advertisement
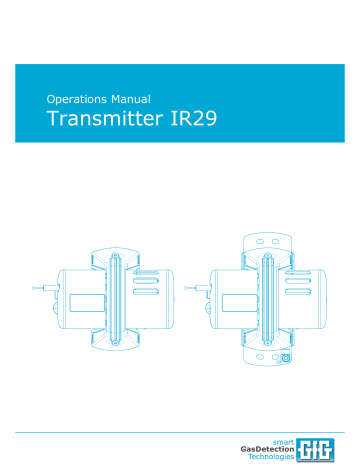
Operations Manual
Transmitter IR29
Table of contents
For Your Safety
Operating Instructions
General Description
Measuring Methods
Device Design
Type Plate
Installation Site of the Transmitter
Assembly
Installing Electrical Connections
Assembly and Operation with Flow Adapter
Using the RC2 or RC3 operator interfaces
Control Buttons
Display and LED test via RC2 or RC3 operator interfaces
Commissioning
Measuring Mode
Changing the Gas Measuring Channel
Under Range
Over Range
Display of Operating Parameters
Measured Value Histogram
Sensor Lifetime
Device Error
Zero Calibration and Adjustment (ZERO)
Activation
Execution
Sensitivity Calibration and Adjustment (SPAN)
Calibration
Adjustment
Service Menu and Advanced Service Menu
Activate Service Menu
Operation
Layout of the Service Menu
Additional Menu Explanations
Displays and Messages
Display of Special Statuses and Malfunctions
Error Messages of the Main CPU
Error Messages of the Sensor CPU
Displays in Measuring Mode
Displays in Service Mode and During Calibration (Status Messages)
Status of the Status LEDs and the Current Output
Initial Commissioning and Maintenance
Maintenance of Stationary Gas Warning Systems
Regular Functional Tests
Repair
Troubleshooting
5
8
8
9
9
9
4
4
10
10
10
11
11
12
12
12
13
13
13
21
21
23
24
24
25
25
26
26
26
27
27
15
15
15
17
17
17
18
19
2
3
3
1
1
2
Accessories
Connections and Terminal Assignment
IR29 i/Di with 4...20mA Interface and Zener barriers
IR29 i/Di with 4...20mA Interface and Zener barriers from MTL
IR29 i/Di with 4...20mA Interface and SB1
IR29 i/Di with 4...20mA Interface & 3-wire cable (e.g. GMA41)
IR29 /D with 4..20mA Interface & 3-wire cable to GMA200
IR29 B/DB; with RS485 Bus & Four-Wire Cable to GMA200
Measuring Gases and Measuring Ranges
Sensor Specification
Technical Data
Notes IR29
Appendix RC3
Field of Application and Intended Use
Operation
Channel Coding
Changing Batteries
Technical Data
Appendix SB1
Operating Instructions
Device Design
Install Electrical Connections
Technical Data
Declarations of Conformity, Type Examination Certificates
33
33
35
28
29
29
29
30
31
32
32
43
43
43
43
45
46
37
41
41
41
41
41
42
For Your Safety
This user manual states the intended use of the product according to the German Product
Safety Act (ProdSG) and helps to prevent accidents and work-related injuries. It must be read and observed by all persons who operate, service, maintain and inspect this product. This product can serve its intended purpose only if it is operated, serviced, maintained and inspected according to the instructions given by GfG Gesellschaft für Gerätebau mbH.
The warranty provided by the company GfG will become void if the product is not operated, serviced, maintained and inspected in accordance with GfG’s instructions. The above declaration does not affect statements regarding warranties and liabilities in the company
GfG's General Terms and Conditions of Sale and Delivery.
Operating Instructions
After installation but before commencing operation, gas warning systems must be inspected by an expert to ensure they operate correctly and in accordance with national standards
(commissioning). In Germany, the rules of the employers' liability insurance associations must be followed, "BGR 500, chapter 2.33 section 4.4.".
The transmitter has been tested for functionality prior to delivery. Calibration and alignment took place with appropriate test or calibration gases.
This however does not release you from the obligation to commission the transmitter
with test or calibration gas after installation.
The IR29 transmitter is approved for use in hazardous areas and has an EC type examination certificate from DEKRA EXAM GmbH in accordance with Directive 2014/34/EU.
Certificate: BVS 09 ATEX E 135 X
For the types IR29 i and IR29 Di applies:
Marking: I M1 Ex ia I Ma
II 1G Ex ia IIC T4 Ga
-25°C≤Ta≤+55°C
-25°C≤Ta≤+55°C
The following applies to types IR29, IR29 D, IR29 B and IR29 DB:
Marking: II 2G Ex eb mb ib [ib] IIC T4 Gb -25°C≤Ta≤+55°C
!
CAUTION:
The supply voltage should under no circumstances exceed 30 V
DC! This also applies to voltage peaks!
Operating Conditions:
The transmitter is only admitted to be used under atmospheric conditions, i.e. the operating parameters for temperature and pressure, according to the Technical
Data in the Annex which has to be complied with.
The electrical safety is tested for the use under atmospheric conditions, i.e. up to an oxygen content of typical 21Vol%.
- 1 -
General Description
A fixed gas warning system consists of a transmitter and an evaluation unit (GMA, not included). The transmitter and the evaluation unit are interconnected via a shielded remote measurement cable. The transmitter converts the gas concentration into an electrical measuring signal. The evaluation of the measuring signal proportional to the existing gas concentration takes place at the evaluation unit (GMA).
The extensive electronics assumes various tasks which, on the one hand, facilitates operation and maintenance and, on the other hand, significantly enhances operational safety and measuring accuracy. The transmitter features the following:
•
Measured value display on the display (optional) or on the RC2 operator panel
•
Settings without opening the housing with the remote control RC 2 or RC 3
•
Compensation of temperature influences
•
Ex-protection in temperature range -25 to +55°C
•
Functional test in the temperature range -25 to +55°C [applied for]
•
Permanent status display (operation/fault) on the transmitter
Measuring Methods
The sensors built into the IR29 transmitter operate according to the infrared absorption principle. Alignment to the gas type being monitored takes place using specific optical filters combined with suitable characteristics. The reduced infrared radiation at the position of the detector is converted into an electrical signal. This signal is amplified in the IR29, filtered and used for the display or measured value transfer. Due to its design with two radiation sources, the measurement assembly offers a powerful signaling function and is less sensitive to interfering influences, such as deterioration of the radiators or temperature deviations. Soiling of the optics can also be compensated up to a certain degree. Due to the said design and additionally available temperature and pressure compensation, influence caused by ambient conditions is almost entirely eliminated.
The electronics of the transmitter IR29 converts the measuring signal into a linear measured value output 4..20 mA.
Depending on the sample gas, cross sensitivities with other gases, especially hydrocarbons, may occur.
Variants
The Transmitter IR29 - Meaning of the short description:
Designation 4..20mA
Interface
RS485
Modbus
IR29i
IR29Di
IR29
IR29D
IR29B
IR29DB yes yes yes yes no no no no no no yes yes
Display no yes no yes no yes
Degree of
Protection
Intrinsically Safe
"i"
Increased Safety
"e
- 2 -
Device Design
Retaining Bracket Impact Protection
Measuring
Space
Gas Entry
Under Protective Cap
Display
(optional)
Diffusion opening
Cable Entry
Status LEDs
Type Plate
Terminal Module
Type Plate
Transmitter version details, serial number and ATEX marking
Transmitter
Type designation & serial number
Type Plate IR29
- 3 -
Installation Site of the Transmitter
When determining the installation site, it is important to know the exact ambient conditions and to take them into consideration. In order to receive representative results, the ventilation conditions must be taken into account.
The position of the transmitter in the room must ensure that the gases still reach the sensor even in the event of unfavorable ventilation. If necessary, carry out a measurement, e.g. with ventilation smoke tubes.
When specifying the site of installation, it must be further observed that the transmitter can be accessed for service and calibration tasks.
External influences must also be considered, e.g.
• rainwater, splash water, dripping water, condensate
• the dust content in the atmosphere
The transmitter is protected against the ingress of water or dust to the greatest possible extent.
Special accessories can protect the transmitter against damage in extremely harsh measurement conditions. If desired, the company GfG will gladly advise you about suitable measures.
!
The warranty may become void if the sensor is exposed to ambient conditions which were unknown to the company GfG during the planning phase or delivery.
!
Transmitter types IR29, IR29 D, IR29 B and IR29 DB:
The housing only fulfils the requirements of the EN 60079-0 (table 13) in combination with the IR29 Protection cover (guard). Therefore, the IR29 Protection cover and the device need to be firmly attached.
Assembly
The assembly is carried out step by step in the following sequence:
A
1
I. Loosen the screws "A" and remove the retaining bracket (1). To do so, slightly pull apart the ends of the bracket until the lugs are free.
2
II.
Remove the transmitter (2) from the socket.
Depending on the type, the electrical plug connection is either disconnected or the plug has to be unplugged manually.
- 4 -
B
3
III.
Loosen screws "B", remove and lift the upper part of the base (3) from the lower part (4).
4
C
4
3
IV.
Fasten the lower part (4) into position at the installation site; use the oval holes "C" and the screws provided for this purpose.
A drilling template is supplied in the Annex to assist in the location of the holes.
Subsequently feed the line through the cable gland (fit the shield) and install the single conductors in the terminals X1-X4 (see next chapter).
Assemble in reverse order (steps III-I).
!
CAUTION:
During assembly, some screws must be tightened to a defined torque. An overview can be found in the appendix.
