- No category
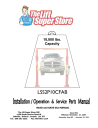
advertisement
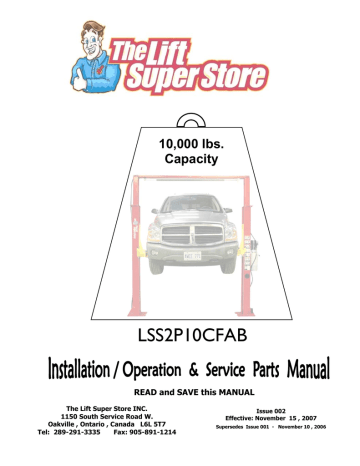
10,000 lbs.
Capacity
LSS2P10CFAB
READ and SAVE this MANUAL
The Lift Super Store INC.
1150 South Service Road W.
Oakville , Ontario , Canada L6L 5T7
Tel: 289-291-3335 Fax: 905-891-1214
Issue 002
Effective: November 15 , 2007
Supersedes Issue 001 - November 10 , 2006
Your new lift will provide years of dependable service if installed, operated and maintained properly. Read and follow all safety, installation, operation, and maintenance instructions in this manual before installing and operating the lift. In addition, read and follow all safety and other information included on and with the lift. Keep this manual in a secure place for
future reference, training and service part identification.
TABLE of CONTENTS
1. Lift Purchase Buyers Agreement page 3
2. Unloading Procedure and Lift Package Contents page 4
3. Warranty and Safety page 5 - 6
4. General Requirements and Lift Specifications page 7 - 8
5. Tools Required and Pre Installation Procedures page 9 - 10
6. Installation Procedures page 10 - 13
7. Operating Instructions and Lift Maintenance page 14
8. Troubleshooting page 15
9. Lift Installation Diagrams and Parts Lists page 16 - 20
IMPORTANT :
It is the shop owner's responsibility to provide a satisfactory installation area for the lift. Lifts should only be installed on level concrete floors with a minimum of 4 inches (102mm) and 3000 psi (20.7MPa) concrete that has been aged a minimum of 30 days. Please consult a qualified individual if any doubt exists concerning proper installation and subsequent safe operation of the lift. Do not install the lift on asphalt.
Prior to installation, it is the shop owner's responsibility to provide constant electrical power in the correct voltage, phase, etc., and all wiring for electrical hook-up of the lift. The shop owner must insure that the electrical installation conforms to local building and safety codes.
Where required, the shop owner will provide an electrical isolation switch located in close proximity to the lift. This switch will have an emergency stop capability and isolate electrical power from the lift for servicing requirements.
Hydraulic oil cannot be shipped with the lift and will be supplied by either the shop owner or the installer. ISO 32 hydraulic oil (10W non detergent hydraulic oil) must be used to fill the reservoir tank before operating the lift.
It is the shop owner's responsibility to train all operators in lift operation and safety.
2
Lift Purchase Buyers Agreement
Warranty
Each Lift Super Store Inc. lift has the following warranty from date of purchase:
Structural Components - 5 years Accessory Items - 90 days
Hydraulic and Other Components - 1 year Labor – owner responsibility
The component and hydraulic parts warranty is limited to defects in workmanship and material. The warranty does not cover misuse, abuse, overloading, lack of maintenance, inappropriate use or
“normal wear and tear”. Warranty parts must be returned to the Lift Super Store Inc. for inspection to qualify for warranty. Shipping costs are the owner’s responsibility.
Freight Damage
Each lift is carefully inspected by our shipping department before loading. Damage incurred during shipping must be noted on the transport companies “bill of lading” and signed by the driver. It is the owner’s responsibility to advise Lift Super Store Inc. within 48 business hours, of any shipping damage.
Installation
At the purchaser's request, the Lift Super Store Inc. will arrange for delivery and installation by a professional contractor. It is the owner’s responsibility to approve completion of all work done and confirm the product is working properly. The owner must advise our office within 24 business hours of incomplete work or product deficiency.
Lift Maintenance
Every lifting product will require ongoing adjustment and maintenance. It is normal for lift cables to require adjustment that ensures level lift operation. Periodic adjustments are the owner’s responsibility.
