequency setting 922 potentiometer bias*7 Motor temperature 925 detection calibration No. 6 terminal gain (speed) 928 No. 6 terminal bias (torque) 929 No. 6 terminal gain (torque) 990 PU buzzer control Additional functions 991 I 990 PU buzzer control 991 PU contrast adjustment 990 PU Buzzer control 990 PU buzzer control 991 PU contrast adjustment 991 PU contrast adjustment n14 PU buzzer sound (990) control n15 PU contrast (991) adjustment PU main display n16 screen data (992) selection E-171 Apx.A Discontinued models PU contrast adjustment Remote Maintenance 927 H Programming Communication No. 6 terminal bias (speed) G Non-Protocol Communication (FX2N-232IF) Built-in frequency setting 923 potentiometer gain*7 926 D E No. 1 terminal 919 bias (torque/ magnetic flux) C Inverter Communication 917 Frequency setting current bias Frequency setting C4 Frequency setting voltage gain (903) voltage gain Computer Link Speed setting No. 2 bias Parallel Link 902 Frequency setting C2 voltage bias Frequency setting (902) frequency 902 voltage bias C3 Frequency setting (902) voltage bias B N:N Network 900 904 Calibration functions Name Common Items FREQROL V500 Series FREQROL F500 Series FREQROL A500 Series FREQROL E500 Series FREQROL S500 Series FX Series PLC User's Manual - Data Communication Edition 12 Related Data Inverter Communication 12.5 FREQROL Inverter Parameter List FREQROL V500 Series FREQROL F500 Series FREQROL A500 Series FREQROL E500 Series FREQROL S500 Series Function Pr No. Name Pr No. Name Pr No. Name Pr No. Name Additional functions Pr No. Name PU disconnection n17 detection/PU (993) setting lock The parameters Pr. 77 and Pr. 79 cannot be written in computer link operation using the FR-A5NR. *1. E-172 Can be read or written when the parameter Pr. 77 is set to "801". *2. Can be read or written when the parameter Pr. 29 is set to "3". *3. Indicates a parameter whose setting is ignored when the advanced magnetic flux vector control mode is selected. *4. Can be set when the parameters Pr. 80 and Pr. 81 are not set to "9999" and the parameter Pr. 60 is set to "7" or "8". *5. Can be read or written when the parameters Pr. 80 and Pr. 81 are not set to "9999" and the parameter Pr. 77 is set to "801". *6. Can be set only in the 200 V/100 V class. *7. Cannot be used in inverter communication. *8. This inverter communication function cannot read or write Pr. 37. Set Pr. 37 to "0" when setting or monitoring the frequency in the PLC. If any value other than "0" is set to Pr. 37 and the instruction code HFF is set to "01", the frequency may not be set or monitored normally (in the 400 V class of the E500 series and S500 series). (In the 200 V and 100 V classes of the E500 series, the frequency may not be set or monitored normally if any value other than "0" is set to Pr. 37 without regard to the setting of the instruction code HFF.) FX Series PLC User's Manual - Data Communication Edition 12 Related Data Inverter Communication 12.5 FREQROL Inverter Parameter List A The following parameters are provided in the F700, A700, E700 and D700 Series inverters. (For details, make sure to refer to the respective inverter manual.) FREQROL F700 Series Name FREQROL D700 Series Pr No. Name Torque boost 0 Torque boost 0 Torque boost 0 Torque boost 1 Maximum frequency 1 Maximum frequency 1 Maximum frequency 1 Maximum frequency 2 Minimum frequency 2 Minimum frequency 2 Minimum frequency 2 Minimum frequency 3 Base frequency 3 Base frequency 3 Base frequency 3 Base frequency 4 Multispeed setting (high speed) 4 Multi-speed setting (high speed) 4 Multi-speed setting (high speed) 4 Multi-speed setting (high speed) 5 Multispeed setting (middle speed) 5 Multi-speed setting (middle speed) 5 Multi-speed setting (middle speed) 5 Multi-speed setting (middle speed) 6 Multispeed setting (low speed) 6 Multi-speed setting (low speed) 6 Multi-speed setting (low speed) 6 Multi-speed setting (low speed) 7 Acceleration time 7 Acceleration time 7 Acceleration time 7 Acceleration time 8 Deceleration time 8 Deceleration time 8 Deceleration time 8 Deceleration time 9 Electronic thermal O/L relay 9 Electronic thermal O/L relay 9 Electronic thermal O/L relay 9 Electronic thermal O/L relay 10 DC injection brake operation frequency 10 DC injection brake operation frequency 10 DC injection brake operation frequency 10 DC injection brake operation frequency 11 DC injection brake operation time 11 DC injection brake operation time 11 DC injection brake operation time 11 DC injection brake operation time 12 DC injection brake operation voltage 12 DC injection brake operation voltage 12 DC injection brake operation voltage 12 DC injection brake operation voltage 13 Starting frequency 13 Starting frequency 13 Starting frequency 13 Starting frequency 14 Load pattern selection 14 Load pattern selection 14 Load pattern selection 14 Load pattern selection 15 Jog frequency 15 Jog frequency 15 Jog frequency 15 Jog frequency 16 Jog acceleration/ deceleration time 16 Jog acceleration/ deceleration time 16 Jog acceleration/ deceleration time 16 Jog acceleration/ deceleration time 17 MRS input selection 18 19 Base frequency voltage 19 Base frequency voltage 19 Base frequency voltage 19 Base frequency voltage Acceleration/ 20 deceleration reference frequency Acceleration/ 20 deceleration reference frequency Acceleration/ 20 deceleration reference frequency Acceleration/ 20 deceleration reference frequency Acceleration/ 21 deceleration time increments Acceleration/ 21 deceleration time increments Acceleration/ 21 deceleration time increments 22 Stall prevention operation level 22 Stall prevention operation level 23 Stall prevention operation level compensation factor at double speed 23 Stall prevention operation level compensation factor at double speed Acceleration/ deceleration times High speed maximum frequency High speed maximum frequency Stall prevention operation level 23 Stall prevention operation level compensation factor at double speed 23 Stall prevention operation level compensation factor at double speed 18 High speed maximum frequency Multi-speed setting 24 (speed 4) 17 MRS input selection 18 High speed maximum frequency H Multi-speed setting 24 (speed 4) Multi-speed setting (speed 5) 25 Multi-speed setting (speed 5) 25 Multi-speed setting (speed 5) 25 Multi-speed setting (speed 5) 26 Multi-speed setting (speed 6) 26 Multi-speed setting (speed 6) 26 Multi-speed setting (speed 6) 26 Multi-speed setting (speed 6) 27 Multi-speed setting (speed 7) 27 Multi-speed setting (speed 7) 27 Multi-speed setting (speed 7) 27 Multi-speed setting (speed 7) 28 Multi-speed input compensation selection 28 Multi-speed input compensation selection E-173 I Apx.A Discontinued models 25 G Remote Maintenance Multi-speed setting 24 (speed 4) 17 MRS input selection F Programming Communication 22 Multi-speed setting 24 (speed 4) 18 Stall prevention 22 operation level (torque limit level ) Stall prevention Multispeed setting 17 MRS input selection E Non-Protocol Communication (FX2N-232IF) D Non-Protocol Communication (RS/RS2 Instruction) Jog operation C Computer Link 0 B Inverter Communication DC injection brake Name FREQROL E700 Series Pr No. Parallel Link Basic functions Name FREQROL A700 Series Pr No. N:N Network Function Pr No. Common Items 12.5.2 Parameters in F700, A700, E700 and D700 Series FX Series PLC User's Manual - Data Communication Edition 12 Related Data Inverter Communication 12.5 FREQROL Inverter Parameter List FREQROL F700 Series Function Pr No. Name Acceleration/ 29 deceleration pattern selection 30 Regenerative function selection FREQROL A700 Series Pr No. Name Acceleration/ 29 deceleration pattern selection 30 Regenerative function selection FREQROL E700 Series Pr No. Name Acceleration/ 29 deceleration pattern selection 30 Regenerative function selection FREQROL D700 Series Pr No. Name Acceleration/ 29 deceleration pattern selection 30 Regenerative function selection 31 Frequency jump 1A 31 Frequency jump 1A 31 Frequency jump 1A 31 Frequency jump 1A 32 Frequency jump 1B 32 Frequency jump 1B 32 Frequency jump 1B 32 Frequency jump 1B 33 Frequency jump 2A 33 Frequency jump 2A 33 Frequency jump 2A 33 Frequency jump 2A 34 Frequency jump 2B 34 Frequency jump 2B 34 Frequency jump 2B 34 Frequency jump 2B 35 Frequency jump 3A 35 Frequency jump 3A 35 Frequency jump 3A 35 Frequency jump 3A 36 Frequency jump 3B 36 Frequency jump 3B 36 Frequency jump 3B 36 Frequency jump 3B 37 Speed display 37 Speed display 37 Speed display*1 37 Speed display*1 40 RUN key rotation direction selection 40 RUN key rotation direction selection Frequency jump Frequency detection Second functions Monitor functions Automatic restart functions 41 Uptofrequency sensitivity 41 Up-to-frequency sensitivity 41 Up-to-frequency sensitivity 41 Up-to-frequency sensitivity 42 Output frequency detection 42 Output frequency detection 42 Output frequency detection 42 Output frequency detection Output frequency 43 detection for reverse rotation Output frequency 43 detection for reverse rotation Output frequency 43 detection for reverse rotation Output frequency 43 detection for reverse rotation 44 Second acceleration/ deceleration time 44 Second acceleration/ deceleration time 44 Second acceleration/ deceleration time 44 Second acceleration/ deceleration time 45 Second deceleration time 45 Second deceleration time 45 Second deceleration time 45 Second deceleration time 46 Second torque boost 46 Second torque boost 46 Second torque boost 46 Second torque boost Second V/F 47 (base frequency) Second V/F 47 (base frequency) Second V/F 47 (base frequency) 47 Second V/F (base frequency) 48 Second stall prevention operation current 48 Second stall prevention operation current 48 Second stall prevention operation current 48 Second stall prevention operation current 49 Second stall prevention operation frequency 49 Second stall prevention operation frequency 50 Second output frequency detection 50 Second output frequency detection 51 Second electronic thermal O/L relay 51 Second electronic thermal O/L relay 51 Second electronic