Installing Electrical Connections
The installation of the remote measuring cables and the connection of the electrical installation may only be carried out by a specialist in compliance with the relevant regulations. The installation must be carried out with a protected cable.
For intrinsically safe devices (IR29 i/Di), e.g. Helukabel OZ-BL-CY 4X1.5 mm2 or Lapp Kabel
ÖLFLEX® EB CY can be used. According to the manufacturer, these exemplarily selected cables meet the requirements of DIN EN 60079-14 or IEC 60079-14 Section 12.2.2 (VDE 0165
Part 1). In addition, mechanical protection of the installed telemetry cable is required if both intrinsically safe circuits are routed in one cable. This is necessary to prevent the two intrinsically safe circuits coming into contact.
Suitable mechanical protection depends on the operating situation, the installation site and the hazard potential. The shielded PVC data cable UNITRONIC® LiYCY 3 x 1.5mm², for example, is suitable for devices with increased safety (IR29 /D/B/DB).
The conductor cross section is determined by the length of the connection line and the version of the transmitter. Remote measurement cables with a conductor cross section of 0.75 mm can be used for short distances of up to 500 m. The conductor cross section must be 1.5 mm for longer distances of up to 1,000 m.
2
2
- 5 -
The shielding is fitted in the M16x1.5 cable gland. Potential equalization may be required for the transmitter IR 29.
Only the transmitter can be installed in a potentially explosive atmosphere – the evaluation unit and the power supply unit must be installed outside this atmosphere.
If potential equalization of the housing is necessary, the potential equalization terminal can be found at the lower section of the wall holder.
!
!
!
The transmitter may only be installed if there is no gas present.
In possibly explosive areas all electrical lines need to be laid stationary from and to the transmitters IR29 (all types).
Each screwed and secured cable and line gland in the housing wall either has to be closed by a cable or by a plug admitted for this application.
Transmitter types IR29 i/ Di:
The user has to make sure that also in case of an error no higher voltage than Ui =
30V DC may apply on the terminal of the IR29.
Transmitter types IR29, IR29 D, IR29 B and IR29 DB:
The user has to make sure that also in case of an error, no higher voltage than the maximum voltage U m terminal of the IR29.
= 45V DC is indicated on the type plate may apply on the
The current interface (4..20mA) of the "i" version requires its own supply voltage. See chapter
Connections and Terminal Assignment.
- 6 -
Connection Diagram IR29 i/Di
X1: 15…30V DC
X2: GND
X3: 15..30V (+)
X4: 4...20mA (-)
Potential Equalization
Potential
Equalization
4 mm2
Potential Equalization Terminal:
This is located on the side next to the cable gland on the lower part of the wall holder.
The potential equalization must be carried out with a cable cross-section of 4 mm 2 .
Potential
Equalization
4 mm2
Potential Equalization Terminal:
(on IR29 Protection cover)
The potential equalization terminal is positioned laterally on the guard (IR29
Protection cover) beside the cable gland
(pressed in threaded bold M5x12).
Potential equalization must take place with a line cross section of 4 mm 2 .
As shown in the diagram, the wall holder must be fixed horizontally with the cable gland facing to the left, fixed to a wall or suitable support. The impact protection should be directed downwards with the diffusion opening. For alignment, loosen the Allen screw slightly, and then turn the protection.
A different mounting of the transmitter may adversely affect the response time or the weather protection.
After the disassembly of the impact protection, a dust filter may be inserted in the measuring space. When using the dust filter, the response time of the transmitter is extended.
In the diffusion mode, the response time for methane is extended by about 50%.
This value may vary for other gases. Depending on the operation site, it is necessary to check in regular intervals if the dust filter is soiled, in order to guarantee the gas entry.
- 7 -
Assembly and Operation with Flow Adapter
It is possible to mount a flow adapter instead of the impact protection (Sketch see Annex).
With that, it is possible to measure gas sampling in the flow via the gas supply on the IR29 and via a gas outlet on the adapter. The gas should be supplied unpressurised with a volume flow of at least 1l∕min (<2l/min). A lower volume flow adversely affects the response time. The use of a flow controller may be useful in this place. The gas supply should be performed via the gas nozzle on the device; the gas outlet is performed via one of the two gas nozzles on the adapter. The two nozzles on the adapter need to be closed.
Gas supply and drain via the two connections on the adapter may adversely influence the response time. The use of the dust filter during the operation with the flow adapter may adversely influence the response time.
The connection to the gas extraction point may be performed e.g. by a PE or PTFE hose.
Delays in the response time due to the hose length need to be considered.
At an inner diameter of the line of 4mm a delay of the response time of one second per 1.3m line length at a flow of 1l/min would result. In the meantime, the pump and any possible other installations (e.g. condensate trap) additionally need to be considered.
The user has to check the sample lines by suitable measures in regular intervals in order to ensure the functionality.
Using the RC2 or RC3 operator interfaces
!
For service tasks, only the remote control RC 2 (BVS 04 ATEX E 212) should be connected to the transmitter, or the remote control RC 3
(BVS 08 ATEX E 006) in conjunction with an integrated display should be used at the transmitter.
The remote control RC 2 and the IR remote control RC 3 can be used in potentially explosive atmospheres.
Settings of the zero point and display sensitivity (adjustment) can be executed directly at the optionally integrated display at the transmitter IR 29 and the remote control RC 3 or with the connected remote control RC 2.
The buttons and functions of the remote control RC 2 are identical to those of the IR remote control RC 3. Output in the transmitter display takes place in plain text format; output in the remote control RC 2 display occurs in abbreviated form.
See operating instructions 206-000.13 for use of the RC2.
In this manual the outputs are mostly given in the form Display/RC2, e.g. Code/ .
- 8 -
Control Buttons
The functions of the buttons at the remote control RC 2 and the IR remote control RC 3 are identical. The designation of the buttons at the RC 3 can be displayed by briefly pressing the central (oval) button at the display of the transmitter IR 29.
Additionaly, there is a sketch with a key label in the appendix.
Display and LED test via RC2 or RC3 operator interfaces
In measuring mode, briefly press the TEST
ZERO button to trigger a display and LED test. All the LEDs are subsequently activated for two seconds and all the segments of the display are shown.
Commissioning
The transmitter IR29 is tested to ensure it is functioning correctly prior to delivery. Calibration and adjustment takes place with a suitable test and calibration gas. Deviations may be identified depending on the transport, assembly and ambient conditions.
Therefore, the gas warning system must be commissioned and tested by the GfG Service to ensure it functions correctly.
After switching on, the transmitter needs, up to four minutes for:
• loading the internal buffer memory
• the self-test, during which the program and main memory are checked
• the reading and evaluation of the device parameters with simultaneous memory check
• the reading and evaluation of the sensor parameters with simultaneous memory check
• the running-in of the sensor
The memory tests occur during the first few seconds of the switch-on phase. The current interface is set to 1.2 mA, the orange and green status LEDs illuminate. During the second step, the current interface is set to 1.6 mA, the fault LED illuminates and the operation LED flashes. The following is initially shown on the display: Einlesen Geräte-Param. (Reading device
param.) ∕ . The measuring unit, the type of gas, the measuring range and the calibration gas concentration are subsequently shown one after the other at the devices equipped with a display or at the remote control RC 2.
The transmitter IR29 switches to the warm-up phase of the sensor, the fault LED flashes and the operation LED indicates readiness at 5 second intervals by flashing briefly – the remaining time is shown on the display in seconds.
The measuring mode is automatically activated after the warm-up phase.
If a device error is detected during the start-up phase, the transmitter IR29 switches to error mode. The current interface is set to 1.2mA, an error message is shown on the display of the transmitter (if available) or via the remote control RC 2 (sees Displaying special statuses and
malfunctions). The fault LED is permanently lit. The display lighting additionally flashes with display versions.
Note:
Initial commissioning demands adjustment of the zero point (AutoCal ZERO) after the warm-up phase and a subsequent sensitivity test, as well as possible adjustment.
(AutoCal SPAN).
- 9 -
Measuring Mode
The gas concentration is measured continuously. The current interface outputs a linear proportional signal in the range 4mA to 20mA. Transfer function: i
0 - 100 % LEL
∝
4 - 20 mA
The current interface is updated every second.
The functions of the electronics such as the parameter memory or the sensor function are monitored continuously. During the trouble-free measuring operation, the green operating LED will flash every 15 seconds, the yellow malfunction LED is off.
For transmitters with a display, the currently measured value is being shown on the display. For transmitters without a display, the measured value is displayed on the connected operating device RC2.
The resolution of the display and the current interface depends on the gas concentration.
Gas concentration x [%UEG] (lower intervention limit) x ≤ 20.0
20.0 > x ≥ 50.0
X > 50.0
Resolution
[%UEG] (lower intervention limit)
0.2
0.5
1.0
When using an IR29 without a display, the display of the remote control RC 2 changes from gas concentration to gas unit and type of gas at one minute intervals.
When using an IR29 with a graphical display, a pending measured value (>0) is shown as a bar graph, which always displays the current measured value in addition to the numerical display (the measuring gas and measuring unit are shown every
30 seconds instead of the bar graph). With display "0.0", the measuring gas and measuring unit are always displayed instead of the bar graph.
Changing the Gas Measuring Channel
For the MK244-3 it is possible to change between the measuring channels, since the measuring value can only be output via the current interface. By simultaneously pressing the buttons
TEST
ZERO and INFO
SPAN
for three seconds, the active gas channel will be displayed such as:
Display:
Choose gas channel
Gas channel 1
RC2:
CHA.1
Then it is possible to choose one of the two other channels by pressing the arrow buttons and INFO
SPAN
which is confirmed by pressing the central button QUIT
MENU
.