If the owner requires the assistance of a lift technician, a service charge will apply for a service call.
The lift is manufactured with a baked on powder coat finish. To maintain this finish it is recommended that scratches are periodically touched up with automotive style paint. All non painted services should be kept clean and lubricated to prevent rust or corrosion.
Service Calls
The Lift Super Store Inc. can provide on site servicing of your lifting product by a qualified lift service technician. The owner is responsible for all costs and direct payment to the contractor at the time the work is completed. It is the owner’s responsibility to return any parts to the Lift Super Store Inc. for warranty consideration as noted above.
The Lift Super Store Inc.
1150 South Service Rd. W.
0akville , Ontario
L6L 5T7
289-291-3335
289-291-3350 fax
866-799-5438 [email protected]
3
UNLOADING PROCEDURE and LIFT PACKAGE CONTENTS
For your information:
All lift components are grouped together in one package held at each end by steel frames.
Unpacking Procedure:
When the lift arrives on site: - If possible have lift unloaded in the installation area.
- Check for freight damage and report immediately to the
trucking company who delivered the lift.
- Check for missing parts and report immediately to:
The Lift Superstore Inc.
1150 South Service Road West
Oakville , Ontario L6L 5T7
1 – 866 – 799 – 5438
Main Components include:
Power Side Column and Carriage Assembly – 1 pc
(c/w equalizing cable and safety decals)
Opposite Side Column and Carriage Assembly – 1 pc
(c/w equalizing cable)
Column Extensions – 2 pc
Overhead Crossmember – 2 pc
(and 2 steel cable pulley assemblies)
Overhead Safety Shutoff Bar – 1 pc
Arms – 4 pc
Powerpack Assembly – 1 pc
Accessory and Hardware Box includes:
Micro-switch for Overhead Safety Shutoff Bar - 1pc
(c/w 2 mounting brackets and hardware)
Baseplate Shims (6mm - 3mm - 1mm assortment) - Anchor Bolt Assemblies - 10 pc
Arm Pins – 4 pc
(c/w roll pins to secure them)
Arm Restraint Component Assemblies (4 pc)
Rubber Stack Pad Assembly – 4 pc
Stack Pad Adapter (3”) – 4 pc
Stack Pad Adapter (6”) – 4 pc
Hydraulic Hose – 1 long & 1 short
(also 1 "T" fitting, 2 90º fittings & 1 powerpack adapter fitting)
Fittings Box (bolts, washers, nuts, screws, cable ties, etc.)
Owner’s Manual
4
WARRANTY and SAFETY
Warranty:
The two post lift listed in this manual has the following warranty from date of
purchase:
Structural Components - 5 years Accessory Items - 90 days
Hydraulic and Other Components - 1 year Labor – owner's responsibility
The above items are warranted to be free of defects in material and workmanship to the original owner of the lift as follows: During the first year
(90 days for accessories)
, those parts proven after inspection to be defective shall be repaired or replaced at the option of the manufacturer. Structural components only are warranted for an extended four years and if proven after inspection to be defective shall be repaired or replaced at the option of the manufacturer. This warranty does not extend to defects caused by ordinary wear, misuse, abuse, improper maintenance, shipping damage or where repairs have been attempted or made by anyone other than the manufacturer or a manufacturer certified technician. This warranty is exclusive and in lieu of all other warranties express or implied. In no event shall the manufacturer be liable for special, incidental or consequential damages for any breach or delay in performance of the warranty. The manufacturer reserves the right to change specifications, designs or add improvements to its product line without incurring any obligation to make such changes to products sold previously.
Safety:
Basic common sense safety precautions should always be followed when
installing and operating the lift. In addition:
1. Read and follow all safety instructions and decals included on and with the lift. Read and
follow all safety instructions in this manual.
2. Only trained and authorized personnel should position a vehicle and operate the lift. Do
not allow customers or bystanders to operate the lift or be in the lift area.
3. Inspect the lift daily. Do not operate if potential problems have been identified or lift
malfunctions. Do not operate if lift has damaged or broken components. Never walk or
work under the lift unless all safety locks are completely engaged.