thermal O/L relay 51 Second electronic thermal O/L relay 52 DU/PU main display data selection 52 DU/PU main display data selection 52 DU/PU main display data selection 52 DU/PU main display data selection 54 FM terminal function selection 54 FM terminal function selection 54 FM terminal function selection 54 FM terminal function selection 55 Frequency monitoring reference 55 Frequency monitoring reference 55 Frequency monitoring reference 55 Frequency monitoring reference 56 Current monitoring reference 56 Current monitoring reference 56 Current monitoring reference 56 Current monitoring reference 57 Restart coasting time 57 Restart coasting time 57 Restart coasting time 57 Restart coasting time 58 Restart cushion time 58 Restart cushion time 58 Restart cushion time 58 Restart cushion time 59 Remote function selection 59 Remote function selection 59 Remote function selection 59 Remote function selection 60 Energy saving control selection 60 Energy saving control selection 60 Energy saving control selection 60 Energy saving control selection E-174 FX Series PLC User's Manual - Data Communication Edition 12 Related Data Inverter Communication 12.5 FREQROL Inverter Parameter List A Function Name FREQROL E700 Series Pr No. Name 61 Reference current 61 Reference current Reference value at 62 acceleration 62 Reference value at 63 deceleration Reference value at 63 deceleration 64 Starting frequency for elevator mode FREQROL D700 Series Pr No. Name Reference value at acceleration B N:N Network Automatic acceleration /deceleration Name FREQROL A700 Series Pr No. 65 Retry selection 65 Retry selection 65 Retry selection 65 Retry selection Stall prevention 66 operation reduction starting frequency Stall prevention 66 operation reduction starting frequency Stall prevention 66 operation reduction starting frequency Stall prevention 66 operation reduction starting frequency Retry Number of retries at alarm occurrence 67 Number of retries at alarm occurrence 67 Number of retries at fault occurrence 67 Number of retries at fault occurrence 68 Retry waiting time 68 Retry waiting time 68 Retry waiting time Retry count display 69 erase Retry count display 69 erase Retry count display 69 erase 69 Retry count display erase 70 Special regenerative brake duty Special regenerative brake duty Special regenerative brake duty Special regenerative brake duty 70 71 Applied motor 71 Applied motor 71 Applied motor 71 Applied motor PWM frequency 72 selection PWM frequency 72 selection PWM frequency 72 selection 72 73 Analog input selection 73 Analog input selection 73 Analog input selection 73 Analog input selection 74 Input filter time constant 74 Input filter time constant 74 Input filter time constant 74 Input filter time constant 75 Reset selection/ disconnected PU detection/PU stop selection 75 Reset selection/ disconnected PU detection/PU stop selection 75 76 Alarm code output selection 76 Alarm code output selection 77 Parameter write selection 77 Parameter write selection 77 Parameter write selection 77 Parameter write selection 78 Reverse rotation prevention selection 78 Reverse rotation prevention selection 78 Reverse rotation prevention selection 78 Reverse rotation prevention selection 79 Operation mode selection 79 Operation mode selection 79 Operation mode selection 79 Operation mode selection F 80 Motor capacity 81 Number of motor poles 81 Number of motor poles 82 Motor excitation current 82 Motor excitation current 82 Motor excitation current 83 Motor rated voltage 83 Motor rated voltage 83 Motor rated voltage 84 Rated motor frequency 84 Rated motor frequency 84 Rated motor frequency Speed control gain 89 (advanced magnetic flux vector) 90 Motor constant (R1) 90 Motor constant (R1) 90 Motor constant (R1) 91 Motor constant (R2) 91 Motor constant (R2) 92 Motor constant (L1) 92 Motor constant (L1) 93 Motor constant (L2) 93 Motor constant (L2) 94 Motor constant (X) 94 Motor constant (X) Speed control gain (magnetic flux vector) Online auto tuning selection 96 Auto tuning setting/ status 96 H I Auto tuning setting/ status 96 Auto tuning setting/ status E-175 Apx.A Discontinued models 95 80 Motor capacity G Remote Maintenance Reset selection/ disconnected PU detection/PU stop selection 80 Motor capacity 89 90 Motor constant (R1) 75 E Programming Communication Reset selection/ disconnected PU detection/PU stop selection PWM frequency selection Non-Protocol Communication (FX2N-232IF) Simple magnetic flux vector control 70 Non-Protocol Communication (RS/RS2 Instruction) Motor capacity 80 (simple magnetic flux vector control) 70 Inverter Communication D Computer Link 68 Retry waiting time C Parallel Link 67 Common Items FREQROL F700 Series Pr No. FX Series PLC User's Manual - Data Communication Edition 12 Related Data Inverter Communication 12.5 FREQROL Inverter Parameter List FREQROL F700 Series Function Adjustable 5 points V/F Pr No. Name FREQROL A700 Series Pr No. Name 100 V/F1 (first frequency) 100 V/F1(first frequency) V/F1 (first frequency 101 voltage) 101 FREQROL E700 Series