Jack JK-T781EK, JK-T782E, JK-T783E Manual
Add to my manuals
22 Pages
Jack JK-T781EK is a versatile sewing machine designed for creating buttonholes in a range of fabrics, including textiles and chemical fiber fabrics. With its ability to handle stitch widths from 2.5 to 4mm and buttonhole lengths from 6.4 to 19mm, this machine offers great flexibility for various sewing projects. It also features an automatic oiling system for ease of maintenance and a maximum sewing speed of 3600 stitches per minute, ensuring efficient operation.
advertisement
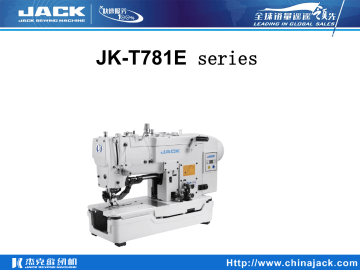
JK-T781E
series
technical parameters and models
Model
Purpos
Buttonhole length
Stitch width
Cutter length
Speed
Needle stroke
Presser foot height
Needle
Refueling mode
Sewing thickness
Needle count
JK-T781E JK-T782E JK-T783E
(Textile, chemical fiber fabric )buttonhole`s sewing lock
22mm 33mm 40mm
JK-T781EK
Knitting
2.5~4mm 2.5~5mm 2.5~5mm
22mm
2.5~4mm
6.4~19mm
(1/4”~3/4”)
6.4~25.4mm
(1/4”~1”)
6.4~31.7mm
(1/4”~1 1/4”)
100~3600rpm/min
34.6mm
10mm
DP × 5 ( #11~#14 )
6.4~19mm
(1/4”~3/4”)
Automatic oiling
4mm
Factory equipped with 4 unitsG(225,83) J(190,100) L(170,110)
N(152,123)
Market has 8 units 54针 ~345 针
1.2 adjust needle and hook
First way:see the no. of 2 in the first picture, put the ruler like this between the Needle plate and needle bar,move the position of needle bar until the distance between needle bar and the ruler is 0. Adjust the hook to make the tip of the hook from the upper end of the pinhole 1.6 ~ 1.8mm, tighten the screw of Rotary hooks to make that the distance between two Tips of the hook is about 0.05 mm.
1.6~1.8mm
0.05mm ruler, this part 14.2mm
requirement for catching thread
2.1
、
adjust the needle bar height
Second way:(observe the hook),Install the needle to make the needle in the middle of the pinhole, move the needle bar to the lowest point, observe and make the upper edge of the pinhole not exceed the needle plate.
lowest point,of the needle needle plate
Front panel of neele plate the middle of the pinhole
2.2
、
adjust needle and hook
Second way: 1、 Turn the handle,until the the pallet moves to the right baseline,
Turn the handwheel until the needle moves to the right baseline,during the period of returning of the needle bar, adjust the Rotary tip util hooking above the pinhole,at the the lowest plat.
2、Adjust the rotary hook positioning screw, util hook tip close to the needle, but not hit the needle (zero distance).3、pls. note when the hook catchs thread, the rotary hook needle plate must be close to the needle, but not squeezed(zero distance). hooking above the pinhole the needle moves to the right baseline requirement for catching thread hook tip close to the needle
3.0
、
adjust buttonhole width and stitching reference position
The movement of the needle is based on the right side of the needle swing. When adjusting, please follow the following steps:
1、Baseline width adjustment: Turn screw 1 and align the baseline pointer to the desired scale on the scale plate.
2 、 Reinforce sewing width adjustment : Tighten screw 2 to align the reinforcement pointer to the baseline pointer.3
、 Right baseline position: twist screw 3, adjust the cutter to cut the screws when the right baseline is not cut.4
、 Left position of the baseline: When screwing the screw 4 so that the blade does not have a left baseline, tighten the screw.
Baseline pointer
Scale plate screw 1 screw 4
Reinforce pointer screw 3 screw 2
4.0 adjust position of feeding control panel when work finished
◆ If the control plate position is not correct, whenever you change the sewing size, the knife will malfunction, the position of the presser foot will change, resulting in broken needle, broken thread.
◆adjustment method: when stopping,make the scale line of plate align the middle position of the roller pin screw. If the position is not correct, move the part A of the right pic. to reaze this .