TEST
ZERO
Under Range
Measured values below the zero point are displayed as numerical values with a negative sign.
The current interface outputs a signal of between 2.8 mA and 3.9 mA according to the measured value.
If the zero point deviation is too high, the current interface is permanently set to 2.8 mA, and transmitters equipped with a display will permanently show ↓↓↓↓/_ _ _ _ .
- 10 -
Over Range
Transmitters equipped with a display, ↑↑↑↑ ∕ and the measured value are displayed alternately if the measuring range has been exceeded by up to 112.0 %. The current interface provides an output signal between 20...22 mA according to the measured value.
If the measured value exceeds 112.0 % of the measuring range, ↑↑↑↑ ∕ will flash on the display . The current interface is set to 22 mA.
Display of Operating Parameters
During measuring mode, briefly press the INFO
SPAN
button at the remote control RC 2 or RC 3 to automatically display the following important operating parameters one after the other:
1)
•
Measuring Gas
•
Measurement Unit
•
Measuring Range /
•
Calibration Gas Concentration /
2)
•
Average value of the last recorded 8 hours
8 h Medium/
•
Average value of the last recorded 15 minutes
15 Min. Average / .
3) If an environmental sensor is installed and activated:
•
Moisture /
•
Print /
•
Temperature /
For transmitters without display, or if it is poorly visible / readable, the parameters can also be displayed in the 7-segment display of the remote control RC2.
For example:
.
.
.
.
.
( .
)
- 11 -
Measured Value Histogram
When using a graphical display, it is possible to change to a different display mode. After triggering the display of the operating parameters via the histogram selection.
INFO
SPAN
, briefly press INFO
SPAN
again to display
It is possible to view data of the last 2 hours, 8 hours or 24 hours (select by pressing the TEST
ZERO or INFO
SPAN
button, press QUIT
MENU
to acknowledge your selection). The histogram display mode subsequently appears. It is possible to display average values, maximum values and minimum values by (briefly) pressing the TEST
ZERO
or INFO
SPAN
button again.
Saved measured values are displayed in graphical form instead of the measured value display.
The currently pending measured value is additionally shown in the top section together with the type of gas and gas unit. The histogram is refreshed at regular intervals and can be used as a permanent display mode.
Briefly press QUIT
MENU
or appearing special messages to exit this display mode.
Sensor Lifetime
The IR emitter used has a limited service life. If the signal level falls below 80% of the original value, the transmitter switches the measuring mode off. The error message Sensor error -115-
(unzur. signal level)/ is shown in the display/RC2 . The current interface is set to
1.2mA, the yellow fault LED lights up and the green operation LED flashes quickly.
The display of the fault message can also be an indication of contamination of the optics.
The signal level at the detector may be decreased by impurities. The optics must be checked for impurities and cleaned if necessary.
To carry out the cleaning, see chapter Initial Commissioning and Maintenance - Repair.
If the transmitter continues to display the error message despite clean optics, the transmitter must be replaced.
Device Error
In the event of a fault in the transmitter, the yellow fault LED lights up permanently, the current interface is set to 1.2mA and an error message appears in the display (see chapter
"Displaying special states and malfunctions").
A fault message occurs if, for example, :
• the sensor or the electronics in the transmitter are defective
•
Errors occur during self-monitoring of the device
As soon as the fault has been eliminated, the yellow fault LED goes out.
- 12 -
Zero Calibration and Adjustment (ZERO)
The prerequisite for this inspection is atmospheric air without influencing gas contents.
Synthetic air can also be used for adjustment if the atmosphere is contaminated.
The calibration adapter shown below must be used for checking or adjusting with synthetic air.
The rubberised area must be tightly stretched over the diffusion openings of the impact protection. The calibration adapter can be used to feed the synthetic air without pressure at a flow rate of approx. 0
.
5l∕min. For the complete flushing of the measuring space, a gas feed for at least 90 seconds is required.
If the zero point display deviates in measuring mode, a zero point adjustment is necessary.
After changing the measuring gas (see Service menu and Advanced Service Menu -
Changing the gas type), the zero point must also be checked and reset if necessary.
The AutoCal program automatically adjusts the zero point signal under the above conditions.
Activation
The zero point can only be set via the remote control RC 2 or RC 3 (only possible with transmitter IR29 with a display).
Automatic zero point offset can only be executed after entering access code if the currently displayed value is 10 % of the maximum measuring range.
An experienced user can activate the zero point setting after entering access code with a display of up to 15 % of the maximum measuring range. This access code should only be used by fully trained staff of the operator.
If the current zero point display exceeds a value of 15 % of the maximum measuring range and it has been ensured that the display was not caused by the presence of gas, a temporary hour code (valid for max. 1 hour) can be read in the Info ∕ submenu of the service menu
(Zero Code ∕ ) and used to activate zero point setting without restrictions.
Note:
The necessity of the latter measure might be an indicator of a defective sensor and thus of the need to replace the sensor as quickly as possible.
Execution
With the RC3 and the IR29 display or the RC2 keypad, the procedure is carried out in three steps:
1.
2.
Press the TEST
ZERO
button for a longer period (at least 3 seconds) to start activation. After activation, the current interface supplies 2.0 mA throughout the entire process and the fault LED flashes at slow intervals. The following appears on the display: Code ∕ .
The numerical access code or must be entered (this access code should only be used by fully trained staff of the operator). Use the TEST
ZERO and INFO
SPAN
buttons to change the number at the current position and QUIT
MENU
to acknowledge the changes. Press the
QUIT
MENU
button for a longer period to delete the last acknowledged number.
3.
After the correct entry, the current measured value and the display Zeroz∕ are alternating on the display . If the measured value remains constant during a time interval of
- 13 -
60 sec., the new zero point is set. The AutoCal program will be automatically terminated with the display Save∕ and changes back to the measuring mode.
Note:
If the current measured value is outside the permissible limits for the respective access code, the display Cal. error no. ∕ .
briefly appears at point 3 .
The AutoCal program can be shortened to a constant measured value TEST
ZERO
by pressing the key for a long time (3 sec.) while waiting. The hardware then starts directly with the zero setting.
To cancel the AutoCal program without zero point adjustment during the waiting time, press the key TEST
ZERO briefly.
The following will appear:
The zero point is outside the permitted tolerance range.
MENU
button to acknowledge it .
The following error messages may occur during zero point adjustment:
Display/RC2 Display
Kal.-Fehler Nr. 2
( Cal. error no. 2) ∕ .
Kal.-Fehler Nr. 3
( Cal. error no. 3) ∕ .
(Cancel) ∕ . Press the QUIT
Remark
The gas signal is unstable.
Malfunction LED fast flashing
All error messages must be acknowledged with QUIT
MENU
. After acknowledgement with the unchanged zero point setting, the transmitter returns to measuring mode.
Calibration adapter for IR29 Only for clarification:
Rubberized area of the adapter via the diffusion orifices, which need to be completely covered.
- 14 -
Sensitivity Calibration and Adjustment (SPAN)
For a device without display, the RC2 operating device is required for calibration and adjustment; for transmitters with display, it is also possible to use the remote control RC3.
!
Always observe special safety precautions when handling toxic gases. MAC values indicate hazards caused by toxic gases.
Calibration
First check the set calibration gas concentration by briefly pressing INFO
SPAN
.
The value of the calibration gas concentration should be at least 20% of the measuring range. It is possible to set 10 to 100% of the measuring range (100% LEL).
If the set value of the calibration gas concentration deviates from the available calibration gas, then the calibration gas setting in IR29 must be changed.
To do so, change to the service mode, numeric access code (or for trained staff).
Set the concentration of the available calibration gas in the sub item cal. gas/ .
Then quit the service menu with Save∕ , in order to adopt the changes.
Use the IR29 calibration adapter shown above to calibrate or adjust the display sensitivity. The rubberised area must be tightly stretched over the diffusion openings of the impact protection.
The calibration gas needs to be supplied unpressurised with a volume flow of about 0.5
l ∕ min.
via the gas supply. The injection needs to be performed for 180 seconds, 90 seconds for flushing the measuring chamber, another 90 seconds for stabilizing the concentration.
It is possible to calibrate the transmitter directly on site using the RC2. If the display deviates from the calibration gas concentration, it might be necessary to adjust it (sensitivity adjustment).
Adjustment
i
The sensor must be free from calibration gas (zero display) prior to each re-adjustment.
Activation
An adjustment can be performed after having entered the access code .
If a measured value of >100% is displayed for the calibration, it is not possible to perform an adjustment with the code 0011. Then, a temporary hour code (valid for max. 1 h) can be read in the Info∕ submenu of the service menu (Code∕ ). By doing this, the adjustment can be activated without restrictions, instead of the code 0011. Then, a repeated calibration and afterwards an adjustment might be necessary, if applicable.
- 15 -
Implementation
With the RC3 and the IR29 with display or the RC2 control unit, the procedure is carried out in four steps:
1.
Activate through pressing the button INFO
SPAN
and holding it for (min. 3 seconds). After the activation, the current interface supplies 2.0 mA throughout the entire following process and the fault LED flashes at slow intervals. The following appears on the display:
Code∕ .
2.
Then, enter the activation code . Use the
TEST
ZERO and
INFO
SPAN
buttons to change the number at the current position and
QUIT
MENU
to acknowledge the changes. Press the button for a longer period to delete the last acknowledged number.