Pr No. FREQROL D700 Series Name Pr No. Name V/F1(first frequency voltage) 102 V/F2 (second frequency) 103 V/F2 (second frequency V/F2(second frequency 103 voltage) voltage) 102 V/F2(second frequency) 104 V/F3 (third frequency) 104 V/F3(third frequency) V/F3 (third frequency 105 voltage) 105 106 V/F4 (fourth frequency) 106 V/F4(fourth frequency) V/F4 (fourth frequency 107 voltage) 107 108 V/F5 (fifth frequency) 108 V/F5(fifth frequency) V/F5 (fifth frequency 109 voltage) 109 V/F5(fifth frequency voltage) 110 Third acceleration/ deceleration time V/F3(third frequency voltage) V/F4(fourth frequency voltage) 111 Third deceleration time 112 Third torque boost Third functions 113 Third V/F (base frequency) 114 Third stall prevention operation current 115 Third stall prevention operation frequency 116 Third output frequency detection 117 PU communication station 117 PU communication station number 117 PU communication station number 117 PU communication station number 118 PU communication speed 118 PU communication speed 118 PU communication speed 118 PU communication speed 119 PU communication stop PU communication stop PU communication stop PU communication stop 119 119 119 bit length. bit length bit length bit length 120 PU communication parity check PU connector communication 121 Number of PU communication retries 120 PU communication parity check 120 PU communication parity check 120 PU communication parity check 121 Number of PU communication retries 121 Number of PU communication retries 121 Number of PU communication retries 122 PU communication check time interval 122 PU communication check time interval 122 PU communication check time interval 122 PU communication check time interval 123 PU communication waiting time setting 123 PU communication waiting time setting 123 PU communication waiting time setting 123 PU communication waiting time setting PU communication CR/ PU communication CR/ PU communication 124 LF presence/absence 124 LF presence/absence 124 CR/LF selection selection selection 124 PU communication CR/LF selection 125 Terminal 2 frequency Terminal 2 frequency 125 setting gain frequency setting gain frequency 125 Terminal 2 frequency setting gain frequency 125 Terminal 2 frequency setting gain frequency 126 Terminal 4 frequency Terminal 4 frequency 126 setting gain frequency setting gain frequency 126 Terminal 4 frequency setting gain frequency 126 Terminal 4 frequency setting gain frequency E-176 FX Series PLC User's Manual - Data Communication Edition 12 Related Data Inverter Communication 12.5 FREQROL Inverter Parameter List A Function 127 PID control automatic switchover frequency 127 Name PID control automatic switchover frequency FREQROL E700 Series Pr No. 127 Name PID control automatic switchover frequency FREQROL D700 Series Pr No. 127 Name PID control automatic switchover frequency 128 PID action selection 128 PID action selection 128 PID action selection 129 PID proportional band 129 PID proportional band 129 PID proportional band 129 PID proportional band 130 PID integral time 130 PID integral time 130 PID integral time 130 PID integral time 131 PID maximum 131 PID upper limit 131 PID upper limit 131 PID upper limit 132 PID minimum 132 PID lower limit 132 PID lower limit 132 PID lower limit 133 PID action set point 133 PID action set point 133 PID action set point 133 PID action set point 134 PID differential time 134 PID differential time 134 PID differential time 134 PID differential time Commercial powersupply switchover 135 sequence output terminal selection 135 136 Electronic bypass sequence selection MC switchover interlock MC switchover interlock 136 time time D 137 Start waiting time 138 Bypass selection at an alarm 139 Automatic switchover Automatic switchover frequency between 139 frequency from inverter inverter and commercial to bypass operation power-supply operation 140 Backlash acceleration stopping frequency 140 Backlash acceleration stopping frequency 141 Backlash acceleration stopping time 141 Backlash acceleration stopping time 142 Backlash deceleration stopping frequency 142 Backlash deceleration stopping frequency 143 Backlash deceleration stopping time 143 Backlash deceleration stopping time 144 Speed setting switchover 144 Speed setting switchover PU 145 PU display language selection 145 PU display language selection 148 Stall prevention level at 0V input. 148 Stall prevention level at 0V input 149 Stall prevention level at 10V input. 