4. Never overload the lift. The rated capacity decal is located on the powerpack column. The
hydraulic system on this lift is not designed to be a load holding devise. Mechanical safety
locks must be engaged before proceeding under the lift, with vehicle servicing, or system
maintenance. Never override operating controls. This is unsafe and will void the warranty.
5. Before driving a vehicle between the columns, position all arms to insure unobstructed
entry. Do not hit or run over arms as this could damage the lift and/or vehicle.
6. Use all 4 arms to raise a vehicle. Position all lift pads to contact vehicle manufacturer's recommended lifting points. Raise lift slowly until all pads contact the vehicle. Check all pads for complete and secure contact with the vehicle. Check all arm restraints to insure they are engaged properly. Check that vehicle is stable on the lift. Only after confirming these procedures, raise the lift to desired working height.
Safety continued on page 5 ……
5
7. Special care must be used when lifting pick-up trucks. Optional truck adapters may be
required to reach manufacturer recommended lifting points. Always use these lifting
points. Running boards and other installed accessories may also require optional
adapters. Insure contents of the cargo box will not affect vehicle balance while on the lift.
8. Important: Removal or installation of heavier parts can change the vehicle's center of gravity on the lift resulting in a critical load shift. The vehicle may then be unstable. Plan ahead for this possibility to insure continued safety and refer to the vehicle manufacturer’s service manual for recommended procedures.
9. Always keep the lift area free of obstructions and debris. Clean up grease and oil spills
immediately.
10. Never raise a vehicle with passengers inside. Before lowering a vehicle, check the lift and
lift area and remove all obstructions. Before removing vehicle from the lift or lift area,
position arms to the drive through position and confirm an unobstructed exit.
Safety Instruction and Information Decals
(included with the lift)
IMPORTANT
Insure All Safety Instructions have been read and understood before the lift is used
Review all safety information daily with all lift operators
LIFT SAFETY and
LIFT MAINTENANCE
MUST BE PART OF
YOUR DAILY ROUTINE
6
GENERAL REQUIREMENTS and LIFT SPECIFICATIONS
LSS2P10CFAB
LSS2P10CFAB
8
TOOLS REQUIRED and PRE INSTALLATION PROCEDURES
Tools Required: Gather all the tools listed below
 4” x 4” Wooden Blocks (for unpacking)
 16ft. Measuring Tape
 Chalk Line and Chalk
 Side Cutters
 Crow Bar
 Metric Wrenches and Ratchet Set
 SAE Wrenches and Ratchet Set
 Metric and SAE Allen Key Sets
 Hammer
 Screwdrivers
 12 ft. Step Ladders - 2
(2 men using 12 ft. ladders should install the overhead crossmember assembly)
 4 ft. Levels - 2
 Rotary Hammer Drill with 3/4” diameter Masonry Drill Bit
Pre Installation Procedures
Before proceeding with installation, read the installation manual and insure all instructions
are fully understood and all component parts are accounted for.
1. In the installation area, identify the center line of the bay and mark the floor. Also mark the center of bay entrance door. Connect these two points with a short chalk line in the area where lift will be located. Draw a second chalk line at 90° to locate the positions of both lift columns
(refer to lift dimensions below)
.
pre installation procedure continued on page 10 ………..
9
Insure each lift column is equal distance from bay centerline and each baseplate maintains a minimum distance of 6 inches from any floor seam. Do not install if floor has cracks or deterioration that could affect lift stability. The shop owner is responsible for confirming there are no obstructions in the installation area like floor drains, under floor piping or electrical conduit that could be damaged or prevent safe lift installation and secure lift anchoring. Check ceiling for beams or heating ducts and walls for protruding structures, etc.. Confirm that the lift overall height will fit in the bay. Insure that the lift can be safely installed in the position you have marked out on the bay floor.
2. Place the lift on wooden blocks so that the steel shipping frames can be removed.
3. Remove protective wrapping. Clear installation area of all packaging materials.
4. Unbolt steel shipping frames and remove from installation area.
5. Carefully remove top column and lay on the floor
(carriage side up)
.
6. Carefully remove column extensions (2 pc), cross-member (2 pc), overhead safety bar,
arms (4 pc), powerpack and hardware box from the lower column.