QUIT
MENU
3.
The display alternates between the current measured value and the display Span∕ .
The instrument now waits until the concentration has risen to at least 80% of the set calibration gas. If the measured value then remains constant during a time interval of
60 seconds, the measured value is automatically used to adjust the sensitivity (display
Speichern (Save)∕ ). The calibration data has now been successfully updated.
4.
However, the transmitter does not switch back to the measuring mode; otherwise, alarms might be triggered by a still pending concentration of calibration gas. The transmitter remains in the adjustment mode, until a decline of the gas concentration and then a stabilization of the display value will be determined. Meanwhile the display
Zero∕ alternating with the current measured value will be displayed. Following the stabilization, the device will switch back to the measuring mode. If no gas decline and stabilization of the measured value is being determined, the device will independently switch back to the measuring mode after three minutes.
Note:
The AutoCal program can be shortened in each phase by pressing the INFO
SPAN
button for a longer period. Speichern ( Save) ∕ appear briefly on the display and the measured value is accepted directly to refresh the sensitivity.
Only press the INFO
SPAN
button briefly to cancel the AutoCal program without setting the sensitivity. Abbruch ( Cancel) ∕ appear on the display and must be acknowledged by pressing the QUIT
MENU
button . Subsequently, it is returned to measuring mode as described under 4.
The following error messages may occur during sensitivity adjustment:
Display/RC2 Display
Kal.-Fehler Nr. 1
( Cal. error no. 1) ∕ .
Kal.-Fehler Nr. 2
( Cal. error no. 2) ∕ .
Kal.-Fehler Nr. 3
( Cal. error no. 3) ∕ .
Remark
No increase in calibration gas has been detected.
The gas signal is unstable
The gas signal is outside the permitted tolerance range.
Malfunction LED fast flashing
Acknowledge the error messages with QUIT
MENU
. The transmitter changes to measuring mode without re-adjustment, the data of the last valid calibration is re-imported, the adjustment must be repeated.
- 16 -
Service Menu and Advanced Service Menu
Activate Service Menu
All-important parameters of the transmitter IR29 can be opened and changed in the service menu. The measuring mode is interrupted when opening the service menu and the device changes to service mode. The special status "Service" is indicated by the slow flashing fault LED and the output signal is set to 2.4 mA. If the user does not press any button, the device automatically exits the service mode after one minute and returns to measuring mode. i
All parameter changes made in the service menu refer to the currently set gas type!
If gas type and parameters are to be changed, the new gas type must first be set before parameter changes for this gas type can take effect. Changing the gas type in the service menu - submenu Gas!
The service menu is available in two different versions.
The standard service menu is opened with access code . It is not possible to change important settings, such as measuring gas or measuring range end value, here. Such attempts are ignored and the message Gesperrt (Locked) ∕ appears.
The advanced service menu is opened with access code . All settings can be carried out without restrictions in the advanced service menu. This access code should only be used by specifically trained staff of the operator.
With the RC3 and the IR29 with display or the RC2 control unit, the procedure is carried out in three steps:
1.
Press the QUIT
MENU
button for at least 3 sec. The transmitter changes to service mode. The following appears on the display: Code ∕ .
2.
Now enter the numerical access code or . Use the TEST
ZERO and the INFO
SPAN
buttons to change the number at the current position and QUIT
MENU the QUIT
MENU
to acknowledge the changes. Press
button for a longer period to delete the last acknowledged number.
3.
After correct entry, the service menu opens with menu item Gas ∕ . Use the the INFO
SPAN
buttons to select other menu items.
TEST
ZERO and
Operation
To select a menu item, use the TEST
ZERO
and INFO
SPAN keys.
The activation of a desired menu item, or the selection of a prameter, takes place after the selection of
Note:
QUIT
MENU
.
The service menu can be exited either with or without saving the changed parameters.
Several parameters can be changed one after the other without having to store them temporarily. All the parameters previously changed in the submenus are saved when exiting the service menu via the menu item “SAVE”
Exceptions:
1) Changing the type of gas:
If a different type of gas is selected in the “Gas” menu, it is saved immediately, the parameters for this type of gas are activated and the transmitter IR29 restarts with the changed parameters.
2) Setting the date and time: These are stored directly.
17
Layout of the Service Menu
Display Indications Statement
RC2 Display
Language/Time/Bus
0
Info
Settings
Query Device
Information
Zero Band
Gas 1
2
Cal. gas Calibration Gas
Concentration
Measuring range 1
Upper Range
Value
Switch Sensor zero band on/off
Sample Gas
Selection
Measured Value
Simulation
Defined values are output to the current interface
Save
Cancel
Exiting the service menu and saving all (changed) parameters
Exiting the service menu without saving all
(changed) parameters
On
Off
Modbus Baud Rate
Modbus Slave Adr 4
Time
4
.
Modbus Format 4
Exit
3
Language
1.2 / 4.0 / 7.8 / 12.0 / 20.0 / 22.0mA/ abort
.
/ .
/ .
/ .
/ .
/ .
/
Baud rates 9600,
19200 and
38400
Slave address
1-249 adjustable
8E1 (standard),
8O1 and 8N2
0 Input menu item
1 Only adjustable in the extended service menu
2 The size of the strip is determined by the sample gas.
3 Adjustable only if supported by the device
4 Only for devices with Modbus interface
Act. Date and time
Display language
Exiting the submenu
Each value individually selectable
18
Additional Menu Explanations
Cancel
Exit the service menu without saving the parameters, changes are discarded.
Save
Exit the service menu and save all changes made to the parameters.
Measured Value Simulation
This menu item can be selected to check the functionality of the current interface without gas supply. One of 6 preset mA values (1.2/4.0/7.8/12.0/20.0/22.0) is selected with the arrow keys and confirmed with the middle button. It will be output for up to 5 minutes via the current interface, and then the transmitter changes back to the measuring mode.
The value remains active within 5 minutes, until another value (or also the same value) is being confirmed, or Cancel/ESC is being confirmed. If a value is only selected, it does not influence the current status.
Gas
With this function, it is possible to explicitly select a type of gas; the corresponding parameters are filled into the device parameter memory and are automatically loaded. Only the gases are displayed for which the data are available in the parameter memory.
Note:
If the change to another gas type is confirmed, the transmitter IR29 directly restarts.
The change to a new gas type always requires a calibration and, if necessary, an adjustment of the zero point (AutoCal ZERO) and subsequently a calibration of the sensitivity and, if necessary, an adjustment (AutoCal SPAN).
There are no restrictions for the first zero adjustment after a gas change.
After a gas change, parameters such as measuring range and calibration gas concentration must be checked and adjusted if necessary, since all changes made to the parameters under the original gas type are not accepted.
Measuring Range
The measuring range of the transmitter is fixed, e.g. 0-100% LEL.
The output range of the current interface can be set to 20.0, 25.0, 30.0, 40.0, 50.0, 75.0,
100.0% of the maximum measuring range.
Note:
The change of the output range is only an adjustment of the output signal. The standardized output signal 4...20mA is used for the set output range (Default = 100%).
When reducing the measuring range, the resolution of the measuring value on the current interface is being increased. This will not change the numerical display on the display indicator/RC2.
Example: Measured value = display indicator = 25% LEL
Output range = 100% -> Iout= 4mA+(16mA * 25 %LEL/100% measuring range) = 8mA
Output range = 50% ->Iout=4mA+(16mA * 25 %LEL/50% measuring range) = 12mA
Note: For the second setting (50%) a signal >20mA will already be output for a measuring value of 51%.
19
Cal.Gas
A standard value is preset in % LEL as calibration gas concentration. It must be compared and adapted to the certificate of the sample gas bottle, where applicable.
For all types of gas, the cal. gas can be set from 10% to 100% LEL.
The following instructions are applied to convert V/V to % LEL. It is rounded to one decimal place.
Gas
Methane CH4*1
Propane
C3H8*1
Acetylene
C2H2*1
Butane
Ethanol
C4H10
C2H6O n-Nonan C9H20
LEL[Vol%]
4.4
1.7
2.3
1.4
3,1
0,7
Standard CalGas
3Vol% = 68,2%LEL
1Vol% = 58,8%LEL
1Vol% = 43,5%LEL
1Vol% = 71,4%LEL
Calibration via cross sensitivities
Zero Band
The zero band (tolerance band) of the sensor can be deactivated as required.
With the zero band a measuring value of
±1.2 %LEL is being suppressed. A measuring value from 1.2 to 2.4 %LEL is mapped to the range from 0 to 2.4 %LEL, thus, an abrupt passage is being avoided.
Possible settings:
•
(red) Zero band activated (On/ )
•
(blue) Zero band deactivated (Off∕ )
Info
Retrievable/displayed device information:
•
Sensor type/MK number(Sensor type∕ .
)
•
Serial number of the sensor (Sensor-Nr.∕ .
Sensor ).
For serial numbers higher than 9999 is displayed on the RC2.
•
Transmitter software version (Transm.-Fw.-Ver.∕ )
•
Sensor software version (Sensor-Fw.-Ver.∕ )
•
Current interface software version (I
•
Hour code (Code∕ )
4
To
20
-Fw.-Ver.∕ )
•
Transmitter serial number (Fert.-Nr./ )
Note:
The figure displayed under Code∕ corresponds to an access code valid limited in time, which can be activated with the zero point and sensitivity adjustment without limitations, refer to Calibration and adjustment (SPAN & ZERO).