大盘刻线
Scale line of plate control plate
18.0
:
Adjustment of the button hole length
Standard : This adjustment is same as 781D serie.
Method :
1. Pull out the part, put up the canning.
:
( The number should be same as length of cutter) Then tighten the screw 。
Feeding Crank
Loose screw
Pointer 781E Machine mode and Number Comparison table
Mode 781E 782E 783E 781EK
Number on dial
1/2 1 5/4 1/2
Notice : After change the number on dial, then should change the presser foot similar as the length of button hole.
19.0
: Adjustment of the position of lower line fixed knife
Adjustment stardard: the distance between fixed knife and needle plate hole is 0.3-0.5mm.
Adjustment influence: if the distance between the fixed knife and the needle plate hole is too close, the thread breakage will happen when you sew. fixed knife fasten screw
Adjustment method:
1.Lose the fixed knife fasten screw.
2. Adjust fixed knife, make the distance between the fixed knife and the needle plate hole to 0.3-0.5mm and then fasten the screw. fixed knife
29.0
:
The sensor chip of automatic foot-lift position adjustment
Adjustment standard: When the machine is in the parked position (the presser foot is in the decentralized state), the motor will automatically find the zero position, so that the mechanical lock between the starting plate and the movement pin left 3mm gap.
Adjustment methods :
1. Loosen the setscrews and adjust the sensor chip up and down relative to the sensor. ( Up to adjust sensor chip, the gap becomes larger after booting to find the zero position, down to adjust the gap smaller.)
2.
Re-boot to find zero position, verify the mechanical lock between the starting plate and the movement pin left 3mm gap.
Larger
Sports pin
Sensor Smaller
Stamp mark
Sensor chip
The sensor chip is aligned with up-side of the stamp mark of sensor
3mm Gap
31.0
:
Adjustment and functions of feeding sensor
◆ The main function of feeding sensor is:prevent foot lifting during sewing, the sensor lamp goes out when entering the sewing state , press , can not lift the foot , when stop sewing, the sensor lamp lights up and presses presser , lift the presser foot
◆ Easy to adjust the presser foot up and down during maintain
Adjustment method ; Loosen the set screws, adjust the sensor up and down, make sure that the distance between sensor and sensor magnet is about 1.5mm, and could be lit up when stop sensor magnet set screw set screws
三、
Parameters and fault codes
1、Operation button
Enter and determine the stored content value
Enter the parameter area function key
Set the value increment / parameter increment
Set the value decrement / parameter decrement
Enter the parameter content value, any changes of the value, need to press the key to save confirmation.
1. In normal boot mode, press the key to enter the user parameter mode
2. Press and hold the key to enter the technician parameter mode
1. In the parameter selection area, as the key to increase the parameter
2. In the parameter contents area, as the key to increase the value
1. In the parameter selection area, as the key to decrease the parameter
2. In the parameter contents area, as the key to decrease the value
2 、 LED display script and actual script comparison table
Digital script part :
Actual value :
LCD :
3 、 Display mode of the LCD screen
English script part :
English alphabet :
LCD :
English alphabet :
LCD :
English alphabet :
LCD :
4 、 Factory reset
Press the up and down key and at the same time boot the machine up, it will show P11.
Press enter key to save it
Press F key and reboot
5、Enter user mode and modify & save(1-10)
In normal case, press F to get into user parameter mode.
Press up and down key to change parameter items.
Press enter key to get the value of this parameter.
Press up and down key to modify the parameter value.
Press enter key to save the value
Press F key to get out of this mode.
6、Enter technician mode * ( 11-25 )
Press F key and at the same time boot the machine up
Press up and down key to change parameter items.
Press enter key to get the value of this parameter.
Press up and down key to modify the parameter value.
Press enter key to save the value
Press F key to get out of this mode.
7 、 System officer mode-limited to item ( 26-27 )
Press F and enter key and at the same time boot the machine up
Press up key to find
P26 (speed limit) and the press ENTER to get the value.
Press up and down key to modify the parameter value and then press enter to save.
Press F key to get out of this mode.
8、Manual up positioning adjustment
Press the up and down key and at the same time boot the machine up
Press up key to find
P27 and the press ENTER to get into it.
Move the hand wheel to adjust and press enter key to save.
Press F key to get out of this mode.