149 Stall prevention level at 10V input 150 Output current detection Output current detection Output current detection Output current detection 150 150 150 level level level level 151 Output current detection Output current detection Output current detection Output current detection 151 151 151 signal delay time signal delay time signal delay time signal delay time 152 Zero current detection level Voltage reduction 154 selection during stall prevention operation Voltage reduction 154 selection during stall prevention operation RT signal function RT signal reflection time 155 155 validity condition selection selection 156 Stall prevention operation selection 156 Stall prevention operation selection 145 PU display language selection 145 PU display language selection 146 Built-in potentiometer switching 146 Built-in potentiometer switching 152 Zero current detection level Zero current detection 153 time 156 Stall prevention operation selection 152 H Zero current detection level Zero current detection 153 time 156 G I Apx.A Stall prevention operation selection E-177 Discontinued models Zero current detection 153 time F Remote Maintenance Zero current detection 153 time E Programming Communication Zero current detection level Non-Protocol Communication (FX2N-232IF) 152 Non-Protocol Communication (RS/RS2 Instruction) Current detection Inverter Communication Backlash measures C Computer Link Commercial 137 Waiting time at a start power Commercial powersupply-inverter supply operation switch-over 138 switchover selection at an alarm B Parallel Link 128 PID action selection N:N Network PID operation Name FREQROL A700 Series Pr No. Common Items FREQROL F700 Series Pr No. FX Series PLC User's Manual - Data Communication Edition 12 Related Data Inverter Communication 12.5 FREQROL Inverter Parameter List FREQROL F700 Series Function Pr No. Name FREQROL A700 Series Pr No. Name FREQROL E700 Series Pr No. Name FREQROL D700 Series Pr No. Name 157 OL signal output timer 157 OL signal output timer AM terminal function 158 selection AM terminal function 158 selection Automatic switchover ON range 159 between commercial powersupply and inverter operation Automatic switchover frequency range from 159 bypass to inverter operation 160 User group read selection 161 Frequency setting/key Frequency setting/key Frequency setting/key Frequency setting/key 161 161 161 lock operation selection lock operation selection lock operation selection lock operation selection Automatic restart after 162 instantaneous power failure selection Automatic restart functions Cumulative monitor clear User group Input terminal function assignment E-178 User group read selection Automatic restart after 162 instantaneous power failure selection 163 First cushion time for restart 164 First cushion voltage for First cushion voltage for 164 restart restart Stall prevention 165 operation level for restart Current detection 160 163 First cushion time for restart Stall prevention 165 operation level for restart 157 OL signal output timer 160 User group read selection Automatic restart after 162 instantaneous power failure selection Stall prevention 165 operation level for restart 166 Output current detection Output current detection 166 signal retention time signal retention time 167 Output current detection Output current detection 167 operation selection operation selection 170 Cumulative power meter clear 170 Watt-hour meter clear 171 Operation hour meter clear 171 Operation hour meter clear 171 Operation hour meter clear 172 User group registered display/batch clear 172 User group registered display/batch clear 172 User group registered display/batch clear 157 OL signal output timer 160 173 User group registration 173 User group registration 173 User group registration 174 User group clear 174 User group clear 174 User group clear Extended function display selection Automatic restart after 162 instantaneous power failure selection Stall prevention 165 operation level for restart 166 Output current detection signal retention time 167 Output current detection operation selection 170 Watt-hour meter clear 170 Watt-hour meter clear 171 Operation hour meter clear 178 STF terminal function selection 178 STF terminal function selection 178 STF terminal function selection 178 STF terminal function selection 179 STR terminal function selection 179 STR terminal function selection 179 STR terminal function selection 179 STR terminal function selection 180 RL terminal function selection 180 RL terminal function selection 180 RL terminal function selection 180 RL terminal function selection 181 RM terminal function selection 181 RM terminal function selection 181 RM terminal function selection 181 RM terminal function selection 182 RH terminal function selection 182 RH terminal function selection 182 RH terminal function selection 182 RH terminal function selection 183 RT terminal function selection 183 RT terminal function selection 183 MRS terminal function selection 184 AU terminal function selection 184 AU terminal function selection 184 RES terminal function selection 185 JOG terminal function selection 185 JOG terminal function selection 186 CS terminal function selection 186 CS terminal function selection 187 MRS terminal function selection 187 MRS terminal function selection 188 STOP terminal function selection 188 STOP terminal function selection 189 RES terminal function selection 189 RES terminal function selection FX Series PLC User's Manual - Data Communication Edition 12 Related Data Inverter Communication 12.5 FREQROL Inverter Parameter List A Function Name FREQROL A700 