Language/Time/Bus Language
Possible language settings:
•
German (Deutsch∕ )
•
English (English∕ )
•
Spanish (Espanol∕ )
Hint:
The setting of the language mainly influences on the display of the IR29. The displays of the RC2 remain unchanged, only the display LEL changes to LEL.
Language/Time/Bus Time
Setting sequence: year, month, day, hour, minute.
20
Language/Time/Bus Bus
Setting of: Modbus format, slave address, baud rate
This menu is only enabled for the IR29 B/DB. This option is not available in the i-variants, where all setting options are disabled.
Modbus format
The three options 8E1(standard), 8O1 and 8N2 are available for choice.
Modbus Slave Adresse
Modbus slave address
The address of the slave devices can be freely selected from 1 to 249.
Modbus baud rate
Three transfer speeds are available:
9600 bauds (9600 / 9.6), 19200 bauds (19200 / 19.2) and 38400 bauds (38400 / 38.4)
Displays and Messages
The following tables describe the special states in which the yellow fault LED lights up permanently and the current interface <4.0mA is set. For a better diagnosis, the transmitter IR29 without display, the error messages must be read out with the RC2 operator interface.
If the transmitter is to be restarted in the event of an error, it must be disconnected from the power supply for a short time. To do this, simply disconnect the transmitter from the socket and reconnect it after 10 seconds.
Display of Special Statuses and Malfunctions
No Display
Display
RC2
001
002
003
Device Test
Reading in Device
Parameters
Sensor Warm-Up
Seconds
Green
LED
To
Yellow
LED
To
Flashing To
Flashing To
Current
Output
1.2mA
1.6mA
1.6mA
Cause
Program and memory tests at the beginning of system start-up
Start up the system (when starting and after changing the type of gas).
Sensor warm-up phase
Note/Explanation
[p] : permanent
Q] : Acknowledgement necessary
[s] : self-resetting
Automatically switches to the “Display of operating parameters”, and then to the sensor heat-up phase
Switches automatically to measuring mode after expiration
Elapsing Seconds
201
211
↑↑↑
„ “
↓↓↓
" "
To
To
To
To
22mA
2.8mA
The gas concentration considerably exceeded the measuring range (≥
112,5% of the measuring range)
[s]
Underrange (< -7.5% of measuring range)
[s]
Zero adjustment is necessary
Note:
The error messages 211 and 201 occur when the extended measuring range (-7.5 to
112.0%LEL) is undercut/exceeded. Before, the "Displays in measuring mode" are displayed according to 210 or 203 or output via the current interface.
21
22
Error Messages of the Main CPU
No. Display
Display
RC2
Green
LED
Yellow
LED
Current
Output
Cause
104 System error -104-
(working memory
defective)
.
105 System error -105
(program memory
defective)
.
106 System error -106-
(param. memory
defective)
.
109 Sensor error -109-
(communication error sensor CPU)
.
110 Sensor error -110-
(communication error
pressure sensor)
.
111 Sensor error -111-
(communication error
humidity sensor)
.
113 System error -113-
(RAM parameter)
.
Off
Off
Off
Off
Off
Off
Off
Flashes quickly
115 Sensor error -115-
(unzur. signal level)
.
116 System error -116-
(error current
measurement)
.
Off
118 System error -118-
(check power supply)
.
130 System error -130-
(error current
measurement)
.
Off
Off
To
To
To
To
To
To
To
To
To
To
To
1.2mA
1.2mA
1.2mA
1.2mA
1.2mA
1.2mA
Error during RAM access
Error during ROM access
Error during EEPROM access
(internal)
[p]
Restart the device.
If error message appears
again, replace device
No/failed communication with sensor
No/failed communication with pressure sensor
No/failed communication with humidity sensor
Note/Explanation
[p] : permanent
[Q] : Acknowledgement required
[s] : self-resetting
[s]
Restart the device.
If error message appears
again, replace device
1.2mA
1.2mA
1.2mA
1.2mA
Depending on resistance
Cyclic check of the operating parameters in the RAM miscarried
The signal level is insufficiently low (< 80%) for an exact measurement.
Output error of the current interface or insufficient power supply
Supply voltage <12V, no measuring operation possible
Reading back the current from the current interface supplies actual value ≠
Setpoint
[p]
Restart the device.
If error message appears
again, replace device
[s]
Check optics for soiling, otherwise
Replace device
[s]
Check supply voltage.
Restart the device.
If error message appears
again, replace device
[s]
Check and readjust supply voltage
[s]
Check load or line resistance in signal path
23
Error Messages of the Sensor CPU
No. Display
Display
RC2
120 SenCpu error -120-
(working memory defective)
.
121 SenCpu error -121-
(program memory
122 defective)
.
ADU error -122-
(Error temperature
measurement)
123
124
125
.
ADU error -123-
("stuck at")
.
ADU error -124-
(Overrange)
.
ADU error -125-
(Underrange)
.
Green
LED
Off
Off
Off
Off
Off
Off
Yellow
LED
To
To
To
To
To
To
Current
Output
1.2mA
1.2mA
1.2mA
1.2mA
1.2mA
1.2mA
Cause
Error during RAM access
Error during ROM access
Error A/D converter
(temperature measurement/NTC)
A/D converter
Multiplexer or AD converter defective
A/D converter
Measured value too high
(upper AD converter limit)
A/D converter
Measured value too small
(lower AD converter limit)
Note/Explanation
[p] : permanent
[Q] : Acknowledgement required
[s] : self-resetting
[p]
Reboot the system.
If the error persists, replace the device.
[s]
Reboot the system.
If the error persists, replace the device.
Displays in Measuring Mode
No. Display
Display
RC2
Green
LED
Yellow
LED
Current
Output
Cause Note/Explanation
[p] : permanent
Q] : Acknowledgement necessary
[s] : self-resetting
[s] 203 Measured value
change with
↑↑↑
Measured value "
Change with
Flashes every
15 sec.
Off 20..22mA The gas concentration has exceeded the measuring range
(100...112.5% of the measuring range).
209
210
„ “
Measured value Flashes every
15 sec.
Measured value Flashes every
15 sec.
Off
Off
4...20mA Trouble-free measuring operation
2.8...4mA Underrange of the measuring range (-7.5...0.0% of the measuring range)
[s]
[s]
Zero adjustment necessary
Note:
The states described under no. 203 and no. 210 concern an extension of the evaluation of the
4...20mA output signal to 2.8...22mA, in order to indicate deviations with consideration of tolerances in the standard measuring range.
24
Displays in Service Mode and During Calibration (Status Messages)
No. Display
Display
RC2
301 Menu Item
302
303
304
305
306
ZERO
SPAN
Cal. error
(No conc. change)
.
Cal. error
(gas not stable)
.
Cal. error
(Cal. not plausible)
.
Green
LED
ON
ON
ON
ON
ON
ON
Yellow
LED
Flashing 2.4mA
Flashing 2.0mA
Flashing 2.0mA
Flashes quickly
Flashes quickly
Flashes quickly
Current
Output
2.0mA
2.0mA
2.0mA
Cause
Service menu was activated via keyboard or RC2
AutoCal setting of zero point was activated via keyboard with RC2 or AutoZero key
AutoCal sensitivity setting has been activated by keyboard or RC2
No increase in calibration gas concentration detected during AutoCal sensitivity adjustment
No stable zero gas or calibration gas concentration was detected during AutoCal adjustment.
The zero point or the sensitivity are outside the permitted tolerance range.
Note/Explanation
[p] : permanent
[Q] : Acknowledgement required
[s] : self-resetting
[s]
Select menu item
If no entry is made for one minute, automatic return to measuring mode
[s]
Automatic termination after successful adjustment
[s]
Automatic termination after successful adjustment
[Q]
Acknowledge with
QUIT
MENU a) Check gas supply b) Gas feed only after calling up the adjustment
[Q]
Acknowledge with
QUIT
MENU a) Stabilize gas supply
[Q]
Acknowledge with QUIT
MENU
Check zero or calibration gas and repeat procedure.
Status of the Status LEDs and the Current Output
For imporved clarity, the following table shows the different displays of both status LEDs and the current output signals as well as their meaning for a transmitter IR29 without a display.
The RC2 keypad is essential for zeroing, adjusting and calling up the service menu on a device without a display.
Green Operation
LED
Yellow Fault
LED on on on on on on flashes every 15 sec. flashes every 15 sec. flashes every 15 sec. flashing flashes quickly from on
Current Output Description see section ... on on
2.8mA
1.2mA
22mA flashes quickly 2.0mA flashing flashing from
2.4mA
2.0mA
20...22mA from from on on on
4...20mA
2.8...4mA
1.6mA
1.2mA
1.2mA
Displaying special states...
Displaying special states...
Displaying special states...
Displays in service mode...
Displays in service mode...
Displays in service mode...
Displays in measuring modeNo.
Displays in measuring modeNo.
Displays in measuring modeNo.
Displaying special states...
Displaying special states...
Displaying special states...
No. 211
No. 001
No. 201
Product No. 304-306
Item No. 301
No. 302, 303.
203
209
210
No. 002, 003
No. 115
No. 104-113, 116-130
25
Fault Messages (system and sensor faults no. 104-130, 201, 211) terminate the measuring mode until they have been eliminated. They appear permanently in the display and are additionally output via the LED code specified above (also for variants without display) and the current interface.
Status Messages are special messages that are triggered by special functions and interrupt the measuring operation. The messages 304, 305, 306 must be acknowledged, all other messages and statuses are self-resetting after a certain time. The transmitter then automatically resumes measuring operation.