7. Identify powerpack column. Move
(carriage side up)
to appropriate location placing the
baseplate end on your floor marks. Similarly, move the second column to the opposite
location.
INSTALLATION PROCEDURE
1. With columns laying on the ground
(carriage side up)
, tightly fasten one column extension
to one column using bolts, washers and nuts provided
.
Fasten one overhead cable pulley
assembly to the top of the column extension. Repeat this procedure with the second
column.
2. Layout both pieces of the overhead crossmember on the floor and fasten tightly together
using bolts, washers and nuts provided
.
3. Identify all parts for overhead safety shut-off bar
.
Tightly fasten these parts to overhead
crossmember with bolts, washers and nuts provided.
installation procedure continued on page 11 ………..
10
4. Raise
(stand up) each column so that its baseplate is located on the floor marking you made
earlier. Confirm that baseplate angles and measurements between columns match lift
specifications on page 9. Use extreme caution to insure the columns do not fall
over. Secure baseplate of the most level column by installing one only anchor bolt.
5. For optimum safety, two installers should lift and secure the overhead crossmember to
both columns using bolts, washers and nuts provided
.
Hand tighten all crossmember
nuts and bolts. Final tightening is completed in step 9.
6. Using two 4 ft. levels and required shims, level each column vertically on all four sides
Use extreme caution to insure the columns do not fall over.
IMPORTANT: When leveling each column using anchor bolts provided, do not use
more than ¾ inch
(19 mm)
of shims under any area of the baseplate. Use a 4 ft. level to
confirm the overhead crossmember is also level and at 90 degrees to both columns.
7. Drill and install all anchor bolts, washers and nuts
(reference diagram below).
Insure that
each nut is torqued to 150 ft-lbs
(204Nm)
.
This should be checked monthly.
8. One equalizing cable comes partially installed on each carriage. Before feeding a cable up
its column to the overhead crossmember, insure the cable is properly seated around the
lower pulley at the base of each column
.
Route each cable up its column, over the
appropriate pulleys in the overhead crossmember, and lower it down to the opposite
carriage. Insure both equalizing cables are properly seated in overhead crossmember
pulleys. Thread one nut to its farthest point on each equalizing cable. Insert threaded
end into appropriate location on the carriage. Install and hand tighten second nut to
secure each cable. Final equalizing cable adjustment is step 17.
installation procedure
continued on page 12
11
Note: Always keep both cables in same tension
9. Completely tighten both sides of the overhead crossmember to its column.
10. Identify parts to install arms and arm restraints
.
Install all 4 arms and arm restraints.
11. Install powerpack on appropriate column
.
13. Identify parts for
hydraulic system
installation
.
Route
the appropriate lines
to cylinders and
powerpack.
Tightly fasten all
hydraulic lines and
secure these lines
to both columns and
and overhead
crossmember using
hardware provided.
Insure that nothing
will rub or wear the
hydraulic lines.
14. Attach microswitch to overhead safety bar bracket on powerpack side of overhead
crossmember
.
NOTE: he following two procedures should be performed by a
certified electrician. Wire overhead safety bar micro-switch to the powerpack. Wire
powerpack to shop electrical system.
installation procedure continued on page 13 ………..
12
15. Fill powerpack reservoir with ISO 32 hydraulic oil.
16. Operate the lift with no vehicle and no other weight. Raise lifting carriages
approximately 30 inches. Confirm that safety locks on both sides engage properly while
lift is being raised. Verify that both lifting cylinders are properly seated in the baseplate
locator hole. Continue raising lift to full height confirming safety locks are engaging.
Lower lift completely. Raise and lower the lift at least three times or until all air in the
hydraulic system is removed.
17. After confirming that all air has been bled from the hydraulic system,
adjust equalizing cable tension as follows:
(Step 1) Hold top of threaded stud with a wrench to prevent
it from rotating.
(Step 2) Tighten nut "B" until all loose slack is removed
from the cable. Do not over tighten.
(Step 3) Firmly tighten nut "A" to lock cable in place. Repeat
this process for the other cable insuring both cables
have the same degree of tightness.