9、user parameters
item description range Initial note value
P01 Max speed ( rpm ) 10 ~ 360 300 Sewing speed ( actual speed=display number
P02 Start sewing speed
( rpm )
*10 )
20 ~ 360 130 Start sewing speed ( actual speed=display number*10 ) for 781E, it doesn’t work
P03 Cutter movement speed
P04 Speed limit for 1 st stitch
P05 Speed limit for 2 nd stitch
P06 Speed limit for 3 rd stitch
P07 Speed limit for 4 th stitch
P08 Speed limit for 5 th stitch ( reserved )
P10 Stitches required
10- 100
10
10
10
10
10
0 - 5 during the cutting.
~
~
~
~
~
360
360
360
360
360
P09 Presser foot protection time ( s )
1 - 120
55
80
80
3
200
250
200
8
The rotation of head during the cutting speed=display number*10
(
(
(
(
(
) actual speed=display number*10 actual speed=display number*10 actual speed=display number*10 actual speed=display number*10 actual speed=display number*10
)
)
)
)
)
( actual
Presser foot will drop after exceeding the continual lifting time set. (Only for
781D)
Stitches required during the cutting.
Coordinated with cutter speed.
item
P16
P22
Protected stitches
P17
P18
Find the up position automatically after booting
Up positioning adjustment
P19 Test working time
P20 Test stop time
P21 A test
B test
P23 C test
P24 Head protection switch
P25
Mechanical lock protection switch
P26 Speed limit
P28
The highest presser foot height
P29 description
Presser middle position range
1 - 990
0 - 1
40 - 180
1 - 250
1 - 250
0 - 1
0 - 1
110
20
20
0
0
Initial value
400
1 note
How many stitched protected if the big board senses nothing
1:Find the up position automatically after booting
0:function closed
Up positioning adjustment, value decreases means stop in advance by 2mm and vice versa
In C test, setting working time.
In C test, setting stop time.
In A test, continual working test with speed P01
In B test, full functional test with speed P01
0 - 1
0 - 1
0 - 1
10~360
0 - 400
0 - 400
0
1
1
300
250
00
In C test, no positioning working with speed P01
0:function closed
1:function
0:function closed
1:function
Speed limit( actual speed=display number*10 )
Adjust the stepper motor angle when it’s in highest presser foot height
Adjust the stepper motor angle when it’s in presser middle position
11、Error code
Error code
E1
E3
E6
E7
E9
E11
Content Solution
1) Power module error code
2)Abnormal overcurrent and overvoltage
Stepper motor communication abnormal
Stepper motor senses abnormal a.
Loose contact of engine plug b.
Position signal abnormal c. Head is blocked d .
Fabric is too heavy . e. module drive efforts abnormal
Module driver efforts and head efforts are both closed. waiting for restart ( check power board ) not frequent
Check the communication line between stepper motor drive board and main board.
1.
Check if stepper motor sensor (optoelectronic switch) is ok
2.
Check if stepper motor’s mechanical structure is right
Module driver efforts and head efforts are both closed. waiting for restart ( check machine head, positioner, engine, module drive)
)
Positioning signal abnormal Check up and down positioning signal and belt pulley
Find the up position automatically after booting. But positioner inserts to
Engine doesn’t work.(Check positioner ) control box, needle signal cannot be outputted.
12、Error code
E12 Power on and no positioner inserted
E13
E14
E15
Power module overheating protection
Encoder signal fault
Power module abnormal overcurrent production
Automatically working in no-positioner mode, and cutting thread, tangent, up positioning and all fixed needle sewing pattern sewing functions have no effect. The motor can work normally.
( check positioner )
Check the power module and cooling fin is good contact
Check whether the encoder signal is right or change the encoder
Module driver efforts and head efforts are both closed. waiting for restart ( check power board function )
E17 Head protection switch is not in its position
Check the head position and the switch.
E18 Mechanical lock protect error code
E19 Big board protect error code
Check mechanical lock position and the switch.
Check the big board position and the switch.
advertisement
* Your assessment is very important for improving the workof artificial intelligence, which forms the content of this project
Key Features
- High speed sewing up to 3600rpm
- Wide range of stitch widths from 2.5mm to 4mm
- Adjustable buttonhole lengths from 22mm to 33mm
- Automatic oiling system for smooth operation
- Built-in cutter for trimming threads
- Easy-to-use control panel with digital display
- Durable construction for long-lasting performance