Initial Commissioning and Maintenance
The DIN EN 60079-29-2 "Gas detectors – Selection, installation, use and maintenance of detectors for flammable gases and oxygen" as well as the relevant national rules and regulations must be observed. In Germany, these include "Explosion Protection Regulations", the leaflet T 023 (BGI 518) "Gas warning devices for explosion protection - use and operation" and the BGR 500, Part 2, Chapter 2.33 "Operation of systems for handling gases", 4.4 Testing of gas warning devices. During initial commissioning, gas warning devices must be checked for function by an expert after installation. (see DIN EN 60079-29-2 Section 8.9 and leaflet BGI 518
/T023 Section 8.1). Maintenance includes inspection, servicing, calibration and adjustment, as well as regular functional tests and repairs. Tests must be carried out by an expert. The result must be confirmed in writing.
According to the instruction sheet BGI 518 / T023 - "Gas warning devices for explosion protection: Application and operation", the application and operation includes the following:
• Maintenance of stationary gas warning systems
• Regular functional test
Maintenance of Stationary Gas Warning Systems
Monthly visual inspection (section 9.1 T023):
- Mechanical damage
- Contamination e.g. by dust
- Condensation due to moisture
As well as control of the:
- Protection devices of the transmitters
- Diffusion orifice of the transmitters
- Gas sampling system, gas processing (if available)
Regular Functional Tests
Tests must be carried out by an expert. The result must be confirmed in writing.
Function checks (section 9.2. T023) Interval: 4 months
Scope of functional checks:
- Calibration (measured value display) using zero and calibration gas
- Adjustment of zero point and sensitivity adjustment with zero or calibration gas
- Response Time
- Output functions (interfaces and displays)
- Error Messages
System checks (section 9.3) Interval: 1 year
26
It is recommended to entrust GfG customer service with these tasks.
Repair
This includes all repair and replacement work. Only use original spare parts and assemblies tested and released by the manufacturer.
If during the regular inspections of the gas warning system or by reviewing a warning or fault message a contamination of the optics of the IR29 is detected, it must be cleaned as described below:
1) Remove the impact protection, if necessary remove the dust filter.
2) Visual inspection of the sapphire disc and mirror
3) It is recommended to use a lint-free cloth and isopropyl in order to clean the mirror and the sapphire disk. If any other cleaning agents are used, first make sure that they are compatible with the device materials (sapphire glass, PA12, PA6 and PE).
Troubleshooting
No measuring signal at current interface:
If no measuring signal is output via the current interface, check the amount of the supply voltage and the polarity of the connections.
If the transmitter is disconnected from the base, the current interface will provide a 1.2mA fault signal if it is connected correctly. Once this state is established, the transmitter can be connected. During the warm-up time the value of the current interface should change to 1.6mA, after the warm-up time to 4mA. If this is not the case, the communication between socket and transmitter may be disturbed. An optical check of the plug connection and cleaning of the contacts with a suitable cleaner (e.g. contact WL Universal cleaner for electronics).
No display indication:
Press the "Test" button on the RC2/RC3. All pixels of the display are controlled. If the display shows no reaction or if areas of the display remain bright, the display is defective. Repairs can only be carried out by the manufacturer or the service staff.
The display is not part of the safety chain, all settings can also be performed via the RC2.
No display in RC2 and no response to key operation:
Replace the RC2 battery. If the error persists, the communication between RC2 and IR29 may be disturbed. Optical control of the connectors, test the connecting cable. If all these points are
“no fault found”, test the RC2 on another transmitter, if applicable.
If the same effect is being observed, the RC2 is probably defective – return the RC2 to the manufacturer. If the RC2 works with another transmitter, the error is in the IR29 – return the
IR29 transmitter.
No bus communication:
•
Check the bus settings in the GMA and in the transmitter (baud rate, address, bus format).
•
Check the measurement loop configuration in the GMA.
•
When using the GfG-GMA, check the selected connection (TRM-Bus1 or TRM-Bus2).
•
Check the voltage supply of the transmitter.
•
Check the polarity of the data lines on the transmitter and on the evaluation unit.
•
Check if there is a cable break or a short circuit on the data line.
•
Check the number and position of the terminating resistors; there may only be one terminating resistor on the last device of the bus.
27
Transmitter does not start / error 116, 118,130
Visual inspection of the contacts in the connector. Check if one of the pins is twisted, soiled or dented in the socket in the base (i.e. shorter than the others).
This can result in no or only poor contact between the socket and the transmitter.
If one of the pins is shortened, the only remedy will be to replace the base.
If contact is poor, clean socket and plug, e.g. with electronic cleaner or isopropanol.
Accessories
Remote Control RC2
Connection cable for RC2 / cable length 2m
Connection cable for RC2 / cable length 5m
Connection cable for RC2 / cable length 8m
Connection cable for RC2 / cable length 10m
Remote control RC3, channel 16 (default)
Remote control RC3, channel 01-15
IR29 calibration adapter to adjust the transmitter
IR29 flow adapter to measure gas samples
Dust Filter 40mm
Dust Filter 20mm
Guard
Supply Module SB1
Best. -No.
2800201
2800210
2800211
2800212
2800213
2910230
On Request
2910220
2910221
2900331
2900332
On Request
2910210
Spare Fuse 63mA for SB1 (F4, F5, F6) 2900381
The storage conditions for RC2, RC3 and SB1 can be found in the corresponding operating instructions or extracts from the operating instructions.
The same temperature ranges apply for the calibration adapter, flow adapter and dust filter as for the IR29 transmitter (-25°C to +60°C; recommended 0°C to +30°C).
Furthermore, the accessories need to be stored clean, dry and free from corrosive influences.
28
Connections and Terminal Assignment
IR29 i/Di with 4...20mA Interface and Zener barriers
IR29 i/Di
Transmitter (+) VCC
X1 15...30V DC (behind the Zener barrier)
X2 Transmitter (-) GND
4...20mA (+)
X3 15...30V DC (behind the Zener barrier)
X4 4...20mA (-) GND
X4
X3
X2
4...20mA
15-30V DC
Supply according to the
Zener barrier spec. mA
X1 max. Resistance see technical data
Supply according to the
Zener barrier spec.
IR29 i/Di with 4...20mA Interface and Zener barriers from MTL
IR29 i/Di
Transmitter (+) VCC
X1 22...27V DC (before of the Zener barrier)
X2 Transmitter (-) GND
4...20mA (+)
X3 22...27V DC (before of the Zener barrier)
X4 4...20mA (-) GND
X4
X3
4...20
Type: MTL 7787P+ / 7728P+
7787P+
4 2
3 1
22-27V DC
Max. Resistance see technical data
X2
X1
7728P+
4 2
3 1
22-27V DC
Transmitter Supply mA
Terminal assignment MTL7700 series according to EPS7700 Rev6
140410
29
IR29 i/Di with 4...20mA Interface and SB1
IR29 i/Di
Supply by SB1
X2 Transmitter (-) GND
X4 4...20mA (-) GND
SB1 see chapter
accessories
X4
X3
X2
X1
4...20 mA
GND
VCC
SB1
X1 VCC
X2 GND
X3 4..20mA
X4 VCC (Transmitter)
X5 GND (Transmitter)
X6 VCC (4...20mA)
X7 Signal (4...20mA)
X7
X6
GfG SB1
X3
X2
X1
Current Interface
Max. 270 Ω
X5
X4
Supply
22-30V DC mA
!
Note on installation:
The transmitter is supplied via terminals X1 and X2. The current interface is supplied via X3 and supplies the 4...20mA signal via X4. Transmitter and current interface are two galvanically separated circuits which communicate via optocouplers. If this communication is disturbed, e.g. because X1 or X2 is not connected or the transmitter is not connected to the socket (terminal), the current interface outputs
1.2 mA if voltage is already present.
30
IR29 i/Di with 4...20mA Interface & 3-wire cable (e.g. GMA41)
IR29i/Di
Supply via the GMA
X2 Transmitter (-) GND
X3 Bridged to X1
X4 4...20 mA output
X4
X3
X2
X1
4...20 mA
GND
VCC
GMA41
AL1
AL2
24V
GND
4-20mA
GND
24V
(+)
(-)
GND
Quit
AL3
Sensor
IN diges
OUT
4...20mA
!
!
CAUTION!
To create the necessary bridge X1-X3, the wiring must be made with stranded wire.
The two conductors in X1 must be professionally pressed into a common, sufficiently dimensioned ferrule.
The use of different conductors (solid wire and stranded wire) is not permitted!
The use of several solid wires in one ferrule is not permitted!
CAUTION!
This type of connection interconnects two intrinsically safe circuits.
The IR29 i/Di thereby loses its intrinsic safety; operation in hazardous areas is not permitted!
31
IR29 /D with 4..20mA Interface & 3-wire cable to GMA200
X1
Transmitter (+) VCC
Supply via the GMA Supply GMA mA
GND
GMA200
X2 Transmitter (-) GND
24V
X5 4...20 mA output 24V
GND
Reset1
Reset2
X5
GND
Iout1
Iout2
X2
X1
4...20 mA
GND
VCC
IN1
24V
GND
IN2
D1+
D0-
DGND
D1+
D0-
DGND
D1+
D0-
DGND
IR29 B/DB; with RS485 Bus & Four-Wire Cable to GMA200
Supply GMA mA
GND
GMA200
X2 GND
X3 D1+
X4 D0-
X5 VCC
X6 GND
X9
X8
X7
X6
X5
X4
24V
24V
GND
Reset1
Reset2
GND
X7 D1+
X8 D0-
X9 terminating resistor
X3
X2
X1
Iout1
Iout2
IN1
24V
GND
IN2
GND
VCC
D0-
D1+
!