13
OPERATING INSTRUCTIONS and LIFT MAINTENANCE
LIFT OPERATION: Before lifting a vehicle, insure all operators are qualified, have
been trained and are following all safety instructions. Insure the vehicle is securely positioned on the lift using manufacturer's recommended lifting points.
Insure all arm restraints are totally engaged. Never allow anyone under the lift when raising or lowering it with or without a vehicle. Always confirm safety locks on both sides of the lift are completely engaged before proceeding under a vehicle.
Lift electrical operating controls are located on the powerpack ( one "up" button for raising the lift and one "down" lever for lowering the lift)
. Before lowering, slightly raise the lifting carriages to release pressure from all safety locks. Manually release each safety lock by pulling the appropriate wire handle. Use extreme care when completing this procedure. Engage the "down" lever to lower the lift. Make certain the safety locks do not accidentally re-engage while lift is being lowered.
LIFT MAINTENANCE : The following is a minimum maintenance schedule:
DAILY: - Raise and lower the lift
(with no vehicle)
at the beginning of each shift to verify it is
operating properly and carriages are level. Confirm all arm restraints engage and
disengage smoothly and totally and telescoping arms have no excessive movement.
- Check all hydraulic fittings and lines for damage or leaks. Check electrical wiring for
damage. Check all moving parts for uneven or excessive wear. Repair or replace all
damaged, worn, or broken components immediately.
- Remove oil/grease on all lift pads.
WEEKLY: - Check hydraulic fluid in powerpack reservoir.
(confirm no leaks before topping up )
- Check equalizing cable adjustment. Check safety lock release cable adjustment.
MONTHLY: - Check that all anchor bolts are torqued to 150 ft-lbs (204Nm).
- Clean and lubricate arm restraints.
(confirm all components are in good condition)
- Lubricate safety locks in both columns.
- Check that overhead safety shutoff is operating properly.
EVERY TWO MONTHS: - Remove and grease arm pins – reinstall insuring secure fit.
- Clean and re-grease slide block channel in both columns.
- Clean and lubricate all cable pulleys.
EVERY YEAR: - Arrange for a certified lift technician to inspect and certify all aspects of the
lift as per "Automotive Lift Operation, Inspection and Maintenance" (ALOIM)
guidelines.
EVERY TWO YEARS: - Change and replace hydraulic oil in cylinders and powerpack.
Lubrication Specifications: - where grease is required use a multi-purpose lithium grease
- where lubricating oil is required use a SAE 30 oil
- where hydraulic oil is required use ISO 32 – 10W non detergent
hydraulic oil.
14
LIFT PROBLEM TROUBLESHOOTING GUIDE
The following are some suggestions to consider if problems are encountered with the lift.
Please call a qualified lift technician for further clarification and information.
1. Lift does not operate:
Possibilities include - blown fuse or tripped circuit breaker – tripped thermal overload on
motor – defective "up" button. Call a qualified electrician for all wiring questions.
2. Motor runs but lift does not rise:
Possibilities include – low hydraulic oil level (check reservoir tank) - dirt under check
valve (press "down" lever and "up" button at the same time for 10-15 seconds. This will
clear small contaminants. If this fails clean check valve ball and seat by removing valve
cover). Call a certified lift technician if problem continues.
3. Motor noise (drone or hum) but will not run:
Possibilities include – low voltage, faulty wiring or faulty capacitor (call electrician to
confirm) – lift is overloaded ( insure vehicle weighs less than rated lift capacity).
4. Lift falters or jerks when it is raised or lowered:
Possibilities include – air in the hydraulic system (cycle lift all the way to the top and
completely lower 3 – 4 times. If this does not solve the problem call a certified lift
technician).
5. Excessive noise when raising or lowering lift:
Possibilities include – pulley assemblies need lubricating – cable is off the pulleys –
carriage sliders need grease – carriage sliders are broken. Do not operate the lift with
broken or damaged carriage sliders or dislodged cable. Replace immediately.
6. Lifting carriages are unequal when raised:
Possibilities include – improperly adjusted equalization cables – air in the hydraulic
system. Adjust cables or call a certified lift technician to correct the problem.
15
10,000 lbs.