Series Pr No. Name FREQROL E700 Series Pr No. Name RUN terminal function selection 190 RUN terminal function selection 190 RUN terminal function selection 191 SU terminal function selection 191 SU terminal function selection 191 FU terminal function selection 192 IPF terminal function selection 192 IPF terminal function selection 192 193 OL terminal function selection 194 FU terminal function selection Output terminal OL terminal function 193 function selection assignment FU terminal function 194 selection ABC1 terminal function selection 195 ABC1 terminal function selection 196 ABC2 terminal function selection 196 ABC2 terminal function selection 232 Multispeed setting (speed 8) 232 Multi-speed setting (speed 8) Multi-speed setting 233 (speed 9) A,B,C terminal function selection 192 A,B,C terminal function selection Multi-speed setting (speed 8) Multi-speed setting 233 (speed 9) 232 C Multi-speed setting (speed 8) Multi-speed setting 233 (speed 9) 234 Multi-speed setting (speed 10) 234 Multi-speed setting (speed 10) 234 Multi-speed setting (speed 10) 235 Multispeed setting (speed 11) 235 Multi-speed setting (speed 11) 235 Multi-speed setting (speed 11) 235 Multi-speed setting (speed 11) 236 Multispeed setting (speed 12) 236 Multi-speed setting (speed 12) 236 Multi-speed setting (speed 12) 236 Multi-speed setting (speed 12) 237 Multispeed setting (speed 13) 237 Multi-speed setting (speed 13) 237 Multi-speed setting (speed 13) 237 Multi-speed setting (speed 13) 238 Multispeed setting (speed 14) 238 Multi-speed setting (speed 14) 238 Multi-speed setting (speed 14) 238 Multi-speed setting (speed 14) 239 Multispeed setting (speed 15) 239 Multi-speed setting (speed 15) 239 Multi-speed setting (speed 15) 239 Multi-speed setting (speed 15) 240 SoftPWM operation selection 240 Soft-PWM operation selection 240 Soft-PWM operation selection 240 Soft-PWM operation selection 241 Analog input display unit switchover 241 Analog input display unit switchover 241 Analog input display unit switchover 241 Analog input display unit switchover Terminal 1 added 242 compensation amount (terminal 2) Terminal 1 added 242 compensation amount (terminal 2) Terminal 1 added 243 compensation amount (terminal 4) Terminal 1 added 243 compensation amount (terminal 4) 244 Slip compensation 245 Rated slip Slip compensation time constant Constant-power region 247 slip compensation selection 250 Stop selection 251 Slip compensation time constant 250 Stop selection 251 Cooling fan operation selection 245 Rated slip Constant-power region 247 slip compensation selection 244 Output phase failure protection selection 252 Override bias 252 Override bias 253 Override gain 253 Override gain 246 Slip compensation time constant Earth (ground) fault detection at start 250 Stop selection 251 244 Cooling fan operation selection 245 Rated slip Constant-power region 247 slip compensation selection 249 Output phase loss protection selection 246 Slip compensation time constant Constant-power range 247 slip compensation selection 249 Earth (ground) fault detection at start 250 Stop selection 251 Output phase loss protection selection H I Apx.A Discontinued models Frequency compensation function Output phase failure protection selection 246 Remote Maintenance 246 Cooling fan operation selection G Programming Communication 245 Rated slip 244 F Non-Protocol Communication (FX2N-232IF) Cooling fan operation selection E Non-Protocol Communication (RS/RS2 Instruction) Multispeed setting (speed 10) D Inverter Communication 234 Multispeed setting B Computer Link Multispeed setting 233 (speed 9) 232 RUN terminal function selection Parallel Link 195 190 Name N:N Network 190 FREQROL D700 Series Pr No. Common Items FREQROL F700 Series Pr No. E-179 FX Series PLC User's Manual - Data Communication Edition 12 Related Data Inverter Communication 12.5 FREQROL Inverter Parameter List FREQROL F700 Series Function Pr No. Name FREQROL A700 Series Pr No. Name FREQROL E700 Series Pr No. Name FREQROL D700 Series Pr No. Name 255 Life alarm status display 255 Life alarm status display 255 Life alarm status display 255 Life alarm status display Life check Power failure stop 256 Inrush current limit circuit life display 257 Control circuit capacitor Control circuit capacitor Control circuit capacitor Control circuit capacitor 257 257 257 life display life display life display life display 258 Main circuit capacitor life display 258 Main circuit capacitor life display 258 Main circuit capacitor life display 258 Main circuit capacitor life display 259 Main circuit capacitor life measuring 259 Main circuit capacitor life measuring 259 Main circuit capacitor life measuring 259 Main circuit capacitor life measuring 260 PWM frequency automatic switchover 260 PWM frequency automatic switchover 261 Power failure stop selection 261 Power failure stop selection 262 Subtracted frequency at Subtracted frequency at 262 deceleration start deceleration start 263 Subtraction starting frequency 263 Subtraction starting frequency 264 Powerfailure deceleration