D1+
D0-
D0-
D1+
D0-
DGND
D1+
DGND
DGND
Transmitter types IR29B and IR29DB:
The non-intrinsically safe internal bus terminating resistor (120Ω) is activated by a jumper at terminals X8 and X9. Only one wire bridge may be connected. No voltage may be applied to terminal X9.
32
Measuring Gases and Measuring Ranges
Measuring Gas methane propane acetylene*
Methane*, propane*, acetylene* n-butane n-Nonan ethanol
2-propanol
Measuring Range
Standard
0 - 100% LEL
0 - 100% LEL
0 - 100% LEL
0 - 100% LEL
0 - 100% LEL
0 - 100% LEL
0 - 100% LEL
0 - 100% LEL
100%UEG according to DIN EN 60079-20-1: 2010
Methane CH4 n-Butane
C4H10 n-Nonan C9H20
2-Propanol
C3H8O
4.4% by volume
1.4% by volume
0.7% by volume
2.0% by volume
Measuring Range Smallest
/ Largest
10% UEG / 100%UEG
10% UEG / 100%UEG
10% UEG / 100%UEG
10% UEG / 100%UEG
10% UEG / 100%UEG
10% UEG / 100%UEG
10% UEG / 100%UEG
10% UEG / 100%UEG
Propane
C3H8
Acetylene
C2H2
Ethanol
C2H6O
MK Number
242-1, 244-3
243-1, 244-3
244-1
244-3
243-1, 244-3
242-1, 244-3
243-1, 244-3
243-1, 244-3
1.7% by volume
2.3% by volume
3.1 % by volume
Sensor Specification
MK242-1 Infrared sensor for flammable gases and vapors
Measuring Range
Disbandment
Tolerance Band
Response Time
Pressure750 ...1200mbar:
Compensated (uncompensated)
Humidity0%
Temperature-25
Cross sensitivities
@ 50%UEG:
...95% r.h.:
...+55°C:
Expected service life
0.0...100%UEG
0.2..1.0%UEG
± 1.2%UEG t50 ≤ 20sect90 ≤ 50 sec @ CH4 (methane)
<1.1%(1.5%) of CH4 indication per 1% change in pressure
(regarding 100kPa) max. ± 2,0 %UEG or ± 10% of the display (with respect to 0%r.F. @40°C) max. ± 2,0 %UEG or ± 10% of the display (regarding 20°C) gas task
0,85Vol% C
3
H
8
CH4-display0
ca.153%UEG
2,20Vol% CH
1,15Vol% C
1,0Vol% C
3
H
0,75Vol% C
1,15Vol% C
0,5Vol% C
6
2
4
H
2
4
= 50%UEG
H
8
O ca.89%UEG
H
H
14
0,7Vol% C
5
H
12
2
ca.0%UEG
8
O ca.43%UEG
6
O ca.105%UEG ca.30%UEG ca.97%UEG
They can vary from sensor to sensor and depend on the gas concentration.
6 years
MK243-1 Infrared sensor for flammable gases and vapors
Measuring Range
Disbandment
Tolerance Band
Response Time
Pressure750 ...1200mbar:
Compensated (uncompensated)
Humidity0%
Temperature-25
Cross sensitivities
@ 50%UEG:
...95% r.h.:
...+55°C:
Expected service life
0.0...100%UEG
0.2..1.0%UEG
± 1.2%UEG t50 ≤ 21sect90 ≤ 50 sec @
C3H8
(propane)
<0.2%(1.2%) of C3H8 display per 1% change in pressure,
(regarding 100kPa) max. ± 2.0 %LEL or ± 10% of the display (relative to 0%R.F. @40°C) max. ± 2.0 %LEL or ± 10% of the display (relative to 20°C) gas task
0,85Vol% C
3
2,20Vol% CH
2
H
4
H
8
C
3
H
8
-Anzeige
= 50%UEG ca.17,6%UEG
2
ca.0%UEG 1,15Vol% C
1,55Vol% C
0,5Vol% C
6
0,7Vol% C
5
2
H
6
O ca.47%UEG
H
14
H
12 ca.19%UEG ca.37%UEG
They can vary from sensor to sensor and depend on the gas concentration.
6 years
33
MK244-1 Infrared sensor for flammable gases and vapors
Measuring Range
Disbandment
Tolerance Band
Response Time
Pressure750...1200mbar:
Compensated (uncompensated)
Humidity0% ...95% r.h.:
Temperature-25...+55°C:
Cross sensitivities
@ 50%UEG:
Expected service life
0.0...100% UEG
0,2..1,0% LEL
± 1.2% LEL t50 ≤ 21sect90 ≤ 50 sec @
C2H2
(acetylene)
<0.6%(1.4%) of C2H2 display per 1% change in pressure, (with respect to
100kPa) max. ± 3,0 % LEL or ± 10% of the display relative to 0% r.h. @40°C) max. ± 2.0 % LEL or ± 10% of the display (regarding 20°C) gas task
0,85Vol% C
3
H
2,20Vol% CH
1,15Vol% C
2
4
H
8
C
2
H
2
-Display
ca.0%UEG ca.0%UEG
2
= 50%UEG
They can vary from sensor to sensor and depend on the gas concentration.
6 years
MK244-3 Infrared sensor for flammable gases and vapors
Measuring Range
Disbandment
Tolerance Band
Response Time
Pressure750 ...1200mbar:
Compensated (uncompensated)
Humidity0% ...95% r.h.:
Temperature-25...+55°C:
Cross sensitivities
@ 50%UEG:
Expected service life
0.0...100% UEG
0,2..1,0% LEL
± 1.2%UEG t50 ≤ 20sect90 ≤ 50 sec @ CH4 (methane) t50 ≤ 26sect90 ≤ 57 sec @ t50 ≤ 21sect90 ≤ 50 sec @
<1,1%(1,5%) the CH
<0,2%(1,2%) the C gas task
0,85Vol% C
3
H
2,20Vol% CH
4
2
H
8
CH
3
H
<0,6%(1,4%) the C
2
4
4
C
3
C
2
-Display
H
8
H
2
(propane)
(acetylene)
C
3
H
8
-display per 1% pressure change, (referred to 100kPa)
8
- display per 1% pressure change, (referred to 100kPa)
H
2
- display per 1% pressure change, (referred to 100kPa) max. ± 3,0 %UEG or ± 10% of the display relative to 0% r.h. @40°C) max. ± 2,0 %UEG or ± 10% of the display (regarding 20°C)
-Display
ca.153%UEG = 50%UEG
C
2
H
2
-Display ca.0%UEG
= 50%UEG ca.17,6%UEG ca.0%UEG
1,15Vol% C
0,5Vol% C
0,7Vol% C
5
6
2
ca.0%UEG ca.0%UEG = 50%UEG
H14 ca.30%UEG ca.19%UEG ca.0%UEG
6 years
H12 ca.97%UEG ca.37%UEG ca.0%UEG
They can vary from sensor to sensor and depend on the gas concentration.
MK247-1 Infrared sensor for CO2
Measuring Range
Disbandment
Tolerance Band
Response Time
Pressure:
Humidity:
Temperature:
Cross sensitivities
@ 50%UEG:
Expected service life
0,00...10,00 Vol%
0.01..0.1 vol%
- t50 ≤ 30sect90 ≤ 130 sec @ CO
2
(carbon dioxide)
750...1200mbar:
0%...95% r.h.
-25...+55°C
Gas task
0,85Vol% C
8
CO
2
-Display
ca.0Vol%
2,20Vol% CH
1,15Vol% C
3
H
2
4
H ca.0Vol%
2
ca.0Vol%
They can vary from sensor to sensor and depend on the gas concentration.
6 years
34
Technical Data
Device Types IR29i and IR29Di
Measurement Function
Measuring principle: infrared absorption
Output signal: 4...20mA (max.load without Zener barrier :500Ω @18V or 800Ω @≥24V)
600Ω @22V - 30V)
Power Supply
(max. load with Zener barrier: 450Ω @22V or 550Ω @≥24V)
(max. load with GfG SB1:
Supply voltage:
Maximum supply current:
18...30V DC @supply intrinsically safe
22...27V DC @supply via Zener barrier (RL* max = 250 Ω)
22...30V DC @supply via GfG transmitter supply module SB1
< 50mA
Climatic Conditions
Temperature (storage): −25...+60°C or 0...+30°C (recommended)
Temperature (operation): −25...+55°C (see also sensor specification)
Air pressure: 750.. 1200mbar (see also sensor specification)
0..100% r.h. (non-condensing)
≤ 21.0% by volume
Humidity:
Oxygen content of the atmosphere:
Case
Dimensions: (132.5 - 152.5) x 75mm (L x Ø) **
Mounting surface min. 161mm x 133mm; height 118mm
Weight: approx. 950 grams
Housing material: stainless steel, polycarbonate, PA12, POM
Housing protection class:
IR29i / Tue: IP 67
IR29Di with rotatable display: IP 40
Approvals and Tests
Marking and type of protection: 0158
I M1 Ex ia I Ma -25°C≤Ta≤+55°C
II 1 G Ex ia IIC T4 Ga -25°C≤Ta≤+55°C
EC type-examination certificate: BVS 09 ATEX E 135 X
Electrical parameters for intrinsically safe connection
Intrinsically safe supply circuit: Connection via terminals X1 and X2
Maximum input voltage: Ui DC 30V
Maximum internal capacity: Ci 11nF
Maximum internal inductance: Li negligible
**)
Intrinsically safe signal circuit: Connection via terminals X3 and X4
Maximum input voltage: Ui DC 30V
Maximum internal capacity: Ci 1.8nF
Maximum internal inductance: Li negligible
The intrinsically safe signal circuit is safely galvanically isolated from the intrinsically safe supply circuit up to a sum of the peak values of the nominal voltages of 60V.