Capacity
LSS2P10CFAB
READ and SAVE this MANUAL
Issue 002 Effective: November 15 , 2007
Supersedes Issue 001 - November 10 , 2006
16
17
18
23
24
25
26
27
28
29
30
19
20
21
22
14
15
16
17
18
7
8
9
10
11
12
13
No.
1
2
3
4
5
6
31
32
33
34
35
36
37
37.1
38
39
40
Chart Number
GB894.1-86
GB819-85
GB5781-86
GB6170-86
GB97.2-85
GB93-87
GB6170-86
GB93-87
GB97.2-85
GB5781-86
GB6170-86
GB93-87
GB97.2-85
GB91-86
GB97.2-85
GB6170-86
GB97.2-85
GB93-87
TPF4-400-07
TPF4-400-01
TPF4-400-03
TPF4-400-03
GB41-86
LSS2P10CFAB Parts List
TPF4-100-00A(B)
TPF4-100-10-05
TPF4-100-12GM
TPF4-700-02-00
TPF4A-700-02-01
TPF4A-700-02-02
TPF4A-700-02-03
TPF4A-700-03-01-00
TPF4A-700-03-02-00
TPF4-200-11-01
TPF4-200-11-02
TPF4-200-11-04
TPF4-200-11-05
TPF4-400-02-00
TPF4-400-05-00M
TPF4-400-06-00
Name Quantity
Base Column 2
Pulley 2
Snap Spring Washer 2
Cover 2
Cross Bolt 4
Hex Bolt C 16
Nut 16
Flat washer 16
Lock Washer
Column Extension
16
2
Equalizing Cable Pulley Bracket 2 each
Nut 4
Spring Washer 4
Spring Washer A 4
Pulley 4
Sheath 6
Spindle 2
Overhead Crossmember (left) 1
Bolt 4
Nut 4
Spring Washer
Flat Washer
4
4
Overhead Crossmember (right)
Arm Restraint Rod
1
4
Spacer 4
Flat Washer A 4
Spring 4
Arm Restraint Rack
Arm Restraint Guide
4
4
Nut 4
Flat Washer
Spring Washer
4
4
Ball Handle 4
Bolt 8
Rubber Lifting Pad
Lifting Pad Weldment
Low Lift Pad Adapter
4
4
4
High Lift Pad Adapter
Lock Nut
Rear Swing Arm
Arm Pin
19
4
8
2
4
64
65
69
70
71
72
73
74
75
76
60
61
62
63
55
56
57
58
59
48
49
50
51
52
53
54
41
42
LSS2P10CFAB Parts List
(continued)
GB819-85
TPF4-400-04-00
43
TPF4-400-05K-00A(B)M
44
GB5781-86
45
46
47
GB6170-86
GB97.2-85
GB93-87
Bolt 4
Arm Pad Weldment 2
Front Swing Arms (Left and Right)
Hex Bolt C
1 each
4
Nut 4
Flat Washer 4
Spring Washer 4
TPF4-500-08
TPF4-500-07
TPF4-500-04
TPF4-500-12
TPF4-500-06
TPF4-500-02
TPF4-500-11
TPF4-200-01-00
TPF4A-200-12
GB91-86
GB97.2-85
TPF4-300-00
TPF4-300-02
GB70-85
TPF4-300-09
TPF4-300-05-01
TPF4-300-05-02
TPF4-500-01
TPF4-100-14-02
TPF4-100-14-01
GB8942-86
TPF4-800
TPF4-900
Powerpack Tank 1
Washer 1
Hydraulic Connector
"T" Fitting
1
1
Hydraulic Hose
90º Elbow Fitting
Hydraulic Line Extension
1
2
2
Powerpack Pump and Motor Assembly
Carriage
Slidder Block
Cotter Pin
Flat Washer
1
2
16
2
2
Safety Lock Weldment
Pull Spring
2
2
Hex Screw 2
Spring 2
Pull Rope 2
Sheath 4
Hydraulic Cylinder 2
Spindle 2
Idler Wheel 2
Spindle Spring Washer 2
Spindle 4
Chain 2
Steel Cable 2
Nut 8
20
advertisement
* Your assessment is very important for improving the workof artificial intelligence, which forms the content of this project
Related manuals
advertisement