time 1 264 Power-failure deceleration time 1 256 261 Inrush current limit circuit life display Power failure stop selection Powerfailure 265 deceleration time 2 Power-failure 265 deceleration time 2 Power failure 266 deceleration time switchover frequency Power failure 266 deceleration time switchover frequency 256 261 Inrush current limit circuit life display Power failure stop selection 256 Inrush current limit circuit life display 267 Terminal 4 input selection 267 Terminal 4 input selection 267 Terminal 4 input selection 267 Terminal 4 input selection 268 Monitor decimal digits selection 268 Monitor decimal digits selection 268 Monitor decimal digits selection 268 Monitor decimal digits selection 270 Stop-on contact control selection Stop-on contact/load torque high speed 270 frequency control selection Load torque high speed frequency control Stop-on contact control E-180 271 High-speed setting maximum current 272 Middle-speed setting minimum current 273 Current averaging range 274 Current averaging filter time constant Stop-on contact Stop-on contact excitation current 275 excitation current low 275 low speed multiplying speed multiplying factor factor 276 PWM carrier frequency at stop-on contact 276 PWM carrier frequency at stop-on contact Stall prevention 277 operation current switchover FX Series PLC User's Manual - Data Communication Edition 12 Related Data Inverter Communication 12.5 FREQROL Inverter Parameter List A Function Name 278 Name Name Brake opening frequency 278 Brake opening frequency 279 Brake opening current 279 Brake opening current Brake opening current 280 detection time Brake opening current 280 detection time Brake operation time at start 281 Brake operation time at start 282 Brake operation frequency 282 Brake operation frequency 283 Brake operation time at stop 283 Brake operation time at stop 284 Deceleration detection function selection Droop control 286 Droop gain Droop filter time 287 constant 287 288 Droop function activation selection 292 Acceleration/ 293 deceleration separate selection 294 UV avoidance voltage gain Rotation direction 299 detection selection at restarting Magnitude of frequency Magnitude of frequency 295 change setting change setting Rotation direction 299 detection selection at restarting Rotation direction 299 detection selection at restarting 301 BCD input gain 302 BIN input bias 302 BIN input bias 303 BIN input gain 303 BIN input gain 305 Read timing operation selection Digital input and analog 304 input compensation enable/disable selection 305 G H Programming Communication 300 BCD input bias 297 Password lock/unlock 298 Frequency search gain 301 BCD input gain 296 Password lock level 298 Frequency search gain 300 BCD input bias Digital input and analog 304 input compensation enable/disable selection F Non-Protocol Communication (FX2N-232IF) Digital input Rotation direction 299 detection selection at restarting E Acceleration/ 293 deceleration separate selection 295 Password function Droop filter time constant Automatic acceleration/ Automatic acceleration/ 292 deceleration deceleration D Non-Protocol Communication (RS/RS2 Instruction) 291 Pulse train I/O selection C Inverter Communication B 286 Droop gain Name Computer Link FREQROL D700 Series Pr No. Parallel Link 281 Overspeed detection frequency (Speed 285 deviation excess detection frequency) FREQROL E700 Series Pr No. N:N Network Brake sequence function FREQROL A700 Series Pr No. Common Items FREQROL F700 Series Pr No. Read timing operation selection I Remote Maintenance Apx.A Discontinued models E-181 FX Series PLC User's Manual - Data Communication Edition 12 Related Data Inverter Communication 12.5 FREQROL Inverter Parameter List FREQROL F700 Series Function Analog output Pr No. Name Analog output 306 Analog output signal selection 307 Setting for zero analog output 307 Setting for zero analog output 308 Setting for maximum analog output 308 Setting for maximum analog output Analog output signal 309 voltage/current switchover FREQROL D700 Series Pr No. Name Analog output signal 309 voltage/current switchover 310 Analog meter voltage output selection 310 Analog meter voltage output selection 311 Setting for zero analog meter voltage output 311 Setting for zero analog meter voltage output Setting for maximum 312 analog meter voltage output 313 DO0 output selection 314 DO1 output selection 314 DO1 output selection 315 DO2 output selection 315 DO2 output selection 316 DO3 output selection 316 DO3 output selection 317 DO4 output selection 317 DO4 output selection 318 DO5 output selection 318 DO5 output selection 319 DO6 output selection 319 DO6 output selection 320 RA1 output selection 320 RA1 output selection 321 RA2 output selection 321 RA2 output selection 322 RA3 output selection 322 RA3 output selection 323 AM0 0V adjustment 323 AM0 0V adjustment 324 AM1 0mA adjustment 324 AM1 0mA adjustment Digital input unit 329 selection 329 331 RS-485 communication RS-485 communication 331 station station number 332 RS-485 communication RS-485 