*) series resistance of the GfG transmitter supply module or the Zener barrier
Length depending on sensor configuration; without sealing plug
35
Device Types IR29, IR29 D, IR29 B and IR29 DB
Measurement Function
Measuring principle: infrared absorption
Output signal for
IR29 and IR29D: 4...20mA (max.load without Zener barrier :500Ω @18V or 800Ω @≥24V)
Power Supply for IR29B and IR29DB RS485 two-wire interface
Supply voltage:
Maximum voltage: 45V DC
Supply voltage: 18V DC ... 30V DC
Maximum supply current: 70mA
Signal circuit (4-20mA) 30V DC Rated voltage
Signal circuit (RS485) 20V DC Rated voltage
Climatic Conditions
Temperature (storage): -25...+60°Cor 0...+30°C (recommended)
Temperature (operation): -25...+55°C (see also sensor specification)
Air pressure: 750..1200mbar (see also sensor specification)
Humidity:
Oxygen content of the atmosphere:
Case
0..100% r.h. (non-condensing)
≤ 21.0% by volume
Dimensions: (132.5 - 152.5) x 75mm (L x Ø) **
Mounting surface min. 161mm x 174mm; height 118mm
Weight: approx. 1100 gram
Housing material: stainless steel, polycarbonate, PA12, POM
Housing protection class:
IR29 / D/ B/ DB: IP 67
IR29 D/ DB with rotatable display: IP 40
Approvals and Tests
Marking and type of protection: 0158
II 2G Ex eb mb ib [ib] IIC T4 Gb -25°C≤Ta≤+55°C
EC type-examination certificate: BVS 09 ATEX E 135 X
**) Length depending on sensor configuration; without sealing plug
GfG Gesellschaft für Gerätebau mbH
Klönnestraße 99 - D-44143 Dortmund
Telephone:
Fax:
Web:
Email:
+49 (0)231 - 564 00-0
+49 (0)231 - 564 00-895 www.gasmessung.de [email protected]
Firmware Version 1.20
224-000.20_BA_IR29.do
Last updated: 09 July 2018 Subject to change
36
Notes IR29
Mounting accessories
Dust Filters
Flow Adapter or Impact Protection
37
Overview Torques
38
39
40
Appendix RC3
Field of Application and Intended Use
The RC3 control unit can only be used to operate the IR29 transmitters with display.
The RC3 operator interface is powered by a lithium battery, which must not be replaced in hazardous areas.
The RC3 operator interface is approved for use in potentially explosive atmospheres and has an EC type-examination certificate issued by DEKRA EXAM GmbH in accordance with
Directive 94/9/EC (ATEX100a) with the following
Certificate: BVS 08 ATEX E 006
Certification: I M1 Ex ia I Ma
II 1G Ex ia IIC T6 Ga -20°C≤Ta≤+55°C
Operation
The button assignment of the RC 3 can be shown on the display of the device by briefly pressing the central button.
Middle Button
Quit
Menu
Left Button
Test
Zero
Right Button
Info
Chip i
The receiver software only responds to activations >0.6 sec. to avoid unintentional or incorrect operation.
Channel Coding
The RC3 is factory coded on channel 16. This allows any IR29 transmitter to be operated.
Channels 1-15 can be factory coded in RC3 and transmitted on request. In this way it is possible to group devices that can only be operated via a separate channel.
The RC2 control unit is not affected by these settings.
Changing Batteries
CAUTION: Never open the device in potentially explosive atmospheres to change the lithium battery.
41
When inserting the new lithium batteries, always observe their polarity. These batteries should only be obtained from the company GfG, i.e. the device manufacturer. Internal monitoring ensures that only batteries which meet the demands of the Type Examination are used. The battery type is: VARTA CR 2430.
Technical Data
Type Designation:
Climatic Conditions:
Power Supply:
Housing:
RC3 for the operation: -20...+55°C | 5...95% r. F. | 700...1300hPa
Lithium battery Typ: VARTA CR 2430
U n
=3V
Material: plastic
C=280mAh
Dimensions: 44 x 61 x 15 mm (W x H x D)
Weight: 20 g
Protection class: min. IP20
Approvals and Tests:
Marking and type of protection: I M1 Ex ia I Ma
II 1G Ex ia IIC T6 Ga -20°C≤Ta≤+55°C
EC type-examination certificate: BVS 08 ATEX E 006 (without measuring function)
42
Appendix SB1
Operating Instructions
The transmitter supply module SB1 is used to limit the voltage and current of nonintrinsically safe circuits to intrinsically safe values. The non-intrinsically safe circuits are galvanically connected to the intrinsically safe circuits.
A transmitter IR29 connected to the transmitter supply module type SB1 is supplied intrinsically safe. The signals of the IR29 transmitter are read out via a 4-20mA interface and forwarded to an evaluation unit outside the hazardous area. The transmitter supply module is optimally designed for the supply of the transmitters IR29i and IR29Di.
The transmitter supply module SB1 must be installed outside hazardous areas and has an
EC type-examination certificate issued by DEKRA EXAM GmbH in accordance with Directive
94/9/EC.
For the SB1 applies:
Certificate: BVS 11 ATEX E 164
Certification: II (1) G [Ex ia Ga] IIC -20°C≤Ta≤+55°C
Device Design
Please refer to the table "Technical data" for the maximum values of the voltage, current and power in the intrinsically safe circuits (U
0
, I
0
, P
0
) as well as the maximum permissible values of the connected capacities and inductances (C
0
und L
0
). The values listed in the table apply to one of the two barrier branches that must be observed separately (relating to PA). Observe the current or voltage additions when interconnecting.
Install Electrical Connections
Input circuit Only for connection to a non-intrinsically safe circuit
(terminals X1, X2 and X3) with a safety-related maximum voltage of U m
= 253 V AC
Output circuit
(terminals X4 and X5)
Signal circuit
(terminals X6 and X7)
In ignition protection class 'intrinsically safe' [Ex ia Ga]
In ignition protection class 'intrinsically safe' [Ex ia Ga]
Interchangeable fuses
From the
Control
Unit
Characteristics of the circuits: linear (see Technical data)
Characteristics of the circuits: linear (see Technical data)
To transmitters
Supply circuit
Signal
circuit
!
When mounting the transmitter supply module please consider that the connector cables of the not intrinsically safe electric circuit in the SB1 are conducted with a distance of at least 6mm clearance in air to the connector cables of the intrinsically safe electric circuit and accordingly the connector of the display (con1).
43
!
!
The transmitter supply module is equipped with three exchangeable prefuses. When replacing the fuses, ensure that only fuse type 164050.0,063
(I
N
=63 mA) from SIBA is used.
(See Technical data)
As the intrinsically safe circuits are galvanically connected to the earth potential, potential equalization must be provided throughout the entire intrinsically safe circuits.
Potential Equalization:
This is located next to the cable entries on the bottom side.
Potential equalization must take place with a line cross section of
4 mm 2 .
Potential Equalization
44
Technical Data
Device types: SB1
Power Supply
Supply voltage: 22V DC...30V DC
Climatic Conditions
Temperature (storage): −25...+60°C
Temperature (operation): −20...+55°C or 0...+30°C (recommended)
Air pressure: 0...200kPa
Humidity: 0...100% r.h. (non-condensing)
Case
Dimensions: 98mm x 96mm x 48mm (L x W x H) without cable entry
Weight: approx. 300 gram
Housing material: ABS
Housing protection class: IP 54
Interchangeable Back-up Fuses
Guy: 164050.0,063
Rated current: 63 mA
Rated breaking capacity: 35A @ 250VAC
Melt integral (I2ts): 0,0007
Checked: IEC 60127
Approvals and Tests
Manufacturer: SIBA
Certification: II (1) G 0158
Ignition protection class: [Ex ia Ga] IIC -20°C≤Ta≤+55°C
EC Type Examination certificate: BVS 11 ATEX E 164
Electrical parameters for non-intrinsically safe connection
Not intrinsically safe supply: X1:
X2:
+22V DC ... +30V DC
GND
Non-intrinsically safe signal circuit: X3: 4...20mA
Maximum fault voltage: Um253V AC
Electrical parameters for intrinsically safe connection
Intrinsically safe supply circuit: X4:
X5:
Maximum output voltage: U
Maximum output current: I
0
Maximum output power: P
Maximum switchable capacity: C
0
0
Maximum switchable inductance: L
0
0
Maximum output current: I
Maximum switchable capacity: C
Maximum switchable inductance: L
0
0
0
0
Maximum output power: P
0
Intrinsically safe signal circuit: X6:
X7:
Maximum output voltage: U
+19V DC
GND
21 V DC
161 mA DC
844 mW
180 nF
1 mH
4…20mA +
4…20mA -
21 V DC
161 mA DC
844 mW
180 nF
1 mH
45
Declarations of Conformity, Type Examination Certificates
46
47
48
49
50
51
52
53
54
advertisement
Related manuals
advertisement