communication 332 speed speed 333 RS-485 communication RS-485 communication 333 stop bit length stop bit length RS-485 communication RS-485 communication RS-485 334 334 parity check selection parity check selection communication E-182 Name Analog output signal selection 313 DO0 output selection Relay output Name FREQROL E700 Series Pr No. 306 Setting for maximum 312 analog meter voltage output Digital output FREQROL A700 Series Pr No. 335 RS-485 communication RS-485 communication 335 number of retries retry count 336 RS-485 communication RS-485 communication 336 check time interval check time interval 337 RS-485 communication RS-485 communication 337 waiting time setting waiting time setting Digital input unit selection FX Series PLC User's Manual - Data Communication Edition 12 Related Data Inverter Communication 12.5 FREQROL Inverter Parameter List A Function Name Communication 338 operation command source Communication 338 operation command source Name Communication 338 operation command source Communication speed command source 339 Communication speed command source 339 Communication speed command source 339 Communication speed command source 340 Communication startup mode selection 340 Communication startup mode selection 340 Communication startup mode selection 340 Communication startup mode selection 341 RS-485 communication RS-485 communication 341 CR/LF selection CR/LF selection Communication error count Communication 342 EEPROM write selection 343 Communication error count Communication 342 EEPROM write selection 343 Communication error count Communication 342 EEPROM write selection 343 Communication error count 345 DeviceNet address 346 DeviceNet baud rate D 380 Acceleration S-pattern 1 381 S-pattern acceleration/ deceleration C 388 Send time interval at heart beat 389 Minimum sending time at heart beat 390 % setting reference frequency 391 Receive time interval at heart beat 392 Event driven detection width Frequency for 0 input pulse 386 Frequency for maximum input pulse F G Non-Protocol Communication (FX2N-232IF) Initial communication delay time 385 Non-Protocol Communication (RS/RS2 Instruction) 387 Input pulse division 384 scaling factor Inverter Communication Pulse train input communication E 382 Acceleration S-pattern 2 LONWORKS Deceleration S-pattern 1 Deceleration S-pattern 383 2 H 450 Second applied motor 450 Second applied motor Second motor control 451 method selection 453 Second motor capacity Number of second motor poles 455 Second motor excitation current 456 Rated second motor voltage 457 Rated second motor frequency I Remote Maintenance 454 Programming Communication 450 Second applied motor Second motor constants C Computer Link Communication reset 349 selection B Parallel Link 343 CCLink Communication 338 operation command source Name FREQROL D700 Series Pr No. 339 Communication 342 EEPROM write selection DeviceNet Name FREQROL E700 Series Pr No. N:N Network RS-485 communication FREQROL A700 Series Pr No. Common Items FREQROL F700 Series Pr No. Apx.A Discontinued models Second motor constant 458 (R1) E-183 FX Series PLC User's Manual - Data Communication Edition 12 Related Data Inverter Communication 12.5 FREQROL Inverter Parameter List FREQROL F700 Series Function Second motor constants Pr No. 495 Remote output Name Remote output selection 459 Second motor constant (R2) 460 Second motor constant (L1) 461 Second motor constant (L2) 462 Second motor constant (X) 463 Second motor auto tuning setting/status 495 Remote output selection 495 Name Name Remote output selection 496 Remote output data 1 496 Remote output data 1 497 Remote output data 2 497 Remote output data 2 Communication error execution waiting time 502 Stop mode selection at communication error 503 Maintenance timer 504 500 Maintenance timer alarm output set time 503 Maintenance timer 504 Maintenance timer alarm output set time 516 S-pattern time at a start of acceleration S-pattern time at a 517 completion of acceleration 518 S-pattern time at a start of deceleration Communication error execution waiting time Communication error 501 occurrence count display 502 Stop mode selection at communication error 503 Maintenance timer 504 FREQROL D700 Series Pr No. 497 Remote output data 2 Communication error Communication 501 occurrence count error display S-pattern acceleration/deceleration D Name FREQROL E700 Series Pr No. 496 Remote output data 1 500 Maintenance FREQROL A700 Series Pr No. Maintenance timer alarm output set time 541 Frequency command sign selection (CC-Link) 542 Communication station number (CCLink) 543 Baud rate selection (CC-Link) 544 CC-Link extended setting 495 Remote output selection 496 Remote output data 1 502 Stop mode selection at communication error 503 Maintenance timer 504 Maintenance timer alarm output set time S-pattern time at a 519 completion of deceleration 542 CCLink Communication station number (C
advertisement
* Your assessment is very important for improving the workof artificial intelligence, which forms the content of this project